Management Accounting Assignment Term 1 2018
VerifiedAdded on 2023/06/12
|9
|2261
|235
AI Summary
This article discusses Management Accounting Assignment Term 1 2018, covering topics such as calculating cost per unit of sewing machines, preparing profit and loss statement, and the benefits and limitations of ABC. It emphasizes the importance of accurate product costing and informed decision making. The article also explains why actual overhead varies from applied overhead. Subject: Management Accounting, Course Code: N/A, Course Name: N/A, College/University: Institution Name
Contribute Materials
Your contribution can guide someone’s learning journey. Share your
documents today.
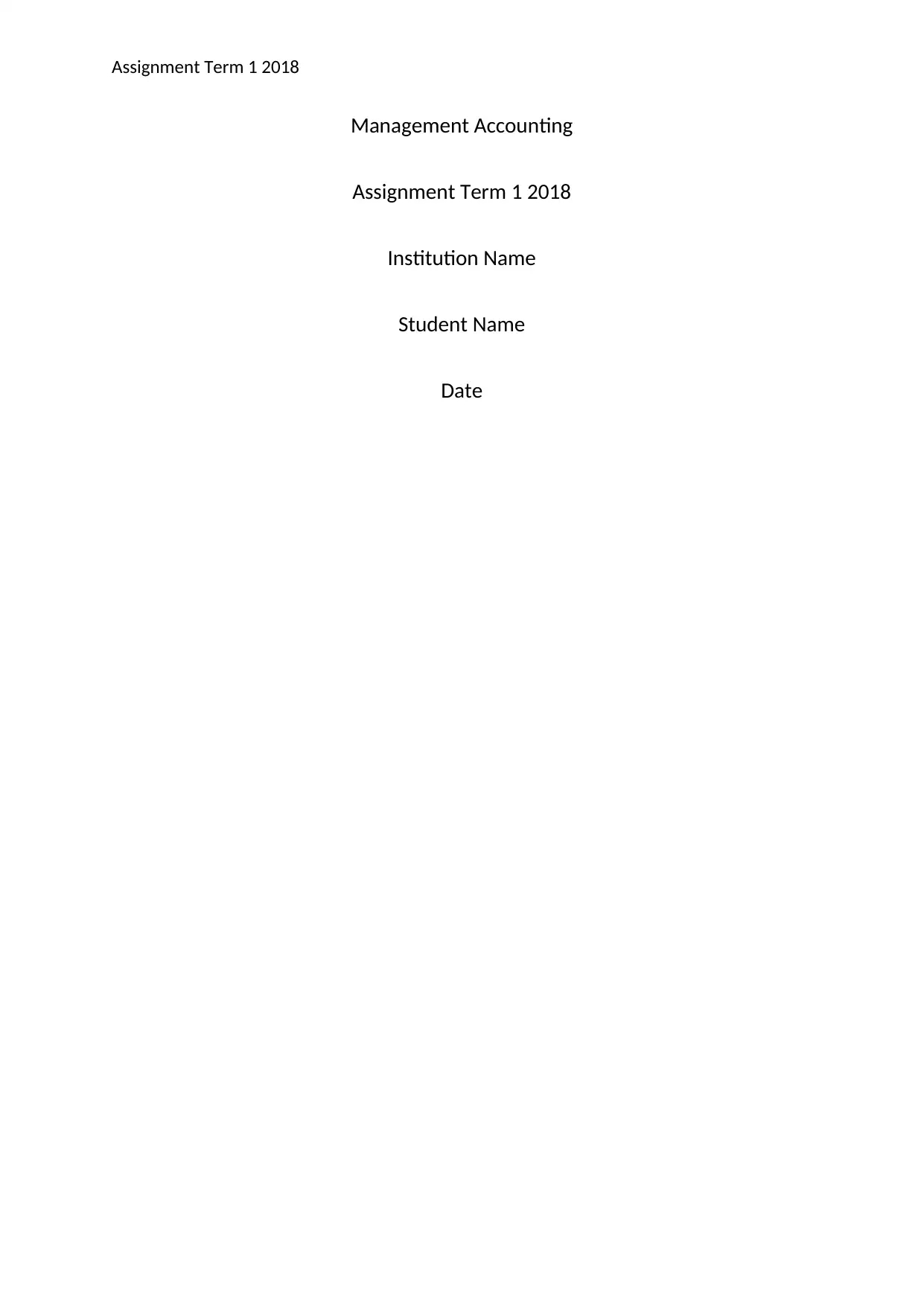
Assignment Term 1 2018
Management Accounting
Assignment Term 1 2018
Institution Name
Student Name
Date
Management Accounting
Assignment Term 1 2018
Institution Name
Student Name
Date
Secure Best Marks with AI Grader
Need help grading? Try our AI Grader for instant feedback on your assignments.
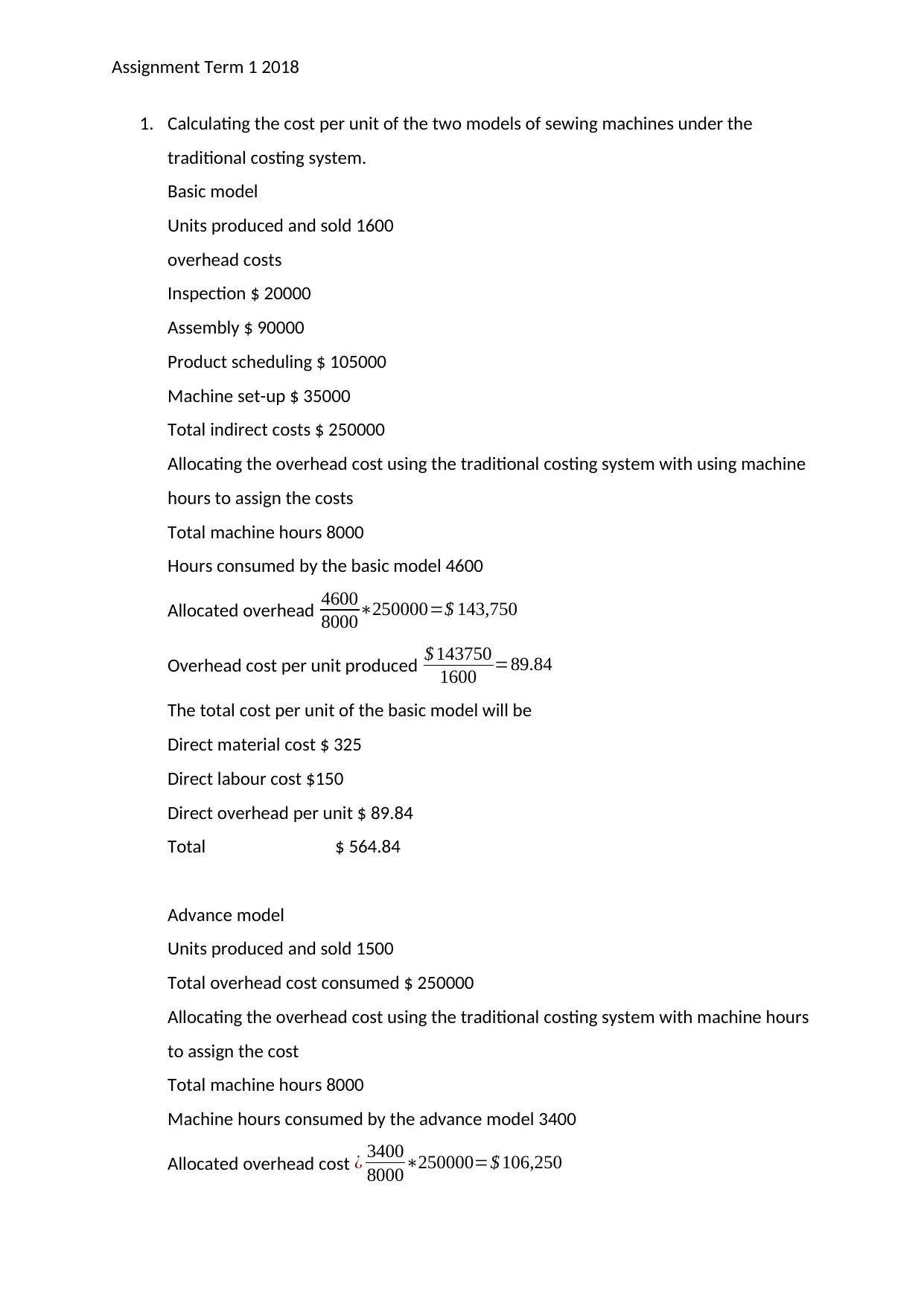
Assignment Term 1 2018
1. Calculating the cost per unit of the two models of sewing machines under the
traditional costing system.
Basic model
Units produced and sold 1600
overhead costs
Inspection $ 20000
Assembly $ 90000
Product scheduling $ 105000
Machine set-up $ 35000
Total indirect costs $ 250000
Allocating the overhead cost using the traditional costing system with using machine
hours to assign the costs
Total machine hours 8000
Hours consumed by the basic model 4600
Allocated overhead 4600
8000∗250000=$ 143,750
Overhead cost per unit produced $ 143750
1600 =89.84
The total cost per unit of the basic model will be
Direct material cost $ 325
Direct labour cost $150
Direct overhead per unit $ 89.84
Total $ 564.84
Advance model
Units produced and sold 1500
Total overhead cost consumed $ 250000
Allocating the overhead cost using the traditional costing system with machine hours
to assign the cost
Total machine hours 8000
Machine hours consumed by the advance model 3400
Allocated overhead cost ¿ 3400
8000∗250000=$ 106,250
1. Calculating the cost per unit of the two models of sewing machines under the
traditional costing system.
Basic model
Units produced and sold 1600
overhead costs
Inspection $ 20000
Assembly $ 90000
Product scheduling $ 105000
Machine set-up $ 35000
Total indirect costs $ 250000
Allocating the overhead cost using the traditional costing system with using machine
hours to assign the costs
Total machine hours 8000
Hours consumed by the basic model 4600
Allocated overhead 4600
8000∗250000=$ 143,750
Overhead cost per unit produced $ 143750
1600 =89.84
The total cost per unit of the basic model will be
Direct material cost $ 325
Direct labour cost $150
Direct overhead per unit $ 89.84
Total $ 564.84
Advance model
Units produced and sold 1500
Total overhead cost consumed $ 250000
Allocating the overhead cost using the traditional costing system with machine hours
to assign the cost
Total machine hours 8000
Machine hours consumed by the advance model 3400
Allocated overhead cost ¿ 3400
8000∗250000=$ 106,250
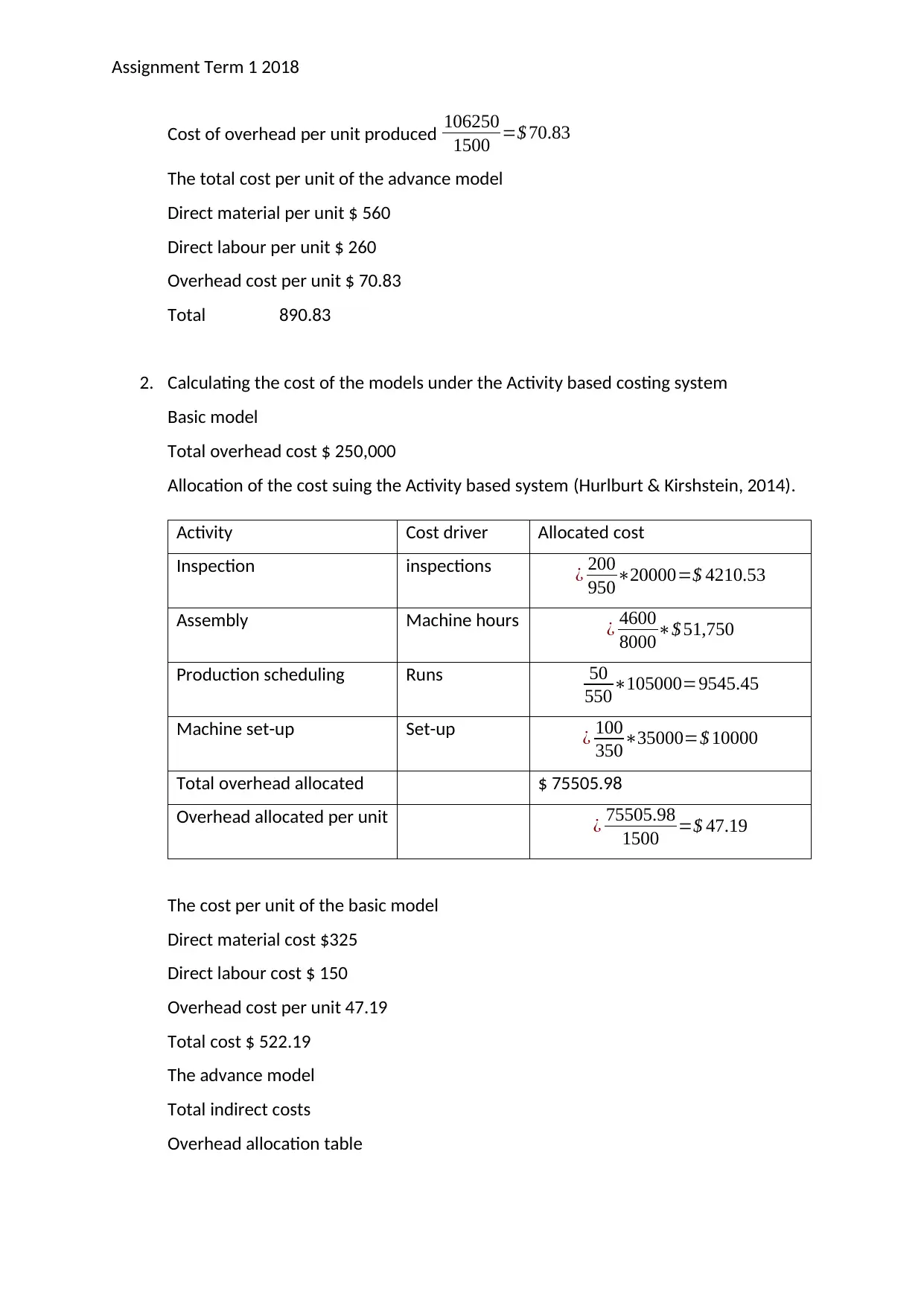
Assignment Term 1 2018
Cost of overhead per unit produced 106250
1500 =$ 70.83
The total cost per unit of the advance model
Direct material per unit $ 560
Direct labour per unit $ 260
Overhead cost per unit $ 70.83
Total 890.83
2. Calculating the cost of the models under the Activity based costing system
Basic model
Total overhead cost $ 250,000
Allocation of the cost suing the Activity based system (Hurlburt & Kirshstein, 2014).
Activity Cost driver Allocated cost
Inspection inspections ¿ 200
950∗20000=$ 4210.53
Assembly Machine hours ¿ 4600
8000∗$ 51,750
Production scheduling Runs 50
550∗105000=9545.45
Machine set-up Set-up ¿ 100
350∗35000=$ 10000
Total overhead allocated $ 75505.98
Overhead allocated per unit ¿ 75505.98
1500 =$ 47.19
The cost per unit of the basic model
Direct material cost $325
Direct labour cost $ 150
Overhead cost per unit 47.19
Total cost $ 522.19
The advance model
Total indirect costs
Overhead allocation table
Cost of overhead per unit produced 106250
1500 =$ 70.83
The total cost per unit of the advance model
Direct material per unit $ 560
Direct labour per unit $ 260
Overhead cost per unit $ 70.83
Total 890.83
2. Calculating the cost of the models under the Activity based costing system
Basic model
Total overhead cost $ 250,000
Allocation of the cost suing the Activity based system (Hurlburt & Kirshstein, 2014).
Activity Cost driver Allocated cost
Inspection inspections ¿ 200
950∗20000=$ 4210.53
Assembly Machine hours ¿ 4600
8000∗$ 51,750
Production scheduling Runs 50
550∗105000=9545.45
Machine set-up Set-up ¿ 100
350∗35000=$ 10000
Total overhead allocated $ 75505.98
Overhead allocated per unit ¿ 75505.98
1500 =$ 47.19
The cost per unit of the basic model
Direct material cost $325
Direct labour cost $ 150
Overhead cost per unit 47.19
Total cost $ 522.19
The advance model
Total indirect costs
Overhead allocation table
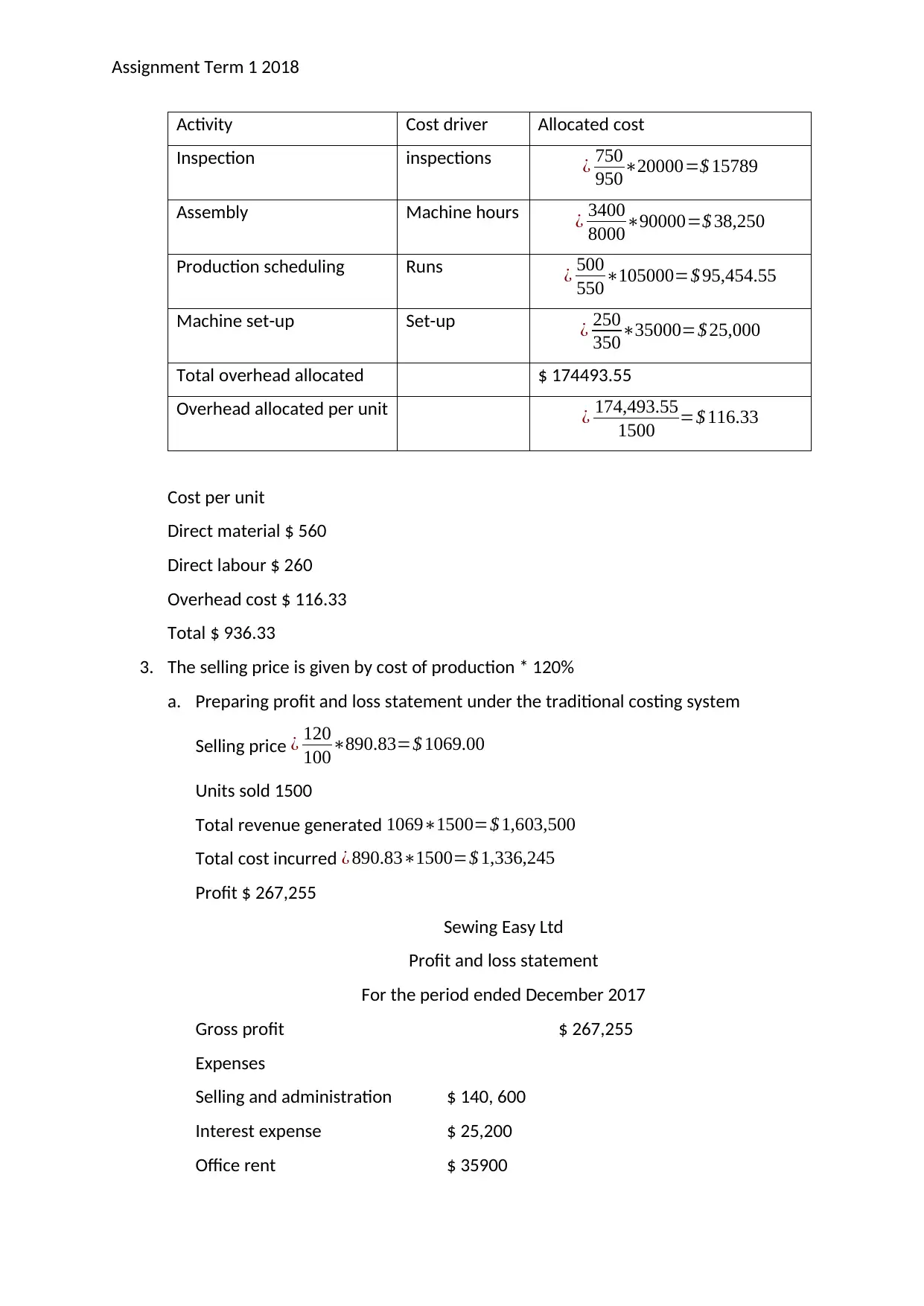
Assignment Term 1 2018
Activity Cost driver Allocated cost
Inspection inspections ¿ 750
950∗20000=$ 15789
Assembly Machine hours ¿ 3400
8000∗90000=$ 38,250
Production scheduling Runs ¿ 500
550∗105000=$ 95,454.55
Machine set-up Set-up ¿ 250
350∗35000=$ 25,000
Total overhead allocated $ 174493.55
Overhead allocated per unit ¿ 174,493.55
1500 =$ 116.33
Cost per unit
Direct material $ 560
Direct labour $ 260
Overhead cost $ 116.33
Total $ 936.33
3. The selling price is given by cost of production * 120%
a. Preparing profit and loss statement under the traditional costing system
Selling price ¿ 120
100∗890.83=$ 1069.00
Units sold 1500
Total revenue generated 1069∗1500=$ 1,603,500
Total cost incurred ¿ 890.83∗1500=$ 1,336,245
Profit $ 267,255
Sewing Easy Ltd
Profit and loss statement
For the period ended December 2017
Gross profit $ 267,255
Expenses
Selling and administration $ 140, 600
Interest expense $ 25,200
Office rent $ 35900
Activity Cost driver Allocated cost
Inspection inspections ¿ 750
950∗20000=$ 15789
Assembly Machine hours ¿ 3400
8000∗90000=$ 38,250
Production scheduling Runs ¿ 500
550∗105000=$ 95,454.55
Machine set-up Set-up ¿ 250
350∗35000=$ 25,000
Total overhead allocated $ 174493.55
Overhead allocated per unit ¿ 174,493.55
1500 =$ 116.33
Cost per unit
Direct material $ 560
Direct labour $ 260
Overhead cost $ 116.33
Total $ 936.33
3. The selling price is given by cost of production * 120%
a. Preparing profit and loss statement under the traditional costing system
Selling price ¿ 120
100∗890.83=$ 1069.00
Units sold 1500
Total revenue generated 1069∗1500=$ 1,603,500
Total cost incurred ¿ 890.83∗1500=$ 1,336,245
Profit $ 267,255
Sewing Easy Ltd
Profit and loss statement
For the period ended December 2017
Gross profit $ 267,255
Expenses
Selling and administration $ 140, 600
Interest expense $ 25,200
Office rent $ 35900
Secure Best Marks with AI Grader
Need help grading? Try our AI Grader for instant feedback on your assignments.
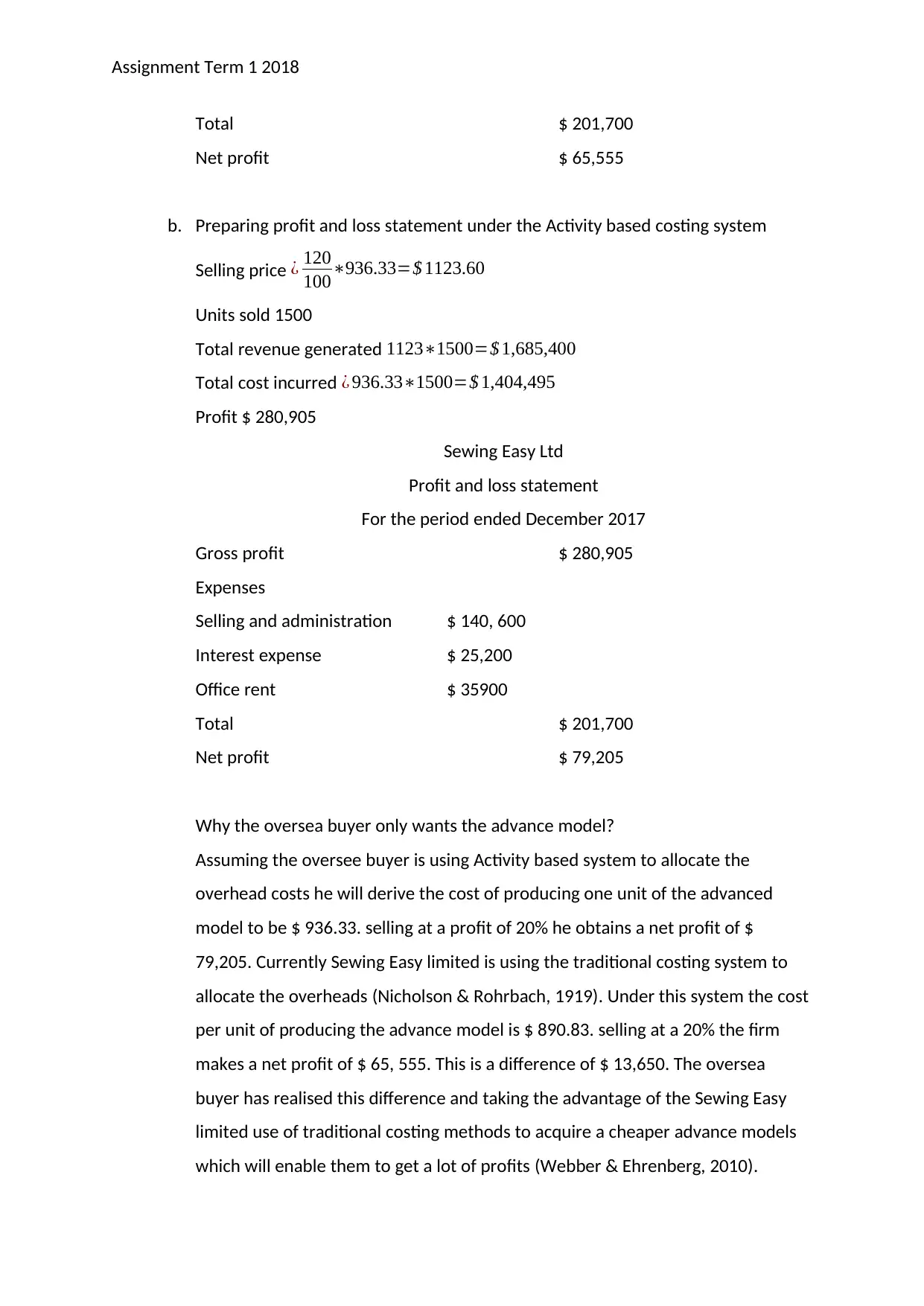
Assignment Term 1 2018
Total $ 201,700
Net profit $ 65,555
b. Preparing profit and loss statement under the Activity based costing system
Selling price ¿ 120
100∗936.33=$ 1123.60
Units sold 1500
Total revenue generated 1123∗1500=$ 1,685,400
Total cost incurred ¿ 936.33∗1500=$ 1,404,495
Profit $ 280,905
Sewing Easy Ltd
Profit and loss statement
For the period ended December 2017
Gross profit $ 280,905
Expenses
Selling and administration $ 140, 600
Interest expense $ 25,200
Office rent $ 35900
Total $ 201,700
Net profit $ 79,205
Why the oversea buyer only wants the advance model?
Assuming the oversee buyer is using Activity based system to allocate the
overhead costs he will derive the cost of producing one unit of the advanced
model to be $ 936.33. selling at a profit of 20% he obtains a net profit of $
79,205. Currently Sewing Easy limited is using the traditional costing system to
allocate the overheads (Nicholson & Rohrbach, 1919). Under this system the cost
per unit of producing the advance model is $ 890.83. selling at a 20% the firm
makes a net profit of $ 65, 555. This is a difference of $ 13,650. The oversea
buyer has realised this difference and taking the advantage of the Sewing Easy
limited use of traditional costing methods to acquire a cheaper advance models
which will enable them to get a lot of profits (Webber & Ehrenberg, 2010).
Total $ 201,700
Net profit $ 65,555
b. Preparing profit and loss statement under the Activity based costing system
Selling price ¿ 120
100∗936.33=$ 1123.60
Units sold 1500
Total revenue generated 1123∗1500=$ 1,685,400
Total cost incurred ¿ 936.33∗1500=$ 1,404,495
Profit $ 280,905
Sewing Easy Ltd
Profit and loss statement
For the period ended December 2017
Gross profit $ 280,905
Expenses
Selling and administration $ 140, 600
Interest expense $ 25,200
Office rent $ 35900
Total $ 201,700
Net profit $ 79,205
Why the oversea buyer only wants the advance model?
Assuming the oversee buyer is using Activity based system to allocate the
overhead costs he will derive the cost of producing one unit of the advanced
model to be $ 936.33. selling at a profit of 20% he obtains a net profit of $
79,205. Currently Sewing Easy limited is using the traditional costing system to
allocate the overheads (Nicholson & Rohrbach, 1919). Under this system the cost
per unit of producing the advance model is $ 890.83. selling at a 20% the firm
makes a net profit of $ 65, 555. This is a difference of $ 13,650. The oversea
buyer has realised this difference and taking the advantage of the Sewing Easy
limited use of traditional costing methods to acquire a cheaper advance models
which will enable them to get a lot of profits (Webber & Ehrenberg, 2010).
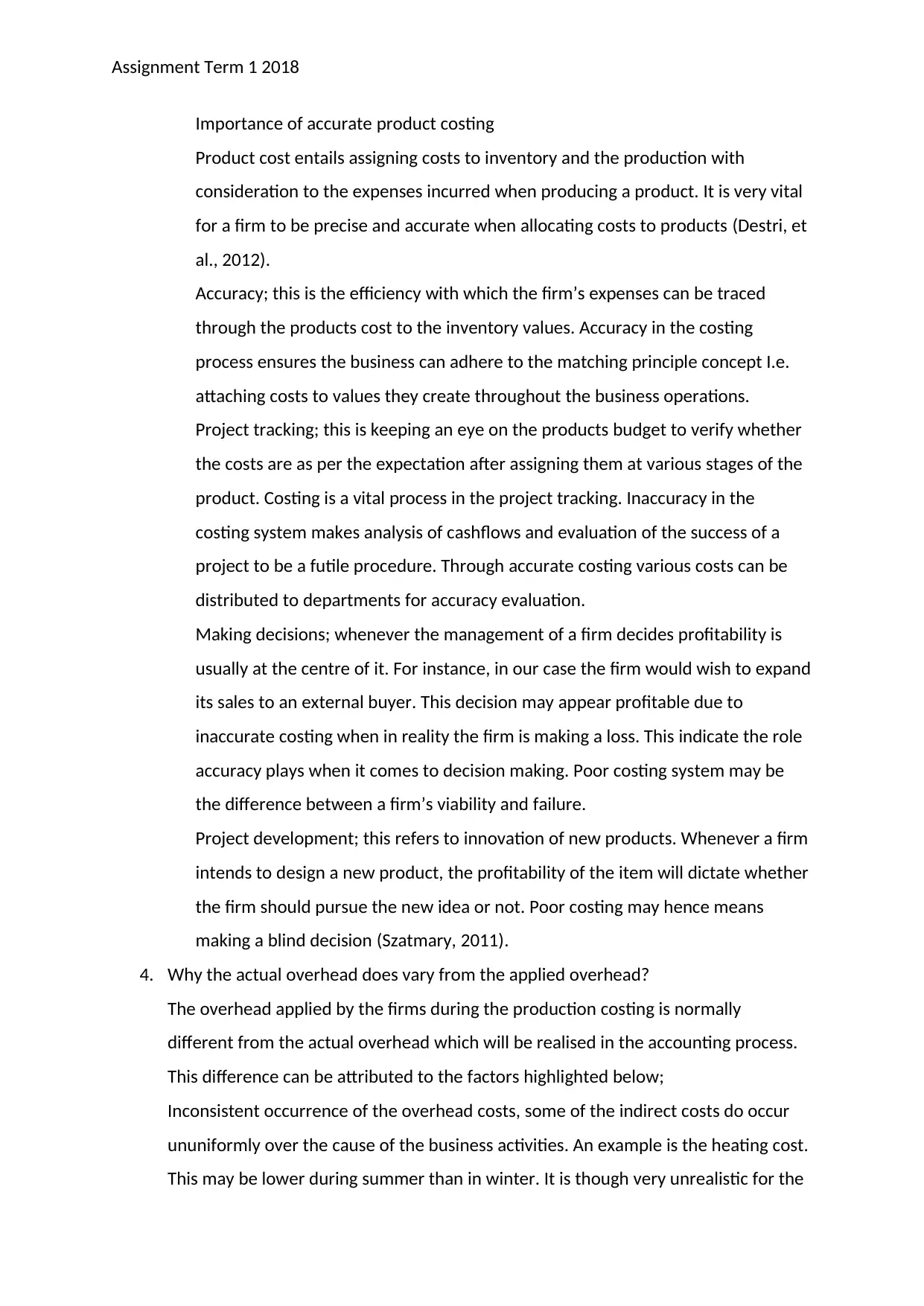
Assignment Term 1 2018
Importance of accurate product costing
Product cost entails assigning costs to inventory and the production with
consideration to the expenses incurred when producing a product. It is very vital
for a firm to be precise and accurate when allocating costs to products (Destri, et
al., 2012).
Accuracy; this is the efficiency with which the firm’s expenses can be traced
through the products cost to the inventory values. Accuracy in the costing
process ensures the business can adhere to the matching principle concept I.e.
attaching costs to values they create throughout the business operations.
Project tracking; this is keeping an eye on the products budget to verify whether
the costs are as per the expectation after assigning them at various stages of the
product. Costing is a vital process in the project tracking. Inaccuracy in the
costing system makes analysis of cashflows and evaluation of the success of a
project to be a futile procedure. Through accurate costing various costs can be
distributed to departments for accuracy evaluation.
Making decisions; whenever the management of a firm decides profitability is
usually at the centre of it. For instance, in our case the firm would wish to expand
its sales to an external buyer. This decision may appear profitable due to
inaccurate costing when in reality the firm is making a loss. This indicate the role
accuracy plays when it comes to decision making. Poor costing system may be
the difference between a firm’s viability and failure.
Project development; this refers to innovation of new products. Whenever a firm
intends to design a new product, the profitability of the item will dictate whether
the firm should pursue the new idea or not. Poor costing may hence means
making a blind decision (Szatmary, 2011).
4. Why the actual overhead does vary from the applied overhead?
The overhead applied by the firms during the production costing is normally
different from the actual overhead which will be realised in the accounting process.
This difference can be attributed to the factors highlighted below;
Inconsistent occurrence of the overhead costs, some of the indirect costs do occur
ununiformly over the cause of the business activities. An example is the heating cost.
This may be lower during summer than in winter. It is though very unrealistic for the
Importance of accurate product costing
Product cost entails assigning costs to inventory and the production with
consideration to the expenses incurred when producing a product. It is very vital
for a firm to be precise and accurate when allocating costs to products (Destri, et
al., 2012).
Accuracy; this is the efficiency with which the firm’s expenses can be traced
through the products cost to the inventory values. Accuracy in the costing
process ensures the business can adhere to the matching principle concept I.e.
attaching costs to values they create throughout the business operations.
Project tracking; this is keeping an eye on the products budget to verify whether
the costs are as per the expectation after assigning them at various stages of the
product. Costing is a vital process in the project tracking. Inaccuracy in the
costing system makes analysis of cashflows and evaluation of the success of a
project to be a futile procedure. Through accurate costing various costs can be
distributed to departments for accuracy evaluation.
Making decisions; whenever the management of a firm decides profitability is
usually at the centre of it. For instance, in our case the firm would wish to expand
its sales to an external buyer. This decision may appear profitable due to
inaccurate costing when in reality the firm is making a loss. This indicate the role
accuracy plays when it comes to decision making. Poor costing system may be
the difference between a firm’s viability and failure.
Project development; this refers to innovation of new products. Whenever a firm
intends to design a new product, the profitability of the item will dictate whether
the firm should pursue the new idea or not. Poor costing may hence means
making a blind decision (Szatmary, 2011).
4. Why the actual overhead does vary from the applied overhead?
The overhead applied by the firms during the production costing is normally
different from the actual overhead which will be realised in the accounting process.
This difference can be attributed to the factors highlighted below;
Inconsistent occurrence of the overhead costs, some of the indirect costs do occur
ununiformly over the cause of the business activities. An example is the heating cost.
This may be lower during summer than in winter. It is though very unrealistic for the
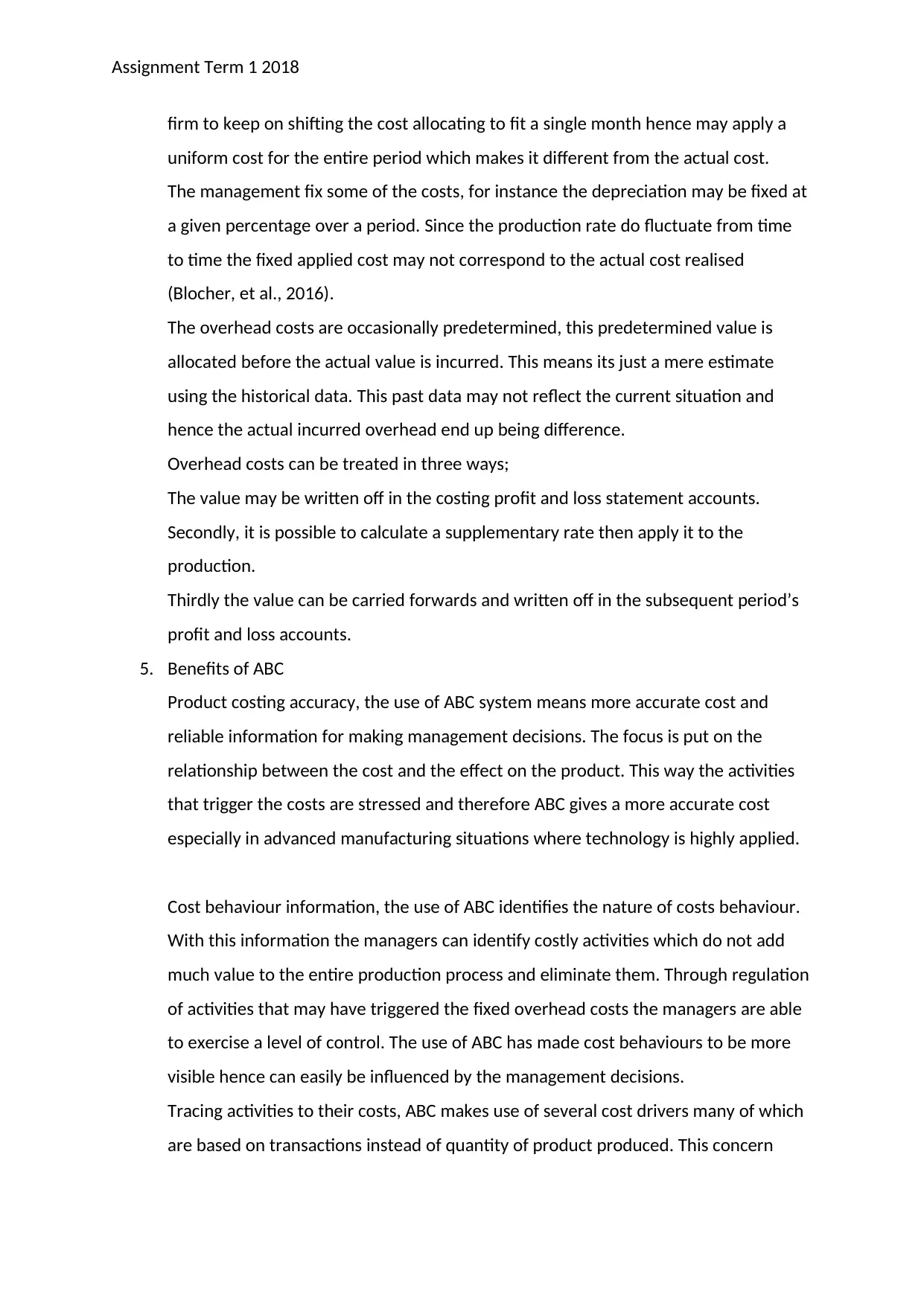
Assignment Term 1 2018
firm to keep on shifting the cost allocating to fit a single month hence may apply a
uniform cost for the entire period which makes it different from the actual cost.
The management fix some of the costs, for instance the depreciation may be fixed at
a given percentage over a period. Since the production rate do fluctuate from time
to time the fixed applied cost may not correspond to the actual cost realised
(Blocher, et al., 2016).
The overhead costs are occasionally predetermined, this predetermined value is
allocated before the actual value is incurred. This means its just a mere estimate
using the historical data. This past data may not reflect the current situation and
hence the actual incurred overhead end up being difference.
Overhead costs can be treated in three ways;
The value may be written off in the costing profit and loss statement accounts.
Secondly, it is possible to calculate a supplementary rate then apply it to the
production.
Thirdly the value can be carried forwards and written off in the subsequent period’s
profit and loss accounts.
5. Benefits of ABC
Product costing accuracy, the use of ABC system means more accurate cost and
reliable information for making management decisions. The focus is put on the
relationship between the cost and the effect on the product. This way the activities
that trigger the costs are stressed and therefore ABC gives a more accurate cost
especially in advanced manufacturing situations where technology is highly applied.
Cost behaviour information, the use of ABC identifies the nature of costs behaviour.
With this information the managers can identify costly activities which do not add
much value to the entire production process and eliminate them. Through regulation
of activities that may have triggered the fixed overhead costs the managers are able
to exercise a level of control. The use of ABC has made cost behaviours to be more
visible hence can easily be influenced by the management decisions.
Tracing activities to their costs, ABC makes use of several cost drivers many of which
are based on transactions instead of quantity of product produced. This concern
firm to keep on shifting the cost allocating to fit a single month hence may apply a
uniform cost for the entire period which makes it different from the actual cost.
The management fix some of the costs, for instance the depreciation may be fixed at
a given percentage over a period. Since the production rate do fluctuate from time
to time the fixed applied cost may not correspond to the actual cost realised
(Blocher, et al., 2016).
The overhead costs are occasionally predetermined, this predetermined value is
allocated before the actual value is incurred. This means its just a mere estimate
using the historical data. This past data may not reflect the current situation and
hence the actual incurred overhead end up being difference.
Overhead costs can be treated in three ways;
The value may be written off in the costing profit and loss statement accounts.
Secondly, it is possible to calculate a supplementary rate then apply it to the
production.
Thirdly the value can be carried forwards and written off in the subsequent period’s
profit and loss accounts.
5. Benefits of ABC
Product costing accuracy, the use of ABC system means more accurate cost and
reliable information for making management decisions. The focus is put on the
relationship between the cost and the effect on the product. This way the activities
that trigger the costs are stressed and therefore ABC gives a more accurate cost
especially in advanced manufacturing situations where technology is highly applied.
Cost behaviour information, the use of ABC identifies the nature of costs behaviour.
With this information the managers can identify costly activities which do not add
much value to the entire production process and eliminate them. Through regulation
of activities that may have triggered the fixed overhead costs the managers are able
to exercise a level of control. The use of ABC has made cost behaviours to be more
visible hence can easily be influenced by the management decisions.
Tracing activities to their costs, ABC makes use of several cost drivers many of which
are based on transactions instead of quantity of product produced. This concern
Paraphrase This Document
Need a fresh take? Get an instant paraphrase of this document with our AI Paraphraser
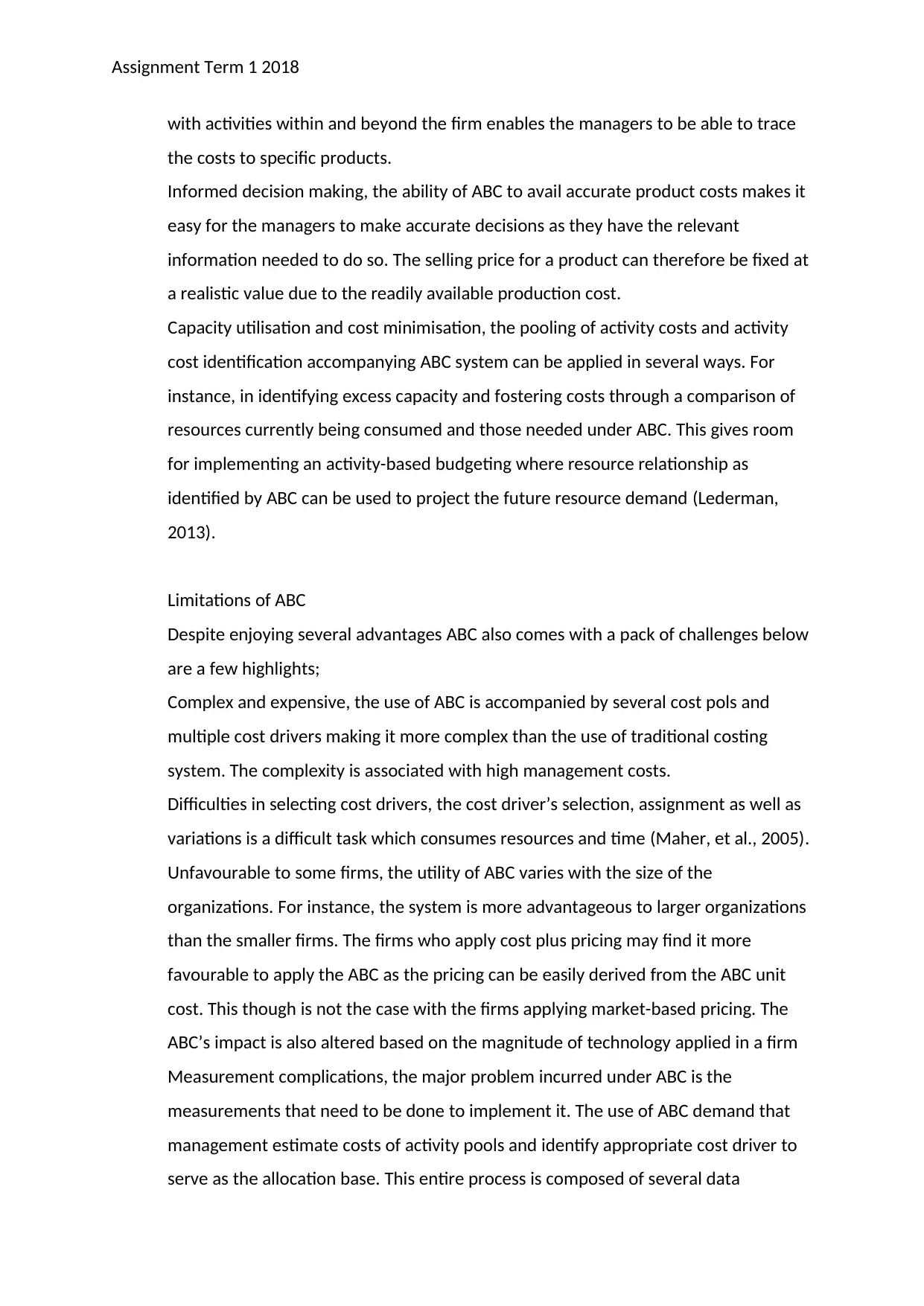
Assignment Term 1 2018
with activities within and beyond the firm enables the managers to be able to trace
the costs to specific products.
Informed decision making, the ability of ABC to avail accurate product costs makes it
easy for the managers to make accurate decisions as they have the relevant
information needed to do so. The selling price for a product can therefore be fixed at
a realistic value due to the readily available production cost.
Capacity utilisation and cost minimisation, the pooling of activity costs and activity
cost identification accompanying ABC system can be applied in several ways. For
instance, in identifying excess capacity and fostering costs through a comparison of
resources currently being consumed and those needed under ABC. This gives room
for implementing an activity-based budgeting where resource relationship as
identified by ABC can be used to project the future resource demand (Lederman,
2013).
Limitations of ABC
Despite enjoying several advantages ABC also comes with a pack of challenges below
are a few highlights;
Complex and expensive, the use of ABC is accompanied by several cost pols and
multiple cost drivers making it more complex than the use of traditional costing
system. The complexity is associated with high management costs.
Difficulties in selecting cost drivers, the cost driver’s selection, assignment as well as
variations is a difficult task which consumes resources and time (Maher, et al., 2005).
Unfavourable to some firms, the utility of ABC varies with the size of the
organizations. For instance, the system is more advantageous to larger organizations
than the smaller firms. The firms who apply cost plus pricing may find it more
favourable to apply the ABC as the pricing can be easily derived from the ABC unit
cost. This though is not the case with the firms applying market-based pricing. The
ABC’s impact is also altered based on the magnitude of technology applied in a firm
Measurement complications, the major problem incurred under ABC is the
measurements that need to be done to implement it. The use of ABC demand that
management estimate costs of activity pools and identify appropriate cost driver to
serve as the allocation base. This entire process is composed of several data
with activities within and beyond the firm enables the managers to be able to trace
the costs to specific products.
Informed decision making, the ability of ABC to avail accurate product costs makes it
easy for the managers to make accurate decisions as they have the relevant
information needed to do so. The selling price for a product can therefore be fixed at
a realistic value due to the readily available production cost.
Capacity utilisation and cost minimisation, the pooling of activity costs and activity
cost identification accompanying ABC system can be applied in several ways. For
instance, in identifying excess capacity and fostering costs through a comparison of
resources currently being consumed and those needed under ABC. This gives room
for implementing an activity-based budgeting where resource relationship as
identified by ABC can be used to project the future resource demand (Lederman,
2013).
Limitations of ABC
Despite enjoying several advantages ABC also comes with a pack of challenges below
are a few highlights;
Complex and expensive, the use of ABC is accompanied by several cost pols and
multiple cost drivers making it more complex than the use of traditional costing
system. The complexity is associated with high management costs.
Difficulties in selecting cost drivers, the cost driver’s selection, assignment as well as
variations is a difficult task which consumes resources and time (Maher, et al., 2005).
Unfavourable to some firms, the utility of ABC varies with the size of the
organizations. For instance, the system is more advantageous to larger organizations
than the smaller firms. The firms who apply cost plus pricing may find it more
favourable to apply the ABC as the pricing can be easily derived from the ABC unit
cost. This though is not the case with the firms applying market-based pricing. The
ABC’s impact is also altered based on the magnitude of technology applied in a firm
Measurement complications, the major problem incurred under ABC is the
measurements that need to be done to implement it. The use of ABC demand that
management estimate costs of activity pools and identify appropriate cost driver to
serve as the allocation base. This entire process is composed of several data
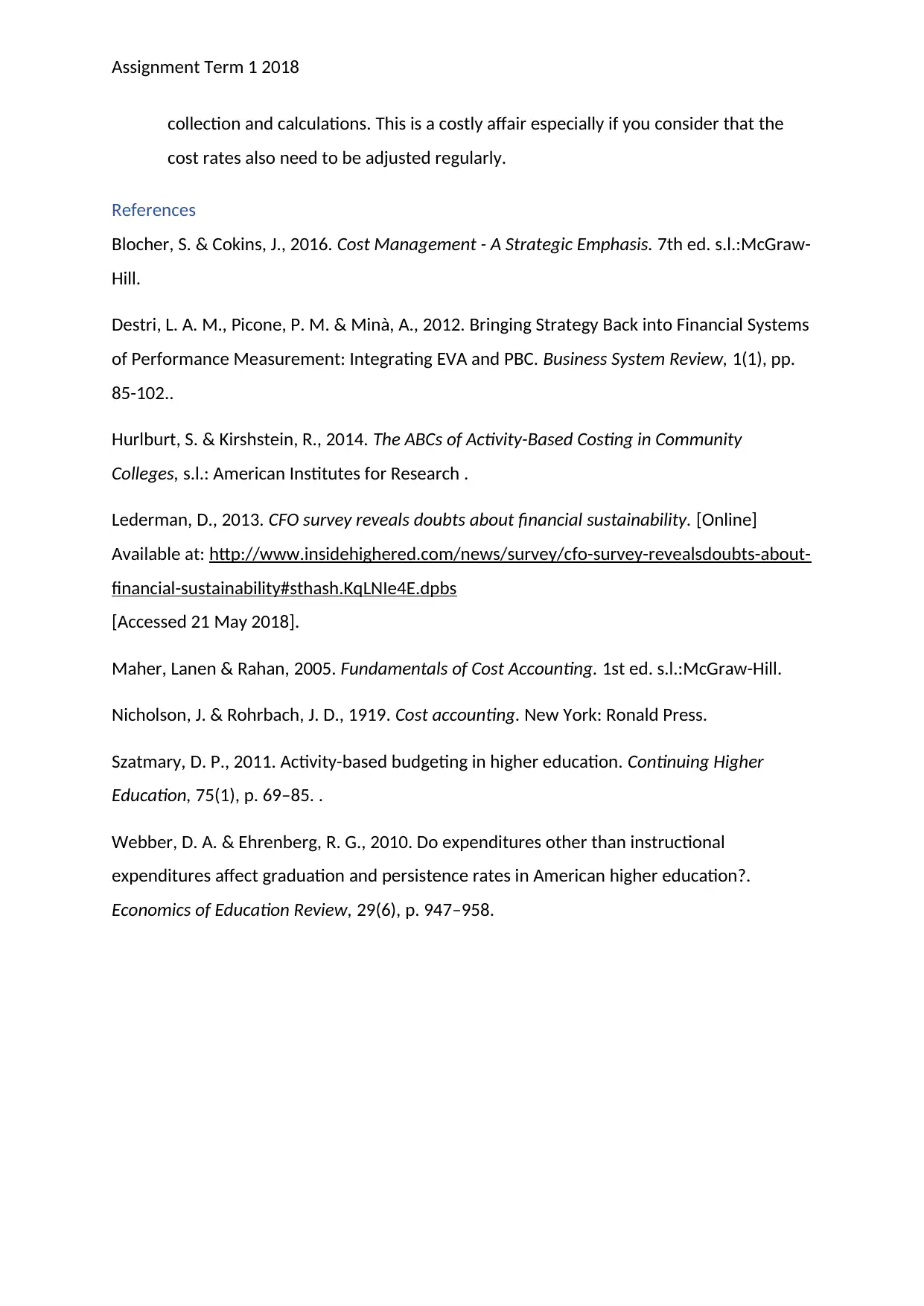
Assignment Term 1 2018
collection and calculations. This is a costly affair especially if you consider that the
cost rates also need to be adjusted regularly.
References
Blocher, S. & Cokins, J., 2016. Cost Management - A Strategic Emphasis. 7th ed. s.l.:McGraw-
Hill.
Destri, L. A. M., Picone, P. M. & Minà, A., 2012. Bringing Strategy Back into Financial Systems
of Performance Measurement: Integrating EVA and PBC. Business System Review, 1(1), pp.
85-102..
Hurlburt, S. & Kirshstein, R., 2014. The ABCs of Activity-Based Costing in Community
Colleges, s.l.: American Institutes for Research .
Lederman, D., 2013. CFO survey reveals doubts about financial sustainability. [Online]
Available at: http://www.insidehighered.com/news/survey/cfo-survey-revealsdoubts-about-
financial-sustainability#sthash.KqLNIe4E.dpbs
[Accessed 21 May 2018].
Maher, Lanen & Rahan, 2005. Fundamentals of Cost Accounting. 1st ed. s.l.:McGraw-Hill.
Nicholson, J. & Rohrbach, J. D., 1919. Cost accounting. New York: Ronald Press.
Szatmary, D. P., 2011. Activity-based budgeting in higher education. Continuing Higher
Education, 75(1), p. 69–85. .
Webber, D. A. & Ehrenberg, R. G., 2010. Do expenditures other than instructional
expenditures affect graduation and persistence rates in American higher education?.
Economics of Education Review, 29(6), p. 947–958.
collection and calculations. This is a costly affair especially if you consider that the
cost rates also need to be adjusted regularly.
References
Blocher, S. & Cokins, J., 2016. Cost Management - A Strategic Emphasis. 7th ed. s.l.:McGraw-
Hill.
Destri, L. A. M., Picone, P. M. & Minà, A., 2012. Bringing Strategy Back into Financial Systems
of Performance Measurement: Integrating EVA and PBC. Business System Review, 1(1), pp.
85-102..
Hurlburt, S. & Kirshstein, R., 2014. The ABCs of Activity-Based Costing in Community
Colleges, s.l.: American Institutes for Research .
Lederman, D., 2013. CFO survey reveals doubts about financial sustainability. [Online]
Available at: http://www.insidehighered.com/news/survey/cfo-survey-revealsdoubts-about-
financial-sustainability#sthash.KqLNIe4E.dpbs
[Accessed 21 May 2018].
Maher, Lanen & Rahan, 2005. Fundamentals of Cost Accounting. 1st ed. s.l.:McGraw-Hill.
Nicholson, J. & Rohrbach, J. D., 1919. Cost accounting. New York: Ronald Press.
Szatmary, D. P., 2011. Activity-based budgeting in higher education. Continuing Higher
Education, 75(1), p. 69–85. .
Webber, D. A. & Ehrenberg, R. G., 2010. Do expenditures other than instructional
expenditures affect graduation and persistence rates in American higher education?.
Economics of Education Review, 29(6), p. 947–958.
1 out of 9
Related Documents
![[object Object]](/_next/image/?url=%2F_next%2Fstatic%2Fmedia%2Flogo.6d15ce61.png&w=640&q=75)
Your All-in-One AI-Powered Toolkit for Academic Success.
+13062052269
info@desklib.com
Available 24*7 on WhatsApp / Email
Unlock your academic potential
© 2024 | Zucol Services PVT LTD | All rights reserved.