Operations Management of Mercedes-Benz
VerifiedAdded on 2023/01/11
|9
|3102
|94
AI Summary
This essay explores the operations management of Mercedes-Benz, focusing on quality management and lean production. It discusses how the company ensures customer satisfaction and efficiency in its manufacturing processes.
Contribute Materials
Your contribution can guide someone’s learning journey. Share your
documents today.
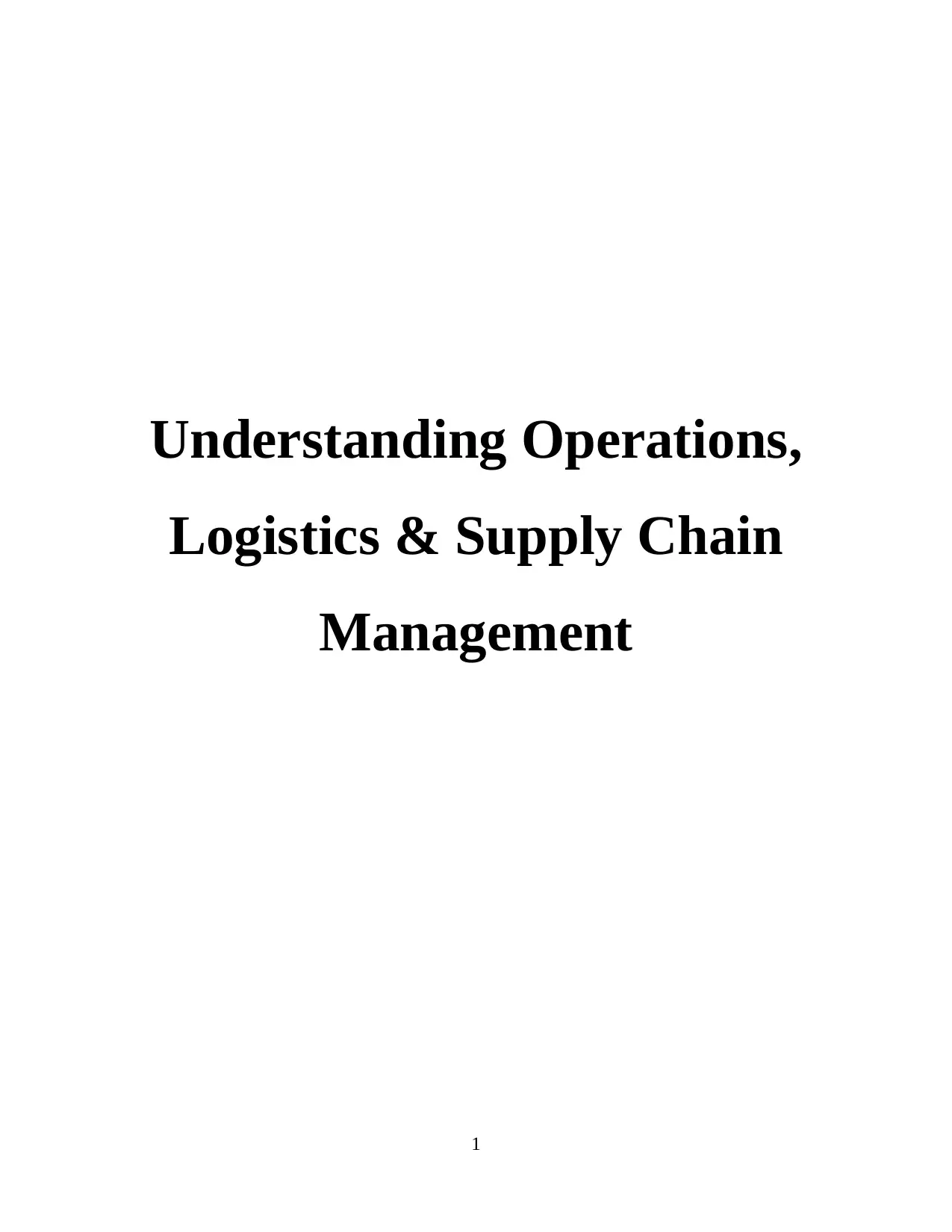
Understanding Operations,
Logistics & Supply Chain
Management
1
Logistics & Supply Chain
Management
1
Secure Best Marks with AI Grader
Need help grading? Try our AI Grader for instant feedback on your assignments.
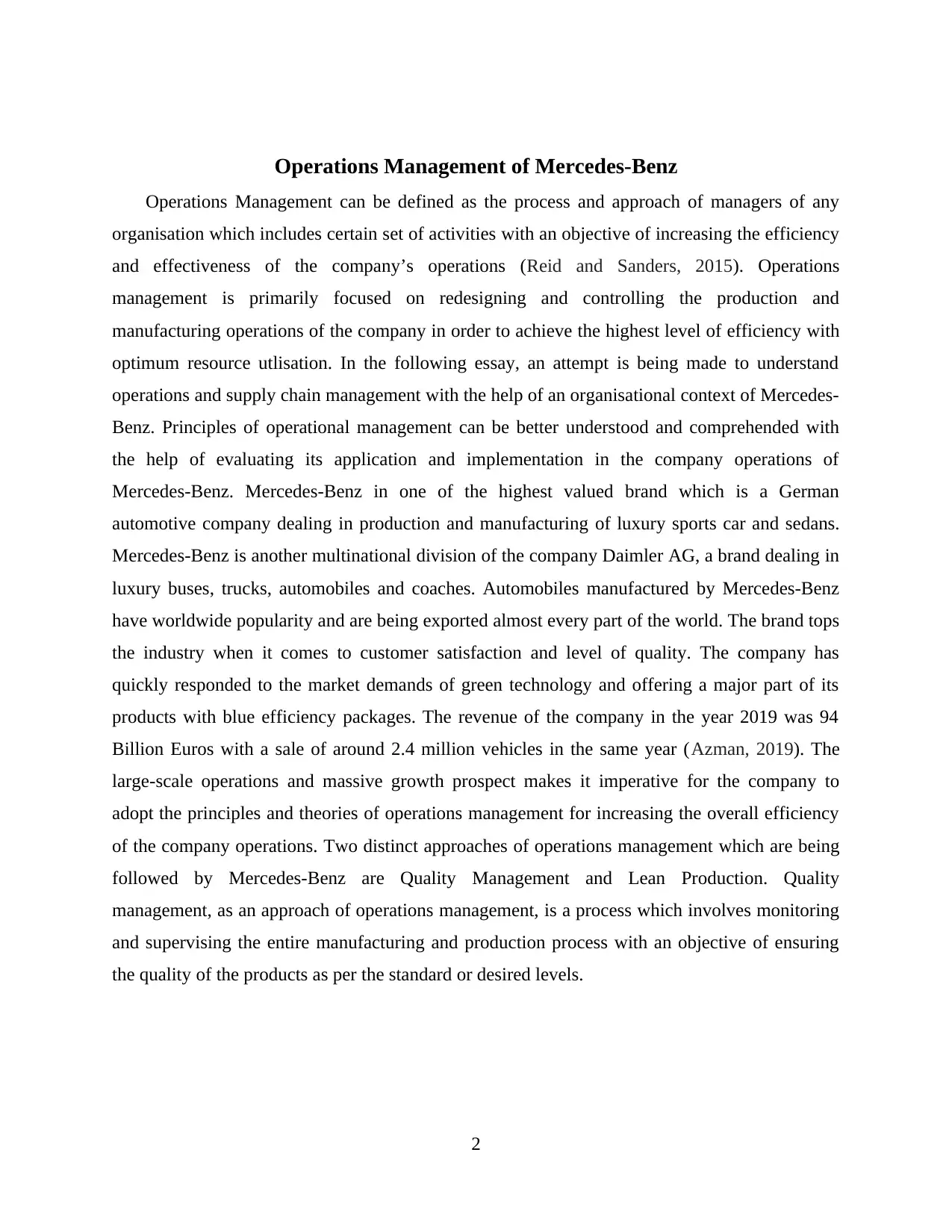
Operations Management of Mercedes-Benz
Operations Management can be defined as the process and approach of managers of any
organisation which includes certain set of activities with an objective of increasing the efficiency
and effectiveness of the company’s operations (Reid and Sanders, 2015). Operations
management is primarily focused on redesigning and controlling the production and
manufacturing operations of the company in order to achieve the highest level of efficiency with
optimum resource utlisation. In the following essay, an attempt is being made to understand
operations and supply chain management with the help of an organisational context of Mercedes-
Benz. Principles of operational management can be better understood and comprehended with
the help of evaluating its application and implementation in the company operations of
Mercedes-Benz. Mercedes-Benz in one of the highest valued brand which is a German
automotive company dealing in production and manufacturing of luxury sports car and sedans.
Mercedes-Benz is another multinational division of the company Daimler AG, a brand dealing in
luxury buses, trucks, automobiles and coaches. Automobiles manufactured by Mercedes-Benz
have worldwide popularity and are being exported almost every part of the world. The brand tops
the industry when it comes to customer satisfaction and level of quality. The company has
quickly responded to the market demands of green technology and offering a major part of its
products with blue efficiency packages. The revenue of the company in the year 2019 was 94
Billion Euros with a sale of around 2.4 million vehicles in the same year (Azman, 2019). The
large-scale operations and massive growth prospect makes it imperative for the company to
adopt the principles and theories of operations management for increasing the overall efficiency
of the company operations. Two distinct approaches of operations management which are being
followed by Mercedes-Benz are Quality Management and Lean Production. Quality
management, as an approach of operations management, is a process which involves monitoring
and supervising the entire manufacturing and production process with an objective of ensuring
the quality of the products as per the standard or desired levels.
2
Operations Management can be defined as the process and approach of managers of any
organisation which includes certain set of activities with an objective of increasing the efficiency
and effectiveness of the company’s operations (Reid and Sanders, 2015). Operations
management is primarily focused on redesigning and controlling the production and
manufacturing operations of the company in order to achieve the highest level of efficiency with
optimum resource utlisation. In the following essay, an attempt is being made to understand
operations and supply chain management with the help of an organisational context of Mercedes-
Benz. Principles of operational management can be better understood and comprehended with
the help of evaluating its application and implementation in the company operations of
Mercedes-Benz. Mercedes-Benz in one of the highest valued brand which is a German
automotive company dealing in production and manufacturing of luxury sports car and sedans.
Mercedes-Benz is another multinational division of the company Daimler AG, a brand dealing in
luxury buses, trucks, automobiles and coaches. Automobiles manufactured by Mercedes-Benz
have worldwide popularity and are being exported almost every part of the world. The brand tops
the industry when it comes to customer satisfaction and level of quality. The company has
quickly responded to the market demands of green technology and offering a major part of its
products with blue efficiency packages. The revenue of the company in the year 2019 was 94
Billion Euros with a sale of around 2.4 million vehicles in the same year (Azman, 2019). The
large-scale operations and massive growth prospect makes it imperative for the company to
adopt the principles and theories of operations management for increasing the overall efficiency
of the company operations. Two distinct approaches of operations management which are being
followed by Mercedes-Benz are Quality Management and Lean Production. Quality
management, as an approach of operations management, is a process which involves monitoring
and supervising the entire manufacturing and production process with an objective of ensuring
the quality of the products as per the standard or desired levels.
2
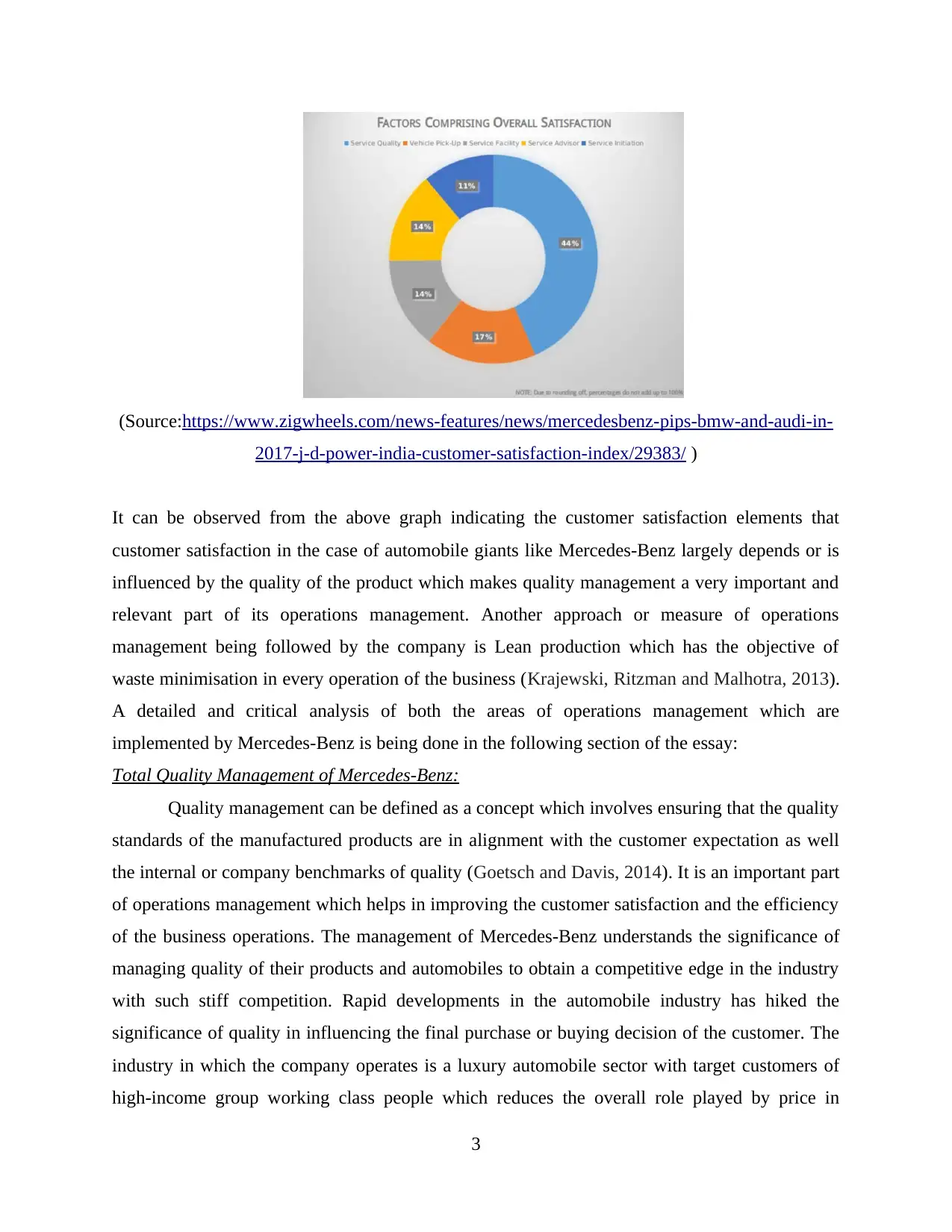
(Source:https://www.zigwheels.com/news-features/news/mercedesbenz-pips-bmw-and-audi-in-
2017-j-d-power-india-customer-satisfaction-index/29383/ )
It can be observed from the above graph indicating the customer satisfaction elements that
customer satisfaction in the case of automobile giants like Mercedes-Benz largely depends or is
influenced by the quality of the product which makes quality management a very important and
relevant part of its operations management. Another approach or measure of operations
management being followed by the company is Lean production which has the objective of
waste minimisation in every operation of the business (Krajewski, Ritzman and Malhotra, 2013).
A detailed and critical analysis of both the areas of operations management which are
implemented by Mercedes-Benz is being done in the following section of the essay:
Total Quality Management of Mercedes-Benz:
Quality management can be defined as a concept which involves ensuring that the quality
standards of the manufactured products are in alignment with the customer expectation as well
the internal or company benchmarks of quality (Goetsch and Davis, 2014). It is an important part
of operations management which helps in improving the customer satisfaction and the efficiency
of the business operations. The management of Mercedes-Benz understands the significance of
managing quality of their products and automobiles to obtain a competitive edge in the industry
with such stiff competition. Rapid developments in the automobile industry has hiked the
significance of quality in influencing the final purchase or buying decision of the customer. The
industry in which the company operates is a luxury automobile sector with target customers of
high-income group working class people which reduces the overall role played by price in
3
2017-j-d-power-india-customer-satisfaction-index/29383/ )
It can be observed from the above graph indicating the customer satisfaction elements that
customer satisfaction in the case of automobile giants like Mercedes-Benz largely depends or is
influenced by the quality of the product which makes quality management a very important and
relevant part of its operations management. Another approach or measure of operations
management being followed by the company is Lean production which has the objective of
waste minimisation in every operation of the business (Krajewski, Ritzman and Malhotra, 2013).
A detailed and critical analysis of both the areas of operations management which are
implemented by Mercedes-Benz is being done in the following section of the essay:
Total Quality Management of Mercedes-Benz:
Quality management can be defined as a concept which involves ensuring that the quality
standards of the manufactured products are in alignment with the customer expectation as well
the internal or company benchmarks of quality (Goetsch and Davis, 2014). It is an important part
of operations management which helps in improving the customer satisfaction and the efficiency
of the business operations. The management of Mercedes-Benz understands the significance of
managing quality of their products and automobiles to obtain a competitive edge in the industry
with such stiff competition. Rapid developments in the automobile industry has hiked the
significance of quality in influencing the final purchase or buying decision of the customer. The
industry in which the company operates is a luxury automobile sector with target customers of
high-income group working class people which reduces the overall role played by price in
3
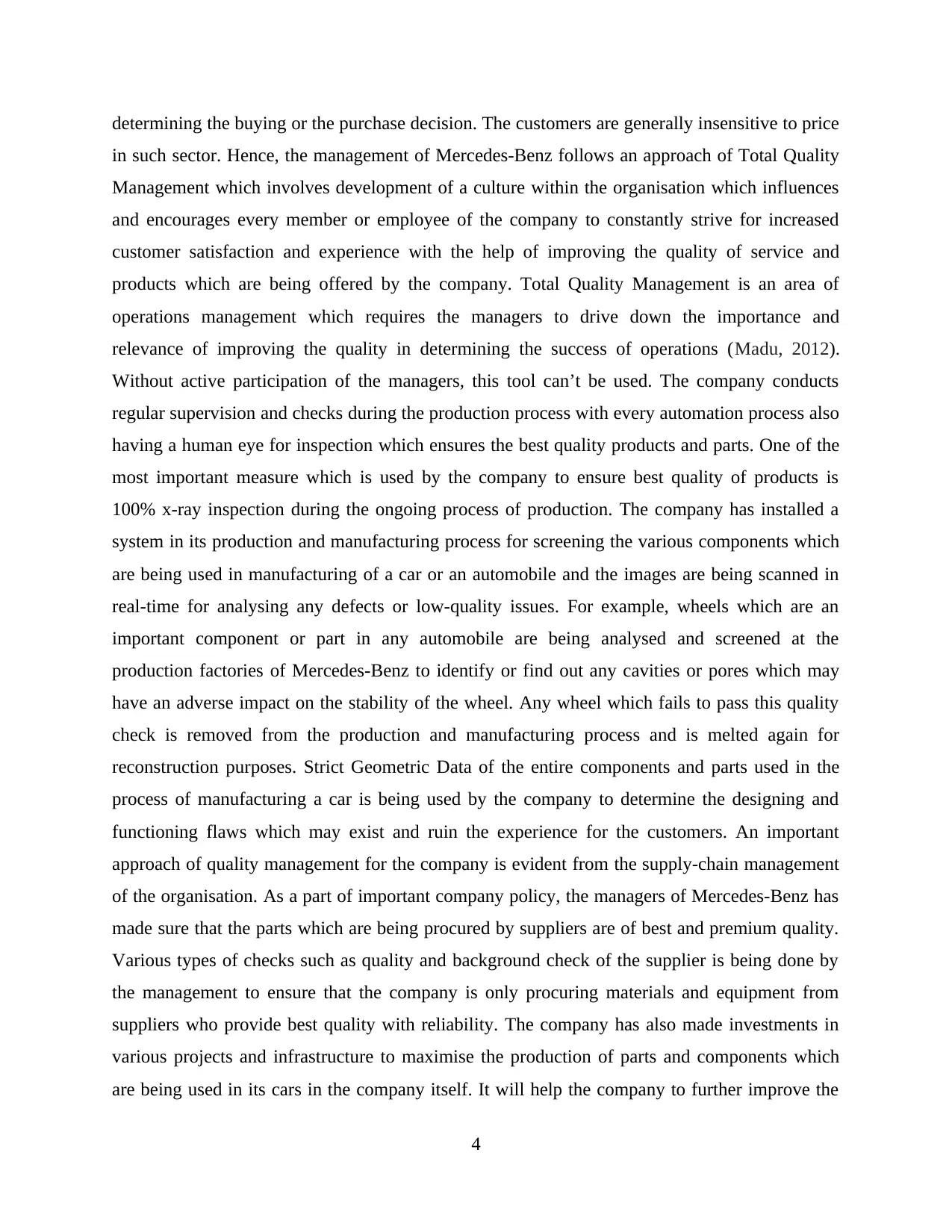
determining the buying or the purchase decision. The customers are generally insensitive to price
in such sector. Hence, the management of Mercedes-Benz follows an approach of Total Quality
Management which involves development of a culture within the organisation which influences
and encourages every member or employee of the company to constantly strive for increased
customer satisfaction and experience with the help of improving the quality of service and
products which are being offered by the company. Total Quality Management is an area of
operations management which requires the managers to drive down the importance and
relevance of improving the quality in determining the success of operations (Madu, 2012).
Without active participation of the managers, this tool can’t be used. The company conducts
regular supervision and checks during the production process with every automation process also
having a human eye for inspection which ensures the best quality products and parts. One of the
most important measure which is used by the company to ensure best quality of products is
100% x-ray inspection during the ongoing process of production. The company has installed a
system in its production and manufacturing process for screening the various components which
are being used in manufacturing of a car or an automobile and the images are being scanned in
real-time for analysing any defects or low-quality issues. For example, wheels which are an
important component or part in any automobile are being analysed and screened at the
production factories of Mercedes-Benz to identify or find out any cavities or pores which may
have an adverse impact on the stability of the wheel. Any wheel which fails to pass this quality
check is removed from the production and manufacturing process and is melted again for
reconstruction purposes. Strict Geometric Data of the entire components and parts used in the
process of manufacturing a car is being used by the company to determine the designing and
functioning flaws which may exist and ruin the experience for the customers. An important
approach of quality management for the company is evident from the supply-chain management
of the organisation. As a part of important company policy, the managers of Mercedes-Benz has
made sure that the parts which are being procured by suppliers are of best and premium quality.
Various types of checks such as quality and background check of the supplier is being done by
the management to ensure that the company is only procuring materials and equipment from
suppliers who provide best quality with reliability. The company has also made investments in
various projects and infrastructure to maximise the production of parts and components which
are being used in its cars in the company itself. It will help the company to further improve the
4
in such sector. Hence, the management of Mercedes-Benz follows an approach of Total Quality
Management which involves development of a culture within the organisation which influences
and encourages every member or employee of the company to constantly strive for increased
customer satisfaction and experience with the help of improving the quality of service and
products which are being offered by the company. Total Quality Management is an area of
operations management which requires the managers to drive down the importance and
relevance of improving the quality in determining the success of operations (Madu, 2012).
Without active participation of the managers, this tool can’t be used. The company conducts
regular supervision and checks during the production process with every automation process also
having a human eye for inspection which ensures the best quality products and parts. One of the
most important measure which is used by the company to ensure best quality of products is
100% x-ray inspection during the ongoing process of production. The company has installed a
system in its production and manufacturing process for screening the various components which
are being used in manufacturing of a car or an automobile and the images are being scanned in
real-time for analysing any defects or low-quality issues. For example, wheels which are an
important component or part in any automobile are being analysed and screened at the
production factories of Mercedes-Benz to identify or find out any cavities or pores which may
have an adverse impact on the stability of the wheel. Any wheel which fails to pass this quality
check is removed from the production and manufacturing process and is melted again for
reconstruction purposes. Strict Geometric Data of the entire components and parts used in the
process of manufacturing a car is being used by the company to determine the designing and
functioning flaws which may exist and ruin the experience for the customers. An important
approach of quality management for the company is evident from the supply-chain management
of the organisation. As a part of important company policy, the managers of Mercedes-Benz has
made sure that the parts which are being procured by suppliers are of best and premium quality.
Various types of checks such as quality and background check of the supplier is being done by
the management to ensure that the company is only procuring materials and equipment from
suppliers who provide best quality with reliability. The company has also made investments in
various projects and infrastructure to maximise the production of parts and components which
are being used in its cars in the company itself. It will help the company to further improve the
4
Secure Best Marks with AI Grader
Need help grading? Try our AI Grader for instant feedback on your assignments.
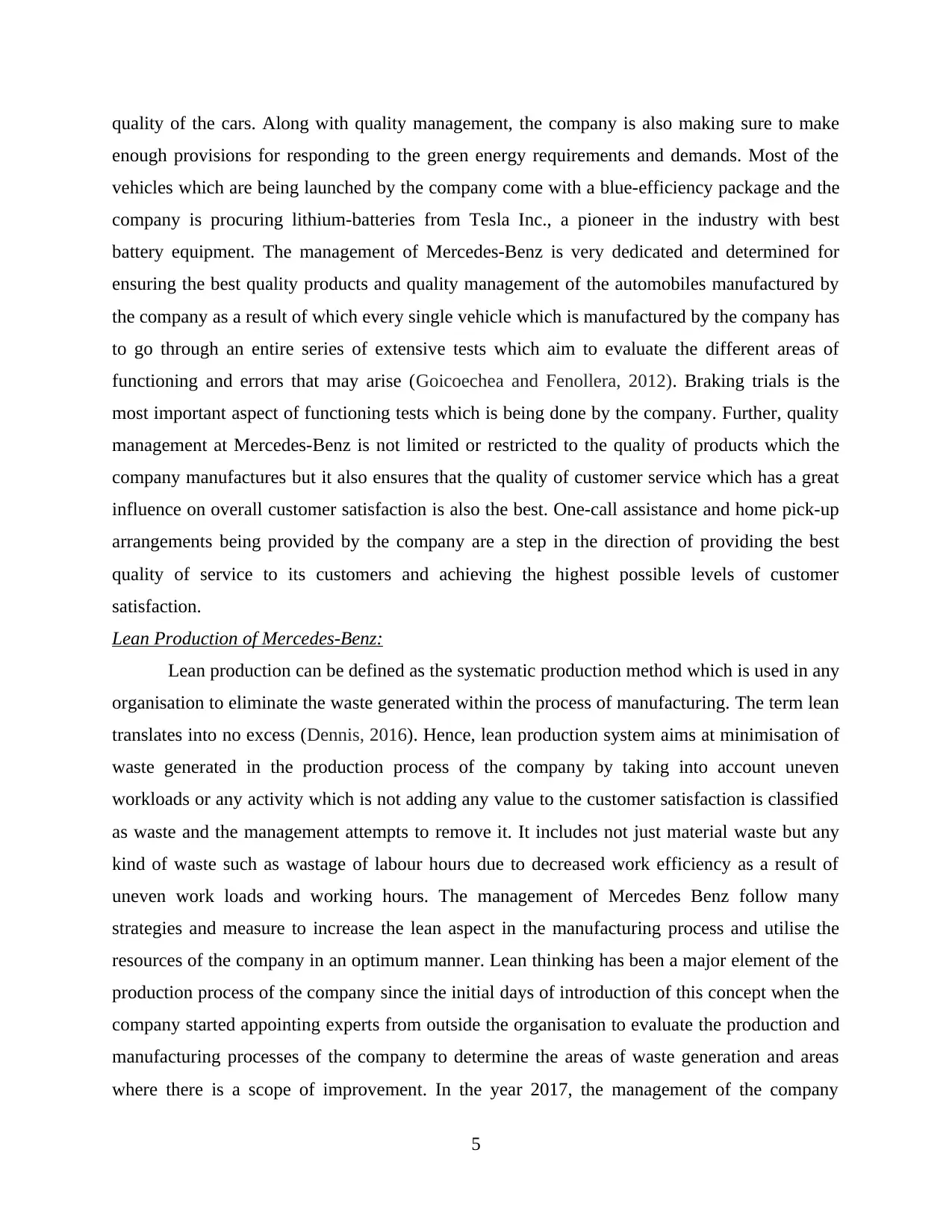
quality of the cars. Along with quality management, the company is also making sure to make
enough provisions for responding to the green energy requirements and demands. Most of the
vehicles which are being launched by the company come with a blue-efficiency package and the
company is procuring lithium-batteries from Tesla Inc., a pioneer in the industry with best
battery equipment. The management of Mercedes-Benz is very dedicated and determined for
ensuring the best quality products and quality management of the automobiles manufactured by
the company as a result of which every single vehicle which is manufactured by the company has
to go through an entire series of extensive tests which aim to evaluate the different areas of
functioning and errors that may arise (Goicoechea and Fenollera, 2012). Braking trials is the
most important aspect of functioning tests which is being done by the company. Further, quality
management at Mercedes-Benz is not limited or restricted to the quality of products which the
company manufactures but it also ensures that the quality of customer service which has a great
influence on overall customer satisfaction is also the best. One-call assistance and home pick-up
arrangements being provided by the company are a step in the direction of providing the best
quality of service to its customers and achieving the highest possible levels of customer
satisfaction.
Lean Production of Mercedes-Benz:
Lean production can be defined as the systematic production method which is used in any
organisation to eliminate the waste generated within the process of manufacturing. The term lean
translates into no excess (Dennis, 2016). Hence, lean production system aims at minimisation of
waste generated in the production process of the company by taking into account uneven
workloads or any activity which is not adding any value to the customer satisfaction is classified
as waste and the management attempts to remove it. It includes not just material waste but any
kind of waste such as wastage of labour hours due to decreased work efficiency as a result of
uneven work loads and working hours. The management of Mercedes Benz follow many
strategies and measure to increase the lean aspect in the manufacturing process and utilise the
resources of the company in an optimum manner. Lean thinking has been a major element of the
production process of the company since the initial days of introduction of this concept when the
company started appointing experts from outside the organisation to evaluate the production and
manufacturing processes of the company to determine the areas of waste generation and areas
where there is a scope of improvement. In the year 2017, the management of the company
5
enough provisions for responding to the green energy requirements and demands. Most of the
vehicles which are being launched by the company come with a blue-efficiency package and the
company is procuring lithium-batteries from Tesla Inc., a pioneer in the industry with best
battery equipment. The management of Mercedes-Benz is very dedicated and determined for
ensuring the best quality products and quality management of the automobiles manufactured by
the company as a result of which every single vehicle which is manufactured by the company has
to go through an entire series of extensive tests which aim to evaluate the different areas of
functioning and errors that may arise (Goicoechea and Fenollera, 2012). Braking trials is the
most important aspect of functioning tests which is being done by the company. Further, quality
management at Mercedes-Benz is not limited or restricted to the quality of products which the
company manufactures but it also ensures that the quality of customer service which has a great
influence on overall customer satisfaction is also the best. One-call assistance and home pick-up
arrangements being provided by the company are a step in the direction of providing the best
quality of service to its customers and achieving the highest possible levels of customer
satisfaction.
Lean Production of Mercedes-Benz:
Lean production can be defined as the systematic production method which is used in any
organisation to eliminate the waste generated within the process of manufacturing. The term lean
translates into no excess (Dennis, 2016). Hence, lean production system aims at minimisation of
waste generated in the production process of the company by taking into account uneven
workloads or any activity which is not adding any value to the customer satisfaction is classified
as waste and the management attempts to remove it. It includes not just material waste but any
kind of waste such as wastage of labour hours due to decreased work efficiency as a result of
uneven work loads and working hours. The management of Mercedes Benz follow many
strategies and measure to increase the lean aspect in the manufacturing process and utilise the
resources of the company in an optimum manner. Lean thinking has been a major element of the
production process of the company since the initial days of introduction of this concept when the
company started appointing experts from outside the organisation to evaluate the production and
manufacturing processes of the company to determine the areas of waste generation and areas
where there is a scope of improvement. In the year 2017, the management of the company
5

introduced the Continuous Improvement Framework with an objective and aim of coordinating
and integrating the many activities and measures which have already been put in place by the
company for lean manufacturing systems. The company followed an intensive approach of Six
Sigma for lean production. Six Sigma is a set of activities or measures used by the management
which is used to reduce the possibility of an event of error occurrence. This approach was
implemented by the company in the production process to reduce and mitigate any chances or
possibility of waste generation within the manufacturing process of the company. The CI
Framework which was implemented by the company had a clear vision and strategy of attaining
business excellence with the help of improvement of process of manufacturing with zero or
minimal waste generation by development of its staff and people involved in the manufacturing
process. The main purpose of this framework was to provide a platform for developing a large
team or set of people with the mindset of continuous improvement of the company’s processes
and solving the various problems which may arise in the manufacturing process related to its
waste generation (McAllister, 2014). Decentralisation of lean production information is the main
aspect of this strategy with creating more and more awareness in the factory and its workers on
how to improve the production efficiency and minimise the generation of waste. The company
also set in place an intensive training program of the employees who were going to be positioned
at closeness with the manufacturing process. Each division and department of the company had a
minimum of 2-3 people supervising the complete production process with an aspect of
minimisation of waste generation. Lean production is not only restricted to mitigation of wastage
of resources but it also ensures that the company is providing the goods which are of best quality.
Customer satisfaction is also a major part of the lean production systems. The management of the
company also accepted the fact that automation of the entire process of manufacturing is also
leading to a lot of waste generation and some parts or processes should be handled by human
resources to achieve maximum efficiency. As a result, the areas of automation were identified
where human resources could have potentially done a better job and improved the efficiency
such as conveyor belts were one such thing or automation aspect which was not as efficient as it
was expected to be. Just-in-time inventory was another major aspect of lean production systems
which had the objective of minimising the wastage and various costs which are associated with
the inventory. The management of Mercedes-Benz applied the principles of Just-in-time
inventory management to determine an adequate level of inventory at which the cost related to
6
and integrating the many activities and measures which have already been put in place by the
company for lean manufacturing systems. The company followed an intensive approach of Six
Sigma for lean production. Six Sigma is a set of activities or measures used by the management
which is used to reduce the possibility of an event of error occurrence. This approach was
implemented by the company in the production process to reduce and mitigate any chances or
possibility of waste generation within the manufacturing process of the company. The CI
Framework which was implemented by the company had a clear vision and strategy of attaining
business excellence with the help of improvement of process of manufacturing with zero or
minimal waste generation by development of its staff and people involved in the manufacturing
process. The main purpose of this framework was to provide a platform for developing a large
team or set of people with the mindset of continuous improvement of the company’s processes
and solving the various problems which may arise in the manufacturing process related to its
waste generation (McAllister, 2014). Decentralisation of lean production information is the main
aspect of this strategy with creating more and more awareness in the factory and its workers on
how to improve the production efficiency and minimise the generation of waste. The company
also set in place an intensive training program of the employees who were going to be positioned
at closeness with the manufacturing process. Each division and department of the company had a
minimum of 2-3 people supervising the complete production process with an aspect of
minimisation of waste generation. Lean production is not only restricted to mitigation of wastage
of resources but it also ensures that the company is providing the goods which are of best quality.
Customer satisfaction is also a major part of the lean production systems. The management of the
company also accepted the fact that automation of the entire process of manufacturing is also
leading to a lot of waste generation and some parts or processes should be handled by human
resources to achieve maximum efficiency. As a result, the areas of automation were identified
where human resources could have potentially done a better job and improved the efficiency
such as conveyor belts were one such thing or automation aspect which was not as efficient as it
was expected to be. Just-in-time inventory was another major aspect of lean production systems
which had the objective of minimising the wastage and various costs which are associated with
the inventory. The management of Mercedes-Benz applied the principles of Just-in-time
inventory management to determine an adequate level of inventory at which the cost related to
6
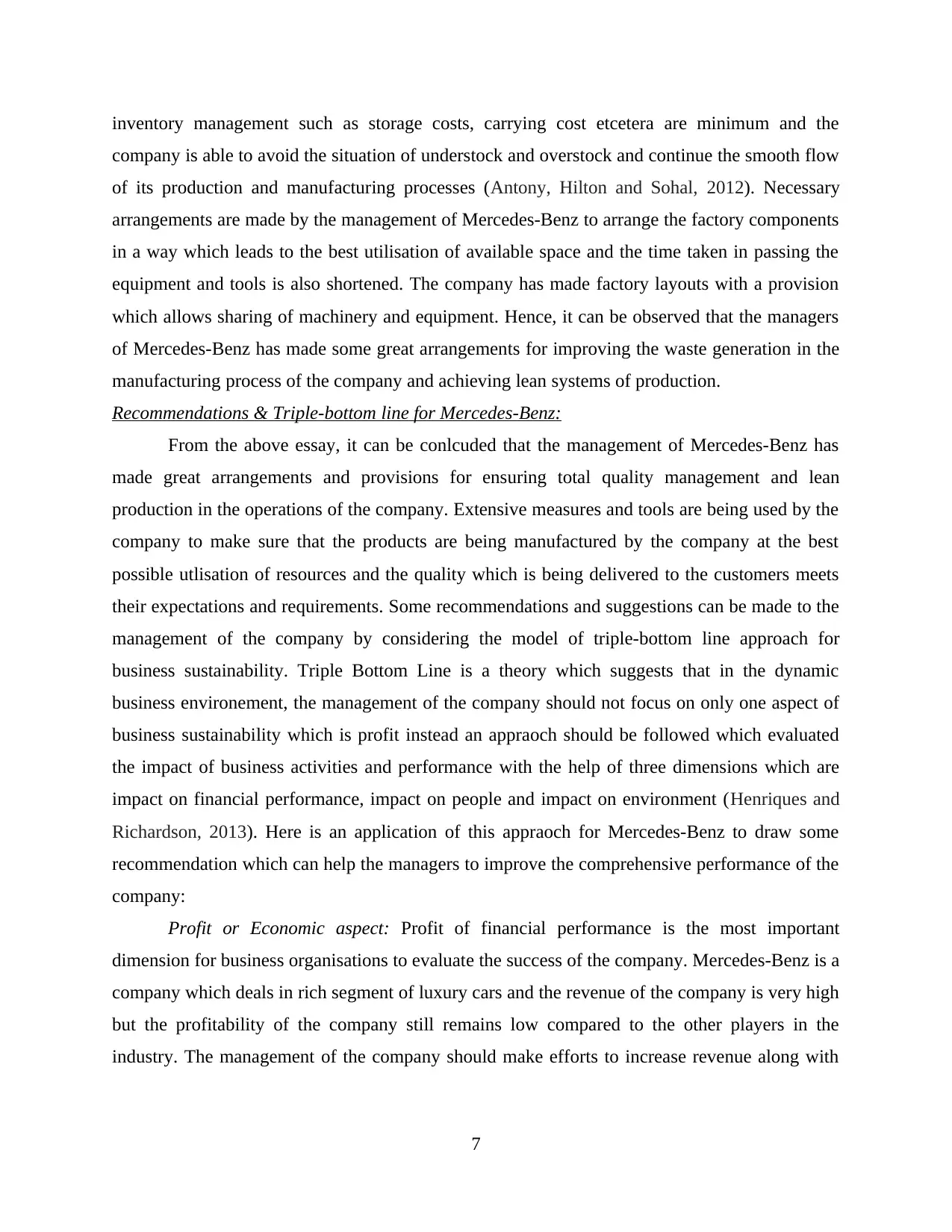
inventory management such as storage costs, carrying cost etcetera are minimum and the
company is able to avoid the situation of understock and overstock and continue the smooth flow
of its production and manufacturing processes (Antony, Hilton and Sohal, 2012). Necessary
arrangements are made by the management of Mercedes-Benz to arrange the factory components
in a way which leads to the best utilisation of available space and the time taken in passing the
equipment and tools is also shortened. The company has made factory layouts with a provision
which allows sharing of machinery and equipment. Hence, it can be observed that the managers
of Mercedes-Benz has made some great arrangements for improving the waste generation in the
manufacturing process of the company and achieving lean systems of production.
Recommendations & Triple-bottom line for Mercedes-Benz:
From the above essay, it can be conlcuded that the management of Mercedes-Benz has
made great arrangements and provisions for ensuring total quality management and lean
production in the operations of the company. Extensive measures and tools are being used by the
company to make sure that the products are being manufactured by the company at the best
possible utlisation of resources and the quality which is being delivered to the customers meets
their expectations and requirements. Some recommendations and suggestions can be made to the
management of the company by considering the model of triple-bottom line approach for
business sustainability. Triple Bottom Line is a theory which suggests that in the dynamic
business environement, the management of the company should not focus on only one aspect of
business sustainability which is profit instead an appraoch should be followed which evaluated
the impact of business activities and performance with the help of three dimensions which are
impact on financial performance, impact on people and impact on environment (Henriques and
Richardson, 2013). Here is an application of this appraoch for Mercedes-Benz to draw some
recommendation which can help the managers to improve the comprehensive performance of the
company:
Profit or Economic aspect: Profit of financial performance is the most important
dimension for business organisations to evaluate the success of the company. Mercedes-Benz is a
company which deals in rich segment of luxury cars and the revenue of the company is very high
but the profitability of the company still remains low compared to the other players in the
industry. The management of the company should make efforts to increase revenue along with
7
company is able to avoid the situation of understock and overstock and continue the smooth flow
of its production and manufacturing processes (Antony, Hilton and Sohal, 2012). Necessary
arrangements are made by the management of Mercedes-Benz to arrange the factory components
in a way which leads to the best utilisation of available space and the time taken in passing the
equipment and tools is also shortened. The company has made factory layouts with a provision
which allows sharing of machinery and equipment. Hence, it can be observed that the managers
of Mercedes-Benz has made some great arrangements for improving the waste generation in the
manufacturing process of the company and achieving lean systems of production.
Recommendations & Triple-bottom line for Mercedes-Benz:
From the above essay, it can be conlcuded that the management of Mercedes-Benz has
made great arrangements and provisions for ensuring total quality management and lean
production in the operations of the company. Extensive measures and tools are being used by the
company to make sure that the products are being manufactured by the company at the best
possible utlisation of resources and the quality which is being delivered to the customers meets
their expectations and requirements. Some recommendations and suggestions can be made to the
management of the company by considering the model of triple-bottom line approach for
business sustainability. Triple Bottom Line is a theory which suggests that in the dynamic
business environement, the management of the company should not focus on only one aspect of
business sustainability which is profit instead an appraoch should be followed which evaluated
the impact of business activities and performance with the help of three dimensions which are
impact on financial performance, impact on people and impact on environment (Henriques and
Richardson, 2013). Here is an application of this appraoch for Mercedes-Benz to draw some
recommendation which can help the managers to improve the comprehensive performance of the
company:
Profit or Economic aspect: Profit of financial performance is the most important
dimension for business organisations to evaluate the success of the company. Mercedes-Benz is a
company which deals in rich segment of luxury cars and the revenue of the company is very high
but the profitability of the company still remains low compared to the other players in the
industry. The management of the company should make efforts to increase revenue along with
7
Paraphrase This Document
Need a fresh take? Get an instant paraphrase of this document with our AI Paraphraser
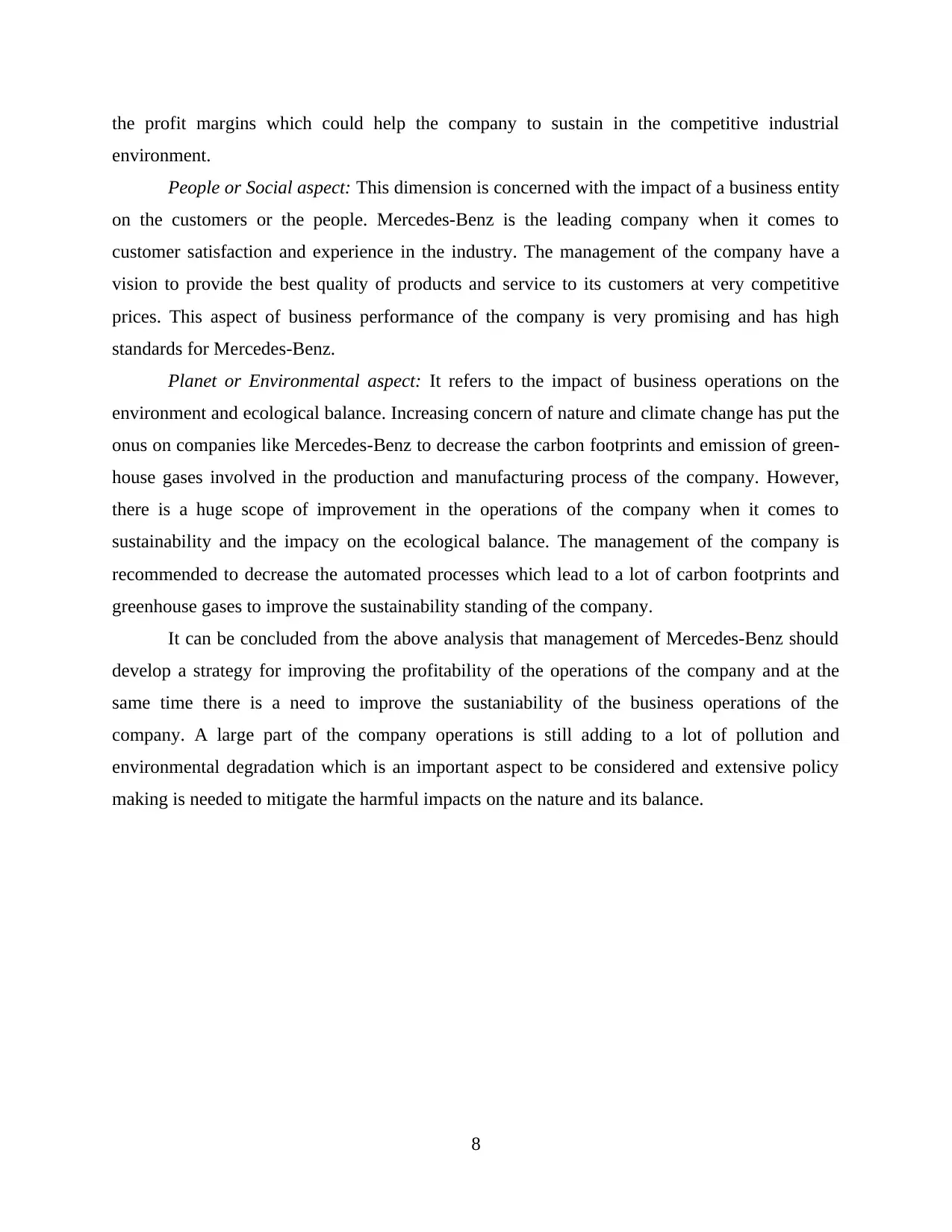
the profit margins which could help the company to sustain in the competitive industrial
environment.
People or Social aspect: This dimension is concerned with the impact of a business entity
on the customers or the people. Mercedes-Benz is the leading company when it comes to
customer satisfaction and experience in the industry. The management of the company have a
vision to provide the best quality of products and service to its customers at very competitive
prices. This aspect of business performance of the company is very promising and has high
standards for Mercedes-Benz.
Planet or Environmental aspect: It refers to the impact of business operations on the
environment and ecological balance. Increasing concern of nature and climate change has put the
onus on companies like Mercedes-Benz to decrease the carbon footprints and emission of green-
house gases involved in the production and manufacturing process of the company. However,
there is a huge scope of improvement in the operations of the company when it comes to
sustainability and the impacy on the ecological balance. The management of the company is
recommended to decrease the automated processes which lead to a lot of carbon footprints and
greenhouse gases to improve the sustainability standing of the company.
It can be concluded from the above analysis that management of Mercedes-Benz should
develop a strategy for improving the profitability of the operations of the company and at the
same time there is a need to improve the sustaniability of the business operations of the
company. A large part of the company operations is still adding to a lot of pollution and
environmental degradation which is an important aspect to be considered and extensive policy
making is needed to mitigate the harmful impacts on the nature and its balance.
8
environment.
People or Social aspect: This dimension is concerned with the impact of a business entity
on the customers or the people. Mercedes-Benz is the leading company when it comes to
customer satisfaction and experience in the industry. The management of the company have a
vision to provide the best quality of products and service to its customers at very competitive
prices. This aspect of business performance of the company is very promising and has high
standards for Mercedes-Benz.
Planet or Environmental aspect: It refers to the impact of business operations on the
environment and ecological balance. Increasing concern of nature and climate change has put the
onus on companies like Mercedes-Benz to decrease the carbon footprints and emission of green-
house gases involved in the production and manufacturing process of the company. However,
there is a huge scope of improvement in the operations of the company when it comes to
sustainability and the impacy on the ecological balance. The management of the company is
recommended to decrease the automated processes which lead to a lot of carbon footprints and
greenhouse gases to improve the sustainability standing of the company.
It can be concluded from the above analysis that management of Mercedes-Benz should
develop a strategy for improving the profitability of the operations of the company and at the
same time there is a need to improve the sustaniability of the business operations of the
company. A large part of the company operations is still adding to a lot of pollution and
environmental degradation which is an important aspect to be considered and extensive policy
making is needed to mitigate the harmful impacts on the nature and its balance.
8
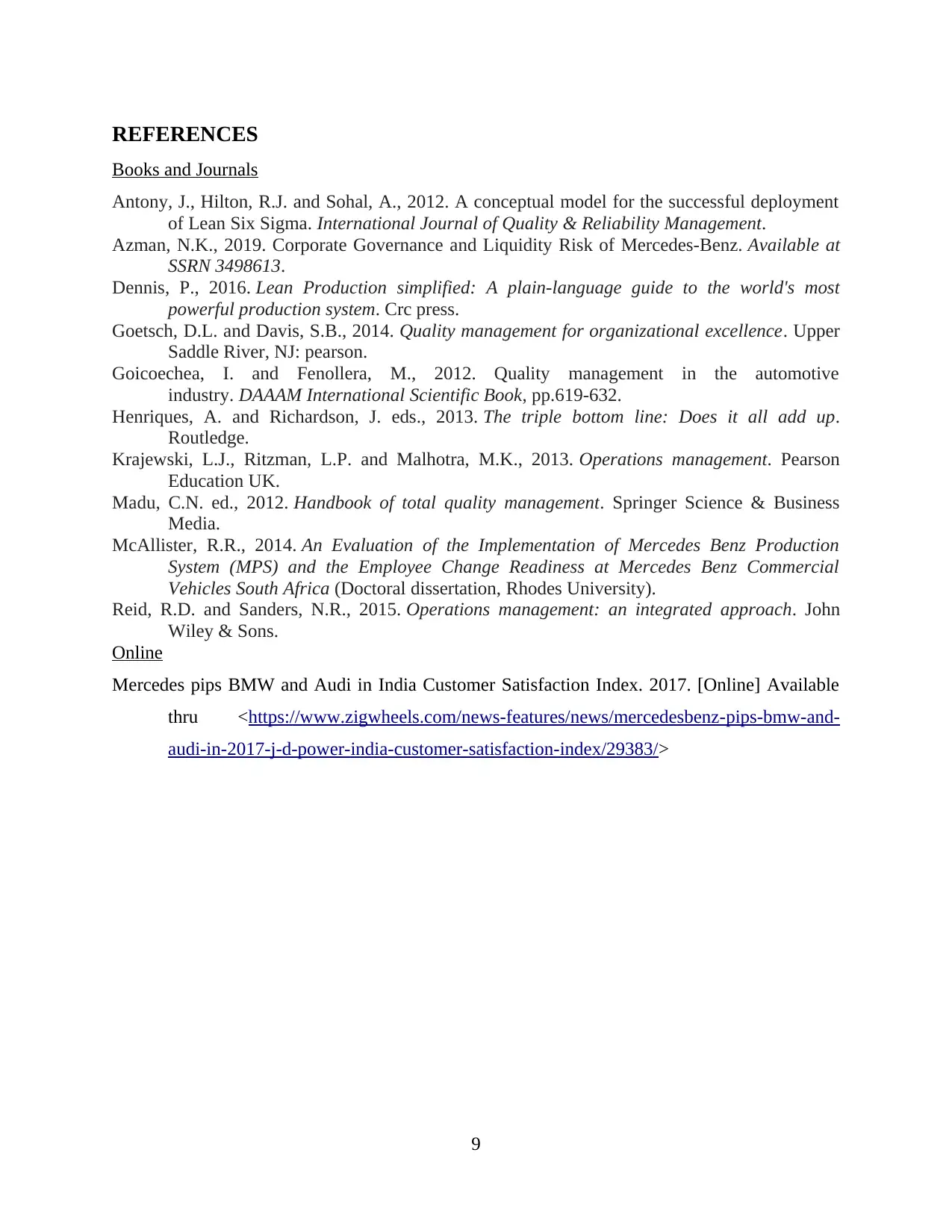
REFERENCES
Books and Journals
Antony, J., Hilton, R.J. and Sohal, A., 2012. A conceptual model for the successful deployment
of Lean Six Sigma. International Journal of Quality & Reliability Management.
Azman, N.K., 2019. Corporate Governance and Liquidity Risk of Mercedes-Benz. Available at
SSRN 3498613.
Dennis, P., 2016. Lean Production simplified: A plain-language guide to the world's most
powerful production system. Crc press.
Goetsch, D.L. and Davis, S.B., 2014. Quality management for organizational excellence. Upper
Saddle River, NJ: pearson.
Goicoechea, I. and Fenollera, M., 2012. Quality management in the automotive
industry. DAAAM International Scientific Book, pp.619-632.
Henriques, A. and Richardson, J. eds., 2013. The triple bottom line: Does it all add up.
Routledge.
Krajewski, L.J., Ritzman, L.P. and Malhotra, M.K., 2013. Operations management. Pearson
Education UK.
Madu, C.N. ed., 2012. Handbook of total quality management. Springer Science & Business
Media.
McAllister, R.R., 2014. An Evaluation of the Implementation of Mercedes Benz Production
System (MPS) and the Employee Change Readiness at Mercedes Benz Commercial
Vehicles South Africa (Doctoral dissertation, Rhodes University).
Reid, R.D. and Sanders, N.R., 2015. Operations management: an integrated approach. John
Wiley & Sons.
Online
Mercedes pips BMW and Audi in India Customer Satisfaction Index. 2017. [Online] Available
thru <https://www.zigwheels.com/news-features/news/mercedesbenz-pips-bmw-and-
audi-in-2017-j-d-power-india-customer-satisfaction-index/29383/>
9
Books and Journals
Antony, J., Hilton, R.J. and Sohal, A., 2012. A conceptual model for the successful deployment
of Lean Six Sigma. International Journal of Quality & Reliability Management.
Azman, N.K., 2019. Corporate Governance and Liquidity Risk of Mercedes-Benz. Available at
SSRN 3498613.
Dennis, P., 2016. Lean Production simplified: A plain-language guide to the world's most
powerful production system. Crc press.
Goetsch, D.L. and Davis, S.B., 2014. Quality management for organizational excellence. Upper
Saddle River, NJ: pearson.
Goicoechea, I. and Fenollera, M., 2012. Quality management in the automotive
industry. DAAAM International Scientific Book, pp.619-632.
Henriques, A. and Richardson, J. eds., 2013. The triple bottom line: Does it all add up.
Routledge.
Krajewski, L.J., Ritzman, L.P. and Malhotra, M.K., 2013. Operations management. Pearson
Education UK.
Madu, C.N. ed., 2012. Handbook of total quality management. Springer Science & Business
Media.
McAllister, R.R., 2014. An Evaluation of the Implementation of Mercedes Benz Production
System (MPS) and the Employee Change Readiness at Mercedes Benz Commercial
Vehicles South Africa (Doctoral dissertation, Rhodes University).
Reid, R.D. and Sanders, N.R., 2015. Operations management: an integrated approach. John
Wiley & Sons.
Online
Mercedes pips BMW and Audi in India Customer Satisfaction Index. 2017. [Online] Available
thru <https://www.zigwheels.com/news-features/news/mercedesbenz-pips-bmw-and-
audi-in-2017-j-d-power-india-customer-satisfaction-index/29383/>
9
1 out of 9
Related Documents
![[object Object]](/_next/image/?url=%2F_next%2Fstatic%2Fmedia%2Flogo.6d15ce61.png&w=640&q=75)
Your All-in-One AI-Powered Toolkit for Academic Success.
+13062052269
info@desklib.com
Available 24*7 on WhatsApp / Email
Unlock your academic potential
© 2024 | Zucol Services PVT LTD | All rights reserved.