Analysis of Six Sigma and Lean Principles
VerifiedAdded on 2020/11/12
|17
|3907
|376
AI Summary
This report discusses the application of six sigma and lean principles in a business setting, focusing on product designing and improvement planning. It also explores the use of various theories, concepts, and models in project management, including the product life cycle. The assignment highlights the significance of these principles in enhancing business operations and success.
Contribute Materials
Your contribution can guide someone’s learning journey. Share your
documents today.
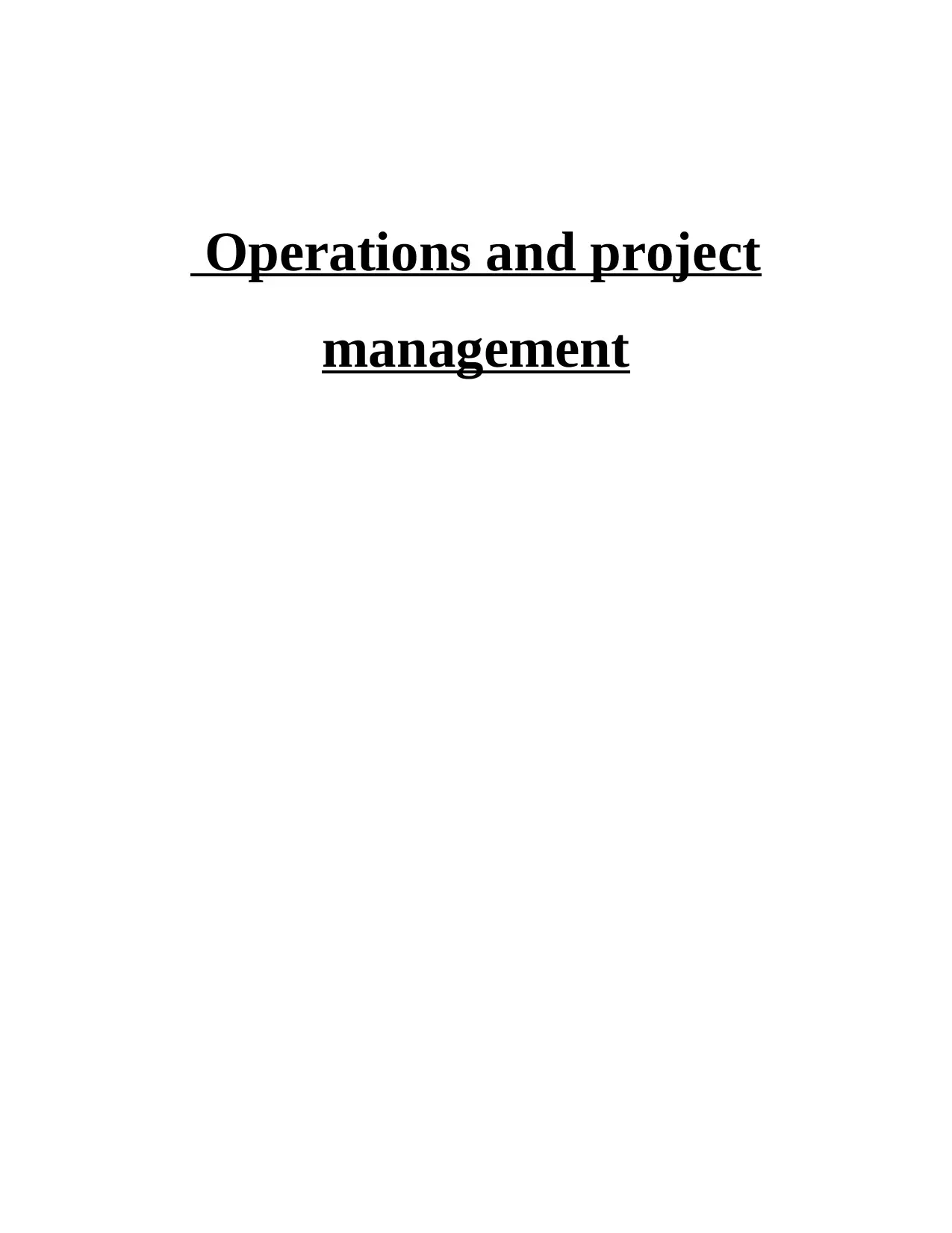
Operations and project
management
management
Secure Best Marks with AI Grader
Need help grading? Try our AI Grader for instant feedback on your assignments.
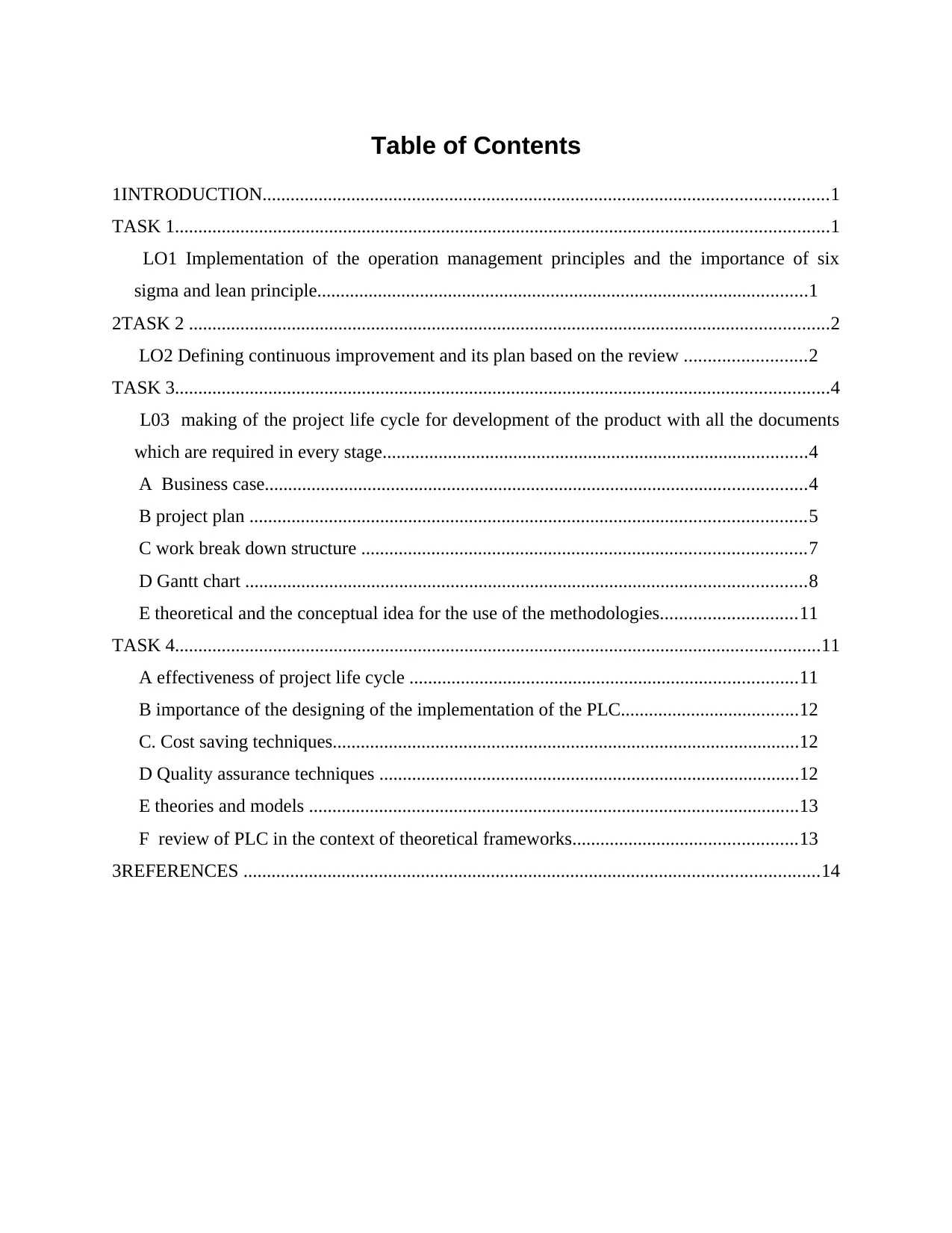
Table of Contents
1INTRODUCTION.........................................................................................................................1
TASK 1............................................................................................................................................1
LO1 Implementation of the operation management principles and the importance of six
sigma and lean principle.........................................................................................................1
2TASK 2 .........................................................................................................................................2
LO2 Defining continuous improvement and its plan based on the review ..........................2
TASK 3............................................................................................................................................4
L03 making of the project life cycle for development of the product with all the documents
which are required in every stage...........................................................................................4
A Business case....................................................................................................................4
B project plan .......................................................................................................................5
C work break down structure ...............................................................................................7
D Gantt chart ........................................................................................................................8
E theoretical and the conceptual idea for the use of the methodologies.............................11
TASK 4..........................................................................................................................................11
A effectiveness of project life cycle ...................................................................................11
B importance of the designing of the implementation of the PLC......................................12
C. Cost saving techniques....................................................................................................12
D Quality assurance techniques ..........................................................................................12
E theories and models .........................................................................................................13
F review of PLC in the context of theoretical frameworks................................................13
3REFERENCES ...........................................................................................................................14
1INTRODUCTION.........................................................................................................................1
TASK 1............................................................................................................................................1
LO1 Implementation of the operation management principles and the importance of six
sigma and lean principle.........................................................................................................1
2TASK 2 .........................................................................................................................................2
LO2 Defining continuous improvement and its plan based on the review ..........................2
TASK 3............................................................................................................................................4
L03 making of the project life cycle for development of the product with all the documents
which are required in every stage...........................................................................................4
A Business case....................................................................................................................4
B project plan .......................................................................................................................5
C work break down structure ...............................................................................................7
D Gantt chart ........................................................................................................................8
E theoretical and the conceptual idea for the use of the methodologies.............................11
TASK 4..........................................................................................................................................11
A effectiveness of project life cycle ...................................................................................11
B importance of the designing of the implementation of the PLC......................................12
C. Cost saving techniques....................................................................................................12
D Quality assurance techniques ..........................................................................................12
E theories and models .........................................................................................................13
F review of PLC in the context of theoretical frameworks................................................13
3REFERENCES ...........................................................................................................................14
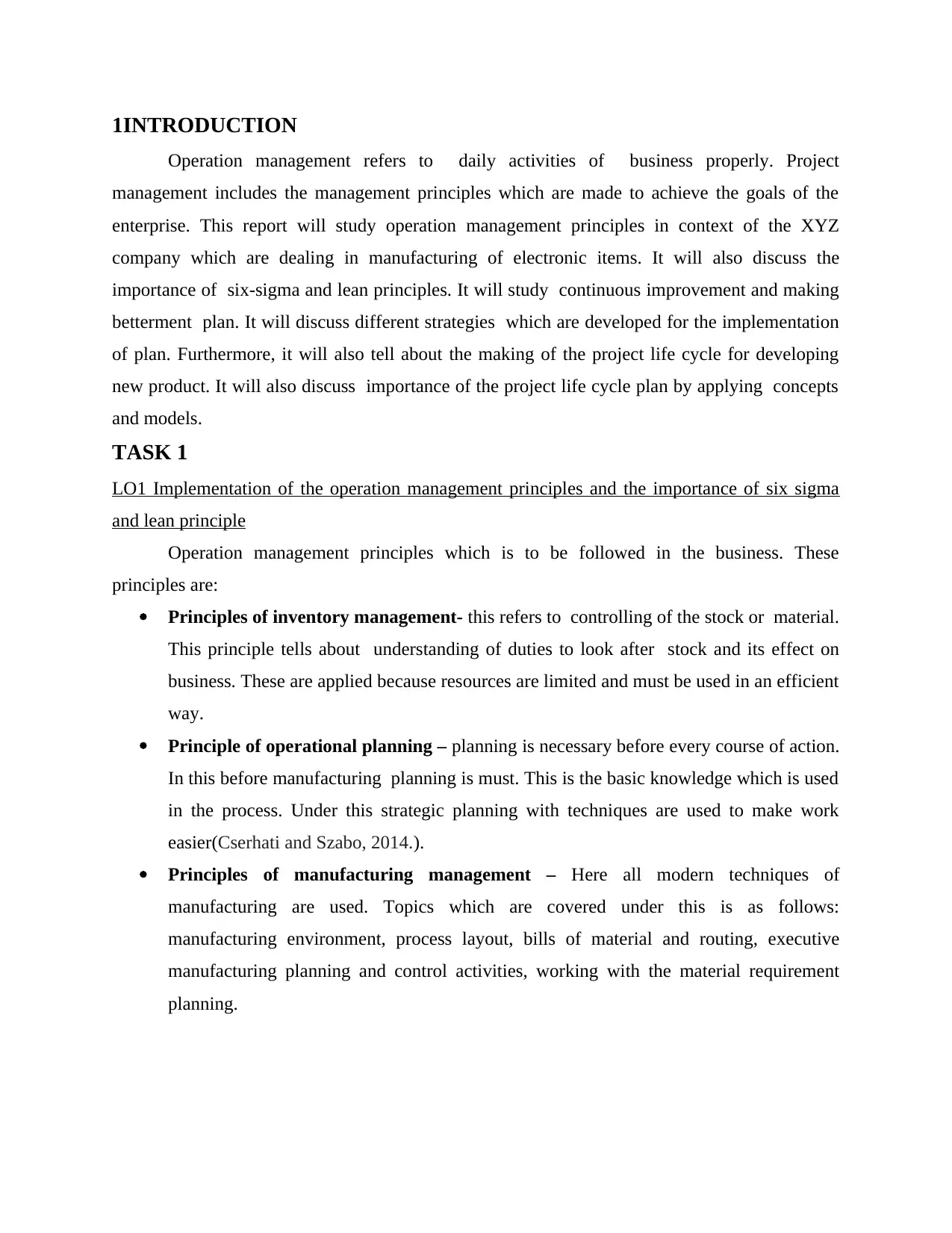
1INTRODUCTION
Operation management refers to daily activities of business properly. Project
management includes the management principles which are made to achieve the goals of the
enterprise. This report will study operation management principles in context of the XYZ
company which are dealing in manufacturing of electronic items. It will also discuss the
importance of six-sigma and lean principles. It will study continuous improvement and making
betterment plan. It will discuss different strategies which are developed for the implementation
of plan. Furthermore, it will also tell about the making of the project life cycle for developing
new product. It will also discuss importance of the project life cycle plan by applying concepts
and models.
TASK 1
LO1 Implementation of the operation management principles and the importance of six sigma
and lean principle
Operation management principles which is to be followed in the business. These
principles are:
Principles of inventory management- this refers to controlling of the stock or material.
This principle tells about understanding of duties to look after stock and its effect on
business. These are applied because resources are limited and must be used in an efficient
way.
Principle of operational planning – planning is necessary before every course of action.
In this before manufacturing planning is must. This is the basic knowledge which is used
in the process. Under this strategic planning with techniques are used to make work
easier(Cserhati and Szabo, 2014.).
Principles of manufacturing management – Here all modern techniques of
manufacturing are used. Topics which are covered under this is as follows:
manufacturing environment, process layout, bills of material and routing, executive
manufacturing planning and control activities, working with the material requirement
planning.
Operation management refers to daily activities of business properly. Project
management includes the management principles which are made to achieve the goals of the
enterprise. This report will study operation management principles in context of the XYZ
company which are dealing in manufacturing of electronic items. It will also discuss the
importance of six-sigma and lean principles. It will study continuous improvement and making
betterment plan. It will discuss different strategies which are developed for the implementation
of plan. Furthermore, it will also tell about the making of the project life cycle for developing
new product. It will also discuss importance of the project life cycle plan by applying concepts
and models.
TASK 1
LO1 Implementation of the operation management principles and the importance of six sigma
and lean principle
Operation management principles which is to be followed in the business. These
principles are:
Principles of inventory management- this refers to controlling of the stock or material.
This principle tells about understanding of duties to look after stock and its effect on
business. These are applied because resources are limited and must be used in an efficient
way.
Principle of operational planning – planning is necessary before every course of action.
In this before manufacturing planning is must. This is the basic knowledge which is used
in the process. Under this strategic planning with techniques are used to make work
easier(Cserhati and Szabo, 2014.).
Principles of manufacturing management – Here all modern techniques of
manufacturing are used. Topics which are covered under this is as follows:
manufacturing environment, process layout, bills of material and routing, executive
manufacturing planning and control activities, working with the material requirement
planning.
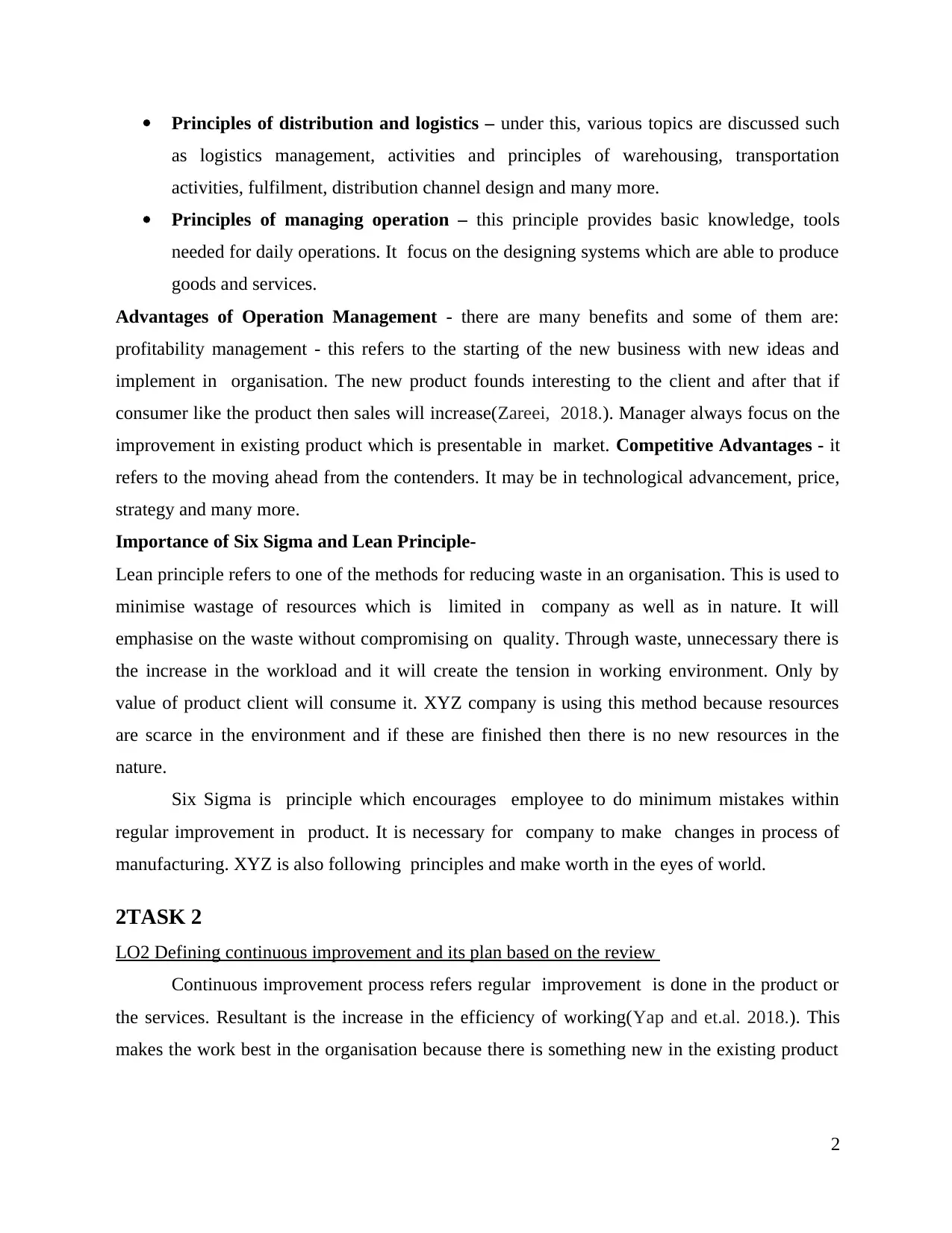
Principles of distribution and logistics – under this, various topics are discussed such
as logistics management, activities and principles of warehousing, transportation
activities, fulfilment, distribution channel design and many more.
Principles of managing operation – this principle provides basic knowledge, tools
needed for daily operations. It focus on the designing systems which are able to produce
goods and services.
Advantages of Operation Management - there are many benefits and some of them are:
profitability management - this refers to the starting of the new business with new ideas and
implement in organisation. The new product founds interesting to the client and after that if
consumer like the product then sales will increase(Zareei, 2018.). Manager always focus on the
improvement in existing product which is presentable in market. Competitive Advantages - it
refers to the moving ahead from the contenders. It may be in technological advancement, price,
strategy and many more.
Importance of Six Sigma and Lean Principle-
Lean principle refers to one of the methods for reducing waste in an organisation. This is used to
minimise wastage of resources which is limited in company as well as in nature. It will
emphasise on the waste without compromising on quality. Through waste, unnecessary there is
the increase in the workload and it will create the tension in working environment. Only by
value of product client will consume it. XYZ company is using this method because resources
are scarce in the environment and if these are finished then there is no new resources in the
nature.
Six Sigma is principle which encourages employee to do minimum mistakes within
regular improvement in product. It is necessary for company to make changes in process of
manufacturing. XYZ is also following principles and make worth in the eyes of world.
2TASK 2
LO2 Defining continuous improvement and its plan based on the review
Continuous improvement process refers regular improvement is done in the product or
the services. Resultant is the increase in the efficiency of working(Yap and et.al. 2018.). This
makes the work best in the organisation because there is something new in the existing product
2
as logistics management, activities and principles of warehousing, transportation
activities, fulfilment, distribution channel design and many more.
Principles of managing operation – this principle provides basic knowledge, tools
needed for daily operations. It focus on the designing systems which are able to produce
goods and services.
Advantages of Operation Management - there are many benefits and some of them are:
profitability management - this refers to the starting of the new business with new ideas and
implement in organisation. The new product founds interesting to the client and after that if
consumer like the product then sales will increase(Zareei, 2018.). Manager always focus on the
improvement in existing product which is presentable in market. Competitive Advantages - it
refers to the moving ahead from the contenders. It may be in technological advancement, price,
strategy and many more.
Importance of Six Sigma and Lean Principle-
Lean principle refers to one of the methods for reducing waste in an organisation. This is used to
minimise wastage of resources which is limited in company as well as in nature. It will
emphasise on the waste without compromising on quality. Through waste, unnecessary there is
the increase in the workload and it will create the tension in working environment. Only by
value of product client will consume it. XYZ company is using this method because resources
are scarce in the environment and if these are finished then there is no new resources in the
nature.
Six Sigma is principle which encourages employee to do minimum mistakes within
regular improvement in product. It is necessary for company to make changes in process of
manufacturing. XYZ is also following principles and make worth in the eyes of world.
2TASK 2
LO2 Defining continuous improvement and its plan based on the review
Continuous improvement process refers regular improvement is done in the product or
the services. Resultant is the increase in the efficiency of working(Yap and et.al. 2018.). This
makes the work best in the organisation because there is something new in the existing product
2
Secure Best Marks with AI Grader
Need help grading? Try our AI Grader for instant feedback on your assignments.
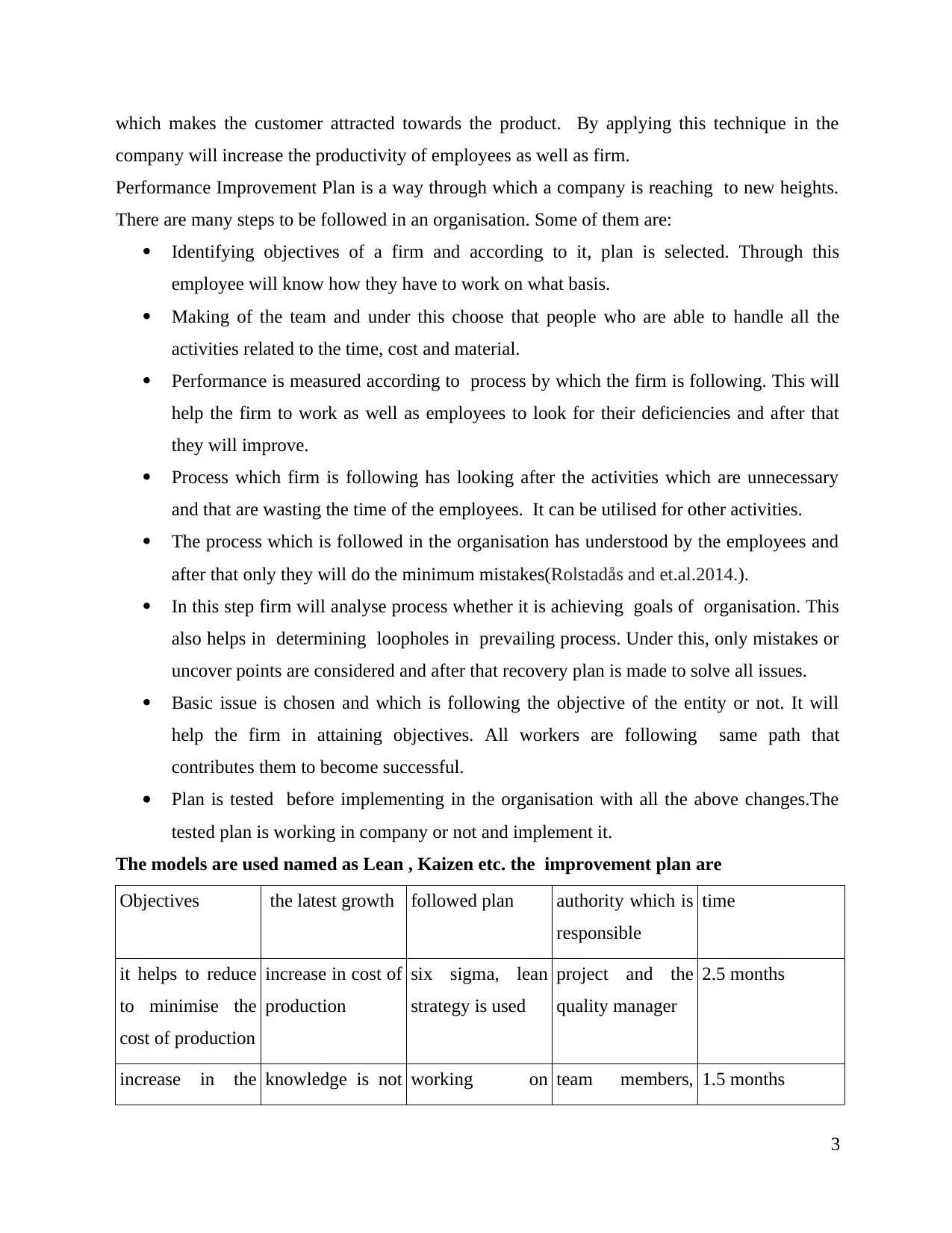
which makes the customer attracted towards the product. By applying this technique in the
company will increase the productivity of employees as well as firm.
Performance Improvement Plan is a way through which a company is reaching to new heights.
There are many steps to be followed in an organisation. Some of them are:
Identifying objectives of a firm and according to it, plan is selected. Through this
employee will know how they have to work on what basis.
Making of the team and under this choose that people who are able to handle all the
activities related to the time, cost and material.
Performance is measured according to process by which the firm is following. This will
help the firm to work as well as employees to look for their deficiencies and after that
they will improve.
Process which firm is following has looking after the activities which are unnecessary
and that are wasting the time of the employees. It can be utilised for other activities.
The process which is followed in the organisation has understood by the employees and
after that only they will do the minimum mistakes(Rolstadås and et.al.2014.).
In this step firm will analyse process whether it is achieving goals of organisation. This
also helps in determining loopholes in prevailing process. Under this, only mistakes or
uncover points are considered and after that recovery plan is made to solve all issues.
Basic issue is chosen and which is following the objective of the entity or not. It will
help the firm in attaining objectives. All workers are following same path that
contributes them to become successful.
Plan is tested before implementing in the organisation with all the above changes.The
tested plan is working in company or not and implement it.
The models are used named as Lean , Kaizen etc. the improvement plan are
Objectives the latest growth followed plan authority which is
responsible
time
it helps to reduce
to minimise the
cost of production
increase in cost of
production
six sigma, lean
strategy is used
project and the
quality manager
2.5 months
increase in the knowledge is not working on team members, 1.5 months
3
company will increase the productivity of employees as well as firm.
Performance Improvement Plan is a way through which a company is reaching to new heights.
There are many steps to be followed in an organisation. Some of them are:
Identifying objectives of a firm and according to it, plan is selected. Through this
employee will know how they have to work on what basis.
Making of the team and under this choose that people who are able to handle all the
activities related to the time, cost and material.
Performance is measured according to process by which the firm is following. This will
help the firm to work as well as employees to look for their deficiencies and after that
they will improve.
Process which firm is following has looking after the activities which are unnecessary
and that are wasting the time of the employees. It can be utilised for other activities.
The process which is followed in the organisation has understood by the employees and
after that only they will do the minimum mistakes(Rolstadås and et.al.2014.).
In this step firm will analyse process whether it is achieving goals of organisation. This
also helps in determining loopholes in prevailing process. Under this, only mistakes or
uncover points are considered and after that recovery plan is made to solve all issues.
Basic issue is chosen and which is following the objective of the entity or not. It will
help the firm in attaining objectives. All workers are following same path that
contributes them to become successful.
Plan is tested before implementing in the organisation with all the above changes.The
tested plan is working in company or not and implement it.
The models are used named as Lean , Kaizen etc. the improvement plan are
Objectives the latest growth followed plan authority which is
responsible
time
it helps to reduce
to minimise the
cost of production
increase in cost of
production
six sigma, lean
strategy is used
project and the
quality manager
2.5 months
increase in the knowledge is not working on team members, 1.5 months
3
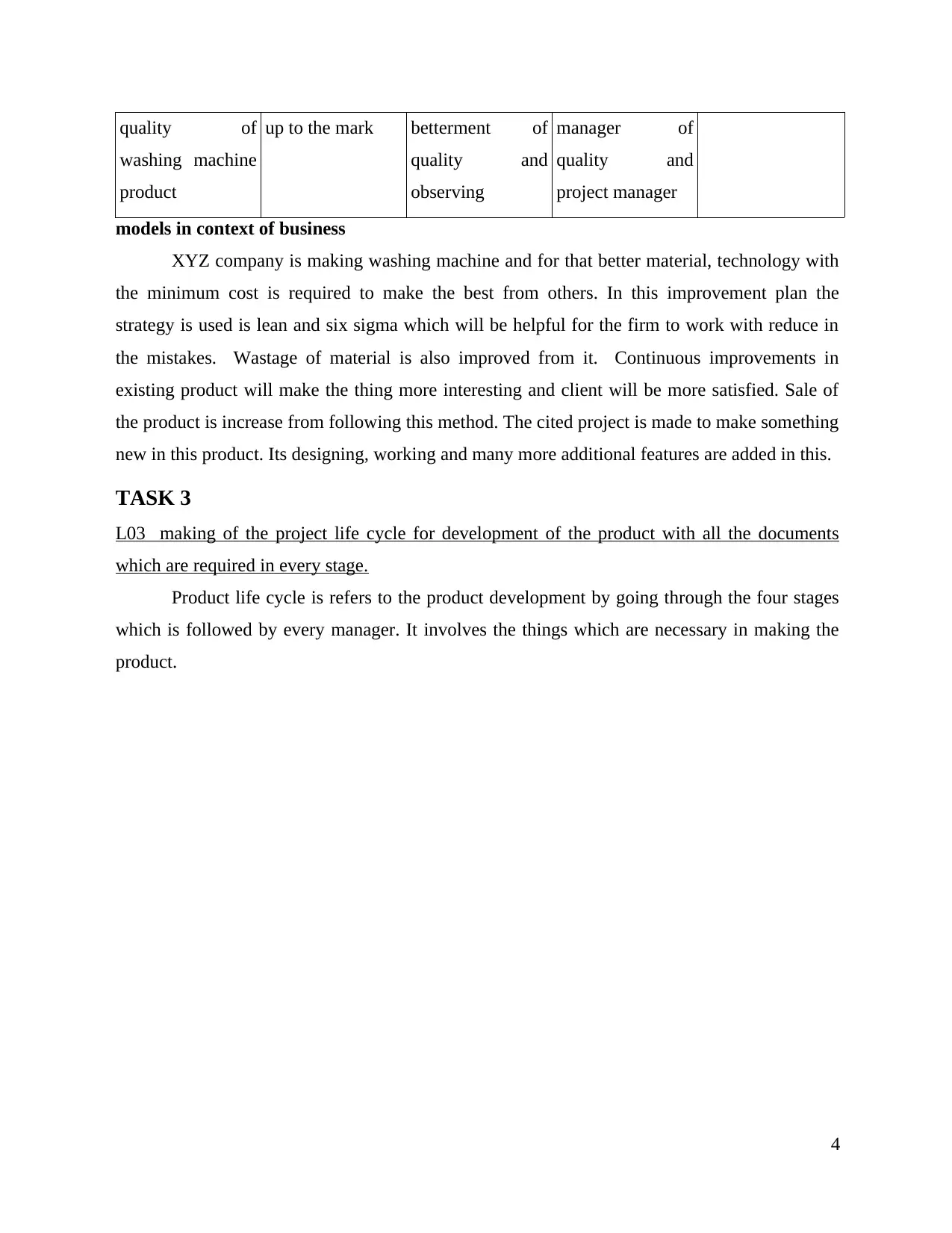
quality of
washing machine
product
up to the mark betterment of
quality and
observing
manager of
quality and
project manager
models in context of business
XYZ company is making washing machine and for that better material, technology with
the minimum cost is required to make the best from others. In this improvement plan the
strategy is used is lean and six sigma which will be helpful for the firm to work with reduce in
the mistakes. Wastage of material is also improved from it. Continuous improvements in
existing product will make the thing more interesting and client will be more satisfied. Sale of
the product is increase from following this method. The cited project is made to make something
new in this product. Its designing, working and many more additional features are added in this.
TASK 3
L03 making of the project life cycle for development of the product with all the documents
which are required in every stage.
Product life cycle is refers to the product development by going through the four stages
which is followed by every manager. It involves the things which are necessary in making the
product.
4
washing machine
product
up to the mark betterment of
quality and
observing
manager of
quality and
project manager
models in context of business
XYZ company is making washing machine and for that better material, technology with
the minimum cost is required to make the best from others. In this improvement plan the
strategy is used is lean and six sigma which will be helpful for the firm to work with reduce in
the mistakes. Wastage of material is also improved from it. Continuous improvements in
existing product will make the thing more interesting and client will be more satisfied. Sale of
the product is increase from following this method. The cited project is made to make something
new in this product. Its designing, working and many more additional features are added in this.
TASK 3
L03 making of the project life cycle for development of the product with all the documents
which are required in every stage.
Product life cycle is refers to the product development by going through the four stages
which is followed by every manager. It involves the things which are necessary in making the
product.
4
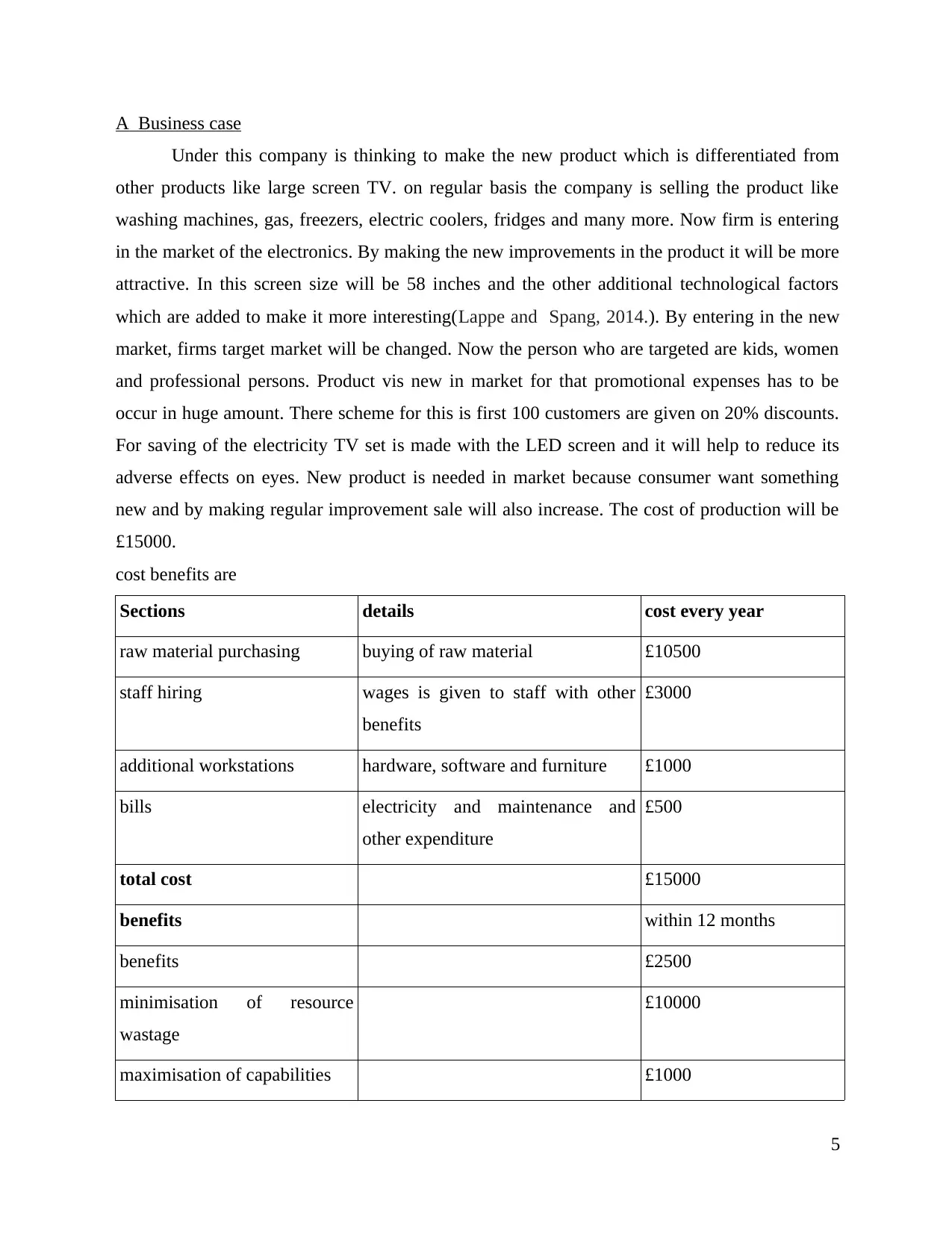
A Business case
Under this company is thinking to make the new product which is differentiated from
other products like large screen TV. on regular basis the company is selling the product like
washing machines, gas, freezers, electric coolers, fridges and many more. Now firm is entering
in the market of the electronics. By making the new improvements in the product it will be more
attractive. In this screen size will be 58 inches and the other additional technological factors
which are added to make it more interesting(Lappe and Spang, 2014.). By entering in the new
market, firms target market will be changed. Now the person who are targeted are kids, women
and professional persons. Product vis new in market for that promotional expenses has to be
occur in huge amount. There scheme for this is first 100 customers are given on 20% discounts.
For saving of the electricity TV set is made with the LED screen and it will help to reduce its
adverse effects on eyes. New product is needed in market because consumer want something
new and by making regular improvement sale will also increase. The cost of production will be
£15000.
cost benefits are
Sections details cost every year
raw material purchasing buying of raw material £10500
staff hiring wages is given to staff with other
benefits
£3000
additional workstations hardware, software and furniture £1000
bills electricity and maintenance and
other expenditure
£500
total cost £15000
benefits within 12 months
benefits £2500
minimisation of resource
wastage
£10000
maximisation of capabilities £1000
5
Under this company is thinking to make the new product which is differentiated from
other products like large screen TV. on regular basis the company is selling the product like
washing machines, gas, freezers, electric coolers, fridges and many more. Now firm is entering
in the market of the electronics. By making the new improvements in the product it will be more
attractive. In this screen size will be 58 inches and the other additional technological factors
which are added to make it more interesting(Lappe and Spang, 2014.). By entering in the new
market, firms target market will be changed. Now the person who are targeted are kids, women
and professional persons. Product vis new in market for that promotional expenses has to be
occur in huge amount. There scheme for this is first 100 customers are given on 20% discounts.
For saving of the electricity TV set is made with the LED screen and it will help to reduce its
adverse effects on eyes. New product is needed in market because consumer want something
new and by making regular improvement sale will also increase. The cost of production will be
£15000.
cost benefits are
Sections details cost every year
raw material purchasing buying of raw material £10500
staff hiring wages is given to staff with other
benefits
£3000
additional workstations hardware, software and furniture £1000
bills electricity and maintenance and
other expenditure
£500
total cost £15000
benefits within 12 months
benefits £2500
minimisation of resource
wastage
£10000
maximisation of capabilities £1000
5
Paraphrase This Document
Need a fresh take? Get an instant paraphrase of this document with our AI Paraphraser
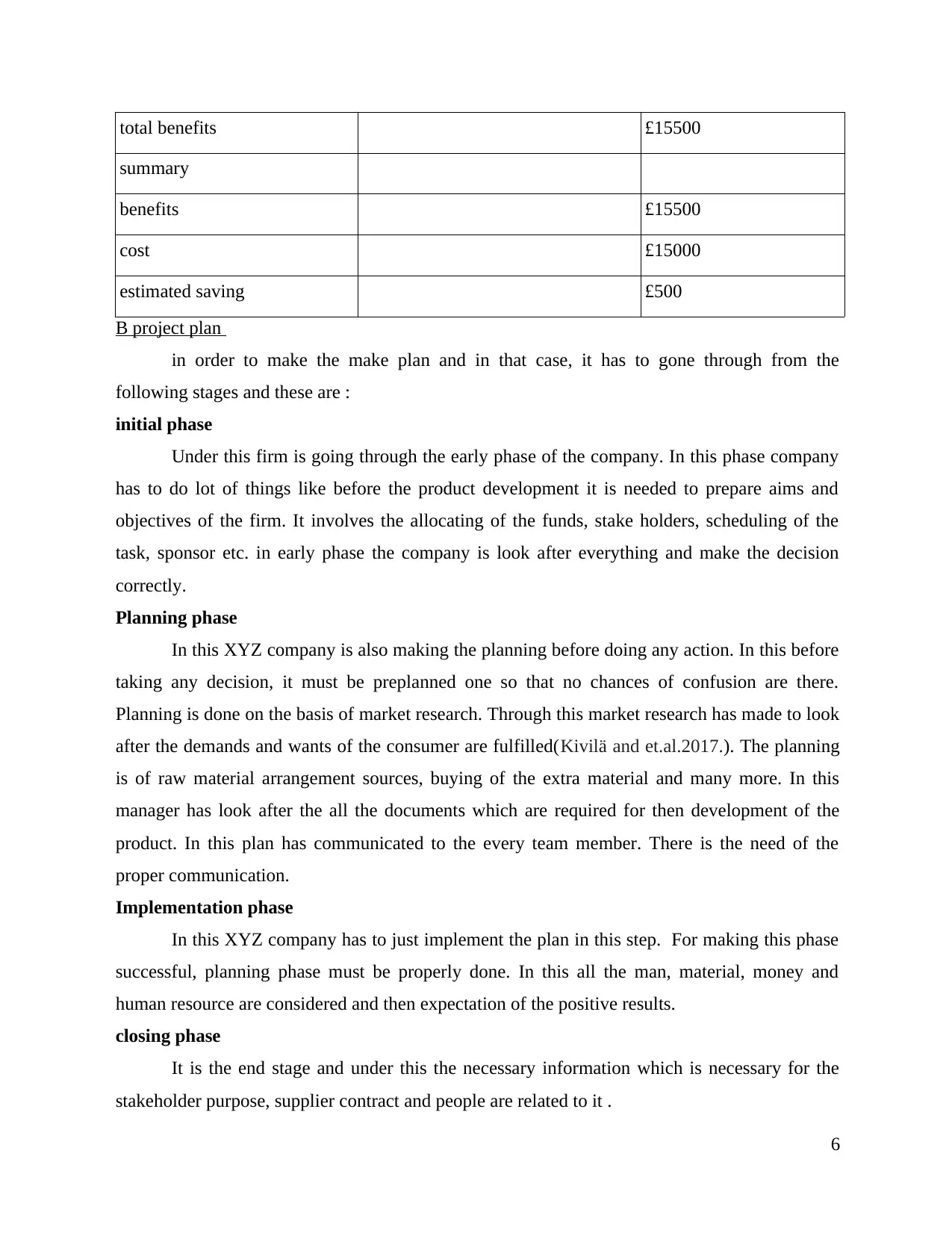
total benefits £15500
summary
benefits £15500
cost £15000
estimated saving £500
B project plan
in order to make the make plan and in that case, it has to gone through from the
following stages and these are :
initial phase
Under this firm is going through the early phase of the company. In this phase company
has to do lot of things like before the product development it is needed to prepare aims and
objectives of the firm. It involves the allocating of the funds, stake holders, scheduling of the
task, sponsor etc. in early phase the company is look after everything and make the decision
correctly.
Planning phase
In this XYZ company is also making the planning before doing any action. In this before
taking any decision, it must be preplanned one so that no chances of confusion are there.
Planning is done on the basis of market research. Through this market research has made to look
after the demands and wants of the consumer are fulfilled(Kivilä and et.al.2017.). The planning
is of raw material arrangement sources, buying of the extra material and many more. In this
manager has look after the all the documents which are required for then development of the
product. In this plan has communicated to the every team member. There is the need of the
proper communication.
Implementation phase
In this XYZ company has to just implement the plan in this step. For making this phase
successful, planning phase must be properly done. In this all the man, material, money and
human resource are considered and then expectation of the positive results.
closing phase
It is the end stage and under this the necessary information which is necessary for the
stakeholder purpose, supplier contract and people are related to it .
6
summary
benefits £15500
cost £15000
estimated saving £500
B project plan
in order to make the make plan and in that case, it has to gone through from the
following stages and these are :
initial phase
Under this firm is going through the early phase of the company. In this phase company
has to do lot of things like before the product development it is needed to prepare aims and
objectives of the firm. It involves the allocating of the funds, stake holders, scheduling of the
task, sponsor etc. in early phase the company is look after everything and make the decision
correctly.
Planning phase
In this XYZ company is also making the planning before doing any action. In this before
taking any decision, it must be preplanned one so that no chances of confusion are there.
Planning is done on the basis of market research. Through this market research has made to look
after the demands and wants of the consumer are fulfilled(Kivilä and et.al.2017.). The planning
is of raw material arrangement sources, buying of the extra material and many more. In this
manager has look after the all the documents which are required for then development of the
product. In this plan has communicated to the every team member. There is the need of the
proper communication.
Implementation phase
In this XYZ company has to just implement the plan in this step. For making this phase
successful, planning phase must be properly done. In this all the man, material, money and
human resource are considered and then expectation of the positive results.
closing phase
It is the end stage and under this the necessary information which is necessary for the
stakeholder purpose, supplier contract and people are related to it .
6
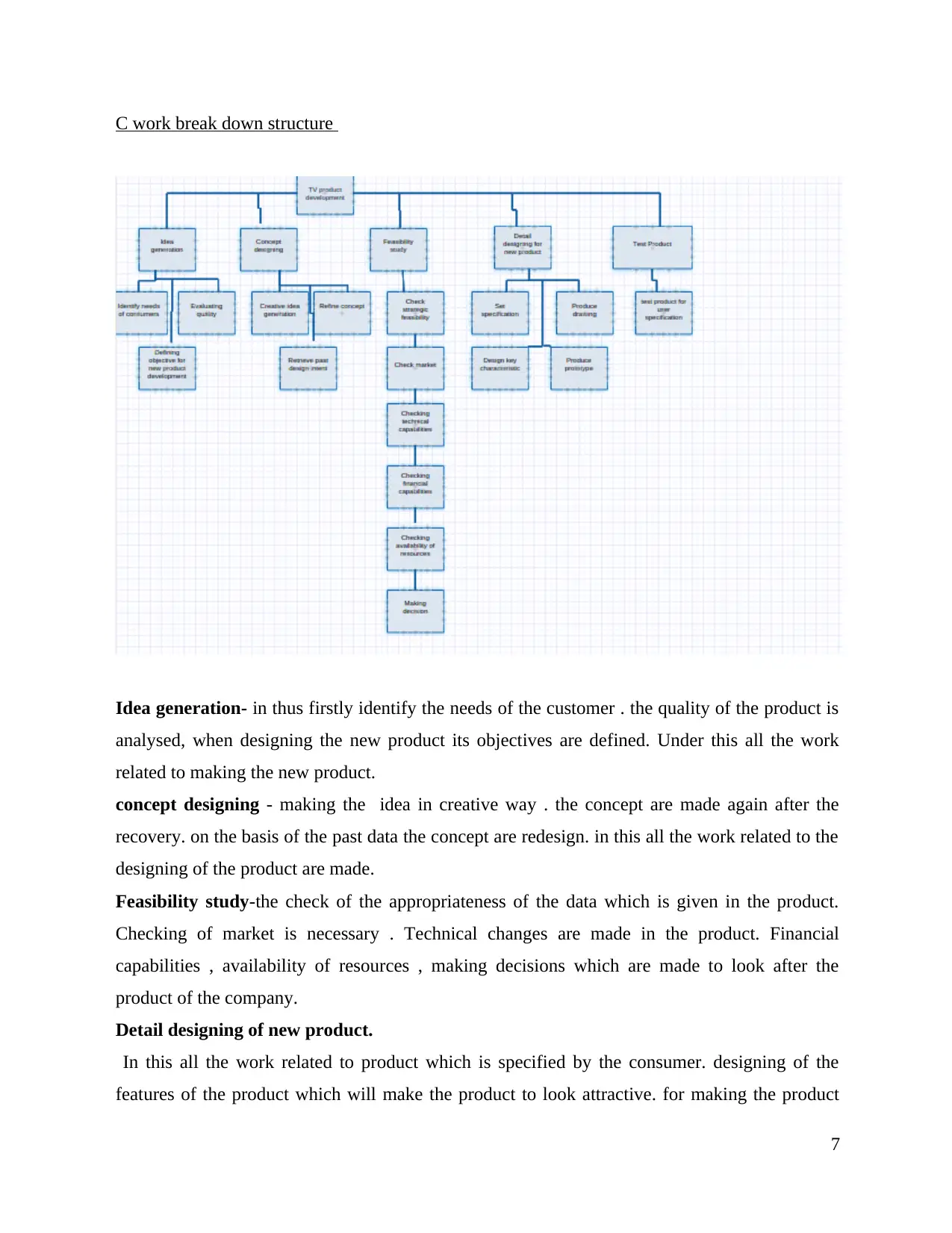
C work break down structure
Idea generation- in thus firstly identify the needs of the customer . the quality of the product is
analysed, when designing the new product its objectives are defined. Under this all the work
related to making the new product.
concept designing - making the idea in creative way . the concept are made again after the
recovery. on the basis of the past data the concept are redesign. in this all the work related to the
designing of the product are made.
Feasibility study-the check of the appropriateness of the data which is given in the product.
Checking of market is necessary . Technical changes are made in the product. Financial
capabilities , availability of resources , making decisions which are made to look after the
product of the company.
Detail designing of new product.
In this all the work related to product which is specified by the consumer. designing of the
features of the product which will make the product to look attractive. for making the product
7
Idea generation- in thus firstly identify the needs of the customer . the quality of the product is
analysed, when designing the new product its objectives are defined. Under this all the work
related to making the new product.
concept designing - making the idea in creative way . the concept are made again after the
recovery. on the basis of the past data the concept are redesign. in this all the work related to the
designing of the product are made.
Feasibility study-the check of the appropriateness of the data which is given in the product.
Checking of market is necessary . Technical changes are made in the product. Financial
capabilities , availability of resources , making decisions which are made to look after the
product of the company.
Detail designing of new product.
In this all the work related to product which is specified by the consumer. designing of the
features of the product which will make the product to look attractive. for making the product
7
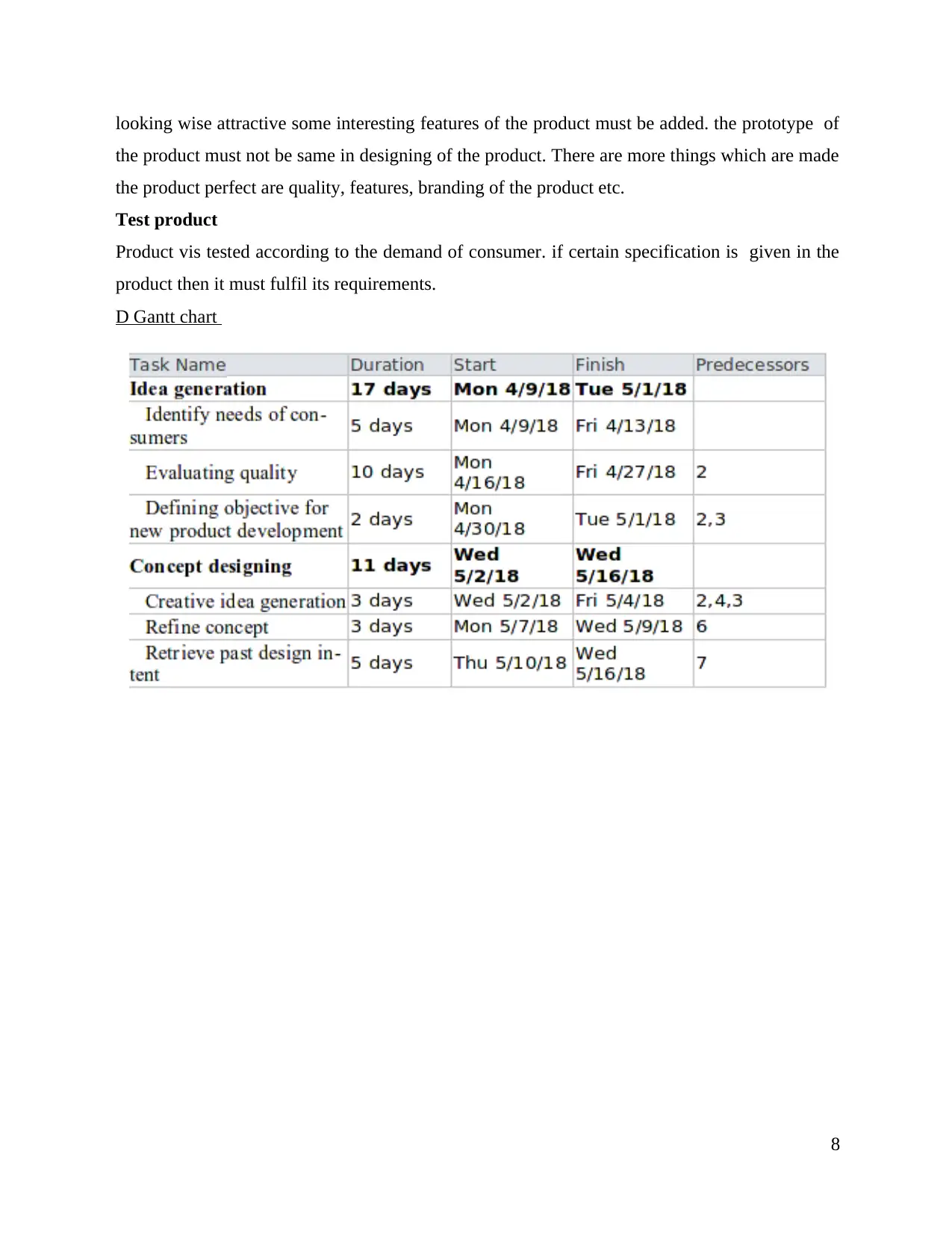
looking wise attractive some interesting features of the product must be added. the prototype of
the product must not be same in designing of the product. There are more things which are made
the product perfect are quality, features, branding of the product etc.
Test product
Product vis tested according to the demand of consumer. if certain specification is given in the
product then it must fulfil its requirements.
D Gantt chart
8
the product must not be same in designing of the product. There are more things which are made
the product perfect are quality, features, branding of the product etc.
Test product
Product vis tested according to the demand of consumer. if certain specification is given in the
product then it must fulfil its requirements.
D Gantt chart
8
Secure Best Marks with AI Grader
Need help grading? Try our AI Grader for instant feedback on your assignments.
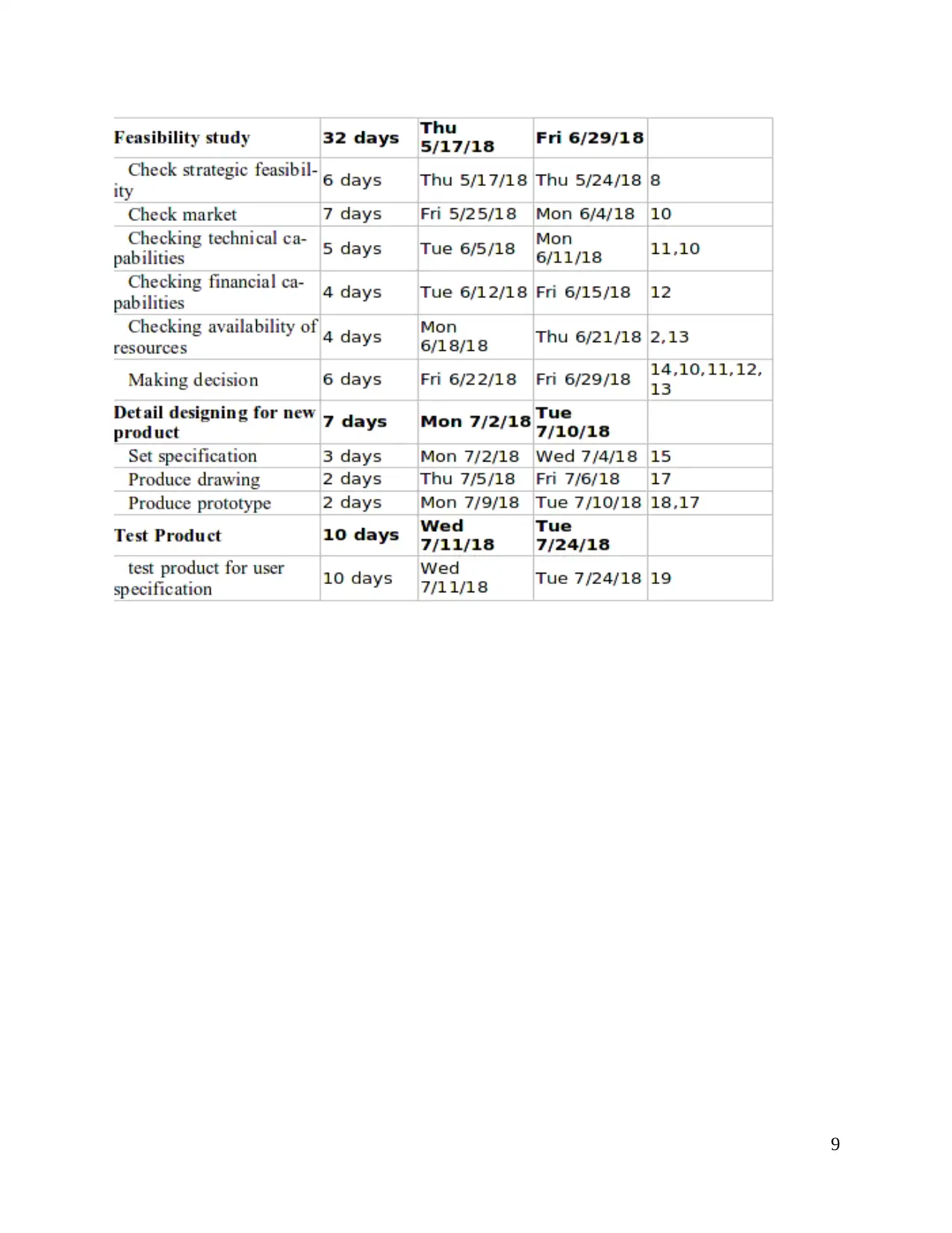
9
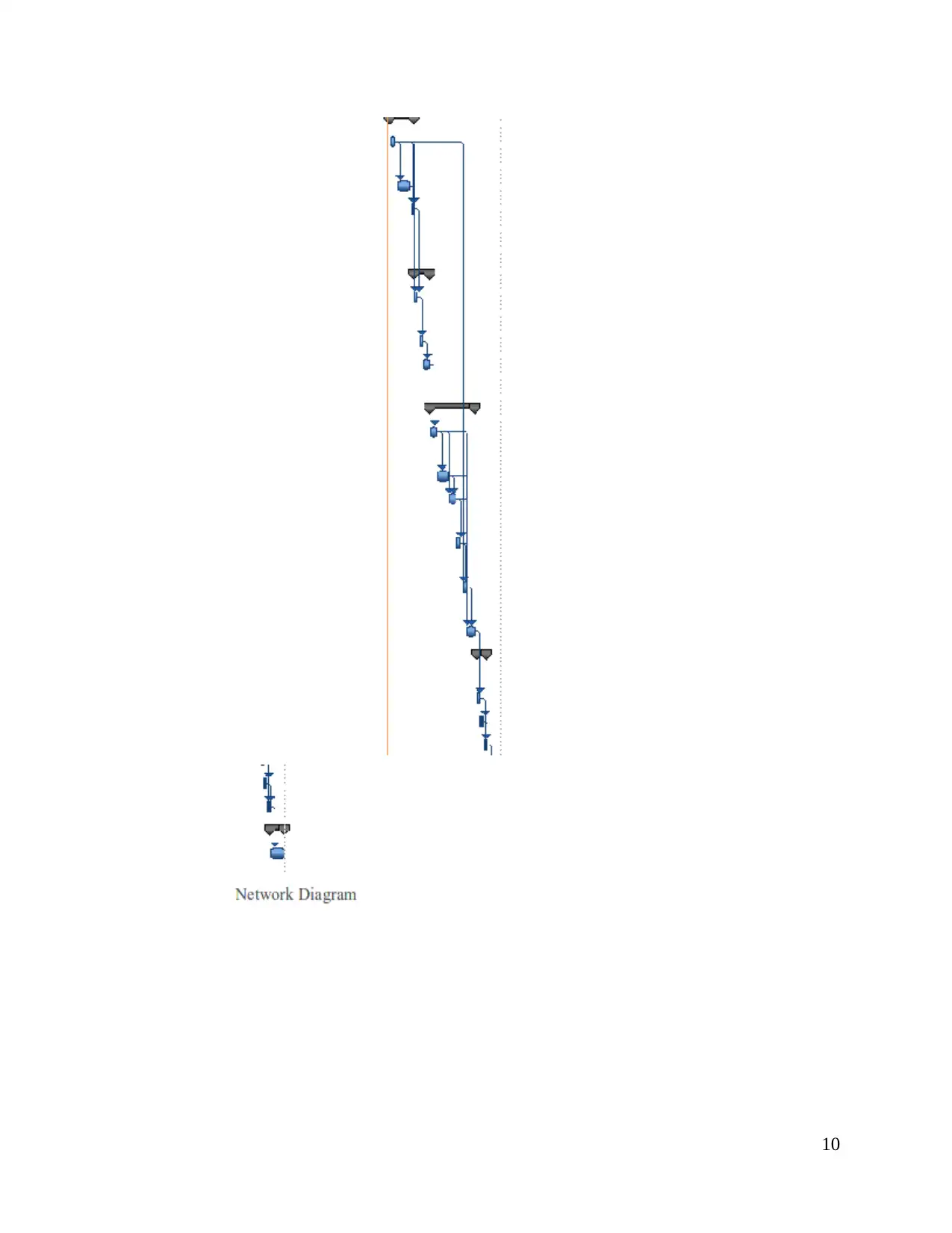
10
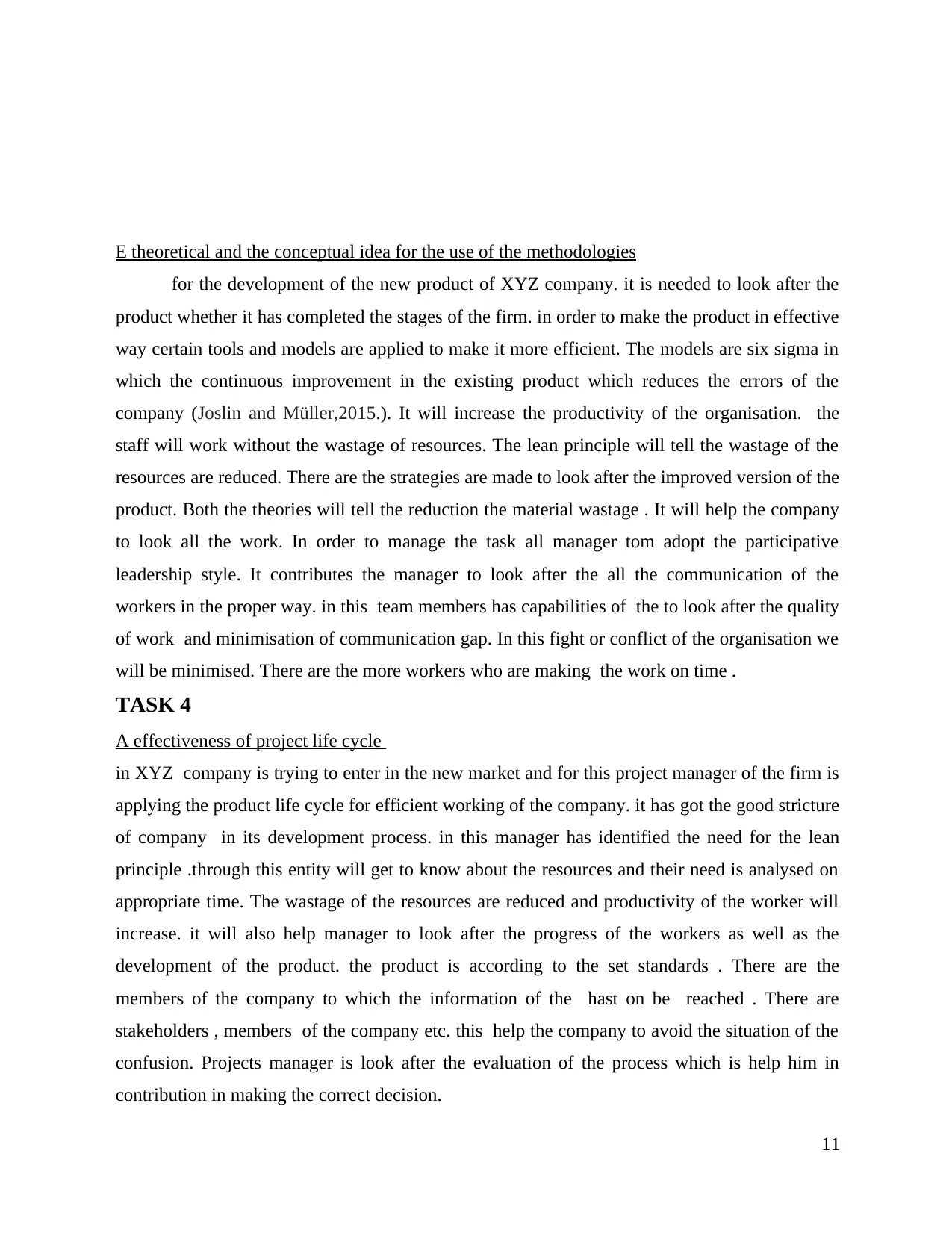
E theoretical and the conceptual idea for the use of the methodologies
for the development of the new product of XYZ company. it is needed to look after the
product whether it has completed the stages of the firm. in order to make the product in effective
way certain tools and models are applied to make it more efficient. The models are six sigma in
which the continuous improvement in the existing product which reduces the errors of the
company (Joslin and Müller,2015.). It will increase the productivity of the organisation. the
staff will work without the wastage of resources. The lean principle will tell the wastage of the
resources are reduced. There are the strategies are made to look after the improved version of the
product. Both the theories will tell the reduction the material wastage . It will help the company
to look all the work. In order to manage the task all manager tom adopt the participative
leadership style. It contributes the manager to look after the all the communication of the
workers in the proper way. in this team members has capabilities of the to look after the quality
of work and minimisation of communication gap. In this fight or conflict of the organisation we
will be minimised. There are the more workers who are making the work on time .
TASK 4
A effectiveness of project life cycle
in XYZ company is trying to enter in the new market and for this project manager of the firm is
applying the product life cycle for efficient working of the company. it has got the good stricture
of company in its development process. in this manager has identified the need for the lean
principle .through this entity will get to know about the resources and their need is analysed on
appropriate time. The wastage of the resources are reduced and productivity of the worker will
increase. it will also help manager to look after the progress of the workers as well as the
development of the product. the product is according to the set standards . There are the
members of the company to which the information of the hast on be reached . There are
stakeholders , members of the company etc. this help the company to avoid the situation of the
confusion. Projects manager is look after the evaluation of the process which is help him in
contribution in making the correct decision.
11
for the development of the new product of XYZ company. it is needed to look after the
product whether it has completed the stages of the firm. in order to make the product in effective
way certain tools and models are applied to make it more efficient. The models are six sigma in
which the continuous improvement in the existing product which reduces the errors of the
company (Joslin and Müller,2015.). It will increase the productivity of the organisation. the
staff will work without the wastage of resources. The lean principle will tell the wastage of the
resources are reduced. There are the strategies are made to look after the improved version of the
product. Both the theories will tell the reduction the material wastage . It will help the company
to look all the work. In order to manage the task all manager tom adopt the participative
leadership style. It contributes the manager to look after the all the communication of the
workers in the proper way. in this team members has capabilities of the to look after the quality
of work and minimisation of communication gap. In this fight or conflict of the organisation we
will be minimised. There are the more workers who are making the work on time .
TASK 4
A effectiveness of project life cycle
in XYZ company is trying to enter in the new market and for this project manager of the firm is
applying the product life cycle for efficient working of the company. it has got the good stricture
of company in its development process. in this manager has identified the need for the lean
principle .through this entity will get to know about the resources and their need is analysed on
appropriate time. The wastage of the resources are reduced and productivity of the worker will
increase. it will also help manager to look after the progress of the workers as well as the
development of the product. the product is according to the set standards . There are the
members of the company to which the information of the hast on be reached . There are
stakeholders , members of the company etc. this help the company to avoid the situation of the
confusion. Projects manager is look after the evaluation of the process which is help him in
contribution in making the correct decision.
11
Paraphrase This Document
Need a fresh take? Get an instant paraphrase of this document with our AI Paraphraser
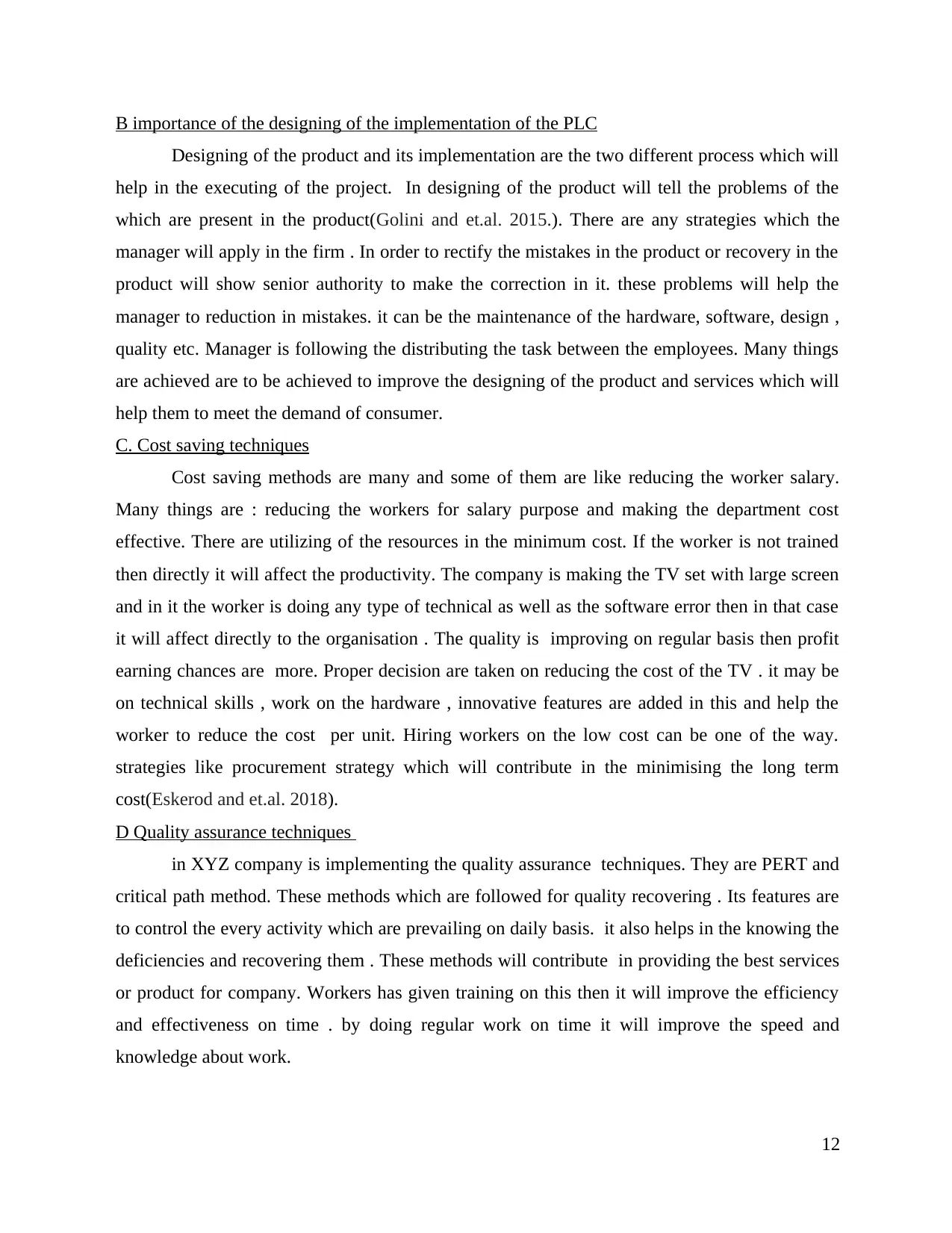
B importance of the designing of the implementation of the PLC
Designing of the product and its implementation are the two different process which will
help in the executing of the project. In designing of the product will tell the problems of the
which are present in the product(Golini and et.al. 2015.). There are any strategies which the
manager will apply in the firm . In order to rectify the mistakes in the product or recovery in the
product will show senior authority to make the correction in it. these problems will help the
manager to reduction in mistakes. it can be the maintenance of the hardware, software, design ,
quality etc. Manager is following the distributing the task between the employees. Many things
are achieved are to be achieved to improve the designing of the product and services which will
help them to meet the demand of consumer.
C. Cost saving techniques
Cost saving methods are many and some of them are like reducing the worker salary.
Many things are : reducing the workers for salary purpose and making the department cost
effective. There are utilizing of the resources in the minimum cost. If the worker is not trained
then directly it will affect the productivity. The company is making the TV set with large screen
and in it the worker is doing any type of technical as well as the software error then in that case
it will affect directly to the organisation . The quality is improving on regular basis then profit
earning chances are more. Proper decision are taken on reducing the cost of the TV . it may be
on technical skills , work on the hardware , innovative features are added in this and help the
worker to reduce the cost per unit. Hiring workers on the low cost can be one of the way.
strategies like procurement strategy which will contribute in the minimising the long term
cost(Eskerod and et.al. 2018).
D Quality assurance techniques
in XYZ company is implementing the quality assurance techniques. They are PERT and
critical path method. These methods which are followed for quality recovering . Its features are
to control the every activity which are prevailing on daily basis. it also helps in the knowing the
deficiencies and recovering them . These methods will contribute in providing the best services
or product for company. Workers has given training on this then it will improve the efficiency
and effectiveness on time . by doing regular work on time it will improve the speed and
knowledge about work.
12
Designing of the product and its implementation are the two different process which will
help in the executing of the project. In designing of the product will tell the problems of the
which are present in the product(Golini and et.al. 2015.). There are any strategies which the
manager will apply in the firm . In order to rectify the mistakes in the product or recovery in the
product will show senior authority to make the correction in it. these problems will help the
manager to reduction in mistakes. it can be the maintenance of the hardware, software, design ,
quality etc. Manager is following the distributing the task between the employees. Many things
are achieved are to be achieved to improve the designing of the product and services which will
help them to meet the demand of consumer.
C. Cost saving techniques
Cost saving methods are many and some of them are like reducing the worker salary.
Many things are : reducing the workers for salary purpose and making the department cost
effective. There are utilizing of the resources in the minimum cost. If the worker is not trained
then directly it will affect the productivity. The company is making the TV set with large screen
and in it the worker is doing any type of technical as well as the software error then in that case
it will affect directly to the organisation . The quality is improving on regular basis then profit
earning chances are more. Proper decision are taken on reducing the cost of the TV . it may be
on technical skills , work on the hardware , innovative features are added in this and help the
worker to reduce the cost per unit. Hiring workers on the low cost can be one of the way.
strategies like procurement strategy which will contribute in the minimising the long term
cost(Eskerod and et.al. 2018).
D Quality assurance techniques
in XYZ company is implementing the quality assurance techniques. They are PERT and
critical path method. These methods which are followed for quality recovering . Its features are
to control the every activity which are prevailing on daily basis. it also helps in the knowing the
deficiencies and recovering them . These methods will contribute in providing the best services
or product for company. Workers has given training on this then it will improve the efficiency
and effectiveness on time . by doing regular work on time it will improve the speed and
knowledge about work.
12
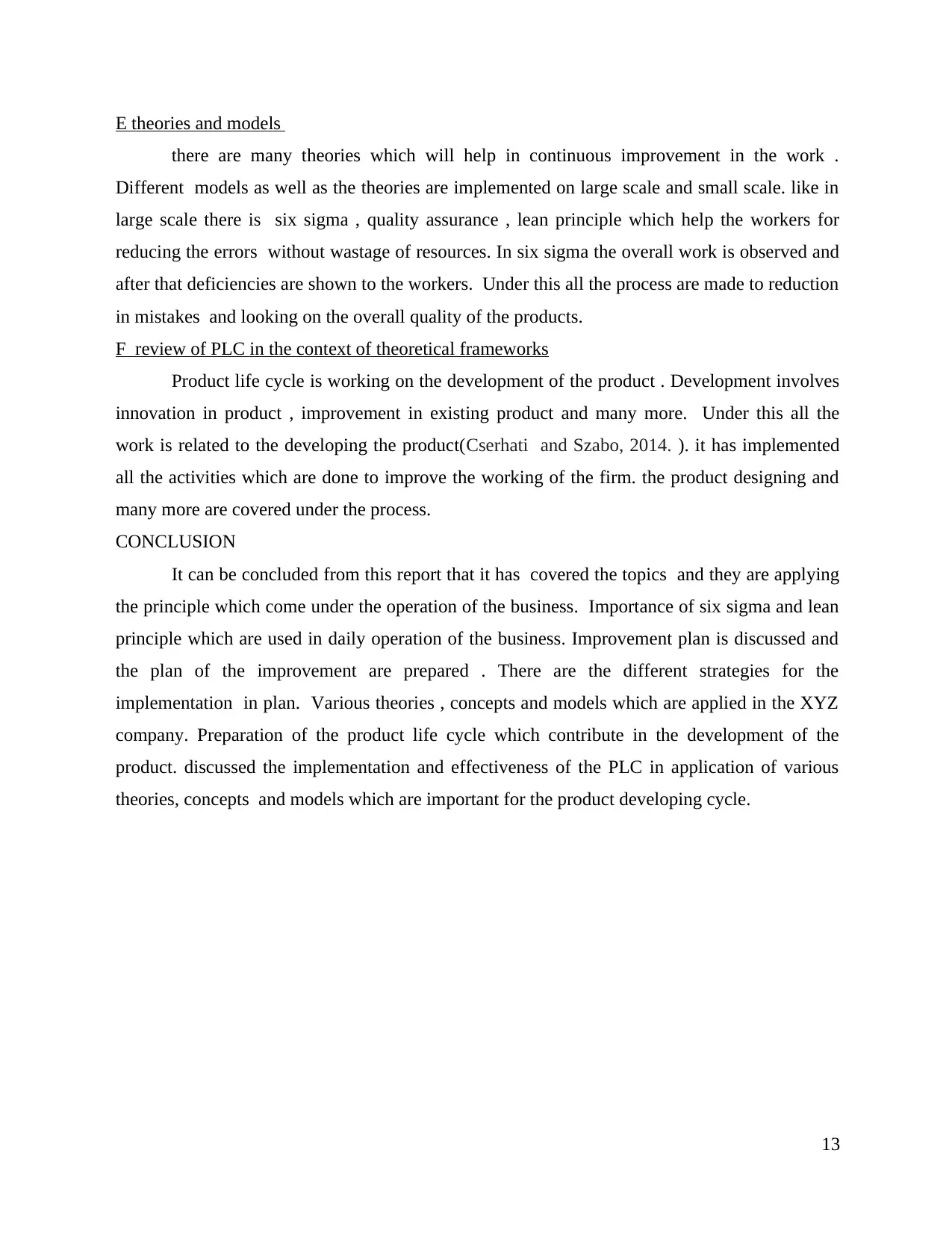
E theories and models
there are many theories which will help in continuous improvement in the work .
Different models as well as the theories are implemented on large scale and small scale. like in
large scale there is six sigma , quality assurance , lean principle which help the workers for
reducing the errors without wastage of resources. In six sigma the overall work is observed and
after that deficiencies are shown to the workers. Under this all the process are made to reduction
in mistakes and looking on the overall quality of the products.
F review of PLC in the context of theoretical frameworks
Product life cycle is working on the development of the product . Development involves
innovation in product , improvement in existing product and many more. Under this all the
work is related to the developing the product(Cserhati and Szabo, 2014. ). it has implemented
all the activities which are done to improve the working of the firm. the product designing and
many more are covered under the process.
CONCLUSION
It can be concluded from this report that it has covered the topics and they are applying
the principle which come under the operation of the business. Importance of six sigma and lean
principle which are used in daily operation of the business. Improvement plan is discussed and
the plan of the improvement are prepared . There are the different strategies for the
implementation in plan. Various theories , concepts and models which are applied in the XYZ
company. Preparation of the product life cycle which contribute in the development of the
product. discussed the implementation and effectiveness of the PLC in application of various
theories, concepts and models which are important for the product developing cycle.
13
there are many theories which will help in continuous improvement in the work .
Different models as well as the theories are implemented on large scale and small scale. like in
large scale there is six sigma , quality assurance , lean principle which help the workers for
reducing the errors without wastage of resources. In six sigma the overall work is observed and
after that deficiencies are shown to the workers. Under this all the process are made to reduction
in mistakes and looking on the overall quality of the products.
F review of PLC in the context of theoretical frameworks
Product life cycle is working on the development of the product . Development involves
innovation in product , improvement in existing product and many more. Under this all the
work is related to the developing the product(Cserhati and Szabo, 2014. ). it has implemented
all the activities which are done to improve the working of the firm. the product designing and
many more are covered under the process.
CONCLUSION
It can be concluded from this report that it has covered the topics and they are applying
the principle which come under the operation of the business. Importance of six sigma and lean
principle which are used in daily operation of the business. Improvement plan is discussed and
the plan of the improvement are prepared . There are the different strategies for the
implementation in plan. Various theories , concepts and models which are applied in the XYZ
company. Preparation of the product life cycle which contribute in the development of the
product. discussed the implementation and effectiveness of the PLC in application of various
theories, concepts and models which are important for the product developing cycle.
13
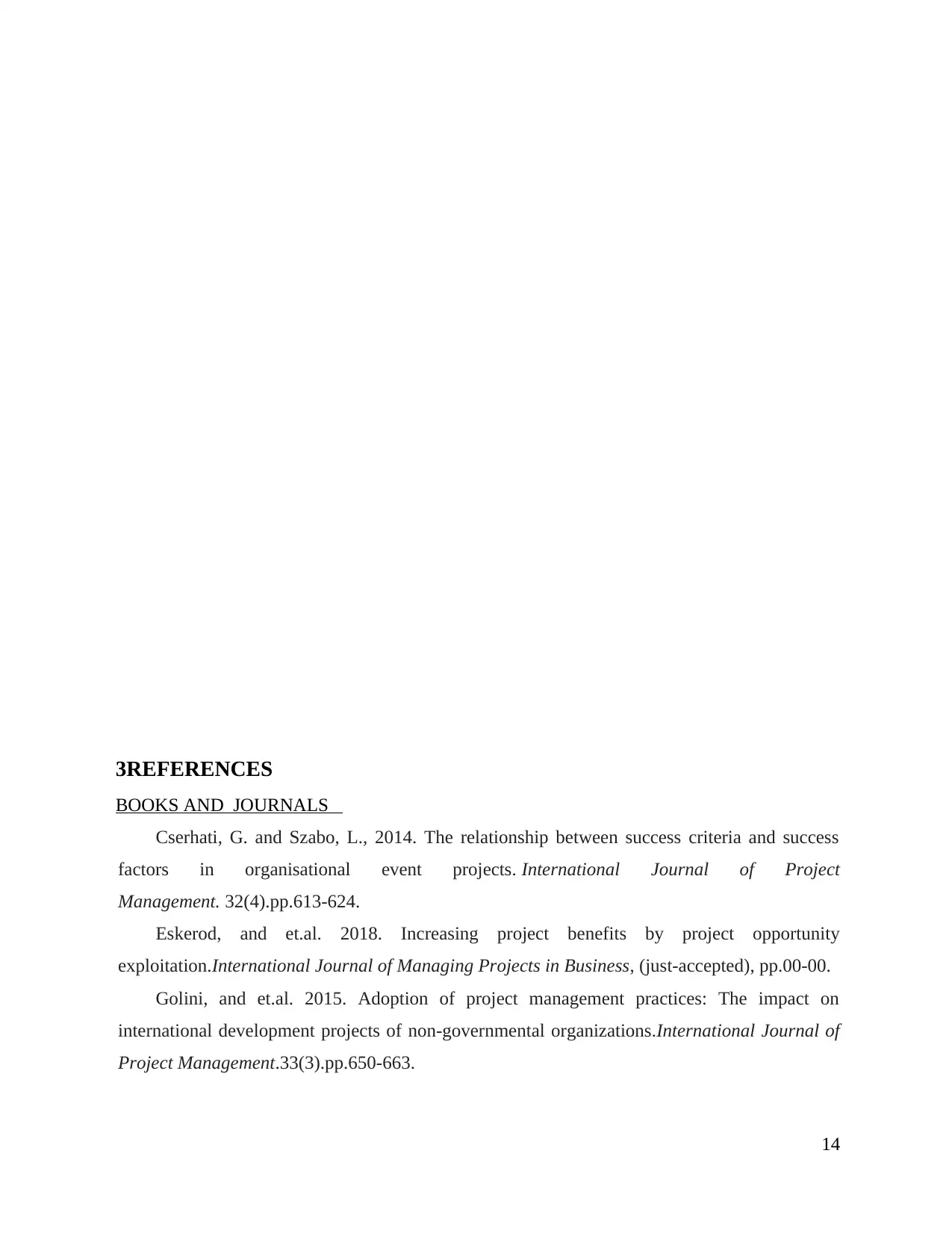
3REFERENCES
BOOKS AND JOURNALS
Cserhati, G. and Szabo, L., 2014. The relationship between success criteria and success
factors in organisational event projects. International Journal of Project
Management. 32(4).pp.613-624.
Eskerod, and et.al. 2018. Increasing project benefits by project opportunity
exploitation.International Journal of Managing Projects in Business, (just-accepted), pp.00-00.
Golini, and et.al. 2015. Adoption of project management practices: The impact on
international development projects of non-governmental organizations.International Journal of
Project Management.33(3).pp.650-663.
14
BOOKS AND JOURNALS
Cserhati, G. and Szabo, L., 2014. The relationship between success criteria and success
factors in organisational event projects. International Journal of Project
Management. 32(4).pp.613-624.
Eskerod, and et.al. 2018. Increasing project benefits by project opportunity
exploitation.International Journal of Managing Projects in Business, (just-accepted), pp.00-00.
Golini, and et.al. 2015. Adoption of project management practices: The impact on
international development projects of non-governmental organizations.International Journal of
Project Management.33(3).pp.650-663.
14
Secure Best Marks with AI Grader
Need help grading? Try our AI Grader for instant feedback on your assignments.
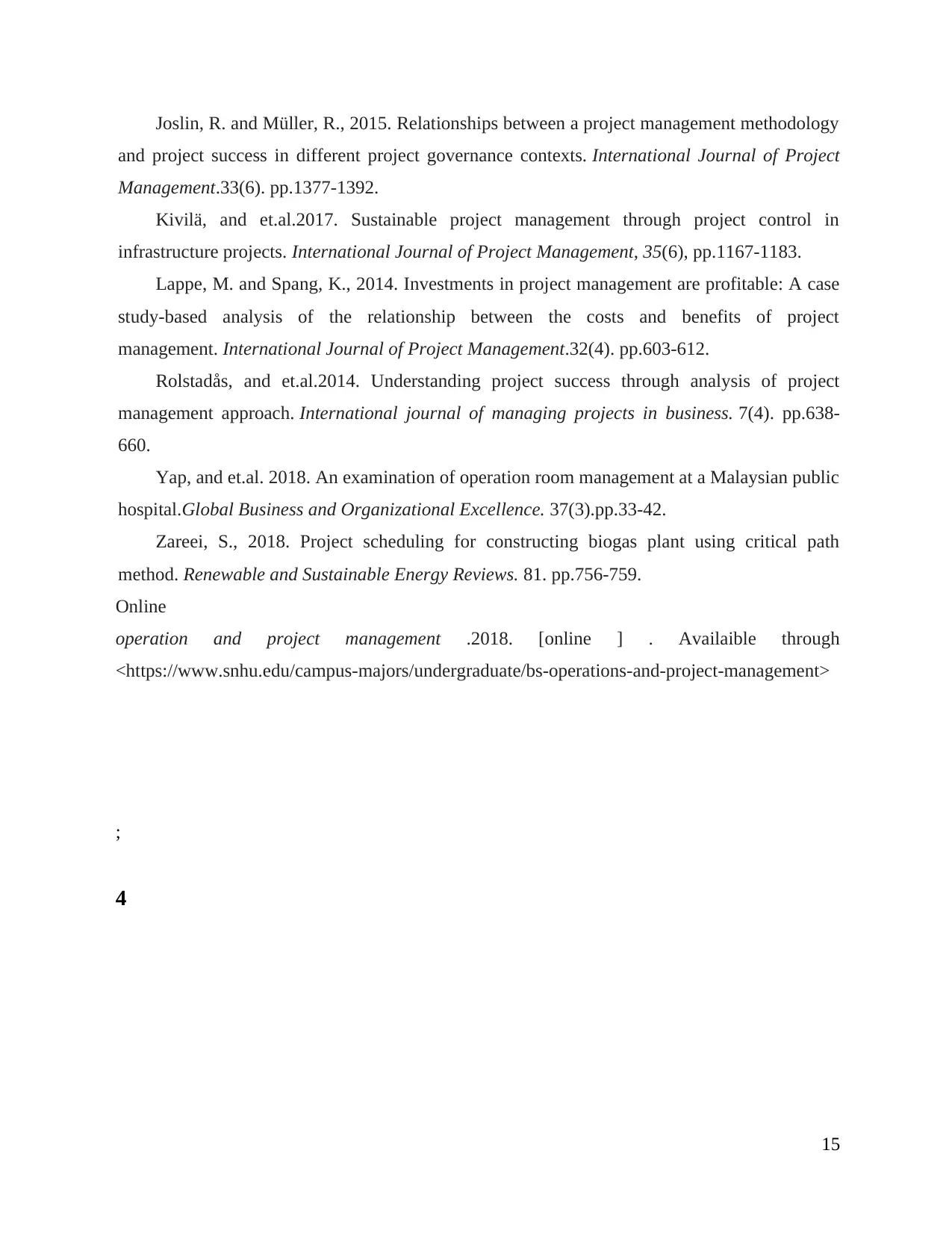
Joslin, R. and Müller, R., 2015. Relationships between a project management methodology
and project success in different project governance contexts. International Journal of Project
Management.33(6). pp.1377-1392.
Kivilä, and et.al.2017. Sustainable project management through project control in
infrastructure projects. International Journal of Project Management, 35(6), pp.1167-1183.
Lappe, M. and Spang, K., 2014. Investments in project management are profitable: A case
study-based analysis of the relationship between the costs and benefits of project
management. International Journal of Project Management.32(4). pp.603-612.
Rolstadås, and et.al.2014. Understanding project success through analysis of project
management approach. International journal of managing projects in business. 7(4). pp.638-
660.
Yap, and et.al. 2018. An examination of operation room management at a Malaysian public
hospital.Global Business and Organizational Excellence. 37(3).pp.33-42.
Zareei, S., 2018. Project scheduling for constructing biogas plant using critical path
method. Renewable and Sustainable Energy Reviews. 81. pp.756-759.
Online
operation and project management .2018. [online ] . Availaible through
<https://www.snhu.edu/campus-majors/undergraduate/bs-operations-and-project-management>
;
4
15
and project success in different project governance contexts. International Journal of Project
Management.33(6). pp.1377-1392.
Kivilä, and et.al.2017. Sustainable project management through project control in
infrastructure projects. International Journal of Project Management, 35(6), pp.1167-1183.
Lappe, M. and Spang, K., 2014. Investments in project management are profitable: A case
study-based analysis of the relationship between the costs and benefits of project
management. International Journal of Project Management.32(4). pp.603-612.
Rolstadås, and et.al.2014. Understanding project success through analysis of project
management approach. International journal of managing projects in business. 7(4). pp.638-
660.
Yap, and et.al. 2018. An examination of operation room management at a Malaysian public
hospital.Global Business and Organizational Excellence. 37(3).pp.33-42.
Zareei, S., 2018. Project scheduling for constructing biogas plant using critical path
method. Renewable and Sustainable Energy Reviews. 81. pp.756-759.
Online
operation and project management .2018. [online ] . Availaible through
<https://www.snhu.edu/campus-majors/undergraduate/bs-operations-and-project-management>
;
4
15
1 out of 17
Related Documents
![[object Object]](/_next/image/?url=%2F_next%2Fstatic%2Fmedia%2Flogo.6d15ce61.png&w=640&q=75)
Your All-in-One AI-Powered Toolkit for Academic Success.
+13062052269
info@desklib.com
Available 24*7 on WhatsApp / Email
Unlock your academic potential
© 2024 | Zucol Services PVT LTD | All rights reserved.