Operations, Quality and Supply Chain Management
VerifiedAdded on 2023/01/05
|17
|6233
|100
AI Summary
This report discusses the various factors, prospects, and impacts of operations and supply chain management on the quality of products and services. It evaluates business operations in different industries, analyzes the contribution of process and lean techniques, explores the role of customer service, and evaluates the range of quality models and systems. The report also covers supply chain theories and models, the impact of logistics, and the requirements and risks of supplier contracts.
Contribute Materials
Your contribution can guide someone’s learning journey. Share your
documents today.
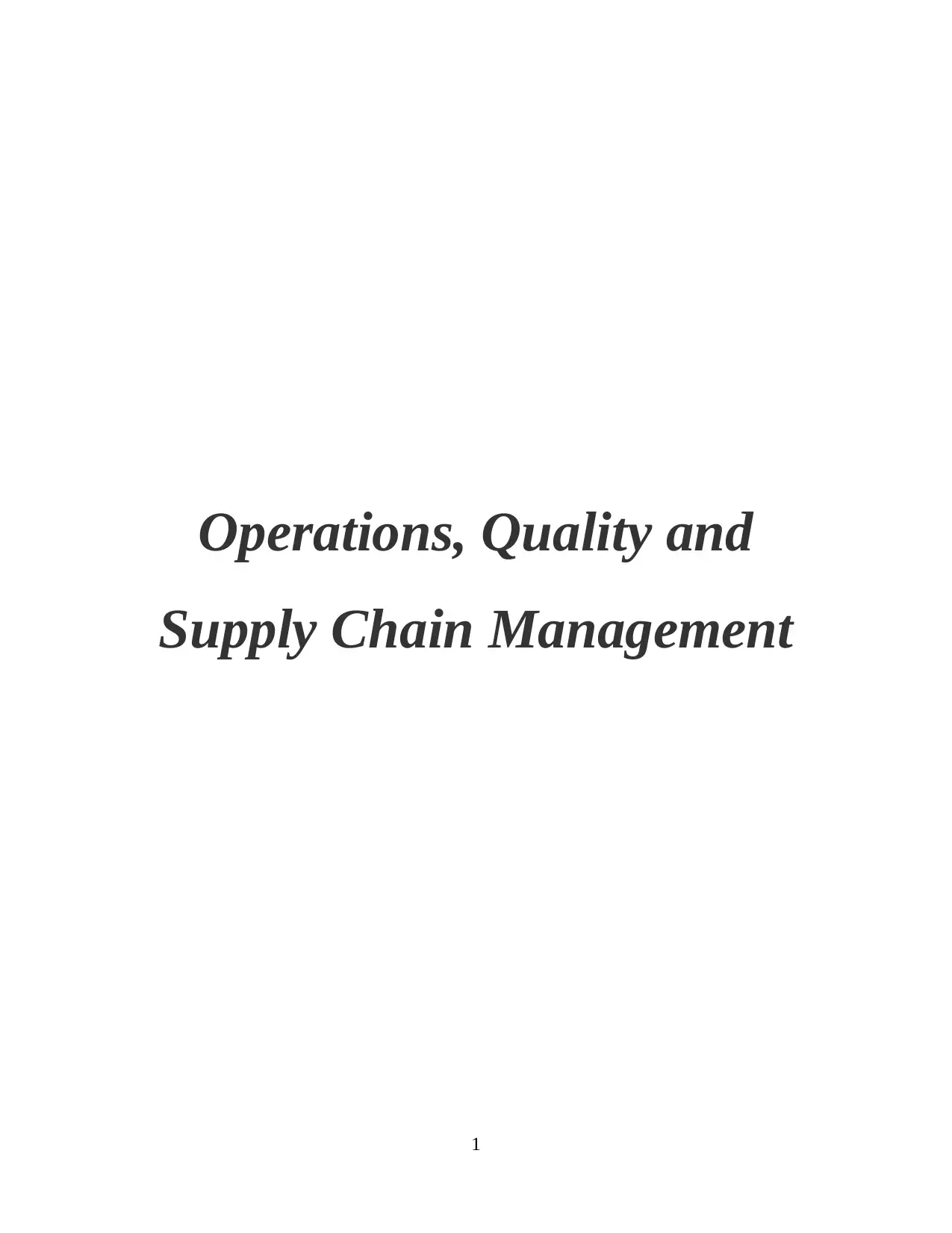
Operations, Quality and
Supply Chain Management
1
Supply Chain Management
1
Secure Best Marks with AI Grader
Need help grading? Try our AI Grader for instant feedback on your assignments.
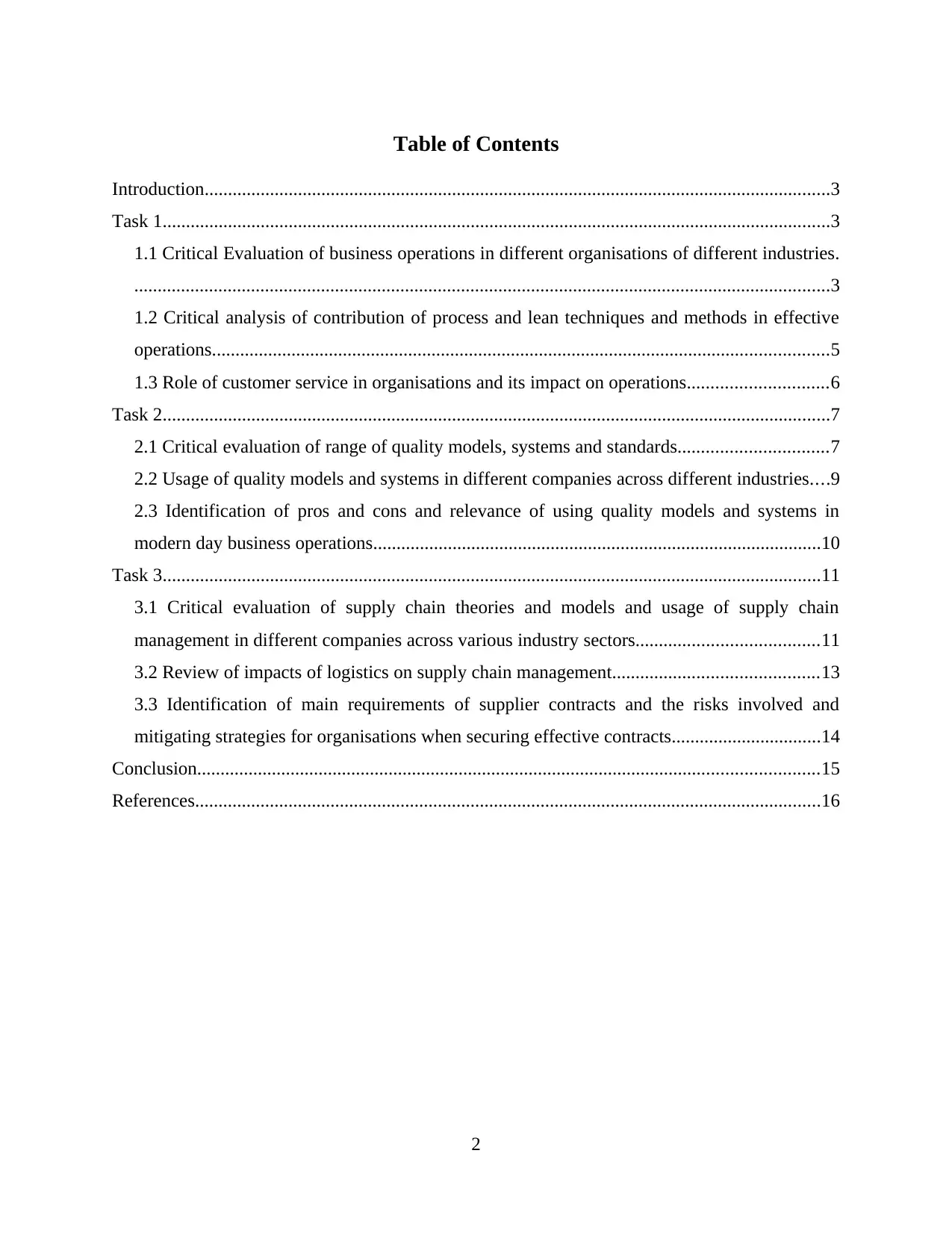
Table of Contents
Introduction......................................................................................................................................3
Task 1...............................................................................................................................................3
1.1 Critical Evaluation of business operations in different organisations of different industries.
.....................................................................................................................................................3
1.2 Critical analysis of contribution of process and lean techniques and methods in effective
operations....................................................................................................................................5
1.3 Role of customer service in organisations and its impact on operations..............................6
Task 2...............................................................................................................................................7
2.1 Critical evaluation of range of quality models, systems and standards................................7
2.2 Usage of quality models and systems in different companies across different industries....9
2.3 Identification of pros and cons and relevance of using quality models and systems in
modern day business operations................................................................................................10
Task 3.............................................................................................................................................11
3.1 Critical evaluation of supply chain theories and models and usage of supply chain
management in different companies across various industry sectors.......................................11
3.2 Review of impacts of logistics on supply chain management............................................13
3.3 Identification of main requirements of supplier contracts and the risks involved and
mitigating strategies for organisations when securing effective contracts................................14
Conclusion.....................................................................................................................................15
References......................................................................................................................................16
2
Introduction......................................................................................................................................3
Task 1...............................................................................................................................................3
1.1 Critical Evaluation of business operations in different organisations of different industries.
.....................................................................................................................................................3
1.2 Critical analysis of contribution of process and lean techniques and methods in effective
operations....................................................................................................................................5
1.3 Role of customer service in organisations and its impact on operations..............................6
Task 2...............................................................................................................................................7
2.1 Critical evaluation of range of quality models, systems and standards................................7
2.2 Usage of quality models and systems in different companies across different industries....9
2.3 Identification of pros and cons and relevance of using quality models and systems in
modern day business operations................................................................................................10
Task 3.............................................................................................................................................11
3.1 Critical evaluation of supply chain theories and models and usage of supply chain
management in different companies across various industry sectors.......................................11
3.2 Review of impacts of logistics on supply chain management............................................13
3.3 Identification of main requirements of supplier contracts and the risks involved and
mitigating strategies for organisations when securing effective contracts................................14
Conclusion.....................................................................................................................................15
References......................................................................................................................................16
2
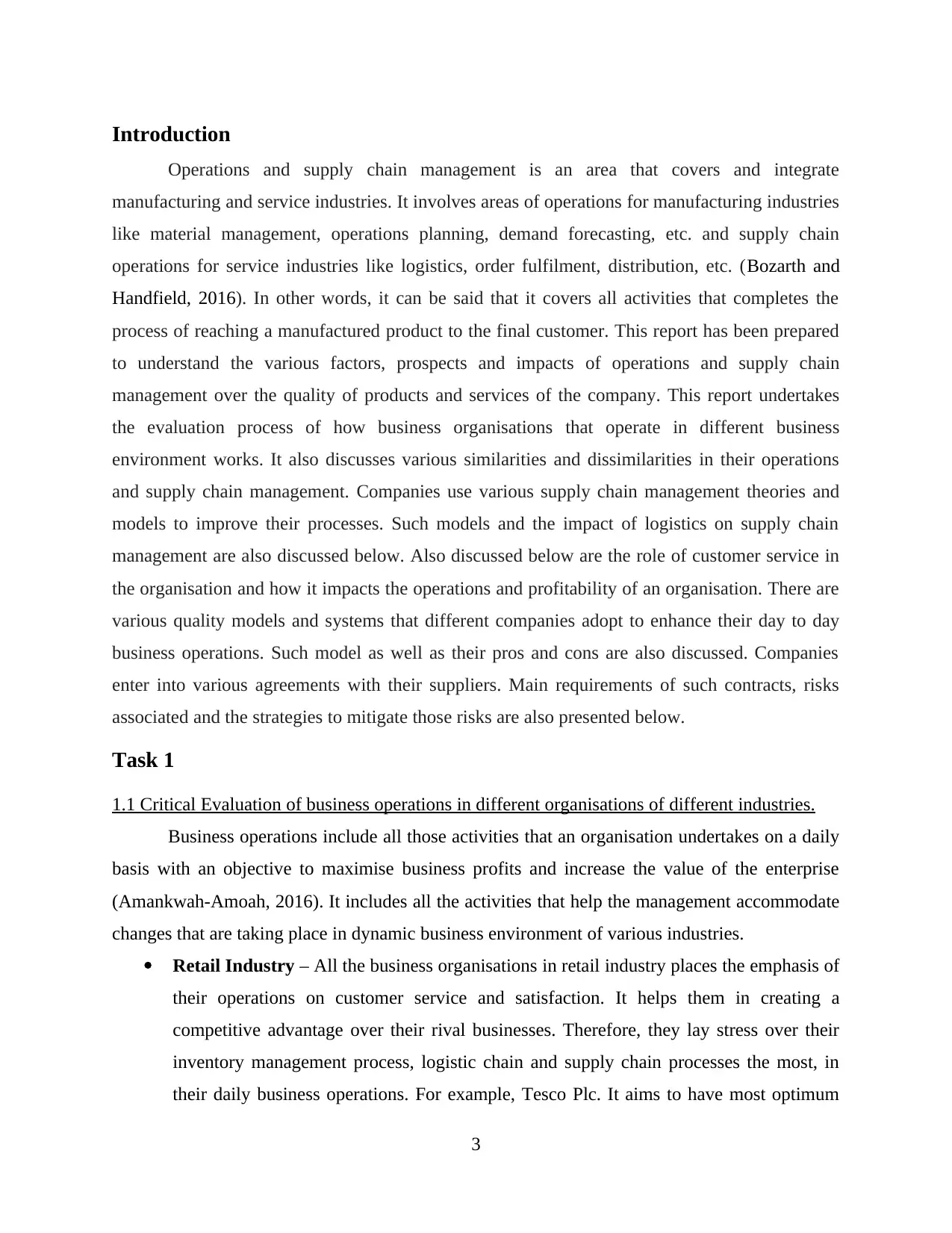
Introduction
Operations and supply chain management is an area that covers and integrate
manufacturing and service industries. It involves areas of operations for manufacturing industries
like material management, operations planning, demand forecasting, etc. and supply chain
operations for service industries like logistics, order fulfilment, distribution, etc. (Bozarth and
Handfield, 2016). In other words, it can be said that it covers all activities that completes the
process of reaching a manufactured product to the final customer. This report has been prepared
to understand the various factors, prospects and impacts of operations and supply chain
management over the quality of products and services of the company. This report undertakes
the evaluation process of how business organisations that operate in different business
environment works. It also discusses various similarities and dissimilarities in their operations
and supply chain management. Companies use various supply chain management theories and
models to improve their processes. Such models and the impact of logistics on supply chain
management are also discussed below. Also discussed below are the role of customer service in
the organisation and how it impacts the operations and profitability of an organisation. There are
various quality models and systems that different companies adopt to enhance their day to day
business operations. Such model as well as their pros and cons are also discussed. Companies
enter into various agreements with their suppliers. Main requirements of such contracts, risks
associated and the strategies to mitigate those risks are also presented below.
Task 1
1.1 Critical Evaluation of business operations in different organisations of different industries.
Business operations include all those activities that an organisation undertakes on a daily
basis with an objective to maximise business profits and increase the value of the enterprise
(Amankwah-Amoah, 2016). It includes all the activities that help the management accommodate
changes that are taking place in dynamic business environment of various industries.
Retail Industry – All the business organisations in retail industry places the emphasis of
their operations on customer service and satisfaction. It helps them in creating a
competitive advantage over their rival businesses. Therefore, they lay stress over their
inventory management process, logistic chain and supply chain processes the most, in
their daily business operations. For example, Tesco Plc. It aims to have most optimum
3
Operations and supply chain management is an area that covers and integrate
manufacturing and service industries. It involves areas of operations for manufacturing industries
like material management, operations planning, demand forecasting, etc. and supply chain
operations for service industries like logistics, order fulfilment, distribution, etc. (Bozarth and
Handfield, 2016). In other words, it can be said that it covers all activities that completes the
process of reaching a manufactured product to the final customer. This report has been prepared
to understand the various factors, prospects and impacts of operations and supply chain
management over the quality of products and services of the company. This report undertakes
the evaluation process of how business organisations that operate in different business
environment works. It also discusses various similarities and dissimilarities in their operations
and supply chain management. Companies use various supply chain management theories and
models to improve their processes. Such models and the impact of logistics on supply chain
management are also discussed below. Also discussed below are the role of customer service in
the organisation and how it impacts the operations and profitability of an organisation. There are
various quality models and systems that different companies adopt to enhance their day to day
business operations. Such model as well as their pros and cons are also discussed. Companies
enter into various agreements with their suppliers. Main requirements of such contracts, risks
associated and the strategies to mitigate those risks are also presented below.
Task 1
1.1 Critical Evaluation of business operations in different organisations of different industries.
Business operations include all those activities that an organisation undertakes on a daily
basis with an objective to maximise business profits and increase the value of the enterprise
(Amankwah-Amoah, 2016). It includes all the activities that help the management accommodate
changes that are taking place in dynamic business environment of various industries.
Retail Industry – All the business organisations in retail industry places the emphasis of
their operations on customer service and satisfaction. It helps them in creating a
competitive advantage over their rival businesses. Therefore, they lay stress over their
inventory management process, logistic chain and supply chain processes the most, in
their daily business operations. For example, Tesco Plc. It aims to have most optimum
3
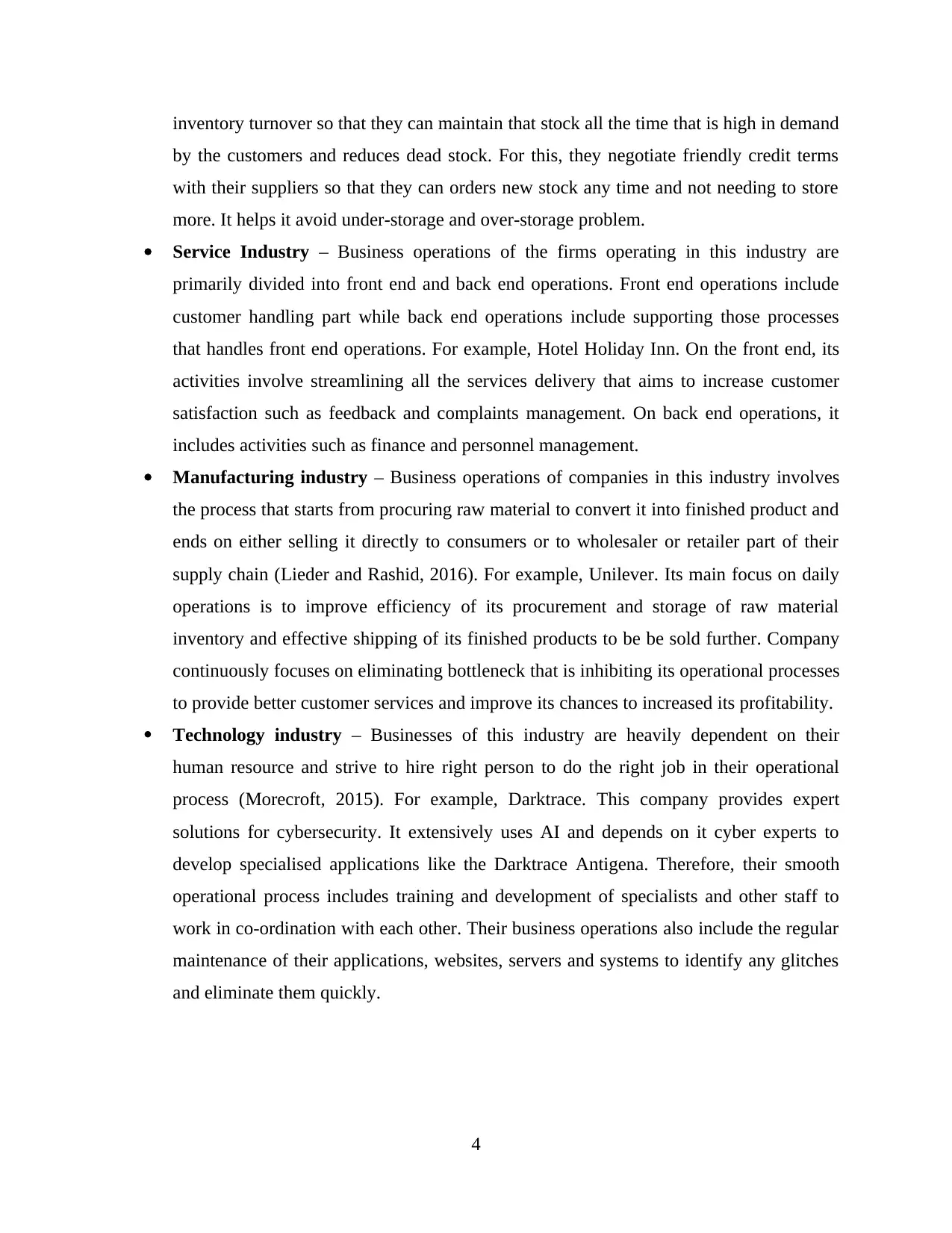
inventory turnover so that they can maintain that stock all the time that is high in demand
by the customers and reduces dead stock. For this, they negotiate friendly credit terms
with their suppliers so that they can orders new stock any time and not needing to store
more. It helps it avoid under-storage and over-storage problem.
Service Industry – Business operations of the firms operating in this industry are
primarily divided into front end and back end operations. Front end operations include
customer handling part while back end operations include supporting those processes
that handles front end operations. For example, Hotel Holiday Inn. On the front end, its
activities involve streamlining all the services delivery that aims to increase customer
satisfaction such as feedback and complaints management. On back end operations, it
includes activities such as finance and personnel management.
Manufacturing industry – Business operations of companies in this industry involves
the process that starts from procuring raw material to convert it into finished product and
ends on either selling it directly to consumers or to wholesaler or retailer part of their
supply chain (Lieder and Rashid, 2016). For example, Unilever. Its main focus on daily
operations is to improve efficiency of its procurement and storage of raw material
inventory and effective shipping of its finished products to be be sold further. Company
continuously focuses on eliminating bottleneck that is inhibiting its operational processes
to provide better customer services and improve its chances to increased its profitability.
Technology industry – Businesses of this industry are heavily dependent on their
human resource and strive to hire right person to do the right job in their operational
process (Morecroft, 2015). For example, Darktrace. This company provides expert
solutions for cybersecurity. It extensively uses AI and depends on it cyber experts to
develop specialised applications like the Darktrace Antigena. Therefore, their smooth
operational process includes training and development of specialists and other staff to
work in co-ordination with each other. Their business operations also include the regular
maintenance of their applications, websites, servers and systems to identify any glitches
and eliminate them quickly.
4
by the customers and reduces dead stock. For this, they negotiate friendly credit terms
with their suppliers so that they can orders new stock any time and not needing to store
more. It helps it avoid under-storage and over-storage problem.
Service Industry – Business operations of the firms operating in this industry are
primarily divided into front end and back end operations. Front end operations include
customer handling part while back end operations include supporting those processes
that handles front end operations. For example, Hotel Holiday Inn. On the front end, its
activities involve streamlining all the services delivery that aims to increase customer
satisfaction such as feedback and complaints management. On back end operations, it
includes activities such as finance and personnel management.
Manufacturing industry – Business operations of companies in this industry involves
the process that starts from procuring raw material to convert it into finished product and
ends on either selling it directly to consumers or to wholesaler or retailer part of their
supply chain (Lieder and Rashid, 2016). For example, Unilever. Its main focus on daily
operations is to improve efficiency of its procurement and storage of raw material
inventory and effective shipping of its finished products to be be sold further. Company
continuously focuses on eliminating bottleneck that is inhibiting its operational processes
to provide better customer services and improve its chances to increased its profitability.
Technology industry – Businesses of this industry are heavily dependent on their
human resource and strive to hire right person to do the right job in their operational
process (Morecroft, 2015). For example, Darktrace. This company provides expert
solutions for cybersecurity. It extensively uses AI and depends on it cyber experts to
develop specialised applications like the Darktrace Antigena. Therefore, their smooth
operational process includes training and development of specialists and other staff to
work in co-ordination with each other. Their business operations also include the regular
maintenance of their applications, websites, servers and systems to identify any glitches
and eliminate them quickly.
4
Secure Best Marks with AI Grader
Need help grading? Try our AI Grader for instant feedback on your assignments.
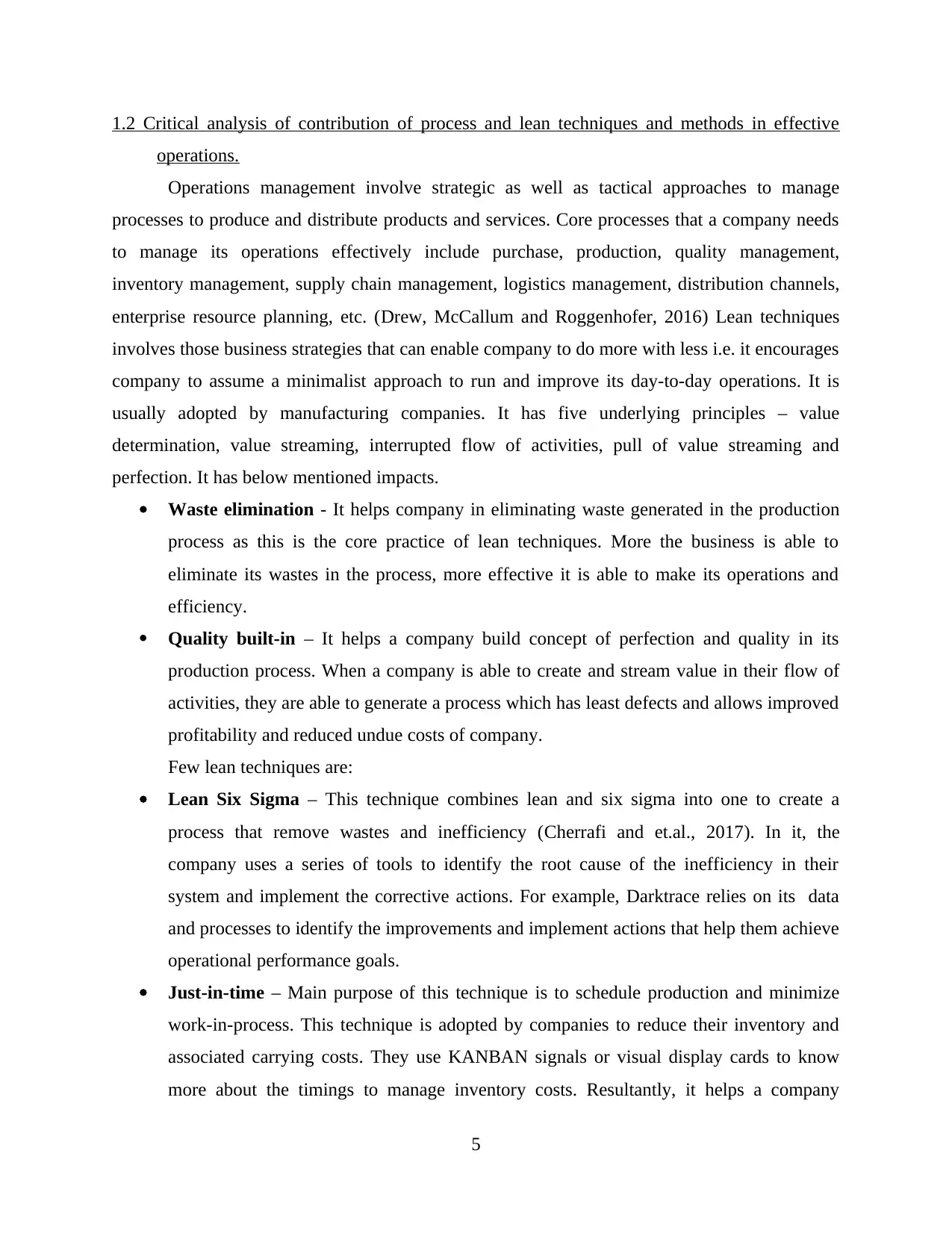
1.2 Critical analysis of contribution of process and lean techniques and methods in effective
operations.
Operations management involve strategic as well as tactical approaches to manage
processes to produce and distribute products and services. Core processes that a company needs
to manage its operations effectively include purchase, production, quality management,
inventory management, supply chain management, logistics management, distribution channels,
enterprise resource planning, etc. (Drew, McCallum and Roggenhofer, 2016) Lean techniques
involves those business strategies that can enable company to do more with less i.e. it encourages
company to assume a minimalist approach to run and improve its day-to-day operations. It is
usually adopted by manufacturing companies. It has five underlying principles – value
determination, value streaming, interrupted flow of activities, pull of value streaming and
perfection. It has below mentioned impacts.
Waste elimination - It helps company in eliminating waste generated in the production
process as this is the core practice of lean techniques. More the business is able to
eliminate its wastes in the process, more effective it is able to make its operations and
efficiency.
Quality built-in – It helps a company build concept of perfection and quality in its
production process. When a company is able to create and stream value in their flow of
activities, they are able to generate a process which has least defects and allows improved
profitability and reduced undue costs of company.
Few lean techniques are:
Lean Six Sigma – This technique combines lean and six sigma into one to create a
process that remove wastes and inefficiency (Cherrafi and et.al., 2017). In it, the
company uses a series of tools to identify the root cause of the inefficiency in their
system and implement the corrective actions. For example, Darktrace relies on its data
and processes to identify the improvements and implement actions that help them achieve
operational performance goals.
Just-in-time – Main purpose of this technique is to schedule production and minimize
work-in-process. This technique is adopted by companies to reduce their inventory and
associated carrying costs. They use KANBAN signals or visual display cards to know
more about the timings to manage inventory costs. Resultantly, it helps a company
5
operations.
Operations management involve strategic as well as tactical approaches to manage
processes to produce and distribute products and services. Core processes that a company needs
to manage its operations effectively include purchase, production, quality management,
inventory management, supply chain management, logistics management, distribution channels,
enterprise resource planning, etc. (Drew, McCallum and Roggenhofer, 2016) Lean techniques
involves those business strategies that can enable company to do more with less i.e. it encourages
company to assume a minimalist approach to run and improve its day-to-day operations. It is
usually adopted by manufacturing companies. It has five underlying principles – value
determination, value streaming, interrupted flow of activities, pull of value streaming and
perfection. It has below mentioned impacts.
Waste elimination - It helps company in eliminating waste generated in the production
process as this is the core practice of lean techniques. More the business is able to
eliminate its wastes in the process, more effective it is able to make its operations and
efficiency.
Quality built-in – It helps a company build concept of perfection and quality in its
production process. When a company is able to create and stream value in their flow of
activities, they are able to generate a process which has least defects and allows improved
profitability and reduced undue costs of company.
Few lean techniques are:
Lean Six Sigma – This technique combines lean and six sigma into one to create a
process that remove wastes and inefficiency (Cherrafi and et.al., 2017). In it, the
company uses a series of tools to identify the root cause of the inefficiency in their
system and implement the corrective actions. For example, Darktrace relies on its data
and processes to identify the improvements and implement actions that help them achieve
operational performance goals.
Just-in-time – Main purpose of this technique is to schedule production and minimize
work-in-process. This technique is adopted by companies to reduce their inventory and
associated carrying costs. They use KANBAN signals or visual display cards to know
more about the timings to manage inventory costs. Resultantly, it helps a company
5
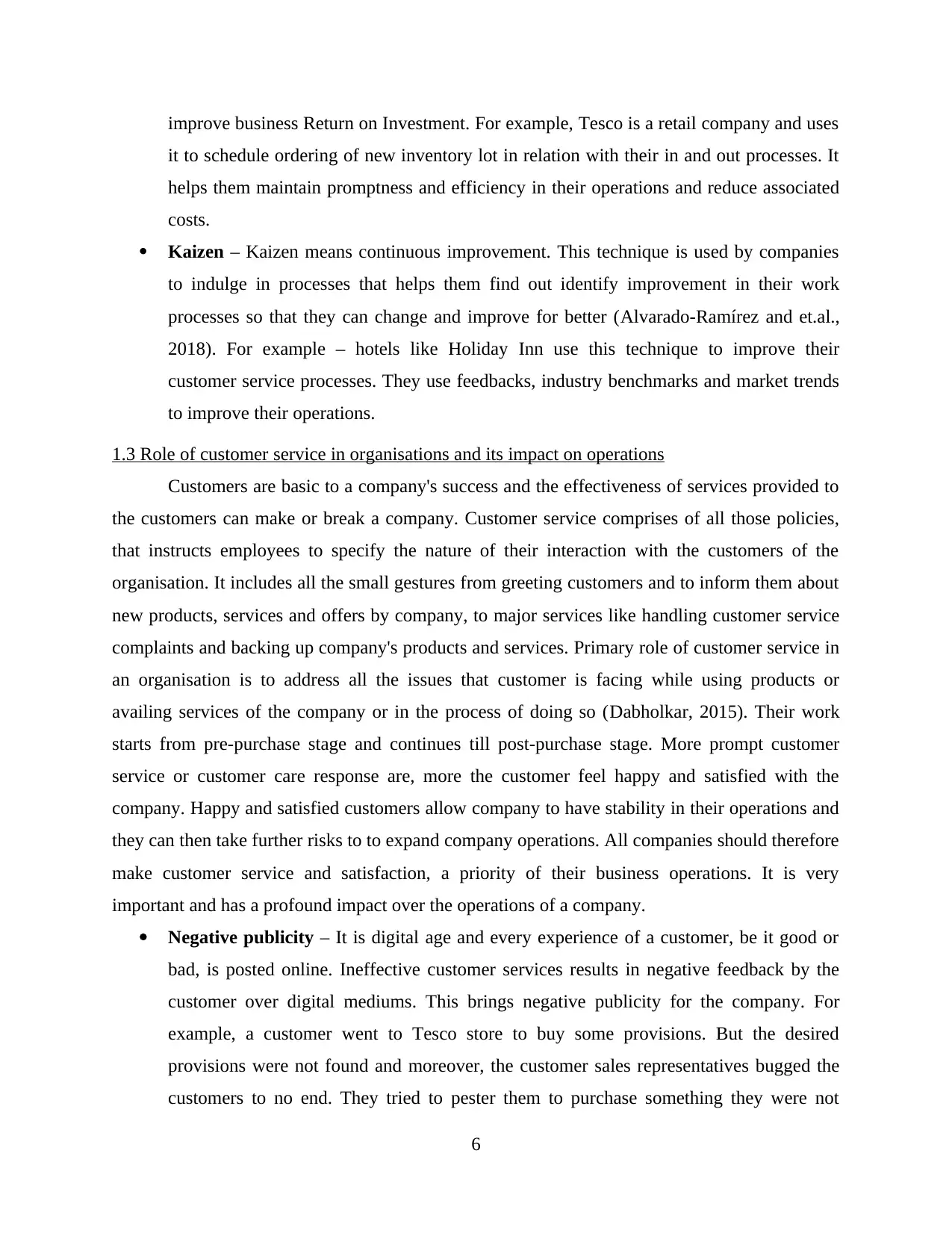
improve business Return on Investment. For example, Tesco is a retail company and uses
it to schedule ordering of new inventory lot in relation with their in and out processes. It
helps them maintain promptness and efficiency in their operations and reduce associated
costs.
Kaizen – Kaizen means continuous improvement. This technique is used by companies
to indulge in processes that helps them find out identify improvement in their work
processes so that they can change and improve for better (Alvarado-Ramírez and et.al.,
2018). For example – hotels like Holiday Inn use this technique to improve their
customer service processes. They use feedbacks, industry benchmarks and market trends
to improve their operations.
1.3 Role of customer service in organisations and its impact on operations
Customers are basic to a company's success and the effectiveness of services provided to
the customers can make or break a company. Customer service comprises of all those policies,
that instructs employees to specify the nature of their interaction with the customers of the
organisation. It includes all the small gestures from greeting customers and to inform them about
new products, services and offers by company, to major services like handling customer service
complaints and backing up company's products and services. Primary role of customer service in
an organisation is to address all the issues that customer is facing while using products or
availing services of the company or in the process of doing so (Dabholkar, 2015). Their work
starts from pre-purchase stage and continues till post-purchase stage. More prompt customer
service or customer care response are, more the customer feel happy and satisfied with the
company. Happy and satisfied customers allow company to have stability in their operations and
they can then take further risks to to expand company operations. All companies should therefore
make customer service and satisfaction, a priority of their business operations. It is very
important and has a profound impact over the operations of a company.
Negative publicity – It is digital age and every experience of a customer, be it good or
bad, is posted online. Ineffective customer services results in negative feedback by the
customer over digital mediums. This brings negative publicity for the company. For
example, a customer went to Tesco store to buy some provisions. But the desired
provisions were not found and moreover, the customer sales representatives bugged the
customers to no end. They tried to pester them to purchase something they were not
6
it to schedule ordering of new inventory lot in relation with their in and out processes. It
helps them maintain promptness and efficiency in their operations and reduce associated
costs.
Kaizen – Kaizen means continuous improvement. This technique is used by companies
to indulge in processes that helps them find out identify improvement in their work
processes so that they can change and improve for better (Alvarado-Ramírez and et.al.,
2018). For example – hotels like Holiday Inn use this technique to improve their
customer service processes. They use feedbacks, industry benchmarks and market trends
to improve their operations.
1.3 Role of customer service in organisations and its impact on operations
Customers are basic to a company's success and the effectiveness of services provided to
the customers can make or break a company. Customer service comprises of all those policies,
that instructs employees to specify the nature of their interaction with the customers of the
organisation. It includes all the small gestures from greeting customers and to inform them about
new products, services and offers by company, to major services like handling customer service
complaints and backing up company's products and services. Primary role of customer service in
an organisation is to address all the issues that customer is facing while using products or
availing services of the company or in the process of doing so (Dabholkar, 2015). Their work
starts from pre-purchase stage and continues till post-purchase stage. More prompt customer
service or customer care response are, more the customer feel happy and satisfied with the
company. Happy and satisfied customers allow company to have stability in their operations and
they can then take further risks to to expand company operations. All companies should therefore
make customer service and satisfaction, a priority of their business operations. It is very
important and has a profound impact over the operations of a company.
Negative publicity – It is digital age and every experience of a customer, be it good or
bad, is posted online. Ineffective customer services results in negative feedback by the
customer over digital mediums. This brings negative publicity for the company. For
example, a customer went to Tesco store to buy some provisions. But the desired
provisions were not found and moreover, the customer sales representatives bugged the
customers to no end. They tried to pester them to purchase something they were not
6
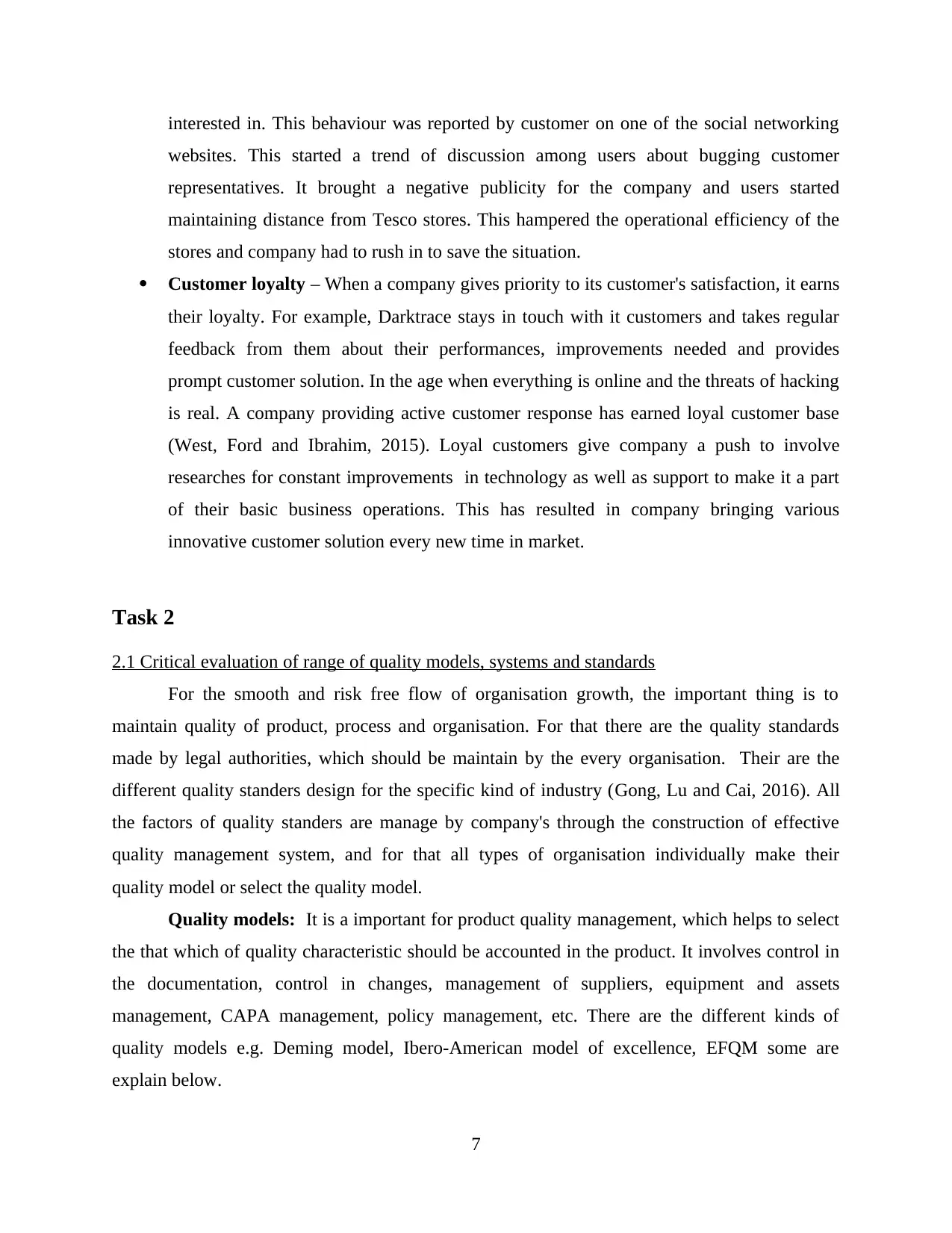
interested in. This behaviour was reported by customer on one of the social networking
websites. This started a trend of discussion among users about bugging customer
representatives. It brought a negative publicity for the company and users started
maintaining distance from Tesco stores. This hampered the operational efficiency of the
stores and company had to rush in to save the situation.
Customer loyalty – When a company gives priority to its customer's satisfaction, it earns
their loyalty. For example, Darktrace stays in touch with it customers and takes regular
feedback from them about their performances, improvements needed and provides
prompt customer solution. In the age when everything is online and the threats of hacking
is real. A company providing active customer response has earned loyal customer base
(West, Ford and Ibrahim, 2015). Loyal customers give company a push to involve
researches for constant improvements in technology as well as support to make it a part
of their basic business operations. This has resulted in company bringing various
innovative customer solution every new time in market.
Task 2
2.1 Critical evaluation of range of quality models, systems and standards
For the smooth and risk free flow of organisation growth, the important thing is to
maintain quality of product, process and organisation. For that there are the quality standards
made by legal authorities, which should be maintain by the every organisation. Their are the
different quality standers design for the specific kind of industry (Gong, Lu and Cai, 2016). All
the factors of quality standers are manage by company's through the construction of effective
quality management system, and for that all types of organisation individually make their
quality model or select the quality model.
Quality models: It is a important for product quality management, which helps to select
the that which of quality characteristic should be accounted in the product. It involves control in
the documentation, control in changes, management of suppliers, equipment and assets
management, CAPA management, policy management, etc. There are the different kinds of
quality models e.g. Deming model, Ibero-American model of excellence, EFQM some are
explain below.
7
websites. This started a trend of discussion among users about bugging customer
representatives. It brought a negative publicity for the company and users started
maintaining distance from Tesco stores. This hampered the operational efficiency of the
stores and company had to rush in to save the situation.
Customer loyalty – When a company gives priority to its customer's satisfaction, it earns
their loyalty. For example, Darktrace stays in touch with it customers and takes regular
feedback from them about their performances, improvements needed and provides
prompt customer solution. In the age when everything is online and the threats of hacking
is real. A company providing active customer response has earned loyal customer base
(West, Ford and Ibrahim, 2015). Loyal customers give company a push to involve
researches for constant improvements in technology as well as support to make it a part
of their basic business operations. This has resulted in company bringing various
innovative customer solution every new time in market.
Task 2
2.1 Critical evaluation of range of quality models, systems and standards
For the smooth and risk free flow of organisation growth, the important thing is to
maintain quality of product, process and organisation. For that there are the quality standards
made by legal authorities, which should be maintain by the every organisation. Their are the
different quality standers design for the specific kind of industry (Gong, Lu and Cai, 2016). All
the factors of quality standers are manage by company's through the construction of effective
quality management system, and for that all types of organisation individually make their
quality model or select the quality model.
Quality models: It is a important for product quality management, which helps to select
the that which of quality characteristic should be accounted in the product. It involves control in
the documentation, control in changes, management of suppliers, equipment and assets
management, CAPA management, policy management, etc. There are the different kinds of
quality models e.g. Deming model, Ibero-American model of excellence, EFQM some are
explain below.
7
Paraphrase This Document
Need a fresh take? Get an instant paraphrase of this document with our AI Paraphraser
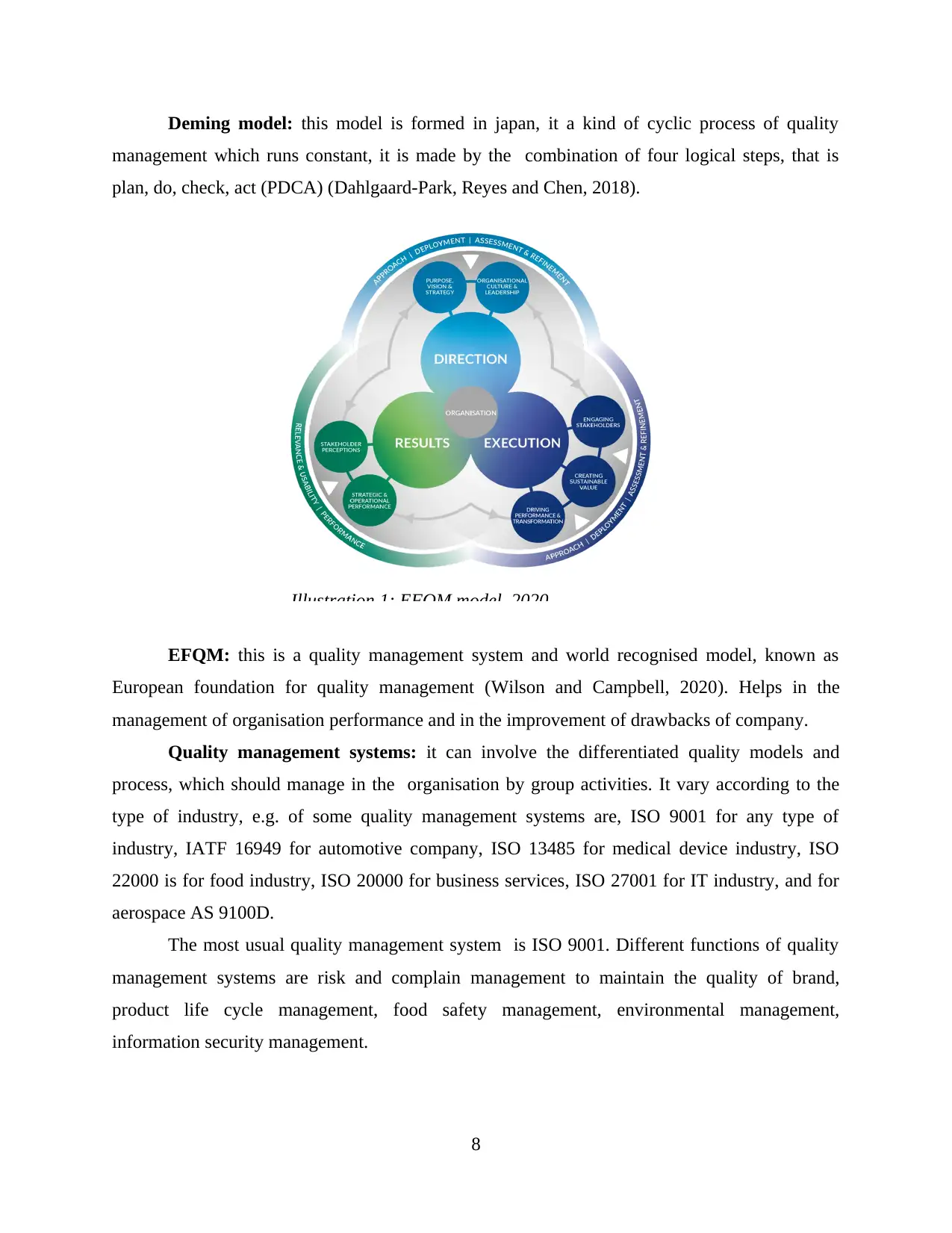
Deming model: this model is formed in japan, it a kind of cyclic process of quality
management which runs constant, it is made by the combination of four logical steps, that is
plan, do, check, act (PDCA) (Dahlgaard-Park, Reyes and Chen, 2018).
EFQM: this is a quality management system and world recognised model, known as
European foundation for quality management (Wilson and Campbell, 2020). Helps in the
management of organisation performance and in the improvement of drawbacks of company.
Quality management systems: it can involve the differentiated quality models and
process, which should manage in the organisation by group activities. It vary according to the
type of industry, e.g. of some quality management systems are, ISO 9001 for any type of
industry, IATF 16949 for automotive company, ISO 13485 for medical device industry, ISO
22000 is for food industry, ISO 20000 for business services, ISO 27001 for IT industry, and for
aerospace AS 9100D.
The most usual quality management system is ISO 9001. Different functions of quality
management systems are risk and complain management to maintain the quality of brand,
product life cycle management, food safety management, environmental management,
information security management.
8
Illustration 1: EFQM model, 2020
management which runs constant, it is made by the combination of four logical steps, that is
plan, do, check, act (PDCA) (Dahlgaard-Park, Reyes and Chen, 2018).
EFQM: this is a quality management system and world recognised model, known as
European foundation for quality management (Wilson and Campbell, 2020). Helps in the
management of organisation performance and in the improvement of drawbacks of company.
Quality management systems: it can involve the differentiated quality models and
process, which should manage in the organisation by group activities. It vary according to the
type of industry, e.g. of some quality management systems are, ISO 9001 for any type of
industry, IATF 16949 for automotive company, ISO 13485 for medical device industry, ISO
22000 is for food industry, ISO 20000 for business services, ISO 27001 for IT industry, and for
aerospace AS 9100D.
The most usual quality management system is ISO 9001. Different functions of quality
management systems are risk and complain management to maintain the quality of brand,
product life cycle management, food safety management, environmental management,
information security management.
8
Illustration 1: EFQM model, 2020
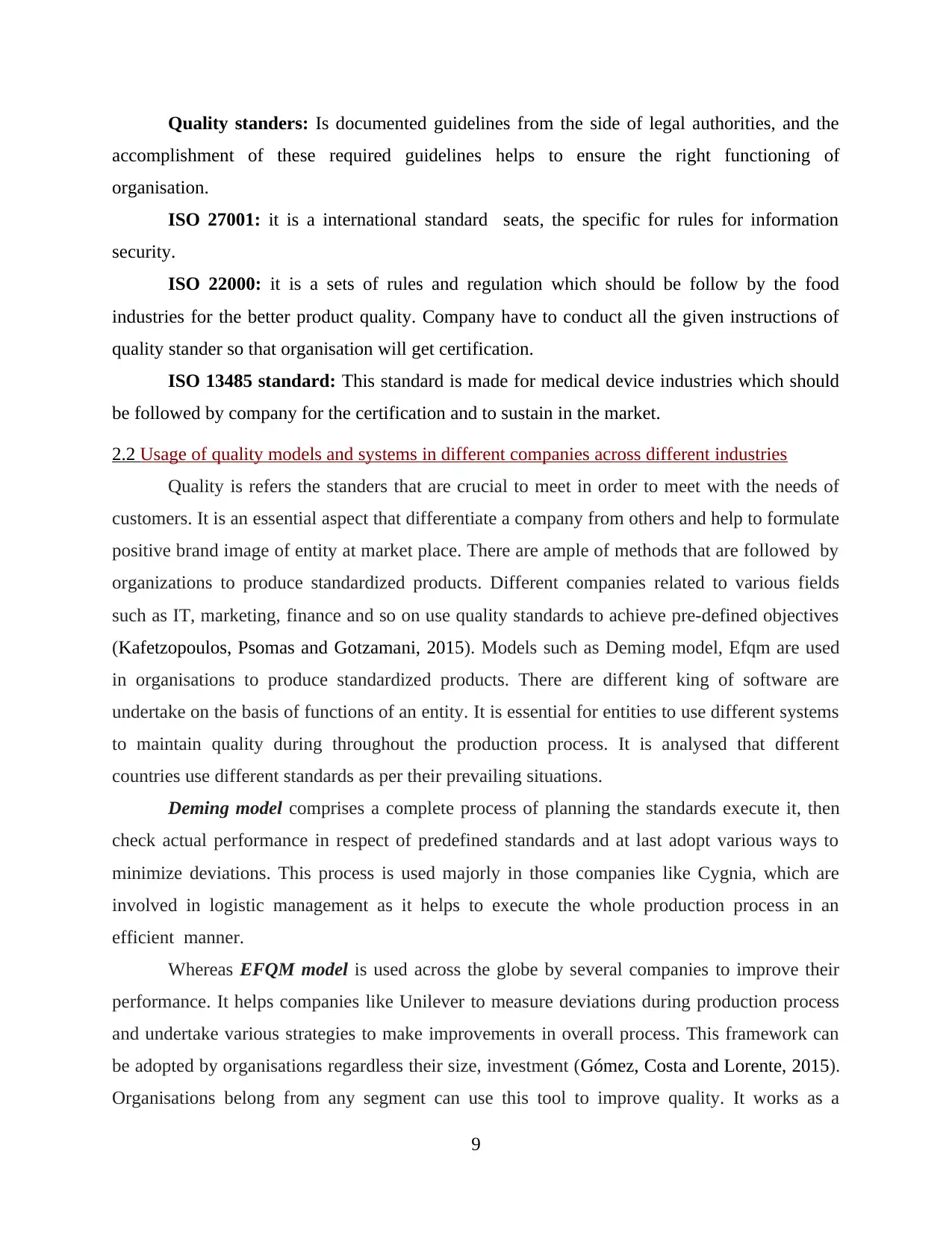
Quality standers: Is documented guidelines from the side of legal authorities, and the
accomplishment of these required guidelines helps to ensure the right functioning of
organisation.
ISO 27001: it is a international standard seats, the specific for rules for information
security.
ISO 22000: it is a sets of rules and regulation which should be follow by the food
industries for the better product quality. Company have to conduct all the given instructions of
quality stander so that organisation will get certification.
ISO 13485 standard: This standard is made for medical device industries which should
be followed by company for the certification and to sustain in the market.
2.2 Usage of quality models and systems in different companies across different industries
Quality is refers the standers that are crucial to meet in order to meet with the needs of
customers. It is an essential aspect that differentiate a company from others and help to formulate
positive brand image of entity at market place. There are ample of methods that are followed by
organizations to produce standardized products. Different companies related to various fields
such as IT, marketing, finance and so on use quality standards to achieve pre-defined objectives
(Kafetzopoulos, Psomas and Gotzamani, 2015). Models such as Deming model, Efqm are used
in organisations to produce standardized products. There are different king of software are
undertake on the basis of functions of an entity. It is essential for entities to use different systems
to maintain quality during throughout the production process. It is analysed that different
countries use different standards as per their prevailing situations.
Deming model comprises a complete process of planning the standards execute it, then
check actual performance in respect of predefined standards and at last adopt various ways to
minimize deviations. This process is used majorly in those companies like Cygnia, which are
involved in logistic management as it helps to execute the whole production process in an
efficient manner.
Whereas EFQM model is used across the globe by several companies to improve their
performance. It helps companies like Unilever to measure deviations during production process
and undertake various strategies to make improvements in overall process. This framework can
be adopted by organisations regardless their size, investment (Gómez, Costa and Lorente, 2015).
Organisations belong from any segment can use this tool to improve quality. It works as a
9
accomplishment of these required guidelines helps to ensure the right functioning of
organisation.
ISO 27001: it is a international standard seats, the specific for rules for information
security.
ISO 22000: it is a sets of rules and regulation which should be follow by the food
industries for the better product quality. Company have to conduct all the given instructions of
quality stander so that organisation will get certification.
ISO 13485 standard: This standard is made for medical device industries which should
be followed by company for the certification and to sustain in the market.
2.2 Usage of quality models and systems in different companies across different industries
Quality is refers the standers that are crucial to meet in order to meet with the needs of
customers. It is an essential aspect that differentiate a company from others and help to formulate
positive brand image of entity at market place. There are ample of methods that are followed by
organizations to produce standardized products. Different companies related to various fields
such as IT, marketing, finance and so on use quality standards to achieve pre-defined objectives
(Kafetzopoulos, Psomas and Gotzamani, 2015). Models such as Deming model, Efqm are used
in organisations to produce standardized products. There are different king of software are
undertake on the basis of functions of an entity. It is essential for entities to use different systems
to maintain quality during throughout the production process. It is analysed that different
countries use different standards as per their prevailing situations.
Deming model comprises a complete process of planning the standards execute it, then
check actual performance in respect of predefined standards and at last adopt various ways to
minimize deviations. This process is used majorly in those companies like Cygnia, which are
involved in logistic management as it helps to execute the whole production process in an
efficient manner.
Whereas EFQM model is used across the globe by several companies to improve their
performance. It helps companies like Unilever to measure deviations during production process
and undertake various strategies to make improvements in overall process. This framework can
be adopted by organisations regardless their size, investment (Gómez, Costa and Lorente, 2015).
Organisations belong from any segment can use this tool to improve quality. It works as a
9
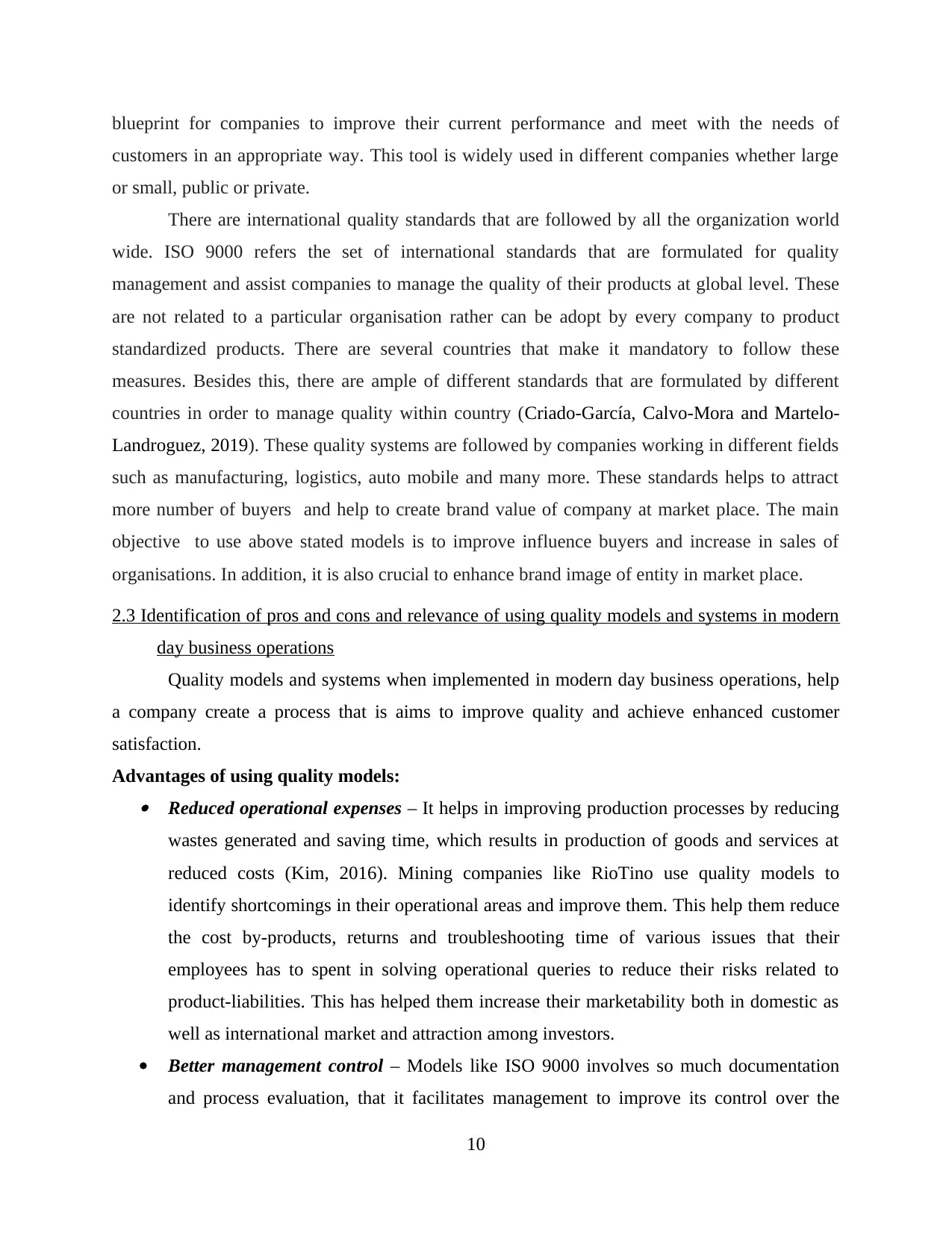
blueprint for companies to improve their current performance and meet with the needs of
customers in an appropriate way. This tool is widely used in different companies whether large
or small, public or private.
There are international quality standards that are followed by all the organization world
wide. ISO 9000 refers the set of international standards that are formulated for quality
management and assist companies to manage the quality of their products at global level. These
are not related to a particular organisation rather can be adopt by every company to product
standardized products. There are several countries that make it mandatory to follow these
measures. Besides this, there are ample of different standards that are formulated by different
countries in order to manage quality within country (Criado-García, Calvo-Mora and Martelo-
Landroguez, 2019). These quality systems are followed by companies working in different fields
such as manufacturing, logistics, auto mobile and many more. These standards helps to attract
more number of buyers and help to create brand value of company at market place. The main
objective to use above stated models is to improve influence buyers and increase in sales of
organisations. In addition, it is also crucial to enhance brand image of entity in market place.
2.3 Identification of pros and cons and relevance of using quality models and systems in modern
day business operations
Quality models and systems when implemented in modern day business operations, help
a company create a process that is aims to improve quality and achieve enhanced customer
satisfaction.
Advantages of using quality models: Reduced operational expenses – It helps in improving production processes by reducing
wastes generated and saving time, which results in production of goods and services at
reduced costs (Kim, 2016). Mining companies like RioTino use quality models to
identify shortcomings in their operational areas and improve them. This help them reduce
the cost by-products, returns and troubleshooting time of various issues that their
employees has to spent in solving operational queries to reduce their risks related to
product-liabilities. This has helped them increase their marketability both in domestic as
well as international market and attraction among investors.
Better management control – Models like ISO 9000 involves so much documentation
and process evaluation, that it facilitates management to improve its control over the
10
customers in an appropriate way. This tool is widely used in different companies whether large
or small, public or private.
There are international quality standards that are followed by all the organization world
wide. ISO 9000 refers the set of international standards that are formulated for quality
management and assist companies to manage the quality of their products at global level. These
are not related to a particular organisation rather can be adopt by every company to product
standardized products. There are several countries that make it mandatory to follow these
measures. Besides this, there are ample of different standards that are formulated by different
countries in order to manage quality within country (Criado-García, Calvo-Mora and Martelo-
Landroguez, 2019). These quality systems are followed by companies working in different fields
such as manufacturing, logistics, auto mobile and many more. These standards helps to attract
more number of buyers and help to create brand value of company at market place. The main
objective to use above stated models is to improve influence buyers and increase in sales of
organisations. In addition, it is also crucial to enhance brand image of entity in market place.
2.3 Identification of pros and cons and relevance of using quality models and systems in modern
day business operations
Quality models and systems when implemented in modern day business operations, help
a company create a process that is aims to improve quality and achieve enhanced customer
satisfaction.
Advantages of using quality models: Reduced operational expenses – It helps in improving production processes by reducing
wastes generated and saving time, which results in production of goods and services at
reduced costs (Kim, 2016). Mining companies like RioTino use quality models to
identify shortcomings in their operational areas and improve them. This help them reduce
the cost by-products, returns and troubleshooting time of various issues that their
employees has to spent in solving operational queries to reduce their risks related to
product-liabilities. This has helped them increase their marketability both in domestic as
well as international market and attraction among investors.
Better management control – Models like ISO 9000 involves so much documentation
and process evaluation, that it facilitates management to improve its control over the
10
Secure Best Marks with AI Grader
Need help grading? Try our AI Grader for instant feedback on your assignments.
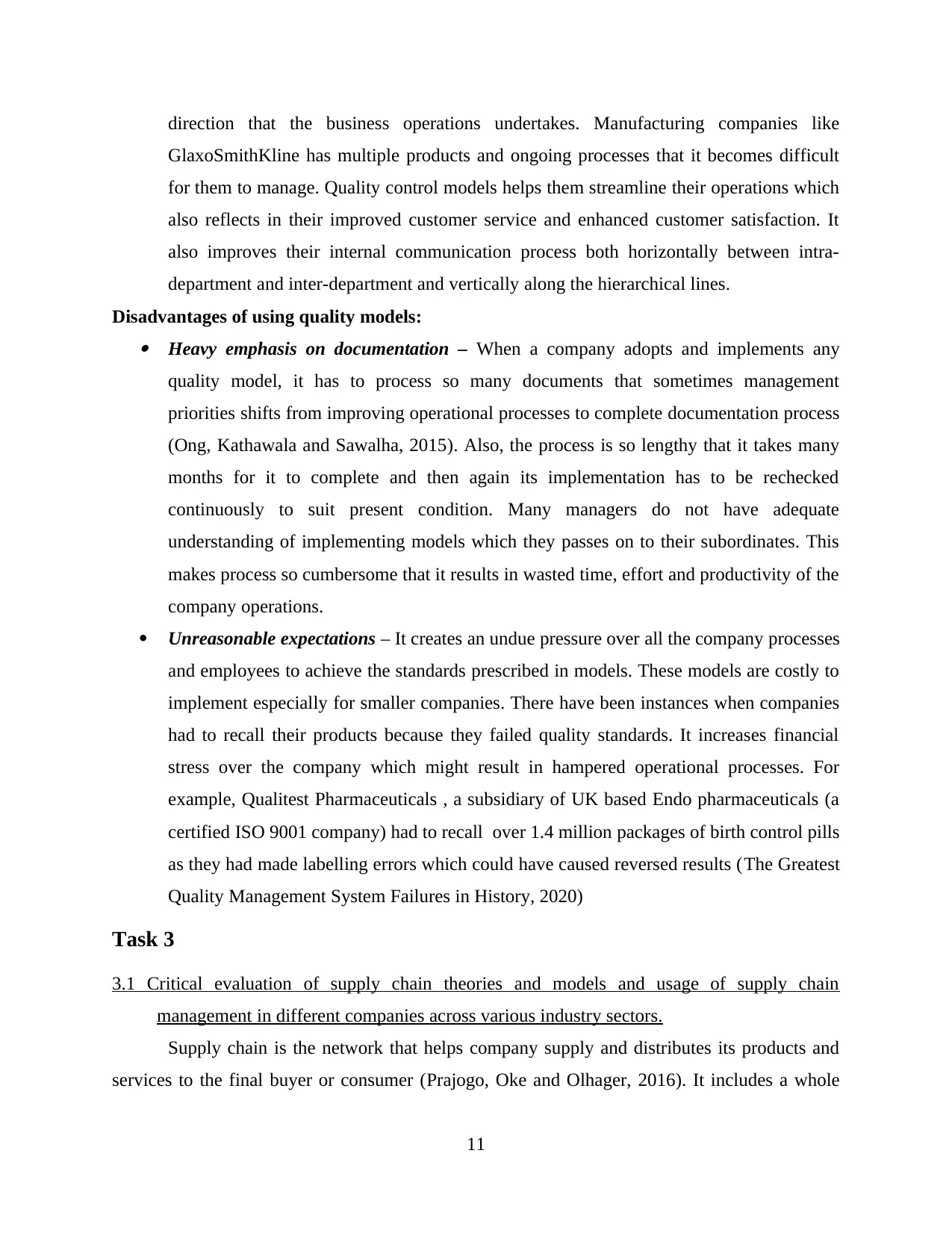
direction that the business operations undertakes. Manufacturing companies like
GlaxoSmithKline has multiple products and ongoing processes that it becomes difficult
for them to manage. Quality control models helps them streamline their operations which
also reflects in their improved customer service and enhanced customer satisfaction. It
also improves their internal communication process both horizontally between intra-
department and inter-department and vertically along the hierarchical lines.
Disadvantages of using quality models: Heavy emphasis on documentation – When a company adopts and implements any
quality model, it has to process so many documents that sometimes management
priorities shifts from improving operational processes to complete documentation process
(Ong, Kathawala and Sawalha, 2015). Also, the process is so lengthy that it takes many
months for it to complete and then again its implementation has to be rechecked
continuously to suit present condition. Many managers do not have adequate
understanding of implementing models which they passes on to their subordinates. This
makes process so cumbersome that it results in wasted time, effort and productivity of the
company operations.
Unreasonable expectations – It creates an undue pressure over all the company processes
and employees to achieve the standards prescribed in models. These models are costly to
implement especially for smaller companies. There have been instances when companies
had to recall their products because they failed quality standards. It increases financial
stress over the company which might result in hampered operational processes. For
example, Qualitest Pharmaceuticals , a subsidiary of UK based Endo pharmaceuticals (a
certified ISO 9001 company) had to recall over 1.4 million packages of birth control pills
as they had made labelling errors which could have caused reversed results (The Greatest
Quality Management System Failures in History, 2020)
Task 3
3.1 Critical evaluation of supply chain theories and models and usage of supply chain
management in different companies across various industry sectors.
Supply chain is the network that helps company supply and distributes its products and
services to the final buyer or consumer (Prajogo, Oke and Olhager, 2016). It includes a whole
11
GlaxoSmithKline has multiple products and ongoing processes that it becomes difficult
for them to manage. Quality control models helps them streamline their operations which
also reflects in their improved customer service and enhanced customer satisfaction. It
also improves their internal communication process both horizontally between intra-
department and inter-department and vertically along the hierarchical lines.
Disadvantages of using quality models: Heavy emphasis on documentation – When a company adopts and implements any
quality model, it has to process so many documents that sometimes management
priorities shifts from improving operational processes to complete documentation process
(Ong, Kathawala and Sawalha, 2015). Also, the process is so lengthy that it takes many
months for it to complete and then again its implementation has to be rechecked
continuously to suit present condition. Many managers do not have adequate
understanding of implementing models which they passes on to their subordinates. This
makes process so cumbersome that it results in wasted time, effort and productivity of the
company operations.
Unreasonable expectations – It creates an undue pressure over all the company processes
and employees to achieve the standards prescribed in models. These models are costly to
implement especially for smaller companies. There have been instances when companies
had to recall their products because they failed quality standards. It increases financial
stress over the company which might result in hampered operational processes. For
example, Qualitest Pharmaceuticals , a subsidiary of UK based Endo pharmaceuticals (a
certified ISO 9001 company) had to recall over 1.4 million packages of birth control pills
as they had made labelling errors which could have caused reversed results (The Greatest
Quality Management System Failures in History, 2020)
Task 3
3.1 Critical evaluation of supply chain theories and models and usage of supply chain
management in different companies across various industry sectors.
Supply chain is the network that helps company supply and distributes its products and
services to the final buyer or consumer (Prajogo, Oke and Olhager, 2016). It includes a whole
11
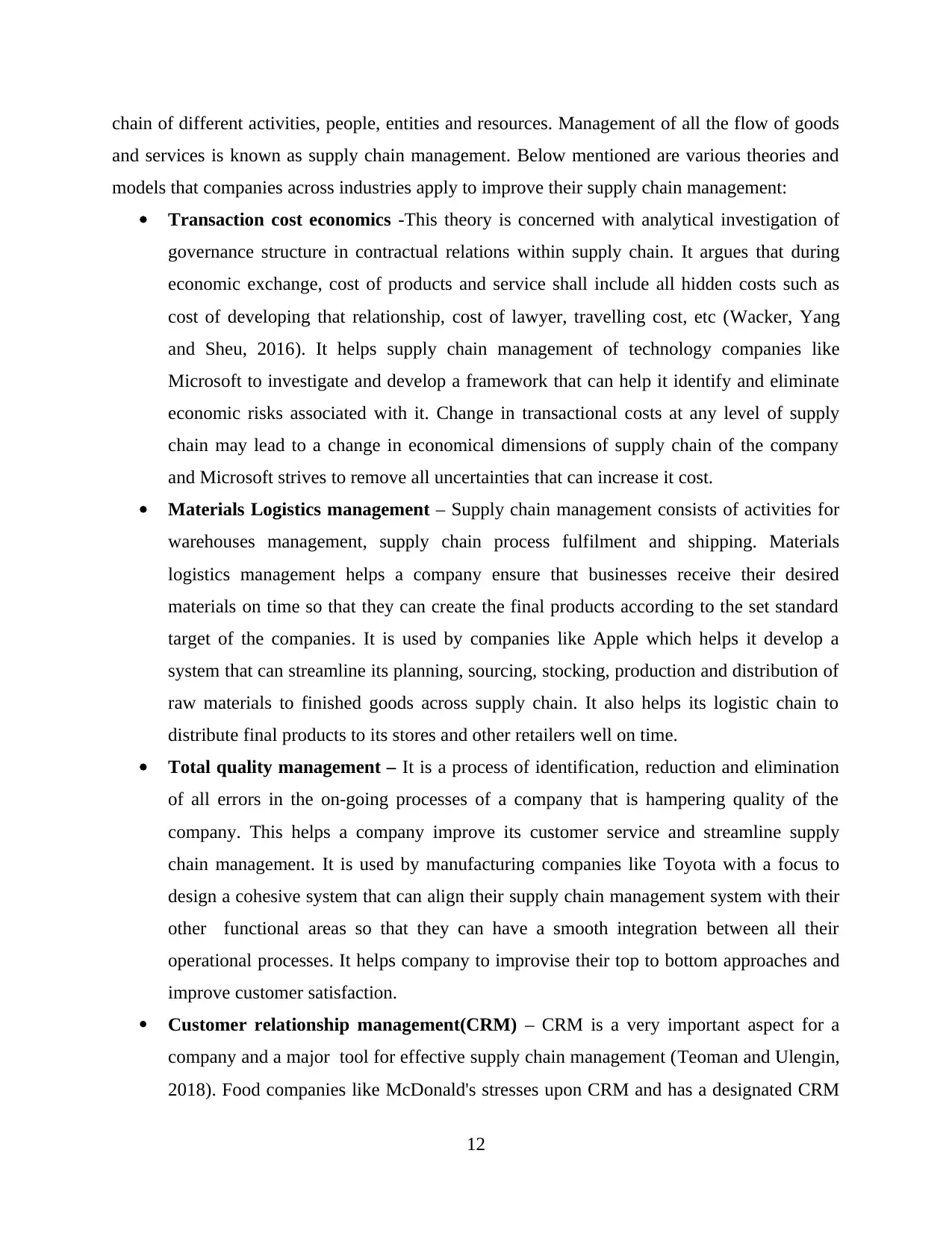
chain of different activities, people, entities and resources. Management of all the flow of goods
and services is known as supply chain management. Below mentioned are various theories and
models that companies across industries apply to improve their supply chain management:
Transaction cost economics -This theory is concerned with analytical investigation of
governance structure in contractual relations within supply chain. It argues that during
economic exchange, cost of products and service shall include all hidden costs such as
cost of developing that relationship, cost of lawyer, travelling cost, etc (Wacker, Yang
and Sheu, 2016). It helps supply chain management of technology companies like
Microsoft to investigate and develop a framework that can help it identify and eliminate
economic risks associated with it. Change in transactional costs at any level of supply
chain may lead to a change in economical dimensions of supply chain of the company
and Microsoft strives to remove all uncertainties that can increase it cost.
Materials Logistics management – Supply chain management consists of activities for
warehouses management, supply chain process fulfilment and shipping. Materials
logistics management helps a company ensure that businesses receive their desired
materials on time so that they can create the final products according to the set standard
target of the companies. It is used by companies like Apple which helps it develop a
system that can streamline its planning, sourcing, stocking, production and distribution of
raw materials to finished goods across supply chain. It also helps its logistic chain to
distribute final products to its stores and other retailers well on time.
Total quality management – It is a process of identification, reduction and elimination
of all errors in the on-going processes of a company that is hampering quality of the
company. This helps a company improve its customer service and streamline supply
chain management. It is used by manufacturing companies like Toyota with a focus to
design a cohesive system that can align their supply chain management system with their
other functional areas so that they can have a smooth integration between all their
operational processes. It helps company to improvise their top to bottom approaches and
improve customer satisfaction.
Customer relationship management(CRM) – CRM is a very important aspect for a
company and a major tool for effective supply chain management (Teoman and Ulengin,
2018). Food companies like McDonald's stresses upon CRM and has a designated CRM
12
and services is known as supply chain management. Below mentioned are various theories and
models that companies across industries apply to improve their supply chain management:
Transaction cost economics -This theory is concerned with analytical investigation of
governance structure in contractual relations within supply chain. It argues that during
economic exchange, cost of products and service shall include all hidden costs such as
cost of developing that relationship, cost of lawyer, travelling cost, etc (Wacker, Yang
and Sheu, 2016). It helps supply chain management of technology companies like
Microsoft to investigate and develop a framework that can help it identify and eliminate
economic risks associated with it. Change in transactional costs at any level of supply
chain may lead to a change in economical dimensions of supply chain of the company
and Microsoft strives to remove all uncertainties that can increase it cost.
Materials Logistics management – Supply chain management consists of activities for
warehouses management, supply chain process fulfilment and shipping. Materials
logistics management helps a company ensure that businesses receive their desired
materials on time so that they can create the final products according to the set standard
target of the companies. It is used by companies like Apple which helps it develop a
system that can streamline its planning, sourcing, stocking, production and distribution of
raw materials to finished goods across supply chain. It also helps its logistic chain to
distribute final products to its stores and other retailers well on time.
Total quality management – It is a process of identification, reduction and elimination
of all errors in the on-going processes of a company that is hampering quality of the
company. This helps a company improve its customer service and streamline supply
chain management. It is used by manufacturing companies like Toyota with a focus to
design a cohesive system that can align their supply chain management system with their
other functional areas so that they can have a smooth integration between all their
operational processes. It helps company to improvise their top to bottom approaches and
improve customer satisfaction.
Customer relationship management(CRM) – CRM is a very important aspect for a
company and a major tool for effective supply chain management (Teoman and Ulengin,
2018). Food companies like McDonald's stresses upon CRM and has a designated CRM
12
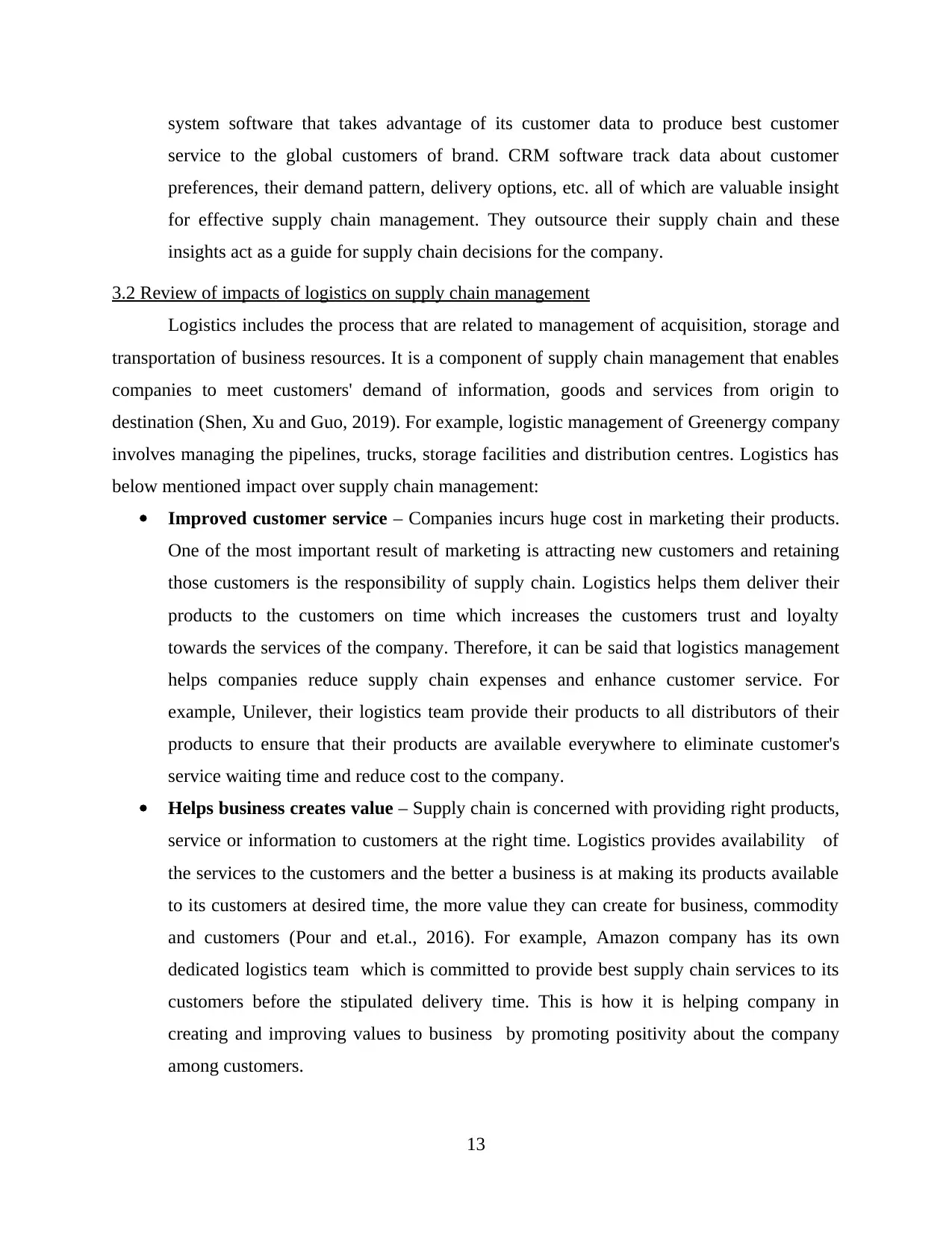
system software that takes advantage of its customer data to produce best customer
service to the global customers of brand. CRM software track data about customer
preferences, their demand pattern, delivery options, etc. all of which are valuable insight
for effective supply chain management. They outsource their supply chain and these
insights act as a guide for supply chain decisions for the company.
3.2 Review of impacts of logistics on supply chain management
Logistics includes the process that are related to management of acquisition, storage and
transportation of business resources. It is a component of supply chain management that enables
companies to meet customers' demand of information, goods and services from origin to
destination (Shen, Xu and Guo, 2019). For example, logistic management of Greenergy company
involves managing the pipelines, trucks, storage facilities and distribution centres. Logistics has
below mentioned impact over supply chain management:
Improved customer service – Companies incurs huge cost in marketing their products.
One of the most important result of marketing is attracting new customers and retaining
those customers is the responsibility of supply chain. Logistics helps them deliver their
products to the customers on time which increases the customers trust and loyalty
towards the services of the company. Therefore, it can be said that logistics management
helps companies reduce supply chain expenses and enhance customer service. For
example, Unilever, their logistics team provide their products to all distributors of their
products to ensure that their products are available everywhere to eliminate customer's
service waiting time and reduce cost to the company.
Helps business creates value – Supply chain is concerned with providing right products,
service or information to customers at the right time. Logistics provides availability of
the services to the customers and the better a business is at making its products available
to its customers at desired time, the more value they can create for business, commodity
and customers (Pour and et.al., 2016). For example, Amazon company has its own
dedicated logistics team which is committed to provide best supply chain services to its
customers before the stipulated delivery time. This is how it is helping company in
creating and improving values to business by promoting positivity about the company
among customers.
13
service to the global customers of brand. CRM software track data about customer
preferences, their demand pattern, delivery options, etc. all of which are valuable insight
for effective supply chain management. They outsource their supply chain and these
insights act as a guide for supply chain decisions for the company.
3.2 Review of impacts of logistics on supply chain management
Logistics includes the process that are related to management of acquisition, storage and
transportation of business resources. It is a component of supply chain management that enables
companies to meet customers' demand of information, goods and services from origin to
destination (Shen, Xu and Guo, 2019). For example, logistic management of Greenergy company
involves managing the pipelines, trucks, storage facilities and distribution centres. Logistics has
below mentioned impact over supply chain management:
Improved customer service – Companies incurs huge cost in marketing their products.
One of the most important result of marketing is attracting new customers and retaining
those customers is the responsibility of supply chain. Logistics helps them deliver their
products to the customers on time which increases the customers trust and loyalty
towards the services of the company. Therefore, it can be said that logistics management
helps companies reduce supply chain expenses and enhance customer service. For
example, Unilever, their logistics team provide their products to all distributors of their
products to ensure that their products are available everywhere to eliminate customer's
service waiting time and reduce cost to the company.
Helps business creates value – Supply chain is concerned with providing right products,
service or information to customers at the right time. Logistics provides availability of
the services to the customers and the better a business is at making its products available
to its customers at desired time, the more value they can create for business, commodity
and customers (Pour and et.al., 2016). For example, Amazon company has its own
dedicated logistics team which is committed to provide best supply chain services to its
customers before the stipulated delivery time. This is how it is helping company in
creating and improving values to business by promoting positivity about the company
among customers.
13
Paraphrase This Document
Need a fresh take? Get an instant paraphrase of this document with our AI Paraphraser
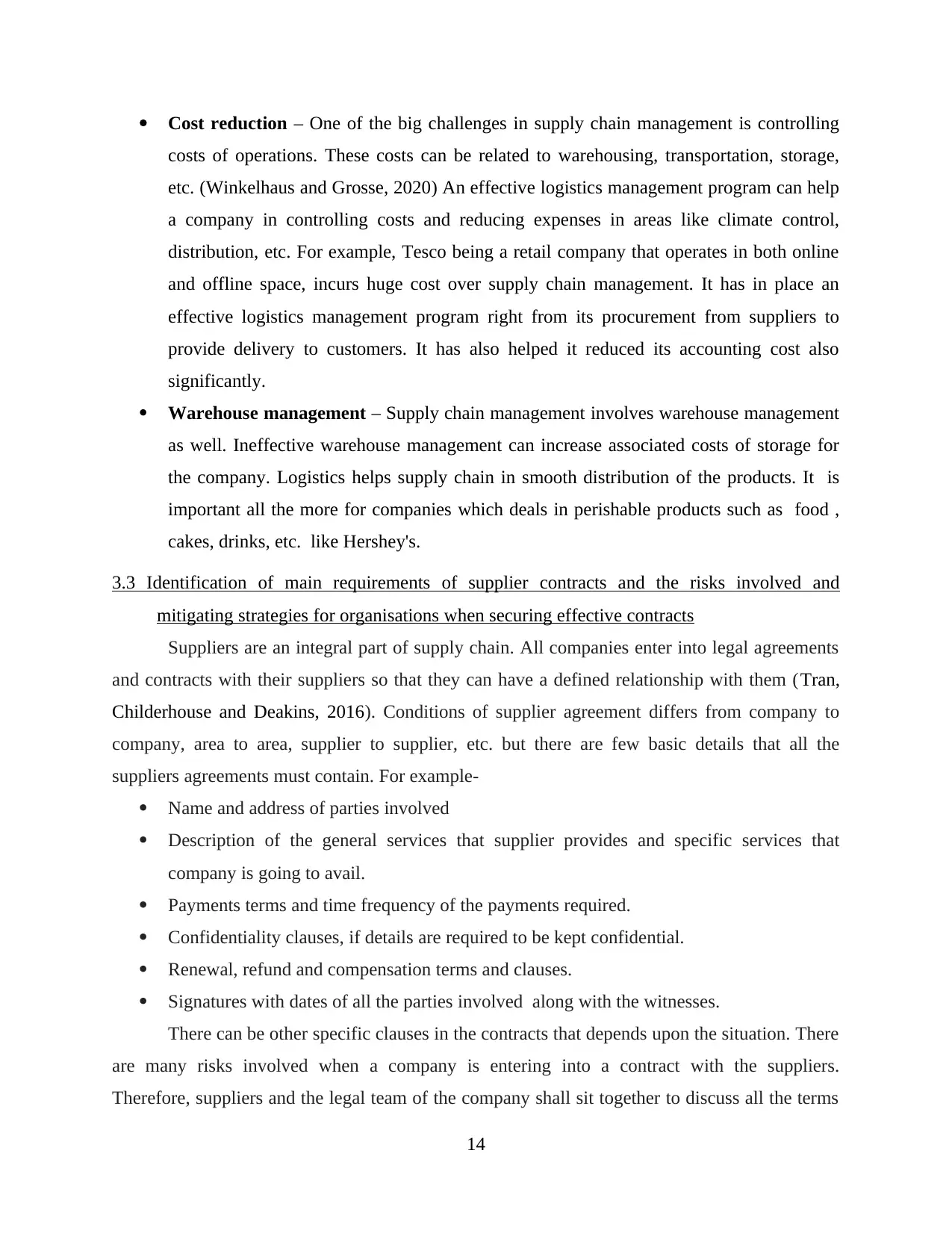
Cost reduction – One of the big challenges in supply chain management is controlling
costs of operations. These costs can be related to warehousing, transportation, storage,
etc. (Winkelhaus and Grosse, 2020) An effective logistics management program can help
a company in controlling costs and reducing expenses in areas like climate control,
distribution, etc. For example, Tesco being a retail company that operates in both online
and offline space, incurs huge cost over supply chain management. It has in place an
effective logistics management program right from its procurement from suppliers to
provide delivery to customers. It has also helped it reduced its accounting cost also
significantly.
Warehouse management – Supply chain management involves warehouse management
as well. Ineffective warehouse management can increase associated costs of storage for
the company. Logistics helps supply chain in smooth distribution of the products. It is
important all the more for companies which deals in perishable products such as food ,
cakes, drinks, etc. like Hershey's.
3.3 Identification of main requirements of supplier contracts and the risks involved and
mitigating strategies for organisations when securing effective contracts
Suppliers are an integral part of supply chain. All companies enter into legal agreements
and contracts with their suppliers so that they can have a defined relationship with them (Tran,
Childerhouse and Deakins, 2016). Conditions of supplier agreement differs from company to
company, area to area, supplier to supplier, etc. but there are few basic details that all the
suppliers agreements must contain. For example-
Name and address of parties involved
Description of the general services that supplier provides and specific services that
company is going to avail.
Payments terms and time frequency of the payments required.
Confidentiality clauses, if details are required to be kept confidential.
Renewal, refund and compensation terms and clauses.
Signatures with dates of all the parties involved along with the witnesses.
There can be other specific clauses in the contracts that depends upon the situation. There
are many risks involved when a company is entering into a contract with the suppliers.
Therefore, suppliers and the legal team of the company shall sit together to discuss all the terms
14
costs of operations. These costs can be related to warehousing, transportation, storage,
etc. (Winkelhaus and Grosse, 2020) An effective logistics management program can help
a company in controlling costs and reducing expenses in areas like climate control,
distribution, etc. For example, Tesco being a retail company that operates in both online
and offline space, incurs huge cost over supply chain management. It has in place an
effective logistics management program right from its procurement from suppliers to
provide delivery to customers. It has also helped it reduced its accounting cost also
significantly.
Warehouse management – Supply chain management involves warehouse management
as well. Ineffective warehouse management can increase associated costs of storage for
the company. Logistics helps supply chain in smooth distribution of the products. It is
important all the more for companies which deals in perishable products such as food ,
cakes, drinks, etc. like Hershey's.
3.3 Identification of main requirements of supplier contracts and the risks involved and
mitigating strategies for organisations when securing effective contracts
Suppliers are an integral part of supply chain. All companies enter into legal agreements
and contracts with their suppliers so that they can have a defined relationship with them (Tran,
Childerhouse and Deakins, 2016). Conditions of supplier agreement differs from company to
company, area to area, supplier to supplier, etc. but there are few basic details that all the
suppliers agreements must contain. For example-
Name and address of parties involved
Description of the general services that supplier provides and specific services that
company is going to avail.
Payments terms and time frequency of the payments required.
Confidentiality clauses, if details are required to be kept confidential.
Renewal, refund and compensation terms and clauses.
Signatures with dates of all the parties involved along with the witnesses.
There can be other specific clauses in the contracts that depends upon the situation. There
are many risks involved when a company is entering into a contract with the suppliers.
Therefore, suppliers and the legal team of the company shall sit together to discuss all the terms
14
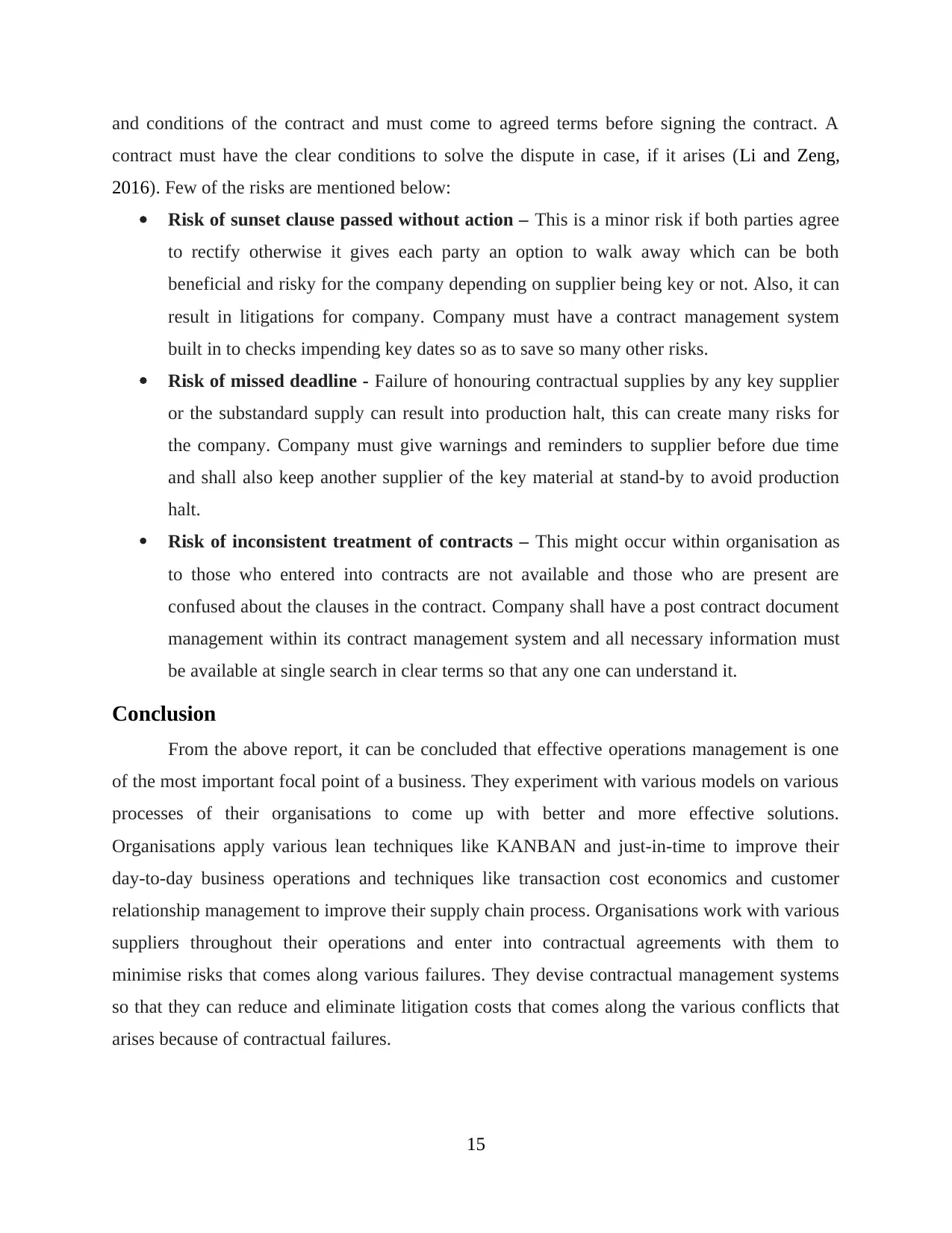
and conditions of the contract and must come to agreed terms before signing the contract. A
contract must have the clear conditions to solve the dispute in case, if it arises (Li and Zeng,
2016). Few of the risks are mentioned below:
Risk of sunset clause passed without action – This is a minor risk if both parties agree
to rectify otherwise it gives each party an option to walk away which can be both
beneficial and risky for the company depending on supplier being key or not. Also, it can
result in litigations for company. Company must have a contract management system
built in to checks impending key dates so as to save so many other risks.
Risk of missed deadline - Failure of honouring contractual supplies by any key supplier
or the substandard supply can result into production halt, this can create many risks for
the company. Company must give warnings and reminders to supplier before due time
and shall also keep another supplier of the key material at stand-by to avoid production
halt.
Risk of inconsistent treatment of contracts – This might occur within organisation as
to those who entered into contracts are not available and those who are present are
confused about the clauses in the contract. Company shall have a post contract document
management within its contract management system and all necessary information must
be available at single search in clear terms so that any one can understand it.
Conclusion
From the above report, it can be concluded that effective operations management is one
of the most important focal point of a business. They experiment with various models on various
processes of their organisations to come up with better and more effective solutions.
Organisations apply various lean techniques like KANBAN and just-in-time to improve their
day-to-day business operations and techniques like transaction cost economics and customer
relationship management to improve their supply chain process. Organisations work with various
suppliers throughout their operations and enter into contractual agreements with them to
minimise risks that comes along various failures. They devise contractual management systems
so that they can reduce and eliminate litigation costs that comes along the various conflicts that
arises because of contractual failures.
15
contract must have the clear conditions to solve the dispute in case, if it arises (Li and Zeng,
2016). Few of the risks are mentioned below:
Risk of sunset clause passed without action – This is a minor risk if both parties agree
to rectify otherwise it gives each party an option to walk away which can be both
beneficial and risky for the company depending on supplier being key or not. Also, it can
result in litigations for company. Company must have a contract management system
built in to checks impending key dates so as to save so many other risks.
Risk of missed deadline - Failure of honouring contractual supplies by any key supplier
or the substandard supply can result into production halt, this can create many risks for
the company. Company must give warnings and reminders to supplier before due time
and shall also keep another supplier of the key material at stand-by to avoid production
halt.
Risk of inconsistent treatment of contracts – This might occur within organisation as
to those who entered into contracts are not available and those who are present are
confused about the clauses in the contract. Company shall have a post contract document
management within its contract management system and all necessary information must
be available at single search in clear terms so that any one can understand it.
Conclusion
From the above report, it can be concluded that effective operations management is one
of the most important focal point of a business. They experiment with various models on various
processes of their organisations to come up with better and more effective solutions.
Organisations apply various lean techniques like KANBAN and just-in-time to improve their
day-to-day business operations and techniques like transaction cost economics and customer
relationship management to improve their supply chain process. Organisations work with various
suppliers throughout their operations and enter into contractual agreements with them to
minimise risks that comes along various failures. They devise contractual management systems
so that they can reduce and eliminate litigation costs that comes along the various conflicts that
arises because of contractual failures.
15
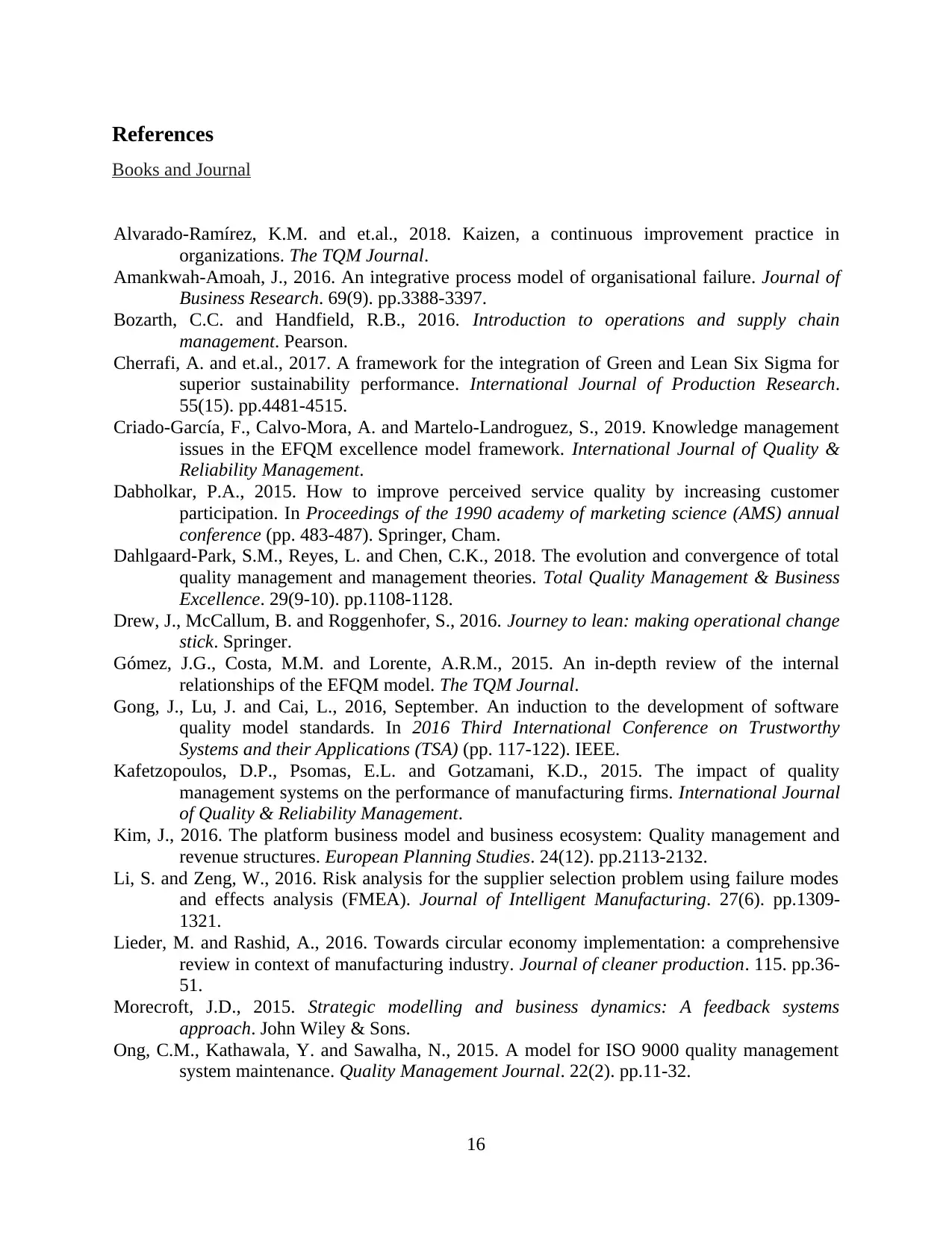
References
Books and Journal
Alvarado-Ramírez, K.M. and et.al., 2018. Kaizen, a continuous improvement practice in
organizations. The TQM Journal.
Amankwah-Amoah, J., 2016. An integrative process model of organisational failure. Journal of
Business Research. 69(9). pp.3388-3397.
Bozarth, C.C. and Handfield, R.B., 2016. Introduction to operations and supply chain
management. Pearson.
Cherrafi, A. and et.al., 2017. A framework for the integration of Green and Lean Six Sigma for
superior sustainability performance. International Journal of Production Research.
55(15). pp.4481-4515.
Criado-García, F., Calvo-Mora, A. and Martelo-Landroguez, S., 2019. Knowledge management
issues in the EFQM excellence model framework. International Journal of Quality &
Reliability Management.
Dabholkar, P.A., 2015. How to improve perceived service quality by increasing customer
participation. In Proceedings of the 1990 academy of marketing science (AMS) annual
conference (pp. 483-487). Springer, Cham.
Dahlgaard-Park, S.M., Reyes, L. and Chen, C.K., 2018. The evolution and convergence of total
quality management and management theories. Total Quality Management & Business
Excellence. 29(9-10). pp.1108-1128.
Drew, J., McCallum, B. and Roggenhofer, S., 2016. Journey to lean: making operational change
stick. Springer.
Gómez, J.G., Costa, M.M. and Lorente, A.R.M., 2015. An in-depth review of the internal
relationships of the EFQM model. The TQM Journal.
Gong, J., Lu, J. and Cai, L., 2016, September. An induction to the development of software
quality model standards. In 2016 Third International Conference on Trustworthy
Systems and their Applications (TSA) (pp. 117-122). IEEE.
Kafetzopoulos, D.P., Psomas, E.L. and Gotzamani, K.D., 2015. The impact of quality
management systems on the performance of manufacturing firms. International Journal
of Quality & Reliability Management.
Kim, J., 2016. The platform business model and business ecosystem: Quality management and
revenue structures. European Planning Studies. 24(12). pp.2113-2132.
Li, S. and Zeng, W., 2016. Risk analysis for the supplier selection problem using failure modes
and effects analysis (FMEA). Journal of Intelligent Manufacturing. 27(6). pp.1309-
1321.
Lieder, M. and Rashid, A., 2016. Towards circular economy implementation: a comprehensive
review in context of manufacturing industry. Journal of cleaner production. 115. pp.36-
51.
Morecroft, J.D., 2015. Strategic modelling and business dynamics: A feedback systems
approach. John Wiley & Sons.
Ong, C.M., Kathawala, Y. and Sawalha, N., 2015. A model for ISO 9000 quality management
system maintenance. Quality Management Journal. 22(2). pp.11-32.
16
Books and Journal
Alvarado-Ramírez, K.M. and et.al., 2018. Kaizen, a continuous improvement practice in
organizations. The TQM Journal.
Amankwah-Amoah, J., 2016. An integrative process model of organisational failure. Journal of
Business Research. 69(9). pp.3388-3397.
Bozarth, C.C. and Handfield, R.B., 2016. Introduction to operations and supply chain
management. Pearson.
Cherrafi, A. and et.al., 2017. A framework for the integration of Green and Lean Six Sigma for
superior sustainability performance. International Journal of Production Research.
55(15). pp.4481-4515.
Criado-García, F., Calvo-Mora, A. and Martelo-Landroguez, S., 2019. Knowledge management
issues in the EFQM excellence model framework. International Journal of Quality &
Reliability Management.
Dabholkar, P.A., 2015. How to improve perceived service quality by increasing customer
participation. In Proceedings of the 1990 academy of marketing science (AMS) annual
conference (pp. 483-487). Springer, Cham.
Dahlgaard-Park, S.M., Reyes, L. and Chen, C.K., 2018. The evolution and convergence of total
quality management and management theories. Total Quality Management & Business
Excellence. 29(9-10). pp.1108-1128.
Drew, J., McCallum, B. and Roggenhofer, S., 2016. Journey to lean: making operational change
stick. Springer.
Gómez, J.G., Costa, M.M. and Lorente, A.R.M., 2015. An in-depth review of the internal
relationships of the EFQM model. The TQM Journal.
Gong, J., Lu, J. and Cai, L., 2016, September. An induction to the development of software
quality model standards. In 2016 Third International Conference on Trustworthy
Systems and their Applications (TSA) (pp. 117-122). IEEE.
Kafetzopoulos, D.P., Psomas, E.L. and Gotzamani, K.D., 2015. The impact of quality
management systems on the performance of manufacturing firms. International Journal
of Quality & Reliability Management.
Kim, J., 2016. The platform business model and business ecosystem: Quality management and
revenue structures. European Planning Studies. 24(12). pp.2113-2132.
Li, S. and Zeng, W., 2016. Risk analysis for the supplier selection problem using failure modes
and effects analysis (FMEA). Journal of Intelligent Manufacturing. 27(6). pp.1309-
1321.
Lieder, M. and Rashid, A., 2016. Towards circular economy implementation: a comprehensive
review in context of manufacturing industry. Journal of cleaner production. 115. pp.36-
51.
Morecroft, J.D., 2015. Strategic modelling and business dynamics: A feedback systems
approach. John Wiley & Sons.
Ong, C.M., Kathawala, Y. and Sawalha, N., 2015. A model for ISO 9000 quality management
system maintenance. Quality Management Journal. 22(2). pp.11-32.
16
Secure Best Marks with AI Grader
Need help grading? Try our AI Grader for instant feedback on your assignments.
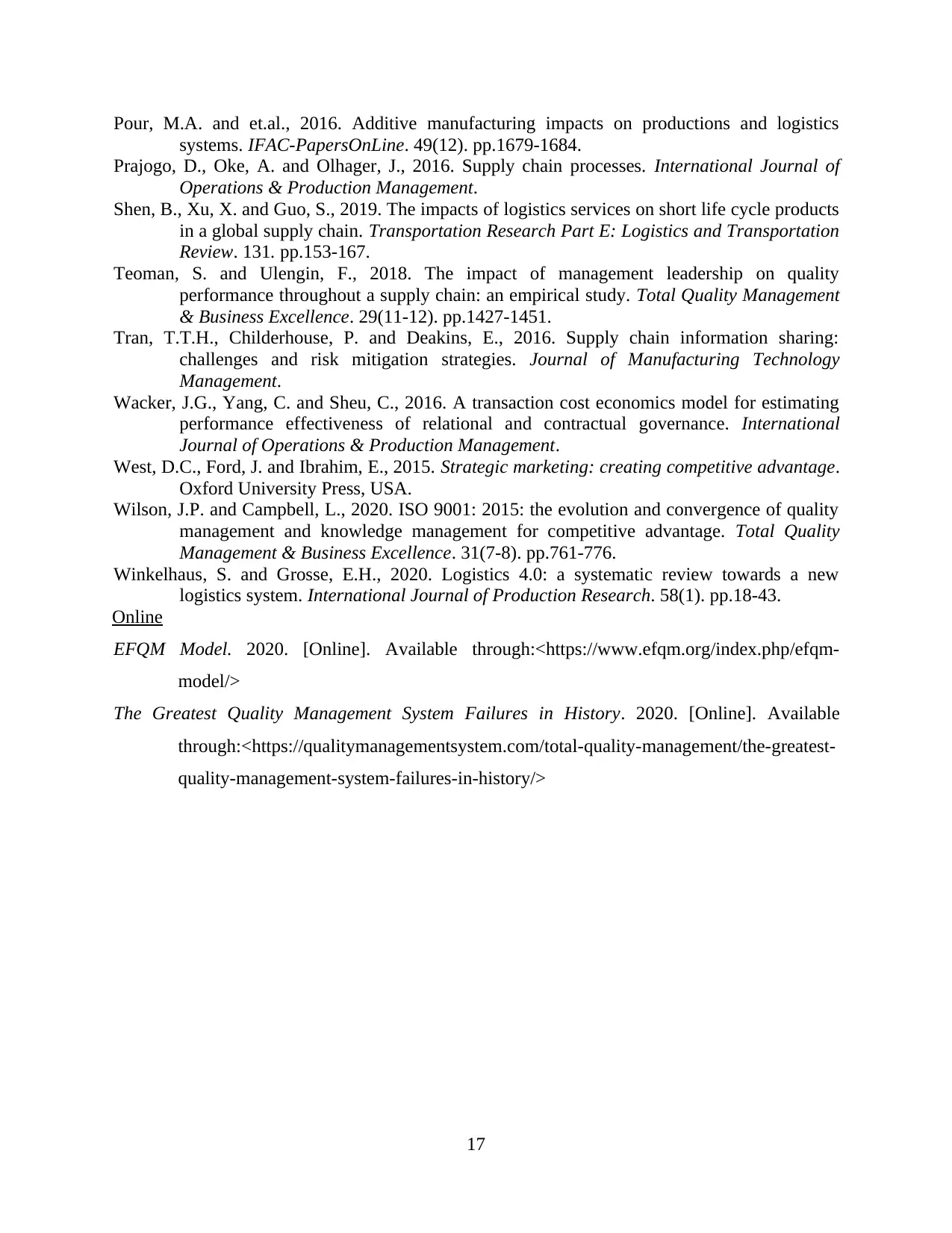
Pour, M.A. and et.al., 2016. Additive manufacturing impacts on productions and logistics
systems. IFAC-PapersOnLine. 49(12). pp.1679-1684.
Prajogo, D., Oke, A. and Olhager, J., 2016. Supply chain processes. International Journal of
Operations & Production Management.
Shen, B., Xu, X. and Guo, S., 2019. The impacts of logistics services on short life cycle products
in a global supply chain. Transportation Research Part E: Logistics and Transportation
Review. 131. pp.153-167.
Teoman, S. and Ulengin, F., 2018. The impact of management leadership on quality
performance throughout a supply chain: an empirical study. Total Quality Management
& Business Excellence. 29(11-12). pp.1427-1451.
Tran, T.T.H., Childerhouse, P. and Deakins, E., 2016. Supply chain information sharing:
challenges and risk mitigation strategies. Journal of Manufacturing Technology
Management.
Wacker, J.G., Yang, C. and Sheu, C., 2016. A transaction cost economics model for estimating
performance effectiveness of relational and contractual governance. International
Journal of Operations & Production Management.
West, D.C., Ford, J. and Ibrahim, E., 2015. Strategic marketing: creating competitive advantage.
Oxford University Press, USA.
Wilson, J.P. and Campbell, L., 2020. ISO 9001: 2015: the evolution and convergence of quality
management and knowledge management for competitive advantage. Total Quality
Management & Business Excellence. 31(7-8). pp.761-776.
Winkelhaus, S. and Grosse, E.H., 2020. Logistics 4.0: a systematic review towards a new
logistics system. International Journal of Production Research. 58(1). pp.18-43.
Online
EFQM Model. 2020. [Online]. Available through:<https://www.efqm.org/index.php/efqm-
model/>
The Greatest Quality Management System Failures in History. 2020. [Online]. Available
through:<https://qualitymanagementsystem.com/total-quality-management/the-greatest-
quality-management-system-failures-in-history/>
17
systems. IFAC-PapersOnLine. 49(12). pp.1679-1684.
Prajogo, D., Oke, A. and Olhager, J., 2016. Supply chain processes. International Journal of
Operations & Production Management.
Shen, B., Xu, X. and Guo, S., 2019. The impacts of logistics services on short life cycle products
in a global supply chain. Transportation Research Part E: Logistics and Transportation
Review. 131. pp.153-167.
Teoman, S. and Ulengin, F., 2018. The impact of management leadership on quality
performance throughout a supply chain: an empirical study. Total Quality Management
& Business Excellence. 29(11-12). pp.1427-1451.
Tran, T.T.H., Childerhouse, P. and Deakins, E., 2016. Supply chain information sharing:
challenges and risk mitigation strategies. Journal of Manufacturing Technology
Management.
Wacker, J.G., Yang, C. and Sheu, C., 2016. A transaction cost economics model for estimating
performance effectiveness of relational and contractual governance. International
Journal of Operations & Production Management.
West, D.C., Ford, J. and Ibrahim, E., 2015. Strategic marketing: creating competitive advantage.
Oxford University Press, USA.
Wilson, J.P. and Campbell, L., 2020. ISO 9001: 2015: the evolution and convergence of quality
management and knowledge management for competitive advantage. Total Quality
Management & Business Excellence. 31(7-8). pp.761-776.
Winkelhaus, S. and Grosse, E.H., 2020. Logistics 4.0: a systematic review towards a new
logistics system. International Journal of Production Research. 58(1). pp.18-43.
Online
EFQM Model. 2020. [Online]. Available through:<https://www.efqm.org/index.php/efqm-
model/>
The Greatest Quality Management System Failures in History. 2020. [Online]. Available
through:<https://qualitymanagementsystem.com/total-quality-management/the-greatest-
quality-management-system-failures-in-history/>
17
1 out of 17
Related Documents
![[object Object]](/_next/image/?url=%2F_next%2Fstatic%2Fmedia%2Flogo.6d15ce61.png&w=640&q=75)
Your All-in-One AI-Powered Toolkit for Academic Success.
+13062052269
info@desklib.com
Available 24*7 on WhatsApp / Email
Unlock your academic potential
© 2024 | Zucol Services PVT LTD | All rights reserved.