Financial Accounting Assignment: Cost Allocation and Manufacturing
VerifiedAdded on  2020/03/01
|13
|2832
|1219
Homework Assignment
AI Summary
This assignment delves into the core concepts of financial accounting, specifically addressing cost allocation within a manufacturing context, using the example of a furniture company. The paper explores the importance of accurately allocating costs for raw materials, labor, and overhead expenses to control manufacturing costs. It emphasizes the need for separate costing of raw materials to identify cost drivers and facilitate cost reduction. The assignment examines different costing methods, including the challenges of quantifying certain materials, and the application of normal costing versus actual costing. It also differentiates between standard products and custom-made products, highlighting how custom products are not included in the manufacturing costs. The paper discusses the use of predetermined overhead rates and the advantages of normal costing. The assignment provides a comprehensive overview of financial accounting principles and their practical application in a manufacturing setting. The assignment concludes by highlighting the importance of predetermined overhead rates in estimating costs and simplifying bookkeeping.
Contribute Materials
Your contribution can guide someone’s learning journey. Share your
documents today.
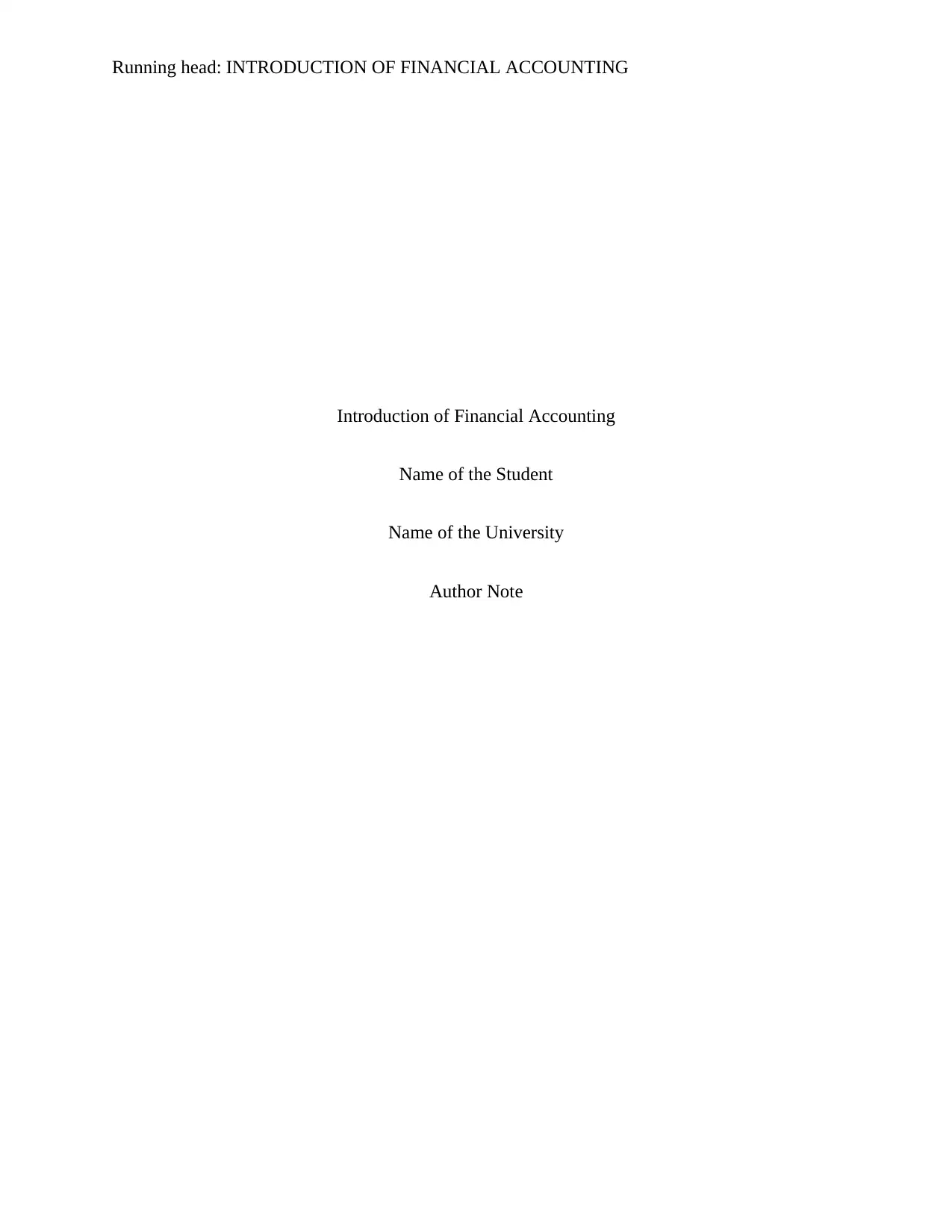
Running head: INTRODUCTION OF FINANCIAL ACCOUNTING
Introduction of Financial Accounting
Name of the Student
Name of the University
Author Note
Introduction of Financial Accounting
Name of the Student
Name of the University
Author Note
Secure Best Marks with AI Grader
Need help grading? Try our AI Grader for instant feedback on your assignments.
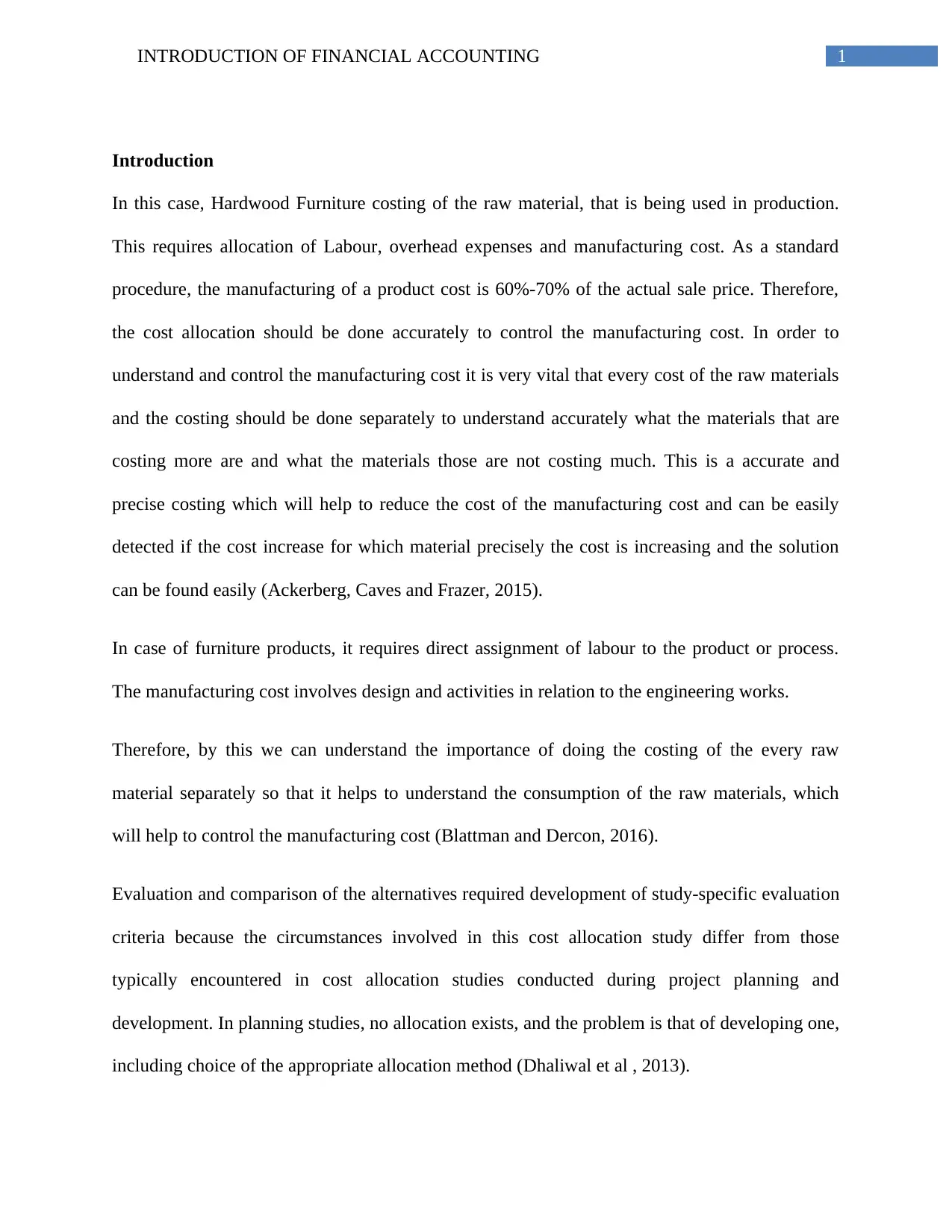
1INTRODUCTION OF FINANCIAL ACCOUNTING
Introduction
In this case, Hardwood Furniture costing of the raw material, that is being used in production.
This requires allocation of Labour, overhead expenses and manufacturing cost. As a standard
procedure, the manufacturing of a product cost is 60%-70% of the actual sale price. Therefore,
the cost allocation should be done accurately to control the manufacturing cost. In order to
understand and control the manufacturing cost it is very vital that every cost of the raw materials
and the costing should be done separately to understand accurately what the materials that are
costing more are and what the materials those are not costing much. This is a accurate and
precise costing which will help to reduce the cost of the manufacturing cost and can be easily
detected if the cost increase for which material precisely the cost is increasing and the solution
can be found easily (Ackerberg, Caves and Frazer, 2015).
In case of furniture products, it requires direct assignment of labour to the product or process.
The manufacturing cost involves design and activities in relation to the engineering works.
Therefore, by this we can understand the importance of doing the costing of the every raw
material separately so that it helps to understand the consumption of the raw materials, which
will help to control the manufacturing cost (Blattman and Dercon, 2016).
Evaluation and comparison of the alternatives required development of study-specific evaluation
criteria because the circumstances involved in this cost allocation study differ from those
typically encountered in cost allocation studies conducted during project planning and
development. In planning studies, no allocation exists, and the problem is that of developing one,
including choice of the appropriate allocation method (Dhaliwal et al , 2013).
Introduction
In this case, Hardwood Furniture costing of the raw material, that is being used in production.
This requires allocation of Labour, overhead expenses and manufacturing cost. As a standard
procedure, the manufacturing of a product cost is 60%-70% of the actual sale price. Therefore,
the cost allocation should be done accurately to control the manufacturing cost. In order to
understand and control the manufacturing cost it is very vital that every cost of the raw materials
and the costing should be done separately to understand accurately what the materials that are
costing more are and what the materials those are not costing much. This is a accurate and
precise costing which will help to reduce the cost of the manufacturing cost and can be easily
detected if the cost increase for which material precisely the cost is increasing and the solution
can be found easily (Ackerberg, Caves and Frazer, 2015).
In case of furniture products, it requires direct assignment of labour to the product or process.
The manufacturing cost involves design and activities in relation to the engineering works.
Therefore, by this we can understand the importance of doing the costing of the every raw
material separately so that it helps to understand the consumption of the raw materials, which
will help to control the manufacturing cost (Blattman and Dercon, 2016).
Evaluation and comparison of the alternatives required development of study-specific evaluation
criteria because the circumstances involved in this cost allocation study differ from those
typically encountered in cost allocation studies conducted during project planning and
development. In planning studies, no allocation exists, and the problem is that of developing one,
including choice of the appropriate allocation method (Dhaliwal et al , 2013).
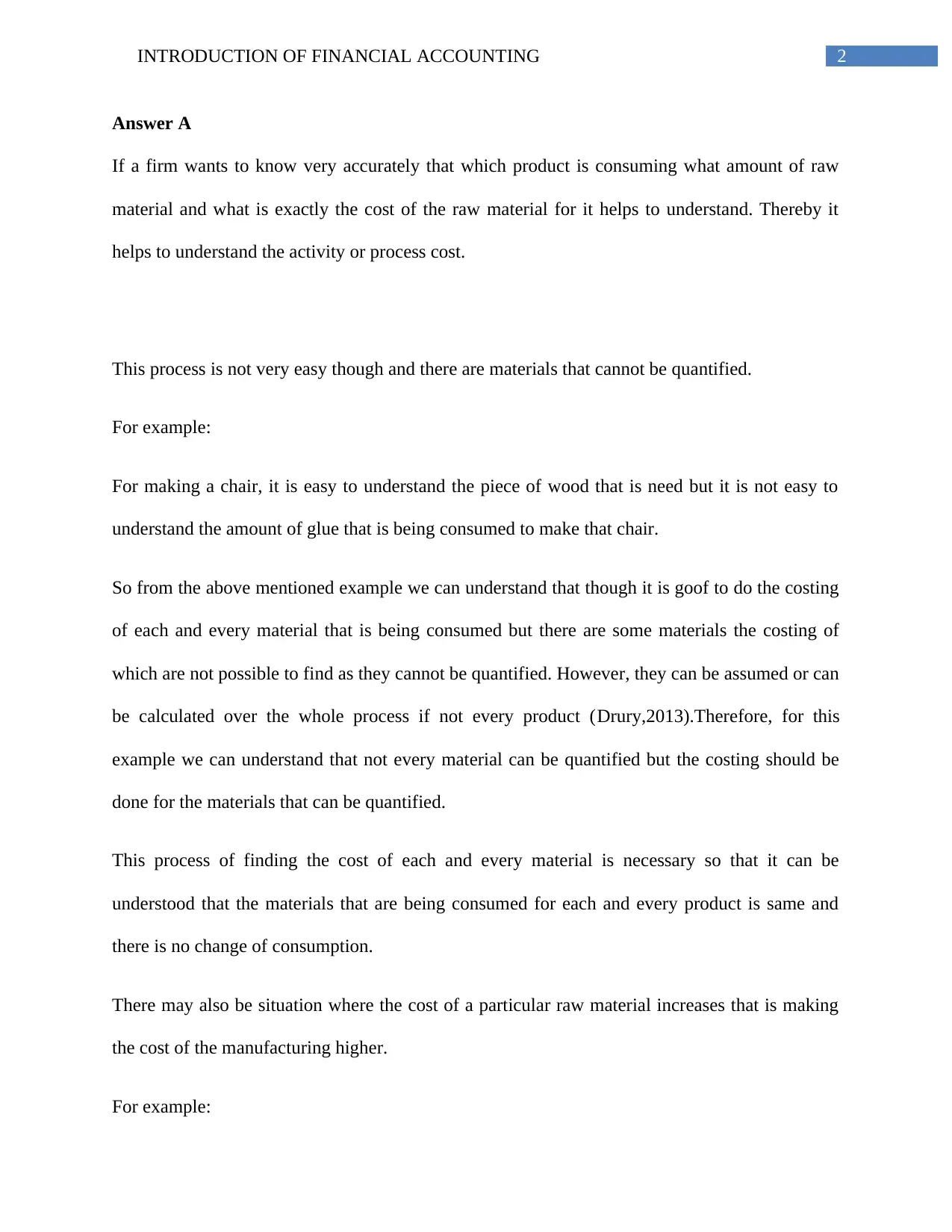
2INTRODUCTION OF FINANCIAL ACCOUNTING
Answer A
If a firm wants to know very accurately that which product is consuming what amount of raw
material and what is exactly the cost of the raw material for it helps to understand. Thereby it
helps to understand the activity or process cost.
This process is not very easy though and there are materials that cannot be quantified.
For example:
For making a chair, it is easy to understand the piece of wood that is need but it is not easy to
understand the amount of glue that is being consumed to make that chair.
So from the above mentioned example we can understand that though it is goof to do the costing
of each and every material that is being consumed but there are some materials the costing of
which are not possible to find as they cannot be quantified. However, they can be assumed or can
be calculated over the whole process if not every product (Drury,2013).Therefore, for this
example we can understand that not every material can be quantified but the costing should be
done for the materials that can be quantified.
This process of finding the cost of each and every material is necessary so that it can be
understood that the materials that are being consumed for each and every product is same and
there is no change of consumption.
There may also be situation where the cost of a particular raw material increases that is making
the cost of the manufacturing higher.
For example:
Answer A
If a firm wants to know very accurately that which product is consuming what amount of raw
material and what is exactly the cost of the raw material for it helps to understand. Thereby it
helps to understand the activity or process cost.
This process is not very easy though and there are materials that cannot be quantified.
For example:
For making a chair, it is easy to understand the piece of wood that is need but it is not easy to
understand the amount of glue that is being consumed to make that chair.
So from the above mentioned example we can understand that though it is goof to do the costing
of each and every material that is being consumed but there are some materials the costing of
which are not possible to find as they cannot be quantified. However, they can be assumed or can
be calculated over the whole process if not every product (Drury,2013).Therefore, for this
example we can understand that not every material can be quantified but the costing should be
done for the materials that can be quantified.
This process of finding the cost of each and every material is necessary so that it can be
understood that the materials that are being consumed for each and every product is same and
there is no change of consumption.
There may also be situation where the cost of a particular raw material increases that is making
the cost of the manufacturing higher.
For example:
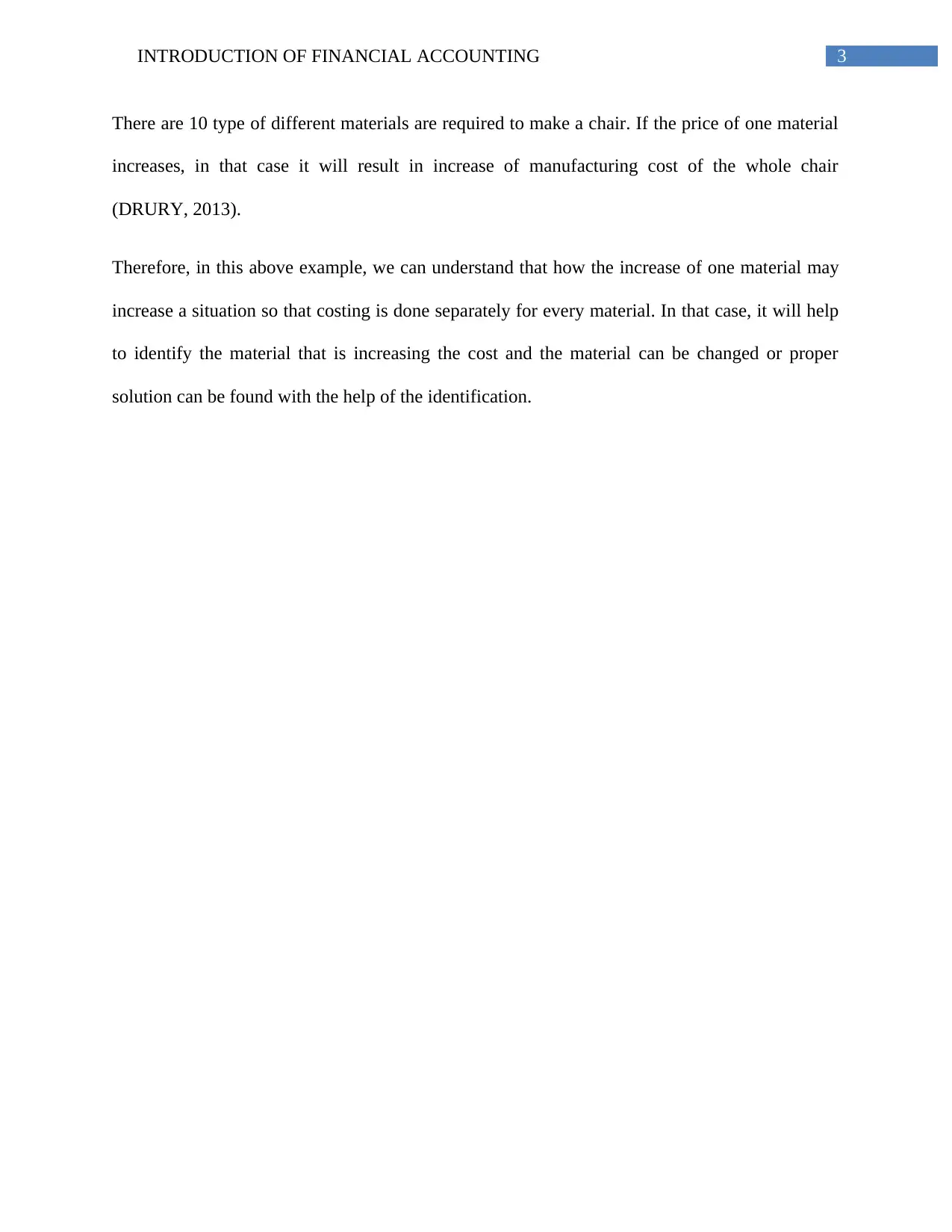
3INTRODUCTION OF FINANCIAL ACCOUNTING
There are 10 type of different materials are required to make a chair. If the price of one material
increases, in that case it will result in increase of manufacturing cost of the whole chair
(DRURY, 2013).
Therefore, in this above example, we can understand that how the increase of one material may
increase a situation so that costing is done separately for every material. In that case, it will help
to identify the material that is increasing the cost and the material can be changed or proper
solution can be found with the help of the identification.
There are 10 type of different materials are required to make a chair. If the price of one material
increases, in that case it will result in increase of manufacturing cost of the whole chair
(DRURY, 2013).
Therefore, in this above example, we can understand that how the increase of one material may
increase a situation so that costing is done separately for every material. In that case, it will help
to identify the material that is increasing the cost and the material can be changed or proper
solution can be found with the help of the identification.
Secure Best Marks with AI Grader
Need help grading? Try our AI Grader for instant feedback on your assignments.
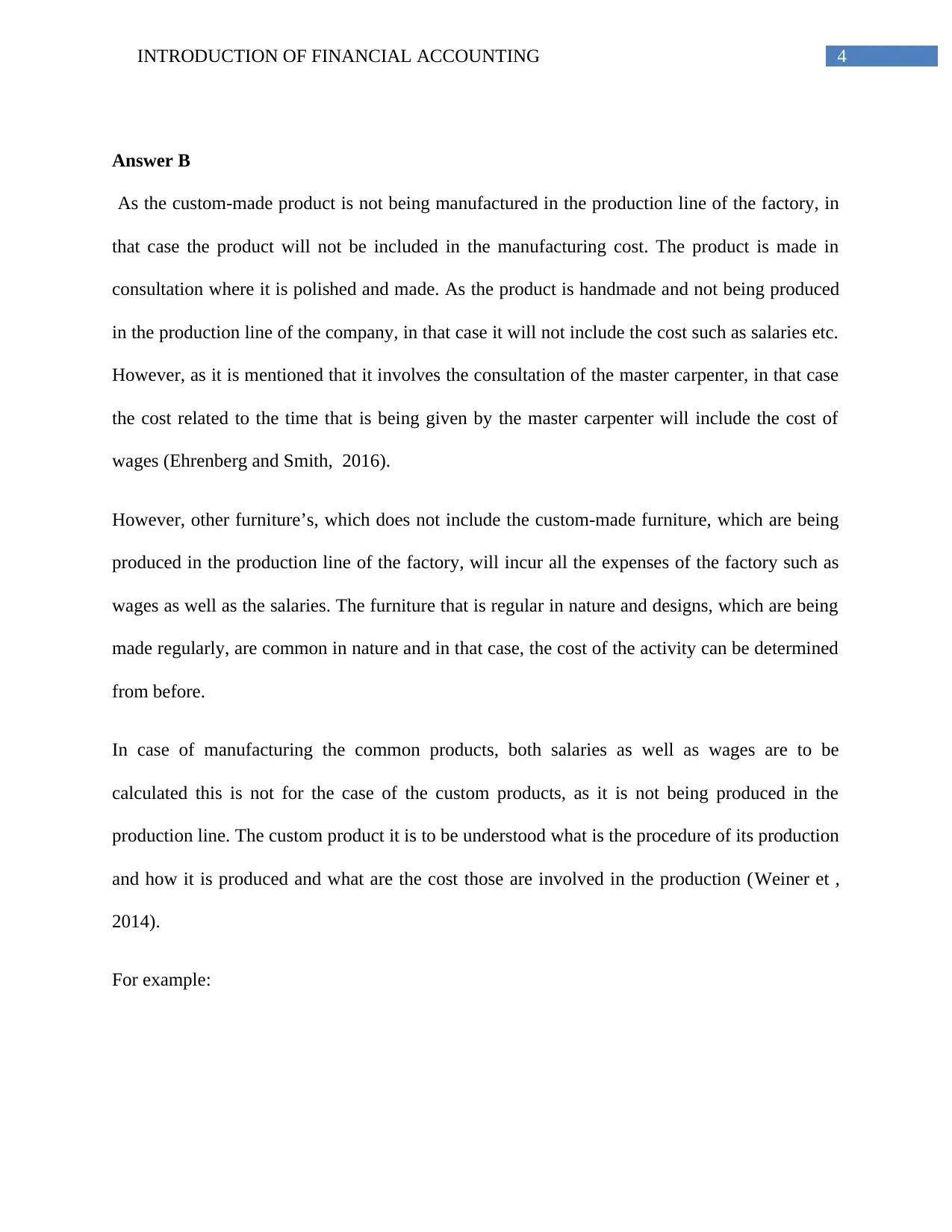
4INTRODUCTION OF FINANCIAL ACCOUNTING
Answer B
As the custom-made product is not being manufactured in the production line of the factory, in
that case the product will not be included in the manufacturing cost. The product is made in
consultation where it is polished and made. As the product is handmade and not being produced
in the production line of the company, in that case it will not include the cost such as salaries etc.
However, as it is mentioned that it involves the consultation of the master carpenter, in that case
the cost related to the time that is being given by the master carpenter will include the cost of
wages (Ehrenberg and Smith, 2016).
However, other furniture’s, which does not include the custom-made furniture, which are being
produced in the production line of the factory, will incur all the expenses of the factory such as
wages as well as the salaries. The furniture that is regular in nature and designs, which are being
made regularly, are common in nature and in that case, the cost of the activity can be determined
from before.
In case of manufacturing the common products, both salaries as well as wages are to be
calculated this is not for the case of the custom products, as it is not being produced in the
production line. The custom product it is to be understood what is the procedure of its production
and how it is produced and what are the cost those are involved in the production (Weiner et ,
2014).
For example:
Answer B
As the custom-made product is not being manufactured in the production line of the factory, in
that case the product will not be included in the manufacturing cost. The product is made in
consultation where it is polished and made. As the product is handmade and not being produced
in the production line of the company, in that case it will not include the cost such as salaries etc.
However, as it is mentioned that it involves the consultation of the master carpenter, in that case
the cost related to the time that is being given by the master carpenter will include the cost of
wages (Ehrenberg and Smith, 2016).
However, other furniture’s, which does not include the custom-made furniture, which are being
produced in the production line of the factory, will incur all the expenses of the factory such as
wages as well as the salaries. The furniture that is regular in nature and designs, which are being
made regularly, are common in nature and in that case, the cost of the activity can be determined
from before.
In case of manufacturing the common products, both salaries as well as wages are to be
calculated this is not for the case of the custom products, as it is not being produced in the
production line. The custom product it is to be understood what is the procedure of its production
and how it is produced and what are the cost those are involved in the production (Weiner et ,
2014).
For example:
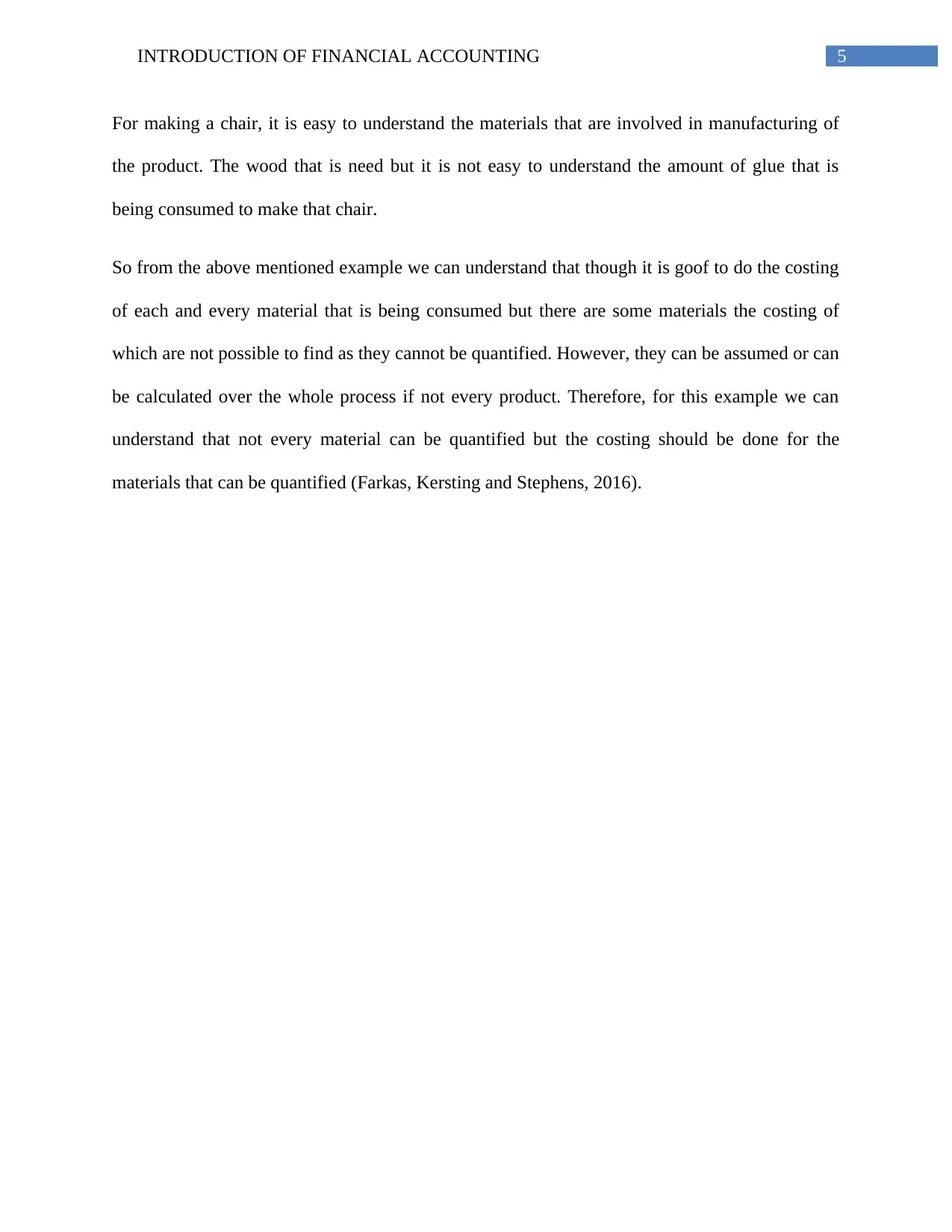
5INTRODUCTION OF FINANCIAL ACCOUNTING
For making a chair, it is easy to understand the materials that are involved in manufacturing of
the product. The wood that is need but it is not easy to understand the amount of glue that is
being consumed to make that chair.
So from the above mentioned example we can understand that though it is goof to do the costing
of each and every material that is being consumed but there are some materials the costing of
which are not possible to find as they cannot be quantified. However, they can be assumed or can
be calculated over the whole process if not every product. Therefore, for this example we can
understand that not every material can be quantified but the costing should be done for the
materials that can be quantified (Farkas, Kersting and Stephens, 2016).
For making a chair, it is easy to understand the materials that are involved in manufacturing of
the product. The wood that is need but it is not easy to understand the amount of glue that is
being consumed to make that chair.
So from the above mentioned example we can understand that though it is goof to do the costing
of each and every material that is being consumed but there are some materials the costing of
which are not possible to find as they cannot be quantified. However, they can be assumed or can
be calculated over the whole process if not every product. Therefore, for this example we can
understand that not every material can be quantified but the costing should be done for the
materials that can be quantified (Farkas, Kersting and Stephens, 2016).
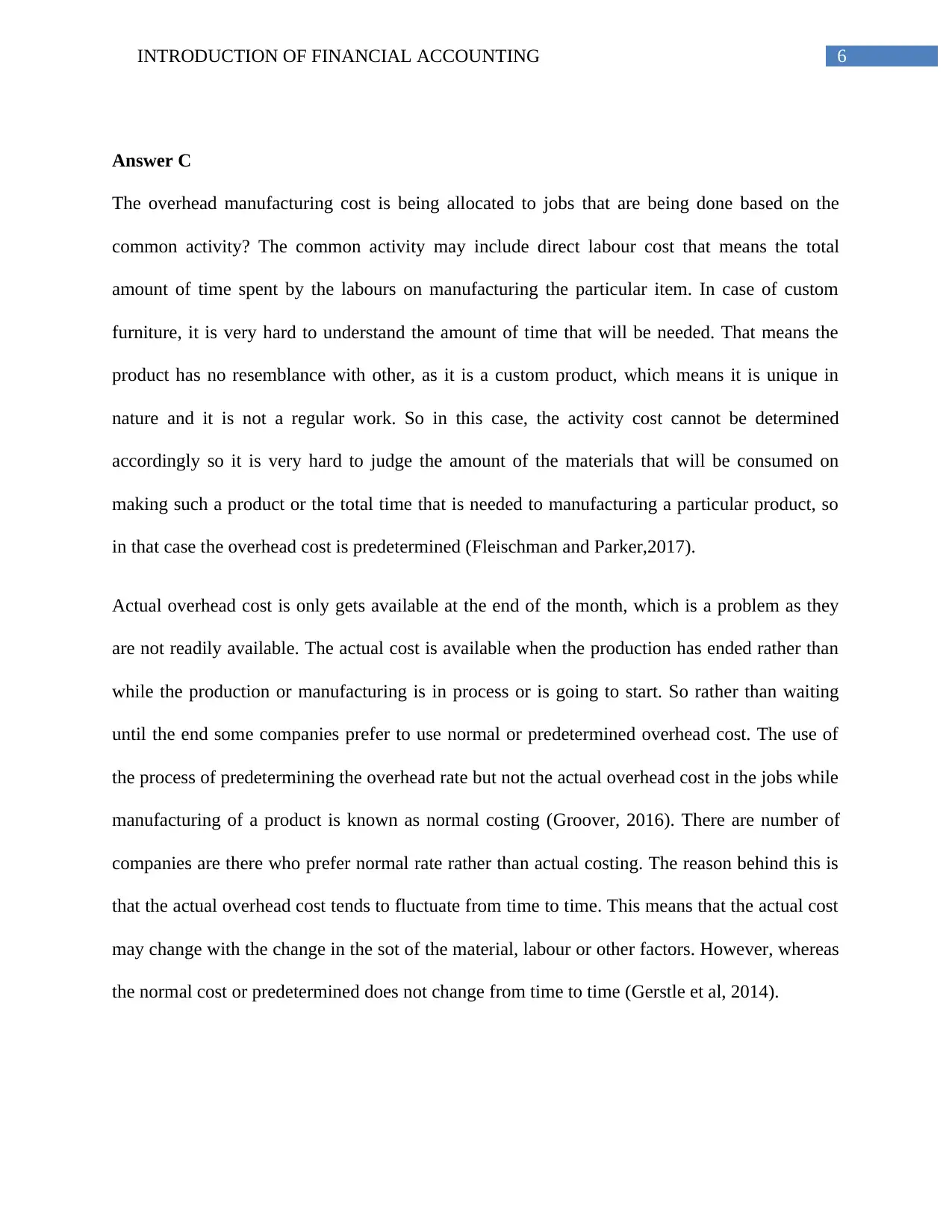
6INTRODUCTION OF FINANCIAL ACCOUNTING
Answer C
The overhead manufacturing cost is being allocated to jobs that are being done based on the
common activity? The common activity may include direct labour cost that means the total
amount of time spent by the labours on manufacturing the particular item. In case of custom
furniture, it is very hard to understand the amount of time that will be needed. That means the
product has no resemblance with other, as it is a custom product, which means it is unique in
nature and it is not a regular work. So in this case, the activity cost cannot be determined
accordingly so it is very hard to judge the amount of the materials that will be consumed on
making such a product or the total time that is needed to manufacturing a particular product, so
in that case the overhead cost is predetermined (Fleischman and Parker,2017).
Actual overhead cost is only gets available at the end of the month, which is a problem as they
are not readily available. The actual cost is available when the production has ended rather than
while the production or manufacturing is in process or is going to start. So rather than waiting
until the end some companies prefer to use normal or predetermined overhead cost. The use of
the process of predetermining the overhead rate but not the actual overhead cost in the jobs while
manufacturing of a product is known as normal costing (Groover, 2016). There are number of
companies are there who prefer normal rate rather than actual costing. The reason behind this is
that the actual overhead cost tends to fluctuate from time to time. This means that the actual cost
may change with the change in the sot of the material, labour or other factors. However, whereas
the normal cost or predetermined does not change from time to time (Gerstle et al, 2014).
Answer C
The overhead manufacturing cost is being allocated to jobs that are being done based on the
common activity? The common activity may include direct labour cost that means the total
amount of time spent by the labours on manufacturing the particular item. In case of custom
furniture, it is very hard to understand the amount of time that will be needed. That means the
product has no resemblance with other, as it is a custom product, which means it is unique in
nature and it is not a regular work. So in this case, the activity cost cannot be determined
accordingly so it is very hard to judge the amount of the materials that will be consumed on
making such a product or the total time that is needed to manufacturing a particular product, so
in that case the overhead cost is predetermined (Fleischman and Parker,2017).
Actual overhead cost is only gets available at the end of the month, which is a problem as they
are not readily available. The actual cost is available when the production has ended rather than
while the production or manufacturing is in process or is going to start. So rather than waiting
until the end some companies prefer to use normal or predetermined overhead cost. The use of
the process of predetermining the overhead rate but not the actual overhead cost in the jobs while
manufacturing of a product is known as normal costing (Groover, 2016). There are number of
companies are there who prefer normal rate rather than actual costing. The reason behind this is
that the actual overhead cost tends to fluctuate from time to time. This means that the actual cost
may change with the change in the sot of the material, labour or other factors. However, whereas
the normal cost or predetermined does not change from time to time (Gerstle et al, 2014).
Paraphrase This Document
Need a fresh take? Get an instant paraphrase of this document with our AI Paraphraser
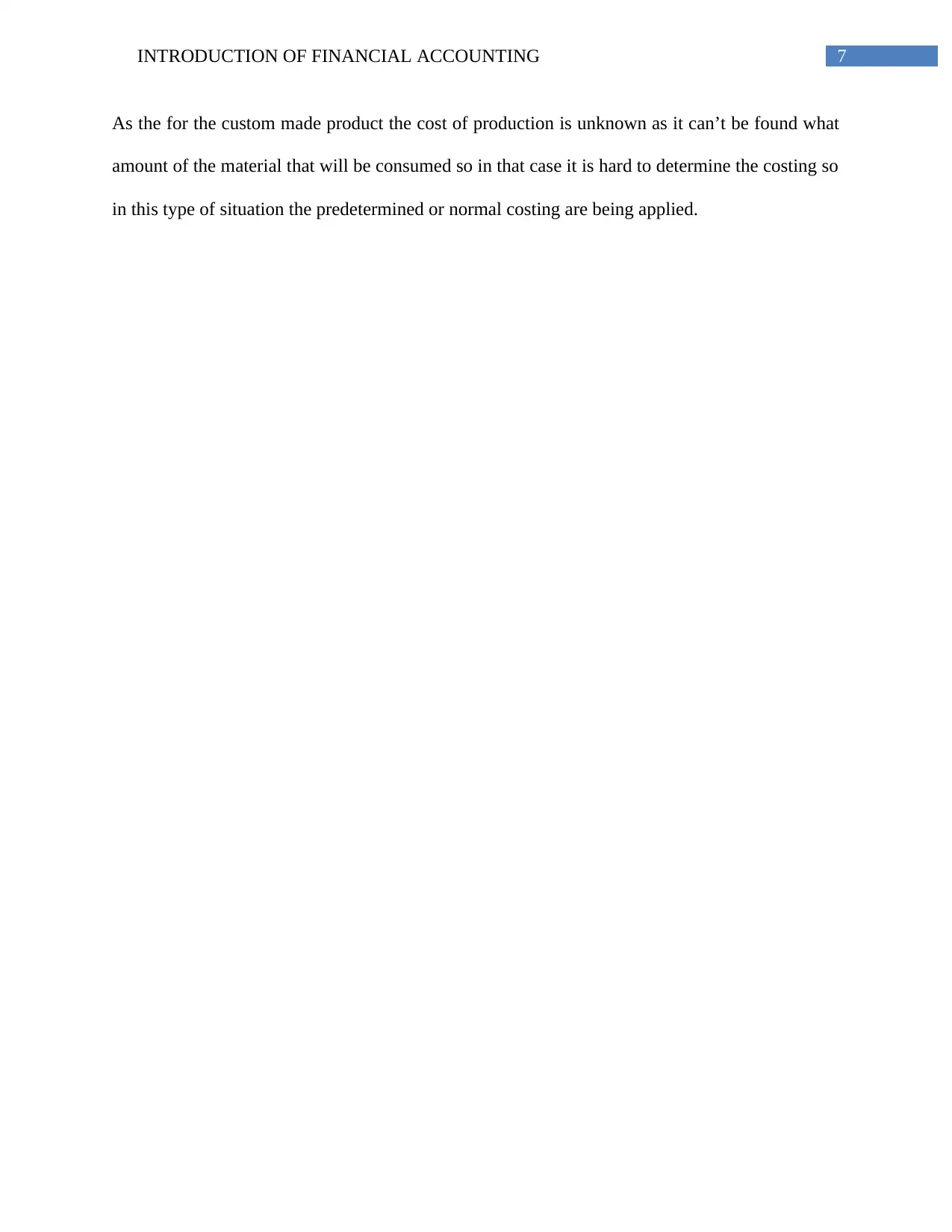
7INTRODUCTION OF FINANCIAL ACCOUNTING
As the for the custom made product the cost of production is unknown as it can’t be found what
amount of the material that will be consumed so in that case it is hard to determine the costing so
in this type of situation the predetermined or normal costing are being applied.
As the for the custom made product the cost of production is unknown as it can’t be found what
amount of the material that will be consumed so in that case it is hard to determine the costing so
in this type of situation the predetermined or normal costing are being applied.
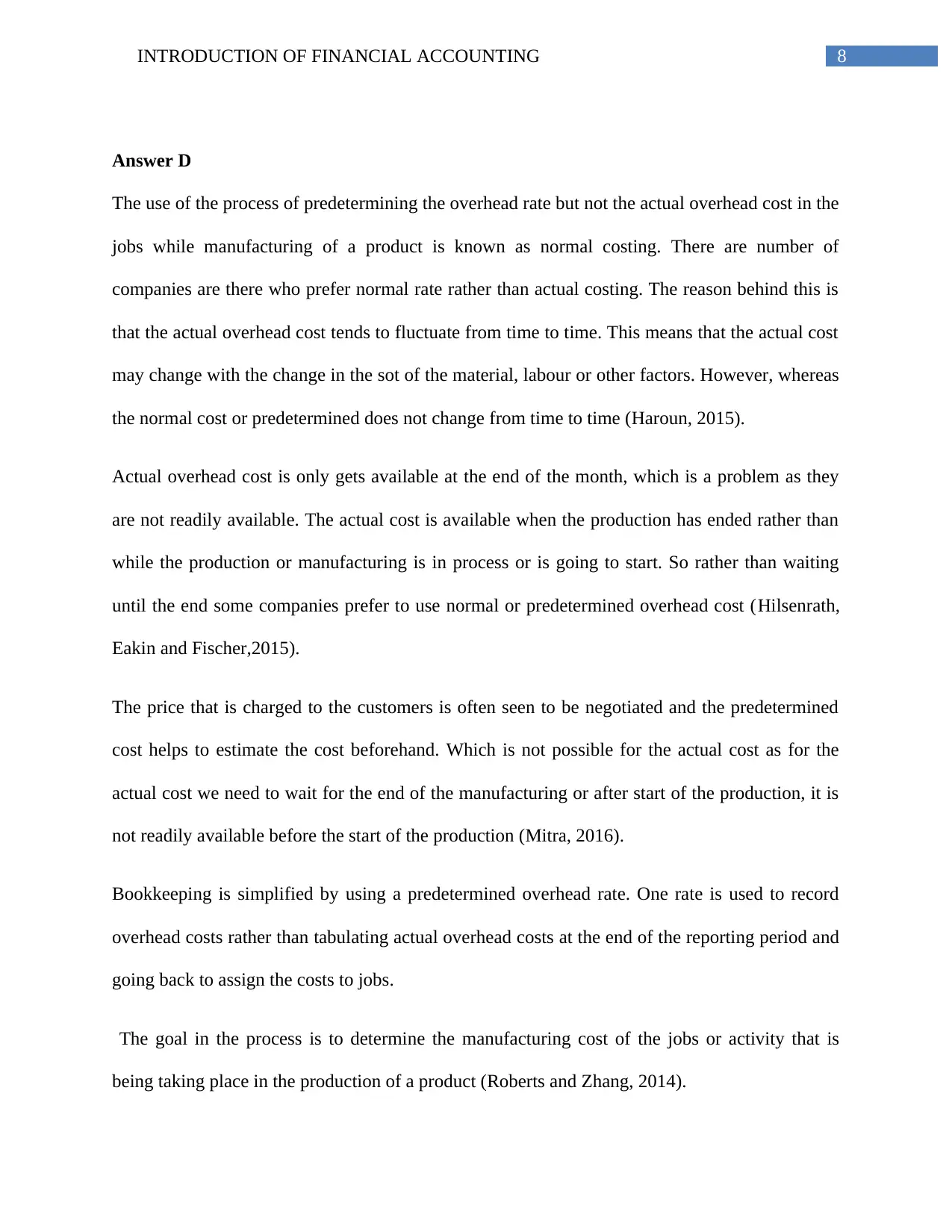
8INTRODUCTION OF FINANCIAL ACCOUNTING
Answer D
The use of the process of predetermining the overhead rate but not the actual overhead cost in the
jobs while manufacturing of a product is known as normal costing. There are number of
companies are there who prefer normal rate rather than actual costing. The reason behind this is
that the actual overhead cost tends to fluctuate from time to time. This means that the actual cost
may change with the change in the sot of the material, labour or other factors. However, whereas
the normal cost or predetermined does not change from time to time (Haroun, 2015).
Actual overhead cost is only gets available at the end of the month, which is a problem as they
are not readily available. The actual cost is available when the production has ended rather than
while the production or manufacturing is in process or is going to start. So rather than waiting
until the end some companies prefer to use normal or predetermined overhead cost (Hilsenrath,
Eakin and Fischer,2015).
The price that is charged to the customers is often seen to be negotiated and the predetermined
cost helps to estimate the cost beforehand. Which is not possible for the actual cost as for the
actual cost we need to wait for the end of the manufacturing or after start of the production, it is
not readily available before the start of the production (Mitra, 2016).
Bookkeeping is simplified by using a predetermined overhead rate. One rate is used to record
overhead costs rather than tabulating actual overhead costs at the end of the reporting period and
going back to assign the costs to jobs.
The goal in the process is to determine the manufacturing cost of the jobs or activity that is
being taking place in the production of a product (Roberts and Zhang, 2014).
Answer D
The use of the process of predetermining the overhead rate but not the actual overhead cost in the
jobs while manufacturing of a product is known as normal costing. There are number of
companies are there who prefer normal rate rather than actual costing. The reason behind this is
that the actual overhead cost tends to fluctuate from time to time. This means that the actual cost
may change with the change in the sot of the material, labour or other factors. However, whereas
the normal cost or predetermined does not change from time to time (Haroun, 2015).
Actual overhead cost is only gets available at the end of the month, which is a problem as they
are not readily available. The actual cost is available when the production has ended rather than
while the production or manufacturing is in process or is going to start. So rather than waiting
until the end some companies prefer to use normal or predetermined overhead cost (Hilsenrath,
Eakin and Fischer,2015).
The price that is charged to the customers is often seen to be negotiated and the predetermined
cost helps to estimate the cost beforehand. Which is not possible for the actual cost as for the
actual cost we need to wait for the end of the manufacturing or after start of the production, it is
not readily available before the start of the production (Mitra, 2016).
Bookkeeping is simplified by using a predetermined overhead rate. One rate is used to record
overhead costs rather than tabulating actual overhead costs at the end of the reporting period and
going back to assign the costs to jobs.
The goal in the process is to determine the manufacturing cost of the jobs or activity that is
being taking place in the production of a product (Roberts and Zhang, 2014).
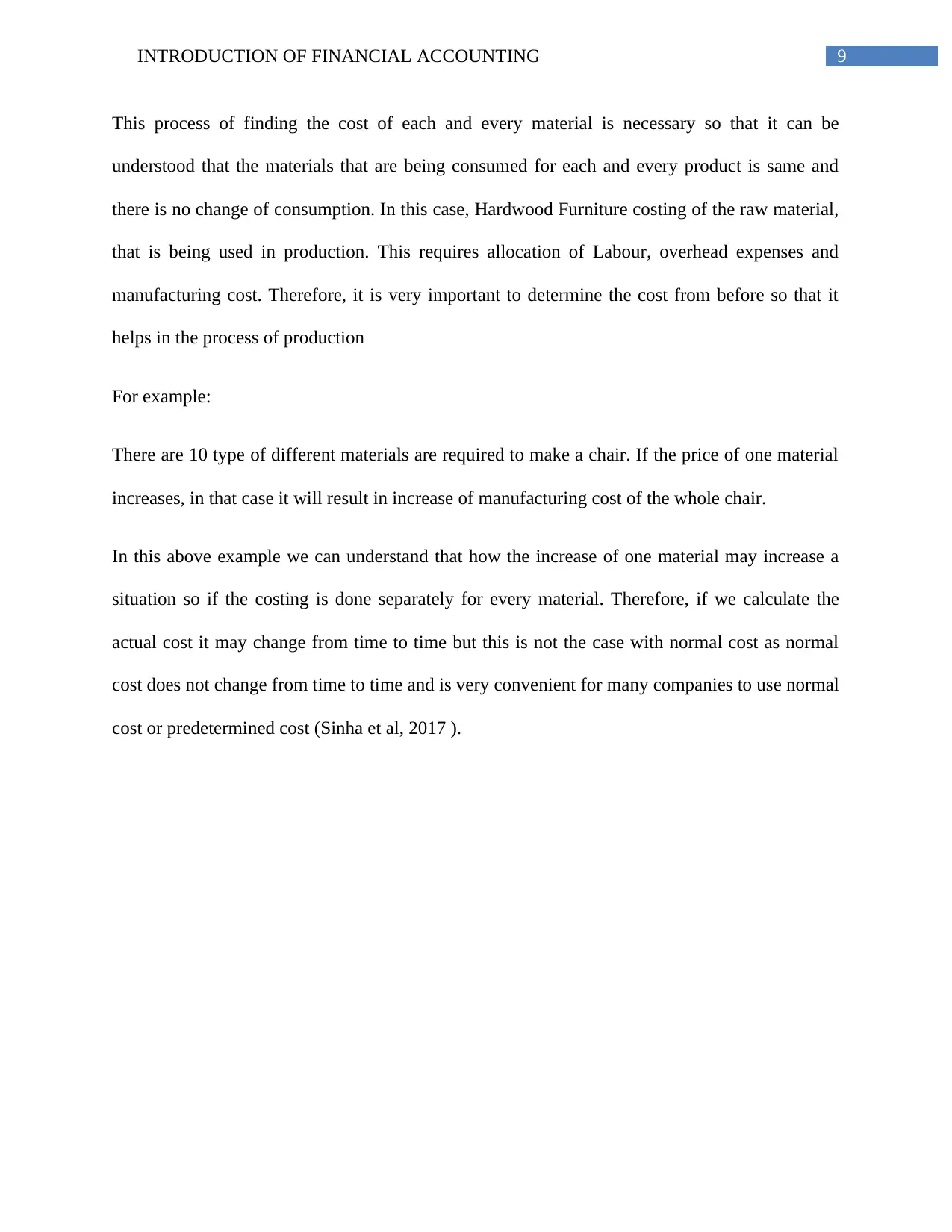
9INTRODUCTION OF FINANCIAL ACCOUNTING
This process of finding the cost of each and every material is necessary so that it can be
understood that the materials that are being consumed for each and every product is same and
there is no change of consumption. In this case, Hardwood Furniture costing of the raw material,
that is being used in production. This requires allocation of Labour, overhead expenses and
manufacturing cost. Therefore, it is very important to determine the cost from before so that it
helps in the process of production
For example:
There are 10 type of different materials are required to make a chair. If the price of one material
increases, in that case it will result in increase of manufacturing cost of the whole chair.
In this above example we can understand that how the increase of one material may increase a
situation so if the costing is done separately for every material. Therefore, if we calculate the
actual cost it may change from time to time but this is not the case with normal cost as normal
cost does not change from time to time and is very convenient for many companies to use normal
cost or predetermined cost (Sinha et al, 2017 ).
This process of finding the cost of each and every material is necessary so that it can be
understood that the materials that are being consumed for each and every product is same and
there is no change of consumption. In this case, Hardwood Furniture costing of the raw material,
that is being used in production. This requires allocation of Labour, overhead expenses and
manufacturing cost. Therefore, it is very important to determine the cost from before so that it
helps in the process of production
For example:
There are 10 type of different materials are required to make a chair. If the price of one material
increases, in that case it will result in increase of manufacturing cost of the whole chair.
In this above example we can understand that how the increase of one material may increase a
situation so if the costing is done separately for every material. Therefore, if we calculate the
actual cost it may change from time to time but this is not the case with normal cost as normal
cost does not change from time to time and is very convenient for many companies to use normal
cost or predetermined cost (Sinha et al, 2017 ).
Secure Best Marks with AI Grader
Need help grading? Try our AI Grader for instant feedback on your assignments.
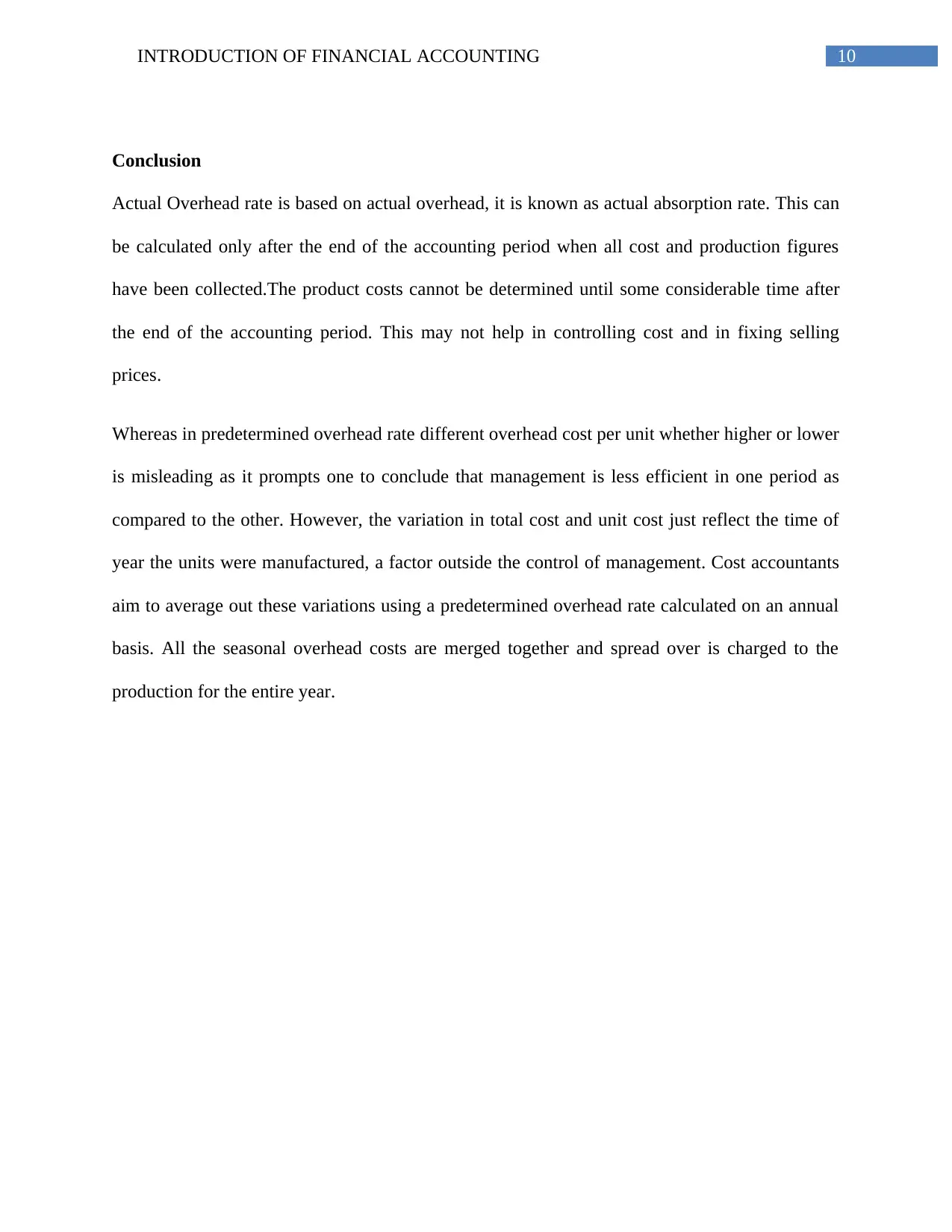
10INTRODUCTION OF FINANCIAL ACCOUNTING
Conclusion
Actual Overhead rate is based on actual overhead, it is known as actual absorption rate. This can
be calculated only after the end of the accounting period when all cost and production figures
have been collected.The product costs cannot be determined until some considerable time after
the end of the accounting period. This may not help in controlling cost and in fixing selling
prices.
Whereas in predetermined overhead rate different overhead cost per unit whether higher or lower
is misleading as it prompts one to conclude that management is less efficient in one period as
compared to the other. However, the variation in total cost and unit cost just reflect the time of
year the units were manufactured, a factor outside the control of management. Cost accountants
aim to average out these variations using a predetermined overhead rate calculated on an annual
basis. All the seasonal overhead costs are merged together and spread over is charged to the
production for the entire year.
Conclusion
Actual Overhead rate is based on actual overhead, it is known as actual absorption rate. This can
be calculated only after the end of the accounting period when all cost and production figures
have been collected.The product costs cannot be determined until some considerable time after
the end of the accounting period. This may not help in controlling cost and in fixing selling
prices.
Whereas in predetermined overhead rate different overhead cost per unit whether higher or lower
is misleading as it prompts one to conclude that management is less efficient in one period as
compared to the other. However, the variation in total cost and unit cost just reflect the time of
year the units were manufactured, a factor outside the control of management. Cost accountants
aim to average out these variations using a predetermined overhead rate calculated on an annual
basis. All the seasonal overhead costs are merged together and spread over is charged to the
production for the entire year.
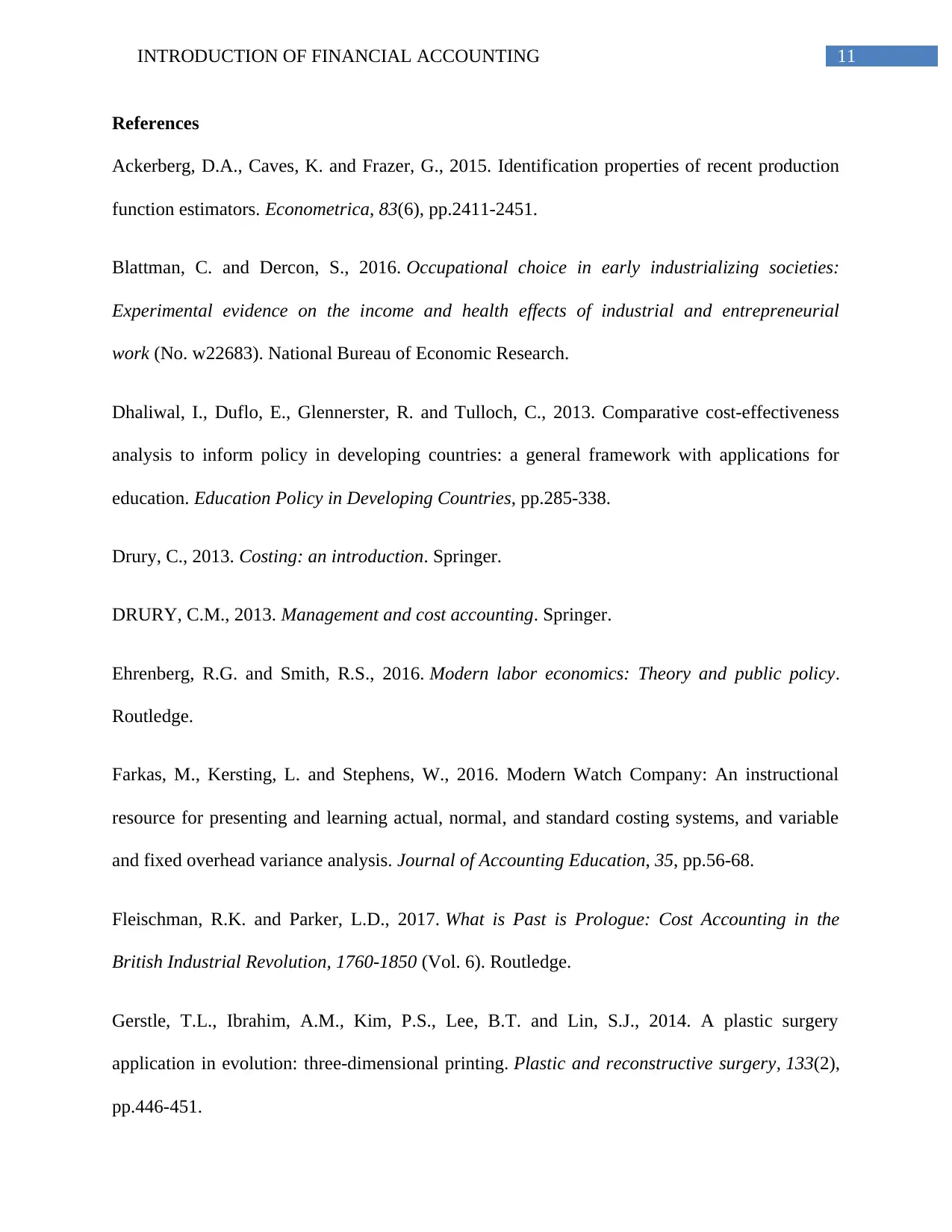
11INTRODUCTION OF FINANCIAL ACCOUNTING
References
Ackerberg, D.A., Caves, K. and Frazer, G., 2015. Identification properties of recent production
function estimators. Econometrica, 83(6), pp.2411-2451.
Blattman, C. and Dercon, S., 2016. Occupational choice in early industrializing societies:
Experimental evidence on the income and health effects of industrial and entrepreneurial
work (No. w22683). National Bureau of Economic Research.
Dhaliwal, I., Duflo, E., Glennerster, R. and Tulloch, C., 2013. Comparative cost-effectiveness
analysis to inform policy in developing countries: a general framework with applications for
education. Education Policy in Developing Countries, pp.285-338.
Drury, C., 2013. Costing: an introduction. Springer.
DRURY, C.M., 2013. Management and cost accounting. Springer.
Ehrenberg, R.G. and Smith, R.S., 2016. Modern labor economics: Theory and public policy.
Routledge.
Farkas, M., Kersting, L. and Stephens, W., 2016. Modern Watch Company: An instructional
resource for presenting and learning actual, normal, and standard costing systems, and variable
and fixed overhead variance analysis. Journal of Accounting Education, 35, pp.56-68.
Fleischman, R.K. and Parker, L.D., 2017. What is Past is Prologue: Cost Accounting in the
British Industrial Revolution, 1760-1850 (Vol. 6). Routledge.
Gerstle, T.L., Ibrahim, A.M., Kim, P.S., Lee, B.T. and Lin, S.J., 2014. A plastic surgery
application in evolution: three-dimensional printing. Plastic and reconstructive surgery, 133(2),
pp.446-451.
References
Ackerberg, D.A., Caves, K. and Frazer, G., 2015. Identification properties of recent production
function estimators. Econometrica, 83(6), pp.2411-2451.
Blattman, C. and Dercon, S., 2016. Occupational choice in early industrializing societies:
Experimental evidence on the income and health effects of industrial and entrepreneurial
work (No. w22683). National Bureau of Economic Research.
Dhaliwal, I., Duflo, E., Glennerster, R. and Tulloch, C., 2013. Comparative cost-effectiveness
analysis to inform policy in developing countries: a general framework with applications for
education. Education Policy in Developing Countries, pp.285-338.
Drury, C., 2013. Costing: an introduction. Springer.
DRURY, C.M., 2013. Management and cost accounting. Springer.
Ehrenberg, R.G. and Smith, R.S., 2016. Modern labor economics: Theory and public policy.
Routledge.
Farkas, M., Kersting, L. and Stephens, W., 2016. Modern Watch Company: An instructional
resource for presenting and learning actual, normal, and standard costing systems, and variable
and fixed overhead variance analysis. Journal of Accounting Education, 35, pp.56-68.
Fleischman, R.K. and Parker, L.D., 2017. What is Past is Prologue: Cost Accounting in the
British Industrial Revolution, 1760-1850 (Vol. 6). Routledge.
Gerstle, T.L., Ibrahim, A.M., Kim, P.S., Lee, B.T. and Lin, S.J., 2014. A plastic surgery
application in evolution: three-dimensional printing. Plastic and reconstructive surgery, 133(2),
pp.446-451.
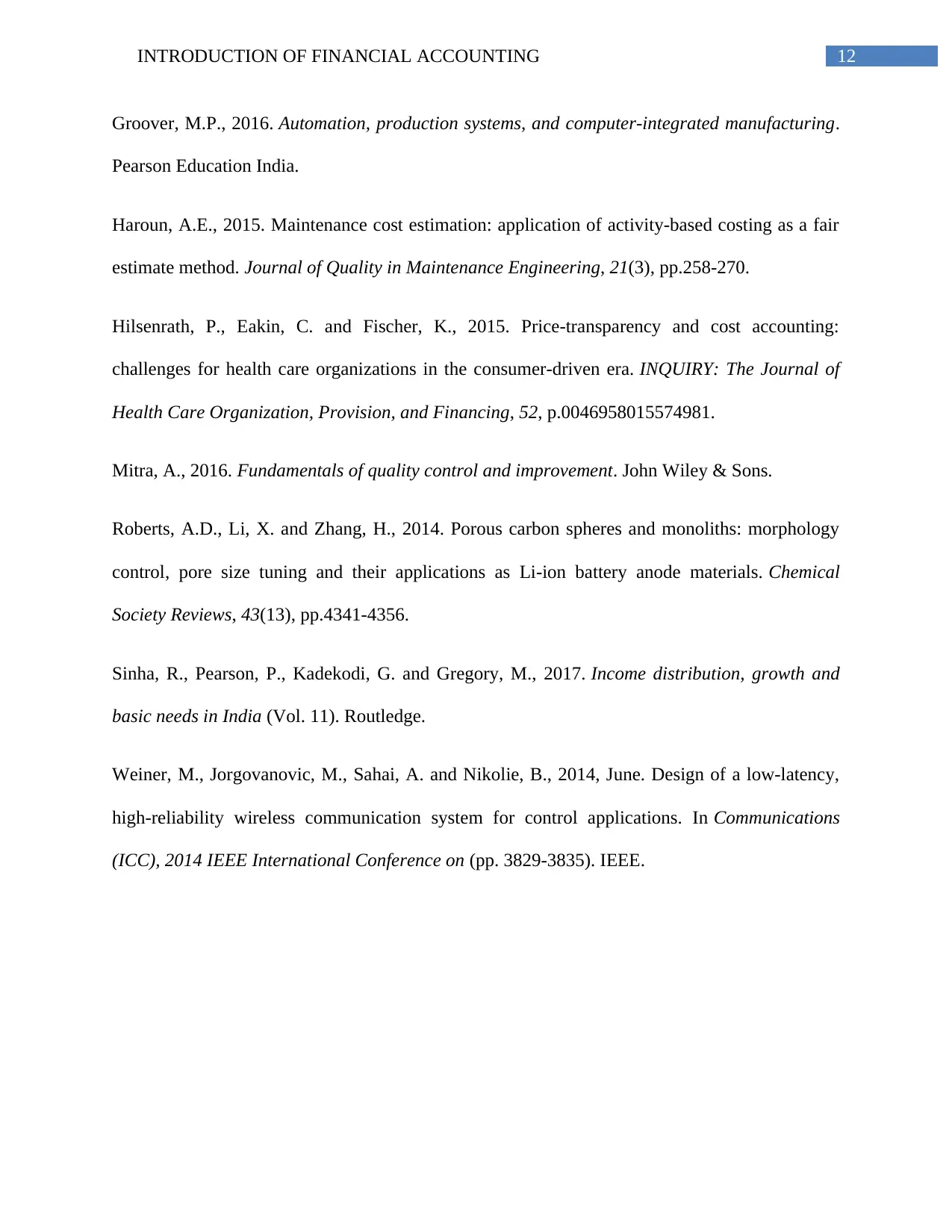
12INTRODUCTION OF FINANCIAL ACCOUNTING
Groover, M.P., 2016. Automation, production systems, and computer-integrated manufacturing.
Pearson Education India.
Haroun, A.E., 2015. Maintenance cost estimation: application of activity-based costing as a fair
estimate method. Journal of Quality in Maintenance Engineering, 21(3), pp.258-270.
Hilsenrath, P., Eakin, C. and Fischer, K., 2015. Price-transparency and cost accounting:
challenges for health care organizations in the consumer-driven era. INQUIRY: The Journal of
Health Care Organization, Provision, and Financing, 52, p.0046958015574981.
Mitra, A., 2016. Fundamentals of quality control and improvement. John Wiley & Sons.
Roberts, A.D., Li, X. and Zhang, H., 2014. Porous carbon spheres and monoliths: morphology
control, pore size tuning and their applications as Li-ion battery anode materials. Chemical
Society Reviews, 43(13), pp.4341-4356.
Sinha, R., Pearson, P., Kadekodi, G. and Gregory, M., 2017. Income distribution, growth and
basic needs in India (Vol. 11). Routledge.
Weiner, M., Jorgovanovic, M., Sahai, A. and Nikolie, B., 2014, June. Design of a low-latency,
high-reliability wireless communication system for control applications. In Communications
(ICC), 2014 IEEE International Conference on (pp. 3829-3835). IEEE.
Groover, M.P., 2016. Automation, production systems, and computer-integrated manufacturing.
Pearson Education India.
Haroun, A.E., 2015. Maintenance cost estimation: application of activity-based costing as a fair
estimate method. Journal of Quality in Maintenance Engineering, 21(3), pp.258-270.
Hilsenrath, P., Eakin, C. and Fischer, K., 2015. Price-transparency and cost accounting:
challenges for health care organizations in the consumer-driven era. INQUIRY: The Journal of
Health Care Organization, Provision, and Financing, 52, p.0046958015574981.
Mitra, A., 2016. Fundamentals of quality control and improvement. John Wiley & Sons.
Roberts, A.D., Li, X. and Zhang, H., 2014. Porous carbon spheres and monoliths: morphology
control, pore size tuning and their applications as Li-ion battery anode materials. Chemical
Society Reviews, 43(13), pp.4341-4356.
Sinha, R., Pearson, P., Kadekodi, G. and Gregory, M., 2017. Income distribution, growth and
basic needs in India (Vol. 11). Routledge.
Weiner, M., Jorgovanovic, M., Sahai, A. and Nikolie, B., 2014, June. Design of a low-latency,
high-reliability wireless communication system for control applications. In Communications
(ICC), 2014 IEEE International Conference on (pp. 3829-3835). IEEE.
1 out of 13
Related Documents

Your All-in-One AI-Powered Toolkit for Academic Success.
 +13062052269
info@desklib.com
Available 24*7 on WhatsApp / Email
Unlock your academic potential
© 2024  |  Zucol Services PVT LTD  |  All rights reserved.