Lean Project Management (LPM) Principles in Project Management Processes
VerifiedAdded on 2023/03/20
|11
|3484
|68
AI Summary
This document presents an assessment of Lean Project Management (LPM) principles in project management processes and evaluates its desirability for implementation in governmental projects. It discusses the reasons for implementing LPM, understanding LPM principles, steps for implementation, critical success factors, benefits to stakeholders, and methods of assessment and training needs.
Contribute Materials
Your contribution can guide someone’s learning journey. Share your
documents today.
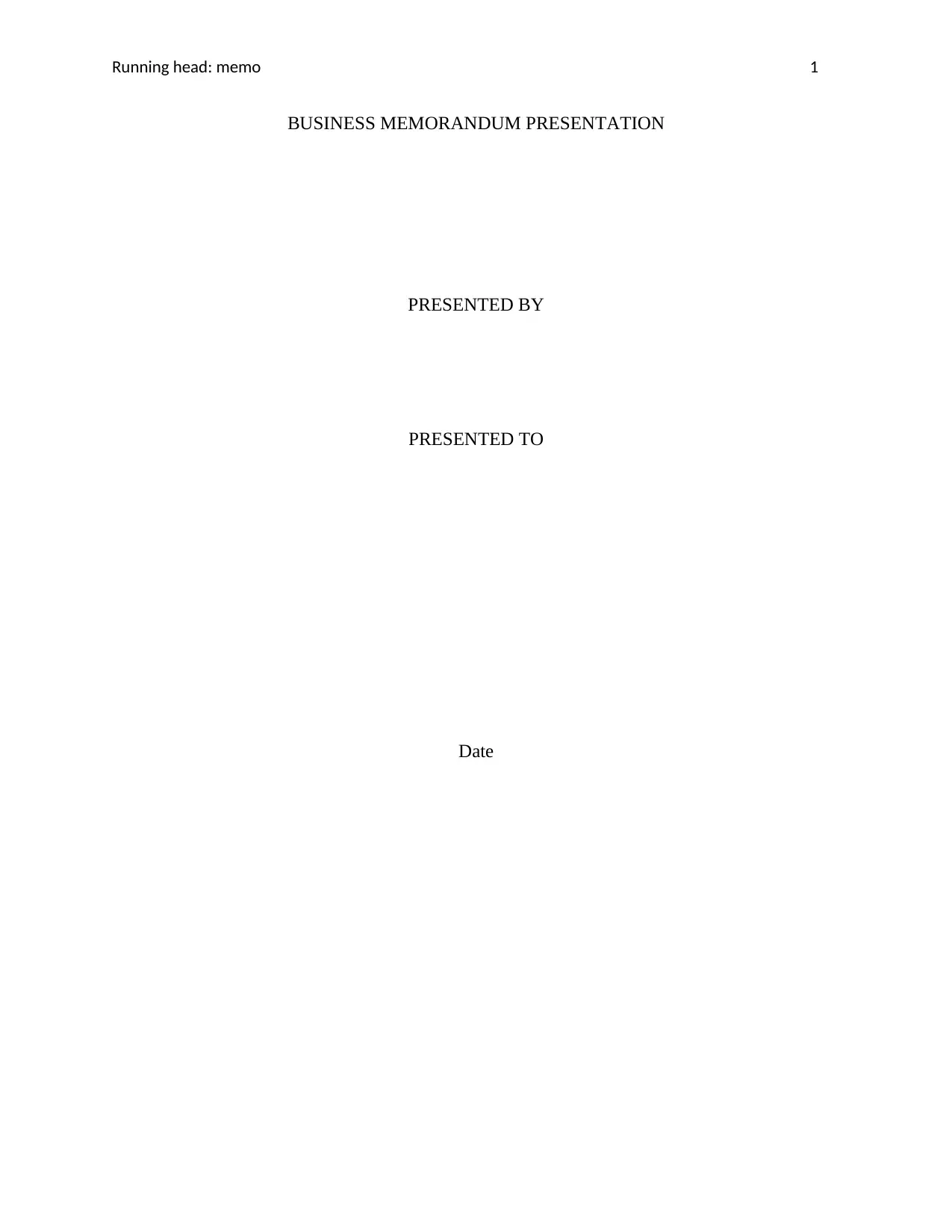
Running head: memo 1
BUSINESS MEMORANDUM PRESENTATION
PRESENTED BY
PRESENTED TO
Date
BUSINESS MEMORANDUM PRESENTATION
PRESENTED BY
PRESENTED TO
Date
Secure Best Marks with AI Grader
Need help grading? Try our AI Grader for instant feedback on your assignments.
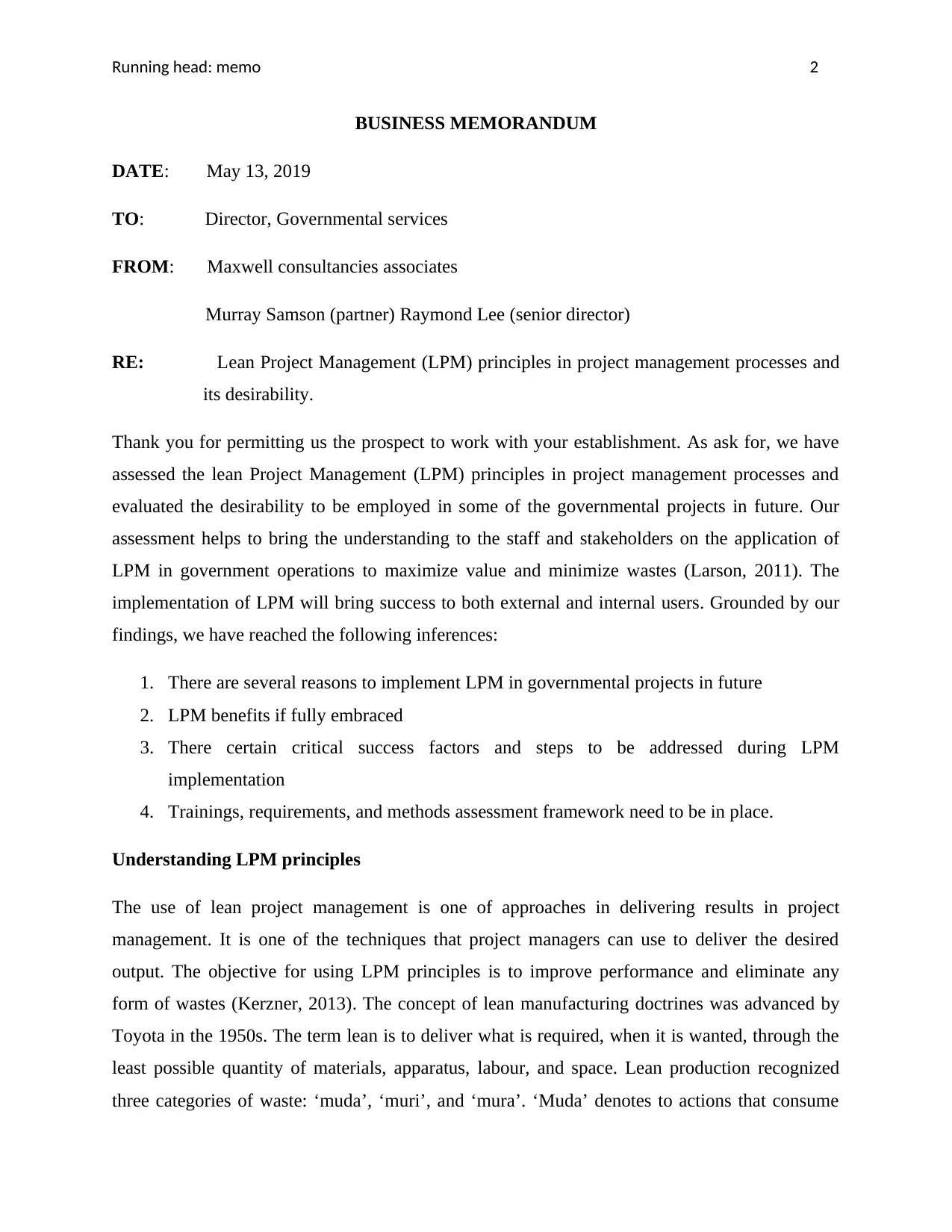
Running head: memo 2
BUSINESS MEMORANDUM
DATE: May 13, 2019
TO: Director, Governmental services
FROM: Maxwell consultancies associates
Murray Samson (partner) Raymond Lee (senior director)
RE: Lean Project Management (LPM) principles in project management processes and
its desirability.
Thank you for permitting us the prospect to work with your establishment. As ask for, we have
assessed the lean Project Management (LPM) principles in project management processes and
evaluated the desirability to be employed in some of the governmental projects in future. Our
assessment helps to bring the understanding to the staff and stakeholders on the application of
LPM in government operations to maximize value and minimize wastes (Larson, 2011). The
implementation of LPM will bring success to both external and internal users. Grounded by our
findings, we have reached the following inferences:
1. There are several reasons to implement LPM in governmental projects in future
2. LPM benefits if fully embraced
3. There certain critical success factors and steps to be addressed during LPM
implementation
4. Trainings, requirements, and methods assessment framework need to be in place.
Understanding LPM principles
The use of lean project management is one of approaches in delivering results in project
management. It is one of the techniques that project managers can use to deliver the desired
output. The objective for using LPM principles is to improve performance and eliminate any
form of wastes (Kerzner, 2013). The concept of lean manufacturing doctrines was advanced by
Toyota in the 1950s. The term lean is to deliver what is required, when it is wanted, through the
least possible quantity of materials, apparatus, labour, and space. Lean production recognized
three categories of waste: ‘muda’, ‘muri’, and ‘mura’. ‘Muda’ denotes to actions that consume
BUSINESS MEMORANDUM
DATE: May 13, 2019
TO: Director, Governmental services
FROM: Maxwell consultancies associates
Murray Samson (partner) Raymond Lee (senior director)
RE: Lean Project Management (LPM) principles in project management processes and
its desirability.
Thank you for permitting us the prospect to work with your establishment. As ask for, we have
assessed the lean Project Management (LPM) principles in project management processes and
evaluated the desirability to be employed in some of the governmental projects in future. Our
assessment helps to bring the understanding to the staff and stakeholders on the application of
LPM in government operations to maximize value and minimize wastes (Larson, 2011). The
implementation of LPM will bring success to both external and internal users. Grounded by our
findings, we have reached the following inferences:
1. There are several reasons to implement LPM in governmental projects in future
2. LPM benefits if fully embraced
3. There certain critical success factors and steps to be addressed during LPM
implementation
4. Trainings, requirements, and methods assessment framework need to be in place.
Understanding LPM principles
The use of lean project management is one of approaches in delivering results in project
management. It is one of the techniques that project managers can use to deliver the desired
output. The objective for using LPM principles is to improve performance and eliminate any
form of wastes (Kerzner, 2013). The concept of lean manufacturing doctrines was advanced by
Toyota in the 1950s. The term lean is to deliver what is required, when it is wanted, through the
least possible quantity of materials, apparatus, labour, and space. Lean production recognized
three categories of waste: ‘muda’, ‘muri’, and ‘mura’. ‘Muda’ denotes to actions that consume

Running head: memo 3
resources devoid of giving extra value. ‘Muri’ denotes to misuse of equipment or workers.
‘Mura’ means reductions of proficiency and output in the long term (Aune, 2013). The key
ideologies that can be used to put on the lean theory to project management: stipulate value, plan
the value stream, value stream, create value flow by reducing waste, and create value movement
at the pull of the customer, clasp uninterrupted development in hunt of precision. The LPM
process is a critical component that can enable effective delivery of governmental functions if
suitably implemented.
Reasons for LPM implementation
The main reasons of implementing the LPM are as follows:
1. For teams to understand the value they are advocating to provide or offer to their
customers or clients
2. To come up with a value stream approach for creating a product or project
3. To come up with ways of eliminating wastes by developing improvement plan
4. To devise ways that would attract customers demand for products or services
5. To adopt a continuous improvement approach to correct problems and focus on
eliminating wastes.
Implementing LPM process
The process to follow when implementing LPM include the use of the following principles
1. Planning need to be centered on long-term viewpoint more than short-term financial
objectives- Individuals in assignment must have a sense of persistence to succeed with
project goals Beecham, 2013). Inspiration generates a flawless vision for supporting them
with these aims. Recognizing openings or waste in their project management procedure.
Project realization derives from experience in creating the project more effective.
2. Focus on problem areas by building an endless process that allows a clear flow of
operations. Management should strive on shaping the entire process rather focusing on
one item or part at intervals (Bigelow, 2016).
resources devoid of giving extra value. ‘Muri’ denotes to misuse of equipment or workers.
‘Mura’ means reductions of proficiency and output in the long term (Aune, 2013). The key
ideologies that can be used to put on the lean theory to project management: stipulate value, plan
the value stream, value stream, create value flow by reducing waste, and create value movement
at the pull of the customer, clasp uninterrupted development in hunt of precision. The LPM
process is a critical component that can enable effective delivery of governmental functions if
suitably implemented.
Reasons for LPM implementation
The main reasons of implementing the LPM are as follows:
1. For teams to understand the value they are advocating to provide or offer to their
customers or clients
2. To come up with a value stream approach for creating a product or project
3. To come up with ways of eliminating wastes by developing improvement plan
4. To devise ways that would attract customers demand for products or services
5. To adopt a continuous improvement approach to correct problems and focus on
eliminating wastes.
Implementing LPM process
The process to follow when implementing LPM include the use of the following principles
1. Planning need to be centered on long-term viewpoint more than short-term financial
objectives- Individuals in assignment must have a sense of persistence to succeed with
project goals Beecham, 2013). Inspiration generates a flawless vision for supporting them
with these aims. Recognizing openings or waste in their project management procedure.
Project realization derives from experience in creating the project more effective.
2. Focus on problem areas by building an endless process that allows a clear flow of
operations. Management should strive on shaping the entire process rather focusing on
one item or part at intervals (Bigelow, 2016).
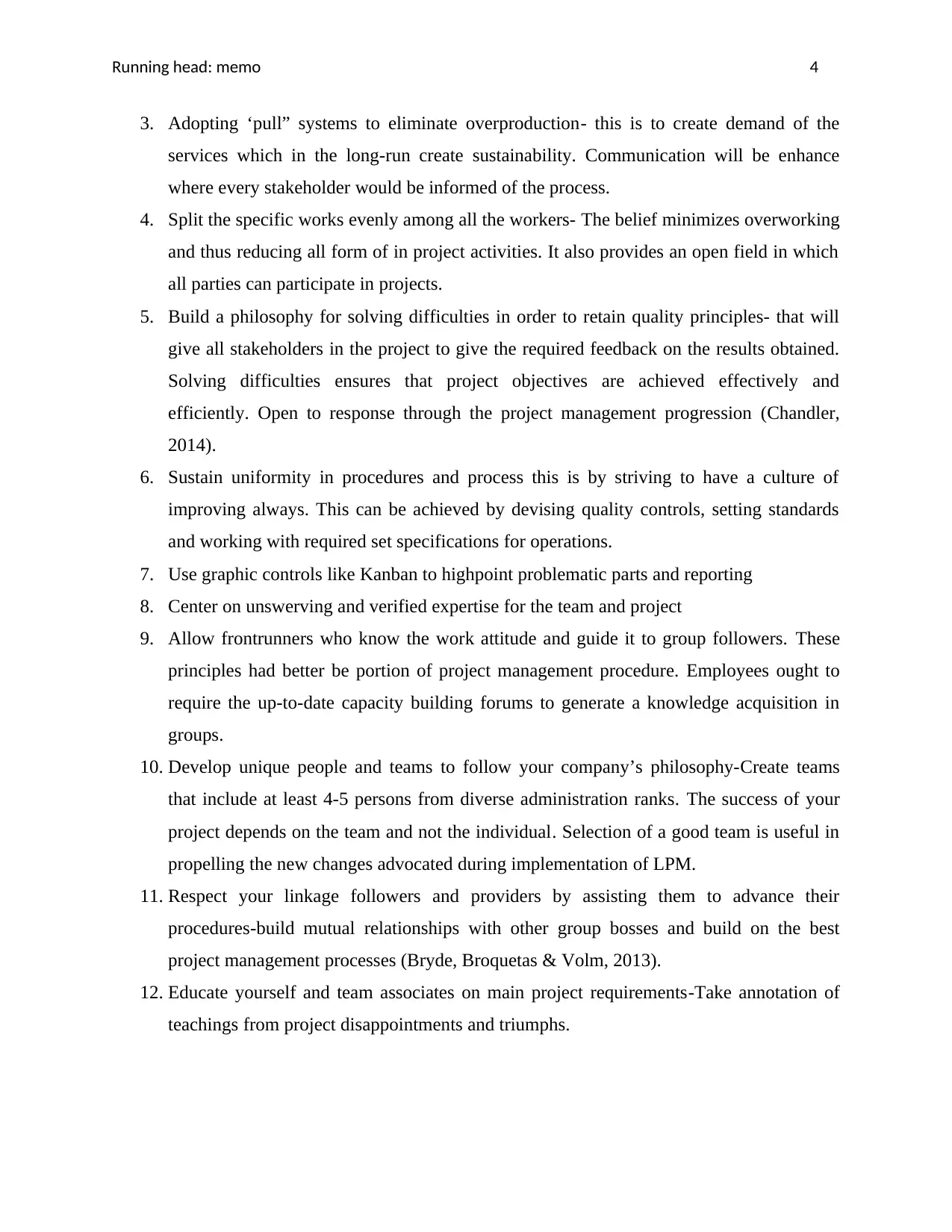
Running head: memo 4
3. Adopting ‘pull” systems to eliminate overproduction- this is to create demand of the
services which in the long-run create sustainability. Communication will be enhance
where every stakeholder would be informed of the process.
4. Split the specific works evenly among all the workers- The belief minimizes overworking
and thus reducing all form of in project activities. It also provides an open field in which
all parties can participate in projects.
5. Build a philosophy for solving difficulties in order to retain quality principles- that will
give all stakeholders in the project to give the required feedback on the results obtained.
Solving difficulties ensures that project objectives are achieved effectively and
efficiently. Open to response through the project management progression (Chandler,
2014).
6. Sustain uniformity in procedures and process this is by striving to have a culture of
improving always. This can be achieved by devising quality controls, setting standards
and working with required set specifications for operations.
7. Use graphic controls like Kanban to highpoint problematic parts and reporting
8. Center on unswerving and verified expertise for the team and project
9. Allow frontrunners who know the work attitude and guide it to group followers. These
principles had better be portion of project management procedure. Employees ought to
require the up-to-date capacity building forums to generate a knowledge acquisition in
groups.
10. Develop unique people and teams to follow your company’s philosophy-Create teams
that include at least 4-5 persons from diverse administration ranks. The success of your
project depends on the team and not the individual. Selection of a good team is useful in
propelling the new changes advocated during implementation of LPM.
11. Respect your linkage followers and providers by assisting them to advance their
procedures-build mutual relationships with other group bosses and build on the best
project management processes (Bryde, Broquetas & Volm, 2013).
12. Educate yourself and team associates on main project requirements-Take annotation of
teachings from project disappointments and triumphs.
3. Adopting ‘pull” systems to eliminate overproduction- this is to create demand of the
services which in the long-run create sustainability. Communication will be enhance
where every stakeholder would be informed of the process.
4. Split the specific works evenly among all the workers- The belief minimizes overworking
and thus reducing all form of in project activities. It also provides an open field in which
all parties can participate in projects.
5. Build a philosophy for solving difficulties in order to retain quality principles- that will
give all stakeholders in the project to give the required feedback on the results obtained.
Solving difficulties ensures that project objectives are achieved effectively and
efficiently. Open to response through the project management progression (Chandler,
2014).
6. Sustain uniformity in procedures and process this is by striving to have a culture of
improving always. This can be achieved by devising quality controls, setting standards
and working with required set specifications for operations.
7. Use graphic controls like Kanban to highpoint problematic parts and reporting
8. Center on unswerving and verified expertise for the team and project
9. Allow frontrunners who know the work attitude and guide it to group followers. These
principles had better be portion of project management procedure. Employees ought to
require the up-to-date capacity building forums to generate a knowledge acquisition in
groups.
10. Develop unique people and teams to follow your company’s philosophy-Create teams
that include at least 4-5 persons from diverse administration ranks. The success of your
project depends on the team and not the individual. Selection of a good team is useful in
propelling the new changes advocated during implementation of LPM.
11. Respect your linkage followers and providers by assisting them to advance their
procedures-build mutual relationships with other group bosses and build on the best
project management processes (Bryde, Broquetas & Volm, 2013).
12. Educate yourself and team associates on main project requirements-Take annotation of
teachings from project disappointments and triumphs.
Secure Best Marks with AI Grader
Need help grading? Try our AI Grader for instant feedback on your assignments.
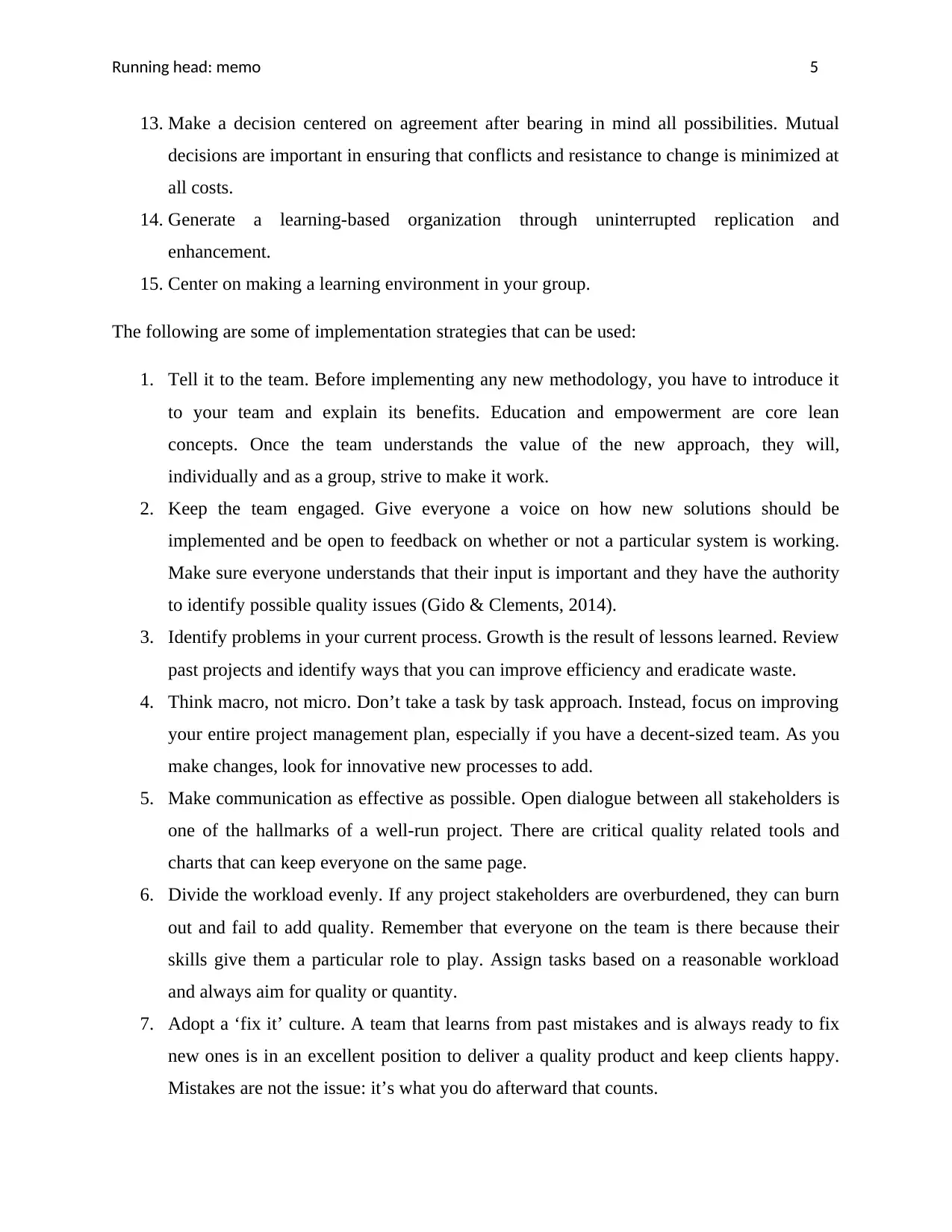
Running head: memo 5
13. Make a decision centered on agreement after bearing in mind all possibilities. Mutual
decisions are important in ensuring that conflicts and resistance to change is minimized at
all costs.
14. Generate a learning-based organization through uninterrupted replication and
enhancement.
15. Center on making a learning environment in your group.
The following are some of implementation strategies that can be used:
1. Tell it to the team. Before implementing any new methodology, you have to introduce it
to your team and explain its benefits. Education and empowerment are core lean
concepts. Once the team understands the value of the new approach, they will,
individually and as a group, strive to make it work.
2. Keep the team engaged. Give everyone a voice on how new solutions should be
implemented and be open to feedback on whether or not a particular system is working.
Make sure everyone understands that their input is important and they have the authority
to identify possible quality issues (Gido & Clements, 2014).
3. Identify problems in your current process. Growth is the result of lessons learned. Review
past projects and identify ways that you can improve efficiency and eradicate waste.
4. Think macro, not micro. Don’t take a task by task approach. Instead, focus on improving
your entire project management plan, especially if you have a decent-sized team. As you
make changes, look for innovative new processes to add.
5. Make communication as effective as possible. Open dialogue between all stakeholders is
one of the hallmarks of a well-run project. There are critical quality related tools and
charts that can keep everyone on the same page.
6. Divide the workload evenly. If any project stakeholders are overburdened, they can burn
out and fail to add quality. Remember that everyone on the team is there because their
skills give them a particular role to play. Assign tasks based on a reasonable workload
and always aim for quality or quantity.
7. Adopt a ‘fix it’ culture. A team that learns from past mistakes and is always ready to fix
new ones is in an excellent position to deliver a quality product and keep clients happy.
Mistakes are not the issue: it’s what you do afterward that counts.
13. Make a decision centered on agreement after bearing in mind all possibilities. Mutual
decisions are important in ensuring that conflicts and resistance to change is minimized at
all costs.
14. Generate a learning-based organization through uninterrupted replication and
enhancement.
15. Center on making a learning environment in your group.
The following are some of implementation strategies that can be used:
1. Tell it to the team. Before implementing any new methodology, you have to introduce it
to your team and explain its benefits. Education and empowerment are core lean
concepts. Once the team understands the value of the new approach, they will,
individually and as a group, strive to make it work.
2. Keep the team engaged. Give everyone a voice on how new solutions should be
implemented and be open to feedback on whether or not a particular system is working.
Make sure everyone understands that their input is important and they have the authority
to identify possible quality issues (Gido & Clements, 2014).
3. Identify problems in your current process. Growth is the result of lessons learned. Review
past projects and identify ways that you can improve efficiency and eradicate waste.
4. Think macro, not micro. Don’t take a task by task approach. Instead, focus on improving
your entire project management plan, especially if you have a decent-sized team. As you
make changes, look for innovative new processes to add.
5. Make communication as effective as possible. Open dialogue between all stakeholders is
one of the hallmarks of a well-run project. There are critical quality related tools and
charts that can keep everyone on the same page.
6. Divide the workload evenly. If any project stakeholders are overburdened, they can burn
out and fail to add quality. Remember that everyone on the team is there because their
skills give them a particular role to play. Assign tasks based on a reasonable workload
and always aim for quality or quantity.
7. Adopt a ‘fix it’ culture. A team that learns from past mistakes and is always ready to fix
new ones is in an excellent position to deliver a quality product and keep clients happy.
Mistakes are not the issue: it’s what you do afterward that counts.
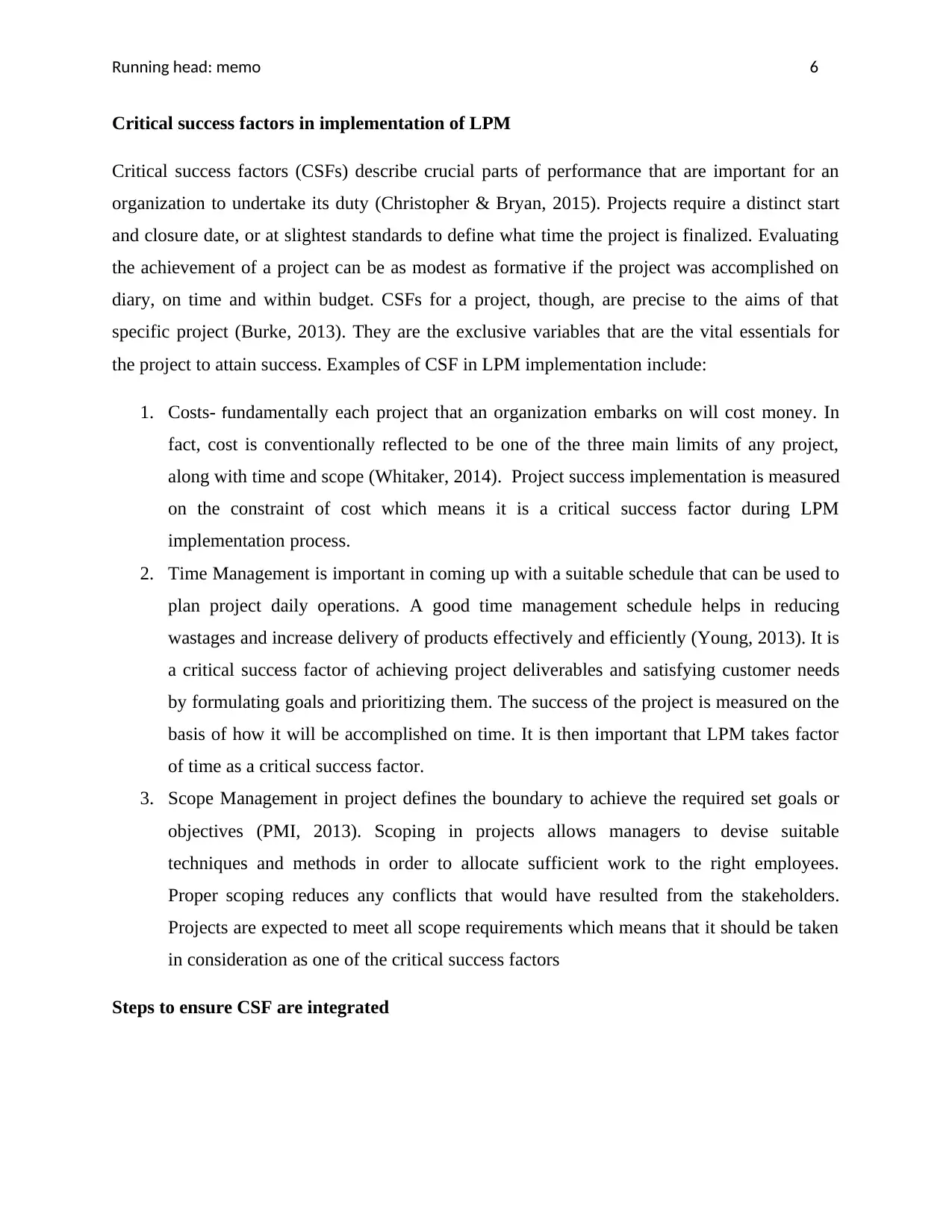
Running head: memo 6
Critical success factors in implementation of LPM
Critical success factors (CSFs) describe crucial parts of performance that are important for an
organization to undertake its duty (Christopher & Bryan, 2015). Projects require a distinct start
and closure date, or at slightest standards to define what time the project is finalized. Evaluating
the achievement of a project can be as modest as formative if the project was accomplished on
diary, on time and within budget. CSFs for a project, though, are precise to the aims of that
specific project (Burke, 2013). They are the exclusive variables that are the vital essentials for
the project to attain success. Examples of CSF in LPM implementation include:
1. Costs- fundamentally each project that an organization embarks on will cost money. In
fact, cost is conventionally reflected to be one of the three main limits of any project,
along with time and scope (Whitaker, 2014). Project success implementation is measured
on the constraint of cost which means it is a critical success factor during LPM
implementation process.
2. Time Management is important in coming up with a suitable schedule that can be used to
plan project daily operations. A good time management schedule helps in reducing
wastages and increase delivery of products effectively and efficiently (Young, 2013). It is
a critical success factor of achieving project deliverables and satisfying customer needs
by formulating goals and prioritizing them. The success of the project is measured on the
basis of how it will be accomplished on time. It is then important that LPM takes factor
of time as a critical success factor.
3. Scope Management in project defines the boundary to achieve the required set goals or
objectives (PMI, 2013). Scoping in projects allows managers to devise suitable
techniques and methods in order to allocate sufficient work to the right employees.
Proper scoping reduces any conflicts that would have resulted from the stakeholders.
Projects are expected to meet all scope requirements which means that it should be taken
in consideration as one of the critical success factors
Steps to ensure CSF are integrated
Critical success factors in implementation of LPM
Critical success factors (CSFs) describe crucial parts of performance that are important for an
organization to undertake its duty (Christopher & Bryan, 2015). Projects require a distinct start
and closure date, or at slightest standards to define what time the project is finalized. Evaluating
the achievement of a project can be as modest as formative if the project was accomplished on
diary, on time and within budget. CSFs for a project, though, are precise to the aims of that
specific project (Burke, 2013). They are the exclusive variables that are the vital essentials for
the project to attain success. Examples of CSF in LPM implementation include:
1. Costs- fundamentally each project that an organization embarks on will cost money. In
fact, cost is conventionally reflected to be one of the three main limits of any project,
along with time and scope (Whitaker, 2014). Project success implementation is measured
on the constraint of cost which means it is a critical success factor during LPM
implementation process.
2. Time Management is important in coming up with a suitable schedule that can be used to
plan project daily operations. A good time management schedule helps in reducing
wastages and increase delivery of products effectively and efficiently (Young, 2013). It is
a critical success factor of achieving project deliverables and satisfying customer needs
by formulating goals and prioritizing them. The success of the project is measured on the
basis of how it will be accomplished on time. It is then important that LPM takes factor
of time as a critical success factor.
3. Scope Management in project defines the boundary to achieve the required set goals or
objectives (PMI, 2013). Scoping in projects allows managers to devise suitable
techniques and methods in order to allocate sufficient work to the right employees.
Proper scoping reduces any conflicts that would have resulted from the stakeholders.
Projects are expected to meet all scope requirements which means that it should be taken
in consideration as one of the critical success factors
Steps to ensure CSF are integrated
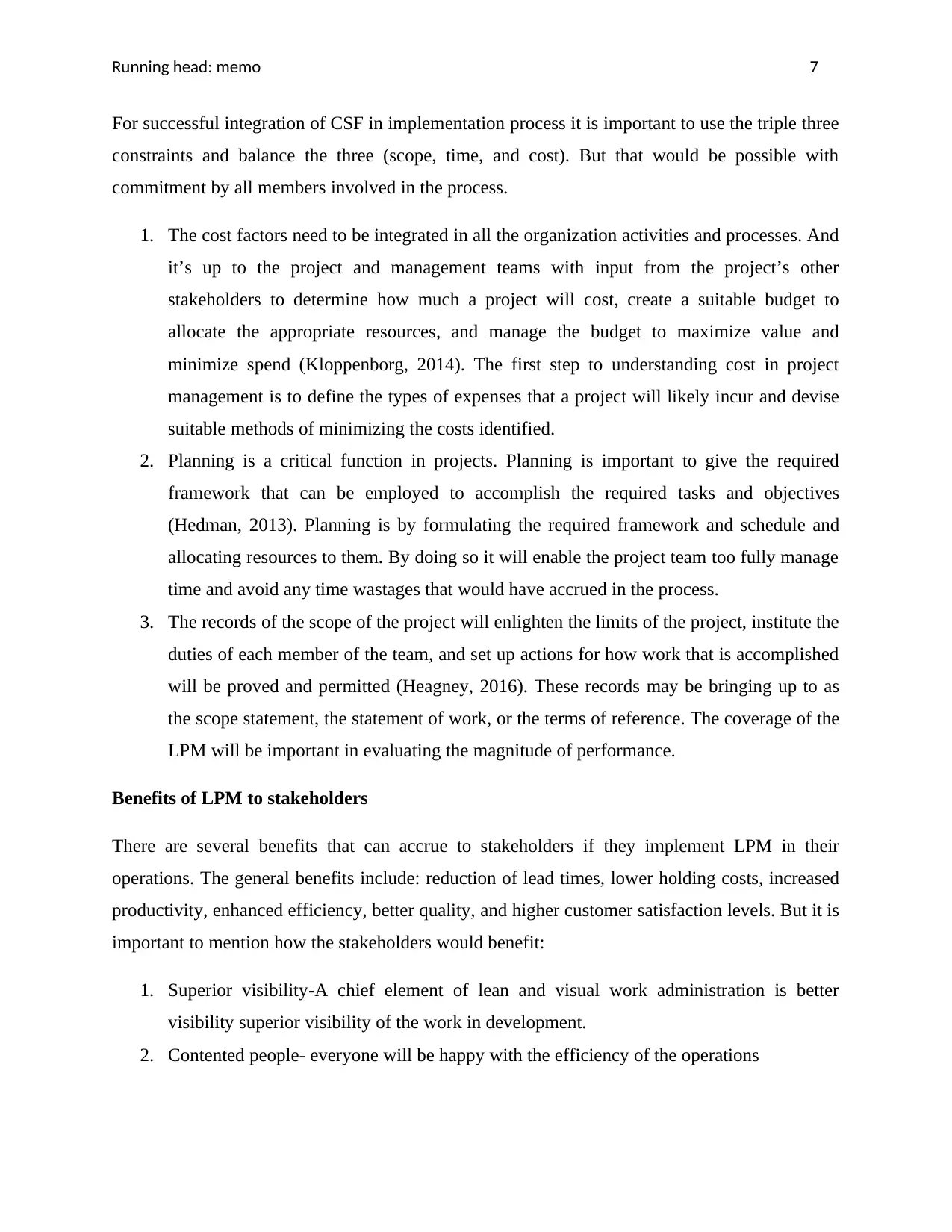
Running head: memo 7
For successful integration of CSF in implementation process it is important to use the triple three
constraints and balance the three (scope, time, and cost). But that would be possible with
commitment by all members involved in the process.
1. The cost factors need to be integrated in all the organization activities and processes. And
it’s up to the project and management teams with input from the project’s other
stakeholders to determine how much a project will cost, create a suitable budget to
allocate the appropriate resources, and manage the budget to maximize value and
minimize spend (Kloppenborg, 2014). The first step to understanding cost in project
management is to define the types of expenses that a project will likely incur and devise
suitable methods of minimizing the costs identified.
2. Planning is a critical function in projects. Planning is important to give the required
framework that can be employed to accomplish the required tasks and objectives
(Hedman, 2013). Planning is by formulating the required framework and schedule and
allocating resources to them. By doing so it will enable the project team too fully manage
time and avoid any time wastages that would have accrued in the process.
3. The records of the scope of the project will enlighten the limits of the project, institute the
duties of each member of the team, and set up actions for how work that is accomplished
will be proved and permitted (Heagney, 2016). These records may be bringing up to as
the scope statement, the statement of work, or the terms of reference. The coverage of the
LPM will be important in evaluating the magnitude of performance.
Benefits of LPM to stakeholders
There are several benefits that can accrue to stakeholders if they implement LPM in their
operations. The general benefits include: reduction of lead times, lower holding costs, increased
productivity, enhanced efficiency, better quality, and higher customer satisfaction levels. But it is
important to mention how the stakeholders would benefit:
1. Superior visibility-A chief element of lean and visual work administration is better
visibility superior visibility of the work in development.
2. Contented people- everyone will be happy with the efficiency of the operations
For successful integration of CSF in implementation process it is important to use the triple three
constraints and balance the three (scope, time, and cost). But that would be possible with
commitment by all members involved in the process.
1. The cost factors need to be integrated in all the organization activities and processes. And
it’s up to the project and management teams with input from the project’s other
stakeholders to determine how much a project will cost, create a suitable budget to
allocate the appropriate resources, and manage the budget to maximize value and
minimize spend (Kloppenborg, 2014). The first step to understanding cost in project
management is to define the types of expenses that a project will likely incur and devise
suitable methods of minimizing the costs identified.
2. Planning is a critical function in projects. Planning is important to give the required
framework that can be employed to accomplish the required tasks and objectives
(Hedman, 2013). Planning is by formulating the required framework and schedule and
allocating resources to them. By doing so it will enable the project team too fully manage
time and avoid any time wastages that would have accrued in the process.
3. The records of the scope of the project will enlighten the limits of the project, institute the
duties of each member of the team, and set up actions for how work that is accomplished
will be proved and permitted (Heagney, 2016). These records may be bringing up to as
the scope statement, the statement of work, or the terms of reference. The coverage of the
LPM will be important in evaluating the magnitude of performance.
Benefits of LPM to stakeholders
There are several benefits that can accrue to stakeholders if they implement LPM in their
operations. The general benefits include: reduction of lead times, lower holding costs, increased
productivity, enhanced efficiency, better quality, and higher customer satisfaction levels. But it is
important to mention how the stakeholders would benefit:
1. Superior visibility-A chief element of lean and visual work administration is better
visibility superior visibility of the work in development.
2. Contented people- everyone will be happy with the efficiency of the operations
Paraphrase This Document
Need a fresh take? Get an instant paraphrase of this document with our AI Paraphraser
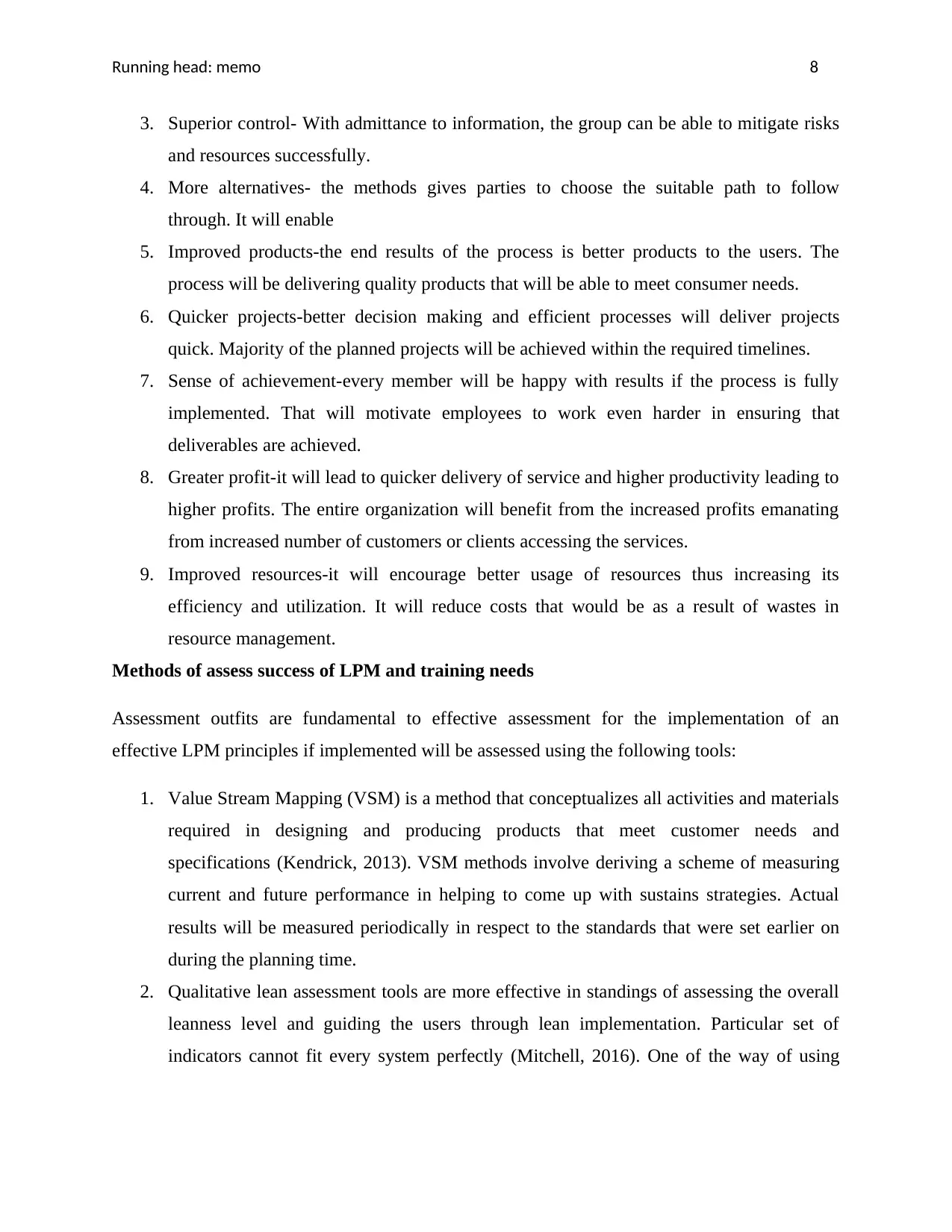
Running head: memo 8
3. Superior control- With admittance to information, the group can be able to mitigate risks
and resources successfully.
4. More alternatives- the methods gives parties to choose the suitable path to follow
through. It will enable
5. Improved products-the end results of the process is better products to the users. The
process will be delivering quality products that will be able to meet consumer needs.
6. Quicker projects-better decision making and efficient processes will deliver projects
quick. Majority of the planned projects will be achieved within the required timelines.
7. Sense of achievement-every member will be happy with results if the process is fully
implemented. That will motivate employees to work even harder in ensuring that
deliverables are achieved.
8. Greater profit-it will lead to quicker delivery of service and higher productivity leading to
higher profits. The entire organization will benefit from the increased profits emanating
from increased number of customers or clients accessing the services.
9. Improved resources-it will encourage better usage of resources thus increasing its
efficiency and utilization. It will reduce costs that would be as a result of wastes in
resource management.
Methods of assess success of LPM and training needs
Assessment outfits are fundamental to effective assessment for the implementation of an
effective LPM principles if implemented will be assessed using the following tools:
1. Value Stream Mapping (VSM) is a method that conceptualizes all activities and materials
required in designing and producing products that meet customer needs and
specifications (Kendrick, 2013). VSM methods involve deriving a scheme of measuring
current and future performance in helping to come up with sustains strategies. Actual
results will be measured periodically in respect to the standards that were set earlier on
during the planning time.
2. Qualitative lean assessment tools are more effective in standings of assessing the overall
leanness level and guiding the users through lean implementation. Particular set of
indicators cannot fit every system perfectly (Mitchell, 2016). One of the way of using
3. Superior control- With admittance to information, the group can be able to mitigate risks
and resources successfully.
4. More alternatives- the methods gives parties to choose the suitable path to follow
through. It will enable
5. Improved products-the end results of the process is better products to the users. The
process will be delivering quality products that will be able to meet consumer needs.
6. Quicker projects-better decision making and efficient processes will deliver projects
quick. Majority of the planned projects will be achieved within the required timelines.
7. Sense of achievement-every member will be happy with results if the process is fully
implemented. That will motivate employees to work even harder in ensuring that
deliverables are achieved.
8. Greater profit-it will lead to quicker delivery of service and higher productivity leading to
higher profits. The entire organization will benefit from the increased profits emanating
from increased number of customers or clients accessing the services.
9. Improved resources-it will encourage better usage of resources thus increasing its
efficiency and utilization. It will reduce costs that would be as a result of wastes in
resource management.
Methods of assess success of LPM and training needs
Assessment outfits are fundamental to effective assessment for the implementation of an
effective LPM principles if implemented will be assessed using the following tools:
1. Value Stream Mapping (VSM) is a method that conceptualizes all activities and materials
required in designing and producing products that meet customer needs and
specifications (Kendrick, 2013). VSM methods involve deriving a scheme of measuring
current and future performance in helping to come up with sustains strategies. Actual
results will be measured periodically in respect to the standards that were set earlier on
during the planning time.
2. Qualitative lean assessment tools are more effective in standings of assessing the overall
leanness level and guiding the users through lean implementation. Particular set of
indicators cannot fit every system perfectly (Mitchell, 2016). One of the way of using
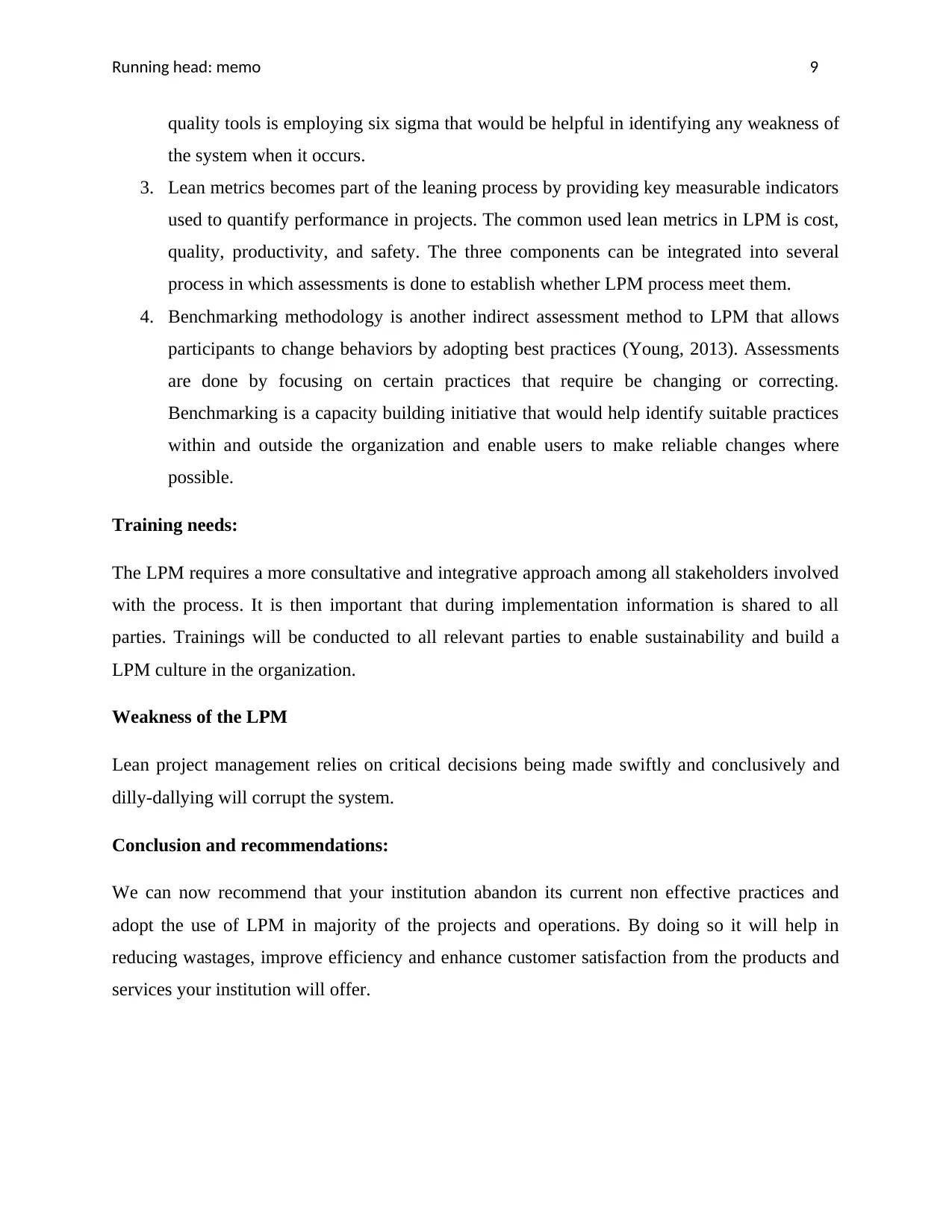
Running head: memo 9
quality tools is employing six sigma that would be helpful in identifying any weakness of
the system when it occurs.
3. Lean metrics becomes part of the leaning process by providing key measurable indicators
used to quantify performance in projects. The common used lean metrics in LPM is cost,
quality, productivity, and safety. The three components can be integrated into several
process in which assessments is done to establish whether LPM process meet them.
4. Benchmarking methodology is another indirect assessment method to LPM that allows
participants to change behaviors by adopting best practices (Young, 2013). Assessments
are done by focusing on certain practices that require be changing or correcting.
Benchmarking is a capacity building initiative that would help identify suitable practices
within and outside the organization and enable users to make reliable changes where
possible.
Training needs:
The LPM requires a more consultative and integrative approach among all stakeholders involved
with the process. It is then important that during implementation information is shared to all
parties. Trainings will be conducted to all relevant parties to enable sustainability and build a
LPM culture in the organization.
Weakness of the LPM
Lean project management relies on critical decisions being made swiftly and conclusively and
dilly-dallying will corrupt the system.
Conclusion and recommendations:
We can now recommend that your institution abandon its current non effective practices and
adopt the use of LPM in majority of the projects and operations. By doing so it will help in
reducing wastages, improve efficiency and enhance customer satisfaction from the products and
services your institution will offer.
quality tools is employing six sigma that would be helpful in identifying any weakness of
the system when it occurs.
3. Lean metrics becomes part of the leaning process by providing key measurable indicators
used to quantify performance in projects. The common used lean metrics in LPM is cost,
quality, productivity, and safety. The three components can be integrated into several
process in which assessments is done to establish whether LPM process meet them.
4. Benchmarking methodology is another indirect assessment method to LPM that allows
participants to change behaviors by adopting best practices (Young, 2013). Assessments
are done by focusing on certain practices that require be changing or correcting.
Benchmarking is a capacity building initiative that would help identify suitable practices
within and outside the organization and enable users to make reliable changes where
possible.
Training needs:
The LPM requires a more consultative and integrative approach among all stakeholders involved
with the process. It is then important that during implementation information is shared to all
parties. Trainings will be conducted to all relevant parties to enable sustainability and build a
LPM culture in the organization.
Weakness of the LPM
Lean project management relies on critical decisions being made swiftly and conclusively and
dilly-dallying will corrupt the system.
Conclusion and recommendations:
We can now recommend that your institution abandon its current non effective practices and
adopt the use of LPM in majority of the projects and operations. By doing so it will help in
reducing wastages, improve efficiency and enhance customer satisfaction from the products and
services your institution will offer.
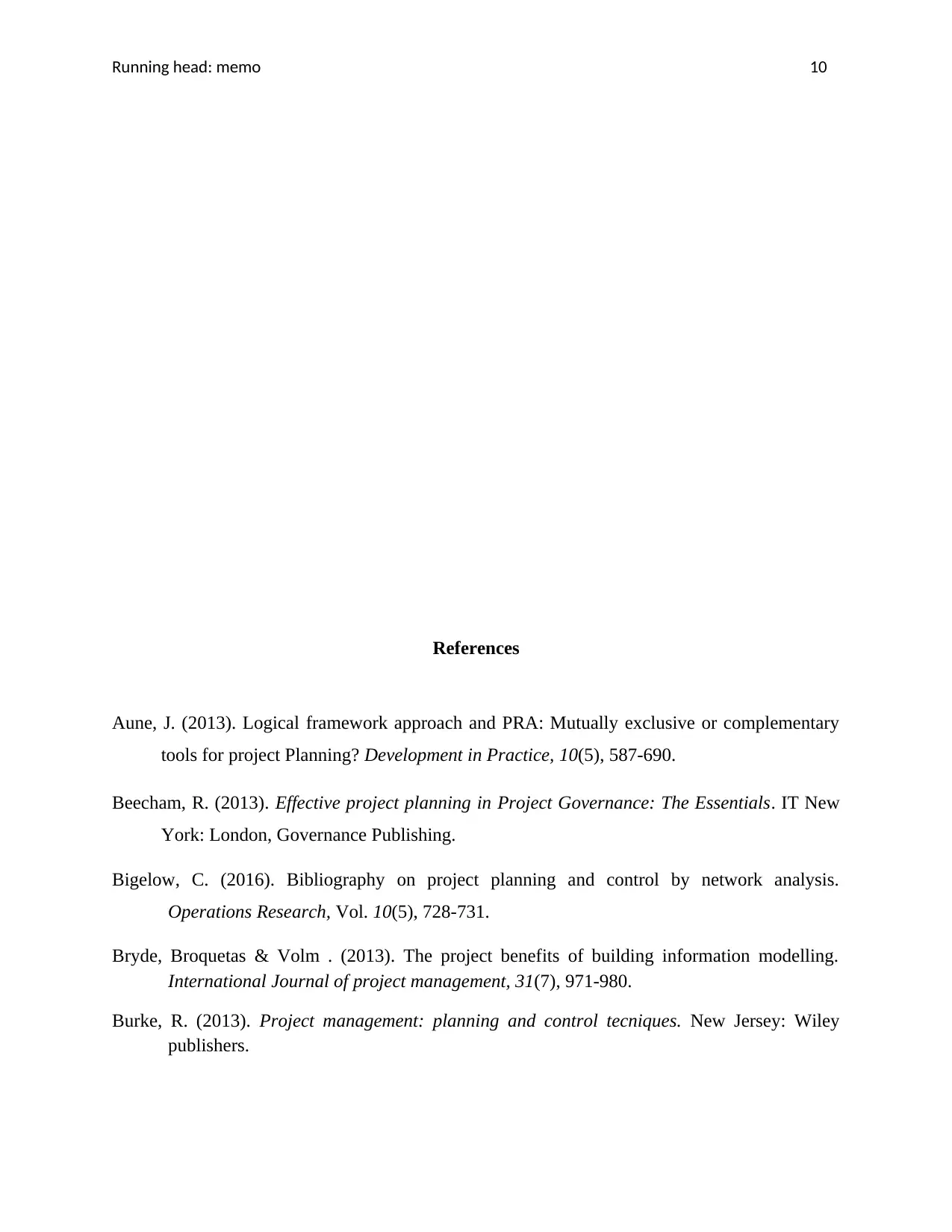
Running head: memo 10
References
Aune, J. (2013). Logical framework approach and PRA: Mutually exclusive or complementary
tools for project Planning? Development in Practice, 10(5), 587-690.
Beecham, R. (2013). Effective project planning in Project Governance: The Essentials. IT New
York: London, Governance Publishing.
Bigelow, C. (2016). Bibliography on project planning and control by network analysis.
Operations Research, Vol. 10(5), 728-731.
Bryde, Broquetas & Volm . (2013). The project benefits of building information modelling.
International Journal of project management, 31(7), 971-980.
Burke, R. (2013). Project management: planning and control tecniques. New Jersey: Wiley
publishers.
References
Aune, J. (2013). Logical framework approach and PRA: Mutually exclusive or complementary
tools for project Planning? Development in Practice, 10(5), 587-690.
Beecham, R. (2013). Effective project planning in Project Governance: The Essentials. IT New
York: London, Governance Publishing.
Bigelow, C. (2016). Bibliography on project planning and control by network analysis.
Operations Research, Vol. 10(5), 728-731.
Bryde, Broquetas & Volm . (2013). The project benefits of building information modelling.
International Journal of project management, 31(7), 971-980.
Burke, R. (2013). Project management: planning and control tecniques. New Jersey: Wiley
publishers.
Secure Best Marks with AI Grader
Need help grading? Try our AI Grader for instant feedback on your assignments.
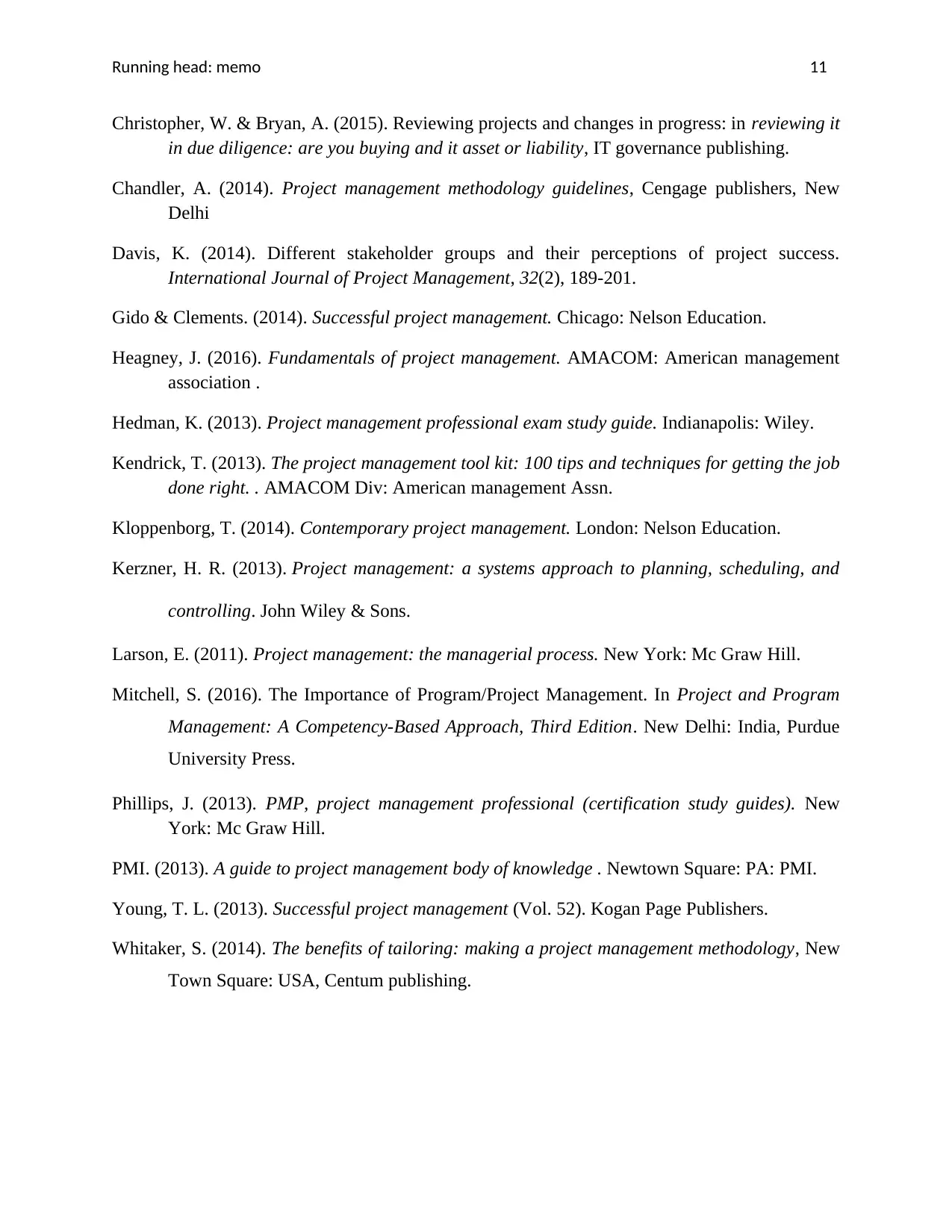
Running head: memo 11
Christopher, W. & Bryan, A. (2015). Reviewing projects and changes in progress: in reviewing it
in due diligence: are you buying and it asset or liability, IT governance publishing.
Chandler, A. (2014). Project management methodology guidelines, Cengage publishers, New
Delhi
Davis, K. (2014). Different stakeholder groups and their perceptions of project success.
International Journal of Project Management, 32(2), 189-201.
Gido & Clements. (2014). Successful project management. Chicago: Nelson Education.
Heagney, J. (2016). Fundamentals of project management. AMACOM: American management
association .
Hedman, K. (2013). Project management professional exam study guide. Indianapolis: Wiley.
Kendrick, T. (2013). The project management tool kit: 100 tips and techniques for getting the job
done right. . AMACOM Div: American management Assn.
Kloppenborg, T. (2014). Contemporary project management. London: Nelson Education.
Kerzner, H. R. (2013). Project management: a systems approach to planning, scheduling, and
controlling. John Wiley & Sons.
Larson, E. (2011). Project management: the managerial process. New York: Mc Graw Hill.
Mitchell, S. (2016). The Importance of Program/Project Management. In Project and Program
Management: A Competency-Based Approach, Third Edition. New Delhi: India, Purdue
University Press.
Phillips, J. (2013). PMP, project management professional (certification study guides). New
York: Mc Graw Hill.
PMI. (2013). A guide to project management body of knowledge . Newtown Square: PA: PMI.
Young, T. L. (2013). Successful project management (Vol. 52). Kogan Page Publishers.
Whitaker, S. (2014). The benefits of tailoring: making a project management methodology, New
Town Square: USA, Centum publishing.
Christopher, W. & Bryan, A. (2015). Reviewing projects and changes in progress: in reviewing it
in due diligence: are you buying and it asset or liability, IT governance publishing.
Chandler, A. (2014). Project management methodology guidelines, Cengage publishers, New
Delhi
Davis, K. (2014). Different stakeholder groups and their perceptions of project success.
International Journal of Project Management, 32(2), 189-201.
Gido & Clements. (2014). Successful project management. Chicago: Nelson Education.
Heagney, J. (2016). Fundamentals of project management. AMACOM: American management
association .
Hedman, K. (2013). Project management professional exam study guide. Indianapolis: Wiley.
Kendrick, T. (2013). The project management tool kit: 100 tips and techniques for getting the job
done right. . AMACOM Div: American management Assn.
Kloppenborg, T. (2014). Contemporary project management. London: Nelson Education.
Kerzner, H. R. (2013). Project management: a systems approach to planning, scheduling, and
controlling. John Wiley & Sons.
Larson, E. (2011). Project management: the managerial process. New York: Mc Graw Hill.
Mitchell, S. (2016). The Importance of Program/Project Management. In Project and Program
Management: A Competency-Based Approach, Third Edition. New Delhi: India, Purdue
University Press.
Phillips, J. (2013). PMP, project management professional (certification study guides). New
York: Mc Graw Hill.
PMI. (2013). A guide to project management body of knowledge . Newtown Square: PA: PMI.
Young, T. L. (2013). Successful project management (Vol. 52). Kogan Page Publishers.
Whitaker, S. (2014). The benefits of tailoring: making a project management methodology, New
Town Square: USA, Centum publishing.
1 out of 11
Related Documents
![[object Object]](/_next/image/?url=%2F_next%2Fstatic%2Fmedia%2Flogo.6d15ce61.png&w=640&q=75)
Your All-in-One AI-Powered Toolkit for Academic Success.
+13062052269
info@desklib.com
Available 24*7 on WhatsApp / Email
Unlock your academic potential
© 2024 | Zucol Services PVT LTD | All rights reserved.