Finance Assignment: Overhead Allocation and Activity Based Costing
VerifiedAdded on 2023/01/18
|6
|1357
|70
Homework Assignment
AI Summary
This assignment analyzes overhead allocation and activity-based costing (ABC) methods, focusing on Dwayne Manufacturing Ltd. Part A calculates departmental and plant-wide overhead rates using provided cost and operational data. It includes the allocation of indirect costs, the computation of overhead rates for machining and assembly departments, and a plan...
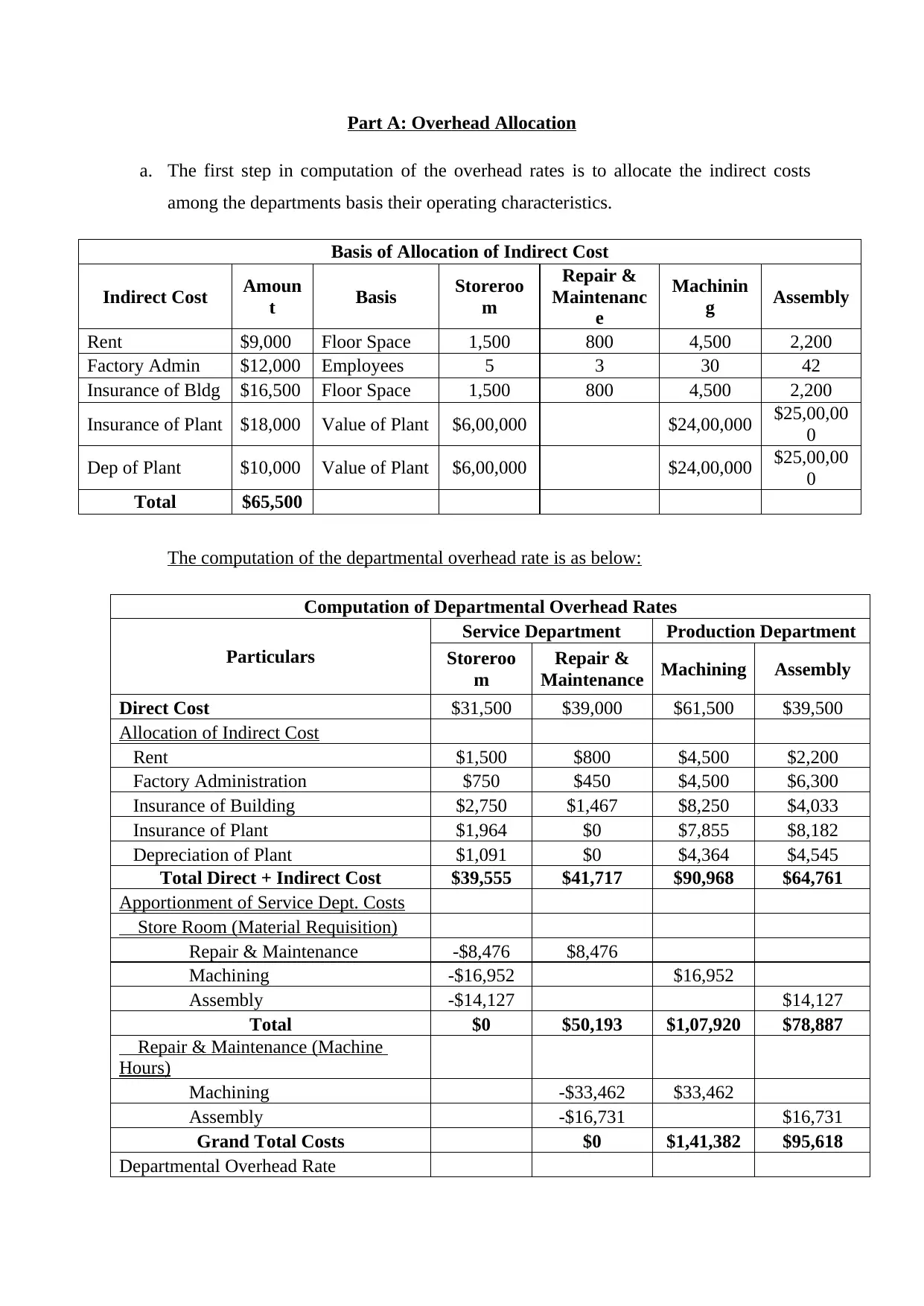
Part A: Overhead Allocation
a. The first step in computation of the overhead rates is to allocate the indirect costs
among the departments basis their operating characteristics.
Basis of Allocation of Indirect Cost
Indirect Cost Amoun
t Basis Storeroo
m
Repair &
Maintenanc
e
Machinin
g Assembly
Rent $9,000 Floor Space 1,500 800 4,500 2,200
Factory Admin $12,000 Employees 5 3 30 42
Insurance of Bldg $16,500 Floor Space 1,500 800 4,500 2,200
Insurance of Plant $18,000 Value of Plant $6,00,000 $24,00,000 $25,00,00
0
Dep of Plant $10,000 Value of Plant $6,00,000 $24,00,000 $25,00,00
0
Total $65,500
The computation of the departmental overhead rate is as below:
Computation of Departmental Overhead Rates
Particulars
Service Department Production Department
Storeroo
m
Repair &
Maintenance Machining Assembly
Direct Cost $31,500 $39,000 $61,500 $39,500
Allocation of Indirect Cost
Rent $1,500 $800 $4,500 $2,200
Factory Administration $750 $450 $4,500 $6,300
Insurance of Building $2,750 $1,467 $8,250 $4,033
Insurance of Plant $1,964 $0 $7,855 $8,182
Depreciation of Plant $1,091 $0 $4,364 $4,545
Total Direct + Indirect Cost $39,555 $41,717 $90,968 $64,761
Apportionment of Service Dept. Costs
Store Room (Material Requisition)
Repair & Maintenance -$8,476 $8,476
Machining -$16,952 $16,952
Assembly -$14,127 $14,127
Total $0 $50,193 $1,07,920 $78,887
Repair & Maintenance (Machine
Hours)
Machining -$33,462 $33,462
Assembly -$16,731 $16,731
Grand Total Costs $0 $1,41,382 $95,618
Departmental Overhead Rate
a. The first step in computation of the overhead rates is to allocate the indirect costs
among the departments basis their operating characteristics.
Basis of Allocation of Indirect Cost
Indirect Cost Amoun
t Basis Storeroo
m
Repair &
Maintenanc
e
Machinin
g Assembly
Rent $9,000 Floor Space 1,500 800 4,500 2,200
Factory Admin $12,000 Employees 5 3 30 42
Insurance of Bldg $16,500 Floor Space 1,500 800 4,500 2,200
Insurance of Plant $18,000 Value of Plant $6,00,000 $24,00,000 $25,00,00
0
Dep of Plant $10,000 Value of Plant $6,00,000 $24,00,000 $25,00,00
0
Total $65,500
The computation of the departmental overhead rate is as below:
Computation of Departmental Overhead Rates
Particulars
Service Department Production Department
Storeroo
m
Repair &
Maintenance Machining Assembly
Direct Cost $31,500 $39,000 $61,500 $39,500
Allocation of Indirect Cost
Rent $1,500 $800 $4,500 $2,200
Factory Administration $750 $450 $4,500 $6,300
Insurance of Building $2,750 $1,467 $8,250 $4,033
Insurance of Plant $1,964 $0 $7,855 $8,182
Depreciation of Plant $1,091 $0 $4,364 $4,545
Total Direct + Indirect Cost $39,555 $41,717 $90,968 $64,761
Apportionment of Service Dept. Costs
Store Room (Material Requisition)
Repair & Maintenance -$8,476 $8,476
Machining -$16,952 $16,952
Assembly -$14,127 $14,127
Total $0 $50,193 $1,07,920 $78,887
Repair & Maintenance (Machine
Hours)
Machining -$33,462 $33,462
Assembly -$16,731 $16,731
Grand Total Costs $0 $1,41,382 $95,618
Departmental Overhead Rate
Paraphrase This Document
Need a fresh take? Get an instant paraphrase of this document with our AI Paraphraser
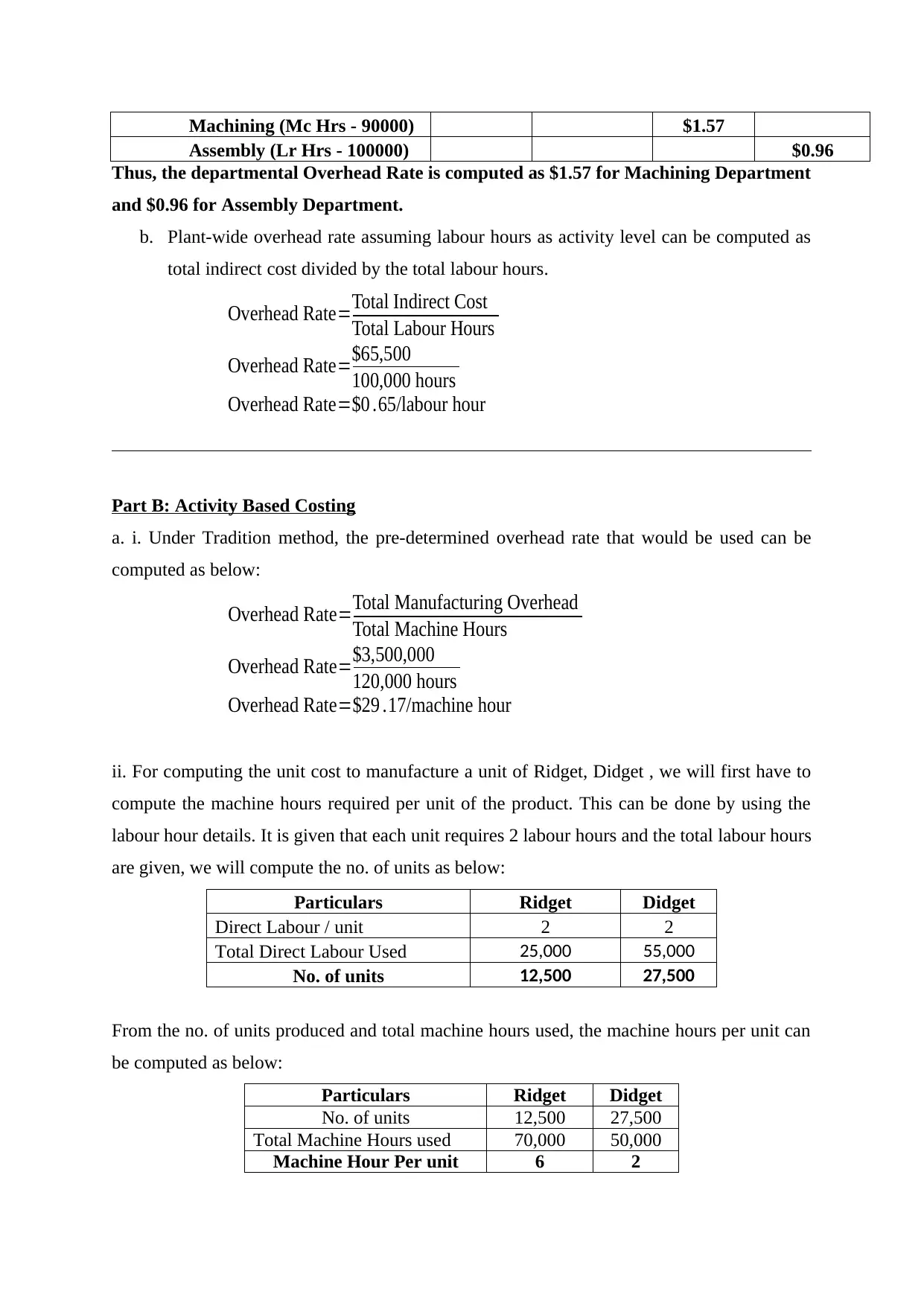
Machining (Mc Hrs - 90000) $1.57
Assembly (Lr Hrs - 100000) $0.96
Thus, the departmental Overhead Rate is computed as $1.57 for Machining Department
and $0.96 for Assembly Department.
b. Plant-wide overhead rate assuming labour hours as activity level can be computed as
total indirect cost divided by the total labour hours.
Overhead Rate=Total Indirect Cost
Total Labour Hours
Overhead Rate=$65,500
100,000 hours
Overhead Rate=$0 .65/labour hour
Part B: Activity Based Costing
a. i. Under Tradition method, the pre-determined overhead rate that would be used can be
computed as below:
Overhead Rate=Total Manufacturing Overhead
Total Machine Hours
Overhead Rate=$3,500,000
120,000 hours
Overhead Rate=$29 .17/machine hour
ii. For computing the unit cost to manufacture a unit of Ridget, Didget , we will first have to
compute the machine hours required per unit of the product. This can be done by using the
labour hour details. It is given that each unit requires 2 labour hours and the total labour hours
are given, we will compute the no. of units as below:
Particulars Ridget Didget
Direct Labour / unit 2 2
Total Direct Labour Used 25,000 55,000
No. of units 12,500 27,500
From the no. of units produced and total machine hours used, the machine hours per unit can
be computed as below:
Particulars Ridget Didget
No. of units 12,500 27,500
Total Machine Hours used 70,000 50,000
Machine Hour Per unit 6 2
Assembly (Lr Hrs - 100000) $0.96
Thus, the departmental Overhead Rate is computed as $1.57 for Machining Department
and $0.96 for Assembly Department.
b. Plant-wide overhead rate assuming labour hours as activity level can be computed as
total indirect cost divided by the total labour hours.
Overhead Rate=Total Indirect Cost
Total Labour Hours
Overhead Rate=$65,500
100,000 hours
Overhead Rate=$0 .65/labour hour
Part B: Activity Based Costing
a. i. Under Tradition method, the pre-determined overhead rate that would be used can be
computed as below:
Overhead Rate=Total Manufacturing Overhead
Total Machine Hours
Overhead Rate=$3,500,000
120,000 hours
Overhead Rate=$29 .17/machine hour
ii. For computing the unit cost to manufacture a unit of Ridget, Didget , we will first have to
compute the machine hours required per unit of the product. This can be done by using the
labour hour details. It is given that each unit requires 2 labour hours and the total labour hours
are given, we will compute the no. of units as below:
Particulars Ridget Didget
Direct Labour / unit 2 2
Total Direct Labour Used 25,000 55,000
No. of units 12,500 27,500
From the no. of units produced and total machine hours used, the machine hours per unit can
be computed as below:
Particulars Ridget Didget
No. of units 12,500 27,500
Total Machine Hours used 70,000 50,000
Machine Hour Per unit 6 2
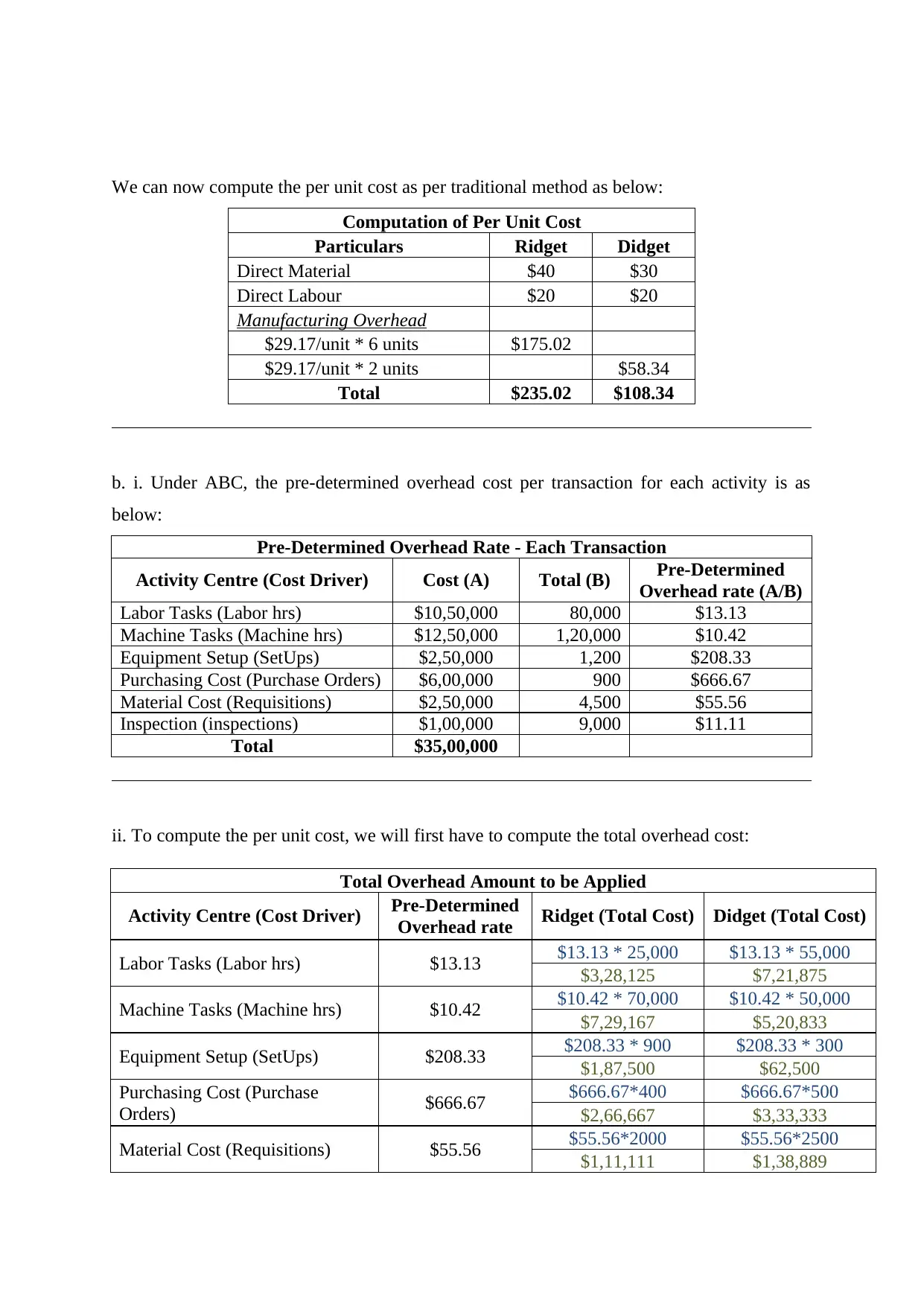
We can now compute the per unit cost as per traditional method as below:
Computation of Per Unit Cost
Particulars Ridget Didget
Direct Material $40 $30
Direct Labour $20 $20
Manufacturing Overhead
$29.17/unit * 6 units $175.02
$29.17/unit * 2 units $58.34
Total $235.02 $108.34
b. i. Under ABC, the pre-determined overhead cost per transaction for each activity is as
below:
Pre-Determined Overhead Rate - Each Transaction
Activity Centre (Cost Driver) Cost (A) Total (B) Pre-Determined
Overhead rate (A/B)
Labor Tasks (Labor hrs) $10,50,000 80,000 $13.13
Machine Tasks (Machine hrs) $12,50,000 1,20,000 $10.42
Equipment Setup (SetUps) $2,50,000 1,200 $208.33
Purchasing Cost (Purchase Orders) $6,00,000 900 $666.67
Material Cost (Requisitions) $2,50,000 4,500 $55.56
Inspection (inspections) $1,00,000 9,000 $11.11
Total $35,00,000
ii. To compute the per unit cost, we will first have to compute the total overhead cost:
Total Overhead Amount to be Applied
Activity Centre (Cost Driver) Pre-Determined
Overhead rate Ridget (Total Cost) Didget (Total Cost)
Labor Tasks (Labor hrs) $13.13 $13.13 * 25,000 $13.13 * 55,000
$3,28,125 $7,21,875
Machine Tasks (Machine hrs) $10.42 $10.42 * 70,000 $10.42 * 50,000
$7,29,167 $5,20,833
Equipment Setup (SetUps) $208.33 $208.33 * 900 $208.33 * 300
$1,87,500 $62,500
Purchasing Cost (Purchase
Orders) $666.67 $666.67*400 $666.67*500
$2,66,667 $3,33,333
Material Cost (Requisitions) $55.56 $55.56*2000 $55.56*2500
$1,11,111 $1,38,889
Computation of Per Unit Cost
Particulars Ridget Didget
Direct Material $40 $30
Direct Labour $20 $20
Manufacturing Overhead
$29.17/unit * 6 units $175.02
$29.17/unit * 2 units $58.34
Total $235.02 $108.34
b. i. Under ABC, the pre-determined overhead cost per transaction for each activity is as
below:
Pre-Determined Overhead Rate - Each Transaction
Activity Centre (Cost Driver) Cost (A) Total (B) Pre-Determined
Overhead rate (A/B)
Labor Tasks (Labor hrs) $10,50,000 80,000 $13.13
Machine Tasks (Machine hrs) $12,50,000 1,20,000 $10.42
Equipment Setup (SetUps) $2,50,000 1,200 $208.33
Purchasing Cost (Purchase Orders) $6,00,000 900 $666.67
Material Cost (Requisitions) $2,50,000 4,500 $55.56
Inspection (inspections) $1,00,000 9,000 $11.11
Total $35,00,000
ii. To compute the per unit cost, we will first have to compute the total overhead cost:
Total Overhead Amount to be Applied
Activity Centre (Cost Driver) Pre-Determined
Overhead rate Ridget (Total Cost) Didget (Total Cost)
Labor Tasks (Labor hrs) $13.13 $13.13 * 25,000 $13.13 * 55,000
$3,28,125 $7,21,875
Machine Tasks (Machine hrs) $10.42 $10.42 * 70,000 $10.42 * 50,000
$7,29,167 $5,20,833
Equipment Setup (SetUps) $208.33 $208.33 * 900 $208.33 * 300
$1,87,500 $62,500
Purchasing Cost (Purchase
Orders) $666.67 $666.67*400 $666.67*500
$2,66,667 $3,33,333
Material Cost (Requisitions) $55.56 $55.56*2000 $55.56*2500
$1,11,111 $1,38,889
⊘ This is a preview!⊘
Do you want full access?
Subscribe today to unlock all pages.

Trusted by 1+ million students worldwide
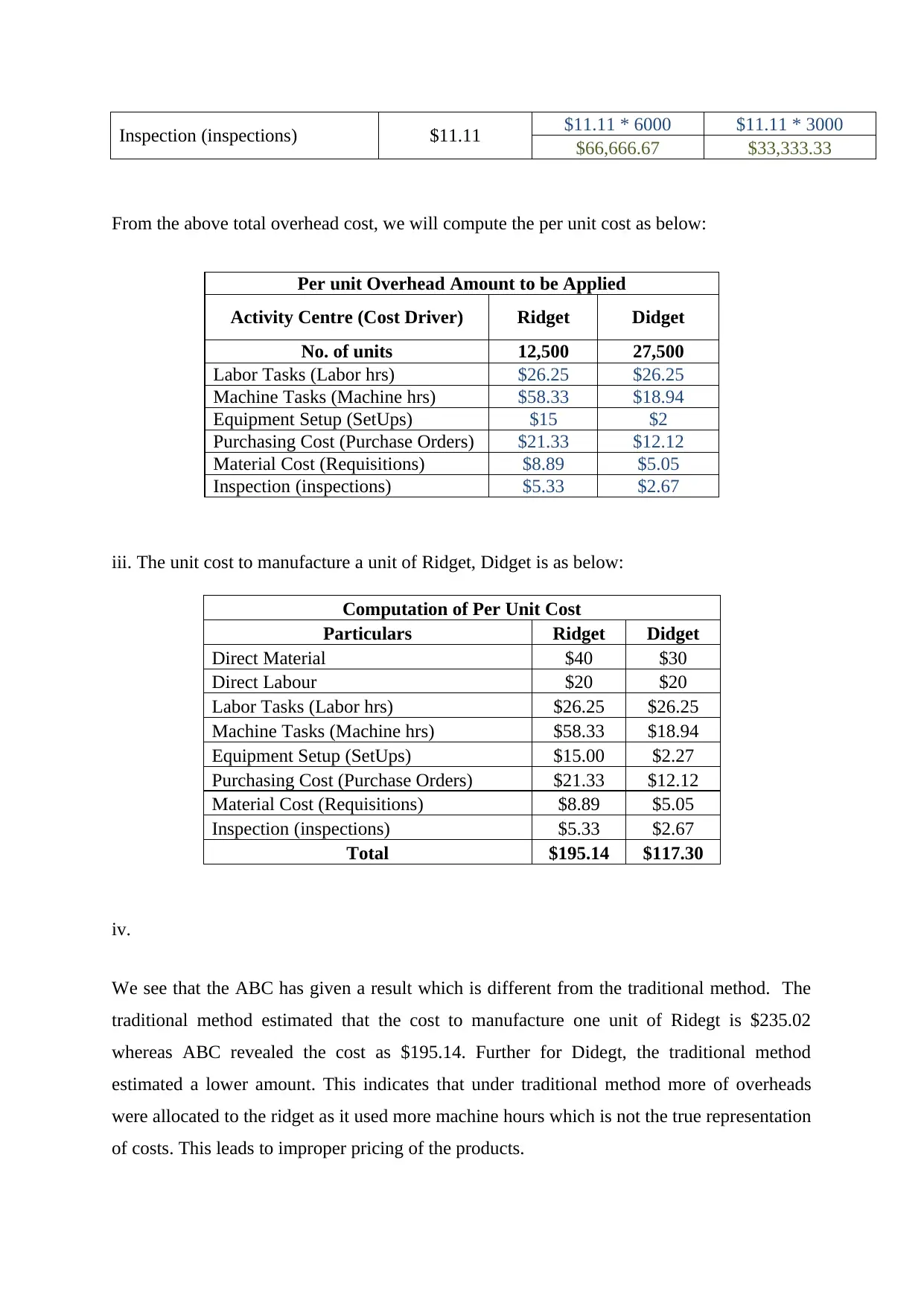
Inspection (inspections) $11.11 $11.11 * 6000 $11.11 * 3000
$66,666.67 $33,333.33
From the above total overhead cost, we will compute the per unit cost as below:
Per unit Overhead Amount to be Applied
Activity Centre (Cost Driver) Ridget Didget
No. of units 12,500 27,500
Labor Tasks (Labor hrs) $26.25 $26.25
Machine Tasks (Machine hrs) $58.33 $18.94
Equipment Setup (SetUps) $15 $2
Purchasing Cost (Purchase Orders) $21.33 $12.12
Material Cost (Requisitions) $8.89 $5.05
Inspection (inspections) $5.33 $2.67
iii. The unit cost to manufacture a unit of Ridget, Didget is as below:
Computation of Per Unit Cost
Particulars Ridget Didget
Direct Material $40 $30
Direct Labour $20 $20
Labor Tasks (Labor hrs) $26.25 $26.25
Machine Tasks (Machine hrs) $58.33 $18.94
Equipment Setup (SetUps) $15.00 $2.27
Purchasing Cost (Purchase Orders) $21.33 $12.12
Material Cost (Requisitions) $8.89 $5.05
Inspection (inspections) $5.33 $2.67
Total $195.14 $117.30
iv.
We see that the ABC has given a result which is different from the traditional method. The
traditional method estimated that the cost to manufacture one unit of Ridegt is $235.02
whereas ABC revealed the cost as $195.14. Further for Didegt, the traditional method
estimated a lower amount. This indicates that under traditional method more of overheads
were allocated to the ridget as it used more machine hours which is not the true representation
of costs. This leads to improper pricing of the products.
$66,666.67 $33,333.33
From the above total overhead cost, we will compute the per unit cost as below:
Per unit Overhead Amount to be Applied
Activity Centre (Cost Driver) Ridget Didget
No. of units 12,500 27,500
Labor Tasks (Labor hrs) $26.25 $26.25
Machine Tasks (Machine hrs) $58.33 $18.94
Equipment Setup (SetUps) $15 $2
Purchasing Cost (Purchase Orders) $21.33 $12.12
Material Cost (Requisitions) $8.89 $5.05
Inspection (inspections) $5.33 $2.67
iii. The unit cost to manufacture a unit of Ridget, Didget is as below:
Computation of Per Unit Cost
Particulars Ridget Didget
Direct Material $40 $30
Direct Labour $20 $20
Labor Tasks (Labor hrs) $26.25 $26.25
Machine Tasks (Machine hrs) $58.33 $18.94
Equipment Setup (SetUps) $15.00 $2.27
Purchasing Cost (Purchase Orders) $21.33 $12.12
Material Cost (Requisitions) $8.89 $5.05
Inspection (inspections) $5.33 $2.67
Total $195.14 $117.30
iv.
We see that the ABC has given a result which is different from the traditional method. The
traditional method estimated that the cost to manufacture one unit of Ridegt is $235.02
whereas ABC revealed the cost as $195.14. Further for Didegt, the traditional method
estimated a lower amount. This indicates that under traditional method more of overheads
were allocated to the ridget as it used more machine hours which is not the true representation
of costs. This leads to improper pricing of the products.
Paraphrase This Document
Need a fresh take? Get an instant paraphrase of this document with our AI Paraphraser
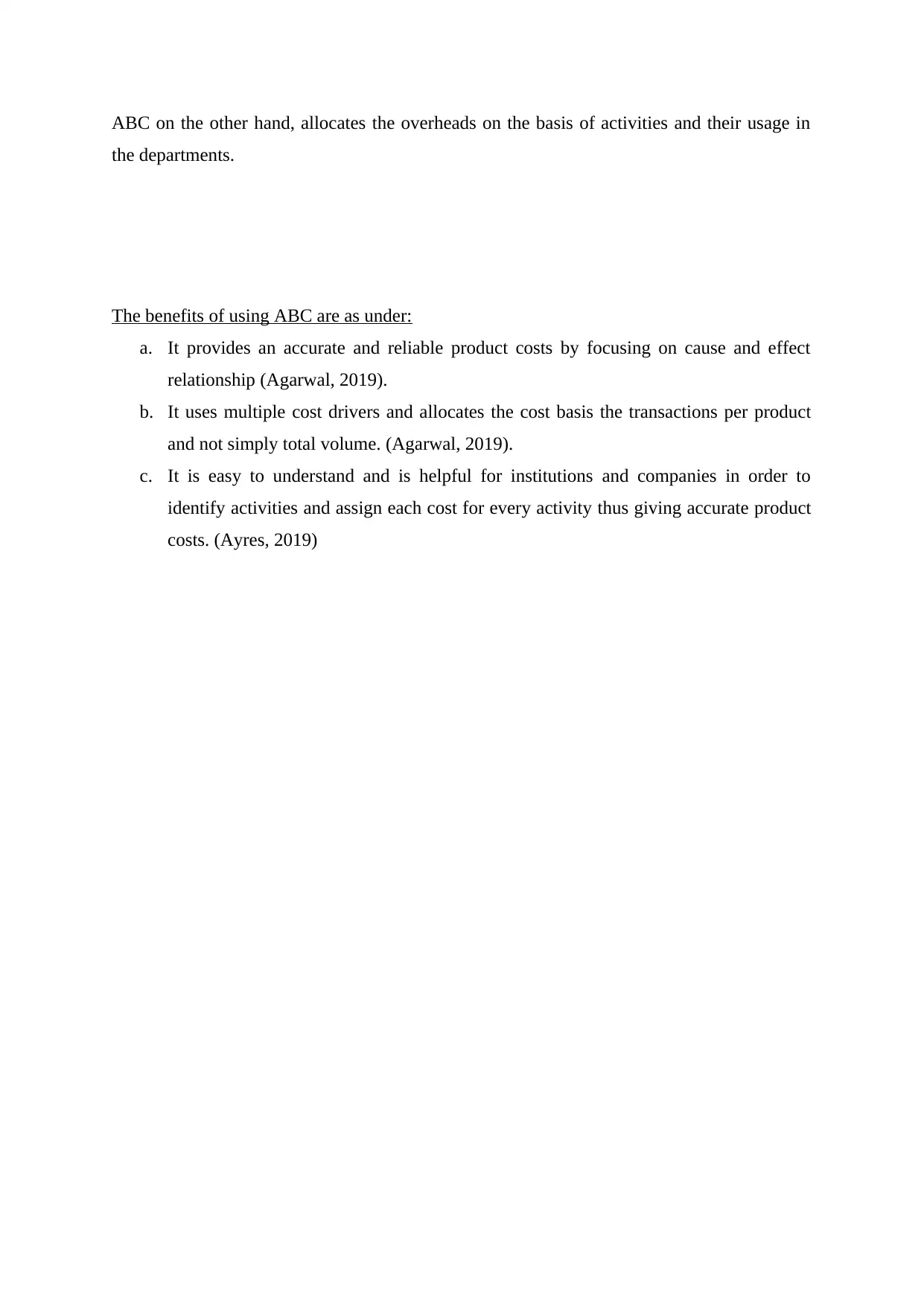
ABC on the other hand, allocates the overheads on the basis of activities and their usage in
the departments.
The benefits of using ABC are as under:
a. It provides an accurate and reliable product costs by focusing on cause and effect
relationship (Agarwal, 2019).
b. It uses multiple cost drivers and allocates the cost basis the transactions per product
and not simply total volume. (Agarwal, 2019).
c. It is easy to understand and is helpful for institutions and companies in order to
identify activities and assign each cost for every activity thus giving accurate product
costs. (Ayres, 2019)
the departments.
The benefits of using ABC are as under:
a. It provides an accurate and reliable product costs by focusing on cause and effect
relationship (Agarwal, 2019).
b. It uses multiple cost drivers and allocates the cost basis the transactions per product
and not simply total volume. (Agarwal, 2019).
c. It is easy to understand and is helpful for institutions and companies in order to
identify activities and assign each cost for every activity thus giving accurate product
costs. (Ayres, 2019)
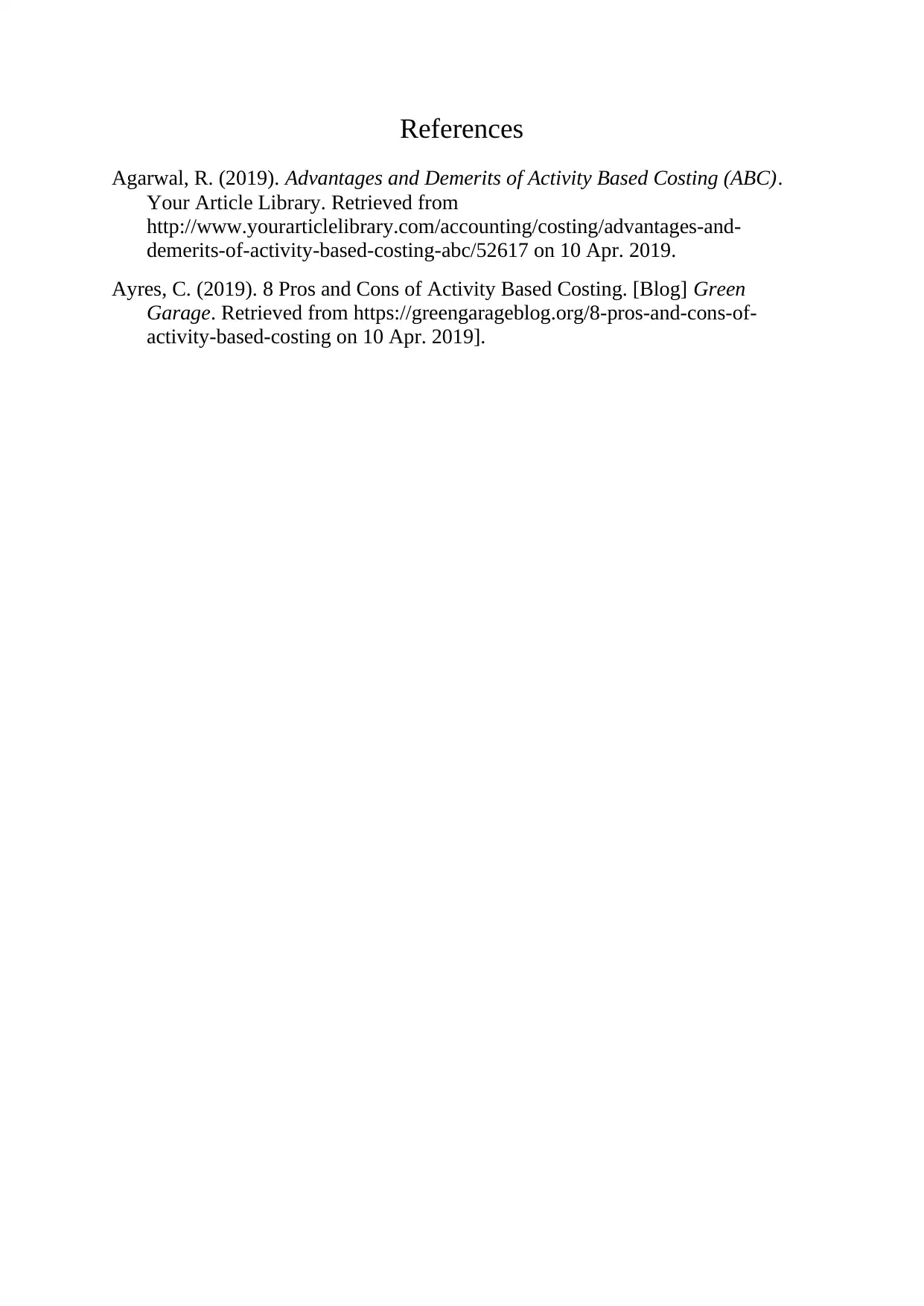
References
Agarwal, R. (2019). Advantages and Demerits of Activity Based Costing (ABC).
Your Article Library. Retrieved from
http://www.yourarticlelibrary.com/accounting/costing/advantages-and-
demerits-of-activity-based-costing-abc/52617 on 10 Apr. 2019.
Ayres, C. (2019). 8 Pros and Cons of Activity Based Costing. [Blog] Green
Garage. Retrieved from https://greengarageblog.org/8-pros-and-cons-of-
activity-based-costing on 10 Apr. 2019].
Agarwal, R. (2019). Advantages and Demerits of Activity Based Costing (ABC).
Your Article Library. Retrieved from
http://www.yourarticlelibrary.com/accounting/costing/advantages-and-
demerits-of-activity-based-costing-abc/52617 on 10 Apr. 2019.
Ayres, C. (2019). 8 Pros and Cons of Activity Based Costing. [Blog] Green
Garage. Retrieved from https://greengarageblog.org/8-pros-and-cons-of-
activity-based-costing on 10 Apr. 2019].
⊘ This is a preview!⊘
Do you want full access?
Subscribe today to unlock all pages.

Trusted by 1+ million students worldwide
1 out of 6

Your All-in-One AI-Powered Toolkit for Academic Success.
+13062052269
info@desklib.com
Available 24*7 on WhatsApp / Email
Unlock your academic potential
© 2024 | Zucol Services PVT LTD | All rights reserved.