KNPC Clean Fuels Project: Delayed Coker Heater for MAA Unit 136 - DCU
VerifiedAdded on 2023/06/11
|7
|1649
|197
AI Summary
This article discusses the KNPC Clean Fuels Project: Delayed Coker Heater for MAA Unit 136 - DCU. It covers the objectives, project group, distinctive activity, and identified issues and their solutions. The project was executed by CB & I Lummus and the author was a team member responsible for documentation and arranging meetings.
Contribute Materials
Your contribution can guide someone’s learning journey. Share your
documents today.
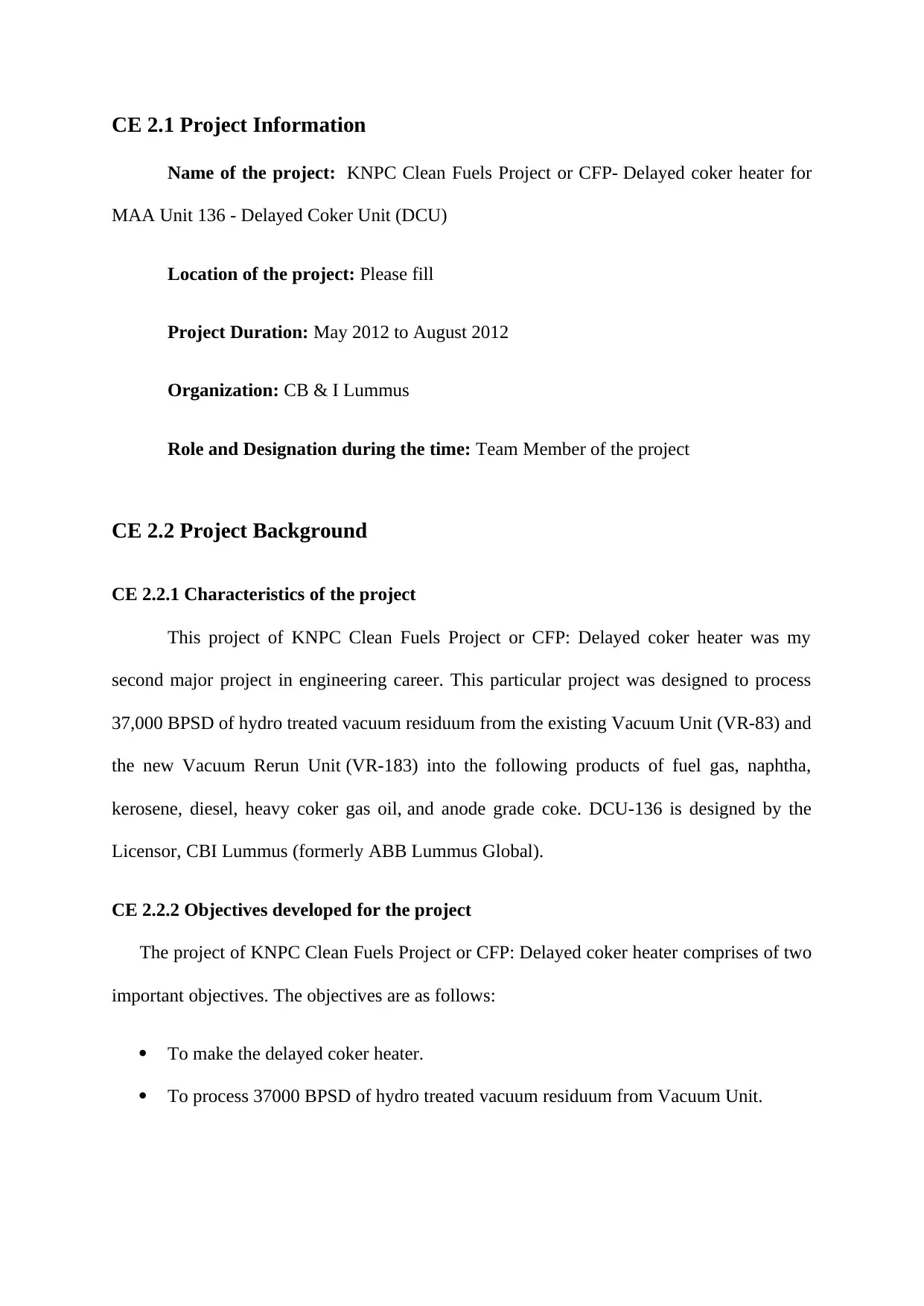
CE 2.1 Project Information
Name of the project: KNPC Clean Fuels Project or CFP- Delayed coker heater for
MAA Unit 136 - Delayed Coker Unit (DCU)
Location of the project: Please fill
Project Duration: May 2012 to August 2012
Organization: CB & I Lummus
Role and Designation during the time: Team Member of the project
CE 2.2 Project Background
CE 2.2.1 Characteristics of the project
This project of KNPC Clean Fuels Project or CFP: Delayed coker heater was my
second major project in engineering career. This particular project was designed to process
37,000 BPSD of hydro treated vacuum residuum from the existing Vacuum Unit (VR-83) and
the new Vacuum Rerun Unit (VR-183) into the following products of fuel gas, naphtha,
kerosene, diesel, heavy coker gas oil, and anode grade coke. DCU-136 is designed by the
Licensor, CBI Lummus (formerly ABB Lummus Global).
CE 2.2.2 Objectives developed for the project
The project of KNPC Clean Fuels Project or CFP: Delayed coker heater comprises of two
important objectives. The objectives are as follows:
To make the delayed coker heater.
To process 37000 BPSD of hydro treated vacuum residuum from Vacuum Unit.
Name of the project: KNPC Clean Fuels Project or CFP- Delayed coker heater for
MAA Unit 136 - Delayed Coker Unit (DCU)
Location of the project: Please fill
Project Duration: May 2012 to August 2012
Organization: CB & I Lummus
Role and Designation during the time: Team Member of the project
CE 2.2 Project Background
CE 2.2.1 Characteristics of the project
This project of KNPC Clean Fuels Project or CFP: Delayed coker heater was my
second major project in engineering career. This particular project was designed to process
37,000 BPSD of hydro treated vacuum residuum from the existing Vacuum Unit (VR-83) and
the new Vacuum Rerun Unit (VR-183) into the following products of fuel gas, naphtha,
kerosene, diesel, heavy coker gas oil, and anode grade coke. DCU-136 is designed by the
Licensor, CBI Lummus (formerly ABB Lummus Global).
CE 2.2.2 Objectives developed for the project
The project of KNPC Clean Fuels Project or CFP: Delayed coker heater comprises of two
important objectives. The objectives are as follows:
To make the delayed coker heater.
To process 37000 BPSD of hydro treated vacuum residuum from Vacuum Unit.
Secure Best Marks with AI Grader
Need help grading? Try our AI Grader for instant feedback on your assignments.
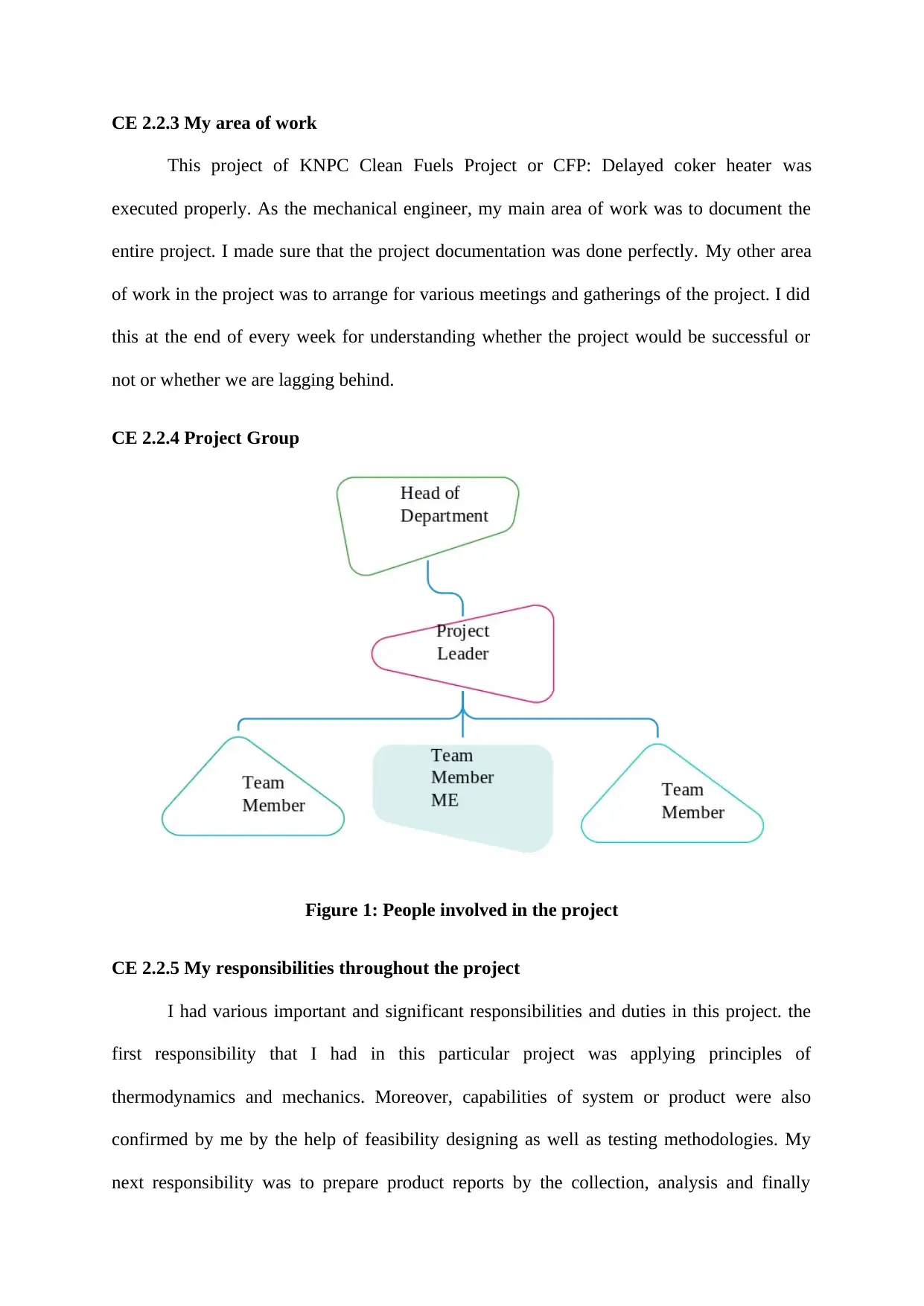
CE 2.2.3 My area of work
This project of KNPC Clean Fuels Project or CFP: Delayed coker heater was
executed properly. As the mechanical engineer, my main area of work was to document the
entire project. I made sure that the project documentation was done perfectly. My other area
of work in the project was to arrange for various meetings and gatherings of the project. I did
this at the end of every week for understanding whether the project would be successful or
not or whether we are lagging behind.
CE 2.2.4 Project Group
Figure 1: People involved in the project
CE 2.2.5 My responsibilities throughout the project
I had various important and significant responsibilities and duties in this project. the
first responsibility that I had in this particular project was applying principles of
thermodynamics and mechanics. Moreover, capabilities of system or product were also
confirmed by me by the help of feasibility designing as well as testing methodologies. My
next responsibility was to prepare product reports by the collection, analysis and finally
This project of KNPC Clean Fuels Project or CFP: Delayed coker heater was
executed properly. As the mechanical engineer, my main area of work was to document the
entire project. I made sure that the project documentation was done perfectly. My other area
of work in the project was to arrange for various meetings and gatherings of the project. I did
this at the end of every week for understanding whether the project would be successful or
not or whether we are lagging behind.
CE 2.2.4 Project Group
Figure 1: People involved in the project
CE 2.2.5 My responsibilities throughout the project
I had various important and significant responsibilities and duties in this project. the
first responsibility that I had in this particular project was applying principles of
thermodynamics and mechanics. Moreover, capabilities of system or product were also
confirmed by me by the help of feasibility designing as well as testing methodologies. My
next responsibility was to prepare product reports by the collection, analysis and finally
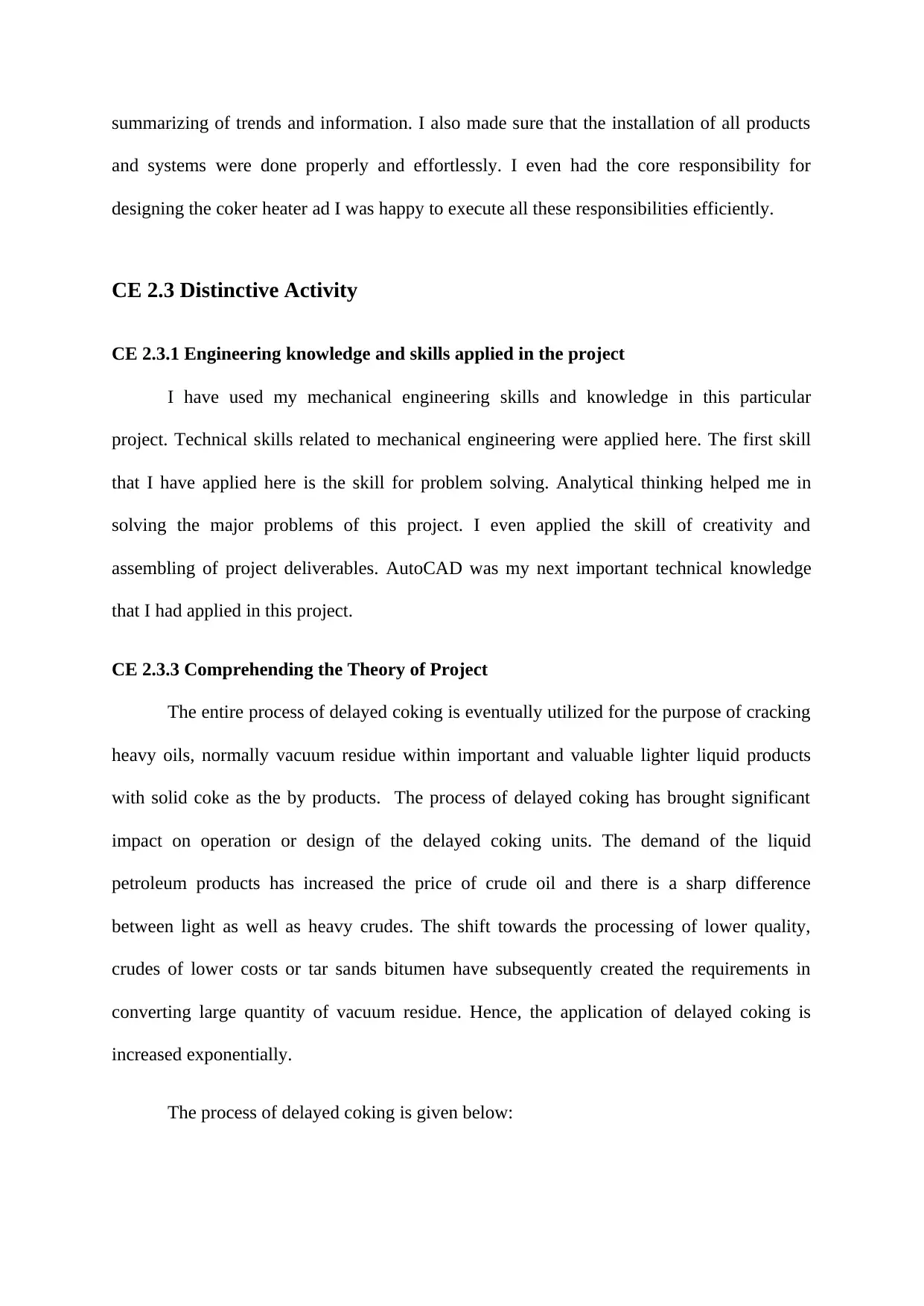
summarizing of trends and information. I also made sure that the installation of all products
and systems were done properly and effortlessly. I even had the core responsibility for
designing the coker heater ad I was happy to execute all these responsibilities efficiently.
CE 2.3 Distinctive Activity
CE 2.3.1 Engineering knowledge and skills applied in the project
I have used my mechanical engineering skills and knowledge in this particular
project. Technical skills related to mechanical engineering were applied here. The first skill
that I have applied here is the skill for problem solving. Analytical thinking helped me in
solving the major problems of this project. I even applied the skill of creativity and
assembling of project deliverables. AutoCAD was my next important technical knowledge
that I had applied in this project.
CE 2.3.3 Comprehending the Theory of Project
The entire process of delayed coking is eventually utilized for the purpose of cracking
heavy oils, normally vacuum residue within important and valuable lighter liquid products
with solid coke as the by products. The process of delayed coking has brought significant
impact on operation or design of the delayed coking units. The demand of the liquid
petroleum products has increased the price of crude oil and there is a sharp difference
between light as well as heavy crudes. The shift towards the processing of lower quality,
crudes of lower costs or tar sands bitumen have subsequently created the requirements in
converting large quantity of vacuum residue. Hence, the application of delayed coking is
increased exponentially.
The process of delayed coking is given below:
and systems were done properly and effortlessly. I even had the core responsibility for
designing the coker heater ad I was happy to execute all these responsibilities efficiently.
CE 2.3 Distinctive Activity
CE 2.3.1 Engineering knowledge and skills applied in the project
I have used my mechanical engineering skills and knowledge in this particular
project. Technical skills related to mechanical engineering were applied here. The first skill
that I have applied here is the skill for problem solving. Analytical thinking helped me in
solving the major problems of this project. I even applied the skill of creativity and
assembling of project deliverables. AutoCAD was my next important technical knowledge
that I had applied in this project.
CE 2.3.3 Comprehending the Theory of Project
The entire process of delayed coking is eventually utilized for the purpose of cracking
heavy oils, normally vacuum residue within important and valuable lighter liquid products
with solid coke as the by products. The process of delayed coking has brought significant
impact on operation or design of the delayed coking units. The demand of the liquid
petroleum products has increased the price of crude oil and there is a sharp difference
between light as well as heavy crudes. The shift towards the processing of lower quality,
crudes of lower costs or tar sands bitumen have subsequently created the requirements in
converting large quantity of vacuum residue. Hence, the application of delayed coking is
increased exponentially.
The process of delayed coking is given below:
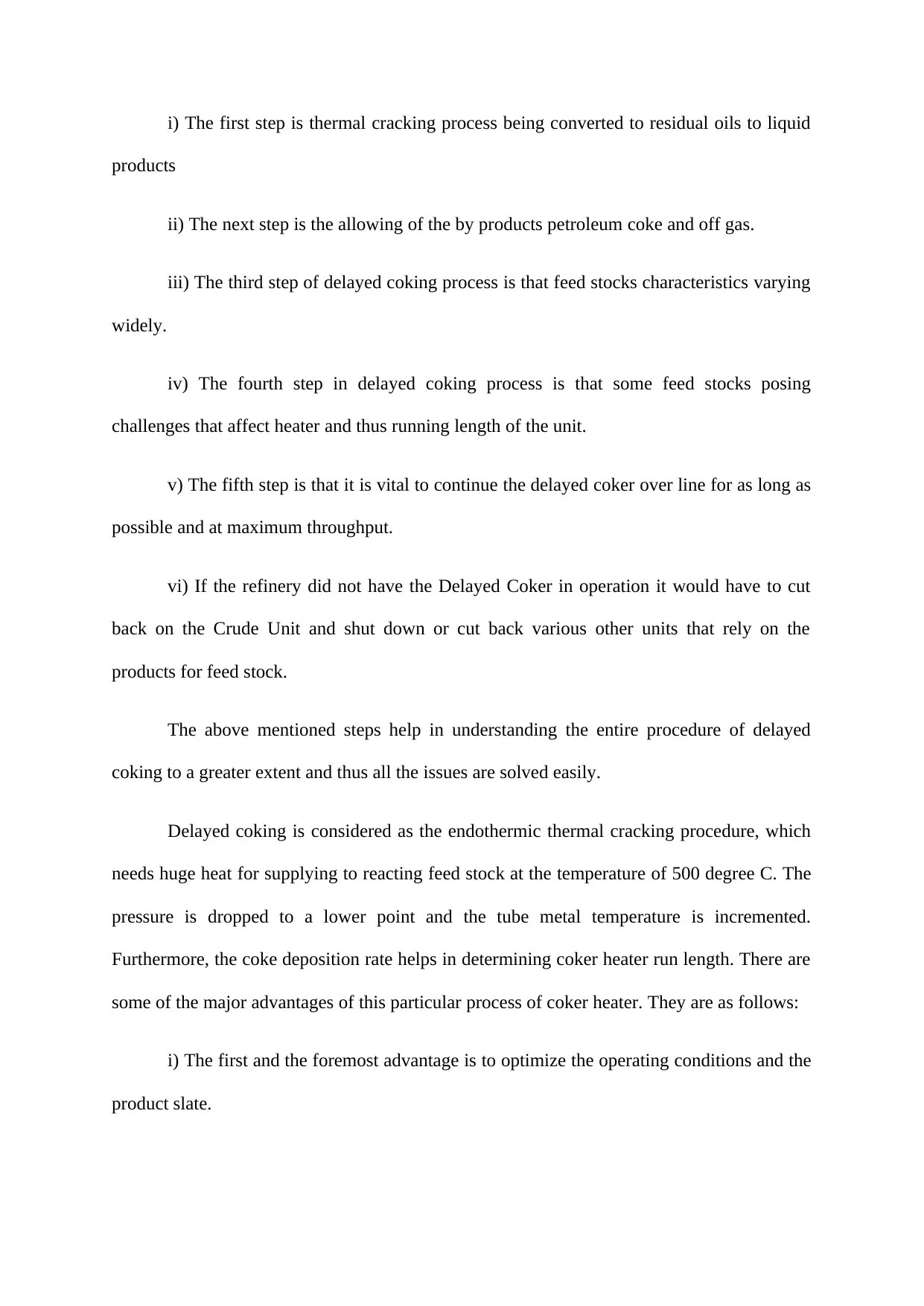
i) The first step is thermal cracking process being converted to residual oils to liquid
products
ii) The next step is the allowing of the by products petroleum coke and off gas.
iii) The third step of delayed coking process is that feed stocks characteristics varying
widely.
iv) The fourth step in delayed coking process is that some feed stocks posing
challenges that affect heater and thus running length of the unit.
v) The fifth step is that it is vital to continue the delayed coker over line for as long as
possible and at maximum throughput.
vi) If the refinery did not have the Delayed Coker in operation it would have to cut
back on the Crude Unit and shut down or cut back various other units that rely on the
products for feed stock.
The above mentioned steps help in understanding the entire procedure of delayed
coking to a greater extent and thus all the issues are solved easily.
Delayed coking is considered as the endothermic thermal cracking procedure, which
needs huge heat for supplying to reacting feed stock at the temperature of 500 degree C. The
pressure is dropped to a lower point and the tube metal temperature is incremented.
Furthermore, the coke deposition rate helps in determining coker heater run length. There are
some of the major advantages of this particular process of coker heater. They are as follows:
i) The first and the foremost advantage is to optimize the operating conditions and the
product slate.
products
ii) The next step is the allowing of the by products petroleum coke and off gas.
iii) The third step of delayed coking process is that feed stocks characteristics varying
widely.
iv) The fourth step in delayed coking process is that some feed stocks posing
challenges that affect heater and thus running length of the unit.
v) The fifth step is that it is vital to continue the delayed coker over line for as long as
possible and at maximum throughput.
vi) If the refinery did not have the Delayed Coker in operation it would have to cut
back on the Crude Unit and shut down or cut back various other units that rely on the
products for feed stock.
The above mentioned steps help in understanding the entire procedure of delayed
coking to a greater extent and thus all the issues are solved easily.
Delayed coking is considered as the endothermic thermal cracking procedure, which
needs huge heat for supplying to reacting feed stock at the temperature of 500 degree C. The
pressure is dropped to a lower point and the tube metal temperature is incremented.
Furthermore, the coke deposition rate helps in determining coker heater run length. There are
some of the major advantages of this particular process of coker heater. They are as follows:
i) The first and the foremost advantage is to optimize the operating conditions and the
product slate.
Secure Best Marks with AI Grader
Need help grading? Try our AI Grader for instant feedback on your assignments.
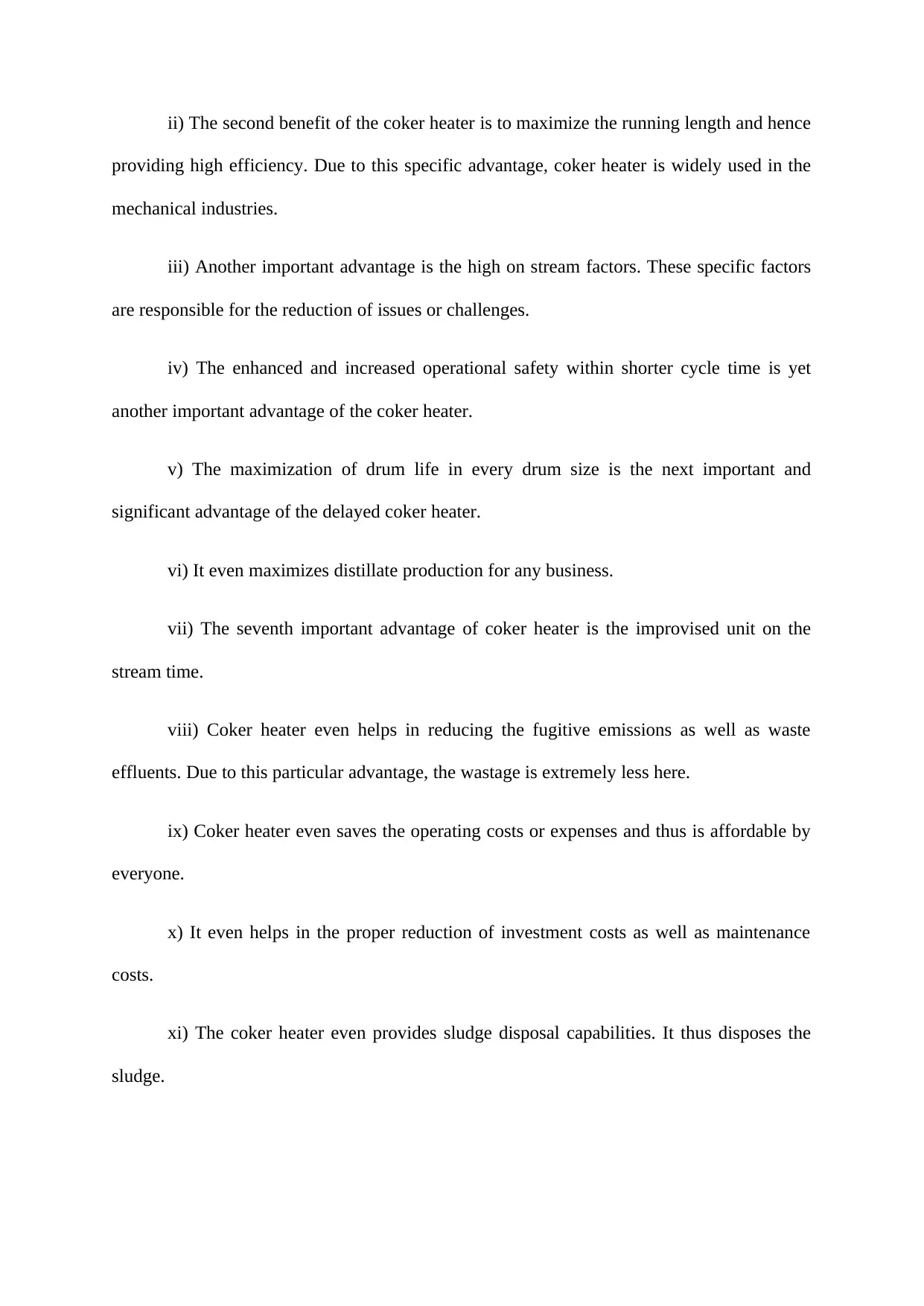
ii) The second benefit of the coker heater is to maximize the running length and hence
providing high efficiency. Due to this specific advantage, coker heater is widely used in the
mechanical industries.
iii) Another important advantage is the high on stream factors. These specific factors
are responsible for the reduction of issues or challenges.
iv) The enhanced and increased operational safety within shorter cycle time is yet
another important advantage of the coker heater.
v) The maximization of drum life in every drum size is the next important and
significant advantage of the delayed coker heater.
vi) It even maximizes distillate production for any business.
vii) The seventh important advantage of coker heater is the improvised unit on the
stream time.
viii) Coker heater even helps in reducing the fugitive emissions as well as waste
effluents. Due to this particular advantage, the wastage is extremely less here.
ix) Coker heater even saves the operating costs or expenses and thus is affordable by
everyone.
x) It even helps in the proper reduction of investment costs as well as maintenance
costs.
xi) The coker heater even provides sludge disposal capabilities. It thus disposes the
sludge.
providing high efficiency. Due to this specific advantage, coker heater is widely used in the
mechanical industries.
iii) Another important advantage is the high on stream factors. These specific factors
are responsible for the reduction of issues or challenges.
iv) The enhanced and increased operational safety within shorter cycle time is yet
another important advantage of the coker heater.
v) The maximization of drum life in every drum size is the next important and
significant advantage of the delayed coker heater.
vi) It even maximizes distillate production for any business.
vii) The seventh important advantage of coker heater is the improvised unit on the
stream time.
viii) Coker heater even helps in reducing the fugitive emissions as well as waste
effluents. Due to this particular advantage, the wastage is extremely less here.
ix) Coker heater even saves the operating costs or expenses and thus is affordable by
everyone.
x) It even helps in the proper reduction of investment costs as well as maintenance
costs.
xi) The coker heater even provides sludge disposal capabilities. It thus disposes the
sludge.
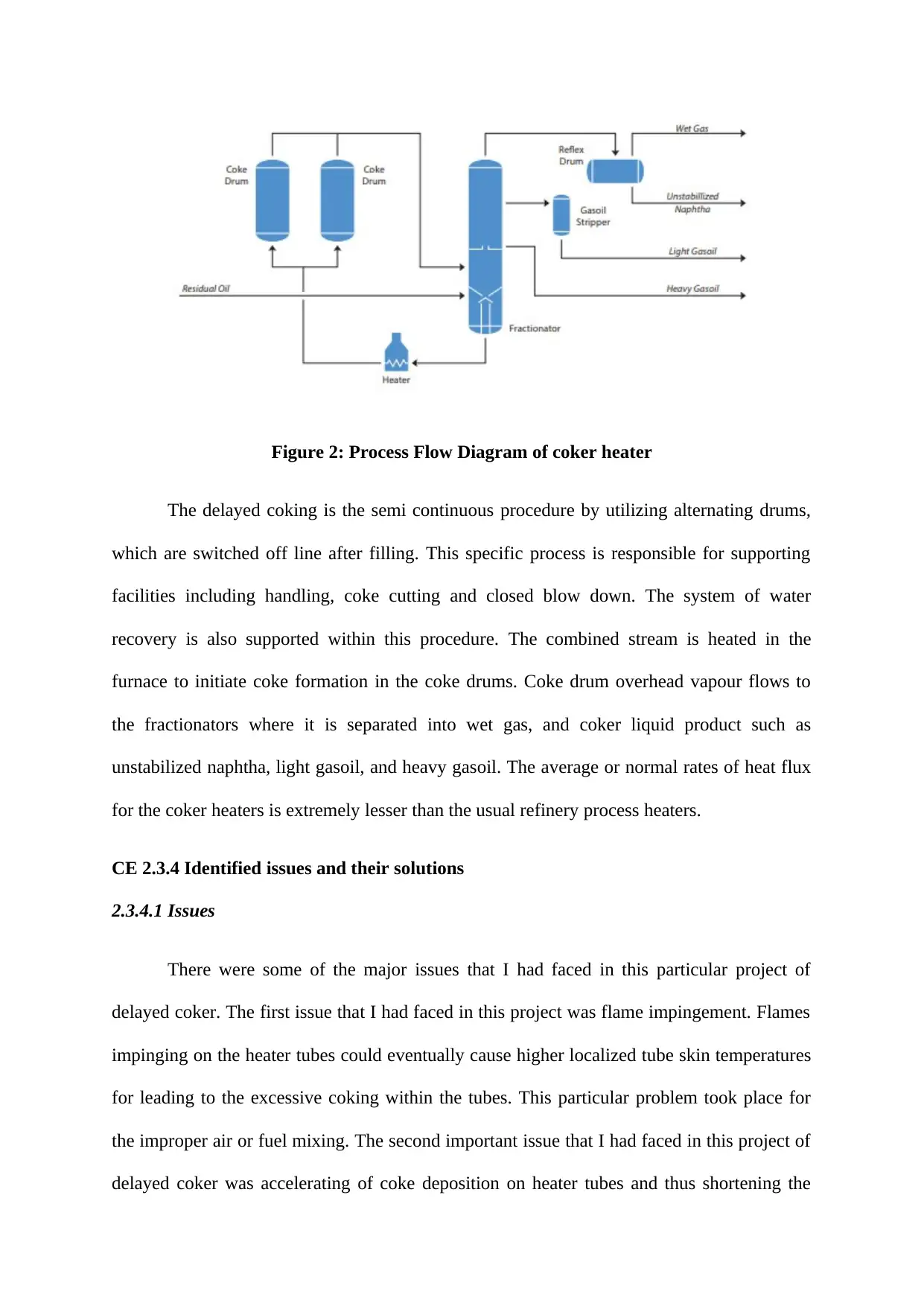
Figure 2: Process Flow Diagram of coker heater
The delayed coking is the semi continuous procedure by utilizing alternating drums,
which are switched off line after filling. This specific process is responsible for supporting
facilities including handling, coke cutting and closed blow down. The system of water
recovery is also supported within this procedure. The combined stream is heated in the
furnace to initiate coke formation in the coke drums. Coke drum overhead vapour flows to
the fractionators where it is separated into wet gas, and coker liquid product such as
unstabilized naphtha, light gasoil, and heavy gasoil. The average or normal rates of heat flux
for the coker heaters is extremely lesser than the usual refinery process heaters.
CE 2.3.4 Identified issues and their solutions
2.3.4.1 Issues
There were some of the major issues that I had faced in this particular project of
delayed coker. The first issue that I had faced in this project was flame impingement. Flames
impinging on the heater tubes could eventually cause higher localized tube skin temperatures
for leading to the excessive coking within the tubes. This particular problem took place for
the improper air or fuel mixing. The second important issue that I had faced in this project of
delayed coker was accelerating of coke deposition on heater tubes and thus shortening the
The delayed coking is the semi continuous procedure by utilizing alternating drums,
which are switched off line after filling. This specific process is responsible for supporting
facilities including handling, coke cutting and closed blow down. The system of water
recovery is also supported within this procedure. The combined stream is heated in the
furnace to initiate coke formation in the coke drums. Coke drum overhead vapour flows to
the fractionators where it is separated into wet gas, and coker liquid product such as
unstabilized naphtha, light gasoil, and heavy gasoil. The average or normal rates of heat flux
for the coker heaters is extremely lesser than the usual refinery process heaters.
CE 2.3.4 Identified issues and their solutions
2.3.4.1 Issues
There were some of the major issues that I had faced in this particular project of
delayed coker. The first issue that I had faced in this project was flame impingement. Flames
impinging on the heater tubes could eventually cause higher localized tube skin temperatures
for leading to the excessive coking within the tubes. This particular problem took place for
the improper air or fuel mixing. The second important issue that I had faced in this project of
delayed coker was accelerating of coke deposition on heater tubes and thus shortening the
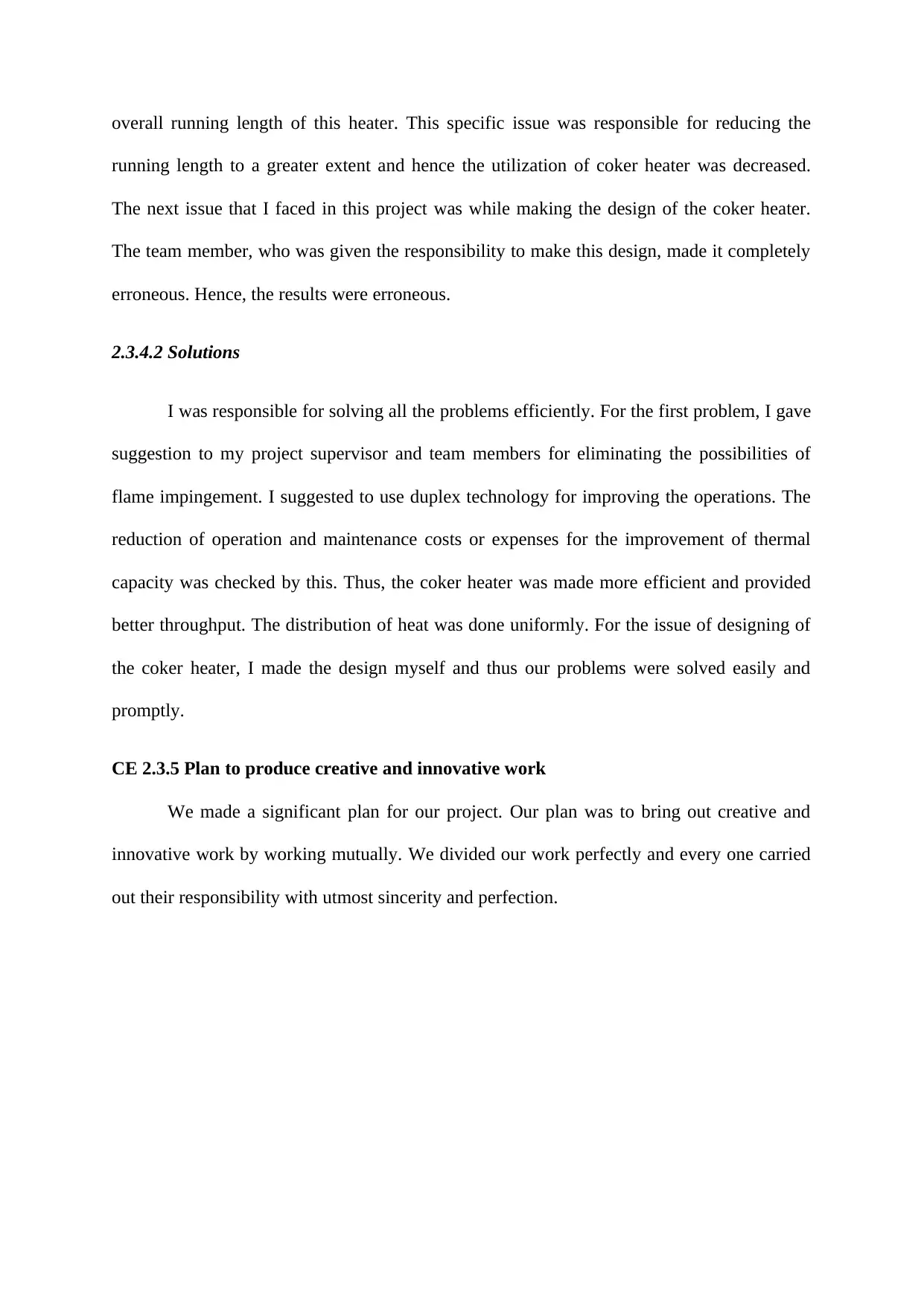
overall running length of this heater. This specific issue was responsible for reducing the
running length to a greater extent and hence the utilization of coker heater was decreased.
The next issue that I faced in this project was while making the design of the coker heater.
The team member, who was given the responsibility to make this design, made it completely
erroneous. Hence, the results were erroneous.
2.3.4.2 Solutions
I was responsible for solving all the problems efficiently. For the first problem, I gave
suggestion to my project supervisor and team members for eliminating the possibilities of
flame impingement. I suggested to use duplex technology for improving the operations. The
reduction of operation and maintenance costs or expenses for the improvement of thermal
capacity was checked by this. Thus, the coker heater was made more efficient and provided
better throughput. The distribution of heat was done uniformly. For the issue of designing of
the coker heater, I made the design myself and thus our problems were solved easily and
promptly.
CE 2.3.5 Plan to produce creative and innovative work
We made a significant plan for our project. Our plan was to bring out creative and
innovative work by working mutually. We divided our work perfectly and every one carried
out their responsibility with utmost sincerity and perfection.
running length to a greater extent and hence the utilization of coker heater was decreased.
The next issue that I faced in this project was while making the design of the coker heater.
The team member, who was given the responsibility to make this design, made it completely
erroneous. Hence, the results were erroneous.
2.3.4.2 Solutions
I was responsible for solving all the problems efficiently. For the first problem, I gave
suggestion to my project supervisor and team members for eliminating the possibilities of
flame impingement. I suggested to use duplex technology for improving the operations. The
reduction of operation and maintenance costs or expenses for the improvement of thermal
capacity was checked by this. Thus, the coker heater was made more efficient and provided
better throughput. The distribution of heat was done uniformly. For the issue of designing of
the coker heater, I made the design myself and thus our problems were solved easily and
promptly.
CE 2.3.5 Plan to produce creative and innovative work
We made a significant plan for our project. Our plan was to bring out creative and
innovative work by working mutually. We divided our work perfectly and every one carried
out their responsibility with utmost sincerity and perfection.
1 out of 7
Related Documents
![[object Object]](/_next/image/?url=%2F_next%2Fstatic%2Fmedia%2Flogo.6d15ce61.png&w=640&q=75)
Your All-in-One AI-Powered Toolkit for Academic Success.
+13062052269
info@desklib.com
Available 24*7 on WhatsApp / Email
Unlock your academic potential
© 2024 | Zucol Services PVT LTD | All rights reserved.