operation and project management Assignment PDF
VerifiedAdded on 2021/05/10
|9
|2430
|30
AI Summary
Contribute Materials
Your contribution can guide someone’s learning journey. Share your
documents today.
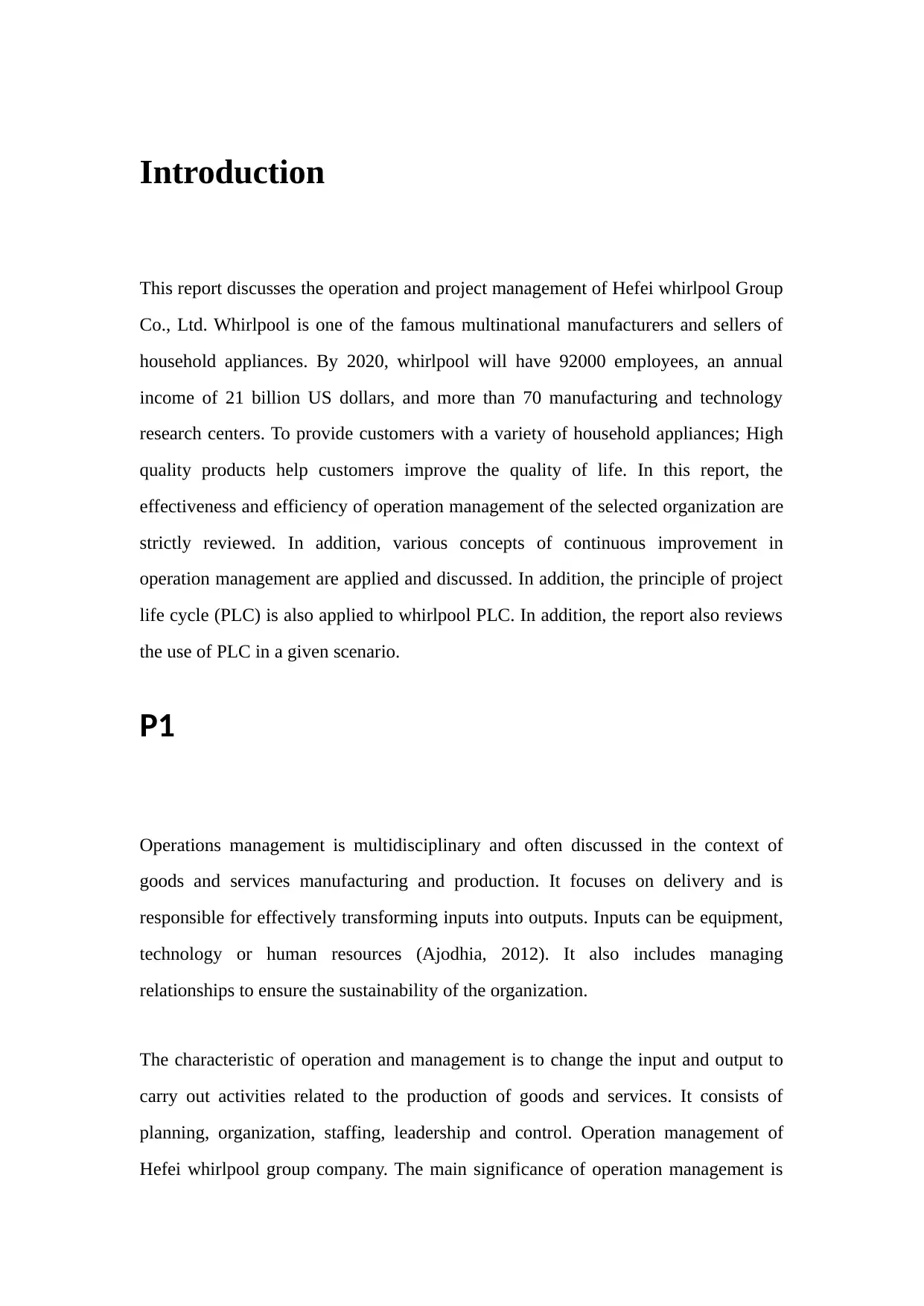
Introduction
This report discusses the operation and project management of Hefei whirlpool Group
Co., Ltd. Whirlpool is one of the famous multinational manufacturers and sellers of
household appliances. By 2020, whirlpool will have 92000 employees, an annual
income of 21 billion US dollars, and more than 70 manufacturing and technology
research centers. To provide customers with a variety of household appliances; High
quality products help customers improve the quality of life. In this report, the
effectiveness and efficiency of operation management of the selected organization are
strictly reviewed. In addition, various concepts of continuous improvement in
operation management are applied and discussed. In addition, the principle of project
life cycle (PLC) is also applied to whirlpool PLC. In addition, the report also reviews
the use of PLC in a given scenario.
P1
Operations management is multidisciplinary and often discussed in the context of
goods and services manufacturing and production. It focuses on delivery and is
responsible for effectively transforming inputs into outputs. Inputs can be equipment,
technology or human resources (Ajodhia, 2012). It also includes managing
relationships to ensure the sustainability of the organization.
The characteristic of operation and management is to change the input and output to
carry out activities related to the production of goods and services. It consists of
planning, organization, staffing, leadership and control. Operation management of
Hefei whirlpool group company. The main significance of operation management is
This report discusses the operation and project management of Hefei whirlpool Group
Co., Ltd. Whirlpool is one of the famous multinational manufacturers and sellers of
household appliances. By 2020, whirlpool will have 92000 employees, an annual
income of 21 billion US dollars, and more than 70 manufacturing and technology
research centers. To provide customers with a variety of household appliances; High
quality products help customers improve the quality of life. In this report, the
effectiveness and efficiency of operation management of the selected organization are
strictly reviewed. In addition, various concepts of continuous improvement in
operation management are applied and discussed. In addition, the principle of project
life cycle (PLC) is also applied to whirlpool PLC. In addition, the report also reviews
the use of PLC in a given scenario.
P1
Operations management is multidisciplinary and often discussed in the context of
goods and services manufacturing and production. It focuses on delivery and is
responsible for effectively transforming inputs into outputs. Inputs can be equipment,
technology or human resources (Ajodhia, 2012). It also includes managing
relationships to ensure the sustainability of the organization.
The characteristic of operation and management is to change the input and output to
carry out activities related to the production of goods and services. It consists of
planning, organization, staffing, leadership and control. Operation management of
Hefei whirlpool group company. The main significance of operation management is
Secure Best Marks with AI Grader
Need help grading? Try our AI Grader for instant feedback on your assignments.
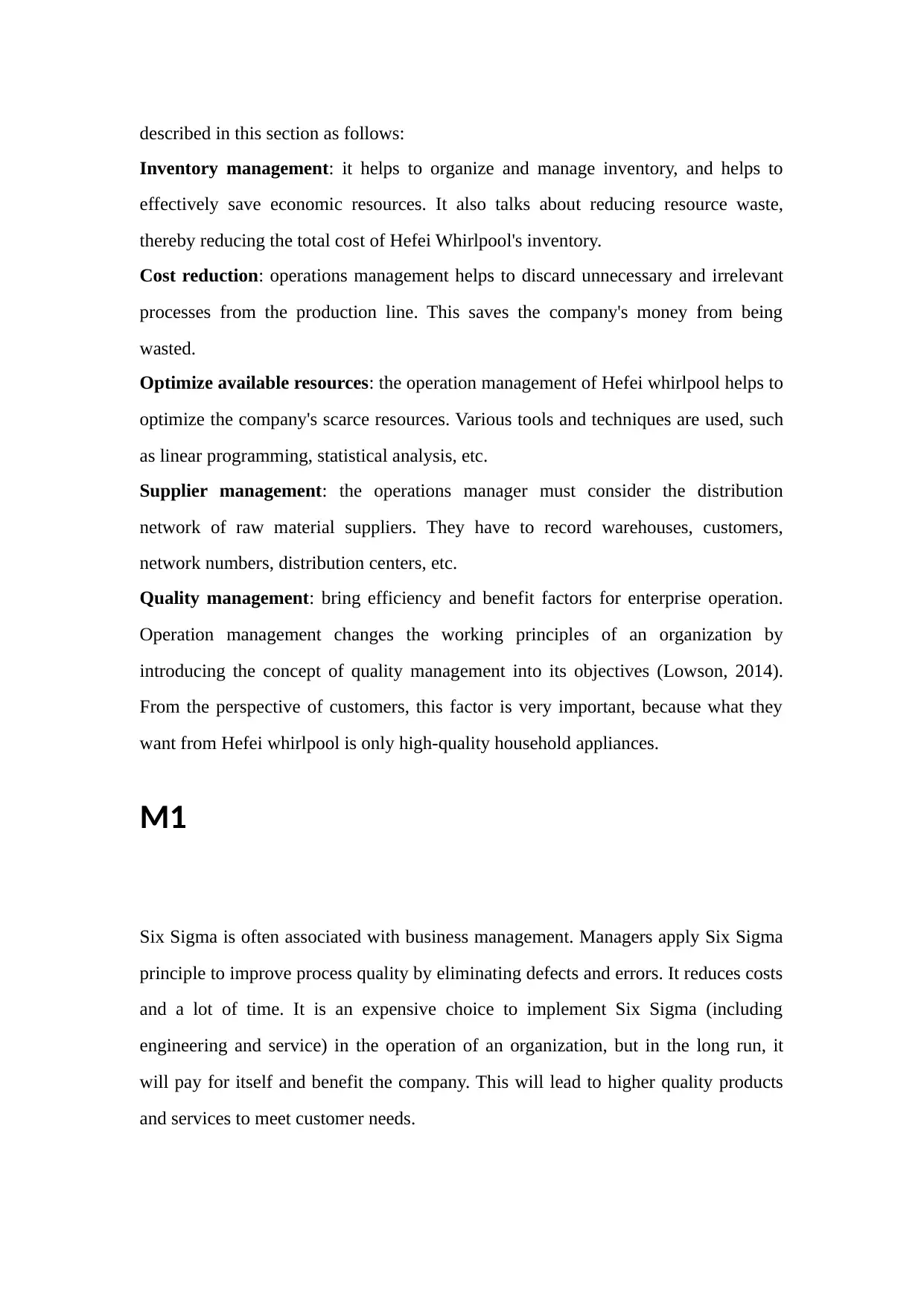
described in this section as follows:
Inventory management: it helps to organize and manage inventory, and helps to
effectively save economic resources. It also talks about reducing resource waste,
thereby reducing the total cost of Hefei Whirlpool's inventory.
Cost reduction: operations management helps to discard unnecessary and irrelevant
processes from the production line. This saves the company's money from being
wasted.
Optimize available resources: the operation management of Hefei whirlpool helps to
optimize the company's scarce resources. Various tools and techniques are used, such
as linear programming, statistical analysis, etc.
Supplier management: the operations manager must consider the distribution
network of raw material suppliers. They have to record warehouses, customers,
network numbers, distribution centers, etc.
Quality management: bring efficiency and benefit factors for enterprise operation.
Operation management changes the working principles of an organization by
introducing the concept of quality management into its objectives (Lowson, 2014).
From the perspective of customers, this factor is very important, because what they
want from Hefei whirlpool is only high-quality household appliances.
M1
Six Sigma is often associated with business management. Managers apply Six Sigma
principle to improve process quality by eliminating defects and errors. It reduces costs
and a lot of time. It is an expensive choice to implement Six Sigma (including
engineering and service) in the operation of an organization, but in the long run, it
will pay for itself and benefit the company. This will lead to higher quality products
and services to meet customer needs.
Inventory management: it helps to organize and manage inventory, and helps to
effectively save economic resources. It also talks about reducing resource waste,
thereby reducing the total cost of Hefei Whirlpool's inventory.
Cost reduction: operations management helps to discard unnecessary and irrelevant
processes from the production line. This saves the company's money from being
wasted.
Optimize available resources: the operation management of Hefei whirlpool helps to
optimize the company's scarce resources. Various tools and techniques are used, such
as linear programming, statistical analysis, etc.
Supplier management: the operations manager must consider the distribution
network of raw material suppliers. They have to record warehouses, customers,
network numbers, distribution centers, etc.
Quality management: bring efficiency and benefit factors for enterprise operation.
Operation management changes the working principles of an organization by
introducing the concept of quality management into its objectives (Lowson, 2014).
From the perspective of customers, this factor is very important, because what they
want from Hefei whirlpool is only high-quality household appliances.
M1
Six Sigma is often associated with business management. Managers apply Six Sigma
principle to improve process quality by eliminating defects and errors. It reduces costs
and a lot of time. It is an expensive choice to implement Six Sigma (including
engineering and service) in the operation of an organization, but in the long run, it
will pay for itself and benefit the company. This will lead to higher quality products
and services to meet customer needs.
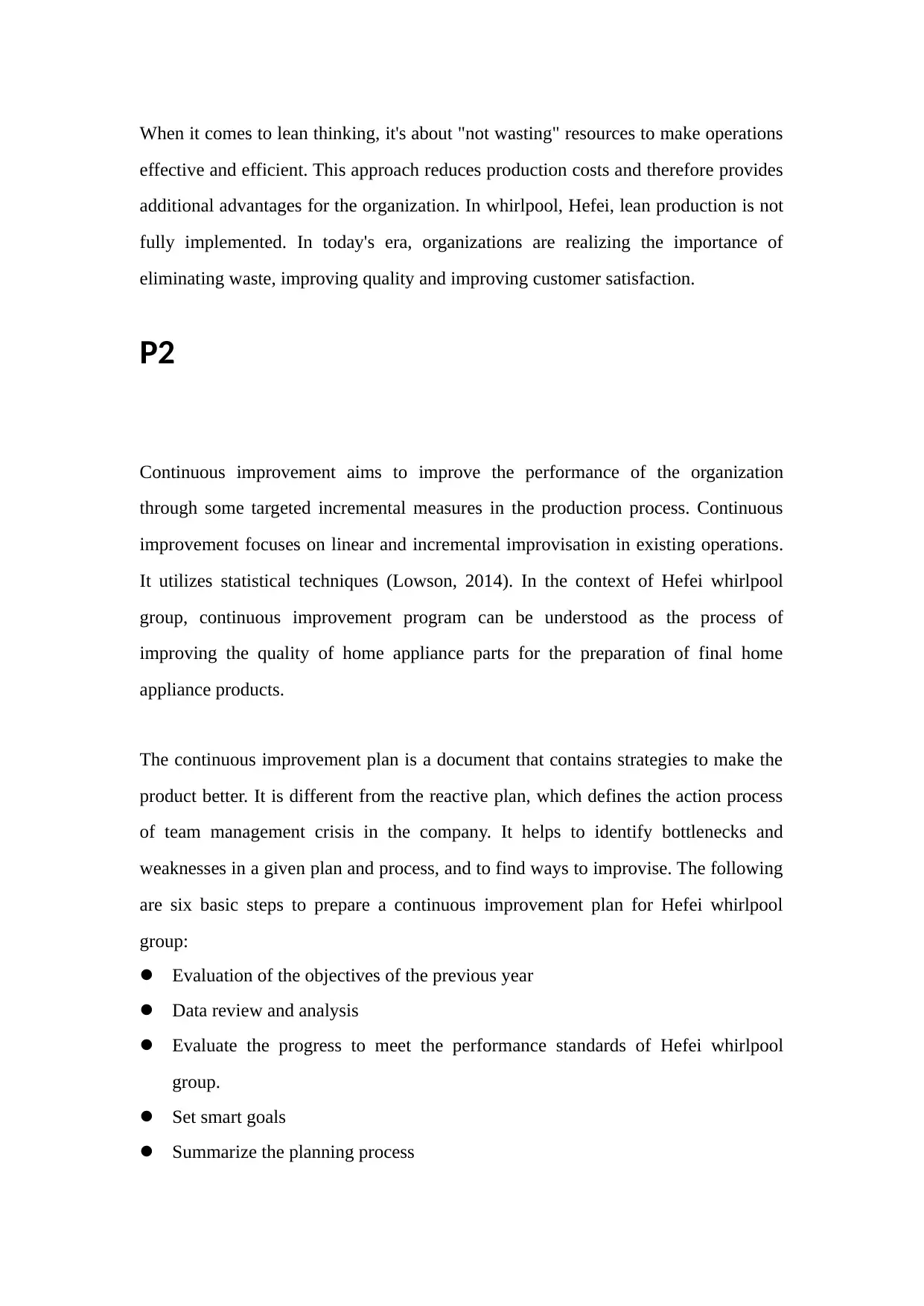
When it comes to lean thinking, it's about "not wasting" resources to make operations
effective and efficient. This approach reduces production costs and therefore provides
additional advantages for the organization. In whirlpool, Hefei, lean production is not
fully implemented. In today's era, organizations are realizing the importance of
eliminating waste, improving quality and improving customer satisfaction.
P2
Continuous improvement aims to improve the performance of the organization
through some targeted incremental measures in the production process. Continuous
improvement focuses on linear and incremental improvisation in existing operations.
It utilizes statistical techniques (Lowson, 2014). In the context of Hefei whirlpool
group, continuous improvement program can be understood as the process of
improving the quality of home appliance parts for the preparation of final home
appliance products.
The continuous improvement plan is a document that contains strategies to make the
product better. It is different from the reactive plan, which defines the action process
of team management crisis in the company. It helps to identify bottlenecks and
weaknesses in a given plan and process, and to find ways to improvise. The following
are six basic steps to prepare a continuous improvement plan for Hefei whirlpool
group:
Evaluation of the objectives of the previous year
Data review and analysis
Evaluate the progress to meet the performance standards of Hefei whirlpool
group.
Set smart goals
Summarize the planning process
effective and efficient. This approach reduces production costs and therefore provides
additional advantages for the organization. In whirlpool, Hefei, lean production is not
fully implemented. In today's era, organizations are realizing the importance of
eliminating waste, improving quality and improving customer satisfaction.
P2
Continuous improvement aims to improve the performance of the organization
through some targeted incremental measures in the production process. Continuous
improvement focuses on linear and incremental improvisation in existing operations.
It utilizes statistical techniques (Lowson, 2014). In the context of Hefei whirlpool
group, continuous improvement program can be understood as the process of
improving the quality of home appliance parts for the preparation of final home
appliance products.
The continuous improvement plan is a document that contains strategies to make the
product better. It is different from the reactive plan, which defines the action process
of team management crisis in the company. It helps to identify bottlenecks and
weaknesses in a given plan and process, and to find ways to improvise. The following
are six basic steps to prepare a continuous improvement plan for Hefei whirlpool
group:
Evaluation of the objectives of the previous year
Data review and analysis
Evaluate the progress to meet the performance standards of Hefei whirlpool
group.
Set smart goals
Summarize the planning process
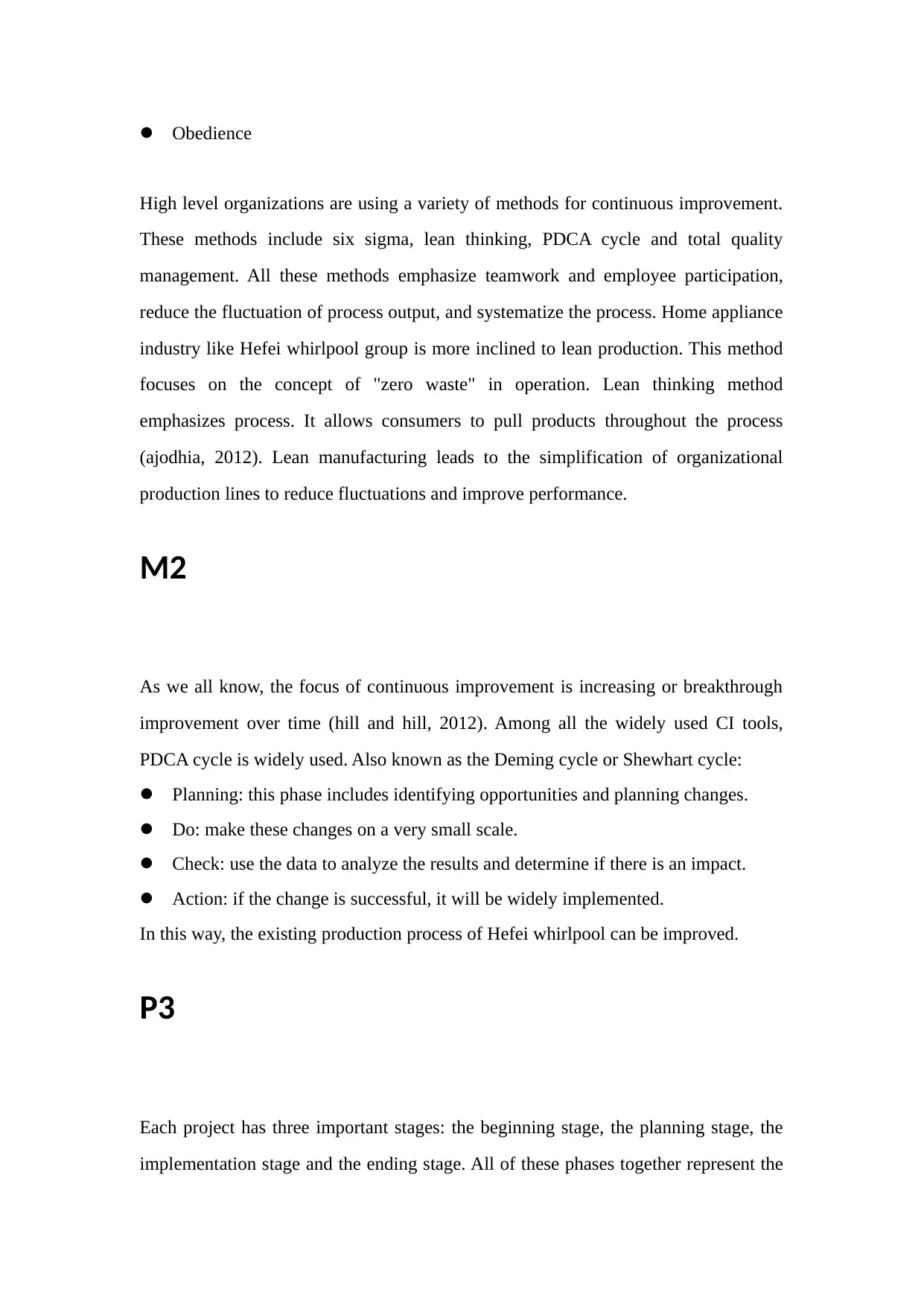
Obedience
High level organizations are using a variety of methods for continuous improvement.
These methods include six sigma, lean thinking, PDCA cycle and total quality
management. All these methods emphasize teamwork and employee participation,
reduce the fluctuation of process output, and systematize the process. Home appliance
industry like Hefei whirlpool group is more inclined to lean production. This method
focuses on the concept of "zero waste" in operation. Lean thinking method
emphasizes process. It allows consumers to pull products throughout the process
(ajodhia, 2012). Lean manufacturing leads to the simplification of organizational
production lines to reduce fluctuations and improve performance.
M2
As we all know, the focus of continuous improvement is increasing or breakthrough
improvement over time (hill and hill, 2012). Among all the widely used CI tools,
PDCA cycle is widely used. Also known as the Deming cycle or Shewhart cycle:
Planning: this phase includes identifying opportunities and planning changes.
Do: make these changes on a very small scale.
Check: use the data to analyze the results and determine if there is an impact.
Action: if the change is successful, it will be widely implemented.
In this way, the existing production process of Hefei whirlpool can be improved.
P3
Each project has three important stages: the beginning stage, the planning stage, the
implementation stage and the ending stage. All of these phases together represent the
High level organizations are using a variety of methods for continuous improvement.
These methods include six sigma, lean thinking, PDCA cycle and total quality
management. All these methods emphasize teamwork and employee participation,
reduce the fluctuation of process output, and systematize the process. Home appliance
industry like Hefei whirlpool group is more inclined to lean production. This method
focuses on the concept of "zero waste" in operation. Lean thinking method
emphasizes process. It allows consumers to pull products throughout the process
(ajodhia, 2012). Lean manufacturing leads to the simplification of organizational
production lines to reduce fluctuations and improve performance.
M2
As we all know, the focus of continuous improvement is increasing or breakthrough
improvement over time (hill and hill, 2012). Among all the widely used CI tools,
PDCA cycle is widely used. Also known as the Deming cycle or Shewhart cycle:
Planning: this phase includes identifying opportunities and planning changes.
Do: make these changes on a very small scale.
Check: use the data to analyze the results and determine if there is an impact.
Action: if the change is successful, it will be widely implemented.
In this way, the existing production process of Hefei whirlpool can be improved.
P3
Each project has three important stages: the beginning stage, the planning stage, the
implementation stage and the ending stage. All of these phases together represent the
Secure Best Marks with AI Grader
Need help grading? Try our AI Grader for instant feedback on your assignments.
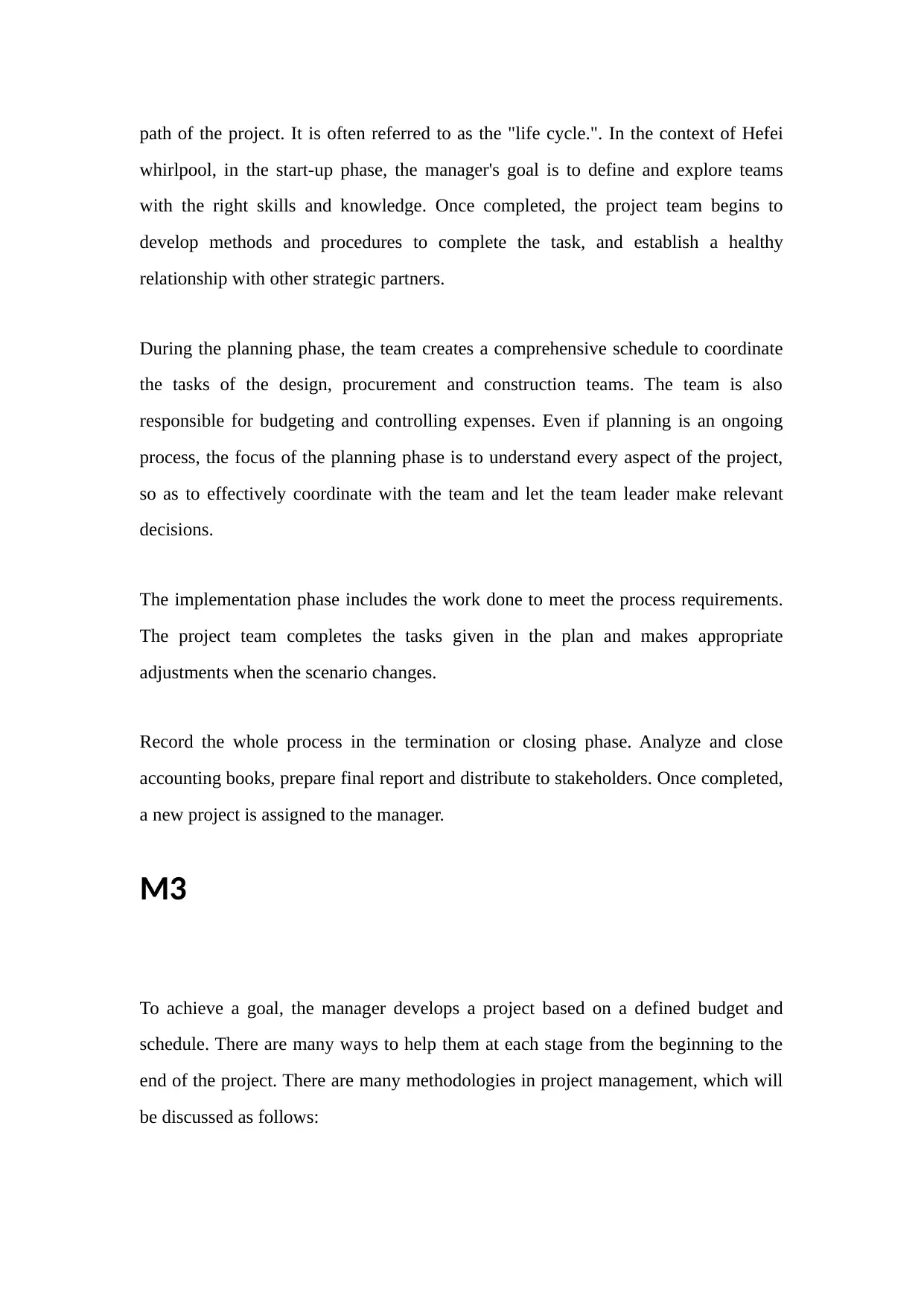
path of the project. It is often referred to as the "life cycle.". In the context of Hefei
whirlpool, in the start-up phase, the manager's goal is to define and explore teams
with the right skills and knowledge. Once completed, the project team begins to
develop methods and procedures to complete the task, and establish a healthy
relationship with other strategic partners.
During the planning phase, the team creates a comprehensive schedule to coordinate
the tasks of the design, procurement and construction teams. The team is also
responsible for budgeting and controlling expenses. Even if planning is an ongoing
process, the focus of the planning phase is to understand every aspect of the project,
so as to effectively coordinate with the team and let the team leader make relevant
decisions.
The implementation phase includes the work done to meet the process requirements.
The project team completes the tasks given in the plan and makes appropriate
adjustments when the scenario changes.
Record the whole process in the termination or closing phase. Analyze and close
accounting books, prepare final report and distribute to stakeholders. Once completed,
a new project is assigned to the manager.
M3
To achieve a goal, the manager develops a project based on a defined budget and
schedule. There are many ways to help them at each stage from the beginning to the
end of the project. There are many methodologies in project management, which will
be discussed as follows:
whirlpool, in the start-up phase, the manager's goal is to define and explore teams
with the right skills and knowledge. Once completed, the project team begins to
develop methods and procedures to complete the task, and establish a healthy
relationship with other strategic partners.
During the planning phase, the team creates a comprehensive schedule to coordinate
the tasks of the design, procurement and construction teams. The team is also
responsible for budgeting and controlling expenses. Even if planning is an ongoing
process, the focus of the planning phase is to understand every aspect of the project,
so as to effectively coordinate with the team and let the team leader make relevant
decisions.
The implementation phase includes the work done to meet the process requirements.
The project team completes the tasks given in the plan and makes appropriate
adjustments when the scenario changes.
Record the whole process in the termination or closing phase. Analyze and close
accounting books, prepare final report and distribute to stakeholders. Once completed,
a new project is assigned to the manager.
M3
To achieve a goal, the manager develops a project based on a defined budget and
schedule. There are many ways to help them at each stage from the beginning to the
end of the project. There are many methodologies in project management, which will
be discussed as follows:
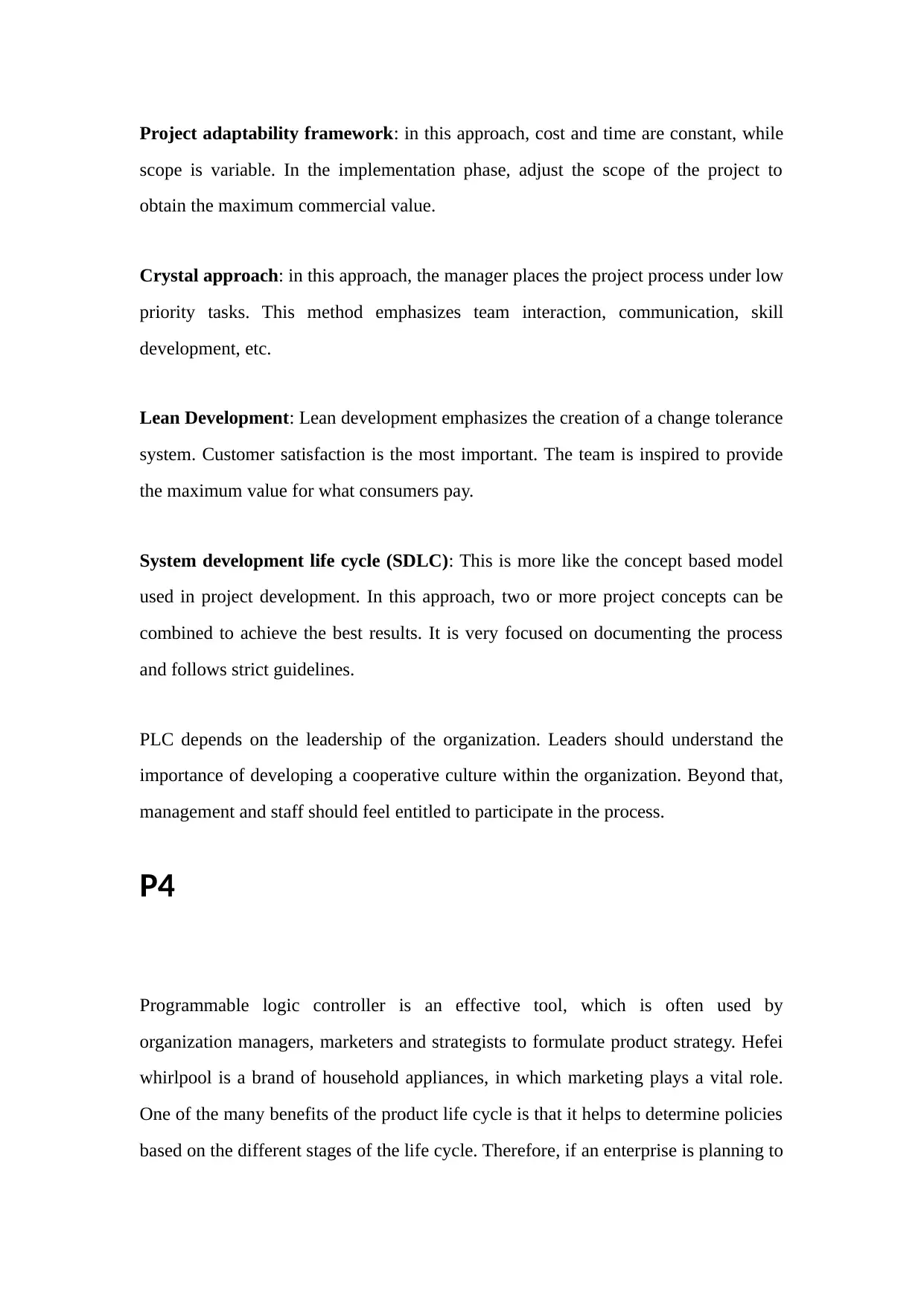
Project adaptability framework: in this approach, cost and time are constant, while
scope is variable. In the implementation phase, adjust the scope of the project to
obtain the maximum commercial value.
Crystal approach: in this approach, the manager places the project process under low
priority tasks. This method emphasizes team interaction, communication, skill
development, etc.
Lean Development: Lean development emphasizes the creation of a change tolerance
system. Customer satisfaction is the most important. The team is inspired to provide
the maximum value for what consumers pay.
System development life cycle (SDLC): This is more like the concept based model
used in project development. In this approach, two or more project concepts can be
combined to achieve the best results. It is very focused on documenting the process
and follows strict guidelines.
PLC depends on the leadership of the organization. Leaders should understand the
importance of developing a cooperative culture within the organization. Beyond that,
management and staff should feel entitled to participate in the process.
P4
Programmable logic controller is an effective tool, which is often used by
organization managers, marketers and strategists to formulate product strategy. Hefei
whirlpool is a brand of household appliances, in which marketing plays a vital role.
One of the many benefits of the product life cycle is that it helps to determine policies
based on the different stages of the life cycle. Therefore, if an enterprise is planning to
scope is variable. In the implementation phase, adjust the scope of the project to
obtain the maximum commercial value.
Crystal approach: in this approach, the manager places the project process under low
priority tasks. This method emphasizes team interaction, communication, skill
development, etc.
Lean Development: Lean development emphasizes the creation of a change tolerance
system. Customer satisfaction is the most important. The team is inspired to provide
the maximum value for what consumers pay.
System development life cycle (SDLC): This is more like the concept based model
used in project development. In this approach, two or more project concepts can be
combined to achieve the best results. It is very focused on documenting the process
and follows strict guidelines.
PLC depends on the leadership of the organization. Leaders should understand the
importance of developing a cooperative culture within the organization. Beyond that,
management and staff should feel entitled to participate in the process.
P4
Programmable logic controller is an effective tool, which is often used by
organization managers, marketers and strategists to formulate product strategy. Hefei
whirlpool is a brand of household appliances, in which marketing plays a vital role.
One of the many benefits of the product life cycle is that it helps to determine policies
based on the different stages of the life cycle. Therefore, if an enterprise is planning to
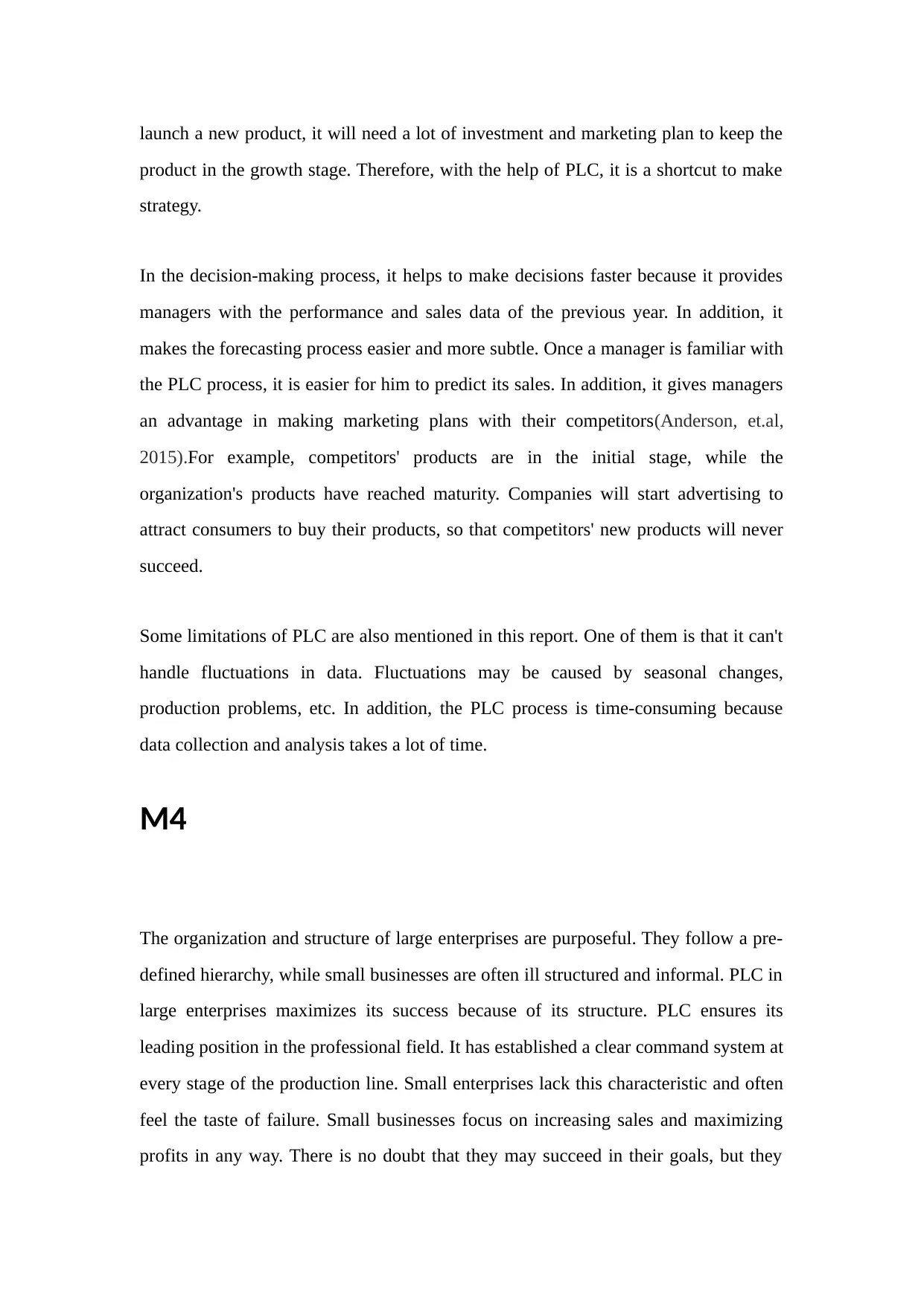
launch a new product, it will need a lot of investment and marketing plan to keep the
product in the growth stage. Therefore, with the help of PLC, it is a shortcut to make
strategy.
In the decision-making process, it helps to make decisions faster because it provides
managers with the performance and sales data of the previous year. In addition, it
makes the forecasting process easier and more subtle. Once a manager is familiar with
the PLC process, it is easier for him to predict its sales. In addition, it gives managers
an advantage in making marketing plans with their competitors(Anderson, et.al,
2015).For example, competitors' products are in the initial stage, while the
organization's products have reached maturity. Companies will start advertising to
attract consumers to buy their products, so that competitors' new products will never
succeed.
Some limitations of PLC are also mentioned in this report. One of them is that it can't
handle fluctuations in data. Fluctuations may be caused by seasonal changes,
production problems, etc. In addition, the PLC process is time-consuming because
data collection and analysis takes a lot of time.
M4
The organization and structure of large enterprises are purposeful. They follow a pre-
defined hierarchy, while small businesses are often ill structured and informal. PLC in
large enterprises maximizes its success because of its structure. PLC ensures its
leading position in the professional field. It has established a clear command system at
every stage of the production line. Small enterprises lack this characteristic and often
feel the taste of failure. Small businesses focus on increasing sales and maximizing
profits in any way. There is no doubt that they may succeed in their goals, but they
product in the growth stage. Therefore, with the help of PLC, it is a shortcut to make
strategy.
In the decision-making process, it helps to make decisions faster because it provides
managers with the performance and sales data of the previous year. In addition, it
makes the forecasting process easier and more subtle. Once a manager is familiar with
the PLC process, it is easier for him to predict its sales. In addition, it gives managers
an advantage in making marketing plans with their competitors(Anderson, et.al,
2015).For example, competitors' products are in the initial stage, while the
organization's products have reached maturity. Companies will start advertising to
attract consumers to buy their products, so that competitors' new products will never
succeed.
Some limitations of PLC are also mentioned in this report. One of them is that it can't
handle fluctuations in data. Fluctuations may be caused by seasonal changes,
production problems, etc. In addition, the PLC process is time-consuming because
data collection and analysis takes a lot of time.
M4
The organization and structure of large enterprises are purposeful. They follow a pre-
defined hierarchy, while small businesses are often ill structured and informal. PLC in
large enterprises maximizes its success because of its structure. PLC ensures its
leading position in the professional field. It has established a clear command system at
every stage of the production line. Small enterprises lack this characteristic and often
feel the taste of failure. Small businesses focus on increasing sales and maximizing
profits in any way. There is no doubt that they may succeed in their goals, but they
Paraphrase This Document
Need a fresh take? Get an instant paraphrase of this document with our AI Paraphraser
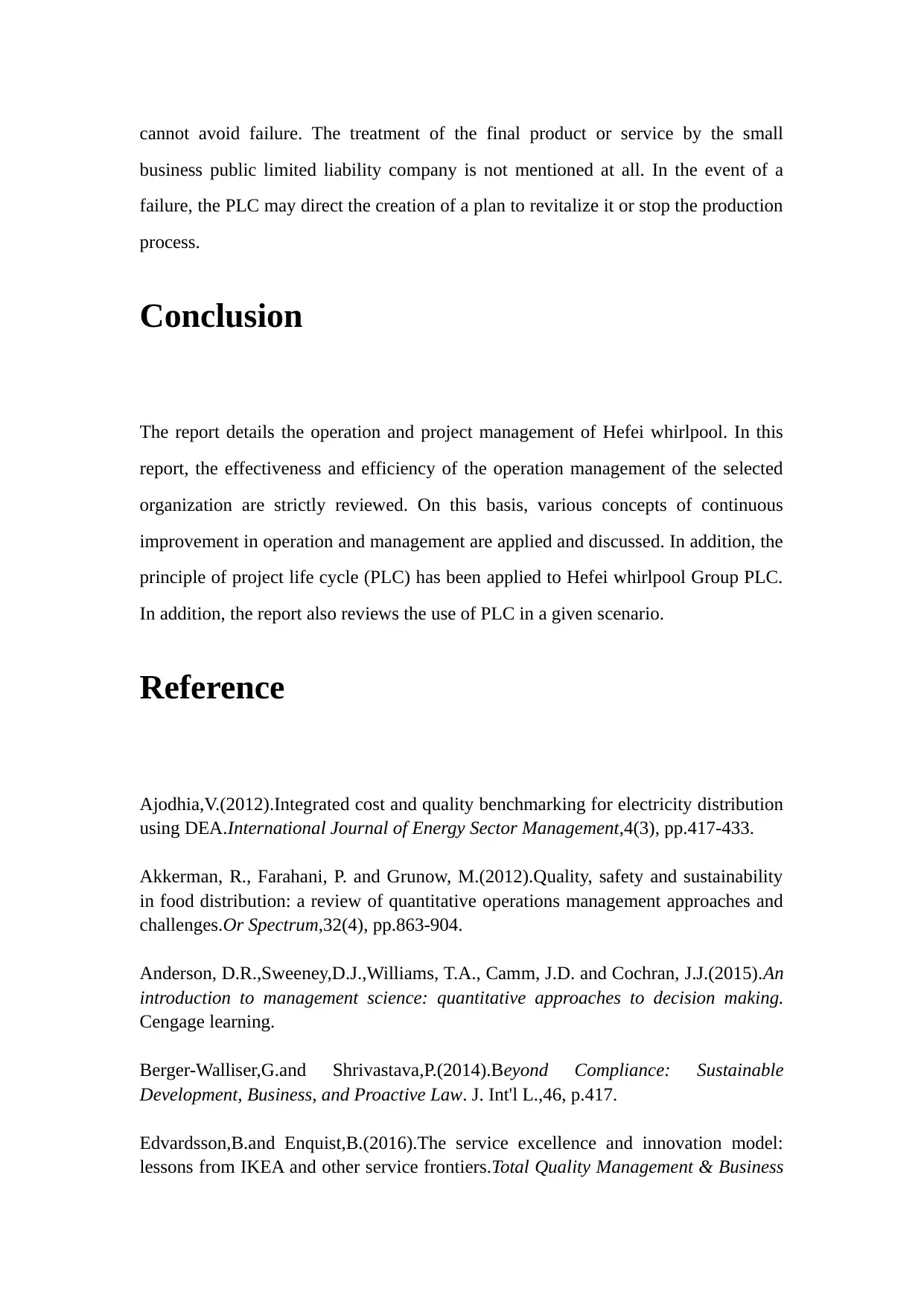
cannot avoid failure. The treatment of the final product or service by the small
business public limited liability company is not mentioned at all. In the event of a
failure, the PLC may direct the creation of a plan to revitalize it or stop the production
process.
Conclusion
The report details the operation and project management of Hefei whirlpool. In this
report, the effectiveness and efficiency of the operation management of the selected
organization are strictly reviewed. On this basis, various concepts of continuous
improvement in operation and management are applied and discussed. In addition, the
principle of project life cycle (PLC) has been applied to Hefei whirlpool Group PLC.
In addition, the report also reviews the use of PLC in a given scenario.
Reference
Ajodhia,V.(2012).Integrated cost and quality benchmarking for electricity distribution
using DEA.International Journal of Energy Sector Management,4(3), pp.417-433.
Akkerman, R., Farahani, P. and Grunow, M.(2012).Quality, safety and sustainability
in food distribution: a review of quantitative operations management approaches and
challenges.Or Spectrum,32(4), pp.863-904.
Anderson, D.R.,Sweeney,D.J.,Williams, T.A., Camm, J.D. and Cochran, J.J.(2015).An
introduction to management science: quantitative approaches to decision making.
Cengage learning.
Berger-Walliser,G.and Shrivastava,P.(2014).Beyond Compliance: Sustainable
Development, Business, and Proactive Law. J. Int'l L.,46, p.417.
Edvardsson,B.and Enquist,B.(2016).The service excellence and innovation model:
lessons from IKEA and other service frontiers.Total Quality Management & Business
business public limited liability company is not mentioned at all. In the event of a
failure, the PLC may direct the creation of a plan to revitalize it or stop the production
process.
Conclusion
The report details the operation and project management of Hefei whirlpool. In this
report, the effectiveness and efficiency of the operation management of the selected
organization are strictly reviewed. On this basis, various concepts of continuous
improvement in operation and management are applied and discussed. In addition, the
principle of project life cycle (PLC) has been applied to Hefei whirlpool Group PLC.
In addition, the report also reviews the use of PLC in a given scenario.
Reference
Ajodhia,V.(2012).Integrated cost and quality benchmarking for electricity distribution
using DEA.International Journal of Energy Sector Management,4(3), pp.417-433.
Akkerman, R., Farahani, P. and Grunow, M.(2012).Quality, safety and sustainability
in food distribution: a review of quantitative operations management approaches and
challenges.Or Spectrum,32(4), pp.863-904.
Anderson, D.R.,Sweeney,D.J.,Williams, T.A., Camm, J.D. and Cochran, J.J.(2015).An
introduction to management science: quantitative approaches to decision making.
Cengage learning.
Berger-Walliser,G.and Shrivastava,P.(2014).Beyond Compliance: Sustainable
Development, Business, and Proactive Law. J. Int'l L.,46, p.417.
Edvardsson,B.and Enquist,B.(2016).The service excellence and innovation model:
lessons from IKEA and other service frontiers.Total Quality Management & Business
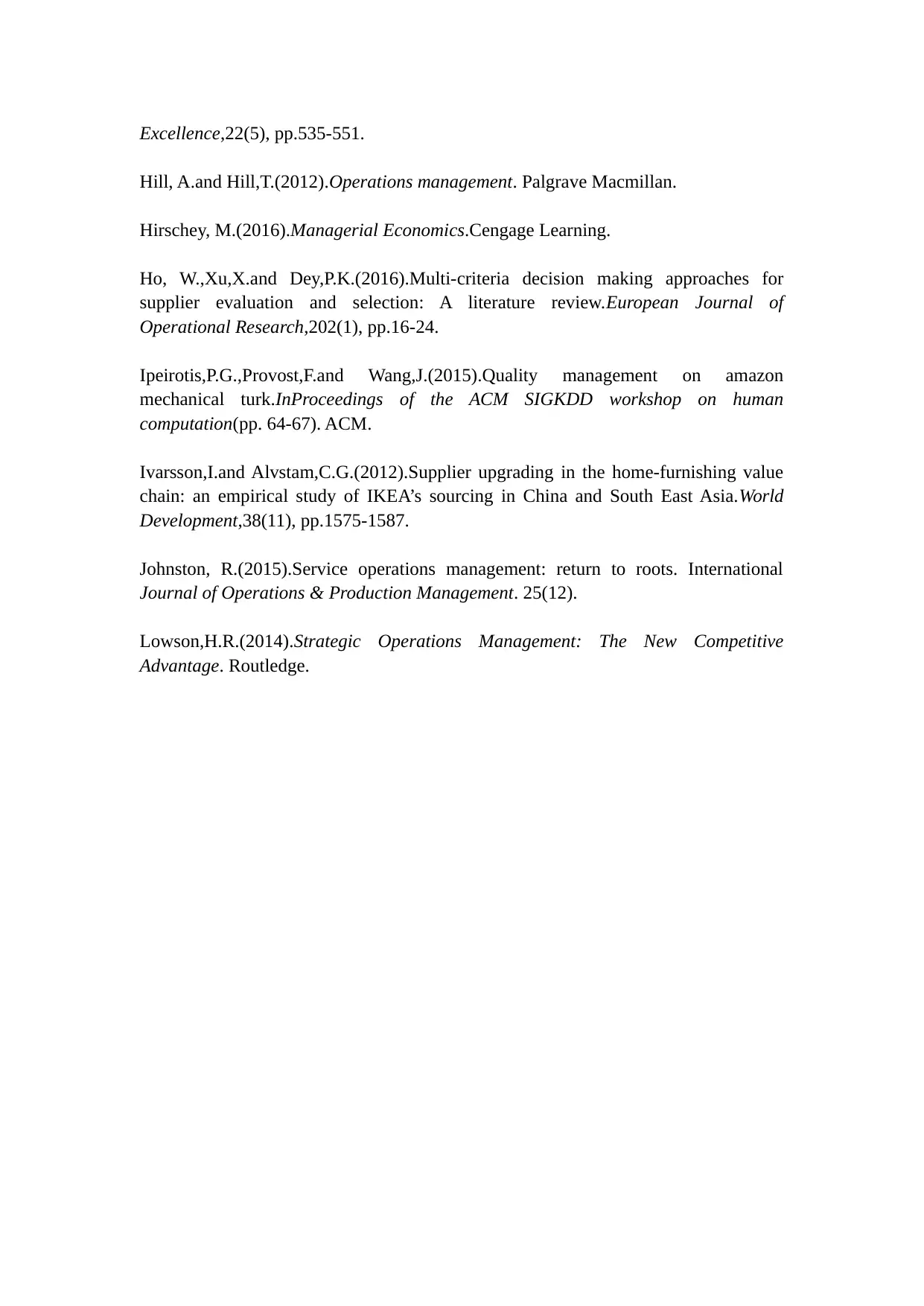
Excellence,22(5), pp.535-551.
Hill, A.and Hill,T.(2012).Operations management. Palgrave Macmillan.
Hirschey, M.(2016).Managerial Economics.Cengage Learning.
Ho, W.,Xu,X.and Dey,P.K.(2016).Multi-criteria decision making approaches for
supplier evaluation and selection: A literature review.European Journal of
Operational Research,202(1), pp.16-24.
Ipeirotis,P.G.,Provost,F.and Wang,J.(2015).Quality management on amazon
mechanical turk.InProceedings of the ACM SIGKDD workshop on human
computation(pp. 64-67). ACM.
Ivarsson,I.and Alvstam,C.G.(2012).Supplier upgrading in the home-furnishing value
chain: an empirical study of IKEA’s sourcing in China and South East Asia.World
Development,38(11), pp.1575-1587.
Johnston, R.(2015).Service operations management: return to roots. International
Journal of Operations & Production Management. 25(12).
Lowson,H.R.(2014).Strategic Operations Management: The New Competitive
Advantage. Routledge.
Hill, A.and Hill,T.(2012).Operations management. Palgrave Macmillan.
Hirschey, M.(2016).Managerial Economics.Cengage Learning.
Ho, W.,Xu,X.and Dey,P.K.(2016).Multi-criteria decision making approaches for
supplier evaluation and selection: A literature review.European Journal of
Operational Research,202(1), pp.16-24.
Ipeirotis,P.G.,Provost,F.and Wang,J.(2015).Quality management on amazon
mechanical turk.InProceedings of the ACM SIGKDD workshop on human
computation(pp. 64-67). ACM.
Ivarsson,I.and Alvstam,C.G.(2012).Supplier upgrading in the home-furnishing value
chain: an empirical study of IKEA’s sourcing in China and South East Asia.World
Development,38(11), pp.1575-1587.
Johnston, R.(2015).Service operations management: return to roots. International
Journal of Operations & Production Management. 25(12).
Lowson,H.R.(2014).Strategic Operations Management: The New Competitive
Advantage. Routledge.
1 out of 9
Related Documents
![[object Object]](/_next/image/?url=%2F_next%2Fstatic%2Fmedia%2Flogo.6d15ce61.png&w=640&q=75)
Your All-in-One AI-Powered Toolkit for Academic Success.
+13062052269
info@desklib.com
Available 24*7 on WhatsApp / Email
Unlock your academic potential
© 2024 | Zucol Services PVT LTD | All rights reserved.