Operational and Project Management: Quality and Capacity Management at Tesco
VerifiedAdded on  2023/06/15
|11
|3256
|344
AI Summary
This project discusses quality and capacity management at Tesco, a multinational grocery and retail company. It covers topics such as inventory management, demand forecasting, and the ABC system theory. The project also explores the interrelation of inventory with marketing and sales departments. Course code and college/university are not mentioned.
Contribute Materials
Your contribution can guide someone’s learning journey. Share your
documents today.
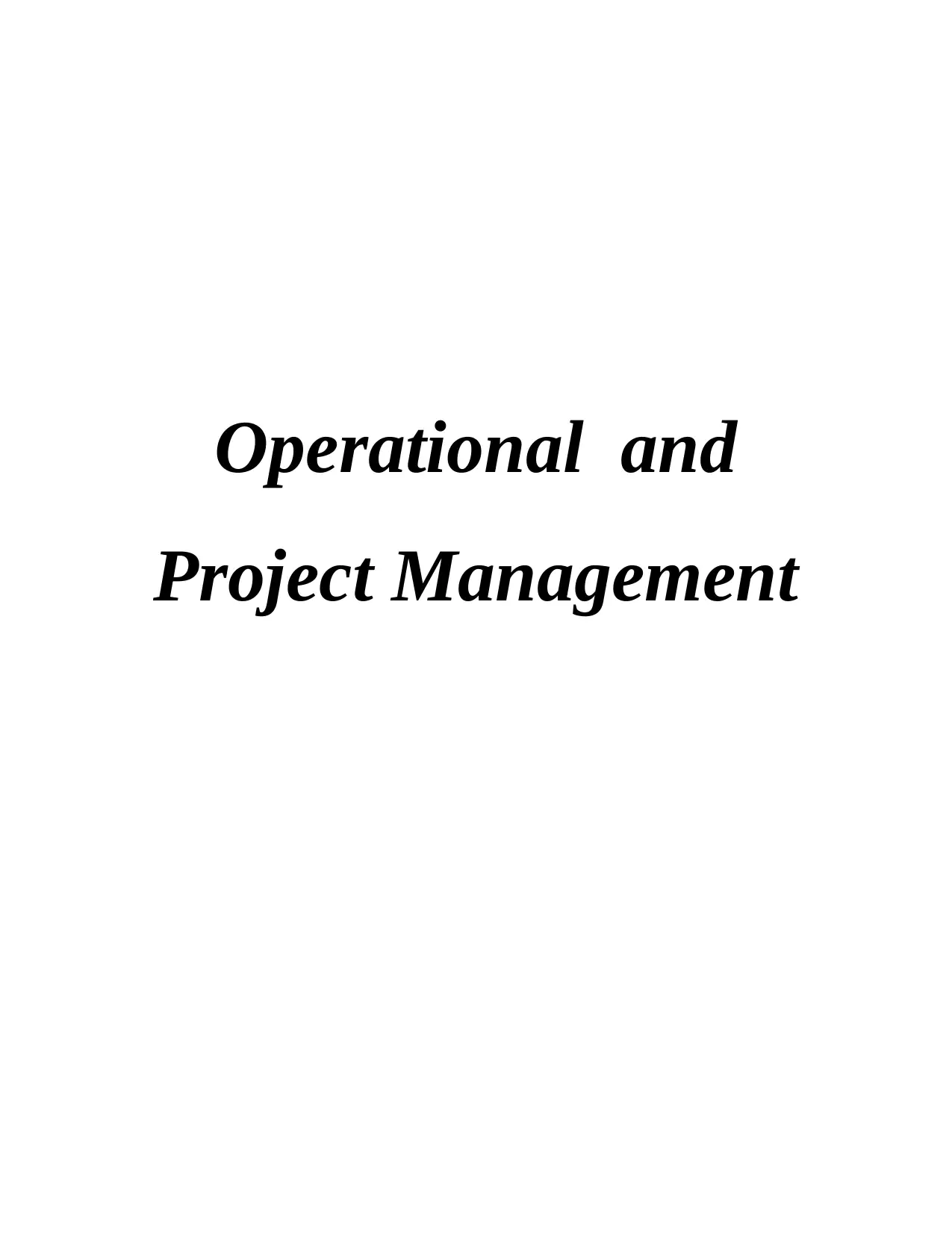
Operational and
Project Management
Project Management
Secure Best Marks with AI Grader
Need help grading? Try our AI Grader for instant feedback on your assignments.
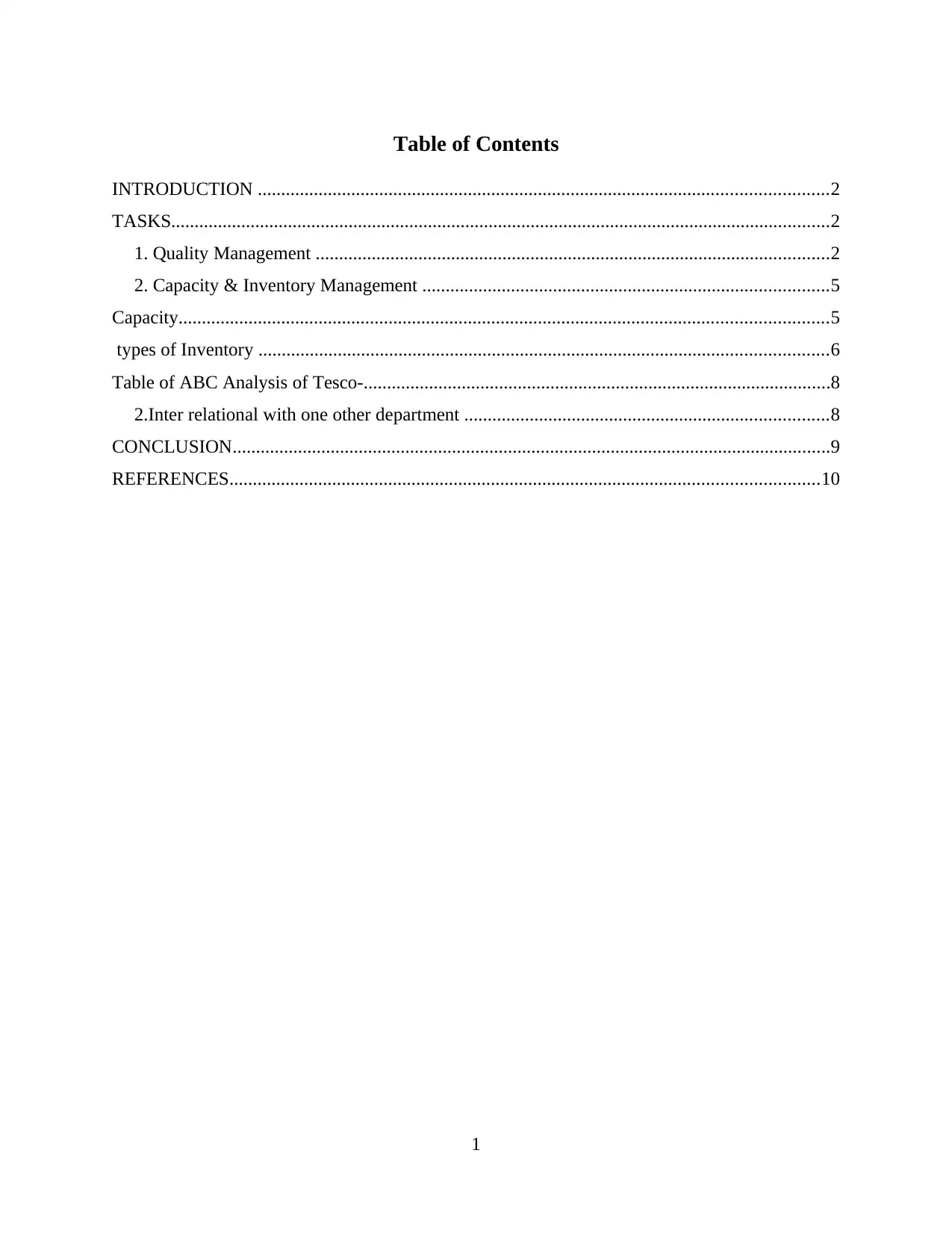
Table of Contents
INTRODUCTION ..........................................................................................................................2
TASKS.............................................................................................................................................2
1. Quality Management ..............................................................................................................2
2. Capacity & Inventory Management .......................................................................................5
Capacity...........................................................................................................................................5
types of Inventory ..........................................................................................................................6
Table of ABC Analysis of Tesco-....................................................................................................8
2.Inter relational with one other department ..............................................................................8
CONCLUSION................................................................................................................................9
REFERENCES..............................................................................................................................10
1
INTRODUCTION ..........................................................................................................................2
TASKS.............................................................................................................................................2
1. Quality Management ..............................................................................................................2
2. Capacity & Inventory Management .......................................................................................5
Capacity...........................................................................................................................................5
types of Inventory ..........................................................................................................................6
Table of ABC Analysis of Tesco-....................................................................................................8
2.Inter relational with one other department ..............................................................................8
CONCLUSION................................................................................................................................9
REFERENCES..............................................................................................................................10
1
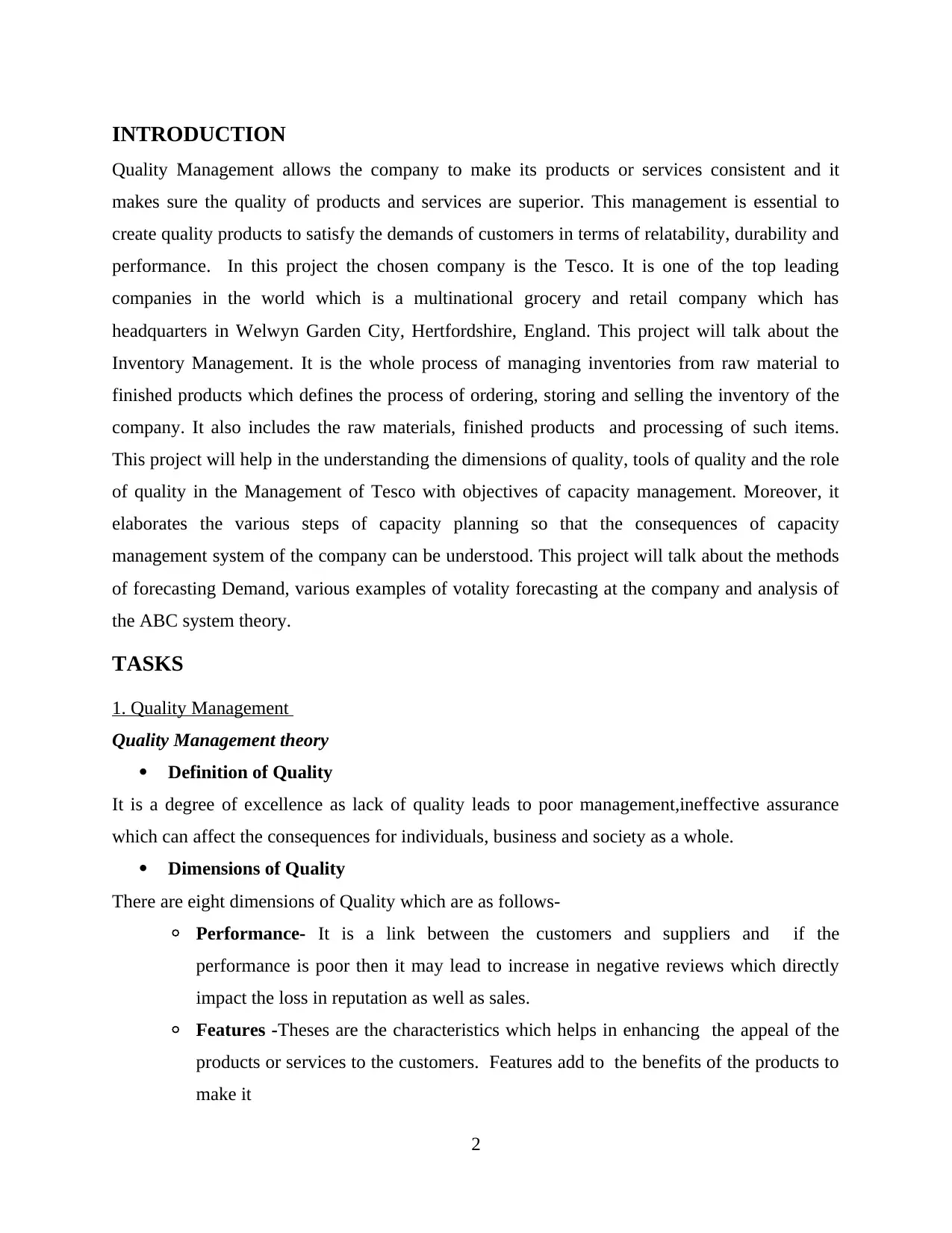
INTRODUCTION
Quality Management allows the company to make its products or services consistent and it
makes sure the quality of products and services are superior. This management is essential to
create quality products to satisfy the demands of customers in terms of relatability, durability and
performance. In this project the chosen company is the Tesco. It is one of the top leading
companies in the world which is a multinational grocery and retail company which has
headquarters in Welwyn Garden City, Hertfordshire, England. This project will talk about the
Inventory Management. It is the whole process of managing inventories from raw material to
finished products which defines the process of ordering, storing and selling the inventory of the
company. It also includes the raw materials, finished products and processing of such items.
This project will help in the understanding the dimensions of quality, tools of quality and the role
of quality in the Management of Tesco with objectives of capacity management. Moreover, it
elaborates the various steps of capacity planning so that the consequences of capacity
management system of the company can be understood. This project will talk about the methods
of forecasting Demand, various examples of votality forecasting at the company and analysis of
the ABC system theory.
TASKS
1. Quality Management
Quality Management theory
ï‚· Definition of Quality
It is a degree of excellence as lack of quality leads to poor management,ineffective assurance
which can affect the consequences for individuals, business and society as a whole.
ï‚· Dimensions of Quality
There are eight dimensions of Quality which are as follows-
â—¦ Performance- It is a link between the customers and suppliers and if the
performance is poor then it may lead to increase in negative reviews which directly
impact the loss in reputation as well as sales.
â—¦ Features -Theses are the characteristics which helps in enhancing the appeal of the
products or services to the customers. Features add to the benefits of the products to
make it
2
Quality Management allows the company to make its products or services consistent and it
makes sure the quality of products and services are superior. This management is essential to
create quality products to satisfy the demands of customers in terms of relatability, durability and
performance. In this project the chosen company is the Tesco. It is one of the top leading
companies in the world which is a multinational grocery and retail company which has
headquarters in Welwyn Garden City, Hertfordshire, England. This project will talk about the
Inventory Management. It is the whole process of managing inventories from raw material to
finished products which defines the process of ordering, storing and selling the inventory of the
company. It also includes the raw materials, finished products and processing of such items.
This project will help in the understanding the dimensions of quality, tools of quality and the role
of quality in the Management of Tesco with objectives of capacity management. Moreover, it
elaborates the various steps of capacity planning so that the consequences of capacity
management system of the company can be understood. This project will talk about the methods
of forecasting Demand, various examples of votality forecasting at the company and analysis of
the ABC system theory.
TASKS
1. Quality Management
Quality Management theory
ï‚· Definition of Quality
It is a degree of excellence as lack of quality leads to poor management,ineffective assurance
which can affect the consequences for individuals, business and society as a whole.
ï‚· Dimensions of Quality
There are eight dimensions of Quality which are as follows-
â—¦ Performance- It is a link between the customers and suppliers and if the
performance is poor then it may lead to increase in negative reviews which directly
impact the loss in reputation as well as sales.
â—¦ Features -Theses are the characteristics which helps in enhancing the appeal of the
products or services to the customers. Features add to the benefits of the products to
make it
2
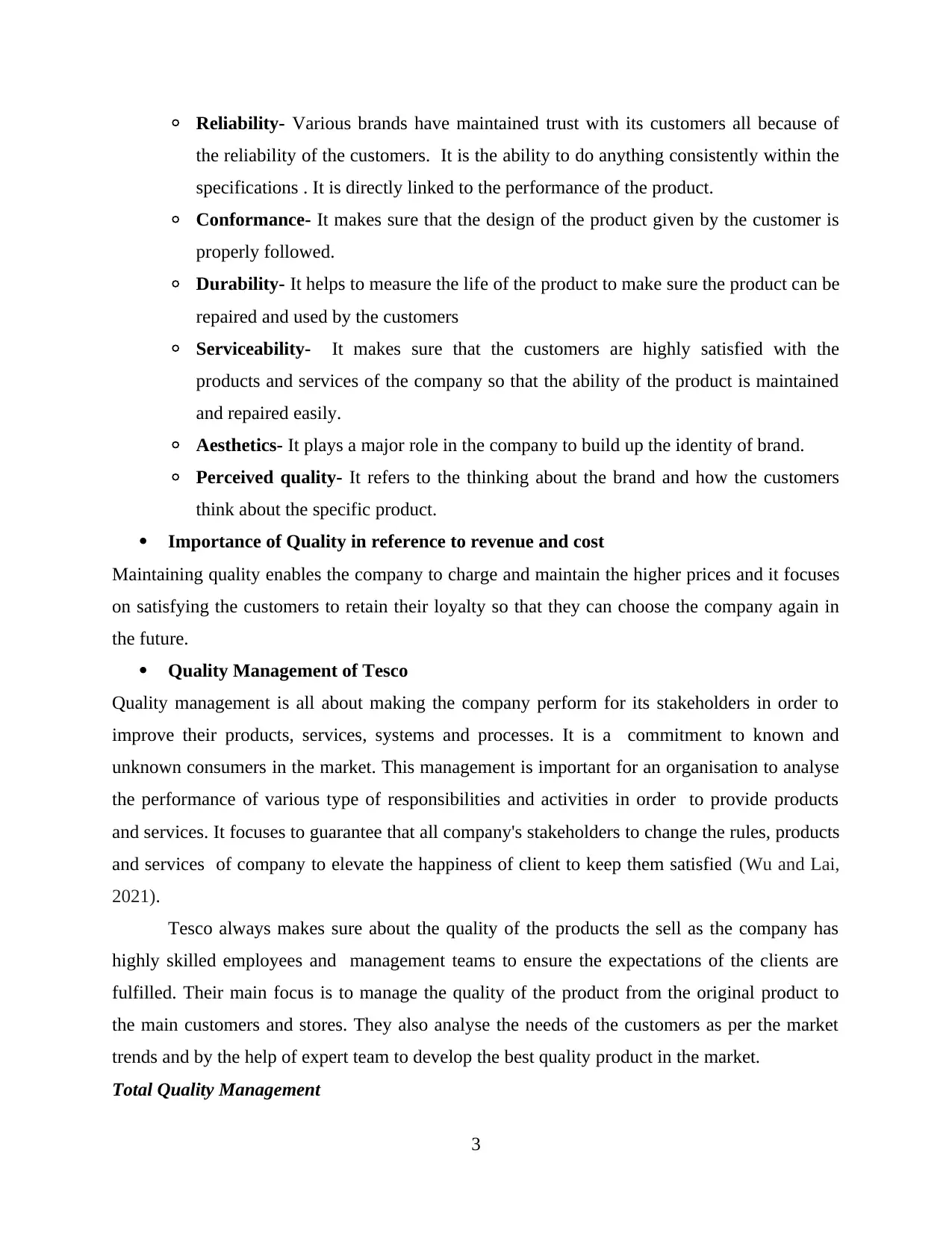
â—¦ Reliability- Various brands have maintained trust with its customers all because of
the reliability of the customers. It is the ability to do anything consistently within the
specifications . It is directly linked to the performance of the product.
â—¦ Conformance- It makes sure that the design of the product given by the customer is
properly followed.
â—¦ Durability- It helps to measure the life of the product to make sure the product can be
repaired and used by the customers
â—¦ Serviceability- It makes sure that the customers are highly satisfied with the
products and services of the company so that the ability of the product is maintained
and repaired easily.
â—¦ Aesthetics- It plays a major role in the company to build up the identity of brand.
â—¦ Perceived quality- It refers to the thinking about the brand and how the customers
think about the specific product.
ï‚· Importance of Quality in reference to revenue and cost
Maintaining quality enables the company to charge and maintain the higher prices and it focuses
on satisfying the customers to retain their loyalty so that they can choose the company again in
the future.
ï‚· Quality Management of Tesco
Quality management is all about making the company perform for its stakeholders in order to
improve their products, services, systems and processes. It is a commitment to known and
unknown consumers in the market. This management is important for an organisation to analyse
the performance of various type of responsibilities and activities in order to provide products
and services. It focuses to guarantee that all company's stakeholders to change the rules, products
and services of company to elevate the happiness of client to keep them satisfied (Wu and Lai,
2021).
Tesco always makes sure about the quality of the products the sell as the company has
highly skilled employees and management teams to ensure the expectations of the clients are
fulfilled. Their main focus is to manage the quality of the product from the original product to
the main customers and stores. They also analyse the needs of the customers as per the market
trends and by the help of expert team to develop the best quality product in the market.
Total Quality Management
3
the reliability of the customers. It is the ability to do anything consistently within the
specifications . It is directly linked to the performance of the product.
â—¦ Conformance- It makes sure that the design of the product given by the customer is
properly followed.
â—¦ Durability- It helps to measure the life of the product to make sure the product can be
repaired and used by the customers
â—¦ Serviceability- It makes sure that the customers are highly satisfied with the
products and services of the company so that the ability of the product is maintained
and repaired easily.
â—¦ Aesthetics- It plays a major role in the company to build up the identity of brand.
â—¦ Perceived quality- It refers to the thinking about the brand and how the customers
think about the specific product.
ï‚· Importance of Quality in reference to revenue and cost
Maintaining quality enables the company to charge and maintain the higher prices and it focuses
on satisfying the customers to retain their loyalty so that they can choose the company again in
the future.
ï‚· Quality Management of Tesco
Quality management is all about making the company perform for its stakeholders in order to
improve their products, services, systems and processes. It is a commitment to known and
unknown consumers in the market. This management is important for an organisation to analyse
the performance of various type of responsibilities and activities in order to provide products
and services. It focuses to guarantee that all company's stakeholders to change the rules, products
and services of company to elevate the happiness of client to keep them satisfied (Wu and Lai,
2021).
Tesco always makes sure about the quality of the products the sell as the company has
highly skilled employees and management teams to ensure the expectations of the clients are
fulfilled. Their main focus is to manage the quality of the product from the original product to
the main customers and stores. They also analyse the needs of the customers as per the market
trends and by the help of expert team to develop the best quality product in the market.
Total Quality Management
3
Secure Best Marks with AI Grader
Need help grading? Try our AI Grader for instant feedback on your assignments.
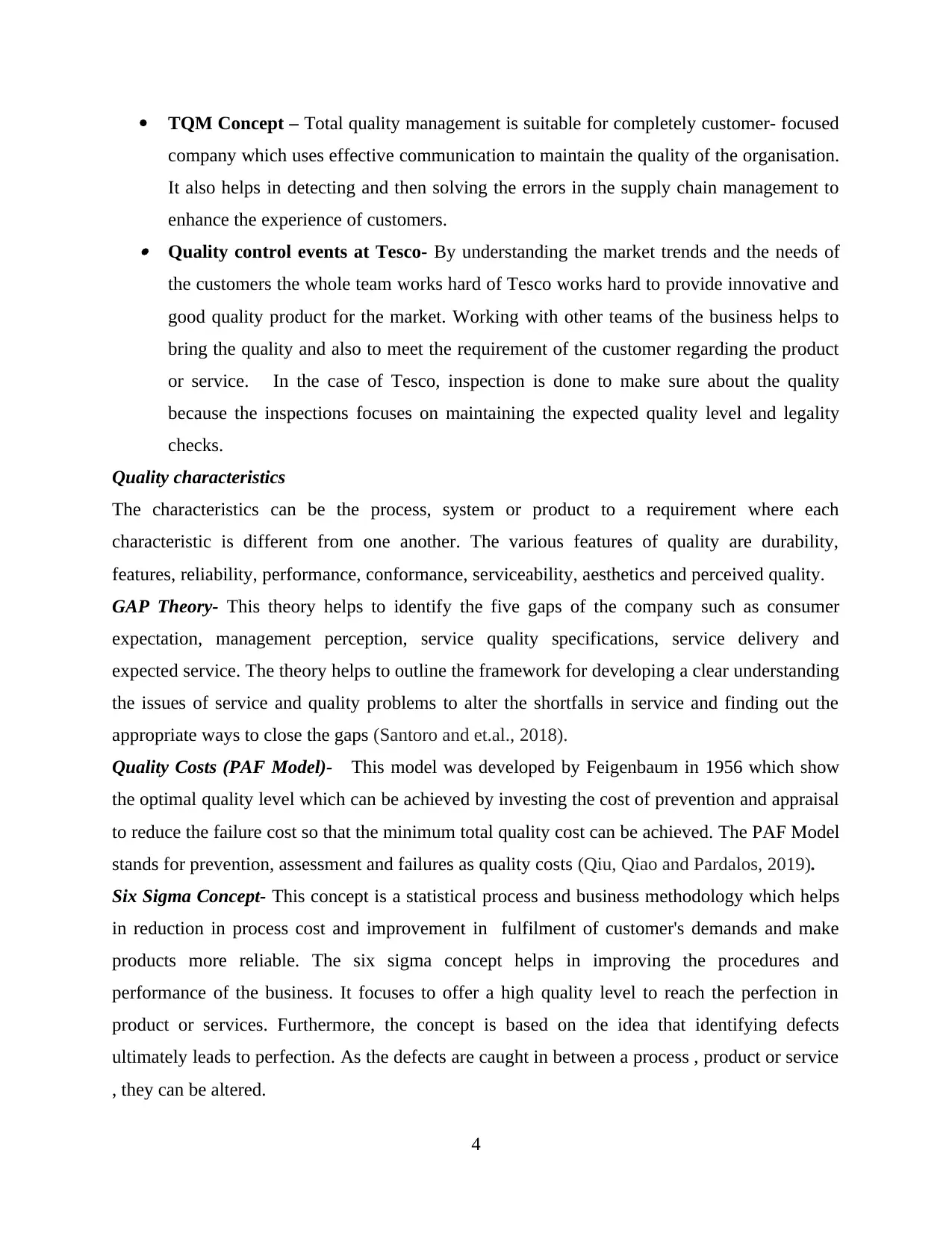
 TQM Concept – Total quality management is suitable for completely customer- focused
company which uses effective communication to maintain the quality of the organisation.
It also helps in detecting and then solving the errors in the supply chain management to
enhance the experience of customers.ï‚· Quality control events at Tesco- By understanding the market trends and the needs of
the customers the whole team works hard of Tesco works hard to provide innovative and
good quality product for the market. Working with other teams of the business helps to
bring the quality and also to meet the requirement of the customer regarding the product
or service. In the case of Tesco, inspection is done to make sure about the quality
because the inspections focuses on maintaining the expected quality level and legality
checks.
Quality characteristics
The characteristics can be the process, system or product to a requirement where each
characteristic is different from one another. The various features of quality are durability,
features, reliability, performance, conformance, serviceability, aesthetics and perceived quality.
GAP Theory- This theory helps to identify the five gaps of the company such as consumer
expectation, management perception, service quality specifications, service delivery and
expected service. The theory helps to outline the framework for developing a clear understanding
the issues of service and quality problems to alter the shortfalls in service and finding out the
appropriate ways to close the gaps (Santoro and et.al., 2018).
Quality Costs (PAF Model)- This model was developed by Feigenbaum in 1956 which show
the optimal quality level which can be achieved by investing the cost of prevention and appraisal
to reduce the failure cost so that the minimum total quality cost can be achieved. The PAF Model
stands for prevention, assessment and failures as quality costs (Qiu, Qiao and Pardalos, 2019).
Six Sigma Concept- This concept is a statistical process and business methodology which helps
in reduction in process cost and improvement in fulfilment of customer's demands and make
products more reliable. The six sigma concept helps in improving the procedures and
performance of the business. It focuses to offer a high quality level to reach the perfection in
product or services. Furthermore, the concept is based on the idea that identifying defects
ultimately leads to perfection. As the defects are caught in between a process , product or service
, they can be altered.
4
company which uses effective communication to maintain the quality of the organisation.
It also helps in detecting and then solving the errors in the supply chain management to
enhance the experience of customers.ï‚· Quality control events at Tesco- By understanding the market trends and the needs of
the customers the whole team works hard of Tesco works hard to provide innovative and
good quality product for the market. Working with other teams of the business helps to
bring the quality and also to meet the requirement of the customer regarding the product
or service. In the case of Tesco, inspection is done to make sure about the quality
because the inspections focuses on maintaining the expected quality level and legality
checks.
Quality characteristics
The characteristics can be the process, system or product to a requirement where each
characteristic is different from one another. The various features of quality are durability,
features, reliability, performance, conformance, serviceability, aesthetics and perceived quality.
GAP Theory- This theory helps to identify the five gaps of the company such as consumer
expectation, management perception, service quality specifications, service delivery and
expected service. The theory helps to outline the framework for developing a clear understanding
the issues of service and quality problems to alter the shortfalls in service and finding out the
appropriate ways to close the gaps (Santoro and et.al., 2018).
Quality Costs (PAF Model)- This model was developed by Feigenbaum in 1956 which show
the optimal quality level which can be achieved by investing the cost of prevention and appraisal
to reduce the failure cost so that the minimum total quality cost can be achieved. The PAF Model
stands for prevention, assessment and failures as quality costs (Qiu, Qiao and Pardalos, 2019).
Six Sigma Concept- This concept is a statistical process and business methodology which helps
in reduction in process cost and improvement in fulfilment of customer's demands and make
products more reliable. The six sigma concept helps in improving the procedures and
performance of the business. It focuses to offer a high quality level to reach the perfection in
product or services. Furthermore, the concept is based on the idea that identifying defects
ultimately leads to perfection. As the defects are caught in between a process , product or service
, they can be altered.
4
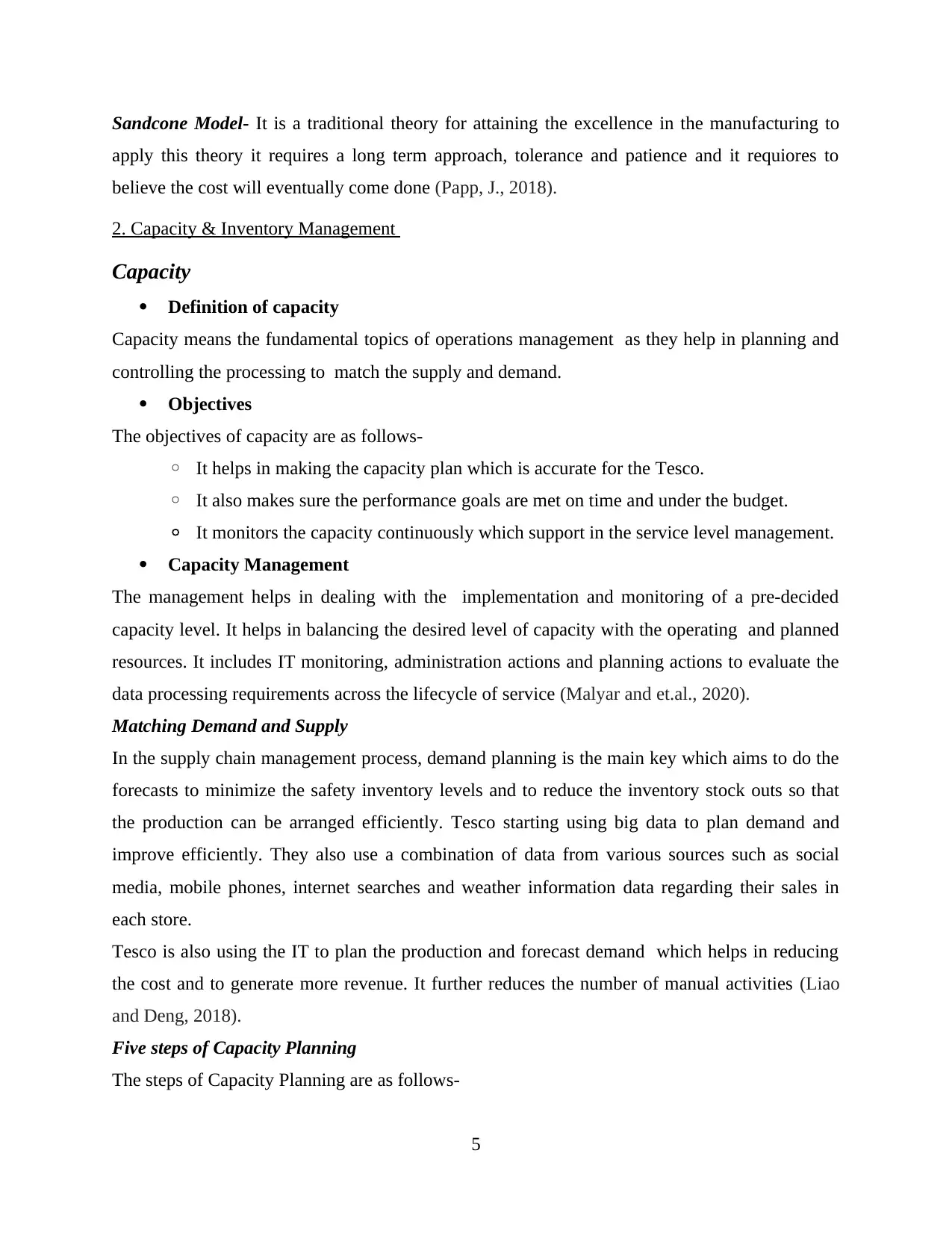
Sandcone Model- It is a traditional theory for attaining the excellence in the manufacturing to
apply this theory it requires a long term approach, tolerance and patience and it requiores to
believe the cost will eventually come done (Papp, J., 2018).
2. Capacity & Inventory Management
Capacity
ï‚· Definition of capacity
Capacity means the fundamental topics of operations management as they help in planning and
controlling the processing to match the supply and demand.
ï‚· Objectives
The objectives of capacity are as follows-
â—¦ It helps in making the capacity plan which is accurate for the Tesco.
â—¦ It also makes sure the performance goals are met on time and under the budget.
â—¦ It monitors the capacity continuously which support in the service level management.
ï‚· Capacity Management
The management helps in dealing with the implementation and monitoring of a pre-decided
capacity level. It helps in balancing the desired level of capacity with the operating and planned
resources. It includes IT monitoring, administration actions and planning actions to evaluate the
data processing requirements across the lifecycle of service (Malyar and et.al., 2020).
Matching Demand and Supply
In the supply chain management process, demand planning is the main key which aims to do the
forecasts to minimize the safety inventory levels and to reduce the inventory stock outs so that
the production can be arranged efficiently. Tesco starting using big data to plan demand and
improve efficiently. They also use a combination of data from various sources such as social
media, mobile phones, internet searches and weather information data regarding their sales in
each store.
Tesco is also using the IT to plan the production and forecast demand which helps in reducing
the cost and to generate more revenue. It further reduces the number of manual activities (Liao
and Deng, 2018).
Five steps of Capacity Planning
The steps of Capacity Planning are as follows-
5
apply this theory it requires a long term approach, tolerance and patience and it requiores to
believe the cost will eventually come done (Papp, J., 2018).
2. Capacity & Inventory Management
Capacity
ï‚· Definition of capacity
Capacity means the fundamental topics of operations management as they help in planning and
controlling the processing to match the supply and demand.
ï‚· Objectives
The objectives of capacity are as follows-
â—¦ It helps in making the capacity plan which is accurate for the Tesco.
â—¦ It also makes sure the performance goals are met on time and under the budget.
â—¦ It monitors the capacity continuously which support in the service level management.
ï‚· Capacity Management
The management helps in dealing with the implementation and monitoring of a pre-decided
capacity level. It helps in balancing the desired level of capacity with the operating and planned
resources. It includes IT monitoring, administration actions and planning actions to evaluate the
data processing requirements across the lifecycle of service (Malyar and et.al., 2020).
Matching Demand and Supply
In the supply chain management process, demand planning is the main key which aims to do the
forecasts to minimize the safety inventory levels and to reduce the inventory stock outs so that
the production can be arranged efficiently. Tesco starting using big data to plan demand and
improve efficiently. They also use a combination of data from various sources such as social
media, mobile phones, internet searches and weather information data regarding their sales in
each store.
Tesco is also using the IT to plan the production and forecast demand which helps in reducing
the cost and to generate more revenue. It further reduces the number of manual activities (Liao
and Deng, 2018).
Five steps of Capacity Planning
The steps of Capacity Planning are as follows-
5
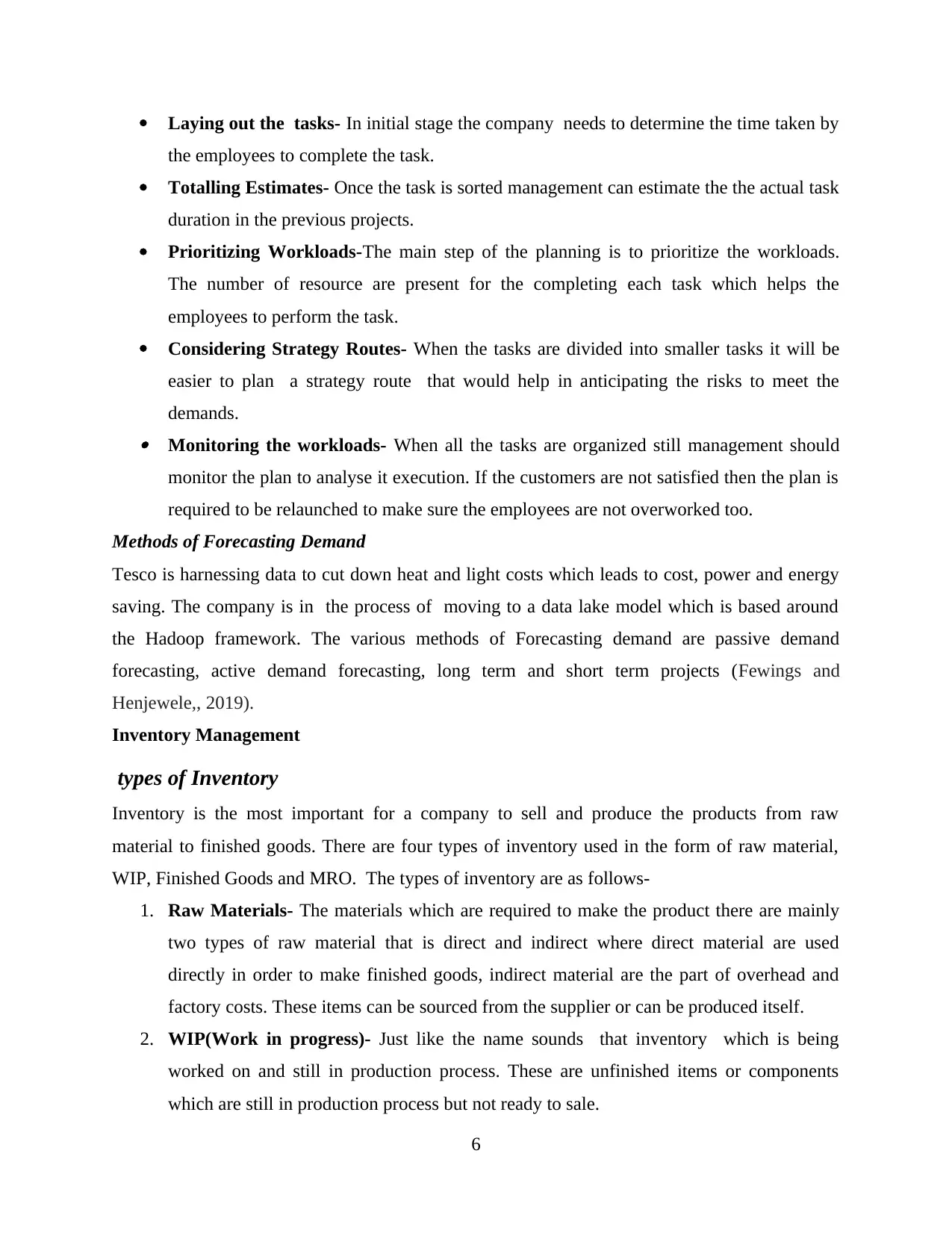
ï‚· Laying out the tasks- In initial stage the company needs to determine the time taken by
the employees to complete the task.
ï‚· Totalling Estimates- Once the task is sorted management can estimate the the actual task
duration in the previous projects.
ï‚· Prioritizing Workloads-The main step of the planning is to prioritize the workloads.
The number of resource are present for the completing each task which helps the
employees to perform the task.
ï‚· Considering Strategy Routes- When the tasks are divided into smaller tasks it will be
easier to plan a strategy route that would help in anticipating the risks to meet the
demands.ï‚· Monitoring the workloads- When all the tasks are organized still management should
monitor the plan to analyse it execution. If the customers are not satisfied then the plan is
required to be relaunched to make sure the employees are not overworked too.
Methods of Forecasting Demand
Tesco is harnessing data to cut down heat and light costs which leads to cost, power and energy
saving. The company is in the process of moving to a data lake model which is based around
the Hadoop framework. The various methods of Forecasting demand are passive demand
forecasting, active demand forecasting, long term and short term projects (Fewings and
Henjewele,, 2019).
Inventory Management
types of Inventory
Inventory is the most important for a company to sell and produce the products from raw
material to finished goods. There are four types of inventory used in the form of raw material,
WIP, Finished Goods and MRO. The types of inventory are as follows-
1. Raw Materials- The materials which are required to make the product there are mainly
two types of raw material that is direct and indirect where direct material are used
directly in order to make finished goods, indirect material are the part of overhead and
factory costs. These items can be sourced from the supplier or can be produced itself.
2. WIP(Work in progress)- Just like the name sounds that inventory which is being
worked on and still in production process. These are unfinished items or components
which are still in production process but not ready to sale.
6
the employees to complete the task.
ï‚· Totalling Estimates- Once the task is sorted management can estimate the the actual task
duration in the previous projects.
ï‚· Prioritizing Workloads-The main step of the planning is to prioritize the workloads.
The number of resource are present for the completing each task which helps the
employees to perform the task.
ï‚· Considering Strategy Routes- When the tasks are divided into smaller tasks it will be
easier to plan a strategy route that would help in anticipating the risks to meet the
demands.ï‚· Monitoring the workloads- When all the tasks are organized still management should
monitor the plan to analyse it execution. If the customers are not satisfied then the plan is
required to be relaunched to make sure the employees are not overworked too.
Methods of Forecasting Demand
Tesco is harnessing data to cut down heat and light costs which leads to cost, power and energy
saving. The company is in the process of moving to a data lake model which is based around
the Hadoop framework. The various methods of Forecasting demand are passive demand
forecasting, active demand forecasting, long term and short term projects (Fewings and
Henjewele,, 2019).
Inventory Management
types of Inventory
Inventory is the most important for a company to sell and produce the products from raw
material to finished goods. There are four types of inventory used in the form of raw material,
WIP, Finished Goods and MRO. The types of inventory are as follows-
1. Raw Materials- The materials which are required to make the product there are mainly
two types of raw material that is direct and indirect where direct material are used
directly in order to make finished goods, indirect material are the part of overhead and
factory costs. These items can be sourced from the supplier or can be produced itself.
2. WIP(Work in progress)- Just like the name sounds that inventory which is being
worked on and still in production process. These are unfinished items or components
which are still in production process but not ready to sale.
6
Paraphrase This Document
Need a fresh take? Get an instant paraphrase of this document with our AI Paraphraser
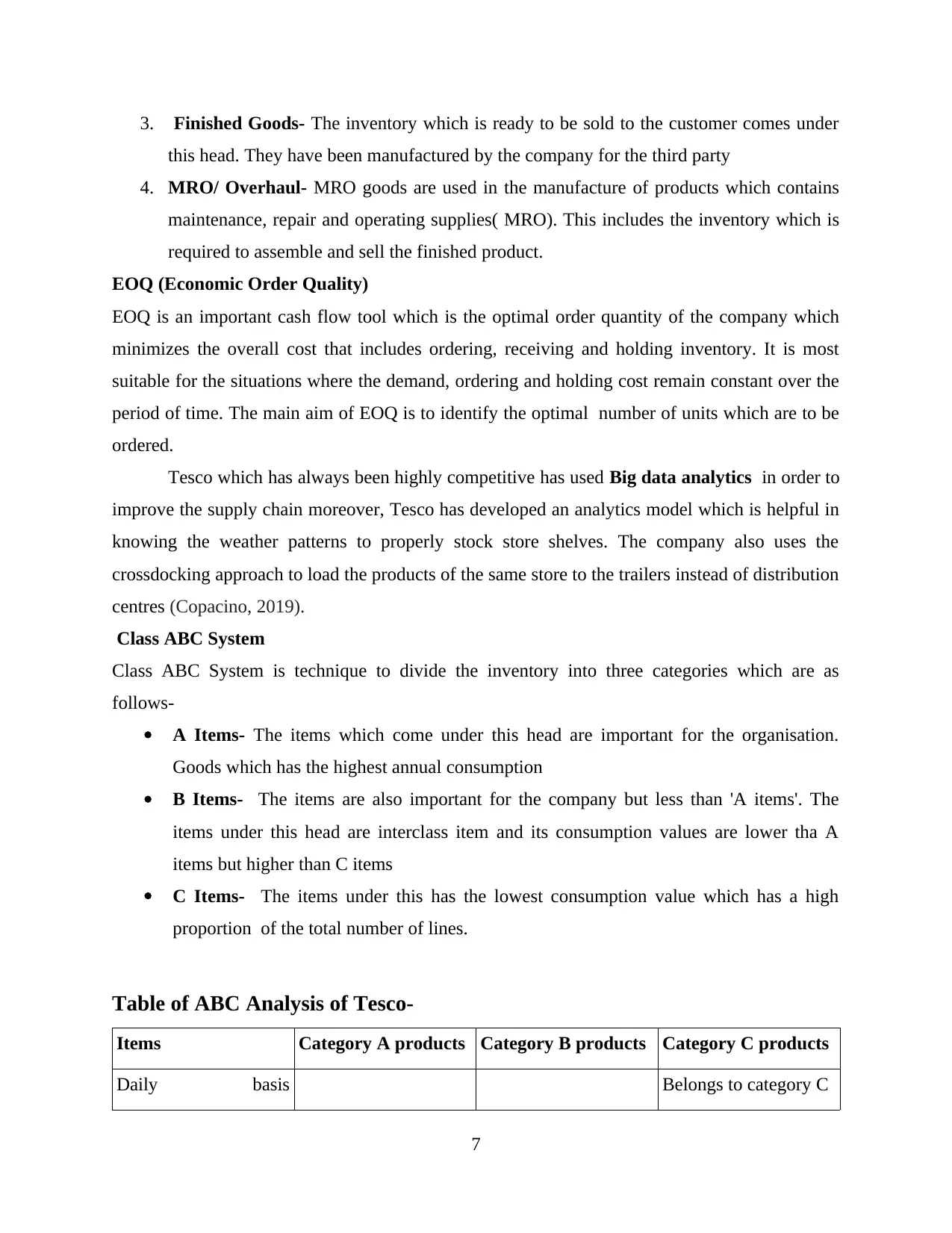
3. Finished Goods- The inventory which is ready to be sold to the customer comes under
this head. They have been manufactured by the company for the third party
4. MRO/ Overhaul- MRO goods are used in the manufacture of products which contains
maintenance, repair and operating supplies( MRO). This includes the inventory which is
required to assemble and sell the finished product.
EOQ (Economic Order Quality)
EOQ is an important cash flow tool which is the optimal order quantity of the company which
minimizes the overall cost that includes ordering, receiving and holding inventory. It is most
suitable for the situations where the demand, ordering and holding cost remain constant over the
period of time. The main aim of EOQ is to identify the optimal number of units which are to be
ordered.
Tesco which has always been highly competitive has used Big data analytics in order to
improve the supply chain moreover, Tesco has developed an analytics model which is helpful in
knowing the weather patterns to properly stock store shelves. The company also uses the
crossdocking approach to load the products of the same store to the trailers instead of distribution
centres (Copacino, 2019).
Class ABC System
Class ABC System is technique to divide the inventory into three categories which are as
follows-
ï‚· A Items- The items which come under this head are important for the organisation.
Goods which has the highest annual consumption
ï‚· B Items- The items are also important for the company but less than 'A items'. The
items under this head are interclass item and its consumption values are lower tha A
items but higher than C items
ï‚· C Items- The items under this has the lowest consumption value which has a high
proportion of the total number of lines.
Table of ABC Analysis of Tesco-
Items Category A products Category B products Category C products
Daily basis Belongs to category C
7
this head. They have been manufactured by the company for the third party
4. MRO/ Overhaul- MRO goods are used in the manufacture of products which contains
maintenance, repair and operating supplies( MRO). This includes the inventory which is
required to assemble and sell the finished product.
EOQ (Economic Order Quality)
EOQ is an important cash flow tool which is the optimal order quantity of the company which
minimizes the overall cost that includes ordering, receiving and holding inventory. It is most
suitable for the situations where the demand, ordering and holding cost remain constant over the
period of time. The main aim of EOQ is to identify the optimal number of units which are to be
ordered.
Tesco which has always been highly competitive has used Big data analytics in order to
improve the supply chain moreover, Tesco has developed an analytics model which is helpful in
knowing the weather patterns to properly stock store shelves. The company also uses the
crossdocking approach to load the products of the same store to the trailers instead of distribution
centres (Copacino, 2019).
Class ABC System
Class ABC System is technique to divide the inventory into three categories which are as
follows-
ï‚· A Items- The items which come under this head are important for the organisation.
Goods which has the highest annual consumption
ï‚· B Items- The items are also important for the company but less than 'A items'. The
items under this head are interclass item and its consumption values are lower tha A
items but higher than C items
ï‚· C Items- The items under this has the lowest consumption value which has a high
proportion of the total number of lines.
Table of ABC Analysis of Tesco-
Items Category A products Category B products Category C products
Daily basis Belongs to category C
7
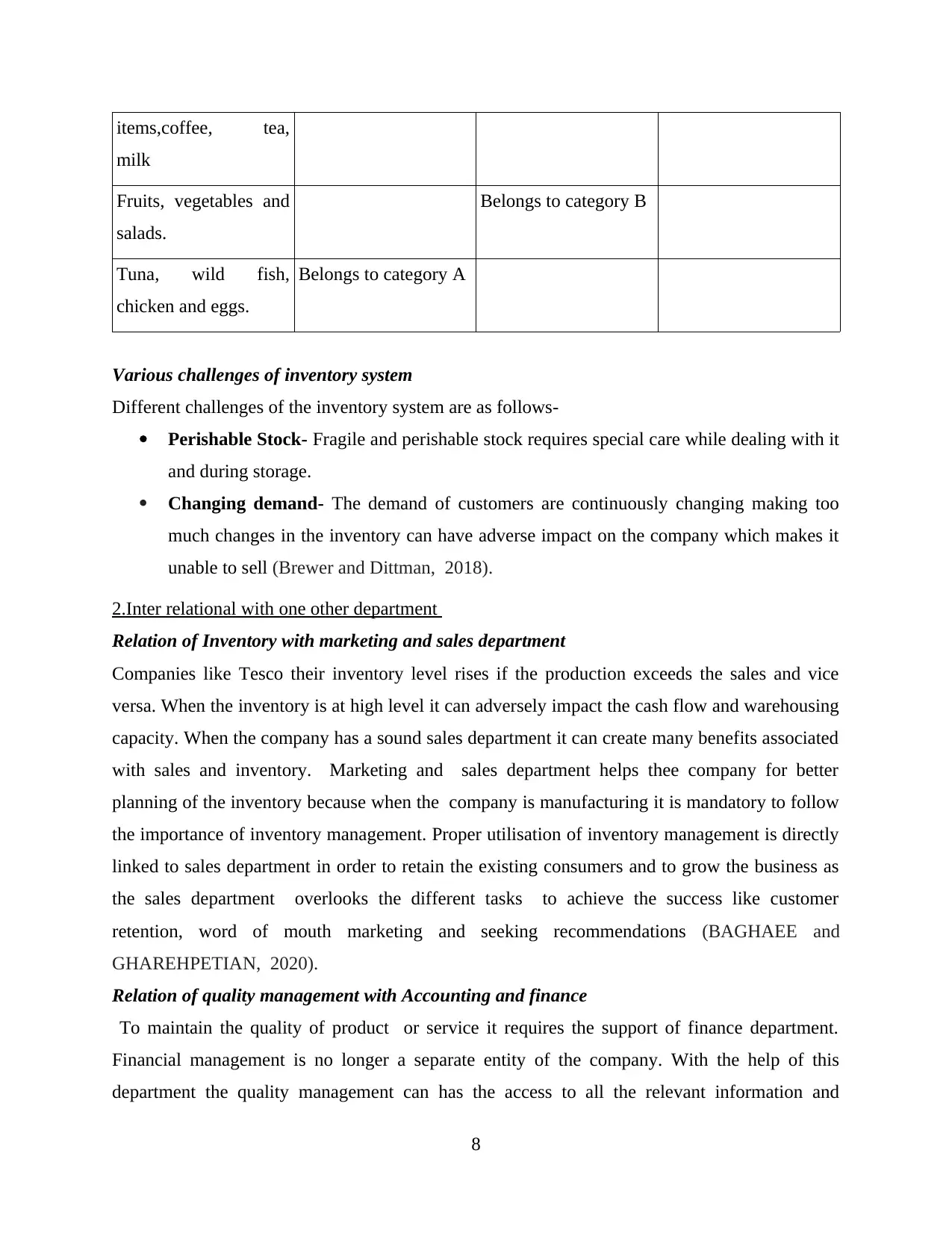
items,coffee, tea,
milk
Fruits, vegetables and
salads.
Belongs to category B
Tuna, wild fish,
chicken and eggs.
Belongs to category A
Various challenges of inventory system
Different challenges of the inventory system are as follows-
ï‚· Perishable Stock- Fragile and perishable stock requires special care while dealing with it
and during storage.
ï‚· Changing demand- The demand of customers are continuously changing making too
much changes in the inventory can have adverse impact on the company which makes it
unable to sell (Brewer and Dittman, 2018).
2.Inter relational with one other department
Relation of Inventory with marketing and sales department
Companies like Tesco their inventory level rises if the production exceeds the sales and vice
versa. When the inventory is at high level it can adversely impact the cash flow and warehousing
capacity. When the company has a sound sales department it can create many benefits associated
with sales and inventory. Marketing and sales department helps thee company for better
planning of the inventory because when the company is manufacturing it is mandatory to follow
the importance of inventory management. Proper utilisation of inventory management is directly
linked to sales department in order to retain the existing consumers and to grow the business as
the sales department overlooks the different tasks to achieve the success like customer
retention, word of mouth marketing and seeking recommendations (BAGHAEE and
GHAREHPETIAN, 2020).
Relation of quality management with Accounting and finance
To maintain the quality of product or service it requires the support of finance department.
Financial management is no longer a separate entity of the company. With the help of this
department the quality management can has the access to all the relevant information and
8
milk
Fruits, vegetables and
salads.
Belongs to category B
Tuna, wild fish,
chicken and eggs.
Belongs to category A
Various challenges of inventory system
Different challenges of the inventory system are as follows-
ï‚· Perishable Stock- Fragile and perishable stock requires special care while dealing with it
and during storage.
ï‚· Changing demand- The demand of customers are continuously changing making too
much changes in the inventory can have adverse impact on the company which makes it
unable to sell (Brewer and Dittman, 2018).
2.Inter relational with one other department
Relation of Inventory with marketing and sales department
Companies like Tesco their inventory level rises if the production exceeds the sales and vice
versa. When the inventory is at high level it can adversely impact the cash flow and warehousing
capacity. When the company has a sound sales department it can create many benefits associated
with sales and inventory. Marketing and sales department helps thee company for better
planning of the inventory because when the company is manufacturing it is mandatory to follow
the importance of inventory management. Proper utilisation of inventory management is directly
linked to sales department in order to retain the existing consumers and to grow the business as
the sales department overlooks the different tasks to achieve the success like customer
retention, word of mouth marketing and seeking recommendations (BAGHAEE and
GHAREHPETIAN, 2020).
Relation of quality management with Accounting and finance
To maintain the quality of product or service it requires the support of finance department.
Financial management is no longer a separate entity of the company. With the help of this
department the quality management can has the access to all the relevant information and
8
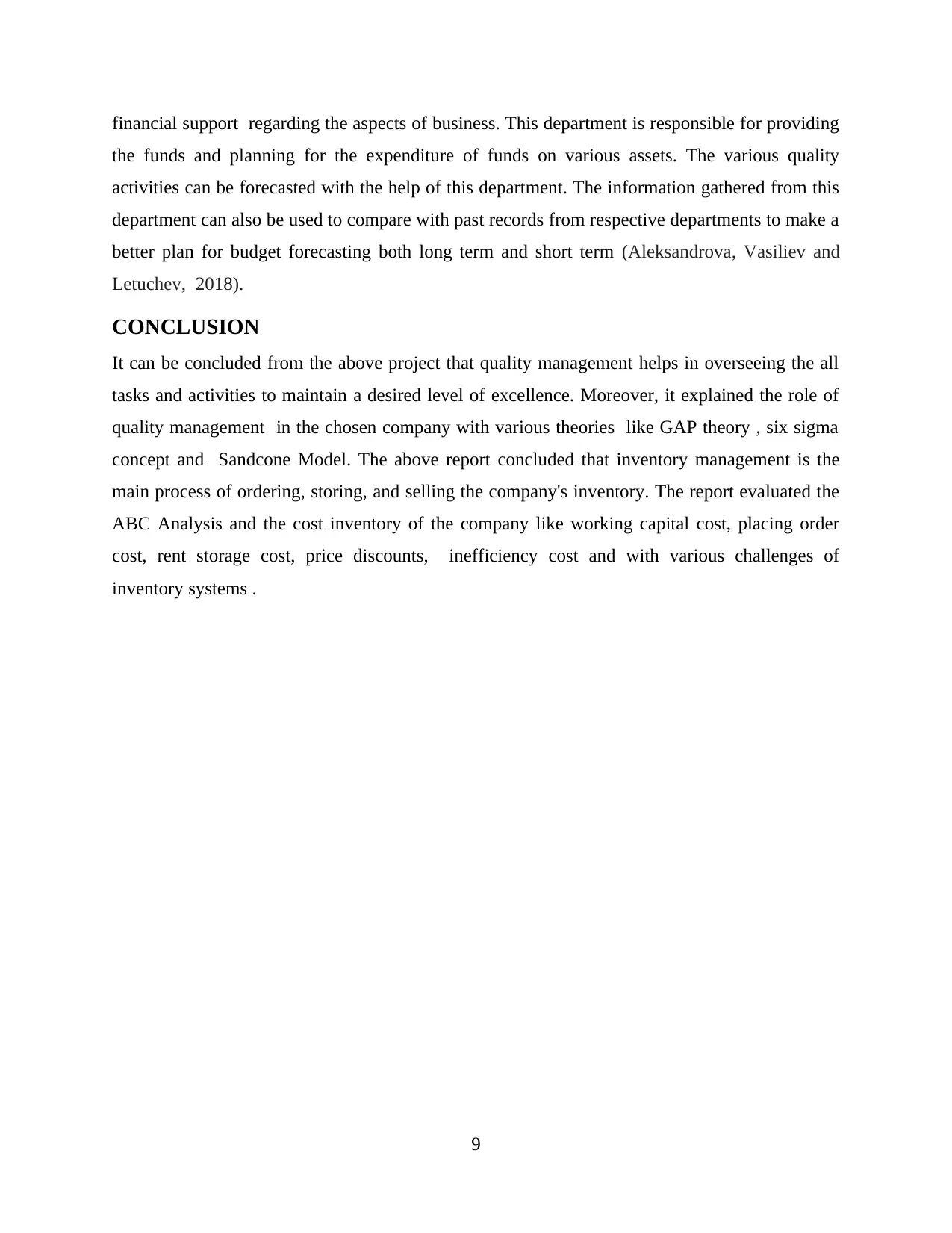
financial support regarding the aspects of business. This department is responsible for providing
the funds and planning for the expenditure of funds on various assets. The various quality
activities can be forecasted with the help of this department. The information gathered from this
department can also be used to compare with past records from respective departments to make a
better plan for budget forecasting both long term and short term (Aleksandrova, Vasiliev and
Letuchev, 2018).
CONCLUSION
It can be concluded from the above project that quality management helps in overseeing the all
tasks and activities to maintain a desired level of excellence. Moreover, it explained the role of
quality management in the chosen company with various theories like GAP theory , six sigma
concept and Sandcone Model. The above report concluded that inventory management is the
main process of ordering, storing, and selling the company's inventory. The report evaluated the
ABC Analysis and the cost inventory of the company like working capital cost, placing order
cost, rent storage cost, price discounts, inefficiency cost and with various challenges of
inventory systems .
9
the funds and planning for the expenditure of funds on various assets. The various quality
activities can be forecasted with the help of this department. The information gathered from this
department can also be used to compare with past records from respective departments to make a
better plan for budget forecasting both long term and short term (Aleksandrova, Vasiliev and
Letuchev, 2018).
CONCLUSION
It can be concluded from the above project that quality management helps in overseeing the all
tasks and activities to maintain a desired level of excellence. Moreover, it explained the role of
quality management in the chosen company with various theories like GAP theory , six sigma
concept and Sandcone Model. The above report concluded that inventory management is the
main process of ordering, storing, and selling the company's inventory. The report evaluated the
ABC Analysis and the cost inventory of the company like working capital cost, placing order
cost, rent storage cost, price discounts, inefficiency cost and with various challenges of
inventory systems .
9
Secure Best Marks with AI Grader
Need help grading? Try our AI Grader for instant feedback on your assignments.
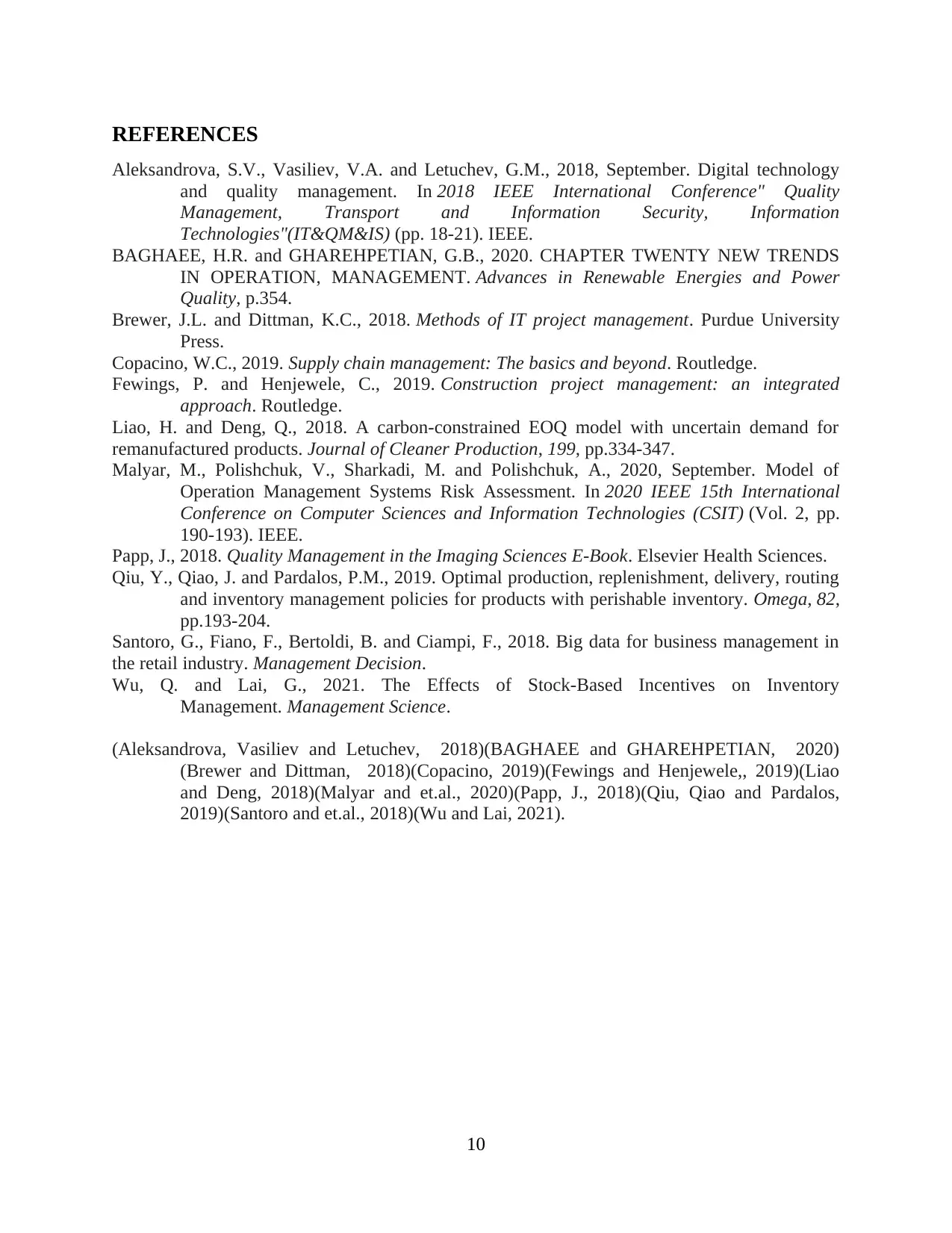
REFERENCES
Aleksandrova, S.V., Vasiliev, V.A. and Letuchev, G.M., 2018, September. Digital technology
and quality management. In 2018 IEEE International Conference" Quality
Management, Transport and Information Security, Information
Technologies"(IT&QM&IS) (pp. 18-21). IEEE.
BAGHAEE, H.R. and GHAREHPETIAN, G.B., 2020. CHAPTER TWENTY NEW TRENDS
IN OPERATION, MANAGEMENT. Advances in Renewable Energies and Power
Quality, p.354.
Brewer, J.L. and Dittman, K.C., 2018. Methods of IT project management. Purdue University
Press.
Copacino, W.C., 2019. Supply chain management: The basics and beyond. Routledge.
Fewings, P. and Henjewele, C., 2019. Construction project management: an integrated
approach. Routledge.
Liao, H. and Deng, Q., 2018. A carbon-constrained EOQ model with uncertain demand for
remanufactured products. Journal of Cleaner Production, 199, pp.334-347.
Malyar, M., Polishchuk, V., Sharkadi, M. and Polishchuk, A., 2020, September. Model of
Operation Management Systems Risk Assessment. In 2020 IEEE 15th International
Conference on Computer Sciences and Information Technologies (CSIT) (Vol. 2, pp.
190-193). IEEE.
Papp, J., 2018. Quality Management in the Imaging Sciences E-Book. Elsevier Health Sciences.
Qiu, Y., Qiao, J. and Pardalos, P.M., 2019. Optimal production, replenishment, delivery, routing
and inventory management policies for products with perishable inventory. Omega, 82,
pp.193-204.
Santoro, G., Fiano, F., Bertoldi, B. and Ciampi, F., 2018. Big data for business management in
the retail industry. Management Decision.
Wu, Q. and Lai, G., 2021. The Effects of Stock-Based Incentives on Inventory
Management. Management Science.
(Aleksandrova, Vasiliev and Letuchev, 2018)(BAGHAEE and GHAREHPETIAN, 2020)
(Brewer and Dittman, 2018)(Copacino, 2019)(Fewings and Henjewele,, 2019)(Liao
and Deng, 2018)(Malyar and et.al., 2020)(Papp, J., 2018)(Qiu, Qiao and Pardalos,
2019)(Santoro and et.al., 2018)(Wu and Lai, 2021).
10
Aleksandrova, S.V., Vasiliev, V.A. and Letuchev, G.M., 2018, September. Digital technology
and quality management. In 2018 IEEE International Conference" Quality
Management, Transport and Information Security, Information
Technologies"(IT&QM&IS) (pp. 18-21). IEEE.
BAGHAEE, H.R. and GHAREHPETIAN, G.B., 2020. CHAPTER TWENTY NEW TRENDS
IN OPERATION, MANAGEMENT. Advances in Renewable Energies and Power
Quality, p.354.
Brewer, J.L. and Dittman, K.C., 2018. Methods of IT project management. Purdue University
Press.
Copacino, W.C., 2019. Supply chain management: The basics and beyond. Routledge.
Fewings, P. and Henjewele, C., 2019. Construction project management: an integrated
approach. Routledge.
Liao, H. and Deng, Q., 2018. A carbon-constrained EOQ model with uncertain demand for
remanufactured products. Journal of Cleaner Production, 199, pp.334-347.
Malyar, M., Polishchuk, V., Sharkadi, M. and Polishchuk, A., 2020, September. Model of
Operation Management Systems Risk Assessment. In 2020 IEEE 15th International
Conference on Computer Sciences and Information Technologies (CSIT) (Vol. 2, pp.
190-193). IEEE.
Papp, J., 2018. Quality Management in the Imaging Sciences E-Book. Elsevier Health Sciences.
Qiu, Y., Qiao, J. and Pardalos, P.M., 2019. Optimal production, replenishment, delivery, routing
and inventory management policies for products with perishable inventory. Omega, 82,
pp.193-204.
Santoro, G., Fiano, F., Bertoldi, B. and Ciampi, F., 2018. Big data for business management in
the retail industry. Management Decision.
Wu, Q. and Lai, G., 2021. The Effects of Stock-Based Incentives on Inventory
Management. Management Science.
(Aleksandrova, Vasiliev and Letuchev, 2018)(BAGHAEE and GHAREHPETIAN, 2020)
(Brewer and Dittman, 2018)(Copacino, 2019)(Fewings and Henjewele,, 2019)(Liao
and Deng, 2018)(Malyar and et.al., 2020)(Papp, J., 2018)(Qiu, Qiao and Pardalos,
2019)(Santoro and et.al., 2018)(Wu and Lai, 2021).
10
1 out of 11
Related Documents
![[object Object]](/_next/image/?url=%2F_next%2Fstatic%2Fmedia%2Flogo.6d15ce61.png&w=640&q=75)
Your All-in-One AI-Powered Toolkit for Academic Success.
 +13062052269
info@desklib.com
Available 24*7 on WhatsApp / Email
Unlock your academic potential
© 2024  |  Zucol Services PVT LTD  |  All rights reserved.