Quality Management systems Coca-cola Company Assignment
Added on 2021-06-17
44 Pages12108 Words63 Views
QUALITY MANAGEMENT SYSTEMS: COCA-COLA COMPANY 1
Quality Management Systems: Coca-Cola Company
Student
Institution
Professor
Quality Management Systems: Coca-Cola Company
Student
Institution
Professor
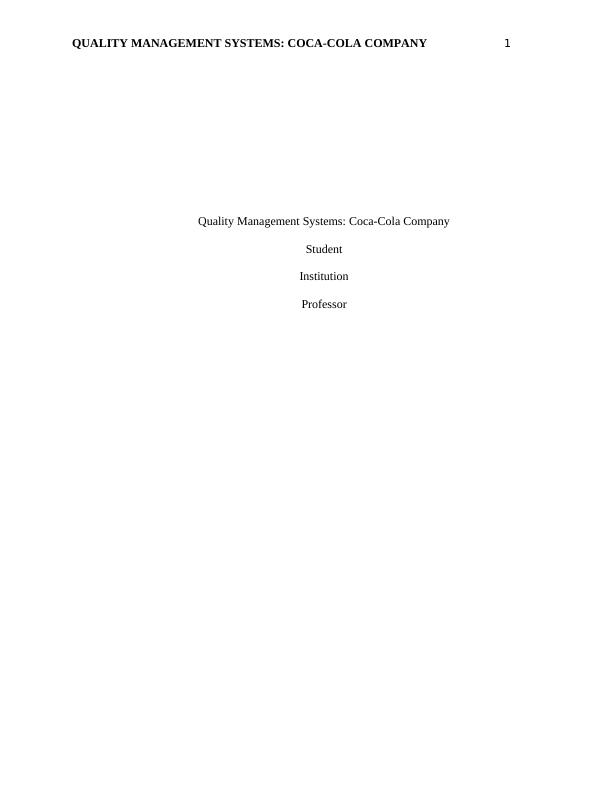
QUALITY MANAGEMENT SYSTEMS: COCA-COLA COMPANY 2
Executive summary
Operations and quality management are key aspects that define organizational
competitiveness. This report has presented an analysis of Quality and operations management
systems in Coca-Cola Company. The company strives to ensure that only high quality and safe
products reach the market through its quality management system dabbed as KORE.
Furthermore, the report has analyzed the role of QMS and OPS in ensuring that an organization
achieves its objectives. About Coca-Cola Company, the company uses SAP software to manage
its inventory. However, this system has some weaknesses making the organization unable to
track its products. Therefore, the report has suggested that the company should implement RFIDs
to help it in tracking its products in the stores and transit. Besides, the report has presented the
change implementation and evaluation plan for Coca-Cola Company and how different
resources, tools, and systems impact on the change management plan. In the final parts of this
report, an analysis of how a quality culture can be incorporated in Coca-Cola Company, the
outcomes of the strategic quality change and recommendations for improvement have been
provided. The recommendations for improvement relate to different gaps that exist in the
strategic quality change that has been implemented.
Executive summary
Operations and quality management are key aspects that define organizational
competitiveness. This report has presented an analysis of Quality and operations management
systems in Coca-Cola Company. The company strives to ensure that only high quality and safe
products reach the market through its quality management system dabbed as KORE.
Furthermore, the report has analyzed the role of QMS and OPS in ensuring that an organization
achieves its objectives. About Coca-Cola Company, the company uses SAP software to manage
its inventory. However, this system has some weaknesses making the organization unable to
track its products. Therefore, the report has suggested that the company should implement RFIDs
to help it in tracking its products in the stores and transit. Besides, the report has presented the
change implementation and evaluation plan for Coca-Cola Company and how different
resources, tools, and systems impact on the change management plan. In the final parts of this
report, an analysis of how a quality culture can be incorporated in Coca-Cola Company, the
outcomes of the strategic quality change and recommendations for improvement have been
provided. The recommendations for improvement relate to different gaps that exist in the
strategic quality change that has been implemented.
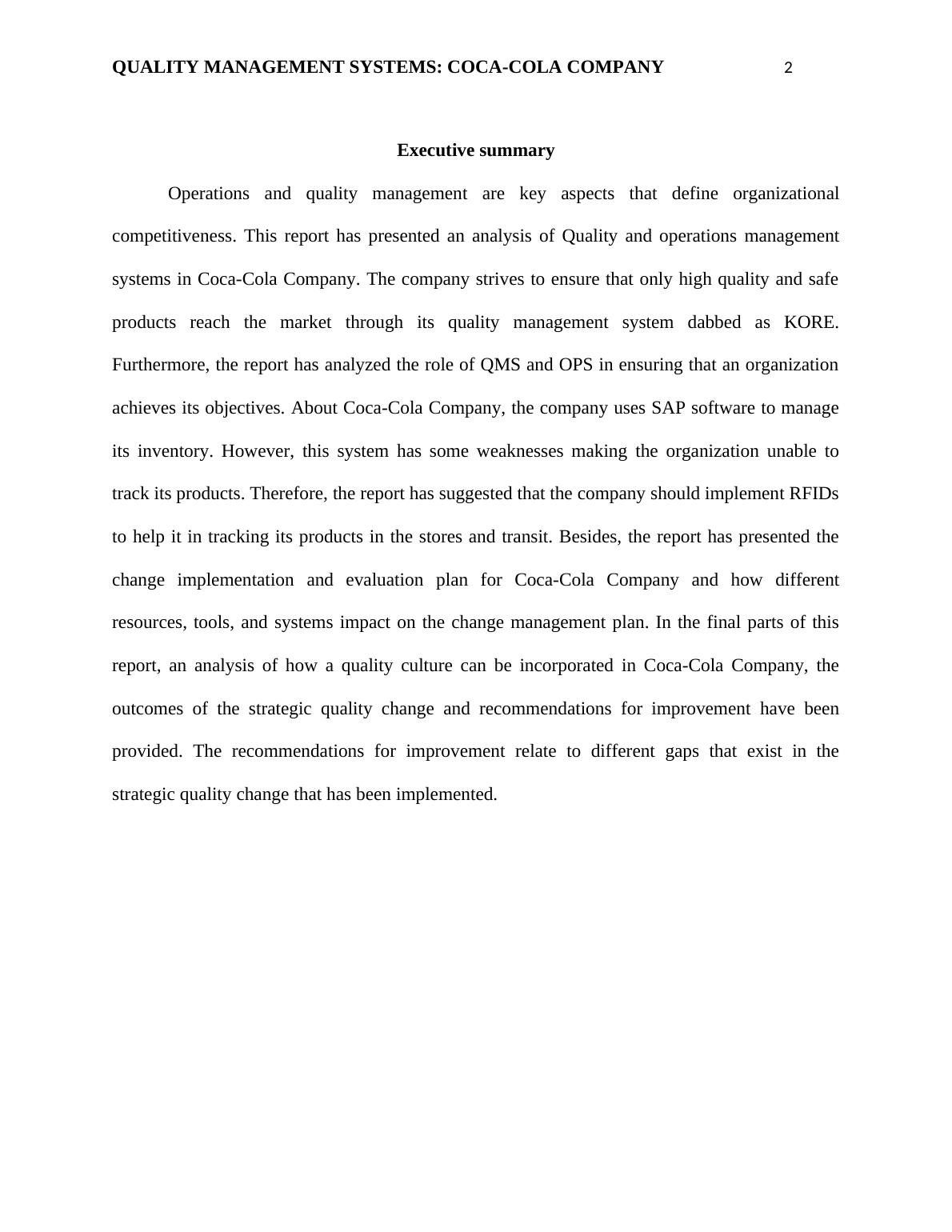
QUALITY MANAGEMENT SYSTEMS: COCA-COLA COMPANY 3
Table of Contents
Executive summary.......................................................................................................................2
Introduction....................................................................................................................................4
Importance of effective operations management and quality management in achieving
organizational objectives...............................................................................................................5
The success of the existing quality and operations management processes in achieving
Coca-Cola’s strategic management objectives............................................................................8
Need for Quality Change.............................................................................................................10
Factors Driving Change..............................................................................................................11
Implications for ignoring the change requirements.................................................................12
Change Implementation Plan.....................................................................................................13
Nature of the Change...............................................................................................................13
Change Perspective..................................................................................................................13
Change Management Model...................................................................................................14
Implementation process...........................................................................................................15
Phase One: Prepare for change...........................................................................................16
Resources Tools and Systems..............................................................................................21
Phase Two: Managing change.............................................................................................22
Resource tools and systems needed.....................................................................................30
Phase Three: Preparing for the change..............................................................................30
Resources, tools and Processes needed...............................................................................31
How the proposed plan will impact on the RTS outlined in each Phase................................32
Resources:.................................................................................................................................32
Tools and Systems....................................................................................................................32
The quality culture of Coca-Cola Company.............................................................................34
Effective Quality Culture that May enable Coca-Cola Company to ensure a continuous
Monitoring and progress.............................................................................................................35
Summary......................................................................................................................................37
Evaluation of the outcomes of the Strategic Quality change...................................................38
Gaps in the change Process.........................................................................................................39
Recommendations: Areas of improvement...............................................................................40
References.....................................................................................................................................41
Table of Contents
Executive summary.......................................................................................................................2
Introduction....................................................................................................................................4
Importance of effective operations management and quality management in achieving
organizational objectives...............................................................................................................5
The success of the existing quality and operations management processes in achieving
Coca-Cola’s strategic management objectives............................................................................8
Need for Quality Change.............................................................................................................10
Factors Driving Change..............................................................................................................11
Implications for ignoring the change requirements.................................................................12
Change Implementation Plan.....................................................................................................13
Nature of the Change...............................................................................................................13
Change Perspective..................................................................................................................13
Change Management Model...................................................................................................14
Implementation process...........................................................................................................15
Phase One: Prepare for change...........................................................................................16
Resources Tools and Systems..............................................................................................21
Phase Two: Managing change.............................................................................................22
Resource tools and systems needed.....................................................................................30
Phase Three: Preparing for the change..............................................................................30
Resources, tools and Processes needed...............................................................................31
How the proposed plan will impact on the RTS outlined in each Phase................................32
Resources:.................................................................................................................................32
Tools and Systems....................................................................................................................32
The quality culture of Coca-Cola Company.............................................................................34
Effective Quality Culture that May enable Coca-Cola Company to ensure a continuous
Monitoring and progress.............................................................................................................35
Summary......................................................................................................................................37
Evaluation of the outcomes of the Strategic Quality change...................................................38
Gaps in the change Process.........................................................................................................39
Recommendations: Areas of improvement...............................................................................40
References.....................................................................................................................................41
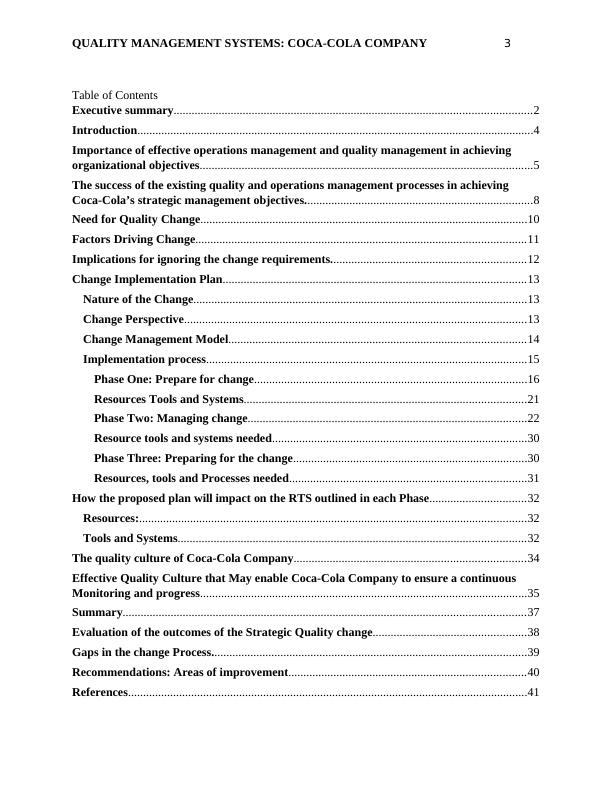
QUALITY MANAGEMENT SYSTEMS: COCA-COLA COMPANY 4
Introduction
The Coca-Cola is an international beverage manufacturer, marketer, and retailer based in
Atlanta, Georgia. The Firm is best recognized for its original brand Coca-Cola, established in
1886 by Pemberton John (Hymson, 2011, p. 2). Since its inception, the company has operated a
franchised distribution system which has seen it rise the ladders to become the world's leading
beverage manufacturer and seller. In its business model, the Company only produces the
concentrate which is then sold to different bottlers worldwide. With the stiff competition and the
global nature of the beverage market, Coca-Cola system has installed the highest processes and
standards to ensure a sustained quality in its entire value chain, ranging from its syrup production
to its bottling and distribution.
Ideally, a Quality Management System (QMS) entails a formalized system that dictates
the procedures, processes, and responsibilities for attaining quality objectives and policies. To
achieve a sustained quality and safety, Coca-Cola has stringent manufacturing sales and
distribution procedures and policies, specifications and requirements which are maintained by an
integrated quality management system termed as “Coca-Cola Operating Requirements (KORE).”
KORE creates an integrated quality management plan for the company which holds on its
system-wide operations (Journey Staff, 2012). With support from leadership throughout the
Company, KORE: integrates preventive actions when introducing new products, integrates
business quality goals and aligns them with the relevant metrics to closely monitor performance,
incorporates critical control points and hazard analysis (HACCP), risk management in the
organization's bottling activities and entire supply chain system, outlines problem-solving
approaches to enhance sustained quality advancements (Journey Staff, 2012). Besides, the
Introduction
The Coca-Cola is an international beverage manufacturer, marketer, and retailer based in
Atlanta, Georgia. The Firm is best recognized for its original brand Coca-Cola, established in
1886 by Pemberton John (Hymson, 2011, p. 2). Since its inception, the company has operated a
franchised distribution system which has seen it rise the ladders to become the world's leading
beverage manufacturer and seller. In its business model, the Company only produces the
concentrate which is then sold to different bottlers worldwide. With the stiff competition and the
global nature of the beverage market, Coca-Cola system has installed the highest processes and
standards to ensure a sustained quality in its entire value chain, ranging from its syrup production
to its bottling and distribution.
Ideally, a Quality Management System (QMS) entails a formalized system that dictates
the procedures, processes, and responsibilities for attaining quality objectives and policies. To
achieve a sustained quality and safety, Coca-Cola has stringent manufacturing sales and
distribution procedures and policies, specifications and requirements which are maintained by an
integrated quality management system termed as “Coca-Cola Operating Requirements (KORE).”
KORE creates an integrated quality management plan for the company which holds on its
system-wide operations (Journey Staff, 2012). With support from leadership throughout the
Company, KORE: integrates preventive actions when introducing new products, integrates
business quality goals and aligns them with the relevant metrics to closely monitor performance,
incorporates critical control points and hazard analysis (HACCP), risk management in the
organization's bottling activities and entire supply chain system, outlines problem-solving
approaches to enhance sustained quality advancements (Journey Staff, 2012). Besides, the
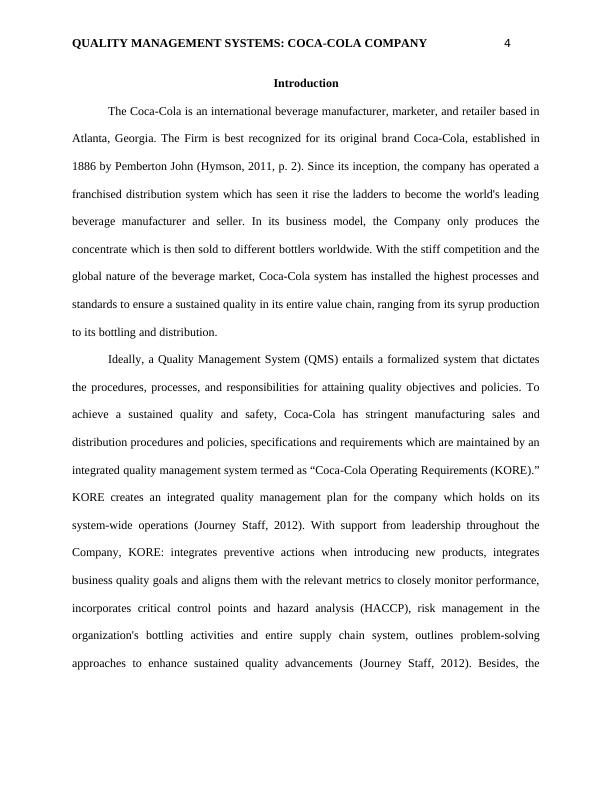
QUALITY MANAGEMENT SYSTEMS: COCA-COLA COMPANY 5
company conducts unannounced audits in its manufacturing facilities and regular inspections to
ensure that its ingredients, are safe, of high quality and sourced from trusted sources.
Importance of effective operations management and quality management in achieving
organizational objectives
As defined by Weinmann (2015, p. 5), operations management entails management
activities and processes that enable a firm to transfer various resources like energy, raw
materials, information, finance and consumer needs into final outputs that transfer the firm’s
primary services and products to the final consumer. Furthermore, Brown & Bessant (2013, p.
12), insist that different factors like supply and logistics, inventory management, design
decisions on capacity planning, management of processes, quality assurance and human capital
act as fundamental components of an effective operations management system. Active OM is
critical in ensuring that the organization achieves its desired objectives. Also, the nature of how
the strategic goals management is designed is largely dependent on the type of organization such
as a wholesale or manufacturing business, an agency or a retail enterprise and a government
authority. As explained by Brown & Bessant (2013, p. 13), the importance of effective
management of operations in achieving organizational strategic goals may be severed into three
primary classes- tactical, strategic and operational decisions.
Strategic decisions: Effective operations management assists the top-level managers in
making different strategic decisions. Strategic decisions may relate to the major problems being
faced by the firm or major strategic and competitive programs being installed by the firm. These
may include acquisitions and merger decisions.
Tactical Decisions: Operations management assists the management to schedule the
available resources effectively and manage its staff members under the legal constraints and
company conducts unannounced audits in its manufacturing facilities and regular inspections to
ensure that its ingredients, are safe, of high quality and sourced from trusted sources.
Importance of effective operations management and quality management in achieving
organizational objectives
As defined by Weinmann (2015, p. 5), operations management entails management
activities and processes that enable a firm to transfer various resources like energy, raw
materials, information, finance and consumer needs into final outputs that transfer the firm’s
primary services and products to the final consumer. Furthermore, Brown & Bessant (2013, p.
12), insist that different factors like supply and logistics, inventory management, design
decisions on capacity planning, management of processes, quality assurance and human capital
act as fundamental components of an effective operations management system. Active OM is
critical in ensuring that the organization achieves its desired objectives. Also, the nature of how
the strategic goals management is designed is largely dependent on the type of organization such
as a wholesale or manufacturing business, an agency or a retail enterprise and a government
authority. As explained by Brown & Bessant (2013, p. 13), the importance of effective
management of operations in achieving organizational strategic goals may be severed into three
primary classes- tactical, strategic and operational decisions.
Strategic decisions: Effective operations management assists the top-level managers in
making different strategic decisions. Strategic decisions may relate to the major problems being
faced by the firm or major strategic and competitive programs being installed by the firm. These
may include acquisitions and merger decisions.
Tactical Decisions: Operations management assists the management to schedule the
available resources effectively and manage its staff members under the legal constraints and
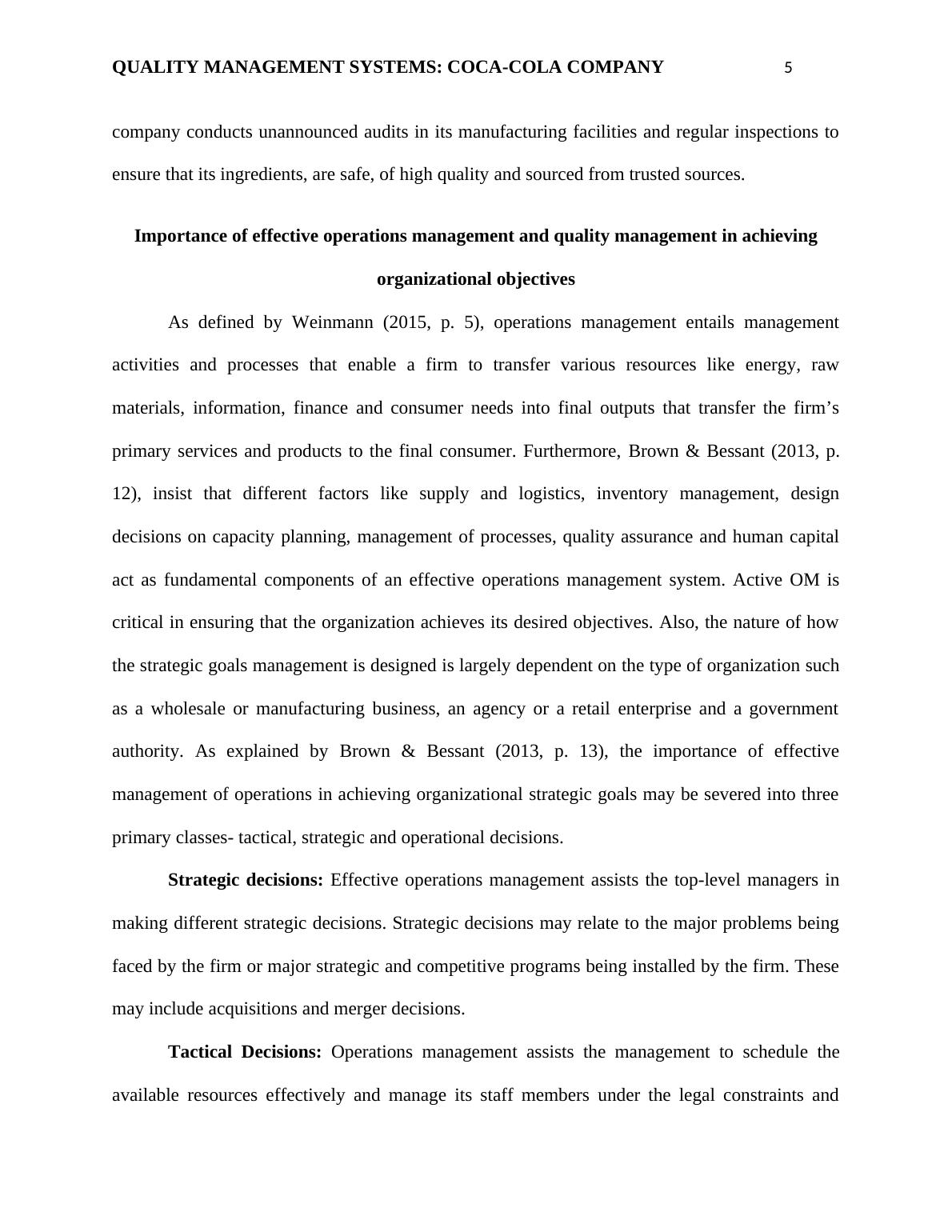
QUALITY MANAGEMENT SYSTEMS: COCA-COLA COMPANY 6
regulations established by the enterprise's strategic plan. For instance, some tactical decisions
made by a firm may entail scheduling raw material delivery and operational shift planning.
Operational Decisions: Following the explanations, given by Mahadevan (2015, p. 20),
OM enables the management to plan properly, control and monitor operational decisions with
regards to the constraints and problems defined by the tactical decisions. Such decisions are
closely related to primary departmental goals and targets and are short-term. Examples of such
decisions entail individual daily operational decisions established by the team managers in an
organization such as planning and defining daily activities and goals.
Apart from effective operations management, quality is an important aspect in firms like
Coca-Cola. Being in the processing and manufacturing sector adds to the firm's responsibility to
manufacture and distribute safe and high-quality products so that it wins the trust and loyalty of
the customers. Furthermore, a Quality Management System plays a pivotal role in ensuring that
the firm's production system is effective. Besides, quality is not related to the manufacturing of
goods alone, but rather it also relates to the quality of different services offered by the firm to the
consumers.
According to Joseph Juran (quality guru), quality management entails three parts-
assurance, planning, and control. To attain excellence, sustained quality management and
improvement should for part of these three roles (Goetsch & Davis, 2014, p. 14). Unreasonable
society and industry behaviors may be corrected by an accurate application of TQM (Total
Quality Management).
Quality management helps an organization to achieve its objectives in two ways- meeting
the requirements of the customers and fulfilling organization's requirements. When an
organization can satisfy the needs of its clients, then the customers will develop confidence in the
regulations established by the enterprise's strategic plan. For instance, some tactical decisions
made by a firm may entail scheduling raw material delivery and operational shift planning.
Operational Decisions: Following the explanations, given by Mahadevan (2015, p. 20),
OM enables the management to plan properly, control and monitor operational decisions with
regards to the constraints and problems defined by the tactical decisions. Such decisions are
closely related to primary departmental goals and targets and are short-term. Examples of such
decisions entail individual daily operational decisions established by the team managers in an
organization such as planning and defining daily activities and goals.
Apart from effective operations management, quality is an important aspect in firms like
Coca-Cola. Being in the processing and manufacturing sector adds to the firm's responsibility to
manufacture and distribute safe and high-quality products so that it wins the trust and loyalty of
the customers. Furthermore, a Quality Management System plays a pivotal role in ensuring that
the firm's production system is effective. Besides, quality is not related to the manufacturing of
goods alone, but rather it also relates to the quality of different services offered by the firm to the
consumers.
According to Joseph Juran (quality guru), quality management entails three parts-
assurance, planning, and control. To attain excellence, sustained quality management and
improvement should for part of these three roles (Goetsch & Davis, 2014, p. 14). Unreasonable
society and industry behaviors may be corrected by an accurate application of TQM (Total
Quality Management).
Quality management helps an organization to achieve its objectives in two ways- meeting
the requirements of the customers and fulfilling organization's requirements. When an
organization can satisfy the needs of its clients, then the customers will develop confidence in the
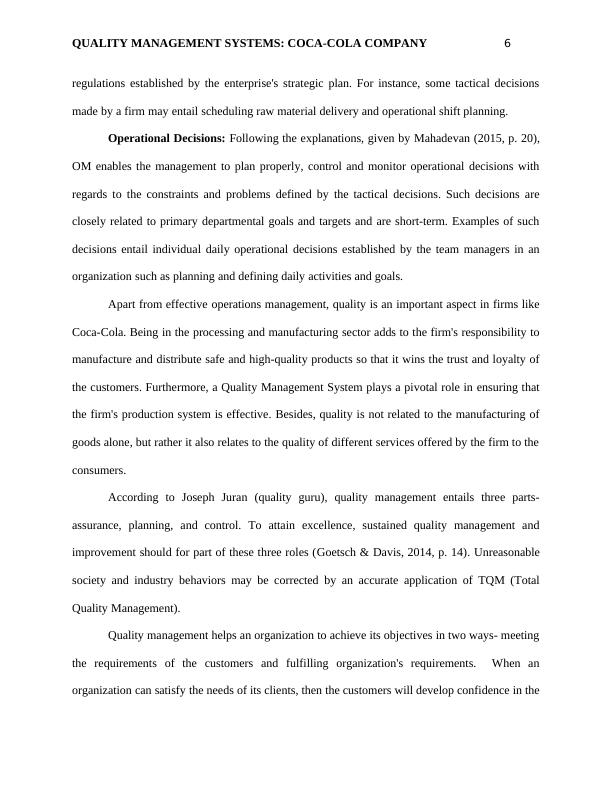
QUALITY MANAGEMENT SYSTEMS: COCA-COLA COMPANY 7
firm which in return may lead to more sales, a large customer base and more repeat business
(Sabella, Kashou & Omran, 2014, p. 1488). Also, effective quality management enables an
organization to meet its requirements such as compliance with regulations and provision of
services and products in the most resource and cost-effective way, creating an opportunity for
growth, expansion, and profitability.
The success of the existing quality and operations management processes in achieving
Coca-Cola’s strategic management objectives.
Operations Decisions Shape
Competencies and Constraints
Performance Objectives
Quality Quality Checks to meet
competencies
Speed Use of
global
Bottling
Partners
Safety Use of
Trusted
suppliers
Use of trusted
Cost Price-Pack
architectur
e strategy
Refranchising its bottling
operations
Flexibility Use of
global
sourcing in
collaborati
on with
bottling
partners
Manufacturing of a
variety of products to
adjust to changing
consumer preferences
Dependab
ility
Use of
different
varieties
and stable
prices
Capacity Supply
Network
Processes and
Technology
firm which in return may lead to more sales, a large customer base and more repeat business
(Sabella, Kashou & Omran, 2014, p. 1488). Also, effective quality management enables an
organization to meet its requirements such as compliance with regulations and provision of
services and products in the most resource and cost-effective way, creating an opportunity for
growth, expansion, and profitability.
The success of the existing quality and operations management processes in achieving
Coca-Cola’s strategic management objectives.
Operations Decisions Shape
Competencies and Constraints
Performance Objectives
Quality Quality Checks to meet
competencies
Speed Use of
global
Bottling
Partners
Safety Use of
Trusted
suppliers
Use of trusted
Cost Price-Pack
architectur
e strategy
Refranchising its bottling
operations
Flexibility Use of
global
sourcing in
collaborati
on with
bottling
partners
Manufacturing of a
variety of products to
adjust to changing
consumer preferences
Dependab
ility
Use of
different
varieties
and stable
prices
Capacity Supply
Network
Processes and
Technology
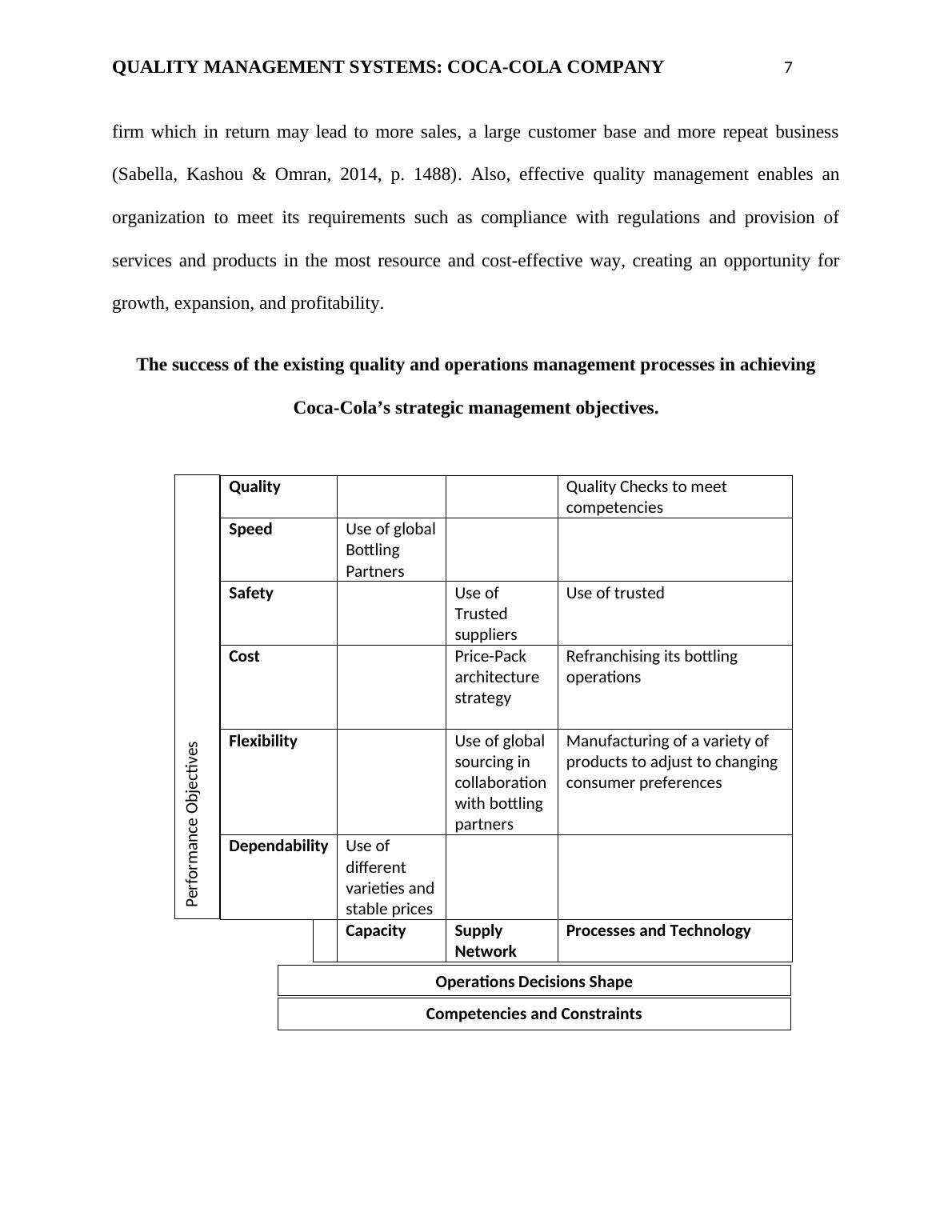
QUALITY MANAGEMENT SYSTEMS: COCA-COLA COMPANY 8
Quality and safety: To maintain its competitive advantage in the global beverages
industry, Coca-cola has tried to observe quality (KORE), safety, speed, low costs and
dependability in its operational processes (Loison, Foch & Boyer, 2014, p. 6). Ideally, through
global sourcing efforts, in partnership with numerous bottling companies, the company has
contracted to source millions of raw materials for its manufacturing processes at lower prices
(Albert, Werhane & Rolph, 2014, p. 4). For instance, in 2016, the company collaborated with
different bottling partners to source one million tons of more sustainable sugar. This achievement
was aimed at positioning the firm at an estimated 15-20% towards its goal to sustainably source
100 percent of its sugar by 2020, hence reducing operational costs.
Cost: Cost-cutting has enabled the company to operate sustainably and make more
profits. Costs entail prices tied to products and services. It may also refer to operational,
manufacturing and overhead expenses incurred by a firm in manufacturing specific products.
Coca Cola’s primary target is to achieve 3 billion US dollars in annual savings in expenses by
2019 and at the same time boost sales by increasing prices and promoting smaller pack sizes
(Journey Staff, 2012). To attain this, the company has adopted a price-pack architecture approach
in the US, whereby it promotes the 8-ounce glass bottle and the mini cans.
Speed: Coca-Cola Company only manufactures the concentrate (Baah & Bohaker, 2015,
p. 17). This concentrate is then distributed to different bottling partners located globally.
Therefore, enabling its customers to gain access and purchase its products from different
locations without delays. Speed is a major consideration for a supply chain system to be
considered as effective (Stadtler, 2015, p. 4). There should be no delays in supplies. Furthermore,
the customers should readily access the products whenever they need them. This is what Coca-
Cola strives to do. The bottlers have stores at strategic places worldwide, where the consumers,
Quality and safety: To maintain its competitive advantage in the global beverages
industry, Coca-cola has tried to observe quality (KORE), safety, speed, low costs and
dependability in its operational processes (Loison, Foch & Boyer, 2014, p. 6). Ideally, through
global sourcing efforts, in partnership with numerous bottling companies, the company has
contracted to source millions of raw materials for its manufacturing processes at lower prices
(Albert, Werhane & Rolph, 2014, p. 4). For instance, in 2016, the company collaborated with
different bottling partners to source one million tons of more sustainable sugar. This achievement
was aimed at positioning the firm at an estimated 15-20% towards its goal to sustainably source
100 percent of its sugar by 2020, hence reducing operational costs.
Cost: Cost-cutting has enabled the company to operate sustainably and make more
profits. Costs entail prices tied to products and services. It may also refer to operational,
manufacturing and overhead expenses incurred by a firm in manufacturing specific products.
Coca Cola’s primary target is to achieve 3 billion US dollars in annual savings in expenses by
2019 and at the same time boost sales by increasing prices and promoting smaller pack sizes
(Journey Staff, 2012). To attain this, the company has adopted a price-pack architecture approach
in the US, whereby it promotes the 8-ounce glass bottle and the mini cans.
Speed: Coca-Cola Company only manufactures the concentrate (Baah & Bohaker, 2015,
p. 17). This concentrate is then distributed to different bottling partners located globally.
Therefore, enabling its customers to gain access and purchase its products from different
locations without delays. Speed is a major consideration for a supply chain system to be
considered as effective (Stadtler, 2015, p. 4). There should be no delays in supplies. Furthermore,
the customers should readily access the products whenever they need them. This is what Coca-
Cola strives to do. The bottlers have stores at strategic places worldwide, where the consumers,
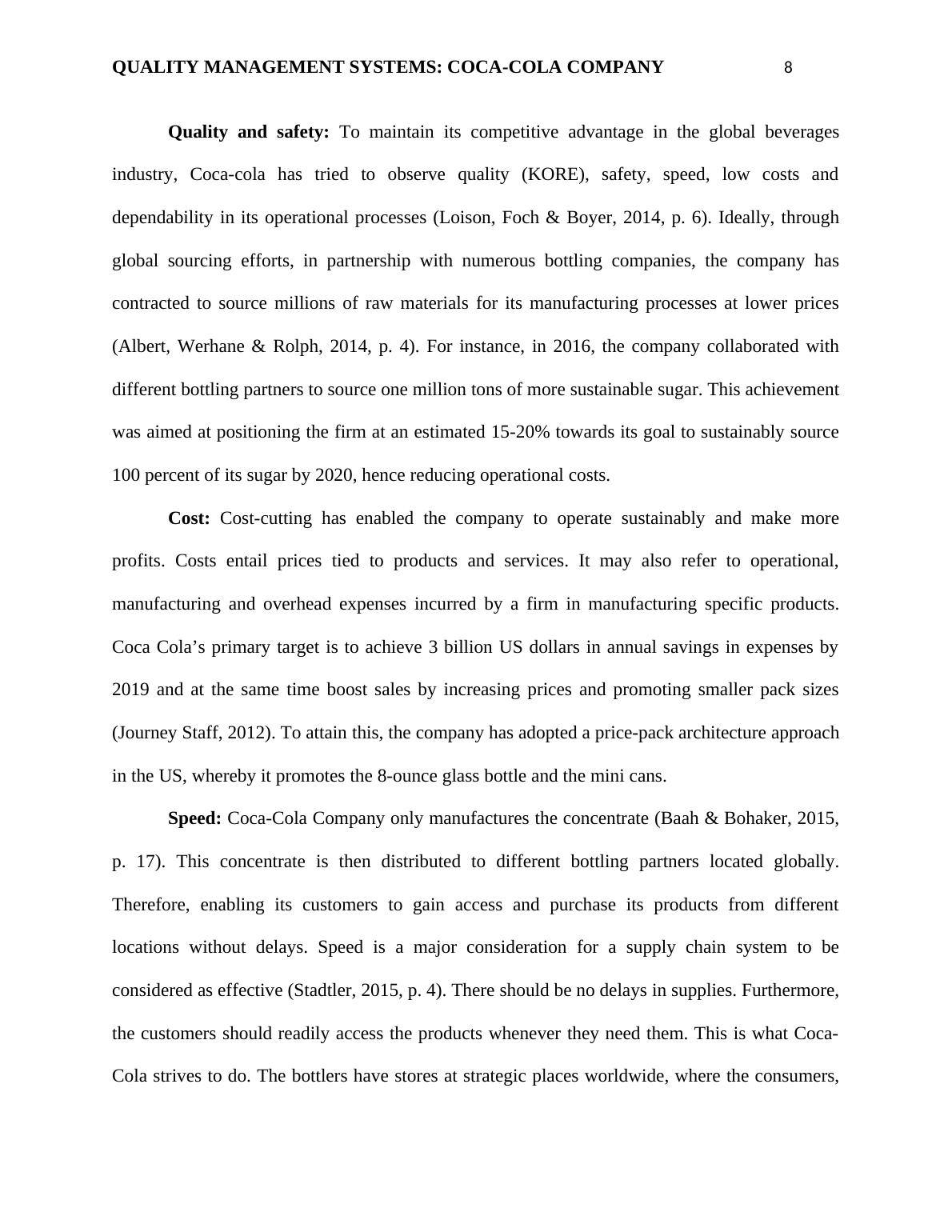
End of preview
Want to access all the pages? Upload your documents or become a member.
Related Documents
Strategic Information Systems Assignment (Doc)lg...
|14
|3019
|240
Strategic Management: Analysis of Coca-Cola's International Strategy and IMI's Business Strategylg...
|16
|4579
|343
ERP System and Accounting Software Packages of Coca-Cola Amatillg...
|12
|3324
|393
CRM Covering Letter to Sponsorlg...
|20
|4594
|21
International Business America Report 2022lg...
|20
|5600
|26
Strategic Management and Information Systems for Coca Cola Amatil Australialg...
|15
|3282
|318