Management and Organization Report: Fordism, Taylorism, Toyota
VerifiedAdded on 2021/06/15
|9
|1773
|129
Report
AI Summary
This report examines the concepts of Fordism and Taylorism, highlighting their impact on production efficiency and the evolution of manufacturing processes. It contrasts these approaches with the corporate culture of Toyota, analyzing its seven dimensions and how they contribute to the company's success. The report discusses the historical context of these management styles, their relevance in contemporary business environments, and their application in various industries, including call centers. It explores the benefits of these approaches, such as increased production and employee motivation, while also addressing potential drawbacks like lack of job security and the need for adaptation in modern workplaces. The report emphasizes the importance of understanding these management concepts for effective leadership and organizational strategy. It also includes an analysis of how Toyota's culture fosters teamwork, innovation, and customer focus.
Contribute Materials
Your contribution can guide someone’s learning journey. Share your
documents today.
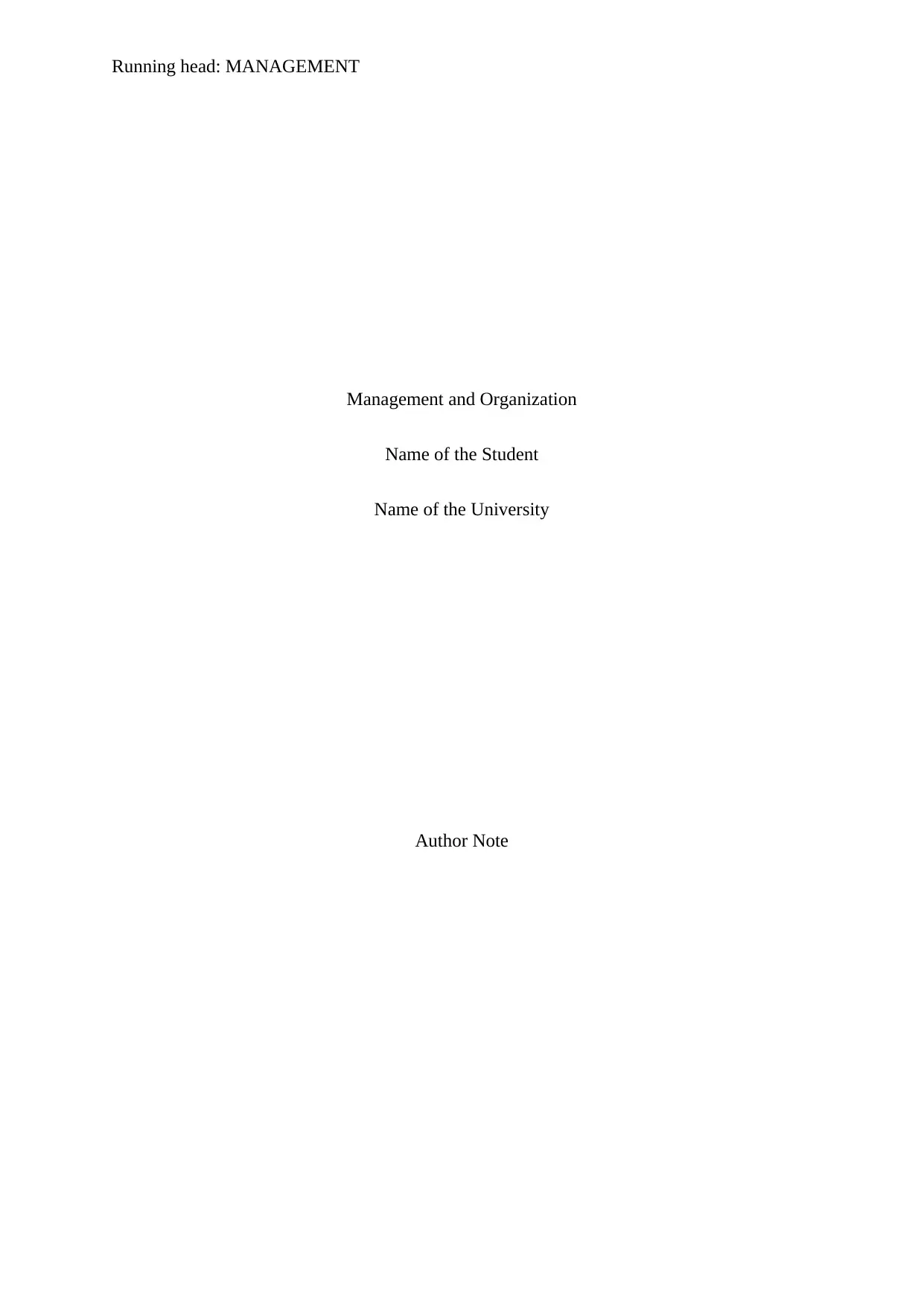
Running head: MANAGEMENT
Management and Organization
Name of the Student
Name of the University
Author Note
Management and Organization
Name of the Student
Name of the University
Author Note
Secure Best Marks with AI Grader
Need help grading? Try our AI Grader for instant feedback on your assignments.
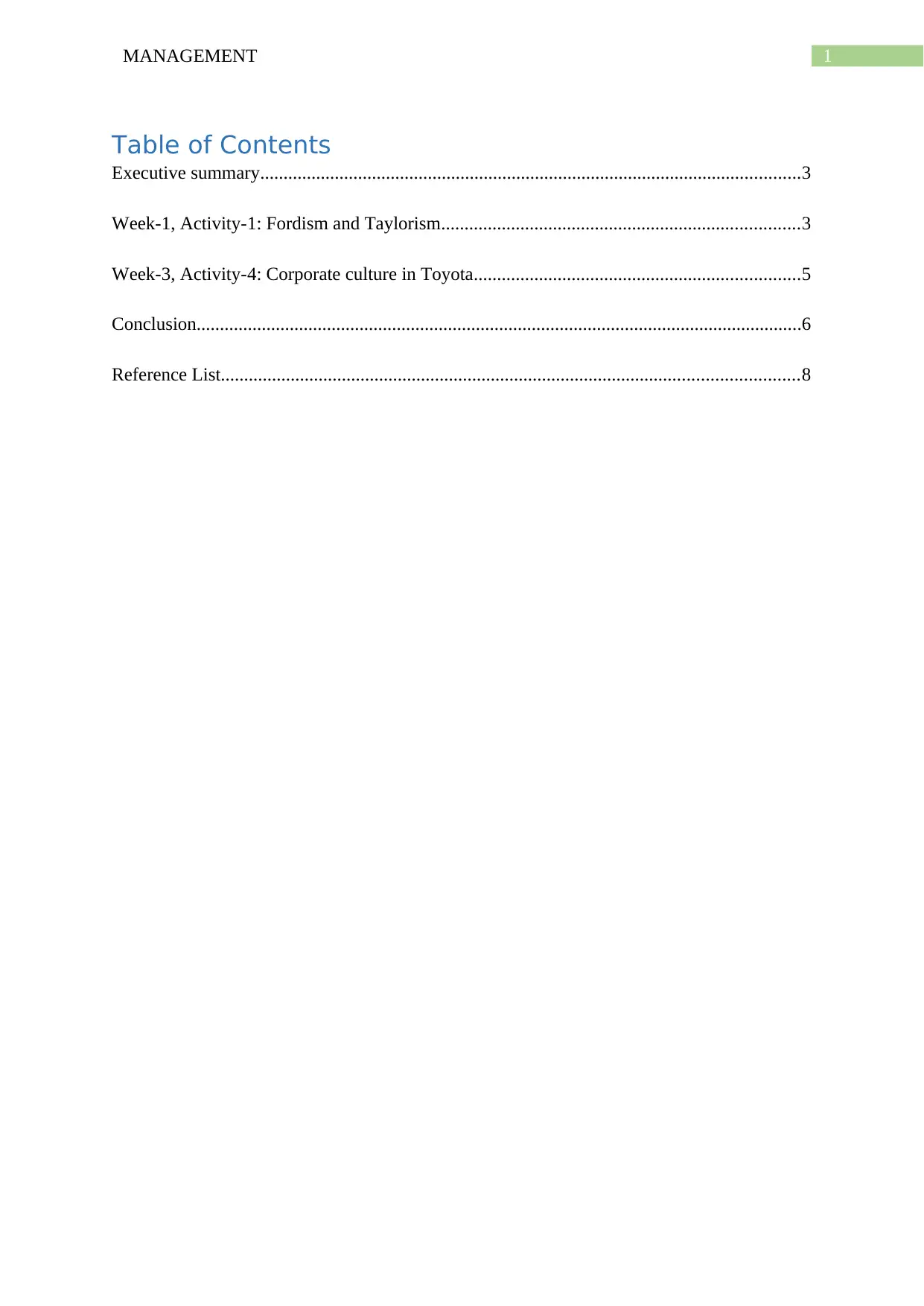
1MANAGEMENT
Table of Contents
Executive summary....................................................................................................................3
Week-1, Activity-1: Fordism and Taylorism.............................................................................3
Week-3, Activity-4: Corporate culture in Toyota......................................................................5
Conclusion..................................................................................................................................6
Reference List............................................................................................................................8
Table of Contents
Executive summary....................................................................................................................3
Week-1, Activity-1: Fordism and Taylorism.............................................................................3
Week-3, Activity-4: Corporate culture in Toyota......................................................................5
Conclusion..................................................................................................................................6
Reference List............................................................................................................................8
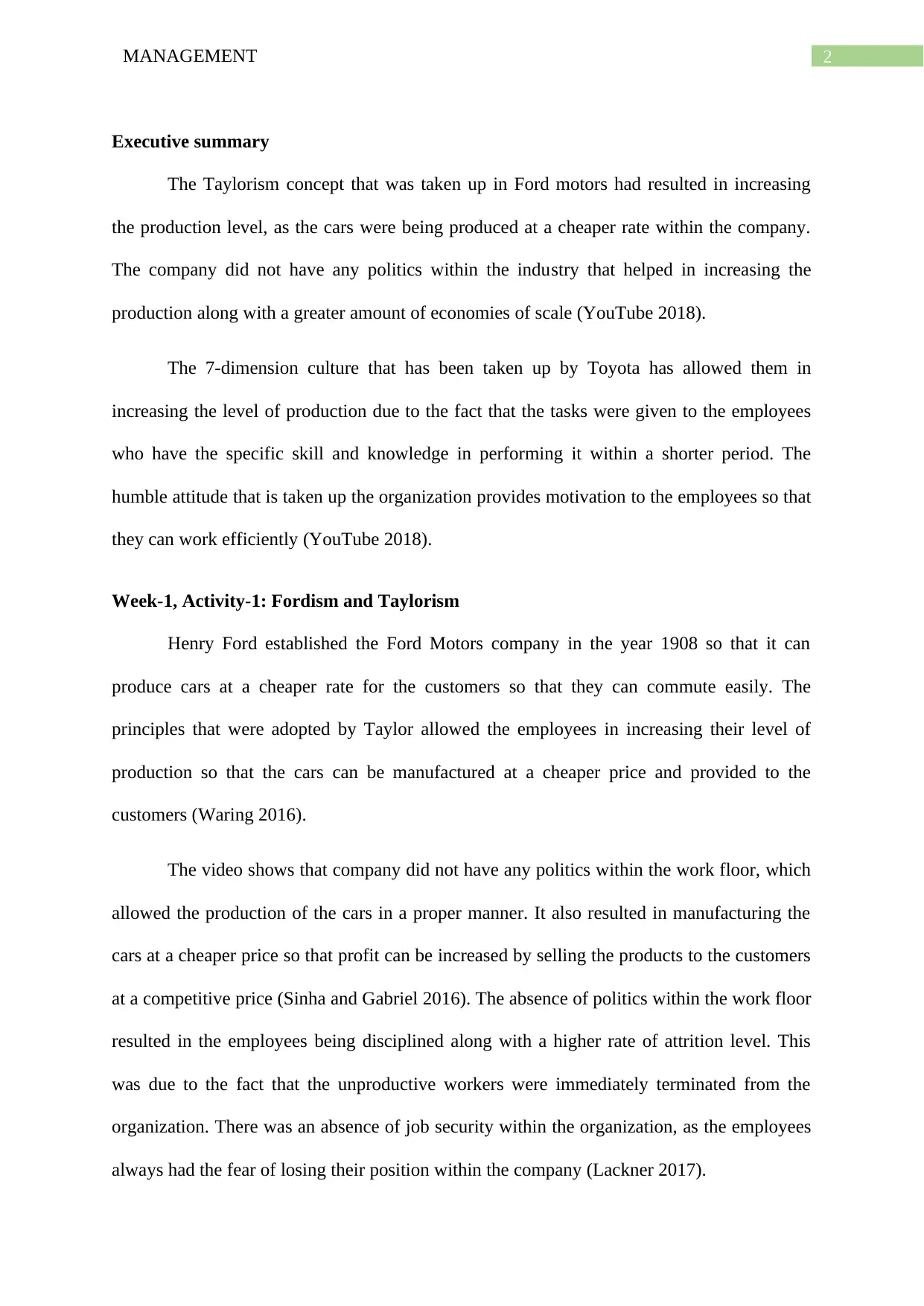
2MANAGEMENT
Executive summary
The Taylorism concept that was taken up in Ford motors had resulted in increasing
the production level, as the cars were being produced at a cheaper rate within the company.
The company did not have any politics within the industry that helped in increasing the
production along with a greater amount of economies of scale (YouTube 2018).
The 7-dimension culture that has been taken up by Toyota has allowed them in
increasing the level of production due to the fact that the tasks were given to the employees
who have the specific skill and knowledge in performing it within a shorter period. The
humble attitude that is taken up the organization provides motivation to the employees so that
they can work efficiently (YouTube 2018).
Week-1, Activity-1: Fordism and Taylorism
Henry Ford established the Ford Motors company in the year 1908 so that it can
produce cars at a cheaper rate for the customers so that they can commute easily. The
principles that were adopted by Taylor allowed the employees in increasing their level of
production so that the cars can be manufactured at a cheaper price and provided to the
customers (Waring 2016).
The video shows that company did not have any politics within the work floor, which
allowed the production of the cars in a proper manner. It also resulted in manufacturing the
cars at a cheaper price so that profit can be increased by selling the products to the customers
at a competitive price (Sinha and Gabriel 2016). The absence of politics within the work floor
resulted in the employees being disciplined along with a higher rate of attrition level. This
was due to the fact that the unproductive workers were immediately terminated from the
organization. There was an absence of job security within the organization, as the employees
always had the fear of losing their position within the company (Lackner 2017).
Executive summary
The Taylorism concept that was taken up in Ford motors had resulted in increasing
the production level, as the cars were being produced at a cheaper rate within the company.
The company did not have any politics within the industry that helped in increasing the
production along with a greater amount of economies of scale (YouTube 2018).
The 7-dimension culture that has been taken up by Toyota has allowed them in
increasing the level of production due to the fact that the tasks were given to the employees
who have the specific skill and knowledge in performing it within a shorter period. The
humble attitude that is taken up the organization provides motivation to the employees so that
they can work efficiently (YouTube 2018).
Week-1, Activity-1: Fordism and Taylorism
Henry Ford established the Ford Motors company in the year 1908 so that it can
produce cars at a cheaper rate for the customers so that they can commute easily. The
principles that were adopted by Taylor allowed the employees in increasing their level of
production so that the cars can be manufactured at a cheaper price and provided to the
customers (Waring 2016).
The video shows that company did not have any politics within the work floor, which
allowed the production of the cars in a proper manner. It also resulted in manufacturing the
cars at a cheaper price so that profit can be increased by selling the products to the customers
at a competitive price (Sinha and Gabriel 2016). The absence of politics within the work floor
resulted in the employees being disciplined along with a higher rate of attrition level. This
was due to the fact that the unproductive workers were immediately terminated from the
organization. There was an absence of job security within the organization, as the employees
always had the fear of losing their position within the company (Lackner 2017).
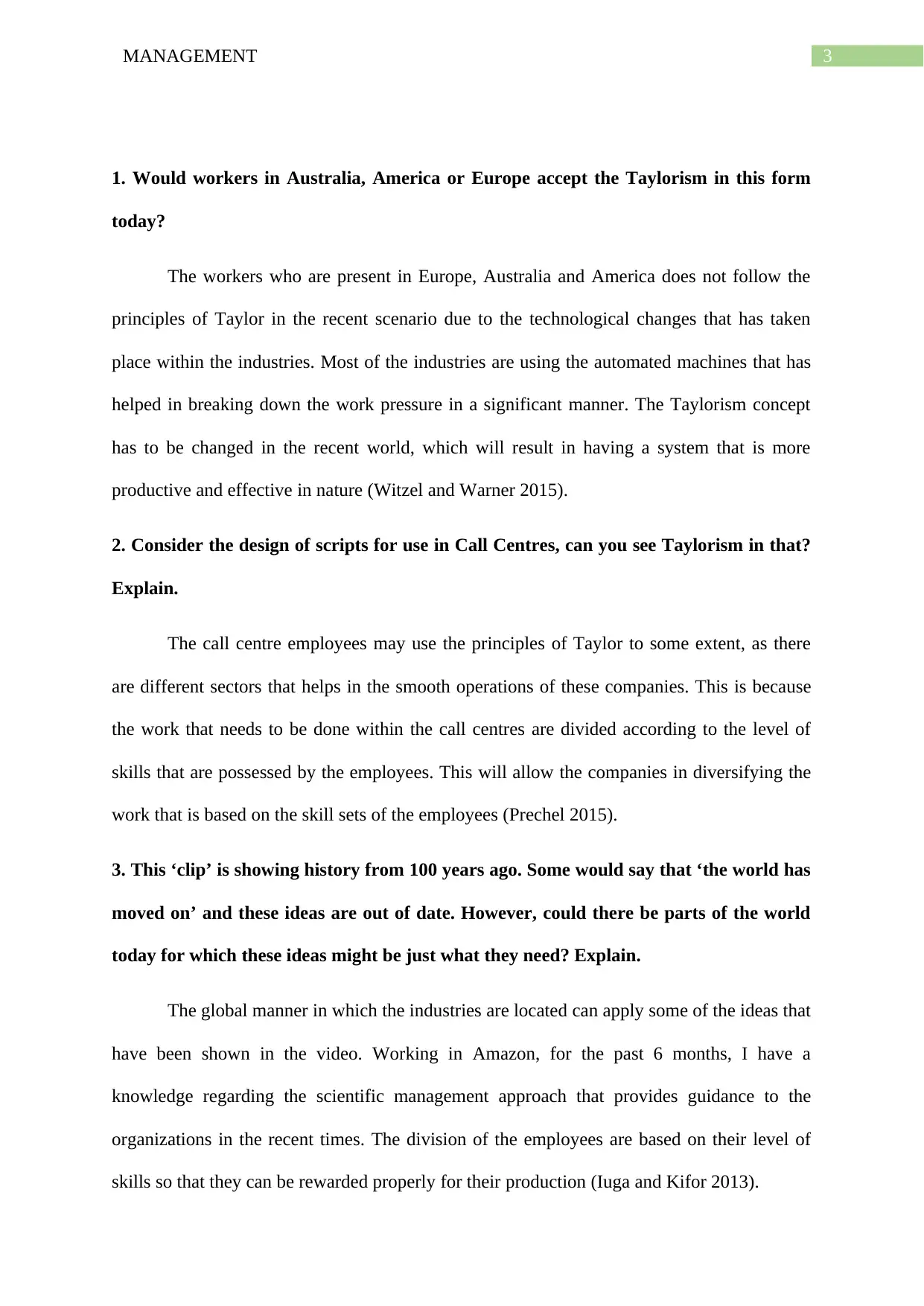
3MANAGEMENT
1. Would workers in Australia, America or Europe accept the Taylorism in this form
today?
The workers who are present in Europe, Australia and America does not follow the
principles of Taylor in the recent scenario due to the technological changes that has taken
place within the industries. Most of the industries are using the automated machines that has
helped in breaking down the work pressure in a significant manner. The Taylorism concept
has to be changed in the recent world, which will result in having a system that is more
productive and effective in nature (Witzel and Warner 2015).
2. Consider the design of scripts for use in Call Centres, can you see Taylorism in that?
Explain.
The call centre employees may use the principles of Taylor to some extent, as there
are different sectors that helps in the smooth operations of these companies. This is because
the work that needs to be done within the call centres are divided according to the level of
skills that are possessed by the employees. This will allow the companies in diversifying the
work that is based on the skill sets of the employees (Prechel 2015).
3. This ‘clip’ is showing history from 100 years ago. Some would say that ‘the world has
moved on’ and these ideas are out of date. However, could there be parts of the world
today for which these ideas might be just what they need? Explain.
The global manner in which the industries are located can apply some of the ideas that
have been shown in the video. Working in Amazon, for the past 6 months, I have a
knowledge regarding the scientific management approach that provides guidance to the
organizations in the recent times. The division of the employees are based on their level of
skills so that they can be rewarded properly for their production (Iuga and Kifor 2013).
1. Would workers in Australia, America or Europe accept the Taylorism in this form
today?
The workers who are present in Europe, Australia and America does not follow the
principles of Taylor in the recent scenario due to the technological changes that has taken
place within the industries. Most of the industries are using the automated machines that has
helped in breaking down the work pressure in a significant manner. The Taylorism concept
has to be changed in the recent world, which will result in having a system that is more
productive and effective in nature (Witzel and Warner 2015).
2. Consider the design of scripts for use in Call Centres, can you see Taylorism in that?
Explain.
The call centre employees may use the principles of Taylor to some extent, as there
are different sectors that helps in the smooth operations of these companies. This is because
the work that needs to be done within the call centres are divided according to the level of
skills that are possessed by the employees. This will allow the companies in diversifying the
work that is based on the skill sets of the employees (Prechel 2015).
3. This ‘clip’ is showing history from 100 years ago. Some would say that ‘the world has
moved on’ and these ideas are out of date. However, could there be parts of the world
today for which these ideas might be just what they need? Explain.
The global manner in which the industries are located can apply some of the ideas that
have been shown in the video. Working in Amazon, for the past 6 months, I have a
knowledge regarding the scientific management approach that provides guidance to the
organizations in the recent times. The division of the employees are based on their level of
skills so that they can be rewarded properly for their production (Iuga and Kifor 2013).
Secure Best Marks with AI Grader
Need help grading? Try our AI Grader for instant feedback on your assignments.
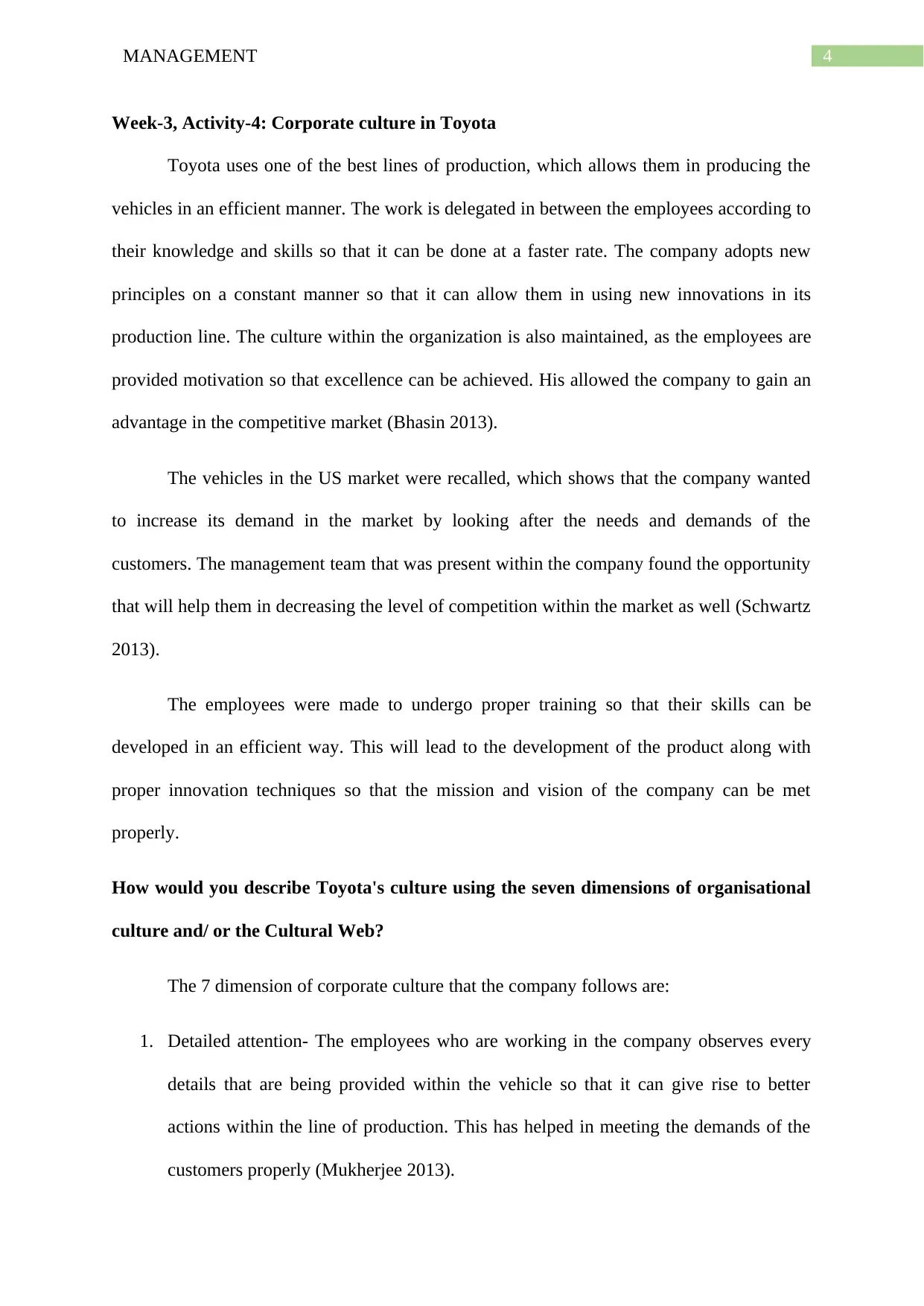
4MANAGEMENT
Week-3, Activity-4: Corporate culture in Toyota
Toyota uses one of the best lines of production, which allows them in producing the
vehicles in an efficient manner. The work is delegated in between the employees according to
their knowledge and skills so that it can be done at a faster rate. The company adopts new
principles on a constant manner so that it can allow them in using new innovations in its
production line. The culture within the organization is also maintained, as the employees are
provided motivation so that excellence can be achieved. His allowed the company to gain an
advantage in the competitive market (Bhasin 2013).
The vehicles in the US market were recalled, which shows that the company wanted
to increase its demand in the market by looking after the needs and demands of the
customers. The management team that was present within the company found the opportunity
that will help them in decreasing the level of competition within the market as well (Schwartz
2013).
The employees were made to undergo proper training so that their skills can be
developed in an efficient way. This will lead to the development of the product along with
proper innovation techniques so that the mission and vision of the company can be met
properly.
How would you describe Toyota's culture using the seven dimensions of organisational
culture and/ or the Cultural Web?
The 7 dimension of corporate culture that the company follows are:
1. Detailed attention- The employees who are working in the company observes every
details that are being provided within the vehicle so that it can give rise to better
actions within the line of production. This has helped in meeting the demands of the
customers properly (Mukherjee 2013).
Week-3, Activity-4: Corporate culture in Toyota
Toyota uses one of the best lines of production, which allows them in producing the
vehicles in an efficient manner. The work is delegated in between the employees according to
their knowledge and skills so that it can be done at a faster rate. The company adopts new
principles on a constant manner so that it can allow them in using new innovations in its
production line. The culture within the organization is also maintained, as the employees are
provided motivation so that excellence can be achieved. His allowed the company to gain an
advantage in the competitive market (Bhasin 2013).
The vehicles in the US market were recalled, which shows that the company wanted
to increase its demand in the market by looking after the needs and demands of the
customers. The management team that was present within the company found the opportunity
that will help them in decreasing the level of competition within the market as well (Schwartz
2013).
The employees were made to undergo proper training so that their skills can be
developed in an efficient way. This will lead to the development of the product along with
proper innovation techniques so that the mission and vision of the company can be met
properly.
How would you describe Toyota's culture using the seven dimensions of organisational
culture and/ or the Cultural Web?
The 7 dimension of corporate culture that the company follows are:
1. Detailed attention- The employees who are working in the company observes every
details that are being provided within the vehicle so that it can give rise to better
actions within the line of production. This has helped in meeting the demands of the
customers properly (Mukherjee 2013).
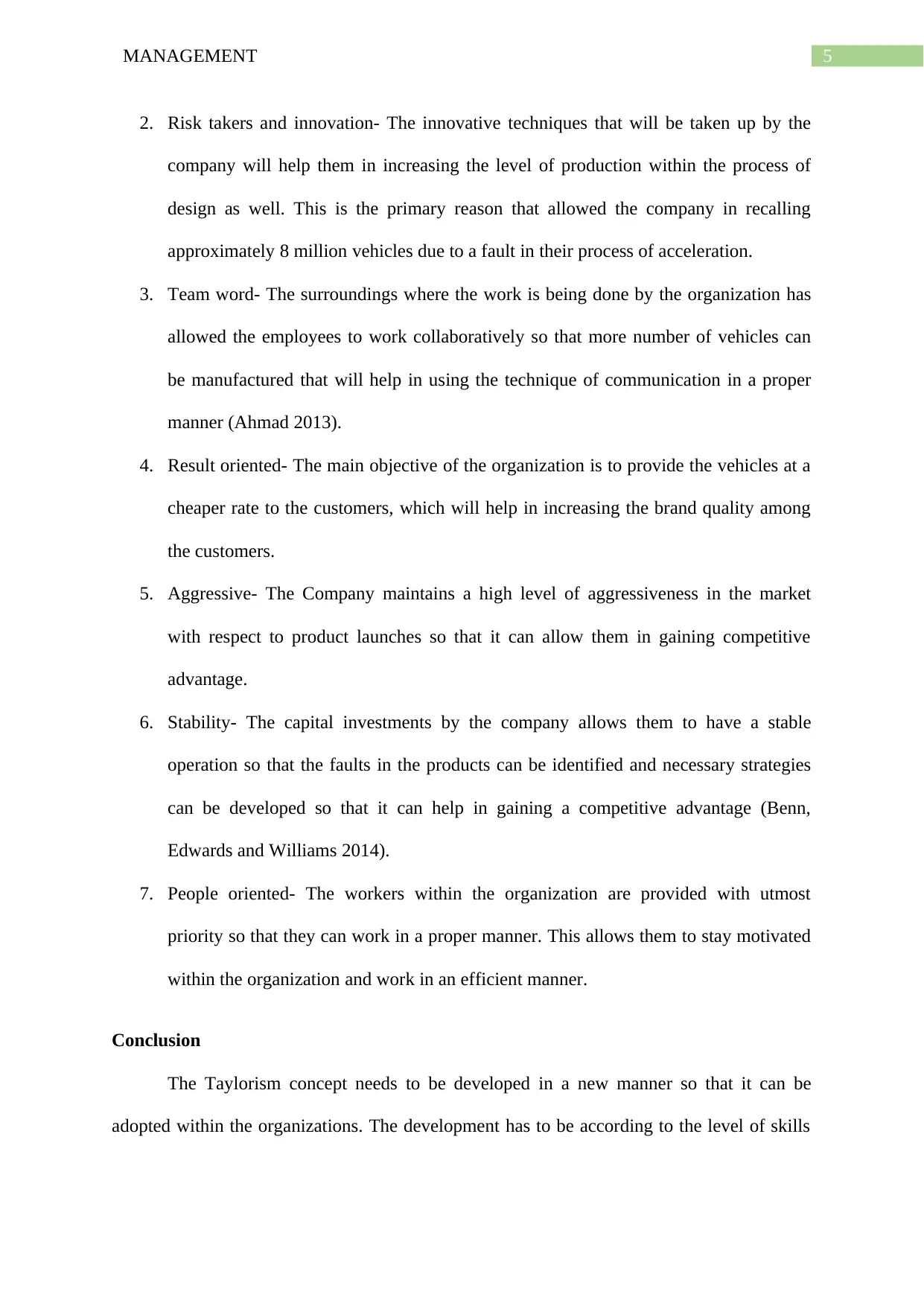
5MANAGEMENT
2. Risk takers and innovation- The innovative techniques that will be taken up by the
company will help them in increasing the level of production within the process of
design as well. This is the primary reason that allowed the company in recalling
approximately 8 million vehicles due to a fault in their process of acceleration.
3. Team word- The surroundings where the work is being done by the organization has
allowed the employees to work collaboratively so that more number of vehicles can
be manufactured that will help in using the technique of communication in a proper
manner (Ahmad 2013).
4. Result oriented- The main objective of the organization is to provide the vehicles at a
cheaper rate to the customers, which will help in increasing the brand quality among
the customers.
5. Aggressive- The Company maintains a high level of aggressiveness in the market
with respect to product launches so that it can allow them in gaining competitive
advantage.
6. Stability- The capital investments by the company allows them to have a stable
operation so that the faults in the products can be identified and necessary strategies
can be developed so that it can help in gaining a competitive advantage (Benn,
Edwards and Williams 2014).
7. People oriented- The workers within the organization are provided with utmost
priority so that they can work in a proper manner. This allows them to stay motivated
within the organization and work in an efficient manner.
Conclusion
The Taylorism concept needs to be developed in a new manner so that it can be
adopted within the organizations. The development has to be according to the level of skills
2. Risk takers and innovation- The innovative techniques that will be taken up by the
company will help them in increasing the level of production within the process of
design as well. This is the primary reason that allowed the company in recalling
approximately 8 million vehicles due to a fault in their process of acceleration.
3. Team word- The surroundings where the work is being done by the organization has
allowed the employees to work collaboratively so that more number of vehicles can
be manufactured that will help in using the technique of communication in a proper
manner (Ahmad 2013).
4. Result oriented- The main objective of the organization is to provide the vehicles at a
cheaper rate to the customers, which will help in increasing the brand quality among
the customers.
5. Aggressive- The Company maintains a high level of aggressiveness in the market
with respect to product launches so that it can allow them in gaining competitive
advantage.
6. Stability- The capital investments by the company allows them to have a stable
operation so that the faults in the products can be identified and necessary strategies
can be developed so that it can help in gaining a competitive advantage (Benn,
Edwards and Williams 2014).
7. People oriented- The workers within the organization are provided with utmost
priority so that they can work in a proper manner. This allows them to stay motivated
within the organization and work in an efficient manner.
Conclusion
The Taylorism concept needs to be developed in a new manner so that it can be
adopted within the organizations. The development has to be according to the level of skills
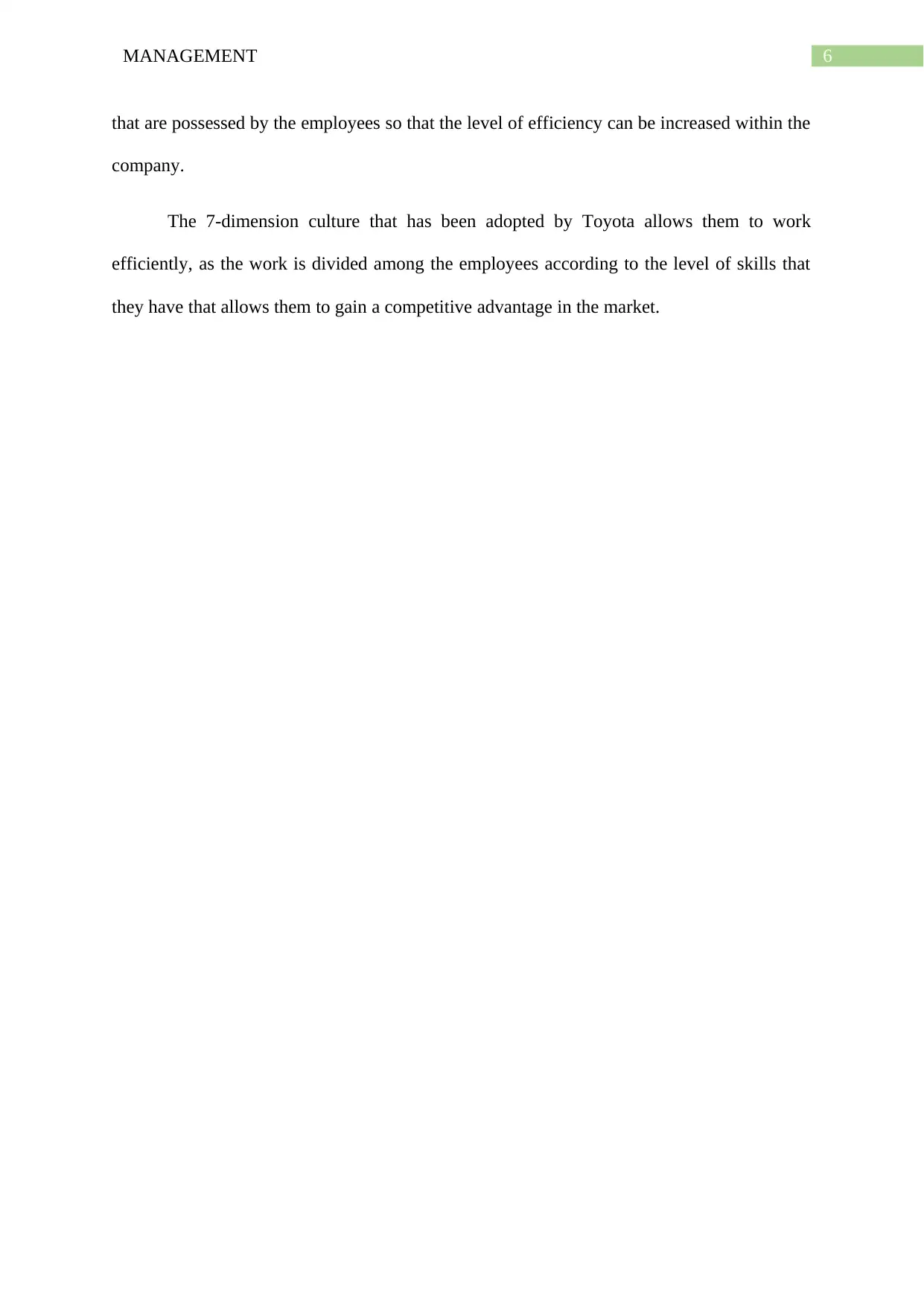
6MANAGEMENT
that are possessed by the employees so that the level of efficiency can be increased within the
company.
The 7-dimension culture that has been adopted by Toyota allows them to work
efficiently, as the work is divided among the employees according to the level of skills that
they have that allows them to gain a competitive advantage in the market.
that are possessed by the employees so that the level of efficiency can be increased within the
company.
The 7-dimension culture that has been adopted by Toyota allows them to work
efficiently, as the work is divided among the employees according to the level of skills that
they have that allows them to gain a competitive advantage in the market.
Paraphrase This Document
Need a fresh take? Get an instant paraphrase of this document with our AI Paraphraser
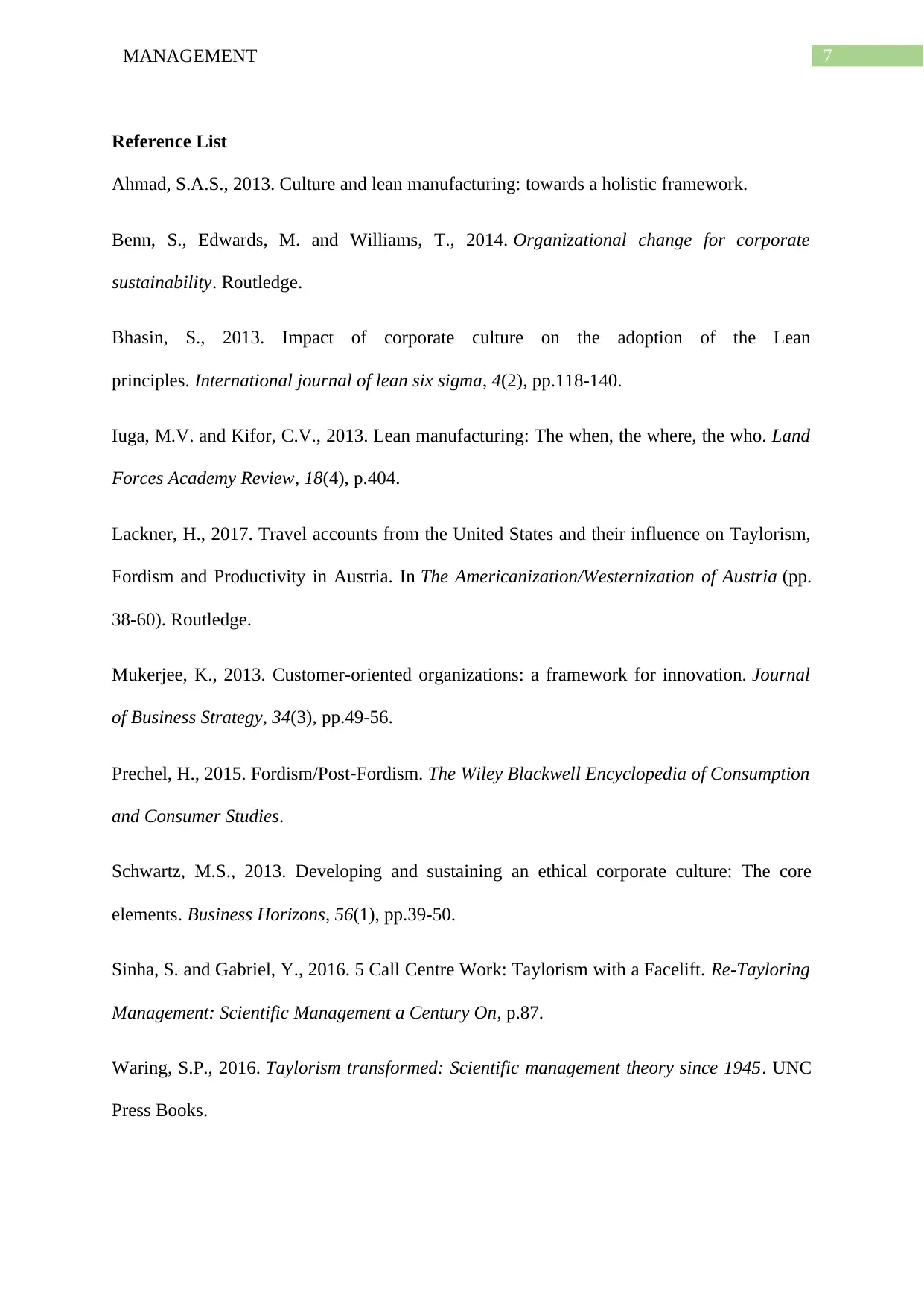
7MANAGEMENT
Reference List
Ahmad, S.A.S., 2013. Culture and lean manufacturing: towards a holistic framework.
Benn, S., Edwards, M. and Williams, T., 2014. Organizational change for corporate
sustainability. Routledge.
Bhasin, S., 2013. Impact of corporate culture on the adoption of the Lean
principles. International journal of lean six sigma, 4(2), pp.118-140.
Iuga, M.V. and Kifor, C.V., 2013. Lean manufacturing: The when, the where, the who. Land
Forces Academy Review, 18(4), p.404.
Lackner, H., 2017. Travel accounts from the United States and their influence on Taylorism,
Fordism and Productivity in Austria. In The Americanization/Westernization of Austria (pp.
38-60). Routledge.
Mukerjee, K., 2013. Customer-oriented organizations: a framework for innovation. Journal
of Business Strategy, 34(3), pp.49-56.
Prechel, H., 2015. Fordism/Post‐Fordism. The Wiley Blackwell Encyclopedia of Consumption
and Consumer Studies.
Schwartz, M.S., 2013. Developing and sustaining an ethical corporate culture: The core
elements. Business Horizons, 56(1), pp.39-50.
Sinha, S. and Gabriel, Y., 2016. 5 Call Centre Work: Taylorism with a Facelift. Re-Tayloring
Management: Scientific Management a Century On, p.87.
Waring, S.P., 2016. Taylorism transformed: Scientific management theory since 1945. UNC
Press Books.
Reference List
Ahmad, S.A.S., 2013. Culture and lean manufacturing: towards a holistic framework.
Benn, S., Edwards, M. and Williams, T., 2014. Organizational change for corporate
sustainability. Routledge.
Bhasin, S., 2013. Impact of corporate culture on the adoption of the Lean
principles. International journal of lean six sigma, 4(2), pp.118-140.
Iuga, M.V. and Kifor, C.V., 2013. Lean manufacturing: The when, the where, the who. Land
Forces Academy Review, 18(4), p.404.
Lackner, H., 2017. Travel accounts from the United States and their influence on Taylorism,
Fordism and Productivity in Austria. In The Americanization/Westernization of Austria (pp.
38-60). Routledge.
Mukerjee, K., 2013. Customer-oriented organizations: a framework for innovation. Journal
of Business Strategy, 34(3), pp.49-56.
Prechel, H., 2015. Fordism/Post‐Fordism. The Wiley Blackwell Encyclopedia of Consumption
and Consumer Studies.
Schwartz, M.S., 2013. Developing and sustaining an ethical corporate culture: The core
elements. Business Horizons, 56(1), pp.39-50.
Sinha, S. and Gabriel, Y., 2016. 5 Call Centre Work: Taylorism with a Facelift. Re-Tayloring
Management: Scientific Management a Century On, p.87.
Waring, S.P., 2016. Taylorism transformed: Scientific management theory since 1945. UNC
Press Books.
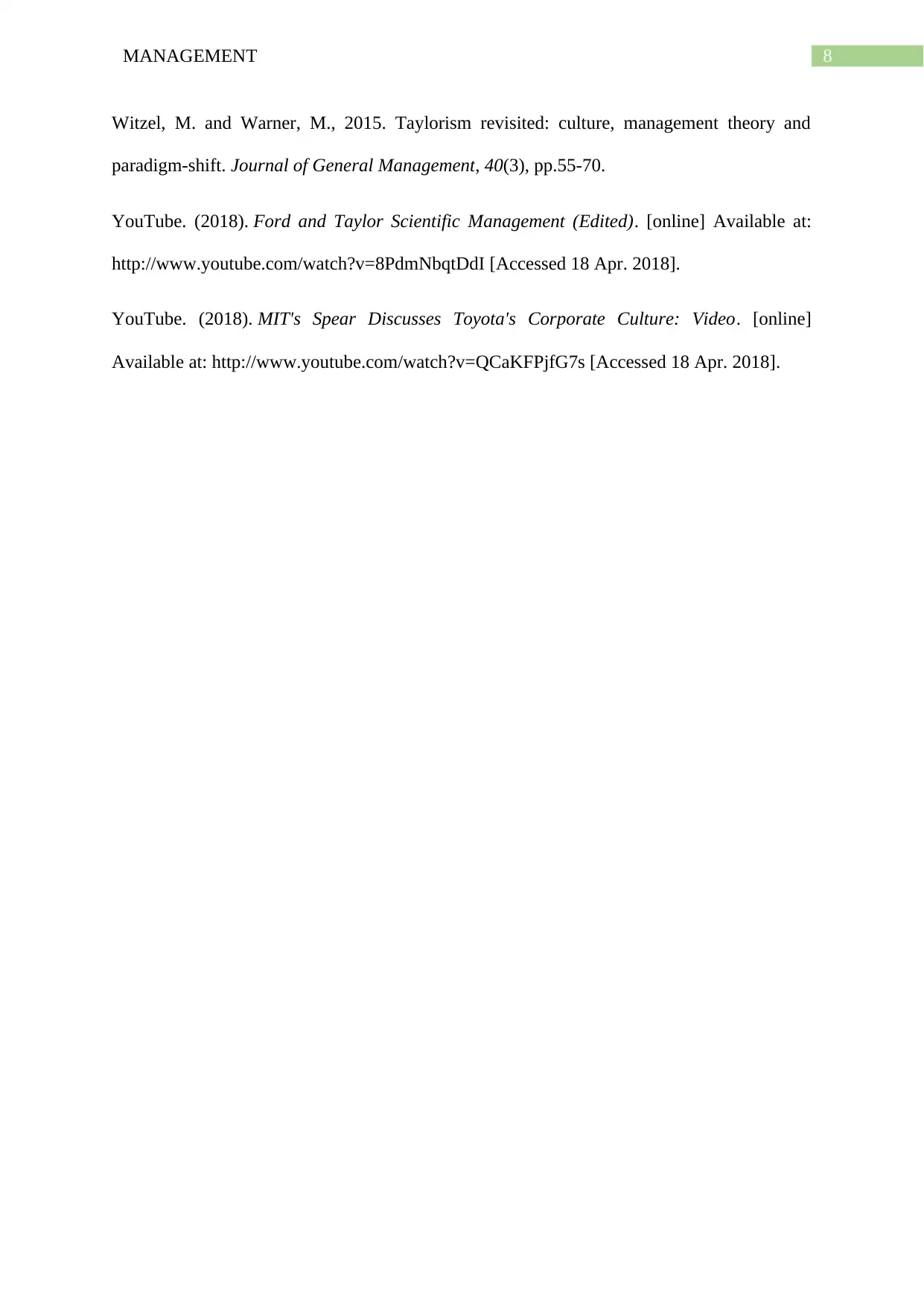
8MANAGEMENT
Witzel, M. and Warner, M., 2015. Taylorism revisited: culture, management theory and
paradigm-shift. Journal of General Management, 40(3), pp.55-70.
YouTube. (2018). Ford and Taylor Scientific Management (Edited). [online] Available at:
http://www.youtube.com/watch?v=8PdmNbqtDdI [Accessed 18 Apr. 2018].
YouTube. (2018). MIT's Spear Discusses Toyota's Corporate Culture: Video. [online]
Available at: http://www.youtube.com/watch?v=QCaKFPjfG7s [Accessed 18 Apr. 2018].
Witzel, M. and Warner, M., 2015. Taylorism revisited: culture, management theory and
paradigm-shift. Journal of General Management, 40(3), pp.55-70.
YouTube. (2018). Ford and Taylor Scientific Management (Edited). [online] Available at:
http://www.youtube.com/watch?v=8PdmNbqtDdI [Accessed 18 Apr. 2018].
YouTube. (2018). MIT's Spear Discusses Toyota's Corporate Culture: Video. [online]
Available at: http://www.youtube.com/watch?v=QCaKFPjfG7s [Accessed 18 Apr. 2018].
1 out of 9
Related Documents

Your All-in-One AI-Powered Toolkit for Academic Success.
+13062052269
info@desklib.com
Available 24*7 on WhatsApp / Email
Unlock your academic potential
© 2024 | Zucol Services PVT LTD | All rights reserved.