Operations and Project Management
VerifiedAdded on 2023/06/11
|20
|6077
|309
AI Summary
This article discusses operations and project management principles with a focus on Dyson, a well-known engineering and manufacturing company. Part 1 covers the introduction of the company, operation versus operations management, review and critique of executing operations management principles, analysis of the extent to which organizational operations management meets the requirements of the company, and continuous improvement as a philosophy. Part 2 includes a project portfolio with a summary of the case study, explanation of each stage of the PLC, analysis of project methodologies and tools used, and a critical evaluation of the effectiveness of PLC in application to the project. The article concludes with a continuous improvement plan that includes justified recommendations for improvement based on the review and critique associated with operations management principles of the company.
Contribute Materials
Your contribution can guide someone’s learning journey. Share your
documents today.
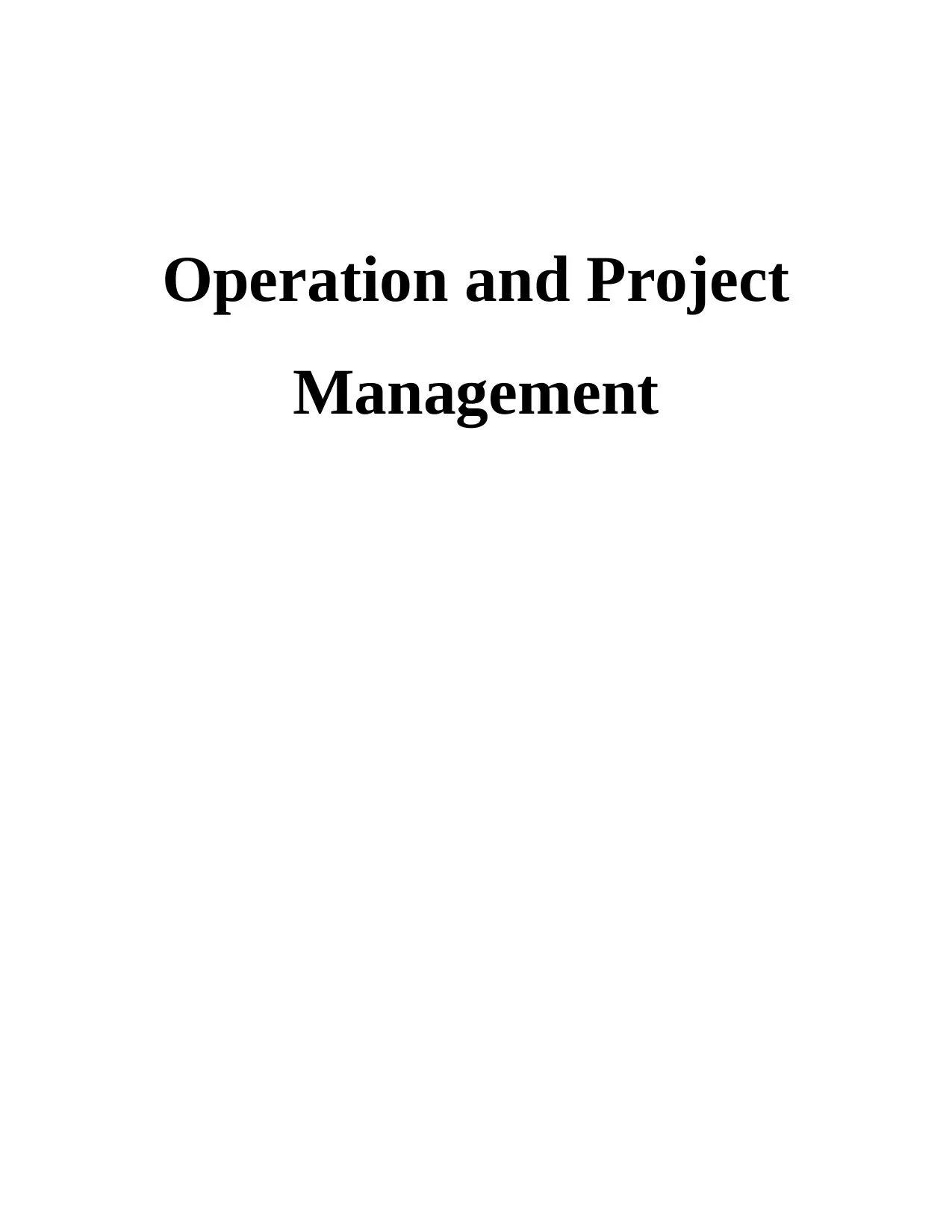
Operation and Project
Management
Management
Secure Best Marks with AI Grader
Need help grading? Try our AI Grader for instant feedback on your assignments.
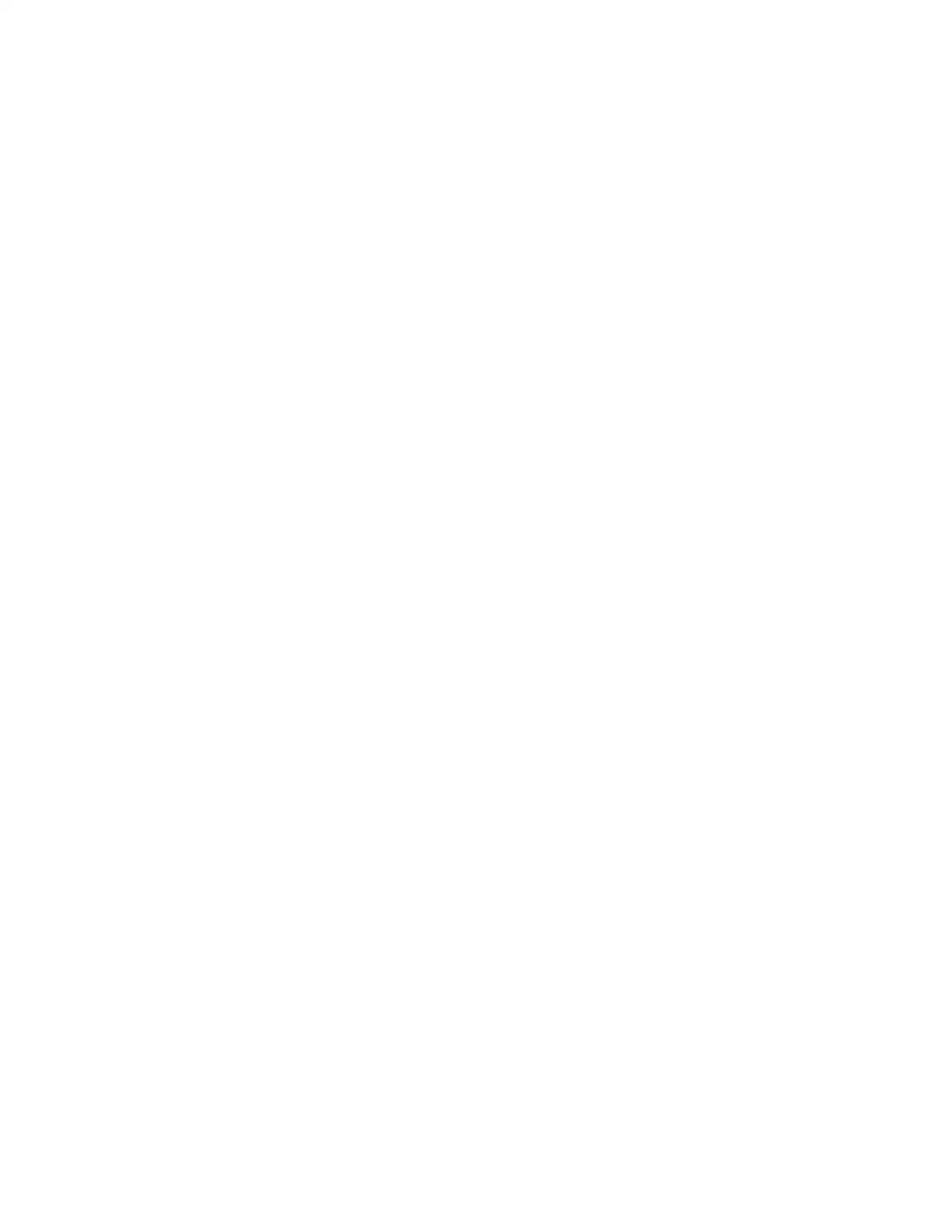
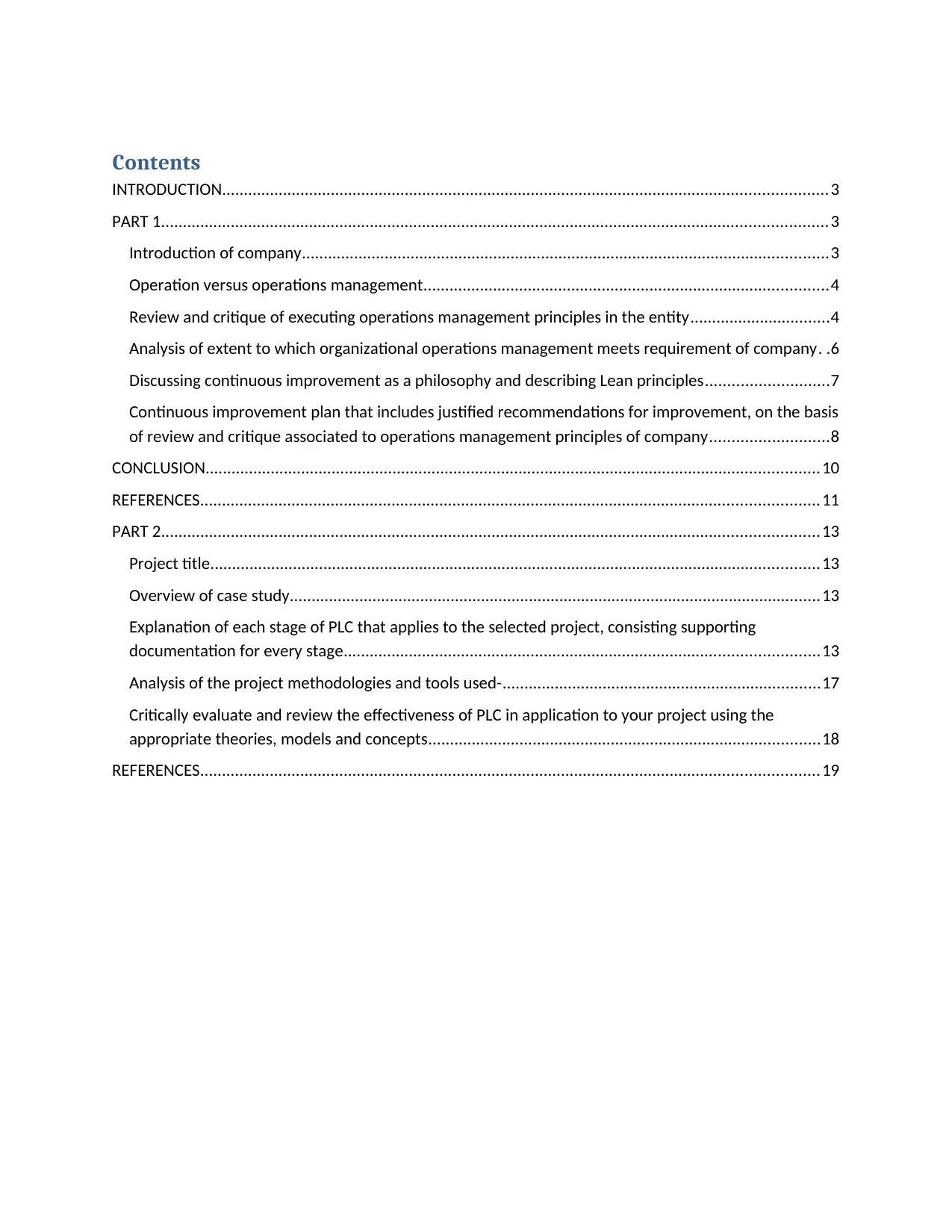
Contents
INTRODUCTION...........................................................................................................................................3
PART 1.........................................................................................................................................................3
Introduction of company.........................................................................................................................3
Operation versus operations management.............................................................................................4
Review and critique of executing operations management principles in the entity................................4
Analysis of extent to which organizational operations management meets requirement of company. .6
Discussing continuous improvement as a philosophy and describing Lean principles............................7
Continuous improvement plan that includes justified recommendations for improvement, on the basis
of review and critique associated to operations management principles of company...........................8
CONCLUSION.............................................................................................................................................10
REFERENCES..............................................................................................................................................11
PART 2.......................................................................................................................................................13
Project title............................................................................................................................................13
Overview of case study..........................................................................................................................13
Explanation of each stage of PLC that applies to the selected project, consisting supporting
documentation for every stage.............................................................................................................13
Analysis of the project methodologies and tools used-.........................................................................17
Critically evaluate and review the effectiveness of PLC in application to your project using the
appropriate theories, models and concepts..........................................................................................18
REFERENCES..............................................................................................................................................19
INTRODUCTION...........................................................................................................................................3
PART 1.........................................................................................................................................................3
Introduction of company.........................................................................................................................3
Operation versus operations management.............................................................................................4
Review and critique of executing operations management principles in the entity................................4
Analysis of extent to which organizational operations management meets requirement of company. .6
Discussing continuous improvement as a philosophy and describing Lean principles............................7
Continuous improvement plan that includes justified recommendations for improvement, on the basis
of review and critique associated to operations management principles of company...........................8
CONCLUSION.............................................................................................................................................10
REFERENCES..............................................................................................................................................11
PART 2.......................................................................................................................................................13
Project title............................................................................................................................................13
Overview of case study..........................................................................................................................13
Explanation of each stage of PLC that applies to the selected project, consisting supporting
documentation for every stage.............................................................................................................13
Analysis of the project methodologies and tools used-.........................................................................17
Critically evaluate and review the effectiveness of PLC in application to your project using the
appropriate theories, models and concepts..........................................................................................18
REFERENCES..............................................................................................................................................19
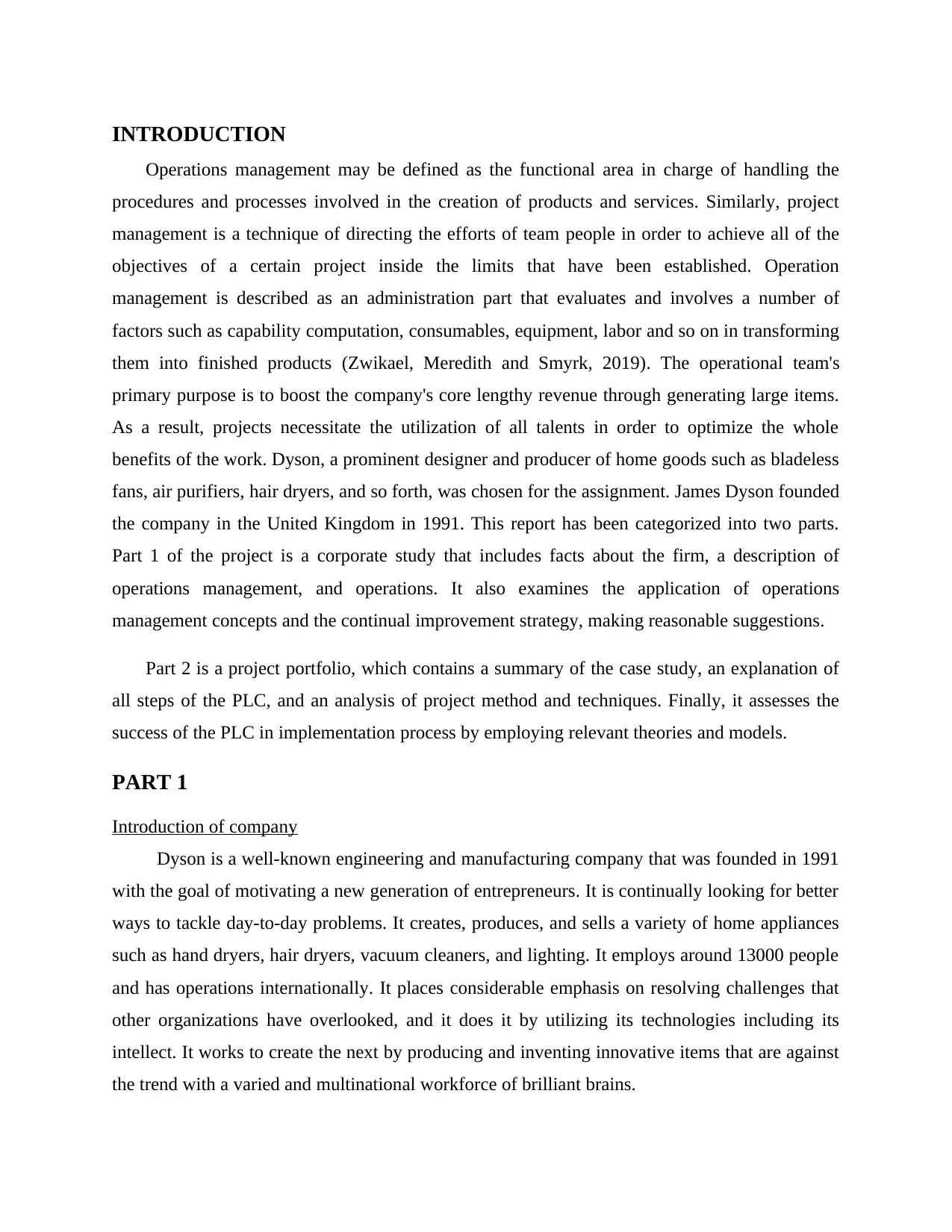
INTRODUCTION
Operations management may be defined as the functional area in charge of handling the
procedures and processes involved in the creation of products and services. Similarly, project
management is a technique of directing the efforts of team people in order to achieve all of the
objectives of a certain project inside the limits that have been established. Operation
management is described as an administration part that evaluates and involves a number of
factors such as capability computation, consumables, equipment, labor and so on in transforming
them into finished products (Zwikael, Meredith and Smyrk, 2019). The operational team's
primary purpose is to boost the company's core lengthy revenue through generating large items.
As a result, projects necessitate the utilization of all talents in order to optimize the whole
benefits of the work. Dyson, a prominent designer and producer of home goods such as bladeless
fans, air purifiers, hair dryers, and so forth, was chosen for the assignment. James Dyson founded
the company in the United Kingdom in 1991. This report has been categorized into two parts.
Part 1 of the project is a corporate study that includes facts about the firm, a description of
operations management, and operations. It also examines the application of operations
management concepts and the continual improvement strategy, making reasonable suggestions.
Part 2 is a project portfolio, which contains a summary of the case study, an explanation of
all steps of the PLC, and an analysis of project method and techniques. Finally, it assesses the
success of the PLC in implementation process by employing relevant theories and models.
PART 1
Introduction of company
Dyson is a well-known engineering and manufacturing company that was founded in 1991
with the goal of motivating a new generation of entrepreneurs. It is continually looking for better
ways to tackle day-to-day problems. It creates, produces, and sells a variety of home appliances
such as hand dryers, hair dryers, vacuum cleaners, and lighting. It employs around 13000 people
and has operations internationally. It places considerable emphasis on resolving challenges that
other organizations have overlooked, and it does it by utilizing its technologies including its
intellect. It works to create the next by producing and inventing innovative items that are against
the trend with a varied and multinational workforce of brilliant brains.
Operations management may be defined as the functional area in charge of handling the
procedures and processes involved in the creation of products and services. Similarly, project
management is a technique of directing the efforts of team people in order to achieve all of the
objectives of a certain project inside the limits that have been established. Operation
management is described as an administration part that evaluates and involves a number of
factors such as capability computation, consumables, equipment, labor and so on in transforming
them into finished products (Zwikael, Meredith and Smyrk, 2019). The operational team's
primary purpose is to boost the company's core lengthy revenue through generating large items.
As a result, projects necessitate the utilization of all talents in order to optimize the whole
benefits of the work. Dyson, a prominent designer and producer of home goods such as bladeless
fans, air purifiers, hair dryers, and so forth, was chosen for the assignment. James Dyson founded
the company in the United Kingdom in 1991. This report has been categorized into two parts.
Part 1 of the project is a corporate study that includes facts about the firm, a description of
operations management, and operations. It also examines the application of operations
management concepts and the continual improvement strategy, making reasonable suggestions.
Part 2 is a project portfolio, which contains a summary of the case study, an explanation of
all steps of the PLC, and an analysis of project method and techniques. Finally, it assesses the
success of the PLC in implementation process by employing relevant theories and models.
PART 1
Introduction of company
Dyson is a well-known engineering and manufacturing company that was founded in 1991
with the goal of motivating a new generation of entrepreneurs. It is continually looking for better
ways to tackle day-to-day problems. It creates, produces, and sells a variety of home appliances
such as hand dryers, hair dryers, vacuum cleaners, and lighting. It employs around 13000 people
and has operations internationally. It places considerable emphasis on resolving challenges that
other organizations have overlooked, and it does it by utilizing its technologies including its
intellect. It works to create the next by producing and inventing innovative items that are against
the trend with a varied and multinational workforce of brilliant brains.
Secure Best Marks with AI Grader
Need help grading? Try our AI Grader for instant feedback on your assignments.
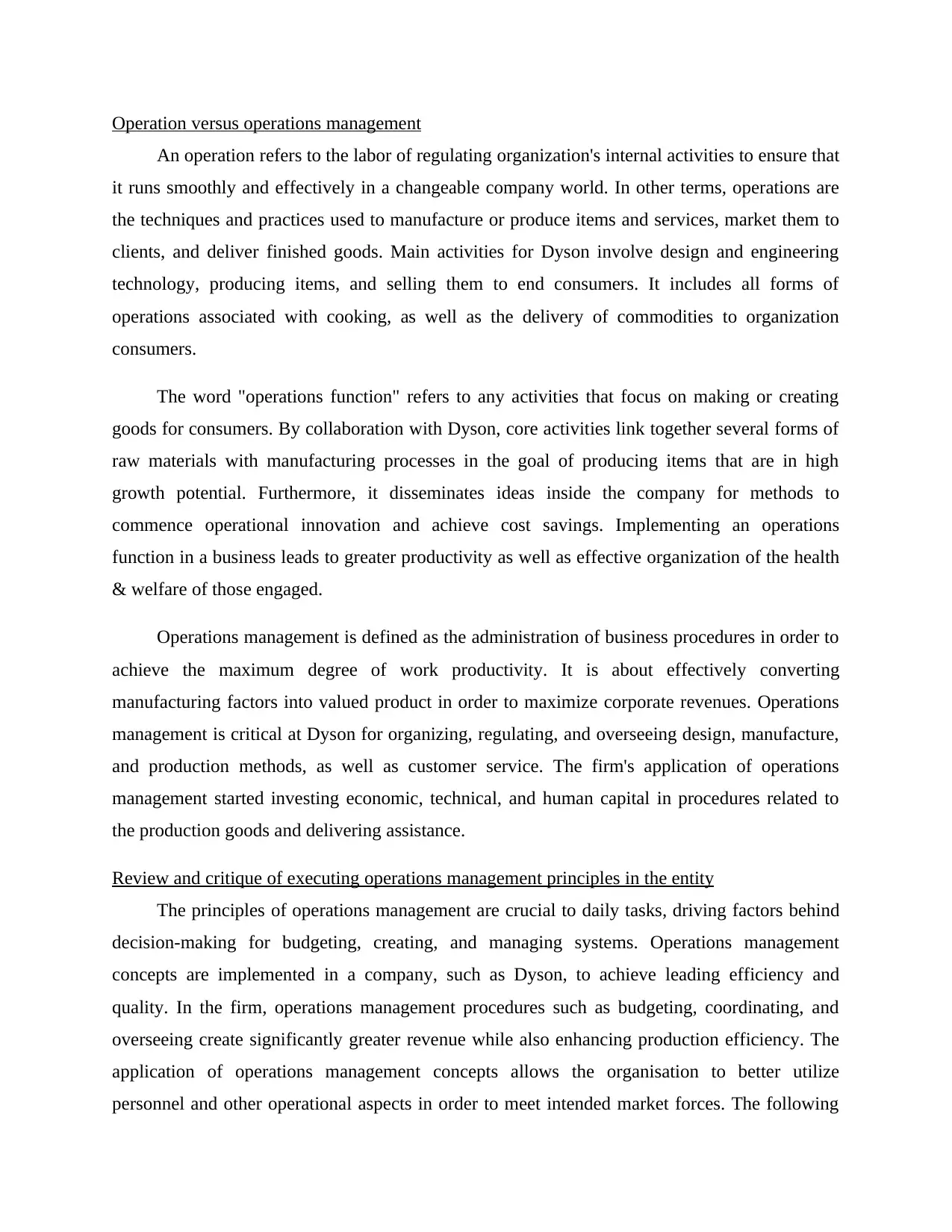
Operation versus operations management
An operation refers to the labor of regulating organization's internal activities to ensure that
it runs smoothly and effectively in a changeable company world. In other terms, operations are
the techniques and practices used to manufacture or produce items and services, market them to
clients, and deliver finished goods. Main activities for Dyson involve design and engineering
technology, producing items, and selling them to end consumers. It includes all forms of
operations associated with cooking, as well as the delivery of commodities to organization
consumers.
The word "operations function" refers to any activities that focus on making or creating
goods for consumers. By collaboration with Dyson, core activities link together several forms of
raw materials with manufacturing processes in the goal of producing items that are in high
growth potential. Furthermore, it disseminates ideas inside the company for methods to
commence operational innovation and achieve cost savings. Implementing an operations
function in a business leads to greater productivity as well as effective organization of the health
& welfare of those engaged.
Operations management is defined as the administration of business procedures in order to
achieve the maximum degree of work productivity. It is about effectively converting
manufacturing factors into valued product in order to maximize corporate revenues. Operations
management is critical at Dyson for organizing, regulating, and overseeing design, manufacture,
and production methods, as well as customer service. The firm's application of operations
management started investing economic, technical, and human capital in procedures related to
the production goods and delivering assistance.
Review and critique of executing operations management principles in the entity
The principles of operations management are crucial to daily tasks, driving factors behind
decision-making for budgeting, creating, and managing systems. Operations management
concepts are implemented in a company, such as Dyson, to achieve leading efficiency and
quality. In the firm, operations management procedures such as budgeting, coordinating, and
overseeing create significantly greater revenue while also enhancing production efficiency. The
application of operations management concepts allows the organisation to better utilize
personnel and other operational aspects in order to meet intended market forces. The following
An operation refers to the labor of regulating organization's internal activities to ensure that
it runs smoothly and effectively in a changeable company world. In other terms, operations are
the techniques and practices used to manufacture or produce items and services, market them to
clients, and deliver finished goods. Main activities for Dyson involve design and engineering
technology, producing items, and selling them to end consumers. It includes all forms of
operations associated with cooking, as well as the delivery of commodities to organization
consumers.
The word "operations function" refers to any activities that focus on making or creating
goods for consumers. By collaboration with Dyson, core activities link together several forms of
raw materials with manufacturing processes in the goal of producing items that are in high
growth potential. Furthermore, it disseminates ideas inside the company for methods to
commence operational innovation and achieve cost savings. Implementing an operations
function in a business leads to greater productivity as well as effective organization of the health
& welfare of those engaged.
Operations management is defined as the administration of business procedures in order to
achieve the maximum degree of work productivity. It is about effectively converting
manufacturing factors into valued product in order to maximize corporate revenues. Operations
management is critical at Dyson for organizing, regulating, and overseeing design, manufacture,
and production methods, as well as customer service. The firm's application of operations
management started investing economic, technical, and human capital in procedures related to
the production goods and delivering assistance.
Review and critique of executing operations management principles in the entity
The principles of operations management are crucial to daily tasks, driving factors behind
decision-making for budgeting, creating, and managing systems. Operations management
concepts are implemented in a company, such as Dyson, to achieve leading efficiency and
quality. In the firm, operations management procedures such as budgeting, coordinating, and
overseeing create significantly greater revenue while also enhancing production efficiency. The
application of operations management concepts allows the organisation to better utilize
personnel and other operational aspects in order to meet intended market forces. The following
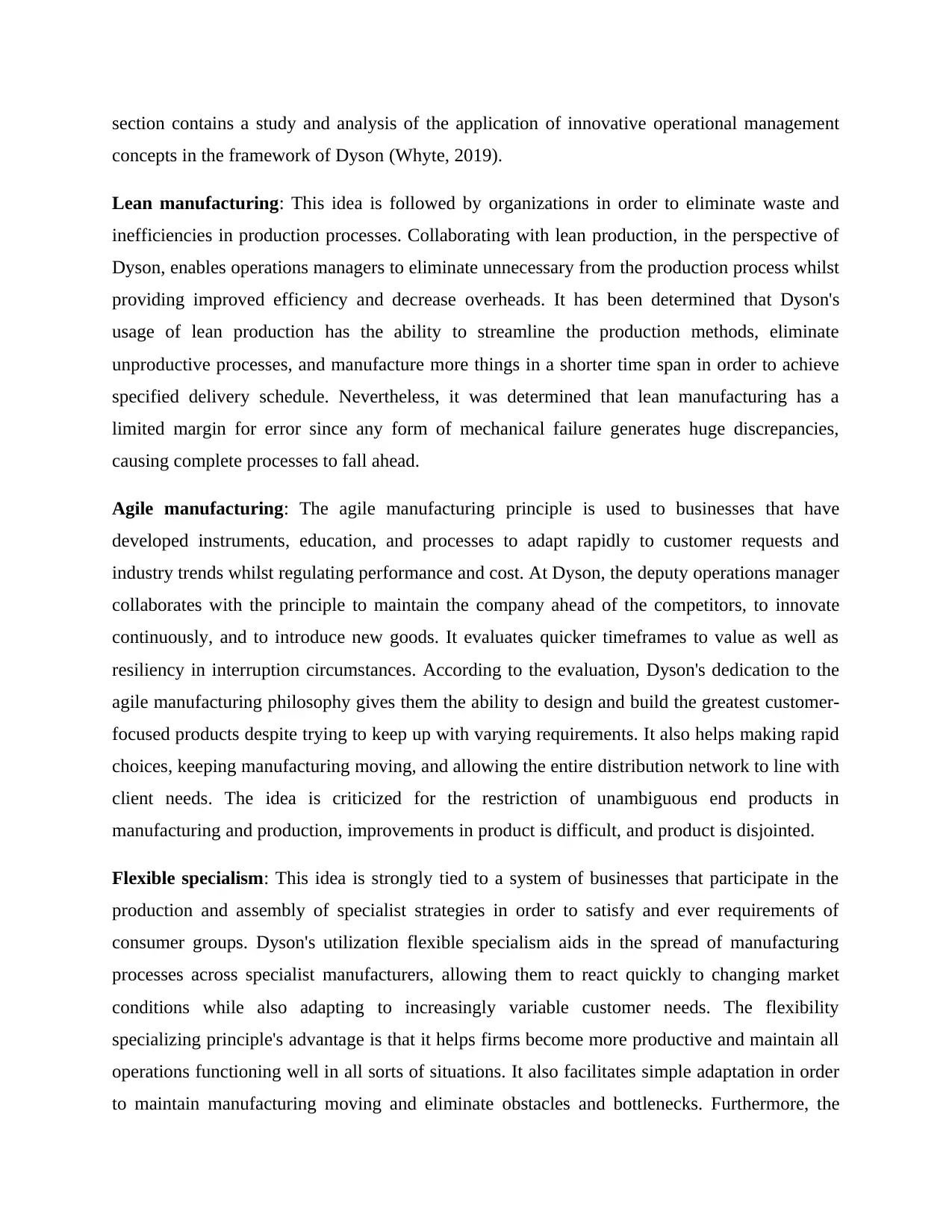
section contains a study and analysis of the application of innovative operational management
concepts in the framework of Dyson (Whyte, 2019).
Lean manufacturing: This idea is followed by organizations in order to eliminate waste and
inefficiencies in production processes. Collaborating with lean production, in the perspective of
Dyson, enables operations managers to eliminate unnecessary from the production process whilst
providing improved efficiency and decrease overheads. It has been determined that Dyson's
usage of lean production has the ability to streamline the production methods, eliminate
unproductive processes, and manufacture more things in a shorter time span in order to achieve
specified delivery schedule. Nevertheless, it was determined that lean manufacturing has a
limited margin for error since any form of mechanical failure generates huge discrepancies,
causing complete processes to fall ahead.
Agile manufacturing: The agile manufacturing principle is used to businesses that have
developed instruments, education, and processes to adapt rapidly to customer requests and
industry trends whilst regulating performance and cost. At Dyson, the deputy operations manager
collaborates with the principle to maintain the company ahead of the competitors, to innovate
continuously, and to introduce new goods. It evaluates quicker timeframes to value as well as
resiliency in interruption circumstances. According to the evaluation, Dyson's dedication to the
agile manufacturing philosophy gives them the ability to design and build the greatest customer-
focused products despite trying to keep up with varying requirements. It also helps making rapid
choices, keeping manufacturing moving, and allowing the entire distribution network to line with
client needs. The idea is criticized for the restriction of unambiguous end products in
manufacturing and production, improvements in product is difficult, and product is disjointed.
Flexible specialism: This idea is strongly tied to a system of businesses that participate in the
production and assembly of specialist strategies in order to satisfy and ever requirements of
consumer groups. Dyson's utilization flexible specialism aids in the spread of manufacturing
processes across specialist manufacturers, allowing them to react quickly to changing market
conditions while also adapting to increasingly variable customer needs. The flexibility
specializing principle's advantage is that it helps firms become more productive and maintain all
operations functioning well in all sorts of situations. It also facilitates simple adaptation in order
to maintain manufacturing moving and eliminate obstacles and bottlenecks. Furthermore, the
concepts in the framework of Dyson (Whyte, 2019).
Lean manufacturing: This idea is followed by organizations in order to eliminate waste and
inefficiencies in production processes. Collaborating with lean production, in the perspective of
Dyson, enables operations managers to eliminate unnecessary from the production process whilst
providing improved efficiency and decrease overheads. It has been determined that Dyson's
usage of lean production has the ability to streamline the production methods, eliminate
unproductive processes, and manufacture more things in a shorter time span in order to achieve
specified delivery schedule. Nevertheless, it was determined that lean manufacturing has a
limited margin for error since any form of mechanical failure generates huge discrepancies,
causing complete processes to fall ahead.
Agile manufacturing: The agile manufacturing principle is used to businesses that have
developed instruments, education, and processes to adapt rapidly to customer requests and
industry trends whilst regulating performance and cost. At Dyson, the deputy operations manager
collaborates with the principle to maintain the company ahead of the competitors, to innovate
continuously, and to introduce new goods. It evaluates quicker timeframes to value as well as
resiliency in interruption circumstances. According to the evaluation, Dyson's dedication to the
agile manufacturing philosophy gives them the ability to design and build the greatest customer-
focused products despite trying to keep up with varying requirements. It also helps making rapid
choices, keeping manufacturing moving, and allowing the entire distribution network to line with
client needs. The idea is criticized for the restriction of unambiguous end products in
manufacturing and production, improvements in product is difficult, and product is disjointed.
Flexible specialism: This idea is strongly tied to a system of businesses that participate in the
production and assembly of specialist strategies in order to satisfy and ever requirements of
consumer groups. Dyson's utilization flexible specialism aids in the spread of manufacturing
processes across specialist manufacturers, allowing them to react quickly to changing market
conditions while also adapting to increasingly variable customer needs. The flexibility
specializing principle's advantage is that it helps firms become more productive and maintain all
operations functioning well in all sorts of situations. It also facilitates simple adaptation in order
to maintain manufacturing moving and eliminate obstacles and bottlenecks. Furthermore, the
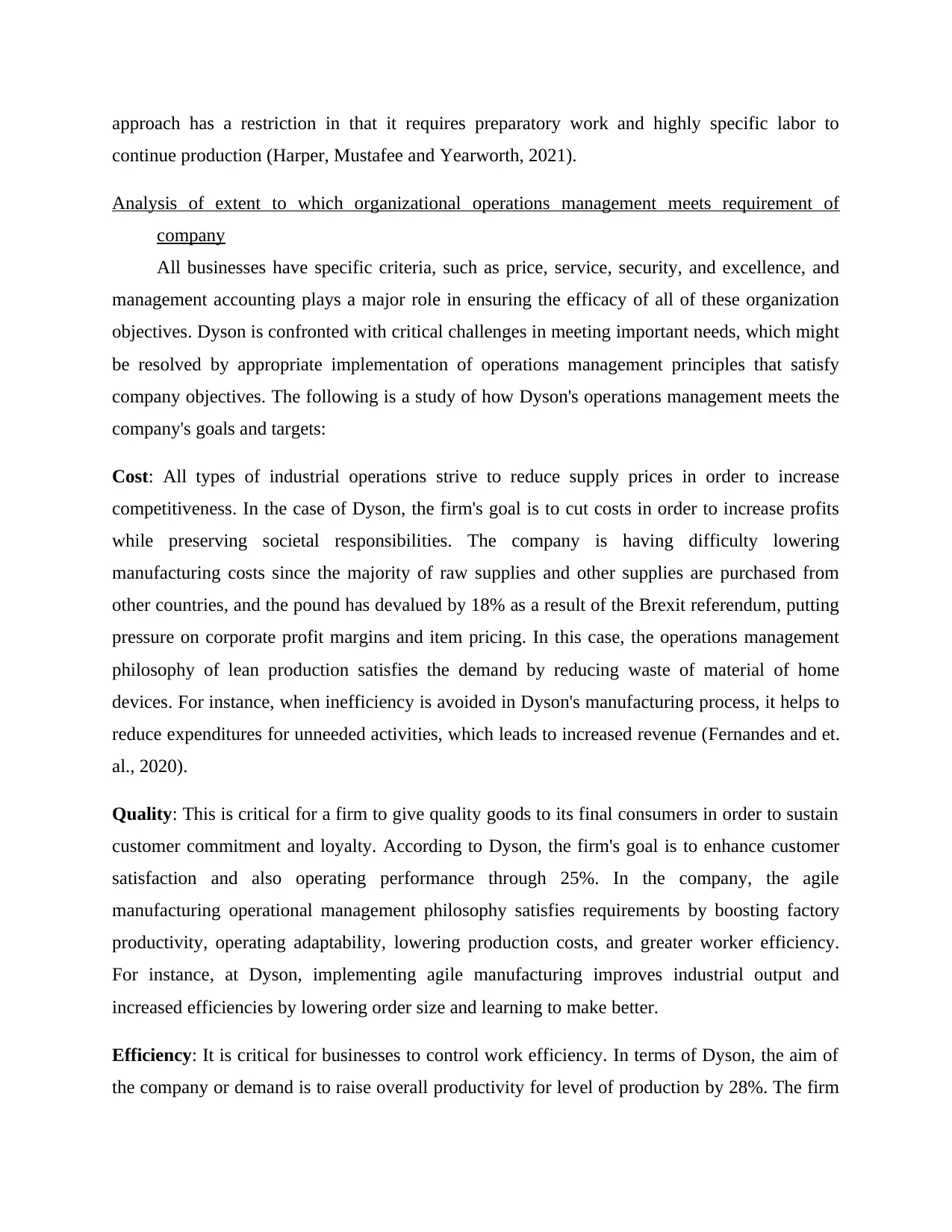
approach has a restriction in that it requires preparatory work and highly specific labor to
continue production (Harper, Mustafee and Yearworth, 2021).
Analysis of extent to which organizational operations management meets requirement of
company
All businesses have specific criteria, such as price, service, security, and excellence, and
management accounting plays a major role in ensuring the efficacy of all of these organization
objectives. Dyson is confronted with critical challenges in meeting important needs, which might
be resolved by appropriate implementation of operations management principles that satisfy
company objectives. The following is a study of how Dyson's operations management meets the
company's goals and targets:
Cost: All types of industrial operations strive to reduce supply prices in order to increase
competitiveness. In the case of Dyson, the firm's goal is to cut costs in order to increase profits
while preserving societal responsibilities. The company is having difficulty lowering
manufacturing costs since the majority of raw supplies and other supplies are purchased from
other countries, and the pound has devalued by 18% as a result of the Brexit referendum, putting
pressure on corporate profit margins and item pricing. In this case, the operations management
philosophy of lean production satisfies the demand by reducing waste of material of home
devices. For instance, when inefficiency is avoided in Dyson's manufacturing process, it helps to
reduce expenditures for unneeded activities, which leads to increased revenue (Fernandes and et.
al., 2020).
Quality: This is critical for a firm to give quality goods to its final consumers in order to sustain
customer commitment and loyalty. According to Dyson, the firm's goal is to enhance customer
satisfaction and also operating performance through 25%. In the company, the agile
manufacturing operational management philosophy satisfies requirements by boosting factory
productivity, operating adaptability, lowering production costs, and greater worker efficiency.
For instance, at Dyson, implementing agile manufacturing improves industrial output and
increased efficiencies by lowering order size and learning to make better.
Efficiency: It is critical for businesses to control work efficiency. In terms of Dyson, the aim of
the company or demand is to raise overall productivity for level of production by 28%. The firm
continue production (Harper, Mustafee and Yearworth, 2021).
Analysis of extent to which organizational operations management meets requirement of
company
All businesses have specific criteria, such as price, service, security, and excellence, and
management accounting plays a major role in ensuring the efficacy of all of these organization
objectives. Dyson is confronted with critical challenges in meeting important needs, which might
be resolved by appropriate implementation of operations management principles that satisfy
company objectives. The following is a study of how Dyson's operations management meets the
company's goals and targets:
Cost: All types of industrial operations strive to reduce supply prices in order to increase
competitiveness. In the case of Dyson, the firm's goal is to cut costs in order to increase profits
while preserving societal responsibilities. The company is having difficulty lowering
manufacturing costs since the majority of raw supplies and other supplies are purchased from
other countries, and the pound has devalued by 18% as a result of the Brexit referendum, putting
pressure on corporate profit margins and item pricing. In this case, the operations management
philosophy of lean production satisfies the demand by reducing waste of material of home
devices. For instance, when inefficiency is avoided in Dyson's manufacturing process, it helps to
reduce expenditures for unneeded activities, which leads to increased revenue (Fernandes and et.
al., 2020).
Quality: This is critical for a firm to give quality goods to its final consumers in order to sustain
customer commitment and loyalty. According to Dyson, the firm's goal is to enhance customer
satisfaction and also operating performance through 25%. In the company, the agile
manufacturing operational management philosophy satisfies requirements by boosting factory
productivity, operating adaptability, lowering production costs, and greater worker efficiency.
For instance, at Dyson, implementing agile manufacturing improves industrial output and
increased efficiencies by lowering order size and learning to make better.
Efficiency: It is critical for businesses to control work efficiency. In terms of Dyson, the aim of
the company or demand is to raise overall productivity for level of production by 28%. The firm
Paraphrase This Document
Need a fresh take? Get an instant paraphrase of this document with our AI Paraphraser
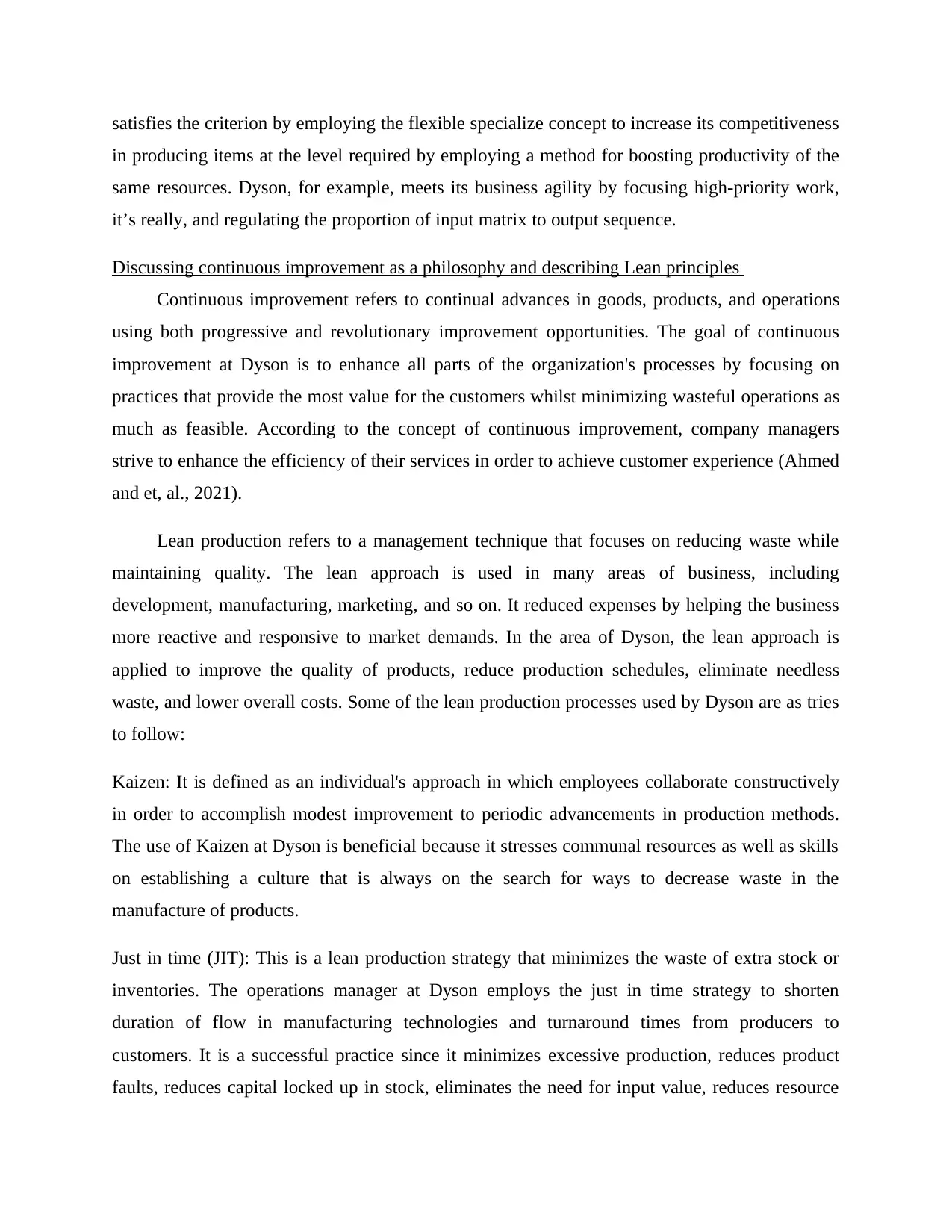
satisfies the criterion by employing the flexible specialize concept to increase its competitiveness
in producing items at the level required by employing a method for boosting productivity of the
same resources. Dyson, for example, meets its business agility by focusing high-priority work,
it’s really, and regulating the proportion of input matrix to output sequence.
Discussing continuous improvement as a philosophy and describing Lean principles
Continuous improvement refers to continual advances in goods, products, and operations
using both progressive and revolutionary improvement opportunities. The goal of continuous
improvement at Dyson is to enhance all parts of the organization's processes by focusing on
practices that provide the most value for the customers whilst minimizing wasteful operations as
much as feasible. According to the concept of continuous improvement, company managers
strive to enhance the efficiency of their services in order to achieve customer experience (Ahmed
and et, al., 2021).
Lean production refers to a management technique that focuses on reducing waste while
maintaining quality. The lean approach is used in many areas of business, including
development, manufacturing, marketing, and so on. It reduced expenses by helping the business
more reactive and responsive to market demands. In the area of Dyson, the lean approach is
applied to improve the quality of products, reduce production schedules, eliminate needless
waste, and lower overall costs. Some of the lean production processes used by Dyson are as tries
to follow:
Kaizen: It is defined as an individual's approach in which employees collaborate constructively
in order to accomplish modest improvement to periodic advancements in production methods.
The use of Kaizen at Dyson is beneficial because it stresses communal resources as well as skills
on establishing a culture that is always on the search for ways to decrease waste in the
manufacture of products.
Just in time (JIT): This is a lean production strategy that minimizes the waste of extra stock or
inventories. The operations manager at Dyson employs the just in time strategy to shorten
duration of flow in manufacturing technologies and turnaround times from producers to
customers. It is a successful practice since it minimizes excessive production, reduces product
faults, reduces capital locked up in stock, eliminates the need for input value, reduces resource
in producing items at the level required by employing a method for boosting productivity of the
same resources. Dyson, for example, meets its business agility by focusing high-priority work,
it’s really, and regulating the proportion of input matrix to output sequence.
Discussing continuous improvement as a philosophy and describing Lean principles
Continuous improvement refers to continual advances in goods, products, and operations
using both progressive and revolutionary improvement opportunities. The goal of continuous
improvement at Dyson is to enhance all parts of the organization's processes by focusing on
practices that provide the most value for the customers whilst minimizing wasteful operations as
much as feasible. According to the concept of continuous improvement, company managers
strive to enhance the efficiency of their services in order to achieve customer experience (Ahmed
and et, al., 2021).
Lean production refers to a management technique that focuses on reducing waste while
maintaining quality. The lean approach is used in many areas of business, including
development, manufacturing, marketing, and so on. It reduced expenses by helping the business
more reactive and responsive to market demands. In the area of Dyson, the lean approach is
applied to improve the quality of products, reduce production schedules, eliminate needless
waste, and lower overall costs. Some of the lean production processes used by Dyson are as tries
to follow:
Kaizen: It is defined as an individual's approach in which employees collaborate constructively
in order to accomplish modest improvement to periodic advancements in production methods.
The use of Kaizen at Dyson is beneficial because it stresses communal resources as well as skills
on establishing a culture that is always on the search for ways to decrease waste in the
manufacture of products.
Just in time (JIT): This is a lean production strategy that minimizes the waste of extra stock or
inventories. The operations manager at Dyson employs the just in time strategy to shorten
duration of flow in manufacturing technologies and turnaround times from producers to
customers. It is a successful practice since it minimizes excessive production, reduces product
faults, reduces capital locked up in stock, eliminates the need for input value, reduces resource
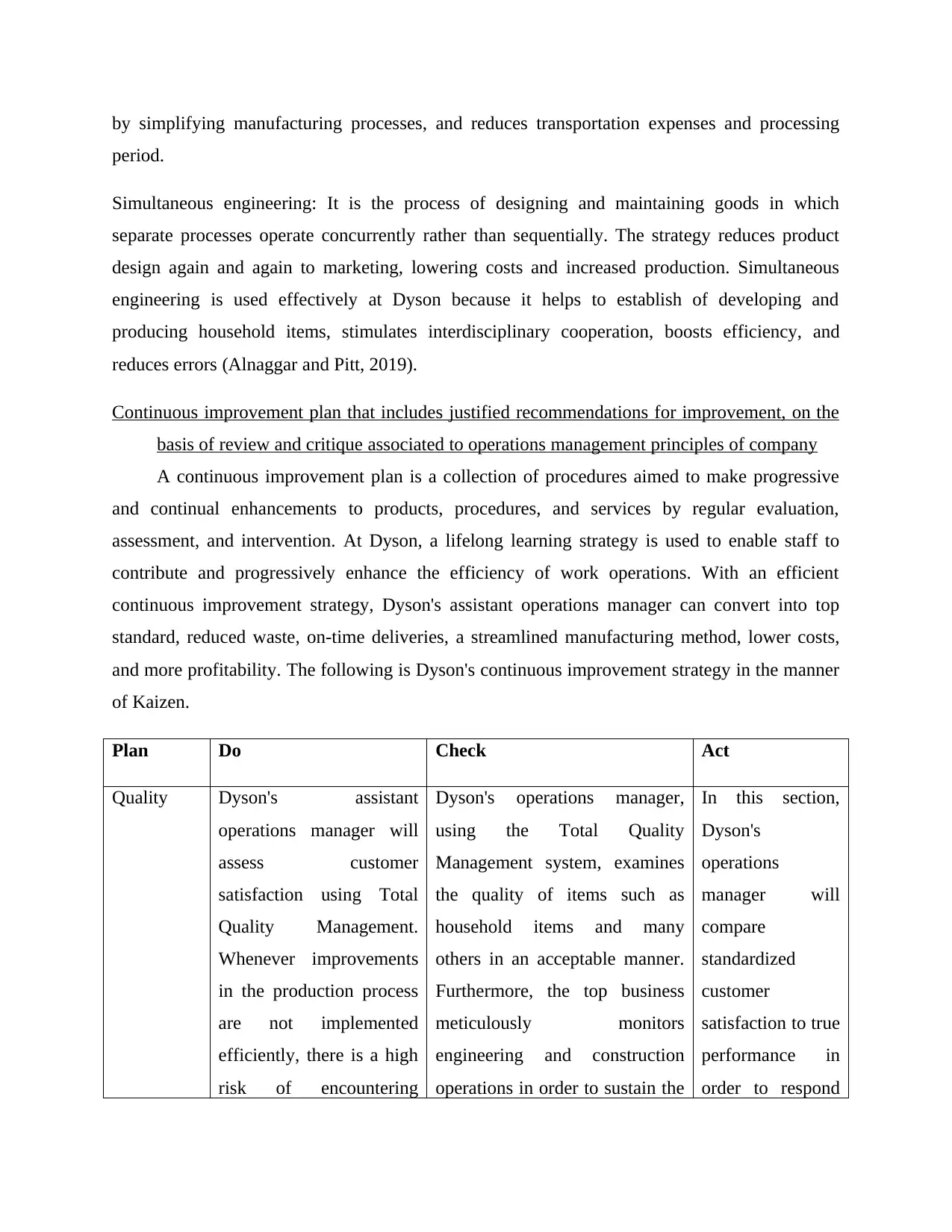
by simplifying manufacturing processes, and reduces transportation expenses and processing
period.
Simultaneous engineering: It is the process of designing and maintaining goods in which
separate processes operate concurrently rather than sequentially. The strategy reduces product
design again and again to marketing, lowering costs and increased production. Simultaneous
engineering is used effectively at Dyson because it helps to establish of developing and
producing household items, stimulates interdisciplinary cooperation, boosts efficiency, and
reduces errors (Alnaggar and Pitt, 2019).
Continuous improvement plan that includes justified recommendations for improvement, on the
basis of review and critique associated to operations management principles of company
A continuous improvement plan is a collection of procedures aimed to make progressive
and continual enhancements to products, procedures, and services by regular evaluation,
assessment, and intervention. At Dyson, a lifelong learning strategy is used to enable staff to
contribute and progressively enhance the efficiency of work operations. With an efficient
continuous improvement strategy, Dyson's assistant operations manager can convert into top
standard, reduced waste, on-time deliveries, a streamlined manufacturing method, lower costs,
and more profitability. The following is Dyson's continuous improvement strategy in the manner
of Kaizen.
Plan Do Check Act
Quality Dyson's assistant
operations manager will
assess customer
satisfaction using Total
Quality Management.
Whenever improvements
in the production process
are not implemented
efficiently, there is a high
risk of encountering
Dyson's operations manager,
using the Total Quality
Management system, examines
the quality of items such as
household items and many
others in an acceptable manner.
Furthermore, the top business
meticulously monitors
engineering and construction
operations in order to sustain the
In this section,
Dyson's
operations
manager will
compare
standardized
customer
satisfaction to true
performance in
order to respond
period.
Simultaneous engineering: It is the process of designing and maintaining goods in which
separate processes operate concurrently rather than sequentially. The strategy reduces product
design again and again to marketing, lowering costs and increased production. Simultaneous
engineering is used effectively at Dyson because it helps to establish of developing and
producing household items, stimulates interdisciplinary cooperation, boosts efficiency, and
reduces errors (Alnaggar and Pitt, 2019).
Continuous improvement plan that includes justified recommendations for improvement, on the
basis of review and critique associated to operations management principles of company
A continuous improvement plan is a collection of procedures aimed to make progressive
and continual enhancements to products, procedures, and services by regular evaluation,
assessment, and intervention. At Dyson, a lifelong learning strategy is used to enable staff to
contribute and progressively enhance the efficiency of work operations. With an efficient
continuous improvement strategy, Dyson's assistant operations manager can convert into top
standard, reduced waste, on-time deliveries, a streamlined manufacturing method, lower costs,
and more profitability. The following is Dyson's continuous improvement strategy in the manner
of Kaizen.
Plan Do Check Act
Quality Dyson's assistant
operations manager will
assess customer
satisfaction using Total
Quality Management.
Whenever improvements
in the production process
are not implemented
efficiently, there is a high
risk of encountering
Dyson's operations manager,
using the Total Quality
Management system, examines
the quality of items such as
household items and many
others in an acceptable manner.
Furthermore, the top business
meticulously monitors
engineering and construction
operations in order to sustain the
In this section,
Dyson's
operations
manager will
compare
standardized
customer
satisfaction to true
performance in
order to respond
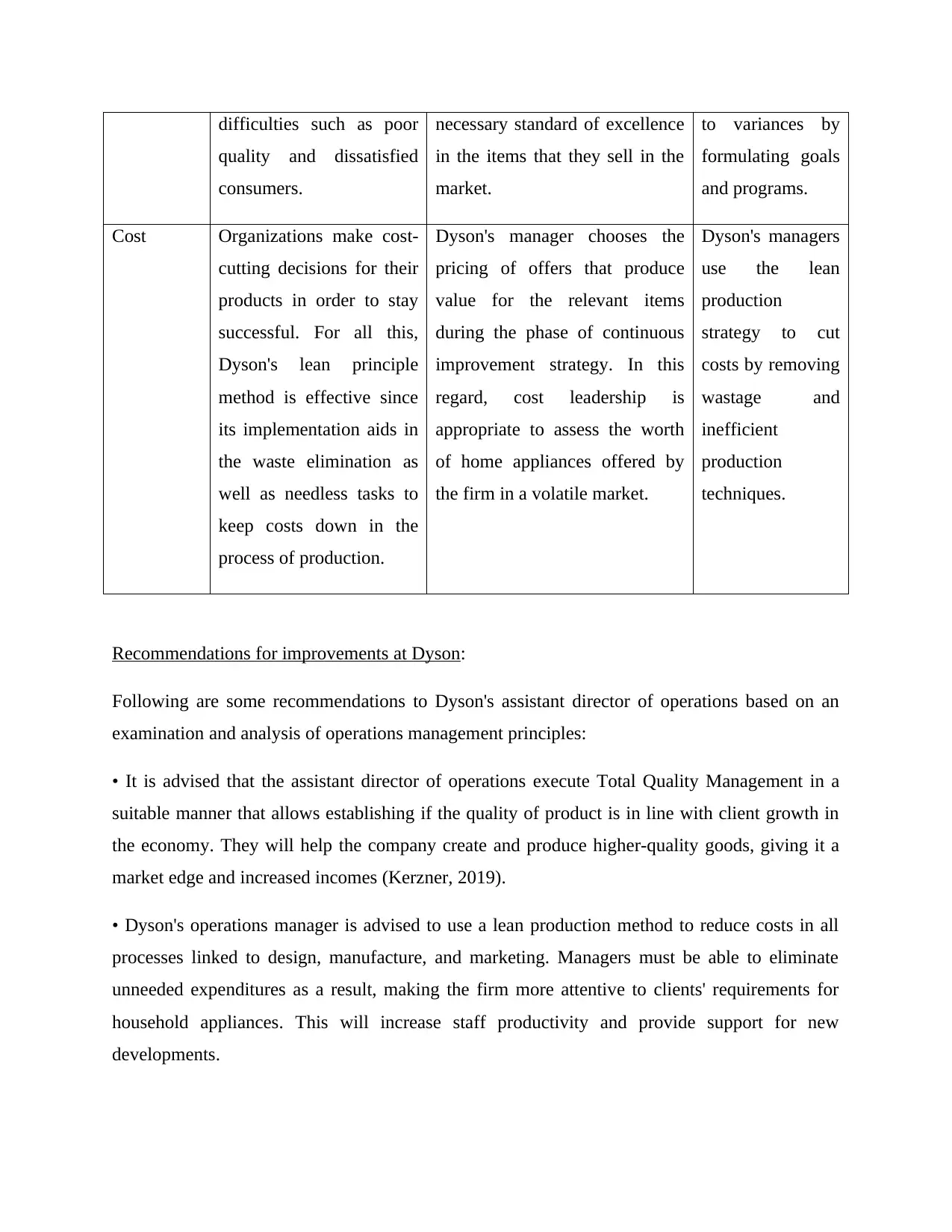
difficulties such as poor
quality and dissatisfied
consumers.
necessary standard of excellence
in the items that they sell in the
market.
to variances by
formulating goals
and programs.
Cost Organizations make cost-
cutting decisions for their
products in order to stay
successful. For all this,
Dyson's lean principle
method is effective since
its implementation aids in
the waste elimination as
well as needless tasks to
keep costs down in the
process of production.
Dyson's manager chooses the
pricing of offers that produce
value for the relevant items
during the phase of continuous
improvement strategy. In this
regard, cost leadership is
appropriate to assess the worth
of home appliances offered by
the firm in a volatile market.
Dyson's managers
use the lean
production
strategy to cut
costs by removing
wastage and
inefficient
production
techniques.
Recommendations for improvements at Dyson:
Following are some recommendations to Dyson's assistant director of operations based on an
examination and analysis of operations management principles:
• It is advised that the assistant director of operations execute Total Quality Management in a
suitable manner that allows establishing if the quality of product is in line with client growth in
the economy. They will help the company create and produce higher-quality goods, giving it a
market edge and increased incomes (Kerzner, 2019).
• Dyson's operations manager is advised to use a lean production method to reduce costs in all
processes linked to design, manufacture, and marketing. Managers must be able to eliminate
unneeded expenditures as a result, making the firm more attentive to clients' requirements for
household appliances. This will increase staff productivity and provide support for new
developments.
quality and dissatisfied
consumers.
necessary standard of excellence
in the items that they sell in the
market.
to variances by
formulating goals
and programs.
Cost Organizations make cost-
cutting decisions for their
products in order to stay
successful. For all this,
Dyson's lean principle
method is effective since
its implementation aids in
the waste elimination as
well as needless tasks to
keep costs down in the
process of production.
Dyson's manager chooses the
pricing of offers that produce
value for the relevant items
during the phase of continuous
improvement strategy. In this
regard, cost leadership is
appropriate to assess the worth
of home appliances offered by
the firm in a volatile market.
Dyson's managers
use the lean
production
strategy to cut
costs by removing
wastage and
inefficient
production
techniques.
Recommendations for improvements at Dyson:
Following are some recommendations to Dyson's assistant director of operations based on an
examination and analysis of operations management principles:
• It is advised that the assistant director of operations execute Total Quality Management in a
suitable manner that allows establishing if the quality of product is in line with client growth in
the economy. They will help the company create and produce higher-quality goods, giving it a
market edge and increased incomes (Kerzner, 2019).
• Dyson's operations manager is advised to use a lean production method to reduce costs in all
processes linked to design, manufacture, and marketing. Managers must be able to eliminate
unneeded expenditures as a result, making the firm more attentive to clients' requirements for
household appliances. This will increase staff productivity and provide support for new
developments.
Secure Best Marks with AI Grader
Need help grading? Try our AI Grader for instant feedback on your assignments.
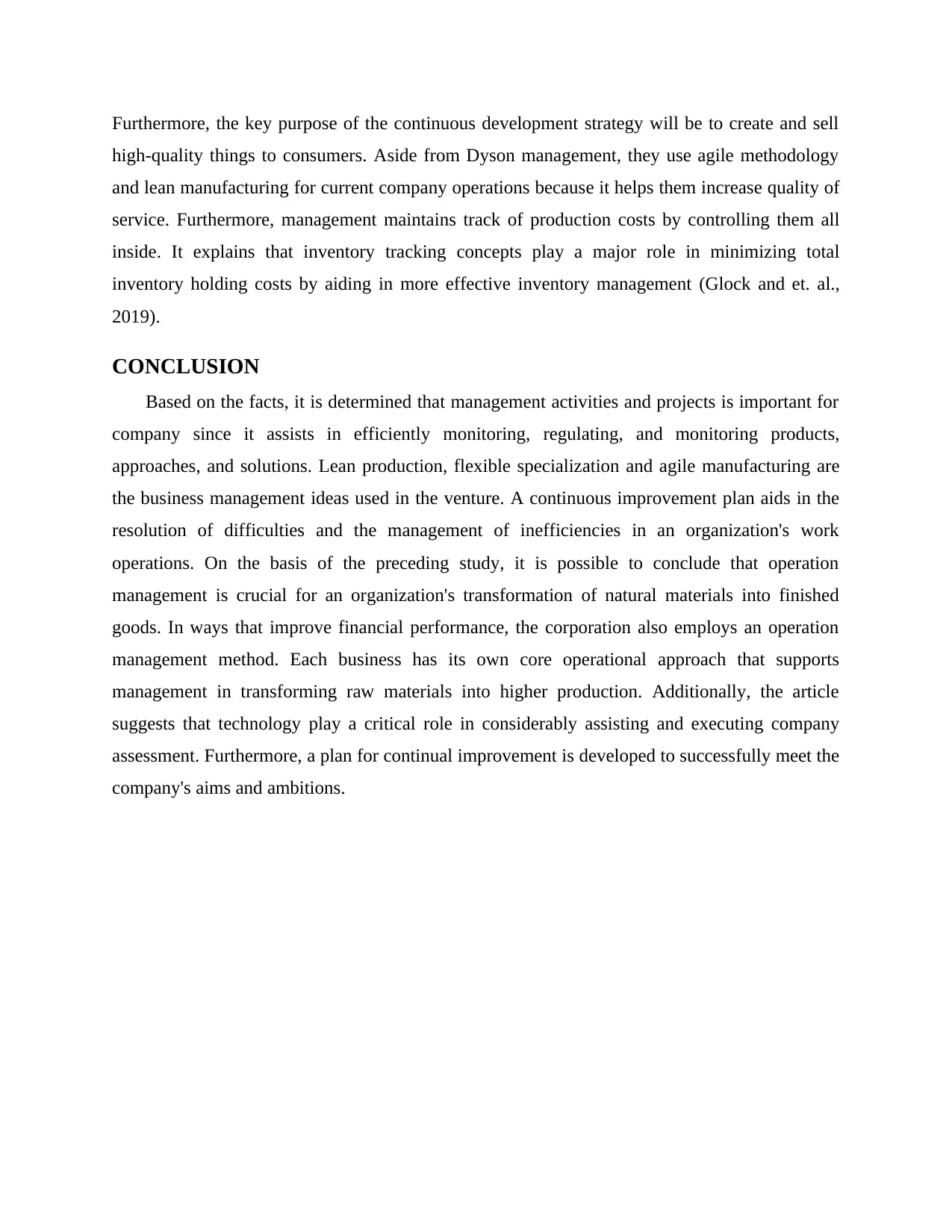
Furthermore, the key purpose of the continuous development strategy will be to create and sell
high-quality things to consumers. Aside from Dyson management, they use agile methodology
and lean manufacturing for current company operations because it helps them increase quality of
service. Furthermore, management maintains track of production costs by controlling them all
inside. It explains that inventory tracking concepts play a major role in minimizing total
inventory holding costs by aiding in more effective inventory management (Glock and et. al.,
2019).
CONCLUSION
Based on the facts, it is determined that management activities and projects is important for
company since it assists in efficiently monitoring, regulating, and monitoring products,
approaches, and solutions. Lean production, flexible specialization and agile manufacturing are
the business management ideas used in the venture. A continuous improvement plan aids in the
resolution of difficulties and the management of inefficiencies in an organization's work
operations. On the basis of the preceding study, it is possible to conclude that operation
management is crucial for an organization's transformation of natural materials into finished
goods. In ways that improve financial performance, the corporation also employs an operation
management method. Each business has its own core operational approach that supports
management in transforming raw materials into higher production. Additionally, the article
suggests that technology play a critical role in considerably assisting and executing company
assessment. Furthermore, a plan for continual improvement is developed to successfully meet the
company's aims and ambitions.
high-quality things to consumers. Aside from Dyson management, they use agile methodology
and lean manufacturing for current company operations because it helps them increase quality of
service. Furthermore, management maintains track of production costs by controlling them all
inside. It explains that inventory tracking concepts play a major role in minimizing total
inventory holding costs by aiding in more effective inventory management (Glock and et. al.,
2019).
CONCLUSION
Based on the facts, it is determined that management activities and projects is important for
company since it assists in efficiently monitoring, regulating, and monitoring products,
approaches, and solutions. Lean production, flexible specialization and agile manufacturing are
the business management ideas used in the venture. A continuous improvement plan aids in the
resolution of difficulties and the management of inefficiencies in an organization's work
operations. On the basis of the preceding study, it is possible to conclude that operation
management is crucial for an organization's transformation of natural materials into finished
goods. In ways that improve financial performance, the corporation also employs an operation
management method. Each business has its own core operational approach that supports
management in transforming raw materials into higher production. Additionally, the article
suggests that technology play a critical role in considerably assisting and executing company
assessment. Furthermore, a plan for continual improvement is developed to successfully meet the
company's aims and ambitions.
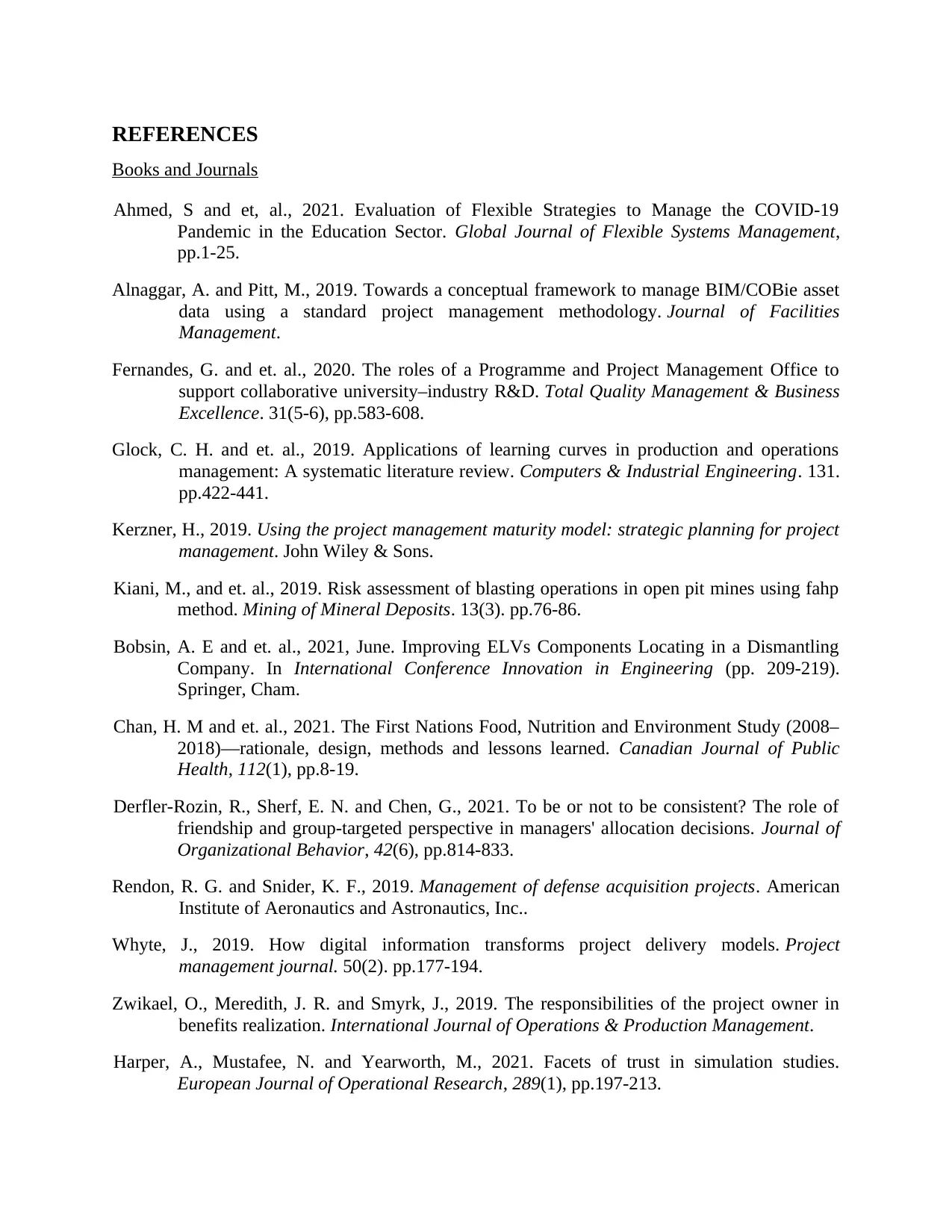
REFERENCES
Books and Journals
Ahmed, S and et, al., 2021. Evaluation of Flexible Strategies to Manage the COVID-19
Pandemic in the Education Sector. Global Journal of Flexible Systems Management,
pp.1-25.
Alnaggar, A. and Pitt, M., 2019. Towards a conceptual framework to manage BIM/COBie asset
data using a standard project management methodology. Journal of Facilities
Management.
Fernandes, G. and et. al., 2020. The roles of a Programme and Project Management Office to
support collaborative university–industry R&D. Total Quality Management & Business
Excellence. 31(5-6), pp.583-608.
Glock, C. H. and et. al., 2019. Applications of learning curves in production and operations
management: A systematic literature review. Computers & Industrial Engineering. 131.
pp.422-441.
Kerzner, H., 2019. Using the project management maturity model: strategic planning for project
management. John Wiley & Sons.
Kiani, M., and et. al., 2019. Risk assessment of blasting operations in open pit mines using fahp
method. Mining of Mineral Deposits. 13(3). pp.76-86.
Bobsin, A. E and et. al., 2021, June. Improving ELVs Components Locating in a Dismantling
Company. In International Conference Innovation in Engineering (pp. 209-219).
Springer, Cham.
Chan, H. M and et. al., 2021. The First Nations Food, Nutrition and Environment Study (2008–
2018)—rationale, design, methods and lessons learned. Canadian Journal of Public
Health, 112(1), pp.8-19.
Derfler-Rozin, R., Sherf, E. N. and Chen, G., 2021. To be or not to be consistent? The role of
friendship and group-targeted perspective in managers' allocation decisions. Journal of
Organizational Behavior, 42(6), pp.814-833.
Rendon, R. G. and Snider, K. F., 2019. Management of defense acquisition projects. American
Institute of Aeronautics and Astronautics, Inc..
Whyte, J., 2019. How digital information transforms project delivery models. Project
management journal. 50(2). pp.177-194.
Zwikael, O., Meredith, J. R. and Smyrk, J., 2019. The responsibilities of the project owner in
benefits realization. International Journal of Operations & Production Management.
Harper, A., Mustafee, N. and Yearworth, M., 2021. Facets of trust in simulation studies.
European Journal of Operational Research, 289(1), pp.197-213.
Books and Journals
Ahmed, S and et, al., 2021. Evaluation of Flexible Strategies to Manage the COVID-19
Pandemic in the Education Sector. Global Journal of Flexible Systems Management,
pp.1-25.
Alnaggar, A. and Pitt, M., 2019. Towards a conceptual framework to manage BIM/COBie asset
data using a standard project management methodology. Journal of Facilities
Management.
Fernandes, G. and et. al., 2020. The roles of a Programme and Project Management Office to
support collaborative university–industry R&D. Total Quality Management & Business
Excellence. 31(5-6), pp.583-608.
Glock, C. H. and et. al., 2019. Applications of learning curves in production and operations
management: A systematic literature review. Computers & Industrial Engineering. 131.
pp.422-441.
Kerzner, H., 2019. Using the project management maturity model: strategic planning for project
management. John Wiley & Sons.
Kiani, M., and et. al., 2019. Risk assessment of blasting operations in open pit mines using fahp
method. Mining of Mineral Deposits. 13(3). pp.76-86.
Bobsin, A. E and et. al., 2021, June. Improving ELVs Components Locating in a Dismantling
Company. In International Conference Innovation in Engineering (pp. 209-219).
Springer, Cham.
Chan, H. M and et. al., 2021. The First Nations Food, Nutrition and Environment Study (2008–
2018)—rationale, design, methods and lessons learned. Canadian Journal of Public
Health, 112(1), pp.8-19.
Derfler-Rozin, R., Sherf, E. N. and Chen, G., 2021. To be or not to be consistent? The role of
friendship and group-targeted perspective in managers' allocation decisions. Journal of
Organizational Behavior, 42(6), pp.814-833.
Rendon, R. G. and Snider, K. F., 2019. Management of defense acquisition projects. American
Institute of Aeronautics and Astronautics, Inc..
Whyte, J., 2019. How digital information transforms project delivery models. Project
management journal. 50(2). pp.177-194.
Zwikael, O., Meredith, J. R. and Smyrk, J., 2019. The responsibilities of the project owner in
benefits realization. International Journal of Operations & Production Management.
Harper, A., Mustafee, N. and Yearworth, M., 2021. Facets of trust in simulation studies.
European Journal of Operational Research, 289(1), pp.197-213.
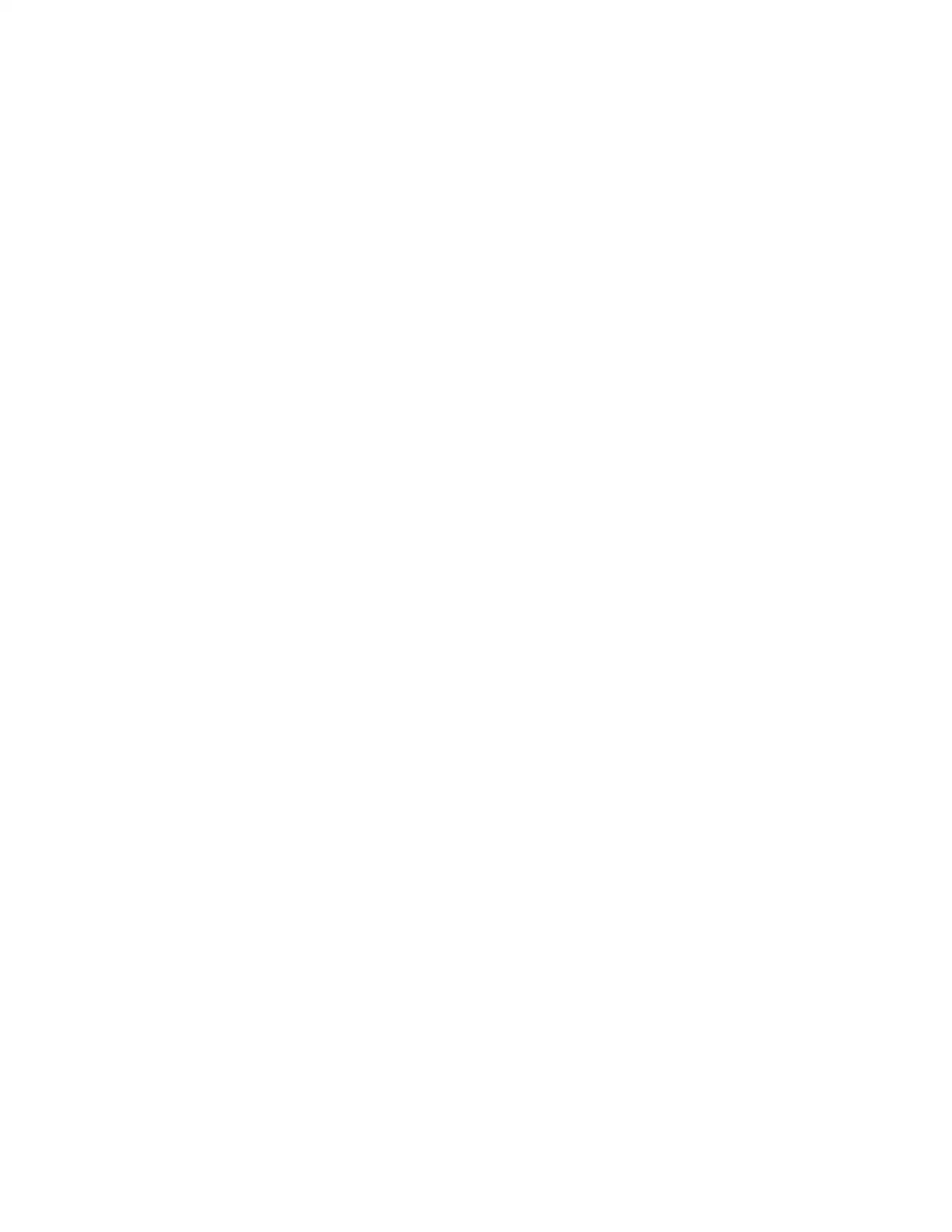
Paraphrase This Document
Need a fresh take? Get an instant paraphrase of this document with our AI Paraphraser
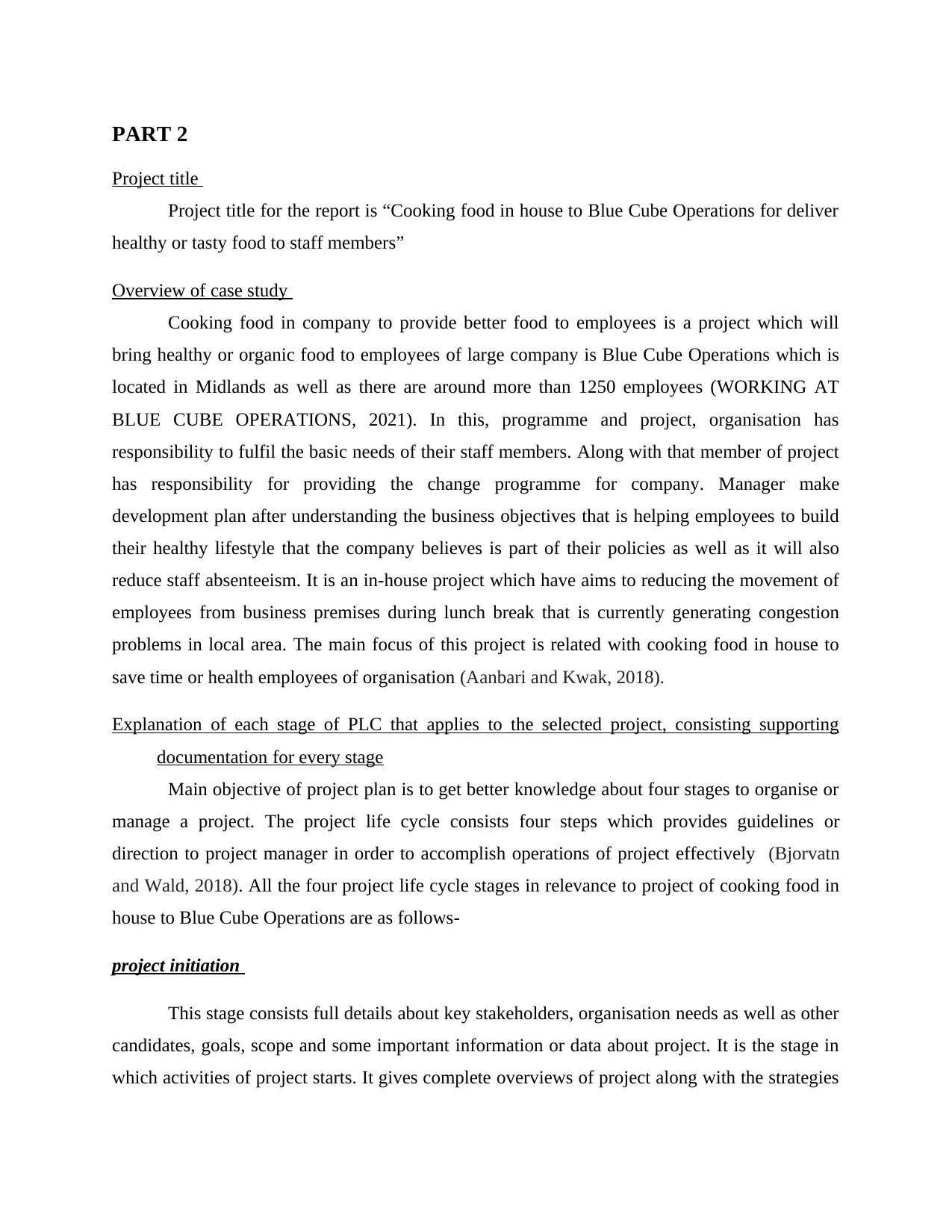
PART 2
Project title
Project title for the report is “Cooking food in house to Blue Cube Operations for deliver
healthy or tasty food to staff members”
Overview of case study
Cooking food in company to provide better food to employees is a project which will
bring healthy or organic food to employees of large company is Blue Cube Operations which is
located in Midlands as well as there are around more than 1250 employees (WORKING AT
BLUE CUBE OPERATIONS, 2021). In this, programme and project, organisation has
responsibility to fulfil the basic needs of their staff members. Along with that member of project
has responsibility for providing the change programme for company. Manager make
development plan after understanding the business objectives that is helping employees to build
their healthy lifestyle that the company believes is part of their policies as well as it will also
reduce staff absenteeism. It is an in-house project which have aims to reducing the movement of
employees from business premises during lunch break that is currently generating congestion
problems in local area. The main focus of this project is related with cooking food in house to
save time or health employees of organisation (Aanbari and Kwak, 2018).
Explanation of each stage of PLC that applies to the selected project, consisting supporting
documentation for every stage
Main objective of project plan is to get better knowledge about four stages to organise or
manage a project. The project life cycle consists four steps which provides guidelines or
direction to project manager in order to accomplish operations of project effectively (Bjorvatn
and Wald, 2018). All the four project life cycle stages in relevance to project of cooking food in
house to Blue Cube Operations are as follows-
project initiation
This stage consists full details about key stakeholders, organisation needs as well as other
candidates, goals, scope and some important information or data about project. It is the stage in
which activities of project starts. It gives complete overviews of project along with the strategies
Project title
Project title for the report is “Cooking food in house to Blue Cube Operations for deliver
healthy or tasty food to staff members”
Overview of case study
Cooking food in company to provide better food to employees is a project which will
bring healthy or organic food to employees of large company is Blue Cube Operations which is
located in Midlands as well as there are around more than 1250 employees (WORKING AT
BLUE CUBE OPERATIONS, 2021). In this, programme and project, organisation has
responsibility to fulfil the basic needs of their staff members. Along with that member of project
has responsibility for providing the change programme for company. Manager make
development plan after understanding the business objectives that is helping employees to build
their healthy lifestyle that the company believes is part of their policies as well as it will also
reduce staff absenteeism. It is an in-house project which have aims to reducing the movement of
employees from business premises during lunch break that is currently generating congestion
problems in local area. The main focus of this project is related with cooking food in house to
save time or health employees of organisation (Aanbari and Kwak, 2018).
Explanation of each stage of PLC that applies to the selected project, consisting supporting
documentation for every stage
Main objective of project plan is to get better knowledge about four stages to organise or
manage a project. The project life cycle consists four steps which provides guidelines or
direction to project manager in order to accomplish operations of project effectively (Bjorvatn
and Wald, 2018). All the four project life cycle stages in relevance to project of cooking food in
house to Blue Cube Operations are as follows-
project initiation
This stage consists full details about key stakeholders, organisation needs as well as other
candidates, goals, scope and some important information or data about project. It is the stage in
which activities of project starts. It gives complete overviews of project along with the strategies
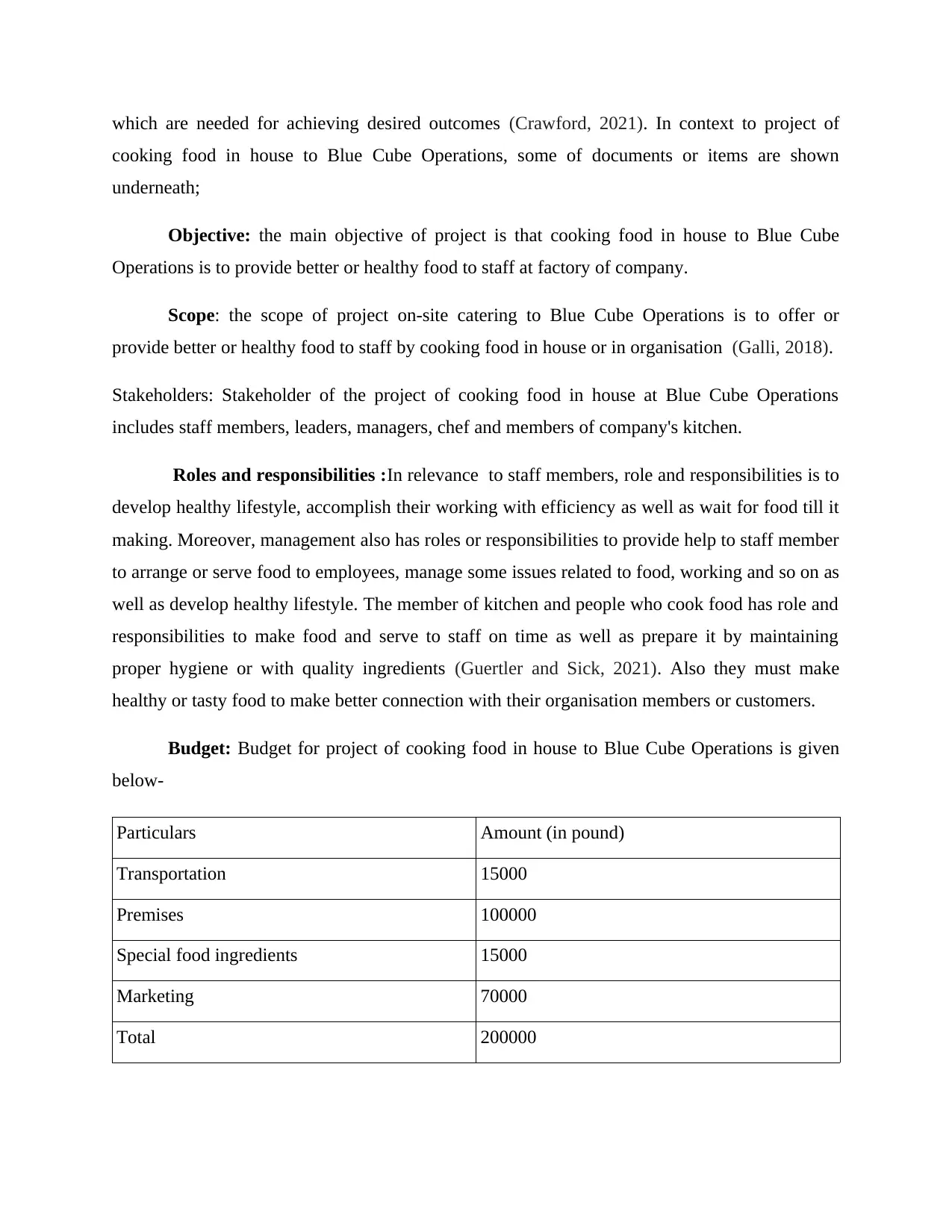
which are needed for achieving desired outcomes (Crawford, 2021). In context to project of
cooking food in house to Blue Cube Operations, some of documents or items are shown
underneath;
Objective: the main objective of project is that cooking food in house to Blue Cube
Operations is to provide better or healthy food to staff at factory of company.
Scope: the scope of project on-site catering to Blue Cube Operations is to offer or
provide better or healthy food to staff by cooking food in house or in organisation (Galli, 2018).
Stakeholders: Stakeholder of the project of cooking food in house at Blue Cube Operations
includes staff members, leaders, managers, chef and members of company's kitchen.
Roles and responsibilities :In relevance to staff members, role and responsibilities is to
develop healthy lifestyle, accomplish their working with efficiency as well as wait for food till it
making. Moreover, management also has roles or responsibilities to provide help to staff member
to arrange or serve food to employees, manage some issues related to food, working and so on as
well as develop healthy lifestyle. The member of kitchen and people who cook food has role and
responsibilities to make food and serve to staff on time as well as prepare it by maintaining
proper hygiene or with quality ingredients (Guertler and Sick, 2021). Also they must make
healthy or tasty food to make better connection with their organisation members or customers.
Budget: Budget for project of cooking food in house to Blue Cube Operations is given
below-
Particulars Amount (in pound)
Transportation 15000
Premises 100000
Special food ingredients 15000
Marketing 70000
Total 200000
cooking food in house to Blue Cube Operations, some of documents or items are shown
underneath;
Objective: the main objective of project is that cooking food in house to Blue Cube
Operations is to provide better or healthy food to staff at factory of company.
Scope: the scope of project on-site catering to Blue Cube Operations is to offer or
provide better or healthy food to staff by cooking food in house or in organisation (Galli, 2018).
Stakeholders: Stakeholder of the project of cooking food in house at Blue Cube Operations
includes staff members, leaders, managers, chef and members of company's kitchen.
Roles and responsibilities :In relevance to staff members, role and responsibilities is to
develop healthy lifestyle, accomplish their working with efficiency as well as wait for food till it
making. Moreover, management also has roles or responsibilities to provide help to staff member
to arrange or serve food to employees, manage some issues related to food, working and so on as
well as develop healthy lifestyle. The member of kitchen and people who cook food has role and
responsibilities to make food and serve to staff on time as well as prepare it by maintaining
proper hygiene or with quality ingredients (Guertler and Sick, 2021). Also they must make
healthy or tasty food to make better connection with their organisation members or customers.
Budget: Budget for project of cooking food in house to Blue Cube Operations is given
below-
Particulars Amount (in pound)
Transportation 15000
Premises 100000
Special food ingredients 15000
Marketing 70000
Total 200000
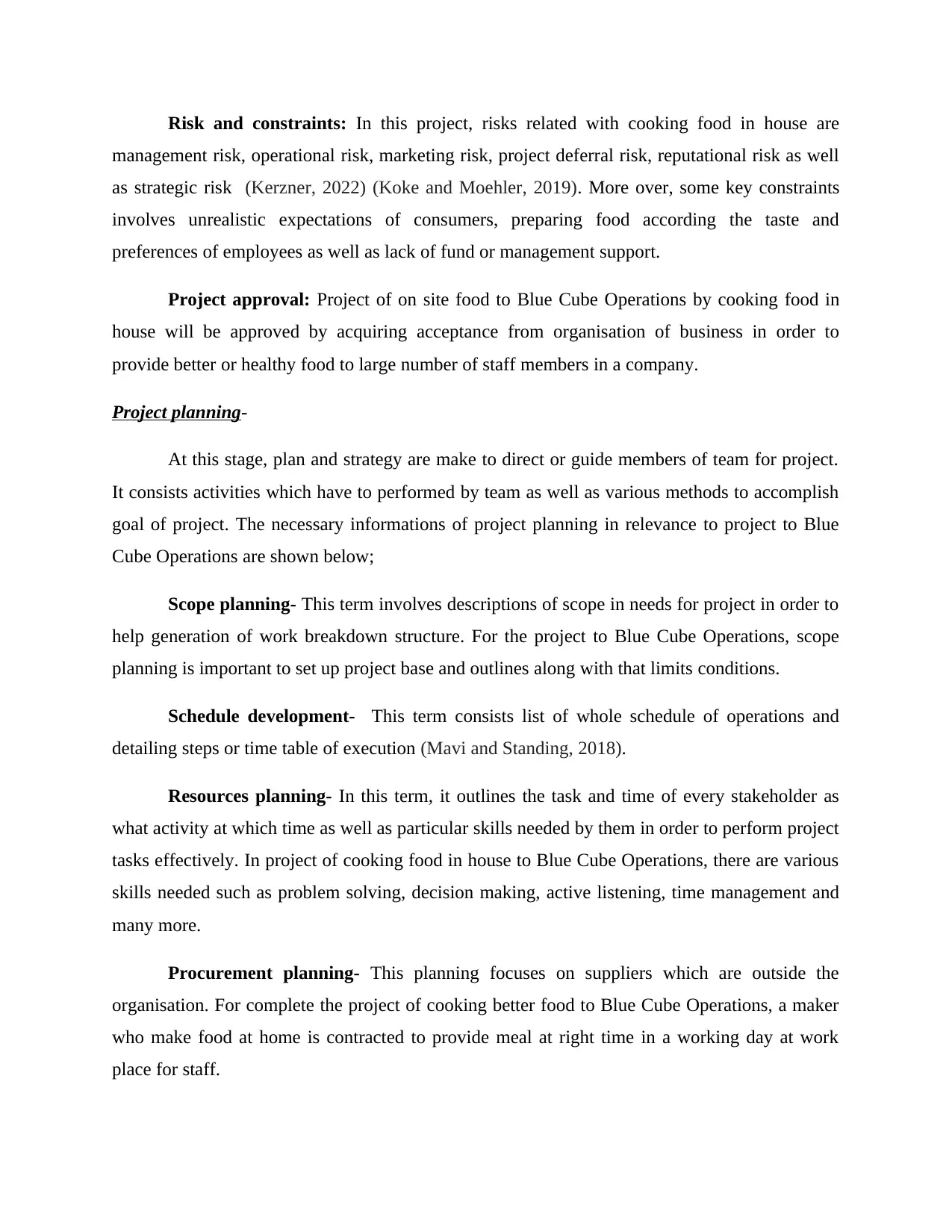
Risk and constraints: In this project, risks related with cooking food in house are
management risk, operational risk, marketing risk, project deferral risk, reputational risk as well
as strategic risk (Kerzner, 2022) (Koke and Moehler, 2019). More over, some key constraints
involves unrealistic expectations of consumers, preparing food according the taste and
preferences of employees as well as lack of fund or management support.
Project approval: Project of on site food to Blue Cube Operations by cooking food in
house will be approved by acquiring acceptance from organisation of business in order to
provide better or healthy food to large number of staff members in a company.
Project planning-
At this stage, plan and strategy are make to direct or guide members of team for project.
It consists activities which have to performed by team as well as various methods to accomplish
goal of project. The necessary informations of project planning in relevance to project to Blue
Cube Operations are shown below;
Scope planning- This term involves descriptions of scope in needs for project in order to
help generation of work breakdown structure. For the project to Blue Cube Operations, scope
planning is important to set up project base and outlines along with that limits conditions.
Schedule development- This term consists list of whole schedule of operations and
detailing steps or time table of execution (Mavi and Standing, 2018).
Resources planning- In this term, it outlines the task and time of every stakeholder as
what activity at which time as well as particular skills needed by them in order to perform project
tasks effectively. In project of cooking food in house to Blue Cube Operations, there are various
skills needed such as problem solving, decision making, active listening, time management and
many more.
Procurement planning- This planning focuses on suppliers which are outside the
organisation. For complete the project of cooking better food to Blue Cube Operations, a maker
who make food at home is contracted to provide meal at right time in a working day at work
place for staff.
management risk, operational risk, marketing risk, project deferral risk, reputational risk as well
as strategic risk (Kerzner, 2022) (Koke and Moehler, 2019). More over, some key constraints
involves unrealistic expectations of consumers, preparing food according the taste and
preferences of employees as well as lack of fund or management support.
Project approval: Project of on site food to Blue Cube Operations by cooking food in
house will be approved by acquiring acceptance from organisation of business in order to
provide better or healthy food to large number of staff members in a company.
Project planning-
At this stage, plan and strategy are make to direct or guide members of team for project.
It consists activities which have to performed by team as well as various methods to accomplish
goal of project. The necessary informations of project planning in relevance to project to Blue
Cube Operations are shown below;
Scope planning- This term involves descriptions of scope in needs for project in order to
help generation of work breakdown structure. For the project to Blue Cube Operations, scope
planning is important to set up project base and outlines along with that limits conditions.
Schedule development- This term consists list of whole schedule of operations and
detailing steps or time table of execution (Mavi and Standing, 2018).
Resources planning- In this term, it outlines the task and time of every stakeholder as
what activity at which time as well as particular skills needed by them in order to perform project
tasks effectively. In project of cooking food in house to Blue Cube Operations, there are various
skills needed such as problem solving, decision making, active listening, time management and
many more.
Procurement planning- This planning focuses on suppliers which are outside the
organisation. For complete the project of cooking better food to Blue Cube Operations, a maker
who make food at home is contracted to provide meal at right time in a working day at work
place for staff.
Secure Best Marks with AI Grader
Need help grading? Try our AI Grader for instant feedback on your assignments.
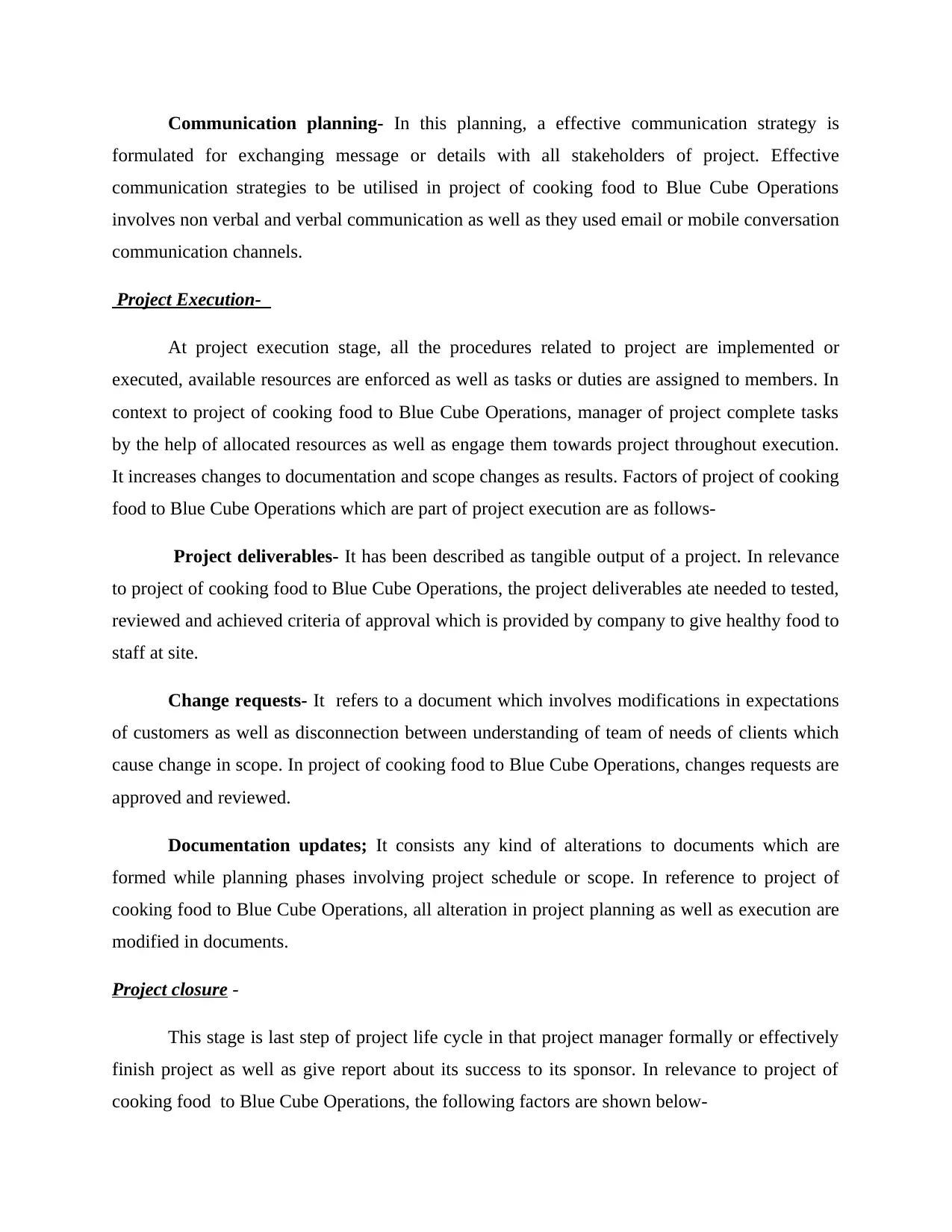
Communication planning- In this planning, a effective communication strategy is
formulated for exchanging message or details with all stakeholders of project. Effective
communication strategies to be utilised in project of cooking food to Blue Cube Operations
involves non verbal and verbal communication as well as they used email or mobile conversation
communication channels.
Project Execution-
At project execution stage, all the procedures related to project are implemented or
executed, available resources are enforced as well as tasks or duties are assigned to members. In
context to project of cooking food to Blue Cube Operations, manager of project complete tasks
by the help of allocated resources as well as engage them towards project throughout execution.
It increases changes to documentation and scope changes as results. Factors of project of cooking
food to Blue Cube Operations which are part of project execution are as follows-
Project deliverables- It has been described as tangible output of a project. In relevance
to project of cooking food to Blue Cube Operations, the project deliverables ate needed to tested,
reviewed and achieved criteria of approval which is provided by company to give healthy food to
staff at site.
Change requests- It refers to a document which involves modifications in expectations
of customers as well as disconnection between understanding of team of needs of clients which
cause change in scope. In project of cooking food to Blue Cube Operations, changes requests are
approved and reviewed.
Documentation updates; It consists any kind of alterations to documents which are
formed while planning phases involving project schedule or scope. In reference to project of
cooking food to Blue Cube Operations, all alteration in project planning as well as execution are
modified in documents.
Project closure -
This stage is last step of project life cycle in that project manager formally or effectively
finish project as well as give report about its success to its sponsor. In relevance to project of
cooking food to Blue Cube Operations, the following factors are shown below-
formulated for exchanging message or details with all stakeholders of project. Effective
communication strategies to be utilised in project of cooking food to Blue Cube Operations
involves non verbal and verbal communication as well as they used email or mobile conversation
communication channels.
Project Execution-
At project execution stage, all the procedures related to project are implemented or
executed, available resources are enforced as well as tasks or duties are assigned to members. In
context to project of cooking food to Blue Cube Operations, manager of project complete tasks
by the help of allocated resources as well as engage them towards project throughout execution.
It increases changes to documentation and scope changes as results. Factors of project of cooking
food to Blue Cube Operations which are part of project execution are as follows-
Project deliverables- It has been described as tangible output of a project. In relevance
to project of cooking food to Blue Cube Operations, the project deliverables ate needed to tested,
reviewed and achieved criteria of approval which is provided by company to give healthy food to
staff at site.
Change requests- It refers to a document which involves modifications in expectations
of customers as well as disconnection between understanding of team of needs of clients which
cause change in scope. In project of cooking food to Blue Cube Operations, changes requests are
approved and reviewed.
Documentation updates; It consists any kind of alterations to documents which are
formed while planning phases involving project schedule or scope. In reference to project of
cooking food to Blue Cube Operations, all alteration in project planning as well as execution are
modified in documents.
Project closure -
This stage is last step of project life cycle in that project manager formally or effectively
finish project as well as give report about its success to its sponsor. In relevance to project of
cooking food to Blue Cube Operations, the following factors are shown below-
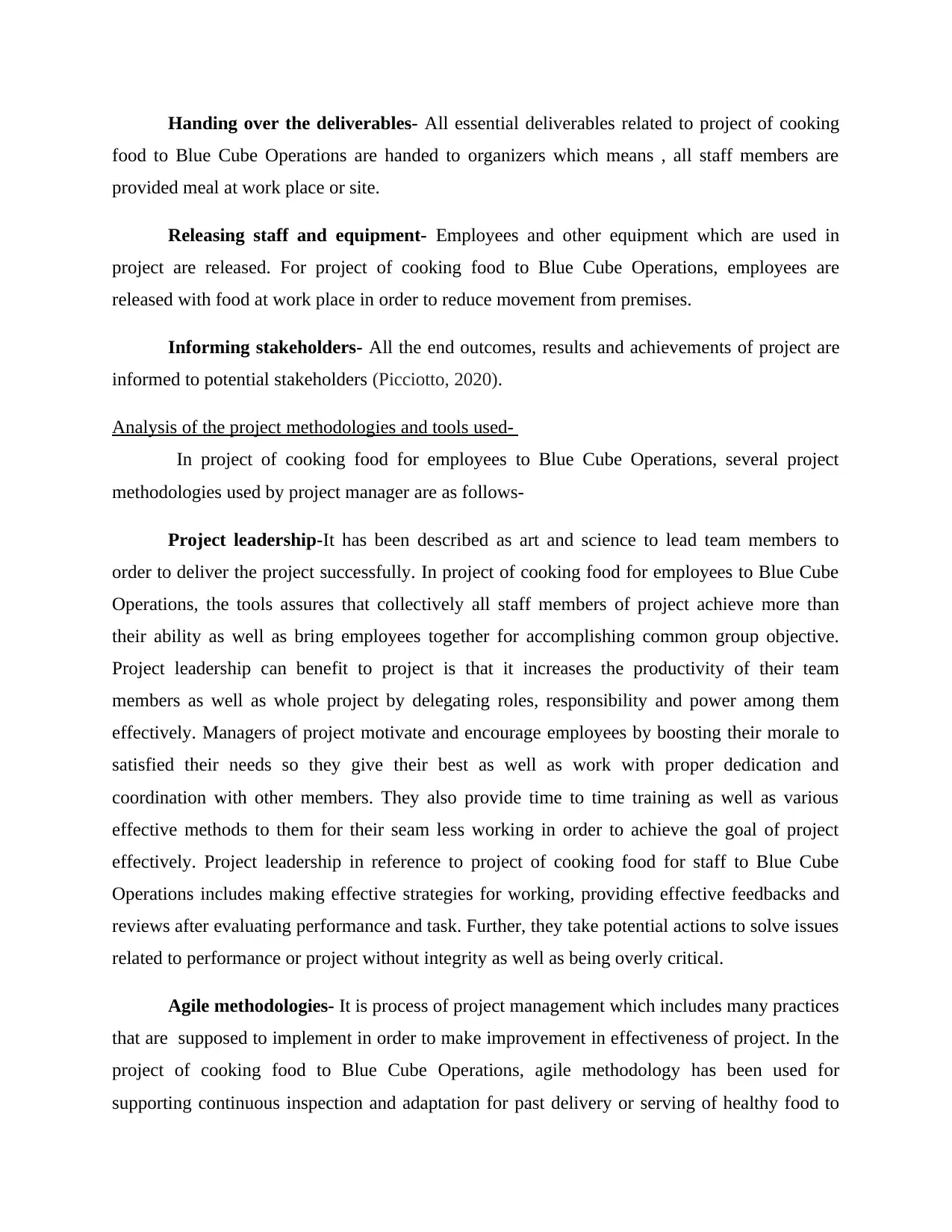
Handing over the deliverables- All essential deliverables related to project of cooking
food to Blue Cube Operations are handed to organizers which means , all staff members are
provided meal at work place or site.
Releasing staff and equipment- Employees and other equipment which are used in
project are released. For project of cooking food to Blue Cube Operations, employees are
released with food at work place in order to reduce movement from premises.
Informing stakeholders- All the end outcomes, results and achievements of project are
informed to potential stakeholders (Picciotto, 2020).
Analysis of the project methodologies and tools used-
In project of cooking food for employees to Blue Cube Operations, several project
methodologies used by project manager are as follows-
Project leadership-It has been described as art and science to lead team members to
order to deliver the project successfully. In project of cooking food for employees to Blue Cube
Operations, the tools assures that collectively all staff members of project achieve more than
their ability as well as bring employees together for accomplishing common group objective.
Project leadership can benefit to project is that it increases the productivity of their team
members as well as whole project by delegating roles, responsibility and power among them
effectively. Managers of project motivate and encourage employees by boosting their morale to
satisfied their needs so they give their best as well as work with proper dedication and
coordination with other members. They also provide time to time training as well as various
effective methods to them for their seam less working in order to achieve the goal of project
effectively. Project leadership in reference to project of cooking food for staff to Blue Cube
Operations includes making effective strategies for working, providing effective feedbacks and
reviews after evaluating performance and task. Further, they take potential actions to solve issues
related to performance or project without integrity as well as being overly critical.
Agile methodologies- It is process of project management which includes many practices
that are supposed to implement in order to make improvement in effectiveness of project. In the
project of cooking food to Blue Cube Operations, agile methodology has been used for
supporting continuous inspection and adaptation for past delivery or serving of healthy food to
food to Blue Cube Operations are handed to organizers which means , all staff members are
provided meal at work place or site.
Releasing staff and equipment- Employees and other equipment which are used in
project are released. For project of cooking food to Blue Cube Operations, employees are
released with food at work place in order to reduce movement from premises.
Informing stakeholders- All the end outcomes, results and achievements of project are
informed to potential stakeholders (Picciotto, 2020).
Analysis of the project methodologies and tools used-
In project of cooking food for employees to Blue Cube Operations, several project
methodologies used by project manager are as follows-
Project leadership-It has been described as art and science to lead team members to
order to deliver the project successfully. In project of cooking food for employees to Blue Cube
Operations, the tools assures that collectively all staff members of project achieve more than
their ability as well as bring employees together for accomplishing common group objective.
Project leadership can benefit to project is that it increases the productivity of their team
members as well as whole project by delegating roles, responsibility and power among them
effectively. Managers of project motivate and encourage employees by boosting their morale to
satisfied their needs so they give their best as well as work with proper dedication and
coordination with other members. They also provide time to time training as well as various
effective methods to them for their seam less working in order to achieve the goal of project
effectively. Project leadership in reference to project of cooking food for staff to Blue Cube
Operations includes making effective strategies for working, providing effective feedbacks and
reviews after evaluating performance and task. Further, they take potential actions to solve issues
related to performance or project without integrity as well as being overly critical.
Agile methodologies- It is process of project management which includes many practices
that are supposed to implement in order to make improvement in effectiveness of project. In the
project of cooking food to Blue Cube Operations, agile methodology has been used for
supporting continuous inspection and adaptation for past delivery or serving of healthy food to
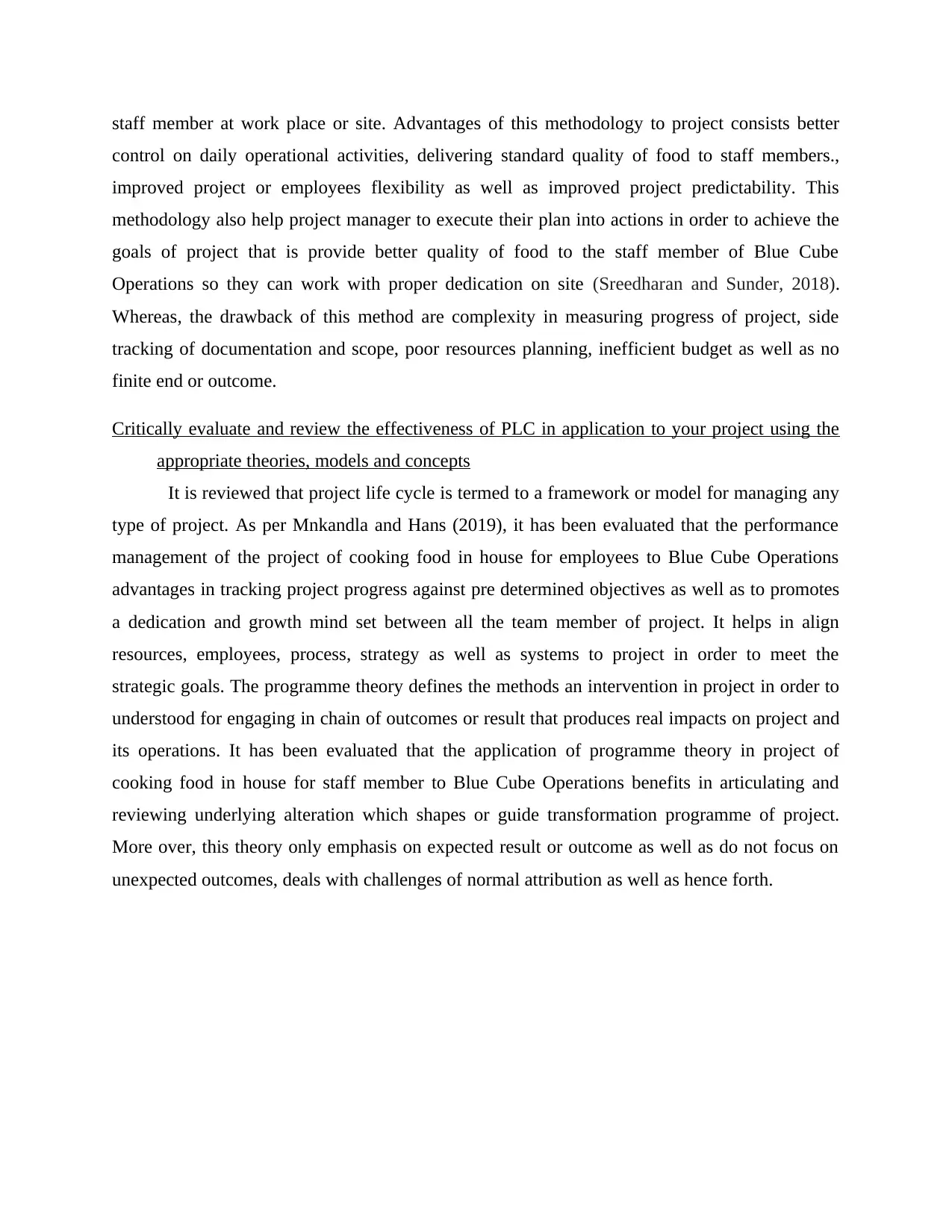
staff member at work place or site. Advantages of this methodology to project consists better
control on daily operational activities, delivering standard quality of food to staff members.,
improved project or employees flexibility as well as improved project predictability. This
methodology also help project manager to execute their plan into actions in order to achieve the
goals of project that is provide better quality of food to the staff member of Blue Cube
Operations so they can work with proper dedication on site (Sreedharan and Sunder, 2018).
Whereas, the drawback of this method are complexity in measuring progress of project, side
tracking of documentation and scope, poor resources planning, inefficient budget as well as no
finite end or outcome.
Critically evaluate and review the effectiveness of PLC in application to your project using the
appropriate theories, models and concepts
It is reviewed that project life cycle is termed to a framework or model for managing any
type of project. As per Mnkandla and Hans (2019), it has been evaluated that the performance
management of the project of cooking food in house for employees to Blue Cube Operations
advantages in tracking project progress against pre determined objectives as well as to promotes
a dedication and growth mind set between all the team member of project. It helps in align
resources, employees, process, strategy as well as systems to project in order to meet the
strategic goals. The programme theory defines the methods an intervention in project in order to
understood for engaging in chain of outcomes or result that produces real impacts on project and
its operations. It has been evaluated that the application of programme theory in project of
cooking food in house for staff member to Blue Cube Operations benefits in articulating and
reviewing underlying alteration which shapes or guide transformation programme of project.
More over, this theory only emphasis on expected result or outcome as well as do not focus on
unexpected outcomes, deals with challenges of normal attribution as well as hence forth.
control on daily operational activities, delivering standard quality of food to staff members.,
improved project or employees flexibility as well as improved project predictability. This
methodology also help project manager to execute their plan into actions in order to achieve the
goals of project that is provide better quality of food to the staff member of Blue Cube
Operations so they can work with proper dedication on site (Sreedharan and Sunder, 2018).
Whereas, the drawback of this method are complexity in measuring progress of project, side
tracking of documentation and scope, poor resources planning, inefficient budget as well as no
finite end or outcome.
Critically evaluate and review the effectiveness of PLC in application to your project using the
appropriate theories, models and concepts
It is reviewed that project life cycle is termed to a framework or model for managing any
type of project. As per Mnkandla and Hans (2019), it has been evaluated that the performance
management of the project of cooking food in house for employees to Blue Cube Operations
advantages in tracking project progress against pre determined objectives as well as to promotes
a dedication and growth mind set between all the team member of project. It helps in align
resources, employees, process, strategy as well as systems to project in order to meet the
strategic goals. The programme theory defines the methods an intervention in project in order to
understood for engaging in chain of outcomes or result that produces real impacts on project and
its operations. It has been evaluated that the application of programme theory in project of
cooking food in house for staff member to Blue Cube Operations benefits in articulating and
reviewing underlying alteration which shapes or guide transformation programme of project.
More over, this theory only emphasis on expected result or outcome as well as do not focus on
unexpected outcomes, deals with challenges of normal attribution as well as hence forth.
Paraphrase This Document
Need a fresh take? Get an instant paraphrase of this document with our AI Paraphraser
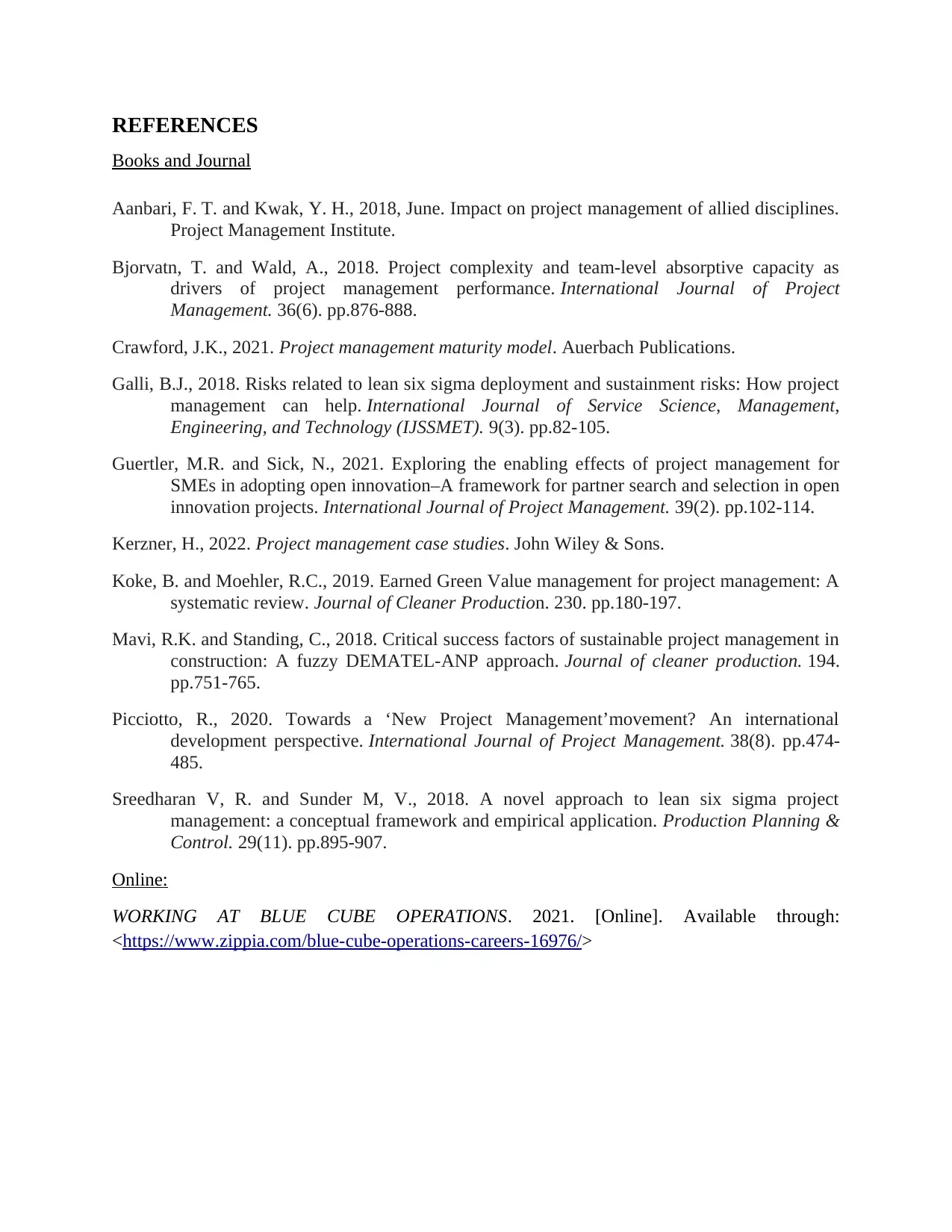
REFERENCES
Books and Journal
Aanbari, F. T. and Kwak, Y. H., 2018, June. Impact on project management of allied disciplines.
Project Management Institute.
Bjorvatn, T. and Wald, A., 2018. Project complexity and team-level absorptive capacity as
drivers of project management performance. International Journal of Project
Management. 36(6). pp.876-888.
Crawford, J.K., 2021. Project management maturity model. Auerbach Publications.
Galli, B.J., 2018. Risks related to lean six sigma deployment and sustainment risks: How project
management can help. International Journal of Service Science, Management,
Engineering, and Technology (IJSSMET). 9(3). pp.82-105.
Guertler, M.R. and Sick, N., 2021. Exploring the enabling effects of project management for
SMEs in adopting open innovation–A framework for partner search and selection in open
innovation projects. International Journal of Project Management. 39(2). pp.102-114.
Kerzner, H., 2022. Project management case studies. John Wiley & Sons.
Koke, B. and Moehler, R.C., 2019. Earned Green Value management for project management: A
systematic review. Journal of Cleaner Production. 230. pp.180-197.
Mavi, R.K. and Standing, C., 2018. Critical success factors of sustainable project management in
construction: A fuzzy DEMATEL-ANP approach. Journal of cleaner production. 194.
pp.751-765.
Picciotto, R., 2020. Towards a ‘New Project Management’movement? An international
development perspective. International Journal of Project Management. 38(8). pp.474-
485.
Sreedharan V, R. and Sunder M, V., 2018. A novel approach to lean six sigma project
management: a conceptual framework and empirical application. Production Planning &
Control. 29(11). pp.895-907.
Online:
WORKING AT BLUE CUBE OPERATIONS. 2021. [Online]. Available through:
<https://www.zippia.com/blue-cube-operations-careers-16976/>
Books and Journal
Aanbari, F. T. and Kwak, Y. H., 2018, June. Impact on project management of allied disciplines.
Project Management Institute.
Bjorvatn, T. and Wald, A., 2018. Project complexity and team-level absorptive capacity as
drivers of project management performance. International Journal of Project
Management. 36(6). pp.876-888.
Crawford, J.K., 2021. Project management maturity model. Auerbach Publications.
Galli, B.J., 2018. Risks related to lean six sigma deployment and sustainment risks: How project
management can help. International Journal of Service Science, Management,
Engineering, and Technology (IJSSMET). 9(3). pp.82-105.
Guertler, M.R. and Sick, N., 2021. Exploring the enabling effects of project management for
SMEs in adopting open innovation–A framework for partner search and selection in open
innovation projects. International Journal of Project Management. 39(2). pp.102-114.
Kerzner, H., 2022. Project management case studies. John Wiley & Sons.
Koke, B. and Moehler, R.C., 2019. Earned Green Value management for project management: A
systematic review. Journal of Cleaner Production. 230. pp.180-197.
Mavi, R.K. and Standing, C., 2018. Critical success factors of sustainable project management in
construction: A fuzzy DEMATEL-ANP approach. Journal of cleaner production. 194.
pp.751-765.
Picciotto, R., 2020. Towards a ‘New Project Management’movement? An international
development perspective. International Journal of Project Management. 38(8). pp.474-
485.
Sreedharan V, R. and Sunder M, V., 2018. A novel approach to lean six sigma project
management: a conceptual framework and empirical application. Production Planning &
Control. 29(11). pp.895-907.
Online:
WORKING AT BLUE CUBE OPERATIONS. 2021. [Online]. Available through:
<https://www.zippia.com/blue-cube-operations-careers-16976/>
1 out of 20
Related Documents
![[object Object]](/_next/image/?url=%2F_next%2Fstatic%2Fmedia%2Flogo.6d15ce61.png&w=640&q=75)
Your All-in-One AI-Powered Toolkit for Academic Success.
+13062052269
info@desklib.com
Available 24*7 on WhatsApp / Email
Unlock your academic potential
© 2024 | Zucol Services PVT LTD | All rights reserved.