Design and Analysis of Leaf Spring
VerifiedAdded on 2023/06/04
|7
|4150
|280
AI Summary
This paper discusses the design and analysis of leaf spring used in automobiles for suspension point of view. It highlights the main characteristics of leaf spring and reviews some previous research work performed on it for increasing the working condition and capacity with load reduction. The paper is based on material composition, experimental testing and load (Steady, Dynamic) study etc.
Contribute Materials
Your contribution can guide someone’s learning journey. Share your
documents today.
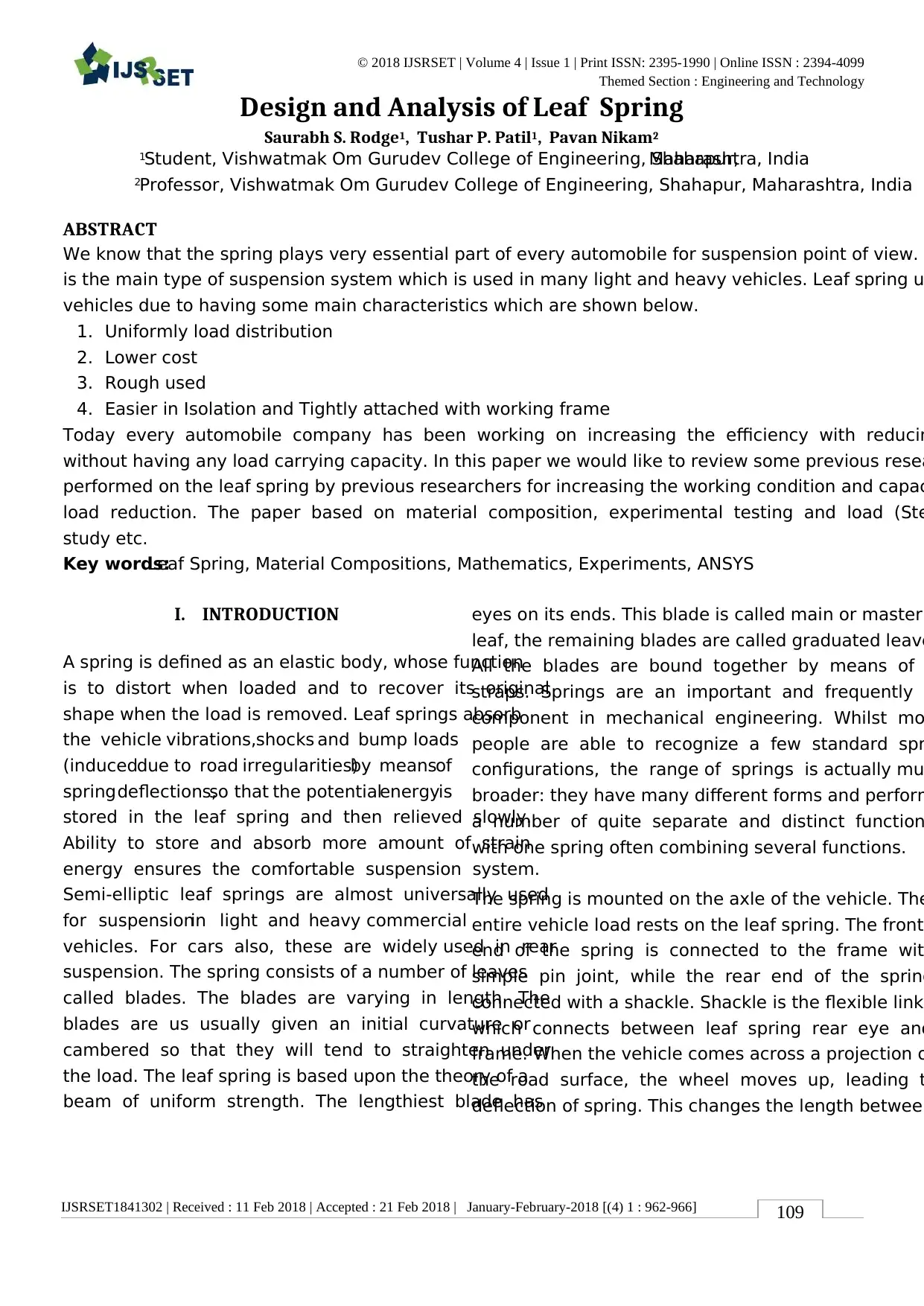
IJSRSET1841302 | Received : 11 Feb 2018 | Accepted : 21 Feb 2018 | January-February-2018 [(4) 1 : 962-966]
© 2018 IJSRSET | Volume 4 | Issue 1 | Print ISSN: 2395-1990 | Online ISSN : 2394-4099
Themed Section : Engineering and Technology
109
Design and Analysis of Leaf Spring
Saurabh S. Rodge1, Tushar P. Patil1, Pavan Nikam2
1Student, Vishwatmak Om Gurudev College of Engineering, Shahapur,Maharashtra, India
2Professor, Vishwatmak Om Gurudev College of Engineering, Shahapur, Maharashtra, India
ABSTRACT
We know that the spring plays very essential part of every automobile for suspension point of view.
is the main type of suspension system which is used in many light and heavy vehicles. Leaf spring u
vehicles due to having some main characteristics which are shown below.
1. Uniformly load distribution
2. Lower cost
3. Rough used
4. Easier in Isolation and Tightly attached with working frame
Today every automobile company has been working on increasing the efficiency with reducin
without having any load carrying capacity. In this paper we would like to review some previous resea
performed on the leaf spring by previous researchers for increasing the working condition and capac
load reduction. The paper based on material composition, experimental testing and load (Ste
study etc.
Key words:Leaf Spring, Material Compositions, Mathematics, Experiments, ANSYS
I. INTRODUCTION
A spring is defined as an elastic body, whose function
is to distort when loaded and to recover its original
shape when the load is removed. Leaf springs absorb
the vehicle vibrations,shocks and bump loads
(induceddue to road irregularities)by meansof
spring deflections,so that the potentialenergyis
stored in the leaf spring and then relieved slowly.
Ability to store and absorb more amount of strain
energy ensures the comfortable suspension system.
Semi-elliptic leaf springs are almost universally used
for suspensionin light and heavy commercial
vehicles. For cars also, these are widely used in rear
suspension. The spring consists of a number of leaves
called blades. The blades are varying in length. The
blades are us usually given an initial curvature or
cambered so that they will tend to straighten under
the load. The leaf spring is based upon the theory of a
beam of uniform strength. The lengthiest blade has
eyes on its ends. This blade is called main or master
leaf, the remaining blades are called graduated leave
All the blades are bound together by means of
straps. Springs are an important and frequently
component in mechanical engineering. Whilst mo
people are able to recognize a few standard spr
configurations, the range of springs is actually mu
broader: they have many different forms and perform
a number of quite separate and distinct function
with one spring often combining several functions.
The spring is mounted on the axle of the vehicle. The
entire vehicle load rests on the leaf spring. The front
end of the spring is connected to the frame wit
simple pin joint, while the rear end of the spring
connected with a shackle. Shackle is the flexible link
which connects between leaf spring rear eye and
frame. When the vehicle comes across a projection o
the road surface, the wheel moves up, leading t
deflection of spring. This changes the length between
© 2018 IJSRSET | Volume 4 | Issue 1 | Print ISSN: 2395-1990 | Online ISSN : 2394-4099
Themed Section : Engineering and Technology
109
Design and Analysis of Leaf Spring
Saurabh S. Rodge1, Tushar P. Patil1, Pavan Nikam2
1Student, Vishwatmak Om Gurudev College of Engineering, Shahapur,Maharashtra, India
2Professor, Vishwatmak Om Gurudev College of Engineering, Shahapur, Maharashtra, India
ABSTRACT
We know that the spring plays very essential part of every automobile for suspension point of view.
is the main type of suspension system which is used in many light and heavy vehicles. Leaf spring u
vehicles due to having some main characteristics which are shown below.
1. Uniformly load distribution
2. Lower cost
3. Rough used
4. Easier in Isolation and Tightly attached with working frame
Today every automobile company has been working on increasing the efficiency with reducin
without having any load carrying capacity. In this paper we would like to review some previous resea
performed on the leaf spring by previous researchers for increasing the working condition and capac
load reduction. The paper based on material composition, experimental testing and load (Ste
study etc.
Key words:Leaf Spring, Material Compositions, Mathematics, Experiments, ANSYS
I. INTRODUCTION
A spring is defined as an elastic body, whose function
is to distort when loaded and to recover its original
shape when the load is removed. Leaf springs absorb
the vehicle vibrations,shocks and bump loads
(induceddue to road irregularities)by meansof
spring deflections,so that the potentialenergyis
stored in the leaf spring and then relieved slowly.
Ability to store and absorb more amount of strain
energy ensures the comfortable suspension system.
Semi-elliptic leaf springs are almost universally used
for suspensionin light and heavy commercial
vehicles. For cars also, these are widely used in rear
suspension. The spring consists of a number of leaves
called blades. The blades are varying in length. The
blades are us usually given an initial curvature or
cambered so that they will tend to straighten under
the load. The leaf spring is based upon the theory of a
beam of uniform strength. The lengthiest blade has
eyes on its ends. This blade is called main or master
leaf, the remaining blades are called graduated leave
All the blades are bound together by means of
straps. Springs are an important and frequently
component in mechanical engineering. Whilst mo
people are able to recognize a few standard spr
configurations, the range of springs is actually mu
broader: they have many different forms and perform
a number of quite separate and distinct function
with one spring often combining several functions.
The spring is mounted on the axle of the vehicle. The
entire vehicle load rests on the leaf spring. The front
end of the spring is connected to the frame wit
simple pin joint, while the rear end of the spring
connected with a shackle. Shackle is the flexible link
which connects between leaf spring rear eye and
frame. When the vehicle comes across a projection o
the road surface, the wheel moves up, leading t
deflection of spring. This changes the length between
Secure Best Marks with AI Grader
Need help grading? Try our AI Grader for instant feedback on your assignments.
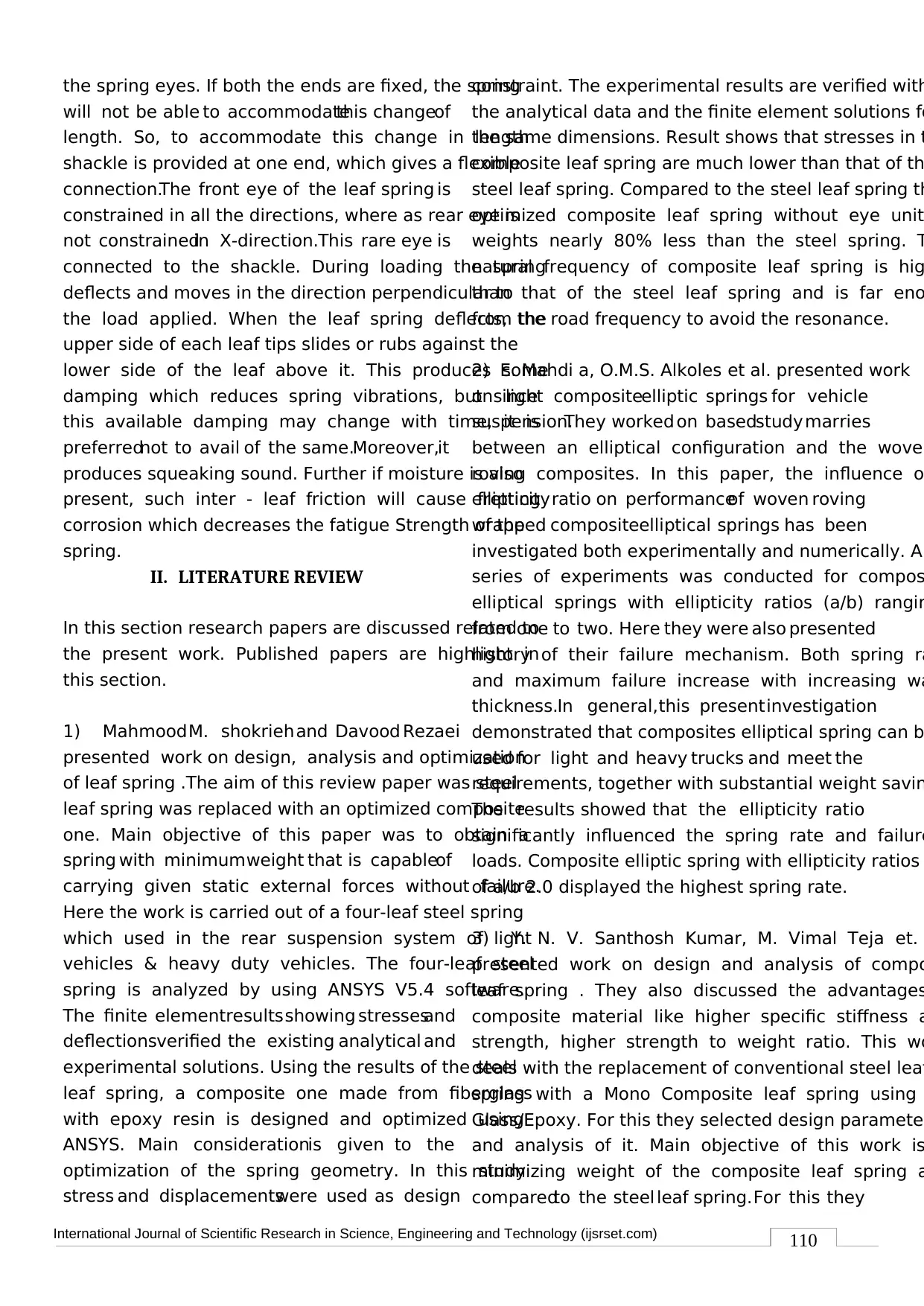
International Journal of Scientific Research in Science, Engineering and Technology (ijsrset.com) 110
the spring eyes. If both the ends are fixed, the spring
will not be able to accommodatethis changeof
length. So, to accommodate this change in length
shackle is provided at one end, which gives a flexible
connection.The front eye of the leaf spring is
constrained in all the directions, where as rear eye is
not constrainedin X-direction.This rare eye is
connected to the shackle. During loading the spring
deflects and moves in the direction perpendicular to
the load applied. When the leaf spring deflects, the
upper side of each leaf tips slides or rubs against the
lower side of the leaf above it. This produces some
damping which reduces spring vibrations, but since
this available damping may change with time, it is
preferrednot to avail of the same.Moreover,it
produces squeaking sound. Further if moisture is also
present, such inter - leaf friction will cause fretting
corrosion which decreases the fatigue Strength of the
spring.
II. LITERATURE REVIEW
In this section research papers are discussed related to
the present work. Published papers are highlight in
this section.
1) Mahmood M. shokrieh and Davood Rezaei
presented work on design, analysis and optimization
of leaf spring .The aim of this review paper was steel
leaf spring was replaced with an optimized composite
one. Main objective of this paper was to obtain a
spring with minimum weight that is capableof
carrying given static external forces without failure.
Here the work is carried out of a four-leaf steel spring
which used in the rear suspension system of light
vehicles & heavy duty vehicles. The four-leaf steel
spring is analyzed by using ANSYS V5.4 software.
The finite elementresults showing stressesand
deflectionsverified the existing analytical and
experimental solutions. Using the results of the steel
leaf spring, a composite one made from fiberglass
with epoxy resin is designed and optimized using
ANSYS. Main considerationis given to the
optimization of the spring geometry. In this study
stress and displacementswere used as design
constraint. The experimental results are verified with
the analytical data and the finite element solutions fo
the same dimensions. Result shows that stresses in t
composite leaf spring are much lower than that of th
steel leaf spring. Compared to the steel leaf spring th
optimized composite leaf spring without eye unit
weights nearly 80% less than the steel spring. T
natural frequency of composite leaf spring is hig
than that of the steel leaf spring and is far eno
from the road frequency to avoid the resonance.
2) E. Mahdi a, O.M.S. Alkoles et al. presented work
on light compositeelliptic springs for vehicle
suspension.They worked on basedstudy marries
between an elliptical configuration and the woven
roving composites. In this paper, the influence o
ellipticity ratio on performanceof woven roving
wrapped compositeelliptical springs has been
investigated both experimentally and numerically. A
series of experiments was conducted for compos
elliptical springs with ellipticity ratios (a/b) rangin
from one to two. Here they were also presented
history of their failure mechanism. Both spring ra
and maximum failure increase with increasing wa
thickness.In general, this present investigation
demonstrated that composites elliptical spring can b
used for light and heavy trucks and meet the
requirements, together with substantial weight savin
The results showed that the ellipticity ratio
significantly influenced the spring rate and failure
loads. Composite elliptic spring with ellipticity ratios
of a/b 2.0 displayed the highest spring rate.
3) Y. N. V. Santhosh Kumar, M. Vimal Teja et.
presented work on design and analysis of compo
leaf spring . They also discussed the advantages
composite material like higher specific stiffness a
strength, higher strength to weight ratio. This wo
deals with the replacement of conventional steel leaf
spring with a Mono Composite leaf spring using
Glass/Epoxy. For this they selected design paramete
and analysis of it. Main objective of this work is
minimizing weight of the composite leaf spring a
comparedto the steel leaf spring. For this they
the spring eyes. If both the ends are fixed, the spring
will not be able to accommodatethis changeof
length. So, to accommodate this change in length
shackle is provided at one end, which gives a flexible
connection.The front eye of the leaf spring is
constrained in all the directions, where as rear eye is
not constrainedin X-direction.This rare eye is
connected to the shackle. During loading the spring
deflects and moves in the direction perpendicular to
the load applied. When the leaf spring deflects, the
upper side of each leaf tips slides or rubs against the
lower side of the leaf above it. This produces some
damping which reduces spring vibrations, but since
this available damping may change with time, it is
preferrednot to avail of the same.Moreover,it
produces squeaking sound. Further if moisture is also
present, such inter - leaf friction will cause fretting
corrosion which decreases the fatigue Strength of the
spring.
II. LITERATURE REVIEW
In this section research papers are discussed related to
the present work. Published papers are highlight in
this section.
1) Mahmood M. shokrieh and Davood Rezaei
presented work on design, analysis and optimization
of leaf spring .The aim of this review paper was steel
leaf spring was replaced with an optimized composite
one. Main objective of this paper was to obtain a
spring with minimum weight that is capableof
carrying given static external forces without failure.
Here the work is carried out of a four-leaf steel spring
which used in the rear suspension system of light
vehicles & heavy duty vehicles. The four-leaf steel
spring is analyzed by using ANSYS V5.4 software.
The finite elementresults showing stressesand
deflectionsverified the existing analytical and
experimental solutions. Using the results of the steel
leaf spring, a composite one made from fiberglass
with epoxy resin is designed and optimized using
ANSYS. Main considerationis given to the
optimization of the spring geometry. In this study
stress and displacementswere used as design
constraint. The experimental results are verified with
the analytical data and the finite element solutions fo
the same dimensions. Result shows that stresses in t
composite leaf spring are much lower than that of th
steel leaf spring. Compared to the steel leaf spring th
optimized composite leaf spring without eye unit
weights nearly 80% less than the steel spring. T
natural frequency of composite leaf spring is hig
than that of the steel leaf spring and is far eno
from the road frequency to avoid the resonance.
2) E. Mahdi a, O.M.S. Alkoles et al. presented work
on light compositeelliptic springs for vehicle
suspension.They worked on basedstudy marries
between an elliptical configuration and the woven
roving composites. In this paper, the influence o
ellipticity ratio on performanceof woven roving
wrapped compositeelliptical springs has been
investigated both experimentally and numerically. A
series of experiments was conducted for compos
elliptical springs with ellipticity ratios (a/b) rangin
from one to two. Here they were also presented
history of their failure mechanism. Both spring ra
and maximum failure increase with increasing wa
thickness.In general, this present investigation
demonstrated that composites elliptical spring can b
used for light and heavy trucks and meet the
requirements, together with substantial weight savin
The results showed that the ellipticity ratio
significantly influenced the spring rate and failure
loads. Composite elliptic spring with ellipticity ratios
of a/b 2.0 displayed the highest spring rate.
3) Y. N. V. Santhosh Kumar, M. Vimal Teja et.
presented work on design and analysis of compo
leaf spring . They also discussed the advantages
composite material like higher specific stiffness a
strength, higher strength to weight ratio. This wo
deals with the replacement of conventional steel leaf
spring with a Mono Composite leaf spring using
Glass/Epoxy. For this they selected design paramete
and analysis of it. Main objective of this work is
minimizing weight of the composite leaf spring a
comparedto the steel leaf spring. For this they
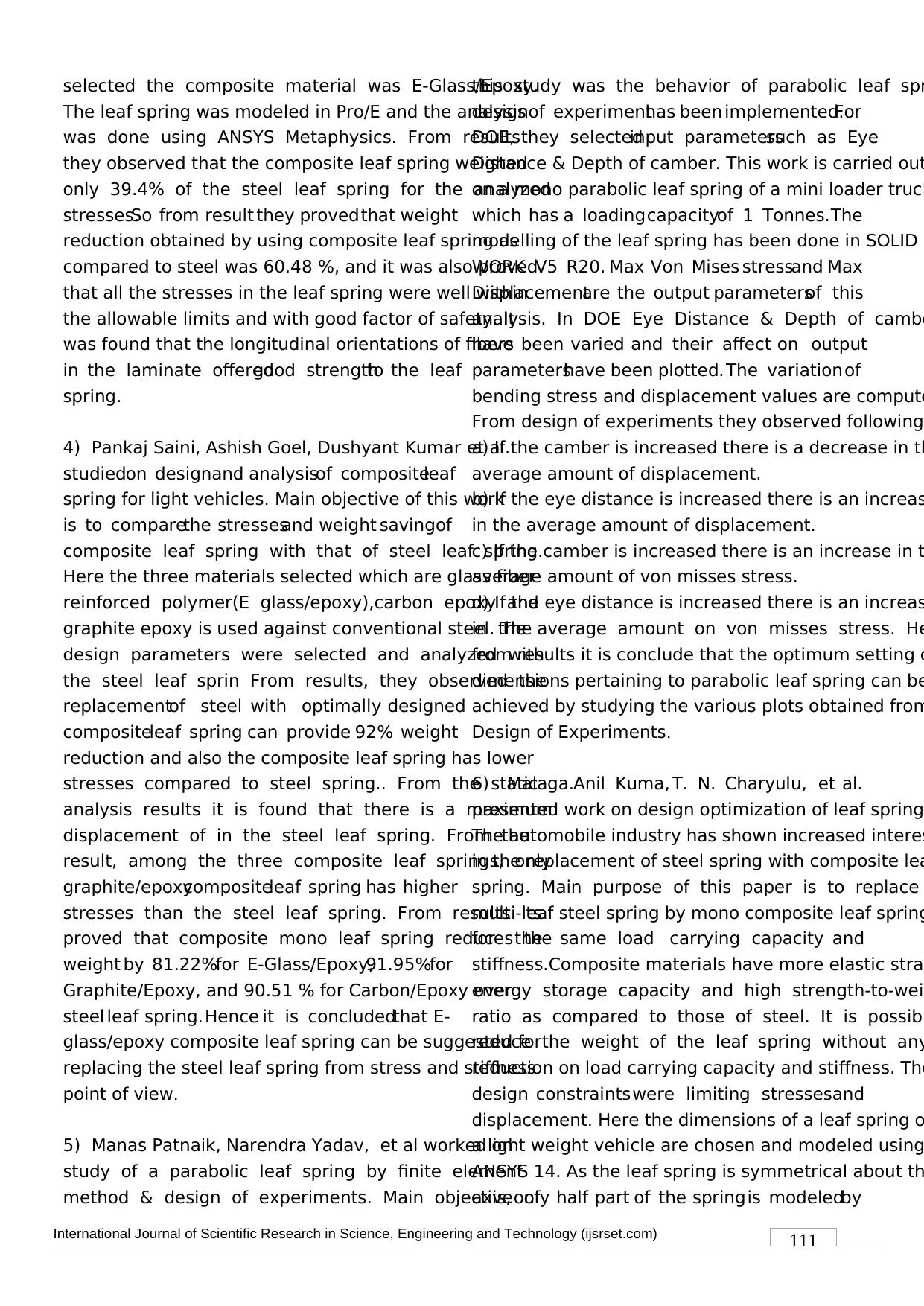
International Journal of Scientific Research in Science, Engineering and Technology (ijsrset.com) 111
selected the composite material was E-Glass/Epoxy.
The leaf spring was modeled in Pro/E and the analysis
was done using ANSYS Metaphysics. From results
they observed that the composite leaf spring weighed
only 39.4% of the steel leaf spring for the analyzed
stresses.So from result they proved that weight
reduction obtained by using composite leaf spring as
compared to steel was 60.48 %, and it was also proved
that all the stresses in the leaf spring were well within
the allowable limits and with good factor of safety. It
was found that the longitudinal orientations of fibers
in the laminate offeredgood strengthto the leaf
spring.
4) Pankaj Saini, Ashish Goel, Dushyant Kumar et al.
studiedon designand analysisof compositeleaf
spring for light vehicles. Main objective of this work
is to comparethe stressesand weight savingof
composite leaf spring with that of steel leaf spring.
Here the three materials selected which are glass fiber
reinforced polymer(E glass/epoxy),carbon epoxy and
graphite epoxy is used against conventional steel. The
design parameters were selected and analyzed with
the steel leaf sprin From results, they observed the
replacementof steel with optimally designed
compositeleaf spring can provide 92% weight
reduction and also the composite leaf spring has lower
stresses compared to steel spring.. From the static
analysis results it is found that there is a maximum
displacement of in the steel leaf spring. From the
result, among the three composite leaf springs, only
graphite/epoxycompositeleaf spring has higher
stresses than the steel leaf spring. From results its
proved that composite mono leaf spring reduces the
weight by 81.22%for E-Glass/Epoxy,91.95%for
Graphite/Epoxy, and 90.51 % for Carbon/Epoxy over
steel leaf spring. Hence it is concludedthat E-
glass/epoxy composite leaf spring can be suggested for
replacing the steel leaf spring from stress and stiffness
point of view.
5) Manas Patnaik, Narendra Yadav, et al worked on
study of a parabolic leaf spring by finite element
method & design of experiments. Main objective of
this study was the behavior of parabolic leaf spr
designof experimenthas been implemented.For
DOE, they selectedinput parameterssuch as Eye
Distance & Depth of camber. This work is carried out
on a mono parabolic leaf spring of a mini loader truck
which has a loading capacityof 1 Tonnes. The
modelling of the leaf spring has been done in SOLID
WORK V5 R20. Max Von Mises stressand Max
Displacementare the output parametersof this
analysis. In DOE Eye Distance & Depth of cambe
have been varied and their affect on output
parametershave been plotted. The variation of
bending stress and displacement values are compute
From design of experiments they observed following
a) If the camber is increased there is a decrease in th
average amount of displacement.
b) If the eye distance is increased there is an increas
in the average amount of displacement.
c) If the camber is increased there is an increase in t
average amount of von misses stress.
d) If the eye distance is increased there is an increas
in the average amount on von misses stress. He
from results it is conclude that the optimum setting o
dimensions pertaining to parabolic leaf spring can be
achieved by studying the various plots obtained from
Design of Experiments.
6) Malaga.Anil Kuma, T. N. Charyulu, et al.
presented work on design optimization of leaf spring
The automobile industry has shown increased interes
in the replacement of steel spring with composite lea
spring. Main purpose of this paper is to replace
multi-leaf steel spring by mono composite leaf spring
for the same load carrying capacity and
stiffness.Composite materials have more elastic stra
energy storage capacity and high strength-to-wei
ratio as compared to those of steel. It is possibl
reduce the weight of the leaf spring without any
reduction on load carrying capacity and stiffness. The
design constraints were limiting stressesand
displacement. Here the dimensions of a leaf spring o
a light weight vehicle are chosen and modeled using
ANSYS 14. As the leaf spring is symmetrical about th
axis, only half part of the spring is modeledby
selected the composite material was E-Glass/Epoxy.
The leaf spring was modeled in Pro/E and the analysis
was done using ANSYS Metaphysics. From results
they observed that the composite leaf spring weighed
only 39.4% of the steel leaf spring for the analyzed
stresses.So from result they proved that weight
reduction obtained by using composite leaf spring as
compared to steel was 60.48 %, and it was also proved
that all the stresses in the leaf spring were well within
the allowable limits and with good factor of safety. It
was found that the longitudinal orientations of fibers
in the laminate offeredgood strengthto the leaf
spring.
4) Pankaj Saini, Ashish Goel, Dushyant Kumar et al.
studiedon designand analysisof compositeleaf
spring for light vehicles. Main objective of this work
is to comparethe stressesand weight savingof
composite leaf spring with that of steel leaf spring.
Here the three materials selected which are glass fiber
reinforced polymer(E glass/epoxy),carbon epoxy and
graphite epoxy is used against conventional steel. The
design parameters were selected and analyzed with
the steel leaf sprin From results, they observed the
replacementof steel with optimally designed
compositeleaf spring can provide 92% weight
reduction and also the composite leaf spring has lower
stresses compared to steel spring.. From the static
analysis results it is found that there is a maximum
displacement of in the steel leaf spring. From the
result, among the three composite leaf springs, only
graphite/epoxycompositeleaf spring has higher
stresses than the steel leaf spring. From results its
proved that composite mono leaf spring reduces the
weight by 81.22%for E-Glass/Epoxy,91.95%for
Graphite/Epoxy, and 90.51 % for Carbon/Epoxy over
steel leaf spring. Hence it is concludedthat E-
glass/epoxy composite leaf spring can be suggested for
replacing the steel leaf spring from stress and stiffness
point of view.
5) Manas Patnaik, Narendra Yadav, et al worked on
study of a parabolic leaf spring by finite element
method & design of experiments. Main objective of
this study was the behavior of parabolic leaf spr
designof experimenthas been implemented.For
DOE, they selectedinput parameterssuch as Eye
Distance & Depth of camber. This work is carried out
on a mono parabolic leaf spring of a mini loader truck
which has a loading capacityof 1 Tonnes. The
modelling of the leaf spring has been done in SOLID
WORK V5 R20. Max Von Mises stressand Max
Displacementare the output parametersof this
analysis. In DOE Eye Distance & Depth of cambe
have been varied and their affect on output
parametershave been plotted. The variation of
bending stress and displacement values are compute
From design of experiments they observed following
a) If the camber is increased there is a decrease in th
average amount of displacement.
b) If the eye distance is increased there is an increas
in the average amount of displacement.
c) If the camber is increased there is an increase in t
average amount of von misses stress.
d) If the eye distance is increased there is an increas
in the average amount on von misses stress. He
from results it is conclude that the optimum setting o
dimensions pertaining to parabolic leaf spring can be
achieved by studying the various plots obtained from
Design of Experiments.
6) Malaga.Anil Kuma, T. N. Charyulu, et al.
presented work on design optimization of leaf spring
The automobile industry has shown increased interes
in the replacement of steel spring with composite lea
spring. Main purpose of this paper is to replace
multi-leaf steel spring by mono composite leaf spring
for the same load carrying capacity and
stiffness.Composite materials have more elastic stra
energy storage capacity and high strength-to-wei
ratio as compared to those of steel. It is possibl
reduce the weight of the leaf spring without any
reduction on load carrying capacity and stiffness. The
design constraints were limiting stressesand
displacement. Here the dimensions of a leaf spring o
a light weight vehicle are chosen and modeled using
ANSYS 14. As the leaf spring is symmetrical about th
axis, only half part of the spring is modeledby
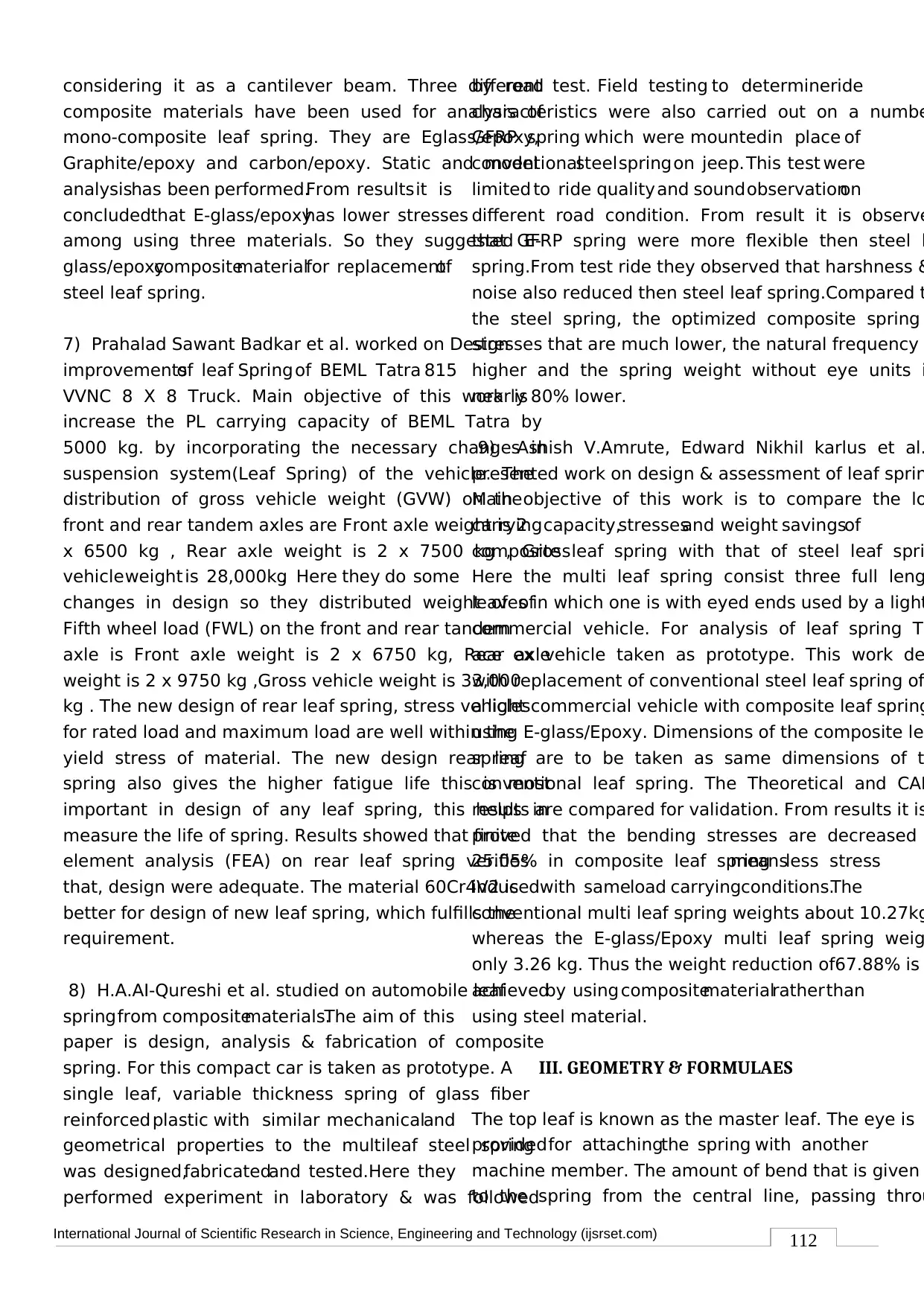
International Journal of Scientific Research in Science, Engineering and Technology (ijsrset.com) 112
considering it as a cantilever beam. Three different
composite materials have been used for analysis of
mono-composite leaf spring. They are Eglass/epoxy,
Graphite/epoxy and carbon/epoxy. Static and model
analysishas been performed.From results it is
concludedthat E-glass/epoxyhas lower stresses
among using three materials. So they suggested E-
glass/epoxycompositematerialfor replacementof
steel leaf spring.
7) Prahalad Sawant Badkar et al. worked on Design
improvementsof leaf Spring of BEML Tatra 815
VVNC 8 X 8 Truck. Main objective of this work is
increase the PL carrying capacity of BEML Tatra by
5000 kg. by incorporating the necessary changes in
suspension system(Leaf Spring) of the vehicle. The
distribution of gross vehicle weight (GVW) on the
front and rear tandem axles are Front axle weight is 2
x 6500 kg , Rear axle weight is 2 x 7500 kg , Gross
vehicle weight is 28,000kg. Here they do some
changes in design so they distributed weight of of
Fifth wheel load (FWL) on the front and rear tandem
axle is Front axle weight is 2 x 6750 kg, Rear axle
weight is 2 x 9750 kg ,Gross vehicle weight is 33,000
kg . The new design of rear leaf spring, stress vehicles
for rated load and maximum load are well within the
yield stress of material. The new design rear leaf
spring also gives the higher fatigue life this is most
important in design of any leaf spring, this helps in
measure the life of spring. Results showed that finite
element analysis (FEA) on rear leaf spring verifies
that, design were adequate. The material 60Cr4V2 is
better for design of new leaf spring, which fulfills the
requirement.
8) H.A.AI-Qureshi et al. studied on automobile leaf
spring from compositematerials.The aim of this
paper is design, analysis & fabrication of composite
spring. For this compact car is taken as prototype. A
single leaf, variable thickness spring of glass fiber
reinforced plastic with similar mechanicaland
geometrical properties to the multileaf steel spring
was designed,fabricatedand tested.Here they
performed experiment in laboratory & was followed
by road test. Field testing to determineride
characteristics were also carried out on a numbe
GFRP spring which were mountedin place of
conventionalsteel spring on jeep. This test were
limited to ride quality and sound observationon
different road condition. From result it is observe
that GFRP spring were more flexible then steel l
spring.From test ride they observed that harshness &
noise also reduced then steel leaf spring.Compared t
the steel spring, the optimized composite spring
stresses that are much lower, the natural frequency
higher and the spring weight without eye units i
nearly 80% lower.
9) Ashish V.Amrute, Edward Nikhil karlus et al.
presented work on design & assessment of leaf sprin
Main objective of this work is to compare the lo
carrying capacity,stressesand weight savingsof
composite leaf spring with that of steel leaf spri
Here the multi leaf spring consist three full leng
leaves in which one is with eyed ends used by a light
commercial vehicle. For analysis of leaf spring Ta
ace ex vehicle taken as prototype. This work de
with replacement of conventional steel leaf spring of
a light commercial vehicle with composite leaf spring
using E-glass/Epoxy. Dimensions of the composite le
spring are to be taken as same dimensions of t
conventional leaf spring. The Theoretical and CAE
results are compared for validation. From results it is
proved that the bending stresses are decreased
25.05% in composite leaf springmeansless stress
inducedwith sameload carryingconditions.The
conventional multi leaf spring weights about 10.27kg
whereas the E-glass/Epoxy multi leaf spring weig
only 3.26 kg. Thus the weight reduction of67.88% is
achievedby using compositematerialrather than
using steel material.
III. GEOMETRY & FORMULAES
The top leaf is known as the master leaf. The eye is
provided for attachingthe spring with another
machine member. The amount of bend that is given
to the spring from the central line, passing throu
considering it as a cantilever beam. Three different
composite materials have been used for analysis of
mono-composite leaf spring. They are Eglass/epoxy,
Graphite/epoxy and carbon/epoxy. Static and model
analysishas been performed.From results it is
concludedthat E-glass/epoxyhas lower stresses
among using three materials. So they suggested E-
glass/epoxycompositematerialfor replacementof
steel leaf spring.
7) Prahalad Sawant Badkar et al. worked on Design
improvementsof leaf Spring of BEML Tatra 815
VVNC 8 X 8 Truck. Main objective of this work is
increase the PL carrying capacity of BEML Tatra by
5000 kg. by incorporating the necessary changes in
suspension system(Leaf Spring) of the vehicle. The
distribution of gross vehicle weight (GVW) on the
front and rear tandem axles are Front axle weight is 2
x 6500 kg , Rear axle weight is 2 x 7500 kg , Gross
vehicle weight is 28,000kg. Here they do some
changes in design so they distributed weight of of
Fifth wheel load (FWL) on the front and rear tandem
axle is Front axle weight is 2 x 6750 kg, Rear axle
weight is 2 x 9750 kg ,Gross vehicle weight is 33,000
kg . The new design of rear leaf spring, stress vehicles
for rated load and maximum load are well within the
yield stress of material. The new design rear leaf
spring also gives the higher fatigue life this is most
important in design of any leaf spring, this helps in
measure the life of spring. Results showed that finite
element analysis (FEA) on rear leaf spring verifies
that, design were adequate. The material 60Cr4V2 is
better for design of new leaf spring, which fulfills the
requirement.
8) H.A.AI-Qureshi et al. studied on automobile leaf
spring from compositematerials.The aim of this
paper is design, analysis & fabrication of composite
spring. For this compact car is taken as prototype. A
single leaf, variable thickness spring of glass fiber
reinforced plastic with similar mechanicaland
geometrical properties to the multileaf steel spring
was designed,fabricatedand tested.Here they
performed experiment in laboratory & was followed
by road test. Field testing to determineride
characteristics were also carried out on a numbe
GFRP spring which were mountedin place of
conventionalsteel spring on jeep. This test were
limited to ride quality and sound observationon
different road condition. From result it is observe
that GFRP spring were more flexible then steel l
spring.From test ride they observed that harshness &
noise also reduced then steel leaf spring.Compared t
the steel spring, the optimized composite spring
stresses that are much lower, the natural frequency
higher and the spring weight without eye units i
nearly 80% lower.
9) Ashish V.Amrute, Edward Nikhil karlus et al.
presented work on design & assessment of leaf sprin
Main objective of this work is to compare the lo
carrying capacity,stressesand weight savingsof
composite leaf spring with that of steel leaf spri
Here the multi leaf spring consist three full leng
leaves in which one is with eyed ends used by a light
commercial vehicle. For analysis of leaf spring Ta
ace ex vehicle taken as prototype. This work de
with replacement of conventional steel leaf spring of
a light commercial vehicle with composite leaf spring
using E-glass/Epoxy. Dimensions of the composite le
spring are to be taken as same dimensions of t
conventional leaf spring. The Theoretical and CAE
results are compared for validation. From results it is
proved that the bending stresses are decreased
25.05% in composite leaf springmeansless stress
inducedwith sameload carryingconditions.The
conventional multi leaf spring weights about 10.27kg
whereas the E-glass/Epoxy multi leaf spring weig
only 3.26 kg. Thus the weight reduction of67.88% is
achievedby using compositematerialrather than
using steel material.
III. GEOMETRY & FORMULAES
The top leaf is known as the master leaf. The eye is
provided for attachingthe spring with another
machine member. The amount of bend that is given
to the spring from the central line, passing throu
Secure Best Marks with AI Grader
Need help grading? Try our AI Grader for instant feedback on your assignments.
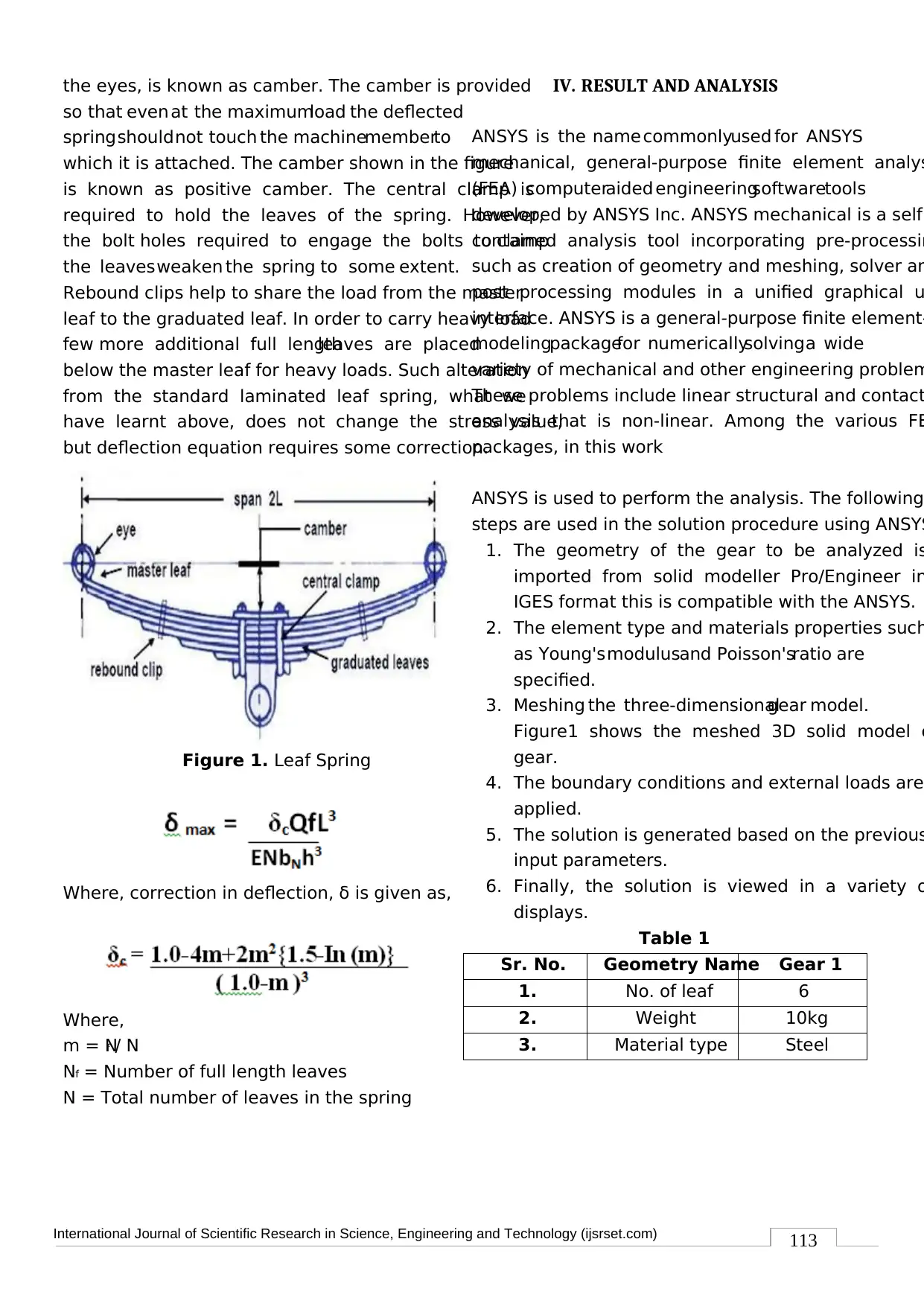
International Journal of Scientific Research in Science, Engineering and Technology (ijsrset.com) 113
the eyes, is known as camber. The camber is provided
so that even at the maximumload the deflected
spring should not touch the machinememberto
which it is attached. The camber shown in the figure
is known as positive camber. The central clamp is
required to hold the leaves of the spring. However,
the bolt holes required to engage the bolts to clamp
the leaves weaken the spring to some extent.
Rebound clips help to share the load from the master
leaf to the graduated leaf. In order to carry heavy load
few more additional full lengthleaves are placed
below the master leaf for heavy loads. Such alteration
from the standard laminated leaf spring, what we
have learnt above, does not change the stress value,
but deflection equation requires some correction.
Figure 1. Leaf Spring
Where, correction in deflection, δ is given as,
Where,
m = Nf / N
Nf = Number of full length leaves
N = Total number of leaves in the spring
IV. RESULT AND ANALYSIS
ANSYS is the name commonlyused for ANSYS
mechanical, general-purpose finite element analys
(FEA) computeraided engineeringsoftwaretools
developed by ANSYS Inc. ANSYS mechanical is a self
contained analysis tool incorporating pre-processin
such as creation of geometry and meshing, solver an
post processing modules in a unified graphical u
interface. ANSYS is a general-purpose finite element-
modelingpackagefor numericallysolving a wide
variety of mechanical and other engineering problem
These problems include linear structural and contact
analysis that is non-linear. Among the various FE
packages, in this work
ANSYS is used to perform the analysis. The following
steps are used in the solution procedure using ANSYS
1. The geometry of the gear to be analyzed is
imported from solid modeller Pro/Engineer in
IGES format this is compatible with the ANSYS.
2. The element type and materials properties such
as Young's modulusand Poisson'sratio are
specified.
3. Meshing the three-dimensionalgear model.
Figure1 shows the meshed 3D solid model o
gear.
4. The boundary conditions and external loads are
applied.
5. The solution is generated based on the previous
input parameters.
6. Finally, the solution is viewed in a variety o
displays.
Table 1
Sr. No. Geometry Name Gear 1
1. No. of leaf 6
2. Weight 10kg
3. Material type Steel
the eyes, is known as camber. The camber is provided
so that even at the maximumload the deflected
spring should not touch the machinememberto
which it is attached. The camber shown in the figure
is known as positive camber. The central clamp is
required to hold the leaves of the spring. However,
the bolt holes required to engage the bolts to clamp
the leaves weaken the spring to some extent.
Rebound clips help to share the load from the master
leaf to the graduated leaf. In order to carry heavy load
few more additional full lengthleaves are placed
below the master leaf for heavy loads. Such alteration
from the standard laminated leaf spring, what we
have learnt above, does not change the stress value,
but deflection equation requires some correction.
Figure 1. Leaf Spring
Where, correction in deflection, δ is given as,
Where,
m = Nf / N
Nf = Number of full length leaves
N = Total number of leaves in the spring
IV. RESULT AND ANALYSIS
ANSYS is the name commonlyused for ANSYS
mechanical, general-purpose finite element analys
(FEA) computeraided engineeringsoftwaretools
developed by ANSYS Inc. ANSYS mechanical is a self
contained analysis tool incorporating pre-processin
such as creation of geometry and meshing, solver an
post processing modules in a unified graphical u
interface. ANSYS is a general-purpose finite element-
modelingpackagefor numericallysolving a wide
variety of mechanical and other engineering problem
These problems include linear structural and contact
analysis that is non-linear. Among the various FE
packages, in this work
ANSYS is used to perform the analysis. The following
steps are used in the solution procedure using ANSYS
1. The geometry of the gear to be analyzed is
imported from solid modeller Pro/Engineer in
IGES format this is compatible with the ANSYS.
2. The element type and materials properties such
as Young's modulusand Poisson'sratio are
specified.
3. Meshing the three-dimensionalgear model.
Figure1 shows the meshed 3D solid model o
gear.
4. The boundary conditions and external loads are
applied.
5. The solution is generated based on the previous
input parameters.
6. Finally, the solution is viewed in a variety o
displays.
Table 1
Sr. No. Geometry Name Gear 1
1. No. of leaf 6
2. Weight 10kg
3. Material type Steel
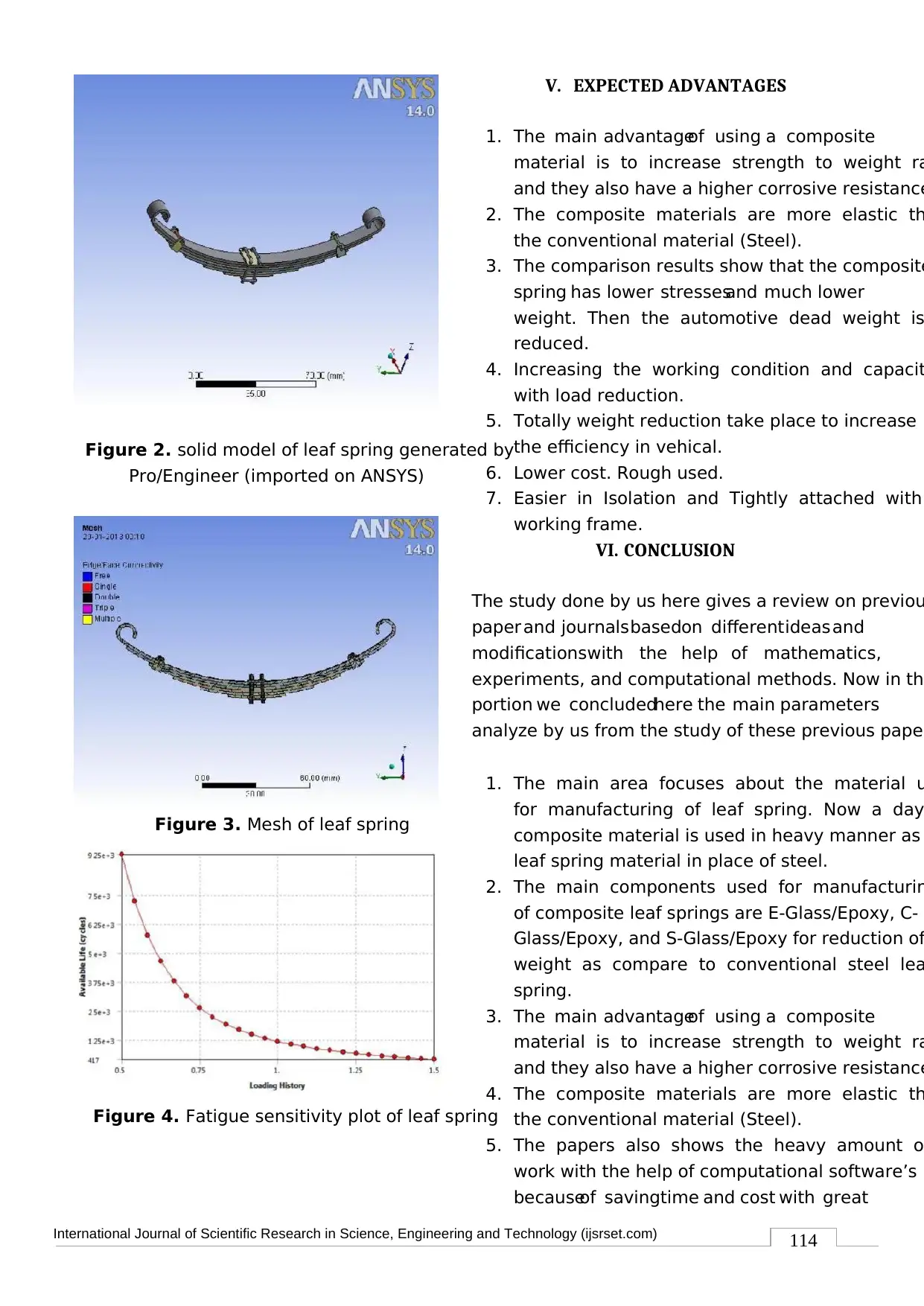
International Journal of Scientific Research in Science, Engineering and Technology (ijsrset.com) 114
Figure 2. solid model of leaf spring generated by
Pro/Engineer (imported on ANSYS)
Figure 3. Mesh of leaf spring
Figure 4. Fatigue sensitivity plot of leaf spring
V. EXPECTED ADVANTAGES
1. The main advantageof using a composite
material is to increase strength to weight ra
and they also have a higher corrosive resistance
2. The composite materials are more elastic th
the conventional material (Steel).
3. The comparison results show that the composite
spring has lower stressesand much lower
weight. Then the automotive dead weight is
reduced.
4. Increasing the working condition and capacit
with load reduction.
5. Totally weight reduction take place to increase
the efficiency in vehical.
6. Lower cost. Rough used.
7. Easier in Isolation and Tightly attached with
working frame.
VI. CONCLUSION
The study done by us here gives a review on previou
paper and journals basedon different ideas and
modificationswith the help of mathematics,
experiments, and computational methods. Now in th
portion we concludedhere the main parameters
analyze by us from the study of these previous paper
1. The main area focuses about the material u
for manufacturing of leaf spring. Now a day
composite material is used in heavy manner as
leaf spring material in place of steel.
2. The main components used for manufacturin
of composite leaf springs are E-Glass/Epoxy, C-
Glass/Epoxy, and S-Glass/Epoxy for reduction of
weight as compare to conventional steel lea
spring.
3. The main advantageof using a composite
material is to increase strength to weight ra
and they also have a higher corrosive resistance
4. The composite materials are more elastic th
the conventional material (Steel).
5. The papers also shows the heavy amount o
work with the help of computational software’s
becauseof savingtime and cost with great
Figure 2. solid model of leaf spring generated by
Pro/Engineer (imported on ANSYS)
Figure 3. Mesh of leaf spring
Figure 4. Fatigue sensitivity plot of leaf spring
V. EXPECTED ADVANTAGES
1. The main advantageof using a composite
material is to increase strength to weight ra
and they also have a higher corrosive resistance
2. The composite materials are more elastic th
the conventional material (Steel).
3. The comparison results show that the composite
spring has lower stressesand much lower
weight. Then the automotive dead weight is
reduced.
4. Increasing the working condition and capacit
with load reduction.
5. Totally weight reduction take place to increase
the efficiency in vehical.
6. Lower cost. Rough used.
7. Easier in Isolation and Tightly attached with
working frame.
VI. CONCLUSION
The study done by us here gives a review on previou
paper and journals basedon different ideas and
modificationswith the help of mathematics,
experiments, and computational methods. Now in th
portion we concludedhere the main parameters
analyze by us from the study of these previous paper
1. The main area focuses about the material u
for manufacturing of leaf spring. Now a day
composite material is used in heavy manner as
leaf spring material in place of steel.
2. The main components used for manufacturin
of composite leaf springs are E-Glass/Epoxy, C-
Glass/Epoxy, and S-Glass/Epoxy for reduction of
weight as compare to conventional steel lea
spring.
3. The main advantageof using a composite
material is to increase strength to weight ra
and they also have a higher corrosive resistance
4. The composite materials are more elastic th
the conventional material (Steel).
5. The papers also shows the heavy amount o
work with the help of computational software’s
becauseof savingtime and cost with great
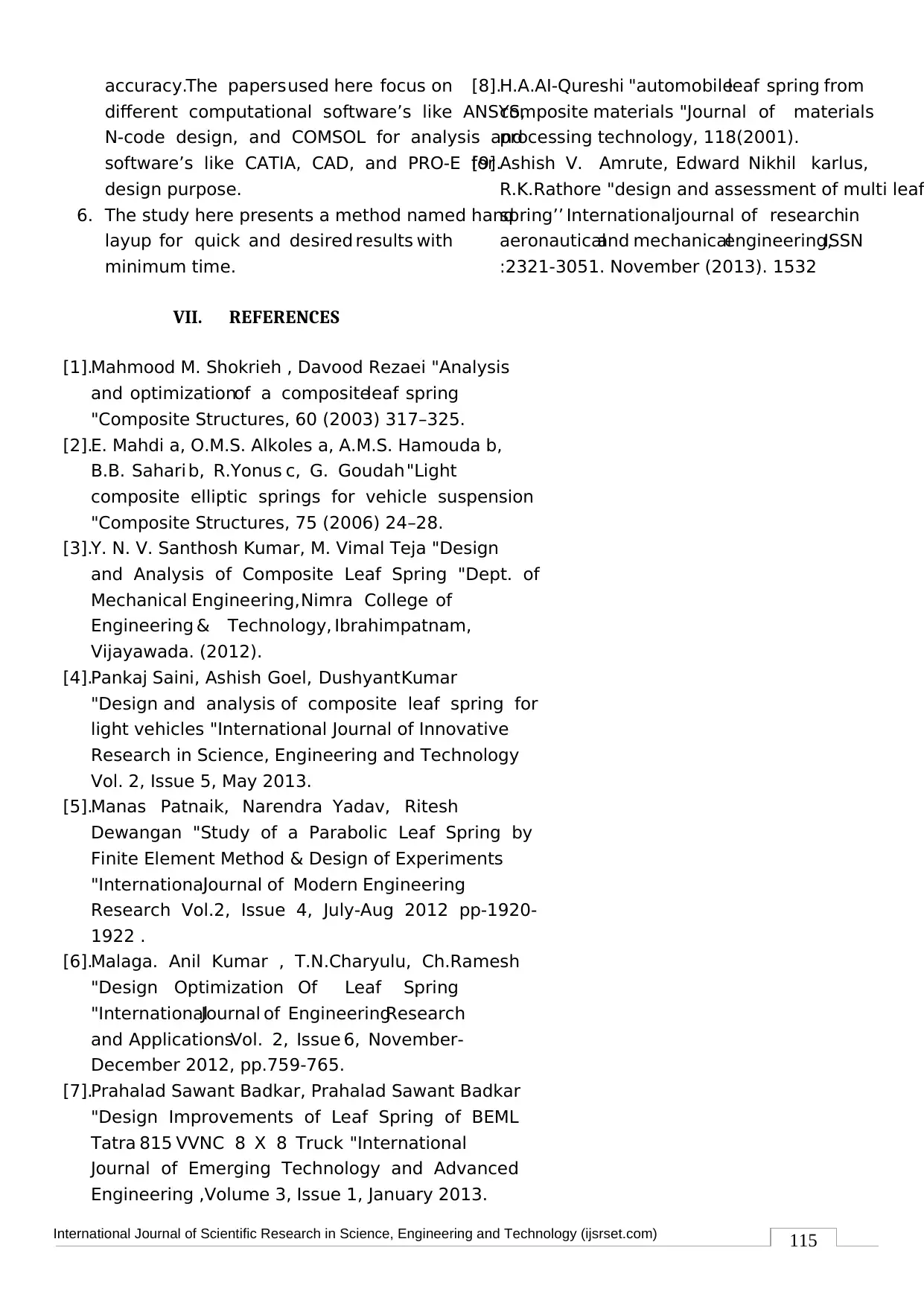
International Journal of Scientific Research in Science, Engineering and Technology (ijsrset.com) 115
accuracy.The papers used here focus on
different computational software’s like ANSYS,
N-code design, and COMSOL for analysis and
software’s like CATIA, CAD, and PRO-E for
design purpose.
6. The study here presents a method named hand
layup for quick and desired results with
minimum time.
VII. REFERENCES
[1].Mahmood M. Shokrieh , Davood Rezaei "Analysis
and optimizationof a compositeleaf spring
"Composite Structures, 60 (2003) 317–325.
[2].E. Mahdi a, O.M.S. Alkoles a, A.M.S. Hamouda b,
B.B. Sahari b, R.Yonus c, G. Goudah "Light
composite elliptic springs for vehicle suspension
"Composite Structures, 75 (2006) 24–28.
[3].Y. N. V. Santhosh Kumar, M. Vimal Teja "Design
and Analysis of Composite Leaf Spring "Dept. of
Mechanical Engineering, Nimra College of
Engineering & Technology, Ibrahimpatnam,
Vijayawada. (2012).
[4].Pankaj Saini, Ashish Goel, Dushyant Kumar
"Design and analysis of composite leaf spring for
light vehicles "International Journal of Innovative
Research in Science, Engineering and Technology
Vol. 2, Issue 5, May 2013.
[5].Manas Patnaik, Narendra Yadav, Ritesh
Dewangan "Study of a Parabolic Leaf Spring by
Finite Element Method & Design of Experiments
"InternationalJournal of Modern Engineering
Research Vol.2, Issue 4, July-Aug 2012 pp-1920-
1922 .
[6].Malaga. Anil Kumar , T.N.Charyulu, Ch.Ramesh
"Design Optimization Of Leaf Spring
"InternationalJournal of EngineeringResearch
and ApplicationsVol. 2, Issue 6, November-
December 2012, pp.759-765.
[7].Prahalad Sawant Badkar, Prahalad Sawant Badkar
"Design Improvements of Leaf Spring of BEML
Tatra 815 VVNC 8 X 8 Truck "International
Journal of Emerging Technology and Advanced
Engineering ,Volume 3, Issue 1, January 2013.
[8].H.A.AI-Qureshi "automobileleaf spring from
composite materials "Journal of materials
processing technology, 118(2001).
[9].Ashish V. Amrute, Edward Nikhil karlus,
R.K.Rathore "design and assessment of multi leaf
spring’’ Internationaljournal of researchin
aeronauticaland mechanicalengineering,ISSN
:2321-3051. November (2013). 1532
accuracy.The papers used here focus on
different computational software’s like ANSYS,
N-code design, and COMSOL for analysis and
software’s like CATIA, CAD, and PRO-E for
design purpose.
6. The study here presents a method named hand
layup for quick and desired results with
minimum time.
VII. REFERENCES
[1].Mahmood M. Shokrieh , Davood Rezaei "Analysis
and optimizationof a compositeleaf spring
"Composite Structures, 60 (2003) 317–325.
[2].E. Mahdi a, O.M.S. Alkoles a, A.M.S. Hamouda b,
B.B. Sahari b, R.Yonus c, G. Goudah "Light
composite elliptic springs for vehicle suspension
"Composite Structures, 75 (2006) 24–28.
[3].Y. N. V. Santhosh Kumar, M. Vimal Teja "Design
and Analysis of Composite Leaf Spring "Dept. of
Mechanical Engineering, Nimra College of
Engineering & Technology, Ibrahimpatnam,
Vijayawada. (2012).
[4].Pankaj Saini, Ashish Goel, Dushyant Kumar
"Design and analysis of composite leaf spring for
light vehicles "International Journal of Innovative
Research in Science, Engineering and Technology
Vol. 2, Issue 5, May 2013.
[5].Manas Patnaik, Narendra Yadav, Ritesh
Dewangan "Study of a Parabolic Leaf Spring by
Finite Element Method & Design of Experiments
"InternationalJournal of Modern Engineering
Research Vol.2, Issue 4, July-Aug 2012 pp-1920-
1922 .
[6].Malaga. Anil Kumar , T.N.Charyulu, Ch.Ramesh
"Design Optimization Of Leaf Spring
"InternationalJournal of EngineeringResearch
and ApplicationsVol. 2, Issue 6, November-
December 2012, pp.759-765.
[7].Prahalad Sawant Badkar, Prahalad Sawant Badkar
"Design Improvements of Leaf Spring of BEML
Tatra 815 VVNC 8 X 8 Truck "International
Journal of Emerging Technology and Advanced
Engineering ,Volume 3, Issue 1, January 2013.
[8].H.A.AI-Qureshi "automobileleaf spring from
composite materials "Journal of materials
processing technology, 118(2001).
[9].Ashish V. Amrute, Edward Nikhil karlus,
R.K.Rathore "design and assessment of multi leaf
spring’’ Internationaljournal of researchin
aeronauticaland mechanicalengineering,ISSN
:2321-3051. November (2013). 1532
1 out of 7
Related Documents
![[object Object]](/_next/image/?url=%2F_next%2Fstatic%2Fmedia%2Flogo.6d15ce61.png&w=640&q=75)
Your All-in-One AI-Powered Toolkit for Academic Success.
+13062052269
info@desklib.com
Available 24*7 on WhatsApp / Email
Unlock your academic potential
© 2024 | Zucol Services PVT LTD | All rights reserved.