Operational Improvement Strategies for Mercedes-Benz, Audi, and BMW
VerifiedAdded on 2023/01/17
|11
|3943
|36
AI Summary
This report discusses the operational improvement strategies that can help Mercedes-Benz, Audi, and BMW solve quality issues and gain market share. It covers lean manufacturing, TQM, Six Sigma, and quality control.
Contribute Materials
Your contribution can guide someone’s learning journey. Share your
documents today.
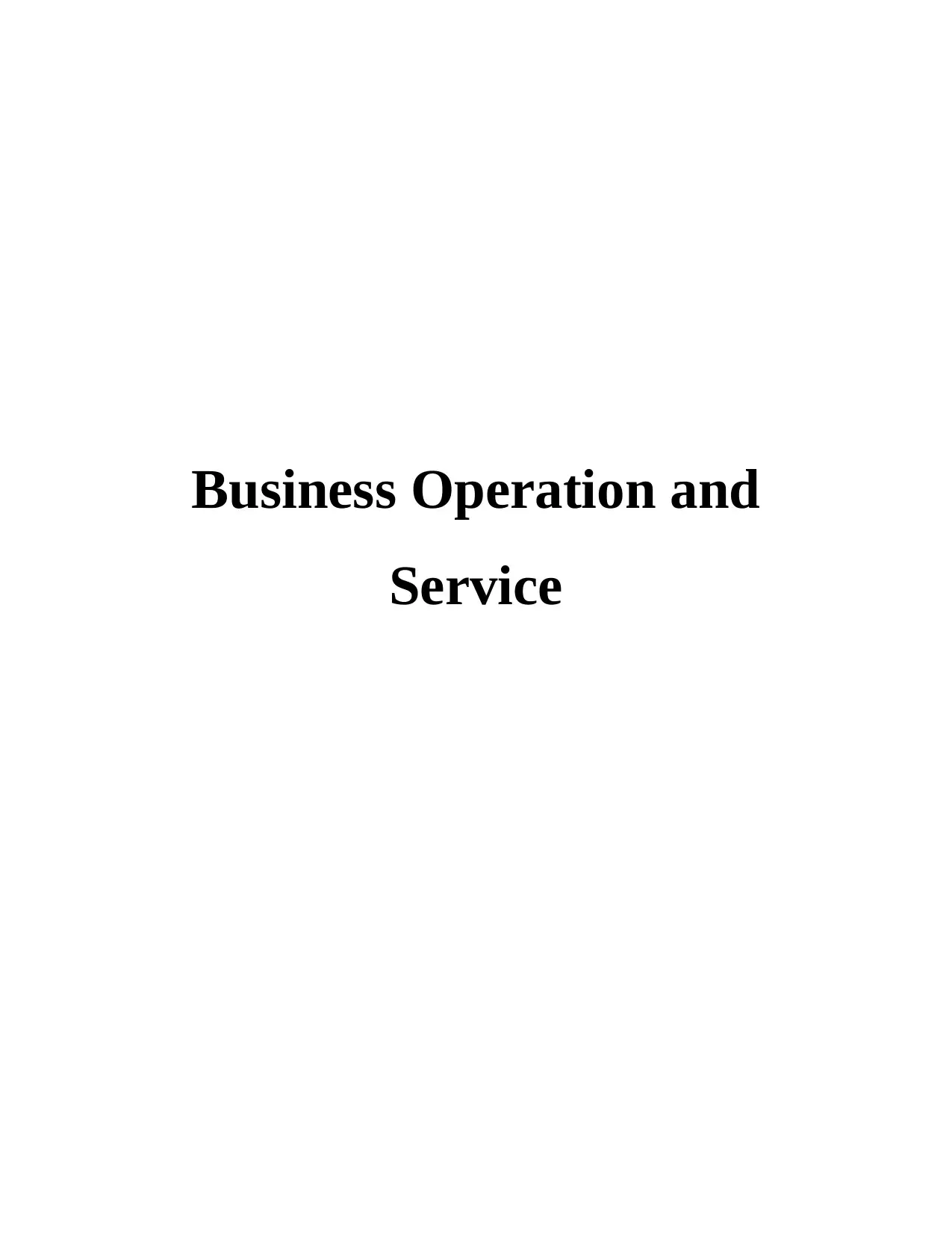
Business Operation and
Service
Service
Secure Best Marks with AI Grader
Need help grading? Try our AI Grader for instant feedback on your assignments.
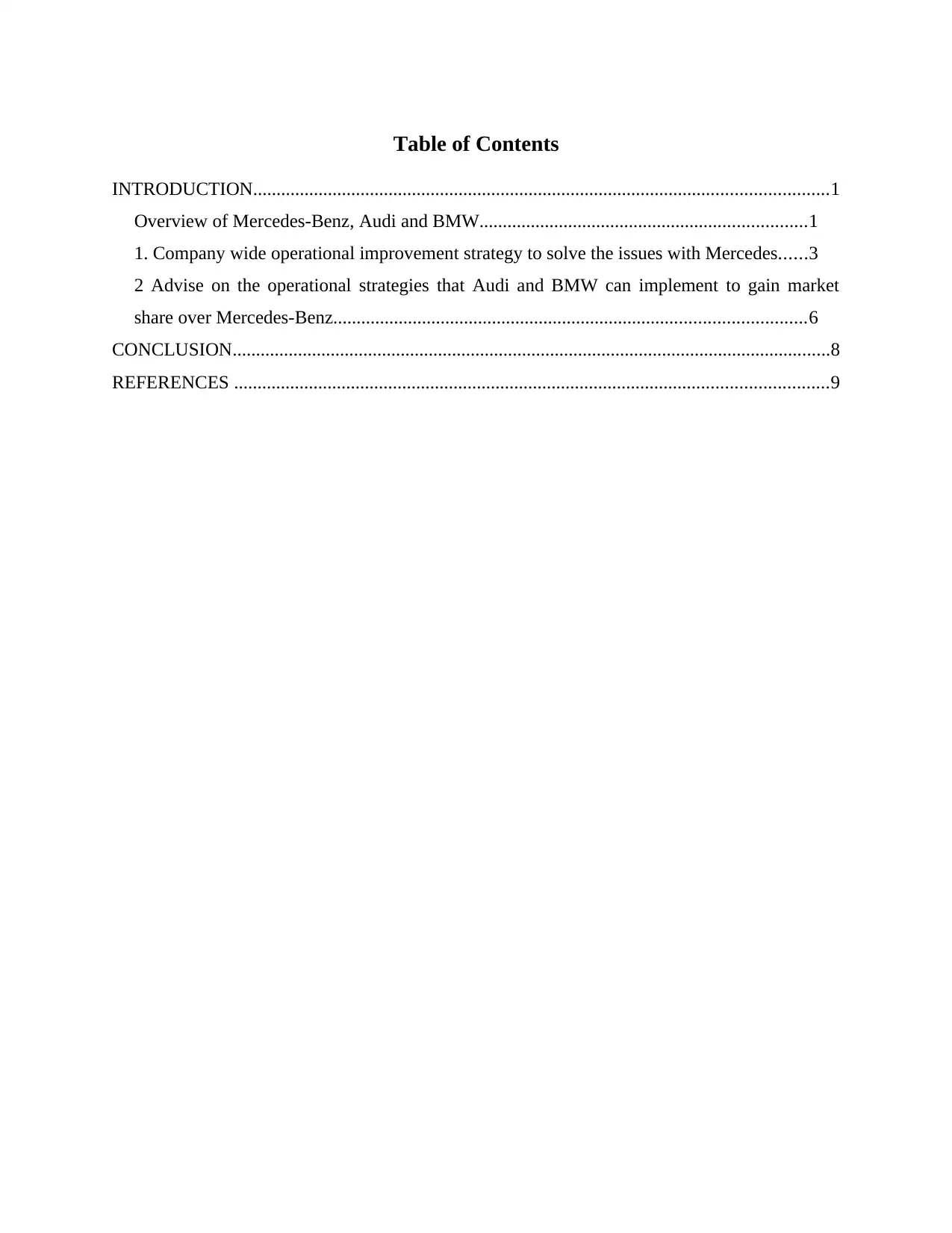
Table of Contents
INTRODUCTION...........................................................................................................................1
Overview of Mercedes-Benz, Audi and BMW......................................................................1
1. Company wide operational improvement strategy to solve the issues with Mercedes......3
2 Advise on the operational strategies that Audi and BMW can implement to gain market
share over Mercedes-Benz.....................................................................................................6
CONCLUSION................................................................................................................................8
REFERENCES ...............................................................................................................................9
INTRODUCTION...........................................................................................................................1
Overview of Mercedes-Benz, Audi and BMW......................................................................1
1. Company wide operational improvement strategy to solve the issues with Mercedes......3
2 Advise on the operational strategies that Audi and BMW can implement to gain market
share over Mercedes-Benz.....................................................................................................6
CONCLUSION................................................................................................................................8
REFERENCES ...............................................................................................................................9
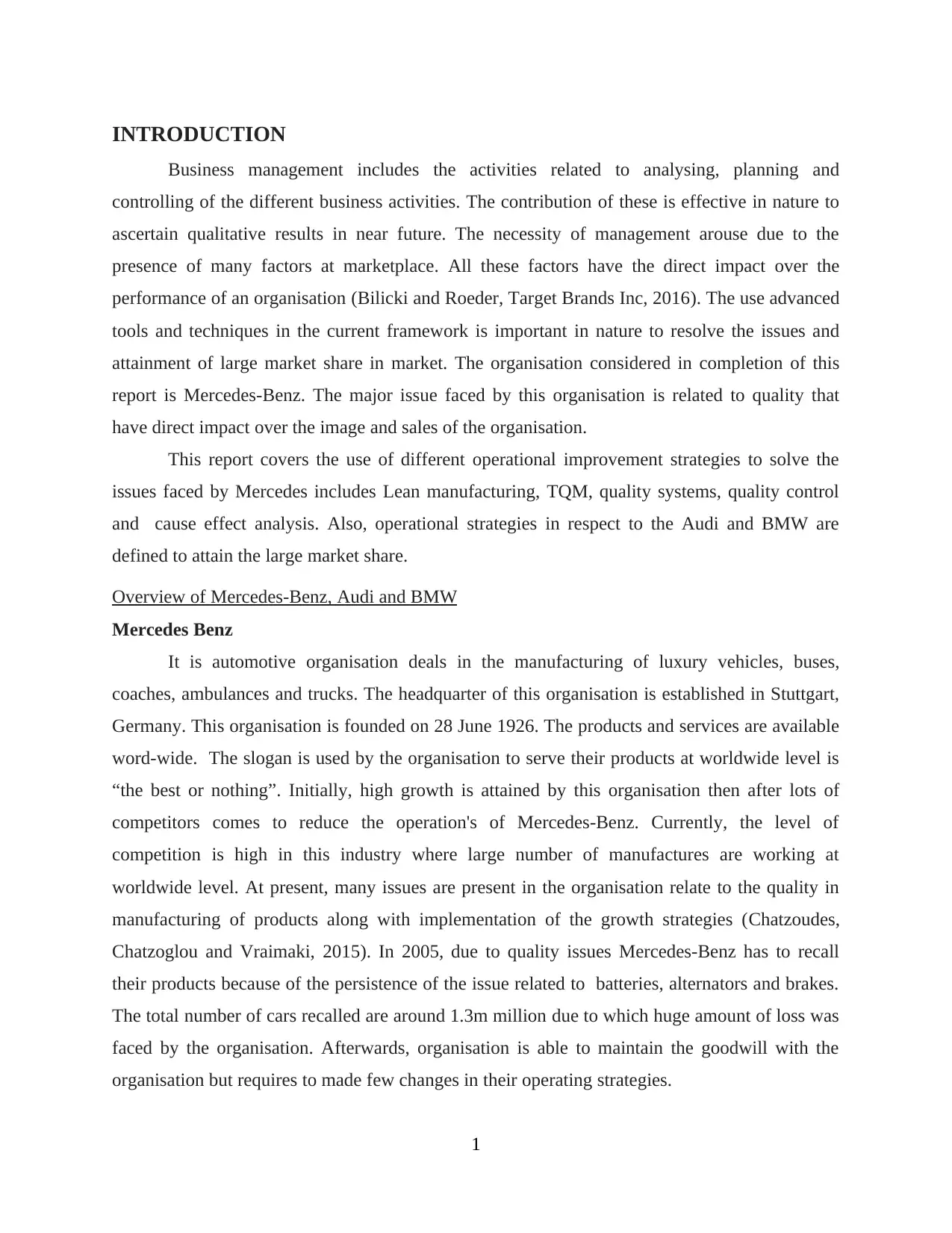
INTRODUCTION
Business management includes the activities related to analysing, planning and
controlling of the different business activities. The contribution of these is effective in nature to
ascertain qualitative results in near future. The necessity of management arouse due to the
presence of many factors at marketplace. All these factors have the direct impact over the
performance of an organisation (Bilicki and Roeder, Target Brands Inc, 2016). The use advanced
tools and techniques in the current framework is important in nature to resolve the issues and
attainment of large market share in market. The organisation considered in completion of this
report is Mercedes-Benz. The major issue faced by this organisation is related to quality that
have direct impact over the image and sales of the organisation.
This report covers the use of different operational improvement strategies to solve the
issues faced by Mercedes includes Lean manufacturing, TQM, quality systems, quality control
and cause effect analysis. Also, operational strategies in respect to the Audi and BMW are
defined to attain the large market share.
Overview of Mercedes-Benz, Audi and BMW
Mercedes Benz
It is automotive organisation deals in the manufacturing of luxury vehicles, buses,
coaches, ambulances and trucks. The headquarter of this organisation is established in Stuttgart,
Germany. This organisation is founded on 28 June 1926. The products and services are available
word-wide. The slogan is used by the organisation to serve their products at worldwide level is
“the best or nothing”. Initially, high growth is attained by this organisation then after lots of
competitors comes to reduce the operation's of Mercedes-Benz. Currently, the level of
competition is high in this industry where large number of manufactures are working at
worldwide level. At present, many issues are present in the organisation relate to the quality in
manufacturing of products along with implementation of the growth strategies (Chatzoudes,
Chatzoglou and Vraimaki, 2015). In 2005, due to quality issues Mercedes-Benz has to recall
their products because of the persistence of the issue related to batteries, alternators and brakes.
The total number of cars recalled are around 1.3m million due to which huge amount of loss was
faced by the organisation. Afterwards, organisation is able to maintain the goodwill with the
organisation but requires to made few changes in their operating strategies.
1
Business management includes the activities related to analysing, planning and
controlling of the different business activities. The contribution of these is effective in nature to
ascertain qualitative results in near future. The necessity of management arouse due to the
presence of many factors at marketplace. All these factors have the direct impact over the
performance of an organisation (Bilicki and Roeder, Target Brands Inc, 2016). The use advanced
tools and techniques in the current framework is important in nature to resolve the issues and
attainment of large market share in market. The organisation considered in completion of this
report is Mercedes-Benz. The major issue faced by this organisation is related to quality that
have direct impact over the image and sales of the organisation.
This report covers the use of different operational improvement strategies to solve the
issues faced by Mercedes includes Lean manufacturing, TQM, quality systems, quality control
and cause effect analysis. Also, operational strategies in respect to the Audi and BMW are
defined to attain the large market share.
Overview of Mercedes-Benz, Audi and BMW
Mercedes Benz
It is automotive organisation deals in the manufacturing of luxury vehicles, buses,
coaches, ambulances and trucks. The headquarter of this organisation is established in Stuttgart,
Germany. This organisation is founded on 28 June 1926. The products and services are available
word-wide. The slogan is used by the organisation to serve their products at worldwide level is
“the best or nothing”. Initially, high growth is attained by this organisation then after lots of
competitors comes to reduce the operation's of Mercedes-Benz. Currently, the level of
competition is high in this industry where large number of manufactures are working at
worldwide level. At present, many issues are present in the organisation relate to the quality in
manufacturing of products along with implementation of the growth strategies (Chatzoudes,
Chatzoglou and Vraimaki, 2015). In 2005, due to quality issues Mercedes-Benz has to recall
their products because of the persistence of the issue related to batteries, alternators and brakes.
The total number of cars recalled are around 1.3m million due to which huge amount of loss was
faced by the organisation. Afterwards, organisation is able to maintain the goodwill with the
organisation but requires to made few changes in their operating strategies.
1
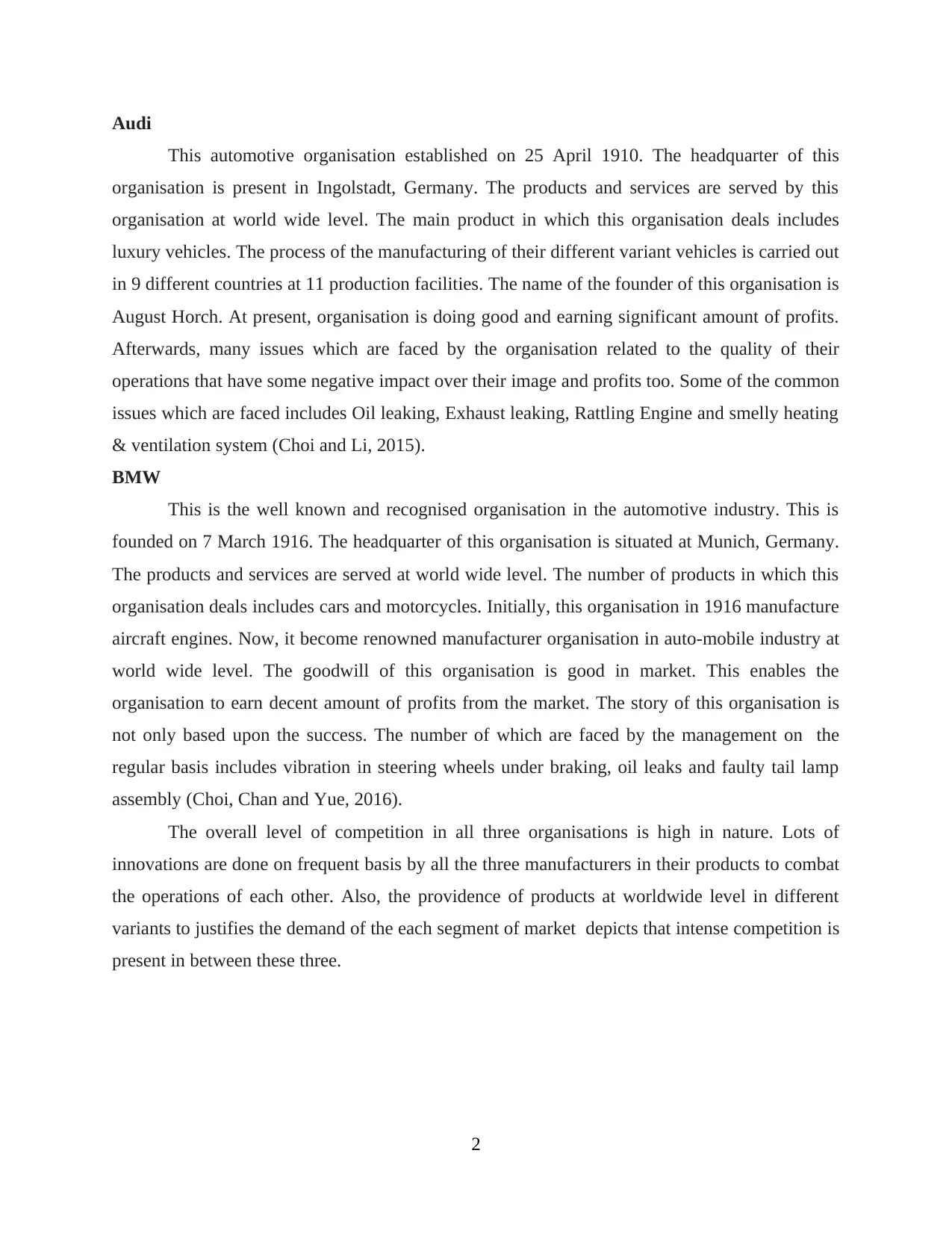
Audi
This automotive organisation established on 25 April 1910. The headquarter of this
organisation is present in Ingolstadt, Germany. The products and services are served by this
organisation at world wide level. The main product in which this organisation deals includes
luxury vehicles. The process of the manufacturing of their different variant vehicles is carried out
in 9 different countries at 11 production facilities. The name of the founder of this organisation is
August Horch. At present, organisation is doing good and earning significant amount of profits.
Afterwards, many issues which are faced by the organisation related to the quality of their
operations that have some negative impact over their image and profits too. Some of the common
issues which are faced includes Oil leaking, Exhaust leaking, Rattling Engine and smelly heating
& ventilation system (Choi and Li, 2015).
BMW
This is the well known and recognised organisation in the automotive industry. This is
founded on 7 March 1916. The headquarter of this organisation is situated at Munich, Germany.
The products and services are served at world wide level. The number of products in which this
organisation deals includes cars and motorcycles. Initially, this organisation in 1916 manufacture
aircraft engines. Now, it become renowned manufacturer organisation in auto-mobile industry at
world wide level. The goodwill of this organisation is good in market. This enables the
organisation to earn decent amount of profits from the market. The story of this organisation is
not only based upon the success. The number of which are faced by the management on the
regular basis includes vibration in steering wheels under braking, oil leaks and faulty tail lamp
assembly (Choi, Chan and Yue, 2016).
The overall level of competition in all three organisations is high in nature. Lots of
innovations are done on frequent basis by all the three manufacturers in their products to combat
the operations of each other. Also, the providence of products at worldwide level in different
variants to justifies the demand of the each segment of market depicts that intense competition is
present in between these three.
2
This automotive organisation established on 25 April 1910. The headquarter of this
organisation is present in Ingolstadt, Germany. The products and services are served by this
organisation at world wide level. The main product in which this organisation deals includes
luxury vehicles. The process of the manufacturing of their different variant vehicles is carried out
in 9 different countries at 11 production facilities. The name of the founder of this organisation is
August Horch. At present, organisation is doing good and earning significant amount of profits.
Afterwards, many issues which are faced by the organisation related to the quality of their
operations that have some negative impact over their image and profits too. Some of the common
issues which are faced includes Oil leaking, Exhaust leaking, Rattling Engine and smelly heating
& ventilation system (Choi and Li, 2015).
BMW
This is the well known and recognised organisation in the automotive industry. This is
founded on 7 March 1916. The headquarter of this organisation is situated at Munich, Germany.
The products and services are served at world wide level. The number of products in which this
organisation deals includes cars and motorcycles. Initially, this organisation in 1916 manufacture
aircraft engines. Now, it become renowned manufacturer organisation in auto-mobile industry at
world wide level. The goodwill of this organisation is good in market. This enables the
organisation to earn decent amount of profits from the market. The story of this organisation is
not only based upon the success. The number of which are faced by the management on the
regular basis includes vibration in steering wheels under braking, oil leaks and faulty tail lamp
assembly (Choi, Chan and Yue, 2016).
The overall level of competition in all three organisations is high in nature. Lots of
innovations are done on frequent basis by all the three manufacturers in their products to combat
the operations of each other. Also, the providence of products at worldwide level in different
variants to justifies the demand of the each segment of market depicts that intense competition is
present in between these three.
2
Secure Best Marks with AI Grader
Need help grading? Try our AI Grader for instant feedback on your assignments.
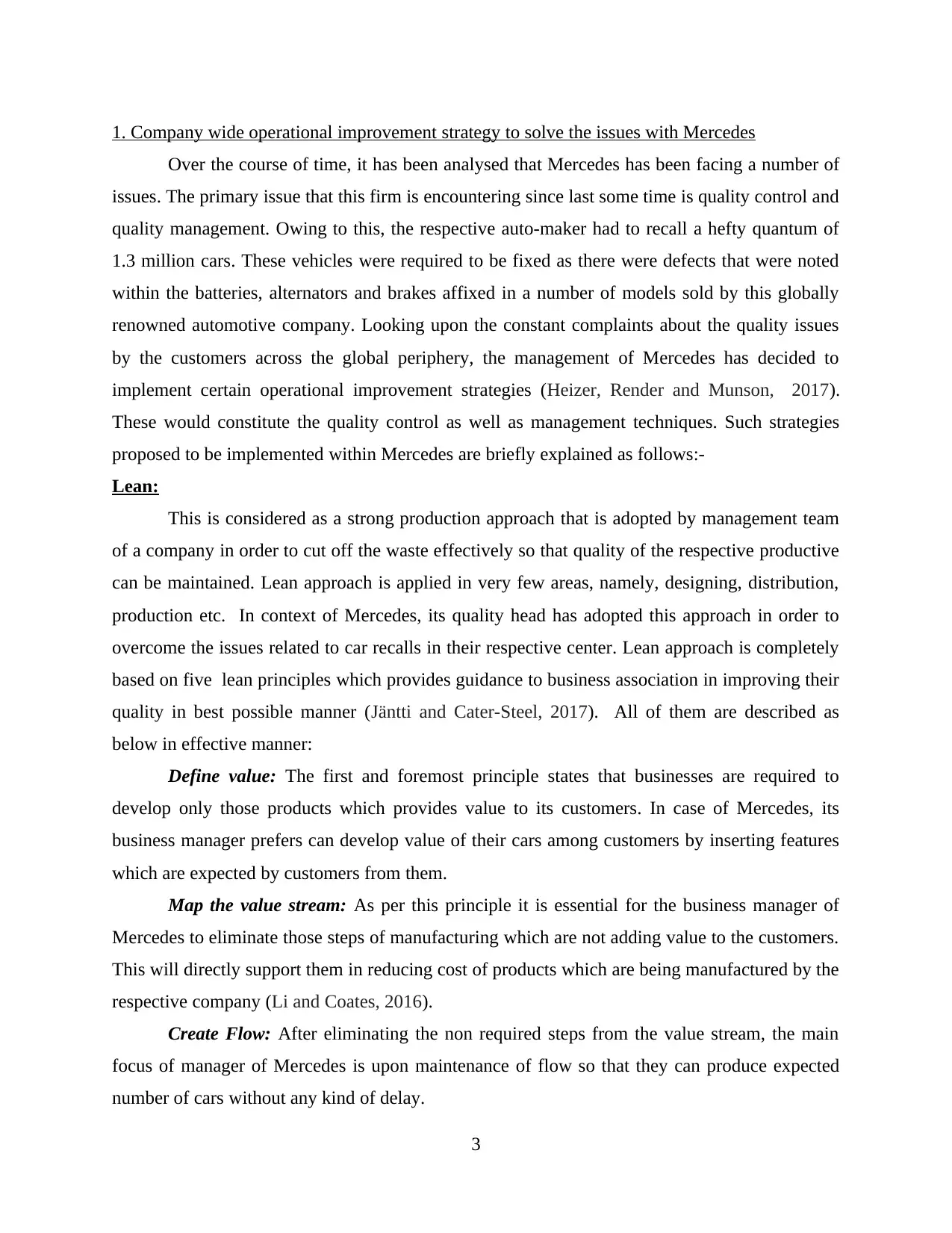
1. Company wide operational improvement strategy to solve the issues with Mercedes
Over the course of time, it has been analysed that Mercedes has been facing a number of
issues. The primary issue that this firm is encountering since last some time is quality control and
quality management. Owing to this, the respective auto-maker had to recall a hefty quantum of
1.3 million cars. These vehicles were required to be fixed as there were defects that were noted
within the batteries, alternators and brakes affixed in a number of models sold by this globally
renowned automotive company. Looking upon the constant complaints about the quality issues
by the customers across the global periphery, the management of Mercedes has decided to
implement certain operational improvement strategies (Heizer, Render and Munson, 2017).
These would constitute the quality control as well as management techniques. Such strategies
proposed to be implemented within Mercedes are briefly explained as follows:-
Lean:
This is considered as a strong production approach that is adopted by management team
of a company in order to cut off the waste effectively so that quality of the respective productive
can be maintained. Lean approach is applied in very few areas, namely, designing, distribution,
production etc. In context of Mercedes, its quality head has adopted this approach in order to
overcome the issues related to car recalls in their respective center. Lean approach is completely
based on five lean principles which provides guidance to business association in improving their
quality in best possible manner (Jäntti and Cater-Steel, 2017). All of them are described as
below in effective manner:
Define value: The first and foremost principle states that businesses are required to
develop only those products which provides value to its customers. In case of Mercedes, its
business manager prefers can develop value of their cars among customers by inserting features
which are expected by customers from them.
Map the value stream: As per this principle it is essential for the business manager of
Mercedes to eliminate those steps of manufacturing which are not adding value to the customers.
This will directly support them in reducing cost of products which are being manufactured by the
respective company (Li and Coates, 2016).
Create Flow: After eliminating the non required steps from the value stream, the main
focus of manager of Mercedes is upon maintenance of flow so that they can produce expected
number of cars without any kind of delay.
3
Over the course of time, it has been analysed that Mercedes has been facing a number of
issues. The primary issue that this firm is encountering since last some time is quality control and
quality management. Owing to this, the respective auto-maker had to recall a hefty quantum of
1.3 million cars. These vehicles were required to be fixed as there were defects that were noted
within the batteries, alternators and brakes affixed in a number of models sold by this globally
renowned automotive company. Looking upon the constant complaints about the quality issues
by the customers across the global periphery, the management of Mercedes has decided to
implement certain operational improvement strategies (Heizer, Render and Munson, 2017).
These would constitute the quality control as well as management techniques. Such strategies
proposed to be implemented within Mercedes are briefly explained as follows:-
Lean:
This is considered as a strong production approach that is adopted by management team
of a company in order to cut off the waste effectively so that quality of the respective productive
can be maintained. Lean approach is applied in very few areas, namely, designing, distribution,
production etc. In context of Mercedes, its quality head has adopted this approach in order to
overcome the issues related to car recalls in their respective center. Lean approach is completely
based on five lean principles which provides guidance to business association in improving their
quality in best possible manner (Jäntti and Cater-Steel, 2017). All of them are described as
below in effective manner:
Define value: The first and foremost principle states that businesses are required to
develop only those products which provides value to its customers. In case of Mercedes, its
business manager prefers can develop value of their cars among customers by inserting features
which are expected by customers from them.
Map the value stream: As per this principle it is essential for the business manager of
Mercedes to eliminate those steps of manufacturing which are not adding value to the customers.
This will directly support them in reducing cost of products which are being manufactured by the
respective company (Li and Coates, 2016).
Create Flow: After eliminating the non required steps from the value stream, the main
focus of manager of Mercedes is upon maintenance of flow so that they can produce expected
number of cars without any kind of delay.
3
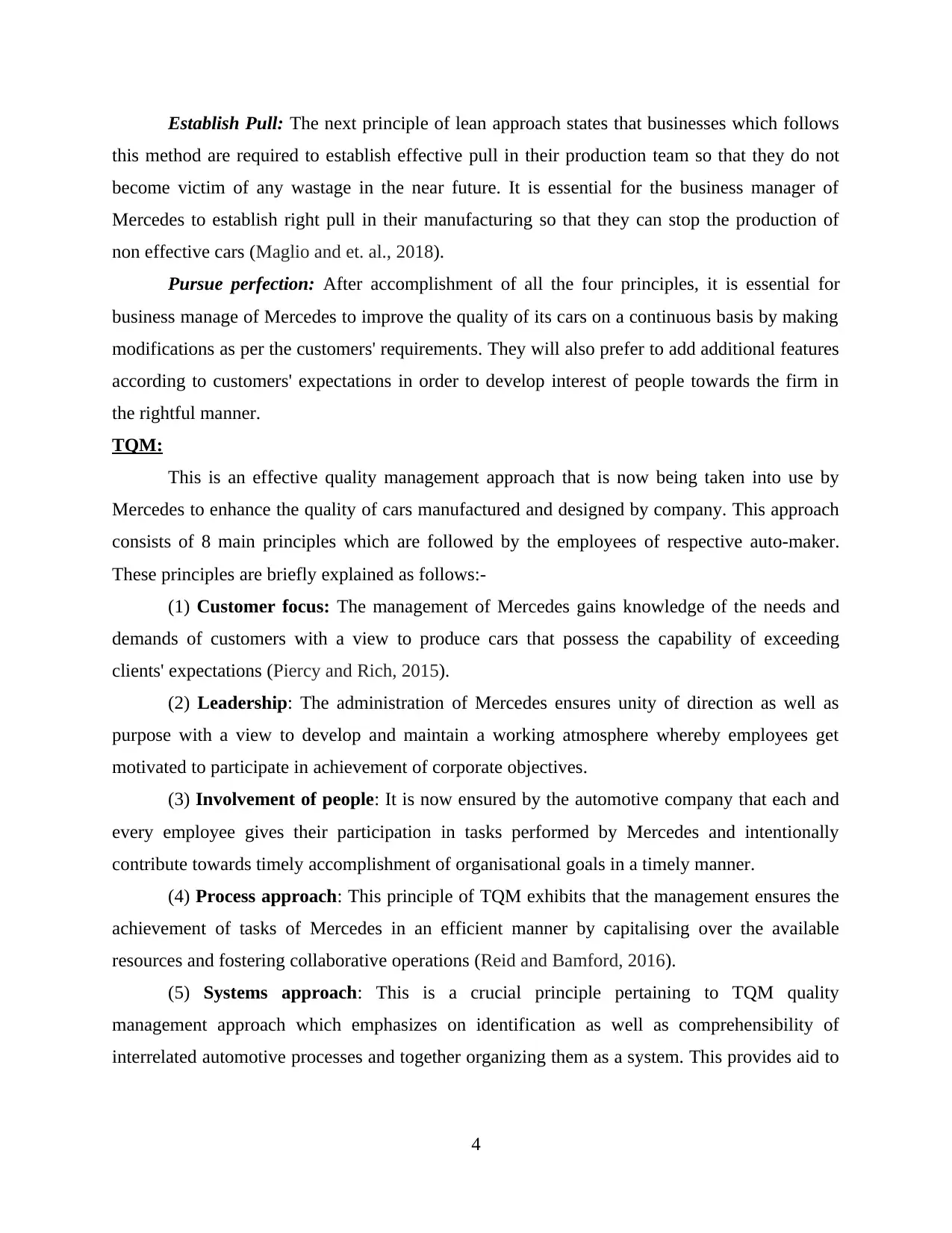
Establish Pull: The next principle of lean approach states that businesses which follows
this method are required to establish effective pull in their production team so that they do not
become victim of any wastage in the near future. It is essential for the business manager of
Mercedes to establish right pull in their manufacturing so that they can stop the production of
non effective cars (Maglio and et. al., 2018).
Pursue perfection: After accomplishment of all the four principles, it is essential for
business manage of Mercedes to improve the quality of its cars on a continuous basis by making
modifications as per the customers' requirements. They will also prefer to add additional features
according to customers' expectations in order to develop interest of people towards the firm in
the rightful manner.
TQM:
This is an effective quality management approach that is now being taken into use by
Mercedes to enhance the quality of cars manufactured and designed by company. This approach
consists of 8 main principles which are followed by the employees of respective auto-maker.
These principles are briefly explained as follows:-
(1) Customer focus: The management of Mercedes gains knowledge of the needs and
demands of customers with a view to produce cars that possess the capability of exceeding
clients' expectations (Piercy and Rich, 2015).
(2) Leadership: The administration of Mercedes ensures unity of direction as well as
purpose with a view to develop and maintain a working atmosphere whereby employees get
motivated to participate in achievement of corporate objectives.
(3) Involvement of people: It is now ensured by the automotive company that each and
every employee gives their participation in tasks performed by Mercedes and intentionally
contribute towards timely accomplishment of organisational goals in a timely manner.
(4) Process approach: This principle of TQM exhibits that the management ensures the
achievement of tasks of Mercedes in an efficient manner by capitalising over the available
resources and fostering collaborative operations (Reid and Bamford, 2016).
(5) Systems approach: This is a crucial principle pertaining to TQM quality
management approach which emphasizes on identification as well as comprehensibility of
interrelated automotive processes and together organizing them as a system. This provides aid to
4
this method are required to establish effective pull in their production team so that they do not
become victim of any wastage in the near future. It is essential for the business manager of
Mercedes to establish right pull in their manufacturing so that they can stop the production of
non effective cars (Maglio and et. al., 2018).
Pursue perfection: After accomplishment of all the four principles, it is essential for
business manage of Mercedes to improve the quality of its cars on a continuous basis by making
modifications as per the customers' requirements. They will also prefer to add additional features
according to customers' expectations in order to develop interest of people towards the firm in
the rightful manner.
TQM:
This is an effective quality management approach that is now being taken into use by
Mercedes to enhance the quality of cars manufactured and designed by company. This approach
consists of 8 main principles which are followed by the employees of respective auto-maker.
These principles are briefly explained as follows:-
(1) Customer focus: The management of Mercedes gains knowledge of the needs and
demands of customers with a view to produce cars that possess the capability of exceeding
clients' expectations (Piercy and Rich, 2015).
(2) Leadership: The administration of Mercedes ensures unity of direction as well as
purpose with a view to develop and maintain a working atmosphere whereby employees get
motivated to participate in achievement of corporate objectives.
(3) Involvement of people: It is now ensured by the automotive company that each and
every employee gives their participation in tasks performed by Mercedes and intentionally
contribute towards timely accomplishment of organisational goals in a timely manner.
(4) Process approach: This principle of TQM exhibits that the management ensures the
achievement of tasks of Mercedes in an efficient manner by capitalising over the available
resources and fostering collaborative operations (Reid and Bamford, 2016).
(5) Systems approach: This is a crucial principle pertaining to TQM quality
management approach which emphasizes on identification as well as comprehensibility of
interrelated automotive processes and together organizing them as a system. This provides aid to
4
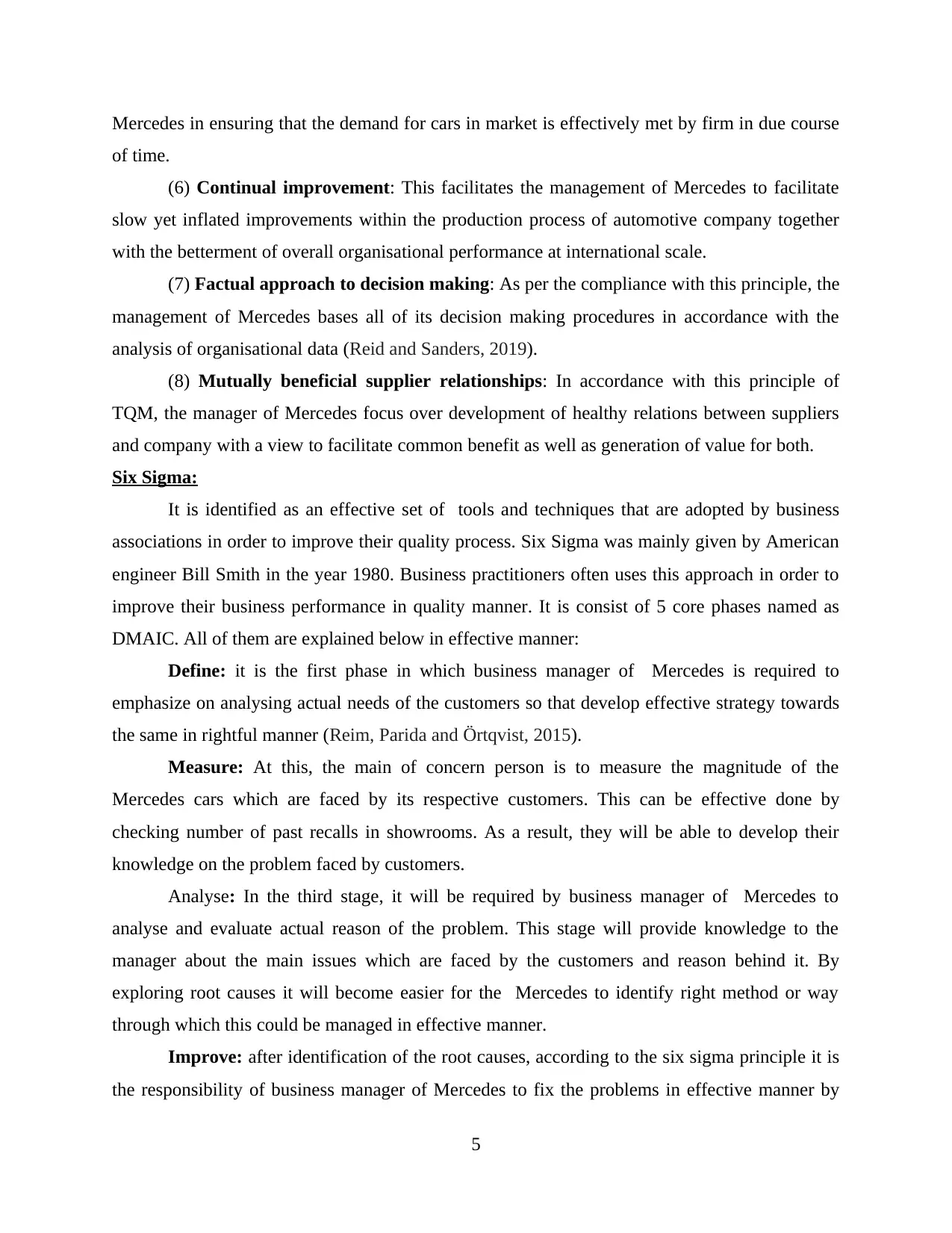
Mercedes in ensuring that the demand for cars in market is effectively met by firm in due course
of time.
(6) Continual improvement: This facilitates the management of Mercedes to facilitate
slow yet inflated improvements within the production process of automotive company together
with the betterment of overall organisational performance at international scale.
(7) Factual approach to decision making: As per the compliance with this principle, the
management of Mercedes bases all of its decision making procedures in accordance with the
analysis of organisational data (Reid and Sanders, 2019).
(8) Mutually beneficial supplier relationships: In accordance with this principle of
TQM, the manager of Mercedes focus over development of healthy relations between suppliers
and company with a view to facilitate common benefit as well as generation of value for both.
Six Sigma:
It is identified as an effective set of tools and techniques that are adopted by business
associations in order to improve their quality process. Six Sigma was mainly given by American
engineer Bill Smith in the year 1980. Business practitioners often uses this approach in order to
improve their business performance in quality manner. It is consist of 5 core phases named as
DMAIC. All of them are explained below in effective manner:
Define: it is the first phase in which business manager of Mercedes is required to
emphasize on analysing actual needs of the customers so that develop effective strategy towards
the same in rightful manner (Reim, Parida and Örtqvist, 2015).
Measure: At this, the main of concern person is to measure the magnitude of the
Mercedes cars which are faced by its respective customers. This can be effective done by
checking number of past recalls in showrooms. As a result, they will be able to develop their
knowledge on the problem faced by customers.
Analyse: In the third stage, it will be required by business manager of Mercedes to
analyse and evaluate actual reason of the problem. This stage will provide knowledge to the
manager about the main issues which are faced by the customers and reason behind it. By
exploring root causes it will become easier for the Mercedes to identify right method or way
through which this could be managed in effective manner.
Improve: after identification of the root causes, according to the six sigma principle it is
the responsibility of business manager of Mercedes to fix the problems in effective manner by
5
of time.
(6) Continual improvement: This facilitates the management of Mercedes to facilitate
slow yet inflated improvements within the production process of automotive company together
with the betterment of overall organisational performance at international scale.
(7) Factual approach to decision making: As per the compliance with this principle, the
management of Mercedes bases all of its decision making procedures in accordance with the
analysis of organisational data (Reid and Sanders, 2019).
(8) Mutually beneficial supplier relationships: In accordance with this principle of
TQM, the manager of Mercedes focus over development of healthy relations between suppliers
and company with a view to facilitate common benefit as well as generation of value for both.
Six Sigma:
It is identified as an effective set of tools and techniques that are adopted by business
associations in order to improve their quality process. Six Sigma was mainly given by American
engineer Bill Smith in the year 1980. Business practitioners often uses this approach in order to
improve their business performance in quality manner. It is consist of 5 core phases named as
DMAIC. All of them are explained below in effective manner:
Define: it is the first phase in which business manager of Mercedes is required to
emphasize on analysing actual needs of the customers so that develop effective strategy towards
the same in rightful manner (Reim, Parida and Örtqvist, 2015).
Measure: At this, the main of concern person is to measure the magnitude of the
Mercedes cars which are faced by its respective customers. This can be effective done by
checking number of past recalls in showrooms. As a result, they will be able to develop their
knowledge on the problem faced by customers.
Analyse: In the third stage, it will be required by business manager of Mercedes to
analyse and evaluate actual reason of the problem. This stage will provide knowledge to the
manager about the main issues which are faced by the customers and reason behind it. By
exploring root causes it will become easier for the Mercedes to identify right method or way
through which this could be managed in effective manner.
Improve: after identification of the root causes, according to the six sigma principle it is
the responsibility of business manager of Mercedes to fix the problems in effective manner by
5
Paraphrase This Document
Need a fresh take? Get an instant paraphrase of this document with our AI Paraphraser
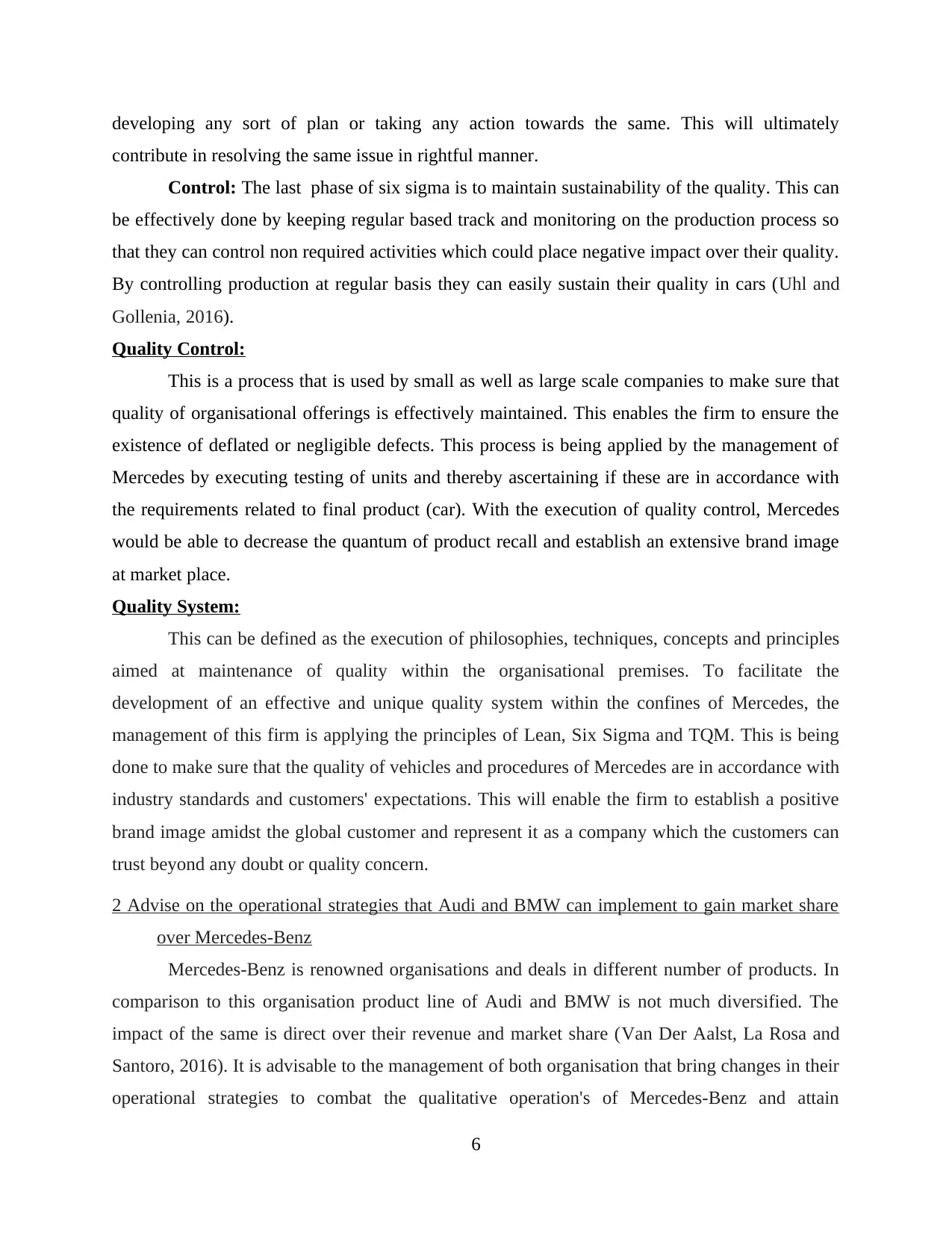
developing any sort of plan or taking any action towards the same. This will ultimately
contribute in resolving the same issue in rightful manner.
Control: The last phase of six sigma is to maintain sustainability of the quality. This can
be effectively done by keeping regular based track and monitoring on the production process so
that they can control non required activities which could place negative impact over their quality.
By controlling production at regular basis they can easily sustain their quality in cars (Uhl and
Gollenia, 2016).
Quality Control:
This is a process that is used by small as well as large scale companies to make sure that
quality of organisational offerings is effectively maintained. This enables the firm to ensure the
existence of deflated or negligible defects. This process is being applied by the management of
Mercedes by executing testing of units and thereby ascertaining if these are in accordance with
the requirements related to final product (car). With the execution of quality control, Mercedes
would be able to decrease the quantum of product recall and establish an extensive brand image
at market place.
Quality System:
This can be defined as the execution of philosophies, techniques, concepts and principles
aimed at maintenance of quality within the organisational premises. To facilitate the
development of an effective and unique quality system within the confines of Mercedes, the
management of this firm is applying the principles of Lean, Six Sigma and TQM. This is being
done to make sure that the quality of vehicles and procedures of Mercedes are in accordance with
industry standards and customers' expectations. This will enable the firm to establish a positive
brand image amidst the global customer and represent it as a company which the customers can
trust beyond any doubt or quality concern.
2 Advise on the operational strategies that Audi and BMW can implement to gain market share
over Mercedes-Benz
Mercedes-Benz is renowned organisations and deals in different number of products. In
comparison to this organisation product line of Audi and BMW is not much diversified. The
impact of the same is direct over their revenue and market share (Van Der Aalst, La Rosa and
Santoro, 2016). It is advisable to the management of both organisation that bring changes in their
operational strategies to combat the qualitative operation's of Mercedes-Benz and attain
6
contribute in resolving the same issue in rightful manner.
Control: The last phase of six sigma is to maintain sustainability of the quality. This can
be effectively done by keeping regular based track and monitoring on the production process so
that they can control non required activities which could place negative impact over their quality.
By controlling production at regular basis they can easily sustain their quality in cars (Uhl and
Gollenia, 2016).
Quality Control:
This is a process that is used by small as well as large scale companies to make sure that
quality of organisational offerings is effectively maintained. This enables the firm to ensure the
existence of deflated or negligible defects. This process is being applied by the management of
Mercedes by executing testing of units and thereby ascertaining if these are in accordance with
the requirements related to final product (car). With the execution of quality control, Mercedes
would be able to decrease the quantum of product recall and establish an extensive brand image
at market place.
Quality System:
This can be defined as the execution of philosophies, techniques, concepts and principles
aimed at maintenance of quality within the organisational premises. To facilitate the
development of an effective and unique quality system within the confines of Mercedes, the
management of this firm is applying the principles of Lean, Six Sigma and TQM. This is being
done to make sure that the quality of vehicles and procedures of Mercedes are in accordance with
industry standards and customers' expectations. This will enable the firm to establish a positive
brand image amidst the global customer and represent it as a company which the customers can
trust beyond any doubt or quality concern.
2 Advise on the operational strategies that Audi and BMW can implement to gain market share
over Mercedes-Benz
Mercedes-Benz is renowned organisations and deals in different number of products. In
comparison to this organisation product line of Audi and BMW is not much diversified. The
impact of the same is direct over their revenue and market share (Van Der Aalst, La Rosa and
Santoro, 2016). It is advisable to the management of both organisation that bring changes in their
operational strategies to combat the qualitative operation's of Mercedes-Benz and attain
6
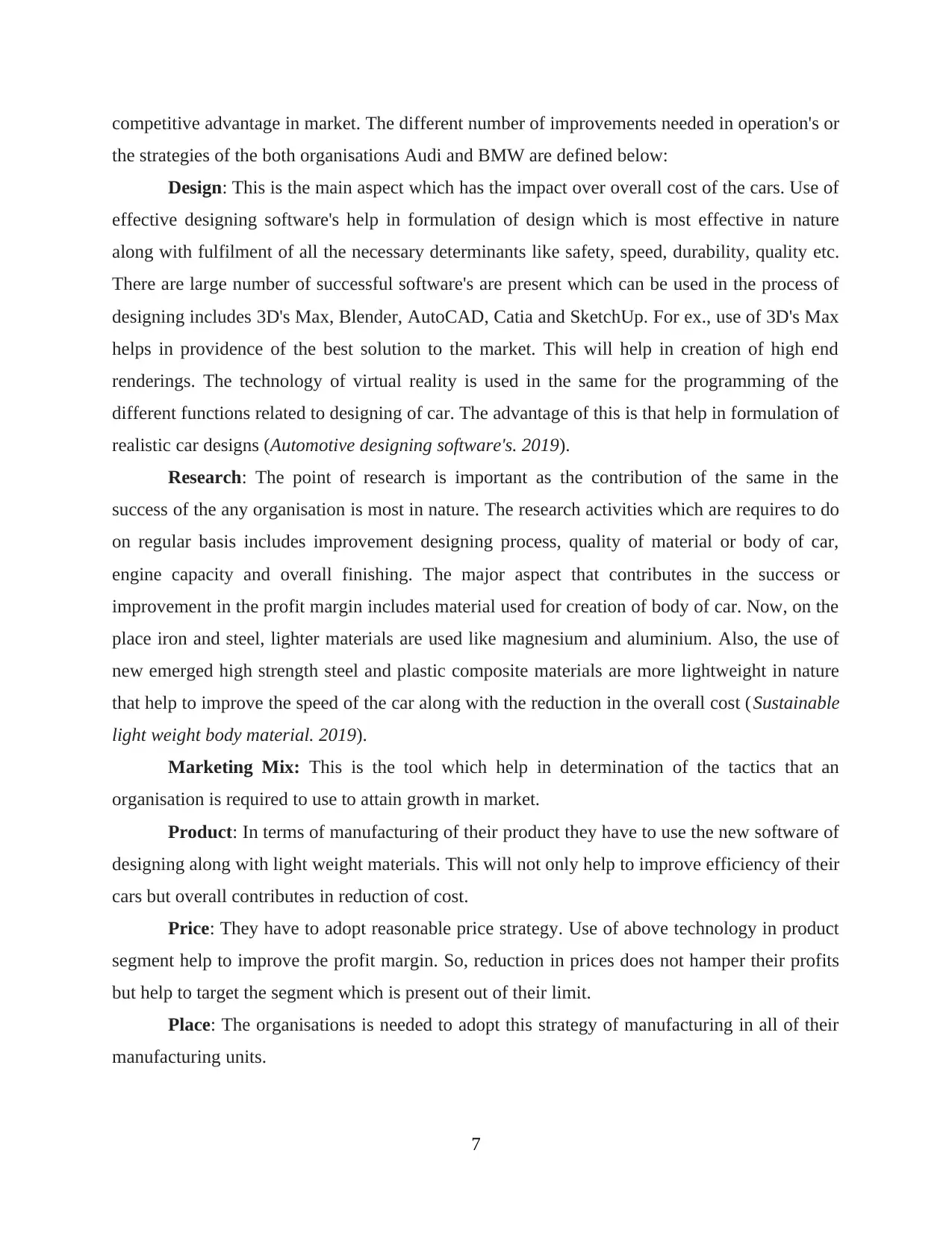
competitive advantage in market. The different number of improvements needed in operation's or
the strategies of the both organisations Audi and BMW are defined below:
Design: This is the main aspect which has the impact over overall cost of the cars. Use of
effective designing software's help in formulation of design which is most effective in nature
along with fulfilment of all the necessary determinants like safety, speed, durability, quality etc.
There are large number of successful software's are present which can be used in the process of
designing includes 3D's Max, Blender, AutoCAD, Catia and SketchUp. For ex., use of 3D's Max
helps in providence of the best solution to the market. This will help in creation of high end
renderings. The technology of virtual reality is used in the same for the programming of the
different functions related to designing of car. The advantage of this is that help in formulation of
realistic car designs (Automotive designing software's. 2019).
Research: The point of research is important as the contribution of the same in the
success of the any organisation is most in nature. The research activities which are requires to do
on regular basis includes improvement designing process, quality of material or body of car,
engine capacity and overall finishing. The major aspect that contributes in the success or
improvement in the profit margin includes material used for creation of body of car. Now, on the
place iron and steel, lighter materials are used like magnesium and aluminium. Also, the use of
new emerged high strength steel and plastic composite materials are more lightweight in nature
that help to improve the speed of the car along with the reduction in the overall cost (Sustainable
light weight body material. 2019).
Marketing Mix: This is the tool which help in determination of the tactics that an
organisation is required to use to attain growth in market.
Product: In terms of manufacturing of their product they have to use the new software of
designing along with light weight materials. This will not only help to improve efficiency of their
cars but overall contributes in reduction of cost.
Price: They have to adopt reasonable price strategy. Use of above technology in product
segment help to improve the profit margin. So, reduction in prices does not hamper their profits
but help to target the segment which is present out of their limit.
Place: The organisations is needed to adopt this strategy of manufacturing in all of their
manufacturing units.
7
the strategies of the both organisations Audi and BMW are defined below:
Design: This is the main aspect which has the impact over overall cost of the cars. Use of
effective designing software's help in formulation of design which is most effective in nature
along with fulfilment of all the necessary determinants like safety, speed, durability, quality etc.
There are large number of successful software's are present which can be used in the process of
designing includes 3D's Max, Blender, AutoCAD, Catia and SketchUp. For ex., use of 3D's Max
helps in providence of the best solution to the market. This will help in creation of high end
renderings. The technology of virtual reality is used in the same for the programming of the
different functions related to designing of car. The advantage of this is that help in formulation of
realistic car designs (Automotive designing software's. 2019).
Research: The point of research is important as the contribution of the same in the
success of the any organisation is most in nature. The research activities which are requires to do
on regular basis includes improvement designing process, quality of material or body of car,
engine capacity and overall finishing. The major aspect that contributes in the success or
improvement in the profit margin includes material used for creation of body of car. Now, on the
place iron and steel, lighter materials are used like magnesium and aluminium. Also, the use of
new emerged high strength steel and plastic composite materials are more lightweight in nature
that help to improve the speed of the car along with the reduction in the overall cost (Sustainable
light weight body material. 2019).
Marketing Mix: This is the tool which help in determination of the tactics that an
organisation is required to use to attain growth in market.
Product: In terms of manufacturing of their product they have to use the new software of
designing along with light weight materials. This will not only help to improve efficiency of their
cars but overall contributes in reduction of cost.
Price: They have to adopt reasonable price strategy. Use of above technology in product
segment help to improve the profit margin. So, reduction in prices does not hamper their profits
but help to target the segment which is present out of their limit.
Place: The organisations is needed to adopt this strategy of manufacturing in all of their
manufacturing units.
7
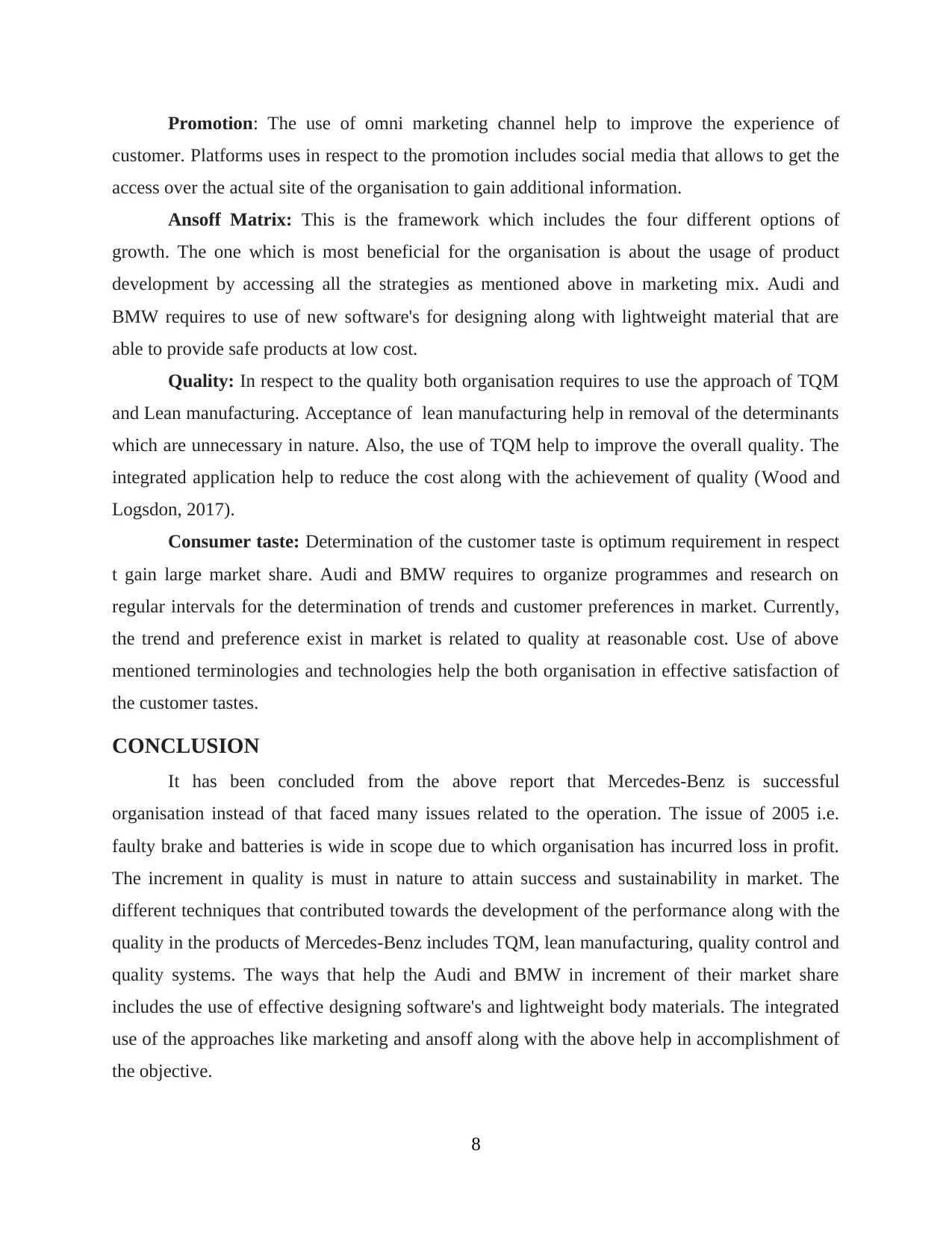
Promotion: The use of omni marketing channel help to improve the experience of
customer. Platforms uses in respect to the promotion includes social media that allows to get the
access over the actual site of the organisation to gain additional information.
Ansoff Matrix: This is the framework which includes the four different options of
growth. The one which is most beneficial for the organisation is about the usage of product
development by accessing all the strategies as mentioned above in marketing mix. Audi and
BMW requires to use of new software's for designing along with lightweight material that are
able to provide safe products at low cost.
Quality: In respect to the quality both organisation requires to use the approach of TQM
and Lean manufacturing. Acceptance of lean manufacturing help in removal of the determinants
which are unnecessary in nature. Also, the use of TQM help to improve the overall quality. The
integrated application help to reduce the cost along with the achievement of quality (Wood and
Logsdon, 2017).
Consumer taste: Determination of the customer taste is optimum requirement in respect
t gain large market share. Audi and BMW requires to organize programmes and research on
regular intervals for the determination of trends and customer preferences in market. Currently,
the trend and preference exist in market is related to quality at reasonable cost. Use of above
mentioned terminologies and technologies help the both organisation in effective satisfaction of
the customer tastes.
CONCLUSION
It has been concluded from the above report that Mercedes-Benz is successful
organisation instead of that faced many issues related to the operation. The issue of 2005 i.e.
faulty brake and batteries is wide in scope due to which organisation has incurred loss in profit.
The increment in quality is must in nature to attain success and sustainability in market. The
different techniques that contributed towards the development of the performance along with the
quality in the products of Mercedes-Benz includes TQM, lean manufacturing, quality control and
quality systems. The ways that help the Audi and BMW in increment of their market share
includes the use of effective designing software's and lightweight body materials. The integrated
use of the approaches like marketing and ansoff along with the above help in accomplishment of
the objective.
8
customer. Platforms uses in respect to the promotion includes social media that allows to get the
access over the actual site of the organisation to gain additional information.
Ansoff Matrix: This is the framework which includes the four different options of
growth. The one which is most beneficial for the organisation is about the usage of product
development by accessing all the strategies as mentioned above in marketing mix. Audi and
BMW requires to use of new software's for designing along with lightweight material that are
able to provide safe products at low cost.
Quality: In respect to the quality both organisation requires to use the approach of TQM
and Lean manufacturing. Acceptance of lean manufacturing help in removal of the determinants
which are unnecessary in nature. Also, the use of TQM help to improve the overall quality. The
integrated application help to reduce the cost along with the achievement of quality (Wood and
Logsdon, 2017).
Consumer taste: Determination of the customer taste is optimum requirement in respect
t gain large market share. Audi and BMW requires to organize programmes and research on
regular intervals for the determination of trends and customer preferences in market. Currently,
the trend and preference exist in market is related to quality at reasonable cost. Use of above
mentioned terminologies and technologies help the both organisation in effective satisfaction of
the customer tastes.
CONCLUSION
It has been concluded from the above report that Mercedes-Benz is successful
organisation instead of that faced many issues related to the operation. The issue of 2005 i.e.
faulty brake and batteries is wide in scope due to which organisation has incurred loss in profit.
The increment in quality is must in nature to attain success and sustainability in market. The
different techniques that contributed towards the development of the performance along with the
quality in the products of Mercedes-Benz includes TQM, lean manufacturing, quality control and
quality systems. The ways that help the Audi and BMW in increment of their market share
includes the use of effective designing software's and lightweight body materials. The integrated
use of the approaches like marketing and ansoff along with the above help in accomplishment of
the objective.
8
Secure Best Marks with AI Grader
Need help grading? Try our AI Grader for instant feedback on your assignments.
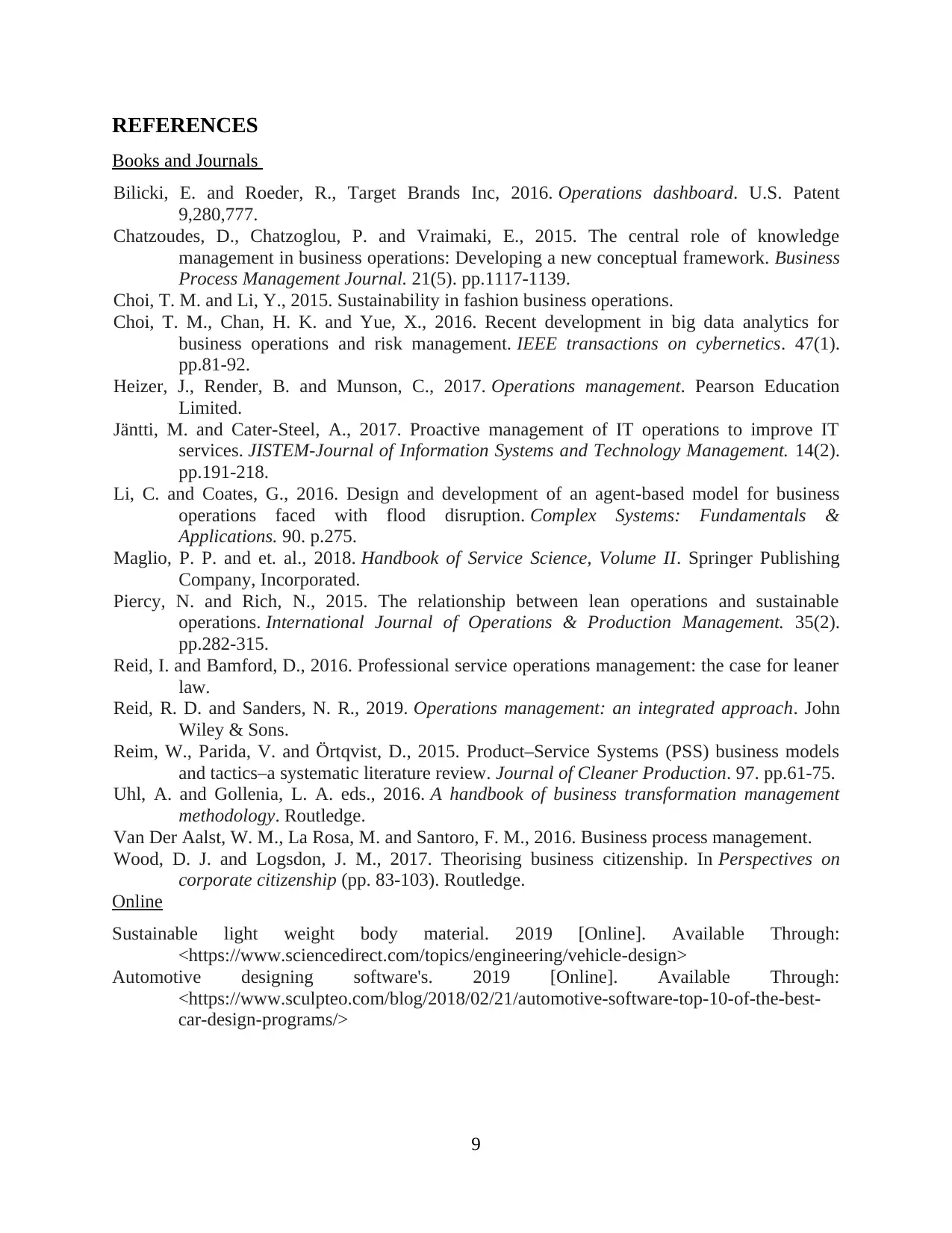
REFERENCES
Books and Journals
Bilicki, E. and Roeder, R., Target Brands Inc, 2016. Operations dashboard. U.S. Patent
9,280,777.
Chatzoudes, D., Chatzoglou, P. and Vraimaki, E., 2015. The central role of knowledge
management in business operations: Developing a new conceptual framework. Business
Process Management Journal. 21(5). pp.1117-1139.
Choi, T. M. and Li, Y., 2015. Sustainability in fashion business operations.
Choi, T. M., Chan, H. K. and Yue, X., 2016. Recent development in big data analytics for
business operations and risk management. IEEE transactions on cybernetics. 47(1).
pp.81-92.
Heizer, J., Render, B. and Munson, C., 2017. Operations management. Pearson Education
Limited.
Jäntti, M. and Cater-Steel, A., 2017. Proactive management of IT operations to improve IT
services. JISTEM-Journal of Information Systems and Technology Management. 14(2).
pp.191-218.
Li, C. and Coates, G., 2016. Design and development of an agent-based model for business
operations faced with flood disruption. Complex Systems: Fundamentals &
Applications. 90. p.275.
Maglio, P. P. and et. al., 2018. Handbook of Service Science, Volume II. Springer Publishing
Company, Incorporated.
Piercy, N. and Rich, N., 2015. The relationship between lean operations and sustainable
operations. International Journal of Operations & Production Management. 35(2).
pp.282-315.
Reid, I. and Bamford, D., 2016. Professional service operations management: the case for leaner
law.
Reid, R. D. and Sanders, N. R., 2019. Operations management: an integrated approach. John
Wiley & Sons.
Reim, W., Parida, V. and Örtqvist, D., 2015. Product–Service Systems (PSS) business models
and tactics–a systematic literature review. Journal of Cleaner Production. 97. pp.61-75.
Uhl, A. and Gollenia, L. A. eds., 2016. A handbook of business transformation management
methodology. Routledge.
Van Der Aalst, W. M., La Rosa, M. and Santoro, F. M., 2016. Business process management.
Wood, D. J. and Logsdon, J. M., 2017. Theorising business citizenship. In Perspectives on
corporate citizenship (pp. 83-103). Routledge.
Online
Sustainable light weight body material. 2019 [Online]. Available Through:
<https://www.sciencedirect.com/topics/engineering/vehicle-design>
Automotive designing software's. 2019 [Online]. Available Through:
<https://www.sculpteo.com/blog/2018/02/21/automotive-software-top-10-of-the-best-
car-design-programs/>
9
Books and Journals
Bilicki, E. and Roeder, R., Target Brands Inc, 2016. Operations dashboard. U.S. Patent
9,280,777.
Chatzoudes, D., Chatzoglou, P. and Vraimaki, E., 2015. The central role of knowledge
management in business operations: Developing a new conceptual framework. Business
Process Management Journal. 21(5). pp.1117-1139.
Choi, T. M. and Li, Y., 2015. Sustainability in fashion business operations.
Choi, T. M., Chan, H. K. and Yue, X., 2016. Recent development in big data analytics for
business operations and risk management. IEEE transactions on cybernetics. 47(1).
pp.81-92.
Heizer, J., Render, B. and Munson, C., 2017. Operations management. Pearson Education
Limited.
Jäntti, M. and Cater-Steel, A., 2017. Proactive management of IT operations to improve IT
services. JISTEM-Journal of Information Systems and Technology Management. 14(2).
pp.191-218.
Li, C. and Coates, G., 2016. Design and development of an agent-based model for business
operations faced with flood disruption. Complex Systems: Fundamentals &
Applications. 90. p.275.
Maglio, P. P. and et. al., 2018. Handbook of Service Science, Volume II. Springer Publishing
Company, Incorporated.
Piercy, N. and Rich, N., 2015. The relationship between lean operations and sustainable
operations. International Journal of Operations & Production Management. 35(2).
pp.282-315.
Reid, I. and Bamford, D., 2016. Professional service operations management: the case for leaner
law.
Reid, R. D. and Sanders, N. R., 2019. Operations management: an integrated approach. John
Wiley & Sons.
Reim, W., Parida, V. and Örtqvist, D., 2015. Product–Service Systems (PSS) business models
and tactics–a systematic literature review. Journal of Cleaner Production. 97. pp.61-75.
Uhl, A. and Gollenia, L. A. eds., 2016. A handbook of business transformation management
methodology. Routledge.
Van Der Aalst, W. M., La Rosa, M. and Santoro, F. M., 2016. Business process management.
Wood, D. J. and Logsdon, J. M., 2017. Theorising business citizenship. In Perspectives on
corporate citizenship (pp. 83-103). Routledge.
Online
Sustainable light weight body material. 2019 [Online]. Available Through:
<https://www.sciencedirect.com/topics/engineering/vehicle-design>
Automotive designing software's. 2019 [Online]. Available Through:
<https://www.sculpteo.com/blog/2018/02/21/automotive-software-top-10-of-the-best-
car-design-programs/>
9
1 out of 11
Related Documents
![[object Object]](/_next/image/?url=%2F_next%2Fstatic%2Fmedia%2Flogo.6d15ce61.png&w=640&q=75)
Your All-in-One AI-Powered Toolkit for Academic Success.
+13062052269
info@desklib.com
Available 24*7 on WhatsApp / Email
Unlock your academic potential
© 2024 | Zucol Services PVT LTD | All rights reserved.