Operations and Project Management: A Case Study of Sainsbury's
VerifiedAdded on 2023/06/04
|15
|5288
|253
AI Summary
This report discusses the operational management principles, Lean principles, continuous improvement plan, Project management life cycle, Six sigma's, Project methodologies and the tools which are used for the particular project with appropriate findings and relevant conclusion. The case study is based on Sainsbury's, a leading retail supermarket organisation in the UK.
Contribute Materials
Your contribution can guide someone’s learning journey. Share your
documents today.
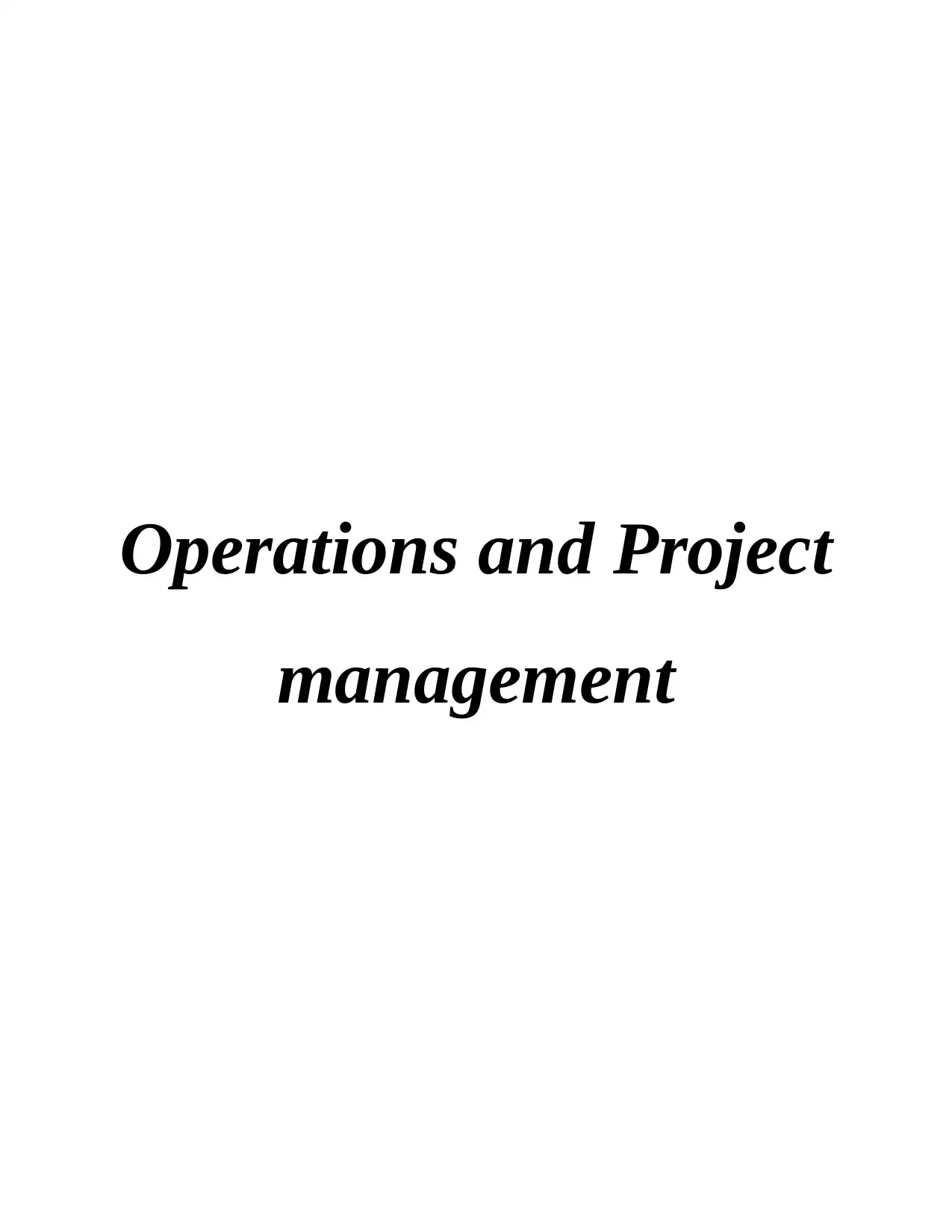
Operations and Project
management
management
Secure Best Marks with AI Grader
Need help grading? Try our AI Grader for instant feedback on your assignments.
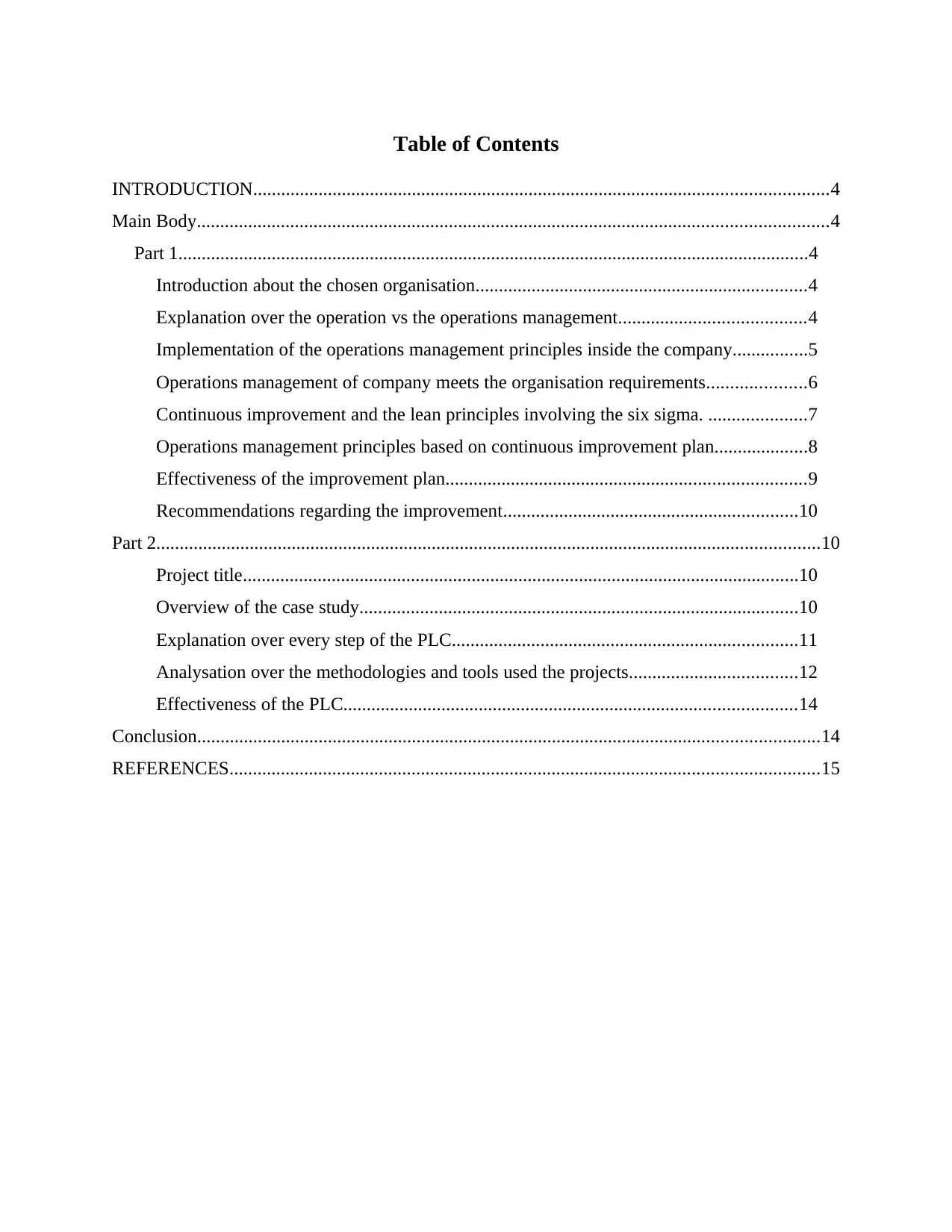
Table of Contents
INTRODUCTION...........................................................................................................................4
Main Body.......................................................................................................................................4
Part 1.......................................................................................................................................4
Introduction about the chosen organisation.......................................................................4
Explanation over the operation vs the operations management........................................4
Implementation of the operations management principles inside the company................5
Operations management of company meets the organisation requirements.....................6
Continuous improvement and the lean principles involving the six sigma. .....................7
Operations management principles based on continuous improvement plan....................8
Effectiveness of the improvement plan.............................................................................9
Recommendations regarding the improvement...............................................................10
Part 2..............................................................................................................................................10
Project title.......................................................................................................................10
Overview of the case study..............................................................................................10
Explanation over every step of the PLC..........................................................................11
Analysation over the methodologies and tools used the projects....................................12
Effectiveness of the PLC.................................................................................................14
Conclusion.....................................................................................................................................14
REFERENCES..............................................................................................................................15
INTRODUCTION...........................................................................................................................4
Main Body.......................................................................................................................................4
Part 1.......................................................................................................................................4
Introduction about the chosen organisation.......................................................................4
Explanation over the operation vs the operations management........................................4
Implementation of the operations management principles inside the company................5
Operations management of company meets the organisation requirements.....................6
Continuous improvement and the lean principles involving the six sigma. .....................7
Operations management principles based on continuous improvement plan....................8
Effectiveness of the improvement plan.............................................................................9
Recommendations regarding the improvement...............................................................10
Part 2..............................................................................................................................................10
Project title.......................................................................................................................10
Overview of the case study..............................................................................................10
Explanation over every step of the PLC..........................................................................11
Analysation over the methodologies and tools used the projects....................................12
Effectiveness of the PLC.................................................................................................14
Conclusion.....................................................................................................................................14
REFERENCES..............................................................................................................................15
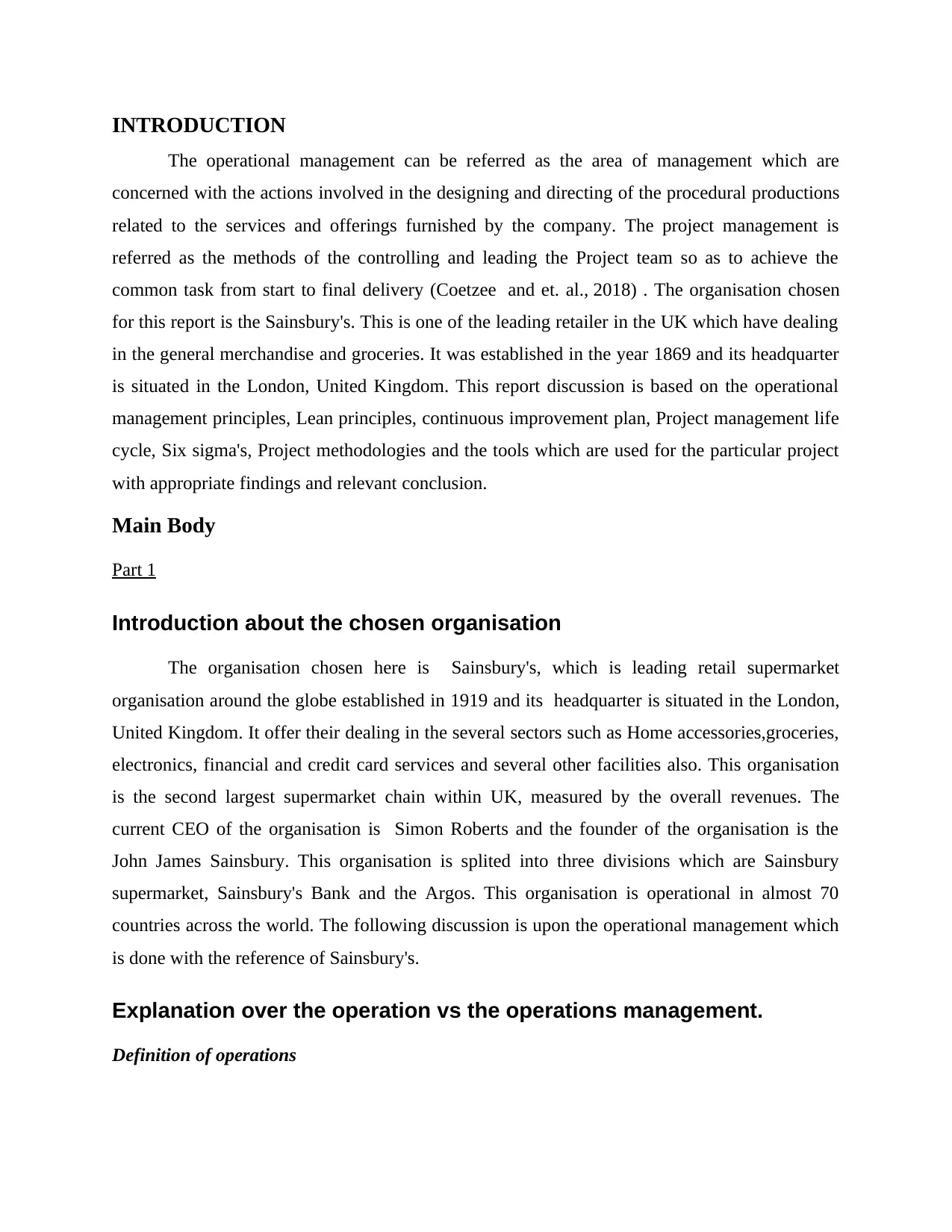
INTRODUCTION
The operational management can be referred as the area of management which are
concerned with the actions involved in the designing and directing of the procedural productions
related to the services and offerings furnished by the company. The project management is
referred as the methods of the controlling and leading the Project team so as to achieve the
common task from start to final delivery (Coetzee and et. al., 2018) . The organisation chosen
for this report is the Sainsbury's. This is one of the leading retailer in the UK which have dealing
in the general merchandise and groceries. It was established in the year 1869 and its headquarter
is situated in the London, United Kingdom. This report discussion is based on the operational
management principles, Lean principles, continuous improvement plan, Project management life
cycle, Six sigma's, Project methodologies and the tools which are used for the particular project
with appropriate findings and relevant conclusion.
Main Body
Part 1
Introduction about the chosen organisation
The organisation chosen here is Sainsbury's, which is leading retail supermarket
organisation around the globe established in 1919 and its headquarter is situated in the London,
United Kingdom. It offer their dealing in the several sectors such as Home accessories,groceries,
electronics, financial and credit card services and several other facilities also. This organisation
is the second largest supermarket chain within UK, measured by the overall revenues. The
current CEO of the organisation is Simon Roberts and the founder of the organisation is the
John James Sainsbury. This organisation is splited into three divisions which are Sainsbury
supermarket, Sainsbury's Bank and the Argos. This organisation is operational in almost 70
countries across the world. The following discussion is upon the operational management which
is done with the reference of Sainsbury's.
Explanation over the operation vs the operations management.
Definition of operations
The operational management can be referred as the area of management which are
concerned with the actions involved in the designing and directing of the procedural productions
related to the services and offerings furnished by the company. The project management is
referred as the methods of the controlling and leading the Project team so as to achieve the
common task from start to final delivery (Coetzee and et. al., 2018) . The organisation chosen
for this report is the Sainsbury's. This is one of the leading retailer in the UK which have dealing
in the general merchandise and groceries. It was established in the year 1869 and its headquarter
is situated in the London, United Kingdom. This report discussion is based on the operational
management principles, Lean principles, continuous improvement plan, Project management life
cycle, Six sigma's, Project methodologies and the tools which are used for the particular project
with appropriate findings and relevant conclusion.
Main Body
Part 1
Introduction about the chosen organisation
The organisation chosen here is Sainsbury's, which is leading retail supermarket
organisation around the globe established in 1919 and its headquarter is situated in the London,
United Kingdom. It offer their dealing in the several sectors such as Home accessories,groceries,
electronics, financial and credit card services and several other facilities also. This organisation
is the second largest supermarket chain within UK, measured by the overall revenues. The
current CEO of the organisation is Simon Roberts and the founder of the organisation is the
John James Sainsbury. This organisation is splited into three divisions which are Sainsbury
supermarket, Sainsbury's Bank and the Argos. This organisation is operational in almost 70
countries across the world. The following discussion is upon the operational management which
is done with the reference of Sainsbury's.
Explanation over the operation vs the operations management.
Definition of operations
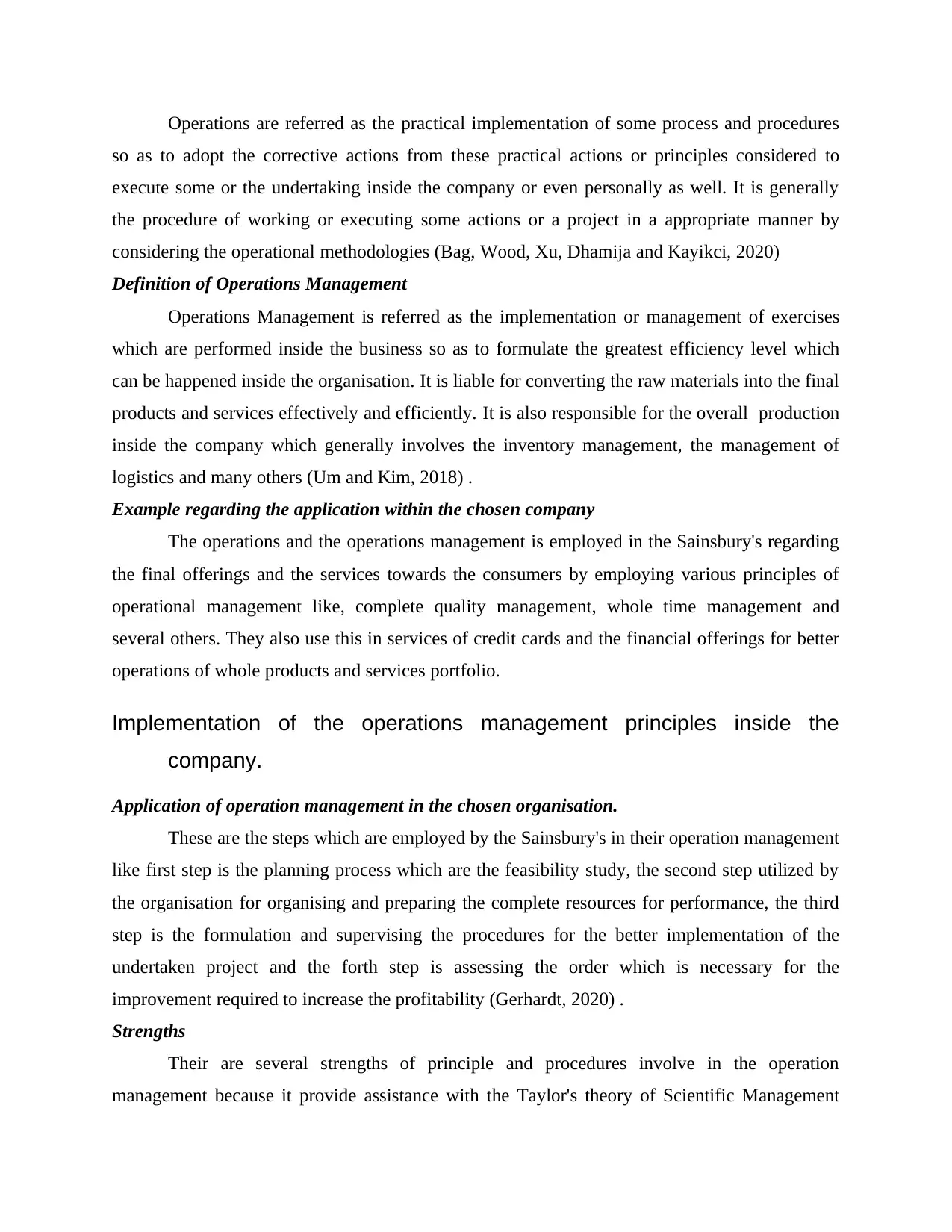
Operations are referred as the practical implementation of some process and procedures
so as to adopt the corrective actions from these practical actions or principles considered to
execute some or the undertaking inside the company or even personally as well. It is generally
the procedure of working or executing some actions or a project in a appropriate manner by
considering the operational methodologies (Bag, Wood, Xu, Dhamija and Kayikci, 2020)
Definition of Operations Management
Operations Management is referred as the implementation or management of exercises
which are performed inside the business so as to formulate the greatest efficiency level which
can be happened inside the organisation. It is liable for converting the raw materials into the final
products and services effectively and efficiently. It is also responsible for the overall production
inside the company which generally involves the inventory management, the management of
logistics and many others (Um and Kim, 2018) .
Example regarding the application within the chosen company
The operations and the operations management is employed in the Sainsbury's regarding
the final offerings and the services towards the consumers by employing various principles of
operational management like, complete quality management, whole time management and
several others. They also use this in services of credit cards and the financial offerings for better
operations of whole products and services portfolio.
Implementation of the operations management principles inside the
company.
Application of operation management in the chosen organisation.
These are the steps which are employed by the Sainsbury's in their operation management
like first step is the planning process which are the feasibility study, the second step utilized by
the organisation for organising and preparing the complete resources for performance, the third
step is the formulation and supervising the procedures for the better implementation of the
undertaken project and the forth step is assessing the order which is necessary for the
improvement required to increase the profitability (Gerhardt, 2020) .
Strengths
Their are several strengths of principle and procedures involve in the operation
management because it provide assistance with the Taylor's theory of Scientific Management
so as to adopt the corrective actions from these practical actions or principles considered to
execute some or the undertaking inside the company or even personally as well. It is generally
the procedure of working or executing some actions or a project in a appropriate manner by
considering the operational methodologies (Bag, Wood, Xu, Dhamija and Kayikci, 2020)
Definition of Operations Management
Operations Management is referred as the implementation or management of exercises
which are performed inside the business so as to formulate the greatest efficiency level which
can be happened inside the organisation. It is liable for converting the raw materials into the final
products and services effectively and efficiently. It is also responsible for the overall production
inside the company which generally involves the inventory management, the management of
logistics and many others (Um and Kim, 2018) .
Example regarding the application within the chosen company
The operations and the operations management is employed in the Sainsbury's regarding
the final offerings and the services towards the consumers by employing various principles of
operational management like, complete quality management, whole time management and
several others. They also use this in services of credit cards and the financial offerings for better
operations of whole products and services portfolio.
Implementation of the operations management principles inside the
company.
Application of operation management in the chosen organisation.
These are the steps which are employed by the Sainsbury's in their operation management
like first step is the planning process which are the feasibility study, the second step utilized by
the organisation for organising and preparing the complete resources for performance, the third
step is the formulation and supervising the procedures for the better implementation of the
undertaken project and the forth step is assessing the order which is necessary for the
improvement required to increase the profitability (Gerhardt, 2020) .
Strengths
Their are several strengths of principle and procedures involve in the operation
management because it provide assistance with the Taylor's theory of Scientific Management
Secure Best Marks with AI Grader
Need help grading? Try our AI Grader for instant feedback on your assignments.
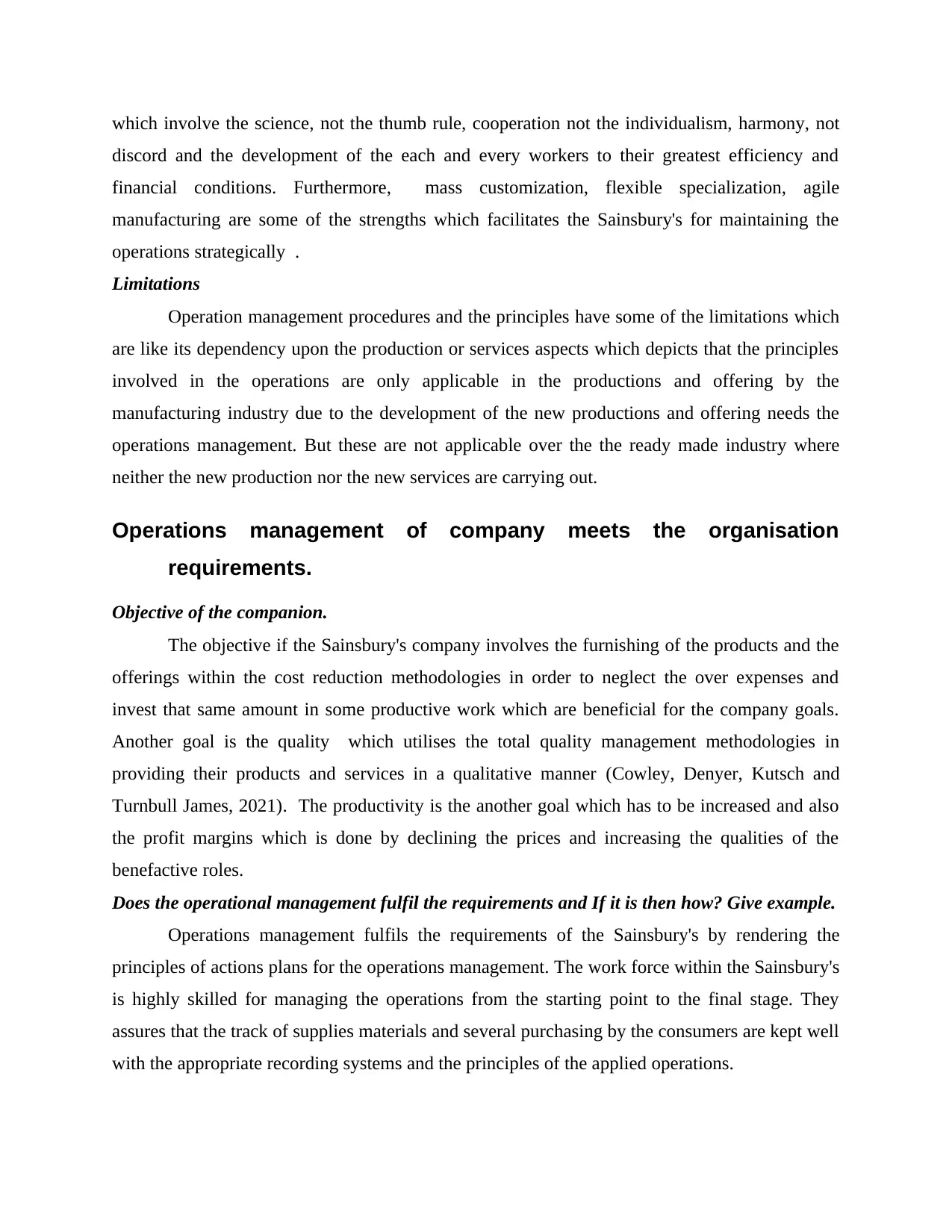
which involve the science, not the thumb rule, cooperation not the individualism, harmony, not
discord and the development of the each and every workers to their greatest efficiency and
financial conditions. Furthermore, mass customization, flexible specialization, agile
manufacturing are some of the strengths which facilitates the Sainsbury's for maintaining the
operations strategically .
Limitations
Operation management procedures and the principles have some of the limitations which
are like its dependency upon the production or services aspects which depicts that the principles
involved in the operations are only applicable in the productions and offering by the
manufacturing industry due to the development of the new productions and offering needs the
operations management. But these are not applicable over the the ready made industry where
neither the new production nor the new services are carrying out.
Operations management of company meets the organisation
requirements.
Objective of the companion.
The objective if the Sainsbury's company involves the furnishing of the products and the
offerings within the cost reduction methodologies in order to neglect the over expenses and
invest that same amount in some productive work which are beneficial for the company goals.
Another goal is the quality which utilises the total quality management methodologies in
providing their products and services in a qualitative manner (Cowley, Denyer, Kutsch and
Turnbull James, 2021). The productivity is the another goal which has to be increased and also
the profit margins which is done by declining the prices and increasing the qualities of the
benefactive roles.
Does the operational management fulfil the requirements and If it is then how? Give example.
Operations management fulfils the requirements of the Sainsbury's by rendering the
principles of actions plans for the operations management. The work force within the Sainsbury's
is highly skilled for managing the operations from the starting point to the final stage. They
assures that the track of supplies materials and several purchasing by the consumers are kept well
with the appropriate recording systems and the principles of the applied operations.
discord and the development of the each and every workers to their greatest efficiency and
financial conditions. Furthermore, mass customization, flexible specialization, agile
manufacturing are some of the strengths which facilitates the Sainsbury's for maintaining the
operations strategically .
Limitations
Operation management procedures and the principles have some of the limitations which
are like its dependency upon the production or services aspects which depicts that the principles
involved in the operations are only applicable in the productions and offering by the
manufacturing industry due to the development of the new productions and offering needs the
operations management. But these are not applicable over the the ready made industry where
neither the new production nor the new services are carrying out.
Operations management of company meets the organisation
requirements.
Objective of the companion.
The objective if the Sainsbury's company involves the furnishing of the products and the
offerings within the cost reduction methodologies in order to neglect the over expenses and
invest that same amount in some productive work which are beneficial for the company goals.
Another goal is the quality which utilises the total quality management methodologies in
providing their products and services in a qualitative manner (Cowley, Denyer, Kutsch and
Turnbull James, 2021). The productivity is the another goal which has to be increased and also
the profit margins which is done by declining the prices and increasing the qualities of the
benefactive roles.
Does the operational management fulfil the requirements and If it is then how? Give example.
Operations management fulfils the requirements of the Sainsbury's by rendering the
principles of actions plans for the operations management. The work force within the Sainsbury's
is highly skilled for managing the operations from the starting point to the final stage. They
assures that the track of supplies materials and several purchasing by the consumers are kept well
with the appropriate recording systems and the principles of the applied operations.
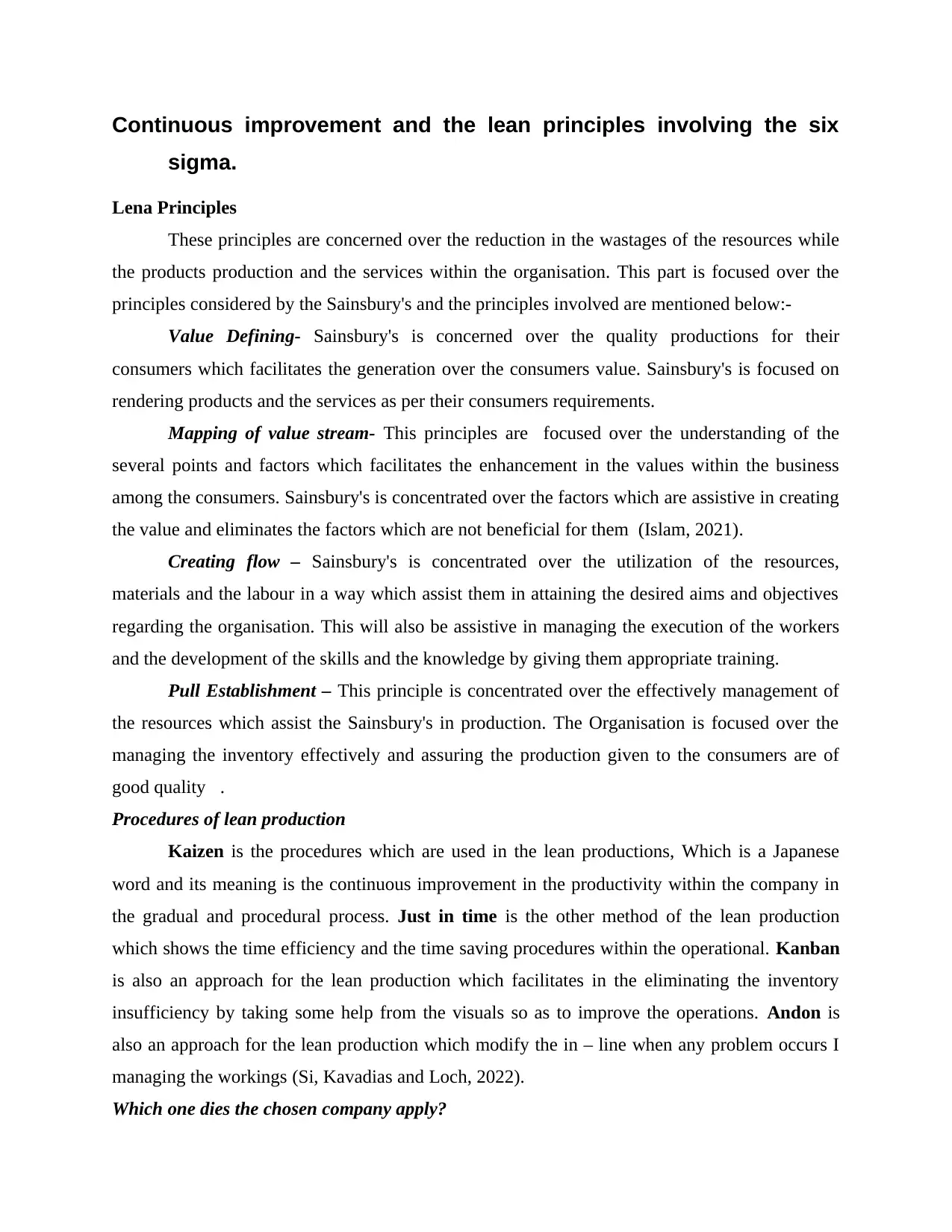
Continuous improvement and the lean principles involving the six
sigma.
Lena Principles
These principles are concerned over the reduction in the wastages of the resources while
the products production and the services within the organisation. This part is focused over the
principles considered by the Sainsbury's and the principles involved are mentioned below:-
Value Defining- Sainsbury's is concerned over the quality productions for their
consumers which facilitates the generation over the consumers value. Sainsbury's is focused on
rendering products and the services as per their consumers requirements.
Mapping of value stream- This principles are focused over the understanding of the
several points and factors which facilitates the enhancement in the values within the business
among the consumers. Sainsbury's is concentrated over the factors which are assistive in creating
the value and eliminates the factors which are not beneficial for them (Islam, 2021).
Creating flow – Sainsbury's is concentrated over the utilization of the resources,
materials and the labour in a way which assist them in attaining the desired aims and objectives
regarding the organisation. This will also be assistive in managing the execution of the workers
and the development of the skills and the knowledge by giving them appropriate training.
Pull Establishment – This principle is concentrated over the effectively management of
the resources which assist the Sainsbury's in production. The Organisation is focused over the
managing the inventory effectively and assuring the production given to the consumers are of
good quality .
Procedures of lean production
Kaizen is the procedures which are used in the lean productions, Which is a Japanese
word and its meaning is the continuous improvement in the productivity within the company in
the gradual and procedural process. Just in time is the other method of the lean production
which shows the time efficiency and the time saving procedures within the operational. Kanban
is also an approach for the lean production which facilitates in the eliminating the inventory
insufficiency by taking some help from the visuals so as to improve the operations. Andon is
also an approach for the lean production which modify the in – line when any problem occurs I
managing the workings (Si, Kavadias and Loch, 2022).
Which one dies the chosen company apply?
sigma.
Lena Principles
These principles are concerned over the reduction in the wastages of the resources while
the products production and the services within the organisation. This part is focused over the
principles considered by the Sainsbury's and the principles involved are mentioned below:-
Value Defining- Sainsbury's is concerned over the quality productions for their
consumers which facilitates the generation over the consumers value. Sainsbury's is focused on
rendering products and the services as per their consumers requirements.
Mapping of value stream- This principles are focused over the understanding of the
several points and factors which facilitates the enhancement in the values within the business
among the consumers. Sainsbury's is concentrated over the factors which are assistive in creating
the value and eliminates the factors which are not beneficial for them (Islam, 2021).
Creating flow – Sainsbury's is concentrated over the utilization of the resources,
materials and the labour in a way which assist them in attaining the desired aims and objectives
regarding the organisation. This will also be assistive in managing the execution of the workers
and the development of the skills and the knowledge by giving them appropriate training.
Pull Establishment – This principle is concentrated over the effectively management of
the resources which assist the Sainsbury's in production. The Organisation is focused over the
managing the inventory effectively and assuring the production given to the consumers are of
good quality .
Procedures of lean production
Kaizen is the procedures which are used in the lean productions, Which is a Japanese
word and its meaning is the continuous improvement in the productivity within the company in
the gradual and procedural process. Just in time is the other method of the lean production
which shows the time efficiency and the time saving procedures within the operational. Kanban
is also an approach for the lean production which facilitates in the eliminating the inventory
insufficiency by taking some help from the visuals so as to improve the operations. Andon is
also an approach for the lean production which modify the in – line when any problem occurs I
managing the workings (Si, Kavadias and Loch, 2022).
Which one dies the chosen company apply?
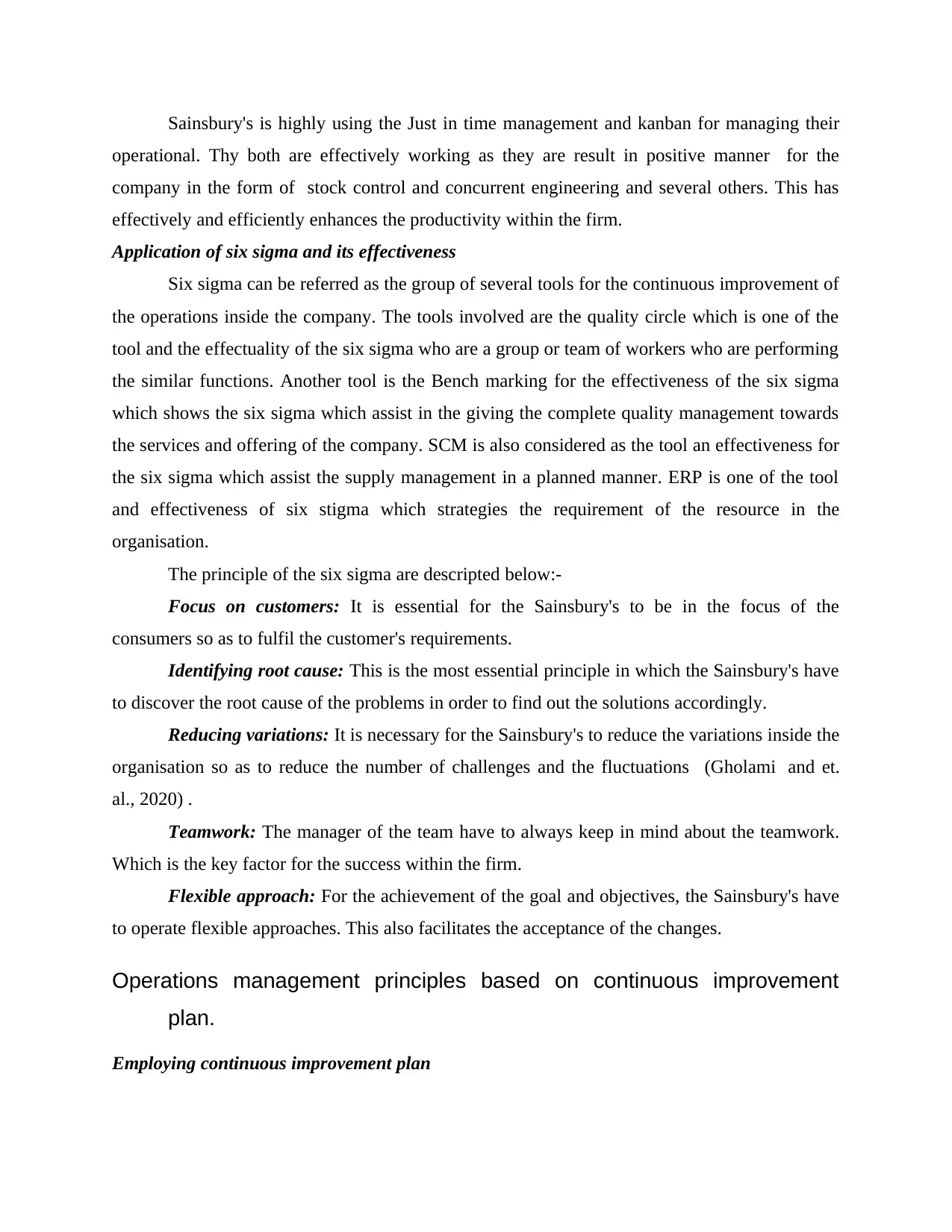
Sainsbury's is highly using the Just in time management and kanban for managing their
operational. Thy both are effectively working as they are result in positive manner for the
company in the form of stock control and concurrent engineering and several others. This has
effectively and efficiently enhances the productivity within the firm.
Application of six sigma and its effectiveness
Six sigma can be referred as the group of several tools for the continuous improvement of
the operations inside the company. The tools involved are the quality circle which is one of the
tool and the effectuality of the six sigma who are a group or team of workers who are performing
the similar functions. Another tool is the Bench marking for the effectiveness of the six sigma
which shows the six sigma which assist in the giving the complete quality management towards
the services and offering of the company. SCM is also considered as the tool an effectiveness for
the six sigma which assist the supply management in a planned manner. ERP is one of the tool
and effectiveness of six stigma which strategies the requirement of the resource in the
organisation.
The principle of the six sigma are descripted below:-
Focus on customers: It is essential for the Sainsbury's to be in the focus of the
consumers so as to fulfil the customer's requirements.
Identifying root cause: This is the most essential principle in which the Sainsbury's have
to discover the root cause of the problems in order to find out the solutions accordingly.
Reducing variations: It is necessary for the Sainsbury's to reduce the variations inside the
organisation so as to reduce the number of challenges and the fluctuations (Gholami and et.
al., 2020) .
Teamwork: The manager of the team have to always keep in mind about the teamwork.
Which is the key factor for the success within the firm.
Flexible approach: For the achievement of the goal and objectives, the Sainsbury's have
to operate flexible approaches. This also facilitates the acceptance of the changes.
Operations management principles based on continuous improvement
plan.
Employing continuous improvement plan
operational. Thy both are effectively working as they are result in positive manner for the
company in the form of stock control and concurrent engineering and several others. This has
effectively and efficiently enhances the productivity within the firm.
Application of six sigma and its effectiveness
Six sigma can be referred as the group of several tools for the continuous improvement of
the operations inside the company. The tools involved are the quality circle which is one of the
tool and the effectuality of the six sigma who are a group or team of workers who are performing
the similar functions. Another tool is the Bench marking for the effectiveness of the six sigma
which shows the six sigma which assist in the giving the complete quality management towards
the services and offering of the company. SCM is also considered as the tool an effectiveness for
the six sigma which assist the supply management in a planned manner. ERP is one of the tool
and effectiveness of six stigma which strategies the requirement of the resource in the
organisation.
The principle of the six sigma are descripted below:-
Focus on customers: It is essential for the Sainsbury's to be in the focus of the
consumers so as to fulfil the customer's requirements.
Identifying root cause: This is the most essential principle in which the Sainsbury's have
to discover the root cause of the problems in order to find out the solutions accordingly.
Reducing variations: It is necessary for the Sainsbury's to reduce the variations inside the
organisation so as to reduce the number of challenges and the fluctuations (Gholami and et.
al., 2020) .
Teamwork: The manager of the team have to always keep in mind about the teamwork.
Which is the key factor for the success within the firm.
Flexible approach: For the achievement of the goal and objectives, the Sainsbury's have
to operate flexible approaches. This also facilitates the acceptance of the changes.
Operations management principles based on continuous improvement
plan.
Employing continuous improvement plan
Paraphrase This Document
Need a fresh take? Get an instant paraphrase of this document with our AI Paraphraser
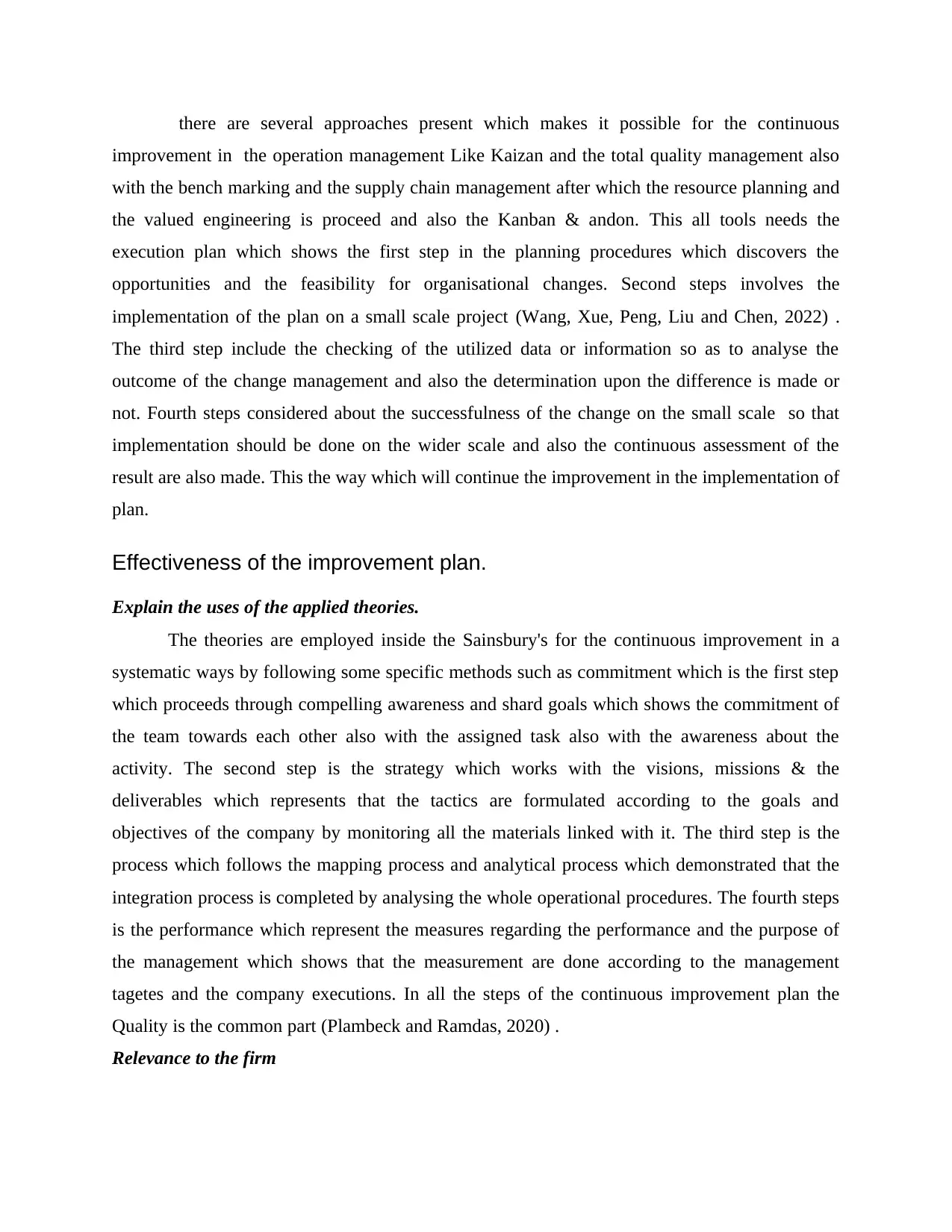
there are several approaches present which makes it possible for the continuous
improvement in the operation management Like Kaizan and the total quality management also
with the bench marking and the supply chain management after which the resource planning and
the valued engineering is proceed and also the Kanban & andon. This all tools needs the
execution plan which shows the first step in the planning procedures which discovers the
opportunities and the feasibility for organisational changes. Second steps involves the
implementation of the plan on a small scale project (Wang, Xue, Peng, Liu and Chen, 2022) .
The third step include the checking of the utilized data or information so as to analyse the
outcome of the change management and also the determination upon the difference is made or
not. Fourth steps considered about the successfulness of the change on the small scale so that
implementation should be done on the wider scale and also the continuous assessment of the
result are also made. This the way which will continue the improvement in the implementation of
plan.
Effectiveness of the improvement plan.
Explain the uses of the applied theories.
The theories are employed inside the Sainsbury's for the continuous improvement in a
systematic ways by following some specific methods such as commitment which is the first step
which proceeds through compelling awareness and shard goals which shows the commitment of
the team towards each other also with the assigned task also with the awareness about the
activity. The second step is the strategy which works with the visions, missions & the
deliverables which represents that the tactics are formulated according to the goals and
objectives of the company by monitoring all the materials linked with it. The third step is the
process which follows the mapping process and analytical process which demonstrated that the
integration process is completed by analysing the whole operational procedures. The fourth steps
is the performance which represent the measures regarding the performance and the purpose of
the management which shows that the measurement are done according to the management
tagetes and the company executions. In all the steps of the continuous improvement plan the
Quality is the common part (Plambeck and Ramdas, 2020) .
Relevance to the firm
improvement in the operation management Like Kaizan and the total quality management also
with the bench marking and the supply chain management after which the resource planning and
the valued engineering is proceed and also the Kanban & andon. This all tools needs the
execution plan which shows the first step in the planning procedures which discovers the
opportunities and the feasibility for organisational changes. Second steps involves the
implementation of the plan on a small scale project (Wang, Xue, Peng, Liu and Chen, 2022) .
The third step include the checking of the utilized data or information so as to analyse the
outcome of the change management and also the determination upon the difference is made or
not. Fourth steps considered about the successfulness of the change on the small scale so that
implementation should be done on the wider scale and also the continuous assessment of the
result are also made. This the way which will continue the improvement in the implementation of
plan.
Effectiveness of the improvement plan.
Explain the uses of the applied theories.
The theories are employed inside the Sainsbury's for the continuous improvement in a
systematic ways by following some specific methods such as commitment which is the first step
which proceeds through compelling awareness and shard goals which shows the commitment of
the team towards each other also with the assigned task also with the awareness about the
activity. The second step is the strategy which works with the visions, missions & the
deliverables which represents that the tactics are formulated according to the goals and
objectives of the company by monitoring all the materials linked with it. The third step is the
process which follows the mapping process and analytical process which demonstrated that the
integration process is completed by analysing the whole operational procedures. The fourth steps
is the performance which represent the measures regarding the performance and the purpose of
the management which shows that the measurement are done according to the management
tagetes and the company executions. In all the steps of the continuous improvement plan the
Quality is the common part (Plambeck and Ramdas, 2020) .
Relevance to the firm
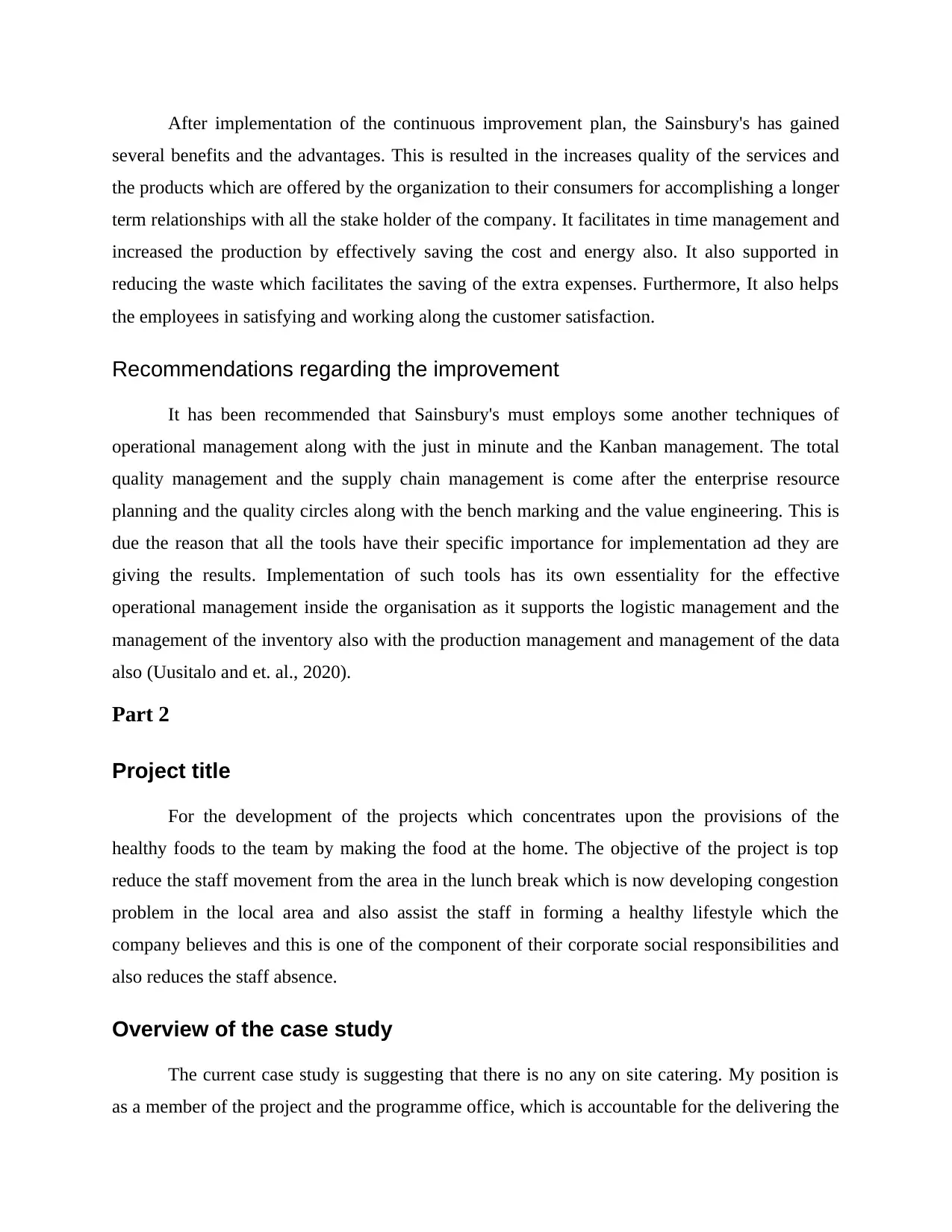
After implementation of the continuous improvement plan, the Sainsbury's has gained
several benefits and the advantages. This is resulted in the increases quality of the services and
the products which are offered by the organization to their consumers for accomplishing a longer
term relationships with all the stake holder of the company. It facilitates in time management and
increased the production by effectively saving the cost and energy also. It also supported in
reducing the waste which facilitates the saving of the extra expenses. Furthermore, It also helps
the employees in satisfying and working along the customer satisfaction.
Recommendations regarding the improvement
It has been recommended that Sainsbury's must employs some another techniques of
operational management along with the just in minute and the Kanban management. The total
quality management and the supply chain management is come after the enterprise resource
planning and the quality circles along with the bench marking and the value engineering. This is
due the reason that all the tools have their specific importance for implementation ad they are
giving the results. Implementation of such tools has its own essentiality for the effective
operational management inside the organisation as it supports the logistic management and the
management of the inventory also with the production management and management of the data
also (Uusitalo and et. al., 2020).
Part 2
Project title
For the development of the projects which concentrates upon the provisions of the
healthy foods to the team by making the food at the home. The objective of the project is top
reduce the staff movement from the area in the lunch break which is now developing congestion
problem in the local area and also assist the staff in forming a healthy lifestyle which the
company believes and this is one of the component of their corporate social responsibilities and
also reduces the staff absence.
Overview of the case study
The current case study is suggesting that there is no any on site catering. My position is
as a member of the project and the programme office, which is accountable for the delivering the
several benefits and the advantages. This is resulted in the increases quality of the services and
the products which are offered by the organization to their consumers for accomplishing a longer
term relationships with all the stake holder of the company. It facilitates in time management and
increased the production by effectively saving the cost and energy also. It also supported in
reducing the waste which facilitates the saving of the extra expenses. Furthermore, It also helps
the employees in satisfying and working along the customer satisfaction.
Recommendations regarding the improvement
It has been recommended that Sainsbury's must employs some another techniques of
operational management along with the just in minute and the Kanban management. The total
quality management and the supply chain management is come after the enterprise resource
planning and the quality circles along with the bench marking and the value engineering. This is
due the reason that all the tools have their specific importance for implementation ad they are
giving the results. Implementation of such tools has its own essentiality for the effective
operational management inside the organisation as it supports the logistic management and the
management of the inventory also with the production management and management of the data
also (Uusitalo and et. al., 2020).
Part 2
Project title
For the development of the projects which concentrates upon the provisions of the
healthy foods to the team by making the food at the home. The objective of the project is top
reduce the staff movement from the area in the lunch break which is now developing congestion
problem in the local area and also assist the staff in forming a healthy lifestyle which the
company believes and this is one of the component of their corporate social responsibilities and
also reduces the staff absence.
Overview of the case study
The current case study is suggesting that there is no any on site catering. My position is
as a member of the project and the programme office, which is accountable for the delivering the
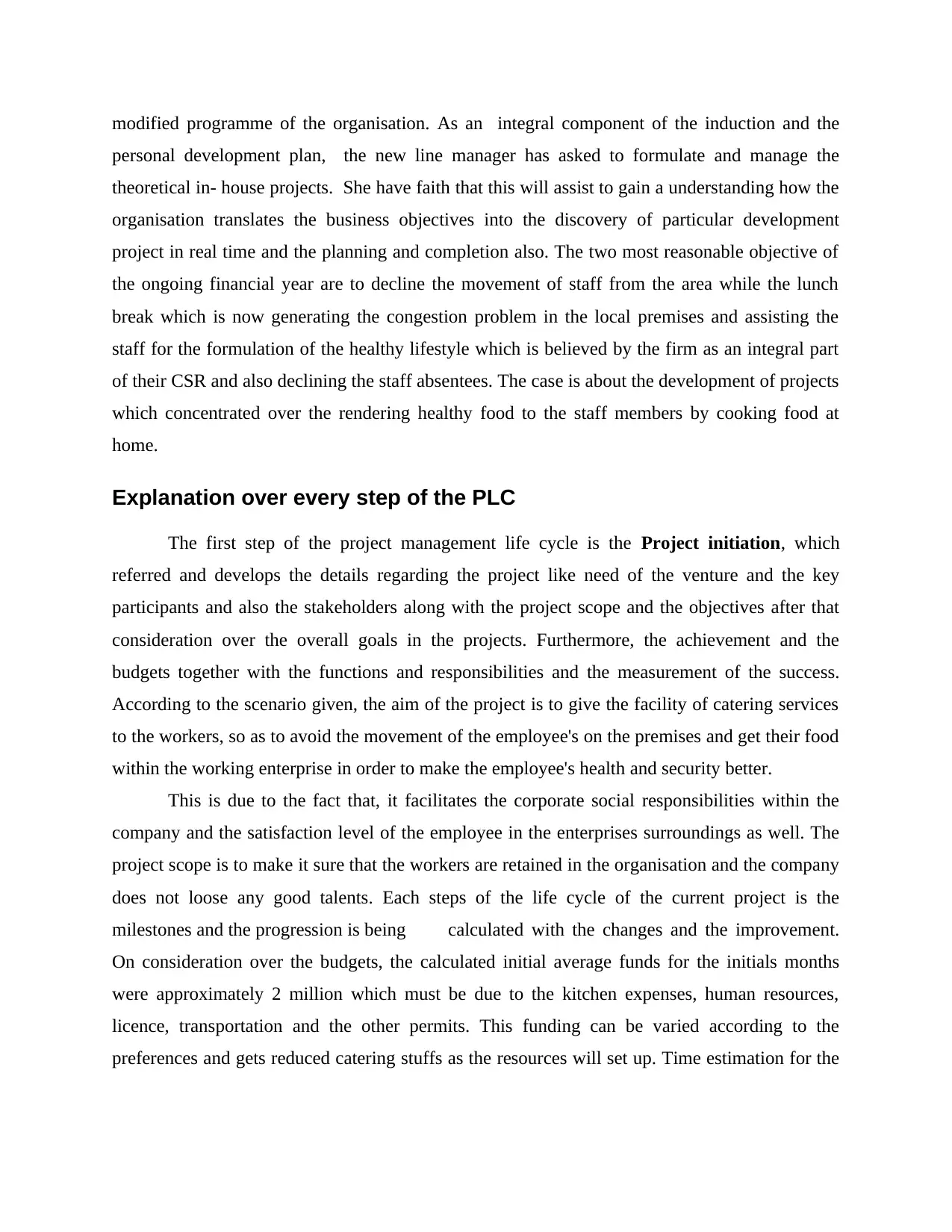
modified programme of the organisation. As an integral component of the induction and the
personal development plan, the new line manager has asked to formulate and manage the
theoretical in- house projects. She have faith that this will assist to gain a understanding how the
organisation translates the business objectives into the discovery of particular development
project in real time and the planning and completion also. The two most reasonable objective of
the ongoing financial year are to decline the movement of staff from the area while the lunch
break which is now generating the congestion problem in the local premises and assisting the
staff for the formulation of the healthy lifestyle which is believed by the firm as an integral part
of their CSR and also declining the staff absentees. The case is about the development of projects
which concentrated over the rendering healthy food to the staff members by cooking food at
home.
Explanation over every step of the PLC
The first step of the project management life cycle is the Project initiation, which
referred and develops the details regarding the project like need of the venture and the key
participants and also the stakeholders along with the project scope and the objectives after that
consideration over the overall goals in the projects. Furthermore, the achievement and the
budgets together with the functions and responsibilities and the measurement of the success.
According to the scenario given, the aim of the project is to give the facility of catering services
to the workers, so as to avoid the movement of the employee's on the premises and get their food
within the working enterprise in order to make the employee's health and security better.
This is due to the fact that, it facilitates the corporate social responsibilities within the
company and the satisfaction level of the employee in the enterprises surroundings as well. The
project scope is to make it sure that the workers are retained in the organisation and the company
does not loose any good talents. Each steps of the life cycle of the current project is the
milestones and the progression is being calculated with the changes and the improvement.
On consideration over the budgets, the calculated initial average funds for the initials months
were approximately 2 million which must be due to the kitchen expenses, human resources,
licence, transportation and the other permits. This funding can be varied according to the
preferences and gets reduced catering stuffs as the resources will set up. Time estimation for the
personal development plan, the new line manager has asked to formulate and manage the
theoretical in- house projects. She have faith that this will assist to gain a understanding how the
organisation translates the business objectives into the discovery of particular development
project in real time and the planning and completion also. The two most reasonable objective of
the ongoing financial year are to decline the movement of staff from the area while the lunch
break which is now generating the congestion problem in the local premises and assisting the
staff for the formulation of the healthy lifestyle which is believed by the firm as an integral part
of their CSR and also declining the staff absentees. The case is about the development of projects
which concentrated over the rendering healthy food to the staff members by cooking food at
home.
Explanation over every step of the PLC
The first step of the project management life cycle is the Project initiation, which
referred and develops the details regarding the project like need of the venture and the key
participants and also the stakeholders along with the project scope and the objectives after that
consideration over the overall goals in the projects. Furthermore, the achievement and the
budgets together with the functions and responsibilities and the measurement of the success.
According to the scenario given, the aim of the project is to give the facility of catering services
to the workers, so as to avoid the movement of the employee's on the premises and get their food
within the working enterprise in order to make the employee's health and security better.
This is due to the fact that, it facilitates the corporate social responsibilities within the
company and the satisfaction level of the employee in the enterprises surroundings as well. The
project scope is to make it sure that the workers are retained in the organisation and the company
does not loose any good talents. Each steps of the life cycle of the current project is the
milestones and the progression is being calculated with the changes and the improvement.
On consideration over the budgets, the calculated initial average funds for the initials months
were approximately 2 million which must be due to the kitchen expenses, human resources,
licence, transportation and the other permits. This funding can be varied according to the
preferences and gets reduced catering stuffs as the resources will set up. Time estimation for the
Secure Best Marks with AI Grader
Need help grading? Try our AI Grader for instant feedback on your assignments.
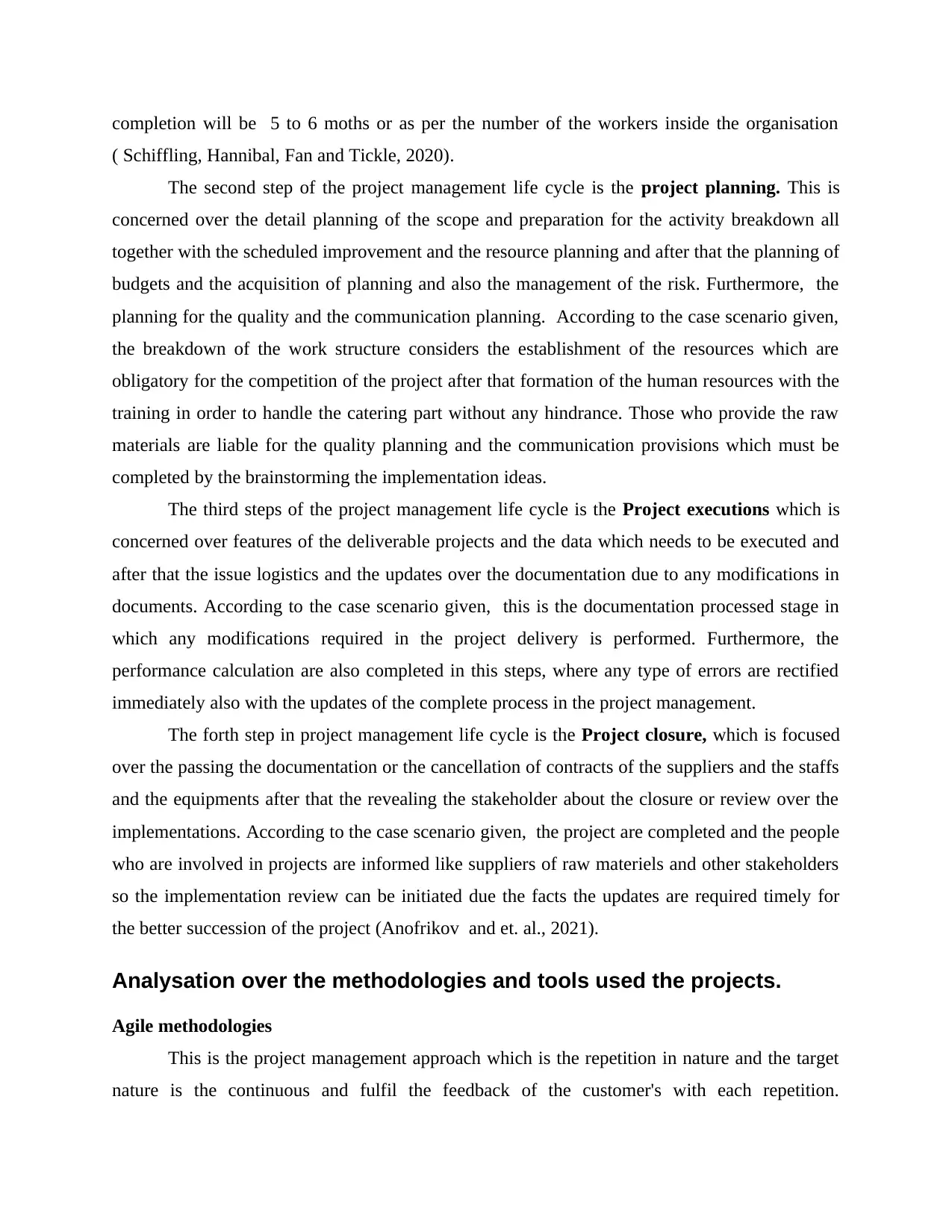
completion will be 5 to 6 moths or as per the number of the workers inside the organisation
( Schiffling, Hannibal, Fan and Tickle, 2020).
The second step of the project management life cycle is the project planning. This is
concerned over the detail planning of the scope and preparation for the activity breakdown all
together with the scheduled improvement and the resource planning and after that the planning of
budgets and the acquisition of planning and also the management of the risk. Furthermore, the
planning for the quality and the communication planning. According to the case scenario given,
the breakdown of the work structure considers the establishment of the resources which are
obligatory for the competition of the project after that formation of the human resources with the
training in order to handle the catering part without any hindrance. Those who provide the raw
materials are liable for the quality planning and the communication provisions which must be
completed by the brainstorming the implementation ideas.
The third steps of the project management life cycle is the Project executions which is
concerned over features of the deliverable projects and the data which needs to be executed and
after that the issue logistics and the updates over the documentation due to any modifications in
documents. According to the case scenario given, this is the documentation processed stage in
which any modifications required in the project delivery is performed. Furthermore, the
performance calculation are also completed in this steps, where any type of errors are rectified
immediately also with the updates of the complete process in the project management.
The forth step in project management life cycle is the Project closure, which is focused
over the passing the documentation or the cancellation of contracts of the suppliers and the staffs
and the equipments after that the revealing the stakeholder about the closure or review over the
implementations. According to the case scenario given, the project are completed and the people
who are involved in projects are informed like suppliers of raw materiels and other stakeholders
so the implementation review can be initiated due the facts the updates are required timely for
the better succession of the project (Anofrikov and et. al., 2021).
Analysation over the methodologies and tools used the projects.
Agile methodologies
This is the project management approach which is the repetition in nature and the target
nature is the continuous and fulfil the feedback of the customer's with each repetition.
( Schiffling, Hannibal, Fan and Tickle, 2020).
The second step of the project management life cycle is the project planning. This is
concerned over the detail planning of the scope and preparation for the activity breakdown all
together with the scheduled improvement and the resource planning and after that the planning of
budgets and the acquisition of planning and also the management of the risk. Furthermore, the
planning for the quality and the communication planning. According to the case scenario given,
the breakdown of the work structure considers the establishment of the resources which are
obligatory for the competition of the project after that formation of the human resources with the
training in order to handle the catering part without any hindrance. Those who provide the raw
materials are liable for the quality planning and the communication provisions which must be
completed by the brainstorming the implementation ideas.
The third steps of the project management life cycle is the Project executions which is
concerned over features of the deliverable projects and the data which needs to be executed and
after that the issue logistics and the updates over the documentation due to any modifications in
documents. According to the case scenario given, this is the documentation processed stage in
which any modifications required in the project delivery is performed. Furthermore, the
performance calculation are also completed in this steps, where any type of errors are rectified
immediately also with the updates of the complete process in the project management.
The forth step in project management life cycle is the Project closure, which is focused
over the passing the documentation or the cancellation of contracts of the suppliers and the staffs
and the equipments after that the revealing the stakeholder about the closure or review over the
implementations. According to the case scenario given, the project are completed and the people
who are involved in projects are informed like suppliers of raw materiels and other stakeholders
so the implementation review can be initiated due the facts the updates are required timely for
the better succession of the project (Anofrikov and et. al., 2021).
Analysation over the methodologies and tools used the projects.
Agile methodologies
This is the project management approach which is the repetition in nature and the target
nature is the continuous and fulfil the feedback of the customer's with each repetition.
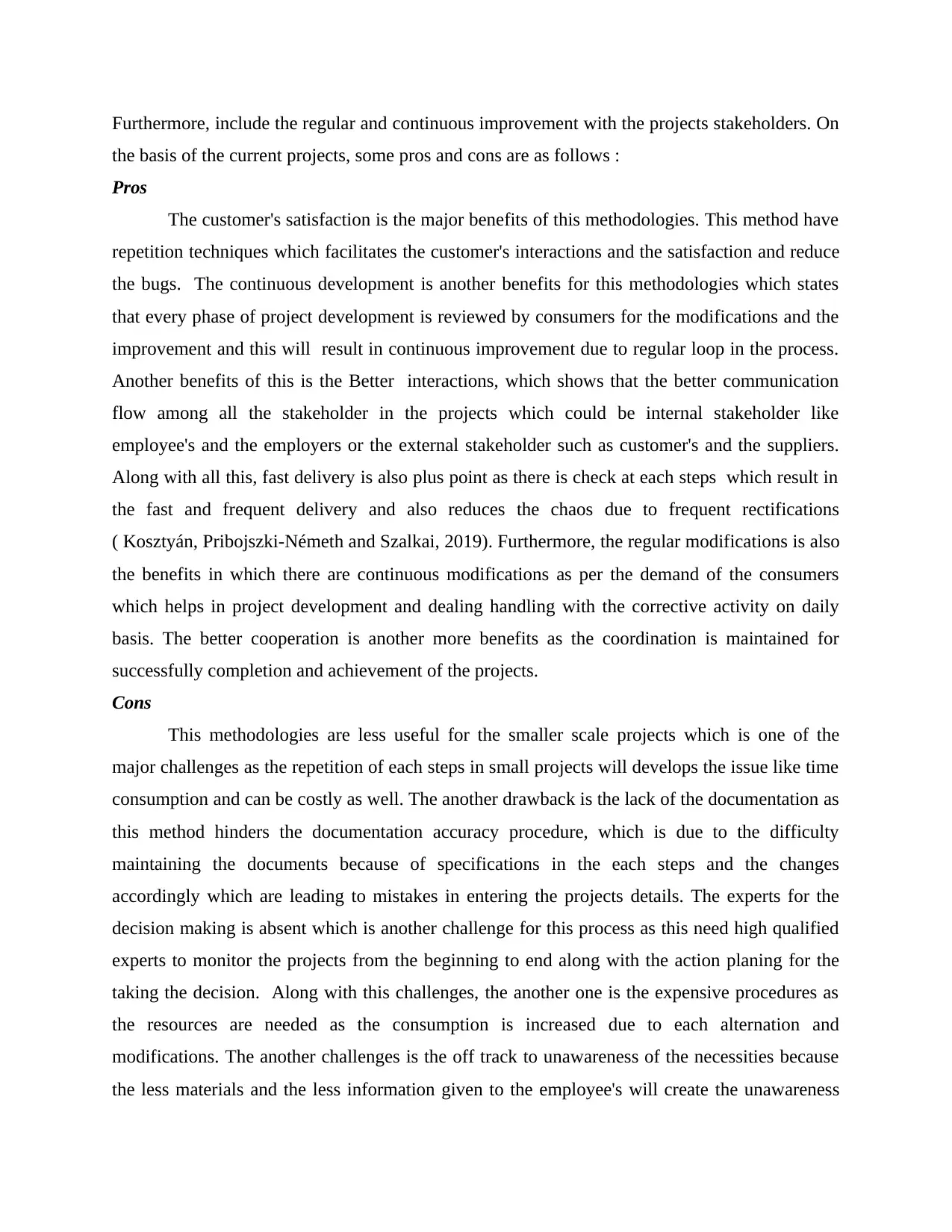
Furthermore, include the regular and continuous improvement with the projects stakeholders. On
the basis of the current projects, some pros and cons are as follows :
Pros
The customer's satisfaction is the major benefits of this methodologies. This method have
repetition techniques which facilitates the customer's interactions and the satisfaction and reduce
the bugs. The continuous development is another benefits for this methodologies which states
that every phase of project development is reviewed by consumers for the modifications and the
improvement and this will result in continuous improvement due to regular loop in the process.
Another benefits of this is the Better interactions, which shows that the better communication
flow among all the stakeholder in the projects which could be internal stakeholder like
employee's and the employers or the external stakeholder such as customer's and the suppliers.
Along with all this, fast delivery is also plus point as there is check at each steps which result in
the fast and frequent delivery and also reduces the chaos due to frequent rectifications
( Kosztyán, Pribojszki-Németh and Szalkai, 2019). Furthermore, the regular modifications is also
the benefits in which there are continuous modifications as per the demand of the consumers
which helps in project development and dealing handling with the corrective activity on daily
basis. The better cooperation is another more benefits as the coordination is maintained for
successfully completion and achievement of the projects.
Cons
This methodologies are less useful for the smaller scale projects which is one of the
major challenges as the repetition of each steps in small projects will develops the issue like time
consumption and can be costly as well. The another drawback is the lack of the documentation as
this method hinders the documentation accuracy procedure, which is due to the difficulty
maintaining the documents because of specifications in the each steps and the changes
accordingly which are leading to mistakes in entering the projects details. The experts for the
decision making is absent which is another challenge for this process as this need high qualified
experts to monitor the projects from the beginning to end along with the action planing for the
taking the decision. Along with this challenges, the another one is the expensive procedures as
the resources are needed as the consumption is increased due to each alternation and
modifications. The another challenges is the off track to unawareness of the necessities because
the less materials and the less information given to the employee's will create the unawareness
the basis of the current projects, some pros and cons are as follows :
Pros
The customer's satisfaction is the major benefits of this methodologies. This method have
repetition techniques which facilitates the customer's interactions and the satisfaction and reduce
the bugs. The continuous development is another benefits for this methodologies which states
that every phase of project development is reviewed by consumers for the modifications and the
improvement and this will result in continuous improvement due to regular loop in the process.
Another benefits of this is the Better interactions, which shows that the better communication
flow among all the stakeholder in the projects which could be internal stakeholder like
employee's and the employers or the external stakeholder such as customer's and the suppliers.
Along with all this, fast delivery is also plus point as there is check at each steps which result in
the fast and frequent delivery and also reduces the chaos due to frequent rectifications
( Kosztyán, Pribojszki-Németh and Szalkai, 2019). Furthermore, the regular modifications is also
the benefits in which there are continuous modifications as per the demand of the consumers
which helps in project development and dealing handling with the corrective activity on daily
basis. The better cooperation is another more benefits as the coordination is maintained for
successfully completion and achievement of the projects.
Cons
This methodologies are less useful for the smaller scale projects which is one of the
major challenges as the repetition of each steps in small projects will develops the issue like time
consumption and can be costly as well. The another drawback is the lack of the documentation as
this method hinders the documentation accuracy procedure, which is due to the difficulty
maintaining the documents because of specifications in the each steps and the changes
accordingly which are leading to mistakes in entering the projects details. The experts for the
decision making is absent which is another challenge for this process as this need high qualified
experts to monitor the projects from the beginning to end along with the action planing for the
taking the decision. Along with this challenges, the another one is the expensive procedures as
the resources are needed as the consumption is increased due to each alternation and
modifications. The another challenges is the off track to unawareness of the necessities because
the less materials and the less information given to the employee's will create the unawareness
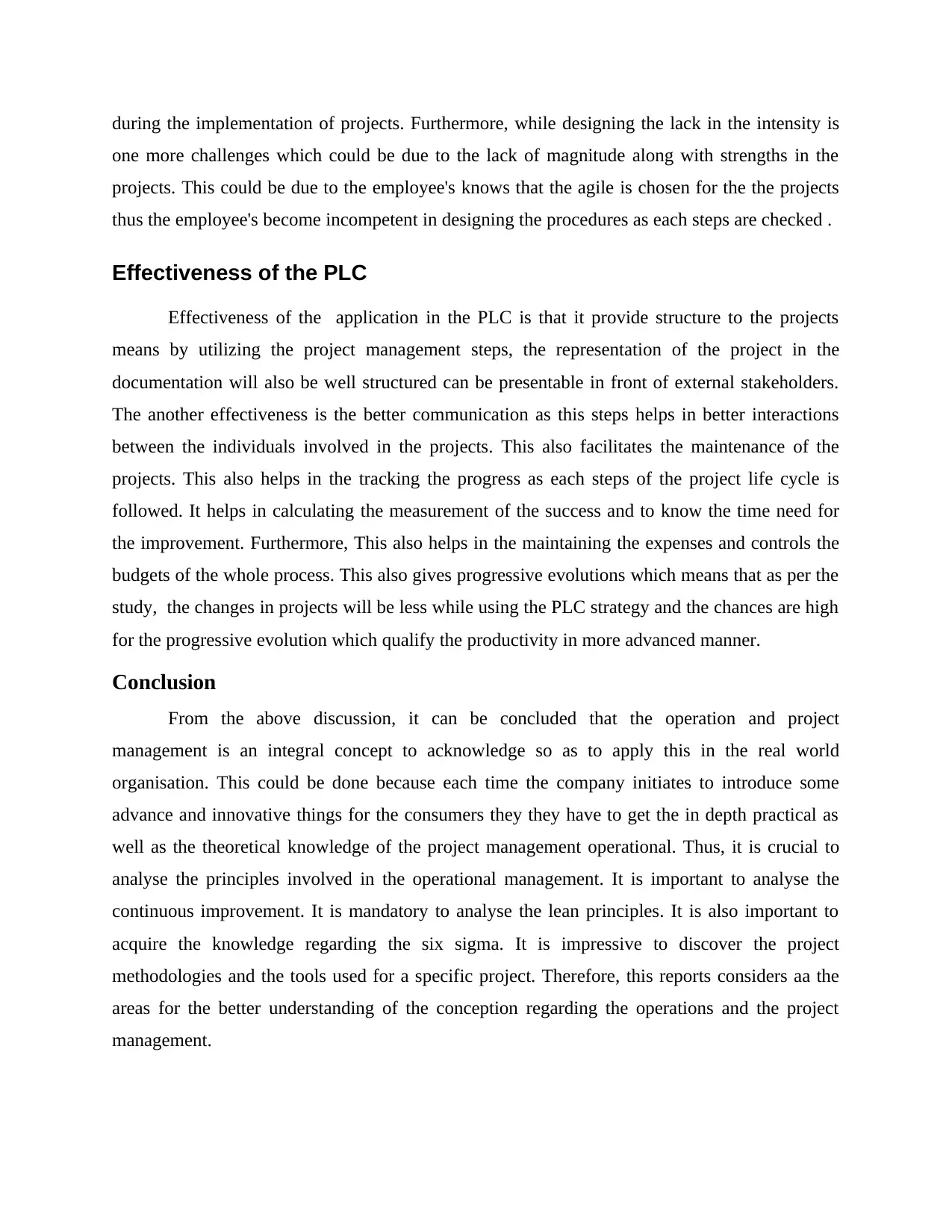
during the implementation of projects. Furthermore, while designing the lack in the intensity is
one more challenges which could be due to the lack of magnitude along with strengths in the
projects. This could be due to the employee's knows that the agile is chosen for the the projects
thus the employee's become incompetent in designing the procedures as each steps are checked .
Effectiveness of the PLC
Effectiveness of the application in the PLC is that it provide structure to the projects
means by utilizing the project management steps, the representation of the project in the
documentation will also be well structured can be presentable in front of external stakeholders.
The another effectiveness is the better communication as this steps helps in better interactions
between the individuals involved in the projects. This also facilitates the maintenance of the
projects. This also helps in the tracking the progress as each steps of the project life cycle is
followed. It helps in calculating the measurement of the success and to know the time need for
the improvement. Furthermore, This also helps in the maintaining the expenses and controls the
budgets of the whole process. This also gives progressive evolutions which means that as per the
study, the changes in projects will be less while using the PLC strategy and the chances are high
for the progressive evolution which qualify the productivity in more advanced manner.
Conclusion
From the above discussion, it can be concluded that the operation and project
management is an integral concept to acknowledge so as to apply this in the real world
organisation. This could be done because each time the company initiates to introduce some
advance and innovative things for the consumers they they have to get the in depth practical as
well as the theoretical knowledge of the project management operational. Thus, it is crucial to
analyse the principles involved in the operational management. It is important to analyse the
continuous improvement. It is mandatory to analyse the lean principles. It is also important to
acquire the knowledge regarding the six sigma. It is impressive to discover the project
methodologies and the tools used for a specific project. Therefore, this reports considers aa the
areas for the better understanding of the conception regarding the operations and the project
management.
one more challenges which could be due to the lack of magnitude along with strengths in the
projects. This could be due to the employee's knows that the agile is chosen for the the projects
thus the employee's become incompetent in designing the procedures as each steps are checked .
Effectiveness of the PLC
Effectiveness of the application in the PLC is that it provide structure to the projects
means by utilizing the project management steps, the representation of the project in the
documentation will also be well structured can be presentable in front of external stakeholders.
The another effectiveness is the better communication as this steps helps in better interactions
between the individuals involved in the projects. This also facilitates the maintenance of the
projects. This also helps in the tracking the progress as each steps of the project life cycle is
followed. It helps in calculating the measurement of the success and to know the time need for
the improvement. Furthermore, This also helps in the maintaining the expenses and controls the
budgets of the whole process. This also gives progressive evolutions which means that as per the
study, the changes in projects will be less while using the PLC strategy and the chances are high
for the progressive evolution which qualify the productivity in more advanced manner.
Conclusion
From the above discussion, it can be concluded that the operation and project
management is an integral concept to acknowledge so as to apply this in the real world
organisation. This could be done because each time the company initiates to introduce some
advance and innovative things for the consumers they they have to get the in depth practical as
well as the theoretical knowledge of the project management operational. Thus, it is crucial to
analyse the principles involved in the operational management. It is important to analyse the
continuous improvement. It is mandatory to analyse the lean principles. It is also important to
acquire the knowledge regarding the six sigma. It is impressive to discover the project
methodologies and the tools used for a specific project. Therefore, this reports considers aa the
areas for the better understanding of the conception regarding the operations and the project
management.
Paraphrase This Document
Need a fresh take? Get an instant paraphrase of this document with our AI Paraphraser
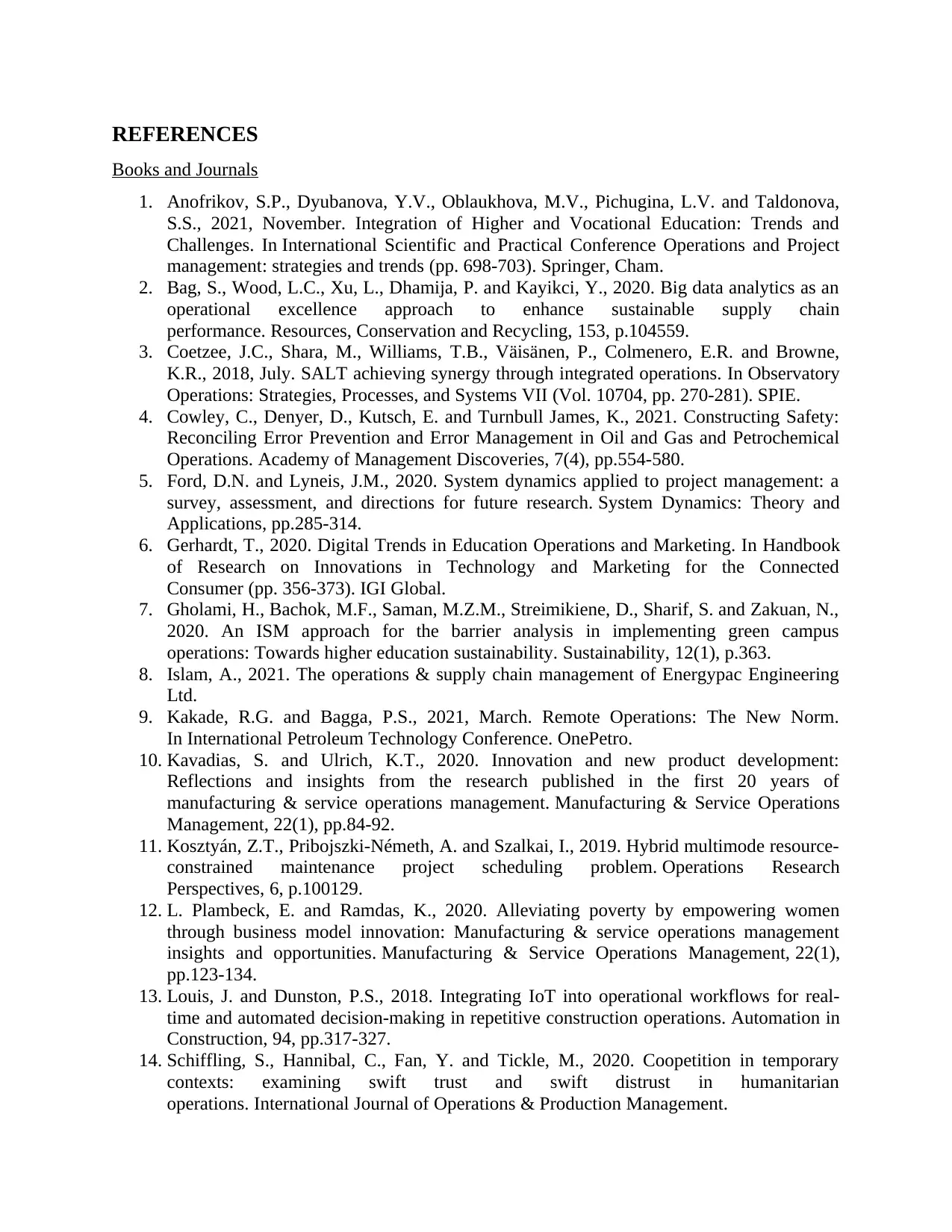
REFERENCES
Books and Journals
1. Anofrikov, S.P., Dyubanova, Y.V., Oblaukhova, M.V., Pichugina, L.V. and Taldonova,
S.S., 2021, November. Integration of Higher and Vocational Education: Trends and
Challenges. In International Scientific and Practical Conference Operations and Project
management: strategies and trends (pp. 698-703). Springer, Cham.
2. Bag, S., Wood, L.C., Xu, L., Dhamija, P. and Kayikci, Y., 2020. Big data analytics as an
operational excellence approach to enhance sustainable supply chain
performance. Resources, Conservation and Recycling, 153, p.104559.
3. Coetzee, J.C., Shara, M., Williams, T.B., Väisänen, P., Colmenero, E.R. and Browne,
K.R., 2018, July. SALT achieving synergy through integrated operations. In Observatory
Operations: Strategies, Processes, and Systems VII (Vol. 10704, pp. 270-281). SPIE.
4. Cowley, C., Denyer, D., Kutsch, E. and Turnbull James, K., 2021. Constructing Safety:
Reconciling Error Prevention and Error Management in Oil and Gas and Petrochemical
Operations. Academy of Management Discoveries, 7(4), pp.554-580.
5. Ford, D.N. and Lyneis, J.M., 2020. System dynamics applied to project management: a
survey, assessment, and directions for future research. System Dynamics: Theory and
Applications, pp.285-314.
6. Gerhardt, T., 2020. Digital Trends in Education Operations and Marketing. In Handbook
of Research on Innovations in Technology and Marketing for the Connected
Consumer (pp. 356-373). IGI Global.
7. Gholami, H., Bachok, M.F., Saman, M.Z.M., Streimikiene, D., Sharif, S. and Zakuan, N.,
2020. An ISM approach for the barrier analysis in implementing green campus
operations: Towards higher education sustainability. Sustainability, 12(1), p.363.
8. Islam, A., 2021. The operations & supply chain management of Energypac Engineering
Ltd.
9. Kakade, R.G. and Bagga, P.S., 2021, March. Remote Operations: The New Norm.
In International Petroleum Technology Conference. OnePetro.
10. Kavadias, S. and Ulrich, K.T., 2020. Innovation and new product development:
Reflections and insights from the research published in the first 20 years of
manufacturing & service operations management. Manufacturing & Service Operations
Management, 22(1), pp.84-92.
11. Kosztyán, Z.T., Pribojszki-Németh, A. and Szalkai, I., 2019. Hybrid multimode resource-
constrained maintenance project scheduling problem. Operations Research
Perspectives, 6, p.100129.
12. L. Plambeck, E. and Ramdas, K., 2020. Alleviating poverty by empowering women
through business model innovation: Manufacturing & service operations management
insights and opportunities. Manufacturing & Service Operations Management, 22(1),
pp.123-134.
13. Louis, J. and Dunston, P.S., 2018. Integrating IoT into operational workflows for real-
time and automated decision-making in repetitive construction operations. Automation in
Construction, 94, pp.317-327.
14. Schiffling, S., Hannibal, C., Fan, Y. and Tickle, M., 2020. Coopetition in temporary
contexts: examining swift trust and swift distrust in humanitarian
operations. International Journal of Operations & Production Management.
Books and Journals
1. Anofrikov, S.P., Dyubanova, Y.V., Oblaukhova, M.V., Pichugina, L.V. and Taldonova,
S.S., 2021, November. Integration of Higher and Vocational Education: Trends and
Challenges. In International Scientific and Practical Conference Operations and Project
management: strategies and trends (pp. 698-703). Springer, Cham.
2. Bag, S., Wood, L.C., Xu, L., Dhamija, P. and Kayikci, Y., 2020. Big data analytics as an
operational excellence approach to enhance sustainable supply chain
performance. Resources, Conservation and Recycling, 153, p.104559.
3. Coetzee, J.C., Shara, M., Williams, T.B., Väisänen, P., Colmenero, E.R. and Browne,
K.R., 2018, July. SALT achieving synergy through integrated operations. In Observatory
Operations: Strategies, Processes, and Systems VII (Vol. 10704, pp. 270-281). SPIE.
4. Cowley, C., Denyer, D., Kutsch, E. and Turnbull James, K., 2021. Constructing Safety:
Reconciling Error Prevention and Error Management in Oil and Gas and Petrochemical
Operations. Academy of Management Discoveries, 7(4), pp.554-580.
5. Ford, D.N. and Lyneis, J.M., 2020. System dynamics applied to project management: a
survey, assessment, and directions for future research. System Dynamics: Theory and
Applications, pp.285-314.
6. Gerhardt, T., 2020. Digital Trends in Education Operations and Marketing. In Handbook
of Research on Innovations in Technology and Marketing for the Connected
Consumer (pp. 356-373). IGI Global.
7. Gholami, H., Bachok, M.F., Saman, M.Z.M., Streimikiene, D., Sharif, S. and Zakuan, N.,
2020. An ISM approach for the barrier analysis in implementing green campus
operations: Towards higher education sustainability. Sustainability, 12(1), p.363.
8. Islam, A., 2021. The operations & supply chain management of Energypac Engineering
Ltd.
9. Kakade, R.G. and Bagga, P.S., 2021, March. Remote Operations: The New Norm.
In International Petroleum Technology Conference. OnePetro.
10. Kavadias, S. and Ulrich, K.T., 2020. Innovation and new product development:
Reflections and insights from the research published in the first 20 years of
manufacturing & service operations management. Manufacturing & Service Operations
Management, 22(1), pp.84-92.
11. Kosztyán, Z.T., Pribojszki-Németh, A. and Szalkai, I., 2019. Hybrid multimode resource-
constrained maintenance project scheduling problem. Operations Research
Perspectives, 6, p.100129.
12. L. Plambeck, E. and Ramdas, K., 2020. Alleviating poverty by empowering women
through business model innovation: Manufacturing & service operations management
insights and opportunities. Manufacturing & Service Operations Management, 22(1),
pp.123-134.
13. Louis, J. and Dunston, P.S., 2018. Integrating IoT into operational workflows for real-
time and automated decision-making in repetitive construction operations. Automation in
Construction, 94, pp.317-327.
14. Schiffling, S., Hannibal, C., Fan, Y. and Tickle, M., 2020. Coopetition in temporary
contexts: examining swift trust and swift distrust in humanitarian
operations. International Journal of Operations & Production Management.
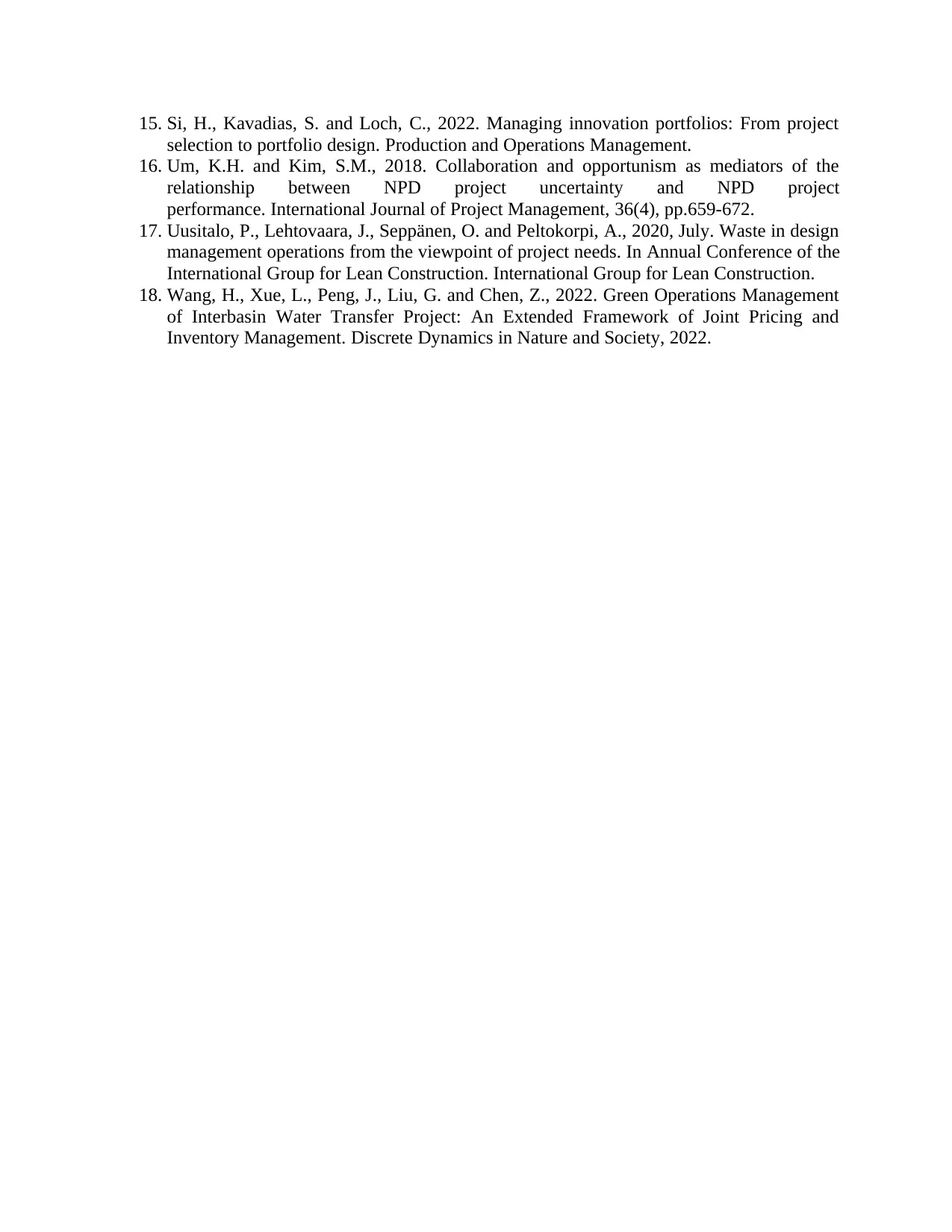
15. Si, H., Kavadias, S. and Loch, C., 2022. Managing innovation portfolios: From project
selection to portfolio design. Production and Operations Management.
16. Um, K.H. and Kim, S.M., 2018. Collaboration and opportunism as mediators of the
relationship between NPD project uncertainty and NPD project
performance. International Journal of Project Management, 36(4), pp.659-672.
17. Uusitalo, P., Lehtovaara, J., Seppänen, O. and Peltokorpi, A., 2020, July. Waste in design
management operations from the viewpoint of project needs. In Annual Conference of the
International Group for Lean Construction. International Group for Lean Construction.
18. Wang, H., Xue, L., Peng, J., Liu, G. and Chen, Z., 2022. Green Operations Management
of Interbasin Water Transfer Project: An Extended Framework of Joint Pricing and
Inventory Management. Discrete Dynamics in Nature and Society, 2022.
selection to portfolio design. Production and Operations Management.
16. Um, K.H. and Kim, S.M., 2018. Collaboration and opportunism as mediators of the
relationship between NPD project uncertainty and NPD project
performance. International Journal of Project Management, 36(4), pp.659-672.
17. Uusitalo, P., Lehtovaara, J., Seppänen, O. and Peltokorpi, A., 2020, July. Waste in design
management operations from the viewpoint of project needs. In Annual Conference of the
International Group for Lean Construction. International Group for Lean Construction.
18. Wang, H., Xue, L., Peng, J., Liu, G. and Chen, Z., 2022. Green Operations Management
of Interbasin Water Transfer Project: An Extended Framework of Joint Pricing and
Inventory Management. Discrete Dynamics in Nature and Society, 2022.
1 out of 15
Related Documents
![[object Object]](/_next/image/?url=%2F_next%2Fstatic%2Fmedia%2Flogo.6d15ce61.png&w=640&q=75)
Your All-in-One AI-Powered Toolkit for Academic Success.
+13062052269
info@desklib.com
Available 24*7 on WhatsApp / Email
Unlock your academic potential
© 2024 | Zucol Services PVT LTD | All rights reserved.