Project Management and Lean Production Techniques
VerifiedAdded on 2020/07/23
|17
|4176
|35
AI Summary
This assignment delves into the realm of project management, highlighting its significance in managing business projects and operational activities. The continuous improvement plans implemented through sig sigma and lean production are also discussed, enabling the analysis of issues and effective strategies for quality product enhancement.
Contribute Materials
Your contribution can guide someone’s learning journey. Share your
documents today.
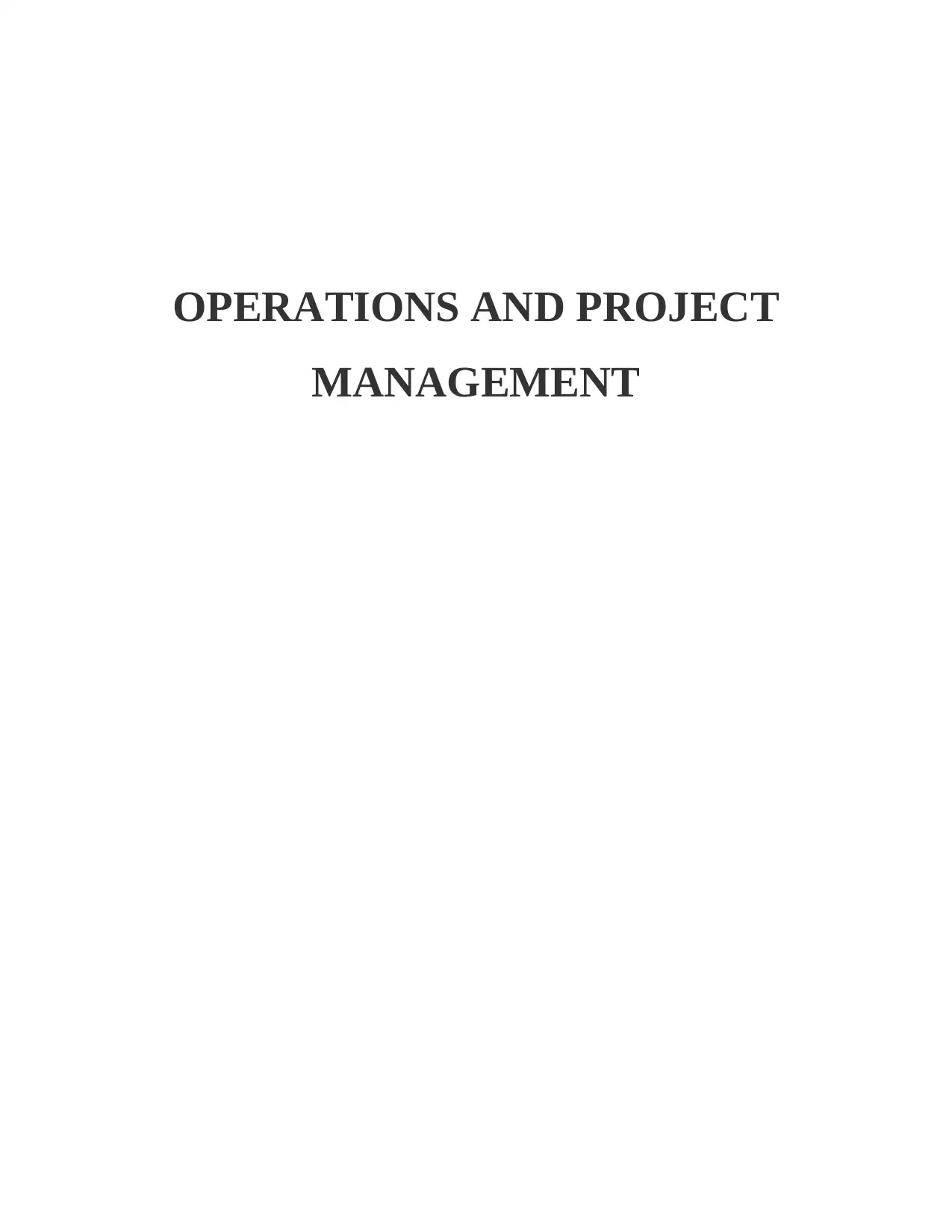
OPERATIONS AND PROJECT
MANAGEMENT
MANAGEMENT
Secure Best Marks with AI Grader
Need help grading? Try our AI Grader for instant feedback on your assignments.

Table of Contents
INTRODUCTION...........................................................................................................................1
TASK 1............................................................................................................................................1
Operation management...............................................................................................................1
Six sigma and lean principles .....................................................................................................2
TASK 2............................................................................................................................................4
Continuous improvements..........................................................................................................4
TASK 3 ...........................................................................................................................................5
A. Business case..........................................................................................................................5
B. Project plan.............................................................................................................................6
C. Work break down structures...................................................................................................7
D. Gantt chart..............................................................................................................................8
E. Theoretical and conceptual idea for use of methodologies..................................................11
TASK 4..........................................................................................................................................11
A. Effectiveness of project life cycle........................................................................................11
B. Importance of designing and implementing PLC.................................................................12
C. Cost saving techniques.........................................................................................................12
D. Quality assurance techniques...............................................................................................12
E. Theories, models...................................................................................................................13
F. Evaluation of PLC within theoretical and practical framework...........................................13
CONCLUSION..............................................................................................................................13
REFERENCES..............................................................................................................................14
INTRODUCTION...........................................................................................................................1
TASK 1............................................................................................................................................1
Operation management...............................................................................................................1
Six sigma and lean principles .....................................................................................................2
TASK 2............................................................................................................................................4
Continuous improvements..........................................................................................................4
TASK 3 ...........................................................................................................................................5
A. Business case..........................................................................................................................5
B. Project plan.............................................................................................................................6
C. Work break down structures...................................................................................................7
D. Gantt chart..............................................................................................................................8
E. Theoretical and conceptual idea for use of methodologies..................................................11
TASK 4..........................................................................................................................................11
A. Effectiveness of project life cycle........................................................................................11
B. Importance of designing and implementing PLC.................................................................12
C. Cost saving techniques.........................................................................................................12
D. Quality assurance techniques...............................................................................................12
E. Theories, models...................................................................................................................13
F. Evaluation of PLC within theoretical and practical framework...........................................13
CONCLUSION..............................................................................................................................13
REFERENCES..............................................................................................................................14
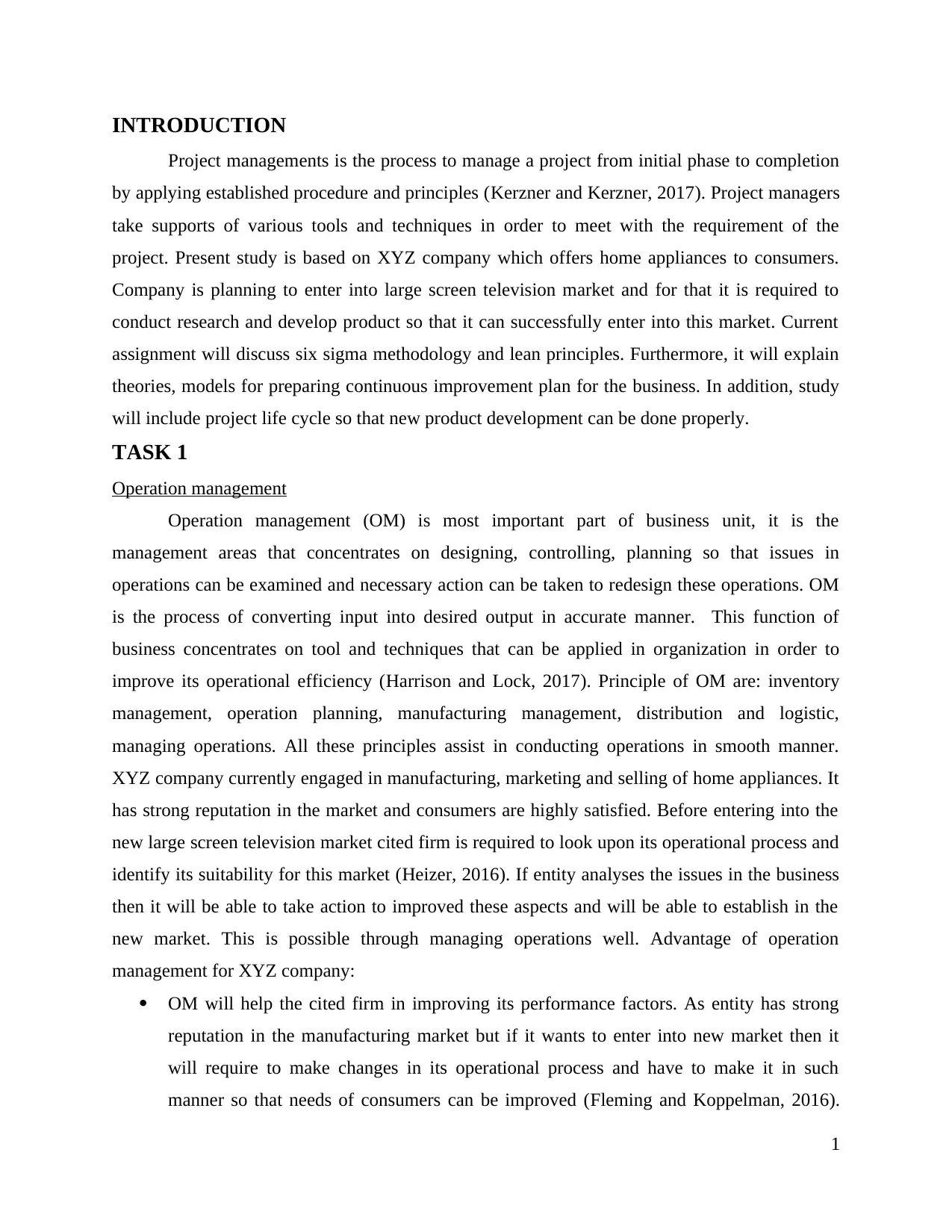
INTRODUCTION
Project managements is the process to manage a project from initial phase to completion
by applying established procedure and principles (Kerzner and Kerzner, 2017). Project managers
take supports of various tools and techniques in order to meet with the requirement of the
project. Present study is based on XYZ company which offers home appliances to consumers.
Company is planning to enter into large screen television market and for that it is required to
conduct research and develop product so that it can successfully enter into this market. Current
assignment will discuss six sigma methodology and lean principles. Furthermore, it will explain
theories, models for preparing continuous improvement plan for the business. In addition, study
will include project life cycle so that new product development can be done properly.
TASK 1
Operation management
Operation management (OM) is most important part of business unit, it is the
management areas that concentrates on designing, controlling, planning so that issues in
operations can be examined and necessary action can be taken to redesign these operations. OM
is the process of converting input into desired output in accurate manner. This function of
business concentrates on tool and techniques that can be applied in organization in order to
improve its operational efficiency (Harrison and Lock, 2017). Principle of OM are: inventory
management, operation planning, manufacturing management, distribution and logistic,
managing operations. All these principles assist in conducting operations in smooth manner.
XYZ company currently engaged in manufacturing, marketing and selling of home appliances. It
has strong reputation in the market and consumers are highly satisfied. Before entering into the
new large screen television market cited firm is required to look upon its operational process and
identify its suitability for this market (Heizer, 2016). If entity analyses the issues in the business
then it will be able to take action to improved these aspects and will be able to establish in the
new market. This is possible through managing operations well. Advantage of operation
management for XYZ company:
OM will help the cited firm in improving its performance factors. As entity has strong
reputation in the manufacturing market but if it wants to enter into new market then it
will require to make changes in its operational process and have to make it in such
manner so that needs of consumers can be improved (Fleming and Koppelman, 2016).
1
Project managements is the process to manage a project from initial phase to completion
by applying established procedure and principles (Kerzner and Kerzner, 2017). Project managers
take supports of various tools and techniques in order to meet with the requirement of the
project. Present study is based on XYZ company which offers home appliances to consumers.
Company is planning to enter into large screen television market and for that it is required to
conduct research and develop product so that it can successfully enter into this market. Current
assignment will discuss six sigma methodology and lean principles. Furthermore, it will explain
theories, models for preparing continuous improvement plan for the business. In addition, study
will include project life cycle so that new product development can be done properly.
TASK 1
Operation management
Operation management (OM) is most important part of business unit, it is the
management areas that concentrates on designing, controlling, planning so that issues in
operations can be examined and necessary action can be taken to redesign these operations. OM
is the process of converting input into desired output in accurate manner. This function of
business concentrates on tool and techniques that can be applied in organization in order to
improve its operational efficiency (Harrison and Lock, 2017). Principle of OM are: inventory
management, operation planning, manufacturing management, distribution and logistic,
managing operations. All these principles assist in conducting operations in smooth manner.
XYZ company currently engaged in manufacturing, marketing and selling of home appliances. It
has strong reputation in the market and consumers are highly satisfied. Before entering into the
new large screen television market cited firm is required to look upon its operational process and
identify its suitability for this market (Heizer, 2016). If entity analyses the issues in the business
then it will be able to take action to improved these aspects and will be able to establish in the
new market. This is possible through managing operations well. Advantage of operation
management for XYZ company:
OM will help the cited firm in improving its performance factors. As entity has strong
reputation in the manufacturing market but if it wants to enter into new market then it
will require to make changes in its operational process and have to make it in such
manner so that needs of consumers can be improved (Fleming and Koppelman, 2016).
1
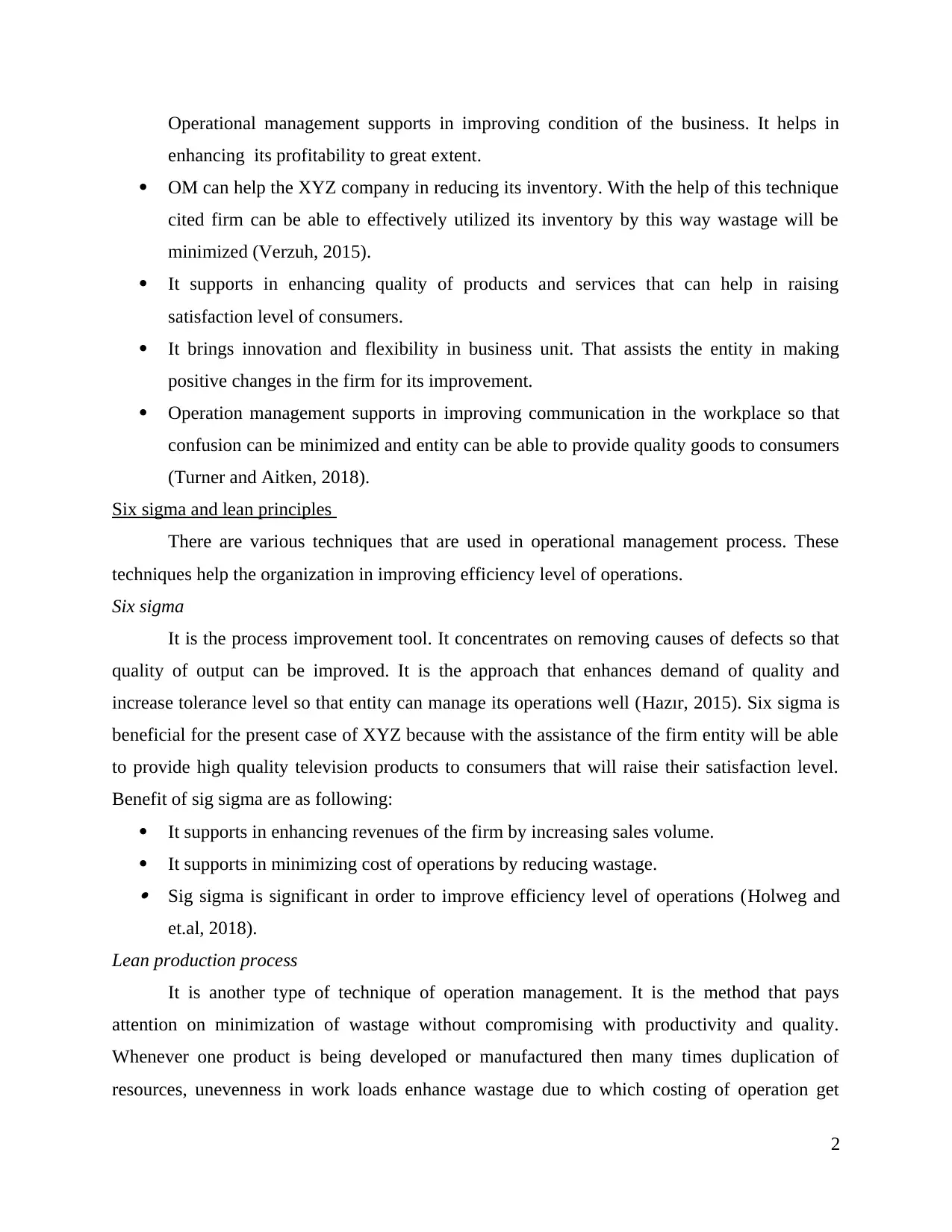
Operational management supports in improving condition of the business. It helps in
enhancing its profitability to great extent.
OM can help the XYZ company in reducing its inventory. With the help of this technique
cited firm can be able to effectively utilized its inventory by this way wastage will be
minimized (Verzuh, 2015).
It supports in enhancing quality of products and services that can help in raising
satisfaction level of consumers.
It brings innovation and flexibility in business unit. That assists the entity in making
positive changes in the firm for its improvement.
Operation management supports in improving communication in the workplace so that
confusion can be minimized and entity can be able to provide quality goods to consumers
(Turner and Aitken, 2018).
Six sigma and lean principles
There are various techniques that are used in operational management process. These
techniques help the organization in improving efficiency level of operations.
Six sigma
It is the process improvement tool. It concentrates on removing causes of defects so that
quality of output can be improved. It is the approach that enhances demand of quality and
increase tolerance level so that entity can manage its operations well (Hazır, 2015). Six sigma is
beneficial for the present case of XYZ because with the assistance of the firm entity will be able
to provide high quality television products to consumers that will raise their satisfaction level.
Benefit of sig sigma are as following:
It supports in enhancing revenues of the firm by increasing sales volume.
It supports in minimizing cost of operations by reducing wastage. Sig sigma is significant in order to improve efficiency level of operations (Holweg and
et.al, 2018).
Lean production process
It is another type of technique of operation management. It is the method that pays
attention on minimization of wastage without compromising with productivity and quality.
Whenever one product is being developed or manufactured then many times duplication of
resources, unevenness in work loads enhance wastage due to which costing of operation get
2
enhancing its profitability to great extent.
OM can help the XYZ company in reducing its inventory. With the help of this technique
cited firm can be able to effectively utilized its inventory by this way wastage will be
minimized (Verzuh, 2015).
It supports in enhancing quality of products and services that can help in raising
satisfaction level of consumers.
It brings innovation and flexibility in business unit. That assists the entity in making
positive changes in the firm for its improvement.
Operation management supports in improving communication in the workplace so that
confusion can be minimized and entity can be able to provide quality goods to consumers
(Turner and Aitken, 2018).
Six sigma and lean principles
There are various techniques that are used in operational management process. These
techniques help the organization in improving efficiency level of operations.
Six sigma
It is the process improvement tool. It concentrates on removing causes of defects so that
quality of output can be improved. It is the approach that enhances demand of quality and
increase tolerance level so that entity can manage its operations well (Hazır, 2015). Six sigma is
beneficial for the present case of XYZ because with the assistance of the firm entity will be able
to provide high quality television products to consumers that will raise their satisfaction level.
Benefit of sig sigma are as following:
It supports in enhancing revenues of the firm by increasing sales volume.
It supports in minimizing cost of operations by reducing wastage. Sig sigma is significant in order to improve efficiency level of operations (Holweg and
et.al, 2018).
Lean production process
It is another type of technique of operation management. It is the method that pays
attention on minimization of wastage without compromising with productivity and quality.
Whenever one product is being developed or manufactured then many times duplication of
resources, unevenness in work loads enhance wastage due to which costing of operation get
2
Secure Best Marks with AI Grader
Need help grading? Try our AI Grader for instant feedback on your assignments.
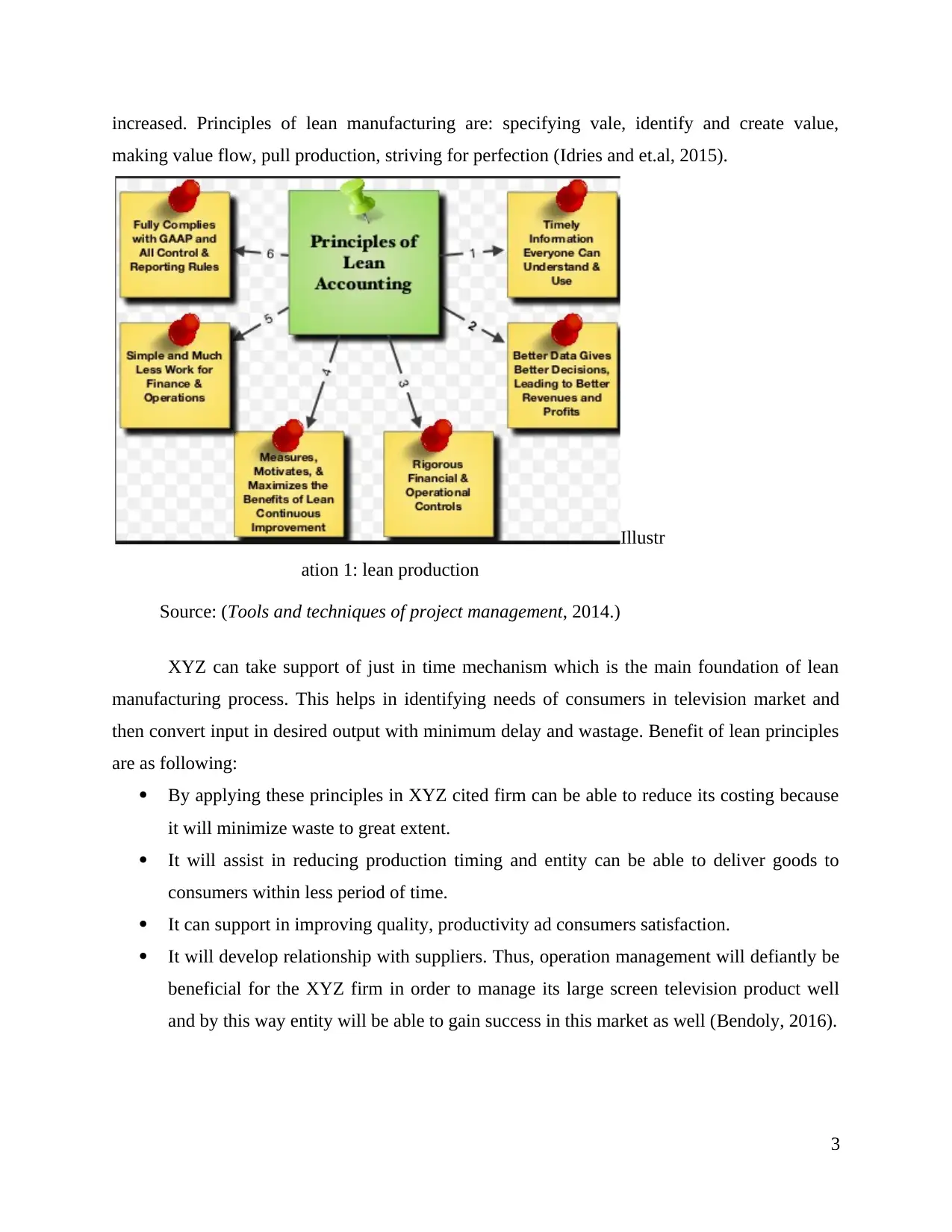
increased. Principles of lean manufacturing are: specifying vale, identify and create value,
making value flow, pull production, striving for perfection (Idries and et.al, 2015).
Illustr
ation 1: lean production
Source: (Tools and techniques of project management, 2014.)
XYZ can take support of just in time mechanism which is the main foundation of lean
manufacturing process. This helps in identifying needs of consumers in television market and
then convert input in desired output with minimum delay and wastage. Benefit of lean principles
are as following:
By applying these principles in XYZ cited firm can be able to reduce its costing because
it will minimize waste to great extent.
It will assist in reducing production timing and entity can be able to deliver goods to
consumers within less period of time.
It can support in improving quality, productivity ad consumers satisfaction.
It will develop relationship with suppliers. Thus, operation management will defiantly be
beneficial for the XYZ firm in order to manage its large screen television product well
and by this way entity will be able to gain success in this market as well (Bendoly, 2016).
3
making value flow, pull production, striving for perfection (Idries and et.al, 2015).
Illustr
ation 1: lean production
Source: (Tools and techniques of project management, 2014.)
XYZ can take support of just in time mechanism which is the main foundation of lean
manufacturing process. This helps in identifying needs of consumers in television market and
then convert input in desired output with minimum delay and wastage. Benefit of lean principles
are as following:
By applying these principles in XYZ cited firm can be able to reduce its costing because
it will minimize waste to great extent.
It will assist in reducing production timing and entity can be able to deliver goods to
consumers within less period of time.
It can support in improving quality, productivity ad consumers satisfaction.
It will develop relationship with suppliers. Thus, operation management will defiantly be
beneficial for the XYZ firm in order to manage its large screen television product well
and by this way entity will be able to gain success in this market as well (Bendoly, 2016).
3
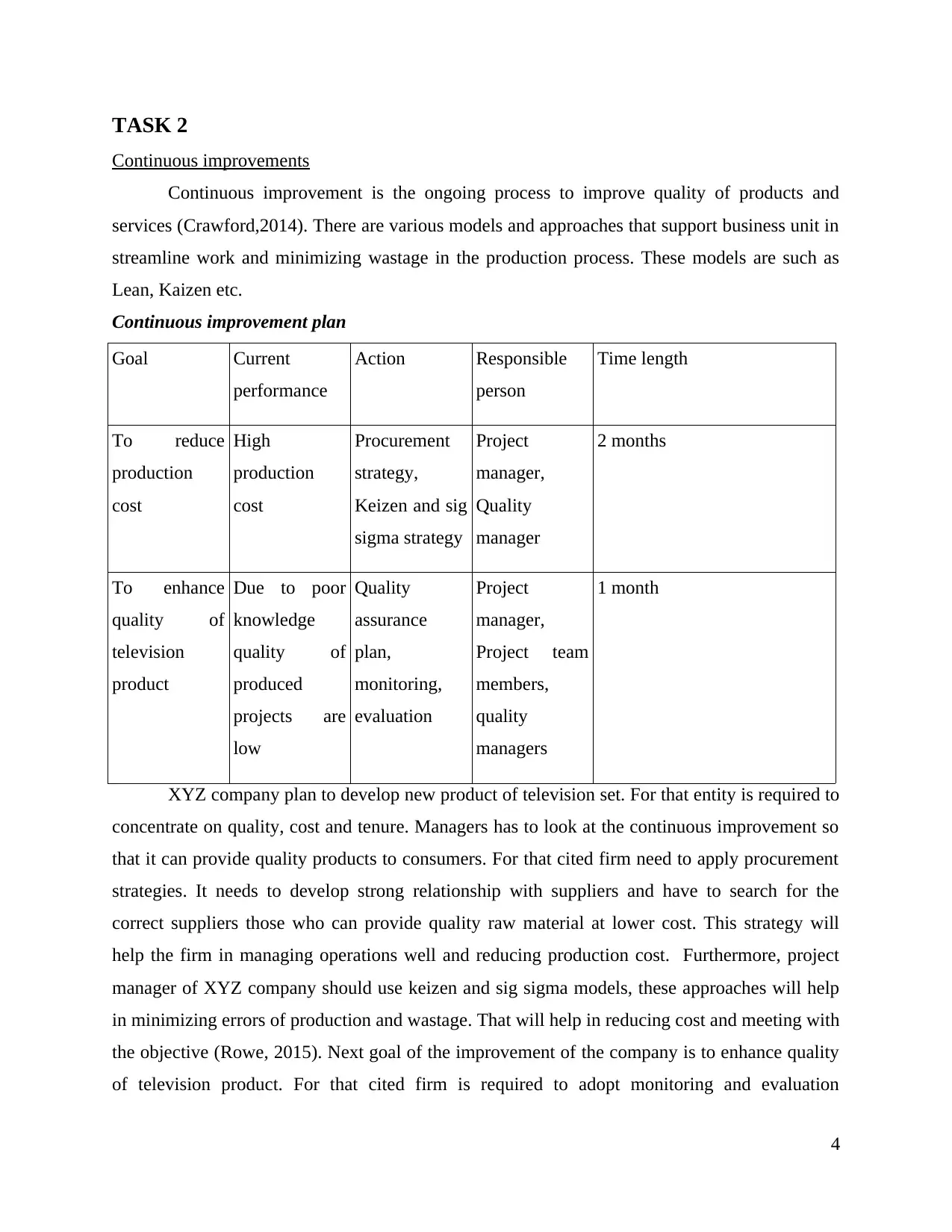
TASK 2
Continuous improvements
Continuous improvement is the ongoing process to improve quality of products and
services (Crawford,2014). There are various models and approaches that support business unit in
streamline work and minimizing wastage in the production process. These models are such as
Lean, Kaizen etc.
Continuous improvement plan
Goal Current
performance
Action Responsible
person
Time length
To reduce
production
cost
High
production
cost
Procurement
strategy,
Keizen and sig
sigma strategy
Project
manager,
Quality
manager
2 months
To enhance
quality of
television
product
Due to poor
knowledge
quality of
produced
projects are
low
Quality
assurance
plan,
monitoring,
evaluation
Project
manager,
Project team
members,
quality
managers
1 month
XYZ company plan to develop new product of television set. For that entity is required to
concentrate on quality, cost and tenure. Managers has to look at the continuous improvement so
that it can provide quality products to consumers. For that cited firm need to apply procurement
strategies. It needs to develop strong relationship with suppliers and have to search for the
correct suppliers those who can provide quality raw material at lower cost. This strategy will
help the firm in managing operations well and reducing production cost. Furthermore, project
manager of XYZ company should use keizen and sig sigma models, these approaches will help
in minimizing errors of production and wastage. That will help in reducing cost and meeting with
the objective (Rowe, 2015). Next goal of the improvement of the company is to enhance quality
of television product. For that cited firm is required to adopt monitoring and evaluation
4
Continuous improvements
Continuous improvement is the ongoing process to improve quality of products and
services (Crawford,2014). There are various models and approaches that support business unit in
streamline work and minimizing wastage in the production process. These models are such as
Lean, Kaizen etc.
Continuous improvement plan
Goal Current
performance
Action Responsible
person
Time length
To reduce
production
cost
High
production
cost
Procurement
strategy,
Keizen and sig
sigma strategy
Project
manager,
Quality
manager
2 months
To enhance
quality of
television
product
Due to poor
knowledge
quality of
produced
projects are
low
Quality
assurance
plan,
monitoring,
evaluation
Project
manager,
Project team
members,
quality
managers
1 month
XYZ company plan to develop new product of television set. For that entity is required to
concentrate on quality, cost and tenure. Managers has to look at the continuous improvement so
that it can provide quality products to consumers. For that cited firm need to apply procurement
strategies. It needs to develop strong relationship with suppliers and have to search for the
correct suppliers those who can provide quality raw material at lower cost. This strategy will
help the firm in managing operations well and reducing production cost. Furthermore, project
manager of XYZ company should use keizen and sig sigma models, these approaches will help
in minimizing errors of production and wastage. That will help in reducing cost and meeting with
the objective (Rowe, 2015). Next goal of the improvement of the company is to enhance quality
of television product. For that cited firm is required to adopt monitoring and evaluation
4
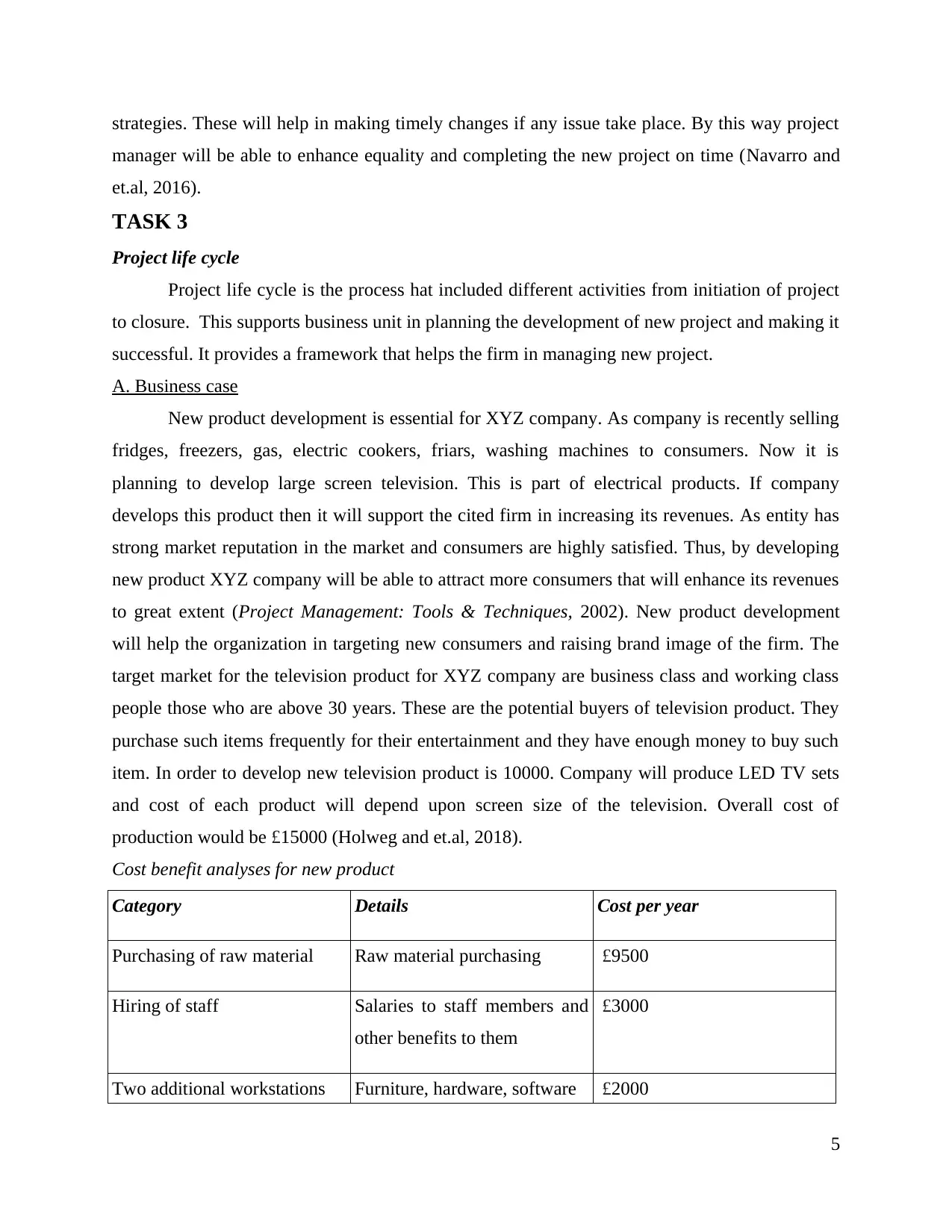
strategies. These will help in making timely changes if any issue take place. By this way project
manager will be able to enhance equality and completing the new project on time (Navarro and
et.al, 2016).
TASK 3
Project life cycle
Project life cycle is the process hat included different activities from initiation of project
to closure. This supports business unit in planning the development of new project and making it
successful. It provides a framework that helps the firm in managing new project.
A. Business case
New product development is essential for XYZ company. As company is recently selling
fridges, freezers, gas, electric cookers, friars, washing machines to consumers. Now it is
planning to develop large screen television. This is part of electrical products. If company
develops this product then it will support the cited firm in increasing its revenues. As entity has
strong market reputation in the market and consumers are highly satisfied. Thus, by developing
new product XYZ company will be able to attract more consumers that will enhance its revenues
to great extent (Project Management: Tools & Techniques, 2002). New product development
will help the organization in targeting new consumers and raising brand image of the firm. The
target market for the television product for XYZ company are business class and working class
people those who are above 30 years. These are the potential buyers of television product. They
purchase such items frequently for their entertainment and they have enough money to buy such
item. In order to develop new television product is 10000. Company will produce LED TV sets
and cost of each product will depend upon screen size of the television. Overall cost of
production would be £15000 (Holweg and et.al, 2018).
Cost benefit analyses for new product
Category Details Cost per year
Purchasing of raw material Raw material purchasing £9500
Hiring of staff Salaries to staff members and
other benefits to them
£3000
Two additional workstations Furniture, hardware, software £2000
5
manager will be able to enhance equality and completing the new project on time (Navarro and
et.al, 2016).
TASK 3
Project life cycle
Project life cycle is the process hat included different activities from initiation of project
to closure. This supports business unit in planning the development of new project and making it
successful. It provides a framework that helps the firm in managing new project.
A. Business case
New product development is essential for XYZ company. As company is recently selling
fridges, freezers, gas, electric cookers, friars, washing machines to consumers. Now it is
planning to develop large screen television. This is part of electrical products. If company
develops this product then it will support the cited firm in increasing its revenues. As entity has
strong market reputation in the market and consumers are highly satisfied. Thus, by developing
new product XYZ company will be able to attract more consumers that will enhance its revenues
to great extent (Project Management: Tools & Techniques, 2002). New product development
will help the organization in targeting new consumers and raising brand image of the firm. The
target market for the television product for XYZ company are business class and working class
people those who are above 30 years. These are the potential buyers of television product. They
purchase such items frequently for their entertainment and they have enough money to buy such
item. In order to develop new television product is 10000. Company will produce LED TV sets
and cost of each product will depend upon screen size of the television. Overall cost of
production would be £15000 (Holweg and et.al, 2018).
Cost benefit analyses for new product
Category Details Cost per year
Purchasing of raw material Raw material purchasing £9500
Hiring of staff Salaries to staff members and
other benefits to them
£3000
Two additional workstations Furniture, hardware, software £2000
5
Paraphrase This Document
Need a fresh take? Get an instant paraphrase of this document with our AI Paraphraser
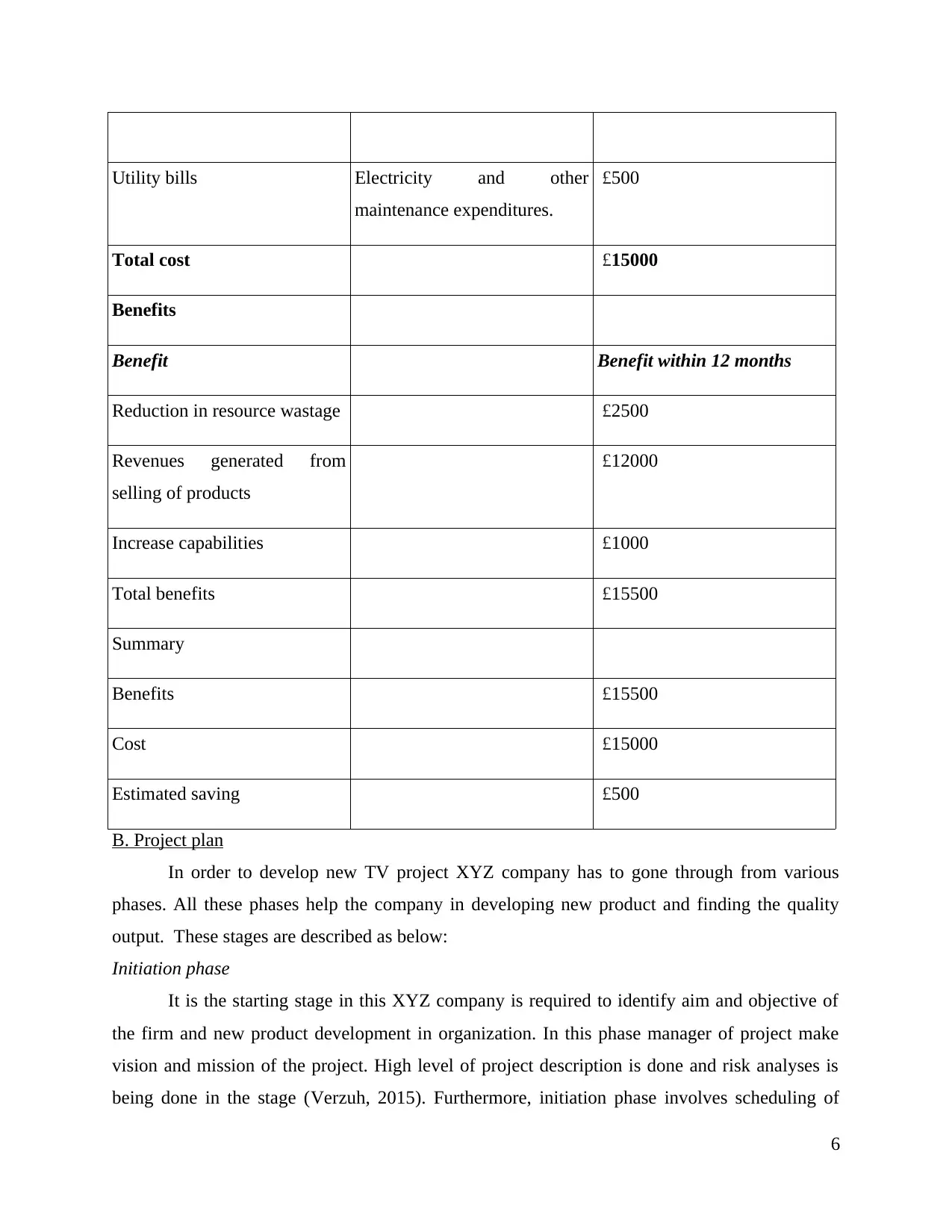
Utility bills Electricity and other
maintenance expenditures.
£500
Total cost £15000
Benefits
Benefit Benefit within 12 months
Reduction in resource wastage £2500
Revenues generated from
selling of products
£12000
Increase capabilities £1000
Total benefits £15500
Summary
Benefits £15500
Cost £15000
Estimated saving £500
B. Project plan
In order to develop new TV project XYZ company has to gone through from various
phases. All these phases help the company in developing new product and finding the quality
output. These stages are described as below:
Initiation phase
It is the starting stage in this XYZ company is required to identify aim and objective of
the firm and new product development in organization. In this phase manager of project make
vision and mission of the project. High level of project description is done and risk analyses is
being done in the stage (Verzuh, 2015). Furthermore, initiation phase involves scheduling of
6
maintenance expenditures.
£500
Total cost £15000
Benefits
Benefit Benefit within 12 months
Reduction in resource wastage £2500
Revenues generated from
selling of products
£12000
Increase capabilities £1000
Total benefits £15500
Summary
Benefits £15500
Cost £15000
Estimated saving £500
B. Project plan
In order to develop new TV project XYZ company has to gone through from various
phases. All these phases help the company in developing new product and finding the quality
output. These stages are described as below:
Initiation phase
It is the starting stage in this XYZ company is required to identify aim and objective of
the firm and new product development in organization. In this phase manager of project make
vision and mission of the project. High level of project description is done and risk analyses is
being done in the stage (Verzuh, 2015). Furthermore, initiation phase involves scheduling of
6
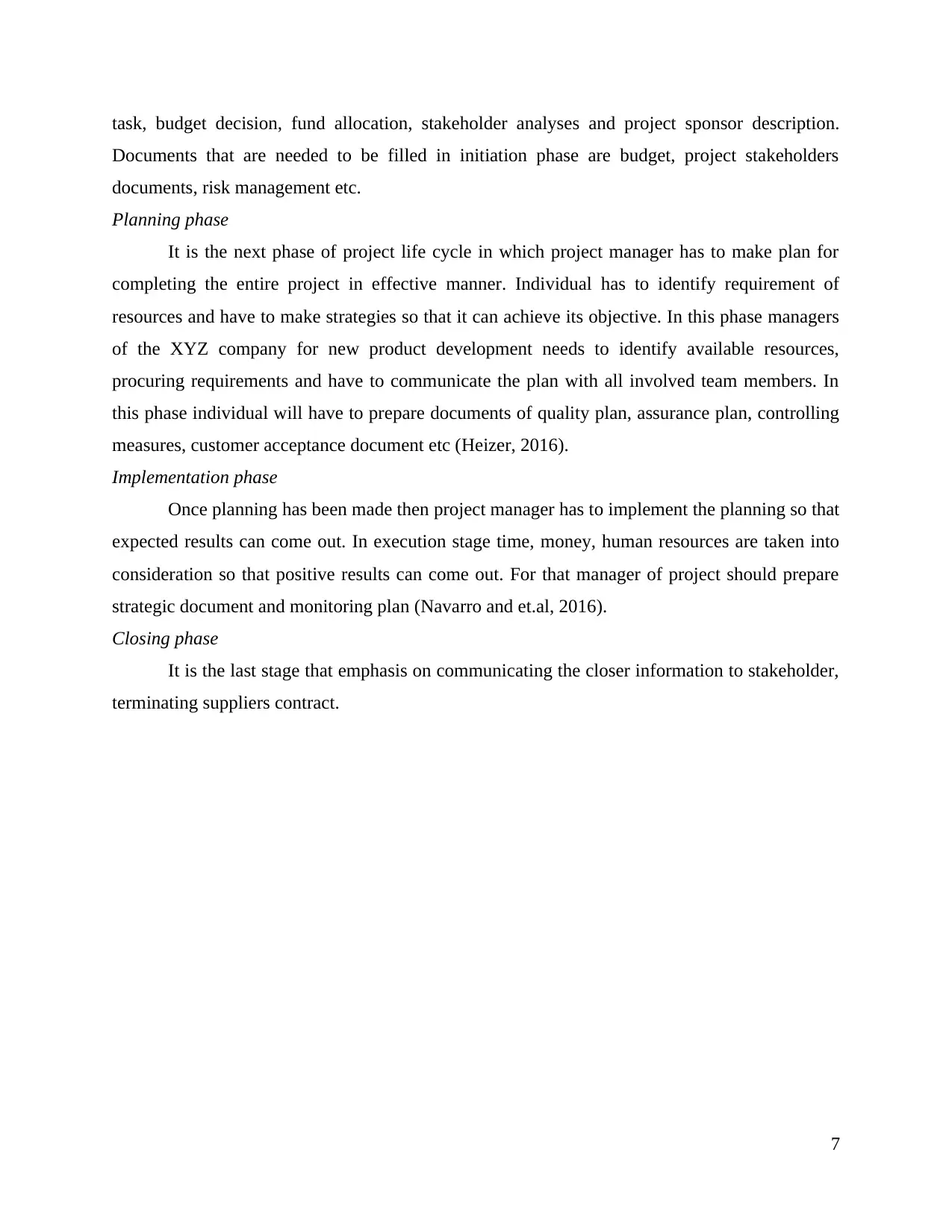
task, budget decision, fund allocation, stakeholder analyses and project sponsor description.
Documents that are needed to be filled in initiation phase are budget, project stakeholders
documents, risk management etc.
Planning phase
It is the next phase of project life cycle in which project manager has to make plan for
completing the entire project in effective manner. Individual has to identify requirement of
resources and have to make strategies so that it can achieve its objective. In this phase managers
of the XYZ company for new product development needs to identify available resources,
procuring requirements and have to communicate the plan with all involved team members. In
this phase individual will have to prepare documents of quality plan, assurance plan, controlling
measures, customer acceptance document etc (Heizer, 2016).
Implementation phase
Once planning has been made then project manager has to implement the planning so that
expected results can come out. In execution stage time, money, human resources are taken into
consideration so that positive results can come out. For that manager of project should prepare
strategic document and monitoring plan (Navarro and et.al, 2016).
Closing phase
It is the last stage that emphasis on communicating the closer information to stakeholder,
terminating suppliers contract.
7
Documents that are needed to be filled in initiation phase are budget, project stakeholders
documents, risk management etc.
Planning phase
It is the next phase of project life cycle in which project manager has to make plan for
completing the entire project in effective manner. Individual has to identify requirement of
resources and have to make strategies so that it can achieve its objective. In this phase managers
of the XYZ company for new product development needs to identify available resources,
procuring requirements and have to communicate the plan with all involved team members. In
this phase individual will have to prepare documents of quality plan, assurance plan, controlling
measures, customer acceptance document etc (Heizer, 2016).
Implementation phase
Once planning has been made then project manager has to implement the planning so that
expected results can come out. In execution stage time, money, human resources are taken into
consideration so that positive results can come out. For that manager of project should prepare
strategic document and monitoring plan (Navarro and et.al, 2016).
Closing phase
It is the last stage that emphasis on communicating the closer information to stakeholder,
terminating suppliers contract.
7
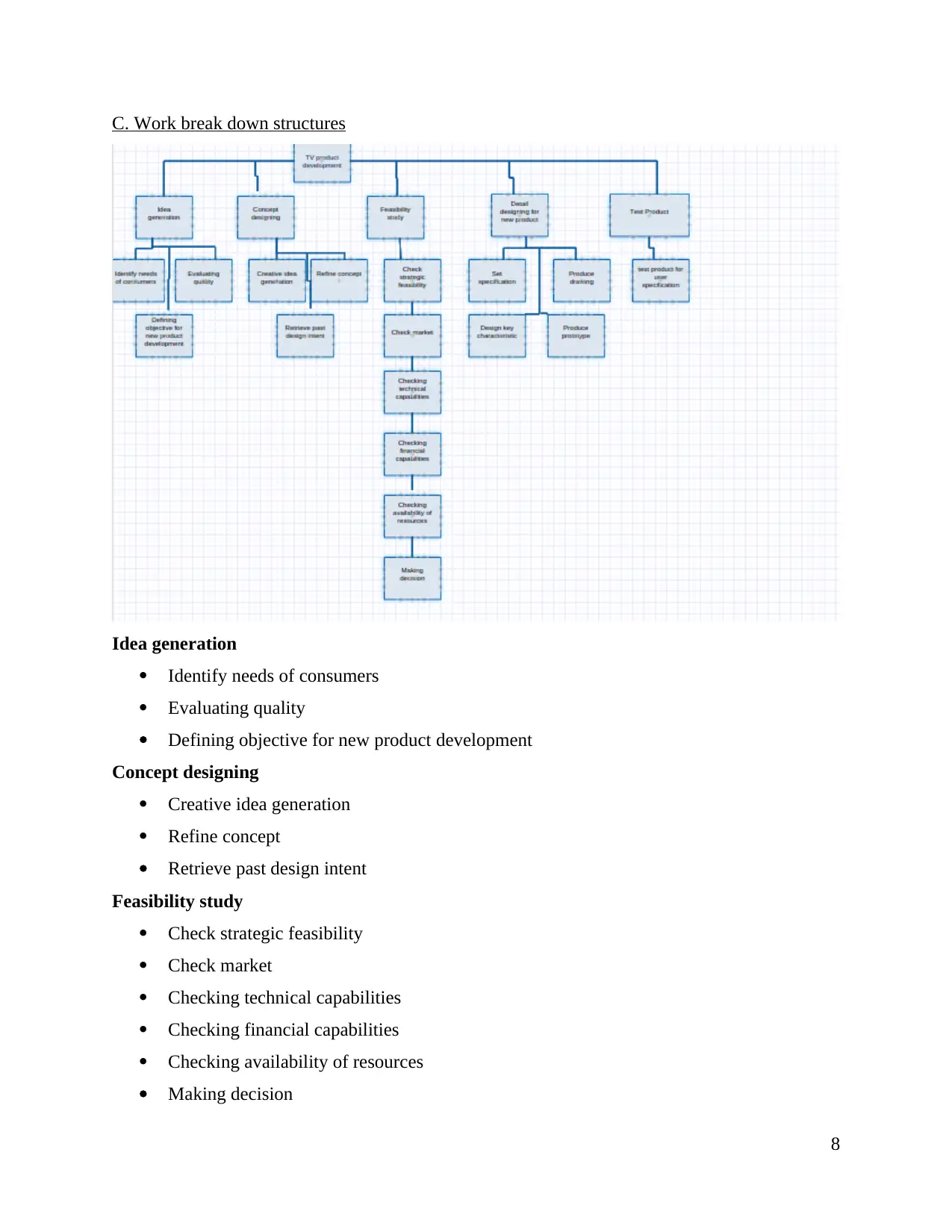
C. Work break down structures
Idea generation
Identify needs of consumers
Evaluating quality
Defining objective for new product development
Concept designing
Creative idea generation
Refine concept
Retrieve past design intent
Feasibility study
Check strategic feasibility
Check market
Checking technical capabilities
Checking financial capabilities
Checking availability of resources
Making decision
8
Idea generation
Identify needs of consumers
Evaluating quality
Defining objective for new product development
Concept designing
Creative idea generation
Refine concept
Retrieve past design intent
Feasibility study
Check strategic feasibility
Check market
Checking technical capabilities
Checking financial capabilities
Checking availability of resources
Making decision
8
Secure Best Marks with AI Grader
Need help grading? Try our AI Grader for instant feedback on your assignments.
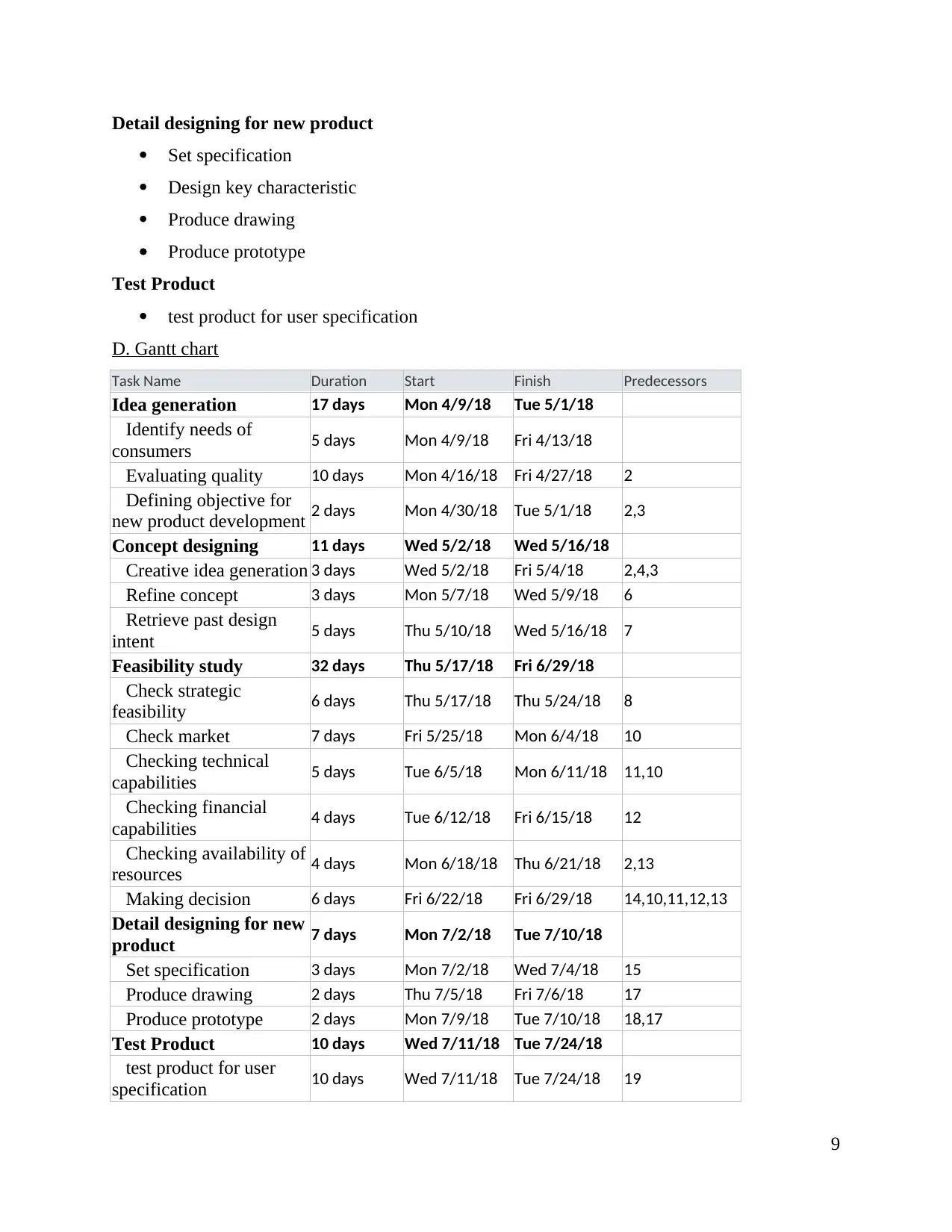
Detail designing for new product
Set specification
Design key characteristic
Produce drawing
Produce prototype
Test Product
test product for user specification
D. Gantt chart
Task Name Duration Start Finish Predecessors
Idea generation 17 days Mon 4/9/18 Tue 5/1/18
Identify needs of
consumers 5 days Mon 4/9/18 Fri 4/13/18
Evaluating quality 10 days Mon 4/16/18 Fri 4/27/18 2
Defining objective for
new product development 2 days Mon 4/30/18 Tue 5/1/18 2,3
Concept designing 11 days Wed 5/2/18 Wed 5/16/18
Creative idea generation 3 days Wed 5/2/18 Fri 5/4/18 2,4,3
Refine concept 3 days Mon 5/7/18 Wed 5/9/18 6
Retrieve past design
intent 5 days Thu 5/10/18 Wed 5/16/18 7
Feasibility study 32 days Thu 5/17/18 Fri 6/29/18
Check strategic
feasibility 6 days Thu 5/17/18 Thu 5/24/18 8
Check market 7 days Fri 5/25/18 Mon 6/4/18 10
Checking technical
capabilities 5 days Tue 6/5/18 Mon 6/11/18 11,10
Checking financial
capabilities 4 days Tue 6/12/18 Fri 6/15/18 12
Checking availability of
resources 4 days Mon 6/18/18 Thu 6/21/18 2,13
Making decision 6 days Fri 6/22/18 Fri 6/29/18 14,10,11,12,13
Detail designing for new
product 7 days Mon 7/2/18 Tue 7/10/18
Set specification 3 days Mon 7/2/18 Wed 7/4/18 15
Produce drawing 2 days Thu 7/5/18 Fri 7/6/18 17
Produce prototype 2 days Mon 7/9/18 Tue 7/10/18 18,17
Test Product 10 days Wed 7/11/18 Tue 7/24/18
test product for user
specification 10 days Wed 7/11/18 Tue 7/24/18 19
9
Set specification
Design key characteristic
Produce drawing
Produce prototype
Test Product
test product for user specification
D. Gantt chart
Task Name Duration Start Finish Predecessors
Idea generation 17 days Mon 4/9/18 Tue 5/1/18
Identify needs of
consumers 5 days Mon 4/9/18 Fri 4/13/18
Evaluating quality 10 days Mon 4/16/18 Fri 4/27/18 2
Defining objective for
new product development 2 days Mon 4/30/18 Tue 5/1/18 2,3
Concept designing 11 days Wed 5/2/18 Wed 5/16/18
Creative idea generation 3 days Wed 5/2/18 Fri 5/4/18 2,4,3
Refine concept 3 days Mon 5/7/18 Wed 5/9/18 6
Retrieve past design
intent 5 days Thu 5/10/18 Wed 5/16/18 7
Feasibility study 32 days Thu 5/17/18 Fri 6/29/18
Check strategic
feasibility 6 days Thu 5/17/18 Thu 5/24/18 8
Check market 7 days Fri 5/25/18 Mon 6/4/18 10
Checking technical
capabilities 5 days Tue 6/5/18 Mon 6/11/18 11,10
Checking financial
capabilities 4 days Tue 6/12/18 Fri 6/15/18 12
Checking availability of
resources 4 days Mon 6/18/18 Thu 6/21/18 2,13
Making decision 6 days Fri 6/22/18 Fri 6/29/18 14,10,11,12,13
Detail designing for new
product 7 days Mon 7/2/18 Tue 7/10/18
Set specification 3 days Mon 7/2/18 Wed 7/4/18 15
Produce drawing 2 days Thu 7/5/18 Fri 7/6/18 17
Produce prototype 2 days Mon 7/9/18 Tue 7/10/18 18,17
Test Product 10 days Wed 7/11/18 Tue 7/24/18
test product for user
specification 10 days Wed 7/11/18 Tue 7/24/18 19
9
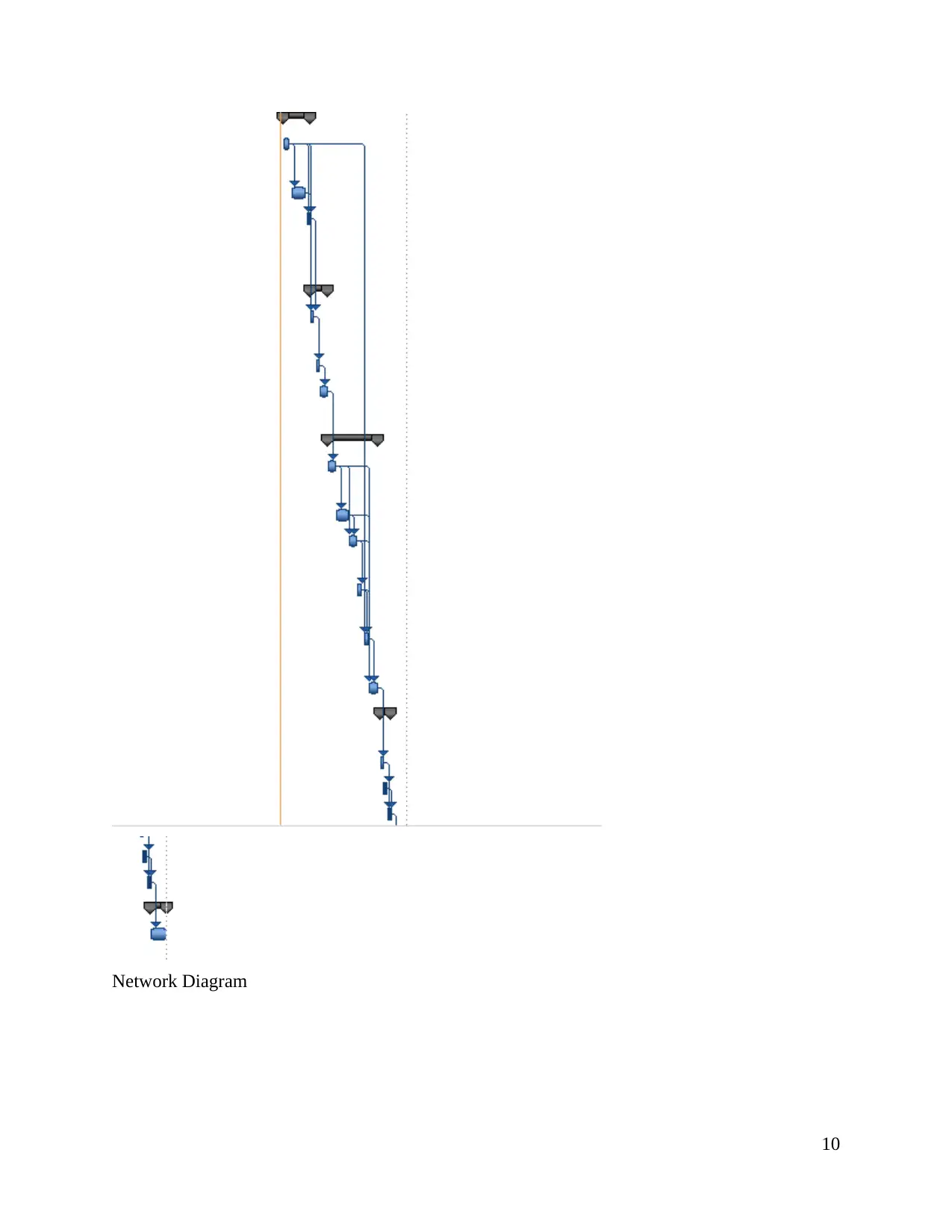
Network Diagram
10
10
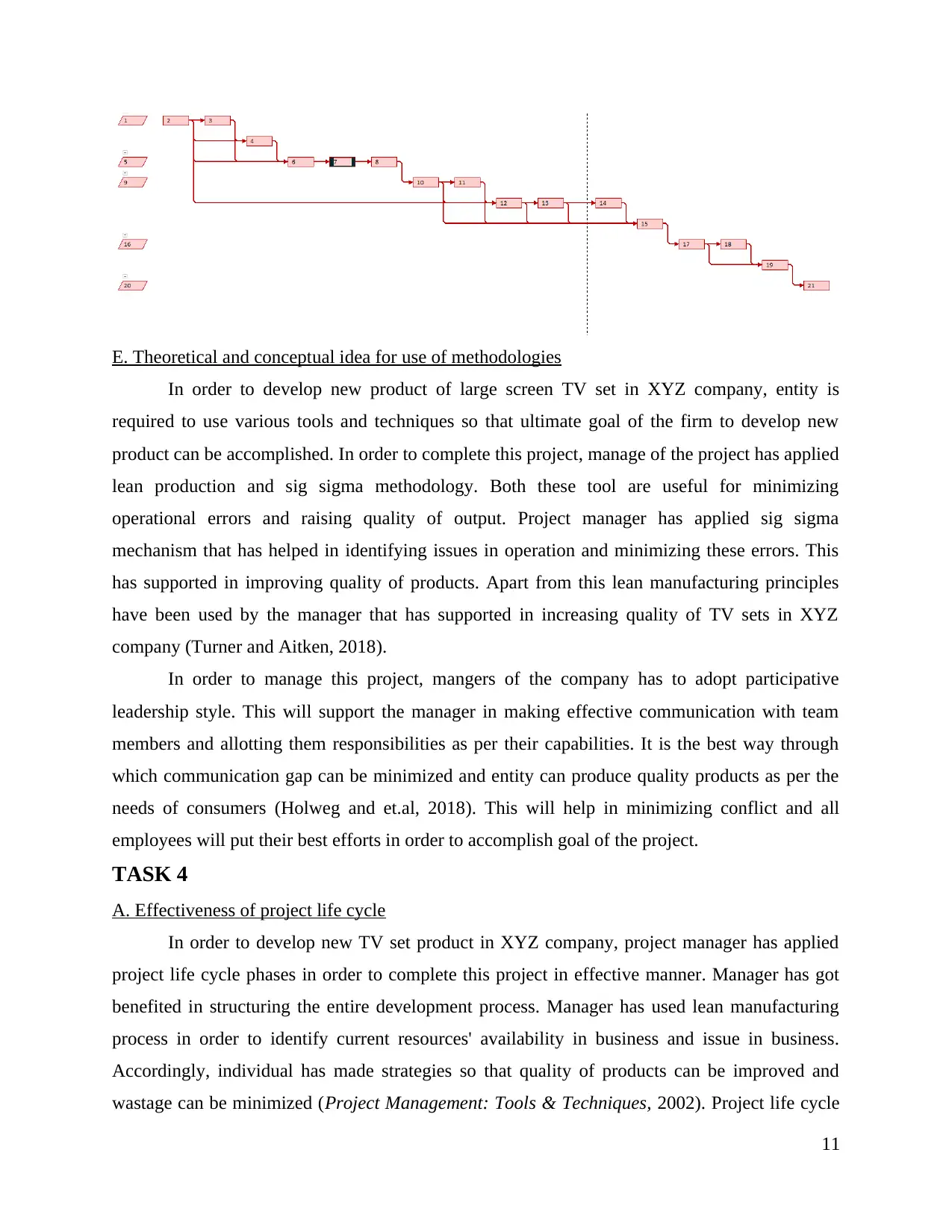
E. Theoretical and conceptual idea for use of methodologies
In order to develop new product of large screen TV set in XYZ company, entity is
required to use various tools and techniques so that ultimate goal of the firm to develop new
product can be accomplished. In order to complete this project, manage of the project has applied
lean production and sig sigma methodology. Both these tool are useful for minimizing
operational errors and raising quality of output. Project manager has applied sig sigma
mechanism that has helped in identifying issues in operation and minimizing these errors. This
has supported in improving quality of products. Apart from this lean manufacturing principles
have been used by the manager that has supported in increasing quality of TV sets in XYZ
company (Turner and Aitken, 2018).
In order to manage this project, mangers of the company has to adopt participative
leadership style. This will support the manager in making effective communication with team
members and allotting them responsibilities as per their capabilities. It is the best way through
which communication gap can be minimized and entity can produce quality products as per the
needs of consumers (Holweg and et.al, 2018). This will help in minimizing conflict and all
employees will put their best efforts in order to accomplish goal of the project.
TASK 4
A. Effectiveness of project life cycle
In order to develop new TV set product in XYZ company, project manager has applied
project life cycle phases in order to complete this project in effective manner. Manager has got
benefited in structuring the entire development process. Manager has used lean manufacturing
process in order to identify current resources' availability in business and issue in business.
Accordingly, individual has made strategies so that quality of products can be improved and
wastage can be minimized (Project Management: Tools & Techniques, 2002). Project life cycle
11
In order to develop new product of large screen TV set in XYZ company, entity is
required to use various tools and techniques so that ultimate goal of the firm to develop new
product can be accomplished. In order to complete this project, manage of the project has applied
lean production and sig sigma methodology. Both these tool are useful for minimizing
operational errors and raising quality of output. Project manager has applied sig sigma
mechanism that has helped in identifying issues in operation and minimizing these errors. This
has supported in improving quality of products. Apart from this lean manufacturing principles
have been used by the manager that has supported in increasing quality of TV sets in XYZ
company (Turner and Aitken, 2018).
In order to manage this project, mangers of the company has to adopt participative
leadership style. This will support the manager in making effective communication with team
members and allotting them responsibilities as per their capabilities. It is the best way through
which communication gap can be minimized and entity can produce quality products as per the
needs of consumers (Holweg and et.al, 2018). This will help in minimizing conflict and all
employees will put their best efforts in order to accomplish goal of the project.
TASK 4
A. Effectiveness of project life cycle
In order to develop new TV set product in XYZ company, project manager has applied
project life cycle phases in order to complete this project in effective manner. Manager has got
benefited in structuring the entire development process. Manager has used lean manufacturing
process in order to identify current resources' availability in business and issue in business.
Accordingly, individual has made strategies so that quality of products can be improved and
wastage can be minimized (Project Management: Tools & Techniques, 2002). Project life cycle
11
Paraphrase This Document
Need a fresh take? Get an instant paraphrase of this document with our AI Paraphraser
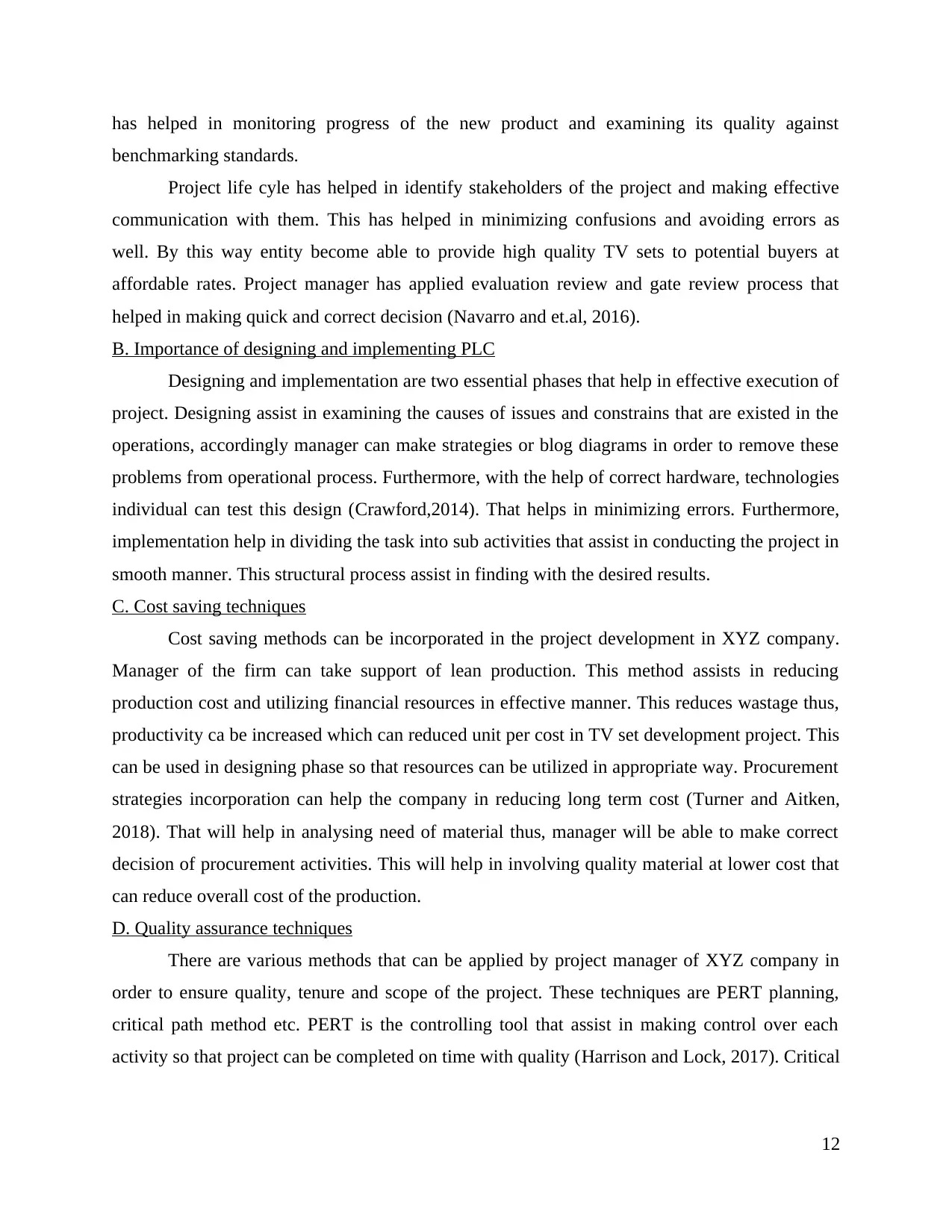
has helped in monitoring progress of the new product and examining its quality against
benchmarking standards.
Project life cyle has helped in identify stakeholders of the project and making effective
communication with them. This has helped in minimizing confusions and avoiding errors as
well. By this way entity become able to provide high quality TV sets to potential buyers at
affordable rates. Project manager has applied evaluation review and gate review process that
helped in making quick and correct decision (Navarro and et.al, 2016).
B. Importance of designing and implementing PLC
Designing and implementation are two essential phases that help in effective execution of
project. Designing assist in examining the causes of issues and constrains that are existed in the
operations, accordingly manager can make strategies or blog diagrams in order to remove these
problems from operational process. Furthermore, with the help of correct hardware, technologies
individual can test this design (Crawford,2014). That helps in minimizing errors. Furthermore,
implementation help in dividing the task into sub activities that assist in conducting the project in
smooth manner. This structural process assist in finding with the desired results.
C. Cost saving techniques
Cost saving methods can be incorporated in the project development in XYZ company.
Manager of the firm can take support of lean production. This method assists in reducing
production cost and utilizing financial resources in effective manner. This reduces wastage thus,
productivity ca be increased which can reduced unit per cost in TV set development project. This
can be used in designing phase so that resources can be utilized in appropriate way. Procurement
strategies incorporation can help the company in reducing long term cost (Turner and Aitken,
2018). That will help in analysing need of material thus, manager will be able to make correct
decision of procurement activities. This will help in involving quality material at lower cost that
can reduce overall cost of the production.
D. Quality assurance techniques
There are various methods that can be applied by project manager of XYZ company in
order to ensure quality, tenure and scope of the project. These techniques are PERT planning,
critical path method etc. PERT is the controlling tool that assist in making control over each
activity so that project can be completed on time with quality (Harrison and Lock, 2017). Critical
12
benchmarking standards.
Project life cyle has helped in identify stakeholders of the project and making effective
communication with them. This has helped in minimizing confusions and avoiding errors as
well. By this way entity become able to provide high quality TV sets to potential buyers at
affordable rates. Project manager has applied evaluation review and gate review process that
helped in making quick and correct decision (Navarro and et.al, 2016).
B. Importance of designing and implementing PLC
Designing and implementation are two essential phases that help in effective execution of
project. Designing assist in examining the causes of issues and constrains that are existed in the
operations, accordingly manager can make strategies or blog diagrams in order to remove these
problems from operational process. Furthermore, with the help of correct hardware, technologies
individual can test this design (Crawford,2014). That helps in minimizing errors. Furthermore,
implementation help in dividing the task into sub activities that assist in conducting the project in
smooth manner. This structural process assist in finding with the desired results.
C. Cost saving techniques
Cost saving methods can be incorporated in the project development in XYZ company.
Manager of the firm can take support of lean production. This method assists in reducing
production cost and utilizing financial resources in effective manner. This reduces wastage thus,
productivity ca be increased which can reduced unit per cost in TV set development project. This
can be used in designing phase so that resources can be utilized in appropriate way. Procurement
strategies incorporation can help the company in reducing long term cost (Turner and Aitken,
2018). That will help in analysing need of material thus, manager will be able to make correct
decision of procurement activities. This will help in involving quality material at lower cost that
can reduce overall cost of the production.
D. Quality assurance techniques
There are various methods that can be applied by project manager of XYZ company in
order to ensure quality, tenure and scope of the project. These techniques are PERT planning,
critical path method etc. PERT is the controlling tool that assist in making control over each
activity so that project can be completed on time with quality (Harrison and Lock, 2017). Critical
12
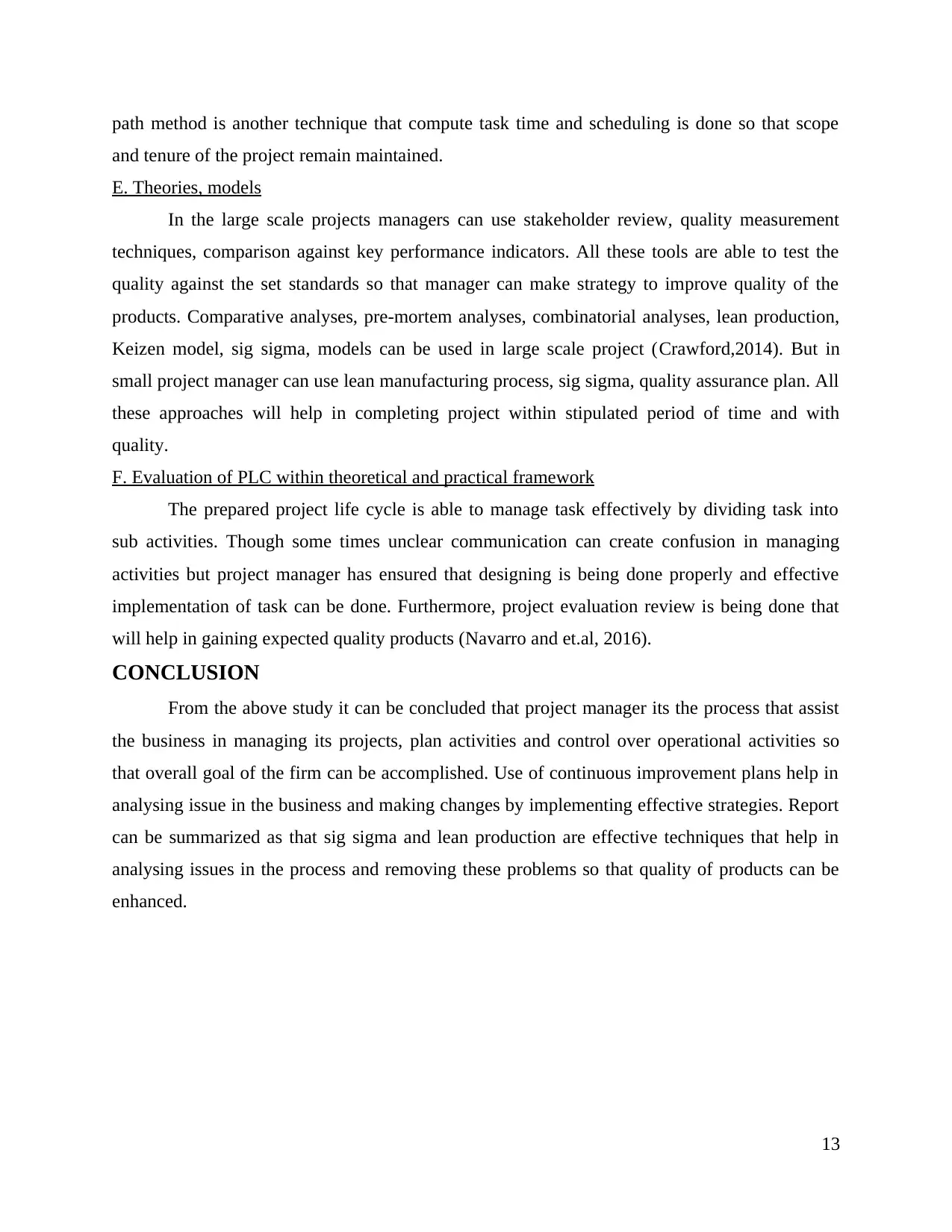
path method is another technique that compute task time and scheduling is done so that scope
and tenure of the project remain maintained.
E. Theories, models
In the large scale projects managers can use stakeholder review, quality measurement
techniques, comparison against key performance indicators. All these tools are able to test the
quality against the set standards so that manager can make strategy to improve quality of the
products. Comparative analyses, pre-mortem analyses, combinatorial analyses, lean production,
Keizen model, sig sigma, models can be used in large scale project (Crawford,2014). But in
small project manager can use lean manufacturing process, sig sigma, quality assurance plan. All
these approaches will help in completing project within stipulated period of time and with
quality.
F. Evaluation of PLC within theoretical and practical framework
The prepared project life cycle is able to manage task effectively by dividing task into
sub activities. Though some times unclear communication can create confusion in managing
activities but project manager has ensured that designing is being done properly and effective
implementation of task can be done. Furthermore, project evaluation review is being done that
will help in gaining expected quality products (Navarro and et.al, 2016).
CONCLUSION
From the above study it can be concluded that project manager its the process that assist
the business in managing its projects, plan activities and control over operational activities so
that overall goal of the firm can be accomplished. Use of continuous improvement plans help in
analysing issue in the business and making changes by implementing effective strategies. Report
can be summarized as that sig sigma and lean production are effective techniques that help in
analysing issues in the process and removing these problems so that quality of products can be
enhanced.
13
and tenure of the project remain maintained.
E. Theories, models
In the large scale projects managers can use stakeholder review, quality measurement
techniques, comparison against key performance indicators. All these tools are able to test the
quality against the set standards so that manager can make strategy to improve quality of the
products. Comparative analyses, pre-mortem analyses, combinatorial analyses, lean production,
Keizen model, sig sigma, models can be used in large scale project (Crawford,2014). But in
small project manager can use lean manufacturing process, sig sigma, quality assurance plan. All
these approaches will help in completing project within stipulated period of time and with
quality.
F. Evaluation of PLC within theoretical and practical framework
The prepared project life cycle is able to manage task effectively by dividing task into
sub activities. Though some times unclear communication can create confusion in managing
activities but project manager has ensured that designing is being done properly and effective
implementation of task can be done. Furthermore, project evaluation review is being done that
will help in gaining expected quality products (Navarro and et.al, 2016).
CONCLUSION
From the above study it can be concluded that project manager its the process that assist
the business in managing its projects, plan activities and control over operational activities so
that overall goal of the firm can be accomplished. Use of continuous improvement plans help in
analysing issue in the business and making changes by implementing effective strategies. Report
can be summarized as that sig sigma and lean production are effective techniques that help in
analysing issues in the process and removing these problems so that quality of products can be
enhanced.
13
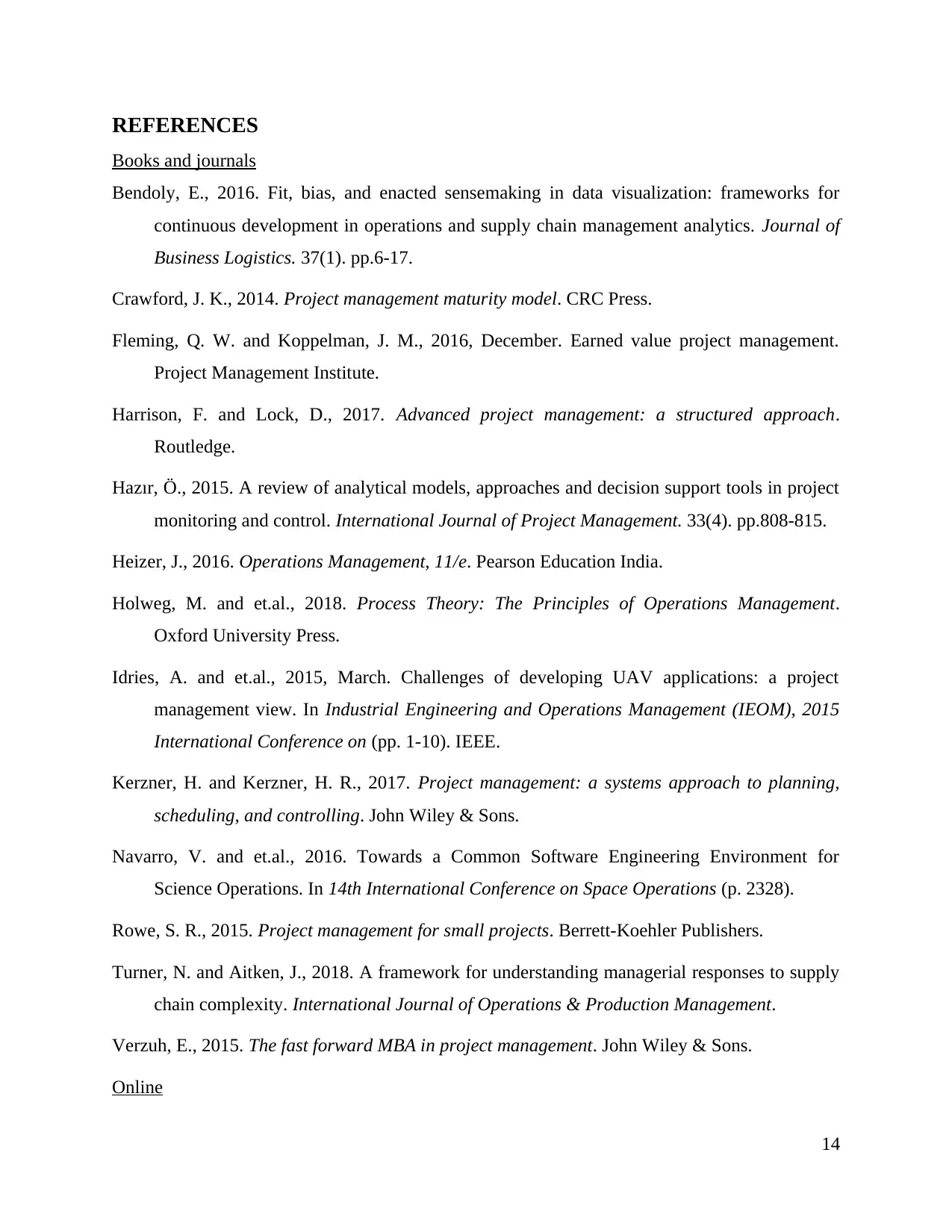
REFERENCES
Books and journals
Bendoly, E., 2016. Fit, bias, and enacted sensemaking in data visualization: frameworks for
continuous development in operations and supply chain management analytics. Journal of
Business Logistics. 37(1). pp.6-17.
Crawford, J. K., 2014. Project management maturity model. CRC Press.
Fleming, Q. W. and Koppelman, J. M., 2016, December. Earned value project management.
Project Management Institute.
Harrison, F. and Lock, D., 2017. Advanced project management: a structured approach.
Routledge.
Hazır, Ö., 2015. A review of analytical models, approaches and decision support tools in project
monitoring and control. International Journal of Project Management. 33(4). pp.808-815.
Heizer, J., 2016. Operations Management, 11/e. Pearson Education India.
Holweg, M. and et.al., 2018. Process Theory: The Principles of Operations Management.
Oxford University Press.
Idries, A. and et.al., 2015, March. Challenges of developing UAV applications: a project
management view. In Industrial Engineering and Operations Management (IEOM), 2015
International Conference on (pp. 1-10). IEEE.
Kerzner, H. and Kerzner, H. R., 2017. Project management: a systems approach to planning,
scheduling, and controlling. John Wiley & Sons.
Navarro, V. and et.al., 2016. Towards a Common Software Engineering Environment for
Science Operations. In 14th International Conference on Space Operations (p. 2328).
Rowe, S. R., 2015. Project management for small projects. Berrett-Koehler Publishers.
Turner, N. and Aitken, J., 2018. A framework for understanding managerial responses to supply
chain complexity. International Journal of Operations & Production Management.
Verzuh, E., 2015. The fast forward MBA in project management. John Wiley & Sons.
Online
14
Books and journals
Bendoly, E., 2016. Fit, bias, and enacted sensemaking in data visualization: frameworks for
continuous development in operations and supply chain management analytics. Journal of
Business Logistics. 37(1). pp.6-17.
Crawford, J. K., 2014. Project management maturity model. CRC Press.
Fleming, Q. W. and Koppelman, J. M., 2016, December. Earned value project management.
Project Management Institute.
Harrison, F. and Lock, D., 2017. Advanced project management: a structured approach.
Routledge.
Hazır, Ö., 2015. A review of analytical models, approaches and decision support tools in project
monitoring and control. International Journal of Project Management. 33(4). pp.808-815.
Heizer, J., 2016. Operations Management, 11/e. Pearson Education India.
Holweg, M. and et.al., 2018. Process Theory: The Principles of Operations Management.
Oxford University Press.
Idries, A. and et.al., 2015, March. Challenges of developing UAV applications: a project
management view. In Industrial Engineering and Operations Management (IEOM), 2015
International Conference on (pp. 1-10). IEEE.
Kerzner, H. and Kerzner, H. R., 2017. Project management: a systems approach to planning,
scheduling, and controlling. John Wiley & Sons.
Navarro, V. and et.al., 2016. Towards a Common Software Engineering Environment for
Science Operations. In 14th International Conference on Space Operations (p. 2328).
Rowe, S. R., 2015. Project management for small projects. Berrett-Koehler Publishers.
Turner, N. and Aitken, J., 2018. A framework for understanding managerial responses to supply
chain complexity. International Journal of Operations & Production Management.
Verzuh, E., 2015. The fast forward MBA in project management. John Wiley & Sons.
Online
14
Secure Best Marks with AI Grader
Need help grading? Try our AI Grader for instant feedback on your assignments.
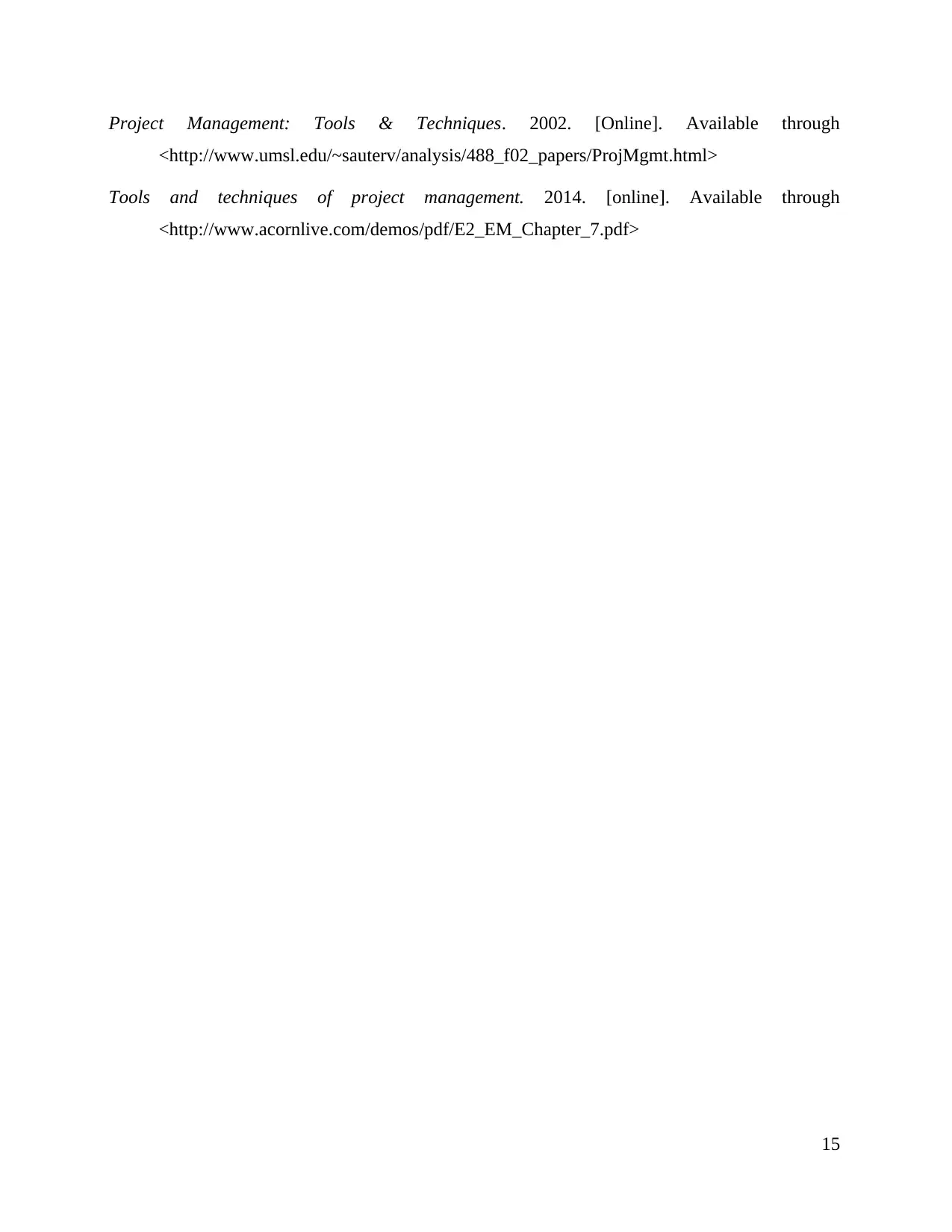
Project Management: Tools & Techniques. 2002. [Online]. Available through
<http://www.umsl.edu/~sauterv/analysis/488_f02_papers/ProjMgmt.html>
Tools and techniques of project management. 2014. [online]. Available through
<http://www.acornlive.com/demos/pdf/E2_EM_Chapter_7.pdf>
15
<http://www.umsl.edu/~sauterv/analysis/488_f02_papers/ProjMgmt.html>
Tools and techniques of project management. 2014. [online]. Available through
<http://www.acornlive.com/demos/pdf/E2_EM_Chapter_7.pdf>
15
1 out of 17
Related Documents
![[object Object]](/_next/image/?url=%2F_next%2Fstatic%2Fmedia%2Flogo.6d15ce61.png&w=640&q=75)
Your All-in-One AI-Powered Toolkit for Academic Success.
+13062052269
info@desklib.com
Available 24*7 on WhatsApp / Email
Unlock your academic potential
© 2024 | Zucol Services PVT LTD | All rights reserved.