Inventory Management and Equipment Cost in Project-Based Organizations
Added on 2023-06-13
15 Pages5155 Words329 Views
PART – 1
Section A
1. The total inventory costs for material resources in a manufacturing industry is the sum of:
b. Total ordering cost + total holding & carrying cost + shortage cost + other related costs
2. In a precast concrete block manufacturing unit, the reorder level of raw materials will
depend upon:
d. All of the above
3. Rider Jessie is a project manger in an airport expansion project. Rider’s project team is
concerned that if they do not have adequate surplus materials, overall project might be
delayed and large cost overruns in some key works are expected. Moreover, the
procurement division alerted that the market forecast for structural steel is not very good.
Rider’s resource strategy should be :
b. Just in case (JIC)
4. High hazard facilities are risky for major accidents - because enormous quantities of
hazardous materials are:
c. both (a) and (b)
5. As a project manager in a construction site, if your current appraisal found that certain
material resources are not used, you would consider this as:
c. Obsolete
6. You are a maintenance contractor for a sports complex facility. Your inventory costs for
material resources would not include:
d. Obsolescence and repair costs for excavation equipment
Section B
Question B1 Question B1 has 3 built-in sub-questions (i), (ii) & (ii). Answer all 3 sub-
questions of B1. A manufacturing factory unit of a large international organization is located
in Victoria. This factory unit requires 12 materials (M1, M2, M3, M4, M5, M6, M7, M8, M9,
M10, M11, and M12) for the production requirements. Assume that you are the manager
responsible for material resources in this production unit.
Sub-question (i) of B1: Prepare an ABC analysis for following materials and suggest
your Pareto principles based material resources planning recommendations in this project
200 tons of Material “M1” (unit cost: $500 per ton)
80 tons of Material “M2” (unit cost: $1800 per ton)
320 m2 of Material “M3” (unit cost: $120 per m2)
2500 m2 of Material “M4” (unit cost: $250 per m2)
Section A
1. The total inventory costs for material resources in a manufacturing industry is the sum of:
b. Total ordering cost + total holding & carrying cost + shortage cost + other related costs
2. In a precast concrete block manufacturing unit, the reorder level of raw materials will
depend upon:
d. All of the above
3. Rider Jessie is a project manger in an airport expansion project. Rider’s project team is
concerned that if they do not have adequate surplus materials, overall project might be
delayed and large cost overruns in some key works are expected. Moreover, the
procurement division alerted that the market forecast for structural steel is not very good.
Rider’s resource strategy should be :
b. Just in case (JIC)
4. High hazard facilities are risky for major accidents - because enormous quantities of
hazardous materials are:
c. both (a) and (b)
5. As a project manager in a construction site, if your current appraisal found that certain
material resources are not used, you would consider this as:
c. Obsolete
6. You are a maintenance contractor for a sports complex facility. Your inventory costs for
material resources would not include:
d. Obsolescence and repair costs for excavation equipment
Section B
Question B1 Question B1 has 3 built-in sub-questions (i), (ii) & (ii). Answer all 3 sub-
questions of B1. A manufacturing factory unit of a large international organization is located
in Victoria. This factory unit requires 12 materials (M1, M2, M3, M4, M5, M6, M7, M8, M9,
M10, M11, and M12) for the production requirements. Assume that you are the manager
responsible for material resources in this production unit.
Sub-question (i) of B1: Prepare an ABC analysis for following materials and suggest
your Pareto principles based material resources planning recommendations in this project
200 tons of Material “M1” (unit cost: $500 per ton)
80 tons of Material “M2” (unit cost: $1800 per ton)
320 m2 of Material “M3” (unit cost: $120 per m2)
2500 m2 of Material “M4” (unit cost: $250 per m2)
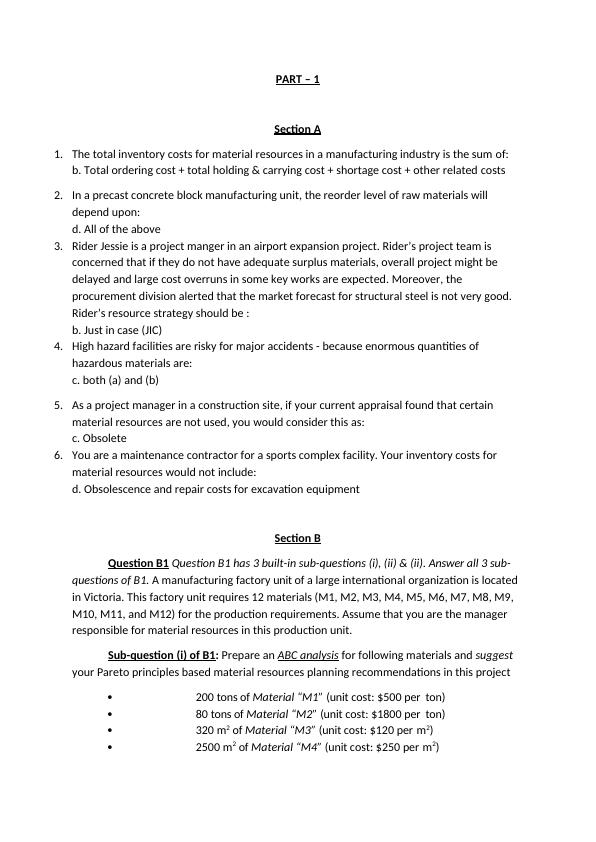
2000 boxes of Material “M5” (unit cost: $50 per box)
10000 m3 of Material “M6” (unit cost: $10 per m3)
5000 liters of Material “M7” (unit cost: $1.5 per liter)
1000 packets of Material “M8” (unit cost: $100 per packet)
100 numbers of Material “M9” (unit cost: $500 per frame)
6000 m3 of Material “M10” (unit cost: $80 per m3)
12000 m of Material “M11” (unit cost: $50 per m)
10000 tons of Material “M12” (unit cost: $110 per ton)
ABC analysis is one of the most commonly used techniques of inventory
management. This tiered method of inventory valuation categorizes inventory based on the
cost per unit and the quantity required over a period of time. This method categorizes
inventory into A as being most valuable, B as being moderately valuable and C as being least
valuable. Usually, the items under category A account for 70% - 80% of the cost of inventory
and are 10% - 20% of the inventory items. Category C accounts for items that are the least
valuable and account for more than 50% of inventory. Category B are items which have a
median value and account for upto 30% of inventory. Below is a table with the
categorization of the given products.
ABC Analysis
Materia
l Cost/Unit Inventory Total Value Category
M1 $500/ton 200 $100,000.00 B
M2 $1800/ton 80 $144,000.00 A
M3 $120/m2 320 $38,400.00 C
M4 $250/m2 2500 $625,000.00 A
M5 $50/box 2000 $100,000.00 B
M6 $10/m3 10000 $100,000.00 B
M7 $1.5/Ltr 5000 $7,500.00 C
M8
$100/
packet 1000 $100,000.00 B
M9 $500/frame 100 $50,000.00 C
10000 m3 of Material “M6” (unit cost: $10 per m3)
5000 liters of Material “M7” (unit cost: $1.5 per liter)
1000 packets of Material “M8” (unit cost: $100 per packet)
100 numbers of Material “M9” (unit cost: $500 per frame)
6000 m3 of Material “M10” (unit cost: $80 per m3)
12000 m of Material “M11” (unit cost: $50 per m)
10000 tons of Material “M12” (unit cost: $110 per ton)
ABC analysis is one of the most commonly used techniques of inventory
management. This tiered method of inventory valuation categorizes inventory based on the
cost per unit and the quantity required over a period of time. This method categorizes
inventory into A as being most valuable, B as being moderately valuable and C as being least
valuable. Usually, the items under category A account for 70% - 80% of the cost of inventory
and are 10% - 20% of the inventory items. Category C accounts for items that are the least
valuable and account for more than 50% of inventory. Category B are items which have a
median value and account for upto 30% of inventory. Below is a table with the
categorization of the given products.
ABC Analysis
Materia
l Cost/Unit Inventory Total Value Category
M1 $500/ton 200 $100,000.00 B
M2 $1800/ton 80 $144,000.00 A
M3 $120/m2 320 $38,400.00 C
M4 $250/m2 2500 $625,000.00 A
M5 $50/box 2000 $100,000.00 B
M6 $10/m3 10000 $100,000.00 B
M7 $1.5/Ltr 5000 $7,500.00 C
M8
$100/
packet 1000 $100,000.00 B
M9 $500/frame 100 $50,000.00 C
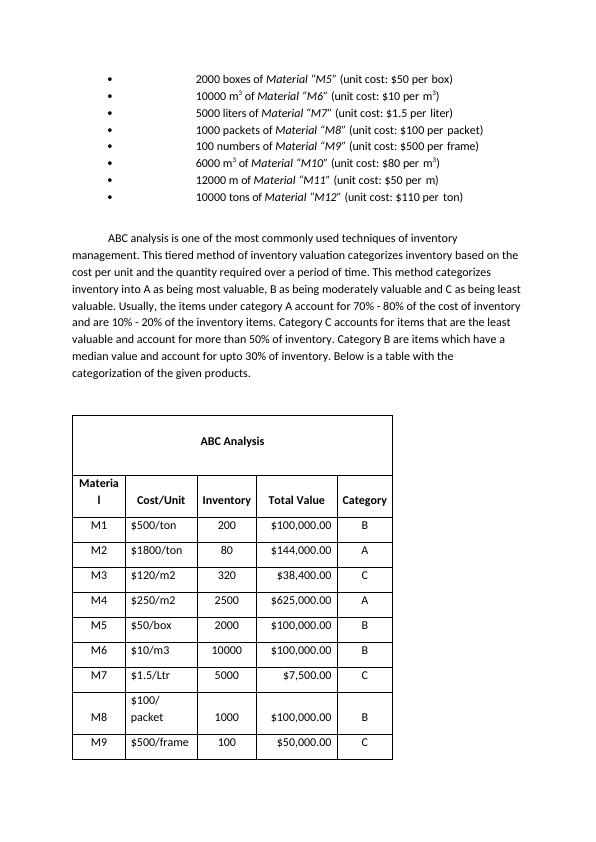
M10 $80/m3 6000 $480,000.00 A
M11 $50/m 12000 $600,000.00 A
M12 $110/ton 10000
$1,100,000.0
0 A
The Pareto Principle was developed by Vilfredo Federico Damaso Pareto. According
to the Pareto Principle, 80% of the overall consumption value is based on only 20% of the
total items (Lokad.com, 2018). This is also known as the 80/20 rule where 80% of the output
in a given system is determined by 20% of the inputs. The ratio is not exactly 80/20, but
close to it. Based on the above data, it is clear that materials M2, M3, M5, M6, M7, M8, and
M9 account for 11.43% of the inventory value, but form almost 50% of the inventory
required for production.
Sub-question (ii) of B1: Discuss your strategies and arrangements for: (a) the
security of costly inventories and (b) buffer stocks of hazardous materials in this factory
warehouse.
(a) The security of costly inventories is an extremely important task in any
organization. According to the Merriam-Webster dictionary, inventory control can be
defined as the “coordination and supervision of the supply, storage, distribution, and
recording of materials to maintain quantities adequate for current customer needs without
excessive supply or loss.” (EazyStock, 2018). There are several ways in which high value
inventory can be safe guarded to ensure loss prevention. Below are listed some of the
inventory safe guard methods:
Periodic Stock Audits: Many organizations conduct an annual stock audit to
get a sense of the stock available and make forecasts for future requirements
based on ongoing projects. In production based organizations, this audit
needs to be done more frequently to spot any theft, spoilage or any other
form of shrinkage.
Automated Inventory Management System: An automated inventory
management system is designed to track stock on a regular basis and makes
it easier to manage high cost goods. There are a lot of tools available which
help in inventory management and when used in conjunction with an
Enterprise Resource Planning system, can make inventory tracking and loss
prevention very easy.
Inventory Conversion Ratios: In this method, the management uses various
methods to calculate the inventory requirements. Based on these
requirements, the management decides on the best policy to follow when
M11 $50/m 12000 $600,000.00 A
M12 $110/ton 10000
$1,100,000.0
0 A
The Pareto Principle was developed by Vilfredo Federico Damaso Pareto. According
to the Pareto Principle, 80% of the overall consumption value is based on only 20% of the
total items (Lokad.com, 2018). This is also known as the 80/20 rule where 80% of the output
in a given system is determined by 20% of the inputs. The ratio is not exactly 80/20, but
close to it. Based on the above data, it is clear that materials M2, M3, M5, M6, M7, M8, and
M9 account for 11.43% of the inventory value, but form almost 50% of the inventory
required for production.
Sub-question (ii) of B1: Discuss your strategies and arrangements for: (a) the
security of costly inventories and (b) buffer stocks of hazardous materials in this factory
warehouse.
(a) The security of costly inventories is an extremely important task in any
organization. According to the Merriam-Webster dictionary, inventory control can be
defined as the “coordination and supervision of the supply, storage, distribution, and
recording of materials to maintain quantities adequate for current customer needs without
excessive supply or loss.” (EazyStock, 2018). There are several ways in which high value
inventory can be safe guarded to ensure loss prevention. Below are listed some of the
inventory safe guard methods:
Periodic Stock Audits: Many organizations conduct an annual stock audit to
get a sense of the stock available and make forecasts for future requirements
based on ongoing projects. In production based organizations, this audit
needs to be done more frequently to spot any theft, spoilage or any other
form of shrinkage.
Automated Inventory Management System: An automated inventory
management system is designed to track stock on a regular basis and makes
it easier to manage high cost goods. There are a lot of tools available which
help in inventory management and when used in conjunction with an
Enterprise Resource Planning system, can make inventory tracking and loss
prevention very easy.
Inventory Conversion Ratios: In this method, the management uses various
methods to calculate the inventory requirements. Based on these
requirements, the management decides on the best policy to follow when
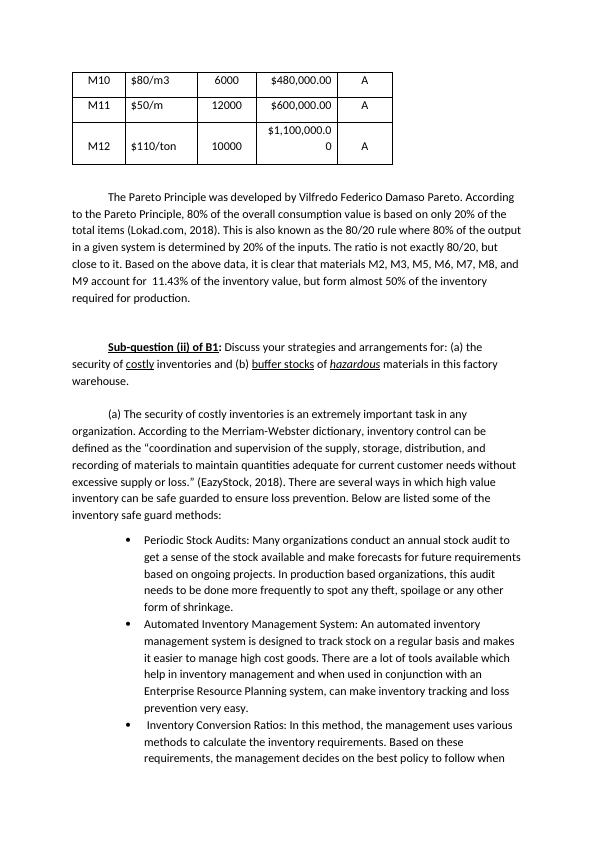
replenishing inventory. One popular method is the Just – In – Time Inventory
system which allows for purchase of inventory just in time that it is required
for production. This way, there is very little time that inventory needs to be
maintained and managed.
Security Personnel & Technology: Security in terms of technology and
personnel can be used to safeguard any high value inventory. Security
cameras and alarms at warehouse entrances, 24/7 security guards posted at
doors, cameras inside the warehouse to discourage employees from misusing
company resources.
ABC Analysis and Classification: ABC analysis is an important tool in inventory
management that helps classify inventory based on their value. The inventory
with the highest value is classified as A and the one with the lowest value is
classified as C. Inventory with a median value falls under category B. By using
this classification method, the management can identify inventory which
needs the highest measure of control and place appropriate measures
accordingly. Inventory with lower values may not require such stringent
control measures.
We have discusses various methods through which high cost inventory can be
safeguarded and protected from theft, damage and other forms of shrinkage.
(b) Buffer stocks of hazardous materials in factories need to be handled with extreme
precaution so as to ensure that there is no incident. These hazardous materials need to be
stored in such a way that there is no spillage, uncontrolled reaction or exposure to
employees. The staff need to ensure that they take proper precautions while handling such
materials to avoid exposure. There should be a set protocol in place on
How much of such materials should be in stock at any given point of time.
Who has access to it?
How are they to handle the material?
The procedure to dispose such material.
These procedures may differ from industry to industry and it is left up to the
management to ensure safety of their employees and their surroundings.
Sub-question (iii) of B1: You are responsible for obsolescence mitigation in this large
international organization. Prepare a set of recommendations to your top management –
i.e. with respect to (a) stock of volatile materials, and (b) equipment spare parts in this
factory.
(a) Volatility is defined as the tendency of a substance to vaporize. It can be related
to the vapor pressure of a substance. At a given temperature, a material with a higher vapor
pressure will vaporize faster than a substance with lower vapor pressure. Volatile
substances are usually considered highly unstable and can easily shrink if not stored
system which allows for purchase of inventory just in time that it is required
for production. This way, there is very little time that inventory needs to be
maintained and managed.
Security Personnel & Technology: Security in terms of technology and
personnel can be used to safeguard any high value inventory. Security
cameras and alarms at warehouse entrances, 24/7 security guards posted at
doors, cameras inside the warehouse to discourage employees from misusing
company resources.
ABC Analysis and Classification: ABC analysis is an important tool in inventory
management that helps classify inventory based on their value. The inventory
with the highest value is classified as A and the one with the lowest value is
classified as C. Inventory with a median value falls under category B. By using
this classification method, the management can identify inventory which
needs the highest measure of control and place appropriate measures
accordingly. Inventory with lower values may not require such stringent
control measures.
We have discusses various methods through which high cost inventory can be
safeguarded and protected from theft, damage and other forms of shrinkage.
(b) Buffer stocks of hazardous materials in factories need to be handled with extreme
precaution so as to ensure that there is no incident. These hazardous materials need to be
stored in such a way that there is no spillage, uncontrolled reaction or exposure to
employees. The staff need to ensure that they take proper precautions while handling such
materials to avoid exposure. There should be a set protocol in place on
How much of such materials should be in stock at any given point of time.
Who has access to it?
How are they to handle the material?
The procedure to dispose such material.
These procedures may differ from industry to industry and it is left up to the
management to ensure safety of their employees and their surroundings.
Sub-question (iii) of B1: You are responsible for obsolescence mitigation in this large
international organization. Prepare a set of recommendations to your top management –
i.e. with respect to (a) stock of volatile materials, and (b) equipment spare parts in this
factory.
(a) Volatility is defined as the tendency of a substance to vaporize. It can be related
to the vapor pressure of a substance. At a given temperature, a material with a higher vapor
pressure will vaporize faster than a substance with lower vapor pressure. Volatile
substances are usually considered highly unstable and can easily shrink if not stored
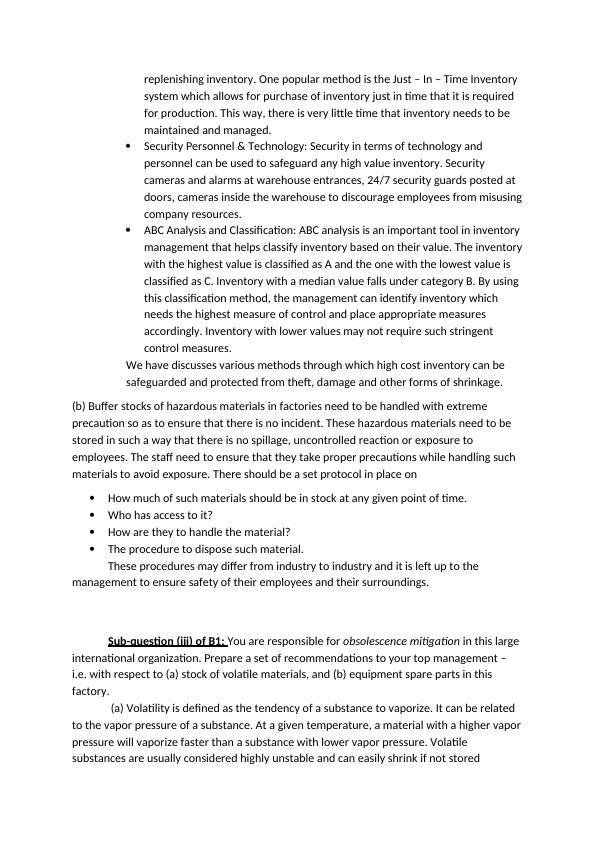
End of preview
Want to access all the pages? Upload your documents or become a member.
Related Documents
Resource Planning and Management - Deskliblg...
|8
|1144
|331
Stakeholder Role and Responsibilities l Assignmentlg...
|14
|1246
|49
Material Wastages Report 2022lg...
|4
|1227
|20