Sheridan AV Case Study 13
VerifiedAdded on 2022/11/01
|14
|3570
|212
AI Summary
Perform tasks related to Sheridan AV's audit for the financial year ended 31 March 2021. Identify inherent risks, assess control risks, propose recommendations, and determine overall risk assessment.
Contribute Materials
Your contribution can guide someone’s learning journey. Share your
documents today.
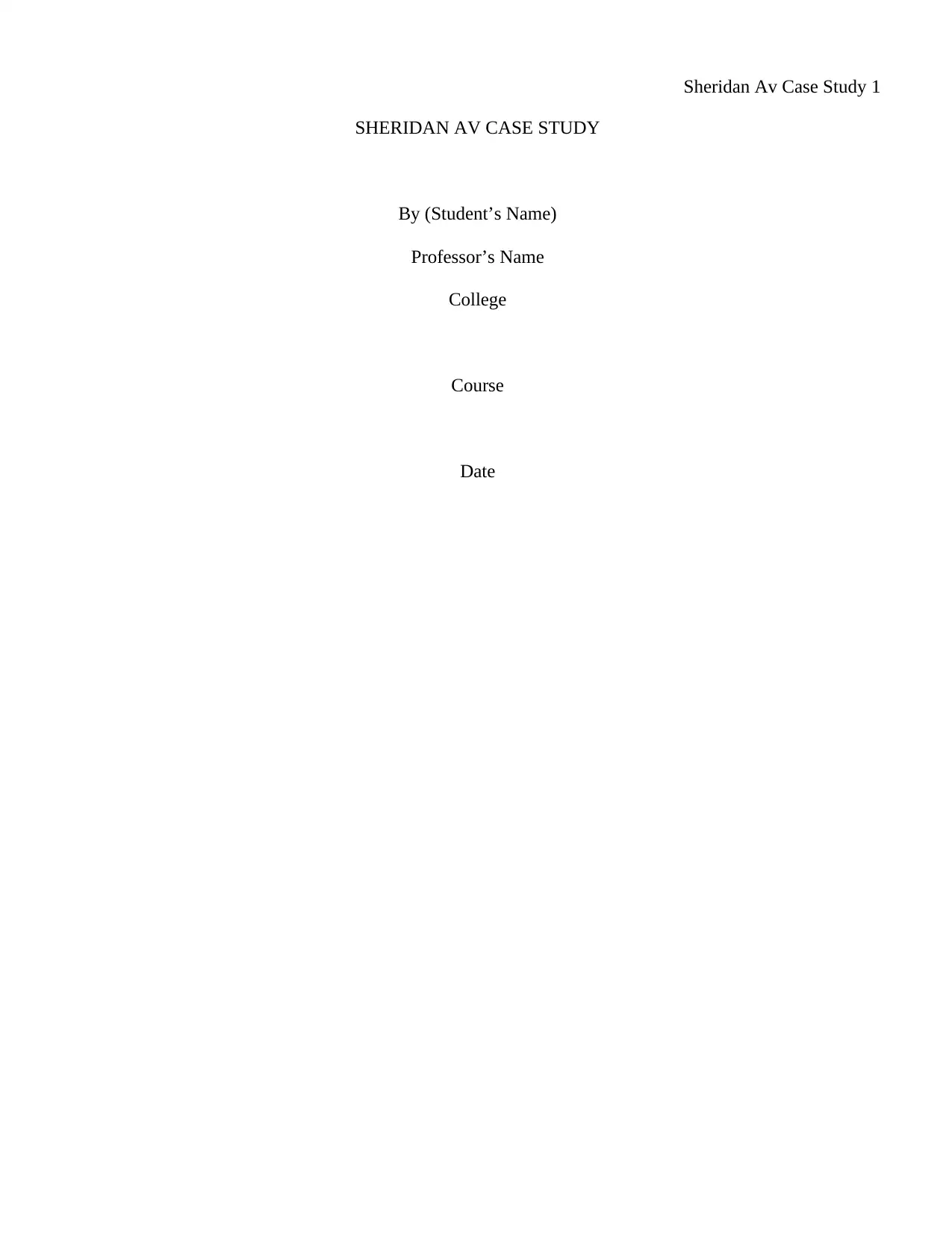
Sheridan Av Case Study 1
SHERIDAN AV CASE STUDY
By (Student’s Name)
Professor’s Name
College
Course
Date
SHERIDAN AV CASE STUDY
By (Student’s Name)
Professor’s Name
College
Course
Date
Secure Best Marks with AI Grader
Need help grading? Try our AI Grader for instant feedback on your assignments.
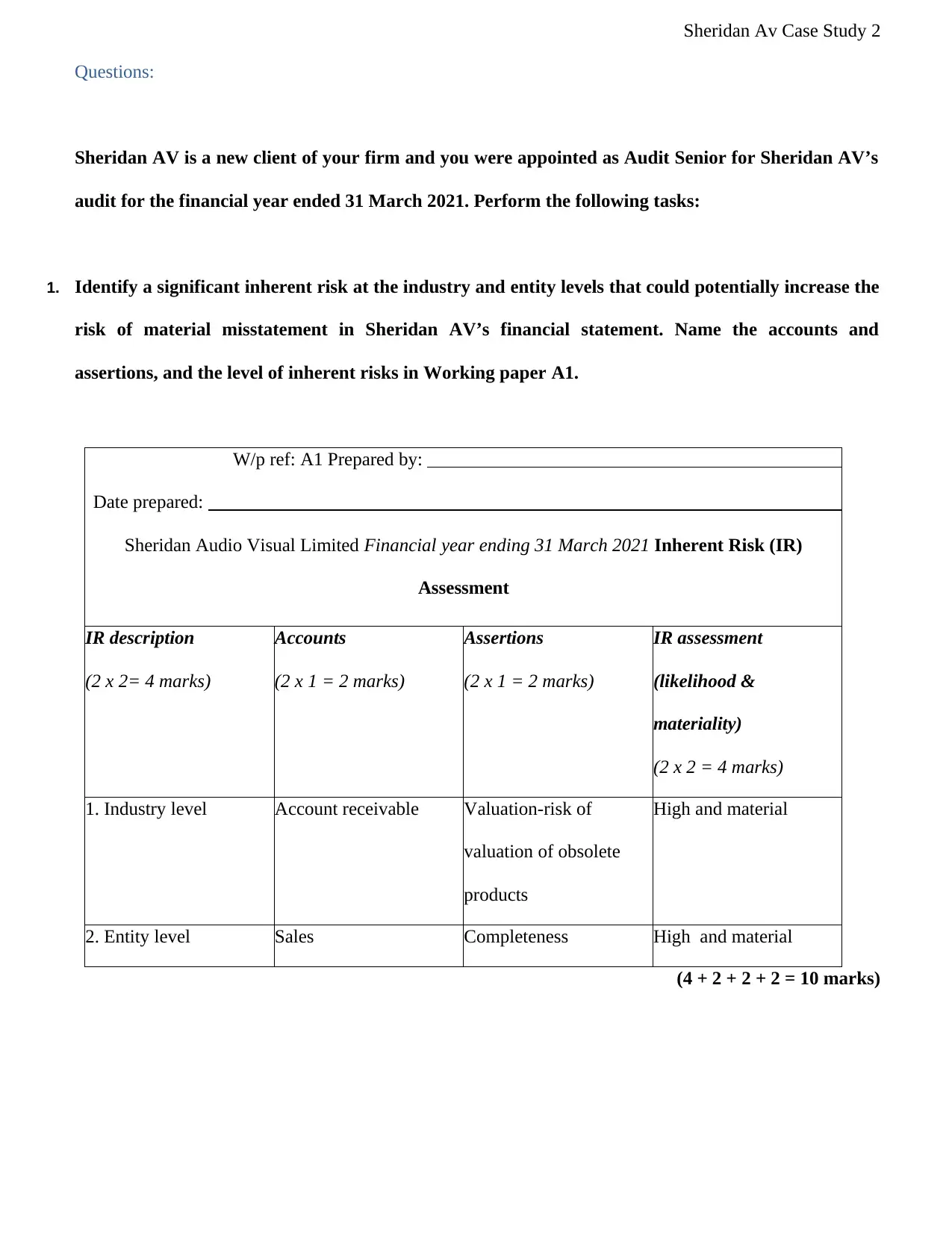
Sheridan Av Case Study 2
Questions:
Sheridan AV is a new client of your firm and you were appointed as Audit Senior for Sheridan AV’s
audit for the financial year ended 31 March 2021. Perform the following tasks:
1. Identify a significant inherent risk at the industry and entity levels that could potentially increase the
risk of material misstatement in Sheridan AV’s financial statement. Name the accounts and
assertions, and the level of inherent risks in Working paper A1.
W/p ref: A1 Prepared by:
Date prepared:
Sheridan Audio Visual Limited Financial year ending 31 March 2021 Inherent Risk (IR)
Assessment
IR description
(2 x 2= 4 marks)
Accounts
(2 x 1 = 2 marks)
Assertions
(2 x 1 = 2 marks)
IR assessment
(likelihood &
materiality)
(2 x 2 = 4 marks)
1. Industry level Account receivable Valuation-risk of
valuation of obsolete
products
High and material
2. Entity level Sales Completeness High and material
(4 + 2 + 2 + 2 = 10 marks)
Questions:
Sheridan AV is a new client of your firm and you were appointed as Audit Senior for Sheridan AV’s
audit for the financial year ended 31 March 2021. Perform the following tasks:
1. Identify a significant inherent risk at the industry and entity levels that could potentially increase the
risk of material misstatement in Sheridan AV’s financial statement. Name the accounts and
assertions, and the level of inherent risks in Working paper A1.
W/p ref: A1 Prepared by:
Date prepared:
Sheridan Audio Visual Limited Financial year ending 31 March 2021 Inherent Risk (IR)
Assessment
IR description
(2 x 2= 4 marks)
Accounts
(2 x 1 = 2 marks)
Assertions
(2 x 1 = 2 marks)
IR assessment
(likelihood &
materiality)
(2 x 2 = 4 marks)
1. Industry level Account receivable Valuation-risk of
valuation of obsolete
products
High and material
2. Entity level Sales Completeness High and material
(4 + 2 + 2 + 2 = 10 marks)
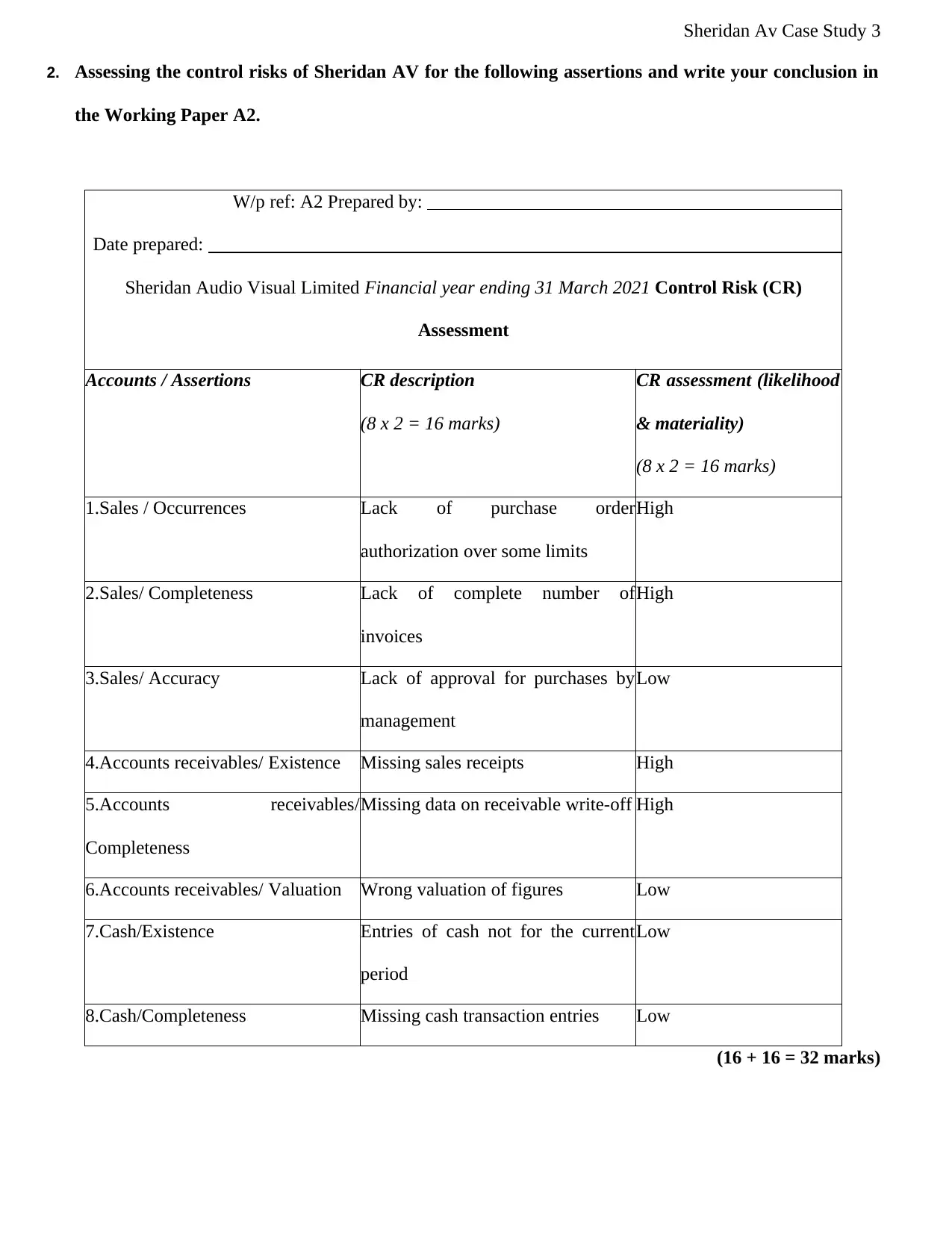
Sheridan Av Case Study 3
2. Assessing the control risks of Sheridan AV for the following assertions and write your conclusion in
the Working Paper A2.
W/p ref: A2 Prepared by:
Date prepared:
Sheridan Audio Visual Limited Financial year ending 31 March 2021 Control Risk (CR)
Assessment
Accounts / Assertions CR description
(8 x 2 = 16 marks)
CR assessment (likelihood
& materiality)
(8 x 2 = 16 marks)
1.Sales / Occurrences Lack of purchase order
authorization over some limits
High
2.Sales/ Completeness Lack of complete number of
invoices
High
3.Sales/ Accuracy Lack of approval for purchases by
management
Low
4.Accounts receivables/ Existence Missing sales receipts High
5.Accounts receivables/
Completeness
Missing data on receivable write-off High
6.Accounts receivables/ Valuation Wrong valuation of figures Low
7.Cash/Existence Entries of cash not for the current
period
Low
8.Cash/Completeness Missing cash transaction entries Low
(16 + 16 = 32 marks)
2. Assessing the control risks of Sheridan AV for the following assertions and write your conclusion in
the Working Paper A2.
W/p ref: A2 Prepared by:
Date prepared:
Sheridan Audio Visual Limited Financial year ending 31 March 2021 Control Risk (CR)
Assessment
Accounts / Assertions CR description
(8 x 2 = 16 marks)
CR assessment (likelihood
& materiality)
(8 x 2 = 16 marks)
1.Sales / Occurrences Lack of purchase order
authorization over some limits
High
2.Sales/ Completeness Lack of complete number of
invoices
High
3.Sales/ Accuracy Lack of approval for purchases by
management
Low
4.Accounts receivables/ Existence Missing sales receipts High
5.Accounts receivables/
Completeness
Missing data on receivable write-off High
6.Accounts receivables/ Valuation Wrong valuation of figures Low
7.Cash/Existence Entries of cash not for the current
period
Low
8.Cash/Completeness Missing cash transaction entries Low
(16 + 16 = 32 marks)
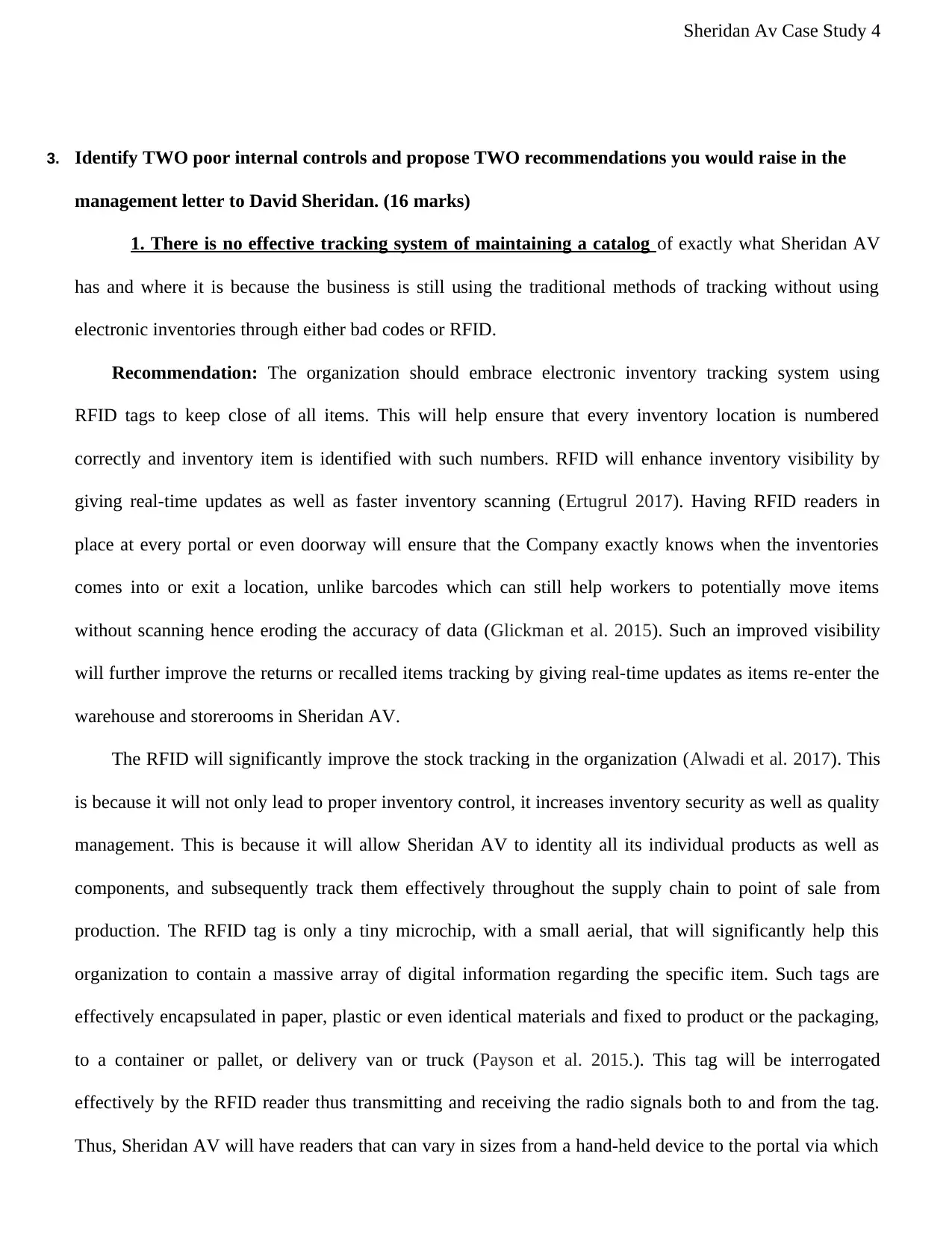
Sheridan Av Case Study 4
3. Identify TWO poor internal controls and propose TWO recommendations you would raise in the
management letter to David Sheridan. (16 marks)
1. There is no effective tracking system of maintaining a catalog of exactly what Sheridan AV
has and where it is because the business is still using the traditional methods of tracking without using
electronic inventories through either bad codes or RFID.
Recommendation: The organization should embrace electronic inventory tracking system using
RFID tags to keep close of all items. This will help ensure that every inventory location is numbered
correctly and inventory item is identified with such numbers. RFID will enhance inventory visibility by
giving real-time updates as well as faster inventory scanning (Ertugrul 2017). Having RFID readers in
place at every portal or even doorway will ensure that the Company exactly knows when the inventories
comes into or exit a location, unlike barcodes which can still help workers to potentially move items
without scanning hence eroding the accuracy of data (Glickman et al. 2015). Such an improved visibility
will further improve the returns or recalled items tracking by giving real-time updates as items re-enter the
warehouse and storerooms in Sheridan AV.
The RFID will significantly improve the stock tracking in the organization (Alwadi et al. 2017). This
is because it will not only lead to proper inventory control, it increases inventory security as well as quality
management. This is because it will allow Sheridan AV to identity all its individual products as well as
components, and subsequently track them effectively throughout the supply chain to point of sale from
production. The RFID tag is only a tiny microchip, with a small aerial, that will significantly help this
organization to contain a massive array of digital information regarding the specific item. Such tags are
effectively encapsulated in paper, plastic or even identical materials and fixed to product or the packaging,
to a container or pallet, or delivery van or truck (Payson et al. 2015.). This tag will be interrogated
effectively by the RFID reader thus transmitting and receiving the radio signals both to and from the tag.
Thus, Sheridan AV will have readers that can vary in sizes from a hand-held device to the portal via which
3. Identify TWO poor internal controls and propose TWO recommendations you would raise in the
management letter to David Sheridan. (16 marks)
1. There is no effective tracking system of maintaining a catalog of exactly what Sheridan AV
has and where it is because the business is still using the traditional methods of tracking without using
electronic inventories through either bad codes or RFID.
Recommendation: The organization should embrace electronic inventory tracking system using
RFID tags to keep close of all items. This will help ensure that every inventory location is numbered
correctly and inventory item is identified with such numbers. RFID will enhance inventory visibility by
giving real-time updates as well as faster inventory scanning (Ertugrul 2017). Having RFID readers in
place at every portal or even doorway will ensure that the Company exactly knows when the inventories
comes into or exit a location, unlike barcodes which can still help workers to potentially move items
without scanning hence eroding the accuracy of data (Glickman et al. 2015). Such an improved visibility
will further improve the returns or recalled items tracking by giving real-time updates as items re-enter the
warehouse and storerooms in Sheridan AV.
The RFID will significantly improve the stock tracking in the organization (Alwadi et al. 2017). This
is because it will not only lead to proper inventory control, it increases inventory security as well as quality
management. This is because it will allow Sheridan AV to identity all its individual products as well as
components, and subsequently track them effectively throughout the supply chain to point of sale from
production. The RFID tag is only a tiny microchip, with a small aerial, that will significantly help this
organization to contain a massive array of digital information regarding the specific item. Such tags are
effectively encapsulated in paper, plastic or even identical materials and fixed to product or the packaging,
to a container or pallet, or delivery van or truck (Payson et al. 2015.). This tag will be interrogated
effectively by the RFID reader thus transmitting and receiving the radio signals both to and from the tag.
Thus, Sheridan AV will have readers that can vary in sizes from a hand-held device to the portal via which
Secure Best Marks with AI Grader
Need help grading? Try our AI Grader for instant feedback on your assignments.
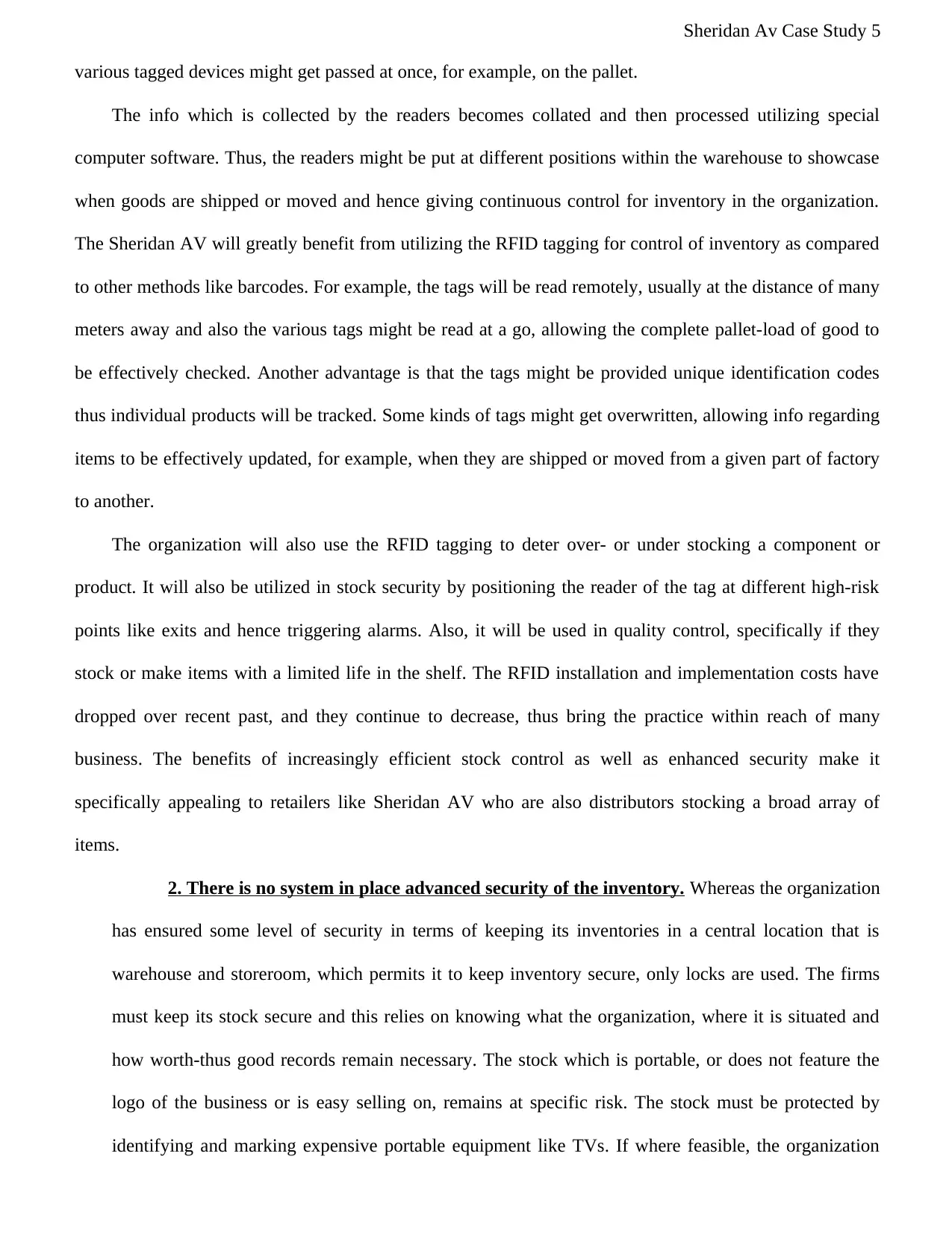
Sheridan Av Case Study 5
various tagged devices might get passed at once, for example, on the pallet.
The info which is collected by the readers becomes collated and then processed utilizing special
computer software. Thus, the readers might be put at different positions within the warehouse to showcase
when goods are shipped or moved and hence giving continuous control for inventory in the organization.
The Sheridan AV will greatly benefit from utilizing the RFID tagging for control of inventory as compared
to other methods like barcodes. For example, the tags will be read remotely, usually at the distance of many
meters away and also the various tags might be read at a go, allowing the complete pallet-load of good to
be effectively checked. Another advantage is that the tags might be provided unique identification codes
thus individual products will be tracked. Some kinds of tags might get overwritten, allowing info regarding
items to be effectively updated, for example, when they are shipped or moved from a given part of factory
to another.
The organization will also use the RFID tagging to deter over- or under stocking a component or
product. It will also be utilized in stock security by positioning the reader of the tag at different high-risk
points like exits and hence triggering alarms. Also, it will be used in quality control, specifically if they
stock or make items with a limited life in the shelf. The RFID installation and implementation costs have
dropped over recent past, and they continue to decrease, thus bring the practice within reach of many
business. The benefits of increasingly efficient stock control as well as enhanced security make it
specifically appealing to retailers like Sheridan AV who are also distributors stocking a broad array of
items.
2. There is no system in place advanced security of the inventory. Whereas the organization
has ensured some level of security in terms of keeping its inventories in a central location that is
warehouse and storeroom, which permits it to keep inventory secure, only locks are used. The firms
must keep its stock secure and this relies on knowing what the organization, where it is situated and
how worth-thus good records remain necessary. The stock which is portable, or does not feature the
logo of the business or is easy selling on, remains at specific risk. The stock must be protected by
identifying and marking expensive portable equipment like TVs. If where feasible, the organization
various tagged devices might get passed at once, for example, on the pallet.
The info which is collected by the readers becomes collated and then processed utilizing special
computer software. Thus, the readers might be put at different positions within the warehouse to showcase
when goods are shipped or moved and hence giving continuous control for inventory in the organization.
The Sheridan AV will greatly benefit from utilizing the RFID tagging for control of inventory as compared
to other methods like barcodes. For example, the tags will be read remotely, usually at the distance of many
meters away and also the various tags might be read at a go, allowing the complete pallet-load of good to
be effectively checked. Another advantage is that the tags might be provided unique identification codes
thus individual products will be tracked. Some kinds of tags might get overwritten, allowing info regarding
items to be effectively updated, for example, when they are shipped or moved from a given part of factory
to another.
The organization will also use the RFID tagging to deter over- or under stocking a component or
product. It will also be utilized in stock security by positioning the reader of the tag at different high-risk
points like exits and hence triggering alarms. Also, it will be used in quality control, specifically if they
stock or make items with a limited life in the shelf. The RFID installation and implementation costs have
dropped over recent past, and they continue to decrease, thus bring the practice within reach of many
business. The benefits of increasingly efficient stock control as well as enhanced security make it
specifically appealing to retailers like Sheridan AV who are also distributors stocking a broad array of
items.
2. There is no system in place advanced security of the inventory. Whereas the organization
has ensured some level of security in terms of keeping its inventories in a central location that is
warehouse and storeroom, which permits it to keep inventory secure, only locks are used. The firms
must keep its stock secure and this relies on knowing what the organization, where it is situated and
how worth-thus good records remain necessary. The stock which is portable, or does not feature the
logo of the business or is easy selling on, remains at specific risk. The stock must be protected by
identifying and marking expensive portable equipment like TVs. If where feasible, the organization
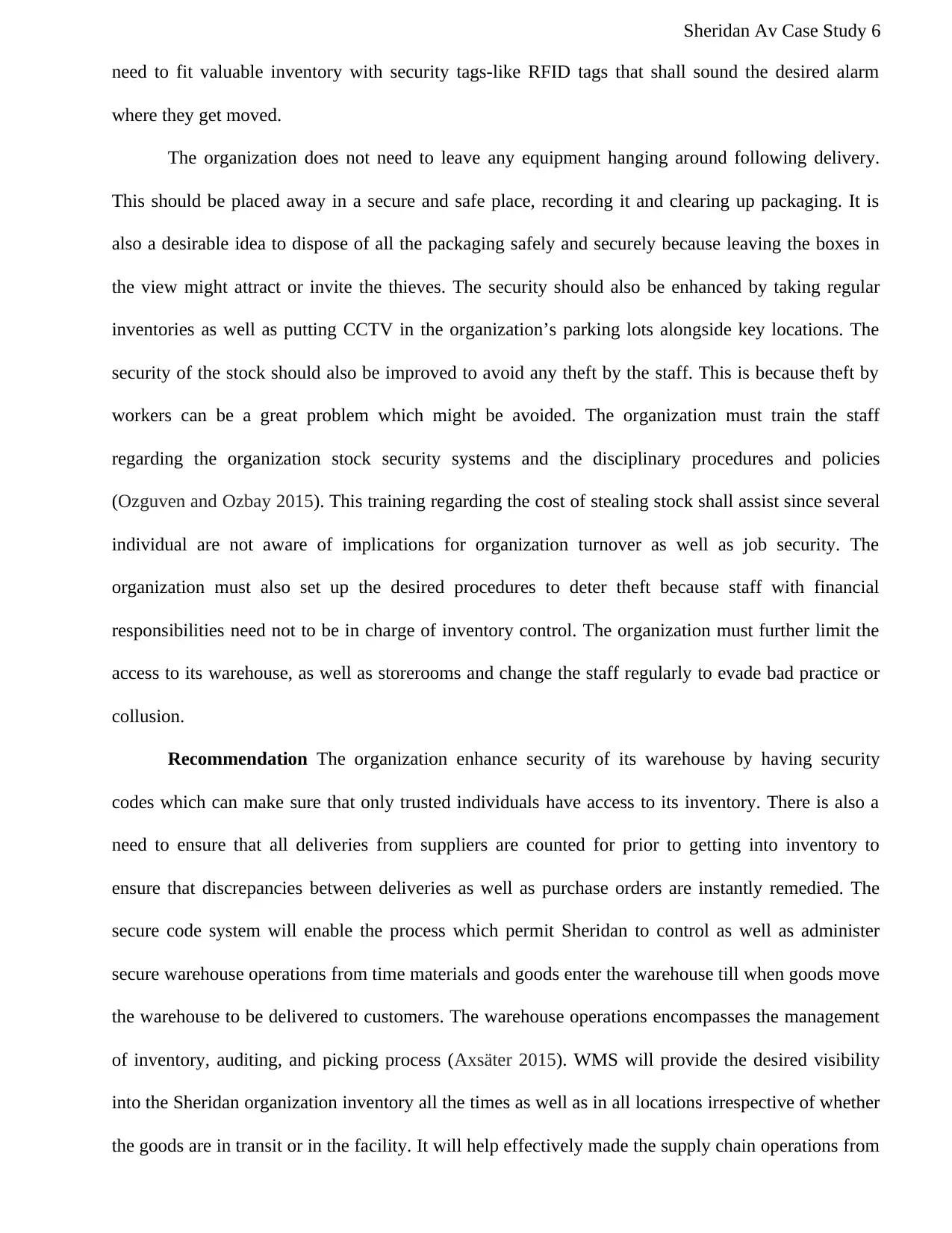
Sheridan Av Case Study 6
need to fit valuable inventory with security tags-like RFID tags that shall sound the desired alarm
where they get moved.
The organization does not need to leave any equipment hanging around following delivery.
This should be placed away in a secure and safe place, recording it and clearing up packaging. It is
also a desirable idea to dispose of all the packaging safely and securely because leaving the boxes in
the view might attract or invite the thieves. The security should also be enhanced by taking regular
inventories as well as putting CCTV in the organization’s parking lots alongside key locations. The
security of the stock should also be improved to avoid any theft by the staff. This is because theft by
workers can be a great problem which might be avoided. The organization must train the staff
regarding the organization stock security systems and the disciplinary procedures and policies
(Ozguven and Ozbay 2015). This training regarding the cost of stealing stock shall assist since several
individual are not aware of implications for organization turnover as well as job security. The
organization must also set up the desired procedures to deter theft because staff with financial
responsibilities need not to be in charge of inventory control. The organization must further limit the
access to its warehouse, as well as storerooms and change the staff regularly to evade bad practice or
collusion.
Recommendation The organization enhance security of its warehouse by having security
codes which can make sure that only trusted individuals have access to its inventory. There is also a
need to ensure that all deliveries from suppliers are counted for prior to getting into inventory to
ensure that discrepancies between deliveries as well as purchase orders are instantly remedied. The
secure code system will enable the process which permit Sheridan to control as well as administer
secure warehouse operations from time materials and goods enter the warehouse till when goods move
the warehouse to be delivered to customers. The warehouse operations encompasses the management
of inventory, auditing, and picking process (Axsäter 2015). WMS will provide the desired visibility
into the Sheridan organization inventory all the times as well as in all locations irrespective of whether
the goods are in transit or in the facility. It will help effectively made the supply chain operations from
need to fit valuable inventory with security tags-like RFID tags that shall sound the desired alarm
where they get moved.
The organization does not need to leave any equipment hanging around following delivery.
This should be placed away in a secure and safe place, recording it and clearing up packaging. It is
also a desirable idea to dispose of all the packaging safely and securely because leaving the boxes in
the view might attract or invite the thieves. The security should also be enhanced by taking regular
inventories as well as putting CCTV in the organization’s parking lots alongside key locations. The
security of the stock should also be improved to avoid any theft by the staff. This is because theft by
workers can be a great problem which might be avoided. The organization must train the staff
regarding the organization stock security systems and the disciplinary procedures and policies
(Ozguven and Ozbay 2015). This training regarding the cost of stealing stock shall assist since several
individual are not aware of implications for organization turnover as well as job security. The
organization must also set up the desired procedures to deter theft because staff with financial
responsibilities need not to be in charge of inventory control. The organization must further limit the
access to its warehouse, as well as storerooms and change the staff regularly to evade bad practice or
collusion.
Recommendation The organization enhance security of its warehouse by having security
codes which can make sure that only trusted individuals have access to its inventory. There is also a
need to ensure that all deliveries from suppliers are counted for prior to getting into inventory to
ensure that discrepancies between deliveries as well as purchase orders are instantly remedied. The
secure code system will enable the process which permit Sheridan to control as well as administer
secure warehouse operations from time materials and goods enter the warehouse till when goods move
the warehouse to be delivered to customers. The warehouse operations encompasses the management
of inventory, auditing, and picking process (Axsäter 2015). WMS will provide the desired visibility
into the Sheridan organization inventory all the times as well as in all locations irrespective of whether
the goods are in transit or in the facility. It will help effectively made the supply chain operations from
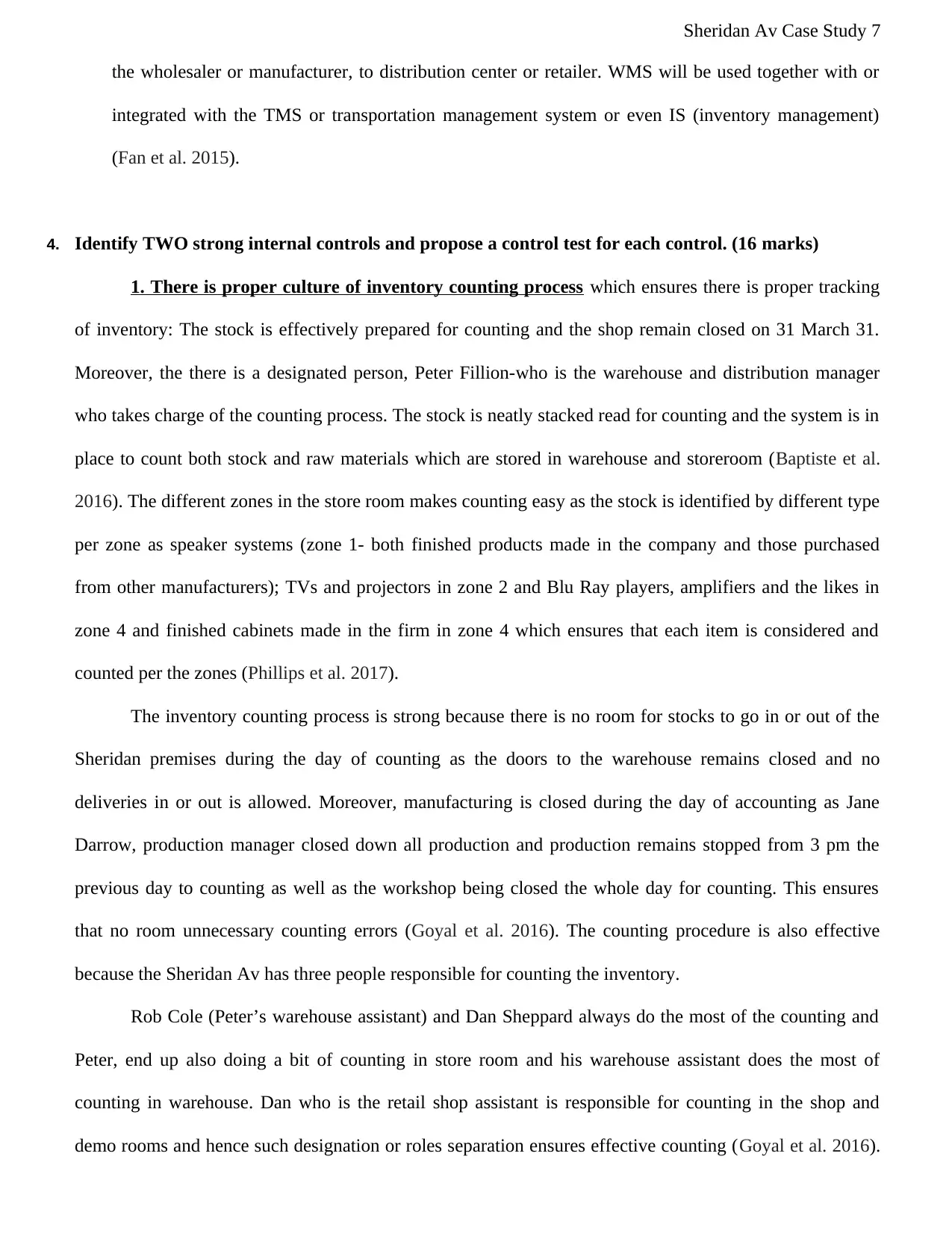
Sheridan Av Case Study 7
the wholesaler or manufacturer, to distribution center or retailer. WMS will be used together with or
integrated with the TMS or transportation management system or even IS (inventory management)
(Fan et al. 2015).
4. Identify TWO strong internal controls and propose a control test for each control. (16 marks)
1. There is proper culture of inventory counting process which ensures there is proper tracking
of inventory: The stock is effectively prepared for counting and the shop remain closed on 31 March 31.
Moreover, the there is a designated person, Peter Fillion-who is the warehouse and distribution manager
who takes charge of the counting process. The stock is neatly stacked read for counting and the system is in
place to count both stock and raw materials which are stored in warehouse and storeroom (Baptiste et al.
2016). The different zones in the store room makes counting easy as the stock is identified by different type
per zone as speaker systems (zone 1- both finished products made in the company and those purchased
from other manufacturers); TVs and projectors in zone 2 and Blu Ray players, amplifiers and the likes in
zone 4 and finished cabinets made in the firm in zone 4 which ensures that each item is considered and
counted per the zones (Phillips et al. 2017).
The inventory counting process is strong because there is no room for stocks to go in or out of the
Sheridan premises during the day of counting as the doors to the warehouse remains closed and no
deliveries in or out is allowed. Moreover, manufacturing is closed during the day of accounting as Jane
Darrow, production manager closed down all production and production remains stopped from 3 pm the
previous day to counting as well as the workshop being closed the whole day for counting. This ensures
that no room unnecessary counting errors (Goyal et al. 2016). The counting procedure is also effective
because the Sheridan Av has three people responsible for counting the inventory.
Rob Cole (Peter’s warehouse assistant) and Dan Sheppard always do the most of the counting and
Peter, end up also doing a bit of counting in store room and his warehouse assistant does the most of
counting in warehouse. Dan who is the retail shop assistant is responsible for counting in the shop and
demo rooms and hence such designation or roles separation ensures effective counting (Goyal et al. 2016).
the wholesaler or manufacturer, to distribution center or retailer. WMS will be used together with or
integrated with the TMS or transportation management system or even IS (inventory management)
(Fan et al. 2015).
4. Identify TWO strong internal controls and propose a control test for each control. (16 marks)
1. There is proper culture of inventory counting process which ensures there is proper tracking
of inventory: The stock is effectively prepared for counting and the shop remain closed on 31 March 31.
Moreover, the there is a designated person, Peter Fillion-who is the warehouse and distribution manager
who takes charge of the counting process. The stock is neatly stacked read for counting and the system is in
place to count both stock and raw materials which are stored in warehouse and storeroom (Baptiste et al.
2016). The different zones in the store room makes counting easy as the stock is identified by different type
per zone as speaker systems (zone 1- both finished products made in the company and those purchased
from other manufacturers); TVs and projectors in zone 2 and Blu Ray players, amplifiers and the likes in
zone 4 and finished cabinets made in the firm in zone 4 which ensures that each item is considered and
counted per the zones (Phillips et al. 2017).
The inventory counting process is strong because there is no room for stocks to go in or out of the
Sheridan premises during the day of counting as the doors to the warehouse remains closed and no
deliveries in or out is allowed. Moreover, manufacturing is closed during the day of accounting as Jane
Darrow, production manager closed down all production and production remains stopped from 3 pm the
previous day to counting as well as the workshop being closed the whole day for counting. This ensures
that no room unnecessary counting errors (Goyal et al. 2016). The counting procedure is also effective
because the Sheridan Av has three people responsible for counting the inventory.
Rob Cole (Peter’s warehouse assistant) and Dan Sheppard always do the most of the counting and
Peter, end up also doing a bit of counting in store room and his warehouse assistant does the most of
counting in warehouse. Dan who is the retail shop assistant is responsible for counting in the shop and
demo rooms and hence such designation or roles separation ensures effective counting (Goyal et al. 2016).
Paraphrase This Document
Need a fresh take? Get an instant paraphrase of this document with our AI Paraphraser
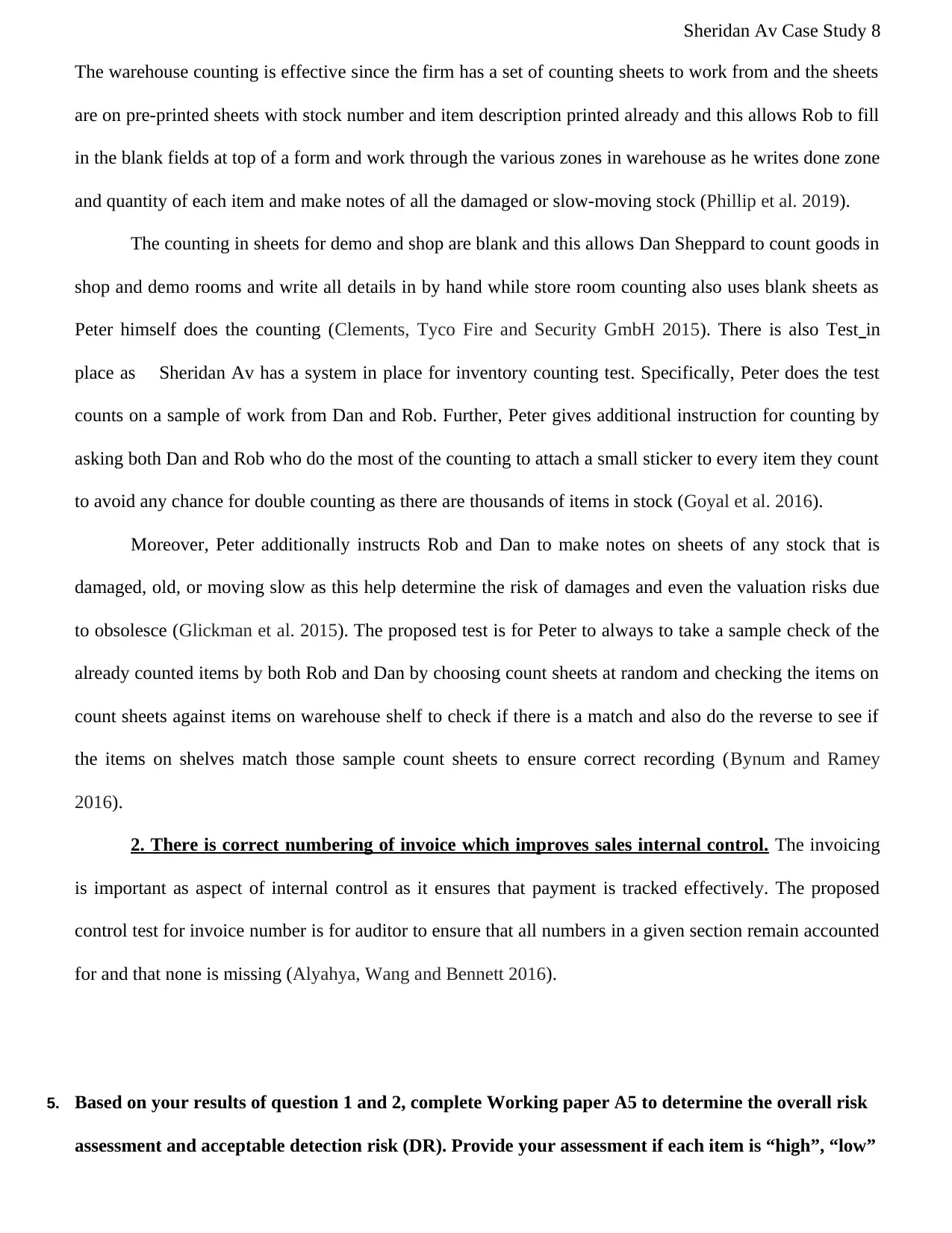
Sheridan Av Case Study 8
The warehouse counting is effective since the firm has a set of counting sheets to work from and the sheets
are on pre-printed sheets with stock number and item description printed already and this allows Rob to fill
in the blank fields at top of a form and work through the various zones in warehouse as he writes done zone
and quantity of each item and make notes of all the damaged or slow-moving stock (Phillip et al. 2019).
The counting in sheets for demo and shop are blank and this allows Dan Sheppard to count goods in
shop and demo rooms and write all details in by hand while store room counting also uses blank sheets as
Peter himself does the counting (Clements, Tyco Fire and Security GmbH 2015). There is also Test in
place as Sheridan Av has a system in place for inventory counting test. Specifically, Peter does the test
counts on a sample of work from Dan and Rob. Further, Peter gives additional instruction for counting by
asking both Dan and Rob who do the most of the counting to attach a small sticker to every item they count
to avoid any chance for double counting as there are thousands of items in stock (Goyal et al. 2016).
Moreover, Peter additionally instructs Rob and Dan to make notes on sheets of any stock that is
damaged, old, or moving slow as this help determine the risk of damages and even the valuation risks due
to obsolesce (Glickman et al. 2015). The proposed test is for Peter to always to take a sample check of the
already counted items by both Rob and Dan by choosing count sheets at random and checking the items on
count sheets against items on warehouse shelf to check if there is a match and also do the reverse to see if
the items on shelves match those sample count sheets to ensure correct recording (Bynum and Ramey
2016).
2. There is correct numbering of invoice which improves sales internal control. The invoicing
is important as aspect of internal control as it ensures that payment is tracked effectively. The proposed
control test for invoice number is for auditor to ensure that all numbers in a given section remain accounted
for and that none is missing (Alyahya, Wang and Bennett 2016).
5. Based on your results of question 1 and 2, complete Working paper A5 to determine the overall risk
assessment and acceptable detection risk (DR). Provide your assessment if each item is “high”, “low”
The warehouse counting is effective since the firm has a set of counting sheets to work from and the sheets
are on pre-printed sheets with stock number and item description printed already and this allows Rob to fill
in the blank fields at top of a form and work through the various zones in warehouse as he writes done zone
and quantity of each item and make notes of all the damaged or slow-moving stock (Phillip et al. 2019).
The counting in sheets for demo and shop are blank and this allows Dan Sheppard to count goods in
shop and demo rooms and write all details in by hand while store room counting also uses blank sheets as
Peter himself does the counting (Clements, Tyco Fire and Security GmbH 2015). There is also Test in
place as Sheridan Av has a system in place for inventory counting test. Specifically, Peter does the test
counts on a sample of work from Dan and Rob. Further, Peter gives additional instruction for counting by
asking both Dan and Rob who do the most of the counting to attach a small sticker to every item they count
to avoid any chance for double counting as there are thousands of items in stock (Goyal et al. 2016).
Moreover, Peter additionally instructs Rob and Dan to make notes on sheets of any stock that is
damaged, old, or moving slow as this help determine the risk of damages and even the valuation risks due
to obsolesce (Glickman et al. 2015). The proposed test is for Peter to always to take a sample check of the
already counted items by both Rob and Dan by choosing count sheets at random and checking the items on
count sheets against items on warehouse shelf to check if there is a match and also do the reverse to see if
the items on shelves match those sample count sheets to ensure correct recording (Bynum and Ramey
2016).
2. There is correct numbering of invoice which improves sales internal control. The invoicing
is important as aspect of internal control as it ensures that payment is tracked effectively. The proposed
control test for invoice number is for auditor to ensure that all numbers in a given section remain accounted
for and that none is missing (Alyahya, Wang and Bennett 2016).
5. Based on your results of question 1 and 2, complete Working paper A5 to determine the overall risk
assessment and acceptable detection risk (DR). Provide your assessment if each item is “high”, “low”
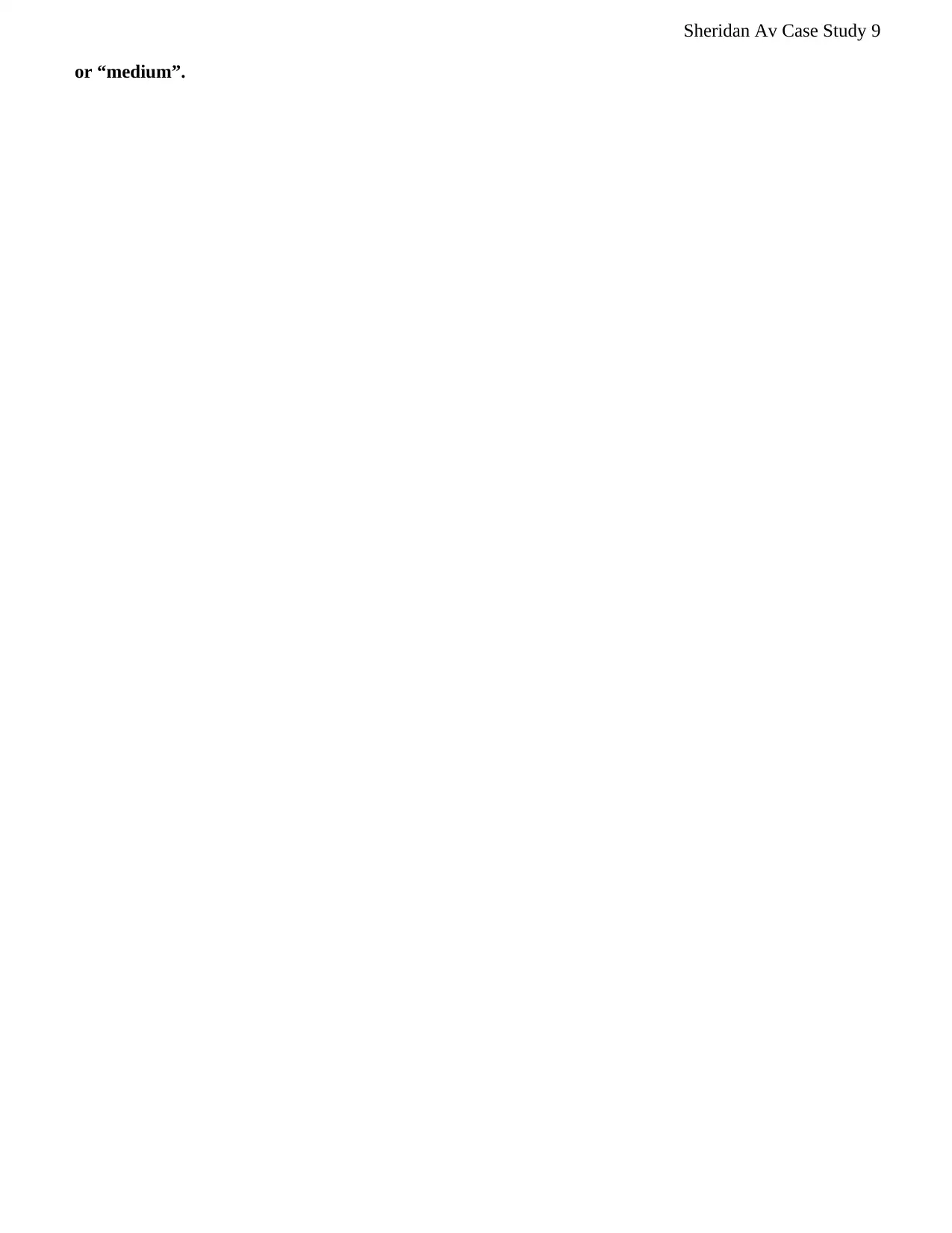
Sheridan Av Case Study 9
or “medium”.
or “medium”.
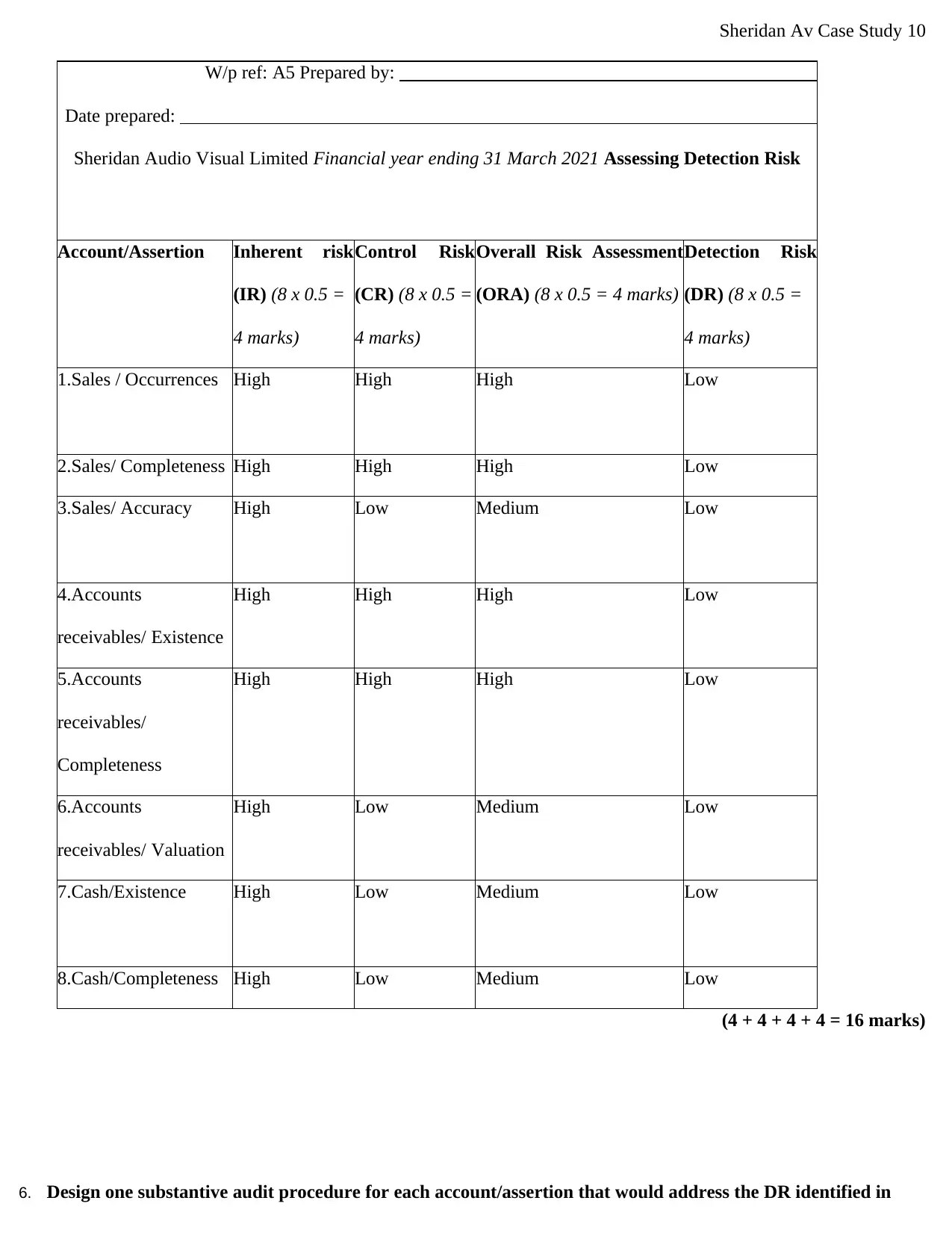
Sheridan Av Case Study 10
W/p ref: A5 Prepared by:
Date prepared:
Sheridan Audio Visual Limited Financial year ending 31 March 2021 Assessing Detection Risk
Account/Assertion Inherent risk
(IR) (8 x 0.5 =
4 marks)
Control Risk
(CR) (8 x 0.5 =
4 marks)
Overall Risk Assessment
(ORA) (8 x 0.5 = 4 marks)
Detection Risk
(DR) (8 x 0.5 =
4 marks)
1.Sales / Occurrences High High High Low
2.Sales/ Completeness High High High Low
3.Sales/ Accuracy High Low Medium Low
4.Accounts
receivables/ Existence
High High High Low
5.Accounts
receivables/
Completeness
High High High Low
6.Accounts
receivables/ Valuation
High Low Medium Low
7.Cash/Existence High Low Medium Low
8.Cash/Completeness High Low Medium Low
(4 + 4 + 4 + 4 = 16 marks)
6. Design one substantive audit procedure for each account/assertion that would address the DR identified in
W/p ref: A5 Prepared by:
Date prepared:
Sheridan Audio Visual Limited Financial year ending 31 March 2021 Assessing Detection Risk
Account/Assertion Inherent risk
(IR) (8 x 0.5 =
4 marks)
Control Risk
(CR) (8 x 0.5 =
4 marks)
Overall Risk Assessment
(ORA) (8 x 0.5 = 4 marks)
Detection Risk
(DR) (8 x 0.5 =
4 marks)
1.Sales / Occurrences High High High Low
2.Sales/ Completeness High High High Low
3.Sales/ Accuracy High Low Medium Low
4.Accounts
receivables/ Existence
High High High Low
5.Accounts
receivables/
Completeness
High High High Low
6.Accounts
receivables/ Valuation
High Low Medium Low
7.Cash/Existence High Low Medium Low
8.Cash/Completeness High Low Medium Low
(4 + 4 + 4 + 4 = 16 marks)
6. Design one substantive audit procedure for each account/assertion that would address the DR identified in
Secure Best Marks with AI Grader
Need help grading? Try our AI Grader for instant feedback on your assignments.
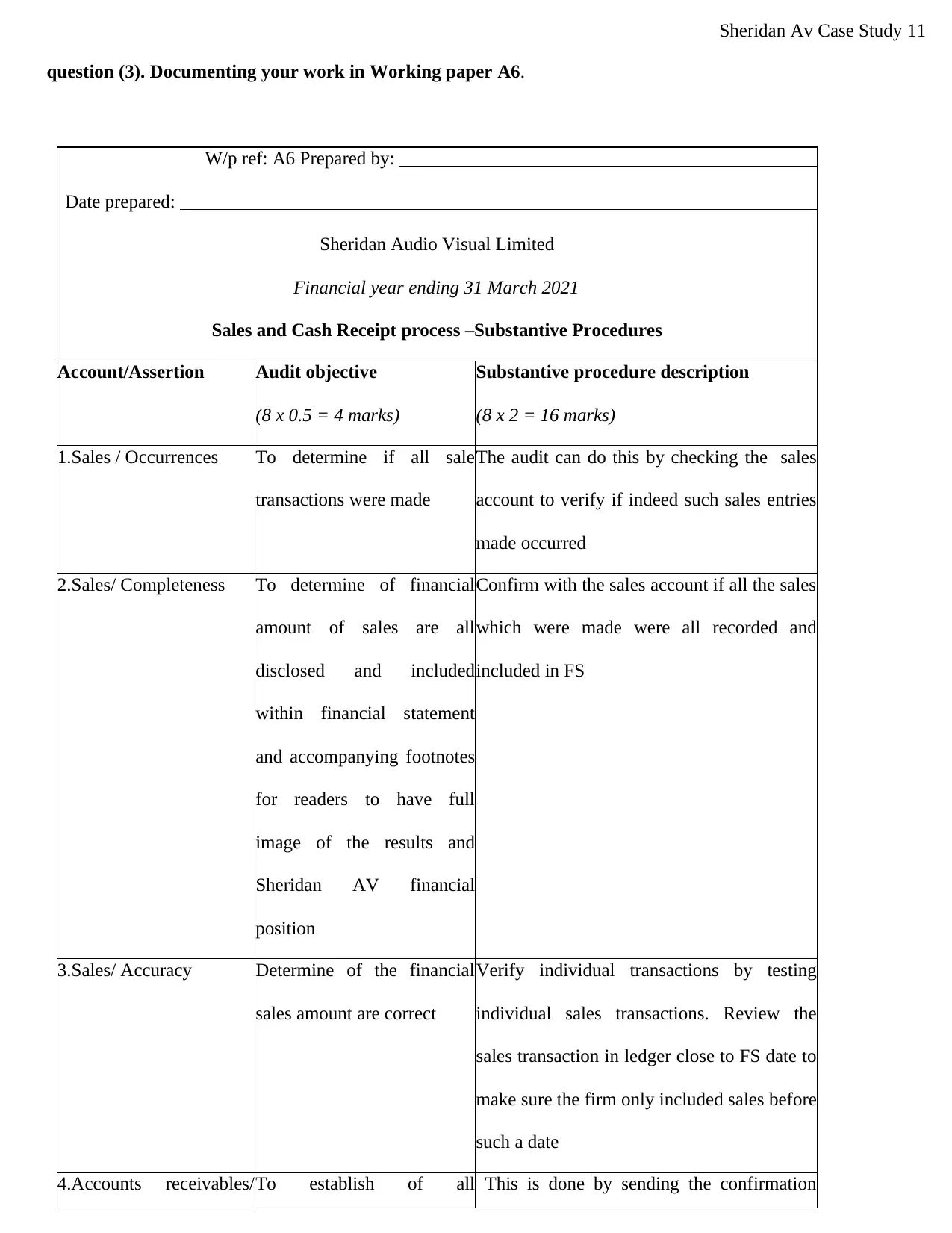
Sheridan Av Case Study 11
question (3). Documenting your work in Working paper A6.
W/p ref: A6 Prepared by:
Date prepared:
Sheridan Audio Visual Limited
Financial year ending 31 March 2021
Sales and Cash Receipt process –Substantive Procedures
Account/Assertion Audit objective
(8 x 0.5 = 4 marks)
Substantive procedure description
(8 x 2 = 16 marks)
1.Sales / Occurrences To determine if all sale
transactions were made
The audit can do this by checking the sales
account to verify if indeed such sales entries
made occurred
2.Sales/ Completeness To determine of financial
amount of sales are all
disclosed and included
within financial statement
and accompanying footnotes
for readers to have full
image of the results and
Sheridan AV financial
position
Confirm with the sales account if all the sales
which were made were all recorded and
included in FS
3.Sales/ Accuracy Determine of the financial
sales amount are correct
Verify individual transactions by testing
individual sales transactions. Review the
sales transaction in ledger close to FS date to
make sure the firm only included sales before
such a date
4.Accounts receivables/To establish of all This is done by sending the confirmation
question (3). Documenting your work in Working paper A6.
W/p ref: A6 Prepared by:
Date prepared:
Sheridan Audio Visual Limited
Financial year ending 31 March 2021
Sales and Cash Receipt process –Substantive Procedures
Account/Assertion Audit objective
(8 x 0.5 = 4 marks)
Substantive procedure description
(8 x 2 = 16 marks)
1.Sales / Occurrences To determine if all sale
transactions were made
The audit can do this by checking the sales
account to verify if indeed such sales entries
made occurred
2.Sales/ Completeness To determine of financial
amount of sales are all
disclosed and included
within financial statement
and accompanying footnotes
for readers to have full
image of the results and
Sheridan AV financial
position
Confirm with the sales account if all the sales
which were made were all recorded and
included in FS
3.Sales/ Accuracy Determine of the financial
sales amount are correct
Verify individual transactions by testing
individual sales transactions. Review the
sales transaction in ledger close to FS date to
make sure the firm only included sales before
such a date
4.Accounts receivables/To establish of all This is done by sending the confirmation
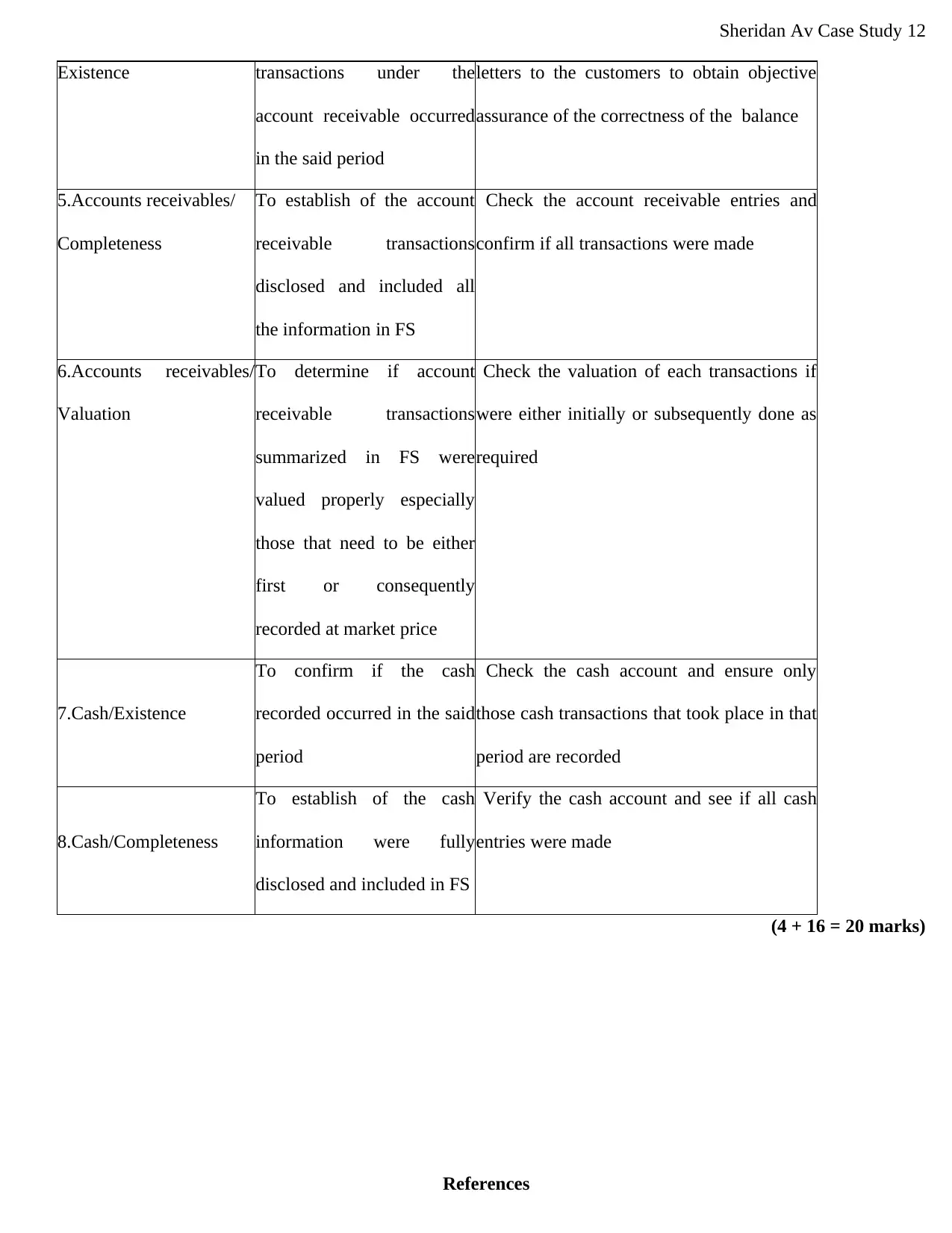
Sheridan Av Case Study 12
Existence transactions under the
account receivable occurred
in the said period
letters to the customers to obtain objective
assurance of the correctness of the balance
5.Accounts receivables/
Completeness
To establish of the account
receivable transactions
disclosed and included all
the information in FS
Check the account receivable entries and
confirm if all transactions were made
6.Accounts receivables/
Valuation
To determine if account
receivable transactions
summarized in FS were
valued properly especially
those that need to be either
first or consequently
recorded at market price
Check the valuation of each transactions if
were either initially or subsequently done as
required
7.Cash/Existence
To confirm if the cash
recorded occurred in the said
period
Check the cash account and ensure only
those cash transactions that took place in that
period are recorded
8.Cash/Completeness
To establish of the cash
information were fully
disclosed and included in FS
Verify the cash account and see if all cash
entries were made
(4 + 16 = 20 marks)
References
Existence transactions under the
account receivable occurred
in the said period
letters to the customers to obtain objective
assurance of the correctness of the balance
5.Accounts receivables/
Completeness
To establish of the account
receivable transactions
disclosed and included all
the information in FS
Check the account receivable entries and
confirm if all transactions were made
6.Accounts receivables/
Valuation
To determine if account
receivable transactions
summarized in FS were
valued properly especially
those that need to be either
first or consequently
recorded at market price
Check the valuation of each transactions if
were either initially or subsequently done as
required
7.Cash/Existence
To confirm if the cash
recorded occurred in the said
period
Check the cash account and ensure only
those cash transactions that took place in that
period are recorded
8.Cash/Completeness
To establish of the cash
information were fully
disclosed and included in FS
Verify the cash account and see if all cash
entries were made
(4 + 16 = 20 marks)
References
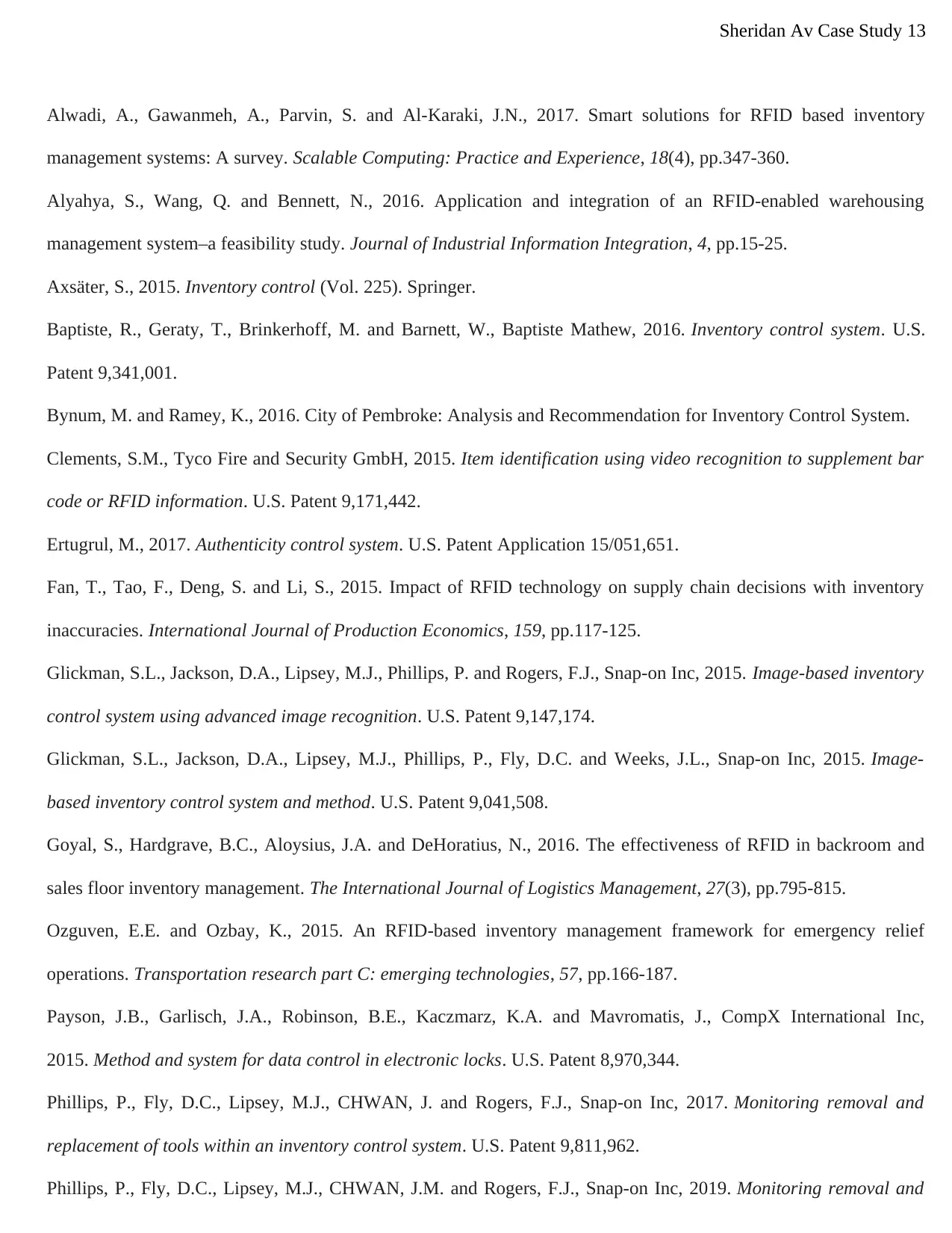
Sheridan Av Case Study 13
Alwadi, A., Gawanmeh, A., Parvin, S. and Al-Karaki, J.N., 2017. Smart solutions for RFID based inventory
management systems: A survey. Scalable Computing: Practice and Experience, 18(4), pp.347-360.
Alyahya, S., Wang, Q. and Bennett, N., 2016. Application and integration of an RFID-enabled warehousing
management system–a feasibility study. Journal of Industrial Information Integration, 4, pp.15-25.
Axsäter, S., 2015. Inventory control (Vol. 225). Springer.
Baptiste, R., Geraty, T., Brinkerhoff, M. and Barnett, W., Baptiste Mathew, 2016. Inventory control system. U.S.
Patent 9,341,001.
Bynum, M. and Ramey, K., 2016. City of Pembroke: Analysis and Recommendation for Inventory Control System.
Clements, S.M., Tyco Fire and Security GmbH, 2015. Item identification using video recognition to supplement bar
code or RFID information. U.S. Patent 9,171,442.
Ertugrul, M., 2017. Authenticity control system. U.S. Patent Application 15/051,651.
Fan, T., Tao, F., Deng, S. and Li, S., 2015. Impact of RFID technology on supply chain decisions with inventory
inaccuracies. International Journal of Production Economics, 159, pp.117-125.
Glickman, S.L., Jackson, D.A., Lipsey, M.J., Phillips, P. and Rogers, F.J., Snap-on Inc, 2015. Image-based inventory
control system using advanced image recognition. U.S. Patent 9,147,174.
Glickman, S.L., Jackson, D.A., Lipsey, M.J., Phillips, P., Fly, D.C. and Weeks, J.L., Snap-on Inc, 2015. Image-
based inventory control system and method. U.S. Patent 9,041,508.
Goyal, S., Hardgrave, B.C., Aloysius, J.A. and DeHoratius, N., 2016. The effectiveness of RFID in backroom and
sales floor inventory management. The International Journal of Logistics Management, 27(3), pp.795-815.
Ozguven, E.E. and Ozbay, K., 2015. An RFID-based inventory management framework for emergency relief
operations. Transportation research part C: emerging technologies, 57, pp.166-187.
Payson, J.B., Garlisch, J.A., Robinson, B.E., Kaczmarz, K.A. and Mavromatis, J., CompX International Inc,
2015. Method and system for data control in electronic locks. U.S. Patent 8,970,344.
Phillips, P., Fly, D.C., Lipsey, M.J., CHWAN, J. and Rogers, F.J., Snap-on Inc, 2017. Monitoring removal and
replacement of tools within an inventory control system. U.S. Patent 9,811,962.
Phillips, P., Fly, D.C., Lipsey, M.J., CHWAN, J.M. and Rogers, F.J., Snap-on Inc, 2019. Monitoring removal and
Alwadi, A., Gawanmeh, A., Parvin, S. and Al-Karaki, J.N., 2017. Smart solutions for RFID based inventory
management systems: A survey. Scalable Computing: Practice and Experience, 18(4), pp.347-360.
Alyahya, S., Wang, Q. and Bennett, N., 2016. Application and integration of an RFID-enabled warehousing
management system–a feasibility study. Journal of Industrial Information Integration, 4, pp.15-25.
Axsäter, S., 2015. Inventory control (Vol. 225). Springer.
Baptiste, R., Geraty, T., Brinkerhoff, M. and Barnett, W., Baptiste Mathew, 2016. Inventory control system. U.S.
Patent 9,341,001.
Bynum, M. and Ramey, K., 2016. City of Pembroke: Analysis and Recommendation for Inventory Control System.
Clements, S.M., Tyco Fire and Security GmbH, 2015. Item identification using video recognition to supplement bar
code or RFID information. U.S. Patent 9,171,442.
Ertugrul, M., 2017. Authenticity control system. U.S. Patent Application 15/051,651.
Fan, T., Tao, F., Deng, S. and Li, S., 2015. Impact of RFID technology on supply chain decisions with inventory
inaccuracies. International Journal of Production Economics, 159, pp.117-125.
Glickman, S.L., Jackson, D.A., Lipsey, M.J., Phillips, P. and Rogers, F.J., Snap-on Inc, 2015. Image-based inventory
control system using advanced image recognition. U.S. Patent 9,147,174.
Glickman, S.L., Jackson, D.A., Lipsey, M.J., Phillips, P., Fly, D.C. and Weeks, J.L., Snap-on Inc, 2015. Image-
based inventory control system and method. U.S. Patent 9,041,508.
Goyal, S., Hardgrave, B.C., Aloysius, J.A. and DeHoratius, N., 2016. The effectiveness of RFID in backroom and
sales floor inventory management. The International Journal of Logistics Management, 27(3), pp.795-815.
Ozguven, E.E. and Ozbay, K., 2015. An RFID-based inventory management framework for emergency relief
operations. Transportation research part C: emerging technologies, 57, pp.166-187.
Payson, J.B., Garlisch, J.A., Robinson, B.E., Kaczmarz, K.A. and Mavromatis, J., CompX International Inc,
2015. Method and system for data control in electronic locks. U.S. Patent 8,970,344.
Phillips, P., Fly, D.C., Lipsey, M.J., CHWAN, J. and Rogers, F.J., Snap-on Inc, 2017. Monitoring removal and
replacement of tools within an inventory control system. U.S. Patent 9,811,962.
Phillips, P., Fly, D.C., Lipsey, M.J., CHWAN, J.M. and Rogers, F.J., Snap-on Inc, 2019. Monitoring removal and
Paraphrase This Document
Need a fresh take? Get an instant paraphrase of this document with our AI Paraphraser
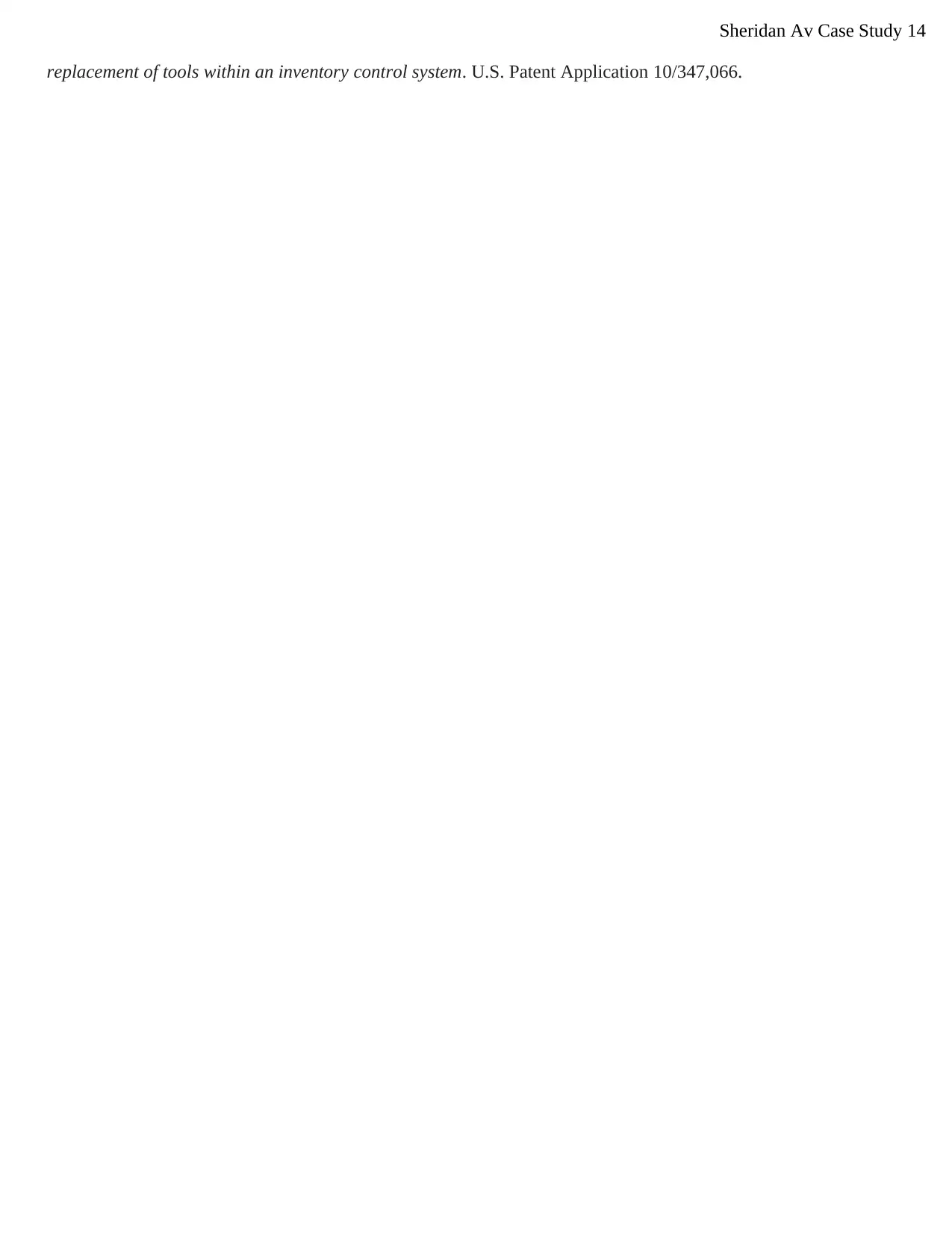
Sheridan Av Case Study 14
replacement of tools within an inventory control system. U.S. Patent Application 10/347,066.
replacement of tools within an inventory control system. U.S. Patent Application 10/347,066.
1 out of 14
![[object Object]](/_next/image/?url=%2F_next%2Fstatic%2Fmedia%2Flogo.6d15ce61.png&w=640&q=75)
Your All-in-One AI-Powered Toolkit for Academic Success.
+13062052269
info@desklib.com
Available 24*7 on WhatsApp / Email
Unlock your academic potential
© 2024 | Zucol Services PVT LTD | All rights reserved.