Teslas Quality Challenge Opeartions Report
VerifiedAdded on 2022/09/09
|13
|3405
|17
AI Summary
Contribute Materials
Your contribution can guide someone’s learning journey. Share your
documents today.
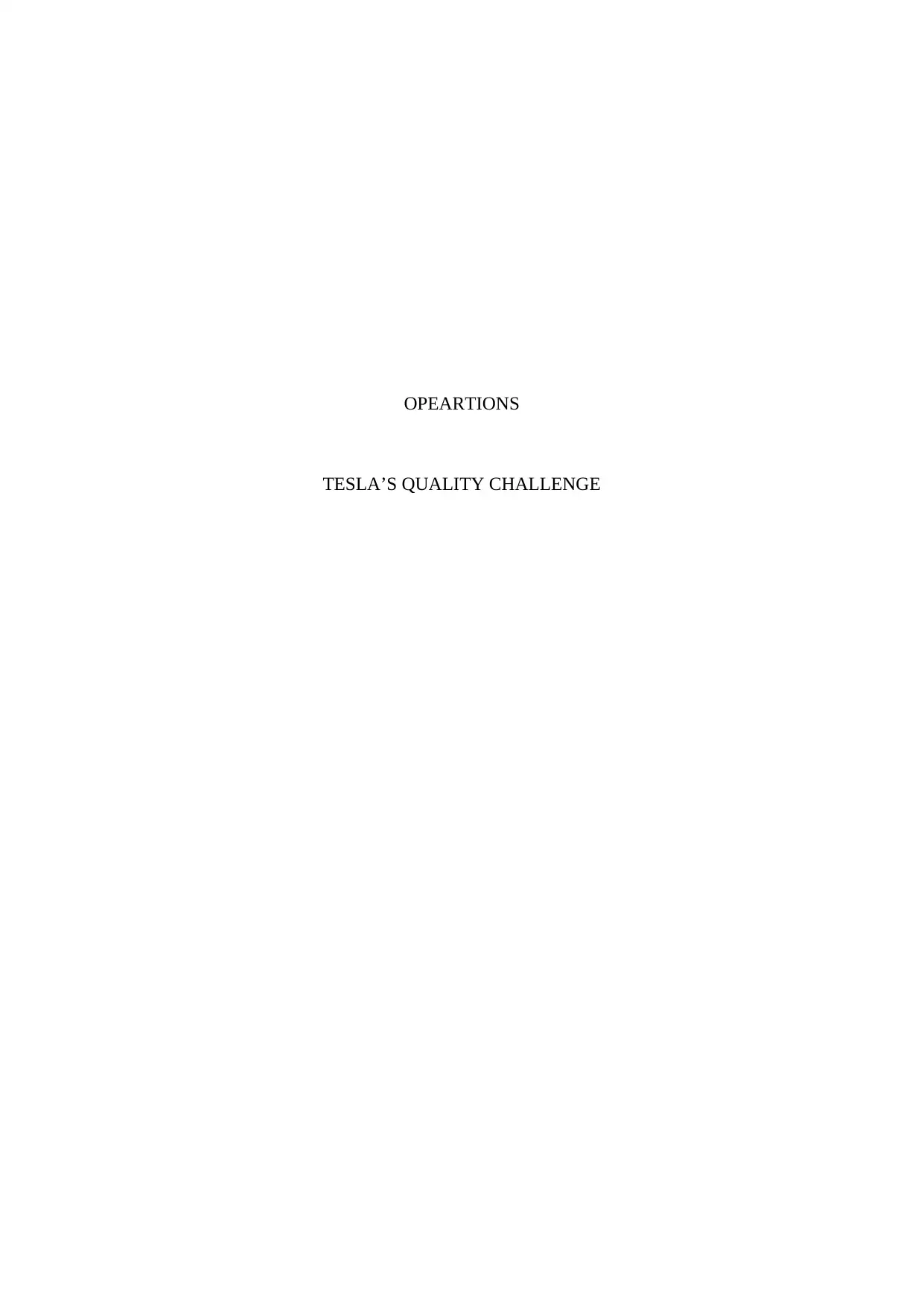
OPEARTIONS
TESLA’S QUALITY CHALLENGE
TESLA’S QUALITY CHALLENGE
Secure Best Marks with AI Grader
Need help grading? Try our AI Grader for instant feedback on your assignments.
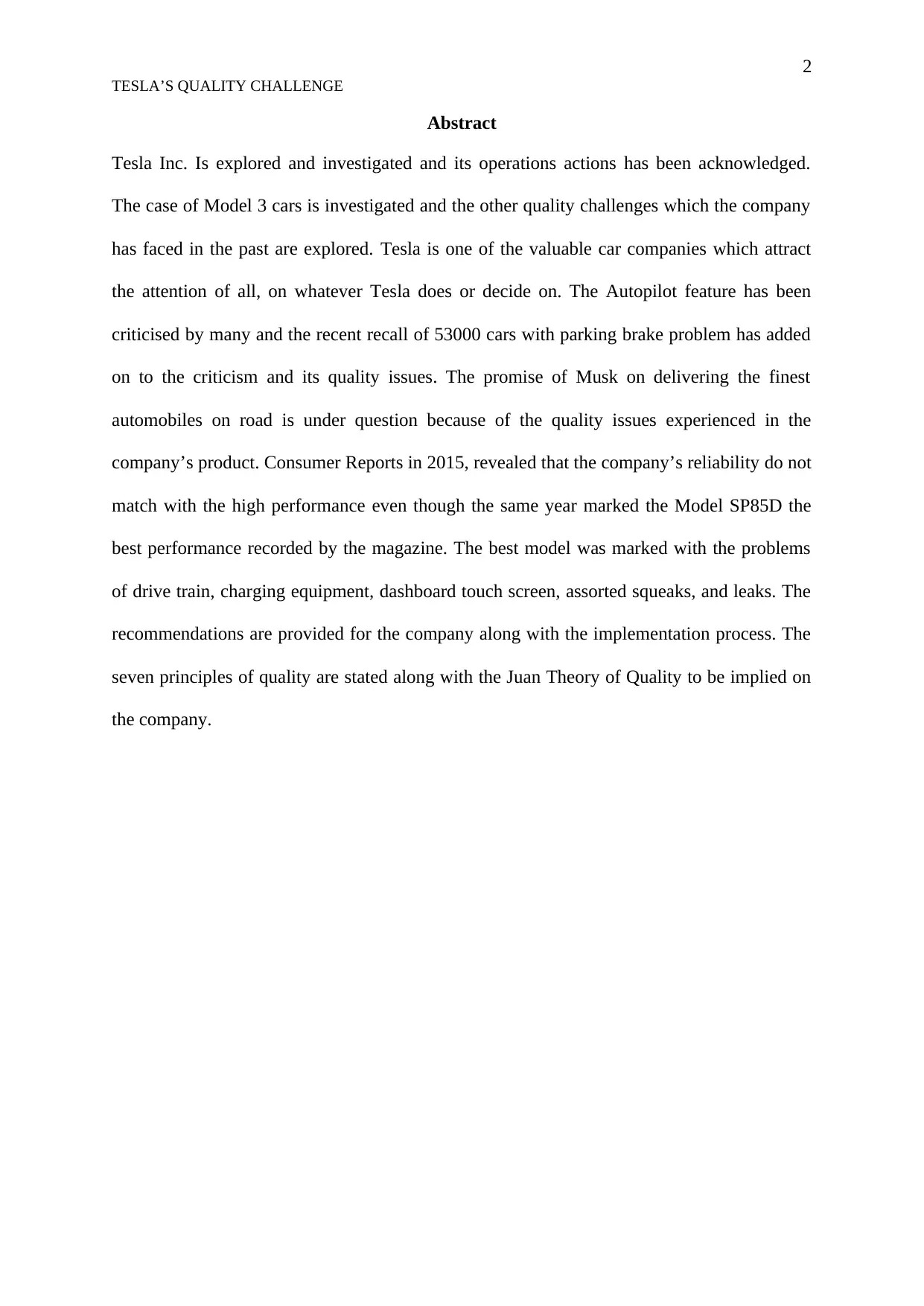
2
TESLA’S QUALITY CHALLENGE
Abstract
Tesla Inc. Is explored and investigated and its operations actions has been acknowledged.
The case of Model 3 cars is investigated and the other quality challenges which the company
has faced in the past are explored. Tesla is one of the valuable car companies which attract
the attention of all, on whatever Tesla does or decide on. The Autopilot feature has been
criticised by many and the recent recall of 53000 cars with parking brake problem has added
on to the criticism and its quality issues. The promise of Musk on delivering the finest
automobiles on road is under question because of the quality issues experienced in the
company’s product. Consumer Reports in 2015, revealed that the company’s reliability do not
match with the high performance even though the same year marked the Model SP85D the
best performance recorded by the magazine. The best model was marked with the problems
of drive train, charging equipment, dashboard touch screen, assorted squeaks, and leaks. The
recommendations are provided for the company along with the implementation process. The
seven principles of quality are stated along with the Juan Theory of Quality to be implied on
the company.
TESLA’S QUALITY CHALLENGE
Abstract
Tesla Inc. Is explored and investigated and its operations actions has been acknowledged.
The case of Model 3 cars is investigated and the other quality challenges which the company
has faced in the past are explored. Tesla is one of the valuable car companies which attract
the attention of all, on whatever Tesla does or decide on. The Autopilot feature has been
criticised by many and the recent recall of 53000 cars with parking brake problem has added
on to the criticism and its quality issues. The promise of Musk on delivering the finest
automobiles on road is under question because of the quality issues experienced in the
company’s product. Consumer Reports in 2015, revealed that the company’s reliability do not
match with the high performance even though the same year marked the Model SP85D the
best performance recorded by the magazine. The best model was marked with the problems
of drive train, charging equipment, dashboard touch screen, assorted squeaks, and leaks. The
recommendations are provided for the company along with the implementation process. The
seven principles of quality are stated along with the Juan Theory of Quality to be implied on
the company.
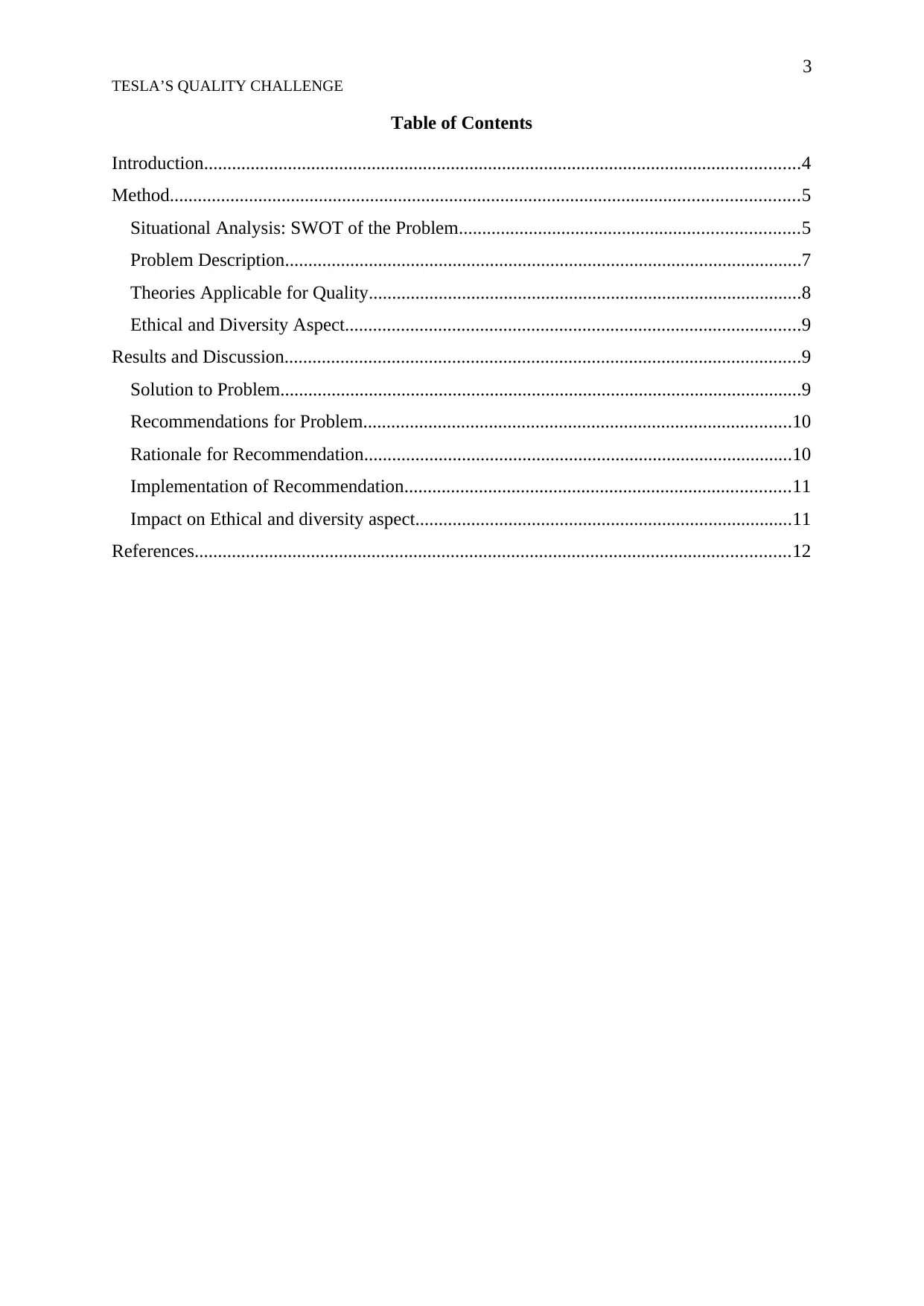
3
TESLA’S QUALITY CHALLENGE
Table of Contents
Introduction................................................................................................................................4
Method.......................................................................................................................................5
Situational Analysis: SWOT of the Problem.........................................................................5
Problem Description...............................................................................................................7
Theories Applicable for Quality.............................................................................................8
Ethical and Diversity Aspect..................................................................................................9
Results and Discussion...............................................................................................................9
Solution to Problem................................................................................................................9
Recommendations for Problem............................................................................................10
Rationale for Recommendation............................................................................................10
Implementation of Recommendation...................................................................................11
Impact on Ethical and diversity aspect.................................................................................11
References................................................................................................................................12
TESLA’S QUALITY CHALLENGE
Table of Contents
Introduction................................................................................................................................4
Method.......................................................................................................................................5
Situational Analysis: SWOT of the Problem.........................................................................5
Problem Description...............................................................................................................7
Theories Applicable for Quality.............................................................................................8
Ethical and Diversity Aspect..................................................................................................9
Results and Discussion...............................................................................................................9
Solution to Problem................................................................................................................9
Recommendations for Problem............................................................................................10
Rationale for Recommendation............................................................................................10
Implementation of Recommendation...................................................................................11
Impact on Ethical and diversity aspect.................................................................................11
References................................................................................................................................12
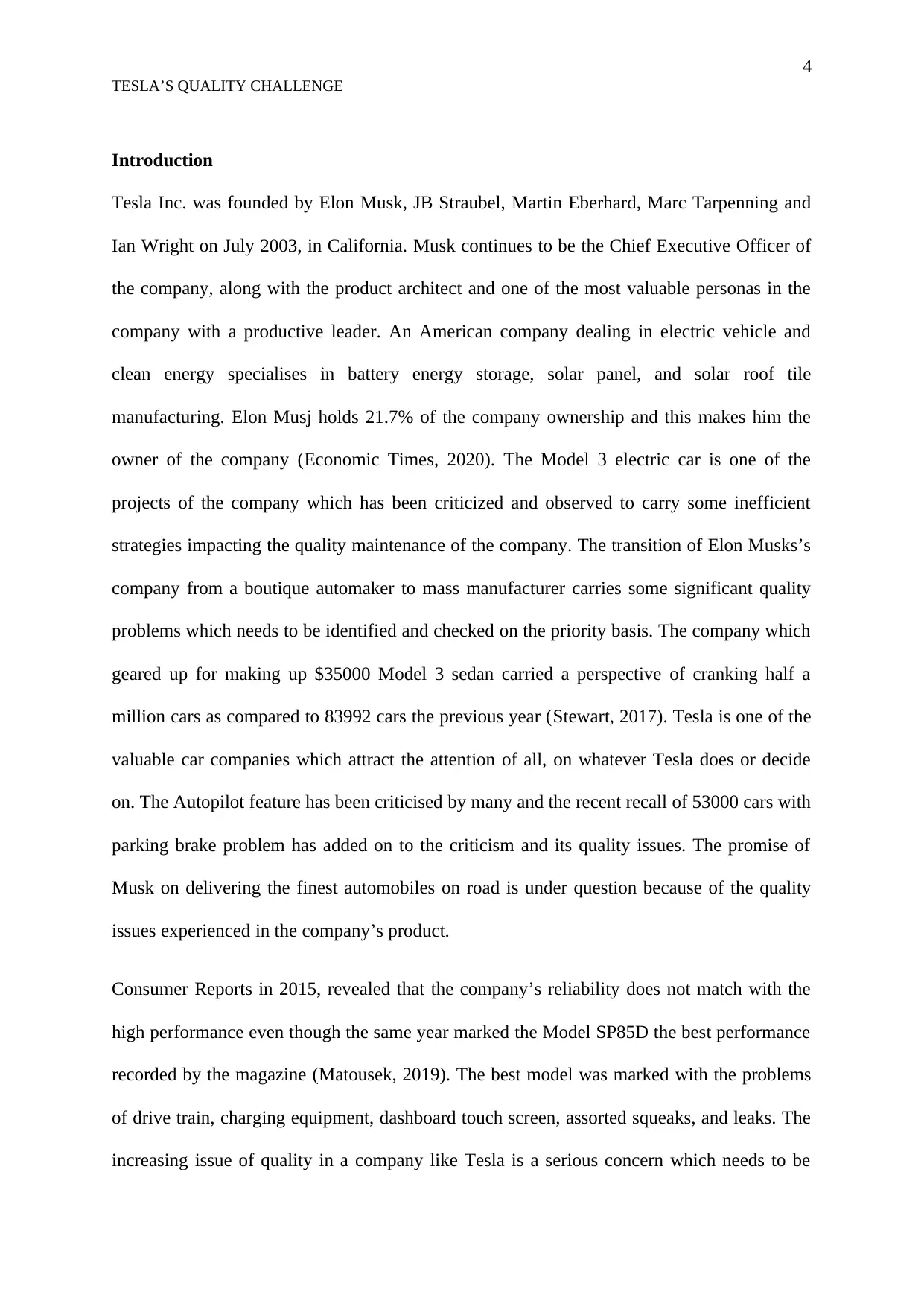
4
TESLA’S QUALITY CHALLENGE
Introduction
Tesla Inc. was founded by Elon Musk, JB Straubel, Martin Eberhard, Marc Tarpenning and
Ian Wright on July 2003, in California. Musk continues to be the Chief Executive Officer of
the company, along with the product architect and one of the most valuable personas in the
company with a productive leader. An American company dealing in electric vehicle and
clean energy specialises in battery energy storage, solar panel, and solar roof tile
manufacturing. Elon Musj holds 21.7% of the company ownership and this makes him the
owner of the company (Economic Times, 2020). The Model 3 electric car is one of the
projects of the company which has been criticized and observed to carry some inefficient
strategies impacting the quality maintenance of the company. The transition of Elon Musks’s
company from a boutique automaker to mass manufacturer carries some significant quality
problems which needs to be identified and checked on the priority basis. The company which
geared up for making up $35000 Model 3 sedan carried a perspective of cranking half a
million cars as compared to 83992 cars the previous year (Stewart, 2017). Tesla is one of the
valuable car companies which attract the attention of all, on whatever Tesla does or decide
on. The Autopilot feature has been criticised by many and the recent recall of 53000 cars with
parking brake problem has added on to the criticism and its quality issues. The promise of
Musk on delivering the finest automobiles on road is under question because of the quality
issues experienced in the company’s product.
Consumer Reports in 2015, revealed that the company’s reliability does not match with the
high performance even though the same year marked the Model SP85D the best performance
recorded by the magazine (Matousek, 2019). The best model was marked with the problems
of drive train, charging equipment, dashboard touch screen, assorted squeaks, and leaks. The
increasing issue of quality in a company like Tesla is a serious concern which needs to be
TESLA’S QUALITY CHALLENGE
Introduction
Tesla Inc. was founded by Elon Musk, JB Straubel, Martin Eberhard, Marc Tarpenning and
Ian Wright on July 2003, in California. Musk continues to be the Chief Executive Officer of
the company, along with the product architect and one of the most valuable personas in the
company with a productive leader. An American company dealing in electric vehicle and
clean energy specialises in battery energy storage, solar panel, and solar roof tile
manufacturing. Elon Musj holds 21.7% of the company ownership and this makes him the
owner of the company (Economic Times, 2020). The Model 3 electric car is one of the
projects of the company which has been criticized and observed to carry some inefficient
strategies impacting the quality maintenance of the company. The transition of Elon Musks’s
company from a boutique automaker to mass manufacturer carries some significant quality
problems which needs to be identified and checked on the priority basis. The company which
geared up for making up $35000 Model 3 sedan carried a perspective of cranking half a
million cars as compared to 83992 cars the previous year (Stewart, 2017). Tesla is one of the
valuable car companies which attract the attention of all, on whatever Tesla does or decide
on. The Autopilot feature has been criticised by many and the recent recall of 53000 cars with
parking brake problem has added on to the criticism and its quality issues. The promise of
Musk on delivering the finest automobiles on road is under question because of the quality
issues experienced in the company’s product.
Consumer Reports in 2015, revealed that the company’s reliability does not match with the
high performance even though the same year marked the Model SP85D the best performance
recorded by the magazine (Matousek, 2019). The best model was marked with the problems
of drive train, charging equipment, dashboard touch screen, assorted squeaks, and leaks. The
increasing issue of quality in a company like Tesla is a serious concern which needs to be
Secure Best Marks with AI Grader
Need help grading? Try our AI Grader for instant feedback on your assignments.
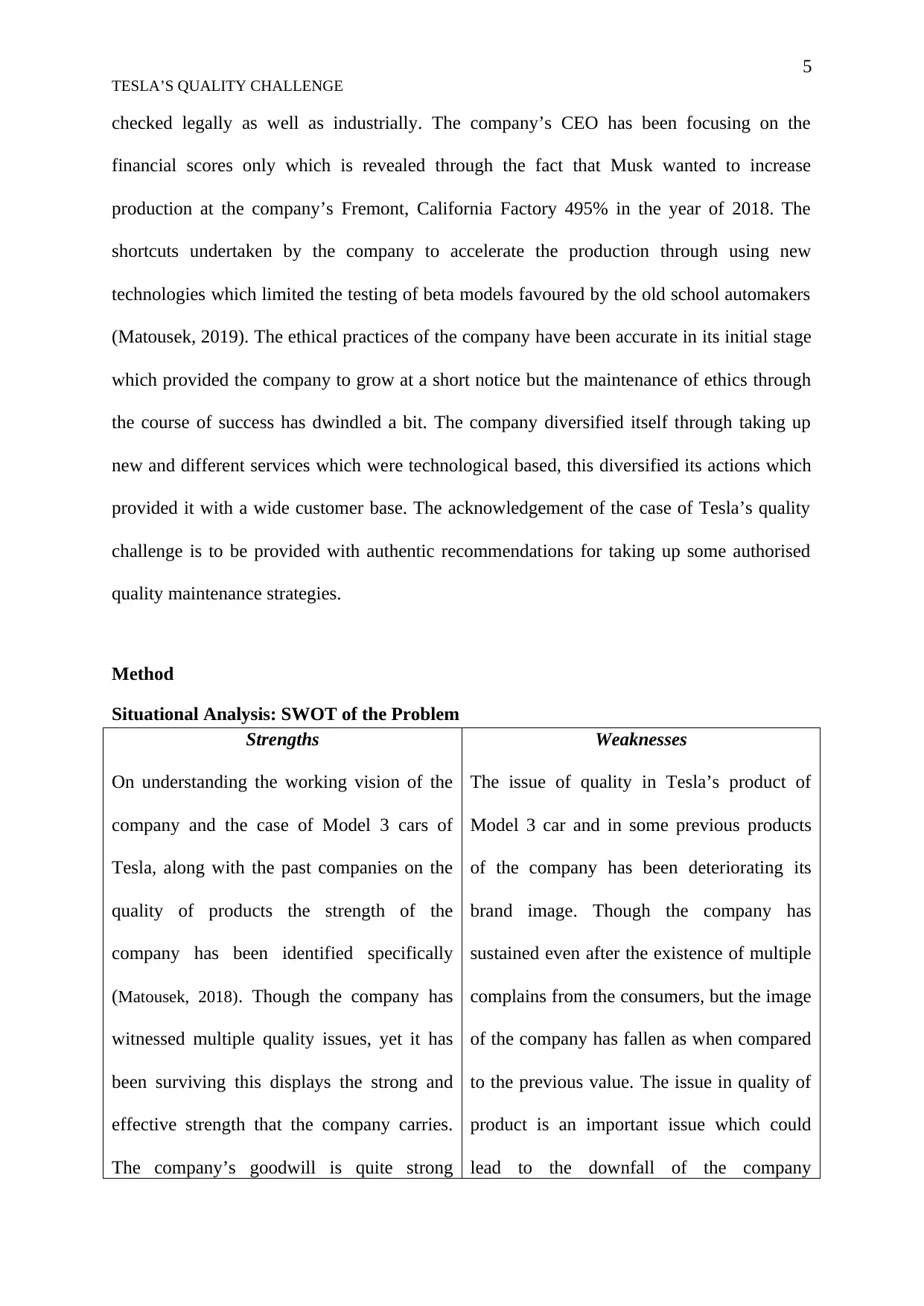
5
TESLA’S QUALITY CHALLENGE
checked legally as well as industrially. The company’s CEO has been focusing on the
financial scores only which is revealed through the fact that Musk wanted to increase
production at the company’s Fremont, California Factory 495% in the year of 2018. The
shortcuts undertaken by the company to accelerate the production through using new
technologies which limited the testing of beta models favoured by the old school automakers
(Matousek, 2019). The ethical practices of the company have been accurate in its initial stage
which provided the company to grow at a short notice but the maintenance of ethics through
the course of success has dwindled a bit. The company diversified itself through taking up
new and different services which were technological based, this diversified its actions which
provided it with a wide customer base. The acknowledgement of the case of Tesla’s quality
challenge is to be provided with authentic recommendations for taking up some authorised
quality maintenance strategies.
Method
Situational Analysis: SWOT of the Problem
Strengths
On understanding the working vision of the
company and the case of Model 3 cars of
Tesla, along with the past companies on the
quality of products the strength of the
company has been identified specifically
(Matousek, 2018). Though the company has
witnessed multiple quality issues, yet it has
been surviving this displays the strong and
effective strength that the company carries.
The company’s goodwill is quite strong
Weaknesses
The issue of quality in Tesla’s product of
Model 3 car and in some previous products
of the company has been deteriorating its
brand image. Though the company has
sustained even after the existence of multiple
complains from the consumers, but the image
of the company has fallen as when compared
to the previous value. The issue in quality of
product is an important issue which could
lead to the downfall of the company
TESLA’S QUALITY CHALLENGE
checked legally as well as industrially. The company’s CEO has been focusing on the
financial scores only which is revealed through the fact that Musk wanted to increase
production at the company’s Fremont, California Factory 495% in the year of 2018. The
shortcuts undertaken by the company to accelerate the production through using new
technologies which limited the testing of beta models favoured by the old school automakers
(Matousek, 2019). The ethical practices of the company have been accurate in its initial stage
which provided the company to grow at a short notice but the maintenance of ethics through
the course of success has dwindled a bit. The company diversified itself through taking up
new and different services which were technological based, this diversified its actions which
provided it with a wide customer base. The acknowledgement of the case of Tesla’s quality
challenge is to be provided with authentic recommendations for taking up some authorised
quality maintenance strategies.
Method
Situational Analysis: SWOT of the Problem
Strengths
On understanding the working vision of the
company and the case of Model 3 cars of
Tesla, along with the past companies on the
quality of products the strength of the
company has been identified specifically
(Matousek, 2018). Though the company has
witnessed multiple quality issues, yet it has
been surviving this displays the strong and
effective strength that the company carries.
The company’s goodwill is quite strong
Weaknesses
The issue of quality in Tesla’s product of
Model 3 car and in some previous products
of the company has been deteriorating its
brand image. Though the company has
sustained even after the existence of multiple
complains from the consumers, but the image
of the company has fallen as when compared
to the previous value. The issue in quality of
product is an important issue which could
lead to the downfall of the company
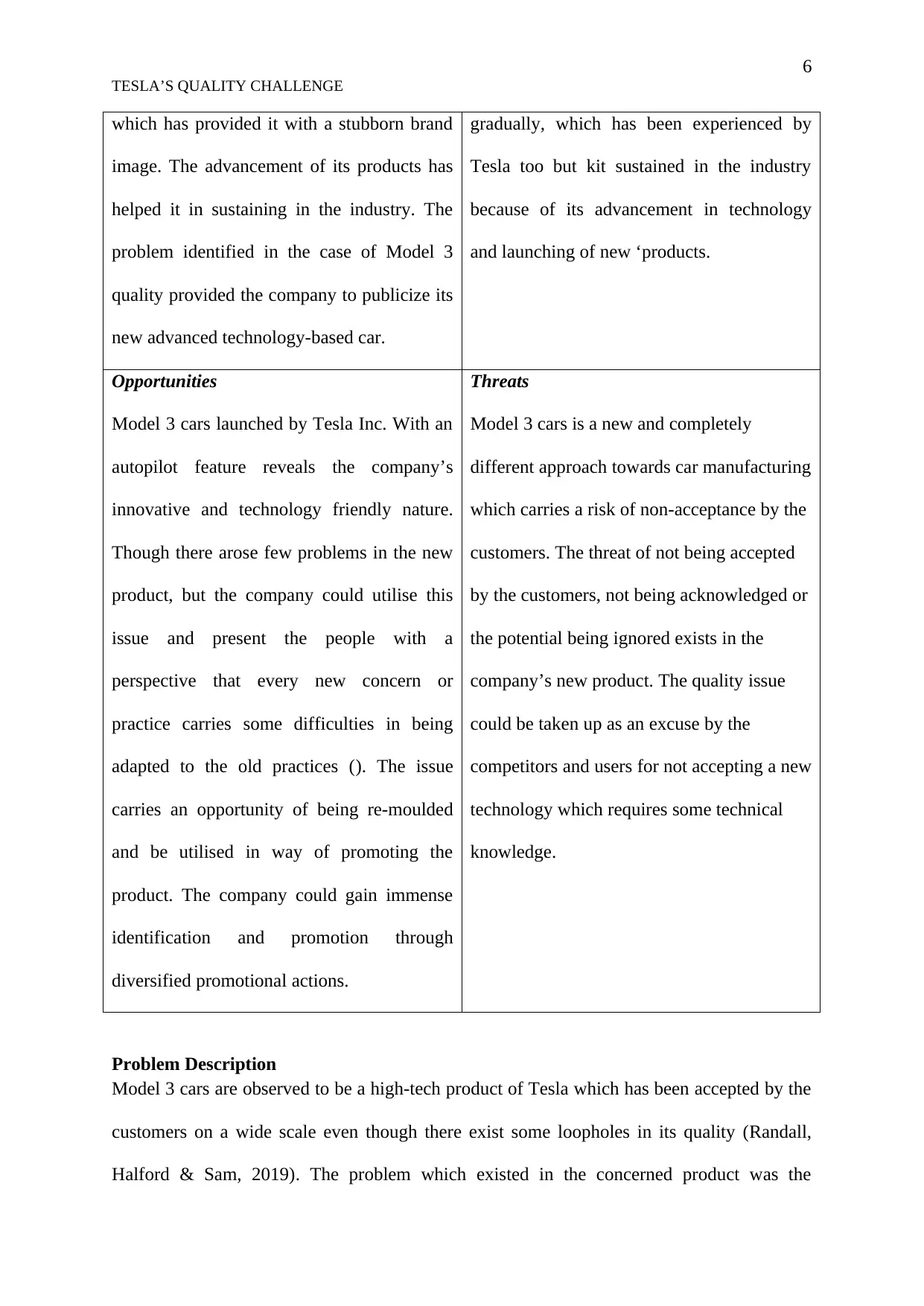
6
TESLA’S QUALITY CHALLENGE
which has provided it with a stubborn brand
image. The advancement of its products has
helped it in sustaining in the industry. The
problem identified in the case of Model 3
quality provided the company to publicize its
new advanced technology-based car.
gradually, which has been experienced by
Tesla too but kit sustained in the industry
because of its advancement in technology
and launching of new ‘products.
Opportunities
Model 3 cars launched by Tesla Inc. With an
autopilot feature reveals the company’s
innovative and technology friendly nature.
Though there arose few problems in the new
product, but the company could utilise this
issue and present the people with a
perspective that every new concern or
practice carries some difficulties in being
adapted to the old practices (). The issue
carries an opportunity of being re-moulded
and be utilised in way of promoting the
product. The company could gain immense
identification and promotion through
diversified promotional actions.
Threats
Model 3 cars is a new and completely
different approach towards car manufacturing
which carries a risk of non-acceptance by the
customers. The threat of not being accepted
by the customers, not being acknowledged or
the potential being ignored exists in the
company’s new product. The quality issue
could be taken up as an excuse by the
competitors and users for not accepting a new
technology which requires some technical
knowledge.
Problem Description
Model 3 cars are observed to be a high-tech product of Tesla which has been accepted by the
customers on a wide scale even though there exist some loopholes in its quality (Randall,
Halford & Sam, 2019). The problem which existed in the concerned product was the
TESLA’S QUALITY CHALLENGE
which has provided it with a stubborn brand
image. The advancement of its products has
helped it in sustaining in the industry. The
problem identified in the case of Model 3
quality provided the company to publicize its
new advanced technology-based car.
gradually, which has been experienced by
Tesla too but kit sustained in the industry
because of its advancement in technology
and launching of new ‘products.
Opportunities
Model 3 cars launched by Tesla Inc. With an
autopilot feature reveals the company’s
innovative and technology friendly nature.
Though there arose few problems in the new
product, but the company could utilise this
issue and present the people with a
perspective that every new concern or
practice carries some difficulties in being
adapted to the old practices (). The issue
carries an opportunity of being re-moulded
and be utilised in way of promoting the
product. The company could gain immense
identification and promotion through
diversified promotional actions.
Threats
Model 3 cars is a new and completely
different approach towards car manufacturing
which carries a risk of non-acceptance by the
customers. The threat of not being accepted
by the customers, not being acknowledged or
the potential being ignored exists in the
company’s new product. The quality issue
could be taken up as an excuse by the
competitors and users for not accepting a new
technology which requires some technical
knowledge.
Problem Description
Model 3 cars are observed to be a high-tech product of Tesla which has been accepted by the
customers on a wide scale even though there exist some loopholes in its quality (Randall,
Halford & Sam, 2019). The problem which existed in the concerned product was the
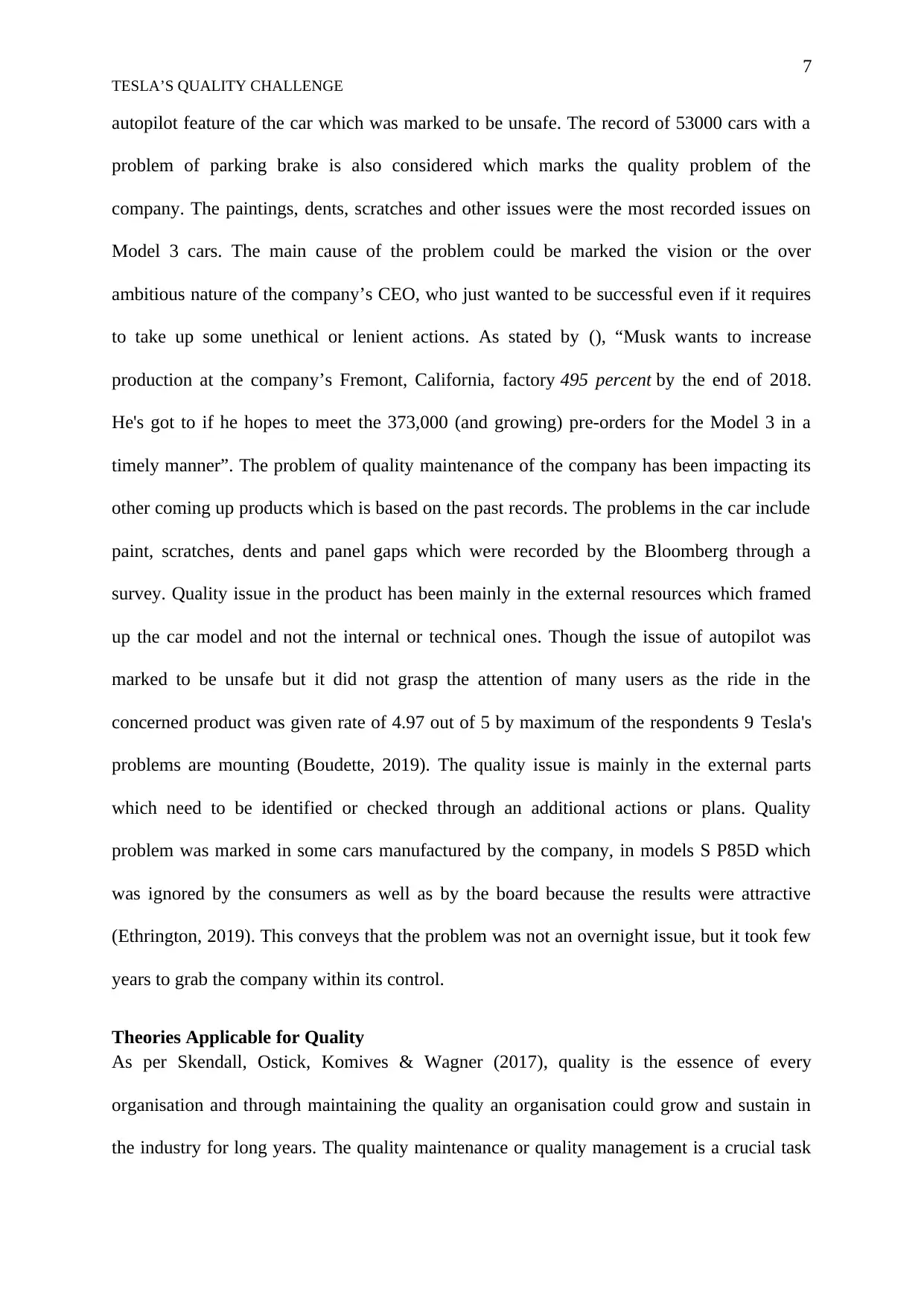
7
TESLA’S QUALITY CHALLENGE
autopilot feature of the car which was marked to be unsafe. The record of 53000 cars with a
problem of parking brake is also considered which marks the quality problem of the
company. The paintings, dents, scratches and other issues were the most recorded issues on
Model 3 cars. The main cause of the problem could be marked the vision or the over
ambitious nature of the company’s CEO, who just wanted to be successful even if it requires
to take up some unethical or lenient actions. As stated by (), “Musk wants to increase
production at the company’s Fremont, California, factory 495 percent by the end of 2018.
He's got to if he hopes to meet the 373,000 (and growing) pre-orders for the Model 3 in a
timely manner”. The problem of quality maintenance of the company has been impacting its
other coming up products which is based on the past records. The problems in the car include
paint, scratches, dents and panel gaps which were recorded by the Bloomberg through a
survey. Quality issue in the product has been mainly in the external resources which framed
up the car model and not the internal or technical ones. Though the issue of autopilot was
marked to be unsafe but it did not grasp the attention of many users as the ride in the
concerned product was given rate of 4.97 out of 5 by maximum of the respondents 9 Tesla's
problems are mounting (Boudette, 2019). The quality issue is mainly in the external parts
which need to be identified or checked through an additional actions or plans. Quality
problem was marked in some cars manufactured by the company, in models S P85D which
was ignored by the consumers as well as by the board because the results were attractive
(Ethrington, 2019). This conveys that the problem was not an overnight issue, but it took few
years to grab the company within its control.
Theories Applicable for Quality
As per Skendall, Ostick, Komives & Wagner (2017), quality is the essence of every
organisation and through maintaining the quality an organisation could grow and sustain in
the industry for long years. The quality maintenance or quality management is a crucial task
TESLA’S QUALITY CHALLENGE
autopilot feature of the car which was marked to be unsafe. The record of 53000 cars with a
problem of parking brake is also considered which marks the quality problem of the
company. The paintings, dents, scratches and other issues were the most recorded issues on
Model 3 cars. The main cause of the problem could be marked the vision or the over
ambitious nature of the company’s CEO, who just wanted to be successful even if it requires
to take up some unethical or lenient actions. As stated by (), “Musk wants to increase
production at the company’s Fremont, California, factory 495 percent by the end of 2018.
He's got to if he hopes to meet the 373,000 (and growing) pre-orders for the Model 3 in a
timely manner”. The problem of quality maintenance of the company has been impacting its
other coming up products which is based on the past records. The problems in the car include
paint, scratches, dents and panel gaps which were recorded by the Bloomberg through a
survey. Quality issue in the product has been mainly in the external resources which framed
up the car model and not the internal or technical ones. Though the issue of autopilot was
marked to be unsafe but it did not grasp the attention of many users as the ride in the
concerned product was given rate of 4.97 out of 5 by maximum of the respondents 9 Tesla's
problems are mounting (Boudette, 2019). The quality issue is mainly in the external parts
which need to be identified or checked through an additional actions or plans. Quality
problem was marked in some cars manufactured by the company, in models S P85D which
was ignored by the consumers as well as by the board because the results were attractive
(Ethrington, 2019). This conveys that the problem was not an overnight issue, but it took few
years to grab the company within its control.
Theories Applicable for Quality
As per Skendall, Ostick, Komives & Wagner (2017), quality is the essence of every
organisation and through maintaining the quality an organisation could grow and sustain in
the industry for long years. The quality maintenance or quality management is a crucial task
Paraphrase This Document
Need a fresh take? Get an instant paraphrase of this document with our AI Paraphraser
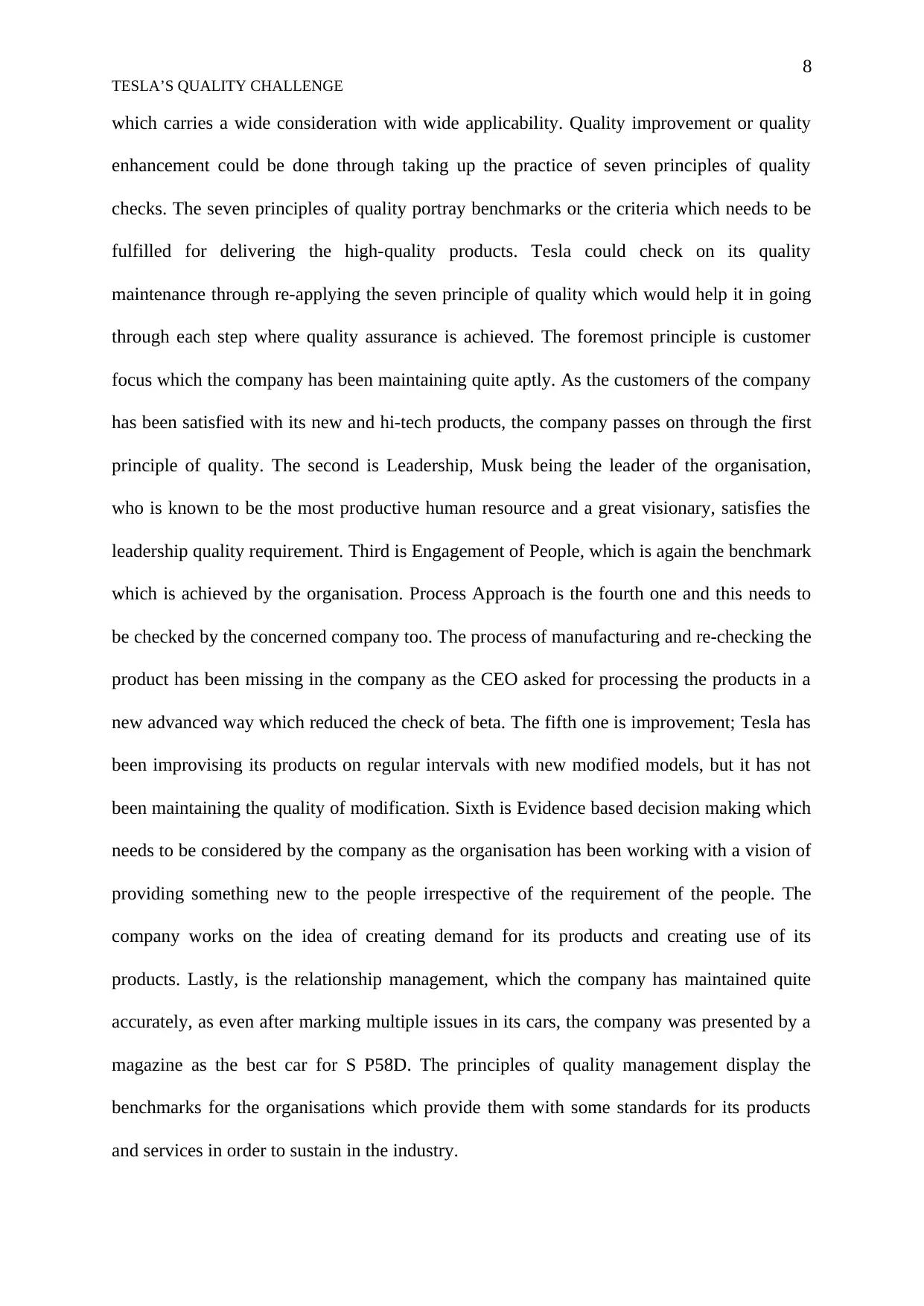
8
TESLA’S QUALITY CHALLENGE
which carries a wide consideration with wide applicability. Quality improvement or quality
enhancement could be done through taking up the practice of seven principles of quality
checks. The seven principles of quality portray benchmarks or the criteria which needs to be
fulfilled for delivering the high-quality products. Tesla could check on its quality
maintenance through re-applying the seven principle of quality which would help it in going
through each step where quality assurance is achieved. The foremost principle is customer
focus which the company has been maintaining quite aptly. As the customers of the company
has been satisfied with its new and hi-tech products, the company passes on through the first
principle of quality. The second is Leadership, Musk being the leader of the organisation,
who is known to be the most productive human resource and a great visionary, satisfies the
leadership quality requirement. Third is Engagement of People, which is again the benchmark
which is achieved by the organisation. Process Approach is the fourth one and this needs to
be checked by the concerned company too. The process of manufacturing and re-checking the
product has been missing in the company as the CEO asked for processing the products in a
new advanced way which reduced the check of beta. The fifth one is improvement; Tesla has
been improvising its products on regular intervals with new modified models, but it has not
been maintaining the quality of modification. Sixth is Evidence based decision making which
needs to be considered by the company as the organisation has been working with a vision of
providing something new to the people irrespective of the requirement of the people. The
company works on the idea of creating demand for its products and creating use of its
products. Lastly, is the relationship management, which the company has maintained quite
accurately, as even after marking multiple issues in its cars, the company was presented by a
magazine as the best car for S P58D. The principles of quality management display the
benchmarks for the organisations which provide them with some standards for its products
and services in order to sustain in the industry.
TESLA’S QUALITY CHALLENGE
which carries a wide consideration with wide applicability. Quality improvement or quality
enhancement could be done through taking up the practice of seven principles of quality
checks. The seven principles of quality portray benchmarks or the criteria which needs to be
fulfilled for delivering the high-quality products. Tesla could check on its quality
maintenance through re-applying the seven principle of quality which would help it in going
through each step where quality assurance is achieved. The foremost principle is customer
focus which the company has been maintaining quite aptly. As the customers of the company
has been satisfied with its new and hi-tech products, the company passes on through the first
principle of quality. The second is Leadership, Musk being the leader of the organisation,
who is known to be the most productive human resource and a great visionary, satisfies the
leadership quality requirement. Third is Engagement of People, which is again the benchmark
which is achieved by the organisation. Process Approach is the fourth one and this needs to
be checked by the concerned company too. The process of manufacturing and re-checking the
product has been missing in the company as the CEO asked for processing the products in a
new advanced way which reduced the check of beta. The fifth one is improvement; Tesla has
been improvising its products on regular intervals with new modified models, but it has not
been maintaining the quality of modification. Sixth is Evidence based decision making which
needs to be considered by the company as the organisation has been working with a vision of
providing something new to the people irrespective of the requirement of the people. The
company works on the idea of creating demand for its products and creating use of its
products. Lastly, is the relationship management, which the company has maintained quite
accurately, as even after marking multiple issues in its cars, the company was presented by a
magazine as the best car for S P58D. The principles of quality management display the
benchmarks for the organisations which provide them with some standards for its products
and services in order to sustain in the industry.
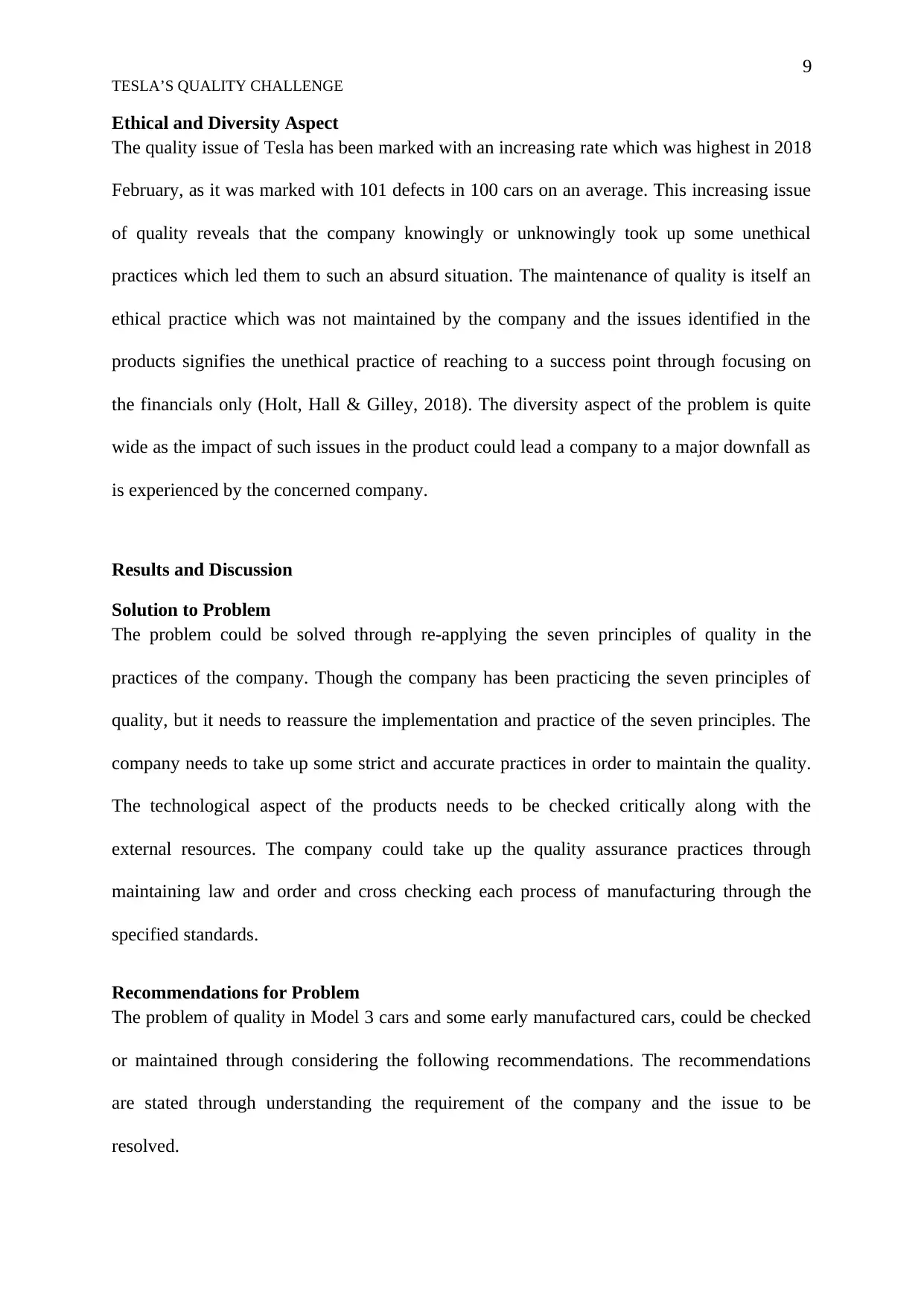
9
TESLA’S QUALITY CHALLENGE
Ethical and Diversity Aspect
The quality issue of Tesla has been marked with an increasing rate which was highest in 2018
February, as it was marked with 101 defects in 100 cars on an average. This increasing issue
of quality reveals that the company knowingly or unknowingly took up some unethical
practices which led them to such an absurd situation. The maintenance of quality is itself an
ethical practice which was not maintained by the company and the issues identified in the
products signifies the unethical practice of reaching to a success point through focusing on
the financials only (Holt, Hall & Gilley, 2018). The diversity aspect of the problem is quite
wide as the impact of such issues in the product could lead a company to a major downfall as
is experienced by the concerned company.
Results and Discussion
Solution to Problem
The problem could be solved through re-applying the seven principles of quality in the
practices of the company. Though the company has been practicing the seven principles of
quality, but it needs to reassure the implementation and practice of the seven principles. The
company needs to take up some strict and accurate practices in order to maintain the quality.
The technological aspect of the products needs to be checked critically along with the
external resources. The company could take up the quality assurance practices through
maintaining law and order and cross checking each process of manufacturing through the
specified standards.
Recommendations for Problem
The problem of quality in Model 3 cars and some early manufactured cars, could be checked
or maintained through considering the following recommendations. The recommendations
are stated through understanding the requirement of the company and the issue to be
resolved.
TESLA’S QUALITY CHALLENGE
Ethical and Diversity Aspect
The quality issue of Tesla has been marked with an increasing rate which was highest in 2018
February, as it was marked with 101 defects in 100 cars on an average. This increasing issue
of quality reveals that the company knowingly or unknowingly took up some unethical
practices which led them to such an absurd situation. The maintenance of quality is itself an
ethical practice which was not maintained by the company and the issues identified in the
products signifies the unethical practice of reaching to a success point through focusing on
the financials only (Holt, Hall & Gilley, 2018). The diversity aspect of the problem is quite
wide as the impact of such issues in the product could lead a company to a major downfall as
is experienced by the concerned company.
Results and Discussion
Solution to Problem
The problem could be solved through re-applying the seven principles of quality in the
practices of the company. Though the company has been practicing the seven principles of
quality, but it needs to reassure the implementation and practice of the seven principles. The
company needs to take up some strict and accurate practices in order to maintain the quality.
The technological aspect of the products needs to be checked critically along with the
external resources. The company could take up the quality assurance practices through
maintaining law and order and cross checking each process of manufacturing through the
specified standards.
Recommendations for Problem
The problem of quality in Model 3 cars and some early manufactured cars, could be checked
or maintained through considering the following recommendations. The recommendations
are stated through understanding the requirement of the company and the issue to be
resolved.
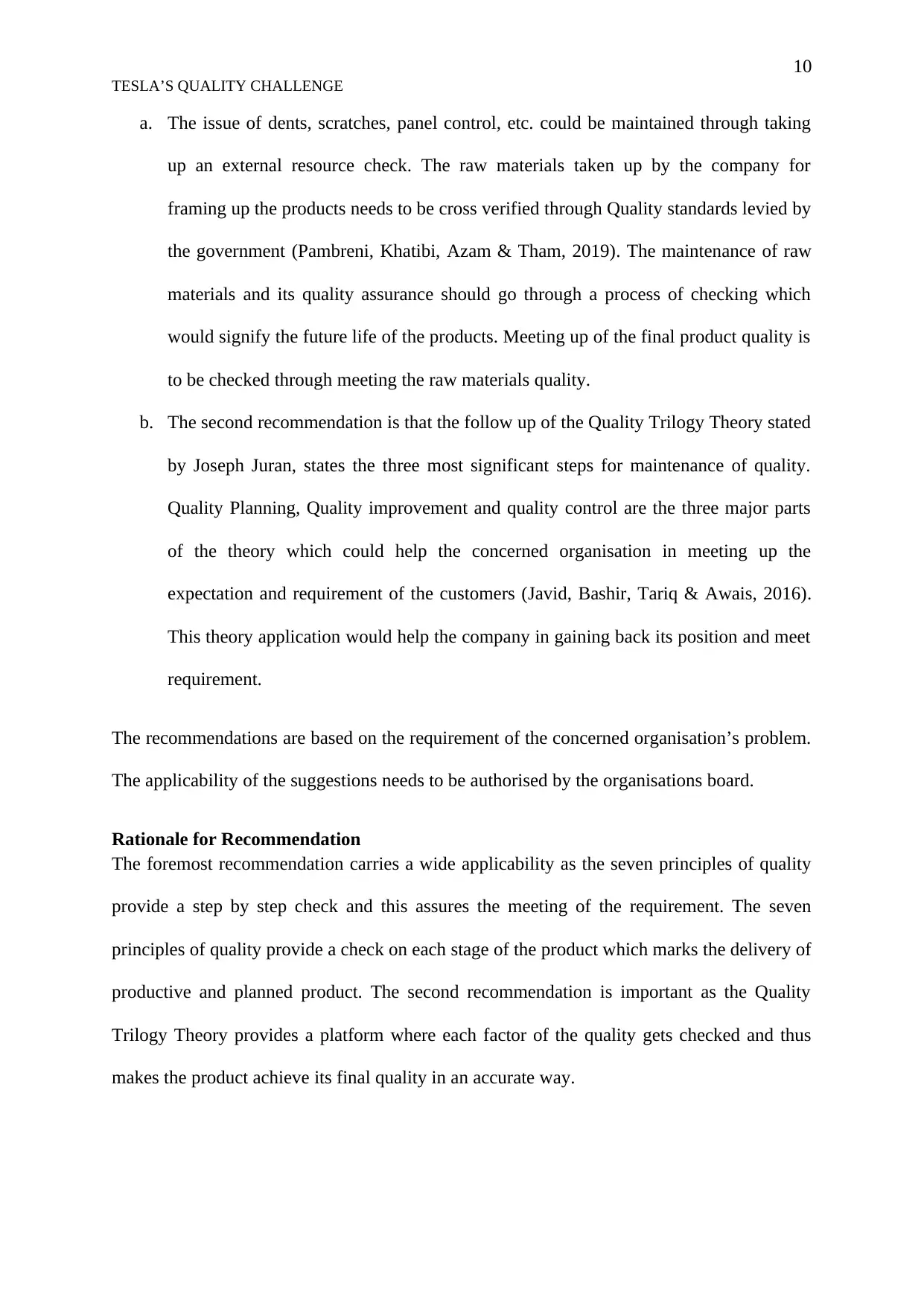
10
TESLA’S QUALITY CHALLENGE
a. The issue of dents, scratches, panel control, etc. could be maintained through taking
up an external resource check. The raw materials taken up by the company for
framing up the products needs to be cross verified through Quality standards levied by
the government (Pambreni, Khatibi, Azam & Tham, 2019). The maintenance of raw
materials and its quality assurance should go through a process of checking which
would signify the future life of the products. Meeting up of the final product quality is
to be checked through meeting the raw materials quality.
b. The second recommendation is that the follow up of the Quality Trilogy Theory stated
by Joseph Juran, states the three most significant steps for maintenance of quality.
Quality Planning, Quality improvement and quality control are the three major parts
of the theory which could help the concerned organisation in meeting up the
expectation and requirement of the customers (Javid, Bashir, Tariq & Awais, 2016).
This theory application would help the company in gaining back its position and meet
requirement.
The recommendations are based on the requirement of the concerned organisation’s problem.
The applicability of the suggestions needs to be authorised by the organisations board.
Rationale for Recommendation
The foremost recommendation carries a wide applicability as the seven principles of quality
provide a step by step check and this assures the meeting of the requirement. The seven
principles of quality provide a check on each stage of the product which marks the delivery of
productive and planned product. The second recommendation is important as the Quality
Trilogy Theory provides a platform where each factor of the quality gets checked and thus
makes the product achieve its final quality in an accurate way.
TESLA’S QUALITY CHALLENGE
a. The issue of dents, scratches, panel control, etc. could be maintained through taking
up an external resource check. The raw materials taken up by the company for
framing up the products needs to be cross verified through Quality standards levied by
the government (Pambreni, Khatibi, Azam & Tham, 2019). The maintenance of raw
materials and its quality assurance should go through a process of checking which
would signify the future life of the products. Meeting up of the final product quality is
to be checked through meeting the raw materials quality.
b. The second recommendation is that the follow up of the Quality Trilogy Theory stated
by Joseph Juran, states the three most significant steps for maintenance of quality.
Quality Planning, Quality improvement and quality control are the three major parts
of the theory which could help the concerned organisation in meeting up the
expectation and requirement of the customers (Javid, Bashir, Tariq & Awais, 2016).
This theory application would help the company in gaining back its position and meet
requirement.
The recommendations are based on the requirement of the concerned organisation’s problem.
The applicability of the suggestions needs to be authorised by the organisations board.
Rationale for Recommendation
The foremost recommendation carries a wide applicability as the seven principles of quality
provide a step by step check and this assures the meeting of the requirement. The seven
principles of quality provide a check on each stage of the product which marks the delivery of
productive and planned product. The second recommendation is important as the Quality
Trilogy Theory provides a platform where each factor of the quality gets checked and thus
makes the product achieve its final quality in an accurate way.
Secure Best Marks with AI Grader
Need help grading? Try our AI Grader for instant feedback on your assignments.

11
TESLA’S QUALITY CHALLENGE
Implementation of Recommendation
The implementation of the seven principles could be done through providing the employees
with a new format of quality check and stating the significance of the new principles
(Tortorella, Giglio, Fogliatto & Sawhney, 2019). The principles of quality need to be
presented to the employees or the executors in a way that they understand the results that
could be achieved through its application and the improvement that could be achieved in the
organisation’s outlook. A team should be framed up for checking on the practice of seven
principles and applications of the same. The second theory of Juan needs to be implemented
through framing up three teams one for quality planning, second for quality enhancement and
thirdly for quality control (Komives & Wagner, 2016). These three teams would be
responsible for execution of each step and thus the quality improvement would be attained.
The follow up of each step in the theory would assure enhancement in quality and thus
improvement in Tesla’s products.
Impact on Ethical and diversity aspect
The impact on the ethical practices of the company would be enhanced too through the
follow up of the new theories and practices. The two new theories or models would provide
the company with a check point of quality on each segment and thus the overall delivery of
the product would be of high quality. The two theories are wide and diverse in nature which
would provide the company with a wide and diversified practice on quality.
TESLA’S QUALITY CHALLENGE
Implementation of Recommendation
The implementation of the seven principles could be done through providing the employees
with a new format of quality check and stating the significance of the new principles
(Tortorella, Giglio, Fogliatto & Sawhney, 2019). The principles of quality need to be
presented to the employees or the executors in a way that they understand the results that
could be achieved through its application and the improvement that could be achieved in the
organisation’s outlook. A team should be framed up for checking on the practice of seven
principles and applications of the same. The second theory of Juan needs to be implemented
through framing up three teams one for quality planning, second for quality enhancement and
thirdly for quality control (Komives & Wagner, 2016). These three teams would be
responsible for execution of each step and thus the quality improvement would be attained.
The follow up of each step in the theory would assure enhancement in quality and thus
improvement in Tesla’s products.
Impact on Ethical and diversity aspect
The impact on the ethical practices of the company would be enhanced too through the
follow up of the new theories and practices. The two new theories or models would provide
the company with a check point of quality on each segment and thus the overall delivery of
the product would be of high quality. The two theories are wide and diverse in nature which
would provide the company with a wide and diversified practice on quality.
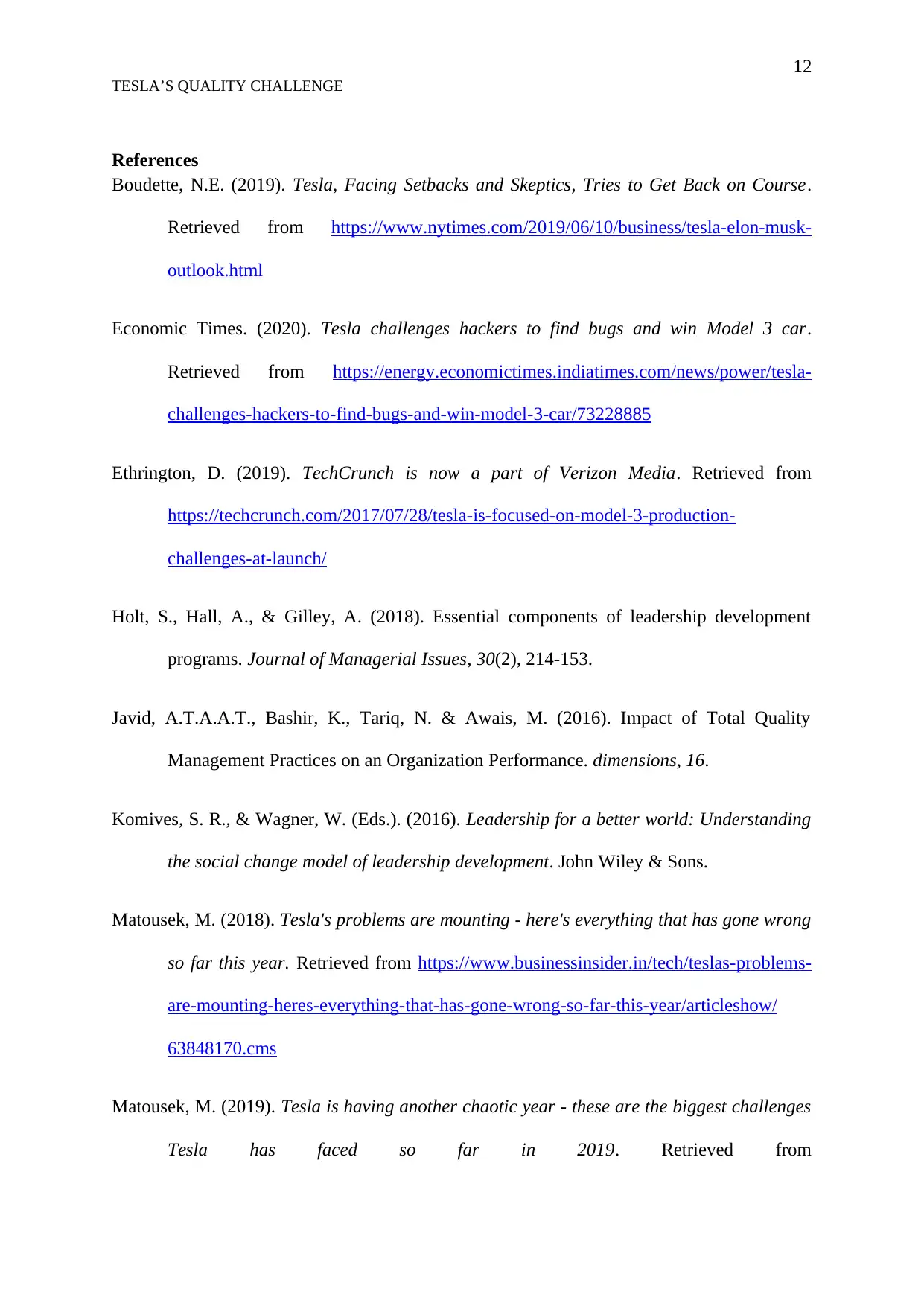
12
TESLA’S QUALITY CHALLENGE
References
Boudette, N.E. (2019). Tesla, Facing Setbacks and Skeptics, Tries to Get Back on Course.
Retrieved from https://www.nytimes.com/2019/06/10/business/tesla-elon-musk-
outlook.html
Economic Times. (2020). Tesla challenges hackers to find bugs and win Model 3 car.
Retrieved from https://energy.economictimes.indiatimes.com/news/power/tesla-
challenges-hackers-to-find-bugs-and-win-model-3-car/73228885
Ethrington, D. (2019). TechCrunch is now a part of Verizon Media. Retrieved from
https://techcrunch.com/2017/07/28/tesla-is-focused-on-model-3-production-
challenges-at-launch/
Holt, S., Hall, A., & Gilley, A. (2018). Essential components of leadership development
programs. Journal of Managerial Issues, 30(2), 214-153.
Javid, A.T.A.A.T., Bashir, K., Tariq, N. & Awais, M. (2016). Impact of Total Quality
Management Practices on an Organization Performance. dimensions, 16.
Komives, S. R., & Wagner, W. (Eds.). (2016). Leadership for a better world: Understanding
the social change model of leadership development. John Wiley & Sons.
Matousek, M. (2018). Tesla's problems are mounting - here's everything that has gone wrong
so far this year. Retrieved from https://www.businessinsider.in/tech/teslas-problems-
are-mounting-heres-everything-that-has-gone-wrong-so-far-this-year/articleshow/
63848170.cms
Matousek, M. (2019). Tesla is having another chaotic year - these are the biggest challenges
Tesla has faced so far in 2019. Retrieved from
TESLA’S QUALITY CHALLENGE
References
Boudette, N.E. (2019). Tesla, Facing Setbacks and Skeptics, Tries to Get Back on Course.
Retrieved from https://www.nytimes.com/2019/06/10/business/tesla-elon-musk-
outlook.html
Economic Times. (2020). Tesla challenges hackers to find bugs and win Model 3 car.
Retrieved from https://energy.economictimes.indiatimes.com/news/power/tesla-
challenges-hackers-to-find-bugs-and-win-model-3-car/73228885
Ethrington, D. (2019). TechCrunch is now a part of Verizon Media. Retrieved from
https://techcrunch.com/2017/07/28/tesla-is-focused-on-model-3-production-
challenges-at-launch/
Holt, S., Hall, A., & Gilley, A. (2018). Essential components of leadership development
programs. Journal of Managerial Issues, 30(2), 214-153.
Javid, A.T.A.A.T., Bashir, K., Tariq, N. & Awais, M. (2016). Impact of Total Quality
Management Practices on an Organization Performance. dimensions, 16.
Komives, S. R., & Wagner, W. (Eds.). (2016). Leadership for a better world: Understanding
the social change model of leadership development. John Wiley & Sons.
Matousek, M. (2018). Tesla's problems are mounting - here's everything that has gone wrong
so far this year. Retrieved from https://www.businessinsider.in/tech/teslas-problems-
are-mounting-heres-everything-that-has-gone-wrong-so-far-this-year/articleshow/
63848170.cms
Matousek, M. (2019). Tesla is having another chaotic year - these are the biggest challenges
Tesla has faced so far in 2019. Retrieved from
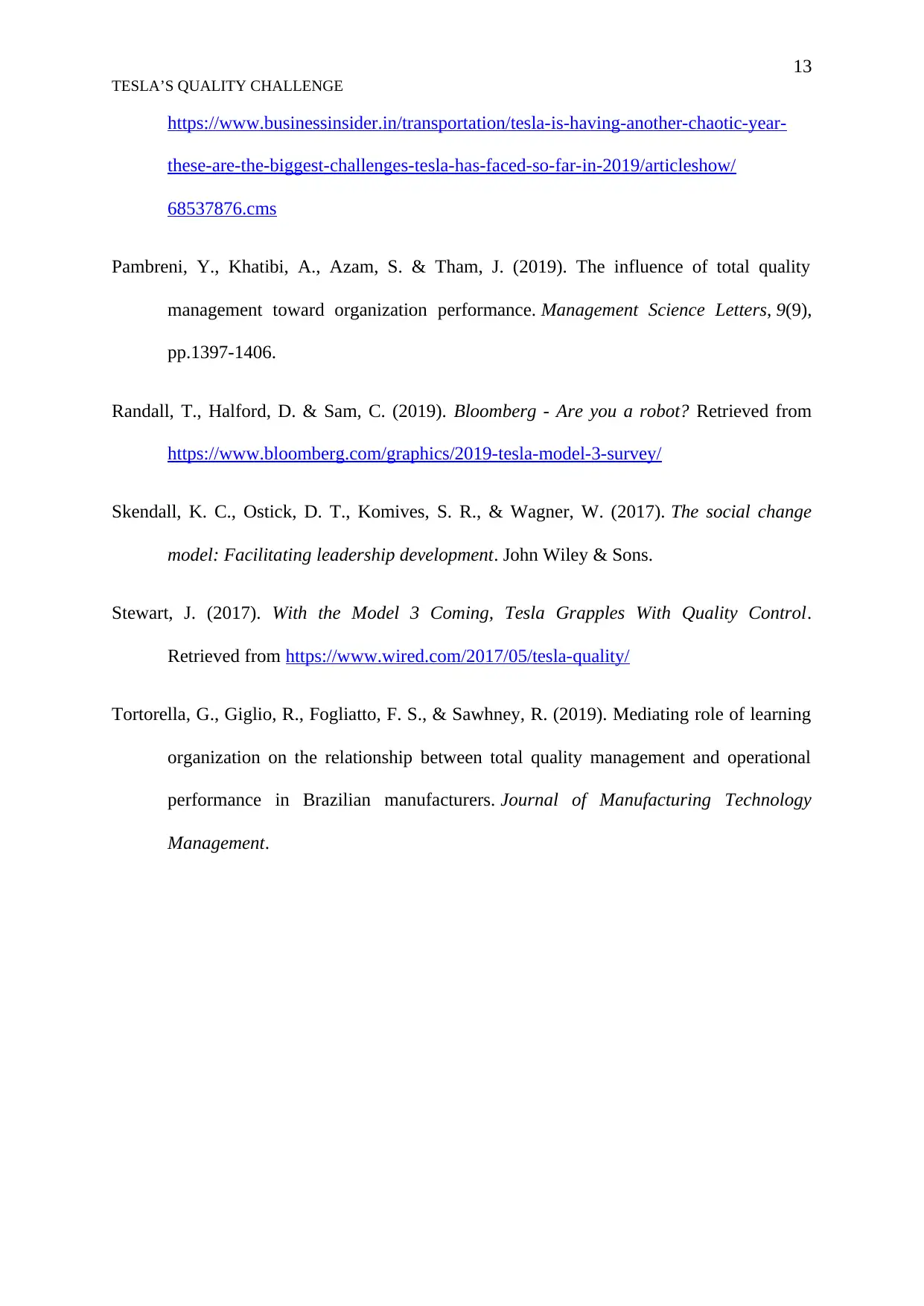
13
TESLA’S QUALITY CHALLENGE
https://www.businessinsider.in/transportation/tesla-is-having-another-chaotic-year-
these-are-the-biggest-challenges-tesla-has-faced-so-far-in-2019/articleshow/
68537876.cms
Pambreni, Y., Khatibi, A., Azam, S. & Tham, J. (2019). The influence of total quality
management toward organization performance. Management Science Letters, 9(9),
pp.1397-1406.
Randall, T., Halford, D. & Sam, C. (2019). Bloomberg - Are you a robot? Retrieved from
https://www.bloomberg.com/graphics/2019-tesla-model-3-survey/
Skendall, K. C., Ostick, D. T., Komives, S. R., & Wagner, W. (2017). The social change
model: Facilitating leadership development. John Wiley & Sons.
Stewart, J. (2017). With the Model 3 Coming, Tesla Grapples With Quality Control.
Retrieved from https://www.wired.com/2017/05/tesla-quality/
Tortorella, G., Giglio, R., Fogliatto, F. S., & Sawhney, R. (2019). Mediating role of learning
organization on the relationship between total quality management and operational
performance in Brazilian manufacturers. Journal of Manufacturing Technology
Management.
TESLA’S QUALITY CHALLENGE
https://www.businessinsider.in/transportation/tesla-is-having-another-chaotic-year-
these-are-the-biggest-challenges-tesla-has-faced-so-far-in-2019/articleshow/
68537876.cms
Pambreni, Y., Khatibi, A., Azam, S. & Tham, J. (2019). The influence of total quality
management toward organization performance. Management Science Letters, 9(9),
pp.1397-1406.
Randall, T., Halford, D. & Sam, C. (2019). Bloomberg - Are you a robot? Retrieved from
https://www.bloomberg.com/graphics/2019-tesla-model-3-survey/
Skendall, K. C., Ostick, D. T., Komives, S. R., & Wagner, W. (2017). The social change
model: Facilitating leadership development. John Wiley & Sons.
Stewart, J. (2017). With the Model 3 Coming, Tesla Grapples With Quality Control.
Retrieved from https://www.wired.com/2017/05/tesla-quality/
Tortorella, G., Giglio, R., Fogliatto, F. S., & Sawhney, R. (2019). Mediating role of learning
organization on the relationship between total quality management and operational
performance in Brazilian manufacturers. Journal of Manufacturing Technology
Management.
1 out of 13
Related Documents
![[object Object]](/_next/image/?url=%2F_next%2Fstatic%2Fmedia%2Flogo.6d15ce61.png&w=640&q=75)
Your All-in-One AI-Powered Toolkit for Academic Success.
+13062052269
info@desklib.com
Available 24*7 on WhatsApp / Email
Unlock your academic potential
© 2024 | Zucol Services PVT LTD | All rights reserved.