Managing Project Quality
VerifiedAdded on 2022/12/28
|12
|2225
|91
AI Summary
This report discusses the importance of managing project quality and provides an overview of various tools and methods used in quality management. It covers topics such as quality standards, quality assurance tools, quality control tools, and the roles and responsibilities of quality management personnel. The report emphasizes the need for effective quality management in order to ensure project success.
Contribute Materials
Your contribution can guide someone’s learning journey. Share your
documents today.
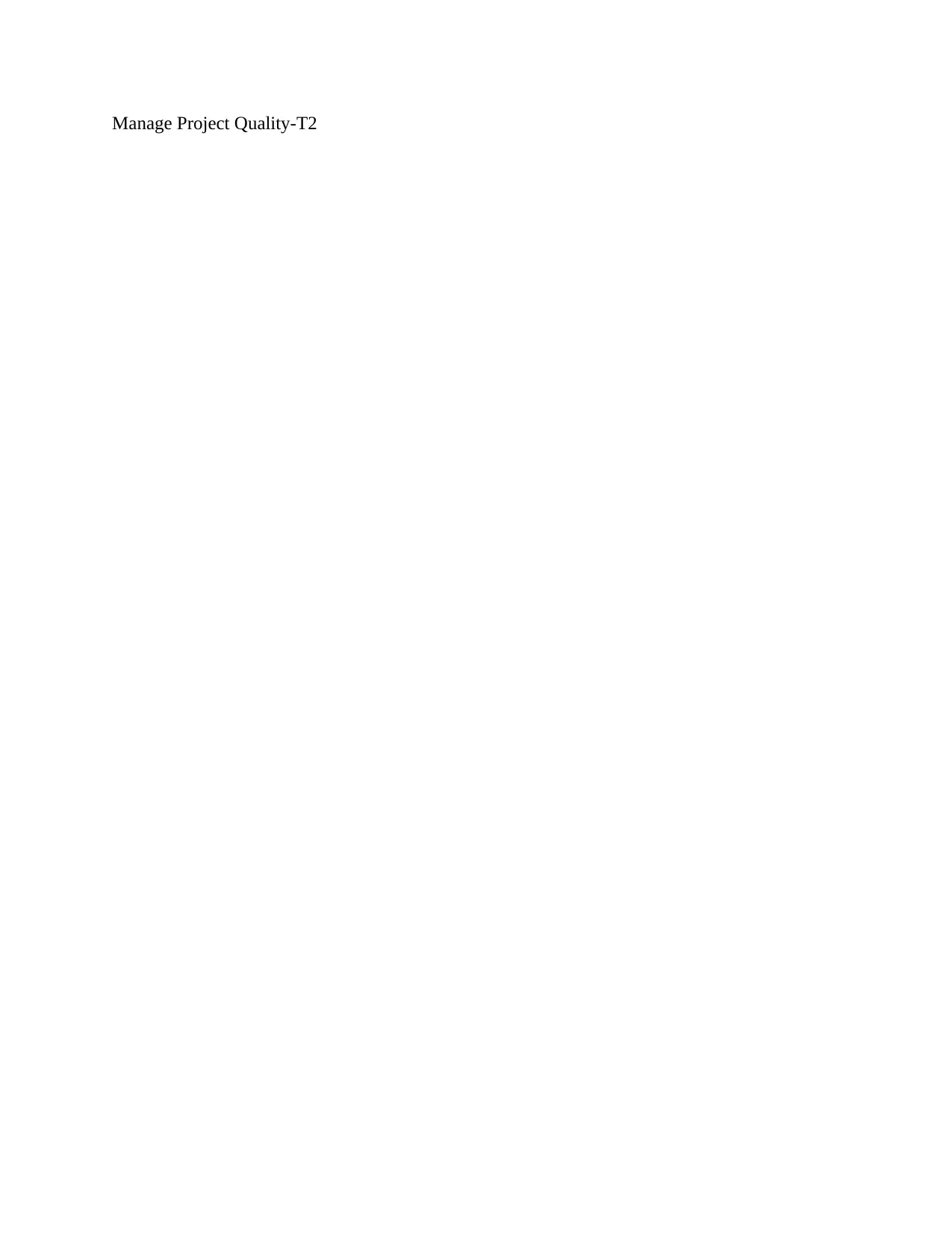
Manage Project Quality-T2
Secure Best Marks with AI Grader
Need help grading? Try our AI Grader for instant feedback on your assignments.
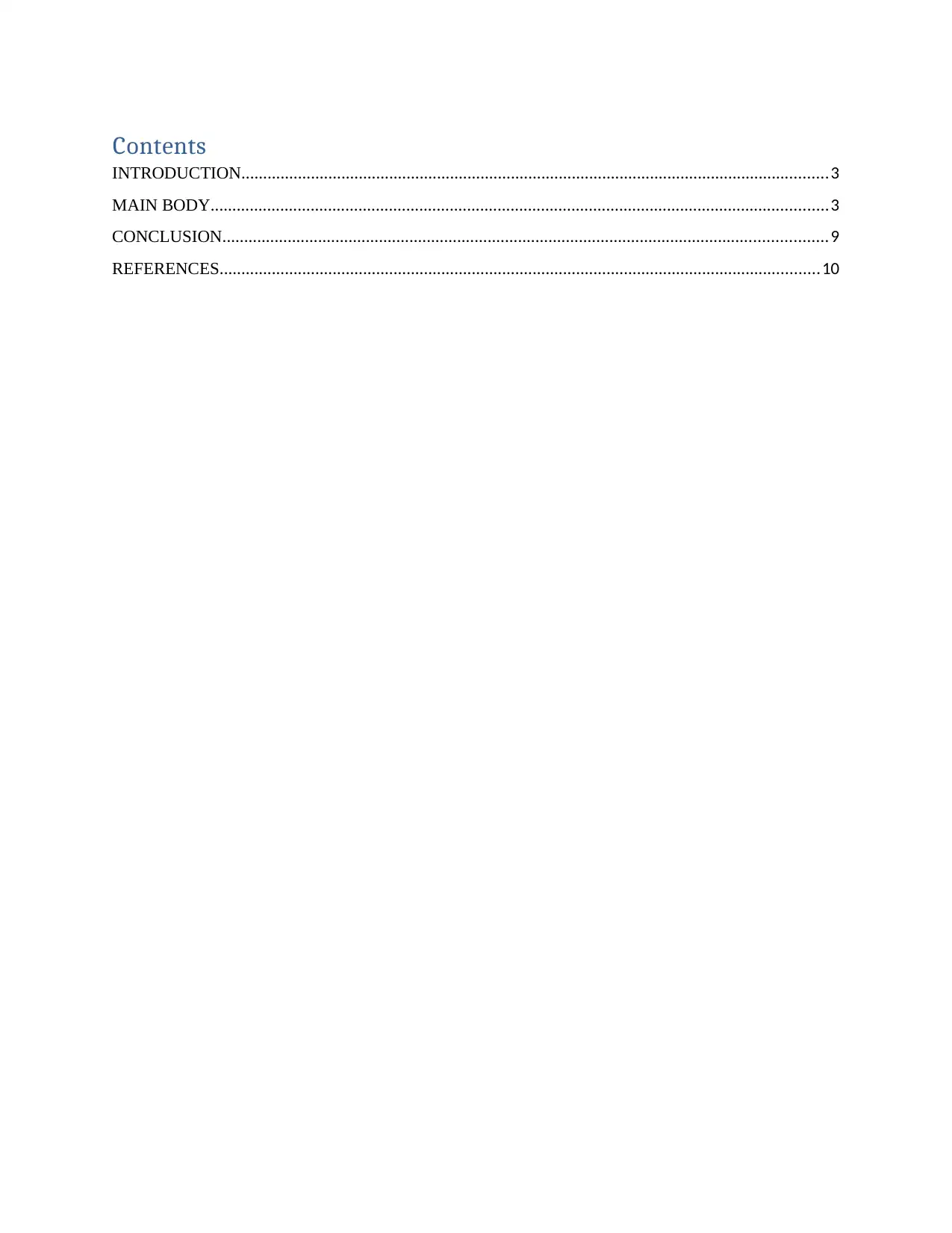
Contents
INTRODUCTION.......................................................................................................................................3
MAIN BODY..............................................................................................................................................3
CONCLUSION...........................................................................................................................................9
REFERENCES..........................................................................................................................................10
INTRODUCTION.......................................................................................................................................3
MAIN BODY..............................................................................................................................................3
CONCLUSION...........................................................................................................................................9
REFERENCES..........................................................................................................................................10
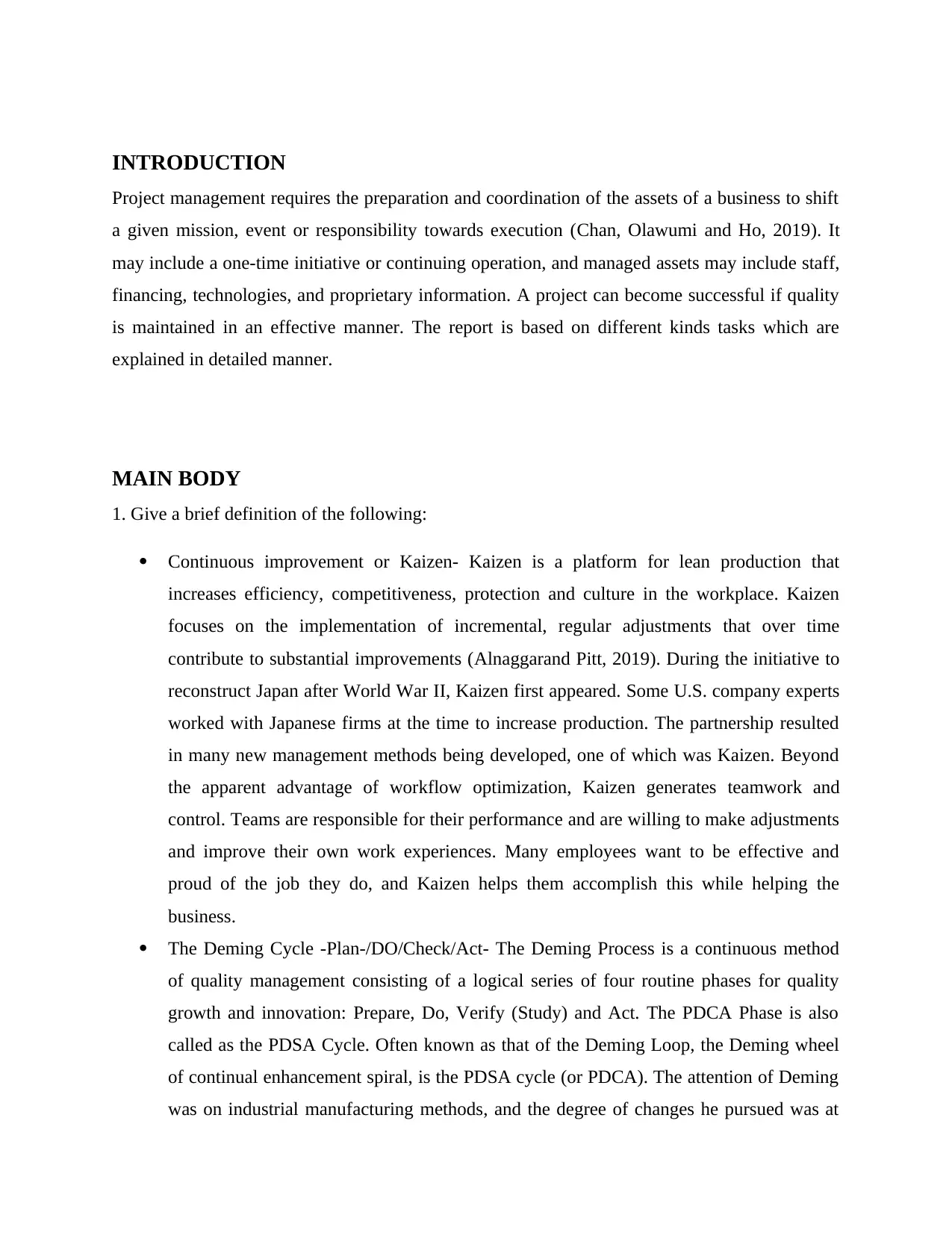
INTRODUCTION
Project management requires the preparation and coordination of the assets of a business to shift
a given mission, event or responsibility towards execution (Chan, Olawumi and Ho, 2019). It
may include a one-time initiative or continuing operation, and managed assets may include staff,
financing, technologies, and proprietary information. A project can become successful if quality
is maintained in an effective manner. The report is based on different kinds tasks which are
explained in detailed manner.
MAIN BODY
1. Give a brief definition of the following:
Continuous improvement or Kaizen- Kaizen is a platform for lean production that
increases efficiency, competitiveness, protection and culture in the workplace. Kaizen
focuses on the implementation of incremental, regular adjustments that over time
contribute to substantial improvements (Alnaggarand Pitt, 2019). During the initiative to
reconstruct Japan after World War II, Kaizen first appeared. Some U.S. company experts
worked with Japanese firms at the time to increase production. The partnership resulted
in many new management methods being developed, one of which was Kaizen. Beyond
the apparent advantage of workflow optimization, Kaizen generates teamwork and
control. Teams are responsible for their performance and are willing to make adjustments
and improve their own work experiences. Many employees want to be effective and
proud of the job they do, and Kaizen helps them accomplish this while helping the
business.
The Deming Cycle -Plan-/DO/Check/Act- The Deming Process is a continuous method
of quality management consisting of a logical series of four routine phases for quality
growth and innovation: Prepare, Do, Verify (Study) and Act. The PDCA Phase is also
called as the PDSA Cycle. Often known as that of the Deming Loop, the Deming wheel
of continual enhancement spiral, is the PDSA cycle (or PDCA). The attention of Deming
was on industrial manufacturing methods, and the degree of changes he pursued was at
Project management requires the preparation and coordination of the assets of a business to shift
a given mission, event or responsibility towards execution (Chan, Olawumi and Ho, 2019). It
may include a one-time initiative or continuing operation, and managed assets may include staff,
financing, technologies, and proprietary information. A project can become successful if quality
is maintained in an effective manner. The report is based on different kinds tasks which are
explained in detailed manner.
MAIN BODY
1. Give a brief definition of the following:
Continuous improvement or Kaizen- Kaizen is a platform for lean production that
increases efficiency, competitiveness, protection and culture in the workplace. Kaizen
focuses on the implementation of incremental, regular adjustments that over time
contribute to substantial improvements (Alnaggarand Pitt, 2019). During the initiative to
reconstruct Japan after World War II, Kaizen first appeared. Some U.S. company experts
worked with Japanese firms at the time to increase production. The partnership resulted
in many new management methods being developed, one of which was Kaizen. Beyond
the apparent advantage of workflow optimization, Kaizen generates teamwork and
control. Teams are responsible for their performance and are willing to make adjustments
and improve their own work experiences. Many employees want to be effective and
proud of the job they do, and Kaizen helps them accomplish this while helping the
business.
The Deming Cycle -Plan-/DO/Check/Act- The Deming Process is a continuous method
of quality management consisting of a logical series of four routine phases for quality
growth and innovation: Prepare, Do, Verify (Study) and Act. The PDCA Phase is also
called as the PDSA Cycle. Often known as that of the Deming Loop, the Deming wheel
of continual enhancement spiral, is the PDSA cycle (or PDCA). The attention of Deming
was on industrial manufacturing methods, and the degree of changes he pursued was at
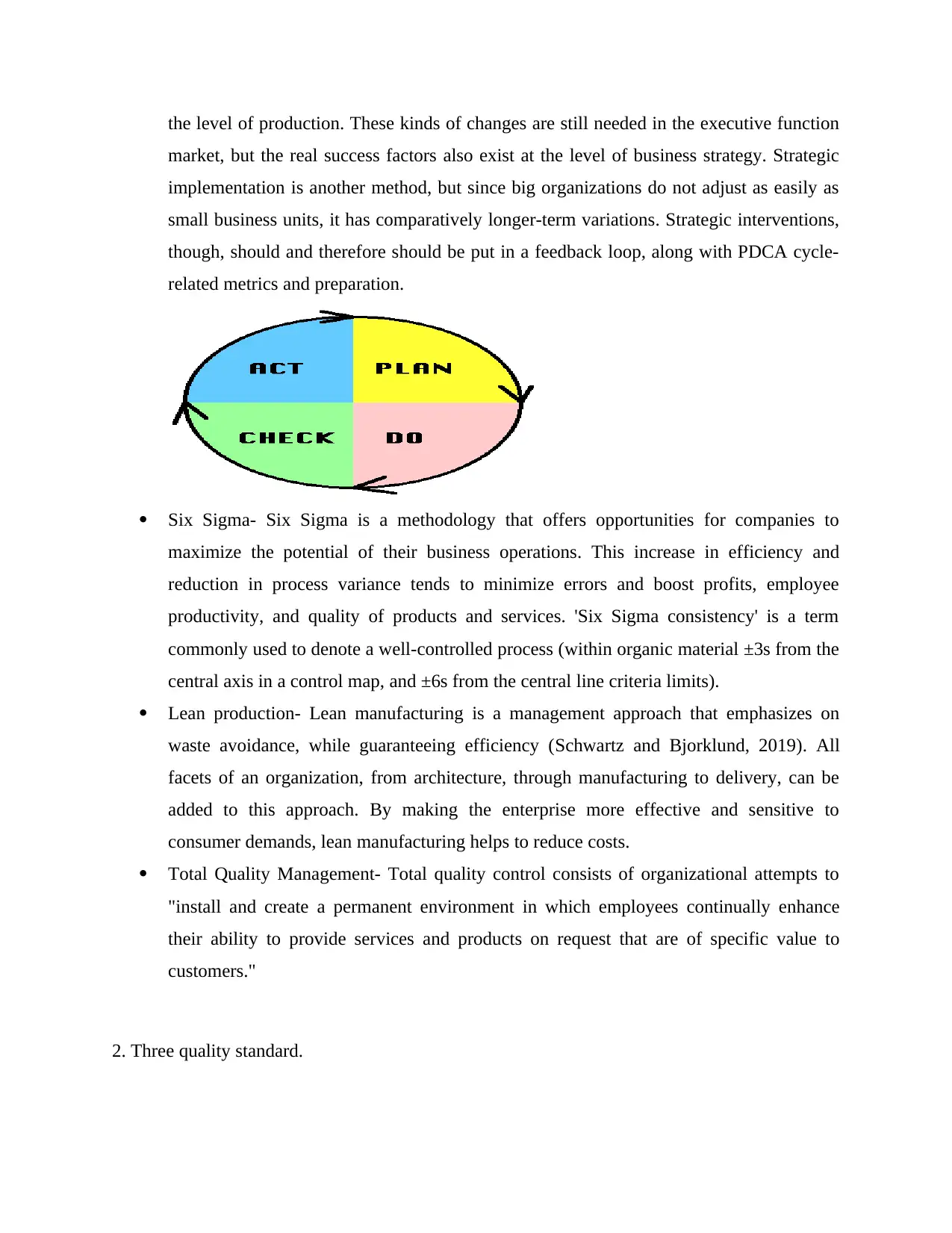
the level of production. These kinds of changes are still needed in the executive function
market, but the real success factors also exist at the level of business strategy. Strategic
implementation is another method, but since big organizations do not adjust as easily as
small business units, it has comparatively longer-term variations. Strategic interventions,
though, should and therefore should be put in a feedback loop, along with PDCA cycle-
related metrics and preparation.
Six Sigma- Six Sigma is a methodology that offers opportunities for companies to
maximize the potential of their business operations. This increase in efficiency and
reduction in process variance tends to minimize errors and boost profits, employee
productivity, and quality of products and services. 'Six Sigma consistency' is a term
commonly used to denote a well-controlled process (within organic material ±3s from the
central axis in a control map, and ±6s from the central line criteria limits).
Lean production- Lean manufacturing is a management approach that emphasizes on
waste avoidance, while guaranteeing efficiency (Schwartz and Bjorklund, 2019). All
facets of an organization, from architecture, through manufacturing to delivery, can be
added to this approach. By making the enterprise more effective and sensitive to
consumer demands, lean manufacturing helps to reduce costs.
Total Quality Management- Total quality control consists of organizational attempts to
"install and create a permanent environment in which employees continually enhance
their ability to provide services and products on request that are of specific value to
customers."
2. Three quality standard.
market, but the real success factors also exist at the level of business strategy. Strategic
implementation is another method, but since big organizations do not adjust as easily as
small business units, it has comparatively longer-term variations. Strategic interventions,
though, should and therefore should be put in a feedback loop, along with PDCA cycle-
related metrics and preparation.
Six Sigma- Six Sigma is a methodology that offers opportunities for companies to
maximize the potential of their business operations. This increase in efficiency and
reduction in process variance tends to minimize errors and boost profits, employee
productivity, and quality of products and services. 'Six Sigma consistency' is a term
commonly used to denote a well-controlled process (within organic material ±3s from the
central axis in a control map, and ±6s from the central line criteria limits).
Lean production- Lean manufacturing is a management approach that emphasizes on
waste avoidance, while guaranteeing efficiency (Schwartz and Bjorklund, 2019). All
facets of an organization, from architecture, through manufacturing to delivery, can be
added to this approach. By making the enterprise more effective and sensitive to
consumer demands, lean manufacturing helps to reduce costs.
Total Quality Management- Total quality control consists of organizational attempts to
"install and create a permanent environment in which employees continually enhance
their ability to provide services and products on request that are of specific value to
customers."
2. Three quality standard.
Secure Best Marks with AI Grader
Need help grading? Try our AI Grader for instant feedback on your assignments.
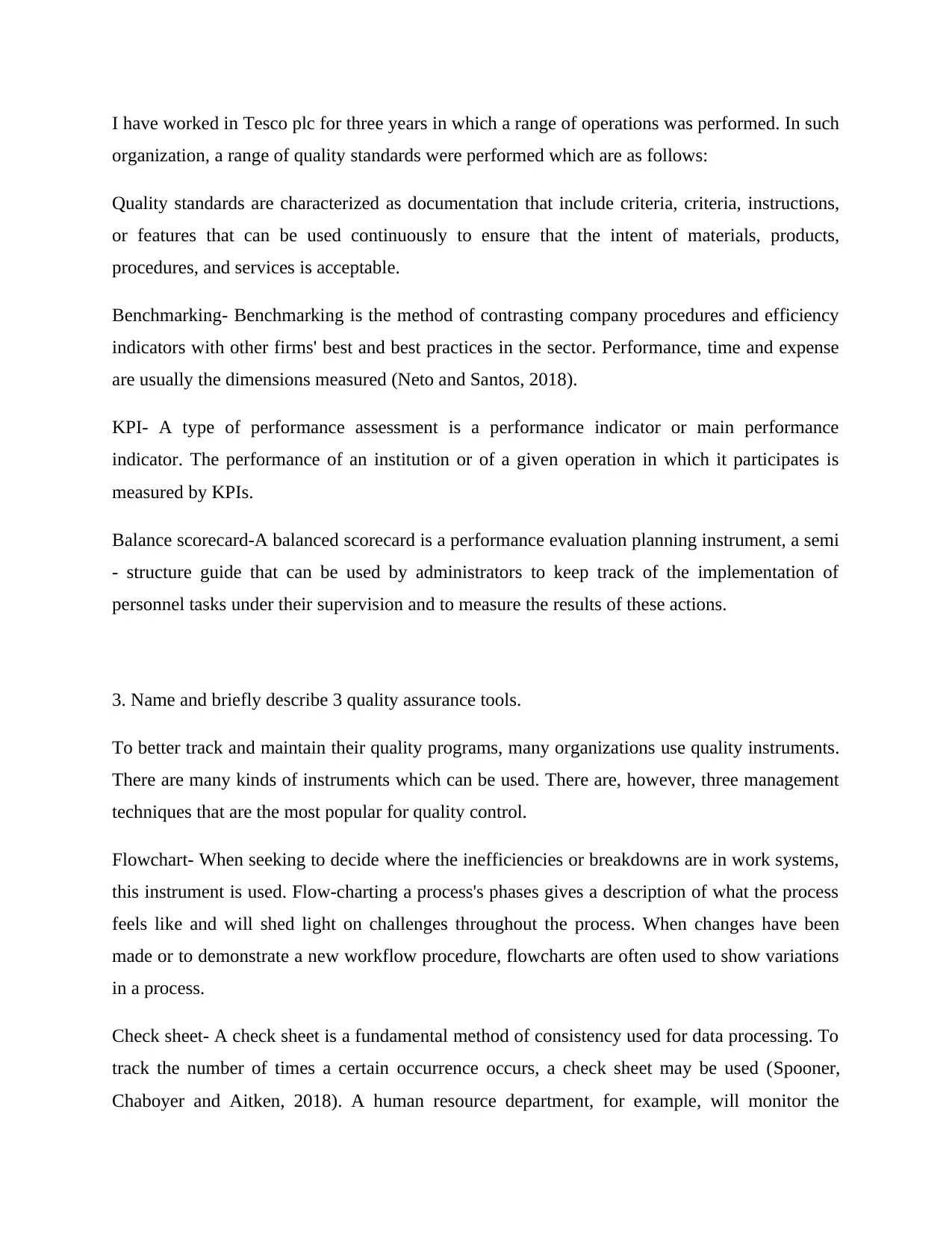
I have worked in Tesco plc for three years in which a range of operations was performed. In such
organization, a range of quality standards were performed which are as follows:
Quality standards are characterized as documentation that include criteria, criteria, instructions,
or features that can be used continuously to ensure that the intent of materials, products,
procedures, and services is acceptable.
Benchmarking- Benchmarking is the method of contrasting company procedures and efficiency
indicators with other firms' best and best practices in the sector. Performance, time and expense
are usually the dimensions measured (Neto and Santos, 2018).
KPI- A type of performance assessment is a performance indicator or main performance
indicator. The performance of an institution or of a given operation in which it participates is
measured by KPIs.
Balance scorecard-A balanced scorecard is a performance evaluation planning instrument, a semi
- structure guide that can be used by administrators to keep track of the implementation of
personnel tasks under their supervision and to measure the results of these actions.
3. Name and briefly describe 3 quality assurance tools.
To better track and maintain their quality programs, many organizations use quality instruments.
There are many kinds of instruments which can be used. There are, however, three management
techniques that are the most popular for quality control.
Flowchart- When seeking to decide where the inefficiencies or breakdowns are in work systems,
this instrument is used. Flow-charting a process's phases gives a description of what the process
feels like and will shed light on challenges throughout the process. When changes have been
made or to demonstrate a new workflow procedure, flowcharts are often used to show variations
in a process.
Check sheet- A check sheet is a fundamental method of consistency used for data processing. To
track the number of times a certain occurrence occurs, a check sheet may be used (Spooner,
Chaboyer and Aitken, 2018). A human resource department, for example, will monitor the
organization, a range of quality standards were performed which are as follows:
Quality standards are characterized as documentation that include criteria, criteria, instructions,
or features that can be used continuously to ensure that the intent of materials, products,
procedures, and services is acceptable.
Benchmarking- Benchmarking is the method of contrasting company procedures and efficiency
indicators with other firms' best and best practices in the sector. Performance, time and expense
are usually the dimensions measured (Neto and Santos, 2018).
KPI- A type of performance assessment is a performance indicator or main performance
indicator. The performance of an institution or of a given operation in which it participates is
measured by KPIs.
Balance scorecard-A balanced scorecard is a performance evaluation planning instrument, a semi
- structure guide that can be used by administrators to keep track of the implementation of
personnel tasks under their supervision and to measure the results of these actions.
3. Name and briefly describe 3 quality assurance tools.
To better track and maintain their quality programs, many organizations use quality instruments.
There are many kinds of instruments which can be used. There are, however, three management
techniques that are the most popular for quality control.
Flowchart- When seeking to decide where the inefficiencies or breakdowns are in work systems,
this instrument is used. Flow-charting a process's phases gives a description of what the process
feels like and will shed light on challenges throughout the process. When changes have been
made or to demonstrate a new workflow procedure, flowcharts are often used to show variations
in a process.
Check sheet- A check sheet is a fundamental method of consistency used for data processing. To
track the number of times a certain occurrence occurs, a check sheet may be used (Spooner,
Chaboyer and Aitken, 2018). A human resource department, for example, will monitor the
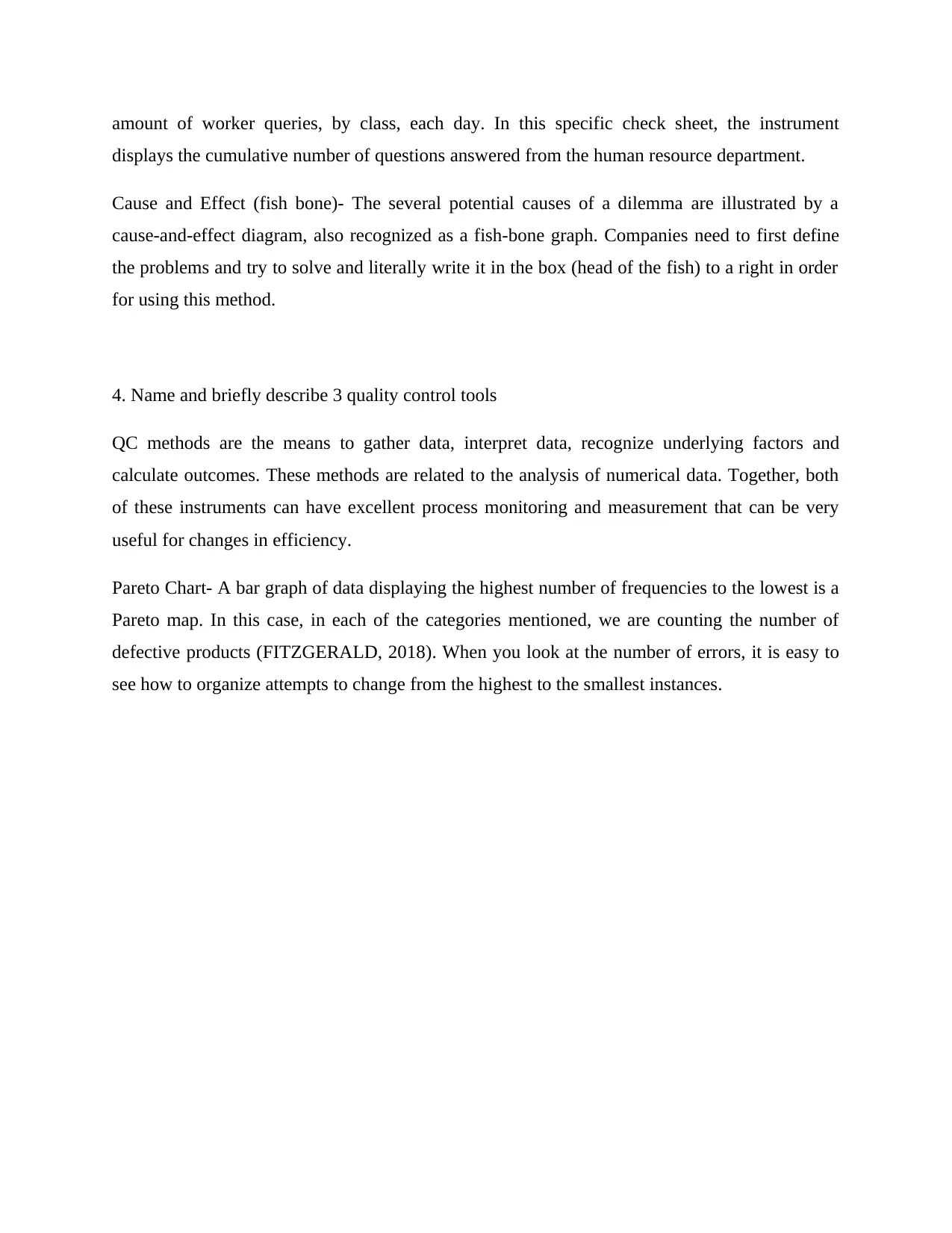
amount of worker queries, by class, each day. In this specific check sheet, the instrument
displays the cumulative number of questions answered from the human resource department.
Cause and Effect (fish bone)- The several potential causes of a dilemma are illustrated by a
cause-and-effect diagram, also recognized as a fish-bone graph. Companies need to first define
the problems and try to solve and literally write it in the box (head of the fish) to a right in order
for using this method.
4. Name and briefly describe 3 quality control tools
QC methods are the means to gather data, interpret data, recognize underlying factors and
calculate outcomes. These methods are related to the analysis of numerical data. Together, both
of these instruments can have excellent process monitoring and measurement that can be very
useful for changes in efficiency.
Pareto Chart- A bar graph of data displaying the highest number of frequencies to the lowest is a
Pareto map. In this case, in each of the categories mentioned, we are counting the number of
defective products (FITZGERALD, 2018). When you look at the number of errors, it is easy to
see how to organize attempts to change from the highest to the smallest instances.
displays the cumulative number of questions answered from the human resource department.
Cause and Effect (fish bone)- The several potential causes of a dilemma are illustrated by a
cause-and-effect diagram, also recognized as a fish-bone graph. Companies need to first define
the problems and try to solve and literally write it in the box (head of the fish) to a right in order
for using this method.
4. Name and briefly describe 3 quality control tools
QC methods are the means to gather data, interpret data, recognize underlying factors and
calculate outcomes. These methods are related to the analysis of numerical data. Together, both
of these instruments can have excellent process monitoring and measurement that can be very
useful for changes in efficiency.
Pareto Chart- A bar graph of data displaying the highest number of frequencies to the lowest is a
Pareto map. In this case, in each of the categories mentioned, we are counting the number of
defective products (FITZGERALD, 2018). When you look at the number of errors, it is easy to
see how to organize attempts to change from the highest to the smallest instances.
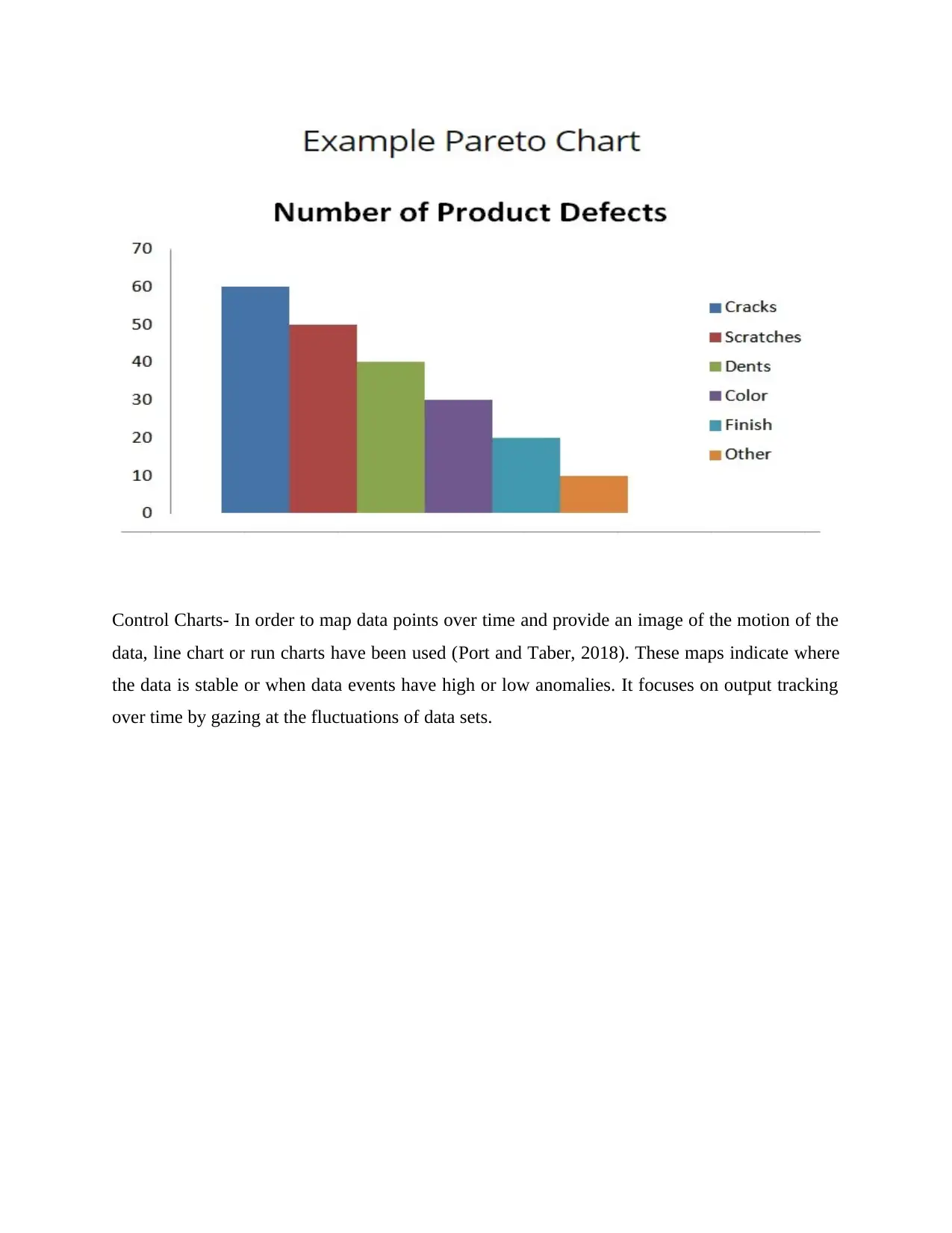
Control Charts- In order to map data points over time and provide an image of the motion of the
data, line chart or run charts have been used (Port and Taber, 2018). These maps indicate where
the data is stable or when data events have high or low anomalies. It focuses on output tracking
over time by gazing at the fluctuations of data sets.
data, line chart or run charts have been used (Port and Taber, 2018). These maps indicate where
the data is stable or when data events have high or low anomalies. It focuses on output tracking
over time by gazing at the fluctuations of data sets.
Paraphrase This Document
Need a fresh take? Get an instant paraphrase of this document with our AI Paraphraser
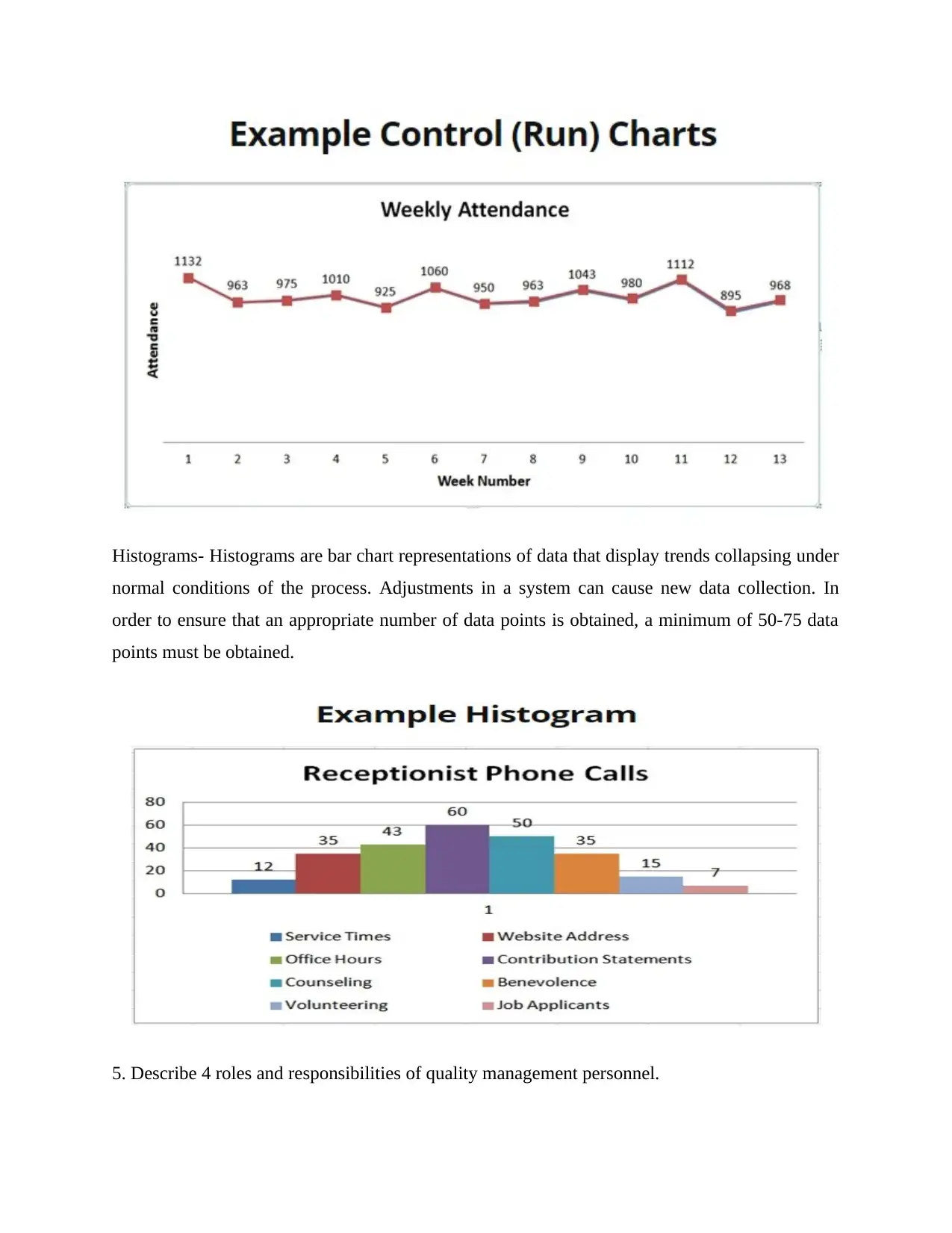
Histograms- Histograms are bar chart representations of data that display trends collapsing under
normal conditions of the process. Adjustments in a system can cause new data collection. In
order to ensure that an appropriate number of data points is obtained, a minimum of 50-75 data
points must be obtained.
5. Describe 4 roles and responsibilities of quality management personnel.
normal conditions of the process. Adjustments in a system can cause new data collection. In
order to ensure that an appropriate number of data points is obtained, a minimum of 50-75 data
points must be obtained.
5. Describe 4 roles and responsibilities of quality management personnel.
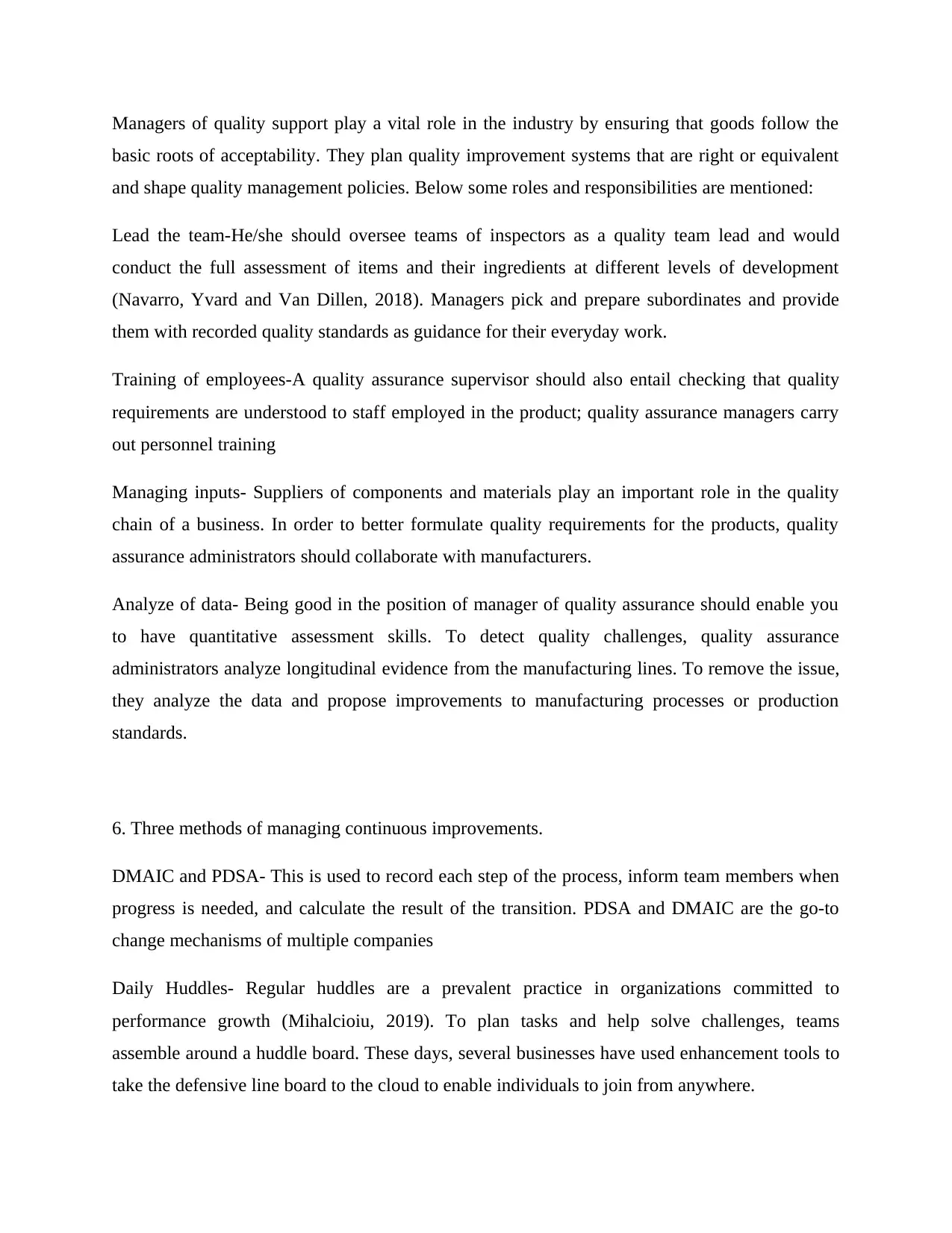
Managers of quality support play a vital role in the industry by ensuring that goods follow the
basic roots of acceptability. They plan quality improvement systems that are right or equivalent
and shape quality management policies. Below some roles and responsibilities are mentioned:
Lead the team-He/she should oversee teams of inspectors as a quality team lead and would
conduct the full assessment of items and their ingredients at different levels of development
(Navarro, Yvard and Van Dillen, 2018). Managers pick and prepare subordinates and provide
them with recorded quality standards as guidance for their everyday work.
Training of employees-A quality assurance supervisor should also entail checking that quality
requirements are understood to staff employed in the product; quality assurance managers carry
out personnel training
Managing inputs- Suppliers of components and materials play an important role in the quality
chain of a business. In order to better formulate quality requirements for the products, quality
assurance administrators should collaborate with manufacturers.
Analyze of data- Being good in the position of manager of quality assurance should enable you
to have quantitative assessment skills. To detect quality challenges, quality assurance
administrators analyze longitudinal evidence from the manufacturing lines. To remove the issue,
they analyze the data and propose improvements to manufacturing processes or production
standards.
6. Three methods of managing continuous improvements.
DMAIC and PDSA- This is used to record each step of the process, inform team members when
progress is needed, and calculate the result of the transition. PDSA and DMAIC are the go-to
change mechanisms of multiple companies
Daily Huddles- Regular huddles are a prevalent practice in organizations committed to
performance growth (Mihalcioiu, 2019). To plan tasks and help solve challenges, teams
assemble around a huddle board. These days, several businesses have used enhancement tools to
take the defensive line board to the cloud to enable individuals to join from anywhere.
basic roots of acceptability. They plan quality improvement systems that are right or equivalent
and shape quality management policies. Below some roles and responsibilities are mentioned:
Lead the team-He/she should oversee teams of inspectors as a quality team lead and would
conduct the full assessment of items and their ingredients at different levels of development
(Navarro, Yvard and Van Dillen, 2018). Managers pick and prepare subordinates and provide
them with recorded quality standards as guidance for their everyday work.
Training of employees-A quality assurance supervisor should also entail checking that quality
requirements are understood to staff employed in the product; quality assurance managers carry
out personnel training
Managing inputs- Suppliers of components and materials play an important role in the quality
chain of a business. In order to better formulate quality requirements for the products, quality
assurance administrators should collaborate with manufacturers.
Analyze of data- Being good in the position of manager of quality assurance should enable you
to have quantitative assessment skills. To detect quality challenges, quality assurance
administrators analyze longitudinal evidence from the manufacturing lines. To remove the issue,
they analyze the data and propose improvements to manufacturing processes or production
standards.
6. Three methods of managing continuous improvements.
DMAIC and PDSA- This is used to record each step of the process, inform team members when
progress is needed, and calculate the result of the transition. PDSA and DMAIC are the go-to
change mechanisms of multiple companies
Daily Huddles- Regular huddles are a prevalent practice in organizations committed to
performance growth (Mihalcioiu, 2019). To plan tasks and help solve challenges, teams
assemble around a huddle board. These days, several businesses have used enhancement tools to
take the defensive line board to the cloud to enable individuals to join from anywhere.
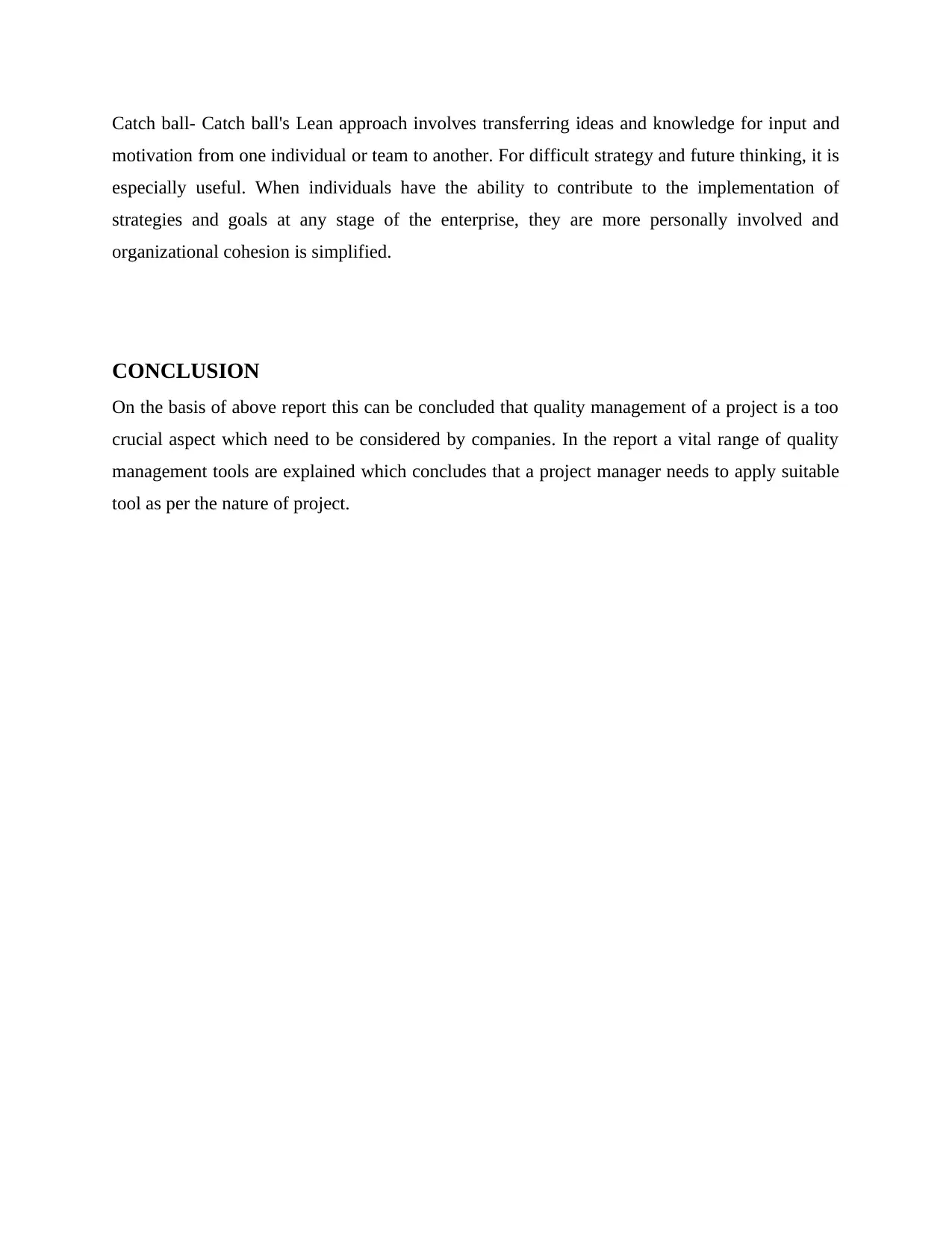
Catch ball- Catch ball's Lean approach involves transferring ideas and knowledge for input and
motivation from one individual or team to another. For difficult strategy and future thinking, it is
especially useful. When individuals have the ability to contribute to the implementation of
strategies and goals at any stage of the enterprise, they are more personally involved and
organizational cohesion is simplified.
CONCLUSION
On the basis of above report this can be concluded that quality management of a project is a too
crucial aspect which need to be considered by companies. In the report a vital range of quality
management tools are explained which concludes that a project manager needs to apply suitable
tool as per the nature of project.
motivation from one individual or team to another. For difficult strategy and future thinking, it is
especially useful. When individuals have the ability to contribute to the implementation of
strategies and goals at any stage of the enterprise, they are more personally involved and
organizational cohesion is simplified.
CONCLUSION
On the basis of above report this can be concluded that quality management of a project is a too
crucial aspect which need to be considered by companies. In the report a vital range of quality
management tools are explained which concludes that a project manager needs to apply suitable
tool as per the nature of project.
Secure Best Marks with AI Grader
Need help grading? Try our AI Grader for instant feedback on your assignments.
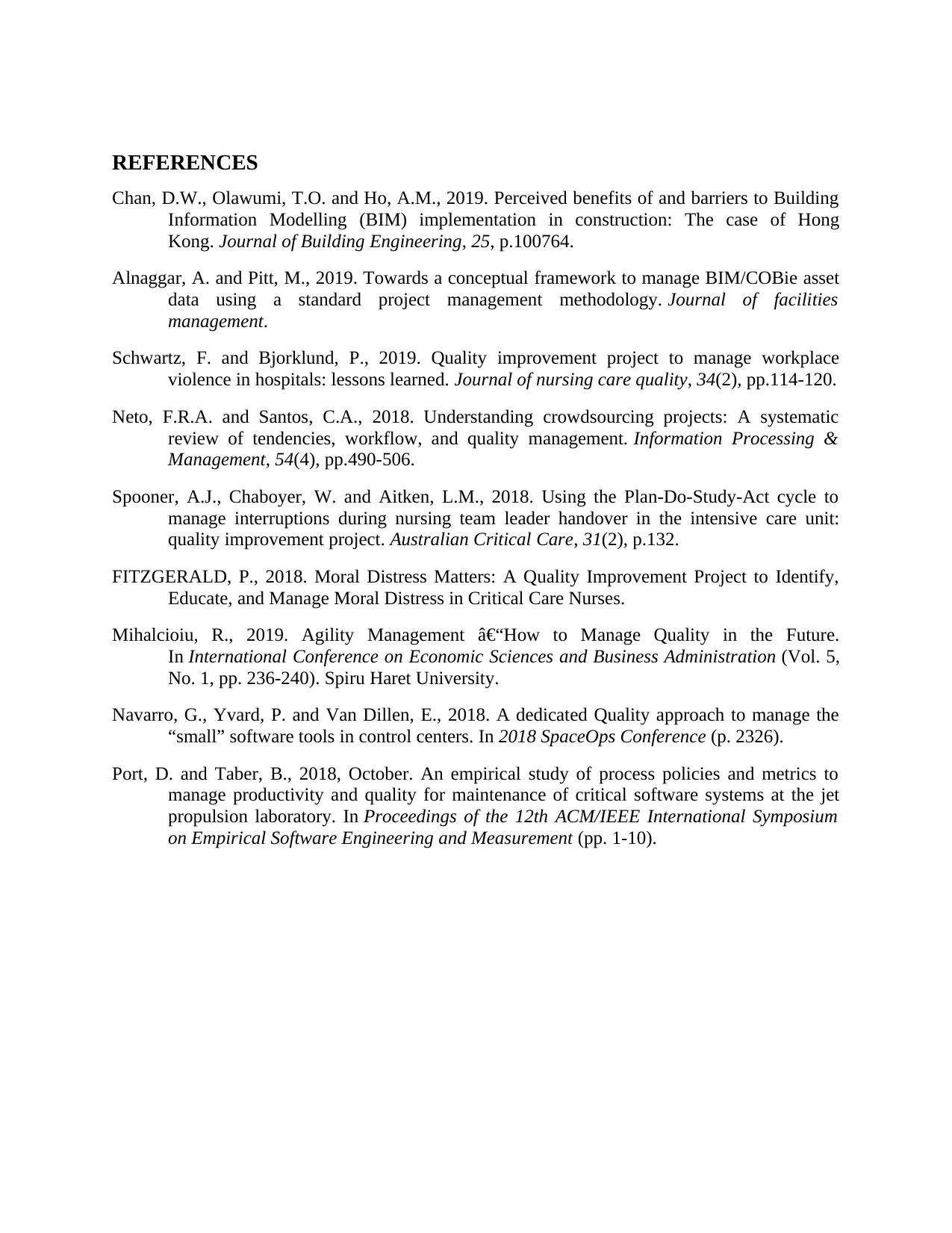
REFERENCES
Chan, D.W., Olawumi, T.O. and Ho, A.M., 2019. Perceived benefits of and barriers to Building
Information Modelling (BIM) implementation in construction: The case of Hong
Kong. Journal of Building Engineering, 25, p.100764.
Alnaggar, A. and Pitt, M., 2019. Towards a conceptual framework to manage BIM/COBie asset
data using a standard project management methodology. Journal of facilities
management.
Schwartz, F. and Bjorklund, P., 2019. Quality improvement project to manage workplace
violence in hospitals: lessons learned. Journal of nursing care quality, 34(2), pp.114-120.
Neto, F.R.A. and Santos, C.A., 2018. Understanding crowdsourcing projects: A systematic
review of tendencies, workflow, and quality management. Information Processing &
Management, 54(4), pp.490-506.
Spooner, A.J., Chaboyer, W. and Aitken, L.M., 2018. Using the Plan-Do-Study-Act cycle to
manage interruptions during nursing team leader handover in the intensive care unit:
quality improvement project. Australian Critical Care, 31(2), p.132.
FITZGERALD, P., 2018. Moral Distress Matters: A Quality Improvement Project to Identify,
Educate, and Manage Moral Distress in Critical Care Nurses.
Mihalcioiu, R., 2019. Agility Management –How to Manage Quality in the Future.
In International Conference on Economic Sciences and Business Administration (Vol. 5,
No. 1, pp. 236-240). Spiru Haret University.
Navarro, G., Yvard, P. and Van Dillen, E., 2018. A dedicated Quality approach to manage the
“small” software tools in control centers. In 2018 SpaceOps Conference (p. 2326).
Port, D. and Taber, B., 2018, October. An empirical study of process policies and metrics to
manage productivity and quality for maintenance of critical software systems at the jet
propulsion laboratory. In Proceedings of the 12th ACM/IEEE International Symposium
on Empirical Software Engineering and Measurement (pp. 1-10).
Chan, D.W., Olawumi, T.O. and Ho, A.M., 2019. Perceived benefits of and barriers to Building
Information Modelling (BIM) implementation in construction: The case of Hong
Kong. Journal of Building Engineering, 25, p.100764.
Alnaggar, A. and Pitt, M., 2019. Towards a conceptual framework to manage BIM/COBie asset
data using a standard project management methodology. Journal of facilities
management.
Schwartz, F. and Bjorklund, P., 2019. Quality improvement project to manage workplace
violence in hospitals: lessons learned. Journal of nursing care quality, 34(2), pp.114-120.
Neto, F.R.A. and Santos, C.A., 2018. Understanding crowdsourcing projects: A systematic
review of tendencies, workflow, and quality management. Information Processing &
Management, 54(4), pp.490-506.
Spooner, A.J., Chaboyer, W. and Aitken, L.M., 2018. Using the Plan-Do-Study-Act cycle to
manage interruptions during nursing team leader handover in the intensive care unit:
quality improvement project. Australian Critical Care, 31(2), p.132.
FITZGERALD, P., 2018. Moral Distress Matters: A Quality Improvement Project to Identify,
Educate, and Manage Moral Distress in Critical Care Nurses.
Mihalcioiu, R., 2019. Agility Management –How to Manage Quality in the Future.
In International Conference on Economic Sciences and Business Administration (Vol. 5,
No. 1, pp. 236-240). Spiru Haret University.
Navarro, G., Yvard, P. and Van Dillen, E., 2018. A dedicated Quality approach to manage the
“small” software tools in control centers. In 2018 SpaceOps Conference (p. 2326).
Port, D. and Taber, B., 2018, October. An empirical study of process policies and metrics to
manage productivity and quality for maintenance of critical software systems at the jet
propulsion laboratory. In Proceedings of the 12th ACM/IEEE International Symposium
on Empirical Software Engineering and Measurement (pp. 1-10).
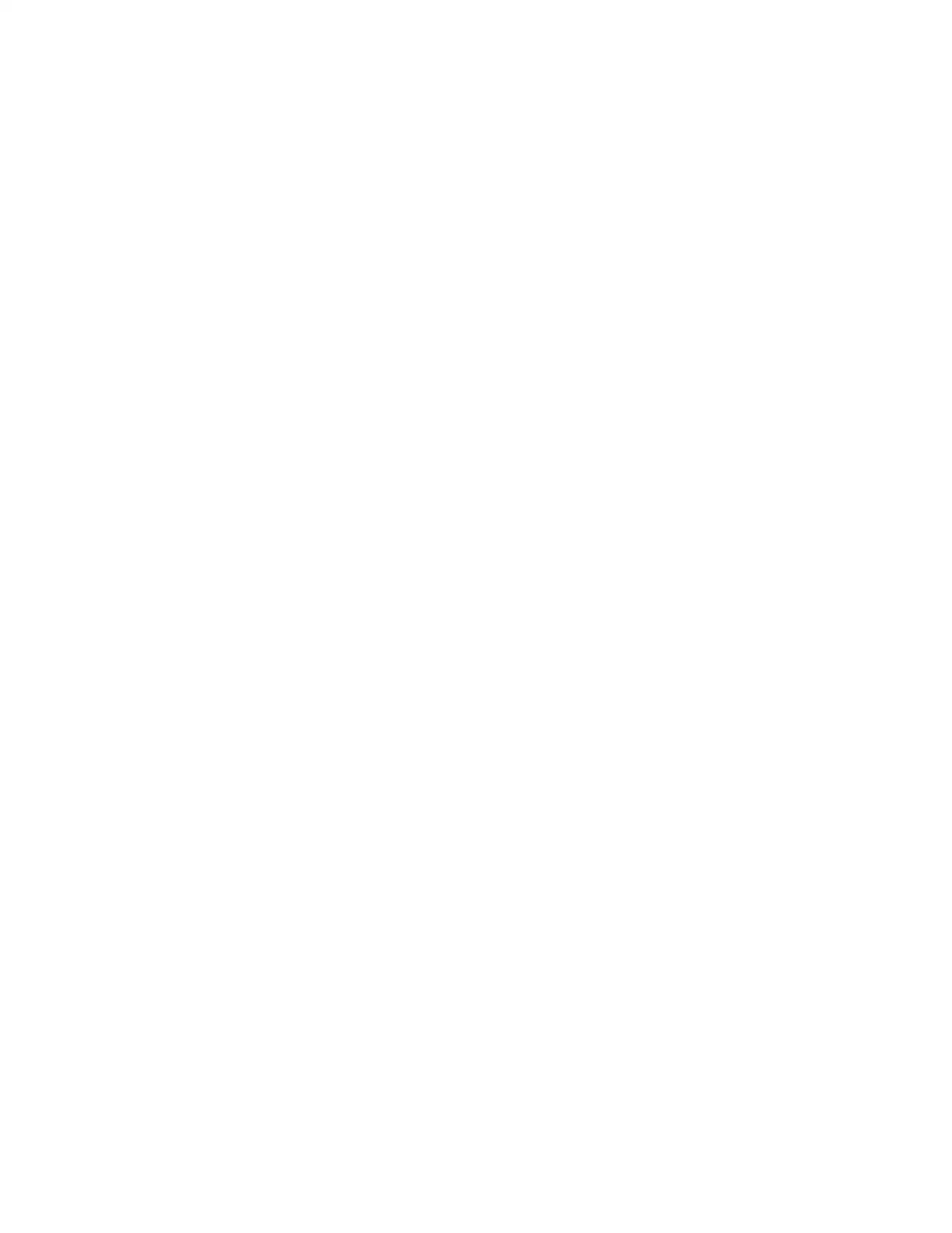
1 out of 12
Related Documents
![[object Object]](/_next/image/?url=%2F_next%2Fstatic%2Fmedia%2Flogo.6d15ce61.png&w=640&q=75)
Your All-in-One AI-Powered Toolkit for Academic Success.
+13062052269
info@desklib.com
Available 24*7 on WhatsApp / Email
Unlock your academic potential
© 2024 | Zucol Services PVT LTD | All rights reserved.