Quality Planning and Analysis - PDF
VerifiedAdded on 2021/06/17
|37
|6994
|219
AI Summary
Contribute Materials
Your contribution can guide someone’s learning journey. Share your
documents today.
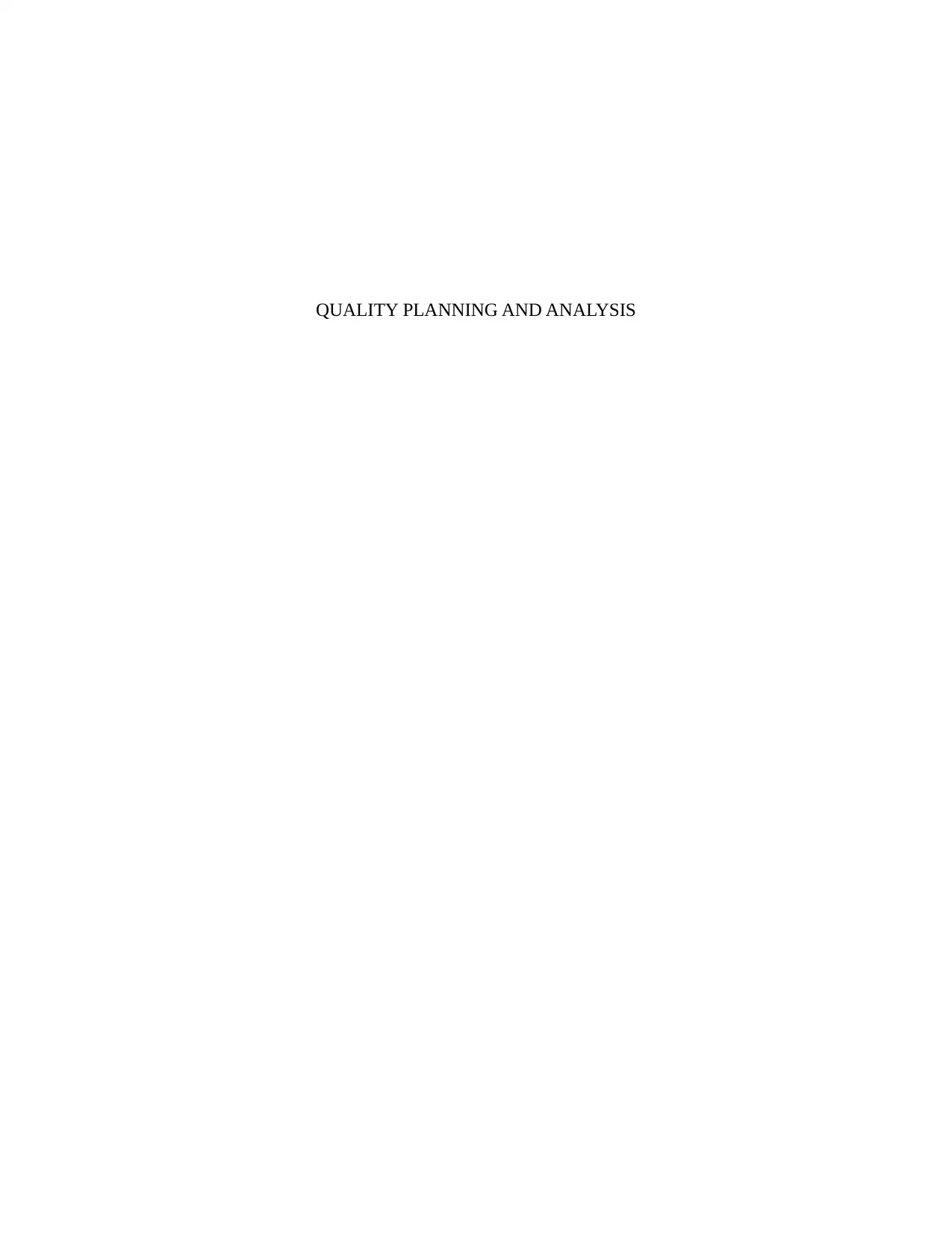
QUALITY PLANNING AND ANALYSIS
Secure Best Marks with AI Grader
Need help grading? Try our AI Grader for instant feedback on your assignments.
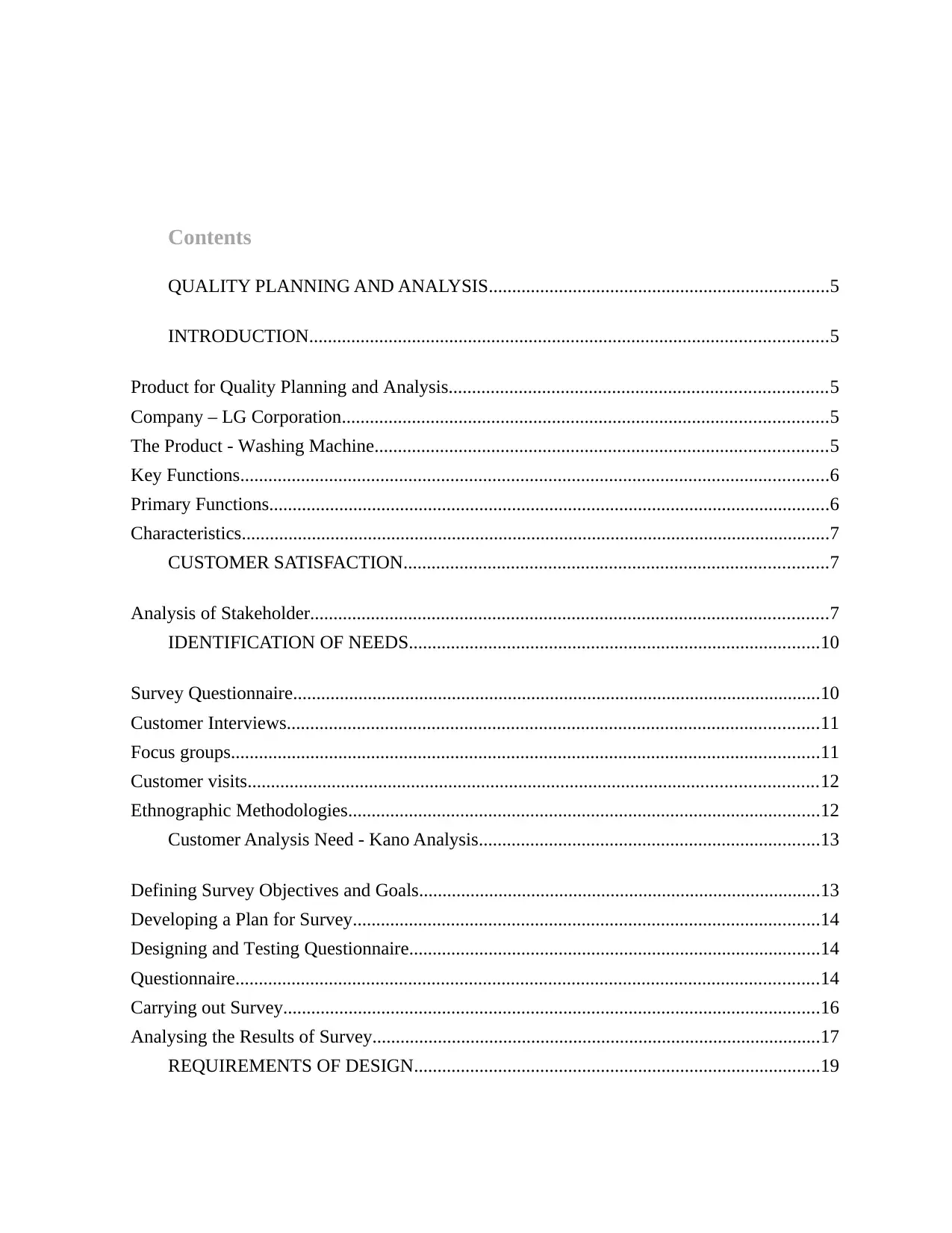
Contents
QUALITY PLANNING AND ANALYSIS.........................................................................5
INTRODUCTION...............................................................................................................5
Product for Quality Planning and Analysis.................................................................................5
Company – LG Corporation........................................................................................................5
The Product - Washing Machine.................................................................................................5
Key Functions..............................................................................................................................6
Primary Functions........................................................................................................................6
Characteristics..............................................................................................................................7
CUSTOMER SATISFACTION...........................................................................................7
Analysis of Stakeholder...............................................................................................................7
IDENTIFICATION OF NEEDS........................................................................................10
Survey Questionnaire.................................................................................................................10
Customer Interviews..................................................................................................................11
Focus groups..............................................................................................................................11
Customer visits..........................................................................................................................12
Ethnographic Methodologies.....................................................................................................12
Customer Analysis Need - Kano Analysis.........................................................................13
Defining Survey Objectives and Goals......................................................................................13
Developing a Plan for Survey....................................................................................................14
Designing and Testing Questionnaire........................................................................................14
Questionnaire.............................................................................................................................14
Carrying out Survey...................................................................................................................16
Analysing the Results of Survey................................................................................................17
REQUIREMENTS OF DESIGN.......................................................................................19
QUALITY PLANNING AND ANALYSIS.........................................................................5
INTRODUCTION...............................................................................................................5
Product for Quality Planning and Analysis.................................................................................5
Company – LG Corporation........................................................................................................5
The Product - Washing Machine.................................................................................................5
Key Functions..............................................................................................................................6
Primary Functions........................................................................................................................6
Characteristics..............................................................................................................................7
CUSTOMER SATISFACTION...........................................................................................7
Analysis of Stakeholder...............................................................................................................7
IDENTIFICATION OF NEEDS........................................................................................10
Survey Questionnaire.................................................................................................................10
Customer Interviews..................................................................................................................11
Focus groups..............................................................................................................................11
Customer visits..........................................................................................................................12
Ethnographic Methodologies.....................................................................................................12
Customer Analysis Need - Kano Analysis.........................................................................13
Defining Survey Objectives and Goals......................................................................................13
Developing a Plan for Survey....................................................................................................14
Designing and Testing Questionnaire........................................................................................14
Questionnaire.............................................................................................................................14
Carrying out Survey...................................................................................................................16
Analysing the Results of Survey................................................................................................17
REQUIREMENTS OF DESIGN.......................................................................................19
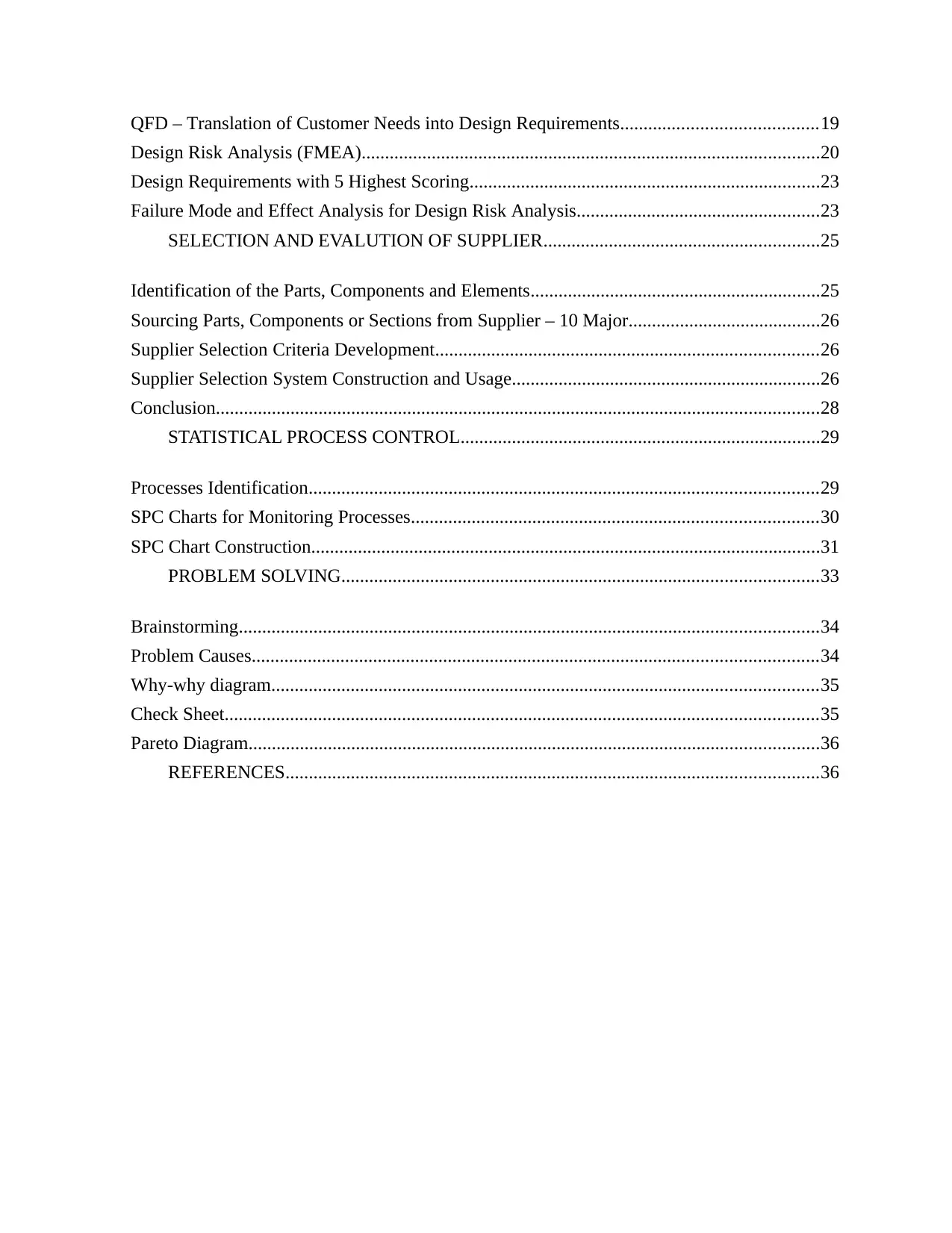
QFD – Translation of Customer Needs into Design Requirements..........................................19
Design Risk Analysis (FMEA)..................................................................................................20
Design Requirements with 5 Highest Scoring...........................................................................23
Failure Mode and Effect Analysis for Design Risk Analysis....................................................23
SELECTION AND EVALUTION OF SUPPLIER...........................................................25
Identification of the Parts, Components and Elements..............................................................25
Sourcing Parts, Components or Sections from Supplier – 10 Major.........................................26
Supplier Selection Criteria Development..................................................................................26
Supplier Selection System Construction and Usage..................................................................26
Conclusion.................................................................................................................................28
STATISTICAL PROCESS CONTROL.............................................................................29
Processes Identification.............................................................................................................29
SPC Charts for Monitoring Processes.......................................................................................30
SPC Chart Construction.............................................................................................................31
PROBLEM SOLVING......................................................................................................33
Brainstorming............................................................................................................................34
Problem Causes.........................................................................................................................34
Why-why diagram.....................................................................................................................35
Check Sheet...............................................................................................................................35
Pareto Diagram..........................................................................................................................36
REFERENCES..................................................................................................................36
Design Risk Analysis (FMEA)..................................................................................................20
Design Requirements with 5 Highest Scoring...........................................................................23
Failure Mode and Effect Analysis for Design Risk Analysis....................................................23
SELECTION AND EVALUTION OF SUPPLIER...........................................................25
Identification of the Parts, Components and Elements..............................................................25
Sourcing Parts, Components or Sections from Supplier – 10 Major.........................................26
Supplier Selection Criteria Development..................................................................................26
Supplier Selection System Construction and Usage..................................................................26
Conclusion.................................................................................................................................28
STATISTICAL PROCESS CONTROL.............................................................................29
Processes Identification.............................................................................................................29
SPC Charts for Monitoring Processes.......................................................................................30
SPC Chart Construction.............................................................................................................31
PROBLEM SOLVING......................................................................................................33
Brainstorming............................................................................................................................34
Problem Causes.........................................................................................................................34
Why-why diagram.....................................................................................................................35
Check Sheet...............................................................................................................................35
Pareto Diagram..........................................................................................................................36
REFERENCES..................................................................................................................36
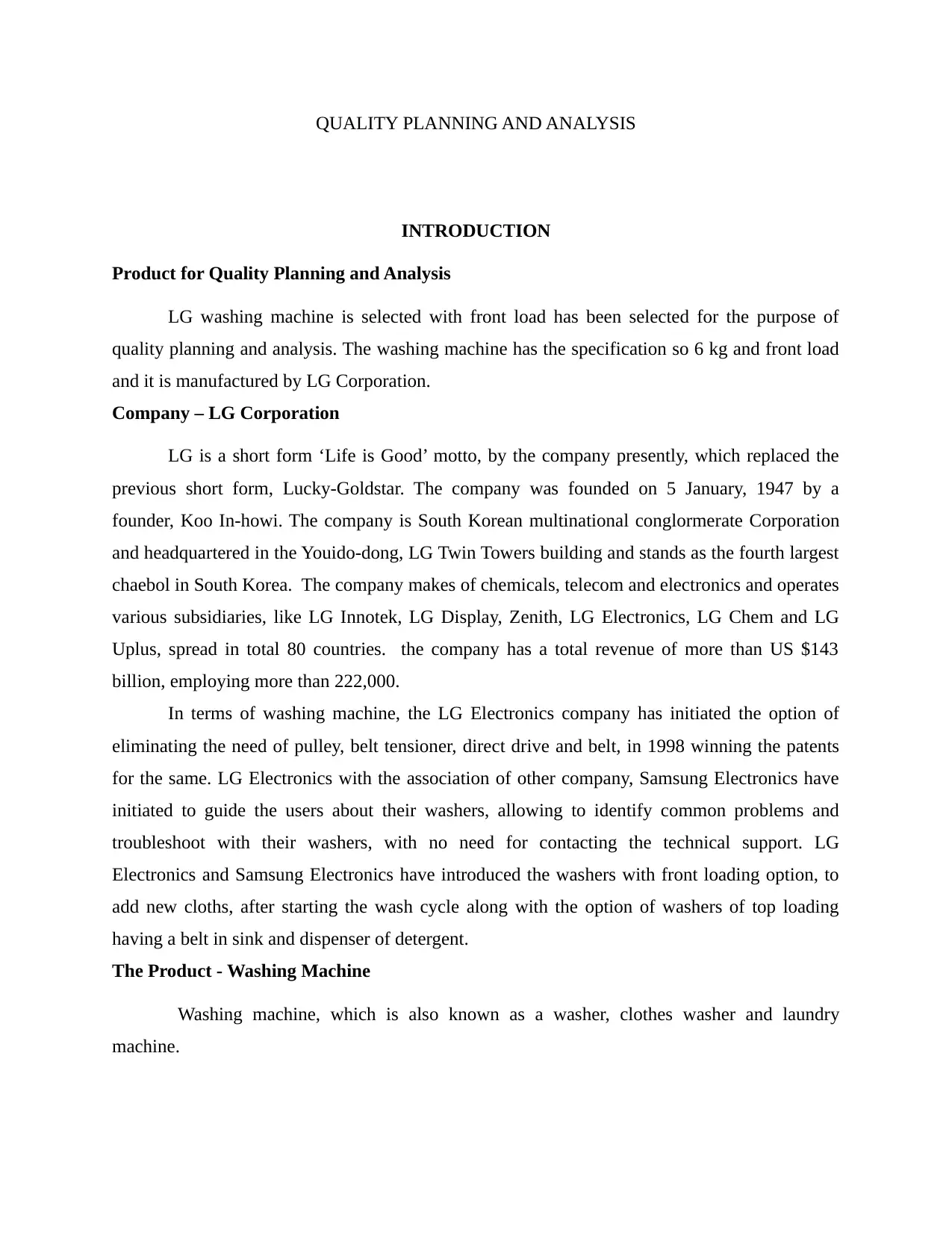
QUALITY PLANNING AND ANALYSIS
INTRODUCTION
Product for Quality Planning and Analysis
LG washing machine is selected with front load has been selected for the purpose of
quality planning and analysis. The washing machine has the specification so 6 kg and front load
and it is manufactured by LG Corporation.
Company – LG Corporation
LG is a short form ‘Life is Good’ motto, by the company presently, which replaced the
previous short form, Lucky-Goldstar. The company was founded on 5 January, 1947 by a
founder, Koo In-howi. The company is South Korean multinational conglormerate Corporation
and headquartered in the Youido-dong, LG Twin Towers building and stands as the fourth largest
chaebol in South Korea. The company makes of chemicals, telecom and electronics and operates
various subsidiaries, like LG Innotek, LG Display, Zenith, LG Electronics, LG Chem and LG
Uplus, spread in total 80 countries. the company has a total revenue of more than US $143
billion, employing more than 222,000.
In terms of washing machine, the LG Electronics company has initiated the option of
eliminating the need of pulley, belt tensioner, direct drive and belt, in 1998 winning the patents
for the same. LG Electronics with the association of other company, Samsung Electronics have
initiated to guide the users about their washers, allowing to identify common problems and
troubleshoot with their washers, with no need for contacting the technical support. LG
Electronics and Samsung Electronics have introduced the washers with front loading option, to
add new cloths, after starting the wash cycle along with the option of washers of top loading
having a belt in sink and dispenser of detergent.
The Product - Washing Machine
Washing machine, which is also known as a washer, clothes washer and laundry
machine.
INTRODUCTION
Product for Quality Planning and Analysis
LG washing machine is selected with front load has been selected for the purpose of
quality planning and analysis. The washing machine has the specification so 6 kg and front load
and it is manufactured by LG Corporation.
Company – LG Corporation
LG is a short form ‘Life is Good’ motto, by the company presently, which replaced the
previous short form, Lucky-Goldstar. The company was founded on 5 January, 1947 by a
founder, Koo In-howi. The company is South Korean multinational conglormerate Corporation
and headquartered in the Youido-dong, LG Twin Towers building and stands as the fourth largest
chaebol in South Korea. The company makes of chemicals, telecom and electronics and operates
various subsidiaries, like LG Innotek, LG Display, Zenith, LG Electronics, LG Chem and LG
Uplus, spread in total 80 countries. the company has a total revenue of more than US $143
billion, employing more than 222,000.
In terms of washing machine, the LG Electronics company has initiated the option of
eliminating the need of pulley, belt tensioner, direct drive and belt, in 1998 winning the patents
for the same. LG Electronics with the association of other company, Samsung Electronics have
initiated to guide the users about their washers, allowing to identify common problems and
troubleshoot with their washers, with no need for contacting the technical support. LG
Electronics and Samsung Electronics have introduced the washers with front loading option, to
add new cloths, after starting the wash cycle along with the option of washers of top loading
having a belt in sink and dispenser of detergent.
The Product - Washing Machine
Washing machine, which is also known as a washer, clothes washer and laundry
machine.
Secure Best Marks with AI Grader
Need help grading? Try our AI Grader for instant feedback on your assignments.
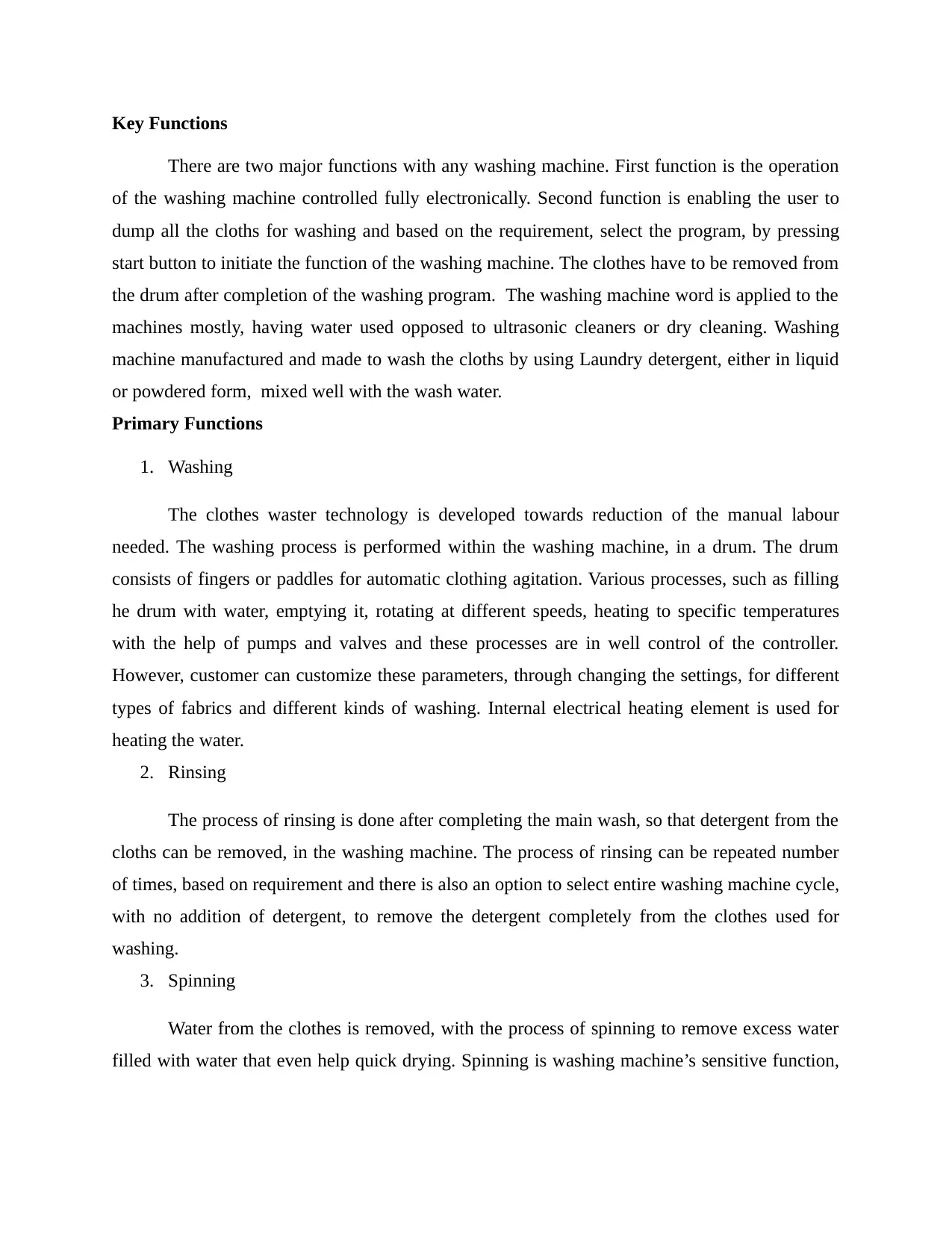
Key Functions
There are two major functions with any washing machine. First function is the operation
of the washing machine controlled fully electronically. Second function is enabling the user to
dump all the cloths for washing and based on the requirement, select the program, by pressing
start button to initiate the function of the washing machine. The clothes have to be removed from
the drum after completion of the washing program. The washing machine word is applied to the
machines mostly, having water used opposed to ultrasonic cleaners or dry cleaning. Washing
machine manufactured and made to wash the cloths by using Laundry detergent, either in liquid
or powdered form, mixed well with the wash water.
Primary Functions
1. Washing
The clothes waster technology is developed towards reduction of the manual labour
needed. The washing process is performed within the washing machine, in a drum. The drum
consists of fingers or paddles for automatic clothing agitation. Various processes, such as filling
he drum with water, emptying it, rotating at different speeds, heating to specific temperatures
with the help of pumps and valves and these processes are in well control of the controller.
However, customer can customize these parameters, through changing the settings, for different
types of fabrics and different kinds of washing. Internal electrical heating element is used for
heating the water.
2. Rinsing
The process of rinsing is done after completing the main wash, so that detergent from the
cloths can be removed, in the washing machine. The process of rinsing can be repeated number
of times, based on requirement and there is also an option to select entire washing machine cycle,
with no addition of detergent, to remove the detergent completely from the clothes used for
washing.
3. Spinning
Water from the clothes is removed, with the process of spinning to remove excess water
filled with water that even help quick drying. Spinning is washing machine’s sensitive function,
There are two major functions with any washing machine. First function is the operation
of the washing machine controlled fully electronically. Second function is enabling the user to
dump all the cloths for washing and based on the requirement, select the program, by pressing
start button to initiate the function of the washing machine. The clothes have to be removed from
the drum after completion of the washing program. The washing machine word is applied to the
machines mostly, having water used opposed to ultrasonic cleaners or dry cleaning. Washing
machine manufactured and made to wash the cloths by using Laundry detergent, either in liquid
or powdered form, mixed well with the wash water.
Primary Functions
1. Washing
The clothes waster technology is developed towards reduction of the manual labour
needed. The washing process is performed within the washing machine, in a drum. The drum
consists of fingers or paddles for automatic clothing agitation. Various processes, such as filling
he drum with water, emptying it, rotating at different speeds, heating to specific temperatures
with the help of pumps and valves and these processes are in well control of the controller.
However, customer can customize these parameters, through changing the settings, for different
types of fabrics and different kinds of washing. Internal electrical heating element is used for
heating the water.
2. Rinsing
The process of rinsing is done after completing the main wash, so that detergent from the
cloths can be removed, in the washing machine. The process of rinsing can be repeated number
of times, based on requirement and there is also an option to select entire washing machine cycle,
with no addition of detergent, to remove the detergent completely from the clothes used for
washing.
3. Spinning
Water from the clothes is removed, with the process of spinning to remove excess water
filled with water that even help quick drying. Spinning is washing machine’s sensitive function,
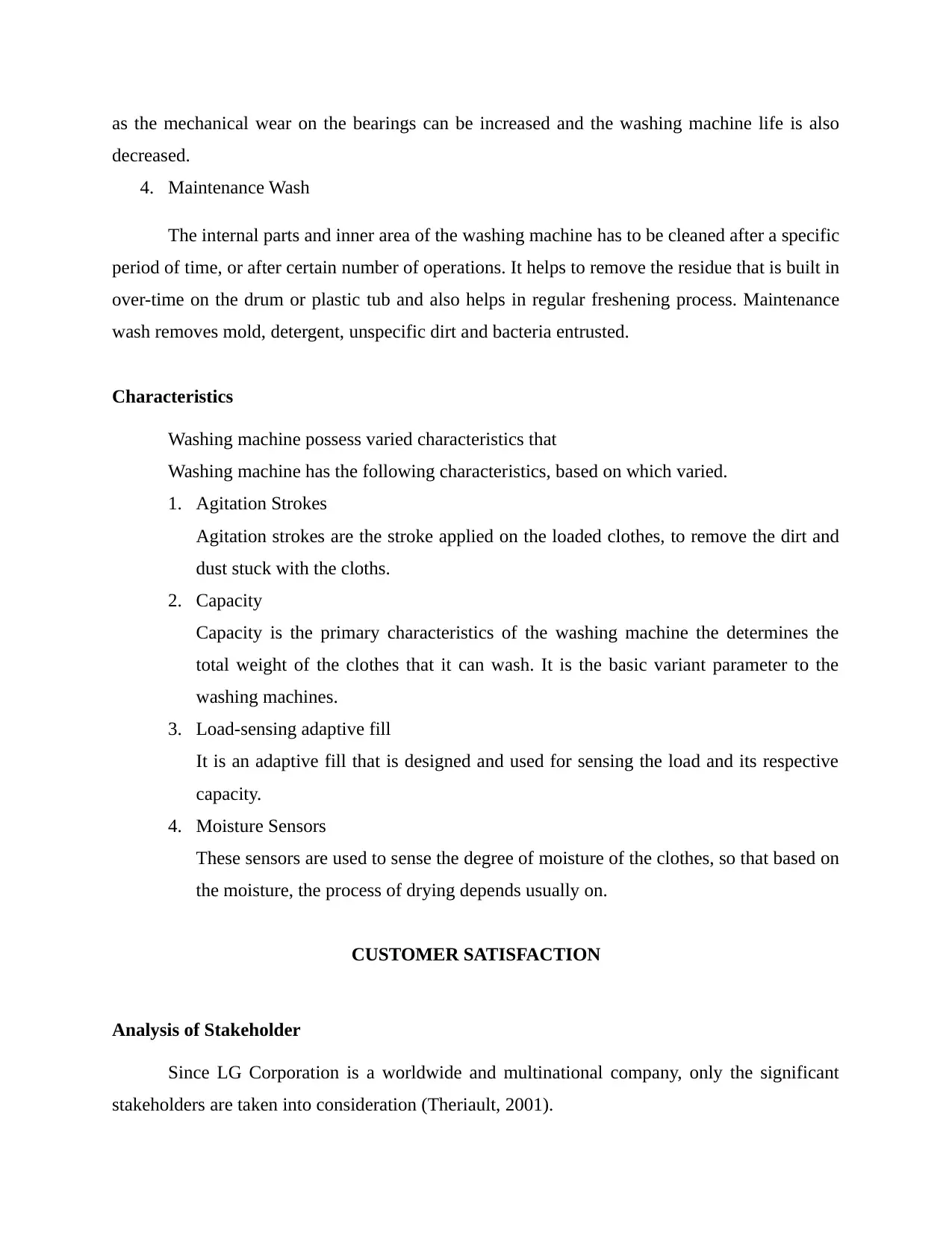
as the mechanical wear on the bearings can be increased and the washing machine life is also
decreased.
4. Maintenance Wash
The internal parts and inner area of the washing machine has to be cleaned after a specific
period of time, or after certain number of operations. It helps to remove the residue that is built in
over-time on the drum or plastic tub and also helps in regular freshening process. Maintenance
wash removes mold, detergent, unspecific dirt and bacteria entrusted.
Characteristics
Washing machine possess varied characteristics that
Washing machine has the following characteristics, based on which varied.
1. Agitation Strokes
Agitation strokes are the stroke applied on the loaded clothes, to remove the dirt and
dust stuck with the cloths.
2. Capacity
Capacity is the primary characteristics of the washing machine the determines the
total weight of the clothes that it can wash. It is the basic variant parameter to the
washing machines.
3. Load-sensing adaptive fill
It is an adaptive fill that is designed and used for sensing the load and its respective
capacity.
4. Moisture Sensors
These sensors are used to sense the degree of moisture of the clothes, so that based on
the moisture, the process of drying depends usually on.
CUSTOMER SATISFACTION
Analysis of Stakeholder
Since LG Corporation is a worldwide and multinational company, only the significant
stakeholders are taken into consideration (Theriault, 2001).
decreased.
4. Maintenance Wash
The internal parts and inner area of the washing machine has to be cleaned after a specific
period of time, or after certain number of operations. It helps to remove the residue that is built in
over-time on the drum or plastic tub and also helps in regular freshening process. Maintenance
wash removes mold, detergent, unspecific dirt and bacteria entrusted.
Characteristics
Washing machine possess varied characteristics that
Washing machine has the following characteristics, based on which varied.
1. Agitation Strokes
Agitation strokes are the stroke applied on the loaded clothes, to remove the dirt and
dust stuck with the cloths.
2. Capacity
Capacity is the primary characteristics of the washing machine the determines the
total weight of the clothes that it can wash. It is the basic variant parameter to the
washing machines.
3. Load-sensing adaptive fill
It is an adaptive fill that is designed and used for sensing the load and its respective
capacity.
4. Moisture Sensors
These sensors are used to sense the degree of moisture of the clothes, so that based on
the moisture, the process of drying depends usually on.
CUSTOMER SATISFACTION
Analysis of Stakeholder
Since LG Corporation is a worldwide and multinational company, only the significant
stakeholders are taken into consideration (Theriault, 2001).
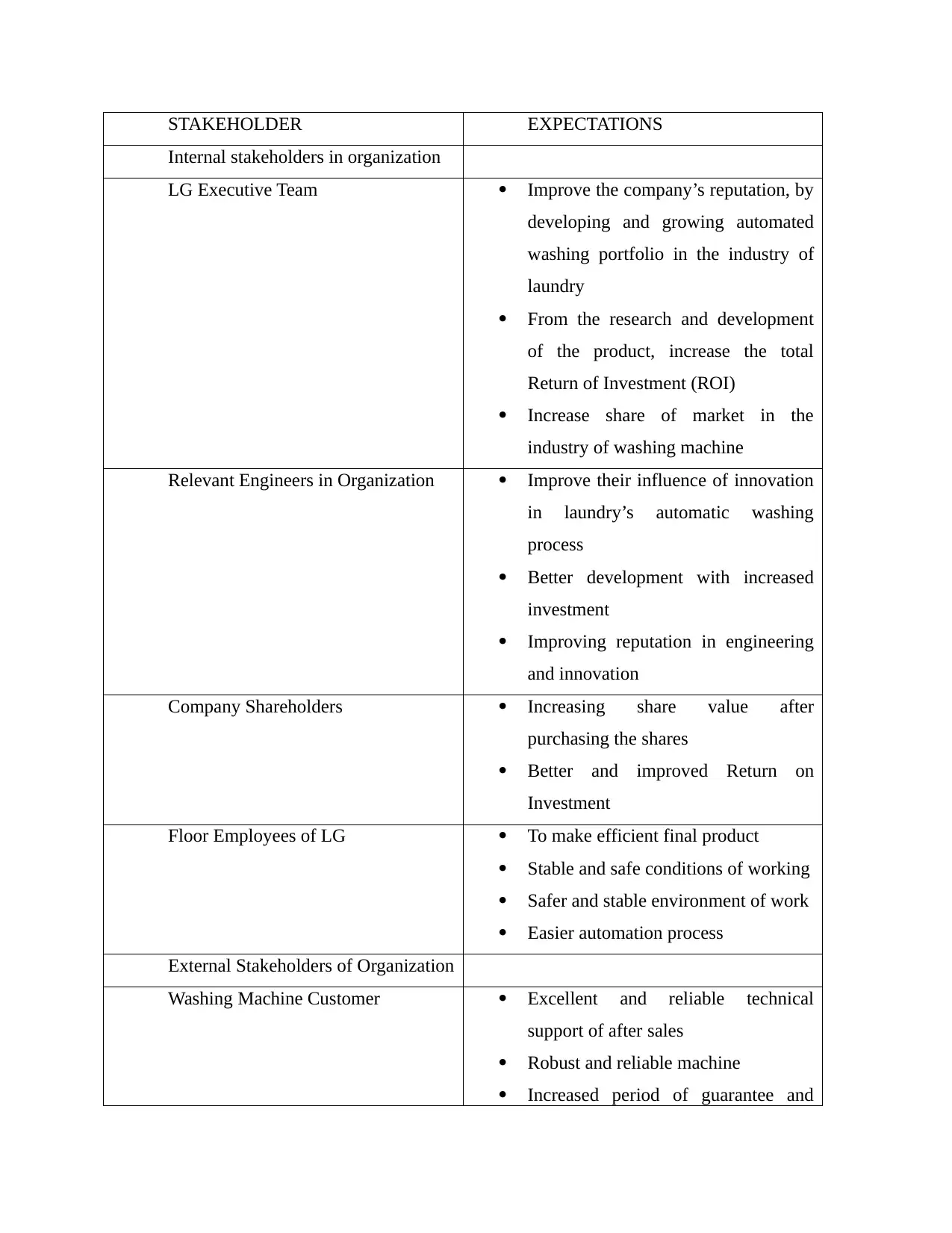
STAKEHOLDER EXPECTATIONS
Internal stakeholders in organization
LG Executive Team Improve the company’s reputation, by
developing and growing automated
washing portfolio in the industry of
laundry
From the research and development
of the product, increase the total
Return of Investment (ROI)
Increase share of market in the
industry of washing machine
Relevant Engineers in Organization Improve their influence of innovation
in laundry’s automatic washing
process
Better development with increased
investment
Improving reputation in engineering
and innovation
Company Shareholders Increasing share value after
purchasing the shares
Better and improved Return on
Investment
Floor Employees of LG To make efficient final product
Stable and safe conditions of working
Safer and stable environment of work
Easier automation process
External Stakeholders of Organization
Washing Machine Customer Excellent and reliable technical
support of after sales
Robust and reliable machine
Increased period of guarantee and
Internal stakeholders in organization
LG Executive Team Improve the company’s reputation, by
developing and growing automated
washing portfolio in the industry of
laundry
From the research and development
of the product, increase the total
Return of Investment (ROI)
Increase share of market in the
industry of washing machine
Relevant Engineers in Organization Improve their influence of innovation
in laundry’s automatic washing
process
Better development with increased
investment
Improving reputation in engineering
and innovation
Company Shareholders Increasing share value after
purchasing the shares
Better and improved Return on
Investment
Floor Employees of LG To make efficient final product
Stable and safe conditions of working
Safer and stable environment of work
Easier automation process
External Stakeholders of Organization
Washing Machine Customer Excellent and reliable technical
support of after sales
Robust and reliable machine
Increased period of guarantee and
Paraphrase This Document
Need a fresh take? Get an instant paraphrase of this document with our AI Paraphraser
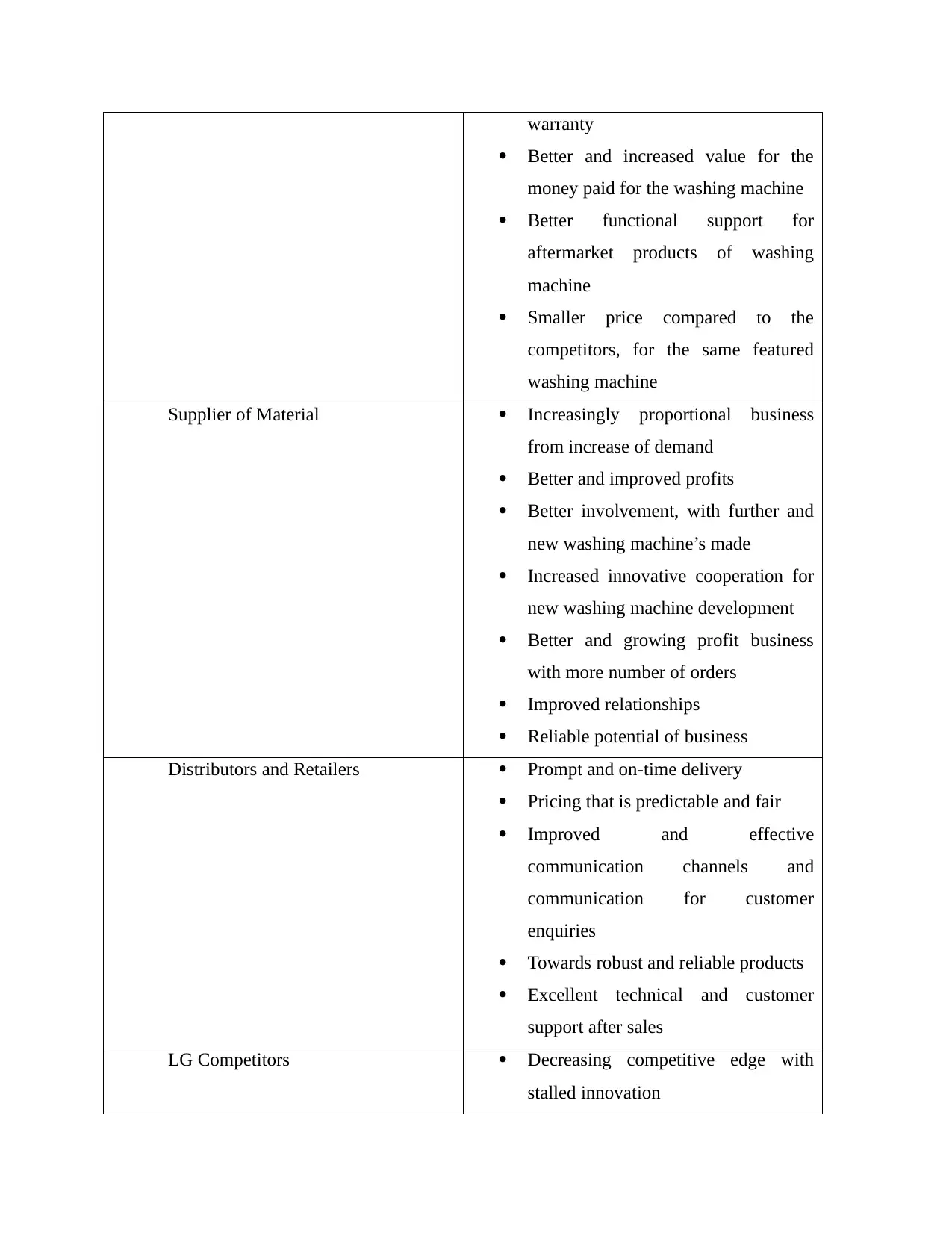
warranty
Better and increased value for the
money paid for the washing machine
Better functional support for
aftermarket products of washing
machine
Smaller price compared to the
competitors, for the same featured
washing machine
Supplier of Material Increasingly proportional business
from increase of demand
Better and improved profits
Better involvement, with further and
new washing machine’s made
Increased innovative cooperation for
new washing machine development
Better and growing profit business
with more number of orders
Improved relationships
Reliable potential of business
Distributors and Retailers Prompt and on-time delivery
Pricing that is predictable and fair
Improved and effective
communication channels and
communication for customer
enquiries
Towards robust and reliable products
Excellent technical and customer
support after sales
LG Competitors Decreasing competitive edge with
stalled innovation
Better and increased value for the
money paid for the washing machine
Better functional support for
aftermarket products of washing
machine
Smaller price compared to the
competitors, for the same featured
washing machine
Supplier of Material Increasingly proportional business
from increase of demand
Better and improved profits
Better involvement, with further and
new washing machine’s made
Increased innovative cooperation for
new washing machine development
Better and growing profit business
with more number of orders
Improved relationships
Reliable potential of business
Distributors and Retailers Prompt and on-time delivery
Pricing that is predictable and fair
Improved and effective
communication channels and
communication for customer
enquiries
Towards robust and reliable products
Excellent technical and customer
support after sales
LG Competitors Decreasing competitive edge with
stalled innovation
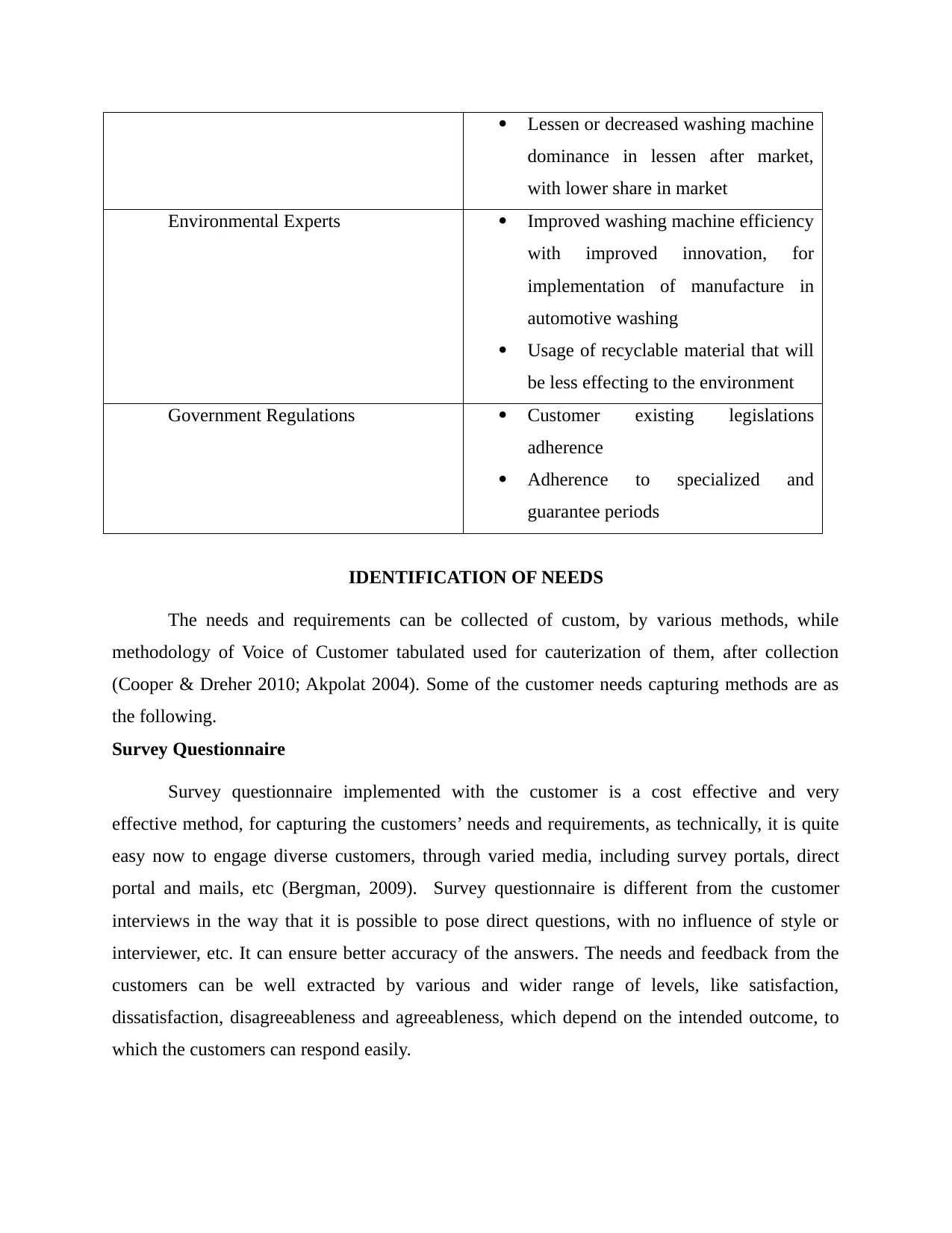
Lessen or decreased washing machine
dominance in lessen after market,
with lower share in market
Environmental Experts Improved washing machine efficiency
with improved innovation, for
implementation of manufacture in
automotive washing
Usage of recyclable material that will
be less effecting to the environment
Government Regulations Customer existing legislations
adherence
Adherence to specialized and
guarantee periods
IDENTIFICATION OF NEEDS
The needs and requirements can be collected of custom, by various methods, while
methodology of Voice of Customer tabulated used for cauterization of them, after collection
(Cooper & Dreher 2010; Akpolat 2004). Some of the customer needs capturing methods are as
the following.
Survey Questionnaire
Survey questionnaire implemented with the customer is a cost effective and very
effective method, for capturing the customers’ needs and requirements, as technically, it is quite
easy now to engage diverse customers, through varied media, including survey portals, direct
portal and mails, etc (Bergman, 2009). Survey questionnaire is different from the customer
interviews in the way that it is possible to pose direct questions, with no influence of style or
interviewer, etc. It can ensure better accuracy of the answers. The needs and feedback from the
customers can be well extracted by various and wider range of levels, like satisfaction,
dissatisfaction, disagreeableness and agreeableness, which depend on the intended outcome, to
which the customers can respond easily.
dominance in lessen after market,
with lower share in market
Environmental Experts Improved washing machine efficiency
with improved innovation, for
implementation of manufacture in
automotive washing
Usage of recyclable material that will
be less effecting to the environment
Government Regulations Customer existing legislations
adherence
Adherence to specialized and
guarantee periods
IDENTIFICATION OF NEEDS
The needs and requirements can be collected of custom, by various methods, while
methodology of Voice of Customer tabulated used for cauterization of them, after collection
(Cooper & Dreher 2010; Akpolat 2004). Some of the customer needs capturing methods are as
the following.
Survey Questionnaire
Survey questionnaire implemented with the customer is a cost effective and very
effective method, for capturing the customers’ needs and requirements, as technically, it is quite
easy now to engage diverse customers, through varied media, including survey portals, direct
portal and mails, etc (Bergman, 2009). Survey questionnaire is different from the customer
interviews in the way that it is possible to pose direct questions, with no influence of style or
interviewer, etc. It can ensure better accuracy of the answers. The needs and feedback from the
customers can be well extracted by various and wider range of levels, like satisfaction,
dissatisfaction, disagreeableness and agreeableness, which depend on the intended outcome, to
which the customers can respond easily.
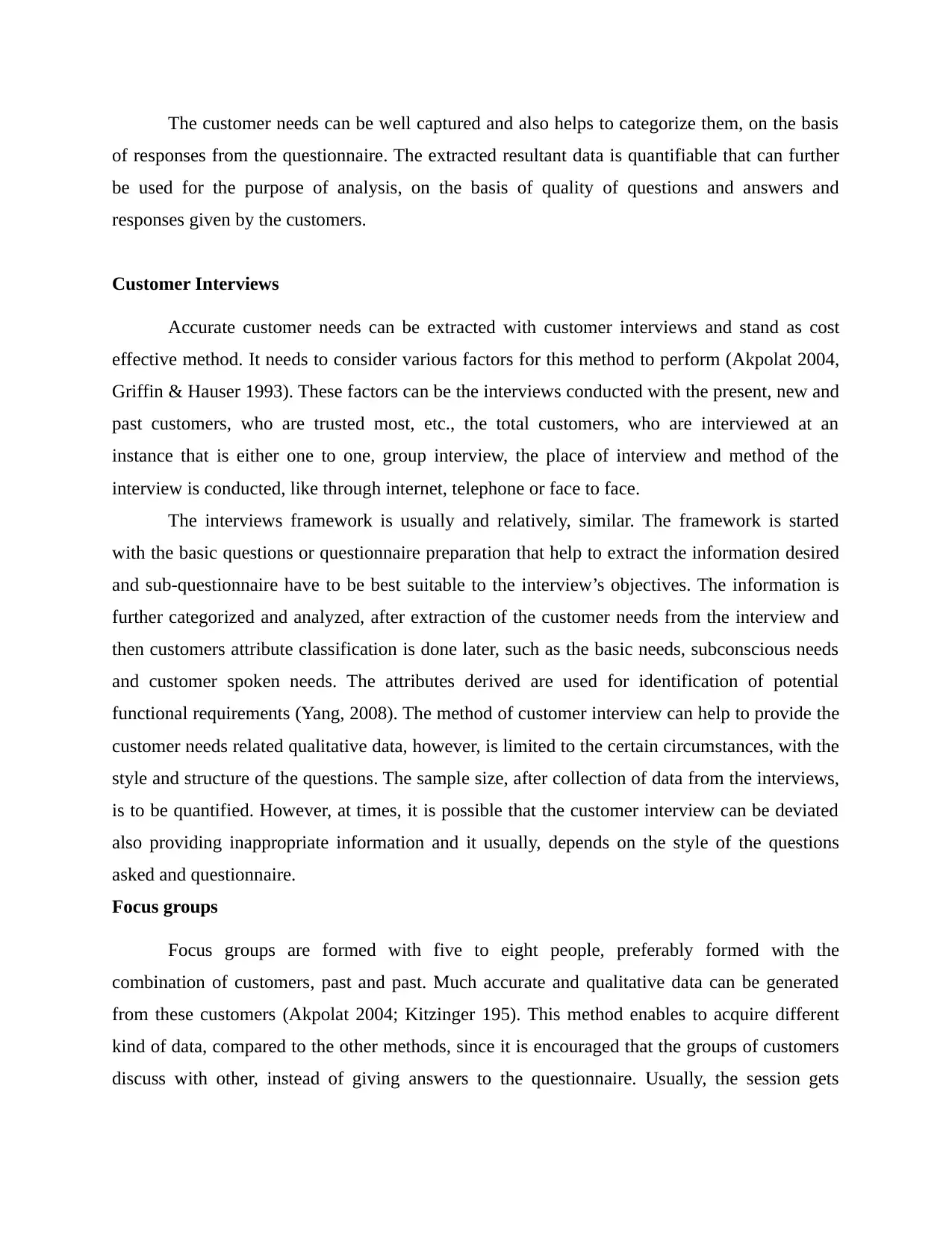
The customer needs can be well captured and also helps to categorize them, on the basis
of responses from the questionnaire. The extracted resultant data is quantifiable that can further
be used for the purpose of analysis, on the basis of quality of questions and answers and
responses given by the customers.
Customer Interviews
Accurate customer needs can be extracted with customer interviews and stand as cost
effective method. It needs to consider various factors for this method to perform (Akpolat 2004,
Griffin & Hauser 1993). These factors can be the interviews conducted with the present, new and
past customers, who are trusted most, etc., the total customers, who are interviewed at an
instance that is either one to one, group interview, the place of interview and method of the
interview is conducted, like through internet, telephone or face to face.
The interviews framework is usually and relatively, similar. The framework is started
with the basic questions or questionnaire preparation that help to extract the information desired
and sub-questionnaire have to be best suitable to the interview’s objectives. The information is
further categorized and analyzed, after extraction of the customer needs from the interview and
then customers attribute classification is done later, such as the basic needs, subconscious needs
and customer spoken needs. The attributes derived are used for identification of potential
functional requirements (Yang, 2008). The method of customer interview can help to provide the
customer needs related qualitative data, however, is limited to the certain circumstances, with the
style and structure of the questions. The sample size, after collection of data from the interviews,
is to be quantified. However, at times, it is possible that the customer interview can be deviated
also providing inappropriate information and it usually, depends on the style of the questions
asked and questionnaire.
Focus groups
Focus groups are formed with five to eight people, preferably formed with the
combination of customers, past and past. Much accurate and qualitative data can be generated
from these customers (Akpolat 2004; Kitzinger 195). This method enables to acquire different
kind of data, compared to the other methods, since it is encouraged that the groups of customers
discuss with other, instead of giving answers to the questionnaire. Usually, the session gets
of responses from the questionnaire. The extracted resultant data is quantifiable that can further
be used for the purpose of analysis, on the basis of quality of questions and answers and
responses given by the customers.
Customer Interviews
Accurate customer needs can be extracted with customer interviews and stand as cost
effective method. It needs to consider various factors for this method to perform (Akpolat 2004,
Griffin & Hauser 1993). These factors can be the interviews conducted with the present, new and
past customers, who are trusted most, etc., the total customers, who are interviewed at an
instance that is either one to one, group interview, the place of interview and method of the
interview is conducted, like through internet, telephone or face to face.
The interviews framework is usually and relatively, similar. The framework is started
with the basic questions or questionnaire preparation that help to extract the information desired
and sub-questionnaire have to be best suitable to the interview’s objectives. The information is
further categorized and analyzed, after extraction of the customer needs from the interview and
then customers attribute classification is done later, such as the basic needs, subconscious needs
and customer spoken needs. The attributes derived are used for identification of potential
functional requirements (Yang, 2008). The method of customer interview can help to provide the
customer needs related qualitative data, however, is limited to the certain circumstances, with the
style and structure of the questions. The sample size, after collection of data from the interviews,
is to be quantified. However, at times, it is possible that the customer interview can be deviated
also providing inappropriate information and it usually, depends on the style of the questions
asked and questionnaire.
Focus groups
Focus groups are formed with five to eight people, preferably formed with the
combination of customers, past and past. Much accurate and qualitative data can be generated
from these customers (Akpolat 2004; Kitzinger 195). This method enables to acquire different
kind of data, compared to the other methods, since it is encouraged that the groups of customers
discuss with other, instead of giving answers to the questionnaire. Usually, the session gets
Secure Best Marks with AI Grader
Need help grading? Try our AI Grader for instant feedback on your assignments.
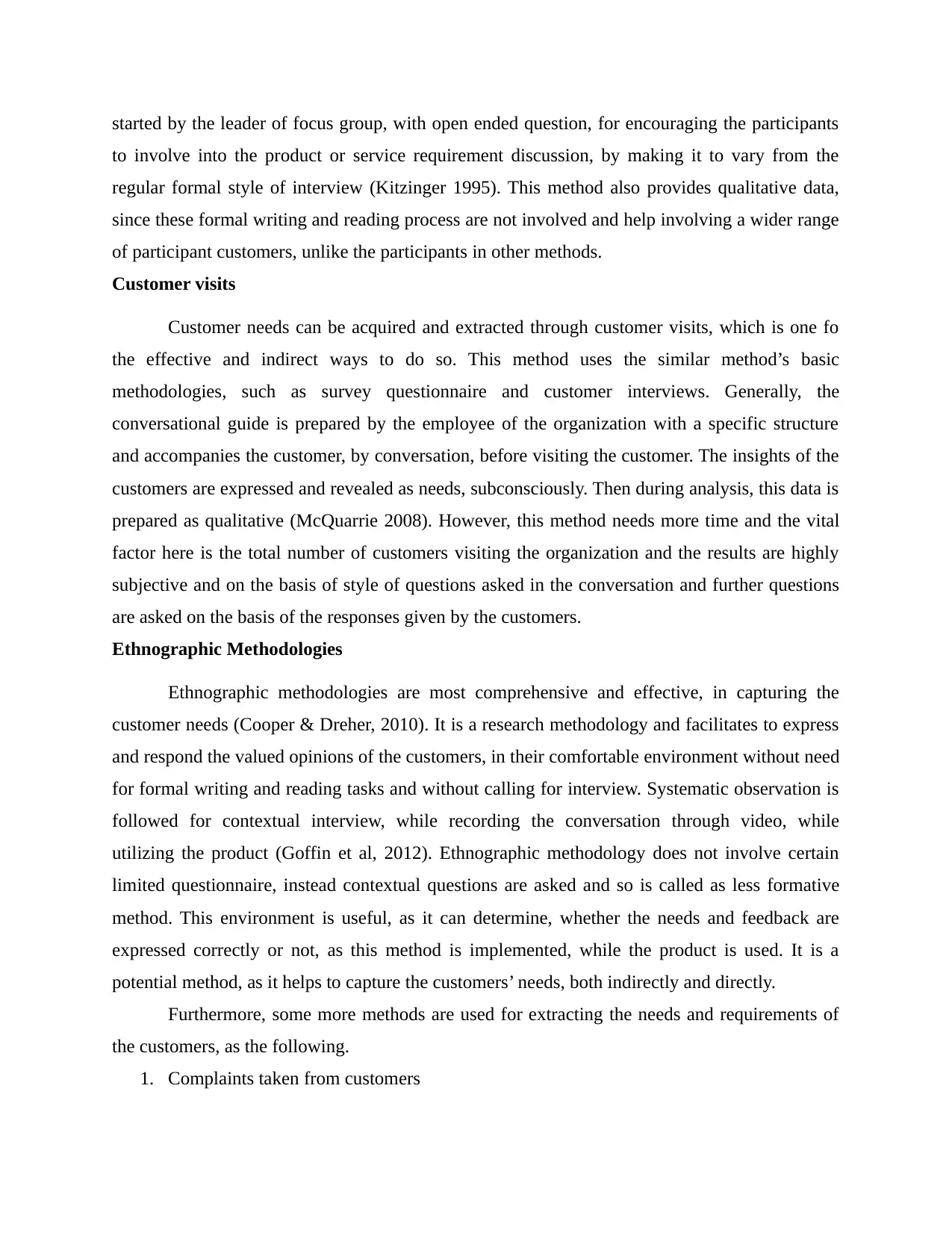
started by the leader of focus group, with open ended question, for encouraging the participants
to involve into the product or service requirement discussion, by making it to vary from the
regular formal style of interview (Kitzinger 1995). This method also provides qualitative data,
since these formal writing and reading process are not involved and help involving a wider range
of participant customers, unlike the participants in other methods.
Customer visits
Customer needs can be acquired and extracted through customer visits, which is one fo
the effective and indirect ways to do so. This method uses the similar method’s basic
methodologies, such as survey questionnaire and customer interviews. Generally, the
conversational guide is prepared by the employee of the organization with a specific structure
and accompanies the customer, by conversation, before visiting the customer. The insights of the
customers are expressed and revealed as needs, subconsciously. Then during analysis, this data is
prepared as qualitative (McQuarrie 2008). However, this method needs more time and the vital
factor here is the total number of customers visiting the organization and the results are highly
subjective and on the basis of style of questions asked in the conversation and further questions
are asked on the basis of the responses given by the customers.
Ethnographic Methodologies
Ethnographic methodologies are most comprehensive and effective, in capturing the
customer needs (Cooper & Dreher, 2010). It is a research methodology and facilitates to express
and respond the valued opinions of the customers, in their comfortable environment without need
for formal writing and reading tasks and without calling for interview. Systematic observation is
followed for contextual interview, while recording the conversation through video, while
utilizing the product (Goffin et al, 2012). Ethnographic methodology does not involve certain
limited questionnaire, instead contextual questions are asked and so is called as less formative
method. This environment is useful, as it can determine, whether the needs and feedback are
expressed correctly or not, as this method is implemented, while the product is used. It is a
potential method, as it helps to capture the customers’ needs, both indirectly and directly.
Furthermore, some more methods are used for extracting the needs and requirements of
the customers, as the following.
1. Complaints taken from customers
to involve into the product or service requirement discussion, by making it to vary from the
regular formal style of interview (Kitzinger 1995). This method also provides qualitative data,
since these formal writing and reading process are not involved and help involving a wider range
of participant customers, unlike the participants in other methods.
Customer visits
Customer needs can be acquired and extracted through customer visits, which is one fo
the effective and indirect ways to do so. This method uses the similar method’s basic
methodologies, such as survey questionnaire and customer interviews. Generally, the
conversational guide is prepared by the employee of the organization with a specific structure
and accompanies the customer, by conversation, before visiting the customer. The insights of the
customers are expressed and revealed as needs, subconsciously. Then during analysis, this data is
prepared as qualitative (McQuarrie 2008). However, this method needs more time and the vital
factor here is the total number of customers visiting the organization and the results are highly
subjective and on the basis of style of questions asked in the conversation and further questions
are asked on the basis of the responses given by the customers.
Ethnographic Methodologies
Ethnographic methodologies are most comprehensive and effective, in capturing the
customer needs (Cooper & Dreher, 2010). It is a research methodology and facilitates to express
and respond the valued opinions of the customers, in their comfortable environment without need
for formal writing and reading tasks and without calling for interview. Systematic observation is
followed for contextual interview, while recording the conversation through video, while
utilizing the product (Goffin et al, 2012). Ethnographic methodology does not involve certain
limited questionnaire, instead contextual questions are asked and so is called as less formative
method. This environment is useful, as it can determine, whether the needs and feedback are
expressed correctly or not, as this method is implemented, while the product is used. It is a
potential method, as it helps to capture the customers’ needs, both indirectly and directly.
Furthermore, some more methods are used for extracting the needs and requirements of
the customers, as the following.
1. Complaints taken from customers
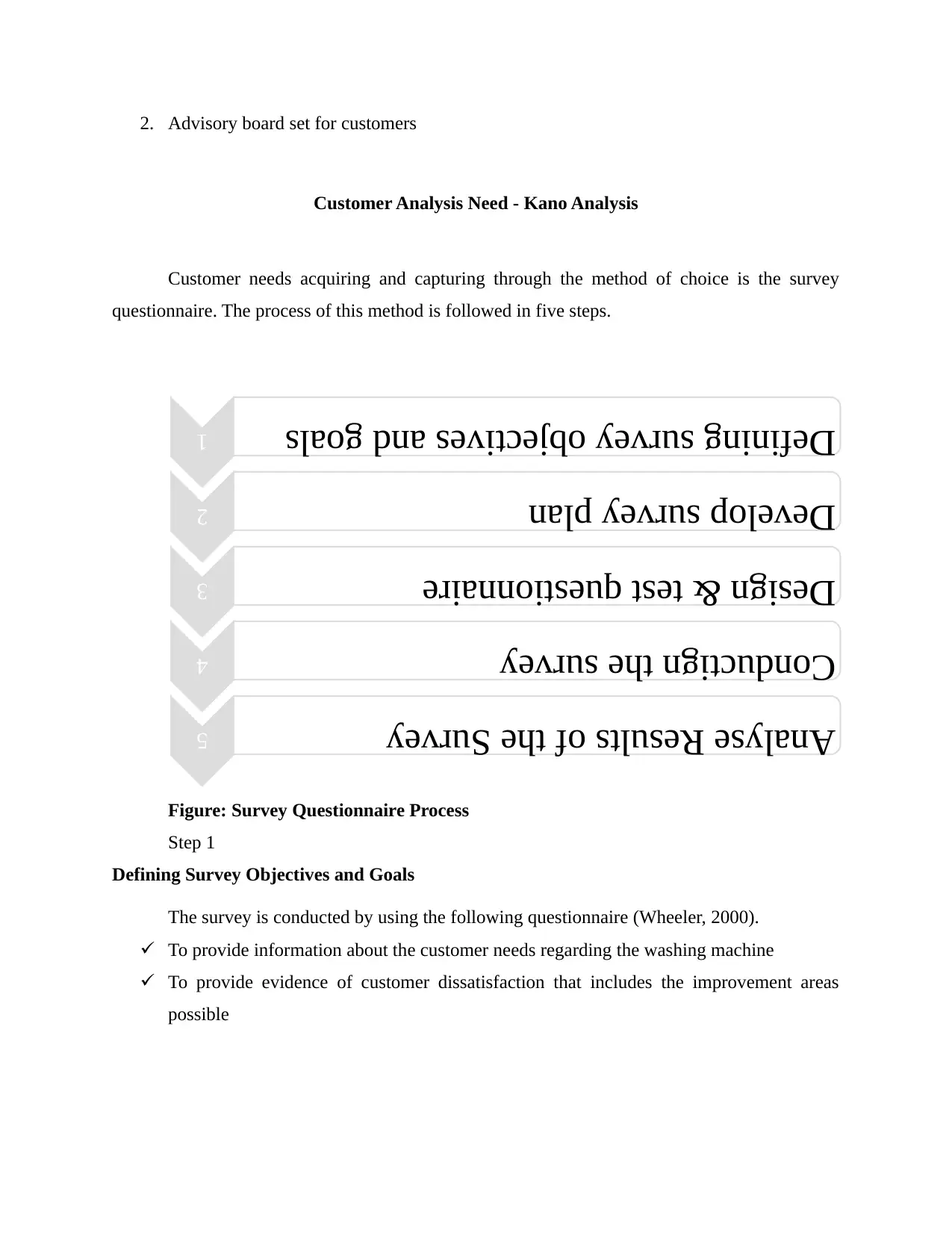
2. Advisory board set for customers
Customer Analysis Need - Kano Analysis
Customer needs acquiring and capturing through the method of choice is the survey
questionnaire. The process of this method is followed in five steps.
Figure: Survey Questionnaire Process
Step 1
Defining Survey Objectives and Goals
The survey is conducted by using the following questionnaire (Wheeler, 2000).
To provide information about the customer needs regarding the washing machine
To provide evidence of customer dissatisfaction that includes the improvement areas
possible
1Defining survey objectives and goals
2Develop survey plan
3Design & test questionnaire
4Conductign the survey
5Analyse Results of the Survey
Customer Analysis Need - Kano Analysis
Customer needs acquiring and capturing through the method of choice is the survey
questionnaire. The process of this method is followed in five steps.
Figure: Survey Questionnaire Process
Step 1
Defining Survey Objectives and Goals
The survey is conducted by using the following questionnaire (Wheeler, 2000).
To provide information about the customer needs regarding the washing machine
To provide evidence of customer dissatisfaction that includes the improvement areas
possible
1Defining survey objectives and goals
2Develop survey plan
3Design & test questionnaire
4Conductign the survey
5Analyse Results of the Survey
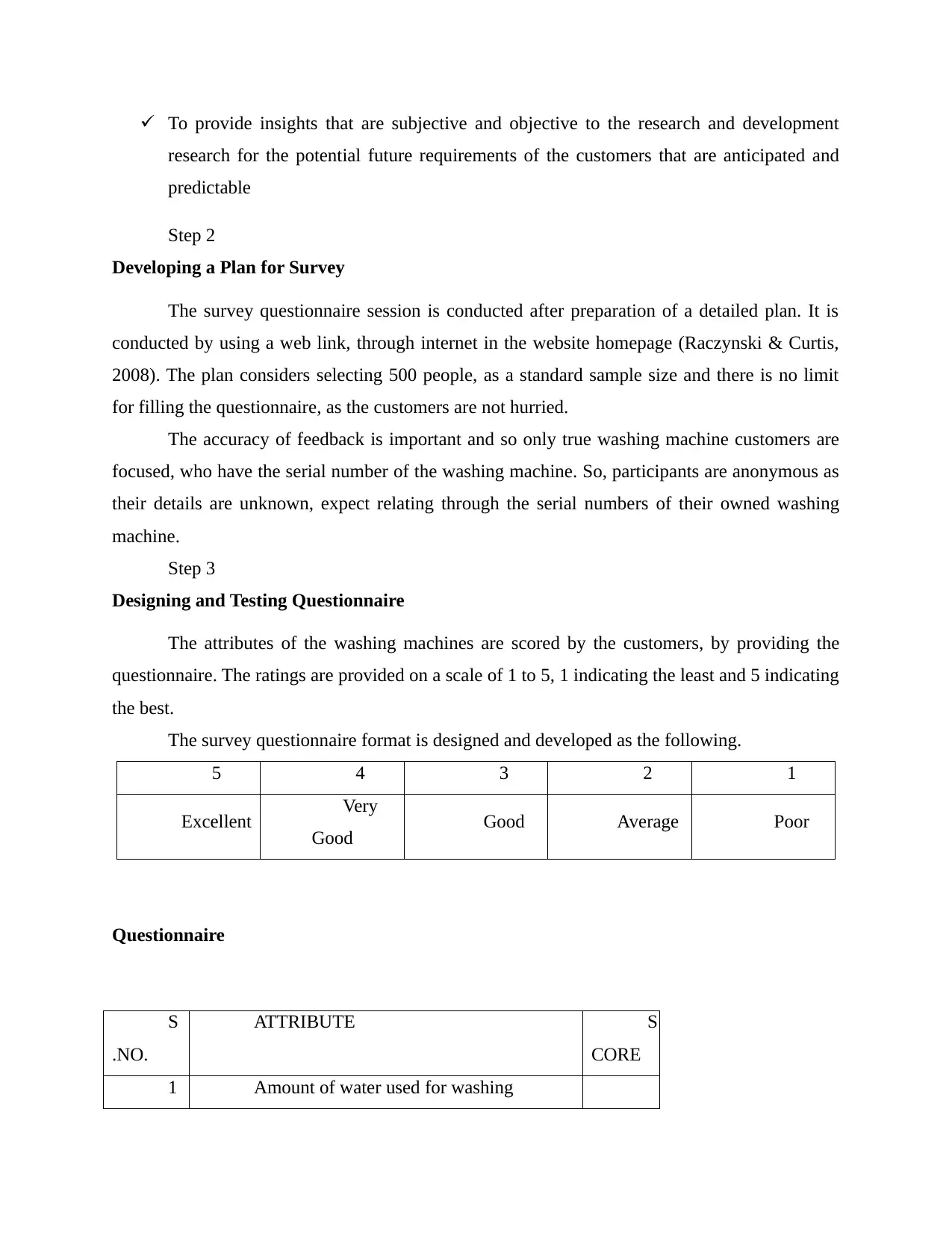
To provide insights that are subjective and objective to the research and development
research for the potential future requirements of the customers that are anticipated and
predictable
Step 2
Developing a Plan for Survey
The survey questionnaire session is conducted after preparation of a detailed plan. It is
conducted by using a web link, through internet in the website homepage (Raczynski & Curtis,
2008). The plan considers selecting 500 people, as a standard sample size and there is no limit
for filling the questionnaire, as the customers are not hurried.
The accuracy of feedback is important and so only true washing machine customers are
focused, who have the serial number of the washing machine. So, participants are anonymous as
their details are unknown, expect relating through the serial numbers of their owned washing
machine.
Step 3
Designing and Testing Questionnaire
The attributes of the washing machines are scored by the customers, by providing the
questionnaire. The ratings are provided on a scale of 1 to 5, 1 indicating the least and 5 indicating
the best.
The survey questionnaire format is designed and developed as the following.
5 4 3 2 1
Excellent Very
Good Good Average Poor
Questionnaire
S
.NO.
ATTRIBUTE S
CORE
1 Amount of water used for washing
research for the potential future requirements of the customers that are anticipated and
predictable
Step 2
Developing a Plan for Survey
The survey questionnaire session is conducted after preparation of a detailed plan. It is
conducted by using a web link, through internet in the website homepage (Raczynski & Curtis,
2008). The plan considers selecting 500 people, as a standard sample size and there is no limit
for filling the questionnaire, as the customers are not hurried.
The accuracy of feedback is important and so only true washing machine customers are
focused, who have the serial number of the washing machine. So, participants are anonymous as
their details are unknown, expect relating through the serial numbers of their owned washing
machine.
Step 3
Designing and Testing Questionnaire
The attributes of the washing machines are scored by the customers, by providing the
questionnaire. The ratings are provided on a scale of 1 to 5, 1 indicating the least and 5 indicating
the best.
The survey questionnaire format is designed and developed as the following.
5 4 3 2 1
Excellent Very
Good Good Average Poor
Questionnaire
S
.NO.
ATTRIBUTE S
CORE
1 Amount of water used for washing
Paraphrase This Document
Need a fresh take? Get an instant paraphrase of this document with our AI Paraphraser
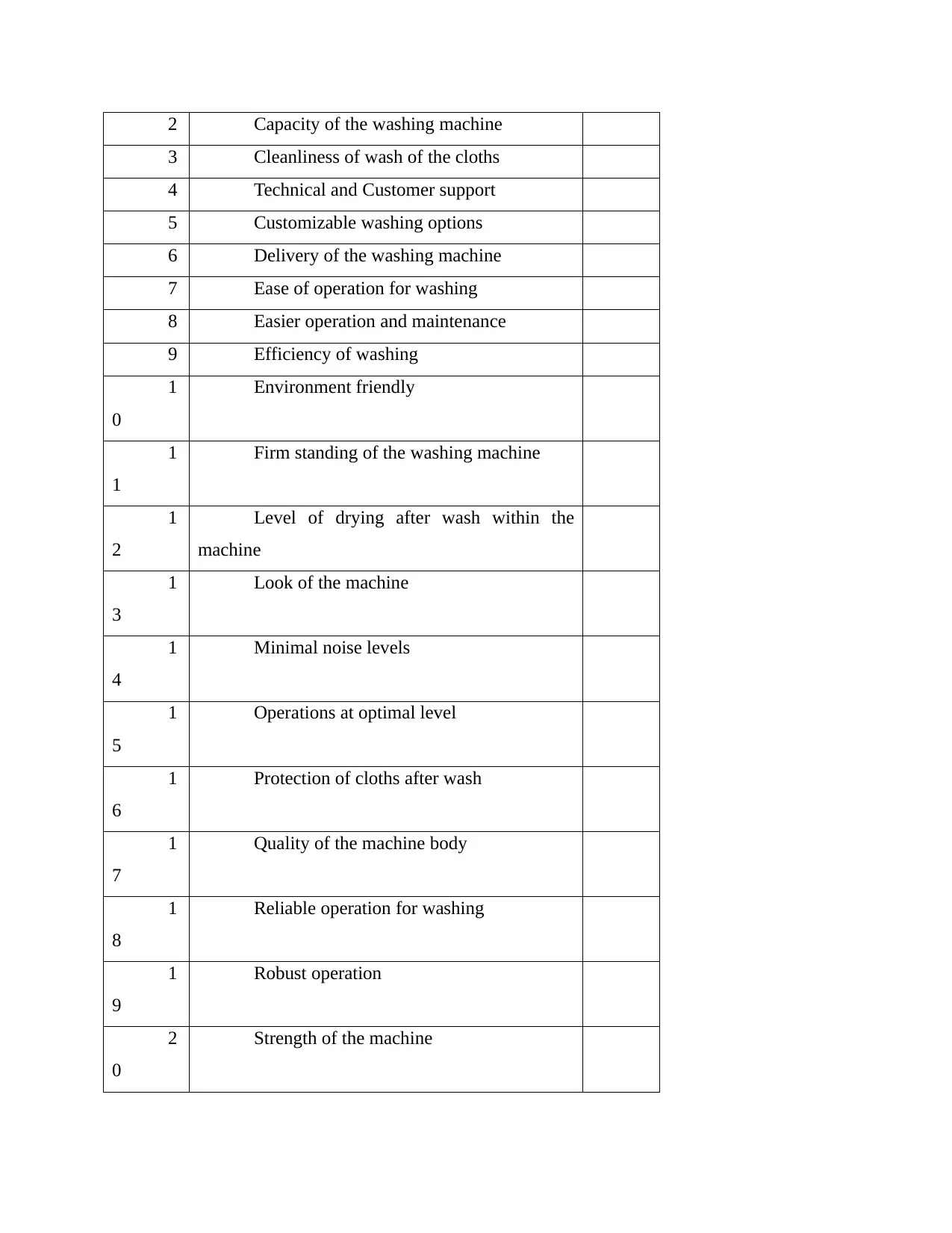
2 Capacity of the washing machine
3 Cleanliness of wash of the cloths
4 Technical and Customer support
5 Customizable washing options
6 Delivery of the washing machine
7 Ease of operation for washing
8 Easier operation and maintenance
9 Efficiency of washing
1
0
Environment friendly
1
1
Firm standing of the washing machine
1
2
Level of drying after wash within the
machine
1
3
Look of the machine
1
4
Minimal noise levels
1
5
Operations at optimal level
1
6
Protection of cloths after wash
1
7
Quality of the machine body
1
8
Reliable operation for washing
1
9
Robust operation
2
0
Strength of the machine
3 Cleanliness of wash of the cloths
4 Technical and Customer support
5 Customizable washing options
6 Delivery of the washing machine
7 Ease of operation for washing
8 Easier operation and maintenance
9 Efficiency of washing
1
0
Environment friendly
1
1
Firm standing of the washing machine
1
2
Level of drying after wash within the
machine
1
3
Look of the machine
1
4
Minimal noise levels
1
5
Operations at optimal level
1
6
Protection of cloths after wash
1
7
Quality of the machine body
1
8
Reliable operation for washing
1
9
Robust operation
2
0
Strength of the machine
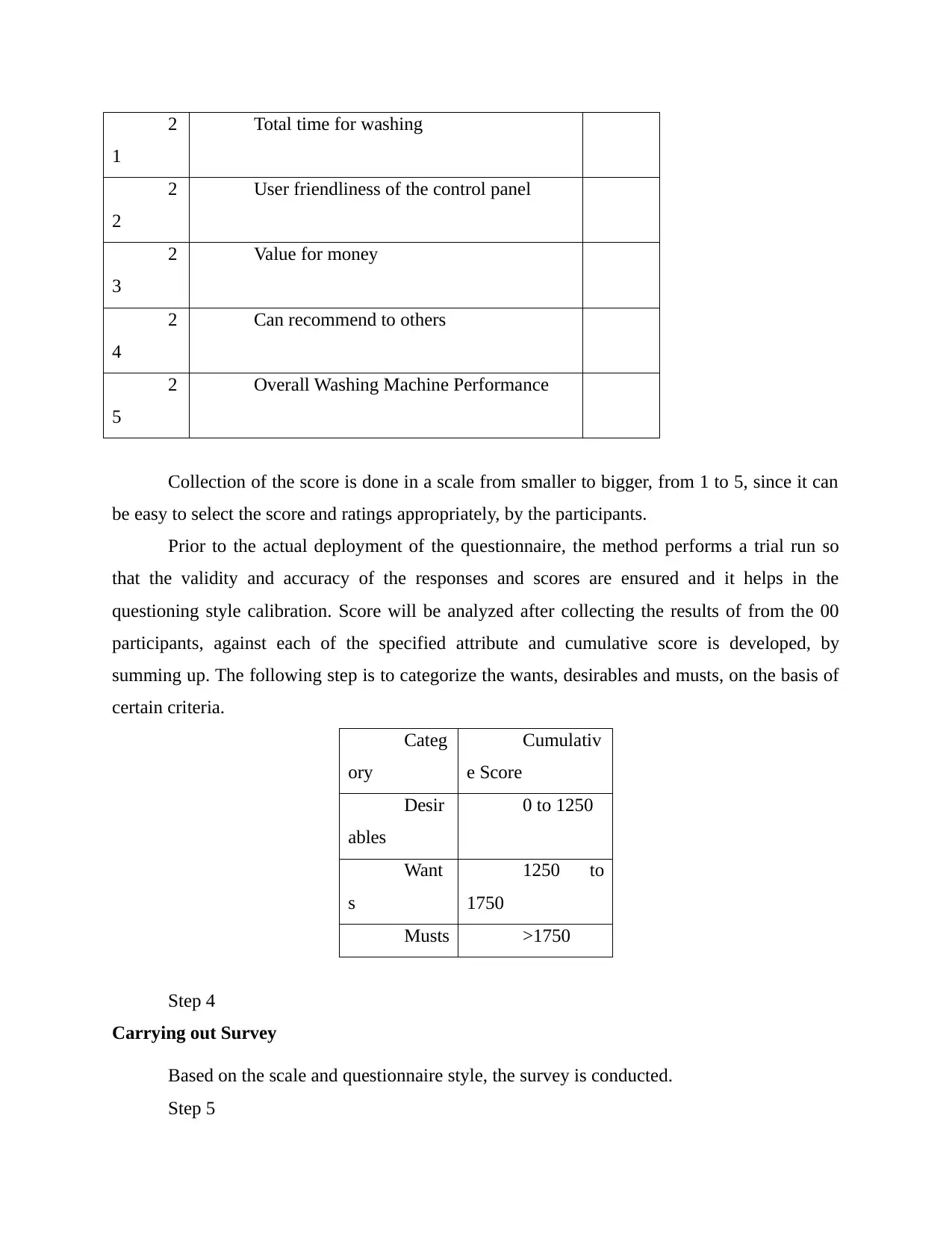
2
1
Total time for washing
2
2
User friendliness of the control panel
2
3
Value for money
2
4
Can recommend to others
2
5
Overall Washing Machine Performance
Collection of the score is done in a scale from smaller to bigger, from 1 to 5, since it can
be easy to select the score and ratings appropriately, by the participants.
Prior to the actual deployment of the questionnaire, the method performs a trial run so
that the validity and accuracy of the responses and scores are ensured and it helps in the
questioning style calibration. Score will be analyzed after collecting the results of from the 00
participants, against each of the specified attribute and cumulative score is developed, by
summing up. The following step is to categorize the wants, desirables and musts, on the basis of
certain criteria.
Categ
ory
Cumulativ
e Score
Desir
ables
0 to 1250
Want
s
1250 to
1750
Musts >1750
Step 4
Carrying out Survey
Based on the scale and questionnaire style, the survey is conducted.
Step 5
1
Total time for washing
2
2
User friendliness of the control panel
2
3
Value for money
2
4
Can recommend to others
2
5
Overall Washing Machine Performance
Collection of the score is done in a scale from smaller to bigger, from 1 to 5, since it can
be easy to select the score and ratings appropriately, by the participants.
Prior to the actual deployment of the questionnaire, the method performs a trial run so
that the validity and accuracy of the responses and scores are ensured and it helps in the
questioning style calibration. Score will be analyzed after collecting the results of from the 00
participants, against each of the specified attribute and cumulative score is developed, by
summing up. The following step is to categorize the wants, desirables and musts, on the basis of
certain criteria.
Categ
ory
Cumulativ
e Score
Desir
ables
0 to 1250
Want
s
1250 to
1750
Musts >1750
Step 4
Carrying out Survey
Based on the scale and questionnaire style, the survey is conducted.
Step 5
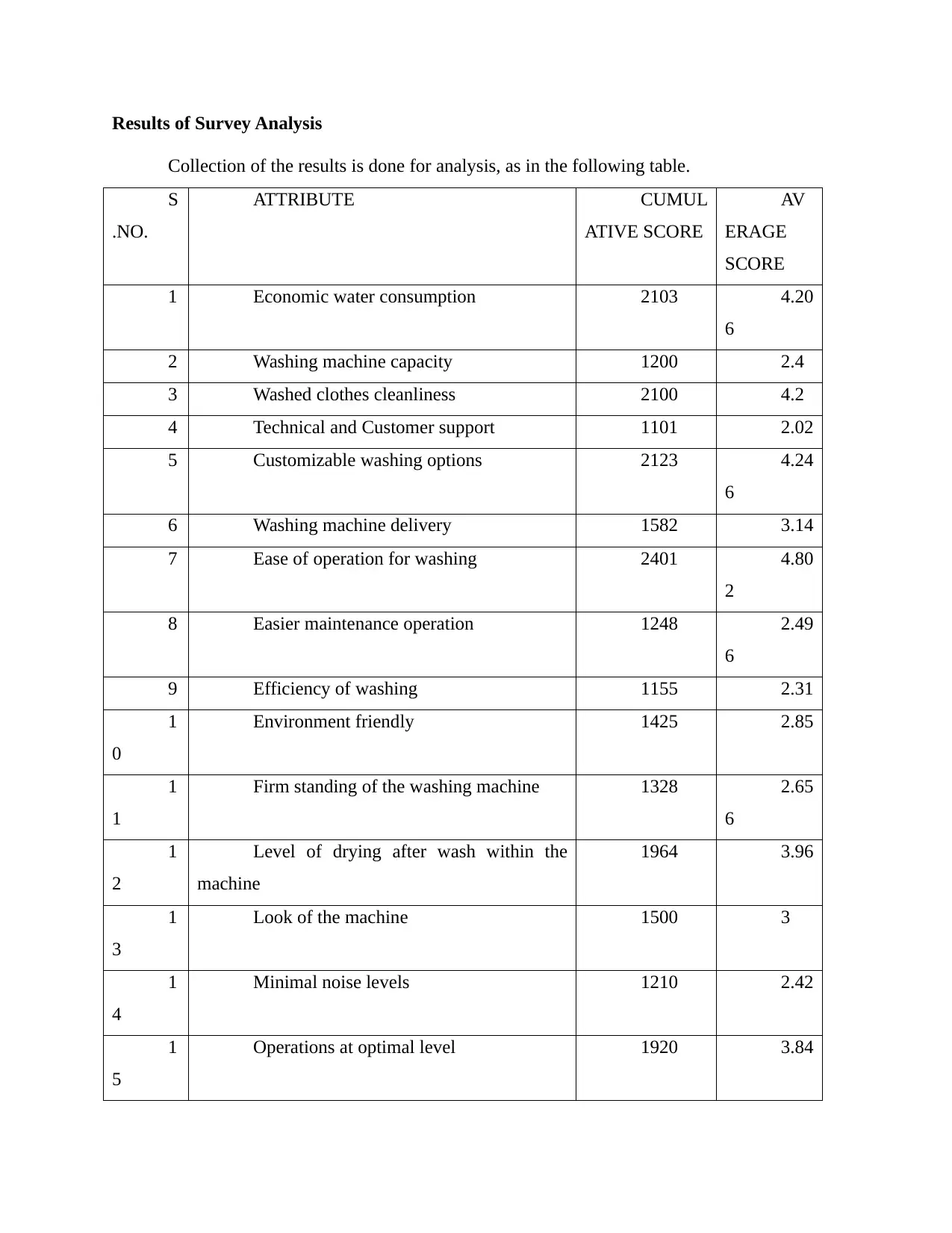
Results of Survey Analysis
Collection of the results is done for analysis, as in the following table.
S
.NO.
ATTRIBUTE CUMUL
ATIVE SCORE
AV
ERAGE
SCORE
1 Economic water consumption 2103 4.20
6
2 Washing machine capacity 1200 2.4
3 Washed clothes cleanliness 2100 4.2
4 Technical and Customer support 1101 2.02
5 Customizable washing options 2123 4.24
6
6 Washing machine delivery 1582 3.14
7 Ease of operation for washing 2401 4.80
2
8 Easier maintenance operation 1248 2.49
6
9 Efficiency of washing 1155 2.31
1
0
Environment friendly 1425 2.85
1
1
Firm standing of the washing machine 1328 2.65
6
1
2
Level of drying after wash within the
machine
1964 3.96
1
3
Look of the machine 1500 3
1
4
Minimal noise levels 1210 2.42
1
5
Operations at optimal level 1920 3.84
Collection of the results is done for analysis, as in the following table.
S
.NO.
ATTRIBUTE CUMUL
ATIVE SCORE
AV
ERAGE
SCORE
1 Economic water consumption 2103 4.20
6
2 Washing machine capacity 1200 2.4
3 Washed clothes cleanliness 2100 4.2
4 Technical and Customer support 1101 2.02
5 Customizable washing options 2123 4.24
6
6 Washing machine delivery 1582 3.14
7 Ease of operation for washing 2401 4.80
2
8 Easier maintenance operation 1248 2.49
6
9 Efficiency of washing 1155 2.31
1
0
Environment friendly 1425 2.85
1
1
Firm standing of the washing machine 1328 2.65
6
1
2
Level of drying after wash within the
machine
1964 3.96
1
3
Look of the machine 1500 3
1
4
Minimal noise levels 1210 2.42
1
5
Operations at optimal level 1920 3.84
Secure Best Marks with AI Grader
Need help grading? Try our AI Grader for instant feedback on your assignments.
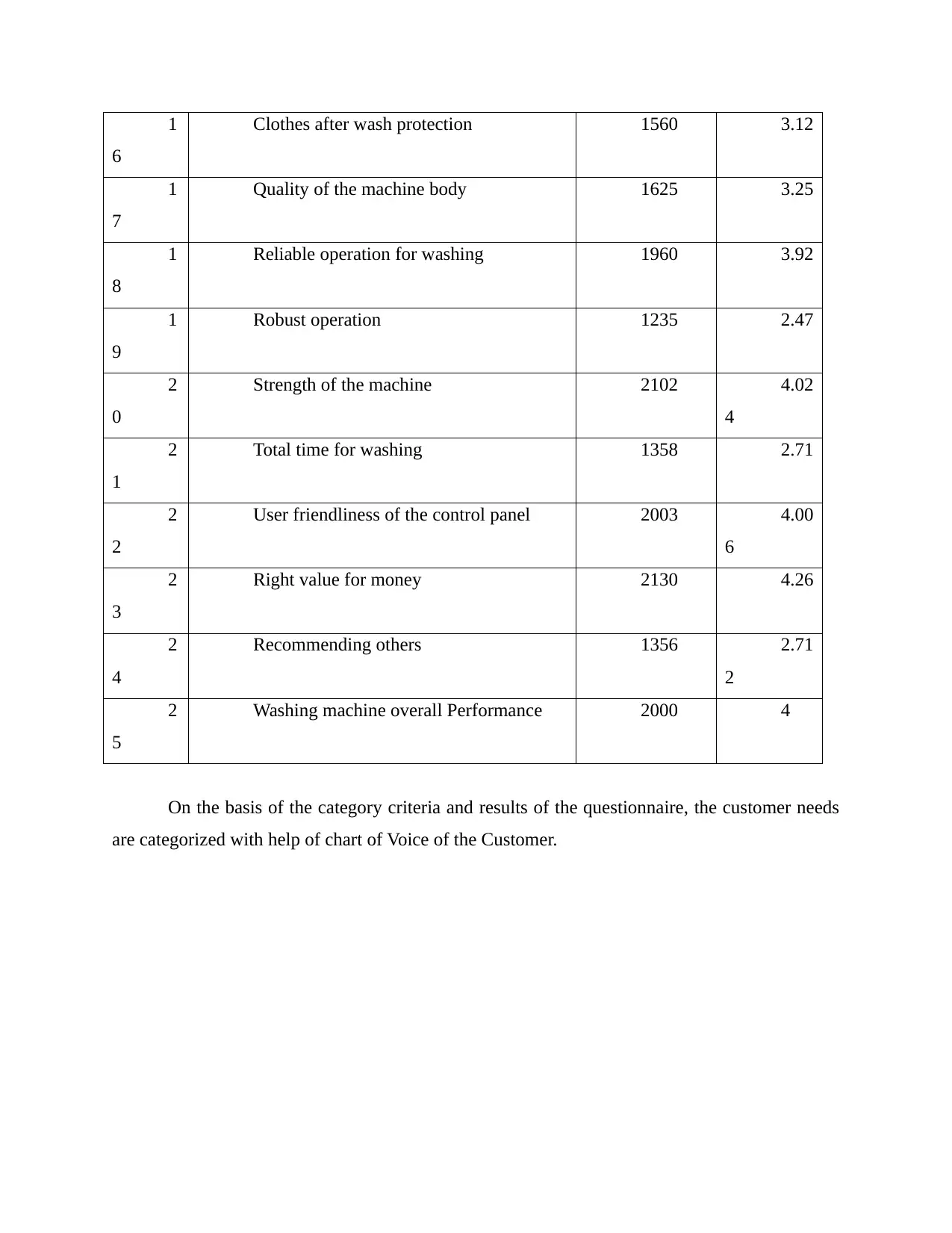
1
6
Clothes after wash protection 1560 3.12
1
7
Quality of the machine body 1625 3.25
1
8
Reliable operation for washing 1960 3.92
1
9
Robust operation 1235 2.47
2
0
Strength of the machine 2102 4.02
4
2
1
Total time for washing 1358 2.71
2
2
User friendliness of the control panel 2003 4.00
6
2
3
Right value for money 2130 4.26
2
4
Recommending others 1356 2.71
2
2
5
Washing machine overall Performance 2000 4
On the basis of the category criteria and results of the questionnaire, the customer needs
are categorized with help of chart of Voice of the Customer.
6
Clothes after wash protection 1560 3.12
1
7
Quality of the machine body 1625 3.25
1
8
Reliable operation for washing 1960 3.92
1
9
Robust operation 1235 2.47
2
0
Strength of the machine 2102 4.02
4
2
1
Total time for washing 1358 2.71
2
2
User friendliness of the control panel 2003 4.00
6
2
3
Right value for money 2130 4.26
2
4
Recommending others 1356 2.71
2
2
5
Washing machine overall Performance 2000 4
On the basis of the category criteria and results of the questionnaire, the customer needs
are categorized with help of chart of Voice of the Customer.
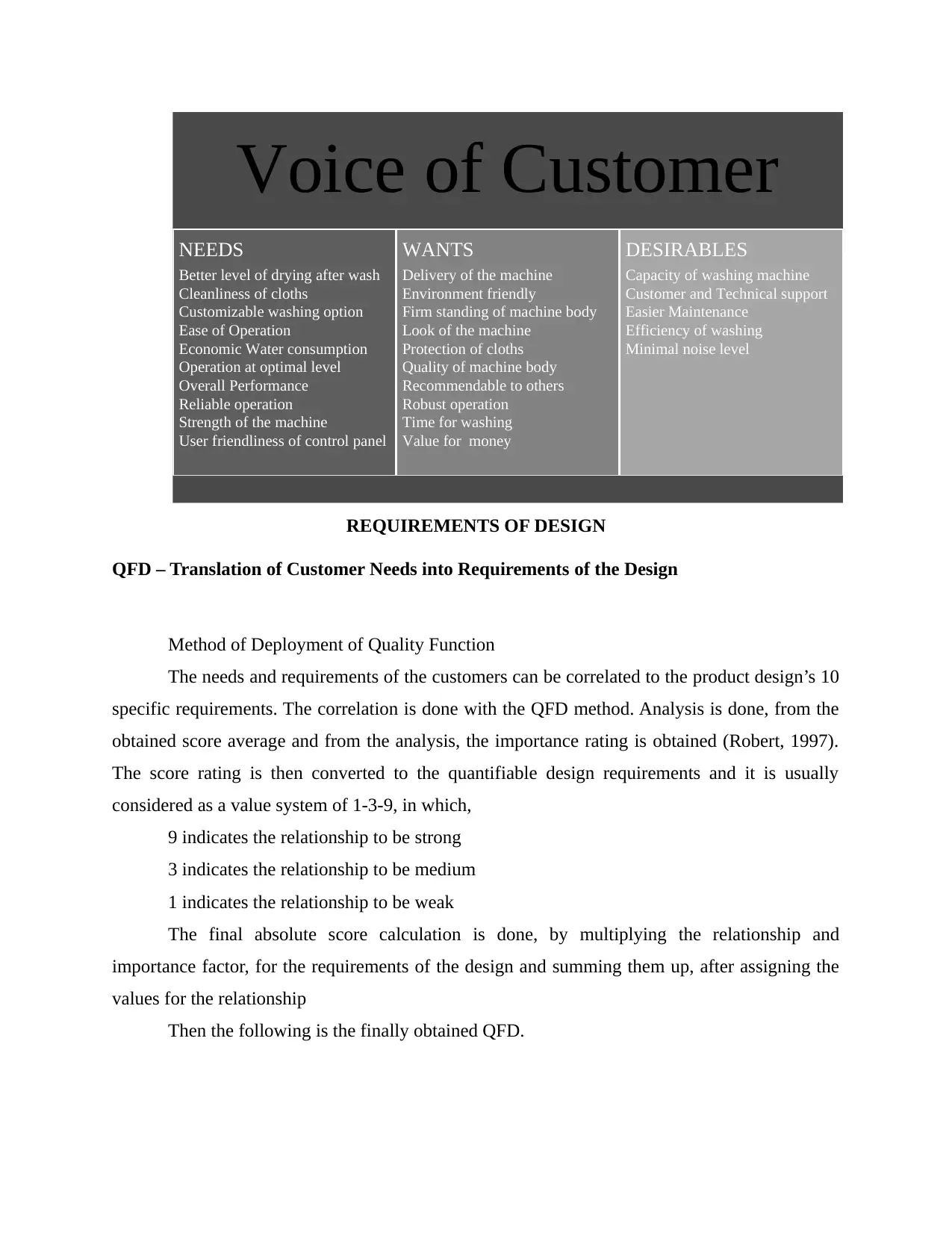
REQUIREMENTS OF DESIGN
QFD – Translation of Customer Needs into Requirements of the Design
Method of Deployment of Quality Function
The needs and requirements of the customers can be correlated to the product design’s 10
specific requirements. The correlation is done with the QFD method. Analysis is done, from the
obtained score average and from the analysis, the importance rating is obtained (Robert, 1997).
The score rating is then converted to the quantifiable design requirements and it is usually
considered as a value system of 1-3-9, in which,
9 indicates the relationship to be strong
3 indicates the relationship to be medium
1 indicates the relationship to be weak
The final absolute score calculation is done, by multiplying the relationship and
importance factor, for the requirements of the design and summing them up, after assigning the
values for the relationship
Then the following is the finally obtained QFD.
Voice of Customer
NEEDS
Better level of drying after wash
Cleanliness of cloths
Customizable washing option
Ease of Operation
Economic Water consumption
Operation at optimal level
Overall Performance
Reliable operation
Strength of the machine
User friendliness of control panel
WANTS
Delivery of the machine
Environment friendly
Firm standing of machine body
Look of the machine
Protection of cloths
Quality of machine body
Recommendable to others
Robust operation
Time for washing
Value for money
DESIRABLES
Capacity of washing machine
Customer and Technical support
Easier Maintenance
Efficiency of washing
Minimal noise level
QFD – Translation of Customer Needs into Requirements of the Design
Method of Deployment of Quality Function
The needs and requirements of the customers can be correlated to the product design’s 10
specific requirements. The correlation is done with the QFD method. Analysis is done, from the
obtained score average and from the analysis, the importance rating is obtained (Robert, 1997).
The score rating is then converted to the quantifiable design requirements and it is usually
considered as a value system of 1-3-9, in which,
9 indicates the relationship to be strong
3 indicates the relationship to be medium
1 indicates the relationship to be weak
The final absolute score calculation is done, by multiplying the relationship and
importance factor, for the requirements of the design and summing them up, after assigning the
values for the relationship
Then the following is the finally obtained QFD.
Voice of Customer
NEEDS
Better level of drying after wash
Cleanliness of cloths
Customizable washing option
Ease of Operation
Economic Water consumption
Operation at optimal level
Overall Performance
Reliable operation
Strength of the machine
User friendliness of control panel
WANTS
Delivery of the machine
Environment friendly
Firm standing of machine body
Look of the machine
Protection of cloths
Quality of machine body
Recommendable to others
Robust operation
Time for washing
Value for money
DESIRABLES
Capacity of washing machine
Customer and Technical support
Easier Maintenance
Efficiency of washing
Minimal noise level
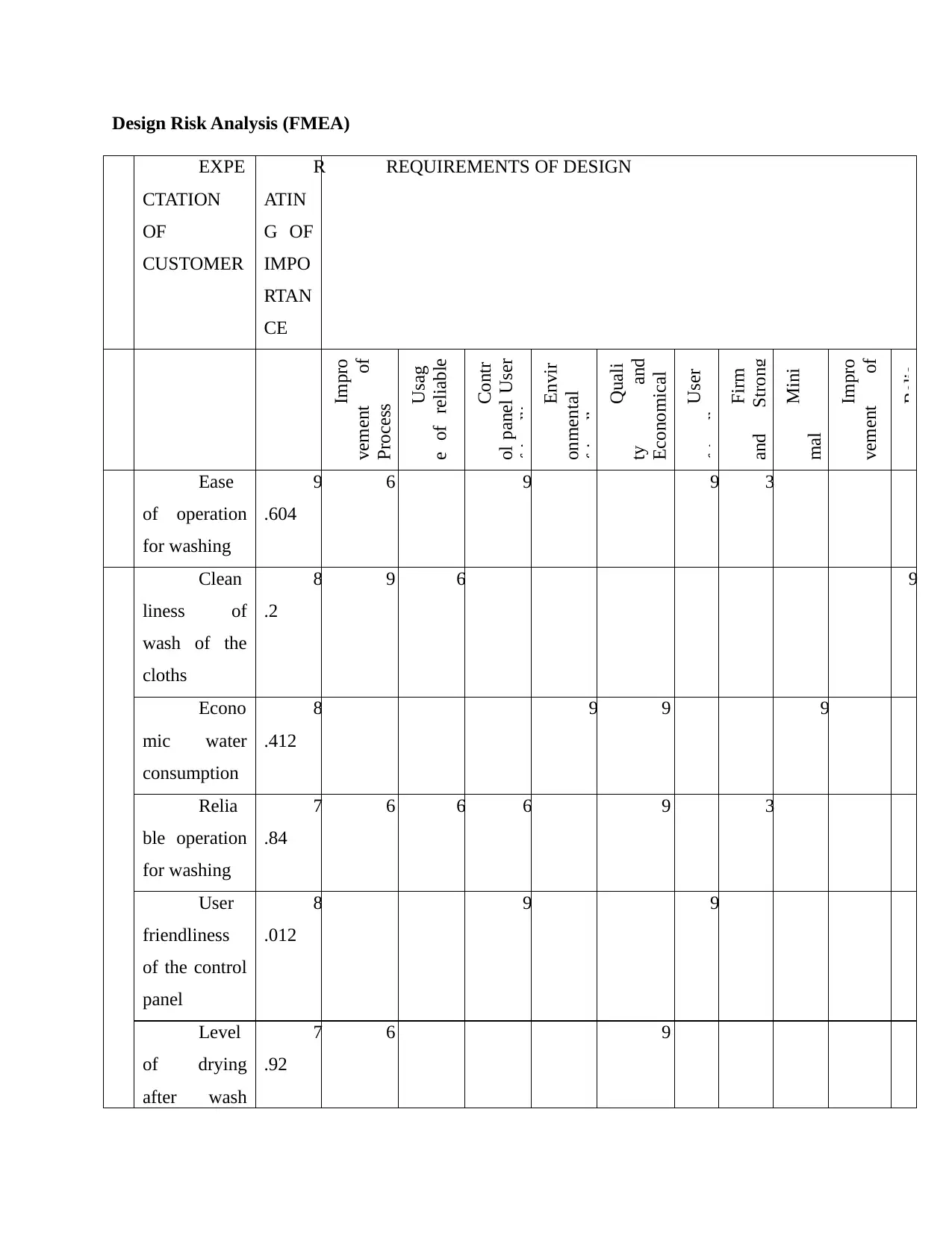
Design Risk Analysis (FMEA)
EXPE
CTATION
OF
CUSTOMER
R
ATIN
G OF
IMPO
RTAN
CE
REQUIREMENTS OF DESIGN
Impro
vement of
Process
Usag
e of reliable
components
Contr
ol panel User
friendliness
Envir
onmental
friendly
Quali
ty and
Economical
User
friendly
Firm
and Strong
Mini
mal
Impro
vement of
Customer
Relia
Ease
of operation
for washing
9
.604
6 9 9 3
Clean
liness of
wash of the
cloths
8
.2
9 6 9
Econo
mic water
consumption
8
.412
9 9 9
Relia
ble operation
for washing
7
.84
6 6 6 9 3
User
friendliness
of the control
panel
8
.012
9 9
Level
of drying
after wash
7
.92
6 9
EXPE
CTATION
OF
CUSTOMER
R
ATIN
G OF
IMPO
RTAN
CE
REQUIREMENTS OF DESIGN
Impro
vement of
Process
Usag
e of reliable
components
Contr
ol panel User
friendliness
Envir
onmental
friendly
Quali
ty and
Economical
User
friendly
Firm
and Strong
Mini
mal
Impro
vement of
Customer
Relia
Ease
of operation
for washing
9
.604
6 9 9 3
Clean
liness of
wash of the
cloths
8
.2
9 6 9
Econo
mic water
consumption
8
.412
9 9 9
Relia
ble operation
for washing
7
.84
6 6 6 9 3
User
friendliness
of the control
panel
8
.012
9 9
Level
of drying
after wash
7
.92
6 9
Paraphrase This Document
Need a fresh take? Get an instant paraphrase of this document with our AI Paraphraser
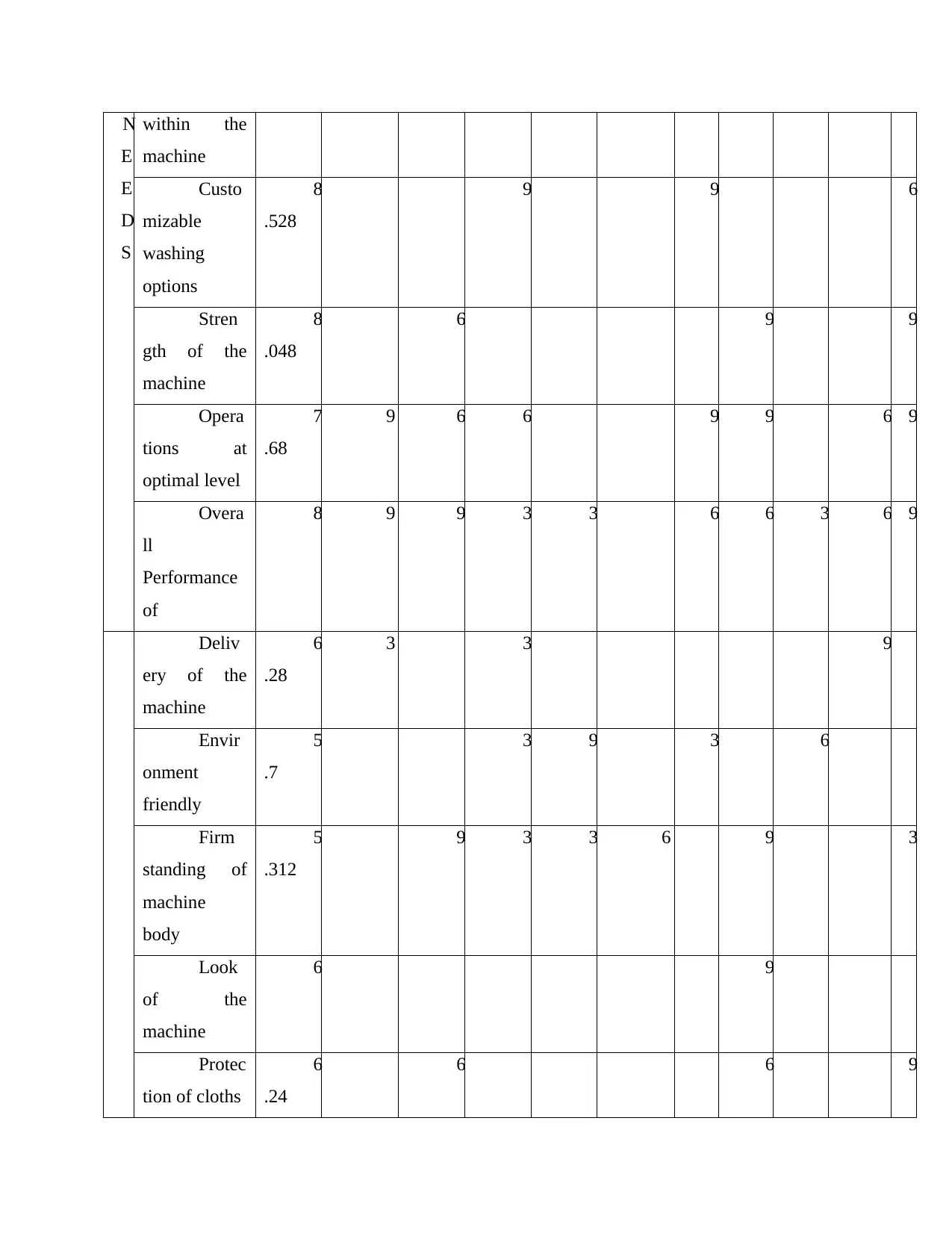
N
E
E
D
S
within the
machine
Custo
mizable
washing
options
8
.528
9 9 6
Stren
gth of the
machine
8
.048
6 9 9
Opera
tions at
optimal level
7
.68
9 6 6 9 9 6 9
Overa
ll
Performance
of
8 9 9 3 3 6 6 3 6 9
Deliv
ery of the
machine
6
.28
3 3 9
Envir
onment
friendly
5
.7
3 9 3 6
Firm
standing of
machine
body
5
.312
9 3 3 6 9 3
Look
of the
machine
6 9
Protec
tion of cloths
6
.24
6 6 9
E
E
D
S
within the
machine
Custo
mizable
washing
options
8
.528
9 9 6
Stren
gth of the
machine
8
.048
6 9 9
Opera
tions at
optimal level
7
.68
9 6 6 9 9 6 9
Overa
ll
Performance
of
8 9 9 3 3 6 6 3 6 9
Deliv
ery of the
machine
6
.28
3 3 9
Envir
onment
friendly
5
.7
3 9 3 6
Firm
standing of
machine
body
5
.312
9 3 3 6 9 3
Look
of the
machine
6 9
Protec
tion of cloths
6
.24
6 6 9
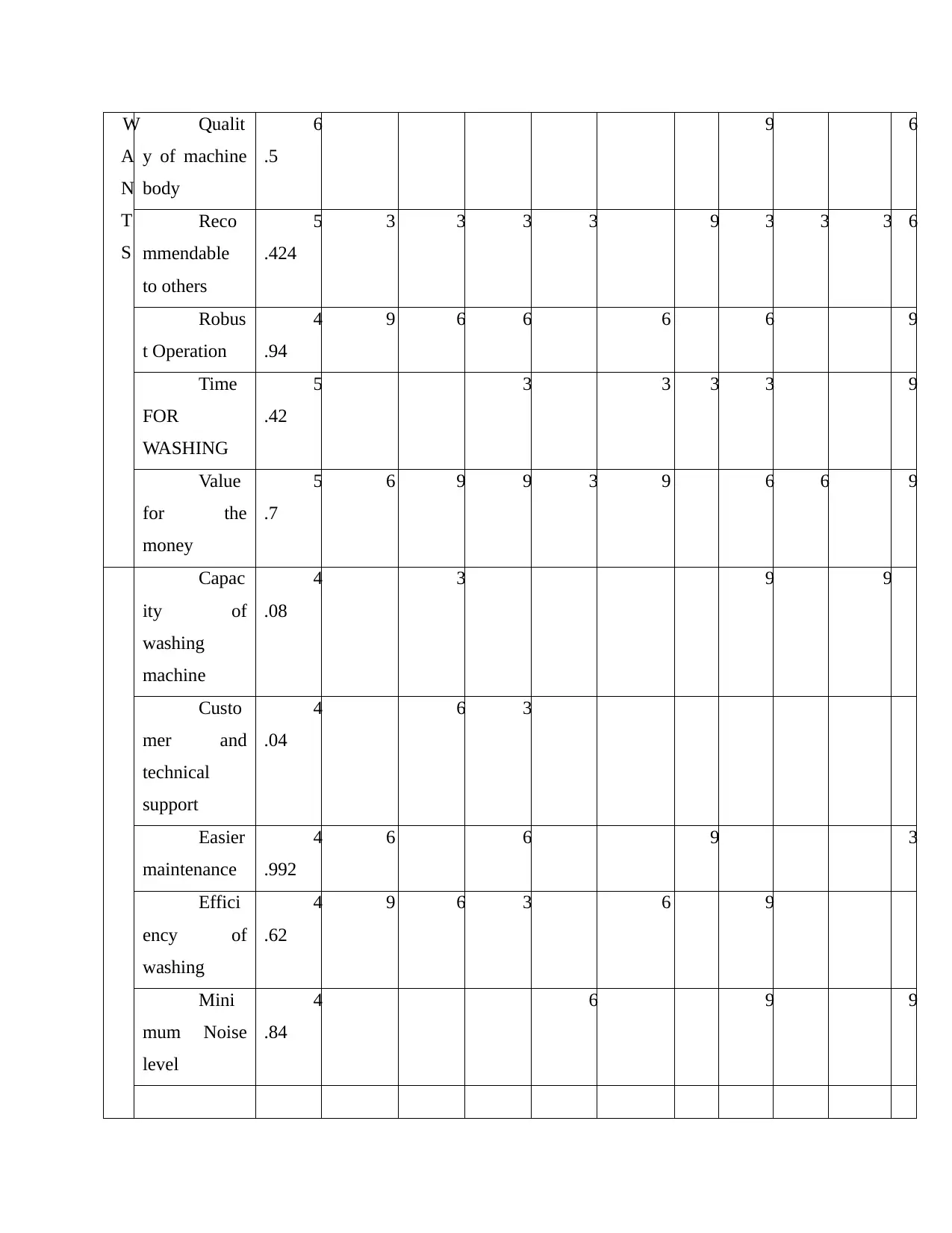
W
A
N
T
S
Qualit
y of machine
body
6
.5
9 6
Reco
mmendable
to others
5
.424
3 3 3 3 9 3 3 3 6
Robus
t Operation
4
.94
9 6 6 6 6 9
Time
FOR
WASHING
5
.42
3 3 3 3 9
Value
for the
money
5
.7
6 9 9 3 9 6 6 9
DESIRABLES
Capac
ity of
washing
machine
4
.08
3 9 9
Custo
mer and
technical
support
4
.04
6 3
Easier
maintenance
4
.992
6 6 9 3
Effici
ency of
washing
4
.62
9 6 3 6 9
Mini
mum Noise
level
4
.84
6 9 9
A
N
T
S
Qualit
y of machine
body
6
.5
9 6
Reco
mmendable
to others
5
.424
3 3 3 3 9 3 3 3 6
Robus
t Operation
4
.94
9 6 6 6 6 9
Time
FOR
WASHING
5
.42
3 3 3 3 9
Value
for the
money
5
.7
6 9 9 3 9 6 6 9
DESIRABLES
Capac
ity of
washing
machine
4
.08
3 9 9
Custo
mer and
technical
support
4
.04
6 3
Easier
maintenance
4
.992
6 6 9 3
Effici
ency of
washing
4
.62
9 6 3 6 9
Mini
mum Noise
level
4
.84
6 9 9
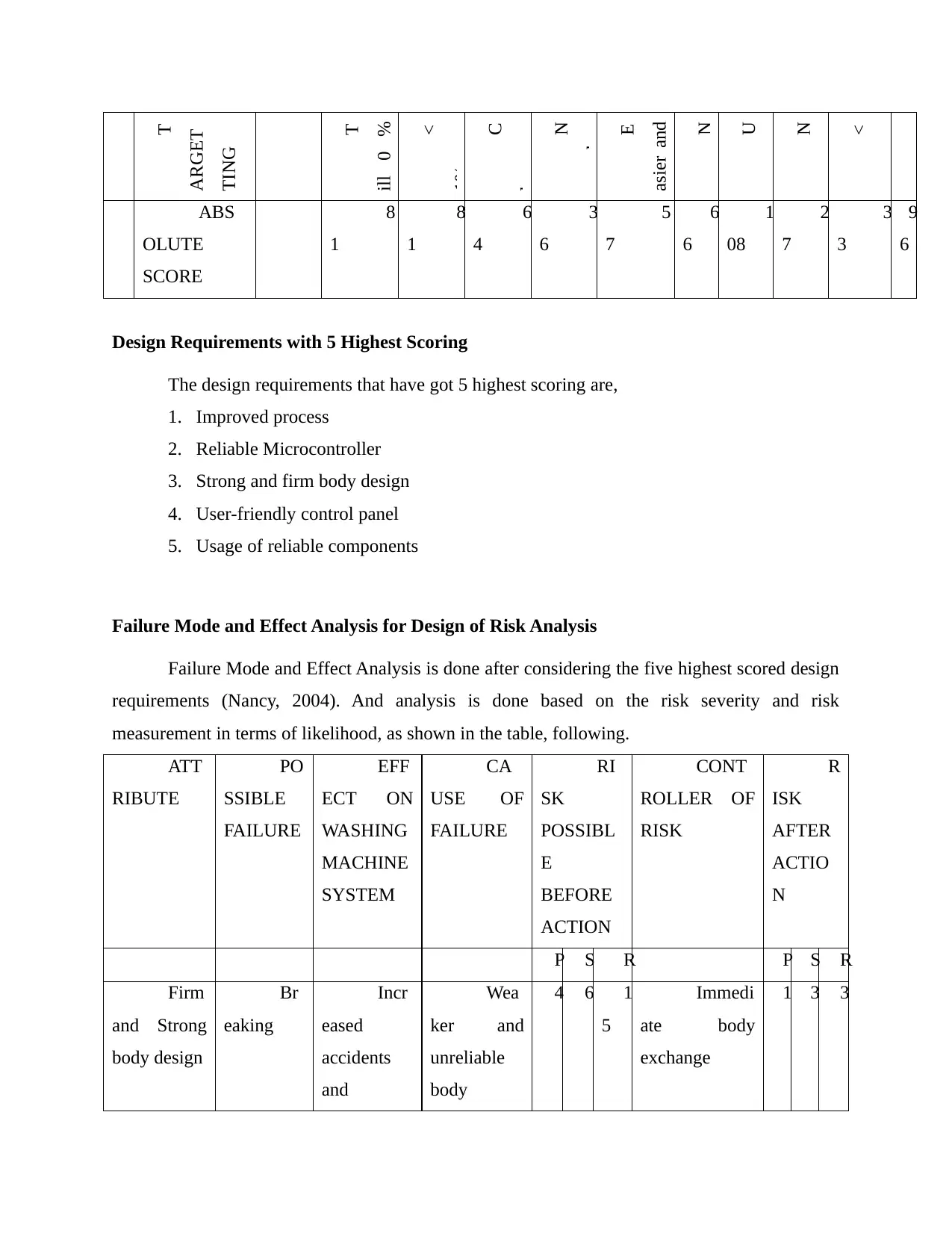
T
ARGET
TING
VALUE
T
ill 0 %
<
1%
C
lear
N
o carbon
E
asier and
N
U
nbreakab
N
ot more
<
5%
ABS
OLUTE
SCORE
8
1
8
1
6
4
3
6
5
7
6
6
1
08
2
7
3
3
9
6
Design Requirements with 5 Highest Scoring
The design requirements that have got 5 highest scoring are,
1. Improved process
2. Reliable Microcontroller
3. Strong and firm body design
4. User-friendly control panel
5. Usage of reliable components
Failure Mode and Effect Analysis for Design of Risk Analysis
Failure Mode and Effect Analysis is done after considering the five highest scored design
requirements (Nancy, 2004). And analysis is done based on the risk severity and risk
measurement in terms of likelihood, as shown in the table, following.
ATT
RIBUTE
PO
SSIBLE
FAILURE
EFF
ECT ON
WASHING
MACHINE
SYSTEM
CA
USE OF
FAILURE
RI
SK
POSSIBL
E
BEFORE
ACTION
CONT
ROLLER OF
RISK
R
ISK
AFTER
ACTIO
N
P S R P S R
Firm
and Strong
body design
Br
eaking
Incr
eased
accidents
and
Wea
ker and
unreliable
body
4 6 1
5
Immedi
ate body
exchange
1 3 3
ARGET
TING
VALUE
T
ill 0 %
<
1%
C
lear
N
o carbon
E
asier and
N
U
nbreakab
N
ot more
<
5%
ABS
OLUTE
SCORE
8
1
8
1
6
4
3
6
5
7
6
6
1
08
2
7
3
3
9
6
Design Requirements with 5 Highest Scoring
The design requirements that have got 5 highest scoring are,
1. Improved process
2. Reliable Microcontroller
3. Strong and firm body design
4. User-friendly control panel
5. Usage of reliable components
Failure Mode and Effect Analysis for Design of Risk Analysis
Failure Mode and Effect Analysis is done after considering the five highest scored design
requirements (Nancy, 2004). And analysis is done based on the risk severity and risk
measurement in terms of likelihood, as shown in the table, following.
ATT
RIBUTE
PO
SSIBLE
FAILURE
EFF
ECT ON
WASHING
MACHINE
SYSTEM
CA
USE OF
FAILURE
RI
SK
POSSIBL
E
BEFORE
ACTION
CONT
ROLLER OF
RISK
R
ISK
AFTER
ACTIO
N
P S R P S R
Firm
and Strong
body design
Br
eaking
Incr
eased
accidents
and
Wea
ker and
unreliable
body
4 6 1
5
Immedi
ate body
exchange
1 3 3
Secure Best Marks with AI Grader
Need help grading? Try our AI Grader for instant feedback on your assignments.
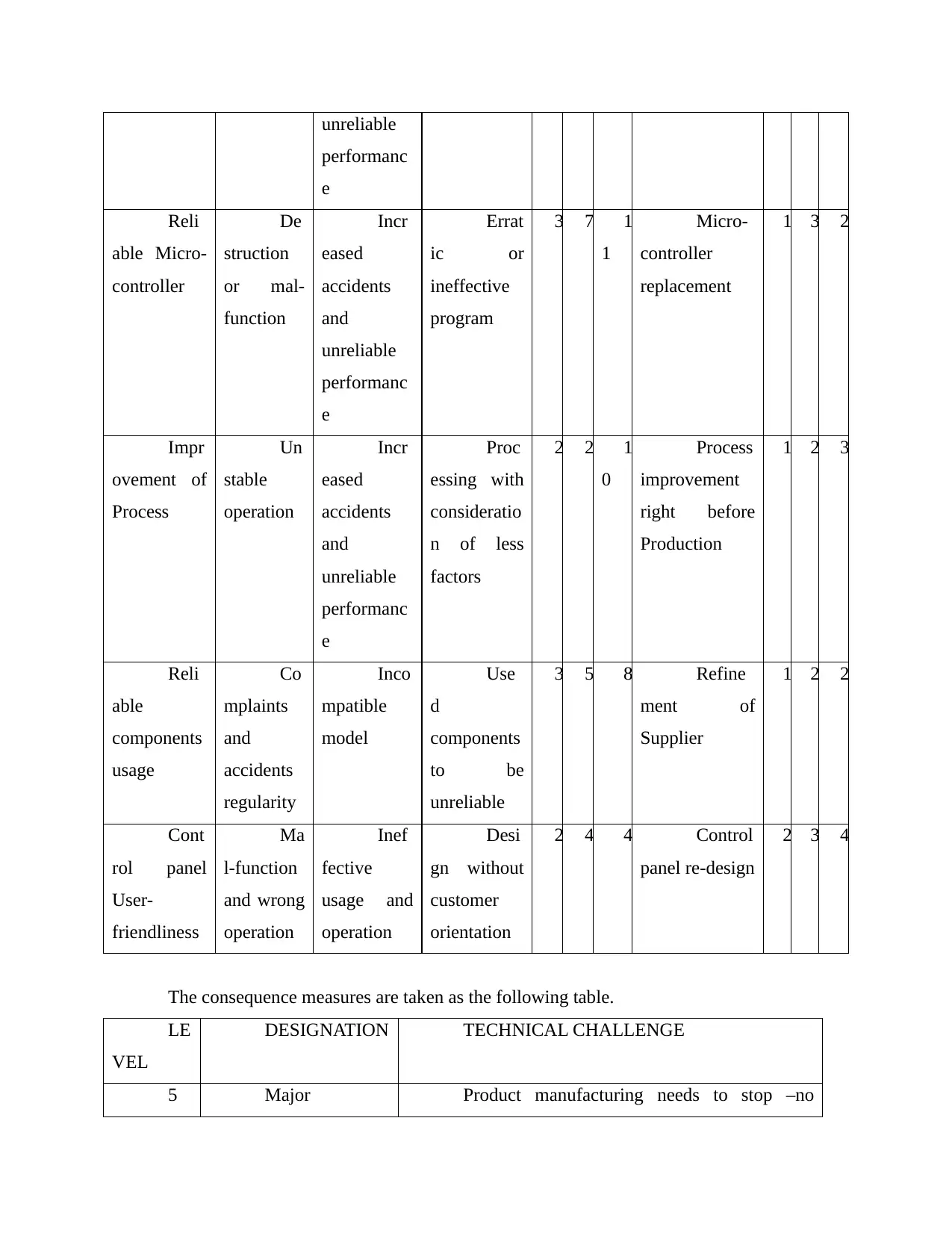
unreliable
performanc
e
Reli
able Micro-
controller
De
struction
or mal-
function
Incr
eased
accidents
and
unreliable
performanc
e
Errat
ic or
ineffective
program
3 7 1
1
Micro-
controller
replacement
1 3 2
Impr
ovement of
Process
Un
stable
operation
Incr
eased
accidents
and
unreliable
performanc
e
Proc
essing with
consideratio
n of less
factors
2 2 1
0
Process
improvement
right before
Production
1 2 3
Reli
able
components
usage
Co
mplaints
and
accidents
regularity
Inco
mpatible
model
Use
d
components
to be
unreliable
3 5 8 Refine
ment of
Supplier
1 2 2
Cont
rol panel
User-
friendliness
Ma
l-function
and wrong
operation
Inef
fective
usage and
operation
Desi
gn without
customer
orientation
2 4 4 Control
panel re-design
2 3 4
The consequence measures are taken as the following table.
LE
VEL
DESIGNATION TECHNICAL CHALLENGE
5 Major Product manufacturing needs to stop –no
performanc
e
Reli
able Micro-
controller
De
struction
or mal-
function
Incr
eased
accidents
and
unreliable
performanc
e
Errat
ic or
ineffective
program
3 7 1
1
Micro-
controller
replacement
1 3 2
Impr
ovement of
Process
Un
stable
operation
Incr
eased
accidents
and
unreliable
performanc
e
Proc
essing with
consideratio
n of less
factors
2 2 1
0
Process
improvement
right before
Production
1 2 3
Reli
able
components
usage
Co
mplaints
and
accidents
regularity
Inco
mpatible
model
Use
d
components
to be
unreliable
3 5 8 Refine
ment of
Supplier
1 2 2
Cont
rol panel
User-
friendliness
Ma
l-function
and wrong
operation
Inef
fective
usage and
operation
Desi
gn without
customer
orientation
2 4 4 Control
panel re-design
2 3 4
The consequence measures are taken as the following table.
LE
VEL
DESIGNATION TECHNICAL CHALLENGE
5 Major Product manufacturing needs to stop –no
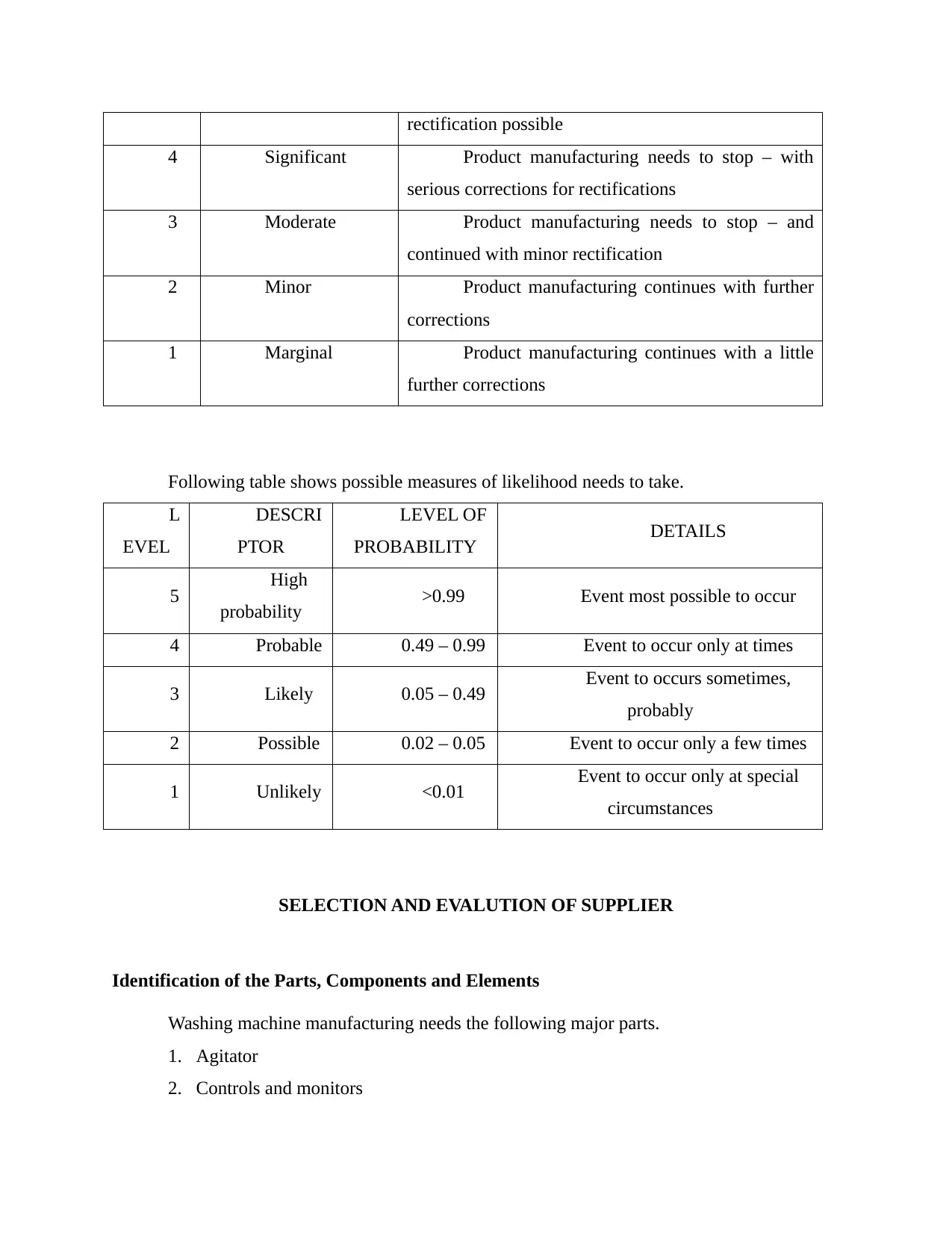
rectification possible
4 Significant Product manufacturing needs to stop – with
serious corrections for rectifications
3 Moderate Product manufacturing needs to stop – and
continued with minor rectification
2 Minor Product manufacturing continues with further
corrections
1 Marginal Product manufacturing continues with a little
further corrections
Following table shows possible measures of likelihood needs to take.
L
EVEL
DESCRI
PTOR
LEVEL OF
PROBABILITY DETAILS
5 High
probability >0.99 Event most possible to occur
4 Probable 0.49 – 0.99 Event to occur only at times
3 Likely 0.05 – 0.49 Event to occurs sometimes,
probably
2 Possible 0.02 – 0.05 Event to occur only a few times
1 Unlikely <0.01 Event to occur only at special
circumstances
SELECTION AND EVALUTION OF SUPPLIER
Identification of the Parts, Components and Elements
Washing machine manufacturing needs the following major parts.
1. Agitator
2. Controls and monitors
4 Significant Product manufacturing needs to stop – with
serious corrections for rectifications
3 Moderate Product manufacturing needs to stop – and
continued with minor rectification
2 Minor Product manufacturing continues with further
corrections
1 Marginal Product manufacturing continues with a little
further corrections
Following table shows possible measures of likelihood needs to take.
L
EVEL
DESCRI
PTOR
LEVEL OF
PROBABILITY DETAILS
5 High
probability >0.99 Event most possible to occur
4 Probable 0.49 – 0.99 Event to occur only at times
3 Likely 0.05 – 0.49 Event to occurs sometimes,
probably
2 Possible 0.02 – 0.05 Event to occur only a few times
1 Unlikely <0.01 Event to occur only at special
circumstances
SELECTION AND EVALUTION OF SUPPLIER
Identification of the Parts, Components and Elements
Washing machine manufacturing needs the following major parts.
1. Agitator
2. Controls and monitors

3. Drum
4. Drum hose
5. External body
6. Levelling feet
7. Lid
8. Lid switch
9. Motor
10. Power supply
11. Standpipe
12. Water inlet valve
13. Water Pump
14. Water supply hose
Sourcing Parts, Components or Sections from Supplier – 10 Major
Among the above fourteen components, parts and sections used for manufacturing, the
following 10 are supplied and sourced from the suppliers.
1. Agitator
2. Controls and monitors
3. Drum
4. External body
5. Hose for Drum and water supply
6. Lid and switch
7. Motor
8. Power supply
9. Water inlet valve
10. Water Pump
Supplier Selection Criteria Development
Housing of the machine has to be done in a body machine made of steel.
Supplier Selection System Construction and Usage
The supplier selection is done according to the following criteria.
4. Drum hose
5. External body
6. Levelling feet
7. Lid
8. Lid switch
9. Motor
10. Power supply
11. Standpipe
12. Water inlet valve
13. Water Pump
14. Water supply hose
Sourcing Parts, Components or Sections from Supplier – 10 Major
Among the above fourteen components, parts and sections used for manufacturing, the
following 10 are supplied and sourced from the suppliers.
1. Agitator
2. Controls and monitors
3. Drum
4. External body
5. Hose for Drum and water supply
6. Lid and switch
7. Motor
8. Power supply
9. Water inlet valve
10. Water Pump
Supplier Selection Criteria Development
Housing of the machine has to be done in a body machine made of steel.
Supplier Selection System Construction and Usage
The supplier selection is done according to the following criteria.
Paraphrase This Document
Need a fresh take? Get an instant paraphrase of this document with our AI Paraphraser
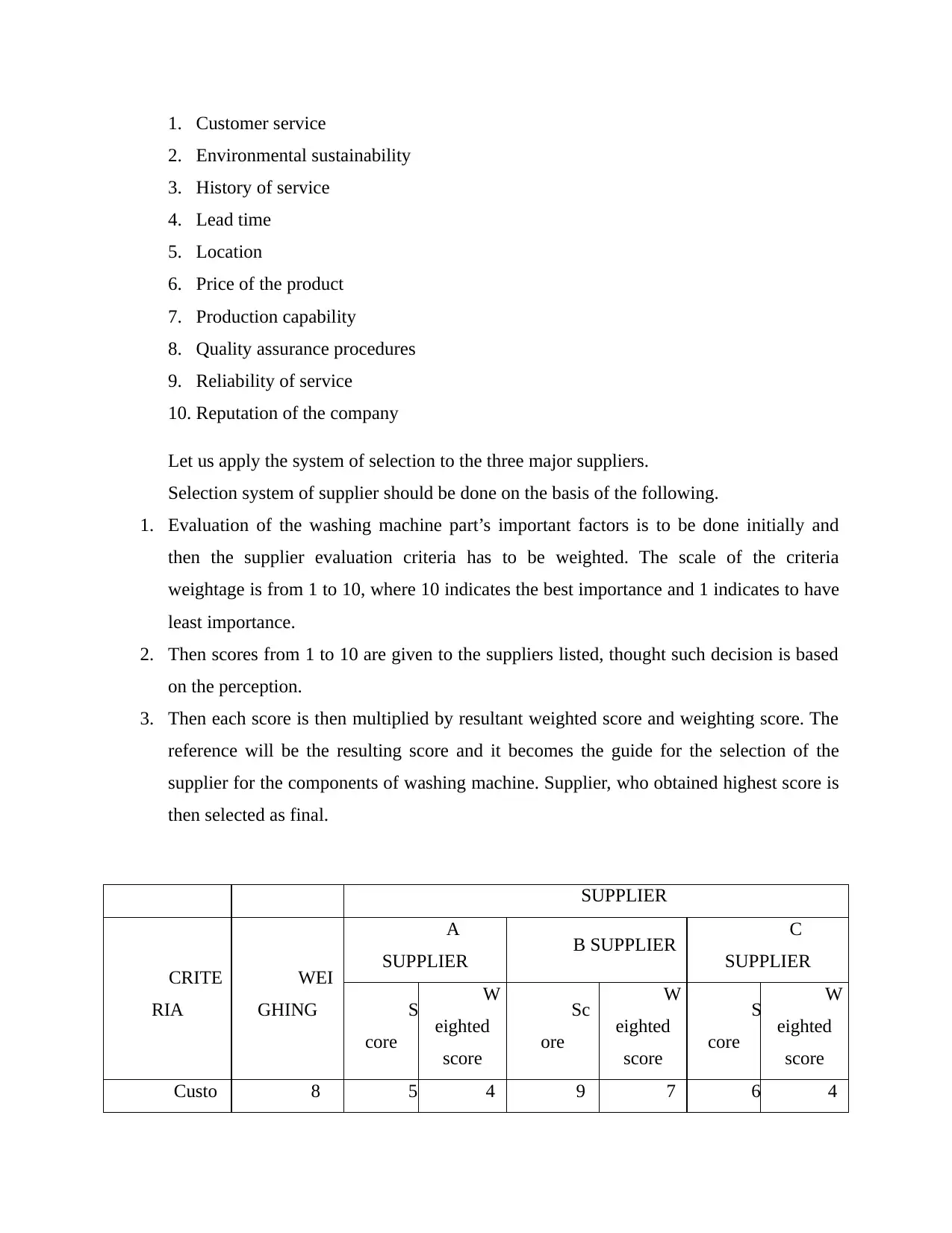
1. Customer service
2. Environmental sustainability
3. History of service
4. Lead time
5. Location
6. Price of the product
7. Production capability
8. Quality assurance procedures
9. Reliability of service
10. Reputation of the company
Let us apply the system of selection to the three major suppliers.
Selection system of supplier should be done on the basis of the following.
1. Evaluation of the washing machine part’s important factors is to be done initially and
then the supplier evaluation criteria has to be weighted. The scale of the criteria
weightage is from 1 to 10, where 10 indicates the best importance and 1 indicates to have
least importance.
2. Then scores from 1 to 10 are given to the suppliers listed, thought such decision is based
on the perception.
3. Then each score is then multiplied by resultant weighted score and weighting score. The
reference will be the resulting score and it becomes the guide for the selection of the
supplier for the components of washing machine. Supplier, who obtained highest score is
then selected as final.
SUPPLIER
CRITE
RIA
WEI
GHING
A
SUPPLIER B SUPPLIER C
SUPPLIER
S
core
W
eighted
score
Sc
ore
W
eighted
score
S
core
W
eighted
score
Custo 8 5 4 9 7 6 4
2. Environmental sustainability
3. History of service
4. Lead time
5. Location
6. Price of the product
7. Production capability
8. Quality assurance procedures
9. Reliability of service
10. Reputation of the company
Let us apply the system of selection to the three major suppliers.
Selection system of supplier should be done on the basis of the following.
1. Evaluation of the washing machine part’s important factors is to be done initially and
then the supplier evaluation criteria has to be weighted. The scale of the criteria
weightage is from 1 to 10, where 10 indicates the best importance and 1 indicates to have
least importance.
2. Then scores from 1 to 10 are given to the suppliers listed, thought such decision is based
on the perception.
3. Then each score is then multiplied by resultant weighted score and weighting score. The
reference will be the resulting score and it becomes the guide for the selection of the
supplier for the components of washing machine. Supplier, who obtained highest score is
then selected as final.
SUPPLIER
CRITE
RIA
WEI
GHING
A
SUPPLIER B SUPPLIER C
SUPPLIER
S
core
W
eighted
score
Sc
ore
W
eighted
score
S
core
W
eighted
score
Custo 8 5 4 9 7 6 4
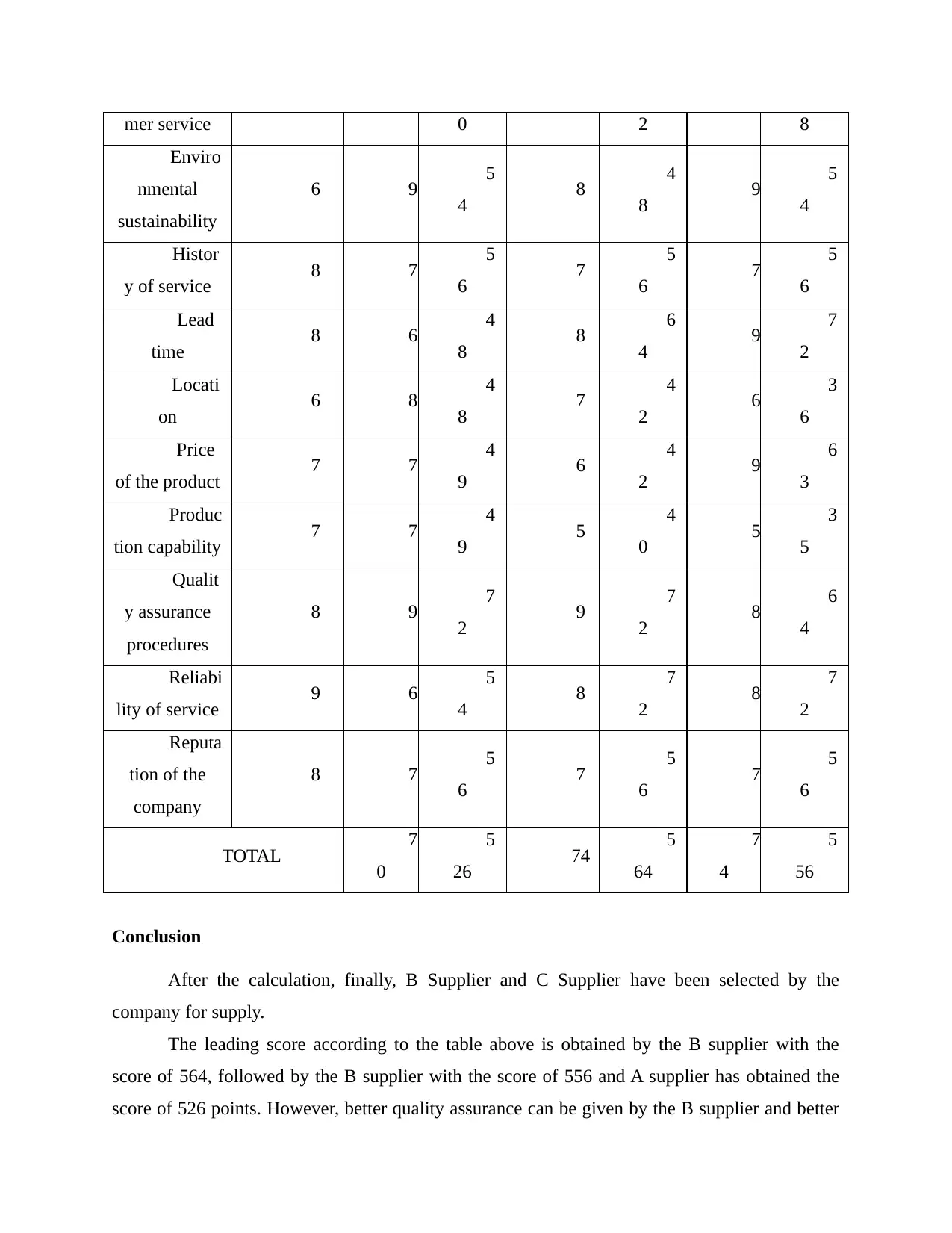
mer service 0 2 8
Enviro
nmental
sustainability
6 9 5
4 8 4
8 9 5
4
Histor
y of service 8 7 5
6 7 5
6 7 5
6
Lead
time 8 6 4
8 8 6
4 9 7
2
Locati
on 6 8 4
8 7 4
2 6 3
6
Price
of the product 7 7 4
9 6 4
2 9 6
3
Produc
tion capability 7 7 4
9 5 4
0 5 3
5
Qualit
y assurance
procedures
8 9 7
2 9 7
2 8 6
4
Reliabi
lity of service 9 6 5
4 8 7
2 8 7
2
Reputa
tion of the
company
8 7 5
6 7 5
6 7 5
6
TOTAL 7
0
5
26 74 5
64
7
4
5
56
Conclusion
After the calculation, finally, B Supplier and C Supplier have been selected by the
company for supply.
The leading score according to the table above is obtained by the B supplier with the
score of 564, followed by the B supplier with the score of 556 and A supplier has obtained the
score of 526 points. However, better quality assurance can be given by the B supplier and better
Enviro
nmental
sustainability
6 9 5
4 8 4
8 9 5
4
Histor
y of service 8 7 5
6 7 5
6 7 5
6
Lead
time 8 6 4
8 8 6
4 9 7
2
Locati
on 6 8 4
8 7 4
2 6 3
6
Price
of the product 7 7 4
9 6 4
2 9 6
3
Produc
tion capability 7 7 4
9 5 4
0 5 3
5
Qualit
y assurance
procedures
8 9 7
2 9 7
2 8 6
4
Reliabi
lity of service 9 6 5
4 8 7
2 8 7
2
Reputa
tion of the
company
8 7 5
6 7 5
6 7 5
6
TOTAL 7
0
5
26 74 5
64
7
4
5
56
Conclusion
After the calculation, finally, B Supplier and C Supplier have been selected by the
company for supply.
The leading score according to the table above is obtained by the B supplier with the
score of 564, followed by the B supplier with the score of 556 and A supplier has obtained the
score of 526 points. However, better quality assurance can be given by the B supplier and better
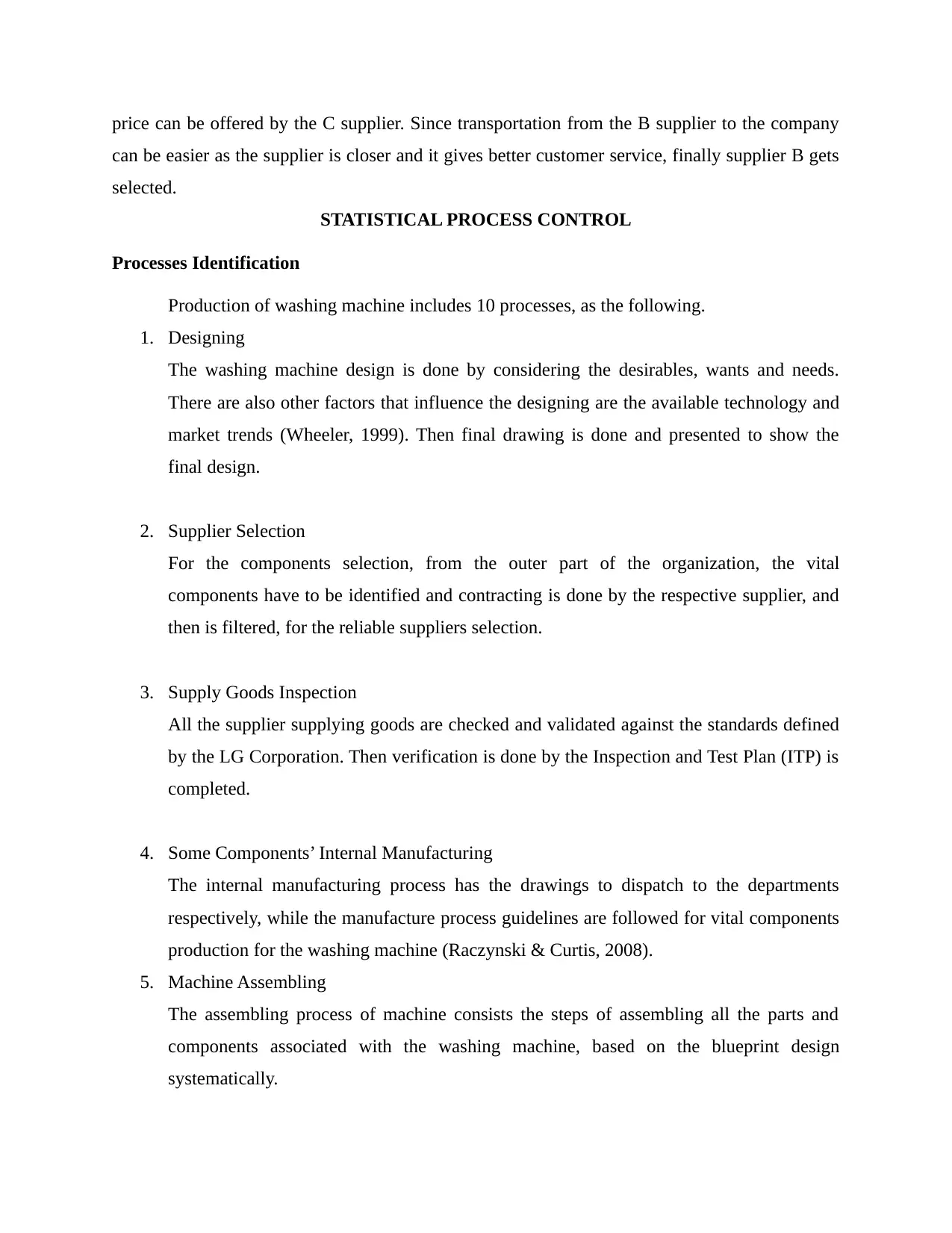
price can be offered by the C supplier. Since transportation from the B supplier to the company
can be easier as the supplier is closer and it gives better customer service, finally supplier B gets
selected.
STATISTICAL PROCESS CONTROL
Processes Identification
Production of washing machine includes 10 processes, as the following.
1. Designing
The washing machine design is done by considering the desirables, wants and needs.
There are also other factors that influence the designing are the available technology and
market trends (Wheeler, 1999). Then final drawing is done and presented to show the
final design.
2. Supplier Selection
For the components selection, from the outer part of the organization, the vital
components have to be identified and contracting is done by the respective supplier, and
then is filtered, for the reliable suppliers selection.
3. Supply Goods Inspection
All the supplier supplying goods are checked and validated against the standards defined
by the LG Corporation. Then verification is done by the Inspection and Test Plan (ITP) is
completed.
4. Some Components’ Internal Manufacturing
The internal manufacturing process has the drawings to dispatch to the departments
respectively, while the manufacture process guidelines are followed for vital components
production for the washing machine (Raczynski & Curtis, 2008).
5. Machine Assembling
The assembling process of machine consists the steps of assembling all the parts and
components associated with the washing machine, based on the blueprint design
systematically.
can be easier as the supplier is closer and it gives better customer service, finally supplier B gets
selected.
STATISTICAL PROCESS CONTROL
Processes Identification
Production of washing machine includes 10 processes, as the following.
1. Designing
The washing machine design is done by considering the desirables, wants and needs.
There are also other factors that influence the designing are the available technology and
market trends (Wheeler, 1999). Then final drawing is done and presented to show the
final design.
2. Supplier Selection
For the components selection, from the outer part of the organization, the vital
components have to be identified and contracting is done by the respective supplier, and
then is filtered, for the reliable suppliers selection.
3. Supply Goods Inspection
All the supplier supplying goods are checked and validated against the standards defined
by the LG Corporation. Then verification is done by the Inspection and Test Plan (ITP) is
completed.
4. Some Components’ Internal Manufacturing
The internal manufacturing process has the drawings to dispatch to the departments
respectively, while the manufacture process guidelines are followed for vital components
production for the washing machine (Raczynski & Curtis, 2008).
5. Machine Assembling
The assembling process of machine consists the steps of assembling all the parts and
components associated with the washing machine, based on the blueprint design
systematically.
Secure Best Marks with AI Grader
Need help grading? Try our AI Grader for instant feedback on your assignments.
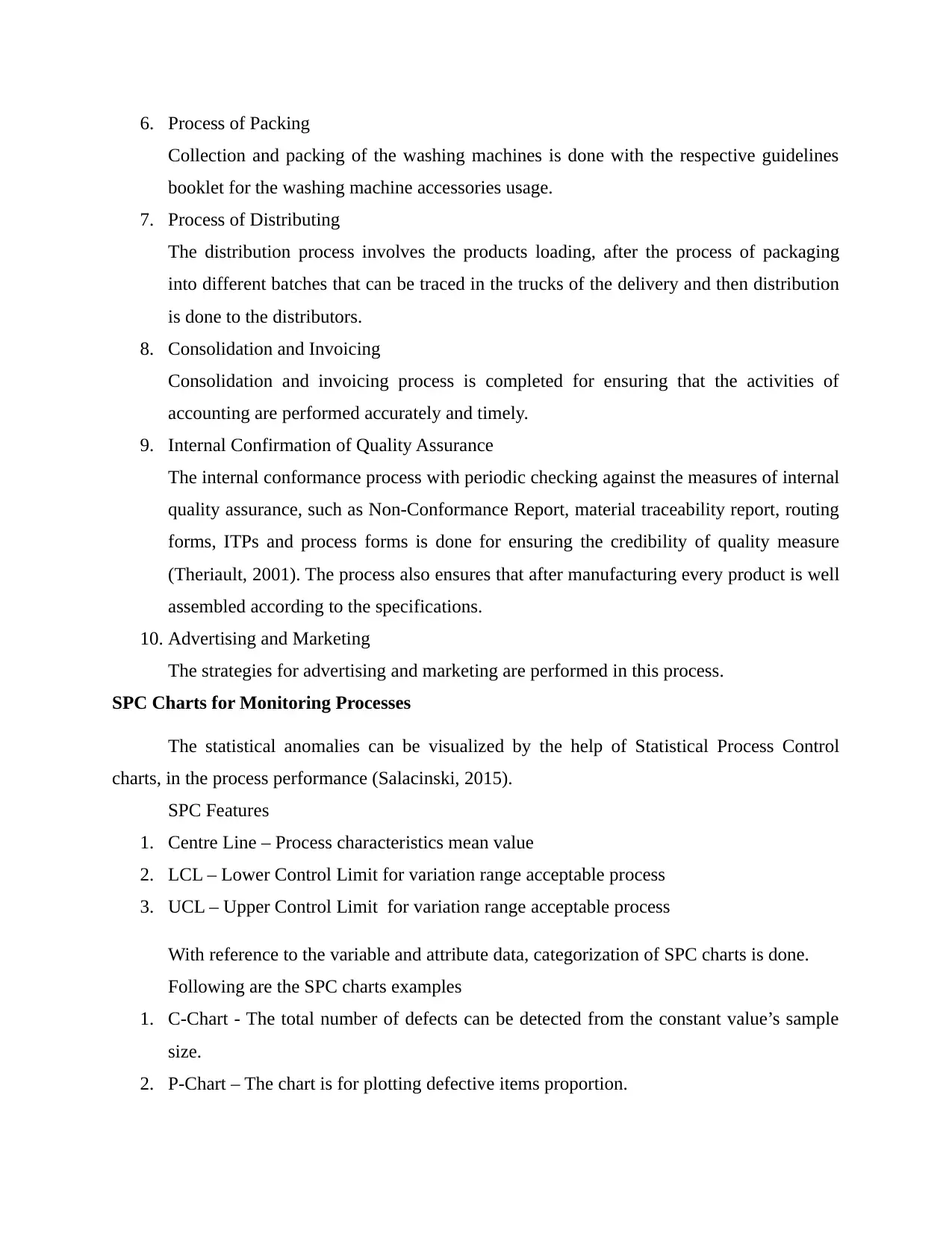
6. Process of Packing
Collection and packing of the washing machines is done with the respective guidelines
booklet for the washing machine accessories usage.
7. Process of Distributing
The distribution process involves the products loading, after the process of packaging
into different batches that can be traced in the trucks of the delivery and then distribution
is done to the distributors.
8. Consolidation and Invoicing
Consolidation and invoicing process is completed for ensuring that the activities of
accounting are performed accurately and timely.
9. Internal Confirmation of Quality Assurance
The internal conformance process with periodic checking against the measures of internal
quality assurance, such as Non-Conformance Report, material traceability report, routing
forms, ITPs and process forms is done for ensuring the credibility of quality measure
(Theriault, 2001). The process also ensures that after manufacturing every product is well
assembled according to the specifications.
10. Advertising and Marketing
The strategies for advertising and marketing are performed in this process.
SPC Charts for Monitoring Processes
The statistical anomalies can be visualized by the help of Statistical Process Control
charts, in the process performance (Salacinski, 2015).
SPC Features
1. Centre Line – Process characteristics mean value
2. LCL – Lower Control Limit for variation range acceptable process
3. UCL – Upper Control Limit for variation range acceptable process
With reference to the variable and attribute data, categorization of SPC charts is done.
Following are the SPC charts examples
1. C-Chart - The total number of defects can be detected from the constant value’s sample
size.
2. P-Chart – The chart is for plotting defective items proportion.
Collection and packing of the washing machines is done with the respective guidelines
booklet for the washing machine accessories usage.
7. Process of Distributing
The distribution process involves the products loading, after the process of packaging
into different batches that can be traced in the trucks of the delivery and then distribution
is done to the distributors.
8. Consolidation and Invoicing
Consolidation and invoicing process is completed for ensuring that the activities of
accounting are performed accurately and timely.
9. Internal Confirmation of Quality Assurance
The internal conformance process with periodic checking against the measures of internal
quality assurance, such as Non-Conformance Report, material traceability report, routing
forms, ITPs and process forms is done for ensuring the credibility of quality measure
(Theriault, 2001). The process also ensures that after manufacturing every product is well
assembled according to the specifications.
10. Advertising and Marketing
The strategies for advertising and marketing are performed in this process.
SPC Charts for Monitoring Processes
The statistical anomalies can be visualized by the help of Statistical Process Control
charts, in the process performance (Salacinski, 2015).
SPC Features
1. Centre Line – Process characteristics mean value
2. LCL – Lower Control Limit for variation range acceptable process
3. UCL – Upper Control Limit for variation range acceptable process
With reference to the variable and attribute data, categorization of SPC charts is done.
Following are the SPC charts examples
1. C-Chart - The total number of defects can be detected from the constant value’s sample
size.
2. P-Chart – The chart is for plotting defective items proportion.
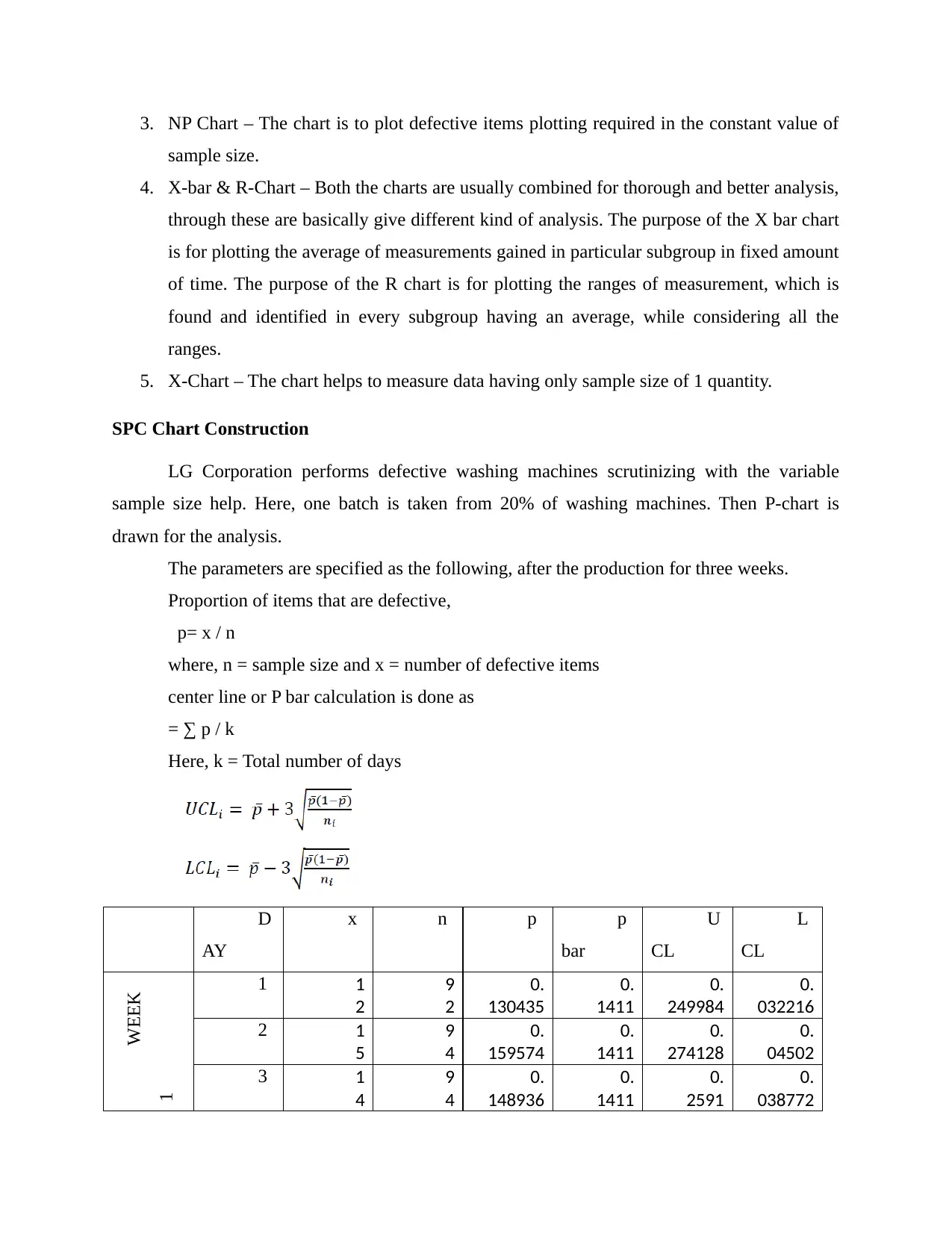
3. NP Chart – The chart is to plot defective items plotting required in the constant value of
sample size.
4. X-bar & R-Chart – Both the charts are usually combined for thorough and better analysis,
through these are basically give different kind of analysis. The purpose of the X bar chart
is for plotting the average of measurements gained in particular subgroup in fixed amount
of time. The purpose of the R chart is for plotting the ranges of measurement, which is
found and identified in every subgroup having an average, while considering all the
ranges.
5. X-Chart – The chart helps to measure data having only sample size of 1 quantity.
SPC Chart Construction
LG Corporation performs defective washing machines scrutinizing with the variable
sample size help. Here, one batch is taken from 20% of washing machines. Then P-chart is
drawn for the analysis.
The parameters are specified as the following, after the production for three weeks.
Proportion of items that are defective,
p= x / n
where, n = sample size and x = number of defective items
center line or P bar calculation is done as
= ∑ p / k
Here, k = Total number of days
D
AY
x n p p
bar
U
CL
L
CL
WEEK
1
1 1
2
9
2
0.
130435
0.
1411
0.
249984
0.
032216
2 1
5
9
4
0.
159574
0.
1411
0.
274128
0.
04502
3 1
4
9
4
0.
148936
0.
1411
0.
2591
0.
038772
sample size.
4. X-bar & R-Chart – Both the charts are usually combined for thorough and better analysis,
through these are basically give different kind of analysis. The purpose of the X bar chart
is for plotting the average of measurements gained in particular subgroup in fixed amount
of time. The purpose of the R chart is for plotting the ranges of measurement, which is
found and identified in every subgroup having an average, while considering all the
ranges.
5. X-Chart – The chart helps to measure data having only sample size of 1 quantity.
SPC Chart Construction
LG Corporation performs defective washing machines scrutinizing with the variable
sample size help. Here, one batch is taken from 20% of washing machines. Then P-chart is
drawn for the analysis.
The parameters are specified as the following, after the production for three weeks.
Proportion of items that are defective,
p= x / n
where, n = sample size and x = number of defective items
center line or P bar calculation is done as
= ∑ p / k
Here, k = Total number of days
D
AY
x n p p
bar
U
CL
L
CL
WEEK
1
1 1
2
9
2
0.
130435
0.
1411
0.
249984
0.
032216
2 1
5
9
4
0.
159574
0.
1411
0.
274128
0.
04502
3 1
4
9
4
0.
148936
0.
1411
0.
2591
0.
038772
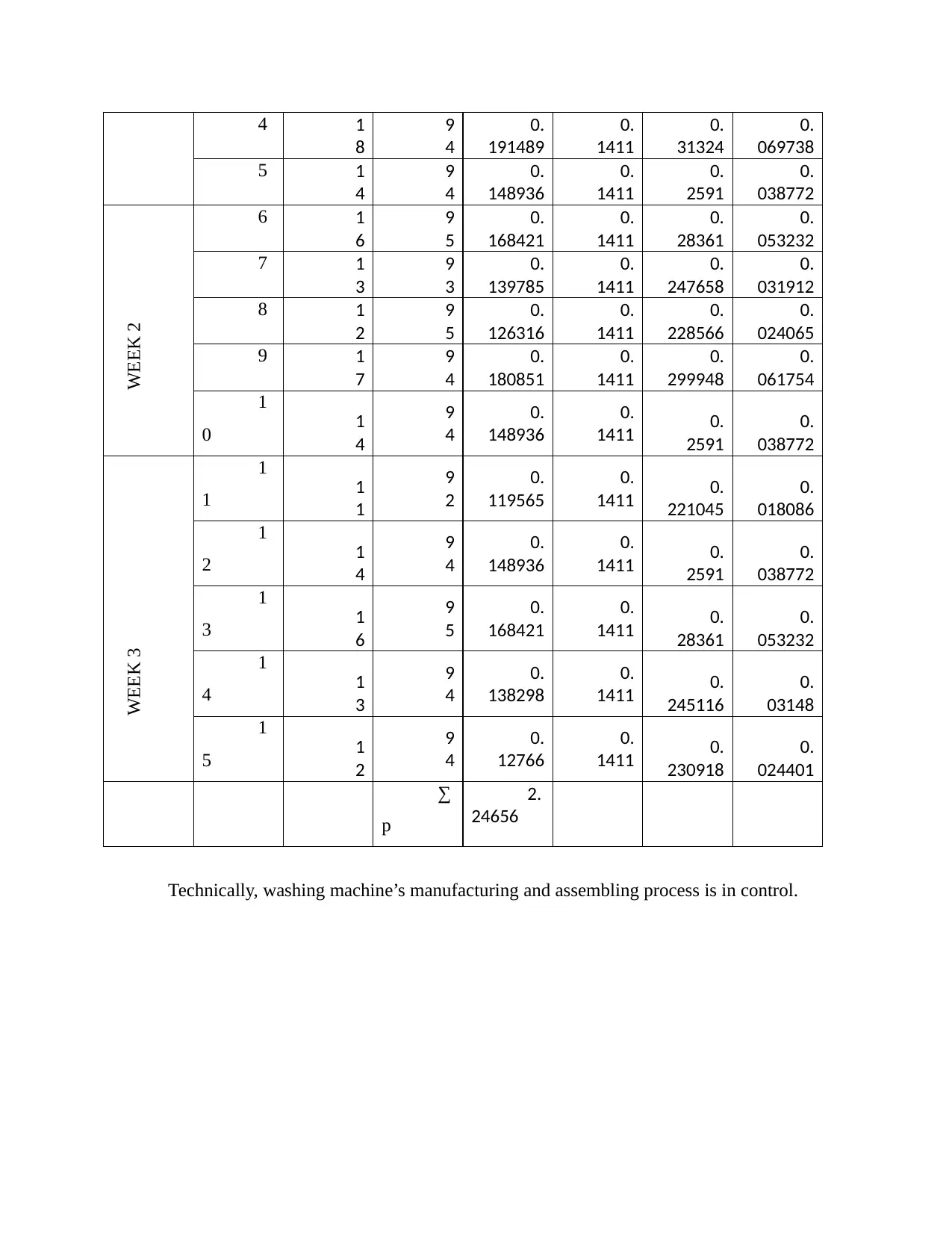
4 1
8
9
4
0.
191489
0.
1411
0.
31324
0.
069738
5 1
4
9
4
0.
148936
0.
1411
0.
2591
0.
038772
WEEK 2
6 1
6
9
5
0.
168421
0.
1411
0.
28361
0.
053232
7 1
3
9
3
0.
139785
0.
1411
0.
247658
0.
031912
8 1
2
9
5
0.
126316
0.
1411
0.
228566
0.
024065
9 1
7
9
4
0.
180851
0.
1411
0.
299948
0.
061754
1
0 1
4
9
4
0.
148936
0.
1411 0.
2591
0.
038772
WEEK 3
1
1 1
1
9
2
0.
119565
0.
1411 0.
221045
0.
018086
1
2 1
4
9
4
0.
148936
0.
1411 0.
2591
0.
038772
1
3 1
6
9
5
0.
168421
0.
1411 0.
28361
0.
053232
1
4 1
3
9
4
0.
138298
0.
1411 0.
245116
0.
03148
1
5 1
2
9
4
0.
12766
0.
1411 0.
230918
0.
024401
∑
p
2.
24656
Technically, washing machine’s manufacturing and assembling process is in control.
8
9
4
0.
191489
0.
1411
0.
31324
0.
069738
5 1
4
9
4
0.
148936
0.
1411
0.
2591
0.
038772
WEEK 2
6 1
6
9
5
0.
168421
0.
1411
0.
28361
0.
053232
7 1
3
9
3
0.
139785
0.
1411
0.
247658
0.
031912
8 1
2
9
5
0.
126316
0.
1411
0.
228566
0.
024065
9 1
7
9
4
0.
180851
0.
1411
0.
299948
0.
061754
1
0 1
4
9
4
0.
148936
0.
1411 0.
2591
0.
038772
WEEK 3
1
1 1
1
9
2
0.
119565
0.
1411 0.
221045
0.
018086
1
2 1
4
9
4
0.
148936
0.
1411 0.
2591
0.
038772
1
3 1
6
9
5
0.
168421
0.
1411 0.
28361
0.
053232
1
4 1
3
9
4
0.
138298
0.
1411 0.
245116
0.
03148
1
5 1
2
9
4
0.
12766
0.
1411 0.
230918
0.
024401
∑
p
2.
24656
Technically, washing machine’s manufacturing and assembling process is in control.
Paraphrase This Document
Need a fresh take? Get an instant paraphrase of this document with our AI Paraphraser
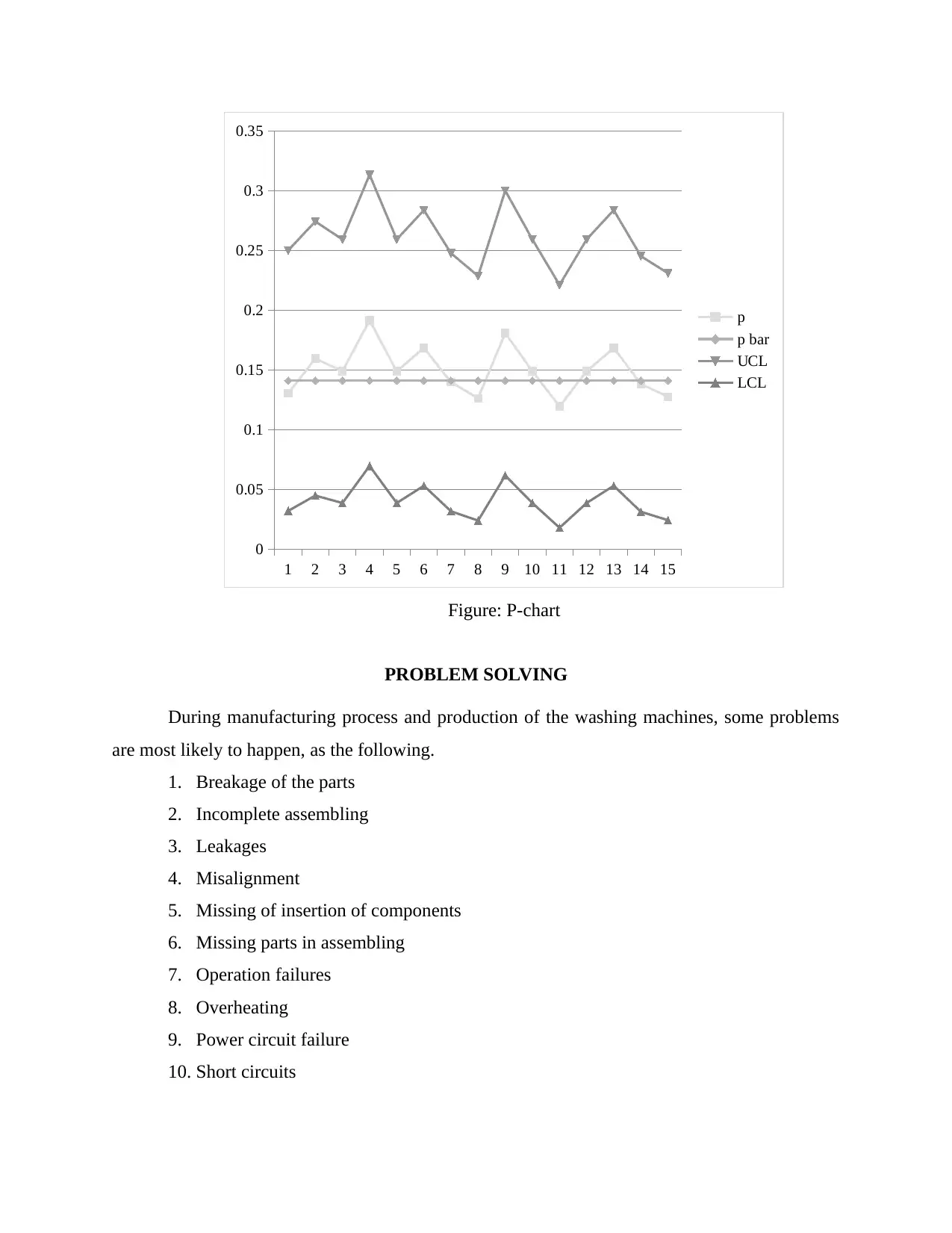
1 2 3 4 5 6 7 8 9 10 11 12 13 14 15
0
0.05
0.1
0.15
0.2
0.25
0.3
0.35
p
p bar
UCL
LCL
Figure: P-chart
PROBLEM SOLVING
During manufacturing process and production of the washing machines, some problems
are most likely to happen, as the following.
1. Breakage of the parts
2. Incomplete assembling
3. Leakages
4. Misalignment
5. Missing of insertion of components
6. Missing parts in assembling
7. Operation failures
8. Overheating
9. Power circuit failure
10. Short circuits
0
0.05
0.1
0.15
0.2
0.25
0.3
0.35
p
p bar
UCL
LCL
Figure: P-chart
PROBLEM SOLVING
During manufacturing process and production of the washing machines, some problems
are most likely to happen, as the following.
1. Breakage of the parts
2. Incomplete assembling
3. Leakages
4. Misalignment
5. Missing of insertion of components
6. Missing parts in assembling
7. Operation failures
8. Overheating
9. Power circuit failure
10. Short circuits
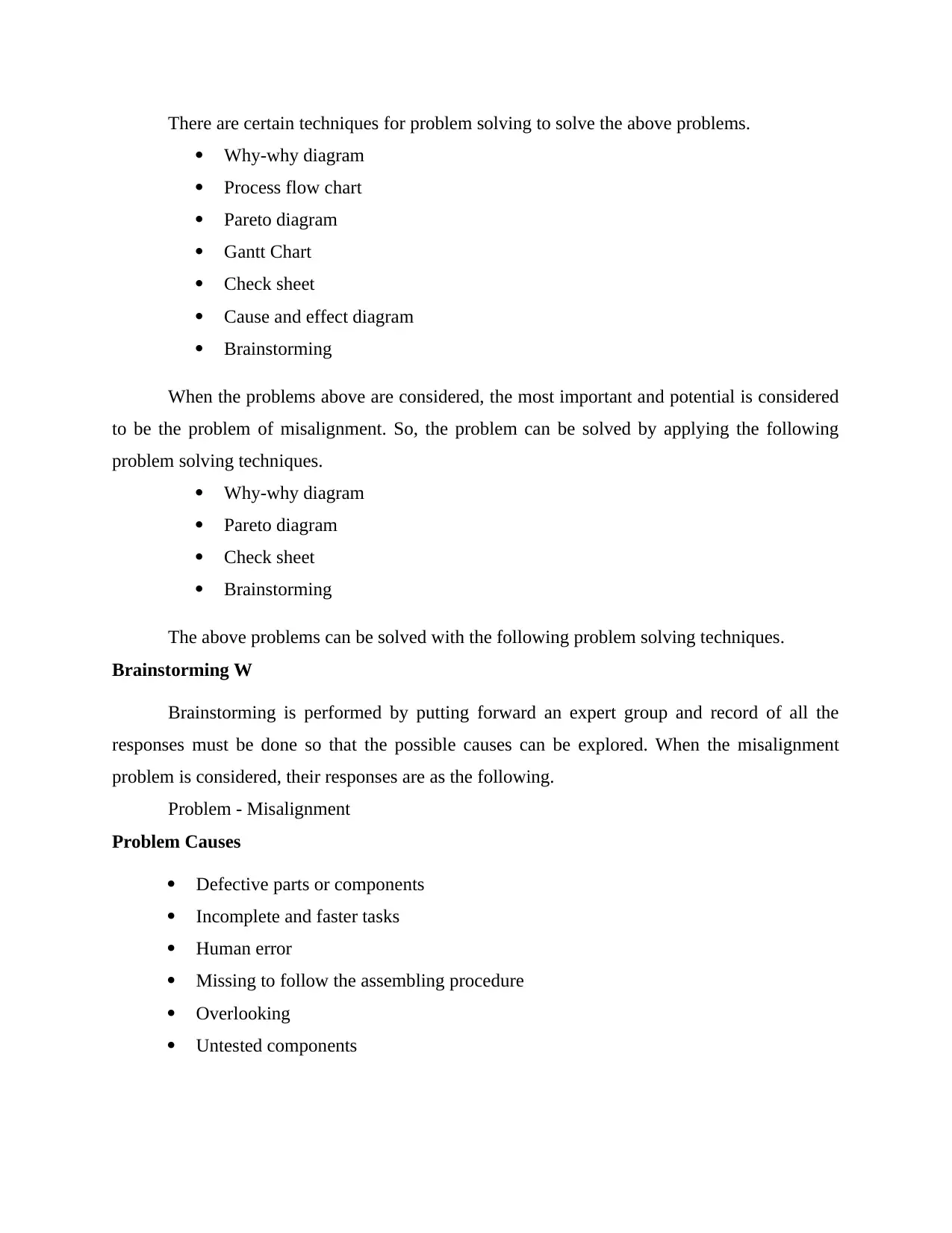
There are certain techniques for problem solving to solve the above problems.
Why-why diagram
Process flow chart
Pareto diagram
Gantt Chart
Check sheet
Cause and effect diagram
Brainstorming
When the problems above are considered, the most important and potential is considered
to be the problem of misalignment. So, the problem can be solved by applying the following
problem solving techniques.
Why-why diagram
Pareto diagram
Check sheet
Brainstorming
The above problems can be solved with the following problem solving techniques.
Brainstorming W
Brainstorming is performed by putting forward an expert group and record of all the
responses must be done so that the possible causes can be explored. When the misalignment
problem is considered, their responses are as the following.
Problem - Misalignment
Problem Causes
Defective parts or components
Incomplete and faster tasks
Human error
Missing to follow the assembling procedure
Overlooking
Untested components
Why-why diagram
Process flow chart
Pareto diagram
Gantt Chart
Check sheet
Cause and effect diagram
Brainstorming
When the problems above are considered, the most important and potential is considered
to be the problem of misalignment. So, the problem can be solved by applying the following
problem solving techniques.
Why-why diagram
Pareto diagram
Check sheet
Brainstorming
The above problems can be solved with the following problem solving techniques.
Brainstorming W
Brainstorming is performed by putting forward an expert group and record of all the
responses must be done so that the possible causes can be explored. When the misalignment
problem is considered, their responses are as the following.
Problem - Misalignment
Problem Causes
Defective parts or components
Incomplete and faster tasks
Human error
Missing to follow the assembling procedure
Overlooking
Untested components
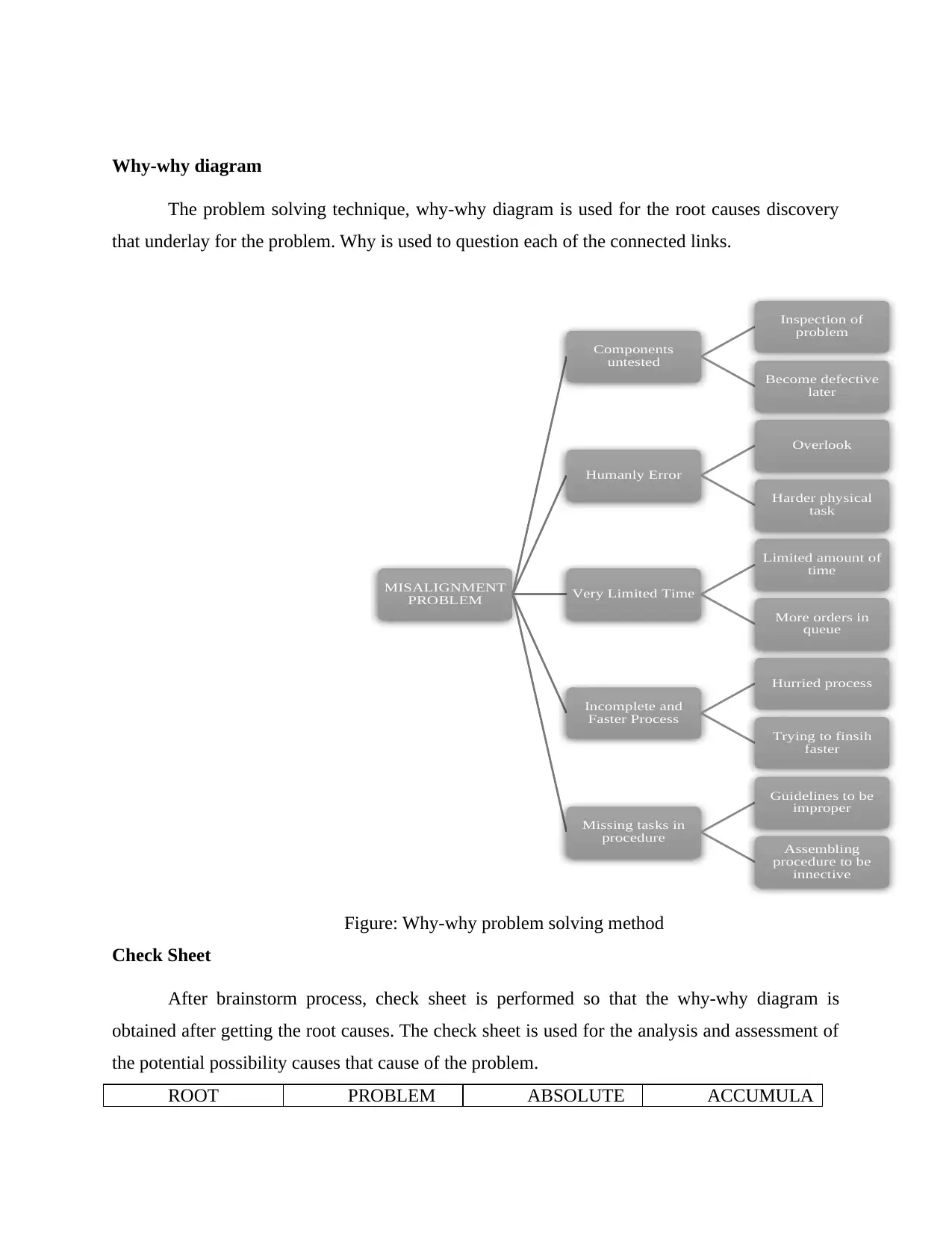
Why-why diagram
The problem solving technique, why-why diagram is used for the root causes discovery
that underlay for the problem. Why is used to question each of the connected links.
Figure: Why-why problem solving method
Check Sheet
After brainstorm process, check sheet is performed so that the why-why diagram is
obtained after getting the root causes. The check sheet is used for the analysis and assessment of
the potential possibility causes that cause of the problem.
ROOT PROBLEM ABSOLUTE ACCUMULA
MISALIGNMENT
PROBLEM
Components
untested
Inspection of
problem
Become defective
later
Humanly Error
Overlook
Harder physical
task
Very Limited Time
Limited amount of
time
More orders in
queue
Incomplete and
Faster Process
Hurried process
Trying to finsih
faster
Missing tasks in
procedure
Guidelines to be
improper
Assembling
procedure to be
innective
The problem solving technique, why-why diagram is used for the root causes discovery
that underlay for the problem. Why is used to question each of the connected links.
Figure: Why-why problem solving method
Check Sheet
After brainstorm process, check sheet is performed so that the why-why diagram is
obtained after getting the root causes. The check sheet is used for the analysis and assessment of
the potential possibility causes that cause of the problem.
ROOT PROBLEM ABSOLUTE ACCUMULA
MISALIGNMENT
PROBLEM
Components
untested
Inspection of
problem
Become defective
later
Humanly Error
Overlook
Harder physical
task
Very Limited Time
Limited amount of
time
More orders in
queue
Incomplete and
Faster Process
Hurried process
Trying to finsih
faster
Missing tasks in
procedure
Guidelines to be
improper
Assembling
procedure to be
innective
Secure Best Marks with AI Grader
Need help grading? Try our AI Grader for instant feedback on your assignments.
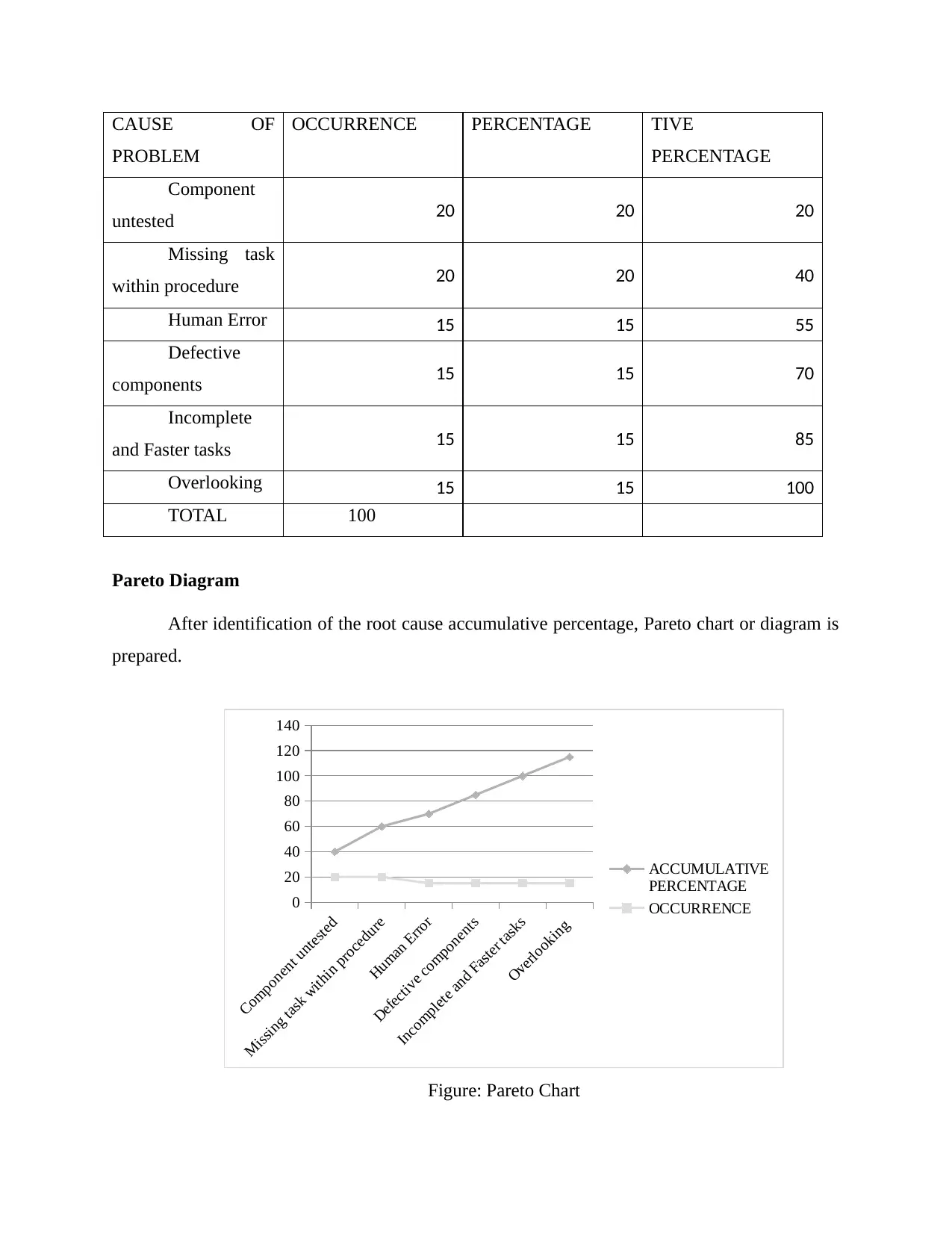
CAUSE OF
PROBLEM
OCCURRENCE PERCENTAGE TIVE
PERCENTAGE
Component
untested 20 20 20
Missing task
within procedure 20 20 40
Human Error 15 15 55
Defective
components 15 15 70
Incomplete
and Faster tasks 15 15 85
Overlooking 15 15 100
TOTAL 100
Pareto Diagram
After identification of the root cause accumulative percentage, Pareto chart or diagram is
prepared.
Component untested
Missing task within procedure
Human Error
Defective components
Incomplete and Faster tasks
Overlooking
0
20
40
60
80
100
120
140
ACCUMULATIVE
PERCENTAGE
OCCURRENCE
Figure: Pareto Chart
PROBLEM
OCCURRENCE PERCENTAGE TIVE
PERCENTAGE
Component
untested 20 20 20
Missing task
within procedure 20 20 40
Human Error 15 15 55
Defective
components 15 15 70
Incomplete
and Faster tasks 15 15 85
Overlooking 15 15 100
TOTAL 100
Pareto Diagram
After identification of the root cause accumulative percentage, Pareto chart or diagram is
prepared.
Component untested
Missing task within procedure
Human Error
Defective components
Incomplete and Faster tasks
Overlooking
0
20
40
60
80
100
120
140
ACCUMULATIVE
PERCENTAGE
OCCURRENCE
Figure: Pareto Chart
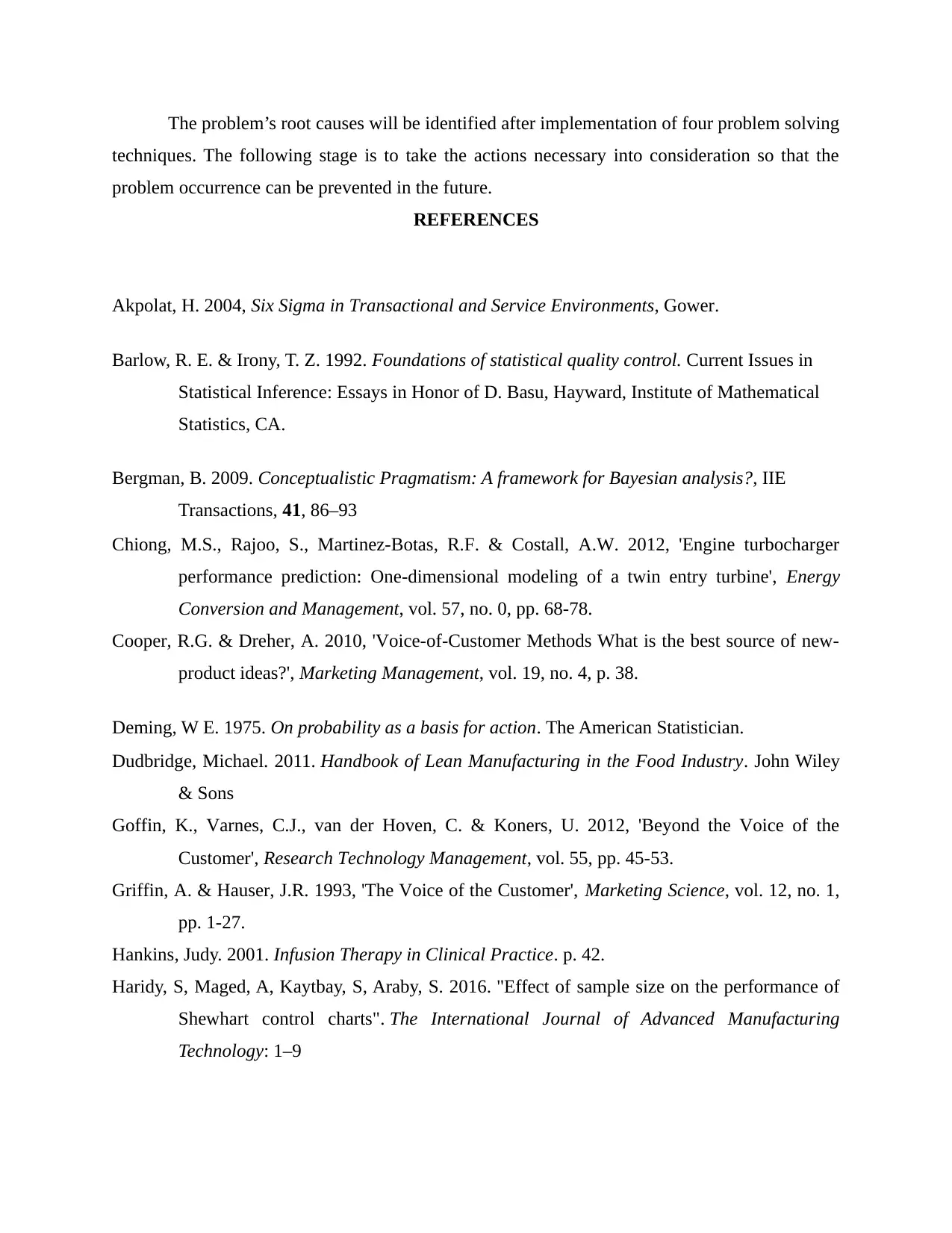
The problem’s root causes will be identified after implementation of four problem solving
techniques. The following stage is to take the actions necessary into consideration so that the
problem occurrence can be prevented in the future.
REFERENCES
Akpolat, H. 2004, Six Sigma in Transactional and Service Environments, Gower.
Barlow, R. E. & Irony, T. Z. 1992. Foundations of statistical quality control. Current Issues in
Statistical Inference: Essays in Honor of D. Basu, Hayward, Institute of Mathematical
Statistics, CA.
Bergman, B. 2009. Conceptualistic Pragmatism: A framework for Bayesian analysis?, IIE
Transactions, 41, 86–93
Chiong, M.S., Rajoo, S., Martinez-Botas, R.F. & Costall, A.W. 2012, 'Engine turbocharger
performance prediction: One-dimensional modeling of a twin entry turbine', Energy
Conversion and Management, vol. 57, no. 0, pp. 68-78.
Cooper, R.G. & Dreher, A. 2010, 'Voice-of-Customer Methods What is the best source of new-
product ideas?', Marketing Management, vol. 19, no. 4, p. 38.
Deming, W E. 1975. On probability as a basis for action. The American Statistician.
Dudbridge, Michael. 2011. Handbook of Lean Manufacturing in the Food Industry. John Wiley
& Sons
Goffin, K., Varnes, C.J., van der Hoven, C. & Koners, U. 2012, 'Beyond the Voice of the
Customer', Research Technology Management, vol. 55, pp. 45-53.
Griffin, A. & Hauser, J.R. 1993, 'The Voice of the Customer', Marketing Science, vol. 12, no. 1,
pp. 1-27.
Hankins, Judy. 2001. Infusion Therapy in Clinical Practice. p. 42.
Haridy, S, Maged, A, Kaytbay, S, Araby, S. 2016. "Effect of sample size on the performance of
Shewhart control charts". The International Journal of Advanced Manufacturing
Technology: 1–9
techniques. The following stage is to take the actions necessary into consideration so that the
problem occurrence can be prevented in the future.
REFERENCES
Akpolat, H. 2004, Six Sigma in Transactional and Service Environments, Gower.
Barlow, R. E. & Irony, T. Z. 1992. Foundations of statistical quality control. Current Issues in
Statistical Inference: Essays in Honor of D. Basu, Hayward, Institute of Mathematical
Statistics, CA.
Bergman, B. 2009. Conceptualistic Pragmatism: A framework for Bayesian analysis?, IIE
Transactions, 41, 86–93
Chiong, M.S., Rajoo, S., Martinez-Botas, R.F. & Costall, A.W. 2012, 'Engine turbocharger
performance prediction: One-dimensional modeling of a twin entry turbine', Energy
Conversion and Management, vol. 57, no. 0, pp. 68-78.
Cooper, R.G. & Dreher, A. 2010, 'Voice-of-Customer Methods What is the best source of new-
product ideas?', Marketing Management, vol. 19, no. 4, p. 38.
Deming, W E. 1975. On probability as a basis for action. The American Statistician.
Dudbridge, Michael. 2011. Handbook of Lean Manufacturing in the Food Industry. John Wiley
& Sons
Goffin, K., Varnes, C.J., van der Hoven, C. & Koners, U. 2012, 'Beyond the Voice of the
Customer', Research Technology Management, vol. 55, pp. 45-53.
Griffin, A. & Hauser, J.R. 1993, 'The Voice of the Customer', Marketing Science, vol. 12, no. 1,
pp. 1-27.
Hankins, Judy. 2001. Infusion Therapy in Clinical Practice. p. 42.
Haridy, S, Maged, A, Kaytbay, S, Araby, S. 2016. "Effect of sample size on the performance of
Shewhart control charts". The International Journal of Advanced Manufacturing
Technology: 1–9
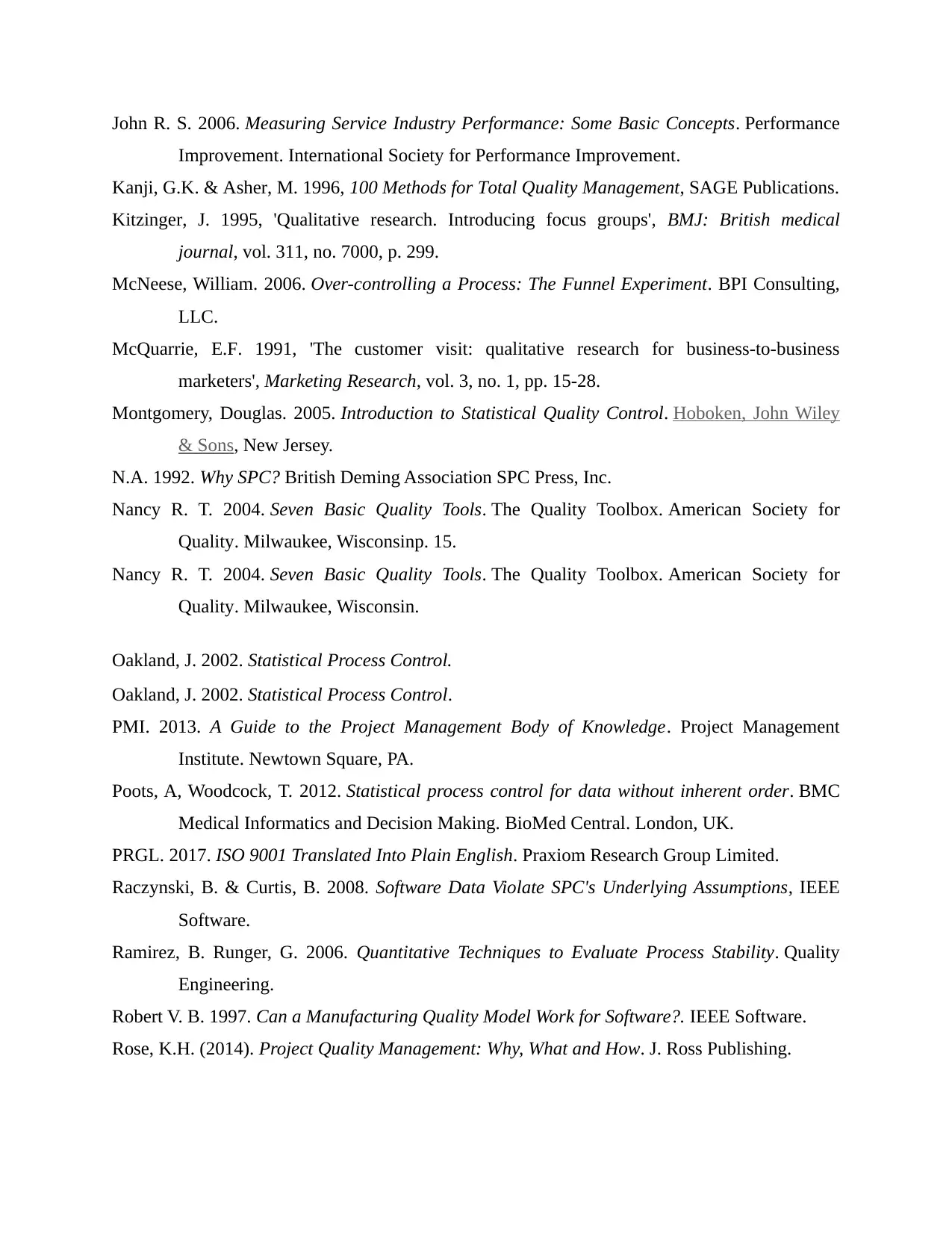
John R. S. 2006. Measuring Service Industry Performance: Some Basic Concepts. Performance
Improvement. International Society for Performance Improvement.
Kanji, G.K. & Asher, M. 1996, 100 Methods for Total Quality Management, SAGE Publications.
Kitzinger, J. 1995, 'Qualitative research. Introducing focus groups', BMJ: British medical
journal, vol. 311, no. 7000, p. 299.
McNeese, William. 2006. Over-controlling a Process: The Funnel Experiment. BPI Consulting,
LLC.
McQuarrie, E.F. 1991, 'The customer visit: qualitative research for business-to-business
marketers', Marketing Research, vol. 3, no. 1, pp. 15-28.
Montgomery, Douglas. 2005. Introduction to Statistical Quality Control. Hoboken, John Wiley
& Sons, New Jersey.
N.A. 1992. Why SPC? British Deming Association SPC Press, Inc.
Nancy R. T. 2004. Seven Basic Quality Tools. The Quality Toolbox. American Society for
Quality. Milwaukee, Wisconsinp. 15.
Nancy R. T. 2004. Seven Basic Quality Tools. The Quality Toolbox. American Society for
Quality. Milwaukee, Wisconsin.
Oakland, J. 2002. Statistical Process Control.
Oakland, J. 2002. Statistical Process Control.
PMI. 2013. A Guide to the Project Management Body of Knowledge. Project Management
Institute. Newtown Square, PA.
Poots, A, Woodcock, T. 2012. Statistical process control for data without inherent order. BMC
Medical Informatics and Decision Making. BioMed Central. London, UK.
PRGL. 2017. ISO 9001 Translated Into Plain English. Praxiom Research Group Limited.
Raczynski, B. & Curtis, B. 2008. Software Data Violate SPC's Underlying Assumptions, IEEE
Software.
Ramirez, B. Runger, G. 2006. Quantitative Techniques to Evaluate Process Stability. Quality
Engineering.
Robert V. B. 1997. Can a Manufacturing Quality Model Work for Software?. IEEE Software.
Rose, K.H. (2014). Project Quality Management: Why, What and How. J. Ross Publishing.
Improvement. International Society for Performance Improvement.
Kanji, G.K. & Asher, M. 1996, 100 Methods for Total Quality Management, SAGE Publications.
Kitzinger, J. 1995, 'Qualitative research. Introducing focus groups', BMJ: British medical
journal, vol. 311, no. 7000, p. 299.
McNeese, William. 2006. Over-controlling a Process: The Funnel Experiment. BPI Consulting,
LLC.
McQuarrie, E.F. 1991, 'The customer visit: qualitative research for business-to-business
marketers', Marketing Research, vol. 3, no. 1, pp. 15-28.
Montgomery, Douglas. 2005. Introduction to Statistical Quality Control. Hoboken, John Wiley
& Sons, New Jersey.
N.A. 1992. Why SPC? British Deming Association SPC Press, Inc.
Nancy R. T. 2004. Seven Basic Quality Tools. The Quality Toolbox. American Society for
Quality. Milwaukee, Wisconsinp. 15.
Nancy R. T. 2004. Seven Basic Quality Tools. The Quality Toolbox. American Society for
Quality. Milwaukee, Wisconsin.
Oakland, J. 2002. Statistical Process Control.
Oakland, J. 2002. Statistical Process Control.
PMI. 2013. A Guide to the Project Management Body of Knowledge. Project Management
Institute. Newtown Square, PA.
Poots, A, Woodcock, T. 2012. Statistical process control for data without inherent order. BMC
Medical Informatics and Decision Making. BioMed Central. London, UK.
PRGL. 2017. ISO 9001 Translated Into Plain English. Praxiom Research Group Limited.
Raczynski, B. & Curtis, B. 2008. Software Data Violate SPC's Underlying Assumptions, IEEE
Software.
Ramirez, B. Runger, G. 2006. Quantitative Techniques to Evaluate Process Stability. Quality
Engineering.
Robert V. B. 1997. Can a Manufacturing Quality Model Work for Software?. IEEE Software.
Rose, K.H. (2014). Project Quality Management: Why, What and How. J. Ross Publishing.
1 out of 37
Related Documents

Your All-in-One AI-Powered Toolkit for Academic Success.
+13062052269
info@desklib.com
Available 24*7 on WhatsApp / Email
Unlock your academic potential
© 2024 | Zucol Services PVT LTD | All rights reserved.