Total Quality Management for Quality Management
VerifiedAdded on  2023/06/15
|15
|3342
|399
AI Summary
This case study analyzes the deficiency of total quality management and quality control in a manufacturing plant. The lack of TQM existed at all levels including the apex level. The evaluation of the faulty manufacturing process shows that the lack of TQM existed in the middle level management due to lack of intervention from the top management. Recommendations are provided to improve the situation.
Contribute Materials
Your contribution can guide someone’s learning journey. Share your
documents today.
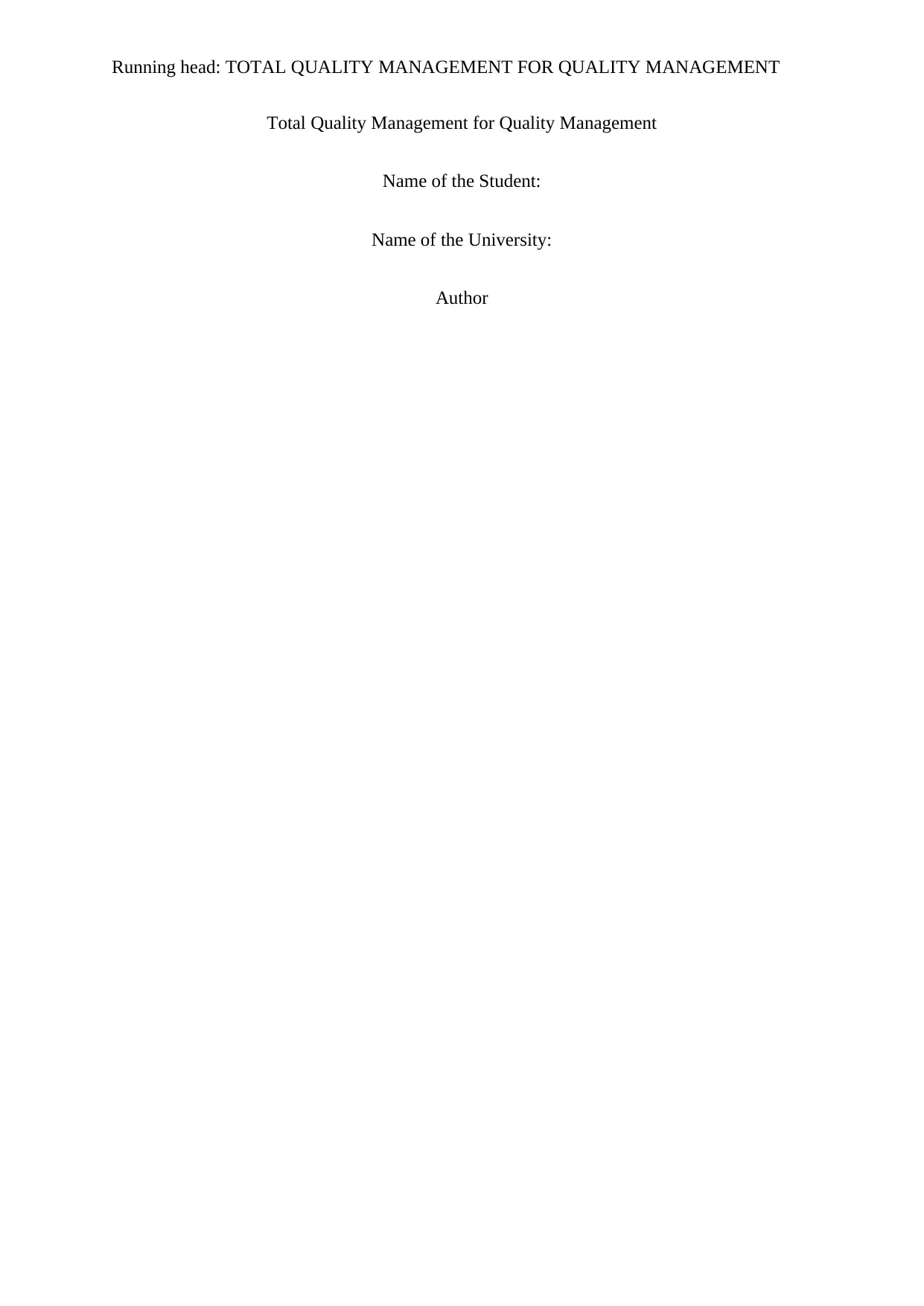
Running head: TOTAL QUALITY MANAGEMENT FOR QUALITY MANAGEMENT
Total Quality Management for Quality Management
Name of the Student:
Name of the University:
Author
Total Quality Management for Quality Management
Name of the Student:
Name of the University:
Author
Secure Best Marks with AI Grader
Need help grading? Try our AI Grader for instant feedback on your assignments.
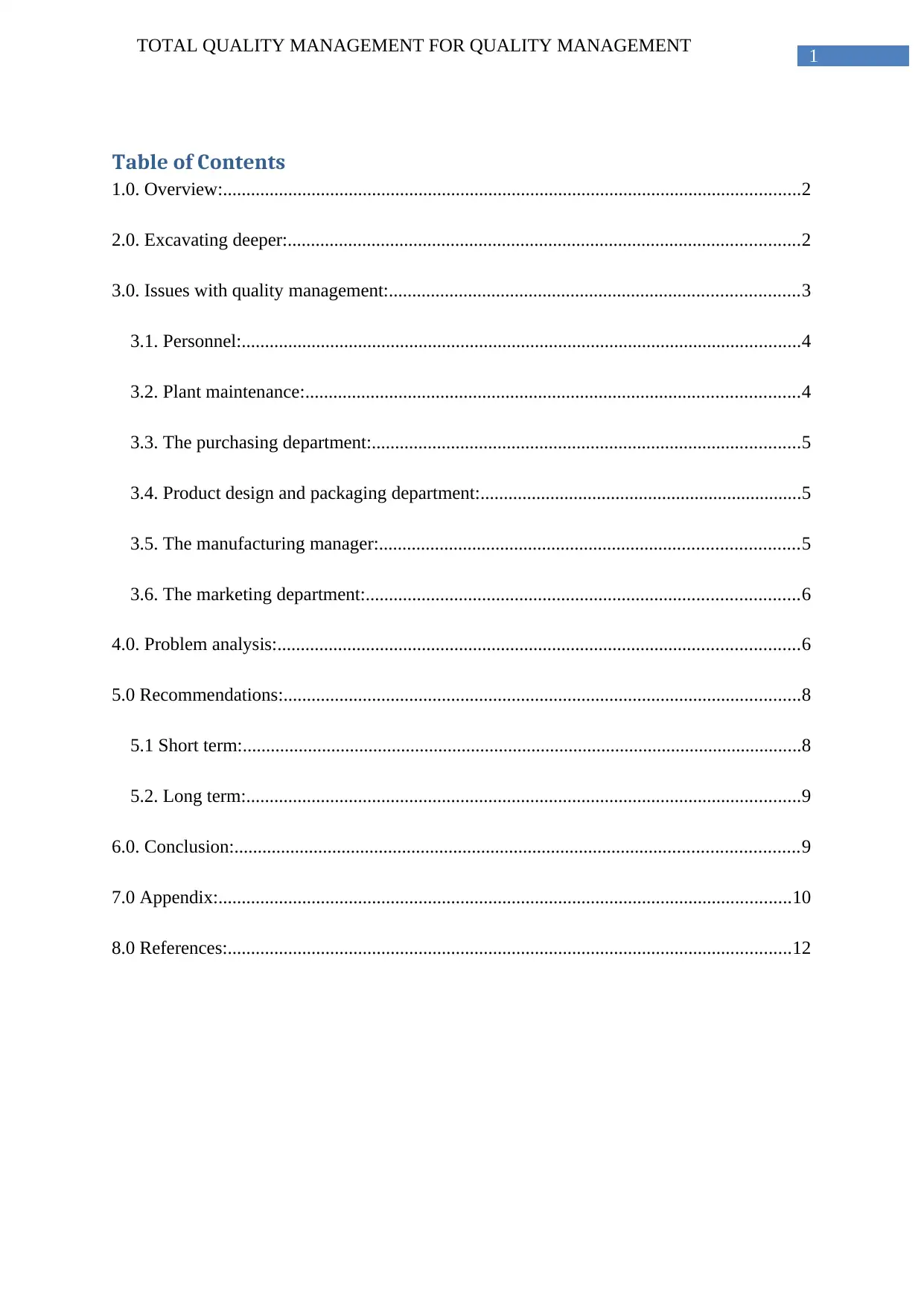
1
TOTAL QUALITY MANAGEMENT FOR QUALITY MANAGEMENT
Table of Contents
1.0. Overview:............................................................................................................................2
2.0. Excavating deeper:..............................................................................................................2
3.0. Issues with quality management:........................................................................................3
3.1. Personnel:........................................................................................................................4
3.2. Plant maintenance:..........................................................................................................4
3.3. The purchasing department:............................................................................................5
3.4. Product design and packaging department:.....................................................................5
3.5. The manufacturing manager:..........................................................................................5
3.6. The marketing department:.............................................................................................6
4.0. Problem analysis:................................................................................................................6
5.0 Recommendations:...............................................................................................................8
5.1 Short term:........................................................................................................................8
5.2. Long term:.......................................................................................................................9
6.0. Conclusion:.........................................................................................................................9
7.0 Appendix:...........................................................................................................................10
8.0 References:.........................................................................................................................12
TOTAL QUALITY MANAGEMENT FOR QUALITY MANAGEMENT
Table of Contents
1.0. Overview:............................................................................................................................2
2.0. Excavating deeper:..............................................................................................................2
3.0. Issues with quality management:........................................................................................3
3.1. Personnel:........................................................................................................................4
3.2. Plant maintenance:..........................................................................................................4
3.3. The purchasing department:............................................................................................5
3.4. Product design and packaging department:.....................................................................5
3.5. The manufacturing manager:..........................................................................................5
3.6. The marketing department:.............................................................................................6
4.0. Problem analysis:................................................................................................................6
5.0 Recommendations:...............................................................................................................8
5.1 Short term:........................................................................................................................8
5.2. Long term:.......................................................................................................................9
6.0. Conclusion:.........................................................................................................................9
7.0 Appendix:...........................................................................................................................10
8.0 References:.........................................................................................................................12
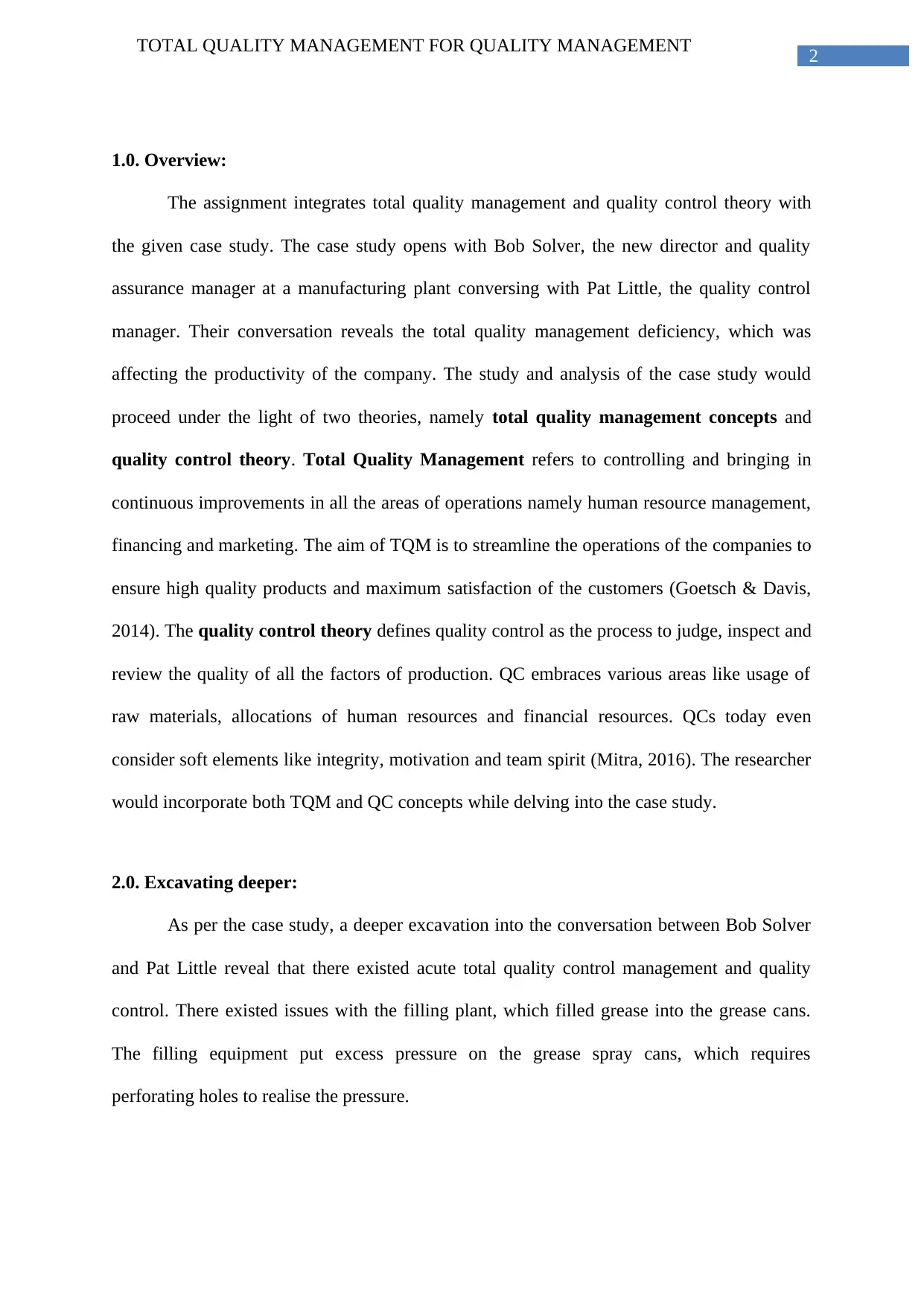
2
TOTAL QUALITY MANAGEMENT FOR QUALITY MANAGEMENT
1.0. Overview:
The assignment integrates total quality management and quality control theory with
the given case study. The case study opens with Bob Solver, the new director and quality
assurance manager at a manufacturing plant conversing with Pat Little, the quality control
manager. Their conversation reveals the total quality management deficiency, which was
affecting the productivity of the company. The study and analysis of the case study would
proceed under the light of two theories, namely total quality management concepts and
quality control theory. Total Quality Management refers to controlling and bringing in
continuous improvements in all the areas of operations namely human resource management,
financing and marketing. The aim of TQM is to streamline the operations of the companies to
ensure high quality products and maximum satisfaction of the customers (Goetsch & Davis,
2014). The quality control theory defines quality control as the process to judge, inspect and
review the quality of all the factors of production. QC embraces various areas like usage of
raw materials, allocations of human resources and financial resources. QCs today even
consider soft elements like integrity, motivation and team spirit (Mitra, 2016). The researcher
would incorporate both TQM and QC concepts while delving into the case study.
2.0. Excavating deeper:
As per the case study, a deeper excavation into the conversation between Bob Solver
and Pat Little reveal that there existed acute total quality control management and quality
control. There existed issues with the filling plant, which filled grease into the grease cans.
The filling equipment put excess pressure on the grease spray cans, which requires
perforating holes to realise the pressure.
TOTAL QUALITY MANAGEMENT FOR QUALITY MANAGEMENT
1.0. Overview:
The assignment integrates total quality management and quality control theory with
the given case study. The case study opens with Bob Solver, the new director and quality
assurance manager at a manufacturing plant conversing with Pat Little, the quality control
manager. Their conversation reveals the total quality management deficiency, which was
affecting the productivity of the company. The study and analysis of the case study would
proceed under the light of two theories, namely total quality management concepts and
quality control theory. Total Quality Management refers to controlling and bringing in
continuous improvements in all the areas of operations namely human resource management,
financing and marketing. The aim of TQM is to streamline the operations of the companies to
ensure high quality products and maximum satisfaction of the customers (Goetsch & Davis,
2014). The quality control theory defines quality control as the process to judge, inspect and
review the quality of all the factors of production. QC embraces various areas like usage of
raw materials, allocations of human resources and financial resources. QCs today even
consider soft elements like integrity, motivation and team spirit (Mitra, 2016). The researcher
would incorporate both TQM and QC concepts while delving into the case study.
2.0. Excavating deeper:
As per the case study, a deeper excavation into the conversation between Bob Solver
and Pat Little reveal that there existed acute total quality control management and quality
control. There existed issues with the filling plant, which filled grease into the grease cans.
The filling equipment put excess pressure on the grease spray cans, which requires
perforating holes to realise the pressure.
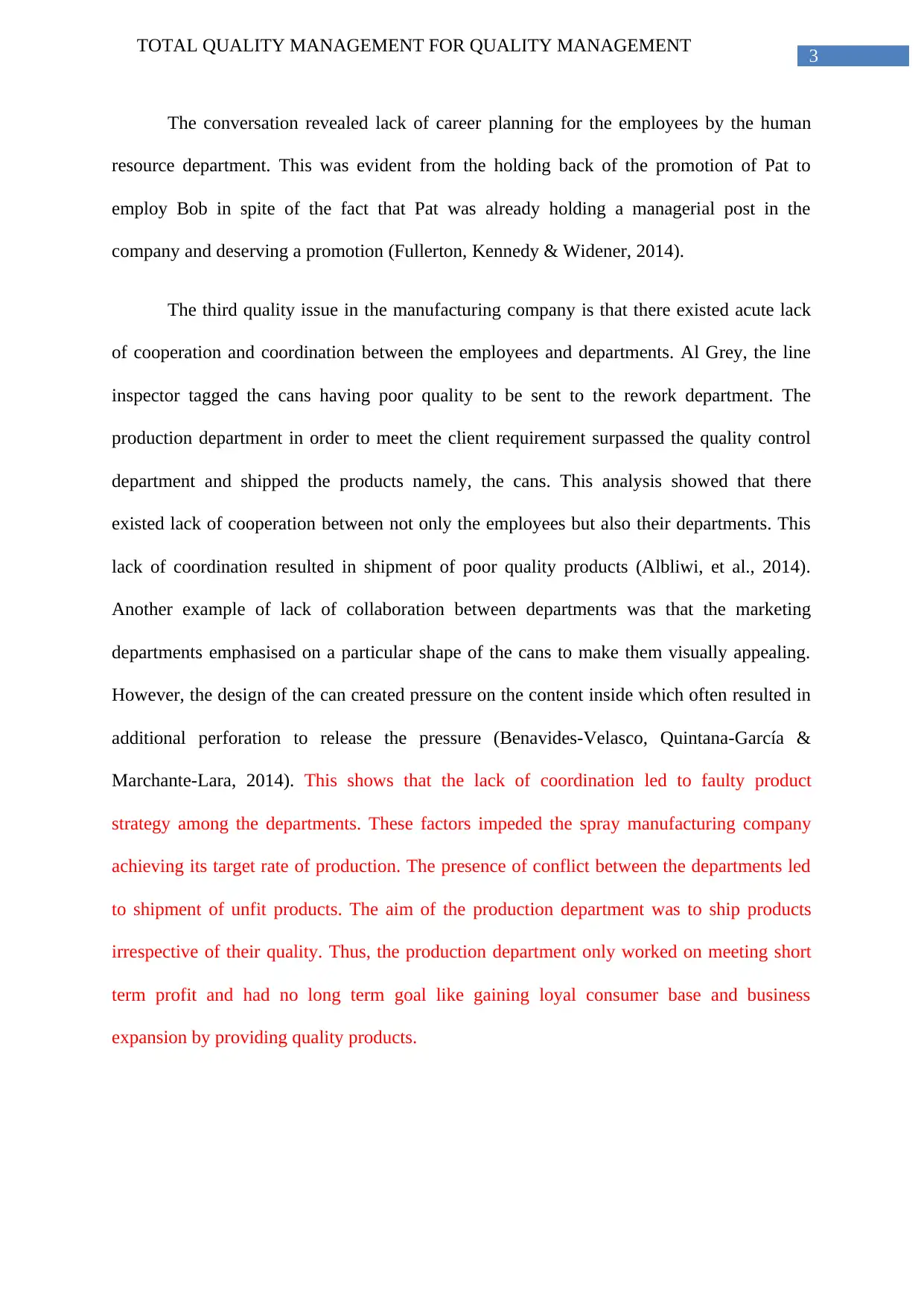
3
TOTAL QUALITY MANAGEMENT FOR QUALITY MANAGEMENT
The conversation revealed lack of career planning for the employees by the human
resource department. This was evident from the holding back of the promotion of Pat to
employ Bob in spite of the fact that Pat was already holding a managerial post in the
company and deserving a promotion (Fullerton, Kennedy & Widener, 2014).
The third quality issue in the manufacturing company is that there existed acute lack
of cooperation and coordination between the employees and departments. Al Grey, the line
inspector tagged the cans having poor quality to be sent to the rework department. The
production department in order to meet the client requirement surpassed the quality control
department and shipped the products namely, the cans. This analysis showed that there
existed lack of cooperation between not only the employees but also their departments. This
lack of coordination resulted in shipment of poor quality products (Albliwi, et al., 2014).
Another example of lack of collaboration between departments was that the marketing
departments emphasised on a particular shape of the cans to make them visually appealing.
However, the design of the can created pressure on the content inside which often resulted in
additional perforation to release the pressure (Benavides-Velasco, Quintana-GarcĂa &
Marchante-Lara, 2014). This shows that the lack of coordination led to faulty product
strategy among the departments. These factors impeded the spray manufacturing company
achieving its target rate of production. The presence of conflict between the departments led
to shipment of unfit products. The aim of the production department was to ship products
irrespective of their quality. Thus, the production department only worked on meeting short
term profit and had no long term goal like gaining loyal consumer base and business
expansion by providing quality products.
TOTAL QUALITY MANAGEMENT FOR QUALITY MANAGEMENT
The conversation revealed lack of career planning for the employees by the human
resource department. This was evident from the holding back of the promotion of Pat to
employ Bob in spite of the fact that Pat was already holding a managerial post in the
company and deserving a promotion (Fullerton, Kennedy & Widener, 2014).
The third quality issue in the manufacturing company is that there existed acute lack
of cooperation and coordination between the employees and departments. Al Grey, the line
inspector tagged the cans having poor quality to be sent to the rework department. The
production department in order to meet the client requirement surpassed the quality control
department and shipped the products namely, the cans. This analysis showed that there
existed lack of cooperation between not only the employees but also their departments. This
lack of coordination resulted in shipment of poor quality products (Albliwi, et al., 2014).
Another example of lack of collaboration between departments was that the marketing
departments emphasised on a particular shape of the cans to make them visually appealing.
However, the design of the can created pressure on the content inside which often resulted in
additional perforation to release the pressure (Benavides-Velasco, Quintana-GarcĂa &
Marchante-Lara, 2014). This shows that the lack of coordination led to faulty product
strategy among the departments. These factors impeded the spray manufacturing company
achieving its target rate of production. The presence of conflict between the departments led
to shipment of unfit products. The aim of the production department was to ship products
irrespective of their quality. Thus, the production department only worked on meeting short
term profit and had no long term goal like gaining loyal consumer base and business
expansion by providing quality products.
Secure Best Marks with AI Grader
Need help grading? Try our AI Grader for instant feedback on your assignments.
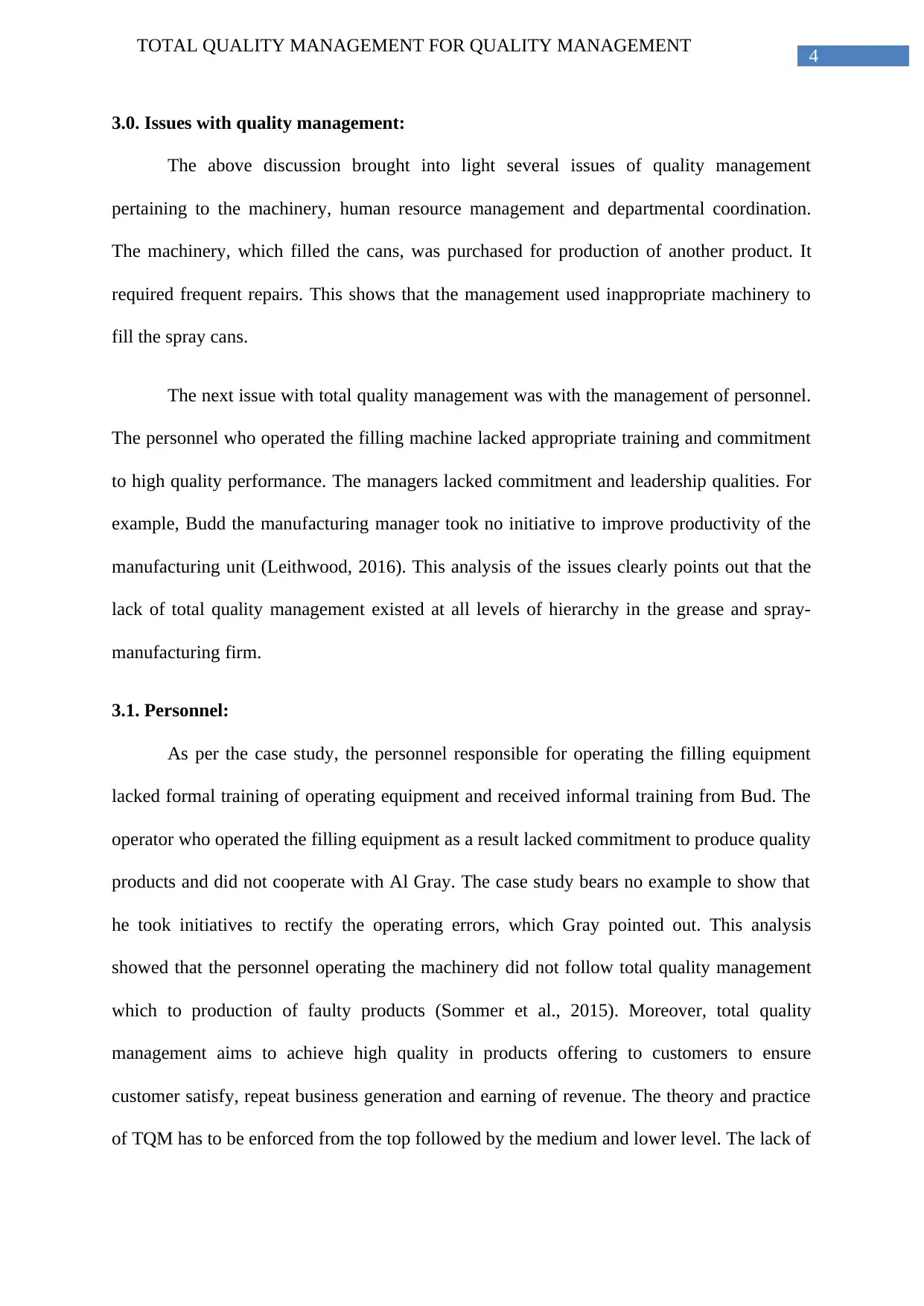
4
TOTAL QUALITY MANAGEMENT FOR QUALITY MANAGEMENT
3.0. Issues with quality management:
The above discussion brought into light several issues of quality management
pertaining to the machinery, human resource management and departmental coordination.
The machinery, which filled the cans, was purchased for production of another product. It
required frequent repairs. This shows that the management used inappropriate machinery to
fill the spray cans.
The next issue with total quality management was with the management of personnel.
The personnel who operated the filling machine lacked appropriate training and commitment
to high quality performance. The managers lacked commitment and leadership qualities. For
example, Budd the manufacturing manager took no initiative to improve productivity of the
manufacturing unit (Leithwood, 2016). This analysis of the issues clearly points out that the
lack of total quality management existed at all levels of hierarchy in the grease and spray-
manufacturing firm.
3.1. Personnel:
As per the case study, the personnel responsible for operating the filling equipment
lacked formal training of operating equipment and received informal training from Bud. The
operator who operated the filling equipment as a result lacked commitment to produce quality
products and did not cooperate with Al Gray. The case study bears no example to show that
he took initiatives to rectify the operating errors, which Gray pointed out. This analysis
showed that the personnel operating the machinery did not follow total quality management
which to production of faulty products (Sommer et al., 2015). Moreover, total quality
management aims to achieve high quality in products offering to customers to ensure
customer satisfy, repeat business generation and earning of revenue. The theory and practice
of TQM has to be enforced from the top followed by the medium and lower level. The lack of
TOTAL QUALITY MANAGEMENT FOR QUALITY MANAGEMENT
3.0. Issues with quality management:
The above discussion brought into light several issues of quality management
pertaining to the machinery, human resource management and departmental coordination.
The machinery, which filled the cans, was purchased for production of another product. It
required frequent repairs. This shows that the management used inappropriate machinery to
fill the spray cans.
The next issue with total quality management was with the management of personnel.
The personnel who operated the filling machine lacked appropriate training and commitment
to high quality performance. The managers lacked commitment and leadership qualities. For
example, Budd the manufacturing manager took no initiative to improve productivity of the
manufacturing unit (Leithwood, 2016). This analysis of the issues clearly points out that the
lack of total quality management existed at all levels of hierarchy in the grease and spray-
manufacturing firm.
3.1. Personnel:
As per the case study, the personnel responsible for operating the filling equipment
lacked formal training of operating equipment and received informal training from Bud. The
operator who operated the filling equipment as a result lacked commitment to produce quality
products and did not cooperate with Al Gray. The case study bears no example to show that
he took initiatives to rectify the operating errors, which Gray pointed out. This analysis
showed that the personnel operating the machinery did not follow total quality management
which to production of faulty products (Sommer et al., 2015). Moreover, total quality
management aims to achieve high quality in products offering to customers to ensure
customer satisfy, repeat business generation and earning of revenue. The theory and practice
of TQM has to be enforced from the top followed by the medium and lower level. The lack of
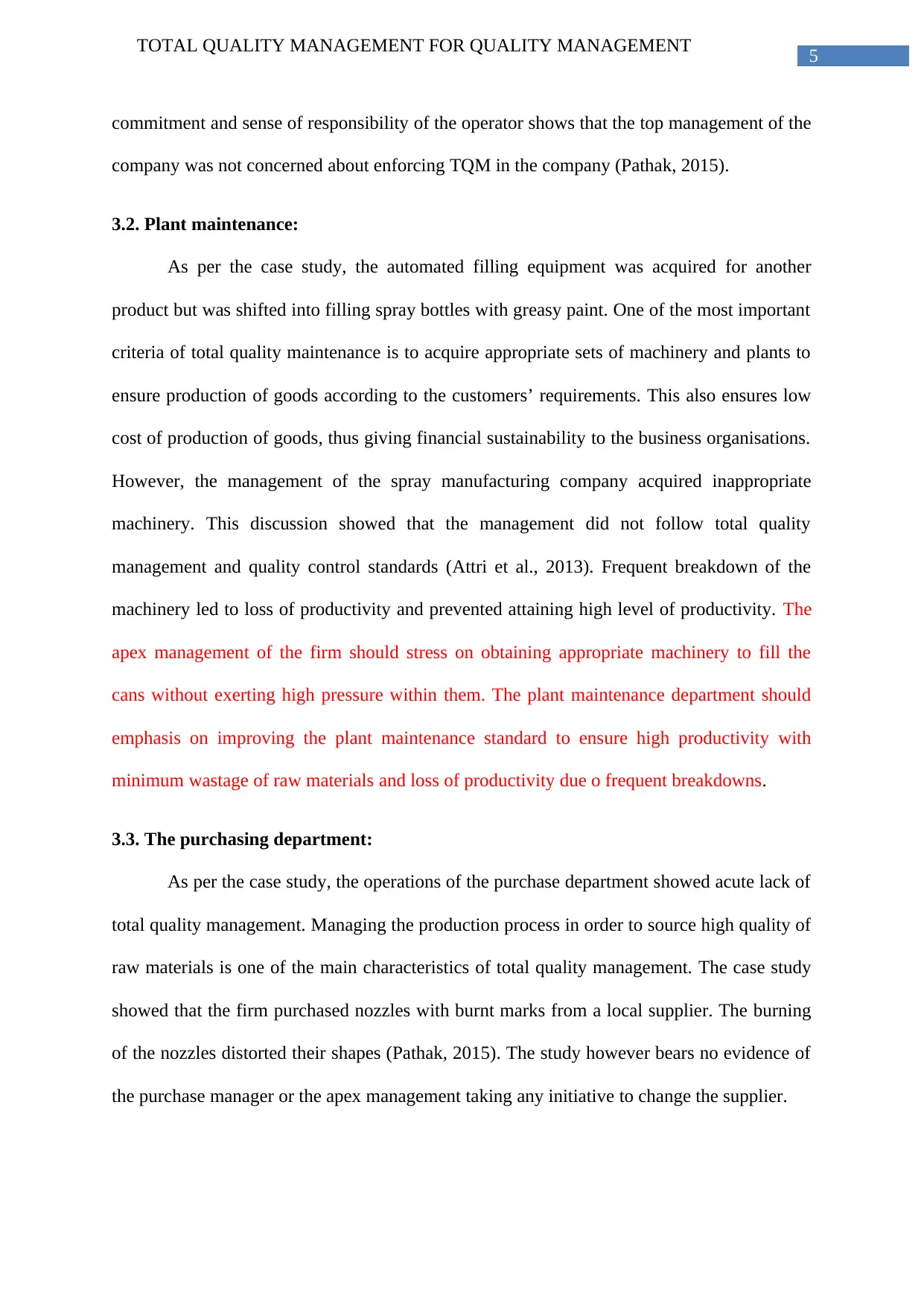
5
TOTAL QUALITY MANAGEMENT FOR QUALITY MANAGEMENT
commitment and sense of responsibility of the operator shows that the top management of the
company was not concerned about enforcing TQM in the company (Pathak, 2015).
3.2. Plant maintenance:
As per the case study, the automated filling equipment was acquired for another
product but was shifted into filling spray bottles with greasy paint. One of the most important
criteria of total quality maintenance is to acquire appropriate sets of machinery and plants to
ensure production of goods according to the customers’ requirements. This also ensures low
cost of production of goods, thus giving financial sustainability to the business organisations.
However, the management of the spray manufacturing company acquired inappropriate
machinery. This discussion showed that the management did not follow total quality
management and quality control standards (Attri et al., 2013). Frequent breakdown of the
machinery led to loss of productivity and prevented attaining high level of productivity. The
apex management of the firm should stress on obtaining appropriate machinery to fill the
cans without exerting high pressure within them. The plant maintenance department should
emphasis on improving the plant maintenance standard to ensure high productivity with
minimum wastage of raw materials and loss of productivity due o frequent breakdowns.
3.3. The purchasing department:
As per the case study, the operations of the purchase department showed acute lack of
total quality management. Managing the production process in order to source high quality of
raw materials is one of the main characteristics of total quality management. The case study
showed that the firm purchased nozzles with burnt marks from a local supplier. The burning
of the nozzles distorted their shapes (Pathak, 2015). The study however bears no evidence of
the purchase manager or the apex management taking any initiative to change the supplier.
TOTAL QUALITY MANAGEMENT FOR QUALITY MANAGEMENT
commitment and sense of responsibility of the operator shows that the top management of the
company was not concerned about enforcing TQM in the company (Pathak, 2015).
3.2. Plant maintenance:
As per the case study, the automated filling equipment was acquired for another
product but was shifted into filling spray bottles with greasy paint. One of the most important
criteria of total quality maintenance is to acquire appropriate sets of machinery and plants to
ensure production of goods according to the customers’ requirements. This also ensures low
cost of production of goods, thus giving financial sustainability to the business organisations.
However, the management of the spray manufacturing company acquired inappropriate
machinery. This discussion showed that the management did not follow total quality
management and quality control standards (Attri et al., 2013). Frequent breakdown of the
machinery led to loss of productivity and prevented attaining high level of productivity. The
apex management of the firm should stress on obtaining appropriate machinery to fill the
cans without exerting high pressure within them. The plant maintenance department should
emphasis on improving the plant maintenance standard to ensure high productivity with
minimum wastage of raw materials and loss of productivity due o frequent breakdowns.
3.3. The purchasing department:
As per the case study, the operations of the purchase department showed acute lack of
total quality management. Managing the production process in order to source high quality of
raw materials is one of the main characteristics of total quality management. The case study
showed that the firm purchased nozzles with burnt marks from a local supplier. The burning
of the nozzles distorted their shapes (Pathak, 2015). The study however bears no evidence of
the purchase manager or the apex management taking any initiative to change the supplier.
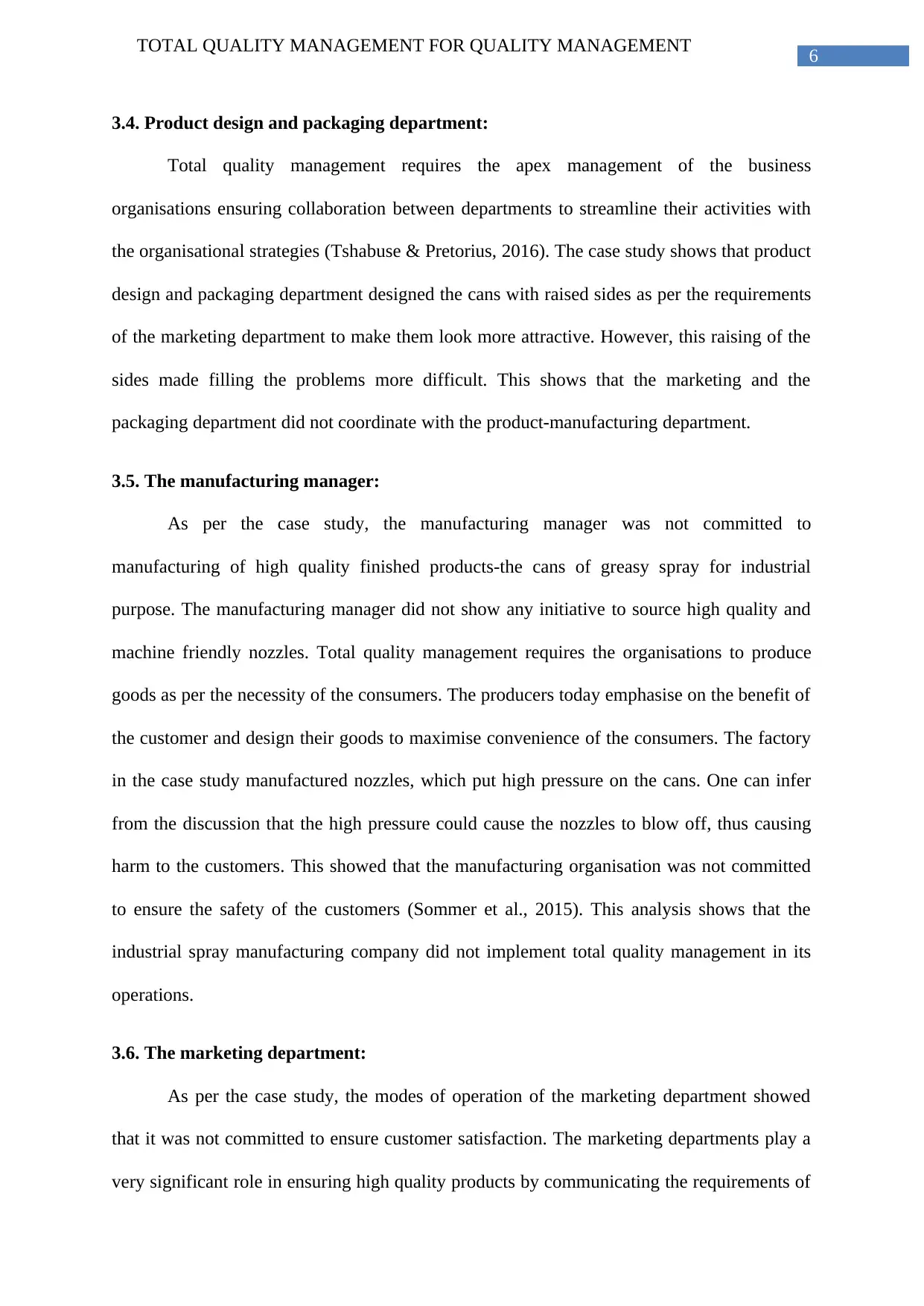
6
TOTAL QUALITY MANAGEMENT FOR QUALITY MANAGEMENT
3.4. Product design and packaging department:
Total quality management requires the apex management of the business
organisations ensuring collaboration between departments to streamline their activities with
the organisational strategies (Tshabuse & Pretorius, 2016). The case study shows that product
design and packaging department designed the cans with raised sides as per the requirements
of the marketing department to make them look more attractive. However, this raising of the
sides made filling the problems more difficult. This shows that the marketing and the
packaging department did not coordinate with the product-manufacturing department.
3.5. The manufacturing manager:
As per the case study, the manufacturing manager was not committed to
manufacturing of high quality finished products-the cans of greasy spray for industrial
purpose. The manufacturing manager did not show any initiative to source high quality and
machine friendly nozzles. Total quality management requires the organisations to produce
goods as per the necessity of the consumers. The producers today emphasise on the benefit of
the customer and design their goods to maximise convenience of the consumers. The factory
in the case study manufactured nozzles, which put high pressure on the cans. One can infer
from the discussion that the high pressure could cause the nozzles to blow off, thus causing
harm to the customers. This showed that the manufacturing organisation was not committed
to ensure the safety of the customers (Sommer et al., 2015). This analysis shows that the
industrial spray manufacturing company did not implement total quality management in its
operations.
3.6. The marketing department:
As per the case study, the modes of operation of the marketing department showed
that it was not committed to ensure customer satisfaction. The marketing departments play a
very significant role in ensuring high quality products by communicating the requirements of
TOTAL QUALITY MANAGEMENT FOR QUALITY MANAGEMENT
3.4. Product design and packaging department:
Total quality management requires the apex management of the business
organisations ensuring collaboration between departments to streamline their activities with
the organisational strategies (Tshabuse & Pretorius, 2016). The case study shows that product
design and packaging department designed the cans with raised sides as per the requirements
of the marketing department to make them look more attractive. However, this raising of the
sides made filling the problems more difficult. This shows that the marketing and the
packaging department did not coordinate with the product-manufacturing department.
3.5. The manufacturing manager:
As per the case study, the manufacturing manager was not committed to
manufacturing of high quality finished products-the cans of greasy spray for industrial
purpose. The manufacturing manager did not show any initiative to source high quality and
machine friendly nozzles. Total quality management requires the organisations to produce
goods as per the necessity of the consumers. The producers today emphasise on the benefit of
the customer and design their goods to maximise convenience of the consumers. The factory
in the case study manufactured nozzles, which put high pressure on the cans. One can infer
from the discussion that the high pressure could cause the nozzles to blow off, thus causing
harm to the customers. This showed that the manufacturing organisation was not committed
to ensure the safety of the customers (Sommer et al., 2015). This analysis shows that the
industrial spray manufacturing company did not implement total quality management in its
operations.
3.6. The marketing department:
As per the case study, the modes of operation of the marketing department showed
that it was not committed to ensure customer satisfaction. The marketing departments play a
very significant role in ensuring high quality products by communicating the requirements of
Paraphrase This Document
Need a fresh take? Get an instant paraphrase of this document with our AI Paraphraser
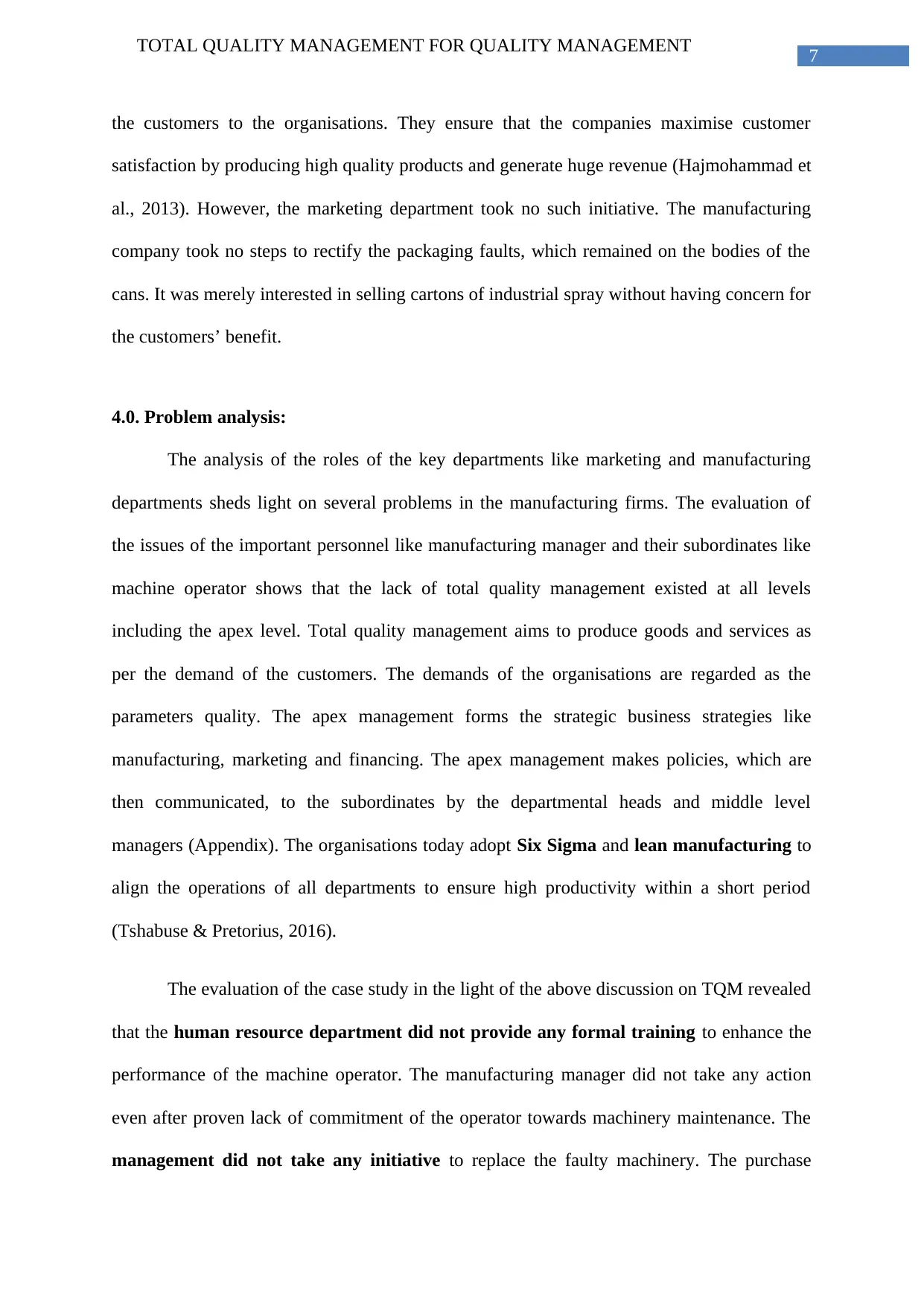
7
TOTAL QUALITY MANAGEMENT FOR QUALITY MANAGEMENT
the customers to the organisations. They ensure that the companies maximise customer
satisfaction by producing high quality products and generate huge revenue (Hajmohammad et
al., 2013). However, the marketing department took no such initiative. The manufacturing
company took no steps to rectify the packaging faults, which remained on the bodies of the
cans. It was merely interested in selling cartons of industrial spray without having concern for
the customers’ benefit.
4.0. Problem analysis:
The analysis of the roles of the key departments like marketing and manufacturing
departments sheds light on several problems in the manufacturing firms. The evaluation of
the issues of the important personnel like manufacturing manager and their subordinates like
machine operator shows that the lack of total quality management existed at all levels
including the apex level. Total quality management aims to produce goods and services as
per the demand of the customers. The demands of the organisations are regarded as the
parameters quality. The apex management forms the strategic business strategies like
manufacturing, marketing and financing. The apex management makes policies, which are
then communicated, to the subordinates by the departmental heads and middle level
managers (Appendix). The organisations today adopt Six Sigma and lean manufacturing to
align the operations of all departments to ensure high productivity within a short period
(Tshabuse & Pretorius, 2016).
The evaluation of the case study in the light of the above discussion on TQM revealed
that the human resource department did not provide any formal training to enhance the
performance of the machine operator. The manufacturing manager did not take any action
even after proven lack of commitment of the operator towards machinery maintenance. The
management did not take any initiative to replace the faulty machinery. The purchase
TOTAL QUALITY MANAGEMENT FOR QUALITY MANAGEMENT
the customers to the organisations. They ensure that the companies maximise customer
satisfaction by producing high quality products and generate huge revenue (Hajmohammad et
al., 2013). However, the marketing department took no such initiative. The manufacturing
company took no steps to rectify the packaging faults, which remained on the bodies of the
cans. It was merely interested in selling cartons of industrial spray without having concern for
the customers’ benefit.
4.0. Problem analysis:
The analysis of the roles of the key departments like marketing and manufacturing
departments sheds light on several problems in the manufacturing firms. The evaluation of
the issues of the important personnel like manufacturing manager and their subordinates like
machine operator shows that the lack of total quality management existed at all levels
including the apex level. Total quality management aims to produce goods and services as
per the demand of the customers. The demands of the organisations are regarded as the
parameters quality. The apex management forms the strategic business strategies like
manufacturing, marketing and financing. The apex management makes policies, which are
then communicated, to the subordinates by the departmental heads and middle level
managers (Appendix). The organisations today adopt Six Sigma and lean manufacturing to
align the operations of all departments to ensure high productivity within a short period
(Tshabuse & Pretorius, 2016).
The evaluation of the case study in the light of the above discussion on TQM revealed
that the human resource department did not provide any formal training to enhance the
performance of the machine operator. The manufacturing manager did not take any action
even after proven lack of commitment of the operator towards machinery maintenance. The
management did not take any initiative to replace the faulty machinery. The purchase
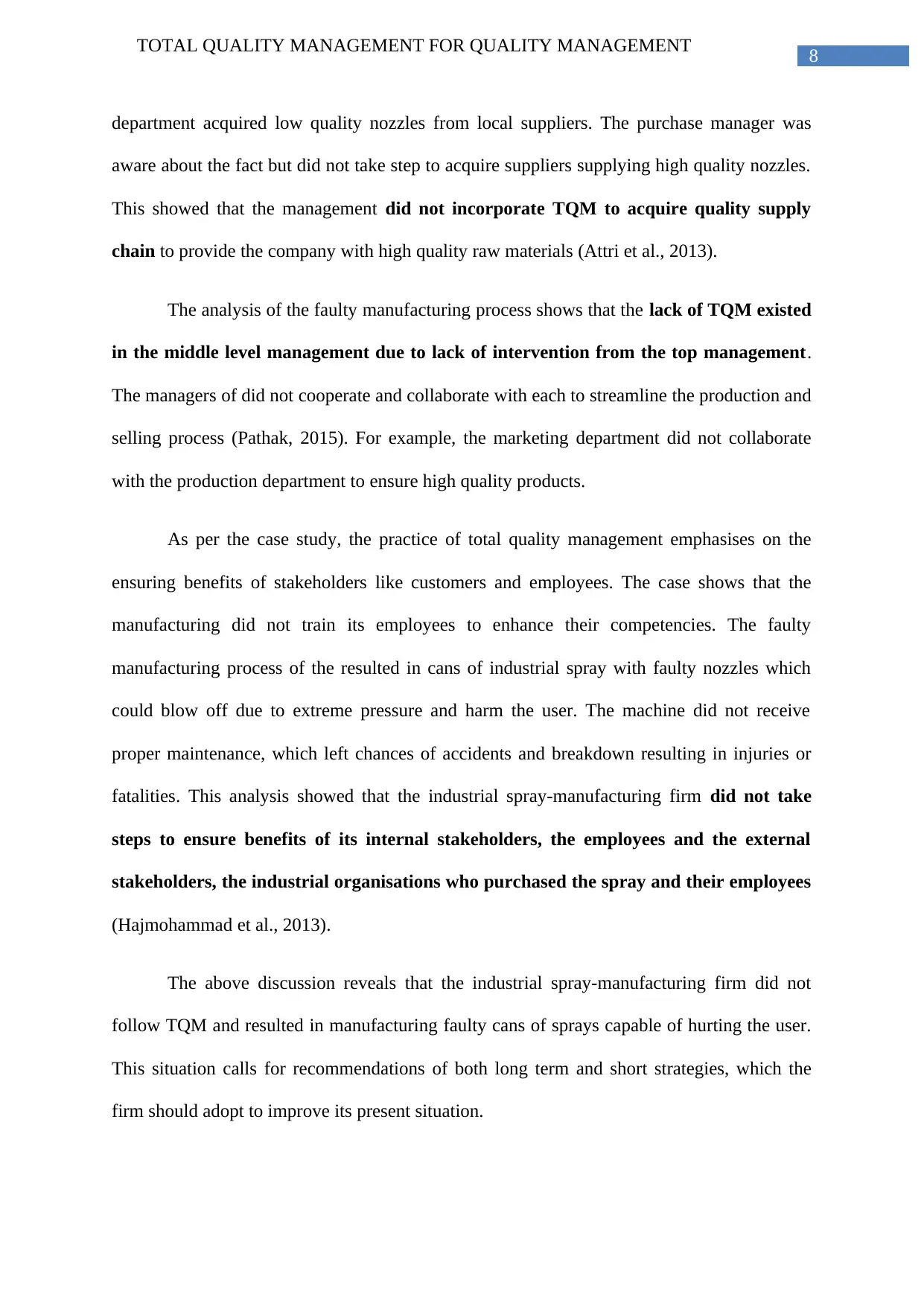
8
TOTAL QUALITY MANAGEMENT FOR QUALITY MANAGEMENT
department acquired low quality nozzles from local suppliers. The purchase manager was
aware about the fact but did not take step to acquire suppliers supplying high quality nozzles.
This showed that the management did not incorporate TQM to acquire quality supply
chain to provide the company with high quality raw materials (Attri et al., 2013).
The analysis of the faulty manufacturing process shows that the lack of TQM existed
in the middle level management due to lack of intervention from the top management.
The managers of did not cooperate and collaborate with each to streamline the production and
selling process (Pathak, 2015). For example, the marketing department did not collaborate
with the production department to ensure high quality products.
As per the case study, the practice of total quality management emphasises on the
ensuring benefits of stakeholders like customers and employees. The case shows that the
manufacturing did not train its employees to enhance their competencies. The faulty
manufacturing process of the resulted in cans of industrial spray with faulty nozzles which
could blow off due to extreme pressure and harm the user. The machine did not receive
proper maintenance, which left chances of accidents and breakdown resulting in injuries or
fatalities. This analysis showed that the industrial spray-manufacturing firm did not take
steps to ensure benefits of its internal stakeholders, the employees and the external
stakeholders, the industrial organisations who purchased the spray and their employees
(Hajmohammad et al., 2013).
The above discussion reveals that the industrial spray-manufacturing firm did not
follow TQM and resulted in manufacturing faulty cans of sprays capable of hurting the user.
This situation calls for recommendations of both long term and short strategies, which the
firm should adopt to improve its present situation.
TOTAL QUALITY MANAGEMENT FOR QUALITY MANAGEMENT
department acquired low quality nozzles from local suppliers. The purchase manager was
aware about the fact but did not take step to acquire suppliers supplying high quality nozzles.
This showed that the management did not incorporate TQM to acquire quality supply
chain to provide the company with high quality raw materials (Attri et al., 2013).
The analysis of the faulty manufacturing process shows that the lack of TQM existed
in the middle level management due to lack of intervention from the top management.
The managers of did not cooperate and collaborate with each to streamline the production and
selling process (Pathak, 2015). For example, the marketing department did not collaborate
with the production department to ensure high quality products.
As per the case study, the practice of total quality management emphasises on the
ensuring benefits of stakeholders like customers and employees. The case shows that the
manufacturing did not train its employees to enhance their competencies. The faulty
manufacturing process of the resulted in cans of industrial spray with faulty nozzles which
could blow off due to extreme pressure and harm the user. The machine did not receive
proper maintenance, which left chances of accidents and breakdown resulting in injuries or
fatalities. This analysis showed that the industrial spray-manufacturing firm did not take
steps to ensure benefits of its internal stakeholders, the employees and the external
stakeholders, the industrial organisations who purchased the spray and their employees
(Hajmohammad et al., 2013).
The above discussion reveals that the industrial spray-manufacturing firm did not
follow TQM and resulted in manufacturing faulty cans of sprays capable of hurting the user.
This situation calls for recommendations of both long term and short strategies, which the
firm should adopt to improve its present situation.
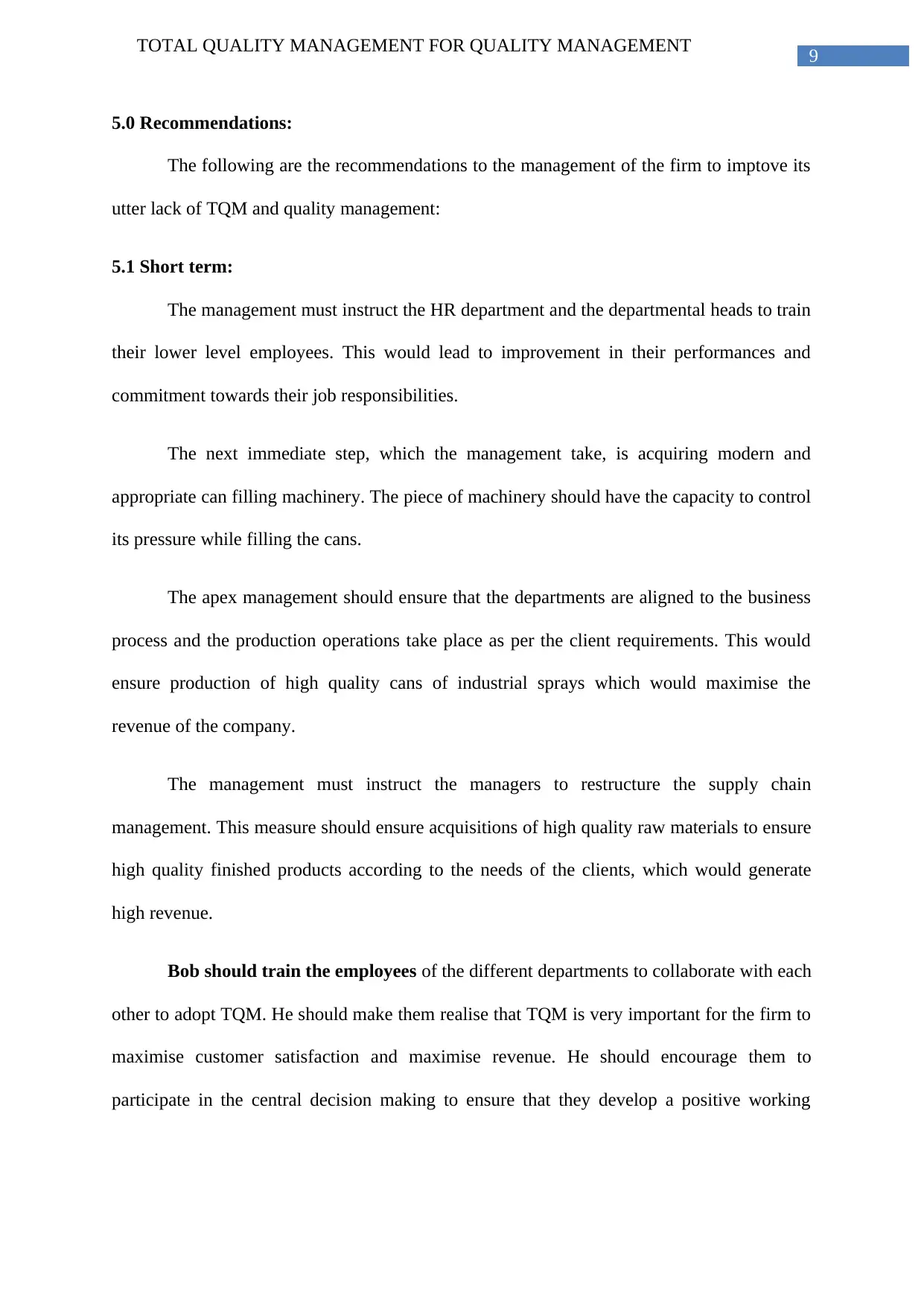
9
TOTAL QUALITY MANAGEMENT FOR QUALITY MANAGEMENT
5.0 Recommendations:
The following are the recommendations to the management of the firm to imptove its
utter lack of TQM and quality management:
5.1 Short term:
The management must instruct the HR department and the departmental heads to train
their lower level employees. This would lead to improvement in their performances and
commitment towards their job responsibilities.
The next immediate step, which the management take, is acquiring modern and
appropriate can filling machinery. The piece of machinery should have the capacity to control
its pressure while filling the cans.
The apex management should ensure that the departments are aligned to the business
process and the production operations take place as per the client requirements. This would
ensure production of high quality cans of industrial sprays which would maximise the
revenue of the company.
The management must instruct the managers to restructure the supply chain
management. This measure should ensure acquisitions of high quality raw materials to ensure
high quality finished products according to the needs of the clients, which would generate
high revenue.
Bob should train the employees of the different departments to collaborate with each
other to adopt TQM. He should make them realise that TQM is very important for the firm to
maximise customer satisfaction and maximise revenue. He should encourage them to
participate in the central decision making to ensure that they develop a positive working
TOTAL QUALITY MANAGEMENT FOR QUALITY MANAGEMENT
5.0 Recommendations:
The following are the recommendations to the management of the firm to imptove its
utter lack of TQM and quality management:
5.1 Short term:
The management must instruct the HR department and the departmental heads to train
their lower level employees. This would lead to improvement in their performances and
commitment towards their job responsibilities.
The next immediate step, which the management take, is acquiring modern and
appropriate can filling machinery. The piece of machinery should have the capacity to control
its pressure while filling the cans.
The apex management should ensure that the departments are aligned to the business
process and the production operations take place as per the client requirements. This would
ensure production of high quality cans of industrial sprays which would maximise the
revenue of the company.
The management must instruct the managers to restructure the supply chain
management. This measure should ensure acquisitions of high quality raw materials to ensure
high quality finished products according to the needs of the clients, which would generate
high revenue.
Bob should train the employees of the different departments to collaborate with each
other to adopt TQM. He should make them realise that TQM is very important for the firm to
maximise customer satisfaction and maximise revenue. He should encourage them to
participate in the central decision making to ensure that they develop a positive working
Secure Best Marks with AI Grader
Need help grading? Try our AI Grader for instant feedback on your assignments.
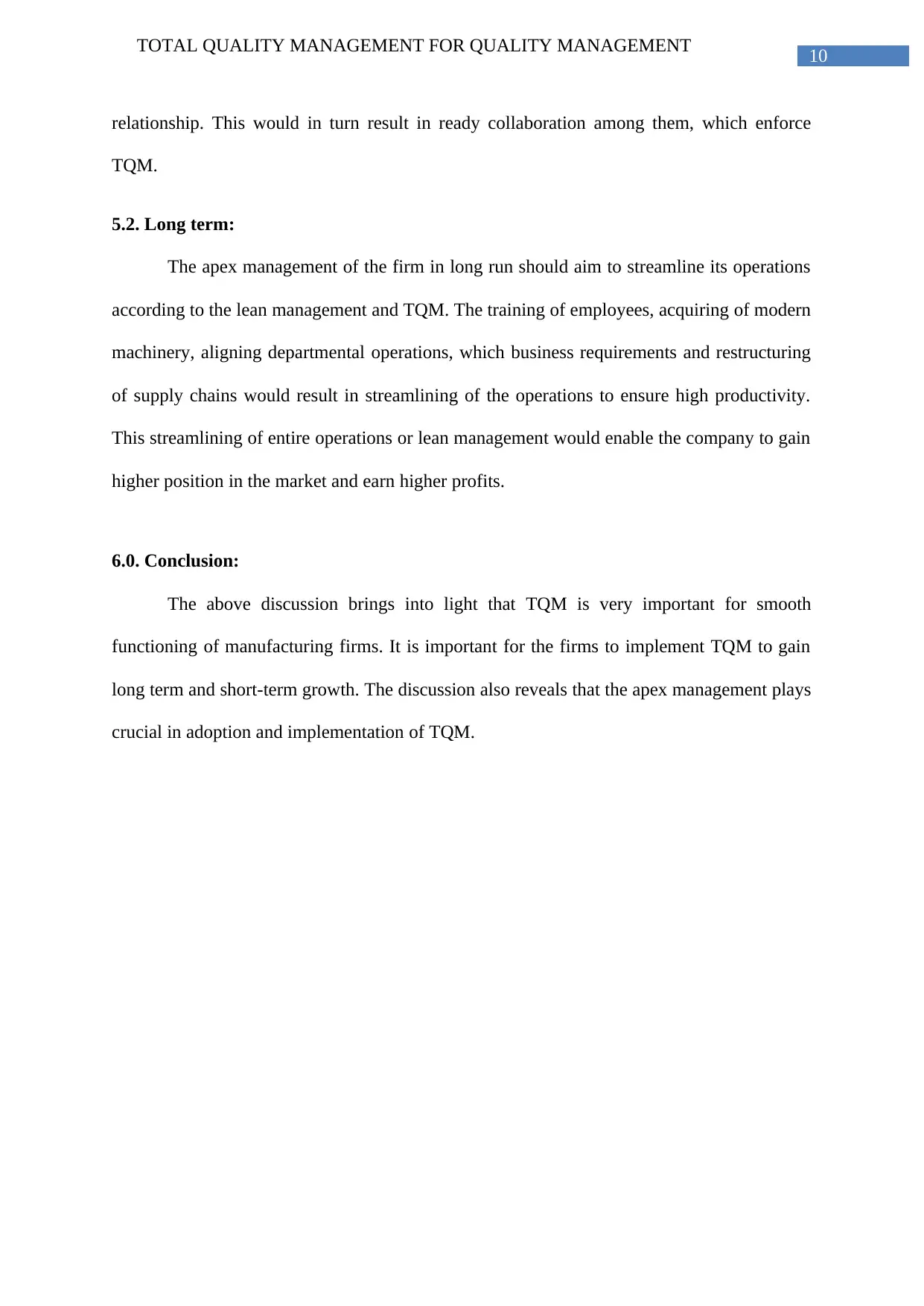
10
TOTAL QUALITY MANAGEMENT FOR QUALITY MANAGEMENT
relationship. This would in turn result in ready collaboration among them, which enforce
TQM.
5.2. Long term:
The apex management of the firm in long run should aim to streamline its operations
according to the lean management and TQM. The training of employees, acquiring of modern
machinery, aligning departmental operations, which business requirements and restructuring
of supply chains would result in streamlining of the operations to ensure high productivity.
This streamlining of entire operations or lean management would enable the company to gain
higher position in the market and earn higher profits.
6.0. Conclusion:
The above discussion brings into light that TQM is very important for smooth
functioning of manufacturing firms. It is important for the firms to implement TQM to gain
long term and short-term growth. The discussion also reveals that the apex management plays
crucial in adoption and implementation of TQM.
TOTAL QUALITY MANAGEMENT FOR QUALITY MANAGEMENT
relationship. This would in turn result in ready collaboration among them, which enforce
TQM.
5.2. Long term:
The apex management of the firm in long run should aim to streamline its operations
according to the lean management and TQM. The training of employees, acquiring of modern
machinery, aligning departmental operations, which business requirements and restructuring
of supply chains would result in streamlining of the operations to ensure high productivity.
This streamlining of entire operations or lean management would enable the company to gain
higher position in the market and earn higher profits.
6.0. Conclusion:
The above discussion brings into light that TQM is very important for smooth
functioning of manufacturing firms. It is important for the firms to implement TQM to gain
long term and short-term growth. The discussion also reveals that the apex management plays
crucial in adoption and implementation of TQM.
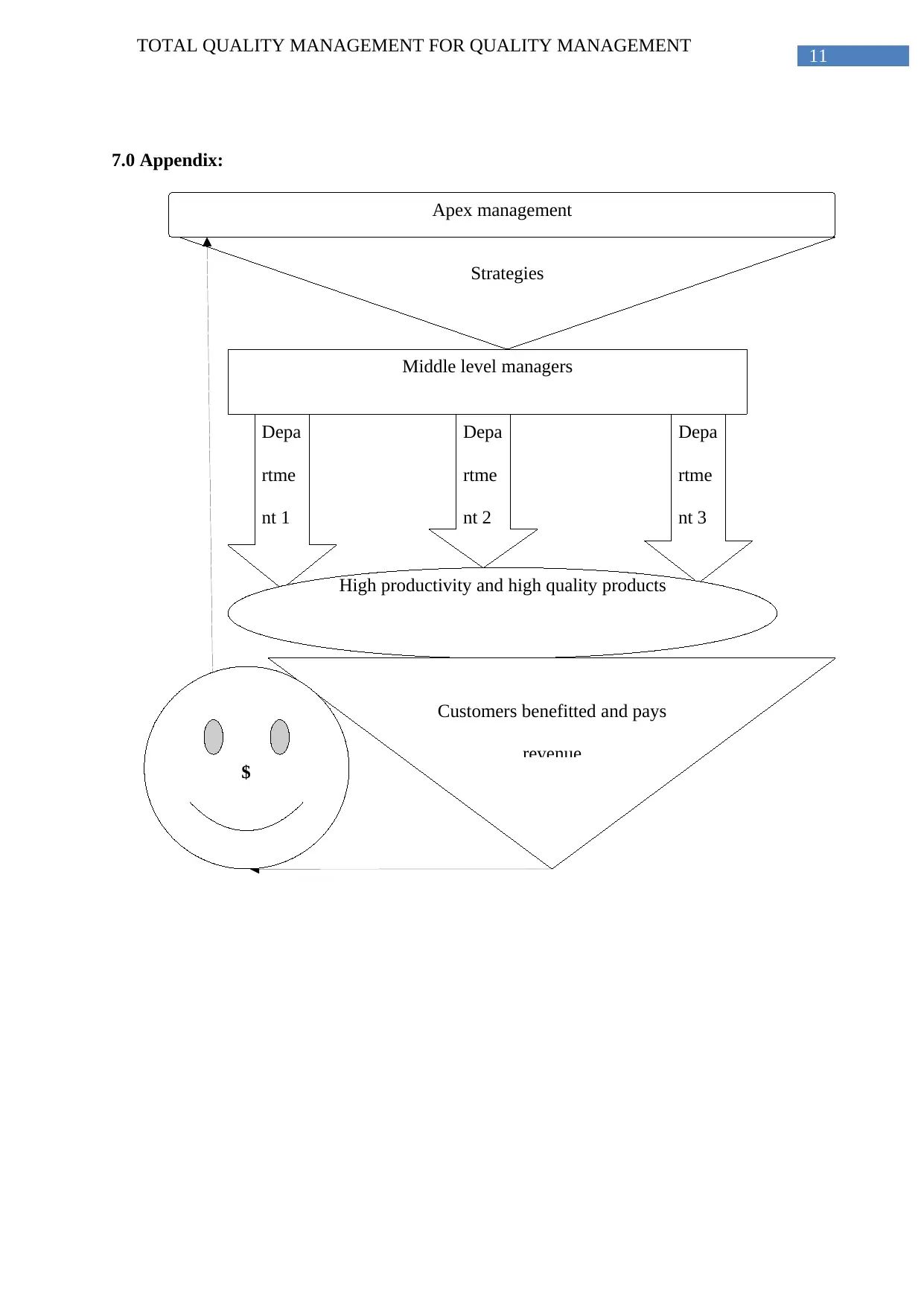
11
TOTAL QUALITY MANAGEMENT FOR QUALITY MANAGEMENT
7.0 Appendix:
Apex management
Middle level managers
Depa
rtme
nt 1
Depa
rtme
nt 2
Depa
rtme
nt 3
High productivity and high quality products
Strategies
Customers benefitted and pays
revenue
$
TOTAL QUALITY MANAGEMENT FOR QUALITY MANAGEMENT
7.0 Appendix:
Apex management
Middle level managers
Depa
rtme
nt 1
Depa
rtme
nt 2
Depa
rtme
nt 3
High productivity and high quality products
Strategies
Customers benefitted and pays
revenue
$
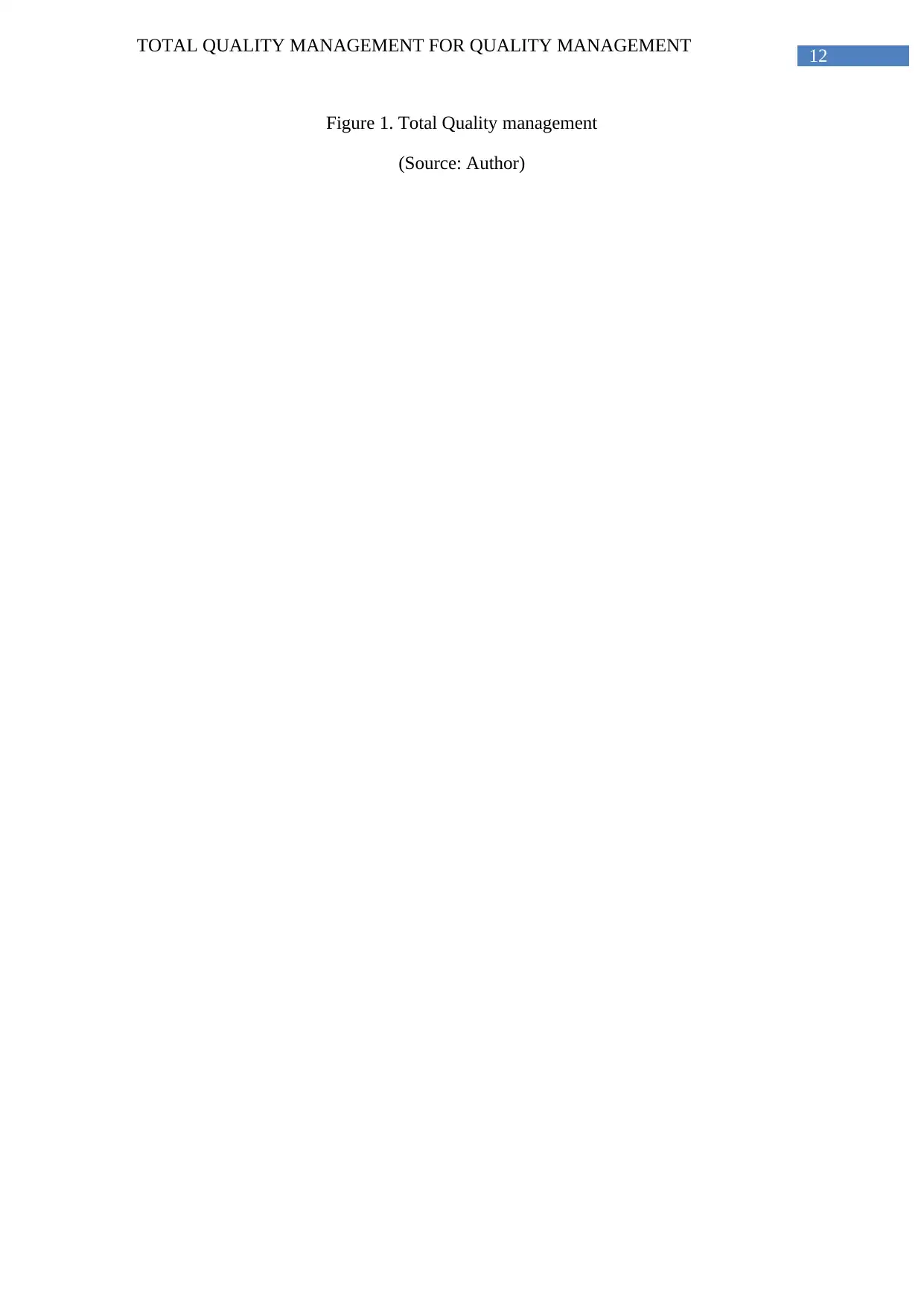
12
TOTAL QUALITY MANAGEMENT FOR QUALITY MANAGEMENT
Figure 1. Total Quality management
(Source: Author)
TOTAL QUALITY MANAGEMENT FOR QUALITY MANAGEMENT
Figure 1. Total Quality management
(Source: Author)
Paraphrase This Document
Need a fresh take? Get an instant paraphrase of this document with our AI Paraphraser
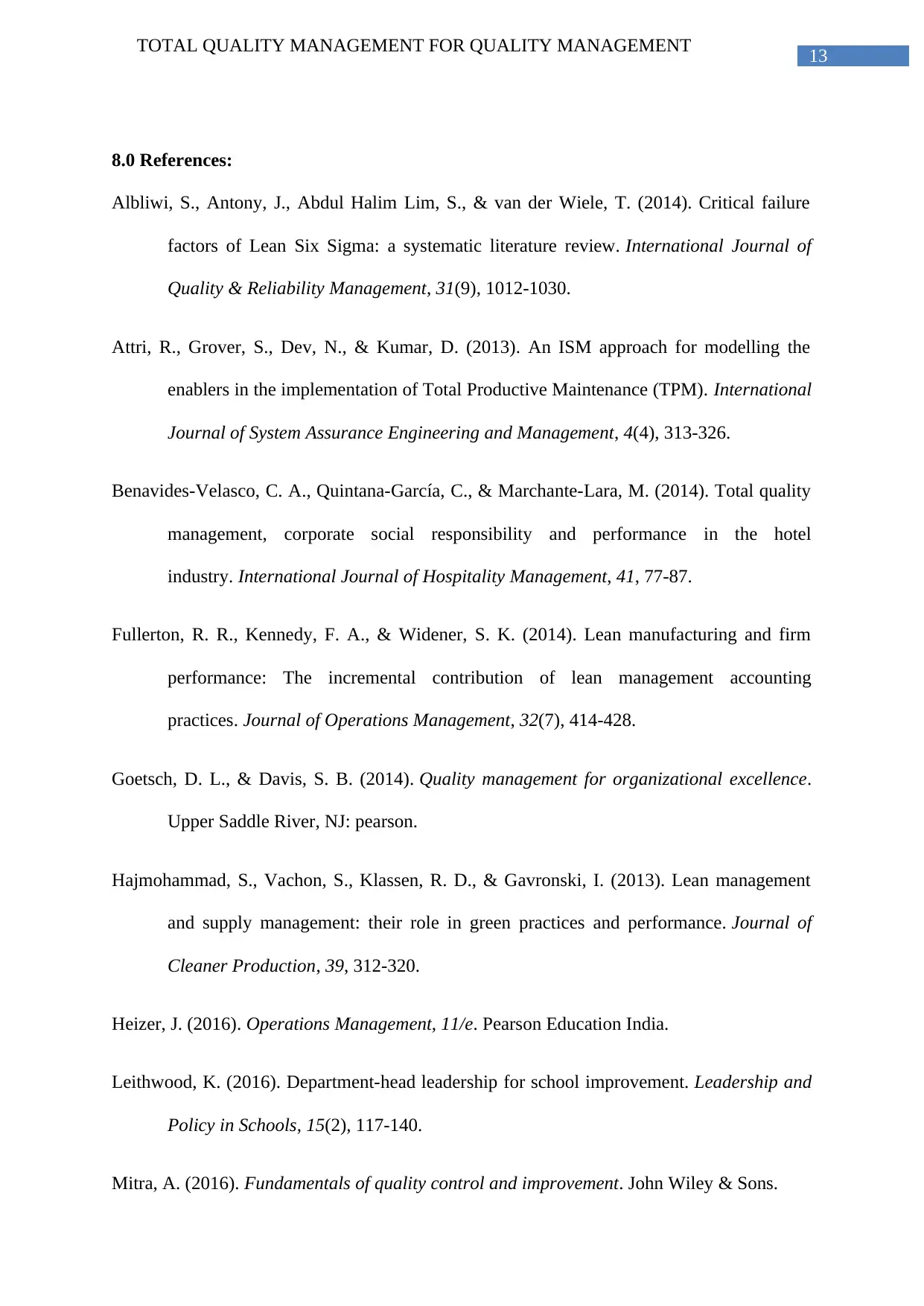
13
TOTAL QUALITY MANAGEMENT FOR QUALITY MANAGEMENT
8.0 References:
Albliwi, S., Antony, J., Abdul Halim Lim, S., & van der Wiele, T. (2014). Critical failure
factors of Lean Six Sigma: a systematic literature review. International Journal of
Quality & Reliability Management, 31(9), 1012-1030.
Attri, R., Grover, S., Dev, N., & Kumar, D. (2013). An ISM approach for modelling the
enablers in the implementation of Total Productive Maintenance (TPM). International
Journal of System Assurance Engineering and Management, 4(4), 313-326.
Benavides-Velasco, C. A., Quintana-GarcĂa, C., & Marchante-Lara, M. (2014). Total quality
management, corporate social responsibility and performance in the hotel
industry. International Journal of Hospitality Management, 41, 77-87.
Fullerton, R. R., Kennedy, F. A., & Widener, S. K. (2014). Lean manufacturing and firm
performance: The incremental contribution of lean management accounting
practices. Journal of Operations Management, 32(7), 414-428.
Goetsch, D. L., & Davis, S. B. (2014). Quality management for organizational excellence.
Upper Saddle River, NJ: pearson.
Hajmohammad, S., Vachon, S., Klassen, R. D., & Gavronski, I. (2013). Lean management
and supply management: their role in green practices and performance. Journal of
Cleaner Production, 39, 312-320.
Heizer, J. (2016). Operations Management, 11/e. Pearson Education India.
Leithwood, K. (2016). Department-head leadership for school improvement. Leadership and
Policy in Schools, 15(2), 117-140.
Mitra, A. (2016). Fundamentals of quality control and improvement. John Wiley & Sons.
TOTAL QUALITY MANAGEMENT FOR QUALITY MANAGEMENT
8.0 References:
Albliwi, S., Antony, J., Abdul Halim Lim, S., & van der Wiele, T. (2014). Critical failure
factors of Lean Six Sigma: a systematic literature review. International Journal of
Quality & Reliability Management, 31(9), 1012-1030.
Attri, R., Grover, S., Dev, N., & Kumar, D. (2013). An ISM approach for modelling the
enablers in the implementation of Total Productive Maintenance (TPM). International
Journal of System Assurance Engineering and Management, 4(4), 313-326.
Benavides-Velasco, C. A., Quintana-GarcĂa, C., & Marchante-Lara, M. (2014). Total quality
management, corporate social responsibility and performance in the hotel
industry. International Journal of Hospitality Management, 41, 77-87.
Fullerton, R. R., Kennedy, F. A., & Widener, S. K. (2014). Lean manufacturing and firm
performance: The incremental contribution of lean management accounting
practices. Journal of Operations Management, 32(7), 414-428.
Goetsch, D. L., & Davis, S. B. (2014). Quality management for organizational excellence.
Upper Saddle River, NJ: pearson.
Hajmohammad, S., Vachon, S., Klassen, R. D., & Gavronski, I. (2013). Lean management
and supply management: their role in green practices and performance. Journal of
Cleaner Production, 39, 312-320.
Heizer, J. (2016). Operations Management, 11/e. Pearson Education India.
Leithwood, K. (2016). Department-head leadership for school improvement. Leadership and
Policy in Schools, 15(2), 117-140.
Mitra, A. (2016). Fundamentals of quality control and improvement. John Wiley & Sons.
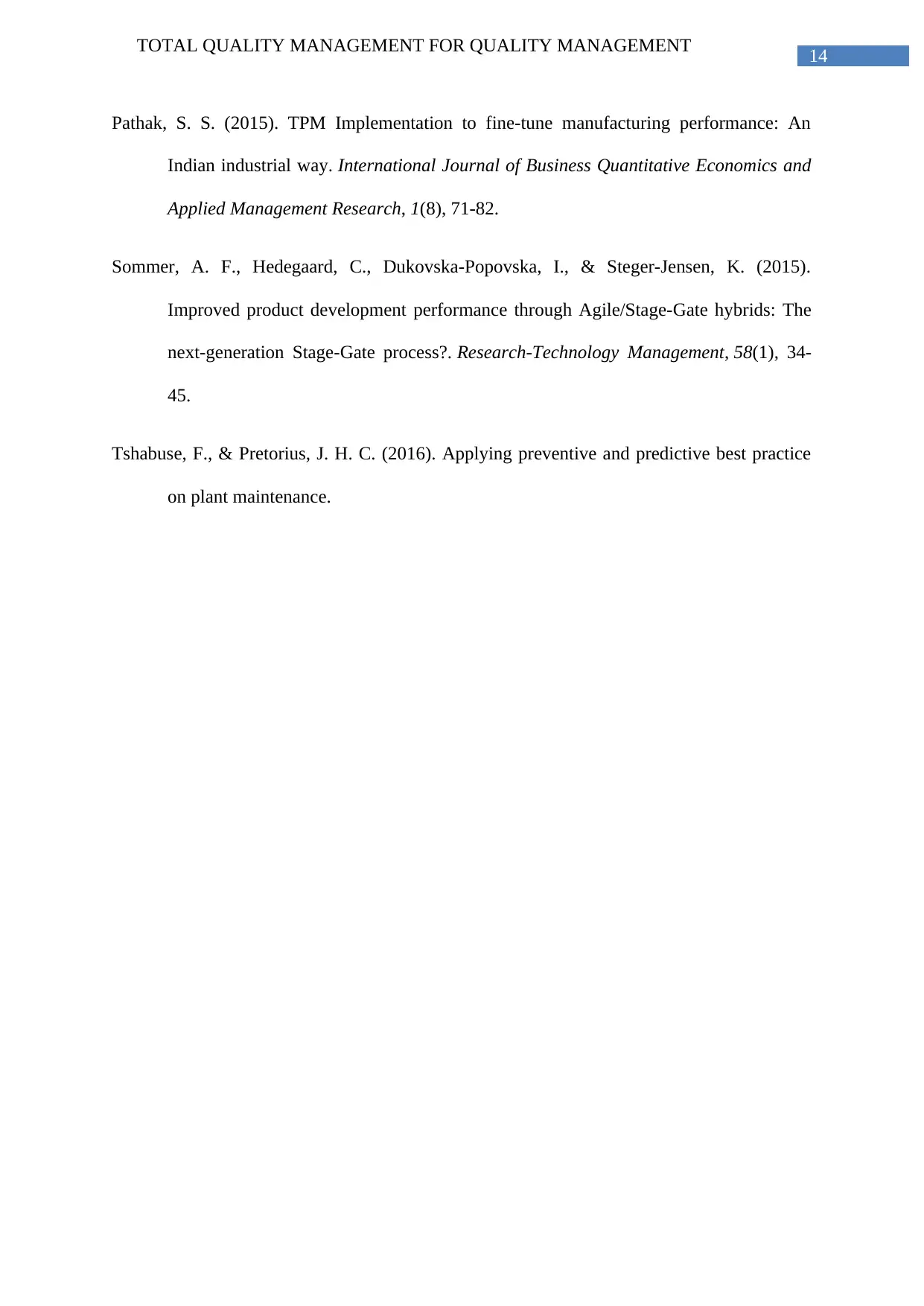
14
TOTAL QUALITY MANAGEMENT FOR QUALITY MANAGEMENT
Pathak, S. S. (2015). TPM Implementation to fine-tune manufacturing performance: An
Indian industrial way. International Journal of Business Quantitative Economics and
Applied Management Research, 1(8), 71-82.
Sommer, A. F., Hedegaard, C., Dukovska-Popovska, I., & Steger-Jensen, K. (2015).
Improved product development performance through Agile/Stage-Gate hybrids: The
next-generation Stage-Gate process?. Research-Technology Management, 58(1), 34-
45.
Tshabuse, F., & Pretorius, J. H. C. (2016). Applying preventive and predictive best practice
on plant maintenance.
TOTAL QUALITY MANAGEMENT FOR QUALITY MANAGEMENT
Pathak, S. S. (2015). TPM Implementation to fine-tune manufacturing performance: An
Indian industrial way. International Journal of Business Quantitative Economics and
Applied Management Research, 1(8), 71-82.
Sommer, A. F., Hedegaard, C., Dukovska-Popovska, I., & Steger-Jensen, K. (2015).
Improved product development performance through Agile/Stage-Gate hybrids: The
next-generation Stage-Gate process?. Research-Technology Management, 58(1), 34-
45.
Tshabuse, F., & Pretorius, J. H. C. (2016). Applying preventive and predictive best practice
on plant maintenance.
1 out of 15
![[object Object]](/_next/image/?url=%2F_next%2Fstatic%2Fmedia%2Flogo.6d15ce61.png&w=640&q=75)
Your All-in-One AI-Powered Toolkit for Academic Success.
 +13062052269
info@desklib.com
Available 24*7 on WhatsApp / Email
Unlock your academic potential
© 2024  |  Zucol Services PVT LTD  |  All rights reserved.