Understanding Operations, Logistics and Supply Chain Management Analysis 2022
VerifiedAdded on 2022/09/14
|10
|3755
|17
AI Summary
Contribute Materials
Your contribution can guide someone’s learning journey. Share your
documents today.
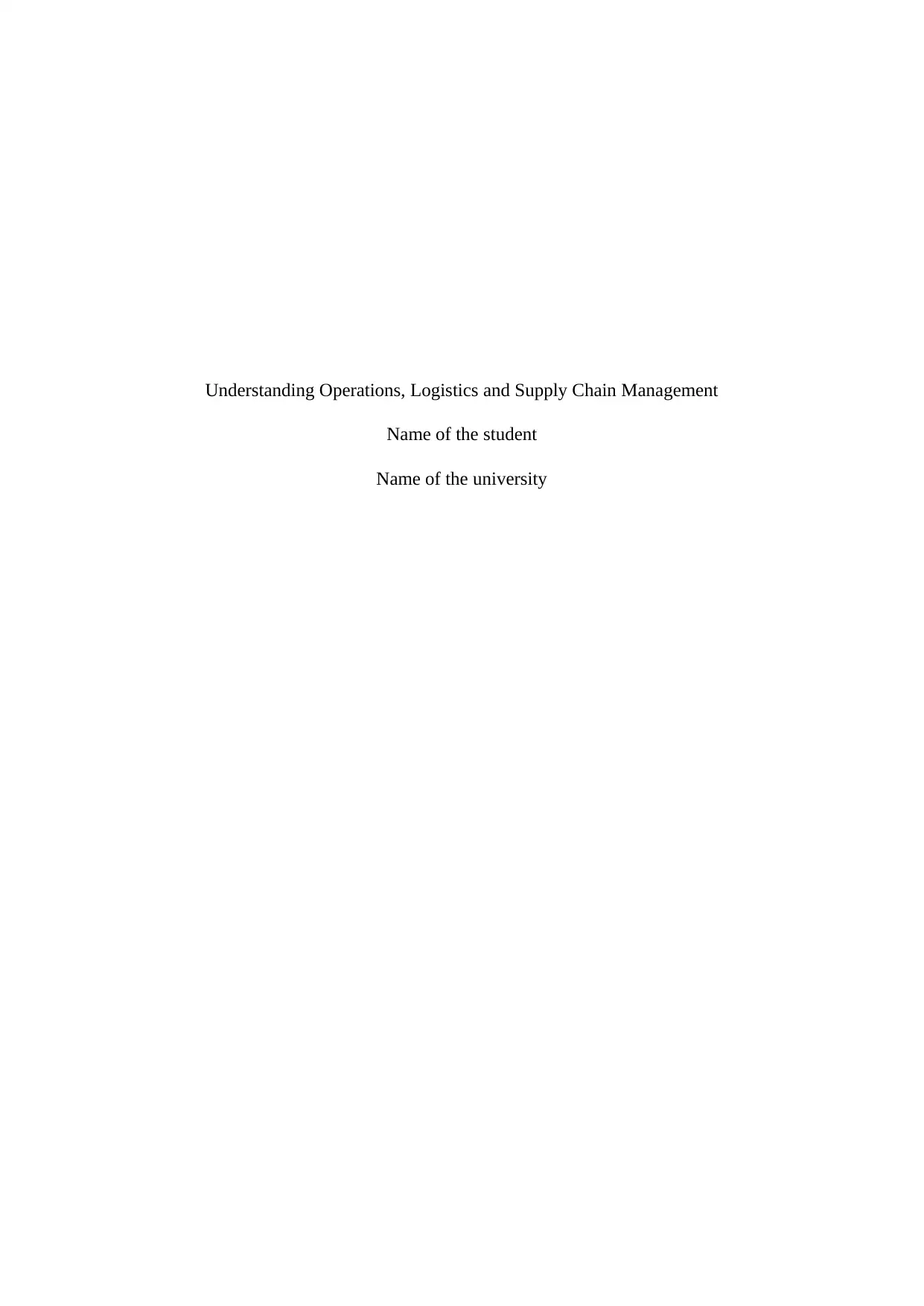
Understanding Operations, Logistics and Supply Chain Management
Name of the student
Name of the university
Name of the student
Name of the university
Secure Best Marks with AI Grader
Need help grading? Try our AI Grader for instant feedback on your assignments.
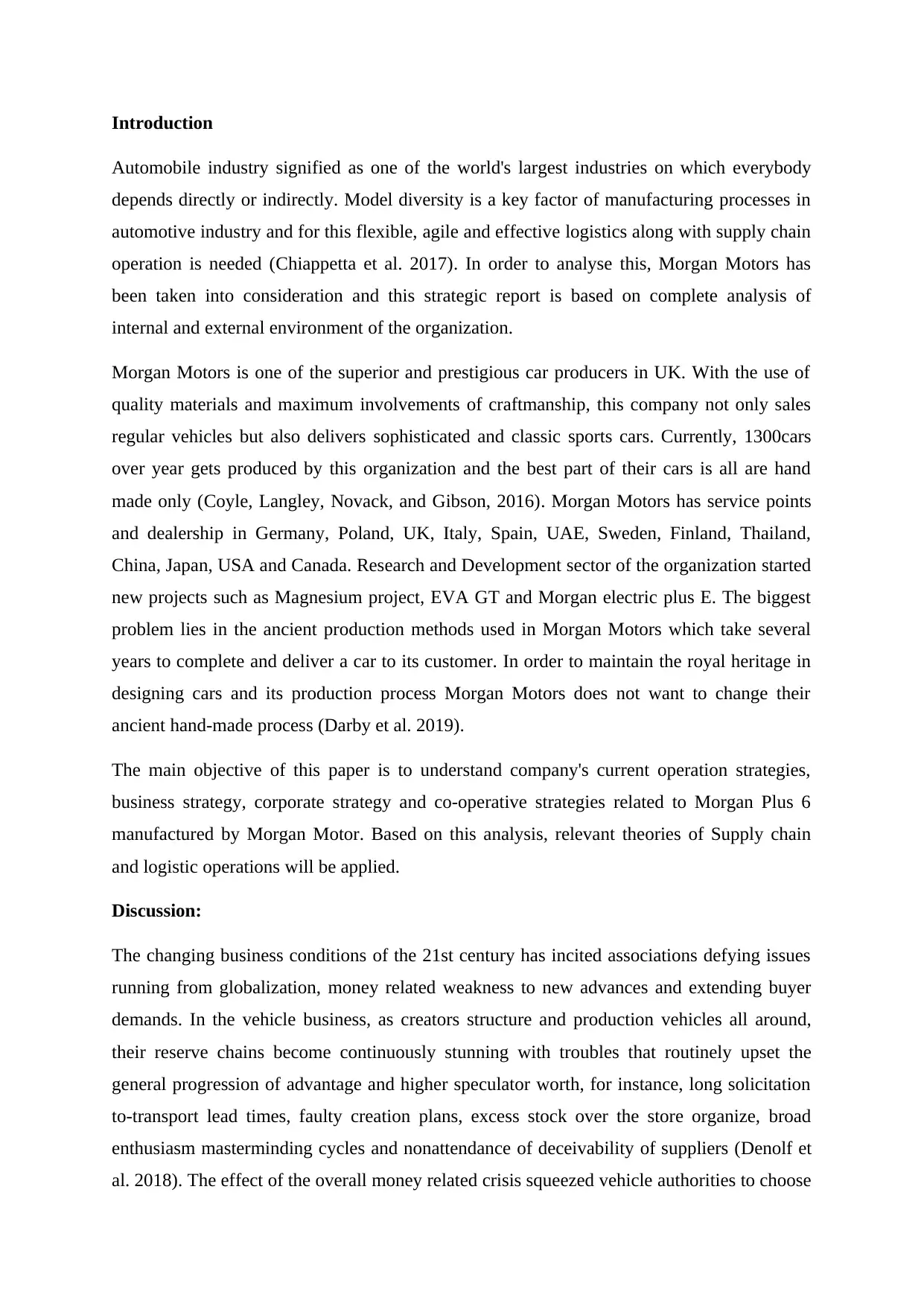
Introduction
Automobile industry signified as one of the world's largest industries on which everybody
depends directly or indirectly. Model diversity is a key factor of manufacturing processes in
automotive industry and for this flexible, agile and effective logistics along with supply chain
operation is needed (Chiappetta et al. 2017). In order to analyse this, Morgan Motors has
been taken into consideration and this strategic report is based on complete analysis of
internal and external environment of the organization.
Morgan Motors is one of the superior and prestigious car producers in UK. With the use of
quality materials and maximum involvements of craftmanship, this company not only sales
regular vehicles but also delivers sophisticated and classic sports cars. Currently, 1300cars
over year gets produced by this organization and the best part of their cars is all are hand
made only (Coyle, Langley, Novack, and Gibson, 2016). Morgan Motors has service points
and dealership in Germany, Poland, UK, Italy, Spain, UAE, Sweden, Finland, Thailand,
China, Japan, USA and Canada. Research and Development sector of the organization started
new projects such as Magnesium project, EVA GT and Morgan electric plus E. The biggest
problem lies in the ancient production methods used in Morgan Motors which take several
years to complete and deliver a car to its customer. In order to maintain the royal heritage in
designing cars and its production process Morgan Motors does not want to change their
ancient hand-made process (Darby et al. 2019).
The main objective of this paper is to understand company's current operation strategies,
business strategy, corporate strategy and co-operative strategies related to Morgan Plus 6
manufactured by Morgan Motor. Based on this analysis, relevant theories of Supply chain
and logistic operations will be applied.
Discussion:
The changing business conditions of the 21st century has incited associations defying issues
running from globalization, money related weakness to new advances and extending buyer
demands. In the vehicle business, as creators structure and production vehicles all around,
their reserve chains become continuously stunning with troubles that routinely upset the
general progression of advantage and higher speculator worth, for instance, long solicitation
to-transport lead times, faulty creation plans, excess stock over the store organize, broad
enthusiasm masterminding cycles and nonattendance of deceivability of suppliers (Denolf et
al. 2018). The effect of the overall money related crisis squeezed vehicle authorities to choose
Automobile industry signified as one of the world's largest industries on which everybody
depends directly or indirectly. Model diversity is a key factor of manufacturing processes in
automotive industry and for this flexible, agile and effective logistics along with supply chain
operation is needed (Chiappetta et al. 2017). In order to analyse this, Morgan Motors has
been taken into consideration and this strategic report is based on complete analysis of
internal and external environment of the organization.
Morgan Motors is one of the superior and prestigious car producers in UK. With the use of
quality materials and maximum involvements of craftmanship, this company not only sales
regular vehicles but also delivers sophisticated and classic sports cars. Currently, 1300cars
over year gets produced by this organization and the best part of their cars is all are hand
made only (Coyle, Langley, Novack, and Gibson, 2016). Morgan Motors has service points
and dealership in Germany, Poland, UK, Italy, Spain, UAE, Sweden, Finland, Thailand,
China, Japan, USA and Canada. Research and Development sector of the organization started
new projects such as Magnesium project, EVA GT and Morgan electric plus E. The biggest
problem lies in the ancient production methods used in Morgan Motors which take several
years to complete and deliver a car to its customer. In order to maintain the royal heritage in
designing cars and its production process Morgan Motors does not want to change their
ancient hand-made process (Darby et al. 2019).
The main objective of this paper is to understand company's current operation strategies,
business strategy, corporate strategy and co-operative strategies related to Morgan Plus 6
manufactured by Morgan Motor. Based on this analysis, relevant theories of Supply chain
and logistic operations will be applied.
Discussion:
The changing business conditions of the 21st century has incited associations defying issues
running from globalization, money related weakness to new advances and extending buyer
demands. In the vehicle business, as creators structure and production vehicles all around,
their reserve chains become continuously stunning with troubles that routinely upset the
general progression of advantage and higher speculator worth, for instance, long solicitation
to-transport lead times, faulty creation plans, excess stock over the store organize, broad
enthusiasm masterminding cycles and nonattendance of deceivability of suppliers (Denolf et
al. 2018). The effect of the overall money related crisis squeezed vehicle authorities to choose
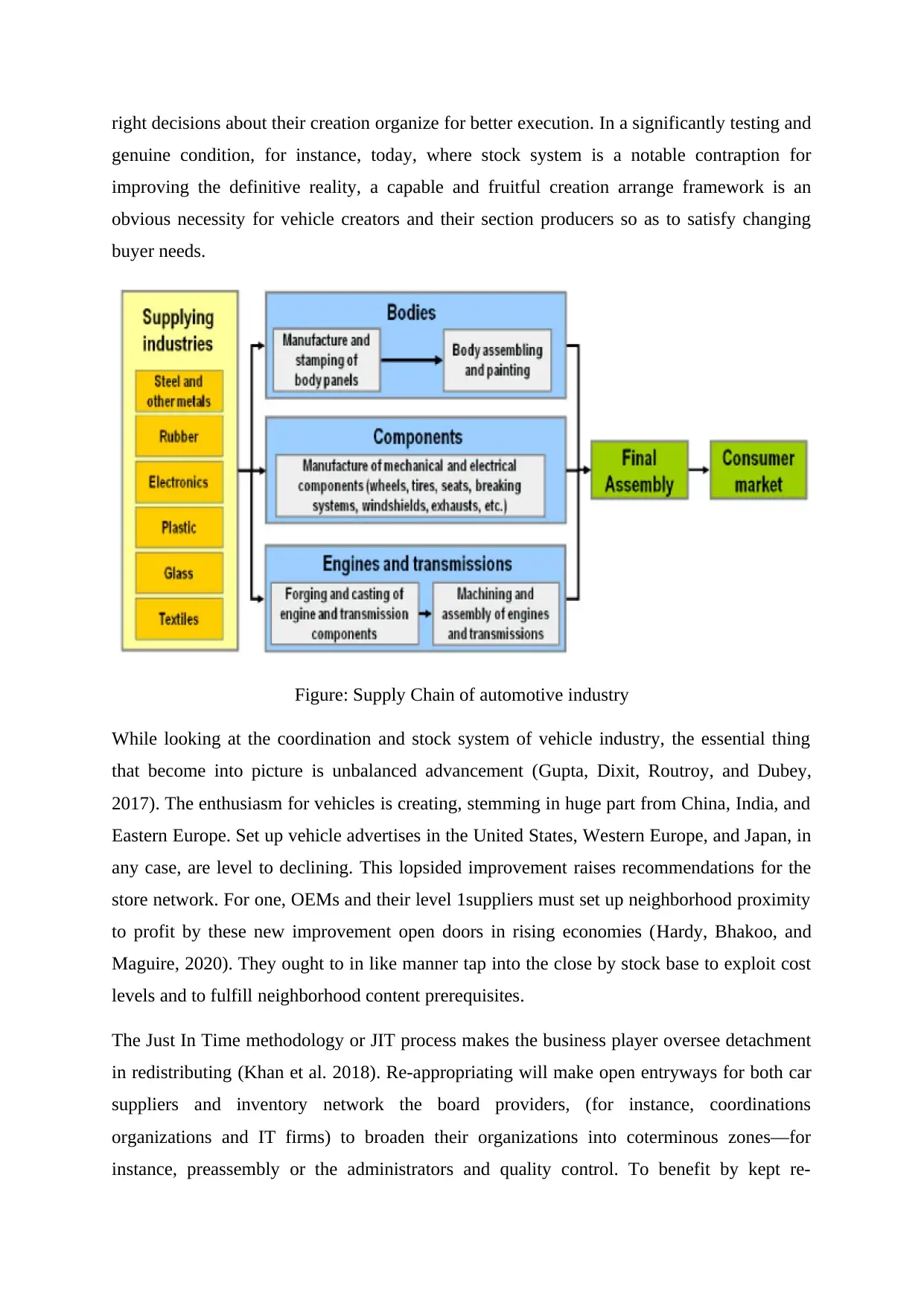
right decisions about their creation organize for better execution. In a significantly testing and
genuine condition, for instance, today, where stock system is a notable contraption for
improving the definitive reality, a capable and fruitful creation arrange framework is an
obvious necessity for vehicle creators and their section producers so as to satisfy changing
buyer needs.
Figure: Supply Chain of automotive industry
While looking at the coordination and stock system of vehicle industry, the essential thing
that become into picture is unbalanced advancement (Gupta, Dixit, Routroy, and Dubey,
2017). The enthusiasm for vehicles is creating, stemming in huge part from China, India, and
Eastern Europe. Set up vehicle advertises in the United States, Western Europe, and Japan, in
any case, are level to declining. This lopsided improvement raises recommendations for the
store network. For one, OEMs and their level 1suppliers must set up neighborhood proximity
to profit by these new improvement open doors in rising economies (Hardy, Bhakoo, and
Maguire, 2020). They ought to in like manner tap into the close by stock base to exploit cost
levels and to fulfill neighborhood content prerequisites.
The Just In Time methodology or JIT process makes the business player oversee detachment
in redistributing (Khan et al. 2018). Re-appropriating will make open entryways for both car
suppliers and inventory network the board providers, (for instance, coordinations
organizations and IT firms) to broaden their organizations into coterminous zones—for
instance, preassembly or the administrators and quality control. To benefit by kept re-
genuine condition, for instance, today, where stock system is a notable contraption for
improving the definitive reality, a capable and fruitful creation arrange framework is an
obvious necessity for vehicle creators and their section producers so as to satisfy changing
buyer needs.
Figure: Supply Chain of automotive industry
While looking at the coordination and stock system of vehicle industry, the essential thing
that become into picture is unbalanced advancement (Gupta, Dixit, Routroy, and Dubey,
2017). The enthusiasm for vehicles is creating, stemming in huge part from China, India, and
Eastern Europe. Set up vehicle advertises in the United States, Western Europe, and Japan, in
any case, are level to declining. This lopsided improvement raises recommendations for the
store network. For one, OEMs and their level 1suppliers must set up neighborhood proximity
to profit by these new improvement open doors in rising economies (Hardy, Bhakoo, and
Maguire, 2020). They ought to in like manner tap into the close by stock base to exploit cost
levels and to fulfill neighborhood content prerequisites.
The Just In Time methodology or JIT process makes the business player oversee detachment
in redistributing (Khan et al. 2018). Re-appropriating will make open entryways for both car
suppliers and inventory network the board providers, (for instance, coordinations
organizations and IT firms) to broaden their organizations into coterminous zones—for
instance, preassembly or the administrators and quality control. To benefit by kept re-
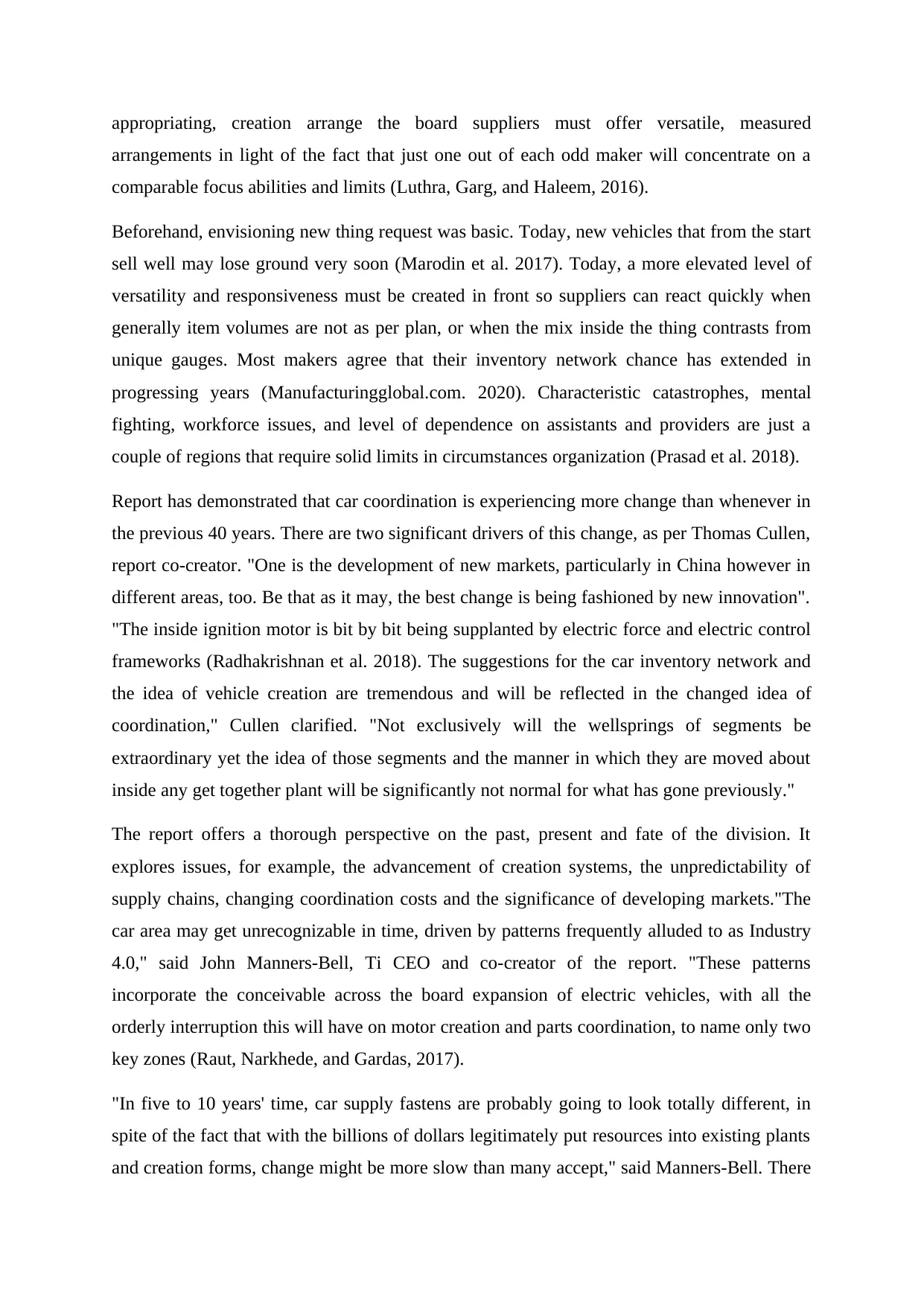
appropriating, creation arrange the board suppliers must offer versatile, measured
arrangements in light of the fact that just one out of each odd maker will concentrate on a
comparable focus abilities and limits (Luthra, Garg, and Haleem, 2016).
Beforehand, envisioning new thing request was basic. Today, new vehicles that from the start
sell well may lose ground very soon (Marodin et al. 2017). Today, a more elevated level of
versatility and responsiveness must be created in front so suppliers can react quickly when
generally item volumes are not as per plan, or when the mix inside the thing contrasts from
unique gauges. Most makers agree that their inventory network chance has extended in
progressing years (Manufacturingglobal.com. 2020). Characteristic catastrophes, mental
fighting, workforce issues, and level of dependence on assistants and providers are just a
couple of regions that require solid limits in circumstances organization (Prasad et al. 2018).
Report has demonstrated that car coordination is experiencing more change than whenever in
the previous 40 years. There are two significant drivers of this change, as per Thomas Cullen,
report co-creator. "One is the development of new markets, particularly in China however in
different areas, too. Be that as it may, the best change is being fashioned by new innovation".
"The inside ignition motor is bit by bit being supplanted by electric force and electric control
frameworks (Radhakrishnan et al. 2018). The suggestions for the car inventory network and
the idea of vehicle creation are tremendous and will be reflected in the changed idea of
coordination," Cullen clarified. "Not exclusively will the wellsprings of segments be
extraordinary yet the idea of those segments and the manner in which they are moved about
inside any get together plant will be significantly not normal for what has gone previously."
The report offers a thorough perspective on the past, present and fate of the division. It
explores issues, for example, the advancement of creation systems, the unpredictability of
supply chains, changing coordination costs and the significance of developing markets."The
car area may get unrecognizable in time, driven by patterns frequently alluded to as Industry
4.0," said John Manners-Bell, Ti CEO and co-creator of the report. "These patterns
incorporate the conceivable across the board expansion of electric vehicles, with all the
orderly interruption this will have on motor creation and parts coordination, to name only two
key zones (Raut, Narkhede, and Gardas, 2017).
"In five to 10 years' time, car supply fastens are probably going to look totally different, in
spite of the fact that with the billions of dollars legitimately put resources into existing plants
and creation forms, change might be more slow than many accept," said Manners-Bell. There
arrangements in light of the fact that just one out of each odd maker will concentrate on a
comparable focus abilities and limits (Luthra, Garg, and Haleem, 2016).
Beforehand, envisioning new thing request was basic. Today, new vehicles that from the start
sell well may lose ground very soon (Marodin et al. 2017). Today, a more elevated level of
versatility and responsiveness must be created in front so suppliers can react quickly when
generally item volumes are not as per plan, or when the mix inside the thing contrasts from
unique gauges. Most makers agree that their inventory network chance has extended in
progressing years (Manufacturingglobal.com. 2020). Characteristic catastrophes, mental
fighting, workforce issues, and level of dependence on assistants and providers are just a
couple of regions that require solid limits in circumstances organization (Prasad et al. 2018).
Report has demonstrated that car coordination is experiencing more change than whenever in
the previous 40 years. There are two significant drivers of this change, as per Thomas Cullen,
report co-creator. "One is the development of new markets, particularly in China however in
different areas, too. Be that as it may, the best change is being fashioned by new innovation".
"The inside ignition motor is bit by bit being supplanted by electric force and electric control
frameworks (Radhakrishnan et al. 2018). The suggestions for the car inventory network and
the idea of vehicle creation are tremendous and will be reflected in the changed idea of
coordination," Cullen clarified. "Not exclusively will the wellsprings of segments be
extraordinary yet the idea of those segments and the manner in which they are moved about
inside any get together plant will be significantly not normal for what has gone previously."
The report offers a thorough perspective on the past, present and fate of the division. It
explores issues, for example, the advancement of creation systems, the unpredictability of
supply chains, changing coordination costs and the significance of developing markets."The
car area may get unrecognizable in time, driven by patterns frequently alluded to as Industry
4.0," said John Manners-Bell, Ti CEO and co-creator of the report. "These patterns
incorporate the conceivable across the board expansion of electric vehicles, with all the
orderly interruption this will have on motor creation and parts coordination, to name only two
key zones (Raut, Narkhede, and Gardas, 2017).
"In five to 10 years' time, car supply fastens are probably going to look totally different, in
spite of the fact that with the billions of dollars legitimately put resources into existing plants
and creation forms, change might be more slow than many accept," said Manners-Bell. There
Secure Best Marks with AI Grader
Need help grading? Try our AI Grader for instant feedback on your assignments.
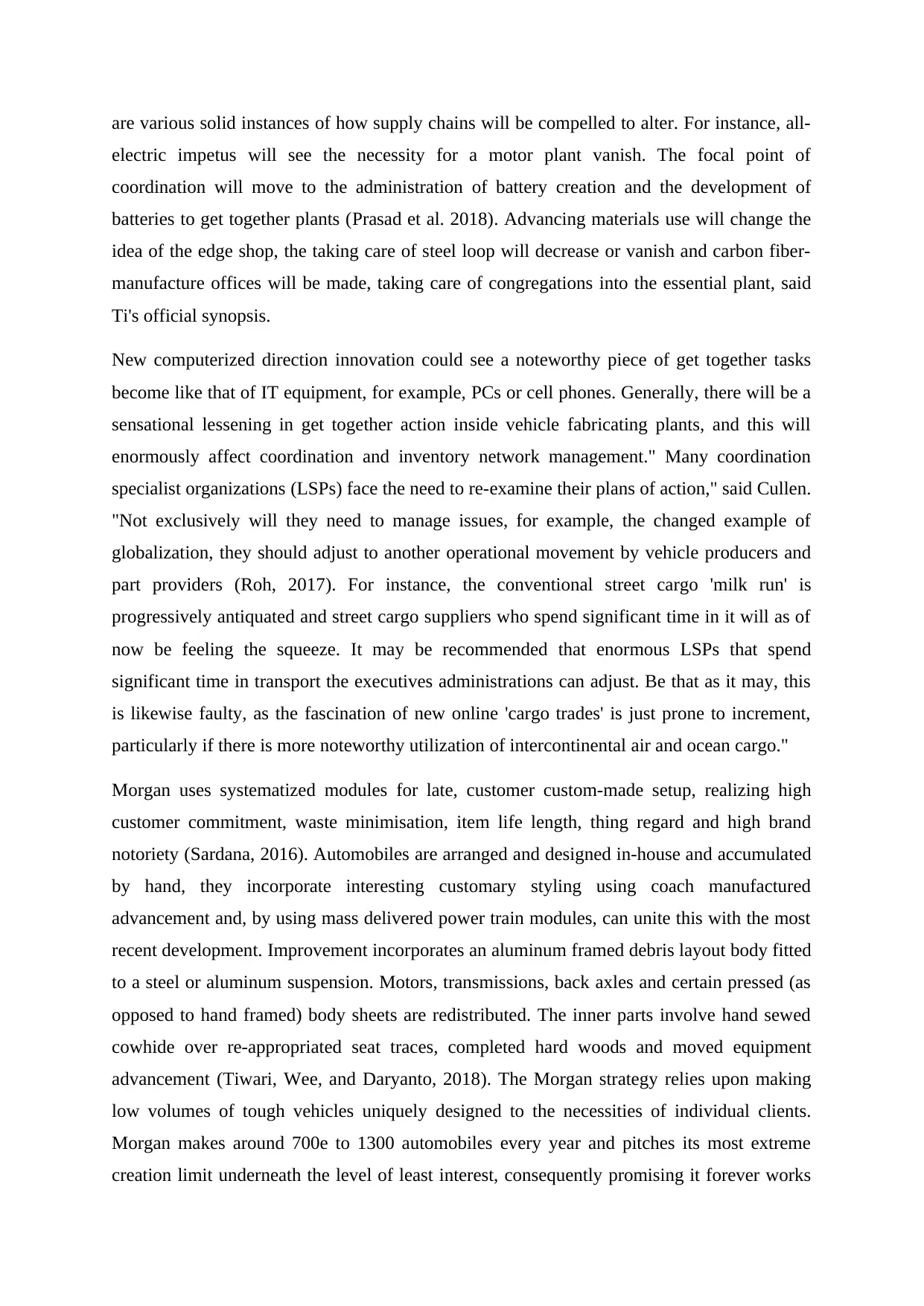
are various solid instances of how supply chains will be compelled to alter. For instance, all-
electric impetus will see the necessity for a motor plant vanish. The focal point of
coordination will move to the administration of battery creation and the development of
batteries to get together plants (Prasad et al. 2018). Advancing materials use will change the
idea of the edge shop, the taking care of steel loop will decrease or vanish and carbon fiber-
manufacture offices will be made, taking care of congregations into the essential plant, said
Ti's official synopsis.
New computerized direction innovation could see a noteworthy piece of get together tasks
become like that of IT equipment, for example, PCs or cell phones. Generally, there will be a
sensational lessening in get together action inside vehicle fabricating plants, and this will
enormously affect coordination and inventory network management." Many coordination
specialist organizations (LSPs) face the need to re-examine their plans of action," said Cullen.
"Not exclusively will they need to manage issues, for example, the changed example of
globalization, they should adjust to another operational movement by vehicle producers and
part providers (Roh, 2017). For instance, the conventional street cargo 'milk run' is
progressively antiquated and street cargo suppliers who spend significant time in it will as of
now be feeling the squeeze. It may be recommended that enormous LSPs that spend
significant time in transport the executives administrations can adjust. Be that as it may, this
is likewise faulty, as the fascination of new online 'cargo trades' is just prone to increment,
particularly if there is more noteworthy utilization of intercontinental air and ocean cargo."
Morgan uses systematized modules for late, customer custom-made setup, realizing high
customer commitment, waste minimisation, item life length, thing regard and high brand
notoriety (Sardana, 2016). Automobiles are arranged and designed in-house and accumulated
by hand, they incorporate interesting customary styling using coach manufactured
advancement and, by using mass delivered power train modules, can unite this with the most
recent development. Improvement incorporates an aluminum framed debris layout body fitted
to a steel or aluminum suspension. Motors, transmissions, back axles and certain pressed (as
opposed to hand framed) body sheets are redistributed. The inner parts involve hand sewed
cowhide over re-appropriated seat traces, completed hard woods and moved equipment
advancement (Tiwari, Wee, and Daryanto, 2018). The Morgan strategy relies upon making
low volumes of tough vehicles uniquely designed to the necessities of individual clients.
Morgan makes around 700e to 1300 automobiles every year and pitches its most extreme
creation limit underneath the level of least interest, consequently promising it forever works
electric impetus will see the necessity for a motor plant vanish. The focal point of
coordination will move to the administration of battery creation and the development of
batteries to get together plants (Prasad et al. 2018). Advancing materials use will change the
idea of the edge shop, the taking care of steel loop will decrease or vanish and carbon fiber-
manufacture offices will be made, taking care of congregations into the essential plant, said
Ti's official synopsis.
New computerized direction innovation could see a noteworthy piece of get together tasks
become like that of IT equipment, for example, PCs or cell phones. Generally, there will be a
sensational lessening in get together action inside vehicle fabricating plants, and this will
enormously affect coordination and inventory network management." Many coordination
specialist organizations (LSPs) face the need to re-examine their plans of action," said Cullen.
"Not exclusively will they need to manage issues, for example, the changed example of
globalization, they should adjust to another operational movement by vehicle producers and
part providers (Roh, 2017). For instance, the conventional street cargo 'milk run' is
progressively antiquated and street cargo suppliers who spend significant time in it will as of
now be feeling the squeeze. It may be recommended that enormous LSPs that spend
significant time in transport the executives administrations can adjust. Be that as it may, this
is likewise faulty, as the fascination of new online 'cargo trades' is just prone to increment,
particularly if there is more noteworthy utilization of intercontinental air and ocean cargo."
Morgan uses systematized modules for late, customer custom-made setup, realizing high
customer commitment, waste minimisation, item life length, thing regard and high brand
notoriety (Sardana, 2016). Automobiles are arranged and designed in-house and accumulated
by hand, they incorporate interesting customary styling using coach manufactured
advancement and, by using mass delivered power train modules, can unite this with the most
recent development. Improvement incorporates an aluminum framed debris layout body fitted
to a steel or aluminum suspension. Motors, transmissions, back axles and certain pressed (as
opposed to hand framed) body sheets are redistributed. The inner parts involve hand sewed
cowhide over re-appropriated seat traces, completed hard woods and moved equipment
advancement (Tiwari, Wee, and Daryanto, 2018). The Morgan strategy relies upon making
low volumes of tough vehicles uniquely designed to the necessities of individual clients.
Morgan makes around 700e to 1300 automobiles every year and pitches its most extreme
creation limit underneath the level of least interest, consequently promising it forever works
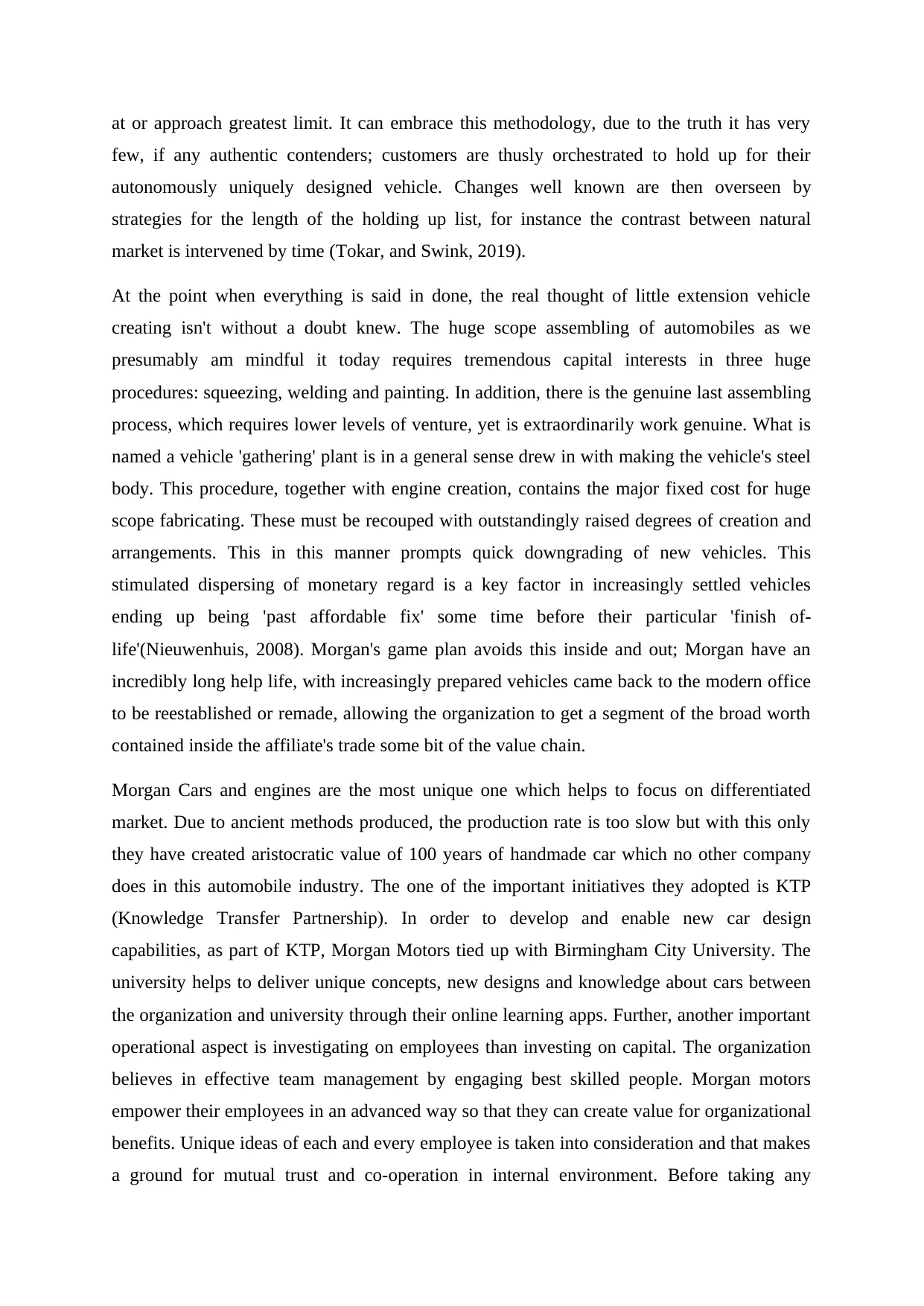
at or approach greatest limit. It can embrace this methodology, due to the truth it has very
few, if any authentic contenders; customers are thusly orchestrated to hold up for their
autonomously uniquely designed vehicle. Changes well known are then overseen by
strategies for the length of the holding up list, for instance the contrast between natural
market is intervened by time (Tokar, and Swink, 2019).
At the point when everything is said in done, the real thought of little extension vehicle
creating isn't without a doubt knew. The huge scope assembling of automobiles as we
presumably am mindful it today requires tremendous capital interests in three huge
procedures: squeezing, welding and painting. In addition, there is the genuine last assembling
process, which requires lower levels of venture, yet is extraordinarily work genuine. What is
named a vehicle 'gathering' plant is in a general sense drew in with making the vehicle's steel
body. This procedure, together with engine creation, contains the major fixed cost for huge
scope fabricating. These must be recouped with outstandingly raised degrees of creation and
arrangements. This in this manner prompts quick downgrading of new vehicles. This
stimulated dispersing of monetary regard is a key factor in increasingly settled vehicles
ending up being 'past affordable fix' some time before their particular 'finish of-
life'(Nieuwenhuis, 2008). Morgan's game plan avoids this inside and out; Morgan have an
incredibly long help life, with increasingly prepared vehicles came back to the modern office
to be reestablished or remade, allowing the organization to get a segment of the broad worth
contained inside the affiliate's trade some bit of the value chain.
Morgan Cars and engines are the most unique one which helps to focus on differentiated
market. Due to ancient methods produced, the production rate is too slow but with this only
they have created aristocratic value of 100 years of handmade car which no other company
does in this automobile industry. The one of the important initiatives they adopted is KTP
(Knowledge Transfer Partnership). In order to develop and enable new car design
capabilities, as part of KTP, Morgan Motors tied up with Birmingham City University. The
university helps to deliver unique concepts, new designs and knowledge about cars between
the organization and university through their online learning apps. Further, another important
operational aspect is investigating on employees than investing on capital. The organization
believes in effective team management by engaging best skilled people. Morgan motors
empower their employees in an advanced way so that they can create value for organizational
benefits. Unique ideas of each and every employee is taken into consideration and that makes
a ground for mutual trust and co-operation in internal environment. Before taking any
few, if any authentic contenders; customers are thusly orchestrated to hold up for their
autonomously uniquely designed vehicle. Changes well known are then overseen by
strategies for the length of the holding up list, for instance the contrast between natural
market is intervened by time (Tokar, and Swink, 2019).
At the point when everything is said in done, the real thought of little extension vehicle
creating isn't without a doubt knew. The huge scope assembling of automobiles as we
presumably am mindful it today requires tremendous capital interests in three huge
procedures: squeezing, welding and painting. In addition, there is the genuine last assembling
process, which requires lower levels of venture, yet is extraordinarily work genuine. What is
named a vehicle 'gathering' plant is in a general sense drew in with making the vehicle's steel
body. This procedure, together with engine creation, contains the major fixed cost for huge
scope fabricating. These must be recouped with outstandingly raised degrees of creation and
arrangements. This in this manner prompts quick downgrading of new vehicles. This
stimulated dispersing of monetary regard is a key factor in increasingly settled vehicles
ending up being 'past affordable fix' some time before their particular 'finish of-
life'(Nieuwenhuis, 2008). Morgan's game plan avoids this inside and out; Morgan have an
incredibly long help life, with increasingly prepared vehicles came back to the modern office
to be reestablished or remade, allowing the organization to get a segment of the broad worth
contained inside the affiliate's trade some bit of the value chain.
Morgan Cars and engines are the most unique one which helps to focus on differentiated
market. Due to ancient methods produced, the production rate is too slow but with this only
they have created aristocratic value of 100 years of handmade car which no other company
does in this automobile industry. The one of the important initiatives they adopted is KTP
(Knowledge Transfer Partnership). In order to develop and enable new car design
capabilities, as part of KTP, Morgan Motors tied up with Birmingham City University. The
university helps to deliver unique concepts, new designs and knowledge about cars between
the organization and university through their online learning apps. Further, another important
operational aspect is investigating on employees than investing on capital. The organization
believes in effective team management by engaging best skilled people. Morgan motors
empower their employees in an advanced way so that they can create value for organizational
benefits. Unique ideas of each and every employee is taken into consideration and that makes
a ground for mutual trust and co-operation in internal environment. Before taking any
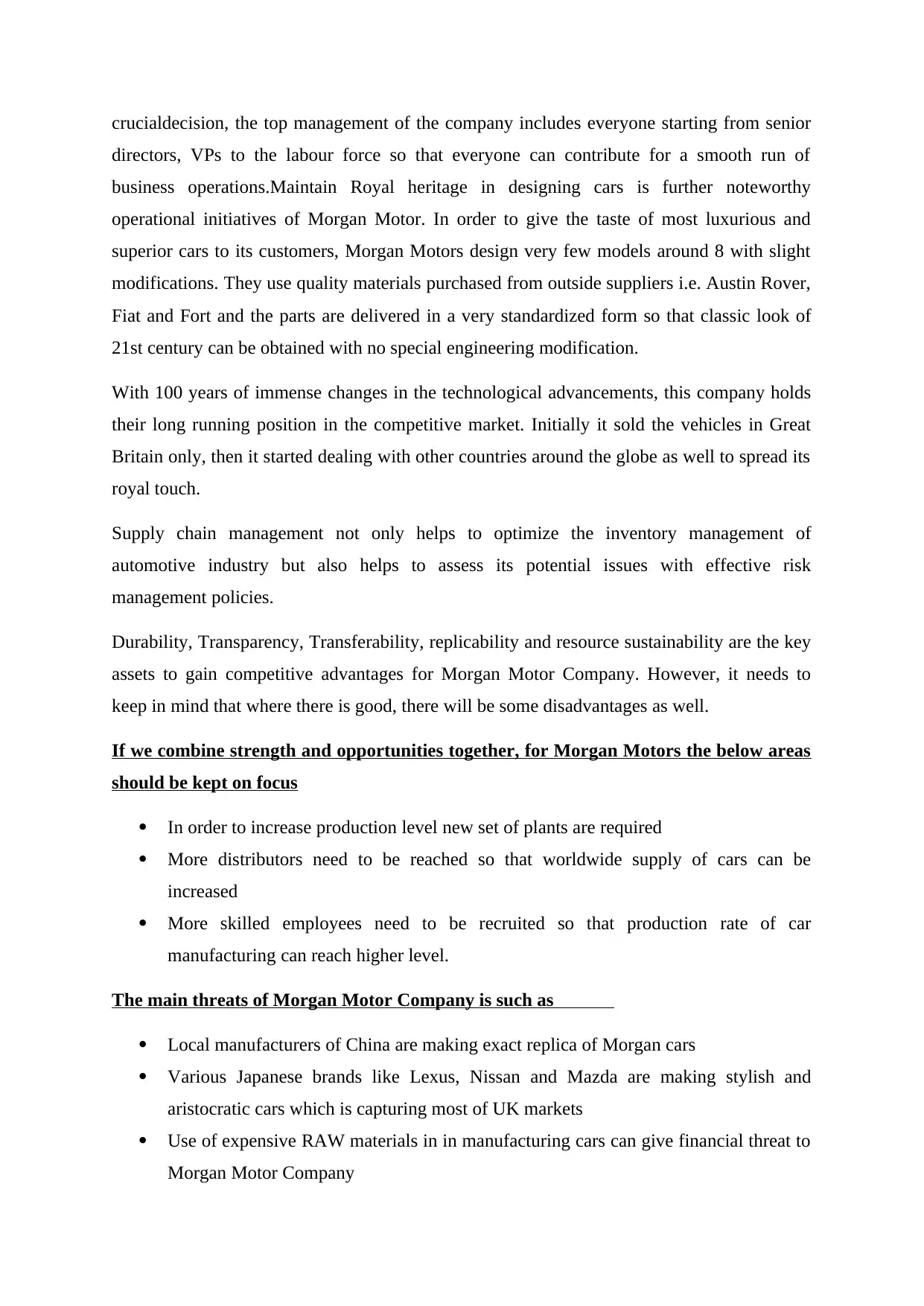
crucialdecision, the top management of the company includes everyone starting from senior
directors, VPs to the labour force so that everyone can contribute for a smooth run of
business operations.Maintain Royal heritage in designing cars is further noteworthy
operational initiatives of Morgan Motor. In order to give the taste of most luxurious and
superior cars to its customers, Morgan Motors design very few models around 8 with slight
modifications. They use quality materials purchased from outside suppliers i.e. Austin Rover,
Fiat and Fort and the parts are delivered in a very standardized form so that classic look of
21st century can be obtained with no special engineering modification.
With 100 years of immense changes in the technological advancements, this company holds
their long running position in the competitive market. Initially it sold the vehicles in Great
Britain only, then it started dealing with other countries around the globe as well to spread its
royal touch.
Supply chain management not only helps to optimize the inventory management of
automotive industry but also helps to assess its potential issues with effective risk
management policies.
Durability, Transparency, Transferability, replicability and resource sustainability are the key
assets to gain competitive advantages for Morgan Motor Company. However, it needs to
keep in mind that where there is good, there will be some disadvantages as well.
If we combine strength and opportunities together, for Morgan Motors the below areas
should be kept on focus
In order to increase production level new set of plants are required
More distributors need to be reached so that worldwide supply of cars can be
increased
More skilled employees need to be recruited so that production rate of car
manufacturing can reach higher level.
The main threats of Morgan Motor Company is such as
Local manufacturers of China are making exact replica of Morgan cars
Various Japanese brands like Lexus, Nissan and Mazda are making stylish and
aristocratic cars which is capturing most of UK markets
Use of expensive RAW materials in in manufacturing cars can give financial threat to
Morgan Motor Company
directors, VPs to the labour force so that everyone can contribute for a smooth run of
business operations.Maintain Royal heritage in designing cars is further noteworthy
operational initiatives of Morgan Motor. In order to give the taste of most luxurious and
superior cars to its customers, Morgan Motors design very few models around 8 with slight
modifications. They use quality materials purchased from outside suppliers i.e. Austin Rover,
Fiat and Fort and the parts are delivered in a very standardized form so that classic look of
21st century can be obtained with no special engineering modification.
With 100 years of immense changes in the technological advancements, this company holds
their long running position in the competitive market. Initially it sold the vehicles in Great
Britain only, then it started dealing with other countries around the globe as well to spread its
royal touch.
Supply chain management not only helps to optimize the inventory management of
automotive industry but also helps to assess its potential issues with effective risk
management policies.
Durability, Transparency, Transferability, replicability and resource sustainability are the key
assets to gain competitive advantages for Morgan Motor Company. However, it needs to
keep in mind that where there is good, there will be some disadvantages as well.
If we combine strength and opportunities together, for Morgan Motors the below areas
should be kept on focus
In order to increase production level new set of plants are required
More distributors need to be reached so that worldwide supply of cars can be
increased
More skilled employees need to be recruited so that production rate of car
manufacturing can reach higher level.
The main threats of Morgan Motor Company is such as
Local manufacturers of China are making exact replica of Morgan cars
Various Japanese brands like Lexus, Nissan and Mazda are making stylish and
aristocratic cars which is capturing most of UK markets
Use of expensive RAW materials in in manufacturing cars can give financial threat to
Morgan Motor Company
Paraphrase This Document
Need a fresh take? Get an instant paraphrase of this document with our AI Paraphraser
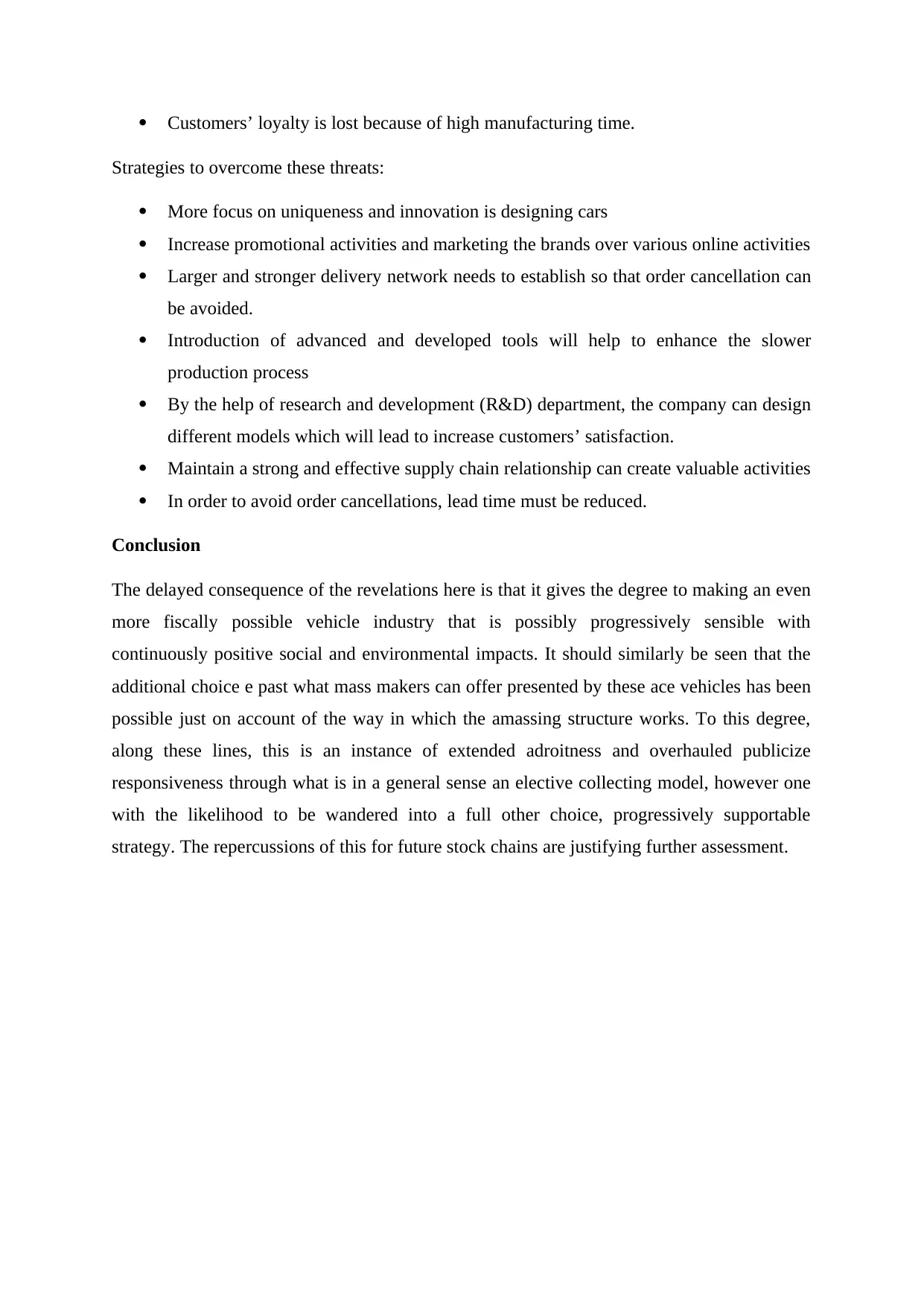
Customers’ loyalty is lost because of high manufacturing time.
Strategies to overcome these threats:
More focus on uniqueness and innovation is designing cars
Increase promotional activities and marketing the brands over various online activities
Larger and stronger delivery network needs to establish so that order cancellation can
be avoided.
Introduction of advanced and developed tools will help to enhance the slower
production process
By the help of research and development (R&D) department, the company can design
different models which will lead to increase customers’ satisfaction.
Maintain a strong and effective supply chain relationship can create valuable activities
In order to avoid order cancellations, lead time must be reduced.
Conclusion
The delayed consequence of the revelations here is that it gives the degree to making an even
more fiscally possible vehicle industry that is possibly progressively sensible with
continuously positive social and environmental impacts. It should similarly be seen that the
additional choice e past what mass makers can offer presented by these ace vehicles has been
possible just on account of the way in which the amassing structure works. To this degree,
along these lines, this is an instance of extended adroitness and overhauled publicize
responsiveness through what is in a general sense an elective collecting model, however one
with the likelihood to be wandered into a full other choice, progressively supportable
strategy. The repercussions of this for future stock chains are justifying further assessment.
Strategies to overcome these threats:
More focus on uniqueness and innovation is designing cars
Increase promotional activities and marketing the brands over various online activities
Larger and stronger delivery network needs to establish so that order cancellation can
be avoided.
Introduction of advanced and developed tools will help to enhance the slower
production process
By the help of research and development (R&D) department, the company can design
different models which will lead to increase customers’ satisfaction.
Maintain a strong and effective supply chain relationship can create valuable activities
In order to avoid order cancellations, lead time must be reduced.
Conclusion
The delayed consequence of the revelations here is that it gives the degree to making an even
more fiscally possible vehicle industry that is possibly progressively sensible with
continuously positive social and environmental impacts. It should similarly be seen that the
additional choice e past what mass makers can offer presented by these ace vehicles has been
possible just on account of the way in which the amassing structure works. To this degree,
along these lines, this is an instance of extended adroitness and overhauled publicize
responsiveness through what is in a general sense an elective collecting model, however one
with the likelihood to be wandered into a full other choice, progressively supportable
strategy. The repercussions of this for future stock chains are justifying further assessment.
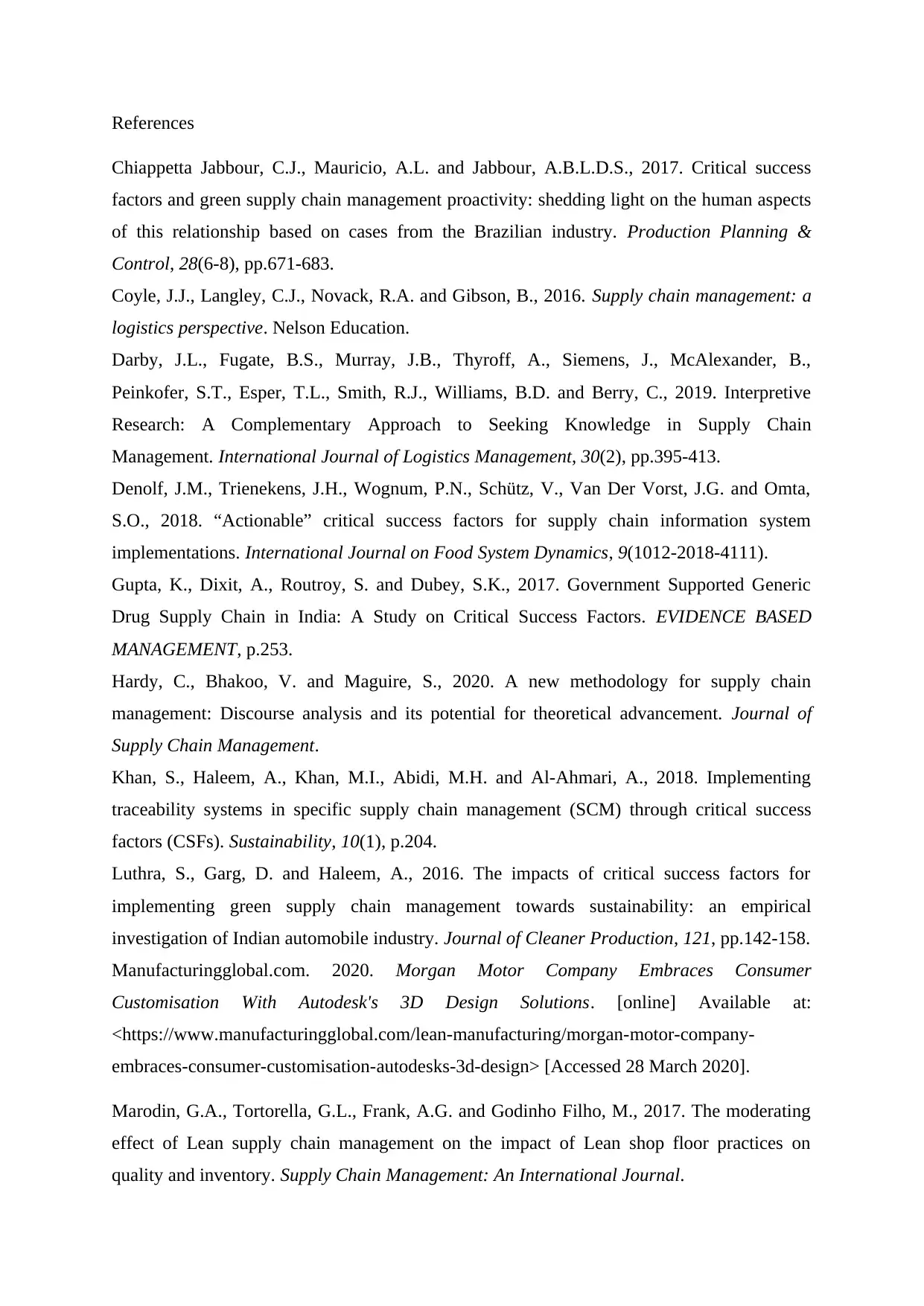
References
Chiappetta Jabbour, C.J., Mauricio, A.L. and Jabbour, A.B.L.D.S., 2017. Critical success
factors and green supply chain management proactivity: shedding light on the human aspects
of this relationship based on cases from the Brazilian industry. Production Planning &
Control, 28(6-8), pp.671-683.
Coyle, J.J., Langley, C.J., Novack, R.A. and Gibson, B., 2016. Supply chain management: a
logistics perspective. Nelson Education.
Darby, J.L., Fugate, B.S., Murray, J.B., Thyroff, A., Siemens, J., McAlexander, B.,
Peinkofer, S.T., Esper, T.L., Smith, R.J., Williams, B.D. and Berry, C., 2019. Interpretive
Research: A Complementary Approach to Seeking Knowledge in Supply Chain
Management. International Journal of Logistics Management, 30(2), pp.395-413.
Denolf, J.M., Trienekens, J.H., Wognum, P.N., Schütz, V., Van Der Vorst, J.G. and Omta,
S.O., 2018. “Actionable” critical success factors for supply chain information system
implementations. International Journal on Food System Dynamics, 9(1012-2018-4111).
Gupta, K., Dixit, A., Routroy, S. and Dubey, S.K., 2017. Government Supported Generic
Drug Supply Chain in India: A Study on Critical Success Factors. EVIDENCE BASED
MANAGEMENT, p.253.
Hardy, C., Bhakoo, V. and Maguire, S., 2020. A new methodology for supply chain
management: Discourse analysis and its potential for theoretical advancement. Journal of
Supply Chain Management.
Khan, S., Haleem, A., Khan, M.I., Abidi, M.H. and Al-Ahmari, A., 2018. Implementing
traceability systems in specific supply chain management (SCM) through critical success
factors (CSFs). Sustainability, 10(1), p.204.
Luthra, S., Garg, D. and Haleem, A., 2016. The impacts of critical success factors for
implementing green supply chain management towards sustainability: an empirical
investigation of Indian automobile industry. Journal of Cleaner Production, 121, pp.142-158.
Manufacturingglobal.com. 2020. Morgan Motor Company Embraces Consumer
Customisation With Autodesk's 3D Design Solutions. [online] Available at:
<https://www.manufacturingglobal.com/lean-manufacturing/morgan-motor-company-
embraces-consumer-customisation-autodesks-3d-design> [Accessed 28 March 2020].
Marodin, G.A., Tortorella, G.L., Frank, A.G. and Godinho Filho, M., 2017. The moderating
effect of Lean supply chain management on the impact of Lean shop floor practices on
quality and inventory. Supply Chain Management: An International Journal.
Chiappetta Jabbour, C.J., Mauricio, A.L. and Jabbour, A.B.L.D.S., 2017. Critical success
factors and green supply chain management proactivity: shedding light on the human aspects
of this relationship based on cases from the Brazilian industry. Production Planning &
Control, 28(6-8), pp.671-683.
Coyle, J.J., Langley, C.J., Novack, R.A. and Gibson, B., 2016. Supply chain management: a
logistics perspective. Nelson Education.
Darby, J.L., Fugate, B.S., Murray, J.B., Thyroff, A., Siemens, J., McAlexander, B.,
Peinkofer, S.T., Esper, T.L., Smith, R.J., Williams, B.D. and Berry, C., 2019. Interpretive
Research: A Complementary Approach to Seeking Knowledge in Supply Chain
Management. International Journal of Logistics Management, 30(2), pp.395-413.
Denolf, J.M., Trienekens, J.H., Wognum, P.N., Schütz, V., Van Der Vorst, J.G. and Omta,
S.O., 2018. “Actionable” critical success factors for supply chain information system
implementations. International Journal on Food System Dynamics, 9(1012-2018-4111).
Gupta, K., Dixit, A., Routroy, S. and Dubey, S.K., 2017. Government Supported Generic
Drug Supply Chain in India: A Study on Critical Success Factors. EVIDENCE BASED
MANAGEMENT, p.253.
Hardy, C., Bhakoo, V. and Maguire, S., 2020. A new methodology for supply chain
management: Discourse analysis and its potential for theoretical advancement. Journal of
Supply Chain Management.
Khan, S., Haleem, A., Khan, M.I., Abidi, M.H. and Al-Ahmari, A., 2018. Implementing
traceability systems in specific supply chain management (SCM) through critical success
factors (CSFs). Sustainability, 10(1), p.204.
Luthra, S., Garg, D. and Haleem, A., 2016. The impacts of critical success factors for
implementing green supply chain management towards sustainability: an empirical
investigation of Indian automobile industry. Journal of Cleaner Production, 121, pp.142-158.
Manufacturingglobal.com. 2020. Morgan Motor Company Embraces Consumer
Customisation With Autodesk's 3D Design Solutions. [online] Available at:
<https://www.manufacturingglobal.com/lean-manufacturing/morgan-motor-company-
embraces-consumer-customisation-autodesks-3d-design> [Accessed 28 March 2020].
Marodin, G.A., Tortorella, G.L., Frank, A.G. and Godinho Filho, M., 2017. The moderating
effect of Lean supply chain management on the impact of Lean shop floor practices on
quality and inventory. Supply Chain Management: An International Journal.
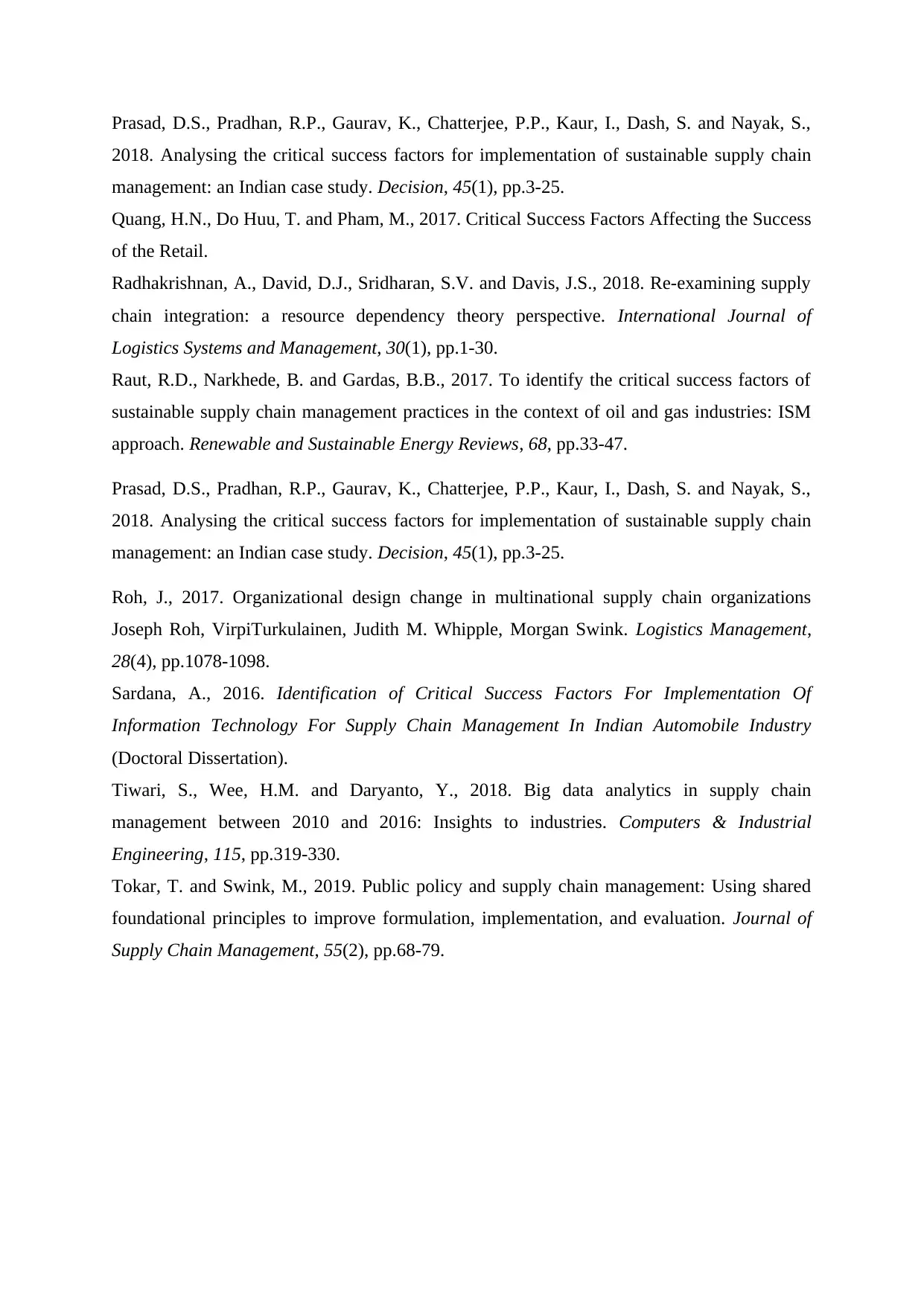
Prasad, D.S., Pradhan, R.P., Gaurav, K., Chatterjee, P.P., Kaur, I., Dash, S. and Nayak, S.,
2018. Analysing the critical success factors for implementation of sustainable supply chain
management: an Indian case study. Decision, 45(1), pp.3-25.
Quang, H.N., Do Huu, T. and Pham, M., 2017. Critical Success Factors Affecting the Success
of the Retail.
Radhakrishnan, A., David, D.J., Sridharan, S.V. and Davis, J.S., 2018. Re-examining supply
chain integration: a resource dependency theory perspective. International Journal of
Logistics Systems and Management, 30(1), pp.1-30.
Raut, R.D., Narkhede, B. and Gardas, B.B., 2017. To identify the critical success factors of
sustainable supply chain management practices in the context of oil and gas industries: ISM
approach. Renewable and Sustainable Energy Reviews, 68, pp.33-47.
Prasad, D.S., Pradhan, R.P., Gaurav, K., Chatterjee, P.P., Kaur, I., Dash, S. and Nayak, S.,
2018. Analysing the critical success factors for implementation of sustainable supply chain
management: an Indian case study. Decision, 45(1), pp.3-25.
Roh, J., 2017. Organizational design change in multinational supply chain organizations
Joseph Roh, VirpiTurkulainen, Judith M. Whipple, Morgan Swink. Logistics Management,
28(4), pp.1078-1098.
Sardana, A., 2016. Identification of Critical Success Factors For Implementation Of
Information Technology For Supply Chain Management In Indian Automobile Industry
(Doctoral Dissertation).
Tiwari, S., Wee, H.M. and Daryanto, Y., 2018. Big data analytics in supply chain
management between 2010 and 2016: Insights to industries. Computers & Industrial
Engineering, 115, pp.319-330.
Tokar, T. and Swink, M., 2019. Public policy and supply chain management: Using shared
foundational principles to improve formulation, implementation, and evaluation. Journal of
Supply Chain Management, 55(2), pp.68-79.
2018. Analysing the critical success factors for implementation of sustainable supply chain
management: an Indian case study. Decision, 45(1), pp.3-25.
Quang, H.N., Do Huu, T. and Pham, M., 2017. Critical Success Factors Affecting the Success
of the Retail.
Radhakrishnan, A., David, D.J., Sridharan, S.V. and Davis, J.S., 2018. Re-examining supply
chain integration: a resource dependency theory perspective. International Journal of
Logistics Systems and Management, 30(1), pp.1-30.
Raut, R.D., Narkhede, B. and Gardas, B.B., 2017. To identify the critical success factors of
sustainable supply chain management practices in the context of oil and gas industries: ISM
approach. Renewable and Sustainable Energy Reviews, 68, pp.33-47.
Prasad, D.S., Pradhan, R.P., Gaurav, K., Chatterjee, P.P., Kaur, I., Dash, S. and Nayak, S.,
2018. Analysing the critical success factors for implementation of sustainable supply chain
management: an Indian case study. Decision, 45(1), pp.3-25.
Roh, J., 2017. Organizational design change in multinational supply chain organizations
Joseph Roh, VirpiTurkulainen, Judith M. Whipple, Morgan Swink. Logistics Management,
28(4), pp.1078-1098.
Sardana, A., 2016. Identification of Critical Success Factors For Implementation Of
Information Technology For Supply Chain Management In Indian Automobile Industry
(Doctoral Dissertation).
Tiwari, S., Wee, H.M. and Daryanto, Y., 2018. Big data analytics in supply chain
management between 2010 and 2016: Insights to industries. Computers & Industrial
Engineering, 115, pp.319-330.
Tokar, T. and Swink, M., 2019. Public policy and supply chain management: Using shared
foundational principles to improve formulation, implementation, and evaluation. Journal of
Supply Chain Management, 55(2), pp.68-79.
1 out of 10
Related Documents
![[object Object]](/_next/image/?url=%2F_next%2Fstatic%2Fmedia%2Flogo.6d15ce61.png&w=640&q=75)
Your All-in-One AI-Powered Toolkit for Academic Success.
+13062052269
info@desklib.com
Available 24*7 on WhatsApp / Email
Unlock your academic potential
© 2024 | Zucol Services PVT LTD | All rights reserved.