Improving Quality of Supply Chain Management
VerifiedAdded on 2020/10/05
|10
|2632
|275
AI Summary
The assignment focuses on improving quality of supply chain management by identifying key factors leading to effective partnerships. It emphasizes the importance of collaboration, open communication, and shared objectives among companies and suppliers to achieve a common goal. The assignment also highlights the need for managing quality of suppliers to ensure timely fulfillment of customer demands.
Contribute Materials
Your contribution can guide someone’s learning journey. Share your
documents today.
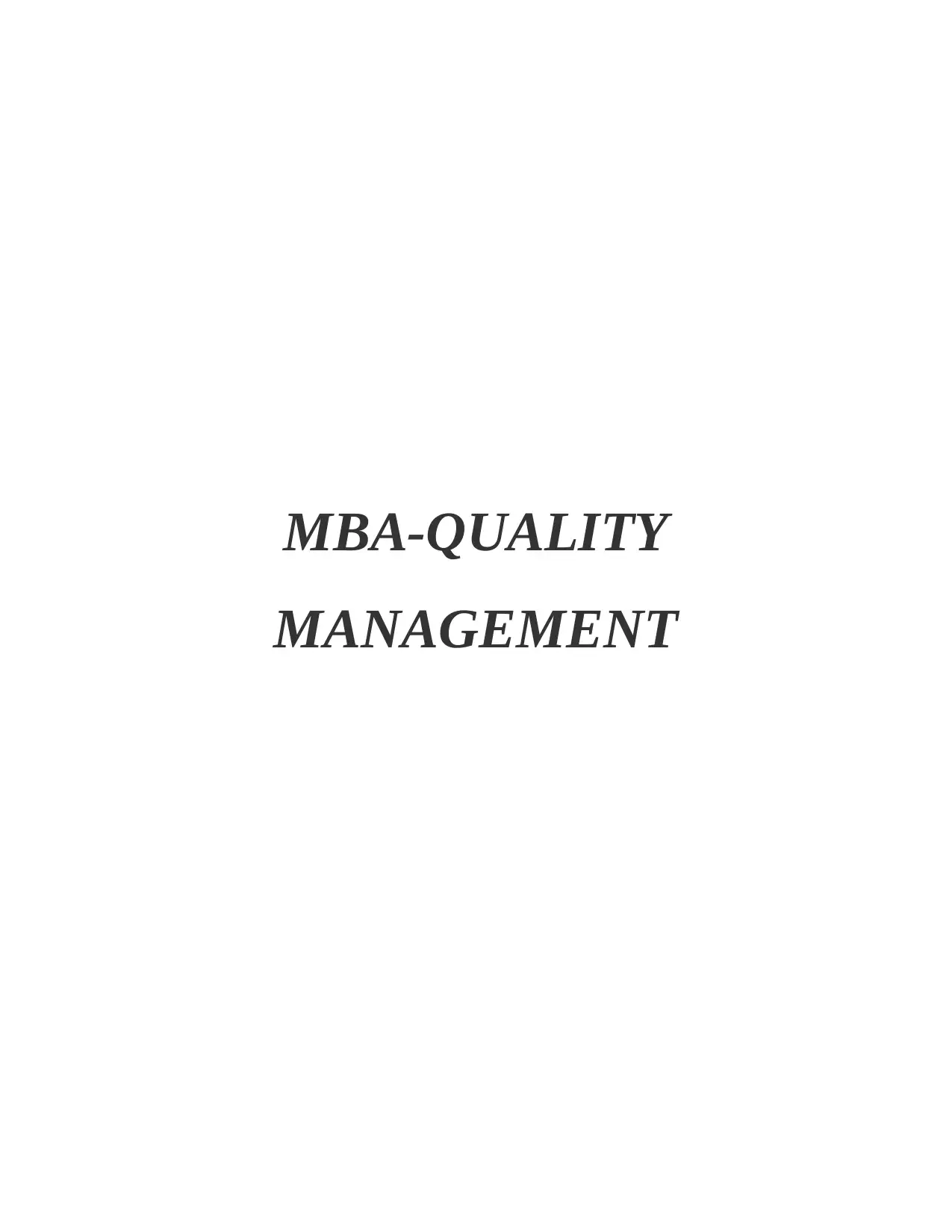
MBA-QUALITY
MANAGEMENT
MANAGEMENT
Secure Best Marks with AI Grader
Need help grading? Try our AI Grader for instant feedback on your assignments.
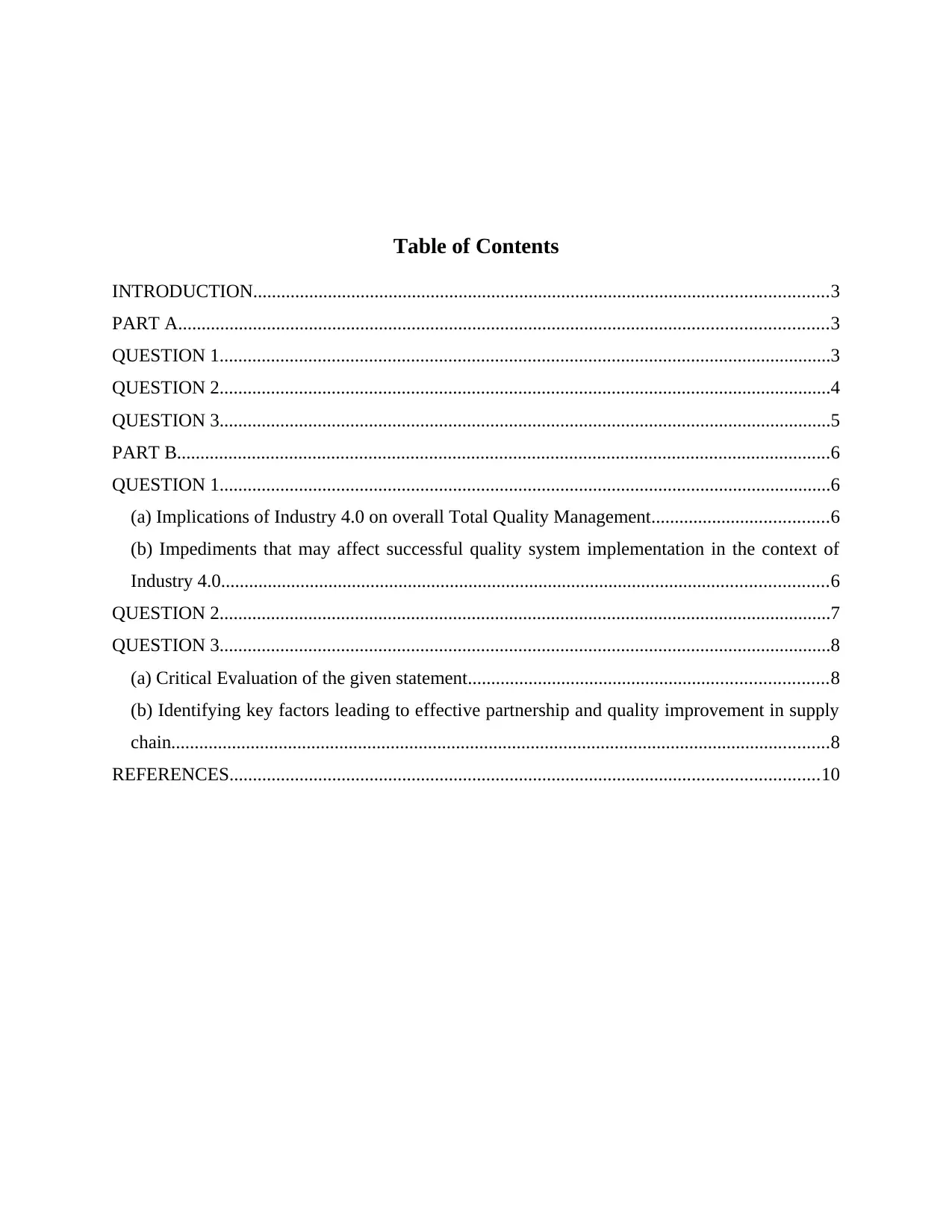
Table of Contents
INTRODUCTION...........................................................................................................................3
PART A...........................................................................................................................................3
QUESTION 1...................................................................................................................................3
QUESTION 2...................................................................................................................................4
QUESTION 3...................................................................................................................................5
PART B............................................................................................................................................6
QUESTION 1...................................................................................................................................6
(a) Implications of Industry 4.0 on overall Total Quality Management......................................6
(b) Impediments that may affect successful quality system implementation in the context of
Industry 4.0..................................................................................................................................6
QUESTION 2...................................................................................................................................7
QUESTION 3...................................................................................................................................8
(a) Critical Evaluation of the given statement.............................................................................8
(b) Identifying key factors leading to effective partnership and quality improvement in supply
chain.............................................................................................................................................8
REFERENCES..............................................................................................................................10
INTRODUCTION...........................................................................................................................3
PART A...........................................................................................................................................3
QUESTION 1...................................................................................................................................3
QUESTION 2...................................................................................................................................4
QUESTION 3...................................................................................................................................5
PART B............................................................................................................................................6
QUESTION 1...................................................................................................................................6
(a) Implications of Industry 4.0 on overall Total Quality Management......................................6
(b) Impediments that may affect successful quality system implementation in the context of
Industry 4.0..................................................................................................................................6
QUESTION 2...................................................................................................................................7
QUESTION 3...................................................................................................................................8
(a) Critical Evaluation of the given statement.............................................................................8
(b) Identifying key factors leading to effective partnership and quality improvement in supply
chain.............................................................................................................................................8
REFERENCES..............................................................................................................................10
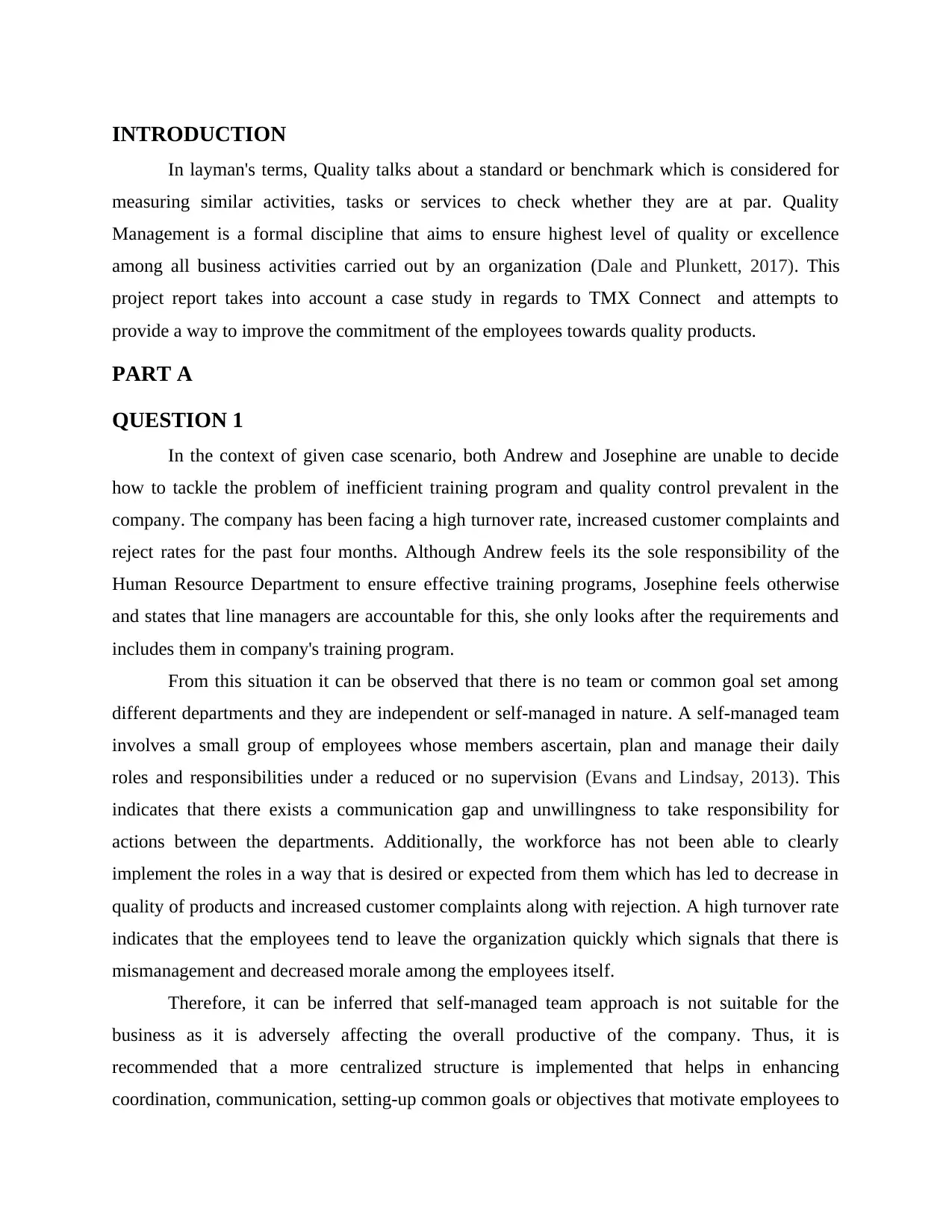
INTRODUCTION
In layman's terms, Quality talks about a standard or benchmark which is considered for
measuring similar activities, tasks or services to check whether they are at par. Quality
Management is a formal discipline that aims to ensure highest level of quality or excellence
among all business activities carried out by an organization (Dale and Plunkett, 2017). This
project report takes into account a case study in regards to TMX Connect and attempts to
provide a way to improve the commitment of the employees towards quality products.
PART A
QUESTION 1
In the context of given case scenario, both Andrew and Josephine are unable to decide
how to tackle the problem of inefficient training program and quality control prevalent in the
company. The company has been facing a high turnover rate, increased customer complaints and
reject rates for the past four months. Although Andrew feels its the sole responsibility of the
Human Resource Department to ensure effective training programs, Josephine feels otherwise
and states that line managers are accountable for this, she only looks after the requirements and
includes them in company's training program.
From this situation it can be observed that there is no team or common goal set among
different departments and they are independent or self-managed in nature. A self-managed team
involves a small group of employees whose members ascertain, plan and manage their daily
roles and responsibilities under a reduced or no supervision (Evans and Lindsay, 2013). This
indicates that there exists a communication gap and unwillingness to take responsibility for
actions between the departments. Additionally, the workforce has not been able to clearly
implement the roles in a way that is desired or expected from them which has led to decrease in
quality of products and increased customer complaints along with rejection. A high turnover rate
indicates that the employees tend to leave the organization quickly which signals that there is
mismanagement and decreased morale among the employees itself.
Therefore, it can be inferred that self-managed team approach is not suitable for the
business as it is adversely affecting the overall productive of the company. Thus, it is
recommended that a more centralized structure is implemented that helps in enhancing
coordination, communication, setting-up common goals or objectives that motivate employees to
In layman's terms, Quality talks about a standard or benchmark which is considered for
measuring similar activities, tasks or services to check whether they are at par. Quality
Management is a formal discipline that aims to ensure highest level of quality or excellence
among all business activities carried out by an organization (Dale and Plunkett, 2017). This
project report takes into account a case study in regards to TMX Connect and attempts to
provide a way to improve the commitment of the employees towards quality products.
PART A
QUESTION 1
In the context of given case scenario, both Andrew and Josephine are unable to decide
how to tackle the problem of inefficient training program and quality control prevalent in the
company. The company has been facing a high turnover rate, increased customer complaints and
reject rates for the past four months. Although Andrew feels its the sole responsibility of the
Human Resource Department to ensure effective training programs, Josephine feels otherwise
and states that line managers are accountable for this, she only looks after the requirements and
includes them in company's training program.
From this situation it can be observed that there is no team or common goal set among
different departments and they are independent or self-managed in nature. A self-managed team
involves a small group of employees whose members ascertain, plan and manage their daily
roles and responsibilities under a reduced or no supervision (Evans and Lindsay, 2013). This
indicates that there exists a communication gap and unwillingness to take responsibility for
actions between the departments. Additionally, the workforce has not been able to clearly
implement the roles in a way that is desired or expected from them which has led to decrease in
quality of products and increased customer complaints along with rejection. A high turnover rate
indicates that the employees tend to leave the organization quickly which signals that there is
mismanagement and decreased morale among the employees itself.
Therefore, it can be inferred that self-managed team approach is not suitable for the
business as it is adversely affecting the overall productive of the company. Thus, it is
recommended that a more centralized structure is implemented that helps in enhancing
coordination, communication, setting-up common goals or objectives that motivate employees to
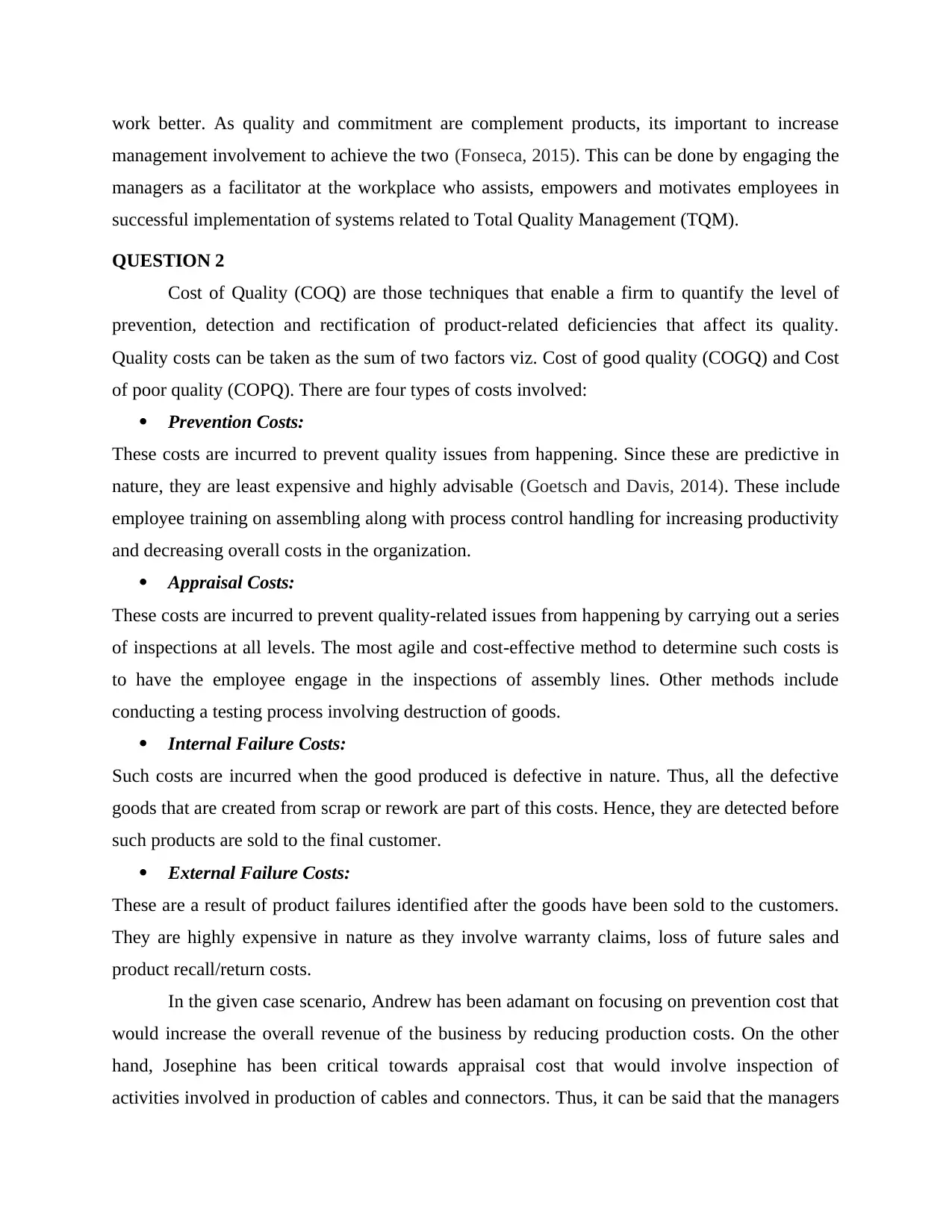
work better. As quality and commitment are complement products, its important to increase
management involvement to achieve the two (Fonseca, 2015). This can be done by engaging the
managers as a facilitator at the workplace who assists, empowers and motivates employees in
successful implementation of systems related to Total Quality Management (TQM).
QUESTION 2
Cost of Quality (COQ) are those techniques that enable a firm to quantify the level of
prevention, detection and rectification of product-related deficiencies that affect its quality.
Quality costs can be taken as the sum of two factors viz. Cost of good quality (COGQ) and Cost
of poor quality (COPQ). There are four types of costs involved:
Prevention Costs:
These costs are incurred to prevent quality issues from happening. Since these are predictive in
nature, they are least expensive and highly advisable (Goetsch and Davis, 2014). These include
employee training on assembling along with process control handling for increasing productivity
and decreasing overall costs in the organization.
Appraisal Costs:
These costs are incurred to prevent quality-related issues from happening by carrying out a series
of inspections at all levels. The most agile and cost-effective method to determine such costs is
to have the employee engage in the inspections of assembly lines. Other methods include
conducting a testing process involving destruction of goods.
Internal Failure Costs:
Such costs are incurred when the good produced is defective in nature. Thus, all the defective
goods that are created from scrap or rework are part of this costs. Hence, they are detected before
such products are sold to the final customer.
External Failure Costs:
These are a result of product failures identified after the goods have been sold to the customers.
They are highly expensive in nature as they involve warranty claims, loss of future sales and
product recall/return costs.
In the given case scenario, Andrew has been adamant on focusing on prevention cost that
would increase the overall revenue of the business by reducing production costs. On the other
hand, Josephine has been critical towards appraisal cost that would involve inspection of
activities involved in production of cables and connectors. Thus, it can be said that the managers
management involvement to achieve the two (Fonseca, 2015). This can be done by engaging the
managers as a facilitator at the workplace who assists, empowers and motivates employees in
successful implementation of systems related to Total Quality Management (TQM).
QUESTION 2
Cost of Quality (COQ) are those techniques that enable a firm to quantify the level of
prevention, detection and rectification of product-related deficiencies that affect its quality.
Quality costs can be taken as the sum of two factors viz. Cost of good quality (COGQ) and Cost
of poor quality (COPQ). There are four types of costs involved:
Prevention Costs:
These costs are incurred to prevent quality issues from happening. Since these are predictive in
nature, they are least expensive and highly advisable (Goetsch and Davis, 2014). These include
employee training on assembling along with process control handling for increasing productivity
and decreasing overall costs in the organization.
Appraisal Costs:
These costs are incurred to prevent quality-related issues from happening by carrying out a series
of inspections at all levels. The most agile and cost-effective method to determine such costs is
to have the employee engage in the inspections of assembly lines. Other methods include
conducting a testing process involving destruction of goods.
Internal Failure Costs:
Such costs are incurred when the good produced is defective in nature. Thus, all the defective
goods that are created from scrap or rework are part of this costs. Hence, they are detected before
such products are sold to the final customer.
External Failure Costs:
These are a result of product failures identified after the goods have been sold to the customers.
They are highly expensive in nature as they involve warranty claims, loss of future sales and
product recall/return costs.
In the given case scenario, Andrew has been adamant on focusing on prevention cost that
would increase the overall revenue of the business by reducing production costs. On the other
hand, Josephine has been critical towards appraisal cost that would involve inspection of
activities involved in production of cables and connectors. Thus, it can be said that the managers
Secure Best Marks with AI Grader
Need help grading? Try our AI Grader for instant feedback on your assignments.
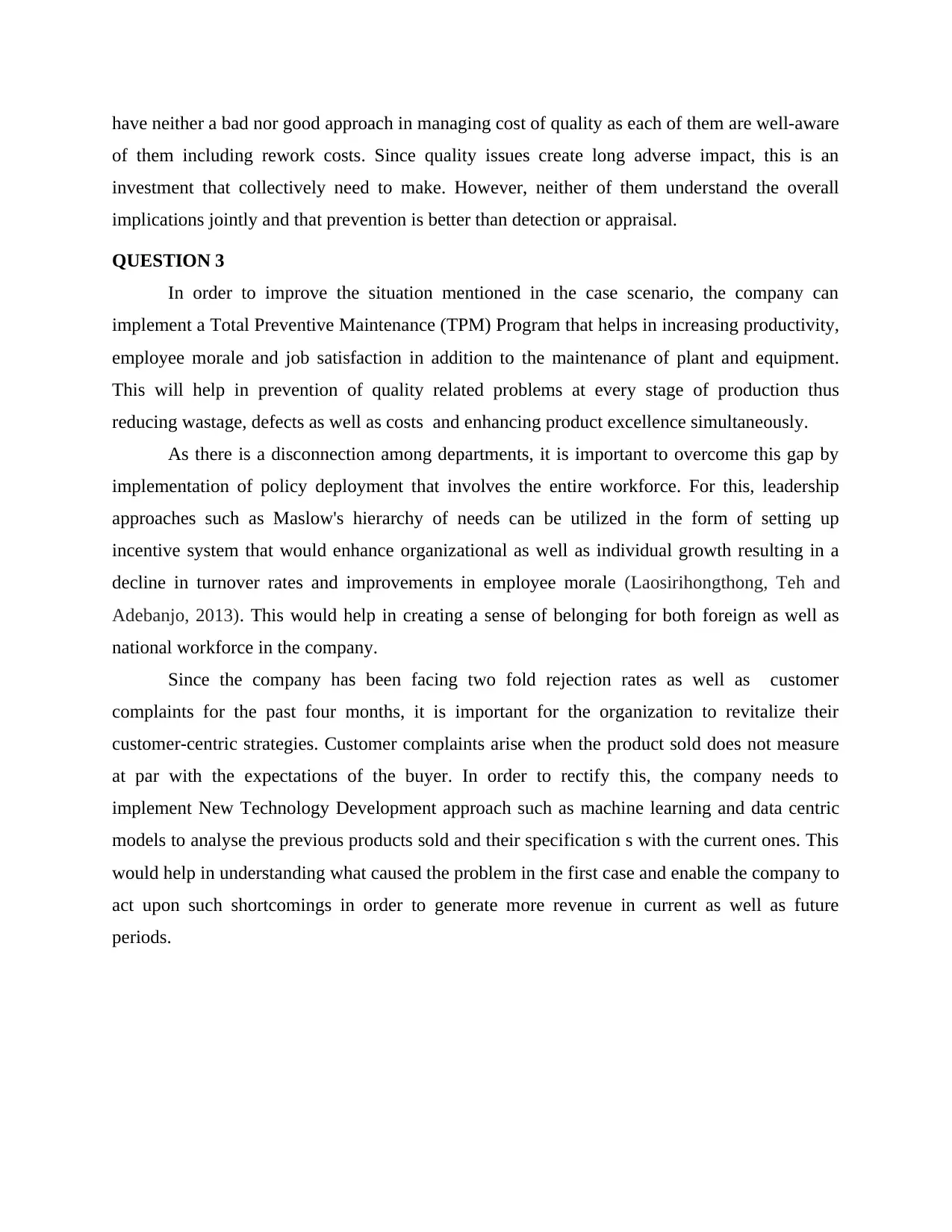
have neither a bad nor good approach in managing cost of quality as each of them are well-aware
of them including rework costs. Since quality issues create long adverse impact, this is an
investment that collectively need to make. However, neither of them understand the overall
implications jointly and that prevention is better than detection or appraisal.
QUESTION 3
In order to improve the situation mentioned in the case scenario, the company can
implement a Total Preventive Maintenance (TPM) Program that helps in increasing productivity,
employee morale and job satisfaction in addition to the maintenance of plant and equipment.
This will help in prevention of quality related problems at every stage of production thus
reducing wastage, defects as well as costs and enhancing product excellence simultaneously.
As there is a disconnection among departments, it is important to overcome this gap by
implementation of policy deployment that involves the entire workforce. For this, leadership
approaches such as Maslow's hierarchy of needs can be utilized in the form of setting up
incentive system that would enhance organizational as well as individual growth resulting in a
decline in turnover rates and improvements in employee morale (Laosirihongthong, Teh and
Adebanjo, 2013). This would help in creating a sense of belonging for both foreign as well as
national workforce in the company.
Since the company has been facing two fold rejection rates as well as customer
complaints for the past four months, it is important for the organization to revitalize their
customer-centric strategies. Customer complaints arise when the product sold does not measure
at par with the expectations of the buyer. In order to rectify this, the company needs to
implement New Technology Development approach such as machine learning and data centric
models to analyse the previous products sold and their specification s with the current ones. This
would help in understanding what caused the problem in the first case and enable the company to
act upon such shortcomings in order to generate more revenue in current as well as future
periods.
of them including rework costs. Since quality issues create long adverse impact, this is an
investment that collectively need to make. However, neither of them understand the overall
implications jointly and that prevention is better than detection or appraisal.
QUESTION 3
In order to improve the situation mentioned in the case scenario, the company can
implement a Total Preventive Maintenance (TPM) Program that helps in increasing productivity,
employee morale and job satisfaction in addition to the maintenance of plant and equipment.
This will help in prevention of quality related problems at every stage of production thus
reducing wastage, defects as well as costs and enhancing product excellence simultaneously.
As there is a disconnection among departments, it is important to overcome this gap by
implementation of policy deployment that involves the entire workforce. For this, leadership
approaches such as Maslow's hierarchy of needs can be utilized in the form of setting up
incentive system that would enhance organizational as well as individual growth resulting in a
decline in turnover rates and improvements in employee morale (Laosirihongthong, Teh and
Adebanjo, 2013). This would help in creating a sense of belonging for both foreign as well as
national workforce in the company.
Since the company has been facing two fold rejection rates as well as customer
complaints for the past four months, it is important for the organization to revitalize their
customer-centric strategies. Customer complaints arise when the product sold does not measure
at par with the expectations of the buyer. In order to rectify this, the company needs to
implement New Technology Development approach such as machine learning and data centric
models to analyse the previous products sold and their specification s with the current ones. This
would help in understanding what caused the problem in the first case and enable the company to
act upon such shortcomings in order to generate more revenue in current as well as future
periods.
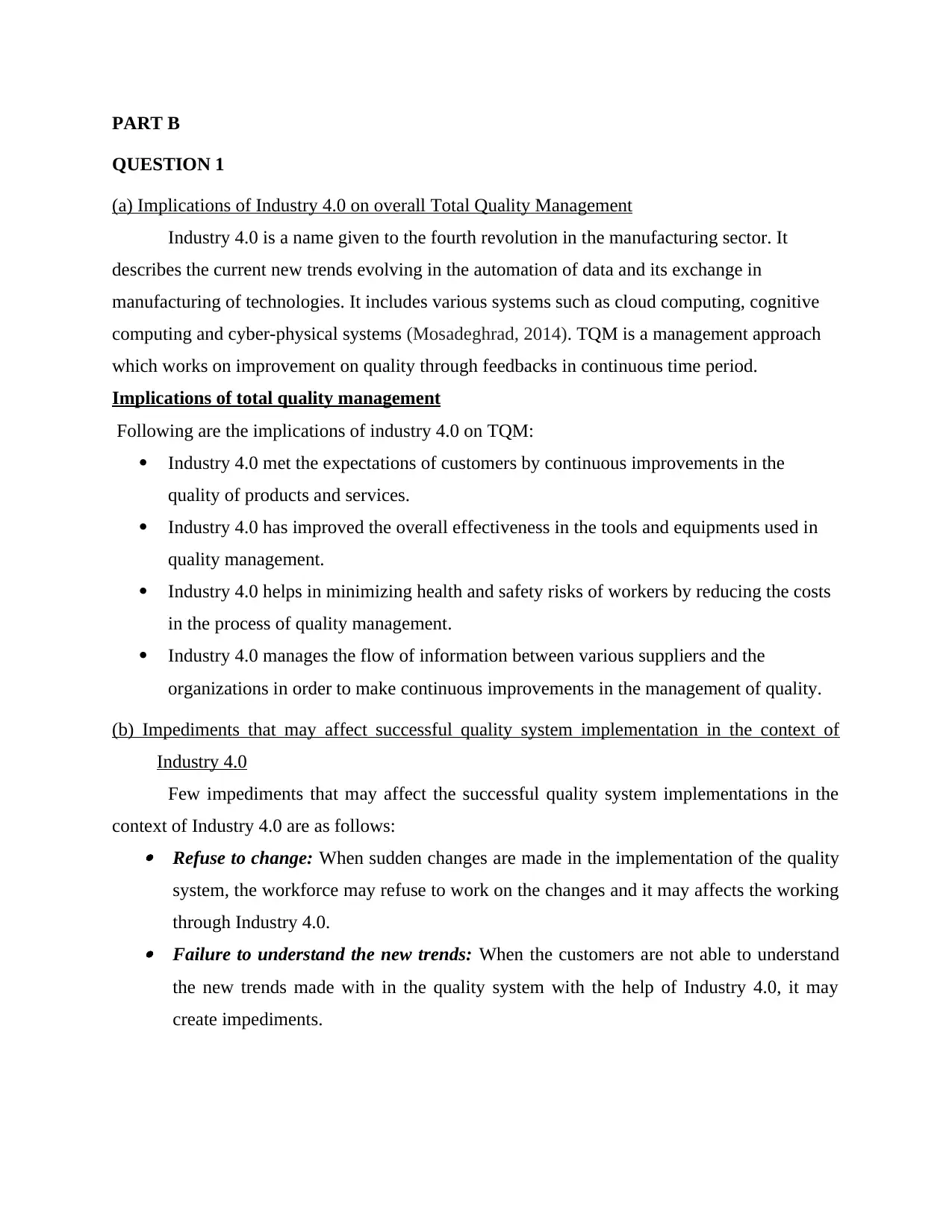
PART B
QUESTION 1
(a) Implications of Industry 4.0 on overall Total Quality Management
Industry 4.0 is a name given to the fourth revolution in the manufacturing sector. It
describes the current new trends evolving in the automation of data and its exchange in
manufacturing of technologies. It includes various systems such as cloud computing, cognitive
computing and cyber-physical systems (Mosadeghrad, 2014). TQM is a management approach
which works on improvement on quality through feedbacks in continuous time period.
Implications of total quality management
Following are the implications of industry 4.0 on TQM:
Industry 4.0 met the expectations of customers by continuous improvements in the
quality of products and services.
Industry 4.0 has improved the overall effectiveness in the tools and equipments used in
quality management.
Industry 4.0 helps in minimizing health and safety risks of workers by reducing the costs
in the process of quality management.
Industry 4.0 manages the flow of information between various suppliers and the
organizations in order to make continuous improvements in the management of quality.
(b) Impediments that may affect successful quality system implementation in the context of
Industry 4.0
Few impediments that may affect the successful quality system implementations in the
context of Industry 4.0 are as follows: Refuse to change: When sudden changes are made in the implementation of the quality
system, the workforce may refuse to work on the changes and it may affects the working
through Industry 4.0. Failure to understand the new trends: When the customers are not able to understand
the new trends made with in the quality system with the help of Industry 4.0, it may
create impediments.
QUESTION 1
(a) Implications of Industry 4.0 on overall Total Quality Management
Industry 4.0 is a name given to the fourth revolution in the manufacturing sector. It
describes the current new trends evolving in the automation of data and its exchange in
manufacturing of technologies. It includes various systems such as cloud computing, cognitive
computing and cyber-physical systems (Mosadeghrad, 2014). TQM is a management approach
which works on improvement on quality through feedbacks in continuous time period.
Implications of total quality management
Following are the implications of industry 4.0 on TQM:
Industry 4.0 met the expectations of customers by continuous improvements in the
quality of products and services.
Industry 4.0 has improved the overall effectiveness in the tools and equipments used in
quality management.
Industry 4.0 helps in minimizing health and safety risks of workers by reducing the costs
in the process of quality management.
Industry 4.0 manages the flow of information between various suppliers and the
organizations in order to make continuous improvements in the management of quality.
(b) Impediments that may affect successful quality system implementation in the context of
Industry 4.0
Few impediments that may affect the successful quality system implementations in the
context of Industry 4.0 are as follows: Refuse to change: When sudden changes are made in the implementation of the quality
system, the workforce may refuse to work on the changes and it may affects the working
through Industry 4.0. Failure to understand the new trends: When the customers are not able to understand
the new trends made with in the quality system with the help of Industry 4.0, it may
create impediments.
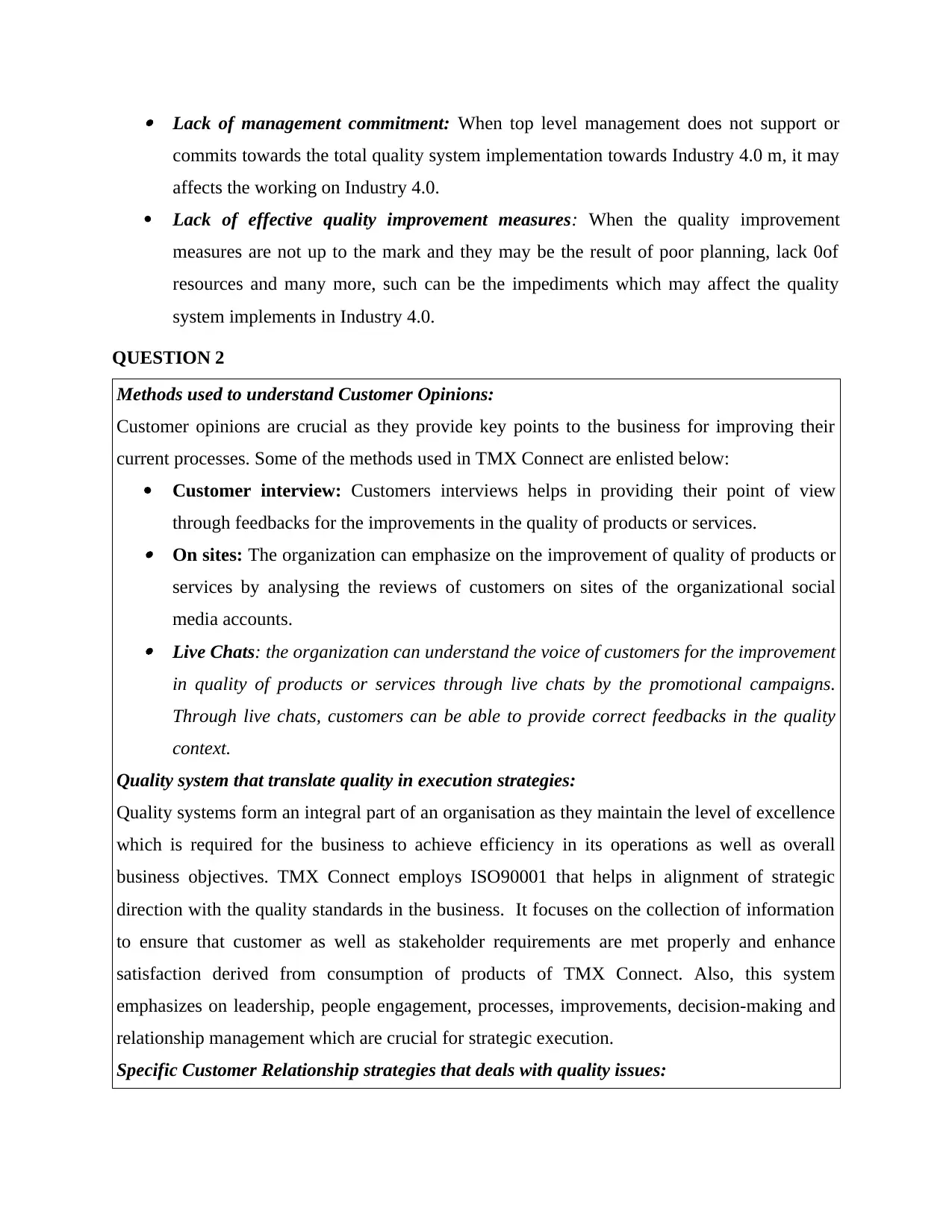
Lack of management commitment: When top level management does not support or
commits towards the total quality system implementation towards Industry 4.0 m, it may
affects the working on Industry 4.0.
Lack of effective quality improvement measures: When the quality improvement
measures are not up to the mark and they may be the result of poor planning, lack 0of
resources and many more, such can be the impediments which may affect the quality
system implements in Industry 4.0.
QUESTION 2
Methods used to understand Customer Opinions:
Customer opinions are crucial as they provide key points to the business for improving their
current processes. Some of the methods used in TMX Connect are enlisted below:
Customer interview: Customers interviews helps in providing their point of view
through feedbacks for the improvements in the quality of products or services. On sites: The organization can emphasize on the improvement of quality of products or
services by analysing the reviews of customers on sites of the organizational social
media accounts. Live Chats: the organization can understand the voice of customers for the improvement
in quality of products or services through live chats by the promotional campaigns.
Through live chats, customers can be able to provide correct feedbacks in the quality
context.
Quality system that translate quality in execution strategies:
Quality systems form an integral part of an organisation as they maintain the level of excellence
which is required for the business to achieve efficiency in its operations as well as overall
business objectives. TMX Connect employs ISO90001 that helps in alignment of strategic
direction with the quality standards in the business. It focuses on the collection of information
to ensure that customer as well as stakeholder requirements are met properly and enhance
satisfaction derived from consumption of products of TMX Connect. Also, this system
emphasizes on leadership, people engagement, processes, improvements, decision-making and
relationship management which are crucial for strategic execution.
Specific Customer Relationship strategies that deals with quality issues:
commits towards the total quality system implementation towards Industry 4.0 m, it may
affects the working on Industry 4.0.
Lack of effective quality improvement measures: When the quality improvement
measures are not up to the mark and they may be the result of poor planning, lack 0of
resources and many more, such can be the impediments which may affect the quality
system implements in Industry 4.0.
QUESTION 2
Methods used to understand Customer Opinions:
Customer opinions are crucial as they provide key points to the business for improving their
current processes. Some of the methods used in TMX Connect are enlisted below:
Customer interview: Customers interviews helps in providing their point of view
through feedbacks for the improvements in the quality of products or services. On sites: The organization can emphasize on the improvement of quality of products or
services by analysing the reviews of customers on sites of the organizational social
media accounts. Live Chats: the organization can understand the voice of customers for the improvement
in quality of products or services through live chats by the promotional campaigns.
Through live chats, customers can be able to provide correct feedbacks in the quality
context.
Quality system that translate quality in execution strategies:
Quality systems form an integral part of an organisation as they maintain the level of excellence
which is required for the business to achieve efficiency in its operations as well as overall
business objectives. TMX Connect employs ISO90001 that helps in alignment of strategic
direction with the quality standards in the business. It focuses on the collection of information
to ensure that customer as well as stakeholder requirements are met properly and enhance
satisfaction derived from consumption of products of TMX Connect. Also, this system
emphasizes on leadership, people engagement, processes, improvements, decision-making and
relationship management which are crucial for strategic execution.
Specific Customer Relationship strategies that deals with quality issues:
Paraphrase This Document
Need a fresh take? Get an instant paraphrase of this document with our AI Paraphraser
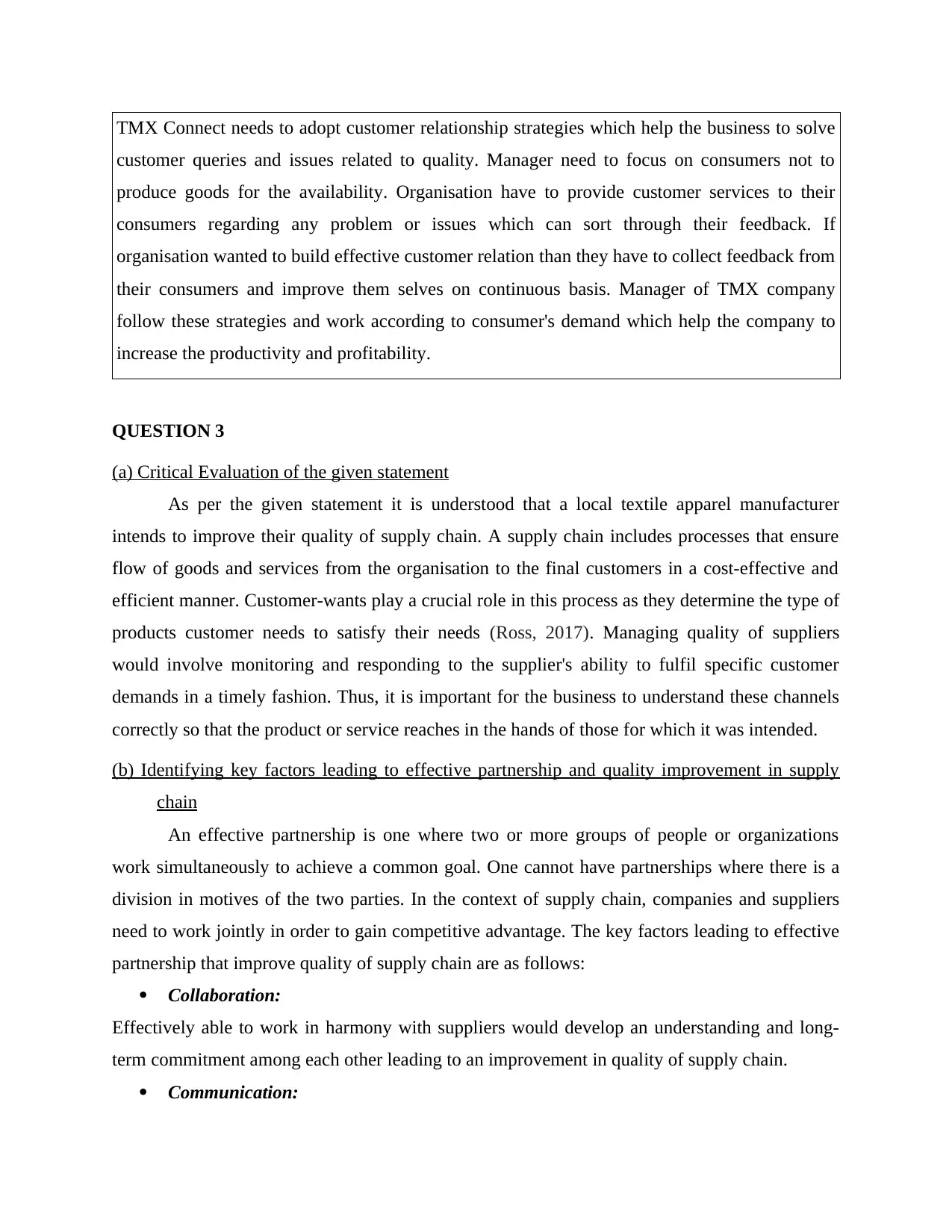
TMX Connect needs to adopt customer relationship strategies which help the business to solve
customer queries and issues related to quality. Manager need to focus on consumers not to
produce goods for the availability. Organisation have to provide customer services to their
consumers regarding any problem or issues which can sort through their feedback. If
organisation wanted to build effective customer relation than they have to collect feedback from
their consumers and improve them selves on continuous basis. Manager of TMX company
follow these strategies and work according to consumer's demand which help the company to
increase the productivity and profitability.
QUESTION 3
(a) Critical Evaluation of the given statement
As per the given statement it is understood that a local textile apparel manufacturer
intends to improve their quality of supply chain. A supply chain includes processes that ensure
flow of goods and services from the organisation to the final customers in a cost-effective and
efficient manner. Customer-wants play a crucial role in this process as they determine the type of
products customer needs to satisfy their needs (Ross, 2017). Managing quality of suppliers
would involve monitoring and responding to the supplier's ability to fulfil specific customer
demands in a timely fashion. Thus, it is important for the business to understand these channels
correctly so that the product or service reaches in the hands of those for which it was intended.
(b) Identifying key factors leading to effective partnership and quality improvement in supply
chain
An effective partnership is one where two or more groups of people or organizations
work simultaneously to achieve a common goal. One cannot have partnerships where there is a
division in motives of the two parties. In the context of supply chain, companies and suppliers
need to work jointly in order to gain competitive advantage. The key factors leading to effective
partnership that improve quality of supply chain are as follows:
Collaboration:
Effectively able to work in harmony with suppliers would develop an understanding and long-
term commitment among each other leading to an improvement in quality of supply chain.
Communication:
customer queries and issues related to quality. Manager need to focus on consumers not to
produce goods for the availability. Organisation have to provide customer services to their
consumers regarding any problem or issues which can sort through their feedback. If
organisation wanted to build effective customer relation than they have to collect feedback from
their consumers and improve them selves on continuous basis. Manager of TMX company
follow these strategies and work according to consumer's demand which help the company to
increase the productivity and profitability.
QUESTION 3
(a) Critical Evaluation of the given statement
As per the given statement it is understood that a local textile apparel manufacturer
intends to improve their quality of supply chain. A supply chain includes processes that ensure
flow of goods and services from the organisation to the final customers in a cost-effective and
efficient manner. Customer-wants play a crucial role in this process as they determine the type of
products customer needs to satisfy their needs (Ross, 2017). Managing quality of suppliers
would involve monitoring and responding to the supplier's ability to fulfil specific customer
demands in a timely fashion. Thus, it is important for the business to understand these channels
correctly so that the product or service reaches in the hands of those for which it was intended.
(b) Identifying key factors leading to effective partnership and quality improvement in supply
chain
An effective partnership is one where two or more groups of people or organizations
work simultaneously to achieve a common goal. One cannot have partnerships where there is a
division in motives of the two parties. In the context of supply chain, companies and suppliers
need to work jointly in order to gain competitive advantage. The key factors leading to effective
partnership that improve quality of supply chain are as follows:
Collaboration:
Effectively able to work in harmony with suppliers would develop an understanding and long-
term commitment among each other leading to an improvement in quality of supply chain.
Communication:
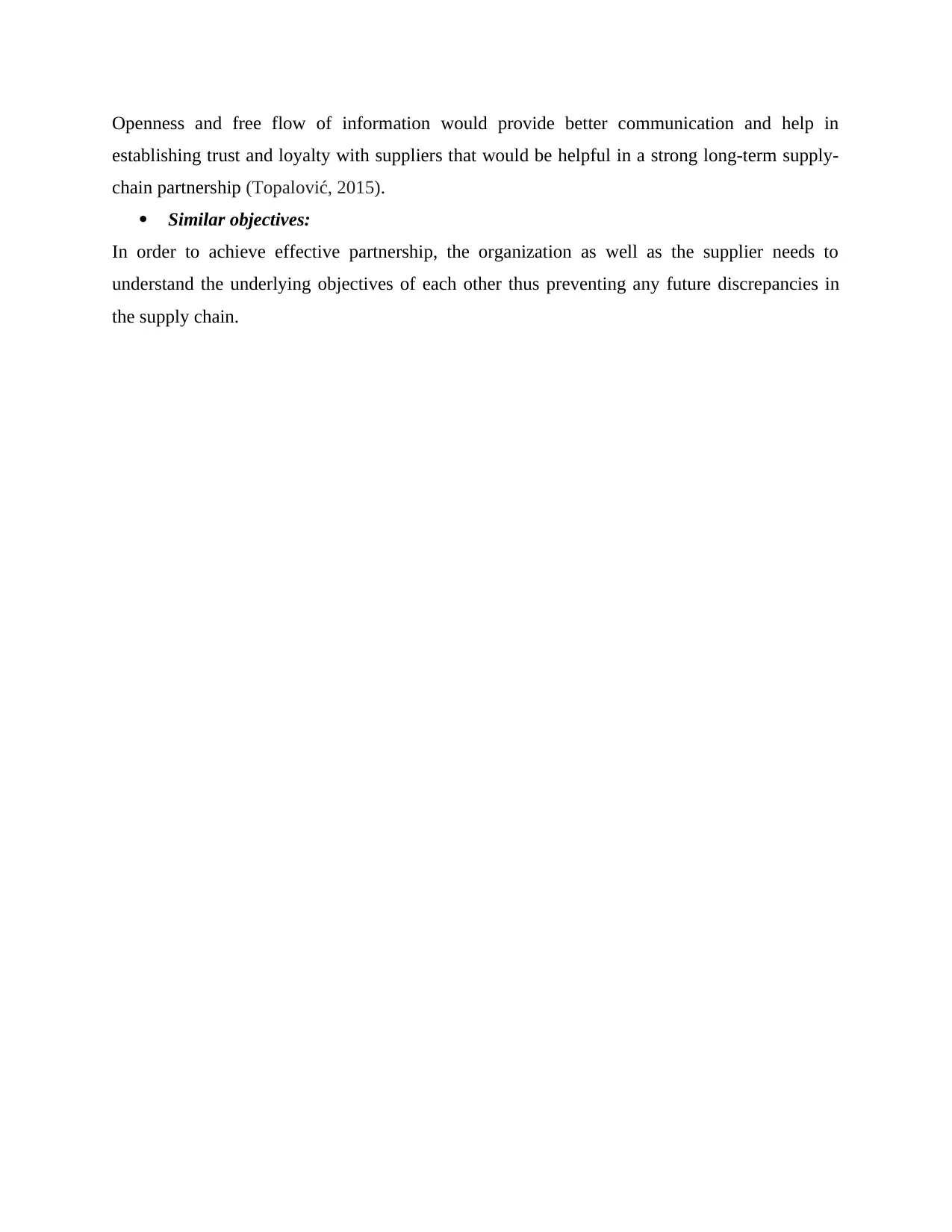
Openness and free flow of information would provide better communication and help in
establishing trust and loyalty with suppliers that would be helpful in a strong long-term supply-
chain partnership (Topalović, 2015).
Similar objectives:
In order to achieve effective partnership, the organization as well as the supplier needs to
understand the underlying objectives of each other thus preventing any future discrepancies in
the supply chain.
establishing trust and loyalty with suppliers that would be helpful in a strong long-term supply-
chain partnership (Topalović, 2015).
Similar objectives:
In order to achieve effective partnership, the organization as well as the supplier needs to
understand the underlying objectives of each other thus preventing any future discrepancies in
the supply chain.
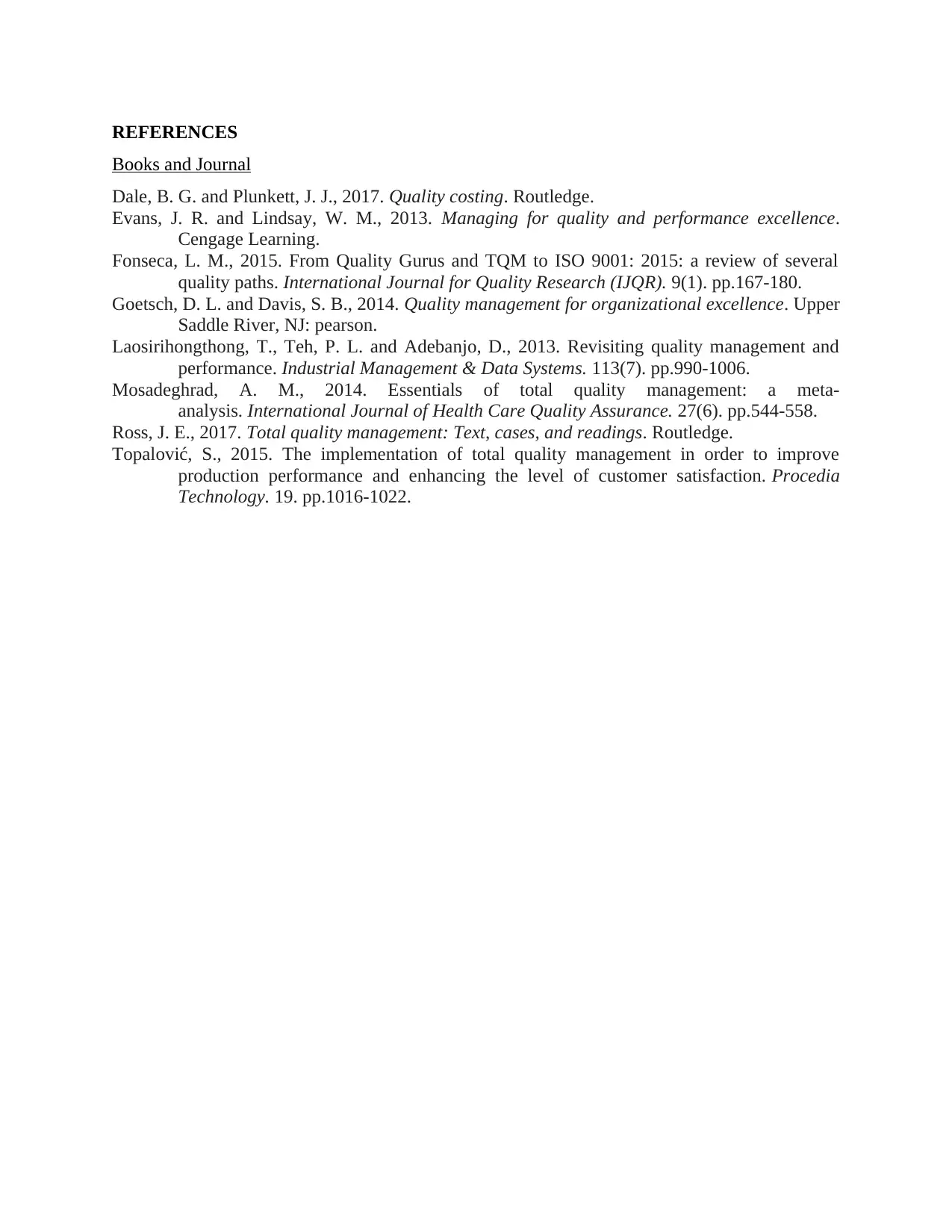
REFERENCES
Books and Journal
Dale, B. G. and Plunkett, J. J., 2017. Quality costing. Routledge.
Evans, J. R. and Lindsay, W. M., 2013. Managing for quality and performance excellence.
Cengage Learning.
Fonseca, L. M., 2015. From Quality Gurus and TQM to ISO 9001: 2015: a review of several
quality paths. International Journal for Quality Research (IJQR). 9(1). pp.167-180.
Goetsch, D. L. and Davis, S. B., 2014. Quality management for organizational excellence. Upper
Saddle River, NJ: pearson.
Laosirihongthong, T., Teh, P. L. and Adebanjo, D., 2013. Revisiting quality management and
performance. Industrial Management & Data Systems. 113(7). pp.990-1006.
Mosadeghrad, A. M., 2014. Essentials of total quality management: a meta-
analysis. International Journal of Health Care Quality Assurance. 27(6). pp.544-558.
Ross, J. E., 2017. Total quality management: Text, cases, and readings. Routledge.
Topalović, S., 2015. The implementation of total quality management in order to improve
production performance and enhancing the level of customer satisfaction. Procedia
Technology. 19. pp.1016-1022.
Books and Journal
Dale, B. G. and Plunkett, J. J., 2017. Quality costing. Routledge.
Evans, J. R. and Lindsay, W. M., 2013. Managing for quality and performance excellence.
Cengage Learning.
Fonseca, L. M., 2015. From Quality Gurus and TQM to ISO 9001: 2015: a review of several
quality paths. International Journal for Quality Research (IJQR). 9(1). pp.167-180.
Goetsch, D. L. and Davis, S. B., 2014. Quality management for organizational excellence. Upper
Saddle River, NJ: pearson.
Laosirihongthong, T., Teh, P. L. and Adebanjo, D., 2013. Revisiting quality management and
performance. Industrial Management & Data Systems. 113(7). pp.990-1006.
Mosadeghrad, A. M., 2014. Essentials of total quality management: a meta-
analysis. International Journal of Health Care Quality Assurance. 27(6). pp.544-558.
Ross, J. E., 2017. Total quality management: Text, cases, and readings. Routledge.
Topalović, S., 2015. The implementation of total quality management in order to improve
production performance and enhancing the level of customer satisfaction. Procedia
Technology. 19. pp.1016-1022.
1 out of 10
Related Documents
![[object Object]](/_next/image/?url=%2F_next%2Fstatic%2Fmedia%2Flogo.6d15ce61.png&w=640&q=75)
Your All-in-One AI-Powered Toolkit for Academic Success.
+13062052269
info@desklib.com
Available 24*7 on WhatsApp / Email
Unlock your academic potential
© 2024 | Zucol Services PVT LTD | All rights reserved.