Total Quality Management: Dimensions, History, and Impact on Organizational Performance
VerifiedAdded on 2023/04/21
|26
|6688
|76
AI Summary
This document provides an overview of Total Quality Management (TQM), including its dimensions, history, and impact on organizational performance. It explains the difference between soft and hard aspects of TQM and discusses how TQM can improve quality and output in corporate establishments. The document also explores the barriers of implementing TQM in industry and highlights the aspects of TQM that still persist in practice.
Contribute Materials
Your contribution can guide someone’s learning journey. Share your
documents today.

Running Head: MANAGEMENT APPROACHES
0
Total Quality Management
Student
0
Total Quality Management
Student
Secure Best Marks with AI Grader
Need help grading? Try our AI Grader for instant feedback on your assignments.
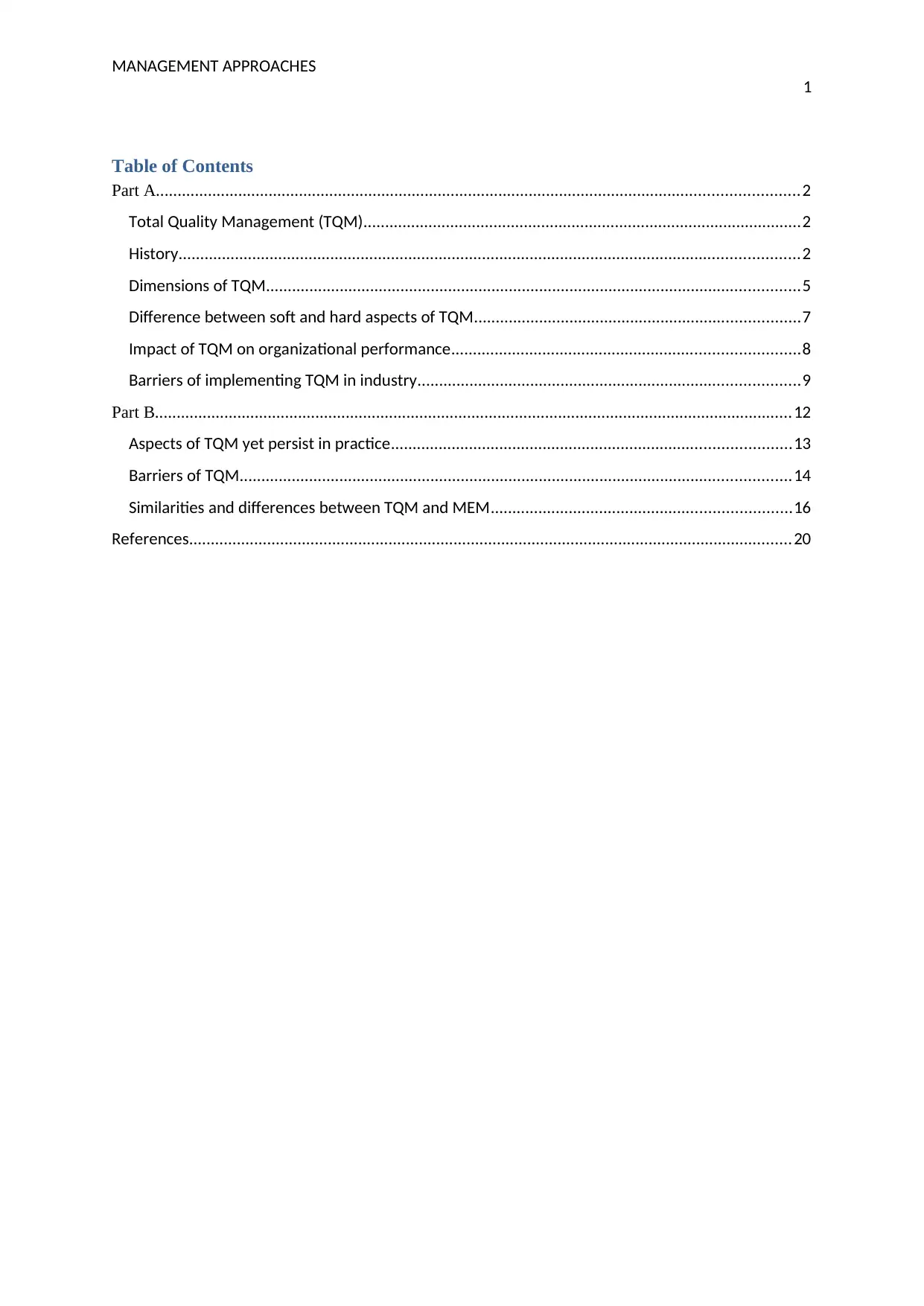
MANAGEMENT APPROACHES
1
Table of Contents
Part A....................................................................................................................................................2
Total Quality Management (TQM).....................................................................................................2
History...............................................................................................................................................2
Dimensions of TQM...........................................................................................................................5
Difference between soft and hard aspects of TQM...........................................................................7
Impact of TQM on organizational performance................................................................................8
Barriers of implementing TQM in industry........................................................................................9
Part B...................................................................................................................................................12
Aspects of TQM yet persist in practice............................................................................................13
Barriers of TQM...............................................................................................................................14
Similarities and differences between TQM and MEM.....................................................................16
References...........................................................................................................................................20
1
Table of Contents
Part A....................................................................................................................................................2
Total Quality Management (TQM).....................................................................................................2
History...............................................................................................................................................2
Dimensions of TQM...........................................................................................................................5
Difference between soft and hard aspects of TQM...........................................................................7
Impact of TQM on organizational performance................................................................................8
Barriers of implementing TQM in industry........................................................................................9
Part B...................................................................................................................................................12
Aspects of TQM yet persist in practice............................................................................................13
Barriers of TQM...............................................................................................................................14
Similarities and differences between TQM and MEM.....................................................................16
References...........................................................................................................................................20
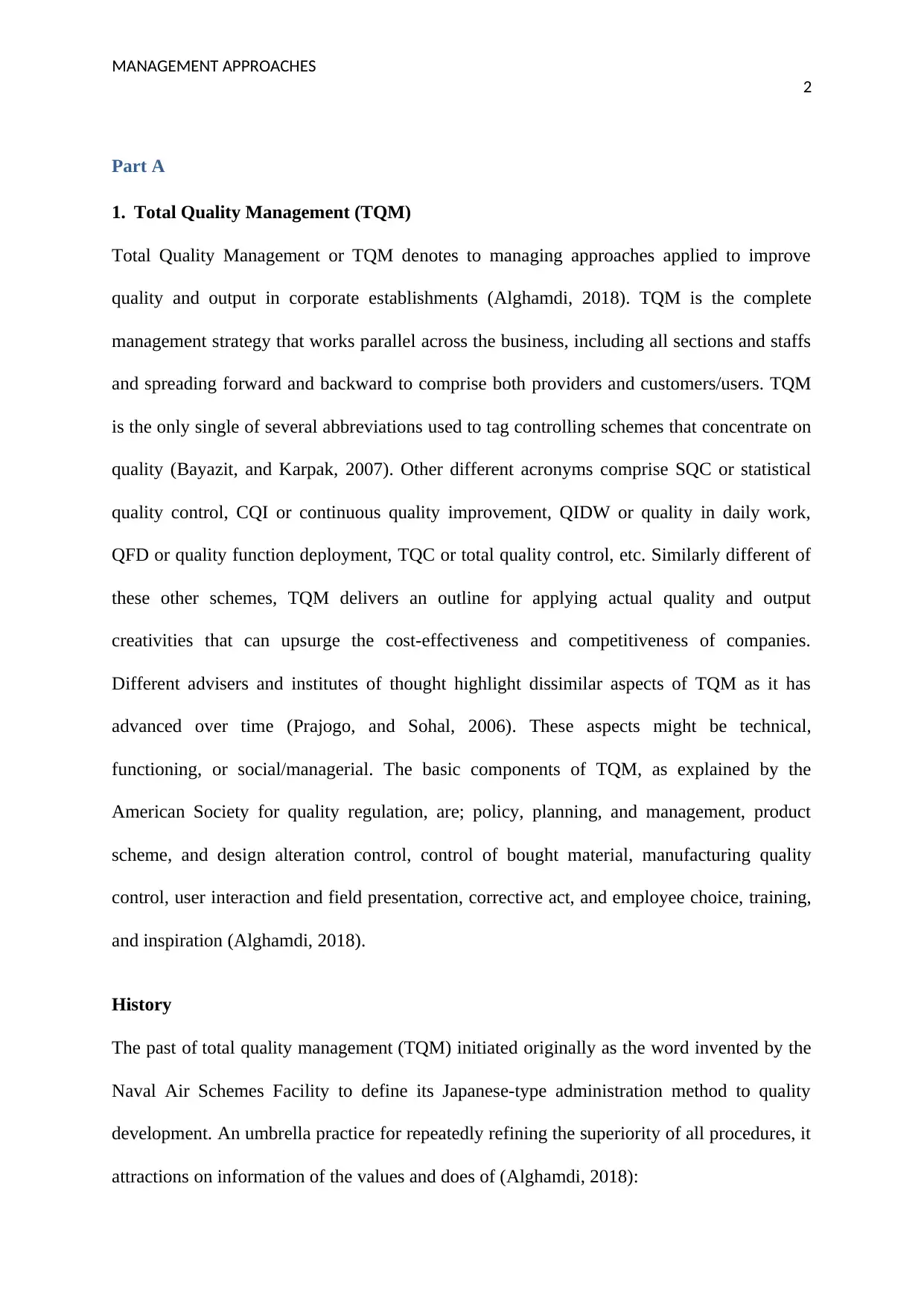
MANAGEMENT APPROACHES
2
Part A
1. Total Quality Management (TQM)
Total Quality Management or TQM denotes to managing approaches applied to improve
quality and output in corporate establishments (Alghamdi, 2018). TQM is the complete
management strategy that works parallel across the business, including all sections and staffs
and spreading forward and backward to comprise both providers and customers/users. TQM
is the only single of several abbreviations used to tag controlling schemes that concentrate on
quality (Bayazit, and Karpak, 2007). Other different acronyms comprise SQC or statistical
quality control, CQI or continuous quality improvement, QIDW or quality in daily work,
QFD or quality function deployment, TQC or total quality control, etc. Similarly different of
these other schemes, TQM delivers an outline for applying actual quality and output
creativities that can upsurge the cost-effectiveness and competitiveness of companies.
Different advisers and institutes of thought highlight dissimilar aspects of TQM as it has
advanced over time (Prajogo, and Sohal, 2006). These aspects might be technical,
functioning, or social/managerial. The basic components of TQM, as explained by the
American Society for quality regulation, are; policy, planning, and management, product
scheme, and design alteration control, control of bought material, manufacturing quality
control, user interaction and field presentation, corrective act, and employee choice, training,
and inspiration (Alghamdi, 2018).
History
The past of total quality management (TQM) initiated originally as the word invented by the
Naval Air Schemes Facility to define its Japanese-type administration method to quality
development. An umbrella practice for repeatedly refining the superiority of all procedures, it
attractions on information of the values and does of (Alghamdi, 2018):
2
Part A
1. Total Quality Management (TQM)
Total Quality Management or TQM denotes to managing approaches applied to improve
quality and output in corporate establishments (Alghamdi, 2018). TQM is the complete
management strategy that works parallel across the business, including all sections and staffs
and spreading forward and backward to comprise both providers and customers/users. TQM
is the only single of several abbreviations used to tag controlling schemes that concentrate on
quality (Bayazit, and Karpak, 2007). Other different acronyms comprise SQC or statistical
quality control, CQI or continuous quality improvement, QIDW or quality in daily work,
QFD or quality function deployment, TQC or total quality control, etc. Similarly different of
these other schemes, TQM delivers an outline for applying actual quality and output
creativities that can upsurge the cost-effectiveness and competitiveness of companies.
Different advisers and institutes of thought highlight dissimilar aspects of TQM as it has
advanced over time (Prajogo, and Sohal, 2006). These aspects might be technical,
functioning, or social/managerial. The basic components of TQM, as explained by the
American Society for quality regulation, are; policy, planning, and management, product
scheme, and design alteration control, control of bought material, manufacturing quality
control, user interaction and field presentation, corrective act, and employee choice, training,
and inspiration (Alghamdi, 2018).
History
The past of total quality management (TQM) initiated originally as the word invented by the
Naval Air Schemes Facility to define its Japanese-type administration method to quality
development. An umbrella practice for repeatedly refining the superiority of all procedures, it
attractions on information of the values and does of (Alghamdi, 2018):
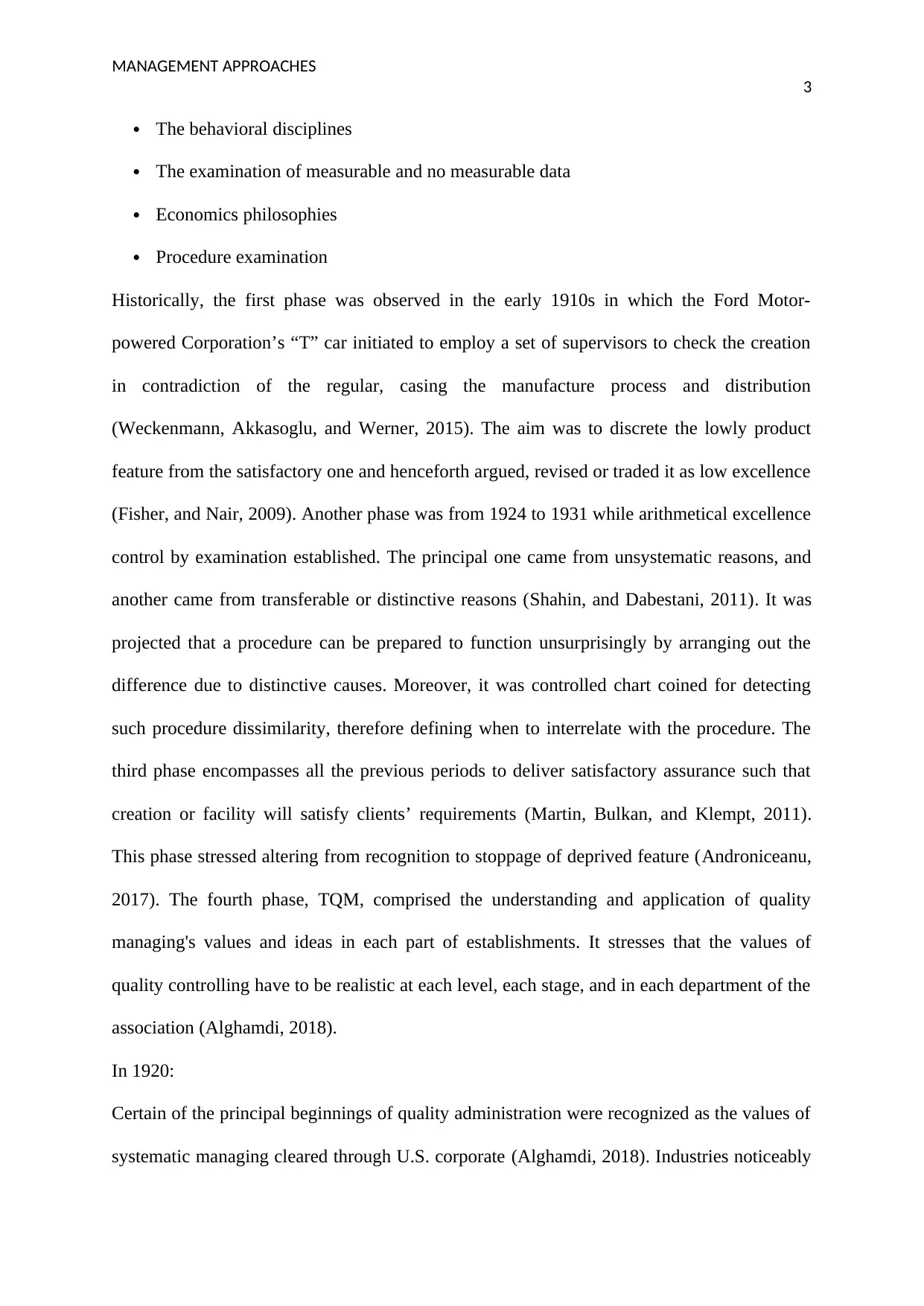
MANAGEMENT APPROACHES
3
The behavioral disciplines
The examination of measurable and no measurable data
Economics philosophies
Procedure examination
Historically, the first phase was observed in the early 1910s in which the Ford Motor-
powered Corporation’s “T” car initiated to employ a set of supervisors to check the creation
in contradiction of the regular, casing the manufacture process and distribution
(Weckenmann, Akkasoglu, and Werner, 2015). The aim was to discrete the lowly product
feature from the satisfactory one and henceforth argued, revised or traded it as low excellence
(Fisher, and Nair, 2009). Another phase was from 1924 to 1931 while arithmetical excellence
control by examination established. The principal one came from unsystematic reasons, and
another came from transferable or distinctive reasons (Shahin, and Dabestani, 2011). It was
projected that a procedure can be prepared to function unsurprisingly by arranging out the
difference due to distinctive causes. Moreover, it was controlled chart coined for detecting
such procedure dissimilarity, therefore defining when to interrelate with the procedure. The
third phase encompasses all the previous periods to deliver satisfactory assurance such that
creation or facility will satisfy clients’ requirements (Martin, Bulkan, and Klempt, 2011).
This phase stressed altering from recognition to stoppage of deprived feature (Androniceanu,
2017). The fourth phase, TQM, comprised the understanding and application of quality
managing's values and ideas in each part of establishments. It stresses that the values of
quality controlling have to be realistic at each level, each stage, and in each department of the
association (Alghamdi, 2018).
In 1920:
Certain of the principal beginnings of quality administration were recognized as the values of
systematic managing cleared through U.S. corporate (Alghamdi, 2018). Industries noticeably
3
The behavioral disciplines
The examination of measurable and no measurable data
Economics philosophies
Procedure examination
Historically, the first phase was observed in the early 1910s in which the Ford Motor-
powered Corporation’s “T” car initiated to employ a set of supervisors to check the creation
in contradiction of the regular, casing the manufacture process and distribution
(Weckenmann, Akkasoglu, and Werner, 2015). The aim was to discrete the lowly product
feature from the satisfactory one and henceforth argued, revised or traded it as low excellence
(Fisher, and Nair, 2009). Another phase was from 1924 to 1931 while arithmetical excellence
control by examination established. The principal one came from unsystematic reasons, and
another came from transferable or distinctive reasons (Shahin, and Dabestani, 2011). It was
projected that a procedure can be prepared to function unsurprisingly by arranging out the
difference due to distinctive causes. Moreover, it was controlled chart coined for detecting
such procedure dissimilarity, therefore defining when to interrelate with the procedure. The
third phase encompasses all the previous periods to deliver satisfactory assurance such that
creation or facility will satisfy clients’ requirements (Martin, Bulkan, and Klempt, 2011).
This phase stressed altering from recognition to stoppage of deprived feature (Androniceanu,
2017). The fourth phase, TQM, comprised the understanding and application of quality
managing's values and ideas in each part of establishments. It stresses that the values of
quality controlling have to be realistic at each level, each stage, and in each department of the
association (Alghamdi, 2018).
In 1920:
Certain of the principal beginnings of quality administration were recognized as the values of
systematic managing cleared through U.S. corporate (Alghamdi, 2018). Industries noticeably
Secure Best Marks with AI Grader
Need help grading? Try our AI Grader for instant feedback on your assignments.
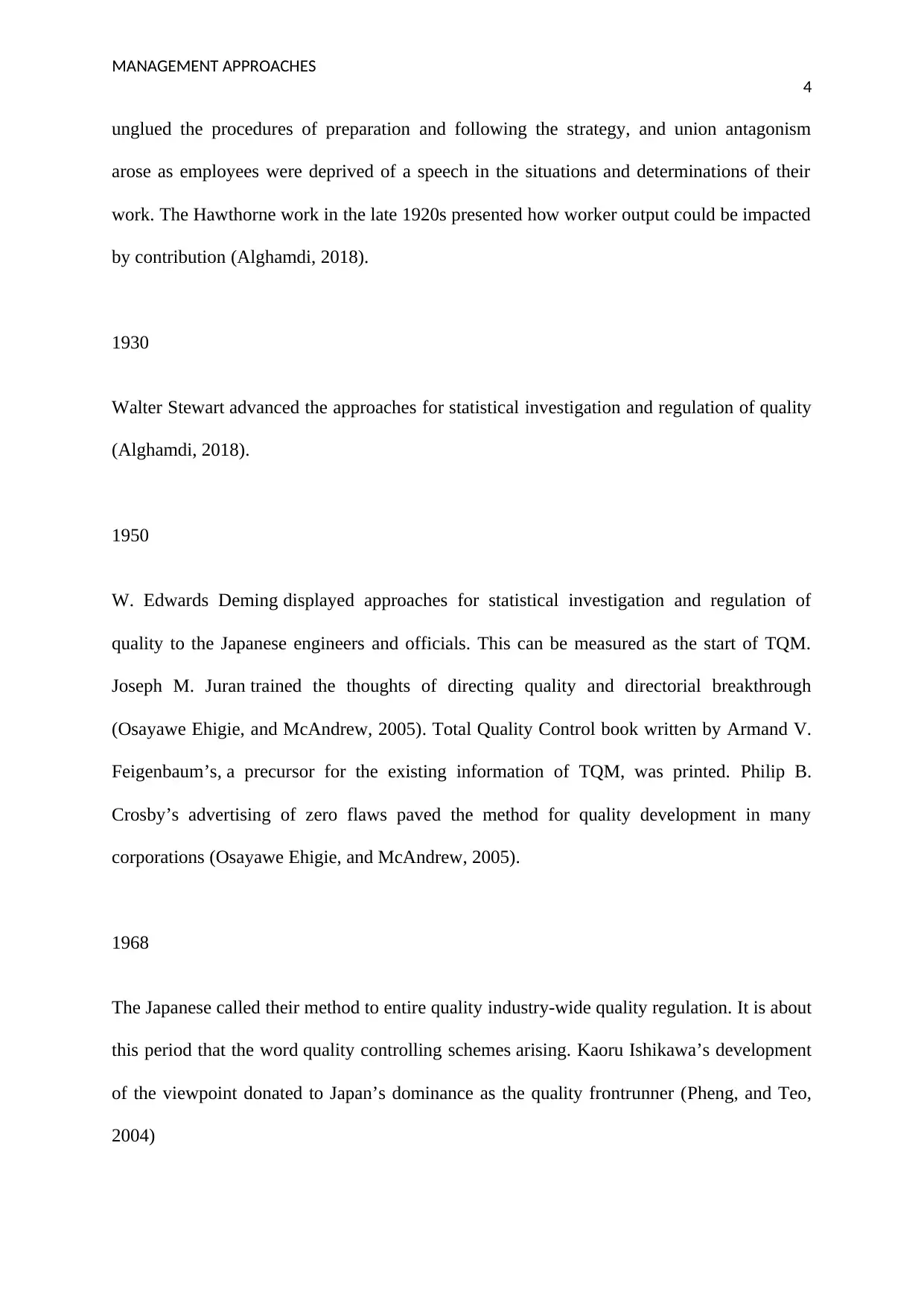
MANAGEMENT APPROACHES
4
unglued the procedures of preparation and following the strategy, and union antagonism
arose as employees were deprived of a speech in the situations and determinations of their
work. The Hawthorne work in the late 1920s presented how worker output could be impacted
by contribution (Alghamdi, 2018).
1930
Walter Stewart advanced the approaches for statistical investigation and regulation of quality
(Alghamdi, 2018).
1950
W. Edwards Deming displayed approaches for statistical investigation and regulation of
quality to the Japanese engineers and officials. This can be measured as the start of TQM.
Joseph M. Juran trained the thoughts of directing quality and directorial breakthrough
(Osayawe Ehigie, and McAndrew, 2005). Total Quality Control book written by Armand V.
Feigenbaum’s, a precursor for the existing information of TQM, was printed. Philip B.
Crosby’s advertising of zero flaws paved the method for quality development in many
corporations (Osayawe Ehigie, and McAndrew, 2005).
1968
The Japanese called their method to entire quality industry-wide quality regulation. It is about
this period that the word quality controlling schemes arising. Kaoru Ishikawa’s development
of the viewpoint donated to Japan’s dominance as the quality frontrunner (Pheng, and Teo,
2004)
4
unglued the procedures of preparation and following the strategy, and union antagonism
arose as employees were deprived of a speech in the situations and determinations of their
work. The Hawthorne work in the late 1920s presented how worker output could be impacted
by contribution (Alghamdi, 2018).
1930
Walter Stewart advanced the approaches for statistical investigation and regulation of quality
(Alghamdi, 2018).
1950
W. Edwards Deming displayed approaches for statistical investigation and regulation of
quality to the Japanese engineers and officials. This can be measured as the start of TQM.
Joseph M. Juran trained the thoughts of directing quality and directorial breakthrough
(Osayawe Ehigie, and McAndrew, 2005). Total Quality Control book written by Armand V.
Feigenbaum’s, a precursor for the existing information of TQM, was printed. Philip B.
Crosby’s advertising of zero flaws paved the method for quality development in many
corporations (Osayawe Ehigie, and McAndrew, 2005).
1968
The Japanese called their method to entire quality industry-wide quality regulation. It is about
this period that the word quality controlling schemes arising. Kaoru Ishikawa’s development
of the viewpoint donated to Japan’s dominance as the quality frontrunner (Pheng, and Teo,
2004)
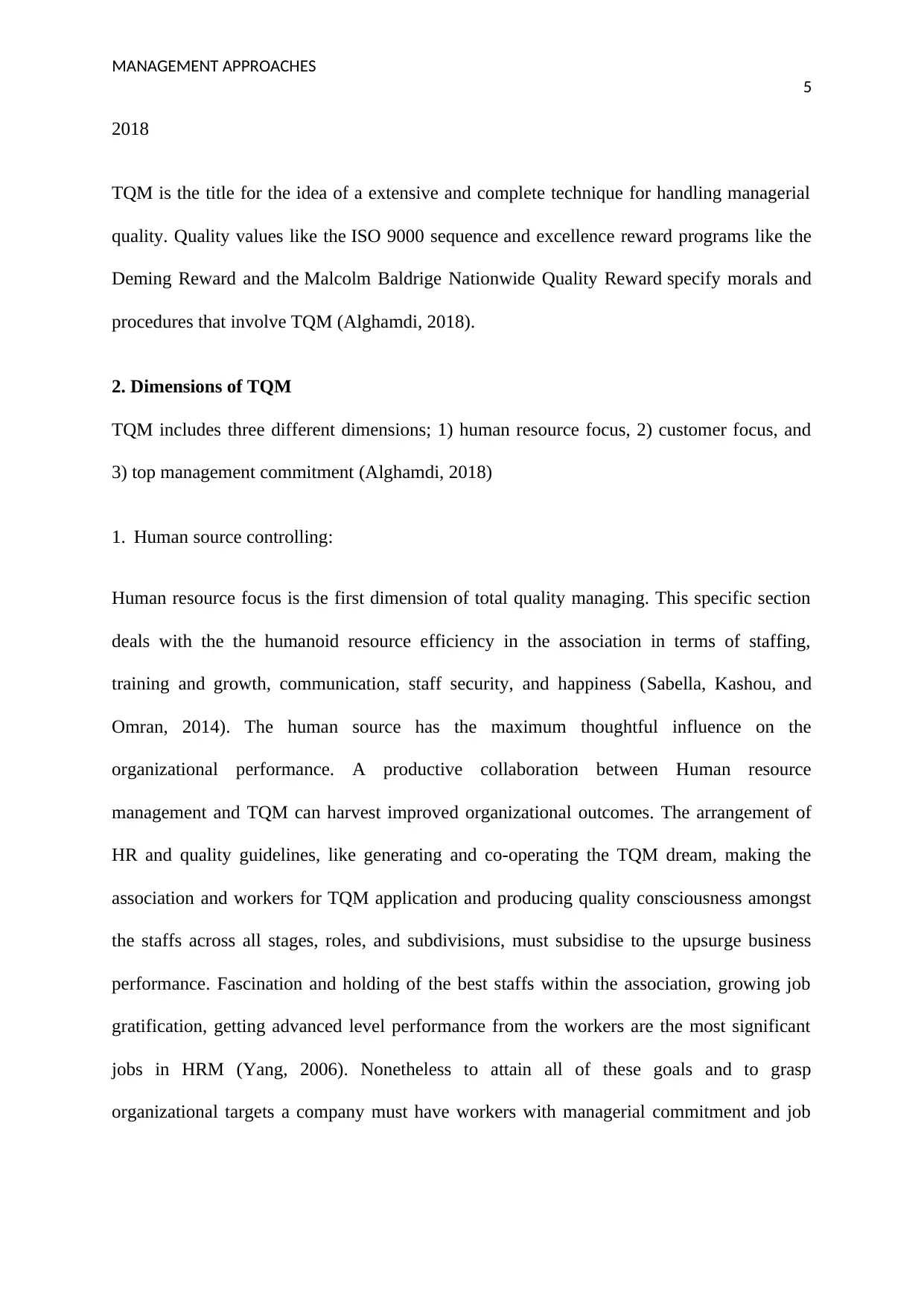
MANAGEMENT APPROACHES
5
2018
TQM is the title for the idea of a extensive and complete technique for handling managerial
quality. Quality values like the ISO 9000 sequence and excellence reward programs like the
Deming Reward and the Malcolm Baldrige Nationwide Quality Reward specify morals and
procedures that involve TQM (Alghamdi, 2018).
2. Dimensions of TQM
TQM includes three different dimensions; 1) human resource focus, 2) customer focus, and
3) top management commitment (Alghamdi, 2018)
1. Human source controlling:
Human resource focus is the first dimension of total quality managing. This specific section
deals with the the humanoid resource efficiency in the association in terms of staffing,
training and growth, communication, staff security, and happiness (Sabella, Kashou, and
Omran, 2014). The human source has the maximum thoughtful influence on the
organizational performance. A productive collaboration between Human resource
management and TQM can harvest improved organizational outcomes. The arrangement of
HR and quality guidelines, like generating and co-operating the TQM dream, making the
association and workers for TQM application and producing quality consciousness amongst
the staffs across all stages, roles, and subdivisions, must subsidise to the upsurge business
performance. Fascination and holding of the best staffs within the association, growing job
gratification, getting advanced level performance from the workers are the most significant
jobs in HRM (Yang, 2006). Nonetheless to attain all of these goals and to grasp
organizational targets a company must have workers with managerial commitment and job
5
2018
TQM is the title for the idea of a extensive and complete technique for handling managerial
quality. Quality values like the ISO 9000 sequence and excellence reward programs like the
Deming Reward and the Malcolm Baldrige Nationwide Quality Reward specify morals and
procedures that involve TQM (Alghamdi, 2018).
2. Dimensions of TQM
TQM includes three different dimensions; 1) human resource focus, 2) customer focus, and
3) top management commitment (Alghamdi, 2018)
1. Human source controlling:
Human resource focus is the first dimension of total quality managing. This specific section
deals with the the humanoid resource efficiency in the association in terms of staffing,
training and growth, communication, staff security, and happiness (Sabella, Kashou, and
Omran, 2014). The human source has the maximum thoughtful influence on the
organizational performance. A productive collaboration between Human resource
management and TQM can harvest improved organizational outcomes. The arrangement of
HR and quality guidelines, like generating and co-operating the TQM dream, making the
association and workers for TQM application and producing quality consciousness amongst
the staffs across all stages, roles, and subdivisions, must subsidise to the upsurge business
performance. Fascination and holding of the best staffs within the association, growing job
gratification, getting advanced level performance from the workers are the most significant
jobs in HRM (Yang, 2006). Nonetheless to attain all of these goals and to grasp
organizational targets a company must have workers with managerial commitment and job
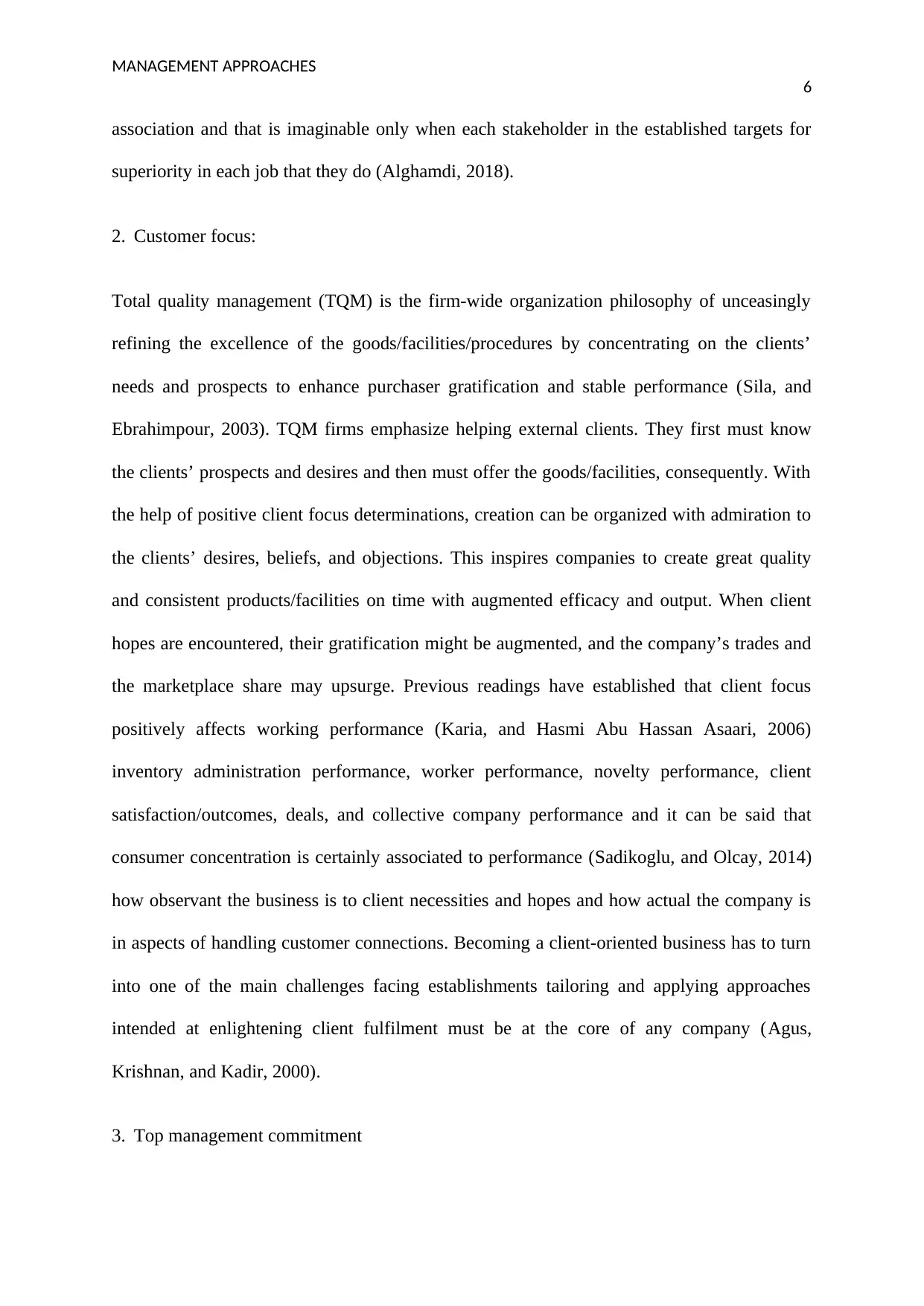
MANAGEMENT APPROACHES
6
association and that is imaginable only when each stakeholder in the established targets for
superiority in each job that they do (Alghamdi, 2018).
2. Customer focus:
Total quality management (TQM) is the firm-wide organization philosophy of unceasingly
refining the excellence of the goods/facilities/procedures by concentrating on the clients’
needs and prospects to enhance purchaser gratification and stable performance (Sila, and
Ebrahimpour, 2003). TQM firms emphasize helping external clients. They first must know
the clients’ prospects and desires and then must offer the goods/facilities, consequently. With
the help of positive client focus determinations, creation can be organized with admiration to
the clients’ desires, beliefs, and objections. This inspires companies to create great quality
and consistent products/facilities on time with augmented efficacy and output. When client
hopes are encountered, their gratification might be augmented, and the company’s trades and
the marketplace share may upsurge. Previous readings have established that client focus
positively affects working performance (Karia, and Hasmi Abu Hassan Asaari, 2006)
inventory administration performance, worker performance, novelty performance, client
satisfaction/outcomes, deals, and collective company performance and it can be said that
consumer concentration is certainly associated to performance (Sadikoglu, and Olcay, 2014)
how observant the business is to client necessities and hopes and how actual the company is
in aspects of handling customer connections. Becoming a client-oriented business has to turn
into one of the main challenges facing establishments tailoring and applying approaches
intended at enlightening client fulfilment must be at the core of any company (Agus,
Krishnan, and Kadir, 2000).
3. Top management commitment
6
association and that is imaginable only when each stakeholder in the established targets for
superiority in each job that they do (Alghamdi, 2018).
2. Customer focus:
Total quality management (TQM) is the firm-wide organization philosophy of unceasingly
refining the excellence of the goods/facilities/procedures by concentrating on the clients’
needs and prospects to enhance purchaser gratification and stable performance (Sila, and
Ebrahimpour, 2003). TQM firms emphasize helping external clients. They first must know
the clients’ prospects and desires and then must offer the goods/facilities, consequently. With
the help of positive client focus determinations, creation can be organized with admiration to
the clients’ desires, beliefs, and objections. This inspires companies to create great quality
and consistent products/facilities on time with augmented efficacy and output. When client
hopes are encountered, their gratification might be augmented, and the company’s trades and
the marketplace share may upsurge. Previous readings have established that client focus
positively affects working performance (Karia, and Hasmi Abu Hassan Asaari, 2006)
inventory administration performance, worker performance, novelty performance, client
satisfaction/outcomes, deals, and collective company performance and it can be said that
consumer concentration is certainly associated to performance (Sadikoglu, and Olcay, 2014)
how observant the business is to client necessities and hopes and how actual the company is
in aspects of handling customer connections. Becoming a client-oriented business has to turn
into one of the main challenges facing establishments tailoring and applying approaches
intended at enlightening client fulfilment must be at the core of any company (Agus,
Krishnan, and Kadir, 2000).
3. Top management commitment
Paraphrase This Document
Need a fresh take? Get an instant paraphrase of this document with our AI Paraphraser
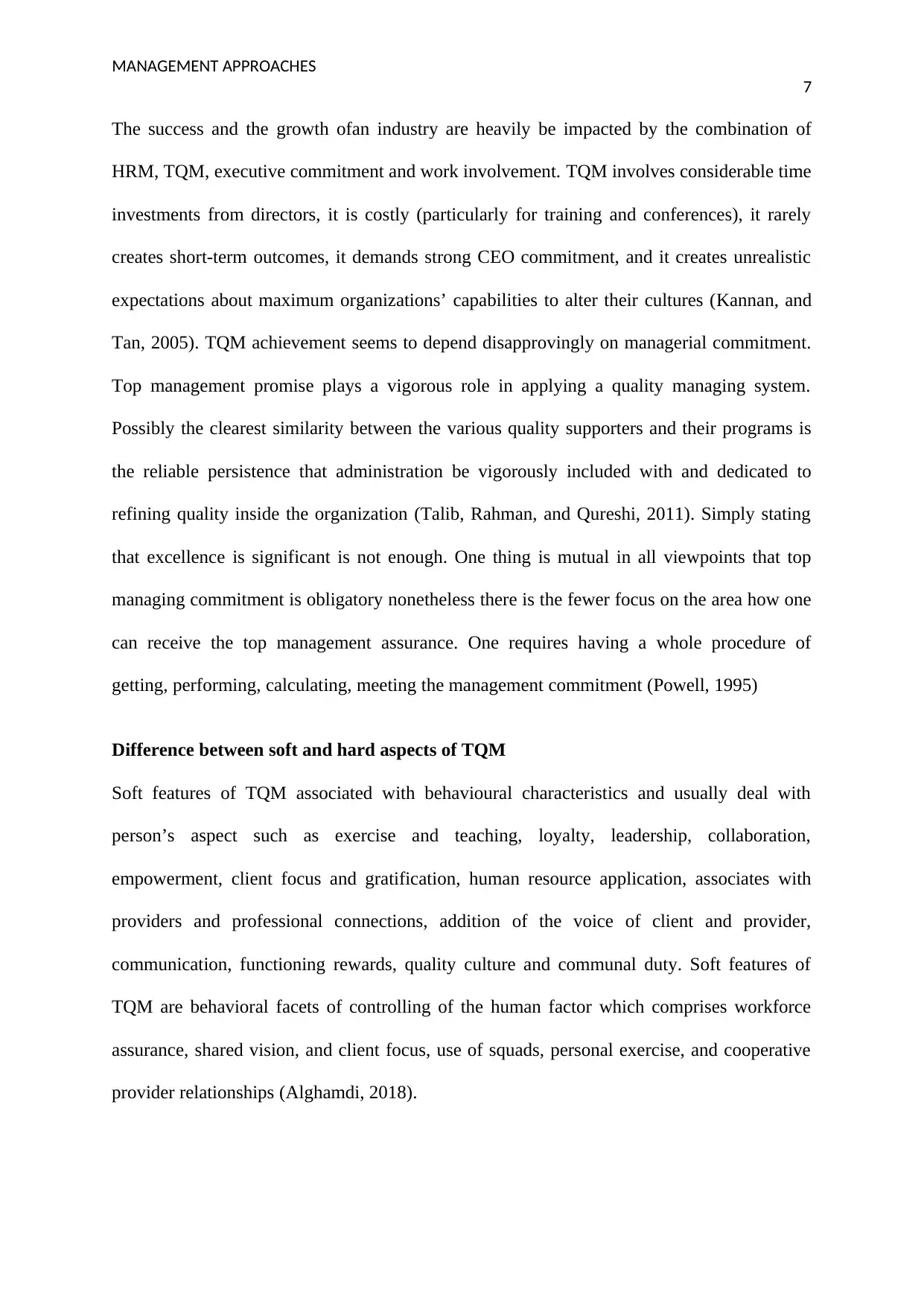
MANAGEMENT APPROACHES
7
The success and the growth ofan industry are heavily be impacted by the combination of
HRM, TQM, executive commitment and work involvement. TQM involves considerable time
investments from directors, it is costly (particularly for training and conferences), it rarely
creates short-term outcomes, it demands strong CEO commitment, and it creates unrealistic
expectations about maximum organizations’ capabilities to alter their cultures (Kannan, and
Tan, 2005). TQM achievement seems to depend disapprovingly on managerial commitment.
Top management promise plays a vigorous role in applying a quality managing system.
Possibly the clearest similarity between the various quality supporters and their programs is
the reliable persistence that administration be vigorously included with and dedicated to
refining quality inside the organization (Talib, Rahman, and Qureshi, 2011). Simply stating
that excellence is significant is not enough. One thing is mutual in all viewpoints that top
managing commitment is obligatory nonetheless there is the fewer focus on the area how one
can receive the top management assurance. One requires having a whole procedure of
getting, performing, calculating, meeting the management commitment (Powell, 1995)
Difference between soft and hard aspects of TQM
Soft features of TQM associated with behavioural characteristics and usually deal with
person’s aspect such as exercise and teaching, loyalty, leadership, collaboration,
empowerment, client focus and gratification, human resource application, associates with
providers and professional connections, addition of the voice of client and provider,
communication, functioning rewards, quality culture and communal duty. Soft features of
TQM are behavioral facets of controlling of the human factor which comprises workforce
assurance, shared vision, and client focus, use of squads, personal exercise, and cooperative
provider relationships (Alghamdi, 2018).
7
The success and the growth ofan industry are heavily be impacted by the combination of
HRM, TQM, executive commitment and work involvement. TQM involves considerable time
investments from directors, it is costly (particularly for training and conferences), it rarely
creates short-term outcomes, it demands strong CEO commitment, and it creates unrealistic
expectations about maximum organizations’ capabilities to alter their cultures (Kannan, and
Tan, 2005). TQM achievement seems to depend disapprovingly on managerial commitment.
Top management promise plays a vigorous role in applying a quality managing system.
Possibly the clearest similarity between the various quality supporters and their programs is
the reliable persistence that administration be vigorously included with and dedicated to
refining quality inside the organization (Talib, Rahman, and Qureshi, 2011). Simply stating
that excellence is significant is not enough. One thing is mutual in all viewpoints that top
managing commitment is obligatory nonetheless there is the fewer focus on the area how one
can receive the top management assurance. One requires having a whole procedure of
getting, performing, calculating, meeting the management commitment (Powell, 1995)
Difference between soft and hard aspects of TQM
Soft features of TQM associated with behavioural characteristics and usually deal with
person’s aspect such as exercise and teaching, loyalty, leadership, collaboration,
empowerment, client focus and gratification, human resource application, associates with
providers and professional connections, addition of the voice of client and provider,
communication, functioning rewards, quality culture and communal duty. Soft features of
TQM are behavioral facets of controlling of the human factor which comprises workforce
assurance, shared vision, and client focus, use of squads, personal exercise, and cooperative
provider relationships (Alghamdi, 2018).
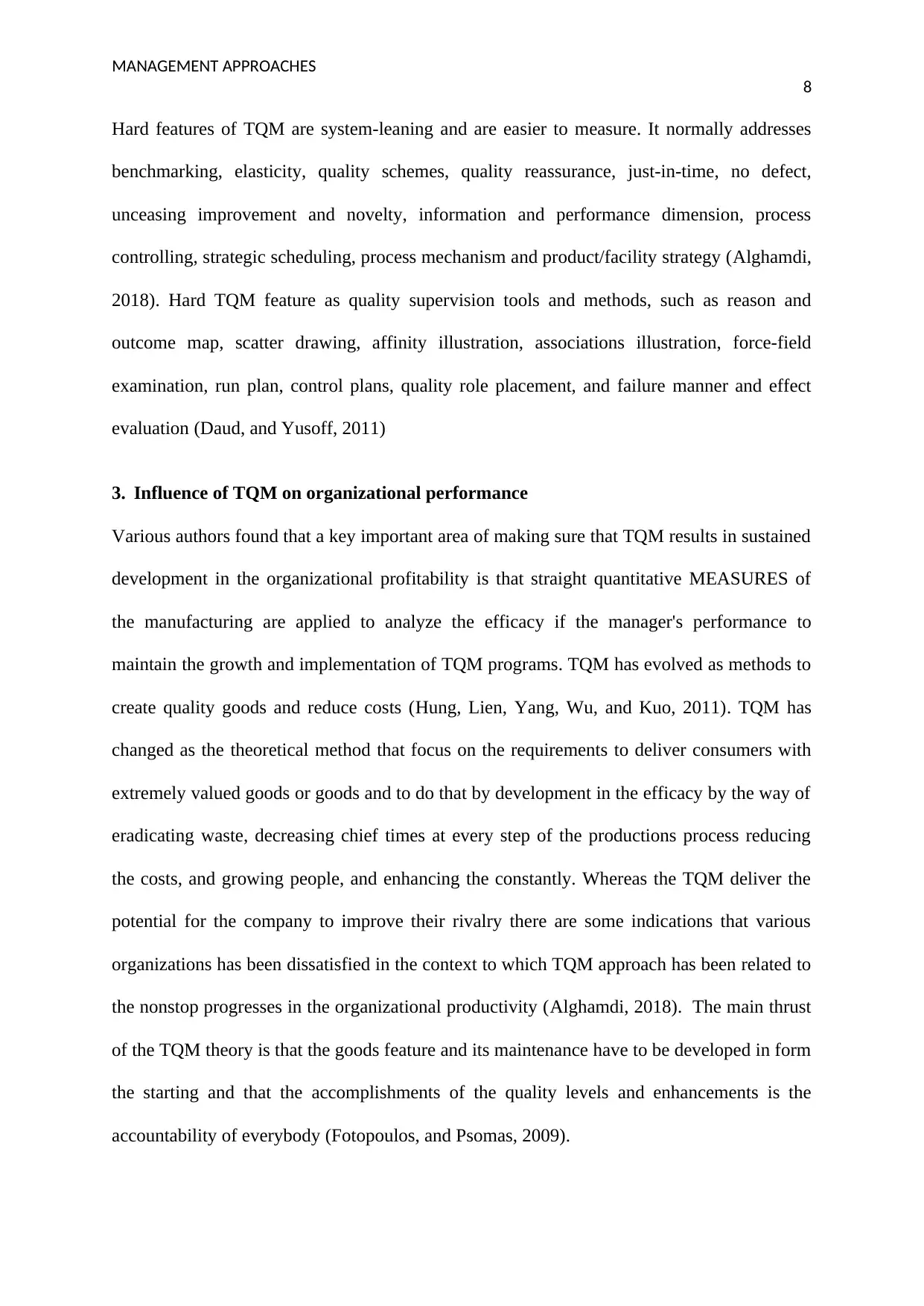
MANAGEMENT APPROACHES
8
Hard features of TQM are system-leaning and are easier to measure. It normally addresses
benchmarking, elasticity, quality schemes, quality reassurance, just-in-time, no defect,
unceasing improvement and novelty, information and performance dimension, process
controlling, strategic scheduling, process mechanism and product/facility strategy (Alghamdi,
2018). Hard TQM feature as quality supervision tools and methods, such as reason and
outcome map, scatter drawing, affinity illustration, associations illustration, force-field
examination, run plan, control plans, quality role placement, and failure manner and effect
evaluation (Daud, and Yusoff, 2011)
3. Influence of TQM on organizational performance
Various authors found that a key important area of making sure that TQM results in sustained
development in the organizational profitability is that straight quantitative MEASURES of
the manufacturing are applied to analyze the efficacy if the manager's performance to
maintain the growth and implementation of TQM programs. TQM has evolved as methods to
create quality goods and reduce costs (Hung, Lien, Yang, Wu, and Kuo, 2011). TQM has
changed as the theoretical method that focus on the requirements to deliver consumers with
extremely valued goods or goods and to do that by development in the efficacy by the way of
eradicating waste, decreasing chief times at every step of the productions process reducing
the costs, and growing people, and enhancing the constantly. Whereas the TQM deliver the
potential for the company to improve their rivalry there are some indications that various
organizations has been dissatisfied in the context to which TQM approach has been related to
the nonstop progresses in the organizational productivity (Alghamdi, 2018). The main thrust
of the TQM theory is that the goods feature and its maintenance have to be developed in form
the starting and that the accomplishments of the quality levels and enhancements is the
accountability of everybody (Fotopoulos, and Psomas, 2009).
8
Hard features of TQM are system-leaning and are easier to measure. It normally addresses
benchmarking, elasticity, quality schemes, quality reassurance, just-in-time, no defect,
unceasing improvement and novelty, information and performance dimension, process
controlling, strategic scheduling, process mechanism and product/facility strategy (Alghamdi,
2018). Hard TQM feature as quality supervision tools and methods, such as reason and
outcome map, scatter drawing, affinity illustration, associations illustration, force-field
examination, run plan, control plans, quality role placement, and failure manner and effect
evaluation (Daud, and Yusoff, 2011)
3. Influence of TQM on organizational performance
Various authors found that a key important area of making sure that TQM results in sustained
development in the organizational profitability is that straight quantitative MEASURES of
the manufacturing are applied to analyze the efficacy if the manager's performance to
maintain the growth and implementation of TQM programs. TQM has evolved as methods to
create quality goods and reduce costs (Hung, Lien, Yang, Wu, and Kuo, 2011). TQM has
changed as the theoretical method that focus on the requirements to deliver consumers with
extremely valued goods or goods and to do that by development in the efficacy by the way of
eradicating waste, decreasing chief times at every step of the productions process reducing
the costs, and growing people, and enhancing the constantly. Whereas the TQM deliver the
potential for the company to improve their rivalry there are some indications that various
organizations has been dissatisfied in the context to which TQM approach has been related to
the nonstop progresses in the organizational productivity (Alghamdi, 2018). The main thrust
of the TQM theory is that the goods feature and its maintenance have to be developed in form
the starting and that the accomplishments of the quality levels and enhancements is the
accountability of everybody (Fotopoulos, and Psomas, 2009).
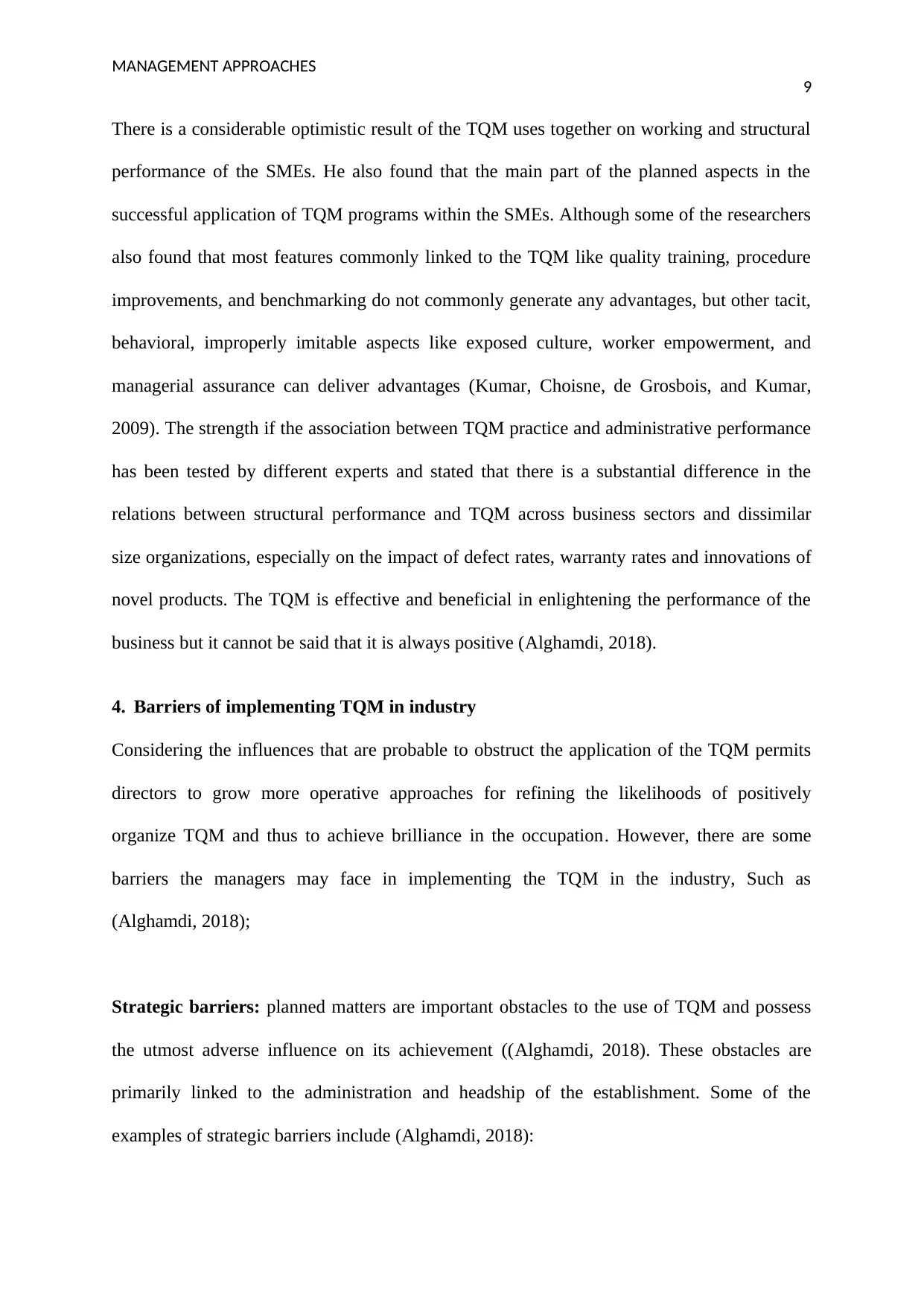
MANAGEMENT APPROACHES
9
There is a considerable optimistic result of the TQM uses together on working and structural
performance of the SMEs. He also found that the main part of the planned aspects in the
successful application of TQM programs within the SMEs. Although some of the researchers
also found that most features commonly linked to the TQM like quality training, procedure
improvements, and benchmarking do not commonly generate any advantages, but other tacit,
behavioral, improperly imitable aspects like exposed culture, worker empowerment, and
managerial assurance can deliver advantages (Kumar, Choisne, de Grosbois, and Kumar,
2009). The strength if the association between TQM practice and administrative performance
has been tested by different experts and stated that there is a substantial difference in the
relations between structural performance and TQM across business sectors and dissimilar
size organizations, especially on the impact of defect rates, warranty rates and innovations of
novel products. The TQM is effective and beneficial in enlightening the performance of the
business but it cannot be said that it is always positive (Alghamdi, 2018).
4. Barriers of implementing TQM in industry
Considering the influences that are probable to obstruct the application of the TQM permits
directors to grow more operative approaches for refining the likelihoods of positively
organize TQM and thus to achieve brilliance in the occupation. However, there are some
barriers the managers may face in implementing the TQM in the industry, Such as
(Alghamdi, 2018);
Strategic barriers: planned matters are important obstacles to the use of TQM and possess
the utmost adverse influence on its achievement ((Alghamdi, 2018). These obstacles are
primarily linked to the administration and headship of the establishment. Some of the
examples of strategic barriers include (Alghamdi, 2018):
9
There is a considerable optimistic result of the TQM uses together on working and structural
performance of the SMEs. He also found that the main part of the planned aspects in the
successful application of TQM programs within the SMEs. Although some of the researchers
also found that most features commonly linked to the TQM like quality training, procedure
improvements, and benchmarking do not commonly generate any advantages, but other tacit,
behavioral, improperly imitable aspects like exposed culture, worker empowerment, and
managerial assurance can deliver advantages (Kumar, Choisne, de Grosbois, and Kumar,
2009). The strength if the association between TQM practice and administrative performance
has been tested by different experts and stated that there is a substantial difference in the
relations between structural performance and TQM across business sectors and dissimilar
size organizations, especially on the impact of defect rates, warranty rates and innovations of
novel products. The TQM is effective and beneficial in enlightening the performance of the
business but it cannot be said that it is always positive (Alghamdi, 2018).
4. Barriers of implementing TQM in industry
Considering the influences that are probable to obstruct the application of the TQM permits
directors to grow more operative approaches for refining the likelihoods of positively
organize TQM and thus to achieve brilliance in the occupation. However, there are some
barriers the managers may face in implementing the TQM in the industry, Such as
(Alghamdi, 2018);
Strategic barriers: planned matters are important obstacles to the use of TQM and possess
the utmost adverse influence on its achievement ((Alghamdi, 2018). These obstacles are
primarily linked to the administration and headship of the establishment. Some of the
examples of strategic barriers include (Alghamdi, 2018):
Secure Best Marks with AI Grader
Need help grading? Try our AI Grader for instant feedback on your assignments.
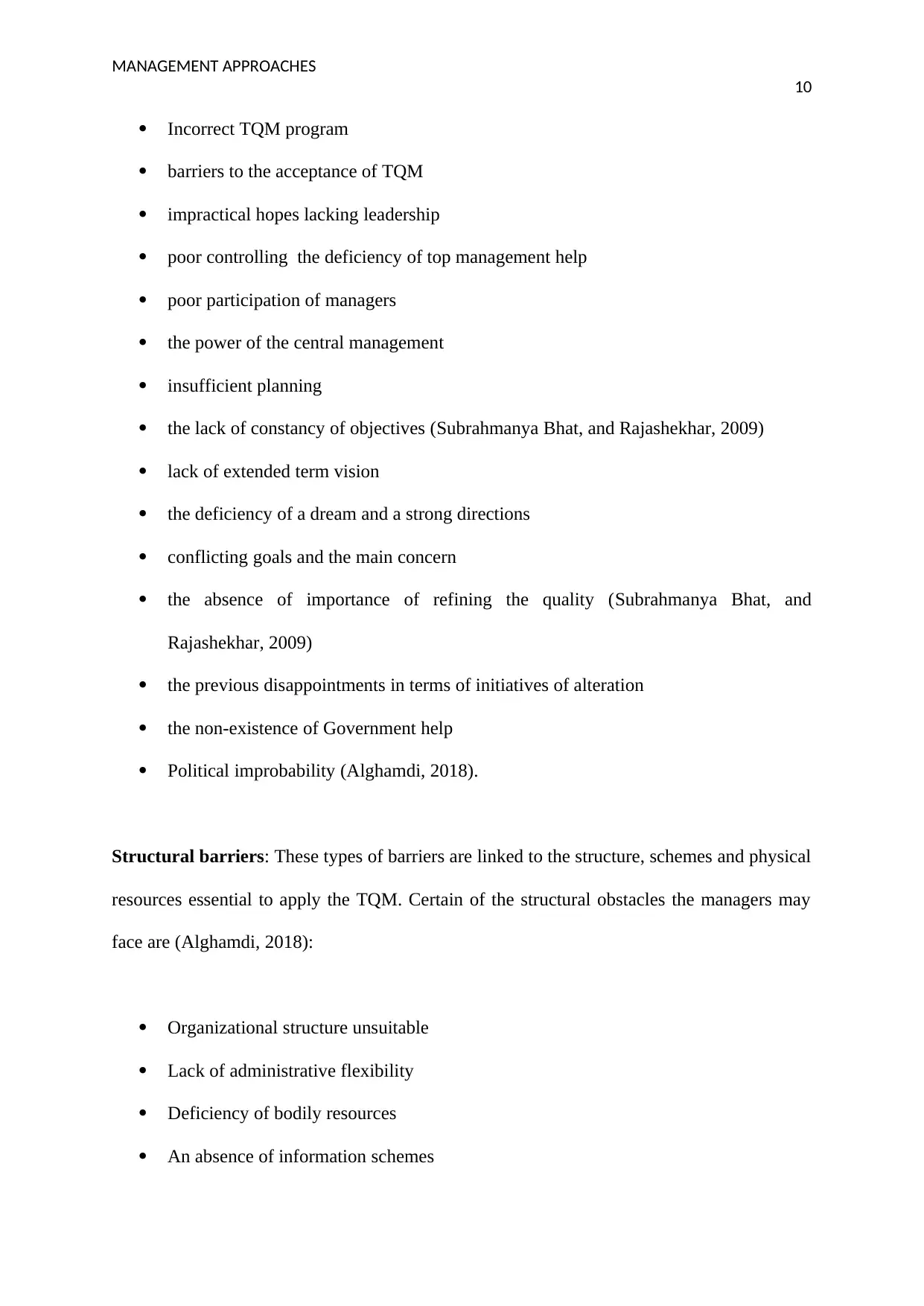
MANAGEMENT APPROACHES
10
Incorrect TQM program
barriers to the acceptance of TQM
impractical hopes lacking leadership
poor controlling the deficiency of top management help
poor participation of managers
the power of the central management
insufficient planning
the lack of constancy of objectives (Subrahmanya Bhat, and Rajashekhar, 2009)
lack of extended term vision
the deficiency of a dream and a strong directions
conflicting goals and the main concern
the absence of importance of refining the quality (Subrahmanya Bhat, and
Rajashekhar, 2009)
the previous disappointments in terms of initiatives of alteration
the non-existence of Government help
Political improbability (Alghamdi, 2018).
Structural barriers: These types of barriers are linked to the structure, schemes and physical
resources essential to apply the TQM. Certain of the structural obstacles the managers may
face are (Alghamdi, 2018):
Organizational structure unsuitable
Lack of administrative flexibility
Deficiency of bodily resources
An absence of information schemes
10
Incorrect TQM program
barriers to the acceptance of TQM
impractical hopes lacking leadership
poor controlling the deficiency of top management help
poor participation of managers
the power of the central management
insufficient planning
the lack of constancy of objectives (Subrahmanya Bhat, and Rajashekhar, 2009)
lack of extended term vision
the deficiency of a dream and a strong directions
conflicting goals and the main concern
the absence of importance of refining the quality (Subrahmanya Bhat, and
Rajashekhar, 2009)
the previous disappointments in terms of initiatives of alteration
the non-existence of Government help
Political improbability (Alghamdi, 2018).
Structural barriers: These types of barriers are linked to the structure, schemes and physical
resources essential to apply the TQM. Certain of the structural obstacles the managers may
face are (Alghamdi, 2018):
Organizational structure unsuitable
Lack of administrative flexibility
Deficiency of bodily resources
An absence of information schemes
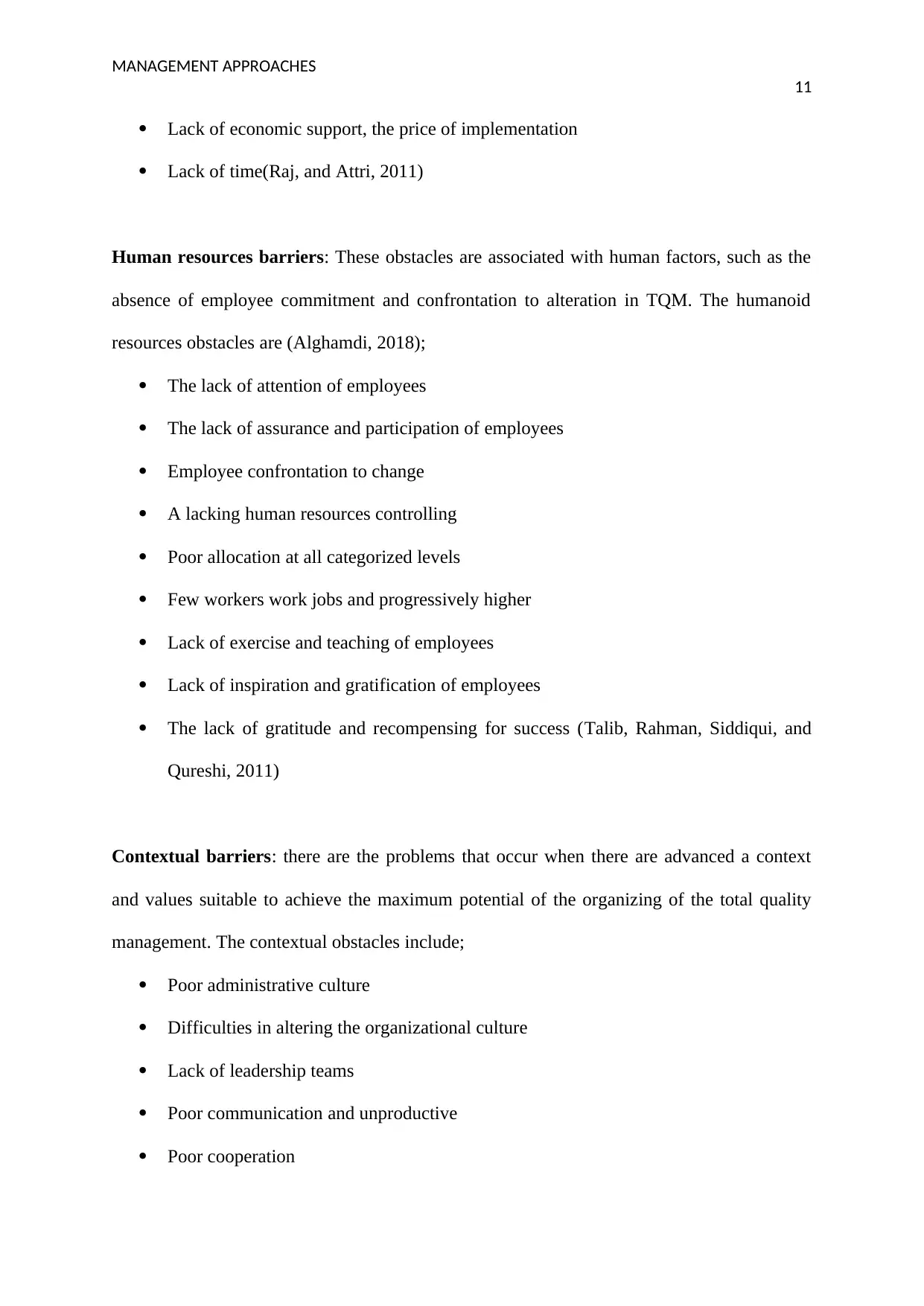
MANAGEMENT APPROACHES
11
Lack of economic support, the price of implementation
Lack of time(Raj, and Attri, 2011)
Human resources barriers: These obstacles are associated with human factors, such as the
absence of employee commitment and confrontation to alteration in TQM. The humanoid
resources obstacles are (Alghamdi, 2018);
The lack of attention of employees
The lack of assurance and participation of employees
Employee confrontation to change
A lacking human resources controlling
Poor allocation at all categorized levels
Few workers work jobs and progressively higher
Lack of exercise and teaching of employees
Lack of inspiration and gratification of employees
The lack of gratitude and recompensing for success (Talib, Rahman, Siddiqui, and
Qureshi, 2011)
Contextual barriers: there are the problems that occur when there are advanced a context
and values suitable to achieve the maximum potential of the organizing of the total quality
management. The contextual obstacles include;
Poor administrative culture
Difficulties in altering the organizational culture
Lack of leadership teams
Poor communication and unproductive
Poor cooperation
11
Lack of economic support, the price of implementation
Lack of time(Raj, and Attri, 2011)
Human resources barriers: These obstacles are associated with human factors, such as the
absence of employee commitment and confrontation to alteration in TQM. The humanoid
resources obstacles are (Alghamdi, 2018);
The lack of attention of employees
The lack of assurance and participation of employees
Employee confrontation to change
A lacking human resources controlling
Poor allocation at all categorized levels
Few workers work jobs and progressively higher
Lack of exercise and teaching of employees
Lack of inspiration and gratification of employees
The lack of gratitude and recompensing for success (Talib, Rahman, Siddiqui, and
Qureshi, 2011)
Contextual barriers: there are the problems that occur when there are advanced a context
and values suitable to achieve the maximum potential of the organizing of the total quality
management. The contextual obstacles include;
Poor administrative culture
Difficulties in altering the organizational culture
Lack of leadership teams
Poor communication and unproductive
Poor cooperation
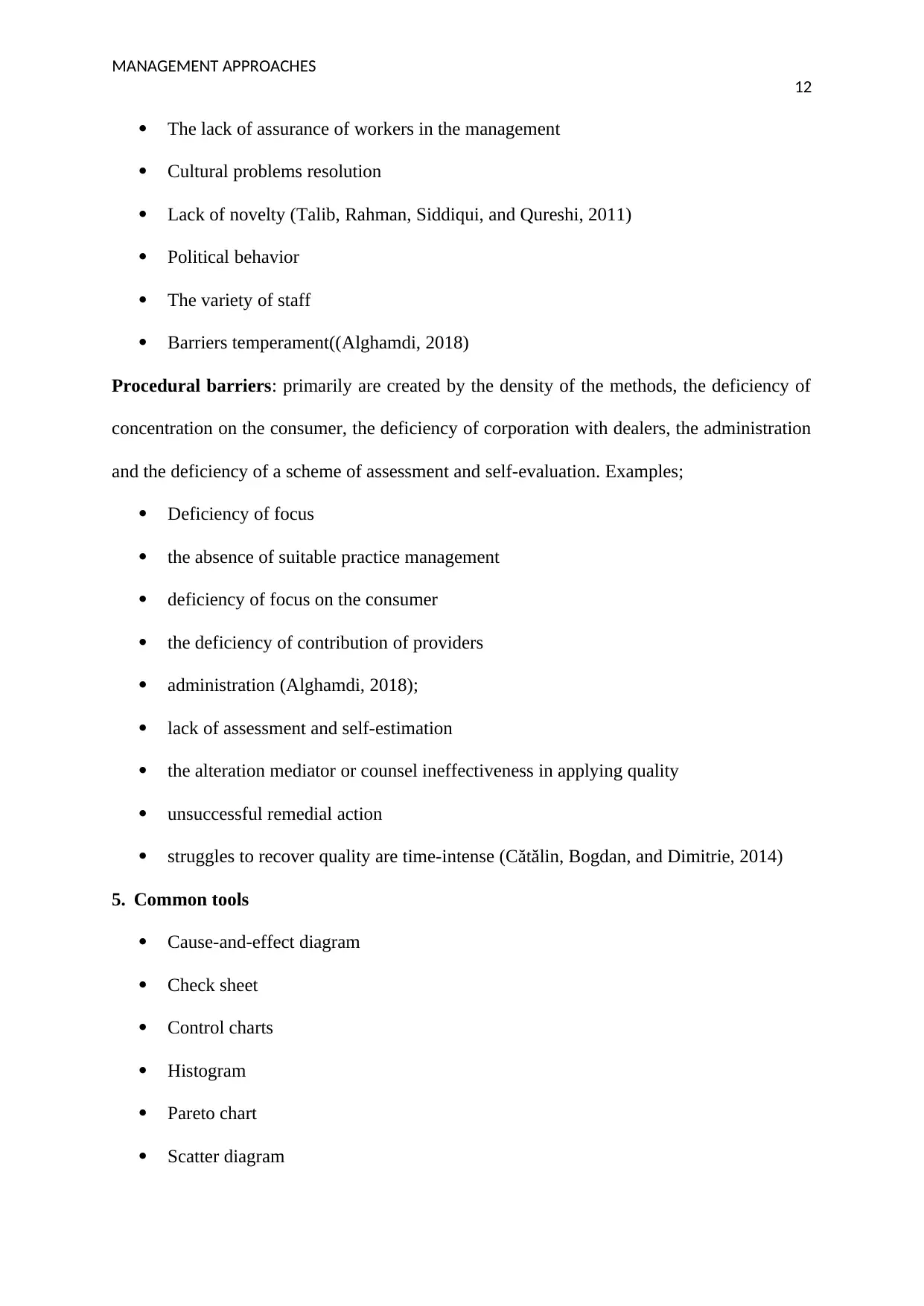
MANAGEMENT APPROACHES
12
The lack of assurance of workers in the management
Cultural problems resolution
Lack of novelty (Talib, Rahman, Siddiqui, and Qureshi, 2011)
Political behavior
The variety of staff
Barriers temperament((Alghamdi, 2018)
Procedural barriers: primarily are created by the density of the methods, the deficiency of
concentration on the consumer, the deficiency of corporation with dealers, the administration
and the deficiency of a scheme of assessment and self-evaluation. Examples;
Deficiency of focus
the absence of suitable practice management
deficiency of focus on the consumer
the deficiency of contribution of providers
administration (Alghamdi, 2018);
lack of assessment and self-estimation
the alteration mediator or counsel ineffectiveness in applying quality
unsuccessful remedial action
struggles to recover quality are time-intense (Cătălin, Bogdan, and Dimitrie, 2014)
5. Common tools
Cause-and-effect diagram
Check sheet
Control charts
Histogram
Pareto chart
Scatter diagram
12
The lack of assurance of workers in the management
Cultural problems resolution
Lack of novelty (Talib, Rahman, Siddiqui, and Qureshi, 2011)
Political behavior
The variety of staff
Barriers temperament((Alghamdi, 2018)
Procedural barriers: primarily are created by the density of the methods, the deficiency of
concentration on the consumer, the deficiency of corporation with dealers, the administration
and the deficiency of a scheme of assessment and self-evaluation. Examples;
Deficiency of focus
the absence of suitable practice management
deficiency of focus on the consumer
the deficiency of contribution of providers
administration (Alghamdi, 2018);
lack of assessment and self-estimation
the alteration mediator or counsel ineffectiveness in applying quality
unsuccessful remedial action
struggles to recover quality are time-intense (Cătălin, Bogdan, and Dimitrie, 2014)
5. Common tools
Cause-and-effect diagram
Check sheet
Control charts
Histogram
Pareto chart
Scatter diagram
Paraphrase This Document
Need a fresh take? Get an instant paraphrase of this document with our AI Paraphraser
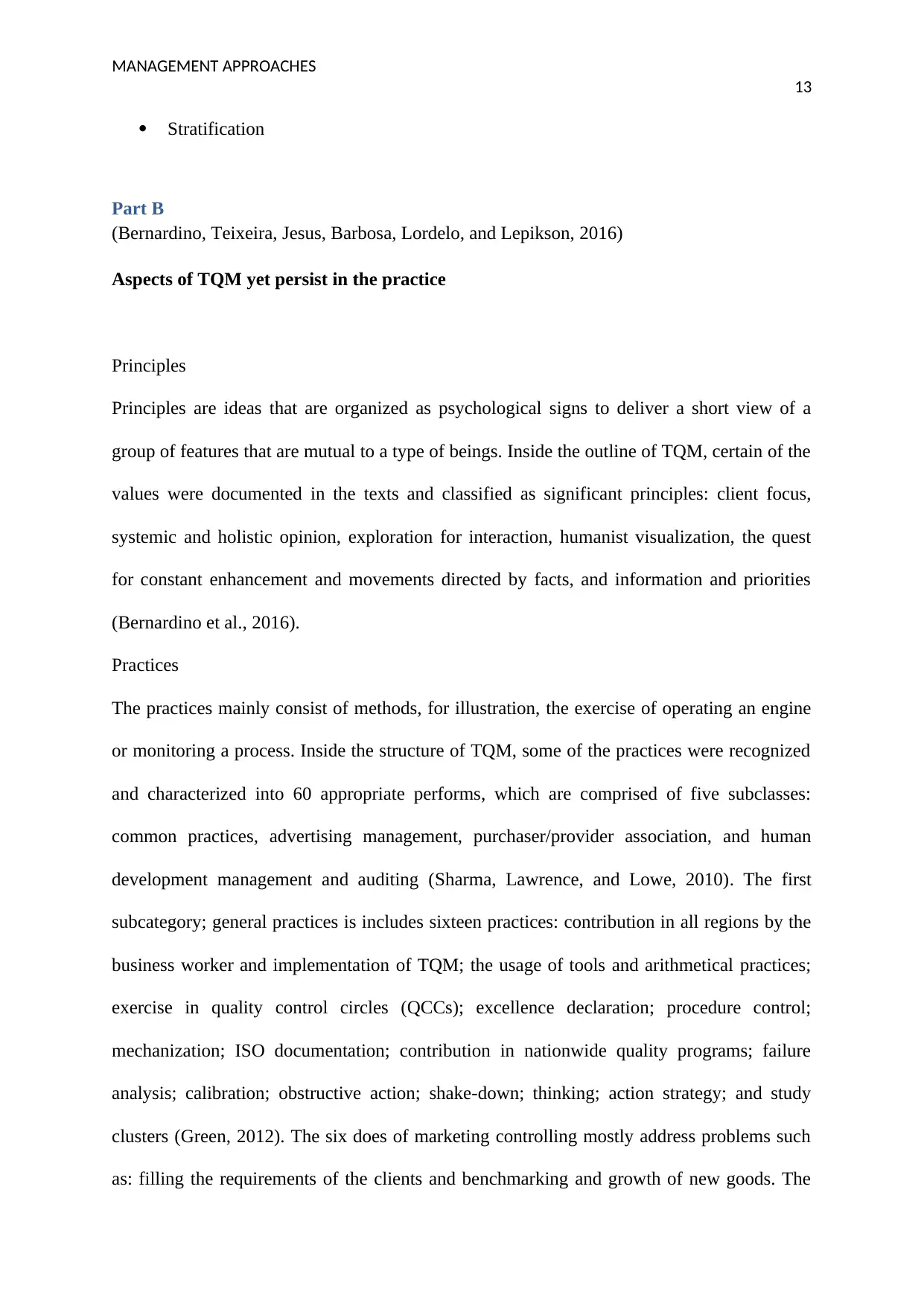
MANAGEMENT APPROACHES
13
Stratification
Part B
(Bernardino, Teixeira, Jesus, Barbosa, Lordelo, and Lepikson, 2016)
Aspects of TQM yet persist in the practice
Principles
Principles are ideas that are organized as psychological signs to deliver a short view of a
group of features that are mutual to a type of beings. Inside the outline of TQM, certain of the
values were documented in the texts and classified as significant principles: client focus,
systemic and holistic opinion, exploration for interaction, humanist visualization, the quest
for constant enhancement and movements directed by facts, and information and priorities
(Bernardino et al., 2016).
Practices
The practices mainly consist of methods, for illustration, the exercise of operating an engine
or monitoring a process. Inside the structure of TQM, some of the practices were recognized
and characterized into 60 appropriate performs, which are comprised of five subclasses:
common practices, advertising management, purchaser/provider association, and human
development management and auditing (Sharma, Lawrence, and Lowe, 2010). The first
subcategory; general practices is includes sixteen practices: contribution in all regions by the
business worker and implementation of TQM; the usage of tools and arithmetical practices;
exercise in quality control circles (QCCs); excellence declaration; procedure control;
mechanization; ISO documentation; contribution in nationwide quality programs; failure
analysis; calibration; obstructive action; shake-down; thinking; action strategy; and study
clusters (Green, 2012). The six does of marketing controlling mostly address problems such
as: filling the requirements of the clients and benchmarking and growth of new goods. The
13
Stratification
Part B
(Bernardino, Teixeira, Jesus, Barbosa, Lordelo, and Lepikson, 2016)
Aspects of TQM yet persist in the practice
Principles
Principles are ideas that are organized as psychological signs to deliver a short view of a
group of features that are mutual to a type of beings. Inside the outline of TQM, certain of the
values were documented in the texts and classified as significant principles: client focus,
systemic and holistic opinion, exploration for interaction, humanist visualization, the quest
for constant enhancement and movements directed by facts, and information and priorities
(Bernardino et al., 2016).
Practices
The practices mainly consist of methods, for illustration, the exercise of operating an engine
or monitoring a process. Inside the structure of TQM, some of the practices were recognized
and characterized into 60 appropriate performs, which are comprised of five subclasses:
common practices, advertising management, purchaser/provider association, and human
development management and auditing (Sharma, Lawrence, and Lowe, 2010). The first
subcategory; general practices is includes sixteen practices: contribution in all regions by the
business worker and implementation of TQM; the usage of tools and arithmetical practices;
exercise in quality control circles (QCCs); excellence declaration; procedure control;
mechanization; ISO documentation; contribution in nationwide quality programs; failure
analysis; calibration; obstructive action; shake-down; thinking; action strategy; and study
clusters (Green, 2012). The six does of marketing controlling mostly address problems such
as: filling the requirements of the clients and benchmarking and growth of new goods. The
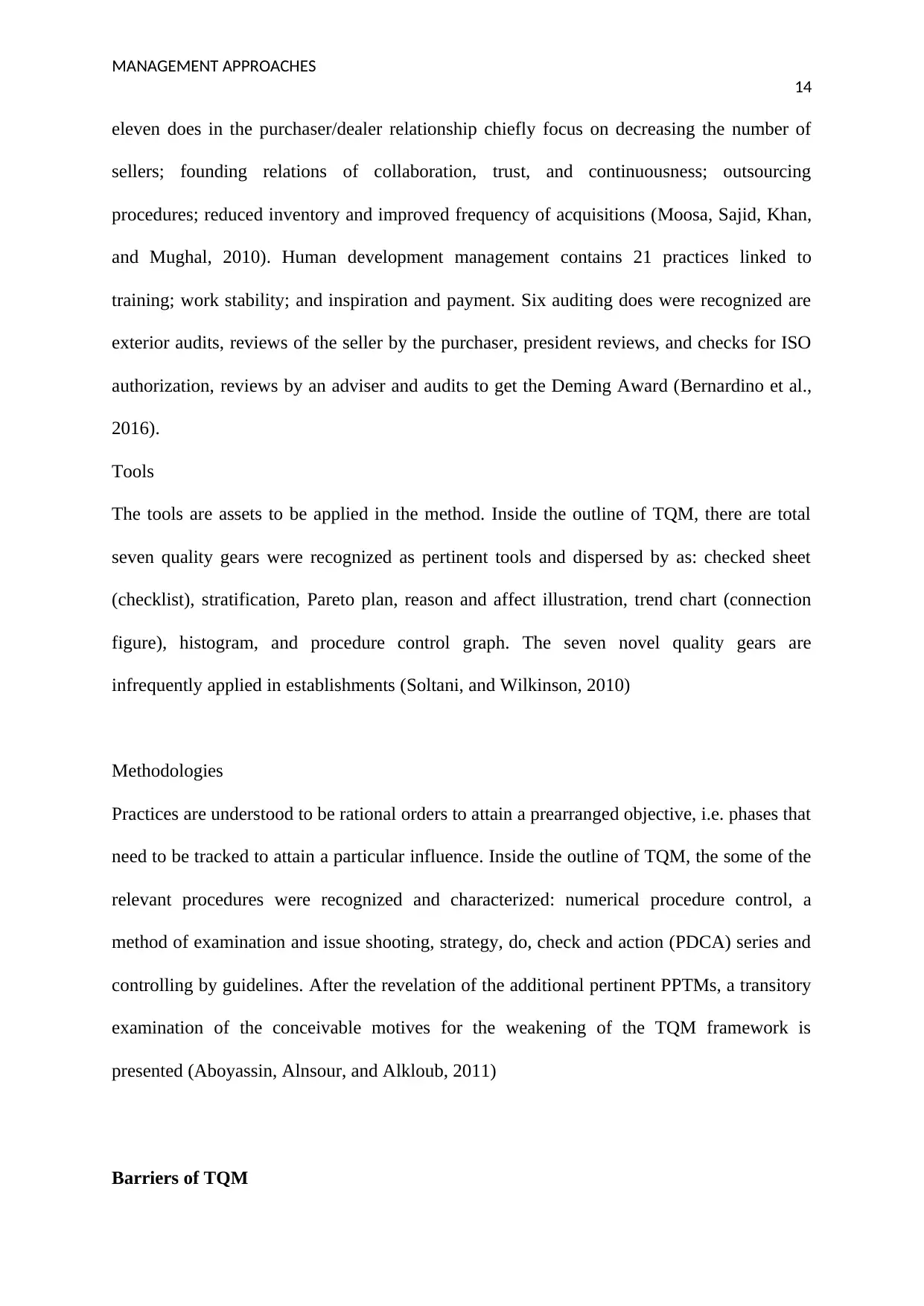
MANAGEMENT APPROACHES
14
eleven does in the purchaser/dealer relationship chiefly focus on decreasing the number of
sellers; founding relations of collaboration, trust, and continuousness; outsourcing
procedures; reduced inventory and improved frequency of acquisitions (Moosa, Sajid, Khan,
and Mughal, 2010). Human development management contains 21 practices linked to
training; work stability; and inspiration and payment. Six auditing does were recognized are
exterior audits, reviews of the seller by the purchaser, president reviews, and checks for ISO
authorization, reviews by an adviser and audits to get the Deming Award (Bernardino et al.,
2016).
Tools
The tools are assets to be applied in the method. Inside the outline of TQM, there are total
seven quality gears were recognized as pertinent tools and dispersed by as: checked sheet
(checklist), stratification, Pareto plan, reason and affect illustration, trend chart (connection
figure), histogram, and procedure control graph. The seven novel quality gears are
infrequently applied in establishments (Soltani, and Wilkinson, 2010)
Methodologies
Practices are understood to be rational orders to attain a prearranged objective, i.e. phases that
need to be tracked to attain a particular influence. Inside the outline of TQM, the some of the
relevant procedures were recognized and characterized: numerical procedure control, a
method of examination and issue shooting, strategy, do, check and action (PDCA) series and
controlling by guidelines. After the revelation of the additional pertinent PPTMs, a transitory
examination of the conceivable motives for the weakening of the TQM framework is
presented (Aboyassin, Alnsour, and Alkloub, 2011)
Barriers of TQM
14
eleven does in the purchaser/dealer relationship chiefly focus on decreasing the number of
sellers; founding relations of collaboration, trust, and continuousness; outsourcing
procedures; reduced inventory and improved frequency of acquisitions (Moosa, Sajid, Khan,
and Mughal, 2010). Human development management contains 21 practices linked to
training; work stability; and inspiration and payment. Six auditing does were recognized are
exterior audits, reviews of the seller by the purchaser, president reviews, and checks for ISO
authorization, reviews by an adviser and audits to get the Deming Award (Bernardino et al.,
2016).
Tools
The tools are assets to be applied in the method. Inside the outline of TQM, there are total
seven quality gears were recognized as pertinent tools and dispersed by as: checked sheet
(checklist), stratification, Pareto plan, reason and affect illustration, trend chart (connection
figure), histogram, and procedure control graph. The seven novel quality gears are
infrequently applied in establishments (Soltani, and Wilkinson, 2010)
Methodologies
Practices are understood to be rational orders to attain a prearranged objective, i.e. phases that
need to be tracked to attain a particular influence. Inside the outline of TQM, the some of the
relevant procedures were recognized and characterized: numerical procedure control, a
method of examination and issue shooting, strategy, do, check and action (PDCA) series and
controlling by guidelines. After the revelation of the additional pertinent PPTMs, a transitory
examination of the conceivable motives for the weakening of the TQM framework is
presented (Aboyassin, Alnsour, and Alkloub, 2011)
Barriers of TQM
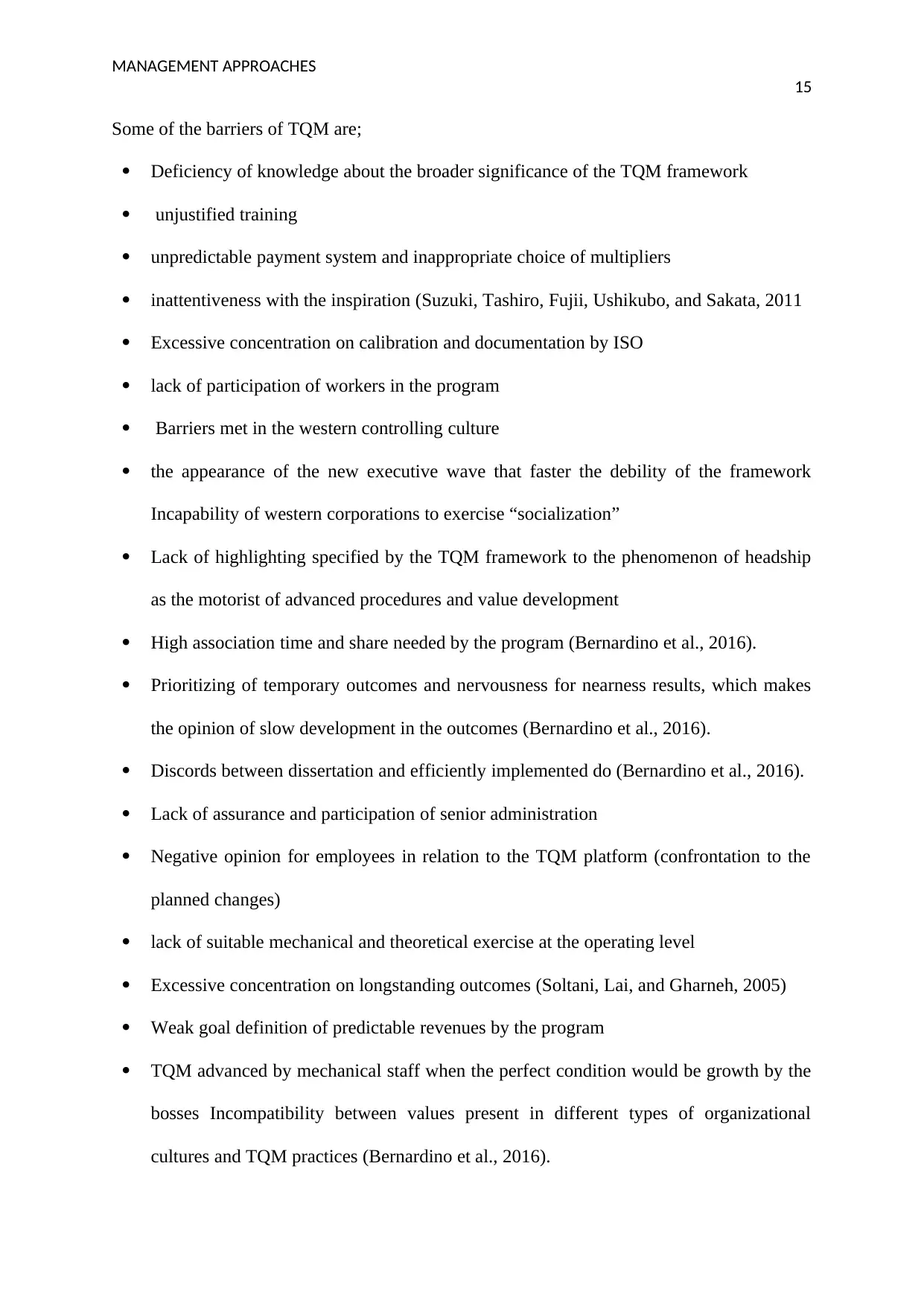
MANAGEMENT APPROACHES
15
Some of the barriers of TQM are;
Deficiency of knowledge about the broader significance of the TQM framework
unjustified training
unpredictable payment system and inappropriate choice of multipliers
inattentiveness with the inspiration (Suzuki, Tashiro, Fujii, Ushikubo, and Sakata, 2011
Excessive concentration on calibration and documentation by ISO
lack of participation of workers in the program
Barriers met in the western controlling culture
the appearance of the new executive wave that faster the debility of the framework
Incapability of western corporations to exercise “socialization”
Lack of highlighting specified by the TQM framework to the phenomenon of headship
as the motorist of advanced procedures and value development
High association time and share needed by the program (Bernardino et al., 2016).
Prioritizing of temporary outcomes and nervousness for nearness results, which makes
the opinion of slow development in the outcomes (Bernardino et al., 2016).
Discords between dissertation and efficiently implemented do (Bernardino et al., 2016).
Lack of assurance and participation of senior administration
Negative opinion for employees in relation to the TQM platform (confrontation to the
planned changes)
lack of suitable mechanical and theoretical exercise at the operating level
Excessive concentration on longstanding outcomes (Soltani, Lai, and Gharneh, 2005)
Weak goal definition of predictable revenues by the program
TQM advanced by mechanical staff when the perfect condition would be growth by the
bosses Incompatibility between values present in different types of organizational
cultures and TQM practices (Bernardino et al., 2016).
15
Some of the barriers of TQM are;
Deficiency of knowledge about the broader significance of the TQM framework
unjustified training
unpredictable payment system and inappropriate choice of multipliers
inattentiveness with the inspiration (Suzuki, Tashiro, Fujii, Ushikubo, and Sakata, 2011
Excessive concentration on calibration and documentation by ISO
lack of participation of workers in the program
Barriers met in the western controlling culture
the appearance of the new executive wave that faster the debility of the framework
Incapability of western corporations to exercise “socialization”
Lack of highlighting specified by the TQM framework to the phenomenon of headship
as the motorist of advanced procedures and value development
High association time and share needed by the program (Bernardino et al., 2016).
Prioritizing of temporary outcomes and nervousness for nearness results, which makes
the opinion of slow development in the outcomes (Bernardino et al., 2016).
Discords between dissertation and efficiently implemented do (Bernardino et al., 2016).
Lack of assurance and participation of senior administration
Negative opinion for employees in relation to the TQM platform (confrontation to the
planned changes)
lack of suitable mechanical and theoretical exercise at the operating level
Excessive concentration on longstanding outcomes (Soltani, Lai, and Gharneh, 2005)
Weak goal definition of predictable revenues by the program
TQM advanced by mechanical staff when the perfect condition would be growth by the
bosses Incompatibility between values present in different types of organizational
cultures and TQM practices (Bernardino et al., 2016).
Secure Best Marks with AI Grader
Need help grading? Try our AI Grader for instant feedback on your assignments.
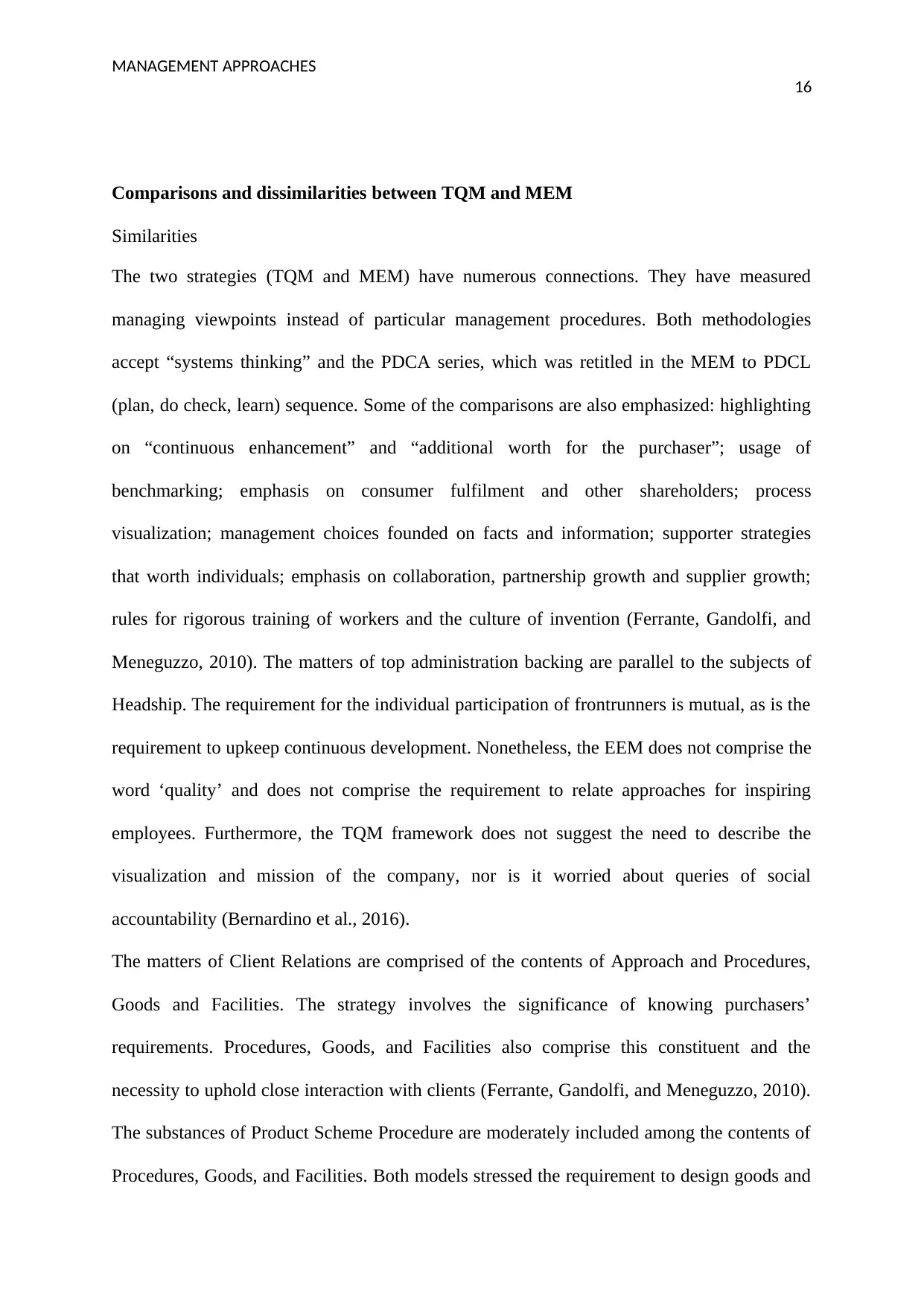
MANAGEMENT APPROACHES
16
Comparisons and dissimilarities between TQM and MEM
Similarities
The two strategies (TQM and MEM) have numerous connections. They have measured
managing viewpoints instead of particular management procedures. Both methodologies
accept “systems thinking” and the PDCA series, which was retitled in the MEM to PDCL
(plan, do check, learn) sequence. Some of the comparisons are also emphasized: highlighting
on “continuous enhancement” and “additional worth for the purchaser”; usage of
benchmarking; emphasis on consumer fulfilment and other shareholders; process
visualization; management choices founded on facts and information; supporter strategies
that worth individuals; emphasis on collaboration, partnership growth and supplier growth;
rules for rigorous training of workers and the culture of invention (Ferrante, Gandolfi, and
Meneguzzo, 2010). The matters of top administration backing are parallel to the subjects of
Headship. The requirement for the individual participation of frontrunners is mutual, as is the
requirement to upkeep continuous development. Nonetheless, the EEM does not comprise the
word ‘quality’ and does not comprise the requirement to relate approaches for inspiring
employees. Furthermore, the TQM framework does not suggest the need to describe the
visualization and mission of the company, nor is it worried about queries of social
accountability (Bernardino et al., 2016).
The matters of Client Relations are comprised of the contents of Approach and Procedures,
Goods and Facilities. The strategy involves the significance of knowing purchasers’
requirements. Procedures, Goods, and Facilities also comprise this constituent and the
necessity to uphold close interaction with clients (Ferrante, Gandolfi, and Meneguzzo, 2010).
The substances of Product Scheme Procedure are moderately included among the contents of
Procedures, Goods, and Facilities. Both models stressed the requirement to design goods and
16
Comparisons and dissimilarities between TQM and MEM
Similarities
The two strategies (TQM and MEM) have numerous connections. They have measured
managing viewpoints instead of particular management procedures. Both methodologies
accept “systems thinking” and the PDCA series, which was retitled in the MEM to PDCL
(plan, do check, learn) sequence. Some of the comparisons are also emphasized: highlighting
on “continuous enhancement” and “additional worth for the purchaser”; usage of
benchmarking; emphasis on consumer fulfilment and other shareholders; process
visualization; management choices founded on facts and information; supporter strategies
that worth individuals; emphasis on collaboration, partnership growth and supplier growth;
rules for rigorous training of workers and the culture of invention (Ferrante, Gandolfi, and
Meneguzzo, 2010). The matters of top administration backing are parallel to the subjects of
Headship. The requirement for the individual participation of frontrunners is mutual, as is the
requirement to upkeep continuous development. Nonetheless, the EEM does not comprise the
word ‘quality’ and does not comprise the requirement to relate approaches for inspiring
employees. Furthermore, the TQM framework does not suggest the need to describe the
visualization and mission of the company, nor is it worried about queries of social
accountability (Bernardino et al., 2016).
The matters of Client Relations are comprised of the contents of Approach and Procedures,
Goods and Facilities. The strategy involves the significance of knowing purchasers’
requirements. Procedures, Goods, and Facilities also comprise this constituent and the
necessity to uphold close interaction with clients (Ferrante, Gandolfi, and Meneguzzo, 2010).
The substances of Product Scheme Procedure are moderately included among the contents of
Procedures, Goods, and Facilities. Both models stressed the requirement to design goods and
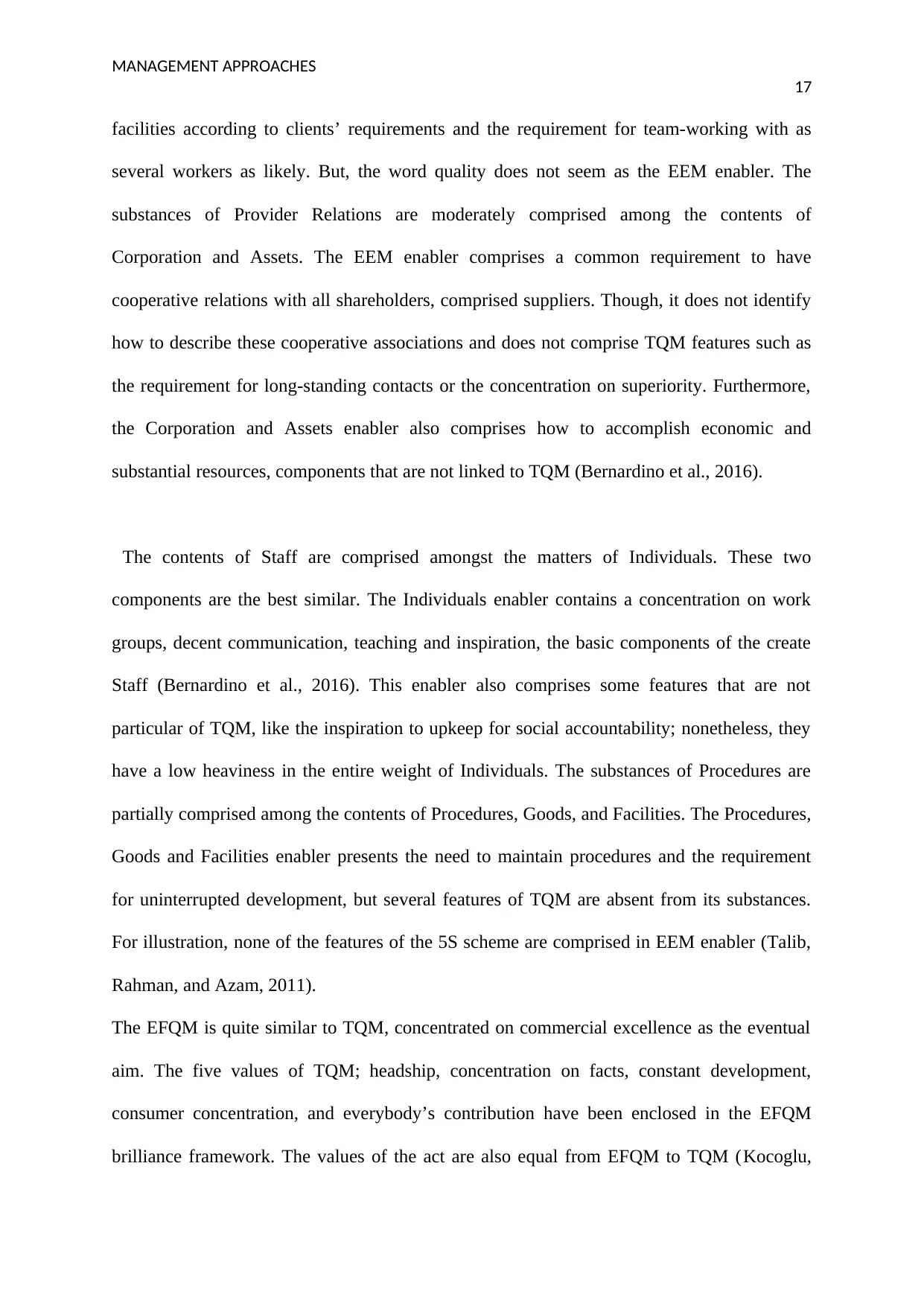
MANAGEMENT APPROACHES
17
facilities according to clients’ requirements and the requirement for team-working with as
several workers as likely. But, the word quality does not seem as the EEM enabler. The
substances of Provider Relations are moderately comprised among the contents of
Corporation and Assets. The EEM enabler comprises a common requirement to have
cooperative relations with all shareholders, comprised suppliers. Though, it does not identify
how to describe these cooperative associations and does not comprise TQM features such as
the requirement for long-standing contacts or the concentration on superiority. Furthermore,
the Corporation and Assets enabler also comprises how to accomplish economic and
substantial resources, components that are not linked to TQM (Bernardino et al., 2016).
The contents of Staff are comprised amongst the matters of Individuals. These two
components are the best similar. The Individuals enabler contains a concentration on work
groups, decent communication, teaching and inspiration, the basic components of the create
Staff (Bernardino et al., 2016). This enabler also comprises some features that are not
particular of TQM, like the inspiration to upkeep for social accountability; nonetheless, they
have a low heaviness in the entire weight of Individuals. The substances of Procedures are
partially comprised among the contents of Procedures, Goods, and Facilities. The Procedures,
Goods and Facilities enabler presents the need to maintain procedures and the requirement
for uninterrupted development, but several features of TQM are absent from its substances.
For illustration, none of the features of the 5S scheme are comprised in EEM enabler (Talib,
Rahman, and Azam, 2011).
The EFQM is quite similar to TQM, concentrated on commercial excellence as the eventual
aim. The five values of TQM; headship, concentration on facts, constant development,
consumer concentration, and everybody’s contribution have been enclosed in the EFQM
brilliance framework. The values of the act are also equal from EFQM to TQM (Kocoglu,
17
facilities according to clients’ requirements and the requirement for team-working with as
several workers as likely. But, the word quality does not seem as the EEM enabler. The
substances of Provider Relations are moderately comprised among the contents of
Corporation and Assets. The EEM enabler comprises a common requirement to have
cooperative relations with all shareholders, comprised suppliers. Though, it does not identify
how to describe these cooperative associations and does not comprise TQM features such as
the requirement for long-standing contacts or the concentration on superiority. Furthermore,
the Corporation and Assets enabler also comprises how to accomplish economic and
substantial resources, components that are not linked to TQM (Bernardino et al., 2016).
The contents of Staff are comprised amongst the matters of Individuals. These two
components are the best similar. The Individuals enabler contains a concentration on work
groups, decent communication, teaching and inspiration, the basic components of the create
Staff (Bernardino et al., 2016). This enabler also comprises some features that are not
particular of TQM, like the inspiration to upkeep for social accountability; nonetheless, they
have a low heaviness in the entire weight of Individuals. The substances of Procedures are
partially comprised among the contents of Procedures, Goods, and Facilities. The Procedures,
Goods and Facilities enabler presents the need to maintain procedures and the requirement
for uninterrupted development, but several features of TQM are absent from its substances.
For illustration, none of the features of the 5S scheme are comprised in EEM enabler (Talib,
Rahman, and Azam, 2011).
The EFQM is quite similar to TQM, concentrated on commercial excellence as the eventual
aim. The five values of TQM; headship, concentration on facts, constant development,
consumer concentration, and everybody’s contribution have been enclosed in the EFQM
brilliance framework. The values of the act are also equal from EFQM to TQM (Kocoglu,
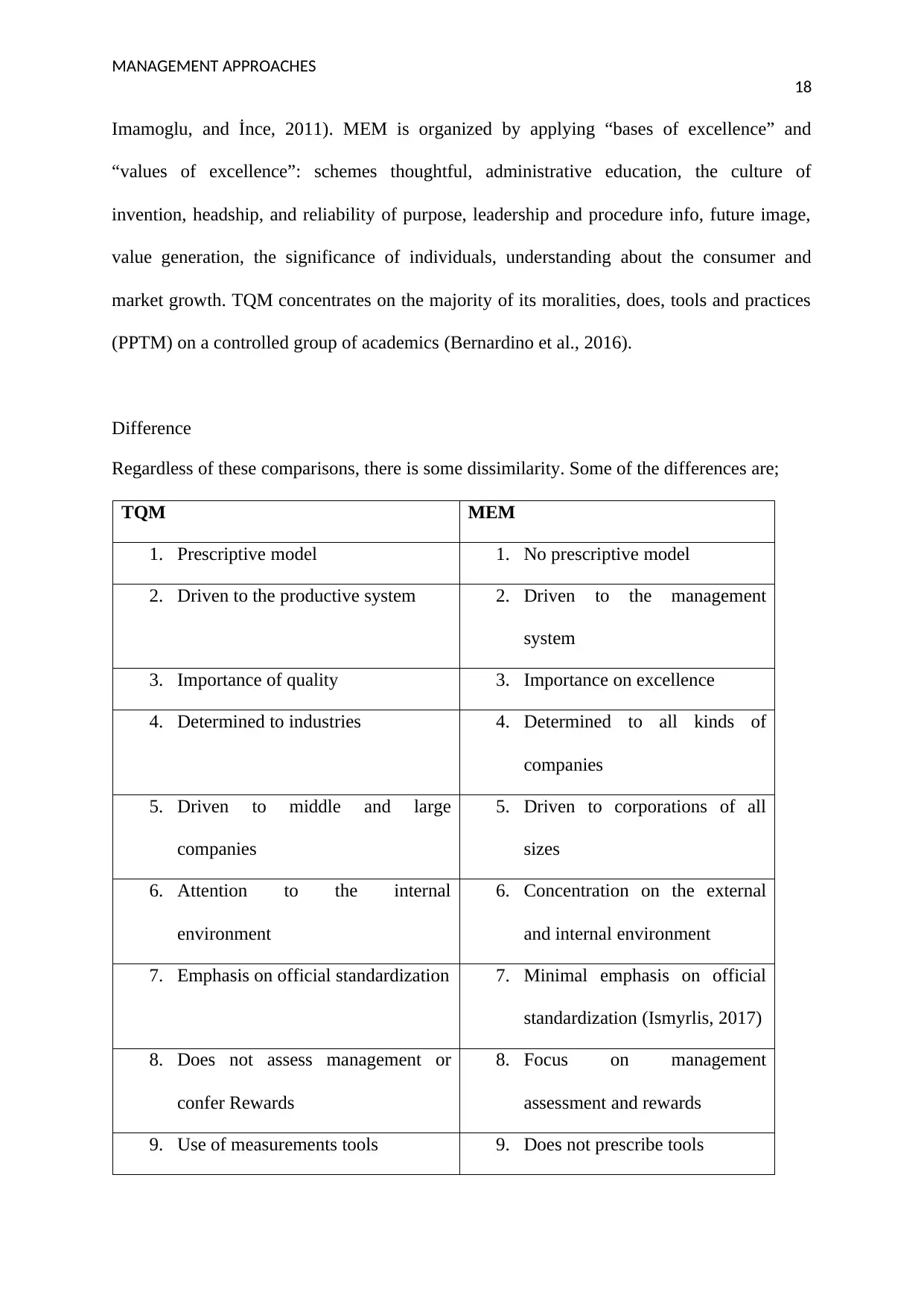
MANAGEMENT APPROACHES
18
Imamoglu, and İnce, 2011). MEM is organized by applying “bases of excellence” and
“values of excellence”: schemes thoughtful, administrative education, the culture of
invention, headship, and reliability of purpose, leadership and procedure info, future image,
value generation, the significance of individuals, understanding about the consumer and
market growth. TQM concentrates on the majority of its moralities, does, tools and practices
(PPTM) on a controlled group of academics (Bernardino et al., 2016).
Difference
Regardless of these comparisons, there is some dissimilarity. Some of the differences are;
TQM MEM
1. Prescriptive model 1. No prescriptive model
2. Driven to the productive system 2. Driven to the management
system
3. Importance of quality 3. Importance on excellence
4. Determined to industries 4. Determined to all kinds of
companies
5. Driven to middle and large
companies
5. Driven to corporations of all
sizes
6. Attention to the internal
environment
6. Concentration on the external
and internal environment
7. Emphasis on official standardization 7. Minimal emphasis on official
standardization (Ismyrlis, 2017)
8. Does not assess management or
confer Rewards
8. Focus on management
assessment and rewards
9. Use of measurements tools 9. Does not prescribe tools
18
Imamoglu, and İnce, 2011). MEM is organized by applying “bases of excellence” and
“values of excellence”: schemes thoughtful, administrative education, the culture of
invention, headship, and reliability of purpose, leadership and procedure info, future image,
value generation, the significance of individuals, understanding about the consumer and
market growth. TQM concentrates on the majority of its moralities, does, tools and practices
(PPTM) on a controlled group of academics (Bernardino et al., 2016).
Difference
Regardless of these comparisons, there is some dissimilarity. Some of the differences are;
TQM MEM
1. Prescriptive model 1. No prescriptive model
2. Driven to the productive system 2. Driven to the management
system
3. Importance of quality 3. Importance on excellence
4. Determined to industries 4. Determined to all kinds of
companies
5. Driven to middle and large
companies
5. Driven to corporations of all
sizes
6. Attention to the internal
environment
6. Concentration on the external
and internal environment
7. Emphasis on official standardization 7. Minimal emphasis on official
standardization (Ismyrlis, 2017)
8. Does not assess management or
confer Rewards
8. Focus on management
assessment and rewards
9. Use of measurements tools 9. Does not prescribe tools
Paraphrase This Document
Need a fresh take? Get an instant paraphrase of this document with our AI Paraphraser

MANAGEMENT APPROACHES
19
10. Focus on reducing nonconformities
(Ivančić, and Bosanac, 2012)
10. Minimal emphasis on reduction
of nonconformities
11. No focus on self-governing and
participative leadership
11. focus on self-governing and
participative leadership
12. No Emphasis on planned planning
(Bernardino et al., 2016).
12. Emphasis on planned planning
(Bernardino et al., 2016).
19
10. Focus on reducing nonconformities
(Ivančić, and Bosanac, 2012)
10. Minimal emphasis on reduction
of nonconformities
11. No focus on self-governing and
participative leadership
11. focus on self-governing and
participative leadership
12. No Emphasis on planned planning
(Bernardino et al., 2016).
12. Emphasis on planned planning
(Bernardino et al., 2016).
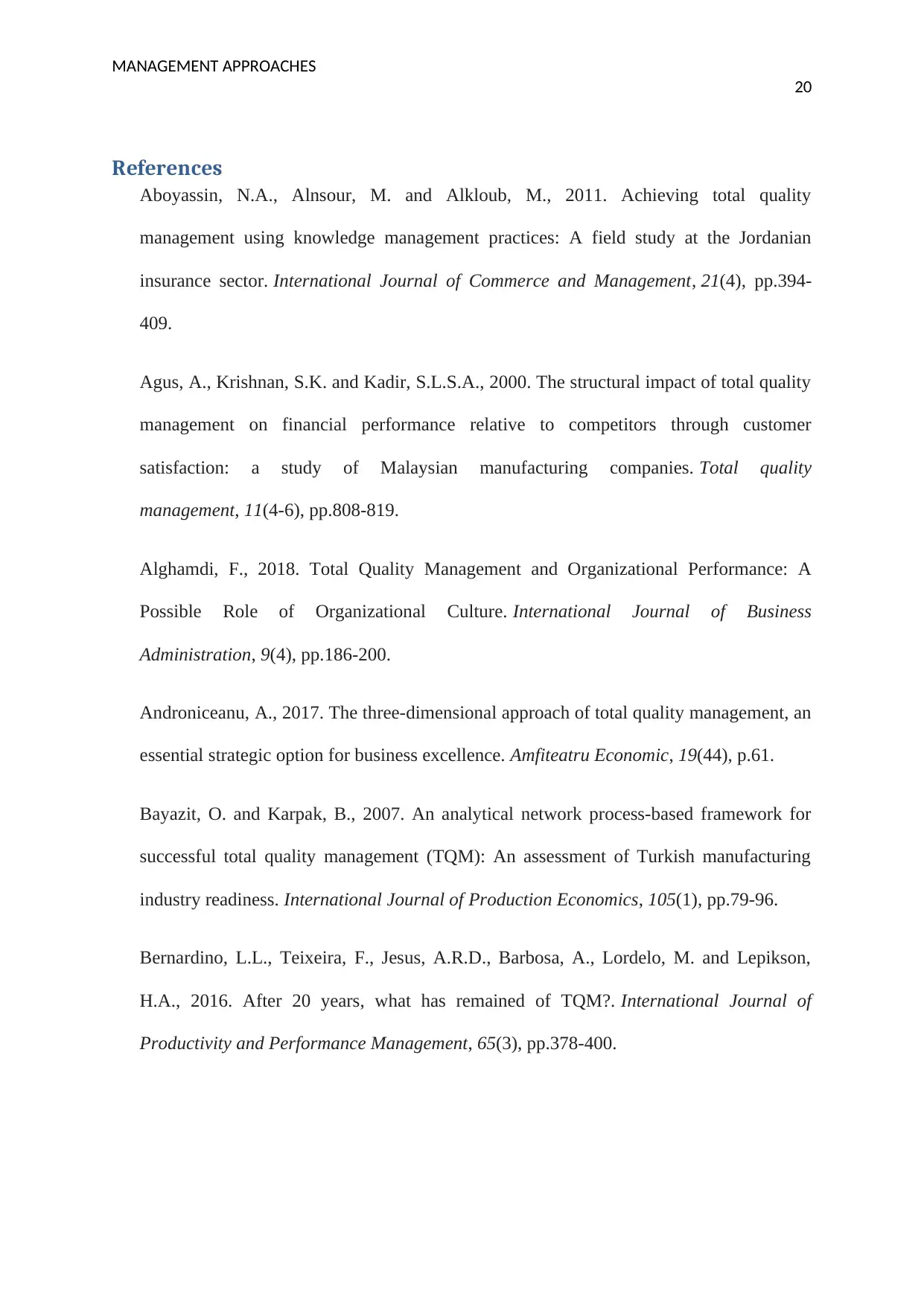
MANAGEMENT APPROACHES
20
References
Aboyassin, N.A., Alnsour, M. and Alkloub, M., 2011. Achieving total quality
management using knowledge management practices: A field study at the Jordanian
insurance sector. International Journal of Commerce and Management, 21(4), pp.394-
409.
Agus, A., Krishnan, S.K. and Kadir, S.L.S.A., 2000. The structural impact of total quality
management on financial performance relative to competitors through customer
satisfaction: a study of Malaysian manufacturing companies. Total quality
management, 11(4-6), pp.808-819.
Alghamdi, F., 2018. Total Quality Management and Organizational Performance: A
Possible Role of Organizational Culture. International Journal of Business
Administration, 9(4), pp.186-200.
Androniceanu, A., 2017. The three-dimensional approach of total quality management, an
essential strategic option for business excellence. Amfiteatru Economic, 19(44), p.61.
Bayazit, O. and Karpak, B., 2007. An analytical network process-based framework for
successful total quality management (TQM): An assessment of Turkish manufacturing
industry readiness. International Journal of Production Economics, 105(1), pp.79-96.
Bernardino, L.L., Teixeira, F., Jesus, A.R.D., Barbosa, A., Lordelo, M. and Lepikson,
H.A., 2016. After 20 years, what has remained of TQM?. International Journal of
Productivity and Performance Management, 65(3), pp.378-400.
20
References
Aboyassin, N.A., Alnsour, M. and Alkloub, M., 2011. Achieving total quality
management using knowledge management practices: A field study at the Jordanian
insurance sector. International Journal of Commerce and Management, 21(4), pp.394-
409.
Agus, A., Krishnan, S.K. and Kadir, S.L.S.A., 2000. The structural impact of total quality
management on financial performance relative to competitors through customer
satisfaction: a study of Malaysian manufacturing companies. Total quality
management, 11(4-6), pp.808-819.
Alghamdi, F., 2018. Total Quality Management and Organizational Performance: A
Possible Role of Organizational Culture. International Journal of Business
Administration, 9(4), pp.186-200.
Androniceanu, A., 2017. The three-dimensional approach of total quality management, an
essential strategic option for business excellence. Amfiteatru Economic, 19(44), p.61.
Bayazit, O. and Karpak, B., 2007. An analytical network process-based framework for
successful total quality management (TQM): An assessment of Turkish manufacturing
industry readiness. International Journal of Production Economics, 105(1), pp.79-96.
Bernardino, L.L., Teixeira, F., Jesus, A.R.D., Barbosa, A., Lordelo, M. and Lepikson,
H.A., 2016. After 20 years, what has remained of TQM?. International Journal of
Productivity and Performance Management, 65(3), pp.378-400.

MANAGEMENT APPROACHES
21
Cătălin, S.H., Bogdan, B. and Dimitrie, G.R., 2014. THE EXISTING BARRIERS IN
IMPLEMENTING TOTAL QUALITY MANAGEMENT. Annals of the University of
Oradea, Economic Science Series, 23(1).
Daud, S. and Yusoff, W.F.W., 2011. The influence of soft and hard TQM factors on
knowledge management: perspective from Malaysia. In International Conference on
Management and Service Science (Vol. 8, pp. 17-22). Singapore: IACSIT Press.
Ferrante, A., Gandolfi, A. and Meneguzzo, M., 2010. Anticipatory strategies for
introducing ISO 26000 in 2010: a comparison between the Italian and Swiss systems of
public administration. Economia Aziendale Online, 1(3), pp.311-321.
Fisher, N.I. and Nair, V.N., 2009. Quality management and quality practice: Perspectives
on their history and their future. Applied Stochastic Models in Business and
Industry, 25(1), pp.1-28.
Fotopoulos, C.B. and Psomas, E.L., 2009. The impact of “soft” and “hard” TQM
elements on quality management results. International Journal of Quality & Reliability
Management, 26(2), pp.150-163.
Green, T.J., 2012. TQM and organisational culture: how do they link?. Total Quality
Management & Business Excellence, 23(2), pp.141-157.
Hung, R.Y.Y., Lien, B.Y.H., Yang, B., Wu, C.M. and Kuo, Y.M., 2011. Impact of TQM
and organizational learning on innovation performance in the high-tech
industry. International business review, 20(2), pp.213-225.
Ismyrlis, V., 2017. The contribution of quality tools and integration of quality
management systems to the organization. The TQM Journal, 29(5), pp.677-689.
21
Cătălin, S.H., Bogdan, B. and Dimitrie, G.R., 2014. THE EXISTING BARRIERS IN
IMPLEMENTING TOTAL QUALITY MANAGEMENT. Annals of the University of
Oradea, Economic Science Series, 23(1).
Daud, S. and Yusoff, W.F.W., 2011. The influence of soft and hard TQM factors on
knowledge management: perspective from Malaysia. In International Conference on
Management and Service Science (Vol. 8, pp. 17-22). Singapore: IACSIT Press.
Ferrante, A., Gandolfi, A. and Meneguzzo, M., 2010. Anticipatory strategies for
introducing ISO 26000 in 2010: a comparison between the Italian and Swiss systems of
public administration. Economia Aziendale Online, 1(3), pp.311-321.
Fisher, N.I. and Nair, V.N., 2009. Quality management and quality practice: Perspectives
on their history and their future. Applied Stochastic Models in Business and
Industry, 25(1), pp.1-28.
Fotopoulos, C.B. and Psomas, E.L., 2009. The impact of “soft” and “hard” TQM
elements on quality management results. International Journal of Quality & Reliability
Management, 26(2), pp.150-163.
Green, T.J., 2012. TQM and organisational culture: how do they link?. Total Quality
Management & Business Excellence, 23(2), pp.141-157.
Hung, R.Y.Y., Lien, B.Y.H., Yang, B., Wu, C.M. and Kuo, Y.M., 2011. Impact of TQM
and organizational learning on innovation performance in the high-tech
industry. International business review, 20(2), pp.213-225.
Ismyrlis, V., 2017. The contribution of quality tools and integration of quality
management systems to the organization. The TQM Journal, 29(5), pp.677-689.
Secure Best Marks with AI Grader
Need help grading? Try our AI Grader for instant feedback on your assignments.
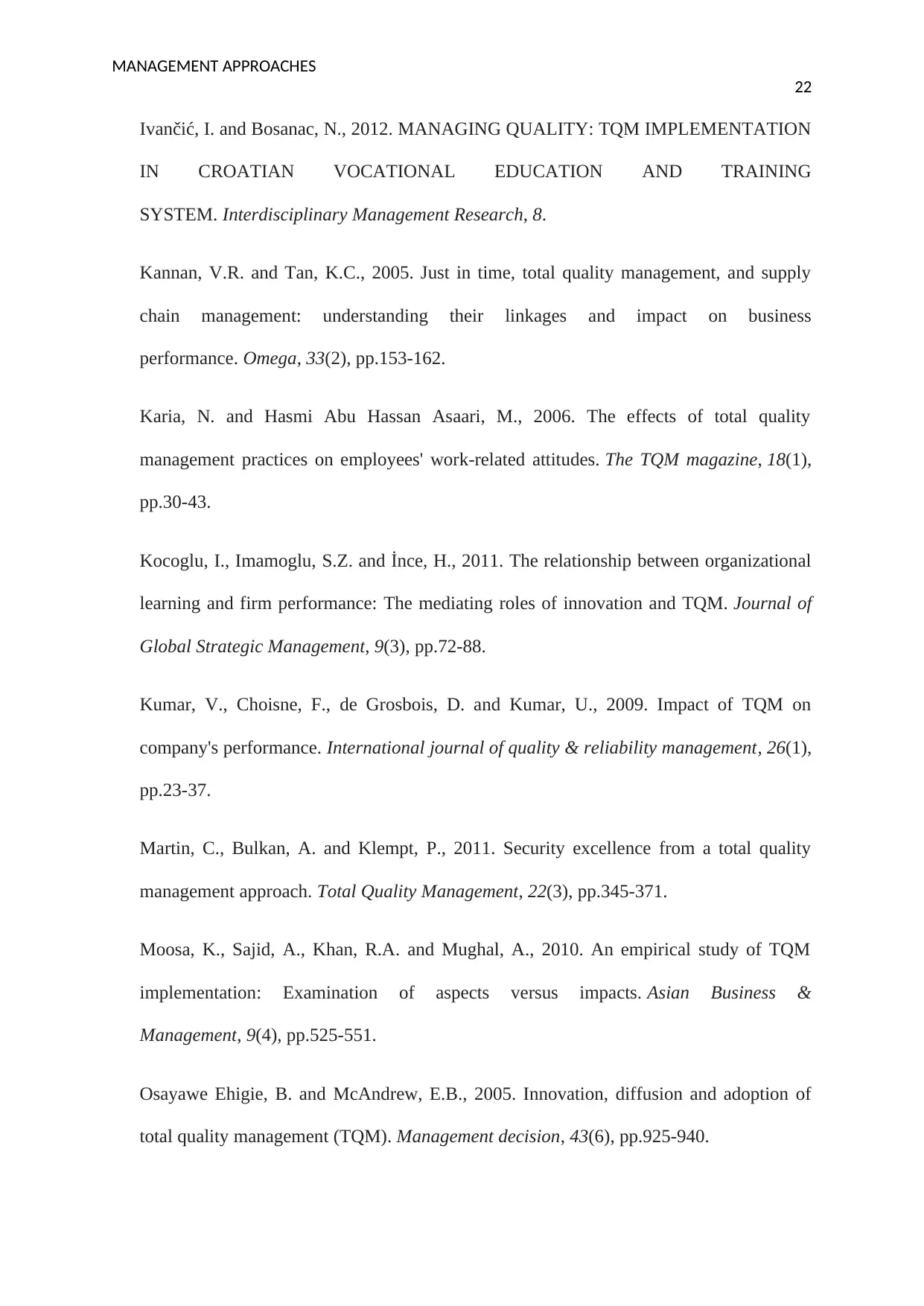
MANAGEMENT APPROACHES
22
Ivančić, I. and Bosanac, N., 2012. MANAGING QUALITY: TQM IMPLEMENTATION
IN CROATIAN VOCATIONAL EDUCATION AND TRAINING
SYSTEM. Interdisciplinary Management Research, 8.
Kannan, V.R. and Tan, K.C., 2005. Just in time, total quality management, and supply
chain management: understanding their linkages and impact on business
performance. Omega, 33(2), pp.153-162.
Karia, N. and Hasmi Abu Hassan Asaari, M., 2006. The effects of total quality
management practices on employees' work-related attitudes. The TQM magazine, 18(1),
pp.30-43.
Kocoglu, I., Imamoglu, S.Z. and İnce, H., 2011. The relationship between organizational
learning and firm performance: The mediating roles of innovation and TQM. Journal of
Global Strategic Management, 9(3), pp.72-88.
Kumar, V., Choisne, F., de Grosbois, D. and Kumar, U., 2009. Impact of TQM on
company's performance. International journal of quality & reliability management, 26(1),
pp.23-37.
Martin, C., Bulkan, A. and Klempt, P., 2011. Security excellence from a total quality
management approach. Total Quality Management, 22(3), pp.345-371.
Moosa, K., Sajid, A., Khan, R.A. and Mughal, A., 2010. An empirical study of TQM
implementation: Examination of aspects versus impacts. Asian Business &
Management, 9(4), pp.525-551.
Osayawe Ehigie, B. and McAndrew, E.B., 2005. Innovation, diffusion and adoption of
total quality management (TQM). Management decision, 43(6), pp.925-940.
22
Ivančić, I. and Bosanac, N., 2012. MANAGING QUALITY: TQM IMPLEMENTATION
IN CROATIAN VOCATIONAL EDUCATION AND TRAINING
SYSTEM. Interdisciplinary Management Research, 8.
Kannan, V.R. and Tan, K.C., 2005. Just in time, total quality management, and supply
chain management: understanding their linkages and impact on business
performance. Omega, 33(2), pp.153-162.
Karia, N. and Hasmi Abu Hassan Asaari, M., 2006. The effects of total quality
management practices on employees' work-related attitudes. The TQM magazine, 18(1),
pp.30-43.
Kocoglu, I., Imamoglu, S.Z. and İnce, H., 2011. The relationship between organizational
learning and firm performance: The mediating roles of innovation and TQM. Journal of
Global Strategic Management, 9(3), pp.72-88.
Kumar, V., Choisne, F., de Grosbois, D. and Kumar, U., 2009. Impact of TQM on
company's performance. International journal of quality & reliability management, 26(1),
pp.23-37.
Martin, C., Bulkan, A. and Klempt, P., 2011. Security excellence from a total quality
management approach. Total Quality Management, 22(3), pp.345-371.
Moosa, K., Sajid, A., Khan, R.A. and Mughal, A., 2010. An empirical study of TQM
implementation: Examination of aspects versus impacts. Asian Business &
Management, 9(4), pp.525-551.
Osayawe Ehigie, B. and McAndrew, E.B., 2005. Innovation, diffusion and adoption of
total quality management (TQM). Management decision, 43(6), pp.925-940.
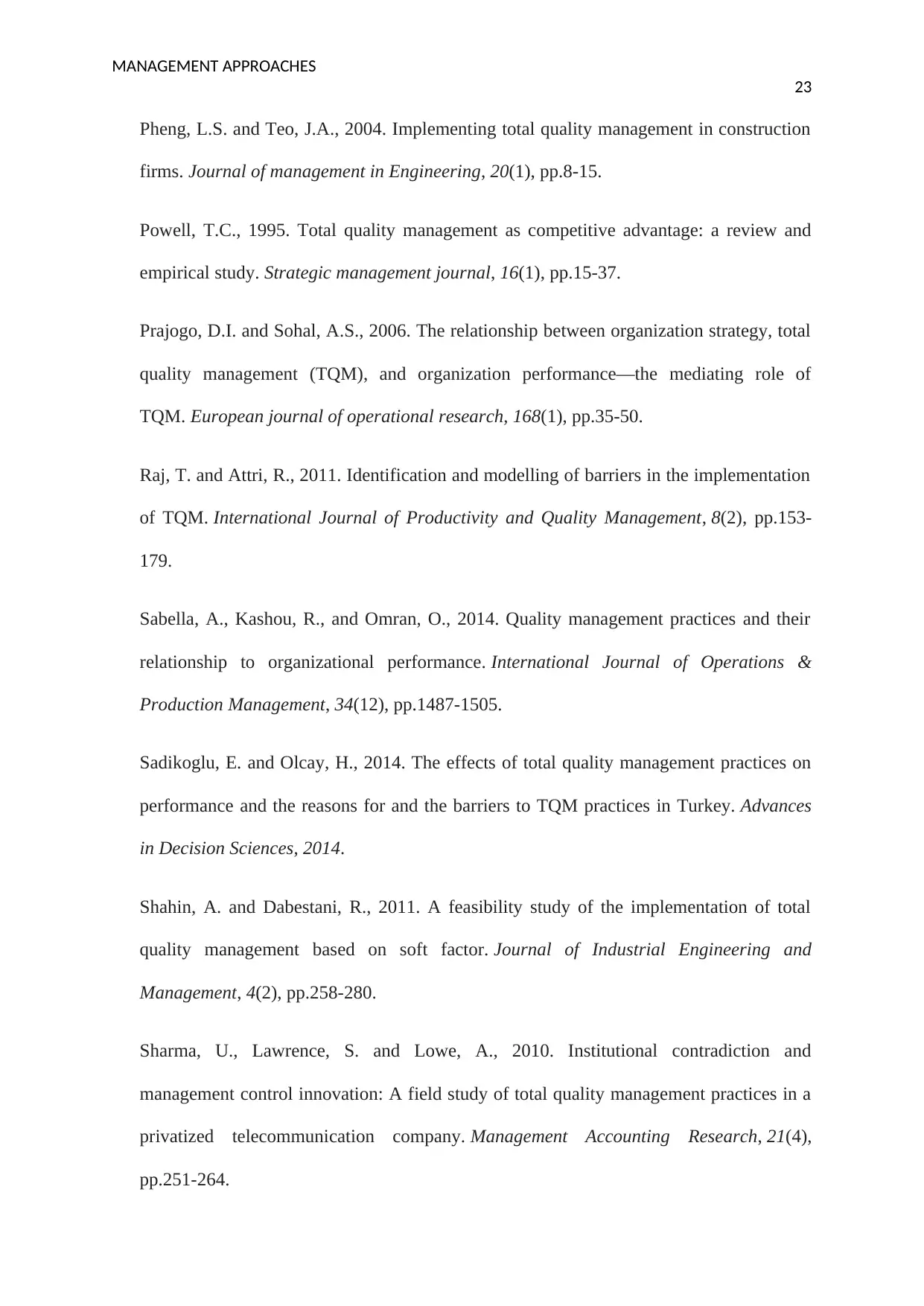
MANAGEMENT APPROACHES
23
Pheng, L.S. and Teo, J.A., 2004. Implementing total quality management in construction
firms. Journal of management in Engineering, 20(1), pp.8-15.
Powell, T.C., 1995. Total quality management as competitive advantage: a review and
empirical study. Strategic management journal, 16(1), pp.15-37.
Prajogo, D.I. and Sohal, A.S., 2006. The relationship between organization strategy, total
quality management (TQM), and organization performance––the mediating role of
TQM. European journal of operational research, 168(1), pp.35-50.
Raj, T. and Attri, R., 2011. Identification and modelling of barriers in the implementation
of TQM. International Journal of Productivity and Quality Management, 8(2), pp.153-
179.
Sabella, A., Kashou, R., and Omran, O., 2014. Quality management practices and their
relationship to organizational performance. International Journal of Operations &
Production Management, 34(12), pp.1487-1505.
Sadikoglu, E. and Olcay, H., 2014. The effects of total quality management practices on
performance and the reasons for and the barriers to TQM practices in Turkey. Advances
in Decision Sciences, 2014.
Shahin, A. and Dabestani, R., 2011. A feasibility study of the implementation of total
quality management based on soft factor. Journal of Industrial Engineering and
Management, 4(2), pp.258-280.
Sharma, U., Lawrence, S. and Lowe, A., 2010. Institutional contradiction and
management control innovation: A field study of total quality management practices in a
privatized telecommunication company. Management Accounting Research, 21(4),
pp.251-264.
23
Pheng, L.S. and Teo, J.A., 2004. Implementing total quality management in construction
firms. Journal of management in Engineering, 20(1), pp.8-15.
Powell, T.C., 1995. Total quality management as competitive advantage: a review and
empirical study. Strategic management journal, 16(1), pp.15-37.
Prajogo, D.I. and Sohal, A.S., 2006. The relationship between organization strategy, total
quality management (TQM), and organization performance––the mediating role of
TQM. European journal of operational research, 168(1), pp.35-50.
Raj, T. and Attri, R., 2011. Identification and modelling of barriers in the implementation
of TQM. International Journal of Productivity and Quality Management, 8(2), pp.153-
179.
Sabella, A., Kashou, R., and Omran, O., 2014. Quality management practices and their
relationship to organizational performance. International Journal of Operations &
Production Management, 34(12), pp.1487-1505.
Sadikoglu, E. and Olcay, H., 2014. The effects of total quality management practices on
performance and the reasons for and the barriers to TQM practices in Turkey. Advances
in Decision Sciences, 2014.
Shahin, A. and Dabestani, R., 2011. A feasibility study of the implementation of total
quality management based on soft factor. Journal of Industrial Engineering and
Management, 4(2), pp.258-280.
Sharma, U., Lawrence, S. and Lowe, A., 2010. Institutional contradiction and
management control innovation: A field study of total quality management practices in a
privatized telecommunication company. Management Accounting Research, 21(4),
pp.251-264.
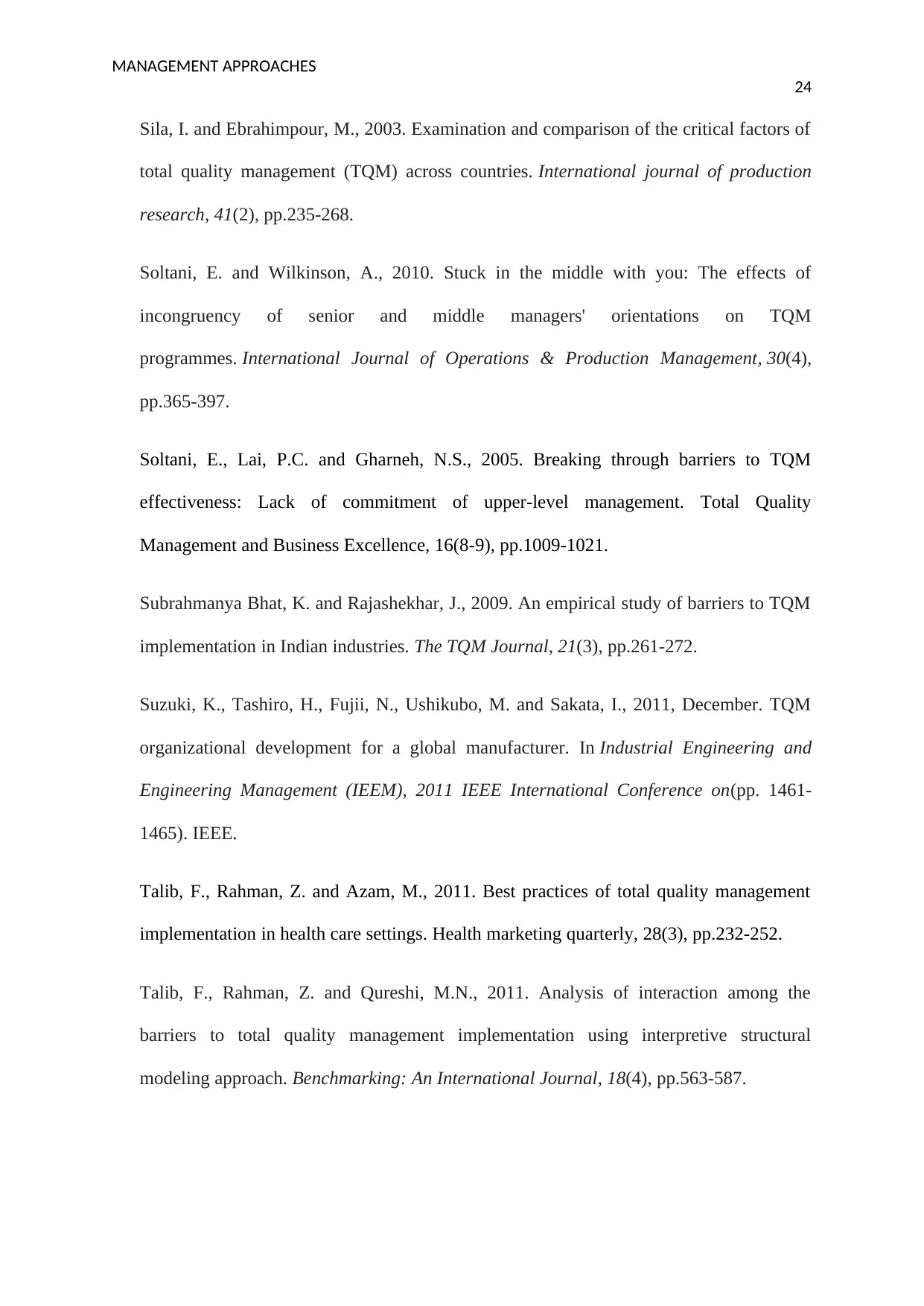
MANAGEMENT APPROACHES
24
Sila, I. and Ebrahimpour, M., 2003. Examination and comparison of the critical factors of
total quality management (TQM) across countries. International journal of production
research, 41(2), pp.235-268.
Soltani, E. and Wilkinson, A., 2010. Stuck in the middle with you: The effects of
incongruency of senior and middle managers' orientations on TQM
programmes. International Journal of Operations & Production Management, 30(4),
pp.365-397.
Soltani, E., Lai, P.C. and Gharneh, N.S., 2005. Breaking through barriers to TQM
effectiveness: Lack of commitment of upper-level management. Total Quality
Management and Business Excellence, 16(8-9), pp.1009-1021.
Subrahmanya Bhat, K. and Rajashekhar, J., 2009. An empirical study of barriers to TQM
implementation in Indian industries. The TQM Journal, 21(3), pp.261-272.
Suzuki, K., Tashiro, H., Fujii, N., Ushikubo, M. and Sakata, I., 2011, December. TQM
organizational development for a global manufacturer. In Industrial Engineering and
Engineering Management (IEEM), 2011 IEEE International Conference on(pp. 1461-
1465). IEEE.
Talib, F., Rahman, Z. and Azam, M., 2011. Best practices of total quality management
implementation in health care settings. Health marketing quarterly, 28(3), pp.232-252.
Talib, F., Rahman, Z. and Qureshi, M.N., 2011. Analysis of interaction among the
barriers to total quality management implementation using interpretive structural
modeling approach. Benchmarking: An International Journal, 18(4), pp.563-587.
24
Sila, I. and Ebrahimpour, M., 2003. Examination and comparison of the critical factors of
total quality management (TQM) across countries. International journal of production
research, 41(2), pp.235-268.
Soltani, E. and Wilkinson, A., 2010. Stuck in the middle with you: The effects of
incongruency of senior and middle managers' orientations on TQM
programmes. International Journal of Operations & Production Management, 30(4),
pp.365-397.
Soltani, E., Lai, P.C. and Gharneh, N.S., 2005. Breaking through barriers to TQM
effectiveness: Lack of commitment of upper-level management. Total Quality
Management and Business Excellence, 16(8-9), pp.1009-1021.
Subrahmanya Bhat, K. and Rajashekhar, J., 2009. An empirical study of barriers to TQM
implementation in Indian industries. The TQM Journal, 21(3), pp.261-272.
Suzuki, K., Tashiro, H., Fujii, N., Ushikubo, M. and Sakata, I., 2011, December. TQM
organizational development for a global manufacturer. In Industrial Engineering and
Engineering Management (IEEM), 2011 IEEE International Conference on(pp. 1461-
1465). IEEE.
Talib, F., Rahman, Z. and Azam, M., 2011. Best practices of total quality management
implementation in health care settings. Health marketing quarterly, 28(3), pp.232-252.
Talib, F., Rahman, Z. and Qureshi, M.N., 2011. Analysis of interaction among the
barriers to total quality management implementation using interpretive structural
modeling approach. Benchmarking: An International Journal, 18(4), pp.563-587.
Paraphrase This Document
Need a fresh take? Get an instant paraphrase of this document with our AI Paraphraser
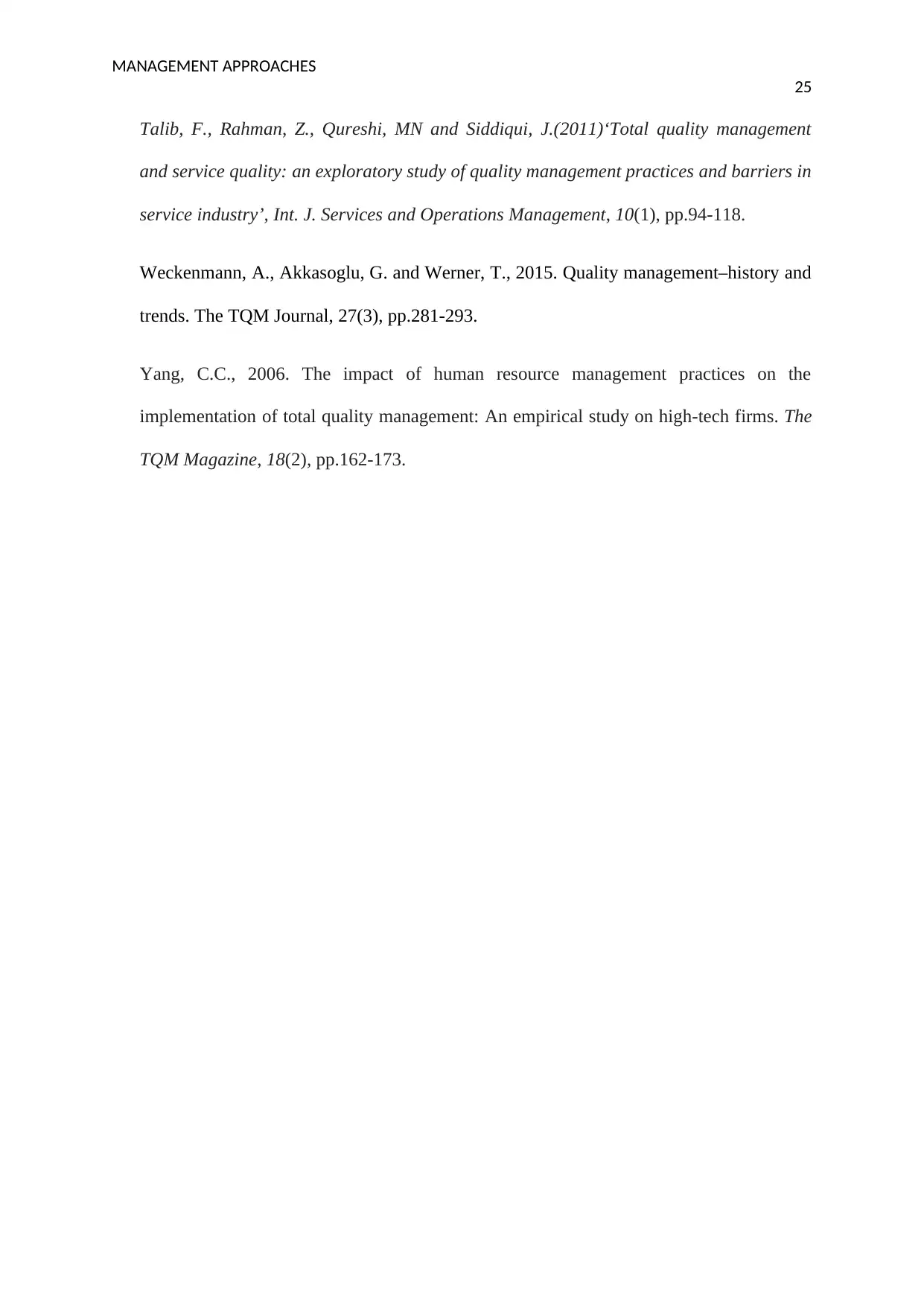
MANAGEMENT APPROACHES
25
Talib, F., Rahman, Z., Qureshi, MN and Siddiqui, J.(2011)‘Total quality management
and service quality: an exploratory study of quality management practices and barriers in
service industry’, Int. J. Services and Operations Management, 10(1), pp.94-118.
Weckenmann, A., Akkasoglu, G. and Werner, T., 2015. Quality management–history and
trends. The TQM Journal, 27(3), pp.281-293.
Yang, C.C., 2006. The impact of human resource management practices on the
implementation of total quality management: An empirical study on high-tech firms. The
TQM Magazine, 18(2), pp.162-173.
25
Talib, F., Rahman, Z., Qureshi, MN and Siddiqui, J.(2011)‘Total quality management
and service quality: an exploratory study of quality management practices and barriers in
service industry’, Int. J. Services and Operations Management, 10(1), pp.94-118.
Weckenmann, A., Akkasoglu, G. and Werner, T., 2015. Quality management–history and
trends. The TQM Journal, 27(3), pp.281-293.
Yang, C.C., 2006. The impact of human resource management practices on the
implementation of total quality management: An empirical study on high-tech firms. The
TQM Magazine, 18(2), pp.162-173.
1 out of 26
Related Documents
![[object Object]](/_next/image/?url=%2F_next%2Fstatic%2Fmedia%2Flogo.6d15ce61.png&w=640&q=75)
Your All-in-One AI-Powered Toolkit for Academic Success.
+13062052269
info@desklib.com
Available 24*7 on WhatsApp / Email
Unlock your academic potential
© 2024 | Zucol Services PVT LTD | All rights reserved.