Project Management - Assignment PDF
VerifiedAdded on 2021/12/22
|18
|3596
|40
AI Summary
Contribute Materials
Your contribution can guide someone’s learning journey. Share your
documents today.
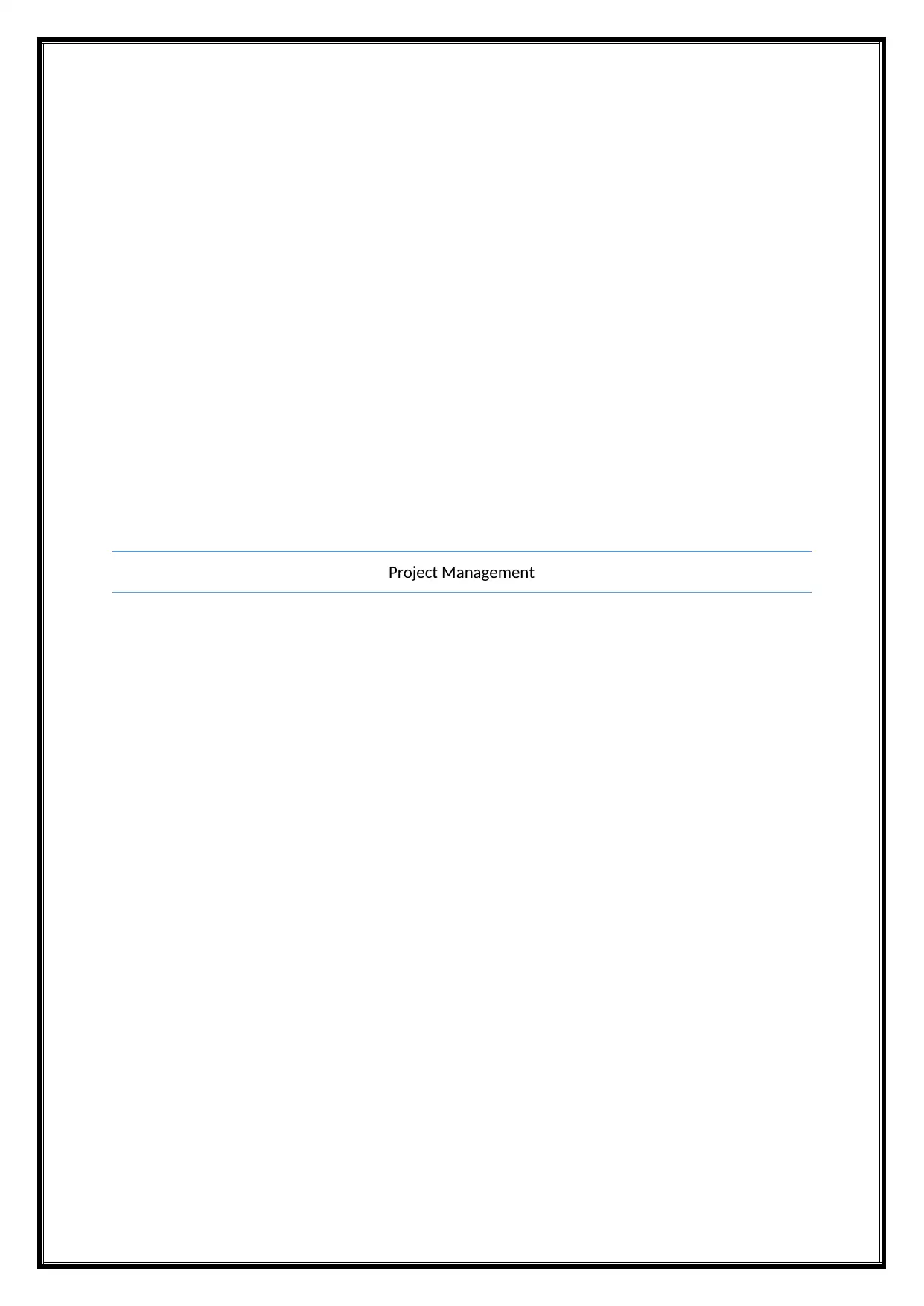
Project Management
Secure Best Marks with AI Grader
Need help grading? Try our AI Grader for instant feedback on your assignments.
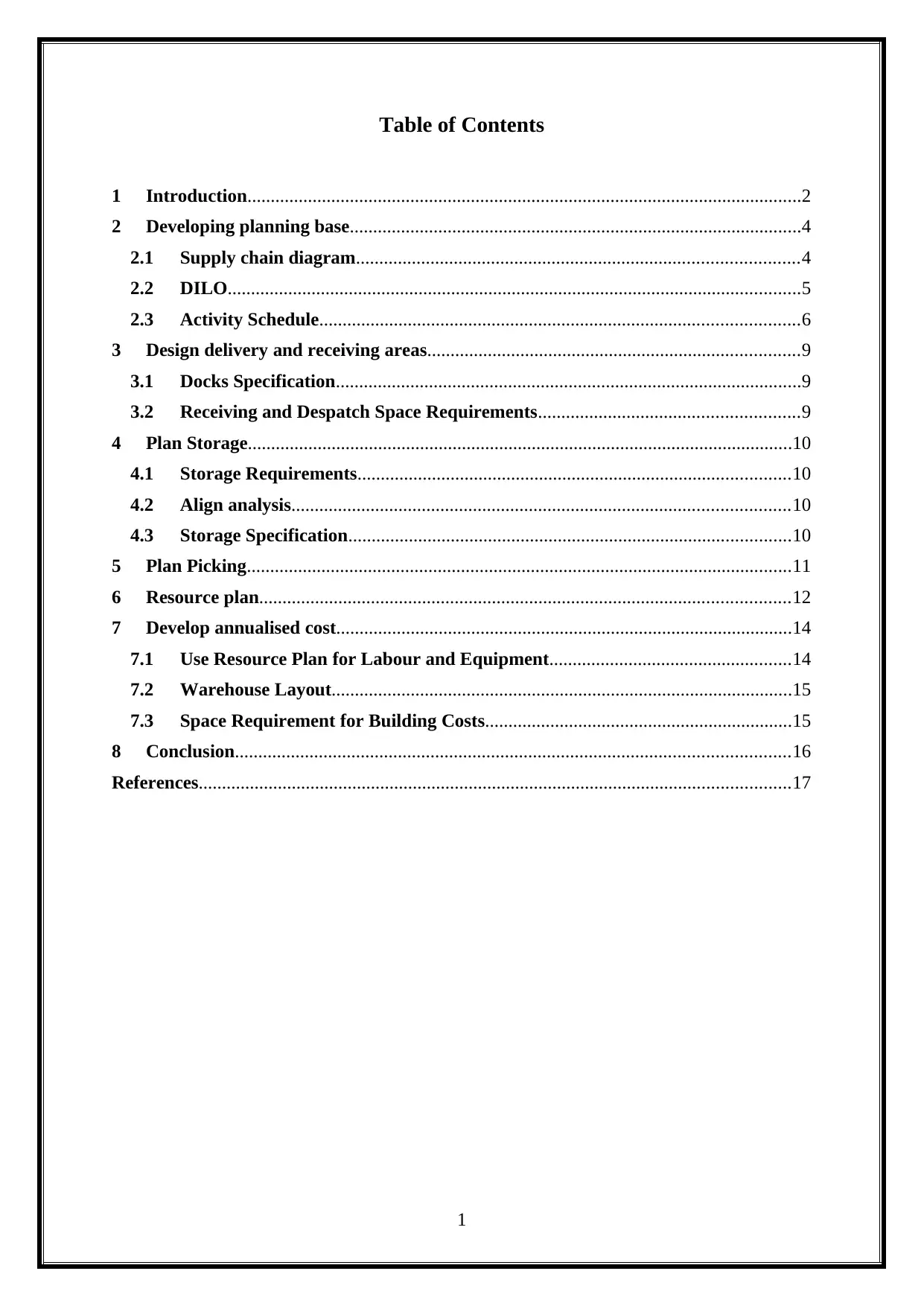
Table of Contents
1 Introduction.......................................................................................................................2
2 Developing planning base.................................................................................................4
2.1 Supply chain diagram...............................................................................................4
2.2 DILO...........................................................................................................................5
2.3 Activity Schedule.......................................................................................................6
3 Design delivery and receiving areas................................................................................9
3.1 Docks Specification....................................................................................................9
3.2 Receiving and Despatch Space Requirements........................................................9
4 Plan Storage.....................................................................................................................10
4.1 Storage Requirements.............................................................................................10
4.2 Align analysis...........................................................................................................10
4.3 Storage Specification...............................................................................................10
5 Plan Picking.....................................................................................................................11
6 Resource plan..................................................................................................................12
7 Develop annualised cost..................................................................................................14
7.1 Use Resource Plan for Labour and Equipment....................................................14
7.2 Warehouse Layout...................................................................................................15
7.3 Space Requirement for Building Costs..................................................................15
8 Conclusion.......................................................................................................................16
References...............................................................................................................................17
1
1 Introduction.......................................................................................................................2
2 Developing planning base.................................................................................................4
2.1 Supply chain diagram...............................................................................................4
2.2 DILO...........................................................................................................................5
2.3 Activity Schedule.......................................................................................................6
3 Design delivery and receiving areas................................................................................9
3.1 Docks Specification....................................................................................................9
3.2 Receiving and Despatch Space Requirements........................................................9
4 Plan Storage.....................................................................................................................10
4.1 Storage Requirements.............................................................................................10
4.2 Align analysis...........................................................................................................10
4.3 Storage Specification...............................................................................................10
5 Plan Picking.....................................................................................................................11
6 Resource plan..................................................................................................................12
7 Develop annualised cost..................................................................................................14
7.1 Use Resource Plan for Labour and Equipment....................................................14
7.2 Warehouse Layout...................................................................................................15
7.3 Space Requirement for Building Costs..................................................................15
8 Conclusion.......................................................................................................................16
References...............................................................................................................................17
1
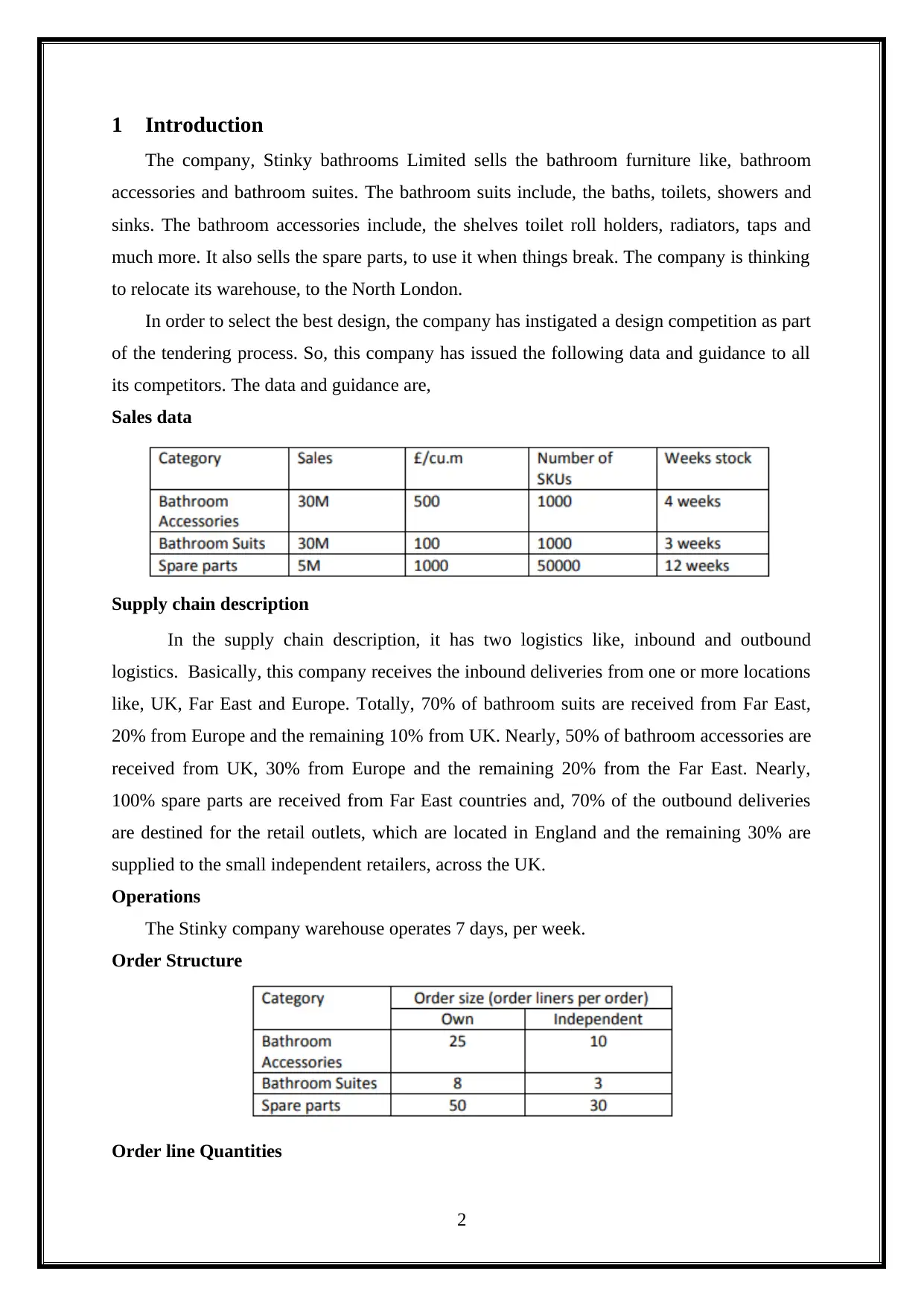
1 Introduction
The company, Stinky bathrooms Limited sells the bathroom furniture like, bathroom
accessories and bathroom suites. The bathroom suits include, the baths, toilets, showers and
sinks. The bathroom accessories include, the shelves toilet roll holders, radiators, taps and
much more. It also sells the spare parts, to use it when things break. The company is thinking
to relocate its warehouse, to the North London.
In order to select the best design, the company has instigated a design competition as part
of the tendering process. So, this company has issued the following data and guidance to all
its competitors. The data and guidance are,
Sales data
Supply chain description
In the supply chain description, it has two logistics like, inbound and outbound
logistics. Basically, this company receives the inbound deliveries from one or more locations
like, UK, Far East and Europe. Totally, 70% of bathroom suits are received from Far East,
20% from Europe and the remaining 10% from UK. Nearly, 50% of bathroom accessories are
received from UK, 30% from Europe and the remaining 20% from the Far East. Nearly,
100% spare parts are received from Far East countries and, 70% of the outbound deliveries
are destined for the retail outlets, which are located in England and the remaining 30% are
supplied to the small independent retailers, across the UK.
Operations
The Stinky company warehouse operates 7 days, per week.
Order Structure
Order line Quantities
2
The company, Stinky bathrooms Limited sells the bathroom furniture like, bathroom
accessories and bathroom suites. The bathroom suits include, the baths, toilets, showers and
sinks. The bathroom accessories include, the shelves toilet roll holders, radiators, taps and
much more. It also sells the spare parts, to use it when things break. The company is thinking
to relocate its warehouse, to the North London.
In order to select the best design, the company has instigated a design competition as part
of the tendering process. So, this company has issued the following data and guidance to all
its competitors. The data and guidance are,
Sales data
Supply chain description
In the supply chain description, it has two logistics like, inbound and outbound
logistics. Basically, this company receives the inbound deliveries from one or more locations
like, UK, Far East and Europe. Totally, 70% of bathroom suits are received from Far East,
20% from Europe and the remaining 10% from UK. Nearly, 50% of bathroom accessories are
received from UK, 30% from Europe and the remaining 20% from the Far East. Nearly,
100% spare parts are received from Far East countries and, 70% of the outbound deliveries
are destined for the retail outlets, which are located in England and the remaining 30% are
supplied to the small independent retailers, across the UK.
Operations
The Stinky company warehouse operates 7 days, per week.
Order Structure
Order line Quantities
2
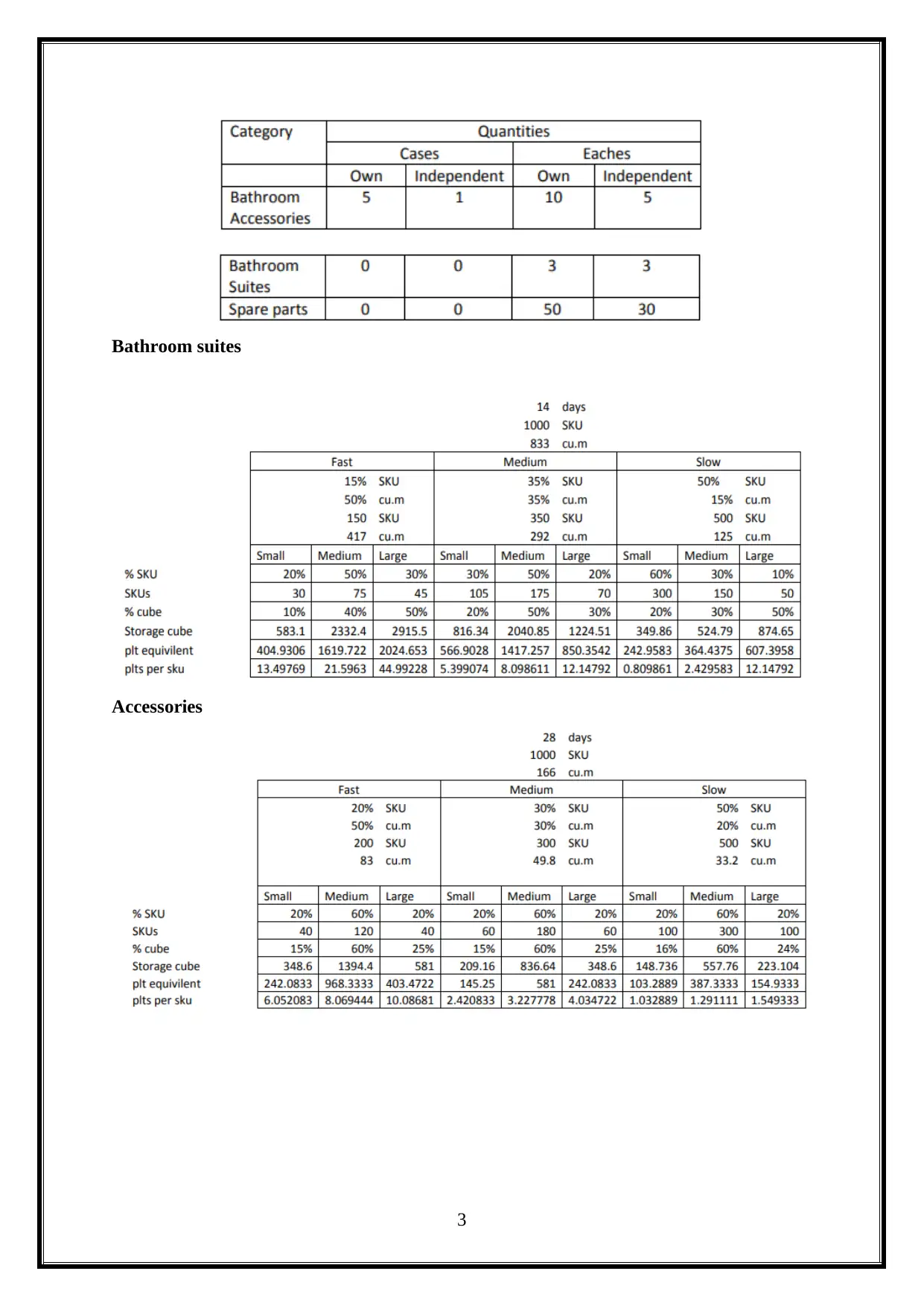
Bathroom suites
Accessories
3
Accessories
3
Secure Best Marks with AI Grader
Need help grading? Try our AI Grader for instant feedback on your assignments.
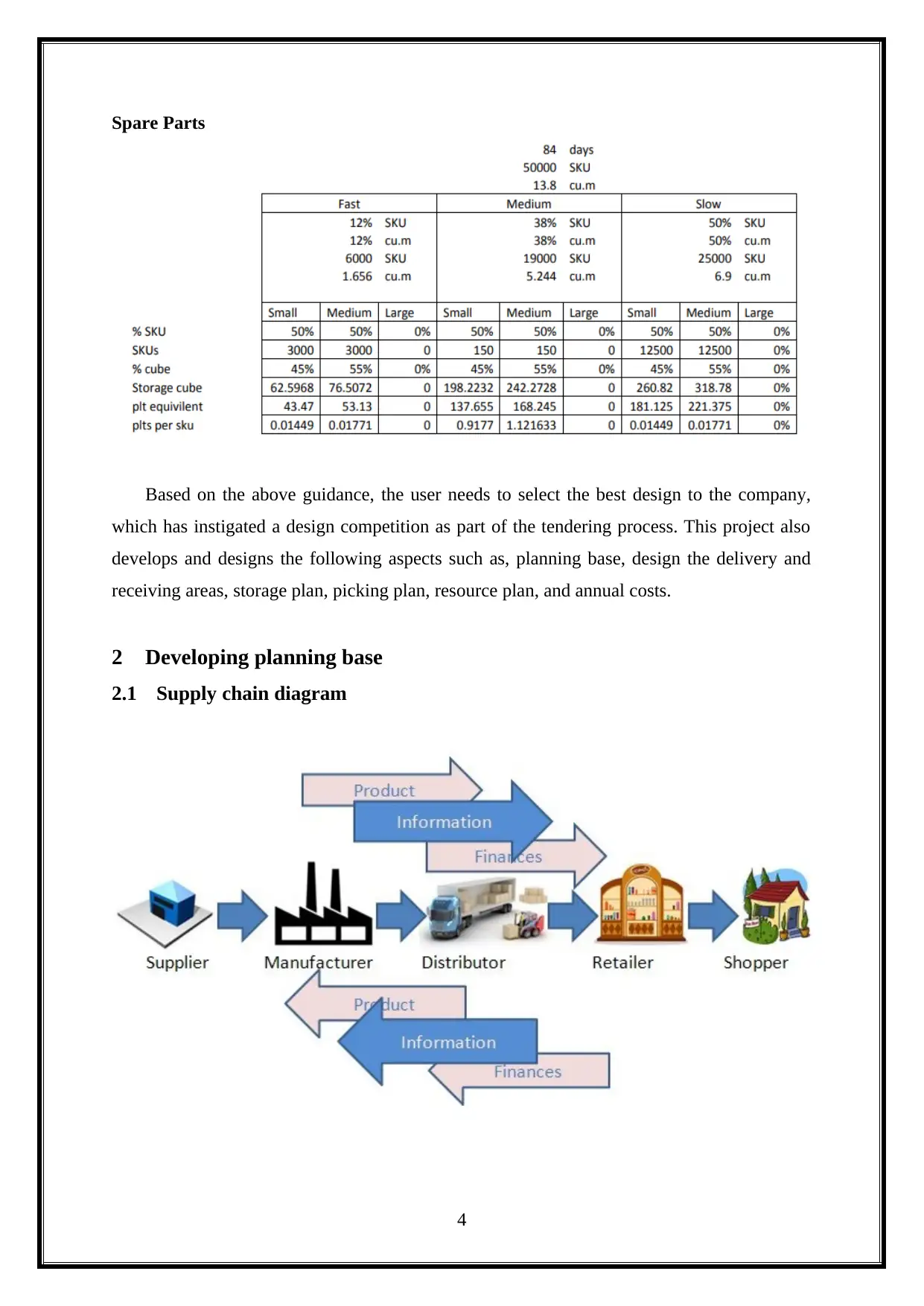
Spare Parts
Based on the above guidance, the user needs to select the best design to the company,
which has instigated a design competition as part of the tendering process. This project also
develops and designs the following aspects such as, planning base, design the delivery and
receiving areas, storage plan, picking plan, resource plan, and annual costs.
2 Developing planning base
2.1 Supply chain diagram
4
Based on the above guidance, the user needs to select the best design to the company,
which has instigated a design competition as part of the tendering process. This project also
develops and designs the following aspects such as, planning base, design the delivery and
receiving areas, storage plan, picking plan, resource plan, and annual costs.
2 Developing planning base
2.1 Supply chain diagram
4
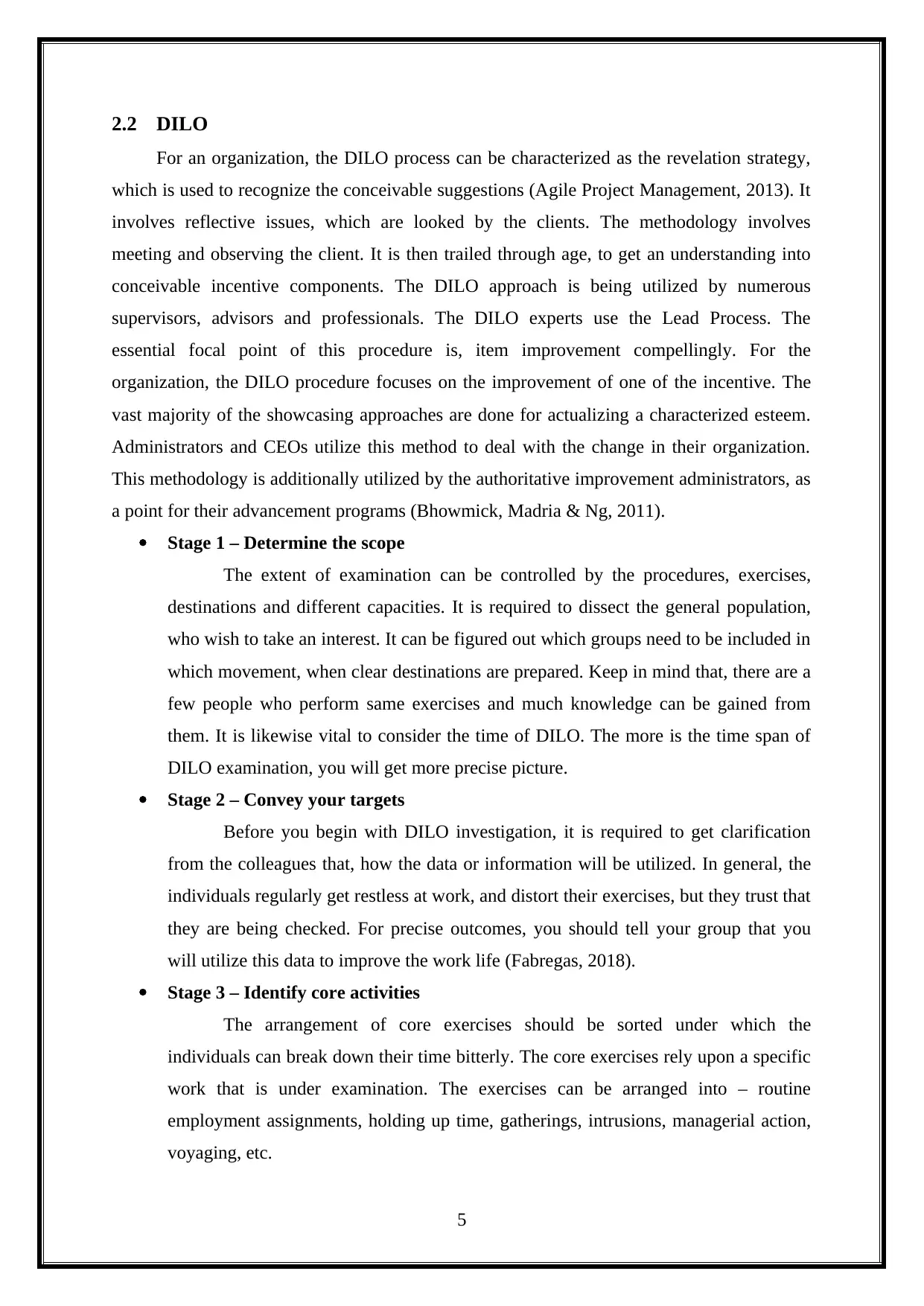
2.2 DILO
For an organization, the DILO process can be characterized as the revelation strategy,
which is used to recognize the conceivable suggestions (Agile Project Management, 2013). It
involves reflective issues, which are looked by the clients. The methodology involves
meeting and observing the client. It is then trailed through age, to get an understanding into
conceivable incentive components. The DILO approach is being utilized by numerous
supervisors, advisors and professionals. The DILO experts use the Lead Process. The
essential focal point of this procedure is, item improvement compellingly. For the
organization, the DILO procedure focuses on the improvement of one of the incentive. The
vast majority of the showcasing approaches are done for actualizing a characterized esteem.
Administrators and CEOs utilize this method to deal with the change in their organization.
This methodology is additionally utilized by the authoritative improvement administrators, as
a point for their advancement programs (Bhowmick, Madria & Ng, 2011).
Stage 1 – Determine the scope
The extent of examination can be controlled by the procedures, exercises,
destinations and different capacities. It is required to dissect the general population,
who wish to take an interest. It can be figured out which groups need to be included in
which movement, when clear destinations are prepared. Keep in mind that, there are a
few people who perform same exercises and much knowledge can be gained from
them. It is likewise vital to consider the time of DILO. The more is the time span of
DILO examination, you will get more precise picture.
Stage 2 – Convey your targets
Before you begin with DILO investigation, it is required to get clarification
from the colleagues that, how the data or information will be utilized. In general, the
individuals regularly get restless at work, and distort their exercises, but they trust that
they are being checked. For precise outcomes, you should tell your group that you
will utilize this data to improve the work life (Fabregas, 2018).
Stage 3 – Identify core activities
The arrangement of core exercises should be sorted under which the
individuals can break down their time bitterly. The core exercises rely upon a specific
work that is under examination. The exercises can be arranged into – routine
employment assignments, holding up time, gatherings, intrusions, managerial action,
voyaging, etc.
5
For an organization, the DILO process can be characterized as the revelation strategy,
which is used to recognize the conceivable suggestions (Agile Project Management, 2013). It
involves reflective issues, which are looked by the clients. The methodology involves
meeting and observing the client. It is then trailed through age, to get an understanding into
conceivable incentive components. The DILO approach is being utilized by numerous
supervisors, advisors and professionals. The DILO experts use the Lead Process. The
essential focal point of this procedure is, item improvement compellingly. For the
organization, the DILO procedure focuses on the improvement of one of the incentive. The
vast majority of the showcasing approaches are done for actualizing a characterized esteem.
Administrators and CEOs utilize this method to deal with the change in their organization.
This methodology is additionally utilized by the authoritative improvement administrators, as
a point for their advancement programs (Bhowmick, Madria & Ng, 2011).
Stage 1 – Determine the scope
The extent of examination can be controlled by the procedures, exercises,
destinations and different capacities. It is required to dissect the general population,
who wish to take an interest. It can be figured out which groups need to be included in
which movement, when clear destinations are prepared. Keep in mind that, there are a
few people who perform same exercises and much knowledge can be gained from
them. It is likewise vital to consider the time of DILO. The more is the time span of
DILO examination, you will get more precise picture.
Stage 2 – Convey your targets
Before you begin with DILO investigation, it is required to get clarification
from the colleagues that, how the data or information will be utilized. In general, the
individuals regularly get restless at work, and distort their exercises, but they trust that
they are being checked. For precise outcomes, you should tell your group that you
will utilize this data to improve the work life (Fabregas, 2018).
Stage 3 – Identify core activities
The arrangement of core exercises should be sorted under which the
individuals can break down their time bitterly. The core exercises rely upon a specific
work that is under examination. The exercises can be arranged into – routine
employment assignments, holding up time, gatherings, intrusions, managerial action,
voyaging, etc.
5
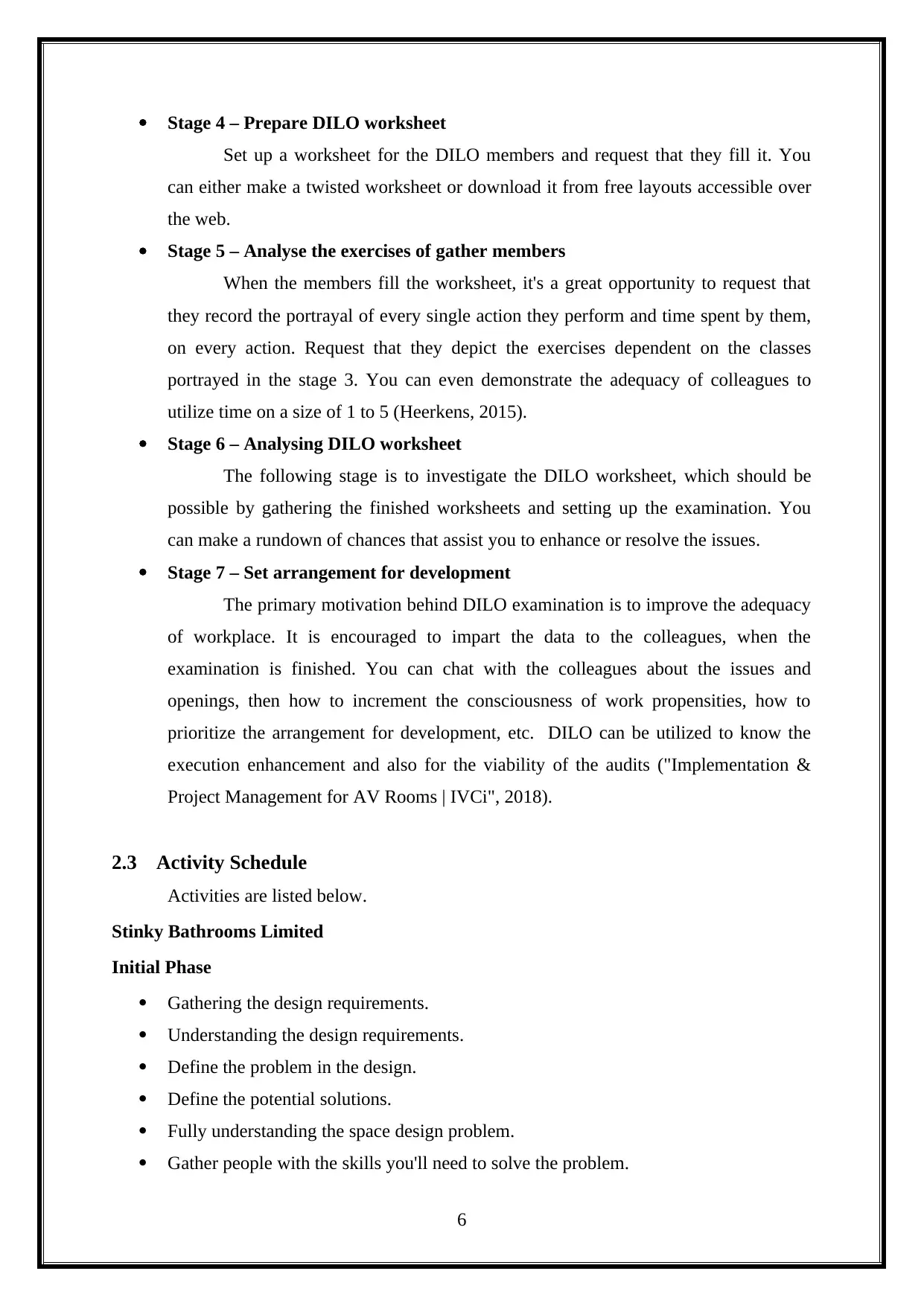
Stage 4 – Prepare DILO worksheet
Set up a worksheet for the DILO members and request that they fill it. You
can either make a twisted worksheet or download it from free layouts accessible over
the web.
Stage 5 – Analyse the exercises of gather members
When the members fill the worksheet, it's a great opportunity to request that
they record the portrayal of every single action they perform and time spent by them,
on every action. Request that they depict the exercises dependent on the classes
portrayed in the stage 3. You can even demonstrate the adequacy of colleagues to
utilize time on a size of 1 to 5 (Heerkens, 2015).
Stage 6 – Analysing DILO worksheet
The following stage is to investigate the DILO worksheet, which should be
possible by gathering the finished worksheets and setting up the examination. You
can make a rundown of chances that assist you to enhance or resolve the issues.
Stage 7 – Set arrangement for development
The primary motivation behind DILO examination is to improve the adequacy
of workplace. It is encouraged to impart the data to the colleagues, when the
examination is finished. You can chat with the colleagues about the issues and
openings, then how to increment the consciousness of work propensities, how to
prioritize the arrangement for development, etc. DILO can be utilized to know the
execution enhancement and also for the viability of the audits ("Implementation &
Project Management for AV Rooms | IVCi", 2018).
2.3 Activity Schedule
Activities are listed below.
Stinky Bathrooms Limited
Initial Phase
Gathering the design requirements.
Understanding the design requirements.
Define the problem in the design.
Define the potential solutions.
Fully understanding the space design problem.
Gather people with the skills you'll need to solve the problem.
6
Set up a worksheet for the DILO members and request that they fill it. You
can either make a twisted worksheet or download it from free layouts accessible over
the web.
Stage 5 – Analyse the exercises of gather members
When the members fill the worksheet, it's a great opportunity to request that
they record the portrayal of every single action they perform and time spent by them,
on every action. Request that they depict the exercises dependent on the classes
portrayed in the stage 3. You can even demonstrate the adequacy of colleagues to
utilize time on a size of 1 to 5 (Heerkens, 2015).
Stage 6 – Analysing DILO worksheet
The following stage is to investigate the DILO worksheet, which should be
possible by gathering the finished worksheets and setting up the examination. You
can make a rundown of chances that assist you to enhance or resolve the issues.
Stage 7 – Set arrangement for development
The primary motivation behind DILO examination is to improve the adequacy
of workplace. It is encouraged to impart the data to the colleagues, when the
examination is finished. You can chat with the colleagues about the issues and
openings, then how to increment the consciousness of work propensities, how to
prioritize the arrangement for development, etc. DILO can be utilized to know the
execution enhancement and also for the viability of the audits ("Implementation &
Project Management for AV Rooms | IVCi", 2018).
2.3 Activity Schedule
Activities are listed below.
Stinky Bathrooms Limited
Initial Phase
Gathering the design requirements.
Understanding the design requirements.
Define the problem in the design.
Define the potential solutions.
Fully understanding the space design problem.
Gather people with the skills you'll need to solve the problem.
6
Paraphrase This Document
Need a fresh take? Get an instant paraphrase of this document with our AI Paraphraser
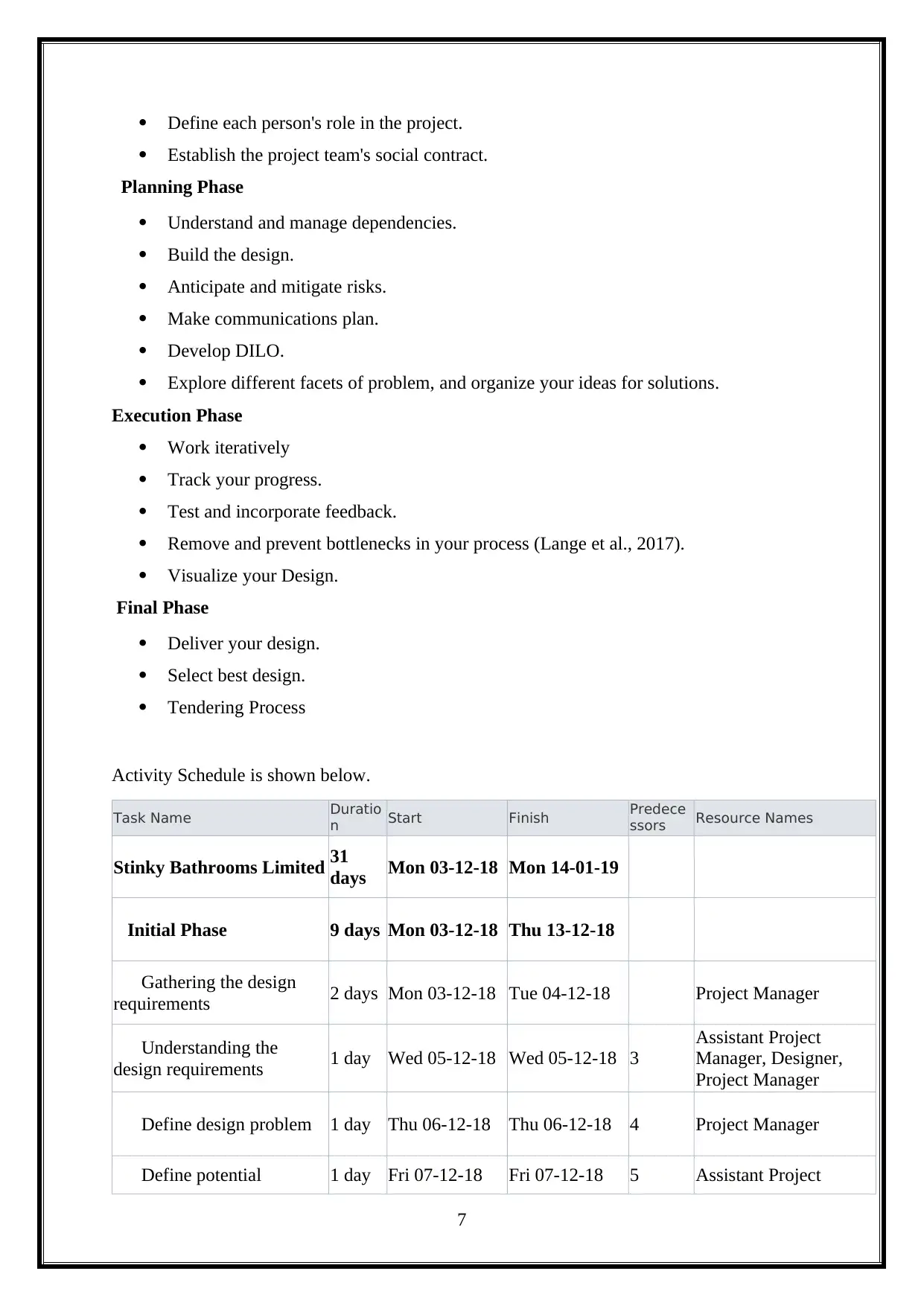
Define each person's role in the project.
Establish the project team's social contract.
Planning Phase
Understand and manage dependencies.
Build the design.
Anticipate and mitigate risks.
Make communications plan.
Develop DILO.
Explore different facets of problem, and organize your ideas for solutions.
Execution Phase
Work iteratively
Track your progress.
Test and incorporate feedback.
Remove and prevent bottlenecks in your process (Lange et al., 2017).
Visualize your Design.
Final Phase
Deliver your design.
Select best design.
Tendering Process
Activity Schedule is shown below.
Task Name Duratio
n Start Finish Predece
ssors Resource Names
Stinky Bathrooms Limited 31
days Mon 03-12-18 Mon 14-01-19
Initial Phase 9 days Mon 03-12-18 Thu 13-12-18
Gathering the design
requirements 2 days Mon 03-12-18 Tue 04-12-18 Project Manager
Understanding the
design requirements 1 day Wed 05-12-18 Wed 05-12-18 3
Assistant Project
Manager, Designer,
Project Manager
Define design problem 1 day Thu 06-12-18 Thu 06-12-18 4 Project Manager
Define potential 1 day Fri 07-12-18 Fri 07-12-18 5 Assistant Project
7
Establish the project team's social contract.
Planning Phase
Understand and manage dependencies.
Build the design.
Anticipate and mitigate risks.
Make communications plan.
Develop DILO.
Explore different facets of problem, and organize your ideas for solutions.
Execution Phase
Work iteratively
Track your progress.
Test and incorporate feedback.
Remove and prevent bottlenecks in your process (Lange et al., 2017).
Visualize your Design.
Final Phase
Deliver your design.
Select best design.
Tendering Process
Activity Schedule is shown below.
Task Name Duratio
n Start Finish Predece
ssors Resource Names
Stinky Bathrooms Limited 31
days Mon 03-12-18 Mon 14-01-19
Initial Phase 9 days Mon 03-12-18 Thu 13-12-18
Gathering the design
requirements 2 days Mon 03-12-18 Tue 04-12-18 Project Manager
Understanding the
design requirements 1 day Wed 05-12-18 Wed 05-12-18 3
Assistant Project
Manager, Designer,
Project Manager
Define design problem 1 day Thu 06-12-18 Thu 06-12-18 4 Project Manager
Define potential 1 day Fri 07-12-18 Fri 07-12-18 5 Assistant Project
7
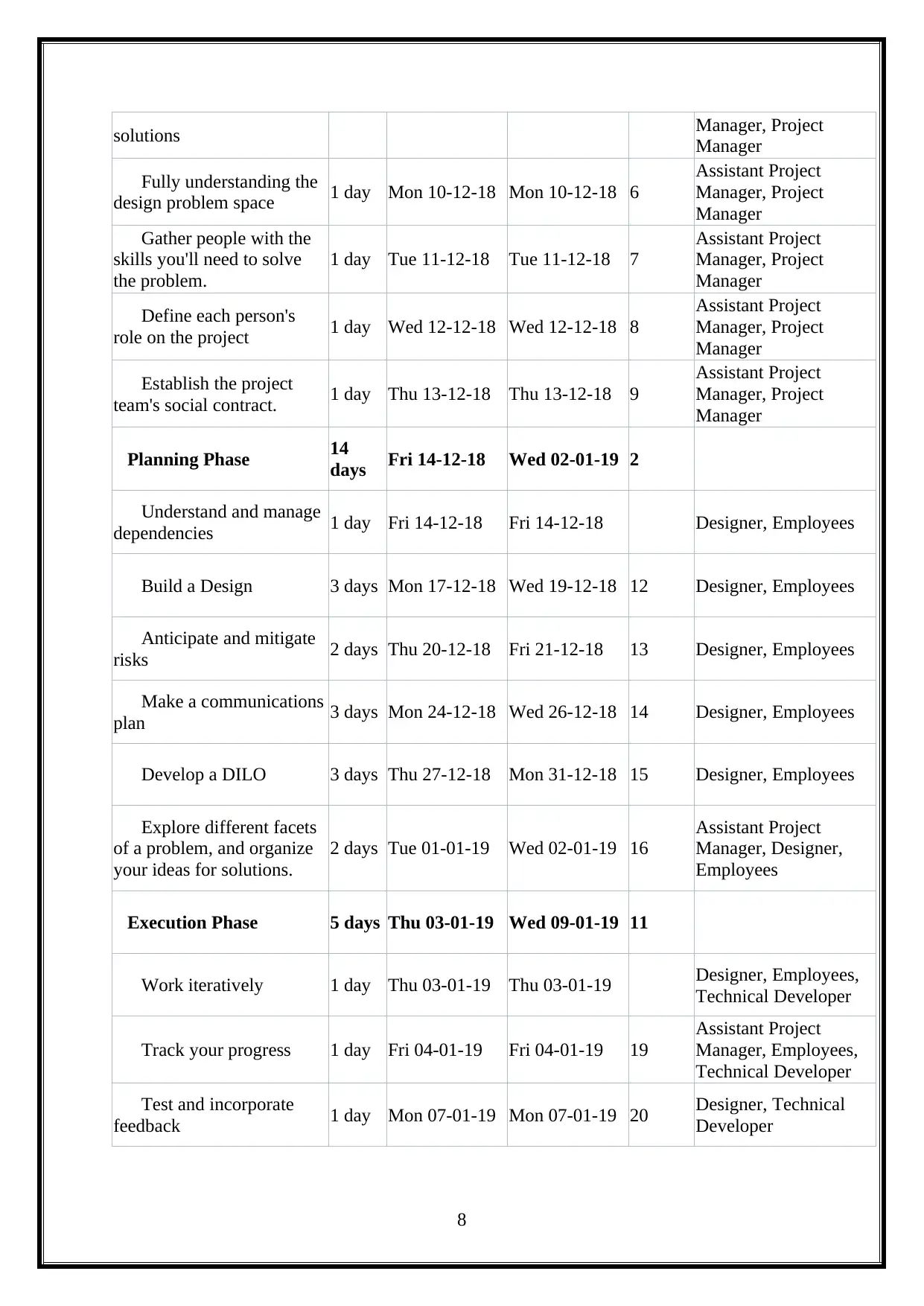
solutions Manager, Project
Manager
Fully understanding the
design problem space 1 day Mon 10-12-18 Mon 10-12-18 6
Assistant Project
Manager, Project
Manager
Gather people with the
skills you'll need to solve
the problem.
1 day Tue 11-12-18 Tue 11-12-18 7
Assistant Project
Manager, Project
Manager
Define each person's
role on the project 1 day Wed 12-12-18 Wed 12-12-18 8
Assistant Project
Manager, Project
Manager
Establish the project
team's social contract. 1 day Thu 13-12-18 Thu 13-12-18 9
Assistant Project
Manager, Project
Manager
Planning Phase 14
days Fri 14-12-18 Wed 02-01-19 2
Understand and manage
dependencies 1 day Fri 14-12-18 Fri 14-12-18 Designer, Employees
Build a Design 3 days Mon 17-12-18 Wed 19-12-18 12 Designer, Employees
Anticipate and mitigate
risks 2 days Thu 20-12-18 Fri 21-12-18 13 Designer, Employees
Make a communications
plan 3 days Mon 24-12-18 Wed 26-12-18 14 Designer, Employees
Develop a DILO 3 days Thu 27-12-18 Mon 31-12-18 15 Designer, Employees
Explore different facets
of a problem, and organize
your ideas for solutions.
2 days Tue 01-01-19 Wed 02-01-19 16
Assistant Project
Manager, Designer,
Employees
Execution Phase 5 days Thu 03-01-19 Wed 09-01-19 11
Work iteratively 1 day Thu 03-01-19 Thu 03-01-19 Designer, Employees,
Technical Developer
Track your progress 1 day Fri 04-01-19 Fri 04-01-19 19
Assistant Project
Manager, Employees,
Technical Developer
Test and incorporate
feedback 1 day Mon 07-01-19 Mon 07-01-19 20 Designer, Technical
Developer
8
Manager
Fully understanding the
design problem space 1 day Mon 10-12-18 Mon 10-12-18 6
Assistant Project
Manager, Project
Manager
Gather people with the
skills you'll need to solve
the problem.
1 day Tue 11-12-18 Tue 11-12-18 7
Assistant Project
Manager, Project
Manager
Define each person's
role on the project 1 day Wed 12-12-18 Wed 12-12-18 8
Assistant Project
Manager, Project
Manager
Establish the project
team's social contract. 1 day Thu 13-12-18 Thu 13-12-18 9
Assistant Project
Manager, Project
Manager
Planning Phase 14
days Fri 14-12-18 Wed 02-01-19 2
Understand and manage
dependencies 1 day Fri 14-12-18 Fri 14-12-18 Designer, Employees
Build a Design 3 days Mon 17-12-18 Wed 19-12-18 12 Designer, Employees
Anticipate and mitigate
risks 2 days Thu 20-12-18 Fri 21-12-18 13 Designer, Employees
Make a communications
plan 3 days Mon 24-12-18 Wed 26-12-18 14 Designer, Employees
Develop a DILO 3 days Thu 27-12-18 Mon 31-12-18 15 Designer, Employees
Explore different facets
of a problem, and organize
your ideas for solutions.
2 days Tue 01-01-19 Wed 02-01-19 16
Assistant Project
Manager, Designer,
Employees
Execution Phase 5 days Thu 03-01-19 Wed 09-01-19 11
Work iteratively 1 day Thu 03-01-19 Thu 03-01-19 Designer, Employees,
Technical Developer
Track your progress 1 day Fri 04-01-19 Fri 04-01-19 19
Assistant Project
Manager, Employees,
Technical Developer
Test and incorporate
feedback 1 day Mon 07-01-19 Mon 07-01-19 20 Designer, Technical
Developer
8
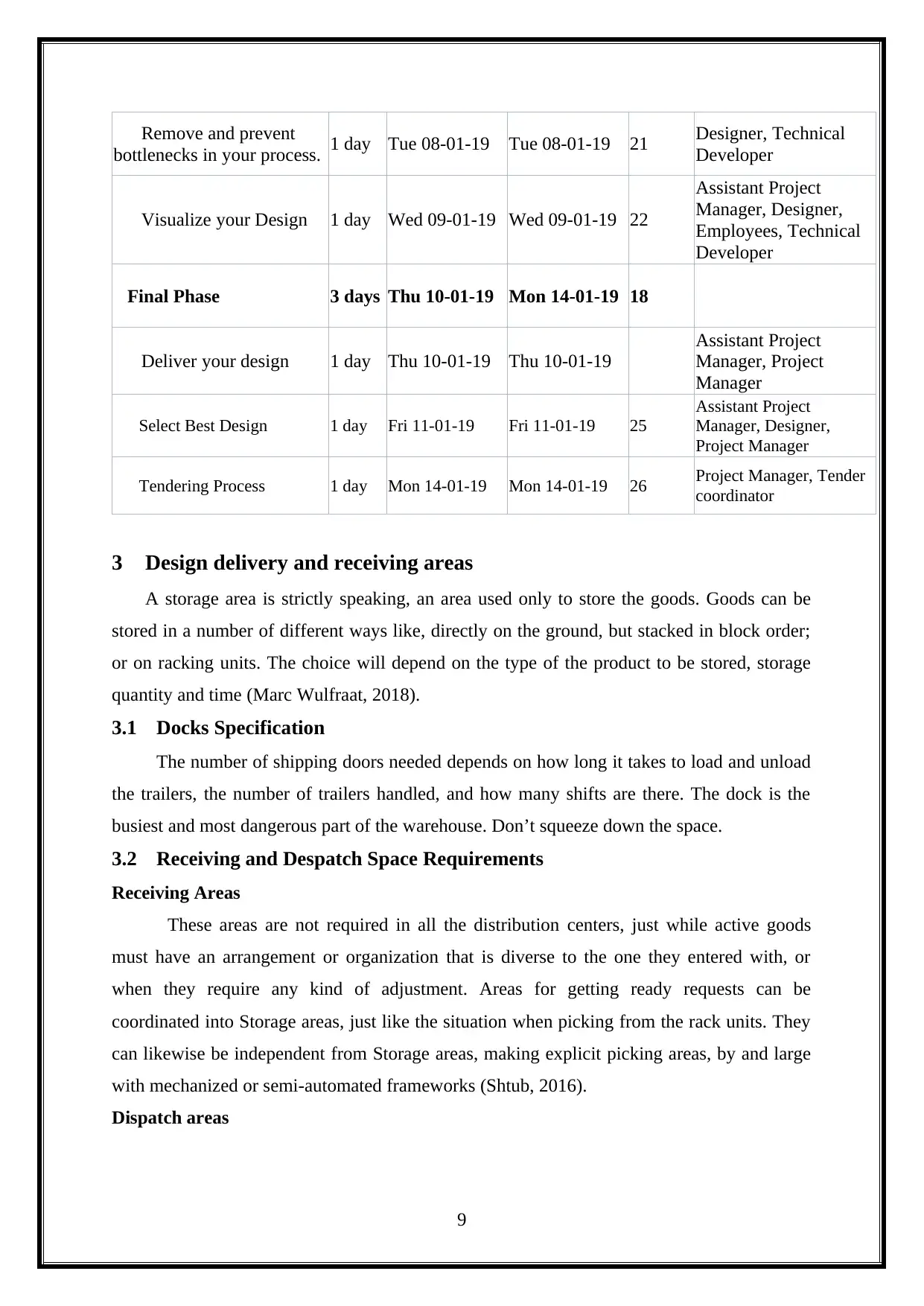
Remove and prevent
bottlenecks in your process. 1 day Tue 08-01-19 Tue 08-01-19 21 Designer, Technical
Developer
Visualize your Design 1 day Wed 09-01-19 Wed 09-01-19 22
Assistant Project
Manager, Designer,
Employees, Technical
Developer
Final Phase 3 days Thu 10-01-19 Mon 14-01-19 18
Deliver your design 1 day Thu 10-01-19 Thu 10-01-19
Assistant Project
Manager, Project
Manager
Select Best Design 1 day Fri 11-01-19 Fri 11-01-19 25
Assistant Project
Manager, Designer,
Project Manager
Tendering Process 1 day Mon 14-01-19 Mon 14-01-19 26 Project Manager, Tender
coordinator
3 Design delivery and receiving areas
A storage area is strictly speaking, an area used only to store the goods. Goods can be
stored in a number of different ways like, directly on the ground, but stacked in block order;
or on racking units. The choice will depend on the type of the product to be stored, storage
quantity and time (Marc Wulfraat, 2018).
3.1 Docks Specification
The number of shipping doors needed depends on how long it takes to load and unload
the trailers, the number of trailers handled, and how many shifts are there. The dock is the
busiest and most dangerous part of the warehouse. Don’t squeeze down the space.
3.2 Receiving and Despatch Space Requirements
Receiving Areas
These areas are not required in all the distribution centers, just while active goods
must have an arrangement or organization that is diverse to the one they entered with, or
when they require any kind of adjustment. Areas for getting ready requests can be
coordinated into Storage areas, just like the situation when picking from the rack units. They
can likewise be independent from Storage areas, making explicit picking areas, by and large
with mechanized or semi-automated frameworks (Shtub, 2016).
Dispatch areas
9
bottlenecks in your process. 1 day Tue 08-01-19 Tue 08-01-19 21 Designer, Technical
Developer
Visualize your Design 1 day Wed 09-01-19 Wed 09-01-19 22
Assistant Project
Manager, Designer,
Employees, Technical
Developer
Final Phase 3 days Thu 10-01-19 Mon 14-01-19 18
Deliver your design 1 day Thu 10-01-19 Thu 10-01-19
Assistant Project
Manager, Project
Manager
Select Best Design 1 day Fri 11-01-19 Fri 11-01-19 25
Assistant Project
Manager, Designer,
Project Manager
Tendering Process 1 day Mon 14-01-19 Mon 14-01-19 26 Project Manager, Tender
coordinator
3 Design delivery and receiving areas
A storage area is strictly speaking, an area used only to store the goods. Goods can be
stored in a number of different ways like, directly on the ground, but stacked in block order;
or on racking units. The choice will depend on the type of the product to be stored, storage
quantity and time (Marc Wulfraat, 2018).
3.1 Docks Specification
The number of shipping doors needed depends on how long it takes to load and unload
the trailers, the number of trailers handled, and how many shifts are there. The dock is the
busiest and most dangerous part of the warehouse. Don’t squeeze down the space.
3.2 Receiving and Despatch Space Requirements
Receiving Areas
These areas are not required in all the distribution centers, just while active goods
must have an arrangement or organization that is diverse to the one they entered with, or
when they require any kind of adjustment. Areas for getting ready requests can be
coordinated into Storage areas, just like the situation when picking from the rack units. They
can likewise be independent from Storage areas, making explicit picking areas, by and large
with mechanized or semi-automated frameworks (Shtub, 2016).
Dispatch areas
9
Secure Best Marks with AI Grader
Need help grading? Try our AI Grader for instant feedback on your assignments.
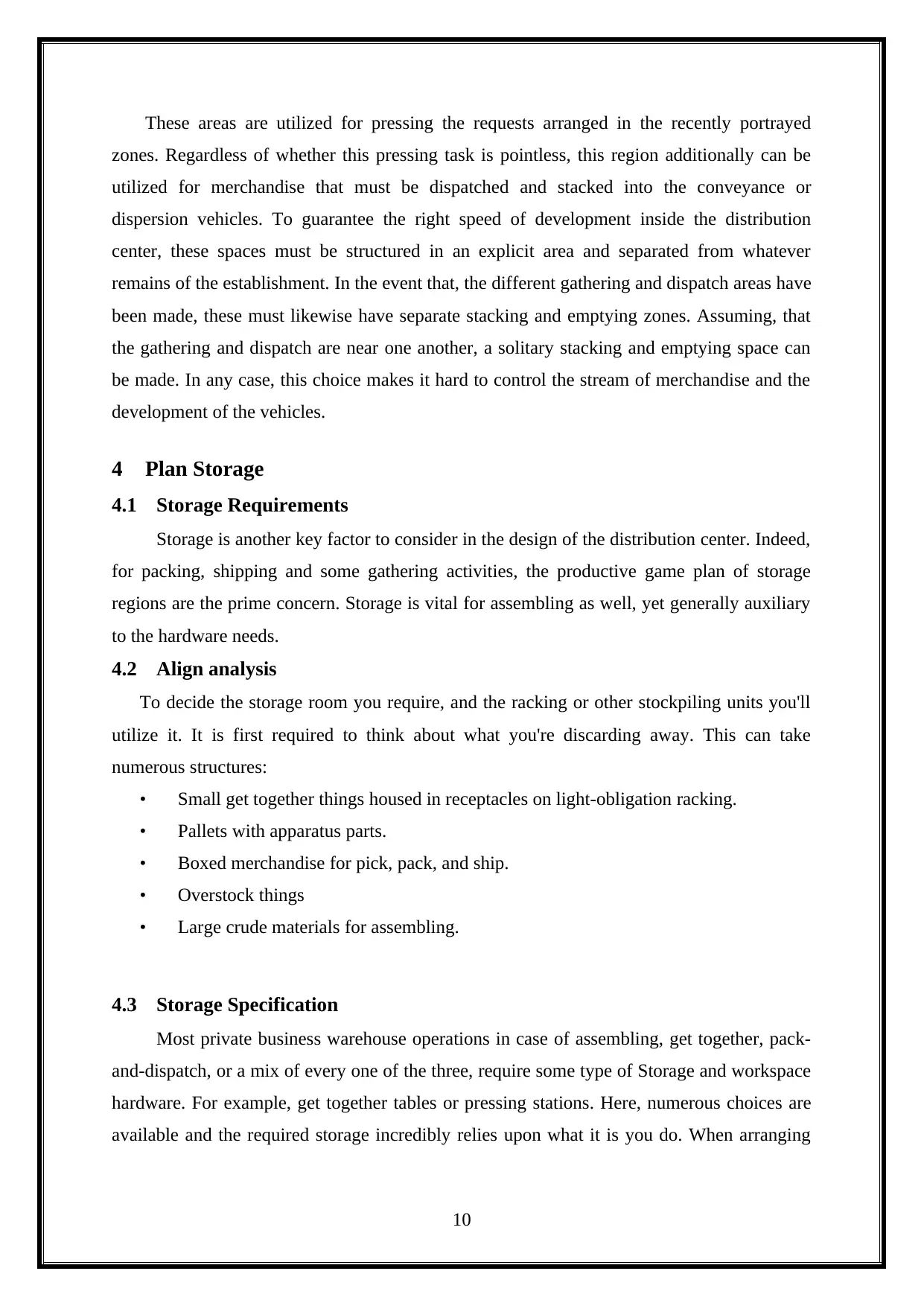
These areas are utilized for pressing the requests arranged in the recently portrayed
zones. Regardless of whether this pressing task is pointless, this region additionally can be
utilized for merchandise that must be dispatched and stacked into the conveyance or
dispersion vehicles. To guarantee the right speed of development inside the distribution
center, these spaces must be structured in an explicit area and separated from whatever
remains of the establishment. In the event that, the different gathering and dispatch areas have
been made, these must likewise have separate stacking and emptying zones. Assuming, that
the gathering and dispatch are near one another, a solitary stacking and emptying space can
be made. In any case, this choice makes it hard to control the stream of merchandise and the
development of the vehicles.
4 Plan Storage
4.1 Storage Requirements
Storage is another key factor to consider in the design of the distribution center. Indeed,
for packing, shipping and some gathering activities, the productive game plan of storage
regions are the prime concern. Storage is vital for assembling as well, yet generally auxiliary
to the hardware needs.
4.2 Align analysis
To decide the storage room you require, and the racking or other stockpiling units you'll
utilize it. It is first required to think about what you're discarding away. This can take
numerous structures:
• Small get together things housed in receptacles on light-obligation racking.
• Pallets with apparatus parts.
• Boxed merchandise for pick, pack, and ship.
• Overstock things
• Large crude materials for assembling.
4.3 Storage Specification
Most private business warehouse operations in case of assembling, get together, pack-
and-dispatch, or a mix of every one of the three, require some type of Storage and workspace
hardware. For example, get together tables or pressing stations. Here, numerous choices are
available and the required storage incredibly relies upon what it is you do. When arranging
10
zones. Regardless of whether this pressing task is pointless, this region additionally can be
utilized for merchandise that must be dispatched and stacked into the conveyance or
dispersion vehicles. To guarantee the right speed of development inside the distribution
center, these spaces must be structured in an explicit area and separated from whatever
remains of the establishment. In the event that, the different gathering and dispatch areas have
been made, these must likewise have separate stacking and emptying zones. Assuming, that
the gathering and dispatch are near one another, a solitary stacking and emptying space can
be made. In any case, this choice makes it hard to control the stream of merchandise and the
development of the vehicles.
4 Plan Storage
4.1 Storage Requirements
Storage is another key factor to consider in the design of the distribution center. Indeed,
for packing, shipping and some gathering activities, the productive game plan of storage
regions are the prime concern. Storage is vital for assembling as well, yet generally auxiliary
to the hardware needs.
4.2 Align analysis
To decide the storage room you require, and the racking or other stockpiling units you'll
utilize it. It is first required to think about what you're discarding away. This can take
numerous structures:
• Small get together things housed in receptacles on light-obligation racking.
• Pallets with apparatus parts.
• Boxed merchandise for pick, pack, and ship.
• Overstock things
• Large crude materials for assembling.
4.3 Storage Specification
Most private business warehouse operations in case of assembling, get together, pack-
and-dispatch, or a mix of every one of the three, require some type of Storage and workspace
hardware. For example, get together tables or pressing stations. Here, numerous choices are
available and the required storage incredibly relies upon what it is you do. When arranging
10
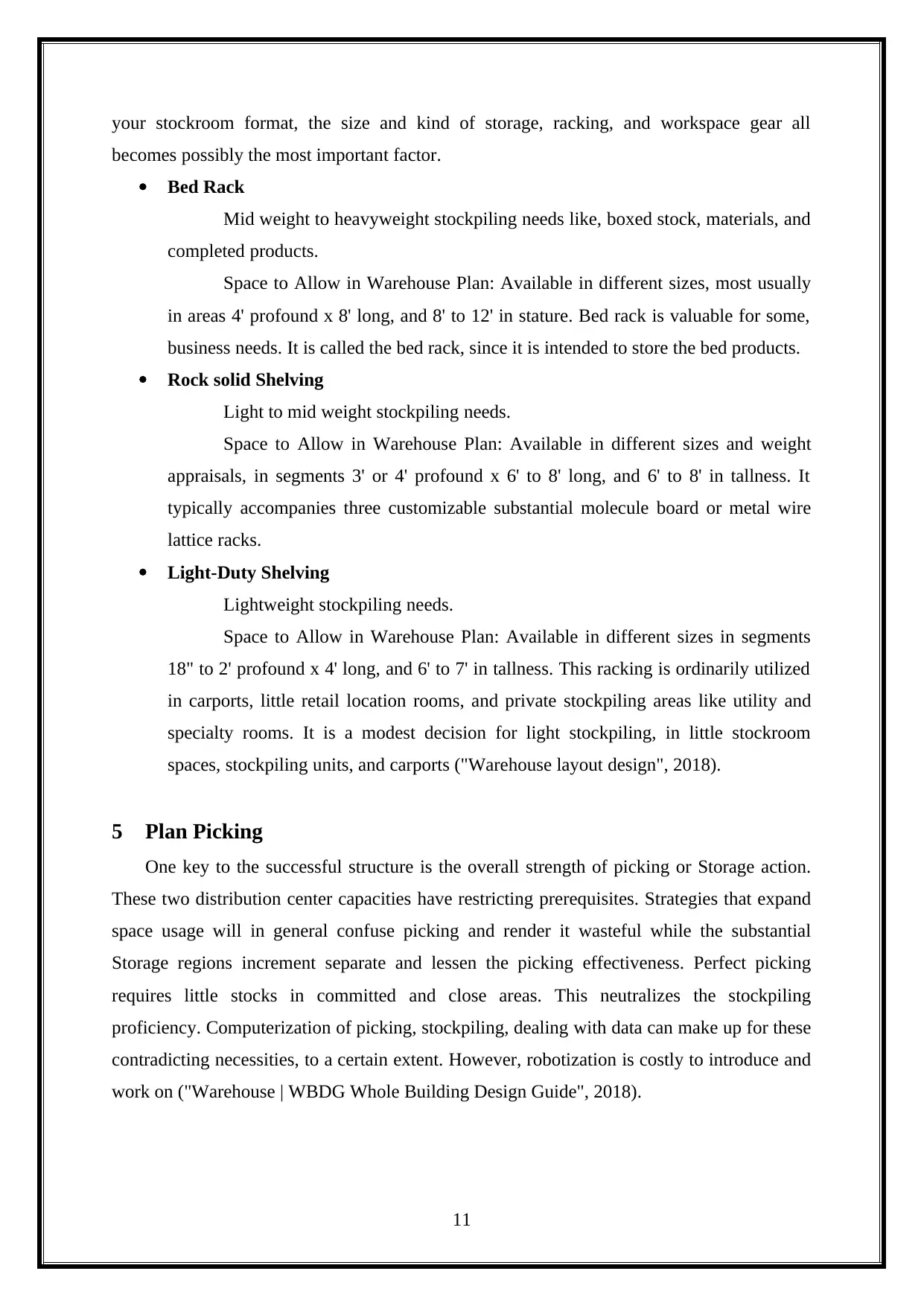
your stockroom format, the size and kind of storage, racking, and workspace gear all
becomes possibly the most important factor.
Bed Rack
Mid weight to heavyweight stockpiling needs like, boxed stock, materials, and
completed products.
Space to Allow in Warehouse Plan: Available in different sizes, most usually
in areas 4' profound x 8' long, and 8' to 12' in stature. Bed rack is valuable for some,
business needs. It is called the bed rack, since it is intended to store the bed products.
Rock solid Shelving
Light to mid weight stockpiling needs.
Space to Allow in Warehouse Plan: Available in different sizes and weight
appraisals, in segments 3' or 4' profound x 6' to 8' long, and 6' to 8' in tallness. It
typically accompanies three customizable substantial molecule board or metal wire
lattice racks.
Light-Duty Shelving
Lightweight stockpiling needs.
Space to Allow in Warehouse Plan: Available in different sizes in segments
18" to 2' profound x 4' long, and 6' to 7' in tallness. This racking is ordinarily utilized
in carports, little retail location rooms, and private stockpiling areas like utility and
specialty rooms. It is a modest decision for light stockpiling, in little stockroom
spaces, stockpiling units, and carports ("Warehouse layout design", 2018).
5 Plan Picking
One key to the successful structure is the overall strength of picking or Storage action.
These two distribution center capacities have restricting prerequisites. Strategies that expand
space usage will in general confuse picking and render it wasteful while the substantial
Storage regions increment separate and lessen the picking effectiveness. Perfect picking
requires little stocks in committed and close areas. This neutralizes the stockpiling
proficiency. Computerization of picking, stockpiling, dealing with data can make up for these
contradicting necessities, to a certain extent. However, robotization is costly to introduce and
work on ("Warehouse | WBDG Whole Building Design Guide", 2018).
11
becomes possibly the most important factor.
Bed Rack
Mid weight to heavyweight stockpiling needs like, boxed stock, materials, and
completed products.
Space to Allow in Warehouse Plan: Available in different sizes, most usually
in areas 4' profound x 8' long, and 8' to 12' in stature. Bed rack is valuable for some,
business needs. It is called the bed rack, since it is intended to store the bed products.
Rock solid Shelving
Light to mid weight stockpiling needs.
Space to Allow in Warehouse Plan: Available in different sizes and weight
appraisals, in segments 3' or 4' profound x 6' to 8' long, and 6' to 8' in tallness. It
typically accompanies three customizable substantial molecule board or metal wire
lattice racks.
Light-Duty Shelving
Lightweight stockpiling needs.
Space to Allow in Warehouse Plan: Available in different sizes in segments
18" to 2' profound x 4' long, and 6' to 7' in tallness. This racking is ordinarily utilized
in carports, little retail location rooms, and private stockpiling areas like utility and
specialty rooms. It is a modest decision for light stockpiling, in little stockroom
spaces, stockpiling units, and carports ("Warehouse layout design", 2018).
5 Plan Picking
One key to the successful structure is the overall strength of picking or Storage action.
These two distribution center capacities have restricting prerequisites. Strategies that expand
space usage will in general confuse picking and render it wasteful while the substantial
Storage regions increment separate and lessen the picking effectiveness. Perfect picking
requires little stocks in committed and close areas. This neutralizes the stockpiling
proficiency. Computerization of picking, stockpiling, dealing with data can make up for these
contradicting necessities, to a certain extent. However, robotization is costly to introduce and
work on ("Warehouse | WBDG Whole Building Design Guide", 2018).
11
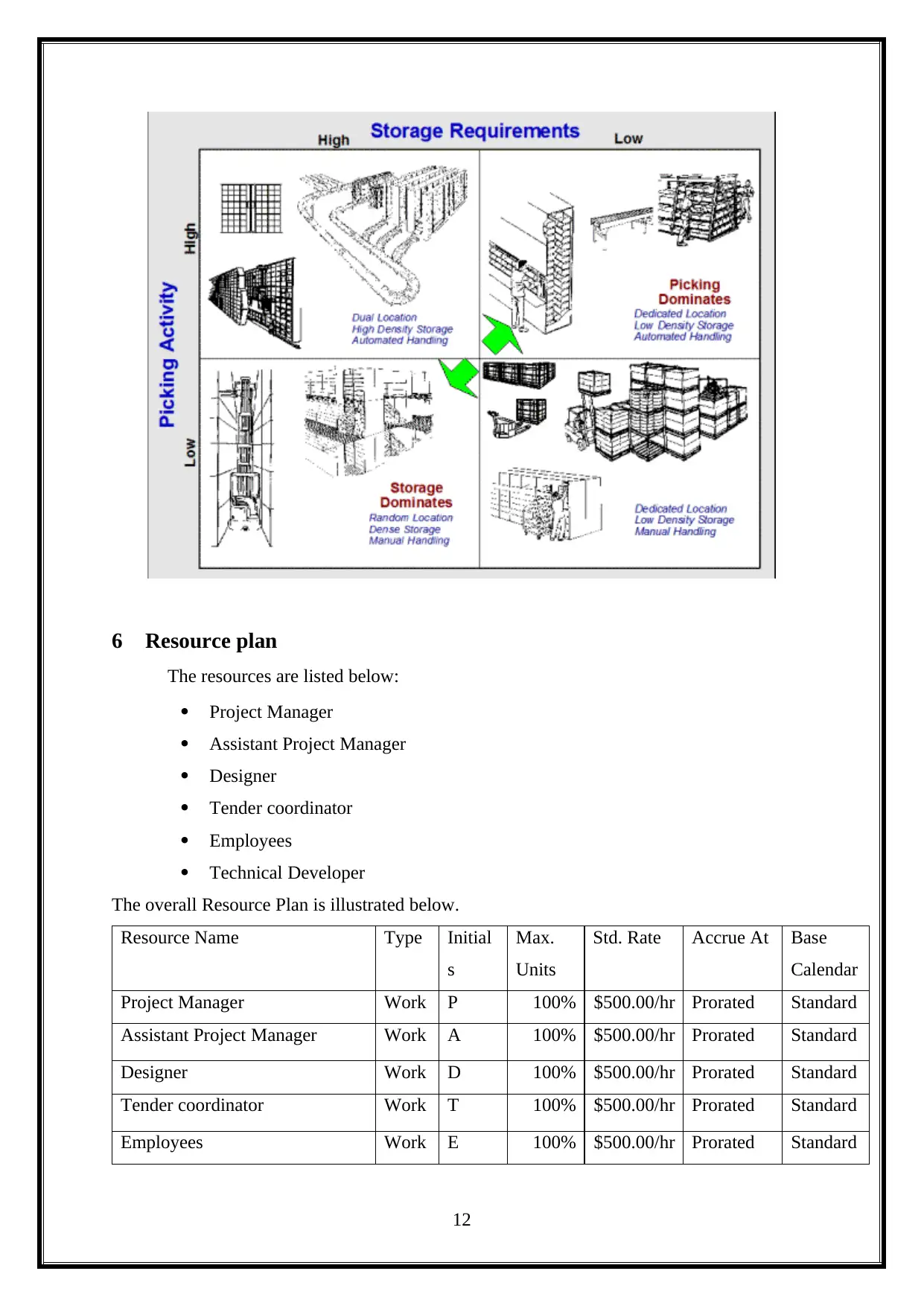
6 Resource plan
The resources are listed below:
Project Manager
Assistant Project Manager
Designer
Tender coordinator
Employees
Technical Developer
The overall Resource Plan is illustrated below.
Resource Name Type Initial
s
Max.
Units
Std. Rate Accrue At Base
Calendar
Project Manager Work P 100% $500.00/hr Prorated Standard
Assistant Project Manager Work A 100% $500.00/hr Prorated Standard
Designer Work D 100% $500.00/hr Prorated Standard
Tender coordinator Work T 100% $500.00/hr Prorated Standard
Employees Work E 100% $500.00/hr Prorated Standard
12
The resources are listed below:
Project Manager
Assistant Project Manager
Designer
Tender coordinator
Employees
Technical Developer
The overall Resource Plan is illustrated below.
Resource Name Type Initial
s
Max.
Units
Std. Rate Accrue At Base
Calendar
Project Manager Work P 100% $500.00/hr Prorated Standard
Assistant Project Manager Work A 100% $500.00/hr Prorated Standard
Designer Work D 100% $500.00/hr Prorated Standard
Tender coordinator Work T 100% $500.00/hr Prorated Standard
Employees Work E 100% $500.00/hr Prorated Standard
12
Paraphrase This Document
Need a fresh take? Get an instant paraphrase of this document with our AI Paraphraser
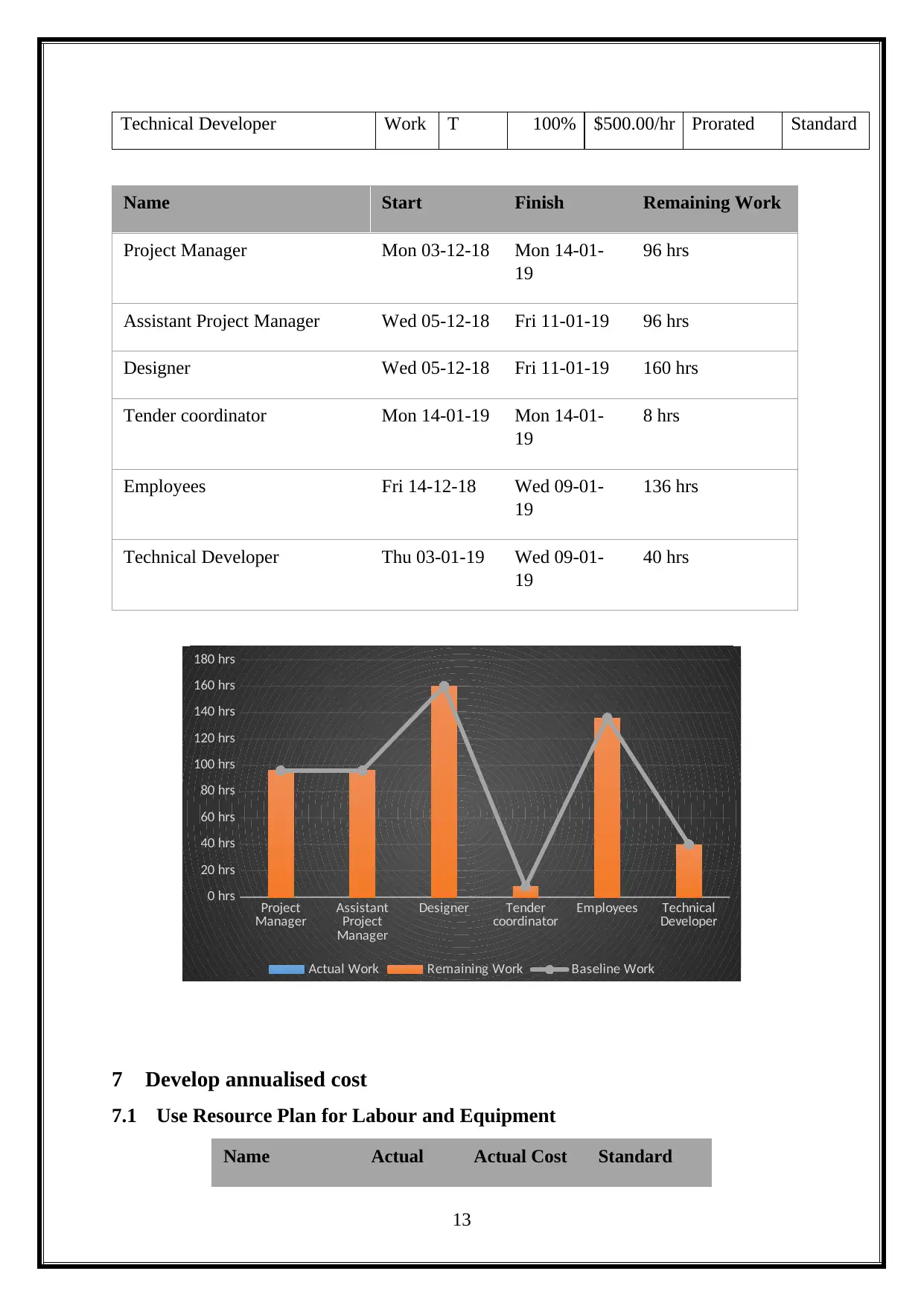
Technical Developer Work T 100% $500.00/hr Prorated Standard
Name Start Finish Remaining Work
Project Manager Mon 03-12-18 Mon 14-01-
19
96 hrs
Assistant Project Manager Wed 05-12-18 Fri 11-01-19 96 hrs
Designer Wed 05-12-18 Fri 11-01-19 160 hrs
Tender coordinator Mon 14-01-19 Mon 14-01-
19
8 hrs
Employees Fri 14-12-18 Wed 09-01-
19
136 hrs
Technical Developer Thu 03-01-19 Wed 09-01-
19
40 hrs
Project
Manager Assistant
Project
Manager
Designer Tender
coordinator Employees Technical
Developer
0 hrs
20 hrs
40 hrs
60 hrs
80 hrs
100 hrs
120 hrs
140 hrs
160 hrs
180 hrs
Actual Work Remaining Work Baseline Work
7 Develop annualised cost
7.1 Use Resource Plan for Labour and Equipment
Name Actual Actual Cost Standard
13
Name Start Finish Remaining Work
Project Manager Mon 03-12-18 Mon 14-01-
19
96 hrs
Assistant Project Manager Wed 05-12-18 Fri 11-01-19 96 hrs
Designer Wed 05-12-18 Fri 11-01-19 160 hrs
Tender coordinator Mon 14-01-19 Mon 14-01-
19
8 hrs
Employees Fri 14-12-18 Wed 09-01-
19
136 hrs
Technical Developer Thu 03-01-19 Wed 09-01-
19
40 hrs
Project
Manager Assistant
Project
Manager
Designer Tender
coordinator Employees Technical
Developer
0 hrs
20 hrs
40 hrs
60 hrs
80 hrs
100 hrs
120 hrs
140 hrs
160 hrs
180 hrs
Actual Work Remaining Work Baseline Work
7 Develop annualised cost
7.1 Use Resource Plan for Labour and Equipment
Name Actual Actual Cost Standard
13
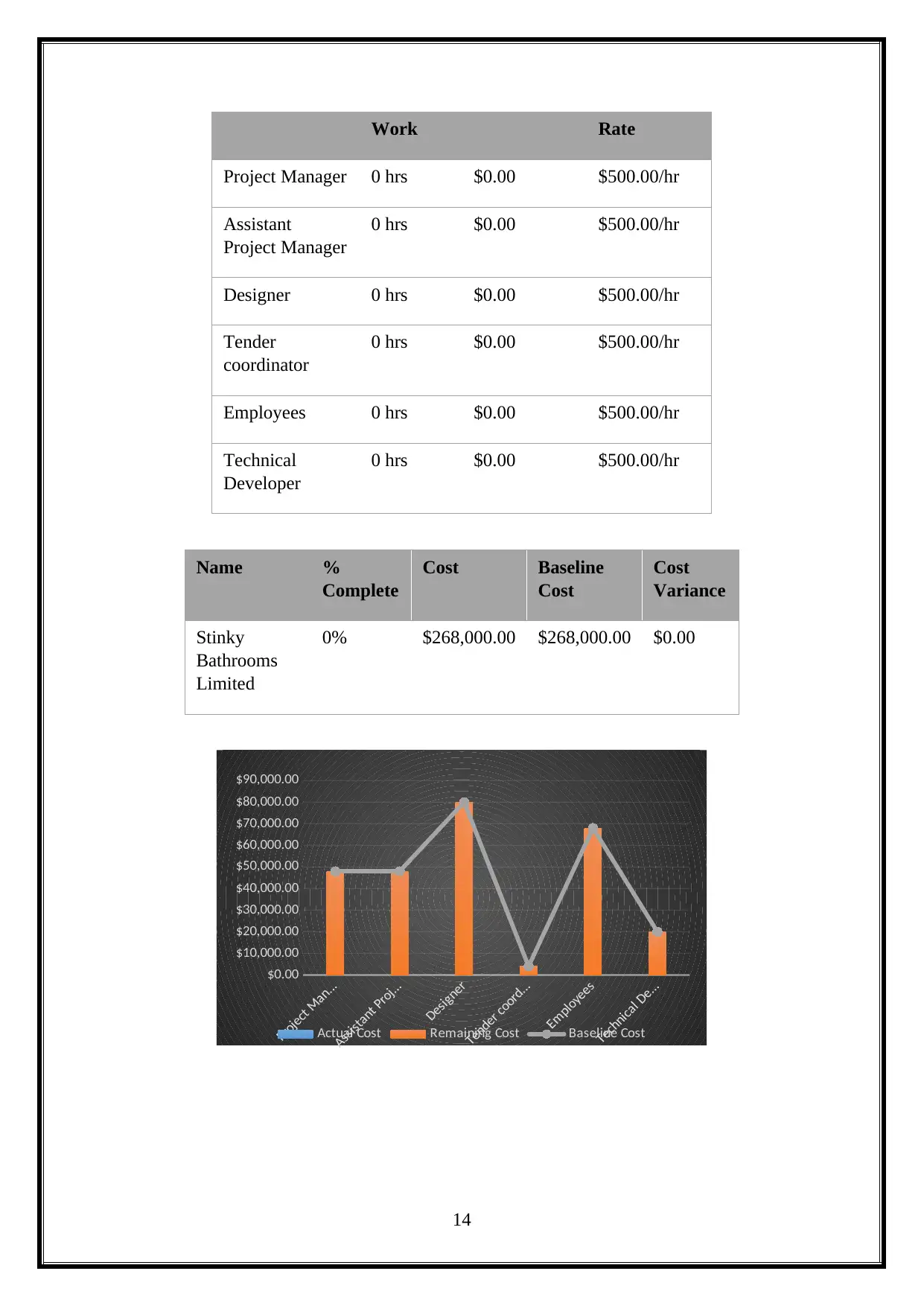
Work Rate
Project Manager 0 hrs $0.00 $500.00/hr
Assistant
Project Manager
0 hrs $0.00 $500.00/hr
Designer 0 hrs $0.00 $500.00/hr
Tender
coordinator
0 hrs $0.00 $500.00/hr
Employees 0 hrs $0.00 $500.00/hr
Technical
Developer
0 hrs $0.00 $500.00/hr
Name %
Complete
Cost Baseline
Cost
Cost
Variance
Stinky
Bathrooms
Limited
0% $268,000.00 $268,000.00 $0.00
$0.00
$10,000.00
$20,000.00
$30,000.00
$40,000.00
$50,000.00
$60,000.00
$70,000.00
$80,000.00
$90,000.00
Actual Cost Remaining Cost Baseline Cost
14
Project Manager 0 hrs $0.00 $500.00/hr
Assistant
Project Manager
0 hrs $0.00 $500.00/hr
Designer 0 hrs $0.00 $500.00/hr
Tender
coordinator
0 hrs $0.00 $500.00/hr
Employees 0 hrs $0.00 $500.00/hr
Technical
Developer
0 hrs $0.00 $500.00/hr
Name %
Complete
Cost Baseline
Cost
Cost
Variance
Stinky
Bathrooms
Limited
0% $268,000.00 $268,000.00 $0.00
$0.00
$10,000.00
$20,000.00
$30,000.00
$40,000.00
$50,000.00
$60,000.00
$70,000.00
$80,000.00
$90,000.00
Actual Cost Remaining Cost Baseline Cost
14
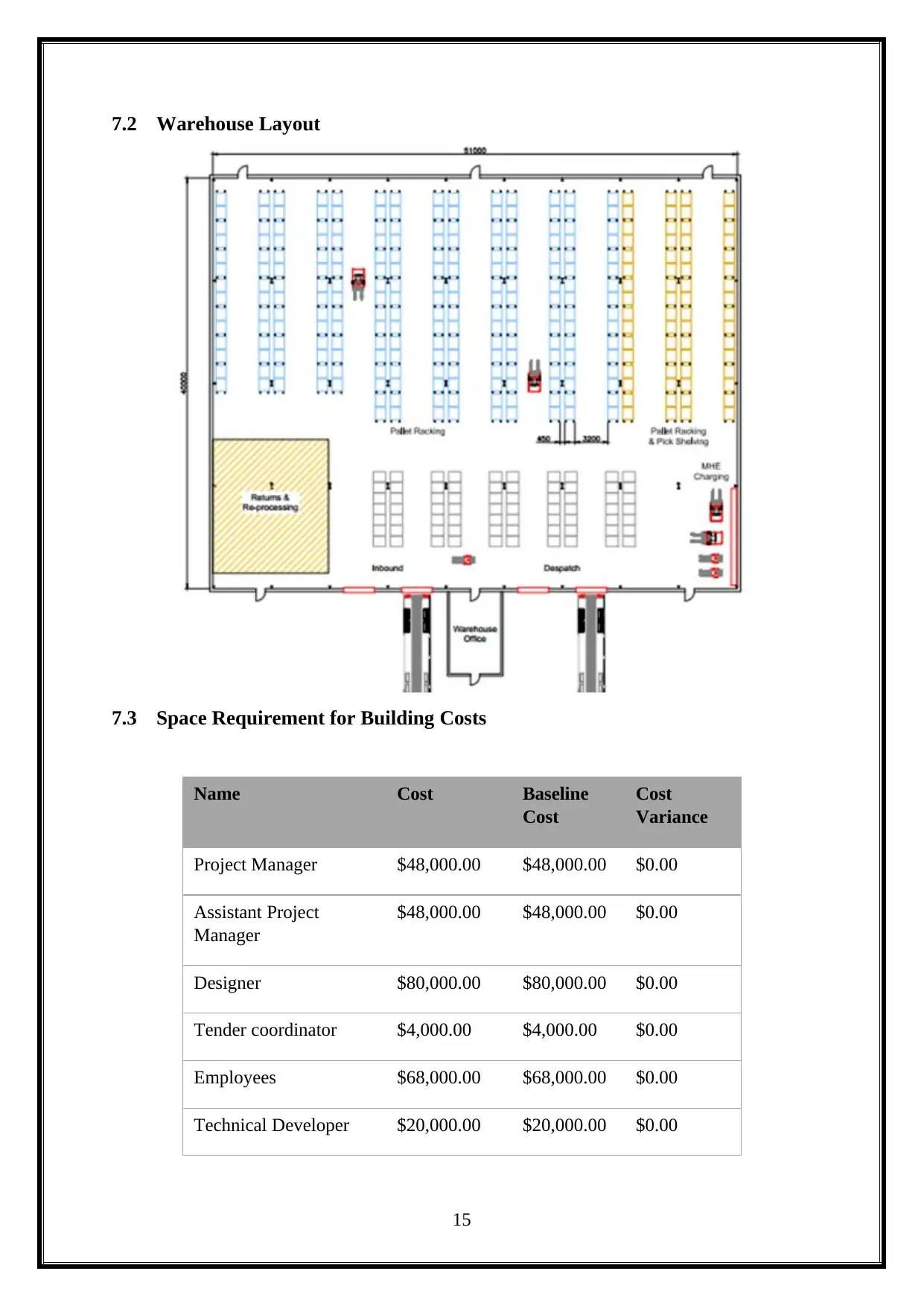
7.2 Warehouse Layout
7.3 Space Requirement for Building Costs
Name Cost Baseline
Cost
Cost
Variance
Project Manager $48,000.00 $48,000.00 $0.00
Assistant Project
Manager
$48,000.00 $48,000.00 $0.00
Designer $80,000.00 $80,000.00 $0.00
Tender coordinator $4,000.00 $4,000.00 $0.00
Employees $68,000.00 $68,000.00 $0.00
Technical Developer $20,000.00 $20,000.00 $0.00
15
7.3 Space Requirement for Building Costs
Name Cost Baseline
Cost
Cost
Variance
Project Manager $48,000.00 $48,000.00 $0.00
Assistant Project
Manager
$48,000.00 $48,000.00 $0.00
Designer $80,000.00 $80,000.00 $0.00
Tender coordinator $4,000.00 $4,000.00 $0.00
Employees $68,000.00 $68,000.00 $0.00
Technical Developer $20,000.00 $20,000.00 $0.00
15
Secure Best Marks with AI Grader
Need help grading? Try our AI Grader for instant feedback on your assignments.
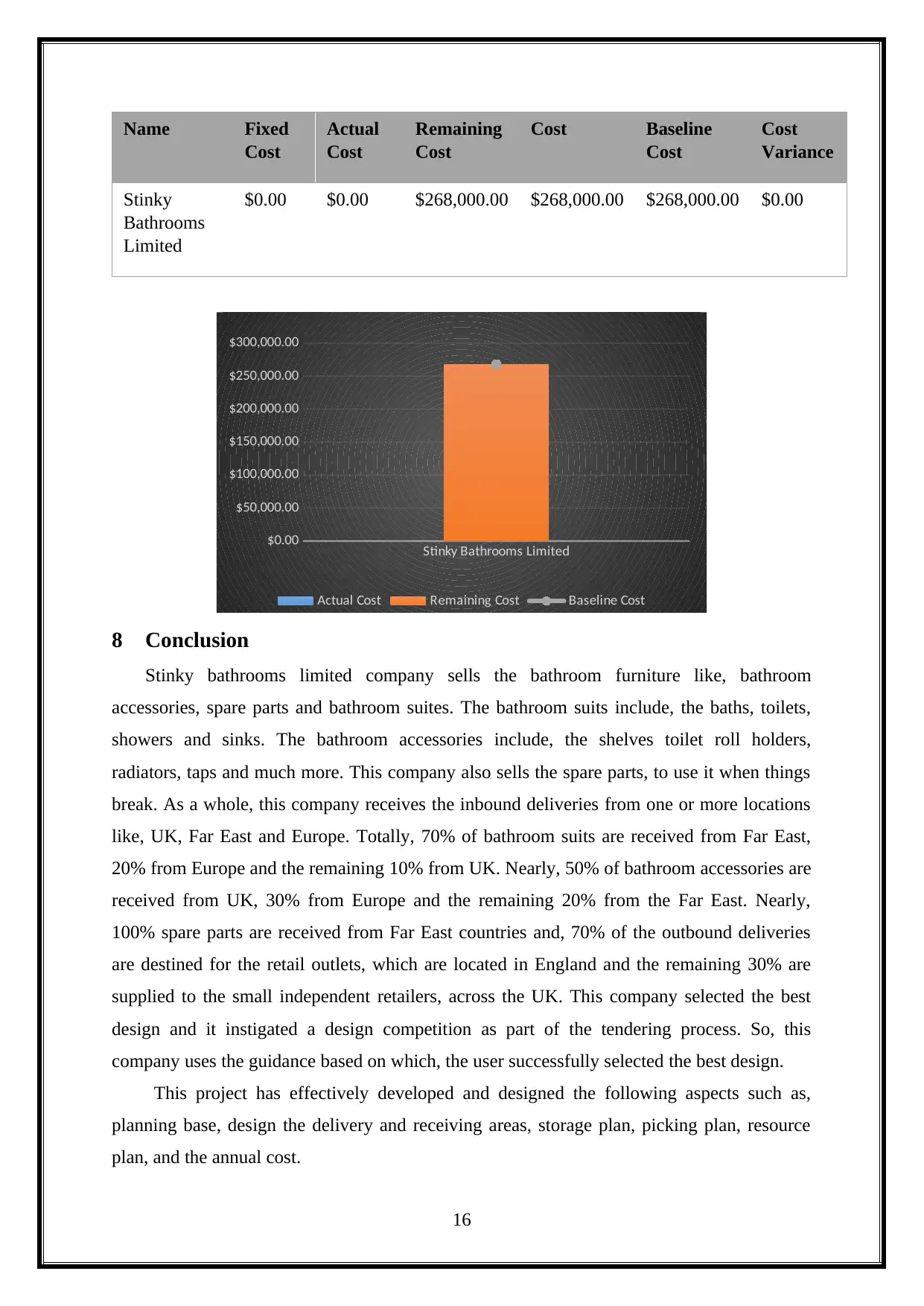
Name Fixed
Cost
Actual
Cost
Remaining
Cost
Cost Baseline
Cost
Cost
Variance
Stinky
Bathrooms
Limited
$0.00 $0.00 $268,000.00 $268,000.00 $268,000.00 $0.00
Stinky Bathrooms Limited
$0.00
$50,000.00
$100,000.00
$150,000.00
$200,000.00
$250,000.00
$300,000.00
Actual Cost Remaining Cost Baseline Cost
8 Conclusion
Stinky bathrooms limited company sells the bathroom furniture like, bathroom
accessories, spare parts and bathroom suites. The bathroom suits include, the baths, toilets,
showers and sinks. The bathroom accessories include, the shelves toilet roll holders,
radiators, taps and much more. This company also sells the spare parts, to use it when things
break. As a whole, this company receives the inbound deliveries from one or more locations
like, UK, Far East and Europe. Totally, 70% of bathroom suits are received from Far East,
20% from Europe and the remaining 10% from UK. Nearly, 50% of bathroom accessories are
received from UK, 30% from Europe and the remaining 20% from the Far East. Nearly,
100% spare parts are received from Far East countries and, 70% of the outbound deliveries
are destined for the retail outlets, which are located in England and the remaining 30% are
supplied to the small independent retailers, across the UK. This company selected the best
design and it instigated a design competition as part of the tendering process. So, this
company uses the guidance based on which, the user successfully selected the best design.
This project has effectively developed and designed the following aspects such as,
planning base, design the delivery and receiving areas, storage plan, picking plan, resource
plan, and the annual cost.
16
Cost
Actual
Cost
Remaining
Cost
Cost Baseline
Cost
Cost
Variance
Stinky
Bathrooms
Limited
$0.00 $0.00 $268,000.00 $268,000.00 $268,000.00 $0.00
Stinky Bathrooms Limited
$0.00
$50,000.00
$100,000.00
$150,000.00
$200,000.00
$250,000.00
$300,000.00
Actual Cost Remaining Cost Baseline Cost
8 Conclusion
Stinky bathrooms limited company sells the bathroom furniture like, bathroom
accessories, spare parts and bathroom suites. The bathroom suits include, the baths, toilets,
showers and sinks. The bathroom accessories include, the shelves toilet roll holders,
radiators, taps and much more. This company also sells the spare parts, to use it when things
break. As a whole, this company receives the inbound deliveries from one or more locations
like, UK, Far East and Europe. Totally, 70% of bathroom suits are received from Far East,
20% from Europe and the remaining 10% from UK. Nearly, 50% of bathroom accessories are
received from UK, 30% from Europe and the remaining 20% from the Far East. Nearly,
100% spare parts are received from Far East countries and, 70% of the outbound deliveries
are destined for the retail outlets, which are located in England and the remaining 30% are
supplied to the small independent retailers, across the UK. This company selected the best
design and it instigated a design competition as part of the tendering process. So, this
company uses the guidance based on which, the user successfully selected the best design.
This project has effectively developed and designed the following aspects such as,
planning base, design the delivery and receiving areas, storage plan, picking plan, resource
plan, and the annual cost.
16
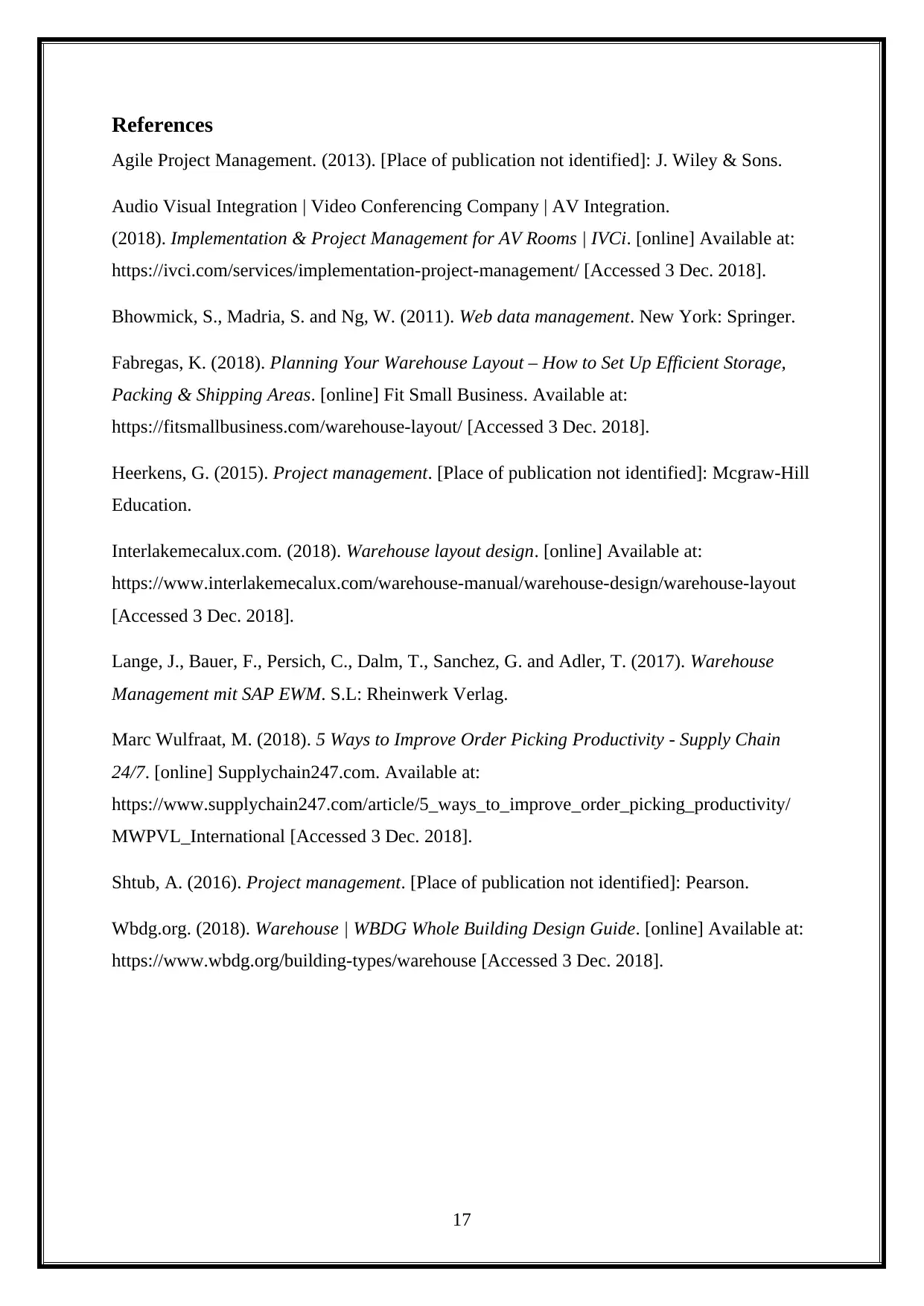
References
Agile Project Management. (2013). [Place of publication not identified]: J. Wiley & Sons.
Audio Visual Integration | Video Conferencing Company | AV Integration.
(2018). Implementation & Project Management for AV Rooms | IVCi. [online] Available at:
https://ivci.com/services/implementation-project-management/ [Accessed 3 Dec. 2018].
Bhowmick, S., Madria, S. and Ng, W. (2011). Web data management. New York: Springer.
Fabregas, K. (2018). Planning Your Warehouse Layout – How to Set Up Efficient Storage,
Packing & Shipping Areas. [online] Fit Small Business. Available at:
https://fitsmallbusiness.com/warehouse-layout/ [Accessed 3 Dec. 2018].
Heerkens, G. (2015). Project management. [Place of publication not identified]: Mcgraw-Hill
Education.
Interlakemecalux.com. (2018). Warehouse layout design. [online] Available at:
https://www.interlakemecalux.com/warehouse-manual/warehouse-design/warehouse-layout
[Accessed 3 Dec. 2018].
Lange, J., Bauer, F., Persich, C., Dalm, T., Sanchez, G. and Adler, T. (2017). Warehouse
Management mit SAP EWM. S.L: Rheinwerk Verlag.
Marc Wulfraat, M. (2018). 5 Ways to Improve Order Picking Productivity - Supply Chain
24/7. [online] Supplychain247.com. Available at:
https://www.supplychain247.com/article/5_ways_to_improve_order_picking_productivity/
MWPVL_International [Accessed 3 Dec. 2018].
Shtub, A. (2016). Project management. [Place of publication not identified]: Pearson.
Wbdg.org. (2018). Warehouse | WBDG Whole Building Design Guide. [online] Available at:
https://www.wbdg.org/building-types/warehouse [Accessed 3 Dec. 2018].
17
Agile Project Management. (2013). [Place of publication not identified]: J. Wiley & Sons.
Audio Visual Integration | Video Conferencing Company | AV Integration.
(2018). Implementation & Project Management for AV Rooms | IVCi. [online] Available at:
https://ivci.com/services/implementation-project-management/ [Accessed 3 Dec. 2018].
Bhowmick, S., Madria, S. and Ng, W. (2011). Web data management. New York: Springer.
Fabregas, K. (2018). Planning Your Warehouse Layout – How to Set Up Efficient Storage,
Packing & Shipping Areas. [online] Fit Small Business. Available at:
https://fitsmallbusiness.com/warehouse-layout/ [Accessed 3 Dec. 2018].
Heerkens, G. (2015). Project management. [Place of publication not identified]: Mcgraw-Hill
Education.
Interlakemecalux.com. (2018). Warehouse layout design. [online] Available at:
https://www.interlakemecalux.com/warehouse-manual/warehouse-design/warehouse-layout
[Accessed 3 Dec. 2018].
Lange, J., Bauer, F., Persich, C., Dalm, T., Sanchez, G. and Adler, T. (2017). Warehouse
Management mit SAP EWM. S.L: Rheinwerk Verlag.
Marc Wulfraat, M. (2018). 5 Ways to Improve Order Picking Productivity - Supply Chain
24/7. [online] Supplychain247.com. Available at:
https://www.supplychain247.com/article/5_ways_to_improve_order_picking_productivity/
MWPVL_International [Accessed 3 Dec. 2018].
Shtub, A. (2016). Project management. [Place of publication not identified]: Pearson.
Wbdg.org. (2018). Warehouse | WBDG Whole Building Design Guide. [online] Available at:
https://www.wbdg.org/building-types/warehouse [Accessed 3 Dec. 2018].
17
1 out of 18
![[object Object]](/_next/image/?url=%2F_next%2Fstatic%2Fmedia%2Flogo.6d15ce61.png&w=640&q=75)
Your All-in-One AI-Powered Toolkit for Academic Success.
+13062052269
info@desklib.com
Available 24*7 on WhatsApp / Email
Unlock your academic potential
© 2024 | Zucol Services PVT LTD | All rights reserved.