Contrasting approaches for operational improvements
VerifiedAdded on 2022/12/21
|15
|3837
|93
AI Summary
This paper discusses the lean thinking and six sigma approaches for operational improvement, with a focus on the digitalization within the selected organization. It also explores the links between operations strategy and operations improvement theories.
Contribute Materials
Your contribution can guide someone’s learning journey. Share your
documents today.
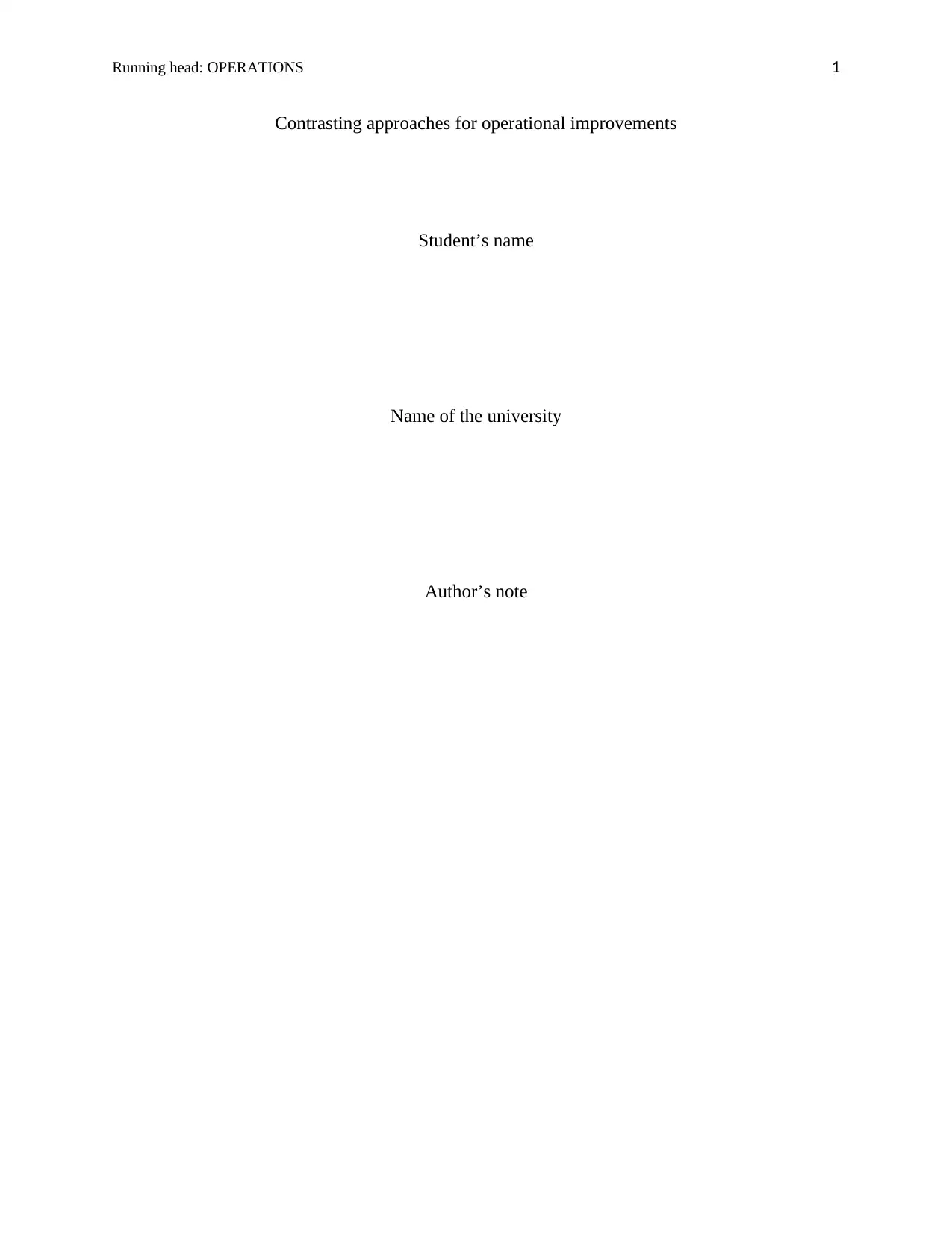
Running head: OPERATIONS 1
Contrasting approaches for operational improvements
Student’s name
Name of the university
Author’s note
Contrasting approaches for operational improvements
Student’s name
Name of the university
Author’s note
Secure Best Marks with AI Grader
Need help grading? Try our AI Grader for instant feedback on your assignments.
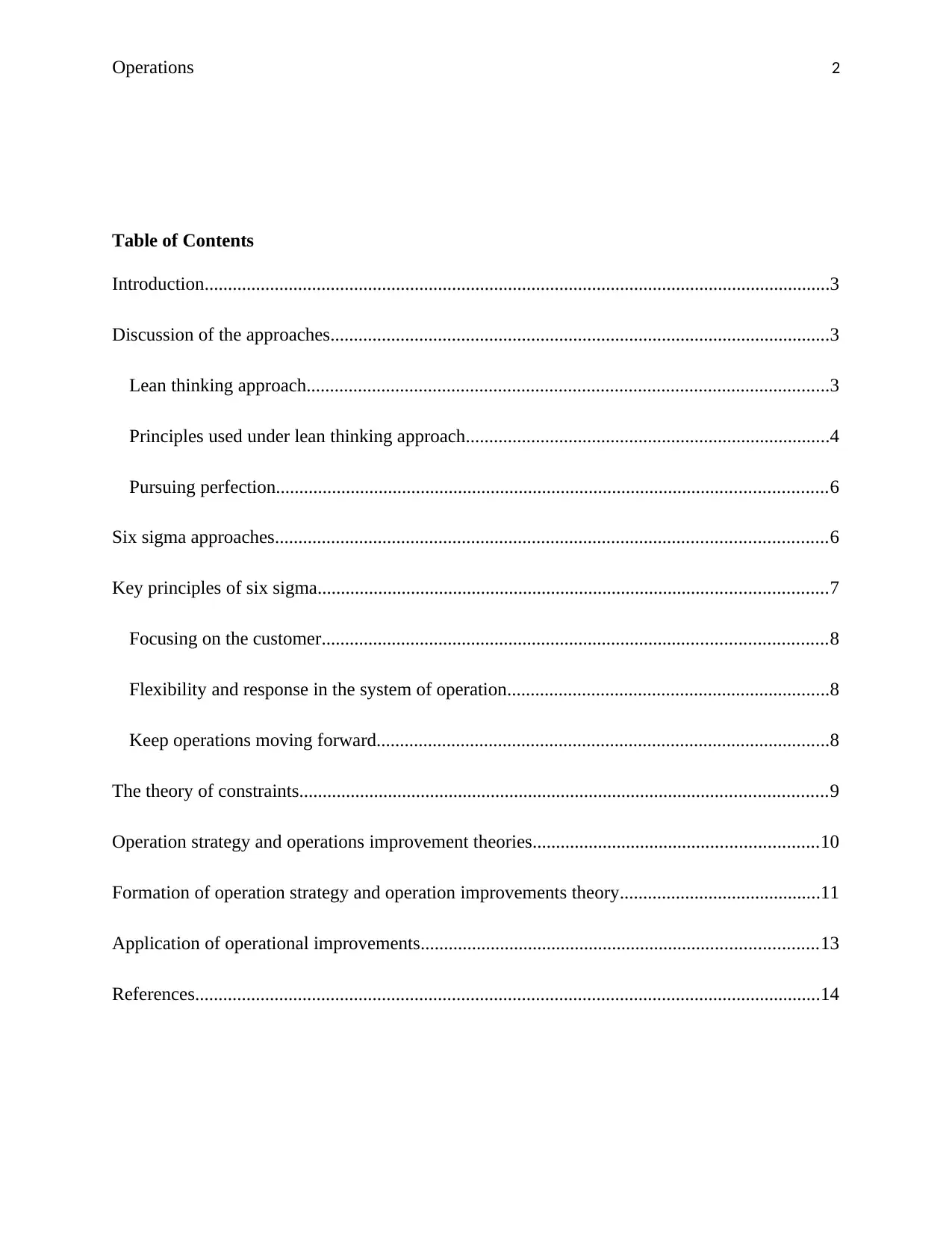
Operations 2
Table of Contents
Introduction......................................................................................................................................3
Discussion of the approaches...........................................................................................................3
Lean thinking approach................................................................................................................3
Principles used under lean thinking approach..............................................................................4
Pursuing perfection......................................................................................................................6
Six sigma approaches......................................................................................................................6
Key principles of six sigma.............................................................................................................7
Focusing on the customer............................................................................................................8
Flexibility and response in the system of operation.....................................................................8
Keep operations moving forward.................................................................................................8
The theory of constraints.................................................................................................................9
Operation strategy and operations improvement theories.............................................................10
Formation of operation strategy and operation improvements theory...........................................11
Application of operational improvements.....................................................................................13
References......................................................................................................................................14
Table of Contents
Introduction......................................................................................................................................3
Discussion of the approaches...........................................................................................................3
Lean thinking approach................................................................................................................3
Principles used under lean thinking approach..............................................................................4
Pursuing perfection......................................................................................................................6
Six sigma approaches......................................................................................................................6
Key principles of six sigma.............................................................................................................7
Focusing on the customer............................................................................................................8
Flexibility and response in the system of operation.....................................................................8
Keep operations moving forward.................................................................................................8
The theory of constraints.................................................................................................................9
Operation strategy and operations improvement theories.............................................................10
Formation of operation strategy and operation improvements theory...........................................11
Application of operational improvements.....................................................................................13
References......................................................................................................................................14
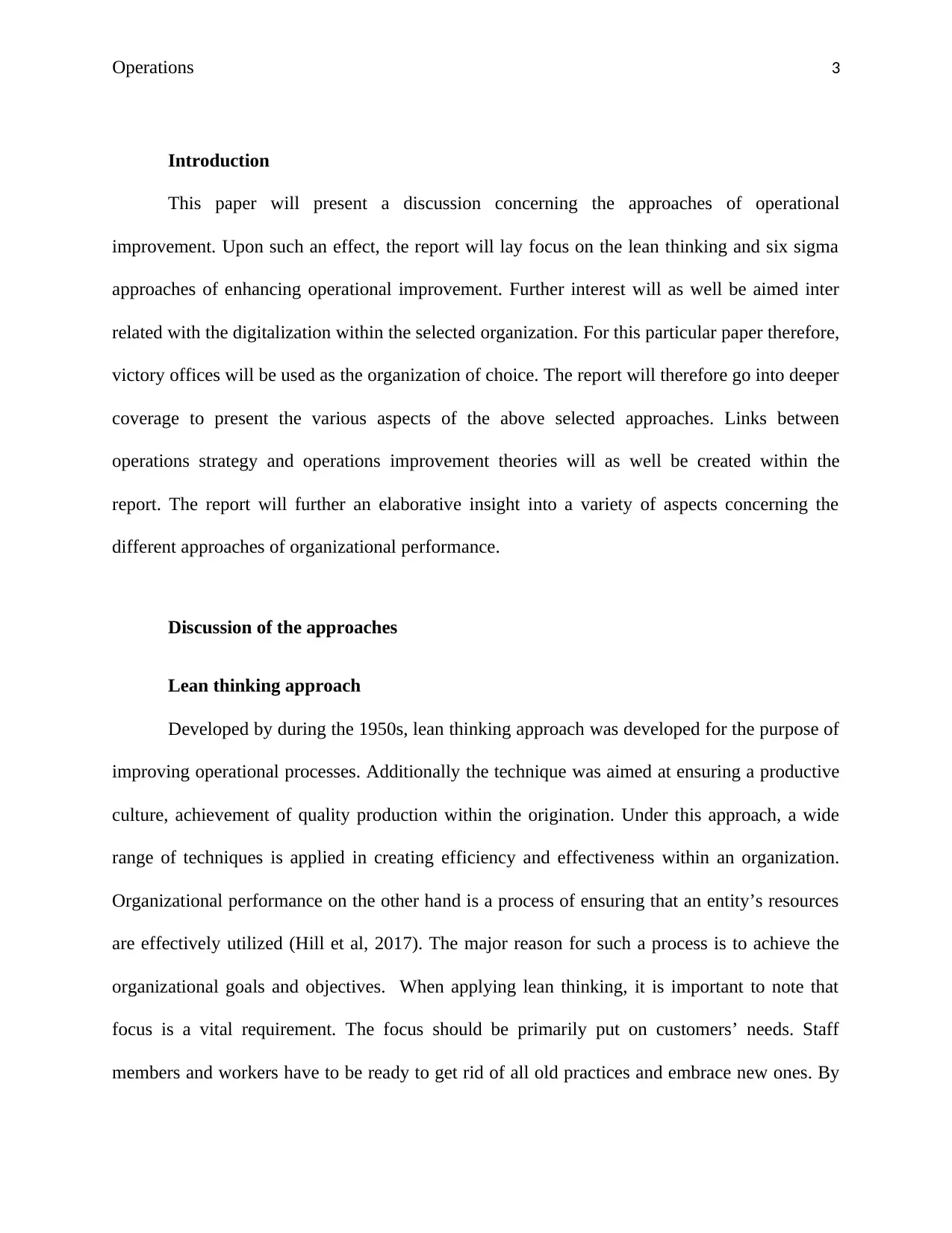
Operations 3
Introduction
This paper will present a discussion concerning the approaches of operational
improvement. Upon such an effect, the report will lay focus on the lean thinking and six sigma
approaches of enhancing operational improvement. Further interest will as well be aimed inter
related with the digitalization within the selected organization. For this particular paper therefore,
victory offices will be used as the organization of choice. The report will therefore go into deeper
coverage to present the various aspects of the above selected approaches. Links between
operations strategy and operations improvement theories will as well be created within the
report. The report will further an elaborative insight into a variety of aspects concerning the
different approaches of organizational performance.
Discussion of the approaches
Lean thinking approach
Developed by during the 1950s, lean thinking approach was developed for the purpose of
improving operational processes. Additionally the technique was aimed at ensuring a productive
culture, achievement of quality production within the origination. Under this approach, a wide
range of techniques is applied in creating efficiency and effectiveness within an organization.
Organizational performance on the other hand is a process of ensuring that an entity’s resources
are effectively utilized (Hill et al, 2017). The major reason for such a process is to achieve the
organizational goals and objectives. When applying lean thinking, it is important to note that
focus is a vital requirement. The focus should be primarily put on customers’ needs. Staff
members and workers have to be ready to get rid of all old practices and embrace new ones. By
Introduction
This paper will present a discussion concerning the approaches of operational
improvement. Upon such an effect, the report will lay focus on the lean thinking and six sigma
approaches of enhancing operational improvement. Further interest will as well be aimed inter
related with the digitalization within the selected organization. For this particular paper therefore,
victory offices will be used as the organization of choice. The report will therefore go into deeper
coverage to present the various aspects of the above selected approaches. Links between
operations strategy and operations improvement theories will as well be created within the
report. The report will further an elaborative insight into a variety of aspects concerning the
different approaches of organizational performance.
Discussion of the approaches
Lean thinking approach
Developed by during the 1950s, lean thinking approach was developed for the purpose of
improving operational processes. Additionally the technique was aimed at ensuring a productive
culture, achievement of quality production within the origination. Under this approach, a wide
range of techniques is applied in creating efficiency and effectiveness within an organization.
Organizational performance on the other hand is a process of ensuring that an entity’s resources
are effectively utilized (Hill et al, 2017). The major reason for such a process is to achieve the
organizational goals and objectives. When applying lean thinking, it is important to note that
focus is a vital requirement. The focus should be primarily put on customers’ needs. Staff
members and workers have to be ready to get rid of all old practices and embrace new ones. By
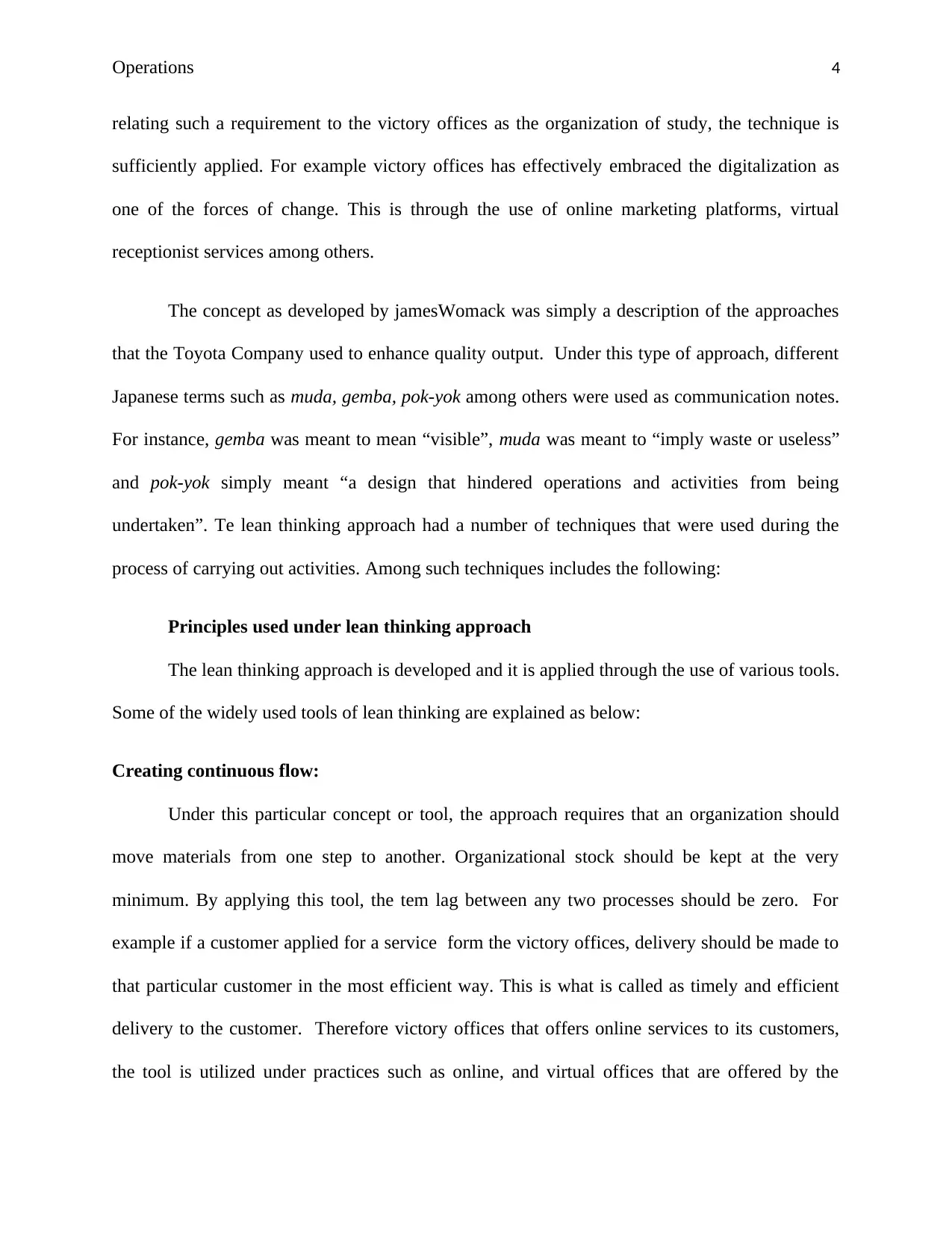
Operations 4
relating such a requirement to the victory offices as the organization of study, the technique is
sufficiently applied. For example victory offices has effectively embraced the digitalization as
one of the forces of change. This is through the use of online marketing platforms, virtual
receptionist services among others.
The concept as developed by jamesWomack was simply a description of the approaches
that the Toyota Company used to enhance quality output. Under this type of approach, different
Japanese terms such as muda, gemba, pok-yok among others were used as communication notes.
For instance, gemba was meant to mean “visible”, muda was meant to “imply waste or useless”
and pok-yok simply meant “a design that hindered operations and activities from being
undertaken”. Te lean thinking approach had a number of techniques that were used during the
process of carrying out activities. Among such techniques includes the following:
Principles used under lean thinking approach
The lean thinking approach is developed and it is applied through the use of various tools.
Some of the widely used tools of lean thinking are explained as below:
Creating continuous flow:
Under this particular concept or tool, the approach requires that an organization should
move materials from one step to another. Organizational stock should be kept at the very
minimum. By applying this tool, the tem lag between any two processes should be zero. For
example if a customer applied for a service form the victory offices, delivery should be made to
that particular customer in the most efficient way. This is what is called as timely and efficient
delivery to the customer. Therefore victory offices that offers online services to its customers,
the tool is utilized under practices such as online, and virtual offices that are offered by the
relating such a requirement to the victory offices as the organization of study, the technique is
sufficiently applied. For example victory offices has effectively embraced the digitalization as
one of the forces of change. This is through the use of online marketing platforms, virtual
receptionist services among others.
The concept as developed by jamesWomack was simply a description of the approaches
that the Toyota Company used to enhance quality output. Under this type of approach, different
Japanese terms such as muda, gemba, pok-yok among others were used as communication notes.
For instance, gemba was meant to mean “visible”, muda was meant to “imply waste or useless”
and pok-yok simply meant “a design that hindered operations and activities from being
undertaken”. Te lean thinking approach had a number of techniques that were used during the
process of carrying out activities. Among such techniques includes the following:
Principles used under lean thinking approach
The lean thinking approach is developed and it is applied through the use of various tools.
Some of the widely used tools of lean thinking are explained as below:
Creating continuous flow:
Under this particular concept or tool, the approach requires that an organization should
move materials from one step to another. Organizational stock should be kept at the very
minimum. By applying this tool, the tem lag between any two processes should be zero. For
example if a customer applied for a service form the victory offices, delivery should be made to
that particular customer in the most efficient way. This is what is called as timely and efficient
delivery to the customer. Therefore victory offices that offers online services to its customers,
the tool is utilized under practices such as online, and virtual offices that are offered by the
Secure Best Marks with AI Grader
Need help grading? Try our AI Grader for instant feedback on your assignments.
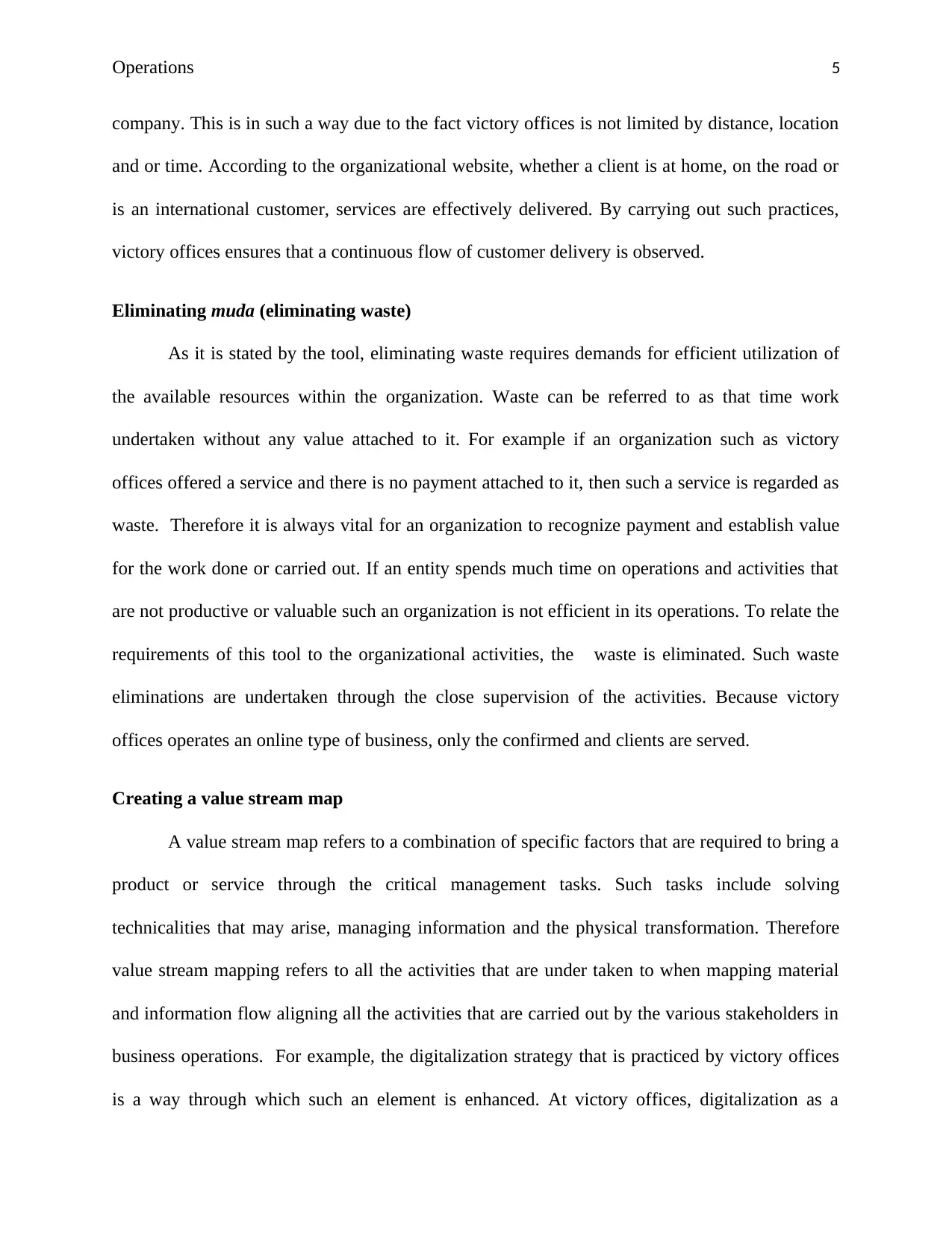
Operations 5
company. This is in such a way due to the fact victory offices is not limited by distance, location
and or time. According to the organizational website, whether a client is at home, on the road or
is an international customer, services are effectively delivered. By carrying out such practices,
victory offices ensures that a continuous flow of customer delivery is observed.
Eliminating muda (eliminating waste)
As it is stated by the tool, eliminating waste requires demands for efficient utilization of
the available resources within the organization. Waste can be referred to as that time work
undertaken without any value attached to it. For example if an organization such as victory
offices offered a service and there is no payment attached to it, then such a service is regarded as
waste. Therefore it is always vital for an organization to recognize payment and establish value
for the work done or carried out. If an entity spends much time on operations and activities that
are not productive or valuable such an organization is not efficient in its operations. To relate the
requirements of this tool to the organizational activities, the waste is eliminated. Such waste
eliminations are undertaken through the close supervision of the activities. Because victory
offices operates an online type of business, only the confirmed and clients are served.
Creating a value stream map
A value stream map refers to a combination of specific factors that are required to bring a
product or service through the critical management tasks. Such tasks include solving
technicalities that may arise, managing information and the physical transformation. Therefore
value stream mapping refers to all the activities that are under taken to when mapping material
and information flow aligning all the activities that are carried out by the various stakeholders in
business operations. For example, the digitalization strategy that is practiced by victory offices
is a way through which such an element is enhanced. At victory offices, digitalization as a
company. This is in such a way due to the fact victory offices is not limited by distance, location
and or time. According to the organizational website, whether a client is at home, on the road or
is an international customer, services are effectively delivered. By carrying out such practices,
victory offices ensures that a continuous flow of customer delivery is observed.
Eliminating muda (eliminating waste)
As it is stated by the tool, eliminating waste requires demands for efficient utilization of
the available resources within the organization. Waste can be referred to as that time work
undertaken without any value attached to it. For example if an organization such as victory
offices offered a service and there is no payment attached to it, then such a service is regarded as
waste. Therefore it is always vital for an organization to recognize payment and establish value
for the work done or carried out. If an entity spends much time on operations and activities that
are not productive or valuable such an organization is not efficient in its operations. To relate the
requirements of this tool to the organizational activities, the waste is eliminated. Such waste
eliminations are undertaken through the close supervision of the activities. Because victory
offices operates an online type of business, only the confirmed and clients are served.
Creating a value stream map
A value stream map refers to a combination of specific factors that are required to bring a
product or service through the critical management tasks. Such tasks include solving
technicalities that may arise, managing information and the physical transformation. Therefore
value stream mapping refers to all the activities that are under taken to when mapping material
and information flow aligning all the activities that are carried out by the various stakeholders in
business operations. For example, the digitalization strategy that is practiced by victory offices
is a way through which such an element is enhanced. At victory offices, digitalization as a
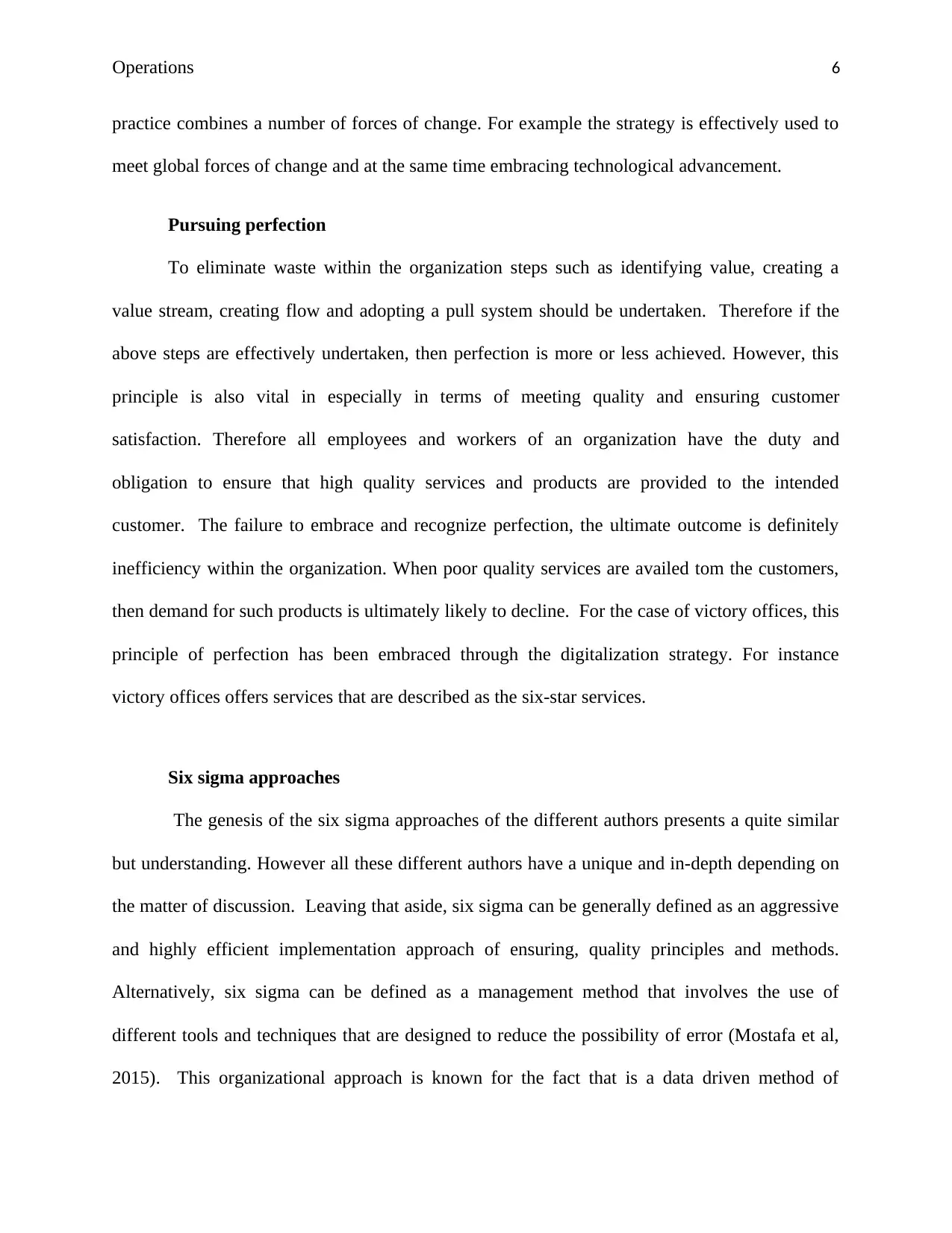
Operations 6
practice combines a number of forces of change. For example the strategy is effectively used to
meet global forces of change and at the same time embracing technological advancement.
Pursuing perfection
To eliminate waste within the organization steps such as identifying value, creating a
value stream, creating flow and adopting a pull system should be undertaken. Therefore if the
above steps are effectively undertaken, then perfection is more or less achieved. However, this
principle is also vital in especially in terms of meeting quality and ensuring customer
satisfaction. Therefore all employees and workers of an organization have the duty and
obligation to ensure that high quality services and products are provided to the intended
customer. The failure to embrace and recognize perfection, the ultimate outcome is definitely
inefficiency within the organization. When poor quality services are availed tom the customers,
then demand for such products is ultimately likely to decline. For the case of victory offices, this
principle of perfection has been embraced through the digitalization strategy. For instance
victory offices offers services that are described as the six-star services.
Six sigma approaches
The genesis of the six sigma approaches of the different authors presents a quite similar
but understanding. However all these different authors have a unique and in-depth depending on
the matter of discussion. Leaving that aside, six sigma can be generally defined as an aggressive
and highly efficient implementation approach of ensuring, quality principles and methods.
Alternatively, six sigma can be defined as a management method that involves the use of
different tools and techniques that are designed to reduce the possibility of error (Mostafa et al,
2015). This organizational approach is known for the fact that is a data driven method of
practice combines a number of forces of change. For example the strategy is effectively used to
meet global forces of change and at the same time embracing technological advancement.
Pursuing perfection
To eliminate waste within the organization steps such as identifying value, creating a
value stream, creating flow and adopting a pull system should be undertaken. Therefore if the
above steps are effectively undertaken, then perfection is more or less achieved. However, this
principle is also vital in especially in terms of meeting quality and ensuring customer
satisfaction. Therefore all employees and workers of an organization have the duty and
obligation to ensure that high quality services and products are provided to the intended
customer. The failure to embrace and recognize perfection, the ultimate outcome is definitely
inefficiency within the organization. When poor quality services are availed tom the customers,
then demand for such products is ultimately likely to decline. For the case of victory offices, this
principle of perfection has been embraced through the digitalization strategy. For instance
victory offices offers services that are described as the six-star services.
Six sigma approaches
The genesis of the six sigma approaches of the different authors presents a quite similar
but understanding. However all these different authors have a unique and in-depth depending on
the matter of discussion. Leaving that aside, six sigma can be generally defined as an aggressive
and highly efficient implementation approach of ensuring, quality principles and methods.
Alternatively, six sigma can be defined as a management method that involves the use of
different tools and techniques that are designed to reduce the possibility of error (Mostafa et al,
2015). This organizational approach is known for the fact that is a data driven method of
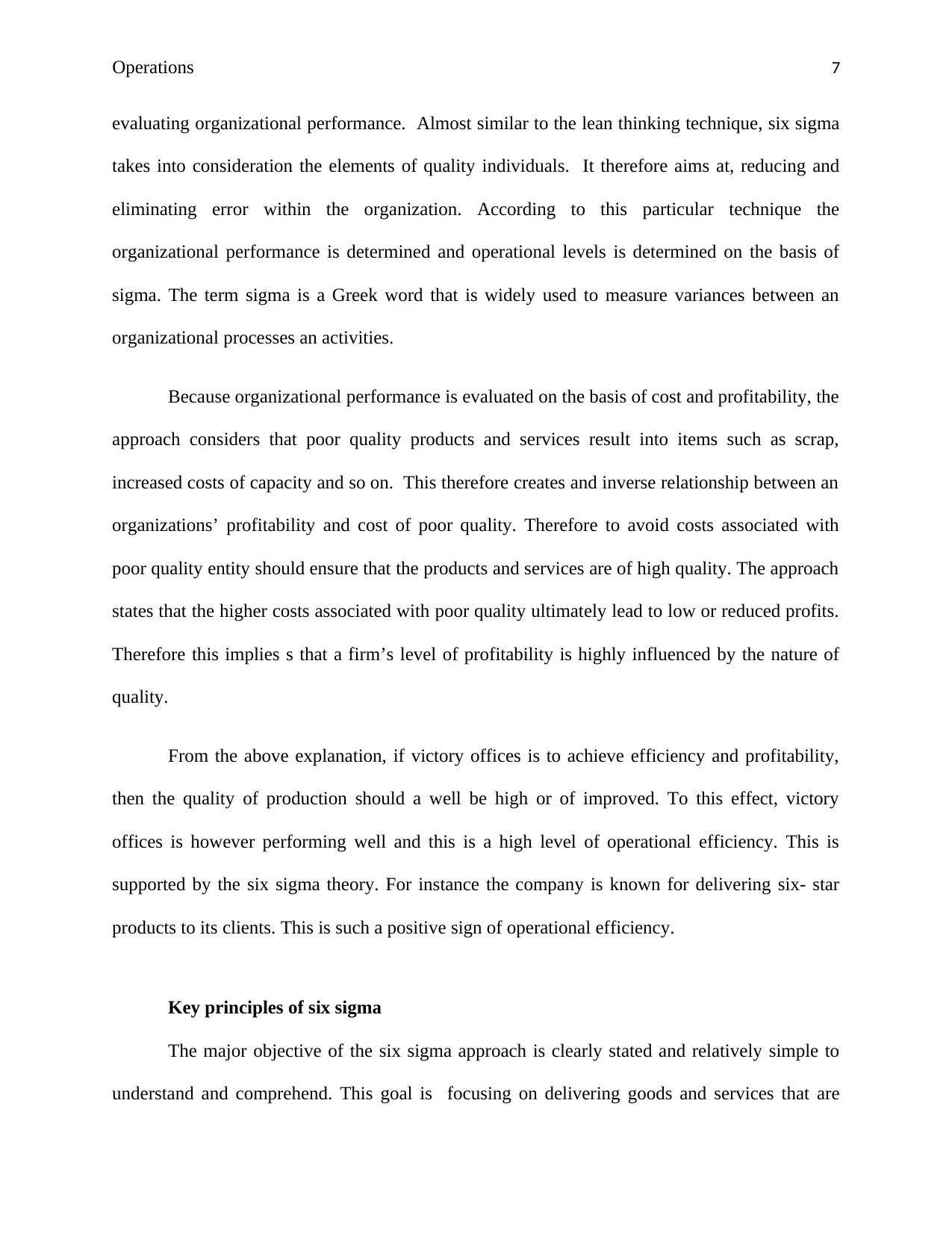
Operations 7
evaluating organizational performance. Almost similar to the lean thinking technique, six sigma
takes into consideration the elements of quality individuals. It therefore aims at, reducing and
eliminating error within the organization. According to this particular technique the
organizational performance is determined and operational levels is determined on the basis of
sigma. The term sigma is a Greek word that is widely used to measure variances between an
organizational processes an activities.
Because organizational performance is evaluated on the basis of cost and profitability, the
approach considers that poor quality products and services result into items such as scrap,
increased costs of capacity and so on. This therefore creates and inverse relationship between an
organizations’ profitability and cost of poor quality. Therefore to avoid costs associated with
poor quality entity should ensure that the products and services are of high quality. The approach
states that the higher costs associated with poor quality ultimately lead to low or reduced profits.
Therefore this implies s that a firm’s level of profitability is highly influenced by the nature of
quality.
From the above explanation, if victory offices is to achieve efficiency and profitability,
then the quality of production should a well be high or of improved. To this effect, victory
offices is however performing well and this is a high level of operational efficiency. This is
supported by the six sigma theory. For instance the company is known for delivering six- star
products to its clients. This is such a positive sign of operational efficiency.
Key principles of six sigma
The major objective of the six sigma approach is clearly stated and relatively simple to
understand and comprehend. This goal is focusing on delivering goods and services that are
evaluating organizational performance. Almost similar to the lean thinking technique, six sigma
takes into consideration the elements of quality individuals. It therefore aims at, reducing and
eliminating error within the organization. According to this particular technique the
organizational performance is determined and operational levels is determined on the basis of
sigma. The term sigma is a Greek word that is widely used to measure variances between an
organizational processes an activities.
Because organizational performance is evaluated on the basis of cost and profitability, the
approach considers that poor quality products and services result into items such as scrap,
increased costs of capacity and so on. This therefore creates and inverse relationship between an
organizations’ profitability and cost of poor quality. Therefore to avoid costs associated with
poor quality entity should ensure that the products and services are of high quality. The approach
states that the higher costs associated with poor quality ultimately lead to low or reduced profits.
Therefore this implies s that a firm’s level of profitability is highly influenced by the nature of
quality.
From the above explanation, if victory offices is to achieve efficiency and profitability,
then the quality of production should a well be high or of improved. To this effect, victory
offices is however performing well and this is a high level of operational efficiency. This is
supported by the six sigma theory. For instance the company is known for delivering six- star
products to its clients. This is such a positive sign of operational efficiency.
Key principles of six sigma
The major objective of the six sigma approach is clearly stated and relatively simple to
understand and comprehend. This goal is focusing on delivering goods and services that are
Paraphrase This Document
Need a fresh take? Get an instant paraphrase of this document with our AI Paraphraser
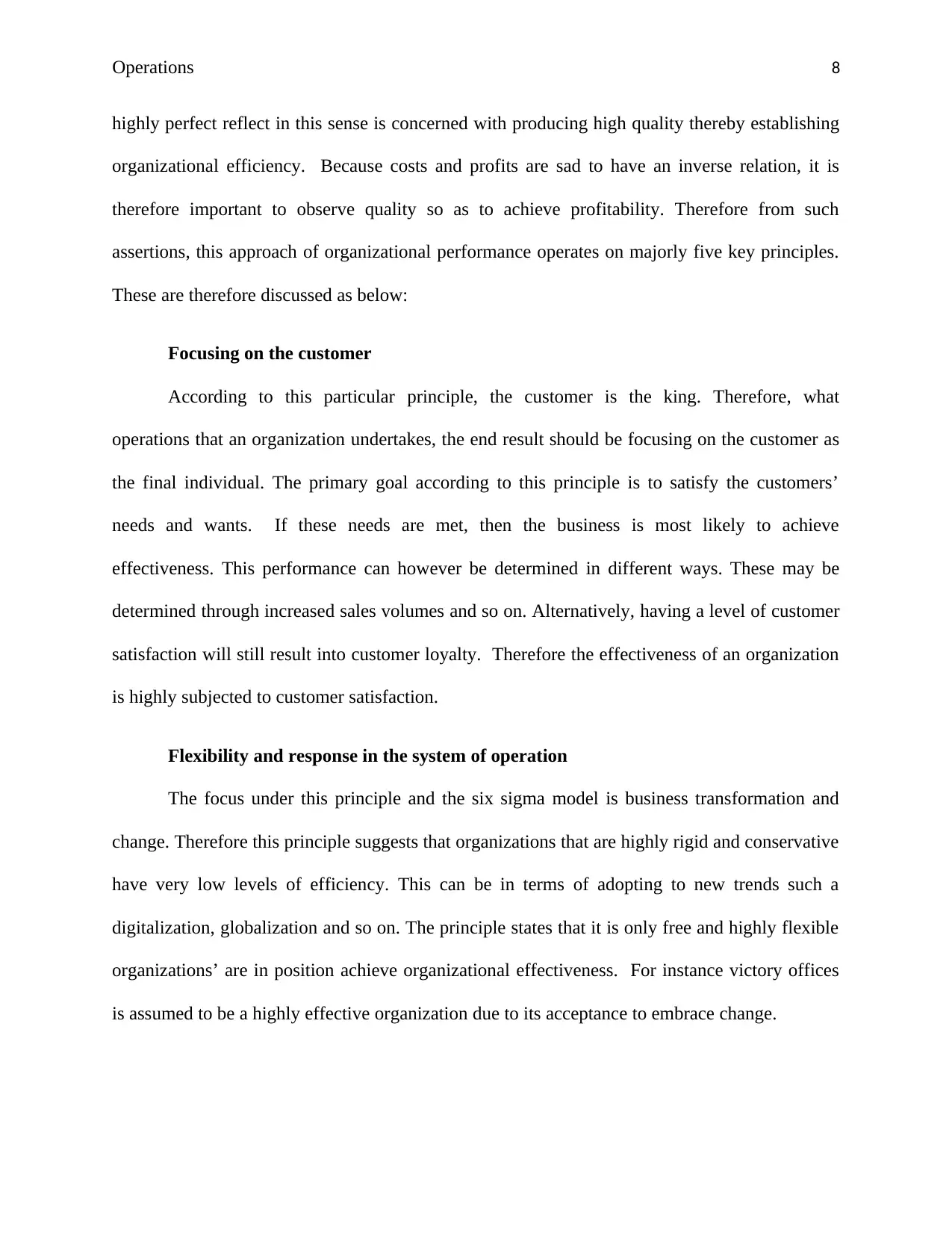
Operations 8
highly perfect reflect in this sense is concerned with producing high quality thereby establishing
organizational efficiency. Because costs and profits are sad to have an inverse relation, it is
therefore important to observe quality so as to achieve profitability. Therefore from such
assertions, this approach of organizational performance operates on majorly five key principles.
These are therefore discussed as below:
Focusing on the customer
According to this particular principle, the customer is the king. Therefore, what
operations that an organization undertakes, the end result should be focusing on the customer as
the final individual. The primary goal according to this principle is to satisfy the customers’
needs and wants. If these needs are met, then the business is most likely to achieve
effectiveness. This performance can however be determined in different ways. These may be
determined through increased sales volumes and so on. Alternatively, having a level of customer
satisfaction will still result into customer loyalty. Therefore the effectiveness of an organization
is highly subjected to customer satisfaction.
Flexibility and response in the system of operation
The focus under this principle and the six sigma model is business transformation and
change. Therefore this principle suggests that organizations that are highly rigid and conservative
have very low levels of efficiency. This can be in terms of adopting to new trends such a
digitalization, globalization and so on. The principle states that it is only free and highly flexible
organizations’ are in position achieve organizational effectiveness. For instance victory offices
is assumed to be a highly effective organization due to its acceptance to embrace change.
highly perfect reflect in this sense is concerned with producing high quality thereby establishing
organizational efficiency. Because costs and profits are sad to have an inverse relation, it is
therefore important to observe quality so as to achieve profitability. Therefore from such
assertions, this approach of organizational performance operates on majorly five key principles.
These are therefore discussed as below:
Focusing on the customer
According to this particular principle, the customer is the king. Therefore, what
operations that an organization undertakes, the end result should be focusing on the customer as
the final individual. The primary goal according to this principle is to satisfy the customers’
needs and wants. If these needs are met, then the business is most likely to achieve
effectiveness. This performance can however be determined in different ways. These may be
determined through increased sales volumes and so on. Alternatively, having a level of customer
satisfaction will still result into customer loyalty. Therefore the effectiveness of an organization
is highly subjected to customer satisfaction.
Flexibility and response in the system of operation
The focus under this principle and the six sigma model is business transformation and
change. Therefore this principle suggests that organizations that are highly rigid and conservative
have very low levels of efficiency. This can be in terms of adopting to new trends such a
digitalization, globalization and so on. The principle states that it is only free and highly flexible
organizations’ are in position achieve organizational effectiveness. For instance victory offices
is assumed to be a highly effective organization due to its acceptance to embrace change.
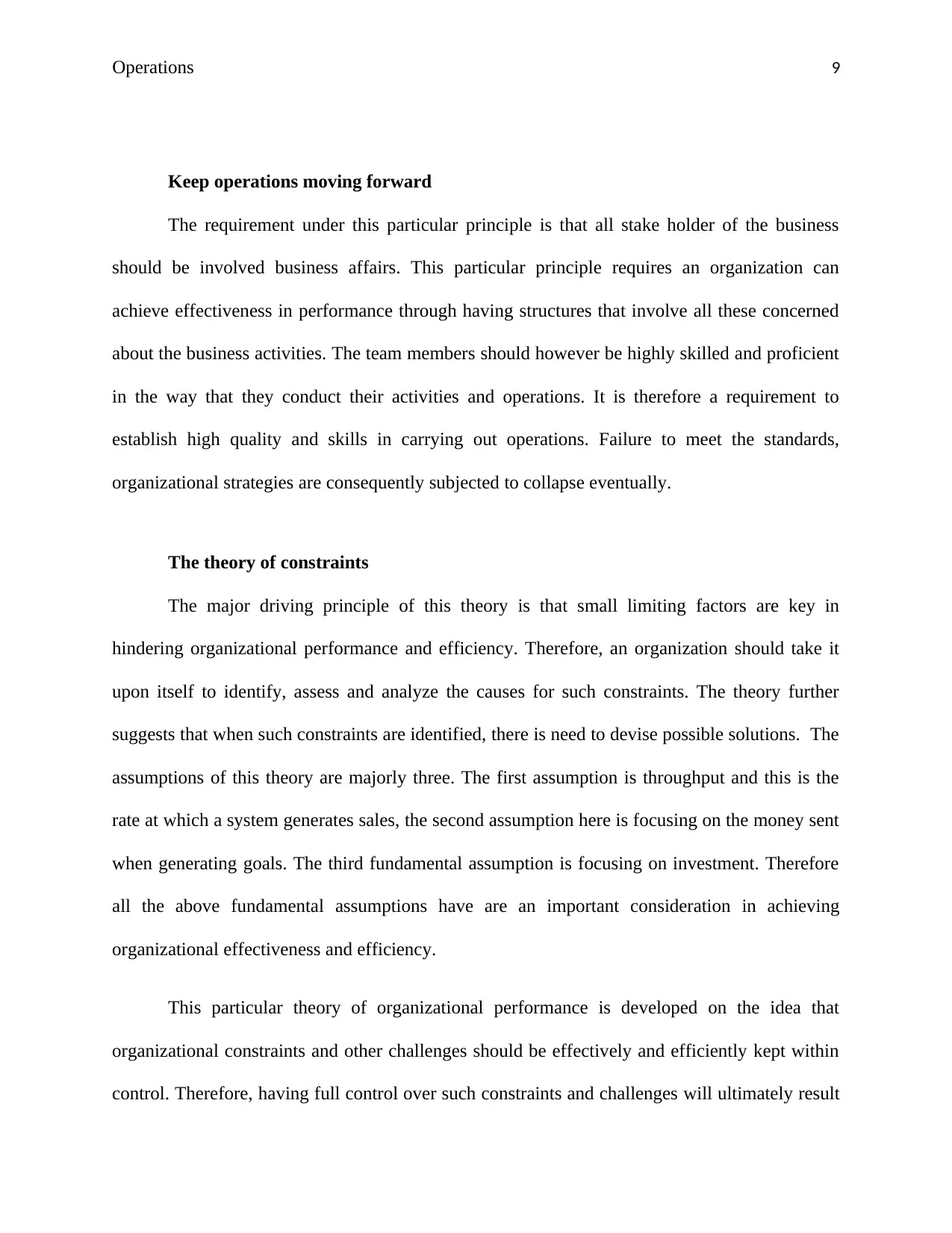
Operations 9
Keep operations moving forward
The requirement under this particular principle is that all stake holder of the business
should be involved business affairs. This particular principle requires an organization can
achieve effectiveness in performance through having structures that involve all these concerned
about the business activities. The team members should however be highly skilled and proficient
in the way that they conduct their activities and operations. It is therefore a requirement to
establish high quality and skills in carrying out operations. Failure to meet the standards,
organizational strategies are consequently subjected to collapse eventually.
The theory of constraints
The major driving principle of this theory is that small limiting factors are key in
hindering organizational performance and efficiency. Therefore, an organization should take it
upon itself to identify, assess and analyze the causes for such constraints. The theory further
suggests that when such constraints are identified, there is need to devise possible solutions. The
assumptions of this theory are majorly three. The first assumption is throughput and this is the
rate at which a system generates sales, the second assumption here is focusing on the money sent
when generating goals. The third fundamental assumption is focusing on investment. Therefore
all the above fundamental assumptions have are an important consideration in achieving
organizational effectiveness and efficiency.
This particular theory of organizational performance is developed on the idea that
organizational constraints and other challenges should be effectively and efficiently kept within
control. Therefore, having full control over such constraints and challenges will ultimately result
Keep operations moving forward
The requirement under this particular principle is that all stake holder of the business
should be involved business affairs. This particular principle requires an organization can
achieve effectiveness in performance through having structures that involve all these concerned
about the business activities. The team members should however be highly skilled and proficient
in the way that they conduct their activities and operations. It is therefore a requirement to
establish high quality and skills in carrying out operations. Failure to meet the standards,
organizational strategies are consequently subjected to collapse eventually.
The theory of constraints
The major driving principle of this theory is that small limiting factors are key in
hindering organizational performance and efficiency. Therefore, an organization should take it
upon itself to identify, assess and analyze the causes for such constraints. The theory further
suggests that when such constraints are identified, there is need to devise possible solutions. The
assumptions of this theory are majorly three. The first assumption is throughput and this is the
rate at which a system generates sales, the second assumption here is focusing on the money sent
when generating goals. The third fundamental assumption is focusing on investment. Therefore
all the above fundamental assumptions have are an important consideration in achieving
organizational effectiveness and efficiency.
This particular theory of organizational performance is developed on the idea that
organizational constraints and other challenges should be effectively and efficiently kept within
control. Therefore, having full control over such constraints and challenges will ultimately result
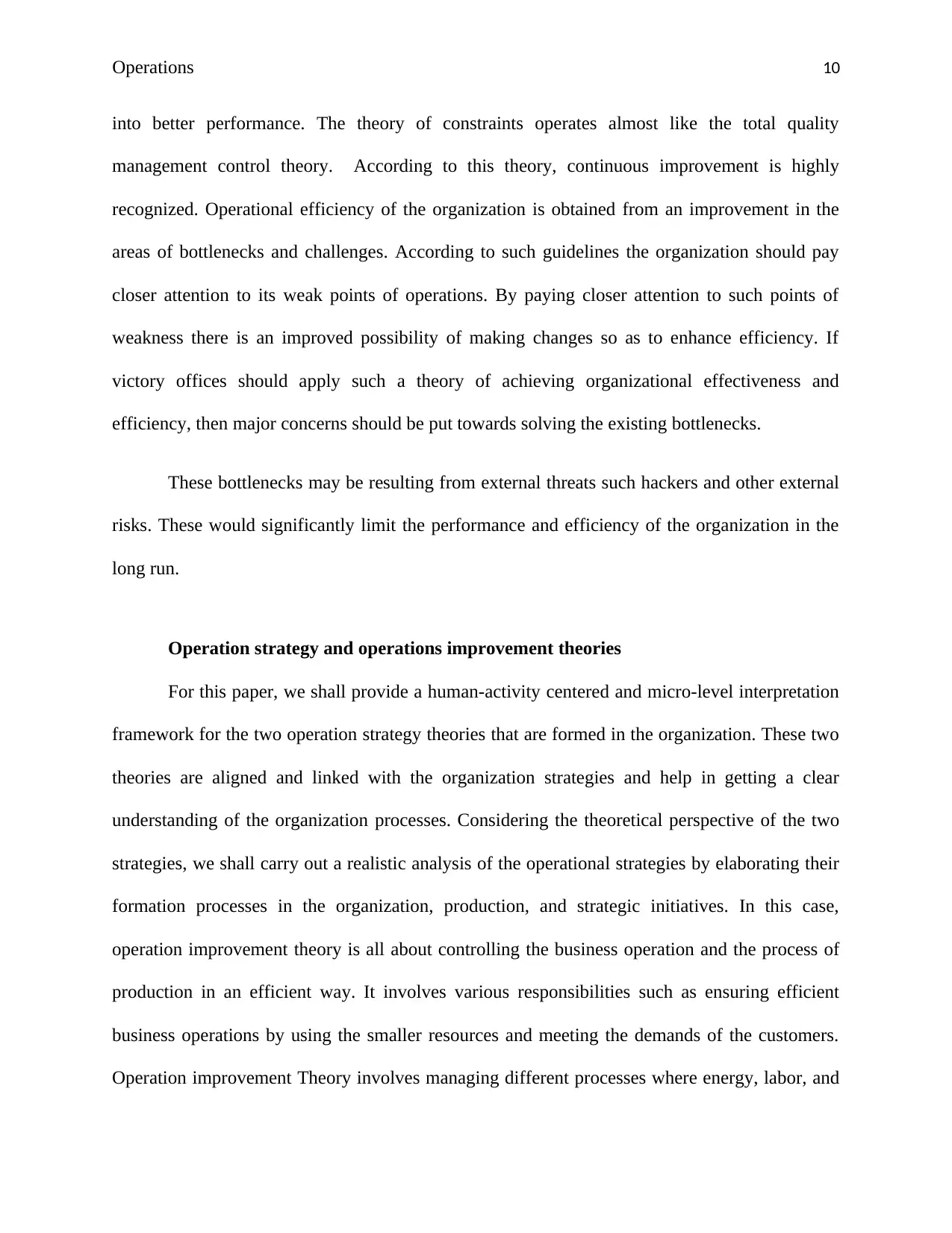
Operations 10
into better performance. The theory of constraints operates almost like the total quality
management control theory. According to this theory, continuous improvement is highly
recognized. Operational efficiency of the organization is obtained from an improvement in the
areas of bottlenecks and challenges. According to such guidelines the organization should pay
closer attention to its weak points of operations. By paying closer attention to such points of
weakness there is an improved possibility of making changes so as to enhance efficiency. If
victory offices should apply such a theory of achieving organizational effectiveness and
efficiency, then major concerns should be put towards solving the existing bottlenecks.
These bottlenecks may be resulting from external threats such hackers and other external
risks. These would significantly limit the performance and efficiency of the organization in the
long run.
Operation strategy and operations improvement theories
For this paper, we shall provide a human-activity centered and micro-level interpretation
framework for the two operation strategy theories that are formed in the organization. These two
theories are aligned and linked with the organization strategies and help in getting a clear
understanding of the organization processes. Considering the theoretical perspective of the two
strategies, we shall carry out a realistic analysis of the operational strategies by elaborating their
formation processes in the organization, production, and strategic initiatives. In this case,
operation improvement theory is all about controlling the business operation and the process of
production in an efficient way. It involves various responsibilities such as ensuring efficient
business operations by using the smaller resources and meeting the demands of the customers.
Operation improvement Theory involves managing different processes where energy, labor, and
into better performance. The theory of constraints operates almost like the total quality
management control theory. According to this theory, continuous improvement is highly
recognized. Operational efficiency of the organization is obtained from an improvement in the
areas of bottlenecks and challenges. According to such guidelines the organization should pay
closer attention to its weak points of operations. By paying closer attention to such points of
weakness there is an improved possibility of making changes so as to enhance efficiency. If
victory offices should apply such a theory of achieving organizational effectiveness and
efficiency, then major concerns should be put towards solving the existing bottlenecks.
These bottlenecks may be resulting from external threats such hackers and other external
risks. These would significantly limit the performance and efficiency of the organization in the
long run.
Operation strategy and operations improvement theories
For this paper, we shall provide a human-activity centered and micro-level interpretation
framework for the two operation strategy theories that are formed in the organization. These two
theories are aligned and linked with the organization strategies and help in getting a clear
understanding of the organization processes. Considering the theoretical perspective of the two
strategies, we shall carry out a realistic analysis of the operational strategies by elaborating their
formation processes in the organization, production, and strategic initiatives. In this case,
operation improvement theory is all about controlling the business operation and the process of
production in an efficient way. It involves various responsibilities such as ensuring efficient
business operations by using the smaller resources and meeting the demands of the customers.
Operation improvement Theory involves managing different processes where energy, labor, and
Secure Best Marks with AI Grader
Need help grading? Try our AI Grader for instant feedback on your assignments.
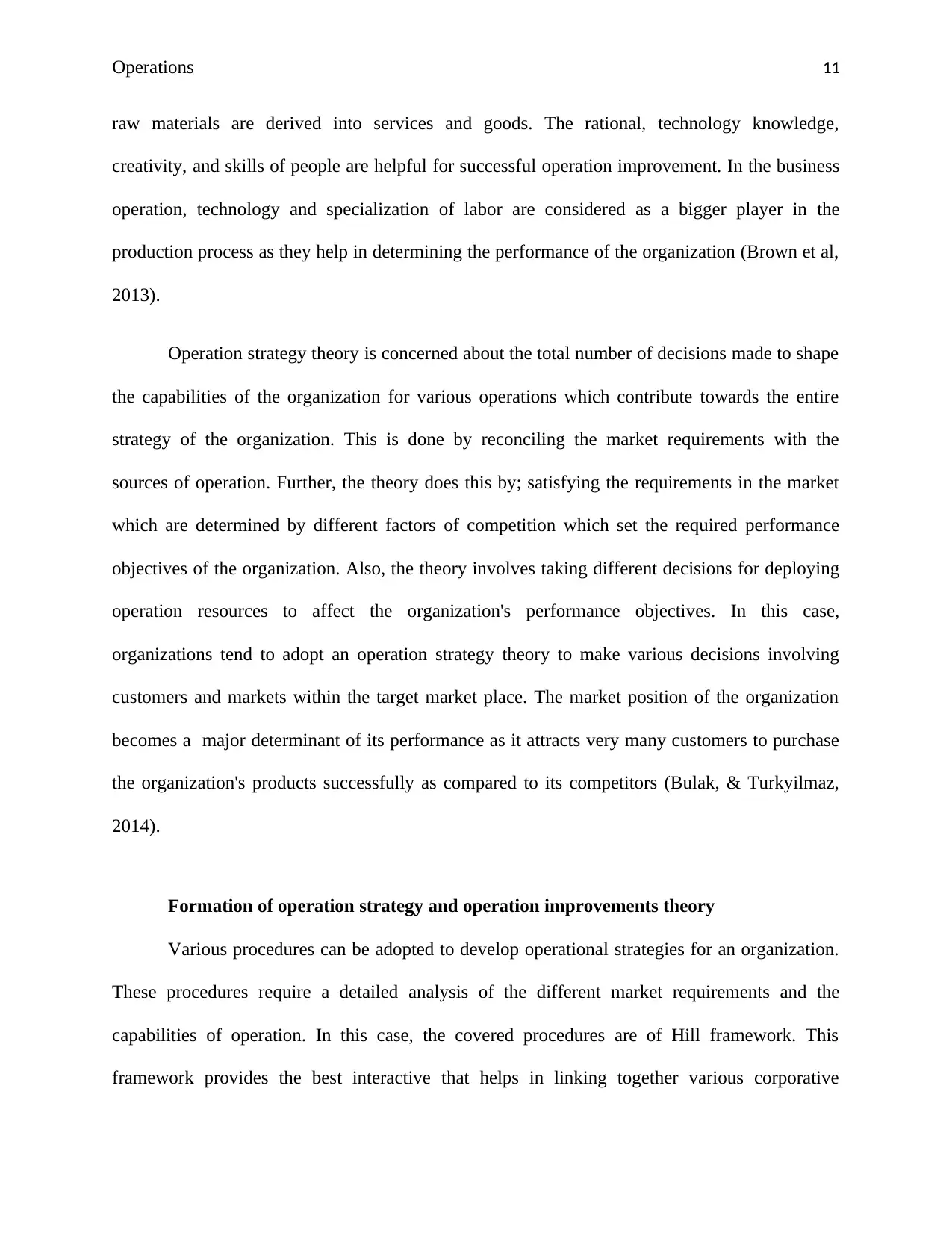
Operations 11
raw materials are derived into services and goods. The rational, technology knowledge,
creativity, and skills of people are helpful for successful operation improvement. In the business
operation, technology and specialization of labor are considered as a bigger player in the
production process as they help in determining the performance of the organization (Brown et al,
2013).
Operation strategy theory is concerned about the total number of decisions made to shape
the capabilities of the organization for various operations which contribute towards the entire
strategy of the organization. This is done by reconciling the market requirements with the
sources of operation. Further, the theory does this by; satisfying the requirements in the market
which are determined by different factors of competition which set the required performance
objectives of the organization. Also, the theory involves taking different decisions for deploying
operation resources to affect the organization's performance objectives. In this case,
organizations tend to adopt an operation strategy theory to make various decisions involving
customers and markets within the target market place. The market position of the organization
becomes a major determinant of its performance as it attracts very many customers to purchase
the organization's products successfully as compared to its competitors (Bulak, & Turkyilmaz,
2014).
Formation of operation strategy and operation improvements theory
Various procedures can be adopted to develop operational strategies for an organization.
These procedures require a detailed analysis of the different market requirements and the
capabilities of operation. In this case, the covered procedures are of Hill framework. This
framework provides the best interactive that helps in linking together various corporative
raw materials are derived into services and goods. The rational, technology knowledge,
creativity, and skills of people are helpful for successful operation improvement. In the business
operation, technology and specialization of labor are considered as a bigger player in the
production process as they help in determining the performance of the organization (Brown et al,
2013).
Operation strategy theory is concerned about the total number of decisions made to shape
the capabilities of the organization for various operations which contribute towards the entire
strategy of the organization. This is done by reconciling the market requirements with the
sources of operation. Further, the theory does this by; satisfying the requirements in the market
which are determined by different factors of competition which set the required performance
objectives of the organization. Also, the theory involves taking different decisions for deploying
operation resources to affect the organization's performance objectives. In this case,
organizations tend to adopt an operation strategy theory to make various decisions involving
customers and markets within the target market place. The market position of the organization
becomes a major determinant of its performance as it attracts very many customers to purchase
the organization's products successfully as compared to its competitors (Bulak, & Turkyilmaz,
2014).
Formation of operation strategy and operation improvements theory
Various procedures can be adopted to develop operational strategies for an organization.
These procedures require a detailed analysis of the different market requirements and the
capabilities of operation. In this case, the covered procedures are of Hill framework. This
framework provides the best interactive that helps in linking together various corporative
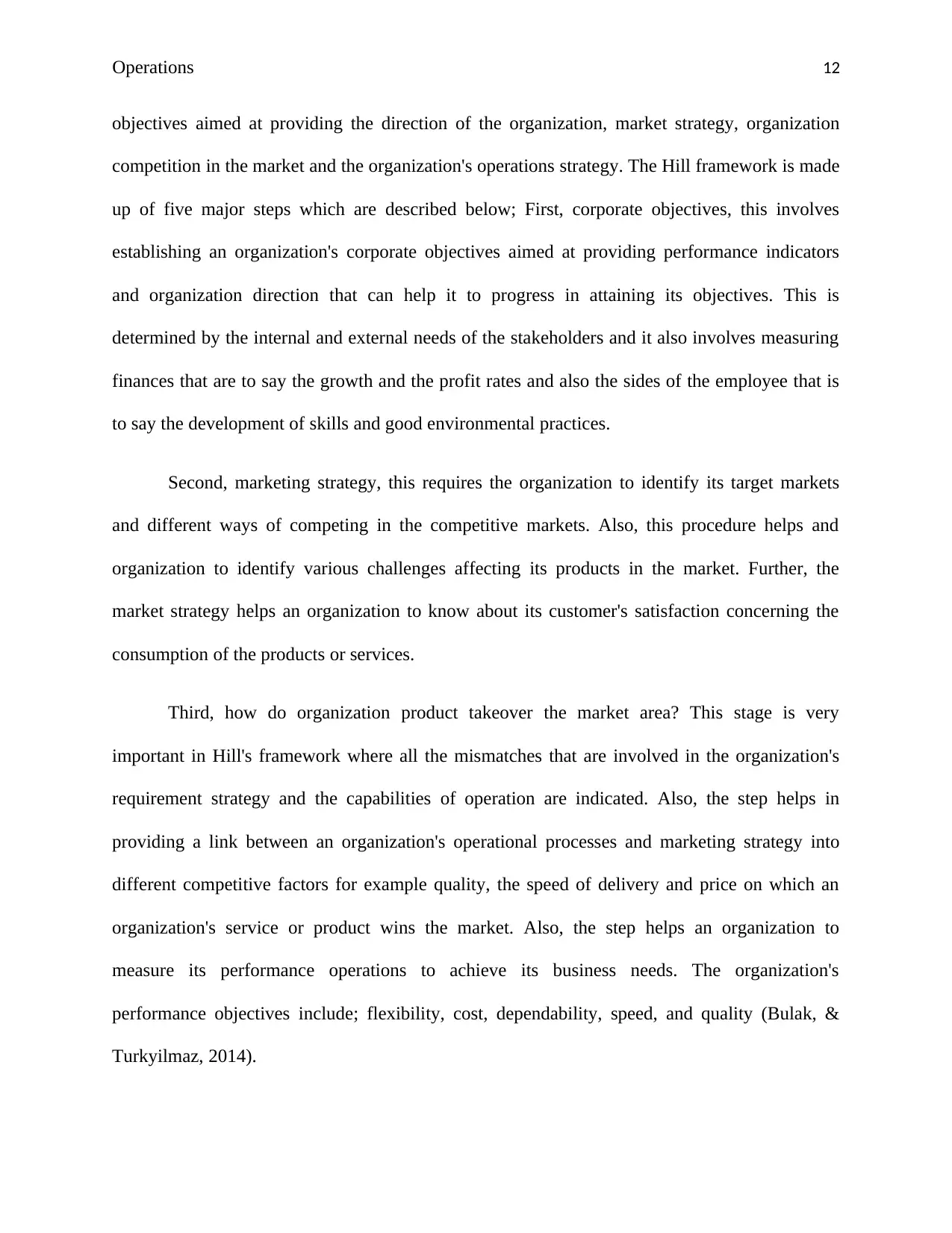
Operations 12
objectives aimed at providing the direction of the organization, market strategy, organization
competition in the market and the organization's operations strategy. The Hill framework is made
up of five major steps which are described below; First, corporate objectives, this involves
establishing an organization's corporate objectives aimed at providing performance indicators
and organization direction that can help it to progress in attaining its objectives. This is
determined by the internal and external needs of the stakeholders and it also involves measuring
finances that are to say the growth and the profit rates and also the sides of the employee that is
to say the development of skills and good environmental practices.
Second, marketing strategy, this requires the organization to identify its target markets
and different ways of competing in the competitive markets. Also, this procedure helps and
organization to identify various challenges affecting its products in the market. Further, the
market strategy helps an organization to know about its customer's satisfaction concerning the
consumption of the products or services.
Third, how do organization product takeover the market area? This stage is very
important in Hill's framework where all the mismatches that are involved in the organization's
requirement strategy and the capabilities of operation are indicated. Also, the step helps in
providing a link between an organization's operational processes and marketing strategy into
different competitive factors for example quality, the speed of delivery and price on which an
organization's service or product wins the market. Also, the step helps an organization to
measure its performance operations to achieve its business needs. The organization's
performance objectives include; flexibility, cost, dependability, speed, and quality (Bulak, &
Turkyilmaz, 2014).
objectives aimed at providing the direction of the organization, market strategy, organization
competition in the market and the organization's operations strategy. The Hill framework is made
up of five major steps which are described below; First, corporate objectives, this involves
establishing an organization's corporate objectives aimed at providing performance indicators
and organization direction that can help it to progress in attaining its objectives. This is
determined by the internal and external needs of the stakeholders and it also involves measuring
finances that are to say the growth and the profit rates and also the sides of the employee that is
to say the development of skills and good environmental practices.
Second, marketing strategy, this requires the organization to identify its target markets
and different ways of competing in the competitive markets. Also, this procedure helps and
organization to identify various challenges affecting its products in the market. Further, the
market strategy helps an organization to know about its customer's satisfaction concerning the
consumption of the products or services.
Third, how do organization product takeover the market area? This stage is very
important in Hill's framework where all the mismatches that are involved in the organization's
requirement strategy and the capabilities of operation are indicated. Also, the step helps in
providing a link between an organization's operational processes and marketing strategy into
different competitive factors for example quality, the speed of delivery and price on which an
organization's service or product wins the market. Also, the step helps an organization to
measure its performance operations to achieve its business needs. The organization's
performance objectives include; flexibility, cost, dependability, speed, and quality (Bulak, &
Turkyilmaz, 2014).
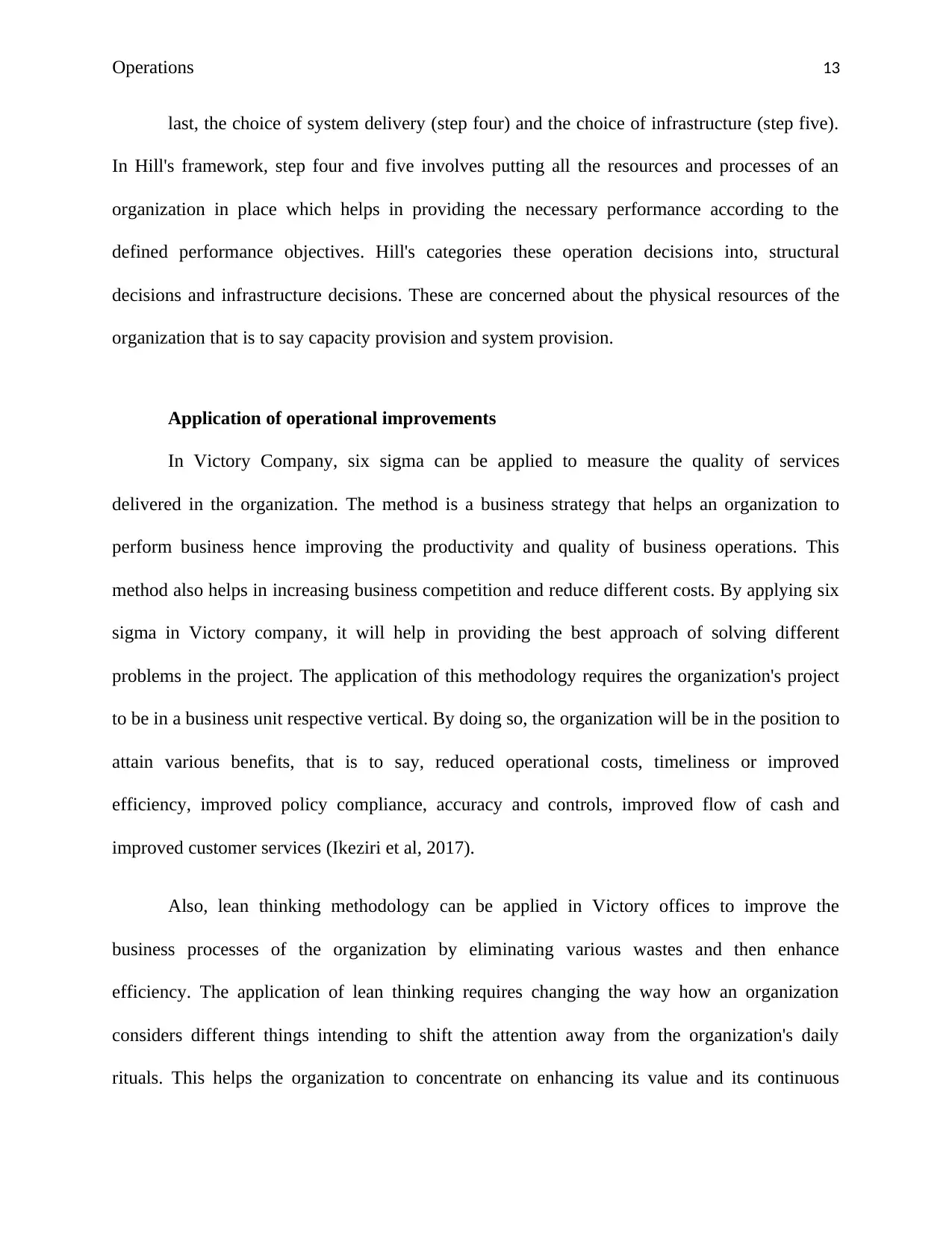
Operations 13
last, the choice of system delivery (step four) and the choice of infrastructure (step five).
In Hill's framework, step four and five involves putting all the resources and processes of an
organization in place which helps in providing the necessary performance according to the
defined performance objectives. Hill's categories these operation decisions into, structural
decisions and infrastructure decisions. These are concerned about the physical resources of the
organization that is to say capacity provision and system provision.
Application of operational improvements
In Victory Company, six sigma can be applied to measure the quality of services
delivered in the organization. The method is a business strategy that helps an organization to
perform business hence improving the productivity and quality of business operations. This
method also helps in increasing business competition and reduce different costs. By applying six
sigma in Victory company, it will help in providing the best approach of solving different
problems in the project. The application of this methodology requires the organization's project
to be in a business unit respective vertical. By doing so, the organization will be in the position to
attain various benefits, that is to say, reduced operational costs, timeliness or improved
efficiency, improved policy compliance, accuracy and controls, improved flow of cash and
improved customer services (Ikeziri et al, 2017).
Also, lean thinking methodology can be applied in Victory offices to improve the
business processes of the organization by eliminating various wastes and then enhance
efficiency. The application of lean thinking requires changing the way how an organization
considers different things intending to shift the attention away from the organization's daily
rituals. This helps the organization to concentrate on enhancing its value and its continuous
last, the choice of system delivery (step four) and the choice of infrastructure (step five).
In Hill's framework, step four and five involves putting all the resources and processes of an
organization in place which helps in providing the necessary performance according to the
defined performance objectives. Hill's categories these operation decisions into, structural
decisions and infrastructure decisions. These are concerned about the physical resources of the
organization that is to say capacity provision and system provision.
Application of operational improvements
In Victory Company, six sigma can be applied to measure the quality of services
delivered in the organization. The method is a business strategy that helps an organization to
perform business hence improving the productivity and quality of business operations. This
method also helps in increasing business competition and reduce different costs. By applying six
sigma in Victory company, it will help in providing the best approach of solving different
problems in the project. The application of this methodology requires the organization's project
to be in a business unit respective vertical. By doing so, the organization will be in the position to
attain various benefits, that is to say, reduced operational costs, timeliness or improved
efficiency, improved policy compliance, accuracy and controls, improved flow of cash and
improved customer services (Ikeziri et al, 2017).
Also, lean thinking methodology can be applied in Victory offices to improve the
business processes of the organization by eliminating various wastes and then enhance
efficiency. The application of lean thinking requires changing the way how an organization
considers different things intending to shift the attention away from the organization's daily
rituals. This helps the organization to concentrate on enhancing its value and its continuous
Paraphrase This Document
Need a fresh take? Get an instant paraphrase of this document with our AI Paraphraser
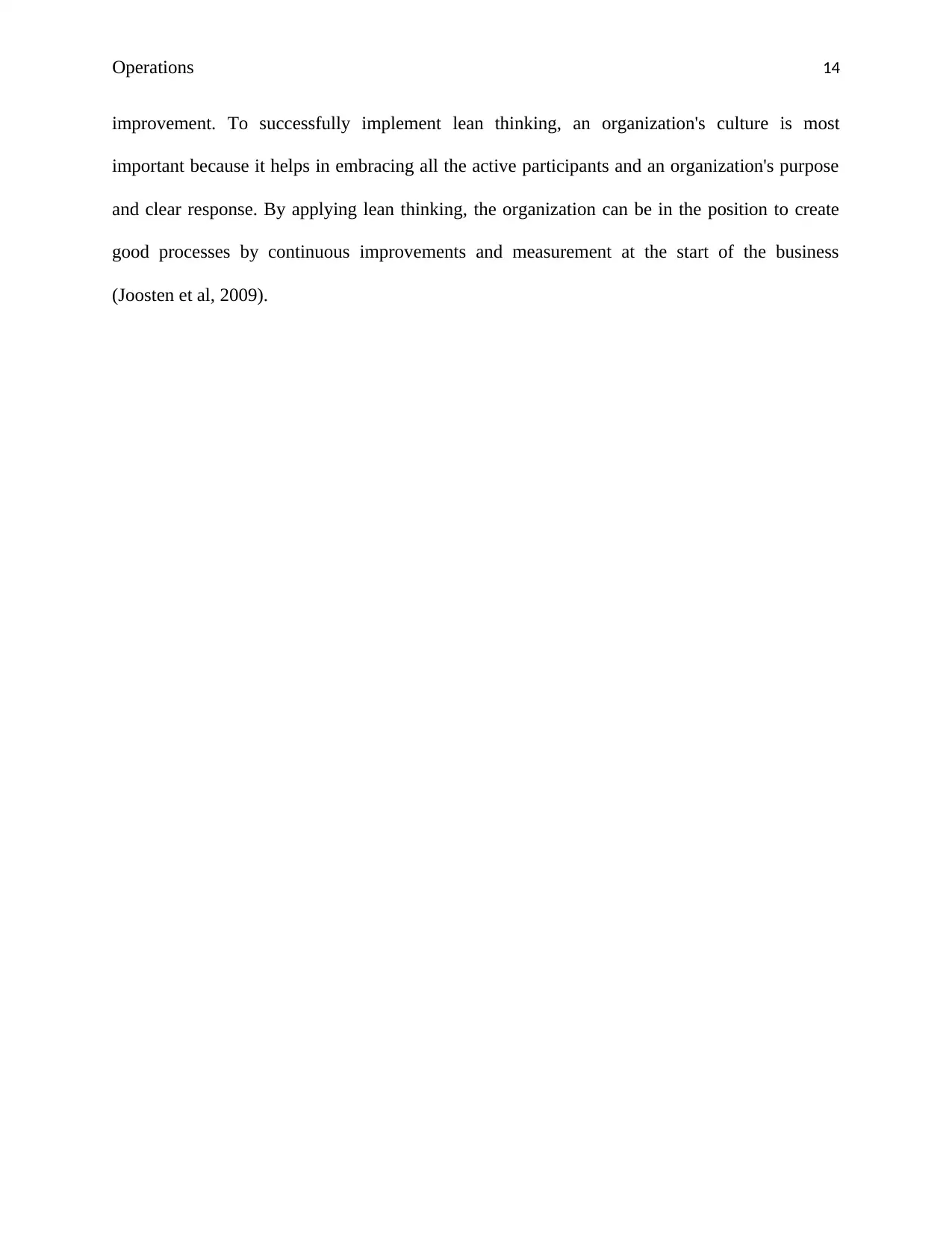
Operations 14
improvement. To successfully implement lean thinking, an organization's culture is most
important because it helps in embracing all the active participants and an organization's purpose
and clear response. By applying lean thinking, the organization can be in the position to create
good processes by continuous improvements and measurement at the start of the business
(Joosten et al, 2009).
improvement. To successfully implement lean thinking, an organization's culture is most
important because it helps in embracing all the active participants and an organization's purpose
and clear response. By applying lean thinking, the organization can be in the position to create
good processes by continuous improvements and measurement at the start of the business
(Joosten et al, 2009).
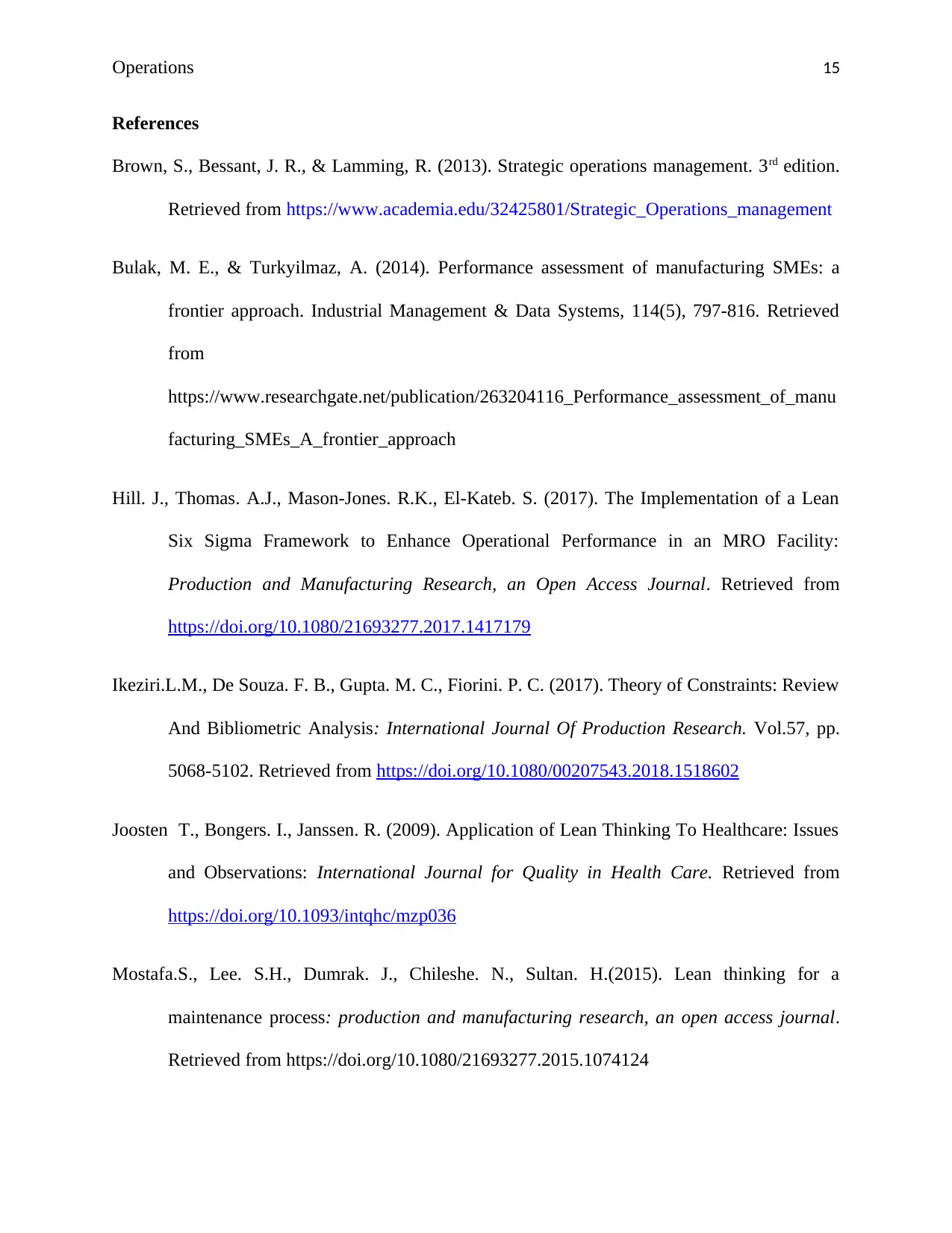
Operations 15
References
Brown, S., Bessant, J. R., & Lamming, R. (2013). Strategic operations management. 3rd edition.
Retrieved from https://www.academia.edu/32425801/Strategic_Operations_management
Bulak, M. E., & Turkyilmaz, A. (2014). Performance assessment of manufacturing SMEs: a
frontier approach. Industrial Management & Data Systems, 114(5), 797-816. Retrieved
from
https://www.researchgate.net/publication/263204116_Performance_assessment_of_manu
facturing_SMEs_A_frontier_approach
Hill. J., Thomas. A.J., Mason-Jones. R.K., El-Kateb. S. (2017). The Implementation of a Lean
Six Sigma Framework to Enhance Operational Performance in an MRO Facility:
Production and Manufacturing Research, an Open Access Journal. Retrieved from
https://doi.org/10.1080/21693277.2017.1417179
Ikeziri.L.M., De Souza. F. B., Gupta. M. C., Fiorini. P. C. (2017). Theory of Constraints: Review
And Bibliometric Analysis: International Journal Of Production Research. Vol.57, pp.
5068-5102. Retrieved from https://doi.org/10.1080/00207543.2018.1518602
Joosten T., Bongers. I., Janssen. R. (2009). Application of Lean Thinking To Healthcare: Issues
and Observations: International Journal for Quality in Health Care. Retrieved from
https://doi.org/10.1093/intqhc/mzp036
Mostafa.S., Lee. S.H., Dumrak. J., Chileshe. N., Sultan. H.(2015). Lean thinking for a
maintenance process: production and manufacturing research, an open access journal.
Retrieved from https://doi.org/10.1080/21693277.2015.1074124
References
Brown, S., Bessant, J. R., & Lamming, R. (2013). Strategic operations management. 3rd edition.
Retrieved from https://www.academia.edu/32425801/Strategic_Operations_management
Bulak, M. E., & Turkyilmaz, A. (2014). Performance assessment of manufacturing SMEs: a
frontier approach. Industrial Management & Data Systems, 114(5), 797-816. Retrieved
from
https://www.researchgate.net/publication/263204116_Performance_assessment_of_manu
facturing_SMEs_A_frontier_approach
Hill. J., Thomas. A.J., Mason-Jones. R.K., El-Kateb. S. (2017). The Implementation of a Lean
Six Sigma Framework to Enhance Operational Performance in an MRO Facility:
Production and Manufacturing Research, an Open Access Journal. Retrieved from
https://doi.org/10.1080/21693277.2017.1417179
Ikeziri.L.M., De Souza. F. B., Gupta. M. C., Fiorini. P. C. (2017). Theory of Constraints: Review
And Bibliometric Analysis: International Journal Of Production Research. Vol.57, pp.
5068-5102. Retrieved from https://doi.org/10.1080/00207543.2018.1518602
Joosten T., Bongers. I., Janssen. R. (2009). Application of Lean Thinking To Healthcare: Issues
and Observations: International Journal for Quality in Health Care. Retrieved from
https://doi.org/10.1093/intqhc/mzp036
Mostafa.S., Lee. S.H., Dumrak. J., Chileshe. N., Sultan. H.(2015). Lean thinking for a
maintenance process: production and manufacturing research, an open access journal.
Retrieved from https://doi.org/10.1080/21693277.2015.1074124
1 out of 15
Related Documents

Your All-in-One AI-Powered Toolkit for Academic Success.
+13062052269
info@desklib.com
Available 24*7 on WhatsApp / Email
Unlock your academic potential
© 2024 | Zucol Services PVT LTD | All rights reserved.