Sand Casting: Manufacturing Process Investigation
VerifiedAdded on 2023/04/10
|10
|2210
|190
AI Summary
This article provides an in-depth investigation into the manufacturing process of sand casting. It covers the main parameters, characteristics, and properties of sand casting, as well as its advantages and disadvantages. The article also discusses the components produced by sand casting and its impact on surface finish and dimensional accuracy. It is a valuable resource for anyone interested in understanding the intricacies of sand casting.
Contribute Materials
Your contribution can guide someone’s learning journey. Share your
documents today.

Manufacturing Process Investigation
Assignment 1b
Topic: Sand Casting
Name:
MG6044 – Manufacturing Processes and Production 2019
Assignment 1b
Topic: Sand Casting
Name:
MG6044 – Manufacturing Processes and Production 2019
Secure Best Marks with AI Grader
Need help grading? Try our AI Grader for instant feedback on your assignments.

SECTION 1
A brief executive summary of manufacturing processes:
Manufacturing is a word derived from Latin, manu factus which means ‘made by hand”.
Manufacturing is involved with the process of making products. Often these manufactured
products may be used to make other products.
(Kang, 2016) pointed out four different modes of manufacturing
1. Moulding – The most common type of moulding is casting, in which the material is
heated till it becomes a liquid, then filling it into a mould. Once the liquid solidifies,
the mould is removed, giving you the desired shape. There are four other kinds of
moulding are as follows:
a. injection moulding,
b. centrifugal moulding
c. blow moulding,
d. pressure die casting,
2. Machining – as stated by (Rao.P.N., 2013), also known as Subtractive manufacturing
in which tools are used to form or shape solid materials, specifically metals. The final
product is made by removing material from the bulk with the use of tools .
3. Joining – At some point of time one has to join 1 or more products together. Such
processes include mechanical fastening, welding, adhesive bonding, soldering,
brazing, and diffusion bonding
4. Forming and shearing – In these processes the part is primarily deformed by various
processes like forging, drawing, Rolling, extrusion, sheet forming, and moulding.
Figure 1: Different types of metal forming processes
A brief executive summary of manufacturing processes:
Manufacturing is a word derived from Latin, manu factus which means ‘made by hand”.
Manufacturing is involved with the process of making products. Often these manufactured
products may be used to make other products.
(Kang, 2016) pointed out four different modes of manufacturing
1. Moulding – The most common type of moulding is casting, in which the material is
heated till it becomes a liquid, then filling it into a mould. Once the liquid solidifies,
the mould is removed, giving you the desired shape. There are four other kinds of
moulding are as follows:
a. injection moulding,
b. centrifugal moulding
c. blow moulding,
d. pressure die casting,
2. Machining – as stated by (Rao.P.N., 2013), also known as Subtractive manufacturing
in which tools are used to form or shape solid materials, specifically metals. The final
product is made by removing material from the bulk with the use of tools .
3. Joining – At some point of time one has to join 1 or more products together. Such
processes include mechanical fastening, welding, adhesive bonding, soldering,
brazing, and diffusion bonding
4. Forming and shearing – In these processes the part is primarily deformed by various
processes like forging, drawing, Rolling, extrusion, sheet forming, and moulding.
Figure 1: Different types of metal forming processes

In this report we shall discuss about Sand casting which comes under moulding techniques.
Sand casting is the oldest manufacturing method know to mankind. And it has been used to
make products since ages.
(Banchhor, 2014) stated the main reason it is still used today is because of its simplicity, low
cost etc. Sand casting falls under expandable mould type, since once the shape is made it
can be changed unlike permanent mould types, that is where is differs from other
processes.
Sand casting is a very common casting process used in production. The upside of utilizing
sand to make components of metal is that sand is exceptionally impervious to high
temperatures practically all metal casting materials can be sant casted. Sand castings can vary
in size from exceptionally little to very large. At present day a few products made in industry
by sand casting process are engine bloacks, machine bases, barrel heads, pump lodgings, and
valves.
(Groover, 2016) explained the procedure of sand casting in detail, on a perfect floor we will
set the drag box then we will put the pattern in the drag box. We will fill the box with the
sand and press or ram the sand into a mould of the shape of the pattern. We place the cope
box on top of the drag box and fill it with the sand and pressed again after putting all the taper
riser and vent patterns. Now, we lift the cope box and remove the patter and risers. We place
the cope box back and seal it. Next we pour the molten metal in the mould cavity.
Sand casting procedure
Sand casting is the oldest manufacturing method know to mankind. And it has been used to
make products since ages.
(Banchhor, 2014) stated the main reason it is still used today is because of its simplicity, low
cost etc. Sand casting falls under expandable mould type, since once the shape is made it
can be changed unlike permanent mould types, that is where is differs from other
processes.
Sand casting is a very common casting process used in production. The upside of utilizing
sand to make components of metal is that sand is exceptionally impervious to high
temperatures practically all metal casting materials can be sant casted. Sand castings can vary
in size from exceptionally little to very large. At present day a few products made in industry
by sand casting process are engine bloacks, machine bases, barrel heads, pump lodgings, and
valves.
(Groover, 2016) explained the procedure of sand casting in detail, on a perfect floor we will
set the drag box then we will put the pattern in the drag box. We will fill the box with the
sand and press or ram the sand into a mould of the shape of the pattern. We place the cope
box on top of the drag box and fill it with the sand and pressed again after putting all the taper
riser and vent patterns. Now, we lift the cope box and remove the patter and risers. We place
the cope box back and seal it. Next we pour the molten metal in the mould cavity.
Sand casting procedure

(Patel, 2012) showed the significant difference between sand casting and pressure die casting,
is that in sand casting the sand mould after the metal cast part is removed is broken and
reused later. But in die casting the tool used to make the shape of product is a permanent tool
and the same mould is reused every time.
SECTION 2
Main parameters of the Sand casting
Temperature - Sand is porous in nature it is required that the material to be molten and
casted should have very high surface tension so that it does not seep into the sand when
poured in molten form. Thus metals are a choice of material used for sand casting. The
solidification happens at room temperature.
Metals have good fluidity, so when molten metal is poured in to the cavity of the sand casting
it can fill the entire volume provided there is enough metal in riser and reservoir.
Characteristics of the Molten metal are as follows:
• Viscosity - Higher viscosity decreases fluidity
• Surface tension - High surface tension reduces fluidity; often caused by oxide film
• Inclusions - Insoluble particles can increase viscosity, reducing fluidity
• Solidification pattern of the alloy - Fluidity is inversely proportional to the freezing
temperature range
Schematic of Sand Casting setup
is that in sand casting the sand mould after the metal cast part is removed is broken and
reused later. But in die casting the tool used to make the shape of product is a permanent tool
and the same mould is reused every time.
SECTION 2
Main parameters of the Sand casting
Temperature - Sand is porous in nature it is required that the material to be molten and
casted should have very high surface tension so that it does not seep into the sand when
poured in molten form. Thus metals are a choice of material used for sand casting. The
solidification happens at room temperature.
Metals have good fluidity, so when molten metal is poured in to the cavity of the sand casting
it can fill the entire volume provided there is enough metal in riser and reservoir.
Characteristics of the Molten metal are as follows:
• Viscosity - Higher viscosity decreases fluidity
• Surface tension - High surface tension reduces fluidity; often caused by oxide film
• Inclusions - Insoluble particles can increase viscosity, reducing fluidity
• Solidification pattern of the alloy - Fluidity is inversely proportional to the freezing
temperature range
Schematic of Sand Casting setup
Secure Best Marks with AI Grader
Need help grading? Try our AI Grader for instant feedback on your assignments.

Effects of Casting Parameters:
• Mold design - The design and size of the sprue, runners, and risers affect fluidity.
• Mold material and surface - Thermal conductivity and roughness decrease fluidity.
• Superheating - The temperature increment above the melting point increases fluidity.
• Pouring time - Lower pouring rates decrease fluidity because of faster cooling.
• Heat transfer - Affects the viscosity of the metal. .
Sand castings are usually done at foundry shops. The main tooling related to sand
casting is:
• Patterns
• Cope and drag box
• Moulding sand
• Mould cavity
• Runner and riser
• Cast product or the casting.
Patterns are the replica of the final product. In small scale foundry shops, wood is commonly
used as the pattern material.
(Kumar, 2011) said sand is the main component in sand casting, there are few properties that
the sand must have to be fit to be used in sand casting processes.
Zones of shrinkages
• Mold design - The design and size of the sprue, runners, and risers affect fluidity.
• Mold material and surface - Thermal conductivity and roughness decrease fluidity.
• Superheating - The temperature increment above the melting point increases fluidity.
• Pouring time - Lower pouring rates decrease fluidity because of faster cooling.
• Heat transfer - Affects the viscosity of the metal. .
Sand castings are usually done at foundry shops. The main tooling related to sand
casting is:
• Patterns
• Cope and drag box
• Moulding sand
• Mould cavity
• Runner and riser
• Cast product or the casting.
Patterns are the replica of the final product. In small scale foundry shops, wood is commonly
used as the pattern material.
(Kumar, 2011) said sand is the main component in sand casting, there are few properties that
the sand must have to be fit to be used in sand casting processes.
Zones of shrinkages
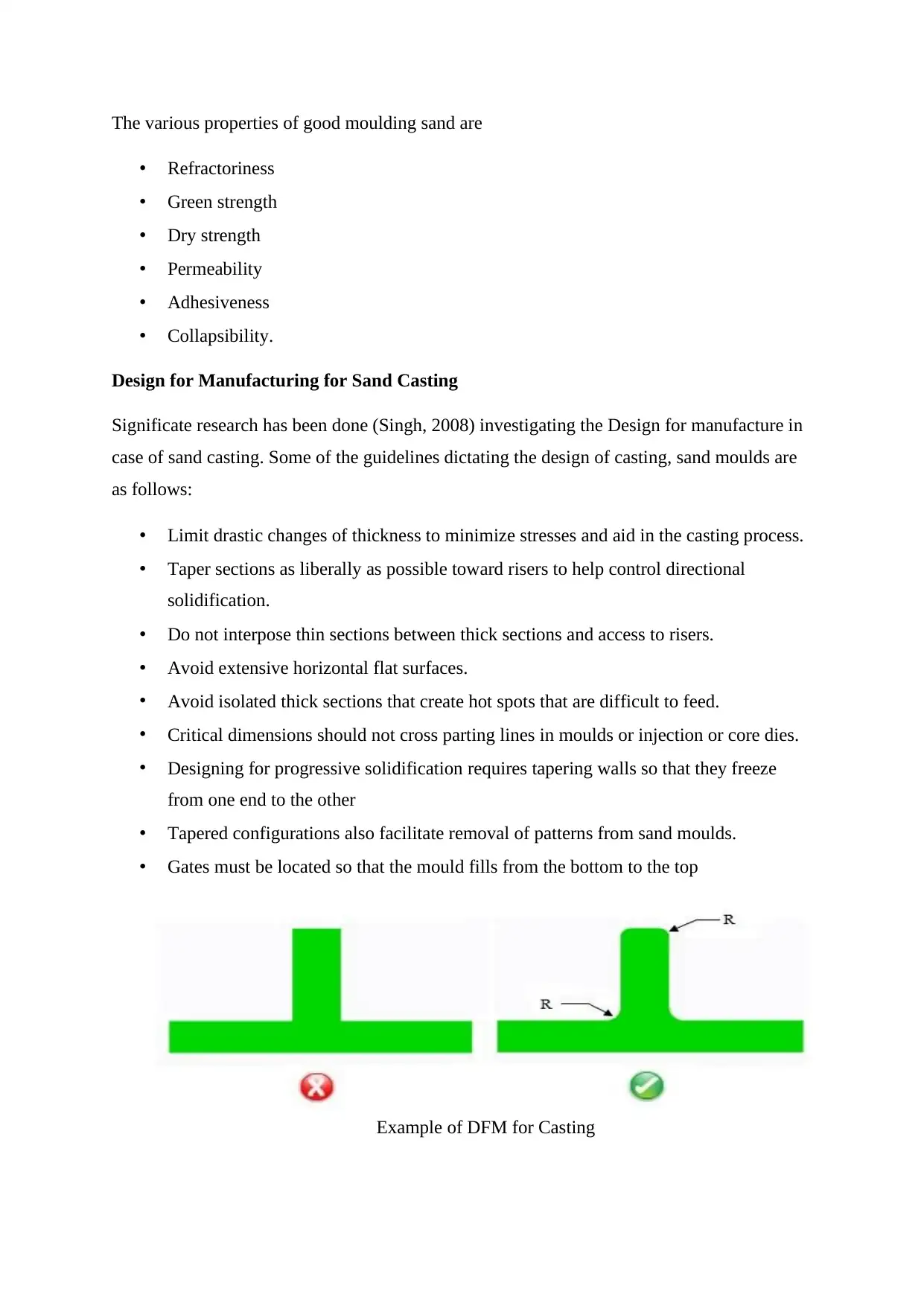
The various properties of good moulding sand are
• Refractoriness
• Green strength
• Dry strength
• Permeability
• Adhesiveness
• Collapsibility.
Design for Manufacturing for Sand Casting
Significate research has been done (Singh, 2008) investigating the Design for manufacture in
case of sand casting. Some of the guidelines dictating the design of casting, sand moulds are
as follows:
• Limit drastic changes of thickness to minimize stresses and aid in the casting process.
• Taper sections as liberally as possible toward risers to help control directional
solidification.
• Do not interpose thin sections between thick sections and access to risers.
• Avoid extensive horizontal flat surfaces.
• Avoid isolated thick sections that create hot spots that are difficult to feed.
• Critical dimensions should not cross parting lines in moulds or injection or core dies.
• Designing for progressive solidification requires tapering walls so that they freeze
from one end to the other
• Tapered configurations also facilitate removal of patterns from sand moulds.
• Gates must be located so that the mould fills from the bottom to the top
Example of DFM for Casting
• Refractoriness
• Green strength
• Dry strength
• Permeability
• Adhesiveness
• Collapsibility.
Design for Manufacturing for Sand Casting
Significate research has been done (Singh, 2008) investigating the Design for manufacture in
case of sand casting. Some of the guidelines dictating the design of casting, sand moulds are
as follows:
• Limit drastic changes of thickness to minimize stresses and aid in the casting process.
• Taper sections as liberally as possible toward risers to help control directional
solidification.
• Do not interpose thin sections between thick sections and access to risers.
• Avoid extensive horizontal flat surfaces.
• Avoid isolated thick sections that create hot spots that are difficult to feed.
• Critical dimensions should not cross parting lines in moulds or injection or core dies.
• Designing for progressive solidification requires tapering walls so that they freeze
from one end to the other
• Tapered configurations also facilitate removal of patterns from sand moulds.
• Gates must be located so that the mould fills from the bottom to the top
Example of DFM for Casting
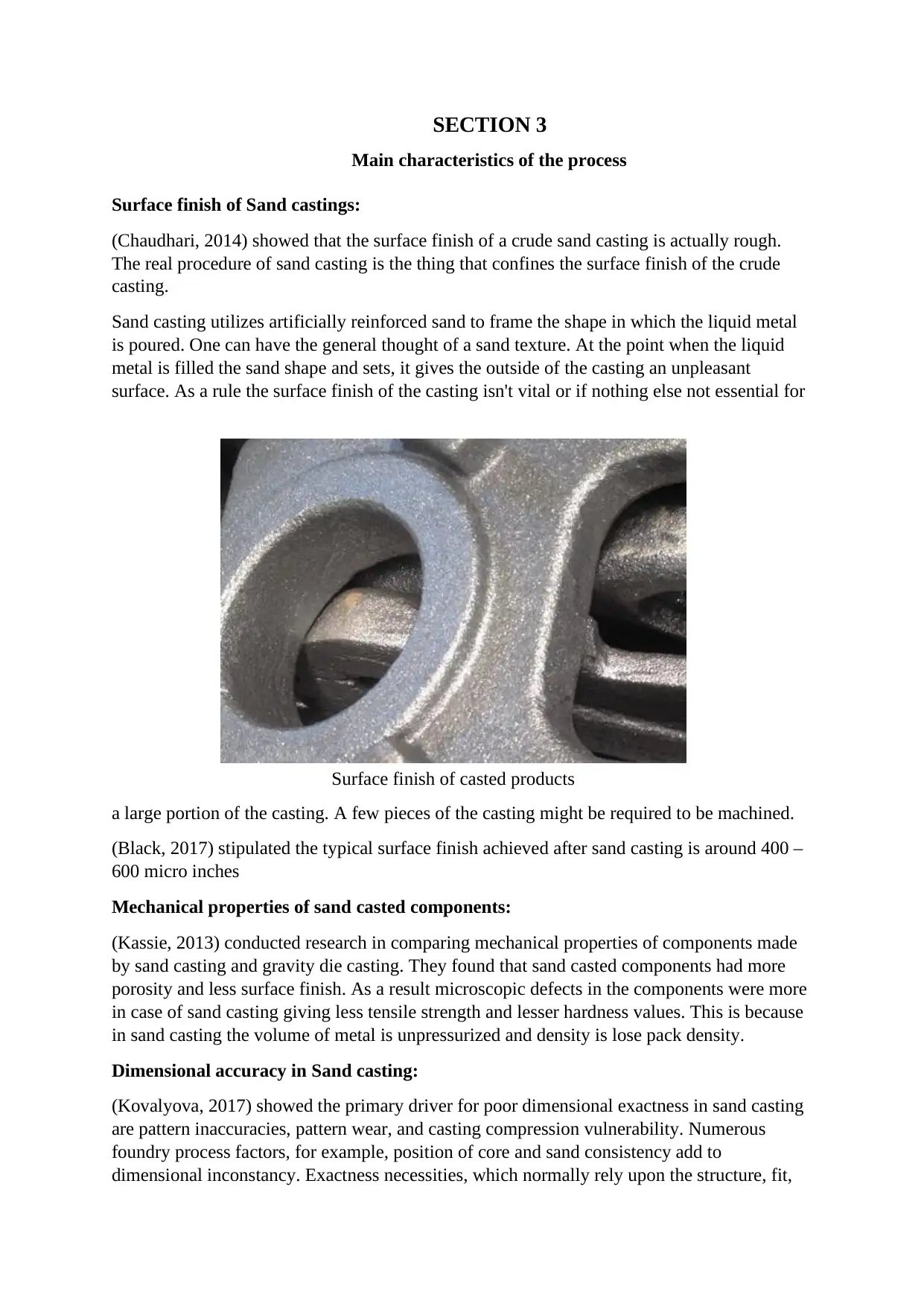
SECTION 3
Main characteristics of the process
Surface finish of Sand castings:
(Chaudhari, 2014) showed that the surface finish of a crude sand casting is actually rough.
The real procedure of sand casting is the thing that confines the surface finish of the crude
casting.
Sand casting utilizes artificially reinforced sand to frame the shape in which the liquid metal
is poured. One can have the general thought of a sand texture. At the point when the liquid
metal is filled the sand shape and sets, it gives the outside of the casting an unpleasant
surface. As a rule the surface finish of the casting isn't vital or if nothing else not essential for
a large portion of the casting. A few pieces of the casting might be required to be machined.
(Black, 2017) stipulated the typical surface finish achieved after sand casting is around 400 –
600 micro inches
Mechanical properties of sand casted components:
(Kassie, 2013) conducted research in comparing mechanical properties of components made
by sand casting and gravity die casting. They found that sand casted components had more
porosity and less surface finish. As a result microscopic defects in the components were more
in case of sand casting giving less tensile strength and lesser hardness values. This is because
in sand casting the volume of metal is unpressurized and density is lose pack density.
Dimensional accuracy in Sand casting:
(Kovalyova, 2017) showed the primary driver for poor dimensional exactness in sand casting
are pattern inaccuracies, pattern wear, and casting compression vulnerability. Numerous
foundry process factors, for example, position of core and sand consistency add to
dimensional inconstancy. Exactness necessities, which normally rely upon the structure, fit,
Surface finish of casted products
Main characteristics of the process
Surface finish of Sand castings:
(Chaudhari, 2014) showed that the surface finish of a crude sand casting is actually rough.
The real procedure of sand casting is the thing that confines the surface finish of the crude
casting.
Sand casting utilizes artificially reinforced sand to frame the shape in which the liquid metal
is poured. One can have the general thought of a sand texture. At the point when the liquid
metal is filled the sand shape and sets, it gives the outside of the casting an unpleasant
surface. As a rule the surface finish of the casting isn't vital or if nothing else not essential for
a large portion of the casting. A few pieces of the casting might be required to be machined.
(Black, 2017) stipulated the typical surface finish achieved after sand casting is around 400 –
600 micro inches
Mechanical properties of sand casted components:
(Kassie, 2013) conducted research in comparing mechanical properties of components made
by sand casting and gravity die casting. They found that sand casted components had more
porosity and less surface finish. As a result microscopic defects in the components were more
in case of sand casting giving less tensile strength and lesser hardness values. This is because
in sand casting the volume of metal is unpressurized and density is lose pack density.
Dimensional accuracy in Sand casting:
(Kovalyova, 2017) showed the primary driver for poor dimensional exactness in sand casting
are pattern inaccuracies, pattern wear, and casting compression vulnerability. Numerous
foundry process factors, for example, position of core and sand consistency add to
dimensional inconstancy. Exactness necessities, which normally rely upon the structure, fit,
Surface finish of casted products
Paraphrase This Document
Need a fresh take? Get an instant paraphrase of this document with our AI Paraphraser

capacity of the casting, are built up as a feature of the casting structure and are determined as
dimensional and structure resistances on the casting drawing.
(Nyembwe, 2012) Accomplished required exactness using rapid prototyping, each
progression of the casting procedure, including tooling structure and creation, shape building,
pouring and solidification, and post treatment of the cast part, must be observed and the
variation controlled.
Lead time in sand casting:
Typical lead time is in many hours and even days. This is because the liquid metal is allowed
to cool at ambient temperatures from its melting point. Lead time will depend upon the
volume of the component, thick and thin sections etc. If the solidification process is
accelerated then chances of defects in casting will also rise.
(Weiss, 2018) showed sand castings can me automated as well with the help of 3D printing.
Flask less sand casting is a variation of sand casting which is automated for high speed output
and consistency.
SECTION 4
Components produced by Sand castings
Some components made by sand casting are:
Engine blocks and manifolds:
Engine blocks are complex in geometry but essentially a single volume body. They can be
made using perishable patterns as pointed out by. (Luo, 2013) The pattern can be made as
complex as required and placed in a space filled with compact sand. Perishable patterns need
not to be removed before the metal is poured.
Gears:
Gears are simple single volume body part
which still involves complex splines and
geometry. The easiest way to make such a
part is to make a replica pattern and use it for
sand casting. By sand casting we can avoid all
the complex machining process and get the
part in one single process.
Machine bases:
Sand casting gives poor surface finish but that
is not a requirement for machine bases.
Machine bases are bulky components
which are heavy and said that there is no
size limitation when it comes to sand
casting; therefore, it is perfect to make huge parts like this.
Sand Casted Products
dimensional and structure resistances on the casting drawing.
(Nyembwe, 2012) Accomplished required exactness using rapid prototyping, each
progression of the casting procedure, including tooling structure and creation, shape building,
pouring and solidification, and post treatment of the cast part, must be observed and the
variation controlled.
Lead time in sand casting:
Typical lead time is in many hours and even days. This is because the liquid metal is allowed
to cool at ambient temperatures from its melting point. Lead time will depend upon the
volume of the component, thick and thin sections etc. If the solidification process is
accelerated then chances of defects in casting will also rise.
(Weiss, 2018) showed sand castings can me automated as well with the help of 3D printing.
Flask less sand casting is a variation of sand casting which is automated for high speed output
and consistency.
SECTION 4
Components produced by Sand castings
Some components made by sand casting are:
Engine blocks and manifolds:
Engine blocks are complex in geometry but essentially a single volume body. They can be
made using perishable patterns as pointed out by. (Luo, 2013) The pattern can be made as
complex as required and placed in a space filled with compact sand. Perishable patterns need
not to be removed before the metal is poured.
Gears:
Gears are simple single volume body part
which still involves complex splines and
geometry. The easiest way to make such a
part is to make a replica pattern and use it for
sand casting. By sand casting we can avoid all
the complex machining process and get the
part in one single process.
Machine bases:
Sand casting gives poor surface finish but that
is not a requirement for machine bases.
Machine bases are bulky components
which are heavy and said that there is no
size limitation when it comes to sand
casting; therefore, it is perfect to make huge parts like this.
Sand Casted Products

SECTION 5
Advantages and disadvantages of Sand casting
Advantages of Sand casting:
• No size limitation of parts
• Bespoke shapes possible
• Plethora of material options
• Low tooling and equipment cost
• All the scraps generated could be recycled
• Lead time reduction with automation.
Disadvantages of Sand casting
• Lower material strength
• High porosity due to lose pack density.
• Poor surface finish and tolerance
• Secondary finishing processes often required to meet specifications
• Low production rate
• High labour cost.
SECTION 6
CONCLUSION
Sand casting is usually applicable in heavy material engineering application like rail,
automobile etc. industries to make components that are made from alloys of iron, cast
iron, bronze etc. In this process the metal is liquefied and used to fill the cavity of a
mould where it solidifies and takes the shape of the cavity, which becomes the
product. Sand casting is adopted as it has a low manufacturing cost and the procedure
is simple. The sand casting process utilizes systems that can make any component of
about any structure, including large parts and those with internal hollow features.
There might be other ideal casting or metalworking options for a particular item, in
view of required constraints, structure complexity, volume, tooling accessibility, or
lead time, however all things considered, a casting in the required setup could be
made utilizing the sand casting.
Advantages and disadvantages of Sand casting
Advantages of Sand casting:
• No size limitation of parts
• Bespoke shapes possible
• Plethora of material options
• Low tooling and equipment cost
• All the scraps generated could be recycled
• Lead time reduction with automation.
Disadvantages of Sand casting
• Lower material strength
• High porosity due to lose pack density.
• Poor surface finish and tolerance
• Secondary finishing processes often required to meet specifications
• Low production rate
• High labour cost.
SECTION 6
CONCLUSION
Sand casting is usually applicable in heavy material engineering application like rail,
automobile etc. industries to make components that are made from alloys of iron, cast
iron, bronze etc. In this process the metal is liquefied and used to fill the cavity of a
mould where it solidifies and takes the shape of the cavity, which becomes the
product. Sand casting is adopted as it has a low manufacturing cost and the procedure
is simple. The sand casting process utilizes systems that can make any component of
about any structure, including large parts and those with internal hollow features.
There might be other ideal casting or metalworking options for a particular item, in
view of required constraints, structure complexity, volume, tooling accessibility, or
lead time, however all things considered, a casting in the required setup could be
made utilizing the sand casting.

SECTION 7
References
Banchhor, R. &. (2014). Optimization in green sand casting process for efficient, economical and
quality casting. Int J Adv Engg Tech/Vol. V/Issue I, 25, 29.
Black, J. T. (2017). DeGarmo's materials and processes in manufacturing. John Wiley & Sons.
Chaudhari, S. &. (2014). Review on analysis of foundry defects for quality improvement of sand
casting. International Journal of Engineering Research and Applications, 615-618.
Groover, M. P. (2016). Automation, production systems, and computer-integrated manufacturing.
Pearson Education India.
Kang, H. S. (2016). Smart manufacturing: Past research, present findings, and future directions.
nternational Journal of Precision Engineering and Manufacturing-Green Technology, 111-
128.
Kassie, A. A. (2013). Minimization of Casting defects. IOSR journal of engineering (IOSRJEN), 31-38.
Kovalyova, T. E. (2017). Enhancing surface roughness of castings when sand-resin mold casting.
Metalurgija, 135-138.
Kumar, S. S. (2011). Optimization of green sand casting process parameters of a foundry by using
Taguchi’s method. The internationa ljournal of advanced manufacturing technology, 23-34.
Luo, A. A. (2013). Magnesium casting technology for structural applications. journal of Magnesium
and Alloys, 2-22.
Nyembwe, K. D. (2012). Assessment of surface finish and dimensional accuracy of tools
manufactured by metal casting in rapid prototyping sand moulds. outh African Journal of
Industrial Engineering, 130-143.
Patel, V. P. (2012). Microstructural and mechanical properties of eutectic Al–Si alloy with grain
refined and modified using gravity-die and sand casting. International Journal of Engineering
Research and Applications, 147-150.
Rao.P.N. (2013). Manufacturing technology: metal cutting and machine tools (Vol. 2). Tata McGraw-
Hill Education.
Singh, K. R. (2008). Junctions in Castings: Simulation-based DFM Analysis and Guidelines. NAE Int.
Conf. on Advances in Manufacturing Technology, 6-8.
Weiss, D. (2018). Advances in the Sand Casting of Aluminium Alloys. Fundamentals of Aluminium
Metallurgy, 159-171.
References
Banchhor, R. &. (2014). Optimization in green sand casting process for efficient, economical and
quality casting. Int J Adv Engg Tech/Vol. V/Issue I, 25, 29.
Black, J. T. (2017). DeGarmo's materials and processes in manufacturing. John Wiley & Sons.
Chaudhari, S. &. (2014). Review on analysis of foundry defects for quality improvement of sand
casting. International Journal of Engineering Research and Applications, 615-618.
Groover, M. P. (2016). Automation, production systems, and computer-integrated manufacturing.
Pearson Education India.
Kang, H. S. (2016). Smart manufacturing: Past research, present findings, and future directions.
nternational Journal of Precision Engineering and Manufacturing-Green Technology, 111-
128.
Kassie, A. A. (2013). Minimization of Casting defects. IOSR journal of engineering (IOSRJEN), 31-38.
Kovalyova, T. E. (2017). Enhancing surface roughness of castings when sand-resin mold casting.
Metalurgija, 135-138.
Kumar, S. S. (2011). Optimization of green sand casting process parameters of a foundry by using
Taguchi’s method. The internationa ljournal of advanced manufacturing technology, 23-34.
Luo, A. A. (2013). Magnesium casting technology for structural applications. journal of Magnesium
and Alloys, 2-22.
Nyembwe, K. D. (2012). Assessment of surface finish and dimensional accuracy of tools
manufactured by metal casting in rapid prototyping sand moulds. outh African Journal of
Industrial Engineering, 130-143.
Patel, V. P. (2012). Microstructural and mechanical properties of eutectic Al–Si alloy with grain
refined and modified using gravity-die and sand casting. International Journal of Engineering
Research and Applications, 147-150.
Rao.P.N. (2013). Manufacturing technology: metal cutting and machine tools (Vol. 2). Tata McGraw-
Hill Education.
Singh, K. R. (2008). Junctions in Castings: Simulation-based DFM Analysis and Guidelines. NAE Int.
Conf. on Advances in Manufacturing Technology, 6-8.
Weiss, D. (2018). Advances in the Sand Casting of Aluminium Alloys. Fundamentals of Aluminium
Metallurgy, 159-171.
1 out of 10
Related Documents
![[object Object]](/_next/image/?url=%2F_next%2Fstatic%2Fmedia%2Flogo.6d15ce61.png&w=640&q=75)
Your All-in-One AI-Powered Toolkit for Academic Success.
+13062052269
info@desklib.com
Available 24*7 on WhatsApp / Email
Unlock your academic potential
© 2024 | Zucol Services PVT LTD | All rights reserved.