Management Accounting Project Report: Answers, Schedules, and List of Activities
VerifiedAdded on 2022/10/19
|15
|3715
|233
AI Summary
This project report covers various topics related to management accounting, including answers, schedules, and a list of activities. It includes information on resource cost categories and drivers, activities and resource drivers used in blending, a list of activities and their associated costs, and more.
Contribute Materials
Your contribution can guide someone’s learning journey. Share your
documents today.

Running Head: Management Accounting
1
Project Report: Management Accounting
1
Project Report: Management Accounting
Secure Best Marks with AI Grader
Need help grading? Try our AI Grader for instant feedback on your assignments.
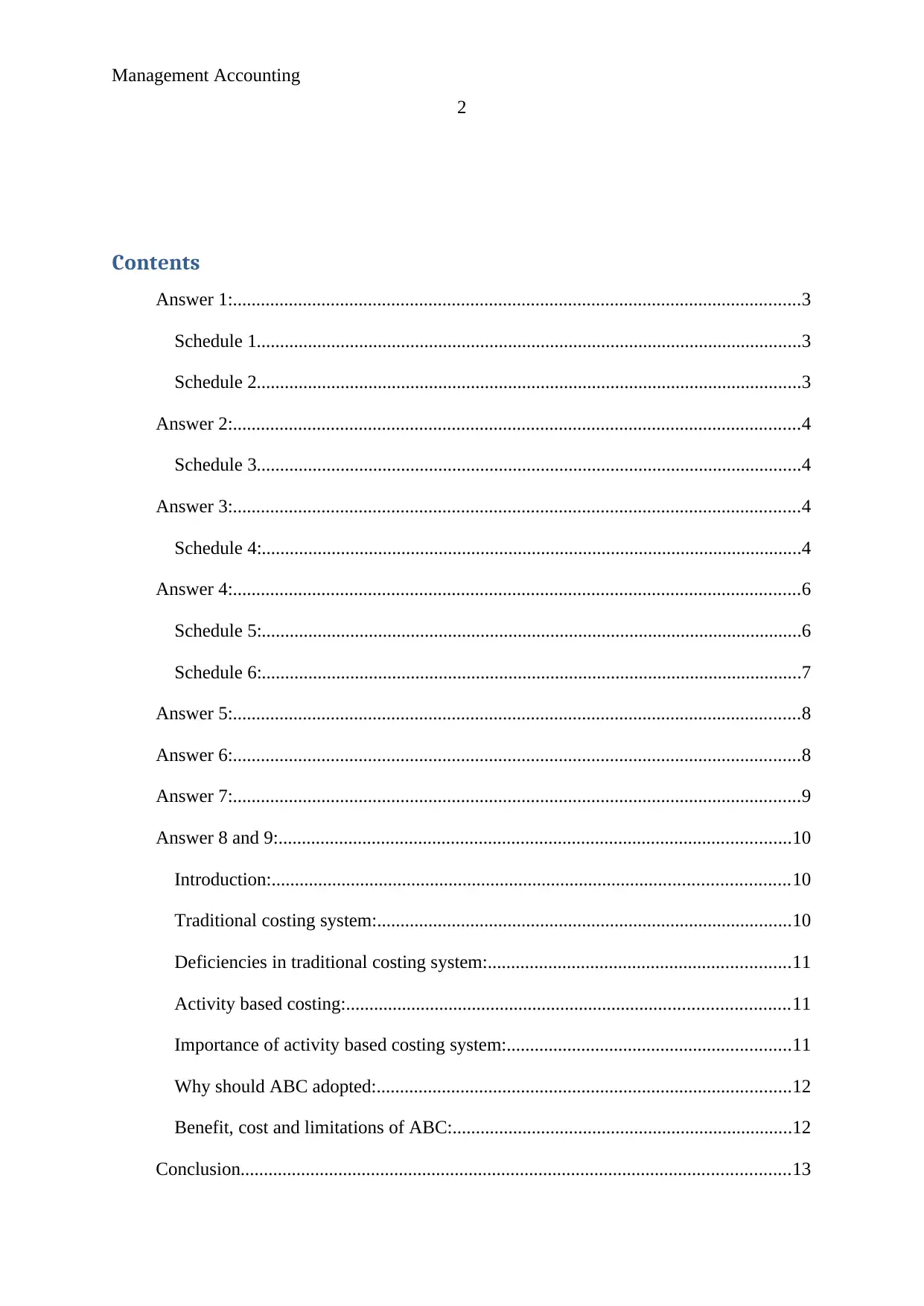
Management Accounting
2
Contents
Answer 1:..........................................................................................................................3
Schedule 1.....................................................................................................................3
Schedule 2.....................................................................................................................3
Answer 2:..........................................................................................................................4
Schedule 3.....................................................................................................................4
Answer 3:..........................................................................................................................4
Schedule 4:....................................................................................................................4
Answer 4:..........................................................................................................................6
Schedule 5:....................................................................................................................6
Schedule 6:....................................................................................................................7
Answer 5:..........................................................................................................................8
Answer 6:..........................................................................................................................8
Answer 7:..........................................................................................................................9
Answer 8 and 9:..............................................................................................................10
Introduction:...............................................................................................................10
Traditional costing system:.........................................................................................10
Deficiencies in traditional costing system:.................................................................11
Activity based costing:...............................................................................................11
Importance of activity based costing system:.............................................................11
Why should ABC adopted:.........................................................................................12
Benefit, cost and limitations of ABC:.........................................................................12
Conclusion......................................................................................................................13
2
Contents
Answer 1:..........................................................................................................................3
Schedule 1.....................................................................................................................3
Schedule 2.....................................................................................................................3
Answer 2:..........................................................................................................................4
Schedule 3.....................................................................................................................4
Answer 3:..........................................................................................................................4
Schedule 4:....................................................................................................................4
Answer 4:..........................................................................................................................6
Schedule 5:....................................................................................................................6
Schedule 6:....................................................................................................................7
Answer 5:..........................................................................................................................8
Answer 6:..........................................................................................................................8
Answer 7:..........................................................................................................................9
Answer 8 and 9:..............................................................................................................10
Introduction:...............................................................................................................10
Traditional costing system:.........................................................................................10
Deficiencies in traditional costing system:.................................................................11
Activity based costing:...............................................................................................11
Importance of activity based costing system:.............................................................11
Why should ABC adopted:.........................................................................................12
Benefit, cost and limitations of ABC:.........................................................................12
Conclusion......................................................................................................................13
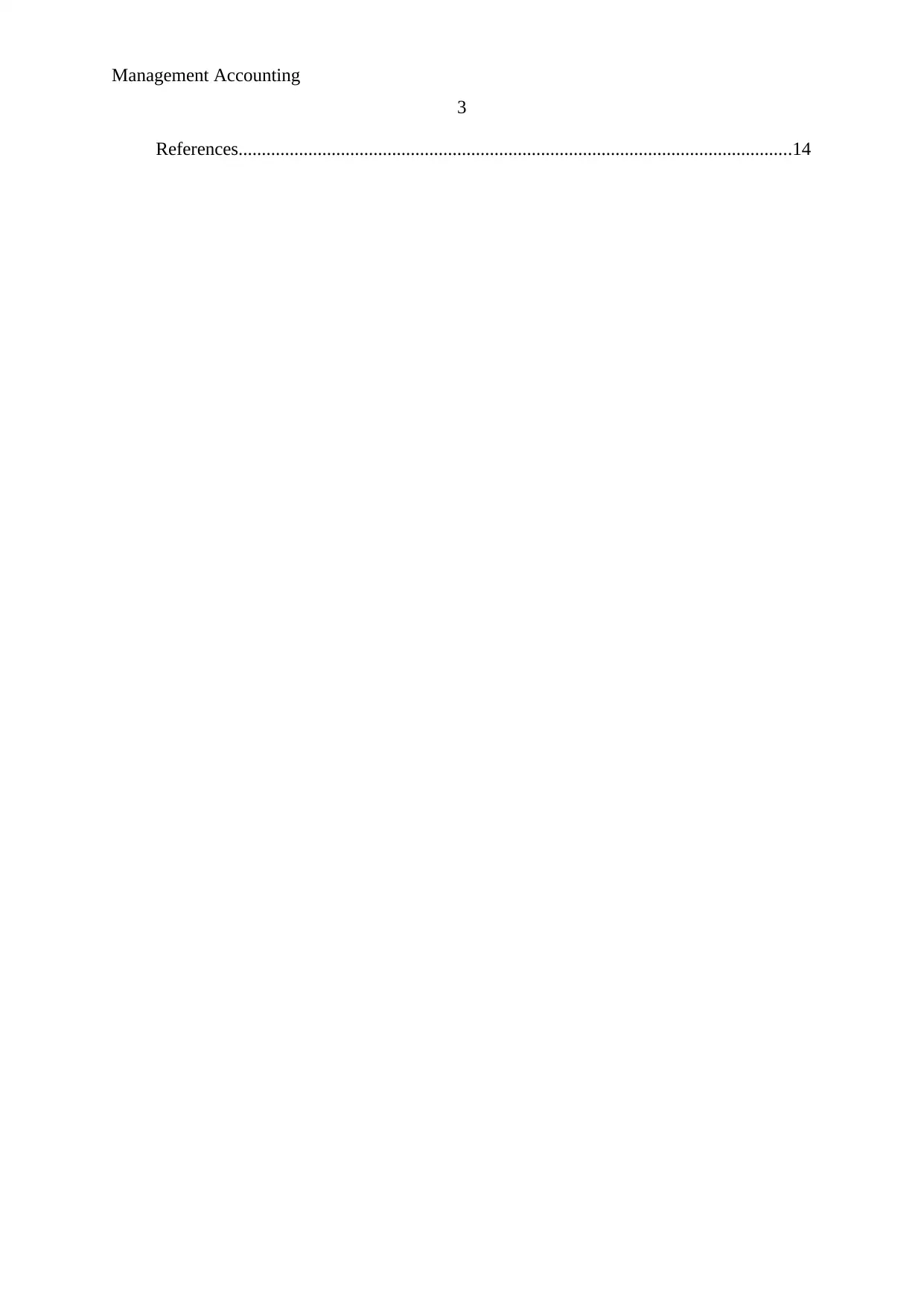
Management Accounting
3
References.......................................................................................................................14
3
References.......................................................................................................................14
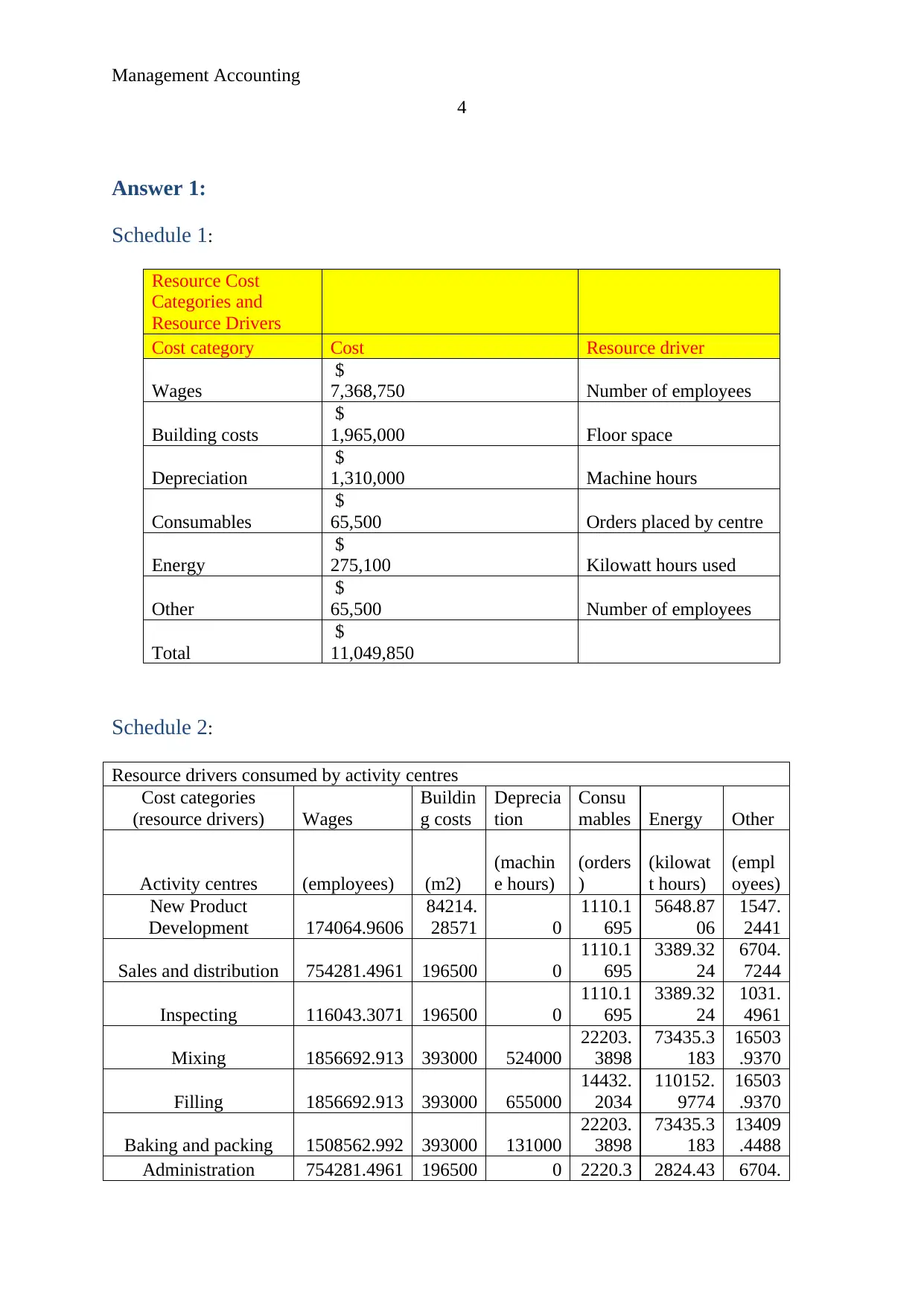
Management Accounting
4
Answer 1:
Schedule 1:
Resource Cost
Categories and
Resource Drivers
Cost category Cost Resource driver
Wages
$
7,368,750 Number of employees
Building costs
$
1,965,000 Floor space
Depreciation
$
1,310,000 Machine hours
Consumables
$
65,500 Orders placed by centre
Energy
$
275,100 Kilowatt hours used
Other
$
65,500 Number of employees
Total
$
11,049,850
Schedule 2:
Resource drivers consumed by activity centres
Cost categories
(resource drivers) Wages
Buildin
g costs
Deprecia
tion
Consu
mables Energy Other
Activity centres (employees) (m2)
(machin
e hours)
(orders
)
(kilowat
t hours)
(empl
oyees)
New Product
Development 174064.9606
84214.
28571 0
1110.1
695
5648.87
06
1547.
2441
Sales and distribution 754281.4961 196500 0
1110.1
695
3389.32
24
6704.
7244
Inspecting 116043.3071 196500 0
1110.1
695
3389.32
24
1031.
4961
Mixing 1856692.913 393000 524000
22203.
3898
73435.3
183
16503
.9370
Filling 1856692.913 393000 655000
14432.
2034
110152.
9774
16503
.9370
Baking and packing 1508562.992 393000 131000
22203.
3898
73435.3
183
13409
.4488
Administration 754281.4961 196500 0 2220.3 2824.43 6704.
4
Answer 1:
Schedule 1:
Resource Cost
Categories and
Resource Drivers
Cost category Cost Resource driver
Wages
$
7,368,750 Number of employees
Building costs
$
1,965,000 Floor space
Depreciation
$
1,310,000 Machine hours
Consumables
$
65,500 Orders placed by centre
Energy
$
275,100 Kilowatt hours used
Other
$
65,500 Number of employees
Total
$
11,049,850
Schedule 2:
Resource drivers consumed by activity centres
Cost categories
(resource drivers) Wages
Buildin
g costs
Deprecia
tion
Consu
mables Energy Other
Activity centres (employees) (m2)
(machin
e hours)
(orders
)
(kilowat
t hours)
(empl
oyees)
New Product
Development 174064.9606
84214.
28571 0
1110.1
695
5648.87
06
1547.
2441
Sales and distribution 754281.4961 196500 0
1110.1
695
3389.32
24
6704.
7244
Inspecting 116043.3071 196500 0
1110.1
695
3389.32
24
1031.
4961
Mixing 1856692.913 393000 524000
22203.
3898
73435.3
183
16503
.9370
Filling 1856692.913 393000 655000
14432.
2034
110152.
9774
16503
.9370
Baking and packing 1508562.992 393000 131000
22203.
3898
73435.3
183
13409
.4488
Administration 754281.4961 196500 0 2220.3 2824.43 6704.
Secure Best Marks with AI Grader
Need help grading? Try our AI Grader for instant feedback on your assignments.
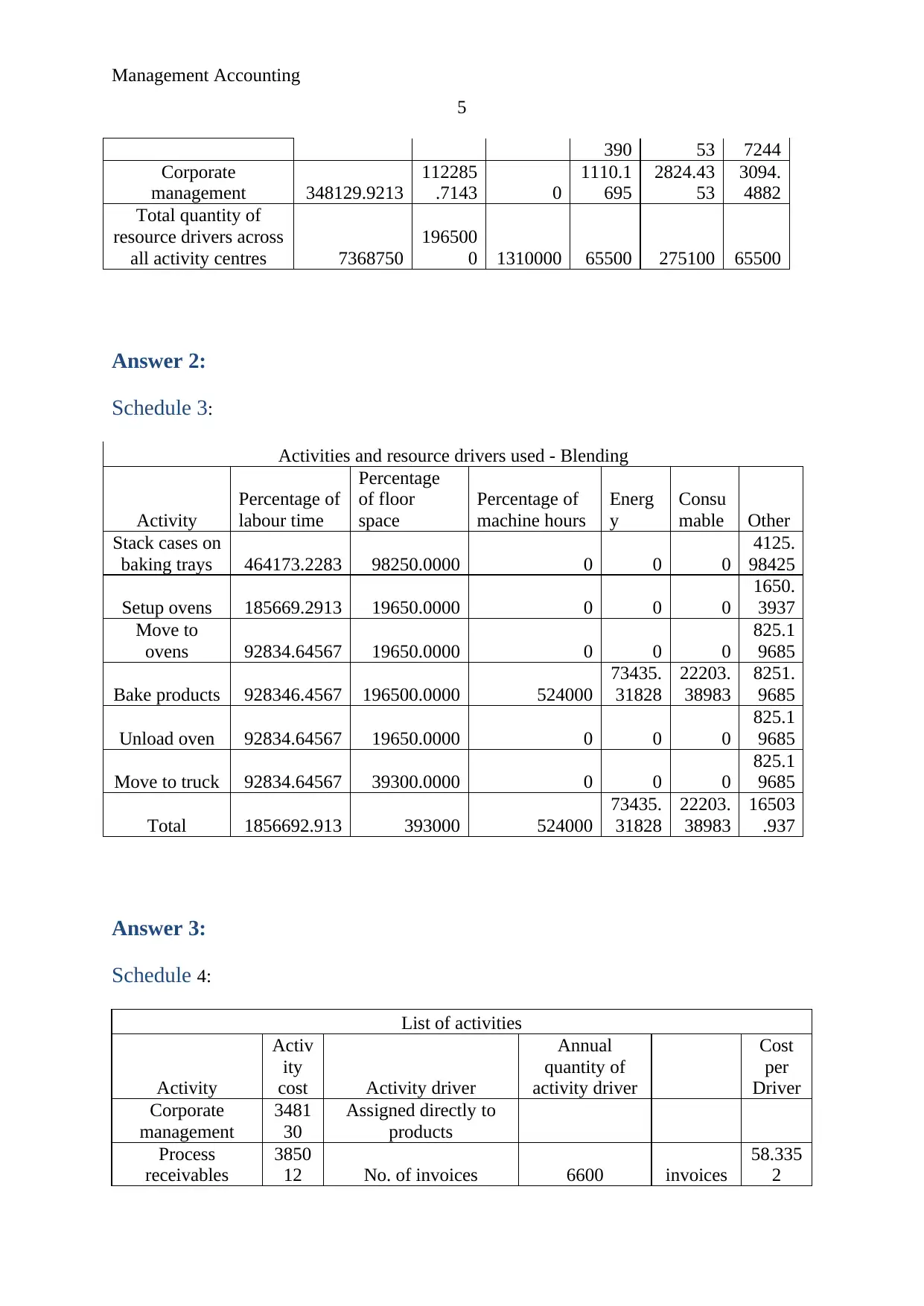
Management Accounting
5
390 53 7244
Corporate
management 348129.9213
112285
.7143 0
1110.1
695
2824.43
53
3094.
4882
Total quantity of
resource drivers across
all activity centres 7368750
196500
0 1310000 65500 275100 65500
Answer 2:
Schedule 3:
Activities and resource drivers used - Blending
Activity
Percentage of
labour time
Percentage
of floor
space
Percentage of
machine hours
Energ
y
Consu
mable Other
Stack cases on
baking trays 464173.2283 98250.0000 0 0 0
4125.
98425
Setup ovens 185669.2913 19650.0000 0 0 0
1650.
3937
Move to
ovens 92834.64567 19650.0000 0 0 0
825.1
9685
Bake products 928346.4567 196500.0000 524000
73435.
31828
22203.
38983
8251.
9685
Unload oven 92834.64567 19650.0000 0 0 0
825.1
9685
Move to truck 92834.64567 39300.0000 0 0 0
825.1
9685
Total 1856692.913 393000 524000
73435.
31828
22203.
38983
16503
.937
Answer 3:
Schedule 4:
List of activities
Activity
Activ
ity
cost Activity driver
Annual
quantity of
activity driver
Cost
per
Driver
Corporate
management
3481
30
Assigned directly to
products
Process
receivables
3850
12 No. of invoices 6600 invoices
58.335
2
5
390 53 7244
Corporate
management 348129.9213
112285
.7143 0
1110.1
695
2824.43
53
3094.
4882
Total quantity of
resource drivers across
all activity centres 7368750
196500
0 1310000 65500 275100 65500
Answer 2:
Schedule 3:
Activities and resource drivers used - Blending
Activity
Percentage of
labour time
Percentage
of floor
space
Percentage of
machine hours
Energ
y
Consu
mable Other
Stack cases on
baking trays 464173.2283 98250.0000 0 0 0
4125.
98425
Setup ovens 185669.2913 19650.0000 0 0 0
1650.
3937
Move to
ovens 92834.64567 19650.0000 0 0 0
825.1
9685
Bake products 928346.4567 196500.0000 524000
73435.
31828
22203.
38983
8251.
9685
Unload oven 92834.64567 19650.0000 0 0 0
825.1
9685
Move to truck 92834.64567 39300.0000 0 0 0
825.1
9685
Total 1856692.913 393000 524000
73435.
31828
22203.
38983
16503
.937
Answer 3:
Schedule 4:
List of activities
Activity
Activ
ity
cost Activity driver
Annual
quantity of
activity driver
Cost
per
Driver
Corporate
management
3481
30
Assigned directly to
products
Process
receivables
3850
12 No. of invoices 6600 invoices
58.335
2
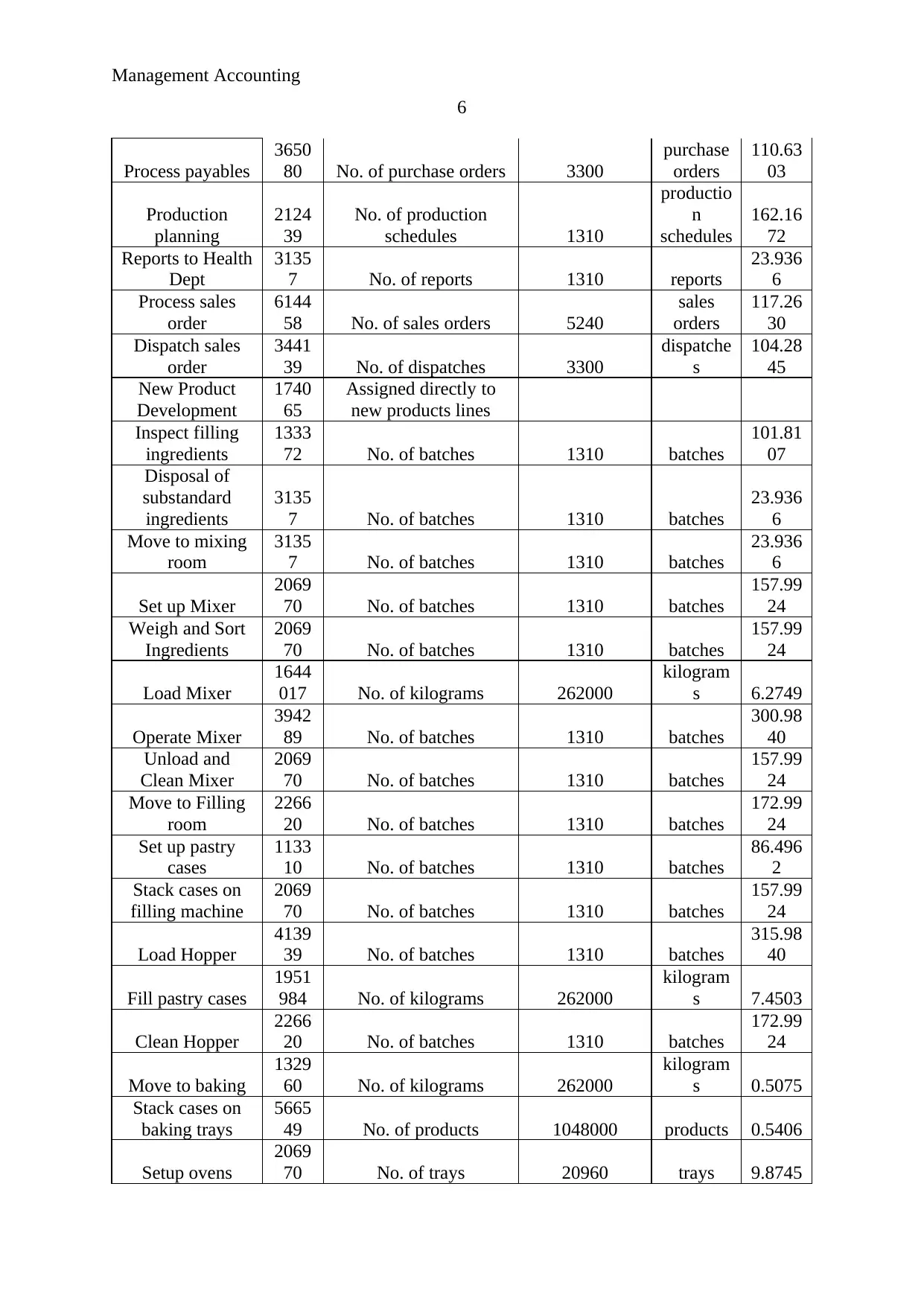
Management Accounting
6
Process payables
3650
80 No. of purchase orders 3300
purchase
orders
110.63
03
Production
planning
2124
39
No. of production
schedules 1310
productio
n
schedules
162.16
72
Reports to Health
Dept
3135
7 No. of reports 1310 reports
23.936
6
Process sales
order
6144
58 No. of sales orders 5240
sales
orders
117.26
30
Dispatch sales
order
3441
39 No. of dispatches 3300
dispatche
s
104.28
45
New Product
Development
1740
65
Assigned directly to
new products lines
Inspect filling
ingredients
1333
72 No. of batches 1310 batches
101.81
07
Disposal of
substandard
ingredients
3135
7 No. of batches 1310 batches
23.936
6
Move to mixing
room
3135
7 No. of batches 1310 batches
23.936
6
Set up Mixer
2069
70 No. of batches 1310 batches
157.99
24
Weigh and Sort
Ingredients
2069
70 No. of batches 1310 batches
157.99
24
Load Mixer
1644
017 No. of kilograms 262000
kilogram
s 6.2749
Operate Mixer
3942
89 No. of batches 1310 batches
300.98
40
Unload and
Clean Mixer
2069
70 No. of batches 1310 batches
157.99
24
Move to Filling
room
2266
20 No. of batches 1310 batches
172.99
24
Set up pastry
cases
1133
10 No. of batches 1310 batches
86.496
2
Stack cases on
filling machine
2069
70 No. of batches 1310 batches
157.99
24
Load Hopper
4139
39 No. of batches 1310 batches
315.98
40
Fill pastry cases
1951
984 No. of kilograms 262000
kilogram
s 7.4503
Clean Hopper
2266
20 No. of batches 1310 batches
172.99
24
Move to baking
1329
60 No. of kilograms 262000
kilogram
s 0.5075
Stack cases on
baking trays
5665
49 No. of products 1048000 products 0.5406
Setup ovens
2069
70 No. of trays 20960 trays 9.8745
6
Process payables
3650
80 No. of purchase orders 3300
purchase
orders
110.63
03
Production
planning
2124
39
No. of production
schedules 1310
productio
n
schedules
162.16
72
Reports to Health
Dept
3135
7 No. of reports 1310 reports
23.936
6
Process sales
order
6144
58 No. of sales orders 5240
sales
orders
117.26
30
Dispatch sales
order
3441
39 No. of dispatches 3300
dispatche
s
104.28
45
New Product
Development
1740
65
Assigned directly to
new products lines
Inspect filling
ingredients
1333
72 No. of batches 1310 batches
101.81
07
Disposal of
substandard
ingredients
3135
7 No. of batches 1310 batches
23.936
6
Move to mixing
room
3135
7 No. of batches 1310 batches
23.936
6
Set up Mixer
2069
70 No. of batches 1310 batches
157.99
24
Weigh and Sort
Ingredients
2069
70 No. of batches 1310 batches
157.99
24
Load Mixer
1644
017 No. of kilograms 262000
kilogram
s 6.2749
Operate Mixer
3942
89 No. of batches 1310 batches
300.98
40
Unload and
Clean Mixer
2069
70 No. of batches 1310 batches
157.99
24
Move to Filling
room
2266
20 No. of batches 1310 batches
172.99
24
Set up pastry
cases
1133
10 No. of batches 1310 batches
86.496
2
Stack cases on
filling machine
2069
70 No. of batches 1310 batches
157.99
24
Load Hopper
4139
39 No. of batches 1310 batches
315.98
40
Fill pastry cases
1951
984 No. of kilograms 262000
kilogram
s 7.4503
Clean Hopper
2266
20 No. of batches 1310 batches
172.99
24
Move to baking
1329
60 No. of kilograms 262000
kilogram
s 0.5075
Stack cases on
baking trays
5665
49 No. of products 1048000 products 0.5406
Setup ovens
2069
70 No. of trays 20960 trays 9.8745
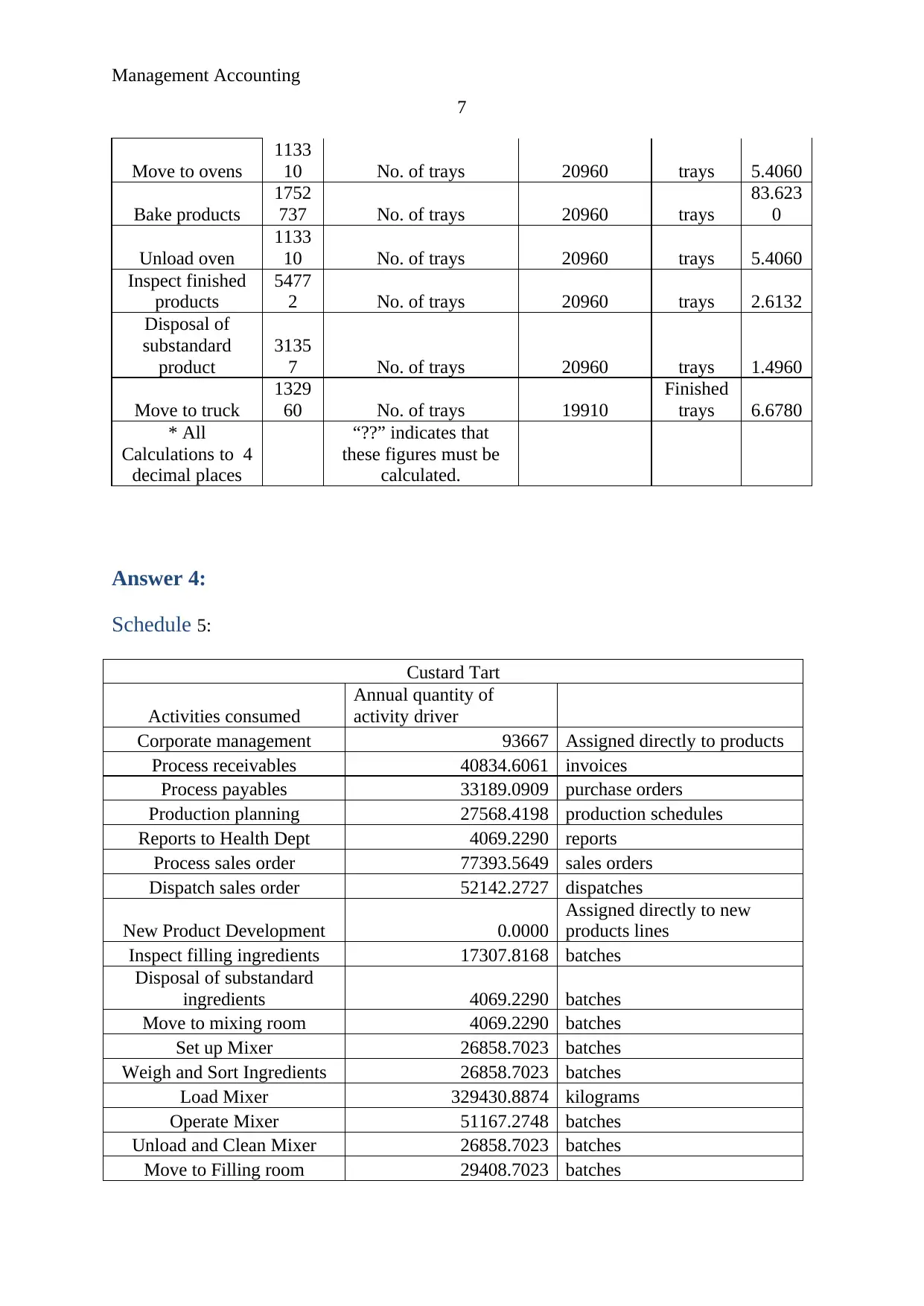
Management Accounting
7
Move to ovens
1133
10 No. of trays 20960 trays 5.4060
Bake products
1752
737 No. of trays 20960 trays
83.623
0
Unload oven
1133
10 No. of trays 20960 trays 5.4060
Inspect finished
products
5477
2 No. of trays 20960 trays 2.6132
Disposal of
substandard
product
3135
7 No. of trays 20960 trays 1.4960
Move to truck
1329
60 No. of trays 19910
Finished
trays 6.6780
* All
Calculations to 4
decimal places
“??” indicates that
these figures must be
calculated.
Answer 4:
Schedule 5:
Custard Tart
Activities consumed
Annual quantity of
activity driver
Corporate management 93667 Assigned directly to products
Process receivables 40834.6061 invoices
Process payables 33189.0909 purchase orders
Production planning 27568.4198 production schedules
Reports to Health Dept 4069.2290 reports
Process sales order 77393.5649 sales orders
Dispatch sales order 52142.2727 dispatches
New Product Development 0.0000
Assigned directly to new
products lines
Inspect filling ingredients 17307.8168 batches
Disposal of substandard
ingredients 4069.2290 batches
Move to mixing room 4069.2290 batches
Set up Mixer 26858.7023 batches
Weigh and Sort Ingredients 26858.7023 batches
Load Mixer 329430.8874 kilograms
Operate Mixer 51167.2748 batches
Unload and Clean Mixer 26858.7023 batches
Move to Filling room 29408.7023 batches
7
Move to ovens
1133
10 No. of trays 20960 trays 5.4060
Bake products
1752
737 No. of trays 20960 trays
83.623
0
Unload oven
1133
10 No. of trays 20960 trays 5.4060
Inspect finished
products
5477
2 No. of trays 20960 trays 2.6132
Disposal of
substandard
product
3135
7 No. of trays 20960 trays 1.4960
Move to truck
1329
60 No. of trays 19910
Finished
trays 6.6780
* All
Calculations to 4
decimal places
“??” indicates that
these figures must be
calculated.
Answer 4:
Schedule 5:
Custard Tart
Activities consumed
Annual quantity of
activity driver
Corporate management 93667 Assigned directly to products
Process receivables 40834.6061 invoices
Process payables 33189.0909 purchase orders
Production planning 27568.4198 production schedules
Reports to Health Dept 4069.2290 reports
Process sales order 77393.5649 sales orders
Dispatch sales order 52142.2727 dispatches
New Product Development 0.0000
Assigned directly to new
products lines
Inspect filling ingredients 17307.8168 batches
Disposal of substandard
ingredients 4069.2290 batches
Move to mixing room 4069.2290 batches
Set up Mixer 26858.7023 batches
Weigh and Sort Ingredients 26858.7023 batches
Load Mixer 329430.8874 kilograms
Operate Mixer 51167.2748 batches
Unload and Clean Mixer 26858.7023 batches
Move to Filling room 29408.7023 batches
Paraphrase This Document
Need a fresh take? Get an instant paraphrase of this document with our AI Paraphraser
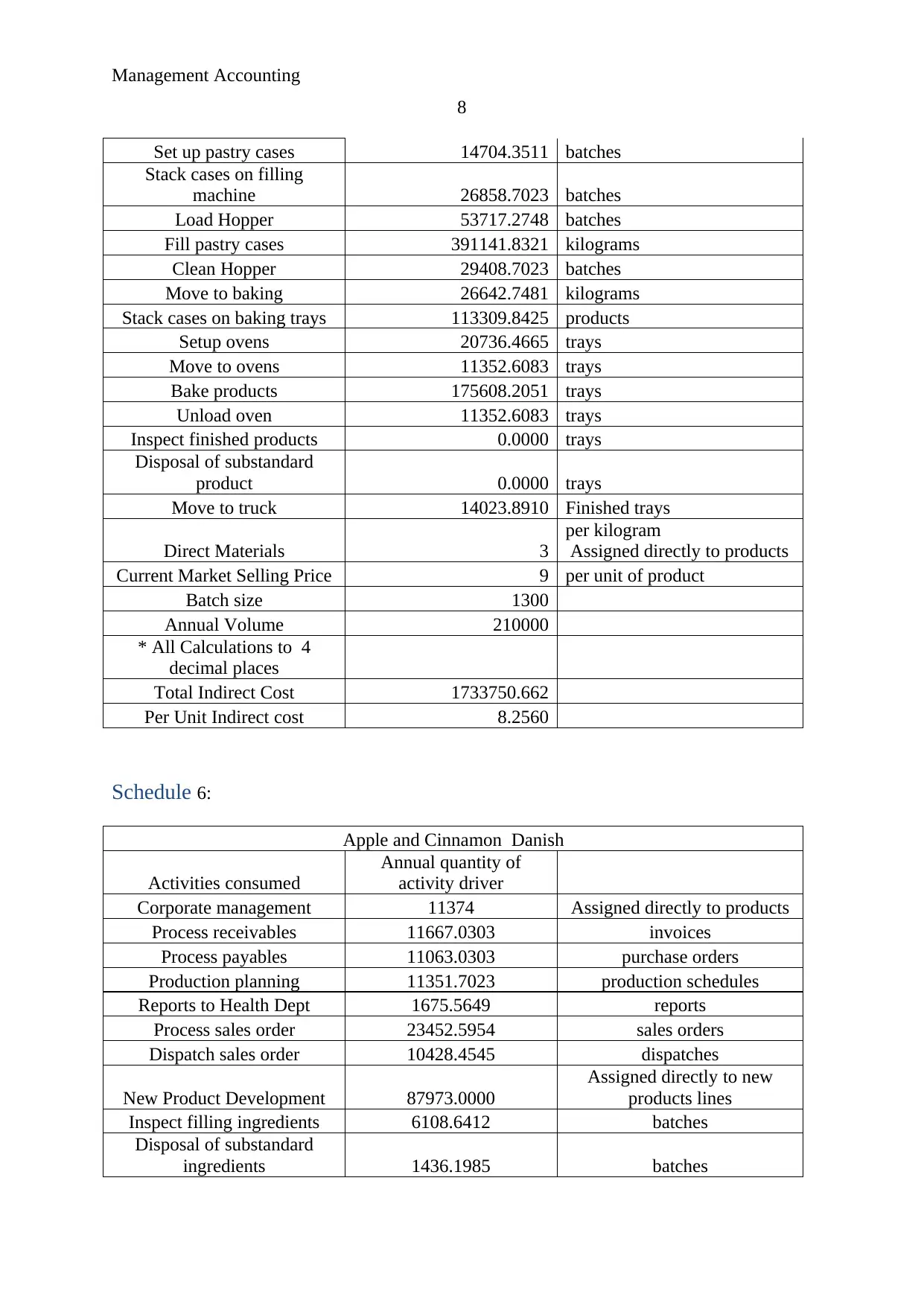
Management Accounting
8
Set up pastry cases 14704.3511 batches
Stack cases on filling
machine 26858.7023 batches
Load Hopper 53717.2748 batches
Fill pastry cases 391141.8321 kilograms
Clean Hopper 29408.7023 batches
Move to baking 26642.7481 kilograms
Stack cases on baking trays 113309.8425 products
Setup ovens 20736.4665 trays
Move to ovens 11352.6083 trays
Bake products 175608.2051 trays
Unload oven 11352.6083 trays
Inspect finished products 0.0000 trays
Disposal of substandard
product 0.0000 trays
Move to truck 14023.8910 Finished trays
Direct Materials 3
per kilogram
Assigned directly to products
Current Market Selling Price 9 per unit of product
Batch size 1300
Annual Volume 210000
* All Calculations to 4
decimal places
Total Indirect Cost 1733750.662
Per Unit Indirect cost 8.2560
Schedule 6:
Apple and Cinnamon Danish
Activities consumed
Annual quantity of
activity driver
Corporate management 11374 Assigned directly to products
Process receivables 11667.0303 invoices
Process payables 11063.0303 purchase orders
Production planning 11351.7023 production schedules
Reports to Health Dept 1675.5649 reports
Process sales order 23452.5954 sales orders
Dispatch sales order 10428.4545 dispatches
New Product Development 87973.0000
Assigned directly to new
products lines
Inspect filling ingredients 6108.6412 batches
Disposal of substandard
ingredients 1436.1985 batches
8
Set up pastry cases 14704.3511 batches
Stack cases on filling
machine 26858.7023 batches
Load Hopper 53717.2748 batches
Fill pastry cases 391141.8321 kilograms
Clean Hopper 29408.7023 batches
Move to baking 26642.7481 kilograms
Stack cases on baking trays 113309.8425 products
Setup ovens 20736.4665 trays
Move to ovens 11352.6083 trays
Bake products 175608.2051 trays
Unload oven 11352.6083 trays
Inspect finished products 0.0000 trays
Disposal of substandard
product 0.0000 trays
Move to truck 14023.8910 Finished trays
Direct Materials 3
per kilogram
Assigned directly to products
Current Market Selling Price 9 per unit of product
Batch size 1300
Annual Volume 210000
* All Calculations to 4
decimal places
Total Indirect Cost 1733750.662
Per Unit Indirect cost 8.2560
Schedule 6:
Apple and Cinnamon Danish
Activities consumed
Annual quantity of
activity driver
Corporate management 11374 Assigned directly to products
Process receivables 11667.0303 invoices
Process payables 11063.0303 purchase orders
Production planning 11351.7023 production schedules
Reports to Health Dept 1675.5649 reports
Process sales order 23452.5954 sales orders
Dispatch sales order 10428.4545 dispatches
New Product Development 87973.0000
Assigned directly to new
products lines
Inspect filling ingredients 6108.6412 batches
Disposal of substandard
ingredients 1436.1985 batches
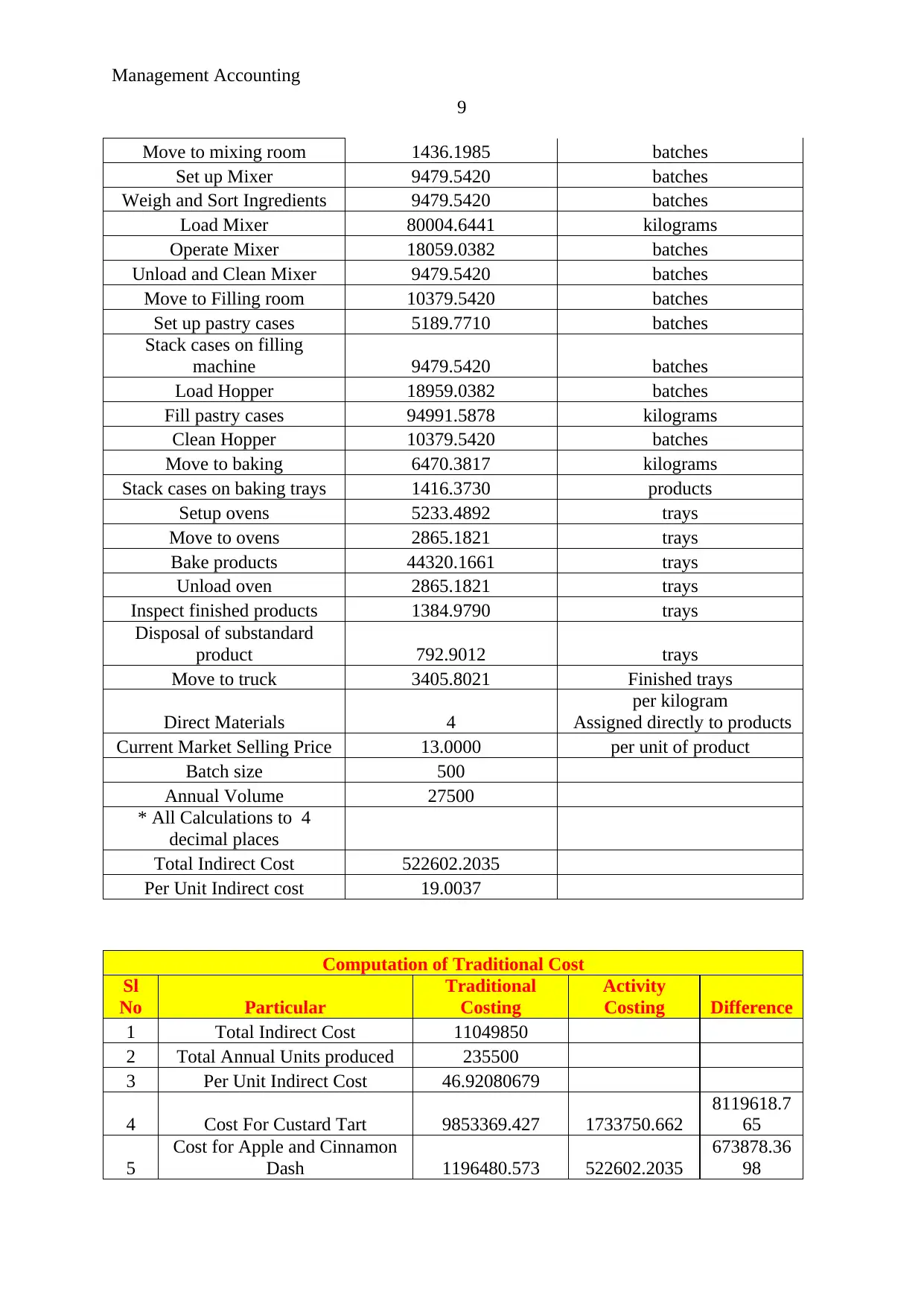
Management Accounting
9
Move to mixing room 1436.1985 batches
Set up Mixer 9479.5420 batches
Weigh and Sort Ingredients 9479.5420 batches
Load Mixer 80004.6441 kilograms
Operate Mixer 18059.0382 batches
Unload and Clean Mixer 9479.5420 batches
Move to Filling room 10379.5420 batches
Set up pastry cases 5189.7710 batches
Stack cases on filling
machine 9479.5420 batches
Load Hopper 18959.0382 batches
Fill pastry cases 94991.5878 kilograms
Clean Hopper 10379.5420 batches
Move to baking 6470.3817 kilograms
Stack cases on baking trays 1416.3730 products
Setup ovens 5233.4892 trays
Move to ovens 2865.1821 trays
Bake products 44320.1661 trays
Unload oven 2865.1821 trays
Inspect finished products 1384.9790 trays
Disposal of substandard
product 792.9012 trays
Move to truck 3405.8021 Finished trays
Direct Materials 4
per kilogram
Assigned directly to products
Current Market Selling Price 13.0000 per unit of product
Batch size 500
Annual Volume 27500
* All Calculations to 4
decimal places
Total Indirect Cost 522602.2035
Per Unit Indirect cost 19.0037
Computation of Traditional Cost
Sl
No Particular
Traditional
Costing
Activity
Costing Difference
1 Total Indirect Cost 11049850
2 Total Annual Units produced 235500
3 Per Unit Indirect Cost 46.92080679
4 Cost For Custard Tart 9853369.427 1733750.662
8119618.7
65
5
Cost for Apple and Cinnamon
Dash 1196480.573 522602.2035
673878.36
98
9
Move to mixing room 1436.1985 batches
Set up Mixer 9479.5420 batches
Weigh and Sort Ingredients 9479.5420 batches
Load Mixer 80004.6441 kilograms
Operate Mixer 18059.0382 batches
Unload and Clean Mixer 9479.5420 batches
Move to Filling room 10379.5420 batches
Set up pastry cases 5189.7710 batches
Stack cases on filling
machine 9479.5420 batches
Load Hopper 18959.0382 batches
Fill pastry cases 94991.5878 kilograms
Clean Hopper 10379.5420 batches
Move to baking 6470.3817 kilograms
Stack cases on baking trays 1416.3730 products
Setup ovens 5233.4892 trays
Move to ovens 2865.1821 trays
Bake products 44320.1661 trays
Unload oven 2865.1821 trays
Inspect finished products 1384.9790 trays
Disposal of substandard
product 792.9012 trays
Move to truck 3405.8021 Finished trays
Direct Materials 4
per kilogram
Assigned directly to products
Current Market Selling Price 13.0000 per unit of product
Batch size 500
Annual Volume 27500
* All Calculations to 4
decimal places
Total Indirect Cost 522602.2035
Per Unit Indirect cost 19.0037
Computation of Traditional Cost
Sl
No Particular
Traditional
Costing
Activity
Costing Difference
1 Total Indirect Cost 11049850
2 Total Annual Units produced 235500
3 Per Unit Indirect Cost 46.92080679
4 Cost For Custard Tart 9853369.427 1733750.662
8119618.7
65
5
Cost for Apple and Cinnamon
Dash 1196480.573 522602.2035
673878.36
98
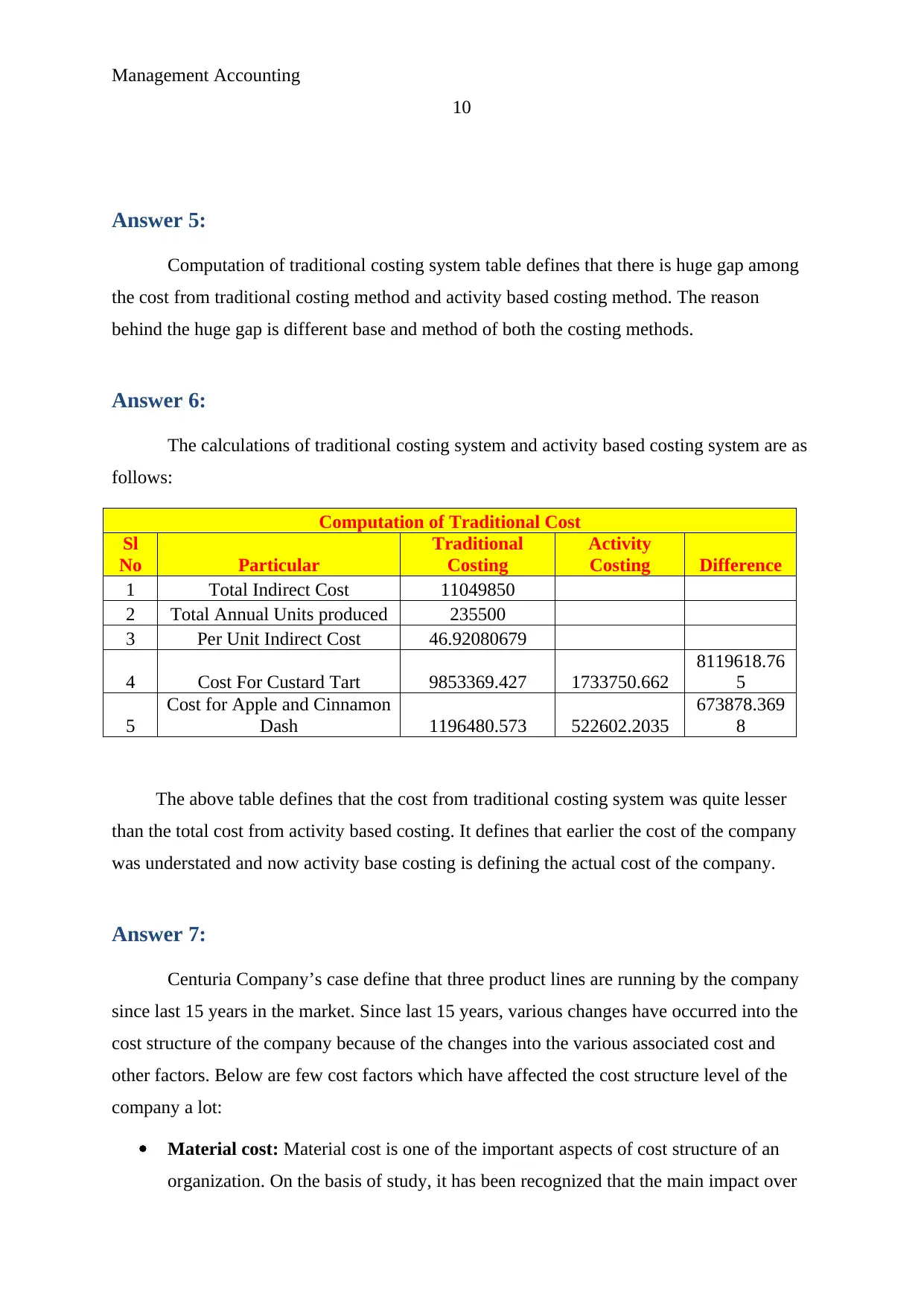
Management Accounting
10
Answer 5:
Computation of traditional costing system table defines that there is huge gap among
the cost from traditional costing method and activity based costing method. The reason
behind the huge gap is different base and method of both the costing methods.
Answer 6:
The calculations of traditional costing system and activity based costing system are as
follows:
Computation of Traditional Cost
Sl
No Particular
Traditional
Costing
Activity
Costing Difference
1 Total Indirect Cost 11049850
2 Total Annual Units produced 235500
3 Per Unit Indirect Cost 46.92080679
4 Cost For Custard Tart 9853369.427 1733750.662
8119618.76
5
5
Cost for Apple and Cinnamon
Dash 1196480.573 522602.2035
673878.369
8
The above table defines that the cost from traditional costing system was quite lesser
than the total cost from activity based costing. It defines that earlier the cost of the company
was understated and now activity base costing is defining the actual cost of the company.
Answer 7:
Centuria Company’s case define that three product lines are running by the company
since last 15 years in the market. Since last 15 years, various changes have occurred into the
cost structure of the company because of the changes into the various associated cost and
other factors. Below are few cost factors which have affected the cost structure level of the
company a lot:
Material cost: Material cost is one of the important aspects of cost structure of an
organization. On the basis of study, it has been recognized that the main impact over
10
Answer 5:
Computation of traditional costing system table defines that there is huge gap among
the cost from traditional costing method and activity based costing method. The reason
behind the huge gap is different base and method of both the costing methods.
Answer 6:
The calculations of traditional costing system and activity based costing system are as
follows:
Computation of Traditional Cost
Sl
No Particular
Traditional
Costing
Activity
Costing Difference
1 Total Indirect Cost 11049850
2 Total Annual Units produced 235500
3 Per Unit Indirect Cost 46.92080679
4 Cost For Custard Tart 9853369.427 1733750.662
8119618.76
5
5
Cost for Apple and Cinnamon
Dash 1196480.573 522602.2035
673878.369
8
The above table defines that the cost from traditional costing system was quite lesser
than the total cost from activity based costing. It defines that earlier the cost of the company
was understated and now activity base costing is defining the actual cost of the company.
Answer 7:
Centuria Company’s case define that three product lines are running by the company
since last 15 years in the market. Since last 15 years, various changes have occurred into the
cost structure of the company because of the changes into the various associated cost and
other factors. Below are few cost factors which have affected the cost structure level of the
company a lot:
Material cost: Material cost is one of the important aspects of cost structure of an
organization. On the basis of study, it has been recognized that the main impact over
Secure Best Marks with AI Grader
Need help grading? Try our AI Grader for instant feedback on your assignments.

Management Accounting
11
the cost structure of an organization is material cost. Hence, changes into material
cost have affected cost structure level at a great extent.
Labour cost: Labour cost is one of the highest and used aspects of cost structure of
an organization. On the basis of study, it has been recognized that the labour cost has
improved a lot in the market from last 15 years (Bhimani, Horngren, Datar & Foster,
2018). Hence, changes into labour cost have affected cost structure level at a great
extent.
High fixed cost: Further the study defines that along with the changes into the
process and machineries, the fixed cost level of the company get also change. On the
basis of study, it has been recognized that the high cost level have affected the
performance of the company at great extent. Hence, changes into fixed cost have
affected cost structure level at a great extent.
Inflation rate: Lastly, inflation rate is the main aspect which affects the cost level of
the business. On the basis of study, it has been recognized that the main impact over
the cost structure of an organization is inflation rate. Hence, changes into inflation
rate have affected cost structure level at a great extent.
Answer 8 and 9:
Introduction:
Costing system is a technique which is used in manufacturing and other organizations
to gather the data and identify the total cost associated with the total production level of the
business. Mainly there are 2 ways to calculate the same: activity based costing and traditional
costing system. Traditional costing system is the oldest technique to calculate the production
cost. Activity based costing is the refined version of traditional costing in which each cost is
allocated on different basis to production department.
In the case, Centuria Company is a manufacturing company and it is manufacturing 3
different products since last 15 years in the market. The company was following the
traditional costing system but now it has been found that there is huge difference between the
costs from traditional costing system in activity based costing. Hence, the company is looking
forward the make the changes in costing system of the company.
11
the cost structure of an organization is material cost. Hence, changes into material
cost have affected cost structure level at a great extent.
Labour cost: Labour cost is one of the highest and used aspects of cost structure of
an organization. On the basis of study, it has been recognized that the labour cost has
improved a lot in the market from last 15 years (Bhimani, Horngren, Datar & Foster,
2018). Hence, changes into labour cost have affected cost structure level at a great
extent.
High fixed cost: Further the study defines that along with the changes into the
process and machineries, the fixed cost level of the company get also change. On the
basis of study, it has been recognized that the high cost level have affected the
performance of the company at great extent. Hence, changes into fixed cost have
affected cost structure level at a great extent.
Inflation rate: Lastly, inflation rate is the main aspect which affects the cost level of
the business. On the basis of study, it has been recognized that the main impact over
the cost structure of an organization is inflation rate. Hence, changes into inflation
rate have affected cost structure level at a great extent.
Answer 8 and 9:
Introduction:
Costing system is a technique which is used in manufacturing and other organizations
to gather the data and identify the total cost associated with the total production level of the
business. Mainly there are 2 ways to calculate the same: activity based costing and traditional
costing system. Traditional costing system is the oldest technique to calculate the production
cost. Activity based costing is the refined version of traditional costing in which each cost is
allocated on different basis to production department.
In the case, Centuria Company is a manufacturing company and it is manufacturing 3
different products since last 15 years in the market. The company was following the
traditional costing system but now it has been found that there is huge difference between the
costs from traditional costing system in activity based costing. Hence, the company is looking
forward the make the changes in costing system of the company.
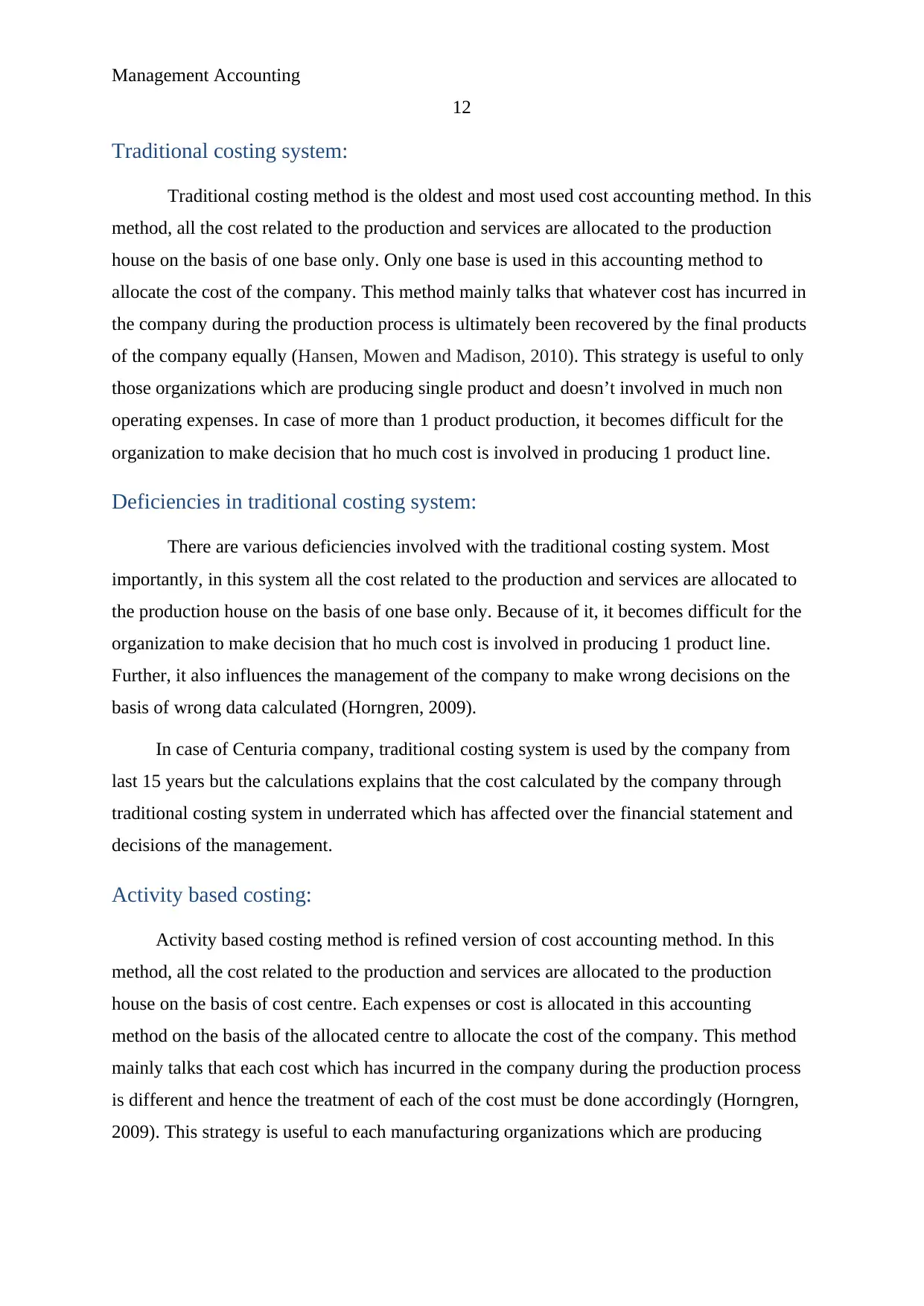
Management Accounting
12
Traditional costing system:
Traditional costing method is the oldest and most used cost accounting method. In this
method, all the cost related to the production and services are allocated to the production
house on the basis of one base only. Only one base is used in this accounting method to
allocate the cost of the company. This method mainly talks that whatever cost has incurred in
the company during the production process is ultimately been recovered by the final products
of the company equally (Hansen, Mowen and Madison, 2010). This strategy is useful to only
those organizations which are producing single product and doesn’t involved in much non
operating expenses. In case of more than 1 product production, it becomes difficult for the
organization to make decision that ho much cost is involved in producing 1 product line.
Deficiencies in traditional costing system:
There are various deficiencies involved with the traditional costing system. Most
importantly, in this system all the cost related to the production and services are allocated to
the production house on the basis of one base only. Because of it, it becomes difficult for the
organization to make decision that ho much cost is involved in producing 1 product line.
Further, it also influences the management of the company to make wrong decisions on the
basis of wrong data calculated (Horngren, 2009).
In case of Centuria company, traditional costing system is used by the company from
last 15 years but the calculations explains that the cost calculated by the company through
traditional costing system in underrated which has affected over the financial statement and
decisions of the management.
Activity based costing:
Activity based costing method is refined version of cost accounting method. In this
method, all the cost related to the production and services are allocated to the production
house on the basis of cost centre. Each expenses or cost is allocated in this accounting
method on the basis of the allocated centre to allocate the cost of the company. This method
mainly talks that each cost which has incurred in the company during the production process
is different and hence the treatment of each of the cost must be done accordingly (Horngren,
2009). This strategy is useful to each manufacturing organizations which are producing
12
Traditional costing system:
Traditional costing method is the oldest and most used cost accounting method. In this
method, all the cost related to the production and services are allocated to the production
house on the basis of one base only. Only one base is used in this accounting method to
allocate the cost of the company. This method mainly talks that whatever cost has incurred in
the company during the production process is ultimately been recovered by the final products
of the company equally (Hansen, Mowen and Madison, 2010). This strategy is useful to only
those organizations which are producing single product and doesn’t involved in much non
operating expenses. In case of more than 1 product production, it becomes difficult for the
organization to make decision that ho much cost is involved in producing 1 product line.
Deficiencies in traditional costing system:
There are various deficiencies involved with the traditional costing system. Most
importantly, in this system all the cost related to the production and services are allocated to
the production house on the basis of one base only. Because of it, it becomes difficult for the
organization to make decision that ho much cost is involved in producing 1 product line.
Further, it also influences the management of the company to make wrong decisions on the
basis of wrong data calculated (Horngren, 2009).
In case of Centuria company, traditional costing system is used by the company from
last 15 years but the calculations explains that the cost calculated by the company through
traditional costing system in underrated which has affected over the financial statement and
decisions of the management.
Activity based costing:
Activity based costing method is refined version of cost accounting method. In this
method, all the cost related to the production and services are allocated to the production
house on the basis of cost centre. Each expenses or cost is allocated in this accounting
method on the basis of the allocated centre to allocate the cost of the company. This method
mainly talks that each cost which has incurred in the company during the production process
is different and hence the treatment of each of the cost must be done accordingly (Horngren,
2009). This strategy is useful to each manufacturing organizations which are producing
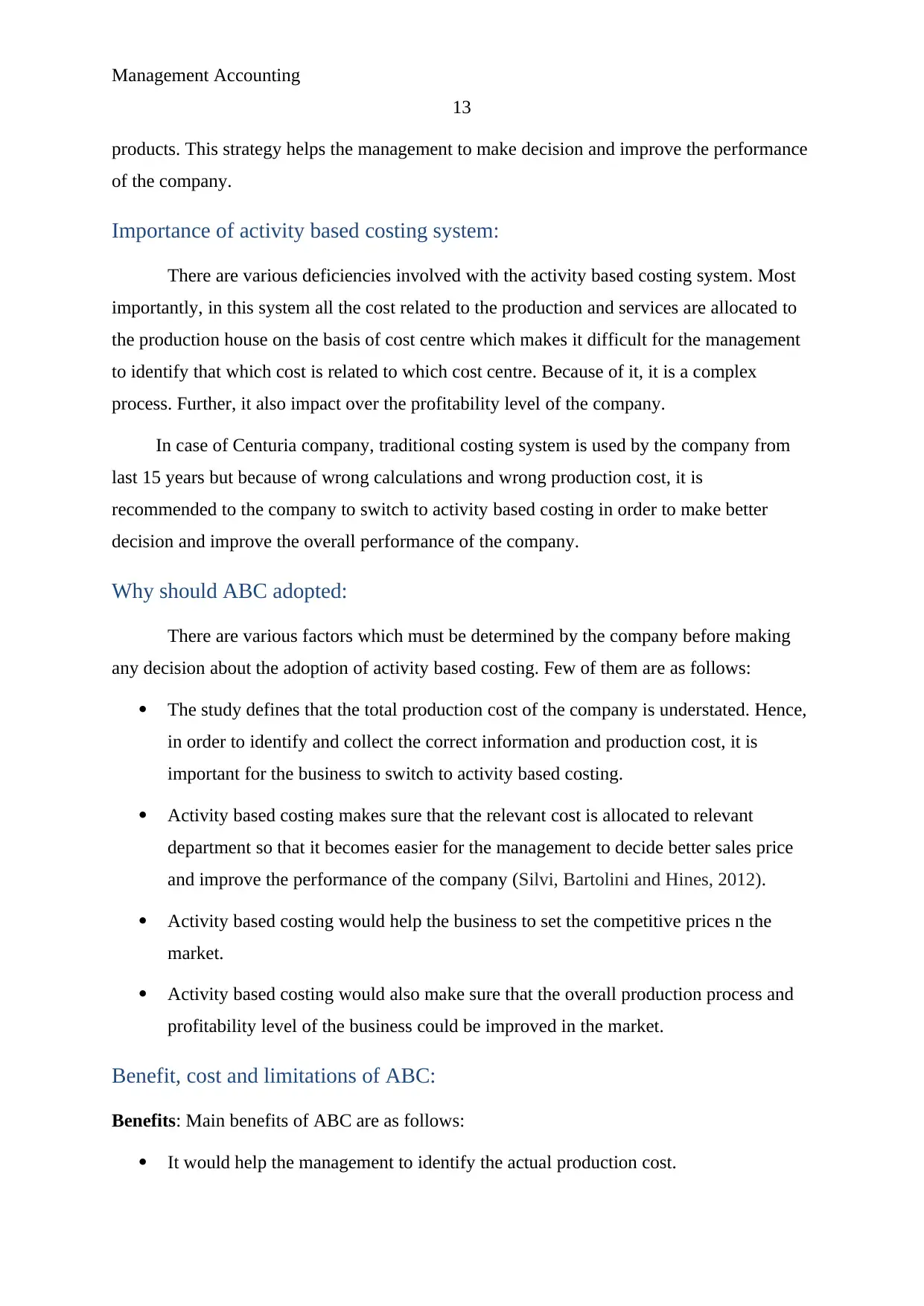
Management Accounting
13
products. This strategy helps the management to make decision and improve the performance
of the company.
Importance of activity based costing system:
There are various deficiencies involved with the activity based costing system. Most
importantly, in this system all the cost related to the production and services are allocated to
the production house on the basis of cost centre which makes it difficult for the management
to identify that which cost is related to which cost centre. Because of it, it is a complex
process. Further, it also impact over the profitability level of the company.
In case of Centuria company, traditional costing system is used by the company from
last 15 years but because of wrong calculations and wrong production cost, it is
recommended to the company to switch to activity based costing in order to make better
decision and improve the overall performance of the company.
Why should ABC adopted:
There are various factors which must be determined by the company before making
any decision about the adoption of activity based costing. Few of them are as follows:
The study defines that the total production cost of the company is understated. Hence,
in order to identify and collect the correct information and production cost, it is
important for the business to switch to activity based costing.
Activity based costing makes sure that the relevant cost is allocated to relevant
department so that it becomes easier for the management to decide better sales price
and improve the performance of the company (Silvi, Bartolini and Hines, 2012).
Activity based costing would help the business to set the competitive prices n the
market.
Activity based costing would also make sure that the overall production process and
profitability level of the business could be improved in the market.
Benefit, cost and limitations of ABC:
Benefits: Main benefits of ABC are as follows:
It would help the management to identify the actual production cost.
13
products. This strategy helps the management to make decision and improve the performance
of the company.
Importance of activity based costing system:
There are various deficiencies involved with the activity based costing system. Most
importantly, in this system all the cost related to the production and services are allocated to
the production house on the basis of cost centre which makes it difficult for the management
to identify that which cost is related to which cost centre. Because of it, it is a complex
process. Further, it also impact over the profitability level of the company.
In case of Centuria company, traditional costing system is used by the company from
last 15 years but because of wrong calculations and wrong production cost, it is
recommended to the company to switch to activity based costing in order to make better
decision and improve the overall performance of the company.
Why should ABC adopted:
There are various factors which must be determined by the company before making
any decision about the adoption of activity based costing. Few of them are as follows:
The study defines that the total production cost of the company is understated. Hence,
in order to identify and collect the correct information and production cost, it is
important for the business to switch to activity based costing.
Activity based costing makes sure that the relevant cost is allocated to relevant
department so that it becomes easier for the management to decide better sales price
and improve the performance of the company (Silvi, Bartolini and Hines, 2012).
Activity based costing would help the business to set the competitive prices n the
market.
Activity based costing would also make sure that the overall production process and
profitability level of the business could be improved in the market.
Benefit, cost and limitations of ABC:
Benefits: Main benefits of ABC are as follows:
It would help the management to identify the actual production cost.
Paraphrase This Document
Need a fresh take? Get an instant paraphrase of this document with our AI Paraphraser
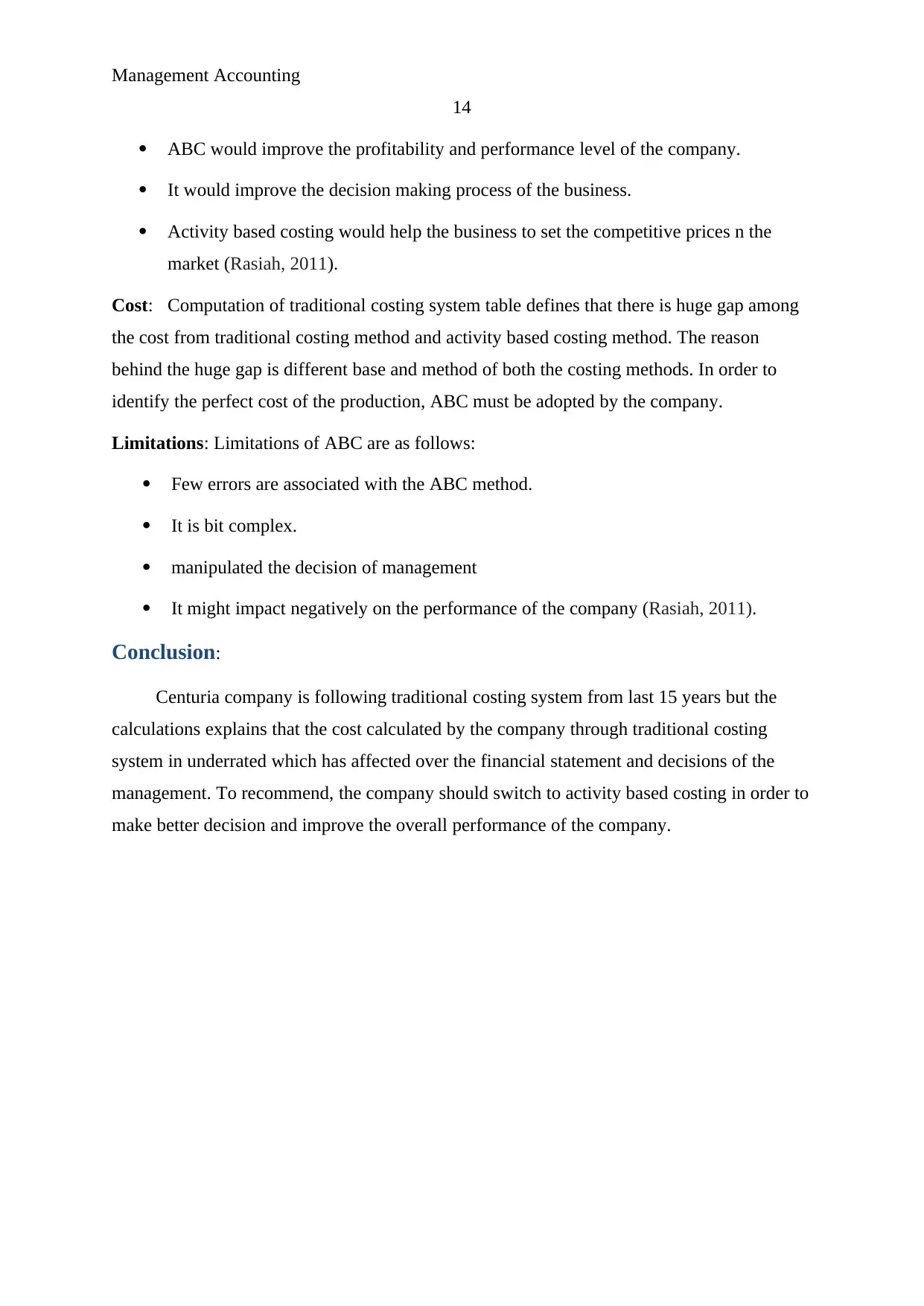
Management Accounting
14
ABC would improve the profitability and performance level of the company.
It would improve the decision making process of the business.
Activity based costing would help the business to set the competitive prices n the
market (Rasiah, 2011).
Cost: Computation of traditional costing system table defines that there is huge gap among
the cost from traditional costing method and activity based costing method. The reason
behind the huge gap is different base and method of both the costing methods. In order to
identify the perfect cost of the production, ABC must be adopted by the company.
Limitations: Limitations of ABC are as follows:
Few errors are associated with the ABC method.
It is bit complex.
manipulated the decision of management
It might impact negatively on the performance of the company (Rasiah, 2011).
Conclusion:
Centuria company is following traditional costing system from last 15 years but the
calculations explains that the cost calculated by the company through traditional costing
system in underrated which has affected over the financial statement and decisions of the
management. To recommend, the company should switch to activity based costing in order to
make better decision and improve the overall performance of the company.
14
ABC would improve the profitability and performance level of the company.
It would improve the decision making process of the business.
Activity based costing would help the business to set the competitive prices n the
market (Rasiah, 2011).
Cost: Computation of traditional costing system table defines that there is huge gap among
the cost from traditional costing method and activity based costing method. The reason
behind the huge gap is different base and method of both the costing methods. In order to
identify the perfect cost of the production, ABC must be adopted by the company.
Limitations: Limitations of ABC are as follows:
Few errors are associated with the ABC method.
It is bit complex.
manipulated the decision of management
It might impact negatively on the performance of the company (Rasiah, 2011).
Conclusion:
Centuria company is following traditional costing system from last 15 years but the
calculations explains that the cost calculated by the company through traditional costing
system in underrated which has affected over the financial statement and decisions of the
management. To recommend, the company should switch to activity based costing in order to
make better decision and improve the overall performance of the company.
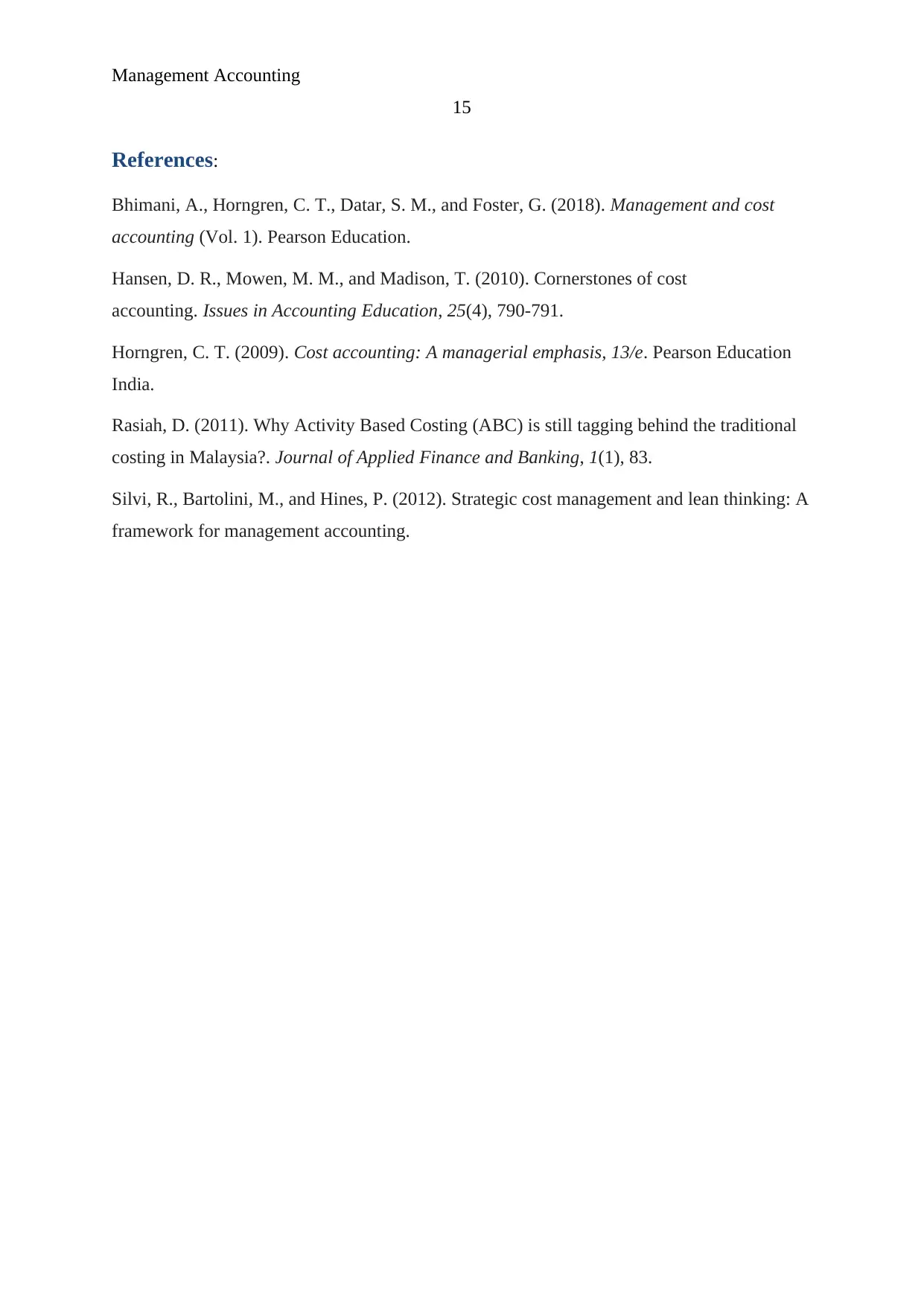
Management Accounting
15
References:
Bhimani, A., Horngren, C. T., Datar, S. M., and Foster, G. (2018). Management and cost
accounting (Vol. 1). Pearson Education.
Hansen, D. R., Mowen, M. M., and Madison, T. (2010). Cornerstones of cost
accounting. Issues in Accounting Education, 25(4), 790-791.
Horngren, C. T. (2009). Cost accounting: A managerial emphasis, 13/e. Pearson Education
India.
Rasiah, D. (2011). Why Activity Based Costing (ABC) is still tagging behind the traditional
costing in Malaysia?. Journal of Applied Finance and Banking, 1(1), 83.
Silvi, R., Bartolini, M., and Hines, P. (2012). Strategic cost management and lean thinking: A
framework for management accounting.
15
References:
Bhimani, A., Horngren, C. T., Datar, S. M., and Foster, G. (2018). Management and cost
accounting (Vol. 1). Pearson Education.
Hansen, D. R., Mowen, M. M., and Madison, T. (2010). Cornerstones of cost
accounting. Issues in Accounting Education, 25(4), 790-791.
Horngren, C. T. (2009). Cost accounting: A managerial emphasis, 13/e. Pearson Education
India.
Rasiah, D. (2011). Why Activity Based Costing (ABC) is still tagging behind the traditional
costing in Malaysia?. Journal of Applied Finance and Banking, 1(1), 83.
Silvi, R., Bartolini, M., and Hines, P. (2012). Strategic cost management and lean thinking: A
framework for management accounting.
1 out of 15
Related Documents
![[object Object]](/_next/image/?url=%2F_next%2Fstatic%2Fmedia%2Flogo.6d15ce61.png&w=640&q=75)
Your All-in-One AI-Powered Toolkit for Academic Success.
+13062052269
info@desklib.com
Available 24*7 on WhatsApp / Email
Unlock your academic potential
© 2024 | Zucol Services PVT LTD | All rights reserved.