Exploring the Feasibility of Recycled PP Filament for 3D Printing
Examine the feasibility of forming 3D printer filaments using waste polypropylene (PP) plastics and address issues relating to polymer shrinkage through use of 'additives' to improve 3D printing potential. Perform mechanical testing of resulting optimised filaments.
37 Pages9403 Words229 Views
Added on 2023-06-11
About This Document
This project explores the feasibility of using recycled PP for 3D printing. It compares the properties of commonly used plastics with PP and measures the mechanical properties and flow index of recycled PP. The aim is to find a more environmentally friendly alternative for 3D printing filament.
Exploring the Feasibility of Recycled PP Filament for 3D Printing
Examine the feasibility of forming 3D printer filaments using waste polypropylene (PP) plastics and address issues relating to polymer shrinkage through use of 'additives' to improve 3D printing potential. Perform mechanical testing of resulting optimised filaments.
Added on 2023-06-11
ShareRelated Documents
Final project report 1
FINAL PROJECT REPORT
By Name
Course
Instructor
Institution
Location
Date
FINAL PROJECT REPORT
By Name
Course
Instructor
Institution
Location
Date
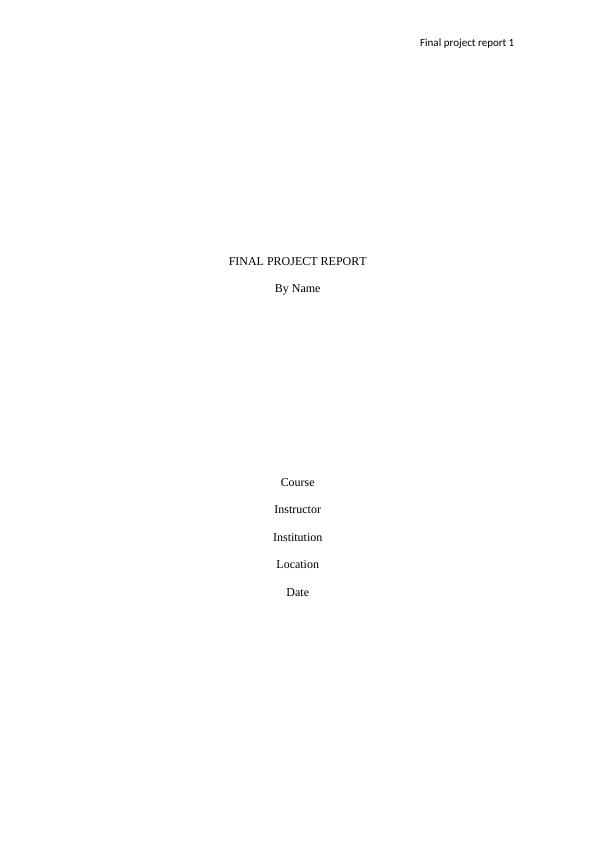
Final project report 2
ABSTRACT
The 3D printing technology that is commonly referred to as the Additive manufacturing
technology has dominated the cell phone industries. This knowledge however, has been taken
from the traditional methods of moulding systems that are used in the plastic industry. The
technology seeks to address different challenges that have existed in the industry before. The
3D printers usually print objects from a digital template to a tangible 3 -dimensional physical
object. This printing is done layer by layer while using plastic, metal, etc. The technology has
been found to be useful in the sectors such as engineering and construction, automotive,
education, in the giving of the geographic information system. The project seeks to explore
how this technology works currently and the possible future applications. The project is
interested in looking at the ways of reducing costs of production.
ABSTRACT
The 3D printing technology that is commonly referred to as the Additive manufacturing
technology has dominated the cell phone industries. This knowledge however, has been taken
from the traditional methods of moulding systems that are used in the plastic industry. The
technology seeks to address different challenges that have existed in the industry before. The
3D printers usually print objects from a digital template to a tangible 3 -dimensional physical
object. This printing is done layer by layer while using plastic, metal, etc. The technology has
been found to be useful in the sectors such as engineering and construction, automotive,
education, in the giving of the geographic information system. The project seeks to explore
how this technology works currently and the possible future applications. The project is
interested in looking at the ways of reducing costs of production.
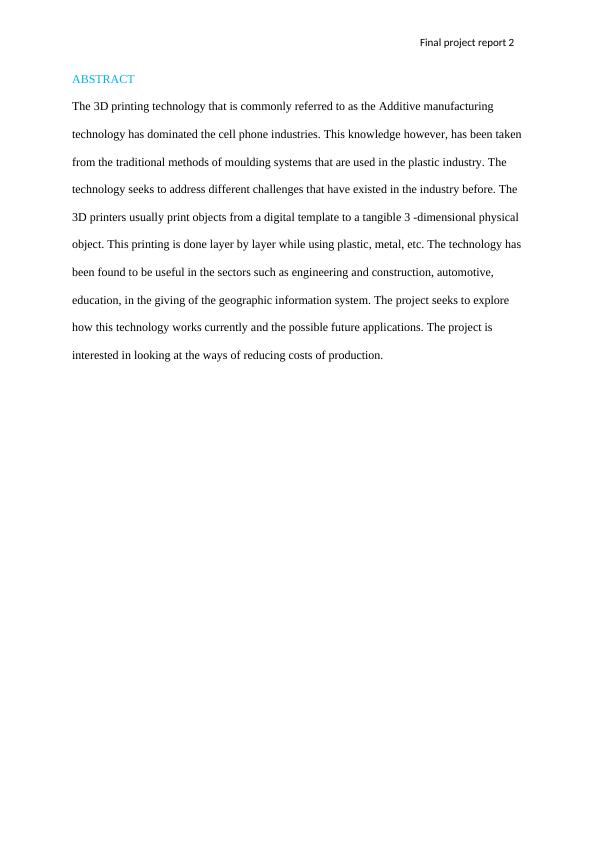
Final project report 3
Table of Contents
ABSTRACT...................................................................................................2
Introduction.................................................................................................3
Cooling........................................................................................................8
Melt and the flow rate.................................................................................8
AIMS AND OBJECTIVES...............................................................................11
Brief Overview of the 3D Printing History..................................................11
THE 3D PRINTING PROCESS.......................................................................12
The 3D Printing Materials..........................................................................13
Plastics...................................................................................................13
Polypropylene.........................................................................................15
The recycled PP.........................................................................................16
The new knowledge used in 3D.................................................................17
The tensile testing.....................................................................................19
Methods..................................................................................................20
Materials.................................................................................................20
Reduction of the shrinkage.....................................................................26
Factors influencing shrinkage.................................................................27
Amorphous materials..........................................................................27
The Semi-crystalline materials............................................................28
The fibres- reinforced and filled materials...........................................28
The Wall Thickness..............................................................................28
Mechanical Properties of recycled waste PP..............................................29
Processing conditions.............................................................................30
Types of Shrinkage.................................................................................30
Volumetric shrinkage...........................................................................30
Conclusion.................................................................................................33
References................................................................................................34
Table of Contents
ABSTRACT...................................................................................................2
Introduction.................................................................................................3
Cooling........................................................................................................8
Melt and the flow rate.................................................................................8
AIMS AND OBJECTIVES...............................................................................11
Brief Overview of the 3D Printing History..................................................11
THE 3D PRINTING PROCESS.......................................................................12
The 3D Printing Materials..........................................................................13
Plastics...................................................................................................13
Polypropylene.........................................................................................15
The recycled PP.........................................................................................16
The new knowledge used in 3D.................................................................17
The tensile testing.....................................................................................19
Methods..................................................................................................20
Materials.................................................................................................20
Reduction of the shrinkage.....................................................................26
Factors influencing shrinkage.................................................................27
Amorphous materials..........................................................................27
The Semi-crystalline materials............................................................28
The fibres- reinforced and filled materials...........................................28
The Wall Thickness..............................................................................28
Mechanical Properties of recycled waste PP..............................................29
Processing conditions.............................................................................30
Types of Shrinkage.................................................................................30
Volumetric shrinkage...........................................................................30
Conclusion.................................................................................................33
References................................................................................................34
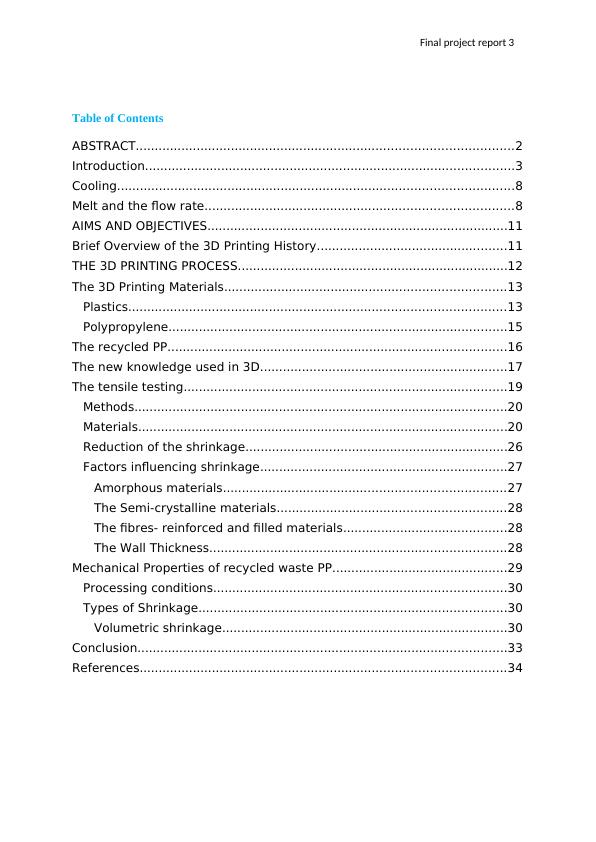
Final project report 4
Introduction
The more plastics seen in the market today ranging from plastic bags, the plastic pipes and
most sheets are products of this technique. The research groups have done evaluation on this
technique and recommended some of the latest improvements being witness today. A mong
the key steps made include the enhancement in the dissolution of the slowly soluble drugs.
This has modified the drug release and the transdermal passage of the drug. The extrusion
refers to a process of converting a raw material into a product of uniform size, density and
shape. This achieved by forcing it through a die but done under controlled conditions. It is
very possible to make this process a continuous one by allowing the temperatures to be
constant. The extruding machine has two parts. The first part consists of the conveying
system whose major task is to transport the material and put a degree of distributive and
dispensation of the mixing. The second part consists of the die itself that forms the material to
the required form of the shape.
The melt extrusion has been broadly classified into a molten system which uses melt under
high temperature and a semi solid viscous system. The application of heat in the molten
system aims at controlling the viscosity and allowing flow into the die. The semi solid
systems are the multiples of the phases which concentrate dispersions containing high
proportions of liquid solid mixture
Operation of the Equipment and the process
Introduction
The more plastics seen in the market today ranging from plastic bags, the plastic pipes and
most sheets are products of this technique. The research groups have done evaluation on this
technique and recommended some of the latest improvements being witness today. A mong
the key steps made include the enhancement in the dissolution of the slowly soluble drugs.
This has modified the drug release and the transdermal passage of the drug. The extrusion
refers to a process of converting a raw material into a product of uniform size, density and
shape. This achieved by forcing it through a die but done under controlled conditions. It is
very possible to make this process a continuous one by allowing the temperatures to be
constant. The extruding machine has two parts. The first part consists of the conveying
system whose major task is to transport the material and put a degree of distributive and
dispensation of the mixing. The second part consists of the die itself that forms the material to
the required form of the shape.
The melt extrusion has been broadly classified into a molten system which uses melt under
high temperature and a semi solid viscous system. The application of heat in the molten
system aims at controlling the viscosity and allowing flow into the die. The semi solid
systems are the multiples of the phases which concentrate dispersions containing high
proportions of liquid solid mixture
Operation of the Equipment and the process
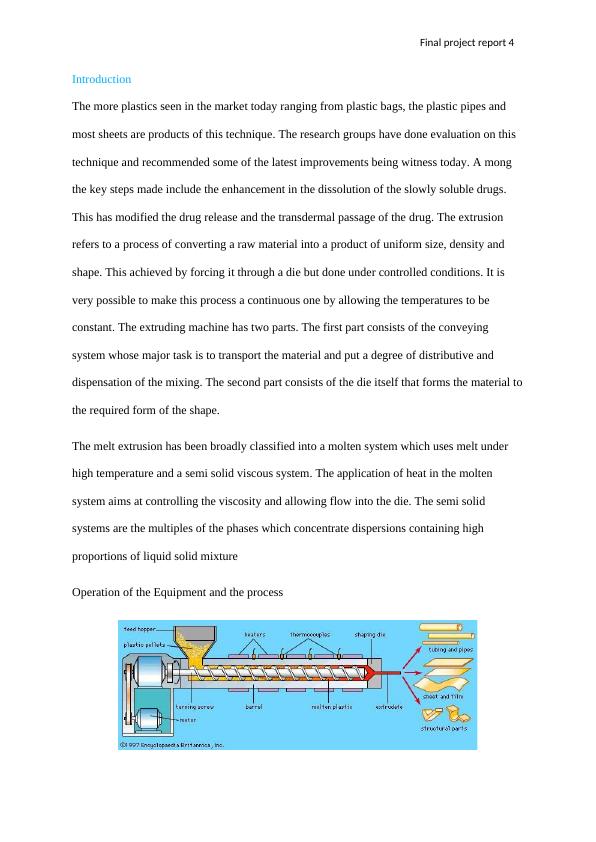
Final project report 5
Fig 1: The extruder layout
The hot melt extrusion equipment is made up of an extruder, the secondary equipment for the
extruder, tools for doing the monitor, lower stream processing equipment and the product
evaluation parts or components. These parts include hopper for the introduction of the
content, barrels, twin screws, the screw and the die Petrick, I.J. and Simpson, T.W., 2012.
The auxiliary equipment for the monitoring processes include a heating or cooling device
installed for barrels, a conveyor belt for cooling down the product and the solvent delivery
pump that pushes the content outside. The parameters to be monitored include the
temperature of the gauges, the speed of the of the screw, the torque of extrusion and the
pressure of the operating system
The extrusion process can be broken down into the following stages in order to enhance the
understanding. These stages may include;
Feeding the extruder
Reduction of the particles in the mixture
The die process of the flow
The down streaming processes.
The extruder
It consists of one or two rotating screw inside a stationary cylindrical barrel. The barrel is
made of a very robust material of sections which are bolted or clamped together. The die is
connected to the end of the barrel. The end of the barrel will always determine the shape of
the product. The required heat to melt the product is provided by the friction between the
melt and the shearing surface. Most of the commercially available extruders have a modular
design. Such designs allow for the choice of the screws or the interchangeable sections that
normally alter the configurations of the feed system. The modification of the process to meet
Fig 1: The extruder layout
The hot melt extrusion equipment is made up of an extruder, the secondary equipment for the
extruder, tools for doing the monitor, lower stream processing equipment and the product
evaluation parts or components. These parts include hopper for the introduction of the
content, barrels, twin screws, the screw and the die Petrick, I.J. and Simpson, T.W., 2012.
The auxiliary equipment for the monitoring processes include a heating or cooling device
installed for barrels, a conveyor belt for cooling down the product and the solvent delivery
pump that pushes the content outside. The parameters to be monitored include the
temperature of the gauges, the speed of the of the screw, the torque of extrusion and the
pressure of the operating system
The extrusion process can be broken down into the following stages in order to enhance the
understanding. These stages may include;
Feeding the extruder
Reduction of the particles in the mixture
The die process of the flow
The down streaming processes.
The extruder
It consists of one or two rotating screw inside a stationary cylindrical barrel. The barrel is
made of a very robust material of sections which are bolted or clamped together. The die is
connected to the end of the barrel. The end of the barrel will always determine the shape of
the product. The required heat to melt the product is provided by the friction between the
melt and the shearing surface. Most of the commercially available extruders have a modular
design. Such designs allow for the choice of the screws or the interchangeable sections that
normally alter the configurations of the feed system. The modification of the process to meet
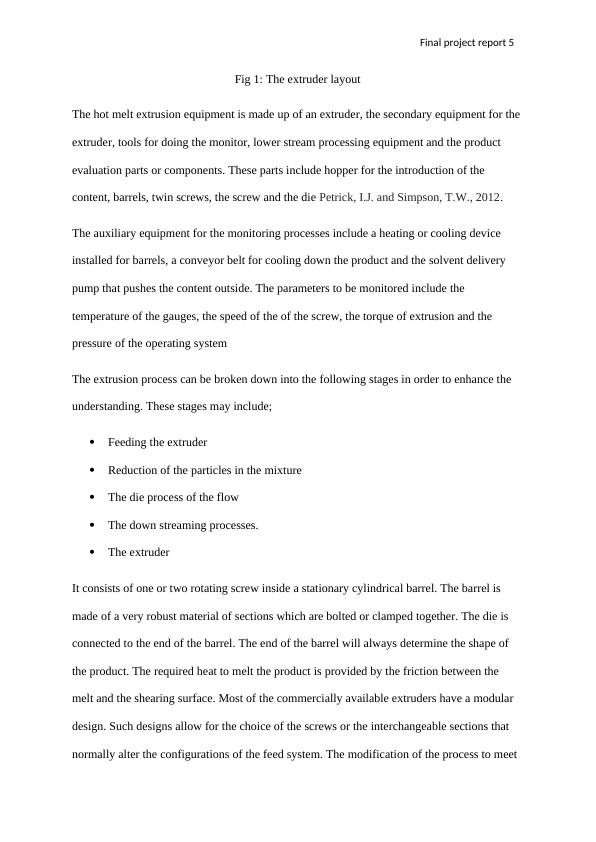
Final project report 6
a specific requirement is thus very possible. These screws allow the extruder to perform a
mixing and reduction of the induced particles.
Fig 2: The configuration of the screws
Conventionally, the extrusion channel is divided int three main sections or channels. These
sections include feed section, transitions zone and finally the metering zone. The raw material
is fed from the hopper directly into the so-called feed section the section has a deeper flight
with greater pitch. This kind of configuration enables the feed material to be fed easily into
the screw. The pitch and the helix angle provide a constant rotation speed of the screws. The
material is usually introduced as a solid plug to the transition zone. In this section the
materials are mixed, melted and compressed before being plasticised
The compression process is achieved through decrease of the thread pitch of the screw while
maintaining the flight depth. The result is an increased pressure as the material move along
the barrel. The transverse flow of the melt is made possible by the helical screw. The drag
flow, pressure flow and leakage are all applied. The material is then introduced at the
metering zone but already in the form of homogenous plastic melt which is ideally suitable
for the extrusion. In order to obtain a uniform thickness, the flow must be kept constant
a specific requirement is thus very possible. These screws allow the extruder to perform a
mixing and reduction of the induced particles.
Fig 2: The configuration of the screws
Conventionally, the extrusion channel is divided int three main sections or channels. These
sections include feed section, transitions zone and finally the metering zone. The raw material
is fed from the hopper directly into the so-called feed section the section has a deeper flight
with greater pitch. This kind of configuration enables the feed material to be fed easily into
the screw. The pitch and the helix angle provide a constant rotation speed of the screws. The
material is usually introduced as a solid plug to the transition zone. In this section the
materials are mixed, melted and compressed before being plasticised
The compression process is achieved through decrease of the thread pitch of the screw while
maintaining the flight depth. The result is an increased pressure as the material move along
the barrel. The transverse flow of the melt is made possible by the helical screw. The drag
flow, pressure flow and leakage are all applied. The material is then introduced at the
metering zone but already in the form of homogenous plastic melt which is ideally suitable
for the extrusion. In order to obtain a uniform thickness, the flow must be kept constant
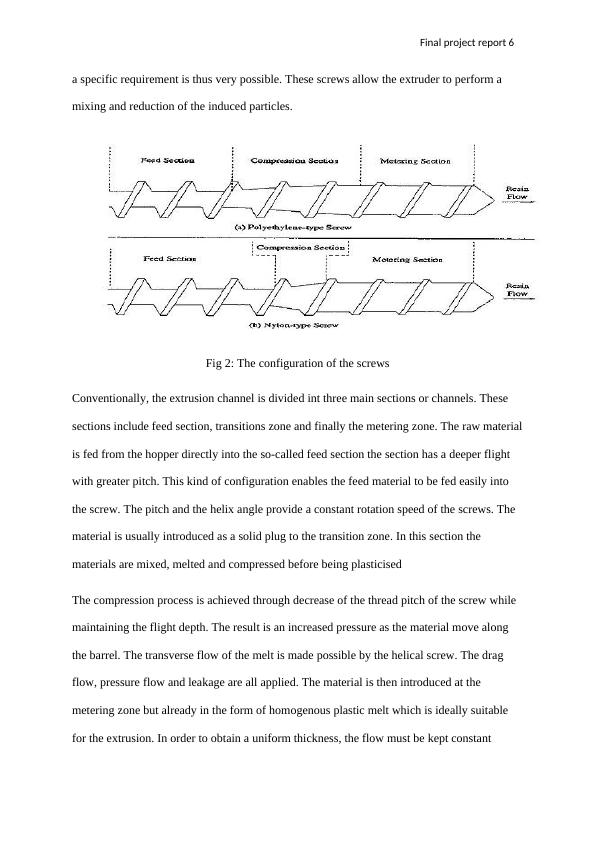
Final project report 7
without any stagnation at any point in the of tube or channel. The metering zone thus serve to
reduce the functioning of pulse activity that may interfere with the delivery rate in the die
cavity.
In the twin screw extruder exist two agitator assemblies mounted on the shafts that are
parallel to each other. These shafts rotate in the same direction or in the opposite direction
corresponding to the position of the material adjacent to the shaft. This arrangement allows
the agitator to wipe on the both sides of the narrow part of the barrel. The co-rotating allows
for the better mixing of the material being mixed as the surfaces usually move against. As the
screw rotate, the flight of one screw element will always wipe the flank of the next screw thus
causing the material transfer from one screw to another. These movements collectively make
the content to move in the barrel.
The features of the twin screw are;
It has a very short time for residence that may range from5 to 10 minutes and this is
recommended.
It has a self-wiping screw file that ensures complete emptying of the of the equipment
and minimises product wastage when shut down.
There are reduced inventories since the time of operation is continuous feeding of the
raw materials and removal of the product. This is very important especially when
processing valuable or potentially harmful product.
The operating parameters can be changed easily and continuously and this makes the
component to be very versatile. The versatility property allows fort the processing of
very many different formulations using the same device or machine.
The superior mixing is allowed in the set up. The screws that are present in the barrel
have various mixing element which impart or put two types of mixing in place that is
without any stagnation at any point in the of tube or channel. The metering zone thus serve to
reduce the functioning of pulse activity that may interfere with the delivery rate in the die
cavity.
In the twin screw extruder exist two agitator assemblies mounted on the shafts that are
parallel to each other. These shafts rotate in the same direction or in the opposite direction
corresponding to the position of the material adjacent to the shaft. This arrangement allows
the agitator to wipe on the both sides of the narrow part of the barrel. The co-rotating allows
for the better mixing of the material being mixed as the surfaces usually move against. As the
screw rotate, the flight of one screw element will always wipe the flank of the next screw thus
causing the material transfer from one screw to another. These movements collectively make
the content to move in the barrel.
The features of the twin screw are;
It has a very short time for residence that may range from5 to 10 minutes and this is
recommended.
It has a self-wiping screw file that ensures complete emptying of the of the equipment
and minimises product wastage when shut down.
There are reduced inventories since the time of operation is continuous feeding of the
raw materials and removal of the product. This is very important especially when
processing valuable or potentially harmful product.
The operating parameters can be changed easily and continuously and this makes the
component to be very versatile. The versatility property allows fort the processing of
very many different formulations using the same device or machine.
The superior mixing is allowed in the set up. The screws that are present in the barrel
have various mixing element which impart or put two types of mixing in place that is
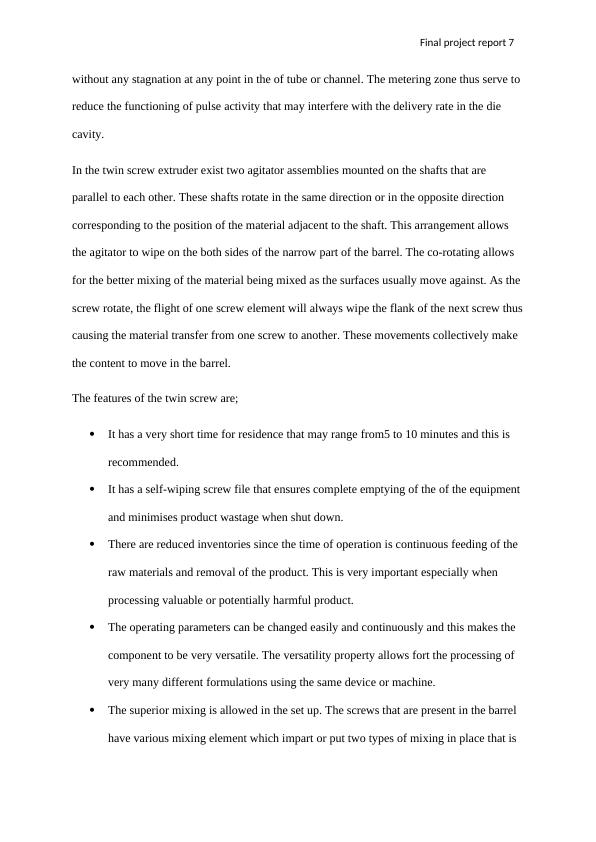
Final project report 8
the distributive and the dispersive. The distributive mixing allows for the division and
recombining of the material while lowering the energy consumption. The most
common Twin screw that is found in our laboratories has a diameter of 26mm-
18mm.The barrels comfortably handle a temperature from 30-300 degrees.
The process of extrusion normally requires a very close monitoring and the
knowledge of the parameters. Some of these parameters include the following;
elasticity, viscosity, temperatures and elasticity. The temperature of the barrel,
federate, motor load among others also need the close monitoring.
The barrel temperatures are taken by a glass transition or polymers. The federate and
screw speed is an important as the two operations affect the efficiency of the extruder.
This is very critical as it will govern the balance between the weak and the vey strong
mass transfer. The melt pressure with the motor load must be taken as well.
Cooling
The hot extrude must be allowed to cool after leaving the die in order to harden it into the
desired dimension. The commonly used way of cooling is by the introduction of the extrudate
int a water bath that is usually circulated or just being sprayed on the product. The
temperature of the cooling water should vary depending in the need for cooling. The
treatment of the extrusion will be an issue of the polymer under investigation.
Melt and the flow rate
The melt flow index is used to analyse and to determine the flow properties of the melted
plastic. This method calculates the flow of the melt out of the die after every 10 minutes. The
grams of the sample polymer are heated and the melt forced to flow through the capillary
using a weighted piston. The weight of the material that has been extruded in the time
interval indicated is the flow rate. It is therefore very obvious that if the MFR is a large value
the distributive and the dispersive. The distributive mixing allows for the division and
recombining of the material while lowering the energy consumption. The most
common Twin screw that is found in our laboratories has a diameter of 26mm-
18mm.The barrels comfortably handle a temperature from 30-300 degrees.
The process of extrusion normally requires a very close monitoring and the
knowledge of the parameters. Some of these parameters include the following;
elasticity, viscosity, temperatures and elasticity. The temperature of the barrel,
federate, motor load among others also need the close monitoring.
The barrel temperatures are taken by a glass transition or polymers. The federate and
screw speed is an important as the two operations affect the efficiency of the extruder.
This is very critical as it will govern the balance between the weak and the vey strong
mass transfer. The melt pressure with the motor load must be taken as well.
Cooling
The hot extrude must be allowed to cool after leaving the die in order to harden it into the
desired dimension. The commonly used way of cooling is by the introduction of the extrudate
int a water bath that is usually circulated or just being sprayed on the product. The
temperature of the cooling water should vary depending in the need for cooling. The
treatment of the extrusion will be an issue of the polymer under investigation.
Melt and the flow rate
The melt flow index is used to analyse and to determine the flow properties of the melted
plastic. This method calculates the flow of the melt out of the die after every 10 minutes. The
grams of the sample polymer are heated and the melt forced to flow through the capillary
using a weighted piston. The weight of the material that has been extruded in the time
interval indicated is the flow rate. It is therefore very obvious that if the MFR is a large value
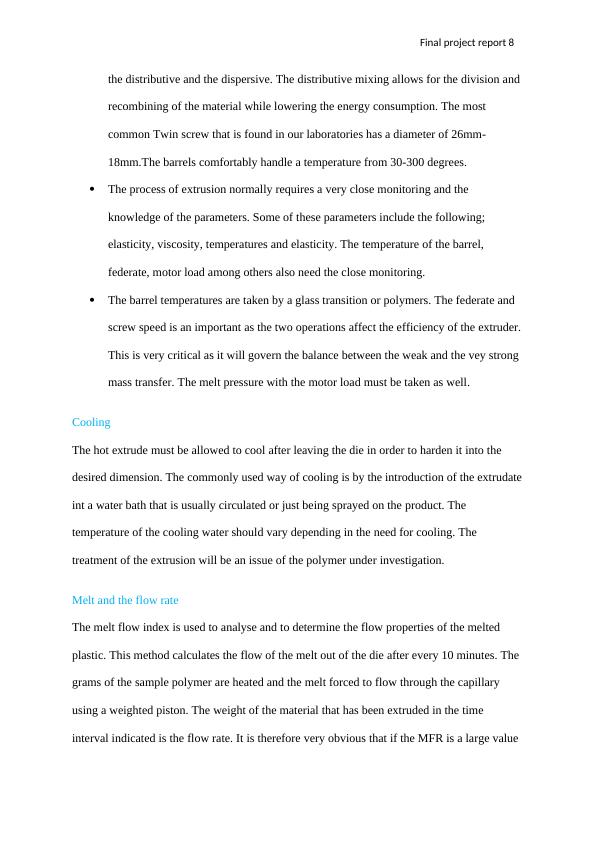
End of preview
Want to access all the pages? Upload your documents or become a member.
Related Documents
3D Zortrax Printers User Guide M Serieslg...
|52
|10500
|19
Recycling of Plastic Bottles by Injection Moldinglg...
|32
|5895
|405