Business Improvement and Performance Excellence Profile of Toyota
VerifiedAdded on 2023/06/15
|10
|2424
|338
AI Summary
This article discusses Toyota's JIT production process, its key tasks, sequence of steps, people involved, equipment used, and more. It also explores the difference between quality and productivity, their impact on profitability, and the role of managers in improving product quality.
Contribute Materials
Your contribution can guide someone’s learning journey. Share your
documents today.
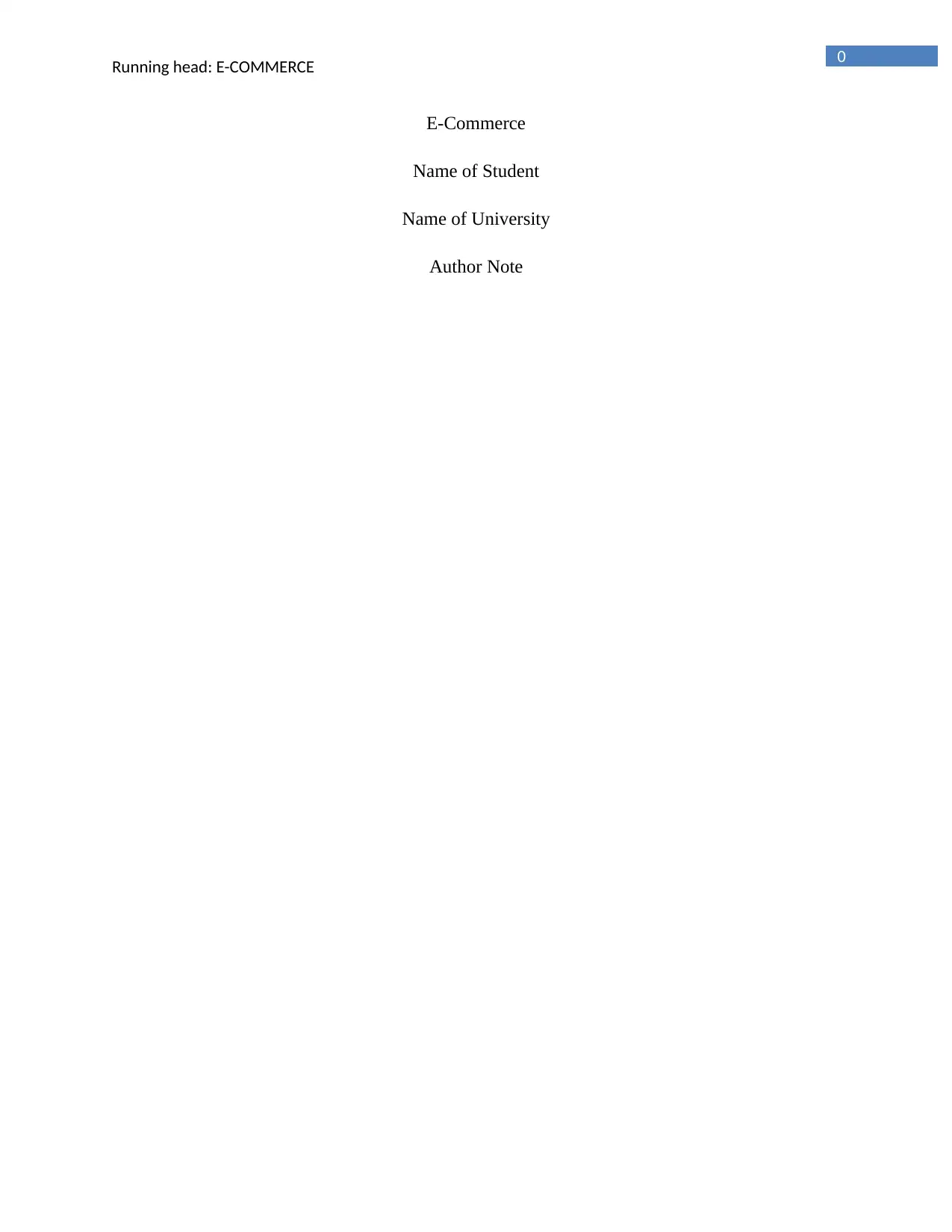
0
Running head: E-COMMERCE
E-Commerce
Name of Student
Name of University
Author Note
Running head: E-COMMERCE
E-Commerce
Name of Student
Name of University
Author Note
Secure Best Marks with AI Grader
Need help grading? Try our AI Grader for instant feedback on your assignments.
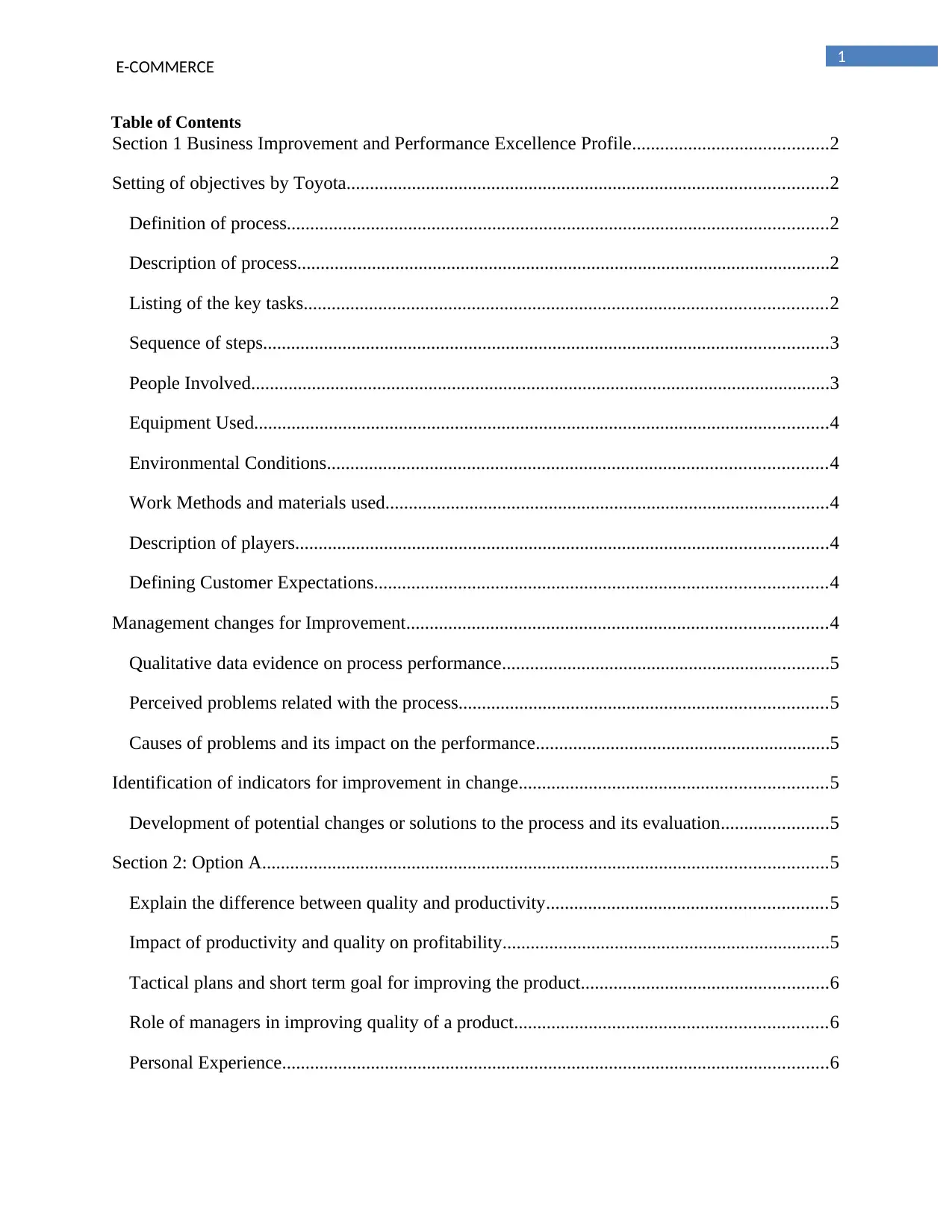
1
E-COMMERCE
Table of Contents
Section 1 Business Improvement and Performance Excellence Profile..........................................2
Setting of objectives by Toyota.......................................................................................................2
Definition of process....................................................................................................................2
Description of process..................................................................................................................2
Listing of the key tasks................................................................................................................2
Sequence of steps.........................................................................................................................3
People Involved............................................................................................................................3
Equipment Used...........................................................................................................................4
Environmental Conditions...........................................................................................................4
Work Methods and materials used...............................................................................................4
Description of players..................................................................................................................4
Defining Customer Expectations.................................................................................................4
Management changes for Improvement..........................................................................................4
Qualitative data evidence on process performance......................................................................5
Perceived problems related with the process...............................................................................5
Causes of problems and its impact on the performance...............................................................5
Identification of indicators for improvement in change..................................................................5
Development of potential changes or solutions to the process and its evaluation.......................5
Section 2: Option A.........................................................................................................................5
Explain the difference between quality and productivity............................................................5
Impact of productivity and quality on profitability......................................................................5
Tactical plans and short term goal for improving the product.....................................................6
Role of managers in improving quality of a product...................................................................6
Personal Experience.....................................................................................................................6
E-COMMERCE
Table of Contents
Section 1 Business Improvement and Performance Excellence Profile..........................................2
Setting of objectives by Toyota.......................................................................................................2
Definition of process....................................................................................................................2
Description of process..................................................................................................................2
Listing of the key tasks................................................................................................................2
Sequence of steps.........................................................................................................................3
People Involved............................................................................................................................3
Equipment Used...........................................................................................................................4
Environmental Conditions...........................................................................................................4
Work Methods and materials used...............................................................................................4
Description of players..................................................................................................................4
Defining Customer Expectations.................................................................................................4
Management changes for Improvement..........................................................................................4
Qualitative data evidence on process performance......................................................................5
Perceived problems related with the process...............................................................................5
Causes of problems and its impact on the performance...............................................................5
Identification of indicators for improvement in change..................................................................5
Development of potential changes or solutions to the process and its evaluation.......................5
Section 2: Option A.........................................................................................................................5
Explain the difference between quality and productivity............................................................5
Impact of productivity and quality on profitability......................................................................5
Tactical plans and short term goal for improving the product.....................................................6
Role of managers in improving quality of a product...................................................................6
Personal Experience.....................................................................................................................6
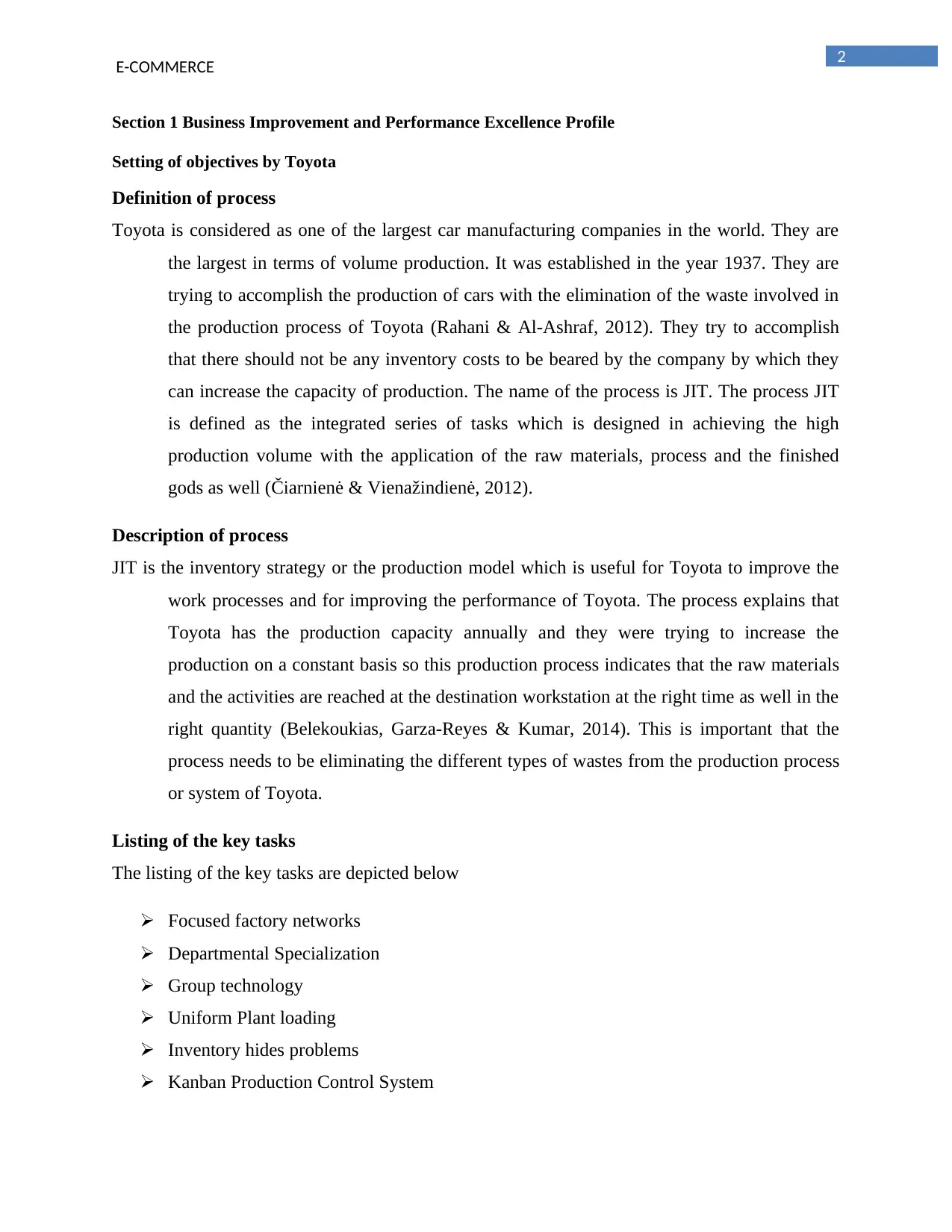
2
E-COMMERCE
Section 1 Business Improvement and Performance Excellence Profile
Setting of objectives by Toyota
Definition of process
Toyota is considered as one of the largest car manufacturing companies in the world. They are
the largest in terms of volume production. It was established in the year 1937. They are
trying to accomplish the production of cars with the elimination of the waste involved in
the production process of Toyota (Rahani & Al-Ashraf, 2012). They try to accomplish
that there should not be any inventory costs to be beared by the company by which they
can increase the capacity of production. The name of the process is JIT. The process JIT
is defined as the integrated series of tasks which is designed in achieving the high
production volume with the application of the raw materials, process and the finished
gods as well (Čiarnienė & Vienažindienė, 2012).
Description of process
JIT is the inventory strategy or the production model which is useful for Toyota to improve the
work processes and for improving the performance of Toyota. The process explains that
Toyota has the production capacity annually and they were trying to increase the
production on a constant basis so this production process indicates that the raw materials
and the activities are reached at the destination workstation at the right time as well in the
right quantity (Belekoukias, Garza-Reyes & Kumar, 2014). This is important that the
process needs to be eliminating the different types of wastes from the production process
or system of Toyota.
Listing of the key tasks
The listing of the key tasks are depicted below
Focused factory networks
Departmental Specialization
Group technology
Uniform Plant loading
Inventory hides problems
Kanban Production Control System
E-COMMERCE
Section 1 Business Improvement and Performance Excellence Profile
Setting of objectives by Toyota
Definition of process
Toyota is considered as one of the largest car manufacturing companies in the world. They are
the largest in terms of volume production. It was established in the year 1937. They are
trying to accomplish the production of cars with the elimination of the waste involved in
the production process of Toyota (Rahani & Al-Ashraf, 2012). They try to accomplish
that there should not be any inventory costs to be beared by the company by which they
can increase the capacity of production. The name of the process is JIT. The process JIT
is defined as the integrated series of tasks which is designed in achieving the high
production volume with the application of the raw materials, process and the finished
gods as well (Čiarnienė & Vienažindienė, 2012).
Description of process
JIT is the inventory strategy or the production model which is useful for Toyota to improve the
work processes and for improving the performance of Toyota. The process explains that
Toyota has the production capacity annually and they were trying to increase the
production on a constant basis so this production process indicates that the raw materials
and the activities are reached at the destination workstation at the right time as well in the
right quantity (Belekoukias, Garza-Reyes & Kumar, 2014). This is important that the
process needs to be eliminating the different types of wastes from the production process
or system of Toyota.
Listing of the key tasks
The listing of the key tasks are depicted below
Focused factory networks
Departmental Specialization
Group technology
Uniform Plant loading
Inventory hides problems
Kanban Production Control System
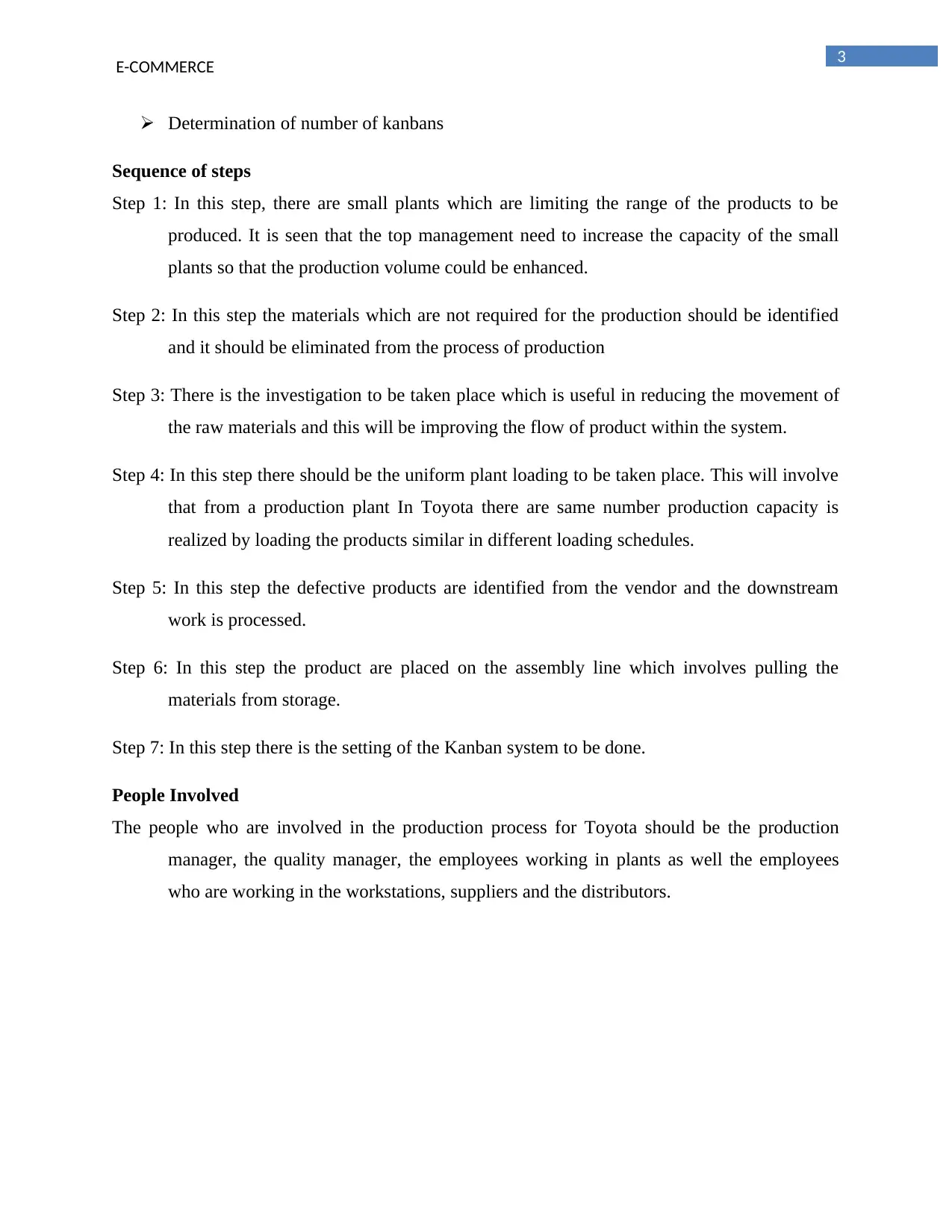
3
E-COMMERCE
Determination of number of kanbans
Sequence of steps
Step 1: In this step, there are small plants which are limiting the range of the products to be
produced. It is seen that the top management need to increase the capacity of the small
plants so that the production volume could be enhanced.
Step 2: In this step the materials which are not required for the production should be identified
and it should be eliminated from the process of production
Step 3: There is the investigation to be taken place which is useful in reducing the movement of
the raw materials and this will be improving the flow of product within the system.
Step 4: In this step there should be the uniform plant loading to be taken place. This will involve
that from a production plant In Toyota there are same number production capacity is
realized by loading the products similar in different loading schedules.
Step 5: In this step the defective products are identified from the vendor and the downstream
work is processed.
Step 6: In this step the product are placed on the assembly line which involves pulling the
materials from storage.
Step 7: In this step there is the setting of the Kanban system to be done.
People Involved
The people who are involved in the production process for Toyota should be the production
manager, the quality manager, the employees working in plants as well the employees
who are working in the workstations, suppliers and the distributors.
E-COMMERCE
Determination of number of kanbans
Sequence of steps
Step 1: In this step, there are small plants which are limiting the range of the products to be
produced. It is seen that the top management need to increase the capacity of the small
plants so that the production volume could be enhanced.
Step 2: In this step the materials which are not required for the production should be identified
and it should be eliminated from the process of production
Step 3: There is the investigation to be taken place which is useful in reducing the movement of
the raw materials and this will be improving the flow of product within the system.
Step 4: In this step there should be the uniform plant loading to be taken place. This will involve
that from a production plant In Toyota there are same number production capacity is
realized by loading the products similar in different loading schedules.
Step 5: In this step the defective products are identified from the vendor and the downstream
work is processed.
Step 6: In this step the product are placed on the assembly line which involves pulling the
materials from storage.
Step 7: In this step there is the setting of the Kanban system to be done.
People Involved
The people who are involved in the production process for Toyota should be the production
manager, the quality manager, the employees working in plants as well the employees
who are working in the workstations, suppliers and the distributors.
Secure Best Marks with AI Grader
Need help grading? Try our AI Grader for instant feedback on your assignments.
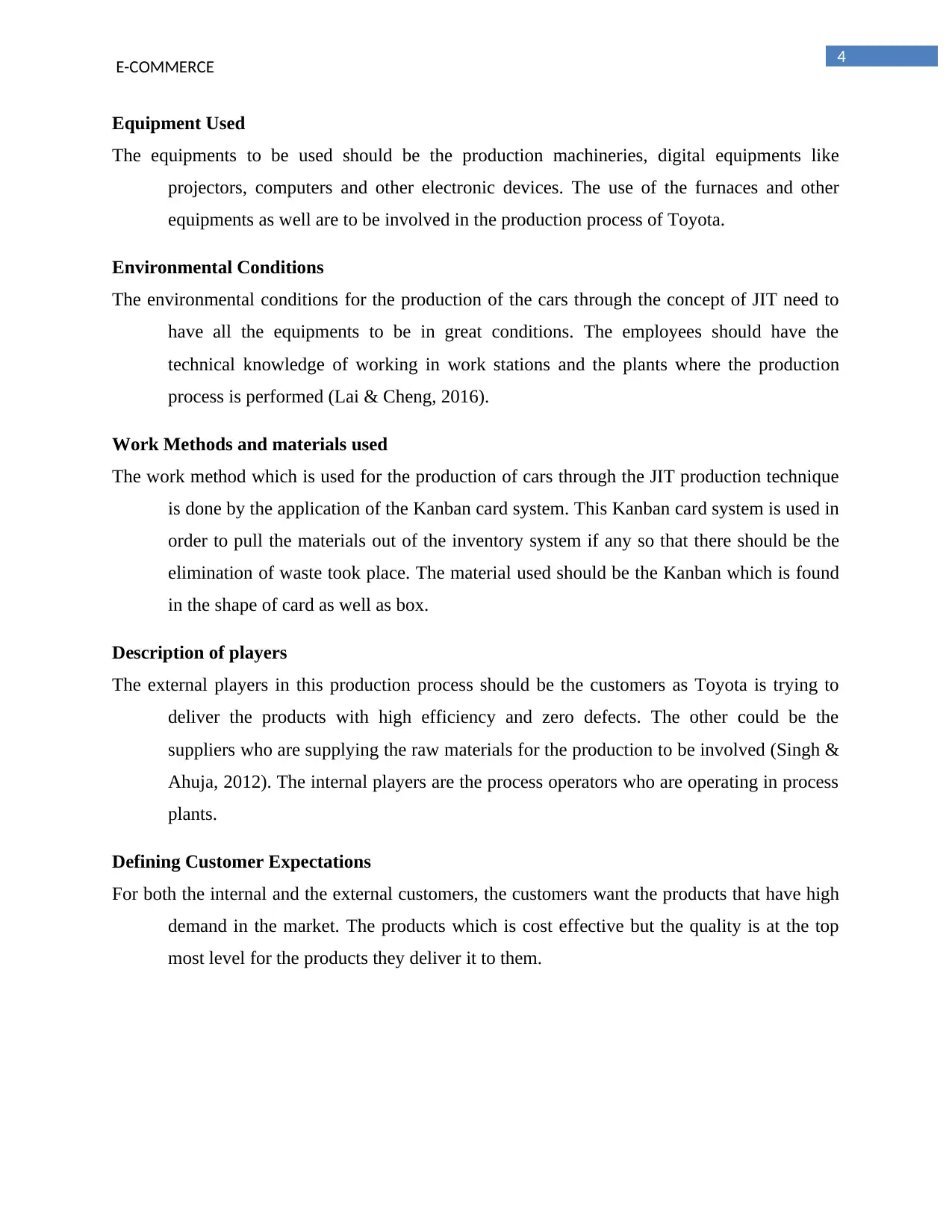
4
E-COMMERCE
Equipment Used
The equipments to be used should be the production machineries, digital equipments like
projectors, computers and other electronic devices. The use of the furnaces and other
equipments as well are to be involved in the production process of Toyota.
Environmental Conditions
The environmental conditions for the production of the cars through the concept of JIT need to
have all the equipments to be in great conditions. The employees should have the
technical knowledge of working in work stations and the plants where the production
process is performed (Lai & Cheng, 2016).
Work Methods and materials used
The work method which is used for the production of cars through the JIT production technique
is done by the application of the Kanban card system. This Kanban card system is used in
order to pull the materials out of the inventory system if any so that there should be the
elimination of waste took place. The material used should be the Kanban which is found
in the shape of card as well as box.
Description of players
The external players in this production process should be the customers as Toyota is trying to
deliver the products with high efficiency and zero defects. The other could be the
suppliers who are supplying the raw materials for the production to be involved (Singh &
Ahuja, 2012). The internal players are the process operators who are operating in process
plants.
Defining Customer Expectations
For both the internal and the external customers, the customers want the products that have high
demand in the market. The products which is cost effective but the quality is at the top
most level for the products they deliver it to them.
E-COMMERCE
Equipment Used
The equipments to be used should be the production machineries, digital equipments like
projectors, computers and other electronic devices. The use of the furnaces and other
equipments as well are to be involved in the production process of Toyota.
Environmental Conditions
The environmental conditions for the production of the cars through the concept of JIT need to
have all the equipments to be in great conditions. The employees should have the
technical knowledge of working in work stations and the plants where the production
process is performed (Lai & Cheng, 2016).
Work Methods and materials used
The work method which is used for the production of cars through the JIT production technique
is done by the application of the Kanban card system. This Kanban card system is used in
order to pull the materials out of the inventory system if any so that there should be the
elimination of waste took place. The material used should be the Kanban which is found
in the shape of card as well as box.
Description of players
The external players in this production process should be the customers as Toyota is trying to
deliver the products with high efficiency and zero defects. The other could be the
suppliers who are supplying the raw materials for the production to be involved (Singh &
Ahuja, 2012). The internal players are the process operators who are operating in process
plants.
Defining Customer Expectations
For both the internal and the external customers, the customers want the products that have high
demand in the market. The products which is cost effective but the quality is at the top
most level for the products they deliver it to them.
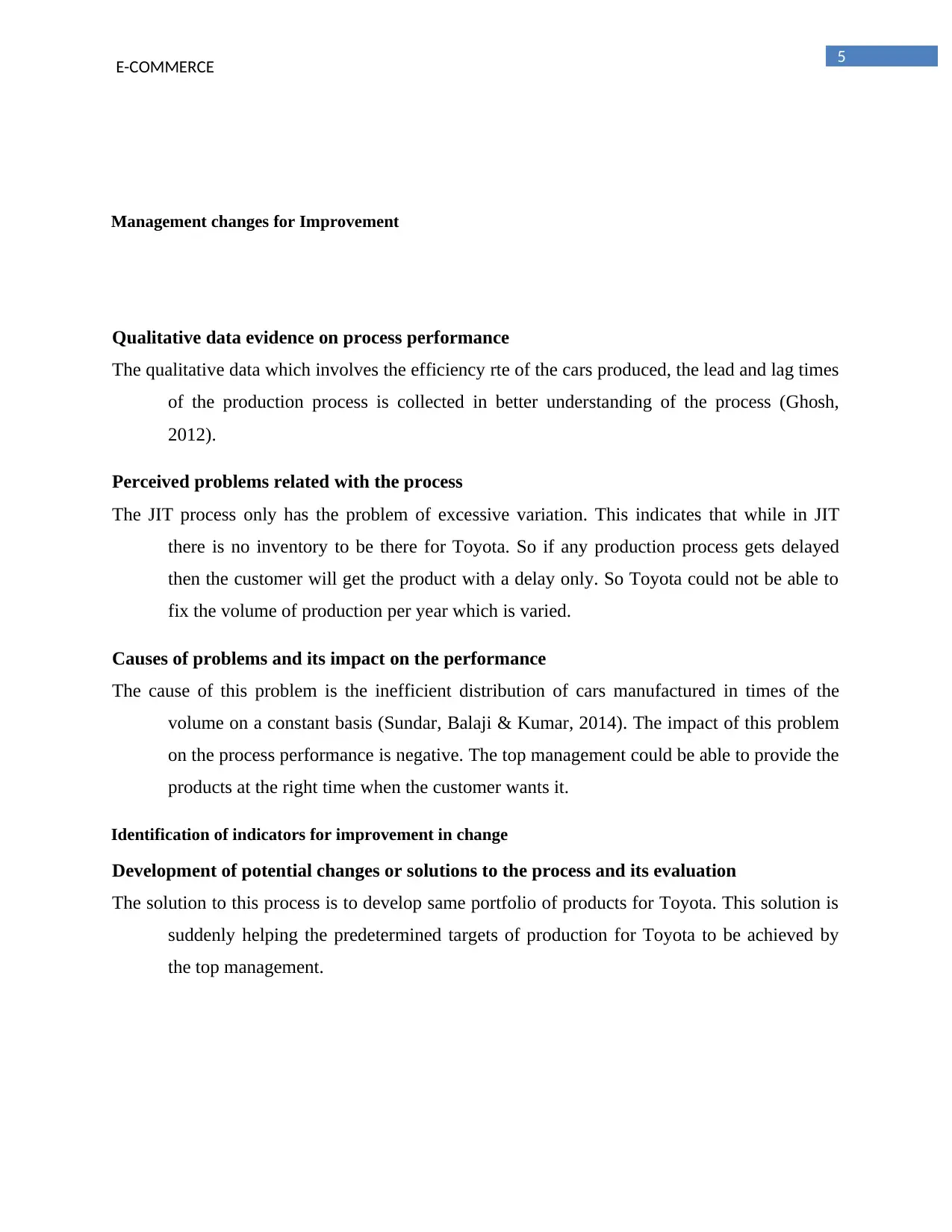
5
E-COMMERCE
Management changes for Improvement
Qualitative data evidence on process performance
The qualitative data which involves the efficiency rte of the cars produced, the lead and lag times
of the production process is collected in better understanding of the process (Ghosh,
2012).
Perceived problems related with the process
The JIT process only has the problem of excessive variation. This indicates that while in JIT
there is no inventory to be there for Toyota. So if any production process gets delayed
then the customer will get the product with a delay only. So Toyota could not be able to
fix the volume of production per year which is varied.
Causes of problems and its impact on the performance
The cause of this problem is the inefficient distribution of cars manufactured in times of the
volume on a constant basis (Sundar, Balaji & Kumar, 2014). The impact of this problem
on the process performance is negative. The top management could be able to provide the
products at the right time when the customer wants it.
Identification of indicators for improvement in change
Development of potential changes or solutions to the process and its evaluation
The solution to this process is to develop same portfolio of products for Toyota. This solution is
suddenly helping the predetermined targets of production for Toyota to be achieved by
the top management.
E-COMMERCE
Management changes for Improvement
Qualitative data evidence on process performance
The qualitative data which involves the efficiency rte of the cars produced, the lead and lag times
of the production process is collected in better understanding of the process (Ghosh,
2012).
Perceived problems related with the process
The JIT process only has the problem of excessive variation. This indicates that while in JIT
there is no inventory to be there for Toyota. So if any production process gets delayed
then the customer will get the product with a delay only. So Toyota could not be able to
fix the volume of production per year which is varied.
Causes of problems and its impact on the performance
The cause of this problem is the inefficient distribution of cars manufactured in times of the
volume on a constant basis (Sundar, Balaji & Kumar, 2014). The impact of this problem
on the process performance is negative. The top management could be able to provide the
products at the right time when the customer wants it.
Identification of indicators for improvement in change
Development of potential changes or solutions to the process and its evaluation
The solution to this process is to develop same portfolio of products for Toyota. This solution is
suddenly helping the predetermined targets of production for Toyota to be achieved by
the top management.
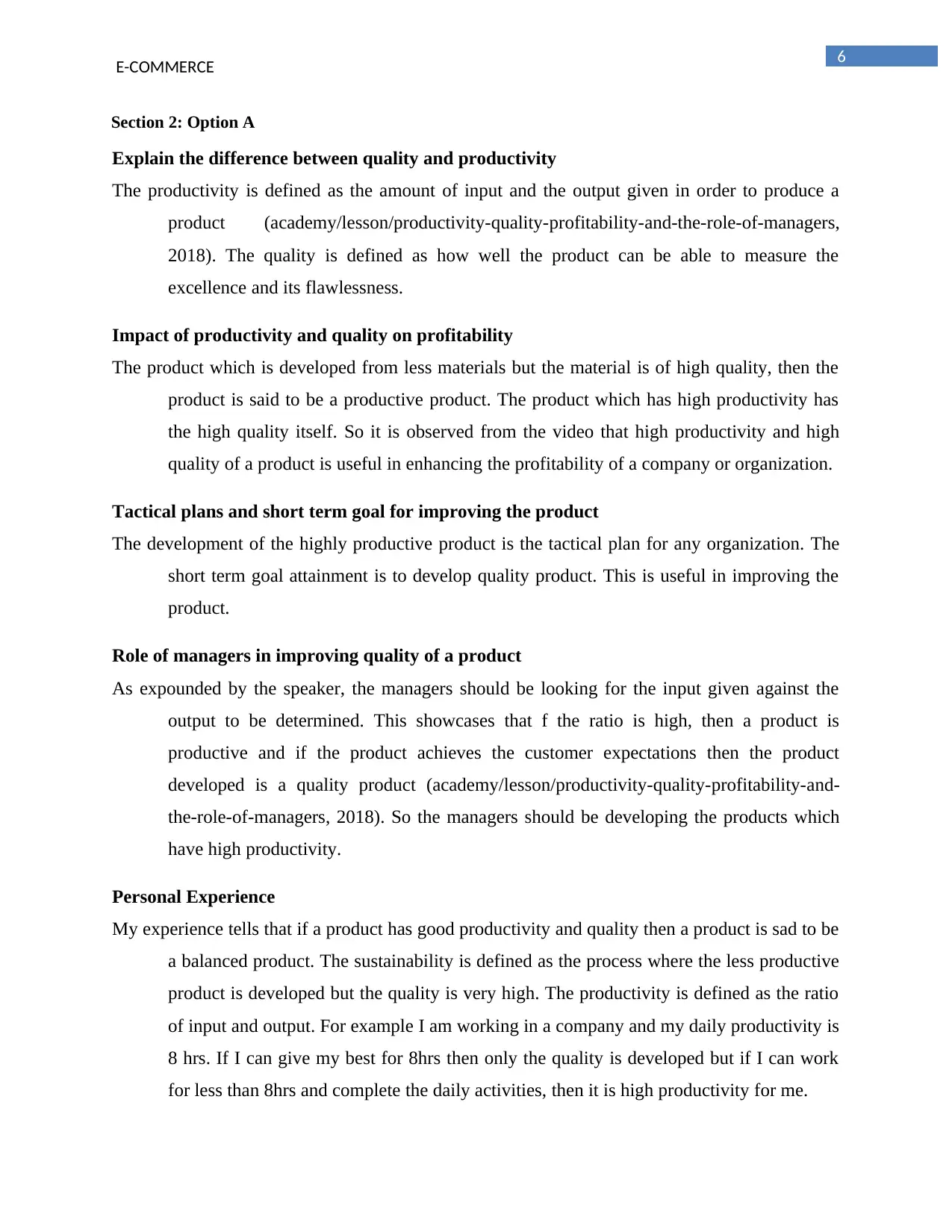
6
E-COMMERCE
Section 2: Option A
Explain the difference between quality and productivity
The productivity is defined as the amount of input and the output given in order to produce a
product (academy/lesson/productivity-quality-profitability-and-the-role-of-managers,
2018). The quality is defined as how well the product can be able to measure the
excellence and its flawlessness.
Impact of productivity and quality on profitability
The product which is developed from less materials but the material is of high quality, then the
product is said to be a productive product. The product which has high productivity has
the high quality itself. So it is observed from the video that high productivity and high
quality of a product is useful in enhancing the profitability of a company or organization.
Tactical plans and short term goal for improving the product
The development of the highly productive product is the tactical plan for any organization. The
short term goal attainment is to develop quality product. This is useful in improving the
product.
Role of managers in improving quality of a product
As expounded by the speaker, the managers should be looking for the input given against the
output to be determined. This showcases that f the ratio is high, then a product is
productive and if the product achieves the customer expectations then the product
developed is a quality product (academy/lesson/productivity-quality-profitability-and-
the-role-of-managers, 2018). So the managers should be developing the products which
have high productivity.
Personal Experience
My experience tells that if a product has good productivity and quality then a product is sad to be
a balanced product. The sustainability is defined as the process where the less productive
product is developed but the quality is very high. The productivity is defined as the ratio
of input and output. For example I am working in a company and my daily productivity is
8 hrs. If I can give my best for 8hrs then only the quality is developed but if I can work
for less than 8hrs and complete the daily activities, then it is high productivity for me.
E-COMMERCE
Section 2: Option A
Explain the difference between quality and productivity
The productivity is defined as the amount of input and the output given in order to produce a
product (academy/lesson/productivity-quality-profitability-and-the-role-of-managers,
2018). The quality is defined as how well the product can be able to measure the
excellence and its flawlessness.
Impact of productivity and quality on profitability
The product which is developed from less materials but the material is of high quality, then the
product is said to be a productive product. The product which has high productivity has
the high quality itself. So it is observed from the video that high productivity and high
quality of a product is useful in enhancing the profitability of a company or organization.
Tactical plans and short term goal for improving the product
The development of the highly productive product is the tactical plan for any organization. The
short term goal attainment is to develop quality product. This is useful in improving the
product.
Role of managers in improving quality of a product
As expounded by the speaker, the managers should be looking for the input given against the
output to be determined. This showcases that f the ratio is high, then a product is
productive and if the product achieves the customer expectations then the product
developed is a quality product (academy/lesson/productivity-quality-profitability-and-
the-role-of-managers, 2018). So the managers should be developing the products which
have high productivity.
Personal Experience
My experience tells that if a product has good productivity and quality then a product is sad to be
a balanced product. The sustainability is defined as the process where the less productive
product is developed but the quality is very high. The productivity is defined as the ratio
of input and output. For example I am working in a company and my daily productivity is
8 hrs. If I can give my best for 8hrs then only the quality is developed but if I can work
for less than 8hrs and complete the daily activities, then it is high productivity for me.
Paraphrase This Document
Need a fresh take? Get an instant paraphrase of this document with our AI Paraphraser
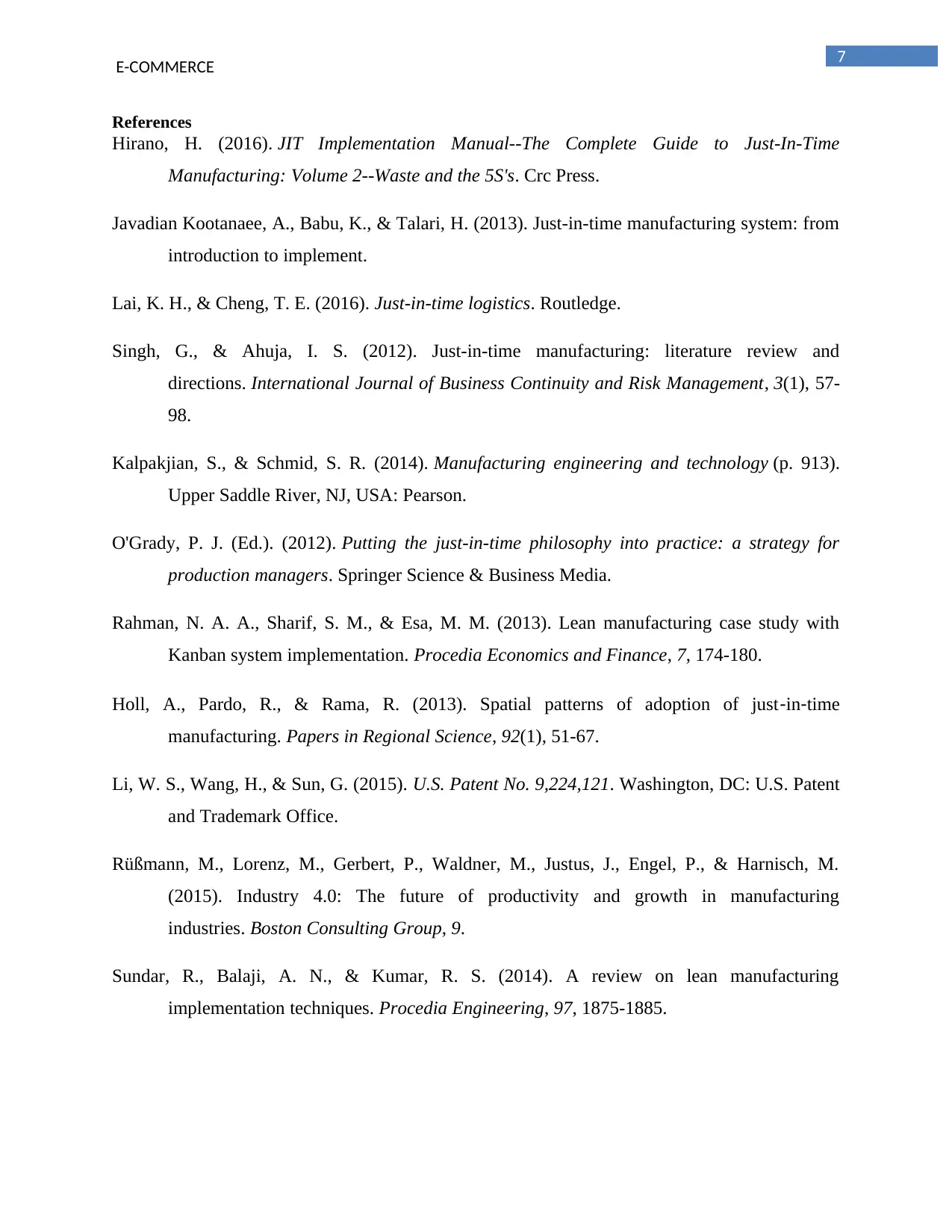
7
E-COMMERCE
References
Hirano, H. (2016). JIT Implementation Manual--The Complete Guide to Just-In-Time
Manufacturing: Volume 2--Waste and the 5S's. Crc Press.
Javadian Kootanaee, A., Babu, K., & Talari, H. (2013). Just-in-time manufacturing system: from
introduction to implement.
Lai, K. H., & Cheng, T. E. (2016). Just-in-time logistics. Routledge.
Singh, G., & Ahuja, I. S. (2012). Just-in-time manufacturing: literature review and
directions. International Journal of Business Continuity and Risk Management, 3(1), 57-
98.
Kalpakjian, S., & Schmid, S. R. (2014). Manufacturing engineering and technology (p. 913).
Upper Saddle River, NJ, USA: Pearson.
O'Grady, P. J. (Ed.). (2012). Putting the just-in-time philosophy into practice: a strategy for
production managers. Springer Science & Business Media.
Rahman, N. A. A., Sharif, S. M., & Esa, M. M. (2013). Lean manufacturing case study with
Kanban system implementation. Procedia Economics and Finance, 7, 174-180.
Holl, A., Pardo, R., & Rama, R. (2013). Spatial patterns of adoption of just‐in‐time
manufacturing. Papers in Regional Science, 92(1), 51-67.
Li, W. S., Wang, H., & Sun, G. (2015). U.S. Patent No. 9,224,121. Washington, DC: U.S. Patent
and Trademark Office.
Rüßmann, M., Lorenz, M., Gerbert, P., Waldner, M., Justus, J., Engel, P., & Harnisch, M.
(2015). Industry 4.0: The future of productivity and growth in manufacturing
industries. Boston Consulting Group, 9.
Sundar, R., Balaji, A. N., & Kumar, R. S. (2014). A review on lean manufacturing
implementation techniques. Procedia Engineering, 97, 1875-1885.
E-COMMERCE
References
Hirano, H. (2016). JIT Implementation Manual--The Complete Guide to Just-In-Time
Manufacturing: Volume 2--Waste and the 5S's. Crc Press.
Javadian Kootanaee, A., Babu, K., & Talari, H. (2013). Just-in-time manufacturing system: from
introduction to implement.
Lai, K. H., & Cheng, T. E. (2016). Just-in-time logistics. Routledge.
Singh, G., & Ahuja, I. S. (2012). Just-in-time manufacturing: literature review and
directions. International Journal of Business Continuity and Risk Management, 3(1), 57-
98.
Kalpakjian, S., & Schmid, S. R. (2014). Manufacturing engineering and technology (p. 913).
Upper Saddle River, NJ, USA: Pearson.
O'Grady, P. J. (Ed.). (2012). Putting the just-in-time philosophy into practice: a strategy for
production managers. Springer Science & Business Media.
Rahman, N. A. A., Sharif, S. M., & Esa, M. M. (2013). Lean manufacturing case study with
Kanban system implementation. Procedia Economics and Finance, 7, 174-180.
Holl, A., Pardo, R., & Rama, R. (2013). Spatial patterns of adoption of just‐in‐time
manufacturing. Papers in Regional Science, 92(1), 51-67.
Li, W. S., Wang, H., & Sun, G. (2015). U.S. Patent No. 9,224,121. Washington, DC: U.S. Patent
and Trademark Office.
Rüßmann, M., Lorenz, M., Gerbert, P., Waldner, M., Justus, J., Engel, P., & Harnisch, M.
(2015). Industry 4.0: The future of productivity and growth in manufacturing
industries. Boston Consulting Group, 9.
Sundar, R., Balaji, A. N., & Kumar, R. S. (2014). A review on lean manufacturing
implementation techniques. Procedia Engineering, 97, 1875-1885.
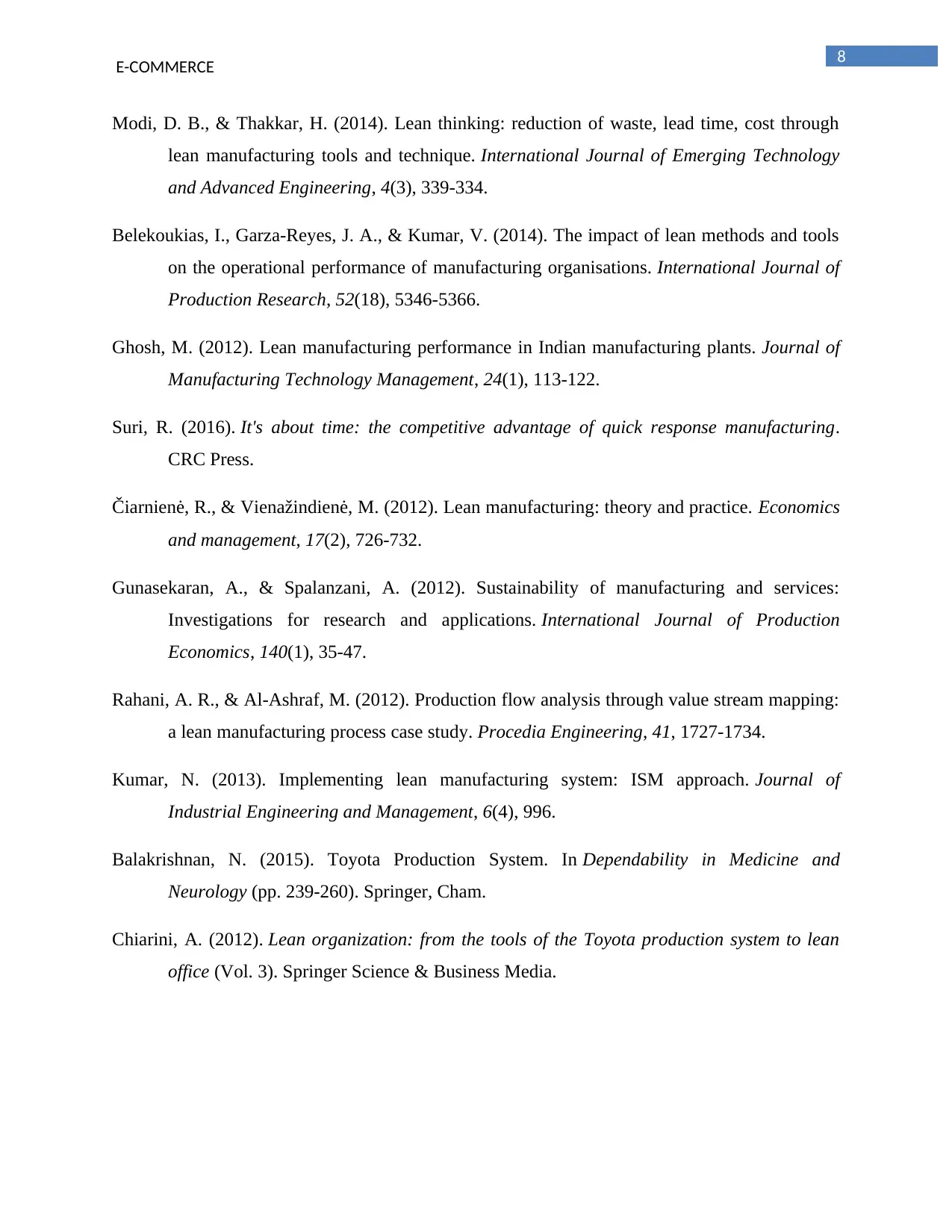
8
E-COMMERCE
Modi, D. B., & Thakkar, H. (2014). Lean thinking: reduction of waste, lead time, cost through
lean manufacturing tools and technique. International Journal of Emerging Technology
and Advanced Engineering, 4(3), 339-334.
Belekoukias, I., Garza-Reyes, J. A., & Kumar, V. (2014). The impact of lean methods and tools
on the operational performance of manufacturing organisations. International Journal of
Production Research, 52(18), 5346-5366.
Ghosh, M. (2012). Lean manufacturing performance in Indian manufacturing plants. Journal of
Manufacturing Technology Management, 24(1), 113-122.
Suri, R. (2016). It's about time: the competitive advantage of quick response manufacturing.
CRC Press.
Čiarnienė, R., & Vienažindienė, M. (2012). Lean manufacturing: theory and practice. Economics
and management, 17(2), 726-732.
Gunasekaran, A., & Spalanzani, A. (2012). Sustainability of manufacturing and services:
Investigations for research and applications. International Journal of Production
Economics, 140(1), 35-47.
Rahani, A. R., & Al-Ashraf, M. (2012). Production flow analysis through value stream mapping:
a lean manufacturing process case study. Procedia Engineering, 41, 1727-1734.
Kumar, N. (2013). Implementing lean manufacturing system: ISM approach. Journal of
Industrial Engineering and Management, 6(4), 996.
Balakrishnan, N. (2015). Toyota Production System. In Dependability in Medicine and
Neurology (pp. 239-260). Springer, Cham.
Chiarini, A. (2012). Lean organization: from the tools of the Toyota production system to lean
office (Vol. 3). Springer Science & Business Media.
E-COMMERCE
Modi, D. B., & Thakkar, H. (2014). Lean thinking: reduction of waste, lead time, cost through
lean manufacturing tools and technique. International Journal of Emerging Technology
and Advanced Engineering, 4(3), 339-334.
Belekoukias, I., Garza-Reyes, J. A., & Kumar, V. (2014). The impact of lean methods and tools
on the operational performance of manufacturing organisations. International Journal of
Production Research, 52(18), 5346-5366.
Ghosh, M. (2012). Lean manufacturing performance in Indian manufacturing plants. Journal of
Manufacturing Technology Management, 24(1), 113-122.
Suri, R. (2016). It's about time: the competitive advantage of quick response manufacturing.
CRC Press.
Čiarnienė, R., & Vienažindienė, M. (2012). Lean manufacturing: theory and practice. Economics
and management, 17(2), 726-732.
Gunasekaran, A., & Spalanzani, A. (2012). Sustainability of manufacturing and services:
Investigations for research and applications. International Journal of Production
Economics, 140(1), 35-47.
Rahani, A. R., & Al-Ashraf, M. (2012). Production flow analysis through value stream mapping:
a lean manufacturing process case study. Procedia Engineering, 41, 1727-1734.
Kumar, N. (2013). Implementing lean manufacturing system: ISM approach. Journal of
Industrial Engineering and Management, 6(4), 996.
Balakrishnan, N. (2015). Toyota Production System. In Dependability in Medicine and
Neurology (pp. 239-260). Springer, Cham.
Chiarini, A. (2012). Lean organization: from the tools of the Toyota production system to lean
office (Vol. 3). Springer Science & Business Media.
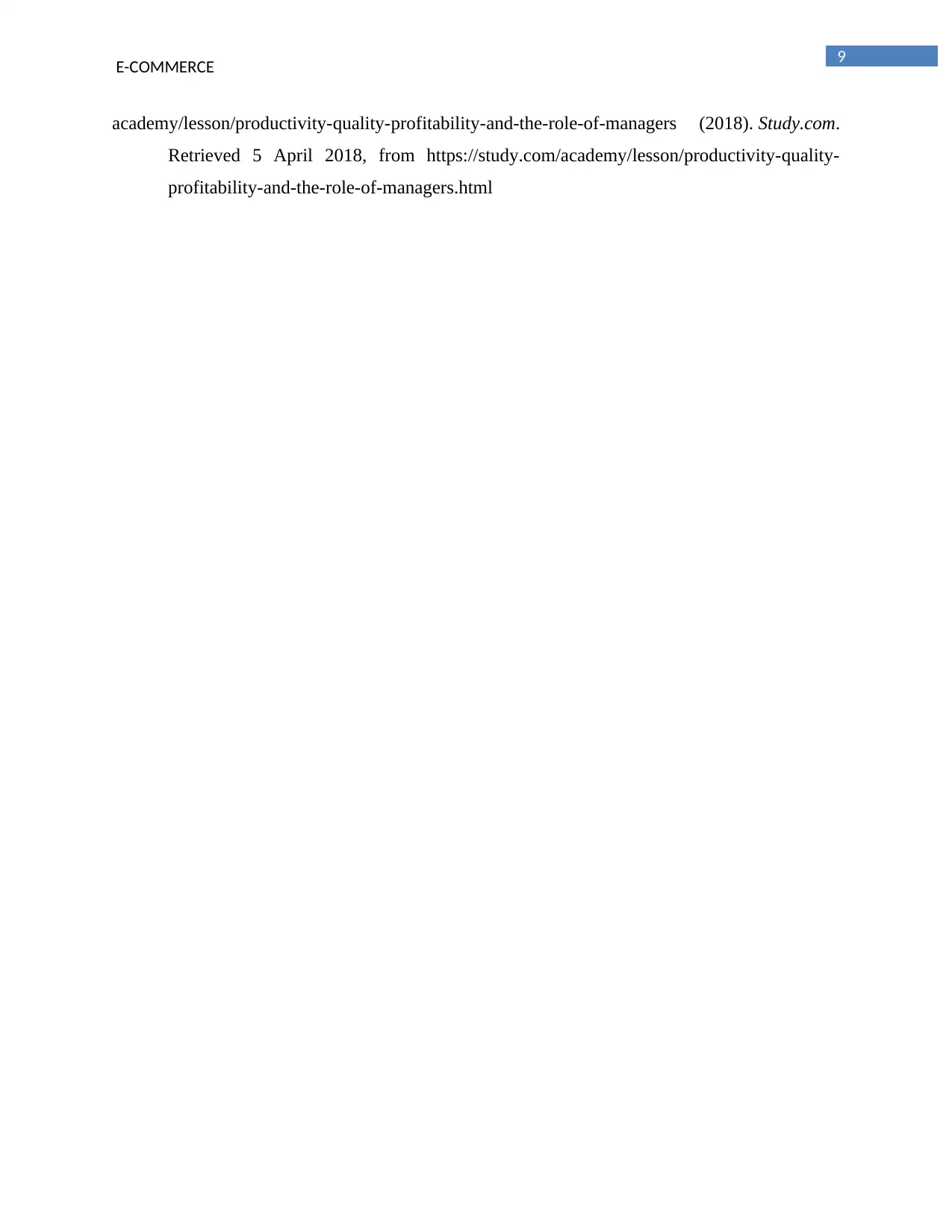
9
E-COMMERCE
academy/lesson/productivity-quality-profitability-and-the-role-of-managers (2018). Study.com.
Retrieved 5 April 2018, from https://study.com/academy/lesson/productivity-quality-
profitability-and-the-role-of-managers.html
E-COMMERCE
academy/lesson/productivity-quality-profitability-and-the-role-of-managers (2018). Study.com.
Retrieved 5 April 2018, from https://study.com/academy/lesson/productivity-quality-
profitability-and-the-role-of-managers.html
1 out of 10
Related Documents
![[object Object]](/_next/image/?url=%2F_next%2Fstatic%2Fmedia%2Flogo.6d15ce61.png&w=640&q=75)
Your All-in-One AI-Powered Toolkit for Academic Success.
+13062052269
info@desklib.com
Available 24*7 on WhatsApp / Email
Unlock your academic potential
© 2024 | Zucol Services PVT LTD | All rights reserved.