OHS/WHS Policies, Duty Holder Responsibilities, Hierarchy of Control, Quality System and WHS Record Keeping
VerifiedAdded on 2023/06/10
|16
|3901
|95
AI Summary
This article covers the importance of OHS/WHS policies, the responsibilities of a duty holder, the hierarchy of control in risk management, the quality system, and WHS record keeping. It explains the benefits of each concept and how they contribute to ensuring a safe workplace.
Contribute Materials
Your contribution can guide someone’s learning journey. Share your
documents today.
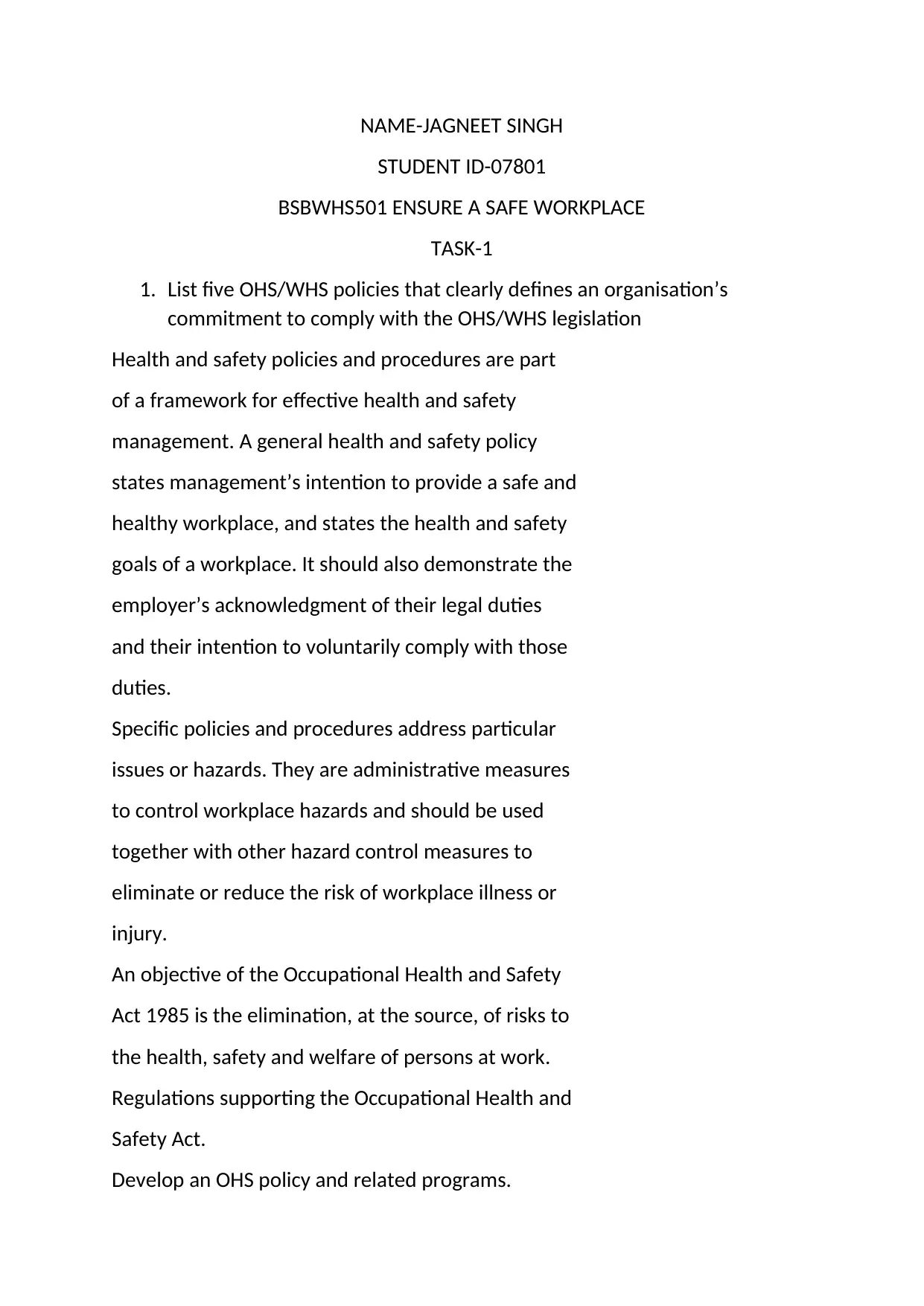
NAME-JAGNEET SINGH
STUDENT ID-07801
BSBWHS501 ENSURE A SAFE WORKPLACE
TASK-1
1. List five OHS/WHS policies that clearly defines an organisation’s
commitment to comply with the OHS/WHS legislation
Health and safety policies and procedures are part
of a framework for effective health and safety
management. A general health and safety policy
states management’s intention to provide a safe and
healthy workplace, and states the health and safety
goals of a workplace. It should also demonstrate the
employer’s acknowledgment of their legal duties
and their intention to voluntarily comply with those
duties.
Specific policies and procedures address particular
issues or hazards. They are administrative measures
to control workplace hazards and should be used
together with other hazard control measures to
eliminate or reduce the risk of workplace illness or
injury.
An objective of the Occupational Health and Safety
Act 1985 is the elimination, at the source, of risks to
the health, safety and welfare of persons at work.
Regulations supporting the Occupational Health and
Safety Act.
Develop an OHS policy and related programs.
STUDENT ID-07801
BSBWHS501 ENSURE A SAFE WORKPLACE
TASK-1
1. List five OHS/WHS policies that clearly defines an organisation’s
commitment to comply with the OHS/WHS legislation
Health and safety policies and procedures are part
of a framework for effective health and safety
management. A general health and safety policy
states management’s intention to provide a safe and
healthy workplace, and states the health and safety
goals of a workplace. It should also demonstrate the
employer’s acknowledgment of their legal duties
and their intention to voluntarily comply with those
duties.
Specific policies and procedures address particular
issues or hazards. They are administrative measures
to control workplace hazards and should be used
together with other hazard control measures to
eliminate or reduce the risk of workplace illness or
injury.
An objective of the Occupational Health and Safety
Act 1985 is the elimination, at the source, of risks to
the health, safety and welfare of persons at work.
Regulations supporting the Occupational Health and
Safety Act.
Develop an OHS policy and related programs.
Secure Best Marks with AI Grader
Need help grading? Try our AI Grader for instant feedback on your assignments.
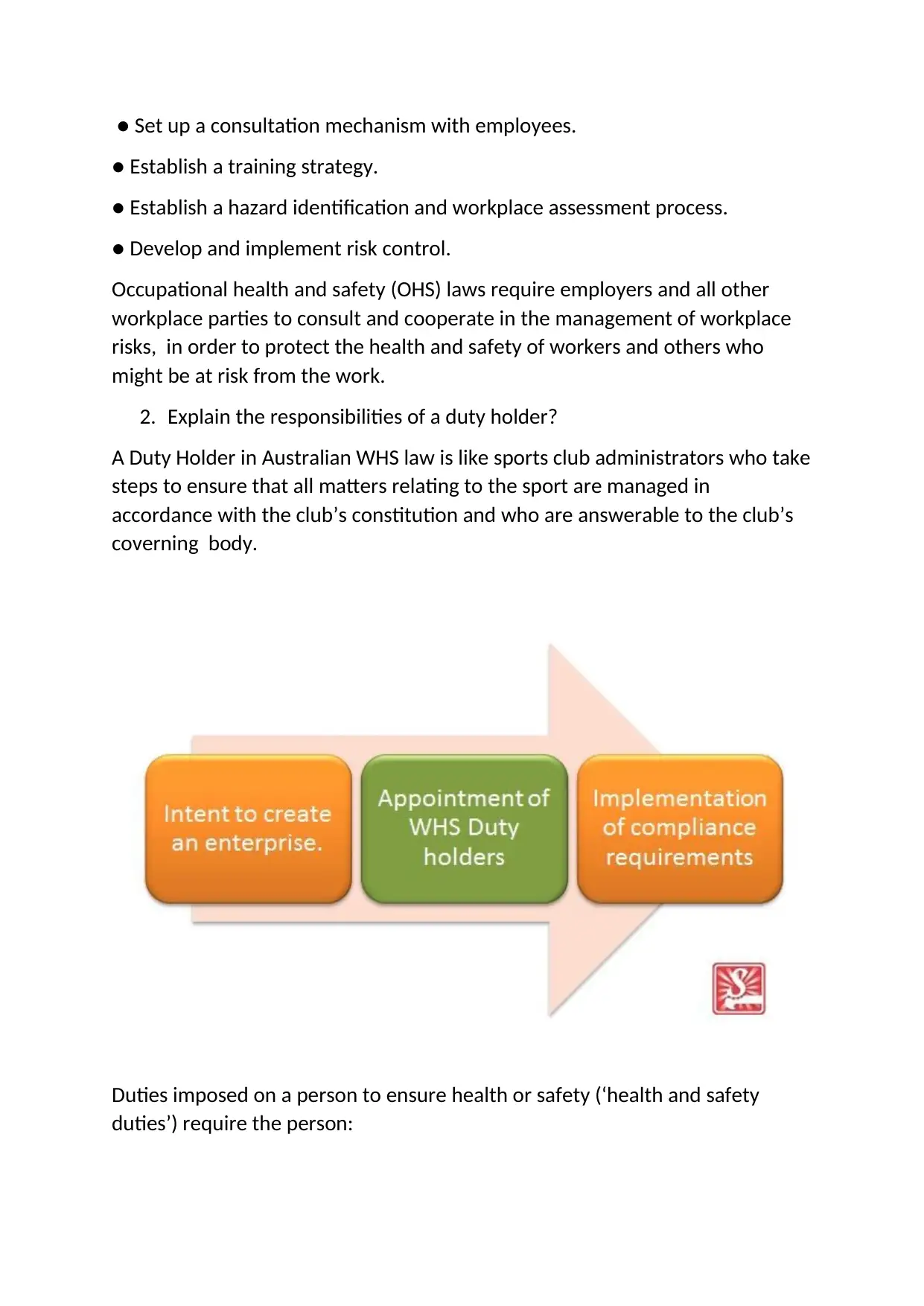
● Set up a consultation mechanism with employees.
● Establish a training strategy.
● Establish a hazard identification and workplace assessment process.
● Develop and implement risk control.
Occupational health and safety (OHS) laws require employers and all other
workplace parties to consult and cooperate in the management of workplace
risks, in order to protect the health and safety of workers and others who
might be at risk from the work.
2. Explain the responsibilities of a duty holder?
A Duty Holder in Australian WHS law is like sports club administrators who take
steps to ensure that all matters relating to the sport are managed in
accordance with the club’s constitution and who are answerable to the club’s
coverning body.
Duties imposed on a person to ensure health or safety (‘health and safety
duties’) require the person:
● Establish a training strategy.
● Establish a hazard identification and workplace assessment process.
● Develop and implement risk control.
Occupational health and safety (OHS) laws require employers and all other
workplace parties to consult and cooperate in the management of workplace
risks, in order to protect the health and safety of workers and others who
might be at risk from the work.
2. Explain the responsibilities of a duty holder?
A Duty Holder in Australian WHS law is like sports club administrators who take
steps to ensure that all matters relating to the sport are managed in
accordance with the club’s constitution and who are answerable to the club’s
coverning body.
Duties imposed on a person to ensure health or safety (‘health and safety
duties’) require the person:
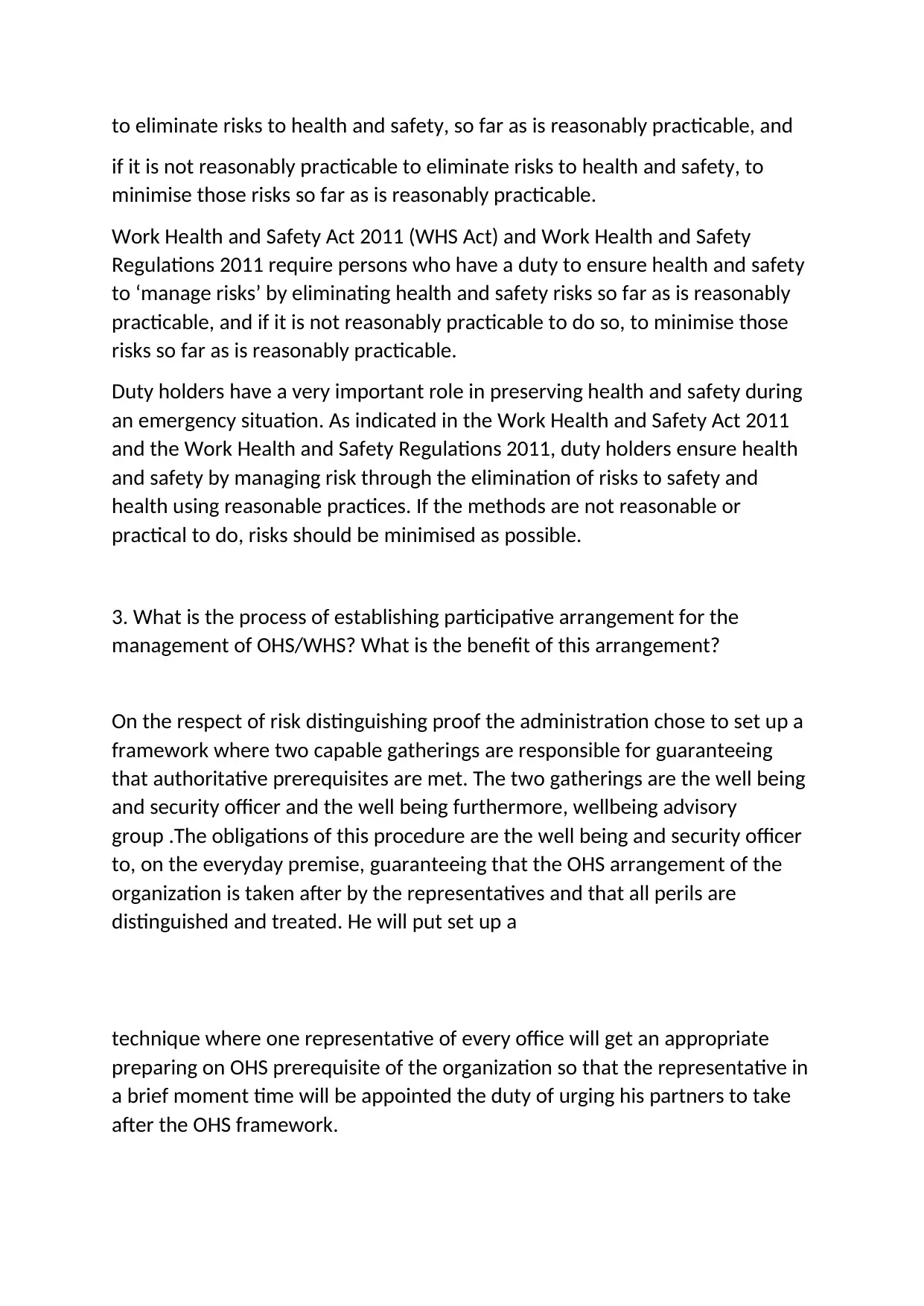
to eliminate risks to health and safety, so far as is reasonably practicable, and
if it is not reasonably practicable to eliminate risks to health and safety, to
minimise those risks so far as is reasonably practicable.
Work Health and Safety Act 2011 (WHS Act) and Work Health and Safety
Regulations 2011 require persons who have a duty to ensure health and safety
to ‘manage risks’ by eliminating health and safety risks so far as is reasonably
practicable, and if it is not reasonably practicable to do so, to minimise those
risks so far as is reasonably practicable.
Duty holders have a very important role in preserving health and safety during
an emergency situation. As indicated in the Work Health and Safety Act 2011
and the Work Health and Safety Regulations 2011, duty holders ensure health
and safety by managing risk through the elimination of risks to safety and
health using reasonable practices. If the methods are not reasonable or
practical to do, risks should be minimised as possible.
3. What is the process of establishing participative arrangement for the
management of OHS/WHS? What is the benefit of this arrangement?
On the respect of risk distinguishing proof the administration chose to set up a
framework where two capable gatherings are responsible for guaranteeing
that authoritative prerequisites are met. The two gatherings are the well being
and security officer and the well being furthermore, wellbeing advisory
group .The obligations of this procedure are the well being and security officer
to, on the everyday premise, guaranteeing that the OHS arrangement of the
organization is taken after by the representatives and that all perils are
distinguished and treated. He will put set up a
technique where one representative of every office will get an appropriate
preparing on OHS prerequisite of the organization so that the representative in
a brief moment time will be appointed the duty of urging his partners to take
after the OHS framework.
if it is not reasonably practicable to eliminate risks to health and safety, to
minimise those risks so far as is reasonably practicable.
Work Health and Safety Act 2011 (WHS Act) and Work Health and Safety
Regulations 2011 require persons who have a duty to ensure health and safety
to ‘manage risks’ by eliminating health and safety risks so far as is reasonably
practicable, and if it is not reasonably practicable to do so, to minimise those
risks so far as is reasonably practicable.
Duty holders have a very important role in preserving health and safety during
an emergency situation. As indicated in the Work Health and Safety Act 2011
and the Work Health and Safety Regulations 2011, duty holders ensure health
and safety by managing risk through the elimination of risks to safety and
health using reasonable practices. If the methods are not reasonable or
practical to do, risks should be minimised as possible.
3. What is the process of establishing participative arrangement for the
management of OHS/WHS? What is the benefit of this arrangement?
On the respect of risk distinguishing proof the administration chose to set up a
framework where two capable gatherings are responsible for guaranteeing
that authoritative prerequisites are met. The two gatherings are the well being
and security officer and the well being furthermore, wellbeing advisory
group .The obligations of this procedure are the well being and security officer
to, on the everyday premise, guaranteeing that the OHS arrangement of the
organization is taken after by the representatives and that all perils are
distinguished and treated. He will put set up a
technique where one representative of every office will get an appropriate
preparing on OHS prerequisite of the organization so that the representative in
a brief moment time will be appointed the duty of urging his partners to take
after the OHS framework.
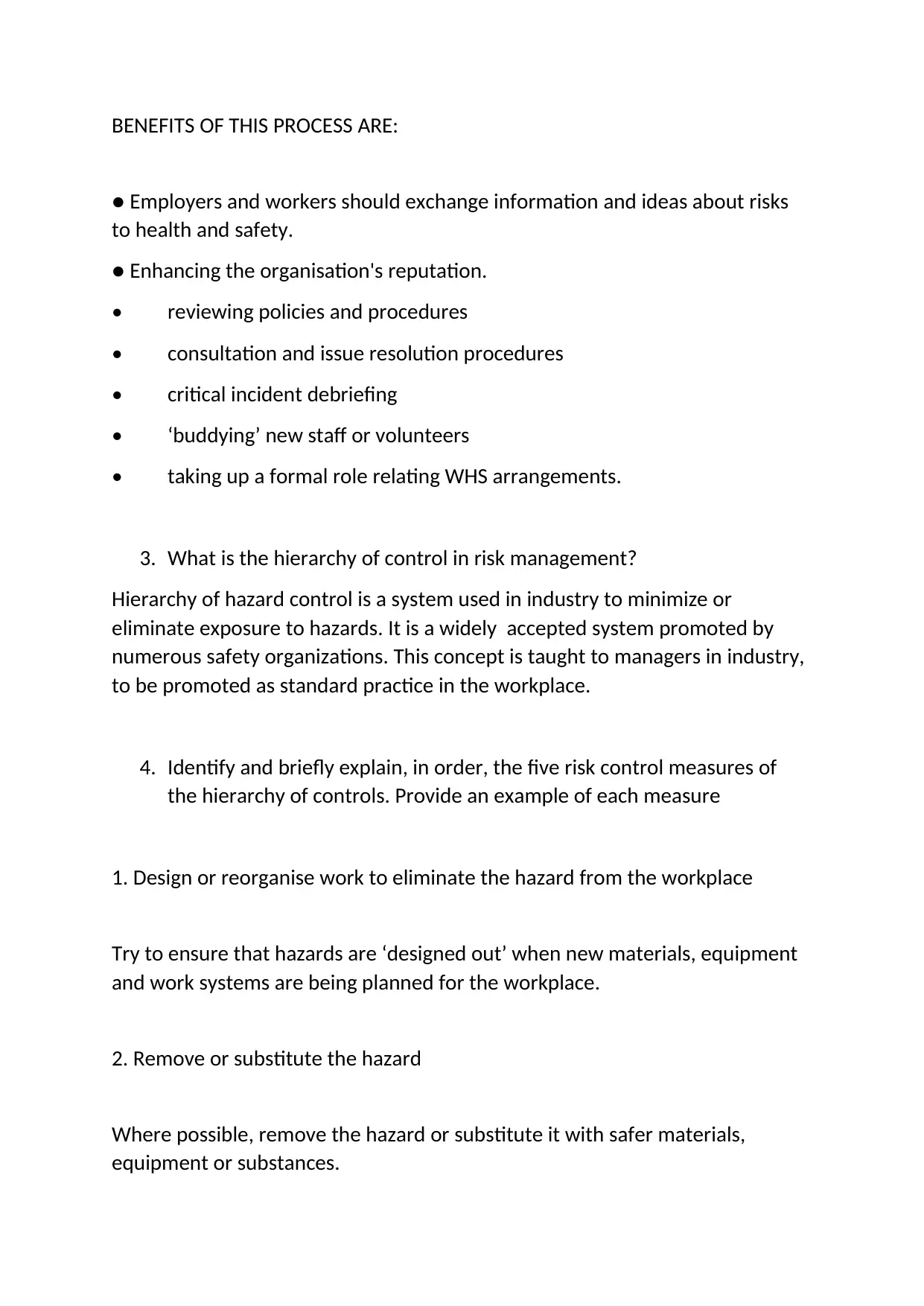
BENEFITS OF THIS PROCESS ARE:
● Employers and workers should exchange information and ideas about risks
to health and safety.
● Enhancing the organisation's reputation.
• reviewing policies and procedures
• consultation and issue resolution procedures
• critical incident debriefing
• ‘buddying’ new staff or volunteers
• taking up a formal role relating WHS arrangements.
3. What is the hierarchy of control in risk management?
Hierarchy of hazard control is a system used in industry to minimize or
eliminate exposure to hazards. It is a widely accepted system promoted by
numerous safety organizations. This concept is taught to managers in industry,
to be promoted as standard practice in the workplace.
4. Identify and briefly explain, in order, the five risk control measures of
the hierarchy of controls. Provide an example of each measure
1. Design or reorganise work to eliminate the hazard from the workplace
Try to ensure that hazards are ‘designed out’ when new materials, equipment
and work systems are being planned for the workplace.
2. Remove or substitute the hazard
Where possible, remove the hazard or substitute it with safer materials,
equipment or substances.
● Employers and workers should exchange information and ideas about risks
to health and safety.
● Enhancing the organisation's reputation.
• reviewing policies and procedures
• consultation and issue resolution procedures
• critical incident debriefing
• ‘buddying’ new staff or volunteers
• taking up a formal role relating WHS arrangements.
3. What is the hierarchy of control in risk management?
Hierarchy of hazard control is a system used in industry to minimize or
eliminate exposure to hazards. It is a widely accepted system promoted by
numerous safety organizations. This concept is taught to managers in industry,
to be promoted as standard practice in the workplace.
4. Identify and briefly explain, in order, the five risk control measures of
the hierarchy of controls. Provide an example of each measure
1. Design or reorganise work to eliminate the hazard from the workplace
Try to ensure that hazards are ‘designed out’ when new materials, equipment
and work systems are being planned for the workplace.
2. Remove or substitute the hazard
Where possible, remove the hazard or substitute it with safer materials,
equipment or substances.
Secure Best Marks with AI Grader
Need help grading? Try our AI Grader for instant feedback on your assignments.
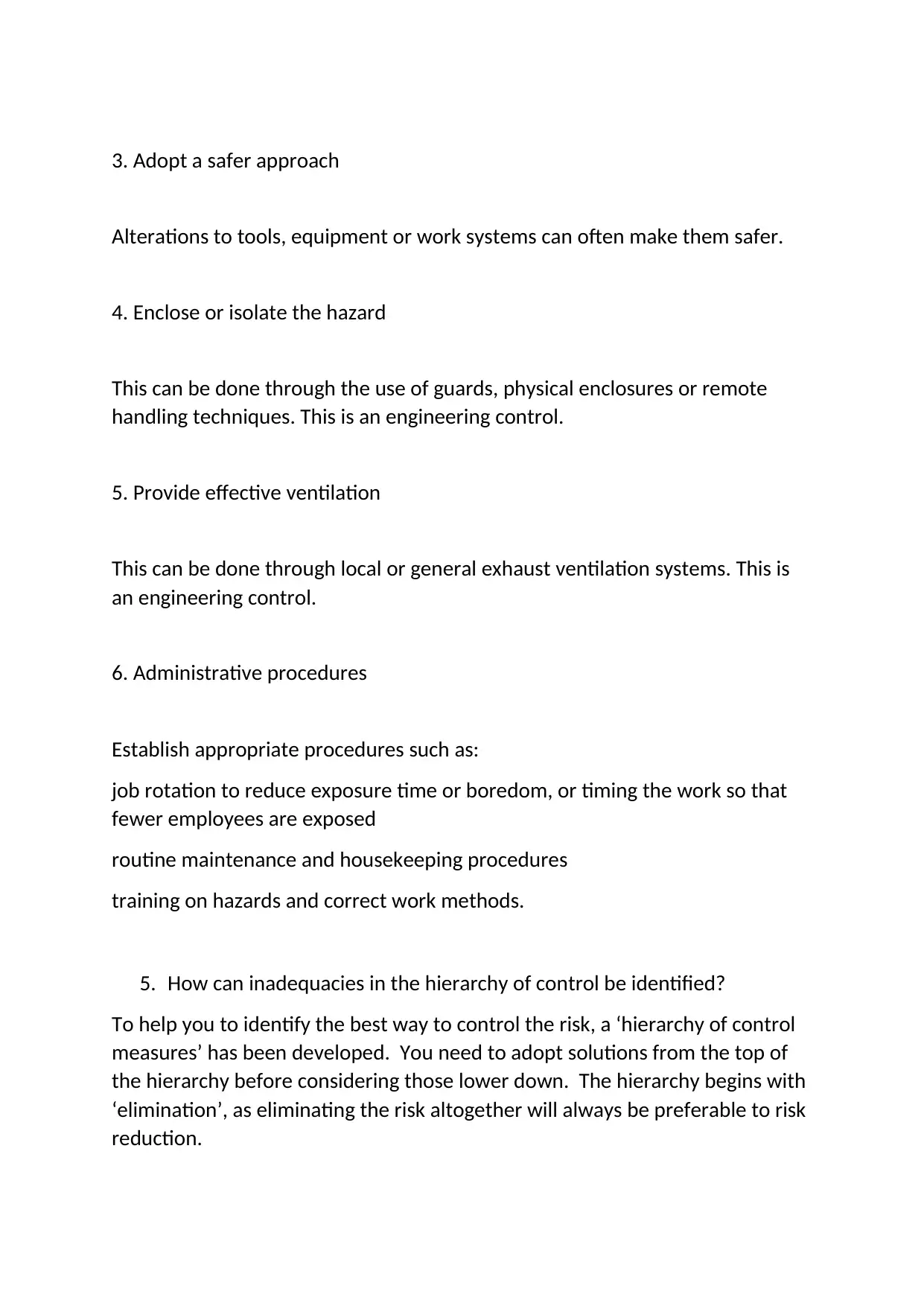
3. Adopt a safer approach
Alterations to tools, equipment or work systems can often make them safer.
4. Enclose or isolate the hazard
This can be done through the use of guards, physical enclosures or remote
handling techniques. This is an engineering control.
5. Provide effective ventilation
This can be done through local or general exhaust ventilation systems. This is
an engineering control.
6. Administrative procedures
Establish appropriate procedures such as:
job rotation to reduce exposure time or boredom, or timing the work so that
fewer employees are exposed
routine maintenance and housekeeping procedures
training on hazards and correct work methods.
5. How can inadequacies in the hierarchy of control be identified?
To help you to identify the best way to control the risk, a ‘hierarchy of control
measures’ has been developed. You need to adopt solutions from the top of
the hierarchy before considering those lower down. The hierarchy begins with
‘elimination’, as eliminating the risk altogether will always be preferable to risk
reduction.
Alterations to tools, equipment or work systems can often make them safer.
4. Enclose or isolate the hazard
This can be done through the use of guards, physical enclosures or remote
handling techniques. This is an engineering control.
5. Provide effective ventilation
This can be done through local or general exhaust ventilation systems. This is
an engineering control.
6. Administrative procedures
Establish appropriate procedures such as:
job rotation to reduce exposure time or boredom, or timing the work so that
fewer employees are exposed
routine maintenance and housekeeping procedures
training on hazards and correct work methods.
5. How can inadequacies in the hierarchy of control be identified?
To help you to identify the best way to control the risk, a ‘hierarchy of control
measures’ has been developed. You need to adopt solutions from the top of
the hierarchy before considering those lower down. The hierarchy begins with
‘elimination’, as eliminating the risk altogether will always be preferable to risk
reduction.
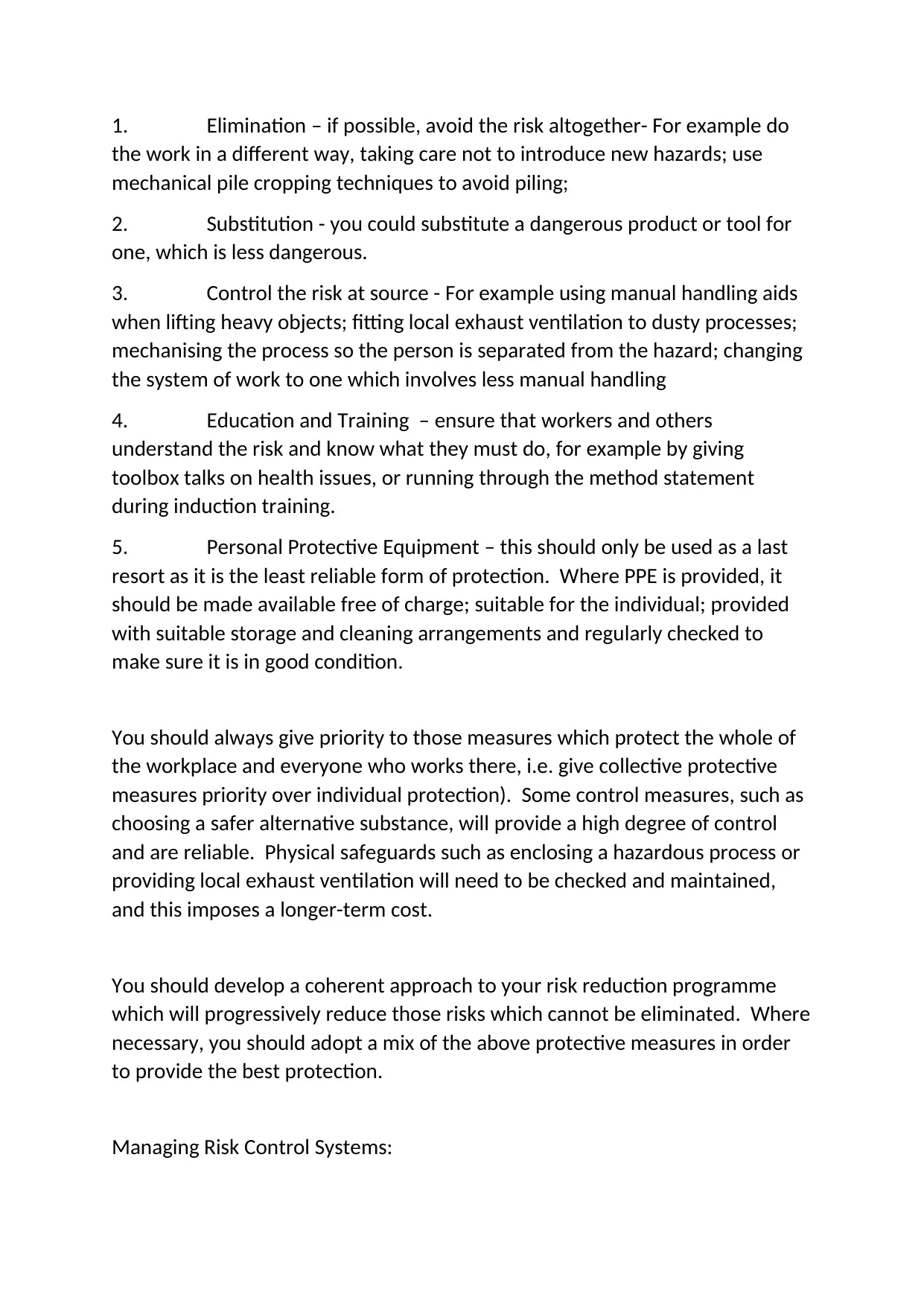
1. Elimination – if possible, avoid the risk altogether- For example do
the work in a different way, taking care not to introduce new hazards; use
mechanical pile cropping techniques to avoid piling;
2. Substitution - you could substitute a dangerous product or tool for
one, which is less dangerous.
3. Control the risk at source - For example using manual handling aids
when lifting heavy objects; fitting local exhaust ventilation to dusty processes;
mechanising the process so the person is separated from the hazard; changing
the system of work to one which involves less manual handling
4. Education and Training – ensure that workers and others
understand the risk and know what they must do, for example by giving
toolbox talks on health issues, or running through the method statement
during induction training.
5. Personal Protective Equipment – this should only be used as a last
resort as it is the least reliable form of protection. Where PPE is provided, it
should be made available free of charge; suitable for the individual; provided
with suitable storage and cleaning arrangements and regularly checked to
make sure it is in good condition.
You should always give priority to those measures which protect the whole of
the workplace and everyone who works there, i.e. give collective protective
measures priority over individual protection). Some control measures, such as
choosing a safer alternative substance, will provide a high degree of control
and are reliable. Physical safeguards such as enclosing a hazardous process or
providing local exhaust ventilation will need to be checked and maintained,
and this imposes a longer-term cost.
You should develop a coherent approach to your risk reduction programme
which will progressively reduce those risks which cannot be eliminated. Where
necessary, you should adopt a mix of the above protective measures in order
to provide the best protection.
Managing Risk Control Systems:
the work in a different way, taking care not to introduce new hazards; use
mechanical pile cropping techniques to avoid piling;
2. Substitution - you could substitute a dangerous product or tool for
one, which is less dangerous.
3. Control the risk at source - For example using manual handling aids
when lifting heavy objects; fitting local exhaust ventilation to dusty processes;
mechanising the process so the person is separated from the hazard; changing
the system of work to one which involves less manual handling
4. Education and Training – ensure that workers and others
understand the risk and know what they must do, for example by giving
toolbox talks on health issues, or running through the method statement
during induction training.
5. Personal Protective Equipment – this should only be used as a last
resort as it is the least reliable form of protection. Where PPE is provided, it
should be made available free of charge; suitable for the individual; provided
with suitable storage and cleaning arrangements and regularly checked to
make sure it is in good condition.
You should always give priority to those measures which protect the whole of
the workplace and everyone who works there, i.e. give collective protective
measures priority over individual protection). Some control measures, such as
choosing a safer alternative substance, will provide a high degree of control
and are reliable. Physical safeguards such as enclosing a hazardous process or
providing local exhaust ventilation will need to be checked and maintained,
and this imposes a longer-term cost.
You should develop a coherent approach to your risk reduction programme
which will progressively reduce those risks which cannot be eliminated. Where
necessary, you should adopt a mix of the above protective measures in order
to provide the best protection.
Managing Risk Control Systems:
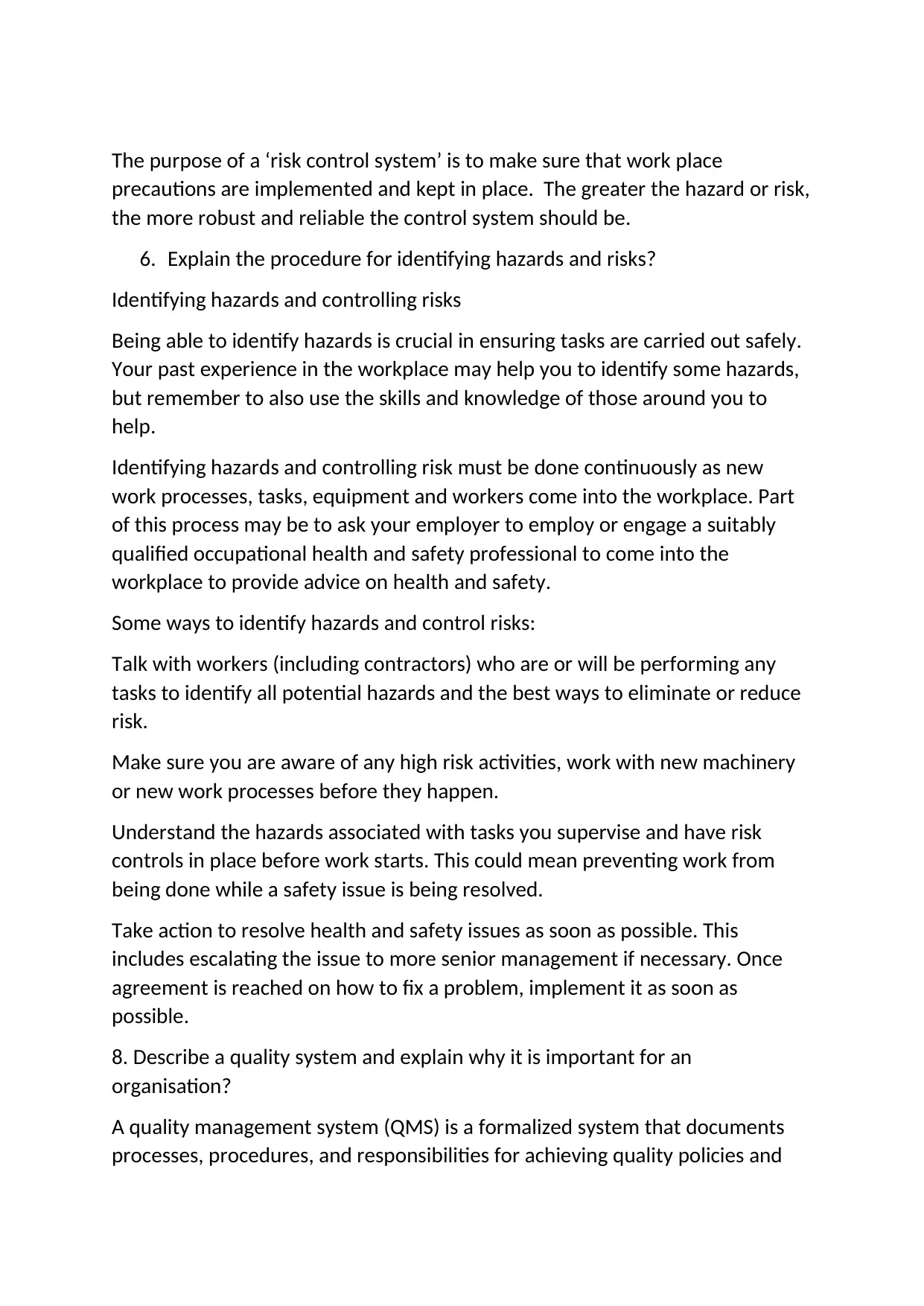
The purpose of a ‘risk control system’ is to make sure that work place
precautions are implemented and kept in place. The greater the hazard or risk,
the more robust and reliable the control system should be.
6. Explain the procedure for identifying hazards and risks?
Identifying hazards and controlling risks
Being able to identify hazards is crucial in ensuring tasks are carried out safely.
Your past experience in the workplace may help you to identify some hazards,
but remember to also use the skills and knowledge of those around you to
help.
Identifying hazards and controlling risk must be done continuously as new
work processes, tasks, equipment and workers come into the workplace. Part
of this process may be to ask your employer to employ or engage a suitably
qualified occupational health and safety professional to come into the
workplace to provide advice on health and safety.
Some ways to identify hazards and control risks:
Talk with workers (including contractors) who are or will be performing any
tasks to identify all potential hazards and the best ways to eliminate or reduce
risk.
Make sure you are aware of any high risk activities, work with new machinery
or new work processes before they happen.
Understand the hazards associated with tasks you supervise and have risk
controls in place before work starts. This could mean preventing work from
being done while a safety issue is being resolved.
Take action to resolve health and safety issues as soon as possible. This
includes escalating the issue to more senior management if necessary. Once
agreement is reached on how to fix a problem, implement it as soon as
possible.
8. Describe a quality system and explain why it is important for an
organisation?
A quality management system (QMS) is a formalized system that documents
processes, procedures, and responsibilities for achieving quality policies and
precautions are implemented and kept in place. The greater the hazard or risk,
the more robust and reliable the control system should be.
6. Explain the procedure for identifying hazards and risks?
Identifying hazards and controlling risks
Being able to identify hazards is crucial in ensuring tasks are carried out safely.
Your past experience in the workplace may help you to identify some hazards,
but remember to also use the skills and knowledge of those around you to
help.
Identifying hazards and controlling risk must be done continuously as new
work processes, tasks, equipment and workers come into the workplace. Part
of this process may be to ask your employer to employ or engage a suitably
qualified occupational health and safety professional to come into the
workplace to provide advice on health and safety.
Some ways to identify hazards and control risks:
Talk with workers (including contractors) who are or will be performing any
tasks to identify all potential hazards and the best ways to eliminate or reduce
risk.
Make sure you are aware of any high risk activities, work with new machinery
or new work processes before they happen.
Understand the hazards associated with tasks you supervise and have risk
controls in place before work starts. This could mean preventing work from
being done while a safety issue is being resolved.
Take action to resolve health and safety issues as soon as possible. This
includes escalating the issue to more senior management if necessary. Once
agreement is reached on how to fix a problem, implement it as soon as
possible.
8. Describe a quality system and explain why it is important for an
organisation?
A quality management system (QMS) is a formalized system that documents
processes, procedures, and responsibilities for achieving quality policies and
Paraphrase This Document
Need a fresh take? Get an instant paraphrase of this document with our AI Paraphraser
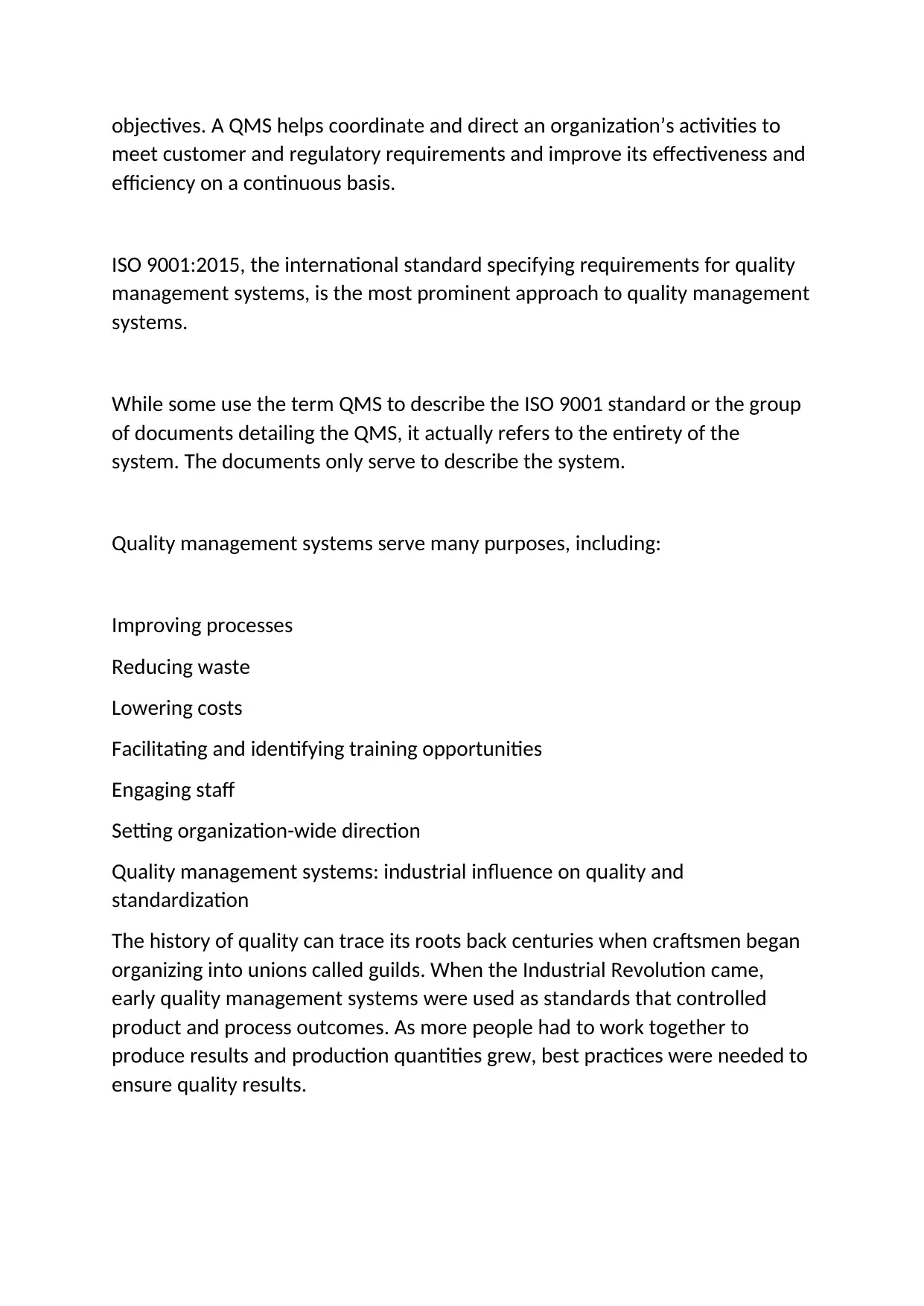
objectives. A QMS helps coordinate and direct an organization’s activities to
meet customer and regulatory requirements and improve its effectiveness and
efficiency on a continuous basis.
ISO 9001:2015, the international standard specifying requirements for quality
management systems, is the most prominent approach to quality management
systems.
While some use the term QMS to describe the ISO 9001 standard or the group
of documents detailing the QMS, it actually refers to the entirety of the
system. The documents only serve to describe the system.
Quality management systems serve many purposes, including:
Improving processes
Reducing waste
Lowering costs
Facilitating and identifying training opportunities
Engaging staff
Setting organization-wide direction
Quality management systems: industrial influence on quality and
standardization
The history of quality can trace its roots back centuries when craftsmen began
organizing into unions called guilds. When the Industrial Revolution came,
early quality management systems were used as standards that controlled
product and process outcomes. As more people had to work together to
produce results and production quantities grew, best practices were needed to
ensure quality results.
meet customer and regulatory requirements and improve its effectiveness and
efficiency on a continuous basis.
ISO 9001:2015, the international standard specifying requirements for quality
management systems, is the most prominent approach to quality management
systems.
While some use the term QMS to describe the ISO 9001 standard or the group
of documents detailing the QMS, it actually refers to the entirety of the
system. The documents only serve to describe the system.
Quality management systems serve many purposes, including:
Improving processes
Reducing waste
Lowering costs
Facilitating and identifying training opportunities
Engaging staff
Setting organization-wide direction
Quality management systems: industrial influence on quality and
standardization
The history of quality can trace its roots back centuries when craftsmen began
organizing into unions called guilds. When the Industrial Revolution came,
early quality management systems were used as standards that controlled
product and process outcomes. As more people had to work together to
produce results and production quantities grew, best practices were needed to
ensure quality results.
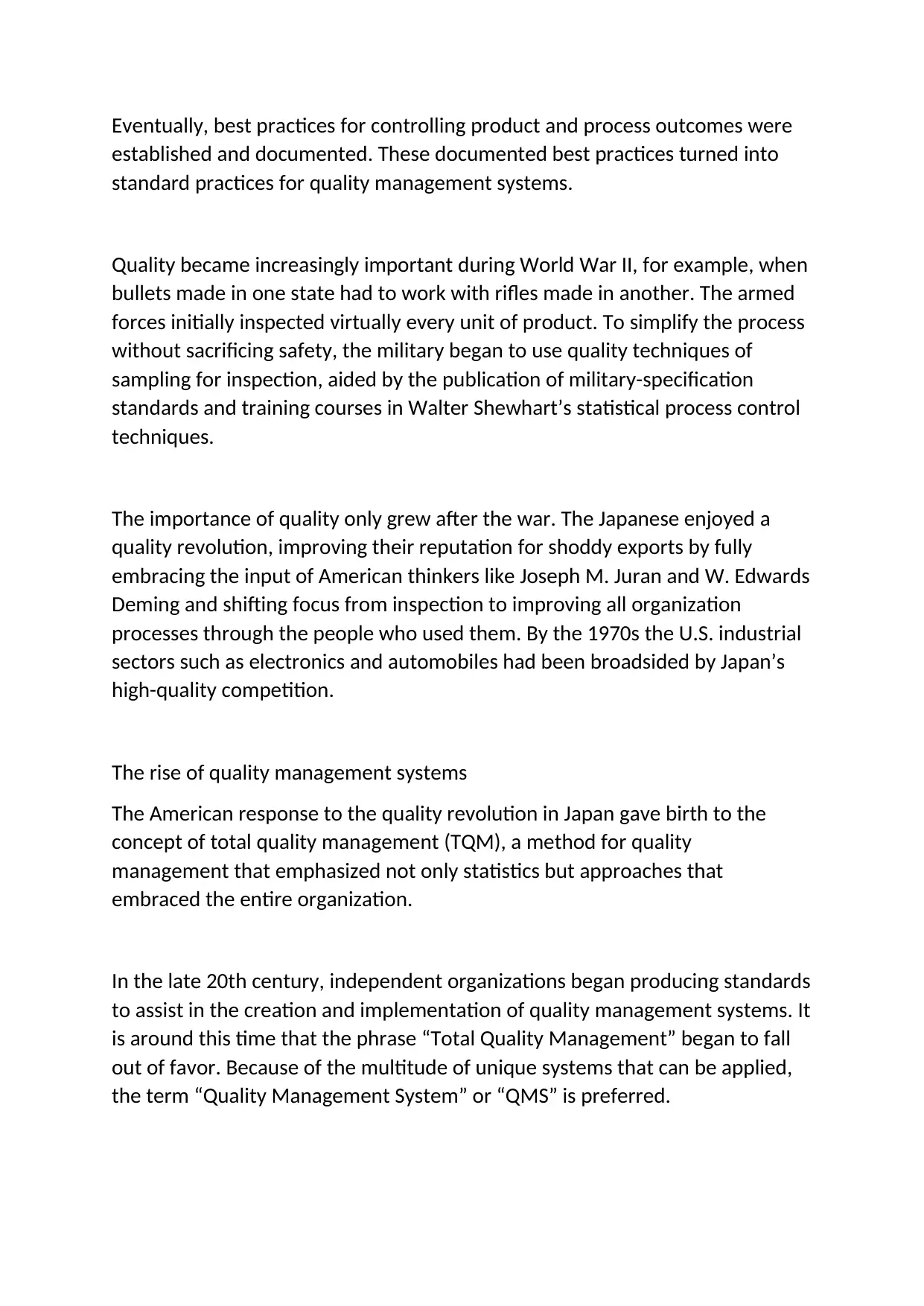
Eventually, best practices for controlling product and process outcomes were
established and documented. These documented best practices turned into
standard practices for quality management systems.
Quality became increasingly important during World War II, for example, when
bullets made in one state had to work with rifles made in another. The armed
forces initially inspected virtually every unit of product. To simplify the process
without sacrificing safety, the military began to use quality techniques of
sampling for inspection, aided by the publication of military-specification
standards and training courses in Walter Shewhart’s statistical process control
techniques.
The importance of quality only grew after the war. The Japanese enjoyed a
quality revolution, improving their reputation for shoddy exports by fully
embracing the input of American thinkers like Joseph M. Juran and W. Edwards
Deming and shifting focus from inspection to improving all organization
processes through the people who used them. By the 1970s the U.S. industrial
sectors such as electronics and automobiles had been broadsided by Japan’s
high-quality competition.
The rise of quality management systems
The American response to the quality revolution in Japan gave birth to the
concept of total quality management (TQM), a method for quality
management that emphasized not only statistics but approaches that
embraced the entire organization.
In the late 20th century, independent organizations began producing standards
to assist in the creation and implementation of quality management systems. It
is around this time that the phrase “Total Quality Management” began to fall
out of favor. Because of the multitude of unique systems that can be applied,
the term “Quality Management System” or “QMS” is preferred.
established and documented. These documented best practices turned into
standard practices for quality management systems.
Quality became increasingly important during World War II, for example, when
bullets made in one state had to work with rifles made in another. The armed
forces initially inspected virtually every unit of product. To simplify the process
without sacrificing safety, the military began to use quality techniques of
sampling for inspection, aided by the publication of military-specification
standards and training courses in Walter Shewhart’s statistical process control
techniques.
The importance of quality only grew after the war. The Japanese enjoyed a
quality revolution, improving their reputation for shoddy exports by fully
embracing the input of American thinkers like Joseph M. Juran and W. Edwards
Deming and shifting focus from inspection to improving all organization
processes through the people who used them. By the 1970s the U.S. industrial
sectors such as electronics and automobiles had been broadsided by Japan’s
high-quality competition.
The rise of quality management systems
The American response to the quality revolution in Japan gave birth to the
concept of total quality management (TQM), a method for quality
management that emphasized not only statistics but approaches that
embraced the entire organization.
In the late 20th century, independent organizations began producing standards
to assist in the creation and implementation of quality management systems. It
is around this time that the phrase “Total Quality Management” began to fall
out of favor. Because of the multitude of unique systems that can be applied,
the term “Quality Management System” or “QMS” is preferred.
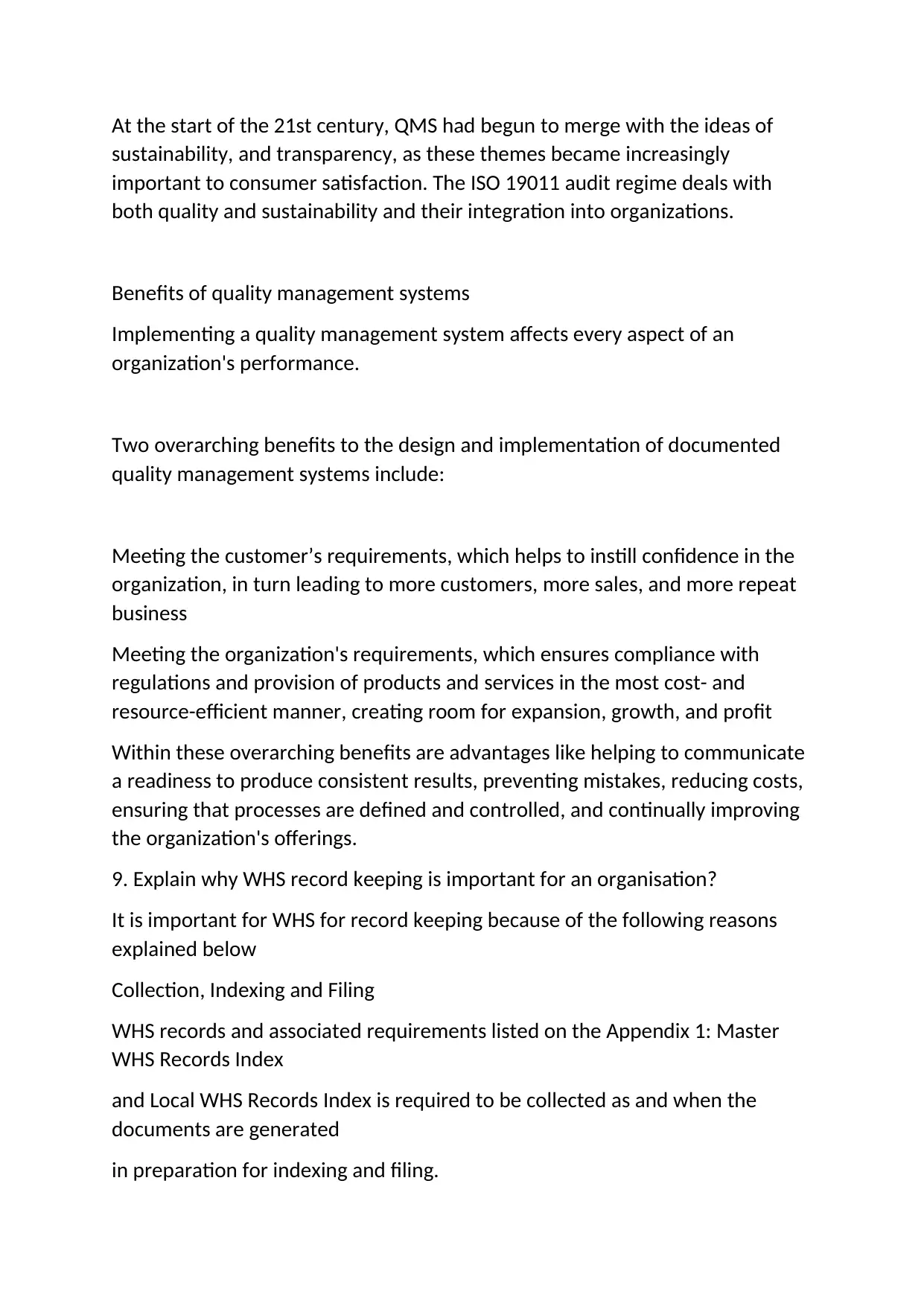
At the start of the 21st century, QMS had begun to merge with the ideas of
sustainability, and transparency, as these themes became increasingly
important to consumer satisfaction. The ISO 19011 audit regime deals with
both quality and sustainability and their integration into organizations.
Benefits of quality management systems
Implementing a quality management system affects every aspect of an
organization's performance.
Two overarching benefits to the design and implementation of documented
quality management systems include:
Meeting the customer’s requirements, which helps to instill confidence in the
organization, in turn leading to more customers, more sales, and more repeat
business
Meeting the organization's requirements, which ensures compliance with
regulations and provision of products and services in the most cost- and
resource-efficient manner, creating room for expansion, growth, and profit
Within these overarching benefits are advantages like helping to communicate
a readiness to produce consistent results, preventing mistakes, reducing costs,
ensuring that processes are defined and controlled, and continually improving
the organization's offerings.
9. Explain why WHS record keeping is important for an organisation?
It is important for WHS for record keeping because of the following reasons
explained below
Collection, Indexing and Filing
WHS records and associated requirements listed on the Appendix 1: Master
WHS Records Index
and Local WHS Records Index is required to be collected as and when the
documents are generated
in preparation for indexing and filing.
sustainability, and transparency, as these themes became increasingly
important to consumer satisfaction. The ISO 19011 audit regime deals with
both quality and sustainability and their integration into organizations.
Benefits of quality management systems
Implementing a quality management system affects every aspect of an
organization's performance.
Two overarching benefits to the design and implementation of documented
quality management systems include:
Meeting the customer’s requirements, which helps to instill confidence in the
organization, in turn leading to more customers, more sales, and more repeat
business
Meeting the organization's requirements, which ensures compliance with
regulations and provision of products and services in the most cost- and
resource-efficient manner, creating room for expansion, growth, and profit
Within these overarching benefits are advantages like helping to communicate
a readiness to produce consistent results, preventing mistakes, reducing costs,
ensuring that processes are defined and controlled, and continually improving
the organization's offerings.
9. Explain why WHS record keeping is important for an organisation?
It is important for WHS for record keeping because of the following reasons
explained below
Collection, Indexing and Filing
WHS records and associated requirements listed on the Appendix 1: Master
WHS Records Index
and Local WHS Records Index is required to be collected as and when the
documents are generated
in preparation for indexing and filing.
Secure Best Marks with AI Grader
Need help grading? Try our AI Grader for instant feedback on your assignments.
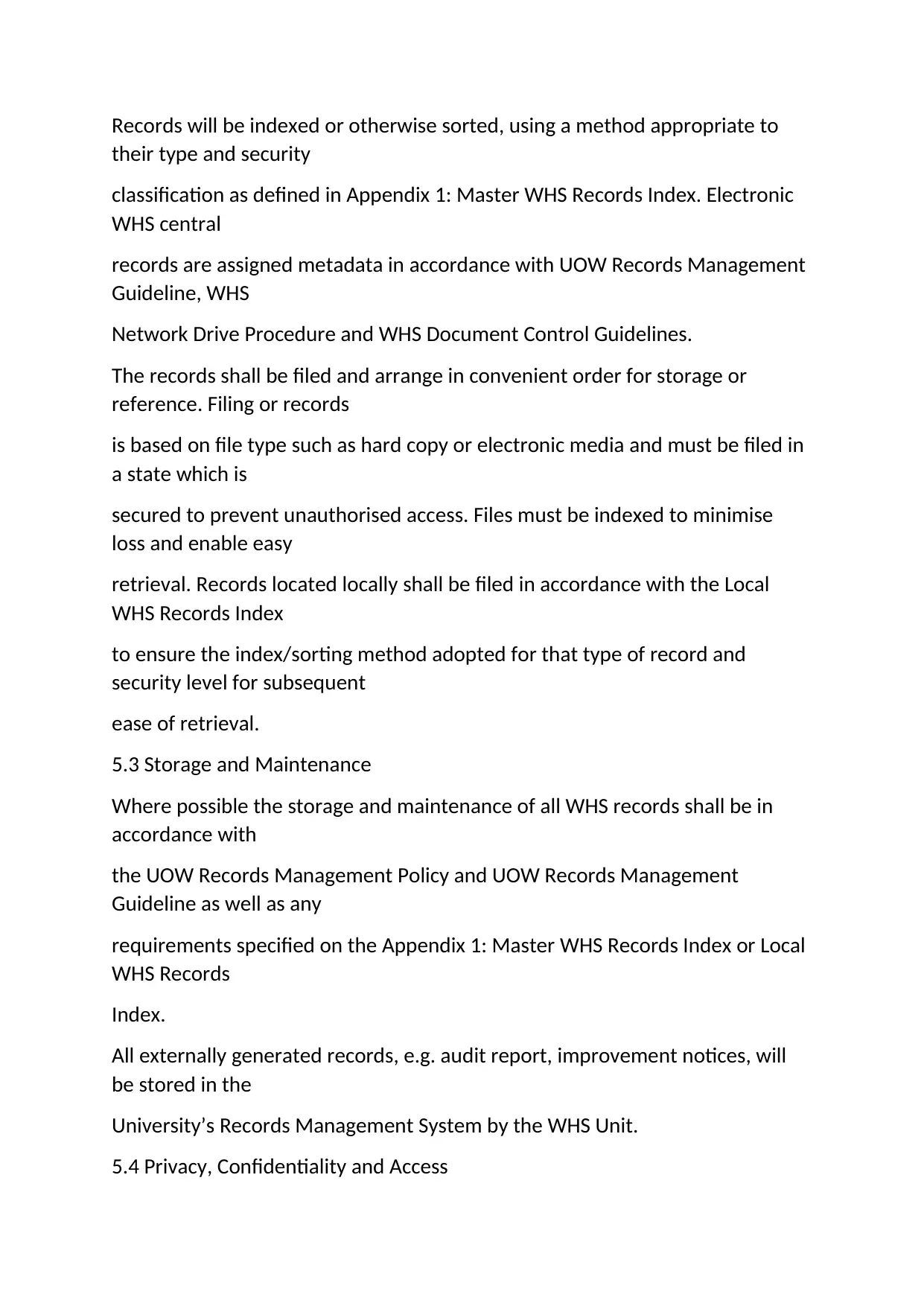
Records will be indexed or otherwise sorted, using a method appropriate to
their type and security
classification as defined in Appendix 1: Master WHS Records Index. Electronic
WHS central
records are assigned metadata in accordance with UOW Records Management
Guideline, WHS
Network Drive Procedure and WHS Document Control Guidelines.
The records shall be filed and arrange in convenient order for storage or
reference. Filing or records
is based on file type such as hard copy or electronic media and must be filed in
a state which is
secured to prevent unauthorised access. Files must be indexed to minimise
loss and enable easy
retrieval. Records located locally shall be filed in accordance with the Local
WHS Records Index
to ensure the index/sorting method adopted for that type of record and
security level for subsequent
ease of retrieval.
5.3 Storage and Maintenance
Where possible the storage and maintenance of all WHS records shall be in
accordance with
the UOW Records Management Policy and UOW Records Management
Guideline as well as any
requirements specified on the Appendix 1: Master WHS Records Index or Local
WHS Records
Index.
All externally generated records, e.g. audit report, improvement notices, will
be stored in the
University’s Records Management System by the WHS Unit.
5.4 Privacy, Confidentiality and Access
their type and security
classification as defined in Appendix 1: Master WHS Records Index. Electronic
WHS central
records are assigned metadata in accordance with UOW Records Management
Guideline, WHS
Network Drive Procedure and WHS Document Control Guidelines.
The records shall be filed and arrange in convenient order for storage or
reference. Filing or records
is based on file type such as hard copy or electronic media and must be filed in
a state which is
secured to prevent unauthorised access. Files must be indexed to minimise
loss and enable easy
retrieval. Records located locally shall be filed in accordance with the Local
WHS Records Index
to ensure the index/sorting method adopted for that type of record and
security level for subsequent
ease of retrieval.
5.3 Storage and Maintenance
Where possible the storage and maintenance of all WHS records shall be in
accordance with
the UOW Records Management Policy and UOW Records Management
Guideline as well as any
requirements specified on the Appendix 1: Master WHS Records Index or Local
WHS Records
Index.
All externally generated records, e.g. audit report, improvement notices, will
be stored in the
University’s Records Management System by the WHS Unit.
5.4 Privacy, Confidentiality and Access
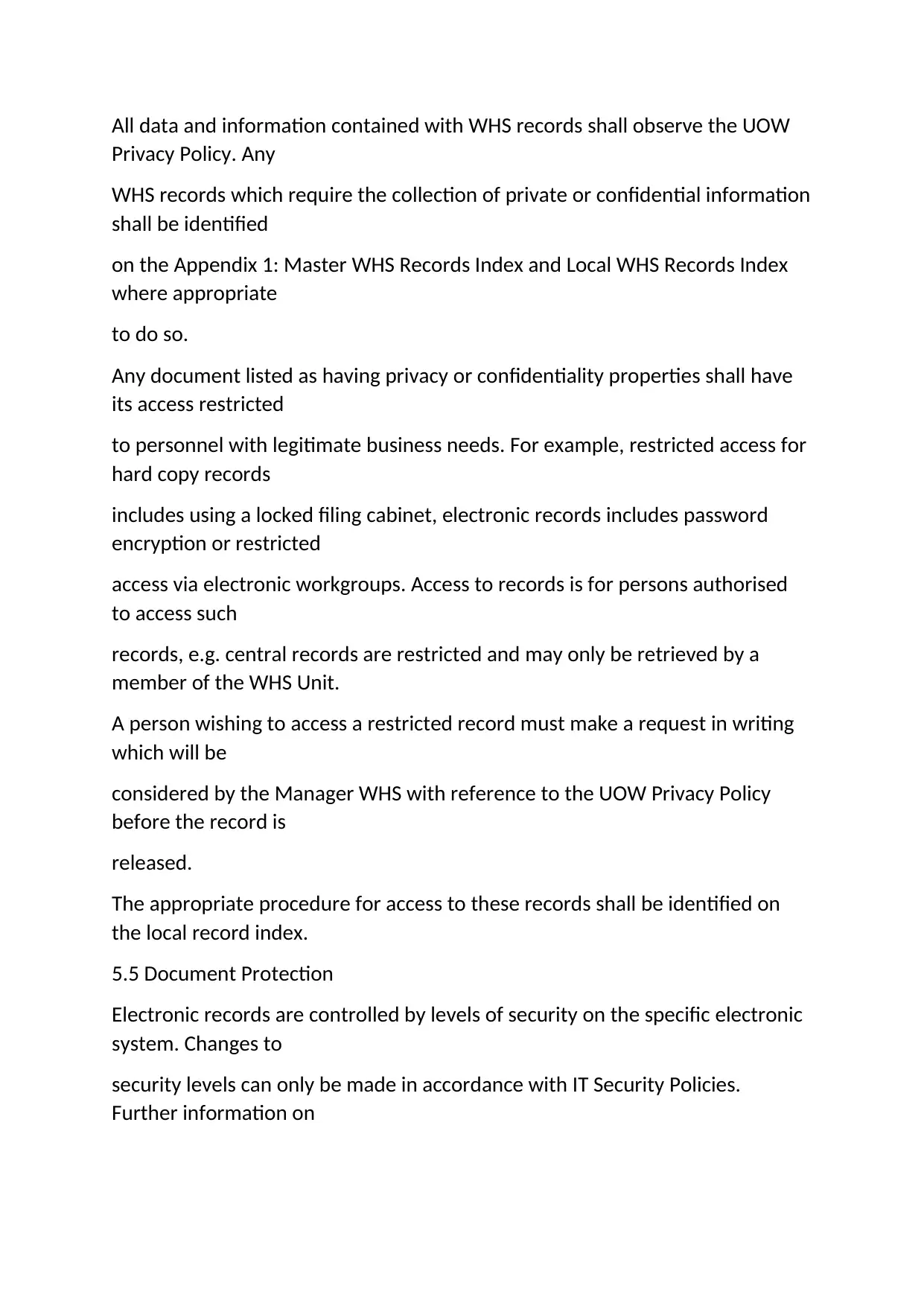
All data and information contained with WHS records shall observe the UOW
Privacy Policy. Any
WHS records which require the collection of private or confidential information
shall be identified
on the Appendix 1: Master WHS Records Index and Local WHS Records Index
where appropriate
to do so.
Any document listed as having privacy or confidentiality properties shall have
its access restricted
to personnel with legitimate business needs. For example, restricted access for
hard copy records
includes using a locked filing cabinet, electronic records includes password
encryption or restricted
access via electronic workgroups. Access to records is for persons authorised
to access such
records, e.g. central records are restricted and may only be retrieved by a
member of the WHS Unit.
A person wishing to access a restricted record must make a request in writing
which will be
considered by the Manager WHS with reference to the UOW Privacy Policy
before the record is
released.
The appropriate procedure for access to these records shall be identified on
the local record index.
5.5 Document Protection
Electronic records are controlled by levels of security on the specific electronic
system. Changes to
security levels can only be made in accordance with IT Security Policies.
Further information on
Privacy Policy. Any
WHS records which require the collection of private or confidential information
shall be identified
on the Appendix 1: Master WHS Records Index and Local WHS Records Index
where appropriate
to do so.
Any document listed as having privacy or confidentiality properties shall have
its access restricted
to personnel with legitimate business needs. For example, restricted access for
hard copy records
includes using a locked filing cabinet, electronic records includes password
encryption or restricted
access via electronic workgroups. Access to records is for persons authorised
to access such
records, e.g. central records are restricted and may only be retrieved by a
member of the WHS Unit.
A person wishing to access a restricted record must make a request in writing
which will be
considered by the Manager WHS with reference to the UOW Privacy Policy
before the record is
released.
The appropriate procedure for access to these records shall be identified on
the local record index.
5.5 Document Protection
Electronic records are controlled by levels of security on the specific electronic
system. Changes to
security levels can only be made in accordance with IT Security Policies.
Further information on
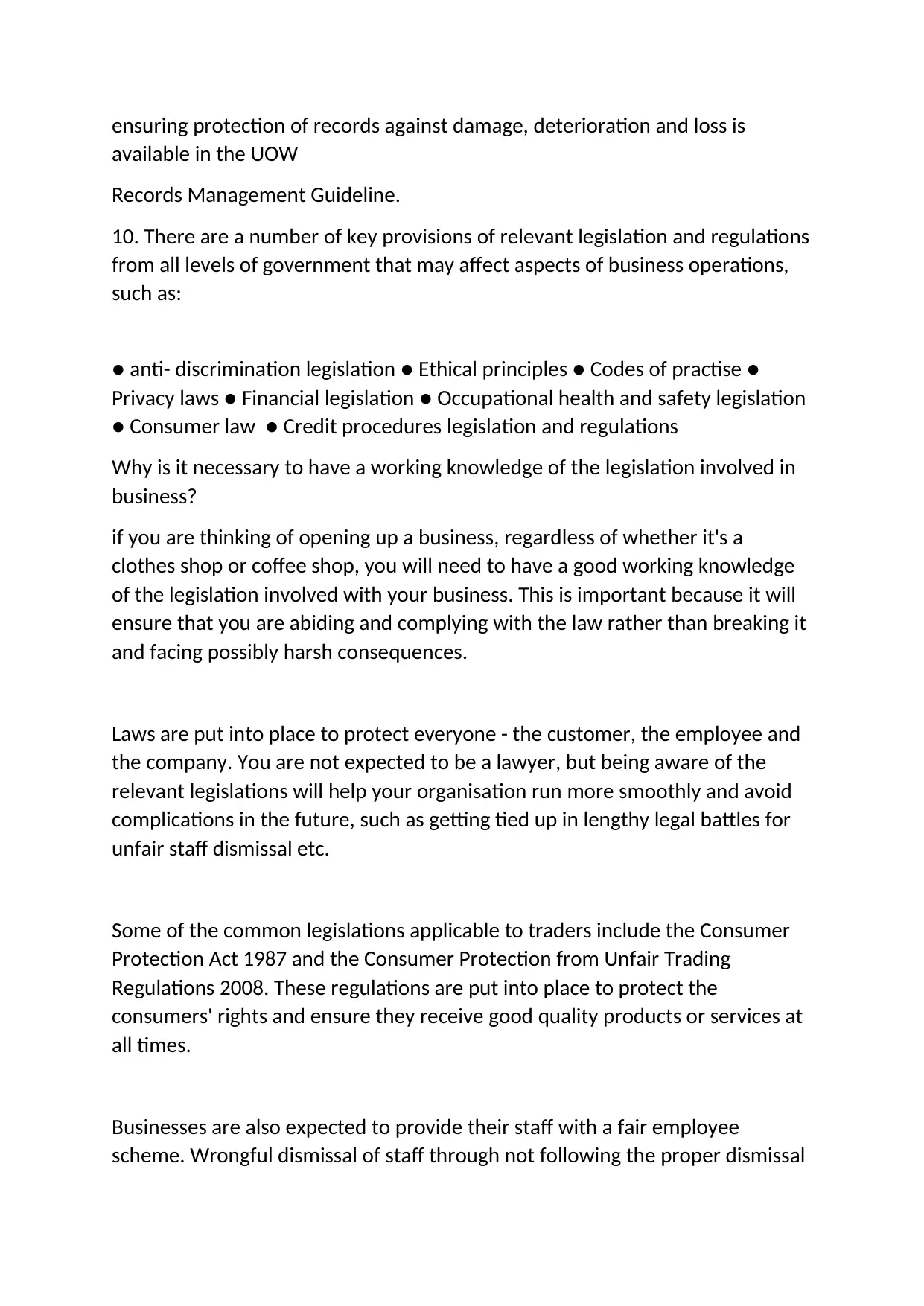
ensuring protection of records against damage, deterioration and loss is
available in the UOW
Records Management Guideline.
10. There are a number of key provisions of relevant legislation and regulations
from all levels of government that may affect aspects of business operations,
such as:
● anti- discrimination legislation ● Ethical principles ● Codes of practise ●
Privacy laws ● Financial legislation ● Occupational health and safety legislation
● Consumer law ● Credit procedures legislation and regulations
Why is it necessary to have a working knowledge of the legislation involved in
business?
if you are thinking of opening up a business, regardless of whether it's a
clothes shop or coffee shop, you will need to have a good working knowledge
of the legislation involved with your business. This is important because it will
ensure that you are abiding and complying with the law rather than breaking it
and facing possibly harsh consequences.
Laws are put into place to protect everyone - the customer, the employee and
the company. You are not expected to be a lawyer, but being aware of the
relevant legislations will help your organisation run more smoothly and avoid
complications in the future, such as getting tied up in lengthy legal battles for
unfair staff dismissal etc.
Some of the common legislations applicable to traders include the Consumer
Protection Act 1987 and the Consumer Protection from Unfair Trading
Regulations 2008. These regulations are put into place to protect the
consumers' rights and ensure they receive good quality products or services at
all times.
Businesses are also expected to provide their staff with a fair employee
scheme. Wrongful dismissal of staff through not following the proper dismissal
available in the UOW
Records Management Guideline.
10. There are a number of key provisions of relevant legislation and regulations
from all levels of government that may affect aspects of business operations,
such as:
● anti- discrimination legislation ● Ethical principles ● Codes of practise ●
Privacy laws ● Financial legislation ● Occupational health and safety legislation
● Consumer law ● Credit procedures legislation and regulations
Why is it necessary to have a working knowledge of the legislation involved in
business?
if you are thinking of opening up a business, regardless of whether it's a
clothes shop or coffee shop, you will need to have a good working knowledge
of the legislation involved with your business. This is important because it will
ensure that you are abiding and complying with the law rather than breaking it
and facing possibly harsh consequences.
Laws are put into place to protect everyone - the customer, the employee and
the company. You are not expected to be a lawyer, but being aware of the
relevant legislations will help your organisation run more smoothly and avoid
complications in the future, such as getting tied up in lengthy legal battles for
unfair staff dismissal etc.
Some of the common legislations applicable to traders include the Consumer
Protection Act 1987 and the Consumer Protection from Unfair Trading
Regulations 2008. These regulations are put into place to protect the
consumers' rights and ensure they receive good quality products or services at
all times.
Businesses are also expected to provide their staff with a fair employee
scheme. Wrongful dismissal of staff through not following the proper dismissal
Paraphrase This Document
Need a fresh take? Get an instant paraphrase of this document with our AI Paraphraser
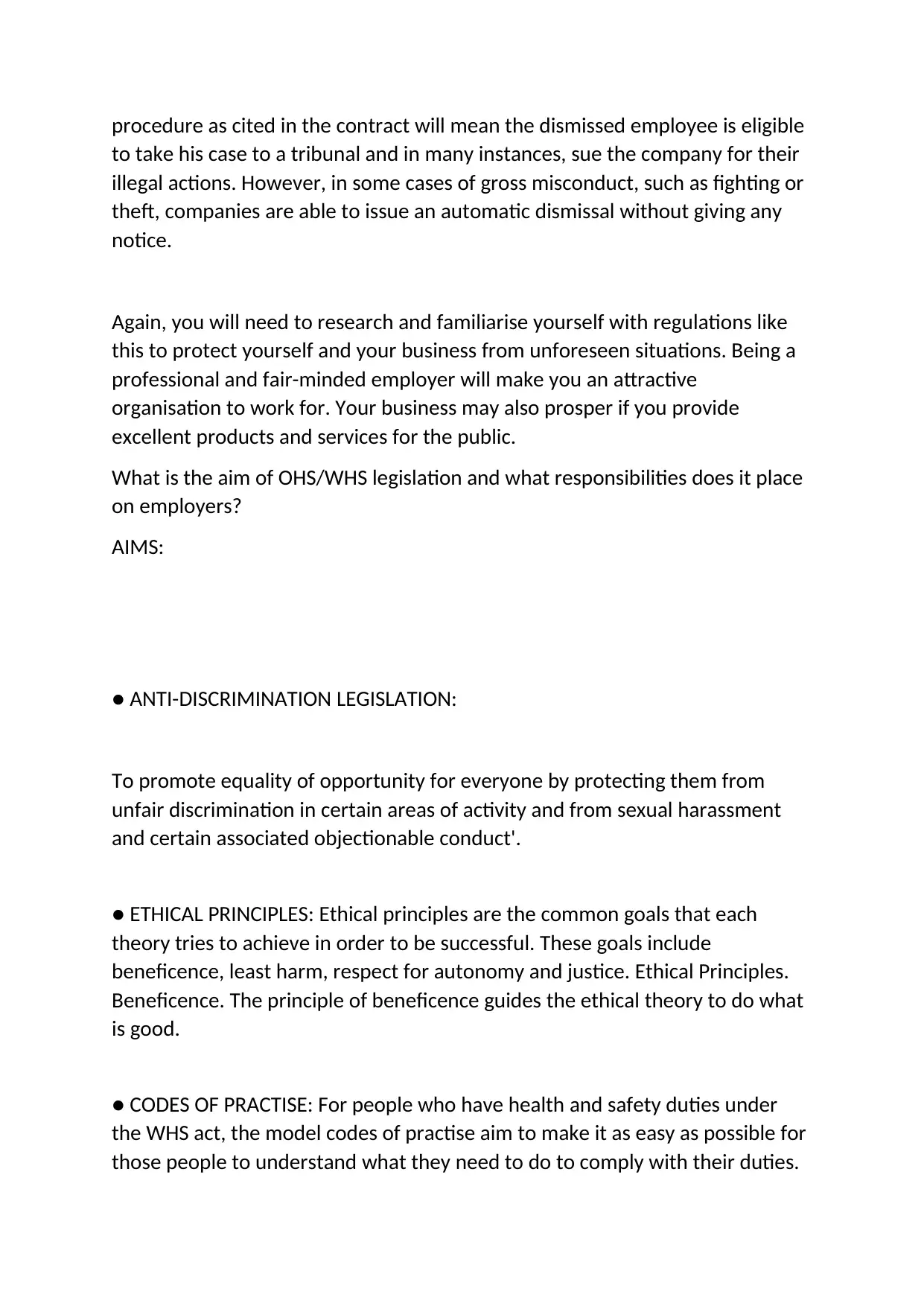
procedure as cited in the contract will mean the dismissed employee is eligible
to take his case to a tribunal and in many instances, sue the company for their
illegal actions. However, in some cases of gross misconduct, such as fighting or
theft, companies are able to issue an automatic dismissal without giving any
notice.
Again, you will need to research and familiarise yourself with regulations like
this to protect yourself and your business from unforeseen situations. Being a
professional and fair-minded employer will make you an attractive
organisation to work for. Your business may also prosper if you provide
excellent products and services for the public.
What is the aim of OHS/WHS legislation and what responsibilities does it place
on employers?
AIMS:
● ANTI-DISCRIMINATION LEGISLATION:
To promote equality of opportunity for everyone by protecting them from
unfair discrimination in certain areas of activity and from sexual harassment
and certain associated objectionable conduct'.
● ETHICAL PRINCIPLES: Ethical principles are the common goals that each
theory tries to achieve in order to be successful. These goals include
beneficence, least harm, respect for autonomy and justice. Ethical Principles.
Beneficence. The principle of beneficence guides the ethical theory to do what
is good.
● CODES OF PRACTISE: For people who have health and safety duties under
the WHS act, the model codes of practise aim to make it as easy as possible for
those people to understand what they need to do to comply with their duties.
to take his case to a tribunal and in many instances, sue the company for their
illegal actions. However, in some cases of gross misconduct, such as fighting or
theft, companies are able to issue an automatic dismissal without giving any
notice.
Again, you will need to research and familiarise yourself with regulations like
this to protect yourself and your business from unforeseen situations. Being a
professional and fair-minded employer will make you an attractive
organisation to work for. Your business may also prosper if you provide
excellent products and services for the public.
What is the aim of OHS/WHS legislation and what responsibilities does it place
on employers?
AIMS:
● ANTI-DISCRIMINATION LEGISLATION:
To promote equality of opportunity for everyone by protecting them from
unfair discrimination in certain areas of activity and from sexual harassment
and certain associated objectionable conduct'.
● ETHICAL PRINCIPLES: Ethical principles are the common goals that each
theory tries to achieve in order to be successful. These goals include
beneficence, least harm, respect for autonomy and justice. Ethical Principles.
Beneficence. The principle of beneficence guides the ethical theory to do what
is good.
● CODES OF PRACTISE: For people who have health and safety duties under
the WHS act, the model codes of practise aim to make it as easy as possible for
those people to understand what they need to do to comply with their duties.
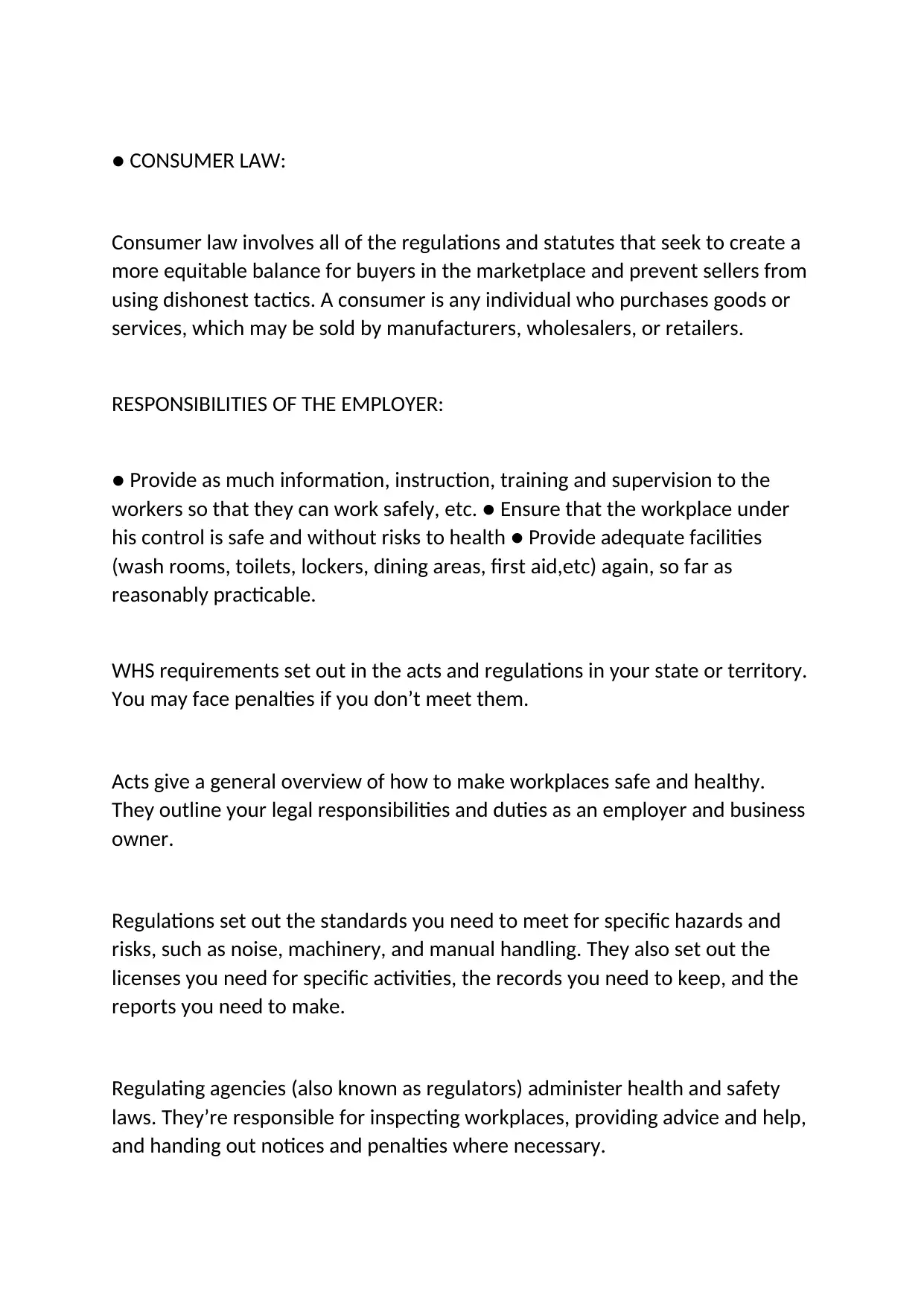
● CONSUMER LAW:
Consumer law involves all of the regulations and statutes that seek to create a
more equitable balance for buyers in the marketplace and prevent sellers from
using dishonest tactics. A consumer is any individual who purchases goods or
services, which may be sold by manufacturers, wholesalers, or retailers.
RESPONSIBILITIES OF THE EMPLOYER:
● Provide as much information, instruction, training and supervision to the
workers so that they can work safely, etc. ● Ensure that the workplace under
his control is safe and without risks to health ● Provide adequate facilities
(wash rooms, toilets, lockers, dining areas, first aid,etc) again, so far as
reasonably practicable.
WHS requirements set out in the acts and regulations in your state or territory.
You may face penalties if you don’t meet them.
Acts give a general overview of how to make workplaces safe and healthy.
They outline your legal responsibilities and duties as an employer and business
owner.
Regulations set out the standards you need to meet for specific hazards and
risks, such as noise, machinery, and manual handling. They also set out the
licenses you need for specific activities, the records you need to keep, and the
reports you need to make.
Regulating agencies (also known as regulators) administer health and safety
laws. They’re responsible for inspecting workplaces, providing advice and help,
and handing out notices and penalties where necessary.
Consumer law involves all of the regulations and statutes that seek to create a
more equitable balance for buyers in the marketplace and prevent sellers from
using dishonest tactics. A consumer is any individual who purchases goods or
services, which may be sold by manufacturers, wholesalers, or retailers.
RESPONSIBILITIES OF THE EMPLOYER:
● Provide as much information, instruction, training and supervision to the
workers so that they can work safely, etc. ● Ensure that the workplace under
his control is safe and without risks to health ● Provide adequate facilities
(wash rooms, toilets, lockers, dining areas, first aid,etc) again, so far as
reasonably practicable.
WHS requirements set out in the acts and regulations in your state or territory.
You may face penalties if you don’t meet them.
Acts give a general overview of how to make workplaces safe and healthy.
They outline your legal responsibilities and duties as an employer and business
owner.
Regulations set out the standards you need to meet for specific hazards and
risks, such as noise, machinery, and manual handling. They also set out the
licenses you need for specific activities, the records you need to keep, and the
reports you need to make.
Regulating agencies (also known as regulators) administer health and safety
laws. They’re responsible for inspecting workplaces, providing advice and help,
and handing out notices and penalties where necessary.

When courts are deciding whether workplace health and safety laws have
been met, they may consider whether you’ve followed the approved codes of
practice for your state or territory. You can get the approved codes of practice,
and advice and support from the regulator in your state or territory listed
below.
Read more about workplace health and safety to understand the benefits to
your business and your rights and obligations as a small business owner.
been met, they may consider whether you’ve followed the approved codes of
practice for your state or territory. You can get the approved codes of practice,
and advice and support from the regulator in your state or territory listed
below.
Read more about workplace health and safety to understand the benefits to
your business and your rights and obligations as a small business owner.
1 out of 16
Related Documents
![[object Object]](/_next/image/?url=%2F_next%2Fstatic%2Fmedia%2Flogo.6d15ce61.png&w=640&q=75)
Your All-in-One AI-Powered Toolkit for Academic Success.
+13062052269
info@desklib.com
Available 24*7 on WhatsApp / Email
Unlock your academic potential
© 2024 | Zucol Services PVT LTD | All rights reserved.