Experimental Analysis of Flow Control Devices
VerifiedAdded on 2019/10/16
|15
|2811
|325
Report
AI Summary
The assignment content discusses the characteristics of various flow control devices, including the iris valve, orifice plate, nozzle, and venturi. The iris valve controls flow linearly with respect to percentage open diameter, while the theoretical equations for pressure drop are confirmed by experiments. Errors in measurement and calculation may cause deviations from straight-line behavior. The article also discusses the merits of each device, their advantages and disadvantages, and provides examples of calculations and applications.
Contribute Materials
Your contribution can guide someone’s learning journey. Share your
documents today.

Last Name 1
Name:
Professor:
Course:
Date: MMDDYYYY
Measurement of Flow Characteristics of Meters and Control Valve
Introduction: Fluid flow is measured and controlled by obstructing the flow with suitable
devices or modification of the internal diameter profile. Five types of devices are studied in
this experiment. Orifice plate, with central hole in a blind flange; Nozzle, like orifice plate
but the hole extended by a short pipe segment; Venturi tube, with converging and diverging
bells; Pitot tube, involving thin L-shaped tube with adjustable radial position, and Iris valve,
like adjustable diameter orifice plate; are studied using controlled delivery air blower. The air
flow creates a pressure drop across the device. The flow rate and corresponding pressure drop
are measured and plotted for the various devices.
Aim: To study pressure drop characteristics of various air flow measuring and controlling
devices and verify theoretical equations.
Experimental Procedure:
Equipment:
a) Two long and one short piece of PVC pipe sections of 84.6mm NB with flanges, a
pipe section with extensions and nut with bolts for connections.
b) An inlet element and an electric blower with potentiometer having settings
between 0 to 90. Air velocity in the pipe was made to vary linearly with
potentiometer setting.
c) 16 manometer panel. Small diameter columns: I and J, were to be used for Pitot
tube.
d) Anemometer to be placed at the centre of inlet element.
e) Flexible hoses for connecting to manometers.
f) Orifice plate and nozzle.
g) Venturi meter.
h) Pitot tube device with adjustable radial position.
i) Iris valve with adjustable opening diameter
Name:
Professor:
Course:
Date: MMDDYYYY
Measurement of Flow Characteristics of Meters and Control Valve
Introduction: Fluid flow is measured and controlled by obstructing the flow with suitable
devices or modification of the internal diameter profile. Five types of devices are studied in
this experiment. Orifice plate, with central hole in a blind flange; Nozzle, like orifice plate
but the hole extended by a short pipe segment; Venturi tube, with converging and diverging
bells; Pitot tube, involving thin L-shaped tube with adjustable radial position, and Iris valve,
like adjustable diameter orifice plate; are studied using controlled delivery air blower. The air
flow creates a pressure drop across the device. The flow rate and corresponding pressure drop
are measured and plotted for the various devices.
Aim: To study pressure drop characteristics of various air flow measuring and controlling
devices and verify theoretical equations.
Experimental Procedure:
Equipment:
a) Two long and one short piece of PVC pipe sections of 84.6mm NB with flanges, a
pipe section with extensions and nut with bolts for connections.
b) An inlet element and an electric blower with potentiometer having settings
between 0 to 90. Air velocity in the pipe was made to vary linearly with
potentiometer setting.
c) 16 manometer panel. Small diameter columns: I and J, were to be used for Pitot
tube.
d) Anemometer to be placed at the centre of inlet element.
e) Flexible hoses for connecting to manometers.
f) Orifice plate and nozzle.
g) Venturi meter.
h) Pitot tube device with adjustable radial position.
i) Iris valve with adjustable opening diameter
Secure Best Marks with AI Grader
Need help grading? Try our AI Grader for instant feedback on your assignments.
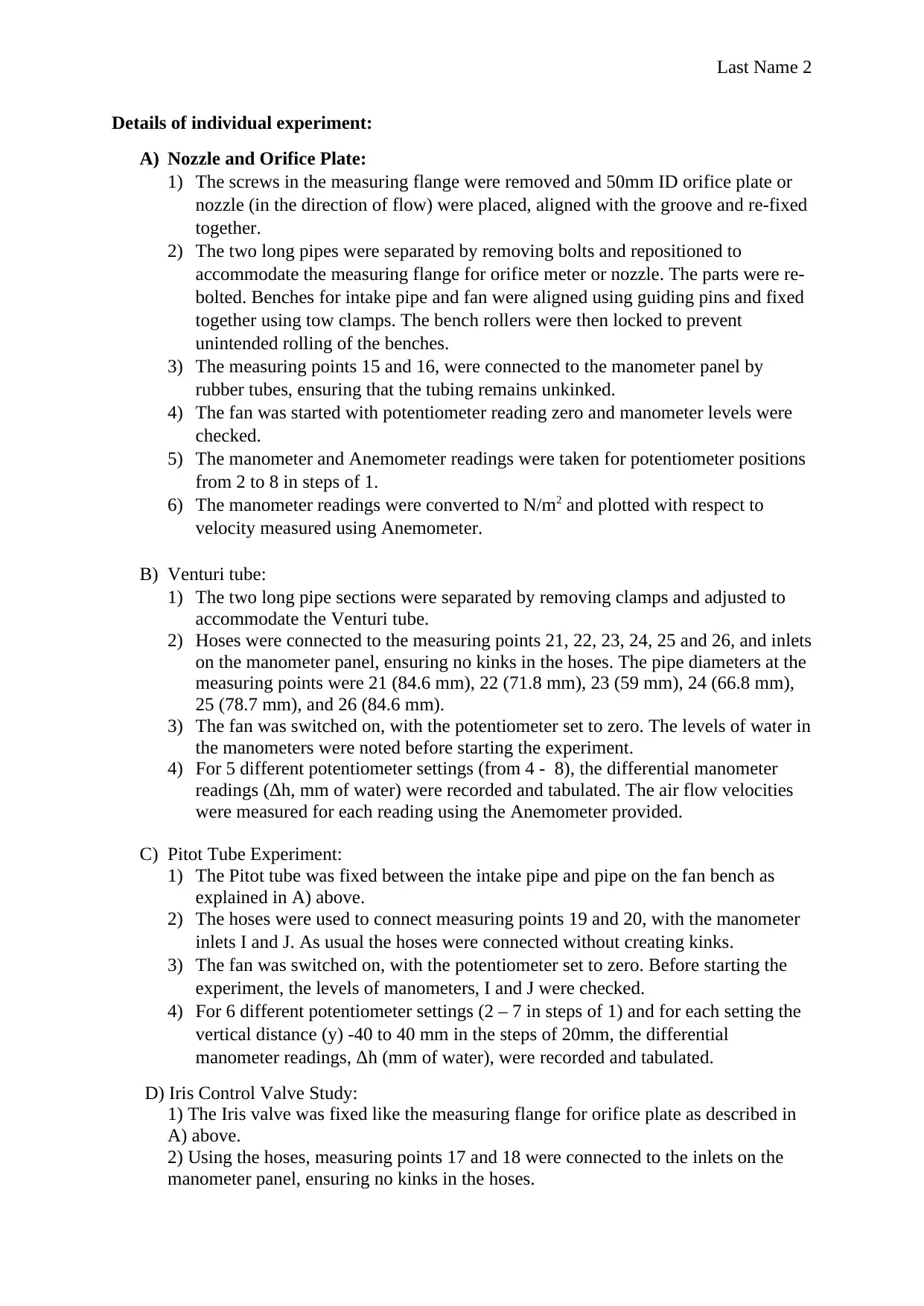
Last Name 2
Details of individual experiment:
A) Nozzle and Orifice Plate:
1) The screws in the measuring flange were removed and 50mm ID orifice plate or
nozzle (in the direction of flow) were placed, aligned with the groove and re-fixed
together.
2) The two long pipes were separated by removing bolts and repositioned to
accommodate the measuring flange for orifice meter or nozzle. The parts were re-
bolted. Benches for intake pipe and fan were aligned using guiding pins and fixed
together using tow clamps. The bench rollers were then locked to prevent
unintended rolling of the benches.
3) The measuring points 15 and 16, were connected to the manometer panel by
rubber tubes, ensuring that the tubing remains unkinked.
4) The fan was started with potentiometer reading zero and manometer levels were
checked.
5) The manometer and Anemometer readings were taken for potentiometer positions
from 2 to 8 in steps of 1.
6) The manometer readings were converted to N/m2 and plotted with respect to
velocity measured using Anemometer.
B) Venturi tube:
1) The two long pipe sections were separated by removing clamps and adjusted to
accommodate the Venturi tube.
2) Hoses were connected to the measuring points 21, 22, 23, 24, 25 and 26, and inlets
on the manometer panel, ensuring no kinks in the hoses. The pipe diameters at the
measuring points were 21 (84.6 mm), 22 (71.8 mm), 23 (59 mm), 24 (66.8 mm),
25 (78.7 mm), and 26 (84.6 mm).
3) The fan was switched on, with the potentiometer set to zero. The levels of water in
the manometers were noted before starting the experiment.
4) For 5 different potentiometer settings (from 4 - 8), the differential manometer
readings (Δh, mm of water) were recorded and tabulated. The air flow velocities
were measured for each reading using the Anemometer provided.
C) Pitot Tube Experiment:
1) The Pitot tube was fixed between the intake pipe and pipe on the fan bench as
explained in A) above.
2) The hoses were used to connect measuring points 19 and 20, with the manometer
inlets I and J. As usual the hoses were connected without creating kinks.
3) The fan was switched on, with the potentiometer set to zero. Before starting the
experiment, the levels of manometers, I and J were checked.
4) For 6 different potentiometer settings (2 – 7 in steps of 1) and for each setting the
vertical distance (y) -40 to 40 mm in the steps of 20mm, the differential
manometer readings, Δh (mm of water), were recorded and tabulated.
D) Iris Control Valve Study:
1) The Iris valve was fixed like the measuring flange for orifice plate as described in
A) above.
2) Using the hoses, measuring points 17 and 18 were connected to the inlets on the
manometer panel, ensuring no kinks in the hoses.
Details of individual experiment:
A) Nozzle and Orifice Plate:
1) The screws in the measuring flange were removed and 50mm ID orifice plate or
nozzle (in the direction of flow) were placed, aligned with the groove and re-fixed
together.
2) The two long pipes were separated by removing bolts and repositioned to
accommodate the measuring flange for orifice meter or nozzle. The parts were re-
bolted. Benches for intake pipe and fan were aligned using guiding pins and fixed
together using tow clamps. The bench rollers were then locked to prevent
unintended rolling of the benches.
3) The measuring points 15 and 16, were connected to the manometer panel by
rubber tubes, ensuring that the tubing remains unkinked.
4) The fan was started with potentiometer reading zero and manometer levels were
checked.
5) The manometer and Anemometer readings were taken for potentiometer positions
from 2 to 8 in steps of 1.
6) The manometer readings were converted to N/m2 and plotted with respect to
velocity measured using Anemometer.
B) Venturi tube:
1) The two long pipe sections were separated by removing clamps and adjusted to
accommodate the Venturi tube.
2) Hoses were connected to the measuring points 21, 22, 23, 24, 25 and 26, and inlets
on the manometer panel, ensuring no kinks in the hoses. The pipe diameters at the
measuring points were 21 (84.6 mm), 22 (71.8 mm), 23 (59 mm), 24 (66.8 mm),
25 (78.7 mm), and 26 (84.6 mm).
3) The fan was switched on, with the potentiometer set to zero. The levels of water in
the manometers were noted before starting the experiment.
4) For 5 different potentiometer settings (from 4 - 8), the differential manometer
readings (Δh, mm of water) were recorded and tabulated. The air flow velocities
were measured for each reading using the Anemometer provided.
C) Pitot Tube Experiment:
1) The Pitot tube was fixed between the intake pipe and pipe on the fan bench as
explained in A) above.
2) The hoses were used to connect measuring points 19 and 20, with the manometer
inlets I and J. As usual the hoses were connected without creating kinks.
3) The fan was switched on, with the potentiometer set to zero. Before starting the
experiment, the levels of manometers, I and J were checked.
4) For 6 different potentiometer settings (2 – 7 in steps of 1) and for each setting the
vertical distance (y) -40 to 40 mm in the steps of 20mm, the differential
manometer readings, Δh (mm of water), were recorded and tabulated.
D) Iris Control Valve Study:
1) The Iris valve was fixed like the measuring flange for orifice plate as described in
A) above.
2) Using the hoses, measuring points 17 and 18 were connected to the inlets on the
manometer panel, ensuring no kinks in the hoses.

Last Name 3
3) The fan was switched on, with the potentiometer set to zero. The level of water in
the manometers was checked before starting the experiment.
4) The blower potentiometer settings from 2 to 6 in steps of 1 were used. For each
setting, readings were taken for 6 valve positions from 1 to 6. The readings were
recorded and tabulated.
3) The fan was switched on, with the potentiometer set to zero. The level of water in
the manometers was checked before starting the experiment.
4) The blower potentiometer settings from 2 to 6 in steps of 1 were used. For each
setting, readings were taken for 6 valve positions from 1 to 6. The readings were
recorded and tabulated.

Last Name 4
Results:
A) Nozzle and Orifice Flows:
Nozzle Characteristics
Potentiomete
r
∆h
(mm)
∆P
(N/m2)
sqrt(∆P
)
(N0.5/m)
Velocit
y (m/s)
2 4 39.2 6.3 1.4
3 8 78.5 8.9 2.1
4 15 147.2 12.1 2.8
5 23 225.6 15.0 3.5
6 33 323.7 18.0 4.2
7 46 451.3 21.2 5.0
8 63 618.0 24.9 6.0
∆h = Manometer Reading, ∆P = Manometer reading converted to Pa or N/m2, Velocity is as
measured by Anemometer.
Orifice Plate Characteristics:
Potentiometer
Setting
∆h
(mm)
∆P
(N/m2)
sqrt(∆P
)
(N0.5/m)
Velocity
(m/s)
2 4 39.2 6.3 1.2
3 9 88.3 9.4 1.9
4 16 157.0 12.5 2.5
5 23 225.6 15.0 3.1
6 35 343.4 18.5 3.8
7 48 470.9 21.7 4.4
8 64 627.8 25.1 5.1
Sample Calculations:
Conversion of (∆h) in mm WC to (∆P) in N/m2:
30 mm WC = (30 m/1000) * (1000 kg/m3) * (9.8 m/s2) = 294 N/m2 (or Pa).
Results:
A) Nozzle and Orifice Flows:
Nozzle Characteristics
Potentiomete
r
∆h
(mm)
∆P
(N/m2)
sqrt(∆P
)
(N0.5/m)
Velocit
y (m/s)
2 4 39.2 6.3 1.4
3 8 78.5 8.9 2.1
4 15 147.2 12.1 2.8
5 23 225.6 15.0 3.5
6 33 323.7 18.0 4.2
7 46 451.3 21.2 5.0
8 63 618.0 24.9 6.0
∆h = Manometer Reading, ∆P = Manometer reading converted to Pa or N/m2, Velocity is as
measured by Anemometer.
Orifice Plate Characteristics:
Potentiometer
Setting
∆h
(mm)
∆P
(N/m2)
sqrt(∆P
)
(N0.5/m)
Velocity
(m/s)
2 4 39.2 6.3 1.2
3 9 88.3 9.4 1.9
4 16 157.0 12.5 2.5
5 23 225.6 15.0 3.1
6 35 343.4 18.5 3.8
7 48 470.9 21.7 4.4
8 64 627.8 25.1 5.1
Sample Calculations:
Conversion of (∆h) in mm WC to (∆P) in N/m2:
30 mm WC = (30 m/1000) * (1000 kg/m3) * (9.8 m/s2) = 294 N/m2 (or Pa).
Secure Best Marks with AI Grader
Need help grading? Try our AI Grader for instant feedback on your assignments.

Last Name 5
Graphs:
5.0 10.0 15.0 20.0 25.0 30.0
0
1
2
3
4
5
6
7
f(x) = 0.236183661084411 x
A1) Nozzle Flow Characteristics
SQRT(DP in Pa)
Velocity in m/s
5.0 10.0 15.0 20.0 25.0 30.0
0
1
2
3
4
5
6
f(x) = 0.20332915291029 x
A2) Orifice Plate Flow Characteristics
SQRT(DP in Pa)
Velocity in m/s
Comments:
1) Nozzle: The points lie in a straight line and the constant of proportionality between
Pipe Velocity to Square root of DP is 0.24.
2) Orifice meter: The points lie in a straight line and the constant correlating the Square
root of ∆P across the meter to Pipe Velocity is 0.2. The constant is lower than the one
for nozzle, as pressure drop is lower for the nozzle.
u0 = CD
√1−β4 ∗
√ 2∗gc∗( pa− pb )
ρ
(McCabe and Smith, p. 219).
Where, CD is constant for the given meter, β is ratio of orifice diameter to pipe
diameter, ρ is density of air and gc is unity in SI units.
Graphs:
5.0 10.0 15.0 20.0 25.0 30.0
0
1
2
3
4
5
6
7
f(x) = 0.236183661084411 x
A1) Nozzle Flow Characteristics
SQRT(DP in Pa)
Velocity in m/s
5.0 10.0 15.0 20.0 25.0 30.0
0
1
2
3
4
5
6
f(x) = 0.20332915291029 x
A2) Orifice Plate Flow Characteristics
SQRT(DP in Pa)
Velocity in m/s
Comments:
1) Nozzle: The points lie in a straight line and the constant of proportionality between
Pipe Velocity to Square root of DP is 0.24.
2) Orifice meter: The points lie in a straight line and the constant correlating the Square
root of ∆P across the meter to Pipe Velocity is 0.2. The constant is lower than the one
for nozzle, as pressure drop is lower for the nozzle.
u0 = CD
√1−β4 ∗
√ 2∗gc∗( pa− pb )
ρ
(McCabe and Smith, p. 219).
Where, CD is constant for the given meter, β is ratio of orifice diameter to pipe
diameter, ρ is density of air and gc is unity in SI units.

Last Name 6
Now by mass balance, u0 = V*β, where V is undisturbed velocity in the pipe and u0 is
orifice exit velocity.
Therefore, V is proportional to sqrt(pa – pb) or √∆P.
This requires, plot of √∆P versus V to be a straight line for orifice meter. The
experiment verifies the theoretical prediction.
Now by mass balance, u0 = V*β, where V is undisturbed velocity in the pipe and u0 is
orifice exit velocity.
Therefore, V is proportional to sqrt(pa – pb) or √∆P.
This requires, plot of √∆P versus V to be a straight line for orifice meter. The
experiment verifies the theoretical prediction.

Last Name 7
B) Venturi Tube Characteristics:
Potentiomet
er
Measurin
g Point
Id
∆h
(mm)
∆P
(N/m2)
sqrt(∆
P)
(
N0.5/m)
Velocit
y (m/s)
4 22 12 117.7 10.8 2.6
4 23 27 264.9 16.3 2.6
4 24 13 127.5 11.3 2.6
4 25 10 98.1 9.9 2.6
4 26 9 88.3 9.4 2.6
5 22 9 88.3 9.4 3.4
5 23 34 333.5 18.3 3.4
5 24 20 196.2 14.0 3.4
5 25 9 88.3 9.4 3.4
5 26 5 49.1 7.0 3.4
6 22 14 137.3 11.7 4.2
6 23 50 490.5 22.1 4.2
6 24 30 294.3 17.2 4.2
6 25 15 147.2 12.1 4.2
6 26 9 88.3 9.4 4.2
7 22 19 186.4 13.7 5.1
7 23 74 725.9 26.9 5.1
7 24 40 392.4 19.8 5.1
7 25 18 176.6 13.3 5.1
7 26 11 107.9 10.4 5.1
8 22 27 264.9 16.3 5.9
8 23 100 981.0 31.3 5.9
8 24 56 549.4 23.4 5.9
8 25 25 245.3 15.7 5.9
8 26 14 137.3 11.7 5.9
B) Venturi Tube Characteristics:
Potentiomet
er
Measurin
g Point
Id
∆h
(mm)
∆P
(N/m2)
sqrt(∆
P)
(
N0.5/m)
Velocit
y (m/s)
4 22 12 117.7 10.8 2.6
4 23 27 264.9 16.3 2.6
4 24 13 127.5 11.3 2.6
4 25 10 98.1 9.9 2.6
4 26 9 88.3 9.4 2.6
5 22 9 88.3 9.4 3.4
5 23 34 333.5 18.3 3.4
5 24 20 196.2 14.0 3.4
5 25 9 88.3 9.4 3.4
5 26 5 49.1 7.0 3.4
6 22 14 137.3 11.7 4.2
6 23 50 490.5 22.1 4.2
6 24 30 294.3 17.2 4.2
6 25 15 147.2 12.1 4.2
6 26 9 88.3 9.4 4.2
7 22 19 186.4 13.7 5.1
7 23 74 725.9 26.9 5.1
7 24 40 392.4 19.8 5.1
7 25 18 176.6 13.3 5.1
7 26 11 107.9 10.4 5.1
8 22 27 264.9 16.3 5.9
8 23 100 981.0 31.3 5.9
8 24 56 549.4 23.4 5.9
8 25 25 245.3 15.7 5.9
8 26 14 137.3 11.7 5.9
Paraphrase This Document
Need a fresh take? Get an instant paraphrase of this document with our AI Paraphraser
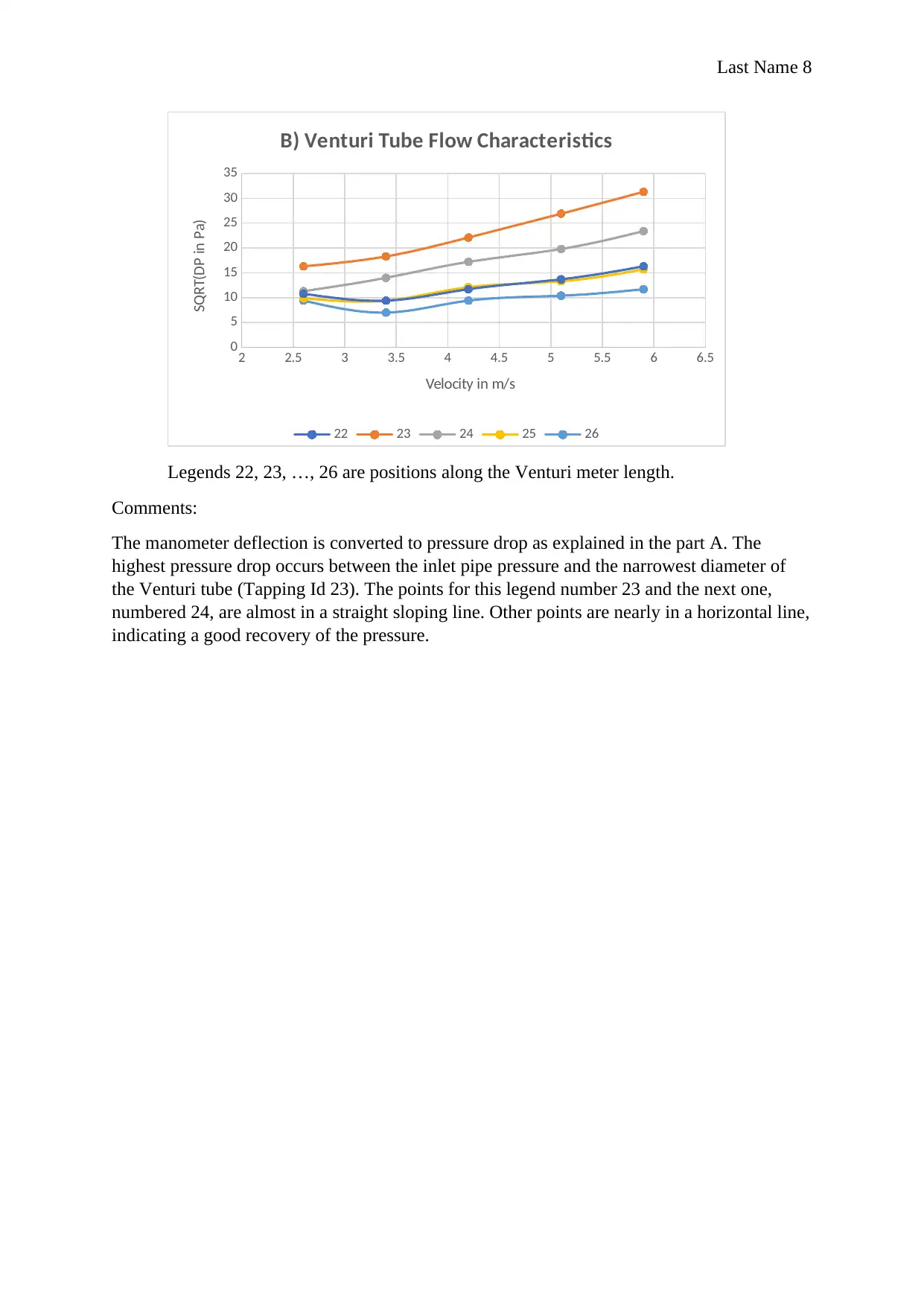
Last Name 8
2 2.5 3 3.5 4 4.5 5 5.5 6 6.5
0
5
10
15
20
25
30
35
B) Venturi Tube Flow Characteristics
22 23 24 25 26
Velocity in m/s
SQRT(DP in Pa)
Legends 22, 23, …, 26 are positions along the Venturi meter length.
Comments:
The manometer deflection is converted to pressure drop as explained in the part A. The
highest pressure drop occurs between the inlet pipe pressure and the narrowest diameter of
the Venturi tube (Tapping Id 23). The points for this legend number 23 and the next one,
numbered 24, are almost in a straight sloping line. Other points are nearly in a horizontal line,
indicating a good recovery of the pressure.
2 2.5 3 3.5 4 4.5 5 5.5 6 6.5
0
5
10
15
20
25
30
35
B) Venturi Tube Flow Characteristics
22 23 24 25 26
Velocity in m/s
SQRT(DP in Pa)
Legends 22, 23, …, 26 are positions along the Venturi meter length.
Comments:
The manometer deflection is converted to pressure drop as explained in the part A. The
highest pressure drop occurs between the inlet pipe pressure and the narrowest diameter of
the Venturi tube (Tapping Id 23). The points for this legend number 23 and the next one,
numbered 24, are almost in a straight sloping line. Other points are nearly in a horizontal line,
indicating a good recovery of the pressure.

Last Name 9
C) Pitot Tube Study of Velocity Profile:
Potentiomet
er
∆h
(mm)
∆P
(N/m2)
sqrt(∆
P)
(
N0.5/m)
Vertica
l
Distanc
e (mm)
Velocit
y x
Consta
nt
2 0 0.0 0.0 -40 0.0
2 1 9.8 3.1 -20 3.1
2 1 9.8 3.1 0 3.1
2 1 9.8 3.1 20 3.1
2 0 0.0 0.0 40 0.0
3 1 9.8 3.1 -40 3.1
3 3 29.4 5.4 -20 5.4
3 3 29.4 5.4 0 5.4
3 3 29.4 5.4 20 5.4
3 1 9.8 3.1 40 3.1
4 3 29.4 5.4 -40 5.4
4 7 68.7 8.3 -20 8.3
4 8 78.5 8.9 0 8.9
4 8 78.5 8.9 20 8.9
4 4 39.2 6.3 40 6.3
5 4 39.2 6.3 -40 6.3
5 10 98.1 9.9 -20 9.9
5 12 117.7 10.8 0 10.8
5 13 127.5 11.3 20 11.3
5 6 58.9 7.7 40 7.7
6 8 78.5 8.9 -40 8.9
6 19 186.4 13.7 -20 13.7
6 20 196.2 14.0 0 14.0
6 20 196.2 14.0 20 14.0
6 7 68.7 8.3 40 8.3
7 13 127.5 11.3 -40 11.3
7 28 274.7 16.6 -20 16.6
7 33 323.7 18.0 0 18.0
7 34 333.5 18.3 20 18.3
7 15 147.2 12.1 40 12.1
C) Pitot Tube Study of Velocity Profile:
Potentiomet
er
∆h
(mm)
∆P
(N/m2)
sqrt(∆
P)
(
N0.5/m)
Vertica
l
Distanc
e (mm)
Velocit
y x
Consta
nt
2 0 0.0 0.0 -40 0.0
2 1 9.8 3.1 -20 3.1
2 1 9.8 3.1 0 3.1
2 1 9.8 3.1 20 3.1
2 0 0.0 0.0 40 0.0
3 1 9.8 3.1 -40 3.1
3 3 29.4 5.4 -20 5.4
3 3 29.4 5.4 0 5.4
3 3 29.4 5.4 20 5.4
3 1 9.8 3.1 40 3.1
4 3 29.4 5.4 -40 5.4
4 7 68.7 8.3 -20 8.3
4 8 78.5 8.9 0 8.9
4 8 78.5 8.9 20 8.9
4 4 39.2 6.3 40 6.3
5 4 39.2 6.3 -40 6.3
5 10 98.1 9.9 -20 9.9
5 12 117.7 10.8 0 10.8
5 13 127.5 11.3 20 11.3
5 6 58.9 7.7 40 7.7
6 8 78.5 8.9 -40 8.9
6 19 186.4 13.7 -20 13.7
6 20 196.2 14.0 0 14.0
6 20 196.2 14.0 20 14.0
6 7 68.7 8.3 40 8.3
7 13 127.5 11.3 -40 11.3
7 28 274.7 16.6 -20 16.6
7 33 323.7 18.0 0 18.0
7 34 333.5 18.3 20 18.3
7 15 147.2 12.1 40 12.1

Last Name 10
Legends 2, 3, …, 7 are the potentiometer settings for the blower.
Comments:
Bernoulli’s equation gives, P + ρgZ + ρV2/2 = constant along a flow-line (McCabe
and Smith, p. 72). As the pressure is constant in a vertical line and neglecting head
due to air column gravity, the reading of the Pitot tube manometer is ρV2/2. Thus, V is
proportional to the square root of water column head in the manometer. The plot of Z
vs V would be therefore, qualitatively similar to Z vs square root of manometer
reading.
The manometer readings can be converted to SI units as indicated in part A above.
The velocity profile is approximately flat in the central region, tapering to zero at the
pipe wall (+/- 42.3 mm). The velocity in the upper region of the centre appears to be
higher than the corresponding velocity in the lower region. This may be due to
position of the blower impeller with respect to the centre line of the discharge pipe,
which allows preferred movement of air in the upper region of pipe.
0 5 10 15 20
-50
-40
-30
-20
-10
0
10
20
30
40
50
Velocity
Radial
Distance in
mm
2
3
4
5
6
7
Legends 2, 3, …, 7 are the potentiometer settings for the blower.
Comments:
Bernoulli’s equation gives, P + ρgZ + ρV2/2 = constant along a flow-line (McCabe
and Smith, p. 72). As the pressure is constant in a vertical line and neglecting head
due to air column gravity, the reading of the Pitot tube manometer is ρV2/2. Thus, V is
proportional to the square root of water column head in the manometer. The plot of Z
vs V would be therefore, qualitatively similar to Z vs square root of manometer
reading.
The manometer readings can be converted to SI units as indicated in part A above.
The velocity profile is approximately flat in the central region, tapering to zero at the
pipe wall (+/- 42.3 mm). The velocity in the upper region of the centre appears to be
higher than the corresponding velocity in the lower region. This may be due to
position of the blower impeller with respect to the centre line of the discharge pipe,
which allows preferred movement of air in the upper region of pipe.
0 5 10 15 20
-50
-40
-30
-20
-10
0
10
20
30
40
50
Velocity
Radial
Distance in
mm
2
3
4
5
6
7
Secure Best Marks with AI Grader
Need help grading? Try our AI Grader for instant feedback on your assignments.

Last Name 11
D) Iris Diaphragm Valve Characteristics:
Potentiomet
er
Setting
∆h
(mm)
∆P
(N/
m2)
Air
Flow
(d
m3/s)
%Valve
Opening
Diamete
r
2 3 29.4 10 53.8
2 7 68.6 18 59.4
2 8 78.4 28 68.8
2 4 39.2 28 76.3
2 4 39.2 36 85.0
2 4 39.2 50 92.5
3 7 68.6 15 53.8
3 8 78.4 21 59.4
3 7 68.6 28 68.8
3 9 88.2 40 76.3
3 8 78.4 50 85.0
3 7 68.6 68 92.5
4 14 137.2 21 53.8
4 15 147.0 30 59.4
4 15 147.0 32 68.8
4 15 147.0 52 76.3
4 20 196.0 78 85.0
4 13 127.4 90 92.5
5 22 215.6 25 53.8
5 23 225.4 34 59.4
5 24 235.2 48 68.8
5 25 245.0 64 76.3
5 24 235.2 85 85.0
5 20 196.0 110 92.5
6 33 323.4 32 53.8
6 34 333.2 42 59.4
6 35 343.0 60 68.8
6 38 372.4 80 76.3
6 36 352.8 100 85.0
6 30 294.0 140 92.5
D) Iris Diaphragm Valve Characteristics:
Potentiomet
er
Setting
∆h
(mm)
∆P
(N/
m2)
Air
Flow
(d
m3/s)
%Valve
Opening
Diamete
r
2 3 29.4 10 53.8
2 7 68.6 18 59.4
2 8 78.4 28 68.8
2 4 39.2 28 76.3
2 4 39.2 36 85.0
2 4 39.2 50 92.5
3 7 68.6 15 53.8
3 8 78.4 21 59.4
3 7 68.6 28 68.8
3 9 88.2 40 76.3
3 8 78.4 50 85.0
3 7 68.6 68 92.5
4 14 137.2 21 53.8
4 15 147.0 30 59.4
4 15 147.0 32 68.8
4 15 147.0 52 76.3
4 20 196.0 78 85.0
4 13 127.4 90 92.5
5 22 215.6 25 53.8
5 23 225.4 34 59.4
5 24 235.2 48 68.8
5 25 245.0 64 76.3
5 24 235.2 85 85.0
5 20 196.0 110 92.5
6 33 323.4 32 53.8
6 34 333.2 42 59.4
6 35 343.0 60 68.8
6 38 372.4 80 76.3
6 36 352.8 100 85.0
6 30 294.0 140 92.5

Last Name 12
20 30 40 50 60 70 80
0
20
40
60
80
100
120
140
160
E) Iris Valve Characteristics
2 3 4 5 6
% Open diameter
Flow Rate in lit/s
Legends 2, 3, …, 6 are potentiometer settings for the blower.
Sample Calculations:
1) Calculation of % Open Diameter in Iris valve:
For position 2 of the valve,
d = 47.5 mm. Fully open diameter = 80 mm.
Therefore, % open diameter = 47.5/80 = 59%.
2) Calculation of Flow rate in Iris Valve:
For potentiometer setting of 6 and the iris valve position of 5, ∆h = 36 mm.
As explained in 1) above, 36 mm WC = (36*9.8) = 353 Pa.
For line number 5 at 300 Pa, flow rate is about 95 dm3/s. So, using judgement, for 353
Pa, the flow rate would be close to 100 dm3/s.
Comments:
The % flow-rate is generally falling in a straight line with respect to % open diameter.
The variation is due to estimating velocity from nomogram. Thus, the Iris valve
controls the flow linearly with respect to % open diameter.
20 30 40 50 60 70 80
0
20
40
60
80
100
120
140
160
E) Iris Valve Characteristics
2 3 4 5 6
% Open diameter
Flow Rate in lit/s
Legends 2, 3, …, 6 are potentiometer settings for the blower.
Sample Calculations:
1) Calculation of % Open Diameter in Iris valve:
For position 2 of the valve,
d = 47.5 mm. Fully open diameter = 80 mm.
Therefore, % open diameter = 47.5/80 = 59%.
2) Calculation of Flow rate in Iris Valve:
For potentiometer setting of 6 and the iris valve position of 5, ∆h = 36 mm.
As explained in 1) above, 36 mm WC = (36*9.8) = 353 Pa.
For line number 5 at 300 Pa, flow rate is about 95 dm3/s. So, using judgement, for 353
Pa, the flow rate would be close to 100 dm3/s.
Comments:
The % flow-rate is generally falling in a straight line with respect to % open diameter.
The variation is due to estimating velocity from nomogram. Thus, the Iris valve
controls the flow linearly with respect to % open diameter.

Last Name 13
Discussion:
Trend of the square root of pressure drop with respect to velocity is linear in all the
experiments, as predicted by theory.
Errors in observation: The measurement of water column difference has an error of 1 mm,
while the readings range from 4 mm to 100 mm. The error in pressure drop is therefore as
high as 25% and in square root of the pressure drop, up to from 12%. The severity of the
errors reduces in the graph, so the graphs look like a reasonable straight line.
Calculation errors: In Iris valve experiment, the flow-rate is calculated using a nomogram on
log-log plot. Some readings required interpolation while some others an extrapolation. On a
linear scale, the errors are much more than the previous experiments. Therefore, the plots
seem to deviate occasionally from a straight-line behaviour.
Conclusion: The theoretical equations are confirmed well for the devices studied in the
experiment. The deviations may be due to the error in measuring pressure drop, in using
nomogram and geometry of the blower.
Discussion:
Trend of the square root of pressure drop with respect to velocity is linear in all the
experiments, as predicted by theory.
Errors in observation: The measurement of water column difference has an error of 1 mm,
while the readings range from 4 mm to 100 mm. The error in pressure drop is therefore as
high as 25% and in square root of the pressure drop, up to from 12%. The severity of the
errors reduces in the graph, so the graphs look like a reasonable straight line.
Calculation errors: In Iris valve experiment, the flow-rate is calculated using a nomogram on
log-log plot. Some readings required interpolation while some others an extrapolation. On a
linear scale, the errors are much more than the previous experiments. Therefore, the plots
seem to deviate occasionally from a straight-line behaviour.
Conclusion: The theoretical equations are confirmed well for the devices studied in the
experiment. The deviations may be due to the error in measuring pressure drop, in using
nomogram and geometry of the blower.
Paraphrase This Document
Need a fresh take? Get an instant paraphrase of this document with our AI Paraphraser

Last Name 14
Questions:
1) Merits of Orifice Plate, Nozzle, Venturi:
Orifice plate is least expensive, most compact, creates more deflection of manometer
but causes more irreversible pressure drop.
Nozzle is more expensive, requires slightly more space and gives less pressure drops.
Venturi is the most expensive item, requires much larger space, gives the highest
reversible pressure drop at the lowest irreversible pressure drop.
2) Assuming density of air to be 1.2 kg/m3,
For nozzle, flow-rate = 1.1377*0.937*0.7854*0.052*sqrt(2*710/1.2)*1000
= 72.0 dm3/s.
For orifice plate, flow-rate = 0.7588*0.9705*0.7854*0.052*sqrt(2*710/1.2)*1000
= 49.7 dm3/s.
3) Pitot tube has a small diameter. To cause deflection of manometer sufficiently fast,
the manometer diameter (and volume) should also be small. Otherwise, much more
air would have to travel through the Pitot tube to cause correct deflection of the
manometer, resulting in a slower response.
4) Anemometer measures velocity of the air (Wind and Weather tools, 2017).
5) Different pipe bends have different lengths and the angle of change in velocity
direction. The three-piece metre bend has gradual change in velocity direction, so it
gives the lowest pressure drop. The round elbow has shorter length but more sudden
turning of the direction giving more pressure drop. The two-piece metre bend has the
sharpest turn of air direction, so it gives the highest pressure drop.
Questions:
1) Merits of Orifice Plate, Nozzle, Venturi:
Orifice plate is least expensive, most compact, creates more deflection of manometer
but causes more irreversible pressure drop.
Nozzle is more expensive, requires slightly more space and gives less pressure drops.
Venturi is the most expensive item, requires much larger space, gives the highest
reversible pressure drop at the lowest irreversible pressure drop.
2) Assuming density of air to be 1.2 kg/m3,
For nozzle, flow-rate = 1.1377*0.937*0.7854*0.052*sqrt(2*710/1.2)*1000
= 72.0 dm3/s.
For orifice plate, flow-rate = 0.7588*0.9705*0.7854*0.052*sqrt(2*710/1.2)*1000
= 49.7 dm3/s.
3) Pitot tube has a small diameter. To cause deflection of manometer sufficiently fast,
the manometer diameter (and volume) should also be small. Otherwise, much more
air would have to travel through the Pitot tube to cause correct deflection of the
manometer, resulting in a slower response.
4) Anemometer measures velocity of the air (Wind and Weather tools, 2017).
5) Different pipe bends have different lengths and the angle of change in velocity
direction. The three-piece metre bend has gradual change in velocity direction, so it
gives the lowest pressure drop. The round elbow has shorter length but more sudden
turning of the direction giving more pressure drop. The two-piece metre bend has the
sharpest turn of air direction, so it gives the highest pressure drop.

Last Name 15
References
1) McCabe, W., J. Smith and P. Harriot (1993). Unit Operations of Chemical
Engineering, 5th edition, London: McGraw-Hill.
2) Wind and Weather Tools (2017). What is an Anemometer and What It is Used for,
https://windandweathertools.com/what-is-an-anemometer-and-what-is-it-used-
for/, Accessed on 30th December 2017.
References
1) McCabe, W., J. Smith and P. Harriot (1993). Unit Operations of Chemical
Engineering, 5th edition, London: McGraw-Hill.
2) Wind and Weather Tools (2017). What is an Anemometer and What It is Used for,
https://windandweathertools.com/what-is-an-anemometer-and-what-is-it-used-
for/, Accessed on 30th December 2017.
1 out of 15
Related Documents
![[object Object]](/_next/image/?url=%2F_next%2Fstatic%2Fmedia%2Flogo.6d15ce61.png&w=640&q=75)
Your All-in-One AI-Powered Toolkit for Academic Success.
+13062052269
info@desklib.com
Available 24*7 on WhatsApp / Email
Unlock your academic potential
© 2024 | Zucol Services PVT LTD | All rights reserved.