Management Accounting: Cost Analysis and Activity Drivers
VerifiedAdded on 2022/11/11
|25
|2530
|370
AI Summary
This document provides a detailed analysis of cost and activity drivers for various activities involved in the production of meat products. It covers topics such as activity centers, relevant costs, and annual quantity of activity drivers.
Contribute Materials
Your contribution can guide someone’s learning journey. Share your
documents today.
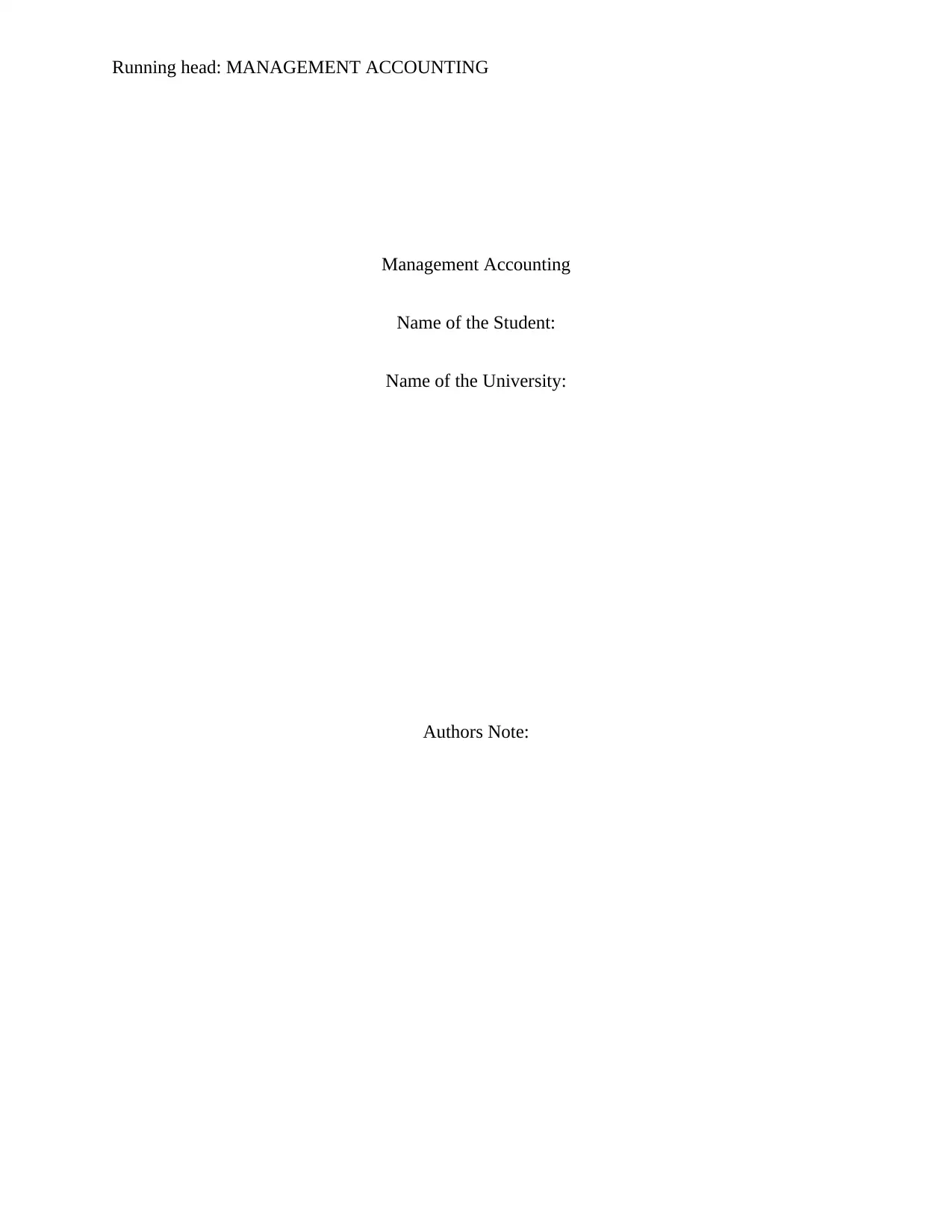
Running head: MANAGEMENT ACCOUNTING
Management Accounting
Name of the Student:
Name of the University:
Authors Note:
Management Accounting
Name of the Student:
Name of the University:
Authors Note:
Secure Best Marks with AI Grader
Need help grading? Try our AI Grader for instant feedback on your assignments.
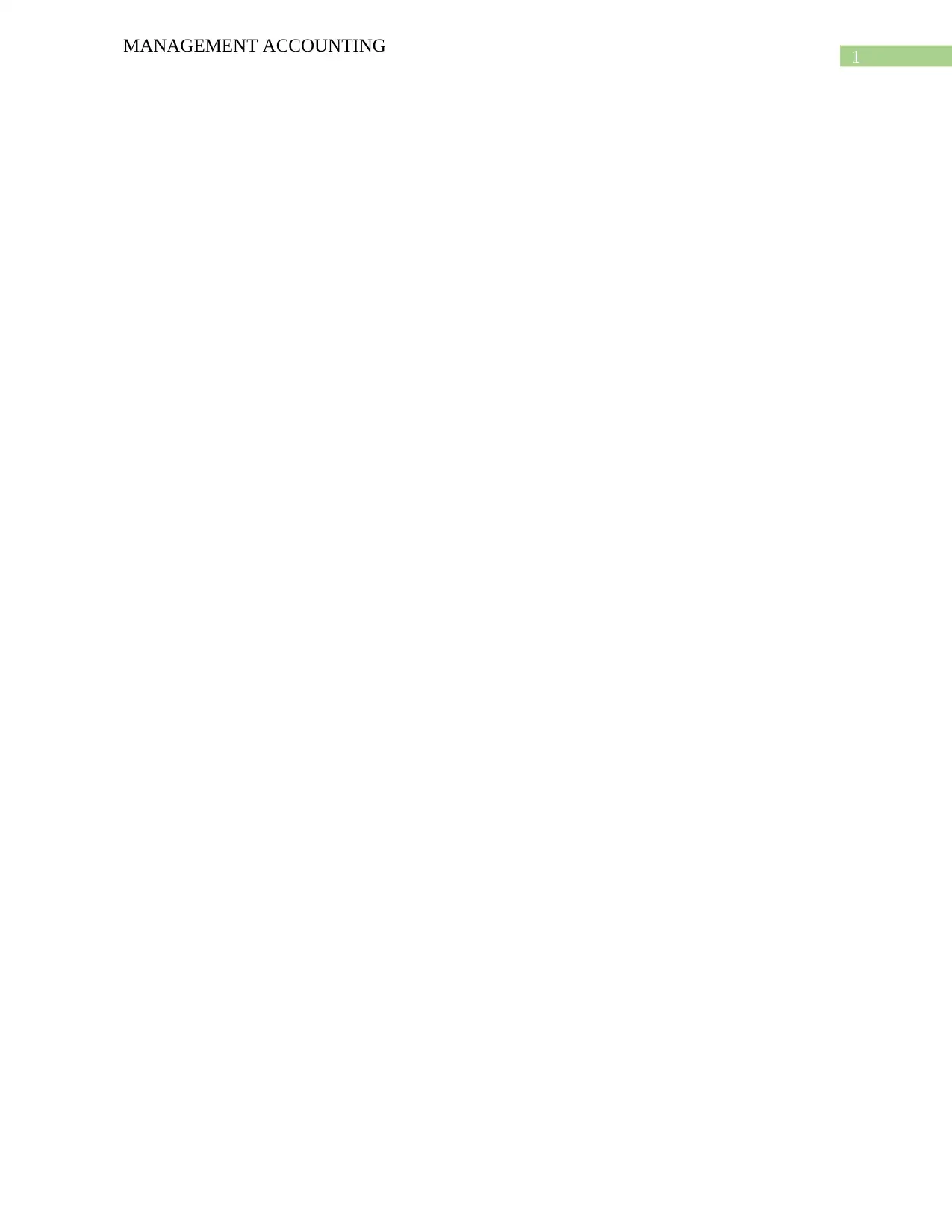
1
MANAGEMENT ACCOUNTING
MANAGEMENT ACCOUNTING
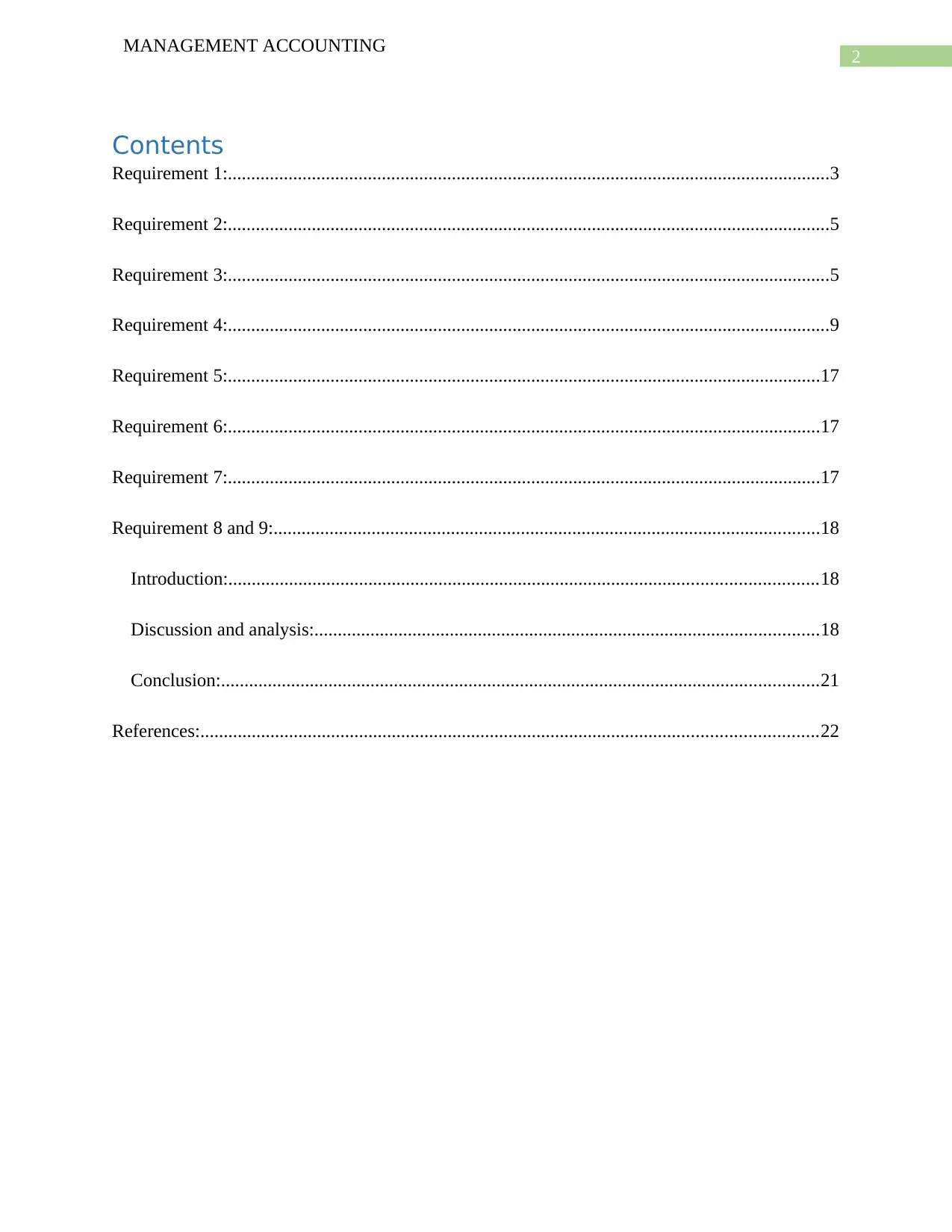
2
MANAGEMENT ACCOUNTING
Contents
Requirement 1:.................................................................................................................................3
Requirement 2:.................................................................................................................................5
Requirement 3:.................................................................................................................................5
Requirement 4:.................................................................................................................................9
Requirement 5:...............................................................................................................................17
Requirement 6:...............................................................................................................................17
Requirement 7:...............................................................................................................................17
Requirement 8 and 9:.....................................................................................................................18
Introduction:..............................................................................................................................18
Discussion and analysis:............................................................................................................18
Conclusion:................................................................................................................................21
References:....................................................................................................................................22
MANAGEMENT ACCOUNTING
Contents
Requirement 1:.................................................................................................................................3
Requirement 2:.................................................................................................................................5
Requirement 3:.................................................................................................................................5
Requirement 4:.................................................................................................................................9
Requirement 5:...............................................................................................................................17
Requirement 6:...............................................................................................................................17
Requirement 7:...............................................................................................................................17
Requirement 8 and 9:.....................................................................................................................18
Introduction:..............................................................................................................................18
Discussion and analysis:............................................................................................................18
Conclusion:................................................................................................................................21
References:....................................................................................................................................22
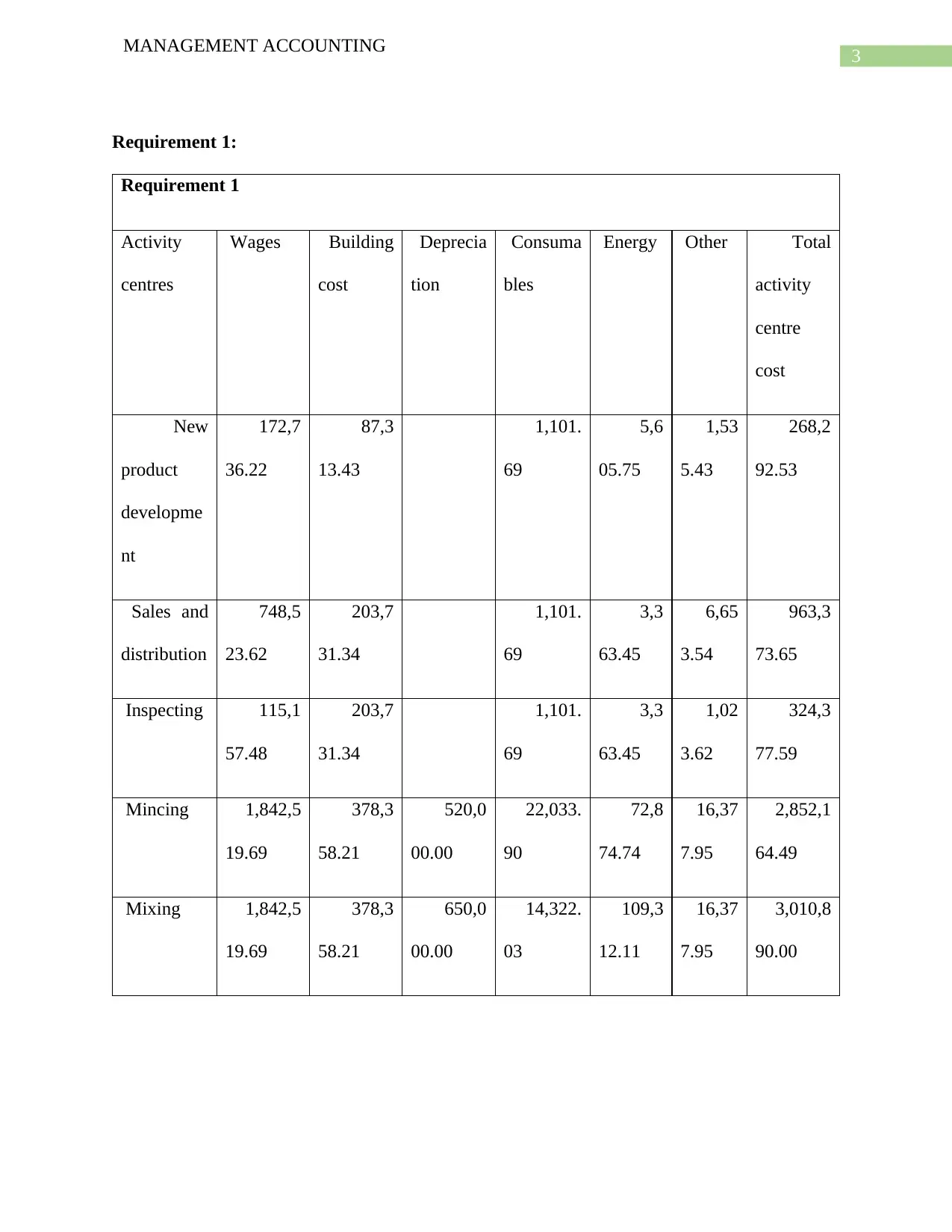
3
MANAGEMENT ACCOUNTING
Requirement 1:
Requirement 1
Activity
centres
Wages Building
cost
Deprecia
tion
Consuma
bles
Energy Other Total
activity
centre
cost
New
product
developme
nt
172,7
36.22
87,3
13.43
1,101.
69
5,6
05.75
1,53
5.43
268,2
92.53
Sales and
distribution
748,5
23.62
203,7
31.34
1,101.
69
3,3
63.45
6,65
3.54
963,3
73.65
Inspecting 115,1
57.48
203,7
31.34
1,101.
69
3,3
63.45
1,02
3.62
324,3
77.59
Mincing 1,842,5
19.69
378,3
58.21
520,0
00.00
22,033.
90
72,8
74.74
16,37
7.95
2,852,1
64.49
Mixing 1,842,5
19.69
378,3
58.21
650,0
00.00
14,322.
03
109,3
12.11
16,37
7.95
3,010,8
90.00
MANAGEMENT ACCOUNTING
Requirement 1:
Requirement 1
Activity
centres
Wages Building
cost
Deprecia
tion
Consuma
bles
Energy Other Total
activity
centre
cost
New
product
developme
nt
172,7
36.22
87,3
13.43
1,101.
69
5,6
05.75
1,53
5.43
268,2
92.53
Sales and
distribution
748,5
23.62
203,7
31.34
1,101.
69
3,3
63.45
6,65
3.54
963,3
73.65
Inspecting 115,1
57.48
203,7
31.34
1,101.
69
3,3
63.45
1,02
3.62
324,3
77.59
Mincing 1,842,5
19.69
378,3
58.21
520,0
00.00
22,033.
90
72,8
74.74
16,37
7.95
2,852,1
64.49
Mixing 1,842,5
19.69
378,3
58.21
650,0
00.00
14,322.
03
109,3
12.11
16,37
7.95
3,010,8
90.00
Secure Best Marks with AI Grader
Need help grading? Try our AI Grader for instant feedback on your assignments.
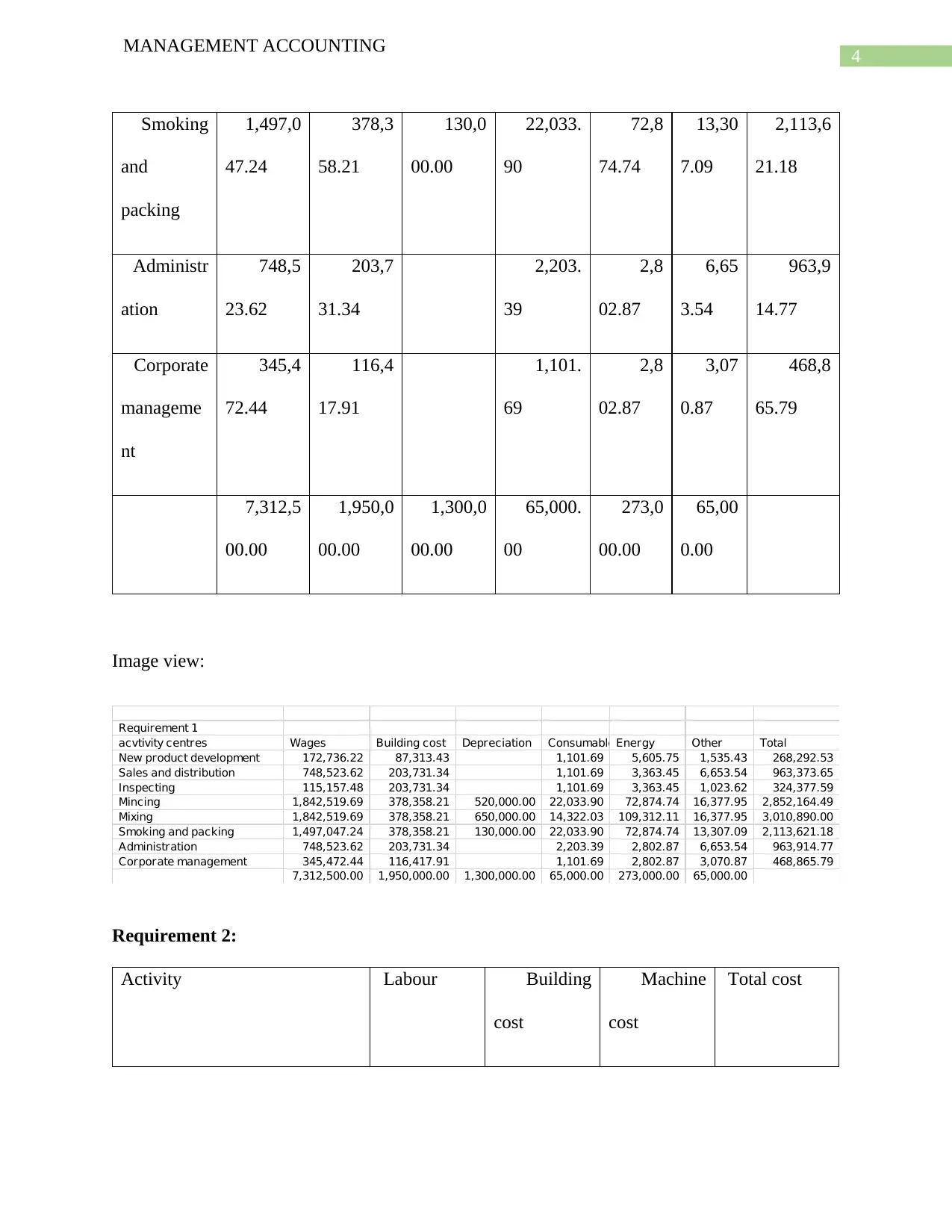
4
MANAGEMENT ACCOUNTING
Smoking
and
packing
1,497,0
47.24
378,3
58.21
130,0
00.00
22,033.
90
72,8
74.74
13,30
7.09
2,113,6
21.18
Administr
ation
748,5
23.62
203,7
31.34
2,203.
39
2,8
02.87
6,65
3.54
963,9
14.77
Corporate
manageme
nt
345,4
72.44
116,4
17.91
1,101.
69
2,8
02.87
3,07
0.87
468,8
65.79
7,312,5
00.00
1,950,0
00.00
1,300,0
00.00
65,000.
00
273,0
00.00
65,00
0.00
Image view:
Requirement 1
acvtivity centres Wages Building cost Depreciation ConsumablesEnergy Other Total
New product development 172,736.22 87,313.43 1,101.69 5,605.75 1,535.43 268,292.53
Sales and distribution 748,523.62 203,731.34 1,101.69 3,363.45 6,653.54 963,373.65
Inspecting 115,157.48 203,731.34 1,101.69 3,363.45 1,023.62 324,377.59
Mincing 1,842,519.69 378,358.21 520,000.00 22,033.90 72,874.74 16,377.95 2,852,164.49
Mixing 1,842,519.69 378,358.21 650,000.00 14,322.03 109,312.11 16,377.95 3,010,890.00
Smoking and packing 1,497,047.24 378,358.21 130,000.00 22,033.90 72,874.74 13,307.09 2,113,621.18
Administration 748,523.62 203,731.34 2,203.39 2,802.87 6,653.54 963,914.77
Corporate management 345,472.44 116,417.91 1,101.69 2,802.87 3,070.87 468,865.79
7,312,500.00 1,950,000.00 1,300,000.00 65,000.00 273,000.00 65,000.00
Requirement 2:
Activity Labour Building
cost
Machine
cost
Total cost
MANAGEMENT ACCOUNTING
Smoking
and
packing
1,497,0
47.24
378,3
58.21
130,0
00.00
22,033.
90
72,8
74.74
13,30
7.09
2,113,6
21.18
Administr
ation
748,5
23.62
203,7
31.34
2,203.
39
2,8
02.87
6,65
3.54
963,9
14.77
Corporate
manageme
nt
345,4
72.44
116,4
17.91
1,101.
69
2,8
02.87
3,07
0.87
468,8
65.79
7,312,5
00.00
1,950,0
00.00
1,300,0
00.00
65,000.
00
273,0
00.00
65,00
0.00
Image view:
Requirement 1
acvtivity centres Wages Building cost Depreciation ConsumablesEnergy Other Total
New product development 172,736.22 87,313.43 1,101.69 5,605.75 1,535.43 268,292.53
Sales and distribution 748,523.62 203,731.34 1,101.69 3,363.45 6,653.54 963,373.65
Inspecting 115,157.48 203,731.34 1,101.69 3,363.45 1,023.62 324,377.59
Mincing 1,842,519.69 378,358.21 520,000.00 22,033.90 72,874.74 16,377.95 2,852,164.49
Mixing 1,842,519.69 378,358.21 650,000.00 14,322.03 109,312.11 16,377.95 3,010,890.00
Smoking and packing 1,497,047.24 378,358.21 130,000.00 22,033.90 72,874.74 13,307.09 2,113,621.18
Administration 748,523.62 203,731.34 2,203.39 2,802.87 6,653.54 963,914.77
Corporate management 345,472.44 116,417.91 1,101.69 2,802.87 3,070.87 468,865.79
7,312,500.00 1,950,000.00 1,300,000.00 65,000.00 273,000.00 65,000.00
Requirement 2:
Activity Labour Building
cost
Machine
cost
Total cost
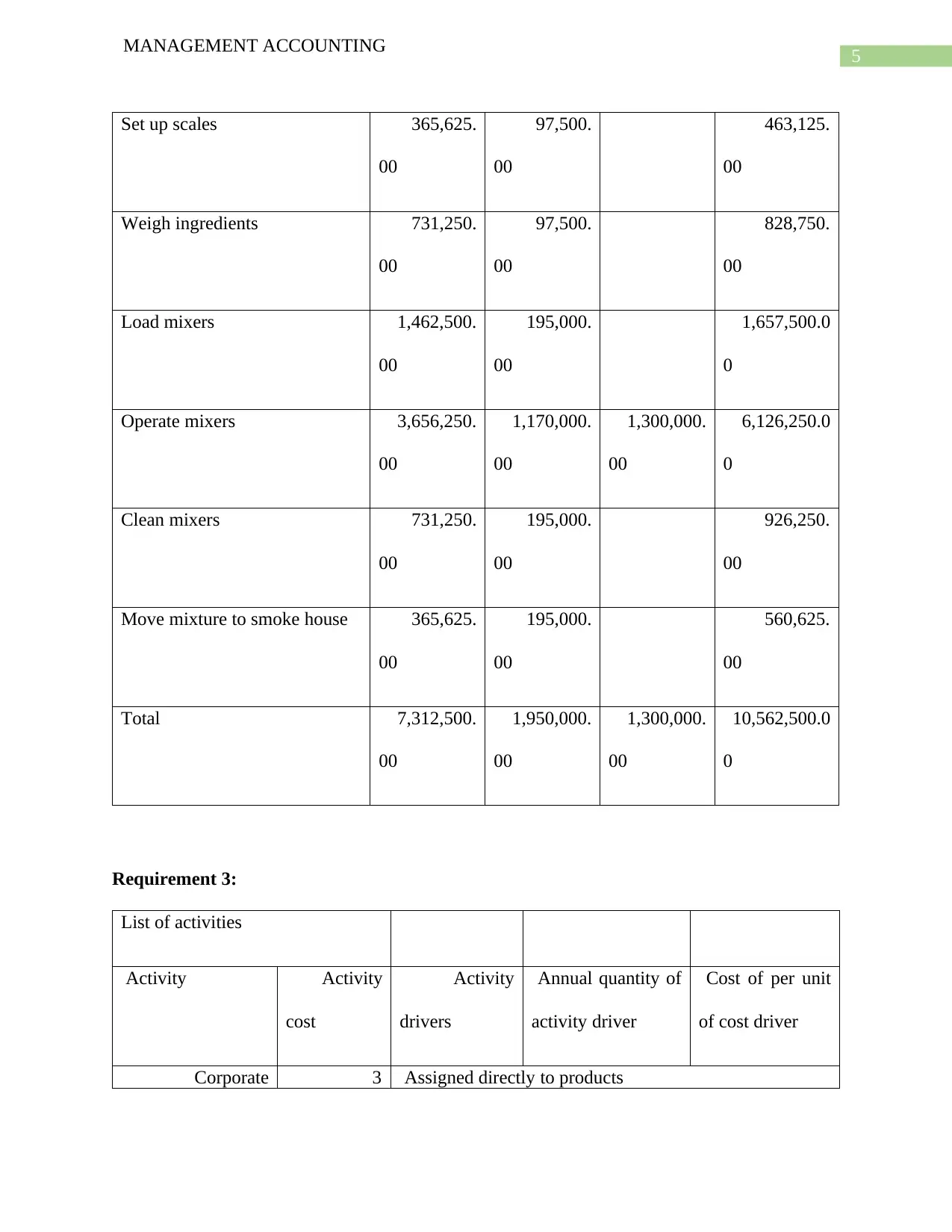
5
MANAGEMENT ACCOUNTING
Set up scales 365,625.
00
97,500.
00
463,125.
00
Weigh ingredients 731,250.
00
97,500.
00
828,750.
00
Load mixers 1,462,500.
00
195,000.
00
1,657,500.0
0
Operate mixers 3,656,250.
00
1,170,000.
00
1,300,000.
00
6,126,250.0
0
Clean mixers 731,250.
00
195,000.
00
926,250.
00
Move mixture to smoke house 365,625.
00
195,000.
00
560,625.
00
Total 7,312,500.
00
1,950,000.
00
1,300,000.
00
10,562,500.0
0
Requirement 3:
List of activities
Activity Activity
cost
Activity
drivers
Annual quantity of
activity driver
Cost of per unit
of cost driver
Corporate 3 Assigned directly to products
MANAGEMENT ACCOUNTING
Set up scales 365,625.
00
97,500.
00
463,125.
00
Weigh ingredients 731,250.
00
97,500.
00
828,750.
00
Load mixers 1,462,500.
00
195,000.
00
1,657,500.0
0
Operate mixers 3,656,250.
00
1,170,000.
00
1,300,000.
00
6,126,250.0
0
Clean mixers 731,250.
00
195,000.
00
926,250.
00
Move mixture to smoke house 365,625.
00
195,000.
00
560,625.
00
Total 7,312,500.
00
1,950,000.
00
1,300,000.
00
10,562,500.0
0
Requirement 3:
List of activities
Activity Activity
cost
Activity
drivers
Annual quantity of
activity driver
Cost of per unit
of cost driver
Corporate 3 Assigned directly to products
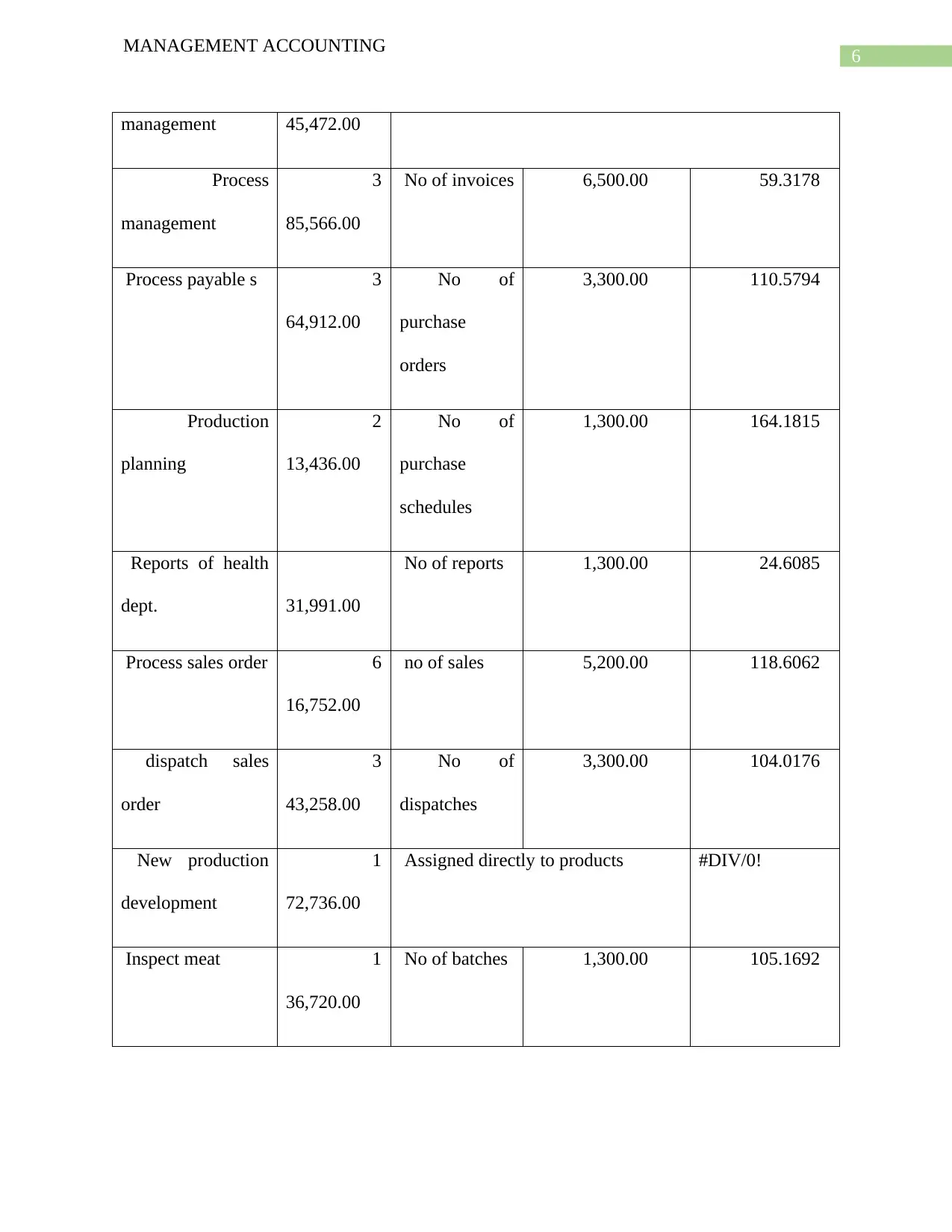
6
MANAGEMENT ACCOUNTING
management 45,472.00
Process
management
3
85,566.00
No of invoices 6,500.00 59.3178
Process payable s 3
64,912.00
No of
purchase
orders
3,300.00 110.5794
Production
planning
2
13,436.00
No of
purchase
schedules
1,300.00 164.1815
Reports of health
dept. 31,991.00
No of reports 1,300.00 24.6085
Process sales order 6
16,752.00
no of sales 5,200.00 118.6062
dispatch sales
order
3
43,258.00
No of
dispatches
3,300.00 104.0176
New production
development
1
72,736.00
Assigned directly to products #DIV/0!
Inspect meat 1
36,720.00
No of batches 1,300.00 105.1692
MANAGEMENT ACCOUNTING
management 45,472.00
Process
management
3
85,566.00
No of invoices 6,500.00 59.3178
Process payable s 3
64,912.00
No of
purchase
orders
3,300.00 110.5794
Production
planning
2
13,436.00
No of
purchase
schedules
1,300.00 164.1815
Reports of health
dept. 31,991.00
No of reports 1,300.00 24.6085
Process sales order 6
16,752.00
no of sales 5,200.00 118.6062
dispatch sales
order
3
43,258.00
No of
dispatches
3,300.00 104.0176
New production
development
1
72,736.00
Assigned directly to products #DIV/0!
Inspect meat 1
36,720.00
No of batches 1,300.00 105.1692
Paraphrase This Document
Need a fresh take? Get an instant paraphrase of this document with our AI Paraphraser
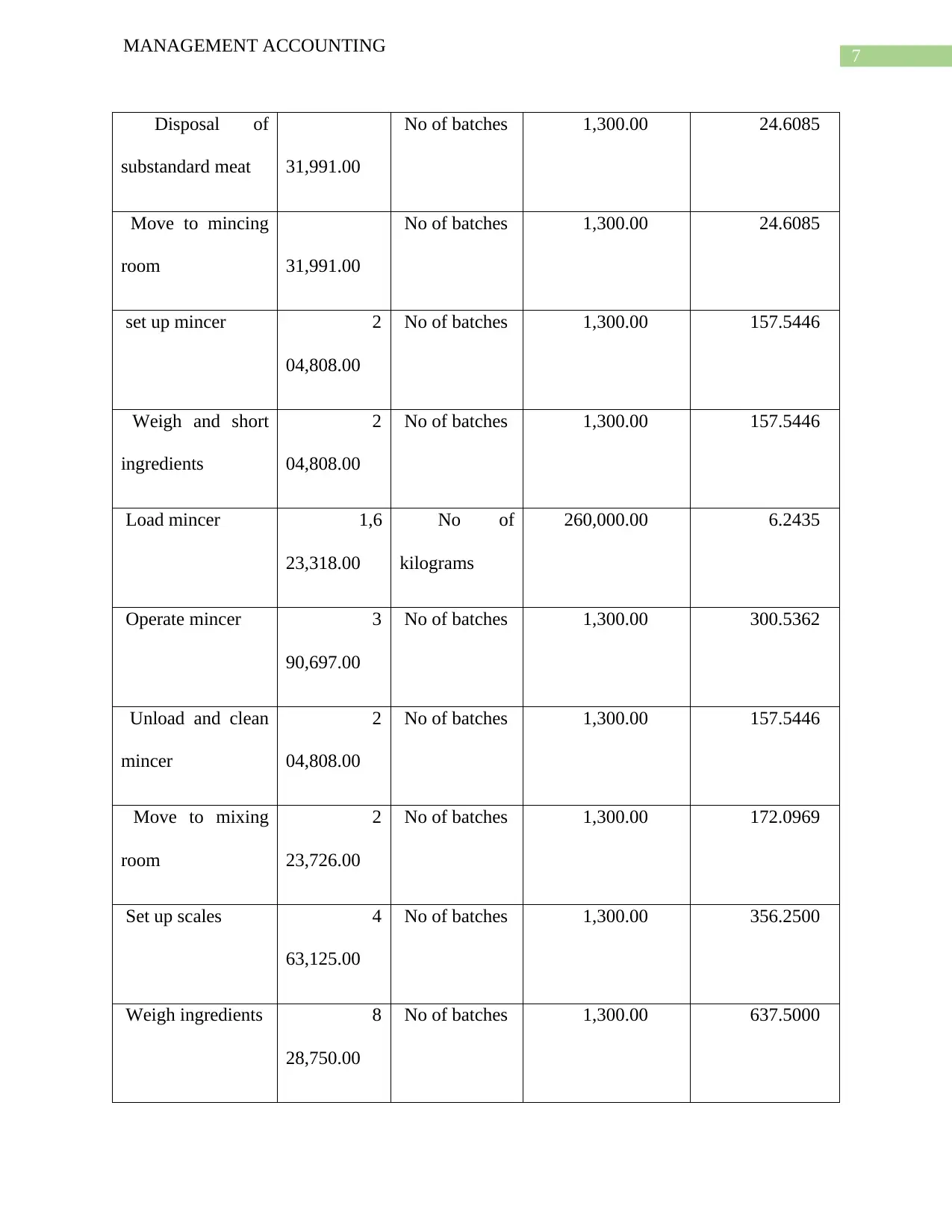
7
MANAGEMENT ACCOUNTING
Disposal of
substandard meat 31,991.00
No of batches 1,300.00 24.6085
Move to mincing
room 31,991.00
No of batches 1,300.00 24.6085
set up mincer 2
04,808.00
No of batches 1,300.00 157.5446
Weigh and short
ingredients
2
04,808.00
No of batches 1,300.00 157.5446
Load mincer 1,6
23,318.00
No of
kilograms
260,000.00 6.2435
Operate mincer 3
90,697.00
No of batches 1,300.00 300.5362
Unload and clean
mincer
2
04,808.00
No of batches 1,300.00 157.5446
Move to mixing
room
2
23,726.00
No of batches 1,300.00 172.0969
Set up scales 4
63,125.00
No of batches 1,300.00 356.2500
Weigh ingredients 8
28,750.00
No of batches 1,300.00 637.5000
MANAGEMENT ACCOUNTING
Disposal of
substandard meat 31,991.00
No of batches 1,300.00 24.6085
Move to mincing
room 31,991.00
No of batches 1,300.00 24.6085
set up mincer 2
04,808.00
No of batches 1,300.00 157.5446
Weigh and short
ingredients
2
04,808.00
No of batches 1,300.00 157.5446
Load mincer 1,6
23,318.00
No of
kilograms
260,000.00 6.2435
Operate mincer 3
90,697.00
No of batches 1,300.00 300.5362
Unload and clean
mincer
2
04,808.00
No of batches 1,300.00 157.5446
Move to mixing
room
2
23,726.00
No of batches 1,300.00 172.0969
Set up scales 4
63,125.00
No of batches 1,300.00 356.2500
Weigh ingredients 8
28,750.00
No of batches 1,300.00 637.5000
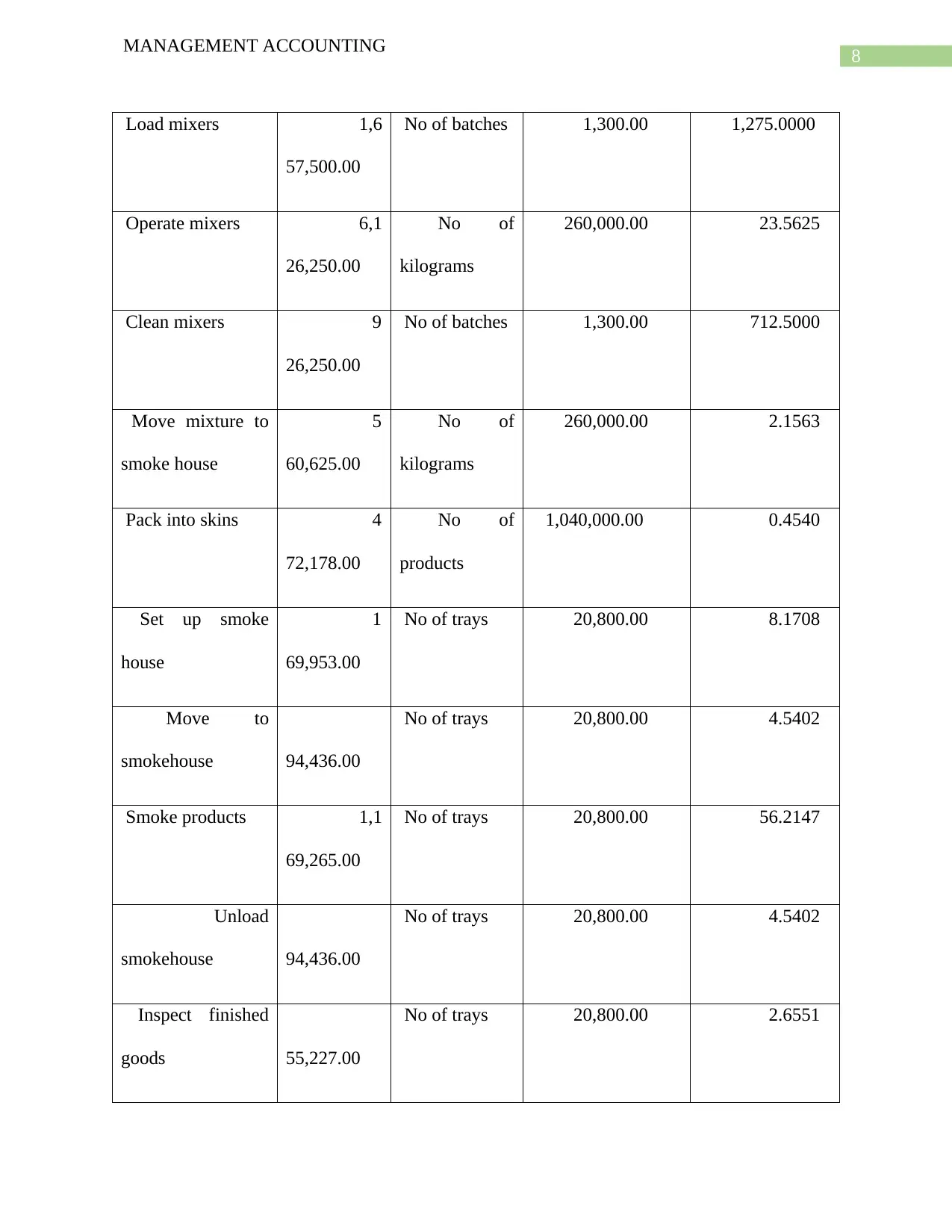
8
MANAGEMENT ACCOUNTING
Load mixers 1,6
57,500.00
No of batches 1,300.00 1,275.0000
Operate mixers 6,1
26,250.00
No of
kilograms
260,000.00 23.5625
Clean mixers 9
26,250.00
No of batches 1,300.00 712.5000
Move mixture to
smoke house
5
60,625.00
No of
kilograms
260,000.00 2.1563
Pack into skins 4
72,178.00
No of
products
1,040,000.00 0.4540
Set up smoke
house
1
69,953.00
No of trays 20,800.00 8.1708
Move to
smokehouse 94,436.00
No of trays 20,800.00 4.5402
Smoke products 1,1
69,265.00
No of trays 20,800.00 56.2147
Unload
smokehouse 94,436.00
No of trays 20,800.00 4.5402
Inspect finished
goods 55,227.00
No of trays 20,800.00 2.6551
MANAGEMENT ACCOUNTING
Load mixers 1,6
57,500.00
No of batches 1,300.00 1,275.0000
Operate mixers 6,1
26,250.00
No of
kilograms
260,000.00 23.5625
Clean mixers 9
26,250.00
No of batches 1,300.00 712.5000
Move mixture to
smoke house
5
60,625.00
No of
kilograms
260,000.00 2.1563
Pack into skins 4
72,178.00
No of
products
1,040,000.00 0.4540
Set up smoke
house
1
69,953.00
No of trays 20,800.00 8.1708
Move to
smokehouse 94,436.00
No of trays 20,800.00 4.5402
Smoke products 1,1
69,265.00
No of trays 20,800.00 56.2147
Unload
smokehouse 94,436.00
No of trays 20,800.00 4.5402
Inspect finished
goods 55,227.00
No of trays 20,800.00 2.6551

9
MANAGEMENT ACCOUNTING
Disposal of
substandard
product
31,991.00
No of trays 20,800.00 1.5380
Move to truck 1
13,354.00
No of trays 19,760.00 5.7365
Requirement 4:
Mettwurst
Activities consumed Annual quantity of activity driver Relevant
cost
Corporate management 93773 Assigned directly to product 93,773.
00
Process receivables 700 Invoices 41,522.
49
Process payables 300 purchase orders 33,173.
82
Production planning 160 Production schedules 26,269.
05
Reports of Health Dept. 160 Reports 3,937.
35
MANAGEMENT ACCOUNTING
Disposal of
substandard
product
31,991.00
No of trays 20,800.00 1.5380
Move to truck 1
13,354.00
No of trays 19,760.00 5.7365
Requirement 4:
Mettwurst
Activities consumed Annual quantity of activity driver Relevant
cost
Corporate management 93773 Assigned directly to product 93,773.
00
Process receivables 700 Invoices 41,522.
49
Process payables 300 purchase orders 33,173.
82
Production planning 160 Production schedules 26,269.
05
Reports of Health Dept. 160 Reports 3,937.
35
Secure Best Marks with AI Grader
Need help grading? Try our AI Grader for instant feedback on your assignments.
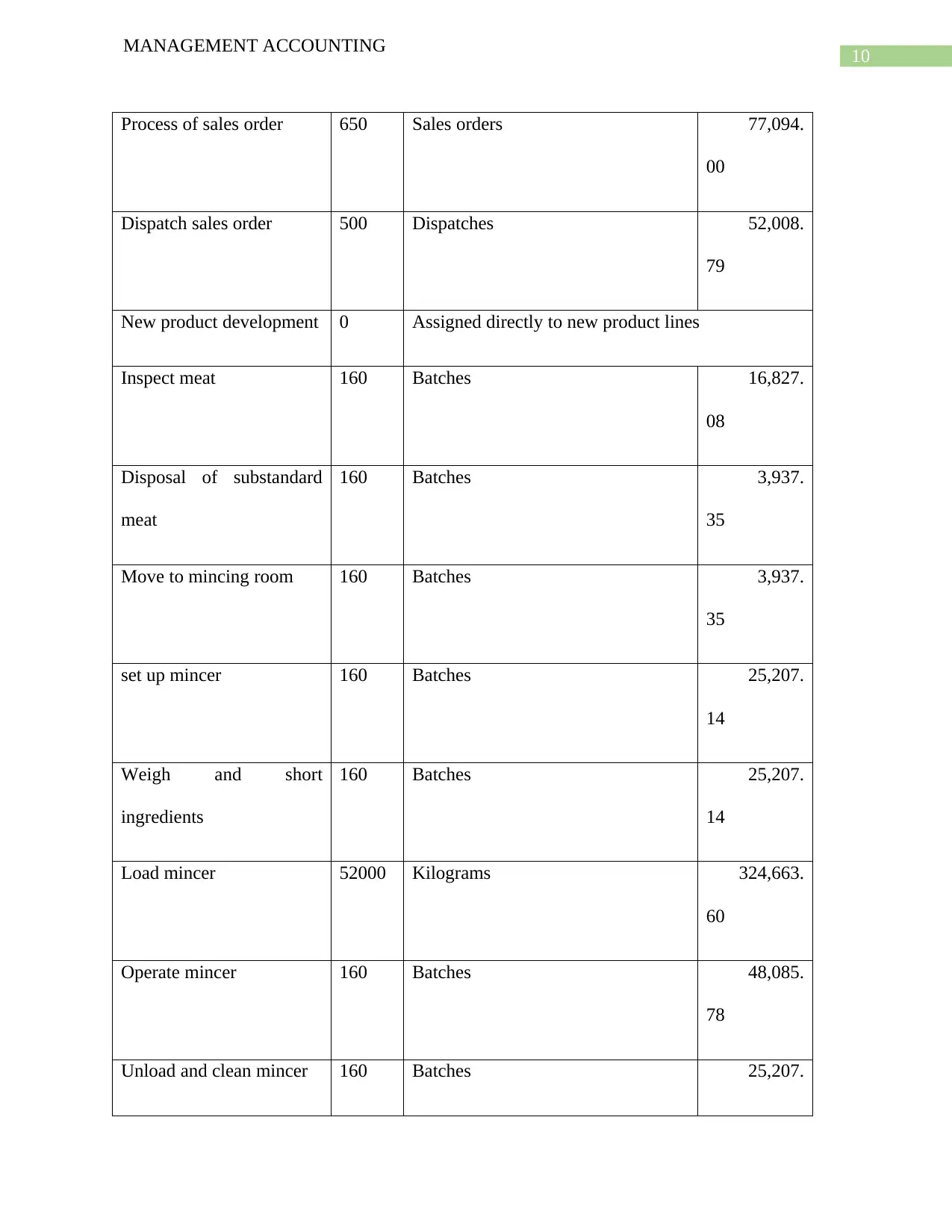
10
MANAGEMENT ACCOUNTING
Process of sales order 650 Sales orders 77,094.
00
Dispatch sales order 500 Dispatches 52,008.
79
New product development 0 Assigned directly to new product lines
Inspect meat 160 Batches 16,827.
08
Disposal of substandard
meat
160 Batches 3,937.
35
Move to mincing room 160 Batches 3,937.
35
set up mincer 160 Batches 25,207.
14
Weigh and short
ingredients
160 Batches 25,207.
14
Load mincer 52000 Kilograms 324,663.
60
Operate mincer 160 Batches 48,085.
78
Unload and clean mincer 160 Batches 25,207.
MANAGEMENT ACCOUNTING
Process of sales order 650 Sales orders 77,094.
00
Dispatch sales order 500 Dispatches 52,008.
79
New product development 0 Assigned directly to new product lines
Inspect meat 160 Batches 16,827.
08
Disposal of substandard
meat
160 Batches 3,937.
35
Move to mincing room 160 Batches 3,937.
35
set up mincer 160 Batches 25,207.
14
Weigh and short
ingredients
160 Batches 25,207.
14
Load mincer 52000 Kilograms 324,663.
60
Operate mincer 160 Batches 48,085.
78
Unload and clean mincer 160 Batches 25,207.
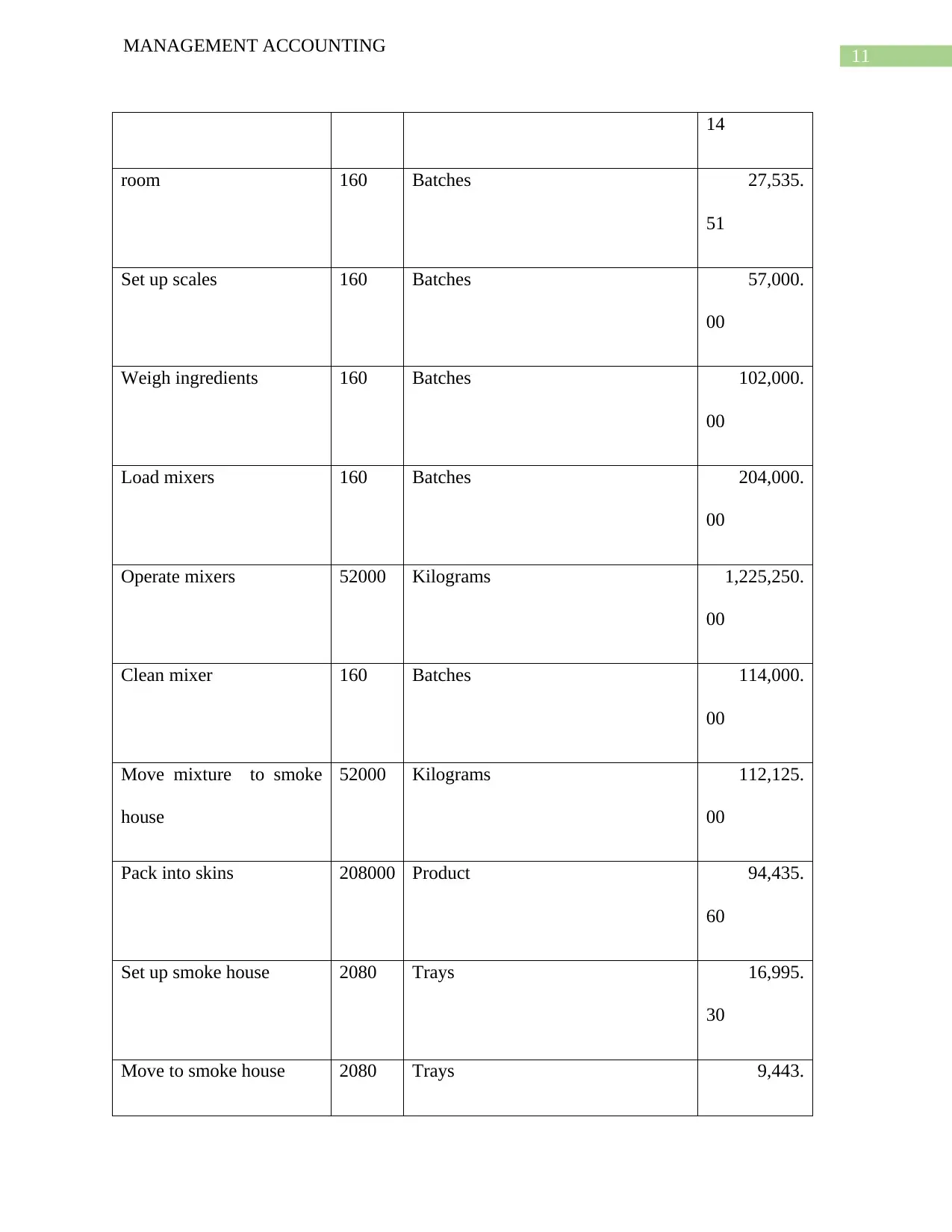
11
MANAGEMENT ACCOUNTING
14
room 160 Batches 27,535.
51
Set up scales 160 Batches 57,000.
00
Weigh ingredients 160 Batches 102,000.
00
Load mixers 160 Batches 204,000.
00
Operate mixers 52000 Kilograms 1,225,250.
00
Clean mixer 160 Batches 114,000.
00
Move mixture to smoke
house
52000 Kilograms 112,125.
00
Pack into skins 208000 Product 94,435.
60
Set up smoke house 2080 Trays 16,995.
30
Move to smoke house 2080 Trays 9,443.
MANAGEMENT ACCOUNTING
14
room 160 Batches 27,535.
51
Set up scales 160 Batches 57,000.
00
Weigh ingredients 160 Batches 102,000.
00
Load mixers 160 Batches 204,000.
00
Operate mixers 52000 Kilograms 1,225,250.
00
Clean mixer 160 Batches 114,000.
00
Move mixture to smoke
house
52000 Kilograms 112,125.
00
Pack into skins 208000 Product 94,435.
60
Set up smoke house 2080 Trays 16,995.
30
Move to smoke house 2080 Trays 9,443.
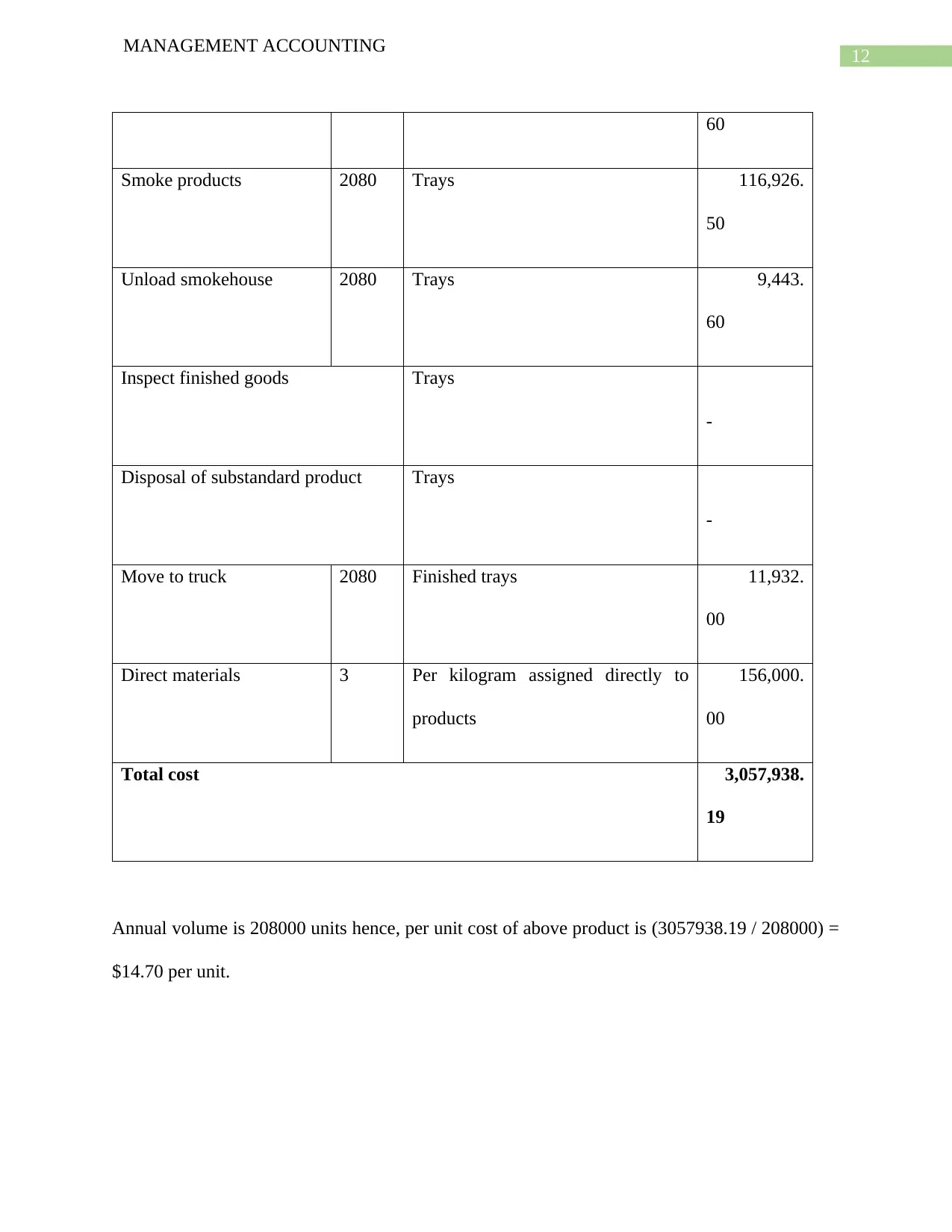
12
MANAGEMENT ACCOUNTING
60
Smoke products 2080 Trays 116,926.
50
Unload smokehouse 2080 Trays 9,443.
60
Inspect finished goods Trays
-
Disposal of substandard product Trays
-
Move to truck 2080 Finished trays 11,932.
00
Direct materials 3 Per kilogram assigned directly to
products
156,000.
00
Total cost 3,057,938.
19
Annual volume is 208000 units hence, per unit cost of above product is (3057938.19 / 208000) =
$14.70 per unit.
MANAGEMENT ACCOUNTING
60
Smoke products 2080 Trays 116,926.
50
Unload smokehouse 2080 Trays 9,443.
60
Inspect finished goods Trays
-
Disposal of substandard product Trays
-
Move to truck 2080 Finished trays 11,932.
00
Direct materials 3 Per kilogram assigned directly to
products
156,000.
00
Total cost 3,057,938.
19
Annual volume is 208000 units hence, per unit cost of above product is (3057938.19 / 208000) =
$14.70 per unit.
Paraphrase This Document
Need a fresh take? Get an instant paraphrase of this document with our AI Paraphraser
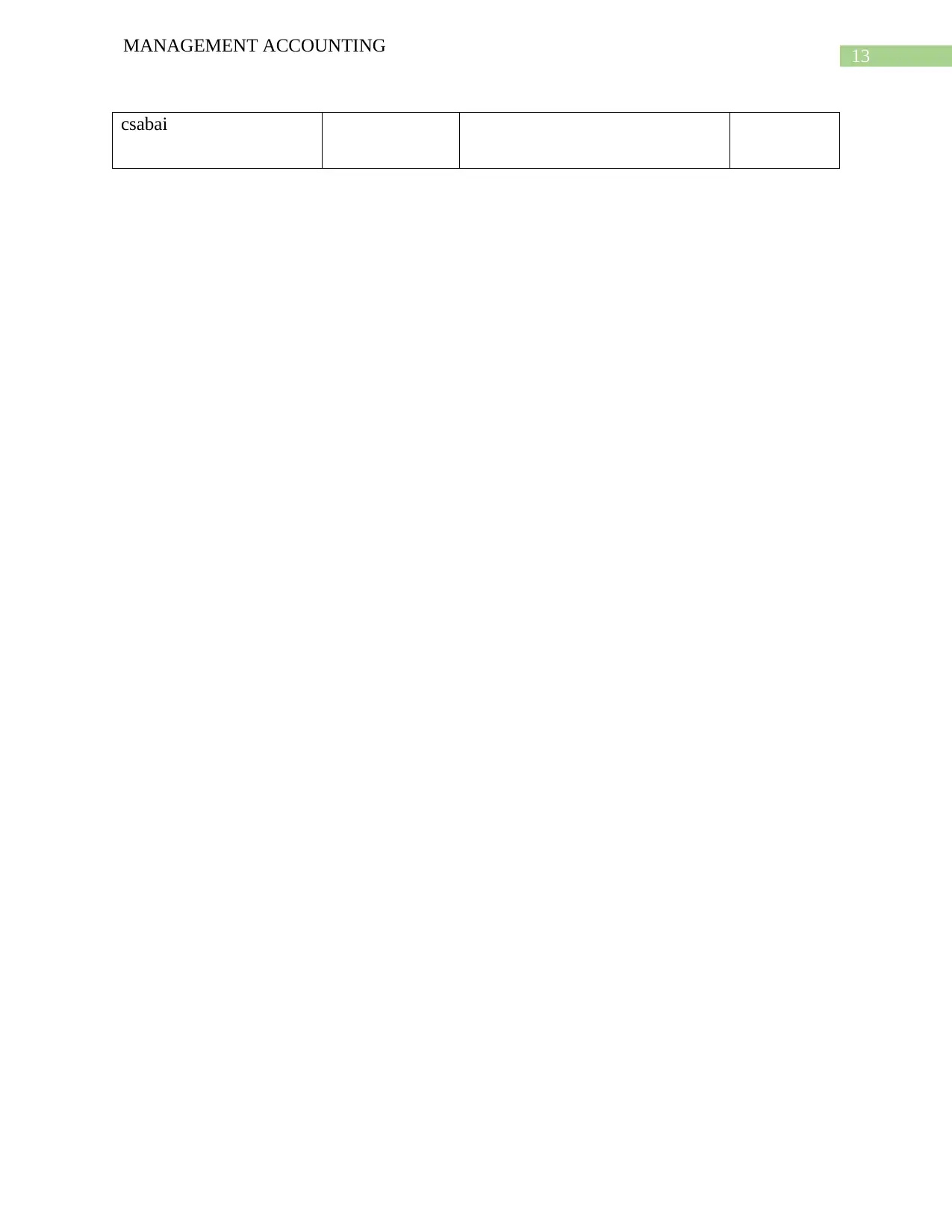
13
MANAGEMENT ACCOUNTING
csabai
MANAGEMENT ACCOUNTING
csabai
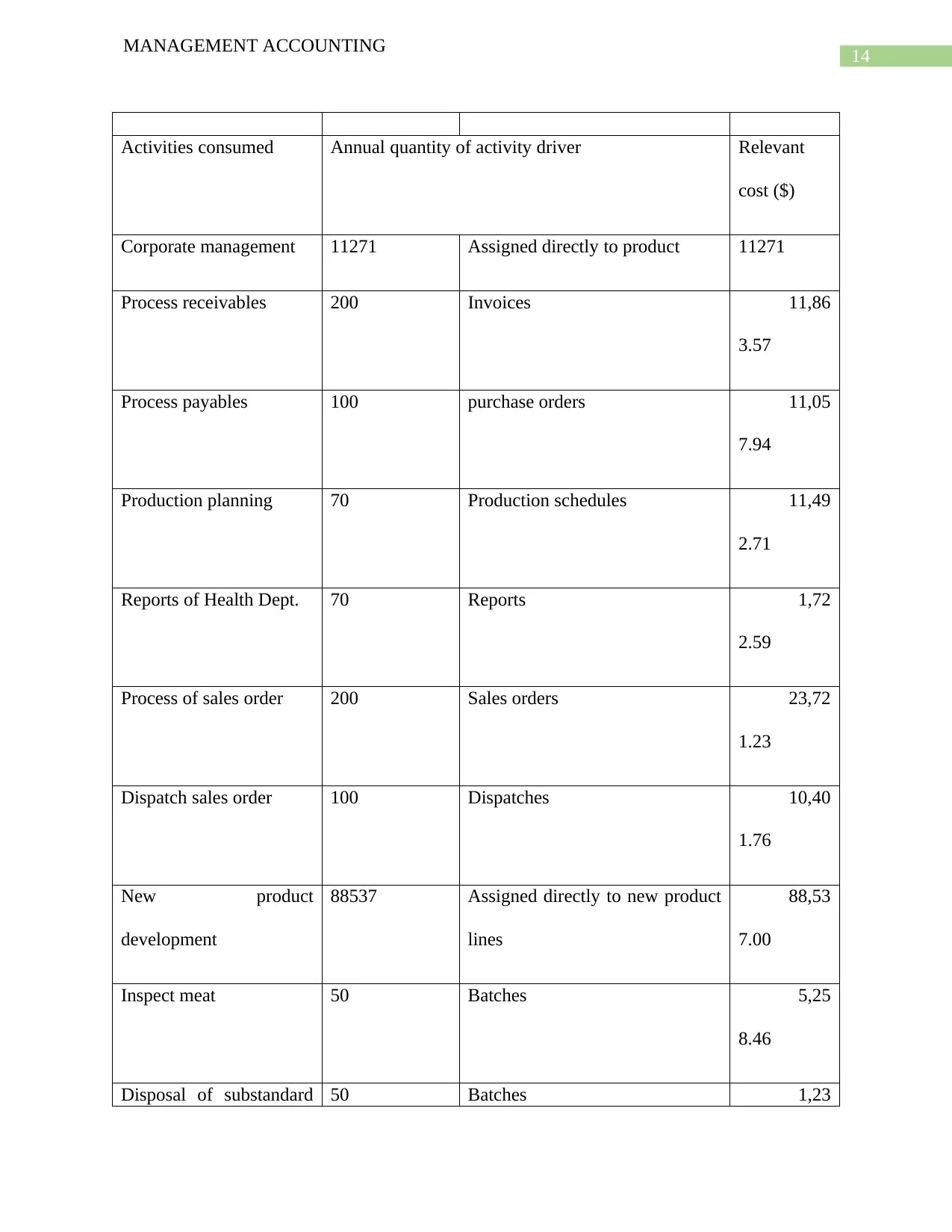
14
MANAGEMENT ACCOUNTING
Activities consumed Annual quantity of activity driver Relevant
cost ($)
Corporate management 11271 Assigned directly to product 11271
Process receivables 200 Invoices 11,86
3.57
Process payables 100 purchase orders 11,05
7.94
Production planning 70 Production schedules 11,49
2.71
Reports of Health Dept. 70 Reports 1,72
2.59
Process of sales order 200 Sales orders 23,72
1.23
Dispatch sales order 100 Dispatches 10,40
1.76
New product
development
88537 Assigned directly to new product
lines
88,53
7.00
Inspect meat 50 Batches 5,25
8.46
Disposal of substandard 50 Batches 1,23
MANAGEMENT ACCOUNTING
Activities consumed Annual quantity of activity driver Relevant
cost ($)
Corporate management 11271 Assigned directly to product 11271
Process receivables 200 Invoices 11,86
3.57
Process payables 100 purchase orders 11,05
7.94
Production planning 70 Production schedules 11,49
2.71
Reports of Health Dept. 70 Reports 1,72
2.59
Process of sales order 200 Sales orders 23,72
1.23
Dispatch sales order 100 Dispatches 10,40
1.76
New product
development
88537 Assigned directly to new product
lines
88,53
7.00
Inspect meat 50 Batches 5,25
8.46
Disposal of substandard 50 Batches 1,23
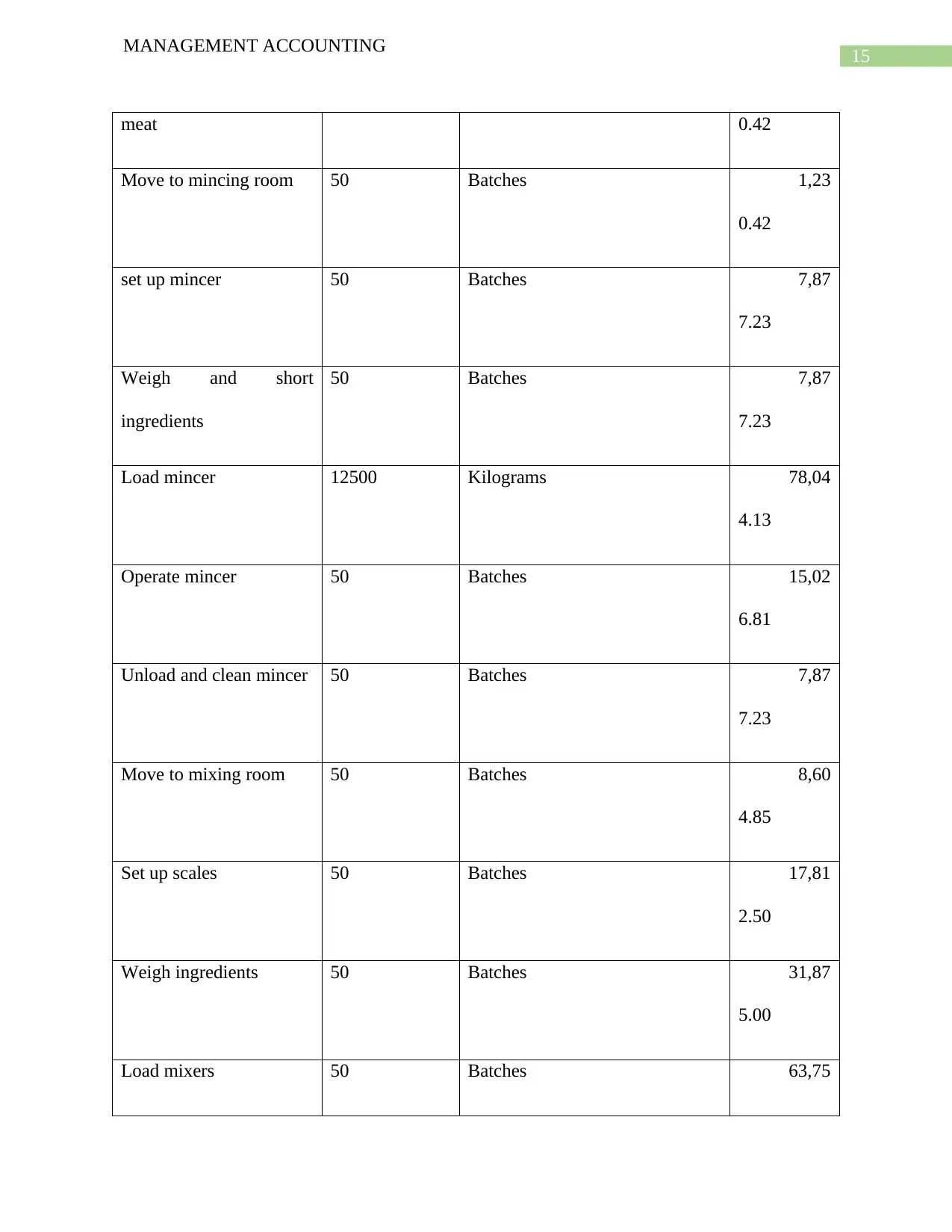
15
MANAGEMENT ACCOUNTING
meat 0.42
Move to mincing room 50 Batches 1,23
0.42
set up mincer 50 Batches 7,87
7.23
Weigh and short
ingredients
50 Batches 7,87
7.23
Load mincer 12500 Kilograms 78,04
4.13
Operate mincer 50 Batches 15,02
6.81
Unload and clean mincer 50 Batches 7,87
7.23
Move to mixing room 50 Batches 8,60
4.85
Set up scales 50 Batches 17,81
2.50
Weigh ingredients 50 Batches 31,87
5.00
Load mixers 50 Batches 63,75
MANAGEMENT ACCOUNTING
meat 0.42
Move to mincing room 50 Batches 1,23
0.42
set up mincer 50 Batches 7,87
7.23
Weigh and short
ingredients
50 Batches 7,87
7.23
Load mincer 12500 Kilograms 78,04
4.13
Operate mincer 50 Batches 15,02
6.81
Unload and clean mincer 50 Batches 7,87
7.23
Move to mixing room 50 Batches 8,60
4.85
Set up scales 50 Batches 17,81
2.50
Weigh ingredients 50 Batches 31,87
5.00
Load mixers 50 Batches 63,75
Secure Best Marks with AI Grader
Need help grading? Try our AI Grader for instant feedback on your assignments.
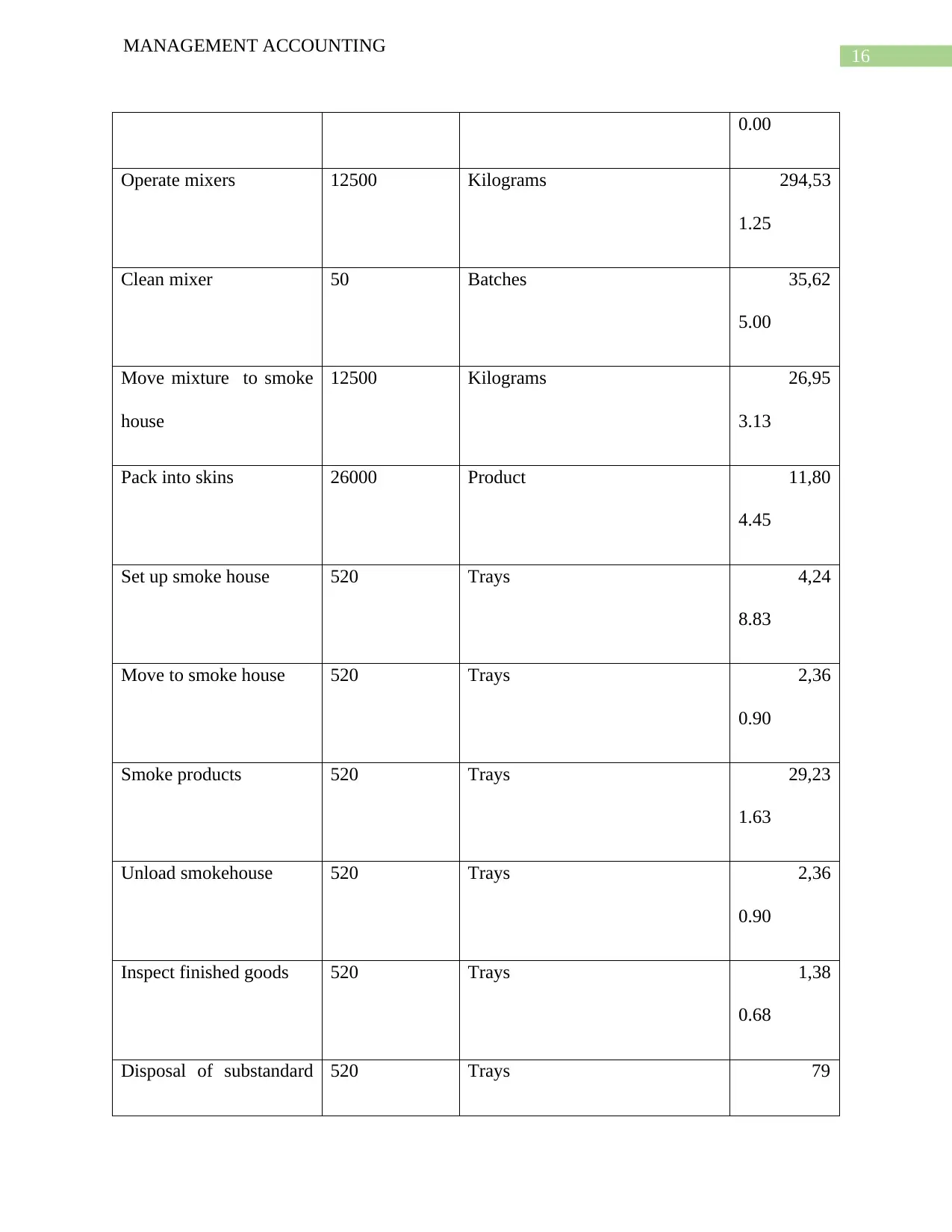
16
MANAGEMENT ACCOUNTING
0.00
Operate mixers 12500 Kilograms 294,53
1.25
Clean mixer 50 Batches 35,62
5.00
Move mixture to smoke
house
12500 Kilograms 26,95
3.13
Pack into skins 26000 Product 11,80
4.45
Set up smoke house 520 Trays 4,24
8.83
Move to smoke house 520 Trays 2,36
0.90
Smoke products 520 Trays 29,23
1.63
Unload smokehouse 520 Trays 2,36
0.90
Inspect finished goods 520 Trays 1,38
0.68
Disposal of substandard 520 Trays 79
MANAGEMENT ACCOUNTING
0.00
Operate mixers 12500 Kilograms 294,53
1.25
Clean mixer 50 Batches 35,62
5.00
Move mixture to smoke
house
12500 Kilograms 26,95
3.13
Pack into skins 26000 Product 11,80
4.45
Set up smoke house 520 Trays 4,24
8.83
Move to smoke house 520 Trays 2,36
0.90
Smoke products 520 Trays 29,23
1.63
Unload smokehouse 520 Trays 2,36
0.90
Inspect finished goods 520 Trays 1,38
0.68
Disposal of substandard 520 Trays 79
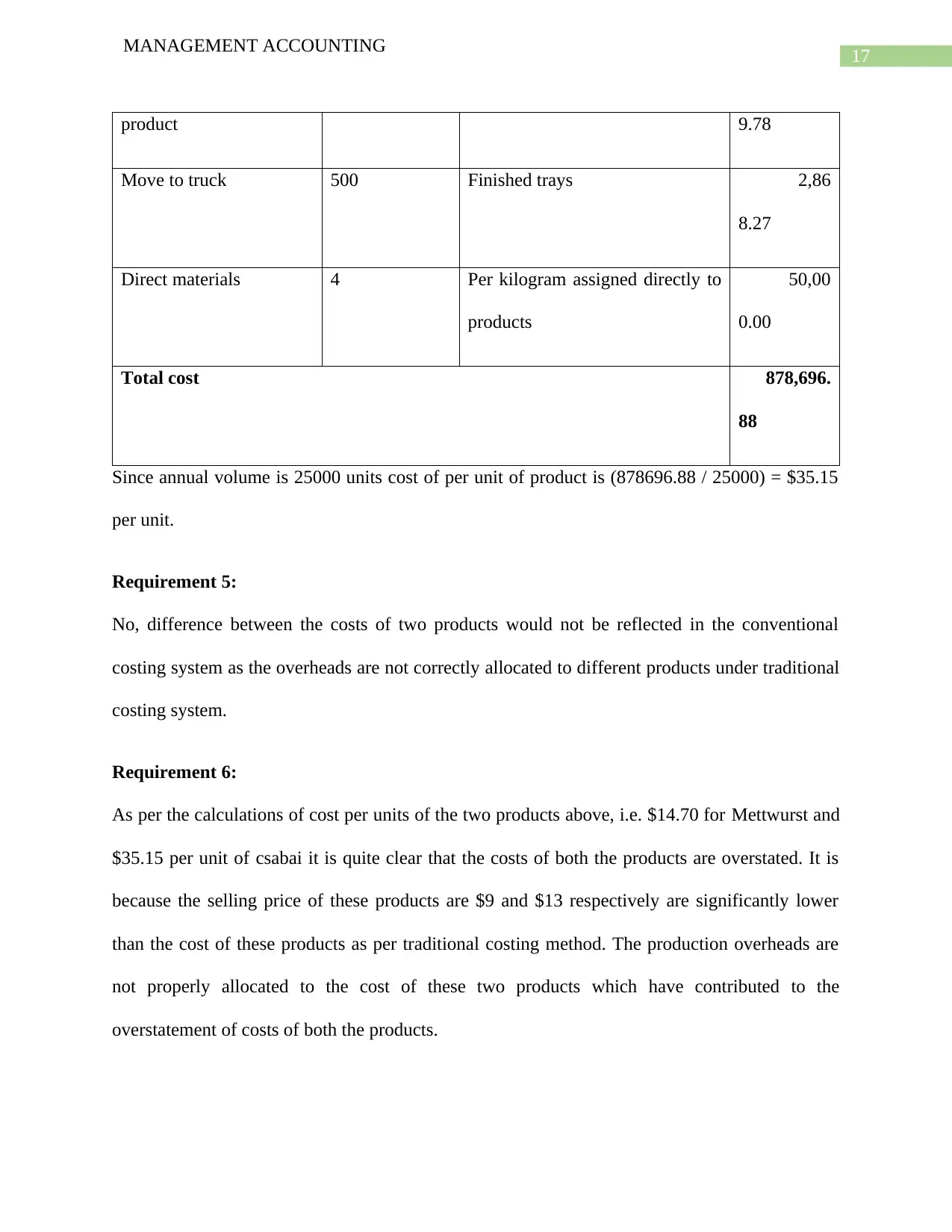
17
MANAGEMENT ACCOUNTING
product 9.78
Move to truck 500 Finished trays 2,86
8.27
Direct materials 4 Per kilogram assigned directly to
products
50,00
0.00
Total cost 878,696.
88
Since annual volume is 25000 units cost of per unit of product is (878696.88 / 25000) = $35.15
per unit.
Requirement 5:
No, difference between the costs of two products would not be reflected in the conventional
costing system as the overheads are not correctly allocated to different products under traditional
costing system.
Requirement 6:
As per the calculations of cost per units of the two products above, i.e. $14.70 for Mettwurst and
$35.15 per unit of csabai it is quite clear that the costs of both the products are overstated. It is
because the selling price of these products are $9 and $13 respectively are significantly lower
than the cost of these products as per traditional costing method. The production overheads are
not properly allocated to the cost of these two products which have contributed to the
overstatement of costs of both the products.
MANAGEMENT ACCOUNTING
product 9.78
Move to truck 500 Finished trays 2,86
8.27
Direct materials 4 Per kilogram assigned directly to
products
50,00
0.00
Total cost 878,696.
88
Since annual volume is 25000 units cost of per unit of product is (878696.88 / 25000) = $35.15
per unit.
Requirement 5:
No, difference between the costs of two products would not be reflected in the conventional
costing system as the overheads are not correctly allocated to different products under traditional
costing system.
Requirement 6:
As per the calculations of cost per units of the two products above, i.e. $14.70 for Mettwurst and
$35.15 per unit of csabai it is quite clear that the costs of both the products are overstated. It is
because the selling price of these products are $9 and $13 respectively are significantly lower
than the cost of these products as per traditional costing method. The production overheads are
not properly allocated to the cost of these two products which have contributed to the
overstatement of costs of both the products.
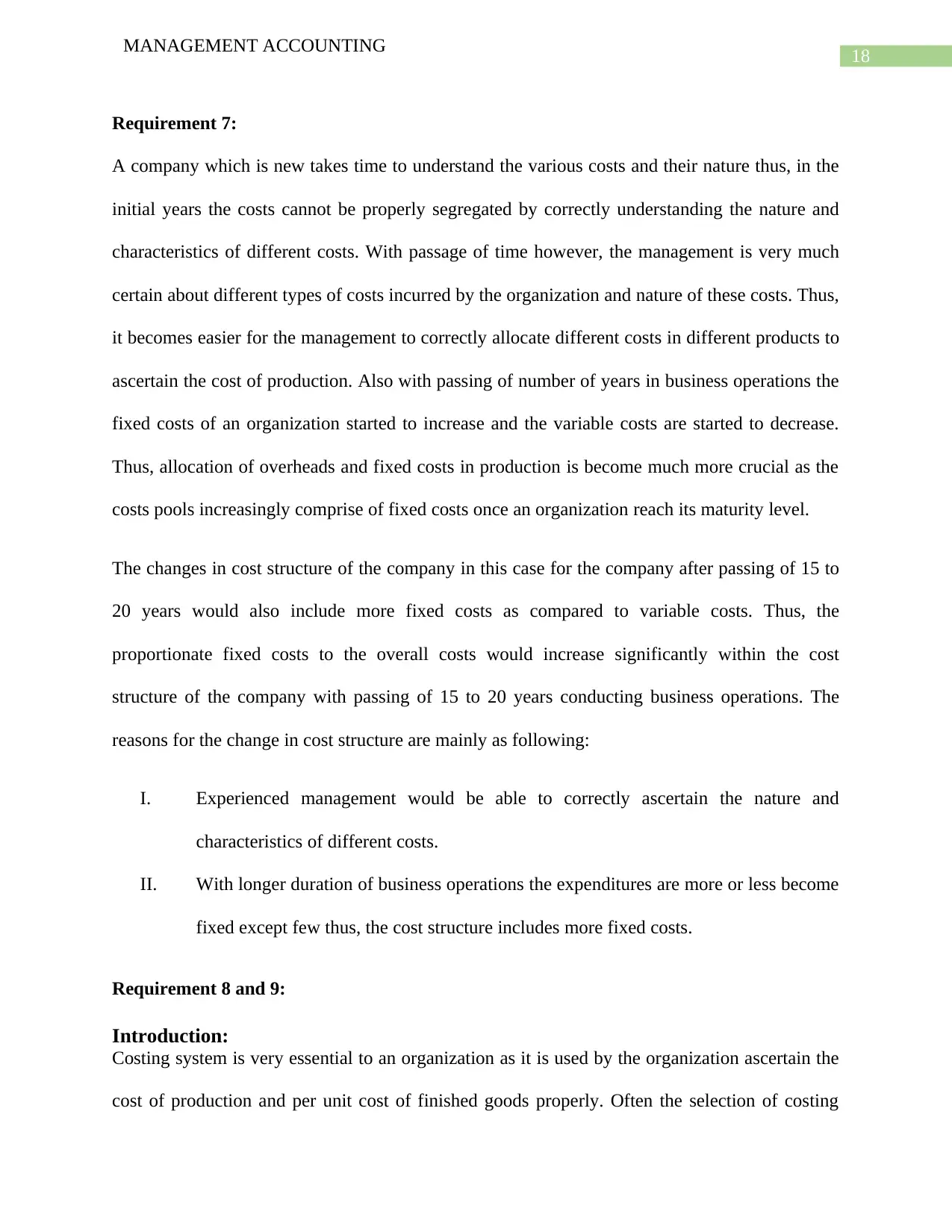
18
MANAGEMENT ACCOUNTING
Requirement 7:
A company which is new takes time to understand the various costs and their nature thus, in the
initial years the costs cannot be properly segregated by correctly understanding the nature and
characteristics of different costs. With passage of time however, the management is very much
certain about different types of costs incurred by the organization and nature of these costs. Thus,
it becomes easier for the management to correctly allocate different costs in different products to
ascertain the cost of production. Also with passing of number of years in business operations the
fixed costs of an organization started to increase and the variable costs are started to decrease.
Thus, allocation of overheads and fixed costs in production is become much more crucial as the
costs pools increasingly comprise of fixed costs once an organization reach its maturity level.
The changes in cost structure of the company in this case for the company after passing of 15 to
20 years would also include more fixed costs as compared to variable costs. Thus, the
proportionate fixed costs to the overall costs would increase significantly within the cost
structure of the company with passing of 15 to 20 years conducting business operations. The
reasons for the change in cost structure are mainly as following:
I. Experienced management would be able to correctly ascertain the nature and
characteristics of different costs.
II. With longer duration of business operations the expenditures are more or less become
fixed except few thus, the cost structure includes more fixed costs.
Requirement 8 and 9:
Introduction:
Costing system is very essential to an organization as it is used by the organization ascertain the
cost of production and per unit cost of finished goods properly. Often the selection of costing
MANAGEMENT ACCOUNTING
Requirement 7:
A company which is new takes time to understand the various costs and their nature thus, in the
initial years the costs cannot be properly segregated by correctly understanding the nature and
characteristics of different costs. With passage of time however, the management is very much
certain about different types of costs incurred by the organization and nature of these costs. Thus,
it becomes easier for the management to correctly allocate different costs in different products to
ascertain the cost of production. Also with passing of number of years in business operations the
fixed costs of an organization started to increase and the variable costs are started to decrease.
Thus, allocation of overheads and fixed costs in production is become much more crucial as the
costs pools increasingly comprise of fixed costs once an organization reach its maturity level.
The changes in cost structure of the company in this case for the company after passing of 15 to
20 years would also include more fixed costs as compared to variable costs. Thus, the
proportionate fixed costs to the overall costs would increase significantly within the cost
structure of the company with passing of 15 to 20 years conducting business operations. The
reasons for the change in cost structure are mainly as following:
I. Experienced management would be able to correctly ascertain the nature and
characteristics of different costs.
II. With longer duration of business operations the expenditures are more or less become
fixed except few thus, the cost structure includes more fixed costs.
Requirement 8 and 9:
Introduction:
Costing system is very essential to an organization as it is used by the organization ascertain the
cost of production and per unit cost of finished goods properly. Often the selection of costing
Paraphrase This Document
Need a fresh take? Get an instant paraphrase of this document with our AI Paraphraser
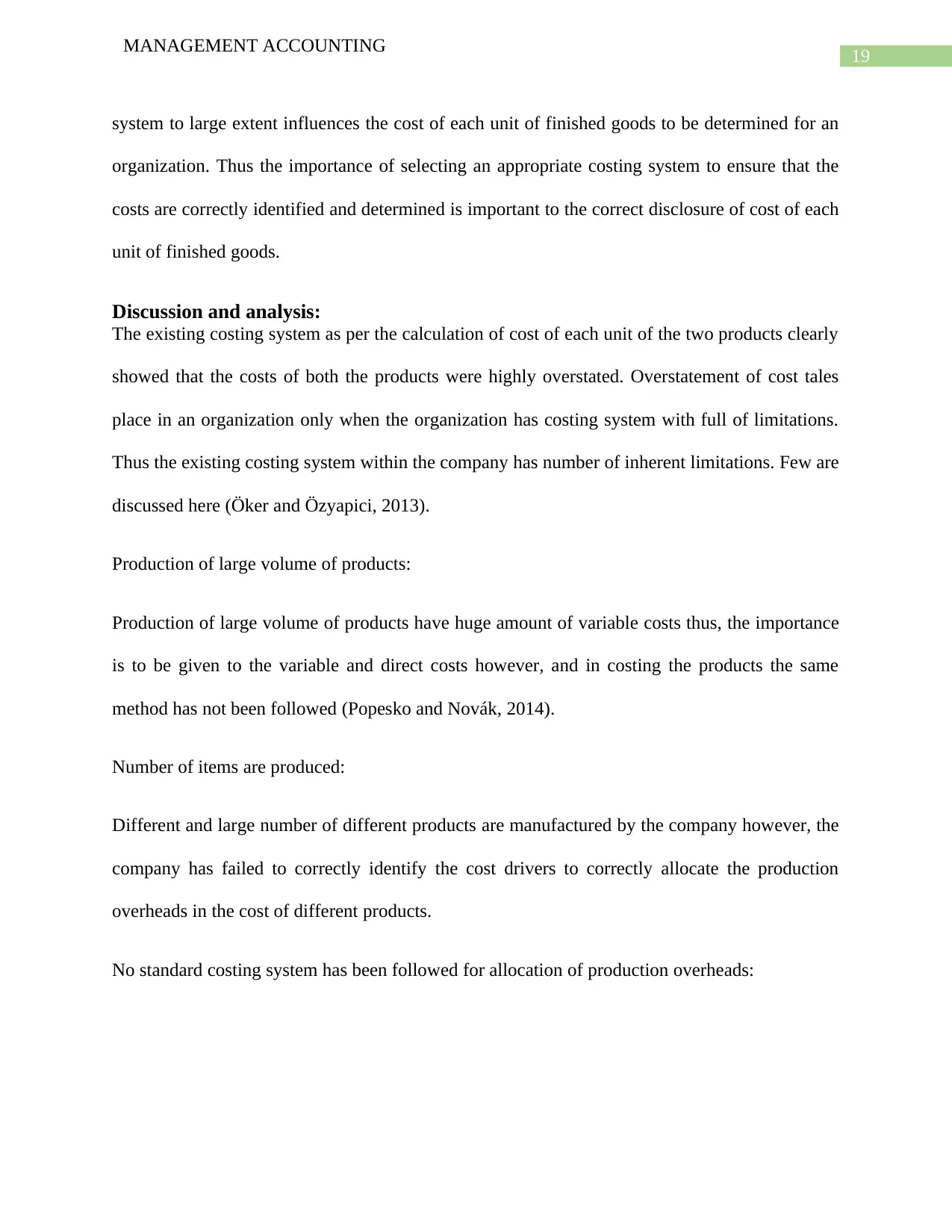
19
MANAGEMENT ACCOUNTING
system to large extent influences the cost of each unit of finished goods to be determined for an
organization. Thus the importance of selecting an appropriate costing system to ensure that the
costs are correctly identified and determined is important to the correct disclosure of cost of each
unit of finished goods.
Discussion and analysis:
The existing costing system as per the calculation of cost of each unit of the two products clearly
showed that the costs of both the products were highly overstated. Overstatement of cost tales
place in an organization only when the organization has costing system with full of limitations.
Thus the existing costing system within the company has number of inherent limitations. Few are
discussed here (Öker and Özyapici, 2013).
Production of large volume of products:
Production of large volume of products have huge amount of variable costs thus, the importance
is to be given to the variable and direct costs however, and in costing the products the same
method has not been followed (Popesko and Novák, 2014).
Number of items are produced:
Different and large number of different products are manufactured by the company however, the
company has failed to correctly identify the cost drivers to correctly allocate the production
overheads in the cost of different products.
No standard costing system has been followed for allocation of production overheads:
MANAGEMENT ACCOUNTING
system to large extent influences the cost of each unit of finished goods to be determined for an
organization. Thus the importance of selecting an appropriate costing system to ensure that the
costs are correctly identified and determined is important to the correct disclosure of cost of each
unit of finished goods.
Discussion and analysis:
The existing costing system as per the calculation of cost of each unit of the two products clearly
showed that the costs of both the products were highly overstated. Overstatement of cost tales
place in an organization only when the organization has costing system with full of limitations.
Thus the existing costing system within the company has number of inherent limitations. Few are
discussed here (Öker and Özyapici, 2013).
Production of large volume of products:
Production of large volume of products have huge amount of variable costs thus, the importance
is to be given to the variable and direct costs however, and in costing the products the same
method has not been followed (Popesko and Novák, 2014).
Number of items are produced:
Different and large number of different products are manufactured by the company however, the
company has failed to correctly identify the cost drivers to correctly allocate the production
overheads in the cost of different products.
No standard costing system has been followed for allocation of production overheads:
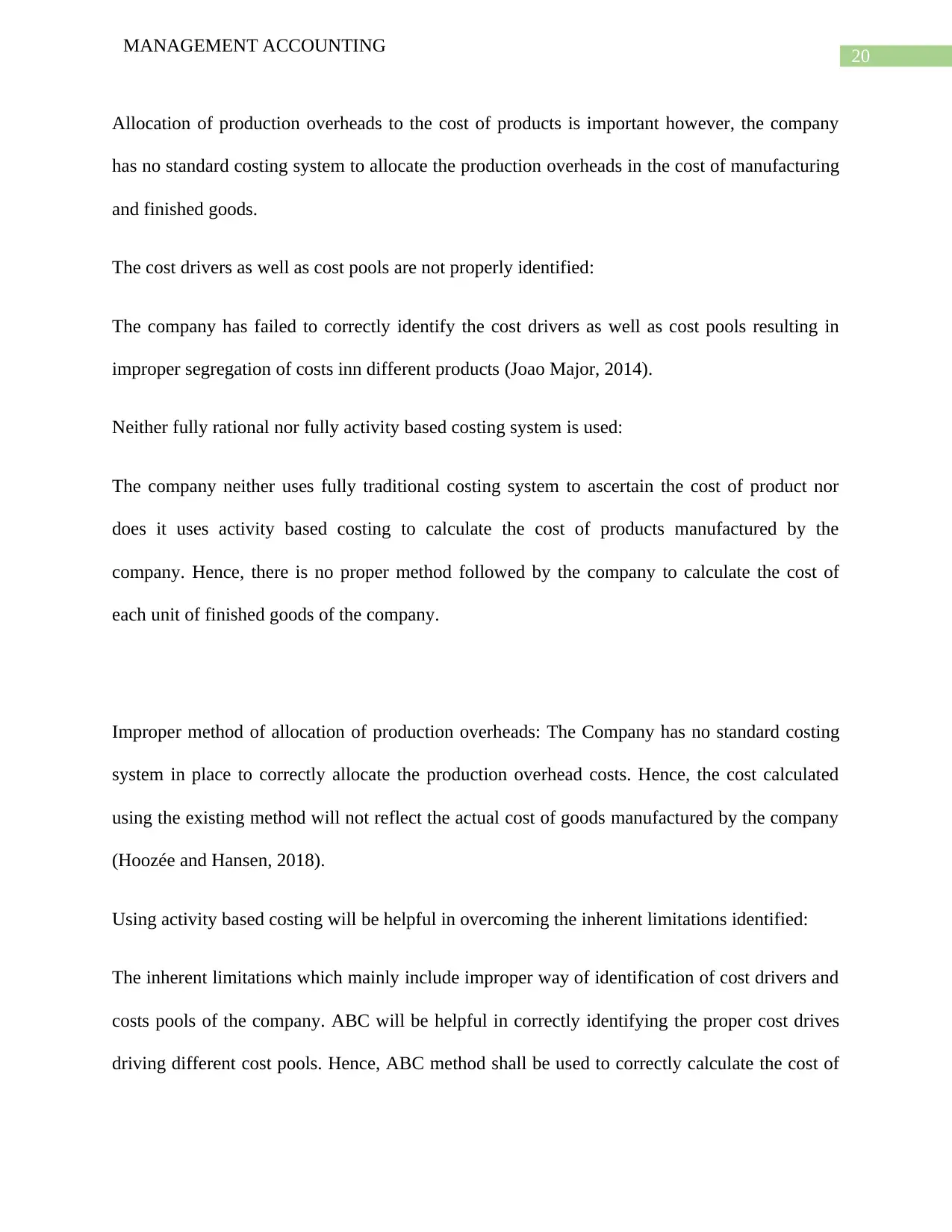
20
MANAGEMENT ACCOUNTING
Allocation of production overheads to the cost of products is important however, the company
has no standard costing system to allocate the production overheads in the cost of manufacturing
and finished goods.
The cost drivers as well as cost pools are not properly identified:
The company has failed to correctly identify the cost drivers as well as cost pools resulting in
improper segregation of costs inn different products (Joao Major, 2014).
Neither fully rational nor fully activity based costing system is used:
The company neither uses fully traditional costing system to ascertain the cost of product nor
does it uses activity based costing to calculate the cost of products manufactured by the
company. Hence, there is no proper method followed by the company to calculate the cost of
each unit of finished goods of the company.
Improper method of allocation of production overheads: The Company has no standard costing
system in place to correctly allocate the production overhead costs. Hence, the cost calculated
using the existing method will not reflect the actual cost of goods manufactured by the company
(Hoozée and Hansen, 2018).
Using activity based costing will be helpful in overcoming the inherent limitations identified:
The inherent limitations which mainly include improper way of identification of cost drivers and
costs pools of the company. ABC will be helpful in correctly identifying the proper cost drives
driving different cost pools. Hence, ABC method shall be used to correctly calculate the cost of
MANAGEMENT ACCOUNTING
Allocation of production overheads to the cost of products is important however, the company
has no standard costing system to allocate the production overheads in the cost of manufacturing
and finished goods.
The cost drivers as well as cost pools are not properly identified:
The company has failed to correctly identify the cost drivers as well as cost pools resulting in
improper segregation of costs inn different products (Joao Major, 2014).
Neither fully rational nor fully activity based costing system is used:
The company neither uses fully traditional costing system to ascertain the cost of product nor
does it uses activity based costing to calculate the cost of products manufactured by the
company. Hence, there is no proper method followed by the company to calculate the cost of
each unit of finished goods of the company.
Improper method of allocation of production overheads: The Company has no standard costing
system in place to correctly allocate the production overhead costs. Hence, the cost calculated
using the existing method will not reflect the actual cost of goods manufactured by the company
(Hoozée and Hansen, 2018).
Using activity based costing will be helpful in overcoming the inherent limitations identified:
The inherent limitations which mainly include improper way of identification of cost drivers and
costs pools of the company. ABC will be helpful in correctly identifying the proper cost drives
driving different cost pools. Hence, ABC method shall be used to correctly calculate the cost of
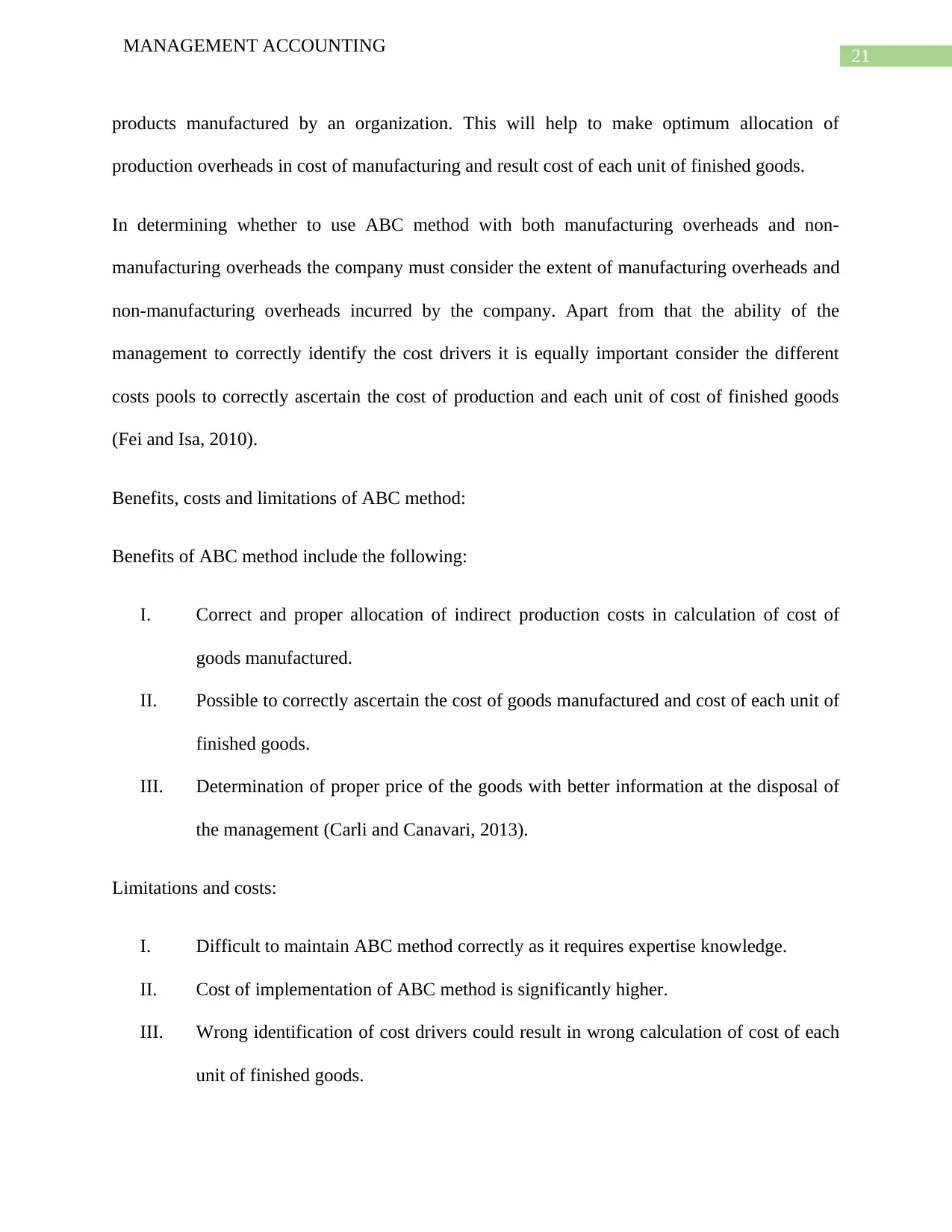
21
MANAGEMENT ACCOUNTING
products manufactured by an organization. This will help to make optimum allocation of
production overheads in cost of manufacturing and result cost of each unit of finished goods.
In determining whether to use ABC method with both manufacturing overheads and non-
manufacturing overheads the company must consider the extent of manufacturing overheads and
non-manufacturing overheads incurred by the company. Apart from that the ability of the
management to correctly identify the cost drivers it is equally important consider the different
costs pools to correctly ascertain the cost of production and each unit of cost of finished goods
(Fei and Isa, 2010).
Benefits, costs and limitations of ABC method:
Benefits of ABC method include the following:
I. Correct and proper allocation of indirect production costs in calculation of cost of
goods manufactured.
II. Possible to correctly ascertain the cost of goods manufactured and cost of each unit of
finished goods.
III. Determination of proper price of the goods with better information at the disposal of
the management (Carli and Canavari, 2013).
Limitations and costs:
I. Difficult to maintain ABC method correctly as it requires expertise knowledge.
II. Cost of implementation of ABC method is significantly higher.
III. Wrong identification of cost drivers could result in wrong calculation of cost of each
unit of finished goods.
MANAGEMENT ACCOUNTING
products manufactured by an organization. This will help to make optimum allocation of
production overheads in cost of manufacturing and result cost of each unit of finished goods.
In determining whether to use ABC method with both manufacturing overheads and non-
manufacturing overheads the company must consider the extent of manufacturing overheads and
non-manufacturing overheads incurred by the company. Apart from that the ability of the
management to correctly identify the cost drivers it is equally important consider the different
costs pools to correctly ascertain the cost of production and each unit of cost of finished goods
(Fei and Isa, 2010).
Benefits, costs and limitations of ABC method:
Benefits of ABC method include the following:
I. Correct and proper allocation of indirect production costs in calculation of cost of
goods manufactured.
II. Possible to correctly ascertain the cost of goods manufactured and cost of each unit of
finished goods.
III. Determination of proper price of the goods with better information at the disposal of
the management (Carli and Canavari, 2013).
Limitations and costs:
I. Difficult to maintain ABC method correctly as it requires expertise knowledge.
II. Cost of implementation of ABC method is significantly higher.
III. Wrong identification of cost drivers could result in wrong calculation of cost of each
unit of finished goods.
Secure Best Marks with AI Grader
Need help grading? Try our AI Grader for instant feedback on your assignments.
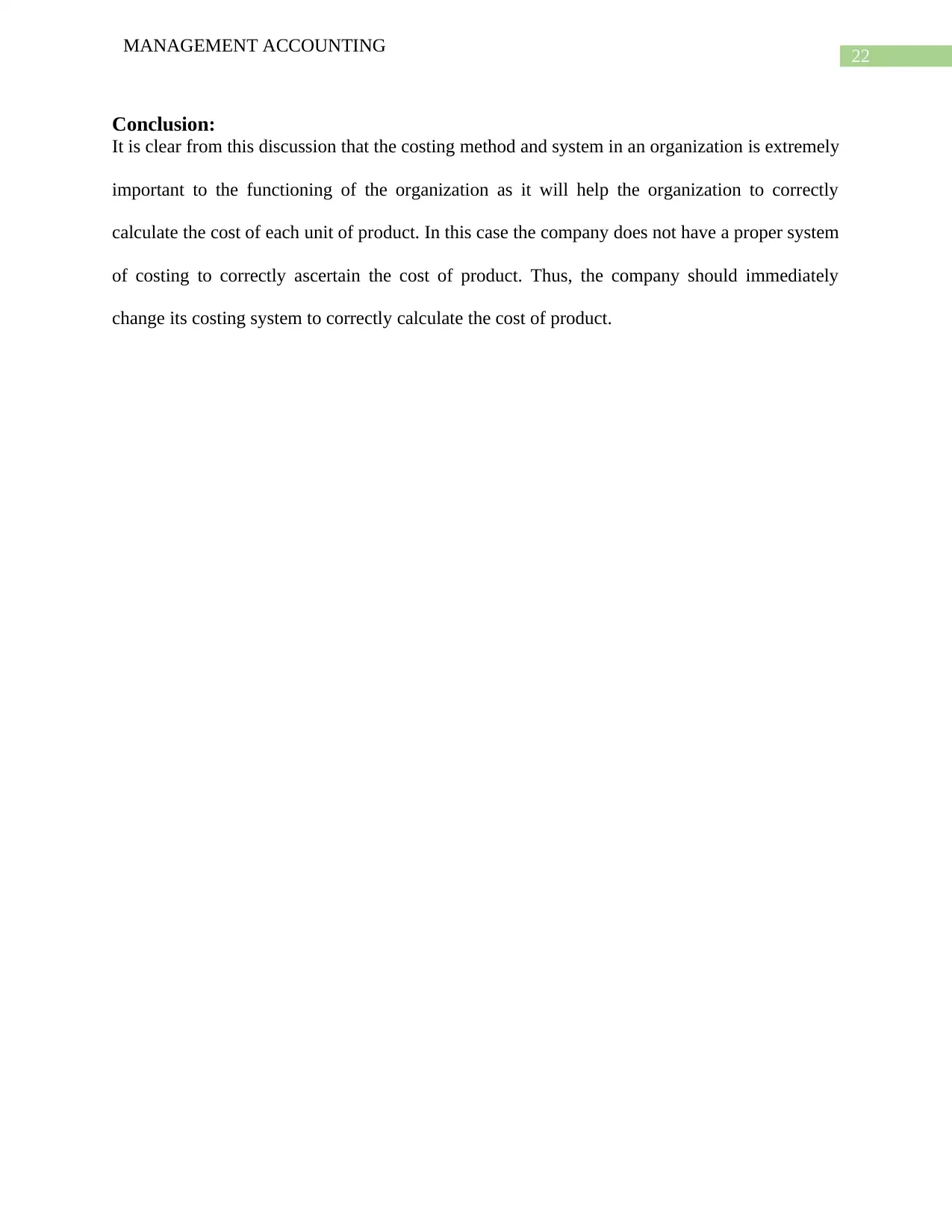
22
MANAGEMENT ACCOUNTING
Conclusion:
It is clear from this discussion that the costing method and system in an organization is extremely
important to the functioning of the organization as it will help the organization to correctly
calculate the cost of each unit of product. In this case the company does not have a proper system
of costing to correctly ascertain the cost of product. Thus, the company should immediately
change its costing system to correctly calculate the cost of product.
MANAGEMENT ACCOUNTING
Conclusion:
It is clear from this discussion that the costing method and system in an organization is extremely
important to the functioning of the organization as it will help the organization to correctly
calculate the cost of each unit of product. In this case the company does not have a proper system
of costing to correctly ascertain the cost of product. Thus, the company should immediately
change its costing system to correctly calculate the cost of product.
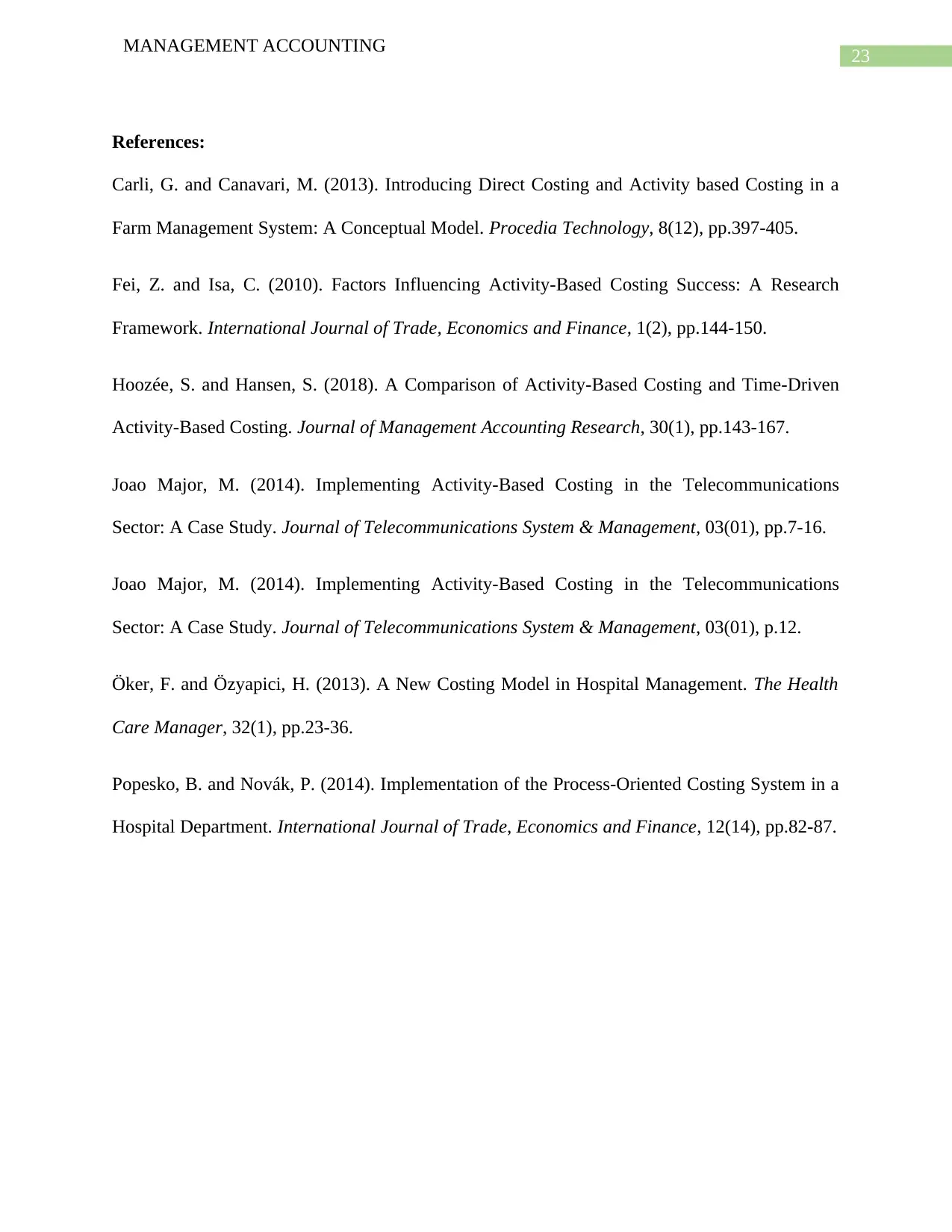
23
MANAGEMENT ACCOUNTING
References:
Carli, G. and Canavari, M. (2013). Introducing Direct Costing and Activity based Costing in a
Farm Management System: A Conceptual Model. Procedia Technology, 8(12), pp.397-405.
Fei, Z. and Isa, C. (2010). Factors Influencing Activity-Based Costing Success: A Research
Framework. International Journal of Trade, Economics and Finance, 1(2), pp.144-150.
Hoozée, S. and Hansen, S. (2018). A Comparison of Activity-Based Costing and Time-Driven
Activity-Based Costing. Journal of Management Accounting Research, 30(1), pp.143-167.
Joao Major, M. (2014). Implementing Activity-Based Costing in the Telecommunications
Sector: A Case Study. Journal of Telecommunications System & Management, 03(01), pp.7-16.
Joao Major, M. (2014). Implementing Activity-Based Costing in the Telecommunications
Sector: A Case Study. Journal of Telecommunications System & Management, 03(01), p.12.
Öker, F. and Özyapici, H. (2013). A New Costing Model in Hospital Management. The Health
Care Manager, 32(1), pp.23-36.
Popesko, B. and Novák, P. (2014). Implementation of the Process-Oriented Costing System in a
Hospital Department. International Journal of Trade, Economics and Finance, 12(14), pp.82-87.
MANAGEMENT ACCOUNTING
References:
Carli, G. and Canavari, M. (2013). Introducing Direct Costing and Activity based Costing in a
Farm Management System: A Conceptual Model. Procedia Technology, 8(12), pp.397-405.
Fei, Z. and Isa, C. (2010). Factors Influencing Activity-Based Costing Success: A Research
Framework. International Journal of Trade, Economics and Finance, 1(2), pp.144-150.
Hoozée, S. and Hansen, S. (2018). A Comparison of Activity-Based Costing and Time-Driven
Activity-Based Costing. Journal of Management Accounting Research, 30(1), pp.143-167.
Joao Major, M. (2014). Implementing Activity-Based Costing in the Telecommunications
Sector: A Case Study. Journal of Telecommunications System & Management, 03(01), pp.7-16.
Joao Major, M. (2014). Implementing Activity-Based Costing in the Telecommunications
Sector: A Case Study. Journal of Telecommunications System & Management, 03(01), p.12.
Öker, F. and Özyapici, H. (2013). A New Costing Model in Hospital Management. The Health
Care Manager, 32(1), pp.23-36.
Popesko, B. and Novák, P. (2014). Implementation of the Process-Oriented Costing System in a
Hospital Department. International Journal of Trade, Economics and Finance, 12(14), pp.82-87.
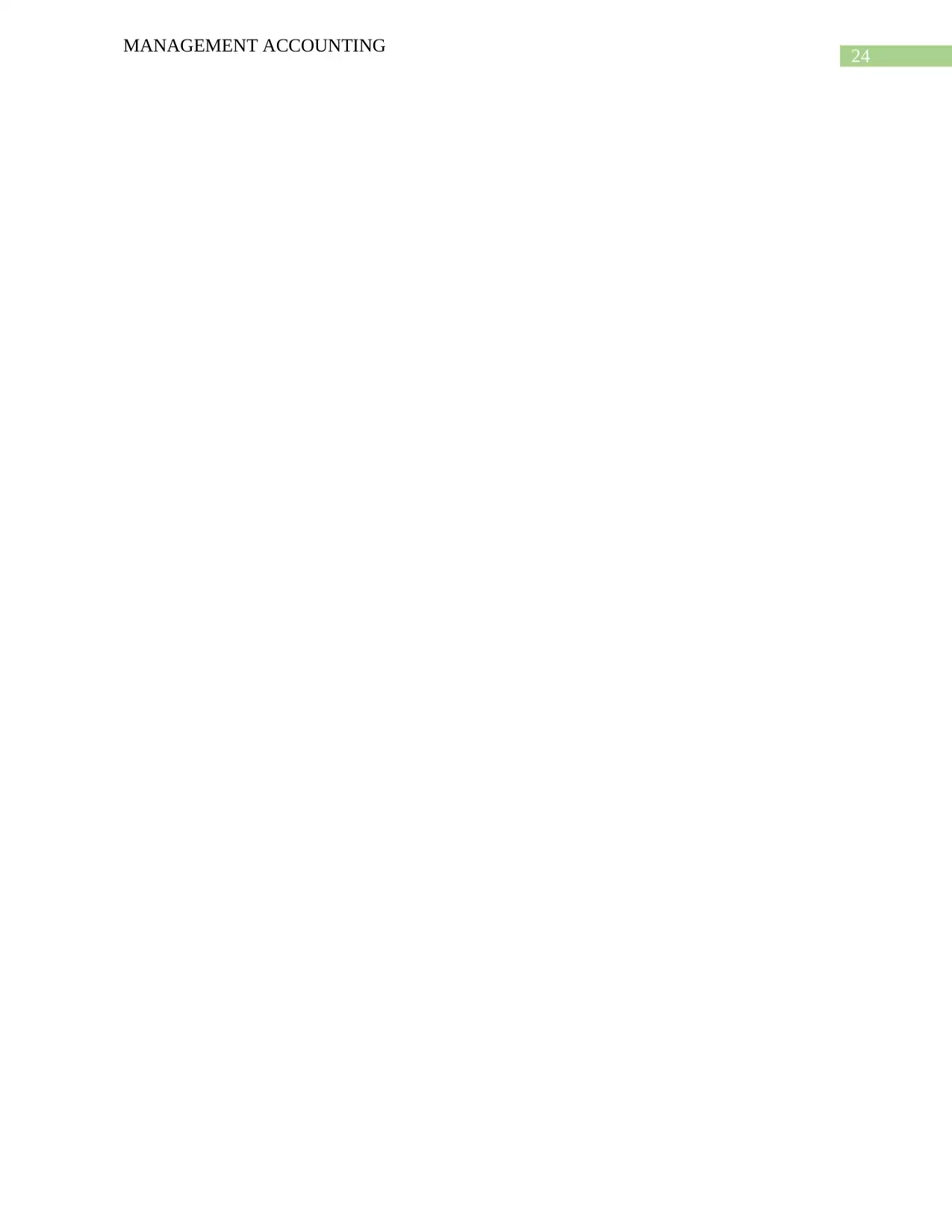
24
MANAGEMENT ACCOUNTING
MANAGEMENT ACCOUNTING
1 out of 25
![[object Object]](/_next/image/?url=%2F_next%2Fstatic%2Fmedia%2Flogo.6d15ce61.png&w=640&q=75)
Your All-in-One AI-Powered Toolkit for Academic Success.
+13062052269
info@desklib.com
Available 24*7 on WhatsApp / Email
Unlock your academic potential
© 2024 | Zucol Services PVT LTD | All rights reserved.