Evaluation of Quality Manuals application within Honda Motors
VerifiedAdded on 2023/04/21
|11
|2753
|268
AI Summary
This essay evaluates the significance of quality manuals in Honda Motors and their impact on product quality. It discusses ISO standards, Six Sigma, Total Quality Management, and other quality management tools.
Contribute Materials
Your contribution can guide someone’s learning journey. Share your
documents today.
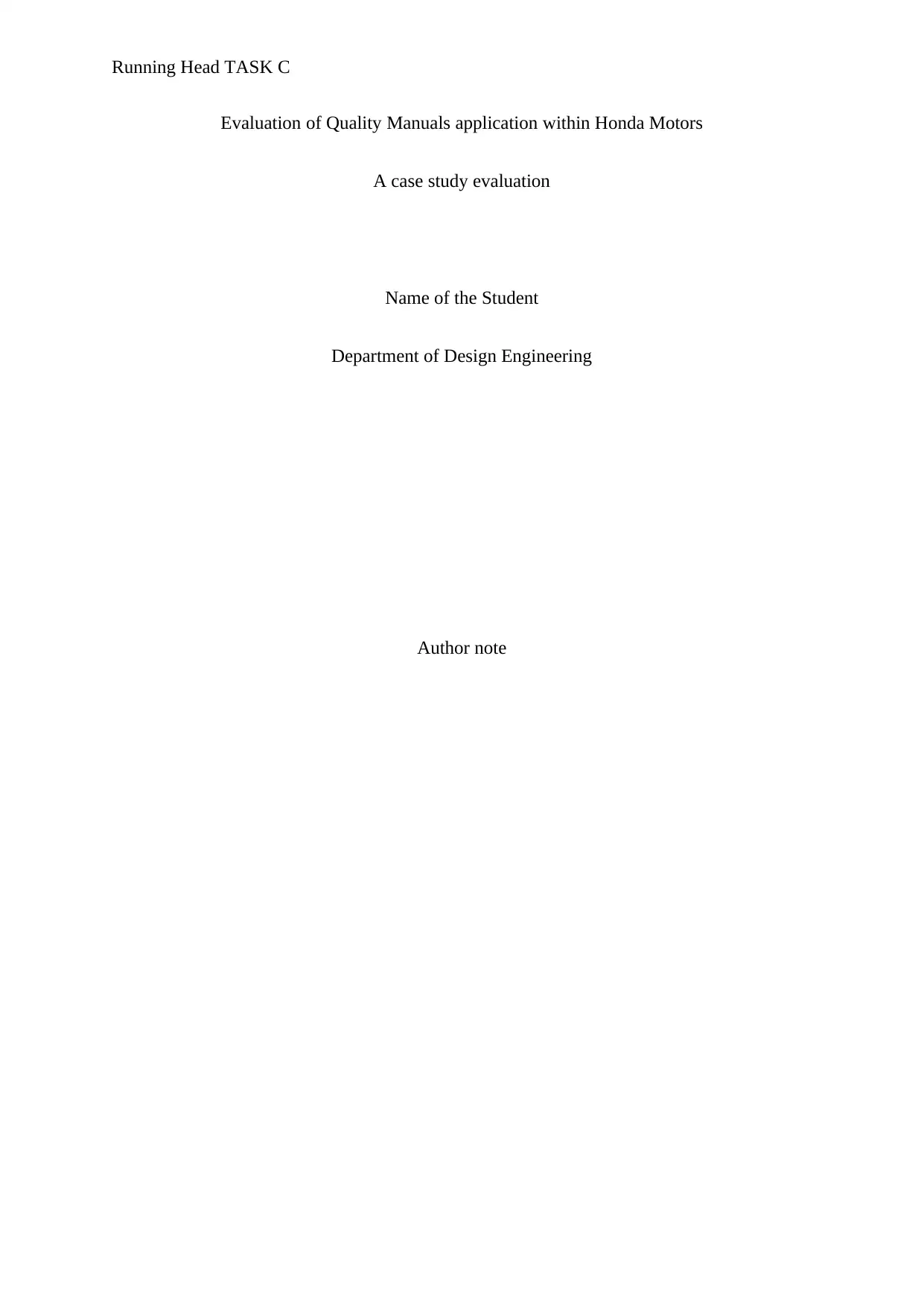
Running Head TASK C
Evaluation of Quality Manuals application within Honda Motors
A case study evaluation
Name of the Student
Department of Design Engineering
Author note
Evaluation of Quality Manuals application within Honda Motors
A case study evaluation
Name of the Student
Department of Design Engineering
Author note
Secure Best Marks with AI Grader
Need help grading? Try our AI Grader for instant feedback on your assignments.
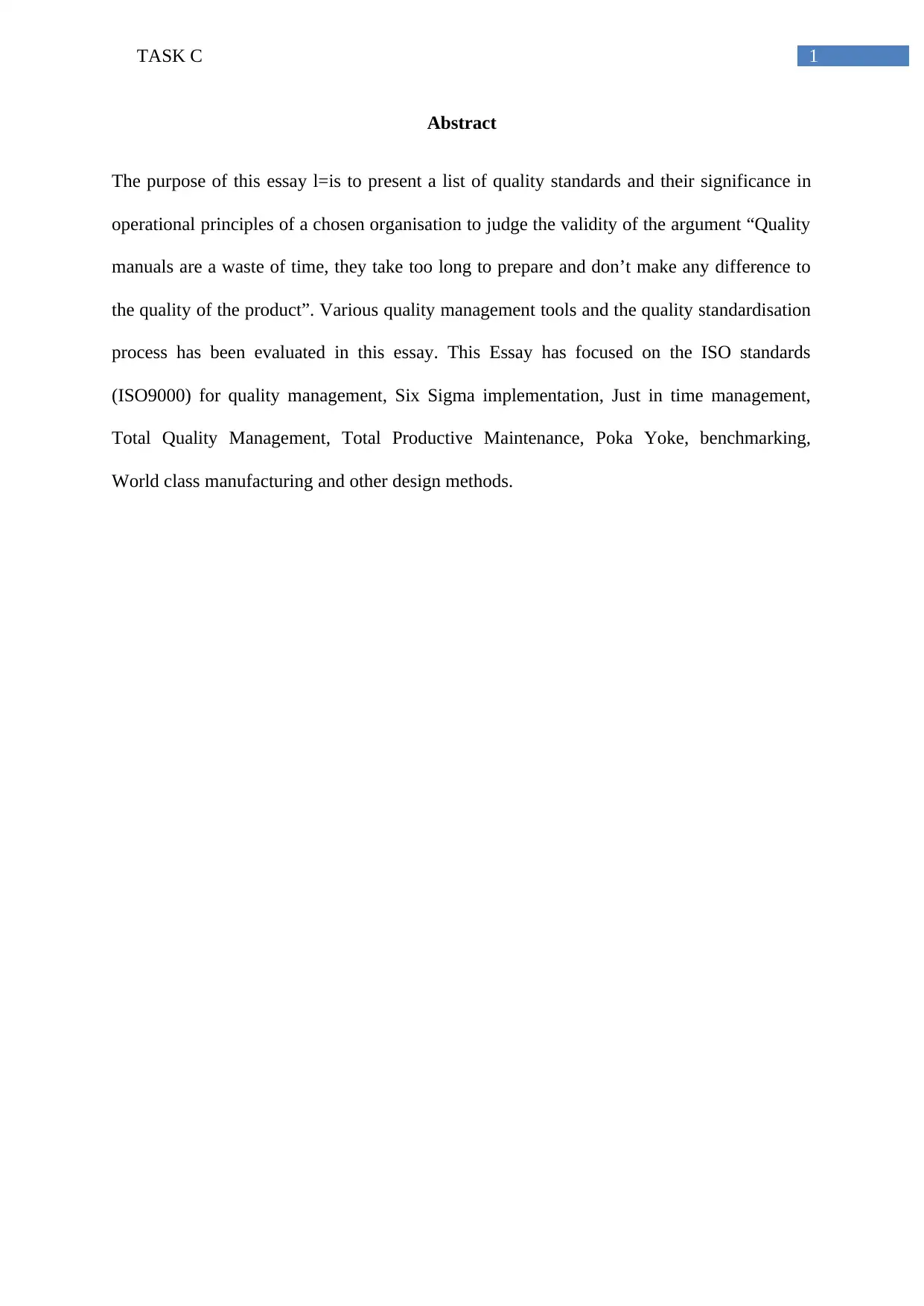
1TASK C
Abstract
The purpose of this essay l=is to present a list of quality standards and their significance in
operational principles of a chosen organisation to judge the validity of the argument “Quality
manuals are a waste of time, they take too long to prepare and don’t make any difference to
the quality of the product”. Various quality management tools and the quality standardisation
process has been evaluated in this essay. This Essay has focused on the ISO standards
(ISO9000) for quality management, Six Sigma implementation, Just in time management,
Total Quality Management, Total Productive Maintenance, Poka Yoke, benchmarking,
World class manufacturing and other design methods.
Abstract
The purpose of this essay l=is to present a list of quality standards and their significance in
operational principles of a chosen organisation to judge the validity of the argument “Quality
manuals are a waste of time, they take too long to prepare and don’t make any difference to
the quality of the product”. Various quality management tools and the quality standardisation
process has been evaluated in this essay. This Essay has focused on the ISO standards
(ISO9000) for quality management, Six Sigma implementation, Just in time management,
Total Quality Management, Total Productive Maintenance, Poka Yoke, benchmarking,
World class manufacturing and other design methods.
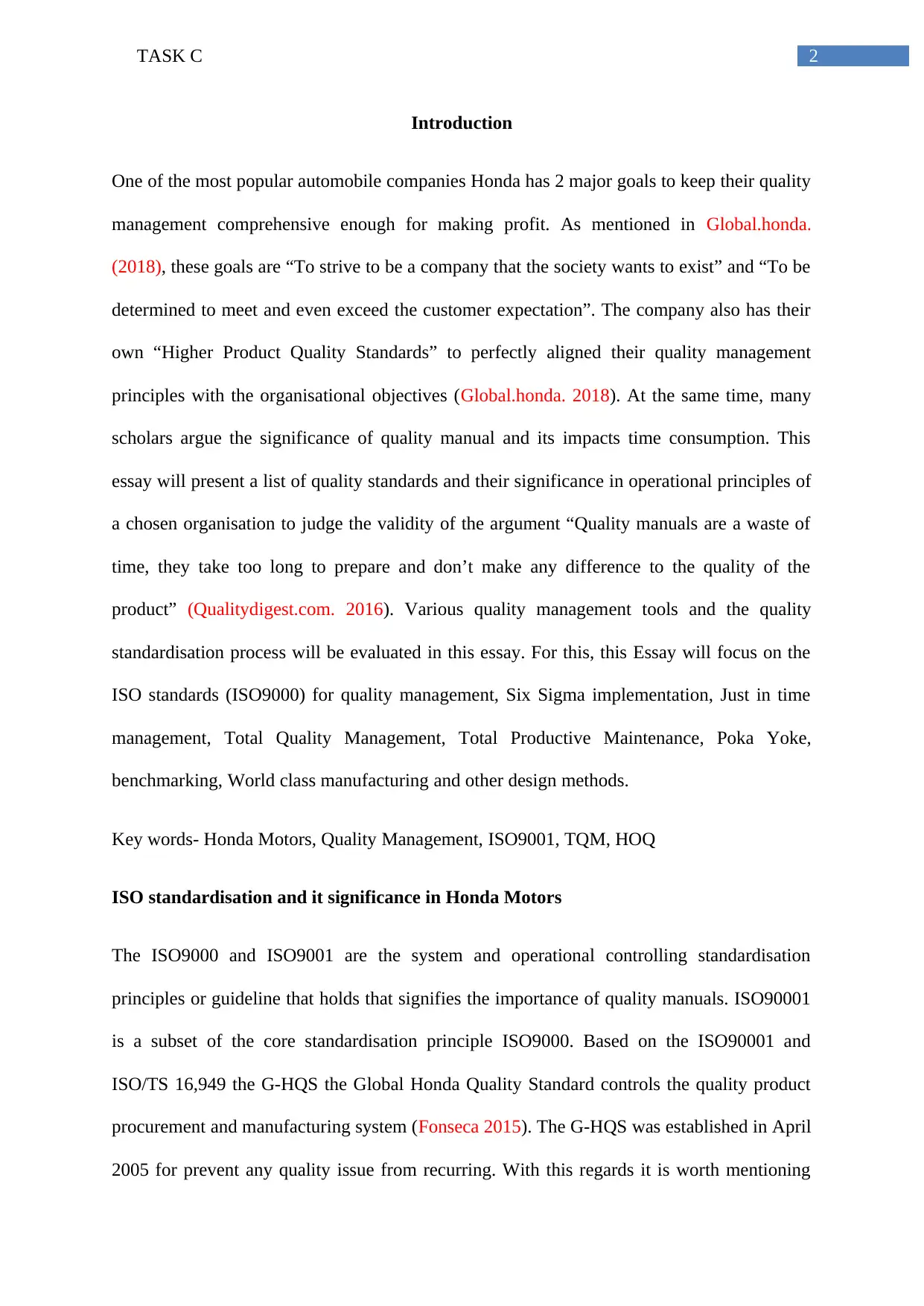
2TASK C
Introduction
One of the most popular automobile companies Honda has 2 major goals to keep their quality
management comprehensive enough for making profit. As mentioned in Global.honda.
(2018), these goals are “To strive to be a company that the society wants to exist” and “To be
determined to meet and even exceed the customer expectation”. The company also has their
own “Higher Product Quality Standards” to perfectly aligned their quality management
principles with the organisational objectives (Global.honda. 2018). At the same time, many
scholars argue the significance of quality manual and its impacts time consumption. This
essay will present a list of quality standards and their significance in operational principles of
a chosen organisation to judge the validity of the argument “Quality manuals are a waste of
time, they take too long to prepare and don’t make any difference to the quality of the
product” (Qualitydigest.com. 2016). Various quality management tools and the quality
standardisation process will be evaluated in this essay. For this, this Essay will focus on the
ISO standards (ISO9000) for quality management, Six Sigma implementation, Just in time
management, Total Quality Management, Total Productive Maintenance, Poka Yoke,
benchmarking, World class manufacturing and other design methods.
Key words- Honda Motors, Quality Management, ISO9001, TQM, HOQ
ISO standardisation and it significance in Honda Motors
The ISO9000 and ISO9001 are the system and operational controlling standardisation
principles or guideline that holds that signifies the importance of quality manuals. ISO90001
is a subset of the core standardisation principle ISO9000. Based on the ISO90001 and
ISO/TS 16,949 the G-HQS the Global Honda Quality Standard controls the quality product
procurement and manufacturing system (Fonseca 2015). The G-HQS was established in April
2005 for prevent any quality issue from recurring. With this regards it is worth mentioning
Introduction
One of the most popular automobile companies Honda has 2 major goals to keep their quality
management comprehensive enough for making profit. As mentioned in Global.honda.
(2018), these goals are “To strive to be a company that the society wants to exist” and “To be
determined to meet and even exceed the customer expectation”. The company also has their
own “Higher Product Quality Standards” to perfectly aligned their quality management
principles with the organisational objectives (Global.honda. 2018). At the same time, many
scholars argue the significance of quality manual and its impacts time consumption. This
essay will present a list of quality standards and their significance in operational principles of
a chosen organisation to judge the validity of the argument “Quality manuals are a waste of
time, they take too long to prepare and don’t make any difference to the quality of the
product” (Qualitydigest.com. 2016). Various quality management tools and the quality
standardisation process will be evaluated in this essay. For this, this Essay will focus on the
ISO standards (ISO9000) for quality management, Six Sigma implementation, Just in time
management, Total Quality Management, Total Productive Maintenance, Poka Yoke,
benchmarking, World class manufacturing and other design methods.
Key words- Honda Motors, Quality Management, ISO9001, TQM, HOQ
ISO standardisation and it significance in Honda Motors
The ISO9000 and ISO9001 are the system and operational controlling standardisation
principles or guideline that holds that signifies the importance of quality manuals. ISO90001
is a subset of the core standardisation principle ISO9000. Based on the ISO90001 and
ISO/TS 16,949 the G-HQS the Global Honda Quality Standard controls the quality product
procurement and manufacturing system (Fonseca 2015). The G-HQS was established in April
2005 for prevent any quality issue from recurring. With this regards it is worth mentioning
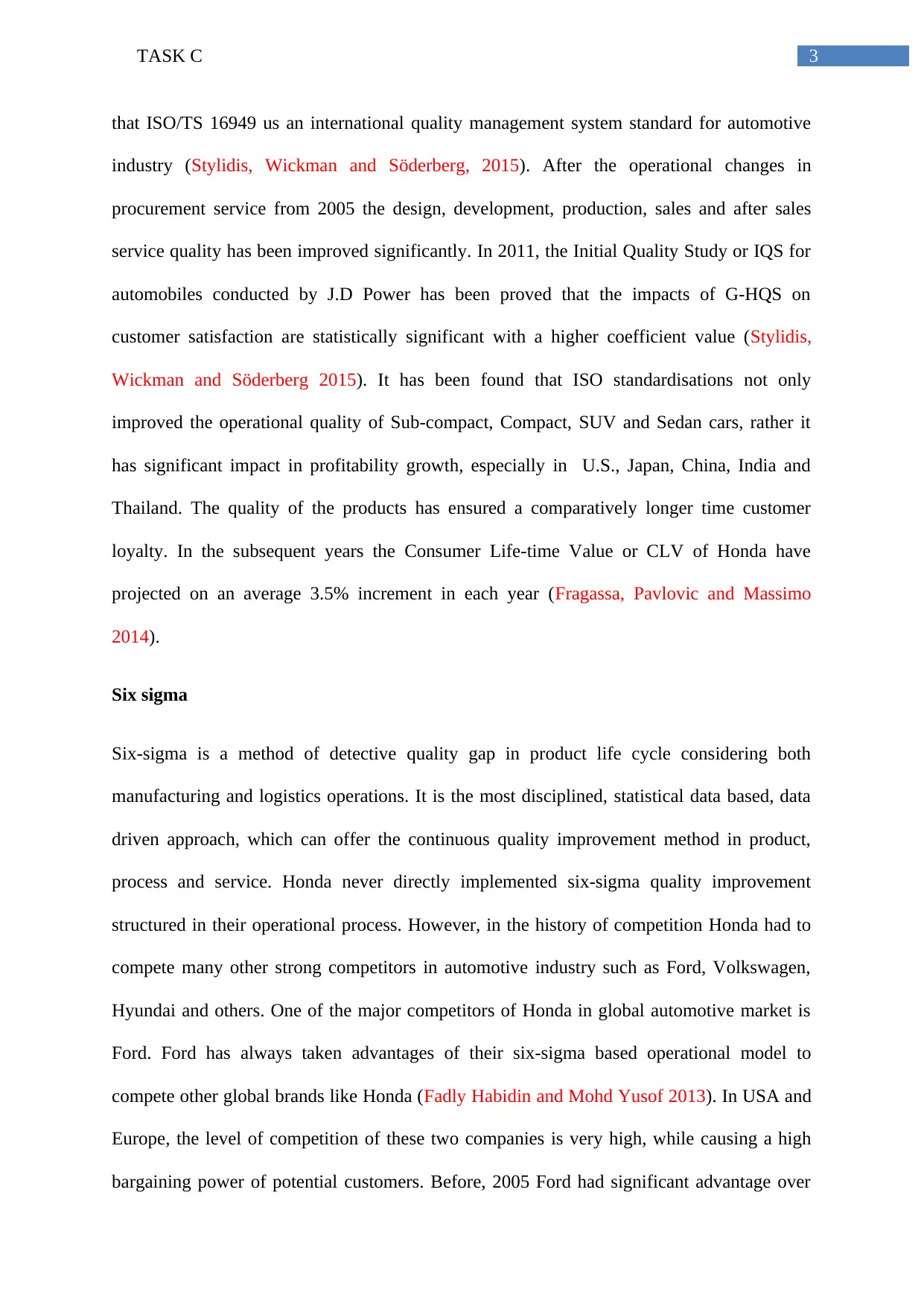
3TASK C
that ISO/TS 16949 us an international quality management system standard for automotive
industry (Stylidis, Wickman and Söderberg, 2015). After the operational changes in
procurement service from 2005 the design, development, production, sales and after sales
service quality has been improved significantly. In 2011, the Initial Quality Study or IQS for
automobiles conducted by J.D Power has been proved that the impacts of G-HQS on
customer satisfaction are statistically significant with a higher coefficient value (Stylidis,
Wickman and Söderberg 2015). It has been found that ISO standardisations not only
improved the operational quality of Sub-compact, Compact, SUV and Sedan cars, rather it
has significant impact in profitability growth, especially in U.S., Japan, China, India and
Thailand. The quality of the products has ensured a comparatively longer time customer
loyalty. In the subsequent years the Consumer Life-time Value or CLV of Honda have
projected on an average 3.5% increment in each year (Fragassa, Pavlovic and Massimo
2014).
Six sigma
Six-sigma is a method of detective quality gap in product life cycle considering both
manufacturing and logistics operations. It is the most disciplined, statistical data based, data
driven approach, which can offer the continuous quality improvement method in product,
process and service. Honda never directly implemented six-sigma quality improvement
structured in their operational process. However, in the history of competition Honda had to
compete many other strong competitors in automotive industry such as Ford, Volkswagen,
Hyundai and others. One of the major competitors of Honda in global automotive market is
Ford. Ford has always taken advantages of their six-sigma based operational model to
compete other global brands like Honda (Fadly Habidin and Mohd Yusof 2013). In USA and
Europe, the level of competition of these two companies is very high, while causing a high
bargaining power of potential customers. Before, 2005 Ford had significant advantage over
that ISO/TS 16949 us an international quality management system standard for automotive
industry (Stylidis, Wickman and Söderberg, 2015). After the operational changes in
procurement service from 2005 the design, development, production, sales and after sales
service quality has been improved significantly. In 2011, the Initial Quality Study or IQS for
automobiles conducted by J.D Power has been proved that the impacts of G-HQS on
customer satisfaction are statistically significant with a higher coefficient value (Stylidis,
Wickman and Söderberg 2015). It has been found that ISO standardisations not only
improved the operational quality of Sub-compact, Compact, SUV and Sedan cars, rather it
has significant impact in profitability growth, especially in U.S., Japan, China, India and
Thailand. The quality of the products has ensured a comparatively longer time customer
loyalty. In the subsequent years the Consumer Life-time Value or CLV of Honda have
projected on an average 3.5% increment in each year (Fragassa, Pavlovic and Massimo
2014).
Six sigma
Six-sigma is a method of detective quality gap in product life cycle considering both
manufacturing and logistics operations. It is the most disciplined, statistical data based, data
driven approach, which can offer the continuous quality improvement method in product,
process and service. Honda never directly implemented six-sigma quality improvement
structured in their operational process. However, in the history of competition Honda had to
compete many other strong competitors in automotive industry such as Ford, Volkswagen,
Hyundai and others. One of the major competitors of Honda in global automotive market is
Ford. Ford has always taken advantages of their six-sigma based operational model to
compete other global brands like Honda (Fadly Habidin and Mohd Yusof 2013). In USA and
Europe, the level of competition of these two companies is very high, while causing a high
bargaining power of potential customers. Before, 2005 Ford had significant advantage over
Secure Best Marks with AI Grader
Need help grading? Try our AI Grader for instant feedback on your assignments.
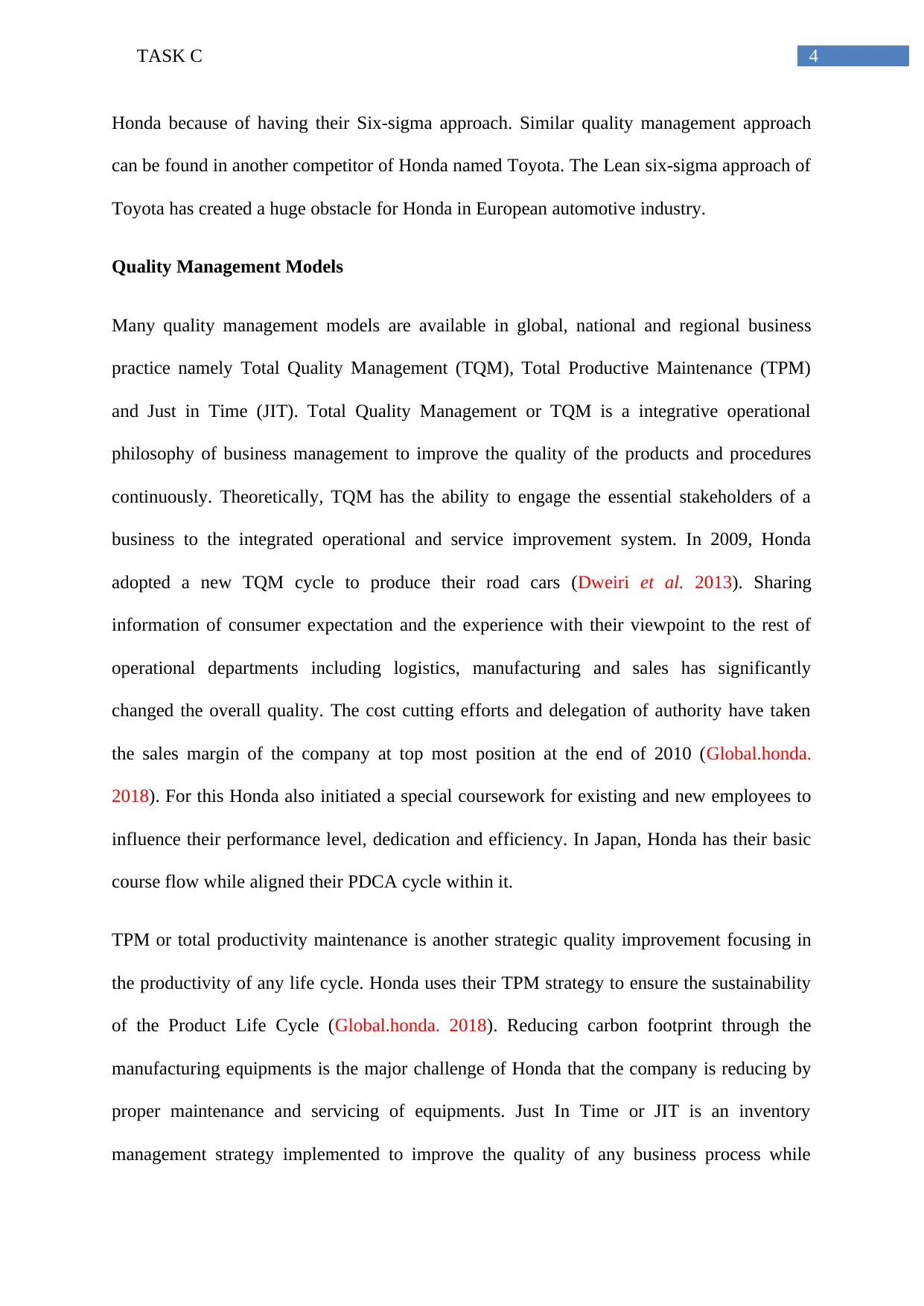
4TASK C
Honda because of having their Six-sigma approach. Similar quality management approach
can be found in another competitor of Honda named Toyota. The Lean six-sigma approach of
Toyota has created a huge obstacle for Honda in European automotive industry.
Quality Management Models
Many quality management models are available in global, national and regional business
practice namely Total Quality Management (TQM), Total Productive Maintenance (TPM)
and Just in Time (JIT). Total Quality Management or TQM is a integrative operational
philosophy of business management to improve the quality of the products and procedures
continuously. Theoretically, TQM has the ability to engage the essential stakeholders of a
business to the integrated operational and service improvement system. In 2009, Honda
adopted a new TQM cycle to produce their road cars (Dweiri et al. 2013). Sharing
information of consumer expectation and the experience with their viewpoint to the rest of
operational departments including logistics, manufacturing and sales has significantly
changed the overall quality. The cost cutting efforts and delegation of authority have taken
the sales margin of the company at top most position at the end of 2010 (Global.honda.
2018). For this Honda also initiated a special coursework for existing and new employees to
influence their performance level, dedication and efficiency. In Japan, Honda has their basic
course flow while aligned their PDCA cycle within it.
TPM or total productivity maintenance is another strategic quality improvement focusing in
the productivity of any life cycle. Honda uses their TPM strategy to ensure the sustainability
of the Product Life Cycle (Global.honda. 2018). Reducing carbon footprint through the
manufacturing equipments is the major challenge of Honda that the company is reducing by
proper maintenance and servicing of equipments. Just In Time or JIT is an inventory
management strategy implemented to improve the quality of any business process while
Honda because of having their Six-sigma approach. Similar quality management approach
can be found in another competitor of Honda named Toyota. The Lean six-sigma approach of
Toyota has created a huge obstacle for Honda in European automotive industry.
Quality Management Models
Many quality management models are available in global, national and regional business
practice namely Total Quality Management (TQM), Total Productive Maintenance (TPM)
and Just in Time (JIT). Total Quality Management or TQM is a integrative operational
philosophy of business management to improve the quality of the products and procedures
continuously. Theoretically, TQM has the ability to engage the essential stakeholders of a
business to the integrated operational and service improvement system. In 2009, Honda
adopted a new TQM cycle to produce their road cars (Dweiri et al. 2013). Sharing
information of consumer expectation and the experience with their viewpoint to the rest of
operational departments including logistics, manufacturing and sales has significantly
changed the overall quality. The cost cutting efforts and delegation of authority have taken
the sales margin of the company at top most position at the end of 2010 (Global.honda.
2018). For this Honda also initiated a special coursework for existing and new employees to
influence their performance level, dedication and efficiency. In Japan, Honda has their basic
course flow while aligned their PDCA cycle within it.
TPM or total productivity maintenance is another strategic quality improvement focusing in
the productivity of any life cycle. Honda uses their TPM strategy to ensure the sustainability
of the Product Life Cycle (Global.honda. 2018). Reducing carbon footprint through the
manufacturing equipments is the major challenge of Honda that the company is reducing by
proper maintenance and servicing of equipments. Just In Time or JIT is an inventory
management strategy implemented to improve the quality of any business process while
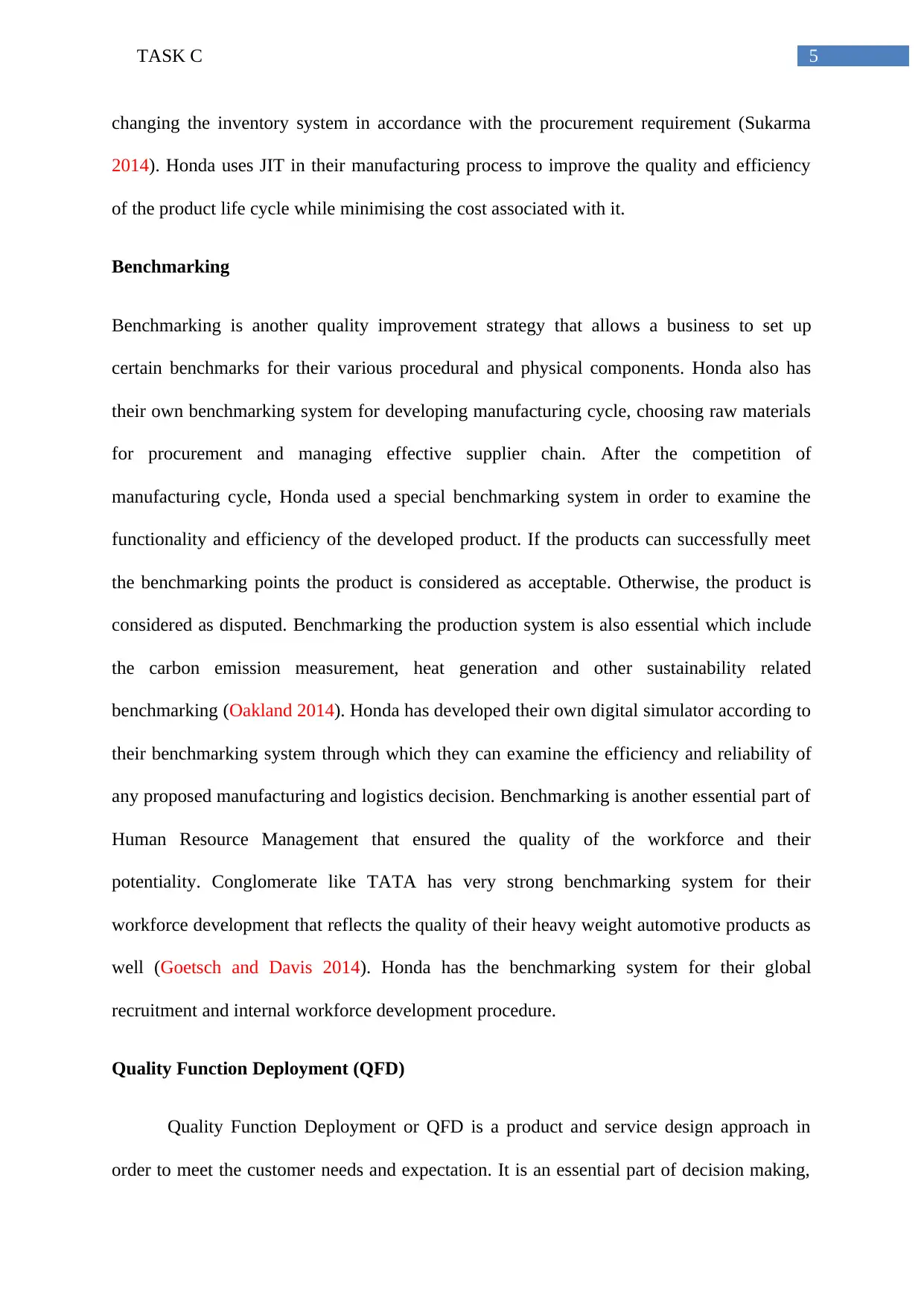
5TASK C
changing the inventory system in accordance with the procurement requirement (Sukarma
2014). Honda uses JIT in their manufacturing process to improve the quality and efficiency
of the product life cycle while minimising the cost associated with it.
Benchmarking
Benchmarking is another quality improvement strategy that allows a business to set up
certain benchmarks for their various procedural and physical components. Honda also has
their own benchmarking system for developing manufacturing cycle, choosing raw materials
for procurement and managing effective supplier chain. After the competition of
manufacturing cycle, Honda used a special benchmarking system in order to examine the
functionality and efficiency of the developed product. If the products can successfully meet
the benchmarking points the product is considered as acceptable. Otherwise, the product is
considered as disputed. Benchmarking the production system is also essential which include
the carbon emission measurement, heat generation and other sustainability related
benchmarking (Oakland 2014). Honda has developed their own digital simulator according to
their benchmarking system through which they can examine the efficiency and reliability of
any proposed manufacturing and logistics decision. Benchmarking is another essential part of
Human Resource Management that ensured the quality of the workforce and their
potentiality. Conglomerate like TATA has very strong benchmarking system for their
workforce development that reflects the quality of their heavy weight automotive products as
well (Goetsch and Davis 2014). Honda has the benchmarking system for their global
recruitment and internal workforce development procedure.
Quality Function Deployment (QFD)
Quality Function Deployment or QFD is a product and service design approach in
order to meet the customer needs and expectation. It is an essential part of decision making,
changing the inventory system in accordance with the procurement requirement (Sukarma
2014). Honda uses JIT in their manufacturing process to improve the quality and efficiency
of the product life cycle while minimising the cost associated with it.
Benchmarking
Benchmarking is another quality improvement strategy that allows a business to set up
certain benchmarks for their various procedural and physical components. Honda also has
their own benchmarking system for developing manufacturing cycle, choosing raw materials
for procurement and managing effective supplier chain. After the competition of
manufacturing cycle, Honda used a special benchmarking system in order to examine the
functionality and efficiency of the developed product. If the products can successfully meet
the benchmarking points the product is considered as acceptable. Otherwise, the product is
considered as disputed. Benchmarking the production system is also essential which include
the carbon emission measurement, heat generation and other sustainability related
benchmarking (Oakland 2014). Honda has developed their own digital simulator according to
their benchmarking system through which they can examine the efficiency and reliability of
any proposed manufacturing and logistics decision. Benchmarking is another essential part of
Human Resource Management that ensured the quality of the workforce and their
potentiality. Conglomerate like TATA has very strong benchmarking system for their
workforce development that reflects the quality of their heavy weight automotive products as
well (Goetsch and Davis 2014). Honda has the benchmarking system for their global
recruitment and internal workforce development procedure.
Quality Function Deployment (QFD)
Quality Function Deployment or QFD is a product and service design approach in
order to meet the customer needs and expectation. It is an essential part of decision making,
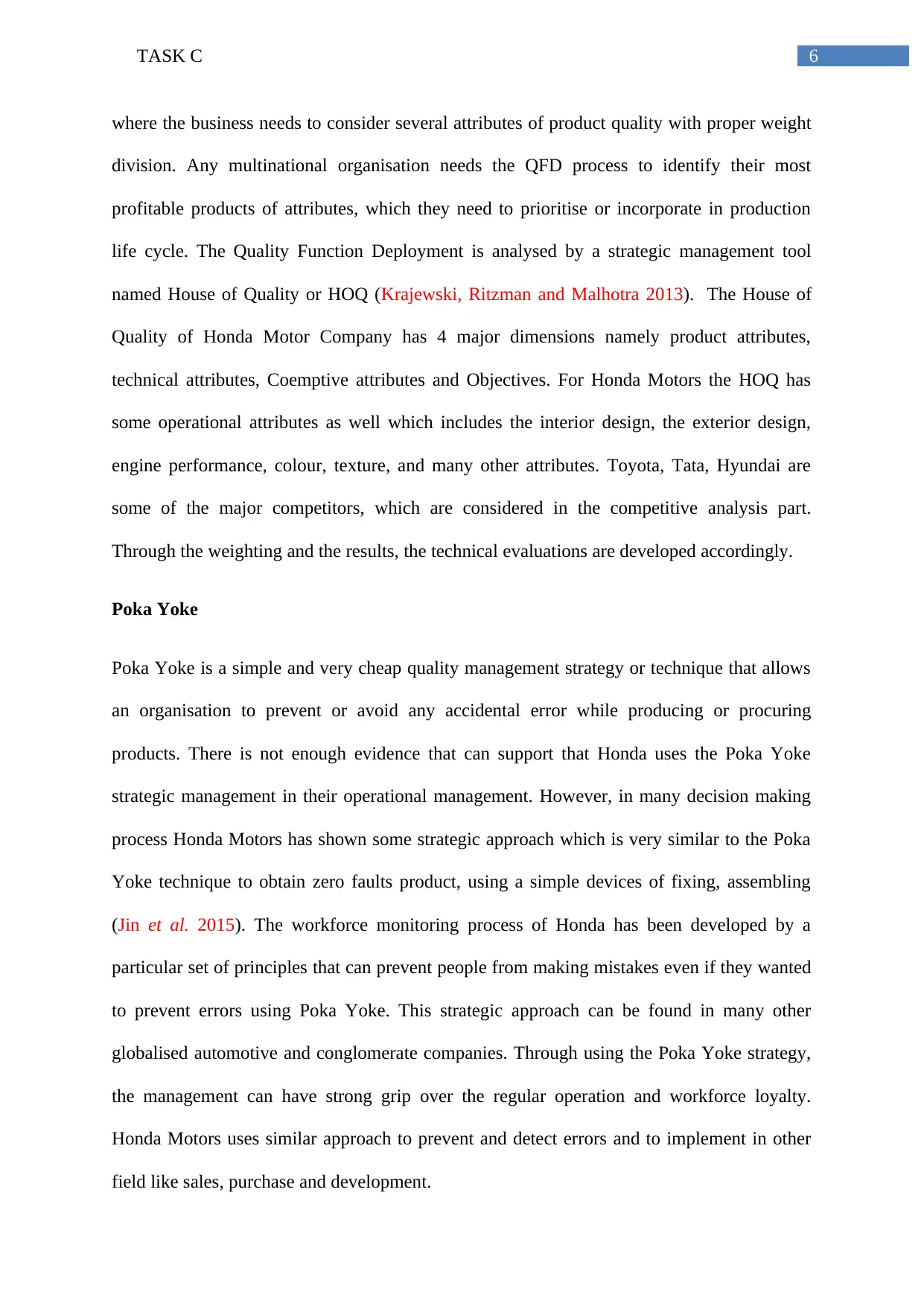
6TASK C
where the business needs to consider several attributes of product quality with proper weight
division. Any multinational organisation needs the QFD process to identify their most
profitable products of attributes, which they need to prioritise or incorporate in production
life cycle. The Quality Function Deployment is analysed by a strategic management tool
named House of Quality or HOQ (Krajewski, Ritzman and Malhotra 2013). The House of
Quality of Honda Motor Company has 4 major dimensions namely product attributes,
technical attributes, Coemptive attributes and Objectives. For Honda Motors the HOQ has
some operational attributes as well which includes the interior design, the exterior design,
engine performance, colour, texture, and many other attributes. Toyota, Tata, Hyundai are
some of the major competitors, which are considered in the competitive analysis part.
Through the weighting and the results, the technical evaluations are developed accordingly.
Poka Yoke
Poka Yoke is a simple and very cheap quality management strategy or technique that allows
an organisation to prevent or avoid any accidental error while producing or procuring
products. There is not enough evidence that can support that Honda uses the Poka Yoke
strategic management in their operational management. However, in many decision making
process Honda Motors has shown some strategic approach which is very similar to the Poka
Yoke technique to obtain zero faults product, using a simple devices of fixing, assembling
(Jin et al. 2015). The workforce monitoring process of Honda has been developed by a
particular set of principles that can prevent people from making mistakes even if they wanted
to prevent errors using Poka Yoke. This strategic approach can be found in many other
globalised automotive and conglomerate companies. Through using the Poka Yoke strategy,
the management can have strong grip over the regular operation and workforce loyalty.
Honda Motors uses similar approach to prevent and detect errors and to implement in other
field like sales, purchase and development.
where the business needs to consider several attributes of product quality with proper weight
division. Any multinational organisation needs the QFD process to identify their most
profitable products of attributes, which they need to prioritise or incorporate in production
life cycle. The Quality Function Deployment is analysed by a strategic management tool
named House of Quality or HOQ (Krajewski, Ritzman and Malhotra 2013). The House of
Quality of Honda Motor Company has 4 major dimensions namely product attributes,
technical attributes, Coemptive attributes and Objectives. For Honda Motors the HOQ has
some operational attributes as well which includes the interior design, the exterior design,
engine performance, colour, texture, and many other attributes. Toyota, Tata, Hyundai are
some of the major competitors, which are considered in the competitive analysis part.
Through the weighting and the results, the technical evaluations are developed accordingly.
Poka Yoke
Poka Yoke is a simple and very cheap quality management strategy or technique that allows
an organisation to prevent or avoid any accidental error while producing or procuring
products. There is not enough evidence that can support that Honda uses the Poka Yoke
strategic management in their operational management. However, in many decision making
process Honda Motors has shown some strategic approach which is very similar to the Poka
Yoke technique to obtain zero faults product, using a simple devices of fixing, assembling
(Jin et al. 2015). The workforce monitoring process of Honda has been developed by a
particular set of principles that can prevent people from making mistakes even if they wanted
to prevent errors using Poka Yoke. This strategic approach can be found in many other
globalised automotive and conglomerate companies. Through using the Poka Yoke strategy,
the management can have strong grip over the regular operation and workforce loyalty.
Honda Motors uses similar approach to prevent and detect errors and to implement in other
field like sales, purchase and development.
Paraphrase This Document
Need a fresh take? Get an instant paraphrase of this document with our AI Paraphraser
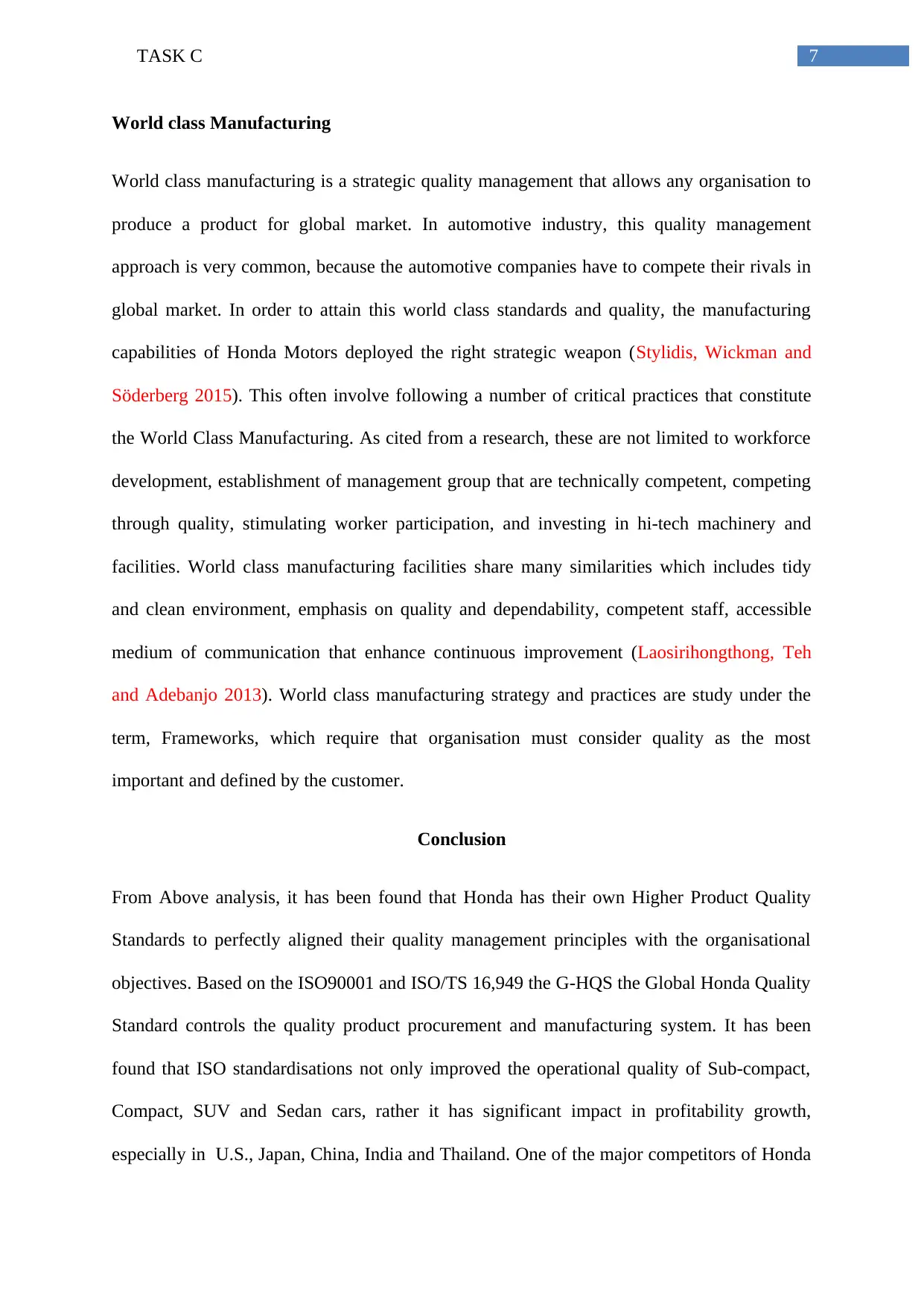
7TASK C
World class Manufacturing
World class manufacturing is a strategic quality management that allows any organisation to
produce a product for global market. In automotive industry, this quality management
approach is very common, because the automotive companies have to compete their rivals in
global market. In order to attain this world class standards and quality, the manufacturing
capabilities of Honda Motors deployed the right strategic weapon (Stylidis, Wickman and
Söderberg 2015). This often involve following a number of critical practices that constitute
the World Class Manufacturing. As cited from a research, these are not limited to workforce
development, establishment of management group that are technically competent, competing
through quality, stimulating worker participation, and investing in hi-tech machinery and
facilities. World class manufacturing facilities share many similarities which includes tidy
and clean environment, emphasis on quality and dependability, competent staff, accessible
medium of communication that enhance continuous improvement (Laosirihongthong, Teh
and Adebanjo 2013). World class manufacturing strategy and practices are study under the
term, Frameworks, which require that organisation must consider quality as the most
important and defined by the customer.
Conclusion
From Above analysis, it has been found that Honda has their own Higher Product Quality
Standards to perfectly aligned their quality management principles with the organisational
objectives. Based on the ISO90001 and ISO/TS 16,949 the G-HQS the Global Honda Quality
Standard controls the quality product procurement and manufacturing system. It has been
found that ISO standardisations not only improved the operational quality of Sub-compact,
Compact, SUV and Sedan cars, rather it has significant impact in profitability growth,
especially in U.S., Japan, China, India and Thailand. One of the major competitors of Honda
World class Manufacturing
World class manufacturing is a strategic quality management that allows any organisation to
produce a product for global market. In automotive industry, this quality management
approach is very common, because the automotive companies have to compete their rivals in
global market. In order to attain this world class standards and quality, the manufacturing
capabilities of Honda Motors deployed the right strategic weapon (Stylidis, Wickman and
Söderberg 2015). This often involve following a number of critical practices that constitute
the World Class Manufacturing. As cited from a research, these are not limited to workforce
development, establishment of management group that are technically competent, competing
through quality, stimulating worker participation, and investing in hi-tech machinery and
facilities. World class manufacturing facilities share many similarities which includes tidy
and clean environment, emphasis on quality and dependability, competent staff, accessible
medium of communication that enhance continuous improvement (Laosirihongthong, Teh
and Adebanjo 2013). World class manufacturing strategy and practices are study under the
term, Frameworks, which require that organisation must consider quality as the most
important and defined by the customer.
Conclusion
From Above analysis, it has been found that Honda has their own Higher Product Quality
Standards to perfectly aligned their quality management principles with the organisational
objectives. Based on the ISO90001 and ISO/TS 16,949 the G-HQS the Global Honda Quality
Standard controls the quality product procurement and manufacturing system. It has been
found that ISO standardisations not only improved the operational quality of Sub-compact,
Compact, SUV and Sedan cars, rather it has significant impact in profitability growth,
especially in U.S., Japan, China, India and Thailand. One of the major competitors of Honda
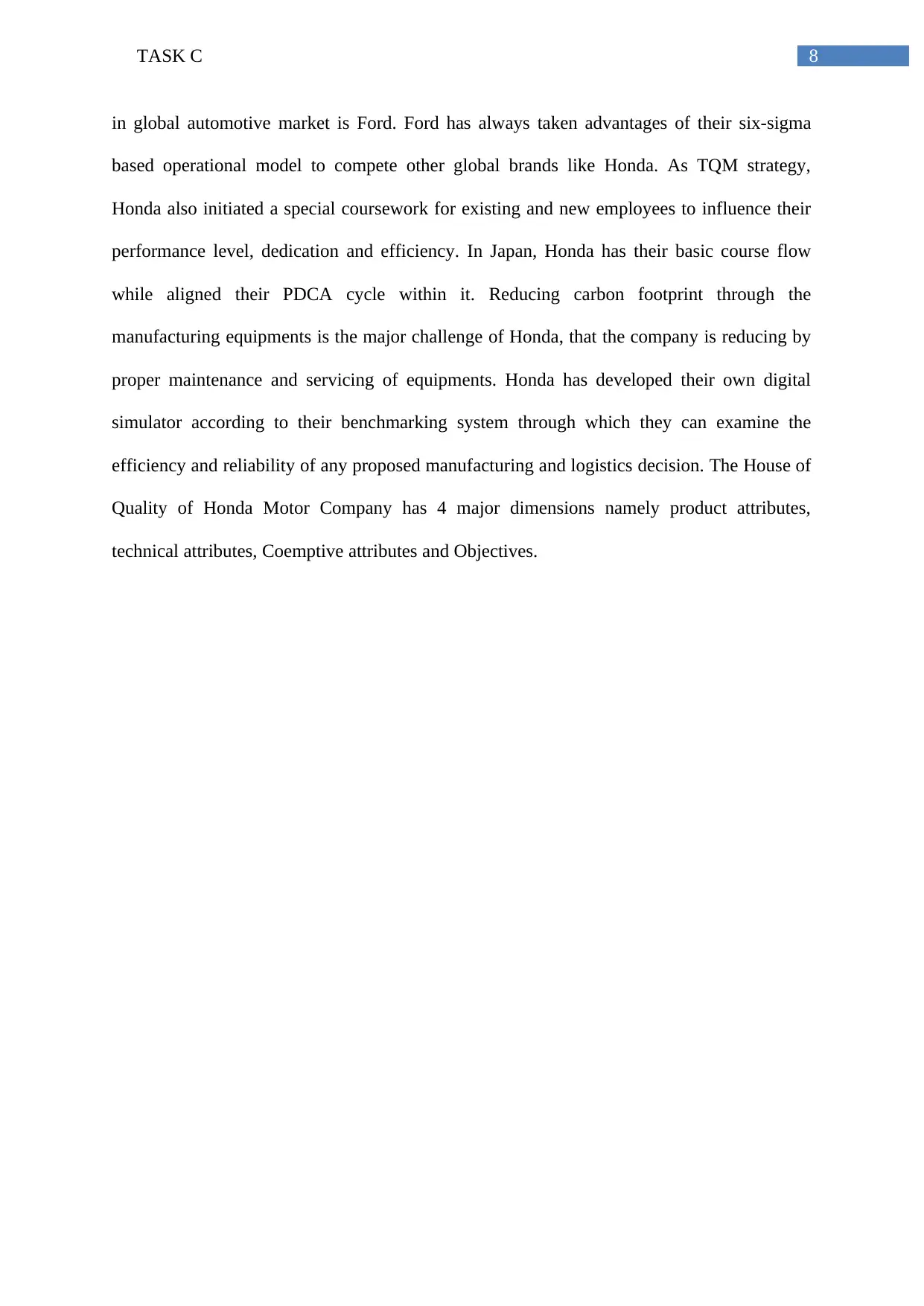
8TASK C
in global automotive market is Ford. Ford has always taken advantages of their six-sigma
based operational model to compete other global brands like Honda. As TQM strategy,
Honda also initiated a special coursework for existing and new employees to influence their
performance level, dedication and efficiency. In Japan, Honda has their basic course flow
while aligned their PDCA cycle within it. Reducing carbon footprint through the
manufacturing equipments is the major challenge of Honda, that the company is reducing by
proper maintenance and servicing of equipments. Honda has developed their own digital
simulator according to their benchmarking system through which they can examine the
efficiency and reliability of any proposed manufacturing and logistics decision. The House of
Quality of Honda Motor Company has 4 major dimensions namely product attributes,
technical attributes, Coemptive attributes and Objectives.
in global automotive market is Ford. Ford has always taken advantages of their six-sigma
based operational model to compete other global brands like Honda. As TQM strategy,
Honda also initiated a special coursework for existing and new employees to influence their
performance level, dedication and efficiency. In Japan, Honda has their basic course flow
while aligned their PDCA cycle within it. Reducing carbon footprint through the
manufacturing equipments is the major challenge of Honda, that the company is reducing by
proper maintenance and servicing of equipments. Honda has developed their own digital
simulator according to their benchmarking system through which they can examine the
efficiency and reliability of any proposed manufacturing and logistics decision. The House of
Quality of Honda Motor Company has 4 major dimensions namely product attributes,
technical attributes, Coemptive attributes and Objectives.

9TASK C
References
Dweiri, F., Kumar, S., Khan, S.A. and Jain, V., 2016. Designing an integrated AHP based
decision support system for supplier selection in automotive industry. Expert Systems with
Applications, 62, pp.273-283.
Fadly Habidin, N. and Mohd Yusof, S.R., 2013. Critical success factors of Lean Six Sigma
for the Malaysian automotive industry. International Journal of Lean Six Sigma, 4(1), pp.60-
82.
Fonseca, L.M., 2015. From Quality Gurus and TQM to ISO 9001: 2015: a review of several
quality paths. International Journal for Quality Research (IJQR), 9(1), pp.167-180.
Fragassa, C., Pavlovic, A. and Massimo, S., 2014. USING A TOTAL QUALITY
STRATEGY IN A NEW PRACTICAL APPROACH FOR IMPROVING THE PRODUCT
RELIABILITY IN AUTOMOTIVE INDUSTRY. International Journal for Quality
Research, 8(3).
Global.honda. 2018. Assuring outstanding product quality. [online] Available at:
https://global.honda/content/dam/site/global/about/cq_img/sustainability/report/pdf/2018/
Honda-SR-2018-en-065-078.pdf [Accessed 25 Mar. 2019].
Goetsch, D.L. and Davis, S.B., 2014. Quality management for organizational excellence.
Upper Saddle River, NJ: pearson.
Jin, J, Ji, P, Liu, Y, and Johnson Lim, S 2015, 'Translating online customer opinions into
engineering characteristics in QFD: A probabilistic language analysis approach', Engineering
Applications Of Artificial Intelligence, 41, pp. 115-127
Krajewski, L.J., Ritzman, L.P. and Malhotra, M.K., 2013. Operations management. Pearson,.
References
Dweiri, F., Kumar, S., Khan, S.A. and Jain, V., 2016. Designing an integrated AHP based
decision support system for supplier selection in automotive industry. Expert Systems with
Applications, 62, pp.273-283.
Fadly Habidin, N. and Mohd Yusof, S.R., 2013. Critical success factors of Lean Six Sigma
for the Malaysian automotive industry. International Journal of Lean Six Sigma, 4(1), pp.60-
82.
Fonseca, L.M., 2015. From Quality Gurus and TQM to ISO 9001: 2015: a review of several
quality paths. International Journal for Quality Research (IJQR), 9(1), pp.167-180.
Fragassa, C., Pavlovic, A. and Massimo, S., 2014. USING A TOTAL QUALITY
STRATEGY IN A NEW PRACTICAL APPROACH FOR IMPROVING THE PRODUCT
RELIABILITY IN AUTOMOTIVE INDUSTRY. International Journal for Quality
Research, 8(3).
Global.honda. 2018. Assuring outstanding product quality. [online] Available at:
https://global.honda/content/dam/site/global/about/cq_img/sustainability/report/pdf/2018/
Honda-SR-2018-en-065-078.pdf [Accessed 25 Mar. 2019].
Goetsch, D.L. and Davis, S.B., 2014. Quality management for organizational excellence.
Upper Saddle River, NJ: pearson.
Jin, J, Ji, P, Liu, Y, and Johnson Lim, S 2015, 'Translating online customer opinions into
engineering characteristics in QFD: A probabilistic language analysis approach', Engineering
Applications Of Artificial Intelligence, 41, pp. 115-127
Krajewski, L.J., Ritzman, L.P. and Malhotra, M.K., 2013. Operations management. Pearson,.
Secure Best Marks with AI Grader
Need help grading? Try our AI Grader for instant feedback on your assignments.
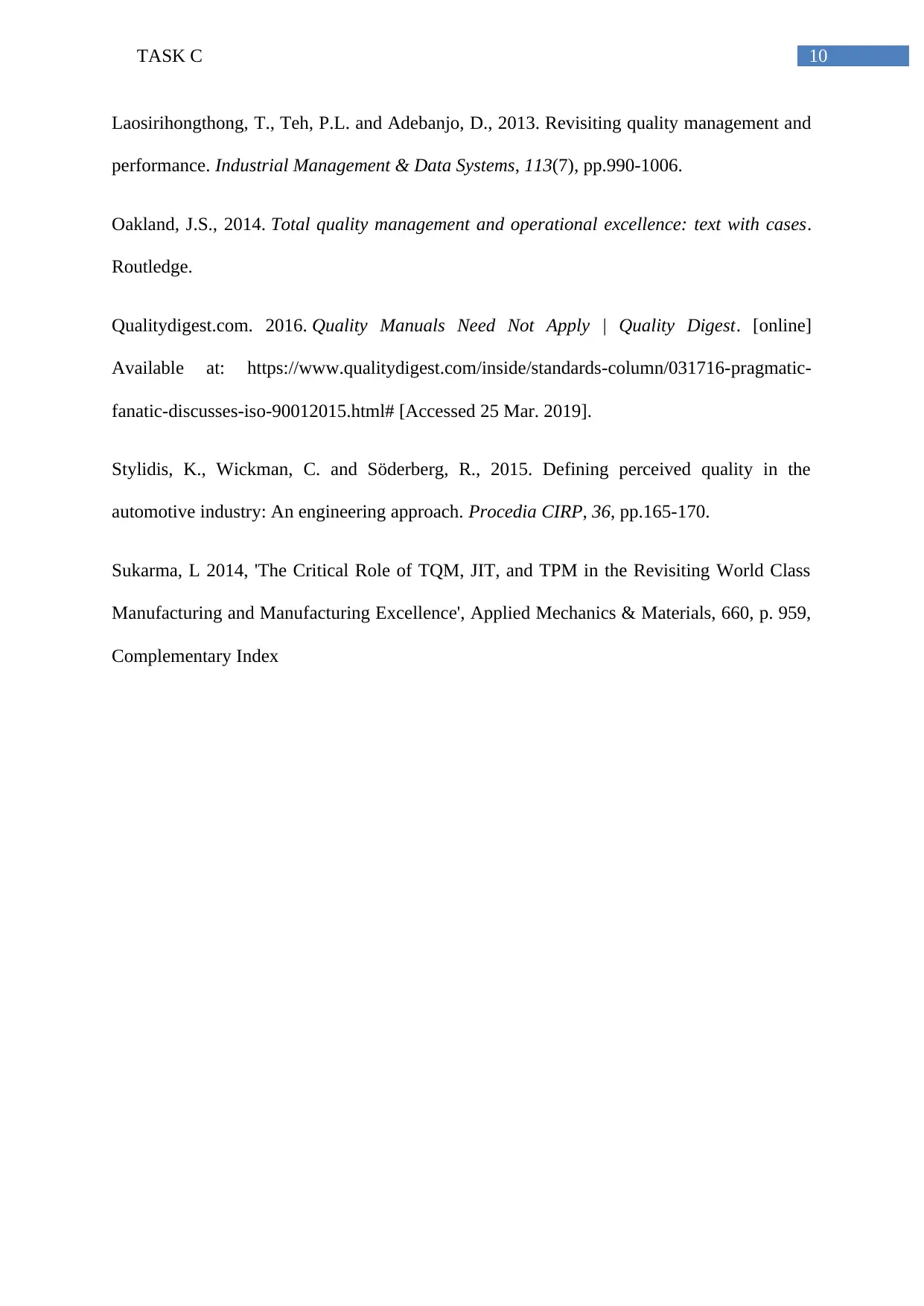
10TASK C
Laosirihongthong, T., Teh, P.L. and Adebanjo, D., 2013. Revisiting quality management and
performance. Industrial Management & Data Systems, 113(7), pp.990-1006.
Oakland, J.S., 2014. Total quality management and operational excellence: text with cases.
Routledge.
Qualitydigest.com. 2016. Quality Manuals Need Not Apply | Quality Digest. [online]
Available at: https://www.qualitydigest.com/inside/standards-column/031716-pragmatic-
fanatic-discusses-iso-90012015.html# [Accessed 25 Mar. 2019].
Stylidis, K., Wickman, C. and Söderberg, R., 2015. Defining perceived quality in the
automotive industry: An engineering approach. Procedia CIRP, 36, pp.165-170.
Sukarma, L 2014, 'The Critical Role of TQM, JIT, and TPM in the Revisiting World Class
Manufacturing and Manufacturing Excellence', Applied Mechanics & Materials, 660, p. 959,
Complementary Index
Laosirihongthong, T., Teh, P.L. and Adebanjo, D., 2013. Revisiting quality management and
performance. Industrial Management & Data Systems, 113(7), pp.990-1006.
Oakland, J.S., 2014. Total quality management and operational excellence: text with cases.
Routledge.
Qualitydigest.com. 2016. Quality Manuals Need Not Apply | Quality Digest. [online]
Available at: https://www.qualitydigest.com/inside/standards-column/031716-pragmatic-
fanatic-discusses-iso-90012015.html# [Accessed 25 Mar. 2019].
Stylidis, K., Wickman, C. and Söderberg, R., 2015. Defining perceived quality in the
automotive industry: An engineering approach. Procedia CIRP, 36, pp.165-170.
Sukarma, L 2014, 'The Critical Role of TQM, JIT, and TPM in the Revisiting World Class
Manufacturing and Manufacturing Excellence', Applied Mechanics & Materials, 660, p. 959,
Complementary Index
1 out of 11
Related Documents
![[object Object]](/_next/image/?url=%2F_next%2Fstatic%2Fmedia%2Flogo.6d15ce61.png&w=640&q=75)
Your All-in-One AI-Powered Toolkit for Academic Success.
+13062052269
info@desklib.com
Available 24*7 on WhatsApp / Email
Unlock your academic potential
© 2024 | Zucol Services PVT LTD | All rights reserved.