Impact of Location on Coca-Cola's Operations
VerifiedAdded on 2019/09/30
|11
|3405
|152
Report
AI Summary
Coca- Cola Company has a strong preference for air freight mode to deliver products to distributors on time and without damage, due to its overstocked inventory. The company's location decision was influenced by various factors such as supply-side (labor cost, transportation cost) and demand-side (image of location, suitability, convenience) considerations, including the need for raw materials, transport facilities, and labor at lower wages. The company analyzed the location decisions of other companies to make the most effective decision for its own location, focusing on factors such as proximity to suppliers, target market, and competitors.
Contribute Materials
Your contribution can guide someone’s learning journey. Share your
documents today.
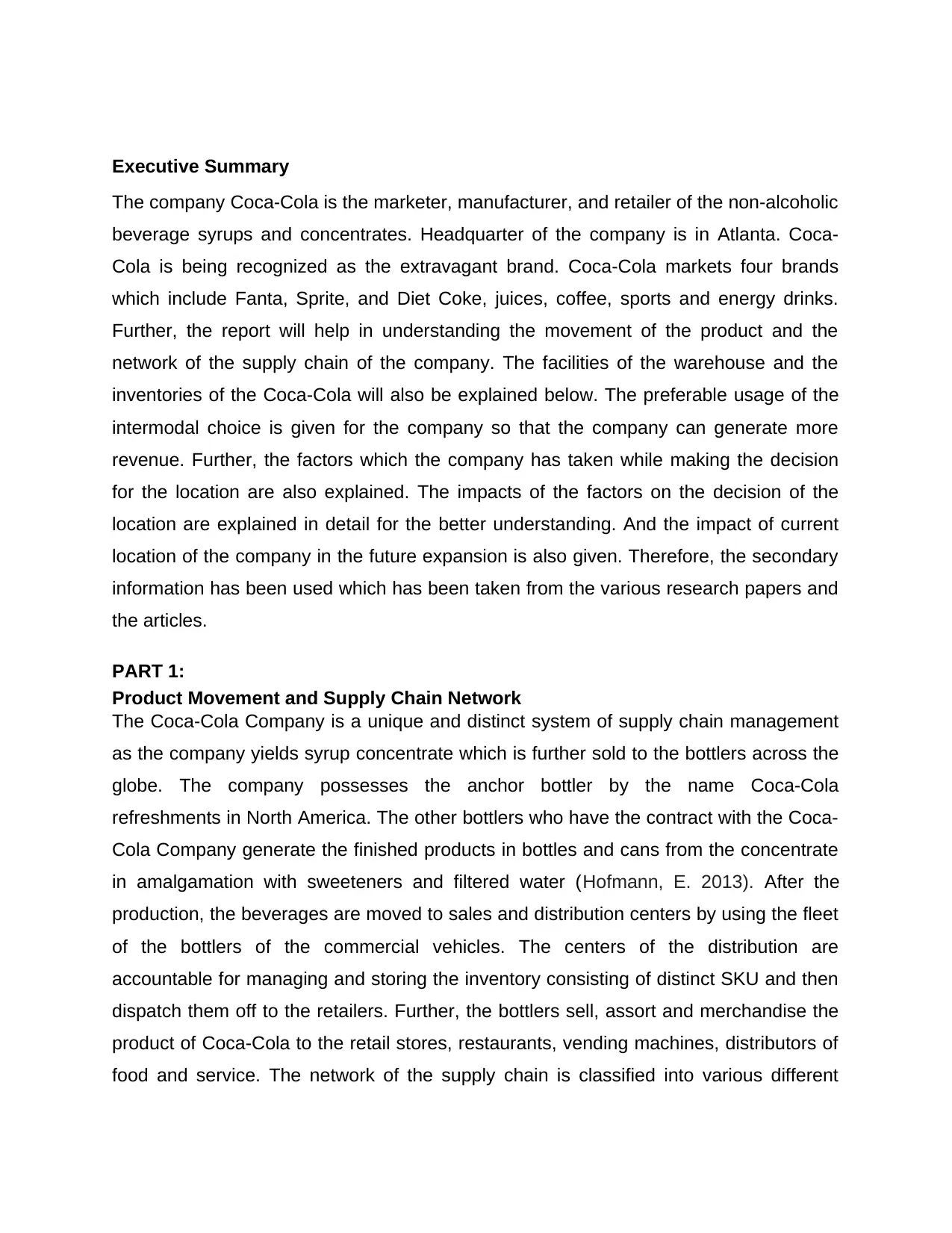
Executive Summary
The company Coca-Cola is the marketer, manufacturer, and retailer of the non-alcoholic
beverage syrups and concentrates. Headquarter of the company is in Atlanta. Coca-
Cola is being recognized as the extravagant brand. Coca-Cola markets four brands
which include Fanta, Sprite, and Diet Coke, juices, coffee, sports and energy drinks.
Further, the report will help in understanding the movement of the product and the
network of the supply chain of the company. The facilities of the warehouse and the
inventories of the Coca-Cola will also be explained below. The preferable usage of the
intermodal choice is given for the company so that the company can generate more
revenue. Further, the factors which the company has taken while making the decision
for the location are also explained. The impacts of the factors on the decision of the
location are explained in detail for the better understanding. And the impact of current
location of the company in the future expansion is also given. Therefore, the secondary
information has been used which has been taken from the various research papers and
the articles.
PART 1:
Product Movement and Supply Chain Network
The Coca-Cola Company is a unique and distinct system of supply chain management
as the company yields syrup concentrate which is further sold to the bottlers across the
globe. The company possesses the anchor bottler by the name Coca-Cola
refreshments in North America. The other bottlers who have the contract with the Coca-
Cola Company generate the finished products in bottles and cans from the concentrate
in amalgamation with sweeteners and filtered water (Hofmann, E. 2013). After the
production, the beverages are moved to sales and distribution centers by using the fleet
of the bottlers of the commercial vehicles. The centers of the distribution are
accountable for managing and storing the inventory consisting of distinct SKU and then
dispatch them off to the retailers. Further, the bottlers sell, assort and merchandise the
product of Coca-Cola to the retail stores, restaurants, vending machines, distributors of
food and service. The network of the supply chain is classified into various different
The company Coca-Cola is the marketer, manufacturer, and retailer of the non-alcoholic
beverage syrups and concentrates. Headquarter of the company is in Atlanta. Coca-
Cola is being recognized as the extravagant brand. Coca-Cola markets four brands
which include Fanta, Sprite, and Diet Coke, juices, coffee, sports and energy drinks.
Further, the report will help in understanding the movement of the product and the
network of the supply chain of the company. The facilities of the warehouse and the
inventories of the Coca-Cola will also be explained below. The preferable usage of the
intermodal choice is given for the company so that the company can generate more
revenue. Further, the factors which the company has taken while making the decision
for the location are also explained. The impacts of the factors on the decision of the
location are explained in detail for the better understanding. And the impact of current
location of the company in the future expansion is also given. Therefore, the secondary
information has been used which has been taken from the various research papers and
the articles.
PART 1:
Product Movement and Supply Chain Network
The Coca-Cola Company is a unique and distinct system of supply chain management
as the company yields syrup concentrate which is further sold to the bottlers across the
globe. The company possesses the anchor bottler by the name Coca-Cola
refreshments in North America. The other bottlers who have the contract with the Coca-
Cola Company generate the finished products in bottles and cans from the concentrate
in amalgamation with sweeteners and filtered water (Hofmann, E. 2013). After the
production, the beverages are moved to sales and distribution centers by using the fleet
of the bottlers of the commercial vehicles. The centers of the distribution are
accountable for managing and storing the inventory consisting of distinct SKU and then
dispatch them off to the retailers. Further, the bottlers sell, assort and merchandise the
product of Coca-Cola to the retail stores, restaurants, vending machines, distributors of
food and service. The network of the supply chain is classified into various different
Secure Best Marks with AI Grader
Need help grading? Try our AI Grader for instant feedback on your assignments.
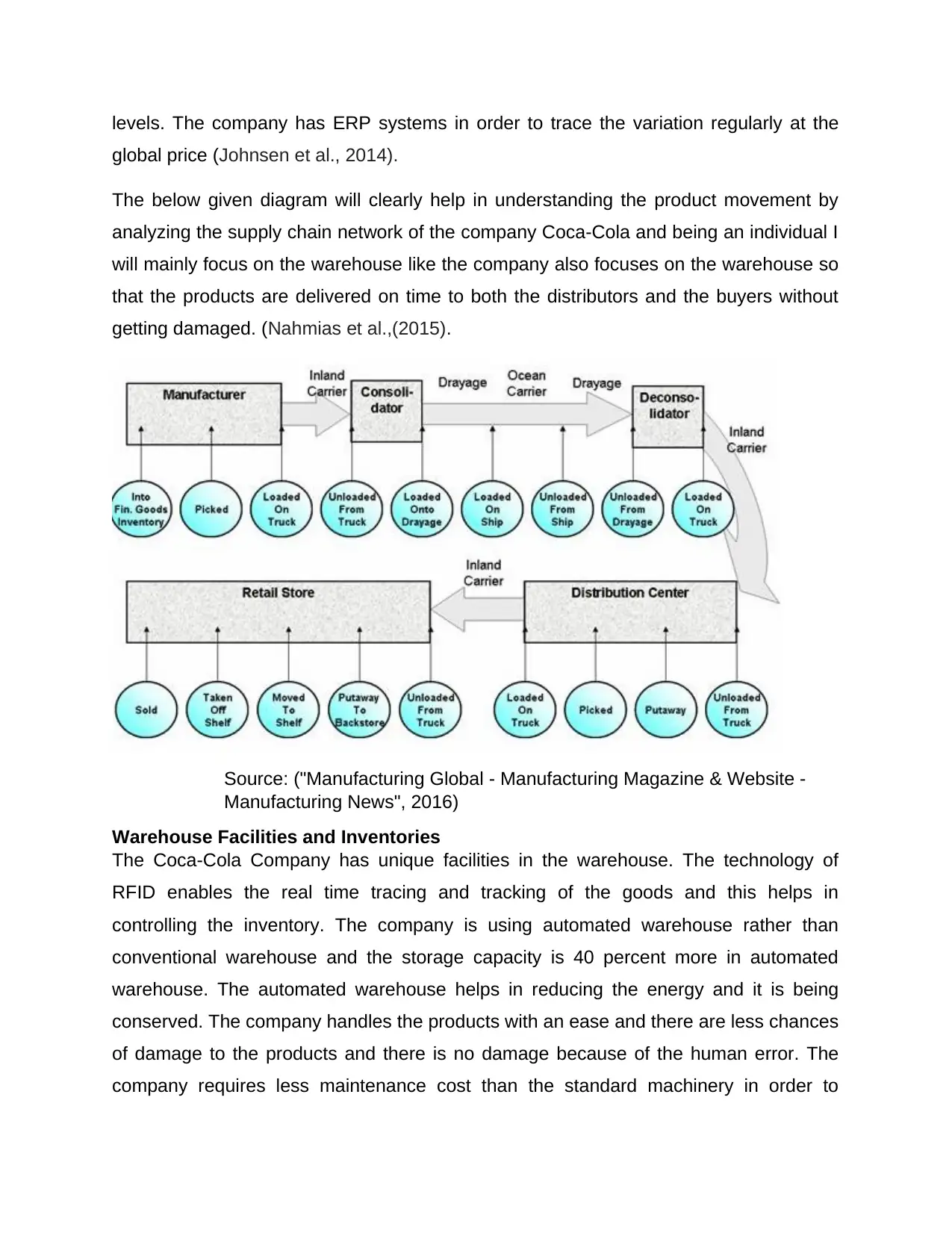
levels. The company has ERP systems in order to trace the variation regularly at the
global price (Johnsen et al., 2014).
The below given diagram will clearly help in understanding the product movement by
analyzing the supply chain network of the company Coca-Cola and being an individual I
will mainly focus on the warehouse like the company also focuses on the warehouse so
that the products are delivered on time to both the distributors and the buyers without
getting damaged. (Nahmias et al.,(2015).
Source: ("Manufacturing Global - Manufacturing Magazine & Website -
Manufacturing News", 2016)
Warehouse Facilities and Inventories
The Coca-Cola Company has unique facilities in the warehouse. The technology of
RFID enables the real time tracing and tracking of the goods and this helps in
controlling the inventory. The company is using automated warehouse rather than
conventional warehouse and the storage capacity is 40 percent more in automated
warehouse. The automated warehouse helps in reducing the energy and it is being
conserved. The company handles the products with an ease and there are less chances
of damage to the products and there is no damage because of the human error. The
company requires less maintenance cost than the standard machinery in order to
global price (Johnsen et al., 2014).
The below given diagram will clearly help in understanding the product movement by
analyzing the supply chain network of the company Coca-Cola and being an individual I
will mainly focus on the warehouse like the company also focuses on the warehouse so
that the products are delivered on time to both the distributors and the buyers without
getting damaged. (Nahmias et al.,(2015).
Source: ("Manufacturing Global - Manufacturing Magazine & Website -
Manufacturing News", 2016)
Warehouse Facilities and Inventories
The Coca-Cola Company has unique facilities in the warehouse. The technology of
RFID enables the real time tracing and tracking of the goods and this helps in
controlling the inventory. The company is using automated warehouse rather than
conventional warehouse and the storage capacity is 40 percent more in automated
warehouse. The automated warehouse helps in reducing the energy and it is being
conserved. The company handles the products with an ease and there are less chances
of damage to the products and there is no damage because of the human error. The
company requires less maintenance cost than the standard machinery in order to
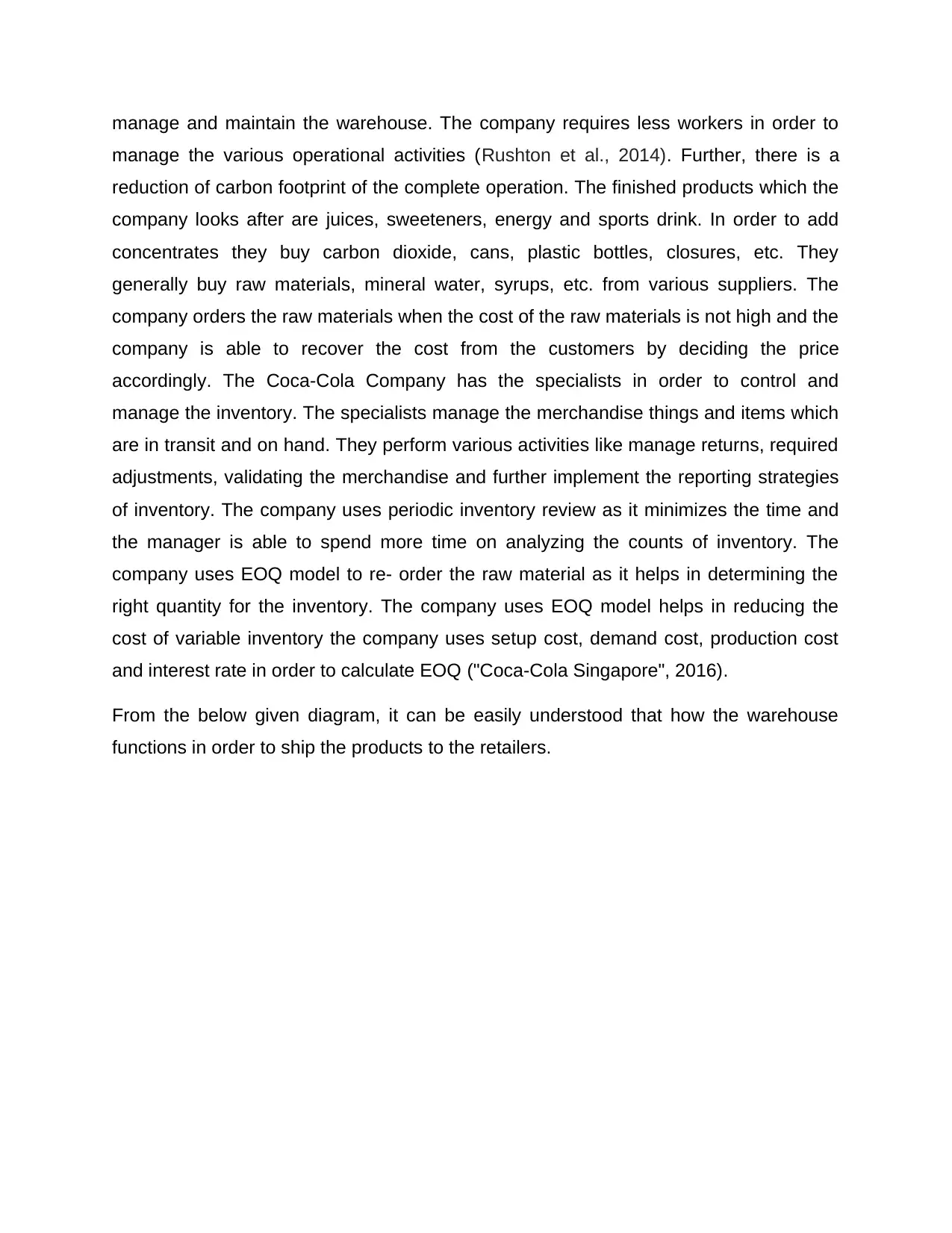
manage and maintain the warehouse. The company requires less workers in order to
manage the various operational activities (Rushton et al., 2014). Further, there is a
reduction of carbon footprint of the complete operation. The finished products which the
company looks after are juices, sweeteners, energy and sports drink. In order to add
concentrates they buy carbon dioxide, cans, plastic bottles, closures, etc. They
generally buy raw materials, mineral water, syrups, etc. from various suppliers. The
company orders the raw materials when the cost of the raw materials is not high and the
company is able to recover the cost from the customers by deciding the price
accordingly. The Coca-Cola Company has the specialists in order to control and
manage the inventory. The specialists manage the merchandise things and items which
are in transit and on hand. They perform various activities like manage returns, required
adjustments, validating the merchandise and further implement the reporting strategies
of inventory. The company uses periodic inventory review as it minimizes the time and
the manager is able to spend more time on analyzing the counts of inventory. The
company uses EOQ model to re- order the raw material as it helps in determining the
right quantity for the inventory. The company uses EOQ model helps in reducing the
cost of variable inventory the company uses setup cost, demand cost, production cost
and interest rate in order to calculate EOQ ("Coca-Cola Singapore", 2016).
From the below given diagram, it can be easily understood that how the warehouse
functions in order to ship the products to the retailers.
manage the various operational activities (Rushton et al., 2014). Further, there is a
reduction of carbon footprint of the complete operation. The finished products which the
company looks after are juices, sweeteners, energy and sports drink. In order to add
concentrates they buy carbon dioxide, cans, plastic bottles, closures, etc. They
generally buy raw materials, mineral water, syrups, etc. from various suppliers. The
company orders the raw materials when the cost of the raw materials is not high and the
company is able to recover the cost from the customers by deciding the price
accordingly. The Coca-Cola Company has the specialists in order to control and
manage the inventory. The specialists manage the merchandise things and items which
are in transit and on hand. They perform various activities like manage returns, required
adjustments, validating the merchandise and further implement the reporting strategies
of inventory. The company uses periodic inventory review as it minimizes the time and
the manager is able to spend more time on analyzing the counts of inventory. The
company uses EOQ model to re- order the raw material as it helps in determining the
right quantity for the inventory. The company uses EOQ model helps in reducing the
cost of variable inventory the company uses setup cost, demand cost, production cost
and interest rate in order to calculate EOQ ("Coca-Cola Singapore", 2016).
From the below given diagram, it can be easily understood that how the warehouse
functions in order to ship the products to the retailers.
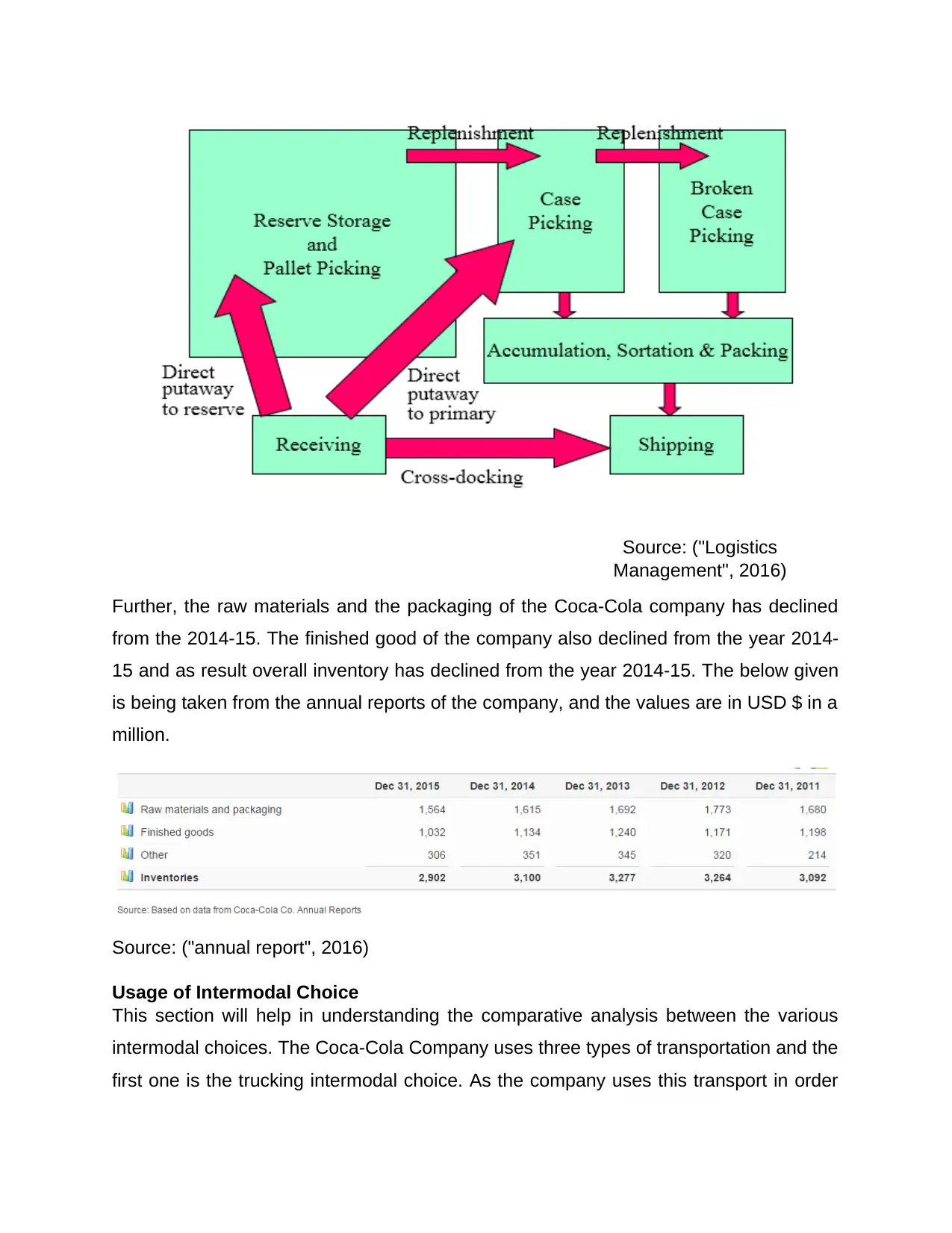
Source: ("Logistics
Management", 2016)
Further, the raw materials and the packaging of the Coca-Cola company has declined
from the 2014-15. The finished good of the company also declined from the year 2014-
15 and as result overall inventory has declined from the year 2014-15. The below given
is being taken from the annual reports of the company, and the values are in USD $ in a
million.
Source: ("annual report", 2016)
Usage of Intermodal Choice
This section will help in understanding the comparative analysis between the various
intermodal choices. The Coca-Cola Company uses three types of transportation and the
first one is the trucking intermodal choice. As the company uses this transport in order
Management", 2016)
Further, the raw materials and the packaging of the Coca-Cola company has declined
from the 2014-15. The finished good of the company also declined from the year 2014-
15 and as result overall inventory has declined from the year 2014-15. The below given
is being taken from the annual reports of the company, and the values are in USD $ in a
million.
Source: ("annual report", 2016)
Usage of Intermodal Choice
This section will help in understanding the comparative analysis between the various
intermodal choices. The Coca-Cola Company uses three types of transportation and the
first one is the trucking intermodal choice. As the company uses this transport in order
Secure Best Marks with AI Grader
Need help grading? Try our AI Grader for instant feedback on your assignments.
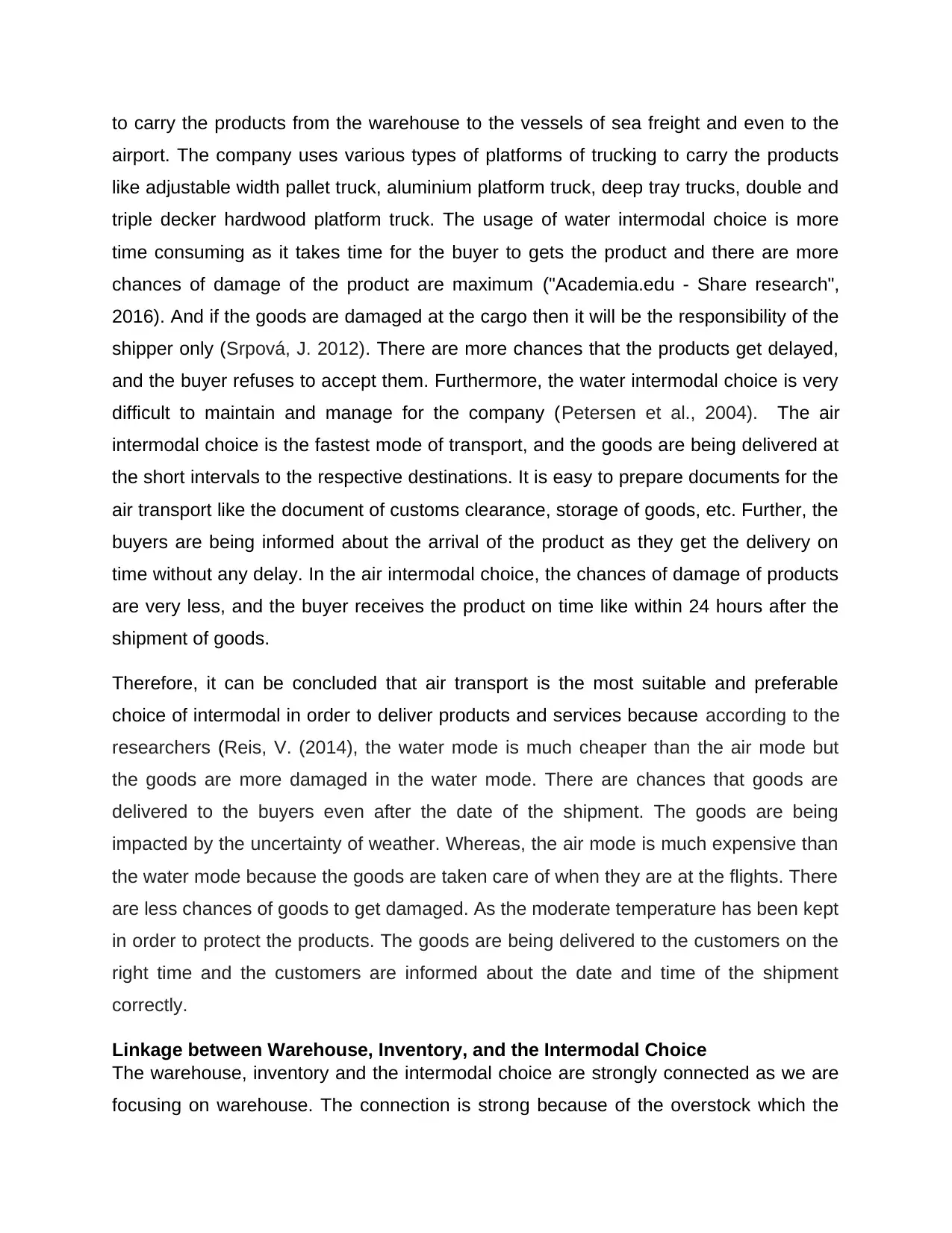
to carry the products from the warehouse to the vessels of sea freight and even to the
airport. The company uses various types of platforms of trucking to carry the products
like adjustable width pallet truck, aluminium platform truck, deep tray trucks, double and
triple decker hardwood platform truck. The usage of water intermodal choice is more
time consuming as it takes time for the buyer to gets the product and there are more
chances of damage of the product are maximum ("Academia.edu - Share research",
2016). And if the goods are damaged at the cargo then it will be the responsibility of the
shipper only (Srpová, J. 2012). There are more chances that the products get delayed,
and the buyer refuses to accept them. Furthermore, the water intermodal choice is very
difficult to maintain and manage for the company (Petersen et al., 2004). The air
intermodal choice is the fastest mode of transport, and the goods are being delivered at
the short intervals to the respective destinations. It is easy to prepare documents for the
air transport like the document of customs clearance, storage of goods, etc. Further, the
buyers are being informed about the arrival of the product as they get the delivery on
time without any delay. In the air intermodal choice, the chances of damage of products
are very less, and the buyer receives the product on time like within 24 hours after the
shipment of goods.
Therefore, it can be concluded that air transport is the most suitable and preferable
choice of intermodal in order to deliver products and services because according to the
researchers (Reis, V. (2014), the water mode is much cheaper than the air mode but
the goods are more damaged in the water mode. There are chances that goods are
delivered to the buyers even after the date of the shipment. The goods are being
impacted by the uncertainty of weather. Whereas, the air mode is much expensive than
the water mode because the goods are taken care of when they are at the flights. There
are less chances of goods to get damaged. As the moderate temperature has been kept
in order to protect the products. The goods are being delivered to the customers on the
right time and the customers are informed about the date and time of the shipment
correctly.
Linkage between Warehouse, Inventory, and the Intermodal Choice
The warehouse, inventory and the intermodal choice are strongly connected as we are
focusing on warehouse. The connection is strong because of the overstock which the
airport. The company uses various types of platforms of trucking to carry the products
like adjustable width pallet truck, aluminium platform truck, deep tray trucks, double and
triple decker hardwood platform truck. The usage of water intermodal choice is more
time consuming as it takes time for the buyer to gets the product and there are more
chances of damage of the product are maximum ("Academia.edu - Share research",
2016). And if the goods are damaged at the cargo then it will be the responsibility of the
shipper only (Srpová, J. 2012). There are more chances that the products get delayed,
and the buyer refuses to accept them. Furthermore, the water intermodal choice is very
difficult to maintain and manage for the company (Petersen et al., 2004). The air
intermodal choice is the fastest mode of transport, and the goods are being delivered at
the short intervals to the respective destinations. It is easy to prepare documents for the
air transport like the document of customs clearance, storage of goods, etc. Further, the
buyers are being informed about the arrival of the product as they get the delivery on
time without any delay. In the air intermodal choice, the chances of damage of products
are very less, and the buyer receives the product on time like within 24 hours after the
shipment of goods.
Therefore, it can be concluded that air transport is the most suitable and preferable
choice of intermodal in order to deliver products and services because according to the
researchers (Reis, V. (2014), the water mode is much cheaper than the air mode but
the goods are more damaged in the water mode. There are chances that goods are
delivered to the buyers even after the date of the shipment. The goods are being
impacted by the uncertainty of weather. Whereas, the air mode is much expensive than
the water mode because the goods are taken care of when they are at the flights. There
are less chances of goods to get damaged. As the moderate temperature has been kept
in order to protect the products. The goods are being delivered to the customers on the
right time and the customers are informed about the date and time of the shipment
correctly.
Linkage between Warehouse, Inventory, and the Intermodal Choice
The warehouse, inventory and the intermodal choice are strongly connected as we are
focusing on warehouse. The connection is strong because of the overstock which the
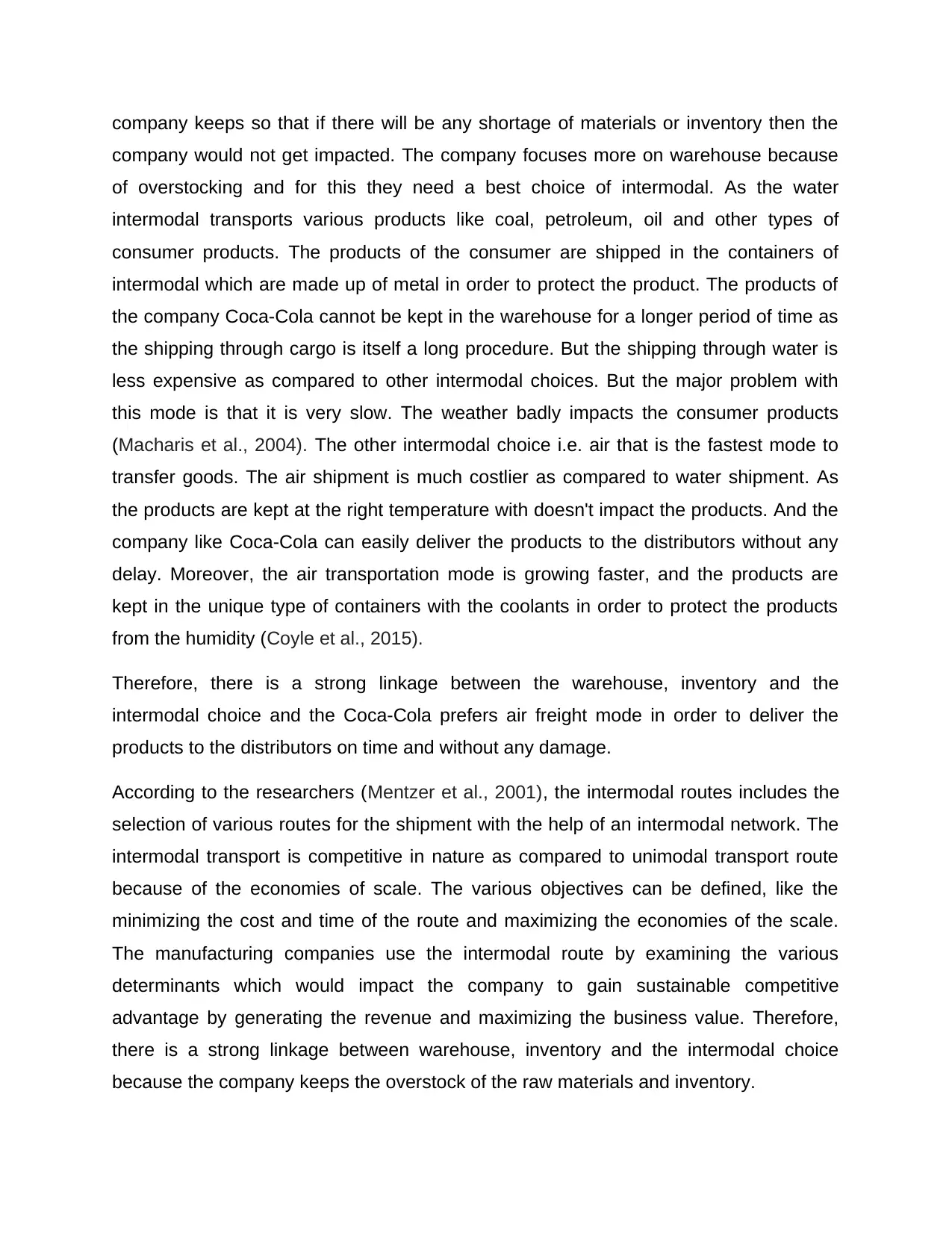
company keeps so that if there will be any shortage of materials or inventory then the
company would not get impacted. The company focuses more on warehouse because
of overstocking and for this they need a best choice of intermodal. As the water
intermodal transports various products like coal, petroleum, oil and other types of
consumer products. The products of the consumer are shipped in the containers of
intermodal which are made up of metal in order to protect the product. The products of
the company Coca-Cola cannot be kept in the warehouse for a longer period of time as
the shipping through cargo is itself a long procedure. But the shipping through water is
less expensive as compared to other intermodal choices. But the major problem with
this mode is that it is very slow. The weather badly impacts the consumer products
(Macharis et al., 2004). The other intermodal choice i.e. air that is the fastest mode to
transfer goods. The air shipment is much costlier as compared to water shipment. As
the products are kept at the right temperature with doesn't impact the products. And the
company like Coca-Cola can easily deliver the products to the distributors without any
delay. Moreover, the air transportation mode is growing faster, and the products are
kept in the unique type of containers with the coolants in order to protect the products
from the humidity (Coyle et al., 2015).
Therefore, there is a strong linkage between the warehouse, inventory and the
intermodal choice and the Coca-Cola prefers air freight mode in order to deliver the
products to the distributors on time and without any damage.
According to the researchers (Mentzer et al., 2001), the intermodal routes includes the
selection of various routes for the shipment with the help of an intermodal network. The
intermodal transport is competitive in nature as compared to unimodal transport route
because of the economies of scale. The various objectives can be defined, like the
minimizing the cost and time of the route and maximizing the economies of the scale.
The manufacturing companies use the intermodal route by examining the various
determinants which would impact the company to gain sustainable competitive
advantage by generating the revenue and maximizing the business value. Therefore,
there is a strong linkage between warehouse, inventory and the intermodal choice
because the company keeps the overstock of the raw materials and inventory.
company would not get impacted. The company focuses more on warehouse because
of overstocking and for this they need a best choice of intermodal. As the water
intermodal transports various products like coal, petroleum, oil and other types of
consumer products. The products of the consumer are shipped in the containers of
intermodal which are made up of metal in order to protect the product. The products of
the company Coca-Cola cannot be kept in the warehouse for a longer period of time as
the shipping through cargo is itself a long procedure. But the shipping through water is
less expensive as compared to other intermodal choices. But the major problem with
this mode is that it is very slow. The weather badly impacts the consumer products
(Macharis et al., 2004). The other intermodal choice i.e. air that is the fastest mode to
transfer goods. The air shipment is much costlier as compared to water shipment. As
the products are kept at the right temperature with doesn't impact the products. And the
company like Coca-Cola can easily deliver the products to the distributors without any
delay. Moreover, the air transportation mode is growing faster, and the products are
kept in the unique type of containers with the coolants in order to protect the products
from the humidity (Coyle et al., 2015).
Therefore, there is a strong linkage between the warehouse, inventory and the
intermodal choice and the Coca-Cola prefers air freight mode in order to deliver the
products to the distributors on time and without any damage.
According to the researchers (Mentzer et al., 2001), the intermodal routes includes the
selection of various routes for the shipment with the help of an intermodal network. The
intermodal transport is competitive in nature as compared to unimodal transport route
because of the economies of scale. The various objectives can be defined, like the
minimizing the cost and time of the route and maximizing the economies of the scale.
The manufacturing companies use the intermodal route by examining the various
determinants which would impact the company to gain sustainable competitive
advantage by generating the revenue and maximizing the business value. Therefore,
there is a strong linkage between warehouse, inventory and the intermodal choice
because the company keeps the overstock of the raw materials and inventory.

Paraphrase This Document
Need a fresh take? Get an instant paraphrase of this document with our AI Paraphraser
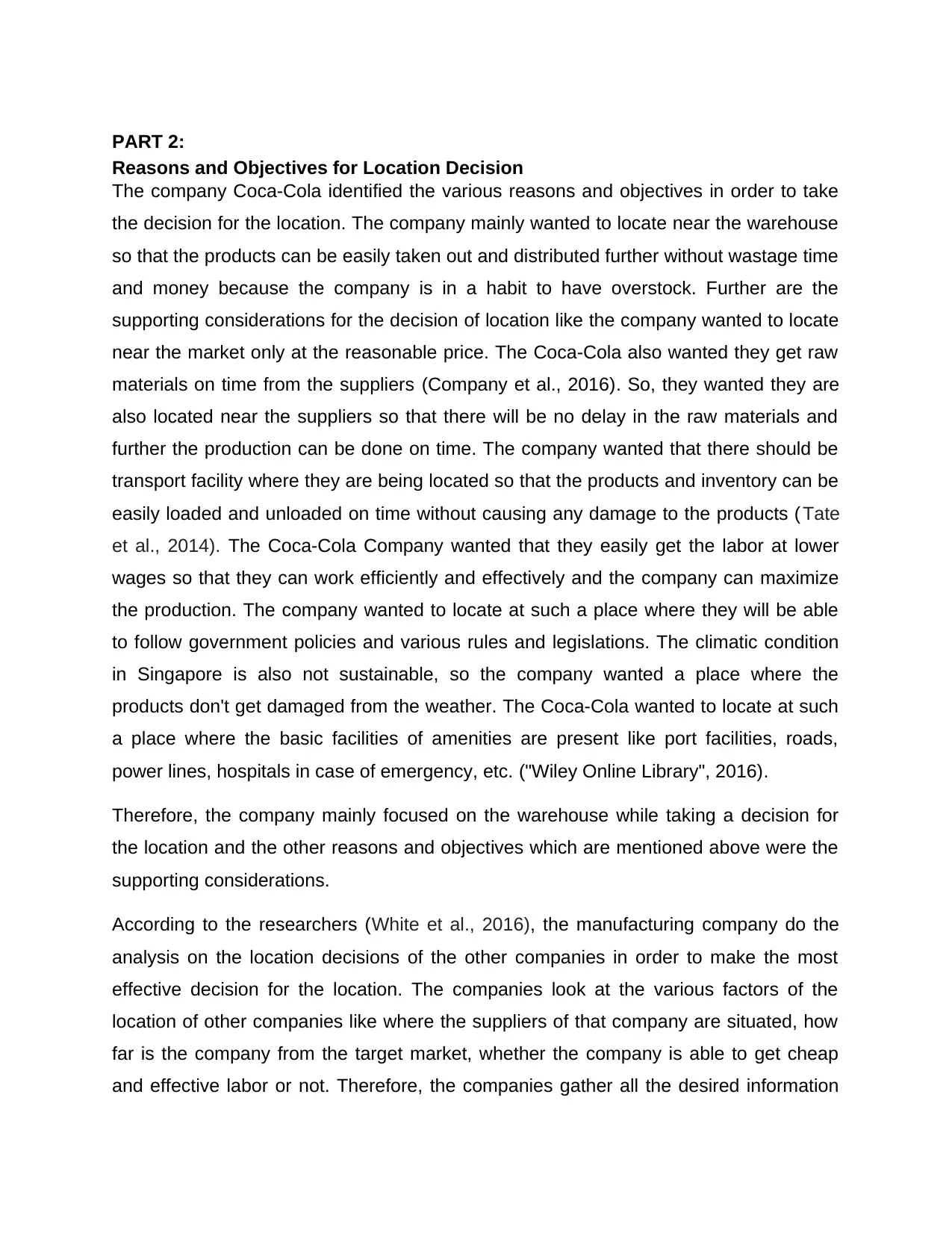
PART 2:
Reasons and Objectives for Location Decision
The company Coca-Cola identified the various reasons and objectives in order to take
the decision for the location. The company mainly wanted to locate near the warehouse
so that the products can be easily taken out and distributed further without wastage time
and money because the company is in a habit to have overstock. Further are the
supporting considerations for the decision of location like the company wanted to locate
near the market only at the reasonable price. The Coca-Cola also wanted they get raw
materials on time from the suppliers (Company et al., 2016). So, they wanted they are
also located near the suppliers so that there will be no delay in the raw materials and
further the production can be done on time. The company wanted that there should be
transport facility where they are being located so that the products and inventory can be
easily loaded and unloaded on time without causing any damage to the products ( Tate
et al., 2014). The Coca-Cola Company wanted that they easily get the labor at lower
wages so that they can work efficiently and effectively and the company can maximize
the production. The company wanted to locate at such a place where they will be able
to follow government policies and various rules and legislations. The climatic condition
in Singapore is also not sustainable, so the company wanted a place where the
products don't get damaged from the weather. The Coca-Cola wanted to locate at such
a place where the basic facilities of amenities are present like port facilities, roads,
power lines, hospitals in case of emergency, etc. ("Wiley Online Library", 2016).
Therefore, the company mainly focused on the warehouse while taking a decision for
the location and the other reasons and objectives which are mentioned above were the
supporting considerations.
According to the researchers (White et al., 2016), the manufacturing company do the
analysis on the location decisions of the other companies in order to make the most
effective decision for the location. The companies look at the various factors of the
location of other companies like where the suppliers of that company are situated, how
far is the company from the target market, whether the company is able to get cheap
and effective labor or not. Therefore, the companies gather all the desired information
Reasons and Objectives for Location Decision
The company Coca-Cola identified the various reasons and objectives in order to take
the decision for the location. The company mainly wanted to locate near the warehouse
so that the products can be easily taken out and distributed further without wastage time
and money because the company is in a habit to have overstock. Further are the
supporting considerations for the decision of location like the company wanted to locate
near the market only at the reasonable price. The Coca-Cola also wanted they get raw
materials on time from the suppliers (Company et al., 2016). So, they wanted they are
also located near the suppliers so that there will be no delay in the raw materials and
further the production can be done on time. The company wanted that there should be
transport facility where they are being located so that the products and inventory can be
easily loaded and unloaded on time without causing any damage to the products ( Tate
et al., 2014). The Coca-Cola Company wanted that they easily get the labor at lower
wages so that they can work efficiently and effectively and the company can maximize
the production. The company wanted to locate at such a place where they will be able
to follow government policies and various rules and legislations. The climatic condition
in Singapore is also not sustainable, so the company wanted a place where the
products don't get damaged from the weather. The Coca-Cola wanted to locate at such
a place where the basic facilities of amenities are present like port facilities, roads,
power lines, hospitals in case of emergency, etc. ("Wiley Online Library", 2016).
Therefore, the company mainly focused on the warehouse while taking a decision for
the location and the other reasons and objectives which are mentioned above were the
supporting considerations.
According to the researchers (White et al., 2016), the manufacturing company do the
analysis on the location decisions of the other companies in order to make the most
effective decision for the location. The companies look at the various factors of the
location of other companies like where the suppliers of that company are situated, how
far is the company from the target market, whether the company is able to get cheap
and effective labor or not. Therefore, the companies gather all the desired information
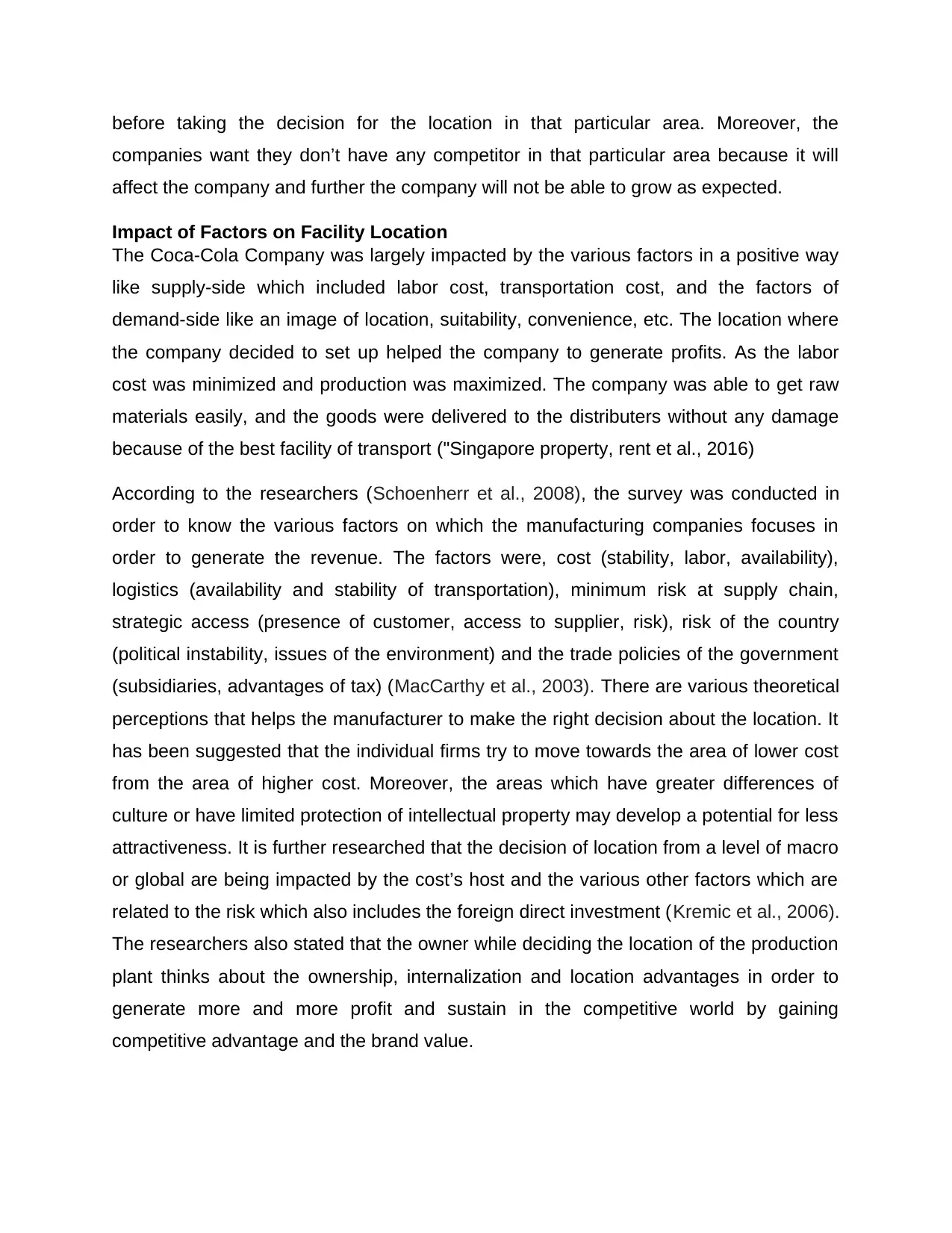
before taking the decision for the location in that particular area. Moreover, the
companies want they don’t have any competitor in that particular area because it will
affect the company and further the company will not be able to grow as expected.
Impact of Factors on Facility Location
The Coca-Cola Company was largely impacted by the various factors in a positive way
like supply-side which included labor cost, transportation cost, and the factors of
demand-side like an image of location, suitability, convenience, etc. The location where
the company decided to set up helped the company to generate profits. As the labor
cost was minimized and production was maximized. The company was able to get raw
materials easily, and the goods were delivered to the distributers without any damage
because of the best facility of transport ("Singapore property, rent et al., 2016)
According to the researchers (Schoenherr et al., 2008), the survey was conducted in
order to know the various factors on which the manufacturing companies focuses in
order to generate the revenue. The factors were, cost (stability, labor, availability),
logistics (availability and stability of transportation), minimum risk at supply chain,
strategic access (presence of customer, access to supplier, risk), risk of the country
(political instability, issues of the environment) and the trade policies of the government
(subsidiaries, advantages of tax) (MacCarthy et al., 2003). There are various theoretical
perceptions that helps the manufacturer to make the right decision about the location. It
has been suggested that the individual firms try to move towards the area of lower cost
from the area of higher cost. Moreover, the areas which have greater differences of
culture or have limited protection of intellectual property may develop a potential for less
attractiveness. It is further researched that the decision of location from a level of macro
or global are being impacted by the cost’s host and the various other factors which are
related to the risk which also includes the foreign direct investment (Kremic et al., 2006).
The researchers also stated that the owner while deciding the location of the production
plant thinks about the ownership, internalization and location advantages in order to
generate more and more profit and sustain in the competitive world by gaining
competitive advantage and the brand value.
companies want they don’t have any competitor in that particular area because it will
affect the company and further the company will not be able to grow as expected.
Impact of Factors on Facility Location
The Coca-Cola Company was largely impacted by the various factors in a positive way
like supply-side which included labor cost, transportation cost, and the factors of
demand-side like an image of location, suitability, convenience, etc. The location where
the company decided to set up helped the company to generate profits. As the labor
cost was minimized and production was maximized. The company was able to get raw
materials easily, and the goods were delivered to the distributers without any damage
because of the best facility of transport ("Singapore property, rent et al., 2016)
According to the researchers (Schoenherr et al., 2008), the survey was conducted in
order to know the various factors on which the manufacturing companies focuses in
order to generate the revenue. The factors were, cost (stability, labor, availability),
logistics (availability and stability of transportation), minimum risk at supply chain,
strategic access (presence of customer, access to supplier, risk), risk of the country
(political instability, issues of the environment) and the trade policies of the government
(subsidiaries, advantages of tax) (MacCarthy et al., 2003). There are various theoretical
perceptions that helps the manufacturer to make the right decision about the location. It
has been suggested that the individual firms try to move towards the area of lower cost
from the area of higher cost. Moreover, the areas which have greater differences of
culture or have limited protection of intellectual property may develop a potential for less
attractiveness. It is further researched that the decision of location from a level of macro
or global are being impacted by the cost’s host and the various other factors which are
related to the risk which also includes the foreign direct investment (Kremic et al., 2006).
The researchers also stated that the owner while deciding the location of the production
plant thinks about the ownership, internalization and location advantages in order to
generate more and more profit and sustain in the competitive world by gaining
competitive advantage and the brand value.
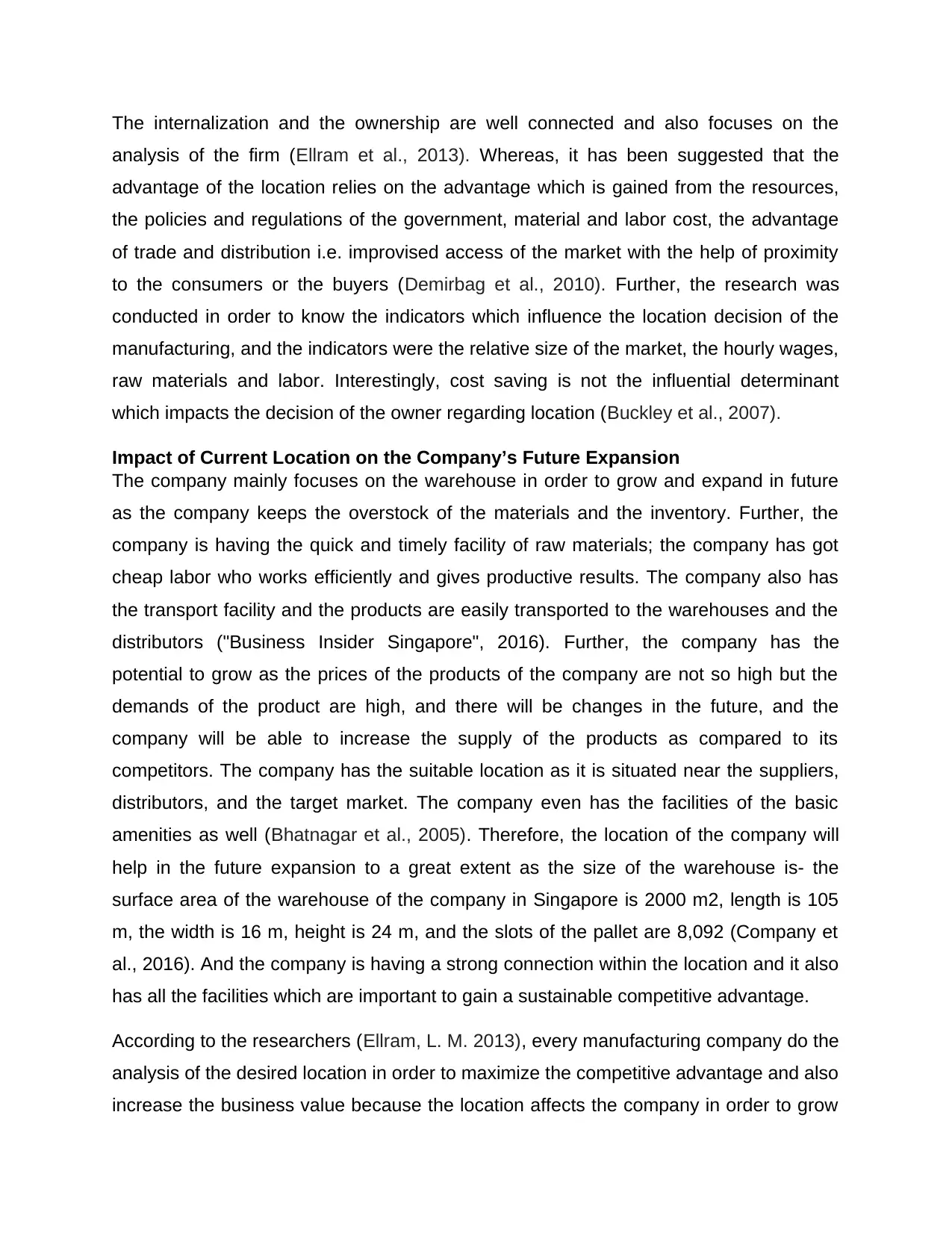
The internalization and the ownership are well connected and also focuses on the
analysis of the firm (Ellram et al., 2013). Whereas, it has been suggested that the
advantage of the location relies on the advantage which is gained from the resources,
the policies and regulations of the government, material and labor cost, the advantage
of trade and distribution i.e. improvised access of the market with the help of proximity
to the consumers or the buyers (Demirbag et al., 2010). Further, the research was
conducted in order to know the indicators which influence the location decision of the
manufacturing, and the indicators were the relative size of the market, the hourly wages,
raw materials and labor. Interestingly, cost saving is not the influential determinant
which impacts the decision of the owner regarding location (Buckley et al., 2007).
Impact of Current Location on the Company’s Future Expansion
The company mainly focuses on the warehouse in order to grow and expand in future
as the company keeps the overstock of the materials and the inventory. Further, the
company is having the quick and timely facility of raw materials; the company has got
cheap labor who works efficiently and gives productive results. The company also has
the transport facility and the products are easily transported to the warehouses and the
distributors ("Business Insider Singapore", 2016). Further, the company has the
potential to grow as the prices of the products of the company are not so high but the
demands of the product are high, and there will be changes in the future, and the
company will be able to increase the supply of the products as compared to its
competitors. The company has the suitable location as it is situated near the suppliers,
distributors, and the target market. The company even has the facilities of the basic
amenities as well (Bhatnagar et al., 2005). Therefore, the location of the company will
help in the future expansion to a great extent as the size of the warehouse is- the
surface area of the warehouse of the company in Singapore is 2000 m2, length is 105
m, the width is 16 m, height is 24 m, and the slots of the pallet are 8,092 (Company et
al., 2016). And the company is having a strong connection within the location and it also
has all the facilities which are important to gain a sustainable competitive advantage.
According to the researchers (Ellram, L. M. 2013), every manufacturing company do the
analysis of the desired location in order to maximize the competitive advantage and also
increase the business value because the location affects the company in order to grow
analysis of the firm (Ellram et al., 2013). Whereas, it has been suggested that the
advantage of the location relies on the advantage which is gained from the resources,
the policies and regulations of the government, material and labor cost, the advantage
of trade and distribution i.e. improvised access of the market with the help of proximity
to the consumers or the buyers (Demirbag et al., 2010). Further, the research was
conducted in order to know the indicators which influence the location decision of the
manufacturing, and the indicators were the relative size of the market, the hourly wages,
raw materials and labor. Interestingly, cost saving is not the influential determinant
which impacts the decision of the owner regarding location (Buckley et al., 2007).
Impact of Current Location on the Company’s Future Expansion
The company mainly focuses on the warehouse in order to grow and expand in future
as the company keeps the overstock of the materials and the inventory. Further, the
company is having the quick and timely facility of raw materials; the company has got
cheap labor who works efficiently and gives productive results. The company also has
the transport facility and the products are easily transported to the warehouses and the
distributors ("Business Insider Singapore", 2016). Further, the company has the
potential to grow as the prices of the products of the company are not so high but the
demands of the product are high, and there will be changes in the future, and the
company will be able to increase the supply of the products as compared to its
competitors. The company has the suitable location as it is situated near the suppliers,
distributors, and the target market. The company even has the facilities of the basic
amenities as well (Bhatnagar et al., 2005). Therefore, the location of the company will
help in the future expansion to a great extent as the size of the warehouse is- the
surface area of the warehouse of the company in Singapore is 2000 m2, length is 105
m, the width is 16 m, height is 24 m, and the slots of the pallet are 8,092 (Company et
al., 2016). And the company is having a strong connection within the location and it also
has all the facilities which are important to gain a sustainable competitive advantage.
According to the researchers (Ellram, L. M. 2013), every manufacturing company do the
analysis of the desired location in order to maximize the competitive advantage and also
increase the business value because the location affects the company in order to grow
Secure Best Marks with AI Grader
Need help grading? Try our AI Grader for instant feedback on your assignments.
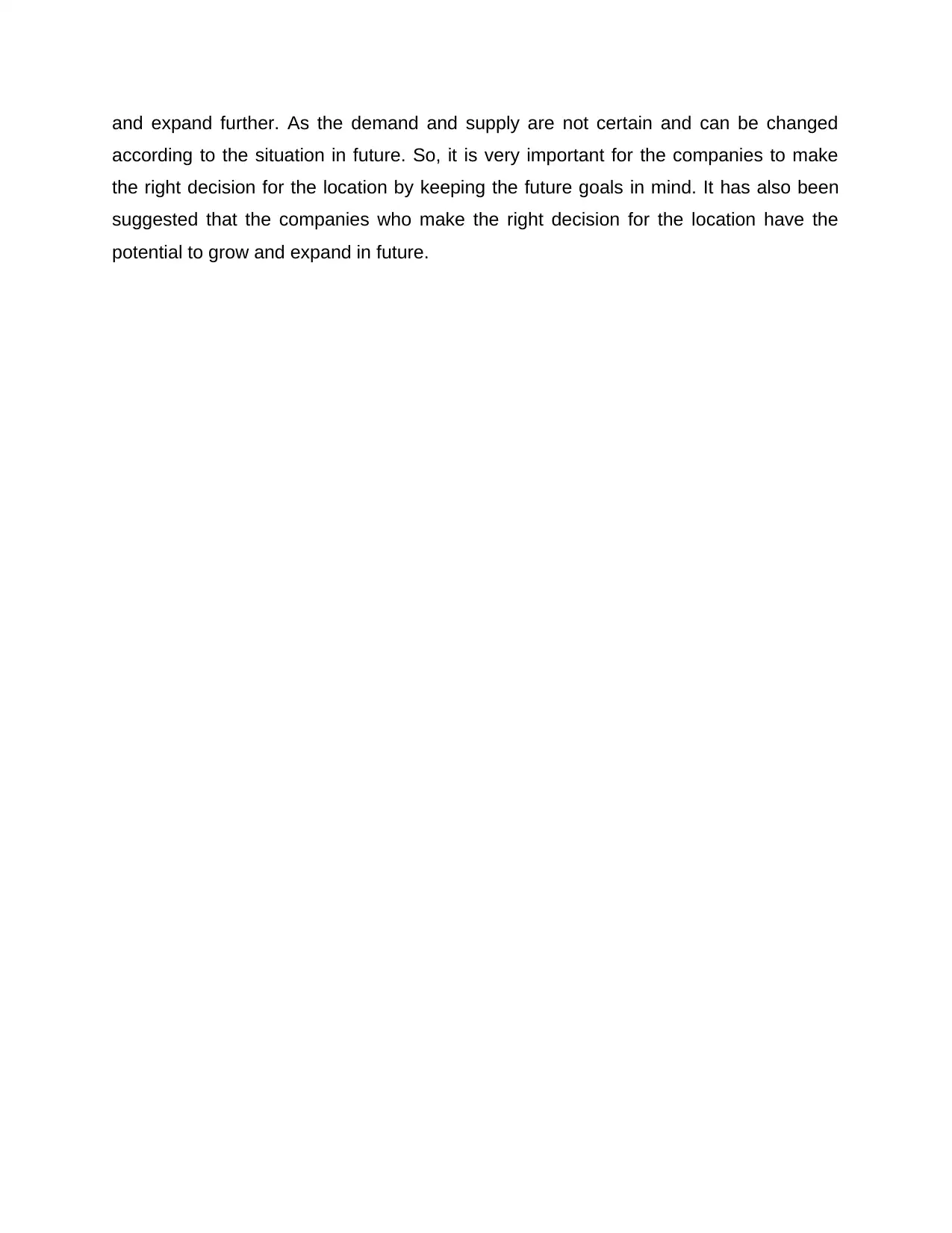
and expand further. As the demand and supply are not certain and can be changed
according to the situation in future. So, it is very important for the companies to make
the right decision for the location by keeping the future goals in mind. It has also been
suggested that the companies who make the right decision for the location have the
potential to grow and expand in future.
according to the situation in future. So, it is very important for the companies to make
the right decision for the location by keeping the future goals in mind. It has also been
suggested that the companies who make the right decision for the location have the
potential to grow and expand in future.
1 out of 11
Related Documents
![[object Object]](/_next/image/?url=%2F_next%2Fstatic%2Fmedia%2Flogo.6d15ce61.png&w=640&q=75)
Your All-in-One AI-Powered Toolkit for Academic Success.
+13062052269
info@desklib.com
Available 24*7 on WhatsApp / Email
Unlock your academic potential
© 2024 | Zucol Services PVT LTD | All rights reserved.