Continuous Improvement Strategies in Construction Industry
VerifiedAdded on 2019/09/22
|30
|7073
|248
Report
AI Summary
The provided content discusses the concept of continuous improvement, particularly in the context of construction companies. It highlights the importance of adopting a lean manufacturing approach to improve processes and reduce waste. The content also touches on the Toyota Production System (TPS) and its principles, such as standardized tasks and processes, visual controls, and proper technology use. Additionally, it emphasizes the role of leaders in fostering a culture of continuous learning and improvement. Overall, the content aims to provide insights and strategies for construction companies seeking to enhance their operations and improve performance.
Contribute Materials
Your contribution can guide someone’s learning journey. Share your
documents today.
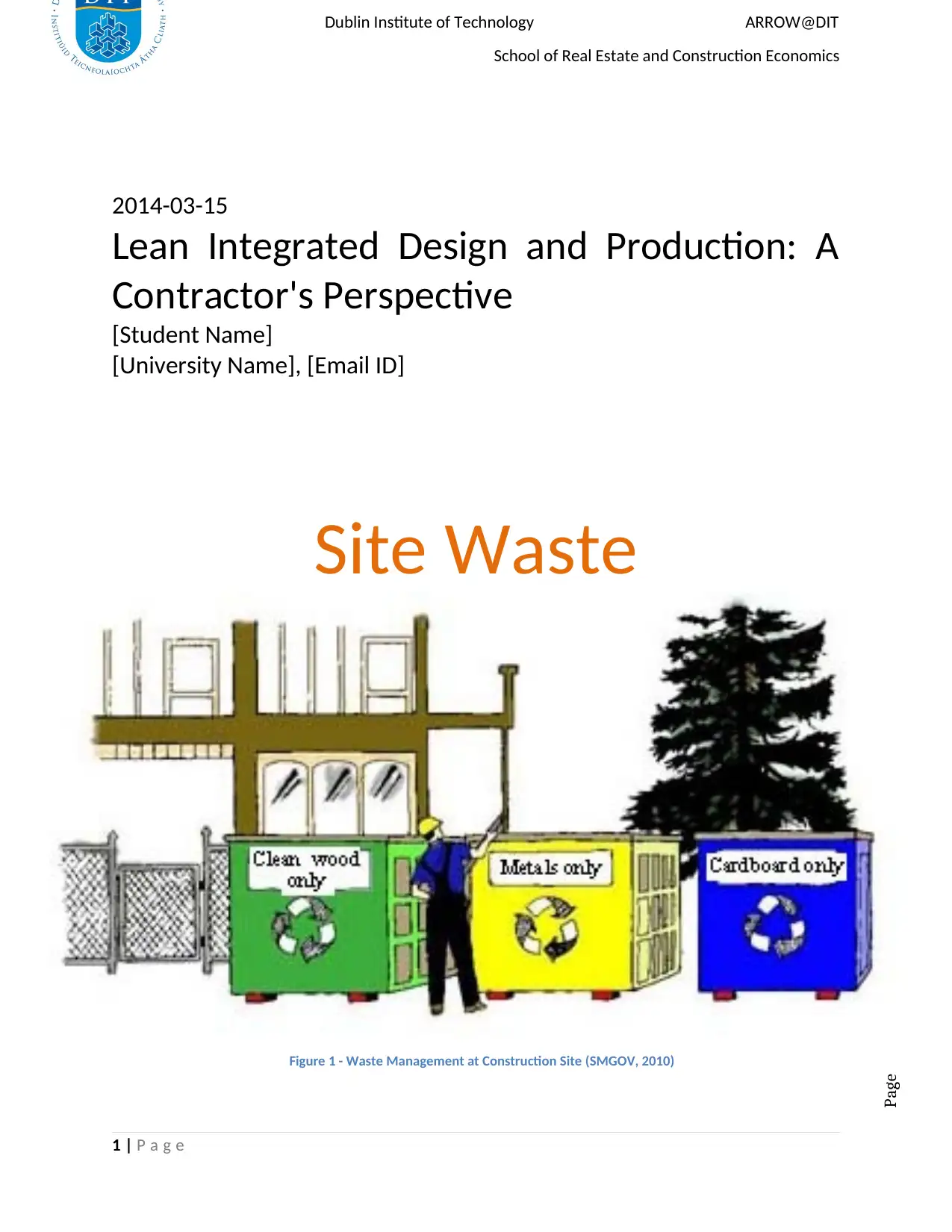
Page1
Dublin Institute of Technology ARROW@DIT
School of Real Estate and Construction Economics
2014-03-15
Lean Integrated Design and Production: A
Contractor's Perspective
[Student Name]
[University Name], [Email ID]
Site Waste
1 | P a g e
Figure 1 - Waste Management at Construction Site (SMGOV, 2010)
Dublin Institute of Technology ARROW@DIT
School of Real Estate and Construction Economics
2014-03-15
Lean Integrated Design and Production: A
Contractor's Perspective
[Student Name]
[University Name], [Email ID]
Site Waste
1 | P a g e
Figure 1 - Waste Management at Construction Site (SMGOV, 2010)
Secure Best Marks with AI Grader
Need help grading? Try our AI Grader for instant feedback on your assignments.

Page2
Table of Contents
Introduction.................................................................................................................................................4
Case Study...................................................................................................................................................5
Toyota Production System.........................................................................................................................16
Applying TPS and Tools for the case study................................................................................................17
Implementing the TPS principles and tools...............................................................................................19
Continuous Improvement..........................................................................................................................20
Conclusion & Recommendation................................................................................................................25
References.................................................................................................................................................27
Table of Contents
Introduction.................................................................................................................................................4
Case Study...................................................................................................................................................5
Toyota Production System.........................................................................................................................16
Applying TPS and Tools for the case study................................................................................................17
Implementing the TPS principles and tools...............................................................................................19
Continuous Improvement..........................................................................................................................20
Conclusion & Recommendation................................................................................................................25
References.................................................................................................................................................27
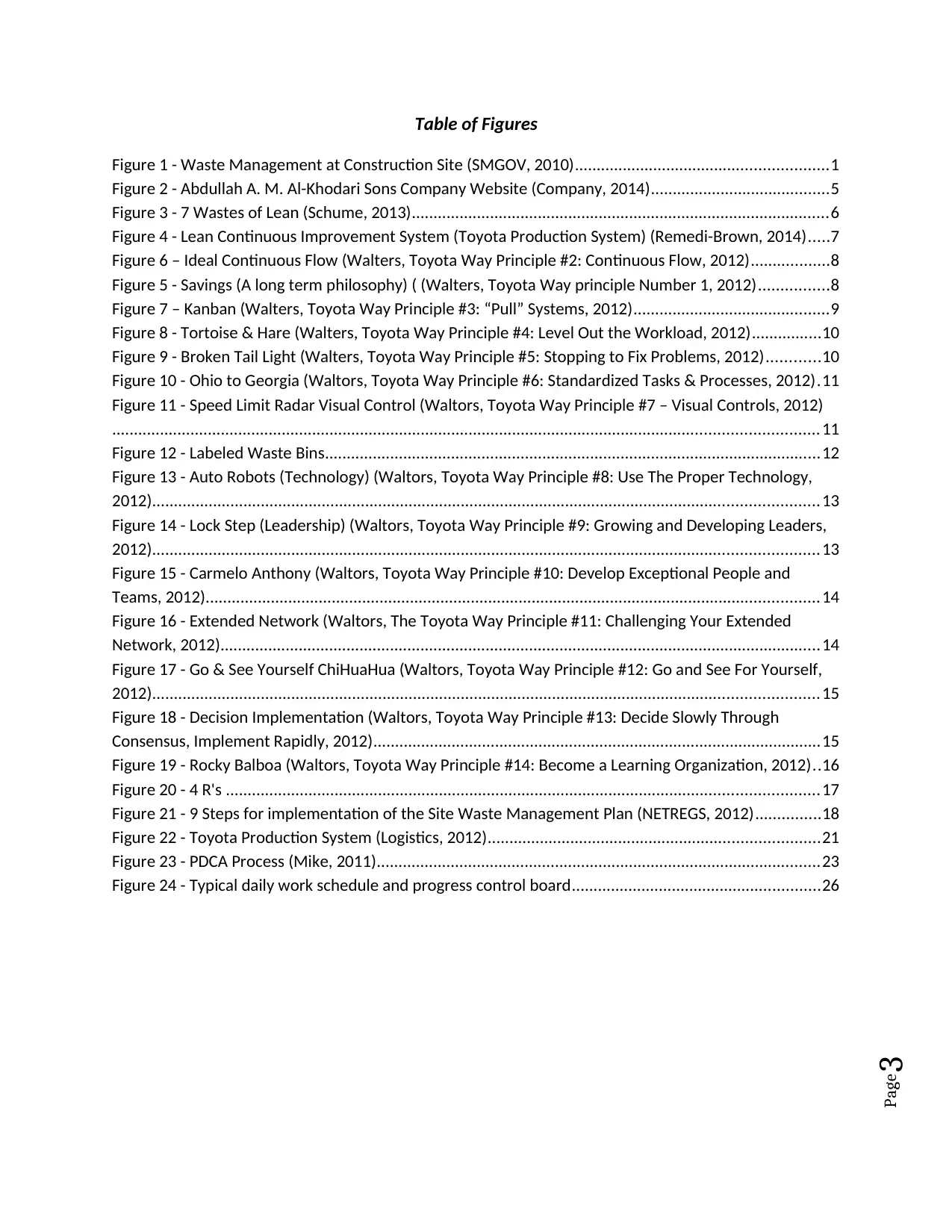
Page3
Table of Figures
Figure 1 - Waste Management at Construction Site (SMGOV, 2010)..........................................................1
Figure 2 - Abdullah A. M. Al-Khodari Sons Company Website (Company, 2014).........................................5
Figure 3 - 7 Wastes of Lean (Schume, 2013)................................................................................................6
Figure 4 - Lean Continuous Improvement System (Toyota Production System) (Remedi-Brown, 2014).....7
Figure 6 – Ideal Continuous Flow (Walters, Toyota Way Principle #2: Continuous Flow, 2012)..................8
Figure 5 - Savings (A long term philosophy) ( (Walters, Toyota Way principle Number 1, 2012)................8
Figure 7 – Kanban (Walters, Toyota Way Principle #3: “Pull” Systems, 2012).............................................9
Figure 8 - Tortoise & Hare (Walters, Toyota Way Principle #4: Level Out the Workload, 2012)................10
Figure 9 - Broken Tail Light (Walters, Toyota Way Principle #5: Stopping to Fix Problems, 2012)............10
Figure 10 - Ohio to Georgia (Waltors, Toyota Way Principle #6: Standardized Tasks & Processes, 2012).11
Figure 11 - Speed Limit Radar Visual Control (Waltors, Toyota Way Principle #7 – Visual Controls, 2012)
.................................................................................................................................................................. 11
Figure 12 - Labeled Waste Bins..................................................................................................................12
Figure 13 - Auto Robots (Technology) (Waltors, Toyota Way Principle #8: Use The Proper Technology,
2012).........................................................................................................................................................13
Figure 14 - Lock Step (Leadership) (Waltors, Toyota Way Principle #9: Growing and Developing Leaders,
2012).........................................................................................................................................................13
Figure 15 - Carmelo Anthony (Waltors, Toyota Way Principle #10: Develop Exceptional People and
Teams, 2012).............................................................................................................................................14
Figure 16 - Extended Network (Waltors, The Toyota Way Principle #11: Challenging Your Extended
Network, 2012)..........................................................................................................................................14
Figure 17 - Go & See Yourself ChiHuaHua (Waltors, Toyota Way Principle #12: Go and See For Yourself,
2012).........................................................................................................................................................15
Figure 18 - Decision Implementation (Waltors, Toyota Way Principle #13: Decide Slowly Through
Consensus, Implement Rapidly, 2012).......................................................................................................15
Figure 19 - Rocky Balboa (Waltors, Toyota Way Principle #14: Become a Learning Organization, 2012)..16
Figure 20 - 4 R's ........................................................................................................................................17
Figure 21 - 9 Steps for implementation of the Site Waste Management Plan (NETREGS, 2012)...............18
Figure 22 - Toyota Production System (Logistics, 2012)............................................................................21
Figure 23 - PDCA Process (Mike, 2011)......................................................................................................23
Figure 24 - Typical daily work schedule and progress control board.........................................................26
Table of Figures
Figure 1 - Waste Management at Construction Site (SMGOV, 2010)..........................................................1
Figure 2 - Abdullah A. M. Al-Khodari Sons Company Website (Company, 2014).........................................5
Figure 3 - 7 Wastes of Lean (Schume, 2013)................................................................................................6
Figure 4 - Lean Continuous Improvement System (Toyota Production System) (Remedi-Brown, 2014).....7
Figure 6 – Ideal Continuous Flow (Walters, Toyota Way Principle #2: Continuous Flow, 2012)..................8
Figure 5 - Savings (A long term philosophy) ( (Walters, Toyota Way principle Number 1, 2012)................8
Figure 7 – Kanban (Walters, Toyota Way Principle #3: “Pull” Systems, 2012).............................................9
Figure 8 - Tortoise & Hare (Walters, Toyota Way Principle #4: Level Out the Workload, 2012)................10
Figure 9 - Broken Tail Light (Walters, Toyota Way Principle #5: Stopping to Fix Problems, 2012)............10
Figure 10 - Ohio to Georgia (Waltors, Toyota Way Principle #6: Standardized Tasks & Processes, 2012).11
Figure 11 - Speed Limit Radar Visual Control (Waltors, Toyota Way Principle #7 – Visual Controls, 2012)
.................................................................................................................................................................. 11
Figure 12 - Labeled Waste Bins..................................................................................................................12
Figure 13 - Auto Robots (Technology) (Waltors, Toyota Way Principle #8: Use The Proper Technology,
2012).........................................................................................................................................................13
Figure 14 - Lock Step (Leadership) (Waltors, Toyota Way Principle #9: Growing and Developing Leaders,
2012).........................................................................................................................................................13
Figure 15 - Carmelo Anthony (Waltors, Toyota Way Principle #10: Develop Exceptional People and
Teams, 2012).............................................................................................................................................14
Figure 16 - Extended Network (Waltors, The Toyota Way Principle #11: Challenging Your Extended
Network, 2012)..........................................................................................................................................14
Figure 17 - Go & See Yourself ChiHuaHua (Waltors, Toyota Way Principle #12: Go and See For Yourself,
2012).........................................................................................................................................................15
Figure 18 - Decision Implementation (Waltors, Toyota Way Principle #13: Decide Slowly Through
Consensus, Implement Rapidly, 2012).......................................................................................................15
Figure 19 - Rocky Balboa (Waltors, Toyota Way Principle #14: Become a Learning Organization, 2012)..16
Figure 20 - 4 R's ........................................................................................................................................17
Figure 21 - 9 Steps for implementation of the Site Waste Management Plan (NETREGS, 2012)...............18
Figure 22 - Toyota Production System (Logistics, 2012)............................................................................21
Figure 23 - PDCA Process (Mike, 2011)......................................................................................................23
Figure 24 - Typical daily work schedule and progress control board.........................................................26

Page4
Introduction
The situation I have picked for my paper focuses on my encounters while utilized as a senior
estimator with Abdullah A. M. Al-Khodari Sons Company in 2009. Abdullah A. M. Al-
Khodari Sons Company was a multifaceted contracting company situated in the Middle East.
The wide extent of exercises compasses: Roads and bridges, railways, structures and framework,
water & waste water treatment, civil engineering, oil & gas and pipelines in backing of
petrochemical generation, city cleaning, ecological control, land transportation and operation &
upkeep exercises. The association being alluded to having a yearly turnover of 1,737$ Millions.
My responsibilities included assessing individual tenders, and gathering all the key
documentation enveloping the acquisition process for that association. (Company, 2014)
Case Study
Report Scenario for Upper Management
Figure 2 - Abdullah A. M. Al-Khodari Sons Company Website (Company, 2014)
Introduction
The situation I have picked for my paper focuses on my encounters while utilized as a senior
estimator with Abdullah A. M. Al-Khodari Sons Company in 2009. Abdullah A. M. Al-
Khodari Sons Company was a multifaceted contracting company situated in the Middle East.
The wide extent of exercises compasses: Roads and bridges, railways, structures and framework,
water & waste water treatment, civil engineering, oil & gas and pipelines in backing of
petrochemical generation, city cleaning, ecological control, land transportation and operation &
upkeep exercises. The association being alluded to having a yearly turnover of 1,737$ Millions.
My responsibilities included assessing individual tenders, and gathering all the key
documentation enveloping the acquisition process for that association. (Company, 2014)
Case Study
Report Scenario for Upper Management
Figure 2 - Abdullah A. M. Al-Khodari Sons Company Website (Company, 2014)
Paraphrase This Document
Need a fresh take? Get an instant paraphrase of this document with our AI Paraphraser

Page5
Brief discussion of Lean Principles
Numerous organizations are battling to make due in today's profoundly focused worldwide
economy. Lean production offers them a proven system to decrease expenses, kill waste, expand
benefit, keep up elevated amounts of value and still make a benefit.
It is a framework that can be utilized as a part of the generation zone as well as some other
territory that you are looking to streamline. It obliges top-down responsibility and base up the
association.
Lean is a technique that enhances forms through continuous improvement (Kaizen) and disposal
of waste. It is the North American likeness the Toyota Production System. The establishment of
Lean Manufacturing is leveling off creation, known as Heijunka. Basically, the work stacks
every day is level. Expanding upon that establishment are two principal pillars which speak to
"Just in time creation" and "Automation with a human touch". (Junction, 2014)
Koskella (2008) tells us that if we don’t notice the problems like waste, resting on the site un-
managed, it will keep increasing at a rapid rate because it will be the “Accepted Waste”. Unless,
we notice it and minimize it by adopting some appropriate principles, it will keep creating itself
more and more. The seven wastes which are relevant to this report are:
Figure 3 - 7 Wastes of Lean (Schume, 2013)
Brief discussion of Lean Principles
Numerous organizations are battling to make due in today's profoundly focused worldwide
economy. Lean production offers them a proven system to decrease expenses, kill waste, expand
benefit, keep up elevated amounts of value and still make a benefit.
It is a framework that can be utilized as a part of the generation zone as well as some other
territory that you are looking to streamline. It obliges top-down responsibility and base up the
association.
Lean is a technique that enhances forms through continuous improvement (Kaizen) and disposal
of waste. It is the North American likeness the Toyota Production System. The establishment of
Lean Manufacturing is leveling off creation, known as Heijunka. Basically, the work stacks
every day is level. Expanding upon that establishment are two principal pillars which speak to
"Just in time creation" and "Automation with a human touch". (Junction, 2014)
Koskella (2008) tells us that if we don’t notice the problems like waste, resting on the site un-
managed, it will keep increasing at a rapid rate because it will be the “Accepted Waste”. Unless,
we notice it and minimize it by adopting some appropriate principles, it will keep creating itself
more and more. The seven wastes which are relevant to this report are:
Figure 3 - 7 Wastes of Lean (Schume, 2013)

Page6
To deal with these wastes to reduce them effectively, we followed the TPS System. Or we can
say, Lean Production System. Here is the complete Lean production System:
We will discuss about it completely later in the report. Before going further in the report, we
need to focus on the major principles required to be followed for a better waste management.
Critical assessment
I have chosen to lead a Critical assessment of the procedure as it existed before tending to the
waste issue by utilizing the 14 principles delineated as a part of TPS as a performance evaluation
system (Liker, 2004). Here are those 14 principles:
Long Term Philosophy
“Base your management decisions on a long-term philosophy, even at the expense of short-term
financial goals.”
Figure 4 - Lean Continuous Improvement System (Toyota Production System) (Remedi-Brown, 2014)
To deal with these wastes to reduce them effectively, we followed the TPS System. Or we can
say, Lean Production System. Here is the complete Lean production System:
We will discuss about it completely later in the report. Before going further in the report, we
need to focus on the major principles required to be followed for a better waste management.
Critical assessment
I have chosen to lead a Critical assessment of the procedure as it existed before tending to the
waste issue by utilizing the 14 principles delineated as a part of TPS as a performance evaluation
system (Liker, 2004). Here are those 14 principles:
Long Term Philosophy
“Base your management decisions on a long-term philosophy, even at the expense of short-term
financial goals.”
Figure 4 - Lean Continuous Improvement System (Toyota Production System) (Remedi-Brown, 2014)

Page7
For an association to be practical, it needs to give worth to its
client base, individuals, employees/members, and suppliers.
A long-term rationality will join giving quality to the
customer and the association. Long-term arrangements may
take years to execute minus all potential limitations degree,
yet their motivation is to make a foundation for long-term
development and maintainability.
Concentrate on the genuine clients in your long-term
philosophy. That is a big start.
The Company managed the Waste on the sites by handling over each unit of the construction site
for individuals. So, as a long term workability thinking, it was a perfect measure.
Continuous Flow
“Create a continuous process flow to bring problems to the surface.”
Figure 6 – Ideal Continuous Flow (Walters, Toyota Way Principle #2: Continuous Flow, 2012)
All lean exercises ought to be sorted out with the expectation of producing continuous flow –
distinguishing problems and solving them, adjusting the load and the lines, decreasing inefficient
activities amid and between process steps.
By attempting to drive the continuous flow of a process, the protection goes away and the issues
rise up to the top – this implies you need to assault those issues as opposed to disregarding them.
Figure 5 - Savings (A long term philosophy)
( (Walters, Toyota Way principle Number 1,
2012)
For an association to be practical, it needs to give worth to its
client base, individuals, employees/members, and suppliers.
A long-term rationality will join giving quality to the
customer and the association. Long-term arrangements may
take years to execute minus all potential limitations degree,
yet their motivation is to make a foundation for long-term
development and maintainability.
Concentrate on the genuine clients in your long-term
philosophy. That is a big start.
The Company managed the Waste on the sites by handling over each unit of the construction site
for individuals. So, as a long term workability thinking, it was a perfect measure.
Continuous Flow
“Create a continuous process flow to bring problems to the surface.”
Figure 6 – Ideal Continuous Flow (Walters, Toyota Way Principle #2: Continuous Flow, 2012)
All lean exercises ought to be sorted out with the expectation of producing continuous flow –
distinguishing problems and solving them, adjusting the load and the lines, decreasing inefficient
activities amid and between process steps.
By attempting to drive the continuous flow of a process, the protection goes away and the issues
rise up to the top – this implies you need to assault those issues as opposed to disregarding them.
Figure 5 - Savings (A long term philosophy)
( (Walters, Toyota Way principle Number 1,
2012)
Secure Best Marks with AI Grader
Need help grading? Try our AI Grader for instant feedback on your assignments.

Page8
You can't have a waste-less process without continuous flow, as it is the genuinely perfect
procedure state. (Liker, 2004)
As there were problems, evaluating the first principle, we couldn’t accomplish the second one
also, efficiently. Continuous flow causes a great flow in the whole process as experienced during
the waste disposal process steps.
Pull Systems
“Use ‘pull’ systems to avoid overproduction.”
The motivation behind the pull system (additionally called "Kanban" system) is to have a
deliberate line of materials (raw materials, work-in-methodology, components, whatever)
prepared to be "pulled" by the following procedure step. After the materials are "pulled", a sign
is sent to the former process venture to replace what was taken.
The Company was very critical about this principle of TPS System. All the materials were
ordered in a very procedural way.
Level Out the Workload
“Level out the workload (work like the tortoise, not the hare.)”
Figure 7 – Kanban (Walters, Toyota Way Principle #3: “Pull” Systems, 2012)
You can't have a waste-less process without continuous flow, as it is the genuinely perfect
procedure state. (Liker, 2004)
As there were problems, evaluating the first principle, we couldn’t accomplish the second one
also, efficiently. Continuous flow causes a great flow in the whole process as experienced during
the waste disposal process steps.
Pull Systems
“Use ‘pull’ systems to avoid overproduction.”
The motivation behind the pull system (additionally called "Kanban" system) is to have a
deliberate line of materials (raw materials, work-in-methodology, components, whatever)
prepared to be "pulled" by the following procedure step. After the materials are "pulled", a sign
is sent to the former process venture to replace what was taken.
The Company was very critical about this principle of TPS System. All the materials were
ordered in a very procedural way.
Level Out the Workload
“Level out the workload (work like the tortoise, not the hare.)”
Figure 7 – Kanban (Walters, Toyota Way Principle #3: “Pull” Systems, 2012)

Page9
Figure 8 - Tortoise & Hare (Walters, Toyota Way Principle #4: Level Out the Workload, 2012)
Like with the tale about the tortoise and the rabbit, "steady minded individuals will win the race
in the end." Maintaining ideal exertion from administrators is important, whether request goes up
or down.
In this present world, not all steps are adjusted and interest doesn't generally scale so effortlessly.
That being said, there are methodologies you can apply to discover intriguing approaches to
balance the workloads.
This was very commonly visible on many of our sites. Mistakes followed by more mistakes
because of an urge of finishing the job as soon as possible. While, at some sites, we could easily
observe the managed process for evaluating the work. (Liker, 2004)
Stopping to Fix Problems
“Build a culture of stopping to fix
problems, to get quality right the
first time.”
The more you assault problems
and fix them, the more the
hierarchical society will start to
Figure 9 - Broken Tail Light (Walters, Toyota Way Principle #5: Stopping to Fix
Problems, 2012)
Figure 8 - Tortoise & Hare (Walters, Toyota Way Principle #4: Level Out the Workload, 2012)
Like with the tale about the tortoise and the rabbit, "steady minded individuals will win the race
in the end." Maintaining ideal exertion from administrators is important, whether request goes up
or down.
In this present world, not all steps are adjusted and interest doesn't generally scale so effortlessly.
That being said, there are methodologies you can apply to discover intriguing approaches to
balance the workloads.
This was very commonly visible on many of our sites. Mistakes followed by more mistakes
because of an urge of finishing the job as soon as possible. While, at some sites, we could easily
observe the managed process for evaluating the work. (Liker, 2004)
Stopping to Fix Problems
“Build a culture of stopping to fix
problems, to get quality right the
first time.”
The more you assault problems
and fix them, the more the
hierarchical society will start to
Figure 9 - Broken Tail Light (Walters, Toyota Way Principle #5: Stopping to Fix
Problems, 2012)

Page10
see the effortlessness in doing as such and the profits acknowledged by not having the same
number of breakdowns or rehashed repairs.
This will build resistance and momentum toward a change in society of not enduring problems
and nonstop repairs. Fixes are speedier, simpler, and less expensive over the long-term.
This varied site-wise throughout the project. If the problem was ignored and just repaired for a
while, it occurred again and again. For example, there was a leak in one of the waste tanks,
which was repaired temporarily by using concrete. But, it created problems later as the size of
the leak increased due to pressure & was problematic to fix.
Standardized tasks & processes
“Standardized tasks and processes are the foundation for
continuous improvement and employee empowerment.”
When you have a standard process and apply
experimentation with adjustments to the standard, you can
make sense of how to improve or with higher rates of value.
Standardize your procedures, whether they are great or
terrible, and afterward begin searching for approaches to
make improvements.
In the internal process of the waste management, it was easy
to determine the exact costing because of the standardization
of the point of origin and the process. Everything was well clear and understandable.
Visual Controls
“Use visual controls so no problems are hidden.”
Visual controls ought to be intended to rapidly impart
information to individuals, showing whether a condition is
worthy/not satisfactory and, similarly as fast, give some bearing
of activity in the interest of individuals.
Figure 10 - Ohio to Georgia (Waltors, Toyota
Way Principle #6: Standardized Tasks &
Processes, 2012)
Figure 11 - Speed Limit Radar Visual Control (Waltors,
Toyota Way Principle #7 – Visual Controls, 2012)
see the effortlessness in doing as such and the profits acknowledged by not having the same
number of breakdowns or rehashed repairs.
This will build resistance and momentum toward a change in society of not enduring problems
and nonstop repairs. Fixes are speedier, simpler, and less expensive over the long-term.
This varied site-wise throughout the project. If the problem was ignored and just repaired for a
while, it occurred again and again. For example, there was a leak in one of the waste tanks,
which was repaired temporarily by using concrete. But, it created problems later as the size of
the leak increased due to pressure & was problematic to fix.
Standardized tasks & processes
“Standardized tasks and processes are the foundation for
continuous improvement and employee empowerment.”
When you have a standard process and apply
experimentation with adjustments to the standard, you can
make sense of how to improve or with higher rates of value.
Standardize your procedures, whether they are great or
terrible, and afterward begin searching for approaches to
make improvements.
In the internal process of the waste management, it was easy
to determine the exact costing because of the standardization
of the point of origin and the process. Everything was well clear and understandable.
Visual Controls
“Use visual controls so no problems are hidden.”
Visual controls ought to be intended to rapidly impart
information to individuals, showing whether a condition is
worthy/not satisfactory and, similarly as fast, give some bearing
of activity in the interest of individuals.
Figure 10 - Ohio to Georgia (Waltors, Toyota
Way Principle #6: Standardized Tasks &
Processes, 2012)
Figure 11 - Speed Limit Radar Visual Control (Waltors,
Toyota Way Principle #7 – Visual Controls, 2012)
Paraphrase This Document
Need a fresh take? Get an instant paraphrase of this document with our AI Paraphraser

Page11
At the site, it was very important to use the visual controls for a better understanding for the co-
workers and also the people around.
There were many areas where the waste was lying un-noticed because of the non labeling of the
waste. But, at some places, it was well maintained and arranged so that it could be recycled
properly.
Use the Proper Technology
“Use only reliable, thoroughly-tested technology that serves your people and process.”
Figure 12 - Labeled Waste Bins
Figure 13 - Auto Robots (Technology) (Waltors, Toyota Way Principle #8: Use
The Proper Technology, 2012)
At the site, it was very important to use the visual controls for a better understanding for the co-
workers and also the people around.
There were many areas where the waste was lying un-noticed because of the non labeling of the
waste. But, at some places, it was well maintained and arranged so that it could be recycled
properly.
Use the Proper Technology
“Use only reliable, thoroughly-tested technology that serves your people and process.”
Figure 12 - Labeled Waste Bins
Figure 13 - Auto Robots (Technology) (Waltors, Toyota Way Principle #8: Use
The Proper Technology, 2012)

Page12
Generally, new technologies are being followed by most of the companies at the sites. They are
first tested on the site itself. At the site, it was pretty focused on that the technology being used is
professionally tested and properly for the following work. (Liker, 2004)
Growing & Developing Leaders
“Grow leaders who thoroughly understand the work, live the philosophy, and teach it to others.”
Leaders truly experience the
rationality and have the capacity to
show it either by immediate strategies
or by "leading by examples." If the
leader maintains a strong philosophy,
backed up by perfect logics, the
Company’s efficiency rises to an
unpredictable level.
Al-Khodari employed the best of the
managers for the job of waste
management on each and every unit of
the construction site. All of them maintained a good respect in their own fields of work and
created a long term philosophy for managing the waste in an appropriate way.
Develop Exceptional People & Teams
“Develop exceptional people and teams who follow your company’s philosophy.”
A philosophy that is taught by leaders that put stock in it and
took after by people and teams has a stronger chance for
accomplishment than an arrangement of people & teams pulling
in diverse directions than their leader.
Figure 14 - Lock Step (Leadership) (Waltors, Toyota Way Principle #9:
Growing and Developing Leaders, 2012)
Figure 15 - Carmelo Anthony
(Waltors, Toyota Way Principle #10:
Develop Exceptional People and
Teams, 2012)
Generally, new technologies are being followed by most of the companies at the sites. They are
first tested on the site itself. At the site, it was pretty focused on that the technology being used is
professionally tested and properly for the following work. (Liker, 2004)
Growing & Developing Leaders
“Grow leaders who thoroughly understand the work, live the philosophy, and teach it to others.”
Leaders truly experience the
rationality and have the capacity to
show it either by immediate strategies
or by "leading by examples." If the
leader maintains a strong philosophy,
backed up by perfect logics, the
Company’s efficiency rises to an
unpredictable level.
Al-Khodari employed the best of the
managers for the job of waste
management on each and every unit of
the construction site. All of them maintained a good respect in their own fields of work and
created a long term philosophy for managing the waste in an appropriate way.
Develop Exceptional People & Teams
“Develop exceptional people and teams who follow your company’s philosophy.”
A philosophy that is taught by leaders that put stock in it and
took after by people and teams has a stronger chance for
accomplishment than an arrangement of people & teams pulling
in diverse directions than their leader.
Figure 14 - Lock Step (Leadership) (Waltors, Toyota Way Principle #9:
Growing and Developing Leaders, 2012)
Figure 15 - Carmelo Anthony
(Waltors, Toyota Way Principle #10:
Develop Exceptional People and
Teams, 2012)

Page13
Once, we developed a strong leadership backbone, Exceptional People & Teams were easily
developed and pursued with. Those teams helped in waste management with a very good
efficiency rate.
Challenging your Extended Network
“Respect your extended network of partners and suppliers by challenging them and helping them
improve.”
For bringing out best administrations and
quality, one Company must go past its
internal methods and recognize the inputs
and yields to further enhance its processes.
This will further make awesome results in
term of project completion furthermore
diminish stress on its contractors &
subcontractors.
In our ongoing project, it played a very
crucial role. We were always focused on providing the best possible help to our co-partners and
contractors during the project. The long built relationships with your contractors and
subcontractors helped the Company rely on the quality and services to be provided by them and
which happened in a very precise manner in the end. (Waltors, The Toyota Way Principle #11:
Challenging Your Extended Network, 2012)
Go and See for Yourself
“Go and see for yourself to thoroughly understand the situation.”
Information can let an individual know a ton of
the story, yet it can't recount the entire story.
Going to see the methodology or movement
Figure 17 - Go & See Yourself ChiHuaHua (Waltors, Toyota Way
Principle #12: Go and See For Yourself, 2012)
Figure 16 - Extended Network (Waltors, The Toyota Way Principle
#11: Challenging Your Extended Network, 2012)
Once, we developed a strong leadership backbone, Exceptional People & Teams were easily
developed and pursued with. Those teams helped in waste management with a very good
efficiency rate.
Challenging your Extended Network
“Respect your extended network of partners and suppliers by challenging them and helping them
improve.”
For bringing out best administrations and
quality, one Company must go past its
internal methods and recognize the inputs
and yields to further enhance its processes.
This will further make awesome results in
term of project completion furthermore
diminish stress on its contractors &
subcontractors.
In our ongoing project, it played a very
crucial role. We were always focused on providing the best possible help to our co-partners and
contractors during the project. The long built relationships with your contractors and
subcontractors helped the Company rely on the quality and services to be provided by them and
which happened in a very precise manner in the end. (Waltors, The Toyota Way Principle #11:
Challenging Your Extended Network, 2012)
Go and See for Yourself
“Go and see for yourself to thoroughly understand the situation.”
Information can let an individual know a ton of
the story, yet it can't recount the entire story.
Going to see the methodology or movement
Figure 17 - Go & See Yourself ChiHuaHua (Waltors, Toyota Way
Principle #12: Go and See For Yourself, 2012)
Figure 16 - Extended Network (Waltors, The Toyota Way Principle
#11: Challenging Your Extended Network, 2012)
Secure Best Marks with AI Grader
Need help grading? Try our AI Grader for instant feedback on your assignments.

Page14
oneself gives him/her a chance to increase a superior comprehension of what's genuinely
happening, data that can rise above the information.
This was another crucial part which obliged consideration. There was infrequently hesitance
from senior administration to invest sufficient time on site to completely admire the issues
concerning waste. They wanted to depend on criticism from project managers who unwittingly
would exhibit that criticism from a one-sided perspective. This brought about choices being
taken without an educated, learning of the genuine hidden problems.
Decide Slowly Through Consensus, Implement Rapidly
“Make decisions slowly by consensus, thoroughly considering all options; implement decisions
rapidly.”
When you've recognized the arrangement that gives
the best advantages at the most negligible of expenses
(negative effect, dollars, and goodwill), now is the
ideal time to place it set up rapidly. On the off chance
that you've got (very nearly) everybody energetic
about the arrangement (practically) everybody accepts
to be the best one. The quicker the right arrangement
is implemented, the speedier procuring of the profits.
Become a Learning Organization
“Become a learning organization through relentless reflection and continuous improvement.”
Figure 18 - Decision Implementation (Waltors,
Toyota Way Principle #13: Decide Slowly Through
Consensus, Implement Rapidly, 2012)
oneself gives him/her a chance to increase a superior comprehension of what's genuinely
happening, data that can rise above the information.
This was another crucial part which obliged consideration. There was infrequently hesitance
from senior administration to invest sufficient time on site to completely admire the issues
concerning waste. They wanted to depend on criticism from project managers who unwittingly
would exhibit that criticism from a one-sided perspective. This brought about choices being
taken without an educated, learning of the genuine hidden problems.
Decide Slowly Through Consensus, Implement Rapidly
“Make decisions slowly by consensus, thoroughly considering all options; implement decisions
rapidly.”
When you've recognized the arrangement that gives
the best advantages at the most negligible of expenses
(negative effect, dollars, and goodwill), now is the
ideal time to place it set up rapidly. On the off chance
that you've got (very nearly) everybody energetic
about the arrangement (practically) everybody accepts
to be the best one. The quicker the right arrangement
is implemented, the speedier procuring of the profits.
Become a Learning Organization
“Become a learning organization through relentless reflection and continuous improvement.”
Figure 18 - Decision Implementation (Waltors,
Toyota Way Principle #13: Decide Slowly Through
Consensus, Implement Rapidly, 2012)

Page15
Figure 19 - Rocky Balboa (Waltors, Toyota Way Principle #14: Become a Learning Organization, 2012)
This principle is established in two different ideas. To start with, it’s critical to glance back at
what changes were actualized and what the outcomes were, in respect to what you anticipated.
Second, backtracking to the Santayana quote, it’s crucial to impart this experiment and its
outcomes to people and gatherings outside so that the data is situated in an association's
knowledge base.
The idea of continuous growth was always a big motivation for the senior management and the
newly entered professionals on the site. So, it was a wave of helping each and every individual in
the Company to improve every next day. (Liker, 2004)
Toyota Production System
Figure 19 - Rocky Balboa (Waltors, Toyota Way Principle #14: Become a Learning Organization, 2012)
This principle is established in two different ideas. To start with, it’s critical to glance back at
what changes were actualized and what the outcomes were, in respect to what you anticipated.
Second, backtracking to the Santayana quote, it’s crucial to impart this experiment and its
outcomes to people and gatherings outside so that the data is situated in an association's
knowledge base.
The idea of continuous growth was always a big motivation for the senior management and the
newly entered professionals on the site. So, it was a wave of helping each and every individual in
the Company to improve every next day. (Liker, 2004)
Toyota Production System

Page16
The generation framework reasoning of Toyota exemplifies an assembling society of constant
change in light of setting norms went for taking out waste through interest of all workers. The
objective of the framework is to lessen the timetable from the time a request is gotten by the time
it is conveyed to the real client. Preferably the framework endeavors to deliver the most elevated
conceivable quality, at the least conceivable expense, with the briefest lead-time conceivable.
There are two essential mainstays of the framework. The primary and most celebrated mainstay
of the framework is being Just In Time (JIT). The JIT ideas, plans to create and convey the right
parts, in the privilege sum, at the opportune time utilizing the base fundamental assets. This
framework diminishes stock, and endeavors avert both early and over generations. (Lean, 2013)
Jidoka (Build in quality) is the second mainstay of the framework. There are two sections to
Jidoka – 1) Building in quality of the procedure and 2) Enabling partition of man from machine
in work situations.
The establishment of TPS is Level Production. By smoothing or leveling client prerequisites
after some time, we can better use our assets and guarantee nonstop creation. Averaging volumes
and model blend obliges littler parts and in the best cases "clump of one" capacity of crude
materials to completed products.
Figure 20 - Toyota Production System (Logistics, 2012)
The generation framework reasoning of Toyota exemplifies an assembling society of constant
change in light of setting norms went for taking out waste through interest of all workers. The
objective of the framework is to lessen the timetable from the time a request is gotten by the time
it is conveyed to the real client. Preferably the framework endeavors to deliver the most elevated
conceivable quality, at the least conceivable expense, with the briefest lead-time conceivable.
There are two essential mainstays of the framework. The primary and most celebrated mainstay
of the framework is being Just In Time (JIT). The JIT ideas, plans to create and convey the right
parts, in the privilege sum, at the opportune time utilizing the base fundamental assets. This
framework diminishes stock, and endeavors avert both early and over generations. (Lean, 2013)
Jidoka (Build in quality) is the second mainstay of the framework. There are two sections to
Jidoka – 1) Building in quality of the procedure and 2) Enabling partition of man from machine
in work situations.
The establishment of TPS is Level Production. By smoothing or leveling client prerequisites
after some time, we can better use our assets and guarantee nonstop creation. Averaging volumes
and model blend obliges littler parts and in the best cases "clump of one" capacity of crude
materials to completed products.
Figure 20 - Toyota Production System (Logistics, 2012)
Paraphrase This Document
Need a fresh take? Get an instant paraphrase of this document with our AI Paraphraser

Page17
The bedrock of this framework is Equipment Reliability. Without dependable gear, we should
fabricate inventories (to be safe), or put resources into more supplies (because of unforeseen
downtime). Legitimate upkeep of gear will guarantee that it is accessible when we require it.
Although the construction industry is too slow to adopt the concept of continuous improvement.
But, it is a very important aspect of industrial growth and is an inherent part of Toyota
Production System. Execution of the Toyota Production System into an element lean production
philosophy, upheld by frameworks and apparatuses, requires predictable effort and training. To
proceed to contend in the worldwide car part showcase and accommodate the needs of clients,
employees and speculators, it is fundamental that all representatives get to be specialists in the
standards of the Toyota Production System. The achievement of the framework requires
everybody's interest. Overseeing continuous change and improvement is fundamental.
In the event that, through the interest of all workers and work teams, we keep up solid gear, level
all production necessities, give extraordinary internal and external quality through In-Station
Process Control and work Just-in-Time, we will give ourselves a safe and the compensating
work environment and extraordinary quality and expense for our clients. The outcome will be an
impartial return for our speculators and secure employment with fair wages and reward for all
representatives. (Liker, 2004)
The bedrock of this framework is Equipment Reliability. Without dependable gear, we should
fabricate inventories (to be safe), or put resources into more supplies (because of unforeseen
downtime). Legitimate upkeep of gear will guarantee that it is accessible when we require it.
Although the construction industry is too slow to adopt the concept of continuous improvement.
But, it is a very important aspect of industrial growth and is an inherent part of Toyota
Production System. Execution of the Toyota Production System into an element lean production
philosophy, upheld by frameworks and apparatuses, requires predictable effort and training. To
proceed to contend in the worldwide car part showcase and accommodate the needs of clients,
employees and speculators, it is fundamental that all representatives get to be specialists in the
standards of the Toyota Production System. The achievement of the framework requires
everybody's interest. Overseeing continuous change and improvement is fundamental.
In the event that, through the interest of all workers and work teams, we keep up solid gear, level
all production necessities, give extraordinary internal and external quality through In-Station
Process Control and work Just-in-Time, we will give ourselves a safe and the compensating
work environment and extraordinary quality and expense for our clients. The outcome will be an
impartial return for our speculators and secure employment with fair wages and reward for all
representatives. (Liker, 2004)
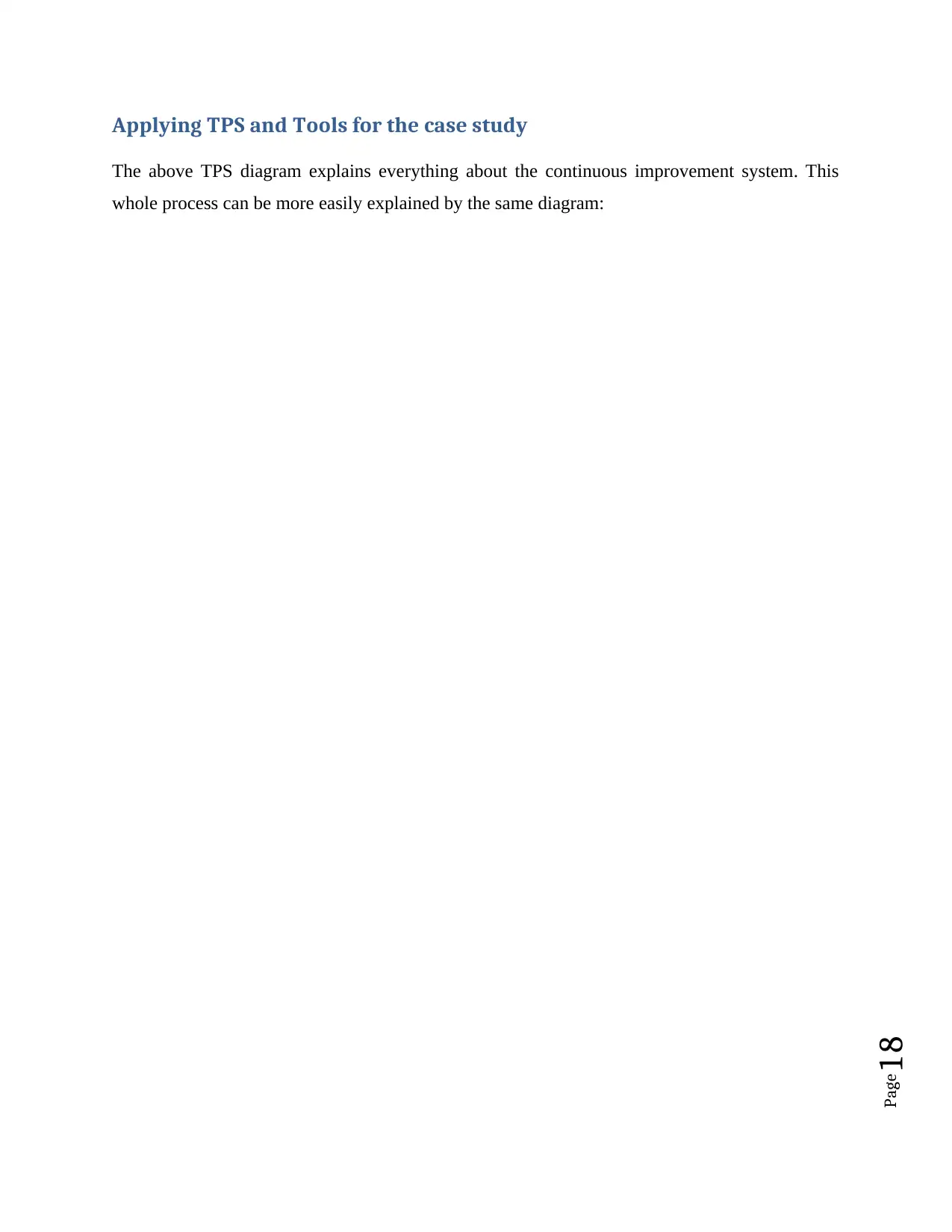
Page18
Applying TPS and Tools for the case study
The above TPS diagram explains everything about the continuous improvement system. This
whole process can be more easily explained by the same diagram:
Applying TPS and Tools for the case study
The above TPS diagram explains everything about the continuous improvement system. This
whole process can be more easily explained by the same diagram:

Page19
Plan: Identifying and analyzing the problem. Because of good planning & Company
policy before commencement of the project on the site, the waste percentages on the unit
was under control.
Do: Developing and testing a potential solution. After planning, the execution plays a
vital role. When it was noticed that waste was non uniformly held in some of the sites,
the Company worked on the process options that could be adopted. They worked on
them, their advantages & disadvantages & then, adopted the most appropriate solution.
Check: Measuring how effective the test solution was, and analyzing whether it could be
improved in any way. Now, the potential of the solution needs to be checked on a regular
basis. A performance measurement survey was scheduled & it was declared that a
company wide policy regarding the waste quantity limit level will be introduced.
Act: Implementing the improved solution fully. After the checking of the solution is
done, the quality is finalized. And better results will be evolved from the following
process.
Figure 21 - PDCA Process (Mike, 2011)
Plan: Identifying and analyzing the problem. Because of good planning & Company
policy before commencement of the project on the site, the waste percentages on the unit
was under control.
Do: Developing and testing a potential solution. After planning, the execution plays a
vital role. When it was noticed that waste was non uniformly held in some of the sites,
the Company worked on the process options that could be adopted. They worked on
them, their advantages & disadvantages & then, adopted the most appropriate solution.
Check: Measuring how effective the test solution was, and analyzing whether it could be
improved in any way. Now, the potential of the solution needs to be checked on a regular
basis. A performance measurement survey was scheduled & it was declared that a
company wide policy regarding the waste quantity limit level will be introduced.
Act: Implementing the improved solution fully. After the checking of the solution is
done, the quality is finalized. And better results will be evolved from the following
process.
Figure 21 - PDCA Process (Mike, 2011)
Secure Best Marks with AI Grader
Need help grading? Try our AI Grader for instant feedback on your assignments.

Page20
Implementing the TPS principles and tools
The four main waste factors which are required to be solved using the TPS Approach are
Conventional Administration, Working without a Plan Overview, Absence of Specialization & Lack of
Communication & Participation. Before using the TPS for solving them, we need to know that
which principle is useful for solving which problem. For that, I have made a matrix table telling
corresponding applicable principle against each waste factor.
The Problems Prn
1
Prn
2
Pr
n
3
Prn
4
Prn
5
Prn
6
Prn
7
Prn
8
Prn
9
Prn
10
Pr
n
11
Prn
12
Prn
13
Prn
14
1 Conventional
Administration 1 2 3 4 5 6 7 8
2 Working without a Plan
Outline 1 2 3 4 5 6 7
3 Absence of
Specialization 1 2 3
4 Lack of
Communication &
Participation
1 2 3 4
Conventional Administration
The traditional approach to the management system leads to a slow process in the construction
project. So, we need to think in terms of a long run. So, for a better approach and efficient
system, we needed to extend the network, build up a team of mix demographic professionals
with both enthusiasm and experience & use of continuous improvement approach. Although the
traditional approach was good in some sectors but overall, it was definitely required to overcome
the backlogs with the help of the principles.
Working Without the Plan Outline
For a good and timely outcome of the project, everyone is required to make a plan and
implement it properly. So, if a plan outline or an overview is not available, it becomes to
complete the project timely and efficiently. For that, we followed the principles in some areas, so
that the problem was solved at the time of the principle followup. Continuous Flow Process, Pull
System, Optimizing the steps, Visual Representation, Learning attitude at every point, and a
grown up team.
Absence of Specialization
Implementing the TPS principles and tools
The four main waste factors which are required to be solved using the TPS Approach are
Conventional Administration, Working without a Plan Overview, Absence of Specialization & Lack of
Communication & Participation. Before using the TPS for solving them, we need to know that
which principle is useful for solving which problem. For that, I have made a matrix table telling
corresponding applicable principle against each waste factor.
The Problems Prn
1
Prn
2
Pr
n
3
Prn
4
Prn
5
Prn
6
Prn
7
Prn
8
Prn
9
Prn
10
Pr
n
11
Prn
12
Prn
13
Prn
14
1 Conventional
Administration 1 2 3 4 5 6 7 8
2 Working without a Plan
Outline 1 2 3 4 5 6 7
3 Absence of
Specialization 1 2 3
4 Lack of
Communication &
Participation
1 2 3 4
Conventional Administration
The traditional approach to the management system leads to a slow process in the construction
project. So, we need to think in terms of a long run. So, for a better approach and efficient
system, we needed to extend the network, build up a team of mix demographic professionals
with both enthusiasm and experience & use of continuous improvement approach. Although the
traditional approach was good in some sectors but overall, it was definitely required to overcome
the backlogs with the help of the principles.
Working Without the Plan Outline
For a good and timely outcome of the project, everyone is required to make a plan and
implement it properly. So, if a plan outline or an overview is not available, it becomes to
complete the project timely and efficiently. For that, we followed the principles in some areas, so
that the problem was solved at the time of the principle followup. Continuous Flow Process, Pull
System, Optimizing the steps, Visual Representation, Learning attitude at every point, and a
grown up team.
Absence of Specialization

Page21
For every task, the professional who specializes in the following tasks, should be assigned. If the
Specialized individual is not available for a particular task, it becomes difficult to fulfil the
conditions and task effective. For that, if we followed the 14 principle rule of the Toyota Way,
we would have managed the time and the quality of the outcome. So, Standardizing the tasks &
processes, developing exceptional leaders & teams & learning for continuous improvement
helped us manage the same in a decent way.
Lack of Communication & Participation
Lack of Communication & Participation causes a huge loss to the quality of the construction. As,
it is required between each and every co-worker to communicate in an efficient way to get to a
decision and bring out the best construction results. At many sites, We observed that the
communication problem occurred and the reason being language & confidence. Thus, we
followed up the principles and optimum distribution of work, visual representation, extended
networks & learning attitude in Each and every co-worker & the labour helped us to some extent.
Continuous Improvement
As the name suggests, Continuous improvement is the improvement of products, services and
processes gradually. It follows a four step model that includes Plan, Do, Check and Act. It is
important to note that continuous improvement should not be used in place of continual
improvement (ASQ, n.d.).
Alternate Approaches to smoothen the Target Process
Implementation Plans
Once the choice was made concerning handling the intemperate waste amounts happening with
respects to material wastage amid production, an execution arrangement must be presented. The
preferences and inconveniences were evaluated. An essential philosophy was created as to
material waste on site, which is outlined in the outline shown below:
For every task, the professional who specializes in the following tasks, should be assigned. If the
Specialized individual is not available for a particular task, it becomes difficult to fulfil the
conditions and task effective. For that, if we followed the 14 principle rule of the Toyota Way,
we would have managed the time and the quality of the outcome. So, Standardizing the tasks &
processes, developing exceptional leaders & teams & learning for continuous improvement
helped us manage the same in a decent way.
Lack of Communication & Participation
Lack of Communication & Participation causes a huge loss to the quality of the construction. As,
it is required between each and every co-worker to communicate in an efficient way to get to a
decision and bring out the best construction results. At many sites, We observed that the
communication problem occurred and the reason being language & confidence. Thus, we
followed up the principles and optimum distribution of work, visual representation, extended
networks & learning attitude in Each and every co-worker & the labour helped us to some extent.
Continuous Improvement
As the name suggests, Continuous improvement is the improvement of products, services and
processes gradually. It follows a four step model that includes Plan, Do, Check and Act. It is
important to note that continuous improvement should not be used in place of continual
improvement (ASQ, n.d.).
Alternate Approaches to smoothen the Target Process
Implementation Plans
Once the choice was made concerning handling the intemperate waste amounts happening with
respects to material wastage amid production, an execution arrangement must be presented. The
preferences and inconveniences were evaluated. An essential philosophy was created as to
material waste on site, which is outlined in the outline shown below:

Page22
Figure 22 - 4 R's
Reduce – Prevent waste in any case; by killing waste at source through better planning and
configuration.
Reuse – Increase creativity on the site – Reuse materials waste at whatever point conceivable;
this is both savvy and decreases waste to landfill Recycle – Secondary material utilization –
Down-cycle in the event that it can't be reused.
Recycle – Ensure a decent partition of waste into "one-material fractions" that can be all the
more effortlessly reused – Enable isolation of no less than 6 fractions: Wood, Concrete,
Gypsum/Plasterboard, Metal, Plastic -delicate and hard, Paper/Cardboard.
Recover – Energy Recovery can be an option, if reusing is not accessible.
Landfill – Waste sent to be disposed in landfills with no 4 R activities taking place. (Skanska,
2012)
The steps needed to create a site waste management plan are represented on a regulated approach
as highlighted beneath. It was concurred that this format would be utilized on every site
preceding commencement of the work. On consummation of any given project, the site waste
Figure 22 - 4 R's
Reduce – Prevent waste in any case; by killing waste at source through better planning and
configuration.
Reuse – Increase creativity on the site – Reuse materials waste at whatever point conceivable;
this is both savvy and decreases waste to landfill Recycle – Secondary material utilization –
Down-cycle in the event that it can't be reused.
Recycle – Ensure a decent partition of waste into "one-material fractions" that can be all the
more effortlessly reused – Enable isolation of no less than 6 fractions: Wood, Concrete,
Gypsum/Plasterboard, Metal, Plastic -delicate and hard, Paper/Cardboard.
Recover – Energy Recovery can be an option, if reusing is not accessible.
Landfill – Waste sent to be disposed in landfills with no 4 R activities taking place. (Skanska,
2012)
The steps needed to create a site waste management plan are represented on a regulated approach
as highlighted beneath. It was concurred that this format would be utilized on every site
preceding commencement of the work. On consummation of any given project, the site waste
Paraphrase This Document
Need a fresh take? Get an instant paraphrase of this document with our AI Paraphraser

Page23
management plan ought to give an exact record of how successfully materials on the site have
been managed and how well the waste management targets have been met.
Figure 23 - 9 Steps for implementation of the Site Waste Management Plan (NETREGS, 2012)
Using the nine steps listed above, each site would now have to follow this procedure
(NETREGS, 2012):
Step 1 – Plan and Prepare
Begin the Site Waste Management Plan (SWMP) amid the idea and outline phase of the
undertaking. Design decisions can add to waste anticipation and reduction. Record all choices
about the undertaking configuration, development systems or materials that will minimize the
waste delivered on site. Guarantee all measures taken to decrease waste are noted. Calendar time
to set up the SWMP while the construction work is being arranged.
Step 2 – Allocate obligation regarding the SWMP
A few individuals can be included in conveying a SWMP, however, somebody must be
designated to assume general liability of the arrangement. This will be the customer in the pre-
construction stage, yet responsibility may exchange to the important foreman when construction
begins. One individual ought to dependably be responsible for the planning and in charge of
redesigning it. That individual needs to obviously comprehend their responsibilities and have the
power to guarantee that others collaborate. The customer and the chief contractor must sign a
management plan ought to give an exact record of how successfully materials on the site have
been managed and how well the waste management targets have been met.
Figure 23 - 9 Steps for implementation of the Site Waste Management Plan (NETREGS, 2012)
Using the nine steps listed above, each site would now have to follow this procedure
(NETREGS, 2012):
Step 1 – Plan and Prepare
Begin the Site Waste Management Plan (SWMP) amid the idea and outline phase of the
undertaking. Design decisions can add to waste anticipation and reduction. Record all choices
about the undertaking configuration, development systems or materials that will minimize the
waste delivered on site. Guarantee all measures taken to decrease waste are noted. Calendar time
to set up the SWMP while the construction work is being arranged.
Step 2 – Allocate obligation regarding the SWMP
A few individuals can be included in conveying a SWMP, however, somebody must be
designated to assume general liability of the arrangement. This will be the customer in the pre-
construction stage, yet responsibility may exchange to the important foreman when construction
begins. One individual ought to dependably be responsible for the planning and in charge of
redesigning it. That individual needs to obviously comprehend their responsibilities and have the
power to guarantee that others collaborate. The customer and the chief contractor must sign a

Page24
declaration that they will handle materials effectively and oversee wastes suitably in accordance
with their obligation of consideration. Perused the guidance on your obligation of consideration
waste obligations here.
Step 3 – Identify the waste
Distinguish the sorts and amounts of waste that the project will deliver. Work out ahead of time
what materials will be utilized at each phase of the project, gauge the amount of waste will be
delivered and set sensible focuses for how a lot of that waste you can reuse, reuse or discard.
Utilize an information sheet or table if vital, including the waste progression, on location and off-
site choices for taking care of the waste, and any uncommon arrangements for dangerous waste.
Utilize the data sheet at the planning phase of the project and after that all through the project,
for instance to report week by week or month to month synopses.
Step 4 – Identify how to deal with the waste
Work out the best alternatives for reusing and discarding all the sorts of waste created. Know
where, when and what kind of materials can be reused, recycled or disposed both on-site and off-
site.
Store and discard all waste capably. Spare time and cash by isolating wastes as they are
created.
Keep marked Waste Transfer Notes (WTNs) or dispatch notes for all waste that is
discarded or exchanged from the site. Keep WTNs for no less than two years and
dispatch notes for no less than three years. For more data see the direction on records for
accepting and exchanging waste here.
Step 5 – Identify where and how to discard waste
Know where and how the waste will be discarded. On the off chance that utilizing a waste
transfer builder guarantee they discard it securely and legitimately.
Watch that:
Anybody transporting waste is enlisted as a waste transporter with the ecological
controller – record their waste bearer enrollment number on the SWMP.
declaration that they will handle materials effectively and oversee wastes suitably in accordance
with their obligation of consideration. Perused the guidance on your obligation of consideration
waste obligations here.
Step 3 – Identify the waste
Distinguish the sorts and amounts of waste that the project will deliver. Work out ahead of time
what materials will be utilized at each phase of the project, gauge the amount of waste will be
delivered and set sensible focuses for how a lot of that waste you can reuse, reuse or discard.
Utilize an information sheet or table if vital, including the waste progression, on location and off-
site choices for taking care of the waste, and any uncommon arrangements for dangerous waste.
Utilize the data sheet at the planning phase of the project and after that all through the project,
for instance to report week by week or month to month synopses.
Step 4 – Identify how to deal with the waste
Work out the best alternatives for reusing and discarding all the sorts of waste created. Know
where, when and what kind of materials can be reused, recycled or disposed both on-site and off-
site.
Store and discard all waste capably. Spare time and cash by isolating wastes as they are
created.
Keep marked Waste Transfer Notes (WTNs) or dispatch notes for all waste that is
discarded or exchanged from the site. Keep WTNs for no less than two years and
dispatch notes for no less than three years. For more data see the direction on records for
accepting and exchanging waste here.
Step 5 – Identify where and how to discard waste
Know where and how the waste will be discarded. On the off chance that utilizing a waste
transfer builder guarantee they discard it securely and legitimately.
Watch that:
Anybody transporting waste is enlisted as a waste transporter with the ecological
controller – record their waste bearer enrollment number on the SWMP.

Page25
All locales, getting waste have a proper allow, permit or enlisted exception from the
ecological controller – record these points of interest (counting the grant or permit
reference number) on the SWMP.
Check waste transporters with your ecological controller: Environment Agency, Northern Ireland
Environment Agency or Scottish Environmental Protection Agency. You can discover
authorized waste locales in your general vicinity utilizing WRAP's Waste Directory.
Step 6 – Organize materials and waste
Make critical reserve funds via painstakingly arranging the materials needed. Dodge over-
requesting to spare cash and decrease site waste. Pre-order materials to detail at the outline stage
to lessen waste made from off-cuts and decrease work costs. Consider utilizing reused or
beforehand utilized materials wherever conceivable. Record all the choices made to minimize
waste, for example, the development routines and materials to be utilized.
Step 7 – Communicate the arrangement and complete preparing
When an arrangement has been framed, convey it to others, particularly subcontractors. Keep the
SWMP on location. Verify everybody taking a shot at the undertaking knows where to discover
it. Verify that all laborers on location have the right preparing and data to do their work as
indicated by the SWMP. Disclose to staff and foremen why the SWMP is imperative.
Incorporate SWMP data in the site actuation, and give customary overhauls.
On the off chance that needed, build up a preparation system to guarantee everybody sees how to
report waste and material utilization. Guarantee that everybody is mindful of the significance of
requesting and recording the right paperwork, receipts, destinations for materials and so forth.
Train specialists on the significance of not blending squanders or sullying skips. Assign skip
zones and mark skips unmistakably. Amid the task, complete spot checks and screen your staff
frequently to verify they are taking after techniques. Designate a 'site champion' with the power
to verify everybody stays on track.
Step 8 – Measure your waste and upgrade your SWMP
When your venture is in progress guarantee the SWMP is redesigned frequently. Stay informed
regarding all developments of waste inside and from the site. Record the sorts of waste taken,
All locales, getting waste have a proper allow, permit or enlisted exception from the
ecological controller – record these points of interest (counting the grant or permit
reference number) on the SWMP.
Check waste transporters with your ecological controller: Environment Agency, Northern Ireland
Environment Agency or Scottish Environmental Protection Agency. You can discover
authorized waste locales in your general vicinity utilizing WRAP's Waste Directory.
Step 6 – Organize materials and waste
Make critical reserve funds via painstakingly arranging the materials needed. Dodge over-
requesting to spare cash and decrease site waste. Pre-order materials to detail at the outline stage
to lessen waste made from off-cuts and decrease work costs. Consider utilizing reused or
beforehand utilized materials wherever conceivable. Record all the choices made to minimize
waste, for example, the development routines and materials to be utilized.
Step 7 – Communicate the arrangement and complete preparing
When an arrangement has been framed, convey it to others, particularly subcontractors. Keep the
SWMP on location. Verify everybody taking a shot at the undertaking knows where to discover
it. Verify that all laborers on location have the right preparing and data to do their work as
indicated by the SWMP. Disclose to staff and foremen why the SWMP is imperative.
Incorporate SWMP data in the site actuation, and give customary overhauls.
On the off chance that needed, build up a preparation system to guarantee everybody sees how to
report waste and material utilization. Guarantee that everybody is mindful of the significance of
requesting and recording the right paperwork, receipts, destinations for materials and so forth.
Train specialists on the significance of not blending squanders or sullying skips. Assign skip
zones and mark skips unmistakably. Amid the task, complete spot checks and screen your staff
frequently to verify they are taking after techniques. Designate a 'site champion' with the power
to verify everybody stays on track.
Step 8 – Measure your waste and upgrade your SWMP
When your venture is in progress guarantee the SWMP is redesigned frequently. Stay informed
regarding all developments of waste inside and from the site. Record the sorts of waste taken,
Secure Best Marks with AI Grader
Need help grading? Try our AI Grader for instant feedback on your assignments.

Page26
who evacuated the waste and where they took the worst. Keep waste reports as an index to the
arrangement and verify it is redesigned with the aggregates of waste took care of two mirrors the
advancement of the task.
Step 9 – Review the achievement and learn lessons about what's to come
Before the end of the undertaking the SWMP ought to give a precise record of how the materials
have been overseen on location and whether waste administration targets have been met. On the
off chance that the undertaking is in England with an expected development expense of in the
middle of £300,000 and £500,000, inside three months of the venture being finished the vital
builder must add more data to the arrangement too:
Affirm the arrangement has been checked and overhauled all the time.
Explain any changes from the original.
Conclusion & Recommendation
Usage of the Toyota Production System into an element lean manufacturing philosophy,
bolstered by frameworks and tools, requires reliable effort and education. So as to proceed to
contend in the worldwide construction segment market and accommodate the needs of clients,
workers and financial specialists, it is key that all representatives get to be specialists in the
principles of the Toyota Production System. The achievement of the framework requires
everybody's support. Overseeing continuous change and improvement is vital. (Doo Hee Lee,
2007)
The Company followed all of these 14 principles combined with the adequate steps for the Site
Waste Management Plan and we could see the difference on the site. The Company Project
Construction Site was as clean like a showroom which made co-workers, visitors and the
contractors & subcontractors really happy. More the cleanliness of the site, so, more was the
motivation for the construction workers. The few measures which were taken are:
1. Straighten and clean up the development site and practice great behavior (counting
welcome). The usage of these exercises is checked and demonstrated every day on the
examination board.
who evacuated the waste and where they took the worst. Keep waste reports as an index to the
arrangement and verify it is redesigned with the aggregates of waste took care of two mirrors the
advancement of the task.
Step 9 – Review the achievement and learn lessons about what's to come
Before the end of the undertaking the SWMP ought to give a precise record of how the materials
have been overseen on location and whether waste administration targets have been met. On the
off chance that the undertaking is in England with an expected development expense of in the
middle of £300,000 and £500,000, inside three months of the venture being finished the vital
builder must add more data to the arrangement too:
Affirm the arrangement has been checked and overhauled all the time.
Explain any changes from the original.
Conclusion & Recommendation
Usage of the Toyota Production System into an element lean manufacturing philosophy,
bolstered by frameworks and tools, requires reliable effort and education. So as to proceed to
contend in the worldwide construction segment market and accommodate the needs of clients,
workers and financial specialists, it is key that all representatives get to be specialists in the
principles of the Toyota Production System. The achievement of the framework requires
everybody's support. Overseeing continuous change and improvement is vital. (Doo Hee Lee,
2007)
The Company followed all of these 14 principles combined with the adequate steps for the Site
Waste Management Plan and we could see the difference on the site. The Company Project
Construction Site was as clean like a showroom which made co-workers, visitors and the
contractors & subcontractors really happy. More the cleanliness of the site, so, more was the
motivation for the construction workers. The few measures which were taken are:
1. Straighten and clean up the development site and practice great behavior (counting
welcome). The usage of these exercises is checked and demonstrated every day on the
examination board.

Page27
2. Post a specialist working position board to help the laborers obviously comprehend the
area, the quantity of specialists, and their exercises in the field.
3. Post a work calendar and advancement control board to help the laborers plainly
comprehend the work progress.
2. Post a specialist working position board to help the laborers obviously comprehend the
area, the quantity of specialists, and their exercises in the field.
3. Post a work calendar and advancement control board to help the laborers plainly
comprehend the work progress.

Page28
4. Post a quality control board to help the laborers unmistakably comprehend the quality
control conditions.
In the event that, through the support of all representatives and work groups, we keep up solid
gear, level all creation prerequisites, give remarkable inward and outside quality through In
Station Procedure Control and work Just-in-Time, we will give ourselves a safe and the
compensating work environment and exceptional quality and expense for our clients. The
outcome will be an evenhanded return for our financial specialists and secure occupation with
impartial wages and reward for all representatives.
Figure 24 - Typical daily work schedule and progress control board
4. Post a quality control board to help the laborers unmistakably comprehend the quality
control conditions.
In the event that, through the support of all representatives and work groups, we keep up solid
gear, level all creation prerequisites, give remarkable inward and outside quality through In
Station Procedure Control and work Just-in-Time, we will give ourselves a safe and the
compensating work environment and exceptional quality and expense for our clients. The
outcome will be an evenhanded return for our financial specialists and secure occupation with
impartial wages and reward for all representatives.
Figure 24 - Typical daily work schedule and progress control board
Paraphrase This Document
Need a fresh take? Get an instant paraphrase of this document with our AI Paraphraser

Page29
References
ASQ. (n.d.). Continuous Improvement. Retrieved 14 03, 2015, from ASQ ORG: http://asq.org/learn-
about-quality/continuous-improvement/overview/overview.html
Company, A. A.-K. (2014, march 10). Retrieved from Abdullah A. M. Al-Khodari Sons Company:
http://www.alkhodari.com/index.html
Doo Hee Lee, Y. W. (2007). CONTINUOUS IMPROVEMENT PLAN OF BUSINESS PROCESS IN
CONSTRUCTION COMPANY. IGLC-15, (pp. 590-596). Michigan.
Junction, L. M. (2014). What is Lean Manufacturing? Retrieved from Lean Manufacturing Junction:
http://www.lean-manufacturing-junction.com/what-is-lean-manufacturing.html
Lean, A. o. (2013). TOYOTA PRODUCTION SYSTEM - BASIC HANDBOOK. Retrieved from Art of Lean:
http://www.artoflean.com/files/Basic_TPS_Handbook_v1.pdf
Liker, J. K. (2004). 14 Management Principles of The Toyota Way. New York: McGraw Hill Education;
Reissue Edition.
Logistics, G. (2012, July). What is Toyota production system, TPS. Retrieved from Global Logistics:
http://logisticsglobal.blogspot.in/2012/07/what-is-toyota-production-system-tps.html
Mike. (2011, March 07). PLAN:DO:CHECK:ACT: TEAM BUILDING PROCESSING & DE-BRIEFING. Retrieved
from Create Learning: http://create-learning.com/article/team-building/plandocheckact-team-
building-processing-de-briefing
NETREGS. (2012). Site waste – it’s criminal. A simple guide to Site Waste Management Plans . Retrieved
from Environmental Guidance For Your Business in Northern Ireland and Scotland (NETREGS):
http://www.netregs.org.uk/pdf/SWMP_simple_guide.pdf
Remedi-Brown, F. (2014, April 9). Toyota Production System Standards Lowered? Retrieved from Liberty
Voice: http://guardianlv.com/2014/04/toyota-production-system-standards-lowered/
Schume, P. (2013, August 28). BPM Voices: BPM and Lean -- a powerful combination for process
improvement. Retrieved from IBM:
http://www.ibm.com/developerworks/bpm/bpmjournal/1308_col_schume/1308_schume.html
Skanska. (2012, April 20). 4R Guide. Retrieved from Skanska Group:
http://www.group.skanska.com/cdn-1cd3d756d843020/Global/sustainability/Materials/
Skanska4RGuide%20April%2016,%202012_external.pdf
SMGOV. (2010, August 02). Construction Management : Site Waste-Management. Retrieved from Office
of Sustainability and the Environment: http://www.smgov.net/WorkArea/linkit.aspx?
LinkIdentifier=id&ItemID=4709
References
ASQ. (n.d.). Continuous Improvement. Retrieved 14 03, 2015, from ASQ ORG: http://asq.org/learn-
about-quality/continuous-improvement/overview/overview.html
Company, A. A.-K. (2014, march 10). Retrieved from Abdullah A. M. Al-Khodari Sons Company:
http://www.alkhodari.com/index.html
Doo Hee Lee, Y. W. (2007). CONTINUOUS IMPROVEMENT PLAN OF BUSINESS PROCESS IN
CONSTRUCTION COMPANY. IGLC-15, (pp. 590-596). Michigan.
Junction, L. M. (2014). What is Lean Manufacturing? Retrieved from Lean Manufacturing Junction:
http://www.lean-manufacturing-junction.com/what-is-lean-manufacturing.html
Lean, A. o. (2013). TOYOTA PRODUCTION SYSTEM - BASIC HANDBOOK. Retrieved from Art of Lean:
http://www.artoflean.com/files/Basic_TPS_Handbook_v1.pdf
Liker, J. K. (2004). 14 Management Principles of The Toyota Way. New York: McGraw Hill Education;
Reissue Edition.
Logistics, G. (2012, July). What is Toyota production system, TPS. Retrieved from Global Logistics:
http://logisticsglobal.blogspot.in/2012/07/what-is-toyota-production-system-tps.html
Mike. (2011, March 07). PLAN:DO:CHECK:ACT: TEAM BUILDING PROCESSING & DE-BRIEFING. Retrieved
from Create Learning: http://create-learning.com/article/team-building/plandocheckact-team-
building-processing-de-briefing
NETREGS. (2012). Site waste – it’s criminal. A simple guide to Site Waste Management Plans . Retrieved
from Environmental Guidance For Your Business in Northern Ireland and Scotland (NETREGS):
http://www.netregs.org.uk/pdf/SWMP_simple_guide.pdf
Remedi-Brown, F. (2014, April 9). Toyota Production System Standards Lowered? Retrieved from Liberty
Voice: http://guardianlv.com/2014/04/toyota-production-system-standards-lowered/
Schume, P. (2013, August 28). BPM Voices: BPM and Lean -- a powerful combination for process
improvement. Retrieved from IBM:
http://www.ibm.com/developerworks/bpm/bpmjournal/1308_col_schume/1308_schume.html
Skanska. (2012, April 20). 4R Guide. Retrieved from Skanska Group:
http://www.group.skanska.com/cdn-1cd3d756d843020/Global/sustainability/Materials/
Skanska4RGuide%20April%2016,%202012_external.pdf
SMGOV. (2010, August 02). Construction Management : Site Waste-Management. Retrieved from Office
of Sustainability and the Environment: http://www.smgov.net/WorkArea/linkit.aspx?
LinkIdentifier=id&ItemID=4709

Page30
Walters, C. (2012, April 23). Toyota Way Principle #2: Continuous Flow. Retrieved from Lean Blitz:
http://leanblitz.net/2012/04/toyota-way-principle-2-continuous-flow/
Walters, C. (2012, may 08). Toyota Way Principle #3: “Pull” Systems. Retrieved from Lean Blitz:
http://leanblitzconsulting.com/2012/05/toyota-way-principle-3-pull-systems/
Walters, C. (2012, May 09). Toyota Way Principle #4: Level Out the Workload. Retrieved from Lean Blitz:
http://leanblitzconsulting.com/2012/05/toyota-way-principle-4-level-out-the-workload/
Walters, C. (2012, May 14). Toyota Way Principle #5: Stopping to Fix Problems. Retrieved from Lean
Blitz: http://leanblitzconsulting.com/2012/05/toyota-way-principle-5-stopping-to-fix-problems/
Walters, C. (2012, April 19). Toyota Way principle Number 1. Retrieved from lean Blitz - Do it Better:
http://leanblitzconsulting.com/2012/04/toyota-way-principle-1/
Waltors, C. (2012, June 25). The Toyota Way Principle #11: Challenging Your Extended Network.
Retrieved from Lean Blitz: http://leanblitzconsulting.com/2012/07/the-toyota-way-principle-11-
challenging-your-extended-network/
Waltors, C. (2012, June 20). Toyota Way Principle #10: Develop Exceptional People and Teams. Retrieved
from Lean Blitz: http://leanblitzconsulting.com/2012/07/toyota-way-principle-10-develop-
exceptional-people-and-teams/
Waltors, C. (2012, July 26). Toyota Way Principle #12: Go and See For Yourself. Retrieved from Lean Blitz:
http://leanblitzconsulting.com/2012/07/toyota-way-principle-12-go-and-see-for-yourself/
Waltors, C. (2012, July 30). Toyota Way Principle #13: Decide Slowly Through Consensus, Implement
Rapidly. Retrieved from Lean Blitz: http://leanblitzconsulting.com/2012/07/toyota-way-
principle-13-decide-slowly-through-consensus-implement-rapidly/
Waltors, C. (2012, August 2). Toyota Way Principle #14: Become a Learning Organization. Retrieved from
Lean Blitz: http://leanblitzconsulting.com/2012/08/toyota-way-principle-14-become-a-learning-
organization/
Waltors, C. (2012, June 01). Toyota Way Principle #6: Standardized Tasks & Processes. Retrieved from
Lean Blitz: http://leanblitzconsulting.com/2012/06/toyota-way-principle-6-standardized-tasks-
processes/
Waltors, C. (2012, June 25). Toyota Way Principle #7 – Visual Controls. Retrieved from Lean Blitz:
http://leanblitzconsulting.com/2012/06/toyota-way-principle-7-visual-controls/
Waltors, C. (2012, June 27). Toyota Way Principle #8: Use The Proper Technology. Retrieved from Lean
Blitz: http://leanblitzconsulting.com/2012/06/toyota-way-principle-8-use-the-proper-
technology/
Walters, C. (2012, April 23). Toyota Way Principle #2: Continuous Flow. Retrieved from Lean Blitz:
http://leanblitz.net/2012/04/toyota-way-principle-2-continuous-flow/
Walters, C. (2012, may 08). Toyota Way Principle #3: “Pull” Systems. Retrieved from Lean Blitz:
http://leanblitzconsulting.com/2012/05/toyota-way-principle-3-pull-systems/
Walters, C. (2012, May 09). Toyota Way Principle #4: Level Out the Workload. Retrieved from Lean Blitz:
http://leanblitzconsulting.com/2012/05/toyota-way-principle-4-level-out-the-workload/
Walters, C. (2012, May 14). Toyota Way Principle #5: Stopping to Fix Problems. Retrieved from Lean
Blitz: http://leanblitzconsulting.com/2012/05/toyota-way-principle-5-stopping-to-fix-problems/
Walters, C. (2012, April 19). Toyota Way principle Number 1. Retrieved from lean Blitz - Do it Better:
http://leanblitzconsulting.com/2012/04/toyota-way-principle-1/
Waltors, C. (2012, June 25). The Toyota Way Principle #11: Challenging Your Extended Network.
Retrieved from Lean Blitz: http://leanblitzconsulting.com/2012/07/the-toyota-way-principle-11-
challenging-your-extended-network/
Waltors, C. (2012, June 20). Toyota Way Principle #10: Develop Exceptional People and Teams. Retrieved
from Lean Blitz: http://leanblitzconsulting.com/2012/07/toyota-way-principle-10-develop-
exceptional-people-and-teams/
Waltors, C. (2012, July 26). Toyota Way Principle #12: Go and See For Yourself. Retrieved from Lean Blitz:
http://leanblitzconsulting.com/2012/07/toyota-way-principle-12-go-and-see-for-yourself/
Waltors, C. (2012, July 30). Toyota Way Principle #13: Decide Slowly Through Consensus, Implement
Rapidly. Retrieved from Lean Blitz: http://leanblitzconsulting.com/2012/07/toyota-way-
principle-13-decide-slowly-through-consensus-implement-rapidly/
Waltors, C. (2012, August 2). Toyota Way Principle #14: Become a Learning Organization. Retrieved from
Lean Blitz: http://leanblitzconsulting.com/2012/08/toyota-way-principle-14-become-a-learning-
organization/
Waltors, C. (2012, June 01). Toyota Way Principle #6: Standardized Tasks & Processes. Retrieved from
Lean Blitz: http://leanblitzconsulting.com/2012/06/toyota-way-principle-6-standardized-tasks-
processes/
Waltors, C. (2012, June 25). Toyota Way Principle #7 – Visual Controls. Retrieved from Lean Blitz:
http://leanblitzconsulting.com/2012/06/toyota-way-principle-7-visual-controls/
Waltors, C. (2012, June 27). Toyota Way Principle #8: Use The Proper Technology. Retrieved from Lean
Blitz: http://leanblitzconsulting.com/2012/06/toyota-way-principle-8-use-the-proper-
technology/
1 out of 30
Related Documents
![[object Object]](/_next/image/?url=%2F_next%2Fstatic%2Fmedia%2Flogo.6d15ce61.png&w=640&q=75)
Your All-in-One AI-Powered Toolkit for Academic Success.
+13062052269
info@desklib.com
Available 24*7 on WhatsApp / Email
Unlock your academic potential
© 2024 | Zucol Services PVT LTD | All rights reserved.