Health and Safety Control Equipment in Construction
Added on 2023-01-10
30 Pages11779 Words66 Views
L2 NVQ in Wood Occupations (Construction) QCF
Knowledge Question Paper
Candidate name:
Candidate signature:
Assessor signature:
Date completed:
A/503/1170
QCF641
Conforming to General Health, Safety and Welfare in the Workplace
R
ef
Assessment Criteria Candidate Response
Version 1
June 2020
pg. 1
Knowledge Question Paper
Candidate name:
Candidate signature:
Assessor signature:
Date completed:
A/503/1170
QCF641
Conforming to General Health, Safety and Welfare in the Workplace
R
ef
Assessment Criteria Candidate Response
Version 1
June 2020
pg. 1
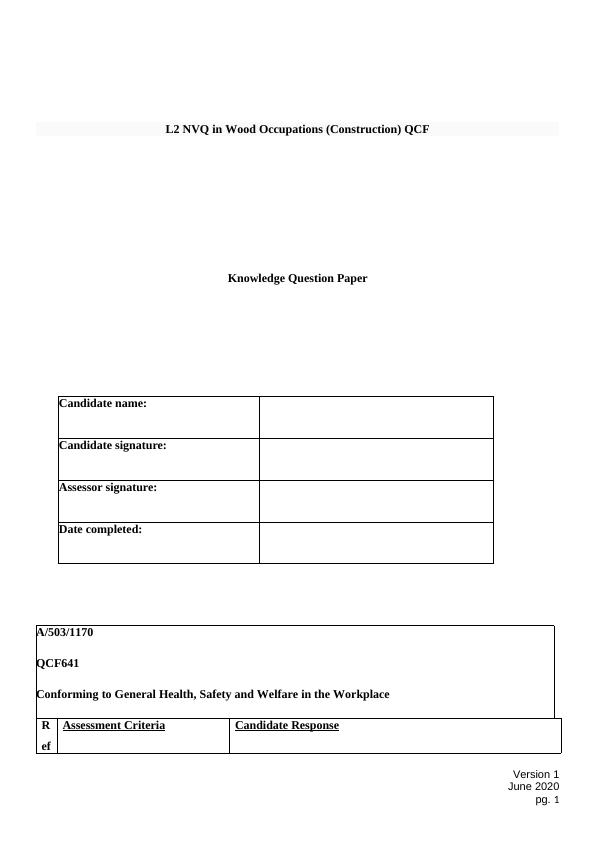
N
o.
1.
4
State why and when health and
safety control equipment,
identified by the principles of
protection, should be used
relating to types, purpose and
limitations of each type, the work
situation, occupational use and
the general work environment, in
relation to:
– collective protective
measures
– personal protective
equipment (PPE)
– respiratory protective
equipment (RPE)
– local exhaust ventilation
(LEV).
In order to ensure the safety and health of workers it is important
that various protective measures must be used so that highest
security and safety of workers is ensured. Some of the effective
measures that can be taken in a construction organisation are:
Collective protective measures: Using warning signs, training
the employees in accordance with usage of tools and equipments,
taking seminars to inform new employees regarding safety
measures, informing about the method to use, use of handrails etc.
The purpose of these measures are to reduce the risks which can
occur at the sites so that safety of workers can be maximised. The
limitations of using this measure can be workers not paying
attention to warning signs and instructions.
PPE: These are the tools which help in protecting an individual
from a hazards like steel toe boots to protect feet from getting
injured, ear defenders to protect ear drums, hard hat to protect
head, goggles to protect eyes, gloves to protect hands from injury
etc.
RPE: Various equipments can be used to prevent respiratory
system from harmful gases and dust like dust masks, self
contained breathing apparatus (SCBA) along with training the
employees so that they can use the equipments efficiently.
LEV: It is an engineering control system which runs on power
and helps in reducing dust, mist, fume, gases etc. which can be
hazardous to the respiratory system.
All the above mentioned measures can help in protecting workers
from any injuries or accident which can occur t the site of work so
that better health conditions can be maintained in organisation.
1.
5
State how the health and safety
control equipment relevant to the
work should be used in
It is important that the health and safety equipments at a
workplace are used as per the given instructions so that the safety
and health of the workers can be ensured. They must also be
Version 1
June 2020
pg. 2
o.
1.
4
State why and when health and
safety control equipment,
identified by the principles of
protection, should be used
relating to types, purpose and
limitations of each type, the work
situation, occupational use and
the general work environment, in
relation to:
– collective protective
measures
– personal protective
equipment (PPE)
– respiratory protective
equipment (RPE)
– local exhaust ventilation
(LEV).
In order to ensure the safety and health of workers it is important
that various protective measures must be used so that highest
security and safety of workers is ensured. Some of the effective
measures that can be taken in a construction organisation are:
Collective protective measures: Using warning signs, training
the employees in accordance with usage of tools and equipments,
taking seminars to inform new employees regarding safety
measures, informing about the method to use, use of handrails etc.
The purpose of these measures are to reduce the risks which can
occur at the sites so that safety of workers can be maximised. The
limitations of using this measure can be workers not paying
attention to warning signs and instructions.
PPE: These are the tools which help in protecting an individual
from a hazards like steel toe boots to protect feet from getting
injured, ear defenders to protect ear drums, hard hat to protect
head, goggles to protect eyes, gloves to protect hands from injury
etc.
RPE: Various equipments can be used to prevent respiratory
system from harmful gases and dust like dust masks, self
contained breathing apparatus (SCBA) along with training the
employees so that they can use the equipments efficiently.
LEV: It is an engineering control system which runs on power
and helps in reducing dust, mist, fume, gases etc. which can be
hazardous to the respiratory system.
All the above mentioned measures can help in protecting workers
from any injuries or accident which can occur t the site of work so
that better health conditions can be maintained in organisation.
1.
5
State how the health and safety
control equipment relevant to the
work should be used in
It is important that the health and safety equipments at a
workplace are used as per the given instructions so that the safety
and health of the workers can be ensured. They must also be
Version 1
June 2020
pg. 2
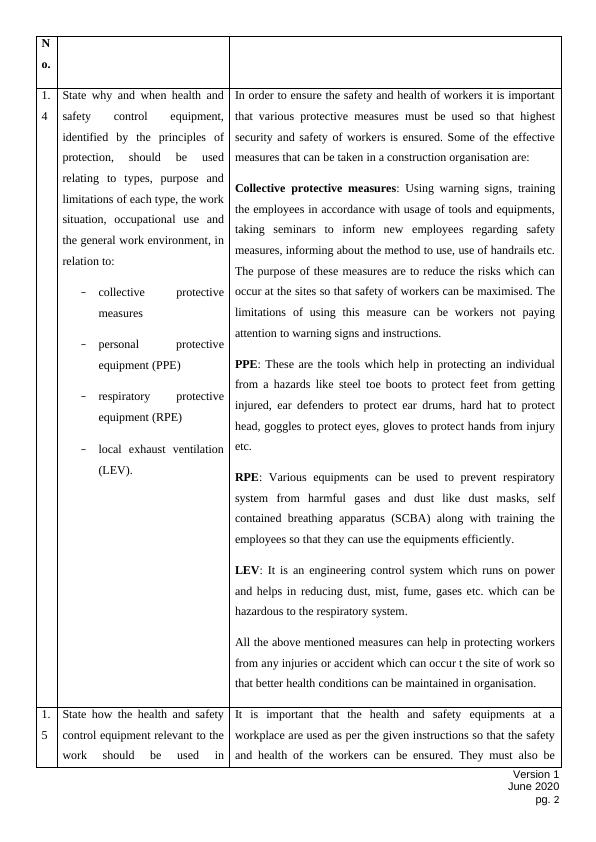
accordance with the given
instructions.
trained regarding the use of these equipments and maintaining the
PPE kits given to them so that they can effectively deal with any
hazardous situations. Also the employees can report any incidence
to their supervisors so that timely corrective actions can be taken,
waste can be disposed off efficiently, switching off lights when
not in use. Should be other measures that can be followed to
ensure high safety and health of the employees. Health and safety
control equipments must be correctly used so that they can
prevent themselves from getting hurt while working on sites from
various types of injuries like head injuries, accidents etc.
1.
6
State which types of health,
safety and welfare legislation,
notices and warning signs are
relevant to the occupational area
and associated equipment.
Various legislations can be followed in construction sites so that
health, safety and welfare at work of the workers can be ensured
like Construction Regulations, 2013, must be implemented in an
organisation so that the safety of workers can be ensured. Use of
warming signs relevant to the sites and hazards associated with
them like mandatory wearing head-gear, eye protection glasses,
shoes etc. It is also important that the equipments related to the
sites must be used so that the workers can be protected from any
unforeseen risks and dangers. It is also important that the workers
are provided with the required equipments so that they can work
efficiently along with reducing the risks.
1.
7
State why health, safety and
welfare legislation, notices and
warning signs are relevant to the
occupational area.
It is important that safety and health legislations are followed
relevant to the occupational area like Health and Safety at Work
etc. Act, 1974, so that the safety of workers can be ensured can
they can use their skills and talents in the most efficient manner so
that the objectives of company can be achieved. It is essential that
workers are provided with clean wash rooms, canteens etc. at the
occupational area so that workers can be prevented from health
issues which can lead to increase in absenteeism in company and
can also lower their capability in achieving company goals on
time. Notices, warning signs, instructions, training etc. must be
provided at the workplace so that any risks can be prevented from
occurring.
Version 1
June 2020
pg. 3
instructions.
trained regarding the use of these equipments and maintaining the
PPE kits given to them so that they can effectively deal with any
hazardous situations. Also the employees can report any incidence
to their supervisors so that timely corrective actions can be taken,
waste can be disposed off efficiently, switching off lights when
not in use. Should be other measures that can be followed to
ensure high safety and health of the employees. Health and safety
control equipments must be correctly used so that they can
prevent themselves from getting hurt while working on sites from
various types of injuries like head injuries, accidents etc.
1.
6
State which types of health,
safety and welfare legislation,
notices and warning signs are
relevant to the occupational area
and associated equipment.
Various legislations can be followed in construction sites so that
health, safety and welfare at work of the workers can be ensured
like Construction Regulations, 2013, must be implemented in an
organisation so that the safety of workers can be ensured. Use of
warming signs relevant to the sites and hazards associated with
them like mandatory wearing head-gear, eye protection glasses,
shoes etc. It is also important that the equipments related to the
sites must be used so that the workers can be protected from any
unforeseen risks and dangers. It is also important that the workers
are provided with the required equipments so that they can work
efficiently along with reducing the risks.
1.
7
State why health, safety and
welfare legislation, notices and
warning signs are relevant to the
occupational area.
It is important that safety and health legislations are followed
relevant to the occupational area like Health and Safety at Work
etc. Act, 1974, so that the safety of workers can be ensured can
they can use their skills and talents in the most efficient manner so
that the objectives of company can be achieved. It is essential that
workers are provided with clean wash rooms, canteens etc. at the
occupational area so that workers can be prevented from health
issues which can lead to increase in absenteeism in company and
can also lower their capability in achieving company goals on
time. Notices, warning signs, instructions, training etc. must be
provided at the workplace so that any risks can be prevented from
occurring.
Version 1
June 2020
pg. 3
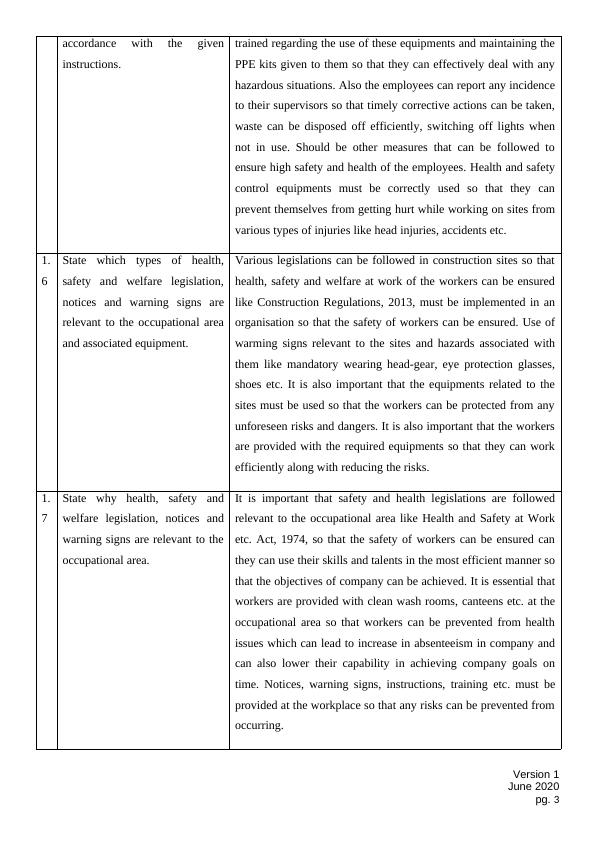
1.
8
State how to comply with control
measures that have been
identified by risk assessments
and safe systems of work.
The risks which have been identified during the risk assessments
needs to be minimised by complying with efficient control
measures so that the risks can be reduced and health and safety of
workers can be ensured. For this following steps can be followed:
Elimination of hazards through re-designing or planning so
that the risks can be minimised like dispose off harmful
chemicals, redesigning the flooring so that even surfaces
can be provided to the workers which can prevent them
from tripping etc.
Substituting hazardous substances with something safe
like using alternatives of solvent based paints, asbestos etc.
Isolating people from areas of risk like putting notices,
warning signs, giving instructions etc.
Using administrative control measures, PPE, engineering
controls etc. so that risks at the workplace can be reduced.
It is important that the control measures are efficiently complied
with which can help in preventing the number of injuries and
accidents at the site of work which can ensure safety of workers.
2.
2
List typical hazards associated
with the work environment and
occupational area in relation to
resources, substances, asbestos,
equipment, obstructions, storage,
services, and work activities.
While working on sites in construction industries, mining
organisations etc. the workers can face various hazards in relation
to the following aspects:
Resources: While working at sites various resources are used by
the workers which must be maintained safely so that safety of
workers can be ensured. Equipments which are too heavy to lift or
which are used in cutting hard materials, equipments poorly
maintained, unavailability or dirty canteens etc. are the ways
which can cause risk to safety of workers.
Substances: Harmful gases, dust from site or sawdust, asbestos
etc. are the substances which can cause respiratory issues among
employees.
Equipments: Noise caused from circular saws or hammer drills
Version 1
June 2020
pg. 4
8
State how to comply with control
measures that have been
identified by risk assessments
and safe systems of work.
The risks which have been identified during the risk assessments
needs to be minimised by complying with efficient control
measures so that the risks can be reduced and health and safety of
workers can be ensured. For this following steps can be followed:
Elimination of hazards through re-designing or planning so
that the risks can be minimised like dispose off harmful
chemicals, redesigning the flooring so that even surfaces
can be provided to the workers which can prevent them
from tripping etc.
Substituting hazardous substances with something safe
like using alternatives of solvent based paints, asbestos etc.
Isolating people from areas of risk like putting notices,
warning signs, giving instructions etc.
Using administrative control measures, PPE, engineering
controls etc. so that risks at the workplace can be reduced.
It is important that the control measures are efficiently complied
with which can help in preventing the number of injuries and
accidents at the site of work which can ensure safety of workers.
2.
2
List typical hazards associated
with the work environment and
occupational area in relation to
resources, substances, asbestos,
equipment, obstructions, storage,
services, and work activities.
While working on sites in construction industries, mining
organisations etc. the workers can face various hazards in relation
to the following aspects:
Resources: While working at sites various resources are used by
the workers which must be maintained safely so that safety of
workers can be ensured. Equipments which are too heavy to lift or
which are used in cutting hard materials, equipments poorly
maintained, unavailability or dirty canteens etc. are the ways
which can cause risk to safety of workers.
Substances: Harmful gases, dust from site or sawdust, asbestos
etc. are the substances which can cause respiratory issues among
employees.
Equipments: Noise caused from circular saws or hammer drills
Version 1
June 2020
pg. 4
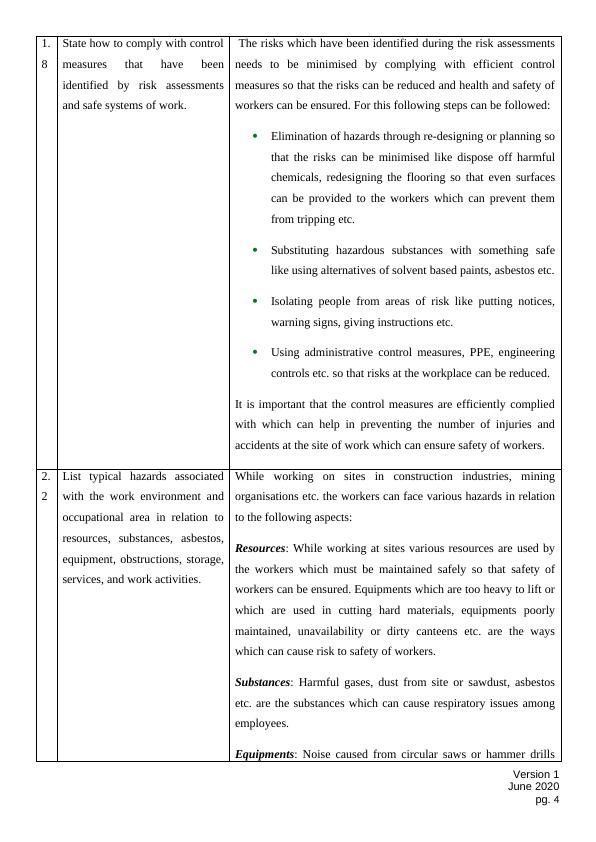
can cause hearing problems, using sharp equipments can cause
injuries etc.
Obstructions: Obstructions like uneven floors can cause falls and
trips, unavailability of proper equipments, ineffective
communication etc. are the obstacles which can affect the health
and safety of workers.
Storage: The sites for storage can be small or located at places
which can cause risks to the health and safety of employees.
Services: While performing various services at the sites like
digging for fountains, drilling walls, removing materials from
sites etc. there are can be risks like electric or gas piping etc.
which can be hazardous.
Work activities: While performing various kinds of work
activities like not using correct lifting technique or equipments,
untidy or uneven workplace, bits of dust or gases going in the eyes
or respiratory systems etc. are various types of hazards.
Thus from above it can be said that the workers at work site can
face various types of hazards and it is important that measures are
taken that can help in preventing such issues so that health and
safety of workers can be maximised.
2.
3
List the current Health and
Safety Executive top ten safety
risks.
There are various safety risks at work like working at height, poor
housekeeping, loose electrical extension cords, forklifts,
chemicals, confined spaces, equipments, lifting weights, sawdust
in eyes or respiratory organs, injuries from using equipments etc.
2.
4
List the current Health and
Safety Executive top five health
risks.
The health risks which can be faced by employees at work are
hearing impairment, breathing issues due to dusty environment,
back pain due to constant sitting position, skin rashes due to
chemicals, vibration of fingers due to using machinery, reduced
well-being, damage to muscles, bones and joints, blood borne
viruses, transmission of diseases like common cold, mental
pressure of workload etc. All these are the issues which are
commonly faced by workers while working on site and must be
Version 1
June 2020
pg. 5
injuries etc.
Obstructions: Obstructions like uneven floors can cause falls and
trips, unavailability of proper equipments, ineffective
communication etc. are the obstacles which can affect the health
and safety of workers.
Storage: The sites for storage can be small or located at places
which can cause risks to the health and safety of employees.
Services: While performing various services at the sites like
digging for fountains, drilling walls, removing materials from
sites etc. there are can be risks like electric or gas piping etc.
which can be hazardous.
Work activities: While performing various kinds of work
activities like not using correct lifting technique or equipments,
untidy or uneven workplace, bits of dust or gases going in the eyes
or respiratory systems etc. are various types of hazards.
Thus from above it can be said that the workers at work site can
face various types of hazards and it is important that measures are
taken that can help in preventing such issues so that health and
safety of workers can be maximised.
2.
3
List the current Health and
Safety Executive top ten safety
risks.
There are various safety risks at work like working at height, poor
housekeeping, loose electrical extension cords, forklifts,
chemicals, confined spaces, equipments, lifting weights, sawdust
in eyes or respiratory organs, injuries from using equipments etc.
2.
4
List the current Health and
Safety Executive top five health
risks.
The health risks which can be faced by employees at work are
hearing impairment, breathing issues due to dusty environment,
back pain due to constant sitting position, skin rashes due to
chemicals, vibration of fingers due to using machinery, reduced
well-being, damage to muscles, bones and joints, blood borne
viruses, transmission of diseases like common cold, mental
pressure of workload etc. All these are the issues which are
commonly faced by workers while working on site and must be
Version 1
June 2020
pg. 5
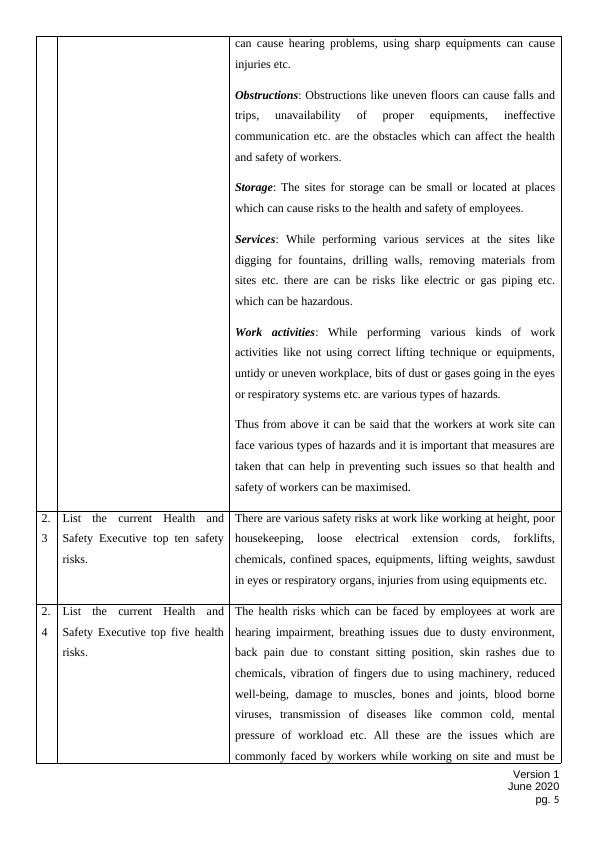
taken care of so that health and safety of workers can be
promoted.
2.
5
State how changing
circumstances within the
workplace could cause hazards.
Due to the changing circumstances there can be various hazards at
the workplace like the employees might face risks due to lack of
knowledge of changes which can impact their safety. It is
important that the employers must inform and update employees
about the change of hazards which change with progress in work.
Also the risk assessments must be regularly done so that
employees can be given knowledge about the risks associated with
work. Changing risks associated with the site must be regularly
informed to the concerned workers so that high safety of workers
can be ensured.
2.
6
State the methods used for
reporting changed circumstances,
hazards, and incidents in the
workplace.
There are various methods which can be used so as to report the
changed circumstances or risks or hazards at a workplace:
Updating risk assessments: It is important that the risks
are regularly assessed so that the employees can be
updated regarding change in risks so that effective
precautions can be taken.
Toolbox talks: It is related with giving information to the
workers on using toolbox so that the equipments can be
used with safety.
Site meetings: Meetings on a regular basis can be
conducted so that the workers can be given information
regarding the change in risks, circumstances etc.
Change in circumstances are important to be informed so that the
workers can be prepared for the associated risks and can take
effective measures so that hazards can be controlled and safety
can be promoted.
3.
6
State the organisational policies
and procedures for health, safety,
and welfare, in relation to:
It is essential that certain policies and procedures should be
applied in the company at the site of work so that workers can be
efficiently protected from hazards and their safety can be ensured:
Version 1
June 2020
pg. 6
promoted.
2.
5
State how changing
circumstances within the
workplace could cause hazards.
Due to the changing circumstances there can be various hazards at
the workplace like the employees might face risks due to lack of
knowledge of changes which can impact their safety. It is
important that the employers must inform and update employees
about the change of hazards which change with progress in work.
Also the risk assessments must be regularly done so that
employees can be given knowledge about the risks associated with
work. Changing risks associated with the site must be regularly
informed to the concerned workers so that high safety of workers
can be ensured.
2.
6
State the methods used for
reporting changed circumstances,
hazards, and incidents in the
workplace.
There are various methods which can be used so as to report the
changed circumstances or risks or hazards at a workplace:
Updating risk assessments: It is important that the risks
are regularly assessed so that the employees can be
updated regarding change in risks so that effective
precautions can be taken.
Toolbox talks: It is related with giving information to the
workers on using toolbox so that the equipments can be
used with safety.
Site meetings: Meetings on a regular basis can be
conducted so that the workers can be given information
regarding the change in risks, circumstances etc.
Change in circumstances are important to be informed so that the
workers can be prepared for the associated risks and can take
effective measures so that hazards can be controlled and safety
can be promoted.
3.
6
State the organisational policies
and procedures for health, safety,
and welfare, in relation to:
It is essential that certain policies and procedures should be
applied in the company at the site of work so that workers can be
efficiently protected from hazards and their safety can be ensured:
Version 1
June 2020
pg. 6
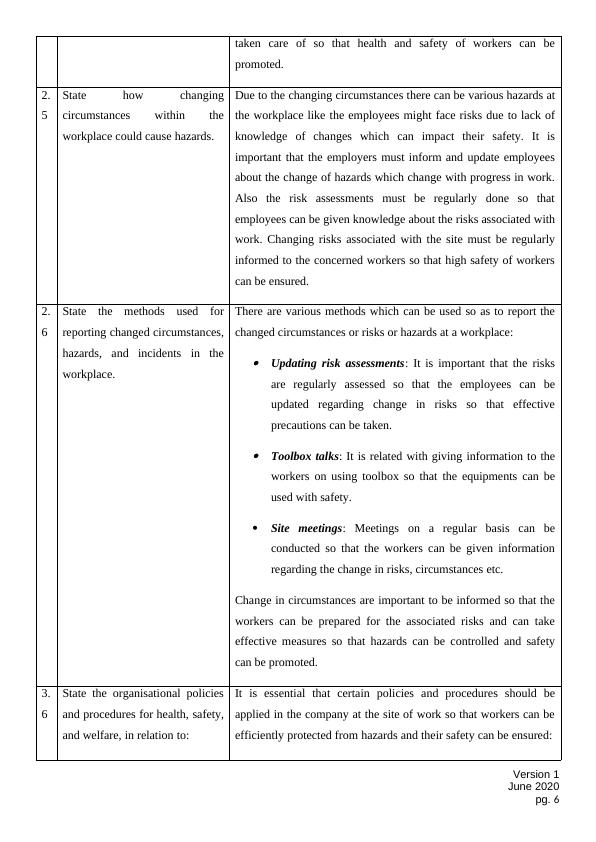
End of preview
Want to access all the pages? Upload your documents or become a member.
Related Documents
Health and Safety Control Measures in Wood Occupationslg...
|33
|10795
|55
Health and Safety Control Measures in Wood Occupationslg...
|25
|9222
|92
L2 NVQ in Wood Occupations (Construction) QCF - Knowledge Question Paperlg...
|23
|9379
|23
Conforming to General Health, Safety and Welfare in the Workplacelg...
|23
|9450
|76
L2 NVQ in Wood Occupations (Construction) QCF - Knowledge Question Paperlg...
|19
|8951
|78
L2 NVQ in Wood Occupations (Construction) QCF - Knowledge Question Paperlg...
|18
|9448
|51