Supply Chain Management (SCM) Assignment
VerifiedAdded on 2021/05/21
|32
|4918
|134
AI Summary
Contribute Materials
Your contribution can guide someone’s learning journey. Share your
documents today.
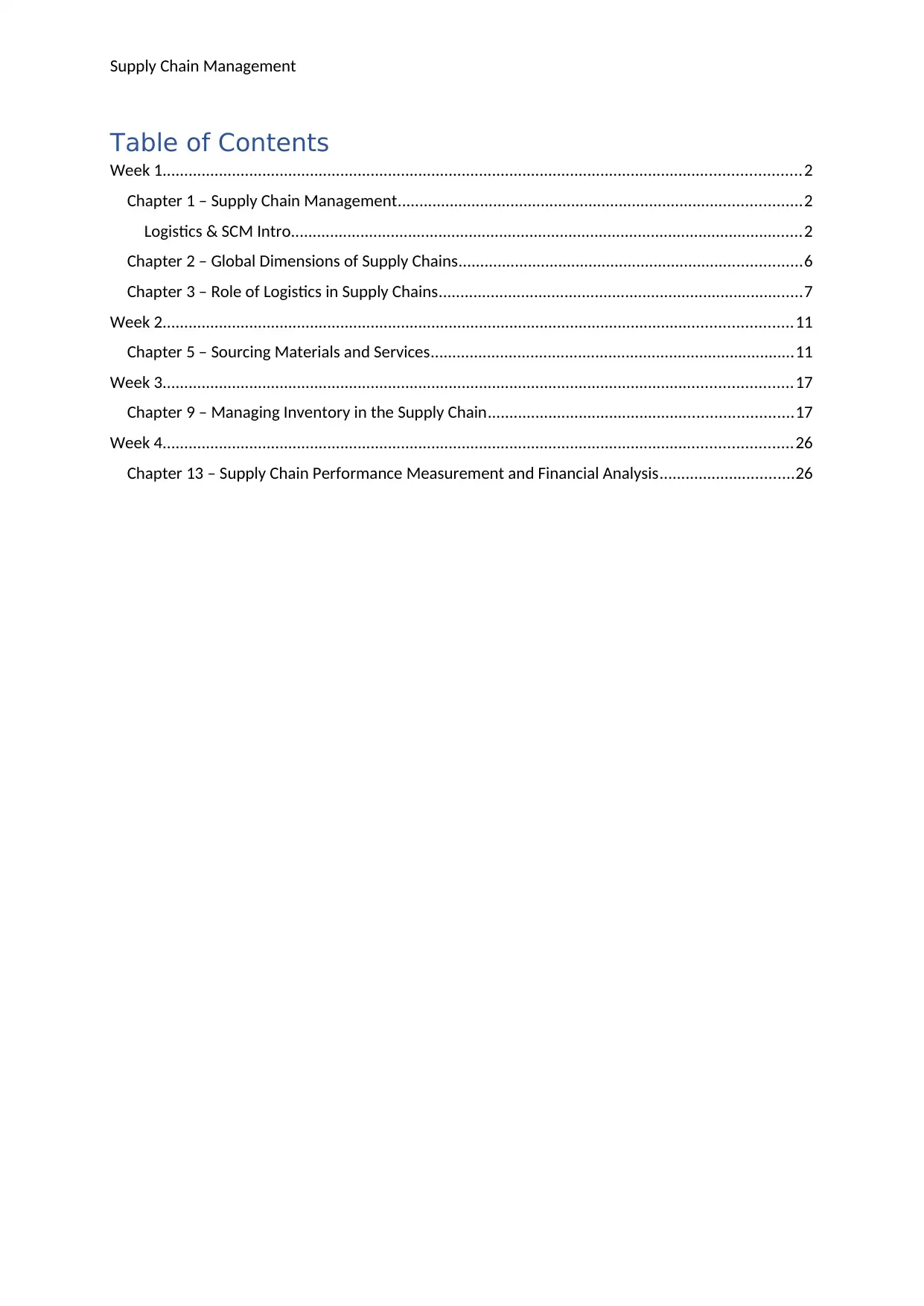
Supply Chain Management
Table of Contents
Week 1...................................................................................................................................................2
Chapter 1 – Supply Chain Management.............................................................................................2
Logistics & SCM Intro......................................................................................................................2
Chapter 2 – Global Dimensions of Supply Chains...............................................................................6
Chapter 3 – Role of Logistics in Supply Chains....................................................................................7
Week 2.................................................................................................................................................11
Chapter 5 – Sourcing Materials and Services....................................................................................11
Week 3.................................................................................................................................................17
Chapter 9 – Managing Inventory in the Supply Chain......................................................................17
Week 4.................................................................................................................................................26
Chapter 13 – Supply Chain Performance Measurement and Financial Analysis...............................26
Table of Contents
Week 1...................................................................................................................................................2
Chapter 1 – Supply Chain Management.............................................................................................2
Logistics & SCM Intro......................................................................................................................2
Chapter 2 – Global Dimensions of Supply Chains...............................................................................6
Chapter 3 – Role of Logistics in Supply Chains....................................................................................7
Week 2.................................................................................................................................................11
Chapter 5 – Sourcing Materials and Services....................................................................................11
Week 3.................................................................................................................................................17
Chapter 9 – Managing Inventory in the Supply Chain......................................................................17
Week 4.................................................................................................................................................26
Chapter 13 – Supply Chain Performance Measurement and Financial Analysis...............................26
Secure Best Marks with AI Grader
Need help grading? Try our AI Grader for instant feedback on your assignments.
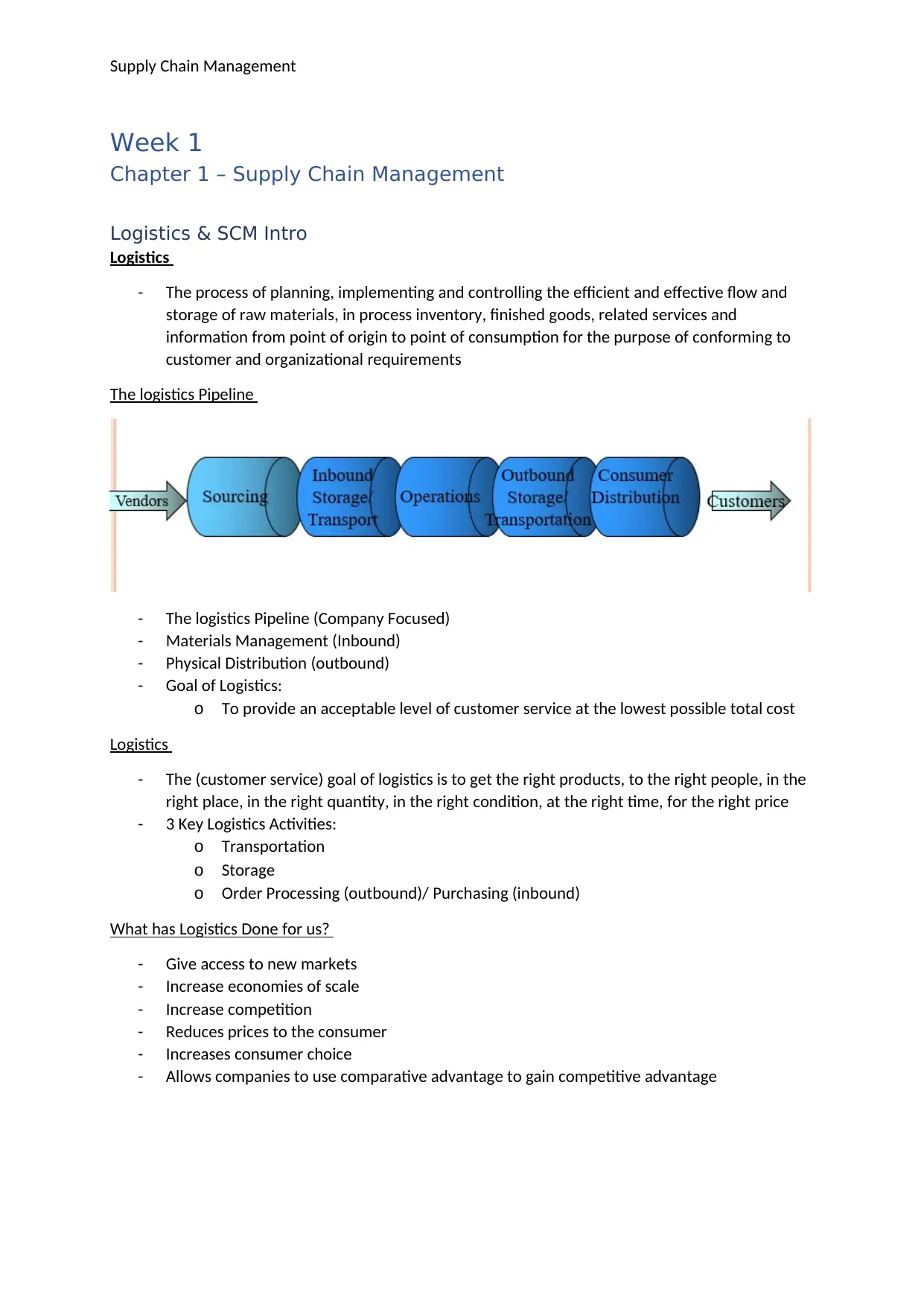
Supply Chain Management
Week 1
Chapter 1 – Supply Chain Management
Logistics & SCM Intro
Logistics
- The process of planning, implementing and controlling the efficient and effective flow and
storage of raw materials, in process inventory, finished goods, related services and
information from point of origin to point of consumption for the purpose of conforming to
customer and organizational requirements
The logistics Pipeline
- The logistics Pipeline (Company Focused)
- Materials Management (Inbound)
- Physical Distribution (outbound)
- Goal of Logistics:
o To provide an acceptable level of customer service at the lowest possible total cost
Logistics
- The (customer service) goal of logistics is to get the right products, to the right people, in the
right place, in the right quantity, in the right condition, at the right time, for the right price
- 3 Key Logistics Activities:
o Transportation
o Storage
o Order Processing (outbound)/ Purchasing (inbound)
What has Logistics Done for us?
- Give access to new markets
- Increase economies of scale
- Increase competition
- Reduces prices to the consumer
- Increases consumer choice
- Allows companies to use comparative advantage to gain competitive advantage
Week 1
Chapter 1 – Supply Chain Management
Logistics & SCM Intro
Logistics
- The process of planning, implementing and controlling the efficient and effective flow and
storage of raw materials, in process inventory, finished goods, related services and
information from point of origin to point of consumption for the purpose of conforming to
customer and organizational requirements
The logistics Pipeline
- The logistics Pipeline (Company Focused)
- Materials Management (Inbound)
- Physical Distribution (outbound)
- Goal of Logistics:
o To provide an acceptable level of customer service at the lowest possible total cost
Logistics
- The (customer service) goal of logistics is to get the right products, to the right people, in the
right place, in the right quantity, in the right condition, at the right time, for the right price
- 3 Key Logistics Activities:
o Transportation
o Storage
o Order Processing (outbound)/ Purchasing (inbound)
What has Logistics Done for us?
- Give access to new markets
- Increase economies of scale
- Increase competition
- Reduces prices to the consumer
- Increases consumer choice
- Allows companies to use comparative advantage to gain competitive advantage
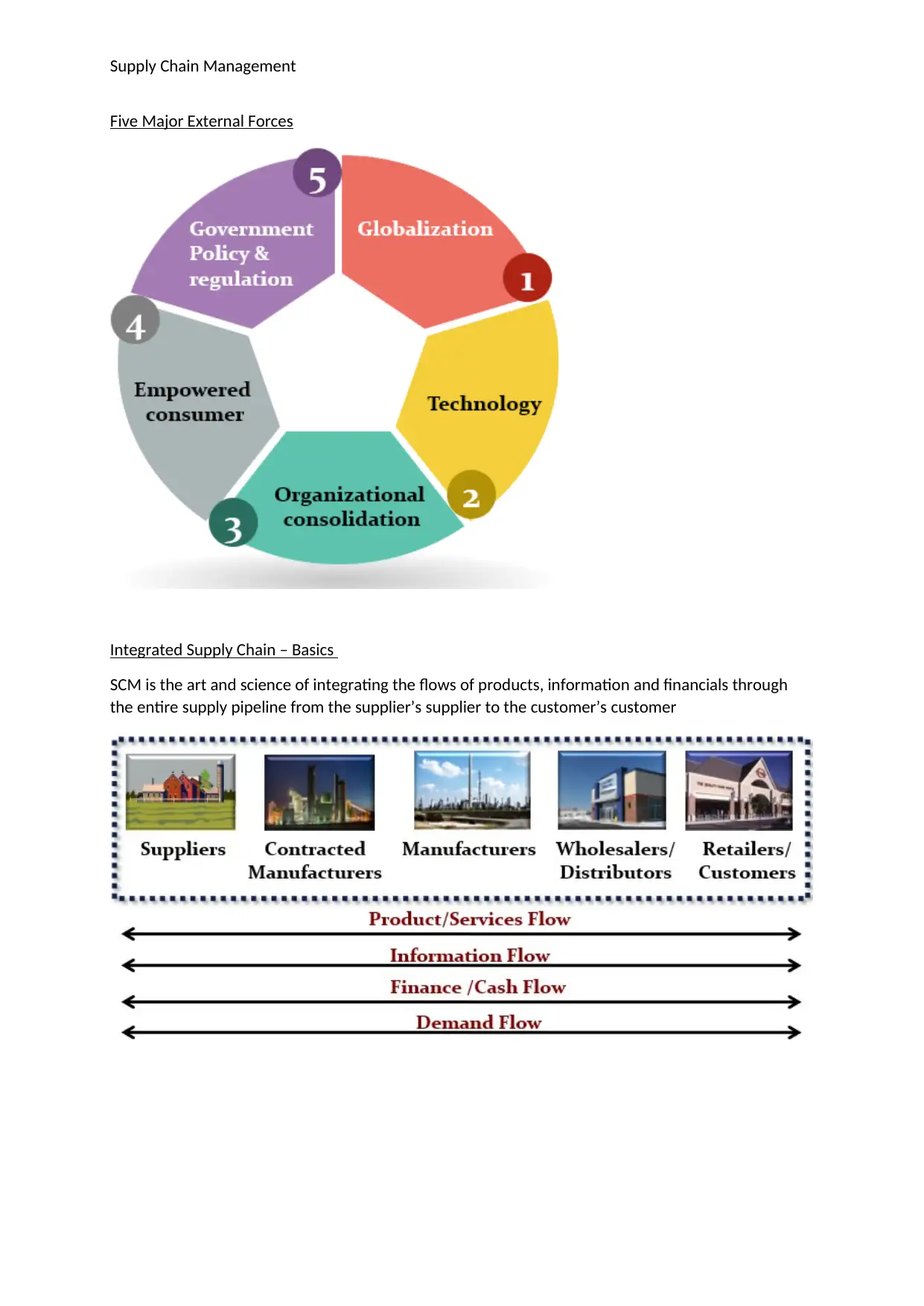
Supply Chain Management
Five Major External Forces
Integrated Supply Chain – Basics
SCM is the art and science of integrating the flows of products, information and financials through
the entire supply pipeline from the supplier’s supplier to the customer’s customer
Five Major External Forces
Integrated Supply Chain – Basics
SCM is the art and science of integrating the flows of products, information and financials through
the entire supply pipeline from the supplier’s supplier to the customer’s customer
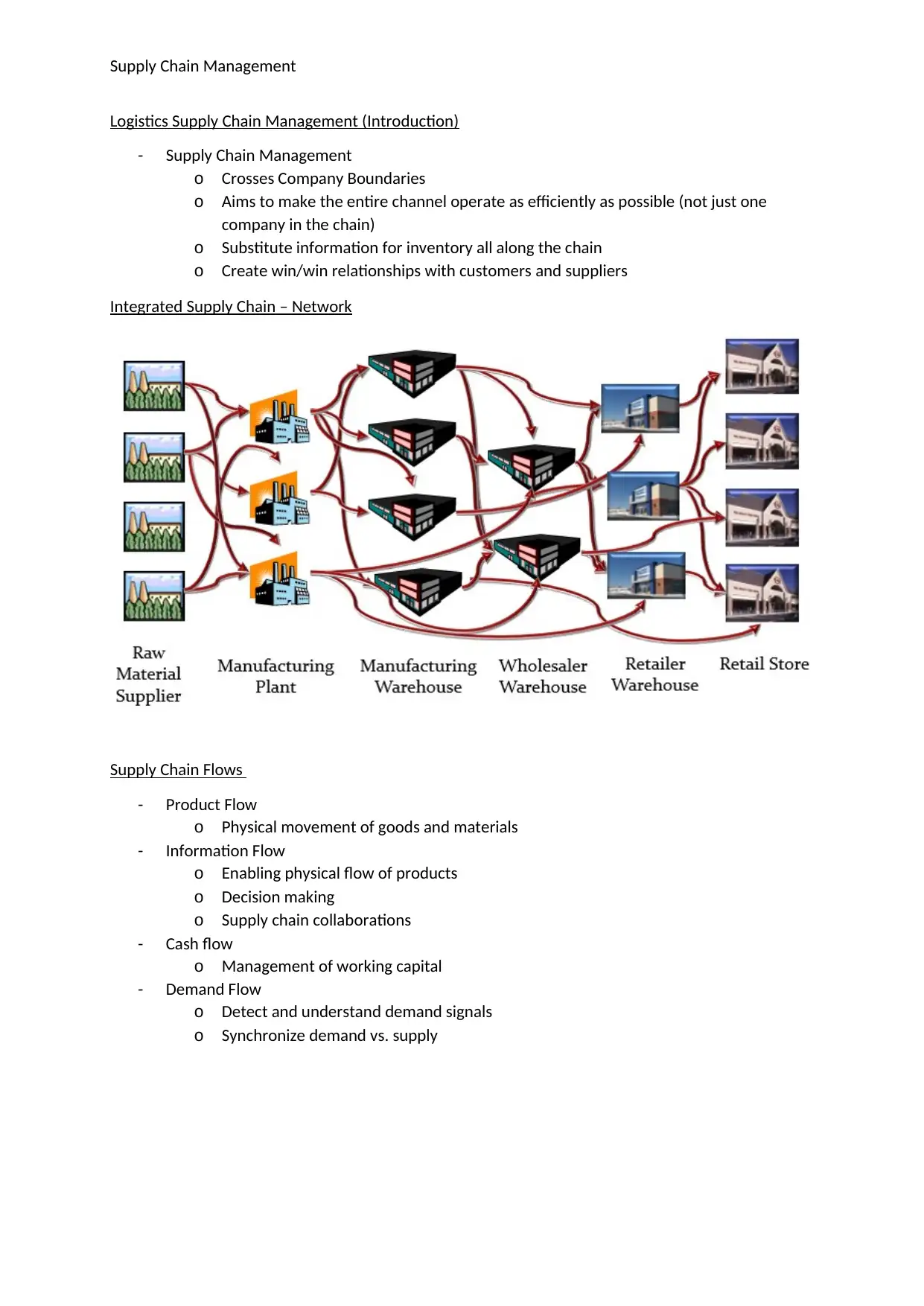
Supply Chain Management
Logistics Supply Chain Management (Introduction)
- Supply Chain Management
o Crosses Company Boundaries
o Aims to make the entire channel operate as efficiently as possible (not just one
company in the chain)
o Substitute information for inventory all along the chain
o Create win/win relationships with customers and suppliers
Integrated Supply Chain – Network
Supply Chain Flows
- Product Flow
o Physical movement of goods and materials
- Information Flow
o Enabling physical flow of products
o Decision making
o Supply chain collaborations
- Cash flow
o Management of working capital
- Demand Flow
o Detect and understand demand signals
o Synchronize demand vs. supply
Logistics Supply Chain Management (Introduction)
- Supply Chain Management
o Crosses Company Boundaries
o Aims to make the entire channel operate as efficiently as possible (not just one
company in the chain)
o Substitute information for inventory all along the chain
o Create win/win relationships with customers and suppliers
Integrated Supply Chain – Network
Supply Chain Flows
- Product Flow
o Physical movement of goods and materials
- Information Flow
o Enabling physical flow of products
o Decision making
o Supply chain collaborations
- Cash flow
o Management of working capital
- Demand Flow
o Detect and understand demand signals
o Synchronize demand vs. supply
Secure Best Marks with AI Grader
Need help grading? Try our AI Grader for instant feedback on your assignments.
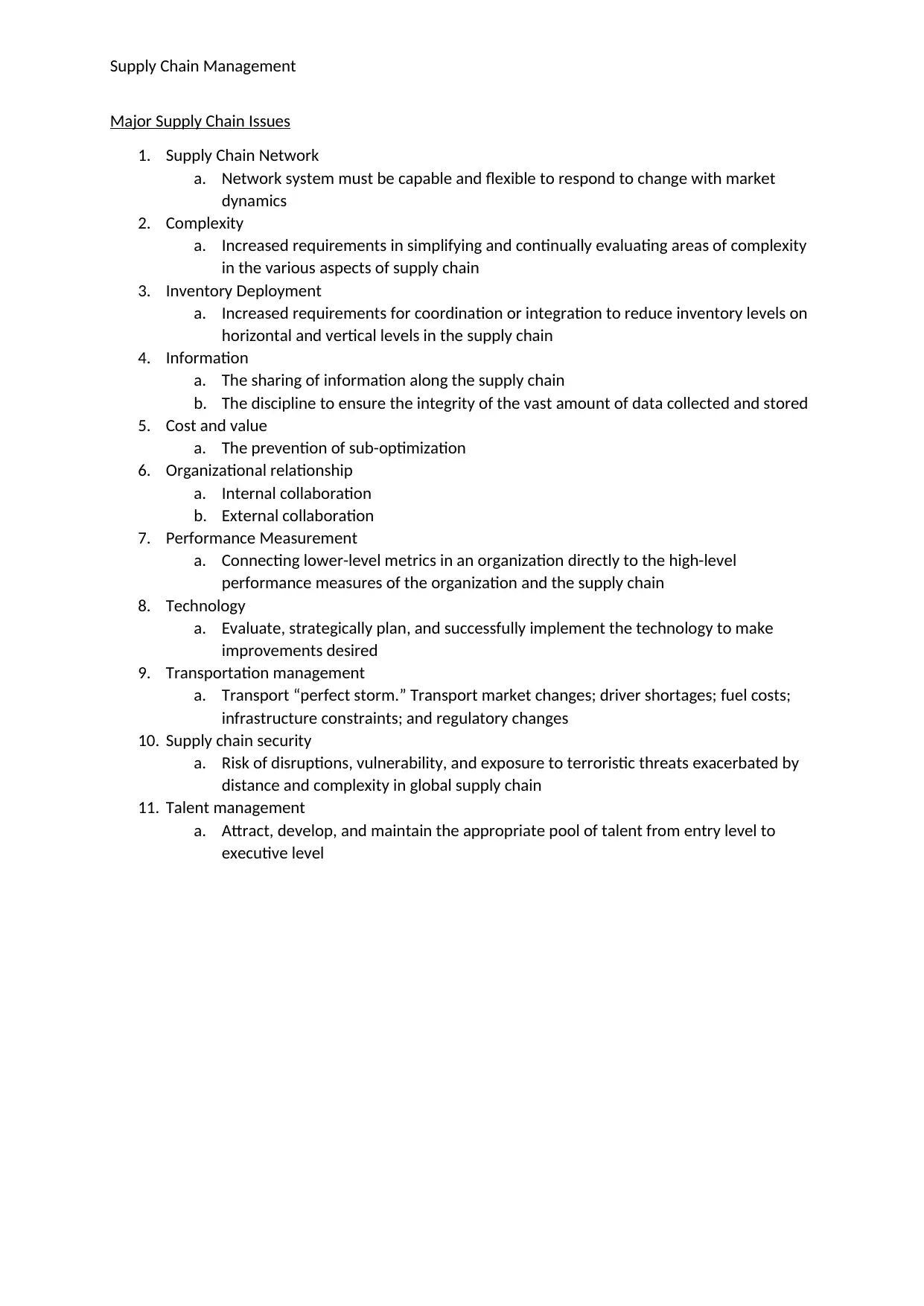
Supply Chain Management
Major Supply Chain Issues
1. Supply Chain Network
a. Network system must be capable and flexible to respond to change with market
dynamics
2. Complexity
a. Increased requirements in simplifying and continually evaluating areas of complexity
in the various aspects of supply chain
3. Inventory Deployment
a. Increased requirements for coordination or integration to reduce inventory levels on
horizontal and vertical levels in the supply chain
4. Information
a. The sharing of information along the supply chain
b. The discipline to ensure the integrity of the vast amount of data collected and stored
5. Cost and value
a. The prevention of sub-optimization
6. Organizational relationship
a. Internal collaboration
b. External collaboration
7. Performance Measurement
a. Connecting lower-level metrics in an organization directly to the high-level
performance measures of the organization and the supply chain
8. Technology
a. Evaluate, strategically plan, and successfully implement the technology to make
improvements desired
9. Transportation management
a. Transport “perfect storm.” Transport market changes; driver shortages; fuel costs;
infrastructure constraints; and regulatory changes
10. Supply chain security
a. Risk of disruptions, vulnerability, and exposure to terroristic threats exacerbated by
distance and complexity in global supply chain
11. Talent management
a. Attract, develop, and maintain the appropriate pool of talent from entry level to
executive level
Major Supply Chain Issues
1. Supply Chain Network
a. Network system must be capable and flexible to respond to change with market
dynamics
2. Complexity
a. Increased requirements in simplifying and continually evaluating areas of complexity
in the various aspects of supply chain
3. Inventory Deployment
a. Increased requirements for coordination or integration to reduce inventory levels on
horizontal and vertical levels in the supply chain
4. Information
a. The sharing of information along the supply chain
b. The discipline to ensure the integrity of the vast amount of data collected and stored
5. Cost and value
a. The prevention of sub-optimization
6. Organizational relationship
a. Internal collaboration
b. External collaboration
7. Performance Measurement
a. Connecting lower-level metrics in an organization directly to the high-level
performance measures of the organization and the supply chain
8. Technology
a. Evaluate, strategically plan, and successfully implement the technology to make
improvements desired
9. Transportation management
a. Transport “perfect storm.” Transport market changes; driver shortages; fuel costs;
infrastructure constraints; and regulatory changes
10. Supply chain security
a. Risk of disruptions, vulnerability, and exposure to terroristic threats exacerbated by
distance and complexity in global supply chain
11. Talent management
a. Attract, develop, and maintain the appropriate pool of talent from entry level to
executive level
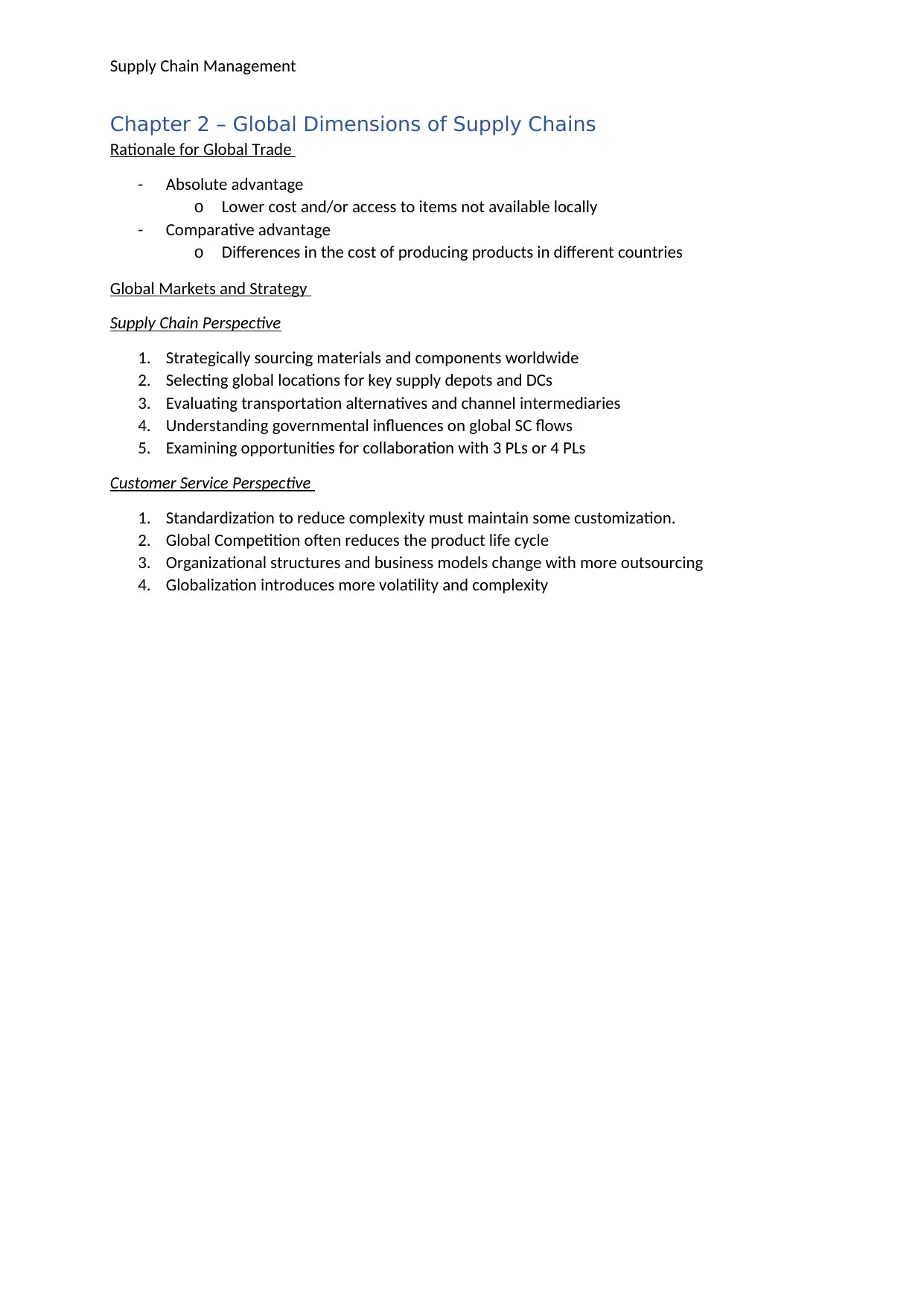
Supply Chain Management
Chapter 2 – Global Dimensions of Supply Chains
Rationale for Global Trade
- Absolute advantage
o Lower cost and/or access to items not available locally
- Comparative advantage
o Differences in the cost of producing products in different countries
Global Markets and Strategy
Supply Chain Perspective
1. Strategically sourcing materials and components worldwide
2. Selecting global locations for key supply depots and DCs
3. Evaluating transportation alternatives and channel intermediaries
4. Understanding governmental influences on global SC flows
5. Examining opportunities for collaboration with 3 PLs or 4 PLs
Customer Service Perspective
1. Standardization to reduce complexity must maintain some customization.
2. Global Competition often reduces the product life cycle
3. Organizational structures and business models change with more outsourcing
4. Globalization introduces more volatility and complexity
Chapter 2 – Global Dimensions of Supply Chains
Rationale for Global Trade
- Absolute advantage
o Lower cost and/or access to items not available locally
- Comparative advantage
o Differences in the cost of producing products in different countries
Global Markets and Strategy
Supply Chain Perspective
1. Strategically sourcing materials and components worldwide
2. Selecting global locations for key supply depots and DCs
3. Evaluating transportation alternatives and channel intermediaries
4. Understanding governmental influences on global SC flows
5. Examining opportunities for collaboration with 3 PLs or 4 PLs
Customer Service Perspective
1. Standardization to reduce complexity must maintain some customization.
2. Global Competition often reduces the product life cycle
3. Organizational structures and business models change with more outsourcing
4. Globalization introduces more volatility and complexity
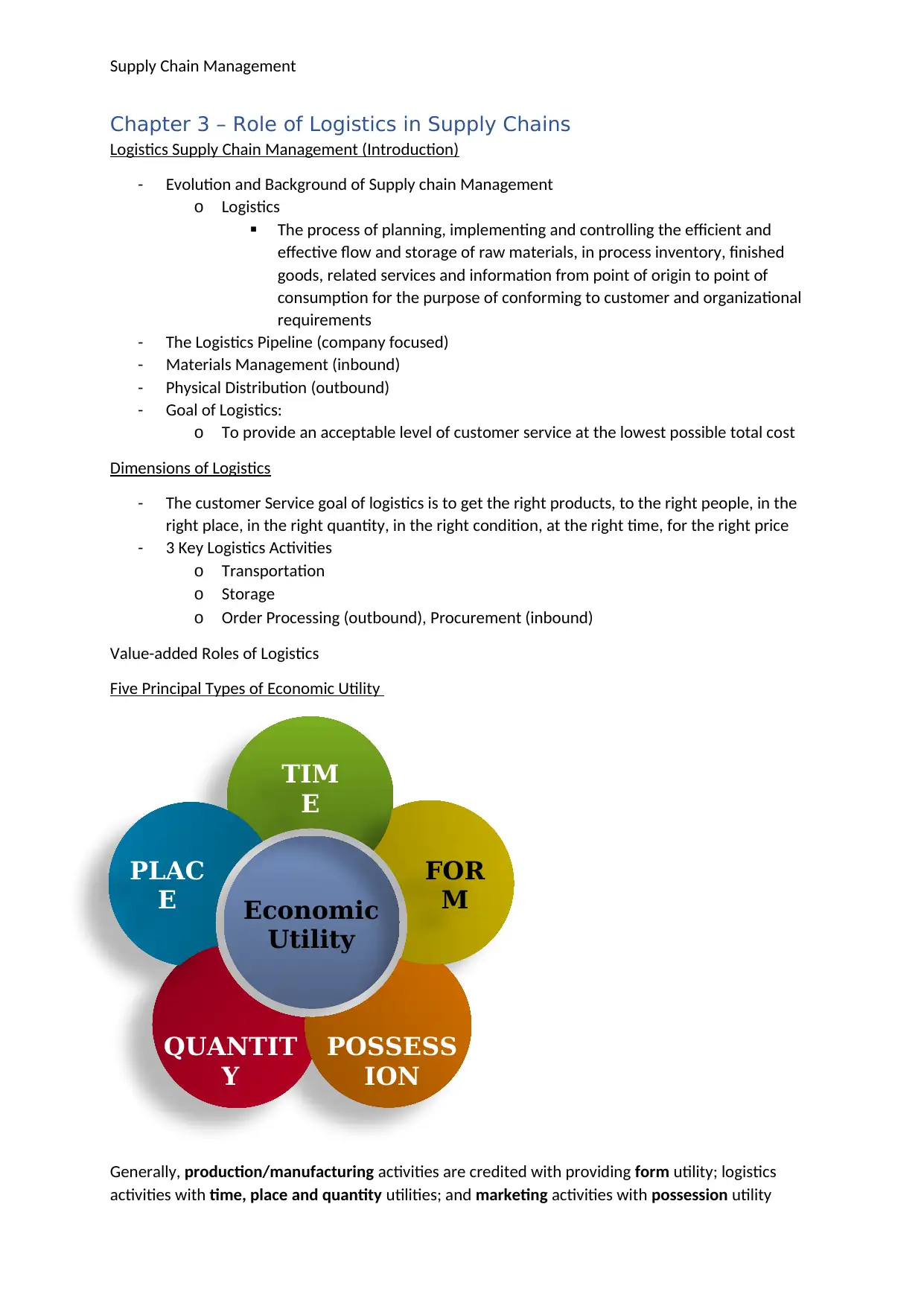
Supply Chain Management
Chapter 3 – Role of Logistics in Supply Chains
Logistics Supply Chain Management (Introduction)
- Evolution and Background of Supply chain Management
o Logistics
The process of planning, implementing and controlling the efficient and
effective flow and storage of raw materials, in process inventory, finished
goods, related services and information from point of origin to point of
consumption for the purpose of conforming to customer and organizational
requirements
- The Logistics Pipeline (company focused)
- Materials Management (inbound)
- Physical Distribution (outbound)
- Goal of Logistics:
o To provide an acceptable level of customer service at the lowest possible total cost
Dimensions of Logistics
- The customer Service goal of logistics is to get the right products, to the right people, in the
right place, in the right quantity, in the right condition, at the right time, for the right price
- 3 Key Logistics Activities
o Transportation
o Storage
o Order Processing (outbound), Procurement (inbound)
Value-added Roles of Logistics
Five Principal Types of Economic Utility
Generally, production/manufacturing activities are credited with providing form utility; logistics
activities with time, place and quantity utilities; and marketing activities with possession utility
TIM
E
FOR
M
PLAC
E Economic
Utility
QUANTIT
Y
POSSESS
ION
Chapter 3 – Role of Logistics in Supply Chains
Logistics Supply Chain Management (Introduction)
- Evolution and Background of Supply chain Management
o Logistics
The process of planning, implementing and controlling the efficient and
effective flow and storage of raw materials, in process inventory, finished
goods, related services and information from point of origin to point of
consumption for the purpose of conforming to customer and organizational
requirements
- The Logistics Pipeline (company focused)
- Materials Management (inbound)
- Physical Distribution (outbound)
- Goal of Logistics:
o To provide an acceptable level of customer service at the lowest possible total cost
Dimensions of Logistics
- The customer Service goal of logistics is to get the right products, to the right people, in the
right place, in the right quantity, in the right condition, at the right time, for the right price
- 3 Key Logistics Activities
o Transportation
o Storage
o Order Processing (outbound), Procurement (inbound)
Value-added Roles of Logistics
Five Principal Types of Economic Utility
Generally, production/manufacturing activities are credited with providing form utility; logistics
activities with time, place and quantity utilities; and marketing activities with possession utility
TIM
E
FOR
M
PLAC
E Economic
Utility
QUANTIT
Y
POSSESS
ION
Paraphrase This Document
Need a fresh take? Get an instant paraphrase of this document with our AI Paraphraser
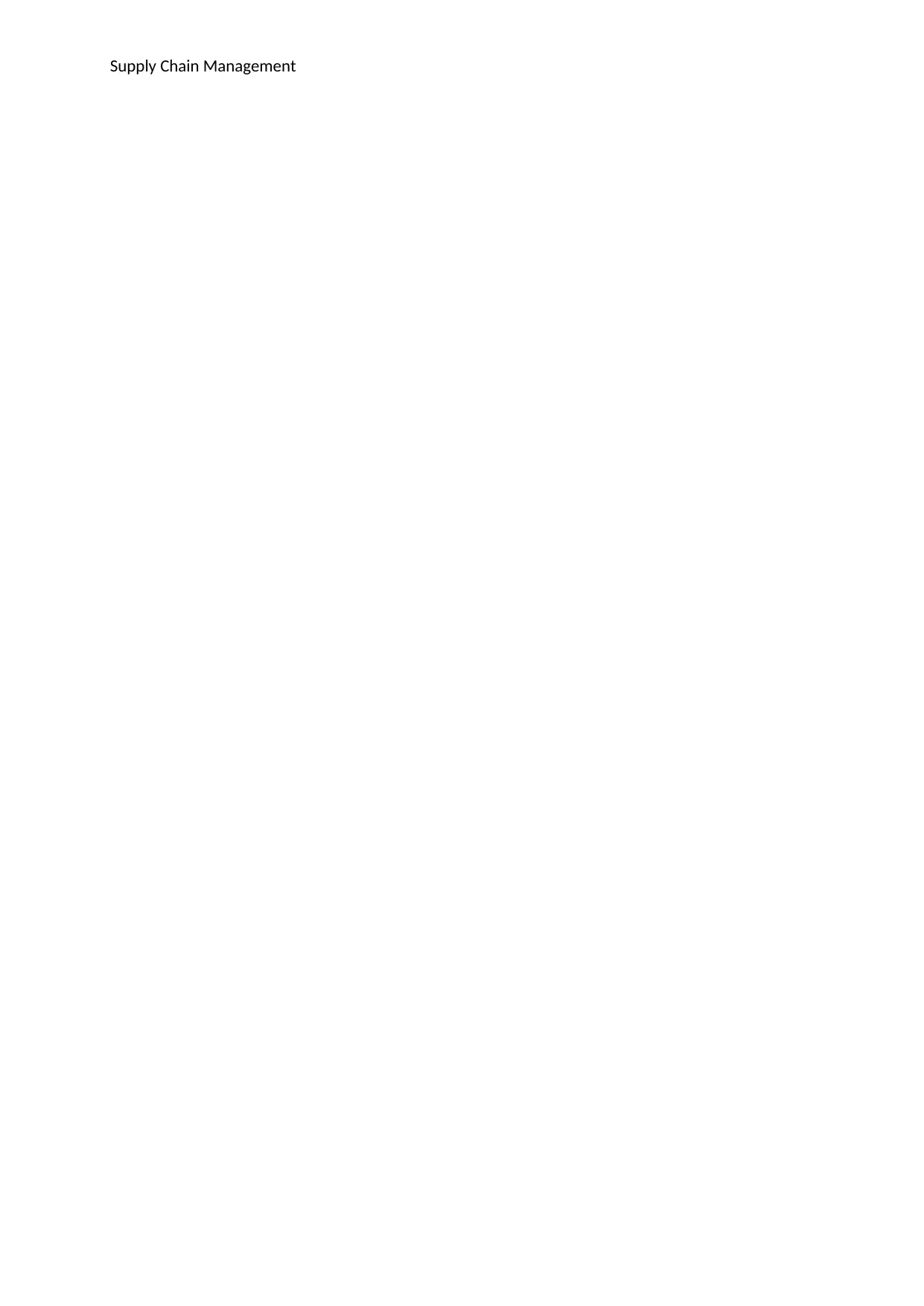
Supply Chain Management
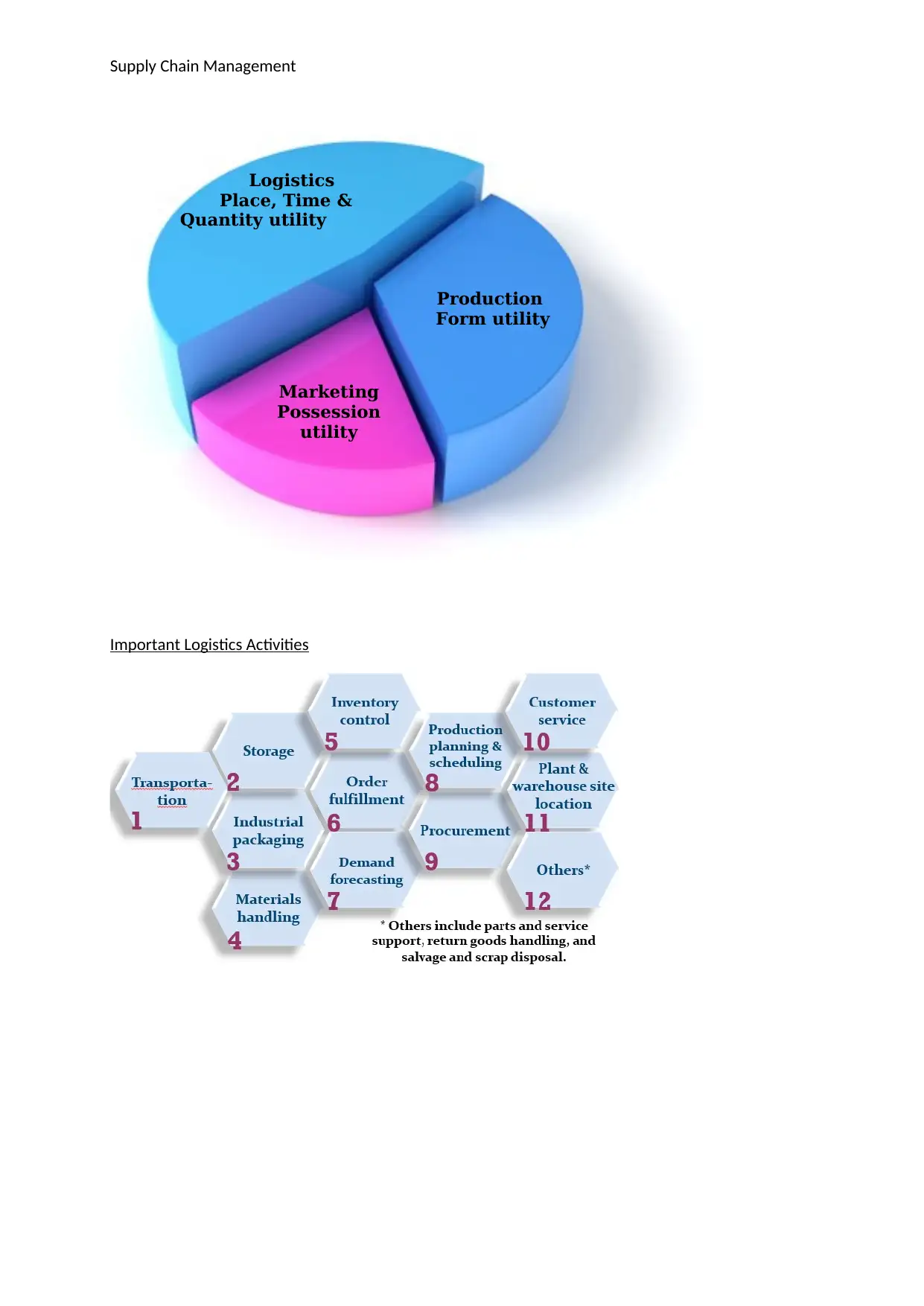
Supply Chain Management
Important Logistics Activities
Production
Form utility
Marketing
Possession
utility
Logistics
Place, Time &
Quantity utility
Important Logistics Activities
Production
Form utility
Marketing
Possession
utility
Logistics
Place, Time &
Quantity utility
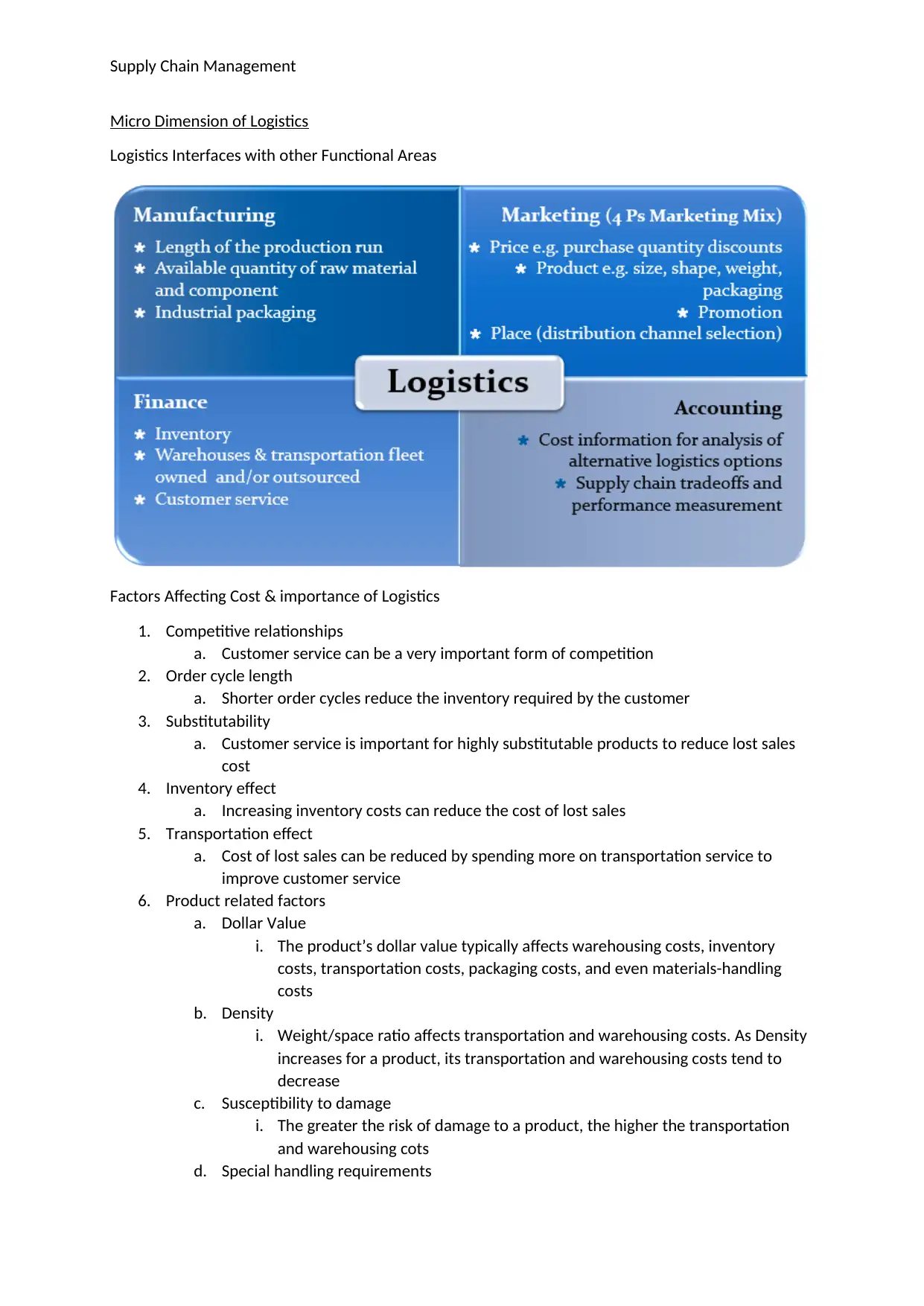
Supply Chain Management
Micro Dimension of Logistics
Logistics Interfaces with other Functional Areas
Factors Affecting Cost & importance of Logistics
1. Competitive relationships
a. Customer service can be a very important form of competition
2. Order cycle length
a. Shorter order cycles reduce the inventory required by the customer
3. Substitutability
a. Customer service is important for highly substitutable products to reduce lost sales
cost
4. Inventory effect
a. Increasing inventory costs can reduce the cost of lost sales
5. Transportation effect
a. Cost of lost sales can be reduced by spending more on transportation service to
improve customer service
6. Product related factors
a. Dollar Value
i. The product’s dollar value typically affects warehousing costs, inventory
costs, transportation costs, packaging costs, and even materials-handling
costs
b. Density
i. Weight/space ratio affects transportation and warehousing costs. As Density
increases for a product, its transportation and warehousing costs tend to
decrease
c. Susceptibility to damage
i. The greater the risk of damage to a product, the higher the transportation
and warehousing cots
d. Special handling requirements
Micro Dimension of Logistics
Logistics Interfaces with other Functional Areas
Factors Affecting Cost & importance of Logistics
1. Competitive relationships
a. Customer service can be a very important form of competition
2. Order cycle length
a. Shorter order cycles reduce the inventory required by the customer
3. Substitutability
a. Customer service is important for highly substitutable products to reduce lost sales
cost
4. Inventory effect
a. Increasing inventory costs can reduce the cost of lost sales
5. Transportation effect
a. Cost of lost sales can be reduced by spending more on transportation service to
improve customer service
6. Product related factors
a. Dollar Value
i. The product’s dollar value typically affects warehousing costs, inventory
costs, transportation costs, packaging costs, and even materials-handling
costs
b. Density
i. Weight/space ratio affects transportation and warehousing costs. As Density
increases for a product, its transportation and warehousing costs tend to
decrease
c. Susceptibility to damage
i. The greater the risk of damage to a product, the higher the transportation
and warehousing cots
d. Special handling requirements
Secure Best Marks with AI Grader
Need help grading? Try our AI Grader for instant feedback on your assignments.
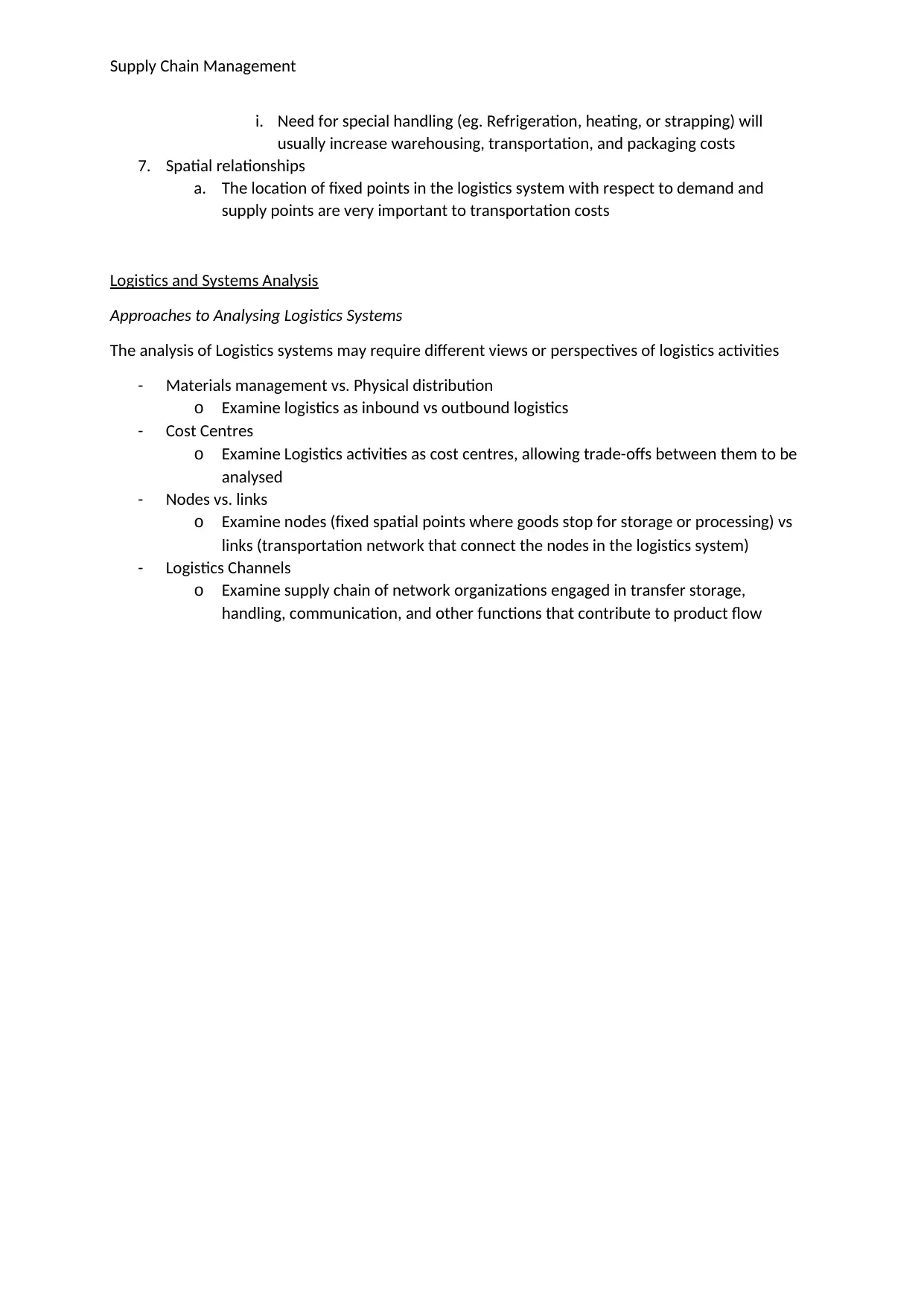
Supply Chain Management
i. Need for special handling (eg. Refrigeration, heating, or strapping) will
usually increase warehousing, transportation, and packaging costs
7. Spatial relationships
a. The location of fixed points in the logistics system with respect to demand and
supply points are very important to transportation costs
Logistics and Systems Analysis
Approaches to Analysing Logistics Systems
The analysis of Logistics systems may require different views or perspectives of logistics activities
- Materials management vs. Physical distribution
o Examine logistics as inbound vs outbound logistics
- Cost Centres
o Examine Logistics activities as cost centres, allowing trade-offs between them to be
analysed
- Nodes vs. links
o Examine nodes (fixed spatial points where goods stop for storage or processing) vs
links (transportation network that connect the nodes in the logistics system)
- Logistics Channels
o Examine supply chain of network organizations engaged in transfer storage,
handling, communication, and other functions that contribute to product flow
i. Need for special handling (eg. Refrigeration, heating, or strapping) will
usually increase warehousing, transportation, and packaging costs
7. Spatial relationships
a. The location of fixed points in the logistics system with respect to demand and
supply points are very important to transportation costs
Logistics and Systems Analysis
Approaches to Analysing Logistics Systems
The analysis of Logistics systems may require different views or perspectives of logistics activities
- Materials management vs. Physical distribution
o Examine logistics as inbound vs outbound logistics
- Cost Centres
o Examine Logistics activities as cost centres, allowing trade-offs between them to be
analysed
- Nodes vs. links
o Examine nodes (fixed spatial points where goods stop for storage or processing) vs
links (transportation network that connect the nodes in the logistics system)
- Logistics Channels
o Examine supply chain of network organizations engaged in transfer storage,
handling, communication, and other functions that contribute to product flow
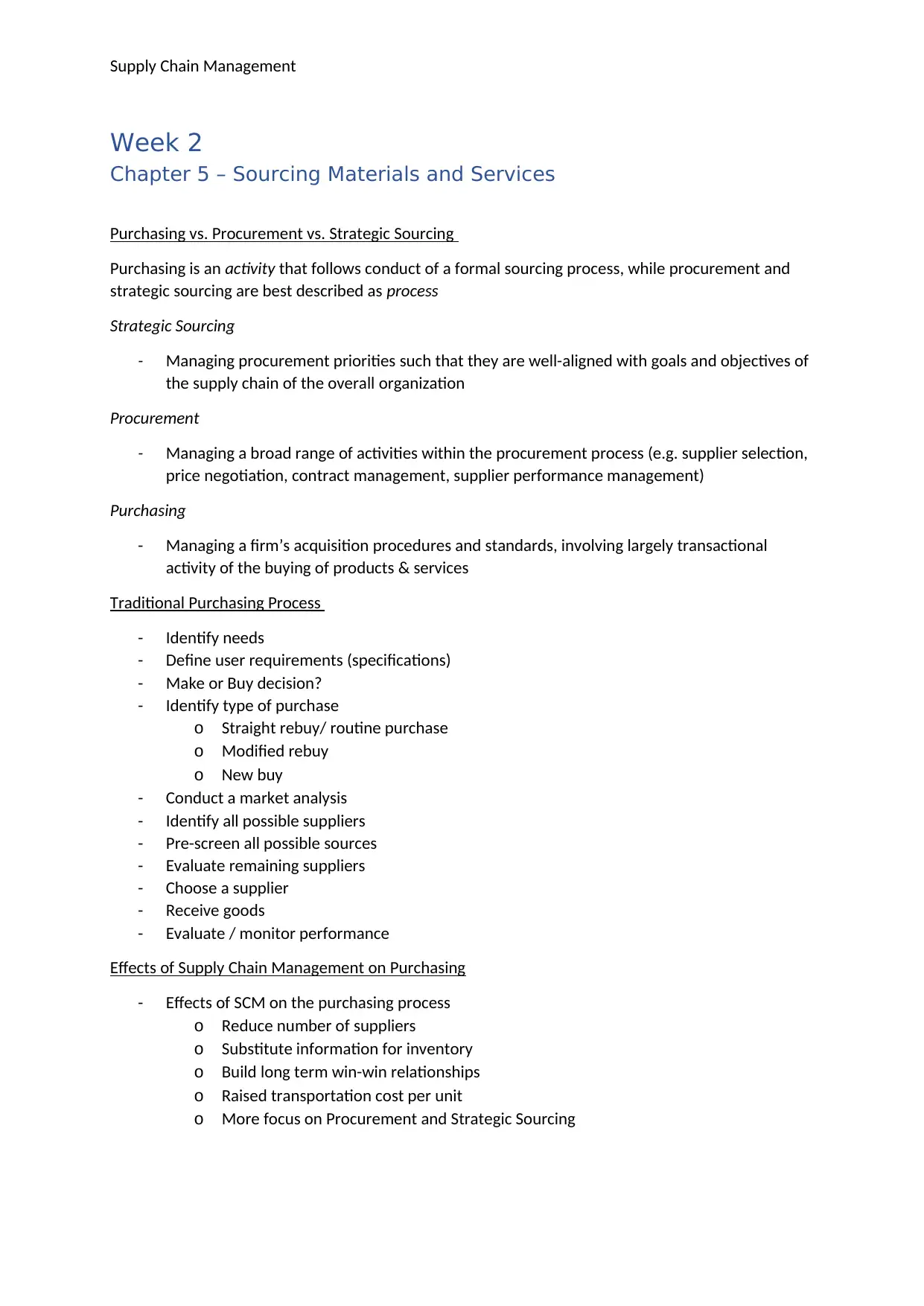
Supply Chain Management
Week 2
Chapter 5 – Sourcing Materials and Services
Purchasing vs. Procurement vs. Strategic Sourcing
Purchasing is an activity that follows conduct of a formal sourcing process, while procurement and
strategic sourcing are best described as process
Strategic Sourcing
- Managing procurement priorities such that they are well-aligned with goals and objectives of
the supply chain of the overall organization
Procurement
- Managing a broad range of activities within the procurement process (e.g. supplier selection,
price negotiation, contract management, supplier performance management)
Purchasing
- Managing a firm’s acquisition procedures and standards, involving largely transactional
activity of the buying of products & services
Traditional Purchasing Process
- Identify needs
- Define user requirements (specifications)
- Make or Buy decision?
- Identify type of purchase
o Straight rebuy/ routine purchase
o Modified rebuy
o New buy
- Conduct a market analysis
- Identify all possible suppliers
- Pre-screen all possible sources
- Evaluate remaining suppliers
- Choose a supplier
- Receive goods
- Evaluate / monitor performance
Effects of Supply Chain Management on Purchasing
- Effects of SCM on the purchasing process
o Reduce number of suppliers
o Substitute information for inventory
o Build long term win-win relationships
o Raised transportation cost per unit
o More focus on Procurement and Strategic Sourcing
Week 2
Chapter 5 – Sourcing Materials and Services
Purchasing vs. Procurement vs. Strategic Sourcing
Purchasing is an activity that follows conduct of a formal sourcing process, while procurement and
strategic sourcing are best described as process
Strategic Sourcing
- Managing procurement priorities such that they are well-aligned with goals and objectives of
the supply chain of the overall organization
Procurement
- Managing a broad range of activities within the procurement process (e.g. supplier selection,
price negotiation, contract management, supplier performance management)
Purchasing
- Managing a firm’s acquisition procedures and standards, involving largely transactional
activity of the buying of products & services
Traditional Purchasing Process
- Identify needs
- Define user requirements (specifications)
- Make or Buy decision?
- Identify type of purchase
o Straight rebuy/ routine purchase
o Modified rebuy
o New buy
- Conduct a market analysis
- Identify all possible suppliers
- Pre-screen all possible sources
- Evaluate remaining suppliers
- Choose a supplier
- Receive goods
- Evaluate / monitor performance
Effects of Supply Chain Management on Purchasing
- Effects of SCM on the purchasing process
o Reduce number of suppliers
o Substitute information for inventory
o Build long term win-win relationships
o Raised transportation cost per unit
o More focus on Procurement and Strategic Sourcing

Supply Chain Management
Unique Aspects of Strategic Sourcing
1. Consolidation and leveraging of purchasing power
2. Emphasis on value
3. More meaningful supplier relationships
4. Attention directed to process improvement
5. Enhanced teamwork and professionalism
Strategic Evolution of Sourcing Process
Three Types of Purchasing Activity
Types of Buys:
1. Capital Goods
2. Rebuy
a. Standard
b. Modified
3. Maintenance, Repair, Operations (MRO)
Unique Aspects of Strategic Sourcing
1. Consolidation and leveraging of purchasing power
2. Emphasis on value
3. More meaningful supplier relationships
4. Attention directed to process improvement
5. Enhanced teamwork and professionalism
Strategic Evolution of Sourcing Process
Three Types of Purchasing Activity
Types of Buys:
1. Capital Goods
2. Rebuy
a. Standard
b. Modified
3. Maintenance, Repair, Operations (MRO)
Paraphrase This Document
Need a fresh take? Get an instant paraphrase of this document with our AI Paraphraser
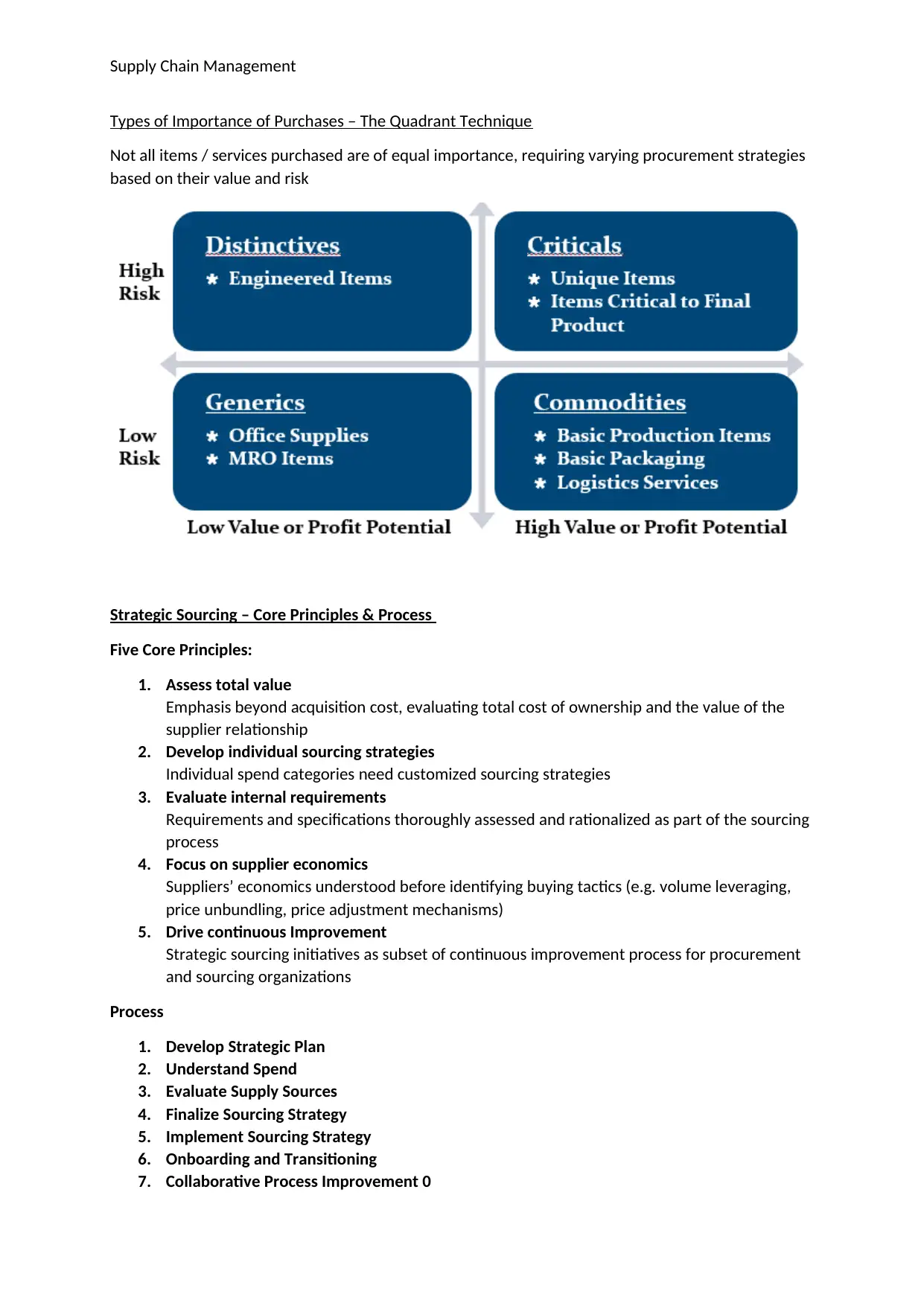
Supply Chain Management
Types of Importance of Purchases – The Quadrant Technique
Not all items / services purchased are of equal importance, requiring varying procurement strategies
based on their value and risk
Strategic Sourcing – Core Principles & Process
Five Core Principles:
1. Assess total value
Emphasis beyond acquisition cost, evaluating total cost of ownership and the value of the
supplier relationship
2. Develop individual sourcing strategies
Individual spend categories need customized sourcing strategies
3. Evaluate internal requirements
Requirements and specifications thoroughly assessed and rationalized as part of the sourcing
process
4. Focus on supplier economics
Suppliers’ economics understood before identifying buying tactics (e.g. volume leveraging,
price unbundling, price adjustment mechanisms)
5. Drive continuous Improvement
Strategic sourcing initiatives as subset of continuous improvement process for procurement
and sourcing organizations
Process
1. Develop Strategic Plan
2. Understand Spend
3. Evaluate Supply Sources
4. Finalize Sourcing Strategy
5. Implement Sourcing Strategy
6. Onboarding and Transitioning
7. Collaborative Process Improvement 0
Types of Importance of Purchases – The Quadrant Technique
Not all items / services purchased are of equal importance, requiring varying procurement strategies
based on their value and risk
Strategic Sourcing – Core Principles & Process
Five Core Principles:
1. Assess total value
Emphasis beyond acquisition cost, evaluating total cost of ownership and the value of the
supplier relationship
2. Develop individual sourcing strategies
Individual spend categories need customized sourcing strategies
3. Evaluate internal requirements
Requirements and specifications thoroughly assessed and rationalized as part of the sourcing
process
4. Focus on supplier economics
Suppliers’ economics understood before identifying buying tactics (e.g. volume leveraging,
price unbundling, price adjustment mechanisms)
5. Drive continuous Improvement
Strategic sourcing initiatives as subset of continuous improvement process for procurement
and sourcing organizations
Process
1. Develop Strategic Plan
2. Understand Spend
3. Evaluate Supply Sources
4. Finalize Sourcing Strategy
5. Implement Sourcing Strategy
6. Onboarding and Transitioning
7. Collaborative Process Improvement 0
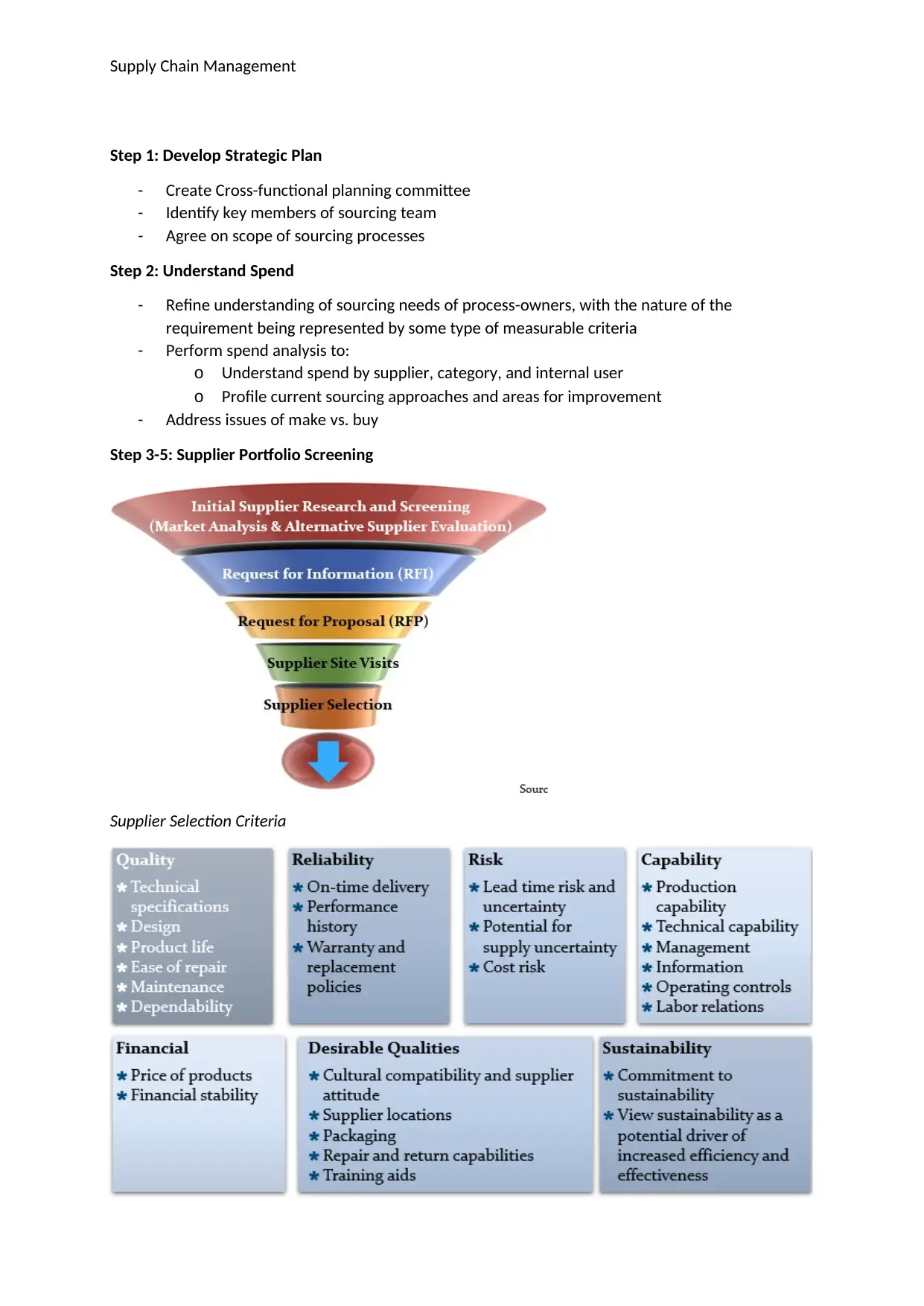
Supply Chain Management
Step 1: Develop Strategic Plan
- Create Cross-functional planning committee
- Identify key members of sourcing team
- Agree on scope of sourcing processes
Step 2: Understand Spend
- Refine understanding of sourcing needs of process-owners, with the nature of the
requirement being represented by some type of measurable criteria
- Perform spend analysis to:
o Understand spend by supplier, category, and internal user
o Profile current sourcing approaches and areas for improvement
- Address issues of make vs. buy
Step 3-5: Supplier Portfolio Screening
Supplier Selection Criteria
Step 1: Develop Strategic Plan
- Create Cross-functional planning committee
- Identify key members of sourcing team
- Agree on scope of sourcing processes
Step 2: Understand Spend
- Refine understanding of sourcing needs of process-owners, with the nature of the
requirement being represented by some type of measurable criteria
- Perform spend analysis to:
o Understand spend by supplier, category, and internal user
o Profile current sourcing approaches and areas for improvement
- Address issues of make vs. buy
Step 3-5: Supplier Portfolio Screening
Supplier Selection Criteria
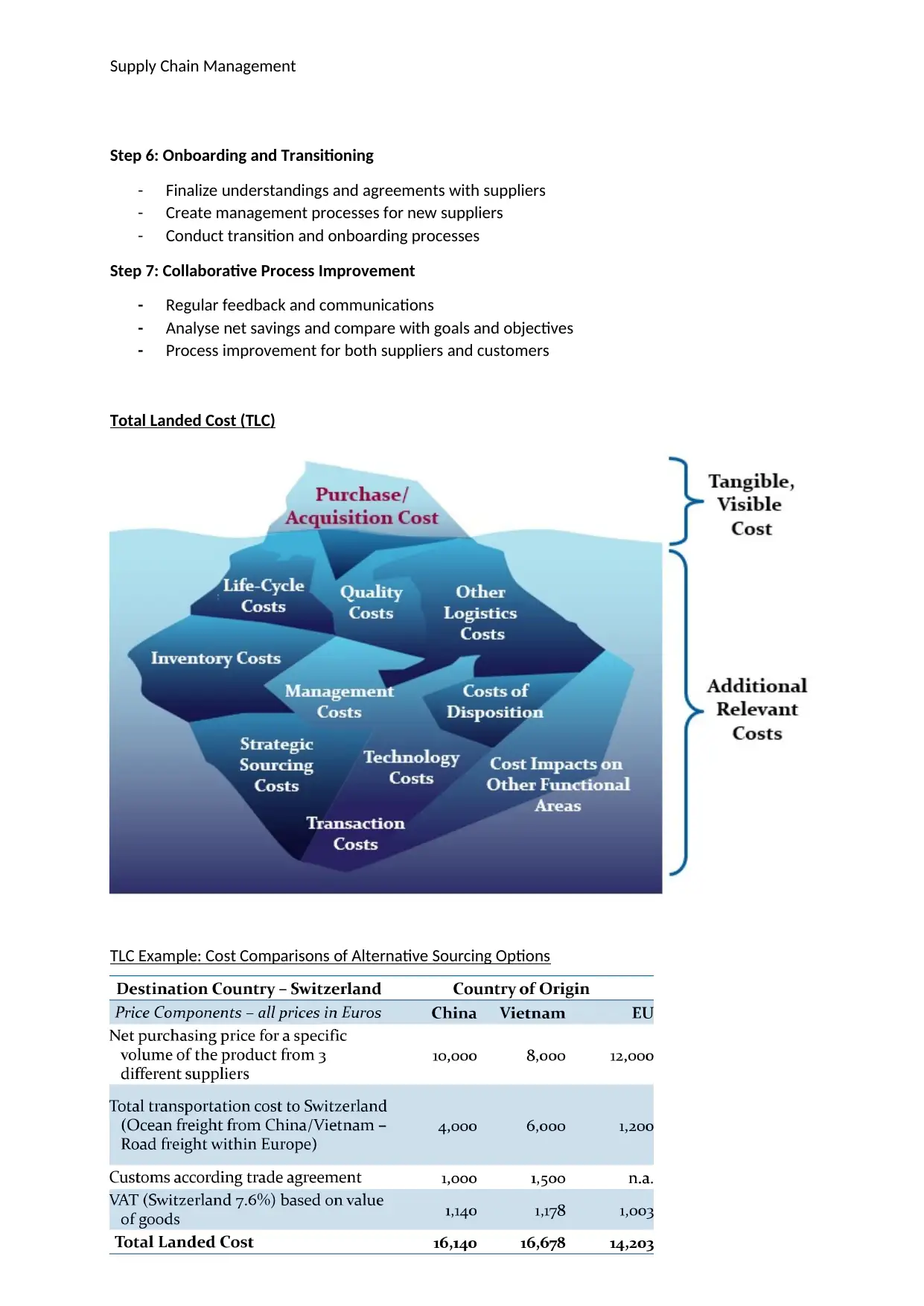
Supply Chain Management
Step 6: Onboarding and Transitioning
- Finalize understandings and agreements with suppliers
- Create management processes for new suppliers
- Conduct transition and onboarding processes
Step 7: Collaborative Process Improvement
- Regular feedback and communications
- Analyse net savings and compare with goals and objectives
- Process improvement for both suppliers and customers
Total Landed Cost (TLC)
TLC Example: Cost Comparisons of Alternative Sourcing Options
Step 6: Onboarding and Transitioning
- Finalize understandings and agreements with suppliers
- Create management processes for new suppliers
- Conduct transition and onboarding processes
Step 7: Collaborative Process Improvement
- Regular feedback and communications
- Analyse net savings and compare with goals and objectives
- Process improvement for both suppliers and customers
Total Landed Cost (TLC)
TLC Example: Cost Comparisons of Alternative Sourcing Options
Secure Best Marks with AI Grader
Need help grading? Try our AI Grader for instant feedback on your assignments.
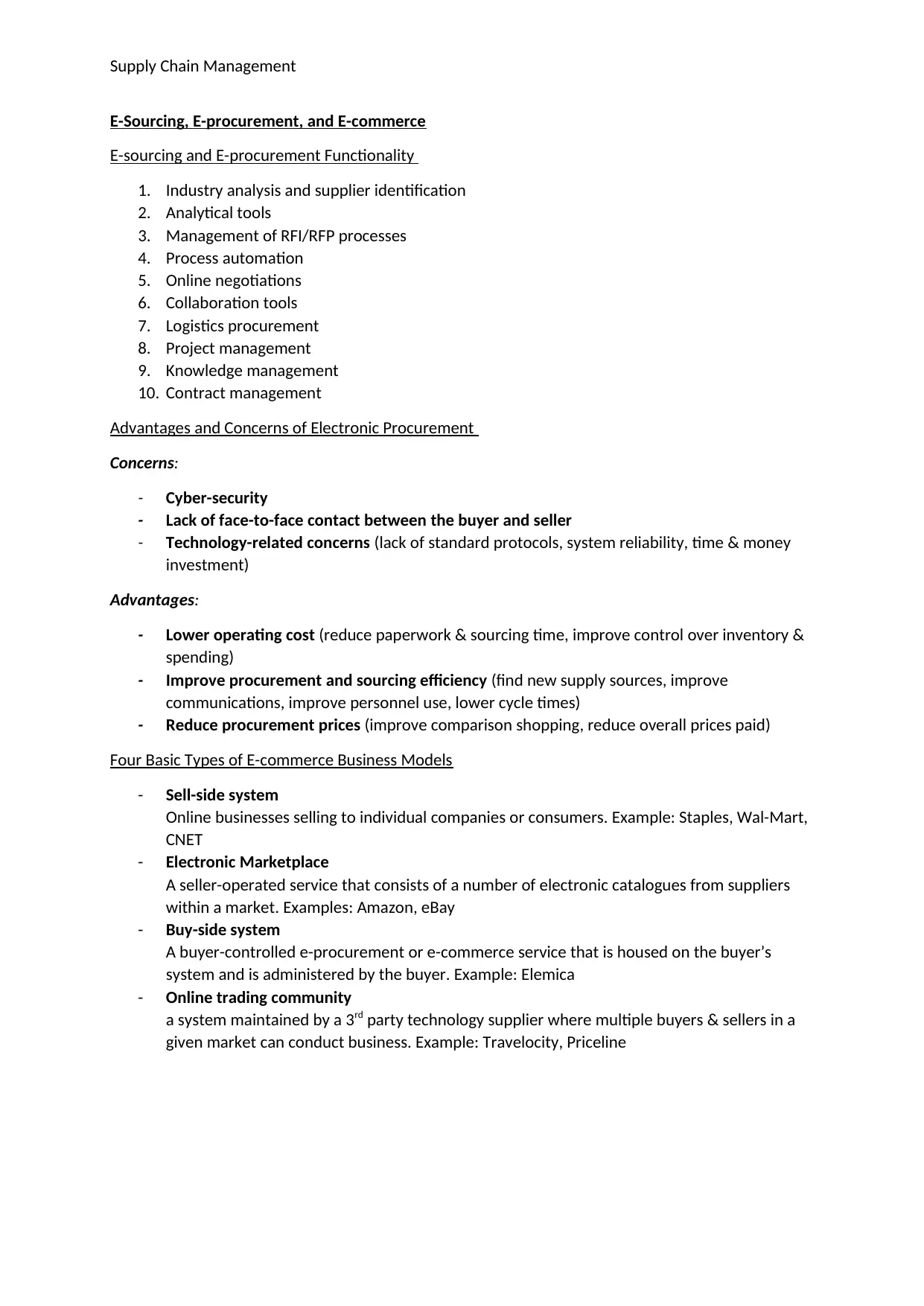
Supply Chain Management
E-Sourcing, E-procurement, and E-commerce
E-sourcing and E-procurement Functionality
1. Industry analysis and supplier identification
2. Analytical tools
3. Management of RFI/RFP processes
4. Process automation
5. Online negotiations
6. Collaboration tools
7. Logistics procurement
8. Project management
9. Knowledge management
10. Contract management
Advantages and Concerns of Electronic Procurement
Concerns:
- Cyber-security
- Lack of face-to-face contact between the buyer and seller
- Technology-related concerns (lack of standard protocols, system reliability, time & money
investment)
Advantages:
- Lower operating cost (reduce paperwork & sourcing time, improve control over inventory &
spending)
- Improve procurement and sourcing efficiency (find new supply sources, improve
communications, improve personnel use, lower cycle times)
- Reduce procurement prices (improve comparison shopping, reduce overall prices paid)
Four Basic Types of E-commerce Business Models
- Sell-side system
Online businesses selling to individual companies or consumers. Example: Staples, Wal-Mart,
CNET
- Electronic Marketplace
A seller-operated service that consists of a number of electronic catalogues from suppliers
within a market. Examples: Amazon, eBay
- Buy-side system
A buyer-controlled e-procurement or e-commerce service that is housed on the buyer’s
system and is administered by the buyer. Example: Elemica
- Online trading community
a system maintained by a 3rd party technology supplier where multiple buyers & sellers in a
given market can conduct business. Example: Travelocity, Priceline
E-Sourcing, E-procurement, and E-commerce
E-sourcing and E-procurement Functionality
1. Industry analysis and supplier identification
2. Analytical tools
3. Management of RFI/RFP processes
4. Process automation
5. Online negotiations
6. Collaboration tools
7. Logistics procurement
8. Project management
9. Knowledge management
10. Contract management
Advantages and Concerns of Electronic Procurement
Concerns:
- Cyber-security
- Lack of face-to-face contact between the buyer and seller
- Technology-related concerns (lack of standard protocols, system reliability, time & money
investment)
Advantages:
- Lower operating cost (reduce paperwork & sourcing time, improve control over inventory &
spending)
- Improve procurement and sourcing efficiency (find new supply sources, improve
communications, improve personnel use, lower cycle times)
- Reduce procurement prices (improve comparison shopping, reduce overall prices paid)
Four Basic Types of E-commerce Business Models
- Sell-side system
Online businesses selling to individual companies or consumers. Example: Staples, Wal-Mart,
CNET
- Electronic Marketplace
A seller-operated service that consists of a number of electronic catalogues from suppliers
within a market. Examples: Amazon, eBay
- Buy-side system
A buyer-controlled e-procurement or e-commerce service that is housed on the buyer’s
system and is administered by the buyer. Example: Elemica
- Online trading community
a system maintained by a 3rd party technology supplier where multiple buyers & sellers in a
given market can conduct business. Example: Travelocity, Priceline
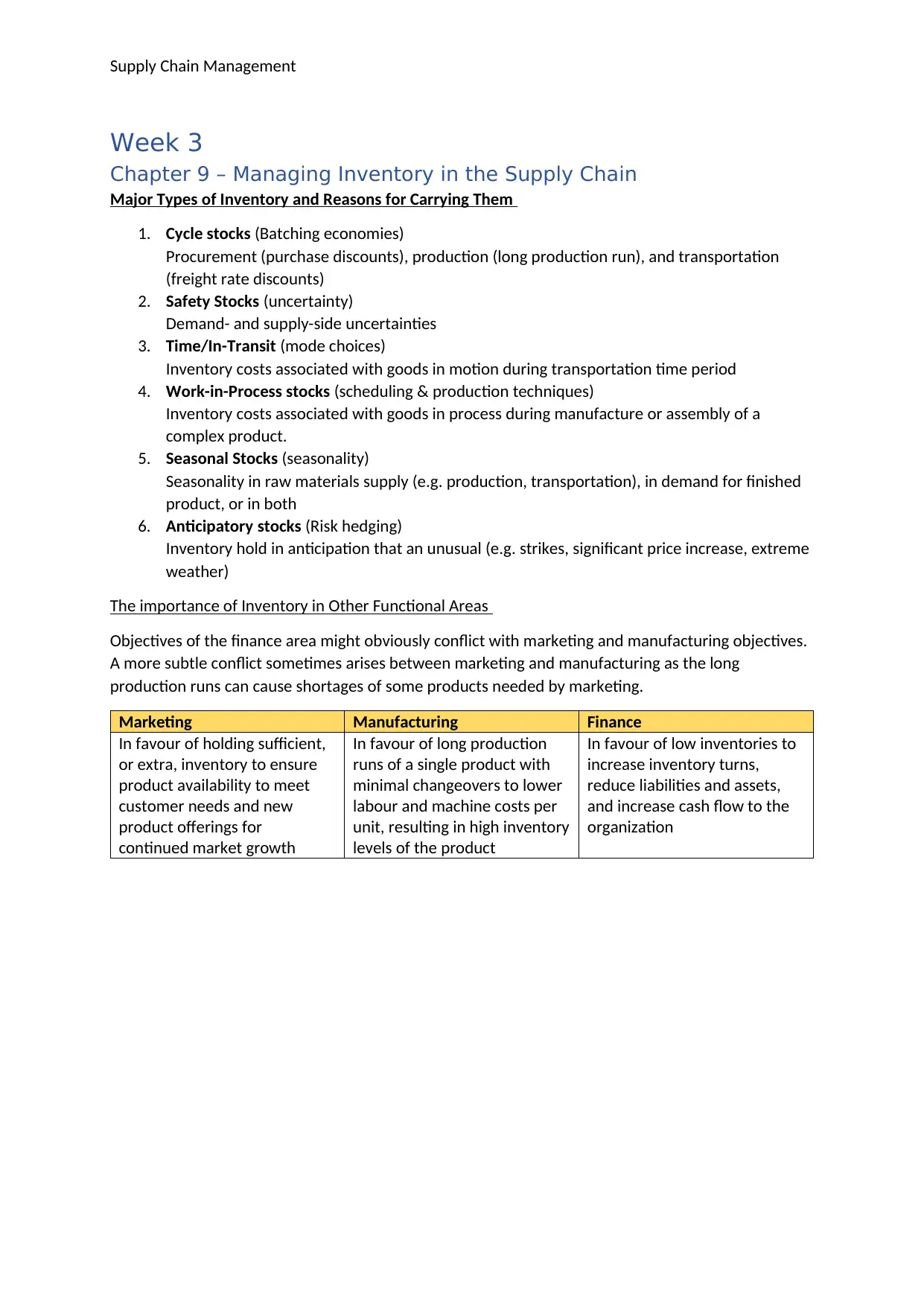
Supply Chain Management
Week 3
Chapter 9 – Managing Inventory in the Supply Chain
Major Types of Inventory and Reasons for Carrying Them
1. Cycle stocks (Batching economies)
Procurement (purchase discounts), production (long production run), and transportation
(freight rate discounts)
2. Safety Stocks (uncertainty)
Demand- and supply-side uncertainties
3. Time/In-Transit (mode choices)
Inventory costs associated with goods in motion during transportation time period
4. Work-in-Process stocks (scheduling & production techniques)
Inventory costs associated with goods in process during manufacture or assembly of a
complex product.
5. Seasonal Stocks (seasonality)
Seasonality in raw materials supply (e.g. production, transportation), in demand for finished
product, or in both
6. Anticipatory stocks (Risk hedging)
Inventory hold in anticipation that an unusual (e.g. strikes, significant price increase, extreme
weather)
The importance of Inventory in Other Functional Areas
Objectives of the finance area might obviously conflict with marketing and manufacturing objectives.
A more subtle conflict sometimes arises between marketing and manufacturing as the long
production runs can cause shortages of some products needed by marketing.
Marketing Manufacturing Finance
In favour of holding sufficient,
or extra, inventory to ensure
product availability to meet
customer needs and new
product offerings for
continued market growth
In favour of long production
runs of a single product with
minimal changeovers to lower
labour and machine costs per
unit, resulting in high inventory
levels of the product
In favour of low inventories to
increase inventory turns,
reduce liabilities and assets,
and increase cash flow to the
organization
Week 3
Chapter 9 – Managing Inventory in the Supply Chain
Major Types of Inventory and Reasons for Carrying Them
1. Cycle stocks (Batching economies)
Procurement (purchase discounts), production (long production run), and transportation
(freight rate discounts)
2. Safety Stocks (uncertainty)
Demand- and supply-side uncertainties
3. Time/In-Transit (mode choices)
Inventory costs associated with goods in motion during transportation time period
4. Work-in-Process stocks (scheduling & production techniques)
Inventory costs associated with goods in process during manufacture or assembly of a
complex product.
5. Seasonal Stocks (seasonality)
Seasonality in raw materials supply (e.g. production, transportation), in demand for finished
product, or in both
6. Anticipatory stocks (Risk hedging)
Inventory hold in anticipation that an unusual (e.g. strikes, significant price increase, extreme
weather)
The importance of Inventory in Other Functional Areas
Objectives of the finance area might obviously conflict with marketing and manufacturing objectives.
A more subtle conflict sometimes arises between marketing and manufacturing as the long
production runs can cause shortages of some products needed by marketing.
Marketing Manufacturing Finance
In favour of holding sufficient,
or extra, inventory to ensure
product availability to meet
customer needs and new
product offerings for
continued market growth
In favour of long production
runs of a single product with
minimal changeovers to lower
labour and machine costs per
unit, resulting in high inventory
levels of the product
In favour of low inventories to
increase inventory turns,
reduce liabilities and assets,
and increase cash flow to the
organization
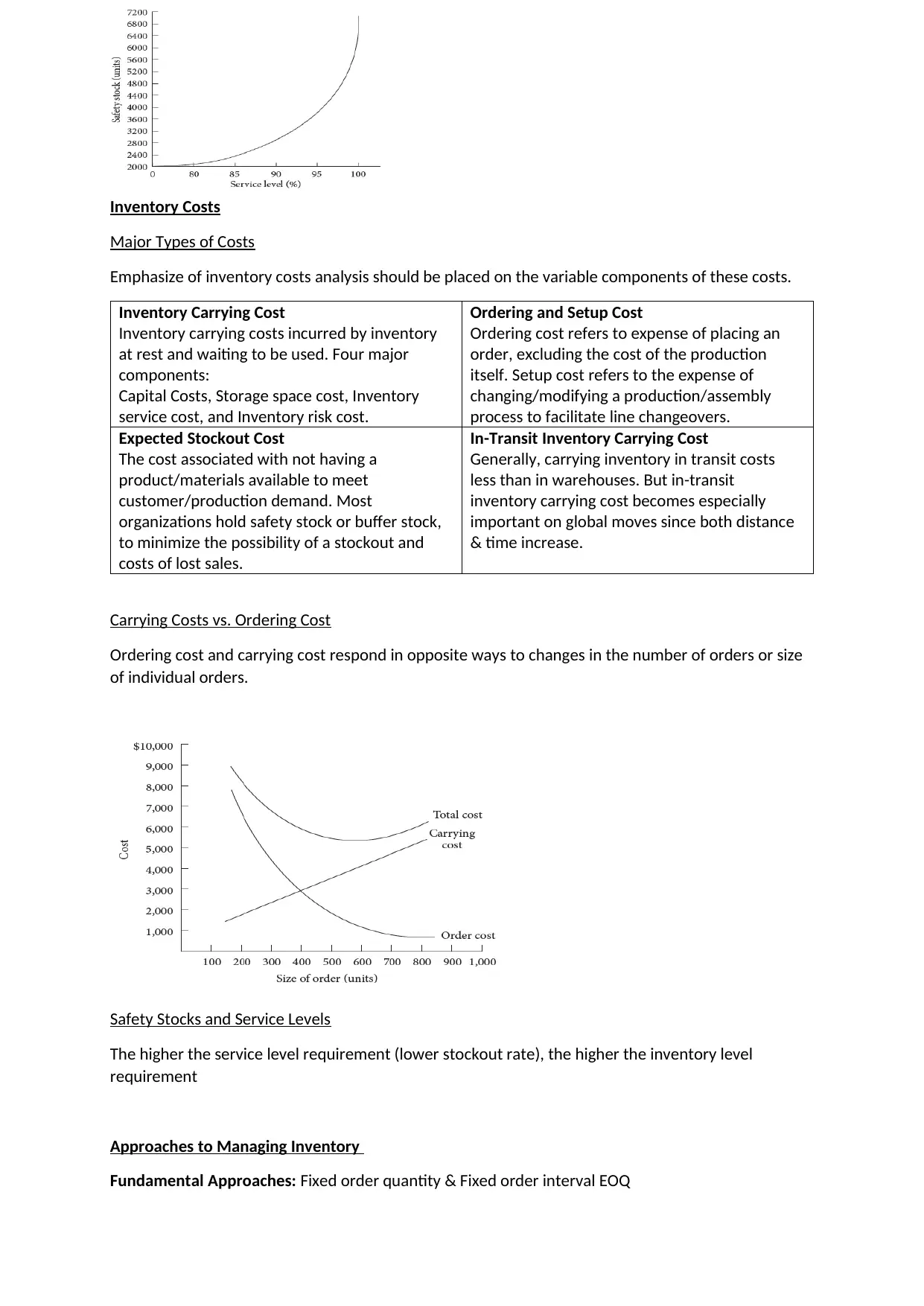
Supply Chain Management
Inventory Costs
Major Types of Costs
Emphasize of inventory costs analysis should be placed on the variable components of these costs.
Inventory Carrying Cost
Inventory carrying costs incurred by inventory
at rest and waiting to be used. Four major
components:
Capital Costs, Storage space cost, Inventory
service cost, and Inventory risk cost.
Ordering and Setup Cost
Ordering cost refers to expense of placing an
order, excluding the cost of the production
itself. Setup cost refers to the expense of
changing/modifying a production/assembly
process to facilitate line changeovers.
Expected Stockout Cost
The cost associated with not having a
product/materials available to meet
customer/production demand. Most
organizations hold safety stock or buffer stock,
to minimize the possibility of a stockout and
costs of lost sales.
In-Transit Inventory Carrying Cost
Generally, carrying inventory in transit costs
less than in warehouses. But in-transit
inventory carrying cost becomes especially
important on global moves since both distance
& time increase.
Carrying Costs vs. Ordering Cost
Ordering cost and carrying cost respond in opposite ways to changes in the number of orders or size
of individual orders.
Safety Stocks and Service Levels
The higher the service level requirement (lower stockout rate), the higher the inventory level
requirement
Approaches to Managing Inventory
Fundamental Approaches: Fixed order quantity & Fixed order interval EOQ
Inventory Costs
Major Types of Costs
Emphasize of inventory costs analysis should be placed on the variable components of these costs.
Inventory Carrying Cost
Inventory carrying costs incurred by inventory
at rest and waiting to be used. Four major
components:
Capital Costs, Storage space cost, Inventory
service cost, and Inventory risk cost.
Ordering and Setup Cost
Ordering cost refers to expense of placing an
order, excluding the cost of the production
itself. Setup cost refers to the expense of
changing/modifying a production/assembly
process to facilitate line changeovers.
Expected Stockout Cost
The cost associated with not having a
product/materials available to meet
customer/production demand. Most
organizations hold safety stock or buffer stock,
to minimize the possibility of a stockout and
costs of lost sales.
In-Transit Inventory Carrying Cost
Generally, carrying inventory in transit costs
less than in warehouses. But in-transit
inventory carrying cost becomes especially
important on global moves since both distance
& time increase.
Carrying Costs vs. Ordering Cost
Ordering cost and carrying cost respond in opposite ways to changes in the number of orders or size
of individual orders.
Safety Stocks and Service Levels
The higher the service level requirement (lower stockout rate), the higher the inventory level
requirement
Approaches to Managing Inventory
Fundamental Approaches: Fixed order quantity & Fixed order interval EOQ
Paraphrase This Document
Need a fresh take? Get an instant paraphrase of this document with our AI Paraphraser
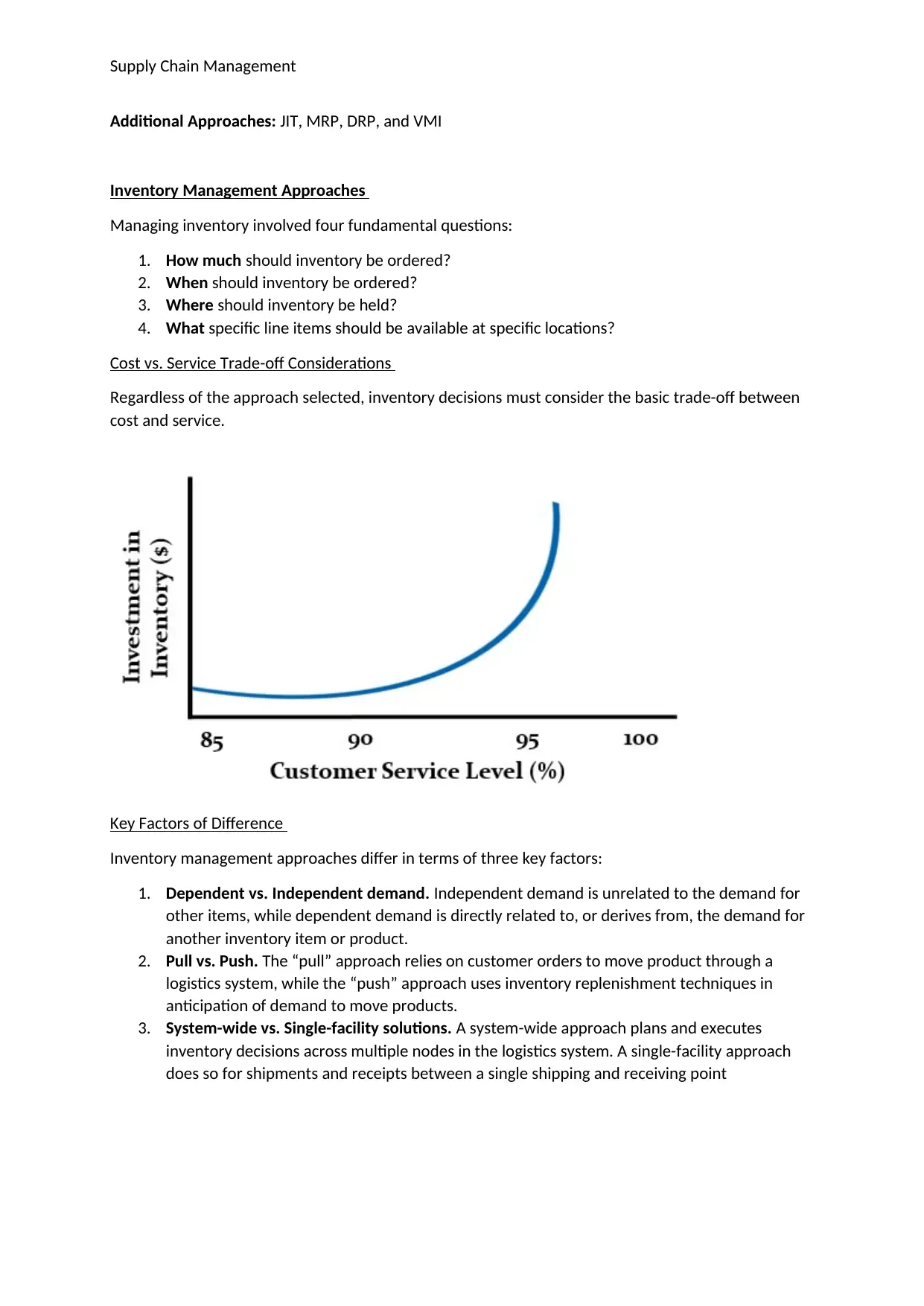
Supply Chain Management
Additional Approaches: JIT, MRP, DRP, and VMI
Inventory Management Approaches
Managing inventory involved four fundamental questions:
1. How much should inventory be ordered?
2. When should inventory be ordered?
3. Where should inventory be held?
4. What specific line items should be available at specific locations?
Cost vs. Service Trade-off Considerations
Regardless of the approach selected, inventory decisions must consider the basic trade-off between
cost and service.
Key Factors of Difference
Inventory management approaches differ in terms of three key factors:
1. Dependent vs. Independent demand. Independent demand is unrelated to the demand for
other items, while dependent demand is directly related to, or derives from, the demand for
another inventory item or product.
2. Pull vs. Push. The “pull” approach relies on customer orders to move product through a
logistics system, while the “push” approach uses inventory replenishment techniques in
anticipation of demand to move products.
3. System-wide vs. Single-facility solutions. A system-wide approach plans and executes
inventory decisions across multiple nodes in the logistics system. A single-facility approach
does so for shipments and receipts between a single shipping and receiving point
Additional Approaches: JIT, MRP, DRP, and VMI
Inventory Management Approaches
Managing inventory involved four fundamental questions:
1. How much should inventory be ordered?
2. When should inventory be ordered?
3. Where should inventory be held?
4. What specific line items should be available at specific locations?
Cost vs. Service Trade-off Considerations
Regardless of the approach selected, inventory decisions must consider the basic trade-off between
cost and service.
Key Factors of Difference
Inventory management approaches differ in terms of three key factors:
1. Dependent vs. Independent demand. Independent demand is unrelated to the demand for
other items, while dependent demand is directly related to, or derives from, the demand for
another inventory item or product.
2. Pull vs. Push. The “pull” approach relies on customer orders to move product through a
logistics system, while the “push” approach uses inventory replenishment techniques in
anticipation of demand to move products.
3. System-wide vs. Single-facility solutions. A system-wide approach plans and executes
inventory decisions across multiple nodes in the logistics system. A single-facility approach
does so for shipments and receipts between a single shipping and receiving point
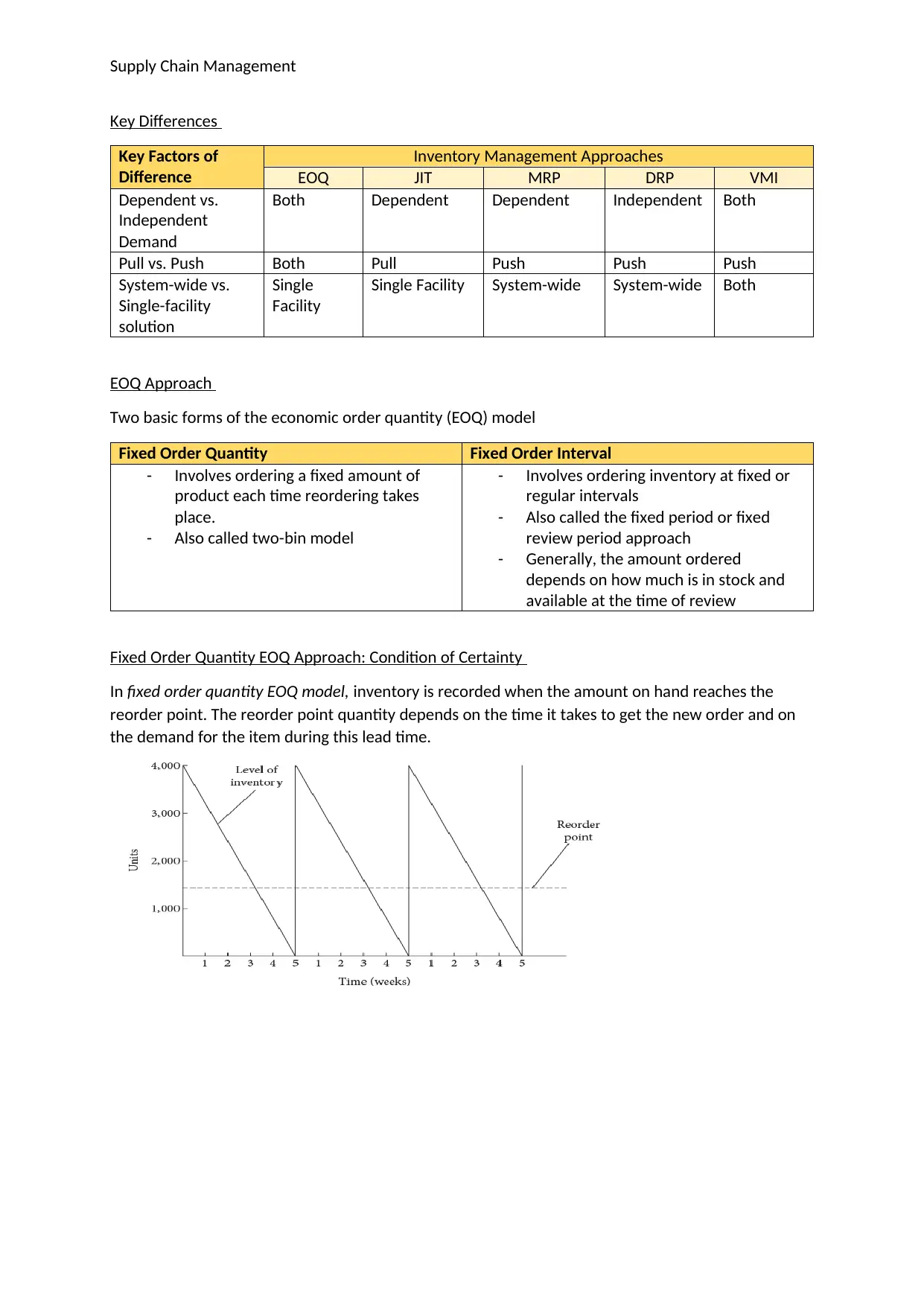
Supply Chain Management
Key Differences
Key Factors of
Difference
Inventory Management Approaches
EOQ JIT MRP DRP VMI
Dependent vs.
Independent
Demand
Both Dependent Dependent Independent Both
Pull vs. Push Both Pull Push Push Push
System-wide vs.
Single-facility
solution
Single
Facility
Single Facility System-wide System-wide Both
EOQ Approach
Two basic forms of the economic order quantity (EOQ) model
Fixed Order Quantity Fixed Order Interval
- Involves ordering a fixed amount of
product each time reordering takes
place.
- Also called two-bin model
- Involves ordering inventory at fixed or
regular intervals
- Also called the fixed period or fixed
review period approach
- Generally, the amount ordered
depends on how much is in stock and
available at the time of review
Fixed Order Quantity EOQ Approach: Condition of Certainty
In fixed order quantity EOQ model, inventory is recorded when the amount on hand reaches the
reorder point. The reorder point quantity depends on the time it takes to get the new order and on
the demand for the item during this lead time.
Key Differences
Key Factors of
Difference
Inventory Management Approaches
EOQ JIT MRP DRP VMI
Dependent vs.
Independent
Demand
Both Dependent Dependent Independent Both
Pull vs. Push Both Pull Push Push Push
System-wide vs.
Single-facility
solution
Single
Facility
Single Facility System-wide System-wide Both
EOQ Approach
Two basic forms of the economic order quantity (EOQ) model
Fixed Order Quantity Fixed Order Interval
- Involves ordering a fixed amount of
product each time reordering takes
place.
- Also called two-bin model
- Involves ordering inventory at fixed or
regular intervals
- Also called the fixed period or fixed
review period approach
- Generally, the amount ordered
depends on how much is in stock and
available at the time of review
Fixed Order Quantity EOQ Approach: Condition of Certainty
In fixed order quantity EOQ model, inventory is recorded when the amount on hand reaches the
reorder point. The reorder point quantity depends on the time it takes to get the new order and on
the demand for the item during this lead time.
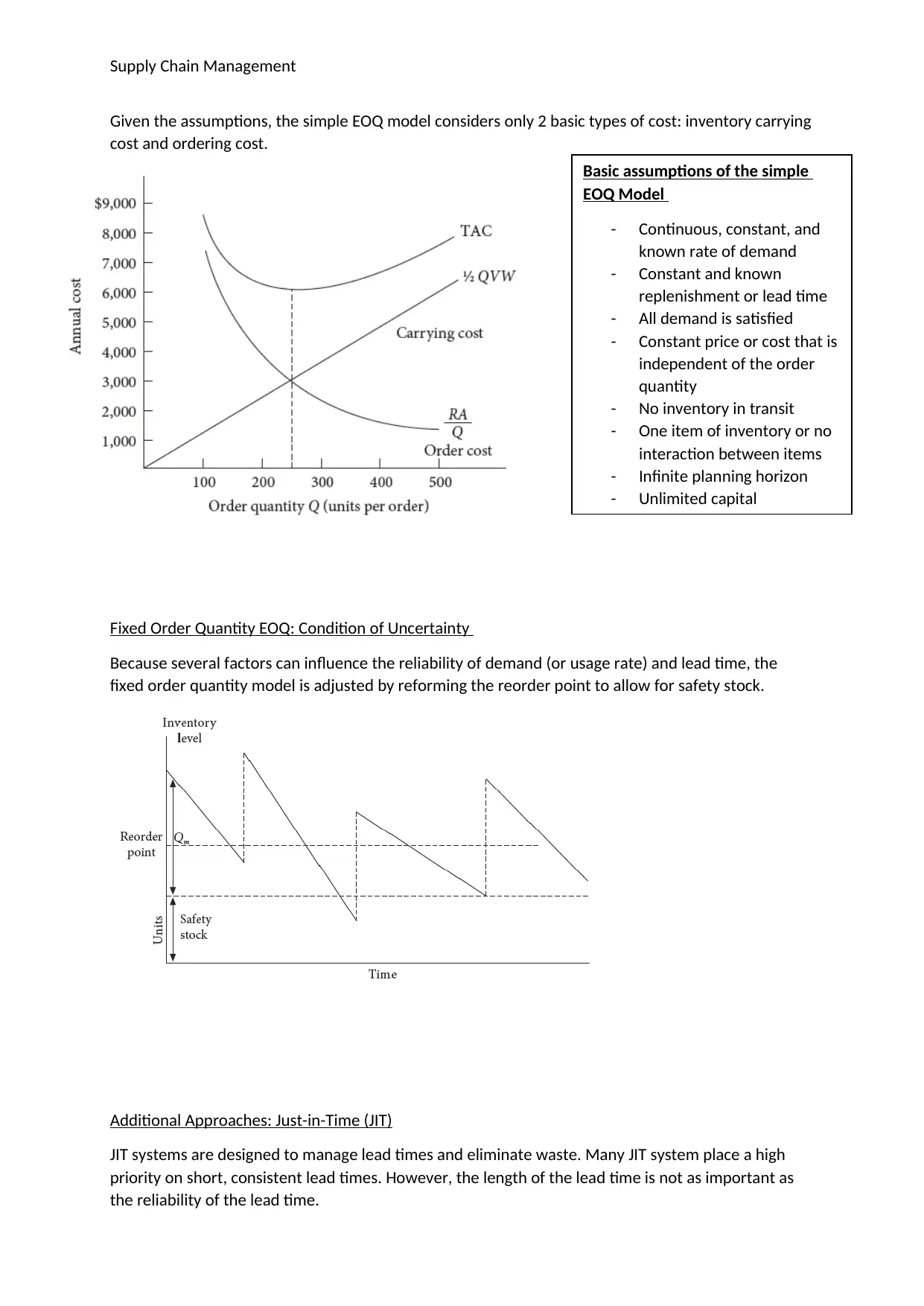
Supply Chain Management
Given the assumptions, the simple EOQ model considers only 2 basic types of cost: inventory carrying
cost and ordering cost.
Fixed Order Quantity EOQ: Condition of Uncertainty
Because several factors can influence the reliability of demand (or usage rate) and lead time, the
fixed order quantity model is adjusted by reforming the reorder point to allow for safety stock.
Additional Approaches: Just-in-Time (JIT)
JIT systems are designed to manage lead times and eliminate waste. Many JIT system place a high
priority on short, consistent lead times. However, the length of the lead time is not as important as
the reliability of the lead time.
Basic assumptions of the simple
EOQ Model
- Continuous, constant, and
known rate of demand
- Constant and known
replenishment or lead time
- All demand is satisfied
- Constant price or cost that is
independent of the order
quantity
- No inventory in transit
- One item of inventory or no
interaction between items
- Infinite planning horizon
- Unlimited capital
Given the assumptions, the simple EOQ model considers only 2 basic types of cost: inventory carrying
cost and ordering cost.
Fixed Order Quantity EOQ: Condition of Uncertainty
Because several factors can influence the reliability of demand (or usage rate) and lead time, the
fixed order quantity model is adjusted by reforming the reorder point to allow for safety stock.
Additional Approaches: Just-in-Time (JIT)
JIT systems are designed to manage lead times and eliminate waste. Many JIT system place a high
priority on short, consistent lead times. However, the length of the lead time is not as important as
the reliability of the lead time.
Basic assumptions of the simple
EOQ Model
- Continuous, constant, and
known rate of demand
- Constant and known
replenishment or lead time
- All demand is satisfied
- Constant price or cost that is
independent of the order
quantity
- No inventory in transit
- One item of inventory or no
interaction between items
- Infinite planning horizon
- Unlimited capital
Secure Best Marks with AI Grader
Need help grading? Try our AI Grader for instant feedback on your assignments.
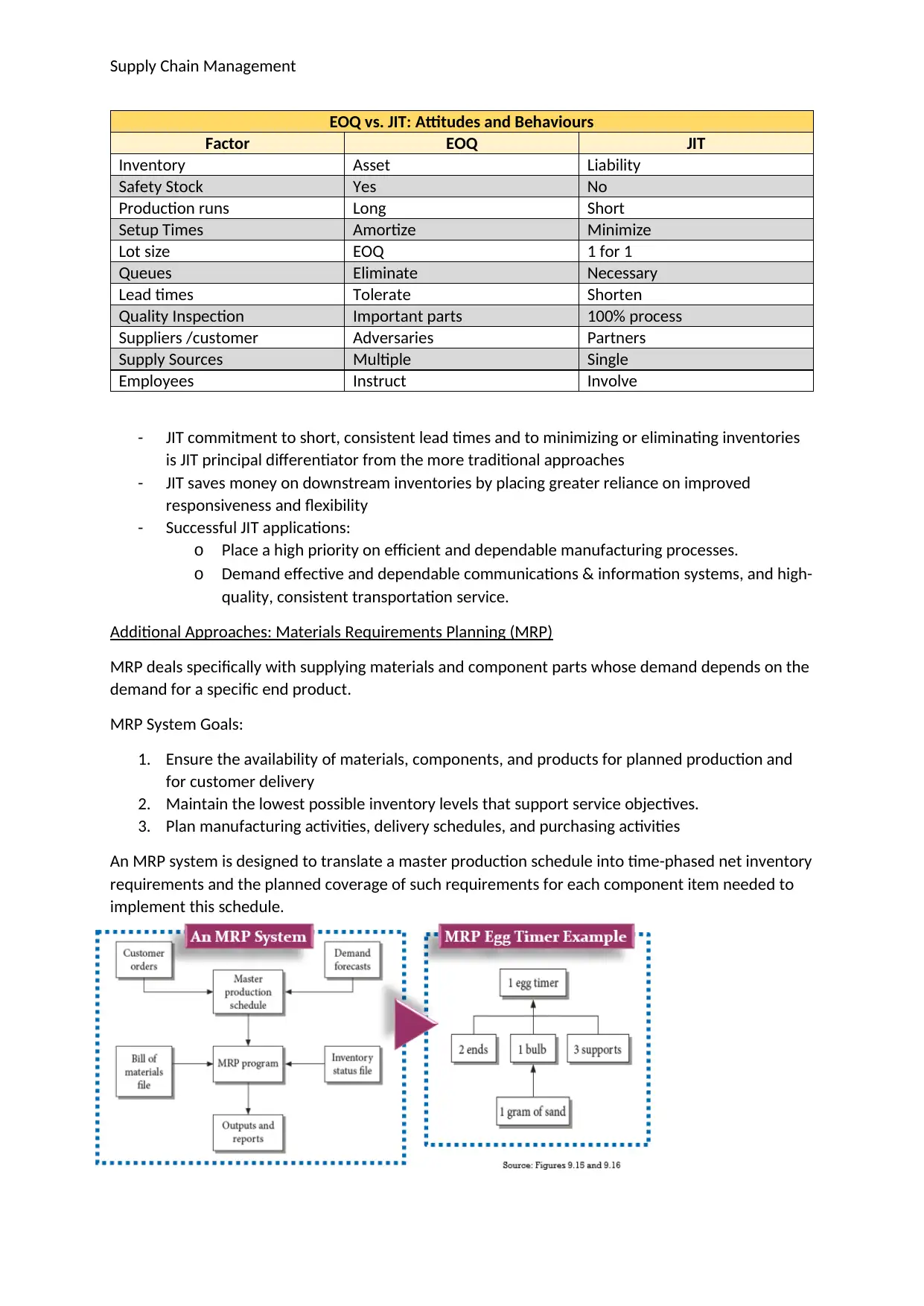
Supply Chain Management
EOQ vs. JIT: Attitudes and Behaviours
Factor EOQ JIT
Inventory Asset Liability
Safety Stock Yes No
Production runs Long Short
Setup Times Amortize Minimize
Lot size EOQ 1 for 1
Queues Eliminate Necessary
Lead times Tolerate Shorten
Quality Inspection Important parts 100% process
Suppliers /customer Adversaries Partners
Supply Sources Multiple Single
Employees Instruct Involve
- JIT commitment to short, consistent lead times and to minimizing or eliminating inventories
is JIT principal differentiator from the more traditional approaches
- JIT saves money on downstream inventories by placing greater reliance on improved
responsiveness and flexibility
- Successful JIT applications:
o Place a high priority on efficient and dependable manufacturing processes.
o Demand effective and dependable communications & information systems, and high-
quality, consistent transportation service.
Additional Approaches: Materials Requirements Planning (MRP)
MRP deals specifically with supplying materials and component parts whose demand depends on the
demand for a specific end product.
MRP System Goals:
1. Ensure the availability of materials, components, and products for planned production and
for customer delivery
2. Maintain the lowest possible inventory levels that support service objectives.
3. Plan manufacturing activities, delivery schedules, and purchasing activities
An MRP system is designed to translate a master production schedule into time-phased net inventory
requirements and the planned coverage of such requirements for each component item needed to
implement this schedule.
EOQ vs. JIT: Attitudes and Behaviours
Factor EOQ JIT
Inventory Asset Liability
Safety Stock Yes No
Production runs Long Short
Setup Times Amortize Minimize
Lot size EOQ 1 for 1
Queues Eliminate Necessary
Lead times Tolerate Shorten
Quality Inspection Important parts 100% process
Suppliers /customer Adversaries Partners
Supply Sources Multiple Single
Employees Instruct Involve
- JIT commitment to short, consistent lead times and to minimizing or eliminating inventories
is JIT principal differentiator from the more traditional approaches
- JIT saves money on downstream inventories by placing greater reliance on improved
responsiveness and flexibility
- Successful JIT applications:
o Place a high priority on efficient and dependable manufacturing processes.
o Demand effective and dependable communications & information systems, and high-
quality, consistent transportation service.
Additional Approaches: Materials Requirements Planning (MRP)
MRP deals specifically with supplying materials and component parts whose demand depends on the
demand for a specific end product.
MRP System Goals:
1. Ensure the availability of materials, components, and products for planned production and
for customer delivery
2. Maintain the lowest possible inventory levels that support service objectives.
3. Plan manufacturing activities, delivery schedules, and purchasing activities
An MRP system is designed to translate a master production schedule into time-phased net inventory
requirements and the planned coverage of such requirements for each component item needed to
implement this schedule.
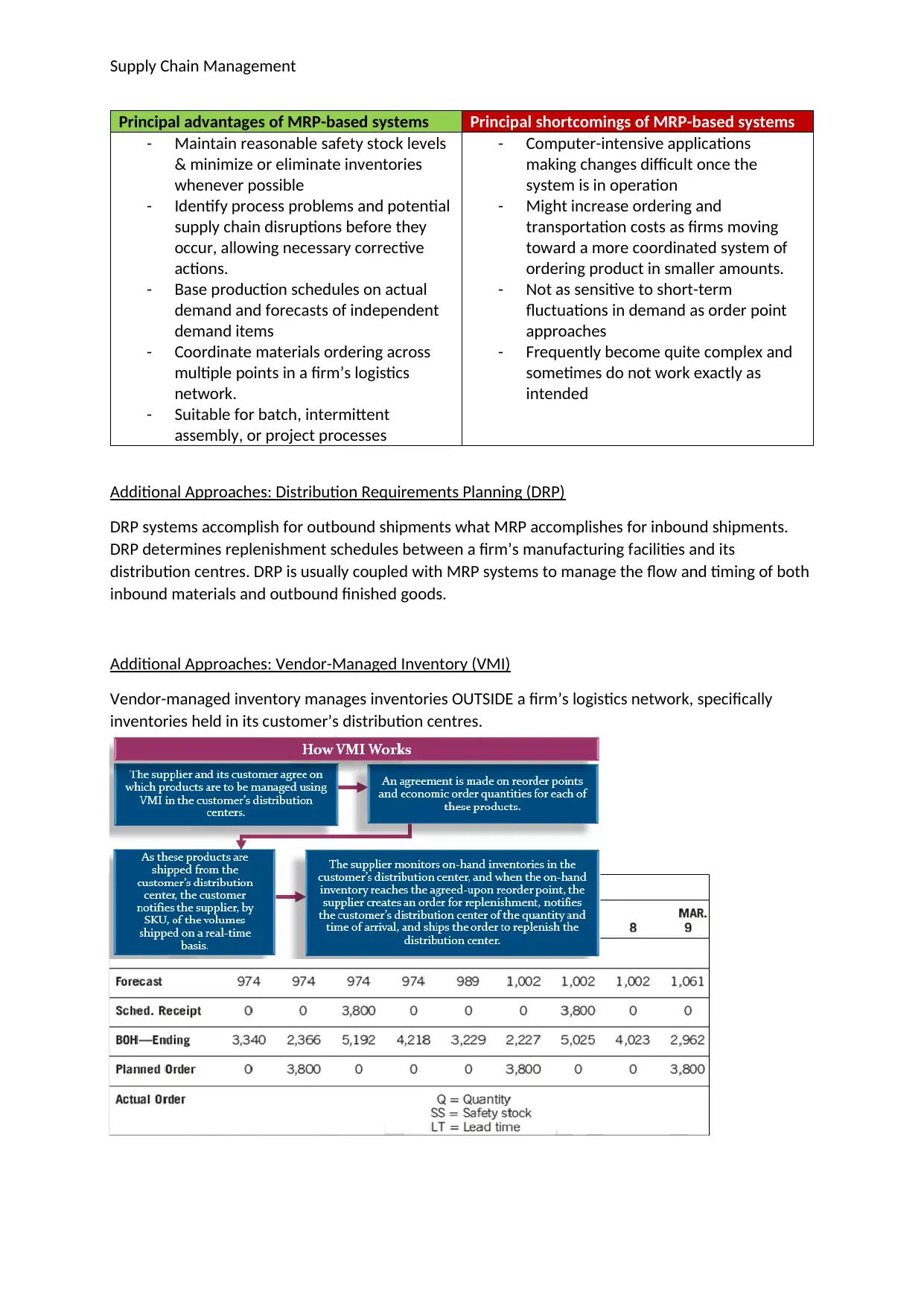
Supply Chain Management
Principal advantages of MRP-based systems Principal shortcomings of MRP-based systems
- Maintain reasonable safety stock levels
& minimize or eliminate inventories
whenever possible
- Identify process problems and potential
supply chain disruptions before they
occur, allowing necessary corrective
actions.
- Base production schedules on actual
demand and forecasts of independent
demand items
- Coordinate materials ordering across
multiple points in a firm’s logistics
network.
- Suitable for batch, intermittent
assembly, or project processes
- Computer-intensive applications
making changes difficult once the
system is in operation
- Might increase ordering and
transportation costs as firms moving
toward a more coordinated system of
ordering product in smaller amounts.
- Not as sensitive to short-term
fluctuations in demand as order point
approaches
- Frequently become quite complex and
sometimes do not work exactly as
intended
Additional Approaches: Distribution Requirements Planning (DRP)
DRP systems accomplish for outbound shipments what MRP accomplishes for inbound shipments.
DRP determines replenishment schedules between a firm’s manufacturing facilities and its
distribution centres. DRP is usually coupled with MRP systems to manage the flow and timing of both
inbound materials and outbound finished goods.
Additional Approaches: Vendor-Managed Inventory (VMI)
Vendor-managed inventory manages inventories OUTSIDE a firm’s logistics network, specifically
inventories held in its customer’s distribution centres.
Principal advantages of MRP-based systems Principal shortcomings of MRP-based systems
- Maintain reasonable safety stock levels
& minimize or eliminate inventories
whenever possible
- Identify process problems and potential
supply chain disruptions before they
occur, allowing necessary corrective
actions.
- Base production schedules on actual
demand and forecasts of independent
demand items
- Coordinate materials ordering across
multiple points in a firm’s logistics
network.
- Suitable for batch, intermittent
assembly, or project processes
- Computer-intensive applications
making changes difficult once the
system is in operation
- Might increase ordering and
transportation costs as firms moving
toward a more coordinated system of
ordering product in smaller amounts.
- Not as sensitive to short-term
fluctuations in demand as order point
approaches
- Frequently become quite complex and
sometimes do not work exactly as
intended
Additional Approaches: Distribution Requirements Planning (DRP)
DRP systems accomplish for outbound shipments what MRP accomplishes for inbound shipments.
DRP determines replenishment schedules between a firm’s manufacturing facilities and its
distribution centres. DRP is usually coupled with MRP systems to manage the flow and timing of both
inbound materials and outbound finished goods.
Additional Approaches: Vendor-Managed Inventory (VMI)
Vendor-managed inventory manages inventories OUTSIDE a firm’s logistics network, specifically
inventories held in its customer’s distribution centres.
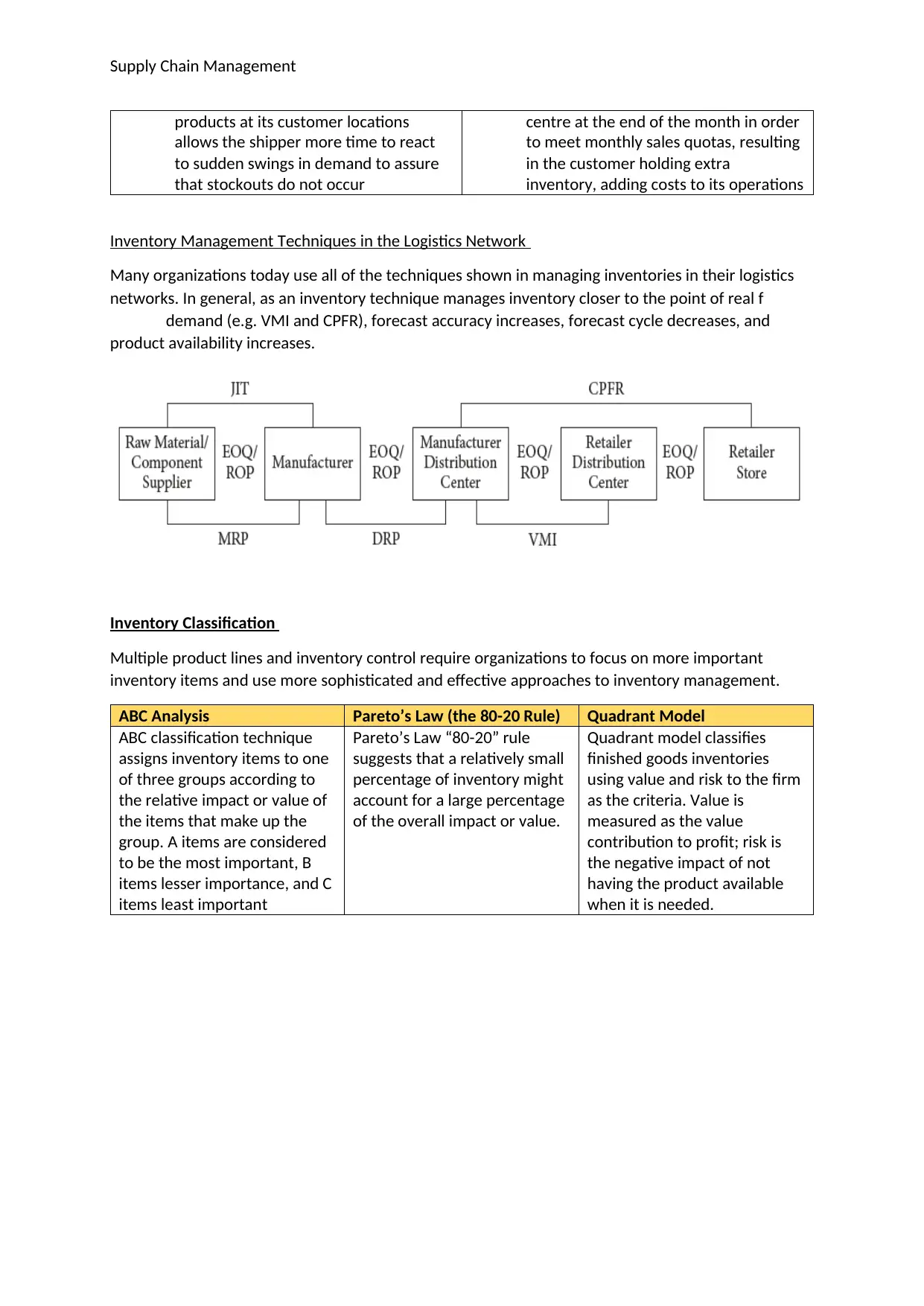
Supply Chain Management
products at its customer locations
allows the shipper more time to react
to sudden swings in demand to assure
that stockouts do not occur
centre at the end of the month in order
to meet monthly sales quotas, resulting
in the customer holding extra
inventory, adding costs to its operations
Inventory Management Techniques in the Logistics Network
Many organizations today use all of the techniques shown in managing inventories in their logistics
networks. In general, as an inventory technique manages inventory closer to the point of real f
demand (e.g. VMI and CPFR), forecast accuracy increases, forecast cycle decreases, and
product availability increases.
Inventory Classification
Multiple product lines and inventory control require organizations to focus on more important
inventory items and use more sophisticated and effective approaches to inventory management.
ABC Analysis Pareto’s Law (the 80-20 Rule) Quadrant Model
ABC classification technique
assigns inventory items to one
of three groups according to
the relative impact or value of
the items that make up the
group. A items are considered
to be the most important, B
items lesser importance, and C
items least important
Pareto’s Law “80-20” rule
suggests that a relatively small
percentage of inventory might
account for a large percentage
of the overall impact or value.
Quadrant model classifies
finished goods inventories
using value and risk to the firm
as the criteria. Value is
measured as the value
contribution to profit; risk is
the negative impact of not
having the product available
when it is needed.
products at its customer locations
allows the shipper more time to react
to sudden swings in demand to assure
that stockouts do not occur
centre at the end of the month in order
to meet monthly sales quotas, resulting
in the customer holding extra
inventory, adding costs to its operations
Inventory Management Techniques in the Logistics Network
Many organizations today use all of the techniques shown in managing inventories in their logistics
networks. In general, as an inventory technique manages inventory closer to the point of real f
demand (e.g. VMI and CPFR), forecast accuracy increases, forecast cycle decreases, and
product availability increases.
Inventory Classification
Multiple product lines and inventory control require organizations to focus on more important
inventory items and use more sophisticated and effective approaches to inventory management.
ABC Analysis Pareto’s Law (the 80-20 Rule) Quadrant Model
ABC classification technique
assigns inventory items to one
of three groups according to
the relative impact or value of
the items that make up the
group. A items are considered
to be the most important, B
items lesser importance, and C
items least important
Pareto’s Law “80-20” rule
suggests that a relatively small
percentage of inventory might
account for a large percentage
of the overall impact or value.
Quadrant model classifies
finished goods inventories
using value and risk to the firm
as the criteria. Value is
measured as the value
contribution to profit; risk is
the negative impact of not
having the product available
when it is needed.
Paraphrase This Document
Need a fresh take? Get an instant paraphrase of this document with our AI Paraphraser
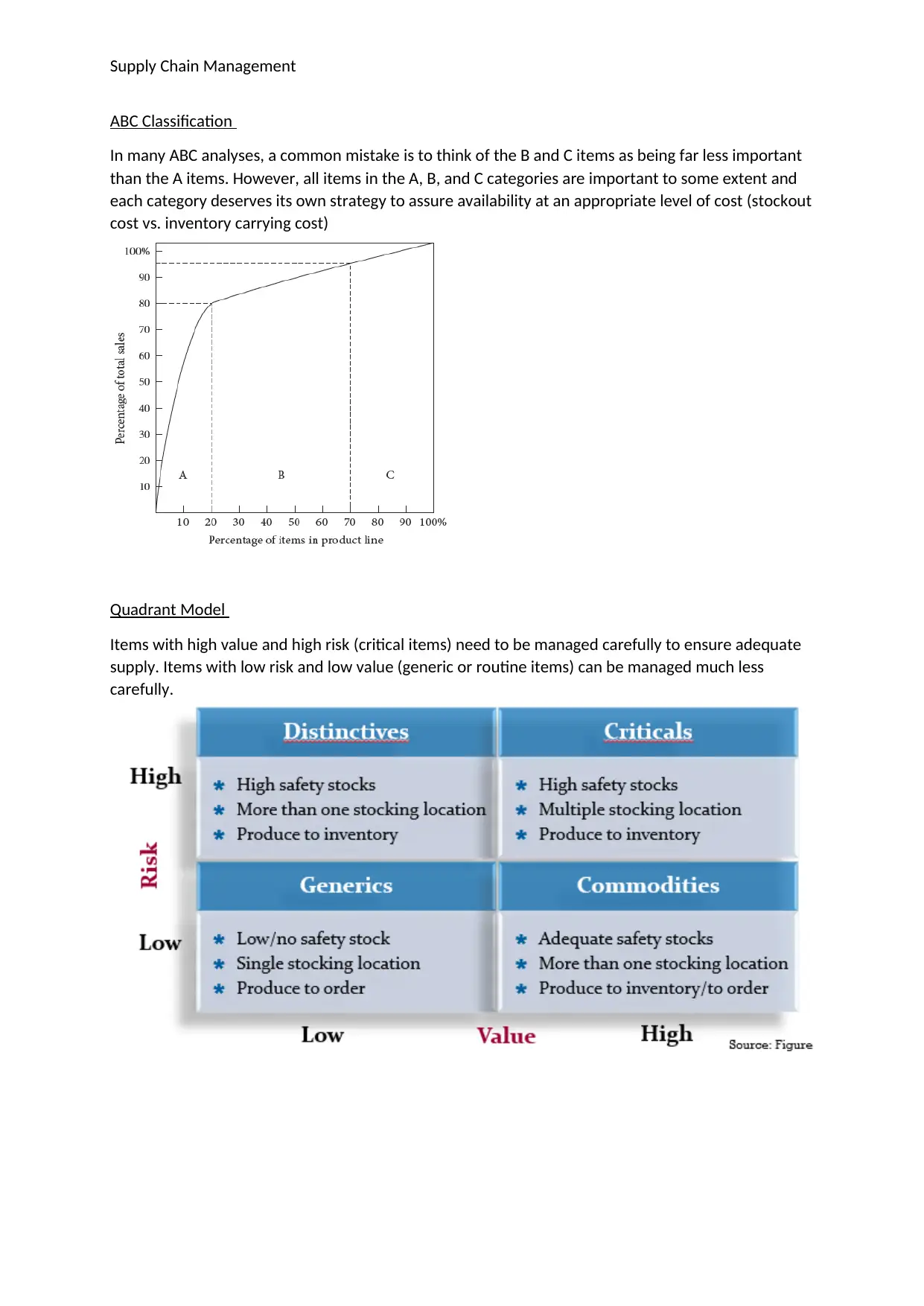
Supply Chain Management
ABC Classification
In many ABC analyses, a common mistake is to think of the B and C items as being far less important
than the A items. However, all items in the A, B, and C categories are important to some extent and
each category deserves its own strategy to assure availability at an appropriate level of cost (stockout
cost vs. inventory carrying cost)
Quadrant Model
Items with high value and high risk (critical items) need to be managed carefully to ensure adequate
supply. Items with low risk and low value (generic or routine items) can be managed much less
carefully.
ABC Classification
In many ABC analyses, a common mistake is to think of the B and C items as being far less important
than the A items. However, all items in the A, B, and C categories are important to some extent and
each category deserves its own strategy to assure availability at an appropriate level of cost (stockout
cost vs. inventory carrying cost)
Quadrant Model
Items with high value and high risk (critical items) need to be managed carefully to ensure adequate
supply. Items with low risk and low value (generic or routine items) can be managed much less
carefully.
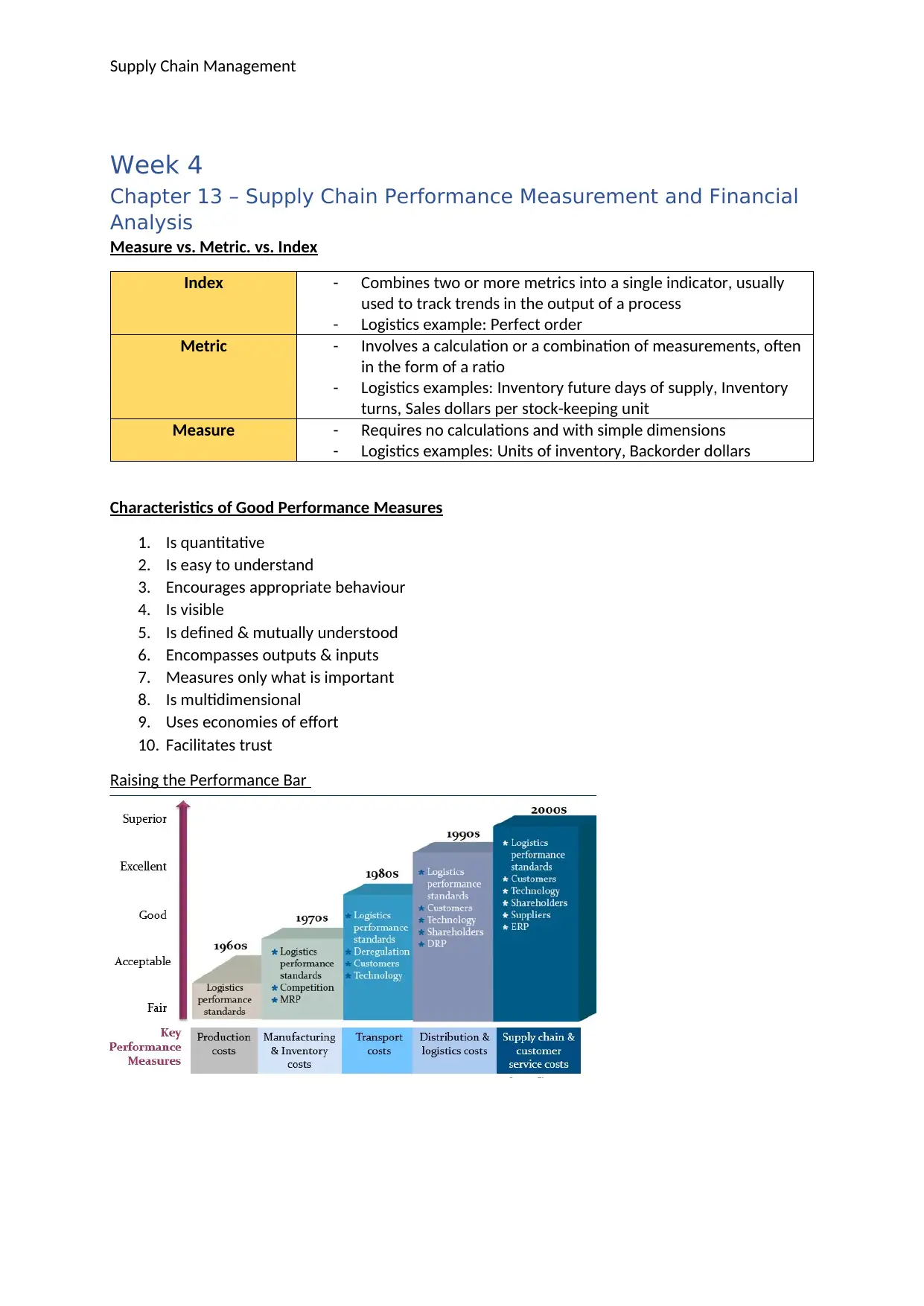
Supply Chain Management
Week 4
Chapter 13 – Supply Chain Performance Measurement and Financial
Analysis
Measure vs. Metric. vs. Index
Index - Combines two or more metrics into a single indicator, usually
used to track trends in the output of a process
- Logistics example: Perfect order
Metric - Involves a calculation or a combination of measurements, often
in the form of a ratio
- Logistics examples: Inventory future days of supply, Inventory
turns, Sales dollars per stock-keeping unit
Measure - Requires no calculations and with simple dimensions
- Logistics examples: Units of inventory, Backorder dollars
Characteristics of Good Performance Measures
1. Is quantitative
2. Is easy to understand
3. Encourages appropriate behaviour
4. Is visible
5. Is defined & mutually understood
6. Encompasses outputs & inputs
7. Measures only what is important
8. Is multidimensional
9. Uses economies of effort
10. Facilitates trust
Raising the Performance Bar
Week 4
Chapter 13 – Supply Chain Performance Measurement and Financial
Analysis
Measure vs. Metric. vs. Index
Index - Combines two or more metrics into a single indicator, usually
used to track trends in the output of a process
- Logistics example: Perfect order
Metric - Involves a calculation or a combination of measurements, often
in the form of a ratio
- Logistics examples: Inventory future days of supply, Inventory
turns, Sales dollars per stock-keeping unit
Measure - Requires no calculations and with simple dimensions
- Logistics examples: Units of inventory, Backorder dollars
Characteristics of Good Performance Measures
1. Is quantitative
2. Is easy to understand
3. Encourages appropriate behaviour
4. Is visible
5. Is defined & mutually understood
6. Encompasses outputs & inputs
7. Measures only what is important
8. Is multidimensional
9. Uses economies of effort
10. Facilitates trust
Raising the Performance Bar
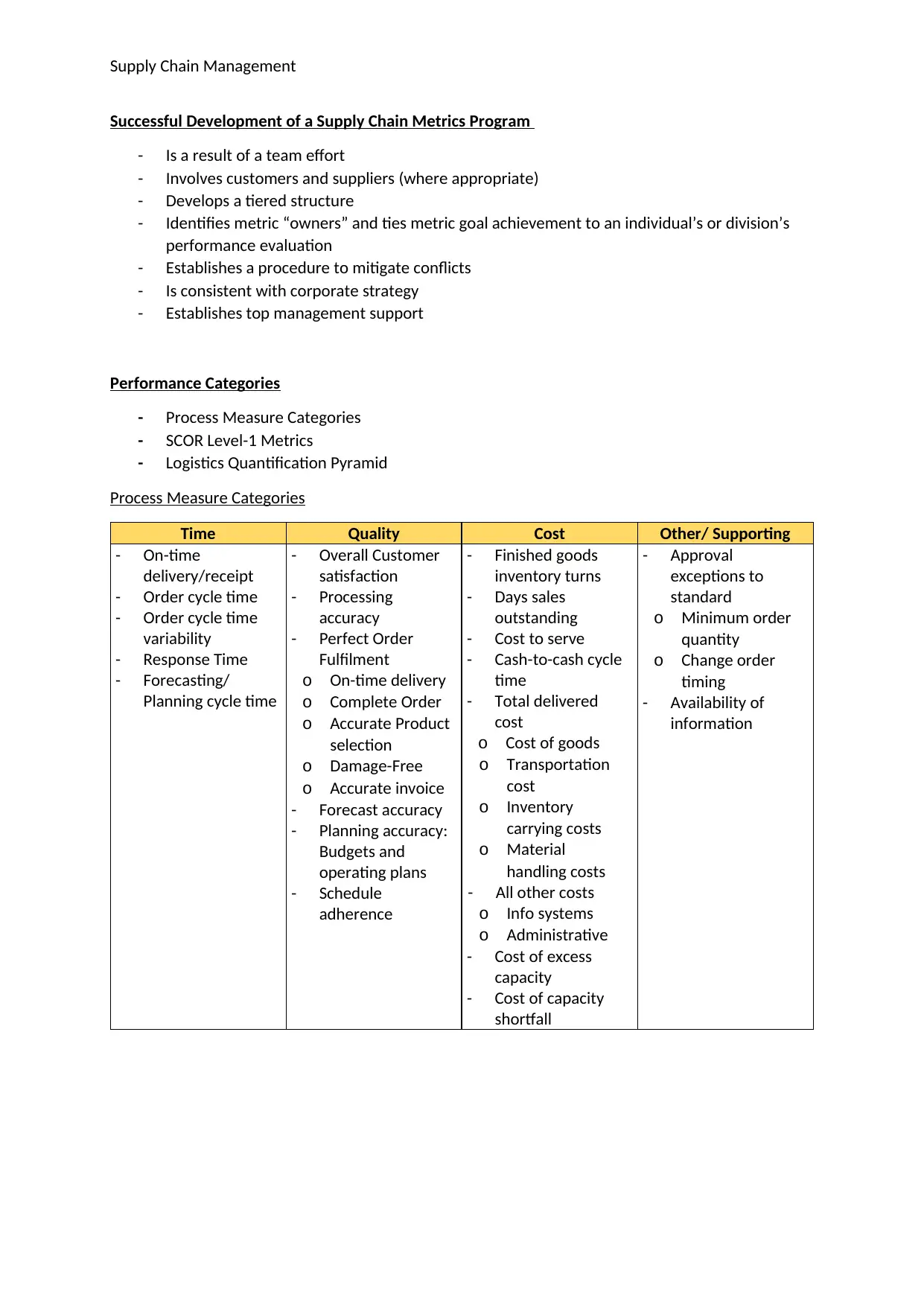
Supply Chain Management
Successful Development of a Supply Chain Metrics Program
- Is a result of a team effort
- Involves customers and suppliers (where appropriate)
- Develops a tiered structure
- Identifies metric “owners” and ties metric goal achievement to an individual’s or division’s
performance evaluation
- Establishes a procedure to mitigate conflicts
- Is consistent with corporate strategy
- Establishes top management support
Performance Categories
- Process Measure Categories
- SCOR Level-1 Metrics
- Logistics Quantification Pyramid
Process Measure Categories
Time Quality Cost Other/ Supporting
- On-time
delivery/receipt
- Order cycle time
- Order cycle time
variability
- Response Time
- Forecasting/
Planning cycle time
- Overall Customer
satisfaction
- Processing
accuracy
- Perfect Order
Fulfilment
o On-time delivery
o Complete Order
o Accurate Product
selection
o Damage-Free
o Accurate invoice
- Forecast accuracy
- Planning accuracy:
Budgets and
operating plans
- Schedule
adherence
- Finished goods
inventory turns
- Days sales
outstanding
- Cost to serve
- Cash-to-cash cycle
time
- Total delivered
cost
o Cost of goods
o Transportation
cost
o Inventory
carrying costs
o Material
handling costs
- All other costs
o Info systems
o Administrative
- Cost of excess
capacity
- Cost of capacity
shortfall
- Approval
exceptions to
standard
o Minimum order
quantity
o Change order
timing
- Availability of
information
Successful Development of a Supply Chain Metrics Program
- Is a result of a team effort
- Involves customers and suppliers (where appropriate)
- Develops a tiered structure
- Identifies metric “owners” and ties metric goal achievement to an individual’s or division’s
performance evaluation
- Establishes a procedure to mitigate conflicts
- Is consistent with corporate strategy
- Establishes top management support
Performance Categories
- Process Measure Categories
- SCOR Level-1 Metrics
- Logistics Quantification Pyramid
Process Measure Categories
Time Quality Cost Other/ Supporting
- On-time
delivery/receipt
- Order cycle time
- Order cycle time
variability
- Response Time
- Forecasting/
Planning cycle time
- Overall Customer
satisfaction
- Processing
accuracy
- Perfect Order
Fulfilment
o On-time delivery
o Complete Order
o Accurate Product
selection
o Damage-Free
o Accurate invoice
- Forecast accuracy
- Planning accuracy:
Budgets and
operating plans
- Schedule
adherence
- Finished goods
inventory turns
- Days sales
outstanding
- Cost to serve
- Cash-to-cash cycle
time
- Total delivered
cost
o Cost of goods
o Transportation
cost
o Inventory
carrying costs
o Material
handling costs
- All other costs
o Info systems
o Administrative
- Cost of excess
capacity
- Cost of capacity
shortfall
- Approval
exceptions to
standard
o Minimum order
quantity
o Change order
timing
- Availability of
information
Secure Best Marks with AI Grader
Need help grading? Try our AI Grader for instant feedback on your assignments.
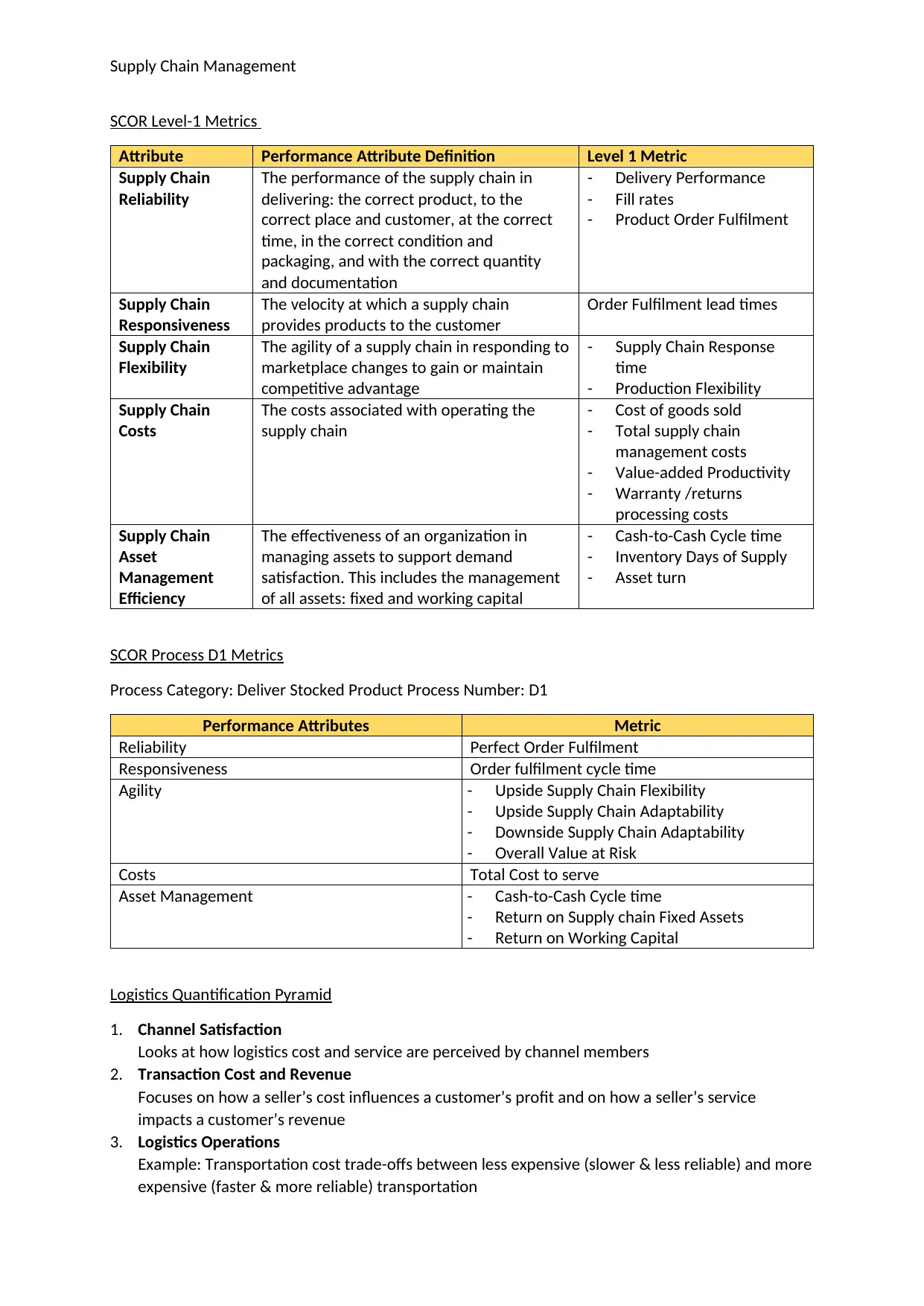
Supply Chain Management
SCOR Level-1 Metrics
Attribute Performance Attribute Definition Level 1 Metric
Supply Chain
Reliability
The performance of the supply chain in
delivering: the correct product, to the
correct place and customer, at the correct
time, in the correct condition and
packaging, and with the correct quantity
and documentation
- Delivery Performance
- Fill rates
- Product Order Fulfilment
Supply Chain
Responsiveness
The velocity at which a supply chain
provides products to the customer
Order Fulfilment lead times
Supply Chain
Flexibility
The agility of a supply chain in responding to
marketplace changes to gain or maintain
competitive advantage
- Supply Chain Response
time
- Production Flexibility
Supply Chain
Costs
The costs associated with operating the
supply chain
- Cost of goods sold
- Total supply chain
management costs
- Value-added Productivity
- Warranty /returns
processing costs
Supply Chain
Asset
Management
Efficiency
The effectiveness of an organization in
managing assets to support demand
satisfaction. This includes the management
of all assets: fixed and working capital
- Cash-to-Cash Cycle time
- Inventory Days of Supply
- Asset turn
SCOR Process D1 Metrics
Process Category: Deliver Stocked Product Process Number: D1
Performance Attributes Metric
Reliability Perfect Order Fulfilment
Responsiveness Order fulfilment cycle time
Agility - Upside Supply Chain Flexibility
- Upside Supply Chain Adaptability
- Downside Supply Chain Adaptability
- Overall Value at Risk
Costs Total Cost to serve
Asset Management - Cash-to-Cash Cycle time
- Return on Supply chain Fixed Assets
- Return on Working Capital
Logistics Quantification Pyramid
1. Channel Satisfaction
Looks at how logistics cost and service are perceived by channel members
2. Transaction Cost and Revenue
Focuses on how a seller’s cost influences a customer’s profit and on how a seller’s service
impacts a customer’s revenue
3. Logistics Operations
Example: Transportation cost trade-offs between less expensive (slower & less reliable) and more
expensive (faster & more reliable) transportation
SCOR Level-1 Metrics
Attribute Performance Attribute Definition Level 1 Metric
Supply Chain
Reliability
The performance of the supply chain in
delivering: the correct product, to the
correct place and customer, at the correct
time, in the correct condition and
packaging, and with the correct quantity
and documentation
- Delivery Performance
- Fill rates
- Product Order Fulfilment
Supply Chain
Responsiveness
The velocity at which a supply chain
provides products to the customer
Order Fulfilment lead times
Supply Chain
Flexibility
The agility of a supply chain in responding to
marketplace changes to gain or maintain
competitive advantage
- Supply Chain Response
time
- Production Flexibility
Supply Chain
Costs
The costs associated with operating the
supply chain
- Cost of goods sold
- Total supply chain
management costs
- Value-added Productivity
- Warranty /returns
processing costs
Supply Chain
Asset
Management
Efficiency
The effectiveness of an organization in
managing assets to support demand
satisfaction. This includes the management
of all assets: fixed and working capital
- Cash-to-Cash Cycle time
- Inventory Days of Supply
- Asset turn
SCOR Process D1 Metrics
Process Category: Deliver Stocked Product Process Number: D1
Performance Attributes Metric
Reliability Perfect Order Fulfilment
Responsiveness Order fulfilment cycle time
Agility - Upside Supply Chain Flexibility
- Upside Supply Chain Adaptability
- Downside Supply Chain Adaptability
- Overall Value at Risk
Costs Total Cost to serve
Asset Management - Cash-to-Cash Cycle time
- Return on Supply chain Fixed Assets
- Return on Working Capital
Logistics Quantification Pyramid
1. Channel Satisfaction
Looks at how logistics cost and service are perceived by channel members
2. Transaction Cost and Revenue
Focuses on how a seller’s cost influences a customer’s profit and on how a seller’s service
impacts a customer’s revenue
3. Logistics Operations
Example: Transportation cost trade-offs between less expensive (slower & less reliable) and more
expensive (faster & more reliable) transportation
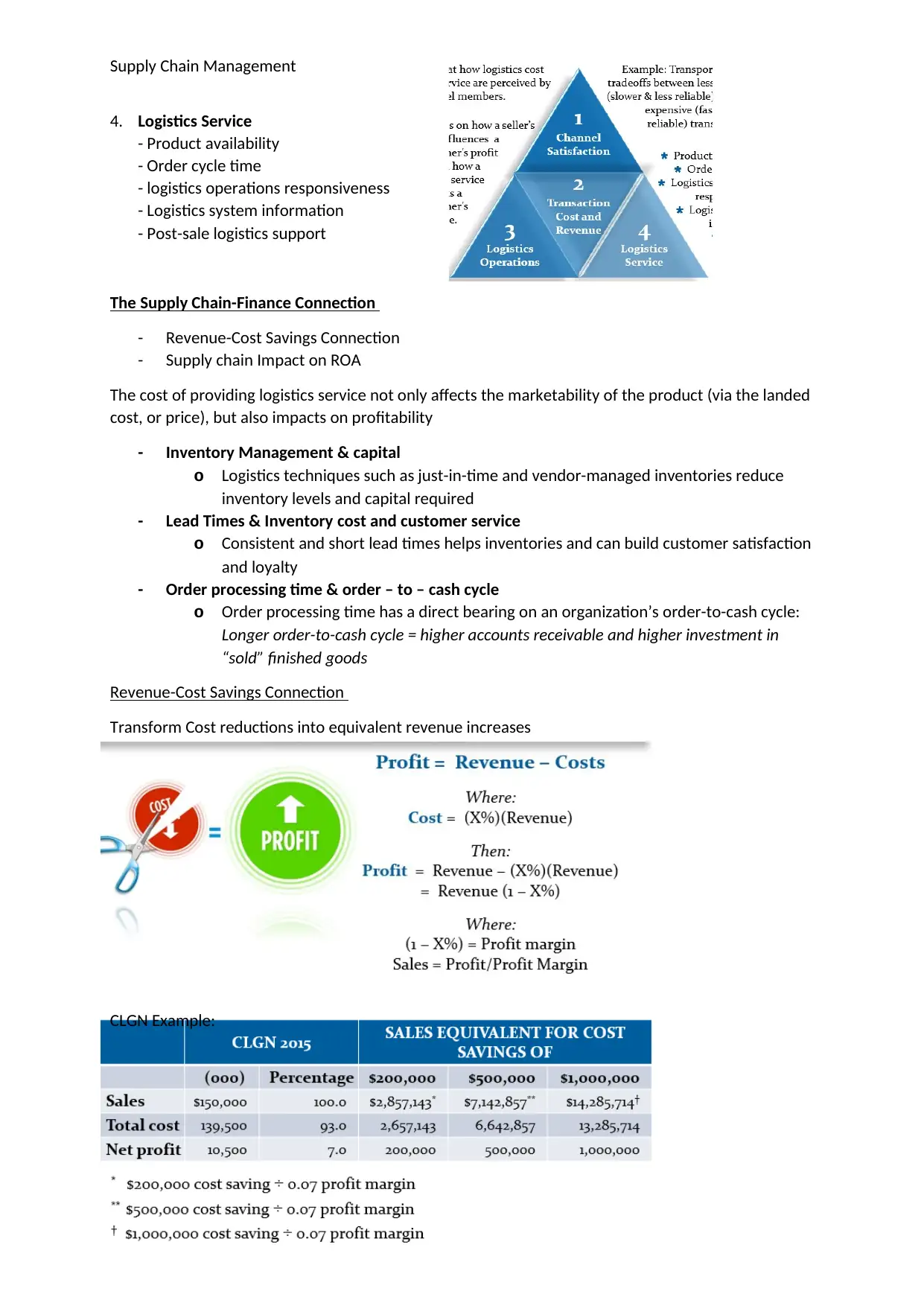
Supply Chain Management
4. Logistics Service
- Product availability
- Order cycle time
- logistics operations responsiveness
- Logistics system information
- Post-sale logistics support
The Supply Chain-Finance Connection
- Revenue-Cost Savings Connection
- Supply chain Impact on ROA
The cost of providing logistics service not only affects the marketability of the product (via the landed
cost, or price), but also impacts on profitability
- Inventory Management & capital
o Logistics techniques such as just-in-time and vendor-managed inventories reduce
inventory levels and capital required
- Lead Times & Inventory cost and customer service
o Consistent and short lead times helps inventories and can build customer satisfaction
and loyalty
- Order processing time & order – to – cash cycle
o Order processing time has a direct bearing on an organization’s order-to-cash cycle:
Longer order-to-cash cycle = higher accounts receivable and higher investment in
“sold” finished goods
Revenue-Cost Savings Connection
Transform Cost reductions into equivalent revenue increases
CLGN Example:
4. Logistics Service
- Product availability
- Order cycle time
- logistics operations responsiveness
- Logistics system information
- Post-sale logistics support
The Supply Chain-Finance Connection
- Revenue-Cost Savings Connection
- Supply chain Impact on ROA
The cost of providing logistics service not only affects the marketability of the product (via the landed
cost, or price), but also impacts on profitability
- Inventory Management & capital
o Logistics techniques such as just-in-time and vendor-managed inventories reduce
inventory levels and capital required
- Lead Times & Inventory cost and customer service
o Consistent and short lead times helps inventories and can build customer satisfaction
and loyalty
- Order processing time & order – to – cash cycle
o Order processing time has a direct bearing on an organization’s order-to-cash cycle:
Longer order-to-cash cycle = higher accounts receivable and higher investment in
“sold” finished goods
Revenue-Cost Savings Connection
Transform Cost reductions into equivalent revenue increases
CLGN Example:
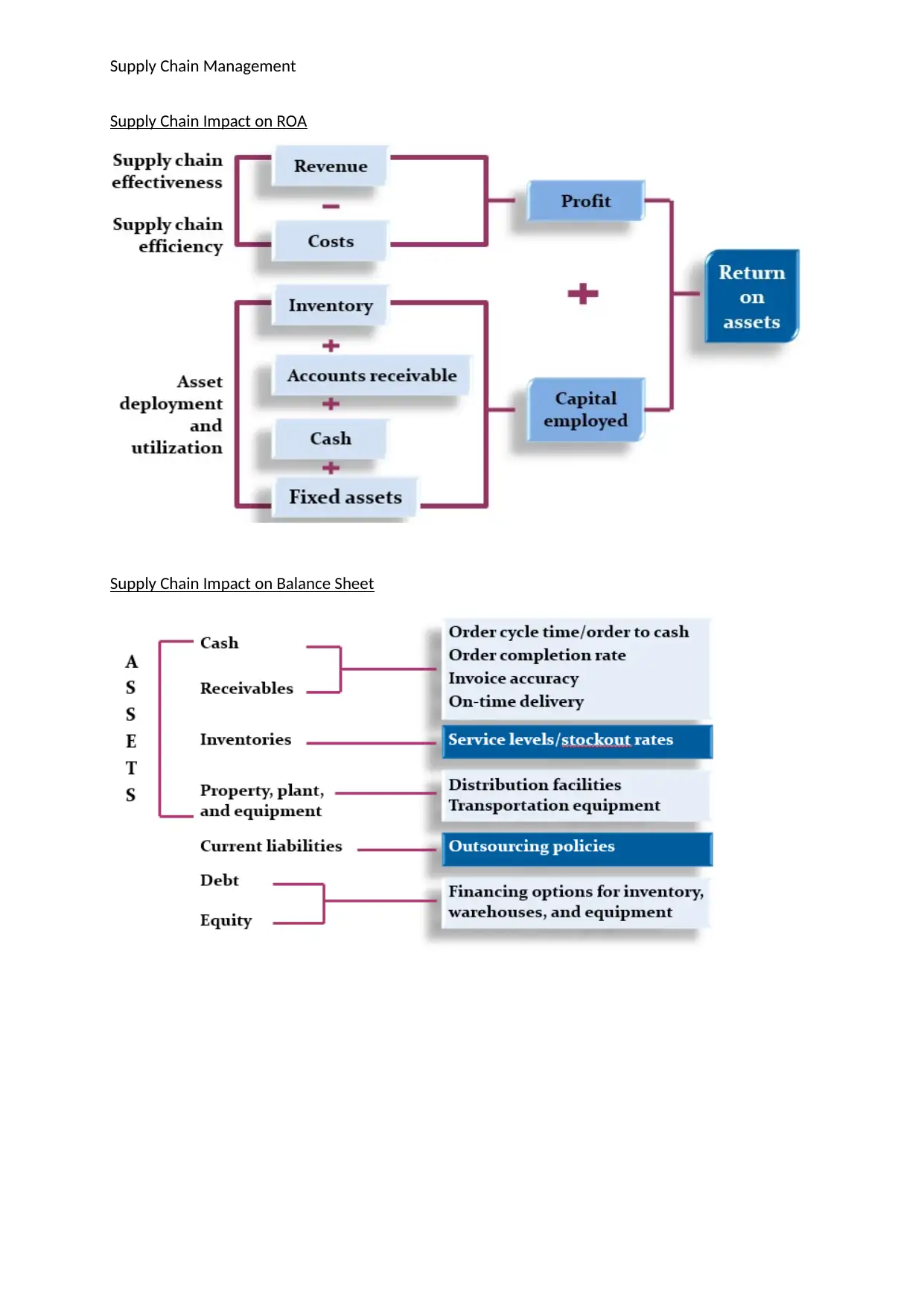
Supply Chain Management
Supply Chain Impact on ROA
Supply Chain Impact on Balance Sheet
Supply Chain Impact on ROA
Supply Chain Impact on Balance Sheet
Paraphrase This Document
Need a fresh take? Get an instant paraphrase of this document with our AI Paraphraser
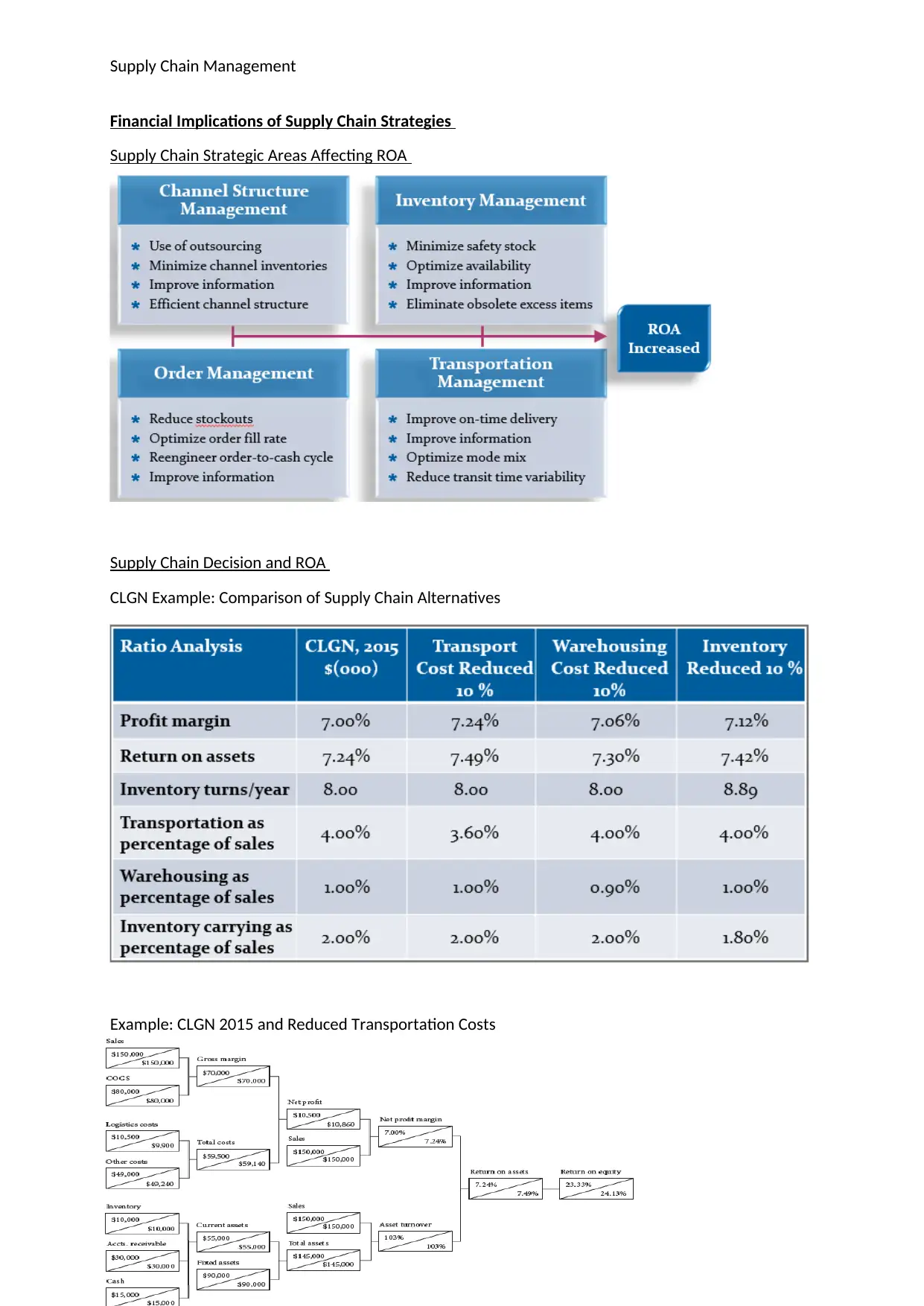
Supply Chain Management
Financial Implications of Supply Chain Strategies
Supply Chain Strategic Areas Affecting ROA
Supply Chain Decision and ROA
CLGN Example: Comparison of Supply Chain Alternatives
Example: CLGN 2015 and Reduced Transportation Costs
Financial Implications of Supply Chain Strategies
Supply Chain Strategic Areas Affecting ROA
Supply Chain Decision and ROA
CLGN Example: Comparison of Supply Chain Alternatives
Example: CLGN 2015 and Reduced Transportation Costs
1 out of 32
Related Documents

Your All-in-One AI-Powered Toolkit for Academic Success.
+13062052269
info@desklib.com
Available 24*7 on WhatsApp / Email
Unlock your academic potential
© 2024 | Zucol Services PVT LTD | All rights reserved.