Implementing Total Quality Management in Ford Motor Company
VerifiedAdded on 2022/08/09
|19
|4085
|53
AI Summary
This report explains how to implement Total Quality Management (TQM) in Ford Motor Company, an Australian subsidiary of the US-based automaker. It covers TQM principles, tools, and techniques like Pareto charts and Ishikawa diagrams, and the benefits of implementing TQM, such as increased productivity and customer satisfaction. The report also outlines the steps to implement TQM, including clarifying the mission and vision, determining critical success factors, and developing an improvement plan. The report is useful for businesses looking to improve their operations and quality of products.
Contribute Materials
Your contribution can guide someone’s learning journey. Share your
documents today.
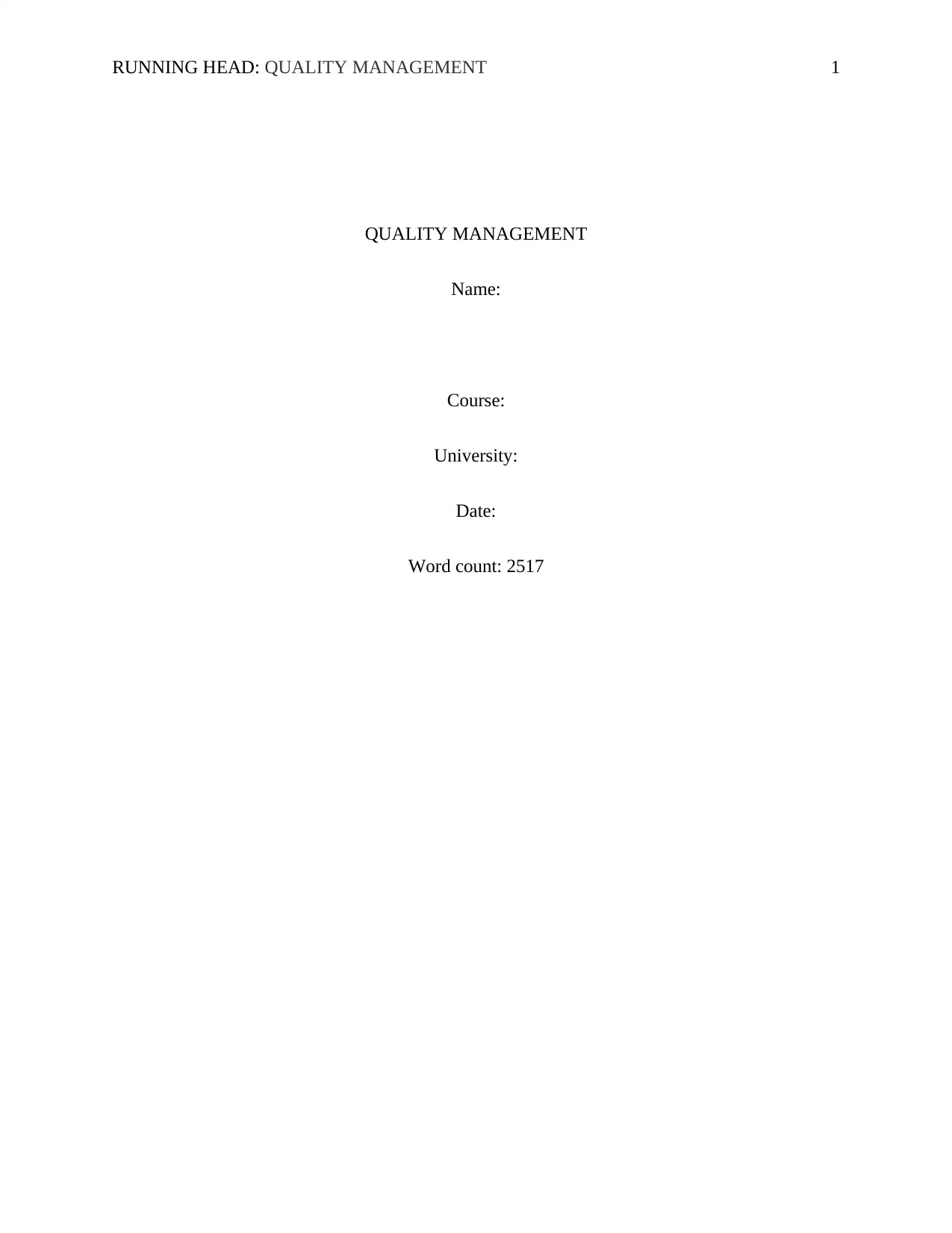
RUNNING HEAD: QUALITY MANAGEMENT 1
QUALITY MANAGEMENT
Name:
Course:
University:
Date:
Word count: 2517
QUALITY MANAGEMENT
Name:
Course:
University:
Date:
Word count: 2517
Secure Best Marks with AI Grader
Need help grading? Try our AI Grader for instant feedback on your assignments.
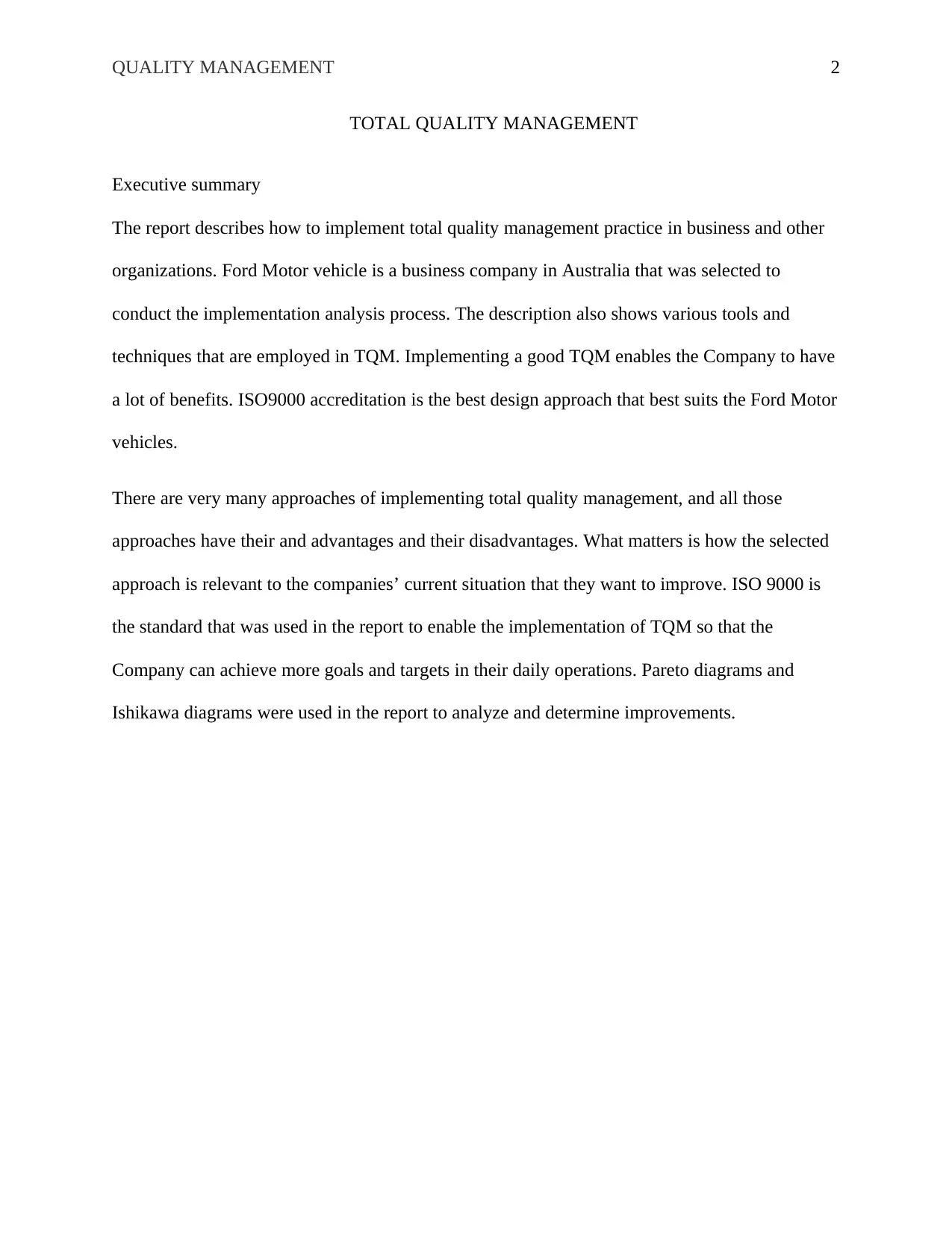
QUALITY MANAGEMENT 2
TOTAL QUALITY MANAGEMENT
Executive summary
The report describes how to implement total quality management practice in business and other
organizations. Ford Motor vehicle is a business company in Australia that was selected to
conduct the implementation analysis process. The description also shows various tools and
techniques that are employed in TQM. Implementing a good TQM enables the Company to have
a lot of benefits. ISO9000 accreditation is the best design approach that best suits the Ford Motor
vehicles.
There are very many approaches of implementing total quality management, and all those
approaches have their and advantages and their disadvantages. What matters is how the selected
approach is relevant to the companies’ current situation that they want to improve. ISO 9000 is
the standard that was used in the report to enable the implementation of TQM so that the
Company can achieve more goals and targets in their daily operations. Pareto diagrams and
Ishikawa diagrams were used in the report to analyze and determine improvements.
TOTAL QUALITY MANAGEMENT
Executive summary
The report describes how to implement total quality management practice in business and other
organizations. Ford Motor vehicle is a business company in Australia that was selected to
conduct the implementation analysis process. The description also shows various tools and
techniques that are employed in TQM. Implementing a good TQM enables the Company to have
a lot of benefits. ISO9000 accreditation is the best design approach that best suits the Ford Motor
vehicles.
There are very many approaches of implementing total quality management, and all those
approaches have their and advantages and their disadvantages. What matters is how the selected
approach is relevant to the companies’ current situation that they want to improve. ISO 9000 is
the standard that was used in the report to enable the implementation of TQM so that the
Company can achieve more goals and targets in their daily operations. Pareto diagrams and
Ishikawa diagrams were used in the report to analyze and determine improvements.
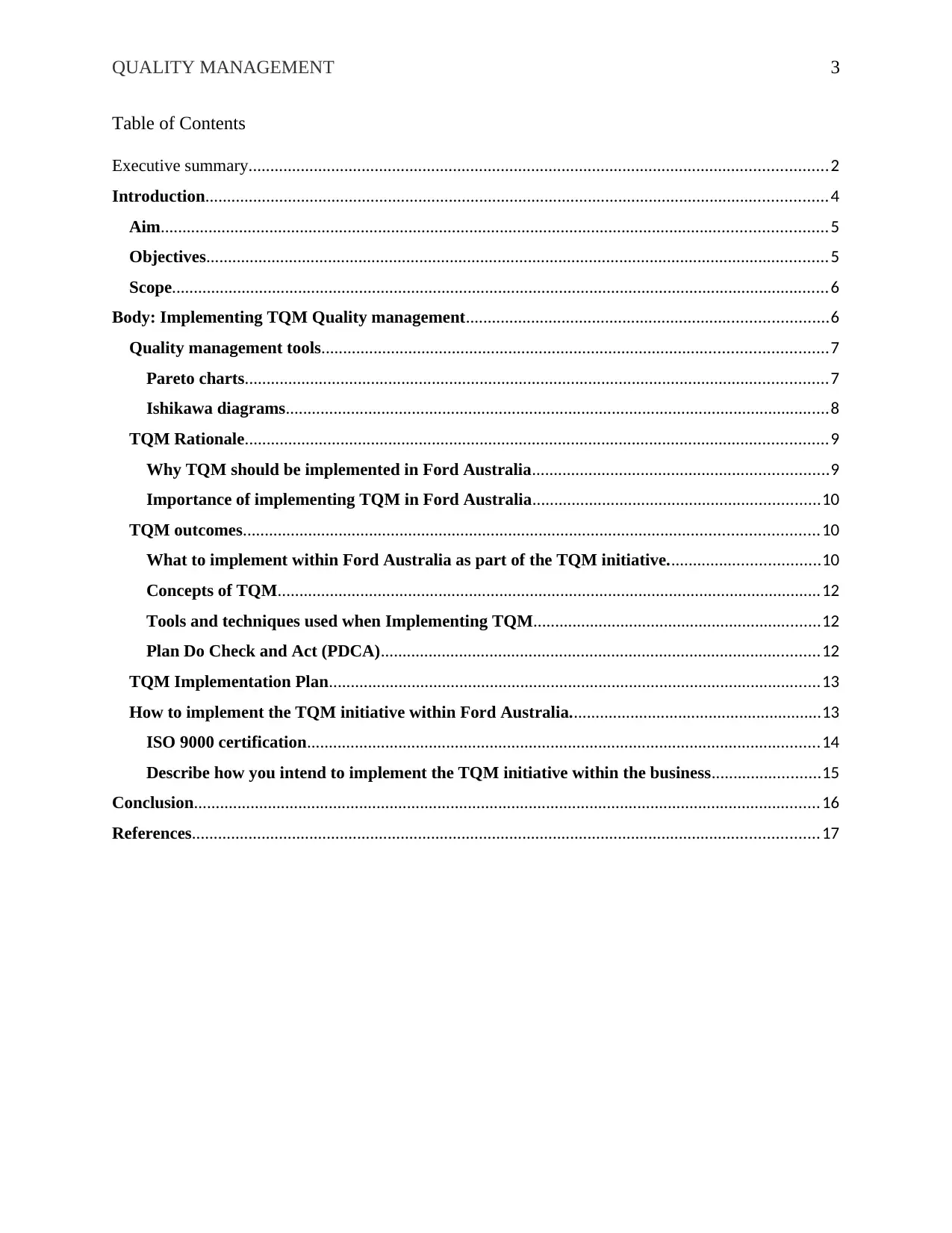
QUALITY MANAGEMENT 3
Table of Contents
Executive summary.....................................................................................................................................2
Introduction...............................................................................................................................................4
Aim.........................................................................................................................................................5
Objectives...............................................................................................................................................5
Scope.......................................................................................................................................................6
Body: Implementing TQM Quality management...................................................................................6
Quality management tools....................................................................................................................7
Pareto charts......................................................................................................................................7
Ishikawa diagrams.............................................................................................................................8
TQM Rationale......................................................................................................................................9
Why TQM should be implemented in Ford Australia....................................................................9
Importance of implementing TQM in Ford Australia..................................................................10
TQM outcomes....................................................................................................................................10
What to implement within Ford Australia as part of the TQM initiative...................................10
Concepts of TQM.............................................................................................................................12
Tools and techniques used when Implementing TQM..................................................................12
Plan Do Check and Act (PDCA).....................................................................................................12
TQM Implementation Plan.................................................................................................................13
How to implement the TQM initiative within Ford Australia..........................................................13
ISO 9000 certification......................................................................................................................14
Describe how you intend to implement the TQM initiative within the business.........................15
Conclusion................................................................................................................................................16
References................................................................................................................................................17
Table of Contents
Executive summary.....................................................................................................................................2
Introduction...............................................................................................................................................4
Aim.........................................................................................................................................................5
Objectives...............................................................................................................................................5
Scope.......................................................................................................................................................6
Body: Implementing TQM Quality management...................................................................................6
Quality management tools....................................................................................................................7
Pareto charts......................................................................................................................................7
Ishikawa diagrams.............................................................................................................................8
TQM Rationale......................................................................................................................................9
Why TQM should be implemented in Ford Australia....................................................................9
Importance of implementing TQM in Ford Australia..................................................................10
TQM outcomes....................................................................................................................................10
What to implement within Ford Australia as part of the TQM initiative...................................10
Concepts of TQM.............................................................................................................................12
Tools and techniques used when Implementing TQM..................................................................12
Plan Do Check and Act (PDCA).....................................................................................................12
TQM Implementation Plan.................................................................................................................13
How to implement the TQM initiative within Ford Australia..........................................................13
ISO 9000 certification......................................................................................................................14
Describe how you intend to implement the TQM initiative within the business.........................15
Conclusion................................................................................................................................................16
References................................................................................................................................................17
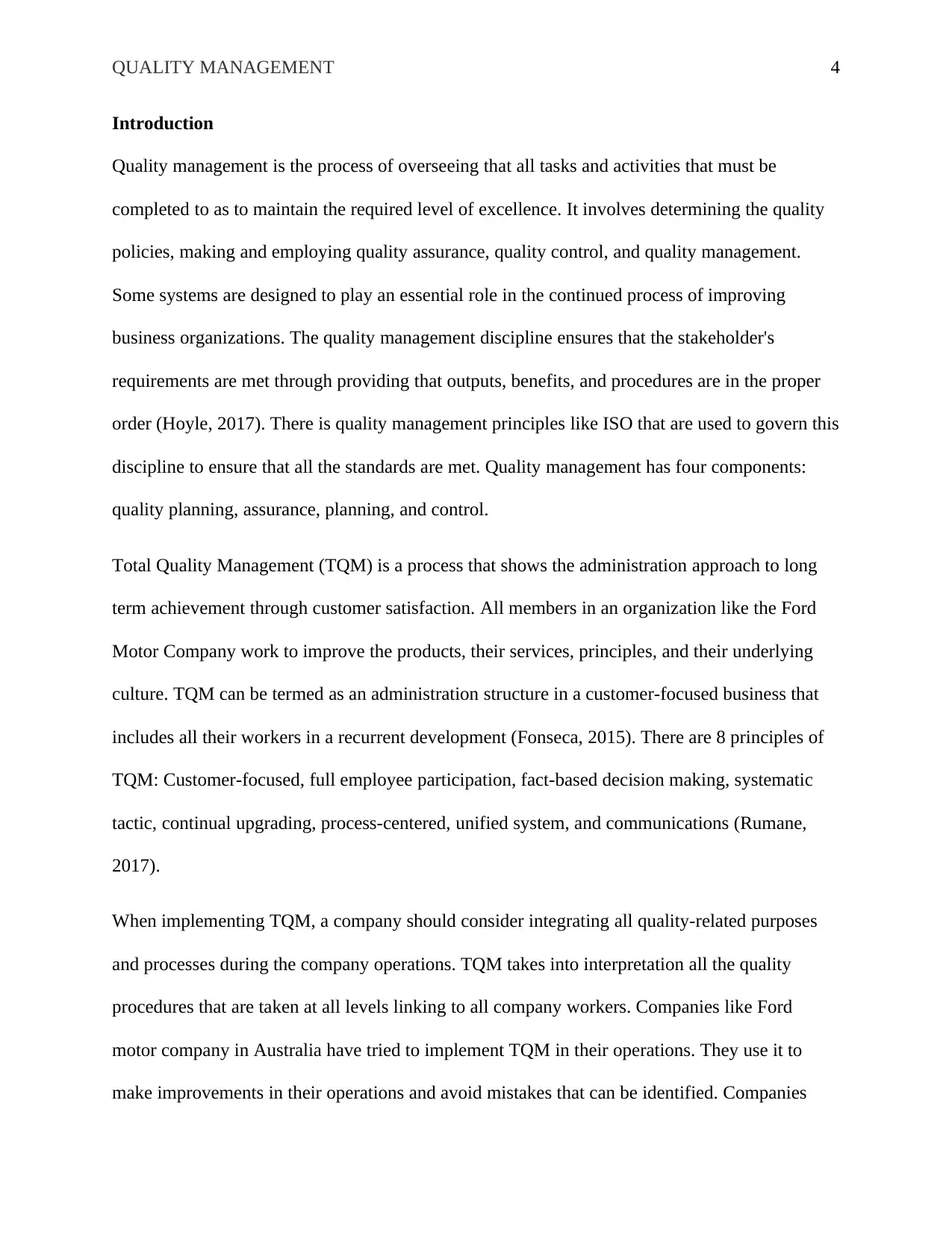
QUALITY MANAGEMENT 4
Introduction
Quality management is the process of overseeing that all tasks and activities that must be
completed to as to maintain the required level of excellence. It involves determining the quality
policies, making and employing quality assurance, quality control, and quality management.
Some systems are designed to play an essential role in the continued process of improving
business organizations. The quality management discipline ensures that the stakeholder's
requirements are met through providing that outputs, benefits, and procedures are in the proper
order (Hoyle, 2017). There is quality management principles like ISO that are used to govern this
discipline to ensure that all the standards are met. Quality management has four components:
quality planning, assurance, planning, and control.
Total Quality Management (TQM) is a process that shows the administration approach to long
term achievement through customer satisfaction. All members in an organization like the Ford
Motor Company work to improve the products, their services, principles, and their underlying
culture. TQM can be termed as an administration structure in a customer-focused business that
includes all their workers in a recurrent development (Fonseca, 2015). There are 8 principles of
TQM: Customer-focused, full employee participation, fact-based decision making, systematic
tactic, continual upgrading, process-centered, unified system, and communications (Rumane,
2017).
When implementing TQM, a company should consider integrating all quality-related purposes
and processes during the company operations. TQM takes into interpretation all the quality
procedures that are taken at all levels linking to all company workers. Companies like Ford
motor company in Australia have tried to implement TQM in their operations. They use it to
make improvements in their operations and avoid mistakes that can be identified. Companies
Introduction
Quality management is the process of overseeing that all tasks and activities that must be
completed to as to maintain the required level of excellence. It involves determining the quality
policies, making and employing quality assurance, quality control, and quality management.
Some systems are designed to play an essential role in the continued process of improving
business organizations. The quality management discipline ensures that the stakeholder's
requirements are met through providing that outputs, benefits, and procedures are in the proper
order (Hoyle, 2017). There is quality management principles like ISO that are used to govern this
discipline to ensure that all the standards are met. Quality management has four components:
quality planning, assurance, planning, and control.
Total Quality Management (TQM) is a process that shows the administration approach to long
term achievement through customer satisfaction. All members in an organization like the Ford
Motor Company work to improve the products, their services, principles, and their underlying
culture. TQM can be termed as an administration structure in a customer-focused business that
includes all their workers in a recurrent development (Fonseca, 2015). There are 8 principles of
TQM: Customer-focused, full employee participation, fact-based decision making, systematic
tactic, continual upgrading, process-centered, unified system, and communications (Rumane,
2017).
When implementing TQM, a company should consider integrating all quality-related purposes
and processes during the company operations. TQM takes into interpretation all the quality
procedures that are taken at all levels linking to all company workers. Companies like Ford
motor company in Australia have tried to implement TQM in their operations. They use it to
make improvements in their operations and avoid mistakes that can be identified. Companies
Secure Best Marks with AI Grader
Need help grading? Try our AI Grader for instant feedback on your assignments.
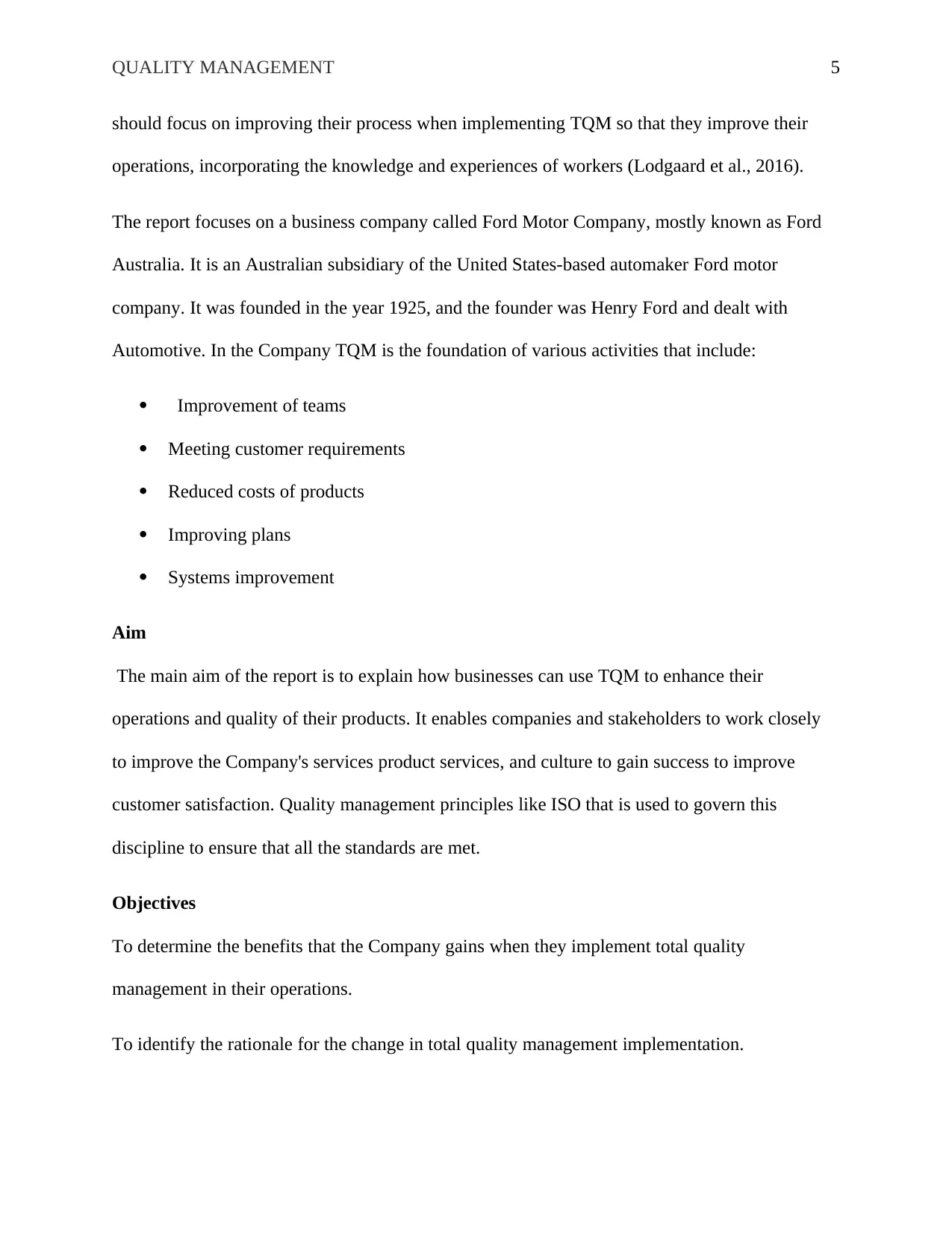
QUALITY MANAGEMENT 5
should focus on improving their process when implementing TQM so that they improve their
operations, incorporating the knowledge and experiences of workers (Lodgaard et al., 2016).
The report focuses on a business company called Ford Motor Company, mostly known as Ford
Australia. It is an Australian subsidiary of the United States-based automaker Ford motor
company. It was founded in the year 1925, and the founder was Henry Ford and dealt with
Automotive. In the Company TQM is the foundation of various activities that include:
Improvement of teams
Meeting customer requirements
Reduced costs of products
Improving plans
Systems improvement
Aim
The main aim of the report is to explain how businesses can use TQM to enhance their
operations and quality of their products. It enables companies and stakeholders to work closely
to improve the Company's services product services, and culture to gain success to improve
customer satisfaction. Quality management principles like ISO that is used to govern this
discipline to ensure that all the standards are met.
Objectives
To determine the benefits that the Company gains when they implement total quality
management in their operations.
To identify the rationale for the change in total quality management implementation.
should focus on improving their process when implementing TQM so that they improve their
operations, incorporating the knowledge and experiences of workers (Lodgaard et al., 2016).
The report focuses on a business company called Ford Motor Company, mostly known as Ford
Australia. It is an Australian subsidiary of the United States-based automaker Ford motor
company. It was founded in the year 1925, and the founder was Henry Ford and dealt with
Automotive. In the Company TQM is the foundation of various activities that include:
Improvement of teams
Meeting customer requirements
Reduced costs of products
Improving plans
Systems improvement
Aim
The main aim of the report is to explain how businesses can use TQM to enhance their
operations and quality of their products. It enables companies and stakeholders to work closely
to improve the Company's services product services, and culture to gain success to improve
customer satisfaction. Quality management principles like ISO that is used to govern this
discipline to ensure that all the standards are met.
Objectives
To determine the benefits that the Company gains when they implement total quality
management in their operations.
To identify the rationale for the change in total quality management implementation.
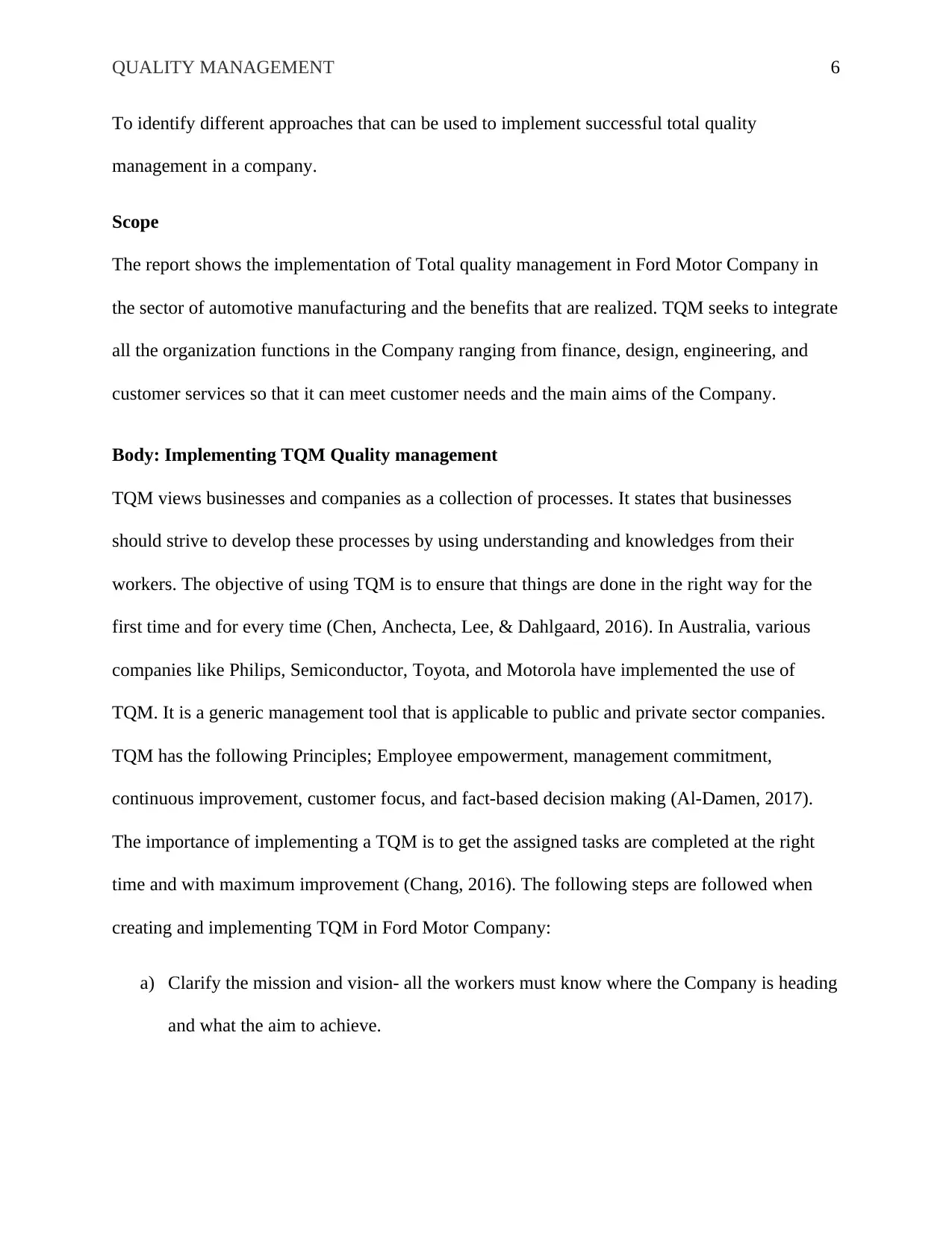
QUALITY MANAGEMENT 6
To identify different approaches that can be used to implement successful total quality
management in a company.
Scope
The report shows the implementation of Total quality management in Ford Motor Company in
the sector of automotive manufacturing and the benefits that are realized. TQM seeks to integrate
all the organization functions in the Company ranging from finance, design, engineering, and
customer services so that it can meet customer needs and the main aims of the Company.
Body: Implementing TQM Quality management
TQM views businesses and companies as a collection of processes. It states that businesses
should strive to develop these processes by using understanding and knowledges from their
workers. The objective of using TQM is to ensure that things are done in the right way for the
first time and for every time (Chen, Anchecta, Lee, & Dahlgaard, 2016). In Australia, various
companies like Philips, Semiconductor, Toyota, and Motorola have implemented the use of
TQM. It is a generic management tool that is applicable to public and private sector companies.
TQM has the following Principles; Employee empowerment, management commitment,
continuous improvement, customer focus, and fact-based decision making (Al-Damen, 2017).
The importance of implementing a TQM is to get the assigned tasks are completed at the right
time and with maximum improvement (Chang, 2016). The following steps are followed when
creating and implementing TQM in Ford Motor Company:
a) Clarify the mission and vision- all the workers must know where the Company is heading
and what the aim to achieve.
To identify different approaches that can be used to implement successful total quality
management in a company.
Scope
The report shows the implementation of Total quality management in Ford Motor Company in
the sector of automotive manufacturing and the benefits that are realized. TQM seeks to integrate
all the organization functions in the Company ranging from finance, design, engineering, and
customer services so that it can meet customer needs and the main aims of the Company.
Body: Implementing TQM Quality management
TQM views businesses and companies as a collection of processes. It states that businesses
should strive to develop these processes by using understanding and knowledges from their
workers. The objective of using TQM is to ensure that things are done in the right way for the
first time and for every time (Chen, Anchecta, Lee, & Dahlgaard, 2016). In Australia, various
companies like Philips, Semiconductor, Toyota, and Motorola have implemented the use of
TQM. It is a generic management tool that is applicable to public and private sector companies.
TQM has the following Principles; Employee empowerment, management commitment,
continuous improvement, customer focus, and fact-based decision making (Al-Damen, 2017).
The importance of implementing a TQM is to get the assigned tasks are completed at the right
time and with maximum improvement (Chang, 2016). The following steps are followed when
creating and implementing TQM in Ford Motor Company:
a) Clarify the mission and vision- all the workers must know where the Company is heading
and what the aim to achieve.
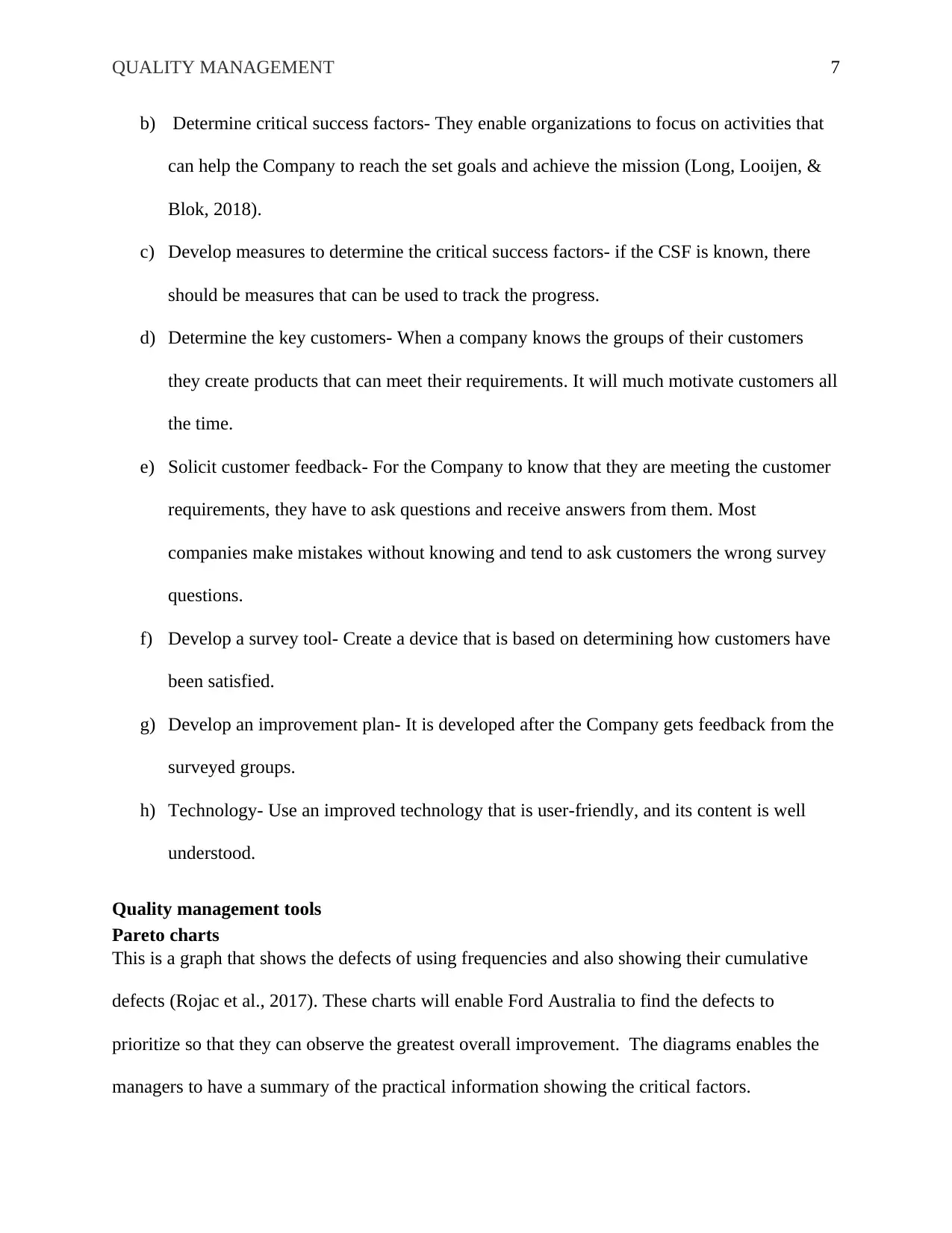
QUALITY MANAGEMENT 7
b) Determine critical success factors- They enable organizations to focus on activities that
can help the Company to reach the set goals and achieve the mission (Long, Looijen, &
Blok, 2018).
c) Develop measures to determine the critical success factors- if the CSF is known, there
should be measures that can be used to track the progress.
d) Determine the key customers- When a company knows the groups of their customers
they create products that can meet their requirements. It will much motivate customers all
the time.
e) Solicit customer feedback- For the Company to know that they are meeting the customer
requirements, they have to ask questions and receive answers from them. Most
companies make mistakes without knowing and tend to ask customers the wrong survey
questions.
f) Develop a survey tool- Create a device that is based on determining how customers have
been satisfied.
g) Develop an improvement plan- It is developed after the Company gets feedback from the
surveyed groups.
h) Technology- Use an improved technology that is user-friendly, and its content is well
understood.
Quality management tools
Pareto charts
This is a graph that shows the defects of using frequencies and also showing their cumulative
defects (Rojac et al., 2017). These charts will enable Ford Australia to find the defects to
prioritize so that they can observe the greatest overall improvement. The diagrams enables the
managers to have a summary of the practical information showing the critical factors.
b) Determine critical success factors- They enable organizations to focus on activities that
can help the Company to reach the set goals and achieve the mission (Long, Looijen, &
Blok, 2018).
c) Develop measures to determine the critical success factors- if the CSF is known, there
should be measures that can be used to track the progress.
d) Determine the key customers- When a company knows the groups of their customers
they create products that can meet their requirements. It will much motivate customers all
the time.
e) Solicit customer feedback- For the Company to know that they are meeting the customer
requirements, they have to ask questions and receive answers from them. Most
companies make mistakes without knowing and tend to ask customers the wrong survey
questions.
f) Develop a survey tool- Create a device that is based on determining how customers have
been satisfied.
g) Develop an improvement plan- It is developed after the Company gets feedback from the
surveyed groups.
h) Technology- Use an improved technology that is user-friendly, and its content is well
understood.
Quality management tools
Pareto charts
This is a graph that shows the defects of using frequencies and also showing their cumulative
defects (Rojac et al., 2017). These charts will enable Ford Australia to find the defects to
prioritize so that they can observe the greatest overall improvement. The diagrams enables the
managers to have a summary of the practical information showing the critical factors.
Paraphrase This Document
Need a fresh take? Get an instant paraphrase of this document with our AI Paraphraser
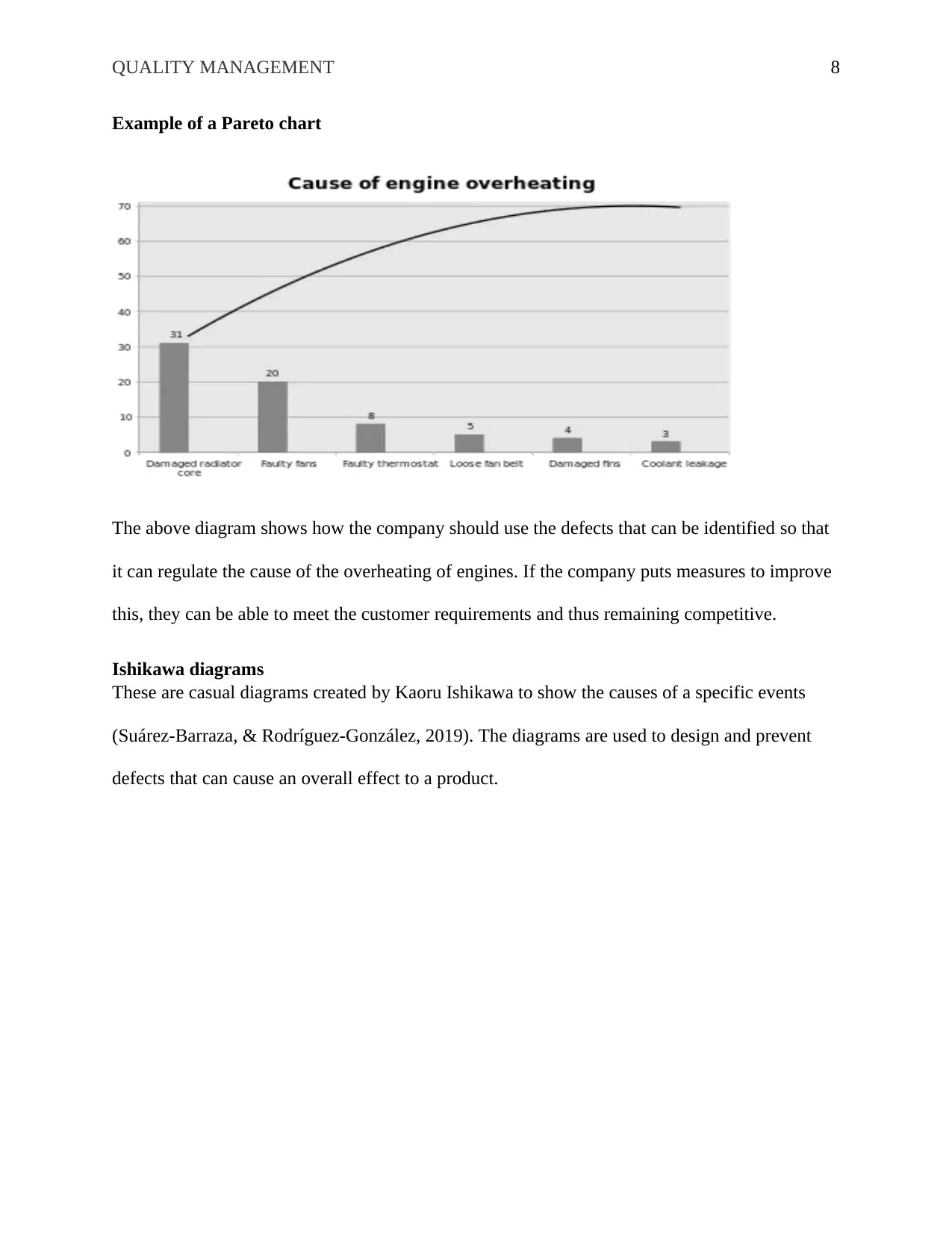
QUALITY MANAGEMENT 8
Example of a Pareto chart
The above diagram shows how the company should use the defects that can be identified so that
it can regulate the cause of the overheating of engines. If the company puts measures to improve
this, they can be able to meet the customer requirements and thus remaining competitive.
Ishikawa diagrams
These are casual diagrams created by Kaoru Ishikawa to show the causes of a specific events
(Suárez-Barraza, & Rodríguez-González, 2019). The diagrams are used to design and prevent
defects that can cause an overall effect to a product.
Example of a Pareto chart
The above diagram shows how the company should use the defects that can be identified so that
it can regulate the cause of the overheating of engines. If the company puts measures to improve
this, they can be able to meet the customer requirements and thus remaining competitive.
Ishikawa diagrams
These are casual diagrams created by Kaoru Ishikawa to show the causes of a specific events
(Suárez-Barraza, & Rodríguez-González, 2019). The diagrams are used to design and prevent
defects that can cause an overall effect to a product.
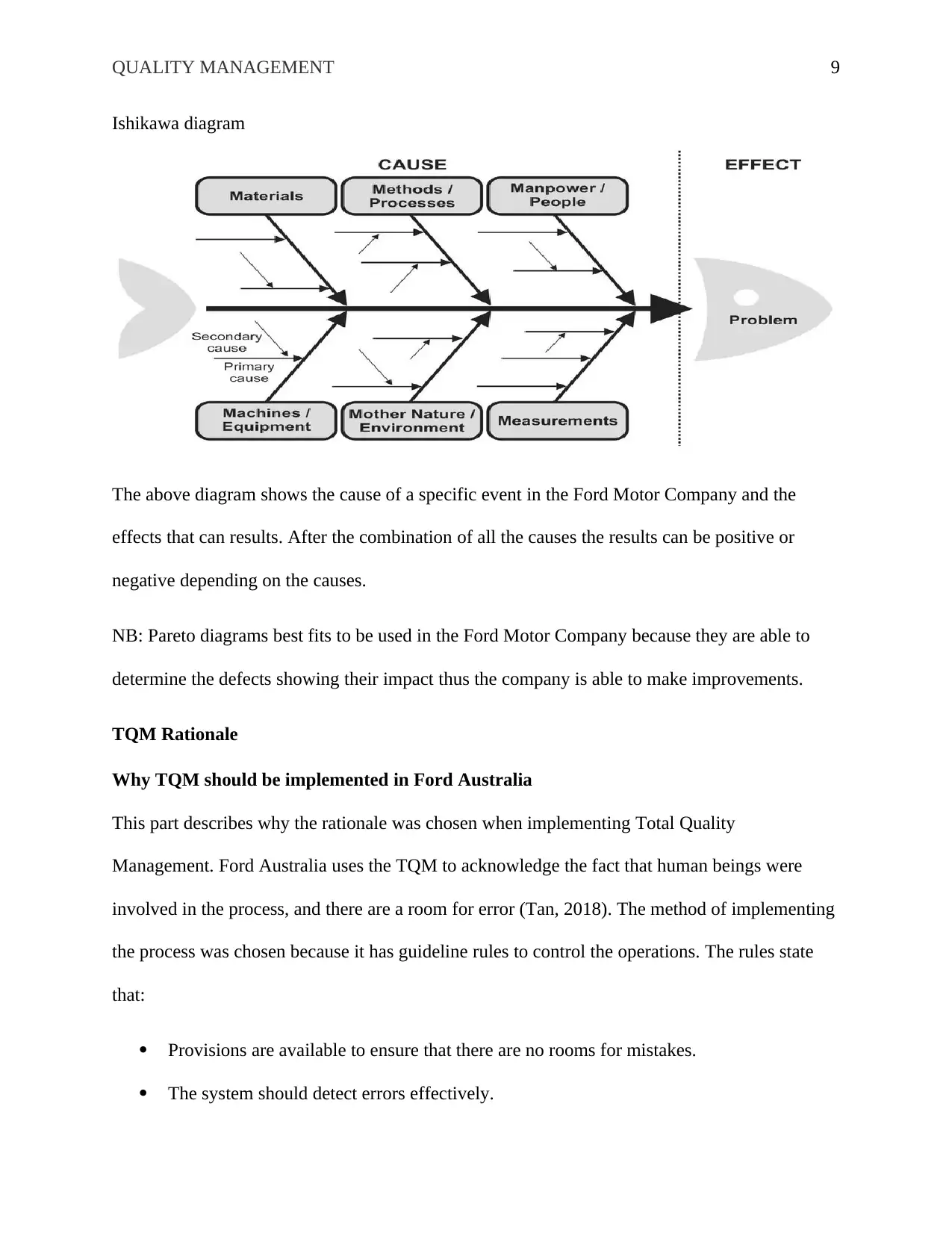
QUALITY MANAGEMENT 9
Ishikawa diagram
The above diagram shows the cause of a specific event in the Ford Motor Company and the
effects that can results. After the combination of all the causes the results can be positive or
negative depending on the causes.
NB: Pareto diagrams best fits to be used in the Ford Motor Company because they are able to
determine the defects showing their impact thus the company is able to make improvements.
TQM Rationale
Why TQM should be implemented in Ford Australia
This part describes why the rationale was chosen when implementing Total Quality
Management. Ford Australia uses the TQM to acknowledge the fact that human beings were
involved in the process, and there are a room for error (Tan, 2018). The method of implementing
the process was chosen because it has guideline rules to control the operations. The rules state
that:
Provisions are available to ensure that there are no rooms for mistakes.
The system should detect errors effectively.
Ishikawa diagram
The above diagram shows the cause of a specific event in the Ford Motor Company and the
effects that can results. After the combination of all the causes the results can be positive or
negative depending on the causes.
NB: Pareto diagrams best fits to be used in the Ford Motor Company because they are able to
determine the defects showing their impact thus the company is able to make improvements.
TQM Rationale
Why TQM should be implemented in Ford Australia
This part describes why the rationale was chosen when implementing Total Quality
Management. Ford Australia uses the TQM to acknowledge the fact that human beings were
involved in the process, and there are a room for error (Tan, 2018). The method of implementing
the process was chosen because it has guideline rules to control the operations. The rules state
that:
Provisions are available to ensure that there are no rooms for mistakes.
The system should detect errors effectively.
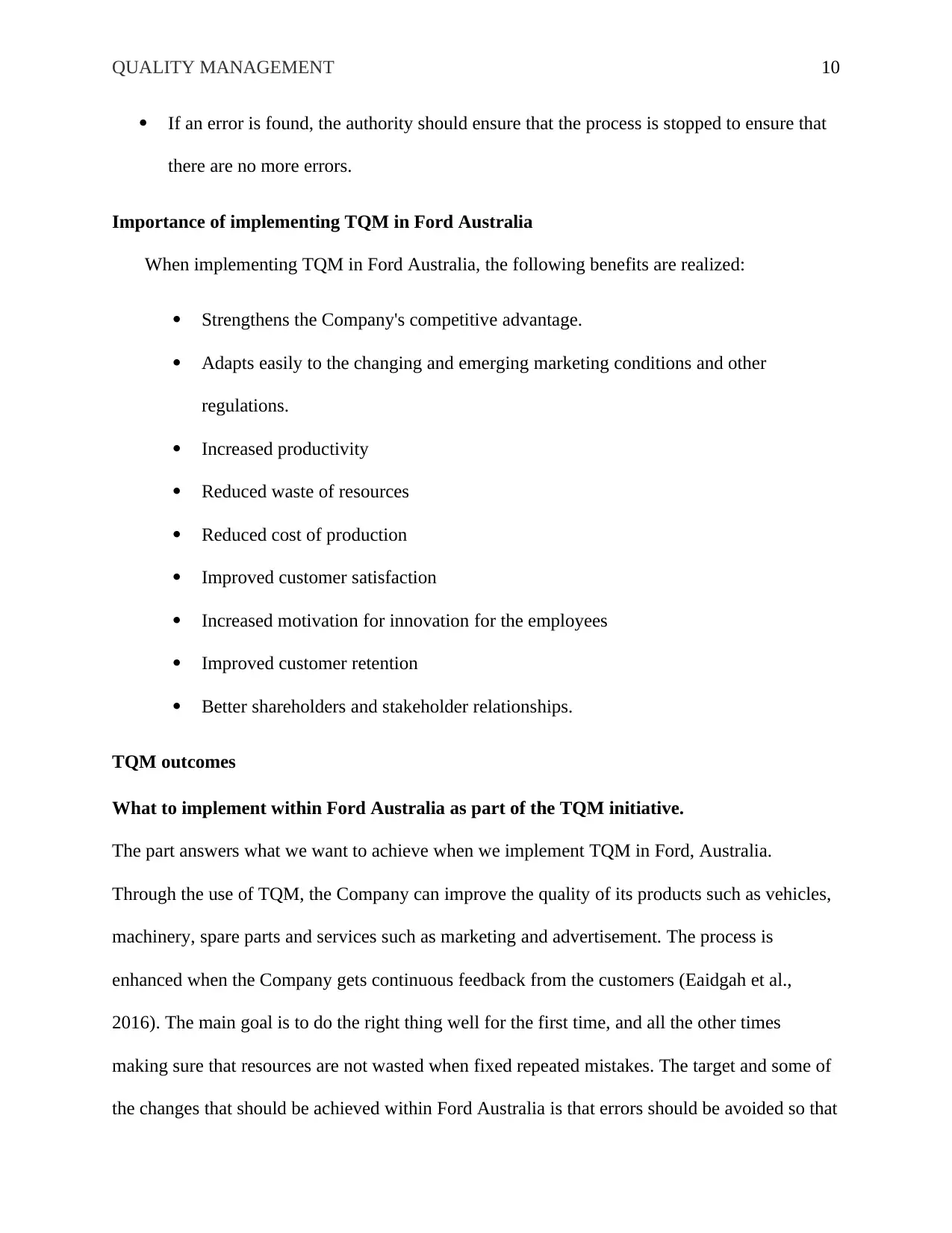
QUALITY MANAGEMENT 10
If an error is found, the authority should ensure that the process is stopped to ensure that
there are no more errors.
Importance of implementing TQM in Ford Australia
When implementing TQM in Ford Australia, the following benefits are realized:
Strengthens the Company's competitive advantage.
Adapts easily to the changing and emerging marketing conditions and other
regulations.
Increased productivity
Reduced waste of resources
Reduced cost of production
Improved customer satisfaction
Increased motivation for innovation for the employees
Improved customer retention
Better shareholders and stakeholder relationships.
TQM outcomes
What to implement within Ford Australia as part of the TQM initiative.
The part answers what we want to achieve when we implement TQM in Ford, Australia.
Through the use of TQM, the Company can improve the quality of its products such as vehicles,
machinery, spare parts and services such as marketing and advertisement. The process is
enhanced when the Company gets continuous feedback from the customers (Eaidgah et al.,
2016). The main goal is to do the right thing well for the first time, and all the other times
making sure that resources are not wasted when fixed repeated mistakes. The target and some of
the changes that should be achieved within Ford Australia is that errors should be avoided so that
If an error is found, the authority should ensure that the process is stopped to ensure that
there are no more errors.
Importance of implementing TQM in Ford Australia
When implementing TQM in Ford Australia, the following benefits are realized:
Strengthens the Company's competitive advantage.
Adapts easily to the changing and emerging marketing conditions and other
regulations.
Increased productivity
Reduced waste of resources
Reduced cost of production
Improved customer satisfaction
Increased motivation for innovation for the employees
Improved customer retention
Better shareholders and stakeholder relationships.
TQM outcomes
What to implement within Ford Australia as part of the TQM initiative.
The part answers what we want to achieve when we implement TQM in Ford, Australia.
Through the use of TQM, the Company can improve the quality of its products such as vehicles,
machinery, spare parts and services such as marketing and advertisement. The process is
enhanced when the Company gets continuous feedback from the customers (Eaidgah et al.,
2016). The main goal is to do the right thing well for the first time, and all the other times
making sure that resources are not wasted when fixed repeated mistakes. The target and some of
the changes that should be achieved within Ford Australia is that errors should be avoided so that
Secure Best Marks with AI Grader
Need help grading? Try our AI Grader for instant feedback on your assignments.

QUALITY MANAGEMENT 11
resources in automotive cannot be wasted when fixing broken processes. Improvements should
be made in the Company through the use of TQM to ensure that activities that are always
repeated based on data and feedback can produce positive changes that will help the Company
grows. The result will impact the vision and business mission of the Ford Motor Company.
The following processes and activities should be implemented within Ford Australia as part of
the Total Quality Management initiative:
Management Audit- It encompasses the rule that are employed by the Company to
institute a culture of total quality management. The Audit should be well managed to take
the full inventory of the available processes (Ross, 2017).
Determining critical success factors- TQM is intangible, and it is found within the
business culture. These factors should be used within the business TQM initiative to
ensure that performance measures are determined.
Improving the process to meet the requirements within the Company- The Company
should be able to determine whether TQM is working well or not. Automated methods
can be used to improve the process of collecting user feedback and improving per the
requirements.
Being data-driven- The feedback received from consumers is correct, even if it does not
favor the Company. TQM emphasizes change, and therefore, changes should be made
where necessary.
Being relentless- The Company should always keep improving, even if the changes are
insignificant. Continuous small improvements will have increased benefits to the
Company (Maskell, Baggaley, & Grasso, 2017).
resources in automotive cannot be wasted when fixing broken processes. Improvements should
be made in the Company through the use of TQM to ensure that activities that are always
repeated based on data and feedback can produce positive changes that will help the Company
grows. The result will impact the vision and business mission of the Ford Motor Company.
The following processes and activities should be implemented within Ford Australia as part of
the Total Quality Management initiative:
Management Audit- It encompasses the rule that are employed by the Company to
institute a culture of total quality management. The Audit should be well managed to take
the full inventory of the available processes (Ross, 2017).
Determining critical success factors- TQM is intangible, and it is found within the
business culture. These factors should be used within the business TQM initiative to
ensure that performance measures are determined.
Improving the process to meet the requirements within the Company- The Company
should be able to determine whether TQM is working well or not. Automated methods
can be used to improve the process of collecting user feedback and improving per the
requirements.
Being data-driven- The feedback received from consumers is correct, even if it does not
favor the Company. TQM emphasizes change, and therefore, changes should be made
where necessary.
Being relentless- The Company should always keep improving, even if the changes are
insignificant. Continuous small improvements will have increased benefits to the
Company (Maskell, Baggaley, & Grasso, 2017).
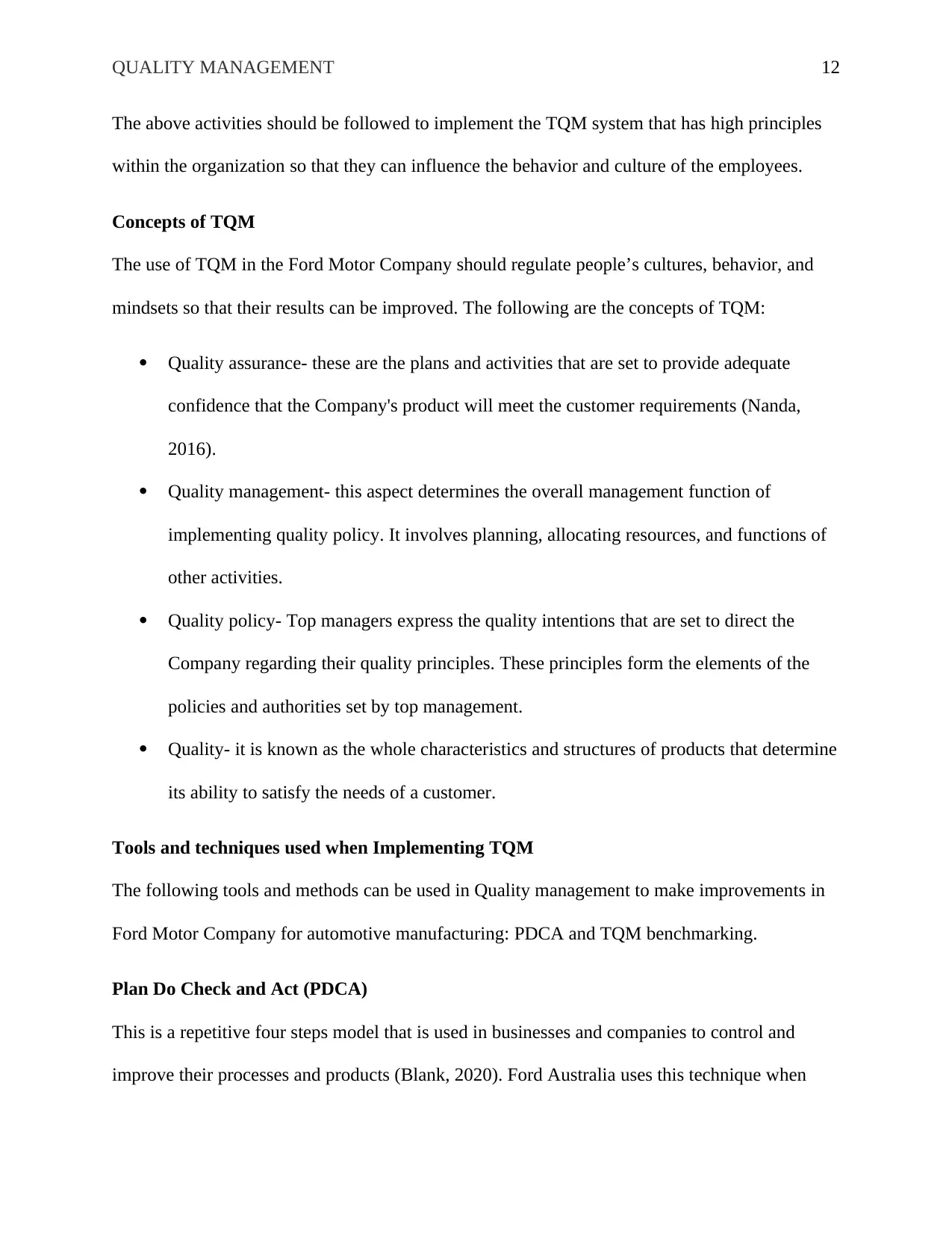
QUALITY MANAGEMENT 12
The above activities should be followed to implement the TQM system that has high principles
within the organization so that they can influence the behavior and culture of the employees.
Concepts of TQM
The use of TQM in the Ford Motor Company should regulate people’s cultures, behavior, and
mindsets so that their results can be improved. The following are the concepts of TQM:
Quality assurance- these are the plans and activities that are set to provide adequate
confidence that the Company's product will meet the customer requirements (Nanda,
2016).
Quality management- this aspect determines the overall management function of
implementing quality policy. It involves planning, allocating resources, and functions of
other activities.
Quality policy- Top managers express the quality intentions that are set to direct the
Company regarding their quality principles. These principles form the elements of the
policies and authorities set by top management.
Quality- it is known as the whole characteristics and structures of products that determine
its ability to satisfy the needs of a customer.
Tools and techniques used when Implementing TQM
The following tools and methods can be used in Quality management to make improvements in
Ford Motor Company for automotive manufacturing: PDCA and TQM benchmarking.
Plan Do Check and Act (PDCA)
This is a repetitive four steps model that is used in businesses and companies to control and
improve their processes and products (Blank, 2020). Ford Australia uses this technique when
The above activities should be followed to implement the TQM system that has high principles
within the organization so that they can influence the behavior and culture of the employees.
Concepts of TQM
The use of TQM in the Ford Motor Company should regulate people’s cultures, behavior, and
mindsets so that their results can be improved. The following are the concepts of TQM:
Quality assurance- these are the plans and activities that are set to provide adequate
confidence that the Company's product will meet the customer requirements (Nanda,
2016).
Quality management- this aspect determines the overall management function of
implementing quality policy. It involves planning, allocating resources, and functions of
other activities.
Quality policy- Top managers express the quality intentions that are set to direct the
Company regarding their quality principles. These principles form the elements of the
policies and authorities set by top management.
Quality- it is known as the whole characteristics and structures of products that determine
its ability to satisfy the needs of a customer.
Tools and techniques used when Implementing TQM
The following tools and methods can be used in Quality management to make improvements in
Ford Motor Company for automotive manufacturing: PDCA and TQM benchmarking.
Plan Do Check and Act (PDCA)
This is a repetitive four steps model that is used in businesses and companies to control and
improve their processes and products (Blank, 2020). Ford Australia uses this technique when
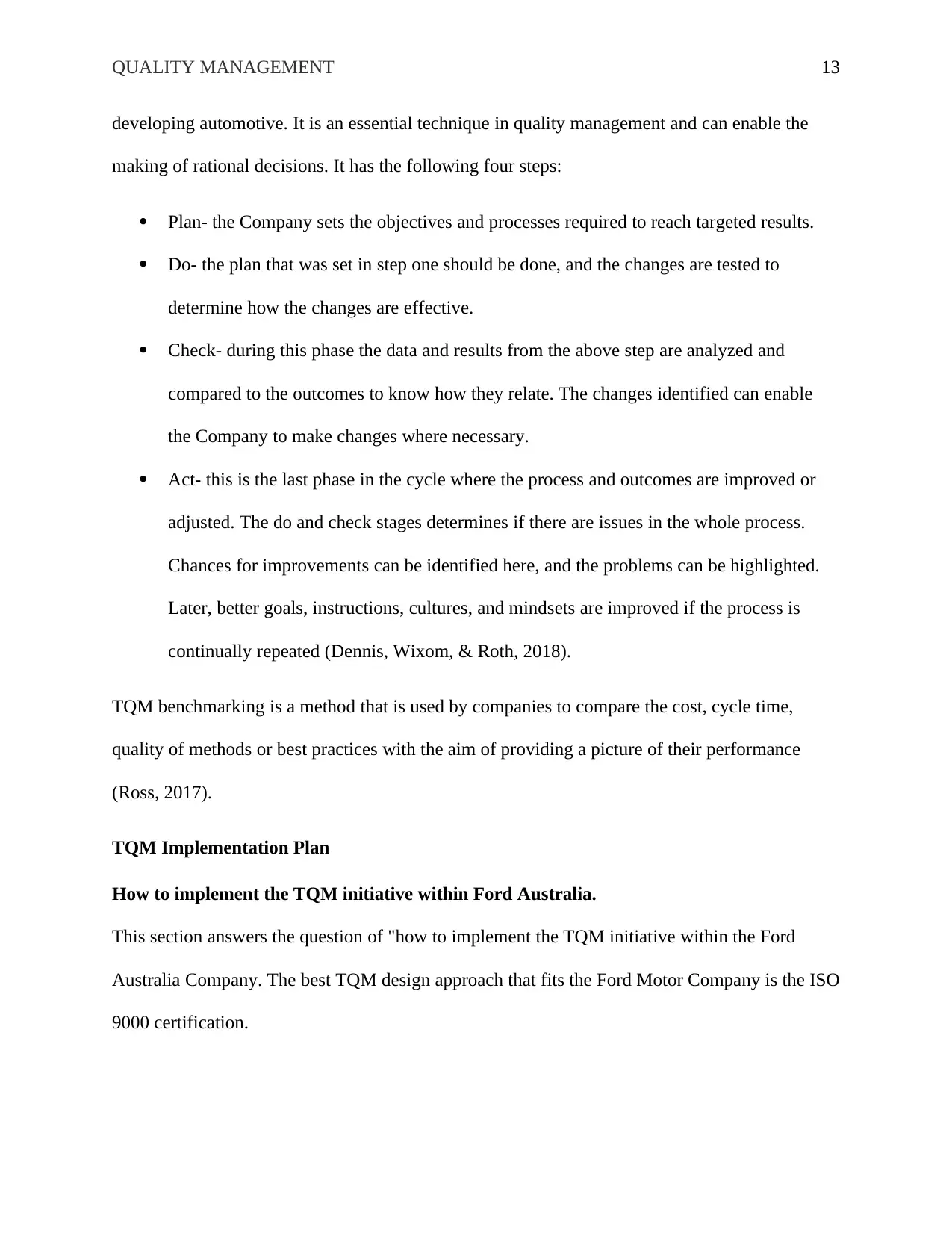
QUALITY MANAGEMENT 13
developing automotive. It is an essential technique in quality management and can enable the
making of rational decisions. It has the following four steps:
Plan- the Company sets the objectives and processes required to reach targeted results.
Do- the plan that was set in step one should be done, and the changes are tested to
determine how the changes are effective.
Check- during this phase the data and results from the above step are analyzed and
compared to the outcomes to know how they relate. The changes identified can enable
the Company to make changes where necessary.
Act- this is the last phase in the cycle where the process and outcomes are improved or
adjusted. The do and check stages determines if there are issues in the whole process.
Chances for improvements can be identified here, and the problems can be highlighted.
Later, better goals, instructions, cultures, and mindsets are improved if the process is
continually repeated (Dennis, Wixom, & Roth, 2018).
TQM benchmarking is a method that is used by companies to compare the cost, cycle time,
quality of methods or best practices with the aim of providing a picture of their performance
(Ross, 2017).
TQM Implementation Plan
How to implement the TQM initiative within Ford Australia.
This section answers the question of "how to implement the TQM initiative within the Ford
Australia Company. The best TQM design approach that fits the Ford Motor Company is the ISO
9000 certification.
developing automotive. It is an essential technique in quality management and can enable the
making of rational decisions. It has the following four steps:
Plan- the Company sets the objectives and processes required to reach targeted results.
Do- the plan that was set in step one should be done, and the changes are tested to
determine how the changes are effective.
Check- during this phase the data and results from the above step are analyzed and
compared to the outcomes to know how they relate. The changes identified can enable
the Company to make changes where necessary.
Act- this is the last phase in the cycle where the process and outcomes are improved or
adjusted. The do and check stages determines if there are issues in the whole process.
Chances for improvements can be identified here, and the problems can be highlighted.
Later, better goals, instructions, cultures, and mindsets are improved if the process is
continually repeated (Dennis, Wixom, & Roth, 2018).
TQM benchmarking is a method that is used by companies to compare the cost, cycle time,
quality of methods or best practices with the aim of providing a picture of their performance
(Ross, 2017).
TQM Implementation Plan
How to implement the TQM initiative within Ford Australia.
This section answers the question of "how to implement the TQM initiative within the Ford
Australia Company. The best TQM design approach that fits the Ford Motor Company is the ISO
9000 certification.
Paraphrase This Document
Need a fresh take? Get an instant paraphrase of this document with our AI Paraphraser
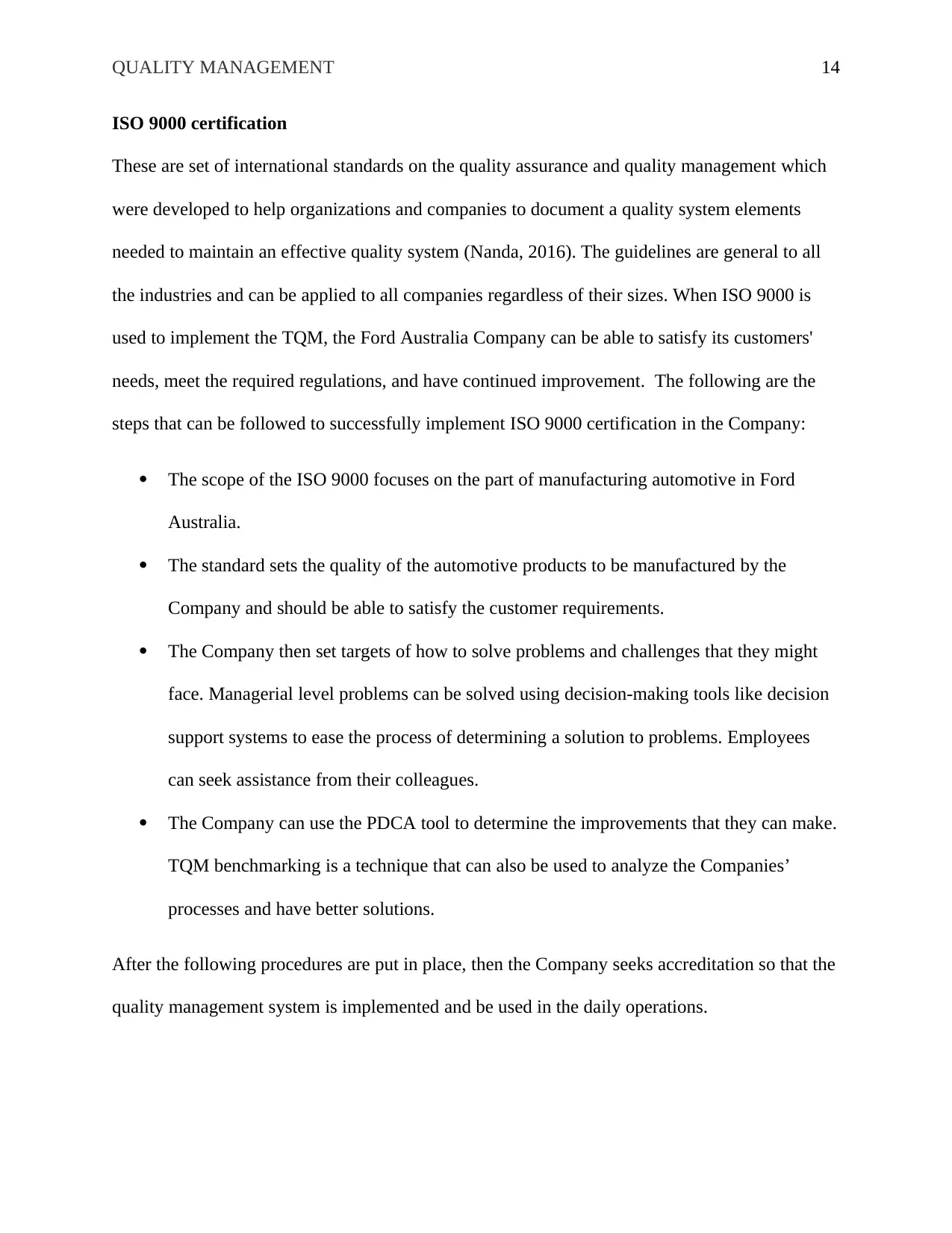
QUALITY MANAGEMENT 14
ISO 9000 certification
These are set of international standards on the quality assurance and quality management which
were developed to help organizations and companies to document a quality system elements
needed to maintain an effective quality system (Nanda, 2016). The guidelines are general to all
the industries and can be applied to all companies regardless of their sizes. When ISO 9000 is
used to implement the TQM, the Ford Australia Company can be able to satisfy its customers'
needs, meet the required regulations, and have continued improvement. The following are the
steps that can be followed to successfully implement ISO 9000 certification in the Company:
The scope of the ISO 9000 focuses on the part of manufacturing automotive in Ford
Australia.
The standard sets the quality of the automotive products to be manufactured by the
Company and should be able to satisfy the customer requirements.
The Company then set targets of how to solve problems and challenges that they might
face. Managerial level problems can be solved using decision-making tools like decision
support systems to ease the process of determining a solution to problems. Employees
can seek assistance from their colleagues.
The Company can use the PDCA tool to determine the improvements that they can make.
TQM benchmarking is a technique that can also be used to analyze the Companies’
processes and have better solutions.
After the following procedures are put in place, then the Company seeks accreditation so that the
quality management system is implemented and be used in the daily operations.
ISO 9000 certification
These are set of international standards on the quality assurance and quality management which
were developed to help organizations and companies to document a quality system elements
needed to maintain an effective quality system (Nanda, 2016). The guidelines are general to all
the industries and can be applied to all companies regardless of their sizes. When ISO 9000 is
used to implement the TQM, the Ford Australia Company can be able to satisfy its customers'
needs, meet the required regulations, and have continued improvement. The following are the
steps that can be followed to successfully implement ISO 9000 certification in the Company:
The scope of the ISO 9000 focuses on the part of manufacturing automotive in Ford
Australia.
The standard sets the quality of the automotive products to be manufactured by the
Company and should be able to satisfy the customer requirements.
The Company then set targets of how to solve problems and challenges that they might
face. Managerial level problems can be solved using decision-making tools like decision
support systems to ease the process of determining a solution to problems. Employees
can seek assistance from their colleagues.
The Company can use the PDCA tool to determine the improvements that they can make.
TQM benchmarking is a technique that can also be used to analyze the Companies’
processes and have better solutions.
After the following procedures are put in place, then the Company seeks accreditation so that the
quality management system is implemented and be used in the daily operations.
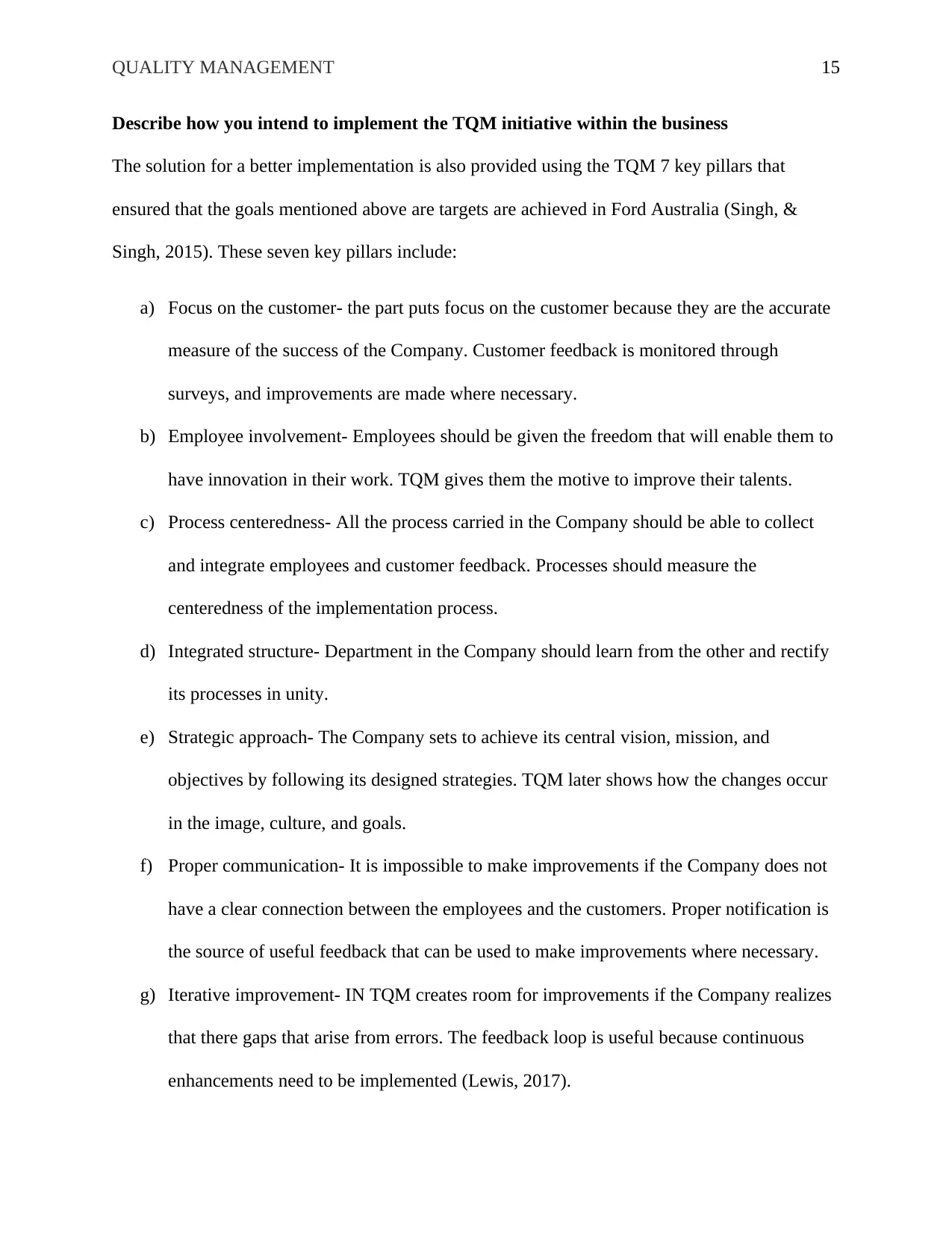
QUALITY MANAGEMENT 15
Describe how you intend to implement the TQM initiative within the business
The solution for a better implementation is also provided using the TQM 7 key pillars that
ensured that the goals mentioned above are targets are achieved in Ford Australia (Singh, &
Singh, 2015). These seven key pillars include:
a) Focus on the customer- the part puts focus on the customer because they are the accurate
measure of the success of the Company. Customer feedback is monitored through
surveys, and improvements are made where necessary.
b) Employee involvement- Employees should be given the freedom that will enable them to
have innovation in their work. TQM gives them the motive to improve their talents.
c) Process centeredness- All the process carried in the Company should be able to collect
and integrate employees and customer feedback. Processes should measure the
centeredness of the implementation process.
d) Integrated structure- Department in the Company should learn from the other and rectify
its processes in unity.
e) Strategic approach- The Company sets to achieve its central vision, mission, and
objectives by following its designed strategies. TQM later shows how the changes occur
in the image, culture, and goals.
f) Proper communication- It is impossible to make improvements if the Company does not
have a clear connection between the employees and the customers. Proper notification is
the source of useful feedback that can be used to make improvements where necessary.
g) Iterative improvement- IN TQM creates room for improvements if the Company realizes
that there gaps that arise from errors. The feedback loop is useful because continuous
enhancements need to be implemented (Lewis, 2017).
Describe how you intend to implement the TQM initiative within the business
The solution for a better implementation is also provided using the TQM 7 key pillars that
ensured that the goals mentioned above are targets are achieved in Ford Australia (Singh, &
Singh, 2015). These seven key pillars include:
a) Focus on the customer- the part puts focus on the customer because they are the accurate
measure of the success of the Company. Customer feedback is monitored through
surveys, and improvements are made where necessary.
b) Employee involvement- Employees should be given the freedom that will enable them to
have innovation in their work. TQM gives them the motive to improve their talents.
c) Process centeredness- All the process carried in the Company should be able to collect
and integrate employees and customer feedback. Processes should measure the
centeredness of the implementation process.
d) Integrated structure- Department in the Company should learn from the other and rectify
its processes in unity.
e) Strategic approach- The Company sets to achieve its central vision, mission, and
objectives by following its designed strategies. TQM later shows how the changes occur
in the image, culture, and goals.
f) Proper communication- It is impossible to make improvements if the Company does not
have a clear connection between the employees and the customers. Proper notification is
the source of useful feedback that can be used to make improvements where necessary.
g) Iterative improvement- IN TQM creates room for improvements if the Company realizes
that there gaps that arise from errors. The feedback loop is useful because continuous
enhancements need to be implemented (Lewis, 2017).
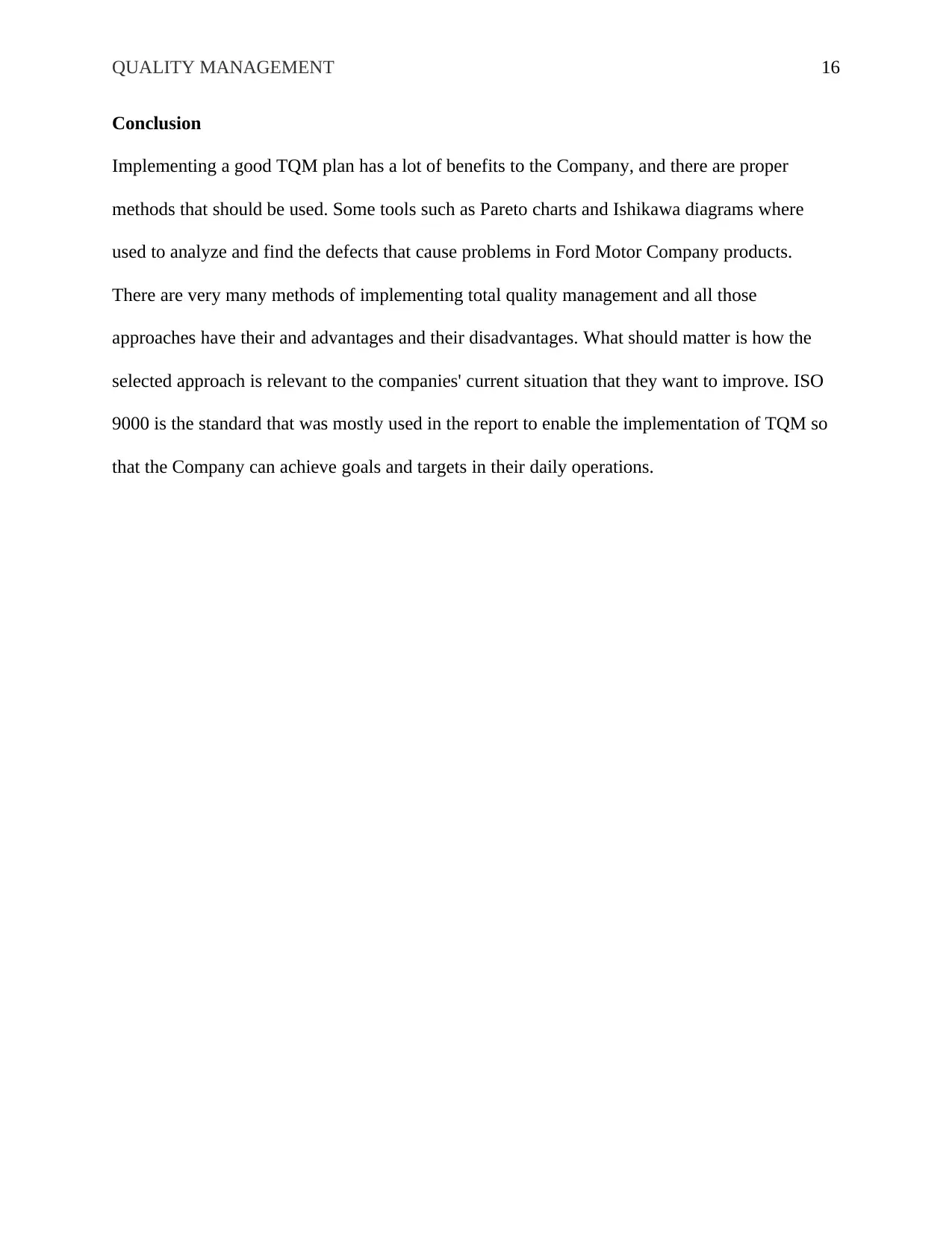
QUALITY MANAGEMENT 16
Conclusion
Implementing a good TQM plan has a lot of benefits to the Company, and there are proper
methods that should be used. Some tools such as Pareto charts and Ishikawa diagrams where
used to analyze and find the defects that cause problems in Ford Motor Company products.
There are very many methods of implementing total quality management and all those
approaches have their and advantages and their disadvantages. What should matter is how the
selected approach is relevant to the companies' current situation that they want to improve. ISO
9000 is the standard that was mostly used in the report to enable the implementation of TQM so
that the Company can achieve goals and targets in their daily operations.
Conclusion
Implementing a good TQM plan has a lot of benefits to the Company, and there are proper
methods that should be used. Some tools such as Pareto charts and Ishikawa diagrams where
used to analyze and find the defects that cause problems in Ford Motor Company products.
There are very many methods of implementing total quality management and all those
approaches have their and advantages and their disadvantages. What should matter is how the
selected approach is relevant to the companies' current situation that they want to improve. ISO
9000 is the standard that was mostly used in the report to enable the implementation of TQM so
that the Company can achieve goals and targets in their daily operations.
Secure Best Marks with AI Grader
Need help grading? Try our AI Grader for instant feedback on your assignments.
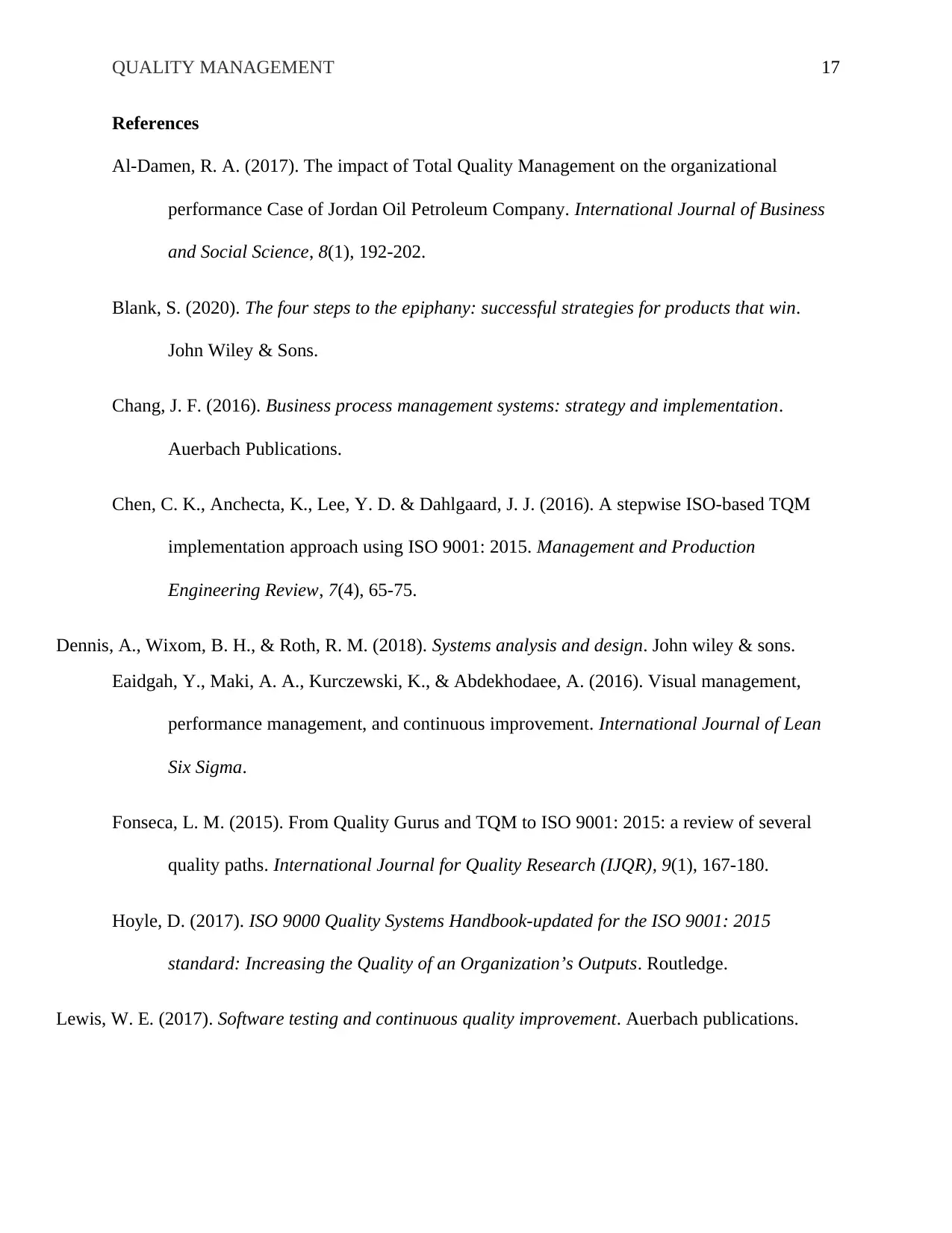
QUALITY MANAGEMENT 17
References
Al-Damen, R. A. (2017). The impact of Total Quality Management on the organizational
performance Case of Jordan Oil Petroleum Company. International Journal of Business
and Social Science, 8(1), 192-202.
Blank, S. (2020). The four steps to the epiphany: successful strategies for products that win.
John Wiley & Sons.
Chang, J. F. (2016). Business process management systems: strategy and implementation.
Auerbach Publications.
Chen, C. K., Anchecta, K., Lee, Y. D. & Dahlgaard, J. J. (2016). A stepwise ISO-based TQM
implementation approach using ISO 9001: 2015. Management and Production
Engineering Review, 7(4), 65-75.
Dennis, A., Wixom, B. H., & Roth, R. M. (2018). Systems analysis and design. John wiley & sons.
Eaidgah, Y., Maki, A. A., Kurczewski, K., & Abdekhodaee, A. (2016). Visual management,
performance management, and continuous improvement. International Journal of Lean
Six Sigma.
Fonseca, L. M. (2015). From Quality Gurus and TQM to ISO 9001: 2015: a review of several
quality paths. International Journal for Quality Research (IJQR), 9(1), 167-180.
Hoyle, D. (2017). ISO 9000 Quality Systems Handbook-updated for the ISO 9001: 2015
standard: Increasing the Quality of an Organization’s Outputs. Routledge.
Lewis, W. E. (2017). Software testing and continuous quality improvement. Auerbach publications.
References
Al-Damen, R. A. (2017). The impact of Total Quality Management on the organizational
performance Case of Jordan Oil Petroleum Company. International Journal of Business
and Social Science, 8(1), 192-202.
Blank, S. (2020). The four steps to the epiphany: successful strategies for products that win.
John Wiley & Sons.
Chang, J. F. (2016). Business process management systems: strategy and implementation.
Auerbach Publications.
Chen, C. K., Anchecta, K., Lee, Y. D. & Dahlgaard, J. J. (2016). A stepwise ISO-based TQM
implementation approach using ISO 9001: 2015. Management and Production
Engineering Review, 7(4), 65-75.
Dennis, A., Wixom, B. H., & Roth, R. M. (2018). Systems analysis and design. John wiley & sons.
Eaidgah, Y., Maki, A. A., Kurczewski, K., & Abdekhodaee, A. (2016). Visual management,
performance management, and continuous improvement. International Journal of Lean
Six Sigma.
Fonseca, L. M. (2015). From Quality Gurus and TQM to ISO 9001: 2015: a review of several
quality paths. International Journal for Quality Research (IJQR), 9(1), 167-180.
Hoyle, D. (2017). ISO 9000 Quality Systems Handbook-updated for the ISO 9001: 2015
standard: Increasing the Quality of an Organization’s Outputs. Routledge.
Lewis, W. E. (2017). Software testing and continuous quality improvement. Auerbach publications.
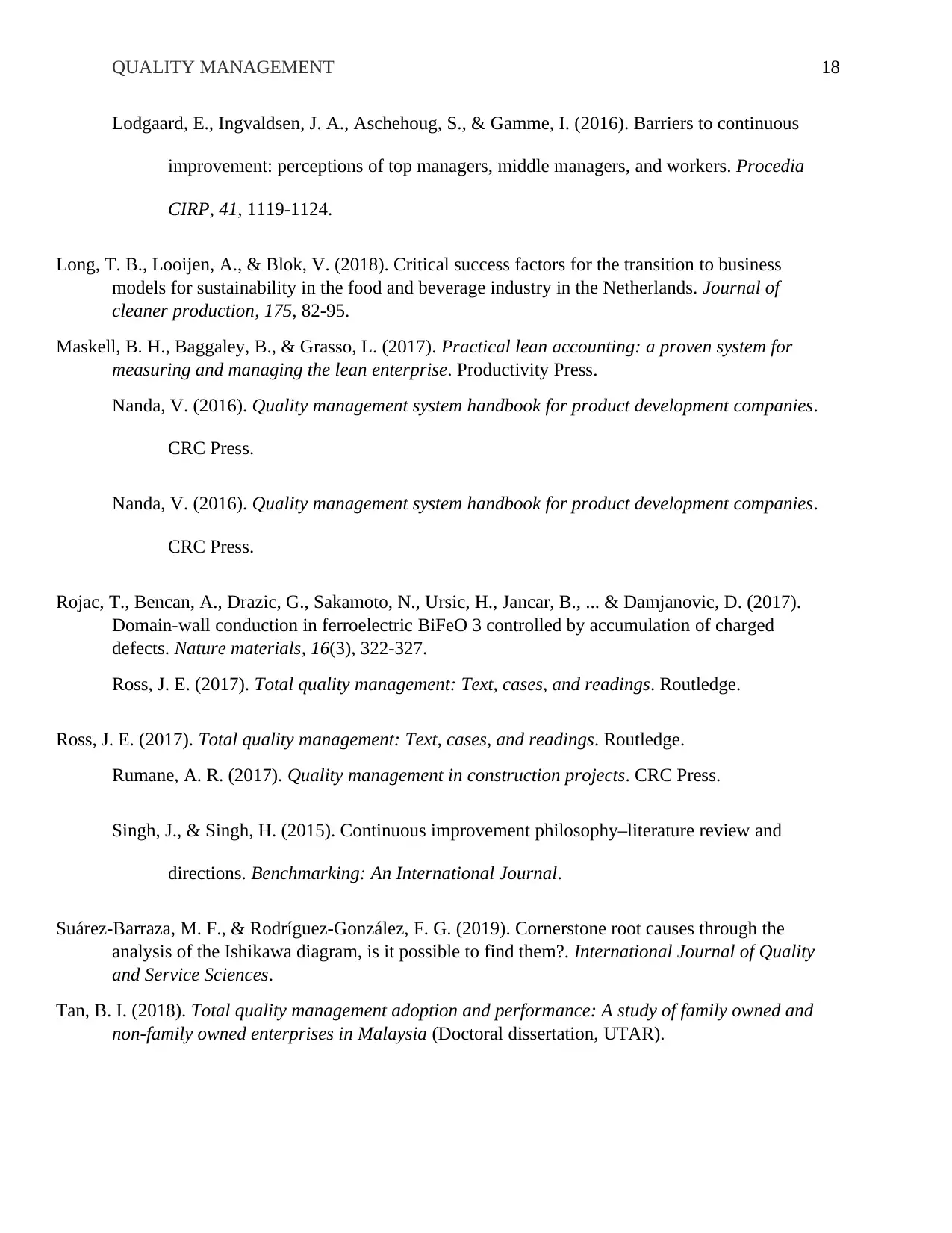
QUALITY MANAGEMENT 18
Lodgaard, E., Ingvaldsen, J. A., Aschehoug, S., & Gamme, I. (2016). Barriers to continuous
improvement: perceptions of top managers, middle managers, and workers. Procedia
CIRP, 41, 1119-1124.
Long, T. B., Looijen, A., & Blok, V. (2018). Critical success factors for the transition to business
models for sustainability in the food and beverage industry in the Netherlands. Journal of
cleaner production, 175, 82-95.
Maskell, B. H., Baggaley, B., & Grasso, L. (2017). Practical lean accounting: a proven system for
measuring and managing the lean enterprise. Productivity Press.
Nanda, V. (2016). Quality management system handbook for product development companies.
CRC Press.
Nanda, V. (2016). Quality management system handbook for product development companies.
CRC Press.
Rojac, T., Bencan, A., Drazic, G., Sakamoto, N., Ursic, H., Jancar, B., ... & Damjanovic, D. (2017).
Domain-wall conduction in ferroelectric BiFeO 3 controlled by accumulation of charged
defects. Nature materials, 16(3), 322-327.
Ross, J. E. (2017). Total quality management: Text, cases, and readings. Routledge.
Ross, J. E. (2017). Total quality management: Text, cases, and readings. Routledge.
Rumane, A. R. (2017). Quality management in construction projects. CRC Press.
Singh, J., & Singh, H. (2015). Continuous improvement philosophy–literature review and
directions. Benchmarking: An International Journal.
Suárez-Barraza, M. F., & Rodríguez-González, F. G. (2019). Cornerstone root causes through the
analysis of the Ishikawa diagram, is it possible to find them?. International Journal of Quality
and Service Sciences.
Tan, B. I. (2018). Total quality management adoption and performance: A study of family owned and
non-family owned enterprises in Malaysia (Doctoral dissertation, UTAR).
Lodgaard, E., Ingvaldsen, J. A., Aschehoug, S., & Gamme, I. (2016). Barriers to continuous
improvement: perceptions of top managers, middle managers, and workers. Procedia
CIRP, 41, 1119-1124.
Long, T. B., Looijen, A., & Blok, V. (2018). Critical success factors for the transition to business
models for sustainability in the food and beverage industry in the Netherlands. Journal of
cleaner production, 175, 82-95.
Maskell, B. H., Baggaley, B., & Grasso, L. (2017). Practical lean accounting: a proven system for
measuring and managing the lean enterprise. Productivity Press.
Nanda, V. (2016). Quality management system handbook for product development companies.
CRC Press.
Nanda, V. (2016). Quality management system handbook for product development companies.
CRC Press.
Rojac, T., Bencan, A., Drazic, G., Sakamoto, N., Ursic, H., Jancar, B., ... & Damjanovic, D. (2017).
Domain-wall conduction in ferroelectric BiFeO 3 controlled by accumulation of charged
defects. Nature materials, 16(3), 322-327.
Ross, J. E. (2017). Total quality management: Text, cases, and readings. Routledge.
Ross, J. E. (2017). Total quality management: Text, cases, and readings. Routledge.
Rumane, A. R. (2017). Quality management in construction projects. CRC Press.
Singh, J., & Singh, H. (2015). Continuous improvement philosophy–literature review and
directions. Benchmarking: An International Journal.
Suárez-Barraza, M. F., & Rodríguez-González, F. G. (2019). Cornerstone root causes through the
analysis of the Ishikawa diagram, is it possible to find them?. International Journal of Quality
and Service Sciences.
Tan, B. I. (2018). Total quality management adoption and performance: A study of family owned and
non-family owned enterprises in Malaysia (Doctoral dissertation, UTAR).
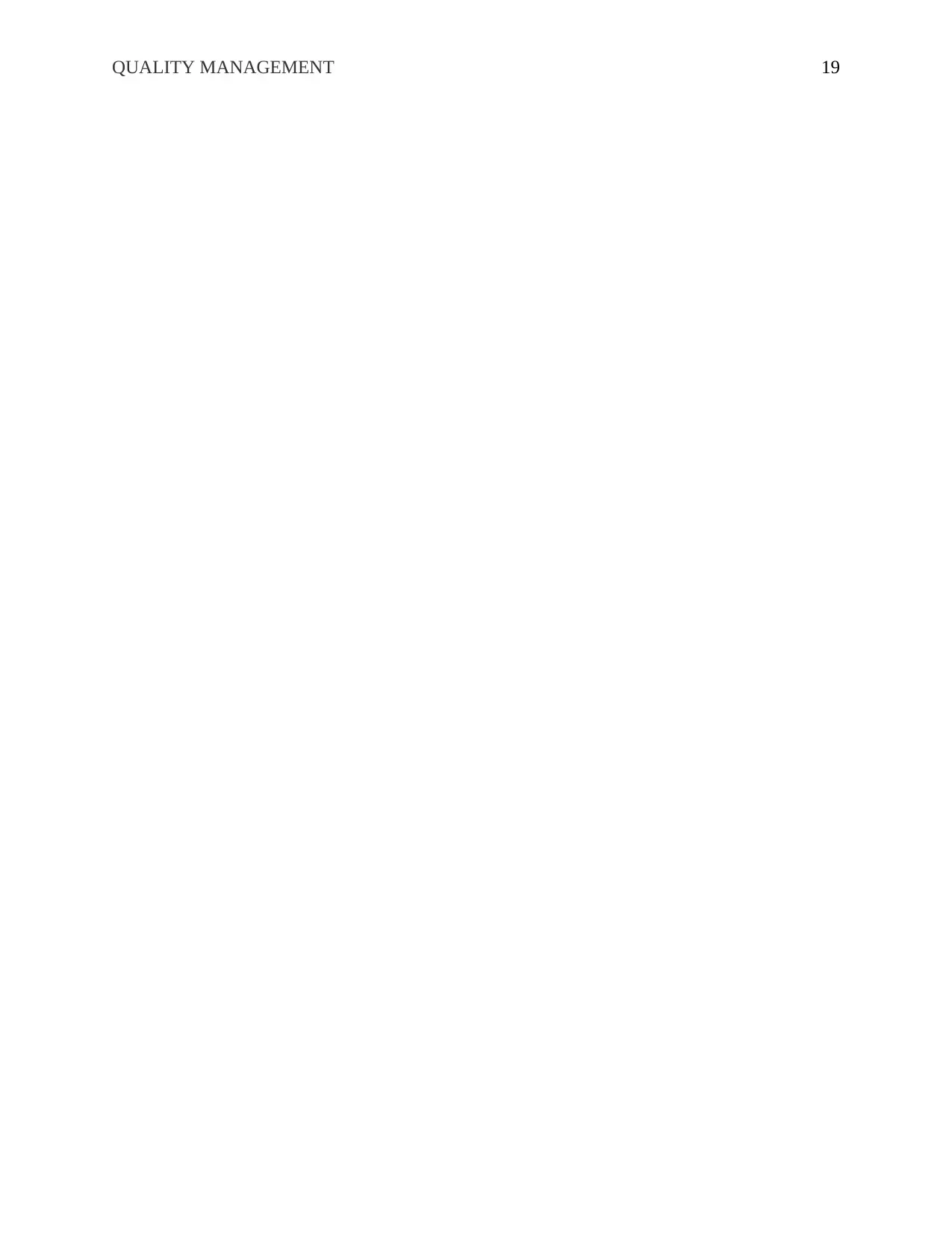
QUALITY MANAGEMENT 19
1 out of 19
Related Documents
![[object Object]](/_next/image/?url=%2F_next%2Fstatic%2Fmedia%2Flogo.6d15ce61.png&w=640&q=75)
Your All-in-One AI-Powered Toolkit for Academic Success.
+13062052269
info@desklib.com
Available 24*7 on WhatsApp / Email
Unlock your academic potential
© 2024 | Zucol Services PVT LTD | All rights reserved.