Operational Functions and Supply Chain Management: A Case Study of Woolworth
VerifiedAdded on 2023/06/17
|12
|3740
|433
AI Summary
This study analyzes the operational functions and supply chain management of Woolworth, a leading Australian supermarket chain. It discusses the role of operational strategy in achieving organizational goals and examines the impact of six sigma on product and service quality. The study also evaluates the supply chain processes of Woolworth and provides recommendations for improvement.
Contribute Materials
Your contribution can guide someone’s learning journey. Share your
documents today.
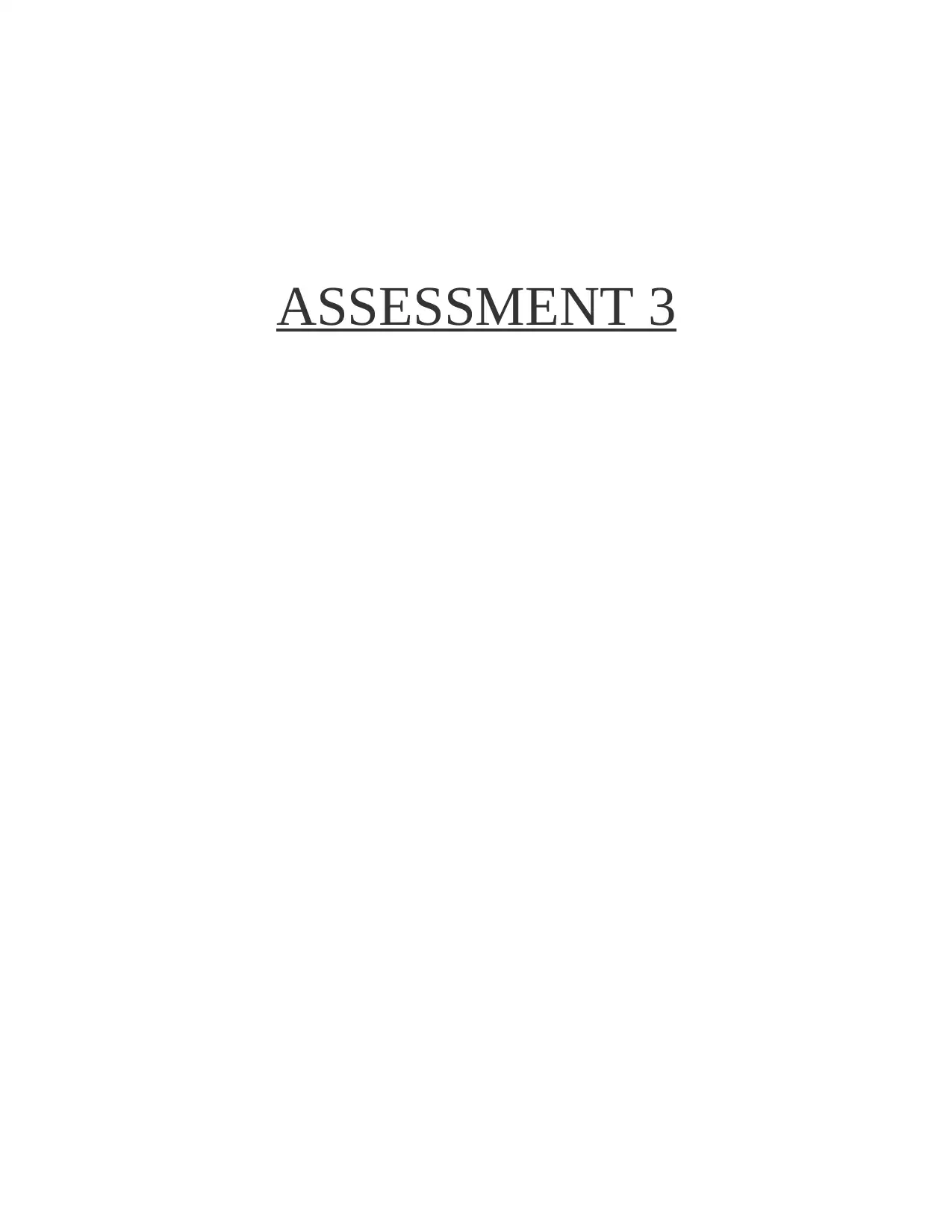
ASSESSMENT 3
Secure Best Marks with AI Grader
Need help grading? Try our AI Grader for instant feedback on your assignments.
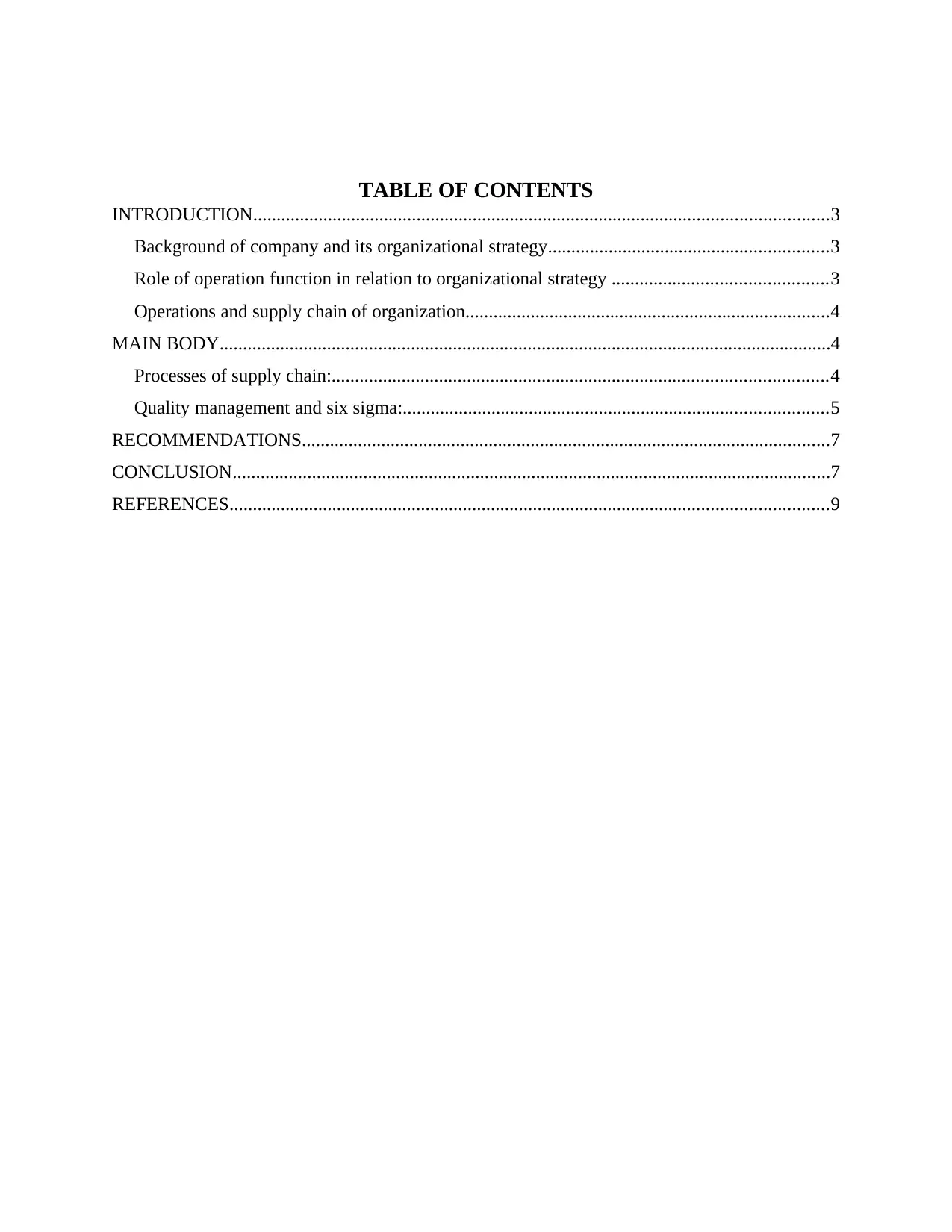
TABLE OF CONTENTS
INTRODUCTION...........................................................................................................................3
Background of company and its organizational strategy............................................................3
Role of operation function in relation to organizational strategy ..............................................3
Operations and supply chain of organization..............................................................................4
MAIN BODY...................................................................................................................................4
Processes of supply chain:..........................................................................................................4
Quality management and six sigma:...........................................................................................5
RECOMMENDATIONS.................................................................................................................7
CONCLUSION................................................................................................................................7
REFERENCES................................................................................................................................9
INTRODUCTION...........................................................................................................................3
Background of company and its organizational strategy............................................................3
Role of operation function in relation to organizational strategy ..............................................3
Operations and supply chain of organization..............................................................................4
MAIN BODY...................................................................................................................................4
Processes of supply chain:..........................................................................................................4
Quality management and six sigma:...........................................................................................5
RECOMMENDATIONS.................................................................................................................7
CONCLUSION................................................................................................................................7
REFERENCES................................................................................................................................9
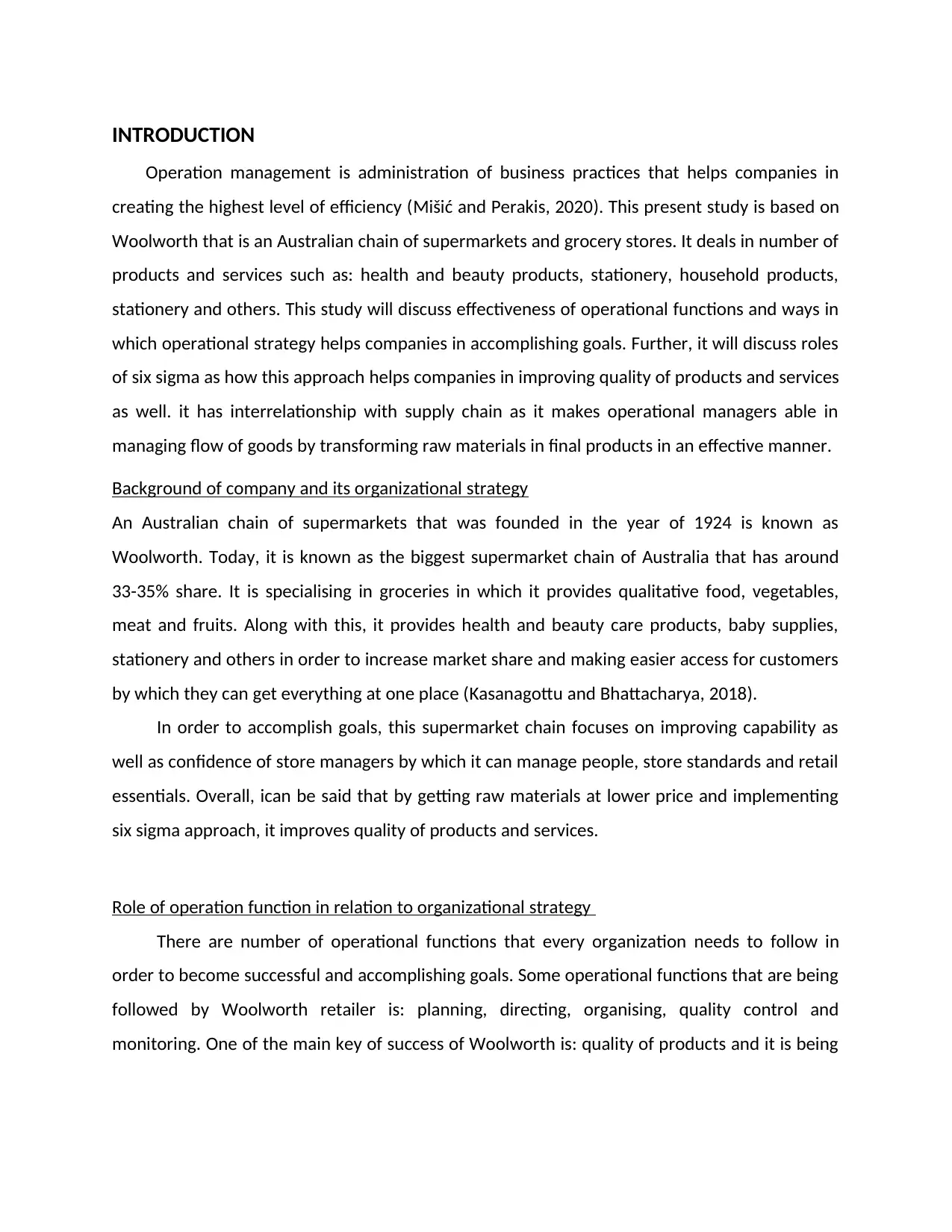
INTRODUCTION
Operation management is administration of business practices that helps companies in
creating the highest level of efficiency (Mišić and Perakis, 2020). This present study is based on
Woolworth that is an Australian chain of supermarkets and grocery stores. It deals in number of
products and services such as: health and beauty products, stationery, household products,
stationery and others. This study will discuss effectiveness of operational functions and ways in
which operational strategy helps companies in accomplishing goals. Further, it will discuss roles
of six sigma as how this approach helps companies in improving quality of products and services
as well. it has interrelationship with supply chain as it makes operational managers able in
managing flow of goods by transforming raw materials in final products in an effective manner.
Background of company and its organizational strategy
An Australian chain of supermarkets that was founded in the year of 1924 is known as
Woolworth. Today, it is known as the biggest supermarket chain of Australia that has around
33-35% share. It is specialising in groceries in which it provides qualitative food, vegetables,
meat and fruits. Along with this, it provides health and beauty care products, baby supplies,
stationery and others in order to increase market share and making easier access for customers
by which they can get everything at one place (Kasanagottu and Bhattacharya, 2018).
In order to accomplish goals, this supermarket chain focuses on improving capability as
well as confidence of store managers by which it can manage people, store standards and retail
essentials. Overall, ican be said that by getting raw materials at lower price and implementing
six sigma approach, it improves quality of products and services.
Role of operation function in relation to organizational strategy
There are number of operational functions that every organization needs to follow in
order to become successful and accomplishing goals. Some operational functions that are being
followed by Woolworth retailer is: planning, directing, organising, quality control and
monitoring. One of the main key of success of Woolworth is: quality of products and it is being
Operation management is administration of business practices that helps companies in
creating the highest level of efficiency (Mišić and Perakis, 2020). This present study is based on
Woolworth that is an Australian chain of supermarkets and grocery stores. It deals in number of
products and services such as: health and beauty products, stationery, household products,
stationery and others. This study will discuss effectiveness of operational functions and ways in
which operational strategy helps companies in accomplishing goals. Further, it will discuss roles
of six sigma as how this approach helps companies in improving quality of products and services
as well. it has interrelationship with supply chain as it makes operational managers able in
managing flow of goods by transforming raw materials in final products in an effective manner.
Background of company and its organizational strategy
An Australian chain of supermarkets that was founded in the year of 1924 is known as
Woolworth. Today, it is known as the biggest supermarket chain of Australia that has around
33-35% share. It is specialising in groceries in which it provides qualitative food, vegetables,
meat and fruits. Along with this, it provides health and beauty care products, baby supplies,
stationery and others in order to increase market share and making easier access for customers
by which they can get everything at one place (Kasanagottu and Bhattacharya, 2018).
In order to accomplish goals, this supermarket chain focuses on improving capability as
well as confidence of store managers by which it can manage people, store standards and retail
essentials. Overall, ican be said that by getting raw materials at lower price and implementing
six sigma approach, it improves quality of products and services.
Role of operation function in relation to organizational strategy
There are number of operational functions that every organization needs to follow in
order to become successful and accomplishing goals. Some operational functions that are being
followed by Woolworth retailer is: planning, directing, organising, quality control and
monitoring. One of the main key of success of Woolworth is: quality of products and it is being
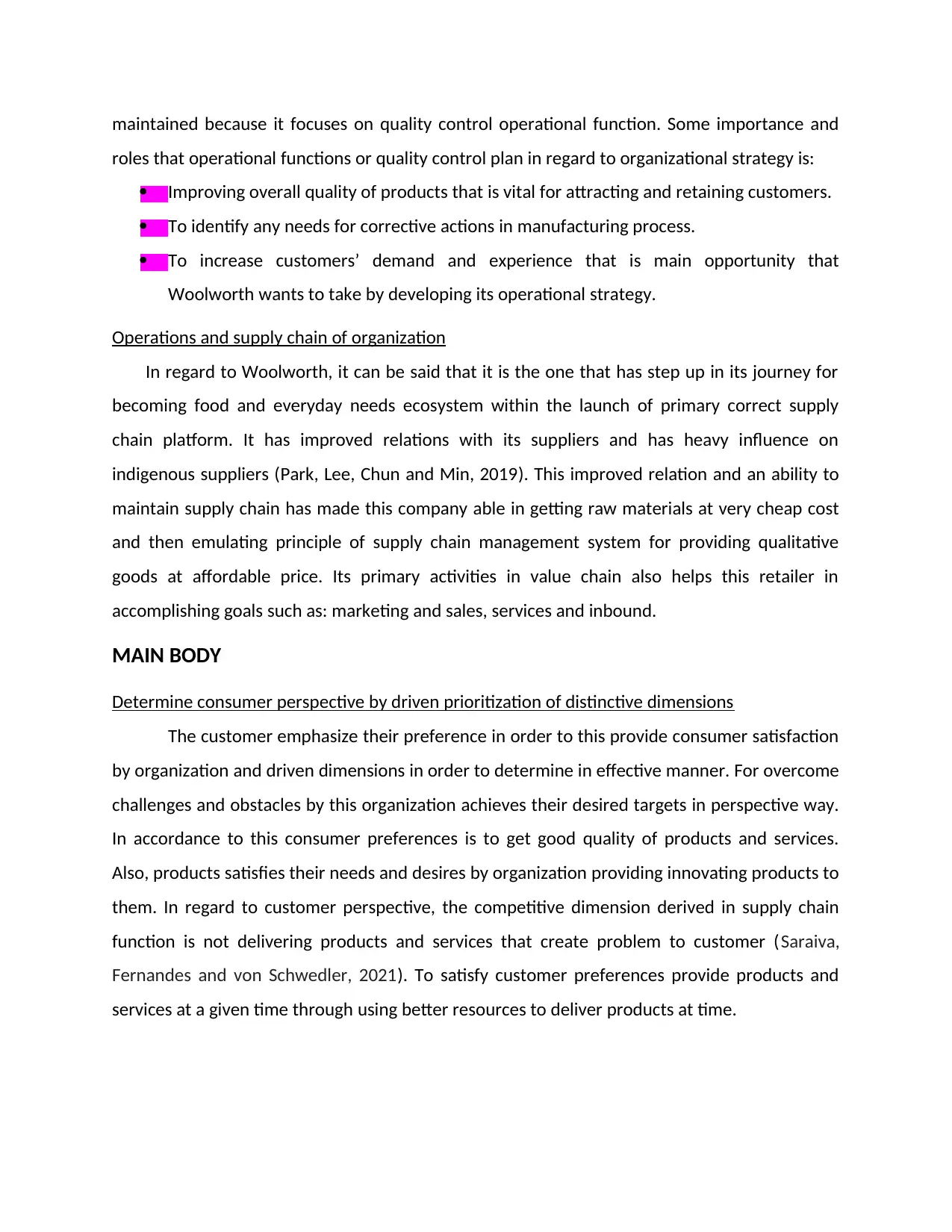
maintained because it focuses on quality control operational function. Some importance and
roles that operational functions or quality control plan in regard to organizational strategy is:
Improving overall quality of products that is vital for attracting and retaining customers.
To identify any needs for corrective actions in manufacturing process.
To increase customers’ demand and experience that is main opportunity that
Woolworth wants to take by developing its operational strategy.
Operations and supply chain of organization
In regard to Woolworth, it can be said that it is the one that has step up in its journey for
becoming food and everyday needs ecosystem within the launch of primary correct supply
chain platform. It has improved relations with its suppliers and has heavy influence on
indigenous suppliers (Park, Lee, Chun and Min, 2019). This improved relation and an ability to
maintain supply chain has made this company able in getting raw materials at very cheap cost
and then emulating principle of supply chain management system for providing qualitative
goods at affordable price. Its primary activities in value chain also helps this retailer in
accomplishing goals such as: marketing and sales, services and inbound.
MAIN BODY
Determine consumer perspective by driven prioritization of distinctive dimensions
The customer emphasize their preference in order to this provide consumer satisfaction
by organization and driven dimensions in order to determine in effective manner. For overcome
challenges and obstacles by this organization achieves their desired targets in perspective way.
In accordance to this consumer preferences is to get good quality of products and services.
Also, products satisfies their needs and desires by organization providing innovating products to
them. In regard to customer perspective, the competitive dimension derived in supply chain
function is not delivering products and services that create problem to customer (Saraiva,
Fernandes and von Schwedler, 2021). To satisfy customer preferences provide products and
services at a given time through using better resources to deliver products at time.
roles that operational functions or quality control plan in regard to organizational strategy is:
Improving overall quality of products that is vital for attracting and retaining customers.
To identify any needs for corrective actions in manufacturing process.
To increase customers’ demand and experience that is main opportunity that
Woolworth wants to take by developing its operational strategy.
Operations and supply chain of organization
In regard to Woolworth, it can be said that it is the one that has step up in its journey for
becoming food and everyday needs ecosystem within the launch of primary correct supply
chain platform. It has improved relations with its suppliers and has heavy influence on
indigenous suppliers (Park, Lee, Chun and Min, 2019). This improved relation and an ability to
maintain supply chain has made this company able in getting raw materials at very cheap cost
and then emulating principle of supply chain management system for providing qualitative
goods at affordable price. Its primary activities in value chain also helps this retailer in
accomplishing goals such as: marketing and sales, services and inbound.
MAIN BODY
Determine consumer perspective by driven prioritization of distinctive dimensions
The customer emphasize their preference in order to this provide consumer satisfaction
by organization and driven dimensions in order to determine in effective manner. For overcome
challenges and obstacles by this organization achieves their desired targets in perspective way.
In accordance to this consumer preferences is to get good quality of products and services.
Also, products satisfies their needs and desires by organization providing innovating products to
them. In regard to customer perspective, the competitive dimension derived in supply chain
function is not delivering products and services that create problem to customer (Saraiva,
Fernandes and von Schwedler, 2021). To satisfy customer preferences provide products and
services at a given time through using better resources to deliver products at time.
Secure Best Marks with AI Grader
Need help grading? Try our AI Grader for instant feedback on your assignments.
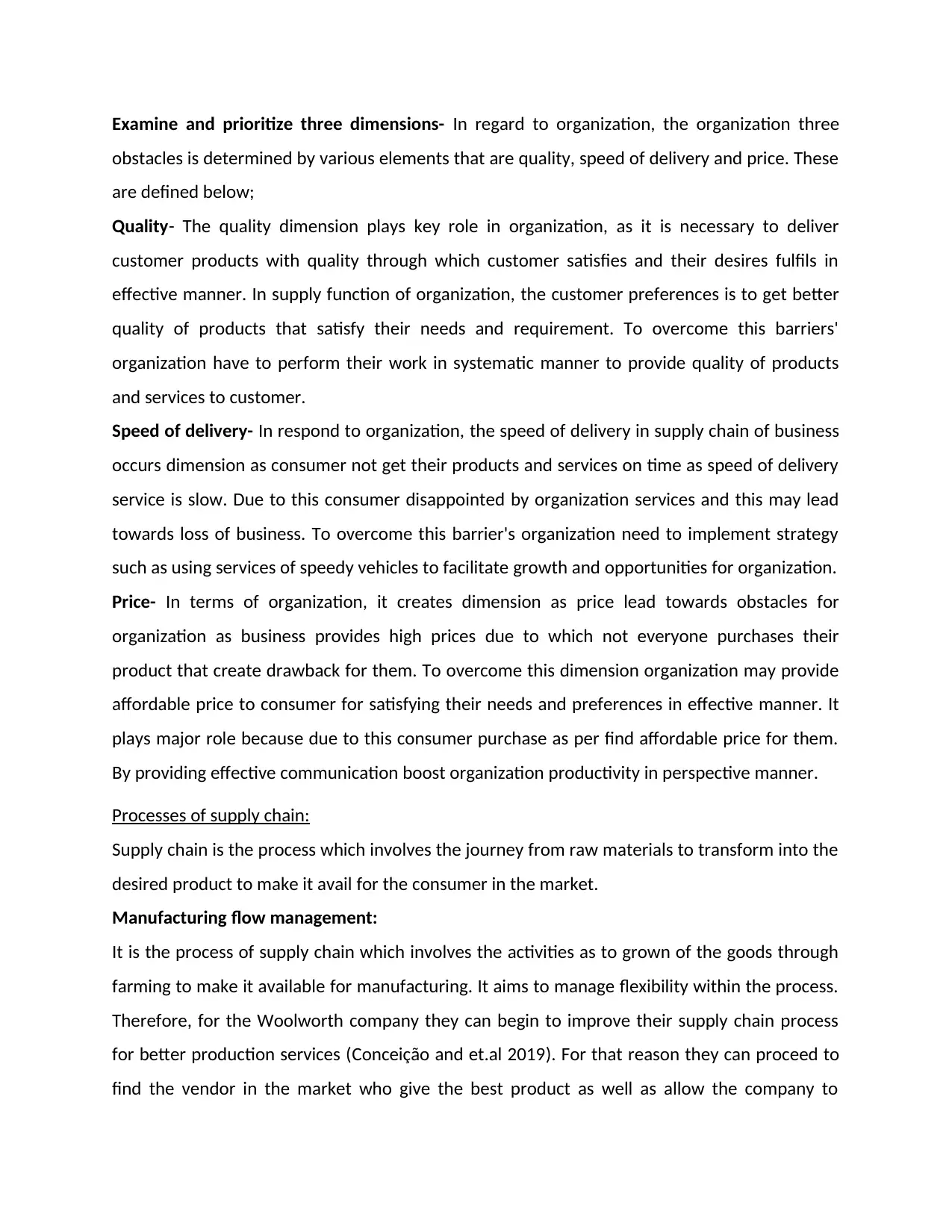
Examine and prioritize three dimensions- In regard to organization, the organization three
obstacles is determined by various elements that are quality, speed of delivery and price. These
are defined below;
Quality- The quality dimension plays key role in organization, as it is necessary to deliver
customer products with quality through which customer satisfies and their desires fulfils in
effective manner. In supply function of organization, the customer preferences is to get better
quality of products that satisfy their needs and requirement. To overcome this barriers'
organization have to perform their work in systematic manner to provide quality of products
and services to customer.
Speed of delivery- In respond to organization, the speed of delivery in supply chain of business
occurs dimension as consumer not get their products and services on time as speed of delivery
service is slow. Due to this consumer disappointed by organization services and this may lead
towards loss of business. To overcome this barrier's organization need to implement strategy
such as using services of speedy vehicles to facilitate growth and opportunities for organization.
Price- In terms of organization, it creates dimension as price lead towards obstacles for
organization as business provides high prices due to which not everyone purchases their
product that create drawback for them. To overcome this dimension organization may provide
affordable price to consumer for satisfying their needs and preferences in effective manner. It
plays major role because due to this consumer purchase as per find affordable price for them.
By providing effective communication boost organization productivity in perspective manner.
Processes of supply chain:
Supply chain is the process which involves the journey from raw materials to transform into the
desired product to make it avail for the consumer in the market.
Manufacturing flow management:
It is the process of supply chain which involves the activities as to grown of the goods through
farming to make it available for manufacturing. It aims to manage flexibility within the process.
Therefore, for the Woolworth company they can begin to improve their supply chain process
for better production services (Conceição and et.al 2019). For that reason they can proceed to
find the vendor in the market who give the best product as well as allow the company to
obstacles is determined by various elements that are quality, speed of delivery and price. These
are defined below;
Quality- The quality dimension plays key role in organization, as it is necessary to deliver
customer products with quality through which customer satisfies and their desires fulfils in
effective manner. In supply function of organization, the customer preferences is to get better
quality of products that satisfy their needs and requirement. To overcome this barriers'
organization have to perform their work in systematic manner to provide quality of products
and services to customer.
Speed of delivery- In respond to organization, the speed of delivery in supply chain of business
occurs dimension as consumer not get their products and services on time as speed of delivery
service is slow. Due to this consumer disappointed by organization services and this may lead
towards loss of business. To overcome this barrier's organization need to implement strategy
such as using services of speedy vehicles to facilitate growth and opportunities for organization.
Price- In terms of organization, it creates dimension as price lead towards obstacles for
organization as business provides high prices due to which not everyone purchases their
product that create drawback for them. To overcome this dimension organization may provide
affordable price to consumer for satisfying their needs and preferences in effective manner. It
plays major role because due to this consumer purchase as per find affordable price for them.
By providing effective communication boost organization productivity in perspective manner.
Processes of supply chain:
Supply chain is the process which involves the journey from raw materials to transform into the
desired product to make it avail for the consumer in the market.
Manufacturing flow management:
It is the process of supply chain which involves the activities as to grown of the goods through
farming to make it available for manufacturing. It aims to manage flexibility within the process.
Therefore, for the Woolworth company they can begin to improve their supply chain process
for better production services (Conceição and et.al 2019). For that reason they can proceed to
find the vendor in the market who give the best product as well as allow the company to
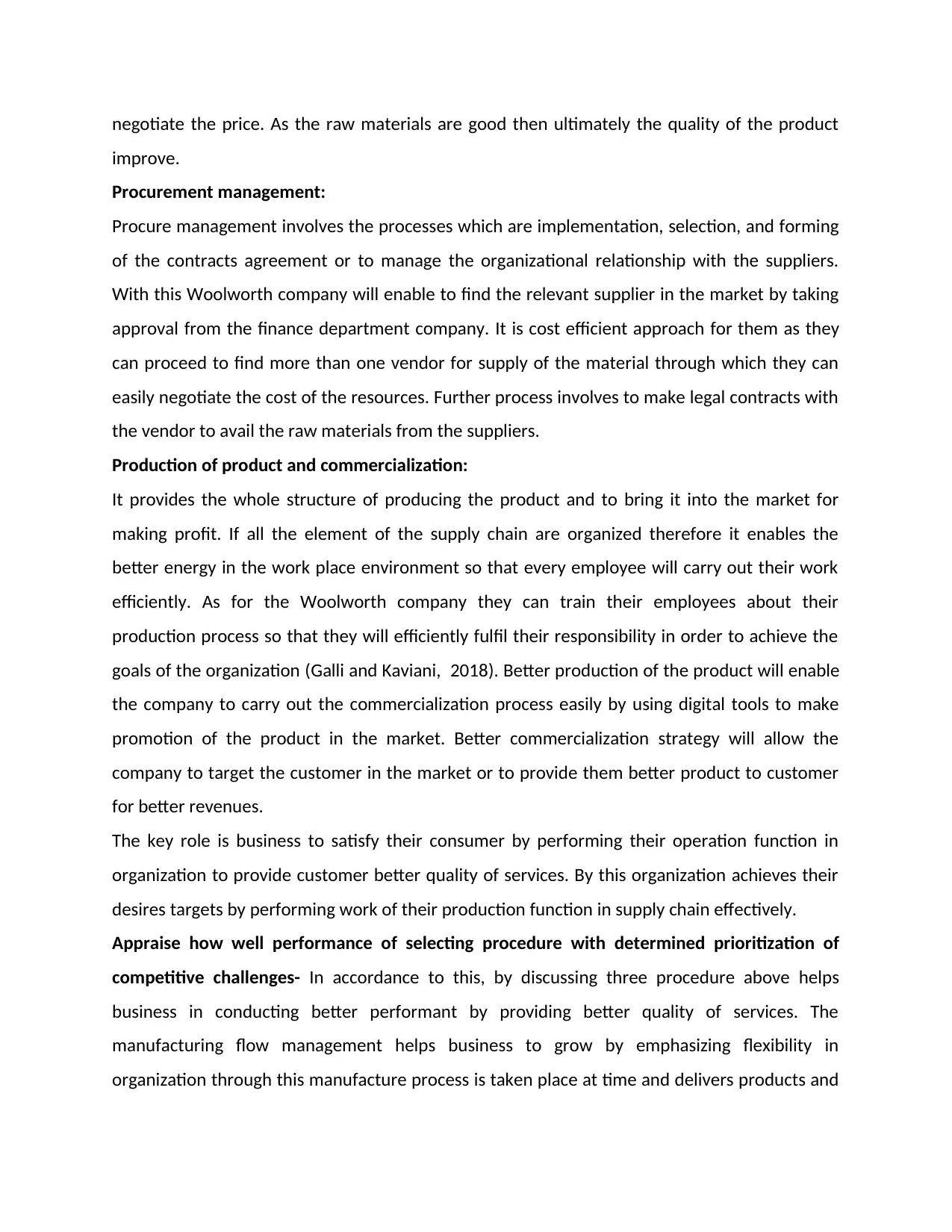
negotiate the price. As the raw materials are good then ultimately the quality of the product
improve.
Procurement management:
Procure management involves the processes which are implementation, selection, and forming
of the contracts agreement or to manage the organizational relationship with the suppliers.
With this Woolworth company will enable to find the relevant supplier in the market by taking
approval from the finance department company. It is cost efficient approach for them as they
can proceed to find more than one vendor for supply of the material through which they can
easily negotiate the cost of the resources. Further process involves to make legal contracts with
the vendor to avail the raw materials from the suppliers.
Production of product and commercialization:
It provides the whole structure of producing the product and to bring it into the market for
making profit. If all the element of the supply chain are organized therefore it enables the
better energy in the work place environment so that every employee will carry out their work
efficiently. As for the Woolworth company they can train their employees about their
production process so that they will efficiently fulfil their responsibility in order to achieve the
goals of the organization (Galli and Kaviani, 2018). Better production of the product will enable
the company to carry out the commercialization process easily by using digital tools to make
promotion of the product in the market. Better commercialization strategy will allow the
company to target the customer in the market or to provide them better product to customer
for better revenues.
The key role is business to satisfy their consumer by performing their operation function in
organization to provide customer better quality of services. By this organization achieves their
desires targets by performing work of their production function in supply chain effectively.
Appraise how well performance of selecting procedure with determined prioritization of
competitive challenges- In accordance to this, by discussing three procedure above helps
business in conducting better performant by providing better quality of services. The
manufacturing flow management helps business to grow by emphasizing flexibility in
organization through this manufacture process is taken place at time and delivers products and
improve.
Procurement management:
Procure management involves the processes which are implementation, selection, and forming
of the contracts agreement or to manage the organizational relationship with the suppliers.
With this Woolworth company will enable to find the relevant supplier in the market by taking
approval from the finance department company. It is cost efficient approach for them as they
can proceed to find more than one vendor for supply of the material through which they can
easily negotiate the cost of the resources. Further process involves to make legal contracts with
the vendor to avail the raw materials from the suppliers.
Production of product and commercialization:
It provides the whole structure of producing the product and to bring it into the market for
making profit. If all the element of the supply chain are organized therefore it enables the
better energy in the work place environment so that every employee will carry out their work
efficiently. As for the Woolworth company they can train their employees about their
production process so that they will efficiently fulfil their responsibility in order to achieve the
goals of the organization (Galli and Kaviani, 2018). Better production of the product will enable
the company to carry out the commercialization process easily by using digital tools to make
promotion of the product in the market. Better commercialization strategy will allow the
company to target the customer in the market or to provide them better product to customer
for better revenues.
The key role is business to satisfy their consumer by performing their operation function in
organization to provide customer better quality of services. By this organization achieves their
desires targets by performing work of their production function in supply chain effectively.
Appraise how well performance of selecting procedure with determined prioritization of
competitive challenges- In accordance to this, by discussing three procedure above helps
business in conducting better performant by providing better quality of services. The
manufacturing flow management helps business to grow by emphasizing flexibility in
organization through this manufacture process is taken place at time and delivers products and
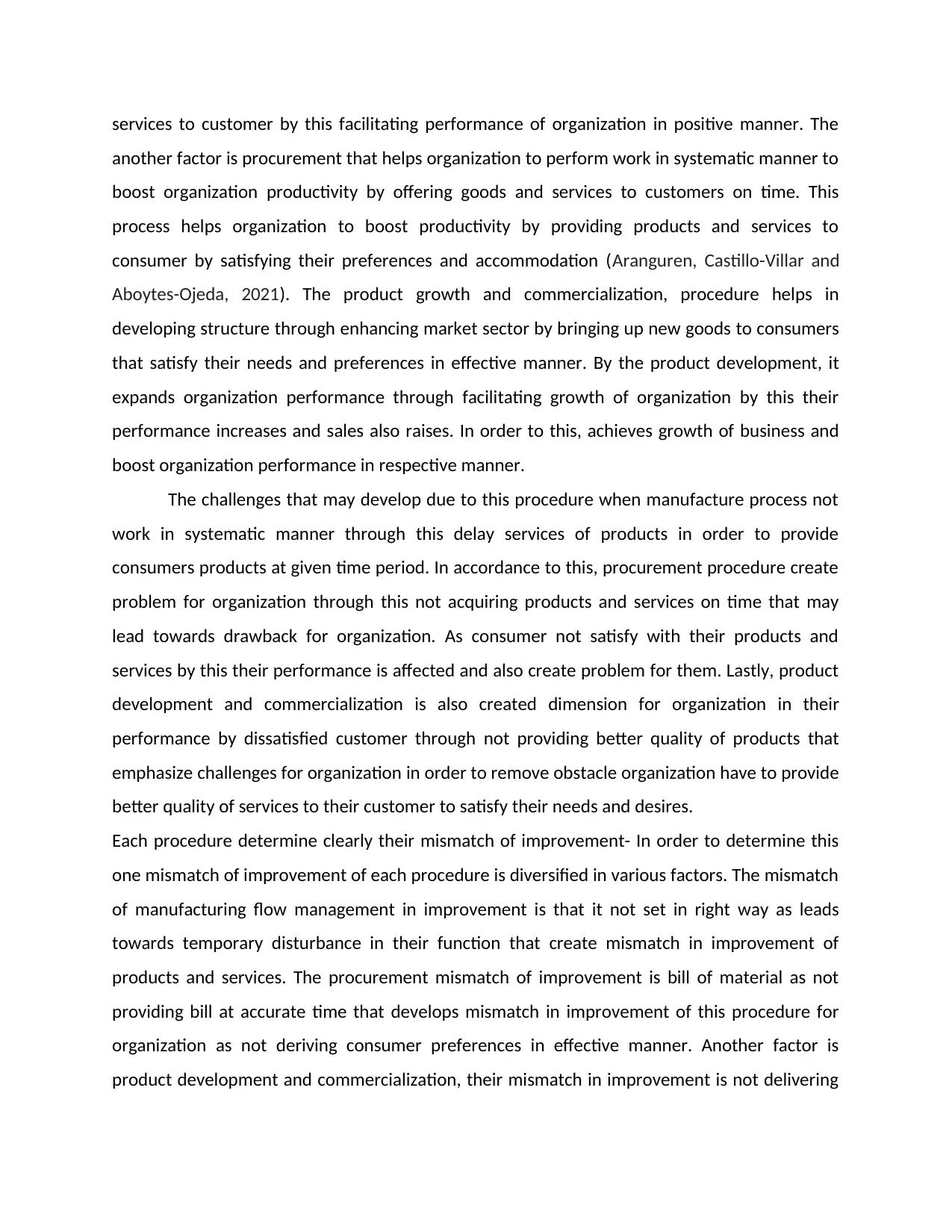
services to customer by this facilitating performance of organization in positive manner. The
another factor is procurement that helps organization to perform work in systematic manner to
boost organization productivity by offering goods and services to customers on time. This
process helps organization to boost productivity by providing products and services to
consumer by satisfying their preferences and accommodation (Aranguren, Castillo-Villar and
Aboytes-Ojeda, 2021). The product growth and commercialization, procedure helps in
developing structure through enhancing market sector by bringing up new goods to consumers
that satisfy their needs and preferences in effective manner. By the product development, it
expands organization performance through facilitating growth of organization by this their
performance increases and sales also raises. In order to this, achieves growth of business and
boost organization performance in respective manner.
The challenges that may develop due to this procedure when manufacture process not
work in systematic manner through this delay services of products in order to provide
consumers products at given time period. In accordance to this, procurement procedure create
problem for organization through this not acquiring products and services on time that may
lead towards drawback for organization. As consumer not satisfy with their products and
services by this their performance is affected and also create problem for them. Lastly, product
development and commercialization is also created dimension for organization in their
performance by dissatisfied customer through not providing better quality of products that
emphasize challenges for organization in order to remove obstacle organization have to provide
better quality of services to their customer to satisfy their needs and desires.
Each procedure determine clearly their mismatch of improvement- In order to determine this
one mismatch of improvement of each procedure is diversified in various factors. The mismatch
of manufacturing flow management in improvement is that it not set in right way as leads
towards temporary disturbance in their function that create mismatch in improvement of
products and services. The procurement mismatch of improvement is bill of material as not
providing bill at accurate time that develops mismatch in improvement of this procedure for
organization as not deriving consumer preferences in effective manner. Another factor is
product development and commercialization, their mismatch in improvement is not delivering
another factor is procurement that helps organization to perform work in systematic manner to
boost organization productivity by offering goods and services to customers on time. This
process helps organization to boost productivity by providing products and services to
consumer by satisfying their preferences and accommodation (Aranguren, Castillo-Villar and
Aboytes-Ojeda, 2021). The product growth and commercialization, procedure helps in
developing structure through enhancing market sector by bringing up new goods to consumers
that satisfy their needs and preferences in effective manner. By the product development, it
expands organization performance through facilitating growth of organization by this their
performance increases and sales also raises. In order to this, achieves growth of business and
boost organization performance in respective manner.
The challenges that may develop due to this procedure when manufacture process not
work in systematic manner through this delay services of products in order to provide
consumers products at given time period. In accordance to this, procurement procedure create
problem for organization through this not acquiring products and services on time that may
lead towards drawback for organization. As consumer not satisfy with their products and
services by this their performance is affected and also create problem for them. Lastly, product
development and commercialization is also created dimension for organization in their
performance by dissatisfied customer through not providing better quality of products that
emphasize challenges for organization in order to remove obstacle organization have to provide
better quality of services to their customer to satisfy their needs and desires.
Each procedure determine clearly their mismatch of improvement- In order to determine this
one mismatch of improvement of each procedure is diversified in various factors. The mismatch
of manufacturing flow management in improvement is that it not set in right way as leads
towards temporary disturbance in their function that create mismatch in improvement of
products and services. The procurement mismatch of improvement is bill of material as not
providing bill at accurate time that develops mismatch in improvement of this procedure for
organization as not deriving consumer preferences in effective manner. Another factor is
product development and commercialization, their mismatch in improvement is not delivering
Paraphrase This Document
Need a fresh take? Get an instant paraphrase of this document with our AI Paraphraser
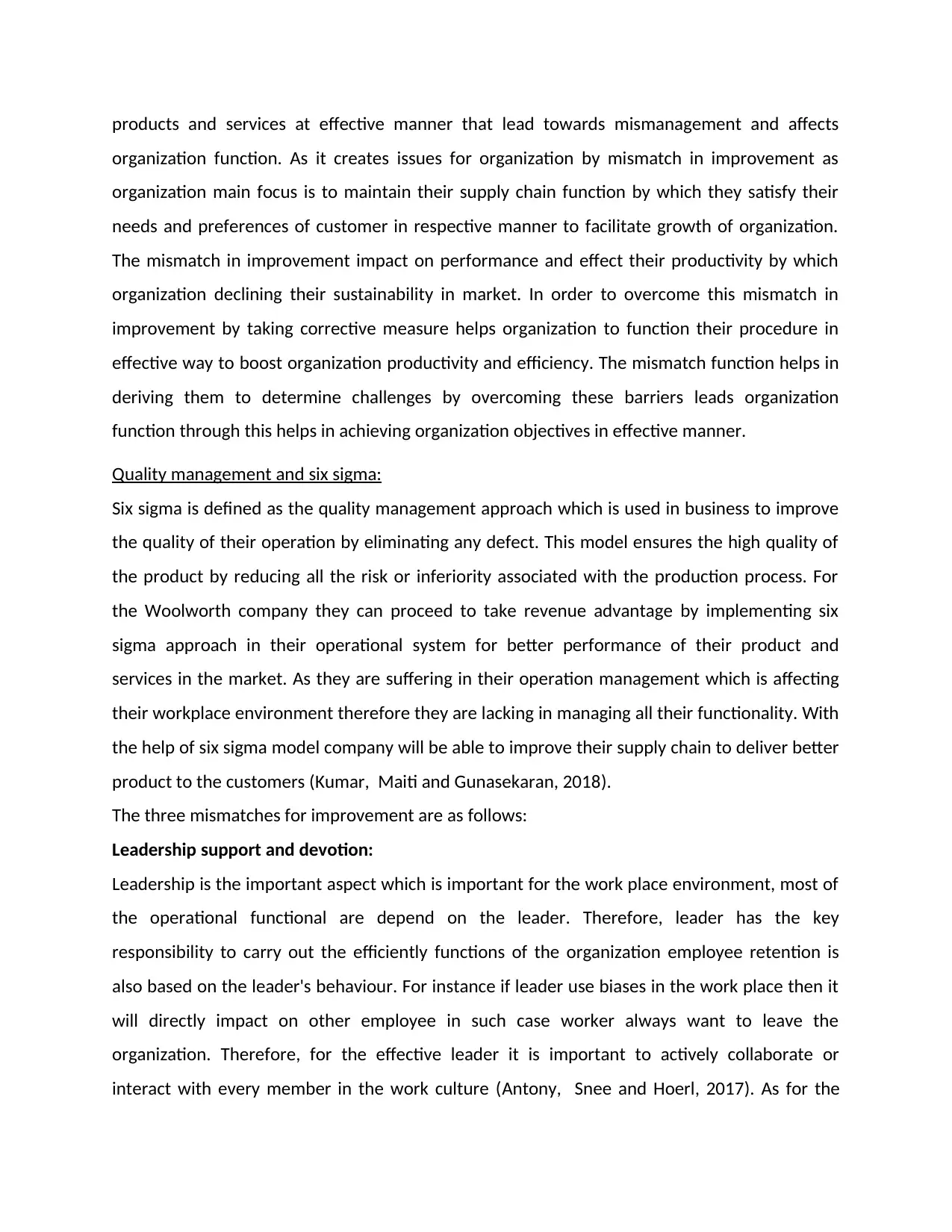
products and services at effective manner that lead towards mismanagement and affects
organization function. As it creates issues for organization by mismatch in improvement as
organization main focus is to maintain their supply chain function by which they satisfy their
needs and preferences of customer in respective manner to facilitate growth of organization.
The mismatch in improvement impact on performance and effect their productivity by which
organization declining their sustainability in market. In order to overcome this mismatch in
improvement by taking corrective measure helps organization to function their procedure in
effective way to boost organization productivity and efficiency. The mismatch function helps in
deriving them to determine challenges by overcoming these barriers leads organization
function through this helps in achieving organization objectives in effective manner.
Quality management and six sigma:
Six sigma is defined as the quality management approach which is used in business to improve
the quality of their operation by eliminating any defect. This model ensures the high quality of
the product by reducing all the risk or inferiority associated with the production process. For
the Woolworth company they can proceed to take revenue advantage by implementing six
sigma approach in their operational system for better performance of their product and
services in the market. As they are suffering in their operation management which is affecting
their workplace environment therefore they are lacking in managing all their functionality. With
the help of six sigma model company will be able to improve their supply chain to deliver better
product to the customers (Kumar, Maiti and Gunasekaran, 2018).
The three mismatches for improvement are as follows:
Leadership support and devotion:
Leadership is the important aspect which is important for the work place environment, most of
the operational functional are depend on the leader. Therefore, leader has the key
responsibility to carry out the efficiently functions of the organization employee retention is
also based on the leader's behaviour. For instance if leader use biases in the work place then it
will directly impact on other employee in such case worker always want to leave the
organization. Therefore, for the effective leader it is important to actively collaborate or
interact with every member in the work culture (Antony, Snee and Hoerl, 2017). As for the
organization function. As it creates issues for organization by mismatch in improvement as
organization main focus is to maintain their supply chain function by which they satisfy their
needs and preferences of customer in respective manner to facilitate growth of organization.
The mismatch in improvement impact on performance and effect their productivity by which
organization declining their sustainability in market. In order to overcome this mismatch in
improvement by taking corrective measure helps organization to function their procedure in
effective way to boost organization productivity and efficiency. The mismatch function helps in
deriving them to determine challenges by overcoming these barriers leads organization
function through this helps in achieving organization objectives in effective manner.
Quality management and six sigma:
Six sigma is defined as the quality management approach which is used in business to improve
the quality of their operation by eliminating any defect. This model ensures the high quality of
the product by reducing all the risk or inferiority associated with the production process. For
the Woolworth company they can proceed to take revenue advantage by implementing six
sigma approach in their operational system for better performance of their product and
services in the market. As they are suffering in their operation management which is affecting
their workplace environment therefore they are lacking in managing all their functionality. With
the help of six sigma model company will be able to improve their supply chain to deliver better
product to the customers (Kumar, Maiti and Gunasekaran, 2018).
The three mismatches for improvement are as follows:
Leadership support and devotion:
Leadership is the important aspect which is important for the work place environment, most of
the operational functional are depend on the leader. Therefore, leader has the key
responsibility to carry out the efficiently functions of the organization employee retention is
also based on the leader's behaviour. For instance if leader use biases in the work place then it
will directly impact on other employee in such case worker always want to leave the
organization. Therefore, for the effective leader it is important to actively collaborate or
interact with every member in the work culture (Antony, Snee and Hoerl, 2017). As for the
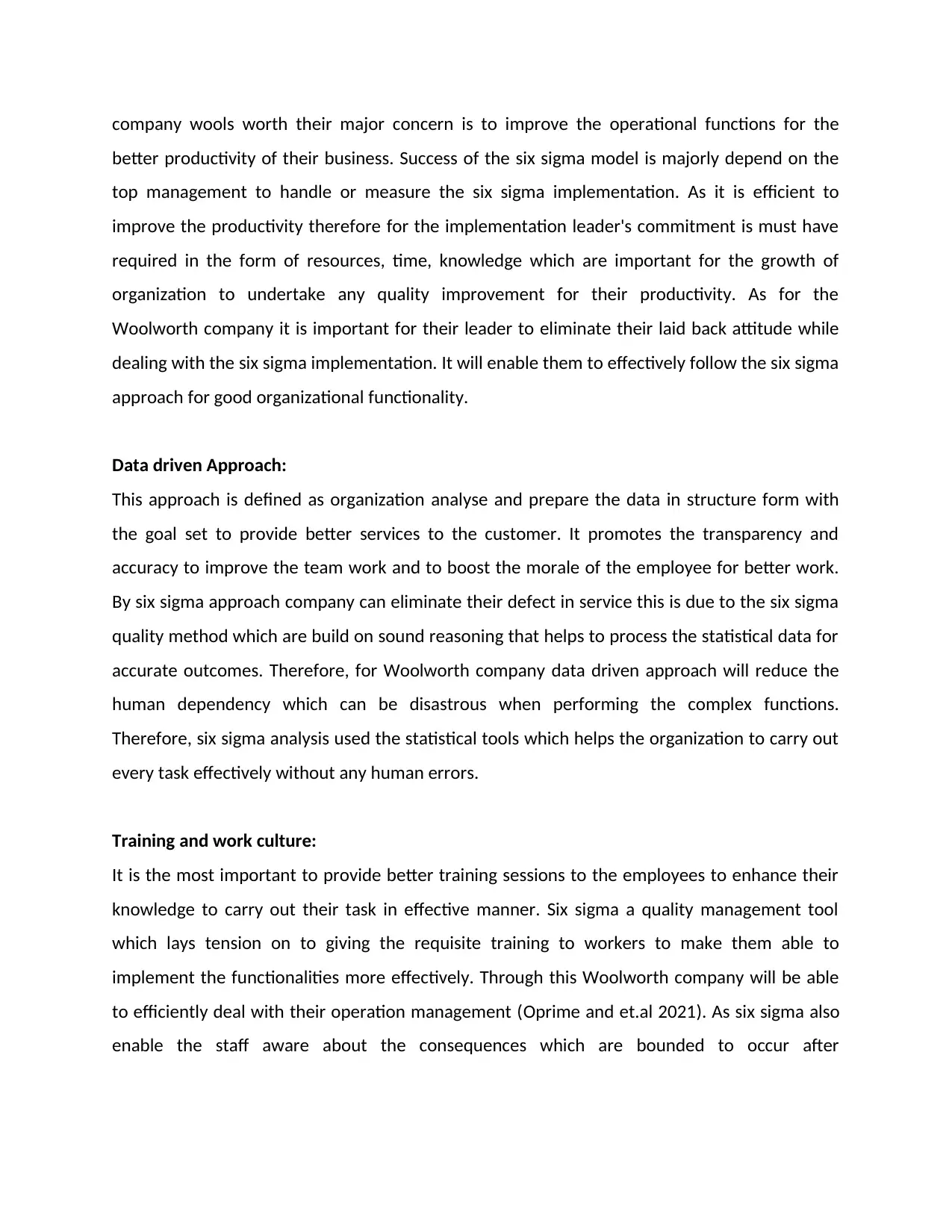
company wools worth their major concern is to improve the operational functions for the
better productivity of their business. Success of the six sigma model is majorly depend on the
top management to handle or measure the six sigma implementation. As it is efficient to
improve the productivity therefore for the implementation leader's commitment is must have
required in the form of resources, time, knowledge which are important for the growth of
organization to undertake any quality improvement for their productivity. As for the
Woolworth company it is important for their leader to eliminate their laid back attitude while
dealing with the six sigma implementation. It will enable them to effectively follow the six sigma
approach for good organizational functionality.
Data driven Approach:
This approach is defined as organization analyse and prepare the data in structure form with
the goal set to provide better services to the customer. It promotes the transparency and
accuracy to improve the team work and to boost the morale of the employee for better work.
By six sigma approach company can eliminate their defect in service this is due to the six sigma
quality method which are build on sound reasoning that helps to process the statistical data for
accurate outcomes. Therefore, for Woolworth company data driven approach will reduce the
human dependency which can be disastrous when performing the complex functions.
Therefore, six sigma analysis used the statistical tools which helps the organization to carry out
every task effectively without any human errors.
Training and work culture:
It is the most important to provide better training sessions to the employees to enhance their
knowledge to carry out their task in effective manner. Six sigma a quality management tool
which lays tension on to giving the requisite training to workers to make them able to
implement the functionalities more effectively. Through this Woolworth company will be able
to efficiently deal with their operation management (Oprime and et.al 2021). As six sigma also
enable the staff aware about the consequences which are bounded to occur after
better productivity of their business. Success of the six sigma model is majorly depend on the
top management to handle or measure the six sigma implementation. As it is efficient to
improve the productivity therefore for the implementation leader's commitment is must have
required in the form of resources, time, knowledge which are important for the growth of
organization to undertake any quality improvement for their productivity. As for the
Woolworth company it is important for their leader to eliminate their laid back attitude while
dealing with the six sigma implementation. It will enable them to effectively follow the six sigma
approach for good organizational functionality.
Data driven Approach:
This approach is defined as organization analyse and prepare the data in structure form with
the goal set to provide better services to the customer. It promotes the transparency and
accuracy to improve the team work and to boost the morale of the employee for better work.
By six sigma approach company can eliminate their defect in service this is due to the six sigma
quality method which are build on sound reasoning that helps to process the statistical data for
accurate outcomes. Therefore, for Woolworth company data driven approach will reduce the
human dependency which can be disastrous when performing the complex functions.
Therefore, six sigma analysis used the statistical tools which helps the organization to carry out
every task effectively without any human errors.
Training and work culture:
It is the most important to provide better training sessions to the employees to enhance their
knowledge to carry out their task in effective manner. Six sigma a quality management tool
which lays tension on to giving the requisite training to workers to make them able to
implement the functionalities more effectively. Through this Woolworth company will be able
to efficiently deal with their operation management (Oprime and et.al 2021). As six sigma also
enable the staff aware about the consequences which are bounded to occur after
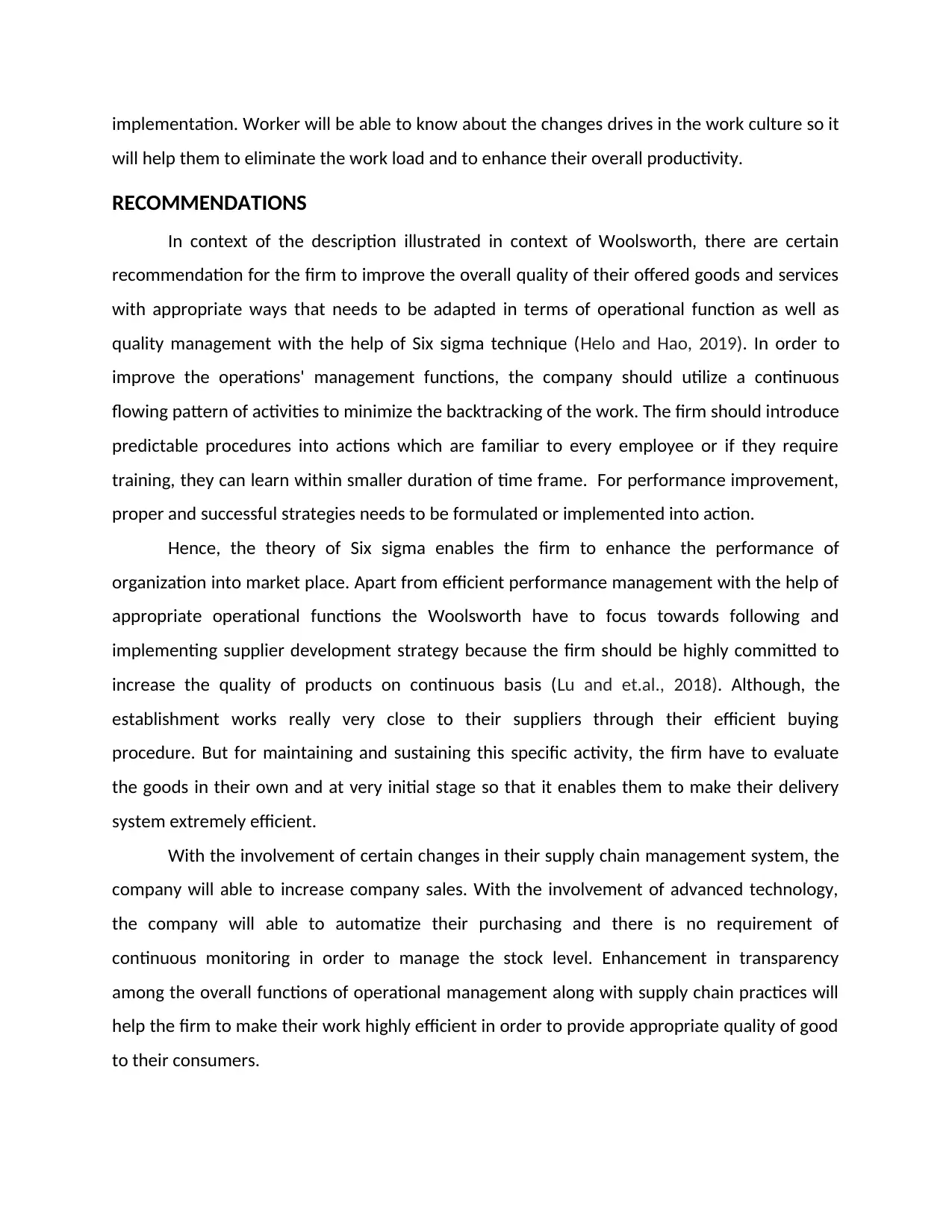
implementation. Worker will be able to know about the changes drives in the work culture so it
will help them to eliminate the work load and to enhance their overall productivity.
RECOMMENDATIONS
In context of the description illustrated in context of Woolsworth, there are certain
recommendation for the firm to improve the overall quality of their offered goods and services
with appropriate ways that needs to be adapted in terms of operational function as well as
quality management with the help of Six sigma technique (Helo and Hao, 2019). In order to
improve the operations' management functions, the company should utilize a continuous
flowing pattern of activities to minimize the backtracking of the work. The firm should introduce
predictable procedures into actions which are familiar to every employee or if they require
training, they can learn within smaller duration of time frame. For performance improvement,
proper and successful strategies needs to be formulated or implemented into action.
Hence, the theory of Six sigma enables the firm to enhance the performance of
organization into market place. Apart from efficient performance management with the help of
appropriate operational functions the Woolsworth have to focus towards following and
implementing supplier development strategy because the firm should be highly committed to
increase the quality of products on continuous basis (Lu and et.al., 2018). Although, the
establishment works really very close to their suppliers through their efficient buying
procedure. But for maintaining and sustaining this specific activity, the firm have to evaluate
the goods in their own and at very initial stage so that it enables them to make their delivery
system extremely efficient.
With the involvement of certain changes in their supply chain management system, the
company will able to increase company sales. With the involvement of advanced technology,
the company will able to automatize their purchasing and there is no requirement of
continuous monitoring in order to manage the stock level. Enhancement in transparency
among the overall functions of operational management along with supply chain practices will
help the firm to make their work highly efficient in order to provide appropriate quality of good
to their consumers.
will help them to eliminate the work load and to enhance their overall productivity.
RECOMMENDATIONS
In context of the description illustrated in context of Woolsworth, there are certain
recommendation for the firm to improve the overall quality of their offered goods and services
with appropriate ways that needs to be adapted in terms of operational function as well as
quality management with the help of Six sigma technique (Helo and Hao, 2019). In order to
improve the operations' management functions, the company should utilize a continuous
flowing pattern of activities to minimize the backtracking of the work. The firm should introduce
predictable procedures into actions which are familiar to every employee or if they require
training, they can learn within smaller duration of time frame. For performance improvement,
proper and successful strategies needs to be formulated or implemented into action.
Hence, the theory of Six sigma enables the firm to enhance the performance of
organization into market place. Apart from efficient performance management with the help of
appropriate operational functions the Woolsworth have to focus towards following and
implementing supplier development strategy because the firm should be highly committed to
increase the quality of products on continuous basis (Lu and et.al., 2018). Although, the
establishment works really very close to their suppliers through their efficient buying
procedure. But for maintaining and sustaining this specific activity, the firm have to evaluate
the goods in their own and at very initial stage so that it enables them to make their delivery
system extremely efficient.
With the involvement of certain changes in their supply chain management system, the
company will able to increase company sales. With the involvement of advanced technology,
the company will able to automatize their purchasing and there is no requirement of
continuous monitoring in order to manage the stock level. Enhancement in transparency
among the overall functions of operational management along with supply chain practices will
help the firm to make their work highly efficient in order to provide appropriate quality of good
to their consumers.
Secure Best Marks with AI Grader
Need help grading? Try our AI Grader for instant feedback on your assignments.
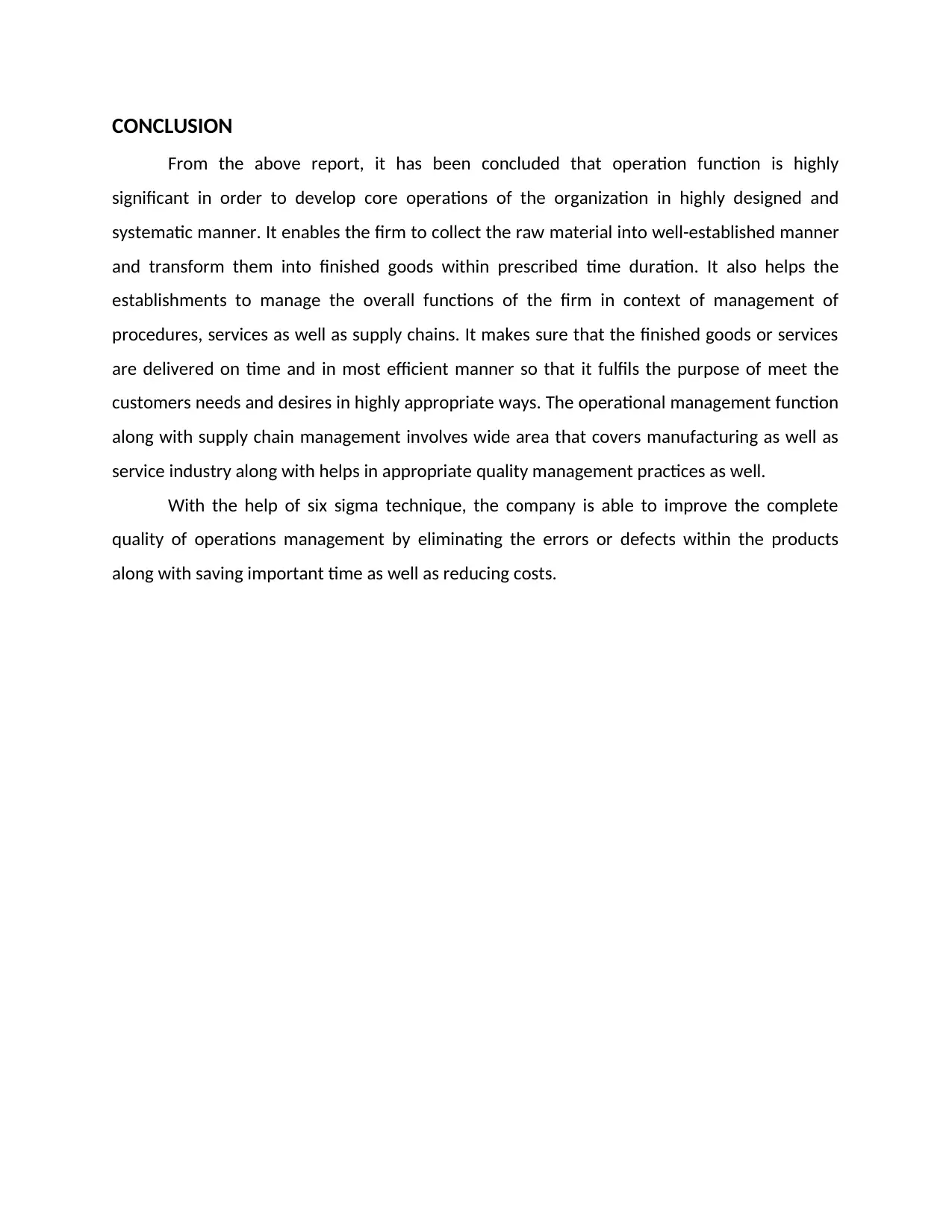
CONCLUSION
From the above report, it has been concluded that operation function is highly
significant in order to develop core operations of the organization in highly designed and
systematic manner. It enables the firm to collect the raw material into well-established manner
and transform them into finished goods within prescribed time duration. It also helps the
establishments to manage the overall functions of the firm in context of management of
procedures, services as well as supply chains. It makes sure that the finished goods or services
are delivered on time and in most efficient manner so that it fulfils the purpose of meet the
customers needs and desires in highly appropriate ways. The operational management function
along with supply chain management involves wide area that covers manufacturing as well as
service industry along with helps in appropriate quality management practices as well.
With the help of six sigma technique, the company is able to improve the complete
quality of operations management by eliminating the errors or defects within the products
along with saving important time as well as reducing costs.
From the above report, it has been concluded that operation function is highly
significant in order to develop core operations of the organization in highly designed and
systematic manner. It enables the firm to collect the raw material into well-established manner
and transform them into finished goods within prescribed time duration. It also helps the
establishments to manage the overall functions of the firm in context of management of
procedures, services as well as supply chains. It makes sure that the finished goods or services
are delivered on time and in most efficient manner so that it fulfils the purpose of meet the
customers needs and desires in highly appropriate ways. The operational management function
along with supply chain management involves wide area that covers manufacturing as well as
service industry along with helps in appropriate quality management practices as well.
With the help of six sigma technique, the company is able to improve the complete
quality of operations management by eliminating the errors or defects within the products
along with saving important time as well as reducing costs.
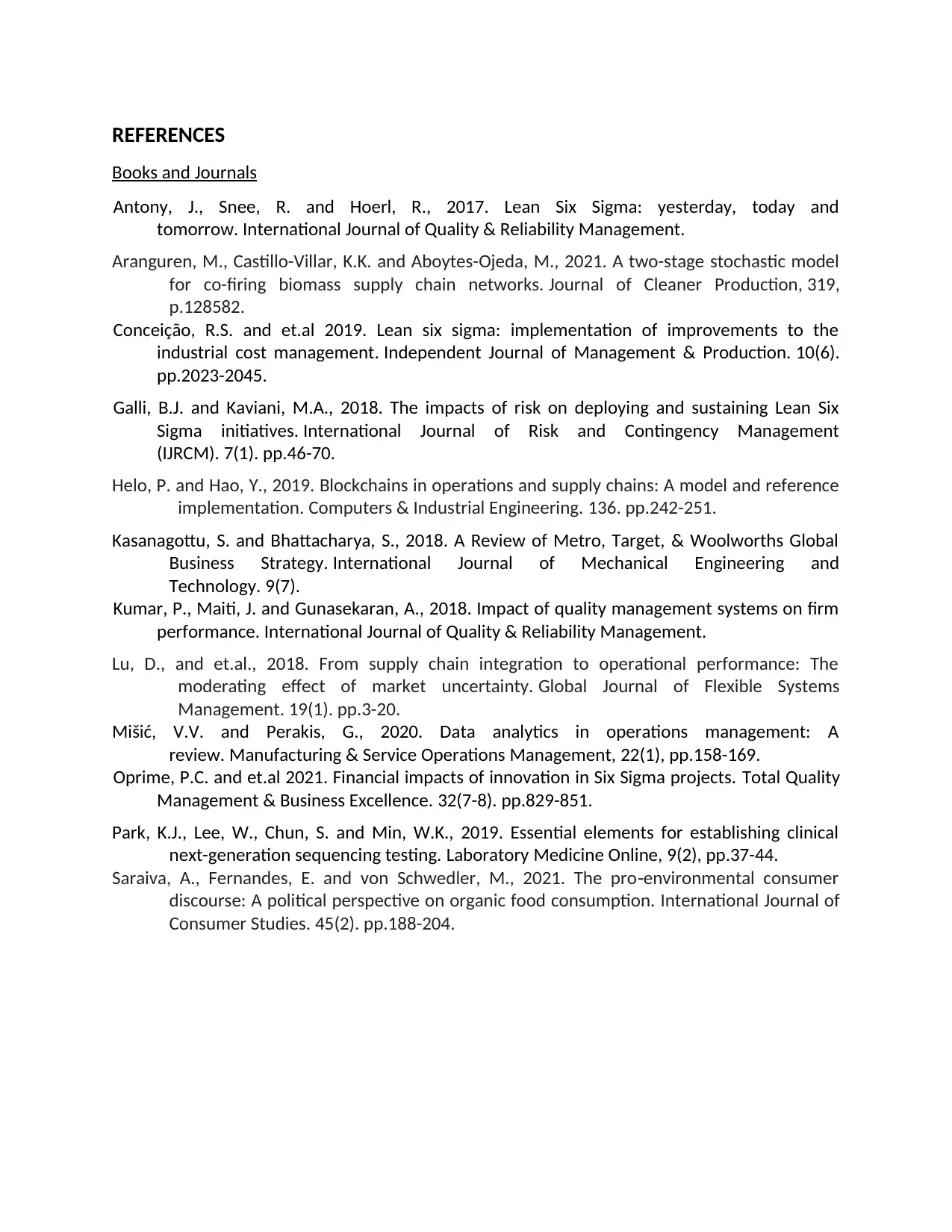
REFERENCES
Books and Journals
Antony, J., Snee, R. and Hoerl, R., 2017. Lean Six Sigma: yesterday, today and
tomorrow. International Journal of Quality & Reliability Management.
Aranguren, M., Castillo-Villar, K.K. and Aboytes-Ojeda, M., 2021. A two-stage stochastic model
for co-firing biomass supply chain networks. Journal of Cleaner Production, 319,
p.128582.
Conceição, R.S. and et.al 2019. Lean six sigma: implementation of improvements to the
industrial cost management. Independent Journal of Management & Production. 10(6).
pp.2023-2045.
Galli, B.J. and Kaviani, M.A., 2018. The impacts of risk on deploying and sustaining Lean Six
Sigma initiatives. International Journal of Risk and Contingency Management
(IJRCM). 7(1). pp.46-70.
Helo, P. and Hao, Y., 2019. Blockchains in operations and supply chains: A model and reference
implementation. Computers & Industrial Engineering. 136. pp.242-251.
Kasanagottu, S. and Bhattacharya, S., 2018. A Review of Metro, Target, & Woolworths Global
Business Strategy. International Journal of Mechanical Engineering and
Technology. 9(7).
Kumar, P., Maiti, J. and Gunasekaran, A., 2018. Impact of quality management systems on firm
performance. International Journal of Quality & Reliability Management.
Lu, D., and et.al., 2018. From supply chain integration to operational performance: The
moderating effect of market uncertainty. Global Journal of Flexible Systems
Management. 19(1). pp.3-20.
Mišić, V.V. and Perakis, G., 2020. Data analytics in operations management: A
review. Manufacturing & Service Operations Management, 22(1), pp.158-169.
Oprime, P.C. and et.al 2021. Financial impacts of innovation in Six Sigma projects. Total Quality
Management & Business Excellence. 32(7-8). pp.829-851.
Park, K.J., Lee, W., Chun, S. and Min, W.K., 2019. Essential elements for establishing clinical
next-generation sequencing testing. Laboratory Medicine Online, 9(2), pp.37-44.
Saraiva, A., Fernandes, E. and von Schwedler, M., 2021. The pro environmental consumer‐
discourse: A political perspective on organic food consumption. International Journal of
Consumer Studies. 45(2). pp.188-204.
Books and Journals
Antony, J., Snee, R. and Hoerl, R., 2017. Lean Six Sigma: yesterday, today and
tomorrow. International Journal of Quality & Reliability Management.
Aranguren, M., Castillo-Villar, K.K. and Aboytes-Ojeda, M., 2021. A two-stage stochastic model
for co-firing biomass supply chain networks. Journal of Cleaner Production, 319,
p.128582.
Conceição, R.S. and et.al 2019. Lean six sigma: implementation of improvements to the
industrial cost management. Independent Journal of Management & Production. 10(6).
pp.2023-2045.
Galli, B.J. and Kaviani, M.A., 2018. The impacts of risk on deploying and sustaining Lean Six
Sigma initiatives. International Journal of Risk and Contingency Management
(IJRCM). 7(1). pp.46-70.
Helo, P. and Hao, Y., 2019. Blockchains in operations and supply chains: A model and reference
implementation. Computers & Industrial Engineering. 136. pp.242-251.
Kasanagottu, S. and Bhattacharya, S., 2018. A Review of Metro, Target, & Woolworths Global
Business Strategy. International Journal of Mechanical Engineering and
Technology. 9(7).
Kumar, P., Maiti, J. and Gunasekaran, A., 2018. Impact of quality management systems on firm
performance. International Journal of Quality & Reliability Management.
Lu, D., and et.al., 2018. From supply chain integration to operational performance: The
moderating effect of market uncertainty. Global Journal of Flexible Systems
Management. 19(1). pp.3-20.
Mišić, V.V. and Perakis, G., 2020. Data analytics in operations management: A
review. Manufacturing & Service Operations Management, 22(1), pp.158-169.
Oprime, P.C. and et.al 2021. Financial impacts of innovation in Six Sigma projects. Total Quality
Management & Business Excellence. 32(7-8). pp.829-851.
Park, K.J., Lee, W., Chun, S. and Min, W.K., 2019. Essential elements for establishing clinical
next-generation sequencing testing. Laboratory Medicine Online, 9(2), pp.37-44.
Saraiva, A., Fernandes, E. and von Schwedler, M., 2021. The pro environmental consumer‐
discourse: A political perspective on organic food consumption. International Journal of
Consumer Studies. 45(2). pp.188-204.
1 out of 12
Related Documents
![[object Object]](/_next/image/?url=%2F_next%2Fstatic%2Fmedia%2Flogo.6d15ce61.png&w=640&q=75)
Your All-in-One AI-Powered Toolkit for Academic Success.
+13062052269
info@desklib.com
Available 24*7 on WhatsApp / Email
Unlock your academic potential
© 2024 | Zucol Services PVT LTD | All rights reserved.