Engineering Planning and Scheduling: Techniques and Capacity Assessment Methods
VerifiedAdded on  2023/06/06
|9
|1614
|366
AI Summary
This essay discusses the importance of engineering planning and scheduling in establishing a proper work breakdown structure, identifying resources, timeline, and budget for each component and group tasks. It covers different process planning techniques such as Gantt charts, PERT charts, critical path analysis, and CAPP. It also explains the capacity assessment methods for engineering processes and the importance of inventory management and shop control systems. Course code and college/university not mentioned.
Contribute Materials
Your contribution can guide someone’s learning journey. Share your
documents today.
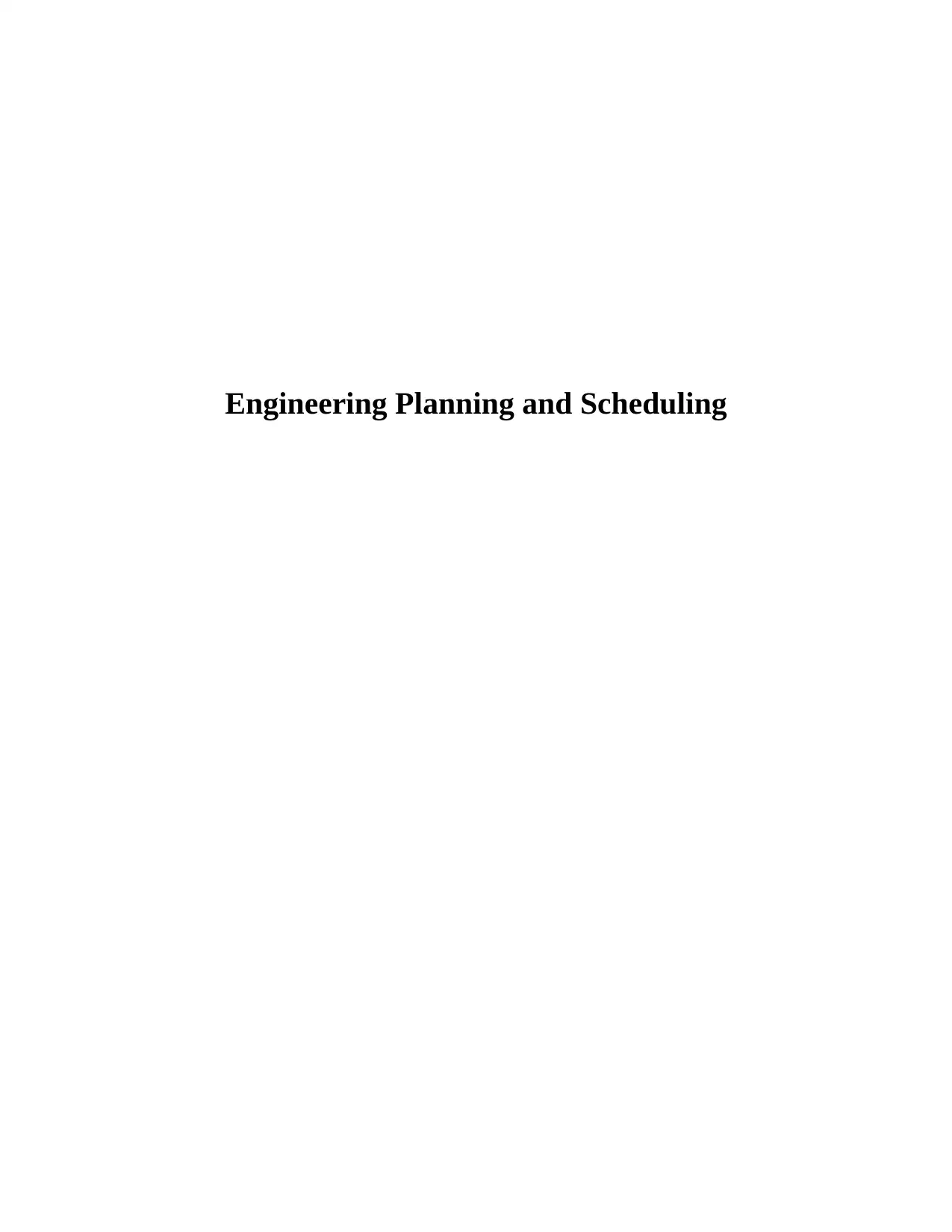
Engineering Planning and Scheduling
Secure Best Marks with AI Grader
Need help grading? Try our AI Grader for instant feedback on your assignments.
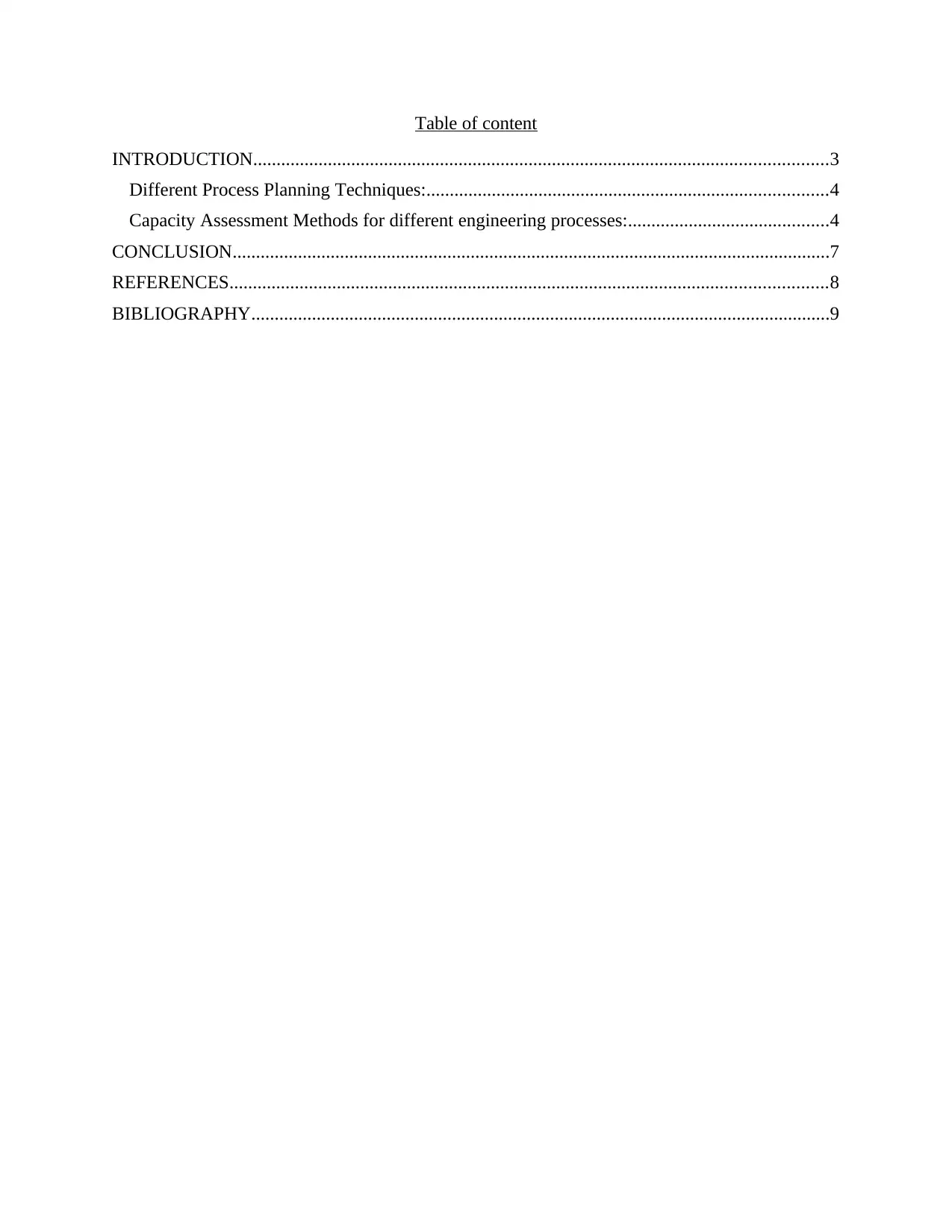
Table of content
INTRODUCTION...........................................................................................................................3
Different Process Planning Techniques:......................................................................................4
Capacity Assessment Methods for different engineering processes:...........................................4
CONCLUSION................................................................................................................................7
REFERENCES................................................................................................................................8
BIBLIOGRAPHY............................................................................................................................9
INTRODUCTION...........................................................................................................................3
Different Process Planning Techniques:......................................................................................4
Capacity Assessment Methods for different engineering processes:...........................................4
CONCLUSION................................................................................................................................7
REFERENCES................................................................................................................................8
BIBLIOGRAPHY............................................................................................................................9
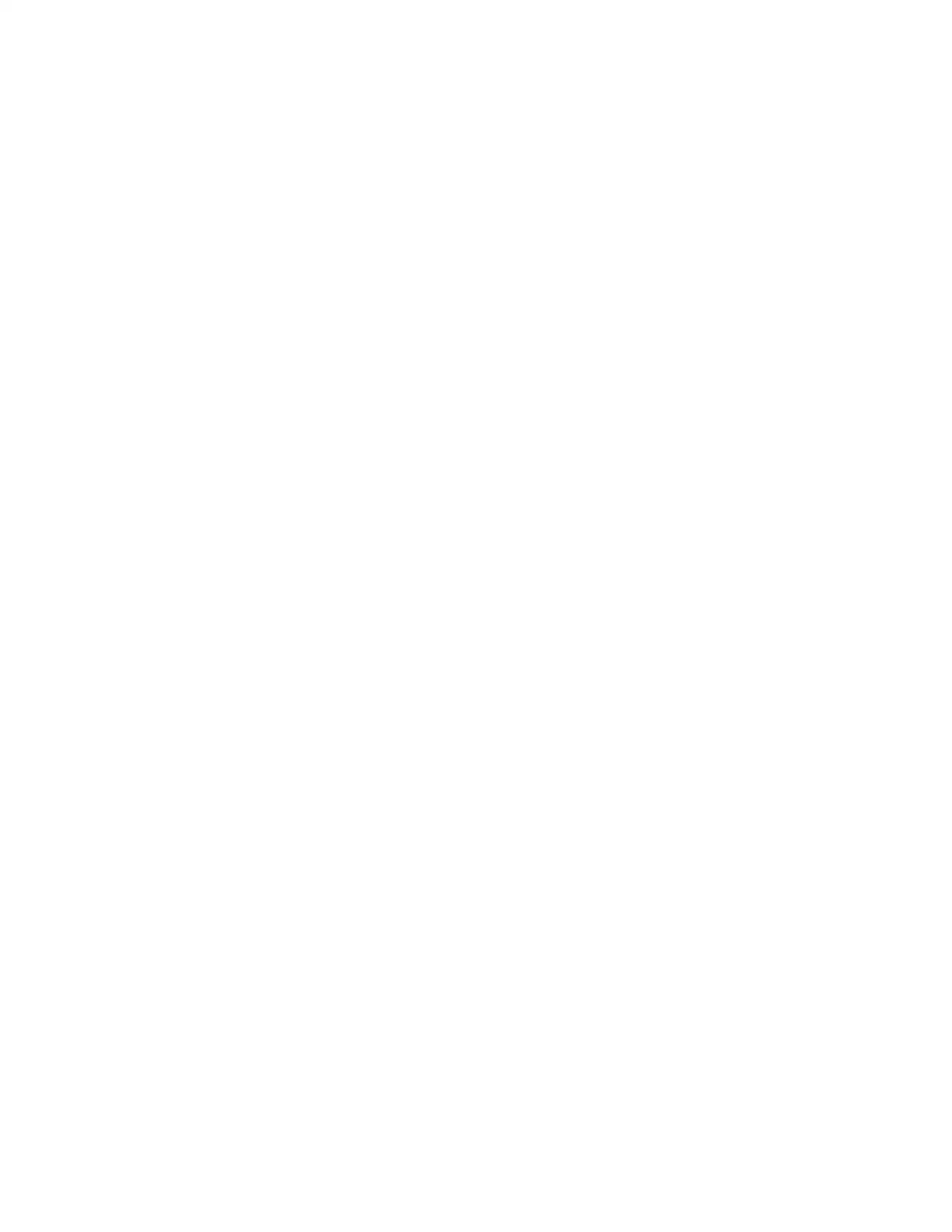
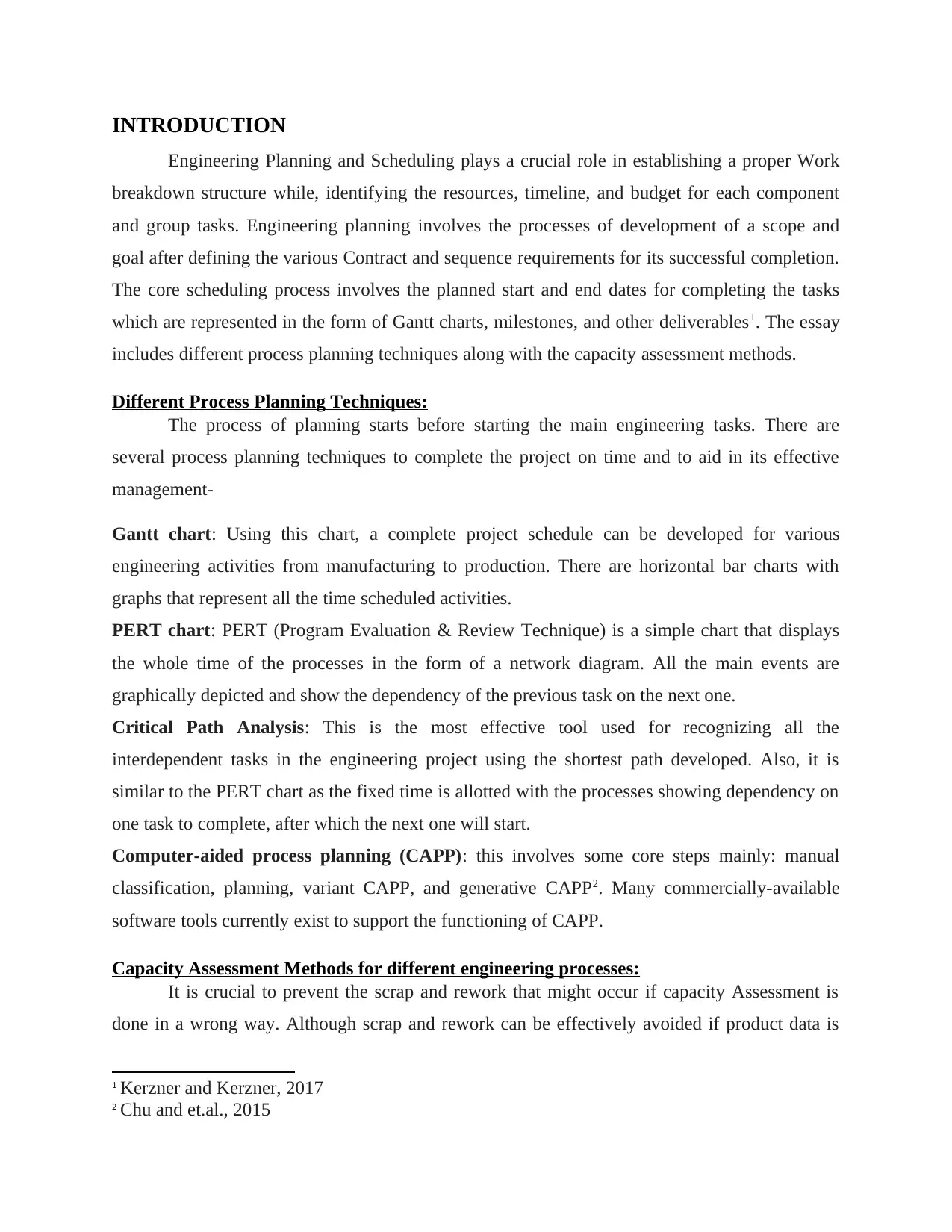
INTRODUCTION
Engineering Planning and Scheduling plays a crucial role in establishing a proper Work
breakdown structure while, identifying the resources, timeline, and budget for each component
and group tasks. Engineering planning involves the processes of development of a scope and
goal after defining the various Contract and sequence requirements for its successful completion.
The core scheduling process involves the planned start and end dates for completing the tasks
which are represented in the form of Gantt charts, milestones, and other deliverables1. The essay
includes different process planning techniques along with the capacity assessment methods.
Different Process Planning Techniques:
The process of planning starts before starting the main engineering tasks. There are
several process planning techniques to complete the project on time and to aid in its effective
management-
Gantt chart: Using this chart, a complete project schedule can be developed for various
engineering activities from manufacturing to production. There are horizontal bar charts with
graphs that represent all the time scheduled activities.
PERT chart: PERT (Program Evaluation & Review Technique) is a simple chart that displays
the whole time of the processes in the form of a network diagram. All the main events are
graphically depicted and show the dependency of the previous task on the next one.
Critical Path Analysis: This is the most effective tool used for recognizing all the
interdependent tasks in the engineering project using the shortest path developed. Also, it is
similar to the PERT chart as the fixed time is allotted with the processes showing dependency on
one task to complete, after which the next one will start.
Computer-aided process planning (CAPP): this involves some core steps mainly: manual
classification, planning, variant CAPP, and generative CAPP2. Many commercially-available
software tools currently exist to support the functioning of CAPP.
Capacity Assessment Methods for different engineering processes:
It is crucial to prevent the scrap and rework that might occur if capacity Assessment is
done in a wrong way. Although scrap and rework can be effectively avoided if product data is
1 Kerzner and Kerzner, 2017
2 Chu and et.al., 2015
Engineering Planning and Scheduling plays a crucial role in establishing a proper Work
breakdown structure while, identifying the resources, timeline, and budget for each component
and group tasks. Engineering planning involves the processes of development of a scope and
goal after defining the various Contract and sequence requirements for its successful completion.
The core scheduling process involves the planned start and end dates for completing the tasks
which are represented in the form of Gantt charts, milestones, and other deliverables1. The essay
includes different process planning techniques along with the capacity assessment methods.
Different Process Planning Techniques:
The process of planning starts before starting the main engineering tasks. There are
several process planning techniques to complete the project on time and to aid in its effective
management-
Gantt chart: Using this chart, a complete project schedule can be developed for various
engineering activities from manufacturing to production. There are horizontal bar charts with
graphs that represent all the time scheduled activities.
PERT chart: PERT (Program Evaluation & Review Technique) is a simple chart that displays
the whole time of the processes in the form of a network diagram. All the main events are
graphically depicted and show the dependency of the previous task on the next one.
Critical Path Analysis: This is the most effective tool used for recognizing all the
interdependent tasks in the engineering project using the shortest path developed. Also, it is
similar to the PERT chart as the fixed time is allotted with the processes showing dependency on
one task to complete, after which the next one will start.
Computer-aided process planning (CAPP): this involves some core steps mainly: manual
classification, planning, variant CAPP, and generative CAPP2. Many commercially-available
software tools currently exist to support the functioning of CAPP.
Capacity Assessment Methods for different engineering processes:
It is crucial to prevent the scrap and rework that might occur if capacity Assessment is
done in a wrong way. Although scrap and rework can be effectively avoided if product data is
1 Kerzner and Kerzner, 2017
2 Chu and et.al., 2015
Secure Best Marks with AI Grader
Need help grading? Try our AI Grader for instant feedback on your assignments.
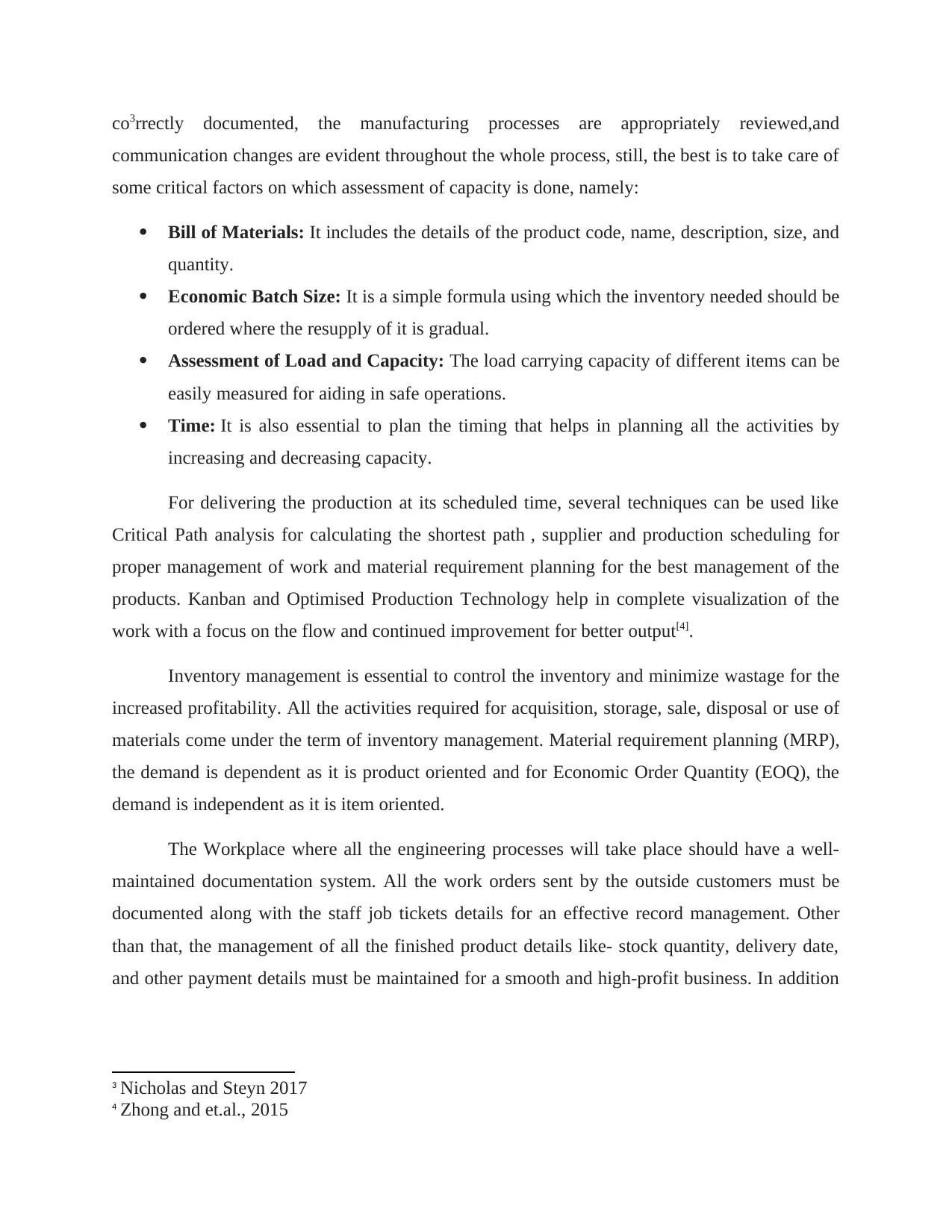
co3rrectly documented, the manufacturing processes are appropriately reviewed,and
communication changes are evident throughout the whole process, still, the best is to take care of
some critical factors on which assessment of capacity is done, namely:
ď‚· Bill of Materials: It includes the details of the product code, name, description, size, and
quantity.
ď‚· Economic Batch Size: It is a simple formula using which the inventory needed should be
ordered where the resupply of it is gradual.
ď‚· Assessment of Load and Capacity: The load carrying capacity of different items can be
easily measured for aiding in safe operations.
ď‚· Time: It is also essential to plan the timing that helps in planning all the activities by
increasing and decreasing capacity.
For delivering the production at its scheduled time, several techniques can be used like
Critical Path analysis for calculating the shortest path , supplier and production scheduling for
proper management of work and material requirement planning for the best management of the
products. Kanban and Optimised Production Technology help in complete visualization of the
work with a focus on the flow and continued improvement for better output[4].
Inventory management is essential to control the inventory and minimize wastage for the
increased profitability. All the activities required for acquisition, storage, sale, disposal or use of
materials come under the term of inventory management. Material requirement planning (MRP),
the demand is dependent as it is product oriented and for Economic Order Quantity (EOQ), the
demand is independent as it is item oriented.
The Workplace where all the engineering processes will take place should have a well-
maintained documentation system. All the work orders sent by the outside customers must be
documented along with the staff job tickets details for an effective record management. Other
than that, the management of all the finished product details like- stock quantity, delivery date,
and other payment details must be maintained for a smooth and high-profit business. In addition
3 Nicholas and Steyn 2017
4 Zhong and et.al., 2015
communication changes are evident throughout the whole process, still, the best is to take care of
some critical factors on which assessment of capacity is done, namely:
ď‚· Bill of Materials: It includes the details of the product code, name, description, size, and
quantity.
ď‚· Economic Batch Size: It is a simple formula using which the inventory needed should be
ordered where the resupply of it is gradual.
ď‚· Assessment of Load and Capacity: The load carrying capacity of different items can be
easily measured for aiding in safe operations.
ď‚· Time: It is also essential to plan the timing that helps in planning all the activities by
increasing and decreasing capacity.
For delivering the production at its scheduled time, several techniques can be used like
Critical Path analysis for calculating the shortest path , supplier and production scheduling for
proper management of work and material requirement planning for the best management of the
products. Kanban and Optimised Production Technology help in complete visualization of the
work with a focus on the flow and continued improvement for better output[4].
Inventory management is essential to control the inventory and minimize wastage for the
increased profitability. All the activities required for acquisition, storage, sale, disposal or use of
materials come under the term of inventory management. Material requirement planning (MRP),
the demand is dependent as it is product oriented and for Economic Order Quantity (EOQ), the
demand is independent as it is item oriented.
The Workplace where all the engineering processes will take place should have a well-
maintained documentation system. All the work orders sent by the outside customers must be
documented along with the staff job tickets details for an effective record management. Other
than that, the management of all the finished product details like- stock quantity, delivery date,
and other payment details must be maintained for a smooth and high-profit business. In addition
3 Nicholas and Steyn 2017
4 Zhong and et.al., 2015
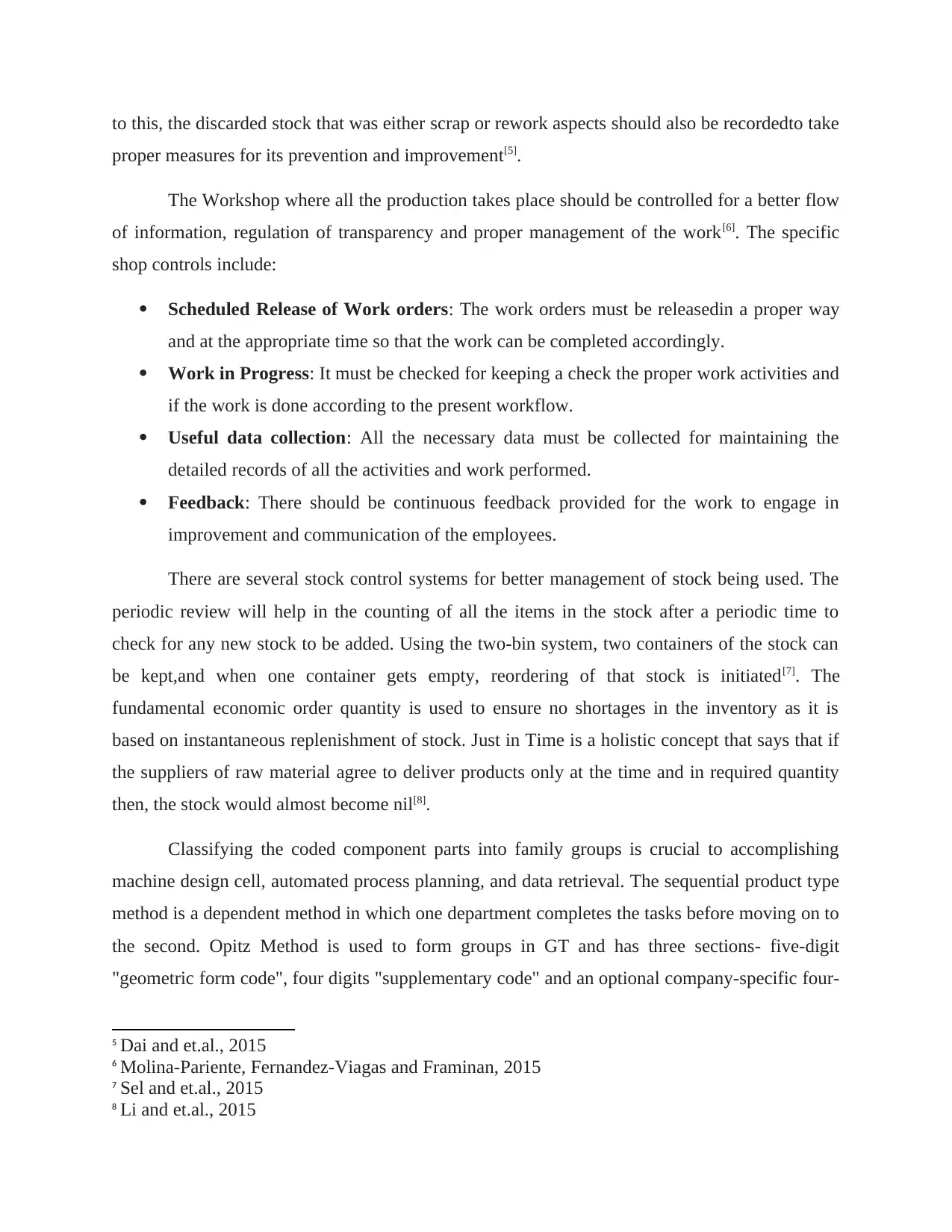
to this, the discarded stock that was either scrap or rework aspects should also be recordedto take
proper measures for its prevention and improvement[5].
The Workshop where all the production takes place should be controlled for a better flow
of information, regulation of transparency and proper management of the work[6]. The specific
shop controls include:
ď‚· Scheduled Release of Work orders: The work orders must be releasedin a proper way
and at the appropriate time so that the work can be completed accordingly.
ď‚· Work in Progress: It must be checked for keeping a check the proper work activities and
if the work is done according to the present workflow.
ď‚· Useful data collection: All the necessary data must be collected for maintaining the
detailed records of all the activities and work performed.
ď‚· Feedback: There should be continuous feedback provided for the work to engage in
improvement and communication of the employees.
There are several stock control systems for better management of stock being used. The
periodic review will help in the counting of all the items in the stock after a periodic time to
check for any new stock to be added. Using the two-bin system, two containers of the stock can
be kept,and when one container gets empty, reordering of that stock is initiated[7]. The
fundamental economic order quantity is used to ensure no shortages in the inventory as it is
based on instantaneous replenishment of stock. Just in Time is a holistic concept that says that if
the suppliers of raw material agree to deliver products only at the time and in required quantity
then, the stock would almost become nil[8].
Classifying the coded component parts into family groups is crucial to accomplishing
machine design cell, automated process planning, and data retrieval. The sequential product type
method is a dependent method in which one department completes the tasks before moving on to
the second. Opitz Method is used to form groups in GT and has three sections- five-digit
"geometric form code", four digits "supplementary code" and an optional company-specific four-
5 Dai and et.al., 2015
6 Molina-Pariente, Fernandez-Viagas and Framinan, 2015
7 Sel and et.al., 2015
8 Li and et.al., 2015
proper measures for its prevention and improvement[5].
The Workshop where all the production takes place should be controlled for a better flow
of information, regulation of transparency and proper management of the work[6]. The specific
shop controls include:
ď‚· Scheduled Release of Work orders: The work orders must be releasedin a proper way
and at the appropriate time so that the work can be completed accordingly.
ď‚· Work in Progress: It must be checked for keeping a check the proper work activities and
if the work is done according to the present workflow.
ď‚· Useful data collection: All the necessary data must be collected for maintaining the
detailed records of all the activities and work performed.
ď‚· Feedback: There should be continuous feedback provided for the work to engage in
improvement and communication of the employees.
There are several stock control systems for better management of stock being used. The
periodic review will help in the counting of all the items in the stock after a periodic time to
check for any new stock to be added. Using the two-bin system, two containers of the stock can
be kept,and when one container gets empty, reordering of that stock is initiated[7]. The
fundamental economic order quantity is used to ensure no shortages in the inventory as it is
based on instantaneous replenishment of stock. Just in Time is a holistic concept that says that if
the suppliers of raw material agree to deliver products only at the time and in required quantity
then, the stock would almost become nil[8].
Classifying the coded component parts into family groups is crucial to accomplishing
machine design cell, automated process planning, and data retrieval. The sequential product type
method is a dependent method in which one department completes the tasks before moving on to
the second. Opitz Method is used to form groups in GT and has three sections- five-digit
"geometric form code", four digits "supplementary code" and an optional company-specific four-
5 Dai and et.al., 2015
6 Molina-Pariente, Fernandez-Viagas and Framinan, 2015
7 Sel and et.al., 2015
8 Li and et.al., 2015
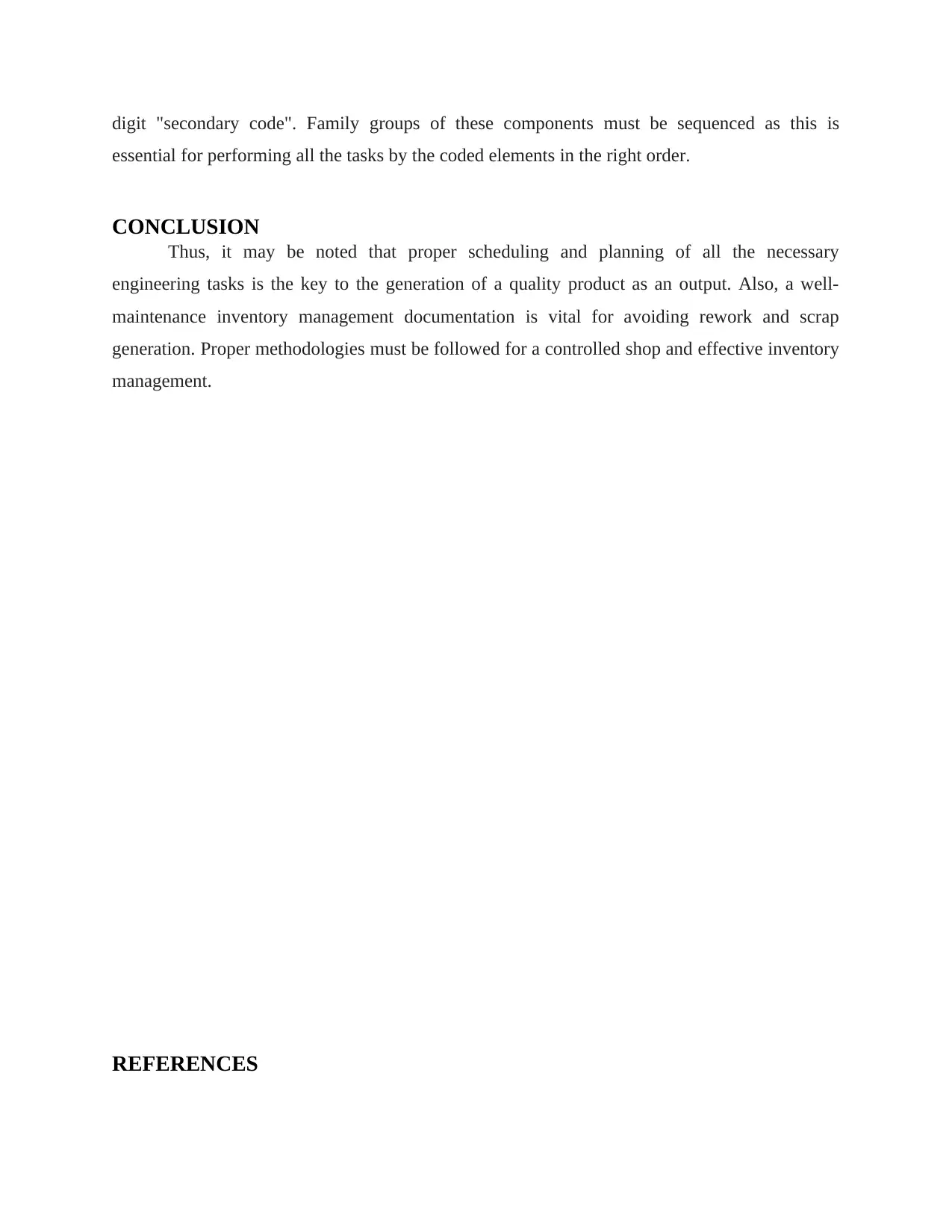
digit "secondary code". Family groups of these components must be sequenced as this is
essential for performing all the tasks by the coded elements in the right order.
CONCLUSION
Thus, it may be noted that proper scheduling and planning of all the necessary
engineering tasks is the key to the generation of a quality product as an output. Also, a well-
maintenance inventory management documentation is vital for avoiding rework and scrap
generation. Proper methodologies must be followed for a controlled shop and effective inventory
management.
REFERENCES
essential for performing all the tasks by the coded elements in the right order.
CONCLUSION
Thus, it may be noted that proper scheduling and planning of all the necessary
engineering tasks is the key to the generation of a quality product as an output. Also, a well-
maintenance inventory management documentation is vital for avoiding rework and scrap
generation. Proper methodologies must be followed for a controlled shop and effective inventory
management.
REFERENCES
Paraphrase This Document
Need a fresh take? Get an instant paraphrase of this document with our AI Paraphraser
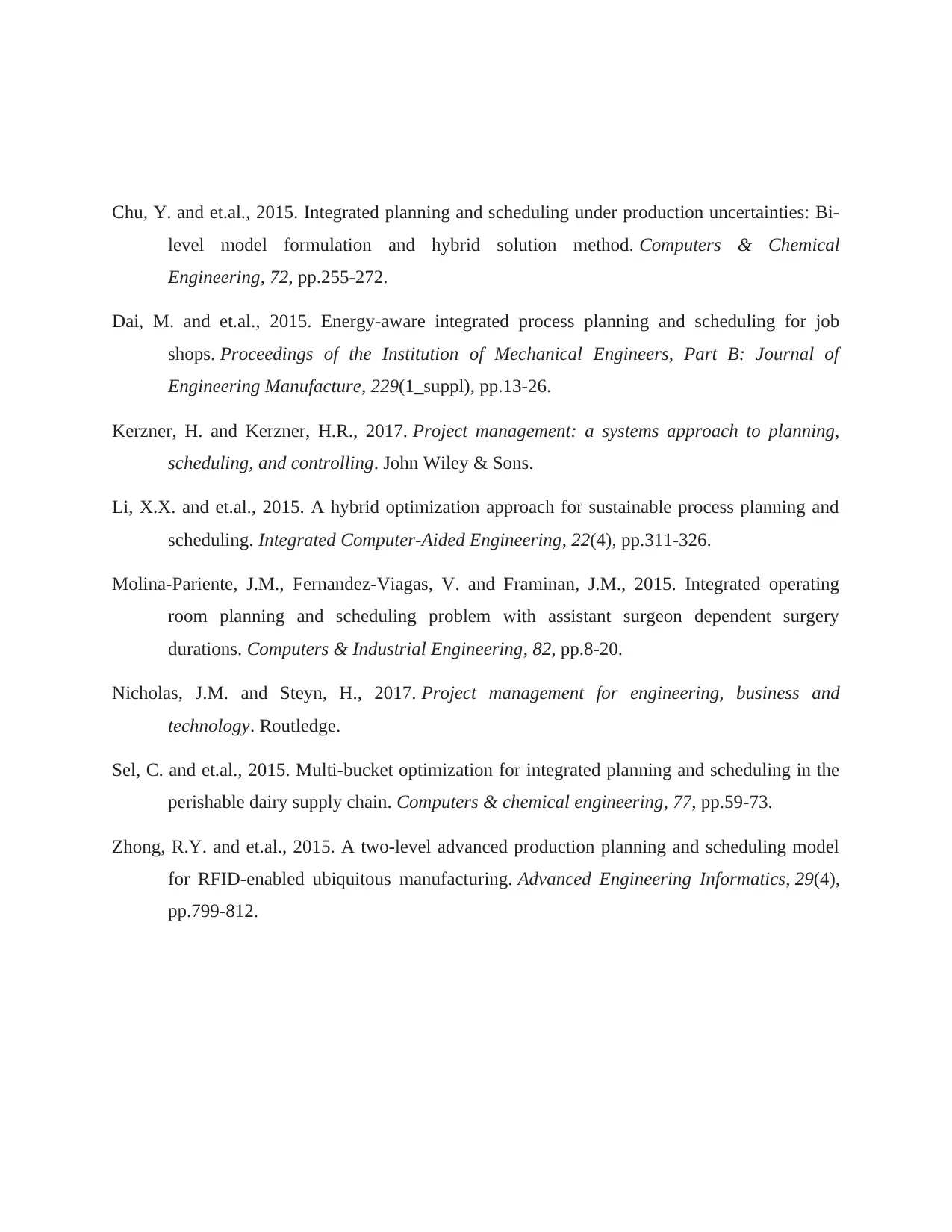
Chu, Y. and et.al., 2015. Integrated planning and scheduling under production uncertainties: Bi-
level model formulation and hybrid solution method. Computers & Chemical
Engineering, 72, pp.255-272.
Dai, M. and et.al., 2015. Energy-aware integrated process planning and scheduling for job
shops. Proceedings of the Institution of Mechanical Engineers, Part B: Journal of
Engineering Manufacture, 229(1_suppl), pp.13-26.
Kerzner, H. and Kerzner, H.R., 2017. Project management: a systems approach to planning,
scheduling, and controlling. John Wiley & Sons.
Li, X.X. and et.al., 2015. A hybrid optimization approach for sustainable process planning and
scheduling. Integrated Computer-Aided Engineering, 22(4), pp.311-326.
Molina-Pariente, J.M., Fernandez-Viagas, V. and Framinan, J.M., 2015. Integrated operating
room planning and scheduling problem with assistant surgeon dependent surgery
durations. Computers & Industrial Engineering, 82, pp.8-20.
Nicholas, J.M. and Steyn, H., 2017. Project management for engineering, business and
technology. Routledge.
Sel, C. and et.al., 2015. Multi-bucket optimization for integrated planning and scheduling in the
perishable dairy supply chain. Computers & chemical engineering, 77, pp.59-73.
Zhong, R.Y. and et.al., 2015. A two-level advanced production planning and scheduling model
for RFID-enabled ubiquitous manufacturing. Advanced Engineering Informatics, 29(4),
pp.799-812.
level model formulation and hybrid solution method. Computers & Chemical
Engineering, 72, pp.255-272.
Dai, M. and et.al., 2015. Energy-aware integrated process planning and scheduling for job
shops. Proceedings of the Institution of Mechanical Engineers, Part B: Journal of
Engineering Manufacture, 229(1_suppl), pp.13-26.
Kerzner, H. and Kerzner, H.R., 2017. Project management: a systems approach to planning,
scheduling, and controlling. John Wiley & Sons.
Li, X.X. and et.al., 2015. A hybrid optimization approach for sustainable process planning and
scheduling. Integrated Computer-Aided Engineering, 22(4), pp.311-326.
Molina-Pariente, J.M., Fernandez-Viagas, V. and Framinan, J.M., 2015. Integrated operating
room planning and scheduling problem with assistant surgeon dependent surgery
durations. Computers & Industrial Engineering, 82, pp.8-20.
Nicholas, J.M. and Steyn, H., 2017. Project management for engineering, business and
technology. Routledge.
Sel, C. and et.al., 2015. Multi-bucket optimization for integrated planning and scheduling in the
perishable dairy supply chain. Computers & chemical engineering, 77, pp.59-73.
Zhong, R.Y. and et.al., 2015. A two-level advanced production planning and scheduling model
for RFID-enabled ubiquitous manufacturing. Advanced Engineering Informatics, 29(4),
pp.799-812.
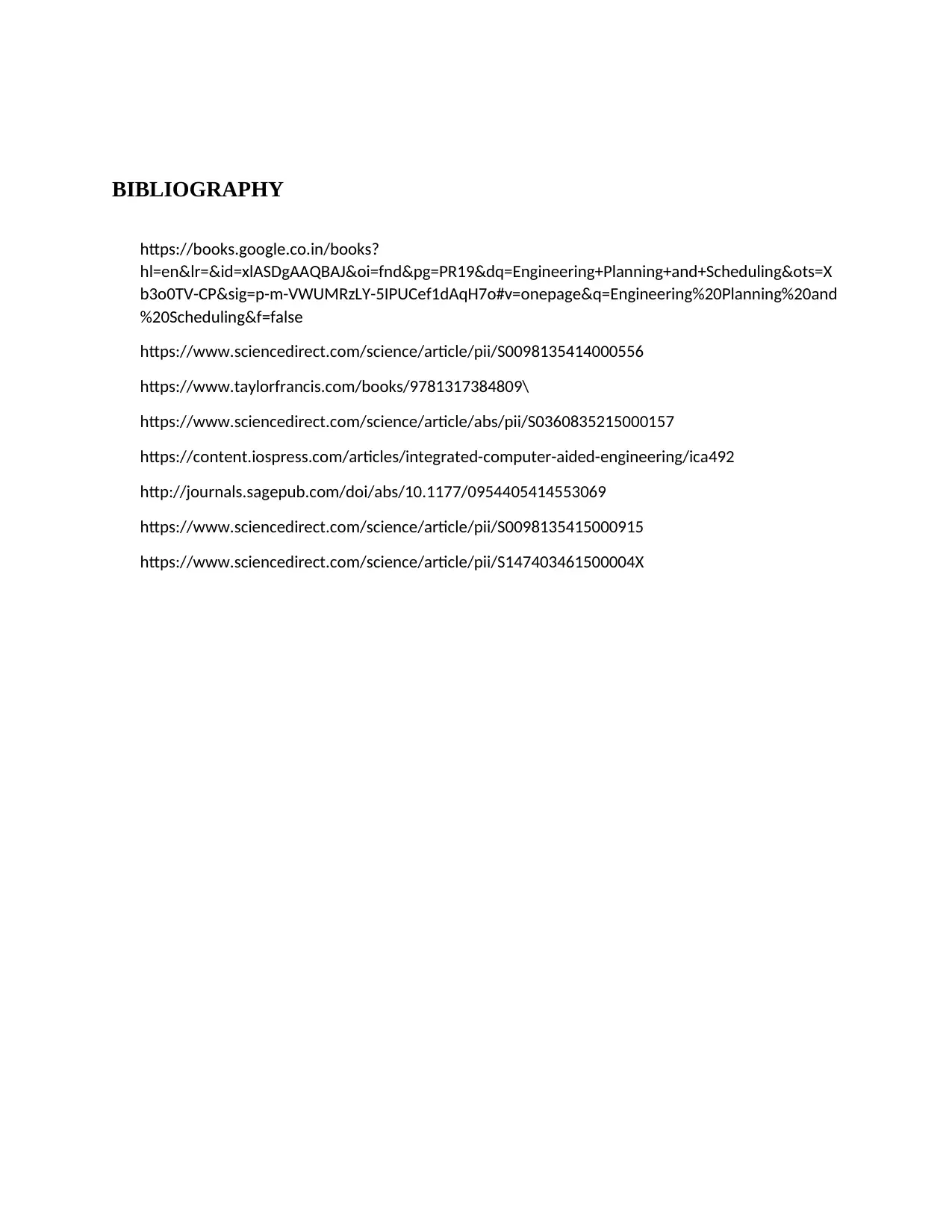
BIBLIOGRAPHY
https://books.google.co.in/books?
hl=en&lr=&id=xlASDgAAQBAJ&oi=fnd&pg=PR19&dq=Engineering+Planning+and+Scheduling&ots=X
b3o0TV-CP&sig=p-m-VWUMRzLY-5IPUCef1dAqH7o#v=onepage&q=Engineering%20Planning%20and
%20Scheduling&f=false
https://www.sciencedirect.com/science/article/pii/S0098135414000556
https://www.taylorfrancis.com/books/9781317384809\
https://www.sciencedirect.com/science/article/abs/pii/S0360835215000157
https://content.iospress.com/articles/integrated-computer-aided-engineering/ica492
http://journals.sagepub.com/doi/abs/10.1177/0954405414553069
https://www.sciencedirect.com/science/article/pii/S0098135415000915
https://www.sciencedirect.com/science/article/pii/S147403461500004X
https://books.google.co.in/books?
hl=en&lr=&id=xlASDgAAQBAJ&oi=fnd&pg=PR19&dq=Engineering+Planning+and+Scheduling&ots=X
b3o0TV-CP&sig=p-m-VWUMRzLY-5IPUCef1dAqH7o#v=onepage&q=Engineering%20Planning%20and
%20Scheduling&f=false
https://www.sciencedirect.com/science/article/pii/S0098135414000556
https://www.taylorfrancis.com/books/9781317384809\
https://www.sciencedirect.com/science/article/abs/pii/S0360835215000157
https://content.iospress.com/articles/integrated-computer-aided-engineering/ica492
http://journals.sagepub.com/doi/abs/10.1177/0954405414553069
https://www.sciencedirect.com/science/article/pii/S0098135415000915
https://www.sciencedirect.com/science/article/pii/S147403461500004X
1 out of 9
Related Documents
![[object Object]](/_next/image/?url=%2F_next%2Fstatic%2Fmedia%2Flogo.6d15ce61.png&w=640&q=75)
Your All-in-One AI-Powered Toolkit for Academic Success.
 +13062052269
info@desklib.com
Available 24*7 on WhatsApp / Email
Unlock your academic potential
© 2024  |  Zucol Services PVT LTD  |  All rights reserved.