Total Quality Management (TQM) Principles and Practices
VerifiedAdded on  2020/07/22
|14
|3772
|32
AI Summary
The provided document is a comprehensive analysis of Total Quality Management (TQM) principles and practices. It includes an overview of TQM fundamentals, key principles, and applications in different industries. The assignment also provides insights into research studies and papers on TQM, its impact on supply chain management, and the importance of quality management in service organizations. Additionally, it covers the European model for business excellence and the holistic approach to TQM. Overall, this document is a valuable resource for students and professionals seeking to understand the principles and applications of Total Quality Management.
Contribute Materials
Your contribution can guide someone’s learning journey. Share your
documents today.
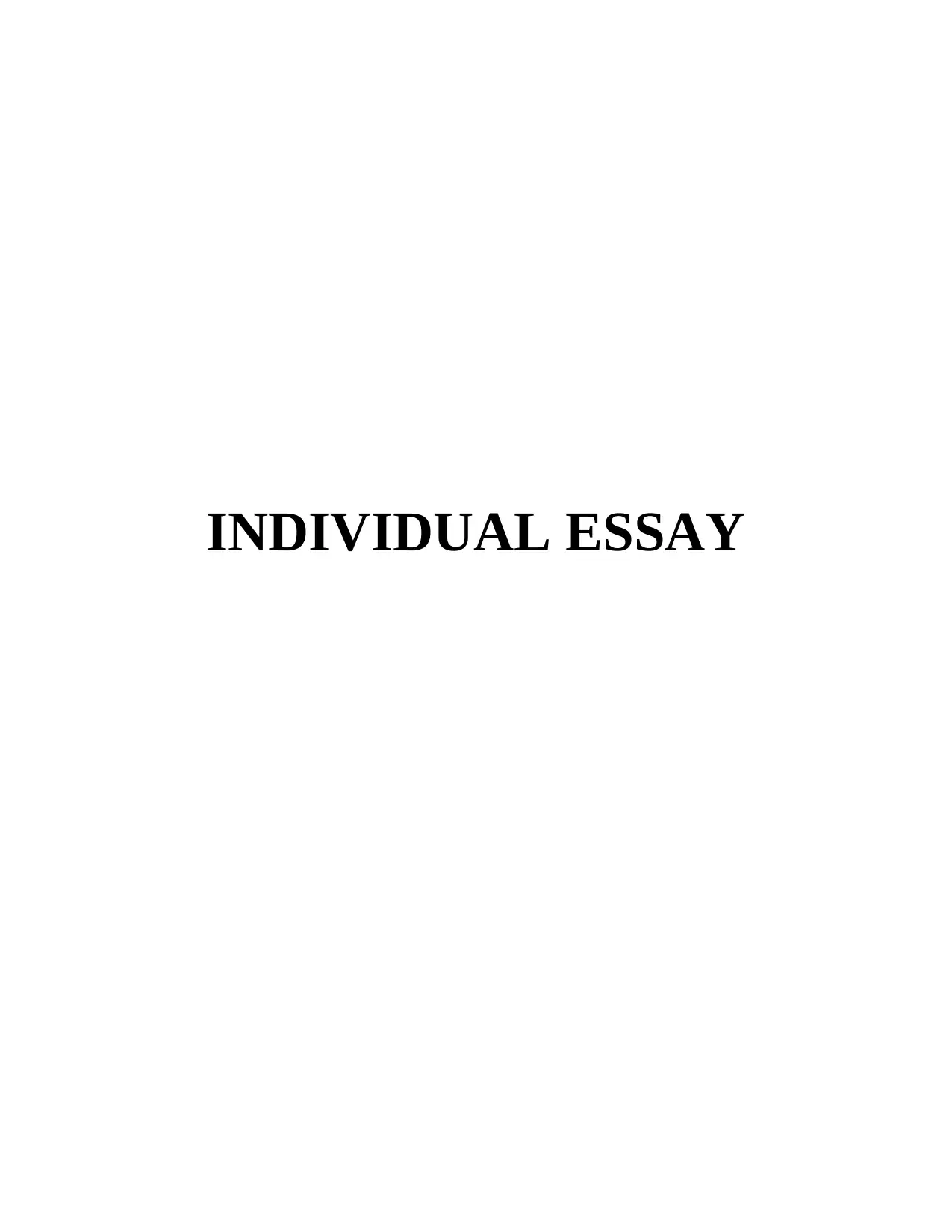
INDIVIDUAL ESSAY
Secure Best Marks with AI Grader
Need help grading? Try our AI Grader for instant feedback on your assignments.
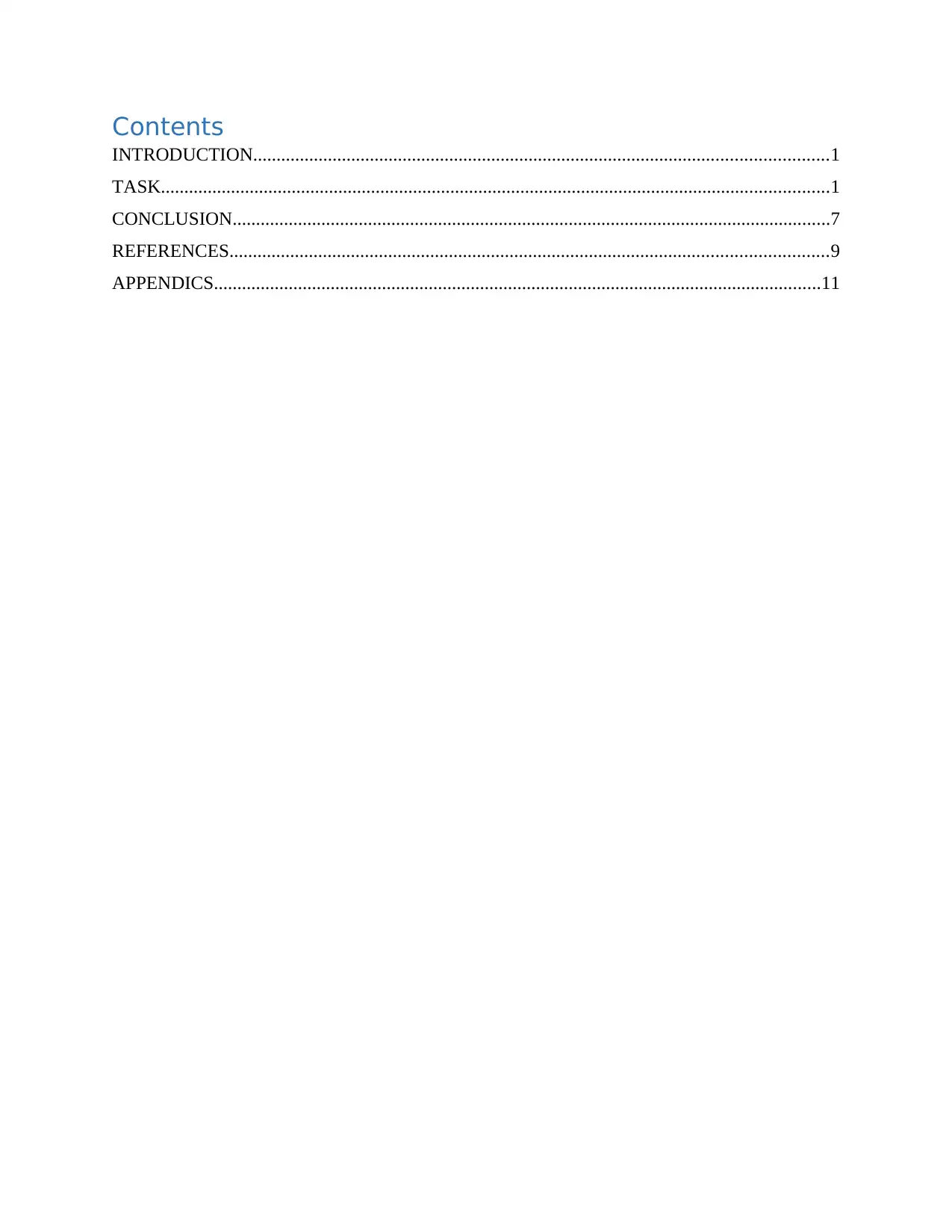
Contents
INTRODUCTION...........................................................................................................................1
TASK...............................................................................................................................................1
CONCLUSION................................................................................................................................7
REFERENCES................................................................................................................................9
APPENDICS..................................................................................................................................11
INTRODUCTION...........................................................................................................................1
TASK...............................................................................................................................................1
CONCLUSION................................................................................................................................7
REFERENCES................................................................................................................................9
APPENDICS..................................................................................................................................11
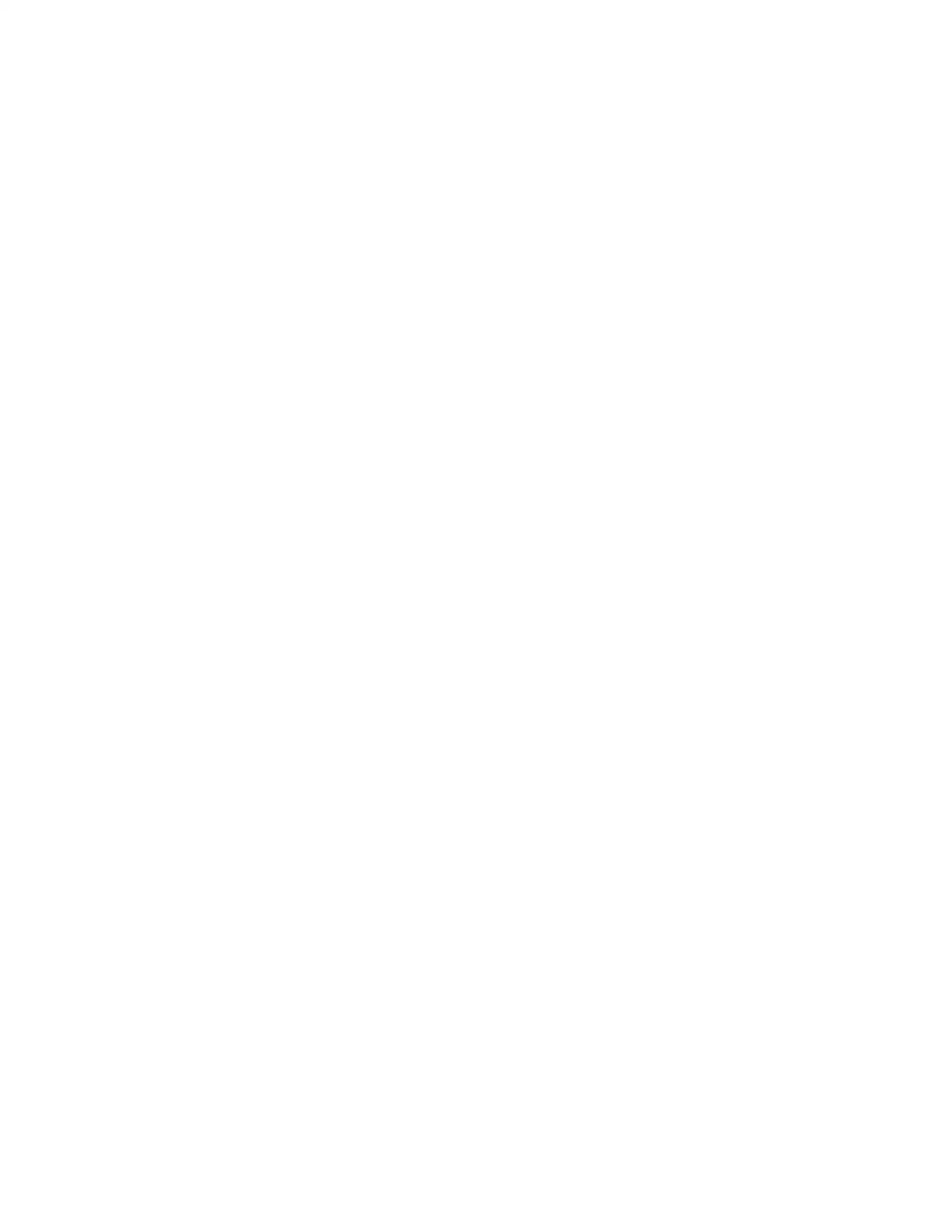
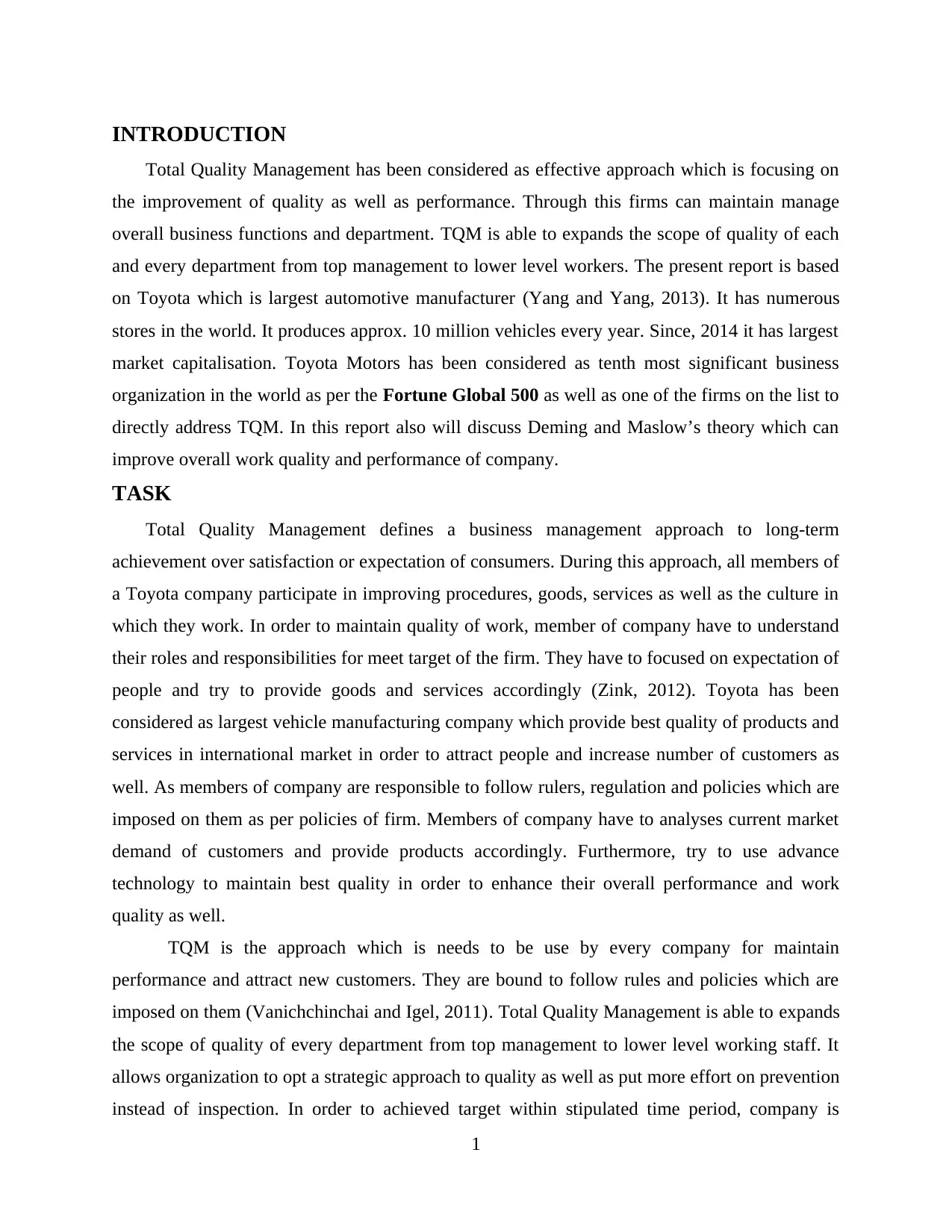
INTRODUCTION
Total Quality Management has been considered as effective approach which is focusing on
the improvement of quality as well as performance. Through this firms can maintain manage
overall business functions and department. TQM is able to expands the scope of quality of each
and every department from top management to lower level workers. The present report is based
on Toyota which is largest automotive manufacturer (Yang and Yang, 2013). It has numerous
stores in the world. It produces approx. 10 million vehicles every year. Since, 2014 it has largest
market capitalisation. Toyota Motors has been considered as tenth most significant business
organization in the world as per the Fortune Global 500 as well as one of the firms on the list to
directly address TQM. In this report also will discuss Deming and Maslow’s theory which can
improve overall work quality and performance of company.
TASK
Total Quality Management defines a business management approach to long-term
achievement over satisfaction or expectation of consumers. During this approach, all members of
a Toyota company participate in improving procedures, goods, services as well as the culture in
which they work. In order to maintain quality of work, member of company have to understand
their roles and responsibilities for meet target of the firm. They have to focused on expectation of
people and try to provide goods and services accordingly (Zink, 2012). Toyota has been
considered as largest vehicle manufacturing company which provide best quality of products and
services in international market in order to attract people and increase number of customers as
well. As members of company are responsible to follow rulers, regulation and policies which are
imposed on them as per policies of firm. Members of company have to analyses current market
demand of customers and provide products accordingly. Furthermore, try to use advance
technology to maintain best quality in order to enhance their overall performance and work
quality as well.
TQM is the approach which is needs to be use by every company for maintain
performance and attract new customers. They are bound to follow rules and policies which are
imposed on them (Vanichchinchai and Igel, 2011). Total Quality Management is able to expands
the scope of quality of every department from top management to lower level working staff. It
allows organization to opt a strategic approach to quality as well as put more effort on prevention
instead of inspection. In order to achieved target within stipulated time period, company is
1
Total Quality Management has been considered as effective approach which is focusing on
the improvement of quality as well as performance. Through this firms can maintain manage
overall business functions and department. TQM is able to expands the scope of quality of each
and every department from top management to lower level workers. The present report is based
on Toyota which is largest automotive manufacturer (Yang and Yang, 2013). It has numerous
stores in the world. It produces approx. 10 million vehicles every year. Since, 2014 it has largest
market capitalisation. Toyota Motors has been considered as tenth most significant business
organization in the world as per the Fortune Global 500 as well as one of the firms on the list to
directly address TQM. In this report also will discuss Deming and Maslow’s theory which can
improve overall work quality and performance of company.
TASK
Total Quality Management defines a business management approach to long-term
achievement over satisfaction or expectation of consumers. During this approach, all members of
a Toyota company participate in improving procedures, goods, services as well as the culture in
which they work. In order to maintain quality of work, member of company have to understand
their roles and responsibilities for meet target of the firm. They have to focused on expectation of
people and try to provide goods and services accordingly (Zink, 2012). Toyota has been
considered as largest vehicle manufacturing company which provide best quality of products and
services in international market in order to attract people and increase number of customers as
well. As members of company are responsible to follow rulers, regulation and policies which are
imposed on them as per policies of firm. Members of company have to analyses current market
demand of customers and provide products accordingly. Furthermore, try to use advance
technology to maintain best quality in order to enhance their overall performance and work
quality as well.
TQM is the approach which is needs to be use by every company for maintain
performance and attract new customers. They are bound to follow rules and policies which are
imposed on them (Vanichchinchai and Igel, 2011). Total Quality Management is able to expands
the scope of quality of every department from top management to lower level working staff. It
allows organization to opt a strategic approach to quality as well as put more effort on prevention
instead of inspection. In order to achieved target within stipulated time period, company is
1
Secure Best Marks with AI Grader
Need help grading? Try our AI Grader for instant feedback on your assignments.
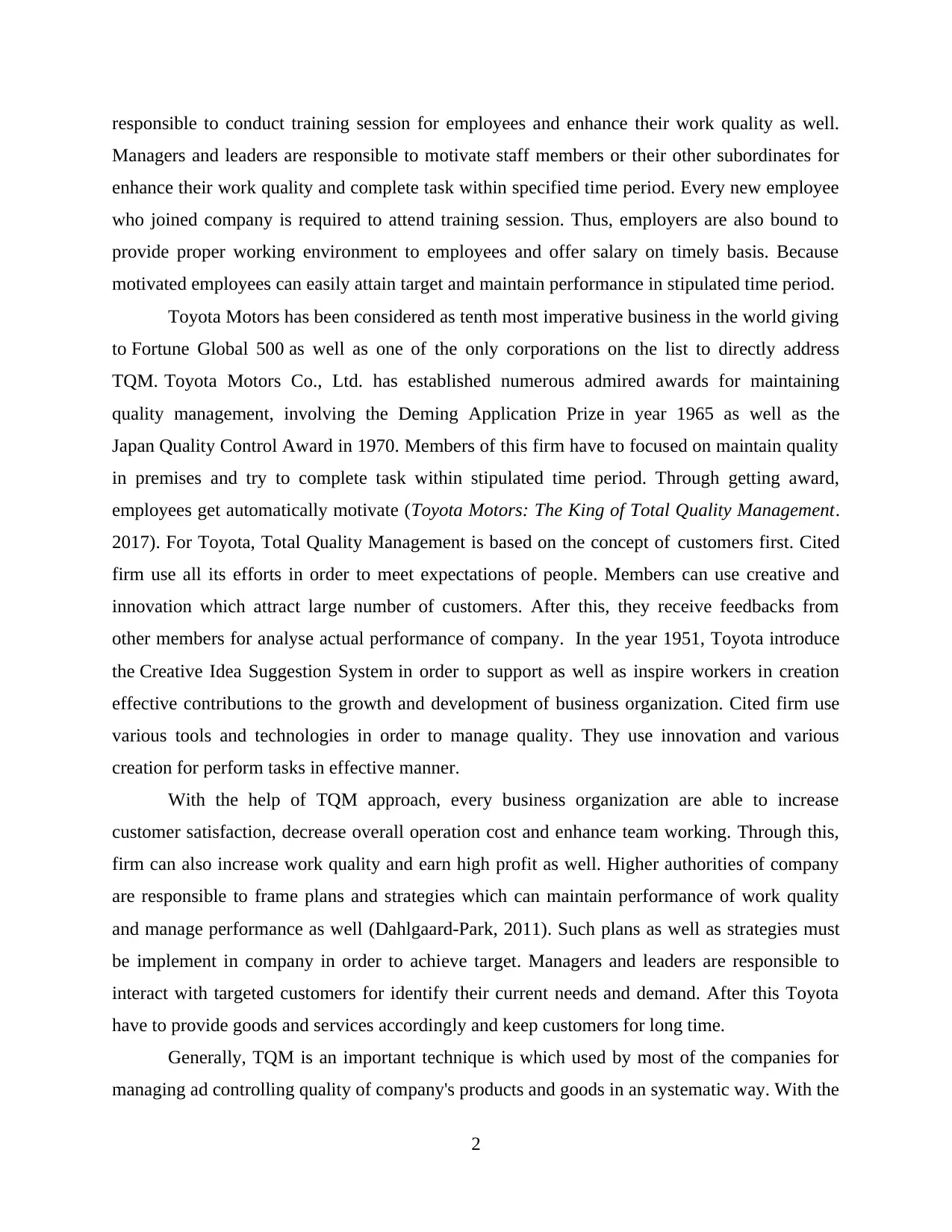
responsible to conduct training session for employees and enhance their work quality as well.
Managers and leaders are responsible to motivate staff members or their other subordinates for
enhance their work quality and complete task within specified time period. Every new employee
who joined company is required to attend training session. Thus, employers are also bound to
provide proper working environment to employees and offer salary on timely basis. Because
motivated employees can easily attain target and maintain performance in stipulated time period.
Toyota Motors has been considered as tenth most imperative business in the world giving
to Fortune Global 500 as well as one of the only corporations on the list to directly address
TQM. Toyota Motors Co., Ltd. has established numerous admired awards for maintaining
quality management, involving the Deming Application Prize in year 1965 as well as the
Japan Quality Control Award in 1970. Members of this firm have to focused on maintain quality
in premises and try to complete task within stipulated time period. Through getting award,
employees get automatically motivate (Toyota Motors: The King of Total Quality Management.
2017). For Toyota, Total Quality Management is based on the concept of customers first. Cited
firm use all its efforts in order to meet expectations of people. Members can use creative and
innovation which attract large number of customers. After this, they receive feedbacks from
other members for analyse actual performance of company. In the year 1951, Toyota introduce
the Creative Idea Suggestion System in order to support as well as inspire workers in creation
effective contributions to the growth and development of business organization. Cited firm use
various tools and technologies in order to manage quality. They use innovation and various
creation for perform tasks in effective manner.
With the help of TQM approach, every business organization are able to increase
customer satisfaction, decrease overall operation cost and enhance team working. Through this,
firm can also increase work quality and earn high profit as well. Higher authorities of company
are responsible to frame plans and strategies which can maintain performance of work quality
and manage performance as well (Dahlgaard-Park, 2011). Such plans as well as strategies must
be implement in company in order to achieve target. Managers and leaders are responsible to
interact with targeted customers for identify their current needs and demand. After this Toyota
have to provide goods and services accordingly and keep customers for long time.
Generally, TQM is an important technique is which used by most of the companies for
managing ad controlling quality of company's products and goods in an systematic way. With the
2
Managers and leaders are responsible to motivate staff members or their other subordinates for
enhance their work quality and complete task within specified time period. Every new employee
who joined company is required to attend training session. Thus, employers are also bound to
provide proper working environment to employees and offer salary on timely basis. Because
motivated employees can easily attain target and maintain performance in stipulated time period.
Toyota Motors has been considered as tenth most imperative business in the world giving
to Fortune Global 500 as well as one of the only corporations on the list to directly address
TQM. Toyota Motors Co., Ltd. has established numerous admired awards for maintaining
quality management, involving the Deming Application Prize in year 1965 as well as the
Japan Quality Control Award in 1970. Members of this firm have to focused on maintain quality
in premises and try to complete task within stipulated time period. Through getting award,
employees get automatically motivate (Toyota Motors: The King of Total Quality Management.
2017). For Toyota, Total Quality Management is based on the concept of customers first. Cited
firm use all its efforts in order to meet expectations of people. Members can use creative and
innovation which attract large number of customers. After this, they receive feedbacks from
other members for analyse actual performance of company. In the year 1951, Toyota introduce
the Creative Idea Suggestion System in order to support as well as inspire workers in creation
effective contributions to the growth and development of business organization. Cited firm use
various tools and technologies in order to manage quality. They use innovation and various
creation for perform tasks in effective manner.
With the help of TQM approach, every business organization are able to increase
customer satisfaction, decrease overall operation cost and enhance team working. Through this,
firm can also increase work quality and earn high profit as well. Higher authorities of company
are responsible to frame plans and strategies which can maintain performance of work quality
and manage performance as well (Dahlgaard-Park, 2011). Such plans as well as strategies must
be implement in company in order to achieve target. Managers and leaders are responsible to
interact with targeted customers for identify their current needs and demand. After this Toyota
have to provide goods and services accordingly and keep customers for long time.
Generally, TQM is an important technique is which used by most of the companies for
managing ad controlling quality of company's products and goods in an systematic way. With the
2
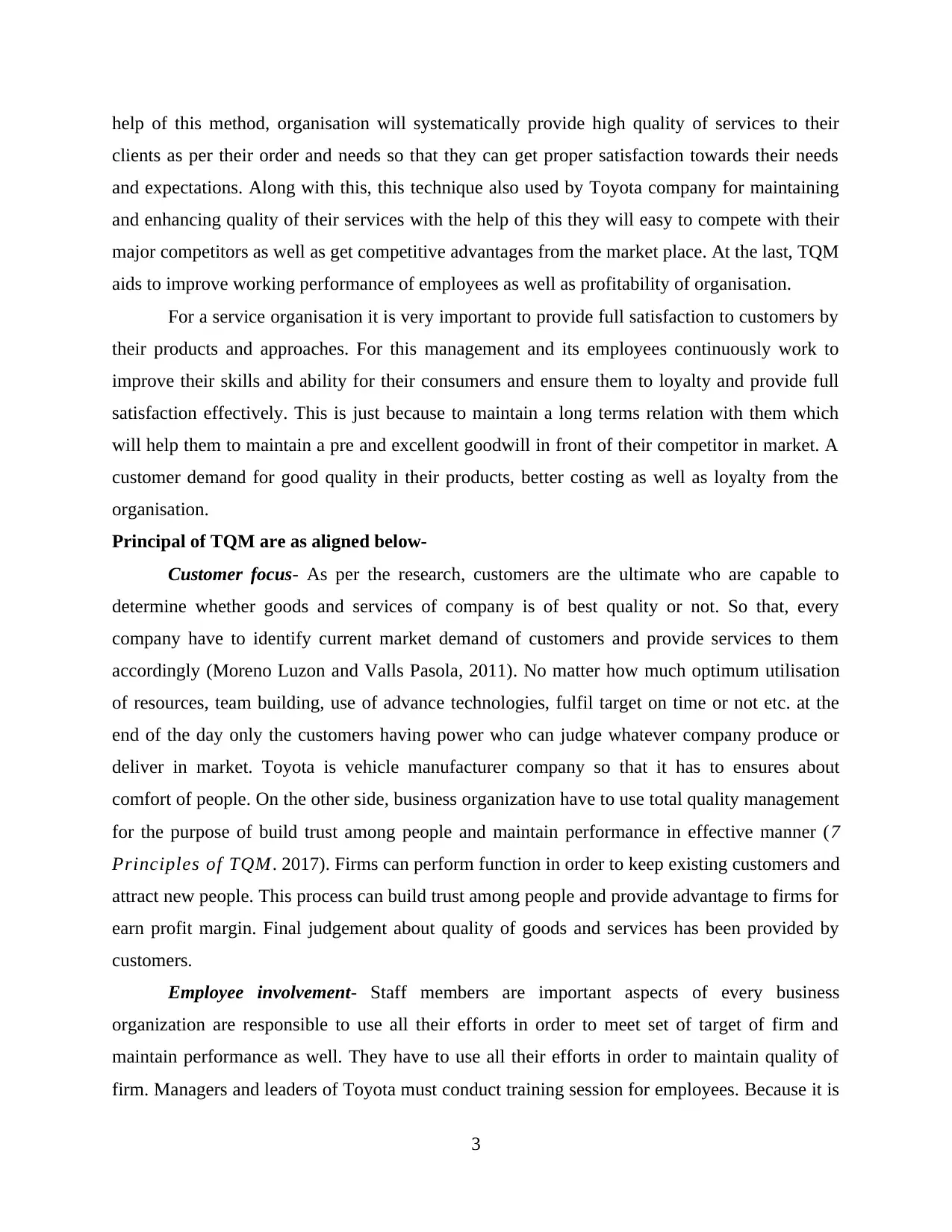
help of this method, organisation will systematically provide high quality of services to their
clients as per their order and needs so that they can get proper satisfaction towards their needs
and expectations. Along with this, this technique also used by Toyota company for maintaining
and enhancing quality of their services with the help of this they will easy to compete with their
major competitors as well as get competitive advantages from the market place. At the last, TQM
aids to improve working performance of employees as well as profitability of organisation.
For a service organisation it is very important to provide full satisfaction to customers by
their products and approaches. For this management and its employees continuously work to
improve their skills and ability for their consumers and ensure them to loyalty and provide full
satisfaction effectively. This is just because to maintain a long terms relation with them which
will help them to maintain a pre and excellent goodwill in front of their competitor in market. A
customer demand for good quality in their products, better costing as well as loyalty from the
organisation.
Principal of TQM are as aligned below-
Customer focus- As per the research, customers are the ultimate who are capable to
determine whether goods and services of company is of best quality or not. So that, every
company have to identify current market demand of customers and provide services to them
accordingly (Moreno Luzon and Valls Pasola, 2011). No matter how much optimum utilisation
of resources, team building, use of advance technologies, fulfil target on time or not etc. at the
end of the day only the customers having power who can judge whatever company produce or
deliver in market. Toyota is vehicle manufacturer company so that it has to ensures about
comfort of people. On the other side, business organization have to use total quality management
for the purpose of build trust among people and maintain performance in effective manner (7
Principles of TQM. 2017). Firms can perform function in order to keep existing customers and
attract new people. This process can build trust among people and provide advantage to firms for
earn profit margin. Final judgement about quality of goods and services has been provided by
customers.
Employee involvement- Staff members are important aspects of every business
organization are responsible to use all their efforts in order to meet set of target of firm and
maintain performance as well. They have to use all their efforts in order to maintain quality of
firm. Managers and leaders of Toyota must conduct training session for employees. Because it is
3
clients as per their order and needs so that they can get proper satisfaction towards their needs
and expectations. Along with this, this technique also used by Toyota company for maintaining
and enhancing quality of their services with the help of this they will easy to compete with their
major competitors as well as get competitive advantages from the market place. At the last, TQM
aids to improve working performance of employees as well as profitability of organisation.
For a service organisation it is very important to provide full satisfaction to customers by
their products and approaches. For this management and its employees continuously work to
improve their skills and ability for their consumers and ensure them to loyalty and provide full
satisfaction effectively. This is just because to maintain a long terms relation with them which
will help them to maintain a pre and excellent goodwill in front of their competitor in market. A
customer demand for good quality in their products, better costing as well as loyalty from the
organisation.
Principal of TQM are as aligned below-
Customer focus- As per the research, customers are the ultimate who are capable to
determine whether goods and services of company is of best quality or not. So that, every
company have to identify current market demand of customers and provide services to them
accordingly (Moreno Luzon and Valls Pasola, 2011). No matter how much optimum utilisation
of resources, team building, use of advance technologies, fulfil target on time or not etc. at the
end of the day only the customers having power who can judge whatever company produce or
deliver in market. Toyota is vehicle manufacturer company so that it has to ensures about
comfort of people. On the other side, business organization have to use total quality management
for the purpose of build trust among people and maintain performance in effective manner (7
Principles of TQM. 2017). Firms can perform function in order to keep existing customers and
attract new people. This process can build trust among people and provide advantage to firms for
earn profit margin. Final judgement about quality of goods and services has been provided by
customers.
Employee involvement- Staff members are important aspects of every business
organization are responsible to use all their efforts in order to meet set of target of firm and
maintain performance as well. They have to use all their efforts in order to maintain quality of
firm. Managers and leaders of Toyota must conduct training session for employees. Because it is
3
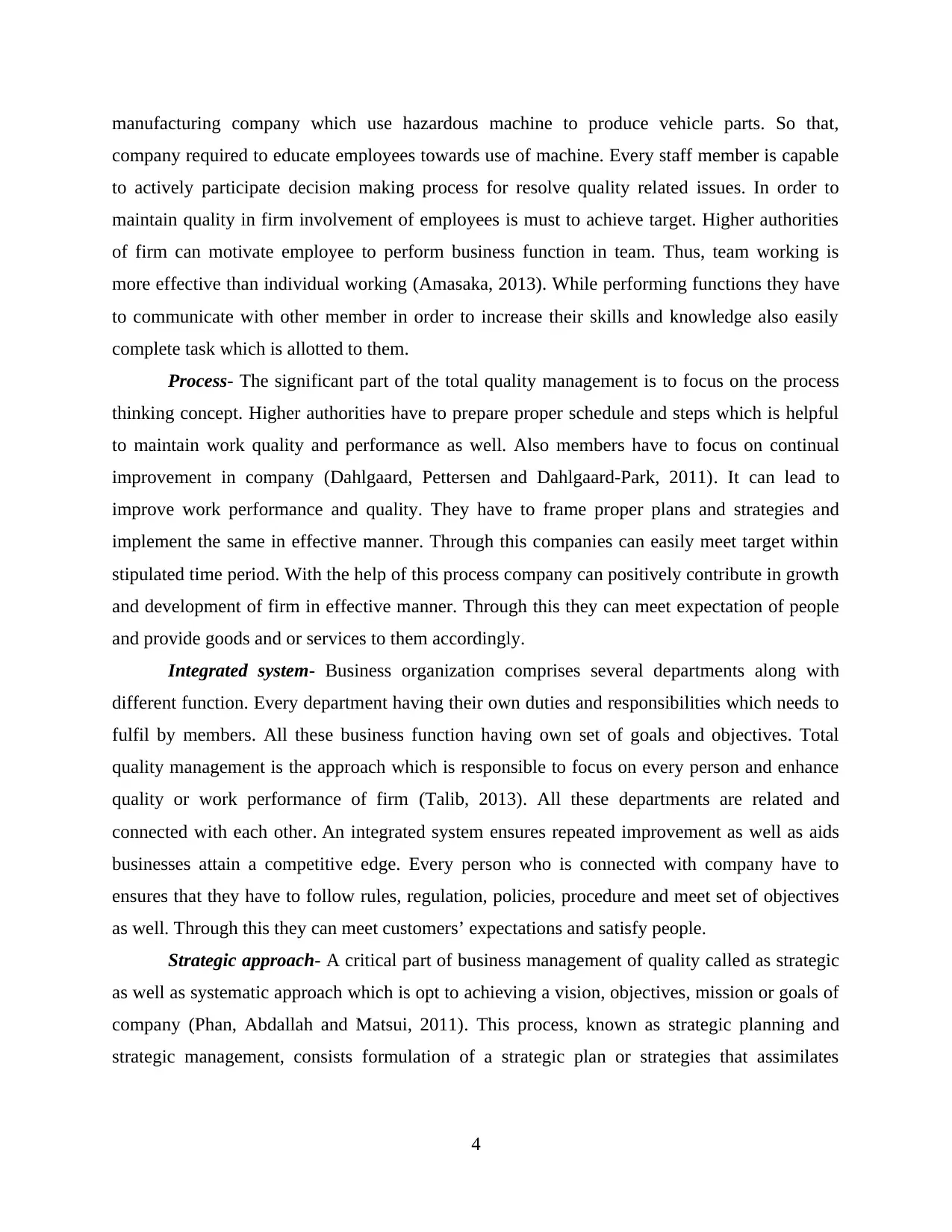
manufacturing company which use hazardous machine to produce vehicle parts. So that,
company required to educate employees towards use of machine. Every staff member is capable
to actively participate decision making process for resolve quality related issues. In order to
maintain quality in firm involvement of employees is must to achieve target. Higher authorities
of firm can motivate employee to perform business function in team. Thus, team working is
more effective than individual working (Amasaka, 2013). While performing functions they have
to communicate with other member in order to increase their skills and knowledge also easily
complete task which is allotted to them.
Process- The significant part of the total quality management is to focus on the process
thinking concept. Higher authorities have to prepare proper schedule and steps which is helpful
to maintain work quality and performance as well. Also members have to focus on continual
improvement in company (Dahlgaard, Pettersen and Dahlgaard-Park, 2011). It can lead to
improve work performance and quality. They have to frame proper plans and strategies and
implement the same in effective manner. Through this companies can easily meet target within
stipulated time period. With the help of this process company can positively contribute in growth
and development of firm in effective manner. Through this they can meet expectation of people
and provide goods and or services to them accordingly.
Integrated system- Business organization comprises several departments along with
different function. Every department having their own duties and responsibilities which needs to
fulfil by members. All these business function having own set of goals and objectives. Total
quality management is the approach which is responsible to focus on every person and enhance
quality or work performance of firm (Talib, 2013). All these departments are related and
connected with each other. An integrated system ensures repeated improvement as well as aids
businesses attain a competitive edge. Every person who is connected with company have to
ensures that they have to follow rules, regulation, policies, procedure and meet set of objectives
as well. Through this they can meet customers’ expectations and satisfy people.
Strategic approach- A critical part of business management of quality called as strategic
as well as systematic approach which is opt to achieving a vision, objectives, mission or goals of
company (Phan, Abdallah and Matsui, 2011). This process, known as strategic planning and
strategic management, consists formulation of a strategic plan or strategies that assimilates
4
company required to educate employees towards use of machine. Every staff member is capable
to actively participate decision making process for resolve quality related issues. In order to
maintain quality in firm involvement of employees is must to achieve target. Higher authorities
of firm can motivate employee to perform business function in team. Thus, team working is
more effective than individual working (Amasaka, 2013). While performing functions they have
to communicate with other member in order to increase their skills and knowledge also easily
complete task which is allotted to them.
Process- The significant part of the total quality management is to focus on the process
thinking concept. Higher authorities have to prepare proper schedule and steps which is helpful
to maintain work quality and performance as well. Also members have to focus on continual
improvement in company (Dahlgaard, Pettersen and Dahlgaard-Park, 2011). It can lead to
improve work performance and quality. They have to frame proper plans and strategies and
implement the same in effective manner. Through this companies can easily meet target within
stipulated time period. With the help of this process company can positively contribute in growth
and development of firm in effective manner. Through this they can meet expectation of people
and provide goods and or services to them accordingly.
Integrated system- Business organization comprises several departments along with
different function. Every department having their own duties and responsibilities which needs to
fulfil by members. All these business function having own set of goals and objectives. Total
quality management is the approach which is responsible to focus on every person and enhance
quality or work performance of firm (Talib, 2013). All these departments are related and
connected with each other. An integrated system ensures repeated improvement as well as aids
businesses attain a competitive edge. Every person who is connected with company have to
ensures that they have to follow rules, regulation, policies, procedure and meet set of objectives
as well. Through this they can meet customers’ expectations and satisfy people.
Strategic approach- A critical part of business management of quality called as strategic
as well as systematic approach which is opt to achieving a vision, objectives, mission or goals of
company (Phan, Abdallah and Matsui, 2011). This process, known as strategic planning and
strategic management, consists formulation of a strategic plan or strategies that assimilates
4
Paraphrase This Document
Need a fresh take? Get an instant paraphrase of this document with our AI Paraphraser
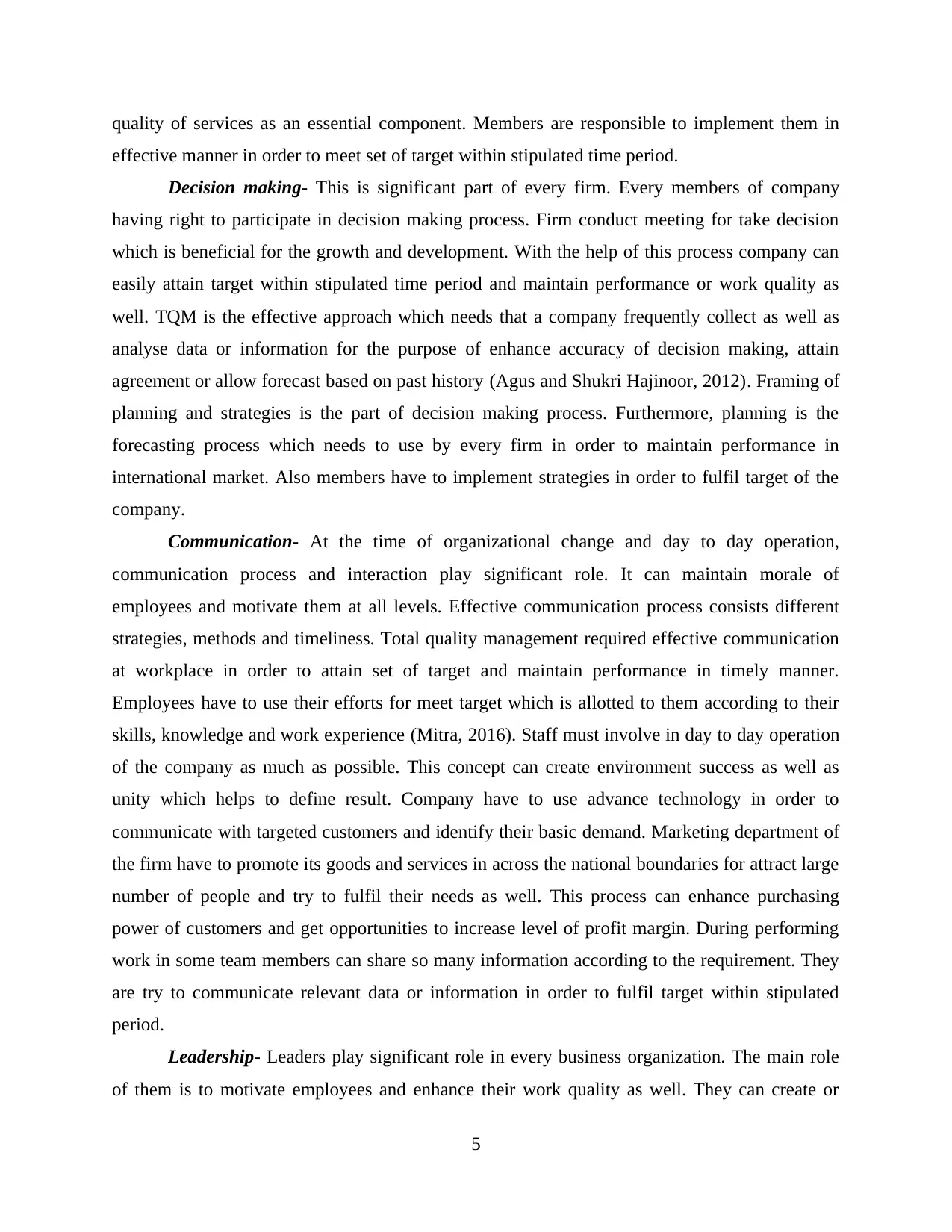
quality of services as an essential component. Members are responsible to implement them in
effective manner in order to meet set of target within stipulated time period.
Decision making- This is significant part of every firm. Every members of company
having right to participate in decision making process. Firm conduct meeting for take decision
which is beneficial for the growth and development. With the help of this process company can
easily attain target within stipulated time period and maintain performance or work quality as
well. TQM is the effective approach which needs that a company frequently collect as well as
analyse data or information for the purpose of enhance accuracy of decision making, attain
agreement or allow forecast based on past history (Agus and Shukri Hajinoor, 2012). Framing of
planning and strategies is the part of decision making process. Furthermore, planning is the
forecasting process which needs to use by every firm in order to maintain performance in
international market. Also members have to implement strategies in order to fulfil target of the
company.
Communication- At the time of organizational change and day to day operation,
communication process and interaction play significant role. It can maintain morale of
employees and motivate them at all levels. Effective communication process consists different
strategies, methods and timeliness. Total quality management required effective communication
at workplace in order to attain set of target and maintain performance in timely manner.
Employees have to use their efforts for meet target which is allotted to them according to their
skills, knowledge and work experience (Mitra, 2016). Staff must involve in day to day operation
of the company as much as possible. This concept can create environment success as well as
unity which helps to define result. Company have to use advance technology in order to
communicate with targeted customers and identify their basic demand. Marketing department of
the firm have to promote its goods and services in across the national boundaries for attract large
number of people and try to fulfil their needs as well. This process can enhance purchasing
power of customers and get opportunities to increase level of profit margin. During performing
work in some team members can share so many information according to the requirement. They
are try to communicate relevant data or information in order to fulfil target within stipulated
period.
Leadership- Leaders play significant role in every business organization. The main role
of them is to motivate employees and enhance their work quality as well. They can create or
5
effective manner in order to meet set of target within stipulated time period.
Decision making- This is significant part of every firm. Every members of company
having right to participate in decision making process. Firm conduct meeting for take decision
which is beneficial for the growth and development. With the help of this process company can
easily attain target within stipulated time period and maintain performance or work quality as
well. TQM is the effective approach which needs that a company frequently collect as well as
analyse data or information for the purpose of enhance accuracy of decision making, attain
agreement or allow forecast based on past history (Agus and Shukri Hajinoor, 2012). Framing of
planning and strategies is the part of decision making process. Furthermore, planning is the
forecasting process which needs to use by every firm in order to maintain performance in
international market. Also members have to implement strategies in order to fulfil target of the
company.
Communication- At the time of organizational change and day to day operation,
communication process and interaction play significant role. It can maintain morale of
employees and motivate them at all levels. Effective communication process consists different
strategies, methods and timeliness. Total quality management required effective communication
at workplace in order to attain set of target and maintain performance in timely manner.
Employees have to use their efforts for meet target which is allotted to them according to their
skills, knowledge and work experience (Mitra, 2016). Staff must involve in day to day operation
of the company as much as possible. This concept can create environment success as well as
unity which helps to define result. Company have to use advance technology in order to
communicate with targeted customers and identify their basic demand. Marketing department of
the firm have to promote its goods and services in across the national boundaries for attract large
number of people and try to fulfil their needs as well. This process can enhance purchasing
power of customers and get opportunities to increase level of profit margin. During performing
work in some team members can share so many information according to the requirement. They
are try to communicate relevant data or information in order to fulfil target within stipulated
period.
Leadership- Leaders play significant role in every business organization. The main role
of them is to motivate employees and enhance their work quality as well. They can create or
5

innovate new things and implement within organization. Total quality management requires that
leaders must understand their roles and responsibilities which are imposed on them as per their
skills and knowledge (Thareja, Sharma and Mahapatra, 2011). Try to motivate employees
towards attain target with stipulated time period and improve work performance as well.
Business result- Companies have to improving several areas of business models which
help them to improve customer service, product performance and consumer satisfaction. Higher
authorities of firm can receive feedbacks from their subordinates (Thareja, Sharma and
Mahapatra, 2011). After this, both types of feedbacks are beneficial for the future growth and
development of firm. with the help of positive feedbacks company can identify its strengths and
maintain the same for long time in order to increase profit level. Through negative feedbacks
firm can identify their weaknesses and try to maintain them as well.
Theories of Total Quality Management (TQM)
Deming's Theory
This is the theory of total quality management which can maintain performance of every
company and improve work quality (Theories in Total Quality Management (TQM). 2017).
Furthermore, members have to use their collective efforts in order to meet target within
stipulated time period and maintain performance as well. Thus, quality is equal to result for
which members of company have to use their efforts. Staff members of Toyota have to focus on
cost and work quality. Deming’s system is able to enhance knowledge of employee who are
working in organization.
An application for system- Deming’s theory needs to be used by Toyota in order to manage
performance in effective manner for the meet target within stipulated time period. For this
purpose, managers and leaders are responsible to motivate employee towards fulfil target within
time period and maintain their work performance along with quality.
Knowledge of variation- Higher authorities of firm are responsible to build trust among
employees and try to educate them towards use of advance technologies for meet target within
stipulated time period. Motivate workers to perform allotted work in team and try to interact
more with other members in a group (Thareja, Sharma and Mahapatra, 2011). With the help of
team building, workers can improve their knowledge, skills and work performance.
Theory of knowledge- This can used to identify current knowledge of employees. In case
members found that workers not having appropriate knowledge according to requirement of
6
leaders must understand their roles and responsibilities which are imposed on them as per their
skills and knowledge (Thareja, Sharma and Mahapatra, 2011). Try to motivate employees
towards attain target with stipulated time period and improve work performance as well.
Business result- Companies have to improving several areas of business models which
help them to improve customer service, product performance and consumer satisfaction. Higher
authorities of firm can receive feedbacks from their subordinates (Thareja, Sharma and
Mahapatra, 2011). After this, both types of feedbacks are beneficial for the future growth and
development of firm. with the help of positive feedbacks company can identify its strengths and
maintain the same for long time in order to increase profit level. Through negative feedbacks
firm can identify their weaknesses and try to maintain them as well.
Theories of Total Quality Management (TQM)
Deming's Theory
This is the theory of total quality management which can maintain performance of every
company and improve work quality (Theories in Total Quality Management (TQM). 2017).
Furthermore, members have to use their collective efforts in order to meet target within
stipulated time period and maintain performance as well. Thus, quality is equal to result for
which members of company have to use their efforts. Staff members of Toyota have to focus on
cost and work quality. Deming’s system is able to enhance knowledge of employee who are
working in organization.
An application for system- Deming’s theory needs to be used by Toyota in order to manage
performance in effective manner for the meet target within stipulated time period. For this
purpose, managers and leaders are responsible to motivate employee towards fulfil target within
time period and maintain their work performance along with quality.
Knowledge of variation- Higher authorities of firm are responsible to build trust among
employees and try to educate them towards use of advance technologies for meet target within
stipulated time period. Motivate workers to perform allotted work in team and try to interact
more with other members in a group (Thareja, Sharma and Mahapatra, 2011). With the help of
team building, workers can improve their knowledge, skills and work performance.
Theory of knowledge- This can used to identify current knowledge of employees. In case
members found that workers not having appropriate knowledge according to requirement of
6
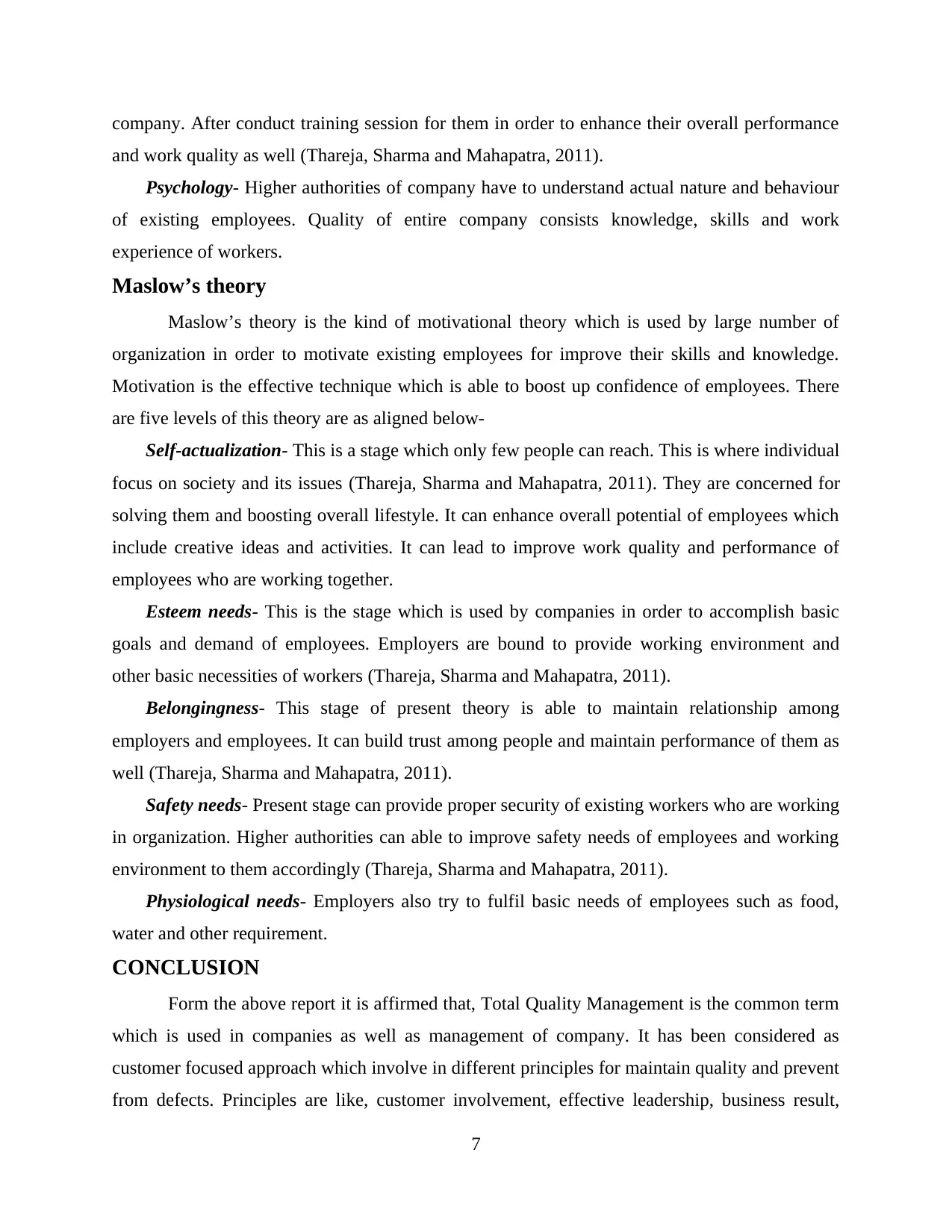
company. After conduct training session for them in order to enhance their overall performance
and work quality as well (Thareja, Sharma and Mahapatra, 2011).
Psychology- Higher authorities of company have to understand actual nature and behaviour
of existing employees. Quality of entire company consists knowledge, skills and work
experience of workers.
Maslow’s theory
Maslow’s theory is the kind of motivational theory which is used by large number of
organization in order to motivate existing employees for improve their skills and knowledge.
Motivation is the effective technique which is able to boost up confidence of employees. There
are five levels of this theory are as aligned below-
Self-actualization- This is a stage which only few people can reach. This is where individual
focus on society and its issues (Thareja, Sharma and Mahapatra, 2011). They are concerned for
solving them and boosting overall lifestyle. It can enhance overall potential of employees which
include creative ideas and activities. It can lead to improve work quality and performance of
employees who are working together.
Esteem needs- This is the stage which is used by companies in order to accomplish basic
goals and demand of employees. Employers are bound to provide working environment and
other basic necessities of workers (Thareja, Sharma and Mahapatra, 2011).
Belongingness- This stage of present theory is able to maintain relationship among
employers and employees. It can build trust among people and maintain performance of them as
well (Thareja, Sharma and Mahapatra, 2011).
Safety needs- Present stage can provide proper security of existing workers who are working
in organization. Higher authorities can able to improve safety needs of employees and working
environment to them accordingly (Thareja, Sharma and Mahapatra, 2011).
Physiological needs- Employers also try to fulfil basic needs of employees such as food,
water and other requirement.
CONCLUSION
Form the above report it is affirmed that, Total Quality Management is the common term
which is used in companies as well as management of company. It has been considered as
customer focused approach which involve in different principles for maintain quality and prevent
from defects. Principles are like, customer involvement, effective leadership, business result,
7
and work quality as well (Thareja, Sharma and Mahapatra, 2011).
Psychology- Higher authorities of company have to understand actual nature and behaviour
of existing employees. Quality of entire company consists knowledge, skills and work
experience of workers.
Maslow’s theory
Maslow’s theory is the kind of motivational theory which is used by large number of
organization in order to motivate existing employees for improve their skills and knowledge.
Motivation is the effective technique which is able to boost up confidence of employees. There
are five levels of this theory are as aligned below-
Self-actualization- This is a stage which only few people can reach. This is where individual
focus on society and its issues (Thareja, Sharma and Mahapatra, 2011). They are concerned for
solving them and boosting overall lifestyle. It can enhance overall potential of employees which
include creative ideas and activities. It can lead to improve work quality and performance of
employees who are working together.
Esteem needs- This is the stage which is used by companies in order to accomplish basic
goals and demand of employees. Employers are bound to provide working environment and
other basic necessities of workers (Thareja, Sharma and Mahapatra, 2011).
Belongingness- This stage of present theory is able to maintain relationship among
employers and employees. It can build trust among people and maintain performance of them as
well (Thareja, Sharma and Mahapatra, 2011).
Safety needs- Present stage can provide proper security of existing workers who are working
in organization. Higher authorities can able to improve safety needs of employees and working
environment to them accordingly (Thareja, Sharma and Mahapatra, 2011).
Physiological needs- Employers also try to fulfil basic needs of employees such as food,
water and other requirement.
CONCLUSION
Form the above report it is affirmed that, Total Quality Management is the common term
which is used in companies as well as management of company. It has been considered as
customer focused approach which involve in different principles for maintain quality and prevent
from defects. Principles are like, customer involvement, effective leadership, business result,
7
Secure Best Marks with AI Grader
Need help grading? Try our AI Grader for instant feedback on your assignments.
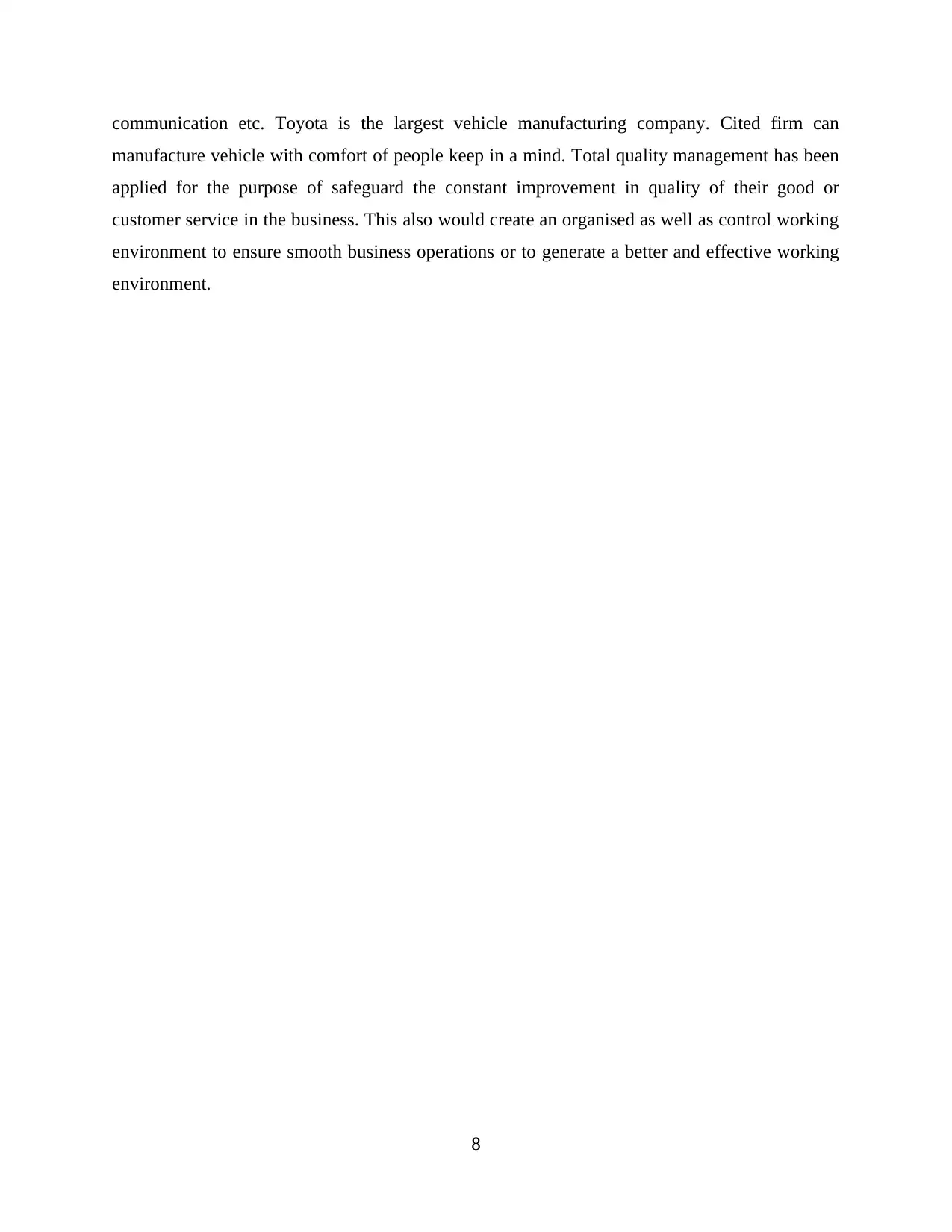
communication etc. Toyota is the largest vehicle manufacturing company. Cited firm can
manufacture vehicle with comfort of people keep in a mind. Total quality management has been
applied for the purpose of safeguard the constant improvement in quality of their good or
customer service in the business. This also would create an organised as well as control working
environment to ensure smooth business operations or to generate a better and effective working
environment.
8
manufacture vehicle with comfort of people keep in a mind. Total quality management has been
applied for the purpose of safeguard the constant improvement in quality of their good or
customer service in the business. This also would create an organised as well as control working
environment to ensure smooth business operations or to generate a better and effective working
environment.
8
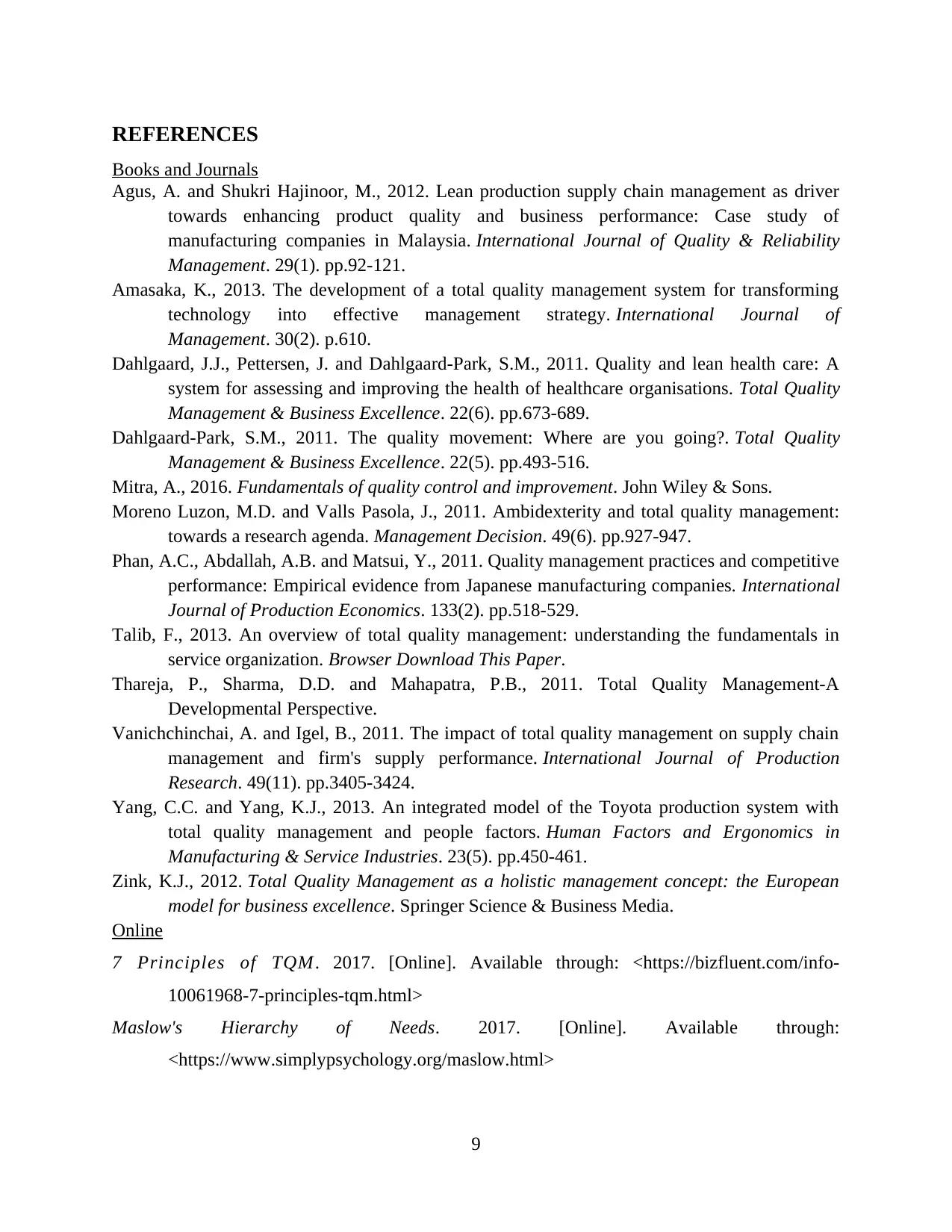
REFERENCES
Books and Journals
Agus, A. and Shukri Hajinoor, M., 2012. Lean production supply chain management as driver
towards enhancing product quality and business performance: Case study of
manufacturing companies in Malaysia. International Journal of Quality & Reliability
Management. 29(1). pp.92-121.
Amasaka, K., 2013. The development of a total quality management system for transforming
technology into effective management strategy. International Journal of
Management. 30(2). p.610.
Dahlgaard, J.J., Pettersen, J. and Dahlgaard-Park, S.M., 2011. Quality and lean health care: A
system for assessing and improving the health of healthcare organisations. Total Quality
Management & Business Excellence. 22(6). pp.673-689.
Dahlgaard-Park, S.M., 2011. The quality movement: Where are you going?. Total Quality
Management & Business Excellence. 22(5). pp.493-516.
Mitra, A., 2016. Fundamentals of quality control and improvement. John Wiley & Sons.
Moreno Luzon, M.D. and Valls Pasola, J., 2011. Ambidexterity and total quality management:
towards a research agenda. Management Decision. 49(6). pp.927-947.
Phan, A.C., Abdallah, A.B. and Matsui, Y., 2011. Quality management practices and competitive
performance: Empirical evidence from Japanese manufacturing companies. International
Journal of Production Economics. 133(2). pp.518-529.
Talib, F., 2013. An overview of total quality management: understanding the fundamentals in
service organization. Browser Download This Paper.
Thareja, P., Sharma, D.D. and Mahapatra, P.B., 2011. Total Quality Management-A
Developmental Perspective.
Vanichchinchai, A. and Igel, B., 2011. The impact of total quality management on supply chain
management and firm's supply performance. International Journal of Production
Research. 49(11). pp.3405-3424.
Yang, C.C. and Yang, K.J., 2013. An integrated model of the Toyota production system with
total quality management and people factors. Human Factors and Ergonomics in
Manufacturing & Service Industries. 23(5). pp.450-461.
Zink, K.J., 2012. Total Quality Management as a holistic management concept: the European
model for business excellence. Springer Science & Business Media.
Online
7 Principles of TQM. 2017. [Online]. Available through: <https://bizfluent.com/info-
10061968-7-principles-tqm.html>
Maslow's Hierarchy of Needs. 2017. [Online]. Available through:
<https://www.simplypsychology.org/maslow.html>
9
Books and Journals
Agus, A. and Shukri Hajinoor, M., 2012. Lean production supply chain management as driver
towards enhancing product quality and business performance: Case study of
manufacturing companies in Malaysia. International Journal of Quality & Reliability
Management. 29(1). pp.92-121.
Amasaka, K., 2013. The development of a total quality management system for transforming
technology into effective management strategy. International Journal of
Management. 30(2). p.610.
Dahlgaard, J.J., Pettersen, J. and Dahlgaard-Park, S.M., 2011. Quality and lean health care: A
system for assessing and improving the health of healthcare organisations. Total Quality
Management & Business Excellence. 22(6). pp.673-689.
Dahlgaard-Park, S.M., 2011. The quality movement: Where are you going?. Total Quality
Management & Business Excellence. 22(5). pp.493-516.
Mitra, A., 2016. Fundamentals of quality control and improvement. John Wiley & Sons.
Moreno Luzon, M.D. and Valls Pasola, J., 2011. Ambidexterity and total quality management:
towards a research agenda. Management Decision. 49(6). pp.927-947.
Phan, A.C., Abdallah, A.B. and Matsui, Y., 2011. Quality management practices and competitive
performance: Empirical evidence from Japanese manufacturing companies. International
Journal of Production Economics. 133(2). pp.518-529.
Talib, F., 2013. An overview of total quality management: understanding the fundamentals in
service organization. Browser Download This Paper.
Thareja, P., Sharma, D.D. and Mahapatra, P.B., 2011. Total Quality Management-A
Developmental Perspective.
Vanichchinchai, A. and Igel, B., 2011. The impact of total quality management on supply chain
management and firm's supply performance. International Journal of Production
Research. 49(11). pp.3405-3424.
Yang, C.C. and Yang, K.J., 2013. An integrated model of the Toyota production system with
total quality management and people factors. Human Factors and Ergonomics in
Manufacturing & Service Industries. 23(5). pp.450-461.
Zink, K.J., 2012. Total Quality Management as a holistic management concept: the European
model for business excellence. Springer Science & Business Media.
Online
7 Principles of TQM. 2017. [Online]. Available through: <https://bizfluent.com/info-
10061968-7-principles-tqm.html>
Maslow's Hierarchy of Needs. 2017. [Online]. Available through:
<https://www.simplypsychology.org/maslow.html>
9
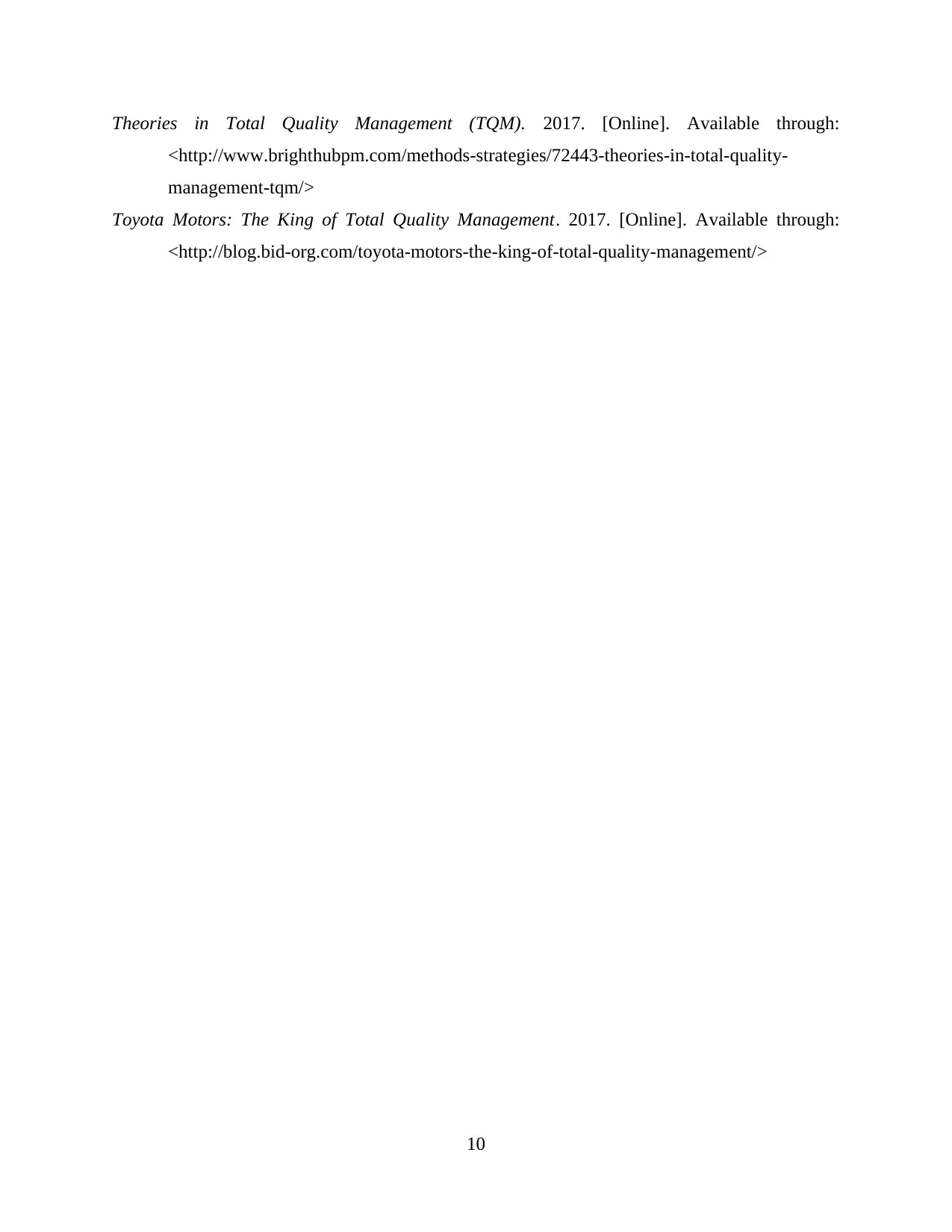
Theories in Total Quality Management (TQM). 2017. [Online]. Available through:
<http://www.brighthubpm.com/methods-strategies/72443-theories-in-total-quality-
management-tqm/>
Toyota Motors: The King of Total Quality Management. 2017. [Online]. Available through:
<http://blog.bid-org.com/toyota-motors-the-king-of-total-quality-management/>
10
<http://www.brighthubpm.com/methods-strategies/72443-theories-in-total-quality-
management-tqm/>
Toyota Motors: The King of Total Quality Management. 2017. [Online]. Available through:
<http://blog.bid-org.com/toyota-motors-the-king-of-total-quality-management/>
10
Paraphrase This Document
Need a fresh take? Get an instant paraphrase of this document with our AI Paraphraser
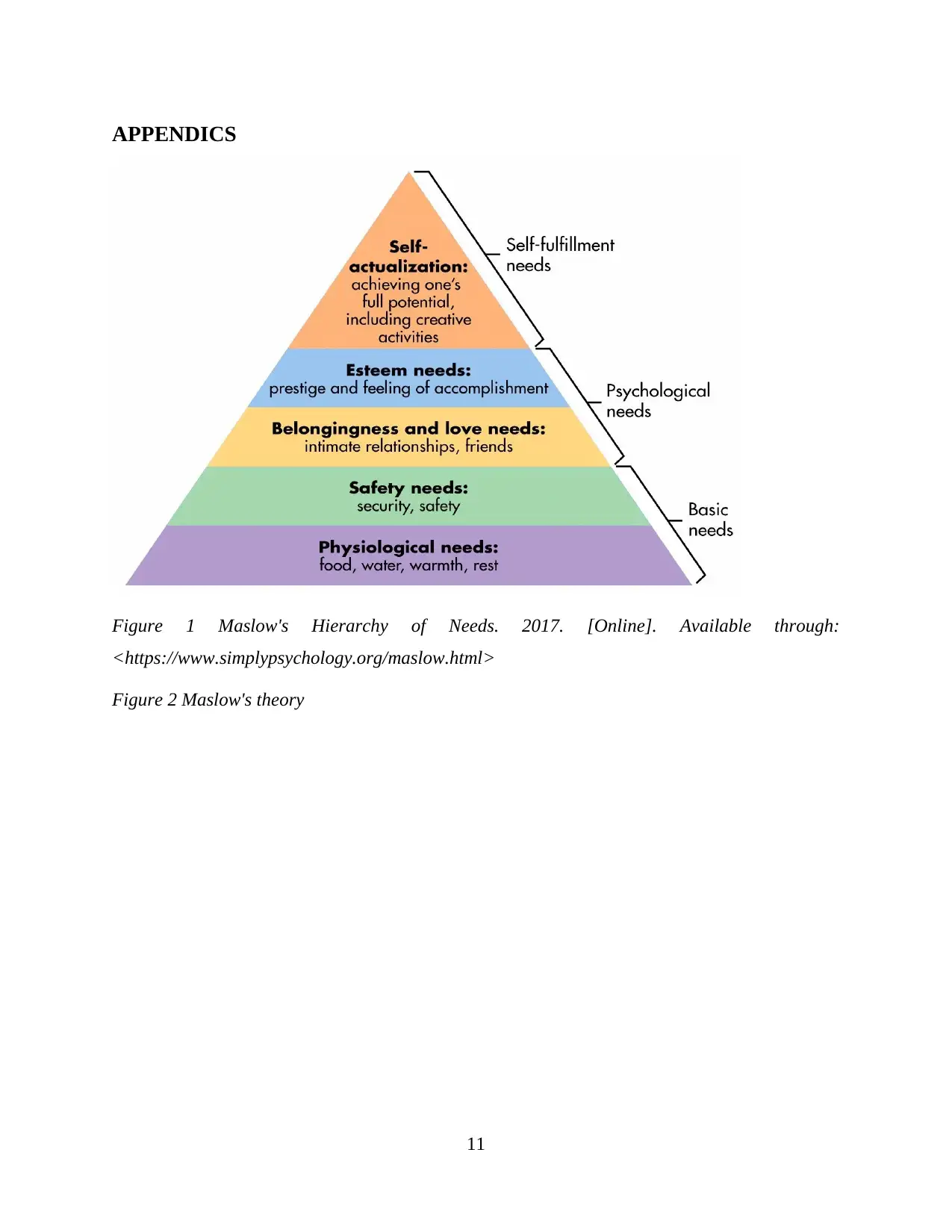
APPENDICS
Figure 1 Maslow's Hierarchy of Needs. 2017. [Online]. Available through:
<https://www.simplypsychology.org/maslow.html>
Figure 2 Maslow's theory
11
Figure 1 Maslow's Hierarchy of Needs. 2017. [Online]. Available through:
<https://www.simplypsychology.org/maslow.html>
Figure 2 Maslow's theory
11
1 out of 14
Related Documents
![[object Object]](/_next/image/?url=%2F_next%2Fstatic%2Fmedia%2Flogo.6d15ce61.png&w=640&q=75)
Your All-in-One AI-Powered Toolkit for Academic Success.
 +13062052269
info@desklib.com
Available 24*7 on WhatsApp / Email
Unlock your academic potential
© 2024  |  Zucol Services PVT LTD  |  All rights reserved.