Operations and Project Management: Principles and Continuous Improvement Plan
VerifiedAdded on 2023/06/18
|20
|6205
|405
AI Summary
This report discusses the principles of operations and project management with Unilever as a case study. It covers the continuous improvement plan and TQM. The report provides study material, solved assignments, essays, and dissertations on Desklib.
Contribute Materials
Your contribution can guide someone’s learning journey. Share your
documents today.
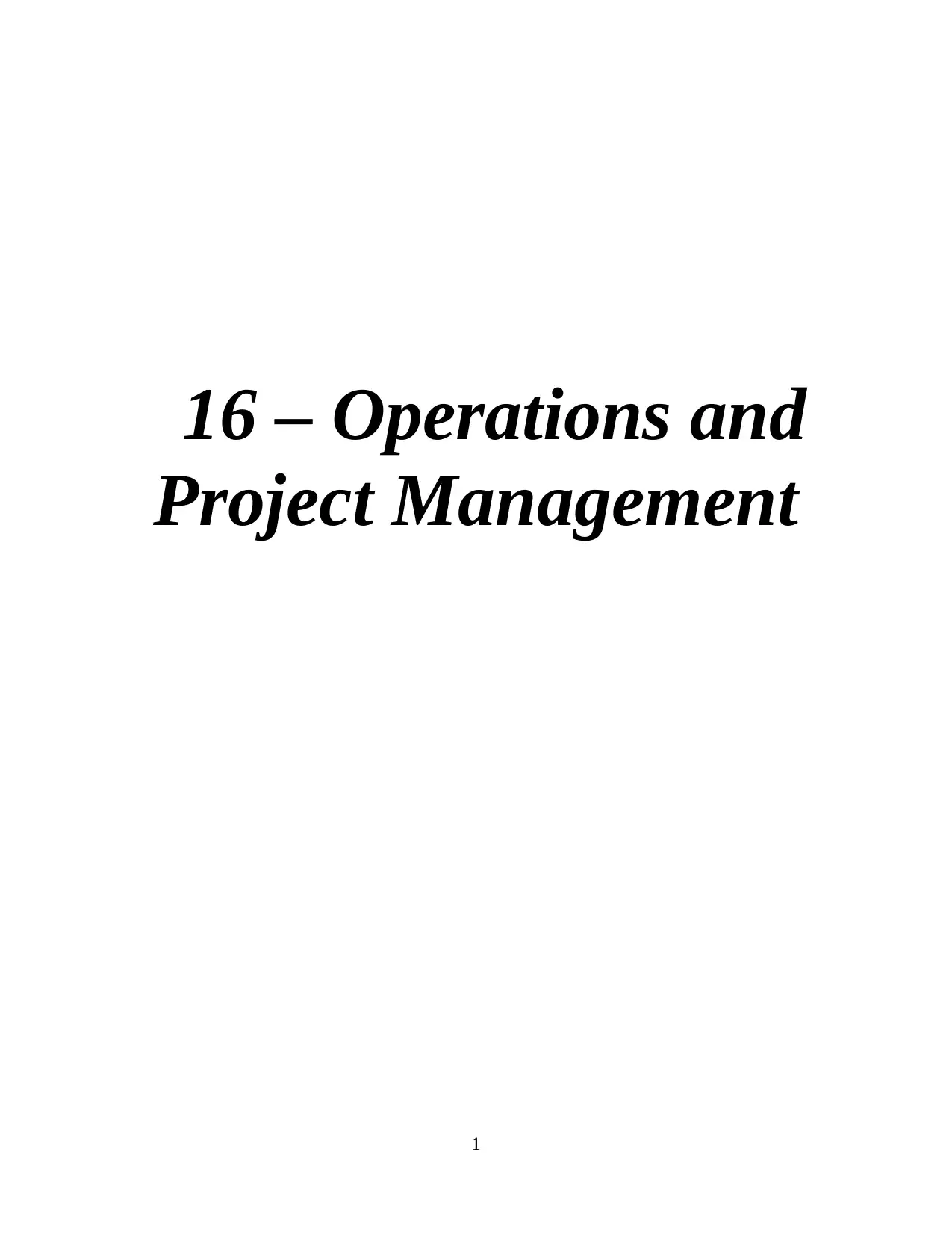
16 – Operations and
Project Management
1
Project Management
1
Secure Best Marks with AI Grader
Need help grading? Try our AI Grader for instant feedback on your assignments.
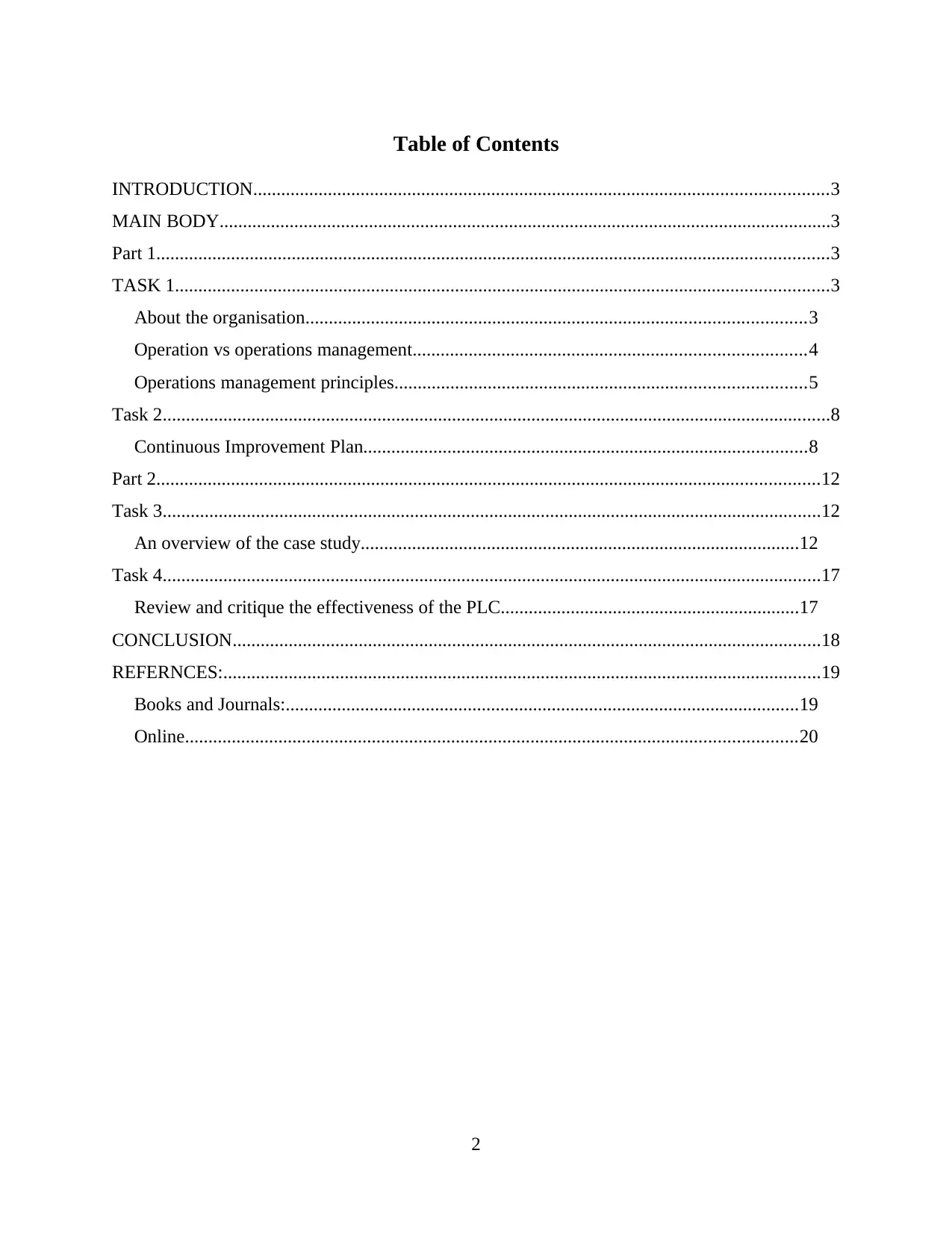
Table of Contents
INTRODUCTION...........................................................................................................................3
MAIN BODY...................................................................................................................................3
Part 1................................................................................................................................................3
TASK 1............................................................................................................................................3
About the organisation...........................................................................................................3
Operation vs operations management....................................................................................4
Operations management principles........................................................................................5
Task 2...............................................................................................................................................8
Continuous Improvement Plan...............................................................................................8
Part 2..............................................................................................................................................12
Task 3.............................................................................................................................................12
An overview of the case study..............................................................................................12
Task 4.............................................................................................................................................17
Review and critique the effectiveness of the PLC................................................................17
CONCLUSION..............................................................................................................................18
REFERNCES:................................................................................................................................19
Books and Journals:..............................................................................................................19
Online...................................................................................................................................20
2
INTRODUCTION...........................................................................................................................3
MAIN BODY...................................................................................................................................3
Part 1................................................................................................................................................3
TASK 1............................................................................................................................................3
About the organisation...........................................................................................................3
Operation vs operations management....................................................................................4
Operations management principles........................................................................................5
Task 2...............................................................................................................................................8
Continuous Improvement Plan...............................................................................................8
Part 2..............................................................................................................................................12
Task 3.............................................................................................................................................12
An overview of the case study..............................................................................................12
Task 4.............................................................................................................................................17
Review and critique the effectiveness of the PLC................................................................17
CONCLUSION..............................................................................................................................18
REFERNCES:................................................................................................................................19
Books and Journals:..............................................................................................................19
Online...................................................................................................................................20
2
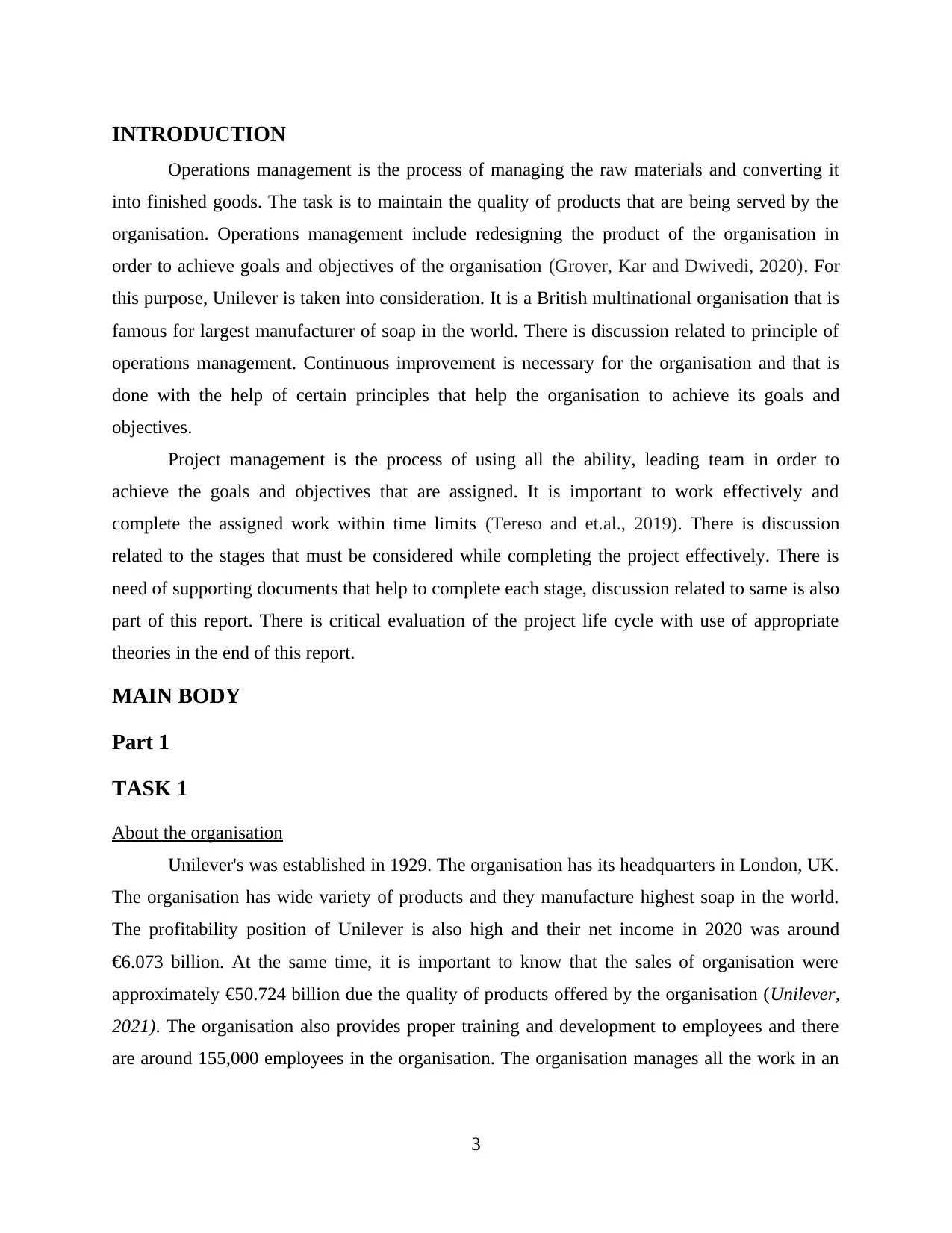
INTRODUCTION
Operations management is the process of managing the raw materials and converting it
into finished goods. The task is to maintain the quality of products that are being served by the
organisation. Operations management include redesigning the product of the organisation in
order to achieve goals and objectives of the organisation (Grover, Kar and Dwivedi, 2020). For
this purpose, Unilever is taken into consideration. It is a British multinational organisation that is
famous for largest manufacturer of soap in the world. There is discussion related to principle of
operations management. Continuous improvement is necessary for the organisation and that is
done with the help of certain principles that help the organisation to achieve its goals and
objectives.
Project management is the process of using all the ability, leading team in order to
achieve the goals and objectives that are assigned. It is important to work effectively and
complete the assigned work within time limits (Tereso and et.al., 2019). There is discussion
related to the stages that must be considered while completing the project effectively. There is
need of supporting documents that help to complete each stage, discussion related to same is also
part of this report. There is critical evaluation of the project life cycle with use of appropriate
theories in the end of this report.
MAIN BODY
Part 1
TASK 1
About the organisation
Unilever's was established in 1929. The organisation has its headquarters in London, UK.
The organisation has wide variety of products and they manufacture highest soap in the world.
The profitability position of Unilever is also high and their net income in 2020 was around
€6.073 billion. At the same time, it is important to know that the sales of organisation were
approximately €50.724 billion due the quality of products offered by the organisation (Unilever,
2021). The organisation also provides proper training and development to employees and there
are around 155,000 employees in the organisation. The organisation manages all the work in an
3
Operations management is the process of managing the raw materials and converting it
into finished goods. The task is to maintain the quality of products that are being served by the
organisation. Operations management include redesigning the product of the organisation in
order to achieve goals and objectives of the organisation (Grover, Kar and Dwivedi, 2020). For
this purpose, Unilever is taken into consideration. It is a British multinational organisation that is
famous for largest manufacturer of soap in the world. There is discussion related to principle of
operations management. Continuous improvement is necessary for the organisation and that is
done with the help of certain principles that help the organisation to achieve its goals and
objectives.
Project management is the process of using all the ability, leading team in order to
achieve the goals and objectives that are assigned. It is important to work effectively and
complete the assigned work within time limits (Tereso and et.al., 2019). There is discussion
related to the stages that must be considered while completing the project effectively. There is
need of supporting documents that help to complete each stage, discussion related to same is also
part of this report. There is critical evaluation of the project life cycle with use of appropriate
theories in the end of this report.
MAIN BODY
Part 1
TASK 1
About the organisation
Unilever's was established in 1929. The organisation has its headquarters in London, UK.
The organisation has wide variety of products and they manufacture highest soap in the world.
The profitability position of Unilever is also high and their net income in 2020 was around
€6.073 billion. At the same time, it is important to know that the sales of organisation were
approximately €50.724 billion due the quality of products offered by the organisation (Unilever,
2021). The organisation also provides proper training and development to employees and there
are around 155,000 employees in the organisation. The organisation manages all the work in an
3

effective manner so as to serve more customers. They plan each and every thing in an
appropriate manner so as to achieve goals and objectives.
Operation vs operations management
Operation includes the day to day activity that the organization performs. It is important
to work in an effective manner as it helps to enhance the value of the organization. Conducting
the operational work effectively is necessary for an organization (Nalliah, Miller and Stefanac,
2019). Management of all the operational work of an organization is known as operations
management. It helps the organization to serve the customer's effectively and attain competitive
advantage. The difference among operations and operations management is discussed
underneath:
Operations Operations Management
Operations includes the business
activities that includes conversion of
raw material into finished goods (Raut
and et.al., 2019). The purpose is to
make them sell able and to earn profit
by satisfying the needs and wants of
customers.
The day to day activity undertaken by
Unilever are called its operations. Each
and every organisation has its own
operations that is called the core
activity done by the business.
To illustrate the activity of
manufacturing goods and selling them
to customers is its operational work.
It is an area of management that is
concerned with the process of
designing and controlling in order to
carry on the business operations of an
organisation. It includes all the aspects
such as quality management,
continuous improvement etc.
Operations management means the
steps followed by the organisation in
order to collect raw materials and
convert it into finished good to provide
best to the customer's (Mišić and
Perakis, 2020).
To illustrate, the organisation manages
its operation's in an effective manner to
achieve success. Soap manufactured by
Unilever are largest in the world.
4
appropriate manner so as to achieve goals and objectives.
Operation vs operations management
Operation includes the day to day activity that the organization performs. It is important
to work in an effective manner as it helps to enhance the value of the organization. Conducting
the operational work effectively is necessary for an organization (Nalliah, Miller and Stefanac,
2019). Management of all the operational work of an organization is known as operations
management. It helps the organization to serve the customer's effectively and attain competitive
advantage. The difference among operations and operations management is discussed
underneath:
Operations Operations Management
Operations includes the business
activities that includes conversion of
raw material into finished goods (Raut
and et.al., 2019). The purpose is to
make them sell able and to earn profit
by satisfying the needs and wants of
customers.
The day to day activity undertaken by
Unilever are called its operations. Each
and every organisation has its own
operations that is called the core
activity done by the business.
To illustrate the activity of
manufacturing goods and selling them
to customers is its operational work.
It is an area of management that is
concerned with the process of
designing and controlling in order to
carry on the business operations of an
organisation. It includes all the aspects
such as quality management,
continuous improvement etc.
Operations management means the
steps followed by the organisation in
order to collect raw materials and
convert it into finished good to provide
best to the customer's (Mišić and
Perakis, 2020).
To illustrate, the organisation manages
its operation's in an effective manner to
achieve success. Soap manufactured by
Unilever are largest in the world.
4
Secure Best Marks with AI Grader
Need help grading? Try our AI Grader for instant feedback on your assignments.
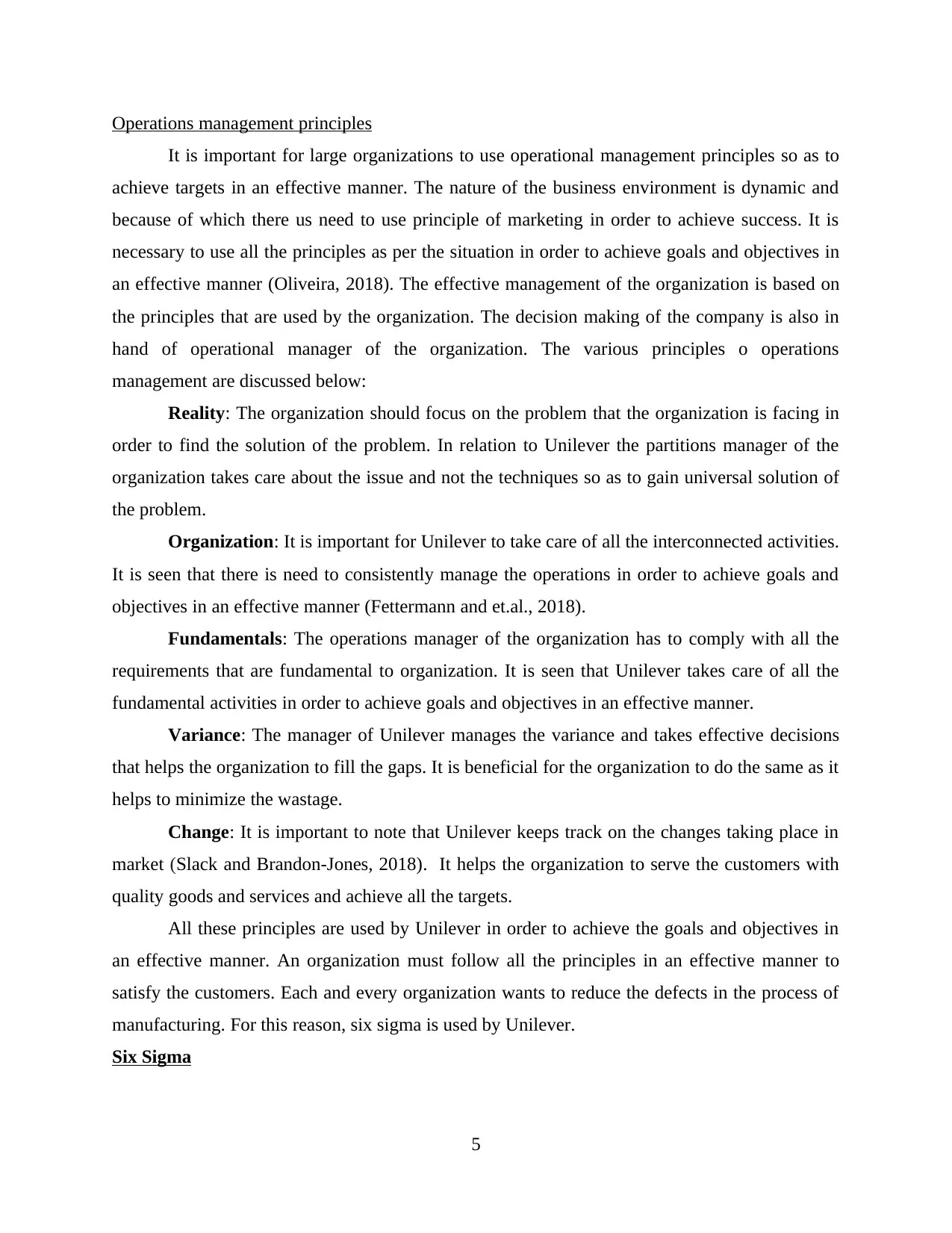
Operations management principles
It is important for large organizations to use operational management principles so as to
achieve targets in an effective manner. The nature of the business environment is dynamic and
because of which there us need to use principle of marketing in order to achieve success. It is
necessary to use all the principles as per the situation in order to achieve goals and objectives in
an effective manner (Oliveira, 2018). The effective management of the organization is based on
the principles that are used by the organization. The decision making of the company is also in
hand of operational manager of the organization. The various principles o operations
management are discussed below:
Reality: The organization should focus on the problem that the organization is facing in
order to find the solution of the problem. In relation to Unilever the partitions manager of the
organization takes care about the issue and not the techniques so as to gain universal solution of
the problem.
Organization: It is important for Unilever to take care of all the interconnected activities.
It is seen that there is need to consistently manage the operations in order to achieve goals and
objectives in an effective manner (Fettermann and et.al., 2018).
Fundamentals: The operations manager of the organization has to comply with all the
requirements that are fundamental to organization. It is seen that Unilever takes care of all the
fundamental activities in order to achieve goals and objectives in an effective manner.
Variance: The manager of Unilever manages the variance and takes effective decisions
that helps the organization to fill the gaps. It is beneficial for the organization to do the same as it
helps to minimize the wastage.
Change: It is important to note that Unilever keeps track on the changes taking place in
market (Slack and Brandon-Jones, 2018). It helps the organization to serve the customers with
quality goods and services and achieve all the targets.
All these principles are used by Unilever in order to achieve the goals and objectives in
an effective manner. An organization must follow all the principles in an effective manner to
satisfy the customers. Each and every organization wants to reduce the defects in the process of
manufacturing. For this reason, six sigma is used by Unilever.
Six Sigma
5
It is important for large organizations to use operational management principles so as to
achieve targets in an effective manner. The nature of the business environment is dynamic and
because of which there us need to use principle of marketing in order to achieve success. It is
necessary to use all the principles as per the situation in order to achieve goals and objectives in
an effective manner (Oliveira, 2018). The effective management of the organization is based on
the principles that are used by the organization. The decision making of the company is also in
hand of operational manager of the organization. The various principles o operations
management are discussed below:
Reality: The organization should focus on the problem that the organization is facing in
order to find the solution of the problem. In relation to Unilever the partitions manager of the
organization takes care about the issue and not the techniques so as to gain universal solution of
the problem.
Organization: It is important for Unilever to take care of all the interconnected activities.
It is seen that there is need to consistently manage the operations in order to achieve goals and
objectives in an effective manner (Fettermann and et.al., 2018).
Fundamentals: The operations manager of the organization has to comply with all the
requirements that are fundamental to organization. It is seen that Unilever takes care of all the
fundamental activities in order to achieve goals and objectives in an effective manner.
Variance: The manager of Unilever manages the variance and takes effective decisions
that helps the organization to fill the gaps. It is beneficial for the organization to do the same as it
helps to minimize the wastage.
Change: It is important to note that Unilever keeps track on the changes taking place in
market (Slack and Brandon-Jones, 2018). It helps the organization to serve the customers with
quality goods and services and achieve all the targets.
All these principles are used by Unilever in order to achieve the goals and objectives in
an effective manner. An organization must follow all the principles in an effective manner to
satisfy the customers. Each and every organization wants to reduce the defects in the process of
manufacturing. For this reason, six sigma is used by Unilever.
Six Sigma
5
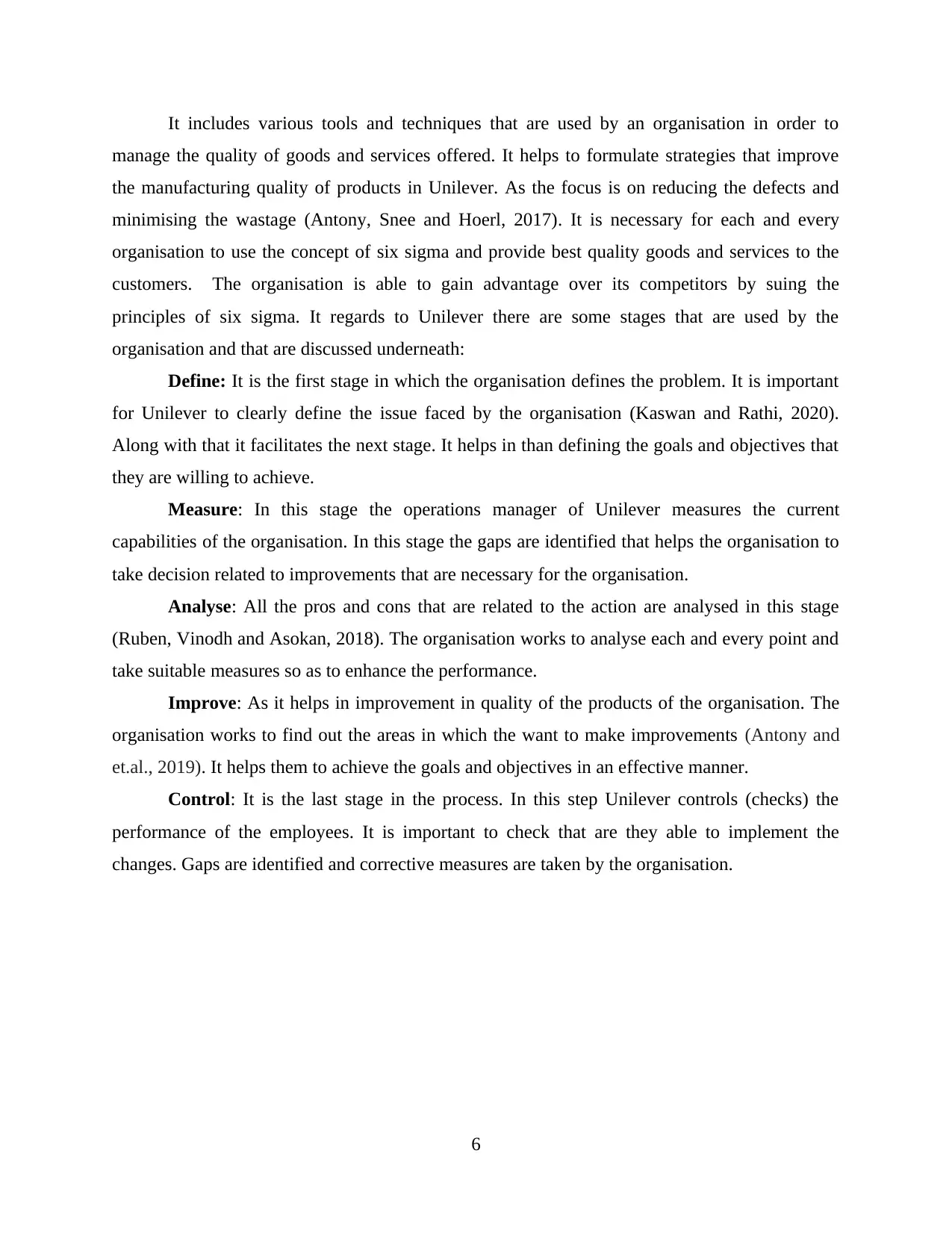
It includes various tools and techniques that are used by an organisation in order to
manage the quality of goods and services offered. It helps to formulate strategies that improve
the manufacturing quality of products in Unilever. As the focus is on reducing the defects and
minimising the wastage (Antony, Snee and Hoerl, 2017). It is necessary for each and every
organisation to use the concept of six sigma and provide best quality goods and services to the
customers. The organisation is able to gain advantage over its competitors by suing the
principles of six sigma. It regards to Unilever there are some stages that are used by the
organisation and that are discussed underneath:
Define: It is the first stage in which the organisation defines the problem. It is important
for Unilever to clearly define the issue faced by the organisation (Kaswan and Rathi, 2020).
Along with that it facilitates the next stage. It helps in than defining the goals and objectives that
they are willing to achieve.
Measure: In this stage the operations manager of Unilever measures the current
capabilities of the organisation. In this stage the gaps are identified that helps the organisation to
take decision related to improvements that are necessary for the organisation.
Analyse: All the pros and cons that are related to the action are analysed in this stage
(Ruben, Vinodh and Asokan, 2018). The organisation works to analyse each and every point and
take suitable measures so as to enhance the performance.
Improve: As it helps in improvement in quality of the products of the organisation. The
organisation works to find out the areas in which the want to make improvements (Antony and
et.al., 2019). It helps them to achieve the goals and objectives in an effective manner.
Control: It is the last stage in the process. In this step Unilever controls (checks) the
performance of the employees. It is important to check that are they able to implement the
changes. Gaps are identified and corrective measures are taken by the organisation.
6
manage the quality of goods and services offered. It helps to formulate strategies that improve
the manufacturing quality of products in Unilever. As the focus is on reducing the defects and
minimising the wastage (Antony, Snee and Hoerl, 2017). It is necessary for each and every
organisation to use the concept of six sigma and provide best quality goods and services to the
customers. The organisation is able to gain advantage over its competitors by suing the
principles of six sigma. It regards to Unilever there are some stages that are used by the
organisation and that are discussed underneath:
Define: It is the first stage in which the organisation defines the problem. It is important
for Unilever to clearly define the issue faced by the organisation (Kaswan and Rathi, 2020).
Along with that it facilitates the next stage. It helps in than defining the goals and objectives that
they are willing to achieve.
Measure: In this stage the operations manager of Unilever measures the current
capabilities of the organisation. In this stage the gaps are identified that helps the organisation to
take decision related to improvements that are necessary for the organisation.
Analyse: All the pros and cons that are related to the action are analysed in this stage
(Ruben, Vinodh and Asokan, 2018). The organisation works to analyse each and every point and
take suitable measures so as to enhance the performance.
Improve: As it helps in improvement in quality of the products of the organisation. The
organisation works to find out the areas in which the want to make improvements (Antony and
et.al., 2019). It helps them to achieve the goals and objectives in an effective manner.
Control: It is the last stage in the process. In this step Unilever controls (checks) the
performance of the employees. It is important to check that are they able to implement the
changes. Gaps are identified and corrective measures are taken by the organisation.
6
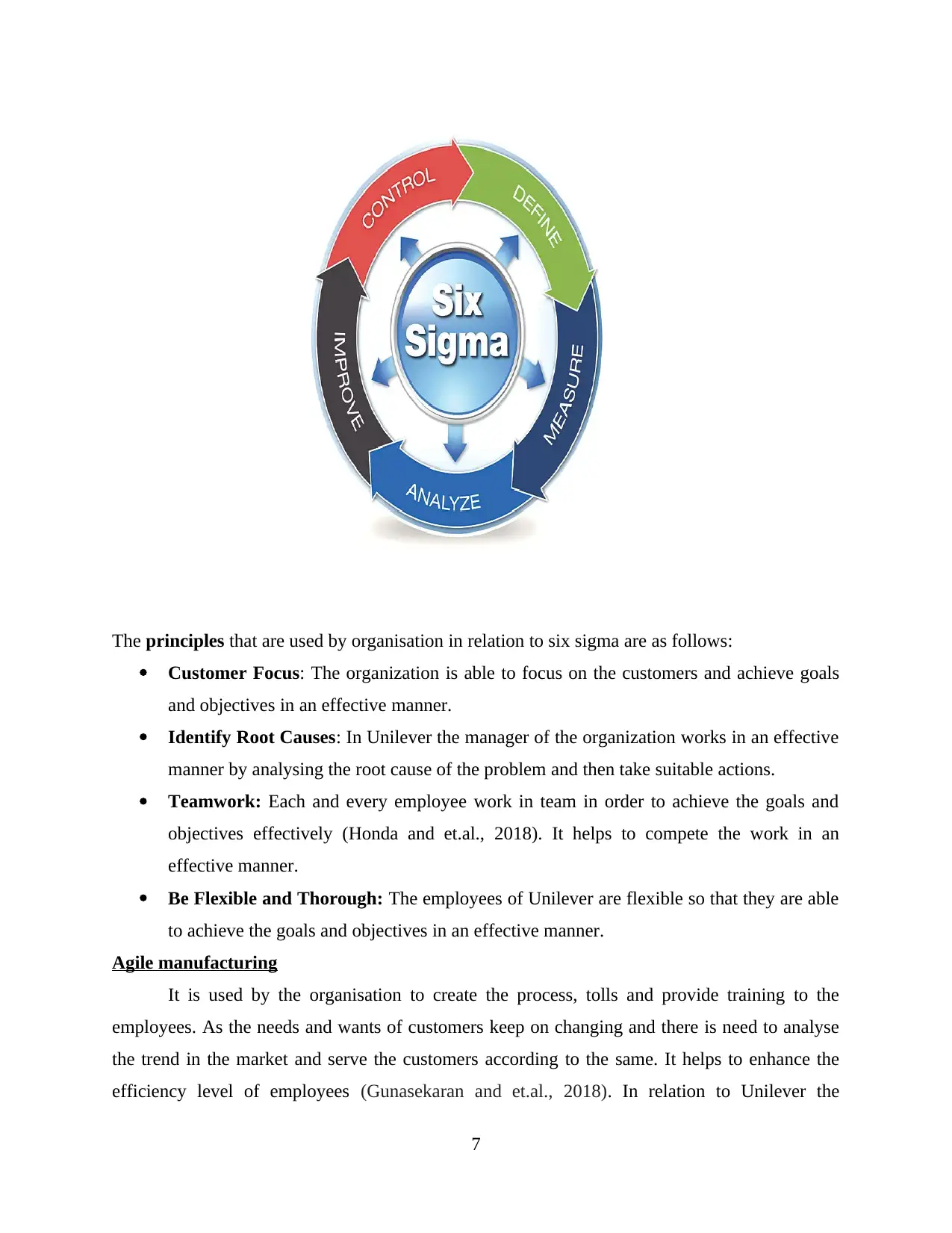
The principles that are used by organisation in relation to six sigma are as follows:
Customer Focus: The organization is able to focus on the customers and achieve goals
and objectives in an effective manner.
Identify Root Causes: In Unilever the manager of the organization works in an effective
manner by analysing the root cause of the problem and then take suitable actions.
Teamwork: Each and every employee work in team in order to achieve the goals and
objectives effectively (Honda and et.al., 2018). It helps to compete the work in an
effective manner.
Be Flexible and Thorough: The employees of Unilever are flexible so that they are able
to achieve the goals and objectives in an effective manner.
Agile manufacturing
It is used by the organisation to create the process, tolls and provide training to the
employees. As the needs and wants of customers keep on changing and there is need to analyse
the trend in the market and serve the customers according to the same. It helps to enhance the
efficiency level of employees (Gunasekaran and et.al., 2018). In relation to Unilever the
7
Customer Focus: The organization is able to focus on the customers and achieve goals
and objectives in an effective manner.
Identify Root Causes: In Unilever the manager of the organization works in an effective
manner by analysing the root cause of the problem and then take suitable actions.
Teamwork: Each and every employee work in team in order to achieve the goals and
objectives effectively (Honda and et.al., 2018). It helps to compete the work in an
effective manner.
Be Flexible and Thorough: The employees of Unilever are flexible so that they are able
to achieve the goals and objectives in an effective manner.
Agile manufacturing
It is used by the organisation to create the process, tolls and provide training to the
employees. As the needs and wants of customers keep on changing and there is need to analyse
the trend in the market and serve the customers according to the same. It helps to enhance the
efficiency level of employees (Gunasekaran and et.al., 2018). In relation to Unilever the
7
Paraphrase This Document
Need a fresh take? Get an instant paraphrase of this document with our AI Paraphraser
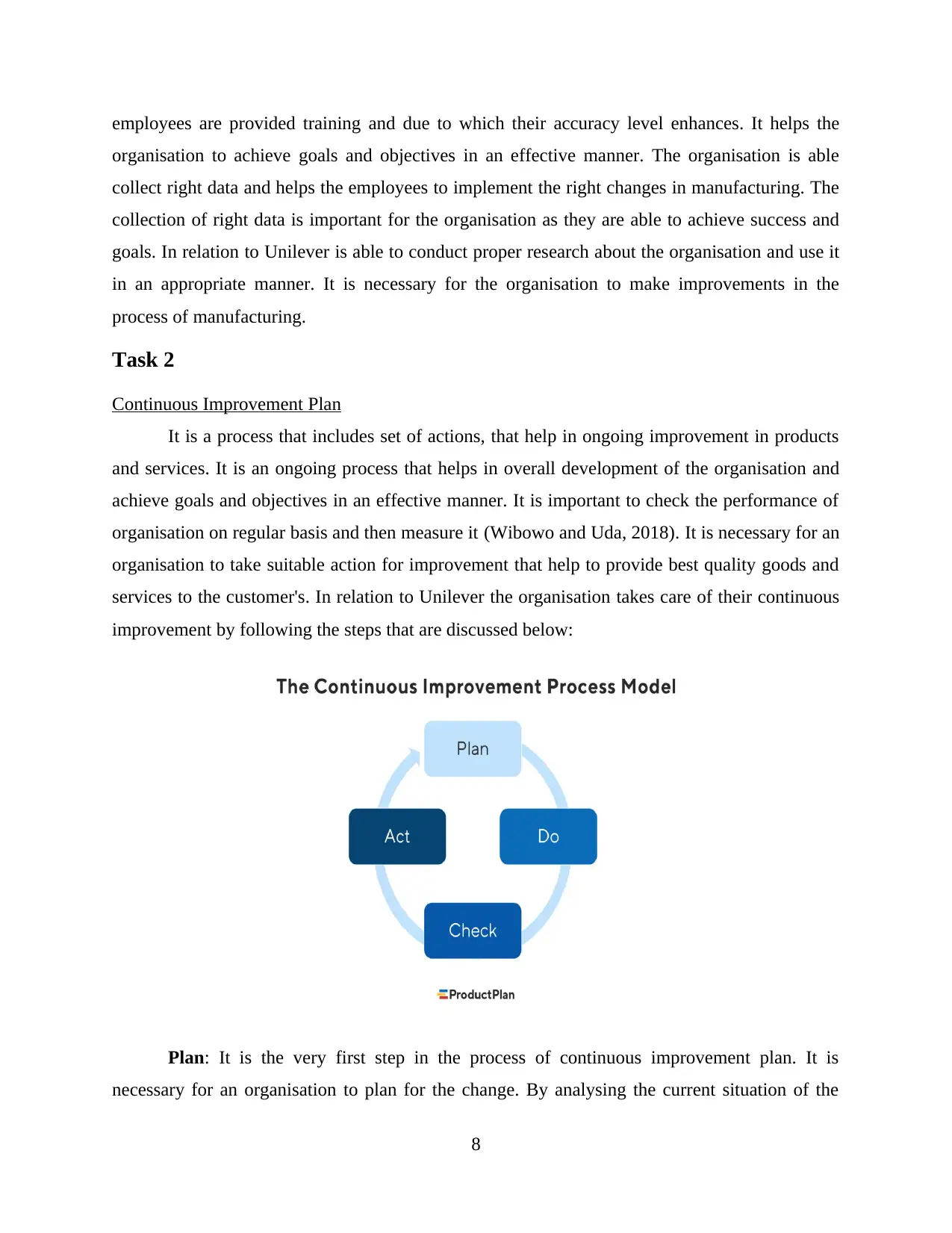
employees are provided training and due to which their accuracy level enhances. It helps the
organisation to achieve goals and objectives in an effective manner. The organisation is able
collect right data and helps the employees to implement the right changes in manufacturing. The
collection of right data is important for the organisation as they are able to achieve success and
goals. In relation to Unilever is able to conduct proper research about the organisation and use it
in an appropriate manner. It is necessary for the organisation to make improvements in the
process of manufacturing.
Task 2
Continuous Improvement Plan
It is a process that includes set of actions, that help in ongoing improvement in products
and services. It is an ongoing process that helps in overall development of the organisation and
achieve goals and objectives in an effective manner. It is important to check the performance of
organisation on regular basis and then measure it (Wibowo and Uda, 2018). It is necessary for an
organisation to take suitable action for improvement that help to provide best quality goods and
services to the customer's. In relation to Unilever the organisation takes care of their continuous
improvement by following the steps that are discussed below:
Plan: It is the very first step in the process of continuous improvement plan. It is
necessary for an organisation to plan for the change. By analysing the current situation of the
8
organisation to achieve goals and objectives in an effective manner. The organisation is able
collect right data and helps the employees to implement the right changes in manufacturing. The
collection of right data is important for the organisation as they are able to achieve success and
goals. In relation to Unilever is able to conduct proper research about the organisation and use it
in an appropriate manner. It is necessary for the organisation to make improvements in the
process of manufacturing.
Task 2
Continuous Improvement Plan
It is a process that includes set of actions, that help in ongoing improvement in products
and services. It is an ongoing process that helps in overall development of the organisation and
achieve goals and objectives in an effective manner. It is important to check the performance of
organisation on regular basis and then measure it (Wibowo and Uda, 2018). It is necessary for an
organisation to take suitable action for improvement that help to provide best quality goods and
services to the customer's. In relation to Unilever the organisation takes care of their continuous
improvement by following the steps that are discussed below:
Plan: It is the very first step in the process of continuous improvement plan. It is
necessary for an organisation to plan for the change. By analysing the current situation of the
8
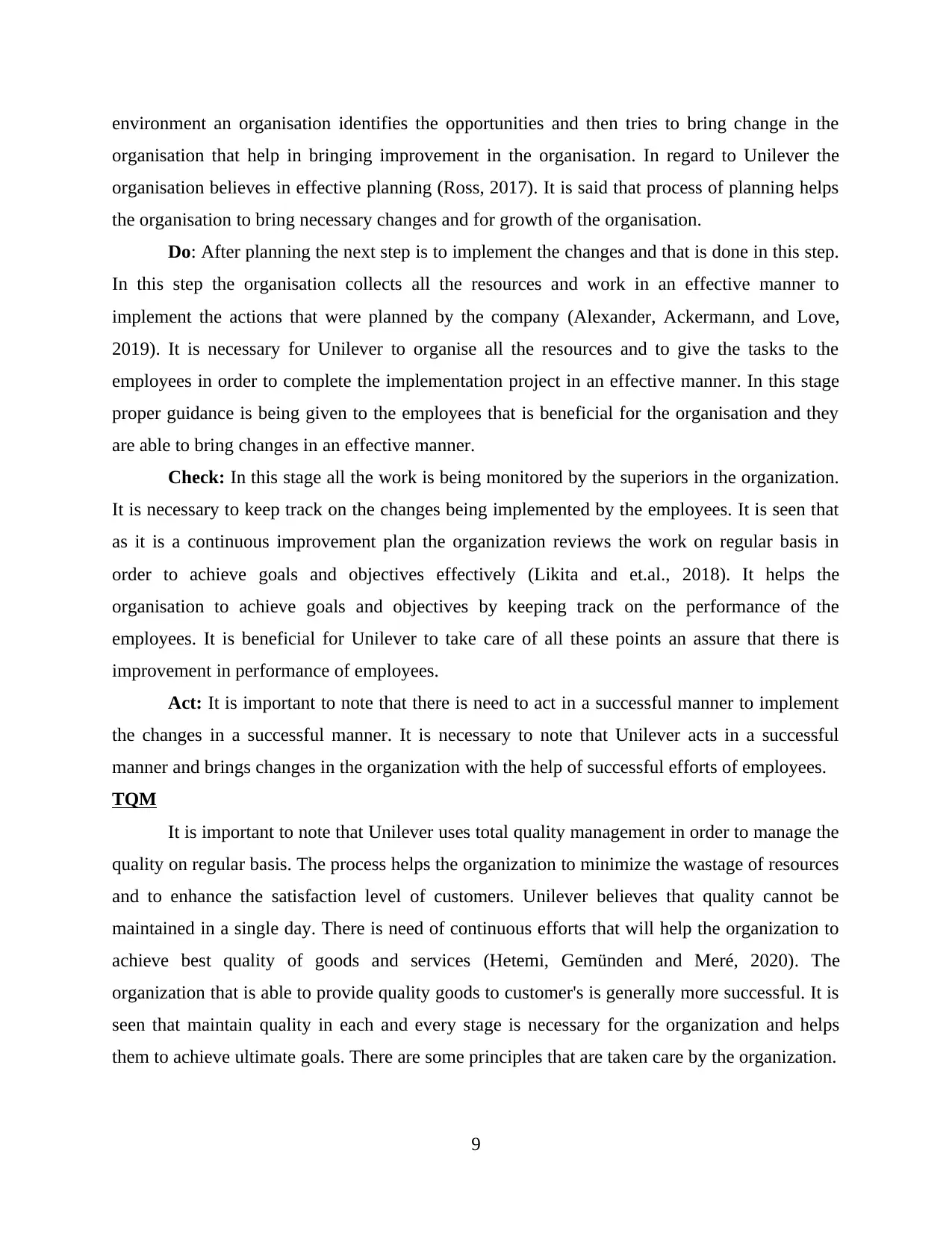
environment an organisation identifies the opportunities and then tries to bring change in the
organisation that help in bringing improvement in the organisation. In regard to Unilever the
organisation believes in effective planning (Ross, 2017). It is said that process of planning helps
the organisation to bring necessary changes and for growth of the organisation.
Do: After planning the next step is to implement the changes and that is done in this step.
In this step the organisation collects all the resources and work in an effective manner to
implement the actions that were planned by the company (Alexander, Ackermann, and Love,
2019). It is necessary for Unilever to organise all the resources and to give the tasks to the
employees in order to complete the implementation project in an effective manner. In this stage
proper guidance is being given to the employees that is beneficial for the organisation and they
are able to bring changes in an effective manner.
Check: In this stage all the work is being monitored by the superiors in the organization.
It is necessary to keep track on the changes being implemented by the employees. It is seen that
as it is a continuous improvement plan the organization reviews the work on regular basis in
order to achieve goals and objectives effectively (Likita and et.al., 2018). It helps the
organisation to achieve goals and objectives by keeping track on the performance of the
employees. It is beneficial for Unilever to take care of all these points an assure that there is
improvement in performance of employees.
Act: It is important to note that there is need to act in a successful manner to implement
the changes in a successful manner. It is necessary to note that Unilever acts in a successful
manner and brings changes in the organization with the help of successful efforts of employees.
TQM
It is important to note that Unilever uses total quality management in order to manage the
quality on regular basis. The process helps the organization to minimize the wastage of resources
and to enhance the satisfaction level of customers. Unilever believes that quality cannot be
maintained in a single day. There is need of continuous efforts that will help the organization to
achieve best quality of goods and services (Hetemi, Gemünden and Meré, 2020). The
organization that is able to provide quality goods to customer's is generally more successful. It is
seen that maintain quality in each and every stage is necessary for the organization and helps
them to achieve ultimate goals. There are some principles that are taken care by the organization.
9
organisation that help in bringing improvement in the organisation. In regard to Unilever the
organisation believes in effective planning (Ross, 2017). It is said that process of planning helps
the organisation to bring necessary changes and for growth of the organisation.
Do: After planning the next step is to implement the changes and that is done in this step.
In this step the organisation collects all the resources and work in an effective manner to
implement the actions that were planned by the company (Alexander, Ackermann, and Love,
2019). It is necessary for Unilever to organise all the resources and to give the tasks to the
employees in order to complete the implementation project in an effective manner. In this stage
proper guidance is being given to the employees that is beneficial for the organisation and they
are able to bring changes in an effective manner.
Check: In this stage all the work is being monitored by the superiors in the organization.
It is necessary to keep track on the changes being implemented by the employees. It is seen that
as it is a continuous improvement plan the organization reviews the work on regular basis in
order to achieve goals and objectives effectively (Likita and et.al., 2018). It helps the
organisation to achieve goals and objectives by keeping track on the performance of the
employees. It is beneficial for Unilever to take care of all these points an assure that there is
improvement in performance of employees.
Act: It is important to note that there is need to act in a successful manner to implement
the changes in a successful manner. It is necessary to note that Unilever acts in a successful
manner and brings changes in the organization with the help of successful efforts of employees.
TQM
It is important to note that Unilever uses total quality management in order to manage the
quality on regular basis. The process helps the organization to minimize the wastage of resources
and to enhance the satisfaction level of customers. Unilever believes that quality cannot be
maintained in a single day. There is need of continuous efforts that will help the organization to
achieve best quality of goods and services (Hetemi, Gemünden and Meré, 2020). The
organization that is able to provide quality goods to customer's is generally more successful. It is
seen that maintain quality in each and every stage is necessary for the organization and helps
them to achieve ultimate goals. There are some principles that are taken care by the organization.
9
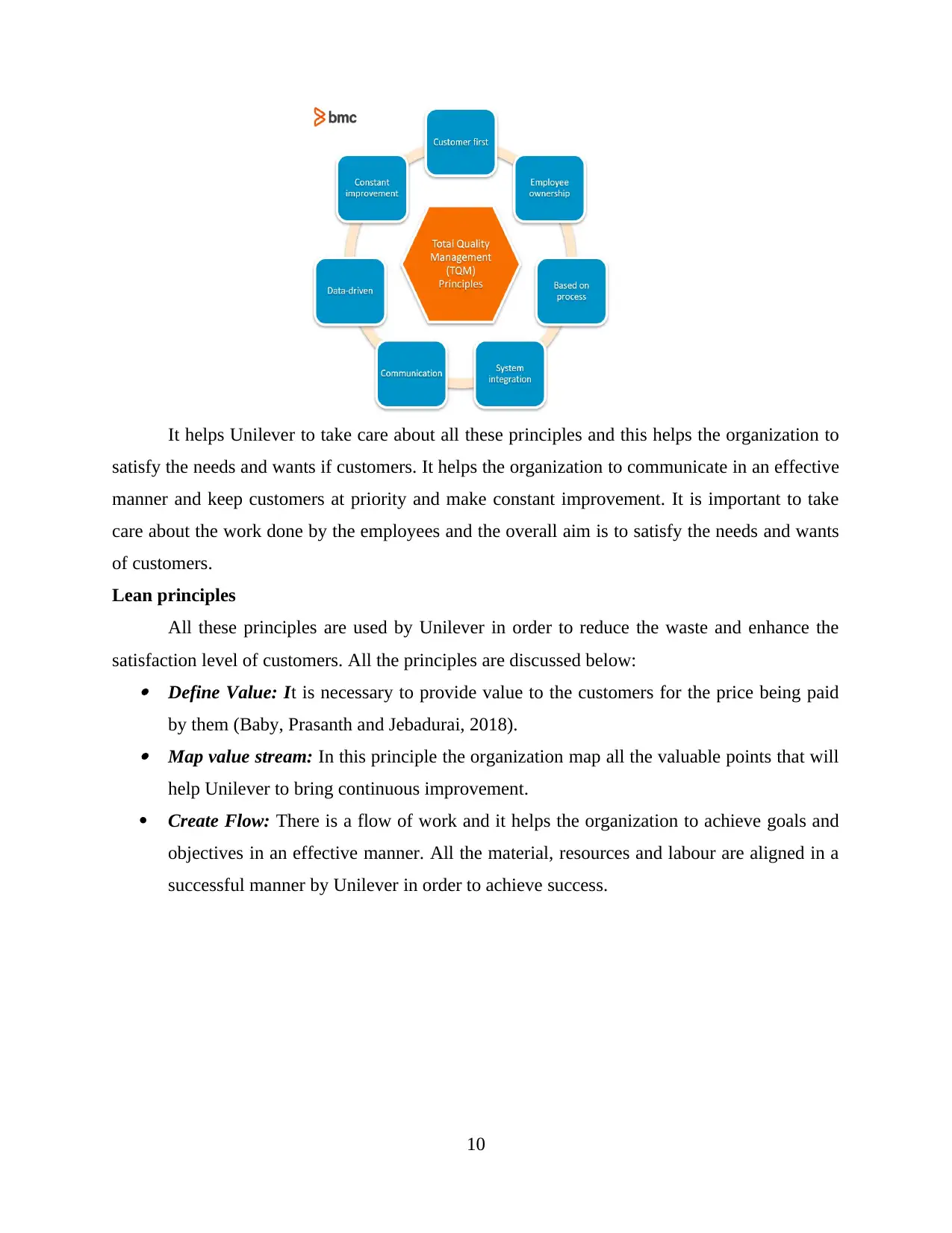
It helps Unilever to take care about all these principles and this helps the organization to
satisfy the needs and wants if customers. It helps the organization to communicate in an effective
manner and keep customers at priority and make constant improvement. It is important to take
care about the work done by the employees and the overall aim is to satisfy the needs and wants
of customers.
Lean principles
All these principles are used by Unilever in order to reduce the waste and enhance the
satisfaction level of customers. All the principles are discussed below: Define Value: It is necessary to provide value to the customers for the price being paid
by them (Baby, Prasanth and Jebadurai, 2018). Map value stream: In this principle the organization map all the valuable points that will
help Unilever to bring continuous improvement.
Create Flow: There is a flow of work and it helps the organization to achieve goals and
objectives in an effective manner. All the material, resources and labour are aligned in a
successful manner by Unilever in order to achieve success.
10
satisfy the needs and wants if customers. It helps the organization to communicate in an effective
manner and keep customers at priority and make constant improvement. It is important to take
care about the work done by the employees and the overall aim is to satisfy the needs and wants
of customers.
Lean principles
All these principles are used by Unilever in order to reduce the waste and enhance the
satisfaction level of customers. All the principles are discussed below: Define Value: It is necessary to provide value to the customers for the price being paid
by them (Baby, Prasanth and Jebadurai, 2018). Map value stream: In this principle the organization map all the valuable points that will
help Unilever to bring continuous improvement.
Create Flow: There is a flow of work and it helps the organization to achieve goals and
objectives in an effective manner. All the material, resources and labour are aligned in a
successful manner by Unilever in order to achieve success.
10
Secure Best Marks with AI Grader
Need help grading? Try our AI Grader for instant feedback on your assignments.
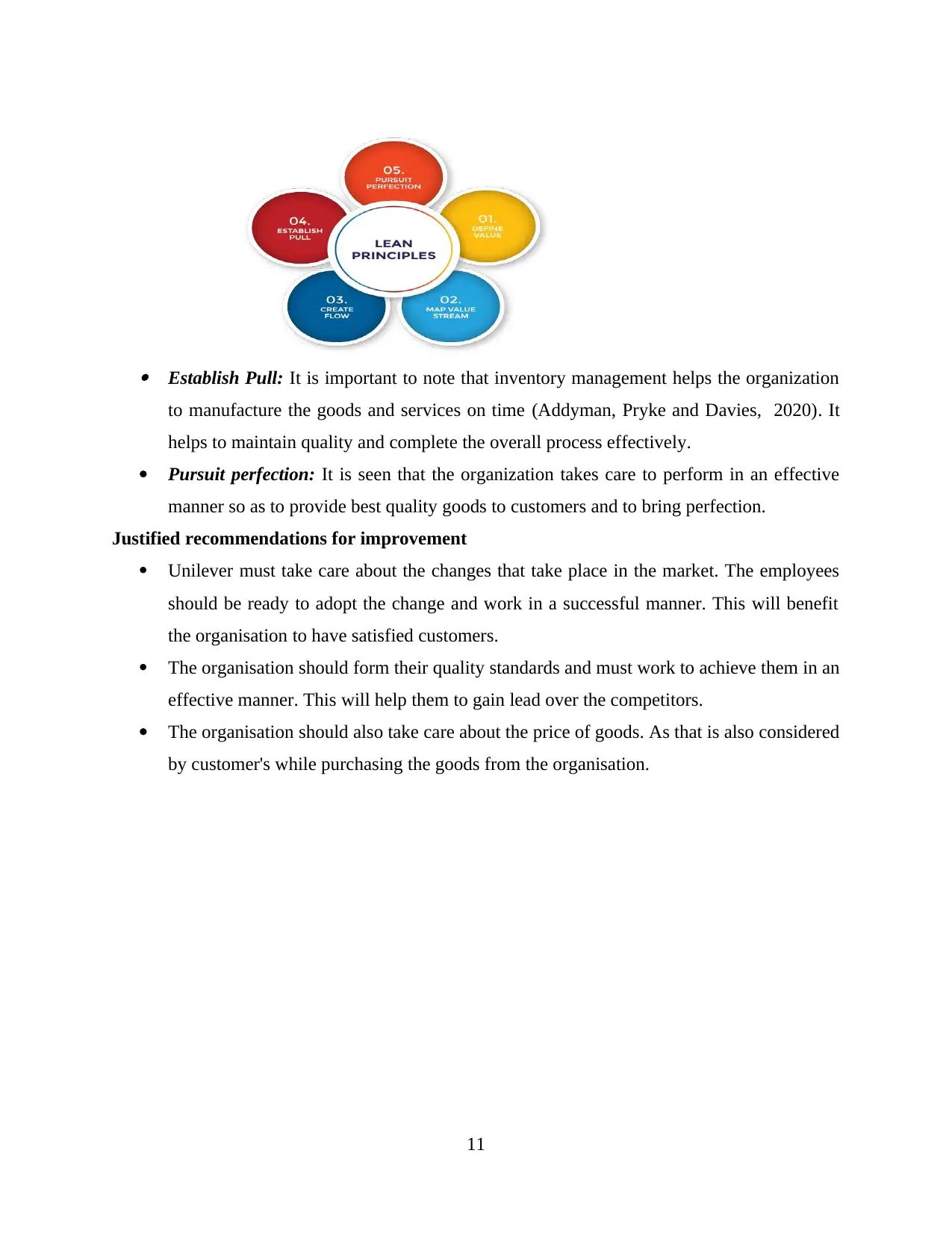
Establish Pull: It is important to note that inventory management helps the organization
to manufacture the goods and services on time (Addyman, Pryke and Davies, 2020). It
helps to maintain quality and complete the overall process effectively.
Pursuit perfection: It is seen that the organization takes care to perform in an effective
manner so as to provide best quality goods to customers and to bring perfection.
Justified recommendations for improvement
Unilever must take care about the changes that take place in the market. The employees
should be ready to adopt the change and work in a successful manner. This will benefit
the organisation to have satisfied customers.
The organisation should form their quality standards and must work to achieve them in an
effective manner. This will help them to gain lead over the competitors.
The organisation should also take care about the price of goods. As that is also considered
by customer's while purchasing the goods from the organisation.
11
to manufacture the goods and services on time (Addyman, Pryke and Davies, 2020). It
helps to maintain quality and complete the overall process effectively.
Pursuit perfection: It is seen that the organization takes care to perform in an effective
manner so as to provide best quality goods to customers and to bring perfection.
Justified recommendations for improvement
Unilever must take care about the changes that take place in the market. The employees
should be ready to adopt the change and work in a successful manner. This will benefit
the organisation to have satisfied customers.
The organisation should form their quality standards and must work to achieve them in an
effective manner. This will help them to gain lead over the competitors.
The organisation should also take care about the price of goods. As that is also considered
by customer's while purchasing the goods from the organisation.
11
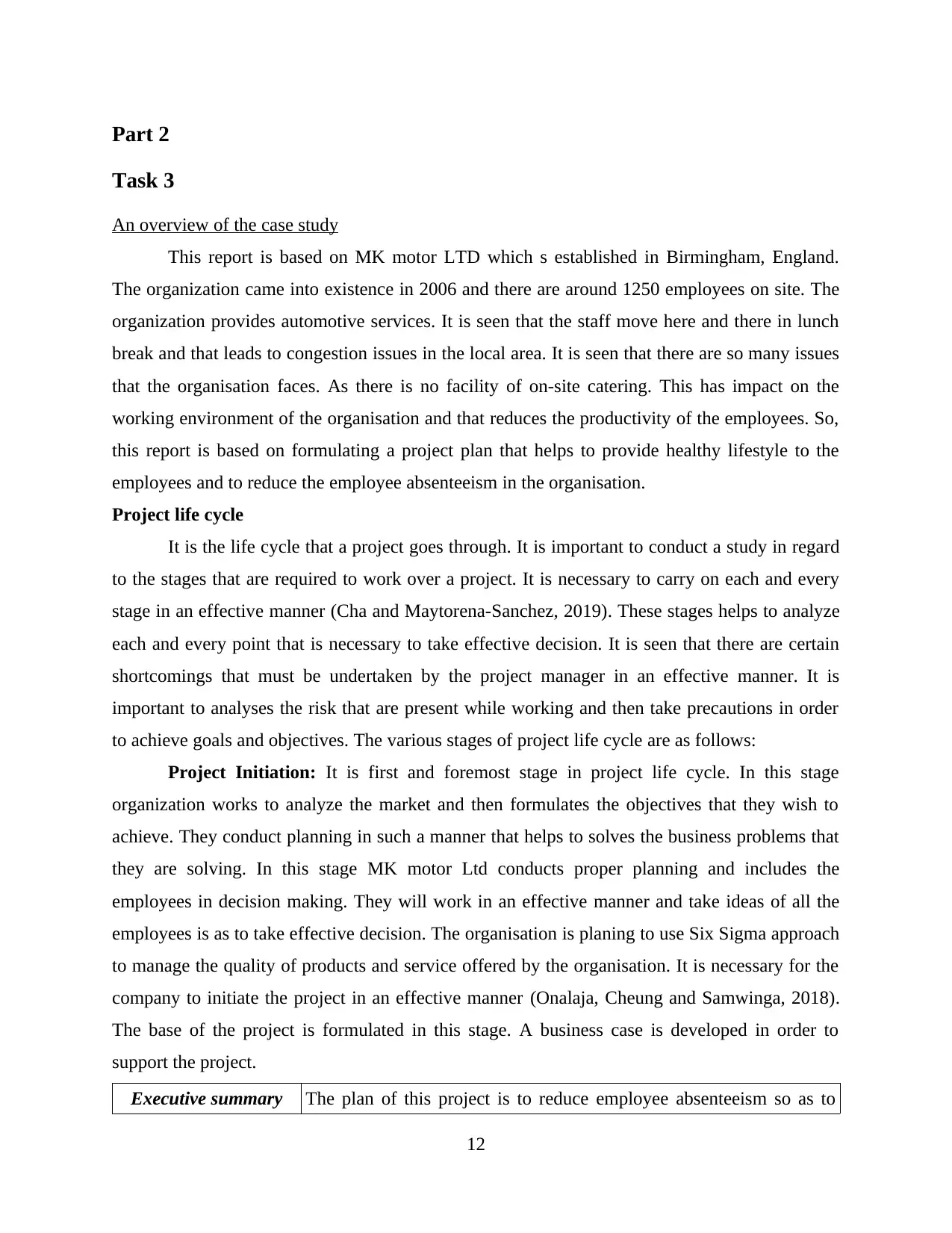
Part 2
Task 3
An overview of the case study
This report is based on MK motor LTD which s established in Birmingham, England.
The organization came into existence in 2006 and there are around 1250 employees on site. The
organization provides automotive services. It is seen that the staff move here and there in lunch
break and that leads to congestion issues in the local area. It is seen that there are so many issues
that the organisation faces. As there is no facility of on-site catering. This has impact on the
working environment of the organisation and that reduces the productivity of the employees. So,
this report is based on formulating a project plan that helps to provide healthy lifestyle to the
employees and to reduce the employee absenteeism in the organisation.
Project life cycle
It is the life cycle that a project goes through. It is important to conduct a study in regard
to the stages that are required to work over a project. It is necessary to carry on each and every
stage in an effective manner (Cha and Maytorena-Sanchez, 2019). These stages helps to analyze
each and every point that is necessary to take effective decision. It is seen that there are certain
shortcomings that must be undertaken by the project manager in an effective manner. It is
important to analyses the risk that are present while working and then take precautions in order
to achieve goals and objectives. The various stages of project life cycle are as follows:
Project Initiation: It is first and foremost stage in project life cycle. In this stage
organization works to analyze the market and then formulates the objectives that they wish to
achieve. They conduct planning in such a manner that helps to solves the business problems that
they are solving. In this stage MK motor Ltd conducts proper planning and includes the
employees in decision making. They will work in an effective manner and take ideas of all the
employees is as to take effective decision. The organisation is planing to use Six Sigma approach
to manage the quality of products and service offered by the organisation. It is necessary for the
company to initiate the project in an effective manner (Onalaja, Cheung and Samwinga, 2018).
The base of the project is formulated in this stage. A business case is developed in order to
support the project.
Executive summary The plan of this project is to reduce employee absenteeism so as to
12
Task 3
An overview of the case study
This report is based on MK motor LTD which s established in Birmingham, England.
The organization came into existence in 2006 and there are around 1250 employees on site. The
organization provides automotive services. It is seen that the staff move here and there in lunch
break and that leads to congestion issues in the local area. It is seen that there are so many issues
that the organisation faces. As there is no facility of on-site catering. This has impact on the
working environment of the organisation and that reduces the productivity of the employees. So,
this report is based on formulating a project plan that helps to provide healthy lifestyle to the
employees and to reduce the employee absenteeism in the organisation.
Project life cycle
It is the life cycle that a project goes through. It is important to conduct a study in regard
to the stages that are required to work over a project. It is necessary to carry on each and every
stage in an effective manner (Cha and Maytorena-Sanchez, 2019). These stages helps to analyze
each and every point that is necessary to take effective decision. It is seen that there are certain
shortcomings that must be undertaken by the project manager in an effective manner. It is
important to analyses the risk that are present while working and then take precautions in order
to achieve goals and objectives. The various stages of project life cycle are as follows:
Project Initiation: It is first and foremost stage in project life cycle. In this stage
organization works to analyze the market and then formulates the objectives that they wish to
achieve. They conduct planning in such a manner that helps to solves the business problems that
they are solving. In this stage MK motor Ltd conducts proper planning and includes the
employees in decision making. They will work in an effective manner and take ideas of all the
employees is as to take effective decision. The organisation is planing to use Six Sigma approach
to manage the quality of products and service offered by the organisation. It is necessary for the
company to initiate the project in an effective manner (Onalaja, Cheung and Samwinga, 2018).
The base of the project is formulated in this stage. A business case is developed in order to
support the project.
Executive summary The plan of this project is to reduce employee absenteeism so as to
12

enhance the productivity of the organisation. Along with that the plan
is to start canteen facility in the organisation so that the employees do
not go out and there is problem of time waste (Orgut and et.al., 2020).
Vision The vision of this project is to serve the employees with best quality
food to maintain the health and hygiene of the employees.
Mission The mission is to create a healthy working environment and start
employee engagement activities that helps to enhance the performance
of employees.
Objectives The objectives of MG Motor Ltd in regard to this project are discussed
below:
Provide in house canteen facility to the employees.
They must provide healthy working environment to the
employees.
To start employee engagement activities to keep employees for
longer duration of time in the organisation.
Opportunity The organisation will identify the opportunities that are present. It is
seen that with help updated technology the organisation is able to
monitor the performance of employees and help to provide them good
working environment.
Improvement The task is to improve the working environment for the employees. To
enhance the facilities provided to them. It will engage the staff in the
organisation and will help the achieve goals and objectives in an
effective manner.
Resources required There is need of infrastructure, man power, latest technology, material
for catering facility (Sartal, Martinez-Senra and Cruz-Machado, 2018).
It will help them to start canteen in the organisation. It is important to
analyse all the resources and then gather them in order to achieve the
goals and objectives in an effective manner. The resources will be
optimally used so as to follow the principles of sustainability.
13
is to start canteen facility in the organisation so that the employees do
not go out and there is problem of time waste (Orgut and et.al., 2020).
Vision The vision of this project is to serve the employees with best quality
food to maintain the health and hygiene of the employees.
Mission The mission is to create a healthy working environment and start
employee engagement activities that helps to enhance the performance
of employees.
Objectives The objectives of MG Motor Ltd in regard to this project are discussed
below:
Provide in house canteen facility to the employees.
They must provide healthy working environment to the
employees.
To start employee engagement activities to keep employees for
longer duration of time in the organisation.
Opportunity The organisation will identify the opportunities that are present. It is
seen that with help updated technology the organisation is able to
monitor the performance of employees and help to provide them good
working environment.
Improvement The task is to improve the working environment for the employees. To
enhance the facilities provided to them. It will engage the staff in the
organisation and will help the achieve goals and objectives in an
effective manner.
Resources required There is need of infrastructure, man power, latest technology, material
for catering facility (Sartal, Martinez-Senra and Cruz-Machado, 2018).
It will help them to start canteen in the organisation. It is important to
analyse all the resources and then gather them in order to achieve the
goals and objectives in an effective manner. The resources will be
optimally used so as to follow the principles of sustainability.
13
Paraphrase This Document
Need a fresh take? Get an instant paraphrase of this document with our AI Paraphraser
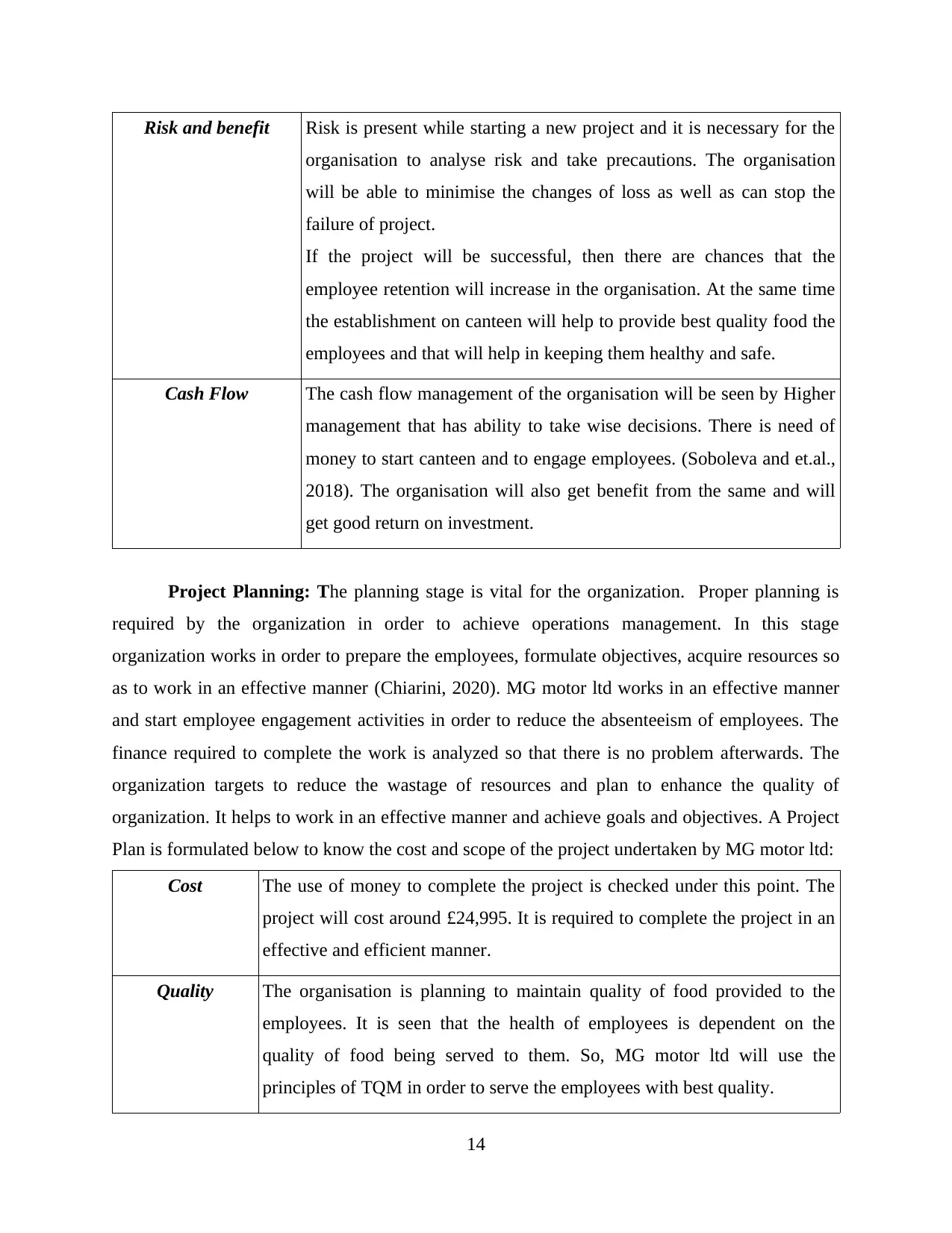
Risk and benefit Risk is present while starting a new project and it is necessary for the
organisation to analyse risk and take precautions. The organisation
will be able to minimise the changes of loss as well as can stop the
failure of project.
If the project will be successful, then there are chances that the
employee retention will increase in the organisation. At the same time
the establishment on canteen will help to provide best quality food the
employees and that will help in keeping them healthy and safe.
Cash Flow The cash flow management of the organisation will be seen by Higher
management that has ability to take wise decisions. There is need of
money to start canteen and to engage employees. (Soboleva and et.al.,
2018). The organisation will also get benefit from the same and will
get good return on investment.
Project Planning: The planning stage is vital for the organization. Proper planning is
required by the organization in order to achieve operations management. In this stage
organization works in order to prepare the employees, formulate objectives, acquire resources so
as to work in an effective manner (Chiarini, 2020). MG motor ltd works in an effective manner
and start employee engagement activities in order to reduce the absenteeism of employees. The
finance required to complete the work is analyzed so that there is no problem afterwards. The
organization targets to reduce the wastage of resources and plan to enhance the quality of
organization. It helps to work in an effective manner and achieve goals and objectives. A Project
Plan is formulated below to know the cost and scope of the project undertaken by MG motor ltd:
Cost The use of money to complete the project is checked under this point. The
project will cost around £24,995. It is required to complete the project in an
effective and efficient manner.
Quality The organisation is planning to maintain quality of food provided to the
employees. It is seen that the health of employees is dependent on the
quality of food being served to them. So, MG motor ltd will use the
principles of TQM in order to serve the employees with best quality.
14
organisation to analyse risk and take precautions. The organisation
will be able to minimise the changes of loss as well as can stop the
failure of project.
If the project will be successful, then there are chances that the
employee retention will increase in the organisation. At the same time
the establishment on canteen will help to provide best quality food the
employees and that will help in keeping them healthy and safe.
Cash Flow The cash flow management of the organisation will be seen by Higher
management that has ability to take wise decisions. There is need of
money to start canteen and to engage employees. (Soboleva and et.al.,
2018). The organisation will also get benefit from the same and will
get good return on investment.
Project Planning: The planning stage is vital for the organization. Proper planning is
required by the organization in order to achieve operations management. In this stage
organization works in order to prepare the employees, formulate objectives, acquire resources so
as to work in an effective manner (Chiarini, 2020). MG motor ltd works in an effective manner
and start employee engagement activities in order to reduce the absenteeism of employees. The
finance required to complete the work is analyzed so that there is no problem afterwards. The
organization targets to reduce the wastage of resources and plan to enhance the quality of
organization. It helps to work in an effective manner and achieve goals and objectives. A Project
Plan is formulated below to know the cost and scope of the project undertaken by MG motor ltd:
Cost The use of money to complete the project is checked under this point. The
project will cost around £24,995. It is required to complete the project in an
effective and efficient manner.
Quality The organisation is planning to maintain quality of food provided to the
employees. It is seen that the health of employees is dependent on the
quality of food being served to them. So, MG motor ltd will use the
principles of TQM in order to serve the employees with best quality.
14
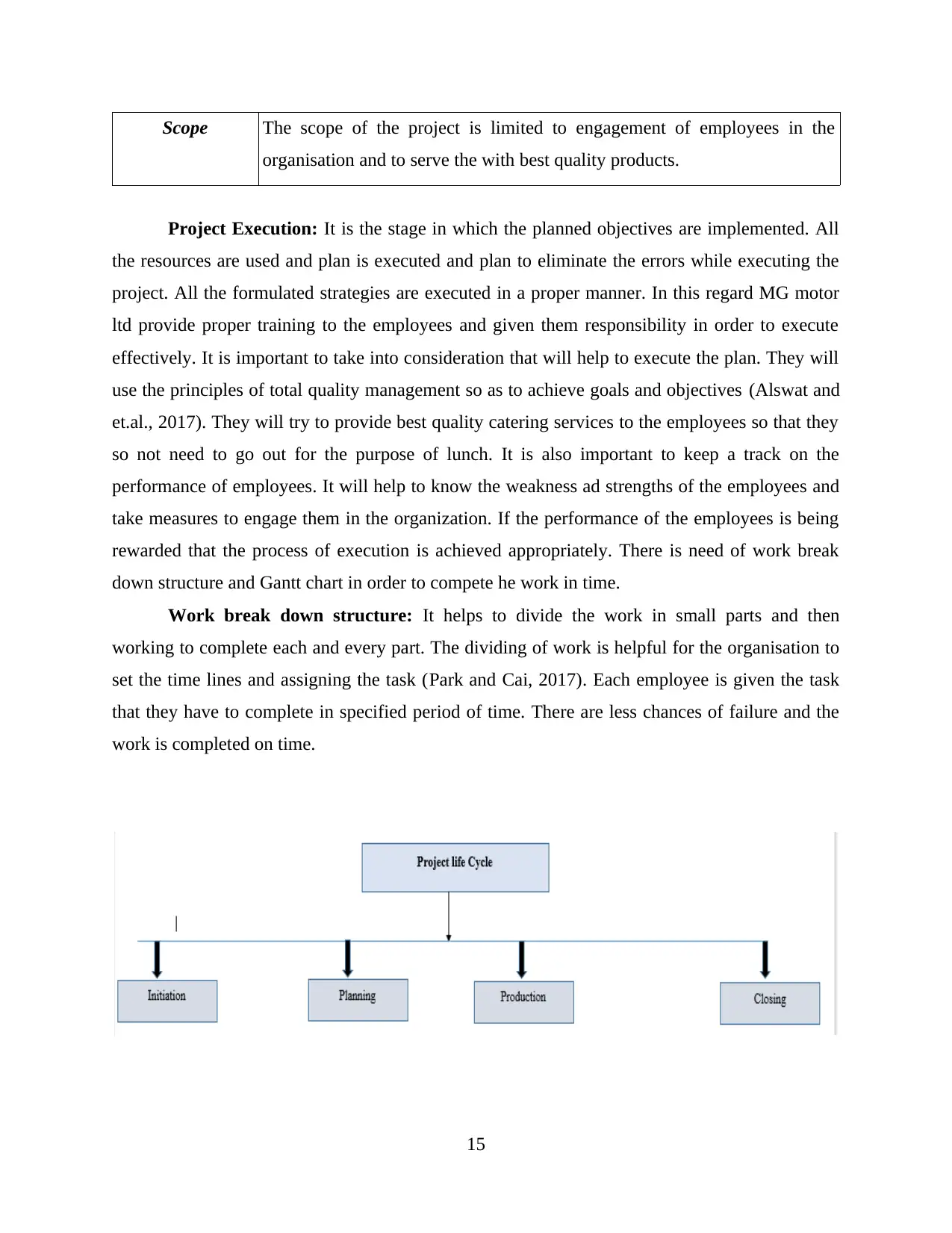
Scope The scope of the project is limited to engagement of employees in the
organisation and to serve the with best quality products.
Project Execution: It is the stage in which the planned objectives are implemented. All
the resources are used and plan is executed and plan to eliminate the errors while executing the
project. All the formulated strategies are executed in a proper manner. In this regard MG motor
ltd provide proper training to the employees and given them responsibility in order to execute
effectively. It is important to take into consideration that will help to execute the plan. They will
use the principles of total quality management so as to achieve goals and objectives (Alswat and
et.al., 2017). They will try to provide best quality catering services to the employees so that they
so not need to go out for the purpose of lunch. It is also important to keep a track on the
performance of employees. It will help to know the weakness ad strengths of the employees and
take measures to engage them in the organization. If the performance of the employees is being
rewarded that the process of execution is achieved appropriately. There is need of work break
down structure and Gantt chart in order to compete he work in time.
Work break down structure: It helps to divide the work in small parts and then
working to complete each and every part. The dividing of work is helpful for the organisation to
set the time lines and assigning the task (Park and Cai, 2017). Each employee is given the task
that they have to complete in specified period of time. There are less chances of failure and the
work is completed on time.
15
organisation and to serve the with best quality products.
Project Execution: It is the stage in which the planned objectives are implemented. All
the resources are used and plan is executed and plan to eliminate the errors while executing the
project. All the formulated strategies are executed in a proper manner. In this regard MG motor
ltd provide proper training to the employees and given them responsibility in order to execute
effectively. It is important to take into consideration that will help to execute the plan. They will
use the principles of total quality management so as to achieve goals and objectives (Alswat and
et.al., 2017). They will try to provide best quality catering services to the employees so that they
so not need to go out for the purpose of lunch. It is also important to keep a track on the
performance of employees. It will help to know the weakness ad strengths of the employees and
take measures to engage them in the organization. If the performance of the employees is being
rewarded that the process of execution is achieved appropriately. There is need of work break
down structure and Gantt chart in order to compete he work in time.
Work break down structure: It helps to divide the work in small parts and then
working to complete each and every part. The dividing of work is helpful for the organisation to
set the time lines and assigning the task (Park and Cai, 2017). Each employee is given the task
that they have to complete in specified period of time. There are less chances of failure and the
work is completed on time.
15
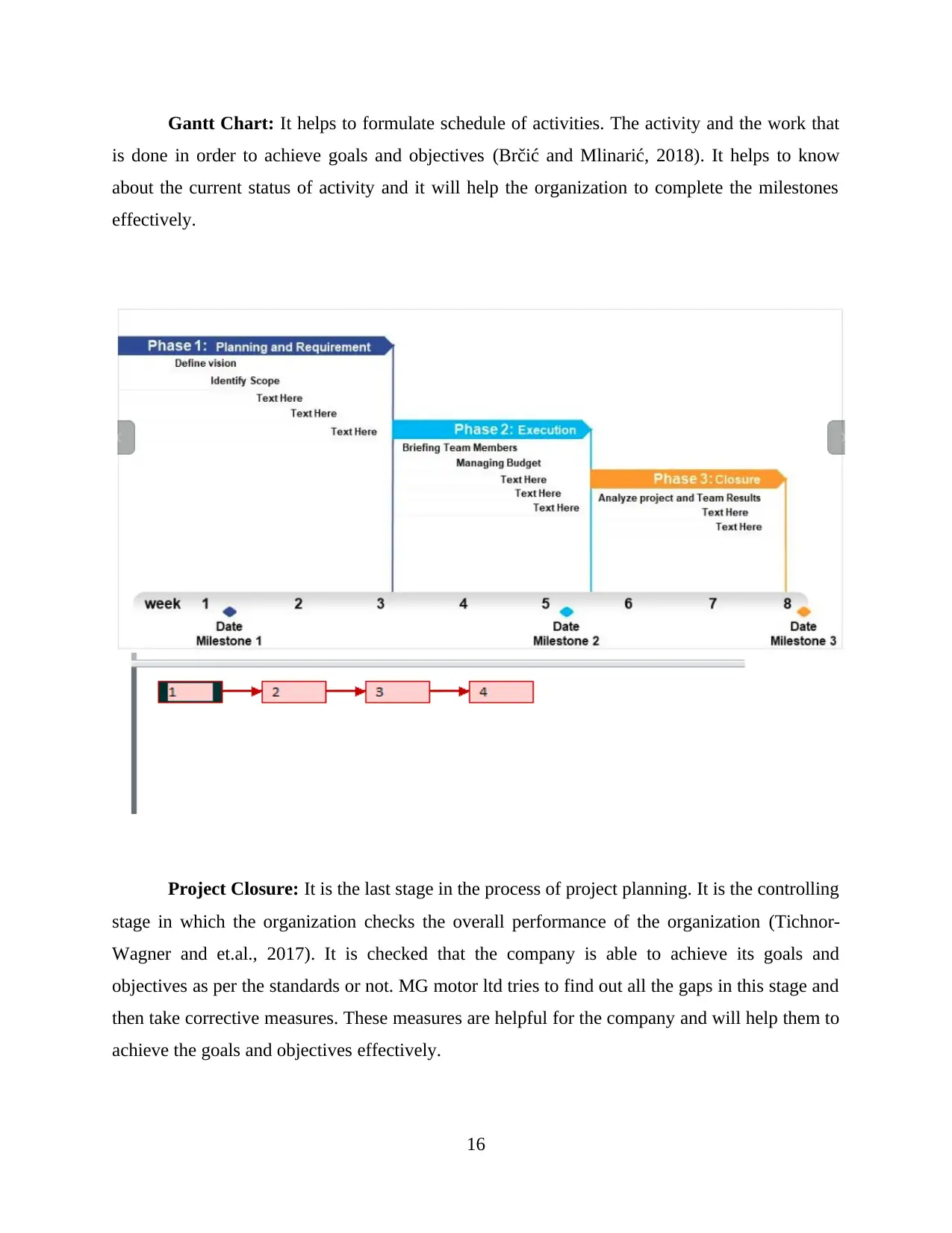
Gantt Chart: It helps to formulate schedule of activities. The activity and the work that
is done in order to achieve goals and objectives (Brčić and Mlinarić, 2018). It helps to know
about the current status of activity and it will help the organization to complete the milestones
effectively.
Project Closure: It is the last stage in the process of project planning. It is the controlling
stage in which the organization checks the overall performance of the organization (Tichnor-
Wagner and et.al., 2017). It is checked that the company is able to achieve its goals and
objectives as per the standards or not. MG motor ltd tries to find out all the gaps in this stage and
then take corrective measures. These measures are helpful for the company and will help them to
achieve the goals and objectives effectively.
16
is done in order to achieve goals and objectives (Brčić and Mlinarić, 2018). It helps to know
about the current status of activity and it will help the organization to complete the milestones
effectively.
Project Closure: It is the last stage in the process of project planning. It is the controlling
stage in which the organization checks the overall performance of the organization (Tichnor-
Wagner and et.al., 2017). It is checked that the company is able to achieve its goals and
objectives as per the standards or not. MG motor ltd tries to find out all the gaps in this stage and
then take corrective measures. These measures are helpful for the company and will help them to
achieve the goals and objectives effectively.
16
Secure Best Marks with AI Grader
Need help grading? Try our AI Grader for instant feedback on your assignments.
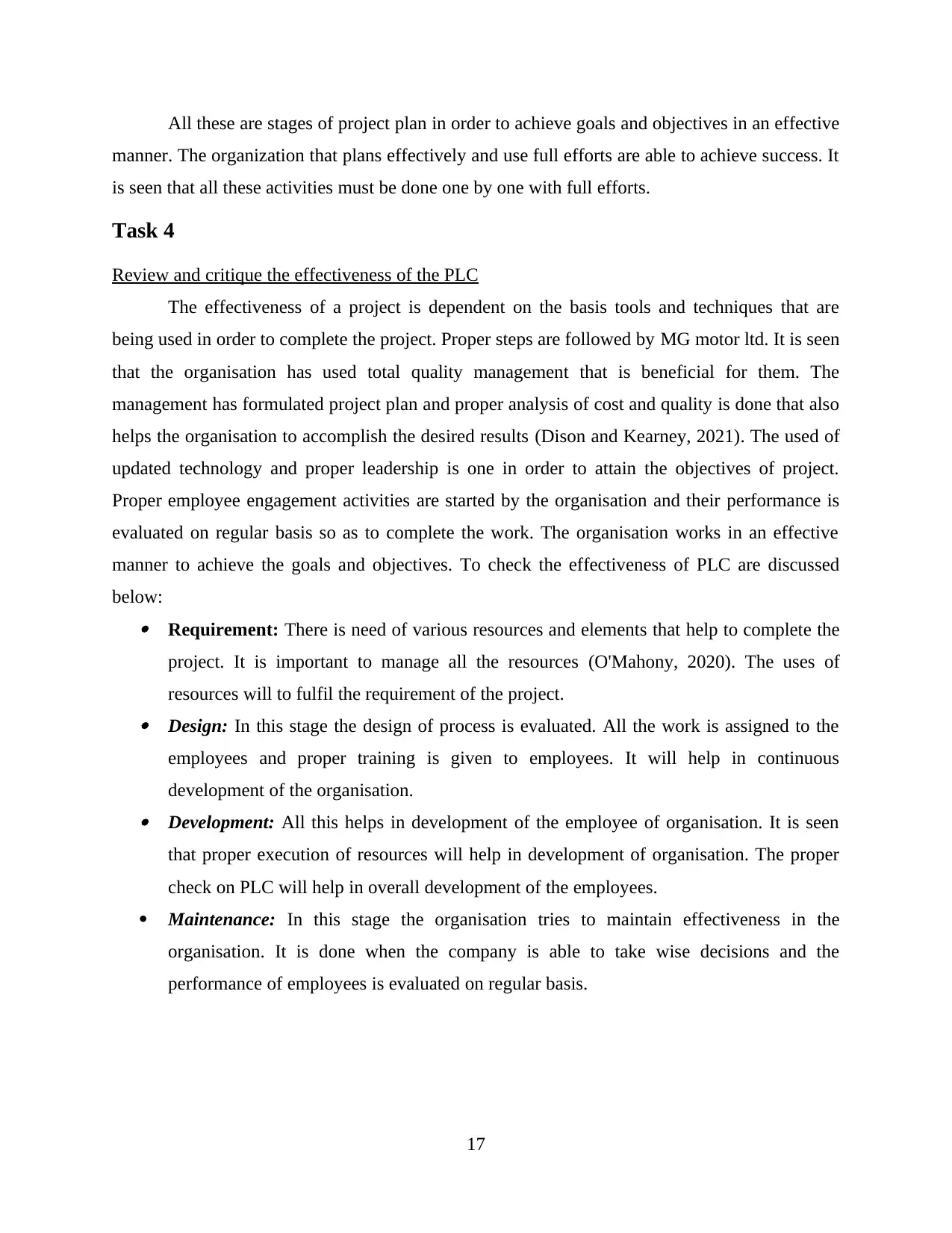
All these are stages of project plan in order to achieve goals and objectives in an effective
manner. The organization that plans effectively and use full efforts are able to achieve success. It
is seen that all these activities must be done one by one with full efforts.
Task 4
Review and critique the effectiveness of the PLC
The effectiveness of a project is dependent on the basis tools and techniques that are
being used in order to complete the project. Proper steps are followed by MG motor ltd. It is seen
that the organisation has used total quality management that is beneficial for them. The
management has formulated project plan and proper analysis of cost and quality is done that also
helps the organisation to accomplish the desired results (Dison and Kearney, 2021). The used of
updated technology and proper leadership is one in order to attain the objectives of project.
Proper employee engagement activities are started by the organisation and their performance is
evaluated on regular basis so as to complete the work. The organisation works in an effective
manner to achieve the goals and objectives. To check the effectiveness of PLC are discussed
below: Requirement: There is need of various resources and elements that help to complete the
project. It is important to manage all the resources (O'Mahony, 2020). The uses of
resources will to fulfil the requirement of the project. Design: In this stage the design of process is evaluated. All the work is assigned to the
employees and proper training is given to employees. It will help in continuous
development of the organisation. Development: All this helps in development of the employee of organisation. It is seen
that proper execution of resources will help in development of organisation. The proper
check on PLC will help in overall development of the employees.
Maintenance: In this stage the organisation tries to maintain effectiveness in the
organisation. It is done when the company is able to take wise decisions and the
performance of employees is evaluated on regular basis.
17
manner. The organization that plans effectively and use full efforts are able to achieve success. It
is seen that all these activities must be done one by one with full efforts.
Task 4
Review and critique the effectiveness of the PLC
The effectiveness of a project is dependent on the basis tools and techniques that are
being used in order to complete the project. Proper steps are followed by MG motor ltd. It is seen
that the organisation has used total quality management that is beneficial for them. The
management has formulated project plan and proper analysis of cost and quality is done that also
helps the organisation to accomplish the desired results (Dison and Kearney, 2021). The used of
updated technology and proper leadership is one in order to attain the objectives of project.
Proper employee engagement activities are started by the organisation and their performance is
evaluated on regular basis so as to complete the work. The organisation works in an effective
manner to achieve the goals and objectives. To check the effectiveness of PLC are discussed
below: Requirement: There is need of various resources and elements that help to complete the
project. It is important to manage all the resources (O'Mahony, 2020). The uses of
resources will to fulfil the requirement of the project. Design: In this stage the design of process is evaluated. All the work is assigned to the
employees and proper training is given to employees. It will help in continuous
development of the organisation. Development: All this helps in development of the employee of organisation. It is seen
that proper execution of resources will help in development of organisation. The proper
check on PLC will help in overall development of the employees.
Maintenance: In this stage the organisation tries to maintain effectiveness in the
organisation. It is done when the company is able to take wise decisions and the
performance of employees is evaluated on regular basis.
17
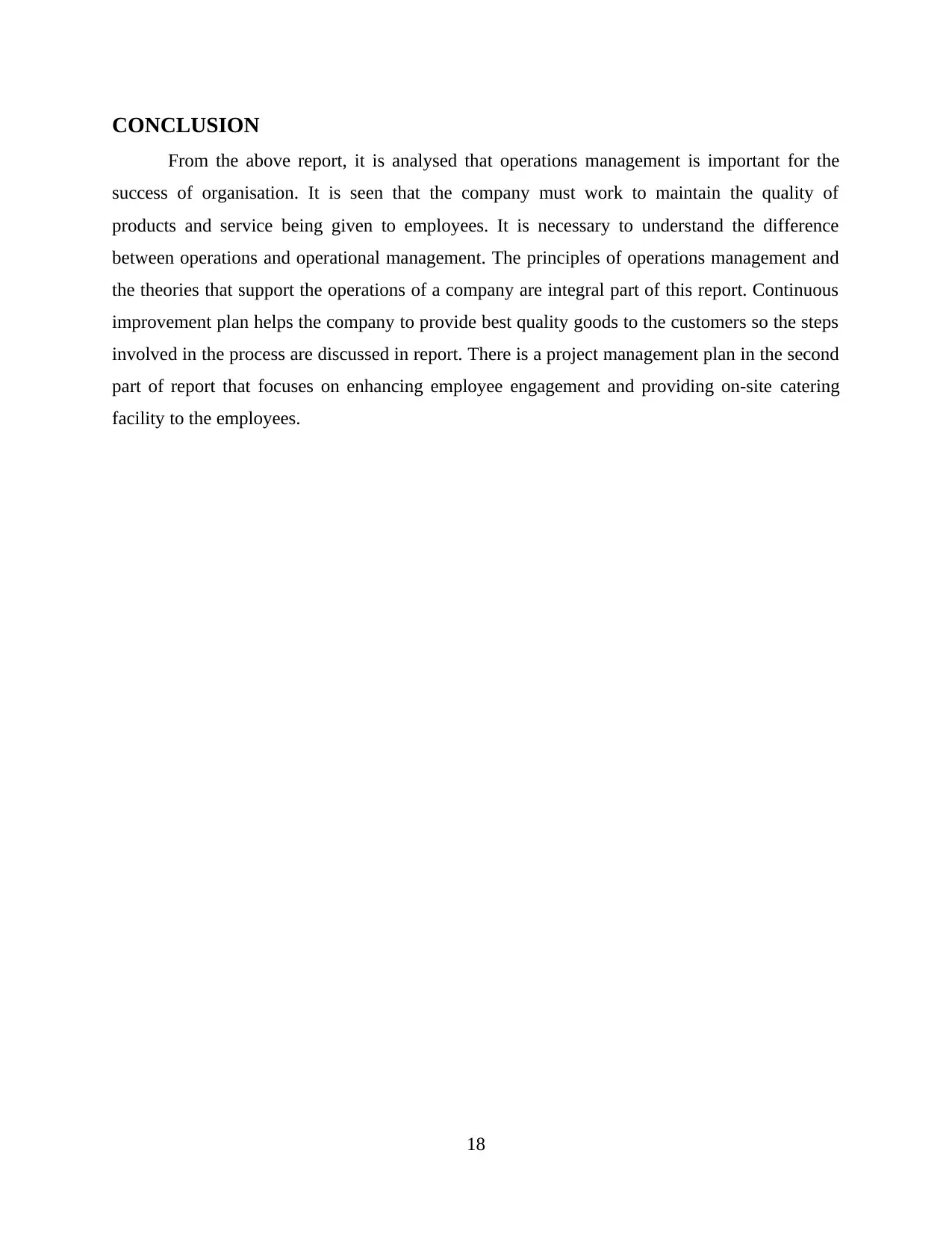
CONCLUSION
From the above report, it is analysed that operations management is important for the
success of organisation. It is seen that the company must work to maintain the quality of
products and service being given to employees. It is necessary to understand the difference
between operations and operational management. The principles of operations management and
the theories that support the operations of a company are integral part of this report. Continuous
improvement plan helps the company to provide best quality goods to the customers so the steps
involved in the process are discussed in report. There is a project management plan in the second
part of report that focuses on enhancing employee engagement and providing on-site catering
facility to the employees.
18
From the above report, it is analysed that operations management is important for the
success of organisation. It is seen that the company must work to maintain the quality of
products and service being given to employees. It is necessary to understand the difference
between operations and operational management. The principles of operations management and
the theories that support the operations of a company are integral part of this report. Continuous
improvement plan helps the company to provide best quality goods to the customers so the steps
involved in the process are discussed in report. There is a project management plan in the second
part of report that focuses on enhancing employee engagement and providing on-site catering
facility to the employees.
18
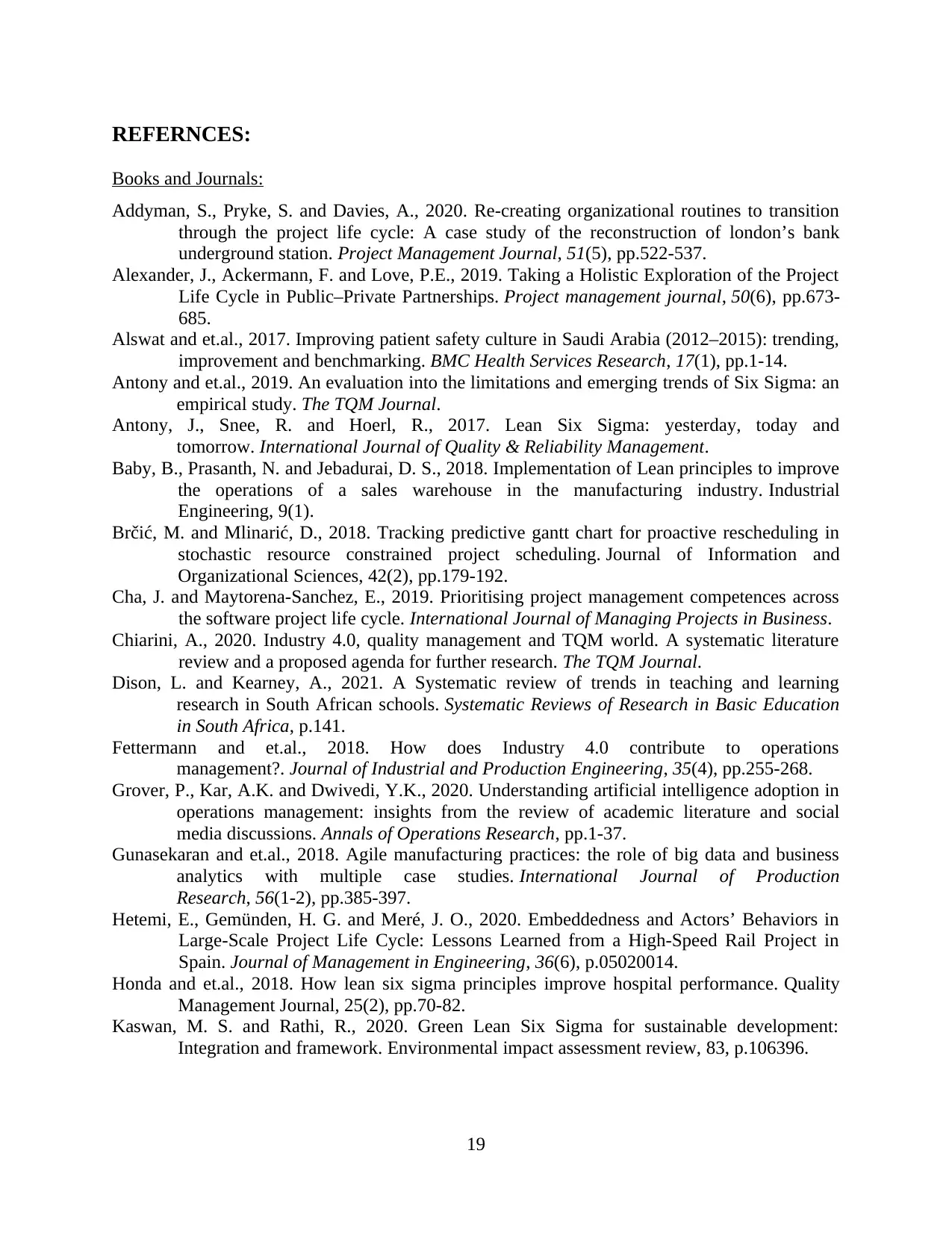
REFERNCES:
Books and Journals:
Addyman, S., Pryke, S. and Davies, A., 2020. Re-creating organizational routines to transition
through the project life cycle: A case study of the reconstruction of london’s bank
underground station. Project Management Journal, 51(5), pp.522-537.
Alexander, J., Ackermann, F. and Love, P.E., 2019. Taking a Holistic Exploration of the Project
Life Cycle in Public–Private Partnerships. Project management journal, 50(6), pp.673-
685.
Alswat and et.al., 2017. Improving patient safety culture in Saudi Arabia (2012–2015): trending,
improvement and benchmarking. BMC Health Services Research, 17(1), pp.1-14.
Antony and et.al., 2019. An evaluation into the limitations and emerging trends of Six Sigma: an
empirical study. The TQM Journal.
Antony, J., Snee, R. and Hoerl, R., 2017. Lean Six Sigma: yesterday, today and
tomorrow. International Journal of Quality & Reliability Management.
Baby, B., Prasanth, N. and Jebadurai, D. S., 2018. Implementation of Lean principles to improve
the operations of a sales warehouse in the manufacturing industry. Industrial
Engineering, 9(1).
Brčić, M. and Mlinarić, D., 2018. Tracking predictive gantt chart for proactive rescheduling in
stochastic resource constrained project scheduling. Journal of Information and
Organizational Sciences, 42(2), pp.179-192.
Cha, J. and Maytorena-Sanchez, E., 2019. Prioritising project management competences across
the software project life cycle. International Journal of Managing Projects in Business.
Chiarini, A., 2020. Industry 4.0, quality management and TQM world. A systematic literature
review and a proposed agenda for further research. The TQM Journal.
Dison, L. and Kearney, A., 2021. A Systematic review of trends in teaching and learning
research in South African schools. Systematic Reviews of Research in Basic Education
in South Africa, p.141.
Fettermann and et.al., 2018. How does Industry 4.0 contribute to operations
management?. Journal of Industrial and Production Engineering, 35(4), pp.255-268.
Grover, P., Kar, A.K. and Dwivedi, Y.K., 2020. Understanding artificial intelligence adoption in
operations management: insights from the review of academic literature and social
media discussions. Annals of Operations Research, pp.1-37.
Gunasekaran and et.al., 2018. Agile manufacturing practices: the role of big data and business
analytics with multiple case studies. International Journal of Production
Research, 56(1-2), pp.385-397.
Hetemi, E., Gemünden, H. G. and Meré, J. O., 2020. Embeddedness and Actors’ Behaviors in
Large-Scale Project Life Cycle: Lessons Learned from a High-Speed Rail Project in
Spain. Journal of Management in Engineering, 36(6), p.05020014.
Honda and et.al., 2018. How lean six sigma principles improve hospital performance. Quality
Management Journal, 25(2), pp.70-82.
Kaswan, M. S. and Rathi, R., 2020. Green Lean Six Sigma for sustainable development:
Integration and framework. Environmental impact assessment review, 83, p.106396.
19
Books and Journals:
Addyman, S., Pryke, S. and Davies, A., 2020. Re-creating organizational routines to transition
through the project life cycle: A case study of the reconstruction of london’s bank
underground station. Project Management Journal, 51(5), pp.522-537.
Alexander, J., Ackermann, F. and Love, P.E., 2019. Taking a Holistic Exploration of the Project
Life Cycle in Public–Private Partnerships. Project management journal, 50(6), pp.673-
685.
Alswat and et.al., 2017. Improving patient safety culture in Saudi Arabia (2012–2015): trending,
improvement and benchmarking. BMC Health Services Research, 17(1), pp.1-14.
Antony and et.al., 2019. An evaluation into the limitations and emerging trends of Six Sigma: an
empirical study. The TQM Journal.
Antony, J., Snee, R. and Hoerl, R., 2017. Lean Six Sigma: yesterday, today and
tomorrow. International Journal of Quality & Reliability Management.
Baby, B., Prasanth, N. and Jebadurai, D. S., 2018. Implementation of Lean principles to improve
the operations of a sales warehouse in the manufacturing industry. Industrial
Engineering, 9(1).
Brčić, M. and Mlinarić, D., 2018. Tracking predictive gantt chart for proactive rescheduling in
stochastic resource constrained project scheduling. Journal of Information and
Organizational Sciences, 42(2), pp.179-192.
Cha, J. and Maytorena-Sanchez, E., 2019. Prioritising project management competences across
the software project life cycle. International Journal of Managing Projects in Business.
Chiarini, A., 2020. Industry 4.0, quality management and TQM world. A systematic literature
review and a proposed agenda for further research. The TQM Journal.
Dison, L. and Kearney, A., 2021. A Systematic review of trends in teaching and learning
research in South African schools. Systematic Reviews of Research in Basic Education
in South Africa, p.141.
Fettermann and et.al., 2018. How does Industry 4.0 contribute to operations
management?. Journal of Industrial and Production Engineering, 35(4), pp.255-268.
Grover, P., Kar, A.K. and Dwivedi, Y.K., 2020. Understanding artificial intelligence adoption in
operations management: insights from the review of academic literature and social
media discussions. Annals of Operations Research, pp.1-37.
Gunasekaran and et.al., 2018. Agile manufacturing practices: the role of big data and business
analytics with multiple case studies. International Journal of Production
Research, 56(1-2), pp.385-397.
Hetemi, E., Gemünden, H. G. and Meré, J. O., 2020. Embeddedness and Actors’ Behaviors in
Large-Scale Project Life Cycle: Lessons Learned from a High-Speed Rail Project in
Spain. Journal of Management in Engineering, 36(6), p.05020014.
Honda and et.al., 2018. How lean six sigma principles improve hospital performance. Quality
Management Journal, 25(2), pp.70-82.
Kaswan, M. S. and Rathi, R., 2020. Green Lean Six Sigma for sustainable development:
Integration and framework. Environmental impact assessment review, 83, p.106396.
19
Paraphrase This Document
Need a fresh take? Get an instant paraphrase of this document with our AI Paraphraser
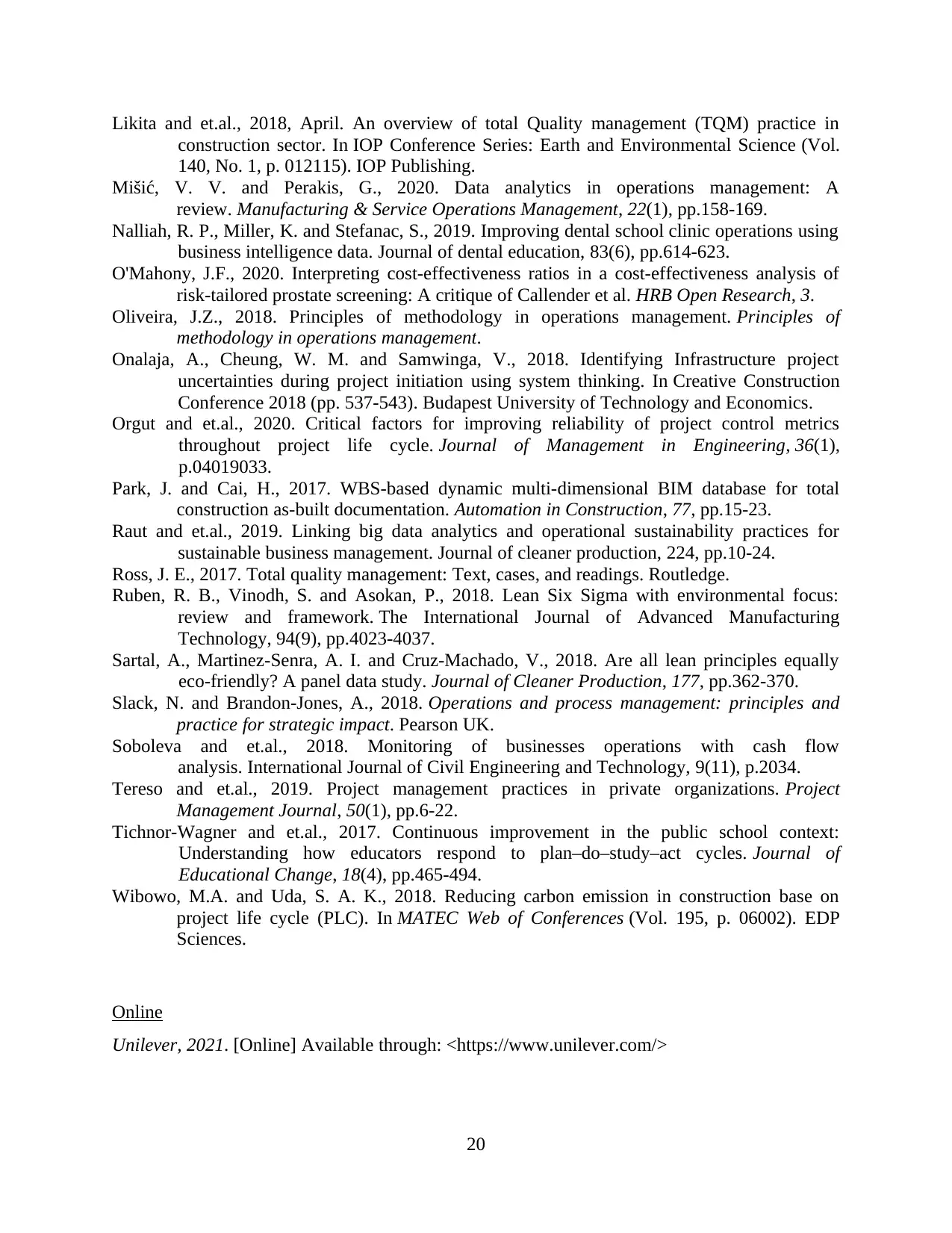
Likita and et.al., 2018, April. An overview of total Quality management (TQM) practice in
construction sector. In IOP Conference Series: Earth and Environmental Science (Vol.
140, No. 1, p. 012115). IOP Publishing.
Mišić, V. V. and Perakis, G., 2020. Data analytics in operations management: A
review. Manufacturing & Service Operations Management, 22(1), pp.158-169.
Nalliah, R. P., Miller, K. and Stefanac, S., 2019. Improving dental school clinic operations using
business intelligence data. Journal of dental education, 83(6), pp.614-623.
O'Mahony, J.F., 2020. Interpreting cost-effectiveness ratios in a cost-effectiveness analysis of
risk-tailored prostate screening: A critique of Callender et al. HRB Open Research, 3.
Oliveira, J.Z., 2018. Principles of methodology in operations management. Principles of
methodology in operations management.
Onalaja, A., Cheung, W. M. and Samwinga, V., 2018. Identifying Infrastructure project
uncertainties during project initiation using system thinking. In Creative Construction
Conference 2018 (pp. 537-543). Budapest University of Technology and Economics.
Orgut and et.al., 2020. Critical factors for improving reliability of project control metrics
throughout project life cycle. Journal of Management in Engineering, 36(1),
p.04019033.
Park, J. and Cai, H., 2017. WBS-based dynamic multi-dimensional BIM database for total
construction as-built documentation. Automation in Construction, 77, pp.15-23.
Raut and et.al., 2019. Linking big data analytics and operational sustainability practices for
sustainable business management. Journal of cleaner production, 224, pp.10-24.
Ross, J. E., 2017. Total quality management: Text, cases, and readings. Routledge.
Ruben, R. B., Vinodh, S. and Asokan, P., 2018. Lean Six Sigma with environmental focus:
review and framework. The International Journal of Advanced Manufacturing
Technology, 94(9), pp.4023-4037.
Sartal, A., Martinez-Senra, A. I. and Cruz-Machado, V., 2018. Are all lean principles equally
eco-friendly? A panel data study. Journal of Cleaner Production, 177, pp.362-370.
Slack, N. and Brandon-Jones, A., 2018. Operations and process management: principles and
practice for strategic impact. Pearson UK.
Soboleva and et.al., 2018. Monitoring of businesses operations with cash flow
analysis. International Journal of Civil Engineering and Technology, 9(11), p.2034.
Tereso and et.al., 2019. Project management practices in private organizations. Project
Management Journal, 50(1), pp.6-22.
Tichnor-Wagner and et.al., 2017. Continuous improvement in the public school context:
Understanding how educators respond to plan–do–study–act cycles. Journal of
Educational Change, 18(4), pp.465-494.
Wibowo, M.A. and Uda, S. A. K., 2018. Reducing carbon emission in construction base on
project life cycle (PLC). In MATEC Web of Conferences (Vol. 195, p. 06002). EDP
Sciences.
Online
Unilever, 2021. [Online] Available through: <https://www.unilever.com/>
20
construction sector. In IOP Conference Series: Earth and Environmental Science (Vol.
140, No. 1, p. 012115). IOP Publishing.
Mišić, V. V. and Perakis, G., 2020. Data analytics in operations management: A
review. Manufacturing & Service Operations Management, 22(1), pp.158-169.
Nalliah, R. P., Miller, K. and Stefanac, S., 2019. Improving dental school clinic operations using
business intelligence data. Journal of dental education, 83(6), pp.614-623.
O'Mahony, J.F., 2020. Interpreting cost-effectiveness ratios in a cost-effectiveness analysis of
risk-tailored prostate screening: A critique of Callender et al. HRB Open Research, 3.
Oliveira, J.Z., 2018. Principles of methodology in operations management. Principles of
methodology in operations management.
Onalaja, A., Cheung, W. M. and Samwinga, V., 2018. Identifying Infrastructure project
uncertainties during project initiation using system thinking. In Creative Construction
Conference 2018 (pp. 537-543). Budapest University of Technology and Economics.
Orgut and et.al., 2020. Critical factors for improving reliability of project control metrics
throughout project life cycle. Journal of Management in Engineering, 36(1),
p.04019033.
Park, J. and Cai, H., 2017. WBS-based dynamic multi-dimensional BIM database for total
construction as-built documentation. Automation in Construction, 77, pp.15-23.
Raut and et.al., 2019. Linking big data analytics and operational sustainability practices for
sustainable business management. Journal of cleaner production, 224, pp.10-24.
Ross, J. E., 2017. Total quality management: Text, cases, and readings. Routledge.
Ruben, R. B., Vinodh, S. and Asokan, P., 2018. Lean Six Sigma with environmental focus:
review and framework. The International Journal of Advanced Manufacturing
Technology, 94(9), pp.4023-4037.
Sartal, A., Martinez-Senra, A. I. and Cruz-Machado, V., 2018. Are all lean principles equally
eco-friendly? A panel data study. Journal of Cleaner Production, 177, pp.362-370.
Slack, N. and Brandon-Jones, A., 2018. Operations and process management: principles and
practice for strategic impact. Pearson UK.
Soboleva and et.al., 2018. Monitoring of businesses operations with cash flow
analysis. International Journal of Civil Engineering and Technology, 9(11), p.2034.
Tereso and et.al., 2019. Project management practices in private organizations. Project
Management Journal, 50(1), pp.6-22.
Tichnor-Wagner and et.al., 2017. Continuous improvement in the public school context:
Understanding how educators respond to plan–do–study–act cycles. Journal of
Educational Change, 18(4), pp.465-494.
Wibowo, M.A. and Uda, S. A. K., 2018. Reducing carbon emission in construction base on
project life cycle (PLC). In MATEC Web of Conferences (Vol. 195, p. 06002). EDP
Sciences.
Online
Unilever, 2021. [Online] Available through: <https://www.unilever.com/>
20
1 out of 20
Related Documents
![[object Object]](/_next/image/?url=%2F_next%2Fstatic%2Fmedia%2Flogo.6d15ce61.png&w=640&q=75)
Your All-in-One AI-Powered Toolkit for Academic Success.
+13062052269
info@desklib.com
Available 24*7 on WhatsApp / Email
Unlock your academic potential
© 2024 | Zucol Services PVT LTD | All rights reserved.