Unit 16 - Operations and Project Management
VerifiedAdded on 2023/06/18
|24
|6555
|451
AI Summary
This report evaluates Unilever's operations management, including the difference between operations and operations management, implementation of operations management principles, and analysis of the extent to which the operations management of the organization meets the requirements of the organization. It also discusses continuous improvement and lean principles, and the effectiveness of six sigma. Additionally, the report provides an overview of project methodologies and tools used by Unilever.
Contribute Materials
Your contribution can guide someone’s learning journey. Share your
documents today.
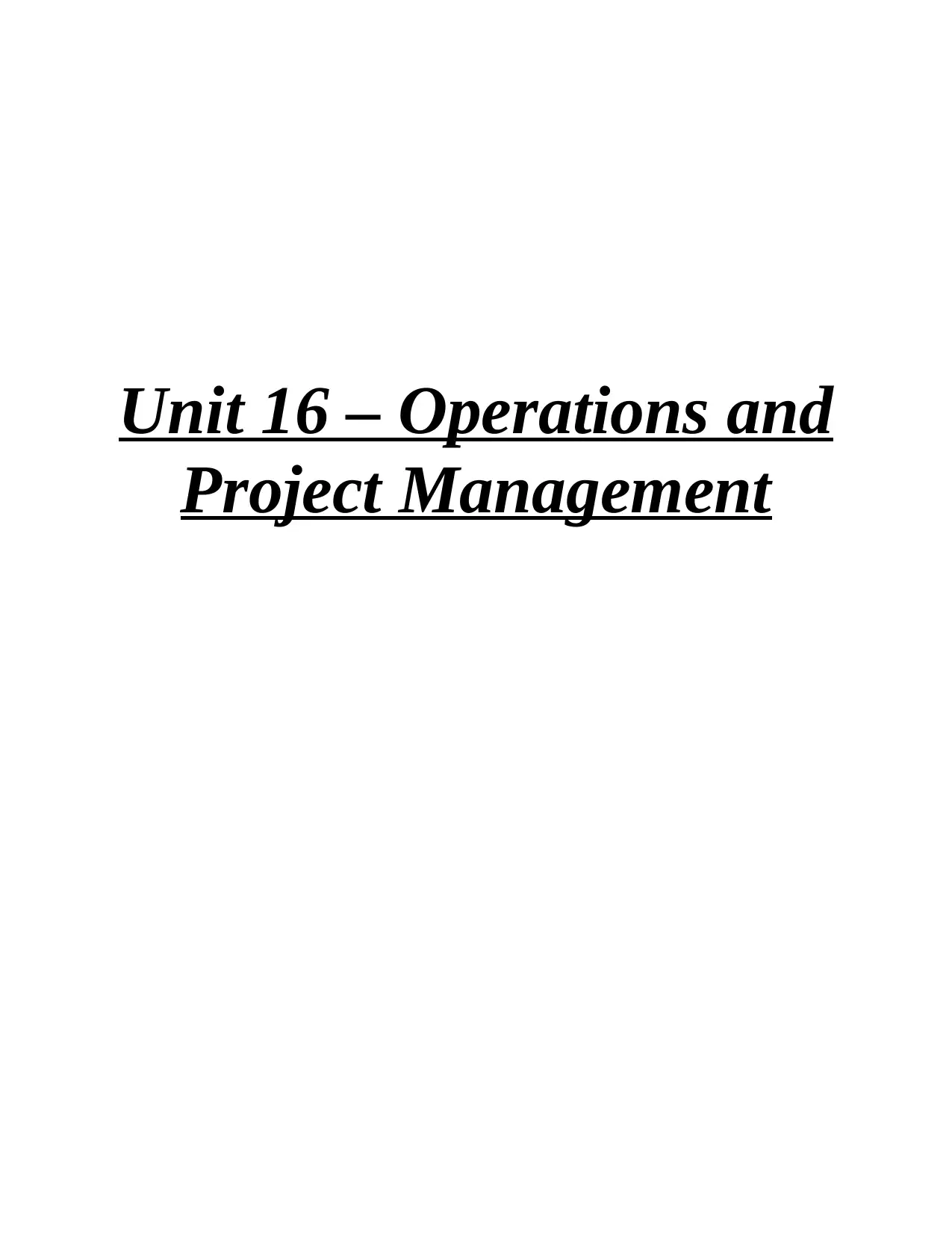
Unit 16 – Operations and
Project Management
Project Management
Secure Best Marks with AI Grader
Need help grading? Try our AI Grader for instant feedback on your assignments.
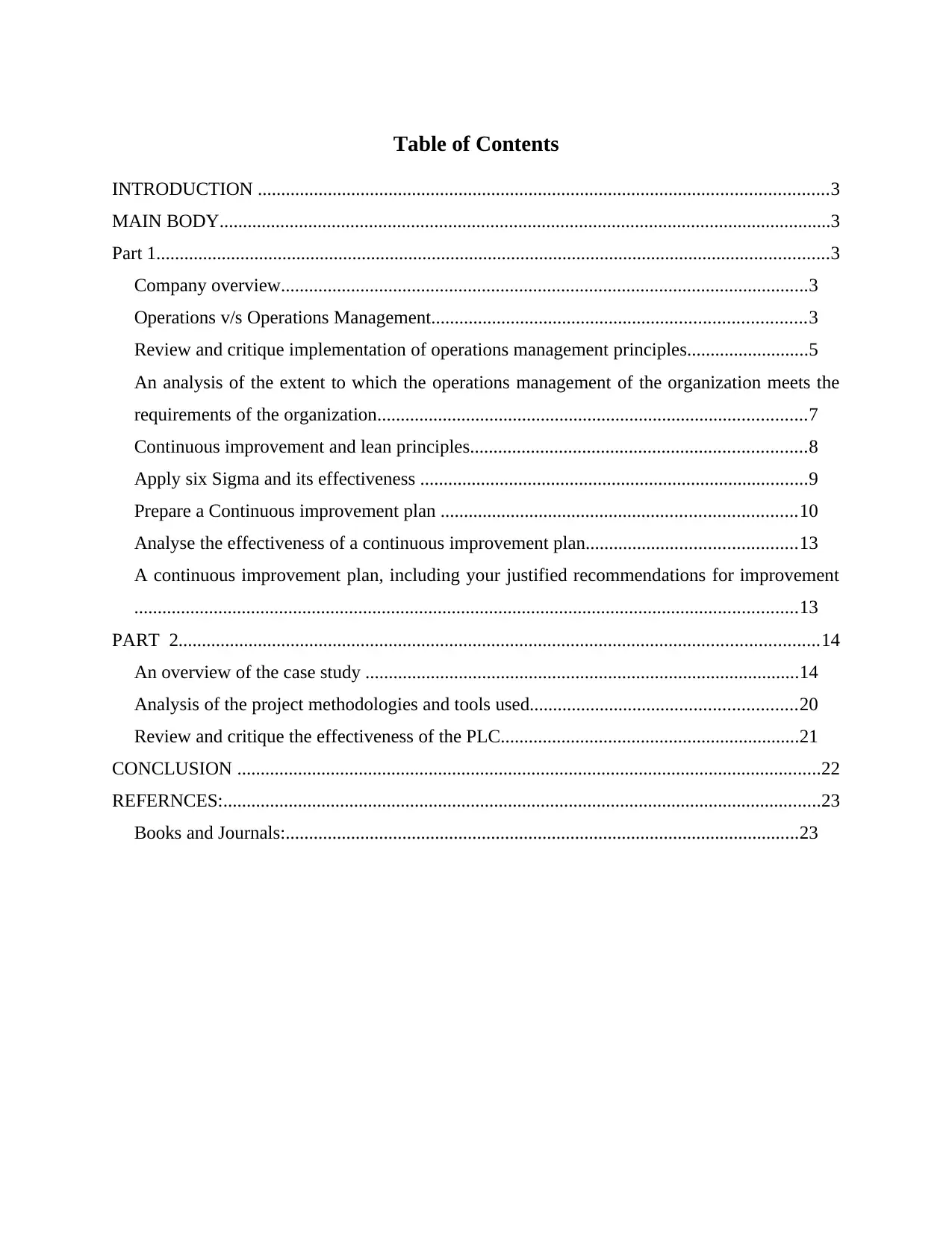
Table of Contents
INTRODUCTION ..........................................................................................................................3
MAIN BODY...................................................................................................................................3
Part 1................................................................................................................................................3
Company overview.................................................................................................................3
Operations v/s Operations Management................................................................................3
Review and critique implementation of operations management principles..........................5
An analysis of the extent to which the operations management of the organization meets the
requirements of the organization............................................................................................7
Continuous improvement and lean principles........................................................................8
Apply six Sigma and its effectiveness ...................................................................................9
Prepare a Continuous improvement plan ............................................................................10
Analyse the effectiveness of a continuous improvement plan.............................................13
A continuous improvement plan, including your justified recommendations for improvement
..............................................................................................................................................13
PART 2.........................................................................................................................................14
An overview of the case study .............................................................................................14
Analysis of the project methodologies and tools used.........................................................20
Review and critique the effectiveness of the PLC................................................................21
CONCLUSION .............................................................................................................................22
REFERNCES:................................................................................................................................23
Books and Journals:..............................................................................................................23
INTRODUCTION ..........................................................................................................................3
MAIN BODY...................................................................................................................................3
Part 1................................................................................................................................................3
Company overview.................................................................................................................3
Operations v/s Operations Management................................................................................3
Review and critique implementation of operations management principles..........................5
An analysis of the extent to which the operations management of the organization meets the
requirements of the organization............................................................................................7
Continuous improvement and lean principles........................................................................8
Apply six Sigma and its effectiveness ...................................................................................9
Prepare a Continuous improvement plan ............................................................................10
Analyse the effectiveness of a continuous improvement plan.............................................13
A continuous improvement plan, including your justified recommendations for improvement
..............................................................................................................................................13
PART 2.........................................................................................................................................14
An overview of the case study .............................................................................................14
Analysis of the project methodologies and tools used.........................................................20
Review and critique the effectiveness of the PLC................................................................21
CONCLUSION .............................................................................................................................22
REFERNCES:................................................................................................................................23
Books and Journals:..............................................................................................................23
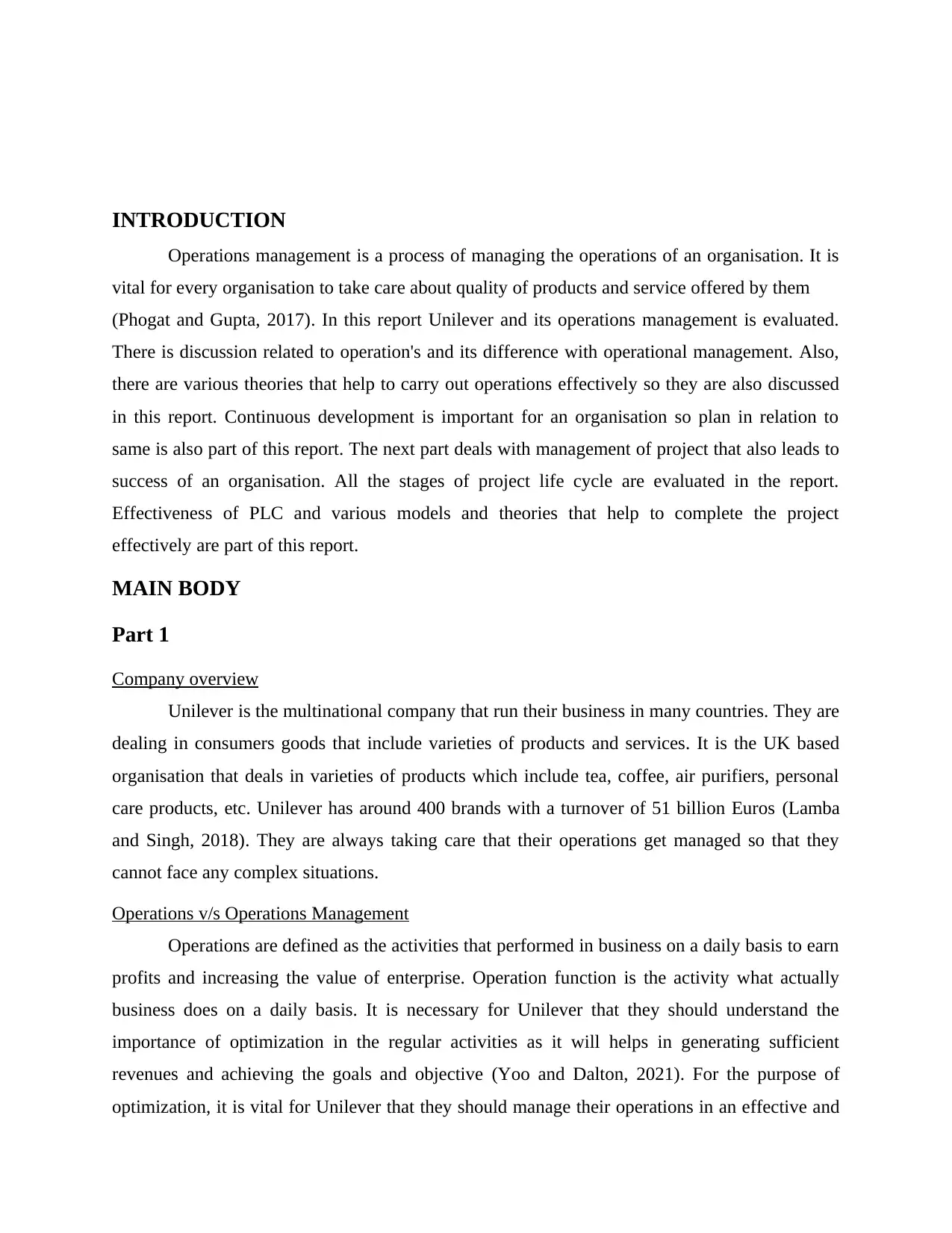
INTRODUCTION
Operations management is a process of managing the operations of an organisation. It is
vital for every organisation to take care about quality of products and service offered by them
(Phogat and Gupta, 2017). In this report Unilever and its operations management is evaluated.
There is discussion related to operation's and its difference with operational management. Also,
there are various theories that help to carry out operations effectively so they are also discussed
in this report. Continuous development is important for an organisation so plan in relation to
same is also part of this report. The next part deals with management of project that also leads to
success of an organisation. All the stages of project life cycle are evaluated in the report.
Effectiveness of PLC and various models and theories that help to complete the project
effectively are part of this report.
MAIN BODY
Part 1
Company overview
Unilever is the multinational company that run their business in many countries. They are
dealing in consumers goods that include varieties of products and services. It is the UK based
organisation that deals in varieties of products which include tea, coffee, air purifiers, personal
care products, etc. Unilever has around 400 brands with a turnover of 51 billion Euros (Lamba
and Singh, 2018). They are always taking care that their operations get managed so that they
cannot face any complex situations.
Operations v/s Operations Management
Operations are defined as the activities that performed in business on a daily basis to earn
profits and increasing the value of enterprise. Operation function is the activity what actually
business does on a daily basis. It is necessary for Unilever that they should understand the
importance of optimization in the regular activities as it will helps in generating sufficient
revenues and achieving the goals and objective (Yoo and Dalton, 2021). For the purpose of
optimization, it is vital for Unilever that they should manage their operations in an effective and
Operations management is a process of managing the operations of an organisation. It is
vital for every organisation to take care about quality of products and service offered by them
(Phogat and Gupta, 2017). In this report Unilever and its operations management is evaluated.
There is discussion related to operation's and its difference with operational management. Also,
there are various theories that help to carry out operations effectively so they are also discussed
in this report. Continuous development is important for an organisation so plan in relation to
same is also part of this report. The next part deals with management of project that also leads to
success of an organisation. All the stages of project life cycle are evaluated in the report.
Effectiveness of PLC and various models and theories that help to complete the project
effectively are part of this report.
MAIN BODY
Part 1
Company overview
Unilever is the multinational company that run their business in many countries. They are
dealing in consumers goods that include varieties of products and services. It is the UK based
organisation that deals in varieties of products which include tea, coffee, air purifiers, personal
care products, etc. Unilever has around 400 brands with a turnover of 51 billion Euros (Lamba
and Singh, 2018). They are always taking care that their operations get managed so that they
cannot face any complex situations.
Operations v/s Operations Management
Operations are defined as the activities that performed in business on a daily basis to earn
profits and increasing the value of enterprise. Operation function is the activity what actually
business does on a daily basis. It is necessary for Unilever that they should understand the
importance of optimization in the regular activities as it will helps in generating sufficient
revenues and achieving the goals and objective (Yoo and Dalton, 2021). For the purpose of
optimization, it is vital for Unilever that they should manage their operations in an effective and
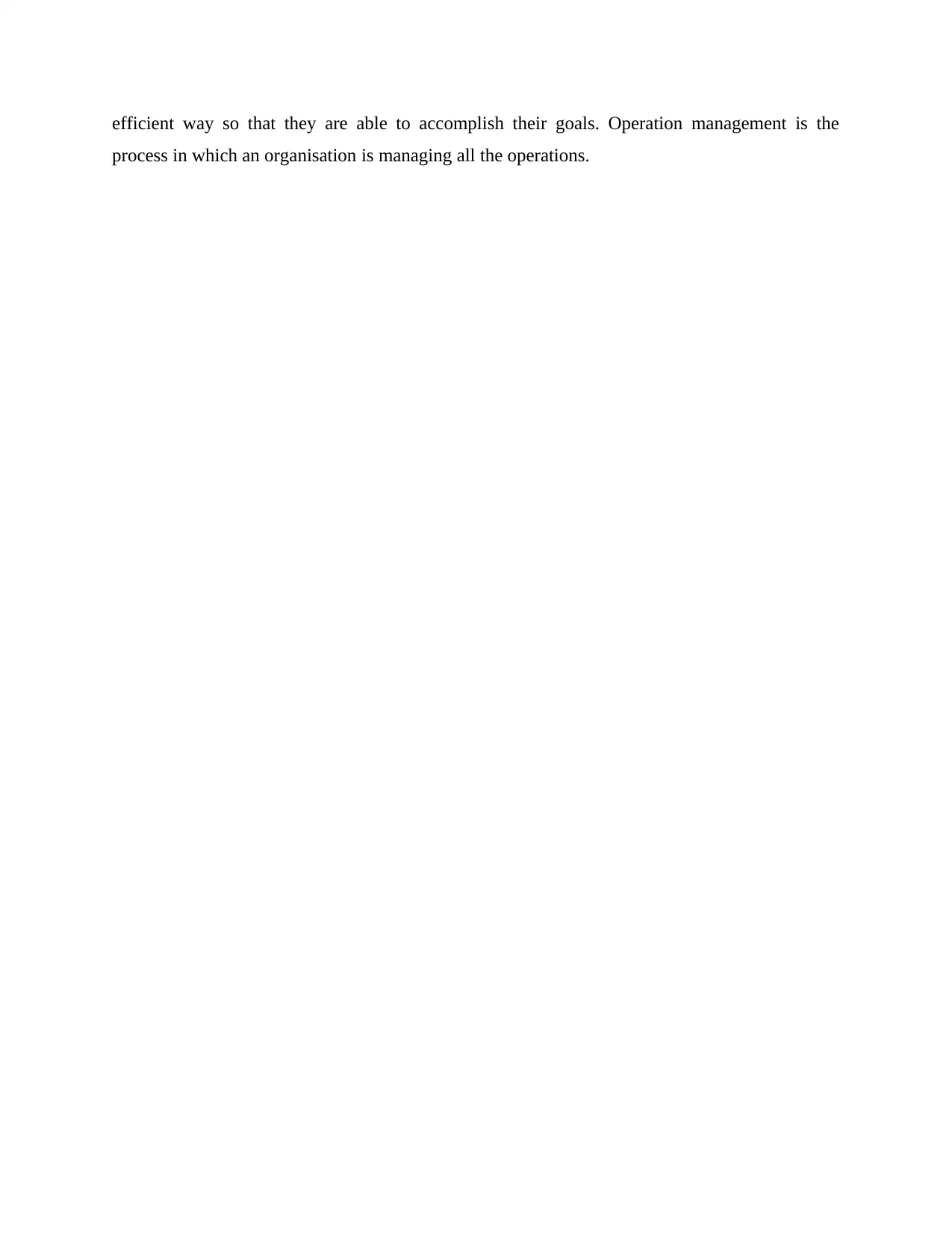
efficient way so that they are able to accomplish their goals. Operation management is the
process in which an organisation is managing all the operations.
process in which an organisation is managing all the operations.
Secure Best Marks with AI Grader
Need help grading? Try our AI Grader for instant feedback on your assignments.
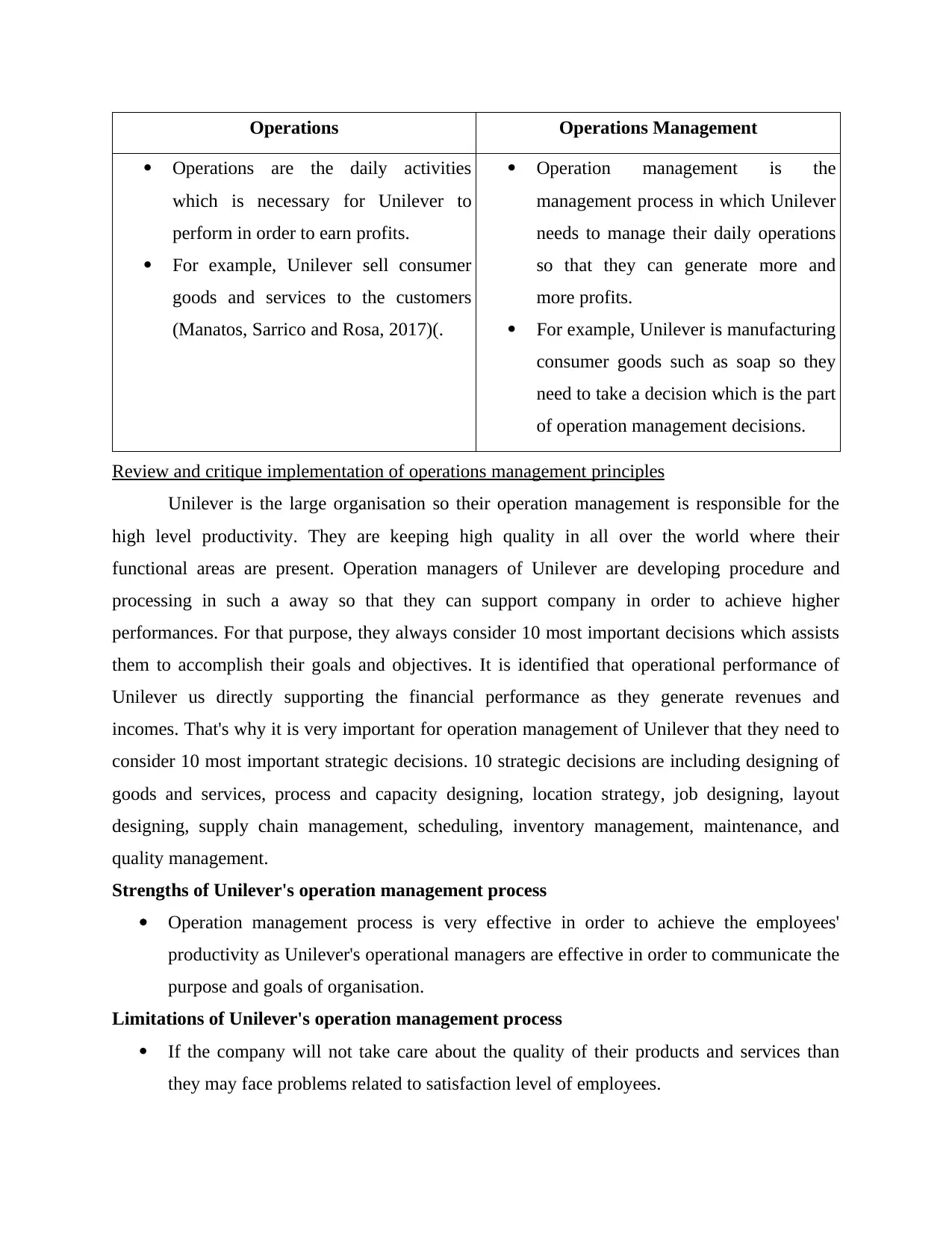
Operations Operations Management
Operations are the daily activities
which is necessary for Unilever to
perform in order to earn profits.
For example, Unilever sell consumer
goods and services to the customers
(Manatos, Sarrico and Rosa, 2017)(.
Operation management is the
management process in which Unilever
needs to manage their daily operations
so that they can generate more and
more profits.
For example, Unilever is manufacturing
consumer goods such as soap so they
need to take a decision which is the part
of operation management decisions.
Review and critique implementation of operations management principles
Unilever is the large organisation so their operation management is responsible for the
high level productivity. They are keeping high quality in all over the world where their
functional areas are present. Operation managers of Unilever are developing procedure and
processing in such a away so that they can support company in order to achieve higher
performances. For that purpose, they always consider 10 most important decisions which assists
them to accomplish their goals and objectives. It is identified that operational performance of
Unilever us directly supporting the financial performance as they generate revenues and
incomes. That's why it is very important for operation management of Unilever that they need to
consider 10 most important strategic decisions. 10 strategic decisions are including designing of
goods and services, process and capacity designing, location strategy, job designing, layout
designing, supply chain management, scheduling, inventory management, maintenance, and
quality management.
Strengths of Unilever's operation management process
Operation management process is very effective in order to achieve the employees'
productivity as Unilever's operational managers are effective in order to communicate the
purpose and goals of organisation.
Limitations of Unilever's operation management process
If the company will not take care about the quality of their products and services than
they may face problems related to satisfaction level of employees.
Operations are the daily activities
which is necessary for Unilever to
perform in order to earn profits.
For example, Unilever sell consumer
goods and services to the customers
(Manatos, Sarrico and Rosa, 2017)(.
Operation management is the
management process in which Unilever
needs to manage their daily operations
so that they can generate more and
more profits.
For example, Unilever is manufacturing
consumer goods such as soap so they
need to take a decision which is the part
of operation management decisions.
Review and critique implementation of operations management principles
Unilever is the large organisation so their operation management is responsible for the
high level productivity. They are keeping high quality in all over the world where their
functional areas are present. Operation managers of Unilever are developing procedure and
processing in such a away so that they can support company in order to achieve higher
performances. For that purpose, they always consider 10 most important decisions which assists
them to accomplish their goals and objectives. It is identified that operational performance of
Unilever us directly supporting the financial performance as they generate revenues and
incomes. That's why it is very important for operation management of Unilever that they need to
consider 10 most important strategic decisions. 10 strategic decisions are including designing of
goods and services, process and capacity designing, location strategy, job designing, layout
designing, supply chain management, scheduling, inventory management, maintenance, and
quality management.
Strengths of Unilever's operation management process
Operation management process is very effective in order to achieve the employees'
productivity as Unilever's operational managers are effective in order to communicate the
purpose and goals of organisation.
Limitations of Unilever's operation management process
If the company will not take care about the quality of their products and services than
they may face problems related to satisfaction level of employees.
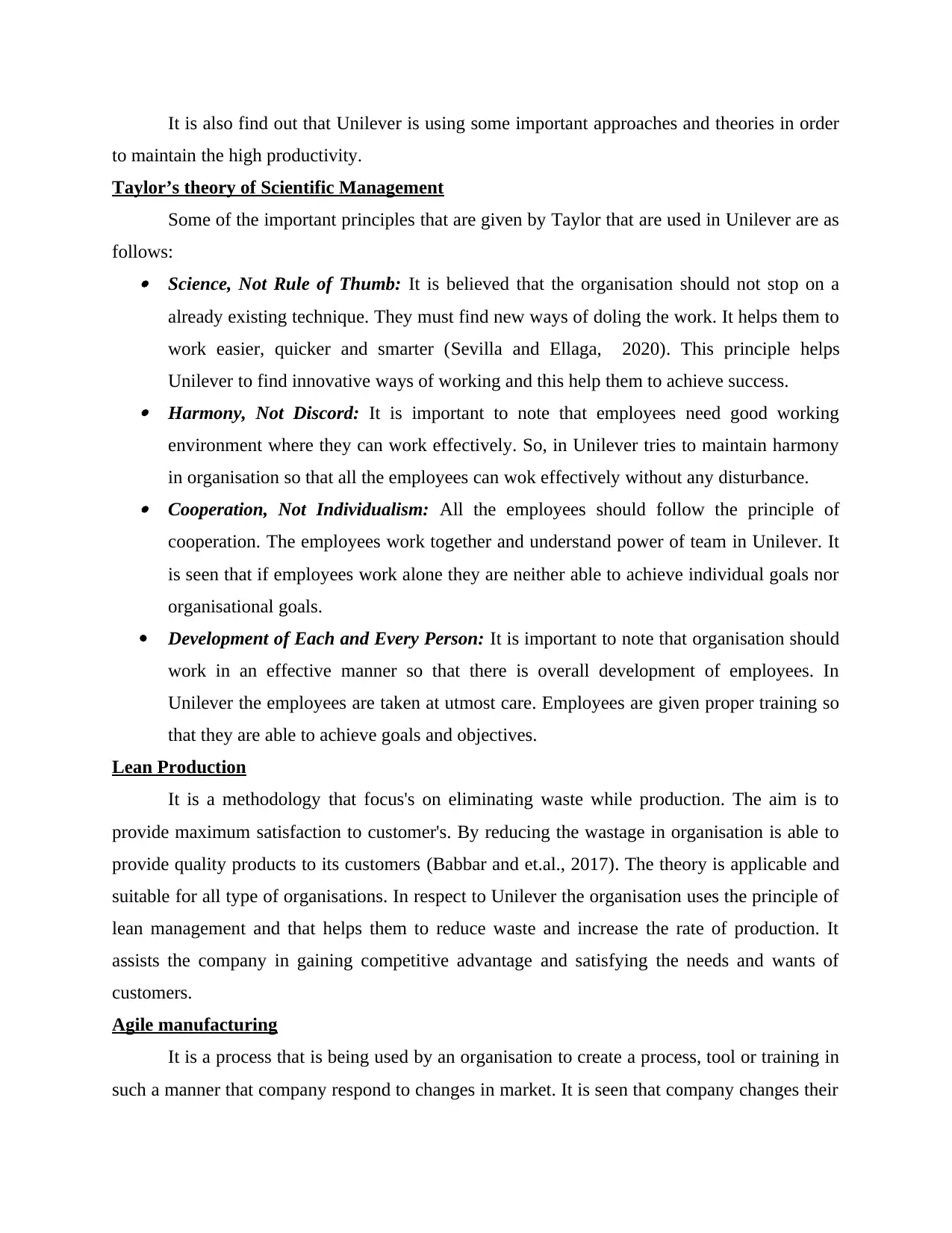
It is also find out that Unilever is using some important approaches and theories in order
to maintain the high productivity.
Taylor’s theory of Scientific Management
Some of the important principles that are given by Taylor that are used in Unilever are as
follows: Science, Not Rule of Thumb: It is believed that the organisation should not stop on a
already existing technique. They must find new ways of doling the work. It helps them to
work easier, quicker and smarter (Sevilla and Ellaga, 2020). This principle helps
Unilever to find innovative ways of working and this help them to achieve success. Harmony, Not Discord: It is important to note that employees need good working
environment where they can work effectively. So, in Unilever tries to maintain harmony
in organisation so that all the employees can wok effectively without any disturbance. Cooperation, Not Individualism: All the employees should follow the principle of
cooperation. The employees work together and understand power of team in Unilever. It
is seen that if employees work alone they are neither able to achieve individual goals nor
organisational goals.
Development of Each and Every Person: It is important to note that organisation should
work in an effective manner so that there is overall development of employees. In
Unilever the employees are taken at utmost care. Employees are given proper training so
that they are able to achieve goals and objectives.
Lean Production
It is a methodology that focus's on eliminating waste while production. The aim is to
provide maximum satisfaction to customer's. By reducing the wastage in organisation is able to
provide quality products to its customers (Babbar and et.al., 2017). The theory is applicable and
suitable for all type of organisations. In respect to Unilever the organisation uses the principle of
lean management and that helps them to reduce waste and increase the rate of production. It
assists the company in gaining competitive advantage and satisfying the needs and wants of
customers.
Agile manufacturing
It is a process that is being used by an organisation to create a process, tool or training in
such a manner that company respond to changes in market. It is seen that company changes their
to maintain the high productivity.
Taylor’s theory of Scientific Management
Some of the important principles that are given by Taylor that are used in Unilever are as
follows: Science, Not Rule of Thumb: It is believed that the organisation should not stop on a
already existing technique. They must find new ways of doling the work. It helps them to
work easier, quicker and smarter (Sevilla and Ellaga, 2020). This principle helps
Unilever to find innovative ways of working and this help them to achieve success. Harmony, Not Discord: It is important to note that employees need good working
environment where they can work effectively. So, in Unilever tries to maintain harmony
in organisation so that all the employees can wok effectively without any disturbance. Cooperation, Not Individualism: All the employees should follow the principle of
cooperation. The employees work together and understand power of team in Unilever. It
is seen that if employees work alone they are neither able to achieve individual goals nor
organisational goals.
Development of Each and Every Person: It is important to note that organisation should
work in an effective manner so that there is overall development of employees. In
Unilever the employees are taken at utmost care. Employees are given proper training so
that they are able to achieve goals and objectives.
Lean Production
It is a methodology that focus's on eliminating waste while production. The aim is to
provide maximum satisfaction to customer's. By reducing the wastage in organisation is able to
provide quality products to its customers (Babbar and et.al., 2017). The theory is applicable and
suitable for all type of organisations. In respect to Unilever the organisation uses the principle of
lean management and that helps them to reduce waste and increase the rate of production. It
assists the company in gaining competitive advantage and satisfying the needs and wants of
customers.
Agile manufacturing
It is a process that is being used by an organisation to create a process, tool or training in
such a manner that company respond to changes in market. It is seen that company changes their
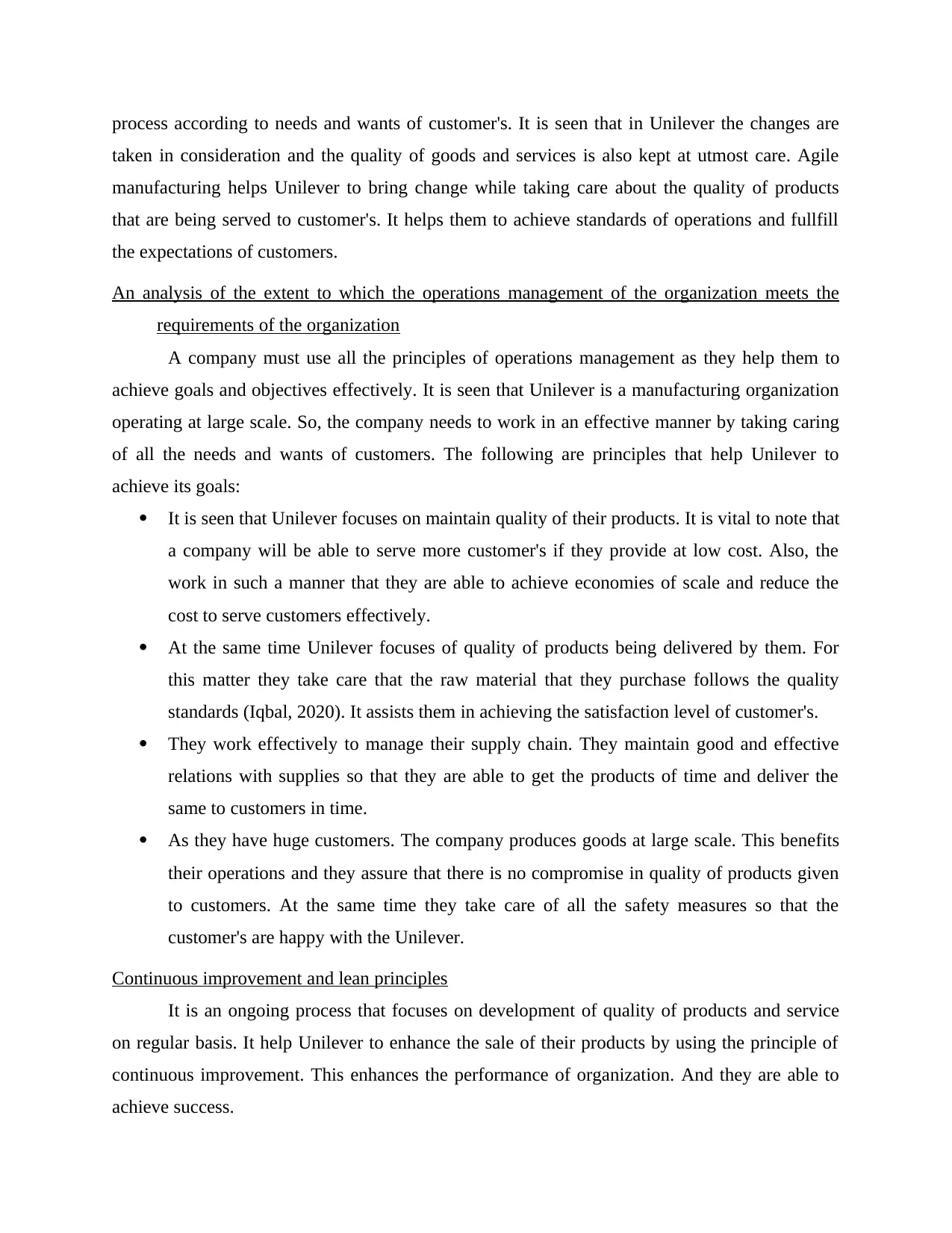
process according to needs and wants of customer's. It is seen that in Unilever the changes are
taken in consideration and the quality of goods and services is also kept at utmost care. Agile
manufacturing helps Unilever to bring change while taking care about the quality of products
that are being served to customer's. It helps them to achieve standards of operations and fullfill
the expectations of customers.
An analysis of the extent to which the operations management of the organization meets the
requirements of the organization
A company must use all the principles of operations management as they help them to
achieve goals and objectives effectively. It is seen that Unilever is a manufacturing organization
operating at large scale. So, the company needs to work in an effective manner by taking caring
of all the needs and wants of customers. The following are principles that help Unilever to
achieve its goals:
It is seen that Unilever focuses on maintain quality of their products. It is vital to note that
a company will be able to serve more customer's if they provide at low cost. Also, the
work in such a manner that they are able to achieve economies of scale and reduce the
cost to serve customers effectively.
At the same time Unilever focuses of quality of products being delivered by them. For
this matter they take care that the raw material that they purchase follows the quality
standards (Iqbal, 2020). It assists them in achieving the satisfaction level of customer's.
They work effectively to manage their supply chain. They maintain good and effective
relations with supplies so that they are able to get the products of time and deliver the
same to customers in time.
As they have huge customers. The company produces goods at large scale. This benefits
their operations and they assure that there is no compromise in quality of products given
to customers. At the same time they take care of all the safety measures so that the
customer's are happy with the Unilever.
Continuous improvement and lean principles
It is an ongoing process that focuses on development of quality of products and service
on regular basis. It help Unilever to enhance the sale of their products by using the principle of
continuous improvement. This enhances the performance of organization. And they are able to
achieve success.
taken in consideration and the quality of goods and services is also kept at utmost care. Agile
manufacturing helps Unilever to bring change while taking care about the quality of products
that are being served to customer's. It helps them to achieve standards of operations and fullfill
the expectations of customers.
An analysis of the extent to which the operations management of the organization meets the
requirements of the organization
A company must use all the principles of operations management as they help them to
achieve goals and objectives effectively. It is seen that Unilever is a manufacturing organization
operating at large scale. So, the company needs to work in an effective manner by taking caring
of all the needs and wants of customers. The following are principles that help Unilever to
achieve its goals:
It is seen that Unilever focuses on maintain quality of their products. It is vital to note that
a company will be able to serve more customer's if they provide at low cost. Also, the
work in such a manner that they are able to achieve economies of scale and reduce the
cost to serve customers effectively.
At the same time Unilever focuses of quality of products being delivered by them. For
this matter they take care that the raw material that they purchase follows the quality
standards (Iqbal, 2020). It assists them in achieving the satisfaction level of customer's.
They work effectively to manage their supply chain. They maintain good and effective
relations with supplies so that they are able to get the products of time and deliver the
same to customers in time.
As they have huge customers. The company produces goods at large scale. This benefits
their operations and they assure that there is no compromise in quality of products given
to customers. At the same time they take care of all the safety measures so that the
customer's are happy with the Unilever.
Continuous improvement and lean principles
It is an ongoing process that focuses on development of quality of products and service
on regular basis. It help Unilever to enhance the sale of their products by using the principle of
continuous improvement. This enhances the performance of organization. And they are able to
achieve success.
Paraphrase This Document
Need a fresh take? Get an instant paraphrase of this document with our AI Paraphraser
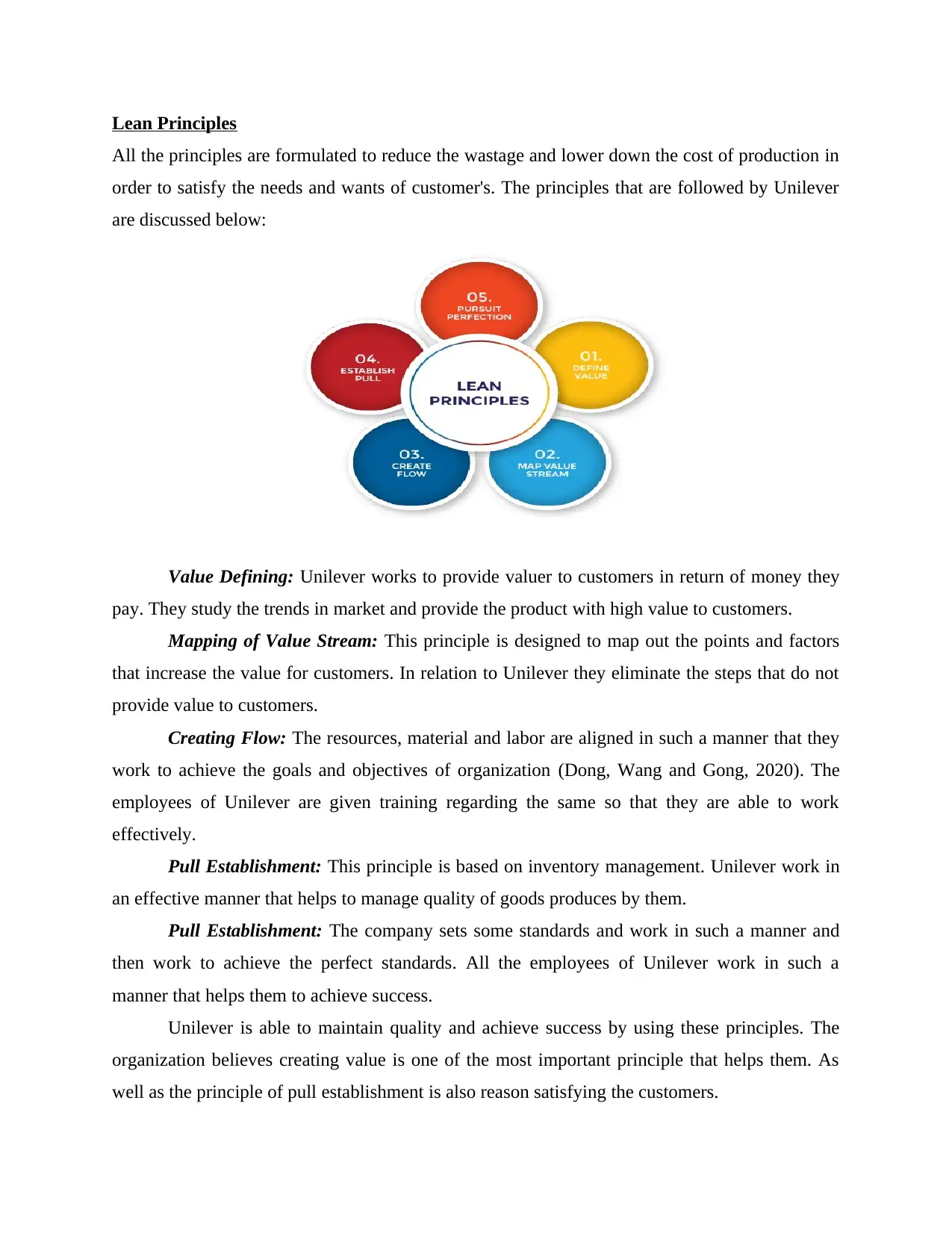
Lean Principles
All the principles are formulated to reduce the wastage and lower down the cost of production in
order to satisfy the needs and wants of customer's. The principles that are followed by Unilever
are discussed below:
Value Defining: Unilever works to provide valuer to customers in return of money they
pay. They study the trends in market and provide the product with high value to customers.
Mapping of Value Stream: This principle is designed to map out the points and factors
that increase the value for customers. In relation to Unilever they eliminate the steps that do not
provide value to customers.
Creating Flow: The resources, material and labor are aligned in such a manner that they
work to achieve the goals and objectives of organization (Dong, Wang and Gong, 2020). The
employees of Unilever are given training regarding the same so that they are able to work
effectively.
Pull Establishment: This principle is based on inventory management. Unilever work in
an effective manner that helps to manage quality of goods produces by them.
Pull Establishment: The company sets some standards and work in such a manner and
then work to achieve the perfect standards. All the employees of Unilever work in such a
manner that helps them to achieve success.
Unilever is able to maintain quality and achieve success by using these principles. The
organization believes creating value is one of the most important principle that helps them. As
well as the principle of pull establishment is also reason satisfying the customers.
All the principles are formulated to reduce the wastage and lower down the cost of production in
order to satisfy the needs and wants of customer's. The principles that are followed by Unilever
are discussed below:
Value Defining: Unilever works to provide valuer to customers in return of money they
pay. They study the trends in market and provide the product with high value to customers.
Mapping of Value Stream: This principle is designed to map out the points and factors
that increase the value for customers. In relation to Unilever they eliminate the steps that do not
provide value to customers.
Creating Flow: The resources, material and labor are aligned in such a manner that they
work to achieve the goals and objectives of organization (Dong, Wang and Gong, 2020). The
employees of Unilever are given training regarding the same so that they are able to work
effectively.
Pull Establishment: This principle is based on inventory management. Unilever work in
an effective manner that helps to manage quality of goods produces by them.
Pull Establishment: The company sets some standards and work in such a manner and
then work to achieve the perfect standards. All the employees of Unilever work in such a
manner that helps them to achieve success.
Unilever is able to maintain quality and achieve success by using these principles. The
organization believes creating value is one of the most important principle that helps them. As
well as the principle of pull establishment is also reason satisfying the customers.
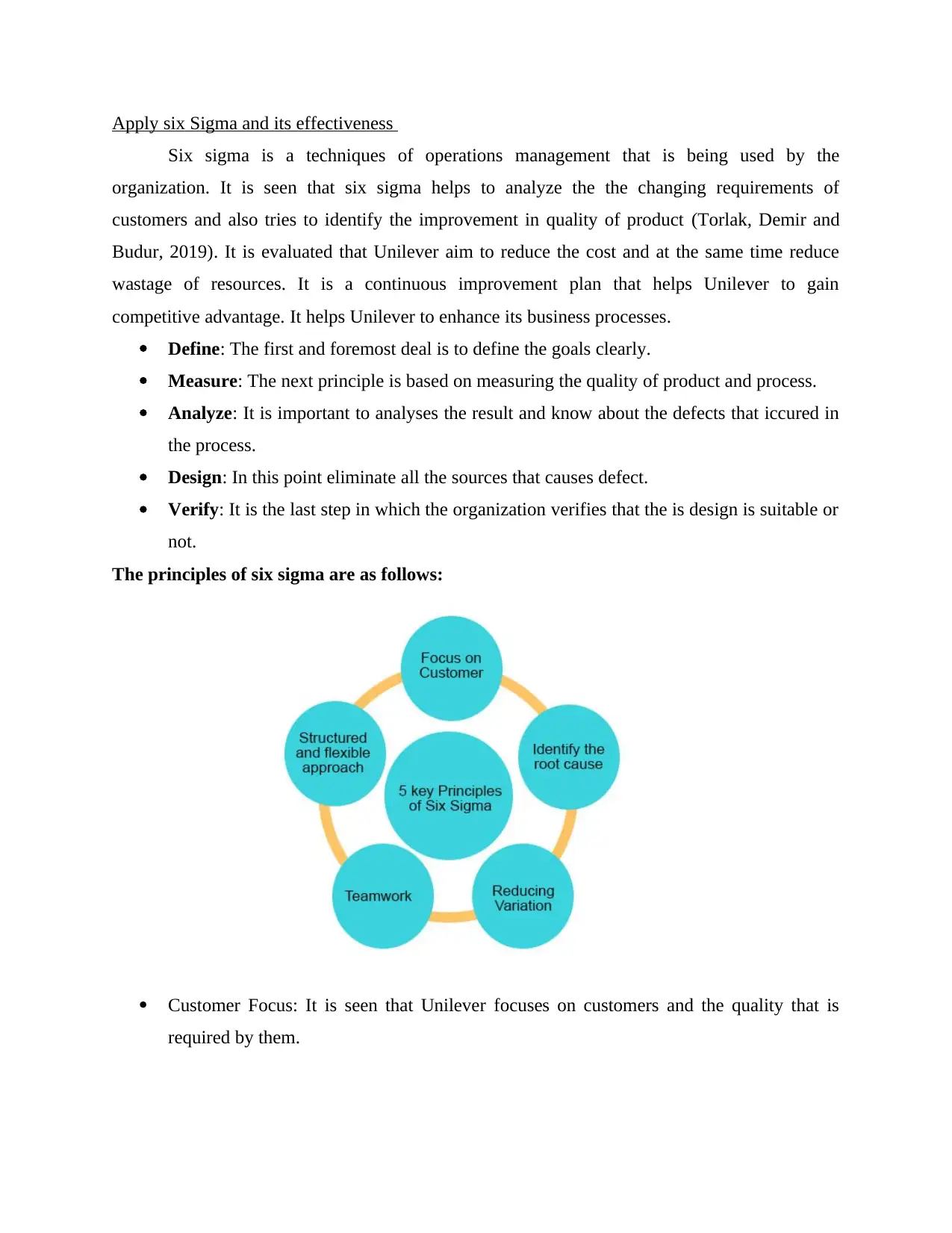
Apply six Sigma and its effectiveness
Six sigma is a techniques of operations management that is being used by the
organization. It is seen that six sigma helps to analyze the the changing requirements of
customers and also tries to identify the improvement in quality of product (Torlak, Demir and
Budur, 2019). It is evaluated that Unilever aim to reduce the cost and at the same time reduce
wastage of resources. It is a continuous improvement plan that helps Unilever to gain
competitive advantage. It helps Unilever to enhance its business processes.
Define: The first and foremost deal is to define the goals clearly.
Measure: The next principle is based on measuring the quality of product and process.
Analyze: It is important to analyses the result and know about the defects that iccured in
the process.
Design: In this point eliminate all the sources that causes defect.
Verify: It is the last step in which the organization verifies that the is design is suitable or
not.
The principles of six sigma are as follows:
Customer Focus: It is seen that Unilever focuses on customers and the quality that is
required by them.
Six sigma is a techniques of operations management that is being used by the
organization. It is seen that six sigma helps to analyze the the changing requirements of
customers and also tries to identify the improvement in quality of product (Torlak, Demir and
Budur, 2019). It is evaluated that Unilever aim to reduce the cost and at the same time reduce
wastage of resources. It is a continuous improvement plan that helps Unilever to gain
competitive advantage. It helps Unilever to enhance its business processes.
Define: The first and foremost deal is to define the goals clearly.
Measure: The next principle is based on measuring the quality of product and process.
Analyze: It is important to analyses the result and know about the defects that iccured in
the process.
Design: In this point eliminate all the sources that causes defect.
Verify: It is the last step in which the organization verifies that the is design is suitable or
not.
The principles of six sigma are as follows:
Customer Focus: It is seen that Unilever focuses on customers and the quality that is
required by them.
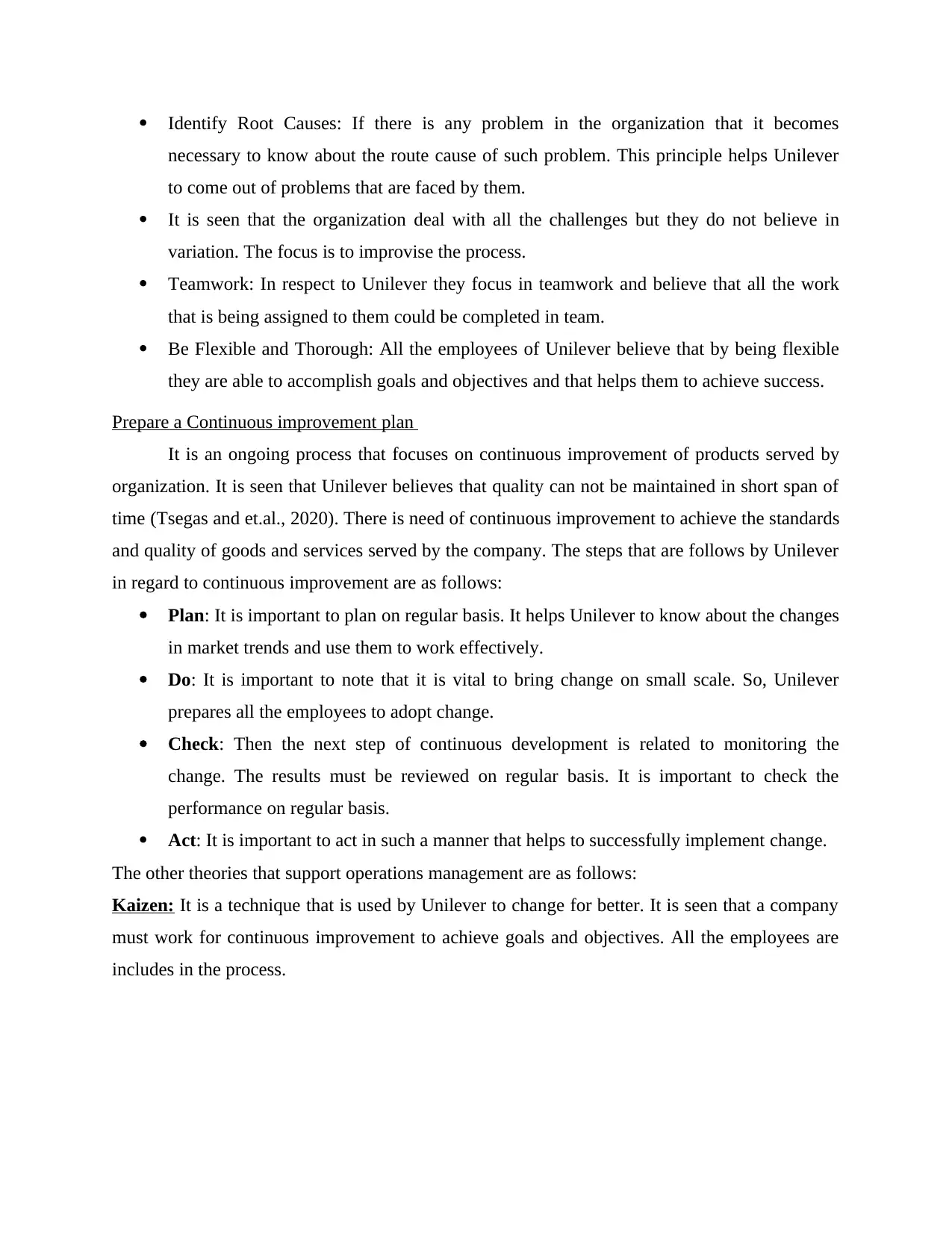
Identify Root Causes: If there is any problem in the organization that it becomes
necessary to know about the route cause of such problem. This principle helps Unilever
to come out of problems that are faced by them.
It is seen that the organization deal with all the challenges but they do not believe in
variation. The focus is to improvise the process.
Teamwork: In respect to Unilever they focus in teamwork and believe that all the work
that is being assigned to them could be completed in team.
Be Flexible and Thorough: All the employees of Unilever believe that by being flexible
they are able to accomplish goals and objectives and that helps them to achieve success.
Prepare a Continuous improvement plan
It is an ongoing process that focuses on continuous improvement of products served by
organization. It is seen that Unilever believes that quality can not be maintained in short span of
time (Tsegas and et.al., 2020). There is need of continuous improvement to achieve the standards
and quality of goods and services served by the company. The steps that are follows by Unilever
in regard to continuous improvement are as follows:
Plan: It is important to plan on regular basis. It helps Unilever to know about the changes
in market trends and use them to work effectively.
Do: It is important to note that it is vital to bring change on small scale. So, Unilever
prepares all the employees to adopt change.
Check: Then the next step of continuous development is related to monitoring the
change. The results must be reviewed on regular basis. It is important to check the
performance on regular basis.
Act: It is important to act in such a manner that helps to successfully implement change.
The other theories that support operations management are as follows:
Kaizen: It is a technique that is used by Unilever to change for better. It is seen that a company
must work for continuous improvement to achieve goals and objectives. All the employees are
includes in the process.
necessary to know about the route cause of such problem. This principle helps Unilever
to come out of problems that are faced by them.
It is seen that the organization deal with all the challenges but they do not believe in
variation. The focus is to improvise the process.
Teamwork: In respect to Unilever they focus in teamwork and believe that all the work
that is being assigned to them could be completed in team.
Be Flexible and Thorough: All the employees of Unilever believe that by being flexible
they are able to accomplish goals and objectives and that helps them to achieve success.
Prepare a Continuous improvement plan
It is an ongoing process that focuses on continuous improvement of products served by
organization. It is seen that Unilever believes that quality can not be maintained in short span of
time (Tsegas and et.al., 2020). There is need of continuous improvement to achieve the standards
and quality of goods and services served by the company. The steps that are follows by Unilever
in regard to continuous improvement are as follows:
Plan: It is important to plan on regular basis. It helps Unilever to know about the changes
in market trends and use them to work effectively.
Do: It is important to note that it is vital to bring change on small scale. So, Unilever
prepares all the employees to adopt change.
Check: Then the next step of continuous development is related to monitoring the
change. The results must be reviewed on regular basis. It is important to check the
performance on regular basis.
Act: It is important to act in such a manner that helps to successfully implement change.
The other theories that support operations management are as follows:
Kaizen: It is a technique that is used by Unilever to change for better. It is seen that a company
must work for continuous improvement to achieve goals and objectives. All the employees are
includes in the process.
Secure Best Marks with AI Grader
Need help grading? Try our AI Grader for instant feedback on your assignments.
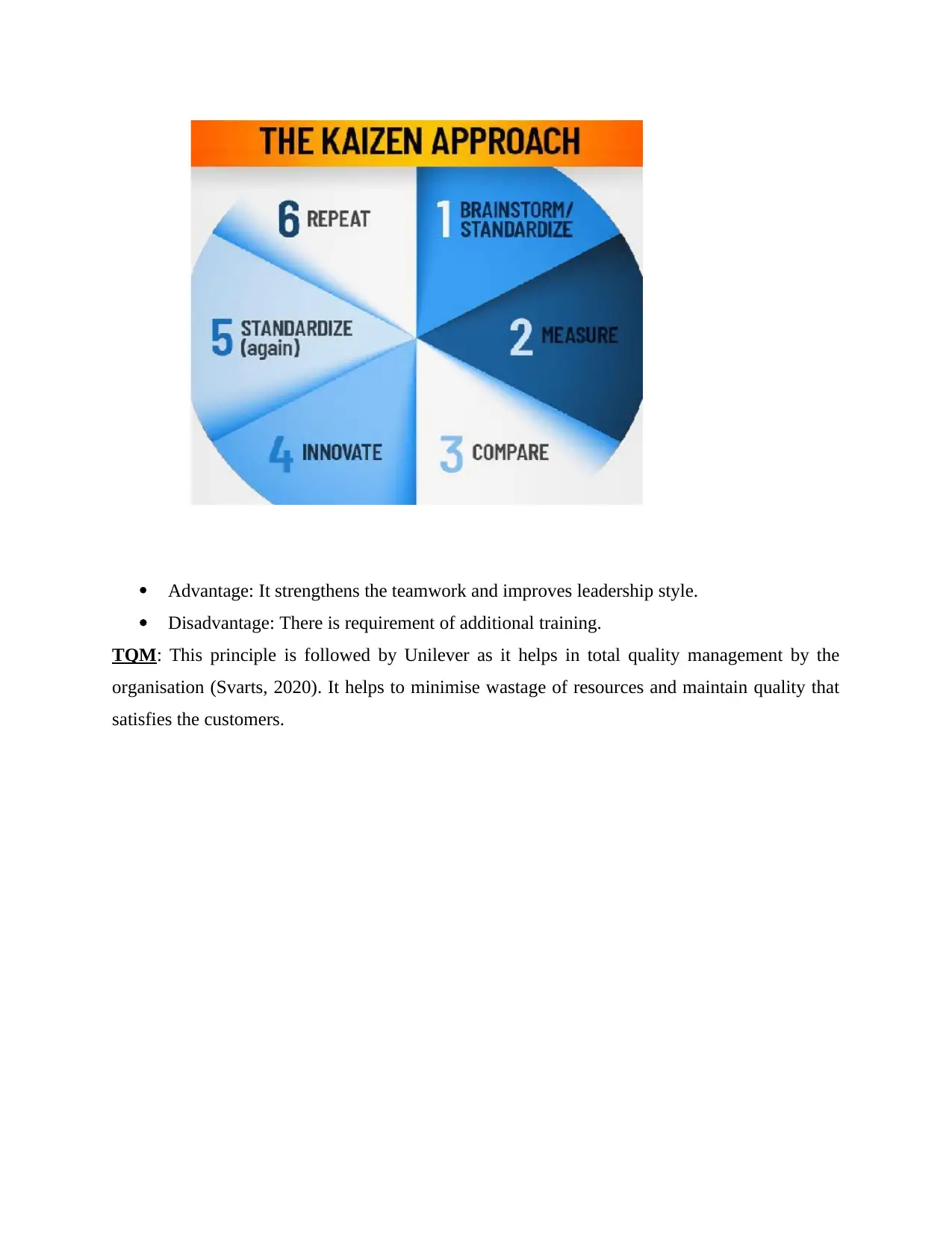
Advantage: It strengthens the teamwork and improves leadership style.
Disadvantage: There is requirement of additional training.
TQM: This principle is followed by Unilever as it helps in total quality management by the
organisation (Svarts, 2020). It helps to minimise wastage of resources and maintain quality that
satisfies the customers.
Disadvantage: There is requirement of additional training.
TQM: This principle is followed by Unilever as it helps in total quality management by the
organisation (Svarts, 2020). It helps to minimise wastage of resources and maintain quality that
satisfies the customers.
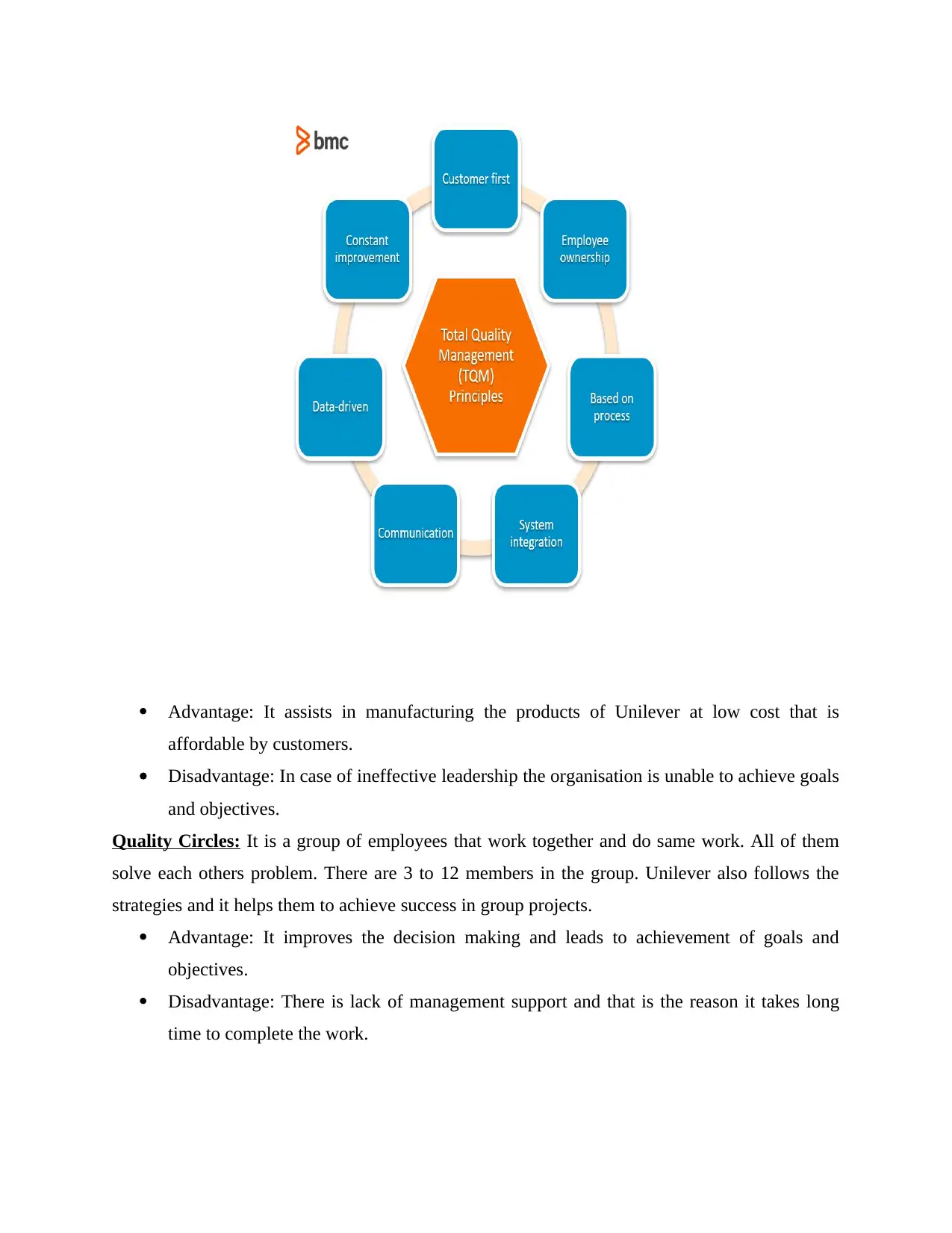
Advantage: It assists in manufacturing the products of Unilever at low cost that is
affordable by customers.
Disadvantage: In case of ineffective leadership the organisation is unable to achieve goals
and objectives.
Quality Circles: It is a group of employees that work together and do same work. All of them
solve each others problem. There are 3 to 12 members in the group. Unilever also follows the
strategies and it helps them to achieve success in group projects.
Advantage: It improves the decision making and leads to achievement of goals and
objectives.
Disadvantage: There is lack of management support and that is the reason it takes long
time to complete the work.
affordable by customers.
Disadvantage: In case of ineffective leadership the organisation is unable to achieve goals
and objectives.
Quality Circles: It is a group of employees that work together and do same work. All of them
solve each others problem. There are 3 to 12 members in the group. Unilever also follows the
strategies and it helps them to achieve success in group projects.
Advantage: It improves the decision making and leads to achievement of goals and
objectives.
Disadvantage: There is lack of management support and that is the reason it takes long
time to complete the work.
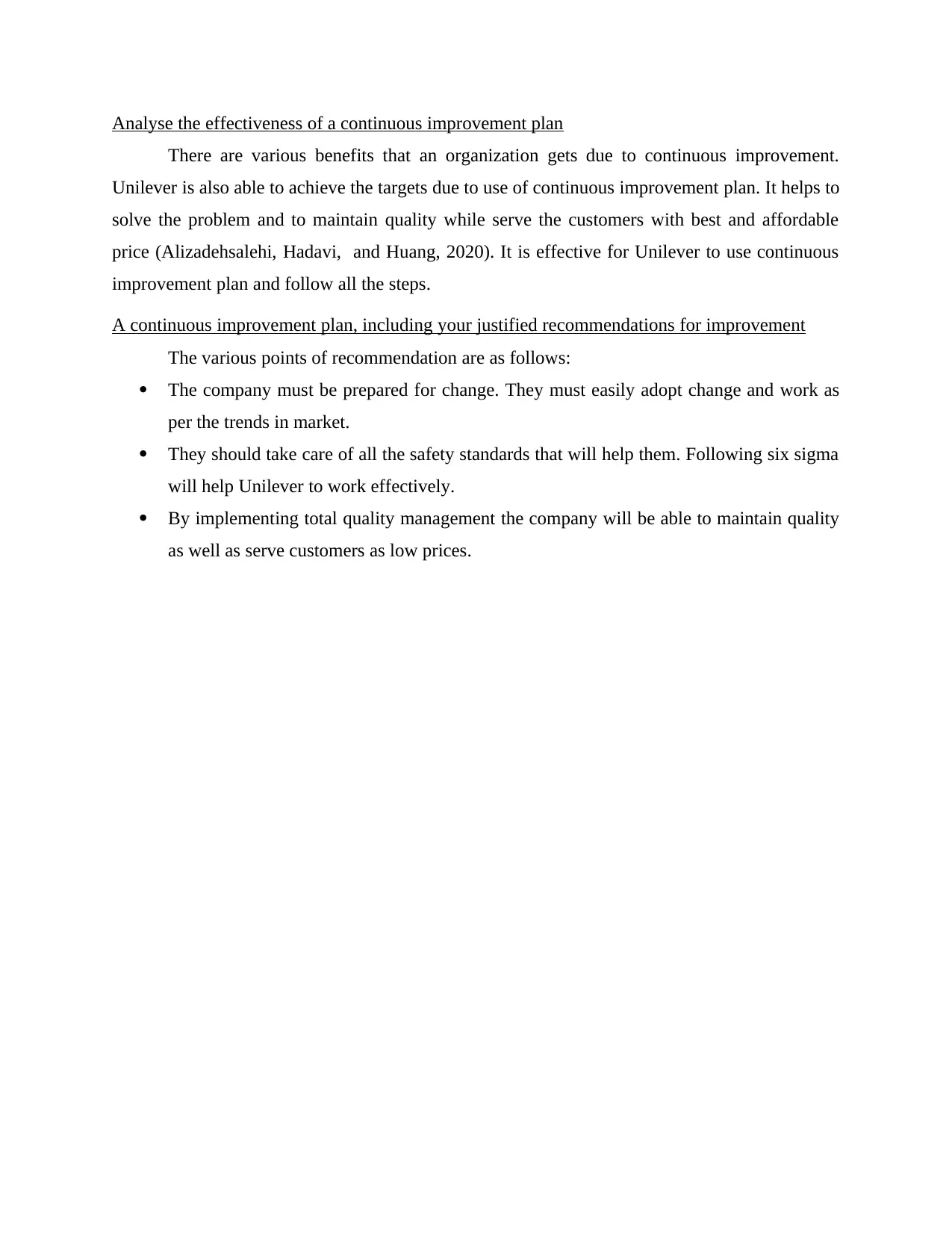
Analyse the effectiveness of a continuous improvement plan
There are various benefits that an organization gets due to continuous improvement.
Unilever is also able to achieve the targets due to use of continuous improvement plan. It helps to
solve the problem and to maintain quality while serve the customers with best and affordable
price (Alizadehsalehi, Hadavi, and Huang, 2020). It is effective for Unilever to use continuous
improvement plan and follow all the steps.
A continuous improvement plan, including your justified recommendations for improvement
The various points of recommendation are as follows:
The company must be prepared for change. They must easily adopt change and work as
per the trends in market.
They should take care of all the safety standards that will help them. Following six sigma
will help Unilever to work effectively.
By implementing total quality management the company will be able to maintain quality
as well as serve customers as low prices.
There are various benefits that an organization gets due to continuous improvement.
Unilever is also able to achieve the targets due to use of continuous improvement plan. It helps to
solve the problem and to maintain quality while serve the customers with best and affordable
price (Alizadehsalehi, Hadavi, and Huang, 2020). It is effective for Unilever to use continuous
improvement plan and follow all the steps.
A continuous improvement plan, including your justified recommendations for improvement
The various points of recommendation are as follows:
The company must be prepared for change. They must easily adopt change and work as
per the trends in market.
They should take care of all the safety standards that will help them. Following six sigma
will help Unilever to work effectively.
By implementing total quality management the company will be able to maintain quality
as well as serve customers as low prices.
Paraphrase This Document
Need a fresh take? Get an instant paraphrase of this document with our AI Paraphraser
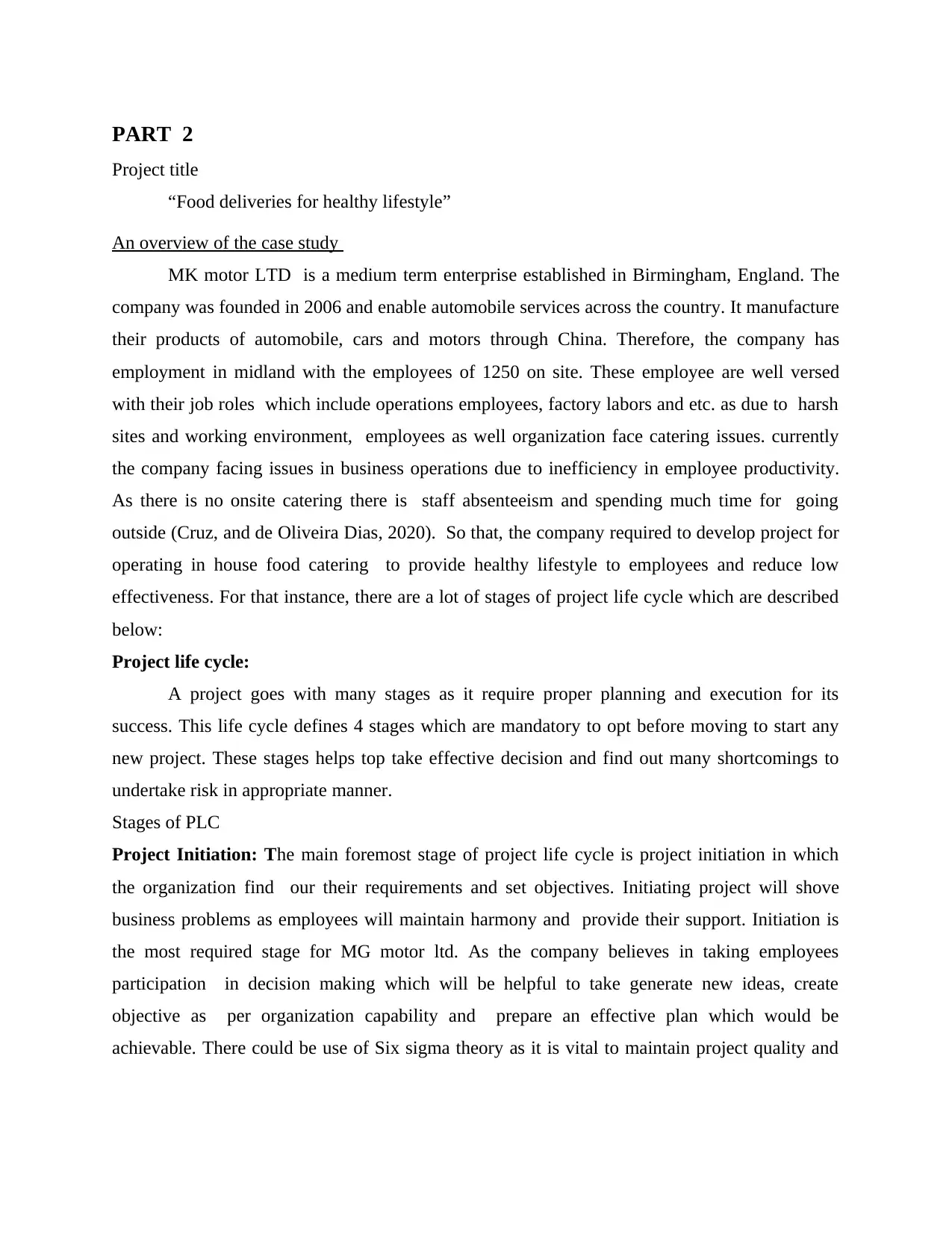
PART 2
Project title
“Food deliveries for healthy lifestyle”
An overview of the case study
MK motor LTD is a medium term enterprise established in Birmingham, England. The
company was founded in 2006 and enable automobile services across the country. It manufacture
their products of automobile, cars and motors through China. Therefore, the company has
employment in midland with the employees of 1250 on site. These employee are well versed
with their job roles which include operations employees, factory labors and etc. as due to harsh
sites and working environment, employees as well organization face catering issues. currently
the company facing issues in business operations due to inefficiency in employee productivity.
As there is no onsite catering there is staff absenteeism and spending much time for going
outside (Cruz, and de Oliveira Dias, 2020). So that, the company required to develop project for
operating in house food catering to provide healthy lifestyle to employees and reduce low
effectiveness. For that instance, there are a lot of stages of project life cycle which are described
below:
Project life cycle:
A project goes with many stages as it require proper planning and execution for its
success. This life cycle defines 4 stages which are mandatory to opt before moving to start any
new project. These stages helps top take effective decision and find out many shortcomings to
undertake risk in appropriate manner.
Stages of PLC
Project Initiation: The main foremost stage of project life cycle is project initiation in which
the organization find our their requirements and set objectives. Initiating project will shove
business problems as employees will maintain harmony and provide their support. Initiation is
the most required stage for MG motor ltd. As the company believes in taking employees
participation in decision making which will be helpful to take generate new ideas, create
objective as per organization capability and prepare an effective plan which would be
achievable. There could be use of Six sigma theory as it is vital to maintain project quality and
Project title
“Food deliveries for healthy lifestyle”
An overview of the case study
MK motor LTD is a medium term enterprise established in Birmingham, England. The
company was founded in 2006 and enable automobile services across the country. It manufacture
their products of automobile, cars and motors through China. Therefore, the company has
employment in midland with the employees of 1250 on site. These employee are well versed
with their job roles which include operations employees, factory labors and etc. as due to harsh
sites and working environment, employees as well organization face catering issues. currently
the company facing issues in business operations due to inefficiency in employee productivity.
As there is no onsite catering there is staff absenteeism and spending much time for going
outside (Cruz, and de Oliveira Dias, 2020). So that, the company required to develop project for
operating in house food catering to provide healthy lifestyle to employees and reduce low
effectiveness. For that instance, there are a lot of stages of project life cycle which are described
below:
Project life cycle:
A project goes with many stages as it require proper planning and execution for its
success. This life cycle defines 4 stages which are mandatory to opt before moving to start any
new project. These stages helps top take effective decision and find out many shortcomings to
undertake risk in appropriate manner.
Stages of PLC
Project Initiation: The main foremost stage of project life cycle is project initiation in which
the organization find our their requirements and set objectives. Initiating project will shove
business problems as employees will maintain harmony and provide their support. Initiation is
the most required stage for MG motor ltd. As the company believes in taking employees
participation in decision making which will be helpful to take generate new ideas, create
objective as per organization capability and prepare an effective plan which would be
achievable. There could be use of Six sigma theory as it is vital to maintain project quality and
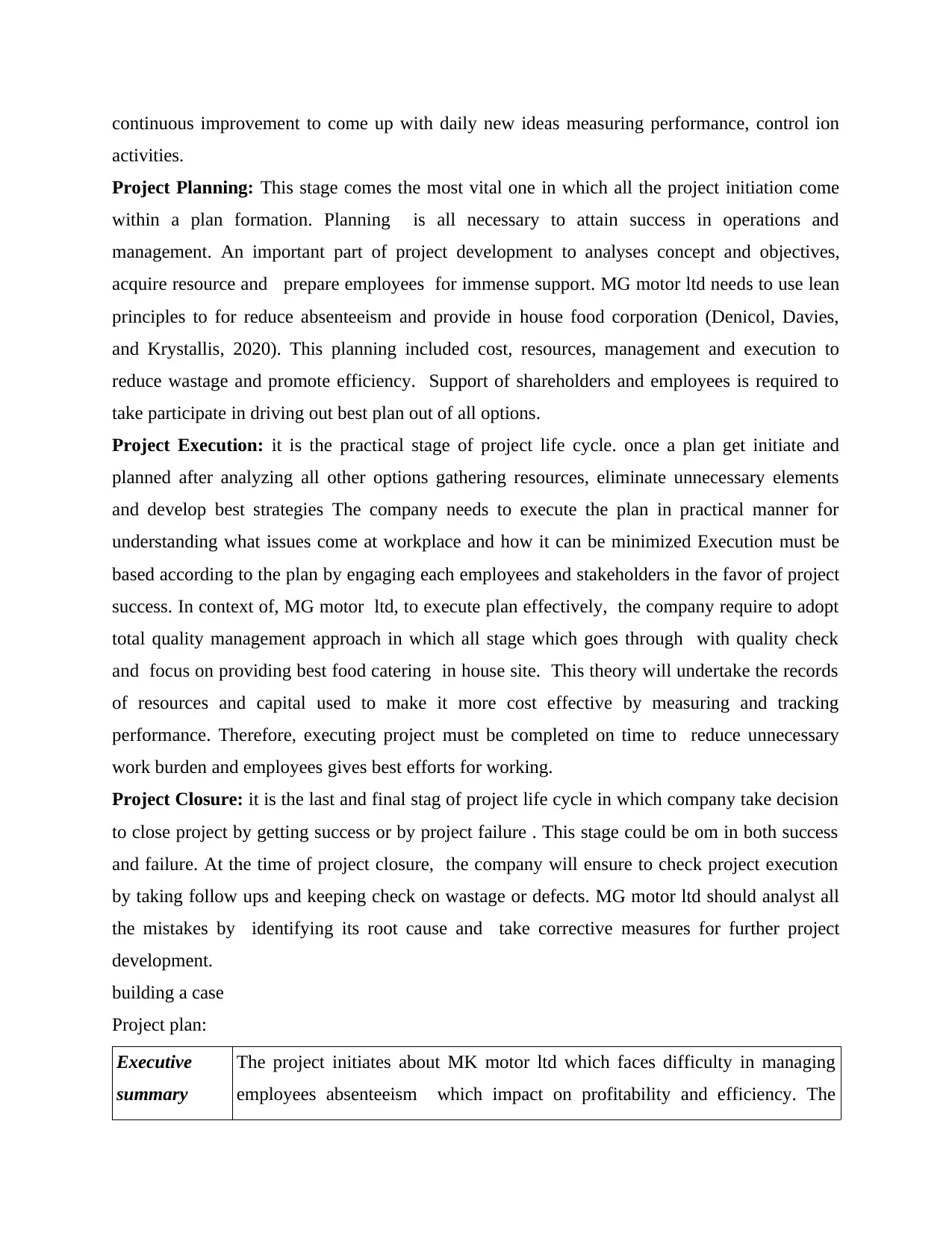
continuous improvement to come up with daily new ideas measuring performance, control ion
activities.
Project Planning: This stage comes the most vital one in which all the project initiation come
within a plan formation. Planning is all necessary to attain success in operations and
management. An important part of project development to analyses concept and objectives,
acquire resource and prepare employees for immense support. MG motor ltd needs to use lean
principles to for reduce absenteeism and provide in house food corporation (Denicol, Davies,
and Krystallis, 2020). This planning included cost, resources, management and execution to
reduce wastage and promote efficiency. Support of shareholders and employees is required to
take participate in driving out best plan out of all options.
Project Execution: it is the practical stage of project life cycle. once a plan get initiate and
planned after analyzing all other options gathering resources, eliminate unnecessary elements
and develop best strategies The company needs to execute the plan in practical manner for
understanding what issues come at workplace and how it can be minimized Execution must be
based according to the plan by engaging each employees and stakeholders in the favor of project
success. In context of, MG motor ltd, to execute plan effectively, the company require to adopt
total quality management approach in which all stage which goes through with quality check
and focus on providing best food catering in house site. This theory will undertake the records
of resources and capital used to make it more cost effective by measuring and tracking
performance. Therefore, executing project must be completed on time to reduce unnecessary
work burden and employees gives best efforts for working.
Project Closure: it is the last and final stag of project life cycle in which company take decision
to close project by getting success or by project failure . This stage could be om in both success
and failure. At the time of project closure, the company will ensure to check project execution
by taking follow ups and keeping check on wastage or defects. MG motor ltd should analyst all
the mistakes by identifying its root cause and take corrective measures for further project
development.
building a case
Project plan:
Executive
summary
The project initiates about MK motor ltd which faces difficulty in managing
employees absenteeism which impact on profitability and efficiency. The
activities.
Project Planning: This stage comes the most vital one in which all the project initiation come
within a plan formation. Planning is all necessary to attain success in operations and
management. An important part of project development to analyses concept and objectives,
acquire resource and prepare employees for immense support. MG motor ltd needs to use lean
principles to for reduce absenteeism and provide in house food corporation (Denicol, Davies,
and Krystallis, 2020). This planning included cost, resources, management and execution to
reduce wastage and promote efficiency. Support of shareholders and employees is required to
take participate in driving out best plan out of all options.
Project Execution: it is the practical stage of project life cycle. once a plan get initiate and
planned after analyzing all other options gathering resources, eliminate unnecessary elements
and develop best strategies The company needs to execute the plan in practical manner for
understanding what issues come at workplace and how it can be minimized Execution must be
based according to the plan by engaging each employees and stakeholders in the favor of project
success. In context of, MG motor ltd, to execute plan effectively, the company require to adopt
total quality management approach in which all stage which goes through with quality check
and focus on providing best food catering in house site. This theory will undertake the records
of resources and capital used to make it more cost effective by measuring and tracking
performance. Therefore, executing project must be completed on time to reduce unnecessary
work burden and employees gives best efforts for working.
Project Closure: it is the last and final stag of project life cycle in which company take decision
to close project by getting success or by project failure . This stage could be om in both success
and failure. At the time of project closure, the company will ensure to check project execution
by taking follow ups and keeping check on wastage or defects. MG motor ltd should analyst all
the mistakes by identifying its root cause and take corrective measures for further project
development.
building a case
Project plan:
Executive
summary
The project initiates about MK motor ltd which faces difficulty in managing
employees absenteeism which impact on profitability and efficiency. The
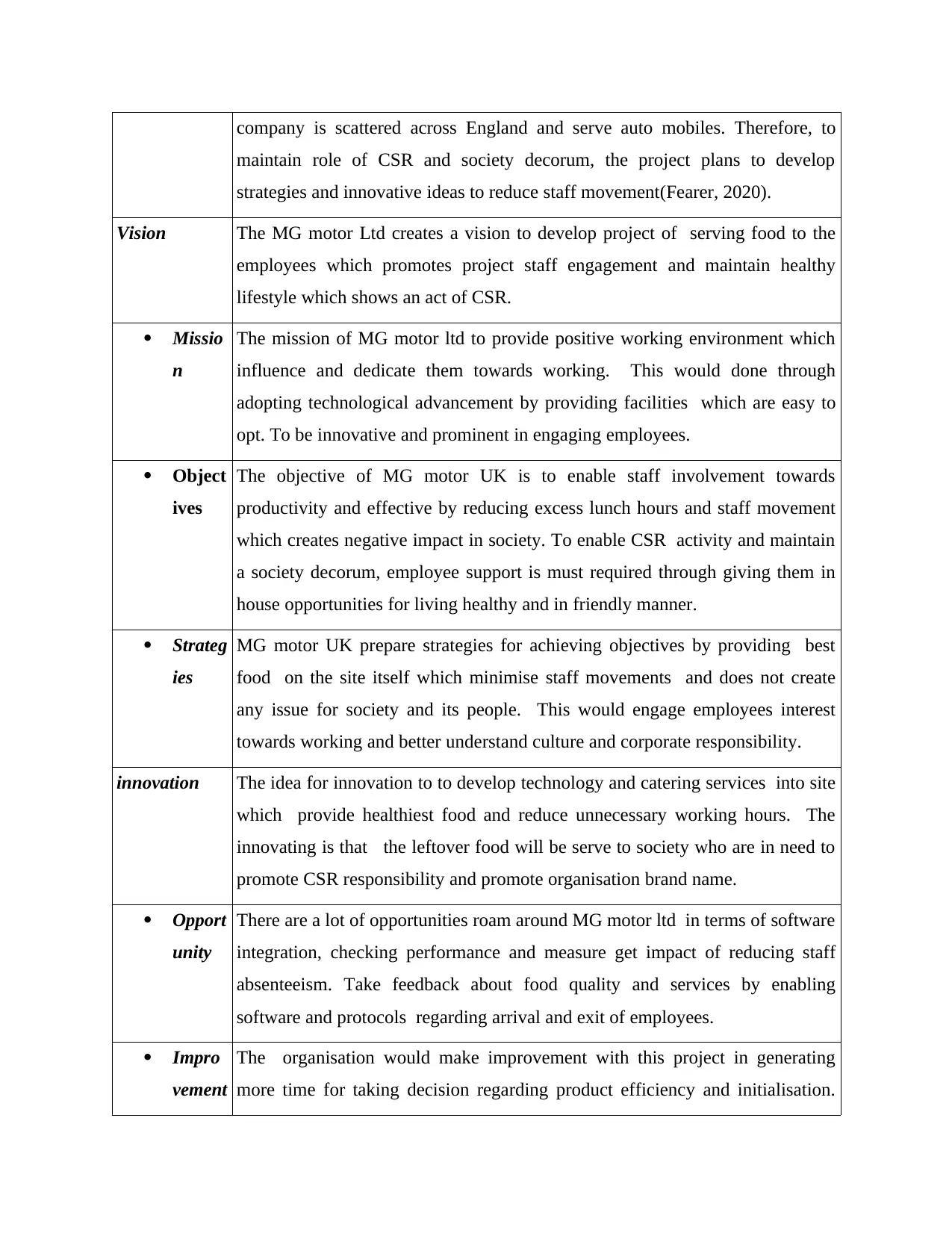
company is scattered across England and serve auto mobiles. Therefore, to
maintain role of CSR and society decorum, the project plans to develop
strategies and innovative ideas to reduce staff movement(Fearer, 2020).
Vision The MG motor Ltd creates a vision to develop project of serving food to the
employees which promotes project staff engagement and maintain healthy
lifestyle which shows an act of CSR.
Missio
n
The mission of MG motor ltd to provide positive working environment which
influence and dedicate them towards working. This would done through
adopting technological advancement by providing facilities which are easy to
opt. To be innovative and prominent in engaging employees.
Object
ives
The objective of MG motor UK is to enable staff involvement towards
productivity and effective by reducing excess lunch hours and staff movement
which creates negative impact in society. To enable CSR activity and maintain
a society decorum, employee support is must required through giving them in
house opportunities for living healthy and in friendly manner.
Strateg
ies
MG motor UK prepare strategies for achieving objectives by providing best
food on the site itself which minimise staff movements and does not create
any issue for society and its people. This would engage employees interest
towards working and better understand culture and corporate responsibility.
innovation The idea for innovation to to develop technology and catering services into site
which provide healthiest food and reduce unnecessary working hours. The
innovating is that the leftover food will be serve to society who are in need to
promote CSR responsibility and promote organisation brand name.
Opport
unity
There are a lot of opportunities roam around MG motor ltd in terms of software
integration, checking performance and measure get impact of reducing staff
absenteeism. Take feedback about food quality and services by enabling
software and protocols regarding arrival and exit of employees.
Impro
vement
The organisation would make improvement with this project in generating
more time for taking decision regarding product efficiency and initialisation.
maintain role of CSR and society decorum, the project plans to develop
strategies and innovative ideas to reduce staff movement(Fearer, 2020).
Vision The MG motor Ltd creates a vision to develop project of serving food to the
employees which promotes project staff engagement and maintain healthy
lifestyle which shows an act of CSR.
Missio
n
The mission of MG motor ltd to provide positive working environment which
influence and dedicate them towards working. This would done through
adopting technological advancement by providing facilities which are easy to
opt. To be innovative and prominent in engaging employees.
Object
ives
The objective of MG motor UK is to enable staff involvement towards
productivity and effective by reducing excess lunch hours and staff movement
which creates negative impact in society. To enable CSR activity and maintain
a society decorum, employee support is must required through giving them in
house opportunities for living healthy and in friendly manner.
Strateg
ies
MG motor UK prepare strategies for achieving objectives by providing best
food on the site itself which minimise staff movements and does not create
any issue for society and its people. This would engage employees interest
towards working and better understand culture and corporate responsibility.
innovation The idea for innovation to to develop technology and catering services into site
which provide healthiest food and reduce unnecessary working hours. The
innovating is that the leftover food will be serve to society who are in need to
promote CSR responsibility and promote organisation brand name.
Opport
unity
There are a lot of opportunities roam around MG motor ltd in terms of software
integration, checking performance and measure get impact of reducing staff
absenteeism. Take feedback about food quality and services by enabling
software and protocols regarding arrival and exit of employees.
Impro
vement
The organisation would make improvement with this project in generating
more time for taking decision regarding product efficiency and initialisation.
Secure Best Marks with AI Grader
Need help grading? Try our AI Grader for instant feedback on your assignments.
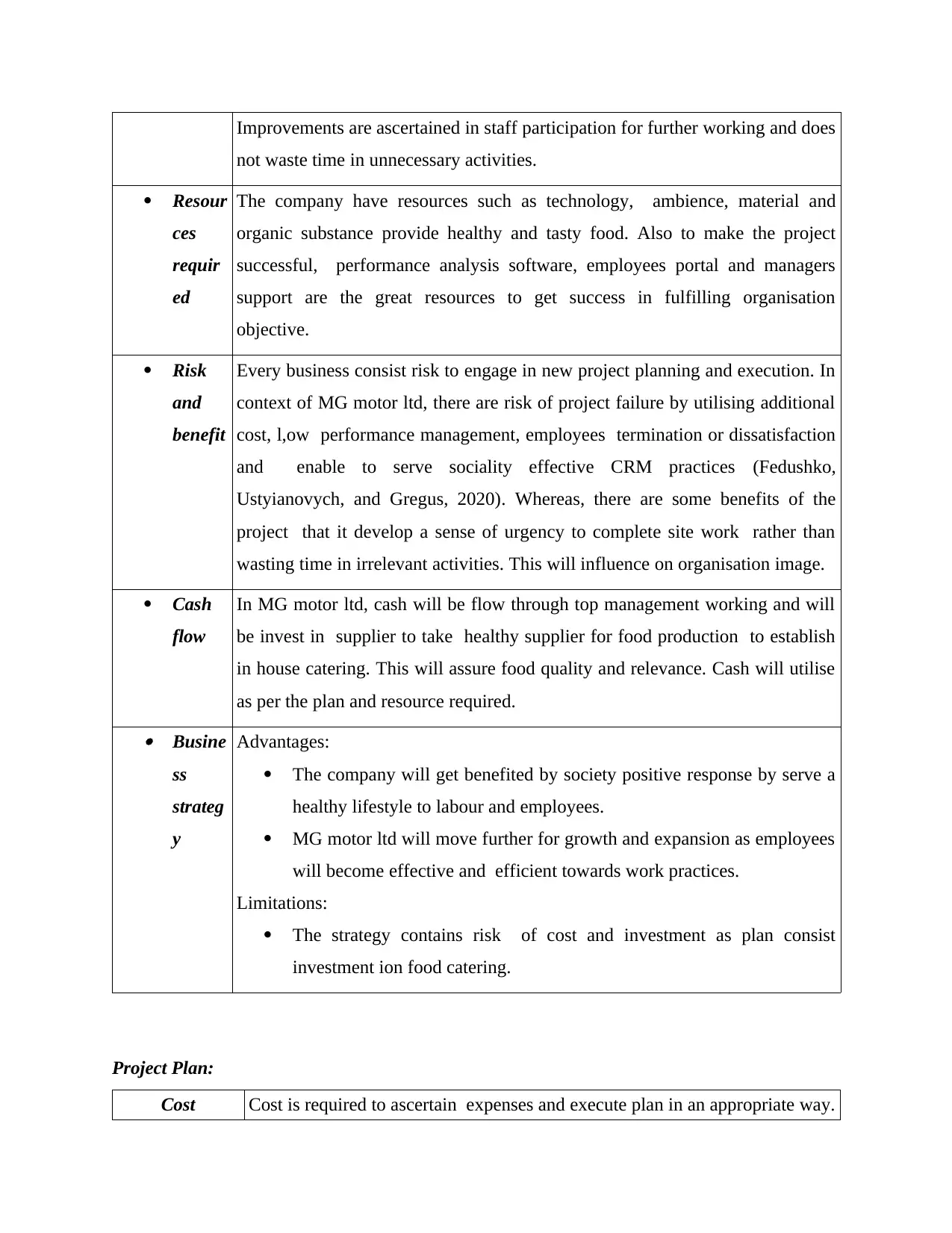
Improvements are ascertained in staff participation for further working and does
not waste time in unnecessary activities.
Resour
ces
requir
ed
The company have resources such as technology, ambience, material and
organic substance provide healthy and tasty food. Also to make the project
successful, performance analysis software, employees portal and managers
support are the great resources to get success in fulfilling organisation
objective.
Risk
and
benefit
Every business consist risk to engage in new project planning and execution. In
context of MG motor ltd, there are risk of project failure by utilising additional
cost, l,ow performance management, employees termination or dissatisfaction
and enable to serve sociality effective CRM practices (Fedushko,
Ustyianovych, and Gregus, 2020). Whereas, there are some benefits of the
project that it develop a sense of urgency to complete site work rather than
wasting time in irrelevant activities. This will influence on organisation image.
Cash
flow
In MG motor ltd, cash will be flow through top management working and will
be invest in supplier to take healthy supplier for food production to establish
in house catering. This will assure food quality and relevance. Cash will utilise
as per the plan and resource required. Busine
ss
strateg
y
Advantages:
The company will get benefited by society positive response by serve a
healthy lifestyle to labour and employees.
MG motor ltd will move further for growth and expansion as employees
will become effective and efficient towards work practices.
Limitations:
The strategy contains risk of cost and investment as plan consist
investment ion food catering.
Project Plan:
Cost Cost is required to ascertain expenses and execute plan in an appropriate way.
not waste time in unnecessary activities.
Resour
ces
requir
ed
The company have resources such as technology, ambience, material and
organic substance provide healthy and tasty food. Also to make the project
successful, performance analysis software, employees portal and managers
support are the great resources to get success in fulfilling organisation
objective.
Risk
and
benefit
Every business consist risk to engage in new project planning and execution. In
context of MG motor ltd, there are risk of project failure by utilising additional
cost, l,ow performance management, employees termination or dissatisfaction
and enable to serve sociality effective CRM practices (Fedushko,
Ustyianovych, and Gregus, 2020). Whereas, there are some benefits of the
project that it develop a sense of urgency to complete site work rather than
wasting time in irrelevant activities. This will influence on organisation image.
Cash
flow
In MG motor ltd, cash will be flow through top management working and will
be invest in supplier to take healthy supplier for food production to establish
in house catering. This will assure food quality and relevance. Cash will utilise
as per the plan and resource required. Busine
ss
strateg
y
Advantages:
The company will get benefited by society positive response by serve a
healthy lifestyle to labour and employees.
MG motor ltd will move further for growth and expansion as employees
will become effective and efficient towards work practices.
Limitations:
The strategy contains risk of cost and investment as plan consist
investment ion food catering.
Project Plan:
Cost Cost is required to ascertain expenses and execute plan in an appropriate way.
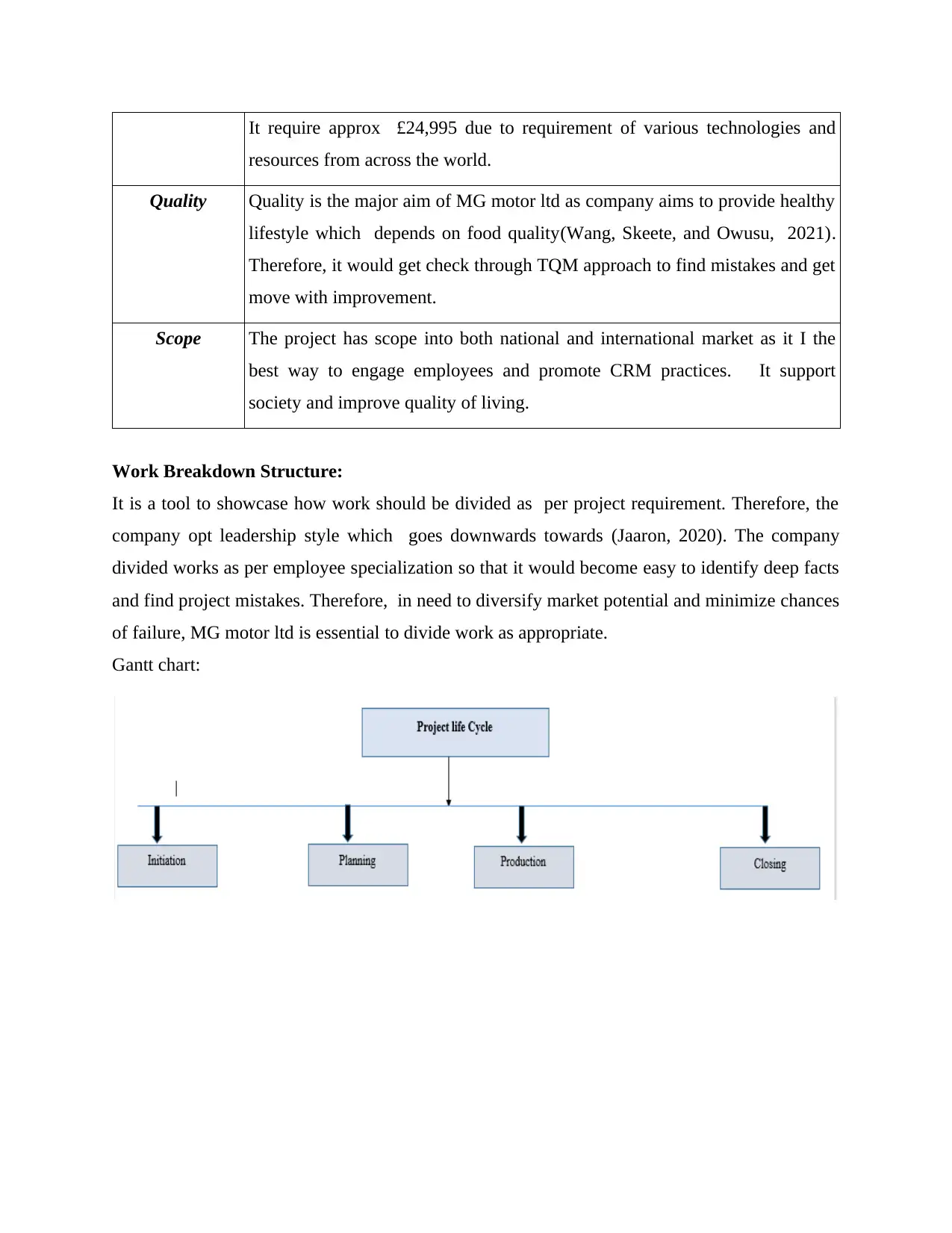
It require approx £24,995 due to requirement of various technologies and
resources from across the world.
Quality Quality is the major aim of MG motor ltd as company aims to provide healthy
lifestyle which depends on food quality(Wang, Skeete, and Owusu, 2021).
Therefore, it would get check through TQM approach to find mistakes and get
move with improvement.
Scope The project has scope into both national and international market as it I the
best way to engage employees and promote CRM practices. It support
society and improve quality of living.
Work Breakdown Structure:
It is a tool to showcase how work should be divided as per project requirement. Therefore, the
company opt leadership style which goes downwards towards (Jaaron, 2020). The company
divided works as per employee specialization so that it would become easy to identify deep facts
and find project mistakes. Therefore, in need to diversify market potential and minimize chances
of failure, MG motor ltd is essential to divide work as appropriate.
Gantt chart:
resources from across the world.
Quality Quality is the major aim of MG motor ltd as company aims to provide healthy
lifestyle which depends on food quality(Wang, Skeete, and Owusu, 2021).
Therefore, it would get check through TQM approach to find mistakes and get
move with improvement.
Scope The project has scope into both national and international market as it I the
best way to engage employees and promote CRM practices. It support
society and improve quality of living.
Work Breakdown Structure:
It is a tool to showcase how work should be divided as per project requirement. Therefore, the
company opt leadership style which goes downwards towards (Jaaron, 2020). The company
divided works as per employee specialization so that it would become easy to identify deep facts
and find project mistakes. Therefore, in need to diversify market potential and minimize chances
of failure, MG motor ltd is essential to divide work as appropriate.
Gantt chart:
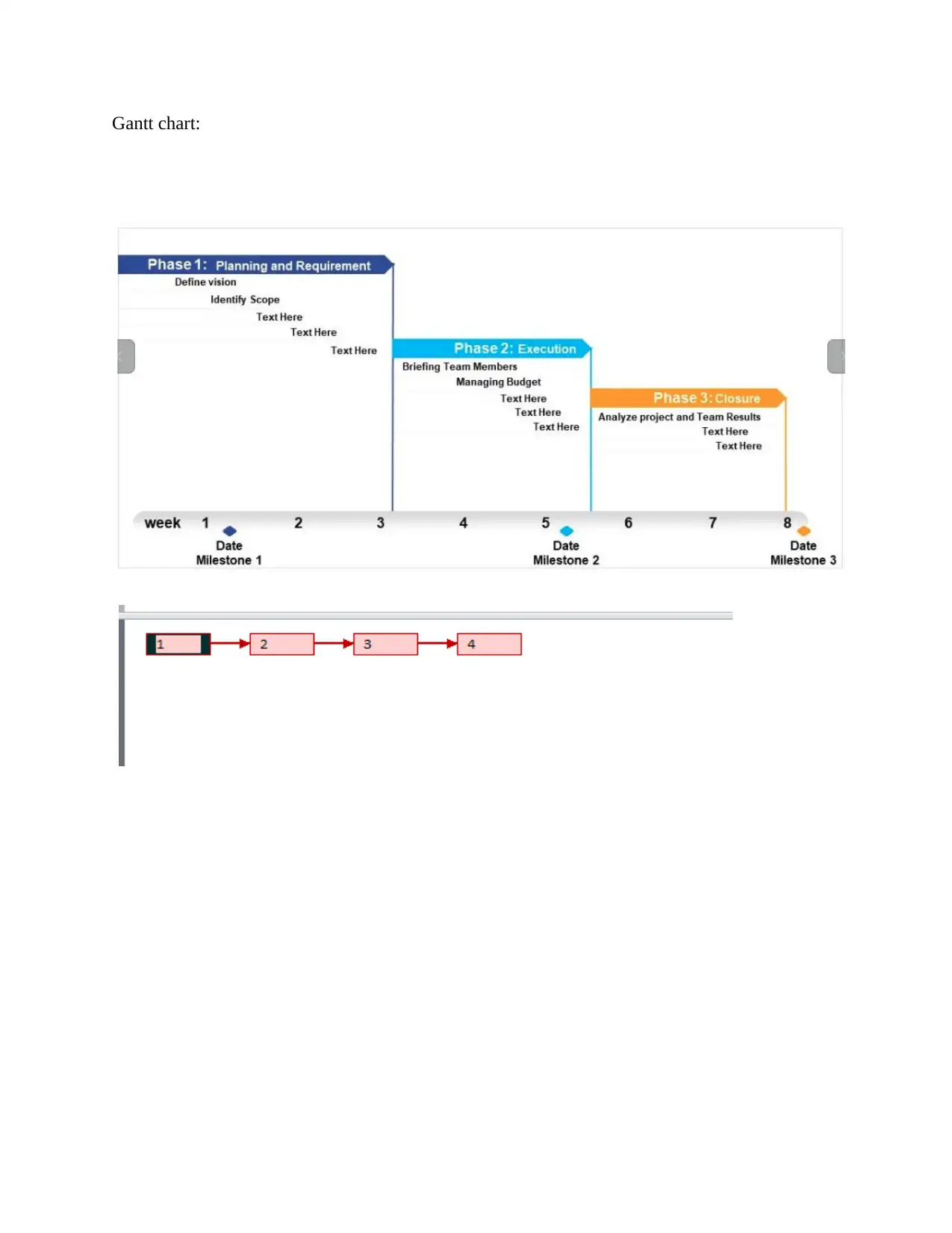
Gantt chart:
Paraphrase This Document
Need a fresh take? Get an instant paraphrase of this document with our AI Paraphraser
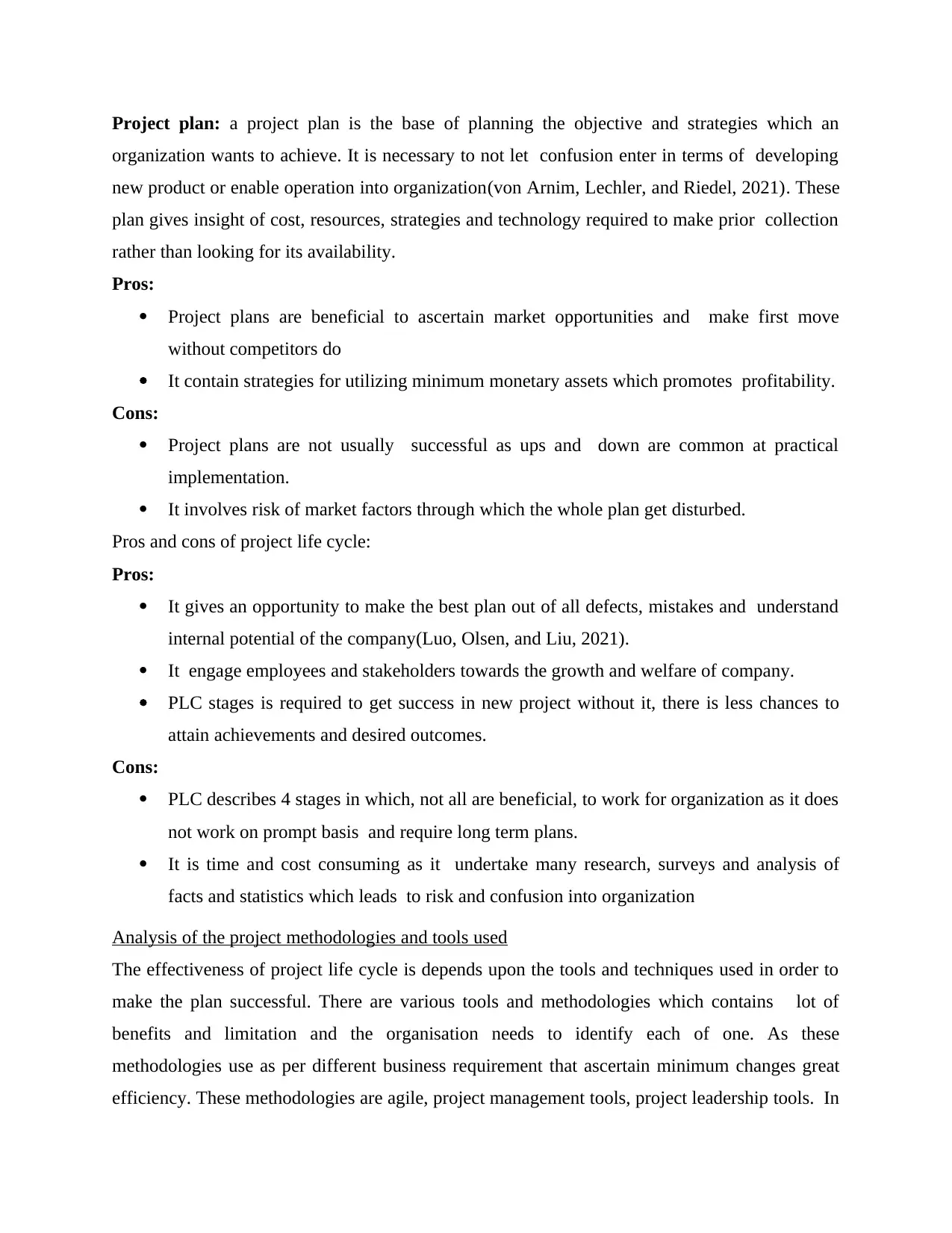
Project plan: a project plan is the base of planning the objective and strategies which an
organization wants to achieve. It is necessary to not let confusion enter in terms of developing
new product or enable operation into organization(von Arnim, Lechler, and Riedel, 2021). These
plan gives insight of cost, resources, strategies and technology required to make prior collection
rather than looking for its availability.
Pros:
Project plans are beneficial to ascertain market opportunities and make first move
without competitors do
It contain strategies for utilizing minimum monetary assets which promotes profitability.
Cons:
Project plans are not usually successful as ups and down are common at practical
implementation.
It involves risk of market factors through which the whole plan get disturbed.
Pros and cons of project life cycle:
Pros:
It gives an opportunity to make the best plan out of all defects, mistakes and understand
internal potential of the company(Luo, Olsen, and Liu, 2021).
It engage employees and stakeholders towards the growth and welfare of company.
PLC stages is required to get success in new project without it, there is less chances to
attain achievements and desired outcomes.
Cons:
PLC describes 4 stages in which, not all are beneficial, to work for organization as it does
not work on prompt basis and require long term plans.
It is time and cost consuming as it undertake many research, surveys and analysis of
facts and statistics which leads to risk and confusion into organization
Analysis of the project methodologies and tools used
The effectiveness of project life cycle is depends upon the tools and techniques used in order to
make the plan successful. There are various tools and methodologies which contains lot of
benefits and limitation and the organisation needs to identify each of one. As these
methodologies use as per different business requirement that ascertain minimum changes great
efficiency. These methodologies are agile, project management tools, project leadership tools. In
organization wants to achieve. It is necessary to not let confusion enter in terms of developing
new product or enable operation into organization(von Arnim, Lechler, and Riedel, 2021). These
plan gives insight of cost, resources, strategies and technology required to make prior collection
rather than looking for its availability.
Pros:
Project plans are beneficial to ascertain market opportunities and make first move
without competitors do
It contain strategies for utilizing minimum monetary assets which promotes profitability.
Cons:
Project plans are not usually successful as ups and down are common at practical
implementation.
It involves risk of market factors through which the whole plan get disturbed.
Pros and cons of project life cycle:
Pros:
It gives an opportunity to make the best plan out of all defects, mistakes and understand
internal potential of the company(Luo, Olsen, and Liu, 2021).
It engage employees and stakeholders towards the growth and welfare of company.
PLC stages is required to get success in new project without it, there is less chances to
attain achievements and desired outcomes.
Cons:
PLC describes 4 stages in which, not all are beneficial, to work for organization as it does
not work on prompt basis and require long term plans.
It is time and cost consuming as it undertake many research, surveys and analysis of
facts and statistics which leads to risk and confusion into organization
Analysis of the project methodologies and tools used
The effectiveness of project life cycle is depends upon the tools and techniques used in order to
make the plan successful. There are various tools and methodologies which contains lot of
benefits and limitation and the organisation needs to identify each of one. As these
methodologies use as per different business requirement that ascertain minimum changes great
efficiency. These methodologies are agile, project management tools, project leadership tools. In
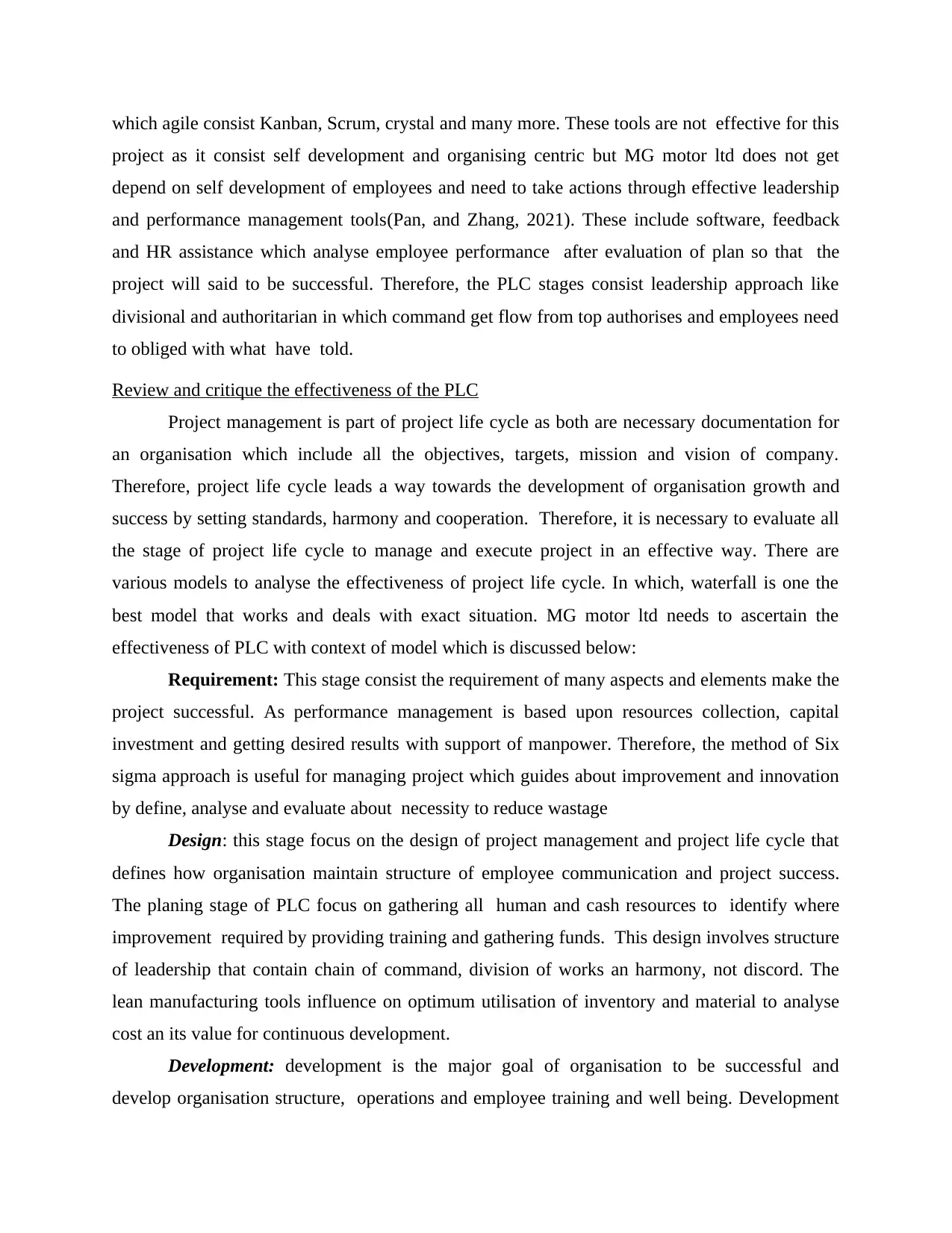
which agile consist Kanban, Scrum, crystal and many more. These tools are not effective for this
project as it consist self development and organising centric but MG motor ltd does not get
depend on self development of employees and need to take actions through effective leadership
and performance management tools(Pan, and Zhang, 2021). These include software, feedback
and HR assistance which analyse employee performance after evaluation of plan so that the
project will said to be successful. Therefore, the PLC stages consist leadership approach like
divisional and authoritarian in which command get flow from top authorises and employees need
to obliged with what have told.
Review and critique the effectiveness of the PLC
Project management is part of project life cycle as both are necessary documentation for
an organisation which include all the objectives, targets, mission and vision of company.
Therefore, project life cycle leads a way towards the development of organisation growth and
success by setting standards, harmony and cooperation. Therefore, it is necessary to evaluate all
the stage of project life cycle to manage and execute project in an effective way. There are
various models to analyse the effectiveness of project life cycle. In which, waterfall is one the
best model that works and deals with exact situation. MG motor ltd needs to ascertain the
effectiveness of PLC with context of model which is discussed below:
Requirement: This stage consist the requirement of many aspects and elements make the
project successful. As performance management is based upon resources collection, capital
investment and getting desired results with support of manpower. Therefore, the method of Six
sigma approach is useful for managing project which guides about improvement and innovation
by define, analyse and evaluate about necessity to reduce wastage
Design: this stage focus on the design of project management and project life cycle that
defines how organisation maintain structure of employee communication and project success.
The planing stage of PLC focus on gathering all human and cash resources to identify where
improvement required by providing training and gathering funds. This design involves structure
of leadership that contain chain of command, division of works an harmony, not discord. The
lean manufacturing tools influence on optimum utilisation of inventory and material to analyse
cost an its value for continuous development.
Development: development is the major goal of organisation to be successful and
develop organisation structure, operations and employee training and well being. Development
project as it consist self development and organising centric but MG motor ltd does not get
depend on self development of employees and need to take actions through effective leadership
and performance management tools(Pan, and Zhang, 2021). These include software, feedback
and HR assistance which analyse employee performance after evaluation of plan so that the
project will said to be successful. Therefore, the PLC stages consist leadership approach like
divisional and authoritarian in which command get flow from top authorises and employees need
to obliged with what have told.
Review and critique the effectiveness of the PLC
Project management is part of project life cycle as both are necessary documentation for
an organisation which include all the objectives, targets, mission and vision of company.
Therefore, project life cycle leads a way towards the development of organisation growth and
success by setting standards, harmony and cooperation. Therefore, it is necessary to evaluate all
the stage of project life cycle to manage and execute project in an effective way. There are
various models to analyse the effectiveness of project life cycle. In which, waterfall is one the
best model that works and deals with exact situation. MG motor ltd needs to ascertain the
effectiveness of PLC with context of model which is discussed below:
Requirement: This stage consist the requirement of many aspects and elements make the
project successful. As performance management is based upon resources collection, capital
investment and getting desired results with support of manpower. Therefore, the method of Six
sigma approach is useful for managing project which guides about improvement and innovation
by define, analyse and evaluate about necessity to reduce wastage
Design: this stage focus on the design of project management and project life cycle that
defines how organisation maintain structure of employee communication and project success.
The planing stage of PLC focus on gathering all human and cash resources to identify where
improvement required by providing training and gathering funds. This design involves structure
of leadership that contain chain of command, division of works an harmony, not discord. The
lean manufacturing tools influence on optimum utilisation of inventory and material to analyse
cost an its value for continuous development.
Development: development is the major goal of organisation to be successful and
develop organisation structure, operations and employee training and well being. Development
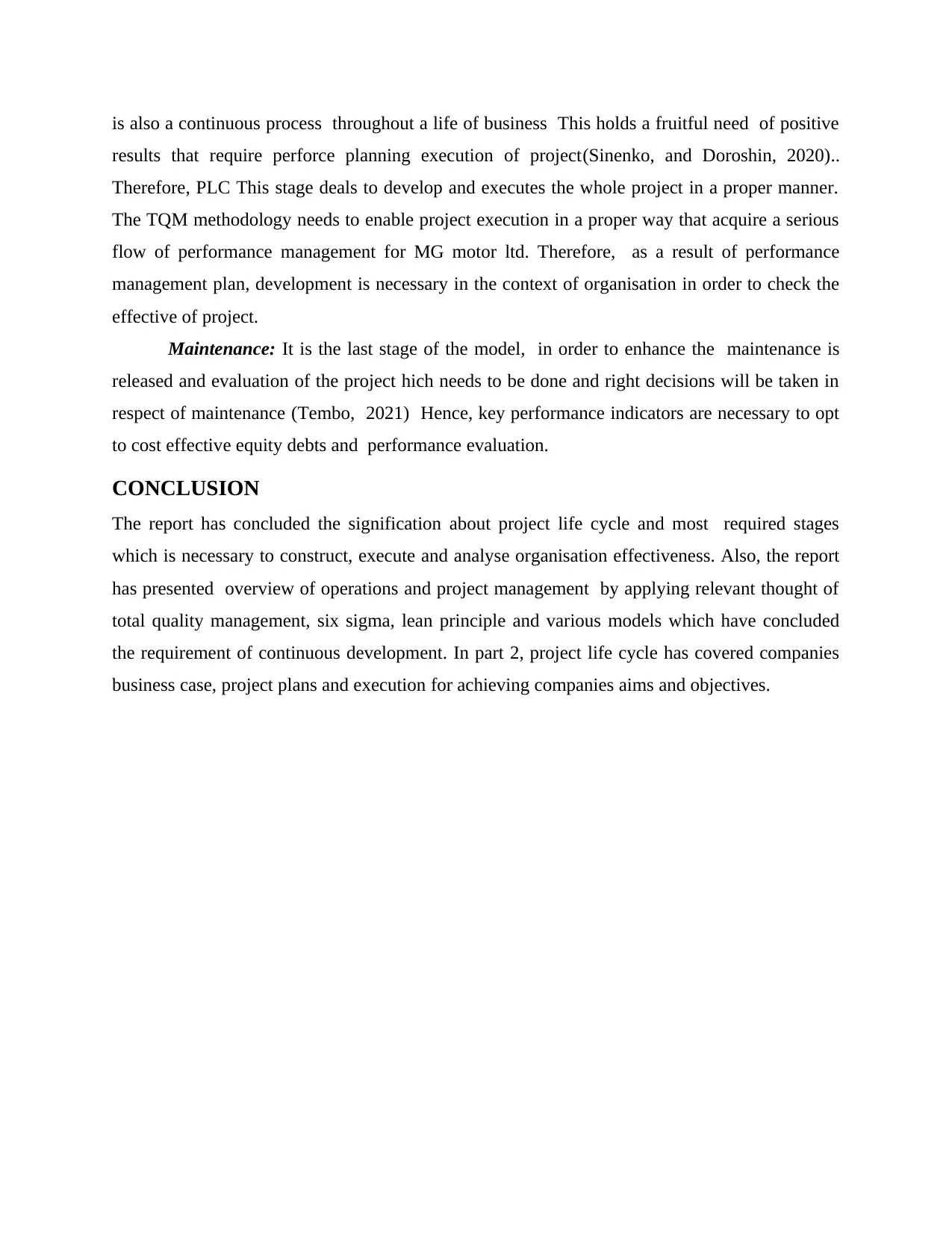
is also a continuous process throughout a life of business This holds a fruitful need of positive
results that require perforce planning execution of project(Sinenko, and Doroshin, 2020)..
Therefore, PLC This stage deals to develop and executes the whole project in a proper manner.
The TQM methodology needs to enable project execution in a proper way that acquire a serious
flow of performance management for MG motor ltd. Therefore, as a result of performance
management plan, development is necessary in the context of organisation in order to check the
effective of project.
Maintenance: It is the last stage of the model, in order to enhance the maintenance is
released and evaluation of the project hich needs to be done and right decisions will be taken in
respect of maintenance (Tembo, 2021) Hence, key performance indicators are necessary to opt
to cost effective equity debts and performance evaluation.
CONCLUSION
The report has concluded the signification about project life cycle and most required stages
which is necessary to construct, execute and analyse organisation effectiveness. Also, the report
has presented overview of operations and project management by applying relevant thought of
total quality management, six sigma, lean principle and various models which have concluded
the requirement of continuous development. In part 2, project life cycle has covered companies
business case, project plans and execution for achieving companies aims and objectives.
results that require perforce planning execution of project(Sinenko, and Doroshin, 2020)..
Therefore, PLC This stage deals to develop and executes the whole project in a proper manner.
The TQM methodology needs to enable project execution in a proper way that acquire a serious
flow of performance management for MG motor ltd. Therefore, as a result of performance
management plan, development is necessary in the context of organisation in order to check the
effective of project.
Maintenance: It is the last stage of the model, in order to enhance the maintenance is
released and evaluation of the project hich needs to be done and right decisions will be taken in
respect of maintenance (Tembo, 2021) Hence, key performance indicators are necessary to opt
to cost effective equity debts and performance evaluation.
CONCLUSION
The report has concluded the signification about project life cycle and most required stages
which is necessary to construct, execute and analyse organisation effectiveness. Also, the report
has presented overview of operations and project management by applying relevant thought of
total quality management, six sigma, lean principle and various models which have concluded
the requirement of continuous development. In part 2, project life cycle has covered companies
business case, project plans and execution for achieving companies aims and objectives.
Secure Best Marks with AI Grader
Need help grading? Try our AI Grader for instant feedback on your assignments.
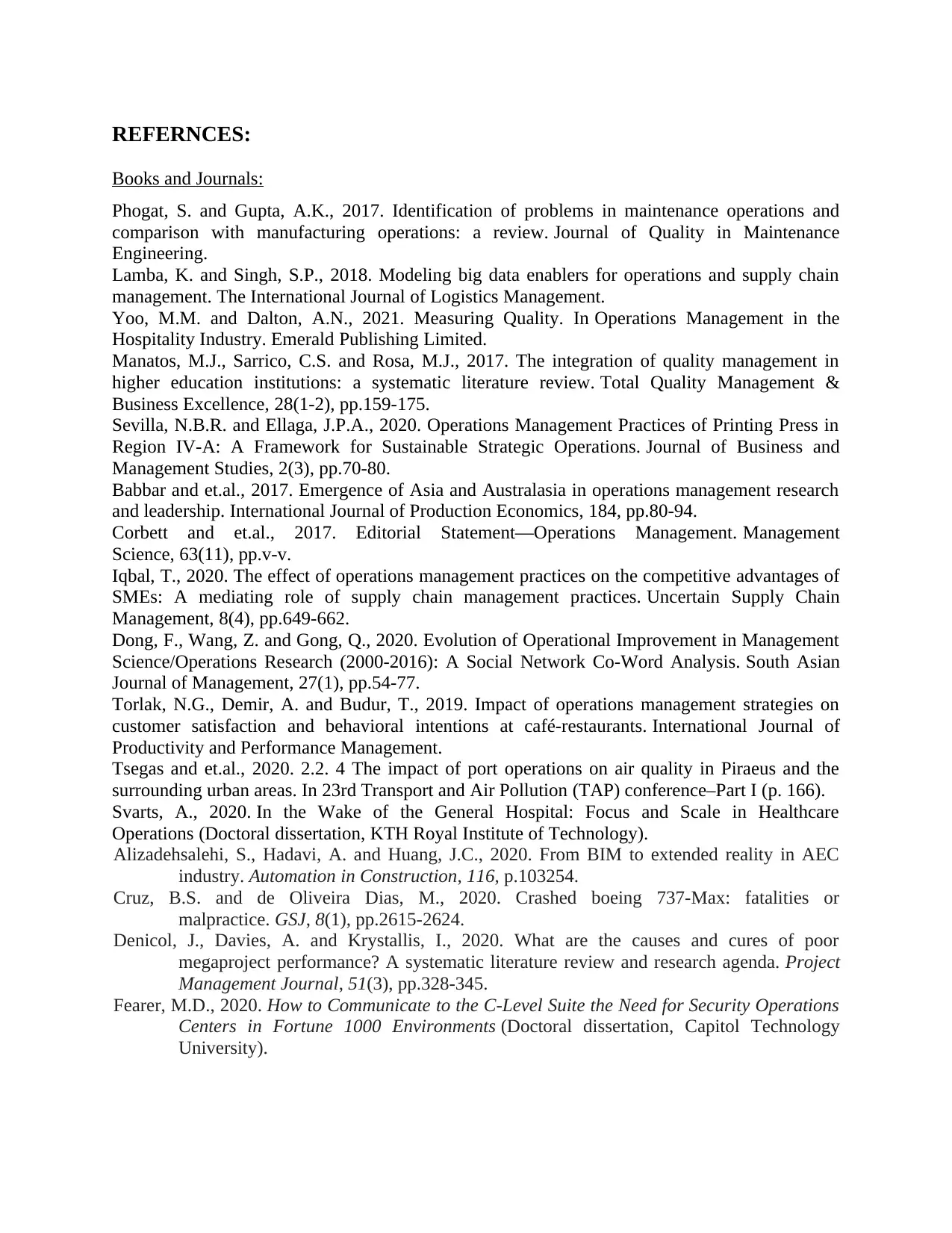
REFERNCES:
Books and Journals:
Phogat, S. and Gupta, A.K., 2017. Identification of problems in maintenance operations and
comparison with manufacturing operations: a review. Journal of Quality in Maintenance
Engineering.
Lamba, K. and Singh, S.P., 2018. Modeling big data enablers for operations and supply chain
management. The International Journal of Logistics Management.
Yoo, M.M. and Dalton, A.N., 2021. Measuring Quality. In Operations Management in the
Hospitality Industry. Emerald Publishing Limited.
Manatos, M.J., Sarrico, C.S. and Rosa, M.J., 2017. The integration of quality management in
higher education institutions: a systematic literature review. Total Quality Management &
Business Excellence, 28(1-2), pp.159-175.
Sevilla, N.B.R. and Ellaga, J.P.A., 2020. Operations Management Practices of Printing Press in
Region IV-A: A Framework for Sustainable Strategic Operations. Journal of Business and
Management Studies, 2(3), pp.70-80.
Babbar and et.al., 2017. Emergence of Asia and Australasia in operations management research
and leadership. International Journal of Production Economics, 184, pp.80-94.
Corbett and et.al., 2017. Editorial Statement—Operations Management. Management
Science, 63(11), pp.v-v.
Iqbal, T., 2020. The effect of operations management practices on the competitive advantages of
SMEs: A mediating role of supply chain management practices. Uncertain Supply Chain
Management, 8(4), pp.649-662.
Dong, F., Wang, Z. and Gong, Q., 2020. Evolution of Operational Improvement in Management
Science/Operations Research (2000-2016): A Social Network Co-Word Analysis. South Asian
Journal of Management, 27(1), pp.54-77.
Torlak, N.G., Demir, A. and Budur, T., 2019. Impact of operations management strategies on
customer satisfaction and behavioral intentions at café-restaurants. International Journal of
Productivity and Performance Management.
Tsegas and et.al., 2020. 2.2. 4 The impact of port operations on air quality in Piraeus and the
surrounding urban areas. In 23rd Transport and Air Pollution (TAP) conference–Part I (p. 166).
Svarts, A., 2020. In the Wake of the General Hospital: Focus and Scale in Healthcare
Operations (Doctoral dissertation, KTH Royal Institute of Technology).
Alizadehsalehi, S., Hadavi, A. and Huang, J.C., 2020. From BIM to extended reality in AEC
industry. Automation in Construction, 116, p.103254.
Cruz, B.S. and de Oliveira Dias, M., 2020. Crashed boeing 737-Max: fatalities or
malpractice. GSJ, 8(1), pp.2615-2624.
Denicol, J., Davies, A. and Krystallis, I., 2020. What are the causes and cures of poor
megaproject performance? A systematic literature review and research agenda. Project
Management Journal, 51(3), pp.328-345.
Fearer, M.D., 2020. How to Communicate to the C-Level Suite the Need for Security Operations
Centers in Fortune 1000 Environments (Doctoral dissertation, Capitol Technology
University).
Books and Journals:
Phogat, S. and Gupta, A.K., 2017. Identification of problems in maintenance operations and
comparison with manufacturing operations: a review. Journal of Quality in Maintenance
Engineering.
Lamba, K. and Singh, S.P., 2018. Modeling big data enablers for operations and supply chain
management. The International Journal of Logistics Management.
Yoo, M.M. and Dalton, A.N., 2021. Measuring Quality. In Operations Management in the
Hospitality Industry. Emerald Publishing Limited.
Manatos, M.J., Sarrico, C.S. and Rosa, M.J., 2017. The integration of quality management in
higher education institutions: a systematic literature review. Total Quality Management &
Business Excellence, 28(1-2), pp.159-175.
Sevilla, N.B.R. and Ellaga, J.P.A., 2020. Operations Management Practices of Printing Press in
Region IV-A: A Framework for Sustainable Strategic Operations. Journal of Business and
Management Studies, 2(3), pp.70-80.
Babbar and et.al., 2017. Emergence of Asia and Australasia in operations management research
and leadership. International Journal of Production Economics, 184, pp.80-94.
Corbett and et.al., 2017. Editorial Statement—Operations Management. Management
Science, 63(11), pp.v-v.
Iqbal, T., 2020. The effect of operations management practices on the competitive advantages of
SMEs: A mediating role of supply chain management practices. Uncertain Supply Chain
Management, 8(4), pp.649-662.
Dong, F., Wang, Z. and Gong, Q., 2020. Evolution of Operational Improvement in Management
Science/Operations Research (2000-2016): A Social Network Co-Word Analysis. South Asian
Journal of Management, 27(1), pp.54-77.
Torlak, N.G., Demir, A. and Budur, T., 2019. Impact of operations management strategies on
customer satisfaction and behavioral intentions at café-restaurants. International Journal of
Productivity and Performance Management.
Tsegas and et.al., 2020. 2.2. 4 The impact of port operations on air quality in Piraeus and the
surrounding urban areas. In 23rd Transport and Air Pollution (TAP) conference–Part I (p. 166).
Svarts, A., 2020. In the Wake of the General Hospital: Focus and Scale in Healthcare
Operations (Doctoral dissertation, KTH Royal Institute of Technology).
Alizadehsalehi, S., Hadavi, A. and Huang, J.C., 2020. From BIM to extended reality in AEC
industry. Automation in Construction, 116, p.103254.
Cruz, B.S. and de Oliveira Dias, M., 2020. Crashed boeing 737-Max: fatalities or
malpractice. GSJ, 8(1), pp.2615-2624.
Denicol, J., Davies, A. and Krystallis, I., 2020. What are the causes and cures of poor
megaproject performance? A systematic literature review and research agenda. Project
Management Journal, 51(3), pp.328-345.
Fearer, M.D., 2020. How to Communicate to the C-Level Suite the Need for Security Operations
Centers in Fortune 1000 Environments (Doctoral dissertation, Capitol Technology
University).
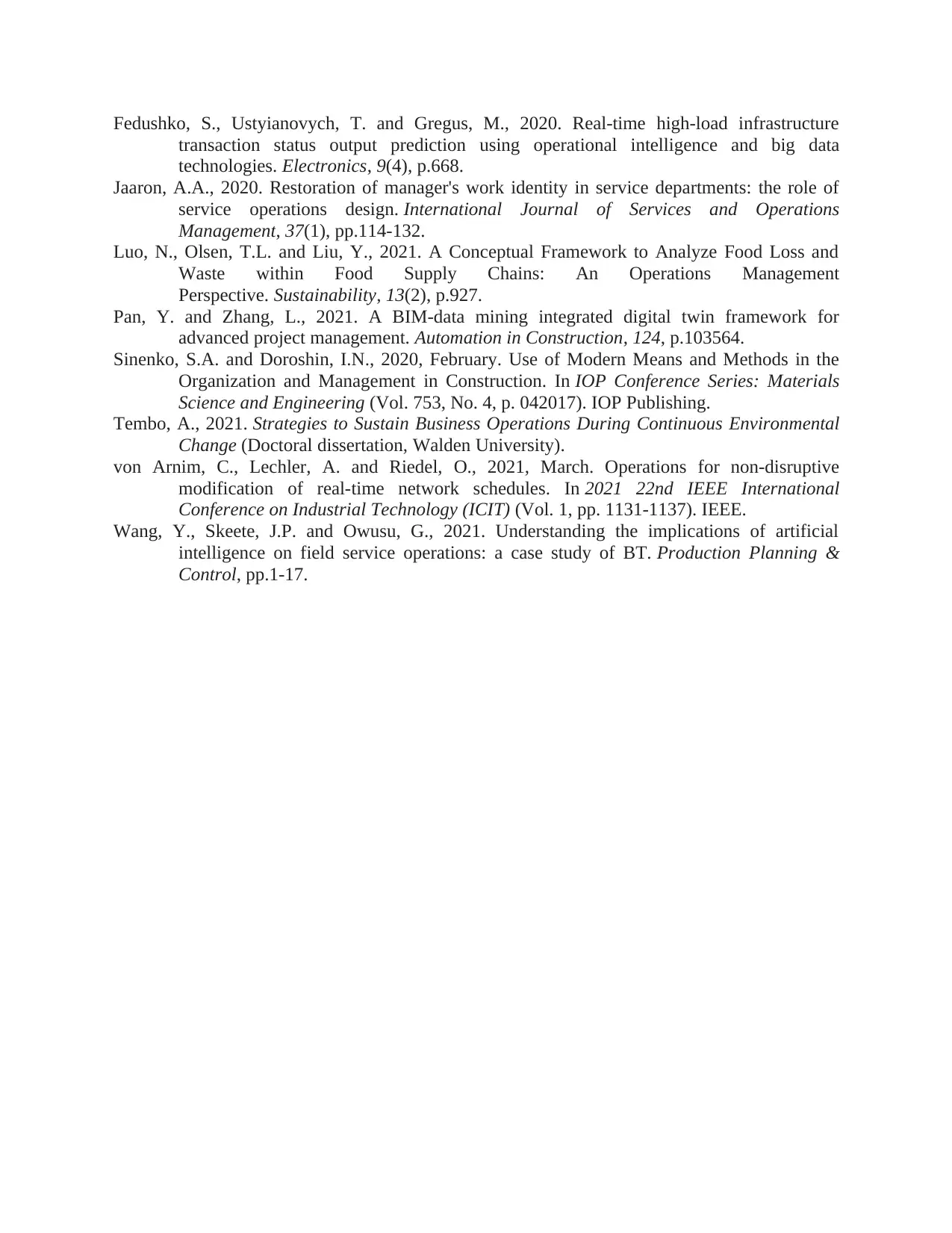
Fedushko, S., Ustyianovych, T. and Gregus, M., 2020. Real-time high-load infrastructure
transaction status output prediction using operational intelligence and big data
technologies. Electronics, 9(4), p.668.
Jaaron, A.A., 2020. Restoration of manager's work identity in service departments: the role of
service operations design. International Journal of Services and Operations
Management, 37(1), pp.114-132.
Luo, N., Olsen, T.L. and Liu, Y., 2021. A Conceptual Framework to Analyze Food Loss and
Waste within Food Supply Chains: An Operations Management
Perspective. Sustainability, 13(2), p.927.
Pan, Y. and Zhang, L., 2021. A BIM-data mining integrated digital twin framework for
advanced project management. Automation in Construction, 124, p.103564.
Sinenko, S.A. and Doroshin, I.N., 2020, February. Use of Modern Means and Methods in the
Organization and Management in Construction. In IOP Conference Series: Materials
Science and Engineering (Vol. 753, No. 4, p. 042017). IOP Publishing.
Tembo, A., 2021. Strategies to Sustain Business Operations During Continuous Environmental
Change (Doctoral dissertation, Walden University).
von Arnim, C., Lechler, A. and Riedel, O., 2021, March. Operations for non-disruptive
modification of real-time network schedules. In 2021 22nd IEEE International
Conference on Industrial Technology (ICIT) (Vol. 1, pp. 1131-1137). IEEE.
Wang, Y., Skeete, J.P. and Owusu, G., 2021. Understanding the implications of artificial
intelligence on field service operations: a case study of BT. Production Planning &
Control, pp.1-17.
transaction status output prediction using operational intelligence and big data
technologies. Electronics, 9(4), p.668.
Jaaron, A.A., 2020. Restoration of manager's work identity in service departments: the role of
service operations design. International Journal of Services and Operations
Management, 37(1), pp.114-132.
Luo, N., Olsen, T.L. and Liu, Y., 2021. A Conceptual Framework to Analyze Food Loss and
Waste within Food Supply Chains: An Operations Management
Perspective. Sustainability, 13(2), p.927.
Pan, Y. and Zhang, L., 2021. A BIM-data mining integrated digital twin framework for
advanced project management. Automation in Construction, 124, p.103564.
Sinenko, S.A. and Doroshin, I.N., 2020, February. Use of Modern Means and Methods in the
Organization and Management in Construction. In IOP Conference Series: Materials
Science and Engineering (Vol. 753, No. 4, p. 042017). IOP Publishing.
Tembo, A., 2021. Strategies to Sustain Business Operations During Continuous Environmental
Change (Doctoral dissertation, Walden University).
von Arnim, C., Lechler, A. and Riedel, O., 2021, March. Operations for non-disruptive
modification of real-time network schedules. In 2021 22nd IEEE International
Conference on Industrial Technology (ICIT) (Vol. 1, pp. 1131-1137). IEEE.
Wang, Y., Skeete, J.P. and Owusu, G., 2021. Understanding the implications of artificial
intelligence on field service operations: a case study of BT. Production Planning &
Control, pp.1-17.
1 out of 24
Related Documents
![[object Object]](/_next/image/?url=%2F_next%2Fstatic%2Fmedia%2Flogo.6d15ce61.png&w=640&q=75)
Your All-in-One AI-Powered Toolkit for Academic Success.
+13062052269
info@desklib.com
Available 24*7 on WhatsApp / Email
Unlock your academic potential
© 2024 | Zucol Services PVT LTD | All rights reserved.