Lean and Agile Manufacturing: Complementary
VerifiedAdded on 2022/09/06
|10
|2122
|20
AI Summary
Contribute Materials
Your contribution can guide someone’s learning journey. Share your
documents today.
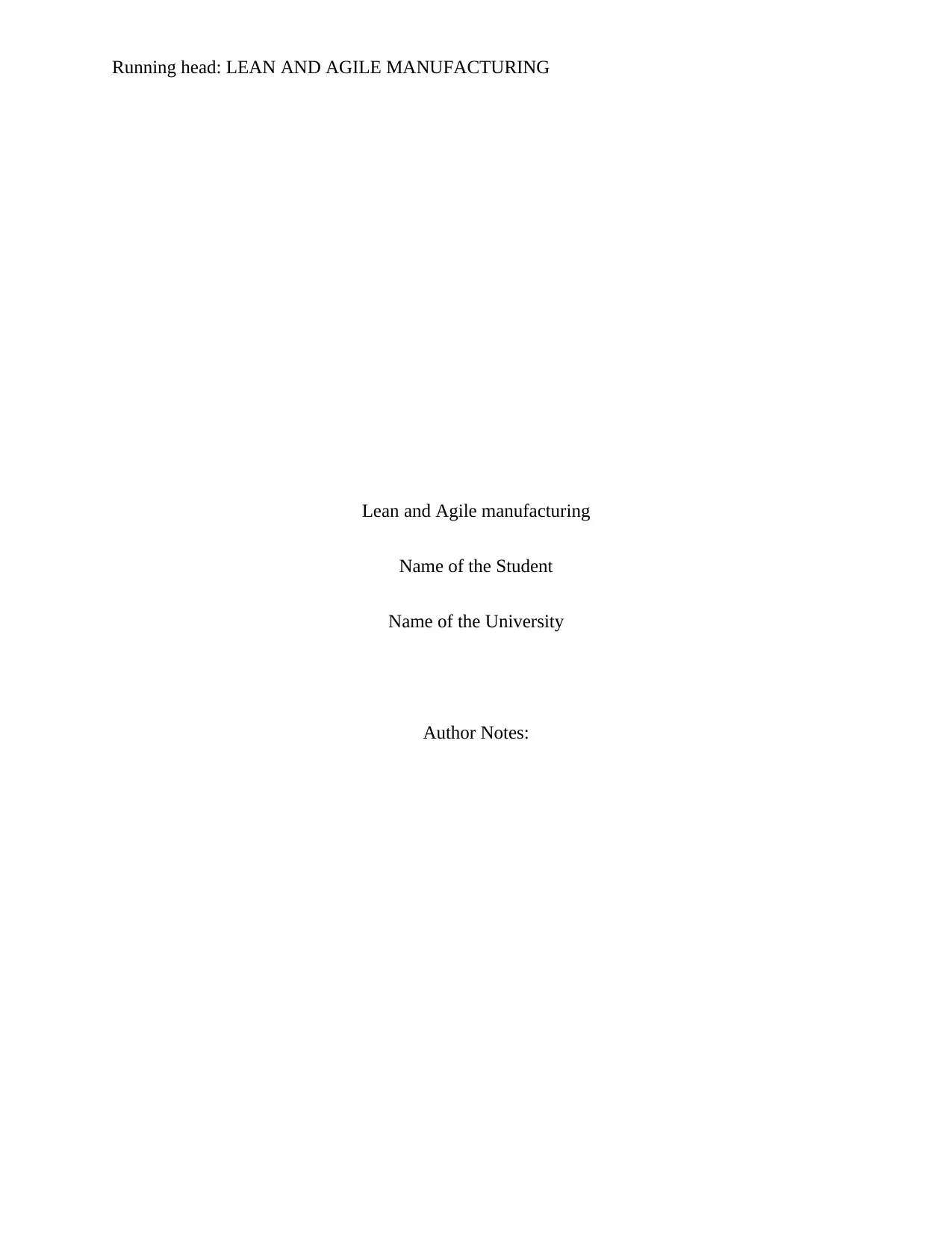
Running head: LEAN AND AGILE MANUFACTURING
Lean and Agile manufacturing
Name of the Student
Name of the University
Author Notes:
Lean and Agile manufacturing
Name of the Student
Name of the University
Author Notes:
Secure Best Marks with AI Grader
Need help grading? Try our AI Grader for instant feedback on your assignments.
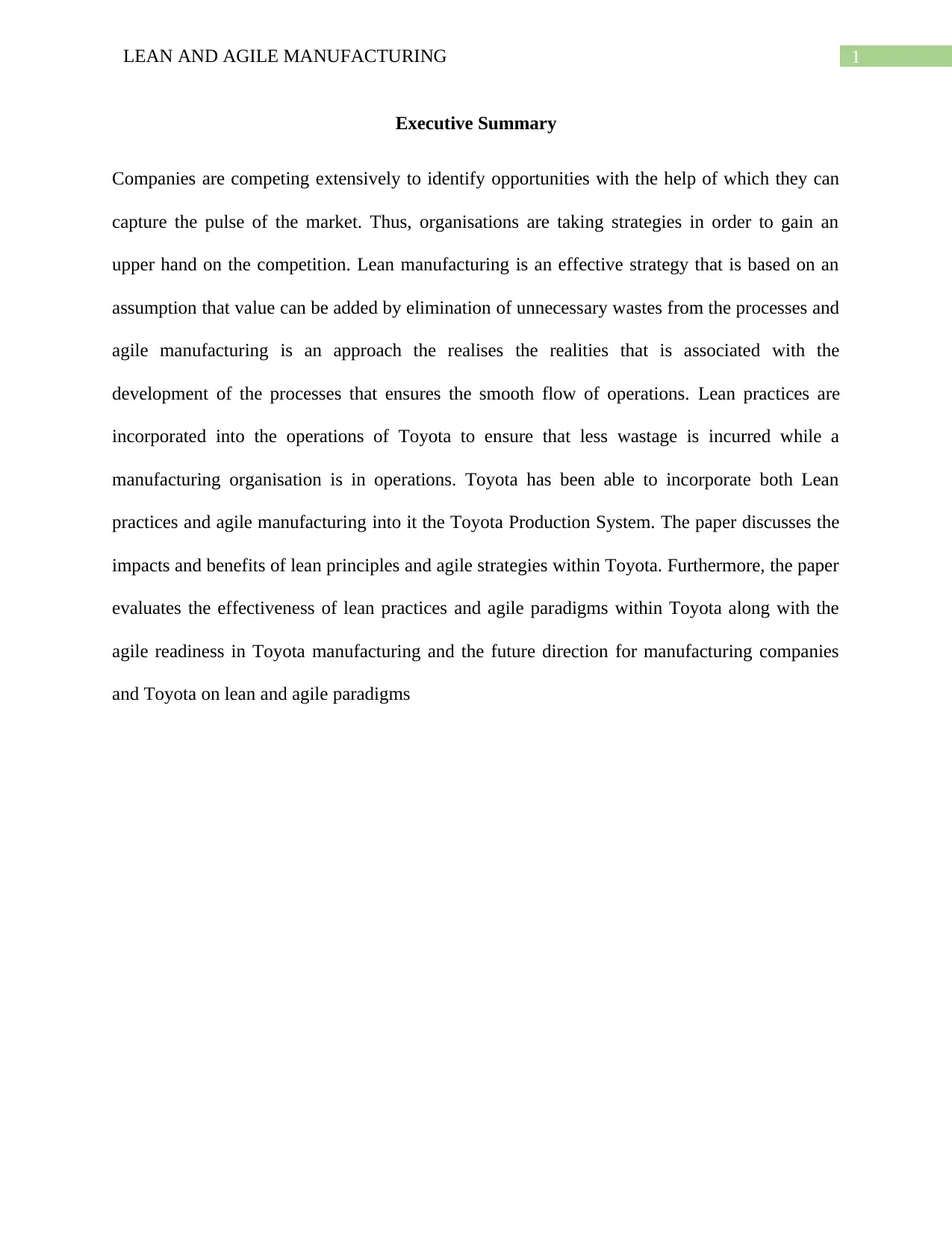
1LEAN AND AGILE MANUFACTURING
Executive Summary
Companies are competing extensively to identify opportunities with the help of which they can
capture the pulse of the market. Thus, organisations are taking strategies in order to gain an
upper hand on the competition. Lean manufacturing is an effective strategy that is based on an
assumption that value can be added by elimination of unnecessary wastes from the processes and
agile manufacturing is an approach the realises the realities that is associated with the
development of the processes that ensures the smooth flow of operations. Lean practices are
incorporated into the operations of Toyota to ensure that less wastage is incurred while a
manufacturing organisation is in operations. Toyota has been able to incorporate both Lean
practices and agile manufacturing into it the Toyota Production System. The paper discusses the
impacts and benefits of lean principles and agile strategies within Toyota. Furthermore, the paper
evaluates the effectiveness of lean practices and agile paradigms within Toyota along with the
agile readiness in Toyota manufacturing and the future direction for manufacturing companies
and Toyota on lean and agile paradigms
Executive Summary
Companies are competing extensively to identify opportunities with the help of which they can
capture the pulse of the market. Thus, organisations are taking strategies in order to gain an
upper hand on the competition. Lean manufacturing is an effective strategy that is based on an
assumption that value can be added by elimination of unnecessary wastes from the processes and
agile manufacturing is an approach the realises the realities that is associated with the
development of the processes that ensures the smooth flow of operations. Lean practices are
incorporated into the operations of Toyota to ensure that less wastage is incurred while a
manufacturing organisation is in operations. Toyota has been able to incorporate both Lean
practices and agile manufacturing into it the Toyota Production System. The paper discusses the
impacts and benefits of lean principles and agile strategies within Toyota. Furthermore, the paper
evaluates the effectiveness of lean practices and agile paradigms within Toyota along with the
agile readiness in Toyota manufacturing and the future direction for manufacturing companies
and Toyota on lean and agile paradigms
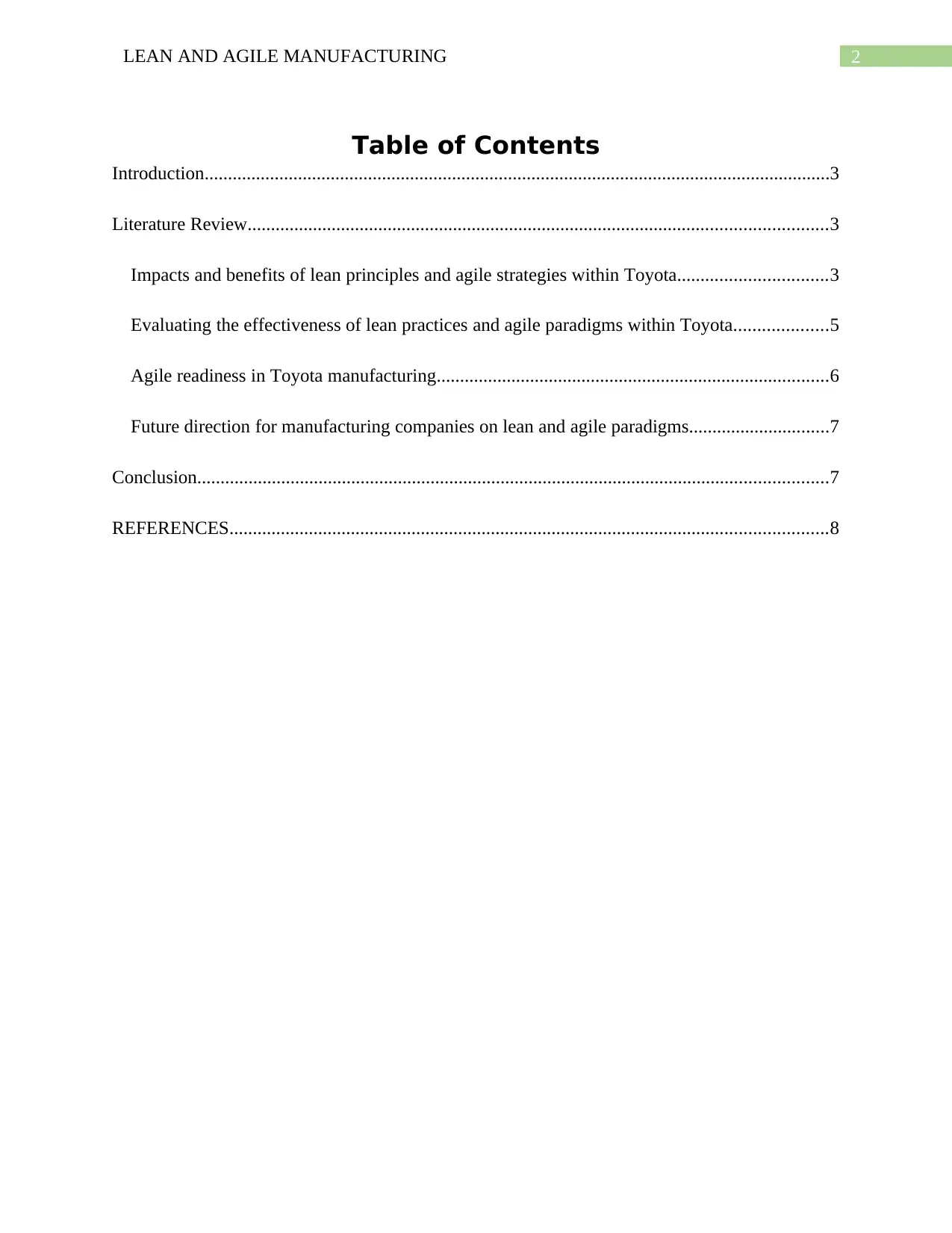
2LEAN AND AGILE MANUFACTURING
Table of Contents
Introduction......................................................................................................................................3
Literature Review............................................................................................................................3
Impacts and benefits of lean principles and agile strategies within Toyota................................3
Evaluating the effectiveness of lean practices and agile paradigms within Toyota....................5
Agile readiness in Toyota manufacturing....................................................................................6
Future direction for manufacturing companies on lean and agile paradigms..............................7
Conclusion.......................................................................................................................................7
REFERENCES................................................................................................................................8
Table of Contents
Introduction......................................................................................................................................3
Literature Review............................................................................................................................3
Impacts and benefits of lean principles and agile strategies within Toyota................................3
Evaluating the effectiveness of lean practices and agile paradigms within Toyota....................5
Agile readiness in Toyota manufacturing....................................................................................6
Future direction for manufacturing companies on lean and agile paradigms..............................7
Conclusion.......................................................................................................................................7
REFERENCES................................................................................................................................8
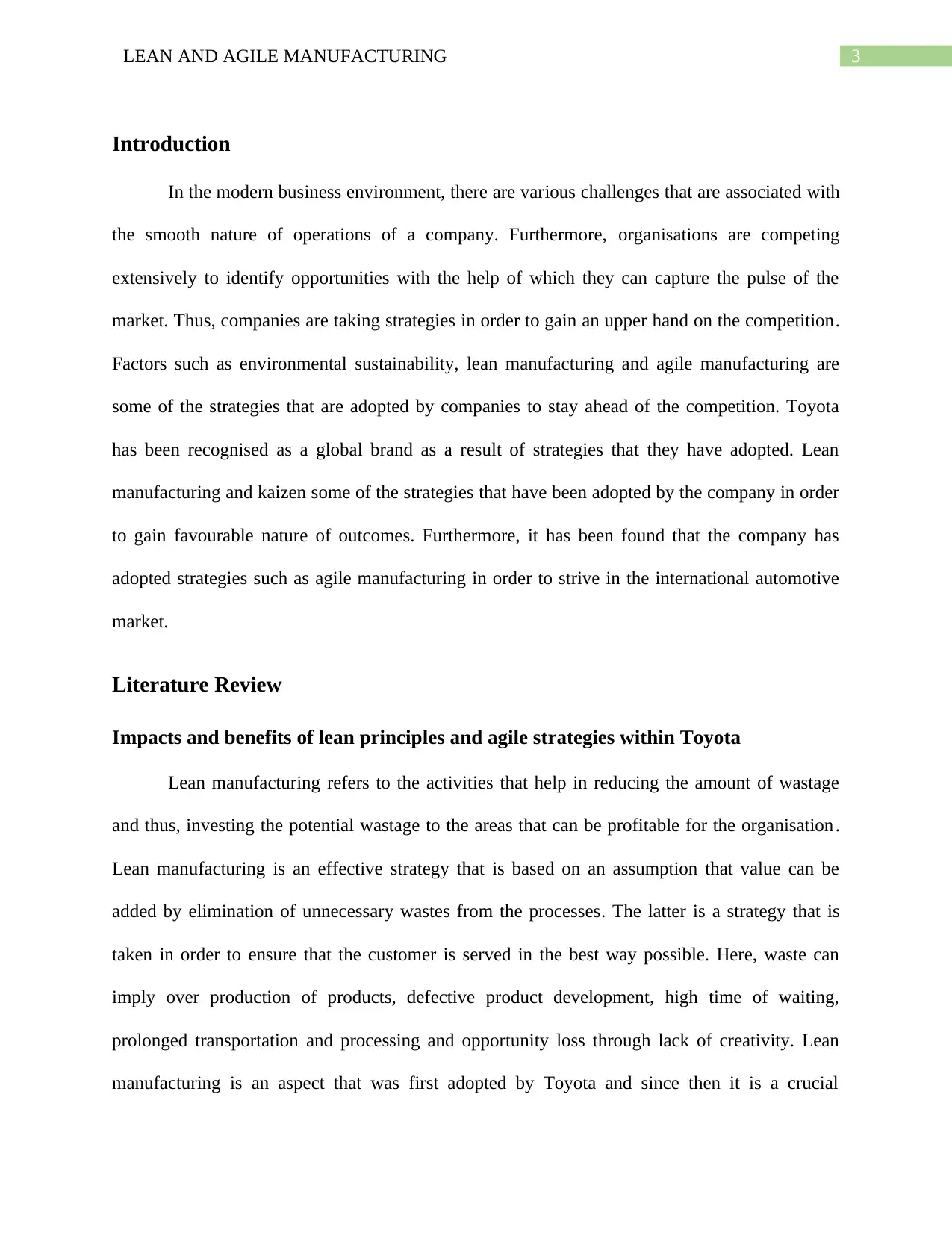
3LEAN AND AGILE MANUFACTURING
Introduction
In the modern business environment, there are various challenges that are associated with
the smooth nature of operations of a company. Furthermore, organisations are competing
extensively to identify opportunities with the help of which they can capture the pulse of the
market. Thus, companies are taking strategies in order to gain an upper hand on the competition.
Factors such as environmental sustainability, lean manufacturing and agile manufacturing are
some of the strategies that are adopted by companies to stay ahead of the competition. Toyota
has been recognised as a global brand as a result of strategies that they have adopted. Lean
manufacturing and kaizen some of the strategies that have been adopted by the company in order
to gain favourable nature of outcomes. Furthermore, it has been found that the company has
adopted strategies such as agile manufacturing in order to strive in the international automotive
market.
Literature Review
Impacts and benefits of lean principles and agile strategies within Toyota
Lean manufacturing refers to the activities that help in reducing the amount of wastage
and thus, investing the potential wastage to the areas that can be profitable for the organisation.
Lean manufacturing is an effective strategy that is based on an assumption that value can be
added by elimination of unnecessary wastes from the processes. The latter is a strategy that is
taken in order to ensure that the customer is served in the best way possible. Here, waste can
imply over production of products, defective product development, high time of waiting,
prolonged transportation and processing and opportunity loss through lack of creativity. Lean
manufacturing is an aspect that was first adopted by Toyota and since then it is a crucial
Introduction
In the modern business environment, there are various challenges that are associated with
the smooth nature of operations of a company. Furthermore, organisations are competing
extensively to identify opportunities with the help of which they can capture the pulse of the
market. Thus, companies are taking strategies in order to gain an upper hand on the competition.
Factors such as environmental sustainability, lean manufacturing and agile manufacturing are
some of the strategies that are adopted by companies to stay ahead of the competition. Toyota
has been recognised as a global brand as a result of strategies that they have adopted. Lean
manufacturing and kaizen some of the strategies that have been adopted by the company in order
to gain favourable nature of outcomes. Furthermore, it has been found that the company has
adopted strategies such as agile manufacturing in order to strive in the international automotive
market.
Literature Review
Impacts and benefits of lean principles and agile strategies within Toyota
Lean manufacturing refers to the activities that help in reducing the amount of wastage
and thus, investing the potential wastage to the areas that can be profitable for the organisation.
Lean manufacturing is an effective strategy that is based on an assumption that value can be
added by elimination of unnecessary wastes from the processes. The latter is a strategy that is
taken in order to ensure that the customer is served in the best way possible. Here, waste can
imply over production of products, defective product development, high time of waiting,
prolonged transportation and processing and opportunity loss through lack of creativity. Lean
manufacturing is an aspect that was first adopted by Toyota and since then it is a crucial
Secure Best Marks with AI Grader
Need help grading? Try our AI Grader for instant feedback on your assignments.
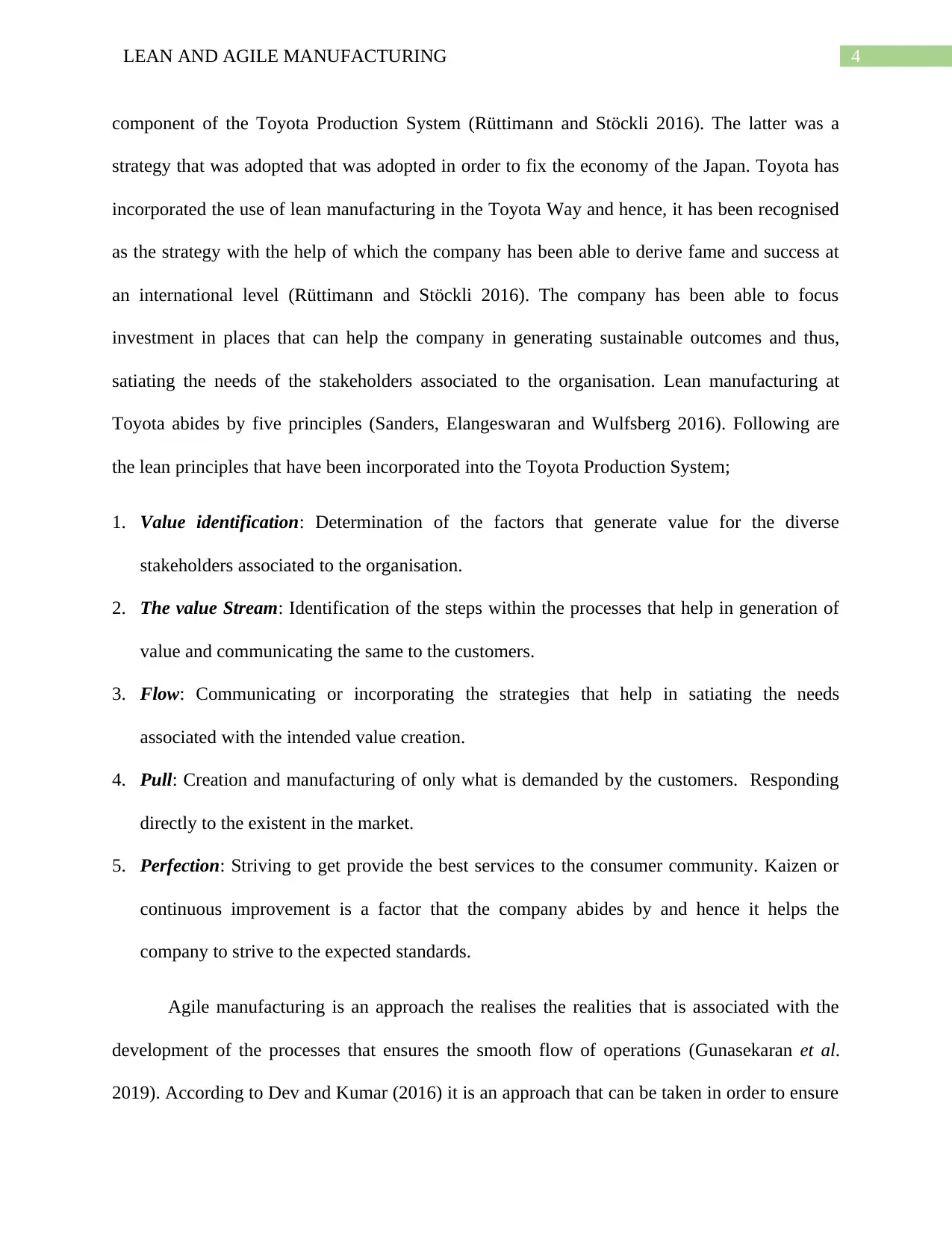
4LEAN AND AGILE MANUFACTURING
component of the Toyota Production System (Rüttimann and Stöckli 2016). The latter was a
strategy that was adopted that was adopted in order to fix the economy of the Japan. Toyota has
incorporated the use of lean manufacturing in the Toyota Way and hence, it has been recognised
as the strategy with the help of which the company has been able to derive fame and success at
an international level (Rüttimann and Stöckli 2016). The company has been able to focus
investment in places that can help the company in generating sustainable outcomes and thus,
satiating the needs of the stakeholders associated to the organisation. Lean manufacturing at
Toyota abides by five principles (Sanders, Elangeswaran and Wulfsberg 2016). Following are
the lean principles that have been incorporated into the Toyota Production System;
1. Value identification: Determination of the factors that generate value for the diverse
stakeholders associated to the organisation.
2. The value Stream: Identification of the steps within the processes that help in generation of
value and communicating the same to the customers.
3. Flow: Communicating or incorporating the strategies that help in satiating the needs
associated with the intended value creation.
4. Pull: Creation and manufacturing of only what is demanded by the customers. Responding
directly to the existent in the market.
5. Perfection: Striving to get provide the best services to the consumer community. Kaizen or
continuous improvement is a factor that the company abides by and hence it helps the
company to strive to the expected standards.
Agile manufacturing is an approach the realises the realities that is associated with the
development of the processes that ensures the smooth flow of operations (Gunasekaran et al.
2019). According to Dev and Kumar (2016) it is an approach that can be taken in order to ensure
component of the Toyota Production System (Rüttimann and Stöckli 2016). The latter was a
strategy that was adopted that was adopted in order to fix the economy of the Japan. Toyota has
incorporated the use of lean manufacturing in the Toyota Way and hence, it has been recognised
as the strategy with the help of which the company has been able to derive fame and success at
an international level (Rüttimann and Stöckli 2016). The company has been able to focus
investment in places that can help the company in generating sustainable outcomes and thus,
satiating the needs of the stakeholders associated to the organisation. Lean manufacturing at
Toyota abides by five principles (Sanders, Elangeswaran and Wulfsberg 2016). Following are
the lean principles that have been incorporated into the Toyota Production System;
1. Value identification: Determination of the factors that generate value for the diverse
stakeholders associated to the organisation.
2. The value Stream: Identification of the steps within the processes that help in generation of
value and communicating the same to the customers.
3. Flow: Communicating or incorporating the strategies that help in satiating the needs
associated with the intended value creation.
4. Pull: Creation and manufacturing of only what is demanded by the customers. Responding
directly to the existent in the market.
5. Perfection: Striving to get provide the best services to the consumer community. Kaizen or
continuous improvement is a factor that the company abides by and hence it helps the
company to strive to the expected standards.
Agile manufacturing is an approach the realises the realities that is associated with the
development of the processes that ensures the smooth flow of operations (Gunasekaran et al.
2019). According to Dev and Kumar (2016) it is an approach that can be taken in order to ensure
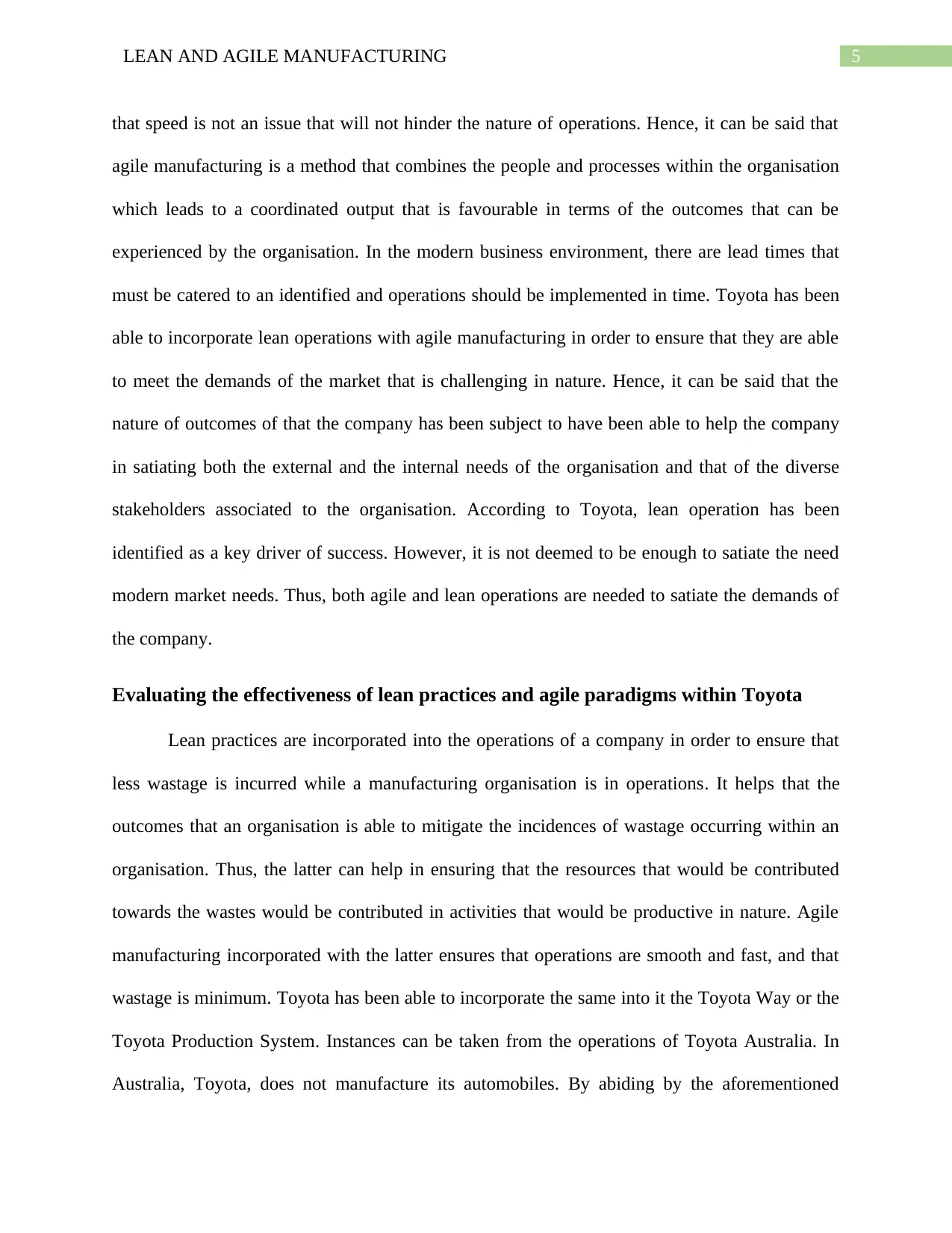
5LEAN AND AGILE MANUFACTURING
that speed is not an issue that will not hinder the nature of operations. Hence, it can be said that
agile manufacturing is a method that combines the people and processes within the organisation
which leads to a coordinated output that is favourable in terms of the outcomes that can be
experienced by the organisation. In the modern business environment, there are lead times that
must be catered to an identified and operations should be implemented in time. Toyota has been
able to incorporate lean operations with agile manufacturing in order to ensure that they are able
to meet the demands of the market that is challenging in nature. Hence, it can be said that the
nature of outcomes of that the company has been subject to have been able to help the company
in satiating both the external and the internal needs of the organisation and that of the diverse
stakeholders associated to the organisation. According to Toyota, lean operation has been
identified as a key driver of success. However, it is not deemed to be enough to satiate the need
modern market needs. Thus, both agile and lean operations are needed to satiate the demands of
the company.
Evaluating the effectiveness of lean practices and agile paradigms within Toyota
Lean practices are incorporated into the operations of a company in order to ensure that
less wastage is incurred while a manufacturing organisation is in operations. It helps that the
outcomes that an organisation is able to mitigate the incidences of wastage occurring within an
organisation. Thus, the latter can help in ensuring that the resources that would be contributed
towards the wastes would be contributed in activities that would be productive in nature. Agile
manufacturing incorporated with the latter ensures that operations are smooth and fast, and that
wastage is minimum. Toyota has been able to incorporate the same into it the Toyota Way or the
Toyota Production System. Instances can be taken from the operations of Toyota Australia. In
Australia, Toyota, does not manufacture its automobiles. By abiding by the aforementioned
that speed is not an issue that will not hinder the nature of operations. Hence, it can be said that
agile manufacturing is a method that combines the people and processes within the organisation
which leads to a coordinated output that is favourable in terms of the outcomes that can be
experienced by the organisation. In the modern business environment, there are lead times that
must be catered to an identified and operations should be implemented in time. Toyota has been
able to incorporate lean operations with agile manufacturing in order to ensure that they are able
to meet the demands of the market that is challenging in nature. Hence, it can be said that the
nature of outcomes of that the company has been subject to have been able to help the company
in satiating both the external and the internal needs of the organisation and that of the diverse
stakeholders associated to the organisation. According to Toyota, lean operation has been
identified as a key driver of success. However, it is not deemed to be enough to satiate the need
modern market needs. Thus, both agile and lean operations are needed to satiate the demands of
the company.
Evaluating the effectiveness of lean practices and agile paradigms within Toyota
Lean practices are incorporated into the operations of a company in order to ensure that
less wastage is incurred while a manufacturing organisation is in operations. It helps that the
outcomes that an organisation is able to mitigate the incidences of wastage occurring within an
organisation. Thus, the latter can help in ensuring that the resources that would be contributed
towards the wastes would be contributed in activities that would be productive in nature. Agile
manufacturing incorporated with the latter ensures that operations are smooth and fast, and that
wastage is minimum. Toyota has been able to incorporate the same into it the Toyota Way or the
Toyota Production System. Instances can be taken from the operations of Toyota Australia. In
Australia, Toyota, does not manufacture its automobiles. By abiding by the aforementioned
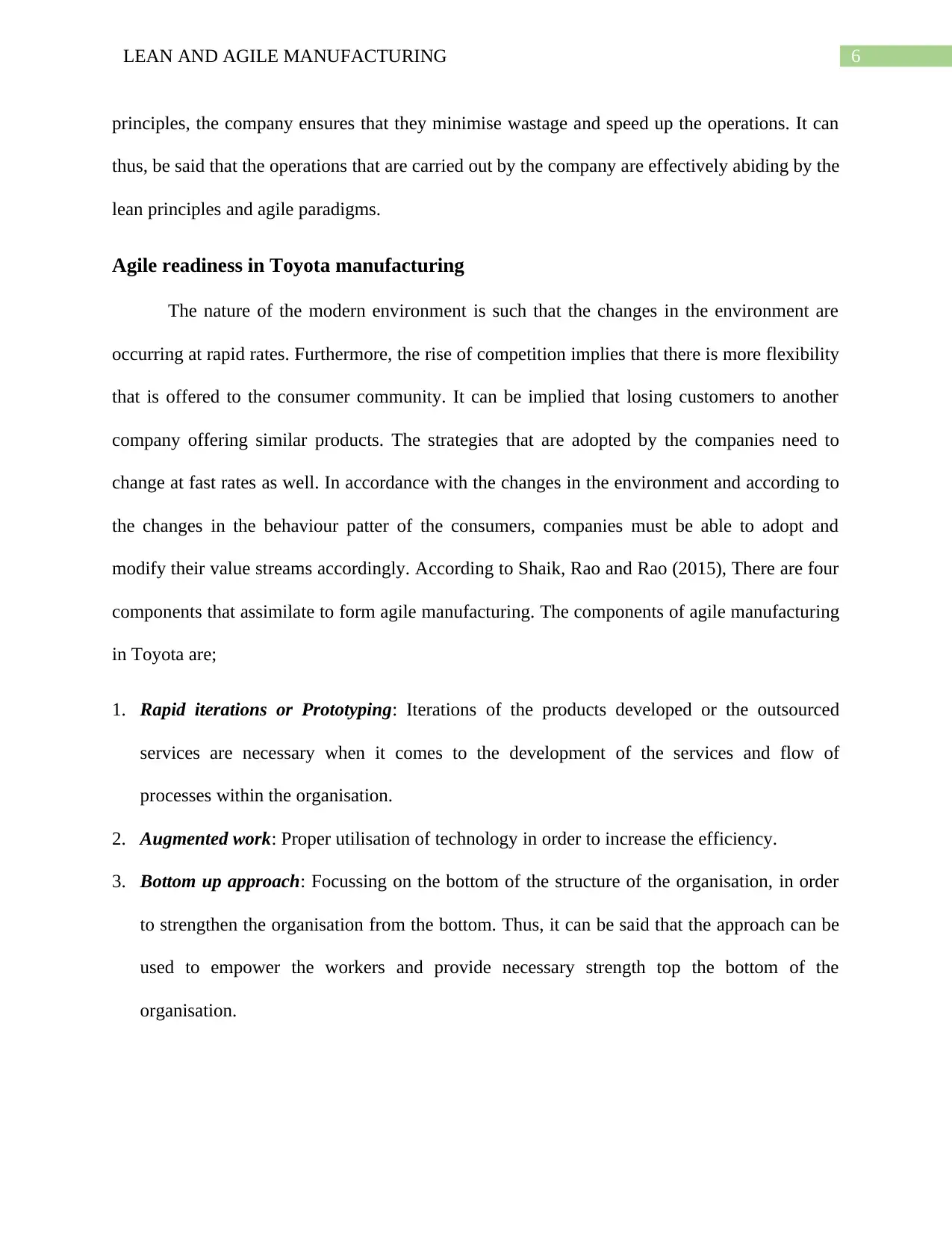
6LEAN AND AGILE MANUFACTURING
principles, the company ensures that they minimise wastage and speed up the operations. It can
thus, be said that the operations that are carried out by the company are effectively abiding by the
lean principles and agile paradigms.
Agile readiness in Toyota manufacturing
The nature of the modern environment is such that the changes in the environment are
occurring at rapid rates. Furthermore, the rise of competition implies that there is more flexibility
that is offered to the consumer community. It can be implied that losing customers to another
company offering similar products. The strategies that are adopted by the companies need to
change at fast rates as well. In accordance with the changes in the environment and according to
the changes in the behaviour patter of the consumers, companies must be able to adopt and
modify their value streams accordingly. According to Shaik, Rao and Rao (2015), There are four
components that assimilate to form agile manufacturing. The components of agile manufacturing
in Toyota are;
1. Rapid iterations or Prototyping: Iterations of the products developed or the outsourced
services are necessary when it comes to the development of the services and flow of
processes within the organisation.
2. Augmented work: Proper utilisation of technology in order to increase the efficiency.
3. Bottom up approach: Focussing on the bottom of the structure of the organisation, in order
to strengthen the organisation from the bottom. Thus, it can be said that the approach can be
used to empower the workers and provide necessary strength top the bottom of the
organisation.
principles, the company ensures that they minimise wastage and speed up the operations. It can
thus, be said that the operations that are carried out by the company are effectively abiding by the
lean principles and agile paradigms.
Agile readiness in Toyota manufacturing
The nature of the modern environment is such that the changes in the environment are
occurring at rapid rates. Furthermore, the rise of competition implies that there is more flexibility
that is offered to the consumer community. It can be implied that losing customers to another
company offering similar products. The strategies that are adopted by the companies need to
change at fast rates as well. In accordance with the changes in the environment and according to
the changes in the behaviour patter of the consumers, companies must be able to adopt and
modify their value streams accordingly. According to Shaik, Rao and Rao (2015), There are four
components that assimilate to form agile manufacturing. The components of agile manufacturing
in Toyota are;
1. Rapid iterations or Prototyping: Iterations of the products developed or the outsourced
services are necessary when it comes to the development of the services and flow of
processes within the organisation.
2. Augmented work: Proper utilisation of technology in order to increase the efficiency.
3. Bottom up approach: Focussing on the bottom of the structure of the organisation, in order
to strengthen the organisation from the bottom. Thus, it can be said that the approach can be
used to empower the workers and provide necessary strength top the bottom of the
organisation.
Paraphrase This Document
Need a fresh take? Get an instant paraphrase of this document with our AI Paraphraser
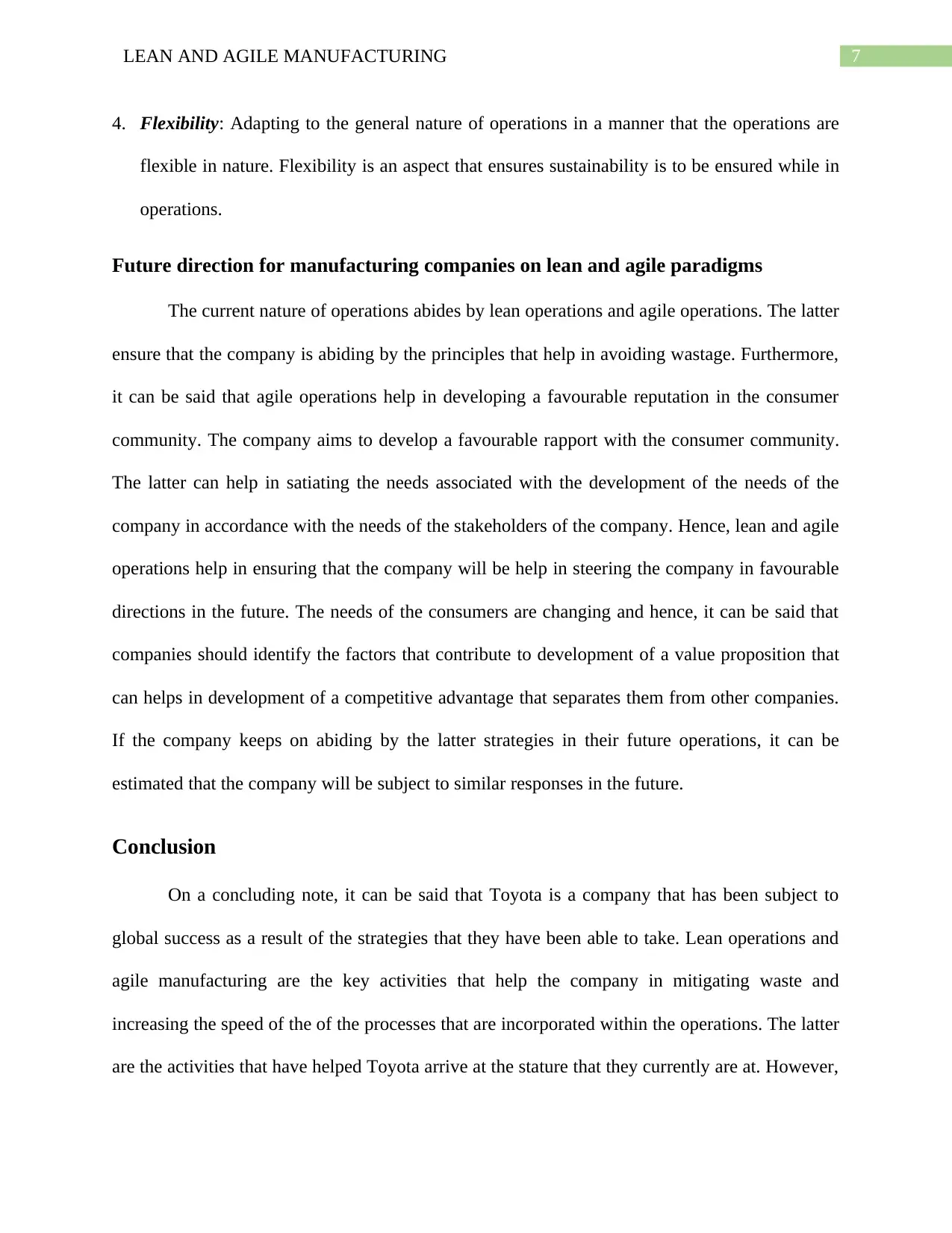
7LEAN AND AGILE MANUFACTURING
4. Flexibility: Adapting to the general nature of operations in a manner that the operations are
flexible in nature. Flexibility is an aspect that ensures sustainability is to be ensured while in
operations.
Future direction for manufacturing companies on lean and agile paradigms
The current nature of operations abides by lean operations and agile operations. The latter
ensure that the company is abiding by the principles that help in avoiding wastage. Furthermore,
it can be said that agile operations help in developing a favourable reputation in the consumer
community. The company aims to develop a favourable rapport with the consumer community.
The latter can help in satiating the needs associated with the development of the needs of the
company in accordance with the needs of the stakeholders of the company. Hence, lean and agile
operations help in ensuring that the company will be help in steering the company in favourable
directions in the future. The needs of the consumers are changing and hence, it can be said that
companies should identify the factors that contribute to development of a value proposition that
can helps in development of a competitive advantage that separates them from other companies.
If the company keeps on abiding by the latter strategies in their future operations, it can be
estimated that the company will be subject to similar responses in the future.
Conclusion
On a concluding note, it can be said that Toyota is a company that has been subject to
global success as a result of the strategies that they have been able to take. Lean operations and
agile manufacturing are the key activities that help the company in mitigating waste and
increasing the speed of the of the processes that are incorporated within the operations. The latter
are the activities that have helped Toyota arrive at the stature that they currently are at. However,
4. Flexibility: Adapting to the general nature of operations in a manner that the operations are
flexible in nature. Flexibility is an aspect that ensures sustainability is to be ensured while in
operations.
Future direction for manufacturing companies on lean and agile paradigms
The current nature of operations abides by lean operations and agile operations. The latter
ensure that the company is abiding by the principles that help in avoiding wastage. Furthermore,
it can be said that agile operations help in developing a favourable reputation in the consumer
community. The company aims to develop a favourable rapport with the consumer community.
The latter can help in satiating the needs associated with the development of the needs of the
company in accordance with the needs of the stakeholders of the company. Hence, lean and agile
operations help in ensuring that the company will be help in steering the company in favourable
directions in the future. The needs of the consumers are changing and hence, it can be said that
companies should identify the factors that contribute to development of a value proposition that
can helps in development of a competitive advantage that separates them from other companies.
If the company keeps on abiding by the latter strategies in their future operations, it can be
estimated that the company will be subject to similar responses in the future.
Conclusion
On a concluding note, it can be said that Toyota is a company that has been subject to
global success as a result of the strategies that they have been able to take. Lean operations and
agile manufacturing are the key activities that help the company in mitigating waste and
increasing the speed of the of the processes that are incorporated within the operations. The latter
are the activities that have helped Toyota arrive at the stature that they currently are at. However,
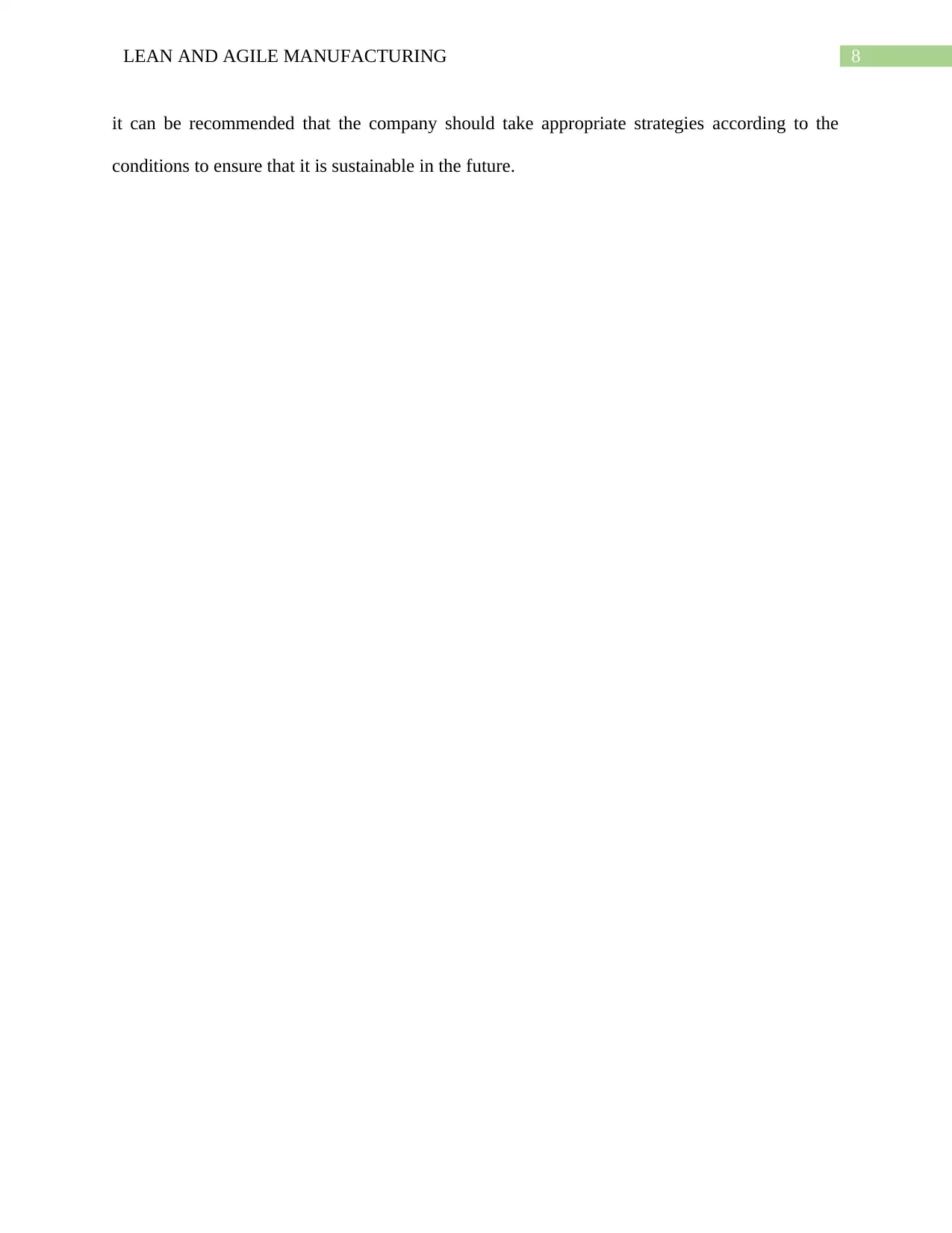
8LEAN AND AGILE MANUFACTURING
it can be recommended that the company should take appropriate strategies according to the
conditions to ensure that it is sustainable in the future.
it can be recommended that the company should take appropriate strategies according to the
conditions to ensure that it is sustainable in the future.
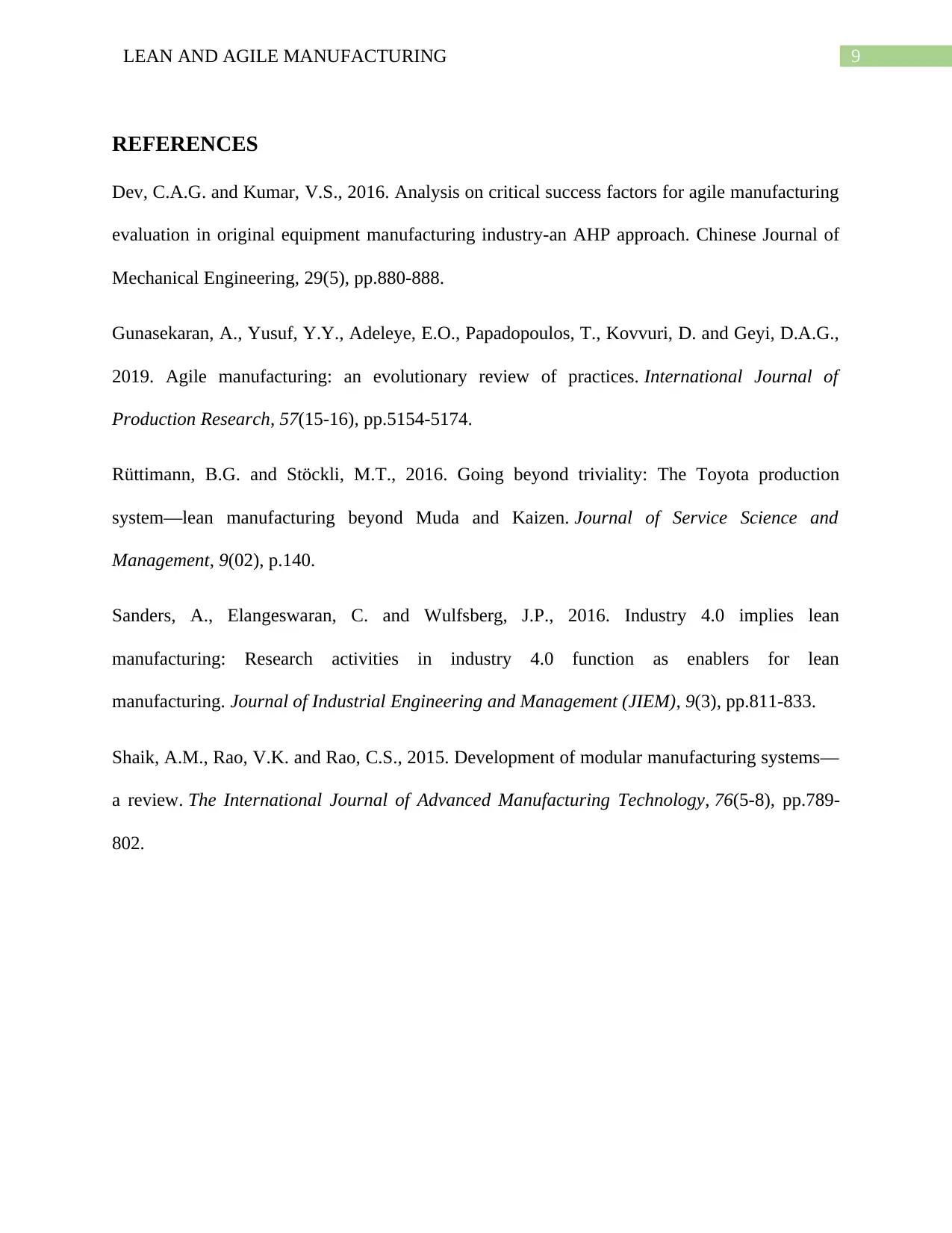
9LEAN AND AGILE MANUFACTURING
REFERENCES
Dev, C.A.G. and Kumar, V.S., 2016. Analysis on critical success factors for agile manufacturing
evaluation in original equipment manufacturing industry-an AHP approach. Chinese Journal of
Mechanical Engineering, 29(5), pp.880-888.
Gunasekaran, A., Yusuf, Y.Y., Adeleye, E.O., Papadopoulos, T., Kovvuri, D. and Geyi, D.A.G.,
2019. Agile manufacturing: an evolutionary review of practices. International Journal of
Production Research, 57(15-16), pp.5154-5174.
Rüttimann, B.G. and Stöckli, M.T., 2016. Going beyond triviality: The Toyota production
system—lean manufacturing beyond Muda and Kaizen. Journal of Service Science and
Management, 9(02), p.140.
Sanders, A., Elangeswaran, C. and Wulfsberg, J.P., 2016. Industry 4.0 implies lean
manufacturing: Research activities in industry 4.0 function as enablers for lean
manufacturing. Journal of Industrial Engineering and Management (JIEM), 9(3), pp.811-833.
Shaik, A.M., Rao, V.K. and Rao, C.S., 2015. Development of modular manufacturing systems—
a review. The International Journal of Advanced Manufacturing Technology, 76(5-8), pp.789-
802.
REFERENCES
Dev, C.A.G. and Kumar, V.S., 2016. Analysis on critical success factors for agile manufacturing
evaluation in original equipment manufacturing industry-an AHP approach. Chinese Journal of
Mechanical Engineering, 29(5), pp.880-888.
Gunasekaran, A., Yusuf, Y.Y., Adeleye, E.O., Papadopoulos, T., Kovvuri, D. and Geyi, D.A.G.,
2019. Agile manufacturing: an evolutionary review of practices. International Journal of
Production Research, 57(15-16), pp.5154-5174.
Rüttimann, B.G. and Stöckli, M.T., 2016. Going beyond triviality: The Toyota production
system—lean manufacturing beyond Muda and Kaizen. Journal of Service Science and
Management, 9(02), p.140.
Sanders, A., Elangeswaran, C. and Wulfsberg, J.P., 2016. Industry 4.0 implies lean
manufacturing: Research activities in industry 4.0 function as enablers for lean
manufacturing. Journal of Industrial Engineering and Management (JIEM), 9(3), pp.811-833.
Shaik, A.M., Rao, V.K. and Rao, C.S., 2015. Development of modular manufacturing systems—
a review. The International Journal of Advanced Manufacturing Technology, 76(5-8), pp.789-
802.
1 out of 10
Related Documents
![[object Object]](/_next/image/?url=%2F_next%2Fstatic%2Fmedia%2Flogo.6d15ce61.png&w=640&q=75)
Your All-in-One AI-Powered Toolkit for Academic Success.
+13062052269
info@desklib.com
Available 24*7 on WhatsApp / Email
Unlock your academic potential
© 2024 | Zucol Services PVT LTD | All rights reserved.