Implementing ISO 9001 for Para Pon X Securities
VerifiedAdded on  2022/11/30
|16
|3192
|55
AI Summary
This study explains the steps to implement ISO 9001 certification for Para Pon X Securities, a private security company. It discusses the importance of ISO certification, the basic requirements before implementation, and the phases of implementation. The study also highlights the benefits of ISO certification for the company.
Contribute Materials
Your contribution can guide someone’s learning journey. Share your
documents today.
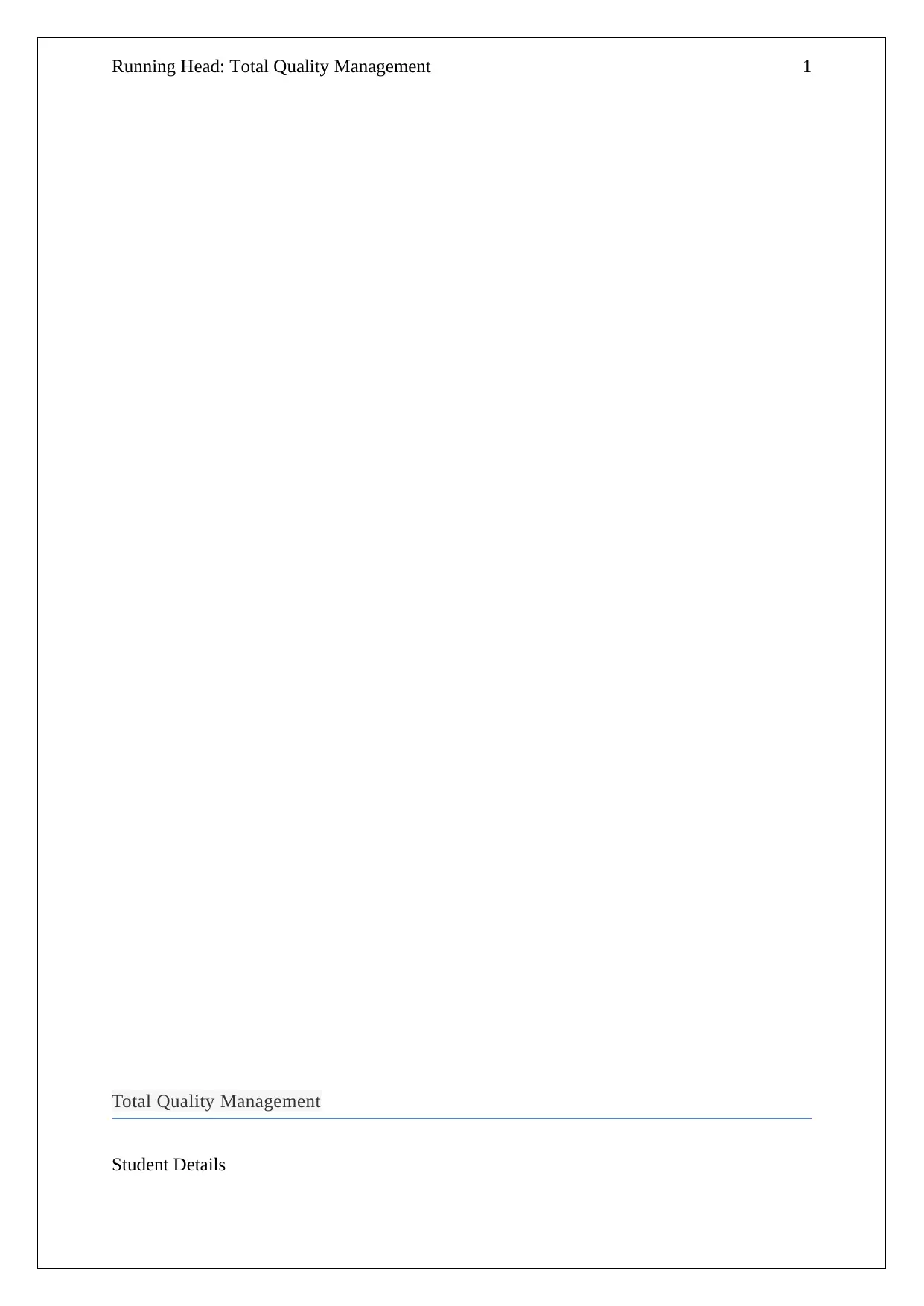
Running Head: Total Quality Management 1
Total Quality Management
Student Details
Total Quality Management
Student Details
Secure Best Marks with AI Grader
Need help grading? Try our AI Grader for instant feedback on your assignments.
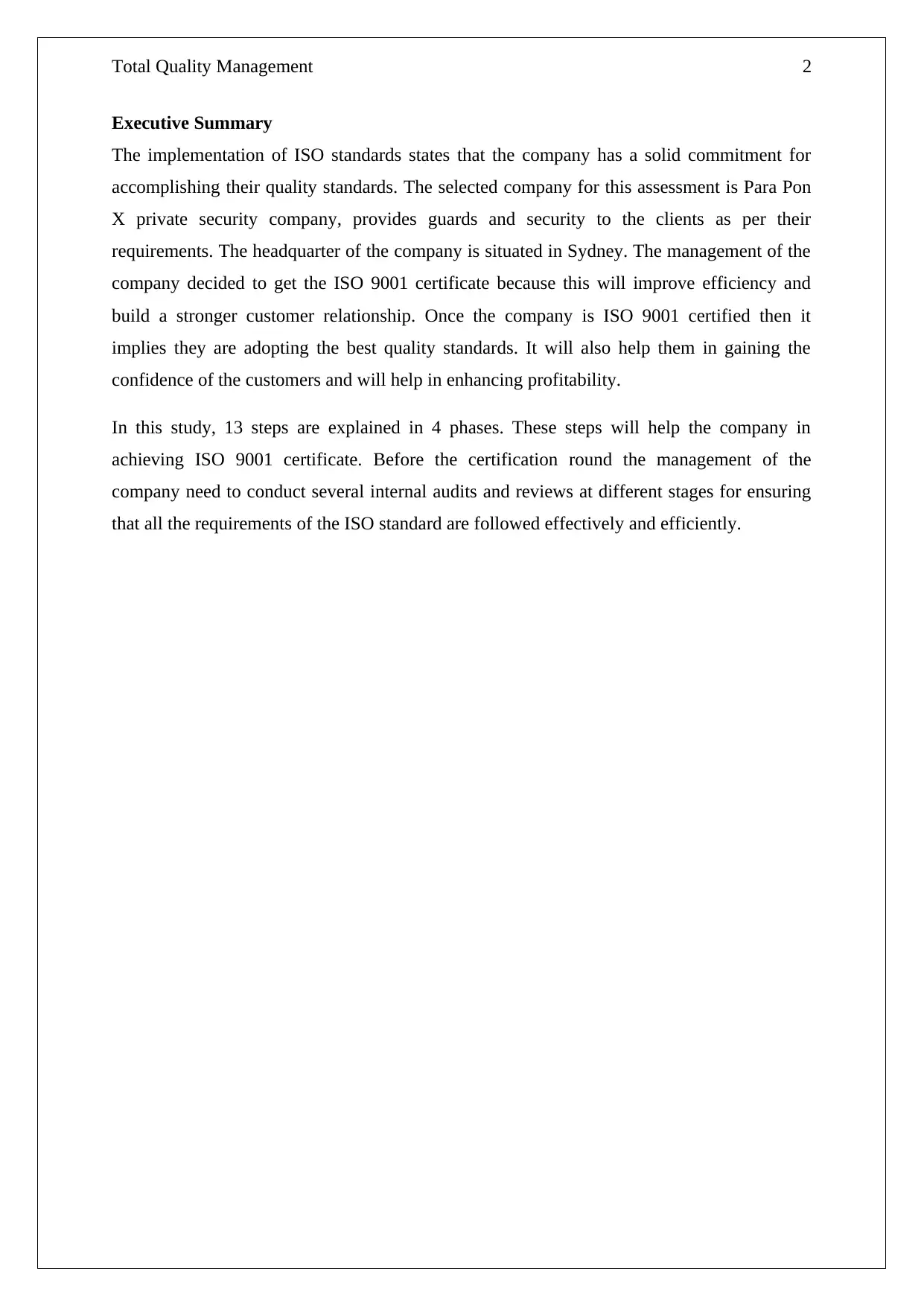
Total Quality Management 2
Executive Summary
The implementation of ISO standards states that the company has a solid commitment for
accomplishing their quality standards. The selected company for this assessment is Para Pon
X private security company, provides guards and security to the clients as per their
requirements. The headquarter of the company is situated in Sydney. The management of the
company decided to get the ISO 9001 certificate because this will improve efficiency and
build a stronger customer relationship. Once the company is ISO 9001 certified then it
implies they are adopting the best quality standards. It will also help them in gaining the
confidence of the customers and will help in enhancing profitability.
In this study, 13 steps are explained in 4 phases. These steps will help the company in
achieving ISO 9001 certificate. Before the certification round the management of the
company need to conduct several internal audits and reviews at different stages for ensuring
that all the requirements of the ISO standard are followed effectively and efficiently.
Executive Summary
The implementation of ISO standards states that the company has a solid commitment for
accomplishing their quality standards. The selected company for this assessment is Para Pon
X private security company, provides guards and security to the clients as per their
requirements. The headquarter of the company is situated in Sydney. The management of the
company decided to get the ISO 9001 certificate because this will improve efficiency and
build a stronger customer relationship. Once the company is ISO 9001 certified then it
implies they are adopting the best quality standards. It will also help them in gaining the
confidence of the customers and will help in enhancing profitability.
In this study, 13 steps are explained in 4 phases. These steps will help the company in
achieving ISO 9001 certificate. Before the certification round the management of the
company need to conduct several internal audits and reviews at different stages for ensuring
that all the requirements of the ISO standard are followed effectively and efficiently.
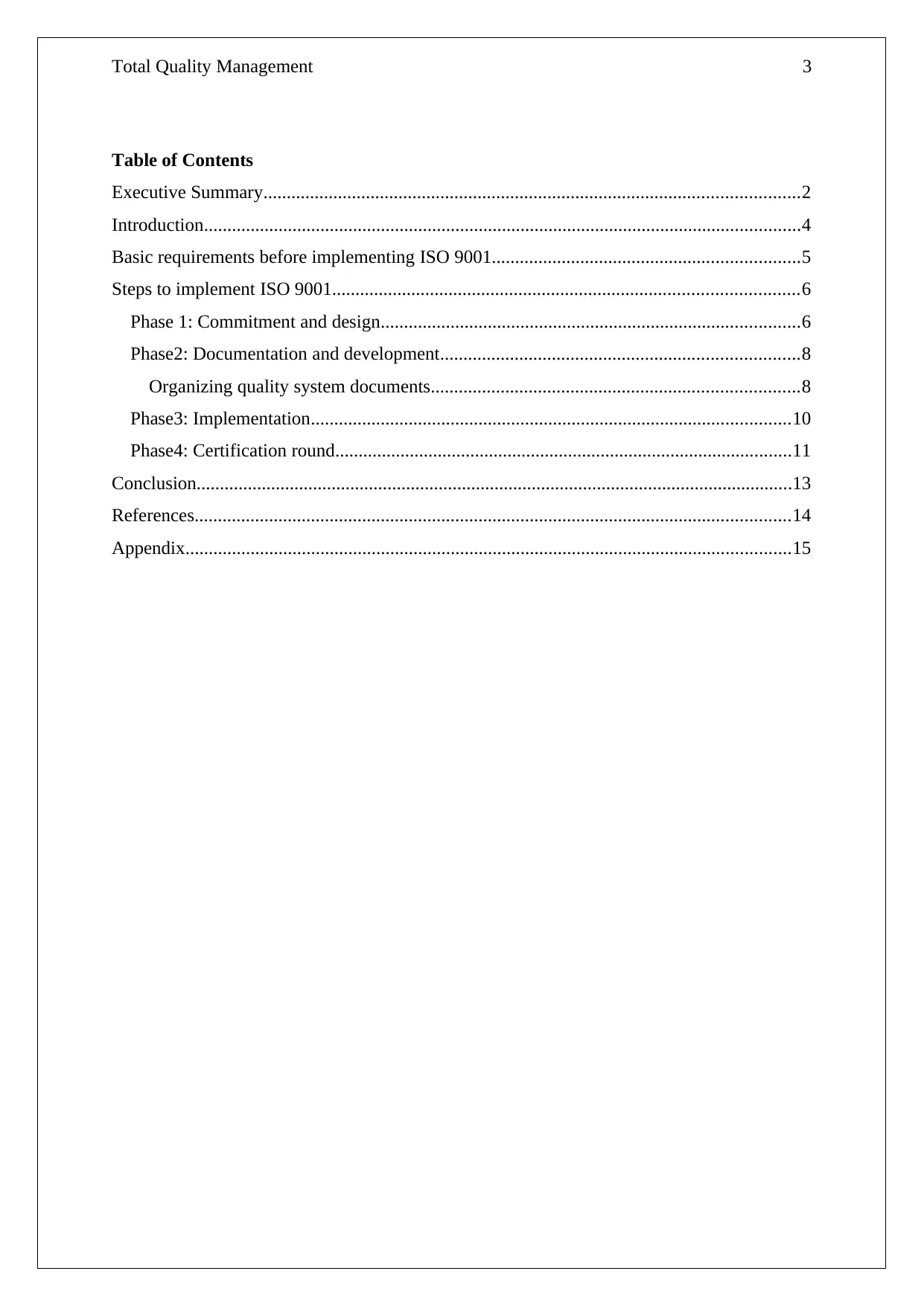
Total Quality Management 3
Table of Contents
Executive Summary...................................................................................................................2
Introduction................................................................................................................................4
Basic requirements before implementing ISO 9001..................................................................5
Steps to implement ISO 9001....................................................................................................6
Phase 1: Commitment and design..........................................................................................6
Phase2: Documentation and development.............................................................................8
Organizing quality system documents...............................................................................8
Phase3: Implementation.......................................................................................................10
Phase4: Certification round..................................................................................................11
Conclusion................................................................................................................................13
References................................................................................................................................14
Appendix..................................................................................................................................15
Table of Contents
Executive Summary...................................................................................................................2
Introduction................................................................................................................................4
Basic requirements before implementing ISO 9001..................................................................5
Steps to implement ISO 9001....................................................................................................6
Phase 1: Commitment and design..........................................................................................6
Phase2: Documentation and development.............................................................................8
Organizing quality system documents...............................................................................8
Phase3: Implementation.......................................................................................................10
Phase4: Certification round..................................................................................................11
Conclusion................................................................................................................................13
References................................................................................................................................14
Appendix..................................................................................................................................15
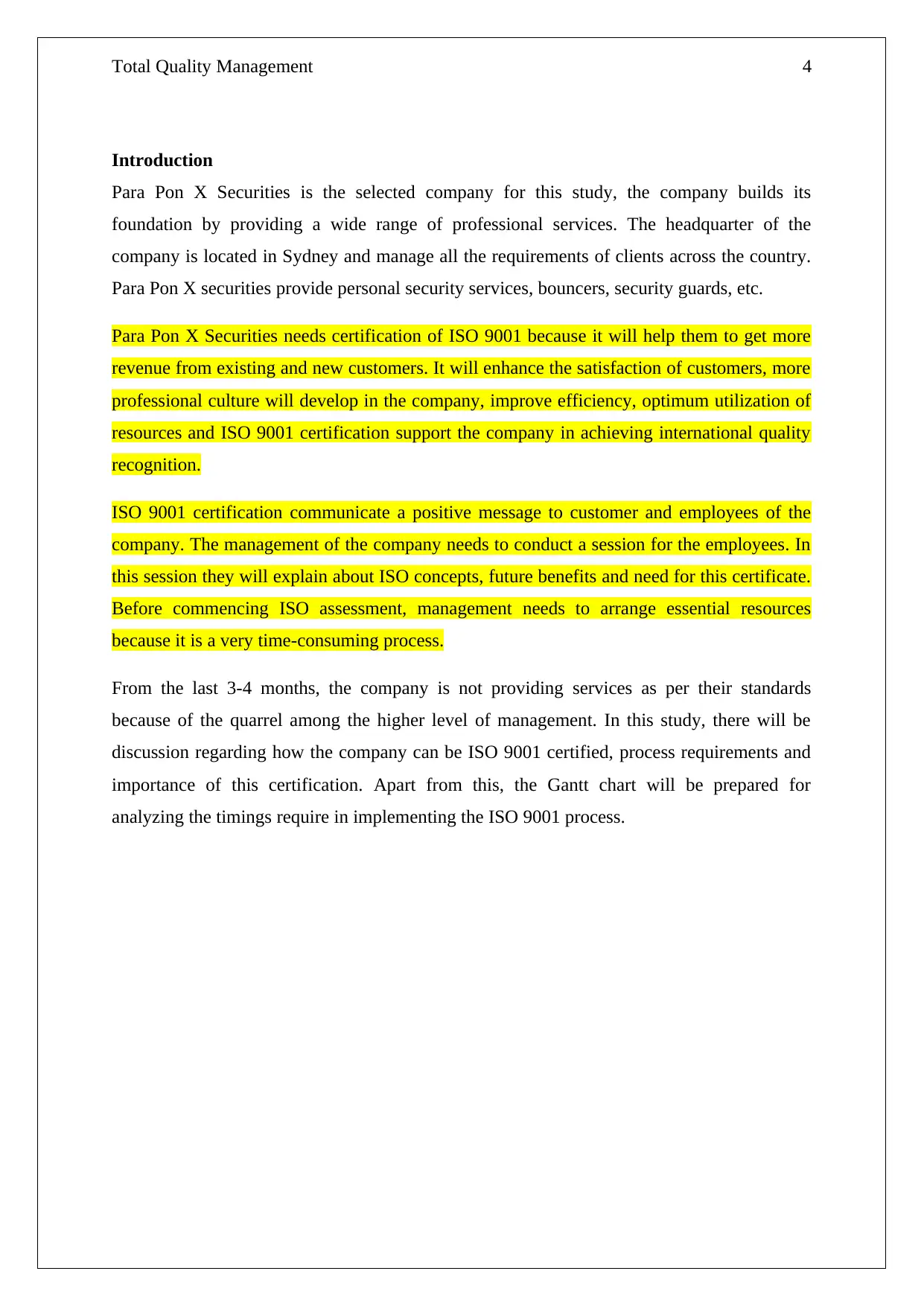
Total Quality Management 4
Introduction
Para Pon X Securities is the selected company for this study, the company builds its
foundation by providing a wide range of professional services. The headquarter of the
company is located in Sydney and manage all the requirements of clients across the country.
Para Pon X securities provide personal security services, bouncers, security guards, etc.
Para Pon X Securities needs certification of ISO 9001 because it will help them to get more
revenue from existing and new customers. It will enhance the satisfaction of customers, more
professional culture will develop in the company, improve efficiency, optimum utilization of
resources and ISO 9001 certification support the company in achieving international quality
recognition.
ISO 9001 certification communicate a positive message to customer and employees of the
company. The management of the company needs to conduct a session for the employees. In
this session they will explain about ISO concepts, future benefits and need for this certificate.
Before commencing ISO assessment, management needs to arrange essential resources
because it is a very time-consuming process.
From the last 3-4 months, the company is not providing services as per their standards
because of the quarrel among the higher level of management. In this study, there will be
discussion regarding how the company can be ISO 9001 certified, process requirements and
importance of this certification. Apart from this, the Gantt chart will be prepared for
analyzing the timings require in implementing the ISO 9001 process.
Introduction
Para Pon X Securities is the selected company for this study, the company builds its
foundation by providing a wide range of professional services. The headquarter of the
company is located in Sydney and manage all the requirements of clients across the country.
Para Pon X securities provide personal security services, bouncers, security guards, etc.
Para Pon X Securities needs certification of ISO 9001 because it will help them to get more
revenue from existing and new customers. It will enhance the satisfaction of customers, more
professional culture will develop in the company, improve efficiency, optimum utilization of
resources and ISO 9001 certification support the company in achieving international quality
recognition.
ISO 9001 certification communicate a positive message to customer and employees of the
company. The management of the company needs to conduct a session for the employees. In
this session they will explain about ISO concepts, future benefits and need for this certificate.
Before commencing ISO assessment, management needs to arrange essential resources
because it is a very time-consuming process.
From the last 3-4 months, the company is not providing services as per their standards
because of the quarrel among the higher level of management. In this study, there will be
discussion regarding how the company can be ISO 9001 certified, process requirements and
importance of this certification. Apart from this, the Gantt chart will be prepared for
analyzing the timings require in implementing the ISO 9001 process.
Secure Best Marks with AI Grader
Need help grading? Try our AI Grader for instant feedback on your assignments.
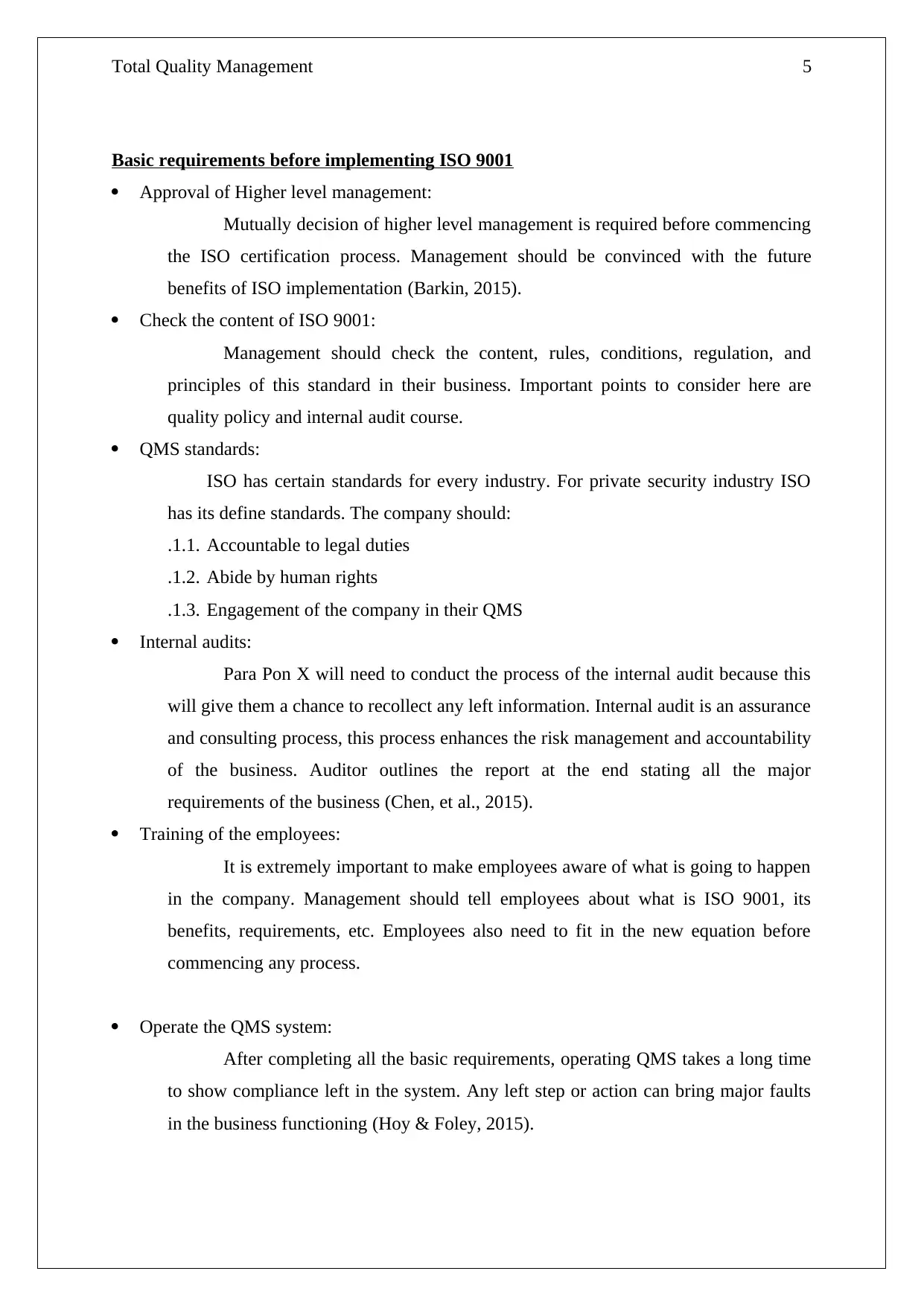
Total Quality Management 5
Basic requirements before implementing ISO 9001
ï‚· Approval of Higher level management:
Mutually decision of higher level management is required before commencing
the ISO certification process. Management should be convinced with the future
benefits of ISO implementation (Barkin, 2015).
ï‚· Check the content of ISO 9001:
Management should check the content, rules, conditions, regulation, and
principles of this standard in their business. Important points to consider here are
quality policy and internal audit course.
ï‚· QMS standards:
ISO has certain standards for every industry. For private security industry ISO
has its define standards. The company should:
.1.1. Accountable to legal duties
.1.2. Abide by human rights
.1.3. Engagement of the company in their QMS
ï‚· Internal audits:
Para Pon X will need to conduct the process of the internal audit because this
will give them a chance to recollect any left information. Internal audit is an assurance
and consulting process, this process enhances the risk management and accountability
of the business. Auditor outlines the report at the end stating all the major
requirements of the business (Chen, et al., 2015).
ï‚· Training of the employees:
It is extremely important to make employees aware of what is going to happen
in the company. Management should tell employees about what is ISO 9001, its
benefits, requirements, etc. Employees also need to fit in the new equation before
commencing any process.
ï‚· Operate the QMS system:
After completing all the basic requirements, operating QMS takes a long time
to show compliance left in the system. Any left step or action can bring major faults
in the business functioning (Hoy & Foley, 2015).
Basic requirements before implementing ISO 9001
ï‚· Approval of Higher level management:
Mutually decision of higher level management is required before commencing
the ISO certification process. Management should be convinced with the future
benefits of ISO implementation (Barkin, 2015).
ï‚· Check the content of ISO 9001:
Management should check the content, rules, conditions, regulation, and
principles of this standard in their business. Important points to consider here are
quality policy and internal audit course.
ï‚· QMS standards:
ISO has certain standards for every industry. For private security industry ISO
has its define standards. The company should:
.1.1. Accountable to legal duties
.1.2. Abide by human rights
.1.3. Engagement of the company in their QMS
ï‚· Internal audits:
Para Pon X will need to conduct the process of the internal audit because this
will give them a chance to recollect any left information. Internal audit is an assurance
and consulting process, this process enhances the risk management and accountability
of the business. Auditor outlines the report at the end stating all the major
requirements of the business (Chen, et al., 2015).
ï‚· Training of the employees:
It is extremely important to make employees aware of what is going to happen
in the company. Management should tell employees about what is ISO 9001, its
benefits, requirements, etc. Employees also need to fit in the new equation before
commencing any process.
ï‚· Operate the QMS system:
After completing all the basic requirements, operating QMS takes a long time
to show compliance left in the system. Any left step or action can bring major faults
in the business functioning (Hoy & Foley, 2015).
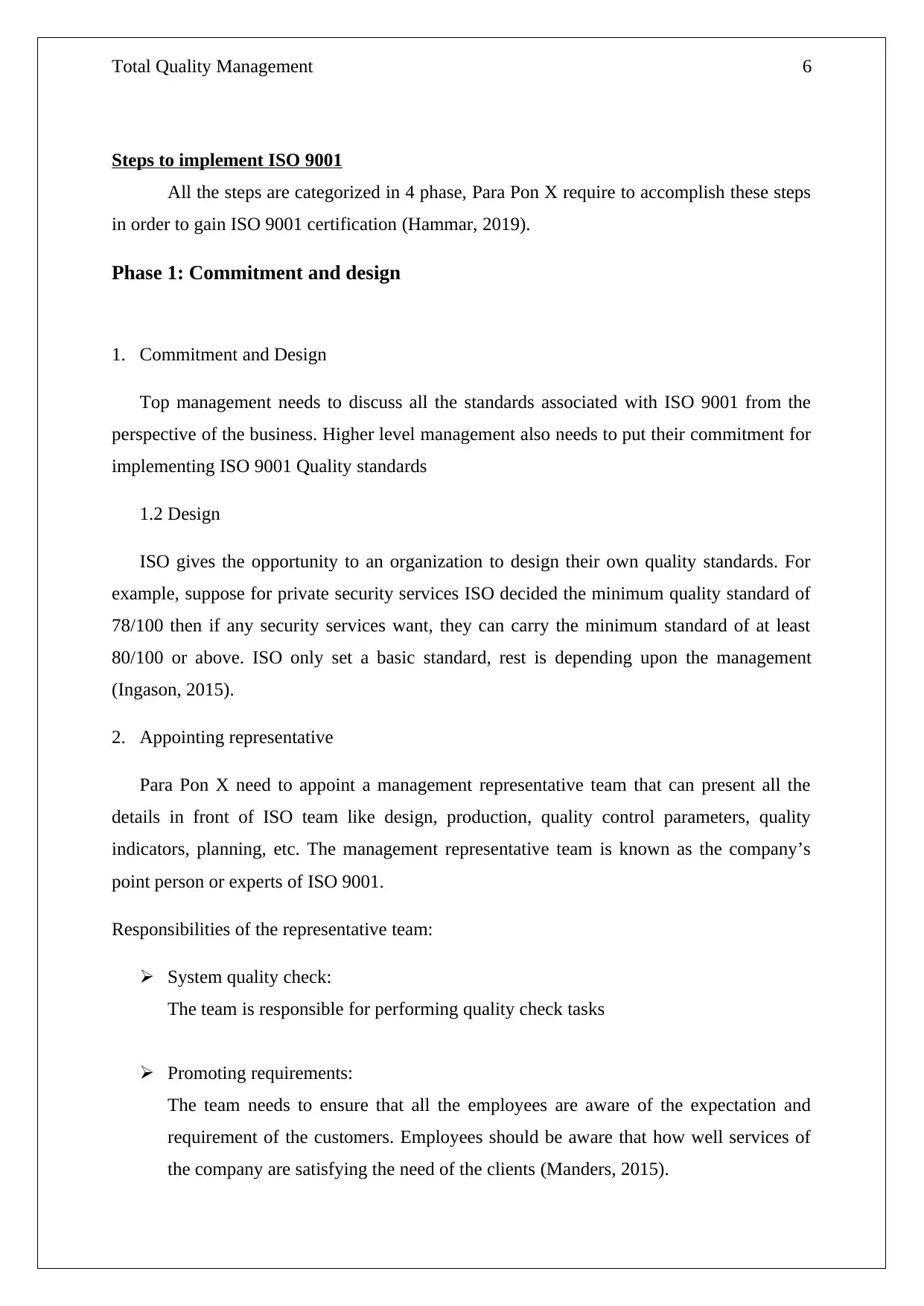
Total Quality Management 6
Steps to implement ISO 9001
All the steps are categorized in 4 phase, Para Pon X require to accomplish these steps
in order to gain ISO 9001 certification (Hammar, 2019).
Phase 1: Commitment and design
1. Commitment and Design
Top management needs to discuss all the standards associated with ISO 9001 from the
perspective of the business. Higher level management also needs to put their commitment for
implementing ISO 9001 Quality standards
1.2 Design
ISO gives the opportunity to an organization to design their own quality standards. For
example, suppose for private security services ISO decided the minimum quality standard of
78/100 then if any security services want, they can carry the minimum standard of at least
80/100 or above. ISO only set a basic standard, rest is depending upon the management
(Ingason, 2015).
2. Appointing representative
Para Pon X need to appoint a management representative team that can present all the
details in front of ISO team like design, production, quality control parameters, quality
indicators, planning, etc. The management representative team is known as the company’s
point person or experts of ISO 9001.
Responsibilities of the representative team:
 System quality check:
The team is responsible for performing quality check tasks
 Promoting requirements:
The team needs to ensure that all the employees are aware of the expectation and
requirement of the customers. Employees should be aware that how well services of
the company are satisfying the need of the clients (Manders, 2015).
Steps to implement ISO 9001
All the steps are categorized in 4 phase, Para Pon X require to accomplish these steps
in order to gain ISO 9001 certification (Hammar, 2019).
Phase 1: Commitment and design
1. Commitment and Design
Top management needs to discuss all the standards associated with ISO 9001 from the
perspective of the business. Higher level management also needs to put their commitment for
implementing ISO 9001 Quality standards
1.2 Design
ISO gives the opportunity to an organization to design their own quality standards. For
example, suppose for private security services ISO decided the minimum quality standard of
78/100 then if any security services want, they can carry the minimum standard of at least
80/100 or above. ISO only set a basic standard, rest is depending upon the management
(Ingason, 2015).
2. Appointing representative
Para Pon X need to appoint a management representative team that can present all the
details in front of ISO team like design, production, quality control parameters, quality
indicators, planning, etc. The management representative team is known as the company’s
point person or experts of ISO 9001.
Responsibilities of the representative team:
 System quality check:
The team is responsible for performing quality check tasks
 Promoting requirements:
The team needs to ensure that all the employees are aware of the expectation and
requirement of the customers. Employees should be aware that how well services of
the company are satisfying the need of the clients (Manders, 2015).
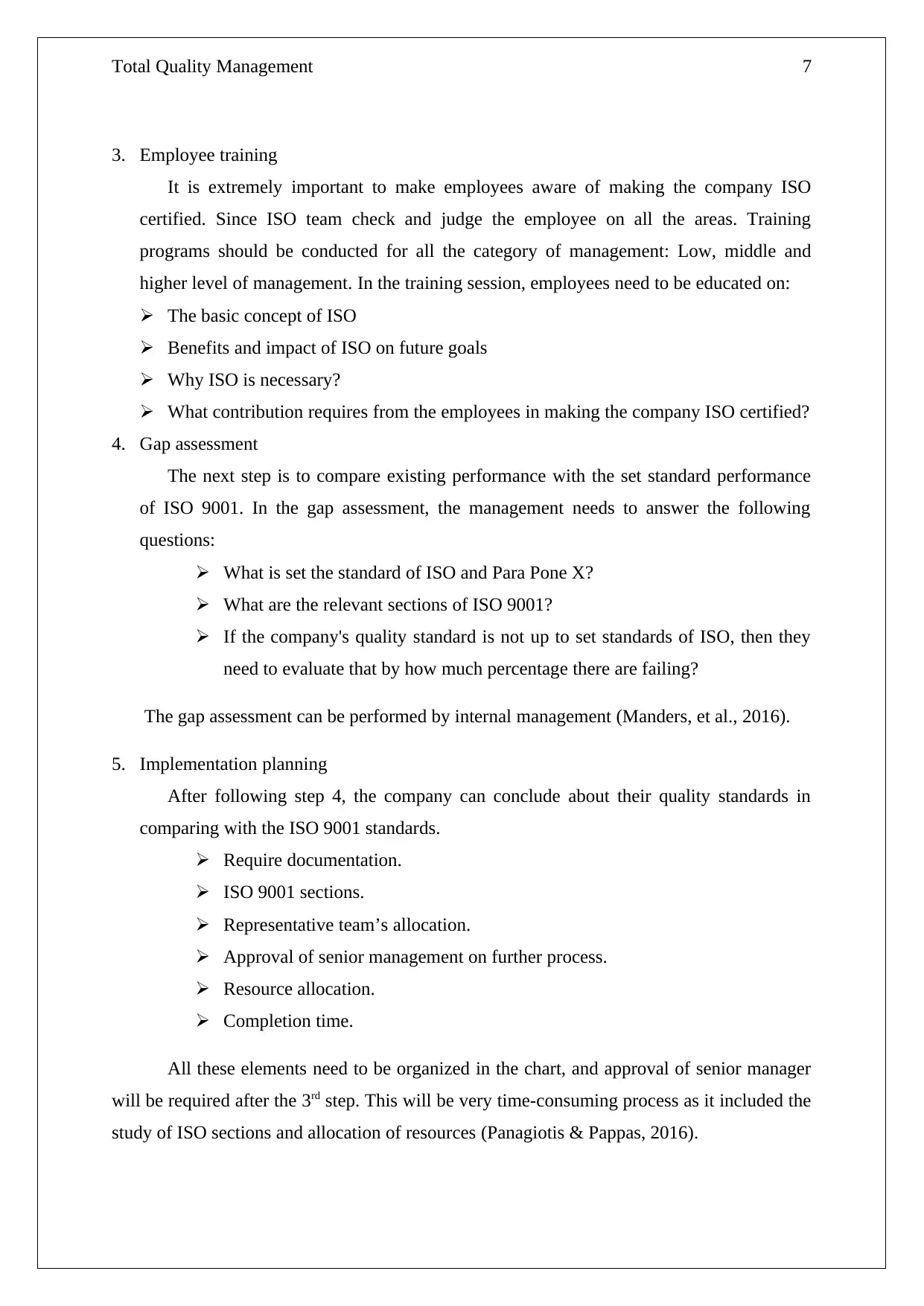
Total Quality Management 7
3. Employee training
It is extremely important to make employees aware of making the company ISO
certified. Since ISO team check and judge the employee on all the areas. Training
programs should be conducted for all the category of management: Low, middle and
higher level of management. In the training session, employees need to be educated on:
 The basic concept of ISO
 Benefits and impact of ISO on future goals
 Why ISO is necessary?
 What contribution requires from the employees in making the company ISO certified?
4. Gap assessment
The next step is to compare existing performance with the set standard performance
of ISO 9001. In the gap assessment, the management needs to answer the following
questions:
 What is set the standard of ISO and Para Pone X?
 What are the relevant sections of ISO 9001?
 If the company's quality standard is not up to set standards of ISO, then they
need to evaluate that by how much percentage there are failing?
The gap assessment can be performed by internal management (Manders, et al., 2016).
5. Implementation planning
After following step 4, the company can conclude about their quality standards in
comparing with the ISO 9001 standards.
 Require documentation.
 ISO 9001 sections.
 Representative team’s allocation.
 Approval of senior management on further process.
 Resource allocation.
 Completion time.
All these elements need to be organized in the chart, and approval of senior manager
will be required after the 3rd step. This will be very time-consuming process as it included the
study of ISO sections and allocation of resources (Panagiotis & Pappas, 2016).
3. Employee training
It is extremely important to make employees aware of making the company ISO
certified. Since ISO team check and judge the employee on all the areas. Training
programs should be conducted for all the category of management: Low, middle and
higher level of management. In the training session, employees need to be educated on:
 The basic concept of ISO
 Benefits and impact of ISO on future goals
 Why ISO is necessary?
 What contribution requires from the employees in making the company ISO certified?
4. Gap assessment
The next step is to compare existing performance with the set standard performance
of ISO 9001. In the gap assessment, the management needs to answer the following
questions:
 What is set the standard of ISO and Para Pone X?
 What are the relevant sections of ISO 9001?
 If the company's quality standard is not up to set standards of ISO, then they
need to evaluate that by how much percentage there are failing?
The gap assessment can be performed by internal management (Manders, et al., 2016).
5. Implementation planning
After following step 4, the company can conclude about their quality standards in
comparing with the ISO 9001 standards.
 Require documentation.
 ISO 9001 sections.
 Representative team’s allocation.
 Approval of senior management on further process.
 Resource allocation.
 Completion time.
All these elements need to be organized in the chart, and approval of senior manager
will be required after the 3rd step. This will be very time-consuming process as it included the
study of ISO sections and allocation of resources (Panagiotis & Pappas, 2016).
Paraphrase This Document
Need a fresh take? Get an instant paraphrase of this document with our AI Paraphraser
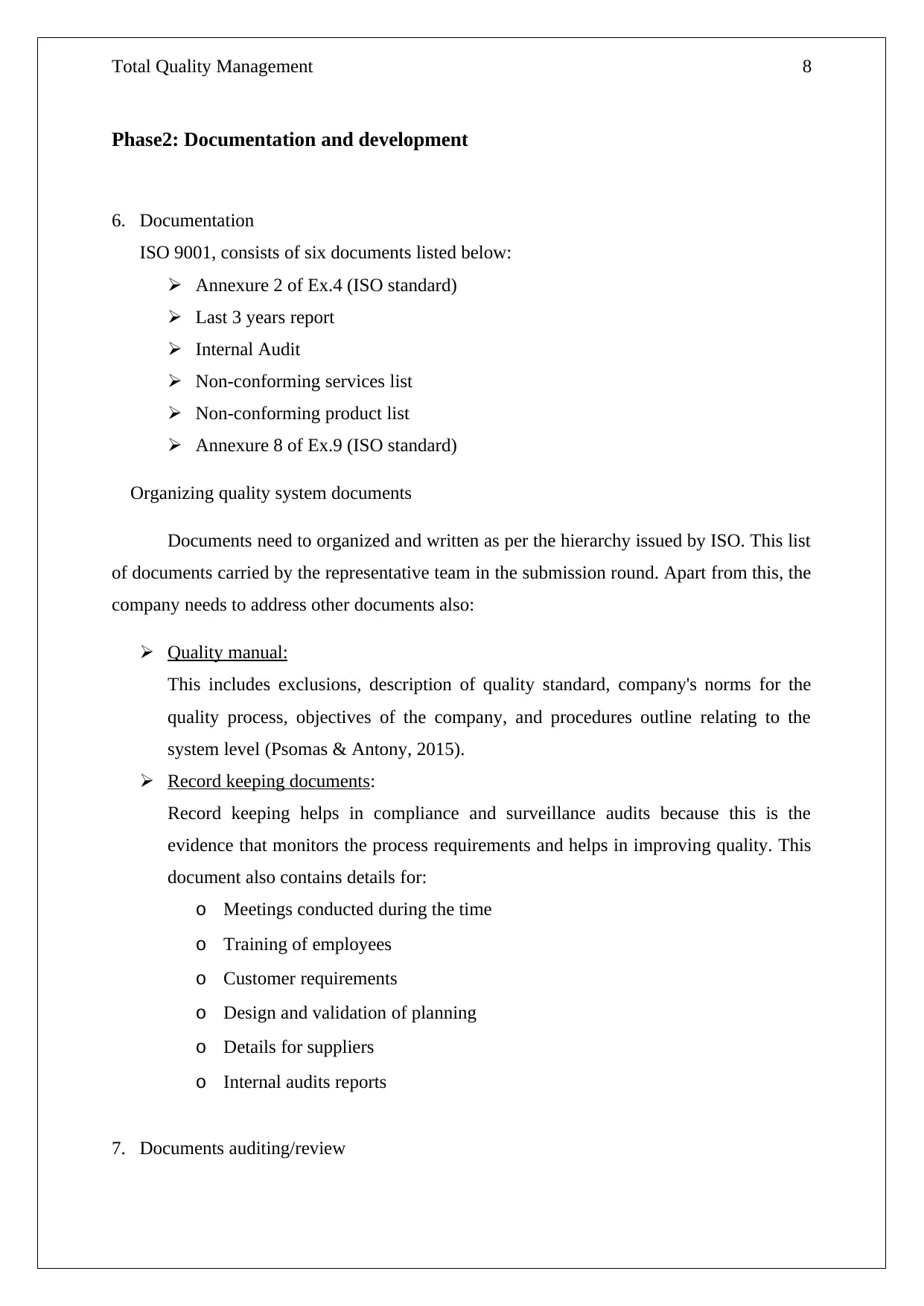
Total Quality Management 8
Phase2: Documentation and development
6. Documentation
ISO 9001, consists of six documents listed below:
 Annexure 2 of Ex.4 (ISO standard)
 Last 3 years report
 Internal Audit
 Non-conforming services list
 Non-conforming product list
 Annexure 8 of Ex.9 (ISO standard)
Organizing quality system documents
Documents need to organized and written as per the hierarchy issued by ISO. This list
of documents carried by the representative team in the submission round. Apart from this, the
company needs to address other documents also:
 Quality manual:
This includes exclusions, description of quality standard, company's norms for the
quality process, objectives of the company, and procedures outline relating to the
system level (Psomas & Antony, 2015).
 Record keeping documents:
Record keeping helps in compliance and surveillance audits because this is the
evidence that monitors the process requirements and helps in improving quality. This
document also contains details for:
o Meetings conducted during the time
o Training of employees
o Customer requirements
o Design and validation of planning
o Details for suppliers
o Internal audits reports
7. Documents auditing/review
Phase2: Documentation and development
6. Documentation
ISO 9001, consists of six documents listed below:
 Annexure 2 of Ex.4 (ISO standard)
 Last 3 years report
 Internal Audit
 Non-conforming services list
 Non-conforming product list
 Annexure 8 of Ex.9 (ISO standard)
Organizing quality system documents
Documents need to organized and written as per the hierarchy issued by ISO. This list
of documents carried by the representative team in the submission round. Apart from this, the
company needs to address other documents also:
 Quality manual:
This includes exclusions, description of quality standard, company's norms for the
quality process, objectives of the company, and procedures outline relating to the
system level (Psomas & Antony, 2015).
 Record keeping documents:
Record keeping helps in compliance and surveillance audits because this is the
evidence that monitors the process requirements and helps in improving quality. This
document also contains details for:
o Meetings conducted during the time
o Training of employees
o Customer requirements
o Design and validation of planning
o Details for suppliers
o Internal audits reports
7. Documents auditing/review
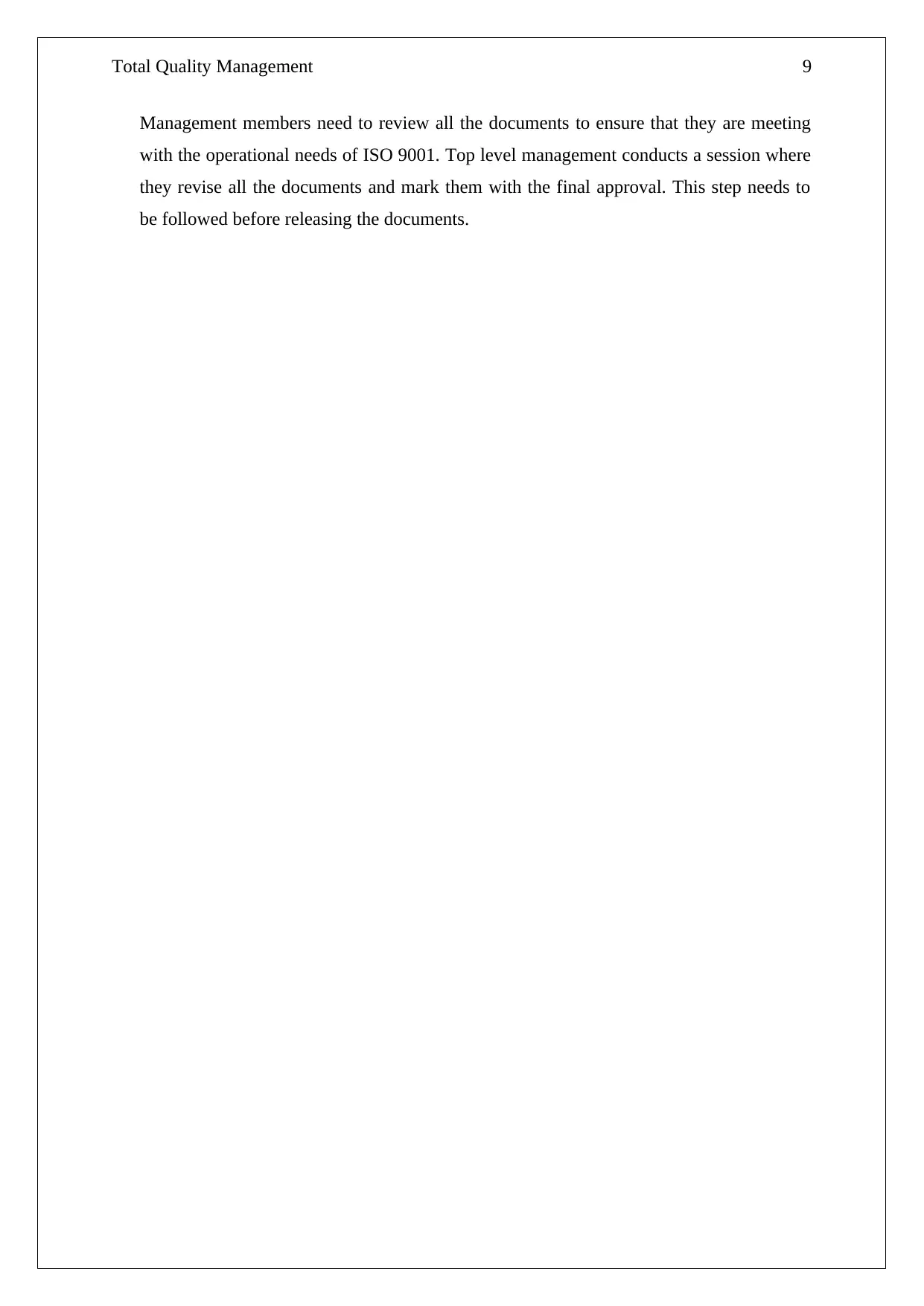
Total Quality Management 9
Management members need to review all the documents to ensure that they are meeting
with the operational needs of ISO 9001. Top level management conducts a session where
they revise all the documents and mark them with the final approval. This step needs to
be followed before releasing the documents.
Management members need to review all the documents to ensure that they are meeting
with the operational needs of ISO 9001. Top level management conducts a session where
they revise all the documents and mark them with the final approval. This step needs to
be followed before releasing the documents.
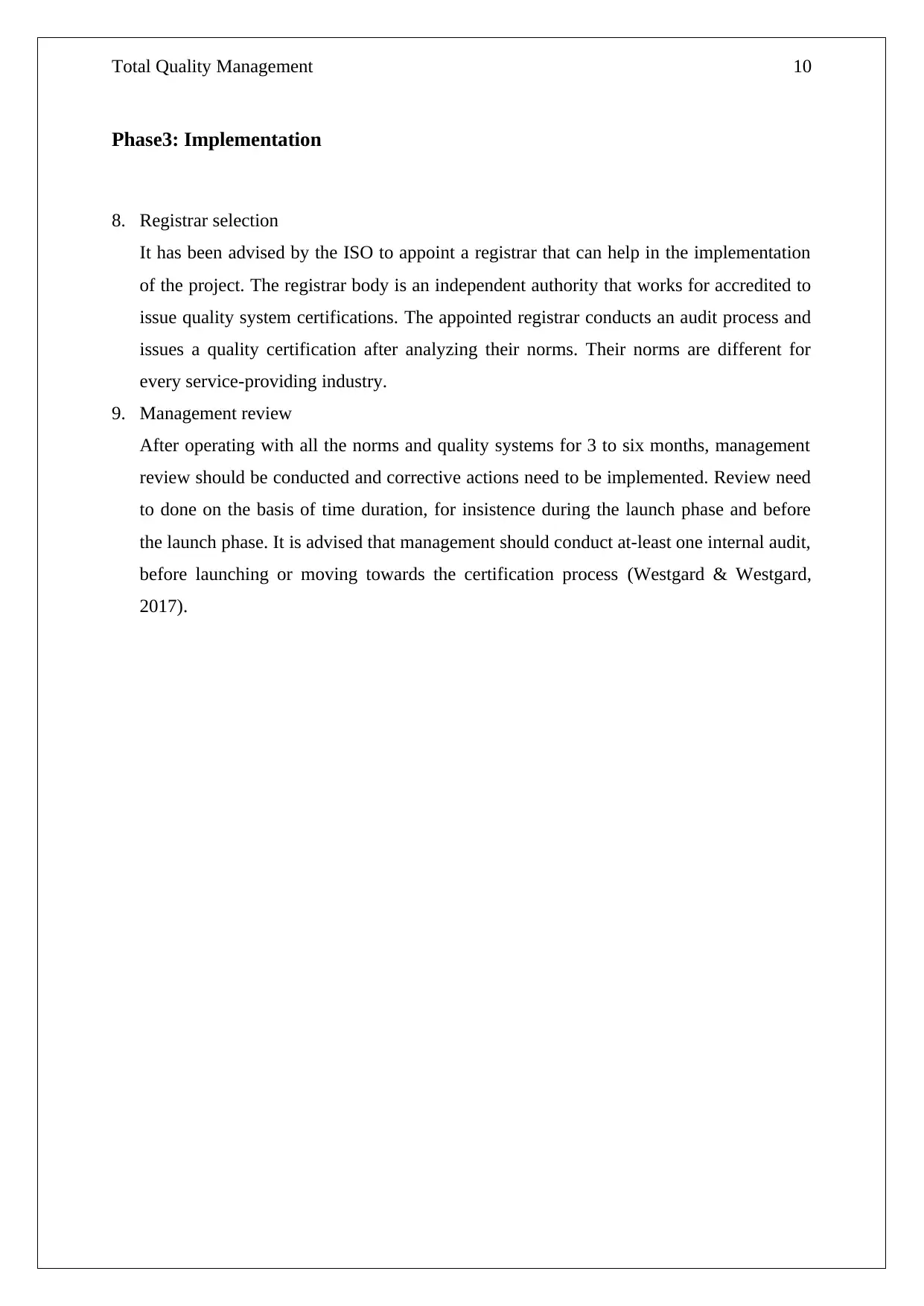
Total Quality Management 10
Phase3: Implementation
8. Registrar selection
It has been advised by the ISO to appoint a registrar that can help in the implementation
of the project. The registrar body is an independent authority that works for accredited to
issue quality system certifications. The appointed registrar conducts an audit process and
issues a quality certification after analyzing their norms. Their norms are different for
every service-providing industry.
9. Management review
After operating with all the norms and quality systems for 3 to six months, management
review should be conducted and corrective actions need to be implemented. Review need
to done on the basis of time duration, for insistence during the launch phase and before
the launch phase. It is advised that management should conduct at-least one internal audit,
before launching or moving towards the certification process (Westgard & Westgard,
2017).
Phase3: Implementation
8. Registrar selection
It has been advised by the ISO to appoint a registrar that can help in the implementation
of the project. The registrar body is an independent authority that works for accredited to
issue quality system certifications. The appointed registrar conducts an audit process and
issues a quality certification after analyzing their norms. Their norms are different for
every service-providing industry.
9. Management review
After operating with all the norms and quality systems for 3 to six months, management
review should be conducted and corrective actions need to be implemented. Review need
to done on the basis of time duration, for insistence during the launch phase and before
the launch phase. It is advised that management should conduct at-least one internal audit,
before launching or moving towards the certification process (Westgard & Westgard,
2017).
Secure Best Marks with AI Grader
Need help grading? Try our AI Grader for instant feedback on your assignments.
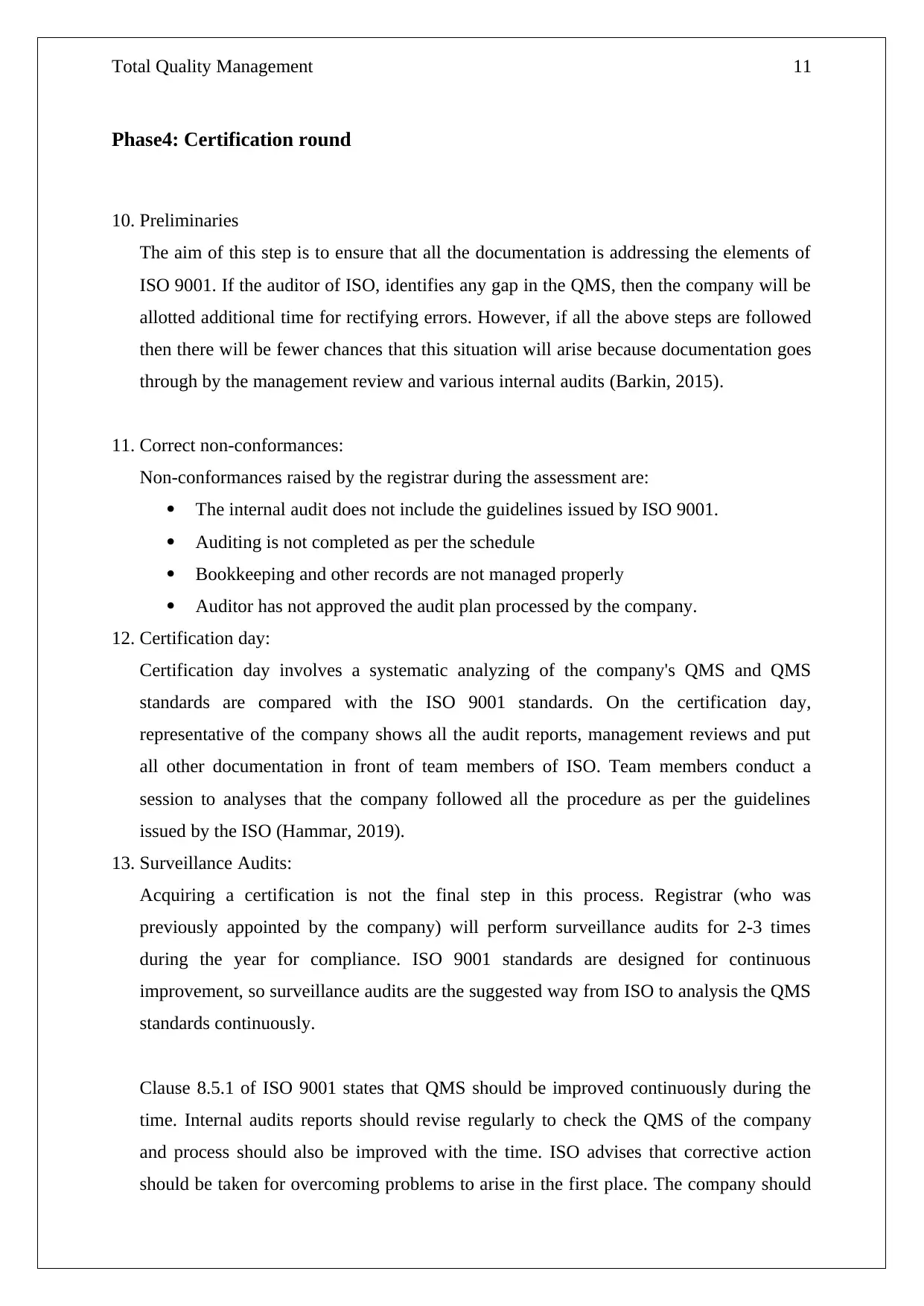
Total Quality Management 11
Phase4: Certification round
10. Preliminaries
The aim of this step is to ensure that all the documentation is addressing the elements of
ISO 9001. If the auditor of ISO, identifies any gap in the QMS, then the company will be
allotted additional time for rectifying errors. However, if all the above steps are followed
then there will be fewer chances that this situation will arise because documentation goes
through by the management review and various internal audits (Barkin, 2015).
11. Correct non-conformances:
Non-conformances raised by the registrar during the assessment are:
ï‚· The internal audit does not include the guidelines issued by ISO 9001.
ï‚· Auditing is not completed as per the schedule
ï‚· Bookkeeping and other records are not managed properly
ï‚· Auditor has not approved the audit plan processed by the company.
12. Certification day:
Certification day involves a systematic analyzing of the company's QMS and QMS
standards are compared with the ISO 9001 standards. On the certification day,
representative of the company shows all the audit reports, management reviews and put
all other documentation in front of team members of ISO. Team members conduct a
session to analyses that the company followed all the procedure as per the guidelines
issued by the ISO (Hammar, 2019).
13. Surveillance Audits:
Acquiring a certification is not the final step in this process. Registrar (who was
previously appointed by the company) will perform surveillance audits for 2-3 times
during the year for compliance. ISO 9001 standards are designed for continuous
improvement, so surveillance audits are the suggested way from ISO to analysis the QMS
standards continuously.
Clause 8.5.1 of ISO 9001 states that QMS should be improved continuously during the
time. Internal audits reports should revise regularly to check the QMS of the company
and process should also be improved with the time. ISO advises that corrective action
should be taken for overcoming problems to arise in the first place. The company should
Phase4: Certification round
10. Preliminaries
The aim of this step is to ensure that all the documentation is addressing the elements of
ISO 9001. If the auditor of ISO, identifies any gap in the QMS, then the company will be
allotted additional time for rectifying errors. However, if all the above steps are followed
then there will be fewer chances that this situation will arise because documentation goes
through by the management review and various internal audits (Barkin, 2015).
11. Correct non-conformances:
Non-conformances raised by the registrar during the assessment are:
ï‚· The internal audit does not include the guidelines issued by ISO 9001.
ï‚· Auditing is not completed as per the schedule
ï‚· Bookkeeping and other records are not managed properly
ï‚· Auditor has not approved the audit plan processed by the company.
12. Certification day:
Certification day involves a systematic analyzing of the company's QMS and QMS
standards are compared with the ISO 9001 standards. On the certification day,
representative of the company shows all the audit reports, management reviews and put
all other documentation in front of team members of ISO. Team members conduct a
session to analyses that the company followed all the procedure as per the guidelines
issued by the ISO (Hammar, 2019).
13. Surveillance Audits:
Acquiring a certification is not the final step in this process. Registrar (who was
previously appointed by the company) will perform surveillance audits for 2-3 times
during the year for compliance. ISO 9001 standards are designed for continuous
improvement, so surveillance audits are the suggested way from ISO to analysis the QMS
standards continuously.
Clause 8.5.1 of ISO 9001 states that QMS should be improved continuously during the
time. Internal audits reports should revise regularly to check the QMS of the company
and process should also be improved with the time. ISO advises that corrective action
should be taken for overcoming problems to arise in the first place. The company should
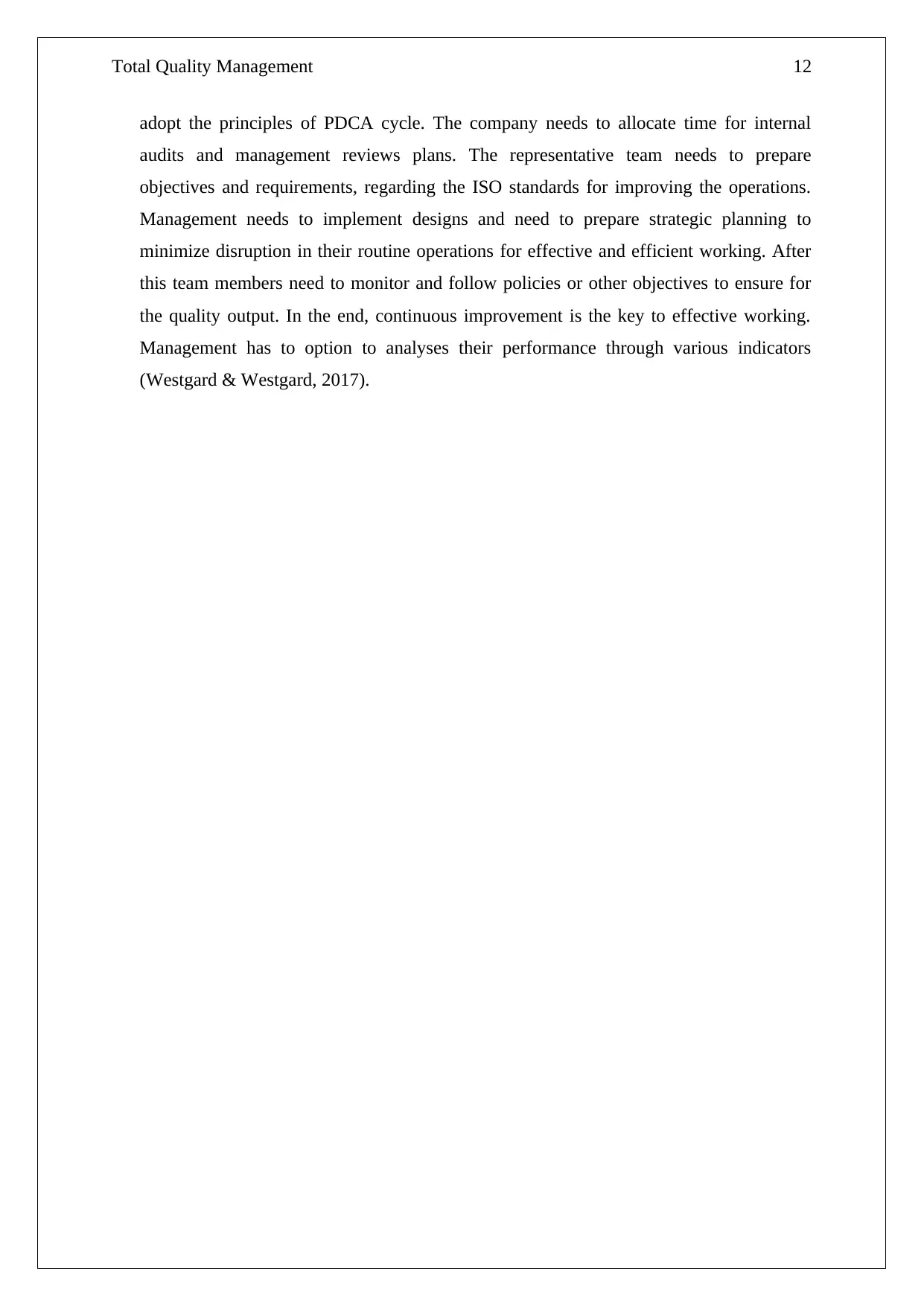
Total Quality Management 12
adopt the principles of PDCA cycle. The company needs to allocate time for internal
audits and management reviews plans. The representative team needs to prepare
objectives and requirements, regarding the ISO standards for improving the operations.
Management needs to implement designs and need to prepare strategic planning to
minimize disruption in their routine operations for effective and efficient working. After
this team members need to monitor and follow policies or other objectives to ensure for
the quality output. In the end, continuous improvement is the key to effective working.
Management has to option to analyses their performance through various indicators
(Westgard & Westgard, 2017).
adopt the principles of PDCA cycle. The company needs to allocate time for internal
audits and management reviews plans. The representative team needs to prepare
objectives and requirements, regarding the ISO standards for improving the operations.
Management needs to implement designs and need to prepare strategic planning to
minimize disruption in their routine operations for effective and efficient working. After
this team members need to monitor and follow policies or other objectives to ensure for
the quality output. In the end, continuous improvement is the key to effective working.
Management has to option to analyses their performance through various indicators
(Westgard & Westgard, 2017).
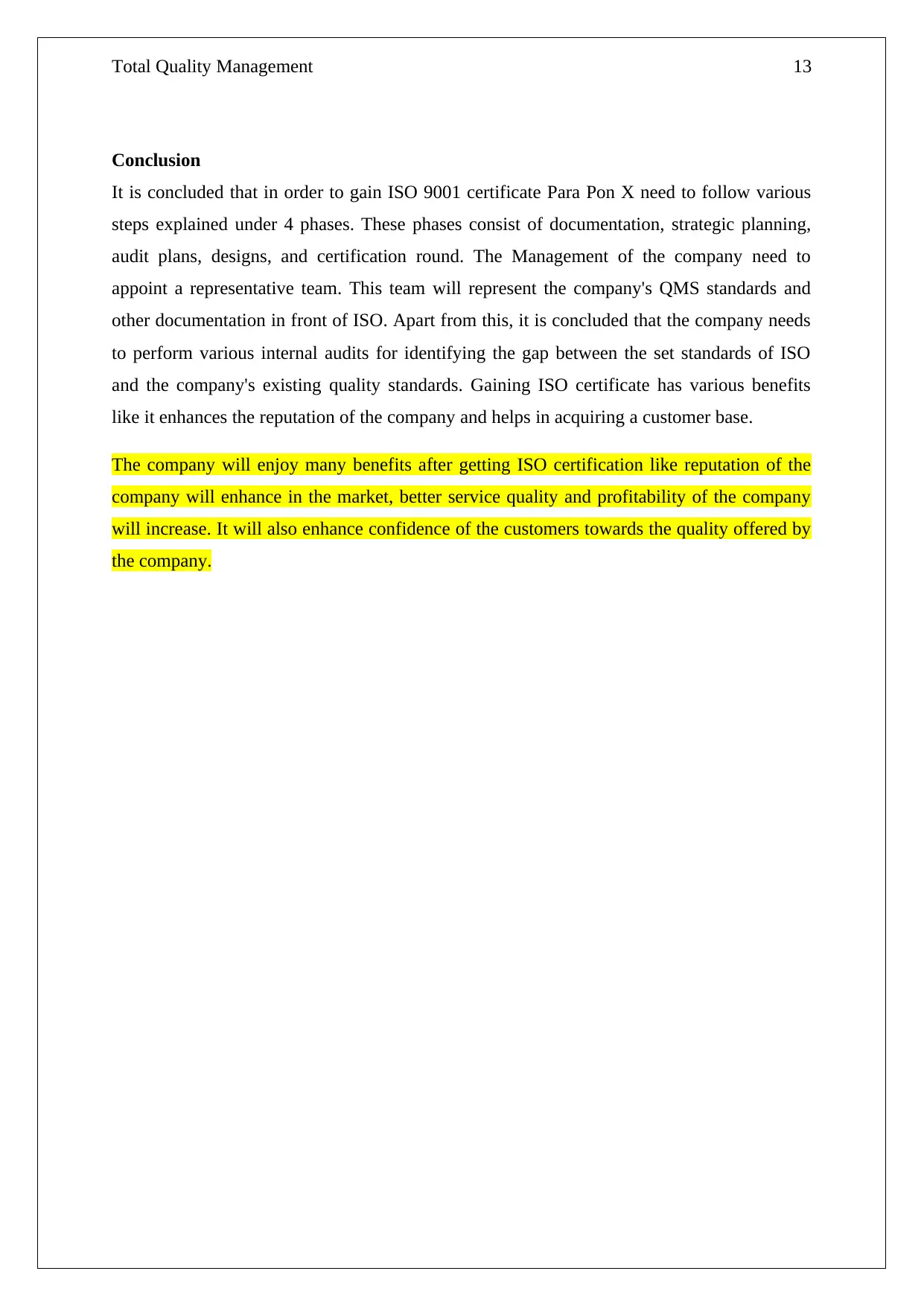
Total Quality Management 13
Conclusion
It is concluded that in order to gain ISO 9001 certificate Para Pon X need to follow various
steps explained under 4 phases. These phases consist of documentation, strategic planning,
audit plans, designs, and certification round. The Management of the company need to
appoint a representative team. This team will represent the company's QMS standards and
other documentation in front of ISO. Apart from this, it is concluded that the company needs
to perform various internal audits for identifying the gap between the set standards of ISO
and the company's existing quality standards. Gaining ISO certificate has various benefits
like it enhances the reputation of the company and helps in acquiring a customer base.
The company will enjoy many benefits after getting ISO certification like reputation of the
company will enhance in the market, better service quality and profitability of the company
will increase. It will also enhance confidence of the customers towards the quality offered by
the company.
Conclusion
It is concluded that in order to gain ISO 9001 certificate Para Pon X need to follow various
steps explained under 4 phases. These phases consist of documentation, strategic planning,
audit plans, designs, and certification round. The Management of the company need to
appoint a representative team. This team will represent the company's QMS standards and
other documentation in front of ISO. Apart from this, it is concluded that the company needs
to perform various internal audits for identifying the gap between the set standards of ISO
and the company's existing quality standards. Gaining ISO certificate has various benefits
like it enhances the reputation of the company and helps in acquiring a customer base.
The company will enjoy many benefits after getting ISO certification like reputation of the
company will enhance in the market, better service quality and profitability of the company
will increase. It will also enhance confidence of the customers towards the quality offered by
the company.
Paraphrase This Document
Need a fresh take? Get an instant paraphrase of this document with our AI Paraphraser
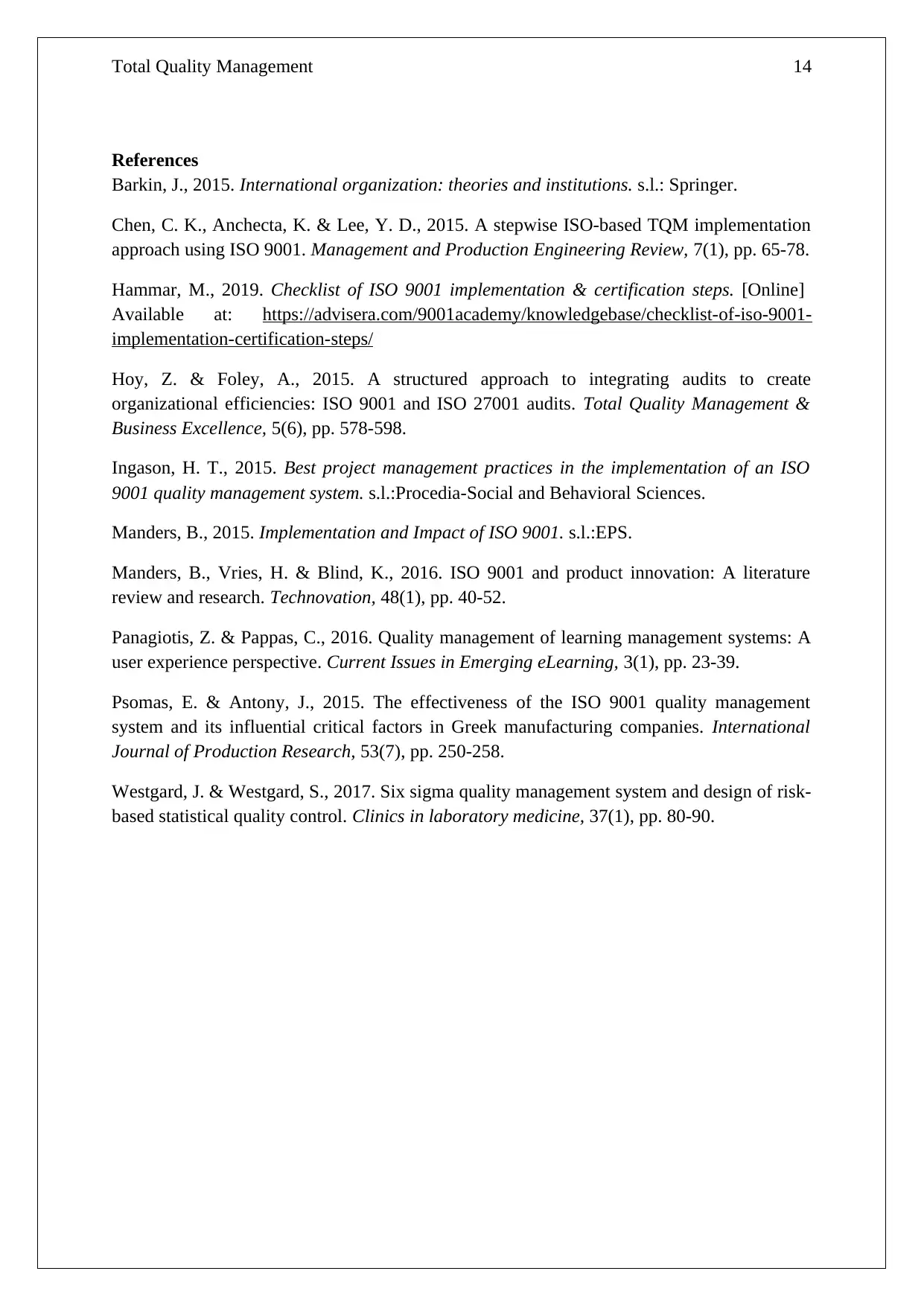
Total Quality Management 14
References
Barkin, J., 2015. International organization: theories and institutions. s.l.: Springer.
Chen, C. K., Anchecta, K. & Lee, Y. D., 2015. A stepwise ISO-based TQM implementation
approach using ISO 9001. Management and Production Engineering Review, 7(1), pp. 65-78.
Hammar, M., 2019. Checklist of ISO 9001 implementation & certification steps. [Online]
Available at: https://advisera.com/9001academy/knowledgebase/checklist-of-iso-9001-
implementation-certification-steps/
Hoy, Z. & Foley, A., 2015. A structured approach to integrating audits to create
organizational efficiencies: ISO 9001 and ISO 27001 audits. Total Quality Management &
Business Excellence, 5(6), pp. 578-598.
Ingason, H. T., 2015. Best project management practices in the implementation of an ISO
9001 quality management system. s.l.:Procedia-Social and Behavioral Sciences.
Manders, B., 2015. Implementation and Impact of ISO 9001. s.l.:EPS.
Manders, B., Vries, H. & Blind, K., 2016. ISO 9001 and product innovation: A literature
review and research. Technovation, 48(1), pp. 40-52.
Panagiotis, Z. & Pappas, C., 2016. Quality management of learning management systems: A
user experience perspective. Current Issues in Emerging eLearning, 3(1), pp. 23-39.
Psomas, E. & Antony, J., 2015. The effectiveness of the ISO 9001 quality management
system and its influential critical factors in Greek manufacturing companies. International
Journal of Production Research, 53(7), pp. 250-258.
Westgard, J. & Westgard, S., 2017. Six sigma quality management system and design of risk-
based statistical quality control. Clinics in laboratory medicine, 37(1), pp. 80-90.
References
Barkin, J., 2015. International organization: theories and institutions. s.l.: Springer.
Chen, C. K., Anchecta, K. & Lee, Y. D., 2015. A stepwise ISO-based TQM implementation
approach using ISO 9001. Management and Production Engineering Review, 7(1), pp. 65-78.
Hammar, M., 2019. Checklist of ISO 9001 implementation & certification steps. [Online]
Available at: https://advisera.com/9001academy/knowledgebase/checklist-of-iso-9001-
implementation-certification-steps/
Hoy, Z. & Foley, A., 2015. A structured approach to integrating audits to create
organizational efficiencies: ISO 9001 and ISO 27001 audits. Total Quality Management &
Business Excellence, 5(6), pp. 578-598.
Ingason, H. T., 2015. Best project management practices in the implementation of an ISO
9001 quality management system. s.l.:Procedia-Social and Behavioral Sciences.
Manders, B., 2015. Implementation and Impact of ISO 9001. s.l.:EPS.
Manders, B., Vries, H. & Blind, K., 2016. ISO 9001 and product innovation: A literature
review and research. Technovation, 48(1), pp. 40-52.
Panagiotis, Z. & Pappas, C., 2016. Quality management of learning management systems: A
user experience perspective. Current Issues in Emerging eLearning, 3(1), pp. 23-39.
Psomas, E. & Antony, J., 2015. The effectiveness of the ISO 9001 quality management
system and its influential critical factors in Greek manufacturing companies. International
Journal of Production Research, 53(7), pp. 250-258.
Westgard, J. & Westgard, S., 2017. Six sigma quality management system and design of risk-
based statistical quality control. Clinics in laboratory medicine, 37(1), pp. 80-90.
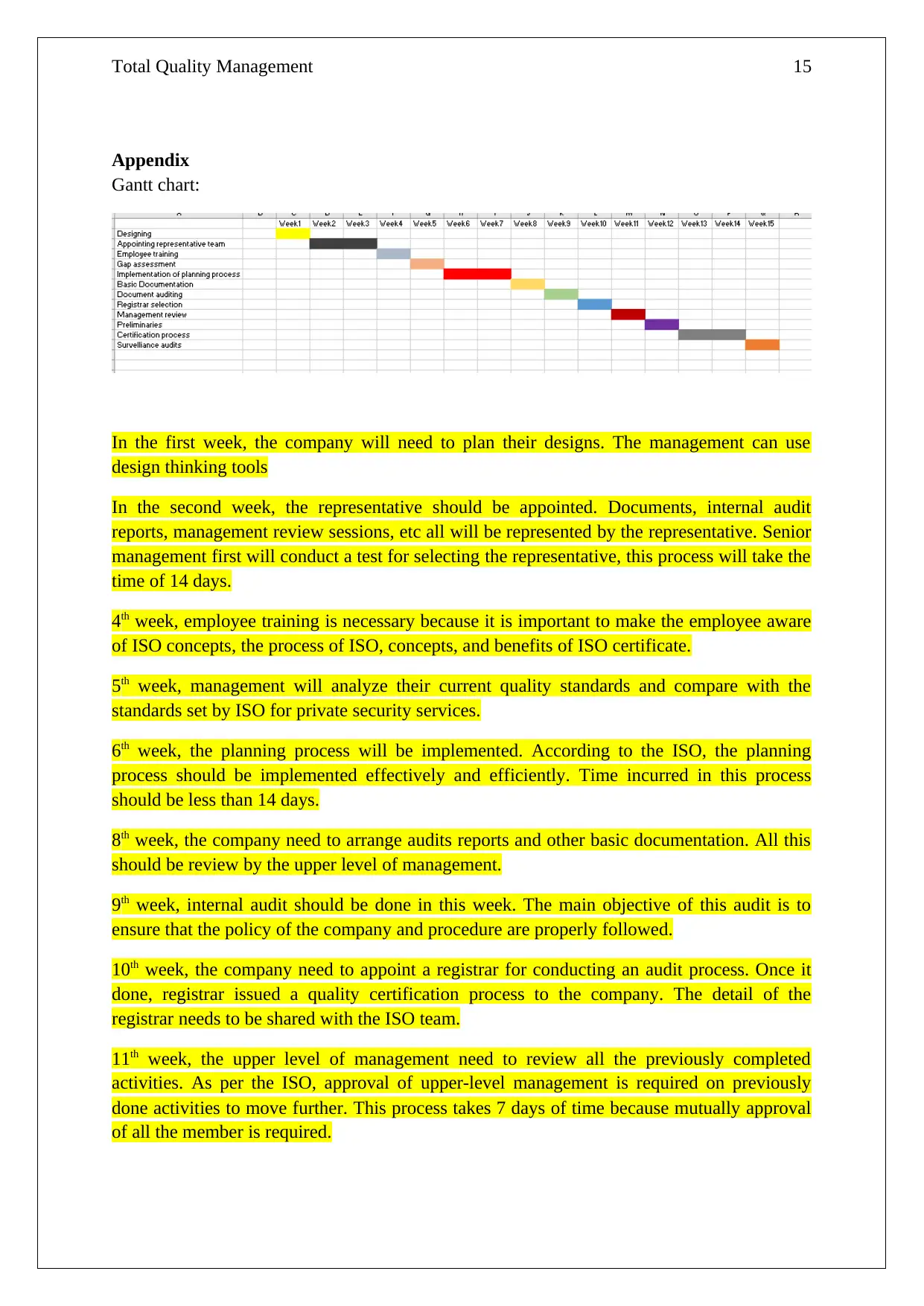
Total Quality Management 15
Appendix
Gantt chart:
In the first week, the company will need to plan their designs. The management can use
design thinking tools
In the second week, the representative should be appointed. Documents, internal audit
reports, management review sessions, etc all will be represented by the representative. Senior
management first will conduct a test for selecting the representative, this process will take the
time of 14 days.
4th week, employee training is necessary because it is important to make the employee aware
of ISO concepts, the process of ISO, concepts, and benefits of ISO certificate.
5th week, management will analyze their current quality standards and compare with the
standards set by ISO for private security services.
6th week, the planning process will be implemented. According to the ISO, the planning
process should be implemented effectively and efficiently. Time incurred in this process
should be less than 14 days.
8th week, the company need to arrange audits reports and other basic documentation. All this
should be review by the upper level of management.
9th week, internal audit should be done in this week. The main objective of this audit is to
ensure that the policy of the company and procedure are properly followed.
10th week, the company need to appoint a registrar for conducting an audit process. Once it
done, registrar issued a quality certification process to the company. The detail of the
registrar needs to be shared with the ISO team.
11th week, the upper level of management need to review all the previously completed
activities. As per the ISO, approval of upper-level management is required on previously
done activities to move further. This process takes 7 days of time because mutually approval
of all the member is required.
Appendix
Gantt chart:
In the first week, the company will need to plan their designs. The management can use
design thinking tools
In the second week, the representative should be appointed. Documents, internal audit
reports, management review sessions, etc all will be represented by the representative. Senior
management first will conduct a test for selecting the representative, this process will take the
time of 14 days.
4th week, employee training is necessary because it is important to make the employee aware
of ISO concepts, the process of ISO, concepts, and benefits of ISO certificate.
5th week, management will analyze their current quality standards and compare with the
standards set by ISO for private security services.
6th week, the planning process will be implemented. According to the ISO, the planning
process should be implemented effectively and efficiently. Time incurred in this process
should be less than 14 days.
8th week, the company need to arrange audits reports and other basic documentation. All this
should be review by the upper level of management.
9th week, internal audit should be done in this week. The main objective of this audit is to
ensure that the policy of the company and procedure are properly followed.
10th week, the company need to appoint a registrar for conducting an audit process. Once it
done, registrar issued a quality certification process to the company. The detail of the
registrar needs to be shared with the ISO team.
11th week, the upper level of management need to review all the previously completed
activities. As per the ISO, approval of upper-level management is required on previously
done activities to move further. This process takes 7 days of time because mutually approval
of all the member is required.
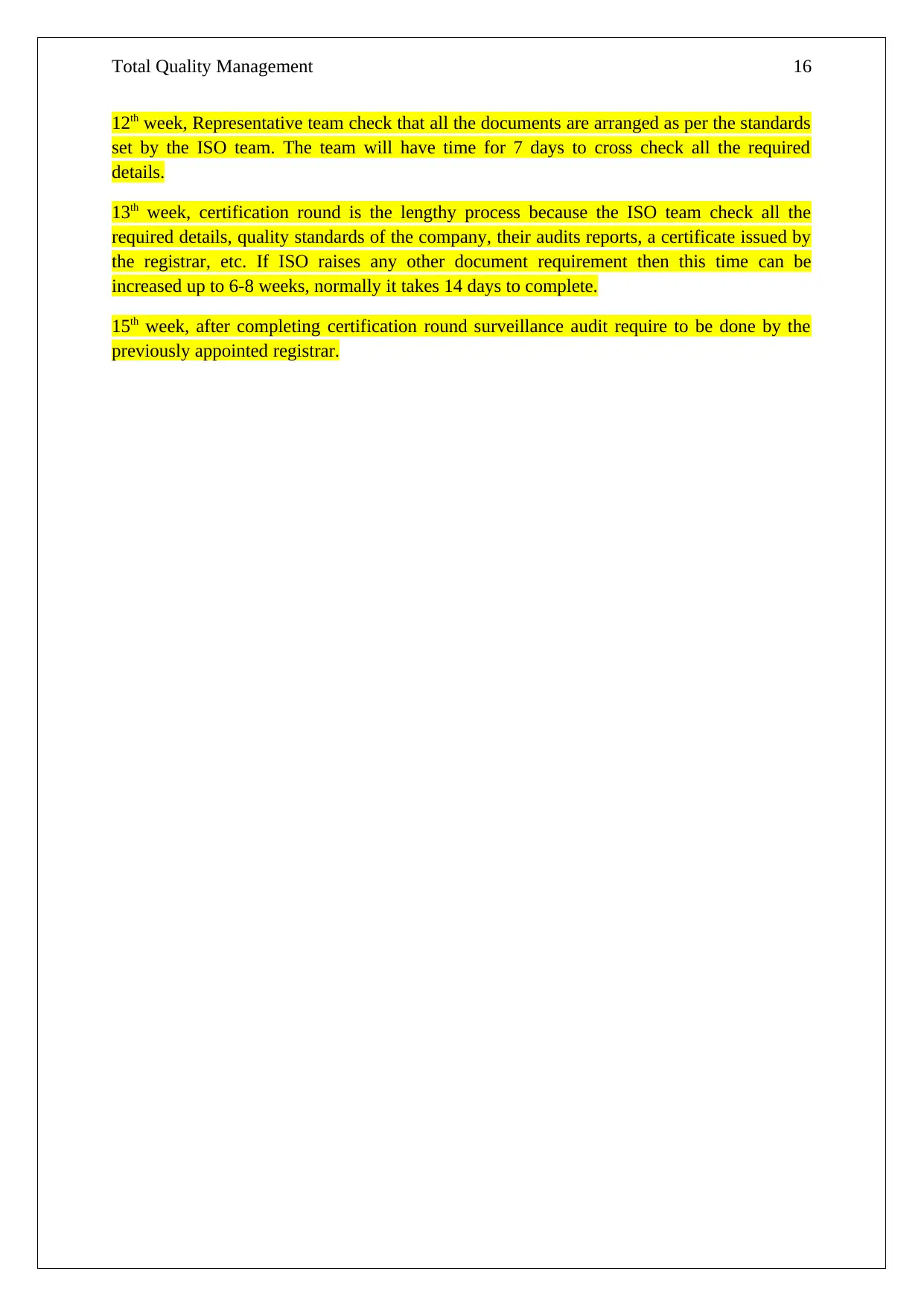
Total Quality Management 16
12th week, Representative team check that all the documents are arranged as per the standards
set by the ISO team. The team will have time for 7 days to cross check all the required
details.
13th week, certification round is the lengthy process because the ISO team check all the
required details, quality standards of the company, their audits reports, a certificate issued by
the registrar, etc. If ISO raises any other document requirement then this time can be
increased up to 6-8 weeks, normally it takes 14 days to complete.
15th week, after completing certification round surveillance audit require to be done by the
previously appointed registrar.
12th week, Representative team check that all the documents are arranged as per the standards
set by the ISO team. The team will have time for 7 days to cross check all the required
details.
13th week, certification round is the lengthy process because the ISO team check all the
required details, quality standards of the company, their audits reports, a certificate issued by
the registrar, etc. If ISO raises any other document requirement then this time can be
increased up to 6-8 weeks, normally it takes 14 days to complete.
15th week, after completing certification round surveillance audit require to be done by the
previously appointed registrar.
1 out of 16
Related Documents
![[object Object]](/_next/image/?url=%2F_next%2Fstatic%2Fmedia%2Flogo.6d15ce61.png&w=640&q=75)
Your All-in-One AI-Powered Toolkit for Academic Success.
 +13062052269
info@desklib.com
Available 24*7 on WhatsApp / Email
Unlock your academic potential
© 2024  |  Zucol Services PVT LTD  |  All rights reserved.