South Qurainat Rumaila Temporary Compression Station Project
VerifiedAdded on 2023/06/11
|7
|1633
|421
AI Summary
The South Qurainat Rumaila Temporary Compression Station project was executed with perfect design and fabrication. The project objectives were to execute the project of gas compressors and understand the entire concept of gas compressors and installation of reciprocating compression. The project involved reciprocating the compressors for processing of gases. The distinctive activities included the application of basic mechanical skills, drafting of standards and geometric, dimension and tolerancing, and utilizing the software of EPDM for Engineering Product Data Management. The identified issues were regarding safety measures and designing of the screw compressors. The solutions included taking up all necessary safety measures and making the design perfectly with the help of AutoCAD. The plan was to produce innovative and creative work by working collaboratively.
Contribute Materials
Your contribution can guide someone’s learning journey. Share your
documents today.
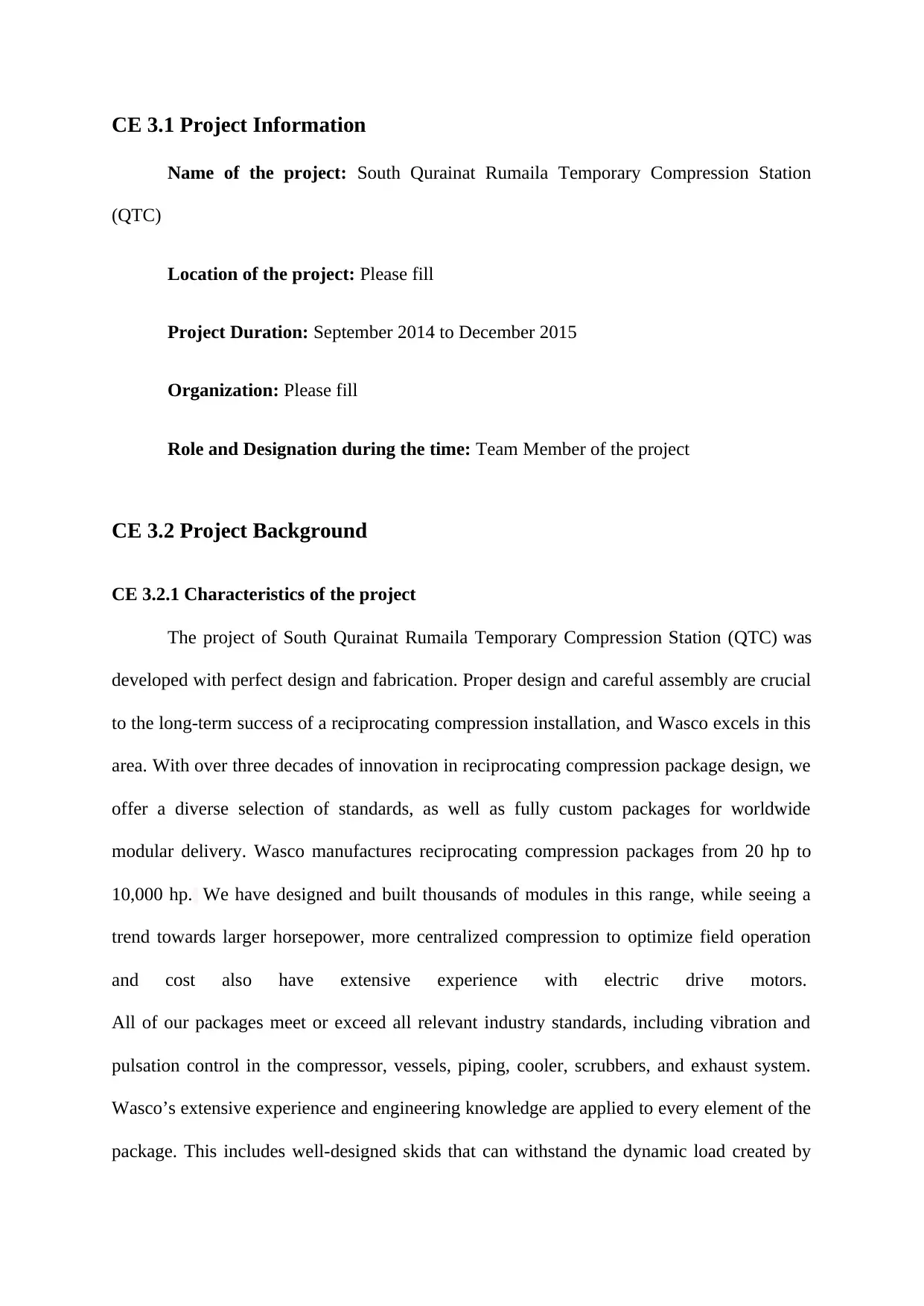
CE 3.1 Project Information
Name of the project: South Qurainat Rumaila Temporary Compression Station
(QTC)
Location of the project: Please fill
Project Duration: September 2014 to December 2015
Organization: Please fill
Role and Designation during the time: Team Member of the project
CE 3.2 Project Background
CE 3.2.1 Characteristics of the project
The project of South Qurainat Rumaila Temporary Compression Station (QTC) was
developed with perfect design and fabrication. Proper design and careful assembly are crucial
to the long-term success of a reciprocating compression installation, and Wasco excels in this
area. With over three decades of innovation in reciprocating compression package design, we
offer a diverse selection of standards, as well as fully custom packages for worldwide
modular delivery. Wasco manufactures reciprocating compression packages from 20 hp to
10,000 hp. We have designed and built thousands of modules in this range, while seeing a
trend towards larger horsepower, more centralized compression to optimize field operation
and cost also have extensive experience with electric drive motors.
All of our packages meet or exceed all relevant industry standards, including vibration and
pulsation control in the compressor, vessels, piping, cooler, scrubbers, and exhaust system.
Wasco’s extensive experience and engineering knowledge are applied to every element of the
package. This includes well-designed skids that can withstand the dynamic load created by
Name of the project: South Qurainat Rumaila Temporary Compression Station
(QTC)
Location of the project: Please fill
Project Duration: September 2014 to December 2015
Organization: Please fill
Role and Designation during the time: Team Member of the project
CE 3.2 Project Background
CE 3.2.1 Characteristics of the project
The project of South Qurainat Rumaila Temporary Compression Station (QTC) was
developed with perfect design and fabrication. Proper design and careful assembly are crucial
to the long-term success of a reciprocating compression installation, and Wasco excels in this
area. With over three decades of innovation in reciprocating compression package design, we
offer a diverse selection of standards, as well as fully custom packages for worldwide
modular delivery. Wasco manufactures reciprocating compression packages from 20 hp to
10,000 hp. We have designed and built thousands of modules in this range, while seeing a
trend towards larger horsepower, more centralized compression to optimize field operation
and cost also have extensive experience with electric drive motors.
All of our packages meet or exceed all relevant industry standards, including vibration and
pulsation control in the compressor, vessels, piping, cooler, scrubbers, and exhaust system.
Wasco’s extensive experience and engineering knowledge are applied to every element of the
package. This includes well-designed skids that can withstand the dynamic load created by
Secure Best Marks with AI Grader
Need help grading? Try our AI Grader for instant feedback on your assignments.

the torque and interaction of the many moving elements.
Wasco packages Ariel, Dresser Rand, and GE compressors along with Caterpillar and
Waukesha engines. We work closely with Howden Thomassen Compressors B.V. in serving
the low-speed traditionally the API 618 reciprocating compressor market.
CE 3.2.2 Objectives developed for the project
This particular project has various significant objectives. They are as follows:
To execute the project of gas compressors.
To understand the entire concept of gas compressors and installation of reciprocating
compression.
CE 3.2.3 My area of work
The project of South Qurainat Rumaila Temporary Compression Station (QTC) was
one of the most important projects in my career. Being a mechanical engineer, I made sure
that the project was executed properly, without any kind of complexities. I was under the
supervision of my project supervisor and the entire project was completed under the control
of our Head of the Department. My major area of work was to reciprocate the compressors
for processing of gases. Moreover, I eve documented the entire project with proper technical
details.
Wasco packages Ariel, Dresser Rand, and GE compressors along with Caterpillar and
Waukesha engines. We work closely with Howden Thomassen Compressors B.V. in serving
the low-speed traditionally the API 618 reciprocating compressor market.
CE 3.2.2 Objectives developed for the project
This particular project has various significant objectives. They are as follows:
To execute the project of gas compressors.
To understand the entire concept of gas compressors and installation of reciprocating
compression.
CE 3.2.3 My area of work
The project of South Qurainat Rumaila Temporary Compression Station (QTC) was
one of the most important projects in my career. Being a mechanical engineer, I made sure
that the project was executed properly, without any kind of complexities. I was under the
supervision of my project supervisor and the entire project was completed under the control
of our Head of the Department. My major area of work was to reciprocate the compressors
for processing of gases. Moreover, I eve documented the entire project with proper technical
details.
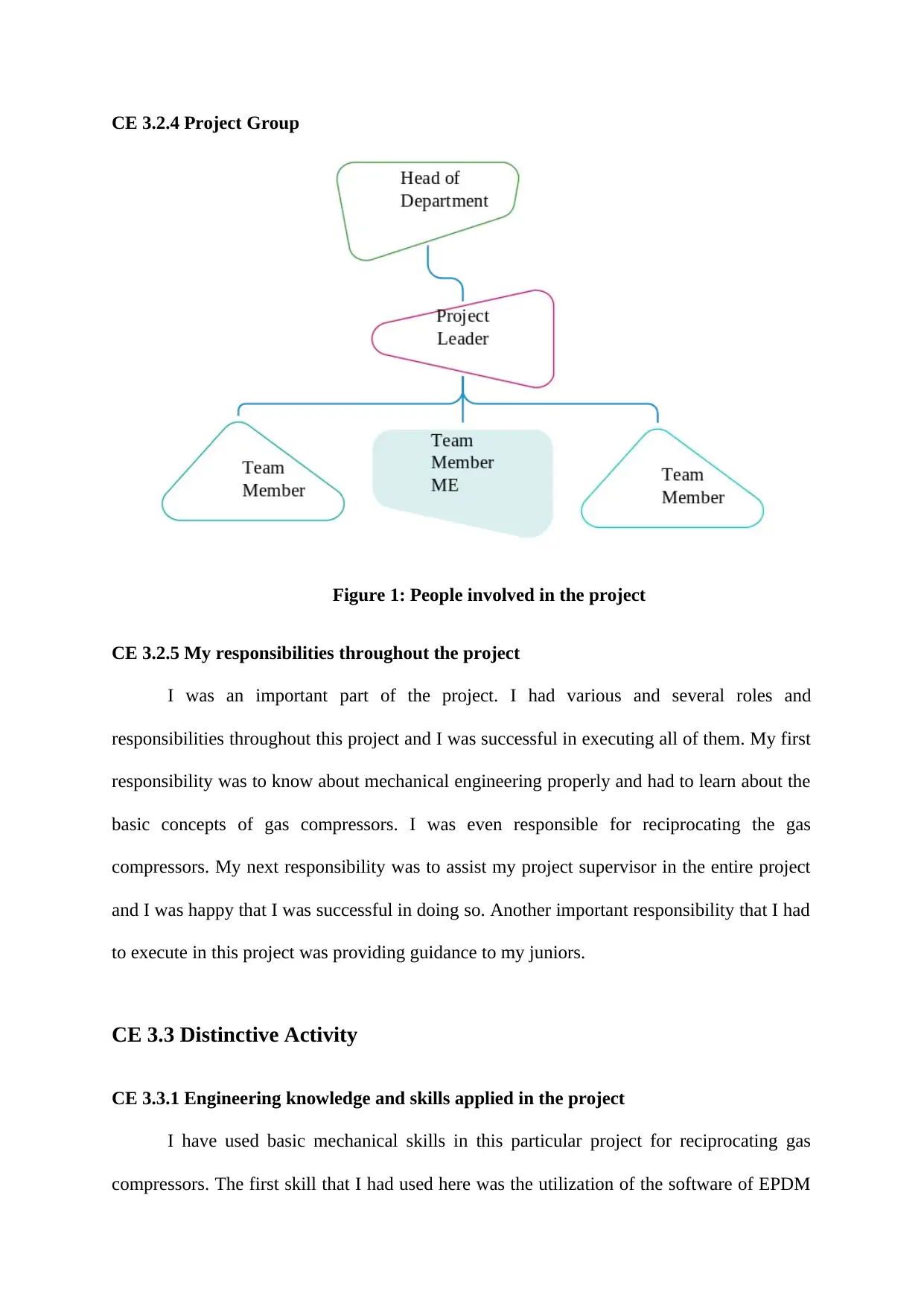
CE 3.2.4 Project Group
Figure 1: People involved in the project
CE 3.2.5 My responsibilities throughout the project
I was an important part of the project. I had various and several roles and
responsibilities throughout this project and I was successful in executing all of them. My first
responsibility was to know about mechanical engineering properly and had to learn about the
basic concepts of gas compressors. I was even responsible for reciprocating the gas
compressors. My next responsibility was to assist my project supervisor in the entire project
and I was happy that I was successful in doing so. Another important responsibility that I had
to execute in this project was providing guidance to my juniors.
CE 3.3 Distinctive Activity
CE 3.3.1 Engineering knowledge and skills applied in the project
I have used basic mechanical skills in this particular project for reciprocating gas
compressors. The first skill that I had used here was the utilization of the software of EPDM
Figure 1: People involved in the project
CE 3.2.5 My responsibilities throughout the project
I was an important part of the project. I had various and several roles and
responsibilities throughout this project and I was successful in executing all of them. My first
responsibility was to know about mechanical engineering properly and had to learn about the
basic concepts of gas compressors. I was even responsible for reciprocating the gas
compressors. My next responsibility was to assist my project supervisor in the entire project
and I was happy that I was successful in doing so. Another important responsibility that I had
to execute in this project was providing guidance to my juniors.
CE 3.3 Distinctive Activity
CE 3.3.1 Engineering knowledge and skills applied in the project
I have used basic mechanical skills in this particular project for reciprocating gas
compressors. The first skill that I had used here was the utilization of the software of EPDM
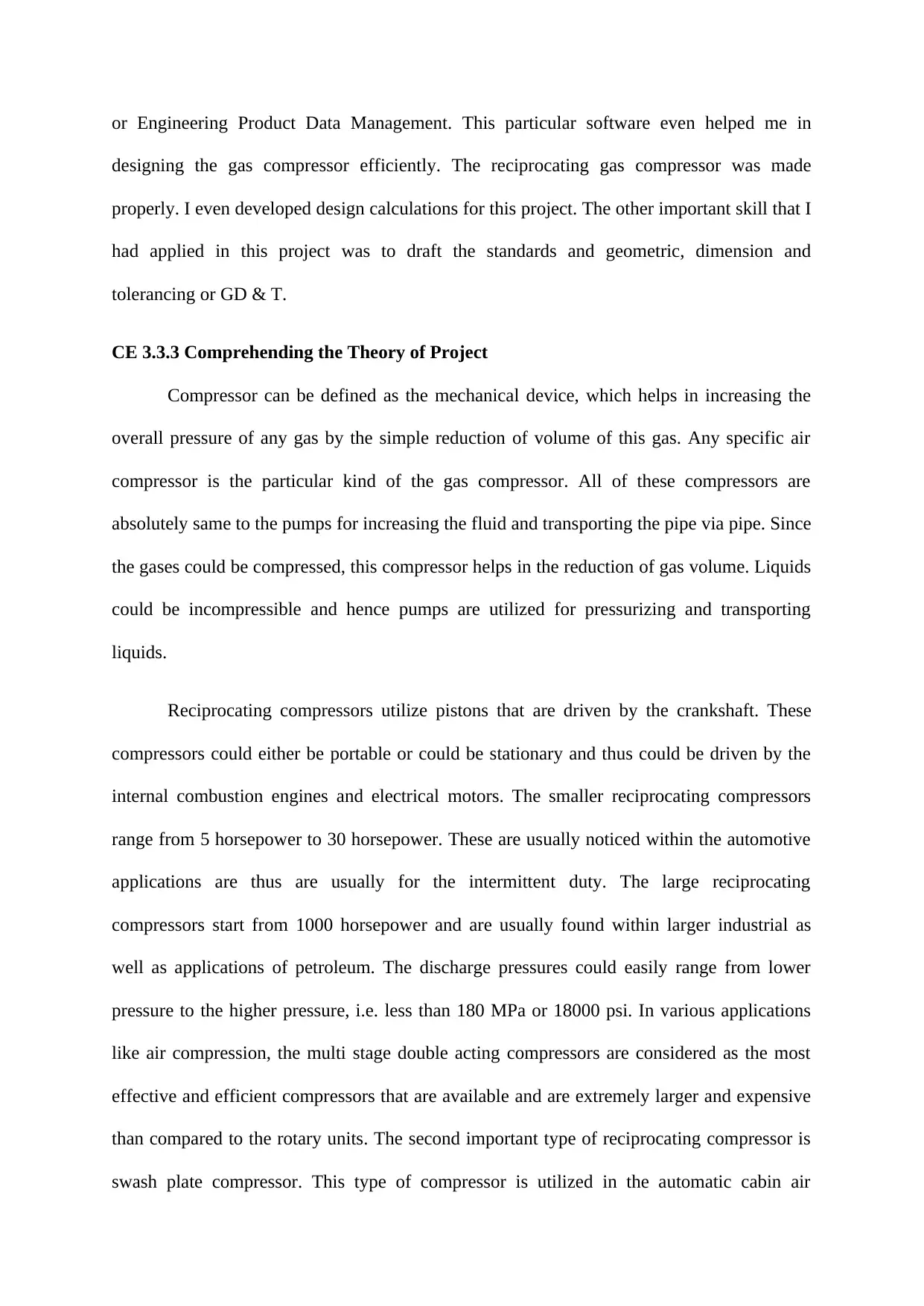
or Engineering Product Data Management. This particular software even helped me in
designing the gas compressor efficiently. The reciprocating gas compressor was made
properly. I even developed design calculations for this project. The other important skill that I
had applied in this project was to draft the standards and geometric, dimension and
tolerancing or GD & T.
CE 3.3.3 Comprehending the Theory of Project
Compressor can be defined as the mechanical device, which helps in increasing the
overall pressure of any gas by the simple reduction of volume of this gas. Any specific air
compressor is the particular kind of the gas compressor. All of these compressors are
absolutely same to the pumps for increasing the fluid and transporting the pipe via pipe. Since
the gases could be compressed, this compressor helps in the reduction of gas volume. Liquids
could be incompressible and hence pumps are utilized for pressurizing and transporting
liquids.
Reciprocating compressors utilize pistons that are driven by the crankshaft. These
compressors could either be portable or could be stationary and thus could be driven by the
internal combustion engines and electrical motors. The smaller reciprocating compressors
range from 5 horsepower to 30 horsepower. These are usually noticed within the automotive
applications are thus are usually for the intermittent duty. The large reciprocating
compressors start from 1000 horsepower and are usually found within larger industrial as
well as applications of petroleum. The discharge pressures could easily range from lower
pressure to the higher pressure, i.e. less than 180 MPa or 18000 psi. In various applications
like air compression, the multi stage double acting compressors are considered as the most
effective and efficient compressors that are available and are extremely larger and expensive
than compared to the rotary units. The second important type of reciprocating compressor is
swash plate compressor. This type of compressor is utilized in the automatic cabin air
designing the gas compressor efficiently. The reciprocating gas compressor was made
properly. I even developed design calculations for this project. The other important skill that I
had applied in this project was to draft the standards and geometric, dimension and
tolerancing or GD & T.
CE 3.3.3 Comprehending the Theory of Project
Compressor can be defined as the mechanical device, which helps in increasing the
overall pressure of any gas by the simple reduction of volume of this gas. Any specific air
compressor is the particular kind of the gas compressor. All of these compressors are
absolutely same to the pumps for increasing the fluid and transporting the pipe via pipe. Since
the gases could be compressed, this compressor helps in the reduction of gas volume. Liquids
could be incompressible and hence pumps are utilized for pressurizing and transporting
liquids.
Reciprocating compressors utilize pistons that are driven by the crankshaft. These
compressors could either be portable or could be stationary and thus could be driven by the
internal combustion engines and electrical motors. The smaller reciprocating compressors
range from 5 horsepower to 30 horsepower. These are usually noticed within the automotive
applications are thus are usually for the intermittent duty. The large reciprocating
compressors start from 1000 horsepower and are usually found within larger industrial as
well as applications of petroleum. The discharge pressures could easily range from lower
pressure to the higher pressure, i.e. less than 180 MPa or 18000 psi. In various applications
like air compression, the multi stage double acting compressors are considered as the most
effective and efficient compressors that are available and are extremely larger and expensive
than compared to the rotary units. The second important type of reciprocating compressor is
swash plate compressor. This type of compressor is utilized in the automatic cabin air
Secure Best Marks with AI Grader
Need help grading? Try our AI Grader for instant feedback on your assignments.
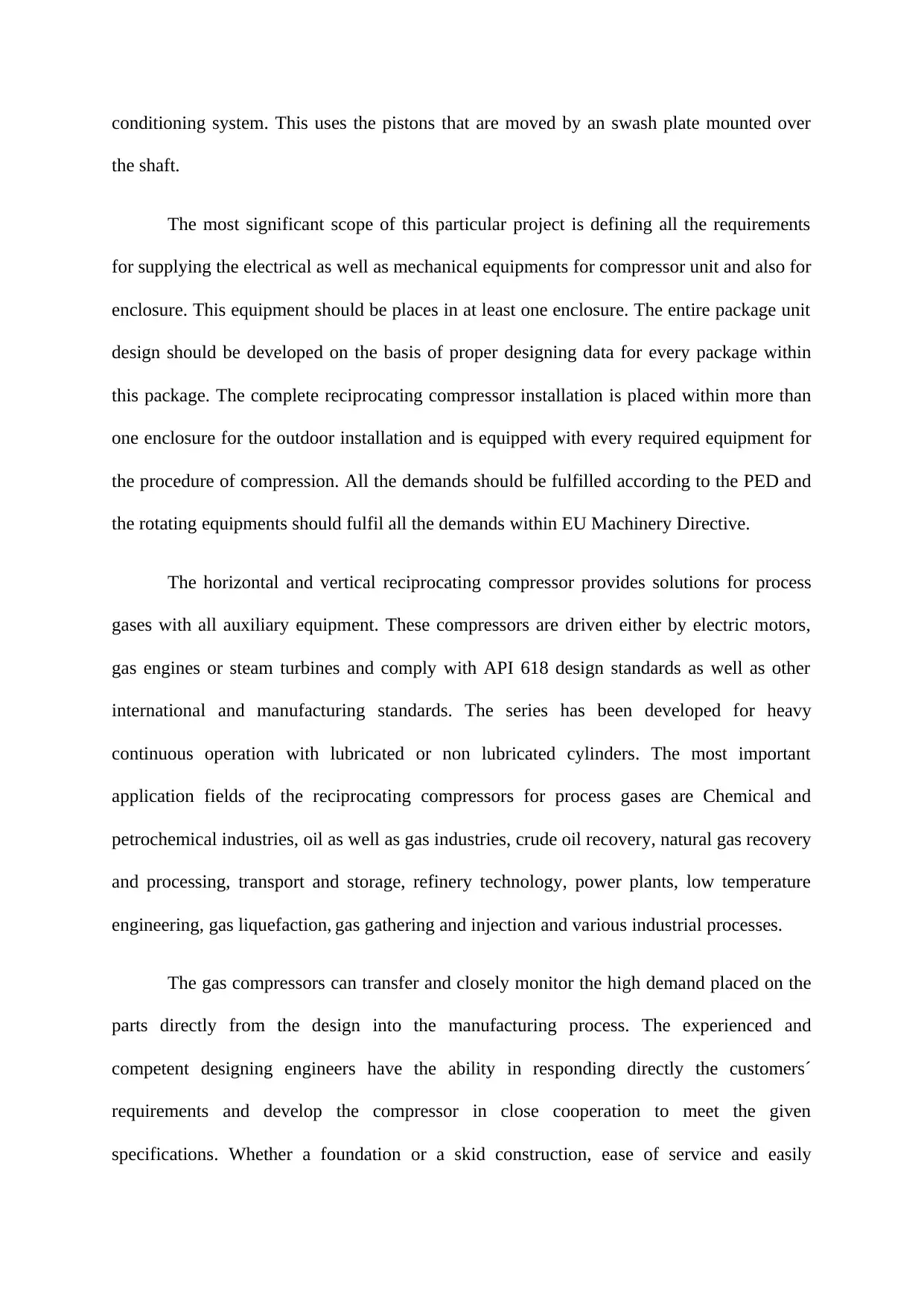
conditioning system. This uses the pistons that are moved by an swash plate mounted over
the shaft.
The most significant scope of this particular project is defining all the requirements
for supplying the electrical as well as mechanical equipments for compressor unit and also for
enclosure. This equipment should be places in at least one enclosure. The entire package unit
design should be developed on the basis of proper designing data for every package within
this package. The complete reciprocating compressor installation is placed within more than
one enclosure for the outdoor installation and is equipped with every required equipment for
the procedure of compression. All the demands should be fulfilled according to the PED and
the rotating equipments should fulfil all the demands within EU Machinery Directive.
The horizontal and vertical reciprocating compressor provides solutions for process
gases with all auxiliary equipment. These compressors are driven either by electric motors,
gas engines or steam turbines and comply with API 618 design standards as well as other
international and manufacturing standards. The series has been developed for heavy
continuous operation with lubricated or non lubricated cylinders. The most important
application fields of the reciprocating compressors for process gases are Chemical and
petrochemical industries, oil as well as gas industries, crude oil recovery, natural gas recovery
and processing, transport and storage, refinery technology, power plants, low temperature
engineering, gas liquefaction, gas gathering and injection and various industrial processes.
The gas compressors can transfer and closely monitor the high demand placed on the
parts directly from the design into the manufacturing process. The experienced and
competent designing engineers have the ability in responding directly the customers´
requirements and develop the compressor in close cooperation to meet the given
specifications. Whether a foundation or a skid construction, ease of service and easily
the shaft.
The most significant scope of this particular project is defining all the requirements
for supplying the electrical as well as mechanical equipments for compressor unit and also for
enclosure. This equipment should be places in at least one enclosure. The entire package unit
design should be developed on the basis of proper designing data for every package within
this package. The complete reciprocating compressor installation is placed within more than
one enclosure for the outdoor installation and is equipped with every required equipment for
the procedure of compression. All the demands should be fulfilled according to the PED and
the rotating equipments should fulfil all the demands within EU Machinery Directive.
The horizontal and vertical reciprocating compressor provides solutions for process
gases with all auxiliary equipment. These compressors are driven either by electric motors,
gas engines or steam turbines and comply with API 618 design standards as well as other
international and manufacturing standards. The series has been developed for heavy
continuous operation with lubricated or non lubricated cylinders. The most important
application fields of the reciprocating compressors for process gases are Chemical and
petrochemical industries, oil as well as gas industries, crude oil recovery, natural gas recovery
and processing, transport and storage, refinery technology, power plants, low temperature
engineering, gas liquefaction, gas gathering and injection and various industrial processes.
The gas compressors can transfer and closely monitor the high demand placed on the
parts directly from the design into the manufacturing process. The experienced and
competent designing engineers have the ability in responding directly the customers´
requirements and develop the compressor in close cooperation to meet the given
specifications. Whether a foundation or a skid construction, ease of service and easily
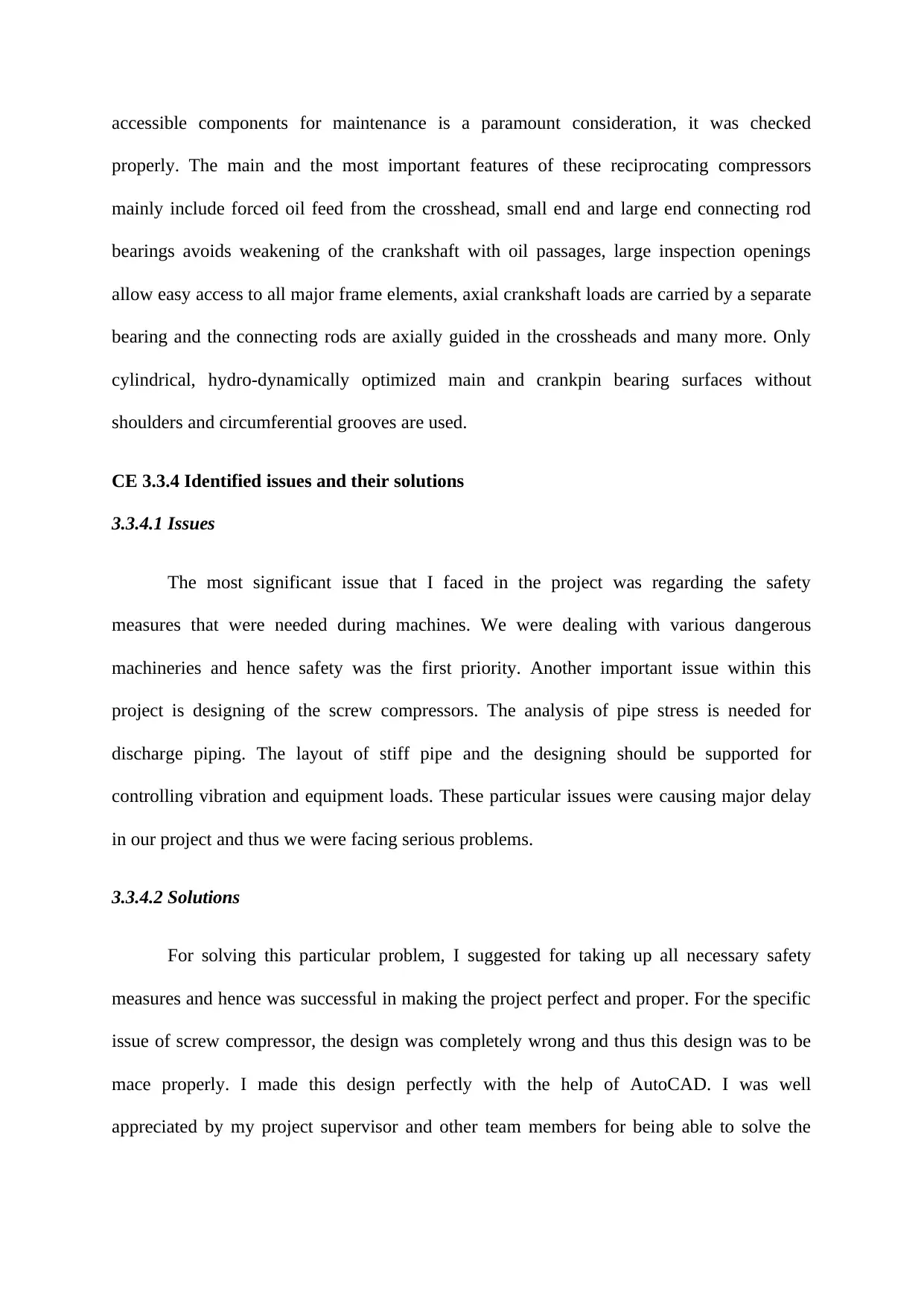
accessible components for maintenance is a paramount consideration, it was checked
properly. The main and the most important features of these reciprocating compressors
mainly include forced oil feed from the crosshead, small end and large end connecting rod
bearings avoids weakening of the crankshaft with oil passages, large inspection openings
allow easy access to all major frame elements, axial crankshaft loads are carried by a separate
bearing and the connecting rods are axially guided in the crossheads and many more. Only
cylindrical, hydro-dynamically optimized main and crankpin bearing surfaces without
shoulders and circumferential grooves are used.
CE 3.3.4 Identified issues and their solutions
3.3.4.1 Issues
The most significant issue that I faced in the project was regarding the safety
measures that were needed during machines. We were dealing with various dangerous
machineries and hence safety was the first priority. Another important issue within this
project is designing of the screw compressors. The analysis of pipe stress is needed for
discharge piping. The layout of stiff pipe and the designing should be supported for
controlling vibration and equipment loads. These particular issues were causing major delay
in our project and thus we were facing serious problems.
3.3.4.2 Solutions
For solving this particular problem, I suggested for taking up all necessary safety
measures and hence was successful in making the project perfect and proper. For the specific
issue of screw compressor, the design was completely wrong and thus this design was to be
mace properly. I made this design perfectly with the help of AutoCAD. I was well
appreciated by my project supervisor and other team members for being able to solve the
properly. The main and the most important features of these reciprocating compressors
mainly include forced oil feed from the crosshead, small end and large end connecting rod
bearings avoids weakening of the crankshaft with oil passages, large inspection openings
allow easy access to all major frame elements, axial crankshaft loads are carried by a separate
bearing and the connecting rods are axially guided in the crossheads and many more. Only
cylindrical, hydro-dynamically optimized main and crankpin bearing surfaces without
shoulders and circumferential grooves are used.
CE 3.3.4 Identified issues and their solutions
3.3.4.1 Issues
The most significant issue that I faced in the project was regarding the safety
measures that were needed during machines. We were dealing with various dangerous
machineries and hence safety was the first priority. Another important issue within this
project is designing of the screw compressors. The analysis of pipe stress is needed for
discharge piping. The layout of stiff pipe and the designing should be supported for
controlling vibration and equipment loads. These particular issues were causing major delay
in our project and thus we were facing serious problems.
3.3.4.2 Solutions
For solving this particular problem, I suggested for taking up all necessary safety
measures and hence was successful in making the project perfect and proper. For the specific
issue of screw compressor, the design was completely wrong and thus this design was to be
mace properly. I made this design perfectly with the help of AutoCAD. I was well
appreciated by my project supervisor and other team members for being able to solve the
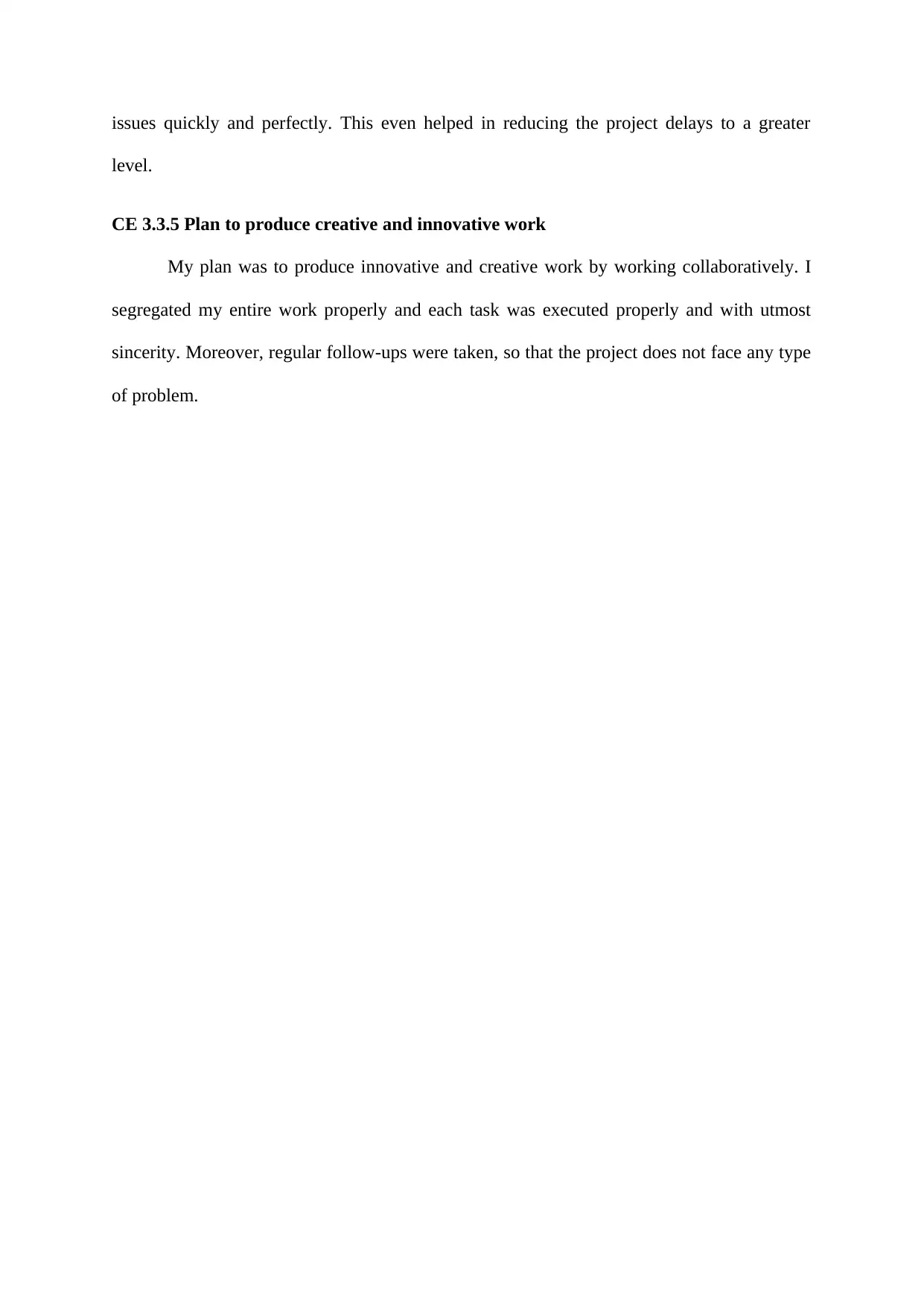
issues quickly and perfectly. This even helped in reducing the project delays to a greater
level.
CE 3.3.5 Plan to produce creative and innovative work
My plan was to produce innovative and creative work by working collaboratively. I
segregated my entire work properly and each task was executed properly and with utmost
sincerity. Moreover, regular follow-ups were taken, so that the project does not face any type
of problem.
level.
CE 3.3.5 Plan to produce creative and innovative work
My plan was to produce innovative and creative work by working collaboratively. I
segregated my entire work properly and each task was executed properly and with utmost
sincerity. Moreover, regular follow-ups were taken, so that the project does not face any type
of problem.
1 out of 7
Related Documents
![[object Object]](/_next/image/?url=%2F_next%2Fstatic%2Fmedia%2Flogo.6d15ce61.png&w=640&q=75)
Your All-in-One AI-Powered Toolkit for Academic Success.
+13062052269
info@desklib.com
Available 24*7 on WhatsApp / Email
Unlock your academic potential
© 2024 | Zucol Services PVT LTD | All rights reserved.