Automation in Paper Industry Warehousing: Strategies and Technologies
Research and analyze different techniques for automation in each stage of warehousing in the paper industry
32 Pages11144 Words68 Views
Added on 2023-06-04
About This Document
This study explores the possibilities of using automation in a paper industry warehouse. It explores the key processes involved in warehousing and the use of different strategies that can be used at each step. Further, the research also explores different technologies like warehouse management system and warehouse control system that can be used for warehousing automation. For each strategy identified for warehouse management, advantages and disadvantages are explored so that most appropriate strategy can be suggested for management of warehouses in the paper industry.
Automation in Paper Industry Warehousing: Strategies and Technologies
Research and analyze different techniques for automation in each stage of warehousing in the paper industry
Added on 2023-06-04
ShareRelated Documents
1
Automation in paper industry warehousing
Executive Summary
This study explores the possibilities of using automation in a paper industry warehouse. It
explores the key processes involved in warehousing and the use of different strategies that
can be used at each step. Further, the research also explores different technologies like
warehouse management system and warehouse control system that can be used for
warehousing automation. For each strategy identified for warehouse management, advantages
and disadvantages are explored so that most appropriate strategy can be suggested for
management of warehouses in the paper industry. The study can help a manager take
decisions on warehousing strategies to use in order to achieve goals of efficient and effective
warehousing. The paper also explores the case of a standard paper industry warehouse that
would need implementation of various technologies and automation equipment’s. The
appropriate technologies and equipment’s have been explored and recommendations have
been made for their selection and appropriate cost implications are accounted in the report.
Automation in paper industry warehousing
Executive Summary
This study explores the possibilities of using automation in a paper industry warehouse. It
explores the key processes involved in warehousing and the use of different strategies that
can be used at each step. Further, the research also explores different technologies like
warehouse management system and warehouse control system that can be used for
warehousing automation. For each strategy identified for warehouse management, advantages
and disadvantages are explored so that most appropriate strategy can be suggested for
management of warehouses in the paper industry. The study can help a manager take
decisions on warehousing strategies to use in order to achieve goals of efficient and effective
warehousing. The paper also explores the case of a standard paper industry warehouse that
would need implementation of various technologies and automation equipment’s. The
appropriate technologies and equipment’s have been explored and recommendations have
been made for their selection and appropriate cost implications are accounted in the report.
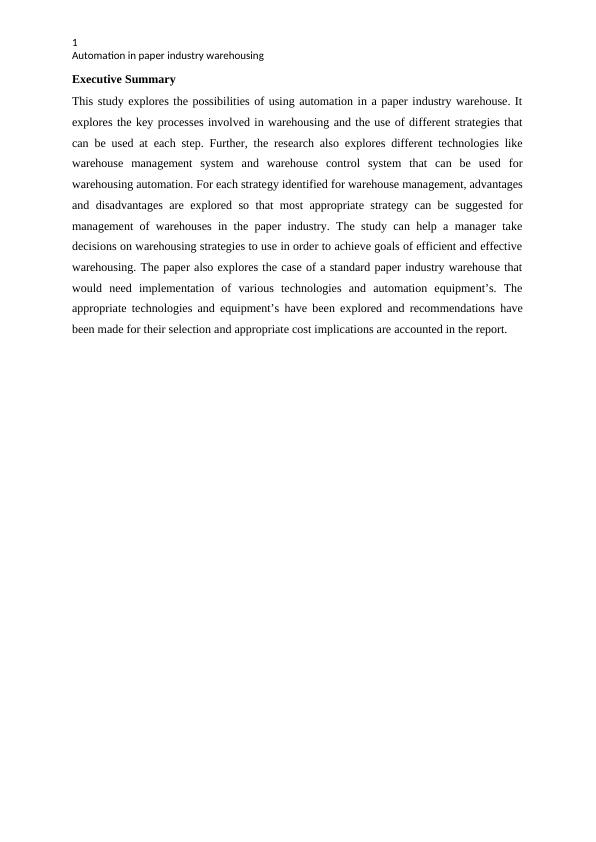
2
Automation in paper industry warehousing
Contents
Introduction...........................................................................................................................................4
Literature Review..................................................................................................................................4
Purpose of Warehousing....................................................................................................................5
Types of Warehouses.........................................................................................................................5
Warehouse operations........................................................................................................................6
Warehouse Designing........................................................................................................................8
Manual Versus Automated Warehouses..........................................................................................10
Warehouse Technologies.................................................................................................................10
Warehouse Automation...................................................................................................................12
Management Tools Analysis...............................................................................................................14
Paper and Pulp Industry...................................................................................................................14
Paper Industry Production & Warehousing.....................................................................................15
Receipt.............................................................................................................................................17
Put Away.........................................................................................................................................18
Storage.............................................................................................................................................18
Picking.............................................................................................................................................22
Packing & Distribution....................................................................................................................24
Integration of stages with Warehouse Management System............................................................25
Cost of Automation.........................................................................................................................26
Conclusions.....................................................................................................................................27
Recommendations...........................................................................................................................28
References...........................................................................................................................................28
Automation in paper industry warehousing
Contents
Introduction...........................................................................................................................................4
Literature Review..................................................................................................................................4
Purpose of Warehousing....................................................................................................................5
Types of Warehouses.........................................................................................................................5
Warehouse operations........................................................................................................................6
Warehouse Designing........................................................................................................................8
Manual Versus Automated Warehouses..........................................................................................10
Warehouse Technologies.................................................................................................................10
Warehouse Automation...................................................................................................................12
Management Tools Analysis...............................................................................................................14
Paper and Pulp Industry...................................................................................................................14
Paper Industry Production & Warehousing.....................................................................................15
Receipt.............................................................................................................................................17
Put Away.........................................................................................................................................18
Storage.............................................................................................................................................18
Picking.............................................................................................................................................22
Packing & Distribution....................................................................................................................24
Integration of stages with Warehouse Management System............................................................25
Cost of Automation.........................................................................................................................26
Conclusions.....................................................................................................................................27
Recommendations...........................................................................................................................28
References...........................................................................................................................................28
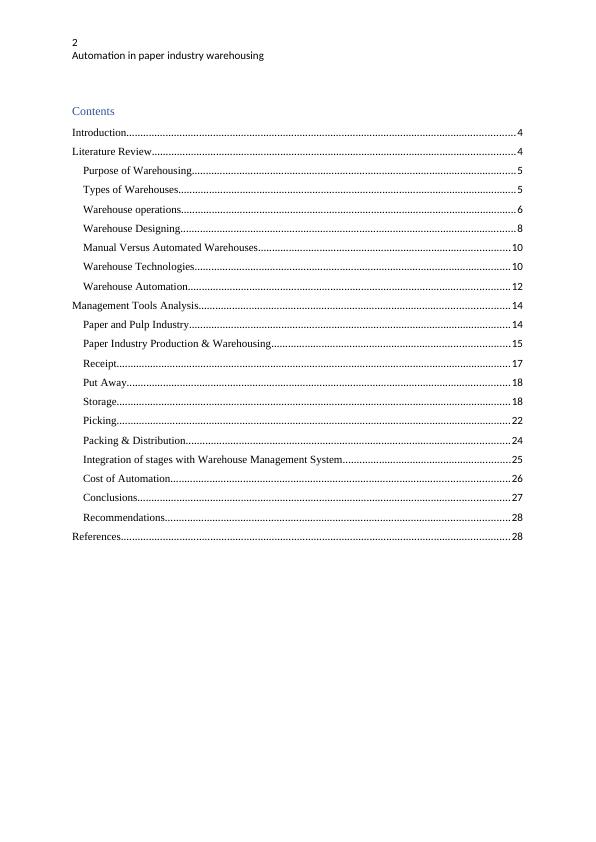
3
Automation in paper industry warehousing
Figure 1:Warehousing Decisions (Mankad & Dholakia, 2013).................................................9
Figure 2: Warehouse component (Blomqvist, 2010)...............................................................11
Figure 3: Warehouse Automation Strategy..............................................................................12
Figure 4: Paper and pulp industry flow (Didone, et al., 2017).................................................14
Figure 5: Paper Manufacturing Process (Carlsonn, Armours, Martel, & ROnnqvvist, 2006).15
Figure 6: Core processes (Sarmiento & Nagi, 2015)...............................................................16
Figure 7: Distribution line (CEPI, 2010)..................................................................................16
Figure 8: Scheduling................................................................................................................21
Figure 9: end-of-aisle OPS.......................................................................................................23
Automation in paper industry warehousing
Figure 1:Warehousing Decisions (Mankad & Dholakia, 2013).................................................9
Figure 2: Warehouse component (Blomqvist, 2010)...............................................................11
Figure 3: Warehouse Automation Strategy..............................................................................12
Figure 4: Paper and pulp industry flow (Didone, et al., 2017).................................................14
Figure 5: Paper Manufacturing Process (Carlsonn, Armours, Martel, & ROnnqvvist, 2006).15
Figure 6: Core processes (Sarmiento & Nagi, 2015)...............................................................16
Figure 7: Distribution line (CEPI, 2010)..................................................................................16
Figure 8: Scheduling................................................................................................................21
Figure 9: end-of-aisle OPS.......................................................................................................23
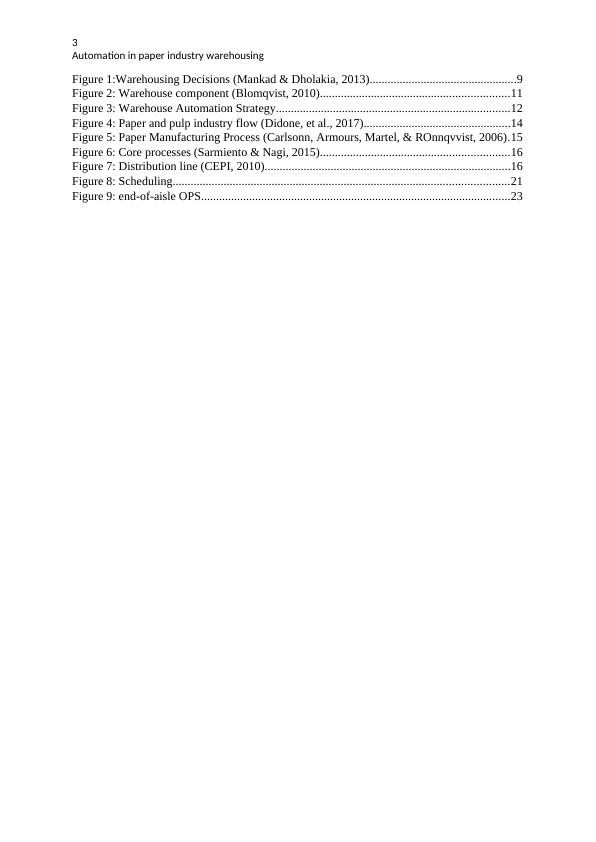
4
Automation in paper industry warehousing
Introduction
Consumer demands are increasing that is driving companies into expansion of their portfolios
where their focus remains on achieving efficiencies in manufacturing and distribution as well
as keep the costs in check at the same time. Manufacturing organizations use warehouse for
storage and logistics. Warehousing processes need a significant amount of investment in
labour and information management. Depending on the capabilities of a warehouse,
companies can adapt to the fast-changing demands of the market. Warehouses provide
consolidation product distribution and logistics such that total transportation costs incurred in
takin products to the market can be reduced. A number of different technologies can be used
in a warehousing unit to make it automated so as to increase productivity and enhance
efficiencies of the systems. In this paper, most of the possible strategies and the automation
capabilities would be explored and recommendations would be made for the automation of a
paper industry warehouse (Martin & Leurent, 2017).
Literature Review
Core functions in warehousing include inbound material processing, inventory management,
and outbound material processing.
Inbound material processing: It involves receipt of paper goods into the warehouse. The
process involved include inbound scheduling, materials receipt, inspection, cross-docking,
and put away. The inbound systems include recept of goods and information with minimum
errors accounted (BR Williams, 2017). In the paper production industry, the inbound
processing activities would include receipt, inspection, and put away.
Inventory Management: It involves purchase requisition, inventory transactions, on-demand
stock information, cycle counting, inventory counting, stock management, job scheduling,
replenishments, material allocation, and vendor management. In the paper production unit
warehouse, the inventory management would involve put away, storage, and retrieval.
Outbound Material Processing: It involves directed picking, packing, loading, shipping,
dispatch planning, shipment tracking, and fleet management. Outbound processing involves
order taking, fulfillment and replenishment of products based on demand forecasts and the
shipment of the product. In a paper manufacturing unit, the outbound logistics would include
picking, packing, and shipment (Andriansyah, 2011).
Automation in paper industry warehousing
Introduction
Consumer demands are increasing that is driving companies into expansion of their portfolios
where their focus remains on achieving efficiencies in manufacturing and distribution as well
as keep the costs in check at the same time. Manufacturing organizations use warehouse for
storage and logistics. Warehousing processes need a significant amount of investment in
labour and information management. Depending on the capabilities of a warehouse,
companies can adapt to the fast-changing demands of the market. Warehouses provide
consolidation product distribution and logistics such that total transportation costs incurred in
takin products to the market can be reduced. A number of different technologies can be used
in a warehousing unit to make it automated so as to increase productivity and enhance
efficiencies of the systems. In this paper, most of the possible strategies and the automation
capabilities would be explored and recommendations would be made for the automation of a
paper industry warehouse (Martin & Leurent, 2017).
Literature Review
Core functions in warehousing include inbound material processing, inventory management,
and outbound material processing.
Inbound material processing: It involves receipt of paper goods into the warehouse. The
process involved include inbound scheduling, materials receipt, inspection, cross-docking,
and put away. The inbound systems include recept of goods and information with minimum
errors accounted (BR Williams, 2017). In the paper production industry, the inbound
processing activities would include receipt, inspection, and put away.
Inventory Management: It involves purchase requisition, inventory transactions, on-demand
stock information, cycle counting, inventory counting, stock management, job scheduling,
replenishments, material allocation, and vendor management. In the paper production unit
warehouse, the inventory management would involve put away, storage, and retrieval.
Outbound Material Processing: It involves directed picking, packing, loading, shipping,
dispatch planning, shipment tracking, and fleet management. Outbound processing involves
order taking, fulfillment and replenishment of products based on demand forecasts and the
shipment of the product. In a paper manufacturing unit, the outbound logistics would include
picking, packing, and shipment (Andriansyah, 2011).
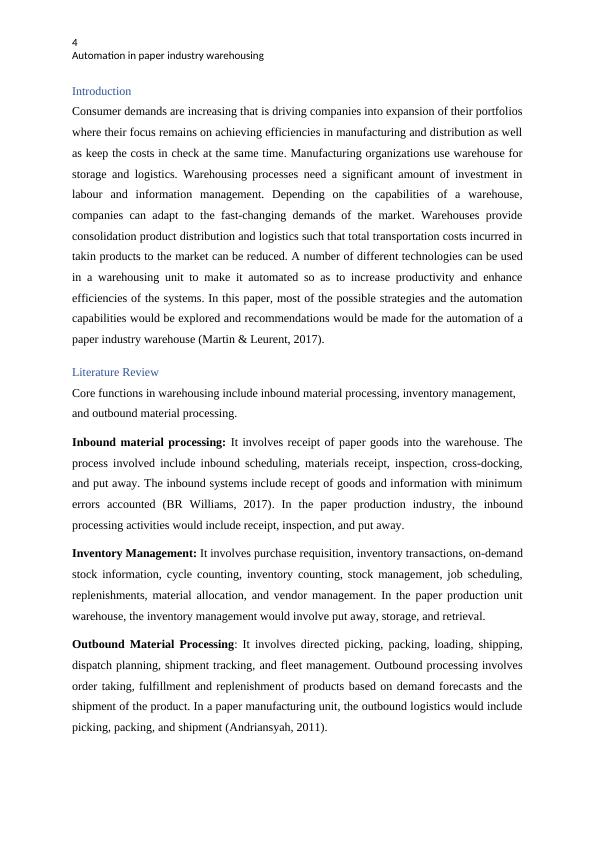
5
Automation in paper industry warehousing
Purpose of Warehousing
Key purpose of a warehouse is to store the goods and one key element of a warehousing
system is order processing which is associated with the flow of goods or products across a
supply chain. Warehousing systems facilitate movement of goods across the supply chain
with the objective of meeting demand in cost effective and timely manner. In old days, large
inventory was the reflection of wealth of an organisation but that is not the case anymore as
holding inventory is a cost to company which can affect the bottom-line. Today, the aim of
organizations remain keeping least inventory and for the shortest time period. However, there
can be other factors that would put constraints on these objectives such as consumer demands
and availability expectations that would make it necessary for organizations to keep certain
level of inventory. Some reasons why companies may need to keep the inventory include
coverage of demand with effective lead time, saving achieved through volume discounts,
coping with seasonal variations, provision of variety in central location, investment stock
keeping, and minimize cost of operations for desired level of service provision.
Traditional warehouses were only intended for storage of goods. However, modern
warehouses have more functions. Warehouse provide storage facility for raw materials,
equipment’s, components, work in progress items, and finished goods. They can be used for
order fulfilment and distribution centre. Warehouse often plays the role of a distribution
centre which provides order consolidation, economic transportation, cross docking,
transhipment, assembling, product fulfilment, returns goods deports for unwanted goods,
customer support, and fulfillment operations.
Types of Warehouses
A warehouse can be production or distribution warehouse. A distribution warehouse stores
the products and fulfils customer orders through a number of different order lines that are
optimized for picking. The aim of such a warehouse is to generate maximum throughput with
minimal costs. Production warehouse stores the raw material needed for production, work-in-
progress material, and at times to the finished goods. Such a warehouse is closely linked to
the assembling or manufacturing facility. Product rate and incoming raw material need to be
well adjusted so that the inventory remains on the low side to make the warehouse efficient in
its operations. The focus of such a warehouse is on building sufficient capacity at low cost.
Either type of warehouse can be automated with the use of appropriate technologies and
equipment. An ideal situation of automation is achieved with the use of information
Automation in paper industry warehousing
Purpose of Warehousing
Key purpose of a warehouse is to store the goods and one key element of a warehousing
system is order processing which is associated with the flow of goods or products across a
supply chain. Warehousing systems facilitate movement of goods across the supply chain
with the objective of meeting demand in cost effective and timely manner. In old days, large
inventory was the reflection of wealth of an organisation but that is not the case anymore as
holding inventory is a cost to company which can affect the bottom-line. Today, the aim of
organizations remain keeping least inventory and for the shortest time period. However, there
can be other factors that would put constraints on these objectives such as consumer demands
and availability expectations that would make it necessary for organizations to keep certain
level of inventory. Some reasons why companies may need to keep the inventory include
coverage of demand with effective lead time, saving achieved through volume discounts,
coping with seasonal variations, provision of variety in central location, investment stock
keeping, and minimize cost of operations for desired level of service provision.
Traditional warehouses were only intended for storage of goods. However, modern
warehouses have more functions. Warehouse provide storage facility for raw materials,
equipment’s, components, work in progress items, and finished goods. They can be used for
order fulfilment and distribution centre. Warehouse often plays the role of a distribution
centre which provides order consolidation, economic transportation, cross docking,
transhipment, assembling, product fulfilment, returns goods deports for unwanted goods,
customer support, and fulfillment operations.
Types of Warehouses
A warehouse can be production or distribution warehouse. A distribution warehouse stores
the products and fulfils customer orders through a number of different order lines that are
optimized for picking. The aim of such a warehouse is to generate maximum throughput with
minimal costs. Production warehouse stores the raw material needed for production, work-in-
progress material, and at times to the finished goods. Such a warehouse is closely linked to
the assembling or manufacturing facility. Product rate and incoming raw material need to be
well adjusted so that the inventory remains on the low side to make the warehouse efficient in
its operations. The focus of such a warehouse is on building sufficient capacity at low cost.
Either type of warehouse can be automated with the use of appropriate technologies and
equipment. An ideal situation of automation is achieved with the use of information
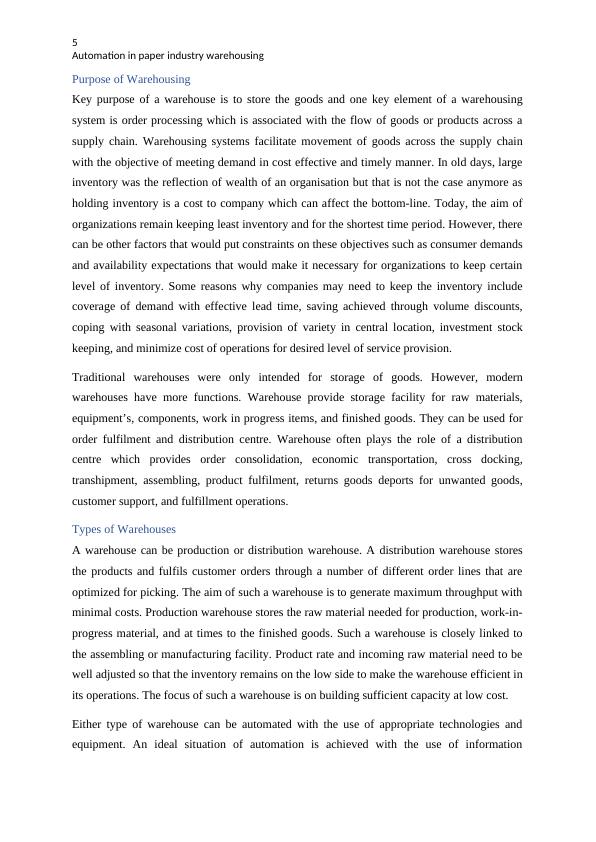
6
Automation in paper industry warehousing
management systems like WMS, WCS, and ERP combined with the automating machines
and equipment used for different stages of warehousing such as receipt, storage, picking, and
packing. The choice of appropriate technologies would depend on the level of automation
that the company chooses which can be manual, automated or automatic. Manual operations
do not make use of any information systems or automated machines while automated
warehouses make use of both. An automatic warehouse would make the highest level of
automation as the human involvement almost get eliminated with the replacement by the
robots. In the current research, the focus would be on the automated warehouse which is
developed using automation equipment’s and technologies.
Warehouse operations
Every warehouse has inbound, inventory, and outbound processes but they may be different
in specific steps used for warehousing. However, there can be some basic steps listed for
warehouse operations that are used in most warehouses as standards. These include receipt,
put away, storage, picking, and shipping.
Receipt: The warehouse management receives an information on the incoming materials or
goods in advance so that receipt and unloading of the goods can be planned before the goods
arrive. In a distribution warehouse, goods are received, scanned and registered when they
arrive. An inspection is done at the time of receipt to check the quality of quantity of goods
received to ensure that they are as per the plan. In a production warehouse, raw materials are
received and normally, the quality check is not required.
Put Away: Every product that is received in the warehouse is allocated a location inside and
this location has to be determined fast so that as soon as the receipt is taken, the goods are put
in the right place in the warehouse. For this to happen, an efficient inventory management is
required. This would involve ad advance knowledge of the available locations, their size, and
the weight they can handle. The location of the storage is scanned to keep the inventory
records and the information is added to the picking lists (Tomé, 2014).
Storage: Storage is one of the most important activities of a warehouse. Storage management
needs three types of decisions to be made that include the count of inventory to be stored in
SKUs, time for replenishment of each SKU, and the storage location of the SKU in the
warehouse. The first two decisions are a part of inventory control while the third decision
deals with the efficiency of storage and access to resources. A warehouse that is well-slotted
can bring efficiencies in storage but many distribution centres do not devote sufficient
Automation in paper industry warehousing
management systems like WMS, WCS, and ERP combined with the automating machines
and equipment used for different stages of warehousing such as receipt, storage, picking, and
packing. The choice of appropriate technologies would depend on the level of automation
that the company chooses which can be manual, automated or automatic. Manual operations
do not make use of any information systems or automated machines while automated
warehouses make use of both. An automatic warehouse would make the highest level of
automation as the human involvement almost get eliminated with the replacement by the
robots. In the current research, the focus would be on the automated warehouse which is
developed using automation equipment’s and technologies.
Warehouse operations
Every warehouse has inbound, inventory, and outbound processes but they may be different
in specific steps used for warehousing. However, there can be some basic steps listed for
warehouse operations that are used in most warehouses as standards. These include receipt,
put away, storage, picking, and shipping.
Receipt: The warehouse management receives an information on the incoming materials or
goods in advance so that receipt and unloading of the goods can be planned before the goods
arrive. In a distribution warehouse, goods are received, scanned and registered when they
arrive. An inspection is done at the time of receipt to check the quality of quantity of goods
received to ensure that they are as per the plan. In a production warehouse, raw materials are
received and normally, the quality check is not required.
Put Away: Every product that is received in the warehouse is allocated a location inside and
this location has to be determined fast so that as soon as the receipt is taken, the goods are put
in the right place in the warehouse. For this to happen, an efficient inventory management is
required. This would involve ad advance knowledge of the available locations, their size, and
the weight they can handle. The location of the storage is scanned to keep the inventory
records and the information is added to the picking lists (Tomé, 2014).
Storage: Storage is one of the most important activities of a warehouse. Storage management
needs three types of decisions to be made that include the count of inventory to be stored in
SKUs, time for replenishment of each SKU, and the storage location of the SKU in the
warehouse. The first two decisions are a part of inventory control while the third decision
deals with the efficiency of storage and access to resources. A warehouse that is well-slotted
can bring efficiencies in storage but many distribution centres do not devote sufficient
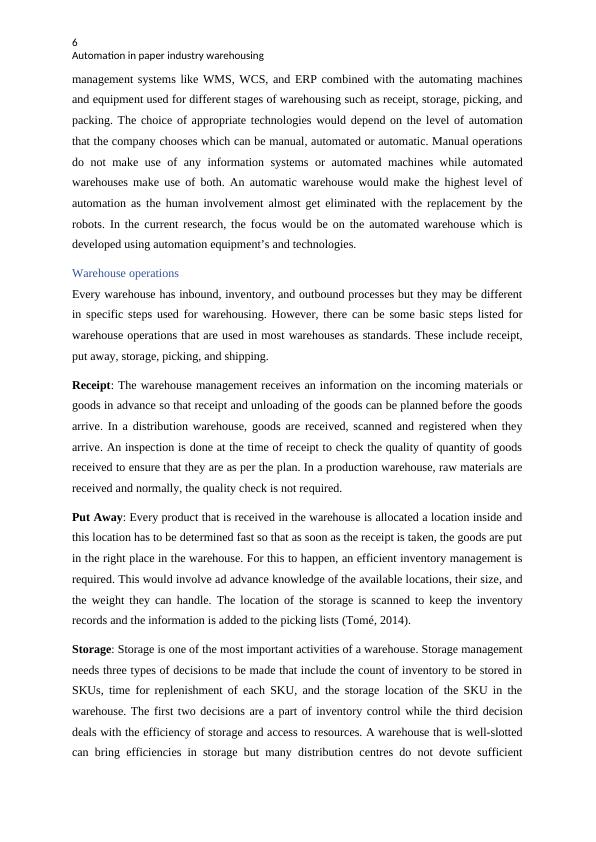
7
Automation in paper industry warehousing
resources for slotting operations. Slotting ensures that products are provided with most
convenient storage equipment and the labour force involved in placing products to assigned
storage location is optimum. It also gives other benefits like good ergonomics for material or
product handling.
The cost that can other occur due to the wrong choice of location of the products of raw
materials are avoided with the use of slotting. Slotting involves creation of assignment
policies that determine the rules for assigning position to SKUs in warehouses. This policy
can be dedicated such that a single location is assigned only to one type of product. This kind
of arrangement is convenient and workers gradually learn the layout and thus, can be fast in
order-picking. However, dedicated assignment ignores the need for optimum space usage and
most of such warehouses have only 50% of the space utilization. Random assignment is more
common approach to defining storage policy and in this approach, multiple locations can be
assigned to same products and the empty location is immediately utilized. However, such
warehouses need a support from software for location assignment and the workers may not
already know where a product should go. This type of warehousing has 66% of space
utilization which is higher than the dedicated arrangement and thus, is more optimum
approach (Borgen & Vaagen, 2011).
Order picking: When an order is received from a customer, the sought products have to be
found in the warehouse which needs verification of their availability in the warehouse. A
picking list is referred to by the workers to check availability. This activity is usually
performed in big warehouses using a warehouse management system that has picking policies
storage based on which grouping of order can also be done. These policies can be different
with different warehouses or products. Common picking policies can be strict-order picking,
batch picking, zone picking, and wave picking (Agrawal, Heragu, & Methapatra, 2016).
In strict-order picking, complete tour of the warehouse is taken by the picker to find out all
SKUs needed for one single order. Batch picking involves clubbing of multiple orders into
single picking which saves the time of the picker by limiting the travel time of the picker.
Wave picking also involves multiple orders picking at one go and is used with scheduled
shipments. Orders can be released from multiple zones within a warehouse for picking
considering the batch sizes that must be adjusted as per the available picking time. The choice
of policy would depend on the volume of activities and the capacity of available trucks. A
strict-order picking is used when the truck size is very small. Wave and batch picking is used
Automation in paper industry warehousing
resources for slotting operations. Slotting ensures that products are provided with most
convenient storage equipment and the labour force involved in placing products to assigned
storage location is optimum. It also gives other benefits like good ergonomics for material or
product handling.
The cost that can other occur due to the wrong choice of location of the products of raw
materials are avoided with the use of slotting. Slotting involves creation of assignment
policies that determine the rules for assigning position to SKUs in warehouses. This policy
can be dedicated such that a single location is assigned only to one type of product. This kind
of arrangement is convenient and workers gradually learn the layout and thus, can be fast in
order-picking. However, dedicated assignment ignores the need for optimum space usage and
most of such warehouses have only 50% of the space utilization. Random assignment is more
common approach to defining storage policy and in this approach, multiple locations can be
assigned to same products and the empty location is immediately utilized. However, such
warehouses need a support from software for location assignment and the workers may not
already know where a product should go. This type of warehousing has 66% of space
utilization which is higher than the dedicated arrangement and thus, is more optimum
approach (Borgen & Vaagen, 2011).
Order picking: When an order is received from a customer, the sought products have to be
found in the warehouse which needs verification of their availability in the warehouse. A
picking list is referred to by the workers to check availability. This activity is usually
performed in big warehouses using a warehouse management system that has picking policies
storage based on which grouping of order can also be done. These policies can be different
with different warehouses or products. Common picking policies can be strict-order picking,
batch picking, zone picking, and wave picking (Agrawal, Heragu, & Methapatra, 2016).
In strict-order picking, complete tour of the warehouse is taken by the picker to find out all
SKUs needed for one single order. Batch picking involves clubbing of multiple orders into
single picking which saves the time of the picker by limiting the travel time of the picker.
Wave picking also involves multiple orders picking at one go and is used with scheduled
shipments. Orders can be released from multiple zones within a warehouse for picking
considering the batch sizes that must be adjusted as per the available picking time. The choice
of policy would depend on the volume of activities and the capacity of available trucks. A
strict-order picking is used when the truck size is very small. Wave and batch picking is used
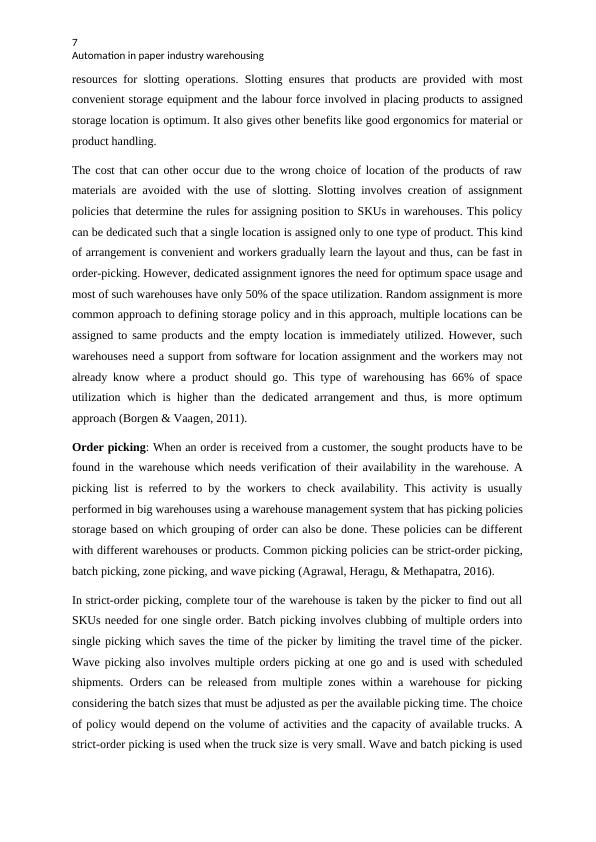
8
Automation in paper industry warehousing
for large number of orders received at the same time that need multiple pickers to do the
picking of multiple orders. Zone picking is most suitable for small products.
Packing and Shipping: Packing is a very labour-intensive activity and needs careful work to
ensure that order is effectively fulfilled which ensures customer satisfaction. Once packaged,
goods are shipped into containers using cases and pallets. The containers are put on the
trailers for transportation but before it is done, containers are scanned for registering them for
departure and the update of the status of order is sent to the customer.
Warehouse Designing
Warehouse design is crucial to warehouse operational efficiencies but not easy as it comes
with several issues and challenges that make decisions tougher. A number of risks may be
involved that are important to considered while taking decisions on the design approaches for
a warehouse. These include market or industry trends that may show dramatic changes,
corporate objectives that warehouse design must fit with, and business plans that have
objectives to make sales and develop markets such that warehousing strategy has to be made
suited to these plans. Warehousing strategies can also depend on other factors like batch sizes
of received goods, characteristics of orders, financial restraints, information technology,
levels of customer service, and regulatory factors (Jindal & Taneja, 2012).
Automation in paper industry warehousing
for large number of orders received at the same time that need multiple pickers to do the
picking of multiple orders. Zone picking is most suitable for small products.
Packing and Shipping: Packing is a very labour-intensive activity and needs careful work to
ensure that order is effectively fulfilled which ensures customer satisfaction. Once packaged,
goods are shipped into containers using cases and pallets. The containers are put on the
trailers for transportation but before it is done, containers are scanned for registering them for
departure and the update of the status of order is sent to the customer.
Warehouse Designing
Warehouse design is crucial to warehouse operational efficiencies but not easy as it comes
with several issues and challenges that make decisions tougher. A number of risks may be
involved that are important to considered while taking decisions on the design approaches for
a warehouse. These include market or industry trends that may show dramatic changes,
corporate objectives that warehouse design must fit with, and business plans that have
objectives to make sales and develop markets such that warehousing strategy has to be made
suited to these plans. Warehousing strategies can also depend on other factors like batch sizes
of received goods, characteristics of orders, financial restraints, information technology,
levels of customer service, and regulatory factors (Jindal & Taneja, 2012).
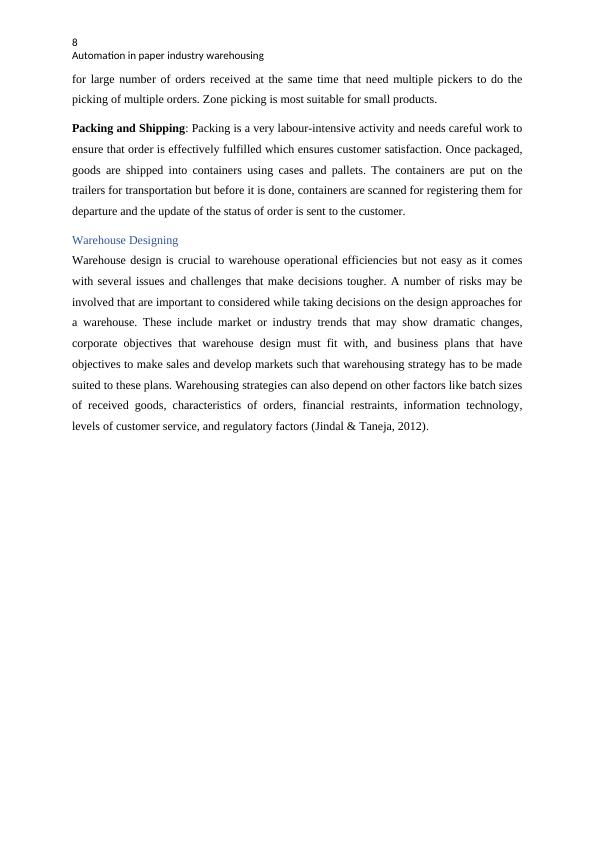
End of preview
Want to access all the pages? Upload your documents or become a member.
Related Documents
Warehouse Performance and Future Trendslg...
|19
|3962
|324
Report on Logistic Managementlg...
|9
|2580
|60
Issues and Challenges in Logistics Companies in Singaporelg...
|59
|12834
|3
Warehousing Functions, Importance, and Benefits -lg...
|9
|1231
|14
Warehousing and Distribution.lg...
|4
|775
|13
Supply Chain Process of Haygrove: A Case Studylg...
|6
|1148
|196